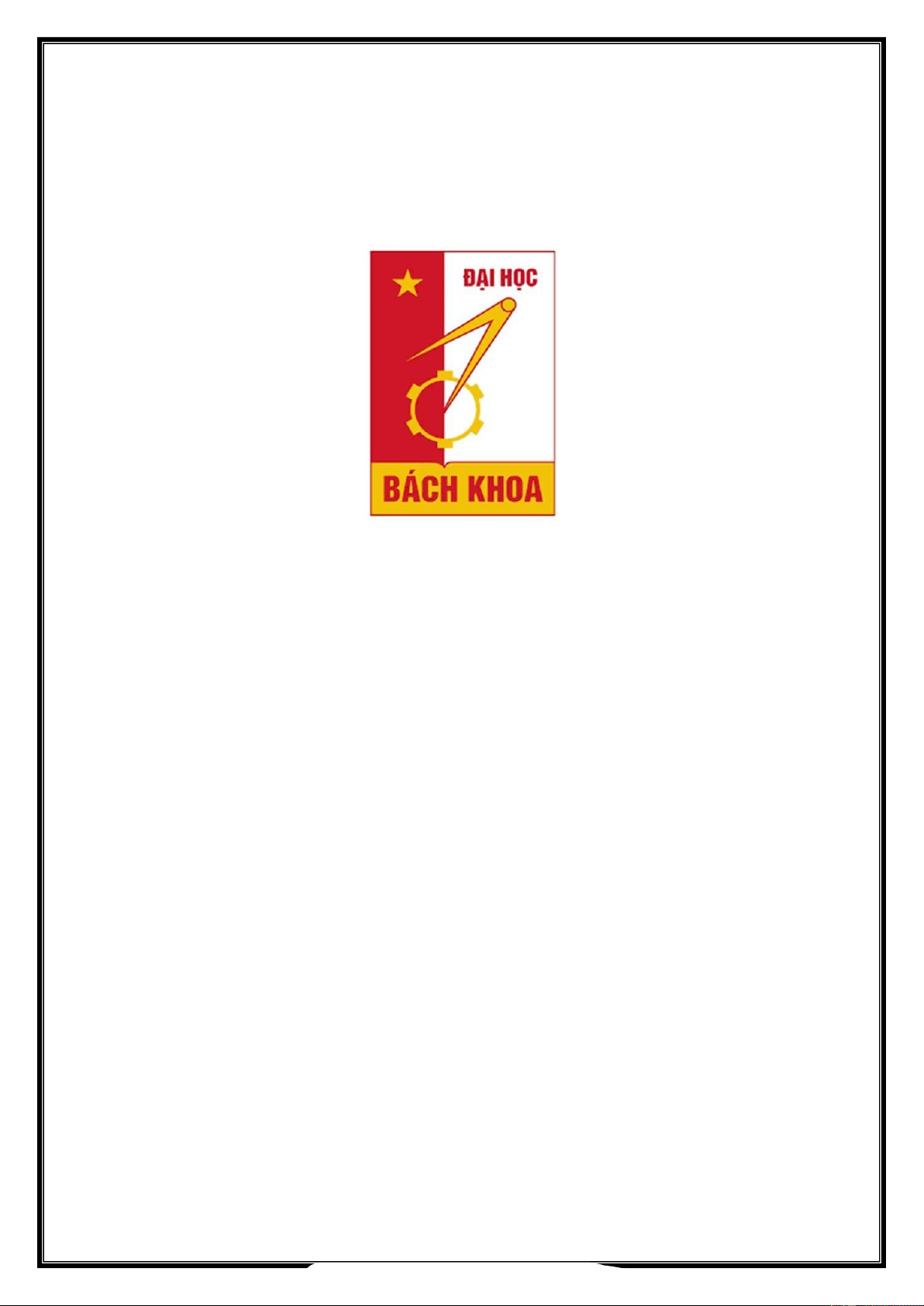
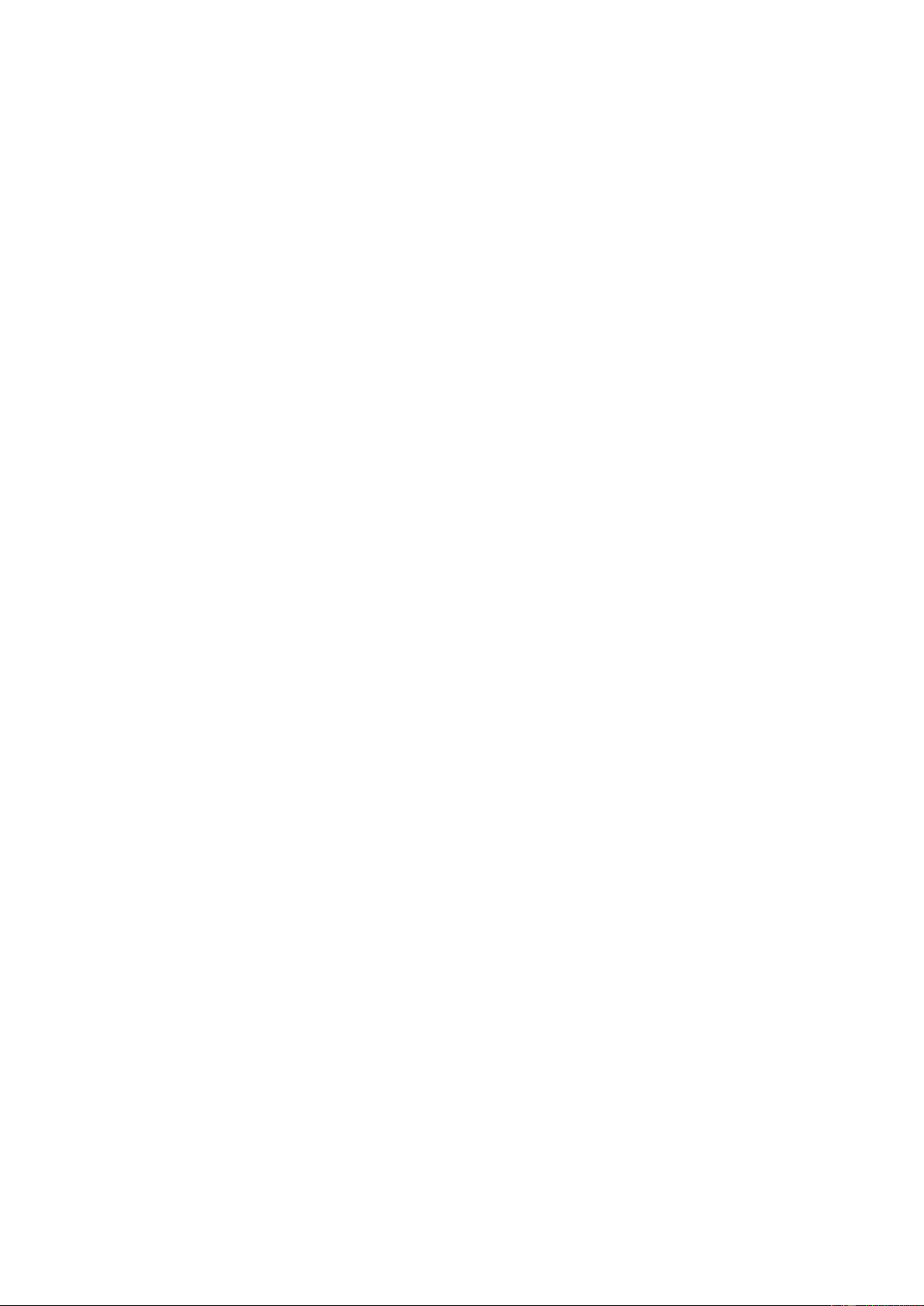
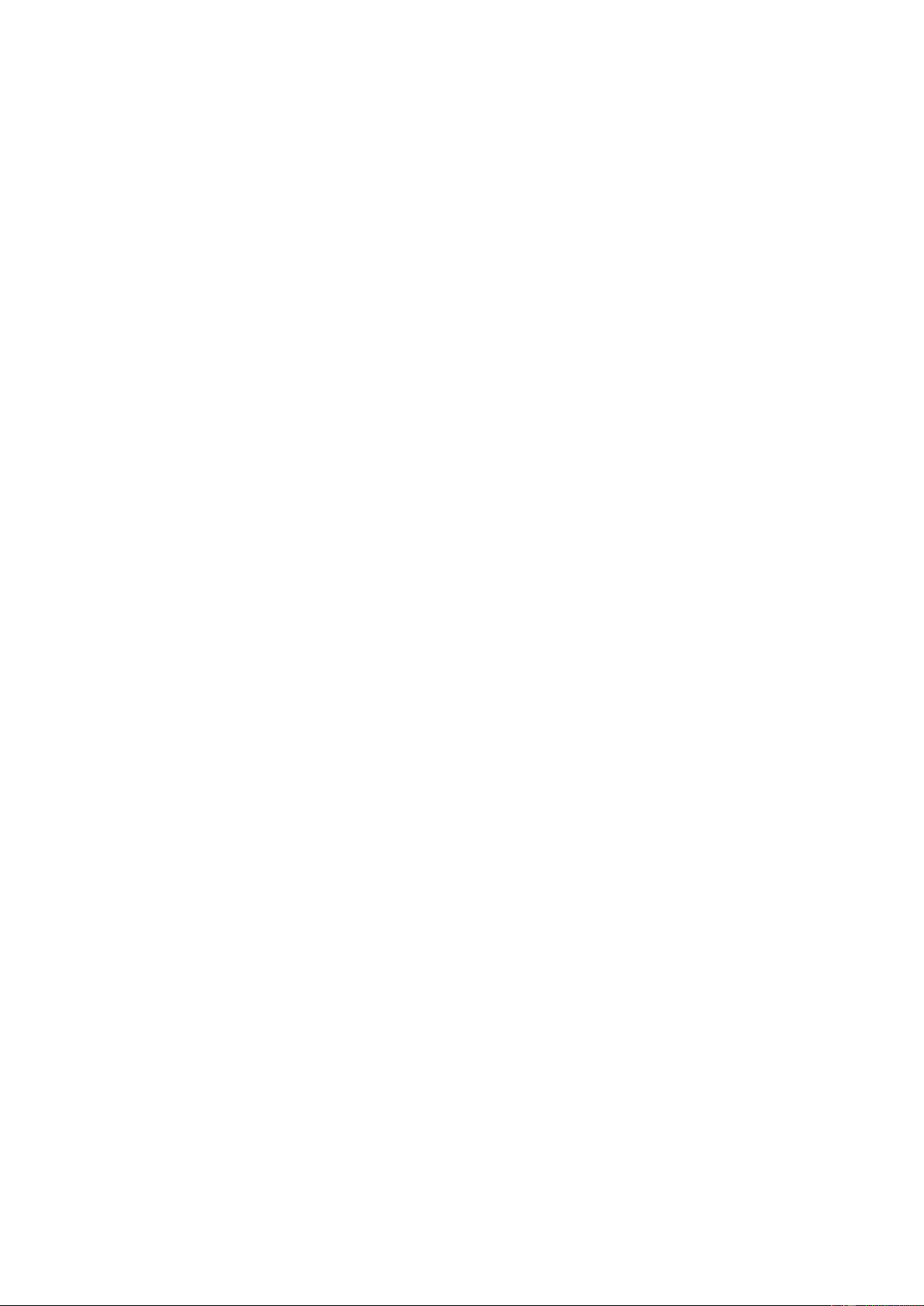
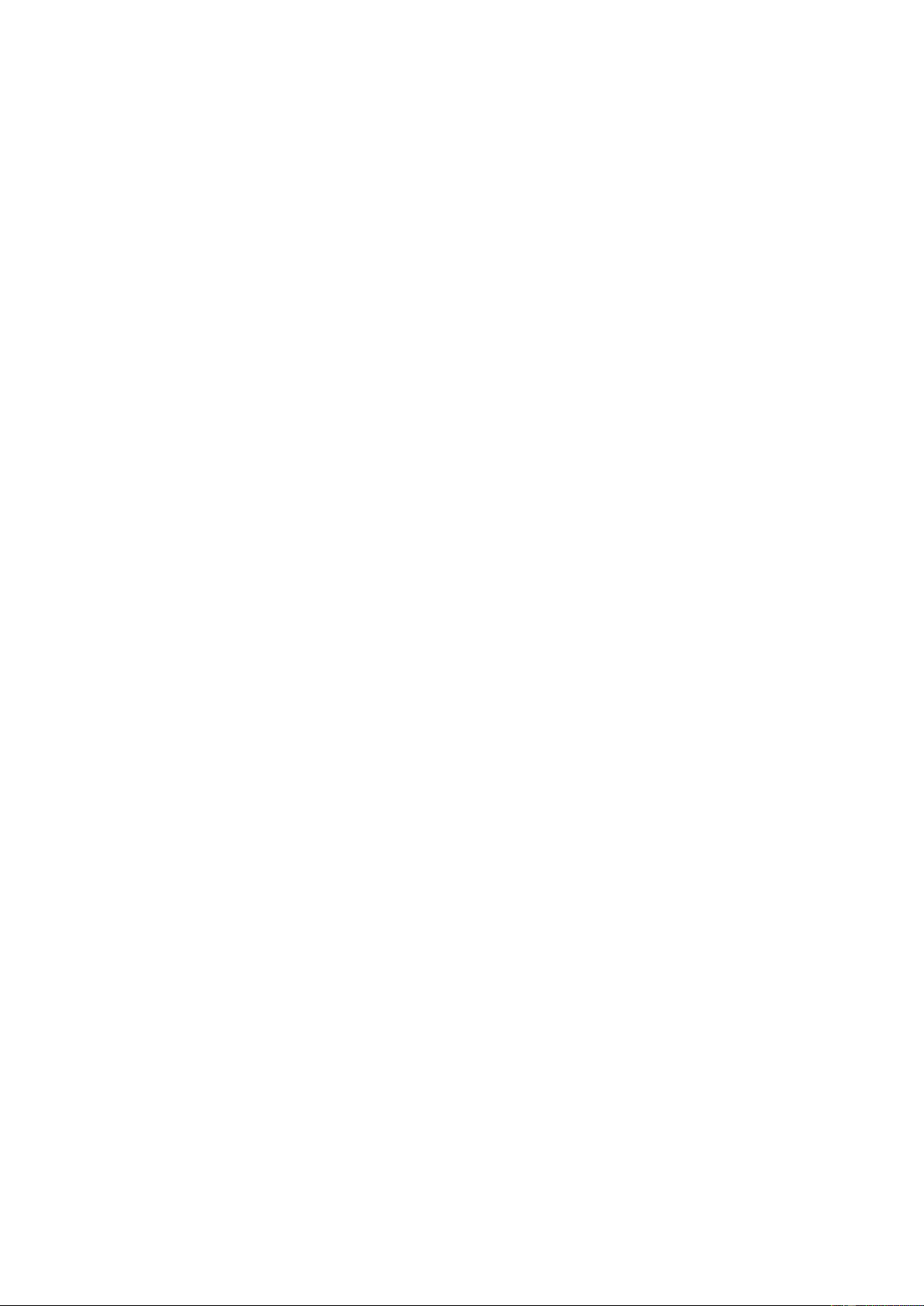
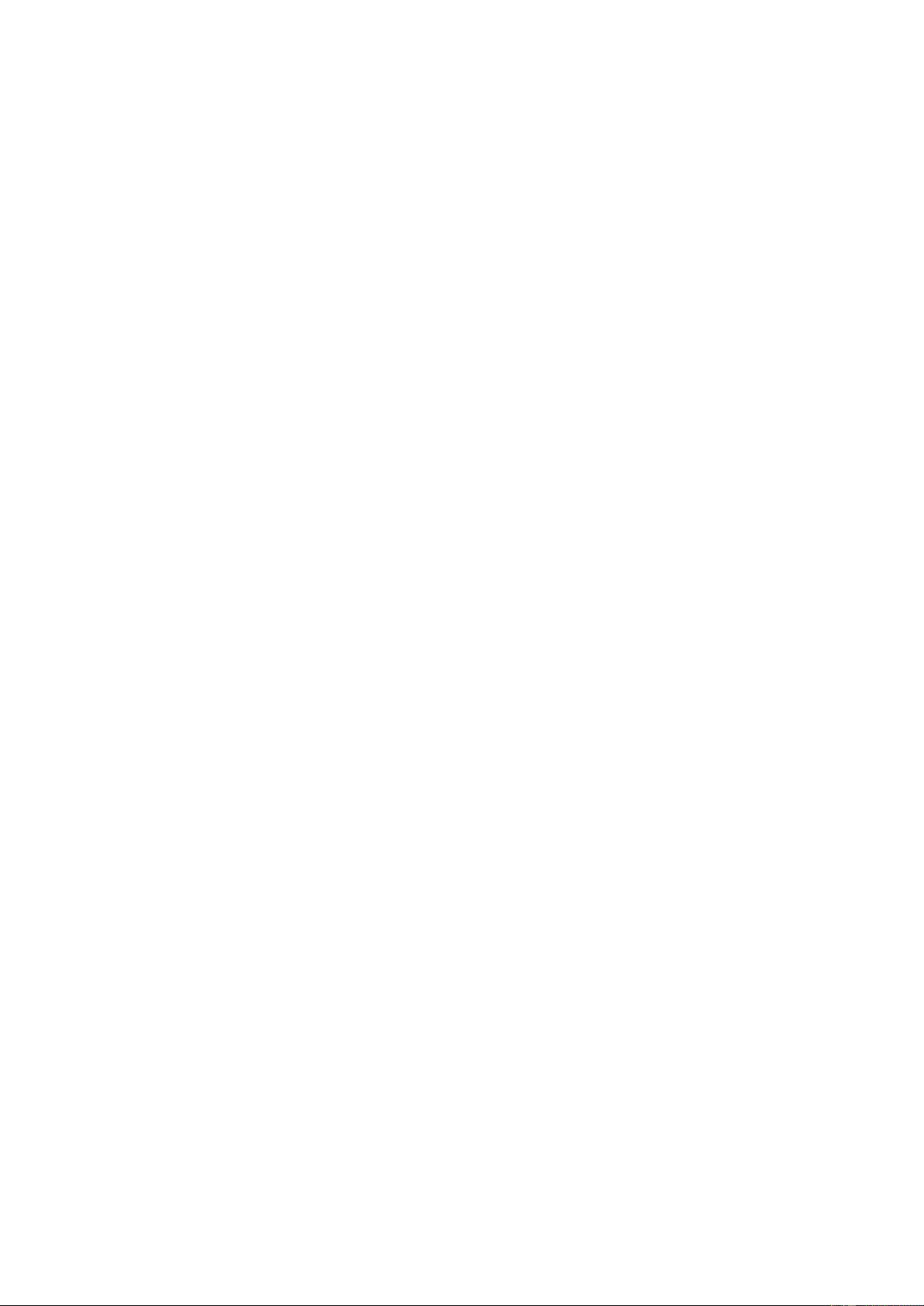
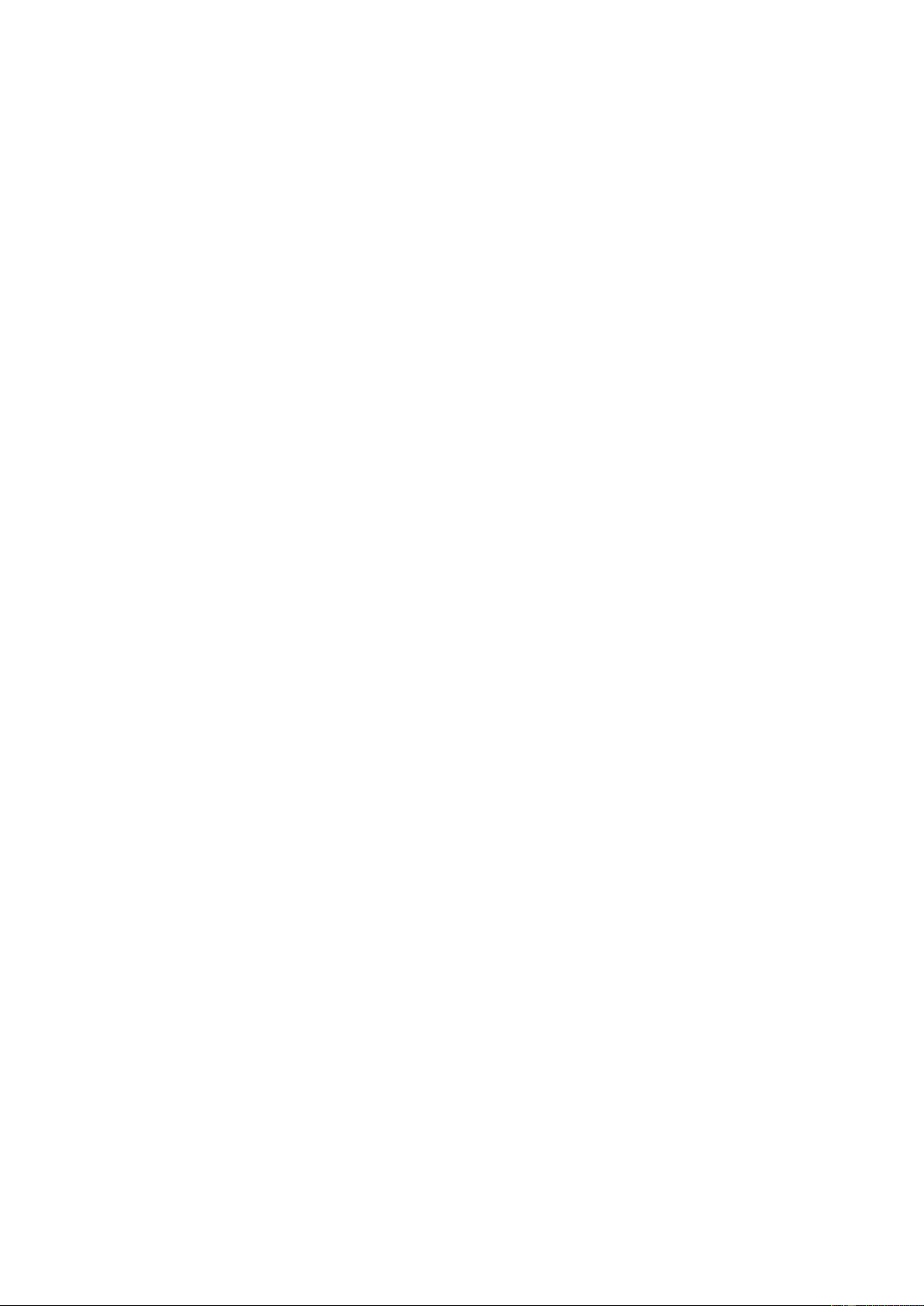
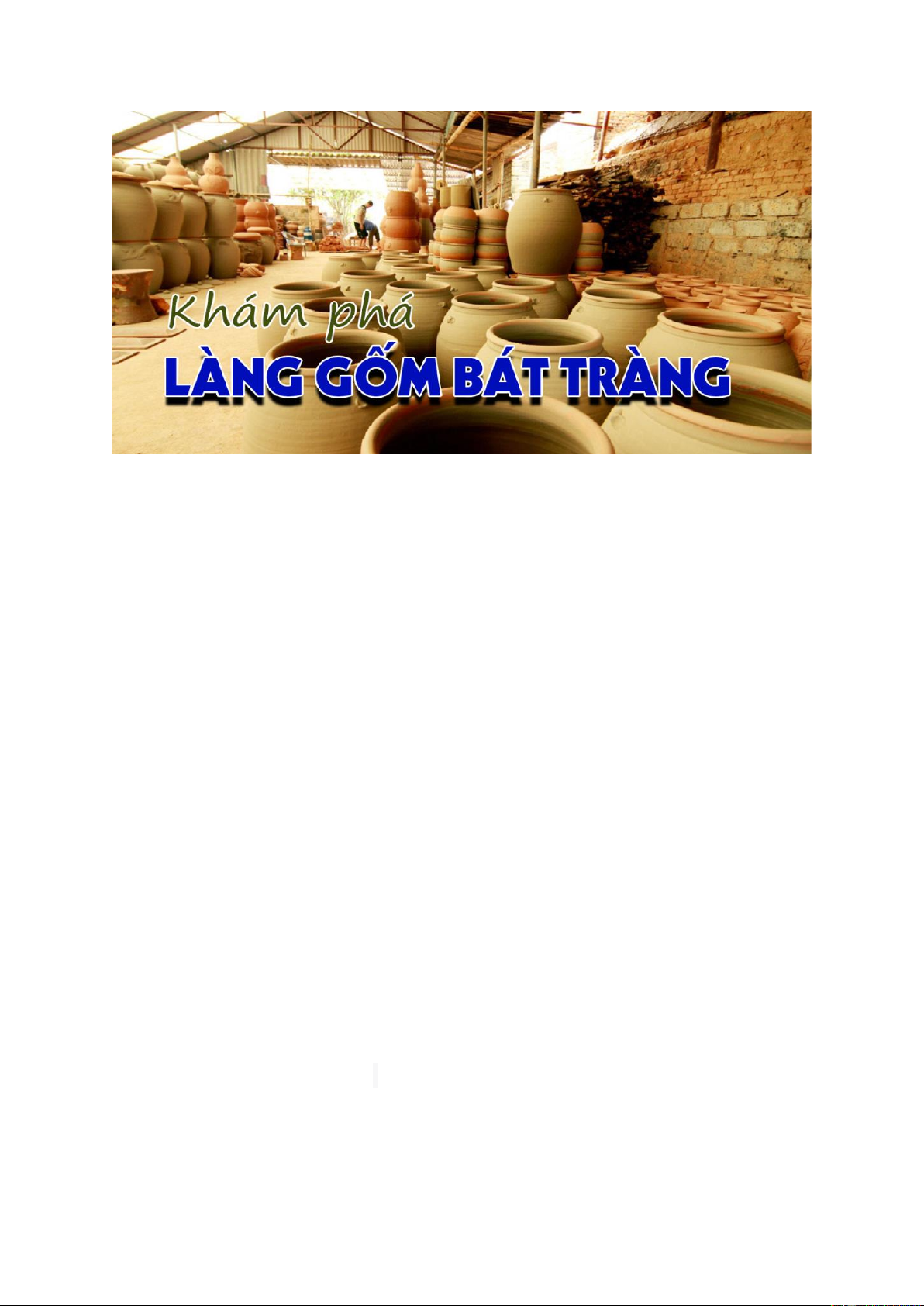
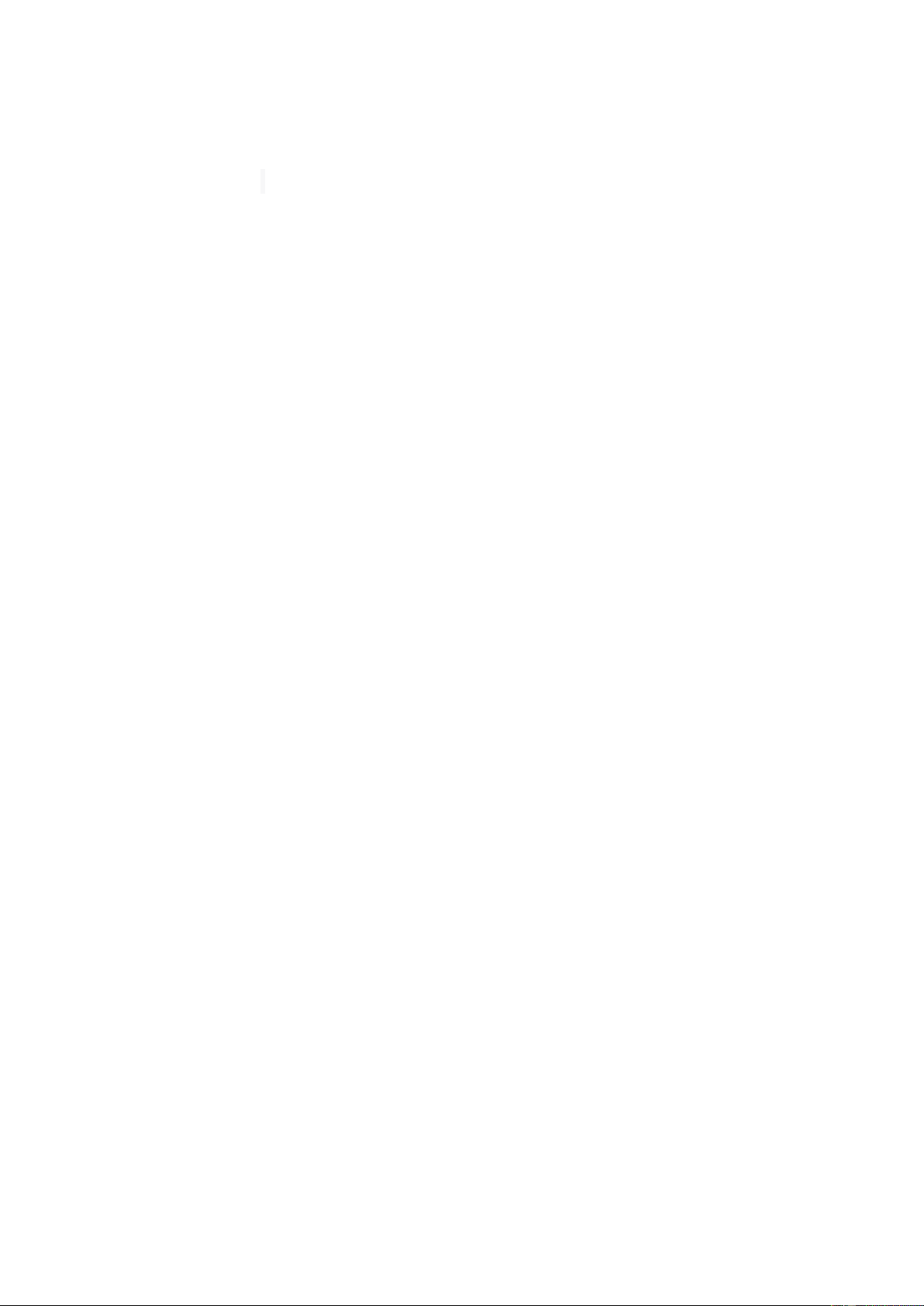
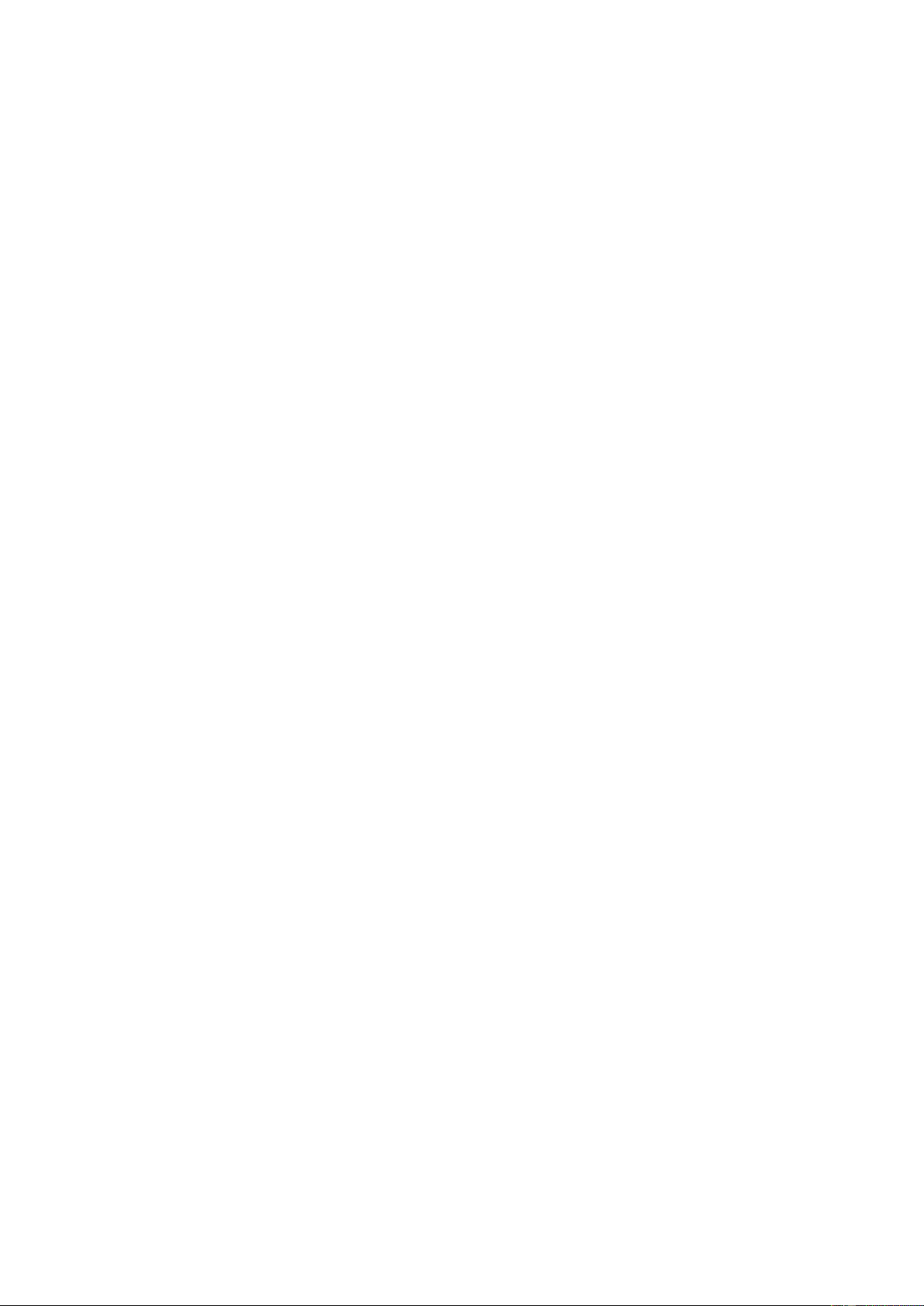
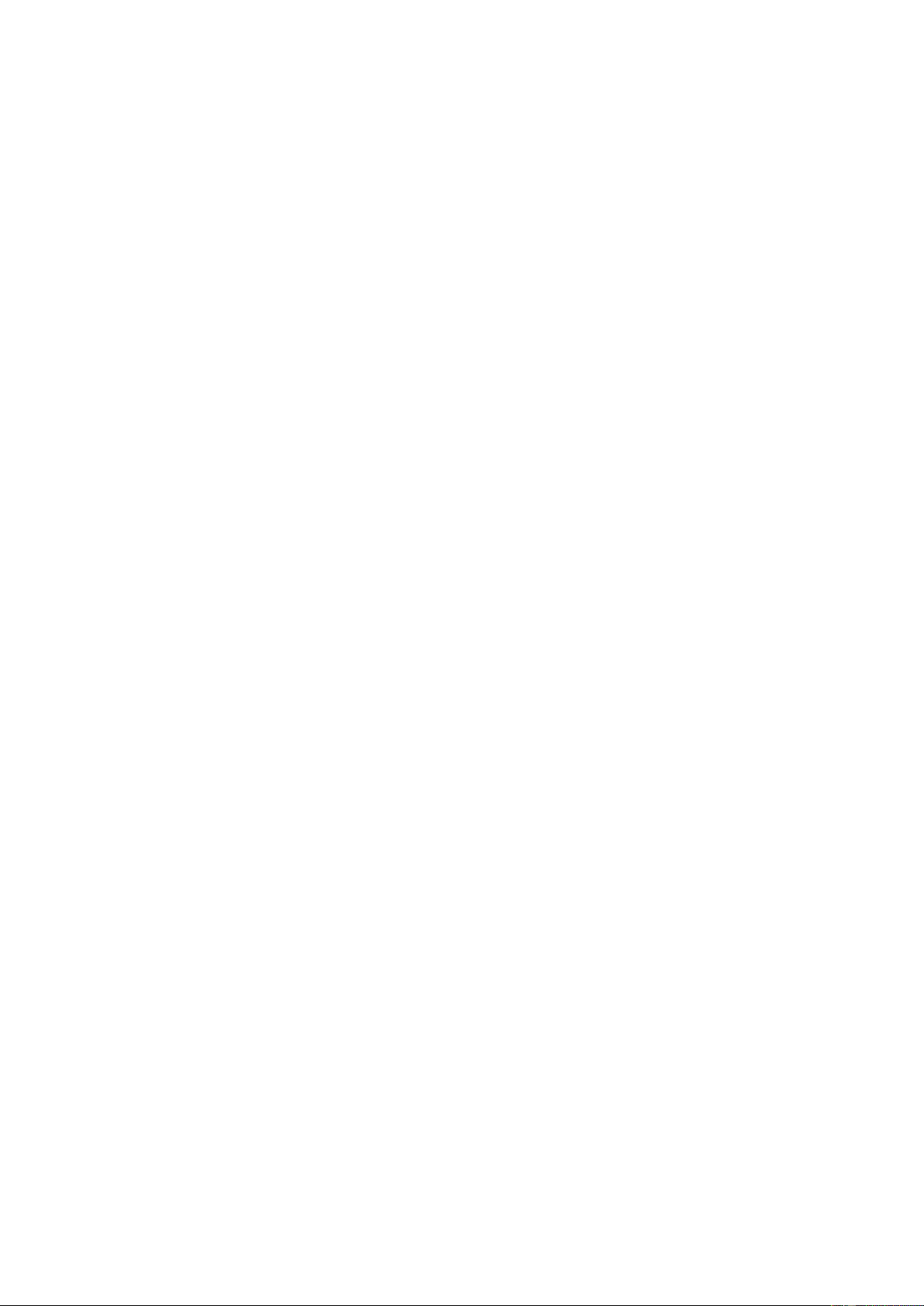
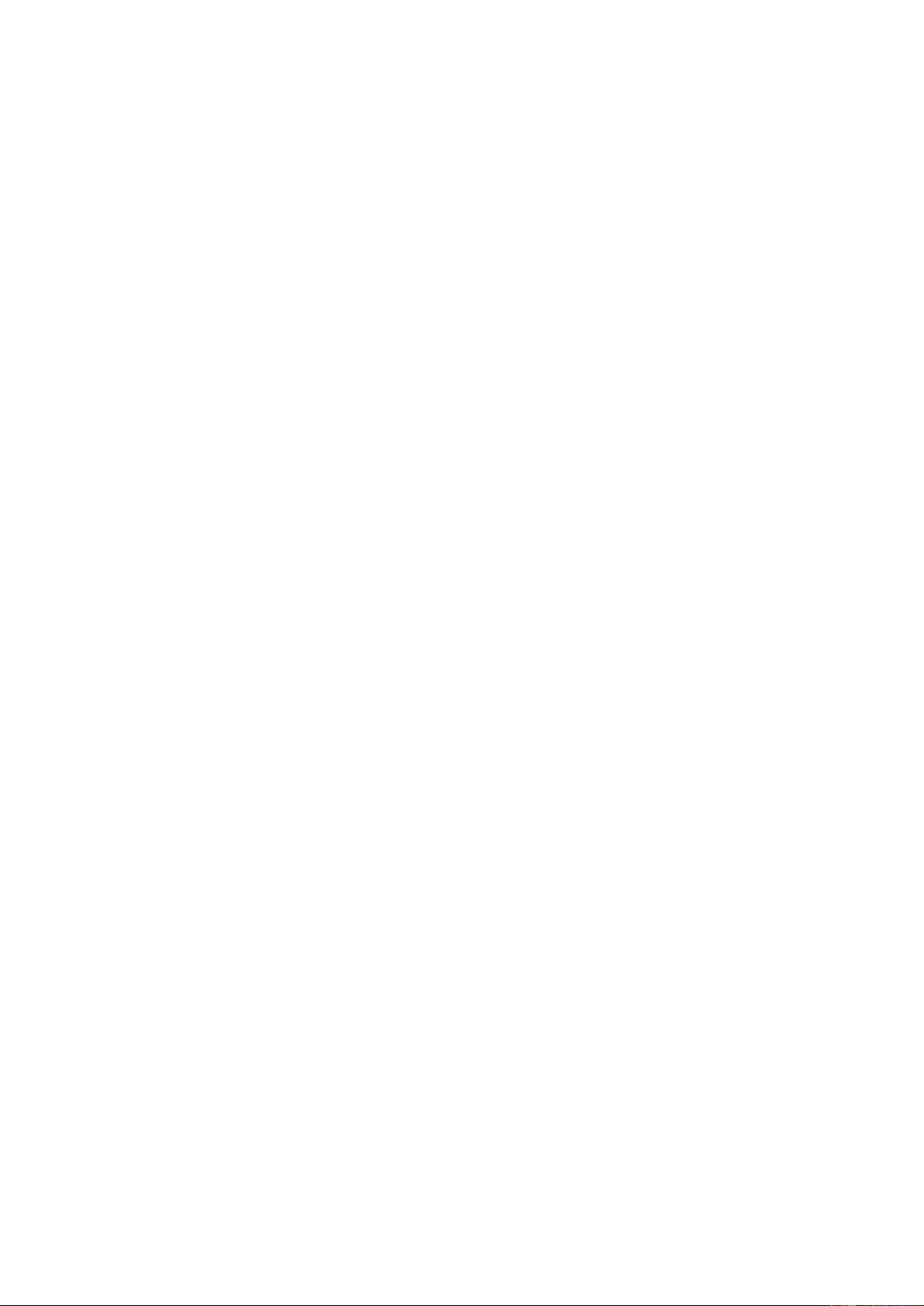
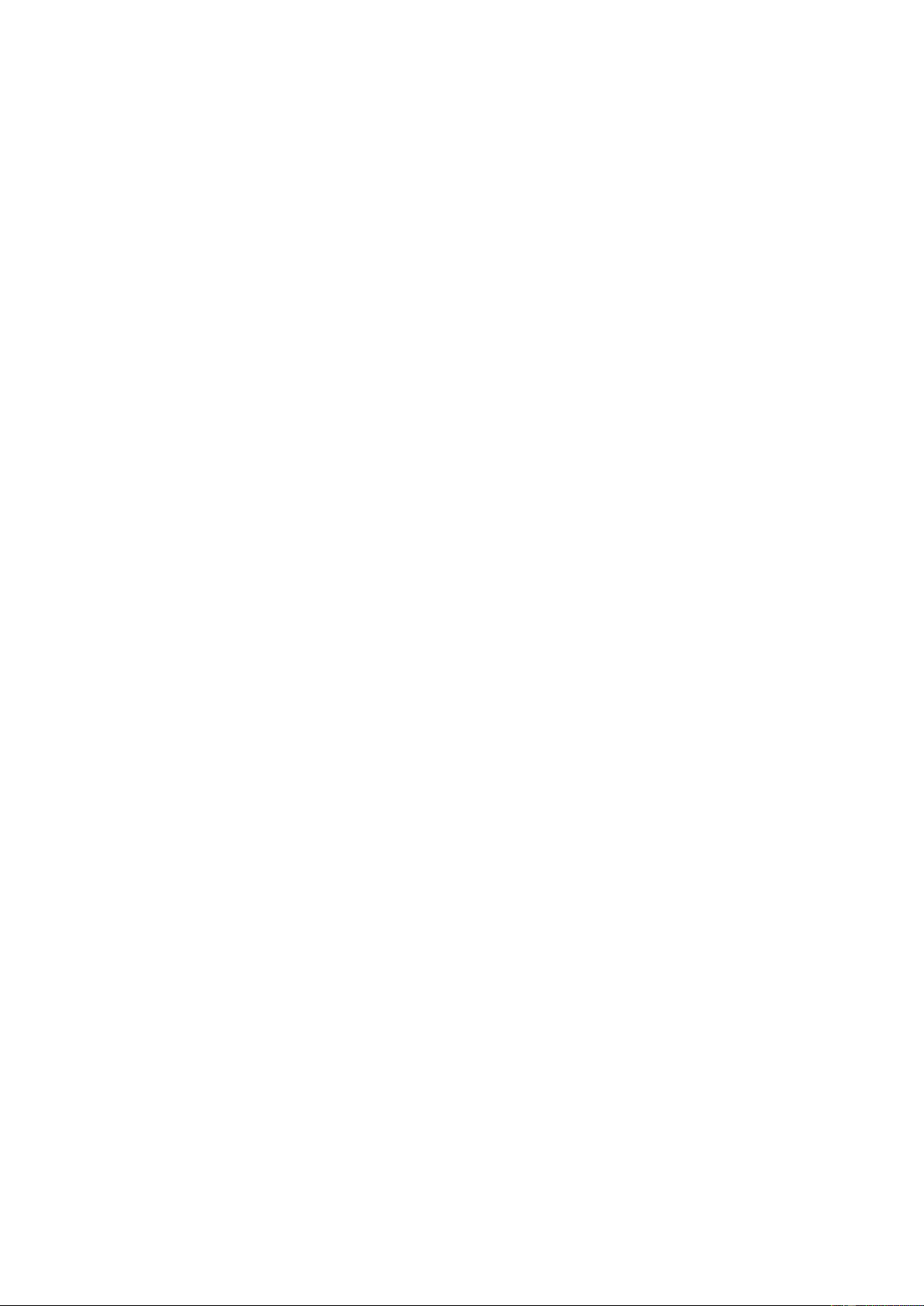
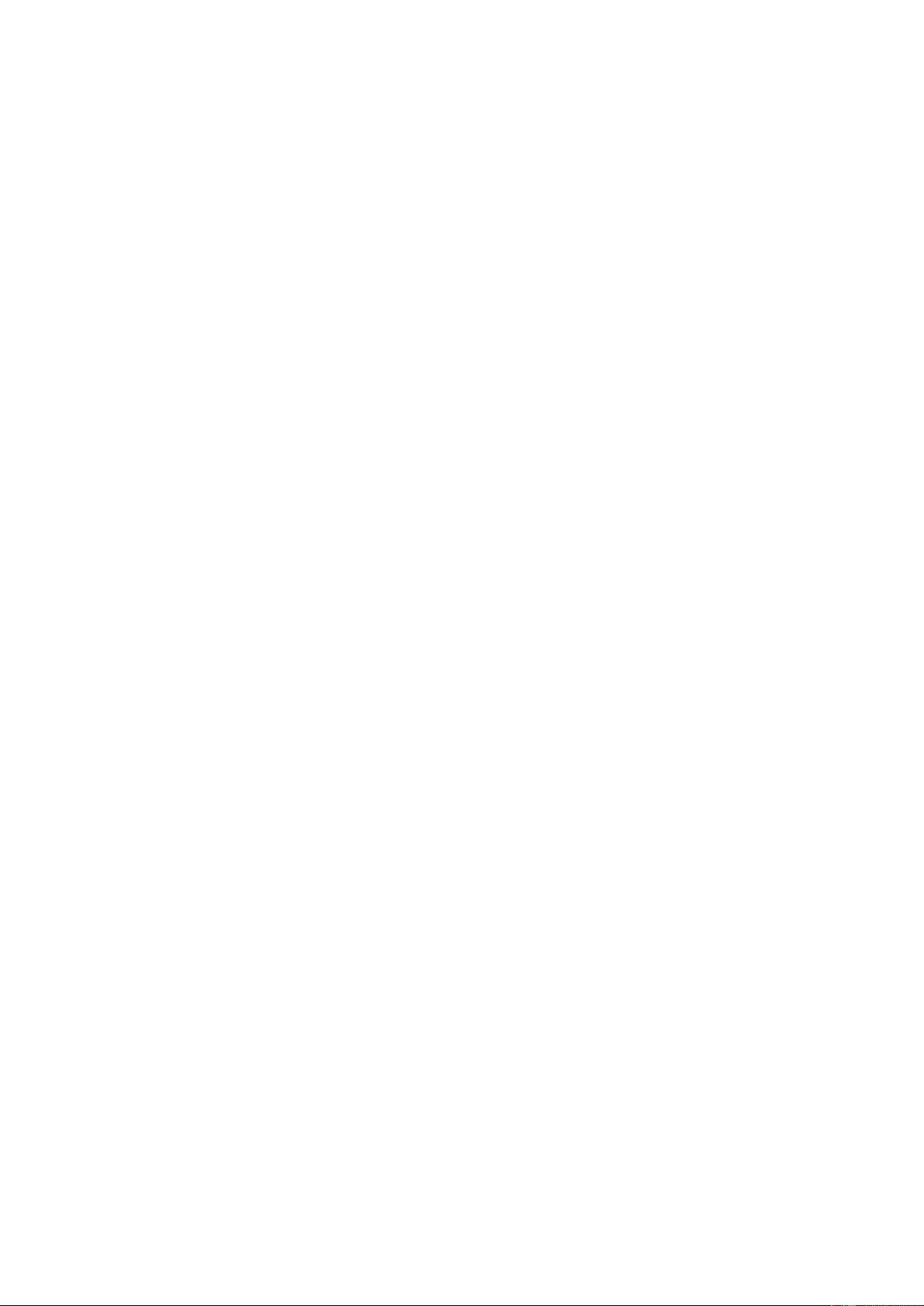
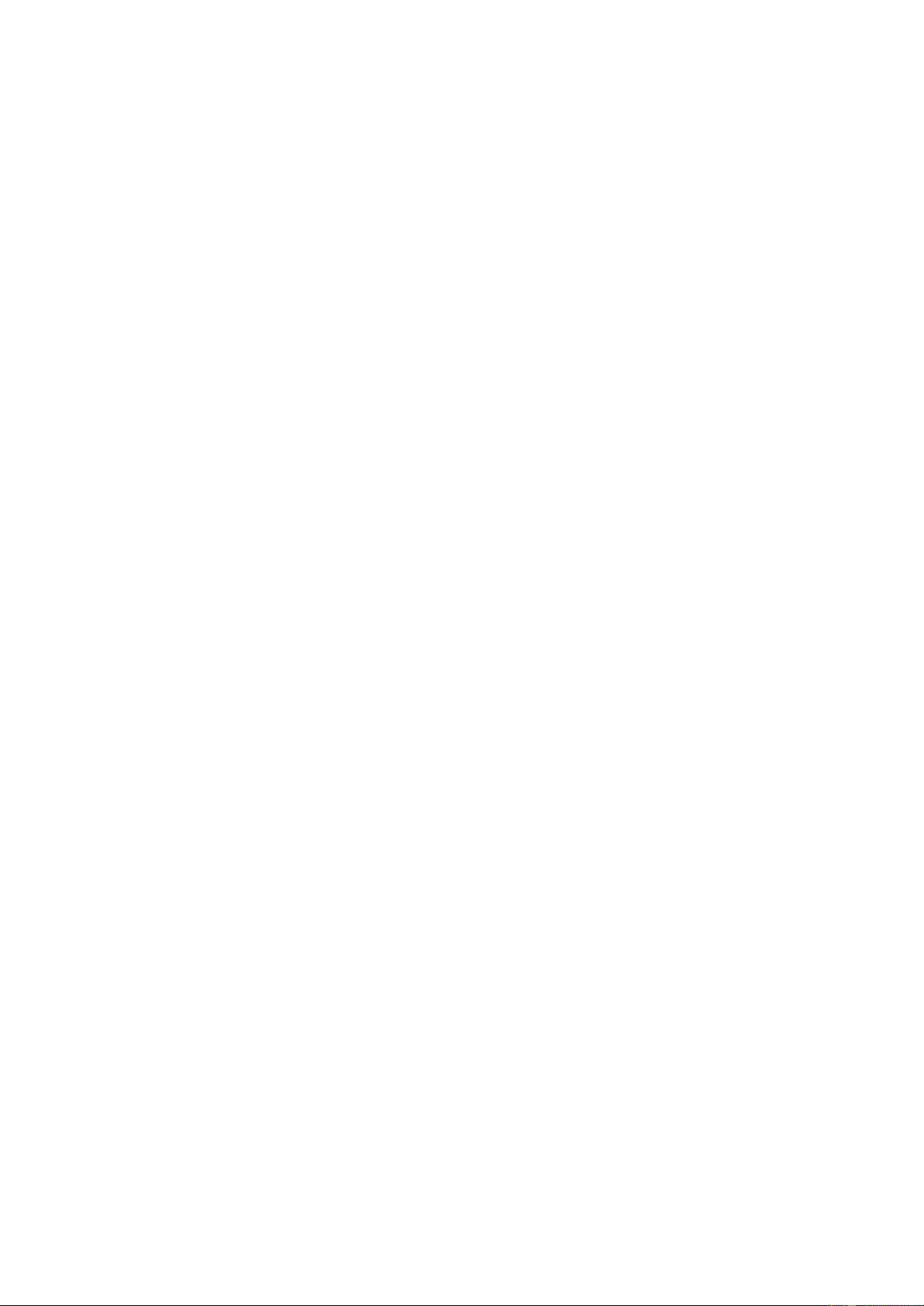
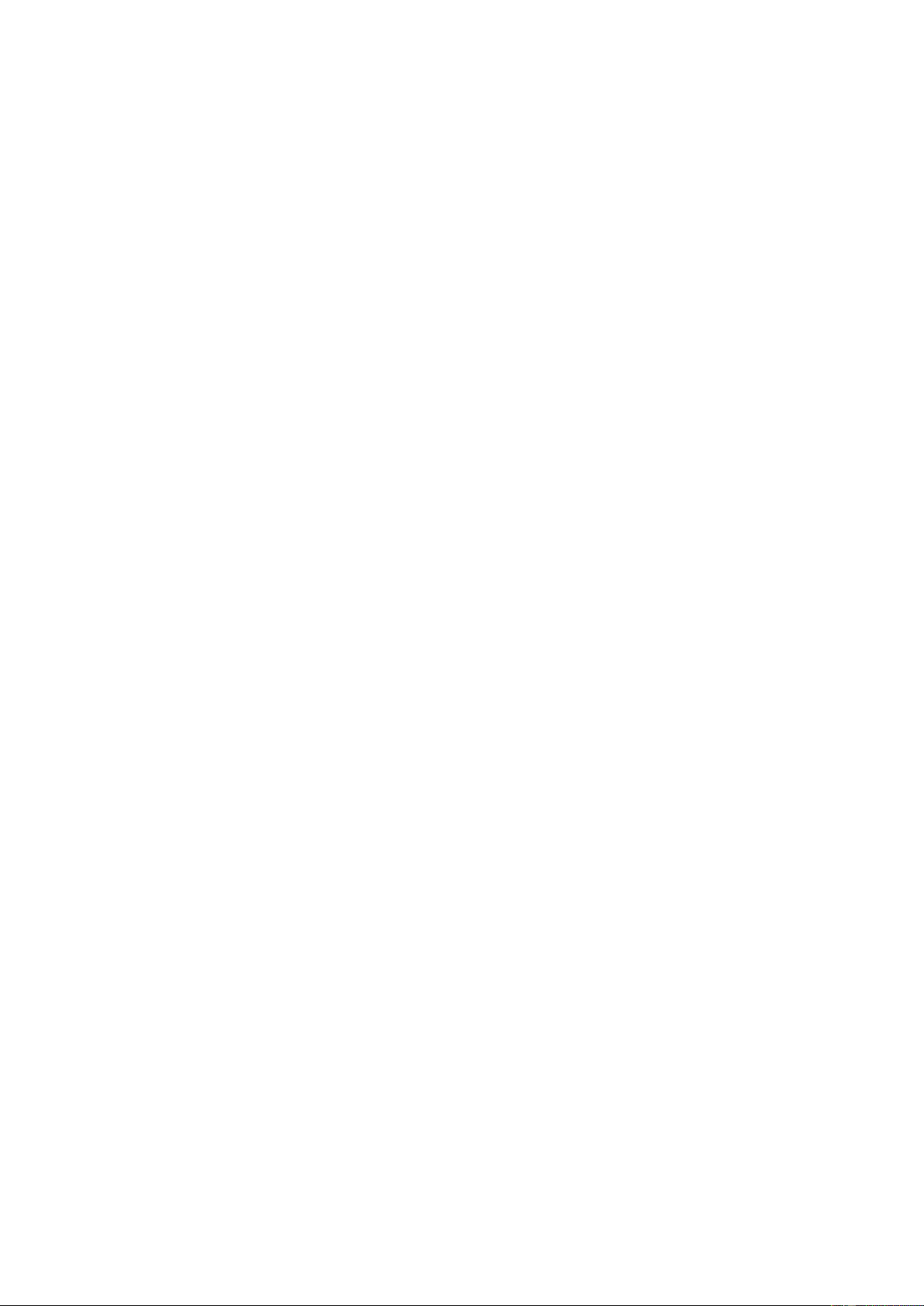
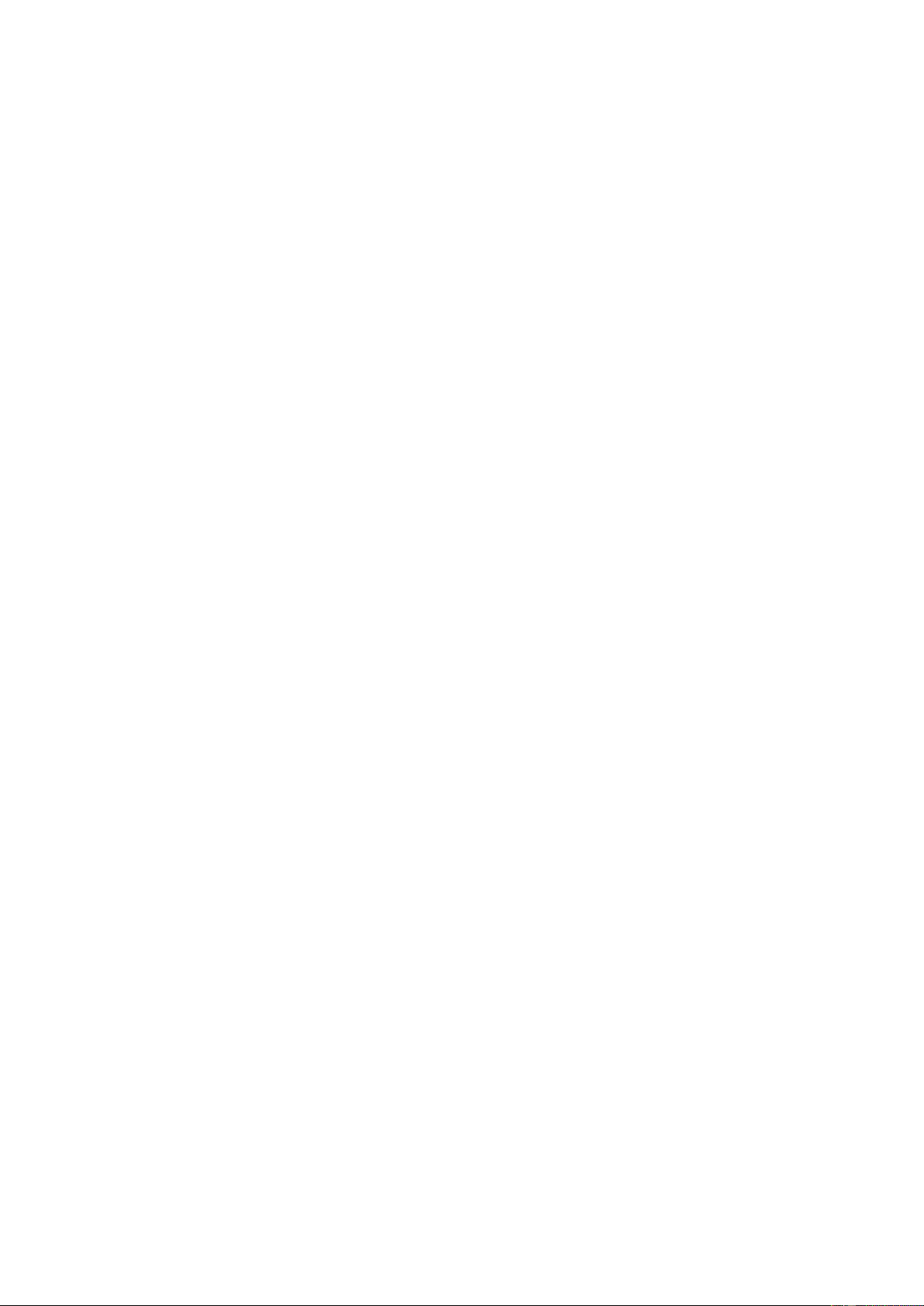
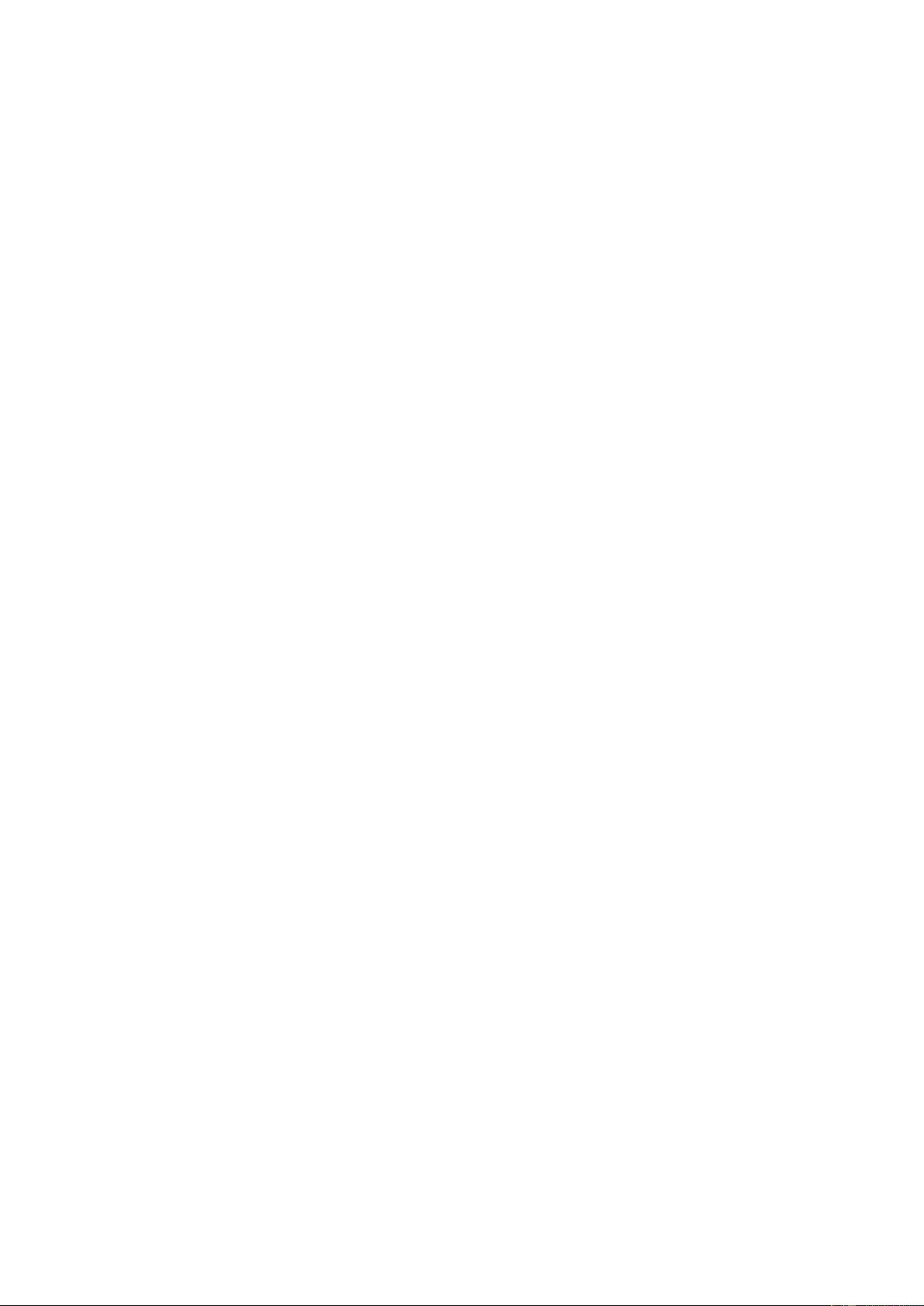
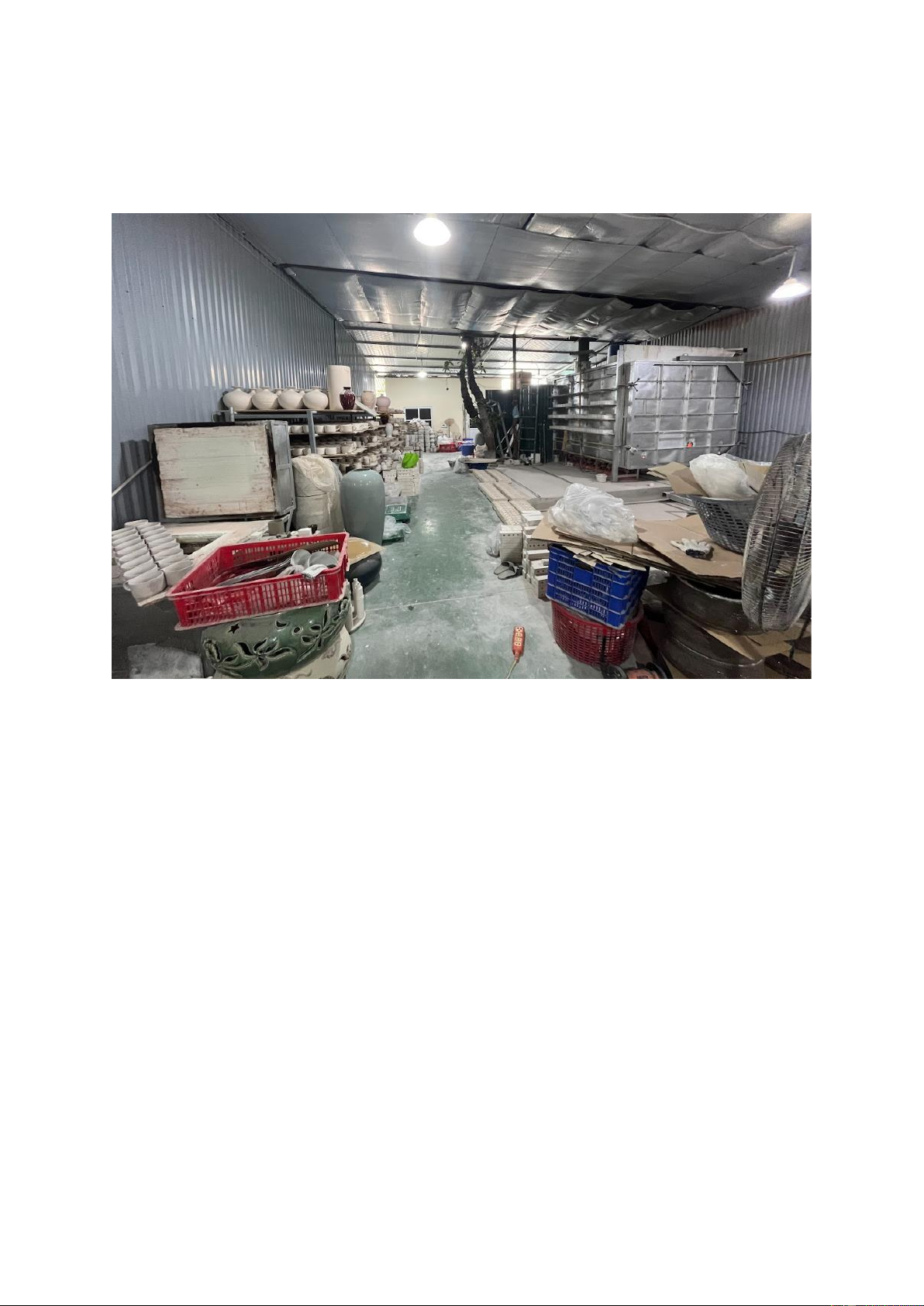
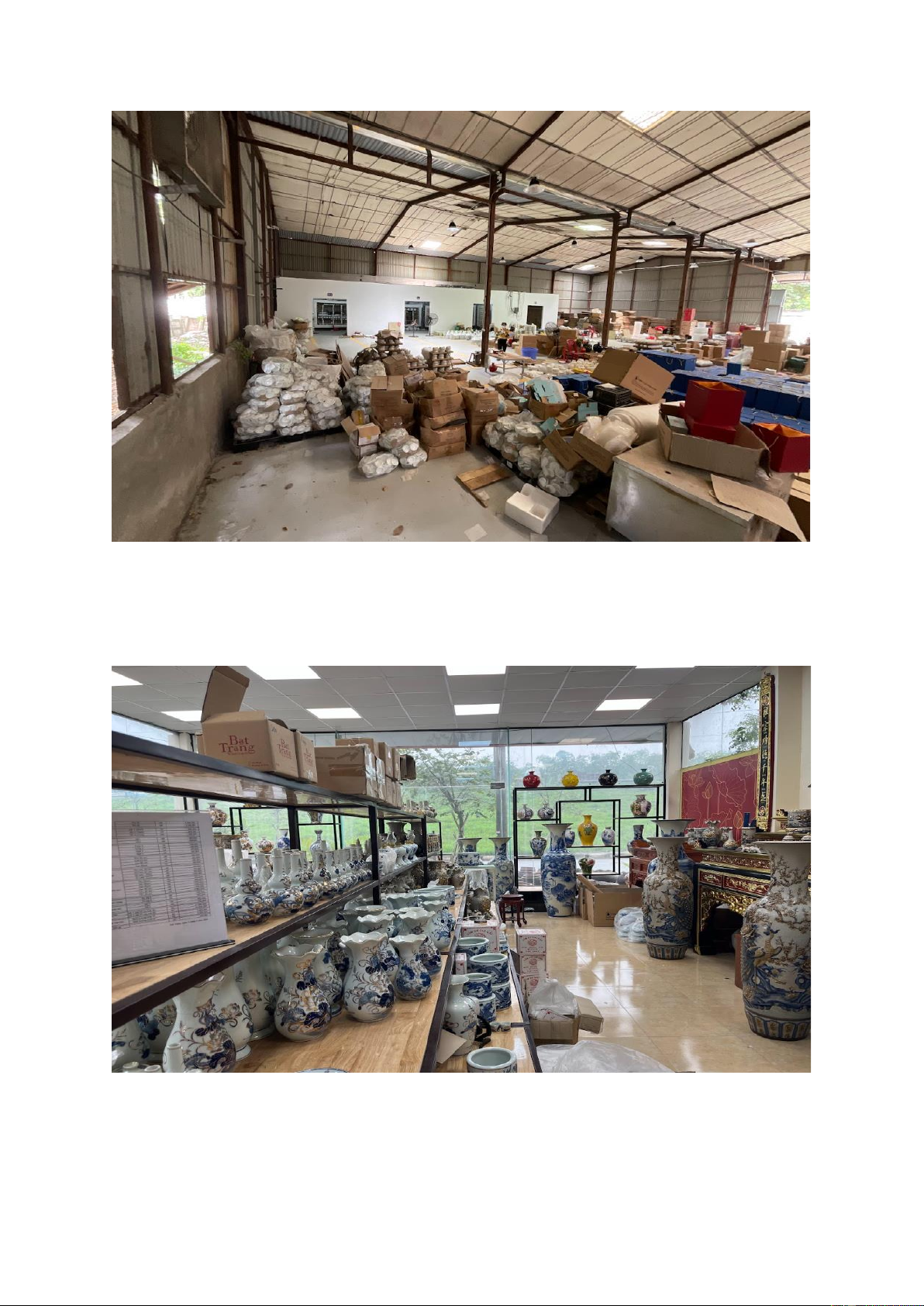
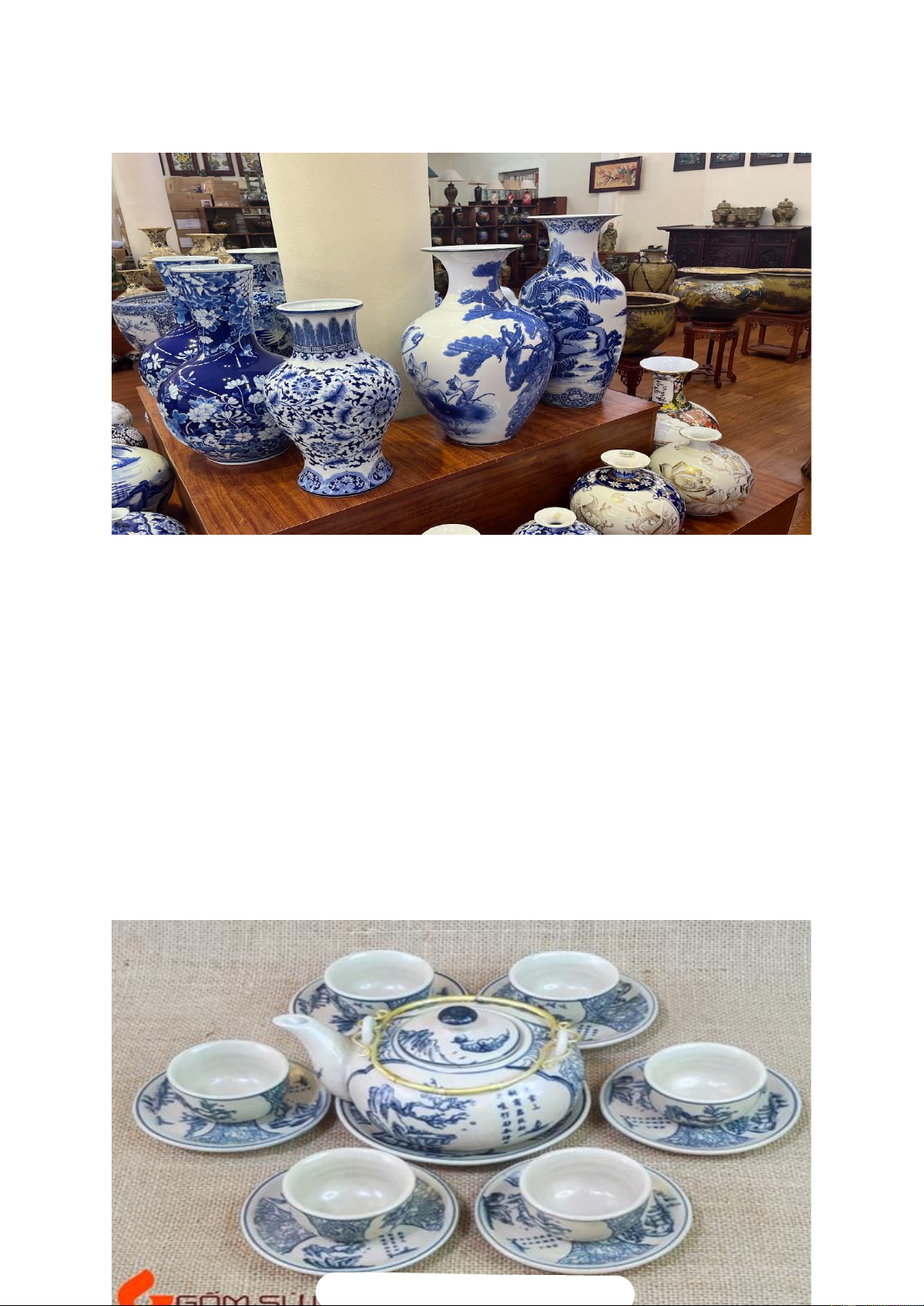
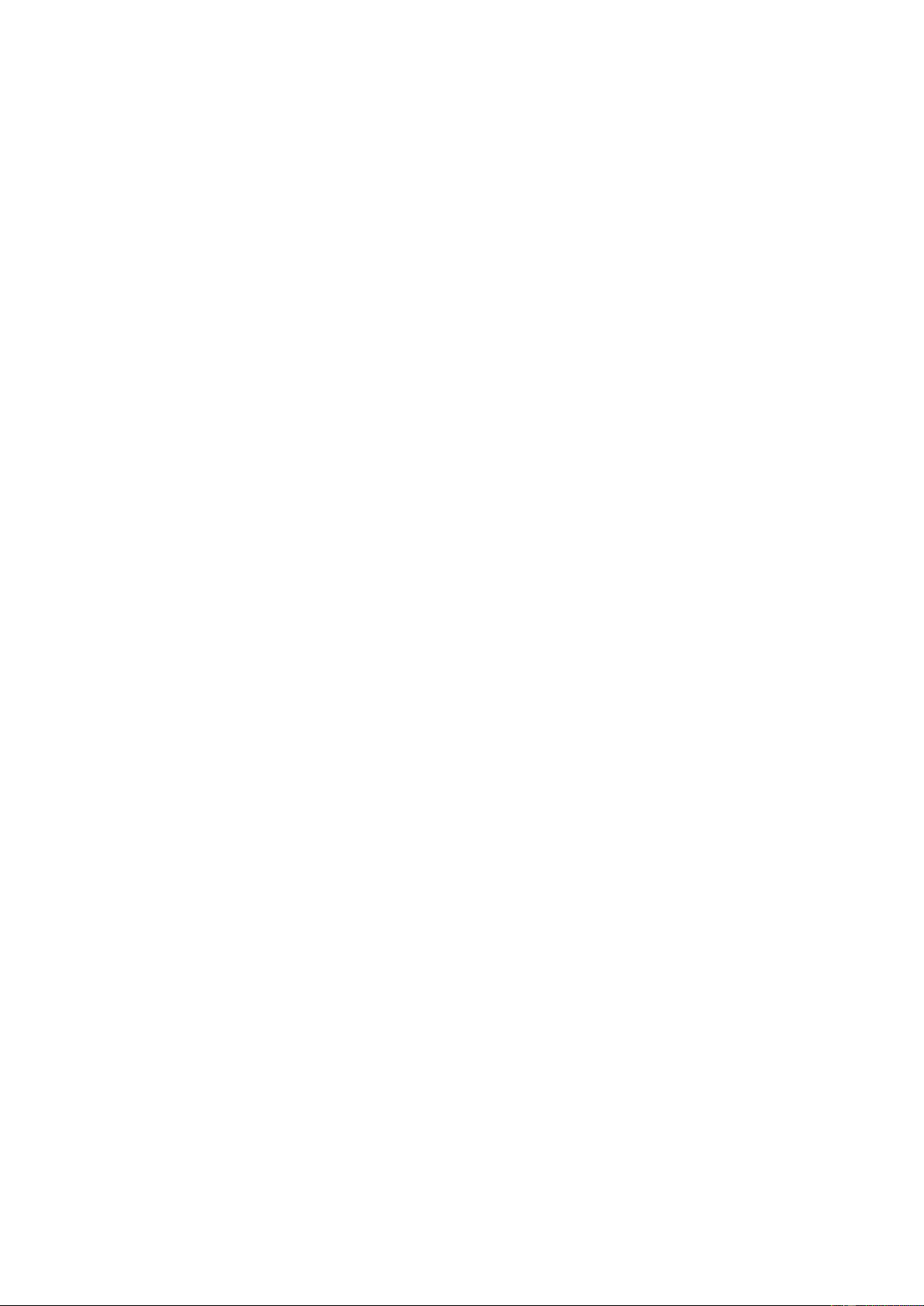
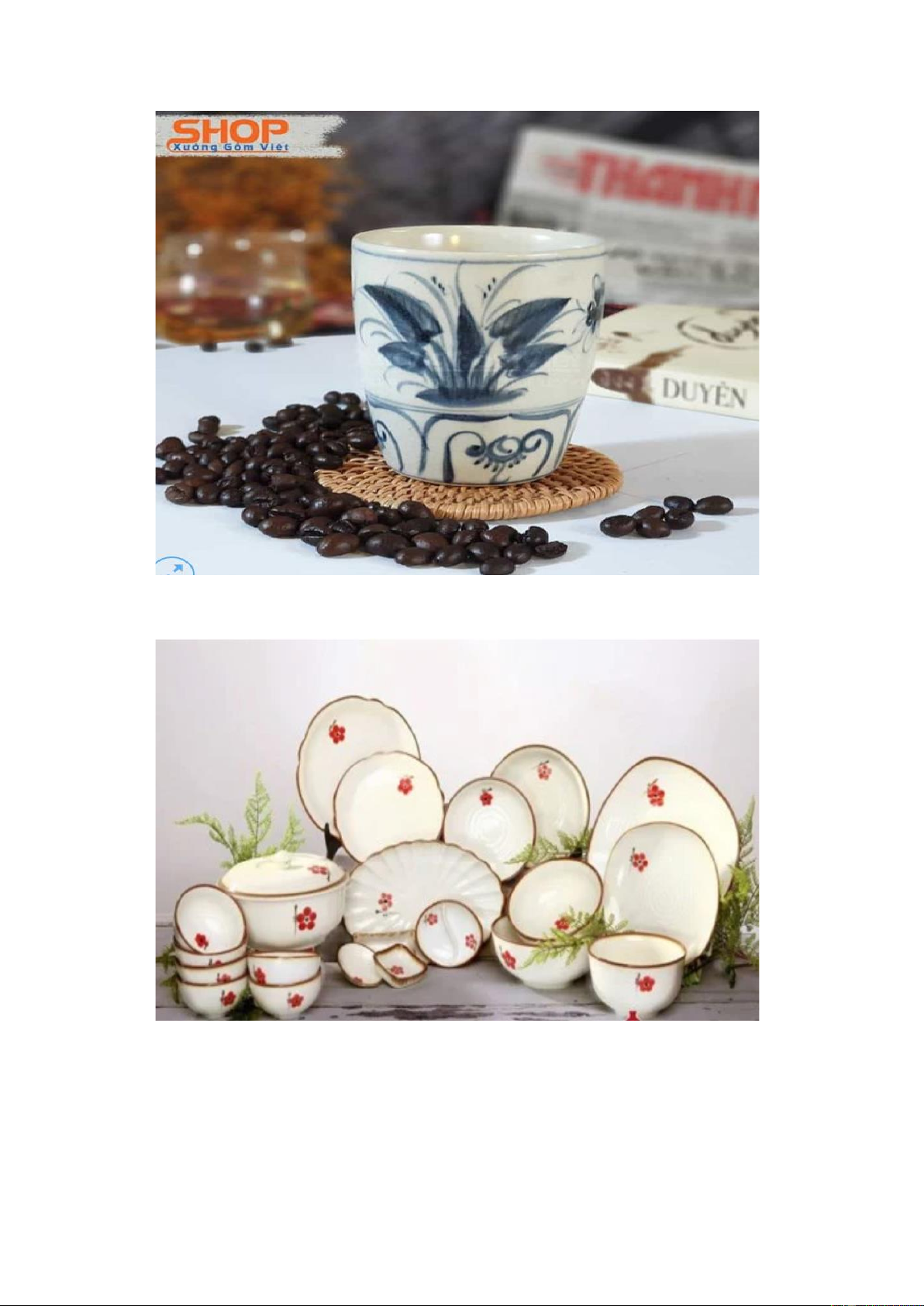
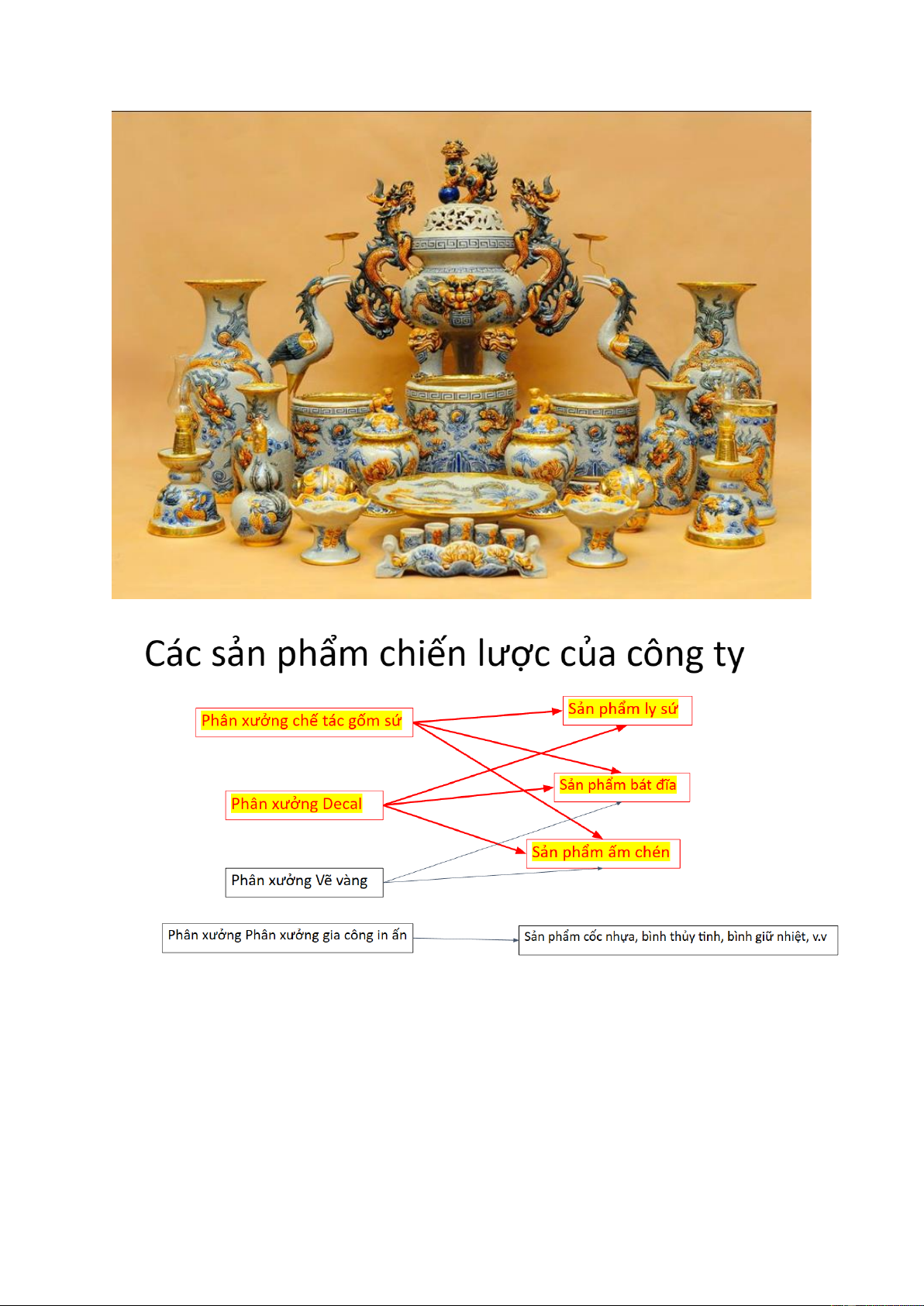
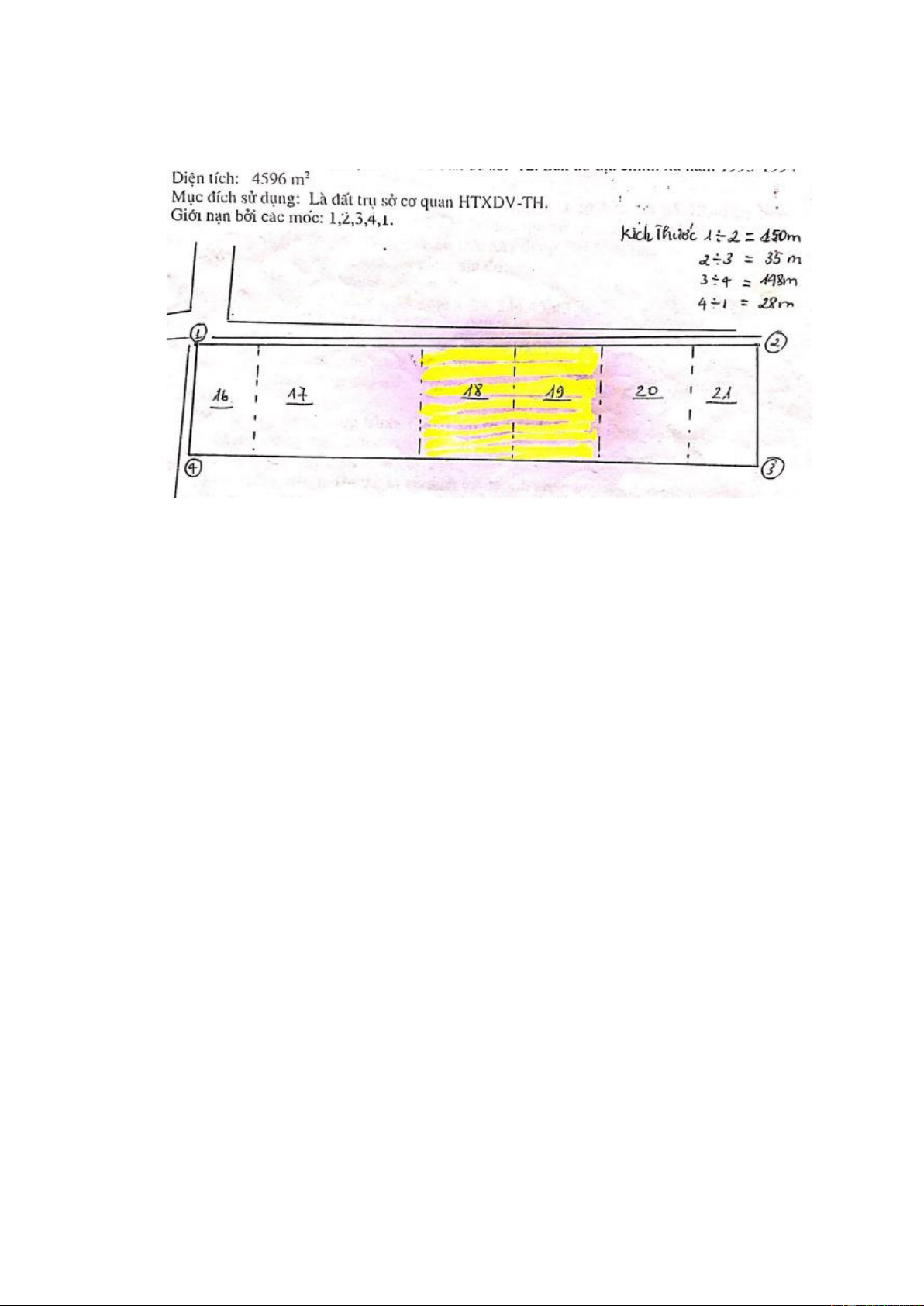
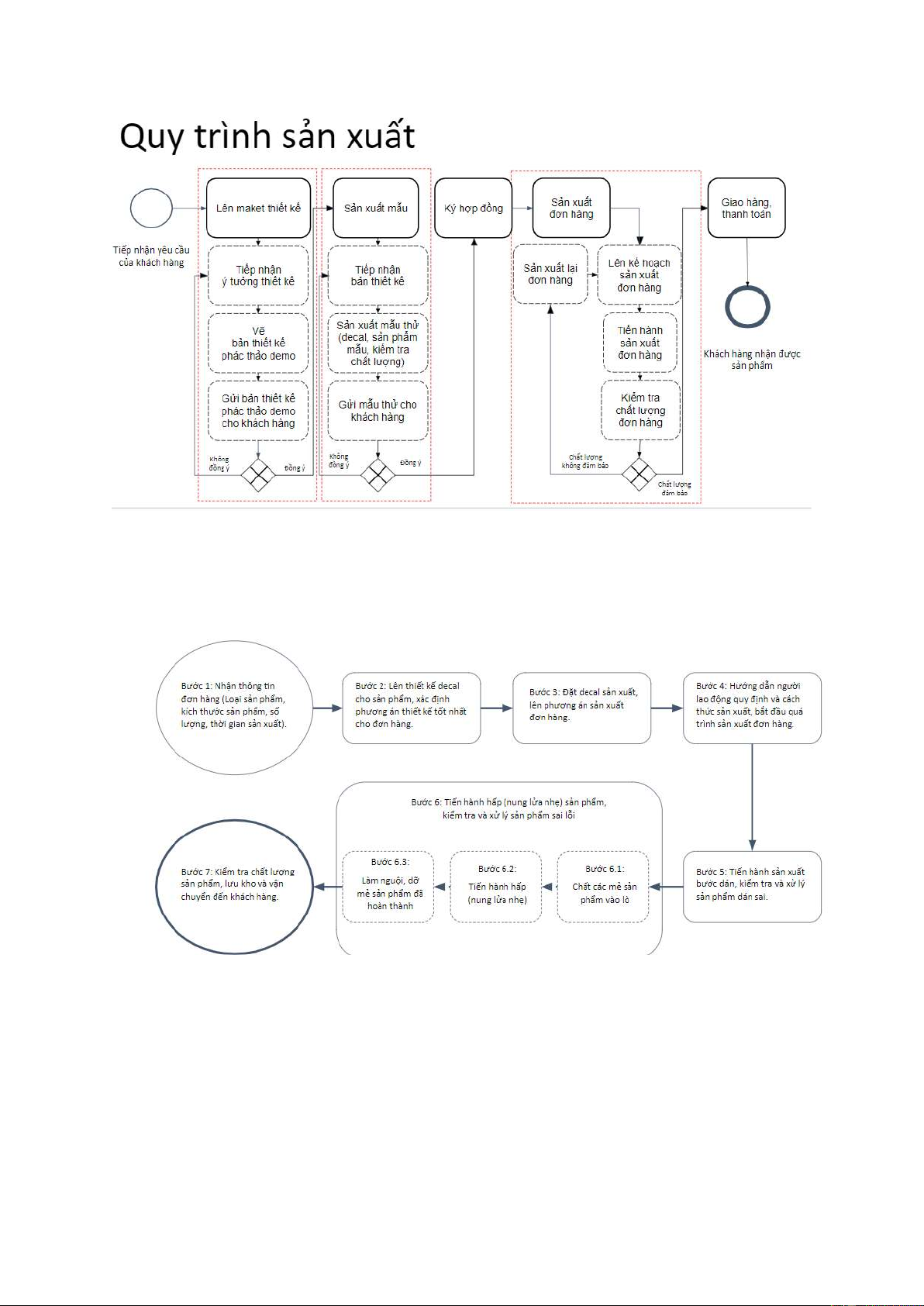

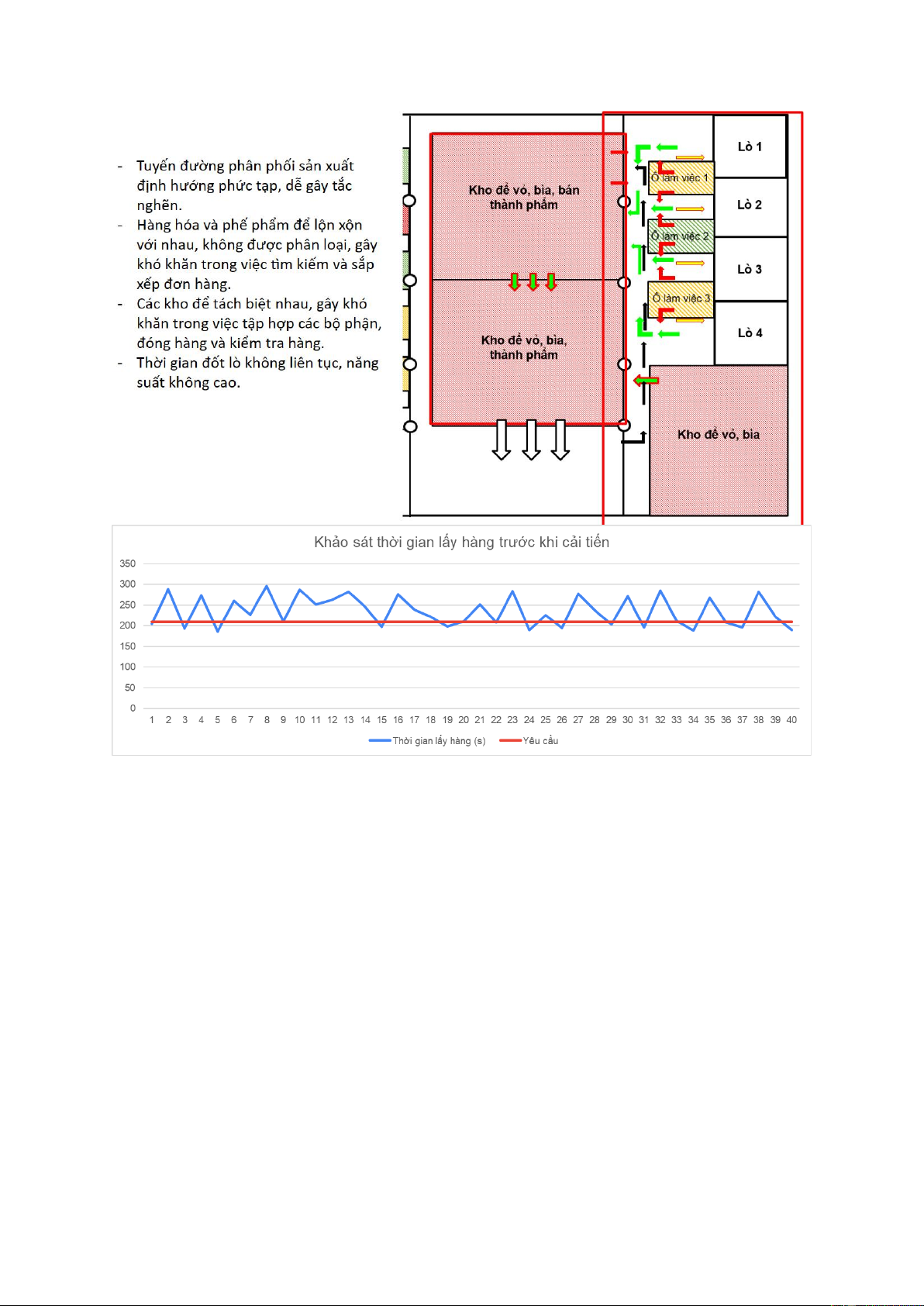
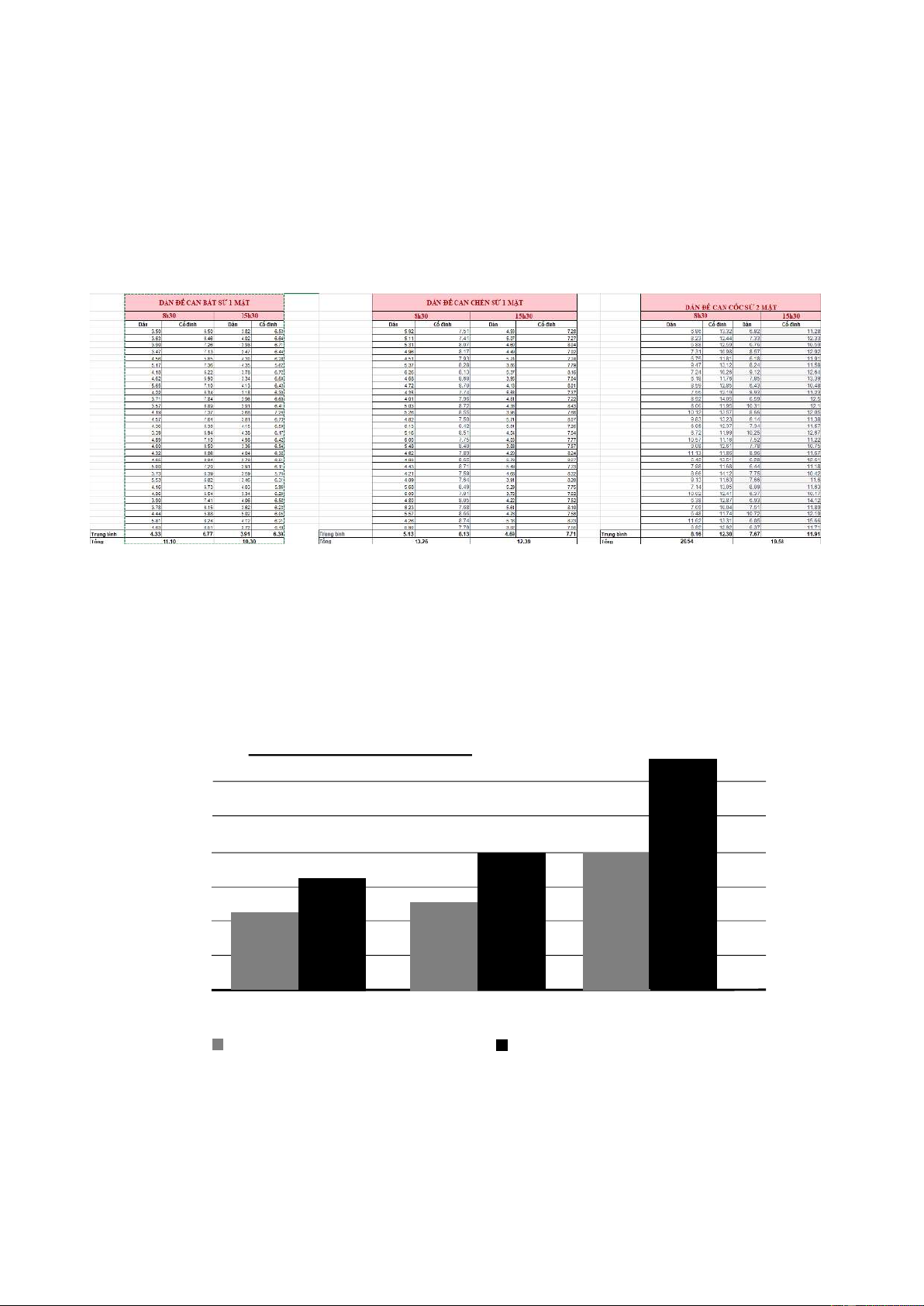
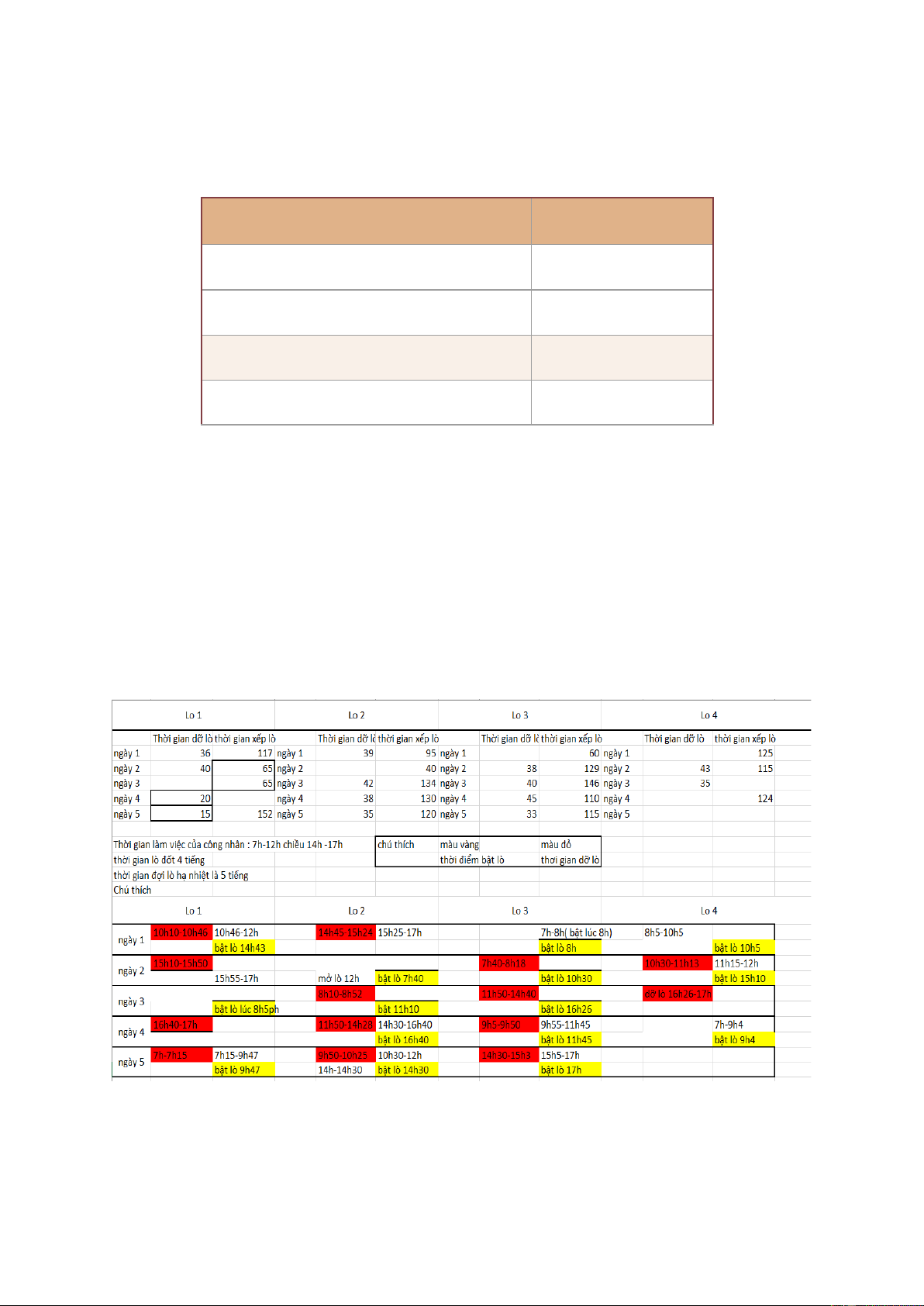
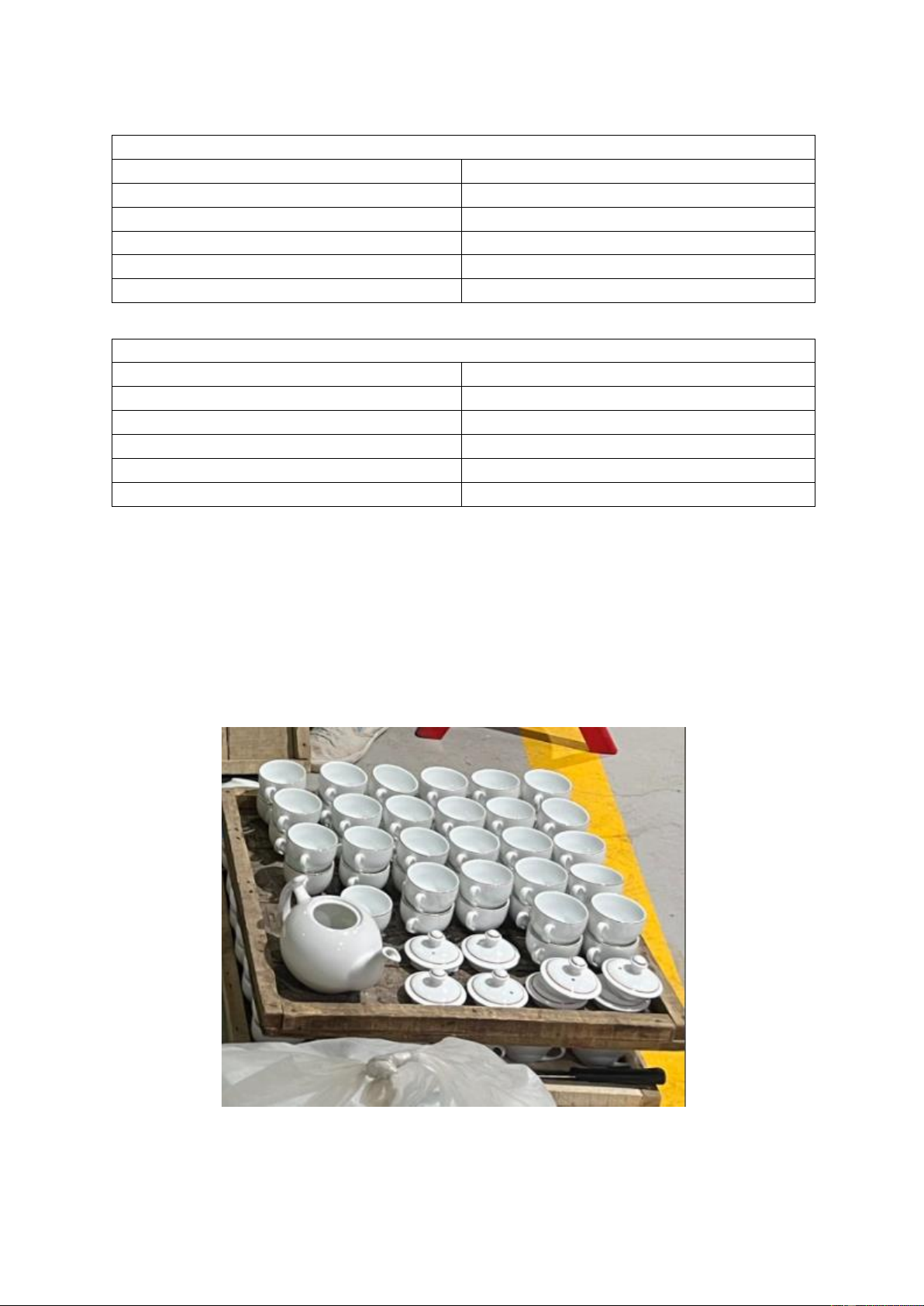
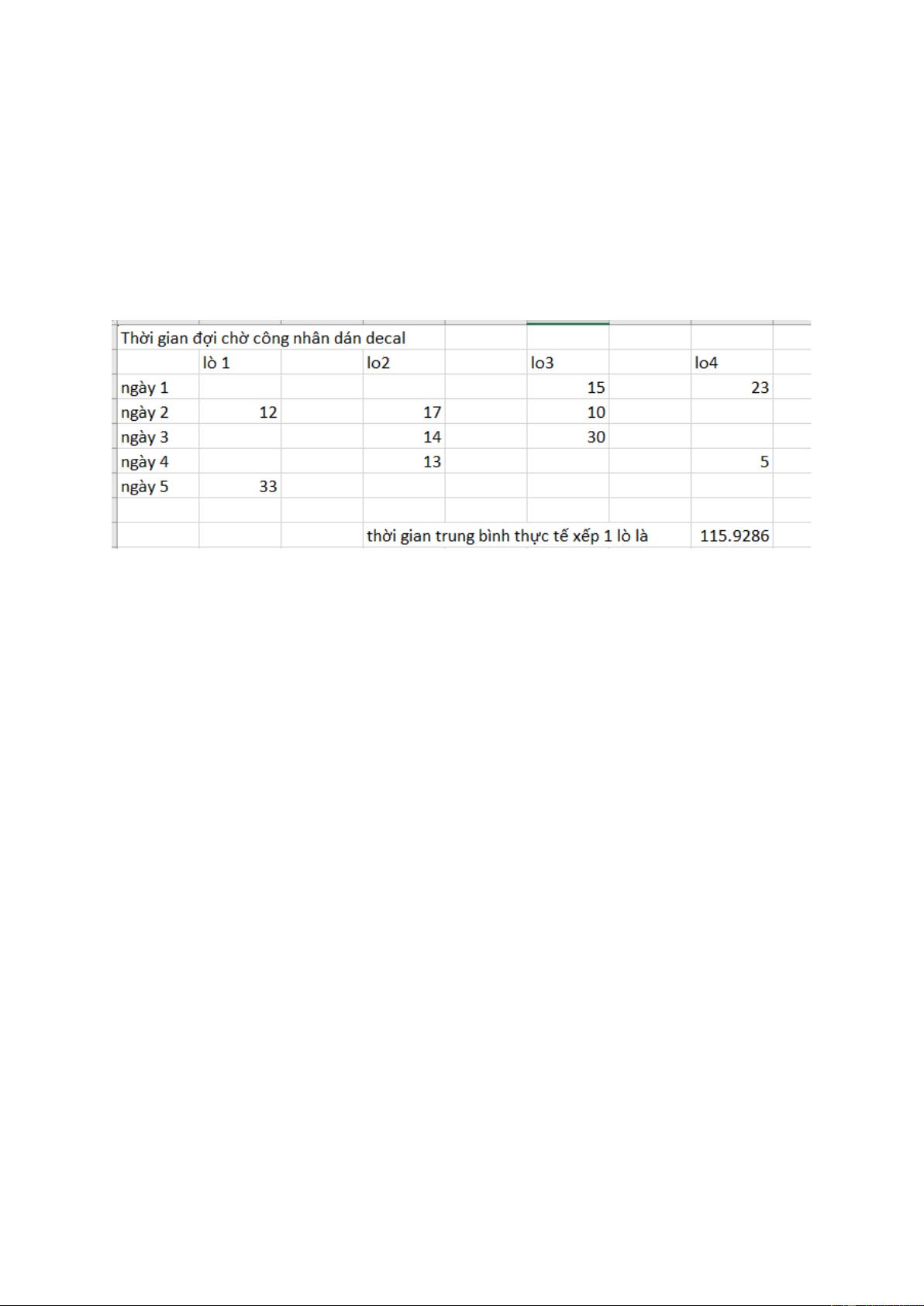
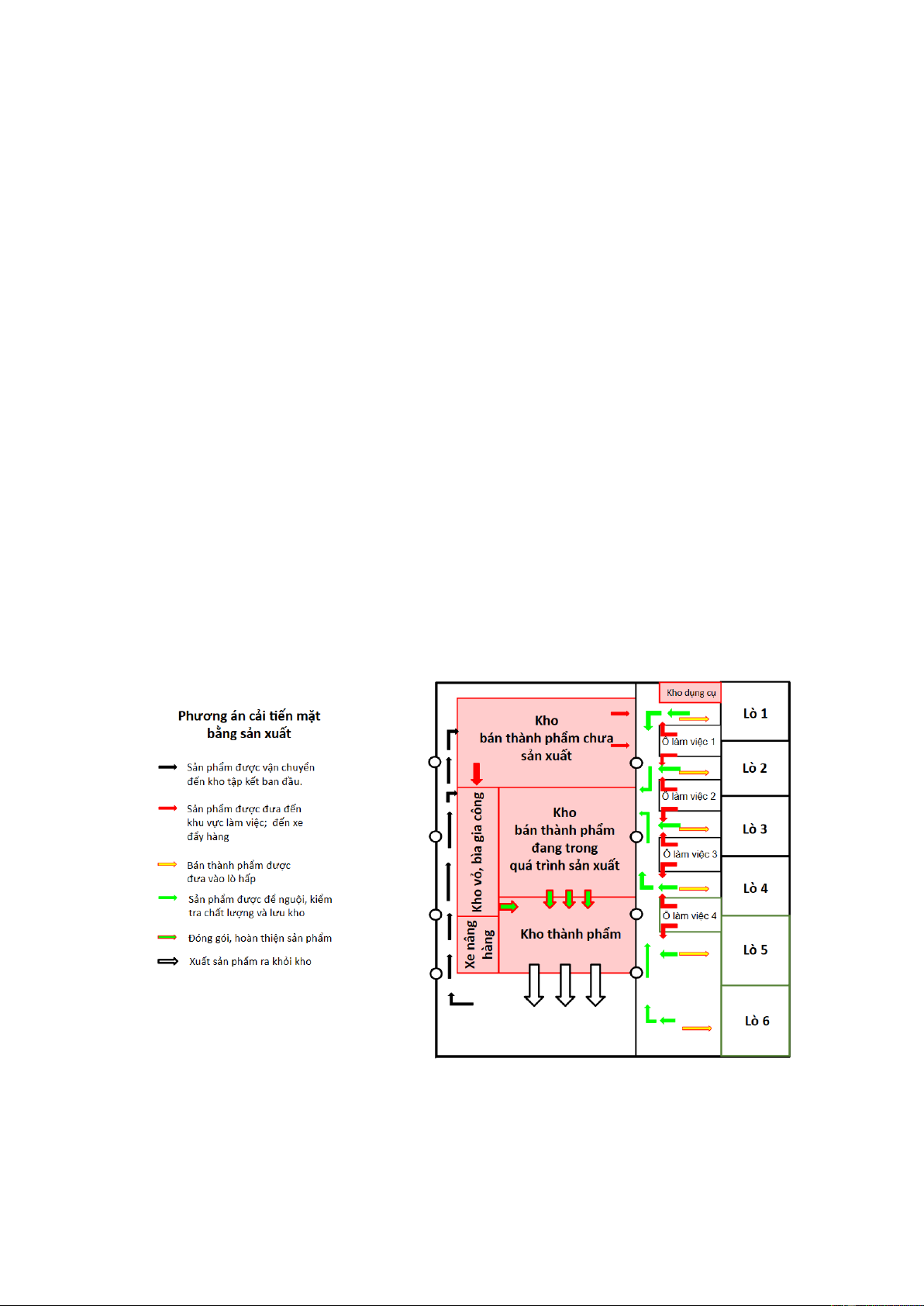
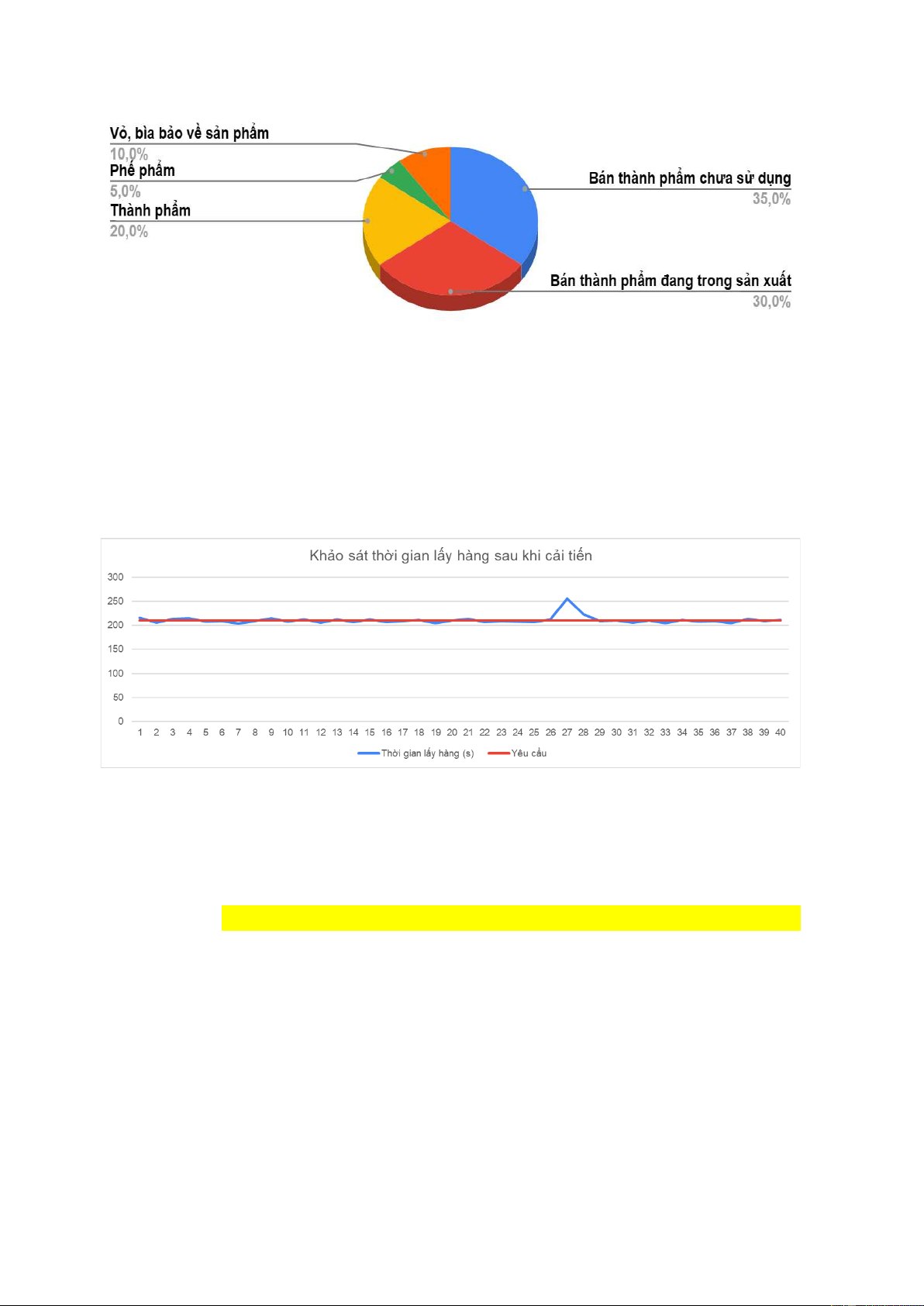
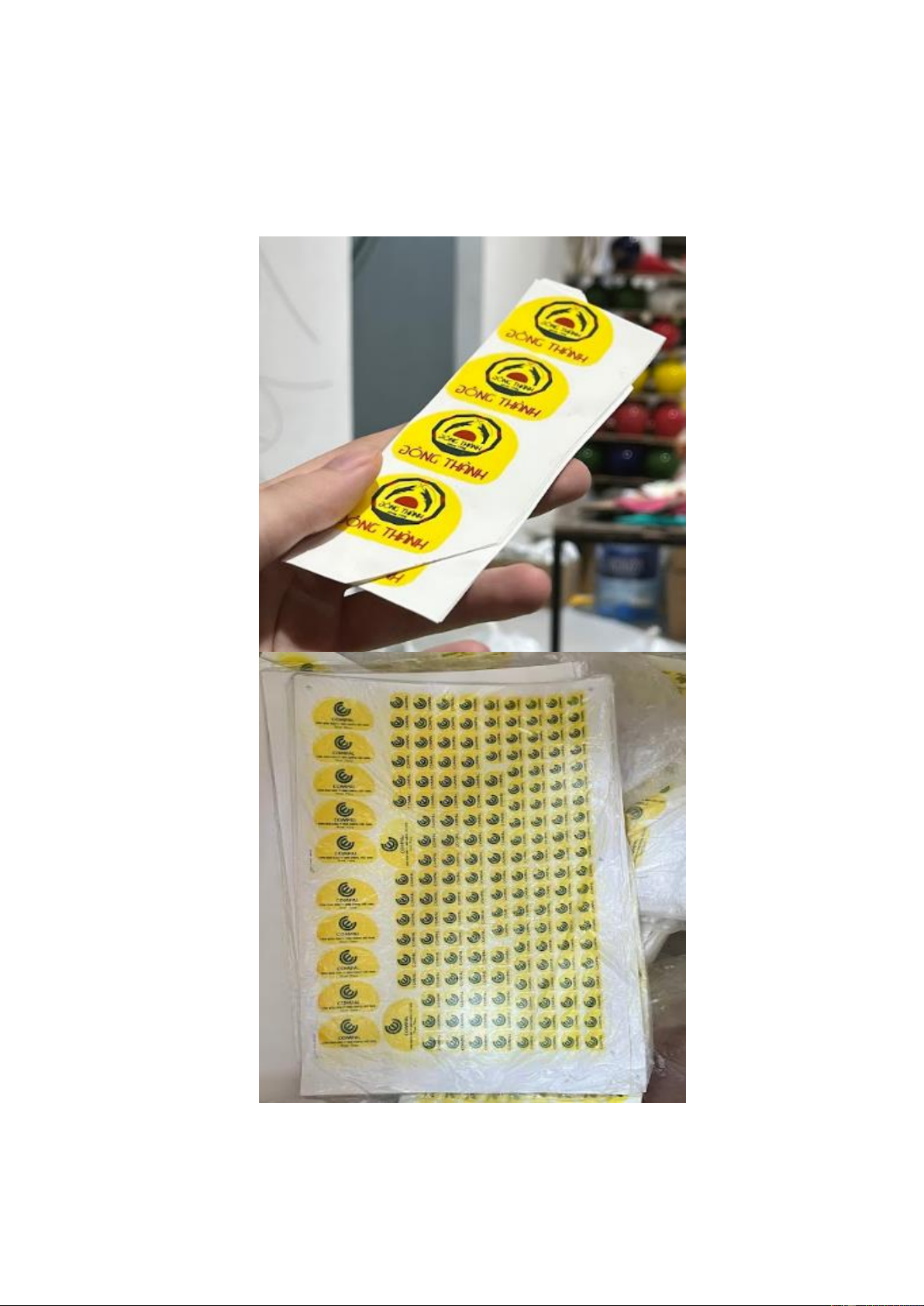
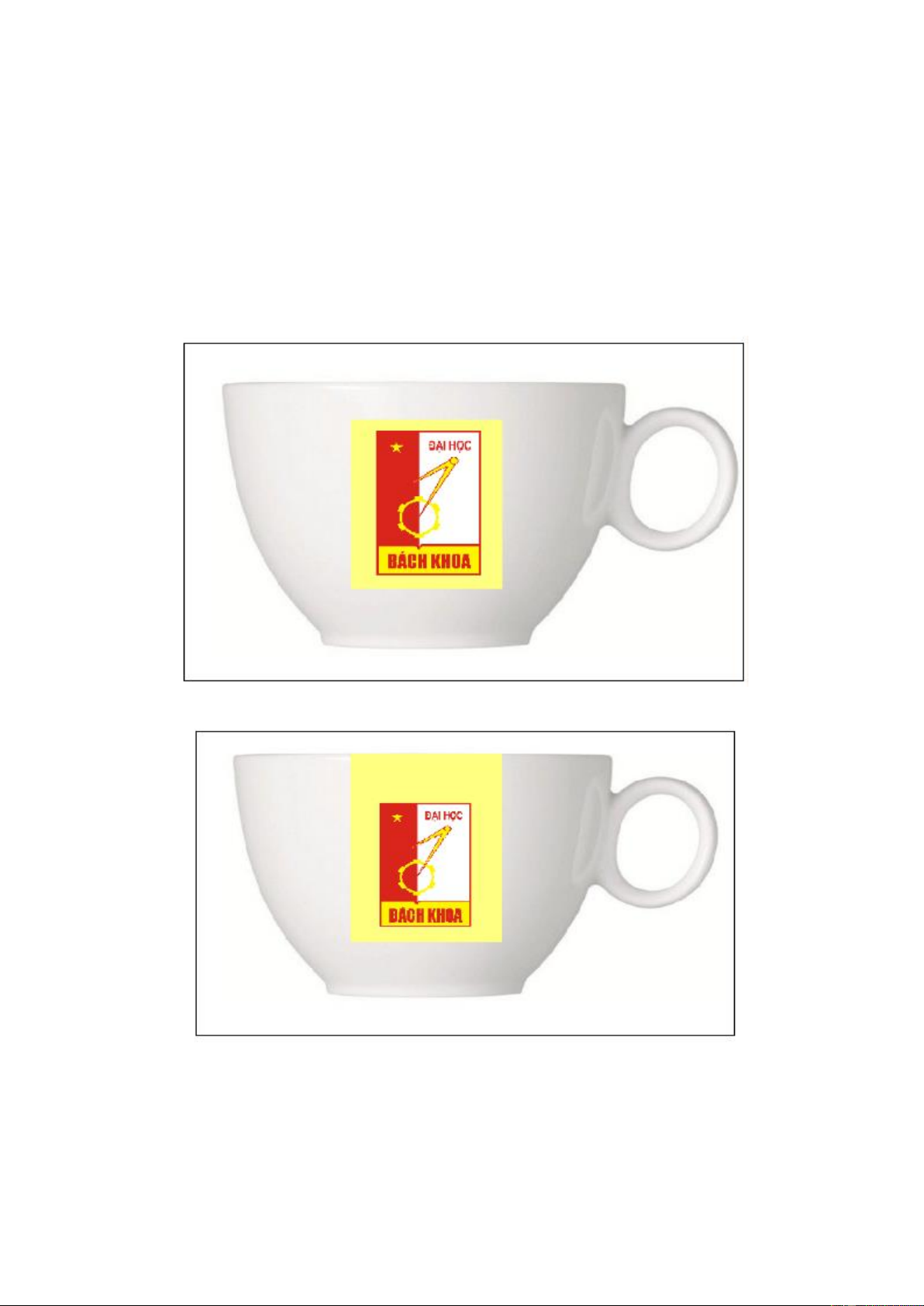
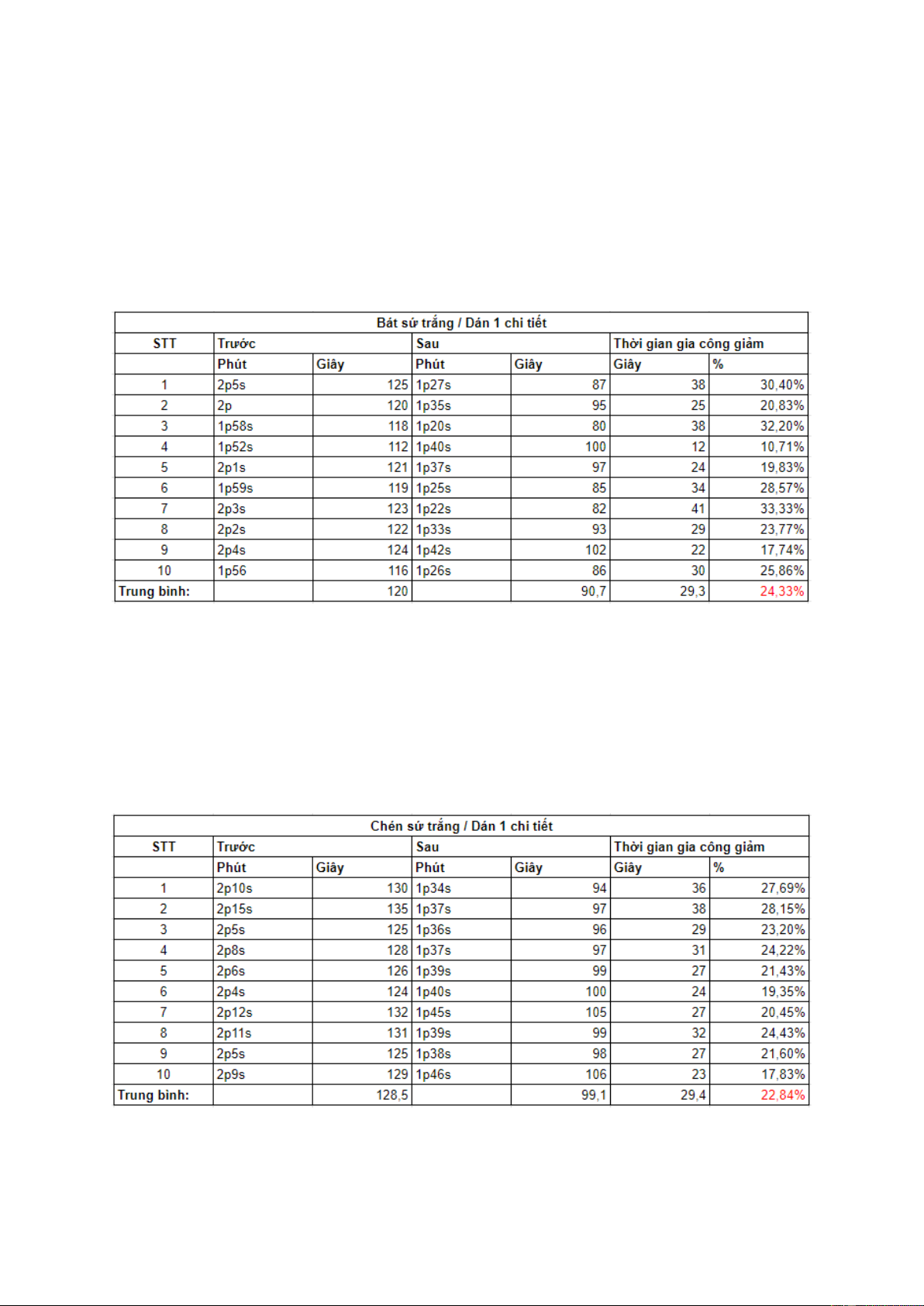
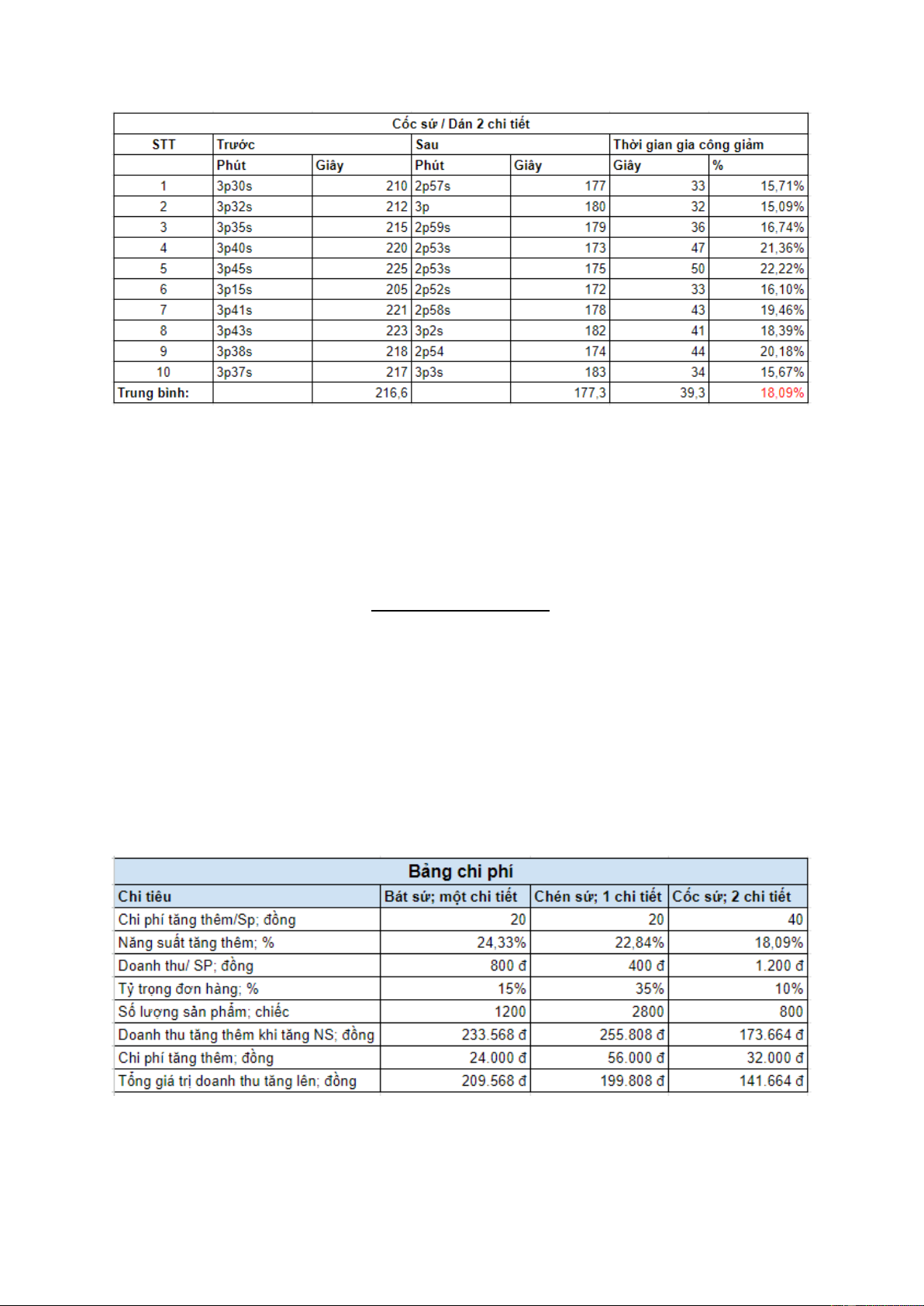
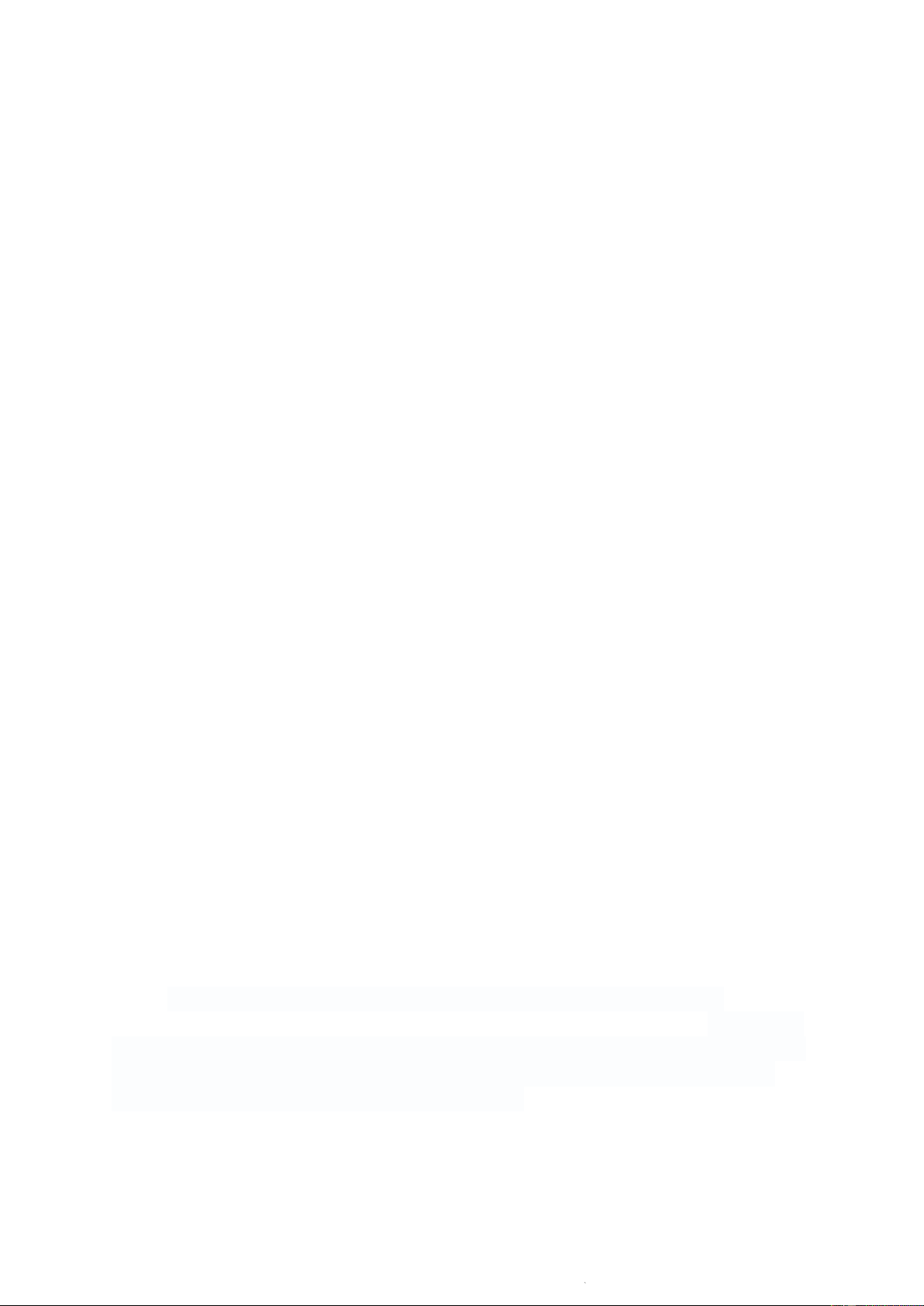
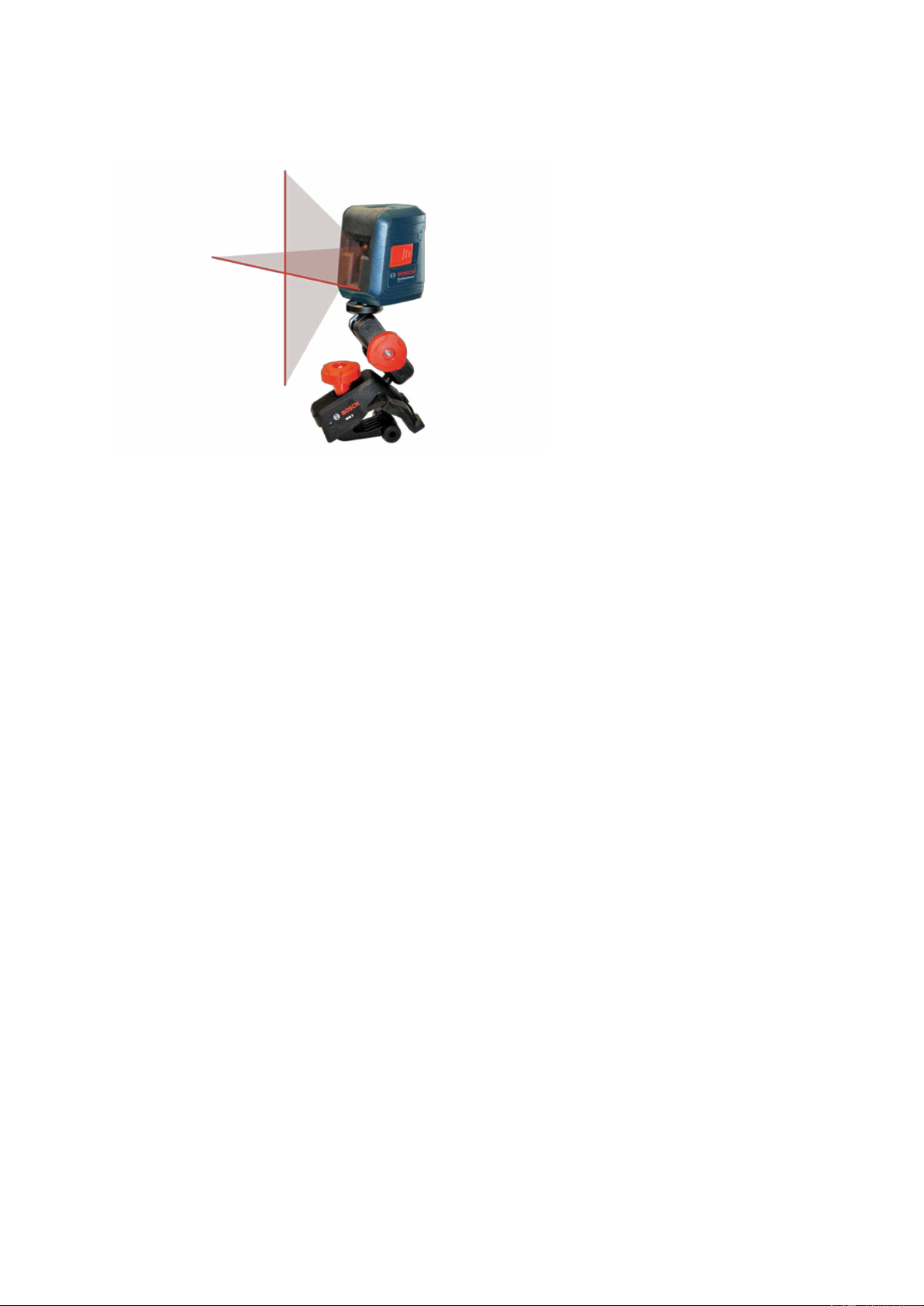
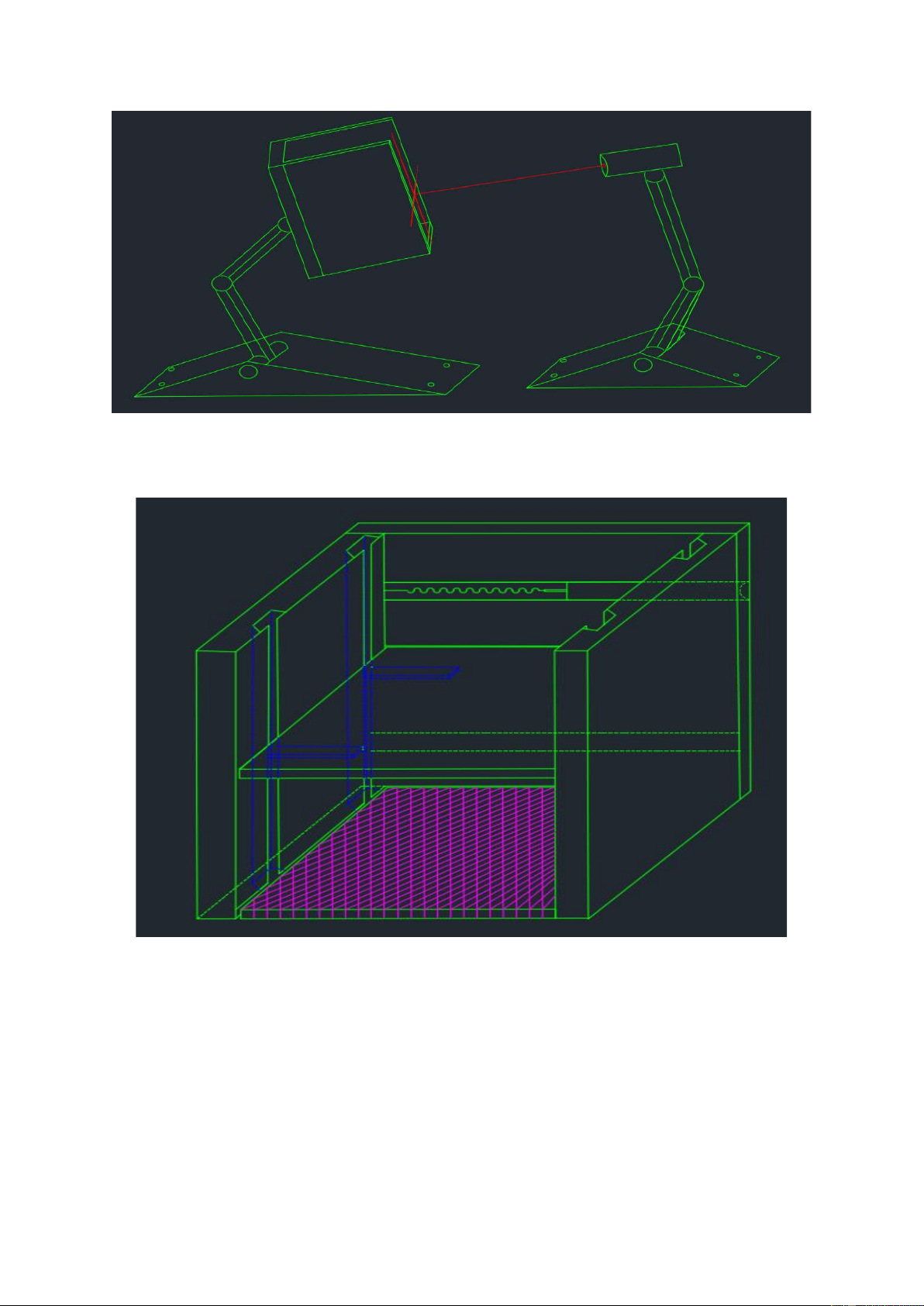
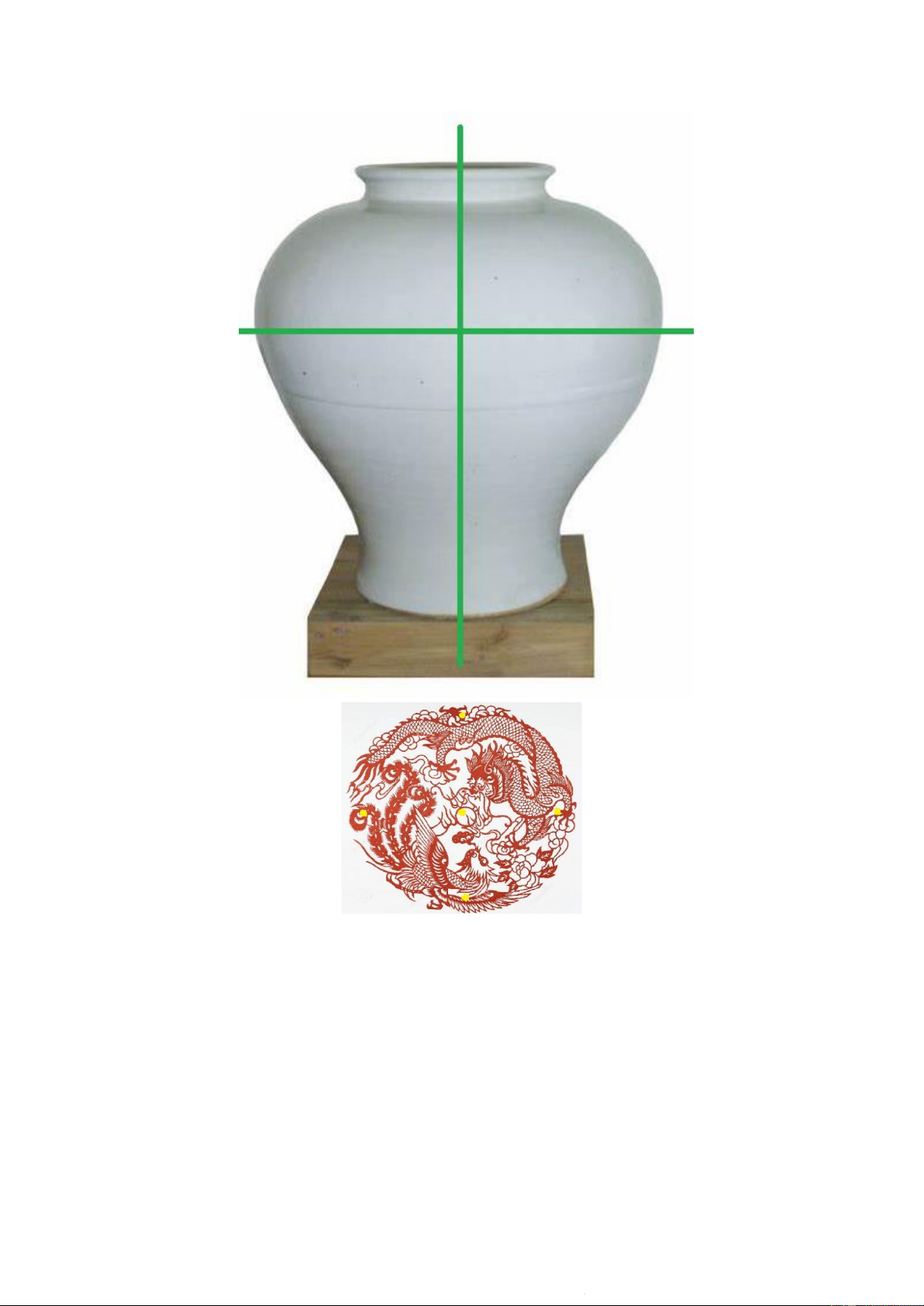
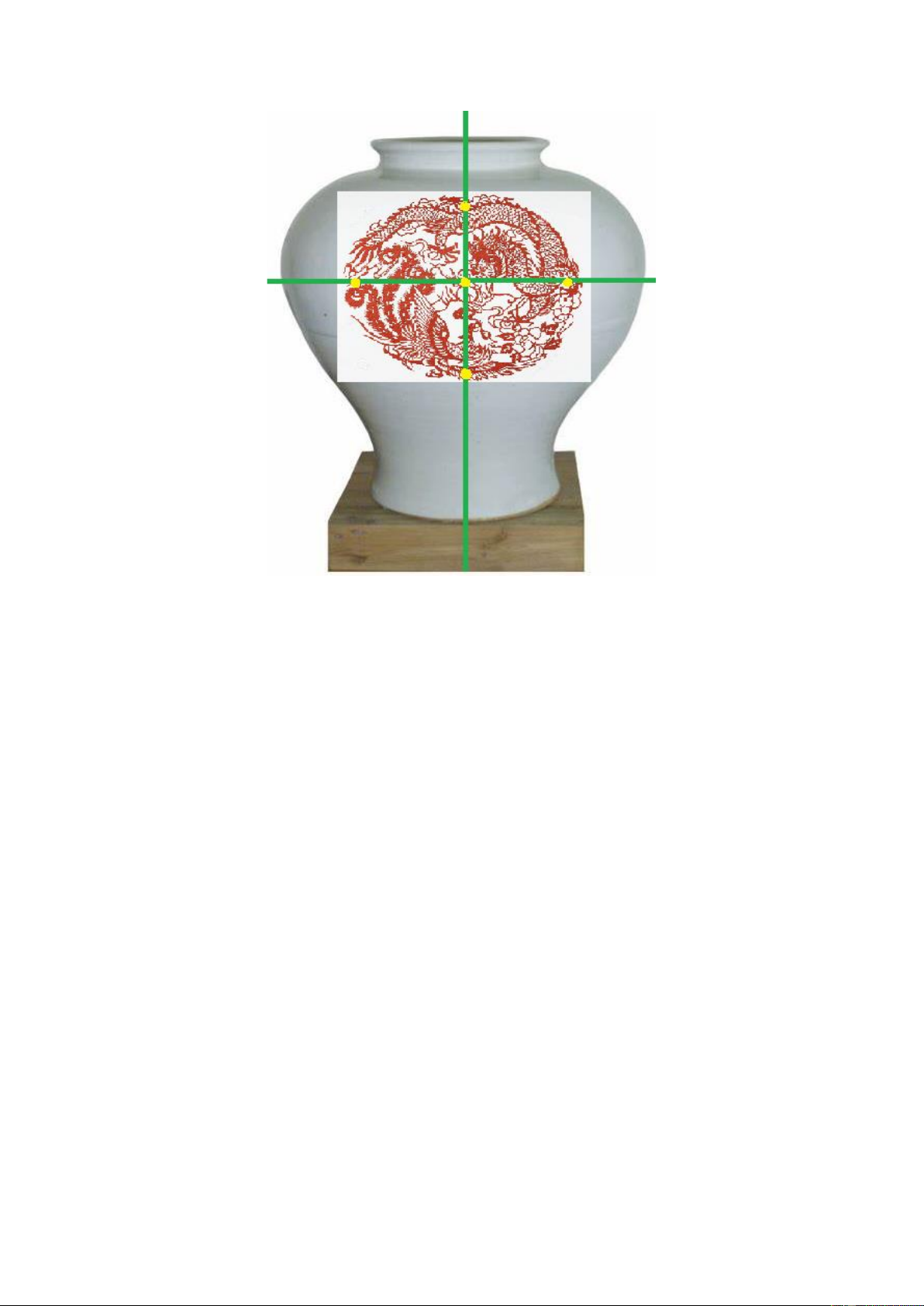
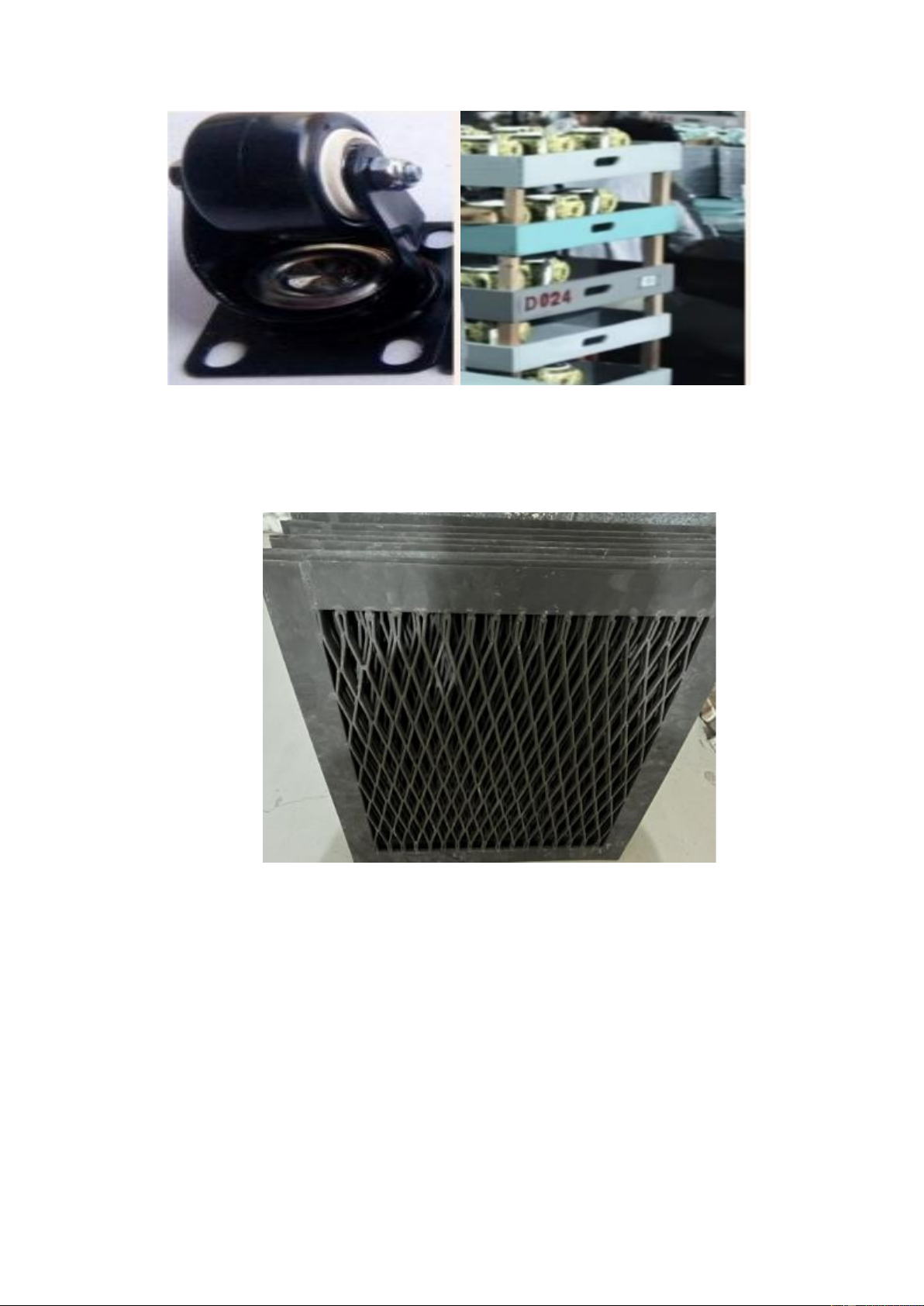

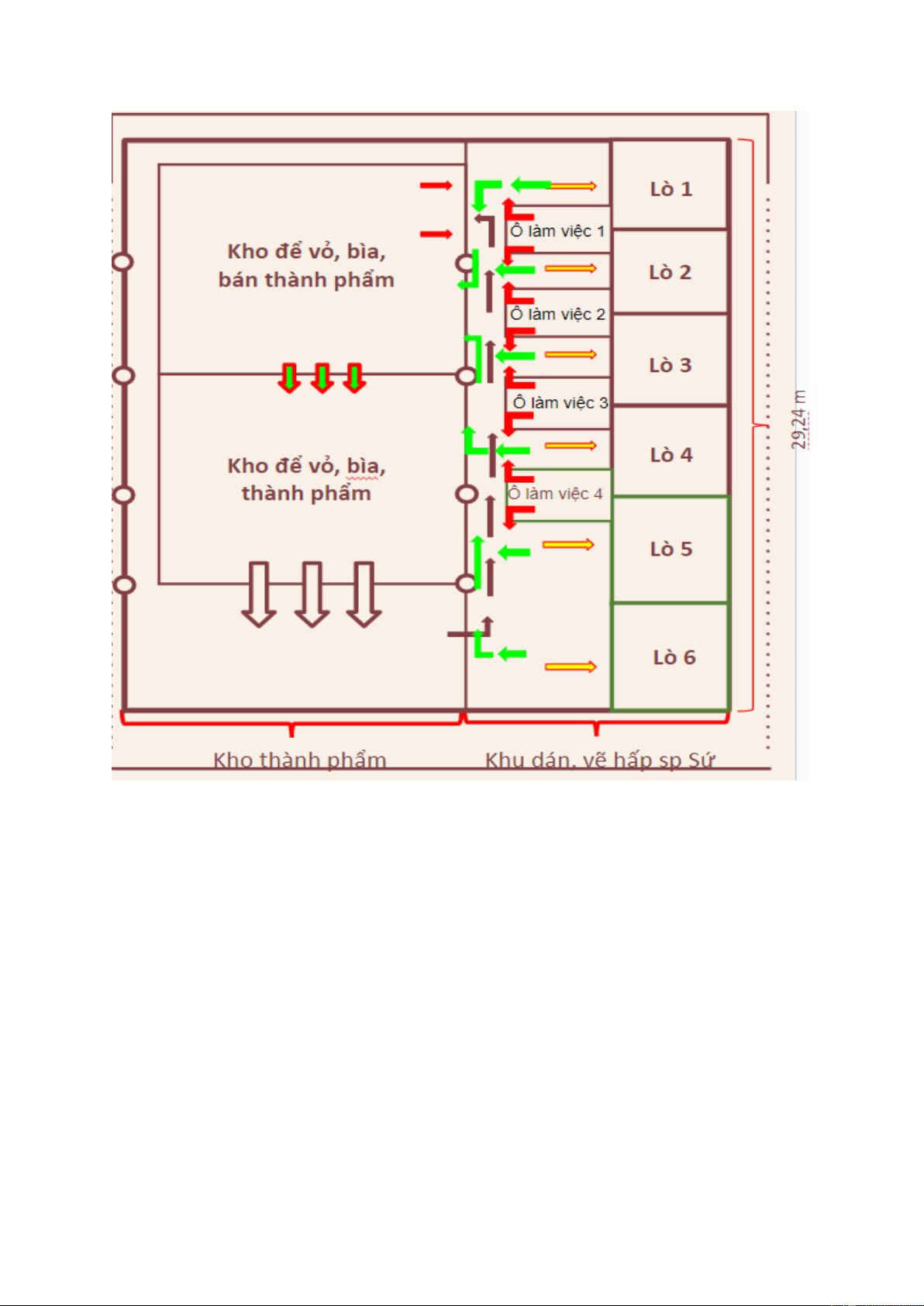
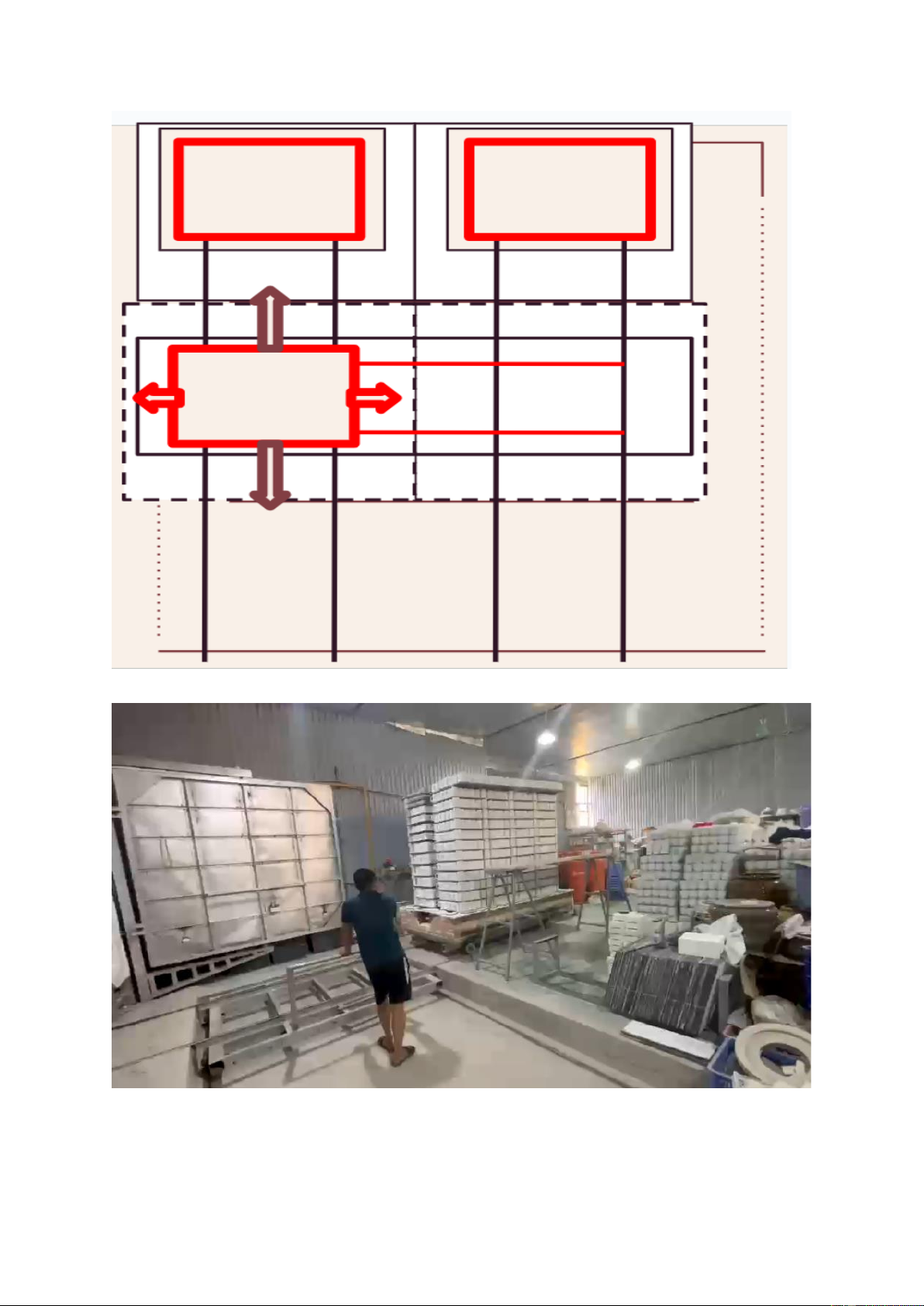
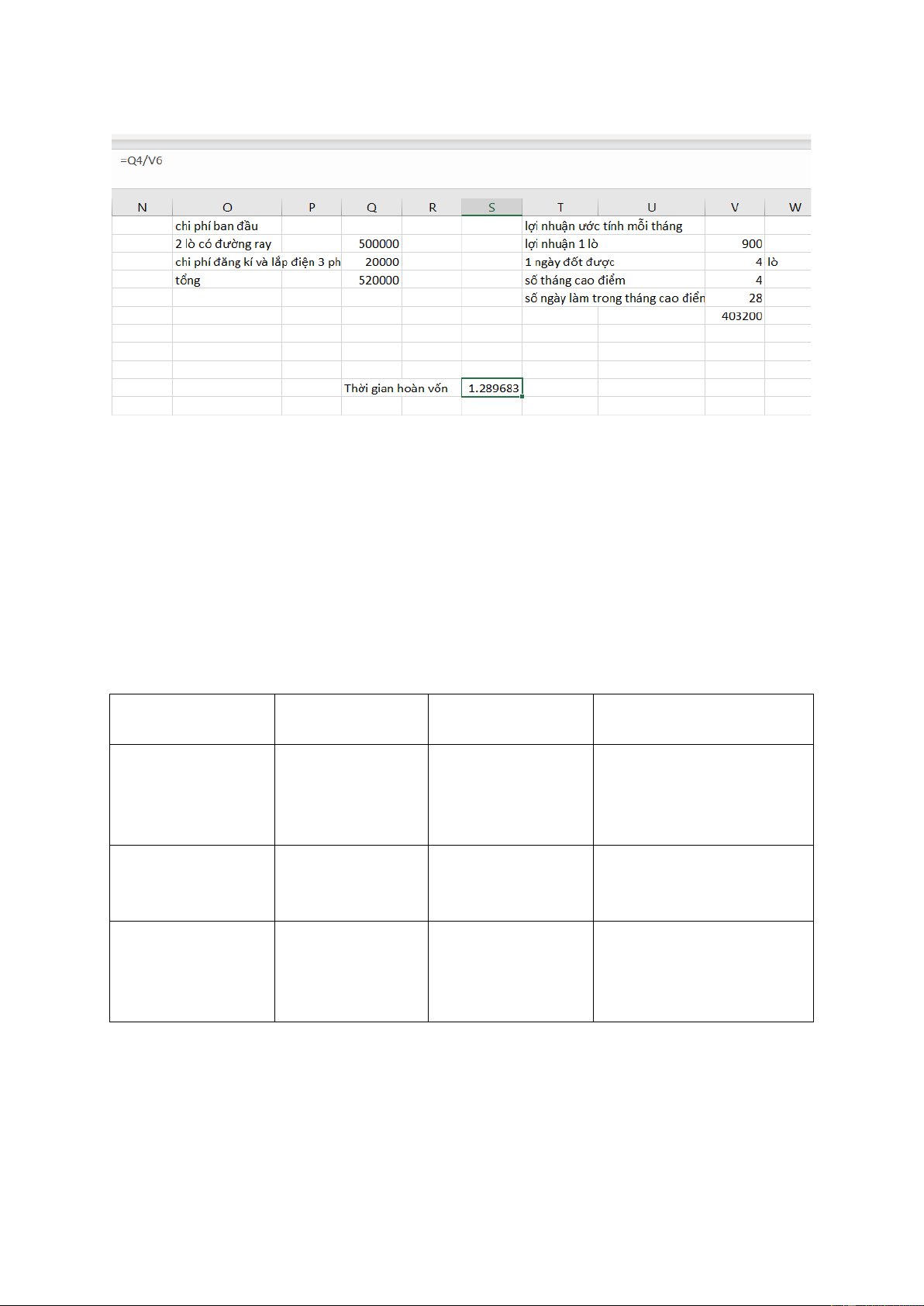
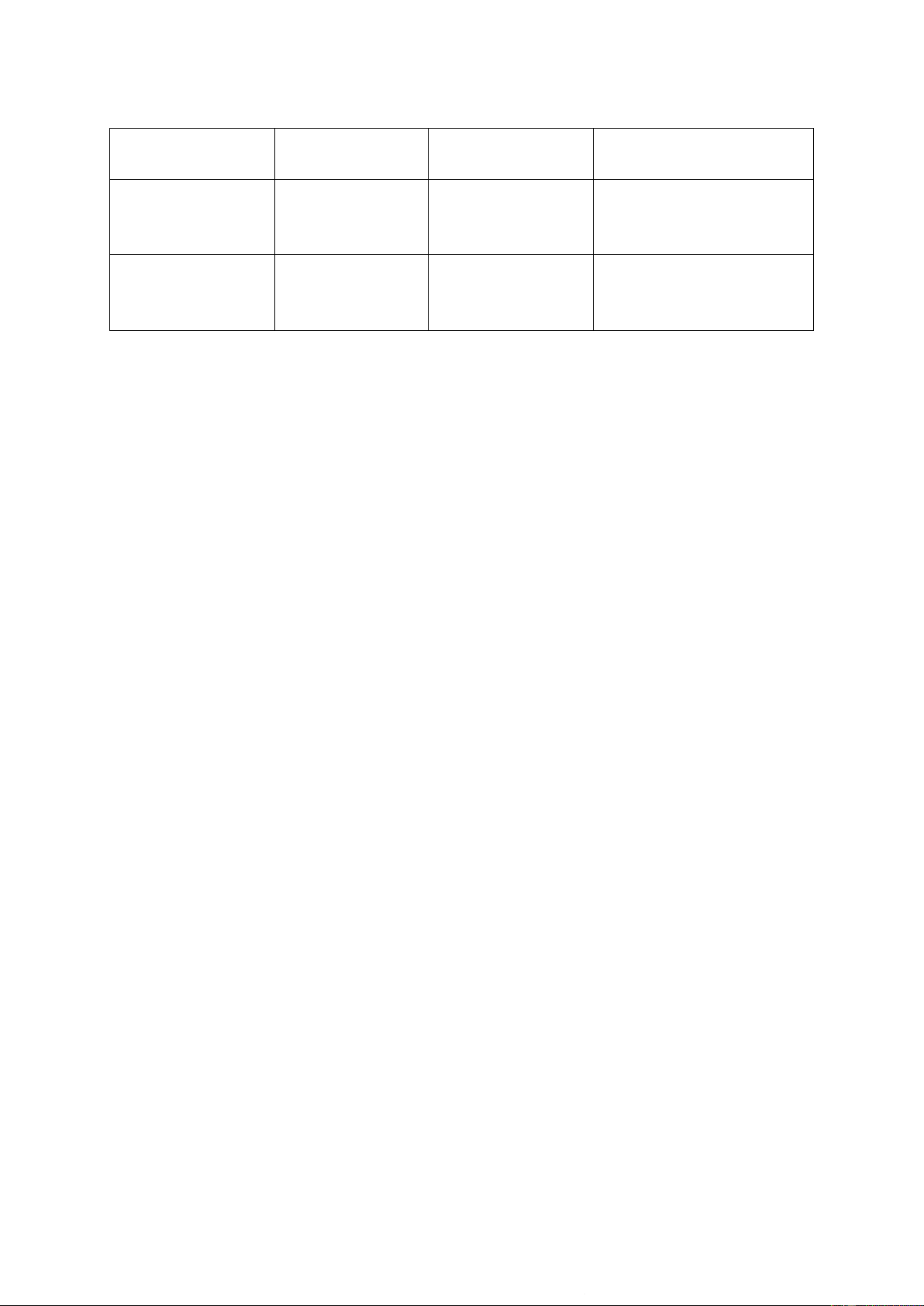
Preview text:
lOMoARcPSD|25518217
TRƯỜNG ĐẠI HỌC BÁCH KHOA HÀ NỘI
VIỆN KINH TẾ - QUẢN LÝ -------o0o-------
HỌC PHẦN: CẢI TIẾN NĂNG SUẤT BÀI TẬP NHÓM
CẢI TIẾN NĂNG SUẤT TẠI XƯỞNG GIA CÔNG GỐM SỨ VIỆT
Giảng viên hướng dẫn: PGS.TS. Nguyễn Danh Nguyên TS. Vũ Hồng Tuấn
Nhóm thực hiện: Nhóm 06 Sinh viên: Nguyễn Thanh Mạnh 20202937 Đậu Trung Hậu 20202914 Trần Xuân Đỉnh 20202902 Phạm Vũ Thịnh 20202965
Nguyễn Xuân Đức Anh 20202888 Trịnh Xuân Thịnh 20202985 Hà Nội, tháng 6 năm 2023 1
Downloaded by Van Le (mrl3v4n@gmail.com) lOMoARcPSD|25518217 LỜI NÓI ĐẦU
"Cải tiến năng suất" là quá trình hoặc hành động nhằm tăng cường hiệu
suất hoặc sản lượng của một quá trình, một hệ thống hoặc một tổ chức. Nó bao
gồm việc áp dụng các biện pháp, phương pháp, công nghệ hoặc quy trình mới
nhằm cải thiện hiệu quả và tăng cường sản xuất.
Cải tiến năng suất có thể áp dụng trong nhiều lĩnh vực, bao gồm công nghiệp,
nông nghiệp, dịch vụ và cả các hoạt động cá nhân. Đây là một quy trình liên tục
và yêu cầu đánh giá, phân tích và cải thiện liên tục để đạt được kết quả tốt hơn.
Cải tiến năng suất có thể bao gồm việc tối ưu hóa quy trình làm việc, cải thiện
công nghệ, nâng cao kỹ năng và đào tạo nhân viên, tăng cường sự tổ chức và
quản lý, áp dụng các phương pháp pháp lý tiết kiệm thời gian và tài nguyên, và
sử dụng công cụ và công nghệ tiên tiến để tăng hiệu quả làm việc.
Cải tiến năng suất là môn học rất cần thiết trong học tập và giảng dạy đối với
giáo dục đại học Việt Nam nói chung và sinh viên các ngành kinh tế nói riêng.
