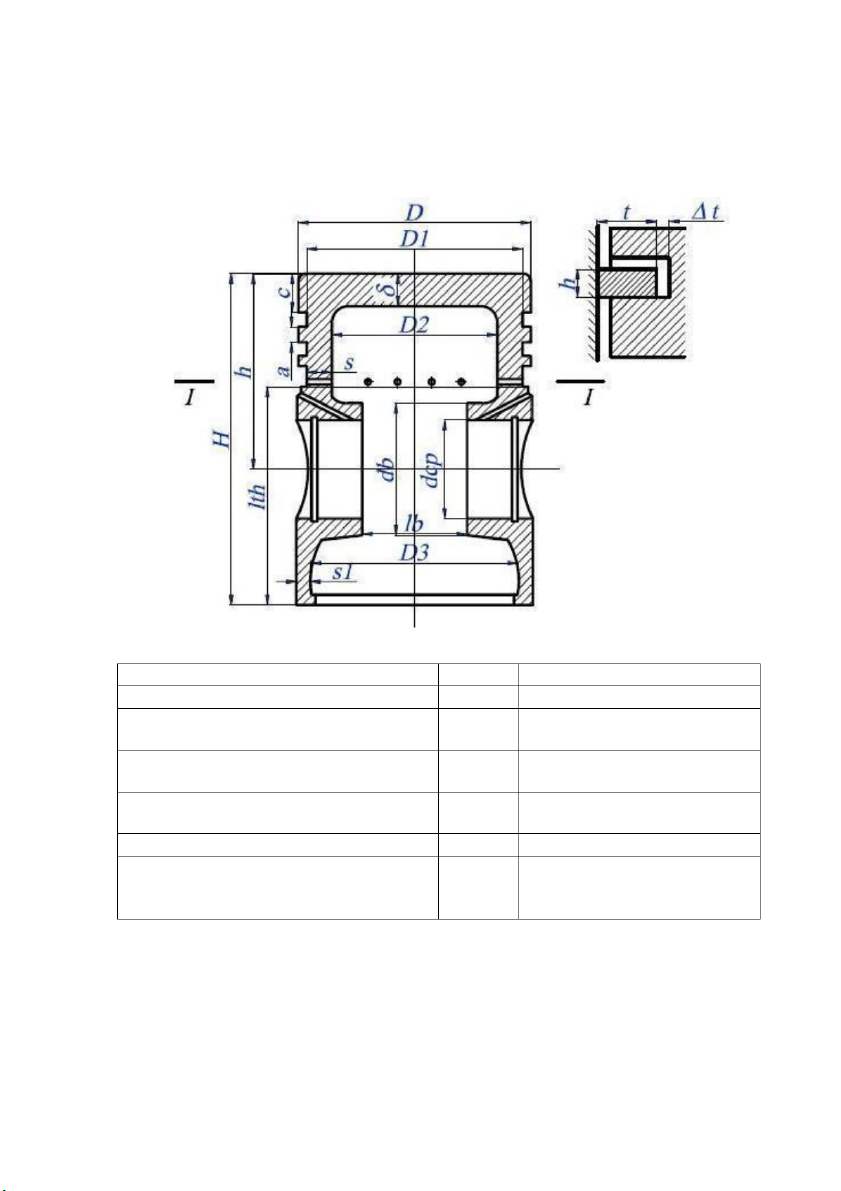
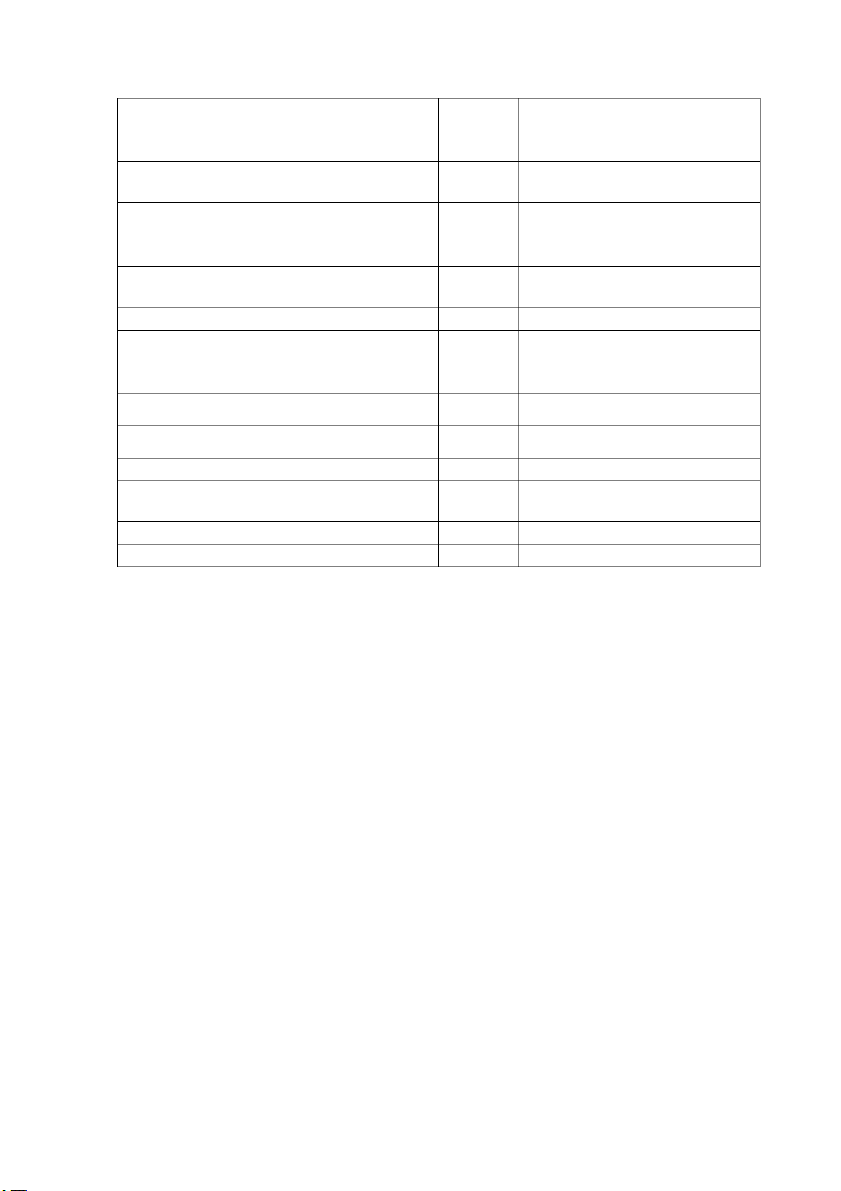
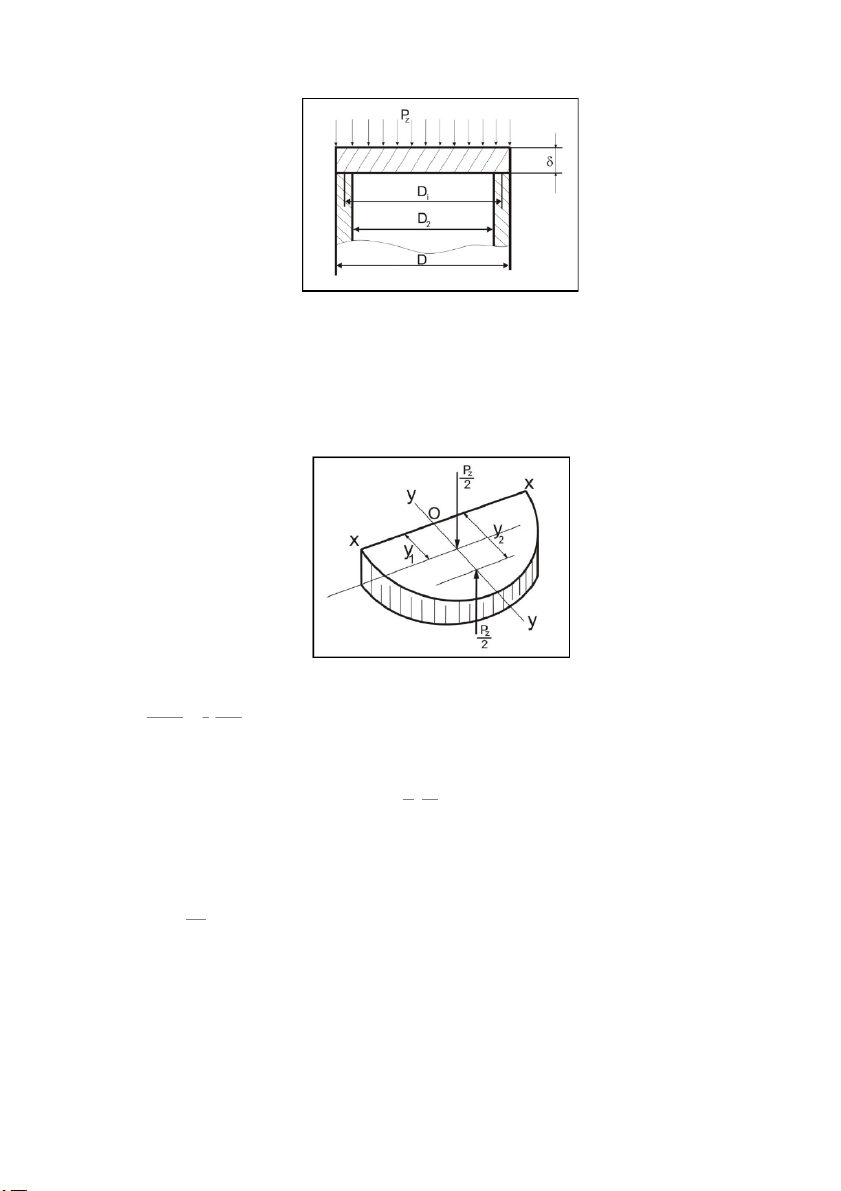
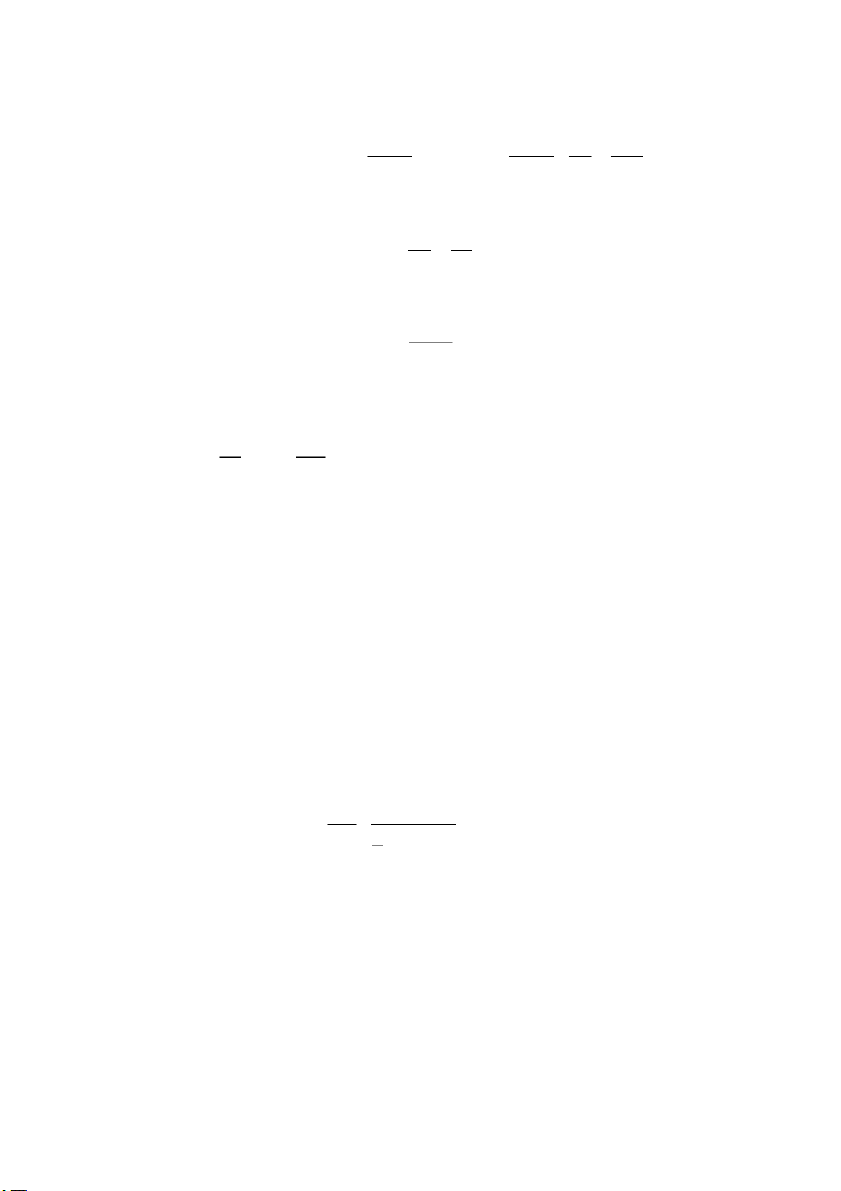
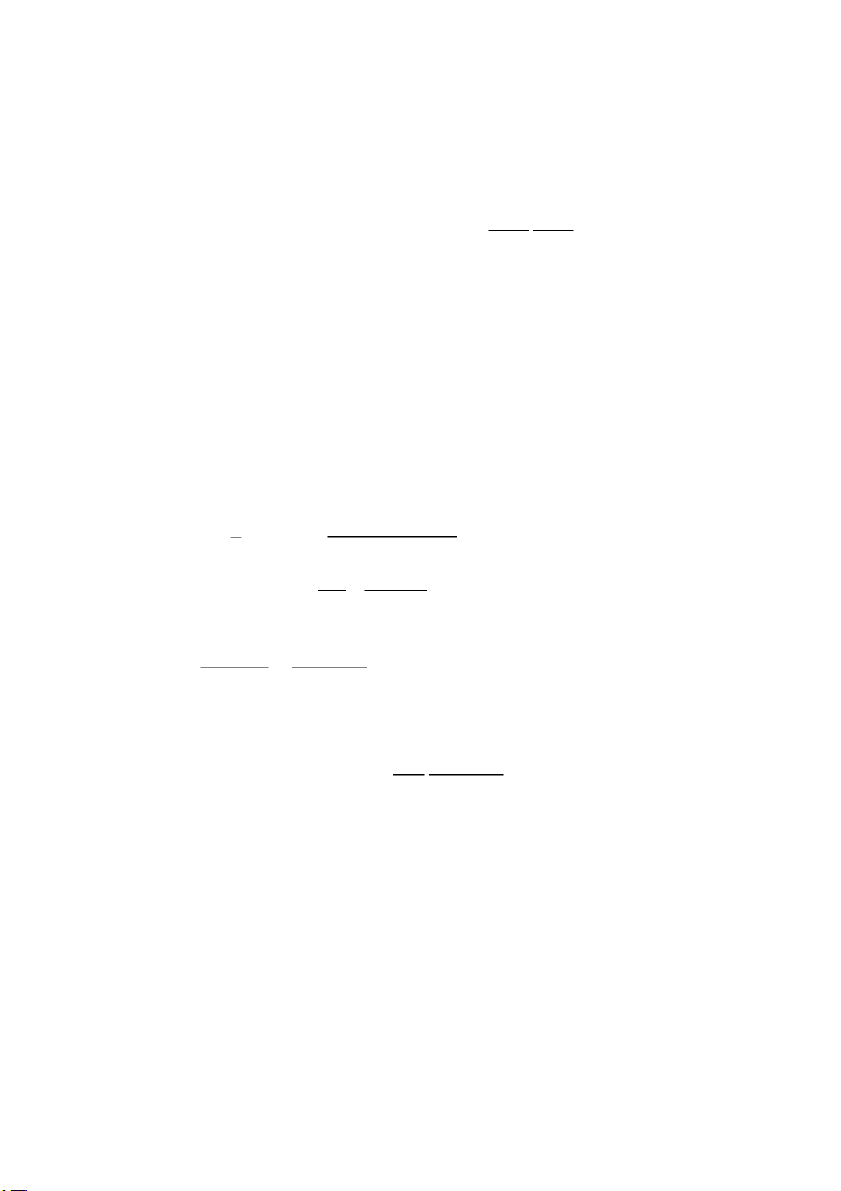
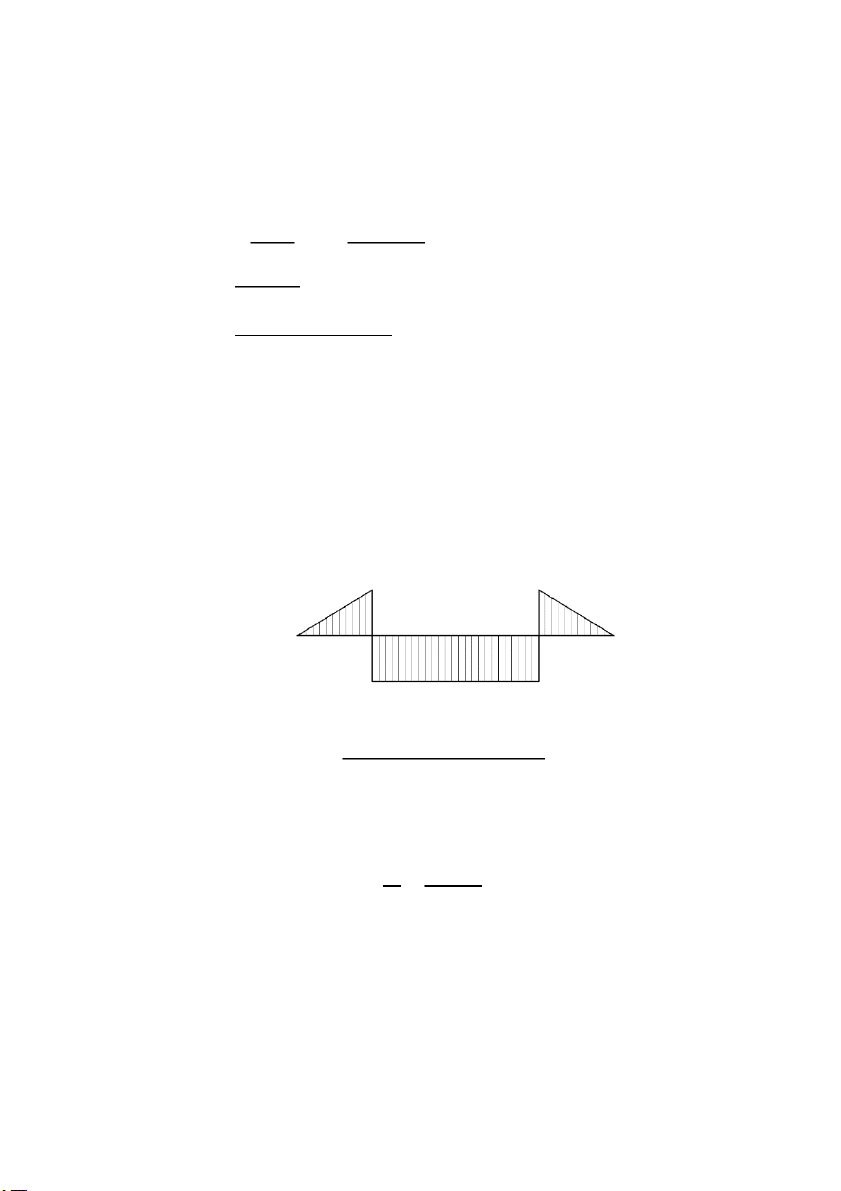
