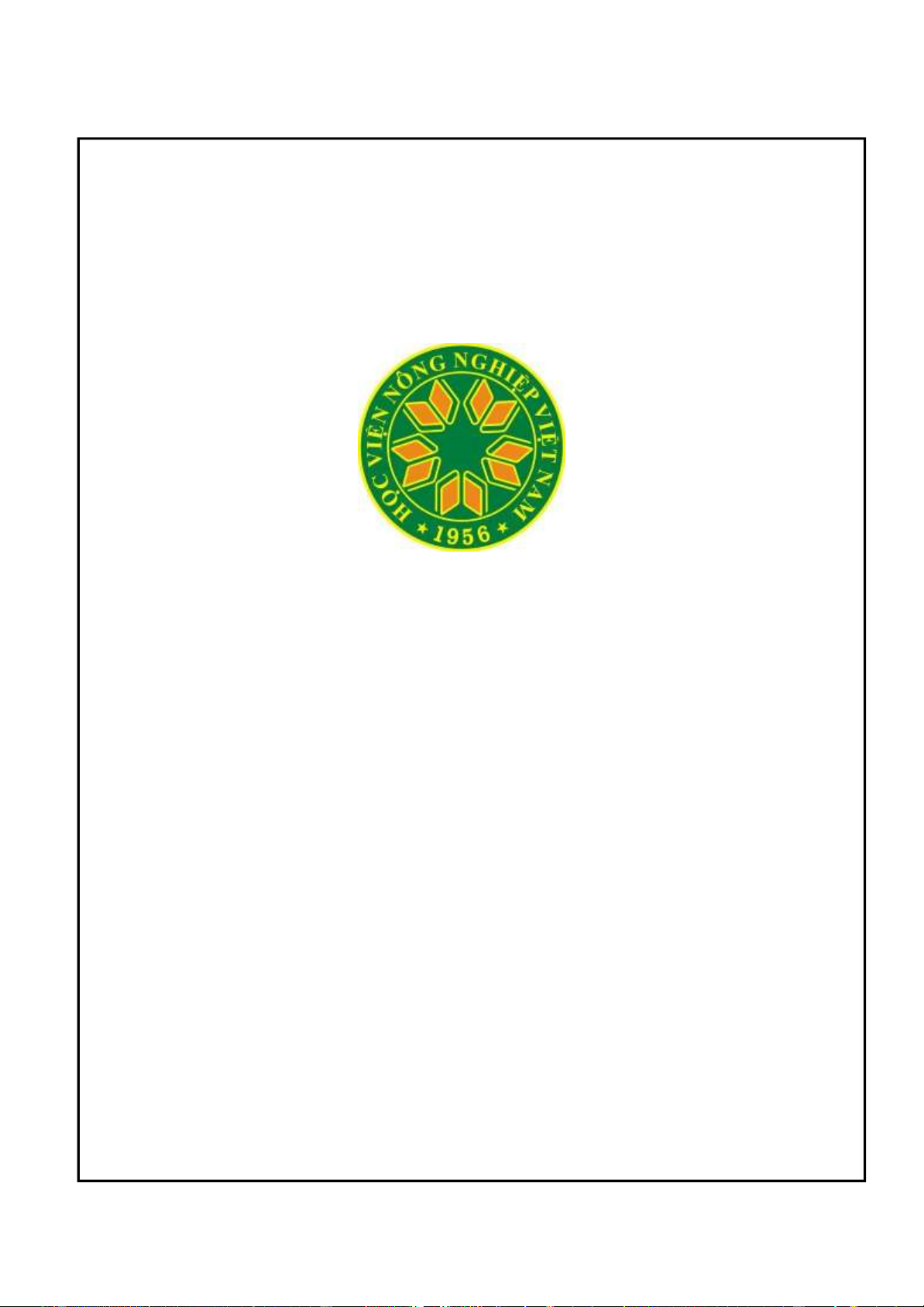
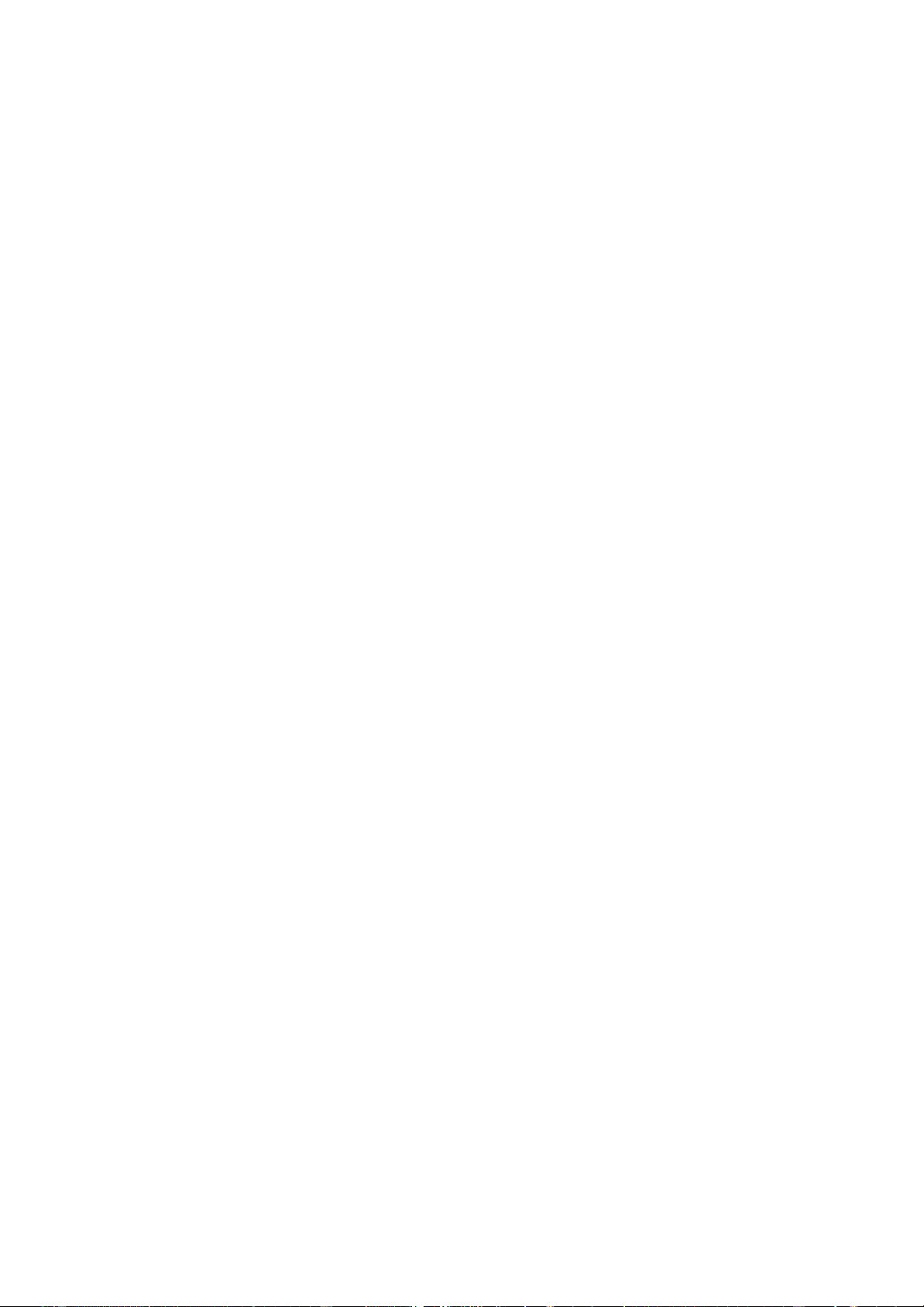
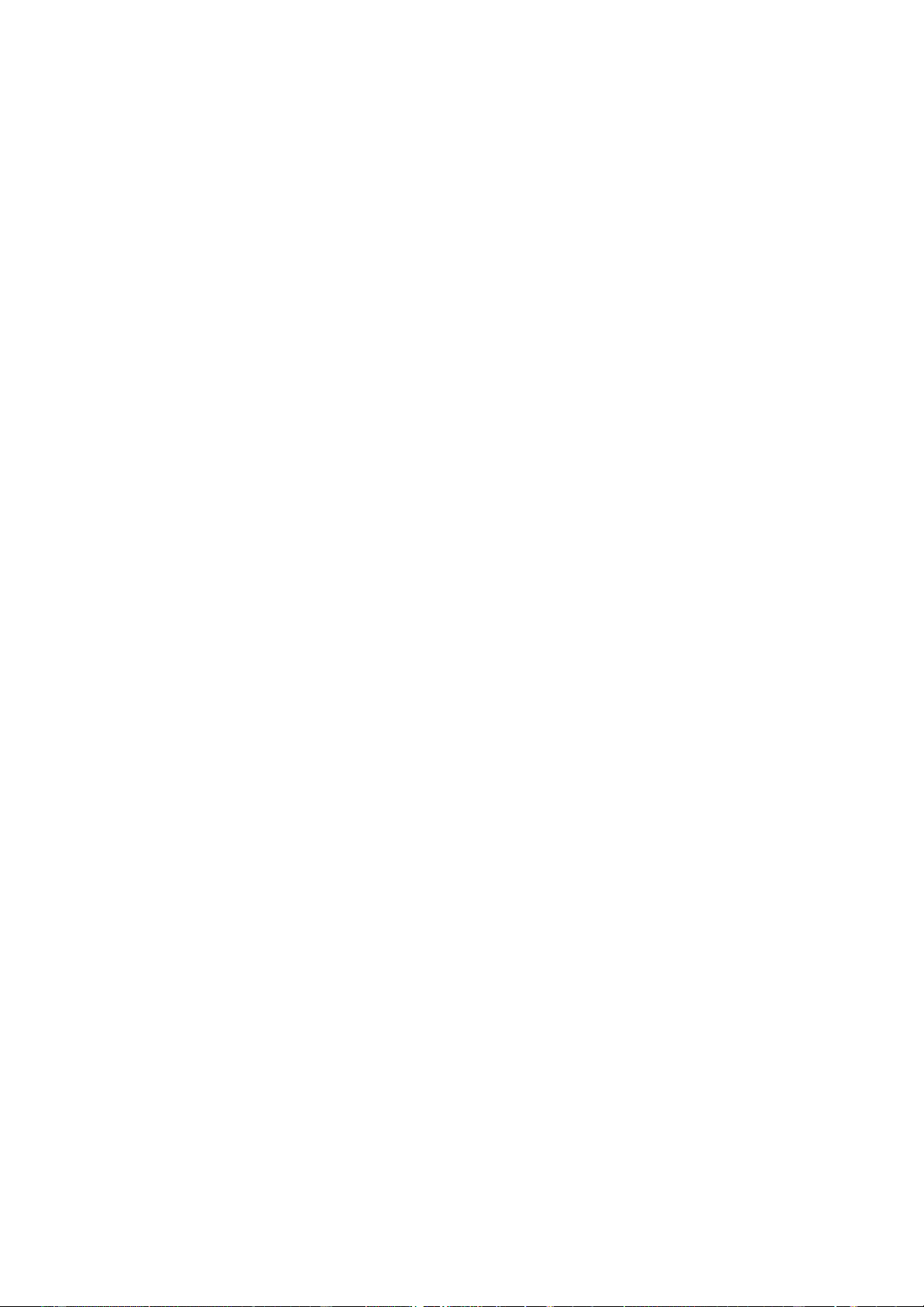
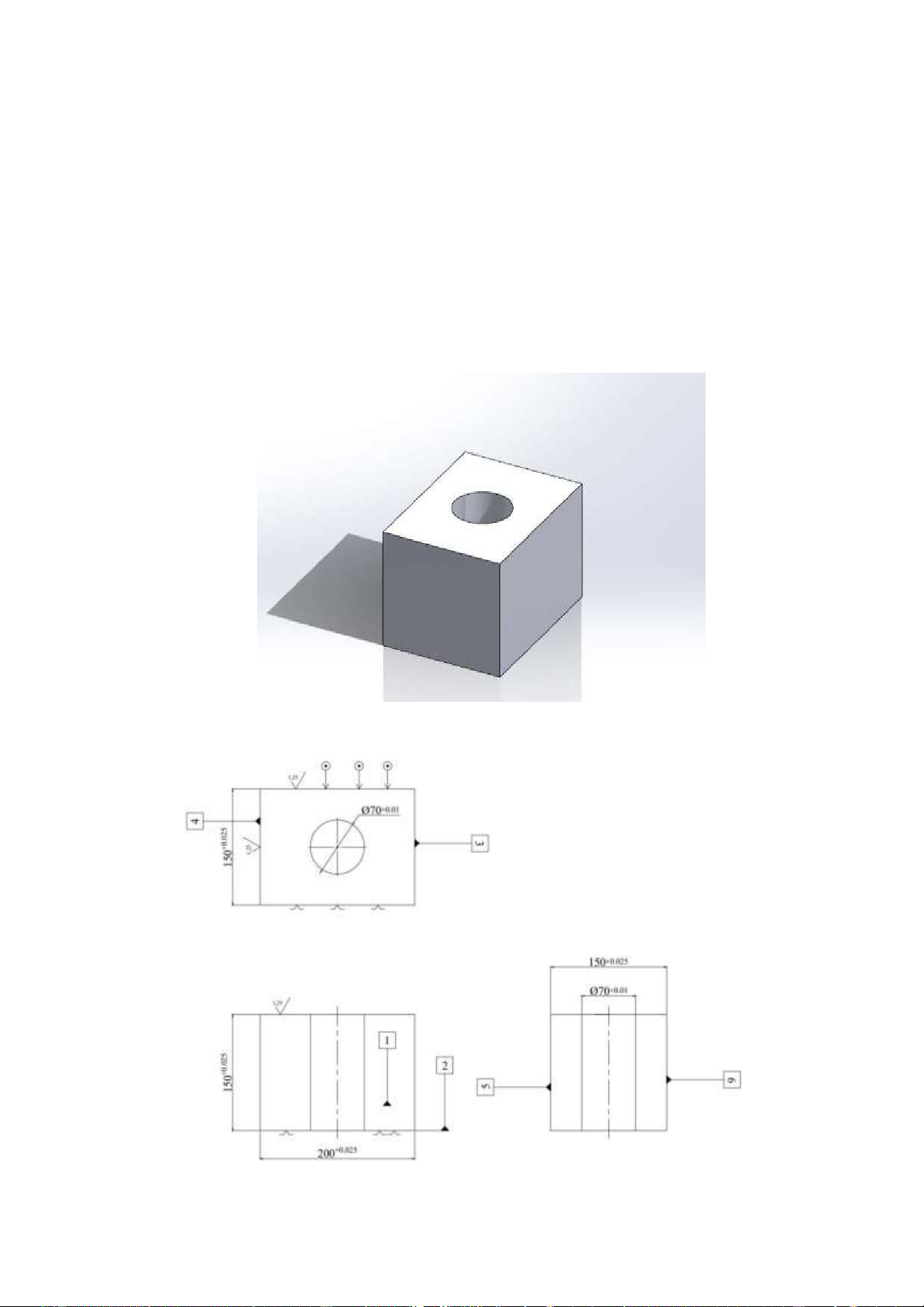
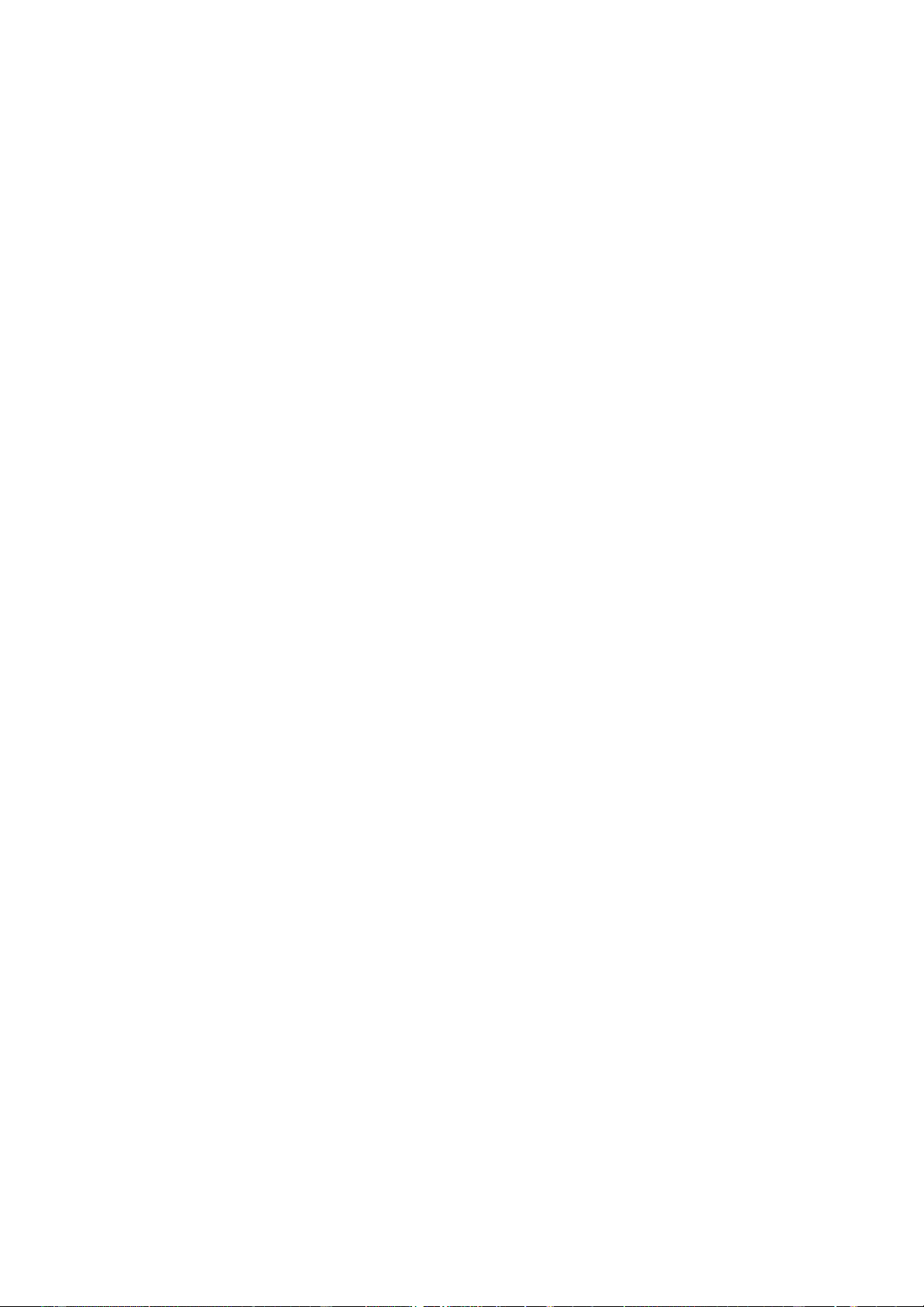
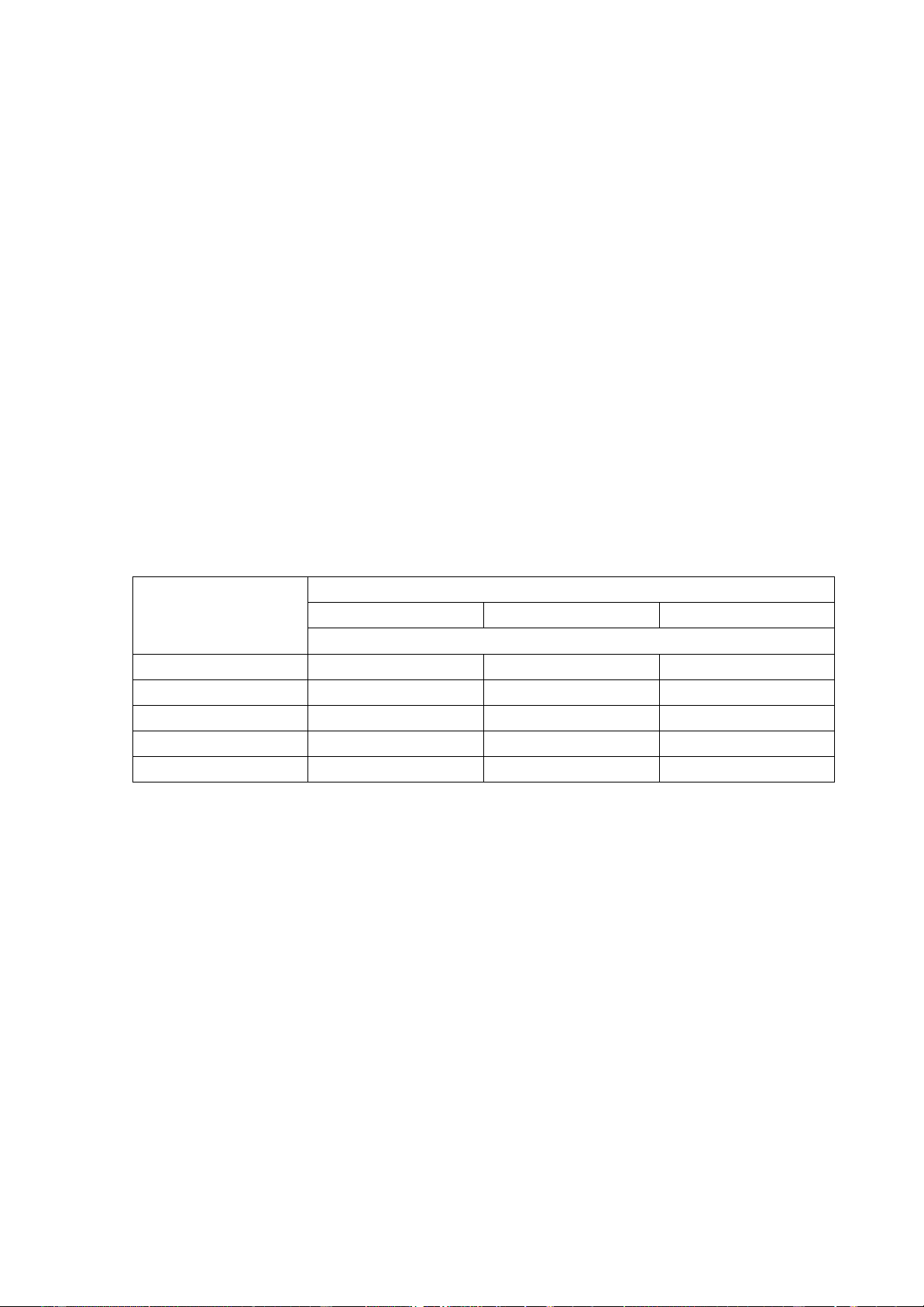
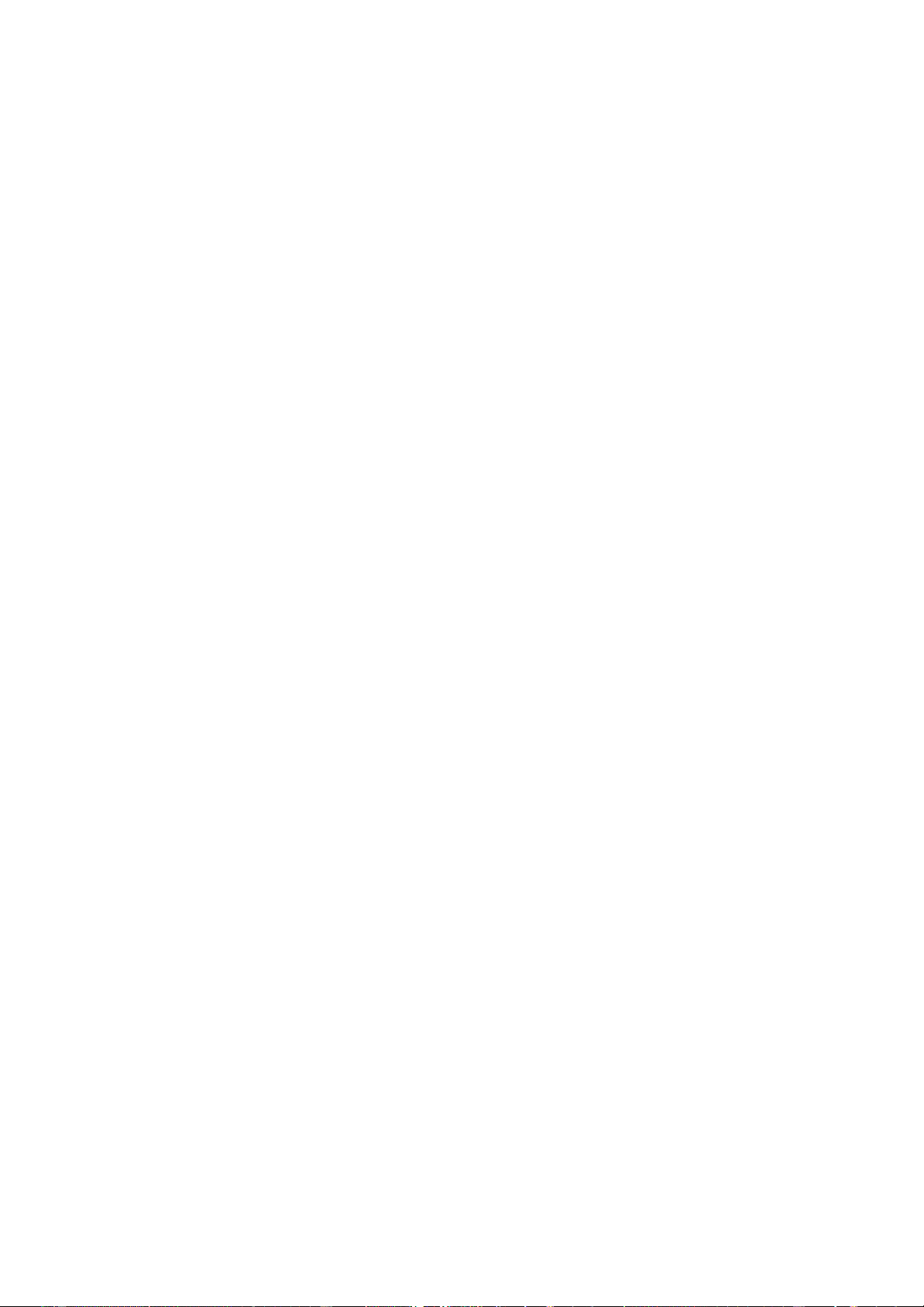
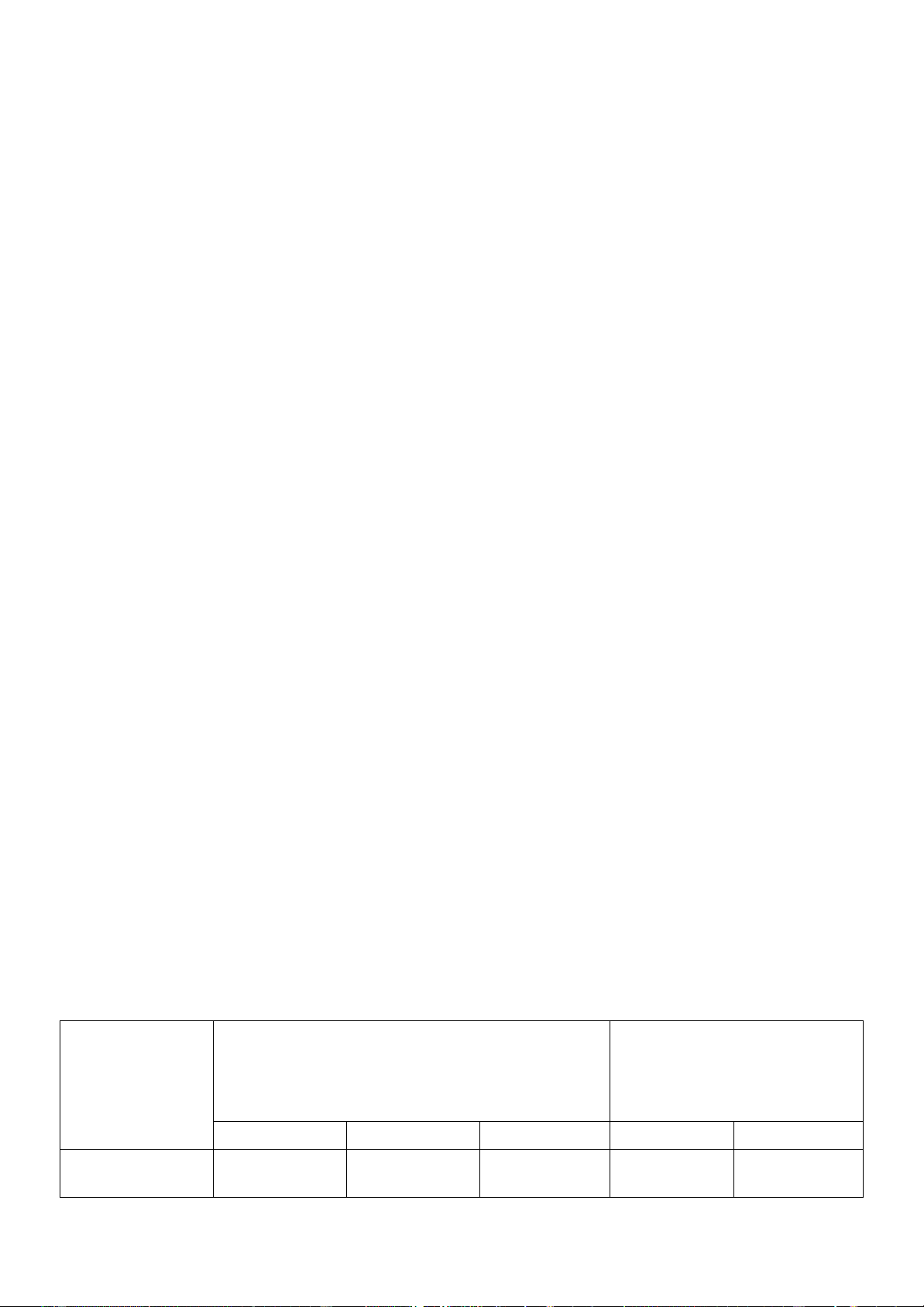
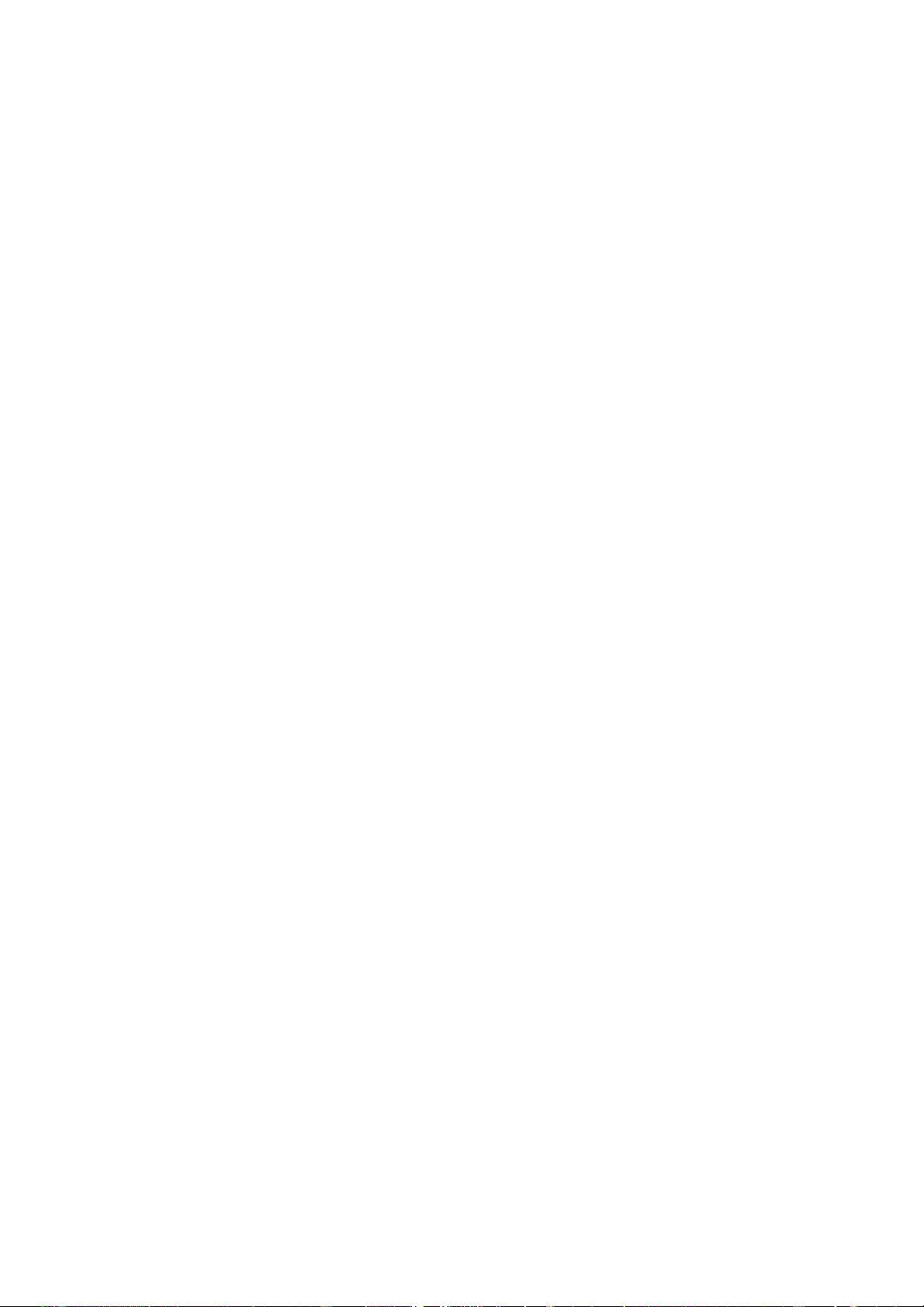
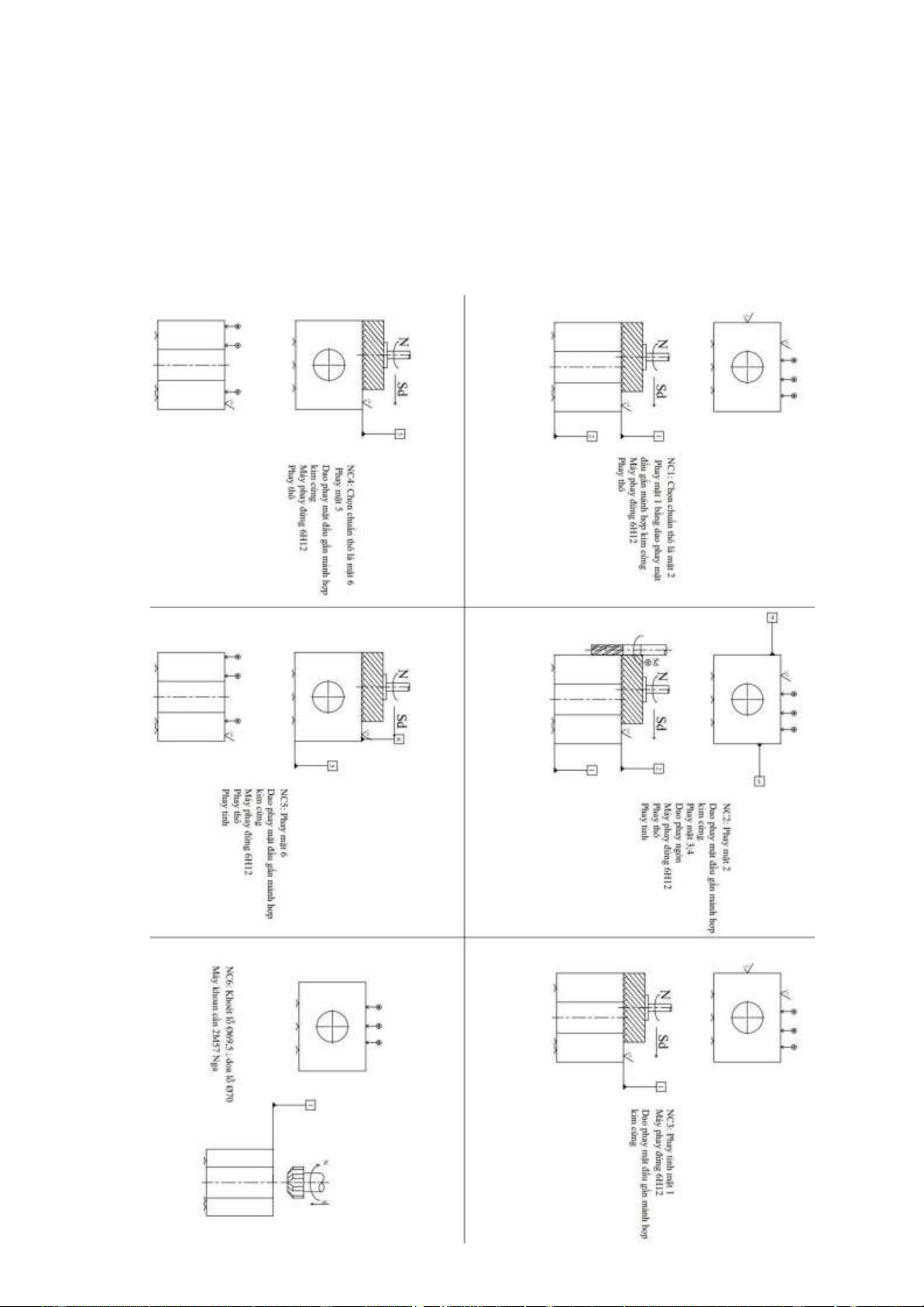
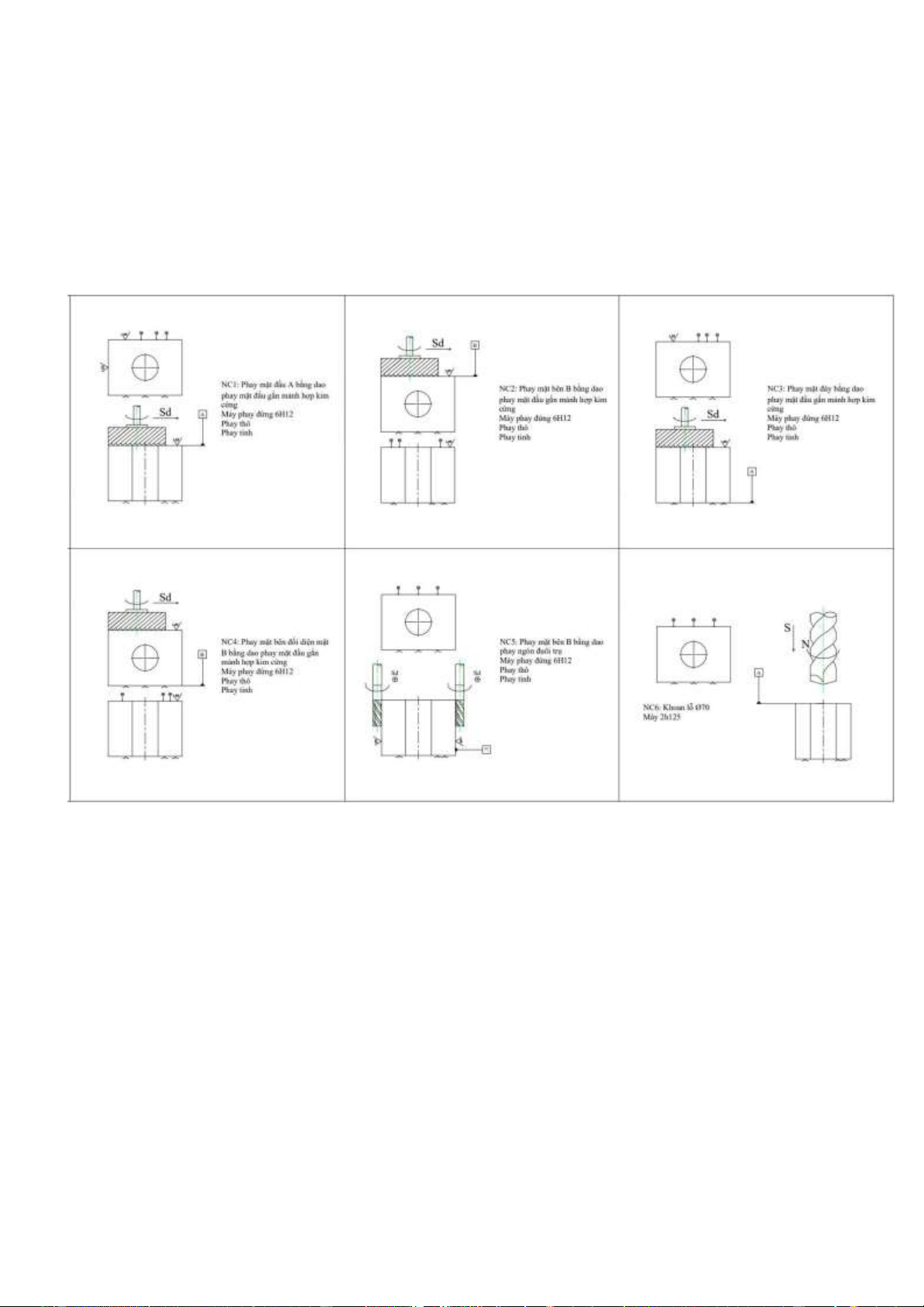
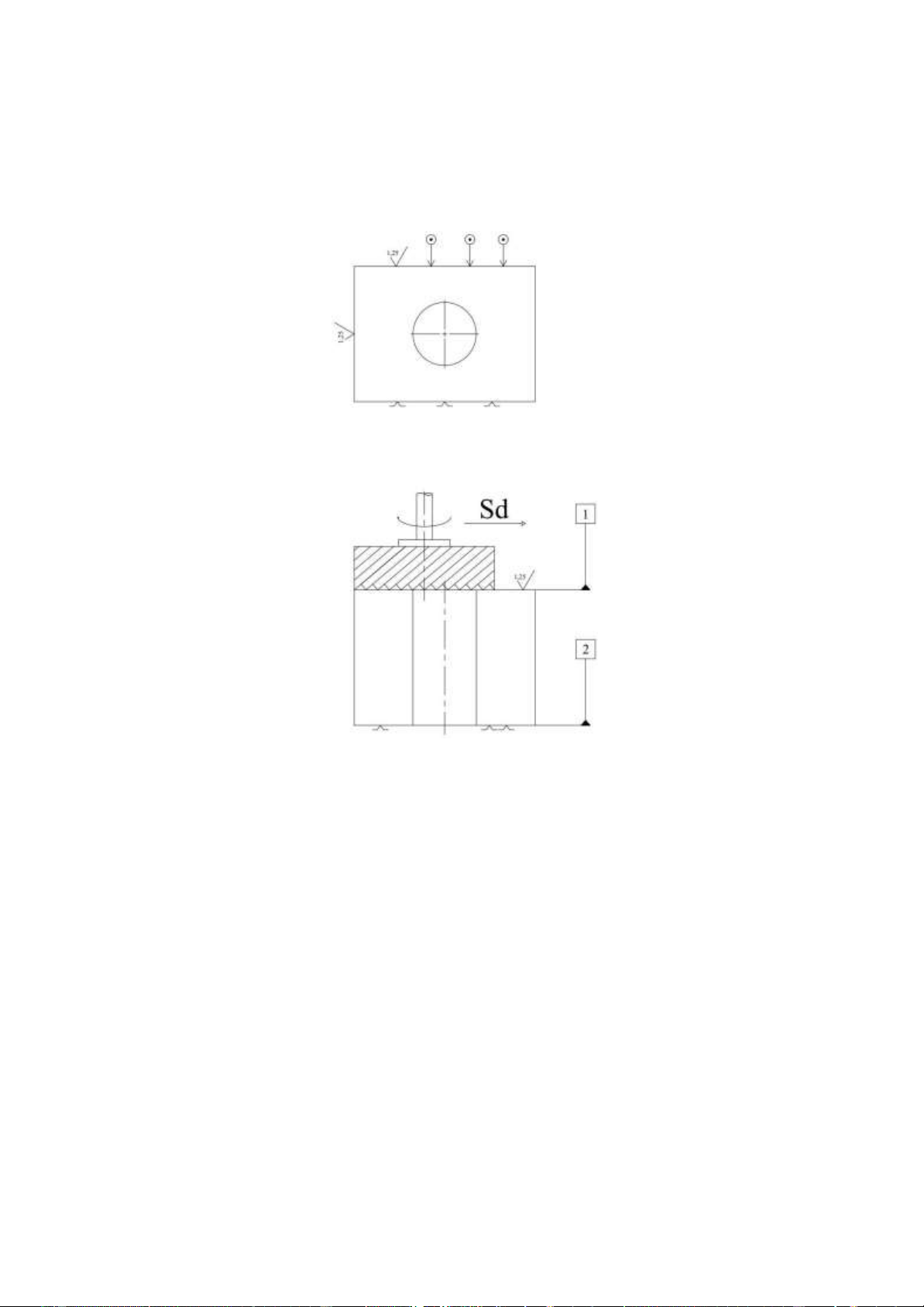
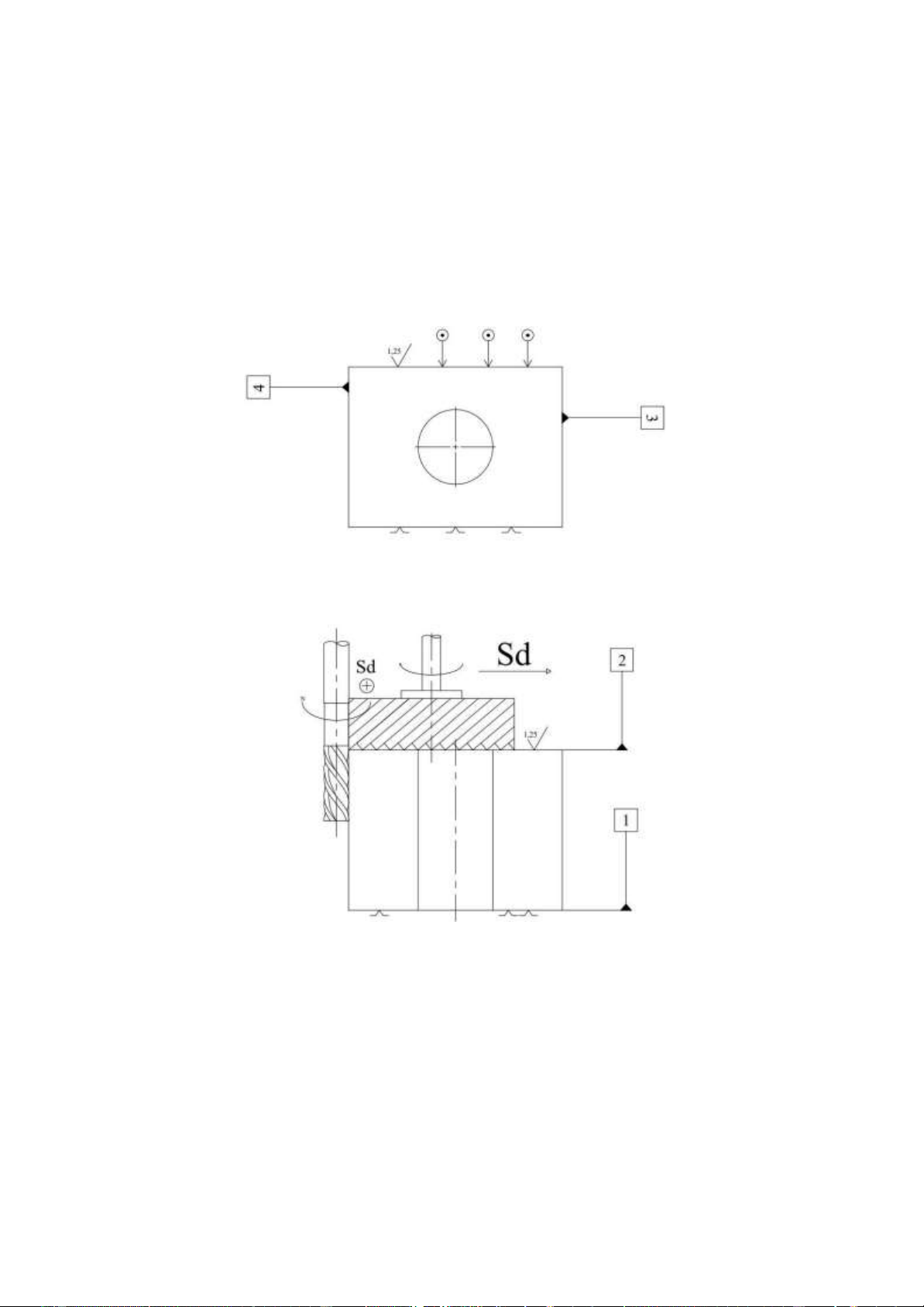
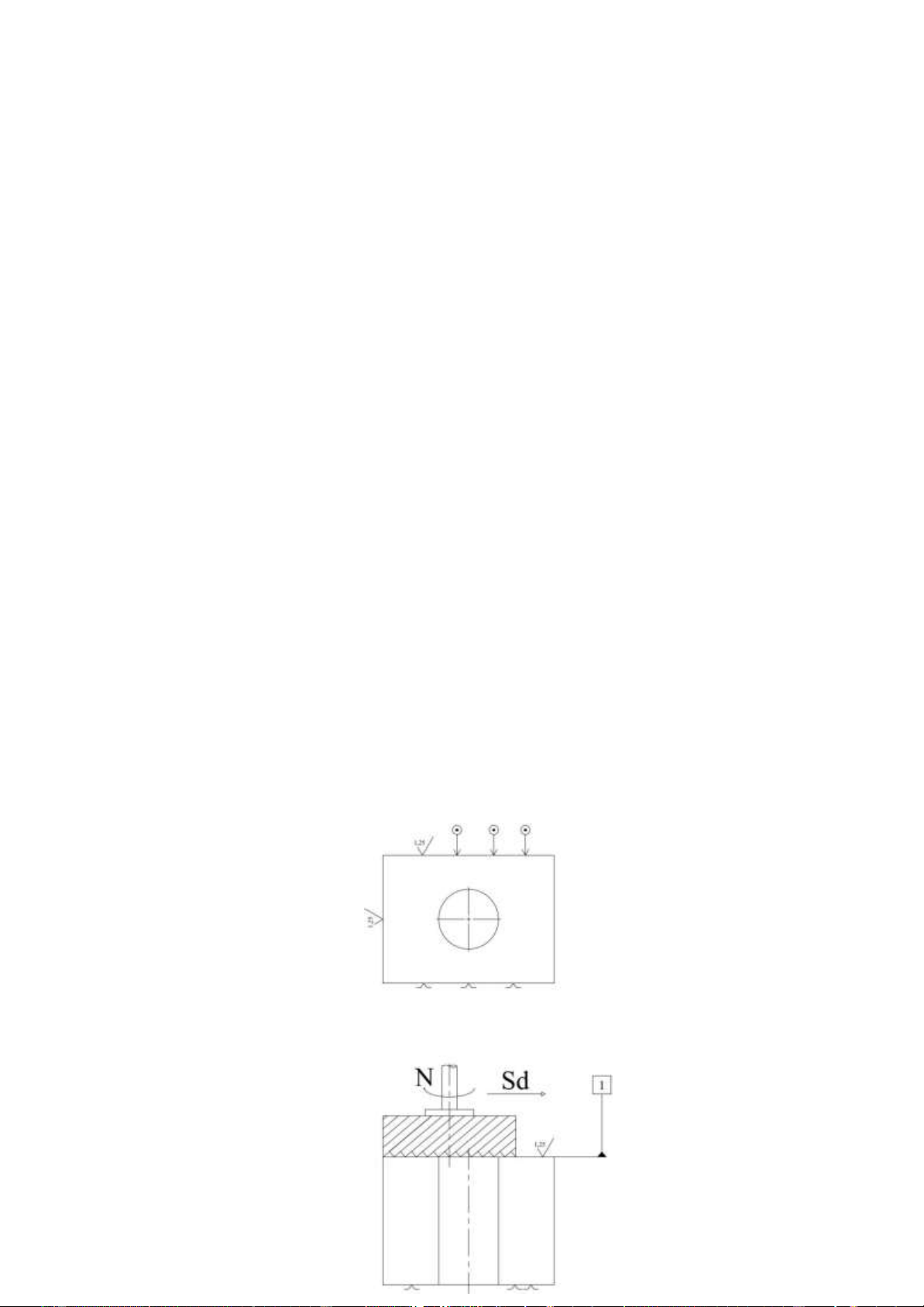
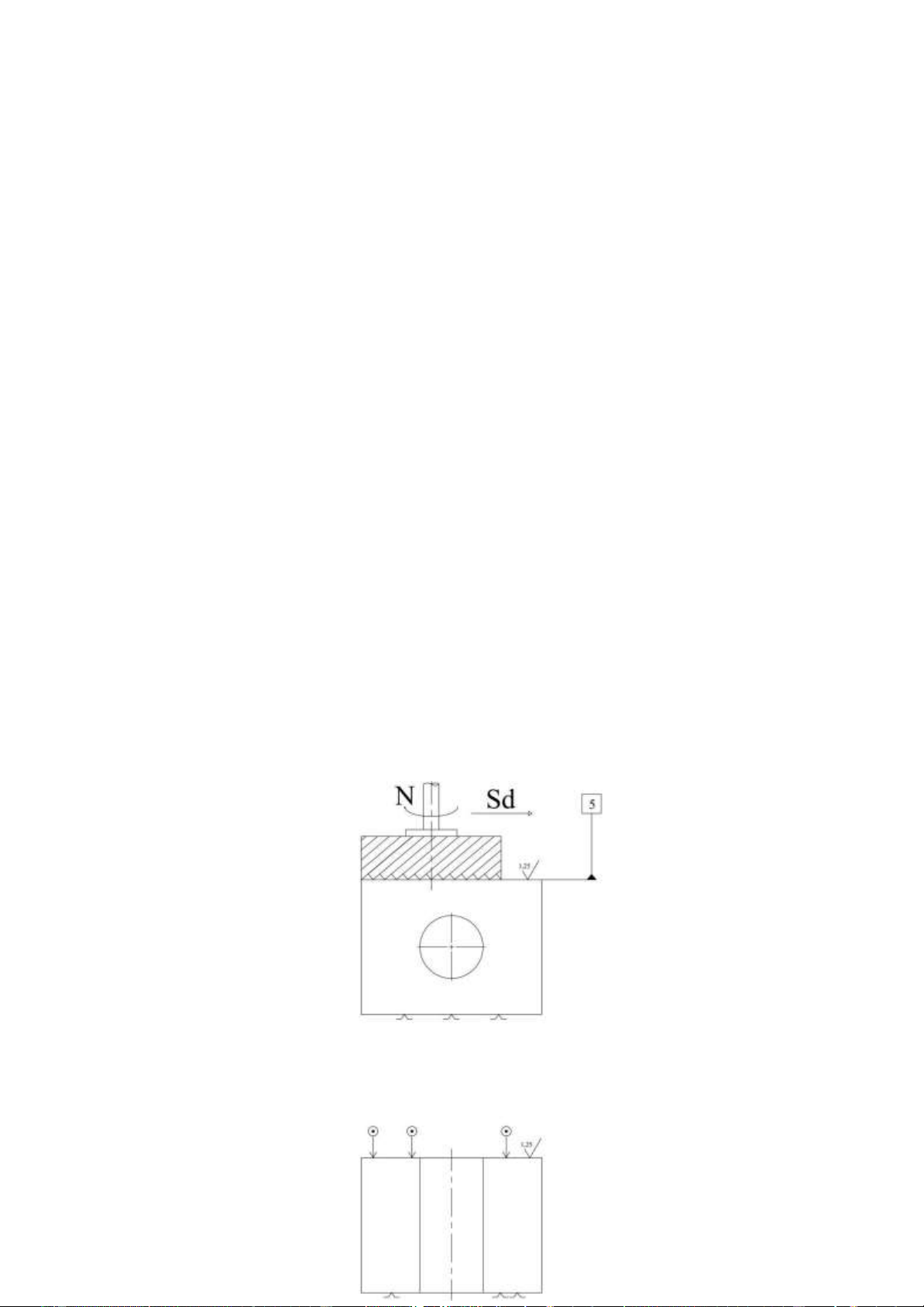
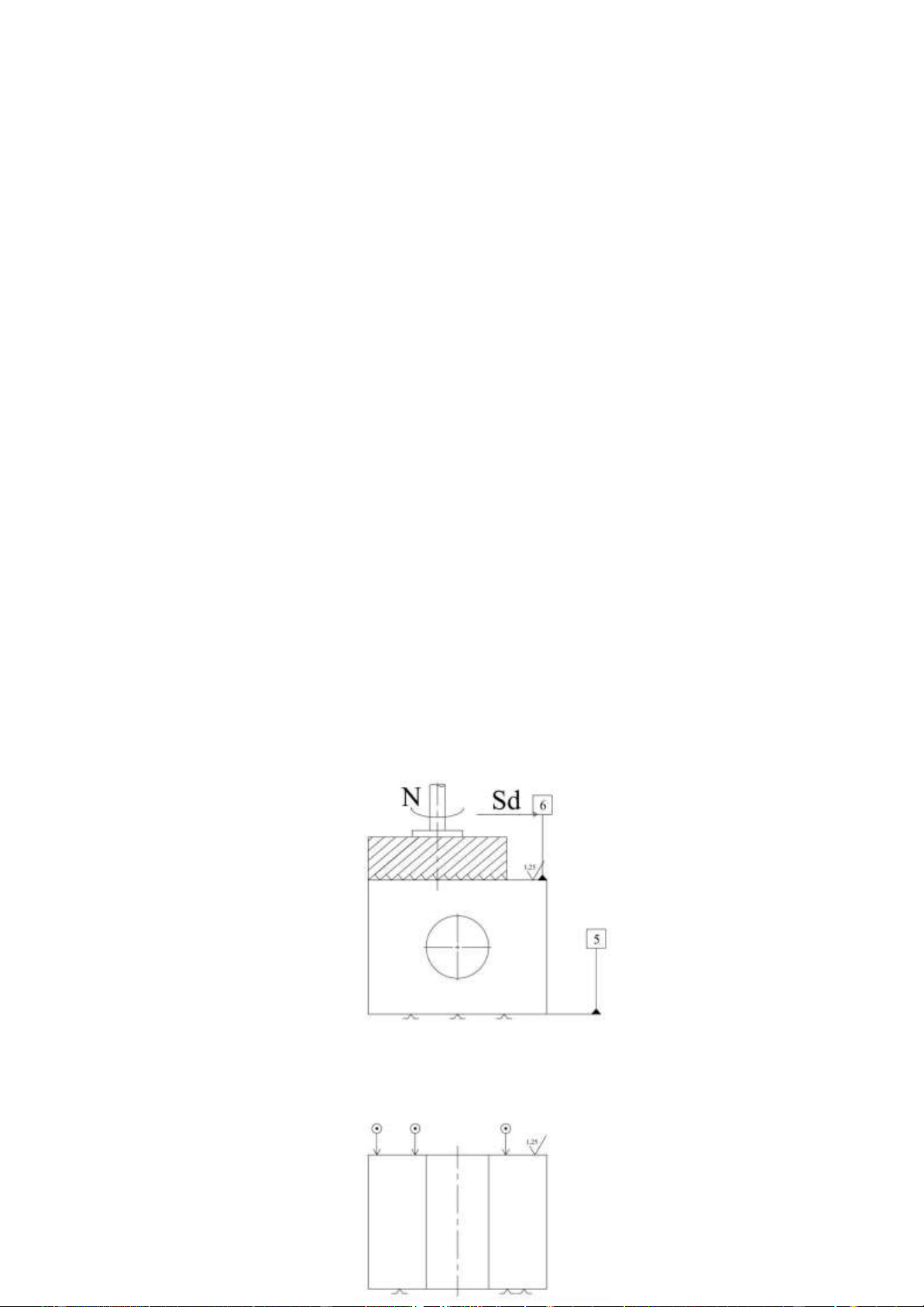
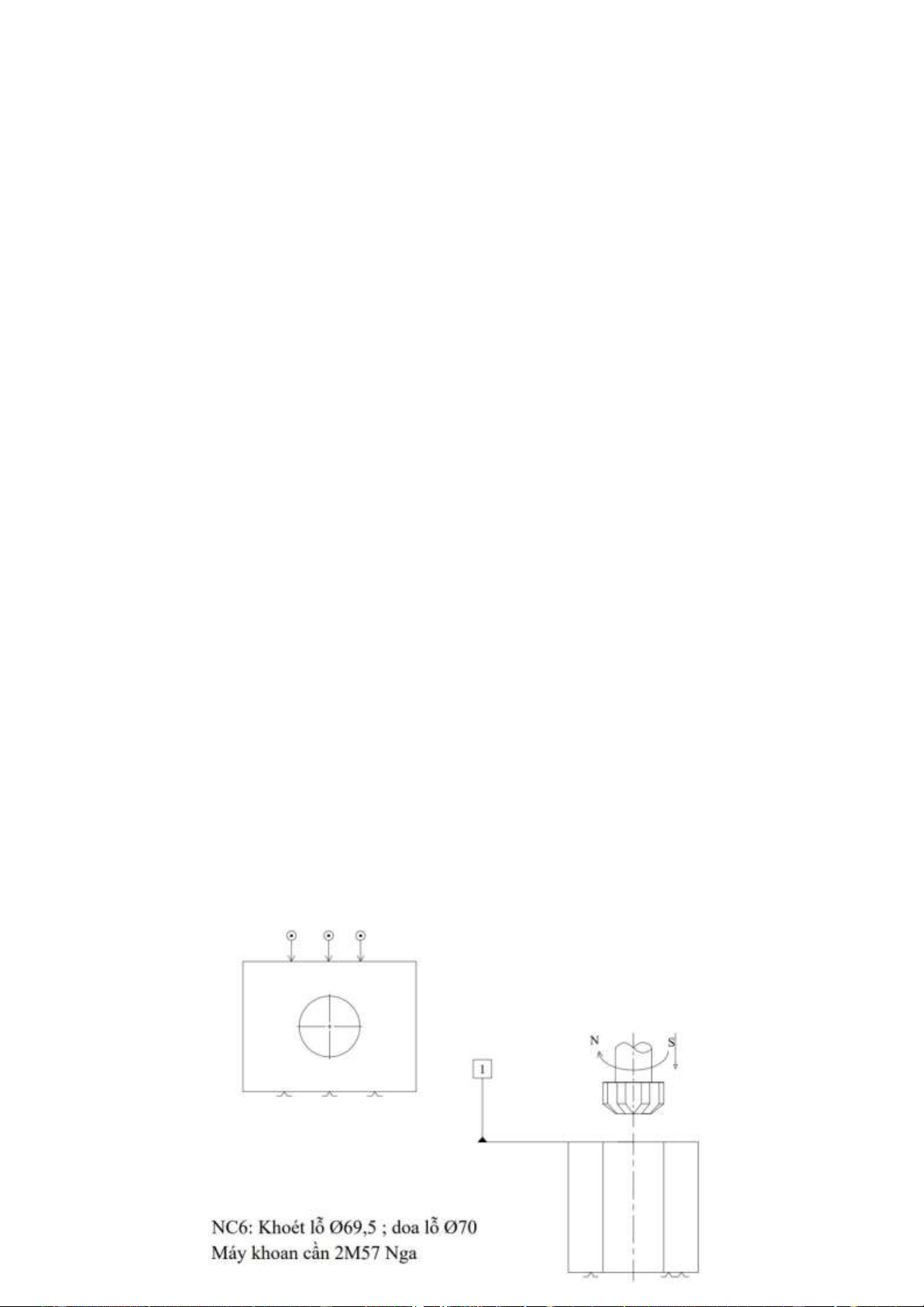
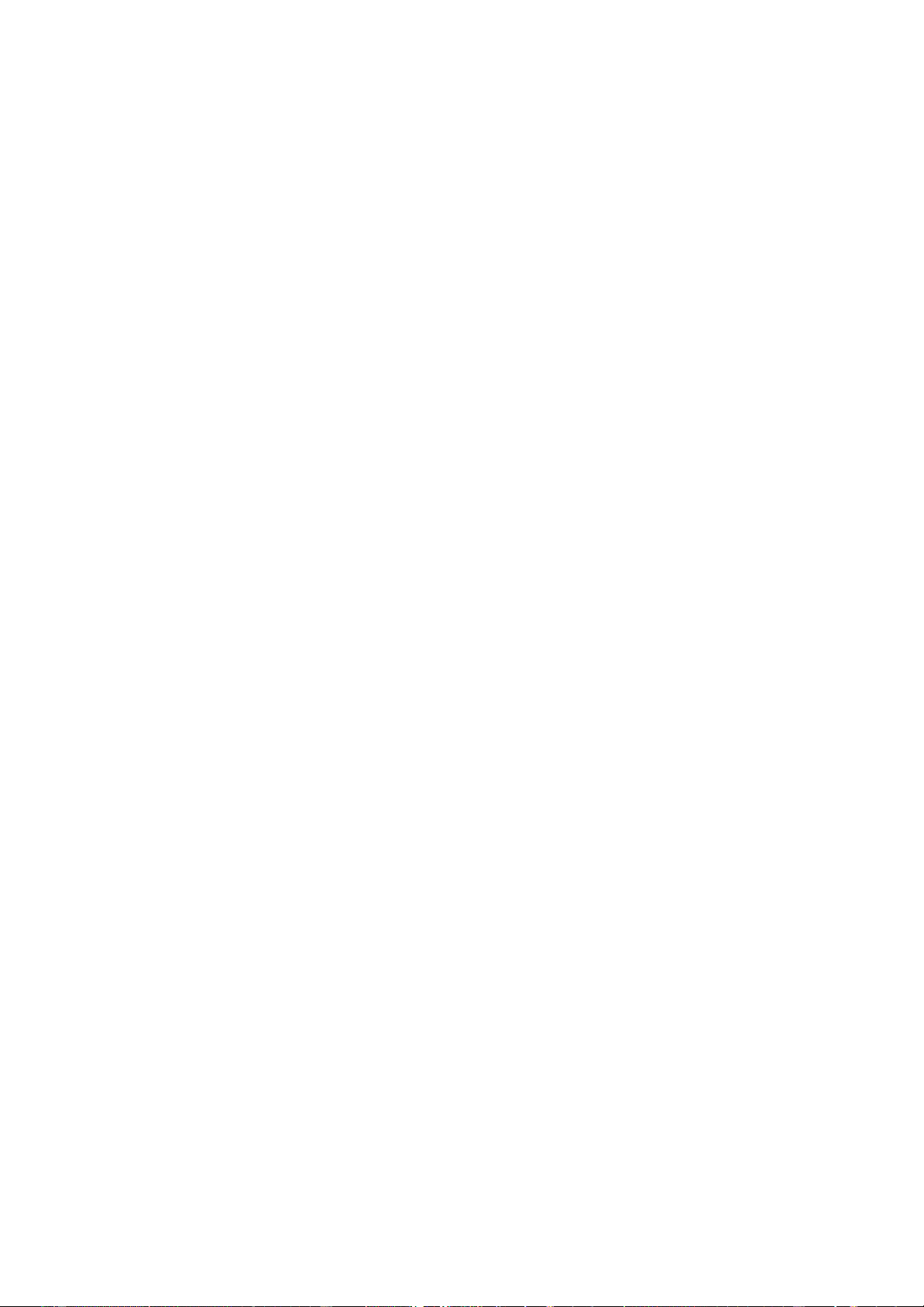
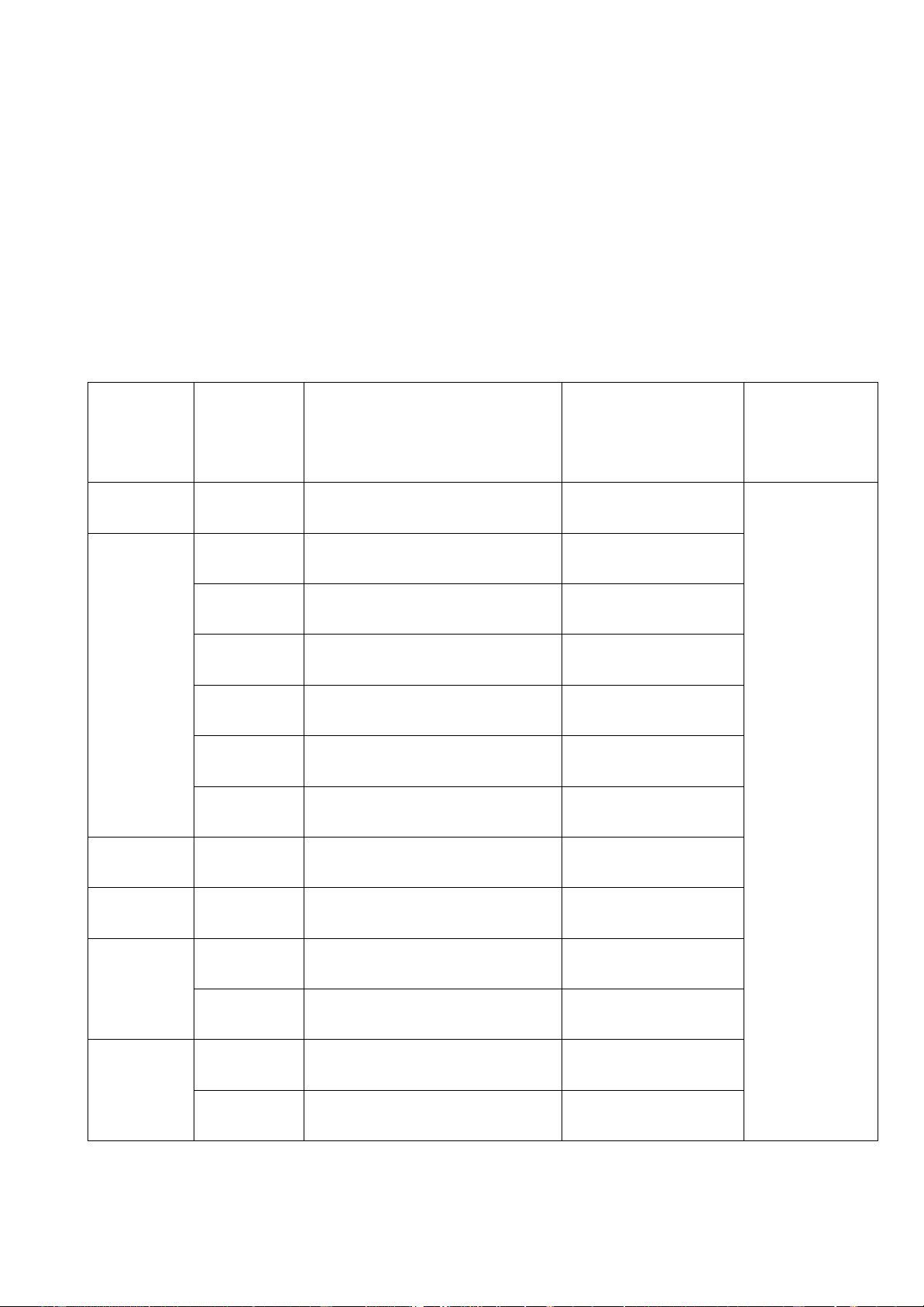
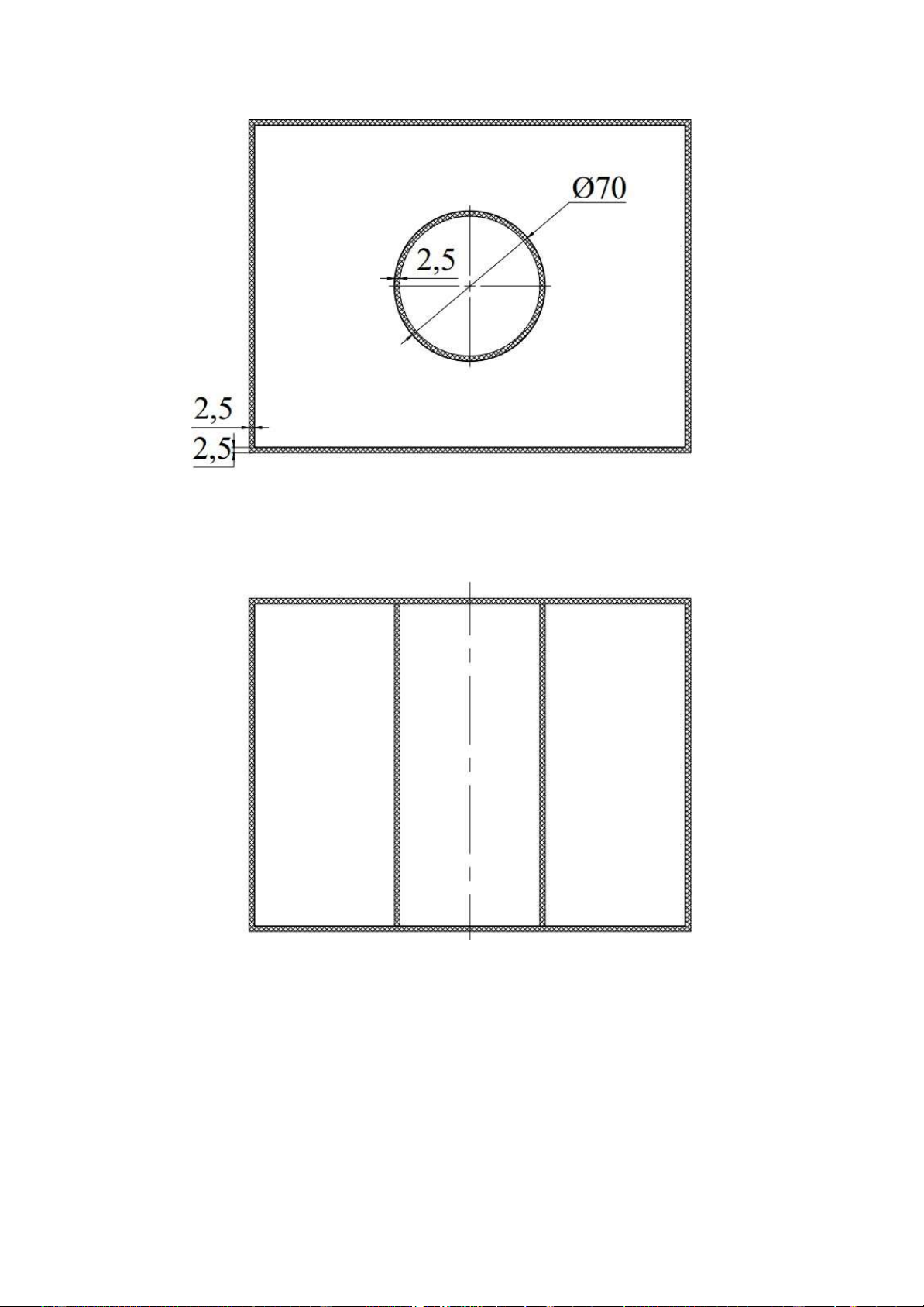
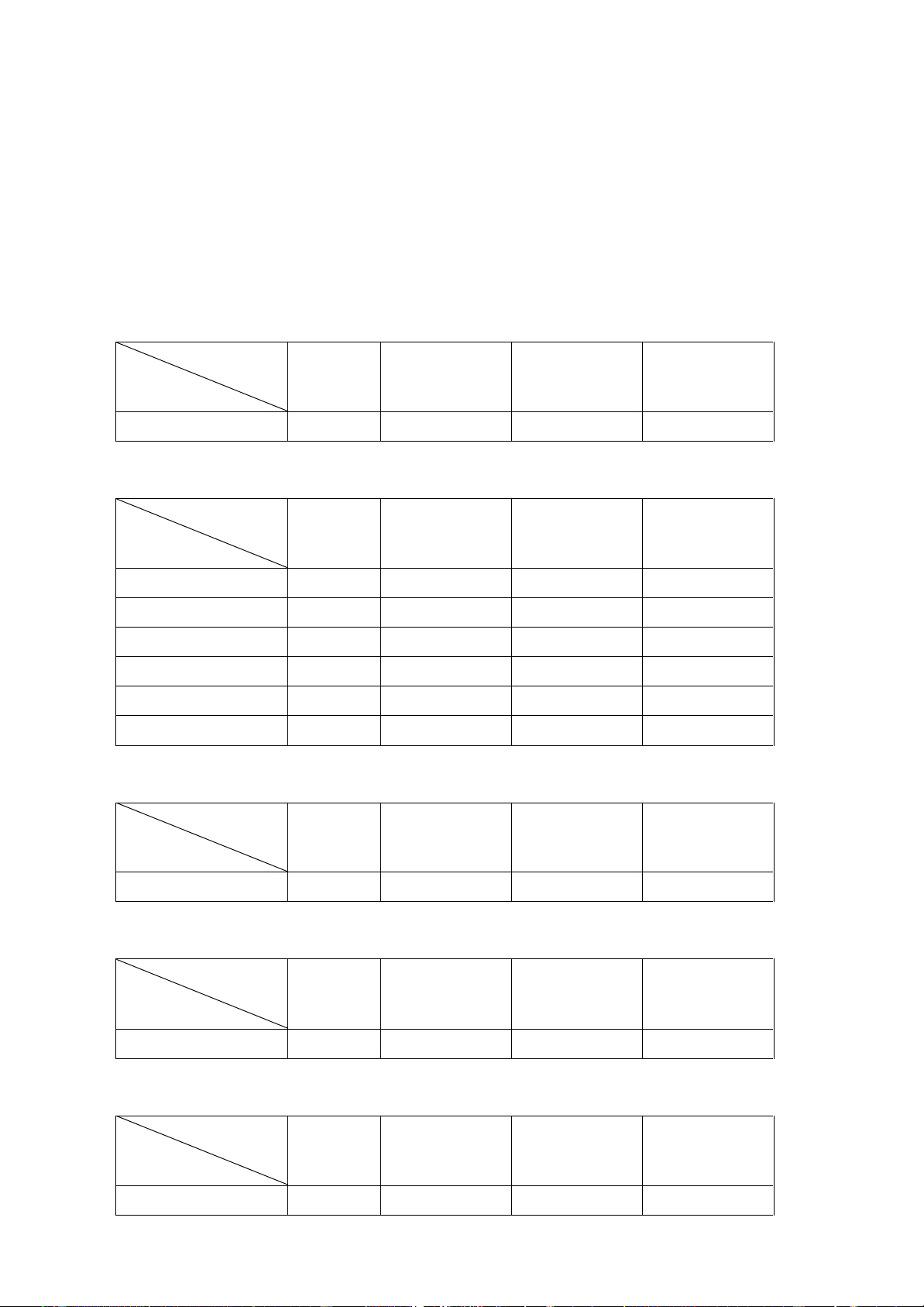
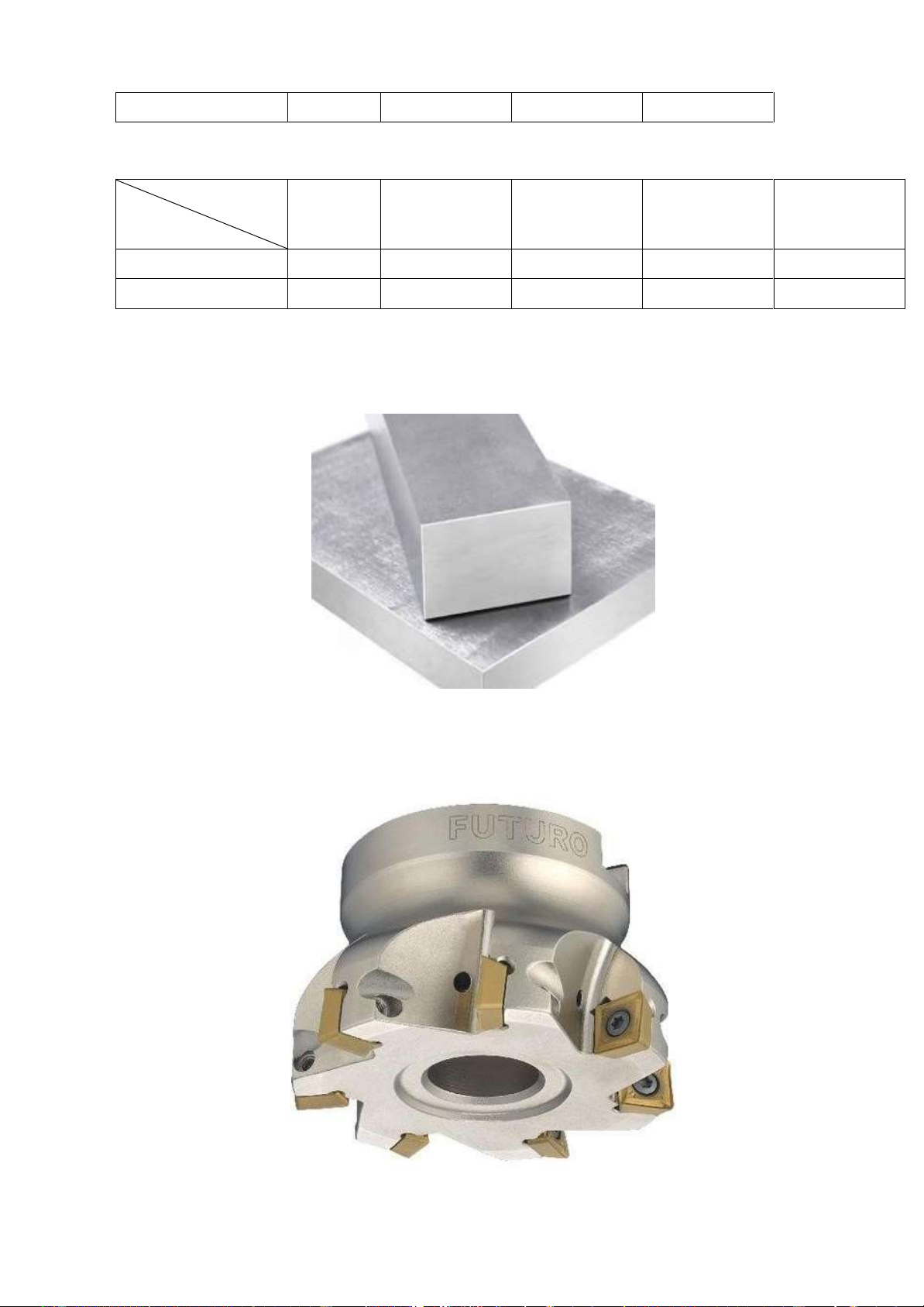
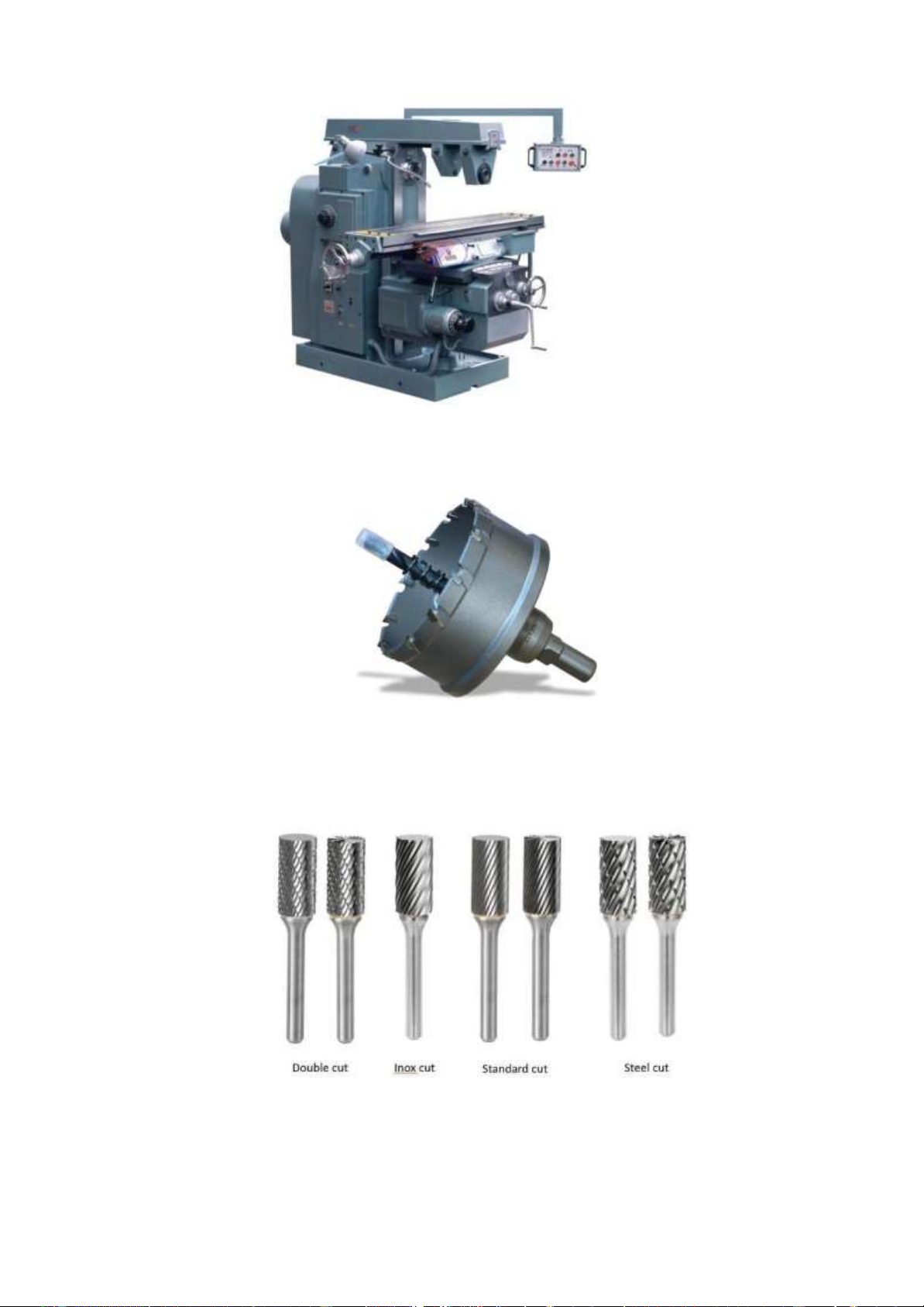
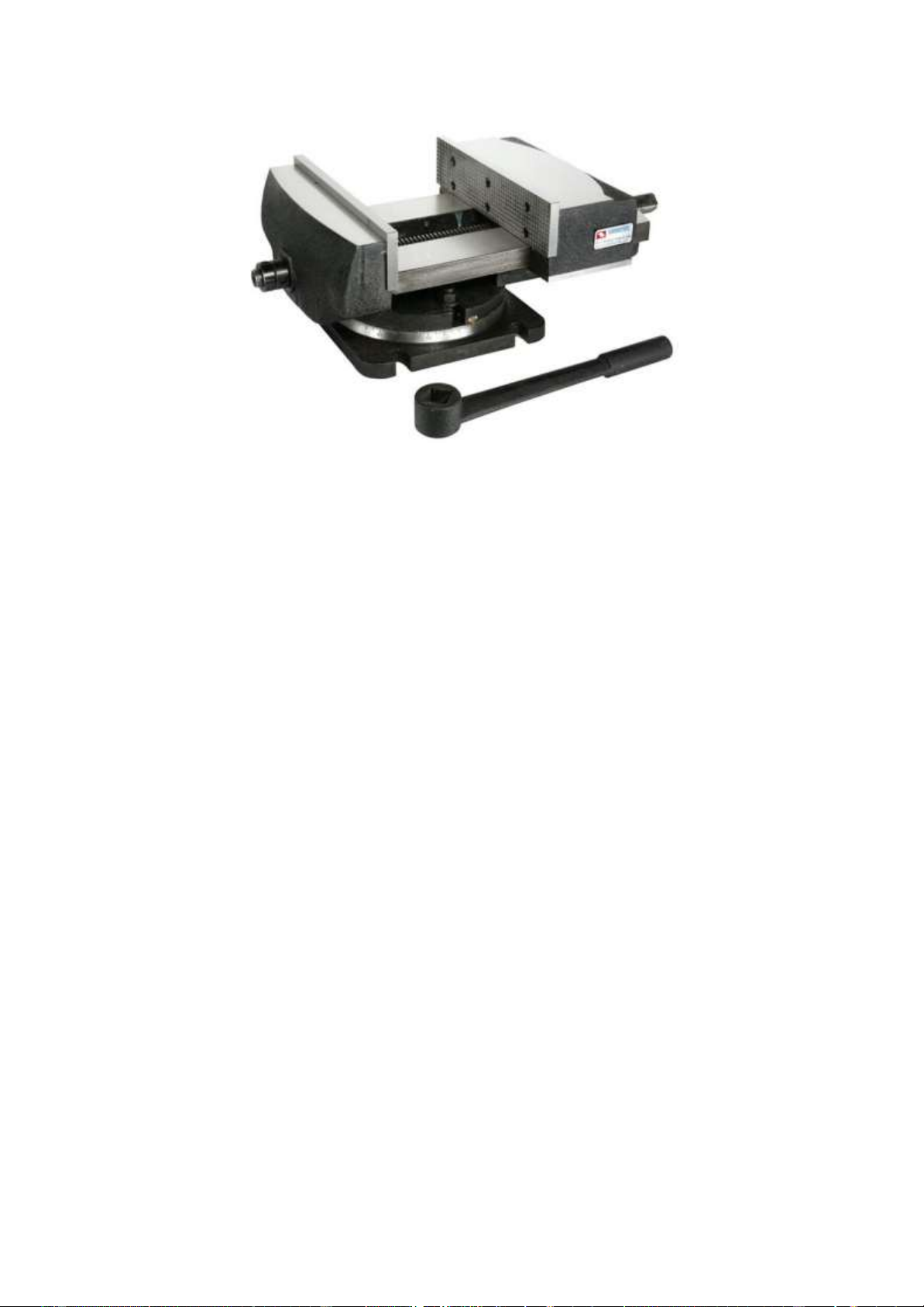
Preview text:
HỌC VIỆN NÔNG NGHIỆP VIỆT NAM KHOA CƠ – ĐIỆN *** ĐỒ ÁN:
CÔNG NGHỆ CHẾ TẠO MÁY HỌ VÀ TÊN SINH VIÊN: Phạm Duy Hinh MÃ SINH VIÊN: 652545 LỚP: K65CKCTM GIẢNG VIÊN HƯỚNG DẪN:
Thầy: Nguyễn Ngọc Cường HÀ NỘI – 2023 MỤC LỤC
Chương I. PHÂN TÍCH SƠ BỘ CHI TIẾT ............................................................... 1
1. Phân tích kết cấu, khả năng làm việc của chi tiết ................................................ 1
1.1. Phân tích kết cấu ............................................................................................. 1
Hình 1. 1: Bản vẽ khối hộp 3D .................................................................................... 1