Đặc biệt là đối với sinh viên của các chuyên ngành khối kinh tế - xã hội.
Những tình huống thực tế sẽ giúp sinh viên hiểu sâu và hiểu kĩ lý thuyết hơn,
có thể vận dụng những gì đã học vào tình huống cụ thể mà sau này có thể sẽ
gặp trong công việc. Làm quen với những thách thức cần phải đưa ra một
quyết định trong dự án kinh doanh của chính mình hoặc của doanh nghiệp mà mình công tác.
Để hoàn thành được bài tập lớn này, nhóm chúng em đã nỗ lực rất nhiều và
chúng em xin gửi lời cảm ơn sâu sắc tới thầy giáo, PGS.TS Nguyễn Danh
Nguyên và TS. Vũ Hồng Tuấn, Trường Đại học Bách khoa Hà Nội đã đồng
hành cùng chúng em suốt quá trình nghiên cứu và học tập, cảm ơn thầy đã tận
tình giảng dạy và truyền thụ kiến thức, kinh nghiệm cũng như phong cách
trình bày, để chúng em có thêm những bài học quý báu.
Do chưa có cơ hội va chạm và tiếp xúc với nhiều tình huống thực tế nên
nhóm chúng em có thể còn gặp nhiều sai sót, rất mong nhận được sự góp ý và
sửa chữa của thầy và các bạn.
Chúng em xin chân thành cảm ơn! Hà Nội, tháng 6 năm 2023 Nhóm thực hiện Nhóm 06 2
Downloaded by Van Le (mrl3v4n@gmail.com) lOMoARcPSD|25518217 MỤC LỤC
LỜI NÓI ĐẦU ....................................................................................................................................... 2 I.
Đặt vấn đề và cơ sở lý thuyết ....................................................................................................... 6
1. Đặt vấn đề ................................................................................................................................... 6 1.1
Lý do chọn đề tài ................................................................................................................. 6
1.2 Mục tiêu nghiên cứu ................................................................................................................. 7
1.3 Đối tượng và phạm vi nghiên cứu ............................................................................................. 7 1.4
Phương pháp nghiên cứu ..................................................................................................... 7 1.5
Dự kiến kết quả nghiên cứu ................................................................................................ 7
2. Cơ sở lý thuyết ............................................................................................................................ 8
2.1 Lý thuyết Kaizen ....................................................................................................................... 8 2.1.1
Khái niệm .................................................................................................................... 8
2.1.2 Đặc điểm của Kaizen ......................................................................................................... 9
2.1.3 Các bước triển khai Kaizen .............................................................................................. 10
2.1.4 Các yếu tố ảnh hưởng đến thành công của hoạt động Kaizen ......................................... 11
2.1.5 Lợi ích của Kaizen ........................................................................................................... 13
2.2 Các chương trình Kaizen cơ bản ............................................................................................. 13