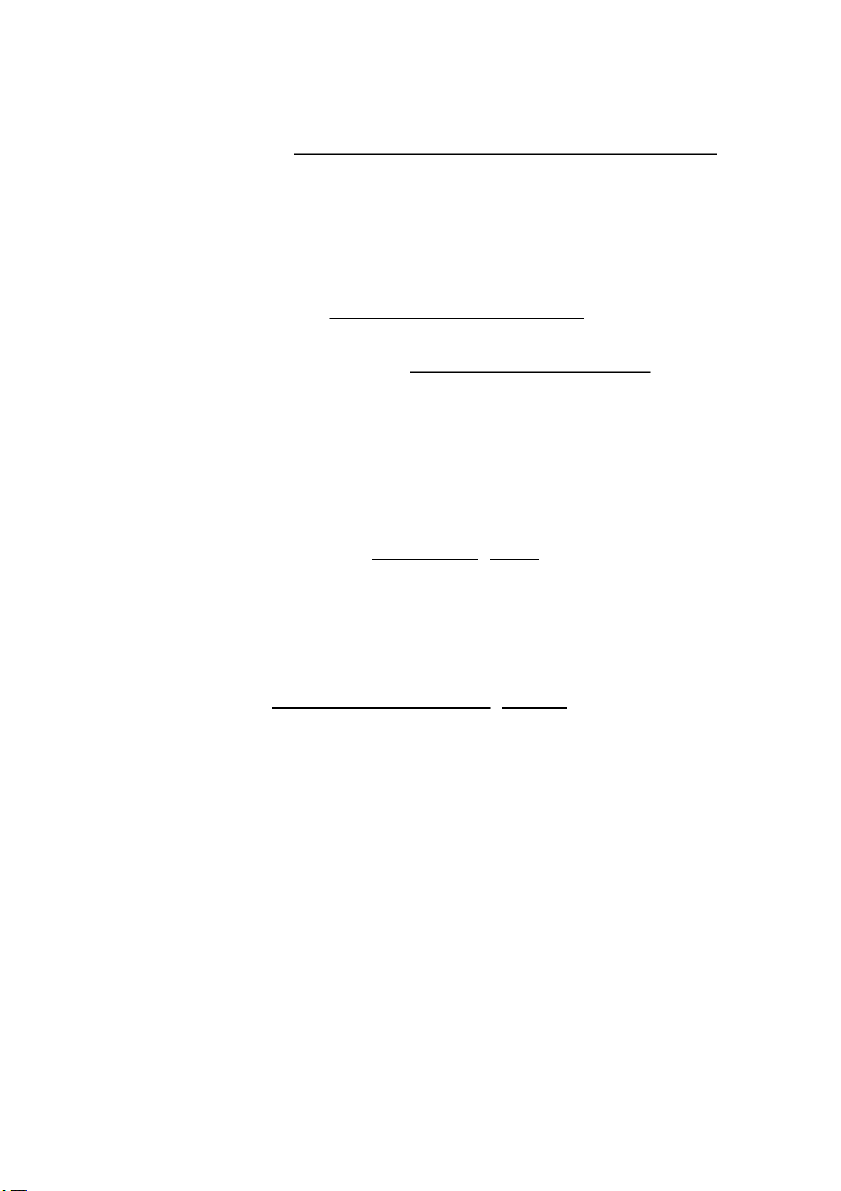
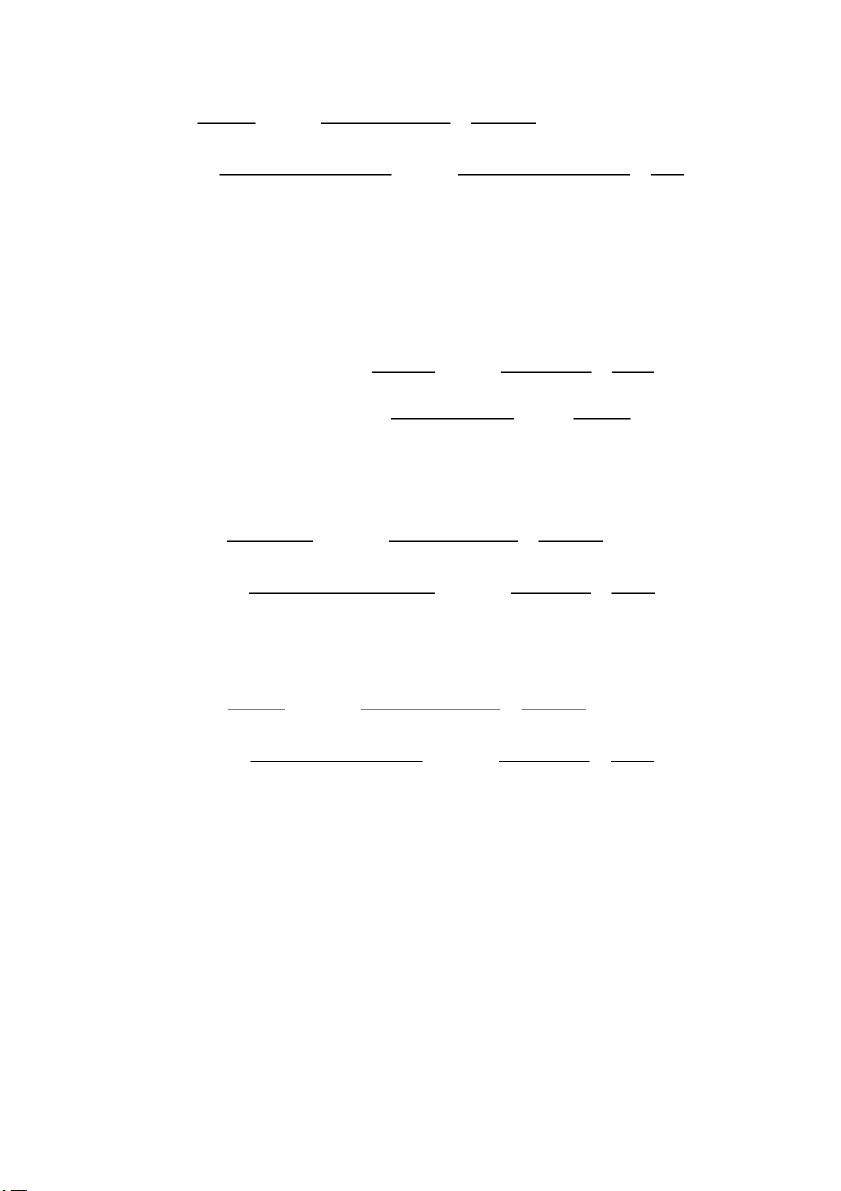
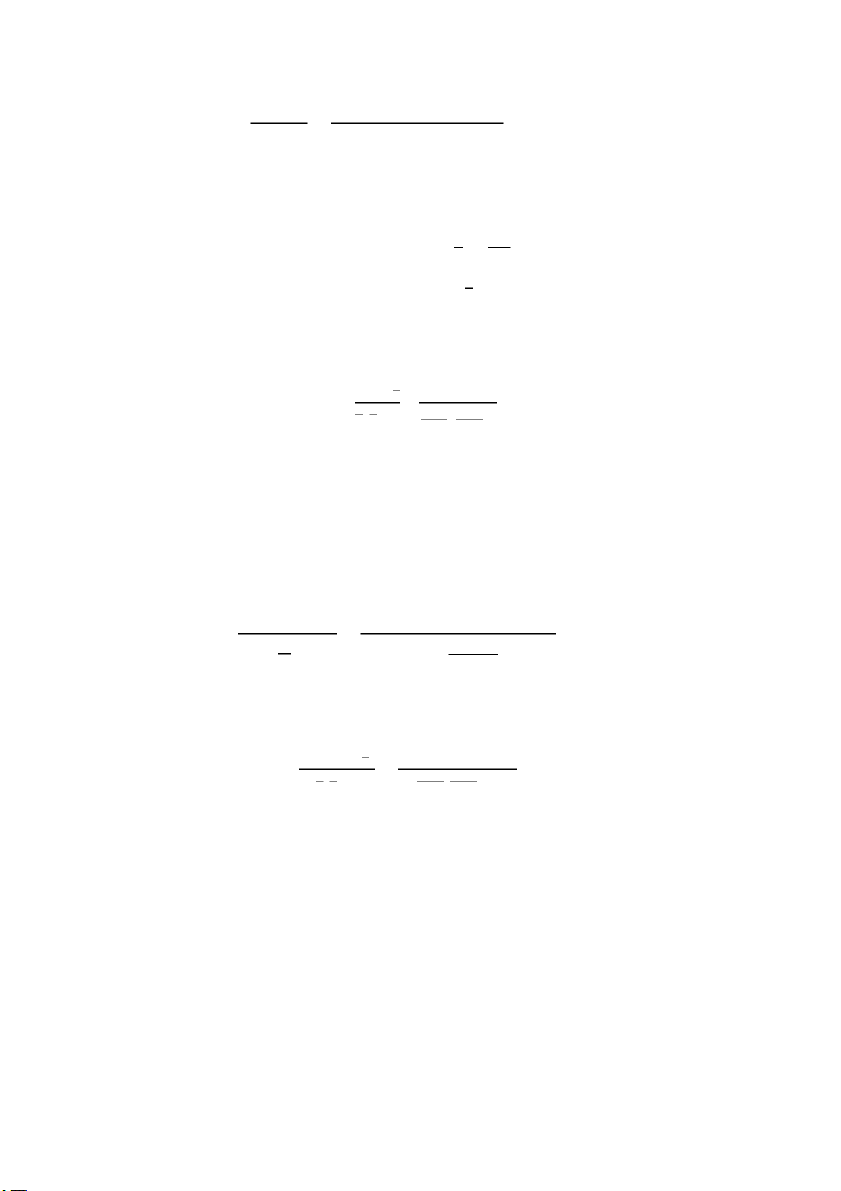
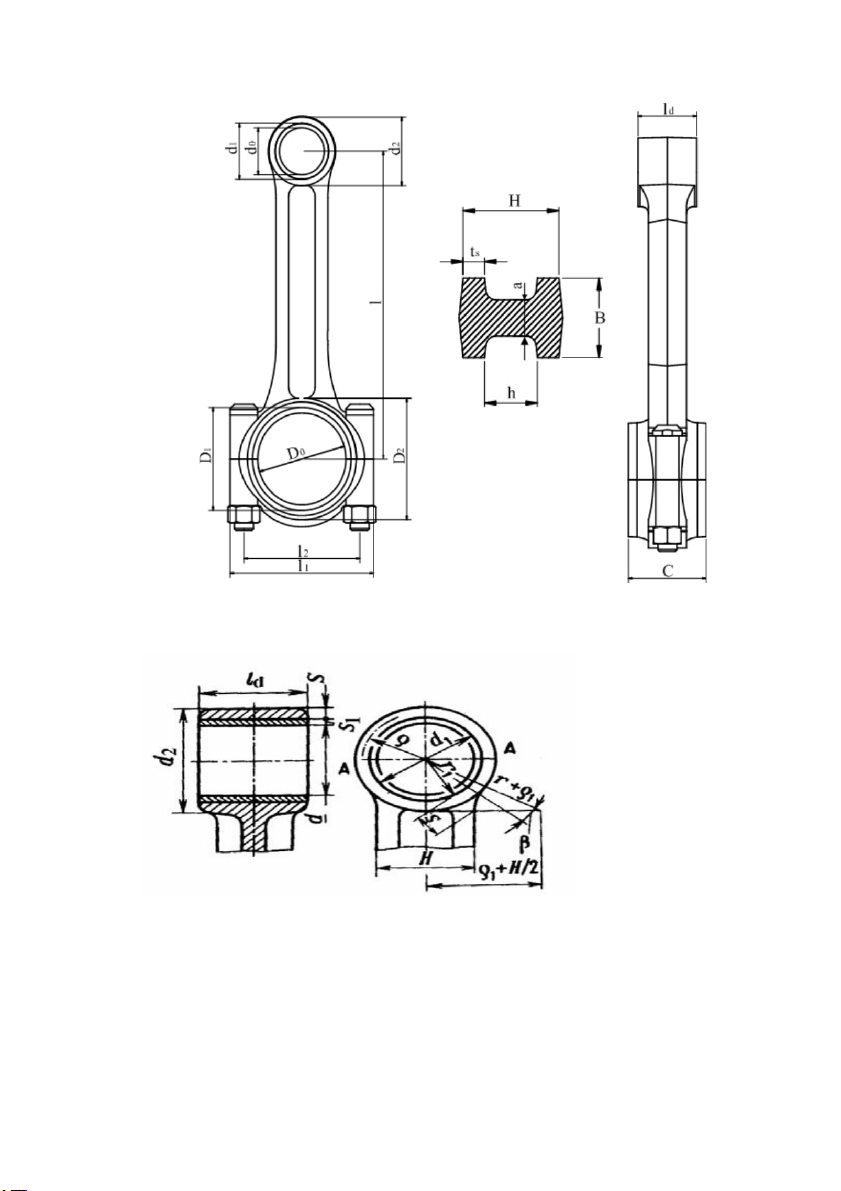
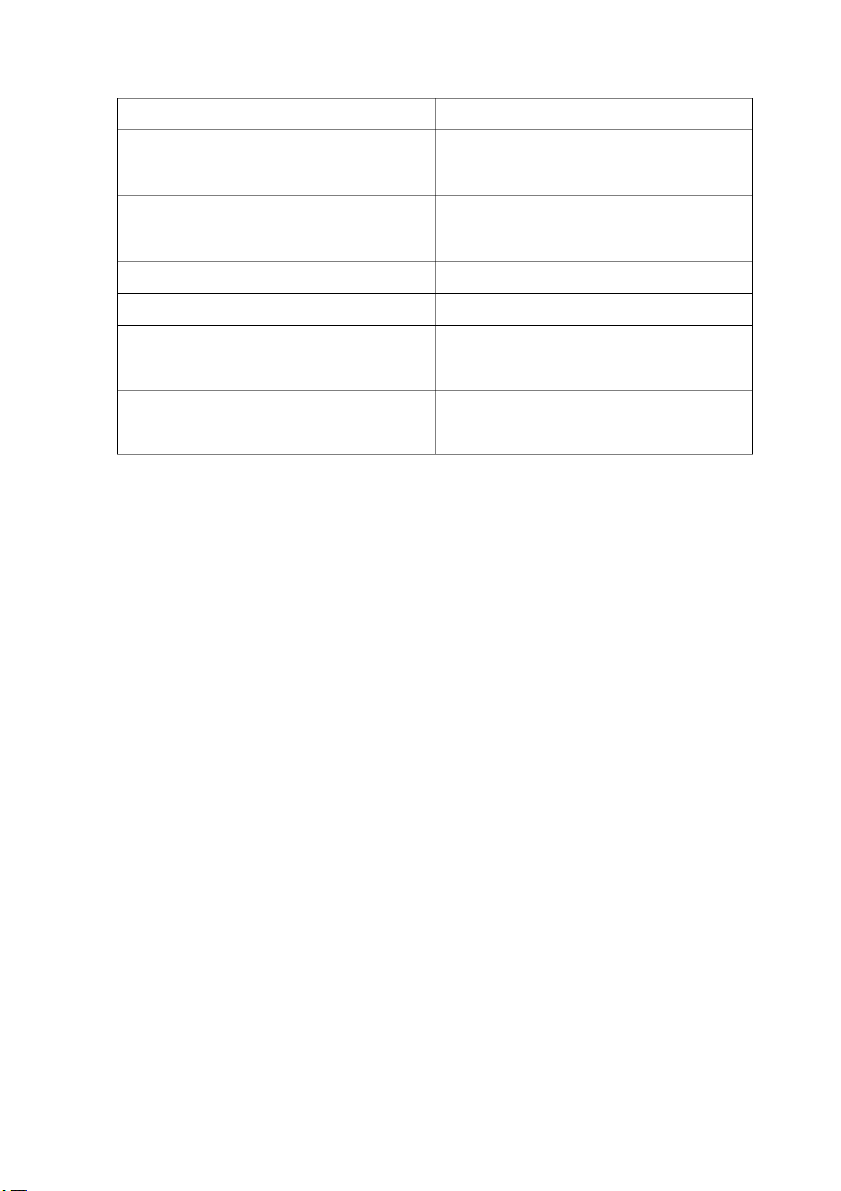