Hình 1. 2: Bản vẽ khối hộp 2D .................................................................................... 1
1.2. Khả năng làm việc của chi tiết máy ................................................................. 2
2. Phân tích tính công nghệ của kết cấu chi tiết ...................................................... 2
Chương II. THIẾT KẾ SƠ BỘ PHƯƠNG ÁN CÔNG NGHỆ ................................. 3
1. Chọn và xác định dạng sản xuất .......................................................................... 3
Bảng 1: Xác định dạng sản xuất ................................................................................. 3
2. Chọn phôi và phương pháp tạo phôi ................................................................... 4
2.1. Chọn phôi ........................................................................................................ 4
2.2 Vật liệu.................................................................................................................. 5
2.3 Phương pháp tạo phôi.......................................................................................... 6
Chương III Thiết kế quy trình công nghệ gia công chi tiết ....................................... 7
1. Chọn phương pháp gia công ................................................................................ 7 1.1
Phương án thứ nhất ........................................................................................ 7
1.2 Phương án hai ..................................................................................................... 8
2. Thiết kế nguyên công ............................................................................................ 9
2.1 Nguyên công 1: phay thô mặt 1 ........................................................................... 9
2.2 Nguyên công 2: Phay các mặt 2,3,4 ................................................................... 10
2.3 Nguyên công 3: Phay mặt tinh mặt 1 ................................................................ 11
2.4 Nguyên công 4: Phay thô mặt 5 ........................................................................ 12
2.5 Nguyên công 5: Phay mặt 6 ............................................................................... 13
2.6 Nguyên công 6: khoét Ø 70,doa Ø 70 ................................................................ 14
3. Xác định lượng dư gia công và chế độ cắt cho các nguyên công ...................... 15
3.1. Tra lượng dư gia công ....................................................................................... 16
3.2. Xác định chế độ cắt cho các bề mặt ................................................................... 17
3.2.2 Tra chế độ cắt cho nguyên công 2 ................................................................. 18
3.2.3 Tra chế độ cắt cho nguyên công 3 ................................................................. 18
3.2.4 Tra chế độ cắt cho nguyên công 4 ................................................................. 18
3.2.5 Tra chế độ cắt cho nguyên công 5 ................................................................. 18
3.2.6 Tra chế độ cắt cho nguyên công 6 ................................................................. 19