2.2.1 5S ..................................................................................................................................... 13
2.2.2 KSS (Kaizen Suggestion System) .................................................................................... 14
2.2.3 QCC (Quality Control Circles) ........................................................................................ 15
2.2.4 JIT (Just In Time) ............................................................................................................. 15
2.2.5 Bảy công cụ thống kê ....................................................................................................... 16 II.
Tổng quan về Xưởng Gốm Sứ Việt ....................................................................................... 17
1. Thông tin doanh nghiệp ............................................................................................................ 17
2. Thông tin về xưởng gia công dán decal Gốm Sứ Việt .............................................................. 23
3. Quy trình thực hiện công việc ................................................................................................... 24 3.1
Quy trình sản xuất chung của doanh nghiệp Gốm Sứ Việt ............................................... 24 3.2
Quy trình sản xuất dán decal nhiệt cho sản phẩm gốm sứ ................................................ 25
4. Thực trạng doanh nghiệp .......................................................................................................... 25
4.1 Thực trạng về mặt bằng .......................................................................................................... 25
4.2 Thực trạng công đoạn dán decal ............................................................................................. 27
4.3 Thực trạng công đoạn xếp dỡ lò nung lửa nhẹ ........................................................................ 29
4.4 Các thực trạng khác ................................................................................................................. 31
5. Xác định điểm cải tiến và thực hiện cải tiến ............................................................................. 32
5.1 Cải tiến mặt bằng .................................................................................................................... 32
5.2 Cải tiến công đoạn dán decal .................................................................................................. 33
5.2.1 Đối với sản phẩm có kích thước bé và hình dáng đơn giản. ........................................... 33 3
Downloaded by Van Le (mrl3v4n@gmail.com) lOMoARcPSD|25518217
5.2.2 Đối với các sản phẩm có kích thước lớn, hình dạng phức tạp. ........................................ 38
5.3 Cải tiến công đoạn xếp, dỡ lò nung lửa nhẹ ............................................................................ 42
KẾT LUẬN .......................................................................................................................................... 47
DANH MỤC HÌNH ẢNH VÀ BẢNG BIỂU
Hình 1 Cơ sở làng gốm Bát Tràng ............................................................................................. 7
Hình 2 Phân xưởng chế tác gốm sứ ......................................................................................... 18
Hình 3 Phân xưởng gia công dán decal ................................................................................... 19