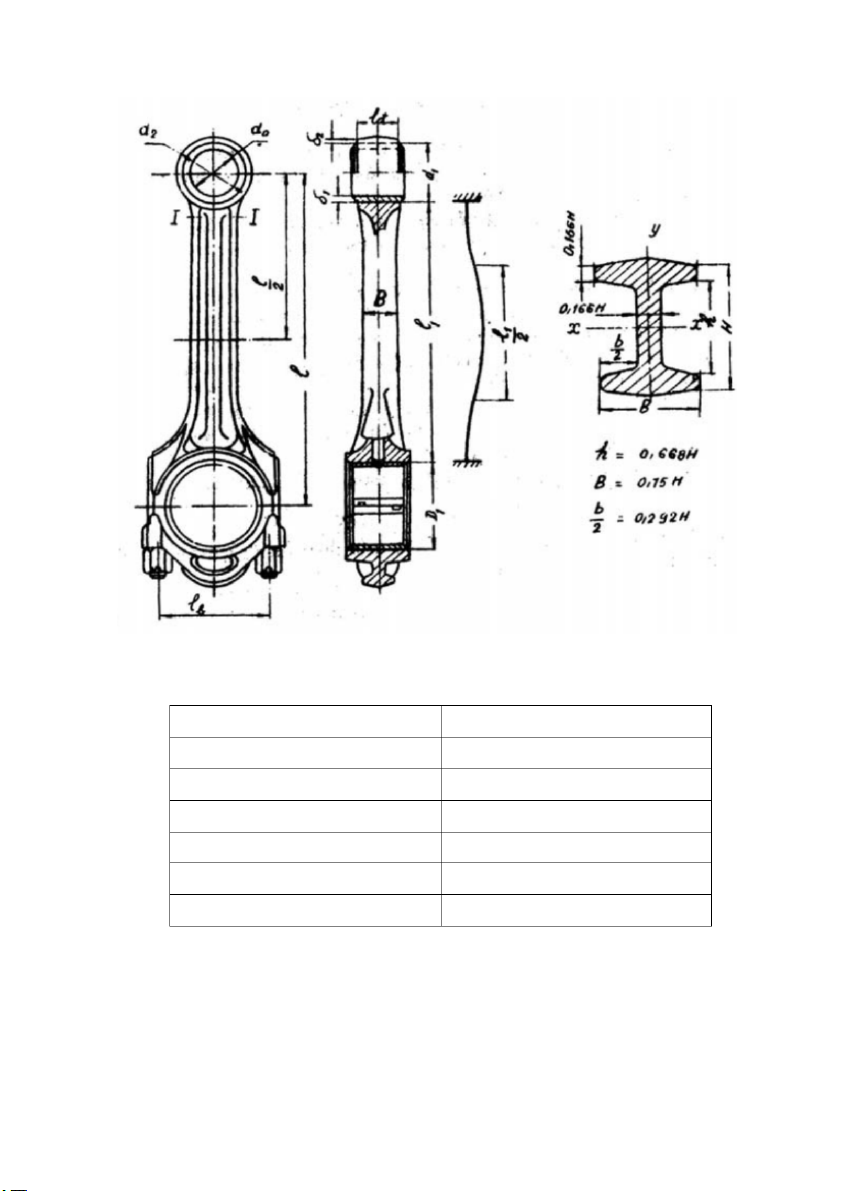
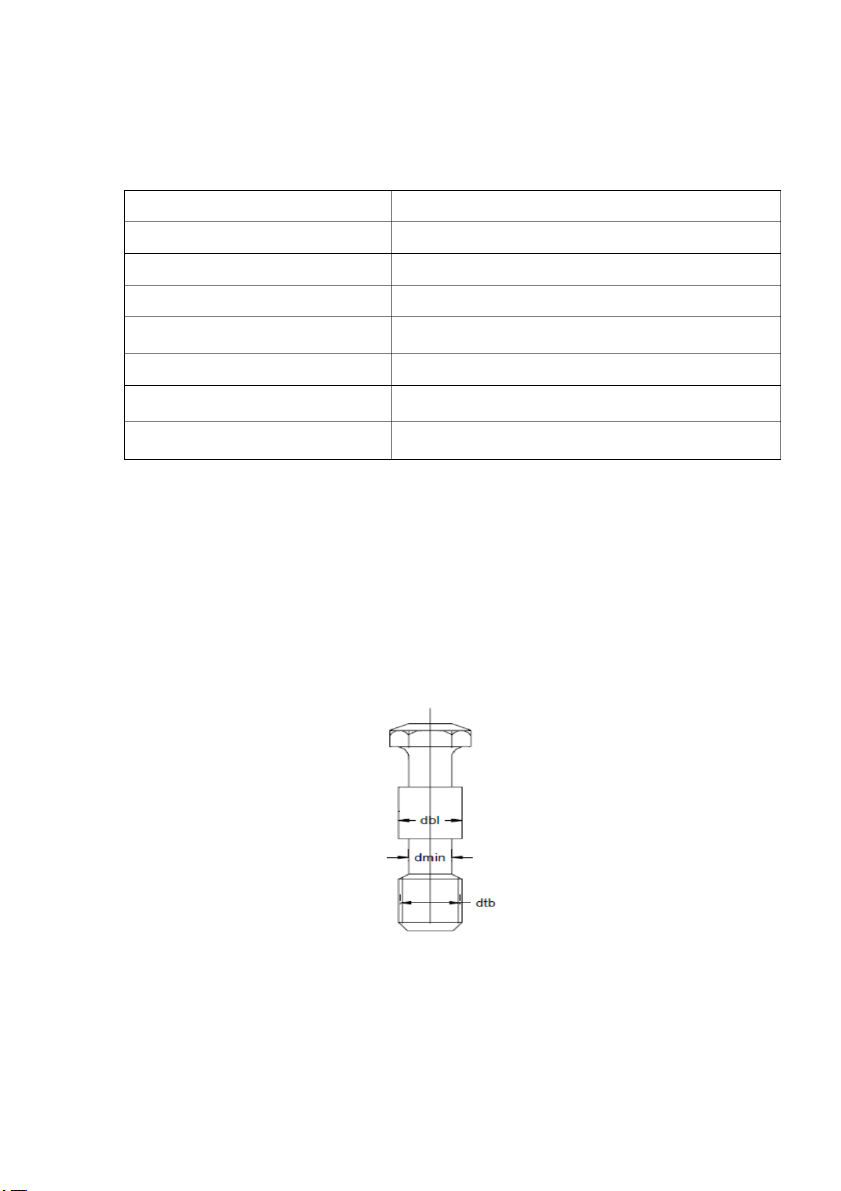
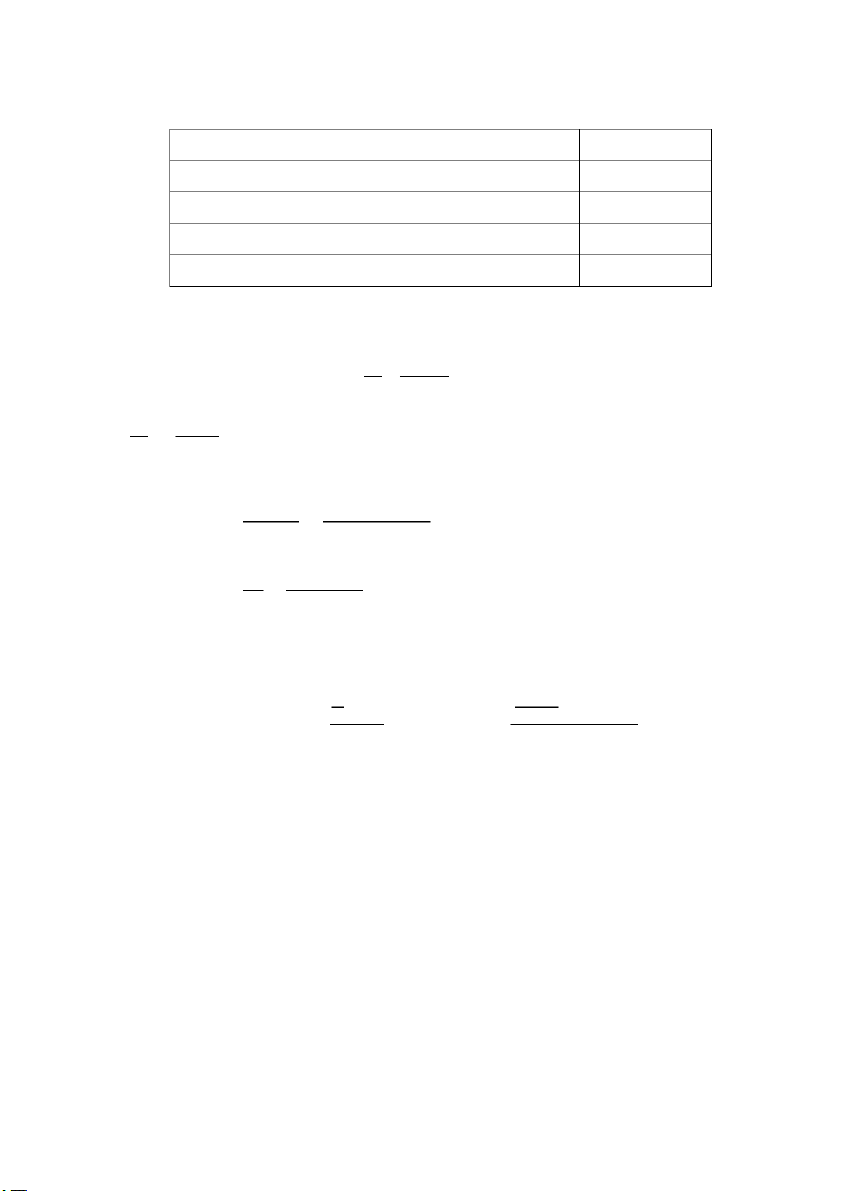
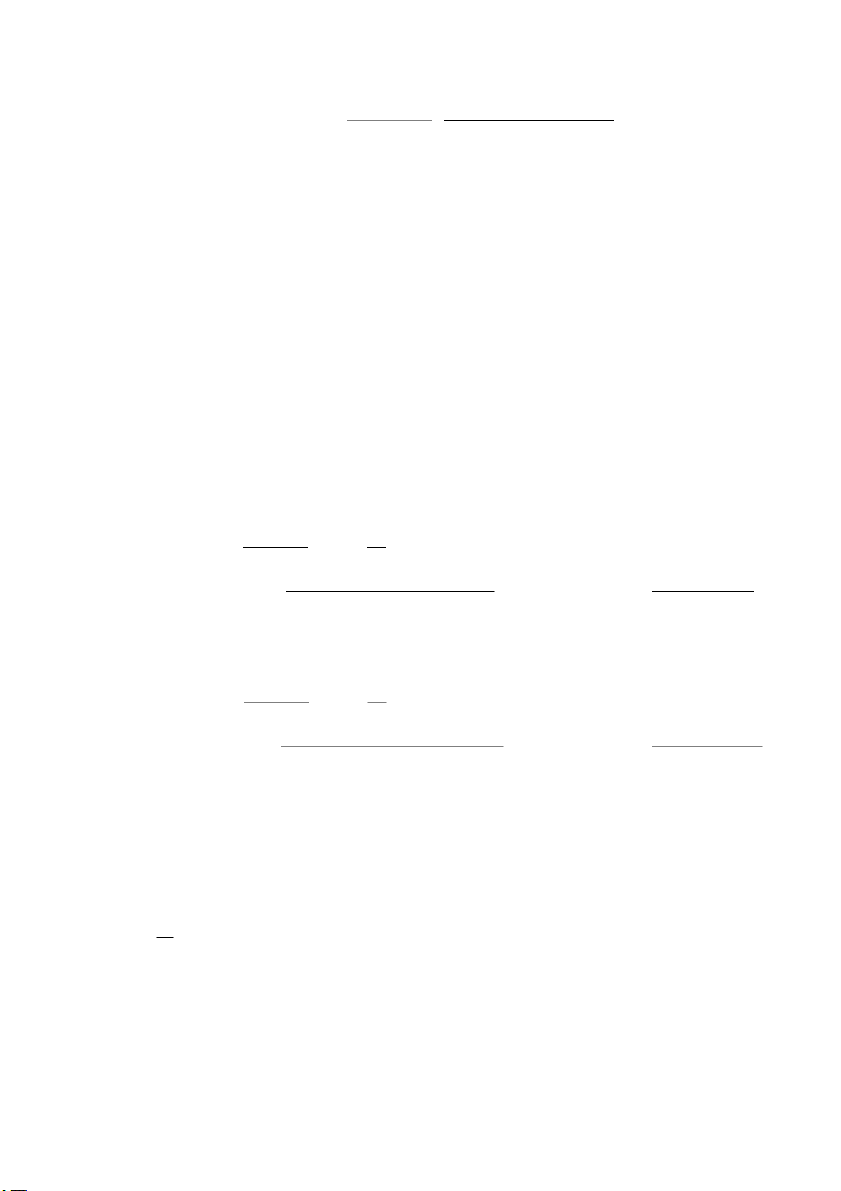
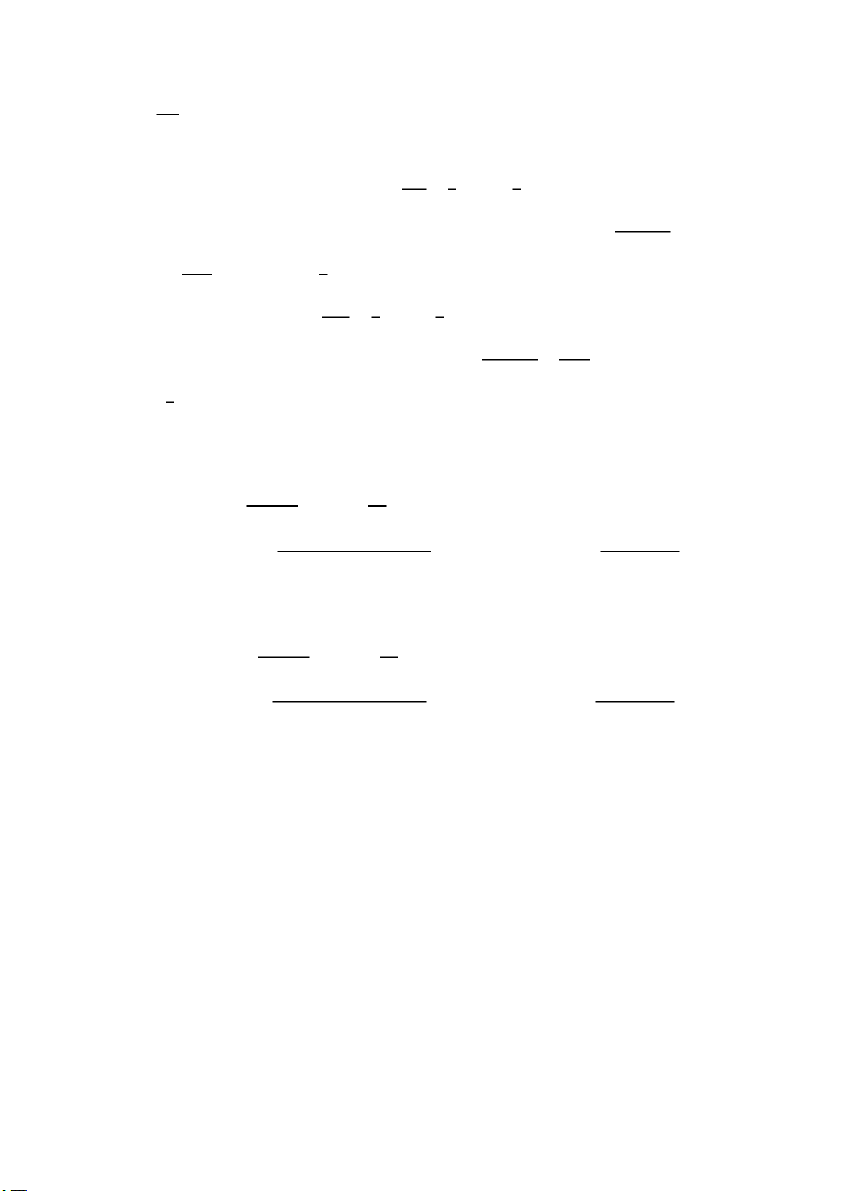
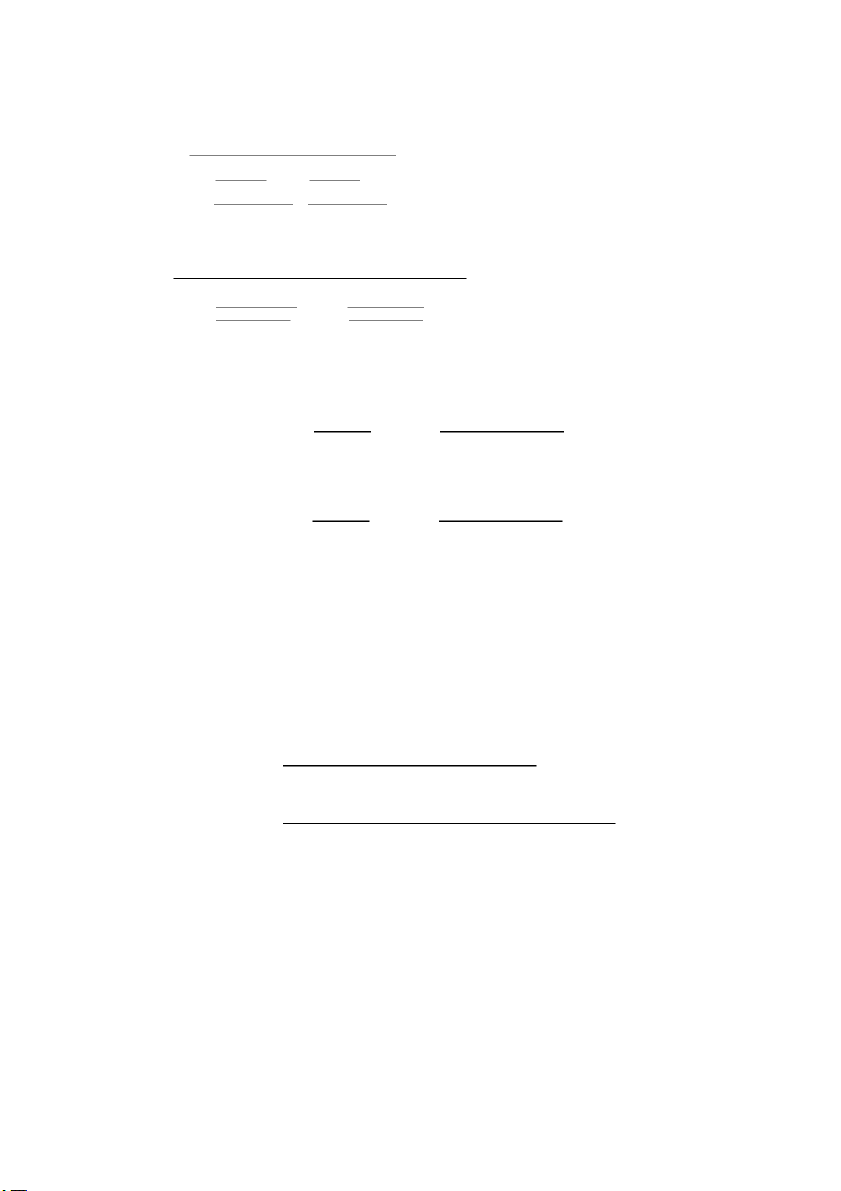