3. Ảnh minh hoạ...................................................................................................... 19
4. Tài liệu tham khảo .............................................................................................. 21
BẢN THUYẾT MINH ĐỒ ÁN
Chương I. PHÂN TÍCH SƠ BỘ CHI TIẾT
1. Phân tích kết cấu, khả năng làm việc của chi tiết
1.1. Phân tích kết cấu
Hình 1. 1: Bản vẽ khối hộp 3D
Hình 1. 2: Bản vẽ khối hộp 2D 1
- Chi tiết có dạng khối hộp chữ nhật dài :200mm,rộng 150mm, cao 150mm,dung sai +0,025mm;
- Trên trục thẳng đứng giữa tâm có lỗ trụ tròn thông suốt d=70mm, dung sai +0,01mm;
- Độ nhám bề mặt cấp độ 7, bán tinh Ra = 1,25µm.
1.2. Khả năng làm việc của chi tiết máy
Chi tiết dạng khối hộp là dạng chi tiết được dùng rất phổ biến trong ngành
công nghệ chế tạo máy, nó có nhiệm vụ làm giá đỡ các trục, hoặc cố định trong cơ cấu máy..
Ở đây chi tiết làm việc chủ yếu ở mặt ∅ 70. Bề mặt này yêu cầu có độ bóng
cần đạt là cấp 7 (Ra = 1,25m) vì vậy phải qua nguyên công mài để gia công đạt
độ chính xác lắp ghép.
Chi tiết được làm bằng hợp kim nhôm
Ta chọn vật liệu là hợp kim nhôm có khối lượng riêng, độ giãn nở nhiệt
nhỏ, không có khuyết tật bên trong và ngoài, tính đúc và tính chống ăn mòn cao
do đó hiệu quả chi phí thấp
2. Phân tích tính công nghệ của kết cấu chi tiết
- Khối hộp dài 300mm, với kết cầu như hình vẽ ta có thể gia công các bề
mặt bằng dao phay mặt đầu gắn mảnh hợp kim cứng
- Khối hộp có lỗ trụ tròn thông suốt trên trục thẳng đứng, ta có thể gia công
bằng mũi khoét và mũi doa
- Độ cứng vững thấp, không cho phép đạt độ chính xác cao.
- Tuỳ theo hàm lượng các nguyên tố mà khối hộp có thể nhiệt luyện hoặc