Hình 4 Trung tâm kinh doanh sản xuất Sứ Việt ...................................................................... 19
Hình 5 Trung tâm kinh doanh phân phối % bán lẻ Sứ Việt ..................................................... 20
Hình 6 Ấm chén Sứ Việt .......................................................... Error! Bookmark not defined.
Hình 7 Ly sứ Sứ Việt ............................................................................................................... 22
Hình 8 Bát đĩa Sứ Việt ............................................................................................................. 22
Hình 9 Đồ thờ Sứ Việt ............................................................................................................. 23
Hình 10 Các sản phẩm chiến lược của công ty ........................................................................ 23
Hình 11 Diện tích mặt bằng xưởng dán decal ......................................................................... 24
Hình 12 Quy trình sản xuất chung ........................................................................................... 25
Hình 13 Quy trình sản xuất dán decal nhiệt ............................................................................. 25
Hình 14 Sơ đồ mặt bằng chức năng hiện tại ............................................................................ 26
Hình 15 Thực trạng công đoạn xếp lò ..................................................................................... 29
Hình 16 Thực trạng đợi dán decal ........................................................................................... 31
Hình 17 Sơ đồ mặt bằng sau cải tiến ....................................................................................... 32
Hình 18 Decal khi chưa in viền rộng hơn ................................................................................ 34
Hình 19 Decal trước cải tiến .................................................................................................... 35
Hình 20 Decal sau cải tiến ....................................................................................................... 35
Hình 21 Tia laser ...................................................................................................................... 39
Hình 22 Bản vẽ mô hình gá đỡ và tia laser .............................................................................. 40
Hình 23 Cấu tạo bên trong gá đỡ ............................................................................................. 40
Hình 24 Bình sứ khi chiếu tia laser và decal được đánh dấu .................................................. 41
Hình 25 Ví trí decal đạt yêu cầu .............................................................................................. 42
Hình 26 Hình ảnh thực tế kệ xếp đồ ........................................................................................ 43
Hình 27 Tấm thép được xuất xứ từ Trung Quốc ..................................................................... 43
Hình 28 Mô phỏng mặt bằng xưởng trong tương lai ............................................................... 45
Hình 29 Sơ đồ 2 lò mới khi có đường ray ............................................................................... 46
Hình 30 Ví dụ thực tế về lò có đường ray................................................................................ 46