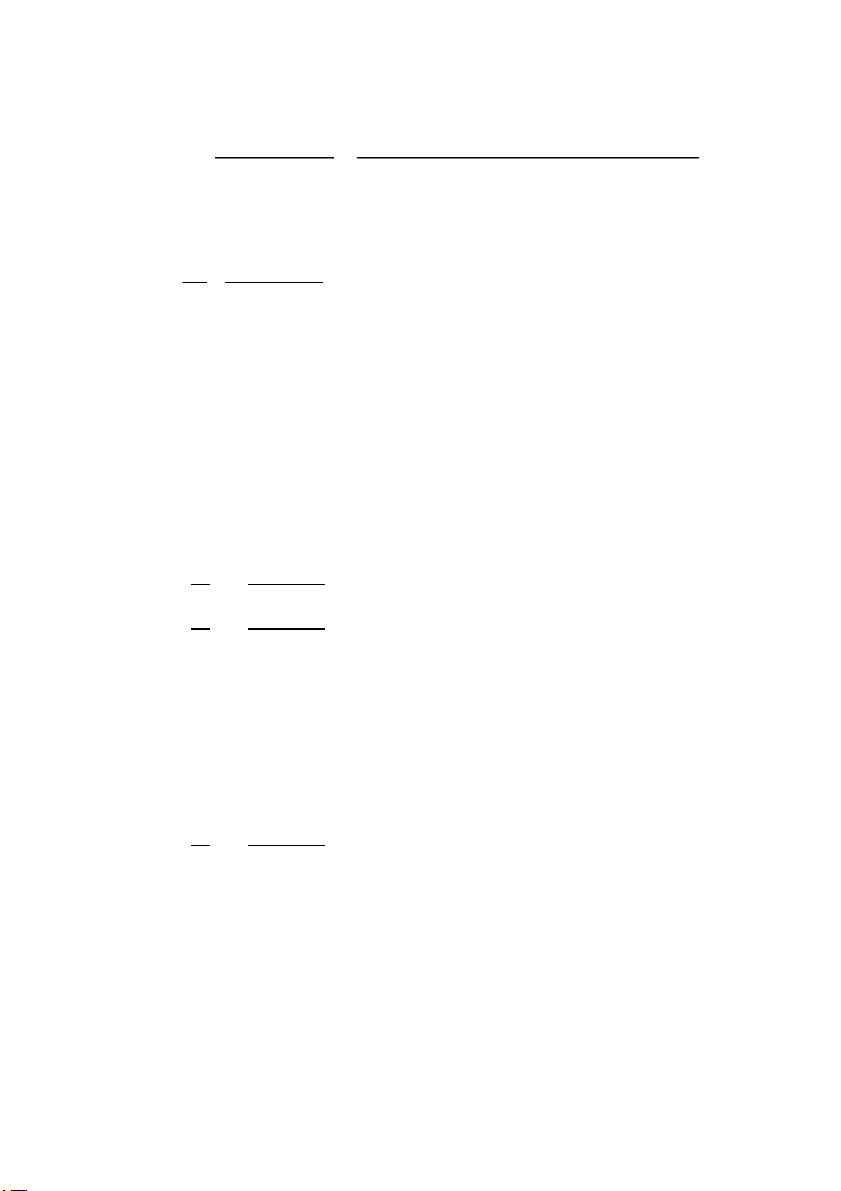
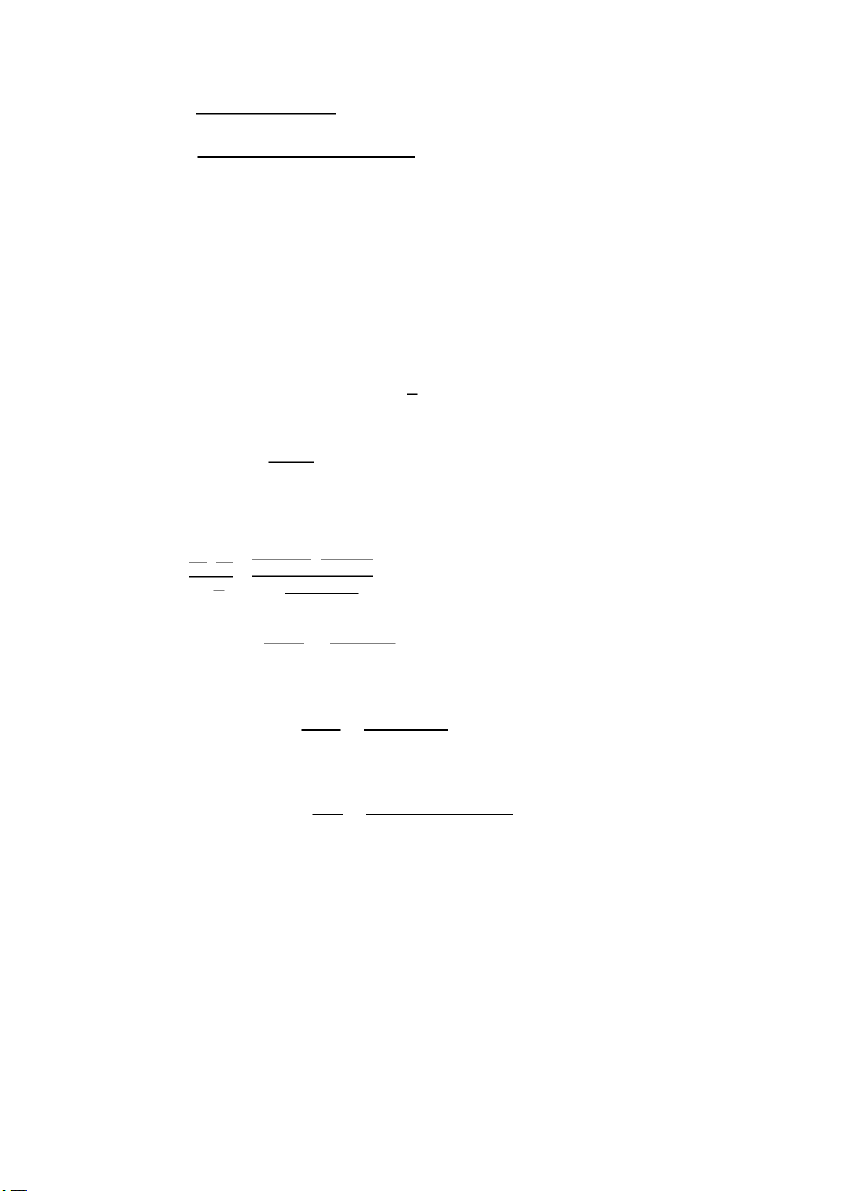
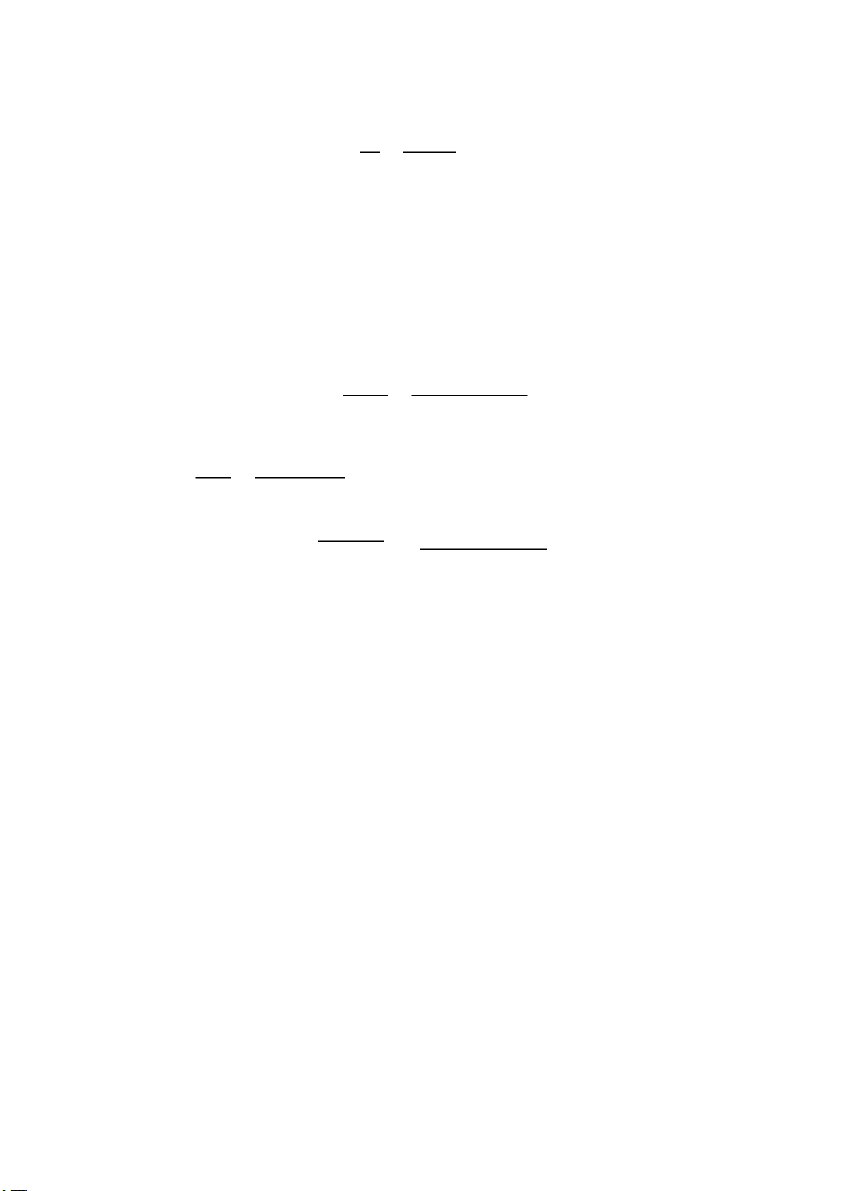
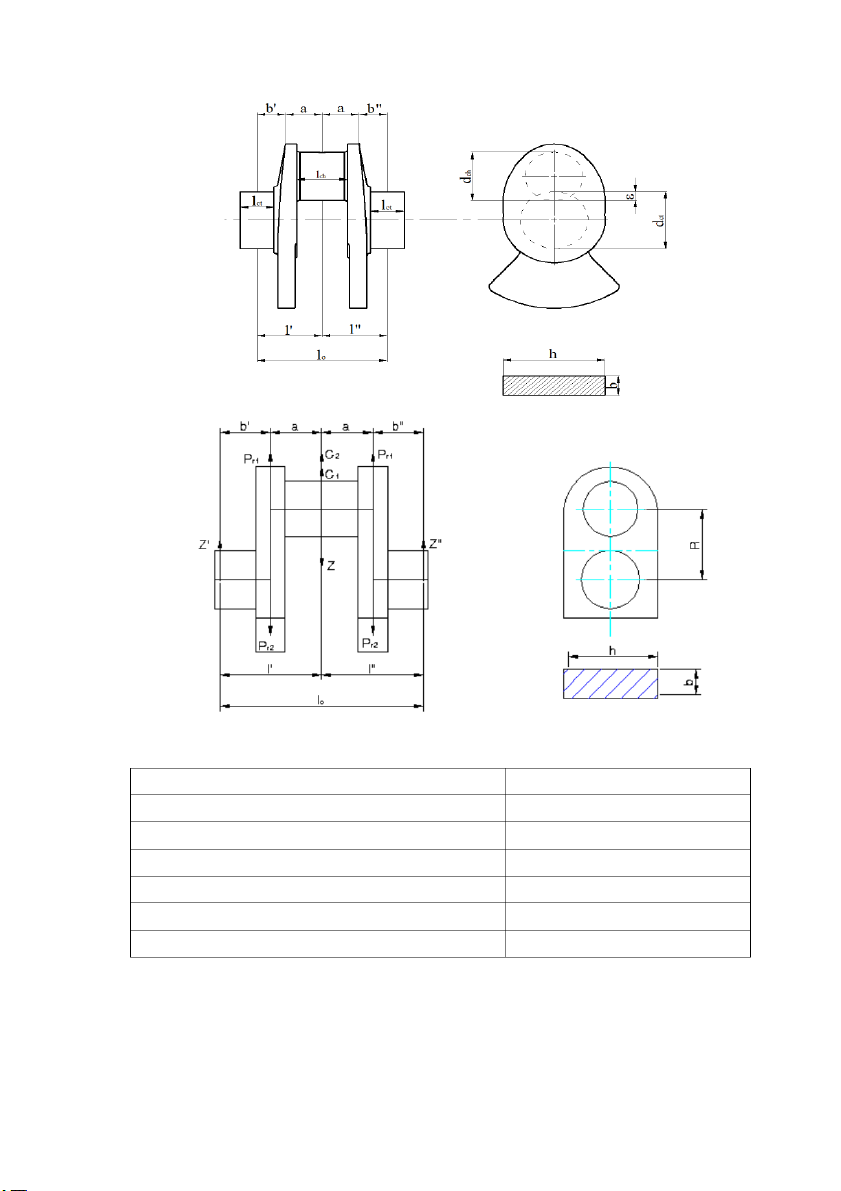
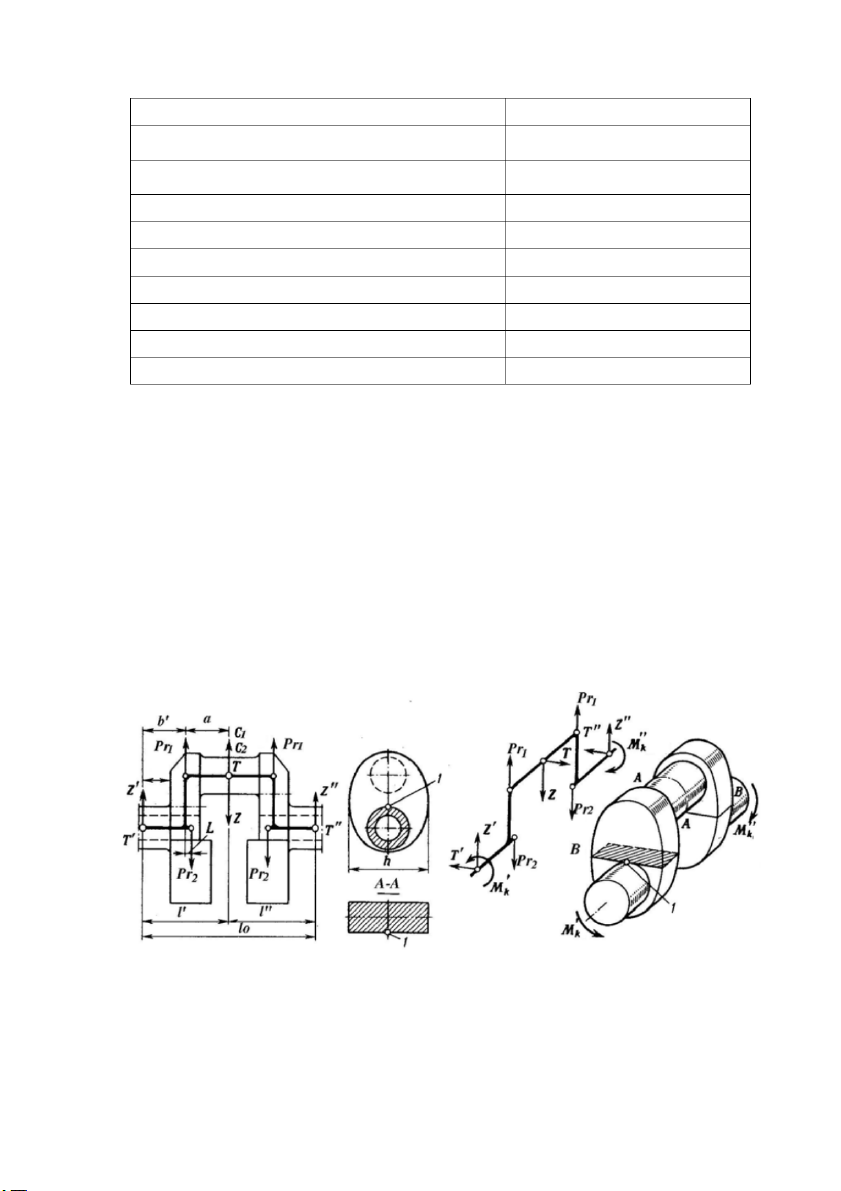