không, cụ thể hàm lượng nhôm trong phôi cao thì không thể hoá bền bằng
phương pháp nhiệt luyện do đó cơ tính thấp, dẻo. Ngược lại với hợp kim nhôm
với hàm lượng Si từ 4 ÷ 10% kết hợp Cu và Mg có thể nhiệt luyện để cải thiện
độ bền. Với nhiệm vụ cụ thể của khối hộp, ta sẽ chọn vật liệu hợp lý để đáp ứng
nhu cầu sử dụng cũng như tiết kiệm chi phí sản xuất.
- Các kết cấu không gây khó khăn trong quá trình gia công. Trong quá trình
gia công, ta sử dụng các phương pháp:phay, khoan hợp lí cho những bề mặt để
đạt được những yêu cầu đặt ra. 2
Chương II. THIẾT KẾ SƠ BỘ PHƯƠNG ÁN CÔNG NGHỆ
1. Chọn và xác định dạng sản xuất
- Sản lượng 10000 chiếc/tháng, 120000 chiếc/năm
- Trọng lượng của chi tiết theo công thức 3 trang 13: Q1= V. (kg) Trong đó:
V – Thể tích của chi tiết (dm3)
V=l*w*h=200*150*150=4500000mm3=4,5 dm3
- Khối lượng riêng của vật liệu (kg/dm3); nhôm = 2,8 kg/dm3 Vậy Q1 = 12,6 kg Dạng sản xuất
Khối lượng chi tiết (kg) < 4 4 ÷ 200 > 200
Sản lượng hàng năm (chiếc) Đơn chiếc < 100 < 10 < 5 Loạt nhỏ 100 ÷ 500 10 ÷ 200 55 ÷ 10 Loạt vừa 500 ÷ 5000 200 ÷ 500 100 ÷ 300 Loạt lớn 5000 ÷ 50000 500 ÷ 1000 300 ÷ 1000 Hàng khối > 50000 > 5000 > 1000
Bảng 1: Xác định dạng sản xuất
Dựa vào bảng 2.1 ta xác định được dạng sản xuất hang khối. 3
2. Chọn phôi và phương pháp tạo phôi 2.1. Chọn phôi Chọn phôi
- Chi tiết trục đỡ có khối lượng là 12,6 kg thuộc dạng sản xuất hang khối
- Khối hộp thuộc chi tiết dạng hộp có hình dạng chi tiết đơn giản.
- Vật liệu chế tạo khối hộp là hợp kim nhôm Alcu5
*Ưu nhược điểm của các loại phôi :
- Phôi đúc : Phôi đúc thường dùng để chế tạo các loại chi tiết như : Các gối đỡ