Bảng 1 Thông tin chi tiết mặt bằng trước cải tiến ................................................................... 26
Bảng 2 Khảo sát thời gian lấy hàng trước cải tiến ................................................................... 27
Bảng 3 Thời gian dỡ lò (phút).................................................................................................. 30
Bảng 4 Thời gian xếp lò (phút) ................................................................................................ 30
Bảng 5 Thông tin chi tiết mặt bằng sau cải tiến ...................................................................... 33
Bảng 6 Khảo sát thời gian lấy hàng sau cải tiến ...................................................................... 33
Bảng 7 Số liệu thu thập từ 10 lần đo đối với sản phẩm Bát sứ trắng ....................................... 36
Bảng 8 Số liệu thua thập từ 10 lần đo đối với sản phẩm chén sứ trắng, dán 1 chi tiết ............ 36
Bảng 9 Số liệu thu thập từ 10 lần đo đối với sản phẩm cốc sứ trắng, dán 2 chi tiết ................ 37
Bảng 10 Bảng chi phí và doanh thu ........................................................................................ 37 4
Downloaded by Van Le (mrl3v4n@gmail.com) lOMoARcPSD|25518217
Bảng 11 Bảng so sánh trước và sau khi có xe nâng và tấm thép (trong 5 ngày thực tế) ......... 44
Bảng 12 Dự kiến thời gian hoàn vốn khi đầu tư thêm lò có đường ray ................................... 47 5
Downloaded by Van Le (mrl3v4n@gmail.com) lOMoARcPSD|25518217
I. Đặt vấn đề và cơ sở lý thuyết 1. Đặt vấn đề 1.1 Lý do chọn đề tài
Xưởng Gốm Bát Tràng đã mang những hạt đất sét đang ngủ yên trong lòng
đất mẹ, hòa với nước, lắng mình dưới ánh nắng mặt trời và cuộn tròn trong bàn
tay “say nghề” của người thợ gốm để tạo nên tác phẩm gốm tâm linh hội tụ đủ
Thiên – Địa – Nhân. Từ đó đưa làng cổ Bát Tràng trở thành nơi sản xuất gốm
tâm linh, phong thủy hàng đầu Việt Nam. Chúng tôi mong muốn giữ gìn truyền
thống “Uống nước nhớ nguồn” của dân tộc, đưa sản phẩm gốm tinh hoa phụng
sự hàng triệu gia đình Việt biết thờ cúng gia tiên và bày trí phong thủy đúng
cách để cuộc sống bình an, vạn sự như ý, hưng thịnh ngàn đời.
Trải qua bao thăng trầm của thời gian, giữa cuộc sống đương đại nhiều sôi
động, làng nghề Bát Tràng đã vươn mình ra khắp năm châu để quảng bá văn
hóa Việt với bạn bè thế giới. Trăn trở, tâm nguyện chắp cánh cho thương hiệu
Gốm Bát Tràng tiếp tục vươn cao trên thị trường trong nước và Quốc tế, Xưởng
Gốm Bát Tràng đã ra đời với sứ mệnh cao cả.
Để tạo nên một sản phẩm hoàn chỉnh, phải trải qua 4 phân xưởng sản
xuất/gia công. Với sự phát triển của xã hội ngày nay, nhu cầu về mặt hàng này
của người tiêu dùng ngày càng cao, xưởng gốm sẽ phải tăng công suất làm việc
và không thể tránh khỏi một số lỗi phát sinh cơ bản khiến năng suất chưa thực
sự đạt hiệu quả tối đa. Chúng em nhận thấy được trực trạng vấn đề này và có
may mắn được trực tiếp trải nghiệm tham quan, đo đạc dữ liệu ở xưởng gia
công (Phân xưởng Decal), nên đã lựa chọn đề tài làm đề tài cải tiến cho môn
học. Hy vọng rằng chúng em sẽ đóng góp được một phần nào đó để cải tiến
năng suất, giúp xưởng decal đạt được tối đa hiệu quả nói riêng, cũng như doanh
nghiệp sẽ càng phát triển hơn nữa, tăng sự hài lòng cho khách hang và nhân
công trong doanh nghiệp, nâng cao hiệu quả kinh doanh.’ 6
Downloaded by Van Le (mrl3v4n@gmail.com) lOMoARcPSD|25518217