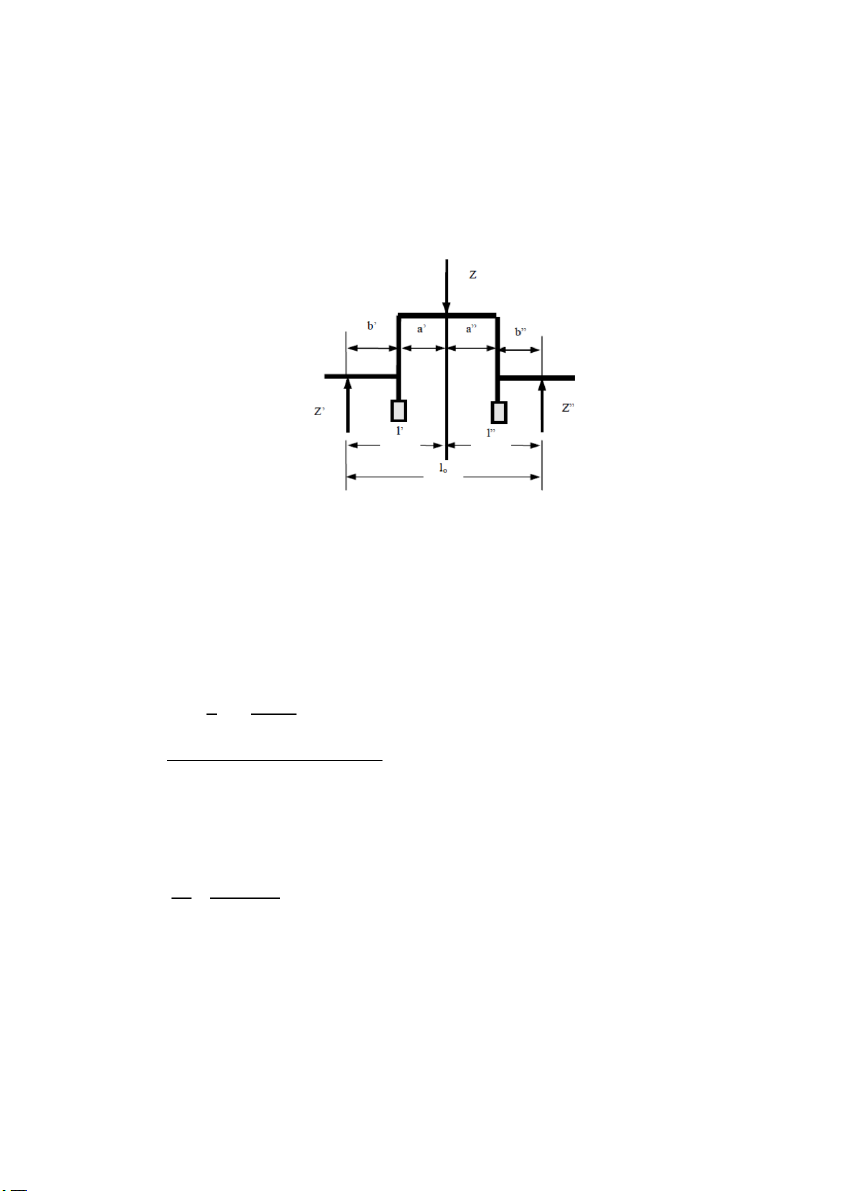
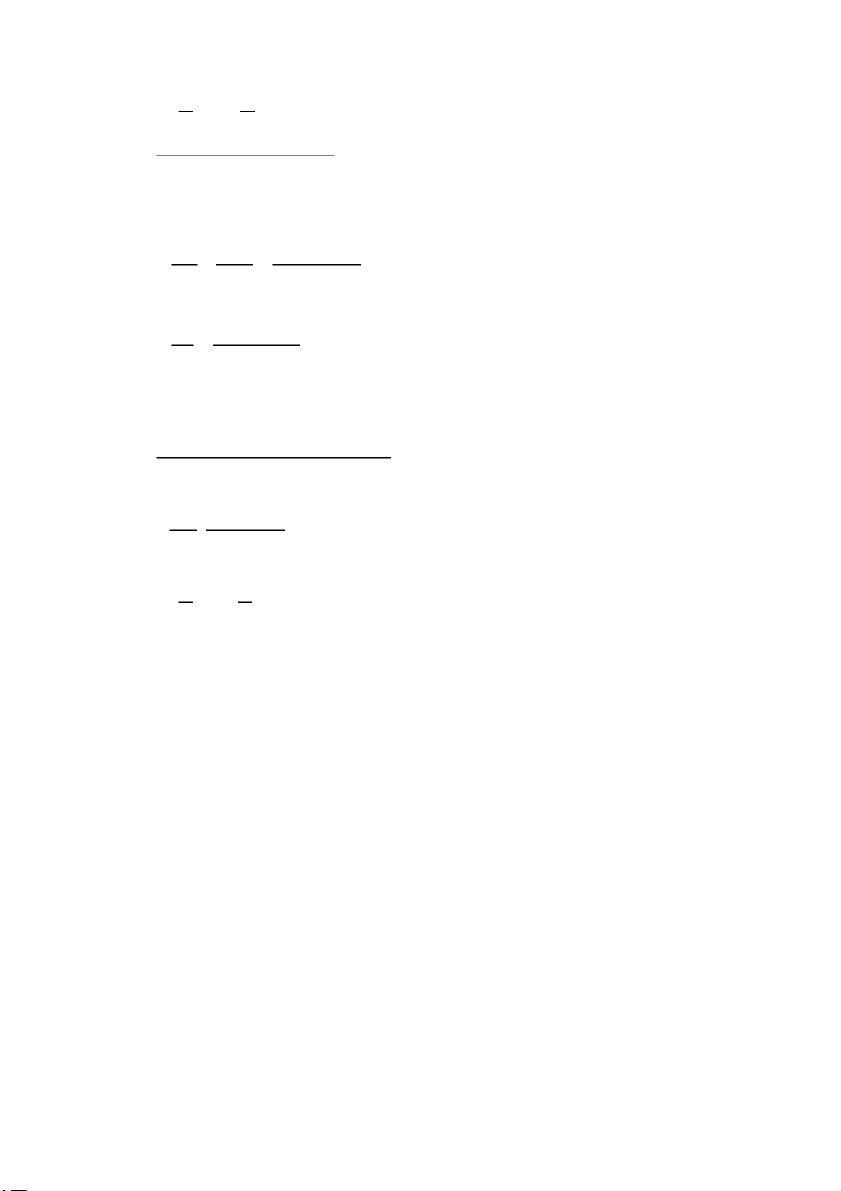
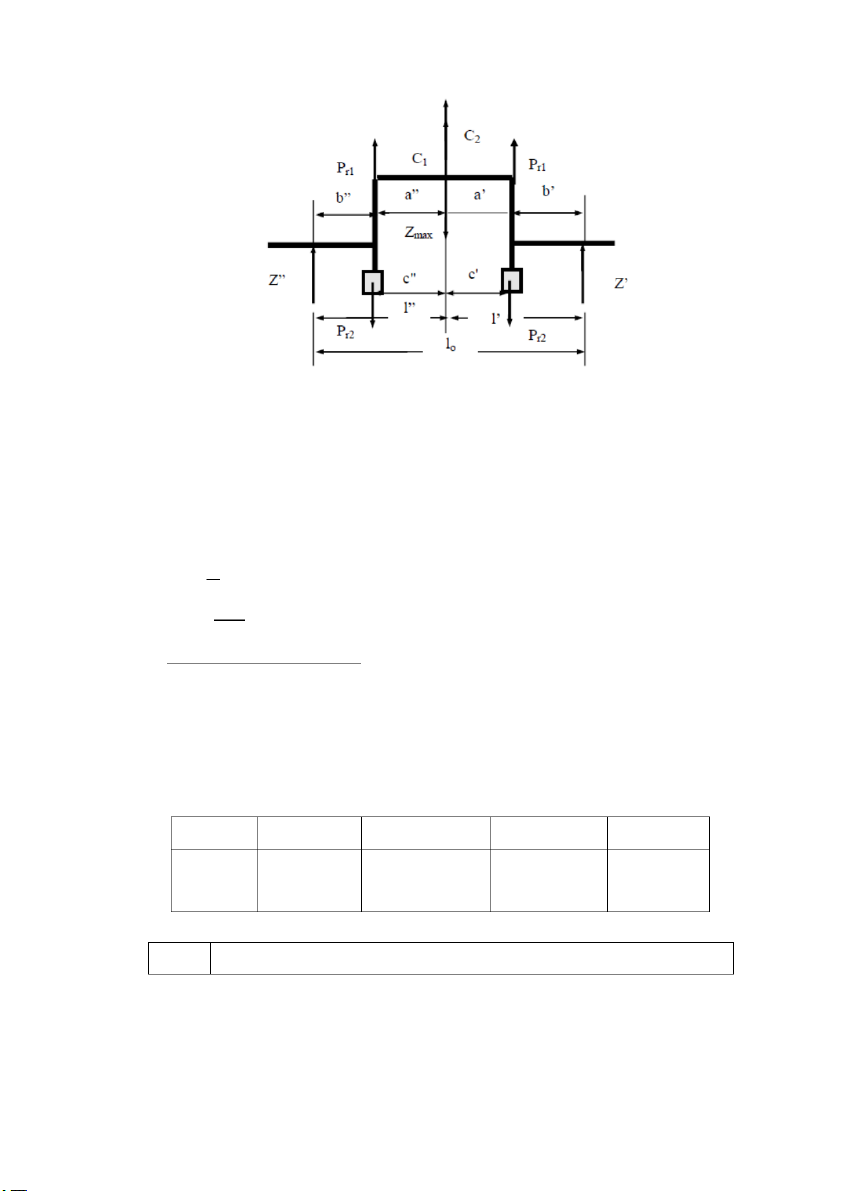
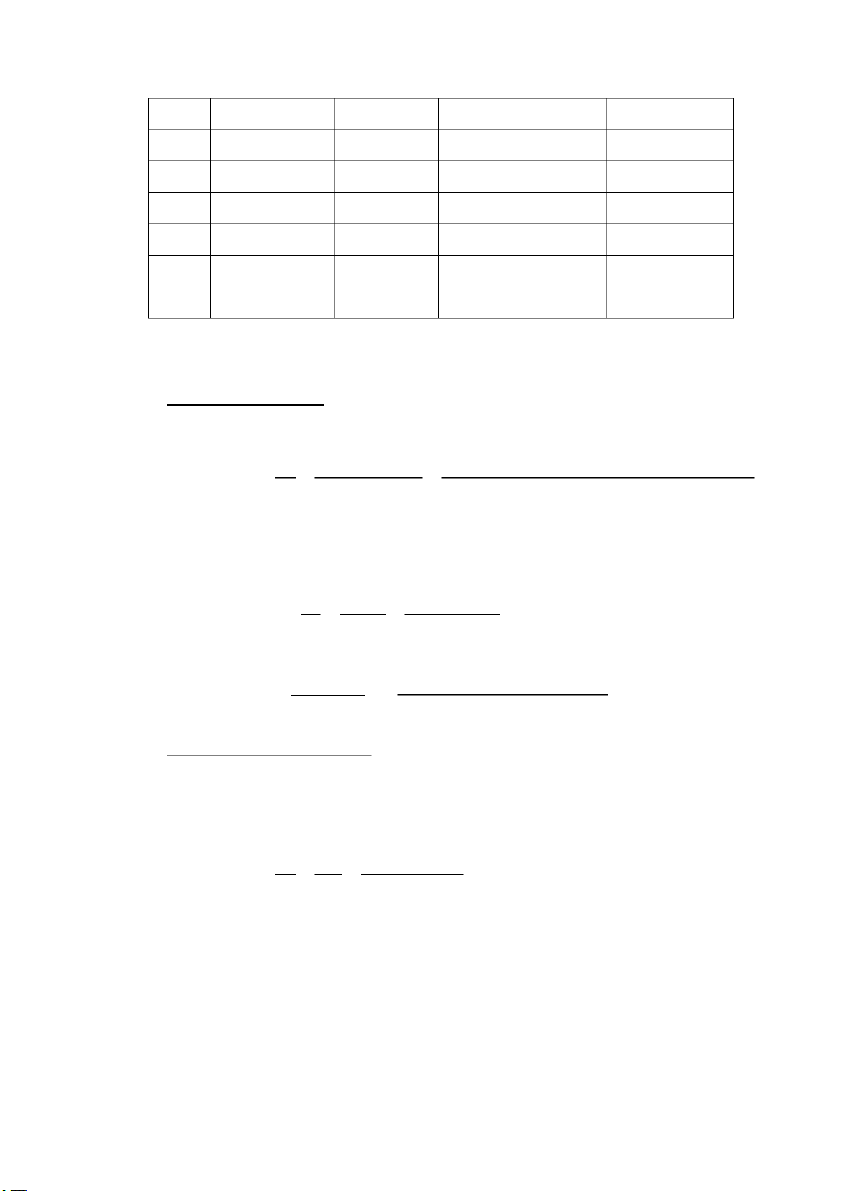
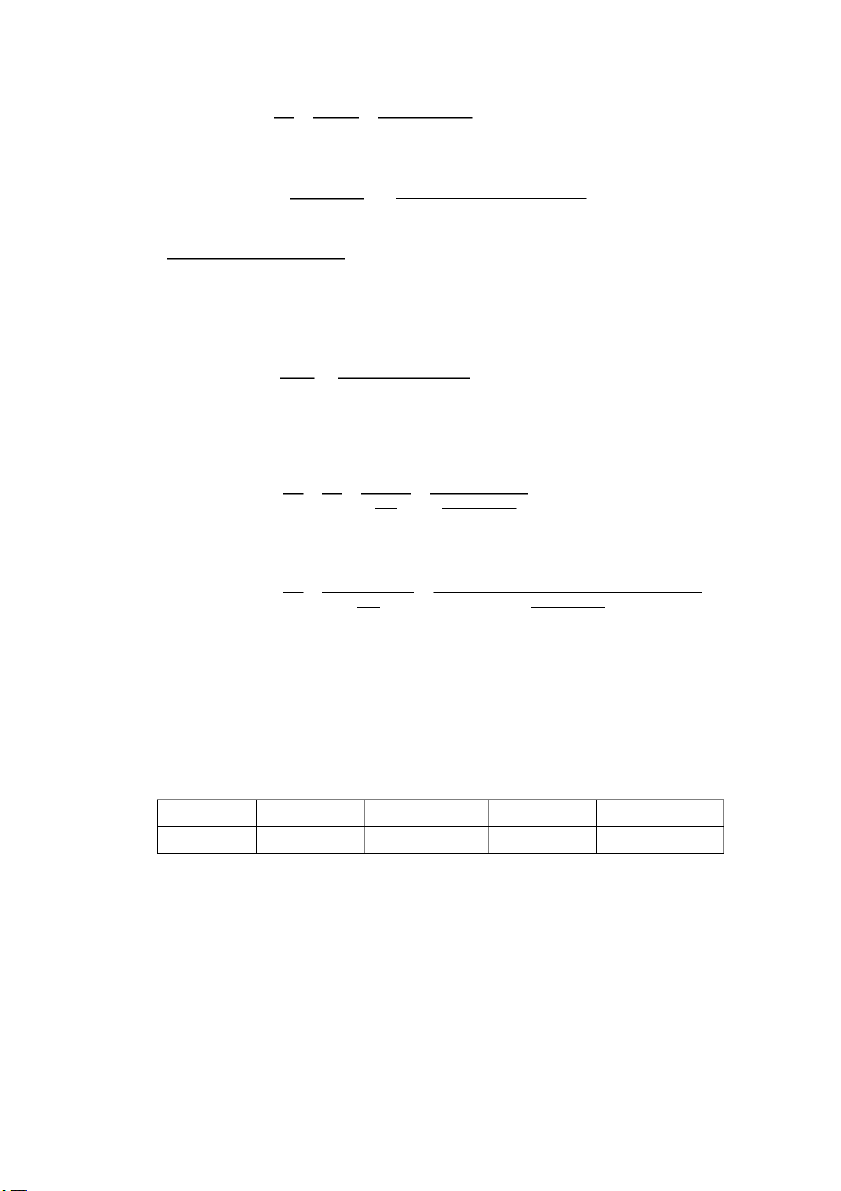
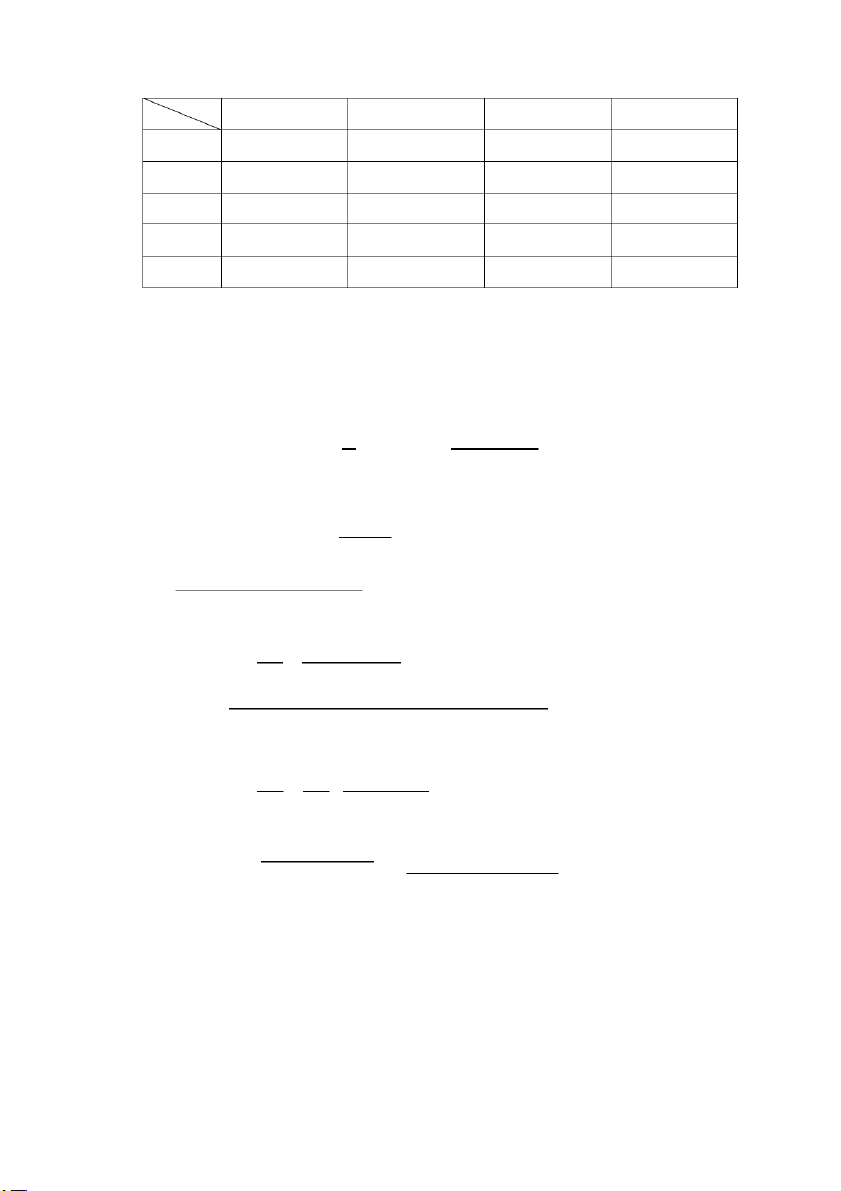