,các chi tiết dạng hộp các loại càng phức tạp các loại trục chữ thập ... Vật
liệu dùng cho phôi đúc là Gang thép đồng nhôm và các loại hợp kim khác . Ưu điểm :
+ Đúc được tất cả các kim loại và hợp kim khác nhau.
+ Có thể đúc được các vật có khối lượng nhỏ và rất lớn.
+ Đúc được các vật đúc có hình dáng phức tạp mà các
phương pháp khác khó thực hiện.
Nhược điểm :Có thể có khuyết tật như rỗ khí, rỗ xỉ, không điền đầy hết
các lòng khuôn, vật đúc bị nứt...
-Phôi dập thường dùng để chế tạo các loại chi tiết sau đây trục răng côn trục
răng thẳng,các loại bánh răng khác, các chi tiết dạng càng, trục chữ thập, trục
Ưu điểm : + Tiết kiệm kim loại do lượng dư gia công nhỏ.
+Giảm thời gian gia công cơ, giữ được mặt ngoài có cơ tính cao
+Năng suất lao động tương đối cao do đó giá thành hạ, thao tác máy dễ dàng.
Nhược điểm : + Lực dập lớn dễ gây nứt chi tiết. +Máy làm việc ổn.
- Phôi cán được chế tạo bằng cách cho phối đi qua hệ thống máy cán với 2
trục cán quay ngược chiều nhau, hình dạng mặt cắt của phôi thay đổi theo mặt
cắt của khe hở giữa 2 trục cán.
Ưu điểm : +Độ chính xác chất lượng bề mặt cao.
+Thành phần hóa học ổn định.
+Gia công được các kích thước, tiết diện ngang và chiều dài theo tiêu chuẩn.
+Tiết kiệm được kim loại.
Nhược điểm :+Không thích hợp cho việc chế tạo phôi chịu tải . 4
+Tồn tại ứng suất dư nhiều.
+Không gia công được các chi tiết phức tạp.
- Rèn là quá trình gia công bằng áp lực (thông qua búa tay hoặc búa máy )để
thay đổi hình dáng của phôi .
Ưu điểm:+Có cơ tính cao
+Tiết kiệm được kim loại và giảm chi phí cho gia công cắt gọt
+Tăng độ bền và độ cứng +Thiết bị đơn giản