H椃nh 1 Cơ sở làng gốm Bát Tràng 1.2 Mục tiêu nghiên cứu
Vận dụng các kiến thức đã học từ lý luận áp dụng vào thực tiễn tại hoạt
động của một phân xưởng decal chuyên nhận gia công các sản phẩm từ gốm.
Đánh giá phân tích thực trạng dịch vụ của xưởng. Từ đó đưa ra các điểm cần cải
tiến, đề xuất các giải pháp nâng cao năng suất và hiệu quả làm việc tại xưởng
gia công làng gốm Bát Tràng.
1.3 Đối tượng và phạm vi nghiên cứu
- Đối tượng nghiên cứu: Quy trình dán decal ( 1 mặt/2 mặt ) và quy
trình nung gốm ở mức lửa nhẹ.
- Phạm vi nghiên cứu: Nghiên cứu tại xưởng gia công làng Gốm Bát Tràng.
1.4 Phương pháp nghiên cứu
- Phương pháp định lượng: Quan sát, bấm giờ hoàn thành 1 thao
tác/công đoạn,ghi chép lại số liệu trực quan,…
- Phương pháp định tính: Phỏng vấn quản lúy và công nhân tại xưởng.
1.5 Dự kiến kết quả nghiên cứu
- Đối với xưởng gia công Gốm Sứ Việt: Tối ưu hóa nguồn nhân lực và
không gian sử dụng, tăng hiệu suất lao động, tối đa hóa năng suất làm
việc, hiệu quả hoàn thành sản phẩm đạt chất lượng theo yêu cầu. 7
Downloaded by Van Le (mrl3v4n@gmail.com) lOMoARcPSD|25518217
- Đối với doanh nghiệp Gốm Sứ Việt: Nâng cao năng suất của một phân
xưởng đồng nghĩa với việc nâng cao năng suất cho toàn bộ doanh
nghiệp. Điều này có thể đảm bảo sự tăng trưởng và lợi nhuận cho doanh nghiệp.
- Đối với sinh viên: Bổ sung, trau dồi thêm các kĩ năng & kiến thức
thực tế cũng như hiểu rõ hơn về lý thuyết và môn học. 2. Cơ sở lý thuyết 2.1 Lý thuyết Kaizen 2.1.1 Khái niệm
Kaizen là một thuật ngữ kinh tế của người Nhật, được ghép bởi từ 改
("kai") có nghĩa là thay đổi và từ 善("zen") có nghĩa là tốt hơn, tức là “thay đổi
để tốt hơn” hoặc “cải tiến liên tục”. Thuật ngữ này trong tiếng Anh là “ongoing
improvement” hoặc “continuous improvement” và trong tiếng Trung, Kaizen
được phát âm là Gansai, nghĩa là hành động liên tục cải tiến, mang lại lợi ích vì
tập thể hơn là lợi ích của cá nhân.
Trong cuốn sách “Kaizen: Chìa khóa thành công của người Nhật”,
Kaizen được định nghĩa như sau: “Kaizen có nghĩa là cải tiến. Hơn nữa, Kaizen
còn có nghĩa là cải tiến liên tục trong đời sống cá nhân, đời sống gia đình, đời
sống xã hội và môi trường làm việc. Khi Kaizen được áp dụng vào nơi làm việc
có nghĩa là sự cải tiến liên tục liên quan tới tất cả mọi người – ban lãnh đạo
cũng như mọi nhân viên”.
Tại Nhật Bản, Kaizen đã có lịch sử hơn 50 năm và Toyota là công ty đầu
tiên triển khai Kaizen. Trước kia, Kaizen chủ yếu được áp dụng trong các công
ty sản xuất như Toyota, Canon, Honda... Sau đó, Kaizen được áp dụng rộng rãi
trong mọi công ty thuộc nhiều lĩnh vực khác nhau và hiện nay, hầu hết các công
ty của Nhật đều đang thực hiện Kaizen. Triết lý này không chỉ giới hạn trong
ngành sản xuất mà còn có thể áp dụng được trong ngành dịch vụ, kinh doanh
bán lẻ và thậm chí là một khóa học bất kì nào đó. Triết lý này cũng thích hợp
đối với đời sống cá nhân của mỗi người.
Trong lần xuất bản năm 1993 của “The New Shorter Oxford English
Dictionary”, từ “Kaizen” cũng được bổ sung và định nghĩa như sau: Kaizen là
sự cải tiến liên tục quá trình làm việc, nâng cao năng suất, ...v.v. như một triết lý
kinh doanh”. Ngày nay, Kaizen được nhắc tới như một triết lý kinh doanh,
phương pháp quản lý hữu hiệu làm nên thành công của các công ty Nhật Bản.
Tuy vậy, những cải tiến trong Kaizen là những cải tiến nhỏ, mang tính chất tăng
dần và quá trình Kaizen mang lại kết quả ấn tượng trong một thời gian dài.