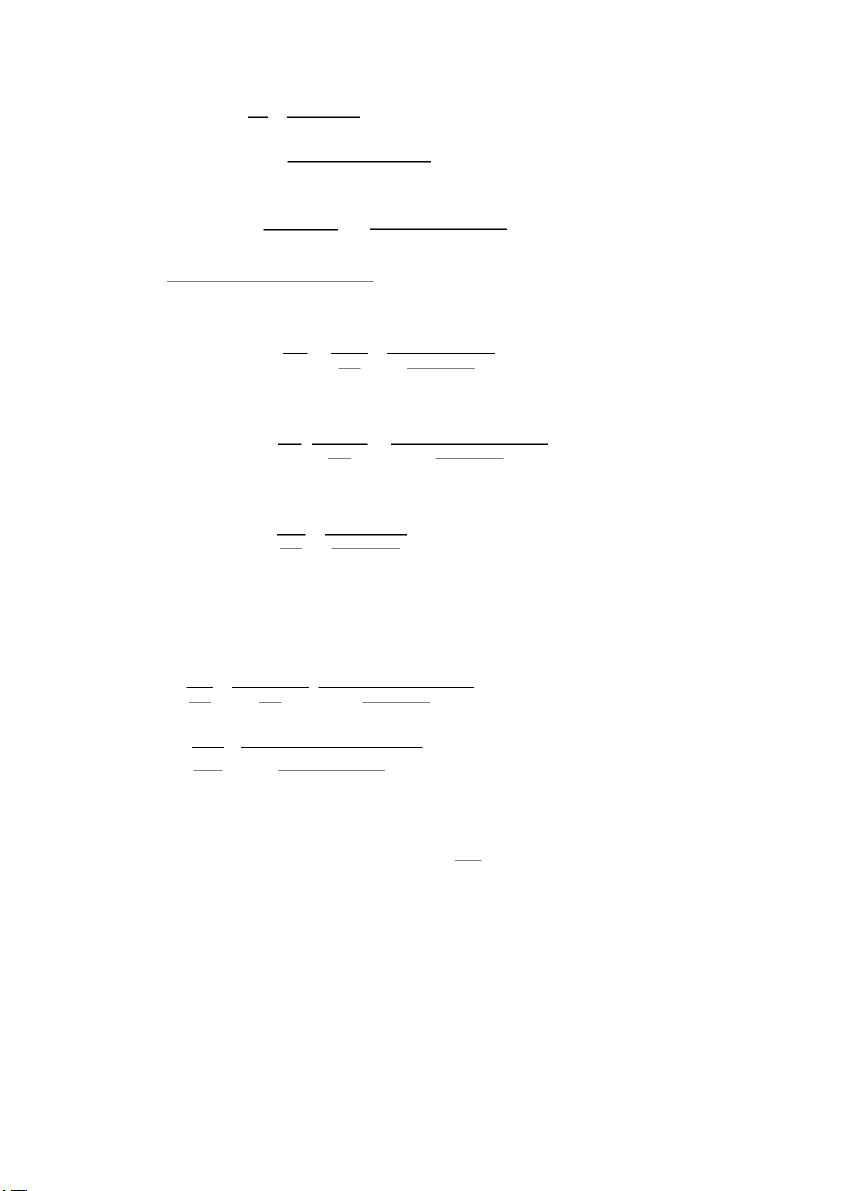
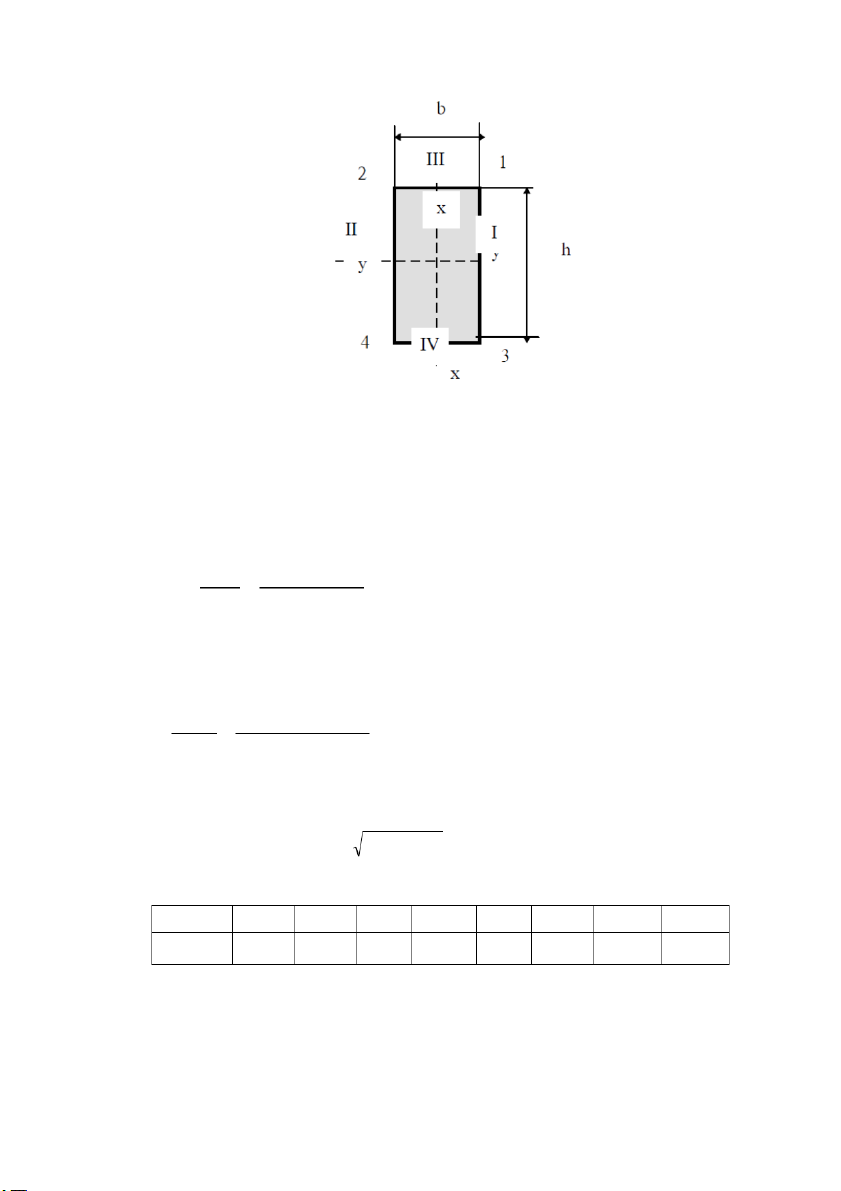
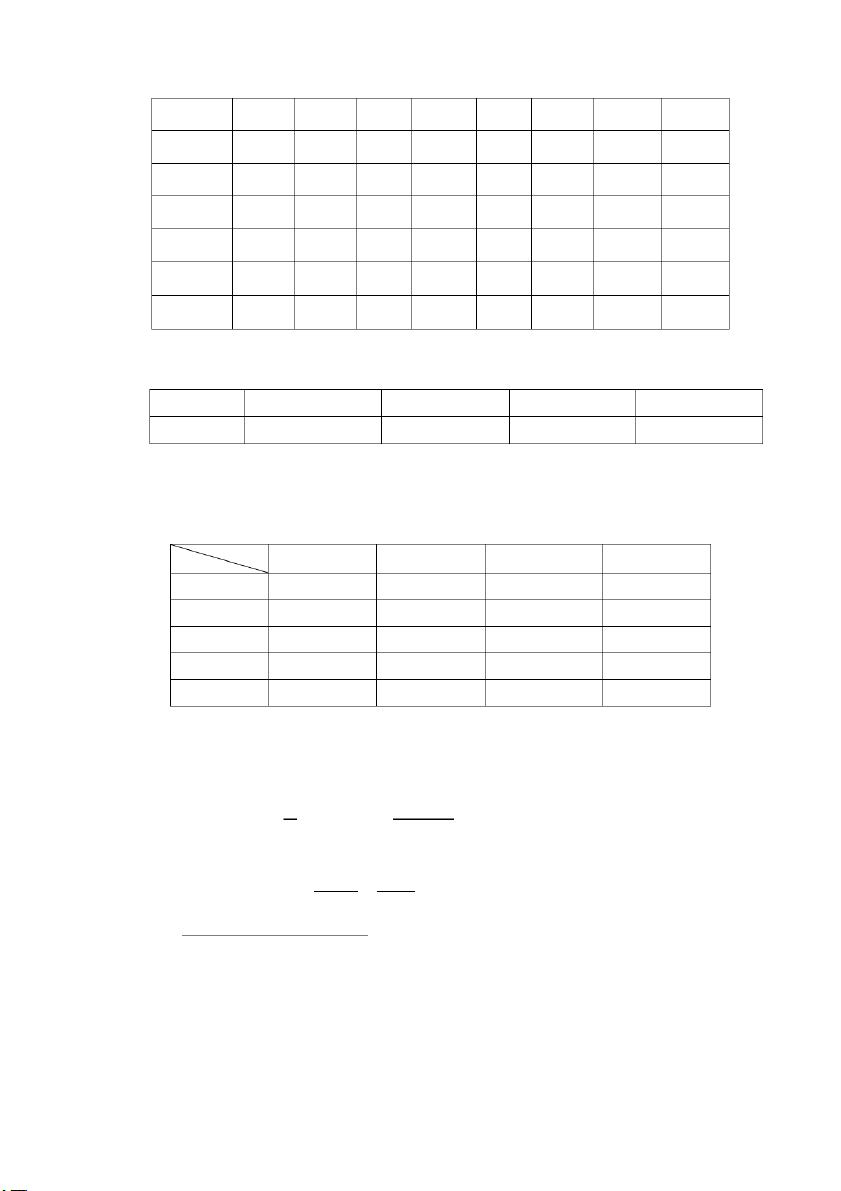
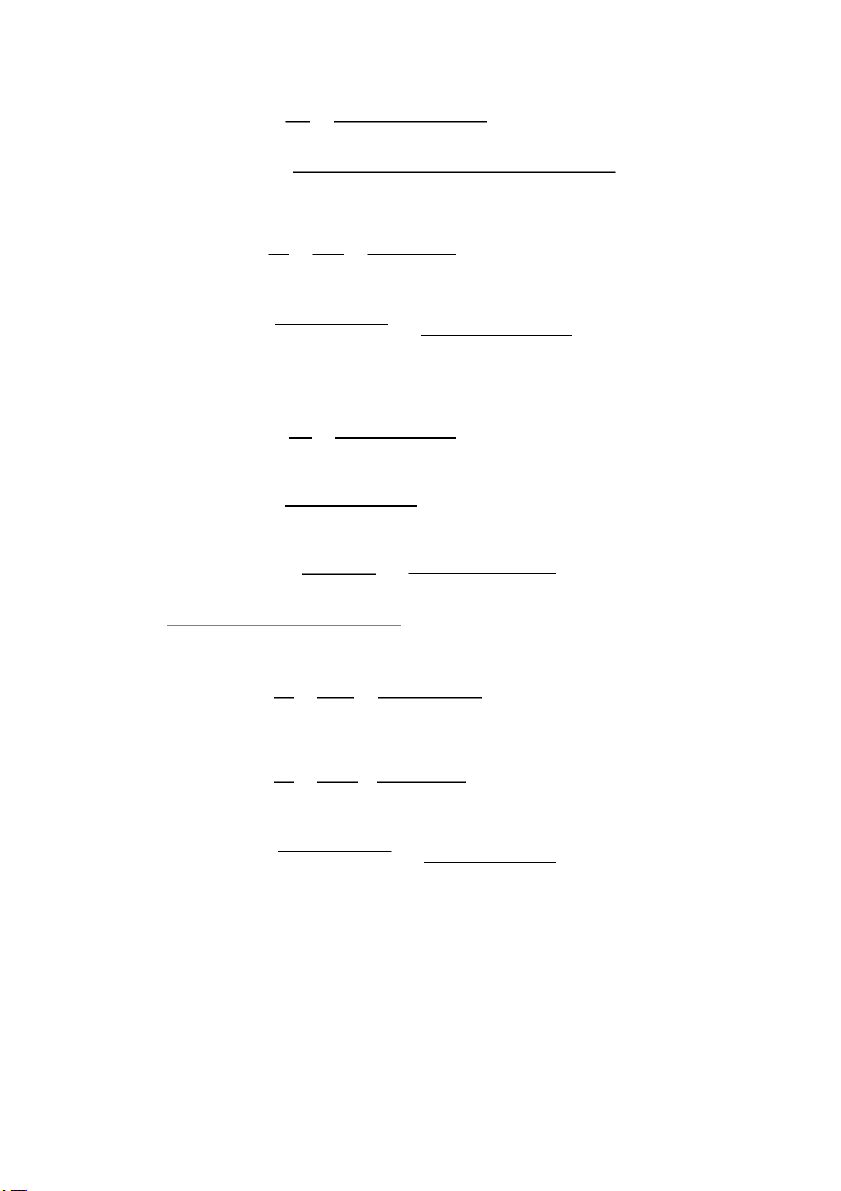
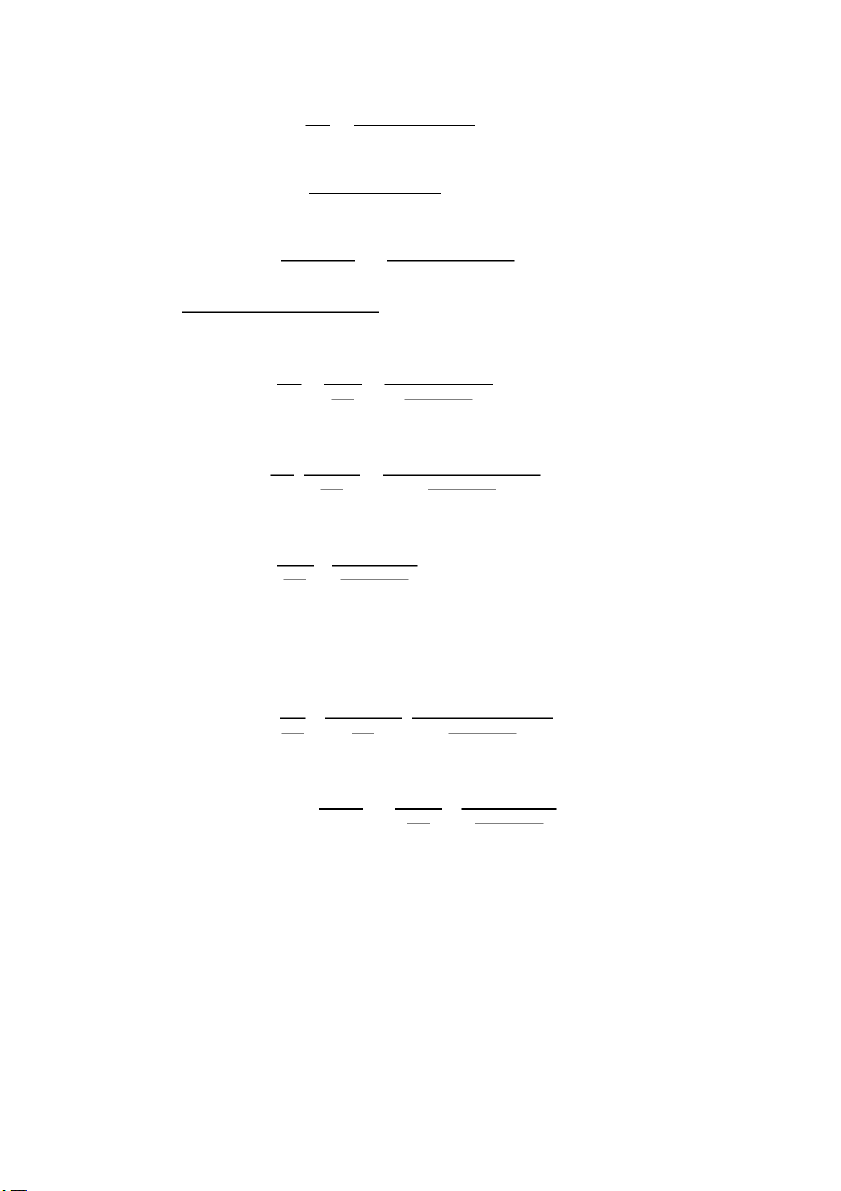