Nhược điểm:+Không chế tạo được các chi tiết phức tạp hoặc quá lớn
+Không gia công được vật liệu giòn (gang )
+Rèn tự do có độ chính xác và năng suất thấp
+Chi tiết dễ bị cong vênh, chất lượng bề mặt thấp dễ gây nứt
-Hàn là phương pháp công nghệ nối các chi tiết máy bằng kim loại hoặc phi
kim bằng cách nung nóng chỗ nối đến trạng thái hàn . Sau đó kim loại lỏng
hóa rắn hoặc kim loại dẻo thông qua lực ép chỗ nối tạo thành mối hàn
Ưu điểm : +Tiết kiệm kim loại. +Thời gian gia công giảm
+Mối hàn có độ bền độ kín tốt, thiết bị đơn giản dễ đầu tư.
Nhược điểm:+Ứng suất nhiệt dư lớn tại lân cận vùng hàn,
+Khó tạo sản phẩm có độ chính xác cao, có tính chất phức tạp.
=> Chọn phôi đúc là thích hợp nhất. 2.2 Vật liệu
Với chi tiết khối hộp này ta chọn vật liệu là hợp kim nhôm Alcu5 với thành phần hóa học là
Cơ tính ( đã nhiệt luyện) Thành phần hóa học Ký hiệu (%) Độ bền Độ dãn dài Độ rắn Al Cu Alcu5 30 5 90 95 5 Thiết kế đúc trang 56 5
2.3 Phương pháp tạo phôi
Phương pháp đúc bằng khuôn kim loại : dùng để đúc kim loại và hợp kim
màu có độ chính xác cao nhưng giá thành thiết bị đầu tư lớn , phôi có hình
dáng gần giống với chi tiết . Gía thành sản phẩm cao . loại này phù hợp với
dạng sản xuất hàng loạt lớn và hàng khối.
Phương pháp đúc ly tâm : Chỉ đúc được những sản phẩm có hình dáng tròn
xoay thành ống mỏng nên không thích hợp.
Phương pháp đúc bằng mẫu chảy : Dùng để đúc chi tiết có hình dáng phức
tạp, việc làm mẫu chảy rất khó khăn và tốn kém vật liệu vì một mẫu chỉ đúc
được một sản phẩm. Thường dùng cho sản xuất đơn chiếc nên không thích hợp.
Phương pháp đúc bằng áp lực : Chủ yếu dùng để đúc kim loại và hợp kim
màu nên không thích hợp.