Thực hiện Kaizen cũng ít tốn kém hơn đổi mới bởi nó nâng cao chất lượng công
việc, ghi nhận sự tham gia của của nhà quản lý cũng như mọi nhân viên, nâng 8
Downloaded by Van Le (mrl3v4n@gmail.com) lOMoARcPSD|25518217
cao chất lượng sản phẩm, dịch vụ và giảm chi phí hoạt động. Đây chính là một
điểm hấp dẫn của Kaizen vì nó không đòi hỏi các kỹ thuật phức tạp hay công nghệ mới.
2.1.2 Đặc điểm của Kaizen
Năm 1997, cuốn sách “Gemba Kaizen – Một cách quản lý thông thường,
chi phí thấp” của ông Masaaki Imai được xuất bản, đã một lần nữa nhấn mạnh
tầm quan trọng của việc cải tiến liên tục tại nơi làm việc. Gemba ở đây nghĩa là
nơi mọi hoạt động thực tế đang diễn ra, ở một nghĩa khác là nơi mà giá trị được
tăng thêm; trong trường hợp ngành sản xuất thì Gemba chính là khu vực chế tạo
hàng hóa trong nhà máy; trong khách sạn thì Gemba chính là khu vực thức ăn
đang được chế biến cho khách và trong ngành dịch vụ thì Gemba là bất cứ nơi
nào. Cuốn sách này đã giới thiệu một phương thức quản lý chất lượng mới nhất,
tập trung vào việc áp dụng nó trong sản xuất sản phẩm và hỗ trợ các hoạt động
chính của việc kinh doanh. Trước tiên, Gemba Kaizen đòi hỏi người tham gia từ
bỏ lối suy nghĩ cứng nhắc theo tập quán. Để có thể cải tiến một quá trình, bạn
cần suy nghĩ, sẵn sàng chất vấn những gì xẩy ra trong hiện tại và bạn cũng đừng
hy vọng kết quả lớn lao.
Bởi Kaizen là một quá trình cải tiến dựa trên những gì sẵn có, có liên
quan tới cán cũng như mọi nhân viên nên đặc điểm chính của Kaizen là: (1)
Luôn được thực hiện liên tục tại nơi làm việc; (2)
Tập trung nâng cao năng suất lao động và thỏa mãn yêu cầu khách hàng
bằng việc giảm lãng phí (thời gian, chi phí...); (3)
Thu hút đông đảo người lao động tham gia cùng cam kết mạnh mẽ của
lãnh đạo và các nhà quản lý; (4)
Yêu cầu cao về hoạt động nhóm; (5)
Công cụ hữu hiệu là thu thập và phân tích dữ liệu.
Do có đặc điểm như vậy, nên quan điểm cơ bản của Kaizen là: (1)
Những hoạt động hiện tại luôn có nhiều cơ hội để cải tiến; (2)
Các phương tiện và phương pháp hiện tại có thể được cải tiến nếu có một nỗ lực nào đó; (3)
Tích lũy những cải tiến nhỏ sẽ tạo ra một sự biến đổi lớn; (4)
Lôi cuốn toàn thể công nhân viên tham gia; (5)
Áp dụng các đề xuất sáng kiến của mọi người.
Các đối tượng cải tiến của Kaizen là tất cả những gì hiện có: phương
pháp làm việc, quan hệ công việc, môi trường làm việc và điều kiện làm việc ở
mọi nơi. Các hoạt động Kaizen có thể được khởi xướng bởi lãnh đạo, một bộ
phận (phòng, ban) của tổ chức, một nhóm làm việc, nhóm kaizen và từng cá 9
Downloaded by Van Le (mrl3v4n@gmail.com) lOMoARcPSD|25518217
nhân. Kaizen cũng được chia ra thành 2 cấp độ: 1.
Kaizen ở cấp độ hệ thống (system or flow kaizen) tập trung vào toàn bộ
chuỗi giá trị, được thực hiện ở cấp quản lý. 2.
Kaizen ở cấp độ quy trình tập trung vào các quy trình, được thực hiện ở
cấp thừa hành (như phòng ban, phân xưởng).
Kaizen được sử dụng phổ biến nhất trong các quy trình sản xuất và tác nghiệp,
ví dụ như tại Toyota, nhưng cũng vẫn được áp dụng ngay tại các môi trường phi
sản xuất. Đối tượng của kaizen có thể là cá nhân, hệ thống, nhóm nhỏ hoặc tổ
chức lớn đều được. Tại Toyota, nó thường sẽ là những thay đổi cục bộ tại phòng
làm việc, nơi làm việc của một nhóm nhỏ để giúp mọi người trong nhóm có thể
cải thiện môi trường làm việc của chính họ cũng như cải thiện hiệu quả công
việc. Nhóm này thường sẽ được hướng dẫn về chu trình kaizen bởi một cấp trên
trực tiếp, đôi khi việc hướng dẫn như vậy được coi là trách nhiệm chính của
người giám sát. Kaizen ở một cấp độ rộng hơn, khi có sự liên kết giữa các
phòng ban trong công ty với nhau, sẽ giúp quản lý chất lượng toàn diện và giải
phóng những nỗ lực của con người thông qua việc cải thiện năng suất bằng cách
sử dụng máy móc và sức mạnh tính toán.
Ngày nay, phương pháp này còn được thiết kế để tìm ra những vấn đề trong quá
trình hoạt động và kinh doanh của doanh nghiệp trong thời gian ngắn, được gọi
là "kaizen chớp nhoáng" (kaizen blitz) hoặc "kaizen sự kiện" (kaizen event).
Người đóng góp lớn trong
2.1.3 Các bước triển khai Kaizen
Kaizen được thực hiện theo 8 bước, tuân thủ theo vòng tròn quản lý chất
lượng PDCA (Plan, Do, Check, Act) của William Edwards Deming được giới
thiệu từ năm 1950. Từ bước 1 đến bước 4 là Plan (lập kế hoạch), bước 5 là Do
(thực hiện), bước 6 là Check (kiểm tra) và bước 7, 8 là Act (hành động khắc
phục hay cải tiến). Dựa trên việc phân tích dữ liệu, chúng ta sẽ giải quyết được
vấn đề thông qua 8 bước được tiêu chuẩn hóa như sau:
- Bước 1: Lựa chọn chủ đề (cho công việc, bộ phận...). Việc lựa chọn được
bắt đầu với lý do tại sao chủ đề trên được lựa chọn. Thông thường, chủ đề
được quyết định cùng với các chính sách quản lý hay dựa trên mức độ ưu
tiên, tầm quan trọng, mức độ khẩn cấp hoặc tình hình kinh tế hiện tại.
- Bước 2: Tìm hiểu tình trạng hiện tại và xác định mục tiêu. Trước khi bắt
đầu một dự án, các trạng thái hiện tại phải được hiểu và xem xét lại. Một
cách để thực hiện những điều trên là con người trực tiếp đến nơi làm việc
(tức là Gemba) và tuân theo 5 nguyên tắc cơ bản của Gemba. Một cách
khác là thu thập dữ liệu.
- Bước 3: Phân tích dữ liệu đã thu thập để xác định nguyên nhân gốc rễ 7
- Bước 4: Xác định biện pháp thực hiện dựa trên cơ sở phân tích dữ liệu 10
Downloaded by Van Le (mrl3v4n@gmail.com) lOMoARcPSD|25518217
- Bước 5: Thực hiện biện pháp
- Bước 6: Xác nhận kết quả thực hiện biện pháp
- Bước 7: Xây dựng hoặc sửa lỗi các tiêu chuẩn để phòng ngừa tái diễn
- Bước 8: Xem xét các quá trình trên và xác định các dự án tiếp theo
Các bước trên sẽ giúp nhà quản lý hình dung và tiếp cận được với quá
trình giải quyết các khó khăn. Đây cũng là một cách hiệu quả để ghi lại các hoạt
động Kaizen. Mỗi một giai đoạn của vòng tròn Deming thường sử dụng các kỹ
thuật hỗ trợ riêng biệt. Vòng tròn Deming được áp dụng một cách liên tục trong
việc quản lý chất lượng nhằm từng bước cải tiến và nâng cao chất lượng sản
phẩm, chất lượng công việc. Bước khởi đầu của vòng tròn mới được dựa trên
kết quả của vòng tròn trước nhằm giải quyết tiếp các vấn đề còn tồn tại... và như
thế sau nhiều lần áp dụng vòng tròn Deming chất lượng sản phẩm sẽ nâng cao
dần và liên tục. Đồng thời, hoạt động Kaizen cũng được cải tiến hơn nữa và tiếp tục được thực hiện.
2.1.4 Các yếu tố ảnh hưởng đến thành công của hoạt động Kaizen
Kaizen được biết đến như một triết lý kinh doanh, cách thức quản lý của
người Nhật. Mặt khác, Kaizen là một hệ thống cải tiến liên tục trong chất lượng,
công nghệ, phương pháp, văn hóa công ty, năng suất, an toàn và khả năng lãnh
đạo. Kaizen là một hệ thống có liên quan tới tất cả mọi người – từ cán bộ quản
lý cấp cao đến những nhân viên bình thường. Mọi người đều được động viên
đưa ra những đề xuất cải tiến một cách thường xuyên. Hoạt động này không chỉ
là một lần trong một tháng hay một lần trong một năm mà là liên tục. Các công
ty của Nhật như Toyota và Canon, trung bình mỗi nhân viên đóng góp 60 đến
70 đề xuất mỗi năm. Các đề xuất đó đều được chia sẻ cho mọi người và triển
khai. Trong hầu hết các trường hợp, những đề xuất đều không mang lại những
thay đổi to lớn. Kaizen dựa trên những thay đổi nhỏ bé tuân theo quy tắc: luôn
luôn cải tiến năng suất, sự an toàn và hiệu quả trong khi giảm thiểu lãng phí.
Kaizen dựa trên những thay đổi ở bất cứ nơi nào mà sự cải tiến được thực
hiện. Các đề xuất không bị giới hạn trong một lĩnh vực riêng biệt như sản xuất
hay tiếp thị. Triết lý của phương Tây có thể được tóm tắt như sau: “Nếu nó
không hỏng, thì đừng sửa nó”. Triết lý Kaizen là “Làm cho nó tốt hơn, chế tạo
ra nó tốt hơn, thúc đẩy nó thậm chí nếu nó chưa đổ vỡ, bởi vì nếu chúng ta
không làm, chúng ta không thể cạnh tranh với những cái của người khác làm”.
Bởi vậy, thái độ đối với triết lý Kaizen, việc hiểu và áp dụng đúng Kaizen đóng
một vai trò quan trọng trong việc triển khai thành công triết lý này. Khi hiểu
triết lý Kaizen, ta mới có thể xây dựng được một hệ thống Kaizen hữu hiệu, áp
dụng Kaizen triệt để, thực hiện Kaizen liên tục và gặt hái được nhiều thành quả 11
Downloaded by Van Le (mrl3v4n@gmail.com) lOMoARcPSD|25518217 tốt đẹp.
Muốn Kaizen thành công thì thái độ của người lao động – từ nhà quản lý
cấp cao đến những nhân viên cấp dưới sẽ cần phải thay đổi. Kaizen cần trở
thành điều mà tất cả nhân viên đều thực hiện bởi họ muốn làm và bởi họ biết
triết lý này không chỉ tốt cho họ mà cho cả công ty của họ. Kaizen không thể là
điều mà người lao động thực hiện khi lãnh đạo ra lệnh. Điều này có nghĩa là nếu
nhà lãnh đạo không sẵn sàng thực hiện Kaizen làm gương thì nó không được
triển khai có hiệu quả. Do đó, người lãnh đạo cao nhất phải hiểu Kaizen và thể
hiện cam kết mạnh mẽ về việc áp dụng Kaizen tại công ty. Đa số các nhân viên
đều ngại thay đổi nên người lãnh đạo, chính là ông chủ cần có ảnh hưởng và
quyền lực hơn đối với họ. Việc nhà quản lý cấp cao nhất của Toyota thường
xuyên có mặt tại khu vực sản xuất trong nhà máy để giải quyết các vấn đề chính
là Gemba Kaizen. Người lãnh đạo hàng đầu phải nghiêm chỉnh tham gia Gemba
Kaizen – Cải tiến liên tục tại nơi làm việc. Nếu không, lợi ích thu được sẽ chỉ là
nhỏ bé và rốt cuộc thì họ sẽ than phiền Kaizen chẳng đem lại kết quả gì. Nhiệm
vụ của người làm quản lý là tạo nên cơ cấu và thúc đẩy sự thay đổi. Đầu tiên sự
thay đổi chỉ mang tính khuyến khích nhưng nếu cần thiết thì họ sẽ đưa ra các quy định bắt buộc.
Năm 1949, người Mỹ đã giới thiệu hệ thống đề xuất ý tưởng cải tiến ESS
(Employee Suggestion System) của mình cho các công ty Nhật. Sau đó, người
Nhật đã ứng dụng, cải tiến và phát triển thành một hệ thống riêng của họ, đặt tên
là Kaizen Teian hay còn gọi Implemented Kaizen Reporting System (Hệ thống
báo cáo thực hiện cải tiến). Họ gọi là Implemented vì muốn chỉ rõ người đề xuất
chính là người thực hiện ý tưởng đó, chứ không phải đề xuất ý tưởng để người
khác thực hiện. Họ đặt Reporting (báo cáo) vì muốn nhấn mạnh tầm quan trọng
của việc viết các đề xuất ra giấy và tường thuật việc thực hiện các ý tưởng cải
tiến. Hầu hết, các công ty Nhật hiện nay đều thành lập Kaizen Teian để thu thập
và thực hiện các đề xuất cải tiến. Bởi họ hiểu rõ: “nếu muốn quản lý tốt công ty
cần quản lý tốt nguồn tài sản quan trọng nhất – nguồn nhân lực”. Những lợi ích
tài chính thu được từ hệ thống này chỉ là một kết quả nhỏ trong mục đích của
nhà quản lý. Điều quan trọng hơn cả là nó tạo cho mọi nhân viên thói quen hàng
ngày suy nghĩ về việc cải tiến công việc của chính họ và thu hút đông đảo được
mọi người tham gia. Tất cả nhân viên cùng tham gia đóng góp ý kiến, thực hiện
Kaizen sẽ tạo nên môi trường làm việc thú vị, hấp dẫn và người lao động càng
có cơ hội để thỏa mãn nhu cầu tự thể hiện. Đáp ứng được điều này thì nhiệm vụ
của nhà lãnh đạo cao nhất và cán bộ quản lý cũng được hoàn thành. Đây chính
là yếu tố cuối cùng quyết định tới sự thành công của hoạt động Kaizen. 12
Downloaded by Van Le (mrl3v4n@gmail.com) lOMoARcPSD|25518217 2.1.5 Lợi ích của Kaizen
Vào những năm 1980 và đầu những năm 1990, rất nhiều các công ty lớn
của Nhật thiết lập cơ sở sản xuất tại miền Bắc nước Mỹ. Khi họ giành được các
công ty lớn ở Bắc Mỹ (như Bridgestone tiếp quản Firestone, Sony tiếp quản
hãng phim Columbia Pictures) cũng là lúc nhà lãnh đạo các tập đoàn của Nhật
truyền bá phương thức quản lý của họ đối với các công ty con và các công ty
nước ngoài khác. Chính thời điểm này, Kaizen cũng được biết đến như chìa
khóa thành công của các doanh nghiệp Nhật Bản trong chiến lược cạnh tranh toàn cầu.
Hiện tại có rất nhiều công ty trên thế giới đang cố gắng áp dụng hiệu quả
triết lý CẢI TIẾN LI䔃ȀN T唃⌀C của người Nhật nhằm đối phó với những thách
thức về môi trường cạnh tranh khắc nghiệt, khó khăn kinh tế tăng lên, sự phát
triển liên tục của công nghệ và các thay đổi về văn hóa – xã hội.
Kaizen thu hút và phát triển những người có khả năng sáng tạo và duy trì
hiệu quả công việc cao. Bởi bản chất của nó, Kaizen lôi cuốn con người từ sự
nhiệt tâm – những người không ngừng tạo ra sự khác biệt, hoàn thiện mọi thứ.
Những con người này tập trung vào công việc của họ, giảm thiểu lãng phí và
thỏa mãn với cơ hội cải thiện những gì mà họ có ưu thế. Việc họ tiếp tục thực
hiện triết lý này sẽ thu hút đông đảo mọi người tham gia, tạo thành một phong
trào trong công ty. Những kết quả thiết thực của việc áp dụng Kaizen tạo ra môi
trường làm việc thoải mái, thúc đẩy họ không ngừng đưa ra nhiều sáng kiến cải
tiến làm lợi cho công ty. Đề xuất ý tưởng cải tiến là một quá trình tự học hỏi và
nâng cao kỹ năng làm việc của nhân viên, giúp họ nâng cao ý thức và phát triển
bản thân cũng như tập thể. Bởi vậy, nhân viên cảm thấy hứng thú hơn trong
công việc, đoàn kết giúp đỡ lẫn nhau. Tất cả những điều đó, càng tạo thêm động
lực thúc đẩy cá nhân có các ý tưởng cải tiến, tạo tinh thần làm việc tập thể, đoàn
kết và tạo ý thức luôn hướng tới giảm thiểu các lãng phí.
Nhà quản lý cũng như mọi nhân viên cần hiểu, tin vào triết lý Kaizen và
cố gắng thực hiện một cách liên tục. Có như vậy, toàn thể nhân viên và lãnh đạo
mới thấm nhuần triết lý CẢI TIẾN LI䔃ȀN T唃⌀C trong suy nghĩ, hành động. Khi
một triết lý được áp dụng hiệu quả thì nó sẽ hình thành nên một nét văn hóa
trong công ty. Tổng biên tập tạp chí AutoWeek nhận định: “Tiết kiệm không chỉ
văn hóa của riêng Toyota. Nó là văn hóa mà người Nhật đem tới nước Mỹ, hay
chí ít cũng là trong các nhà máy sản xuất của họ”.
2.2 Các chương trình Kaizen cơ bản 2.2.1 5S
Đây là nền tảng cơ bản để thực hiện hệ thống đảm bảo chất lượng của
người Nhật, gồm các từ sau:
- Seiri (整理Sàng lọc): tức là lọc ra những vật không cần thiết tại nơi làm 13
Downloaded by Van Le (mrl3v4n@gmail.com) lOMoARcPSD|25518217
việc và loại bỏ chúng. Nơi làm việc khác nhau và đối tượng khác nhau sẽ
có những tiêu chuẩn khác nhau.
- Seiton (整頓 Sắp xếp): tức là sắp xếp ngăn nắp, có trật tự những vật cần
thiết sao cho có thể dễ dàng lấy chúng ra để sử dụng. Điều này nhằm sắp
xếp những vật cần thiết luôn ở trong “điều kiện tốt” (sẵn sàng để dùng),
“đảm bảo an toàn” (không bị dùng sai để ngăn ngừa sự cố) và “dễ làm theo” ở mọi lúc.
- Seiso (清掃 Sạch sẽ): tức là dọn, vệ sinh sạch sẽ hoàn toàn mọi chỗ tại
nơi làm việc để không còn rác, bụi bẩm bám trên sàn nhà, máy móc và
trang thiết bị. Nguyên tắc này đòi hỏi người công nhân luôn phải dọn vệ
sinh sạch sẽ tại khu vực làm việc của họ, kiểm tra máy móc xem có bụi bẩn hay không?
- Seiketsu (清潔 Săn sóc): tức là duy trì tiêu chuẩn cao về giữ gìn vệ sinh
và sắp xếp nơi làm việc gọn gàng vào mọi lúc bằng cách liên tục thực
hiện Seiri, Seiton và Seiso.
- Shitsuke (躾 Sẵn sàng): tức là đào tạo mọi người tự giác làm việc tốt và
luôn tuân thủ 4 nguyên tắc trên tại nơi làm việc. Hoạt động này hướng
tới cấp độ tự phát triển rất cao và không hề dễ dàng.
Chương trình 5S được coi là nền tảng của triết lý Kaizen bởi nó đòi hỏi
sự tham gia của tất cả mọi người trong công ty. Mặt khác, đây là một phương
pháp rất hiệu quả để huy động nguồn lực con người, cải tiến môi trường làm
việc và nâng cao năng suất lao động.
Khi một công ty thực hiện thành công 5S có nghĩa là công ty đó cũng
thành công trong việc nâng cao tinh thần bên trong cũng như bên ngoài. Khi nhà
máy, công ty đã sạch sẽ, ngăn nắp thì mọi nhân viên đều cảm thấy thoải mái khi
làm việc trong một môi trường tốt. Nâng cao tinh thần nội bộ là cơ sở để xây
dựng một công ty, nhà máy hoạt động năng suất cao. Ngoài ra, khi đó họ cũng
sẽ thu hút được khách hàng đến tham quan. Kết quả là công ty sẽ có thêm cơ hội
để bán sản phẩm, dịch vụ cho khách hàng, tăng doanh thu bán hàng, tăng lợi
nhuận. Và môi trường làm việc tốt cũng sẽ thu hút được những nhân viên có
năng lực, nhiệt tình cùng làm việc với họ trong tương lai.
2.2.2 KSS (Kaizen Suggestion System)
Đây là hệ thống khuyến nghị Kaizen, gồm hệ thống tiếp nhận, xử lý, phản
hồi và hỗ trợ thực hiện ý tưởng (phiếu đề xuất ý tưởng, bản tin, hộp thư...), hệ
thống đào tạo tại chỗ (phương pháp não công giải quyết các vấn đề, tư duy sáng
tạo...) và hệ thống quảng bá, xúc tiến, khen thưởng (bản tin Kaizen, Tạp chí
Kaizen,...) tới nhà quản lý, yêu cầu sự tài trợ và chấp thuận từ ban lãnh đạo 14
Downloaded by Van Le (mrl3v4n@gmail.com) lOMoARcPSD|25518217
cũng như sự áp dụng tiếp theo cho mỗi cải tiến của một sản phẩm. Người lao
động sẽ nhận được tiền thưởng hoặc phần thưởng vì đã giúp tiết kiệm chi phí sản xuất sản phẩm.
Hệ thống chỉ dẫn này là một bộ phận quan trọng trong hệ thống quản lý
được xây dựng nhằm hướng dẫn mọi nhân viên thực hiện trong nguyên tắc Kaizen.
2.2.3 QCC (Quality Control Circles)
Nhóm chất lượng là một nhóm nhỏ tình nguyện thực hiện các hoạt động
kiểm soát chất lượng tại nơi làm việc, thực hiện công việc liên tục như một phần
trong chương trình kiểm soát chất lượng toàn công ty, tự phát triển, giáo dục lẫn
nhau và Kaizen trong nơi làm việc.
Với nhiệm vụ tăng cường sự đoàn kết, phối hợp công tác và phát huy sự
chủ động, sáng tạo của người lao động trong các hoạt động cải tiến năng suất
chất lượng, hoạt động của nhóm chất lượng xuất phát từ nhu cầu kiểm soát chất
lượng, chống lãng phí, tăng năng suất... thông qua việc sử dụng các công cụ xác
định và giải quyết vấn đề tồn tại trong tổ chức. Nhóm chất lượng hoạt động trên
tinh thần tự nguyện và dựa trên quan điểm: “Mọi người sẽ quan tâm và tự hào
hơn về công việc nếu họ có quyền tham gia vào việc quyết định đến công việc
hay cách thức tiến hành công việc của mình”.
Nhóm gồm từ 8 đến 10 người, bao gồm các thành viên: nhà tài trợ, hỗ trợ
cho hoạt động của nhóm chính là lãnh đạo công ty; nhóm trưởng; nhân viên thu
thập, xử lý thông tin và các thành viên khác (nhân viên công ty, chuyên gia...).
Nhóm chất lượng được huấn luyện các phương pháp kiểm tra chất lượng, tư duy
sáng tạo, giải quyết vấn đề như phương pháp não công (brainstorming), 6 mũ tư duy (Six Thinking Hat)...
Lợi ích cơ bản của nhóm chất lượng là khai thác khả năng và tiềm tàng to
lớn của người lao động. Ngoài ra, nhóm còn tạo ra môi trường làm việc tốt trên
cơ sở tôn trọng người lao động, đóng góp cho sự phát triển không ngừng của tổ
chức. Thông qua hoạt động Nhóm chất lượng, các thành viên có thể tự xử lý
được những khó khăn vướng mắc trong công việc hàng ngày. Bởi vậy, nhóm
chất lượng là một yếu tố không thể thiếu khi công ty thực hiện phương pháp
quản lý Kaizen. Nhóm chất lượng hoạt động hiệu quả cũng giúp Kaizen được
thực hiện hiệu quả, vì Kaizen là cải tiến liên tục, là nâng cao chất lượng công việc. 2.2.4 JIT (Just In Time)
JIT là một kỹ thuật kiểm soát hàng tồn kho và sản xuất của người Nhật.
Nó là một hệ thống được thiết kế nhằm đạt được chất lượng, chi phí và thời gian
giao hàng tốt nhất của hàng hóa và dịch vụ bằng cách loại trừ các loại lãng phí 15
Downloaded by Van Le (mrl3v4n@gmail.com) lOMoARcPSD|25518217
trong quá trình sản xuất và giao hàng đúng lúc, đáp ứng đầy đủ các yêu cầu của
khách hàng. Đây là một phần trong hệ thống sản xuất của Toyota, được Taiichi
Ohno thiết kế và hoàn thiện tại công ty Toyota, chủ yếu nhằm giảm thiểu lãng
phí khi sản xuất. JIT còn có tên gọi khác là hệ thống sản xuất Toyota, hệ thống
sản xuất tinh gọn và hệ thống kanban.
夃Ā tưởng chính của hệ thống “Just in time” (JIT) có được từ khái niệm của
“hệ thống kéo” từ hệ thống siêu thị Mỹ. Theo đó, mỗi món hàng sẽ được cung
cấp thêm khi mà chúng bắt đầu vơi đi trên kệ. Tại các quốc gia khác, các nhà
công nghiệp luôn sản xuất các bộ phận sản phẩm rồi chất đống trong kho, thùng
chứa nhiều ngày, hàng tháng, gây tốn kém, tăng chi phí bảo quản. Đến khi
khách hàng cần, họ mới tung sản phẩm đã nằm phủ bụi ra thị trường. Trong khi
đó, người Nhật chỉ sản xuất các bộ phận vào “đúng lúc”, đó là khi chúng được
thực sự cần tới. Các bộ phận sẽ được chuyển tới đúng thời điểm mà chúng cần
được sử dụng trong dây chuyền sản xuất.
Hệ thống “Just In Time” (JIT) là một hệ thống sản xuất linh hoạt, có những đặc điểm sau: (1)
Cung cấp cho khách hàng những gì họ muốn, khi nào và số lượng mà khách hàng cần; (2)
Nguyên liệu được cung cấp thêm tùy vào sự tiêu thụ, giảm thiểu công
việc trong quy trình và sự sắp xếp hàng hóa tồn kho nên bạn chỉ phải dự trữ một
khối lượng nhỏ cho mỗi sản phẩm và thường xuyên bổ sung chúng dựa trên
những gì mà khách hàng thật sự lấy đi.
Bởi vậy, đúng thời hạn (JIT) đã được nhiều công ty Nhật cũng như nước
ngoài áp dụng. Kỹ thuật sản xuất này không chỉ tiết kiệm chi phí (nguyên vật
liệu, bảo quản...) mà còn tiết kiệm thời gian. Cách thức sản xuất này cũng nâng
cao tinh thần làm việc của nhân viên vì họ cảm thấy họ lao động bằng trí óc với
sự thông minh khéo léo của mình. Họ có thể thấy được kết quả lao động của
mình – tốt hay xấu – ngay trong quá trình sản xuất của công ty. Nâng cao tinh
thần lao động của nhân viên và giãm lãng phí (thời gian, nguyên liệu, tiền
bạc...) là những lợi ích chính của cách thức sản xuất này trong phương pháp quản lý Kaizen.
2.2.5 Bảy công cụ thống kê
Là các phương pháp thu thập và phân tích dữ liệu làm căn cứ để ra các quyết định, bao
- Lưu đồ (Flow chart) được sử dụng để phác hoạ các hoạt động hoặc các công đoạn tạo 16
Downloaded by Van Le (mrl3v4n@gmail.com) lOMoARcPSD|25518217
ra sản phẩm theo một trình tự nhất định từ lúc tiếp nhận đầu vào đến khi kết thúc quá trình.
- Phiếu kiểm tra (Checksheet) được sử dụng để thu thập, sắp xếp và trình
bày các thông tin/dữ liệu. Các bảng này thường được dùng để đếm các loại lỗi khác nhau.
- Biểu đồ nhân quả (Cause and Effect Diagram) là một công cụ được sử
dụng để biểu thị mối quan hệ giữa đặc tính chất lượng và các nhân tố ảnh
hưởng đến đặc tính đó.
- Biểu đồ Pareto (Pareto Diagram) là một biểu đồ hình cột được sử dụng để
phân loại các nguyên nhân/nhân tố ảnh hưởng có tính đến tầm quan trọng
của chúng đối với sản phẩm. Lợi ích của việc sử dụng biểu đồ Pareto là
phân tích nguyên nhân cần phải tập trung xử lý và chi phí do các nguyên nhân đó gây ra.
- Biểu đồ phân bố (Histogram) được sử dụng để theo dõi sự phân bố của
các thông số của sản phẩm/quá trình và từ đó đánh giá được năng lực của
quá trình đó. Quá trình có đáp ứng được yêu cầu sản xuất sản phẩm hay không?
- Biểu đồ kiểm soát (Control Chart) được sử dụng để theo dõi sự biến động
của các thông số về đặc tính chất lượng của sản phẩm/quá trình.
- Biểu đồ phân tán (Scatter Diagram) được sử dụng để phân tích mối quan
hệ giữa 2 nhân tố. Dựa vào việc phân tích biểu đồ có thể thấy được nhân
tố này phụ thuộc như thế nào vào một nhân tố khác như thế nào và mức
độ phụ thuộc giữa chúng.
=> Khi thực hiện Kaizen, nhà quản lý có thể sử dụng một hay một nhiều công
cụ thống kê để phân tích và giải quyết các khó khăn trong cải tiến chất lượng
sản phẩm. Việc này cũng giúp tìm được nguyên nhân của vấn đề dễ dàng hơn.
II. Tổng quan về Xưởng Gốm Sứ Việt 1. Thông tin doanh nghiệp
- Là trung tâm sản xuất gốm sứ Bát Tràng tại khu công nghiệp làng
nghề truyền thống gốm sứ Bát Tràng.
- Có lịch sử 10 năm phát triển với bước đầu là một phân xưởng sản xuất
gồm 10 công nhân, đến hiện nay đã phát triển thành một trung tâm sản
xuất & thương mại quy mô lớn gồm 4 phân xưởng sản xuất, 2 trung
tâm kinh doanh và hơn 200 cán bộ công nhân viên đang làm việc.
- 4 Phân xưởng sản xuất bao gồm:
• Phân xưởng chế tác gốm sứ.
• Phân xưởng sản xuất decal 17
Downloaded by Van Le (mrl3v4n@gmail.com) lOMoARcPSD|25518217
• Phân xưởng Vẽ vàng.
• Phân xưởng gia công dán decal •
H椃nh 2 Phân xưởng chế tác gốm sứ 18
Downloaded by Van Le (mrl3v4n@gmail.com) lOMoARcPSD|25518217
H椃nh 3 Phân xưởng gia công dán decal
2 Trung tâm kinh doanh bao gồm:
• Trung tâm kinh doanh sản xuất Sứ Việt.
H椃nh 4 Trung tâm kinh doanh sản xuất Sứ Việt 19
Downloaded by Van Le (mrl3v4n@gmail.com) lOMoARcPSD|25518217
• Trung tâm kinh doanh phân phối % bán lẻ Sứ Việt.
H椃nh 5 Trung tâm kinh doanh phân phối % bán lẻ Sứ Việt
5 Mảng sản xuất và kinh doanh cốt lõi của Sứ Việt:
• Chế tác sản xuất các sản phẩm gốm sứ phục vụ thị trường trong
nước và xuất khẩu: Ly cốc sứ, bát đĩa, ấm chén, bình lọ decor, đồ thờ,...