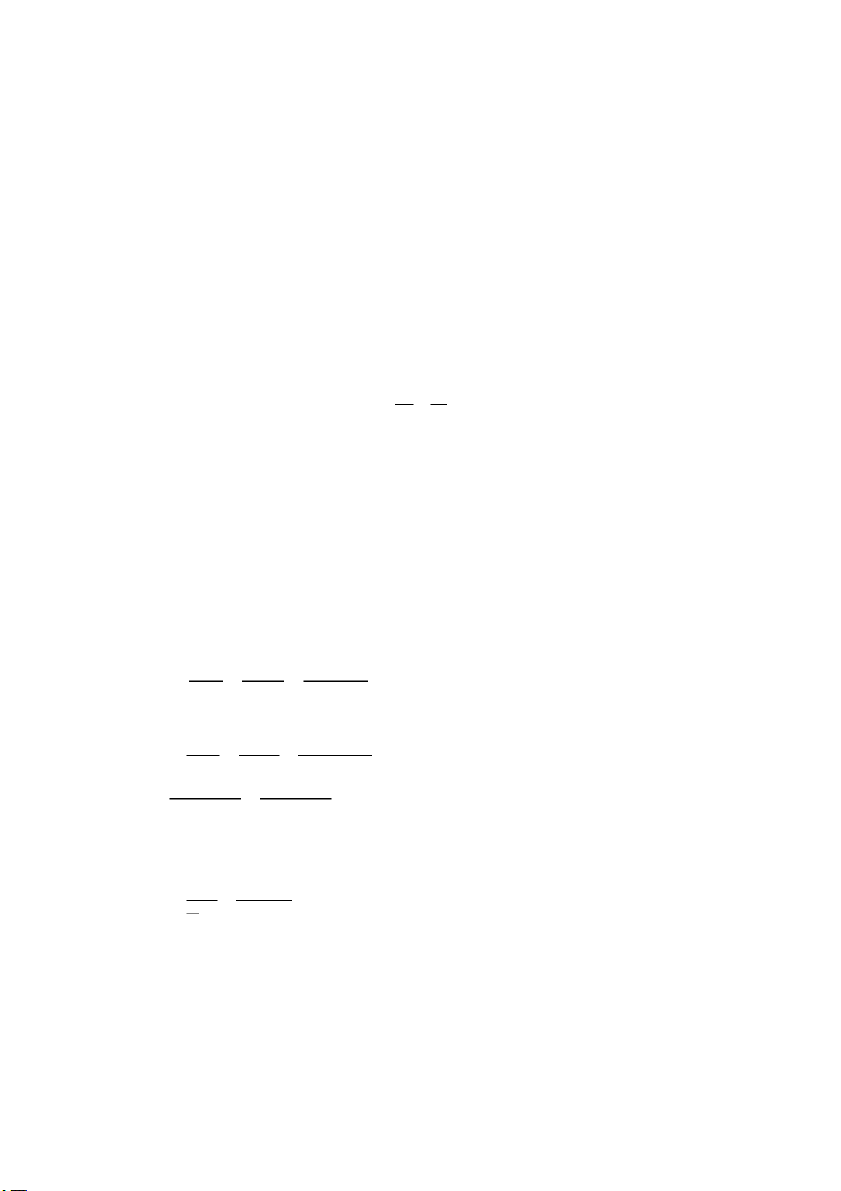
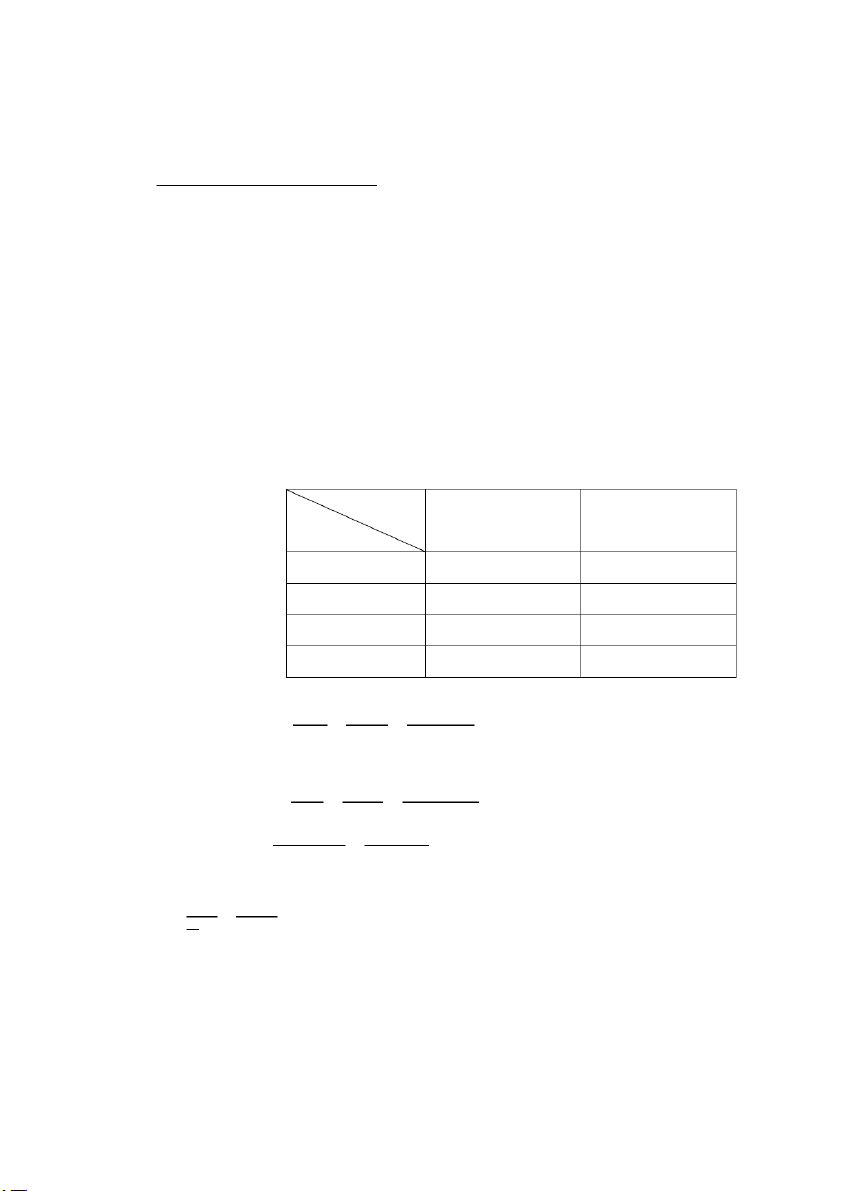
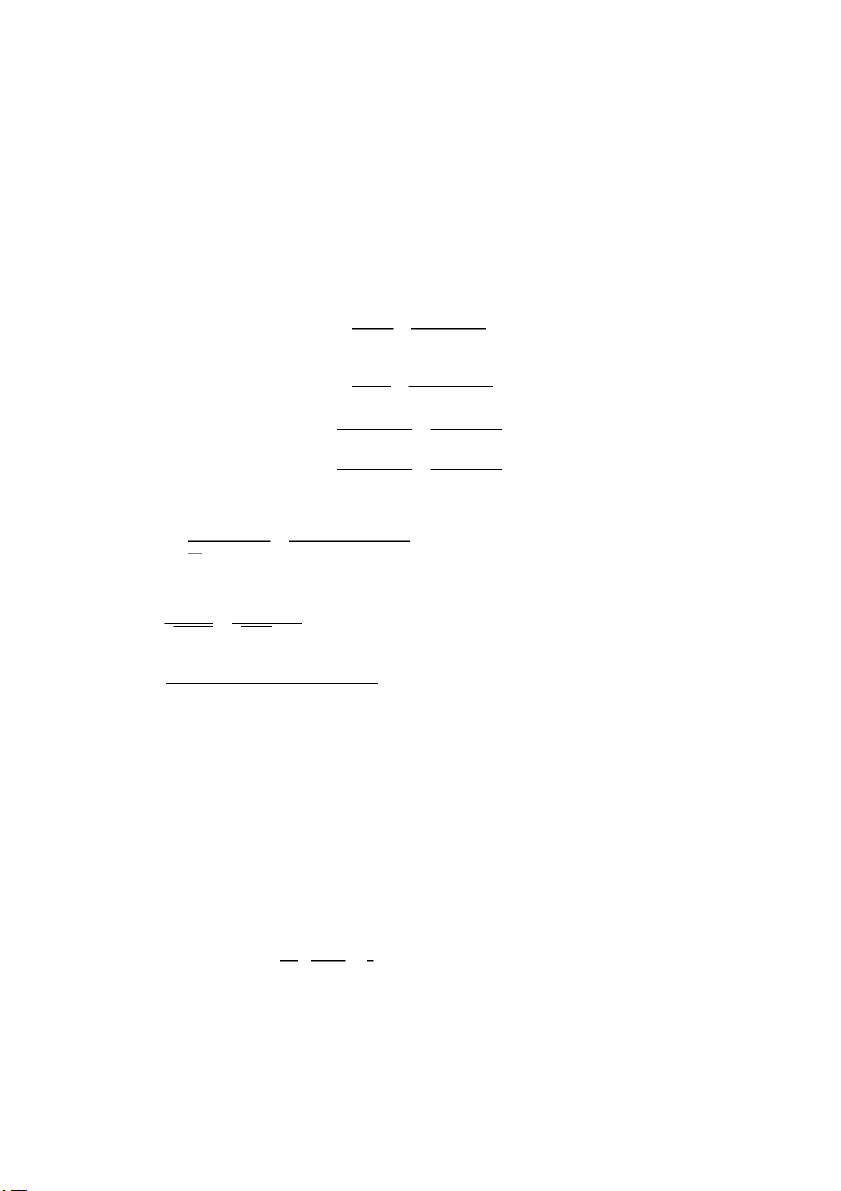
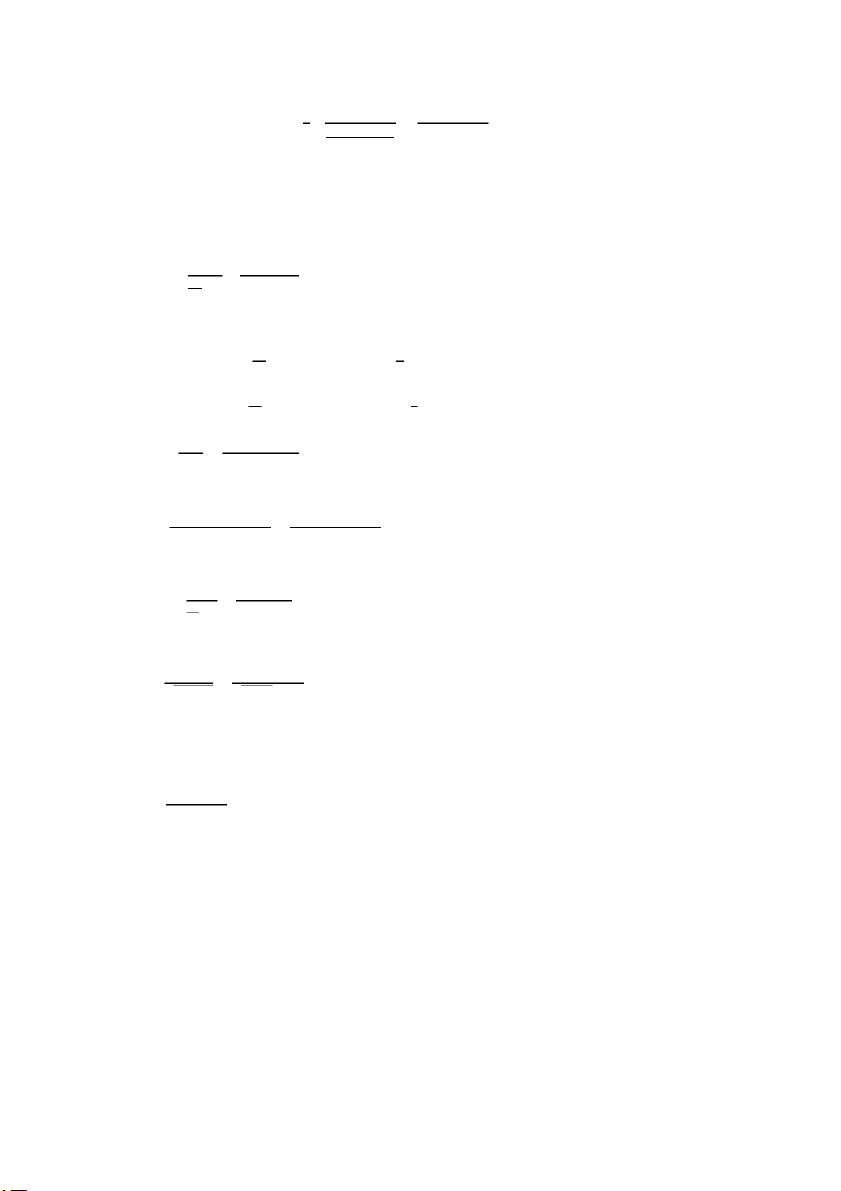
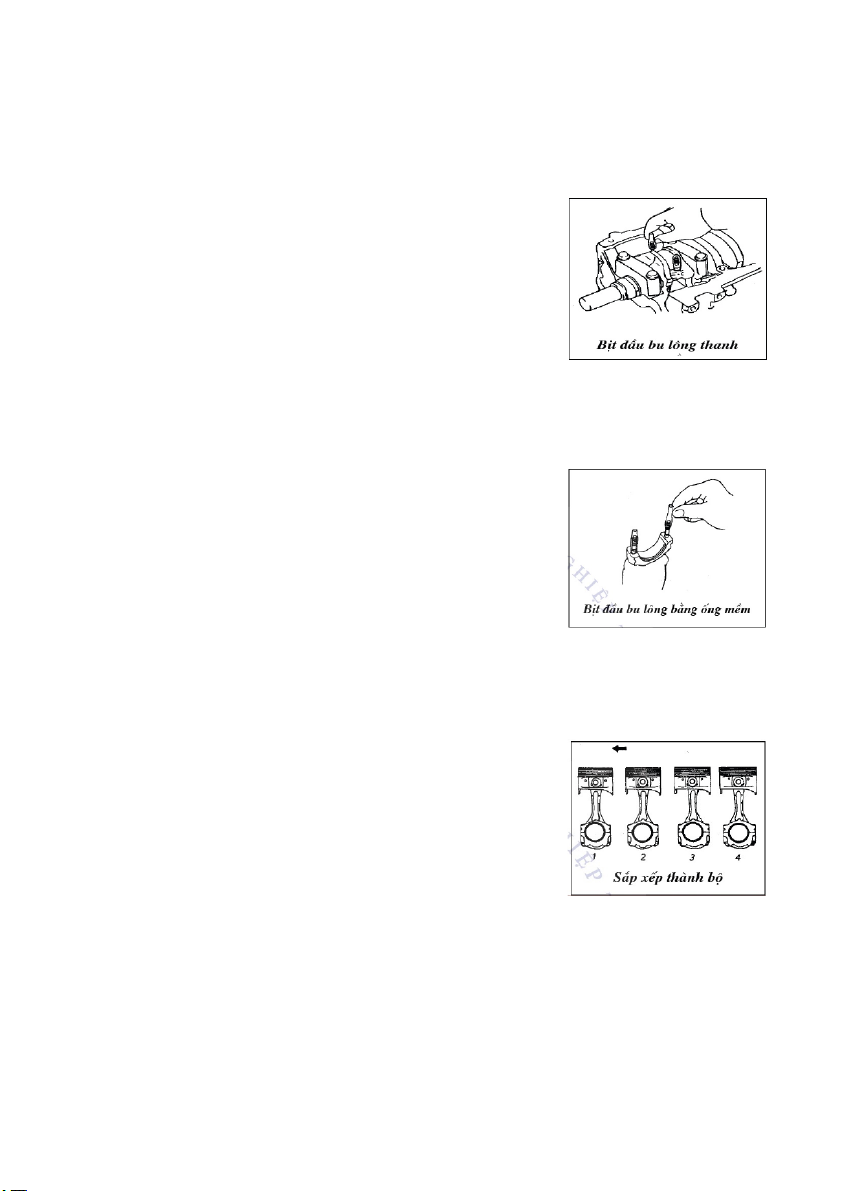