Phương pháp đúc trong khuôn cát : Đúc được tất cả các vật liệu có tính nóng
chảy, thích hợp cho dạng sản xuất đơn chiếc hàng loạt nhỏ và hàng loạt vừa,
đúc được những hình dạng phức tạp. Vật liệu làm hòm khuôn CT3, hỗn hợp
làm khuôn : cát, đất sét ( chất kết dính) vật liệu phụ, nước... nên thích hợp cho
việc chế tạo phôi bằng gang, độ chính xác tương đối cao, phù hợp cho dạng sản xuất hàng loạt vừa.
=> Kết luận ta chọn phương pháp đúc bằng khuôn kim loại do yêu cầu sản xuất hàng khối 6
Chương III Thiết kế quy trình công nghệ gia công chi tiết
1. Chọn phương pháp gia công
1.1 Phương án thứ nhất 7 1.2 Phương án hai
Từ 2 phương án ta thấy :
Phương án thứ nhất dùng chẩn thô phay thô rồi mới lật lại gia công thô và tinh mặt đối
diện điều này giúp đảm bảo yêu cầu của đề bài khi dung sai kích thước các mặt là 0,025
. Còn phương án hai gia công khó để đạt được dung sai cho phép
Kết luận : Chọn phương án 1 là phương án tối ưu nhất 8
2. Thiết kế nguyên công:
2.1 Nguyên công 1: phay thô mặt 1 Sơ đồ gia công:
-Định vị và kẹp chặt:
Dùng êtô, ta hạn chế 5 bậc tự do.
Dùng phiến tỳ khống chế 3 bậc tự do. -Chọn máy:
- Dùng máy phay đứng 6H12
- Các thông số cơ bản của máy : Máy phay đứng 6H12
Công suất máy �� = 7 Kw
Số vòng quay trục chính n = 18 cấp ( 30 – 1500 vòng/ phút)
Kích thước bàn máy là 320 x 1250 ( bảng 9-38 trang 75 CNCTM3). - Dụng cụ đo :
Dụng cụ đo : thước cặp 1/20, thước dài, bộ lấy dấu.. -Chọn dụng cụ cắt :
Dao phay mặt đầu chắp mảnh hợp kim cứng (t376 bảng 4.95 STCNCTM 1) .Mác hợp kim là BK8
Đường kính dao phay : D = 160 mm Bề rộng dao : B = 60MM Số răng :10 9
Đường kính lỗ dao : 50mm
Số lượng và trình tự các bước công nghệ: Số lần gá: 1
Các bước: Phay thô mặt 1
2.2 Nguyên công 2: Phay các mặt 2,3,4 Sơ đồ gia công:
-Định vị và kẹp chặt:
Dùng êtô, ta hạn chế 5 bậc tự do.
Dùng phiến tỳ khống chế 3 bậc tự do. -Chọn máy: Dùng máy phay đứng 6H12
- Các thông số cơ bản của máy : Máy phay đứng 6H12
Công suất máy �� = 7 Kw
Số vòng quay trục chính n = 18 cấp ( 30 – 1500 vòng/ phút)
Kích thước bàn máy là 320 x 1250 ( bảng 9-38 trang 75 CNCTM3). - Dụng cụ đo : 10
Dụng cụ đo : thước cặp 1/20, thước dài, bộ lấy dấu.. Chọn dụng cụ cắt :
Dao phay mặt đầu chắp mảnh hợp kim cứng (t376 bảng 4.95 STCNCTM 1) .Mác hợp kim là BK8
Đường kính dao phay : D = 160 mm Bề rộng dao : B = 60MM Số răng :10
Đường kính lỗ dao : 50mm
Dao phay ngón đôi trụ Đường kính dao : d=22mm
Chiều dài chuôi dao: L=104mm
Chiều dài lưỡi dao: l=38mm Số rang: Z=6
-Số lượng và trình tự các bước công nghệ: Số lần gá: 1 Các bước: Bước 1: Phay thô mặt 2 Bước 2: Phay tinh mặt 2 Bước 3:Phay thô mặt 3 Bước 4: Phay tinh mặt 3 Bước 5: Phay thô mặt 4 Bước 6: Phay tinh mặt 4
2.3 Nguyên công 3: Phay mặt tinh mặt 1 Sơ đồ gia công: 11
Dùng êtô, ta hạn chế 5 bậc tự do.
Dùng phiến tỳ khống chế 3 bậc tự do. -Chọn máy: Dùng máy phay đứng 6H12
- Các thông số cơ bản của máy : Máy phay đứng 6H12
Công suất máy �� = 7 Kw
Số vòng quay trục chính n = 18 cấp ( 30 – 1500 vòng/ phút)
Kích thước bàn máy là 320 x 1250 ( bảng 9-38 trang 75 CNCTM3). - Dụng cụ đo :
Dụng cụ đo : thước cặp 1/20, thước dài, bộ lấy dấu.. Chọn dụng cụ cắt :
Dao phay mặt đầu chắp mảnh hợp kim cứng (t376 bảng 4.95 STCNCTM 1) .Mác hợp kim là BK8
Đường kính dao phay : D = 160 mm Bề rộng dao : B = 60MM Số răng :10
Đường kính lỗ dao : 50mm
-Số lượng và trình tự các bước công nghệ: Số lần gá: 1 Các bước: Bước 1: Phay tinh mặt 1
2.4 Nguyên công 4: Phay thô mặt 5 Sơ đồ gia công: 12
Dùng êtô, ta hạn chế 5 bậc tự do.
Dùng phiến tỳ khống chế 3 bậc tự do. -Chọn máy: Dùng máy phay đứng 6H12
- Các thông số cơ bản của máy : Máy phay đứng 6H12
Công suất máy �� = 7 Kw
Số vòng quay trục chính n = 18 cấp ( 30 – 1500 vòng/ phút)
Kích thước bàn máy là 320 x 1250 ( bảng 9-38 trang 75 CNCTM3). - Dụng cụ đo :
Dụng cụ đo : thước cặp 1/20, thước dài, bộ lấy dấu.. Chọn dụng cụ cắt :
Dao phay mặt đầu chắp mảnh hợp kim cứng (t376 bảng 4.95 STCNCTM 1) .Mác hợp kim là BK8
Đường kính dao phay : D = 160 mm Bề rộng dao : B = 60MM Số răng :10
Đường kính lỗ dao : 50mm
-Số lượng và trình tự các bước công nghệ: Số lần gá: 1 Các bước: Bước 1: Phay thô mặt 5
2.5 Nguyên công 5: Phay mặt 6 Sơ đồ gia công: 13
Dùng êtô, ta hạn chế 5 bậc tự do.
Dùng phiến tỳ khống chế 3 bậc tự do. -Chọn máy: Dùng máy phay đứng 6H12
- Các thông số cơ bản của máy : Máy phay đứng 6H12
Công suất máy �� = 7 Kw
Số vòng quay trục chính n = 18 cấp ( 30 – 1500 vòng/ phút)
Kích thước bàn máy là 320 x 1250 ( bảng 9-38 trang 75 CNCTM3). - Dụng cụ đo :
Dụng cụ đo : thước cặp 1/20, thước dài, bộ lấy dấu.. Chọn dụng cụ cắt :
Dao phay mặt đầu chắp mảnh hợp kim cứng (t376 bảng 4.95 STCNCTM 1) .Mác hợp kim là BK8
Đường kính dao phay : D = 160 mm Bề rộng dao : B = 60MM Số răng :10
Đường kính lỗ dao : 50mm
-Số lượng và trình tự các bước công nghệ: Số lần gá: 1 Các bước: Bước 1: Phay thô mặt 6 Bước 2: Phay tinh mặt 6
2.6 Nguyên công 6: khoét Ø 70,doa Ø 70 Sơ đồ gia công: 14 -Định vị: Để gia công, ta dùng:
+Hai phiến tỳ hạn chế 3 bậc tự do. -Kẹp chặt:
+ Dùng êtô, ta hạn chế 5 bậc tự do. -Chọn máy:
Theo bảng 9-22 trang 46 STCNCTM Tập 3
Chọn máy khoan cần 2M57 của Nga, có các thông số sau:
Đường kính lớn nhất khoan được, 75 mm
Khoảng cách từ đường tâm trục chính tới trụ, 500-2000 mm
Khoảng cách lớn nhất từ mút trục chính tới bàn:420 - 1800mm
Kích thước bề mặt làm việc của bàn máy: 1300 x 2065 mm
Dịch chuyển lớn nhất của trục chính: 450 mm
Số cấp tốc độ trục chính: 18
Phạm vi tốc độ trục chính 12,5 /1600 vg/ph Số cấp bước tiến: 18
Phạm vi bước tiến: 0,006/1,22 mm/vg
Góc quay lớn nhất của cần xung quanh trục thẳng đứng, độ: 360
Công suất động cơ chính,7,5 kW: -Chọn dao : Dụng cụ cắt : - Mũi khoét :
• Vật liệu phần cắt thép gió .
Kích thước dao :D *L *l=69,5 * 76 * 80
Tuổi bền của dao: T = 100 ph(Bảng 5.30 - [ 3.1 ]). - Mũi doa :
Chọn mũi doa liền khối, chuôi lắp (Bảng 4.49 - [ 3.1]).
Vật liệu phần cắt thép gió .
Kích thước dao: D * L* 1 = 70 *90 * 50 .
• Tuổi bền của dao: T = 120 ph (Bảng 5.30 - [ 3.1]).
-Số lượng và trình tự các bước công nghệ : - Số lần gá : 1 Các bước: Bước 1: Khoét Ø69.5 Bước 2: Doa tinh Ø70
3. Xác định lượng dư gia công và chế độ cắt cho các nguyên công:
- Xác định lượng dư gia công cho các bề mặt căn cứ vào : • Vật liệu chi tiết .
Phôi và phương pháp chế tạo phôi.
Tiến trình công nghệ gia công các bề mặt 15
• Sơ đồ gá đặt chi tiết khi gia công bề mặt .
Kích thước, yêu cầu kỹ thuật đối với bề mặt gia công.
3.1. Tra lượng dư gia công
Căn cứ vào phương pháp chế tạo phôi và các kích thước của phôi,ta có bảng tra
lượng dư cho các nguyên công như sau:
- Xác định lượng dư gia công cho các bề mặt căn cứ vào : • Vật liệu chi tiết .
• Phôi và phương pháp chế tạo phôi.
• Tiến trình công nghệ gia công các bề mặt .
• Sơ đồ gá đặt chi tiết khi gia công bề mặt .
Kích thước, yêu cầu kỹ thuật đối với bề mặt gia công . Nguyên Bước Nội dung các bước Lượng dư(mm) Ghi chú công 1 1 Phay thô mặt 1 2 1 Phay thô mặt 2 0.5 2 Phay tinh mặt 2 0.5 3 Phay thô mặt bên 3 2 2 4 Phay tinh mặt bên 3 0.5 Các giá trị 5 Phay thô mặt bên 4 2 được tra bảng trong 6 Phay tinh mặt bên 4 0.5 (Sổ tay công 3 1 Phay tinh mặt 2 0.5 nghệ chế tạo 4 1 Phay thô mặt 5 2 máy) 5 1 Phay thô mặt 6 2 2 Phay tinh mặt 6 0.5 6 1 Khoét lỗ Ø 69.5 2,25 2 Doa lỗ Ø 70 0,25 16
Bản vẽ lồng phôi
3.2. Xác định chế độ cắt cho các bề mặt:
Quá trình tra chế độ cắt được tiến hành như sau:
-Đầu tiên ta tiến hành chọn chiều sâu cắt phù hợp với các yêu cầu về độ nhám bề
mặt(cho gia công tinh), yêu cầu nâng cao về năng suất(cho gia công thô)...
-Tra lượng chạy dao : tuỳ thuộc vào độ cứng vững của hệ thống công nghệ, độ bền
của dụng cụ cắt, công suất động cơ (khi gia công thô) và độ chính xác kích thước
,nhám bề mặt gia công(cho gia công tinh) để chọn lượng chạy dao phù hợp. Khi tra
được lượng chạy dao đã tính đến các hệ số điều chỉnh, thì kết quả này phỉ làm tròn
theo giá trị thực của máy 17
Tra tốc độ cắt: được tra theo các bảng trong các sổ tay hoặc được tính theo các công
thực nghiệm đã được xác lập cho từng phương pháp công nghệ.Khi tra được tốc độ cắt
ta tính ra số vòng quay tính toán, sau đó chọn số vòng quay theo máy
Từ các thông số trên ta tra công suất cắt cần thiết cho chế độ cắt đã cho
-So sánh công suất cắt cần thiết với công suất của máy nếu thấy nhỏ hơn thì thoả
mãn, nếu không thì phải chọn lại. -Tính thời gian máy :
Theo trình tự như vậy, ta tiến hành tra chế độ cắt lần lượt cho các nguyên công
như sau, kết quả sau khi tính toán đã thoả mãn được cho dưới dạng bảng :
3.2.1 Tra chế độ cắt cho nguyên công 1 Chế độ cắt T(mm) Sz(mm/r) V(vg/ph) n(vg/ph) Bước Phay thô mặt 2 2 0,2 500 800
3.2.2 Tra chế độ cắt cho nguyên công 2 Chế độ cắt T(mm) Sz(mm/r) V(vg/ph) n(vg/ph) Bước Phay thô mặt 1 2 0,2 500 800 Phay tinh mặt 1 0.5 0,2 600 950 Phay thô mặt 3 2 0,2 500 800 Phay tinh mặt 3 0.5 0,2 600 950 Phay thô mặt 4 2 0,2 500 800 Phay tinh mặt 4 0.5 0,2 600 950
3.2.3 Tra chế độ cắt cho nguyên công 3 Chế độ cắt T(mm) Sz(mm/r) V(vg/ph) n(vg/ph) Bước Phay tinh mặt 2 2 0,2 600 950
3.2.4 Tra chế độ cắt cho nguyên công 4 Chế độ cắt T(mm) Sz(mm/r) V(vg/ph) n(vg/ph) Bước Phay thô mặt 5 2 0,2 500 800
3.2.5 Tra chế độ cắt cho nguyên công 5 Chế độ cắt T(mm) Sz(mm/r) V(vg/ph) n(vg/ph) Bước Phay thô mặt 5 2 0,2 500 800 18 Phay tinh mặt 5 0.5 0,2 600 950
3.2.6 Tra chế độ cắt cho nguyên công 6 Chế độ cắt T(mm) Sz(mm/r) n(vg/ph) Nc(Kw) T0(ph) Bước Khoét lỗ Ø 69.5 2.25 0,5 250 1.1 0.7 Doa lỗ Ø 70 0.25 0,4 560 1.06 1.2 3. Ảnh minh hoạ Phôi hợp kim nhôm
Dao phay gắn mảnh hợp kim 19 Máy phay đứng 6H12 Mũi khoét Mũi doa 20 Ê tô máy phay
4. Tài liệu tham khảo
- Thiết kế đồ án công nghệ chế tạo máy ;
- Sổ tay công nghệ chế tạo máy 1, 2, 3
- Hướng dẫn thiết kế đồ án công nghệ chế tạo máy ; - Công nghệ đúc 21