• Sản xuất chế tác decal hoạc tiết lên các sản phẩm gốm sứ.
• Gia công in ấn và vẽ vàng lên các sản phẩm gốm sứ.
• Cung cấp giải pháp quà tặng doanh nghiệp cho các tổ chức, doanh nghiệp lớn.
• Chế tác sản xuất theo yêu cầu cho các đơn hàng xuất khẩu.
- Cung cấp các dịch vụ : • Sản xuất ấm chén. 20
Downloaded by Van Le (mrl3v4n@gmail.com) lOMoARcPSD|25518217
H椃nh 6 Ấm chén Sứ Việt • Sản xuất ly sứ 21
Downloaded by Van Le (mrl3v4n@gmail.com) lOMoARcPSD|25518217
H椃nh 7 Ly sứ Sứ Việt • Sản xuất bát đĩa.
H椃nh 8 Bát đĩa Sứ Việt • Sản xuất đồ thờ. 22
Downloaded by Van Le (mrl3v4n@gmail.com) lOMoARcPSD|25518217
H椃nh 9 Đồ thờ Sứ Việt
H椃nh 10 Các sản phẩm chiến lược của công ty
2. Thông tin về xưởng gia công dán decal Gốm Sứ Việt
- Địa chỉ : Lô A2 KCN Bát Tràng, Gia Lâm, Hà Nội
- Thông tin về diện tích mặt bằng: •
Tổng diện tích mặt bằng của xưởng gồm lô 18, 19 (hình ) : 23
Downloaded by Van Le (mrl3v4n@gmail.com) lOMoARcPSD|25518217 844,45m2 (29,24mx14,44mx2)
H椃nh 11 Diện tích mặt bằng xưởng dán decal •
Diện tích làm việc khu vực dán decal sản phẩm sứ: ~250m2 (chưa bao gồm kho) •
Tổng diện tích làm việc khu vực dán decal sản phẩm sứ: ~500m2 (bao gồm kho) •
Nhân công thuộc xưởng gia công gồm:
+ 4 công nhân được chia thành 2 tổ dán decal.
+ 2 công nhân xếp/dỡ lò. •
Công việc thực hiện: Nhận gia công các loại mặt hàng gốm sứ ( dán decal, nung lửa nhẹ )
3. Quy trình thực hiện công việc
3.1 Quy trình sản xuất chung của doanh nghiệp Gốm Sứ Việt 24
Downloaded by Van Le (mrl3v4n@gmail.com) lOMoARcPSD|25518217
H椃nh 12 Quy tr椃nh sản xuất chung
3.2 Quy trình sản xuất dán decal nhiệt cho sản phẩm gốm sứ
H椃nh 13 Quy tr椃nh sản xuất dán decal nhiệt
4. Thực trạng doanh nghiệp
4.1 Thực trạng về mặt bằng
- Mặt bằng nằm trong dự án chưa tối ưu.
• Mặt bằng kho chưa có sự sắp xếp hiệu quả, phần lớn là sắp xếp tự
phát, không có kế hoạch sắp xếp cụ thể, khoa học. 25
Downloaded by Van Le (mrl3v4n@gmail.com) lOMoARcPSD|25518217
• Quá trình tìm kiếm, lấy hàng sản xuất mất nhiều thời gian.
• Quá trình sản xuất mất thời gian tìm kiếm chỗ để bán thành phẩm.
• Các bán thành phẩm, thành phẩm sắp xếp hỗn loạn, gây rối loạn cho người lao động.
H椃nh 14 Sơ đồ mặt bằng chức năng hiện tại
- Thông tin chi tiết về mặt bằng: (350,3m2)
o Bán thành phẩm chưa sử dụng: 129,57m2
o Bán thành phẩm đang trong sản xuất: 105,05m2 o Thành phẩm: 52,45m2 o Phế phẩm: 28,15m2
o Vỏ, bìa bảo về sản phẩm: 35,08m2
Bảng 1 Thông tin chi tiết mặt bằng trước cải tiến
Theo yêu cầu của Công ty sẽ bổ sung thêm 2 lò hấp, diện
tích kho giảm từ 350,3m2 xuống 250m2 26
Downloaded by Van Le (mrl3v4n@gmail.com) lOMoARcPSD|25518217
Bảng 2 Khảo sát thời gian lấy hàng trước cải tiến
• Tổng thời gian lấy hàng trong 4 tiếng: 9411 giây
• Thời gian trung bình lấy 1 đơn hàng: 235,275 giây
• Thời gian yêu cầu : 210 giây
Thời gian lãng phí: 1194,9 giây.
4.2 Thực trạng công đoạn dán decal
Sau khi quan sát quá trình làm việc của các công nhân tại phân xưởng. Nhóm
nhận thấy rằng ở công đoạn dán decal, các công nhân thường mất rất nhiều thời gian
để căn chỉnh cho vị trí decal không bị lệch. Sản phẩm công ty nhận gia công bao gồm
hàng trong nước và hàng xuất khẩu. Nhiều khách hàng đặt ra những tiệu chuẩn và yêu
cầu khắt khe. Theo số liệu hiện tại, có khoảng 30% đơn hàng yêu cầu dán đúng vị trí
họ chỉ định. Chính vì thế công đoạn này đòi hỏi sự tỷ mỉ và độ chính xác cao. Tuy
nhiên hiện tại công đoạn này ở phân xưởng đang hoàn toàn làm thủ công, không có 27
Downloaded by Van Le (mrl3v4n@gmail.com) lOMoARcPSD|25518217
một công nghệ hộ trợ nào. Việc xác định vị trí của decal hoàn toàn là bằng mắt thường
và cảm quan của người dán, đây có thể xem là một trong những hạn chế mà phân
xưởng cần phải thay đổi.
Trong công đoạn dán Decal có hai thao tác quan trọng chính là dán Decal lên
sản phẩm và căn chỉnh cố định sản phẩm. Trong quá trình quan sát và đo thời gian làm
giữa các công đoạn trong dán Decal, thời gian căn chỉnh cố định tấm Decal lâu hơn so
với thời gian dán Decal ở trên 3 loại sản phẩm Bát Sứ, Chén Sứ và Cốc Sứ.
Hình X.X Biểu đồ thể hiện thời gian giữa các lần đo của các loại sản phẩm
Ở đây nhóm đo 3 loại sản phẩm với mỗi loại sản phẩm là 30 lần đo vào hai
khung giờ làm việc là 8h30 và 15h30. Nhìn vào số liệu có thể thấy thời gian trung
bình để cố định các loại sản phẩm ở 8h30 cao hơn so với 15h30. Điều này có thể giải
thích được do 8h30 là vào lúc đầu ca làm, lúc đấy người công nhân chưa có cảm giác
căn chỉnh nên việc căn chỉnh mất nhiều thời gian hơn. Ta lấy thời gian trung bình giữa
hai khung giờ 8h30 và 15h30 cho từng sản phẩm, ta có so sánh giữa dán và cố định của 3 loại sản phẩm: 10 8 6 4 2 0 Bát sứ Chén sứ Cốc sứ Thời gian dán Decal Thời gian cố định 28
Downloaded by Van Le (mrl3v4n@gmail.com) lOMoARcPSD|25518217
Sau đó ta lấy thời gian trung bình của sản phẩm dán Decal một mặt - Bát sứ và
Chén sứ, thời gian của sản phẩm dán Decal hai mặt – Cốc sứ, ta được kết quả:
Bảng X.X: Bảng phân tích thời gian dán và cố định Decal 1 mặt và 2 mặt
Chỉ tiêu phân tích Kết quả
Thời gian dán Decal 1 mặt 5,00 giây
Thời gian cố định Decal 1 mặt 7,13 giây
Thời gian dán Decal 2 mặt 8 giây
Thời gian cố định Decal 2 mặt 12,15 giây
Kết luận: Khi đo cả ba sản phẩm, ta có thể thấy thời gian cố định Decal chiếm
nhiều thời gian trong công đoạn.
4.3 Thực trạng công đoạn xếp dỡ lò nung lửa nhẹ
Thời gian làm việc của công nhân 7h-12h chiều 14h-17h với 2 công nhân xếp
dỡ và 4 công nhân dán decal.
Thời gian đốt lò là 4 tiếng , thời gian đợi lò hạ nhiệt để dỡ lò là 5 tiếng .
khi bắt đầu ngày làm việc công nhân xếp dỡ phải tắt các lò đã bật từ chiều tối hôm trước.
H椃nh 15 Thực trạng công đoạn xếp lò 29
Downloaded by Van Le (mrl3v4n@gmail.com) lOMoARcPSD|25518217 Thời gian dỡ lò (phút) Ngày 1 37.5 Ngày 2 40.33 Ngày 3 39 Ngày 4 39.33 Ngày 5 34 Trung bình 38.03
Bảng 3 Thời gian dỡ lò (phút) Thời gian xếp lò (phút) Ngày 1 130.67 Ngày 2 124.67 Ngày 3 140 Ngày 4 121.33 Ngày 5 129 Trung bình 129.13
Bảng 4 Thời gian xếp lò (phút)
Trung bình theo thực tế thời gian dỡ lò là 38.03 phút ( dao dộng từ 33’ - 45’ )
và thời gian trung bình xếp lò là 129,13’ ( dao động từ 110’ - 152’ ) người công nhân
xếp dỡ xếp được lò nào thì sẽ bật luôn lò đó.
Thời gian dỡ lò có sự chênh lệch như vậy thường là do vào khoảng thời gian
gần trưa hoặc mới bắt đầu ca làm thì nhân viên còn chưa được tập trung.
Các lò đo được là 1 lò khoảng 300 bộ ấm chén với 2000 sản phẩm trong 1 lò
với 28 khay, 1 khay 72 cốc.
Thời gian thực tế người công nhân xếp trung bình từ 110p – 120p ( Trung bình 115p ) 30
Downloaded by Van Le (mrl3v4n@gmail.com) lOMoARcPSD|25518217
Theo thực trạng hiện nay xưởng đốt 3 trên 4 lò do không có nhiều đơn hàng và nhân viên làm còn chậm.
Với năng suất trong 5 ngày đo được tính theo sản phẩm đã hoàn thành là 12.75 ( sản phẩm / 1 phút ).
- Với nhân viên xếp dỡ khi mang sản phẩm và lò để xếp còn bỏ ra nhiều sức như
thế làm ảnh hưởng đến năng suất xếp lò không những thế với một số đỡ đặt
hàng cốc dán 2 mặt người công nhân xếp dỡ còn phải đợi chờ công nhân dán decal.
H椃nh 16 Thực trạng đợi dán decal
- Với nhân viên dán decal trong khi dán cần phải căn chỉnh tỷ mỉ với độ chính
xác cao chưa có các phương pháp để giúp đỡ người công nhân dán ( họ chỉ dựa
vào kinh nghiệm để chỉnh dẫn đến chậm và có khi ảnh hưởng đến chất lượng sản phẩm.
- Thời gian chờ lò nguội và chờ dán decal trung bình gần 20p. 4.4 Các thực trạng khác
- Công nhân chưa quen việc thay đổi.
• Người lao động chưa thích nghi được với cách thưc làm việc mới.
• Người lao động có xu hướng quay lại làm việc theo phương thức cũ.
• Việc này ảnh hưởng đến quy trình sản xuất khi làm việc không đúng chỗ.
• Làm quá trình sản xuất bị gián đoạn do dòng bán thành phẩm di
chuyển bị chậm lại ở khu vực sai vị trí. - Quản lý chưa sát sao.
• Quản lý chưa nắm được các phương thức sản xuất mới.
• Quản lý chưa nhận ra lợi ích khi thay đổi phương thức sản xuất mới.
• Người quản lý chưa có sự thay đổi, làm gương cho người lao động.
• Cơ chế quản lý, tính lương theo ngày, chưa có cơ chế tính lương thưởng theo sản phẩm. 31
Downloaded by Van Le (mrl3v4n@gmail.com) lOMoARcPSD|25518217
- Chưa tối ưu được thời gian sử dụng lò.
• Thời gian sử dụng lò trung bình 8-10 tiếng/ngày.
• Người lao động chưa quen với thao tác
- Chất hàng, dỡ hàng trong lò hấp chiếm nhiều thời gian.
• Thao tác chất, dỡ hàng trong lò theo chồng, chiếc riêng lẻ, mất nhiều
thời gian và nhân công để thực hiện công việc
• Số lượng, chủng loại sản phẩm tương đối lớn, khó đồng bộ thao tác trên quy mô công nghiệp.
• Khối lượng tấm đỡ lớn, gây khó khăn trong việc chất, dỡ hàng.
• Thời gian lao động trong khu vực lò có nhiệt độ cao kéo dài làm ảnh
hưởng đến sức khỏe của người lao động.
- Sắp xếp tủ đồ chưa gọn gàng.
• Công cụ để lộn xộn, người lao động mất nhiều thời gian để tìm được
công cụ sản xuất thích hợp.
• Thiếu công cụ thích hợp với từng sản phẩm khác nhau.
5. Xác định điểm cải tiến và thực hiện cải tiến 5.1 Cải tiến mặt bằng (*) Sau khi cải tiến:
H椃nh 17 Sơ đồ mặt bằng sau cải tiến 32
Downloaded by Van Le (mrl3v4n@gmail.com) lOMoARcPSD|25518217
Bảng 5 Thông tin chi tiết mặt bằng sau cải tiến
- Thông tin chi tiết về mặt bằng: (250 m2)
o Bán thành phẩm chưa sử dụng: 87,5m2
o Bán thành phẩm đang trong sản xuất: 75m2 o Thành phẩm: 50m2 o Phế phẩm: 12,5m2
o Vỏ, bìa bảo về sản phẩm: 25m2
Bảng 6 Khảo sát thời gian lấy hàng sau cải tiến
• Tổng thời gian lấy hàng trong 4 tiếng: 8437,2 giây
• Thời gian trung bình lấy 1 đơn hàng: 210,93 giây
• Thời gian yêu cầu : 210 giây
Thời gian lãng phí: 96,2 giây.
Giảm thời gian lãng phí 1098,7 giây ~7,63% thời gian lấy hàng
5.2 Cải tiến công đoạn dán decal
Nhận thấy được sự hạn chế của công đoạn dán decal, nhóm đã tìm hiểu
và đề xuất một số giải pháp để khắc phục những yếu điểm đó, nhằm tối ưu được
thời gian của công đoạn này.
5.2.1 Đối với sản phẩm có kích thước bé và hình dáng đơn giản.
Đối với các sản phẩm có kích thước nhỏ, có hình dáng đơn giản sẽ tận
dụng đường giới hạn trên của decal để làm thước căn chỉnh vị trí dán. 33
Downloaded by Van Le (mrl3v4n@gmail.com) lOMoARcPSD|25518217
Hiện tại các decal sau khi được nhập về công nhân sẽ dùng kéo cắt thành
từng dải, sau đó sẽ ngâm decal trong nước một thời gian để decal phân tách khỏi
lớp giấy kèm. Tùy vào kích thước của chi tiết decal sẽ được cắt theo kích cỡ đó.
Công nhân ở công đoạn dán sẽ dùng tay dán các decal này lên vị trí sản phẩm.
H椃nh 18 Decal khi chưa in viền rộng hơn 34
Downloaded by Van Le (mrl3v4n@gmail.com) lOMoARcPSD|25518217
Để công nhân có thể chính xác hơn trong việc xác định vị trí dán, thay vì
chỉ in vừa theo chi tiết sẽ in rộng hơn và tận dụng đường giới hạn của decal để
căn chỉnh. Sao cho đường giới hạn của decal sẽ trùng với mép trên của sản
phẩm, điều này sẽ khắc phục tình trạng lệch lên trên hoặc xuống dưới. Đồng
thời cũng giảm thời gian thao tác của công nhân. Hạn chế của giải pháp này là
chỉ áp dụng đc với các sản phẩm có kích thước bé, đối với sản phẩm kích thước
lớn, phần in thừa sẽ tốn kém chi phí và không mang lại hiệu quả kinh tế.
H椃nh 19 Decal trước cải tiến
H椃nh 20 Decal sau cải tiến 35
Downloaded by Van Le (mrl3v4n@gmail.com) lOMoARcPSD|25518217
Để kiểm chứng hiệu quả của giải pháp này, nhóm tiến hành thử nghiệm để thu thập kết quả.
- Sản phẩm thử nghiệm: chén sứ
- Yêu cầu: Dán một mặt, 1 deacl/ 1 sản phẩm
- Số lượng/ lần đo : 10 - Số lần đo : 10
Sau khi tiến hành tiến thử nghiệm thử và đo đạc thì nhóm thu được kết quả như sau :
Bảng 7 Số liệu thu thập từ 10 lần đo đối với sản phẩm Bát sứ trắng
Thời gian gia công trung bình trước và sau khi cải tiến là 120s và 90,7s.
So với ban đầu thời gian gia công trung bình đã giảm 29,3s tương đương 24,33%.
Thực hiện phương pháp đo tương tự đối với một số sản phẩm khác nhóm thu được kết quả sau:
Bảng 8 Số liệu thua thập từ 10 lần đo đối với sản phẩm chén sứ trắng, dán 1 chi tiết 36
Downloaded by Van Le (mrl3v4n@gmail.com) lOMoARcPSD|25518217
Bảng 9 Số liệu thu thập từ 10 lần đo đối với sản phẩm cốc sứ trắng, dán 2 chi tiết
Đối với sản phẩm chén sứ trắng dán 1 chi tiết thời gian gia công giảm
22.84 %, đối với cốc sứ giảm dán 2 chi tiết giảm 18.09% cả hai lần đo đều thu
được kết quả nhỏ hơn so với sản phầm bát sứ nhưng ở cả hai đều cho thấy có
sự thay đổi rõ rệt từ trước và sau khi thực hiện cải tiến. Ta có công thức sau: Công suất Thời gian làm việc/ngày dán decal = Thời gian gia công/SP
Sau khi tiến hành đo đạc trên 3 sản phẩm khác nhau nhóm thu được giá
trị thời gian gia công giảm lần lượt là 24,33%, 22,84% và 18,09% . Lấy trung
bình kết quả ba lần đo là 22,26 %, đồng nghĩa công suất làm việc sẽ tăng 22,26 %.
Con số này phần nào đã giải quyết được bài toán: phân xưởng chỉ nhận
tối đa 60% đơn hàng vào đợt cao điểm.
- Tính toán chi phí và doanh thu:
Bảng 10 Bảng chi phí và doanh thu 37
Downloaded by Van Le (mrl3v4n@gmail.com) lOMoARcPSD|25518217
Đối với chi phí tăng lên khi công ty áp dụng phương án in viền rộng hơn
là 20 đồng/ decal. Tổng số sản phẩm trung bình công ty nhận gia công một ngày
là 8000 sản phẩm. Cùng với một số dữ liệu nhóm thu thập được đã tính toán các
chi phí và doanh thu khi áp dụng phương án như bảng trên. Kết quả tính toán
cho thấy đối với 3 sản phẩm doanh thu tăng lên trong một ngày lần lượt là
209.568 đồng, 199.808 đồng, 142.664 đồng. Tương đương một ngày tổng giá trị
doanh thu công ty tăng lên khi áp dụng phương án này là 551.040 đồng.
Thử nghiệm trên mục đích chính là chứng minh có sự thay đổi năng suất
khi sử dụng phương án đã đề xuất. Trong thực tế, tại phân xưởng có nhiều mẫu
loại khác nhau, tuy thuộc vào đặc điểm của mỗi sản phẩm sẽ có kết quả khác
nhau. Ngoài ra, mẫu mã và yêu cầu cũng sẽ thay đổi theo từng đơn hàng tùy thuộc khách hàng.
5.2.2 Đối với các sản phẩm có kích thước lớn, hình dạng phức tạp.
Sản phẩm của phân xưởng nhận đa công rất đa dạng, từ kích cỡ đến mẫu
loại. Với những sản phẩm có kích thước lớn và hình dạng phức tạp nếu áp dụng
phương pháp trên là không khả thi. Tìm hiểu và tham khảo các công nghệ đã áp
dụng trong ngành nhóm có ý tưởng sử dụng sự hỗ của tia laser để xác định điểm
chuẩn. Cách thức chung: Sử dụng tia laser xác định vị trí trên sản phẩm, đặt
decal được đánh dấu lên sản phẩm theo vị trí đã được xác định. Căn chỉnh để
điểm đánh dấu trên decal trùng khớp với vị trí đã được xác định trên sản phẩm.
a. Các yêu cầu cần thực hiện:
- Thiết kế rá đỡ linh hoạt và có thể điều chỉnh để cố định được nhiều loại
sản phẩm. Mỗi lần thực hiện với 1 loại sản phẩm sẽ điều chỉnh gá phù
hợp để giữ cố định sản phẩm không bị lệch.
- Sử dụng tia laser chiếu sáng vào sản phẩm để xác định vị trí cần dán decal.
- Dán decal đã được đánh dấu lên sản phẩm , nếu điểm đánh dấu trùng với tia laser, đạt yêu cầu.
b. Các yêu cầu về vật liệu:
- Tia laser: Tia laser phải chiếu được góc nhìn linh hoạt, tùy vào mỗi lần
làm việc, công nhân sẽ tùy chỉnh để phù hợp với từng sản phẩm. Thứ hai
là ánh sáng phải an toàn, không có hại cho mắt, không gây lóa hay mỏi mắt cho công nhân.
Theo tiêu chuẩn mới về mức độ an toàn của laser ANSI Z136.1,Hiệp hội
Quang học Hoa Kỳ (American National Standards Institute - ANSI). mức độ an
toàn của laser được phân thành 4 cấp chính: Cấp 1 và cấp 1M, cấp 2 và cấp 2M,
Cấp 3R và cấp 3B và cấp 4. Trong đó chỉ có cấp 1 và cấp 1M là được chứng
nhận là an toàn không gây nguy hiểm cho mắt. Tiêu chuẩn này đặt ra các giới 38
Downloaded by Van Le (mrl3v4n@gmail.com) lOMoARcPSD|25518217
hạn an toàn cho mắt dựa trên bước sóng và công suất của laser. Theo đó, các
giới hạn an toàn cho mắt với tia laser có bước sóng từ 1.4 µm đến 2 µm. H椃nh 21 Tia laser
- Hợp chất sử dụng để đánh dấu trên decal:
Để không bị ảnh hưởng đến chất lượng decal các hợp chất sử dụng đánh
dấu phải là hợp chất thường được sử dụng trong in ấn decal. Thứ hai, hợp chất
phải bị mất màu khi nung ở nhiệt độ của lò. Đây là yêu tố rất quan trọng, nếu
trong quá trình hấp màu của các dấu không bị bay màu sẽ ảnh hưởng đến hình
ảnh họa tiết trên decal, làm mất đi tính thẩm mỹ. Và cuối cùng là giá thành hợp
lý. Mục đích lớn nhất của tất cả các doanh nghiệp là lợi nhuận, nếu phương án
đưa ra không khả thi về tính kinh tế, nó sẽ không được triển khai. - Về gá đỡ:
Thiết kế được gá đỡ cố định giữ chắc sản phẩm nhưng phải linh hoạt để
công nhân thao tác nhanh trong quá trình thay thế sản phẩm khác vào gá. Đối
với mỗi loại sản phẩm công nhân sẽ điều chỉnh gá đỡ và góc chiếu của tia laser
phù hợp. Trong quá trình làm việc, các sản phẩm sẽ lần lượt được đưa vào gá
và thay ra liên tục, chính vì thế sự linh hoạt của gá đỡ là vô cùng quan trọng. Mô hình minh họa: 39
Downloaded by Van Le (mrl3v4n@gmail.com) lOMoARcPSD|25518217
H椃nh 22 Bản vẽ mô h椃nh gá đỡ và tia laser
H椃nh 23 Cấu tạo bên trong gá đỡ 40
Downloaded by Van Le (mrl3v4n@gmail.com) lOMoARcPSD|25518217 c
H椃nh 24 B椃nh sứ khi chiếu tia laser và decal được đánh dấu 41
Downloaded by Van Le (mrl3v4n@gmail.com) lOMoARcPSD|25518217
H椃nh 25 Ví trí decal đạt yêu cầu
Hiện tại, phương pháp được nhóm đưa ra vẫn đang là phương án đề xuất,
chưa được triển khai thử nghiệm trên sản phẩm thực tế. Nhưng xét về tính thực
tiễn phương án có khả thi.
Với một sản phẩm hiện tại công nhân lành nghề đòi hỏi phải mất từ 10-15 phút
để hoàn thiện, tùy thuộc vào độ phức tạp của sản phẩm và chất lượng decal. Nếu triển
khai phương án này dự tính có thể giảm thời gian xuống 5-6 phút/ sản phẩm.
5.3 Cải tiến công đoạn xếp, dỡ lò nung lửa nhẹ Các giải pháp :
- Đầu tư kệ xếp đồ chi phí 6,8 triệu ( trong đó chi phí giá bánh xe là 2 triệu và
chi phí kệ xếp đồ là 4,8 triệu ) độ bền trung bình là 5 năm để giúp đỡ công nhân
xếp dỡ thuận tiện không mất thời gian bê lên xe và giảm thời gian để lấy sản
phẩm xếp lên lò giảm nguy cơ rơi vỡ sản phẩm và những vấn đề về chất lượng
sản phẩm như bị nứt và bị xước ở sản phẩm gốm sứ. 42
Downloaded by Van Le (mrl3v4n@gmail.com) lOMoARcPSD|25518217
H椃nh 26 H椃nh ảnh thực tế kệ xếp đồ
Hình ảnh thực tế về kệ xếp đồ
- Đầu tư mua tấm thép chịu nhiệt ( với chi phí 2,5 tr giảm được 40kwh =50k giá
điện công nghiệp và vấn đề quan trọng nhất là giảm được hơn 60 phút thời gian chờ lò
H椃nh 27 Tấm thép được xuất xứ từ Trung Quốc
Hình ảnh về tấm thép được xuất xứ từ Trung Quốc
=> Dự kiến : giảm thời gian xếp là 20 phút và thời gian dỡ lò 3 phút.
- Thời gian làm nhanh hơn 5 tiếng 15 phút tính theo số liệu 5 ngày đo được và
năng suất dự kiến 14,21 sản phẩm / phút tăng hơn 11 % 43
Downloaded by Van Le (mrl3v4n@gmail.com) lOMoARcPSD|25518217
Bảng 11 Bảng so sánh trước và sau khi có xe nâng và tấm thép (trong 5 ngày thực tế)
Thời gian hoàn vốn khi đầu tư là hơn 2 năm
Vào thời gian cao điểm
Với dịp lễ tết với công suất max của xưởng thì xưởng chỉ đốt được 6 lần /4 lò
cho nên vì năng lực sản xuất như vậy xưởng chỉ nhận 60% / 100 % đơn đặt hàng ( 4
nhân viên xếp dỡ và 8 nhân viên dán và có khi làm đến hơn 10h đêm ) -
Vấn đề lớn nhất của xưởng hiện tại là năng lực của lò ( bởi vì điện cung cấp để
bật lò chỉ tối đa đáp ứng được cho cùng lúc 2 lò ) -
Khi đầu tư thêm xe nâng tay và tấm thép thì sẽ giảm được tiền thuê thêm công
nhân xếp dỡ và thời gian hạ nhiệt đã giảm hơn 60 phút => xưởng sẽ đốt được
8 lò /1 ngày đáp ứng được 80% đơn đặt hàng -
xưởng có ý định muốn mở thêm 2 lò và như vậy cần đăng kí thêm nguồn điện
kinh doanh 3 pha chi phí khoảng 15-20 triệu đồng => giảm được thời gian thuê
nhân công ngoài giờ làm việc ( ca đêm ) và có thể đáp ứng được 100 % đơn
hàng với tổng chi phí 2 lò mới là 500 triệu đồng -
Sơ đồ mặt bằng chức năng dự định trong tương lai :
• Sản phẩm được vận chuyển đến kho tập kết ban đầu.
• Thời gian chuẩn bị để người công nhân xếp chỉ mất 45 phút
• Sản phẩm được đưa đến khu vực làm việc; đến xe đẩy hàng
• Bán thành phẩm được đưa vào lò hấp
• Sản phẩm được để nguội, kiểm tra chất lượng và lưu kho
• Đóng gói, hoàn thiện sản phẩm
• Xuất sản phẩm ra khỏi kho 44
Downloaded by Van Le (mrl3v4n@gmail.com) lOMoARcPSD|25518217
H椃nh 28 Mô phỏng mặt bằng xưởng trong tương lai 45
Downloaded by Van Le (mrl3v4n@gmail.com) lOMoARcPSD|25518217
H椃nh 29 Sơ đồ 2 lò mới khi có đường ray
H椃nh 30 Ví dụ thực tế về lò có đường ray 46
Downloaded by Van Le (mrl3v4n@gmail.com) lOMoARcPSD|25518217
Bảng 12 Dự kiến thời gian hoàn vốn khi đầu tư thêm lò có đường ray Dự kiến - Dỡ lò 30 phút - Xếp lò : 40-60 phút -
Lợi nhuận 1 lò ước tính là 900 nghìn đồng - 1 ngày đốt được 4 lò -
4 tháng cao điểm trong năm -
Số ngày làm việc trong tháng cao điểm là 28 ngày
=> Thời gian hoàn vốn khi đầu tư thêm lò có đường ray là hơn 1 năm. KẾT LUẬN Chỉ tiêu đánh
Trước cải tiến Sau cải tiến Tăng giảm (± %) giá Thời gian dán cố 6,00 5,00 - 16,7% định 1 sản phẩm/1 mặt (giây) Thời gian cố 15 6 - 60% định áp dụng tia Laser (phút) Thời gian dán cố 12,15 9,82 - 19,2% định 1 sản phẩm/2 mặt (giây) 47
Downloaded by Van Le (mrl3v4n@gmail.com) lOMoARcPSD|25518217 Chỉ tiêu đánh
Chi phí đầu tư Dự kiến thu hồi Thời gian hoàn vốn giá (năm)
Phương án giảm 336.800.000 155.400.000 2,17 thời gian chờ lò (đồng) Phương án xây 520.000.000 403.200.000 1,3 thêm 2 lò mới (đồng)
Thông qua phân tích thực trạng tại xưởng gia công decal công ty gốm Sứ Việt,
nhóm chúng em đã đưa ra một số giải pháp và đề xuất cải tiến nhằm tăng cường
năng suất và cải thiện hiệu quả sản xuất thông qua việc giảm thiểu thời gian cố
định decal và giảm thiểu thời gian chờ lò.
Một trong những vấn đề mà xưởng gặp phải là thời gian cố định decal. Quá
trình này đã tốn nhiều thời gian và công sức, dẫn đến việc làm chậm quá trình
sản xuất tổng thể. Bằng cách tận dụng đường giới hạn của các miếng decal và
áp dụng công nghệ tia laser, thời gian cố định có thể được giảm thiểu, giúp quá
trình này diễn ra nhanh chóng và hiệu quả hơn.
Ngoài ra, thời gian chờ lò cũng là một vấn đề đáng kể mà chúng em đã tập trung
giải quyết. Việc chờ đợi trong quá trình sản xuất đôi khi gây ra sự gián đoạn và
gây tổn hại đáng kể cho năng suất. Tuy nhiên, thông qua việc đầu tư các tấm
thép và kệ xếp đồ cũng như đề xuất xây thêm 2 lò mới với hệ thống đường ray,
chúng em hướng việc giảm thiểu thời gian chờ và nâng cao năng suất chung của xưởng.
Những đề xuất và giải pháp trên không chỉ có thể giúp xưởng cải thiện năng
suất mà còn giúp tăng tính cạnh tranh và đáp ứng nhanh chóng nhu cầu của thị
trường. Sự tối ưu hóa quy trình và sắp xếp mặt bằng một cách hiệu quả cũng có
tiềm năng lớn trong việc nâng cao hiệu suất sản xuất. 48
Downloaded by Van Le (mrl3v4n@gmail.com)