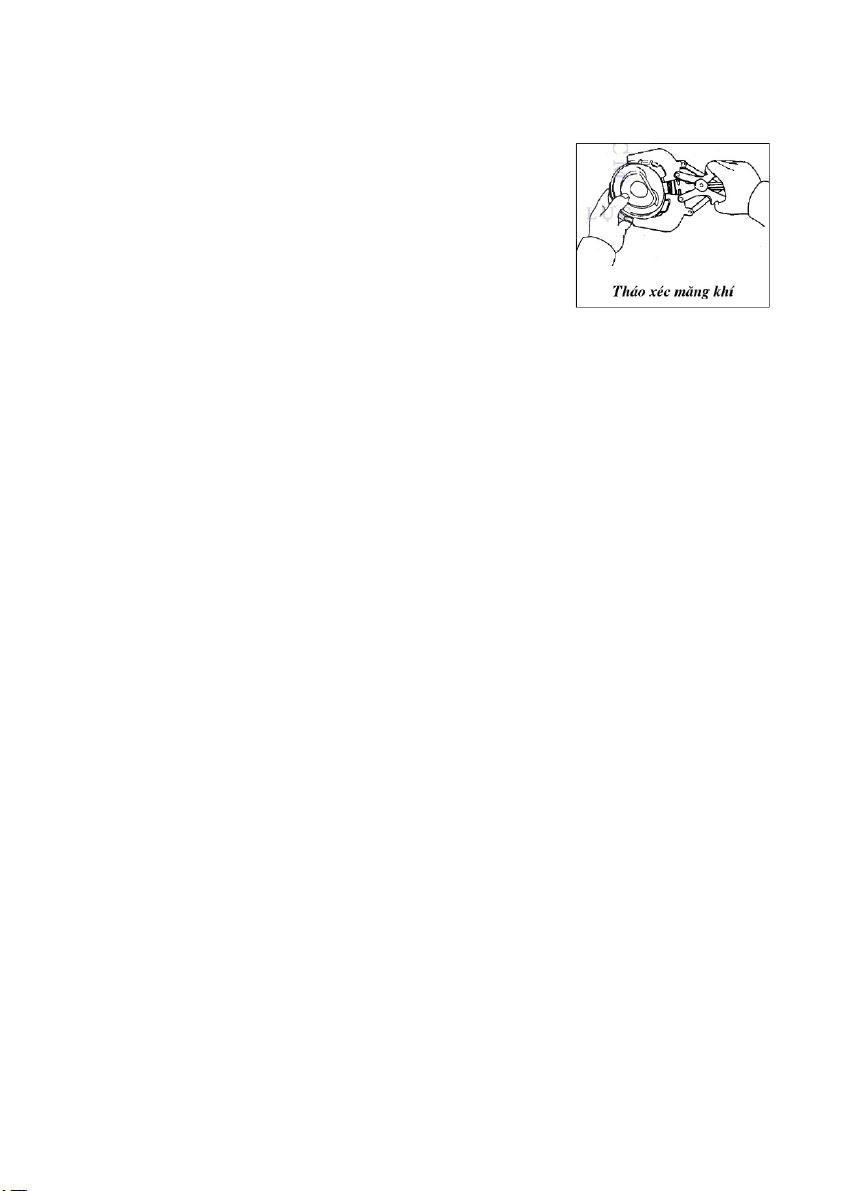
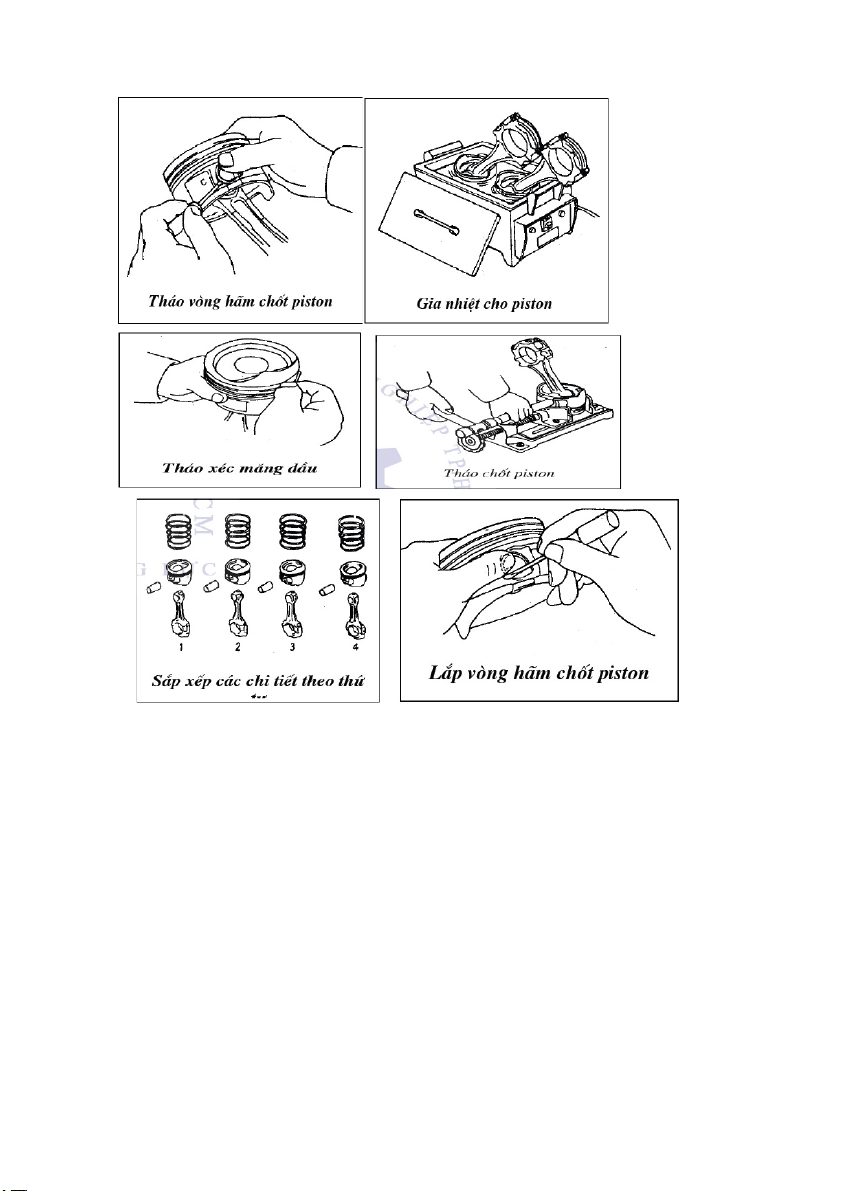
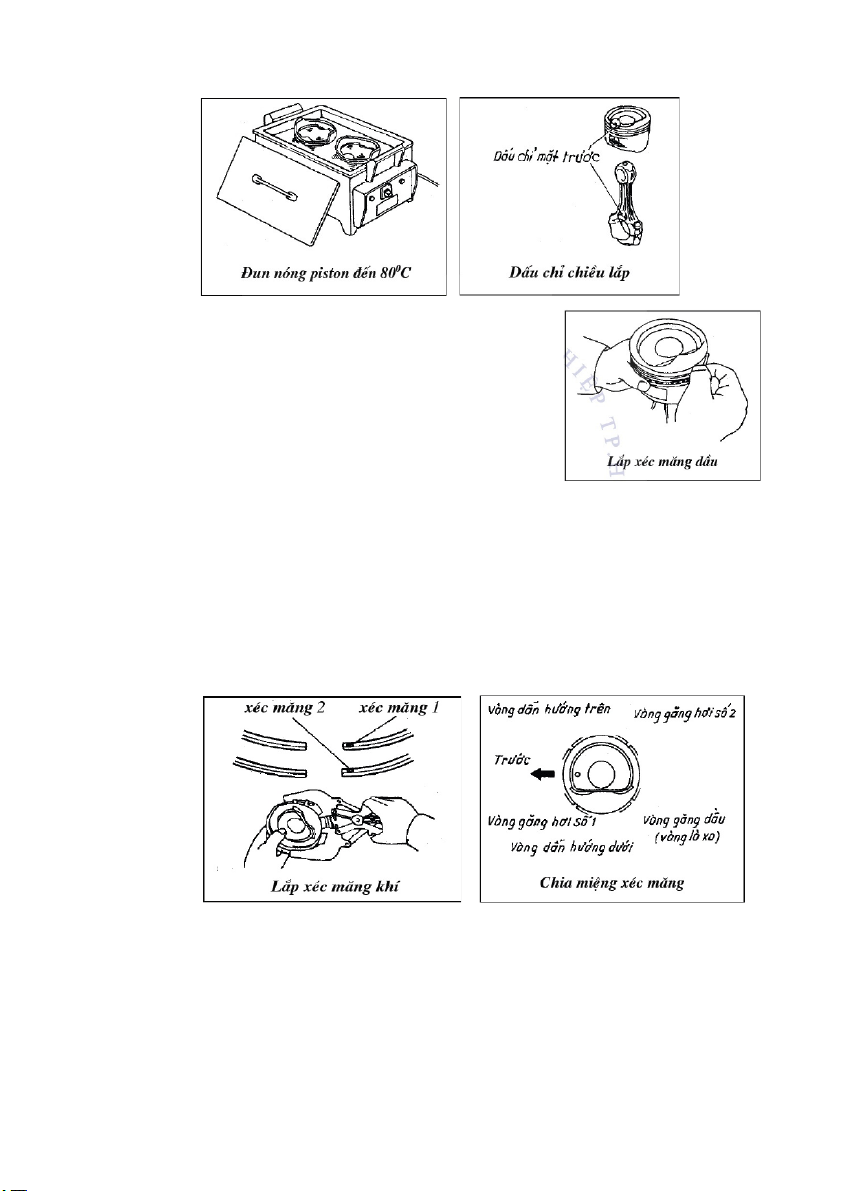
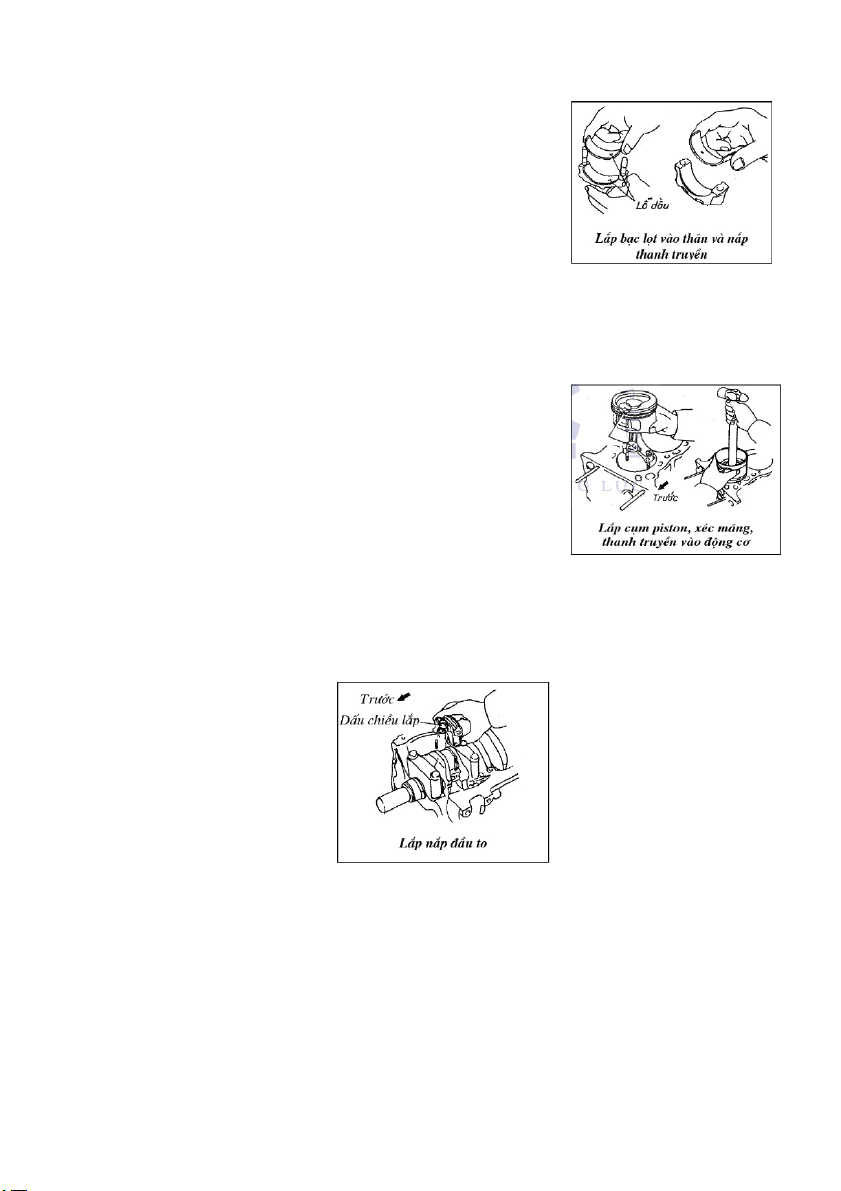
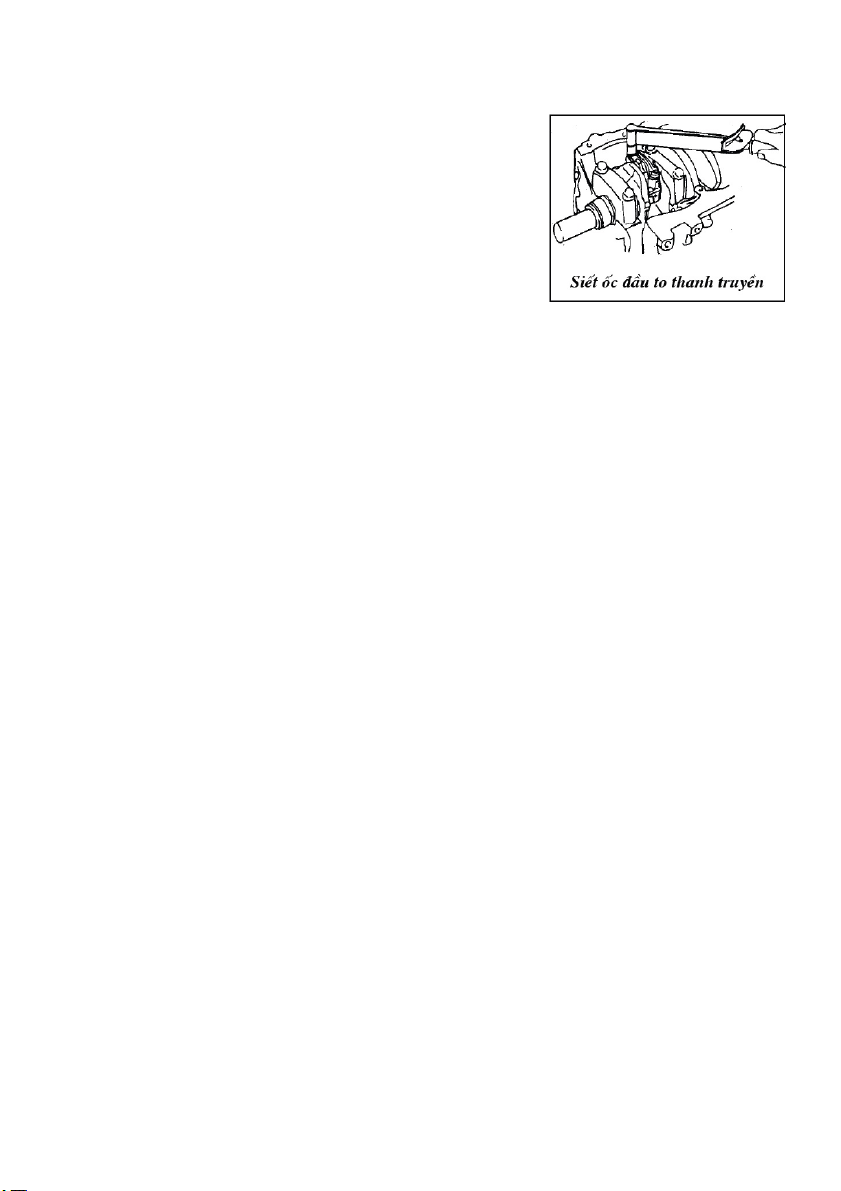
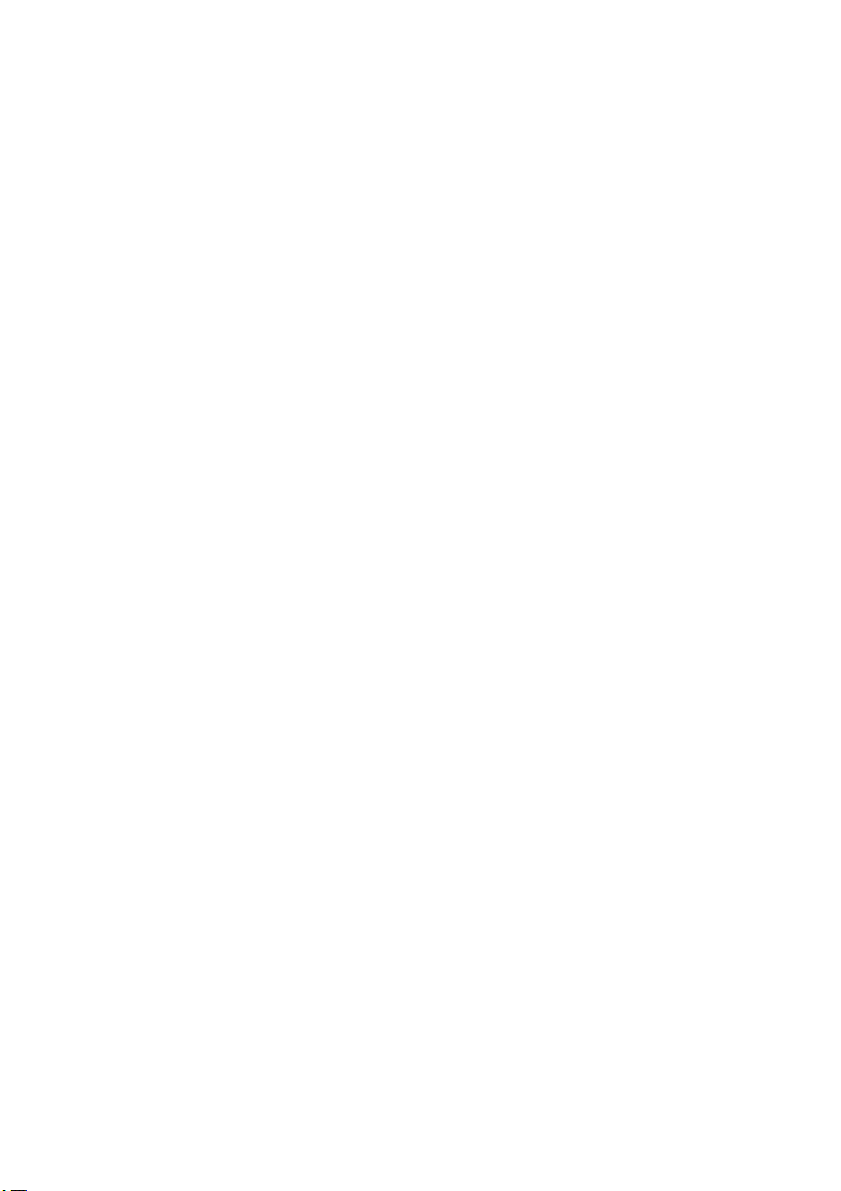
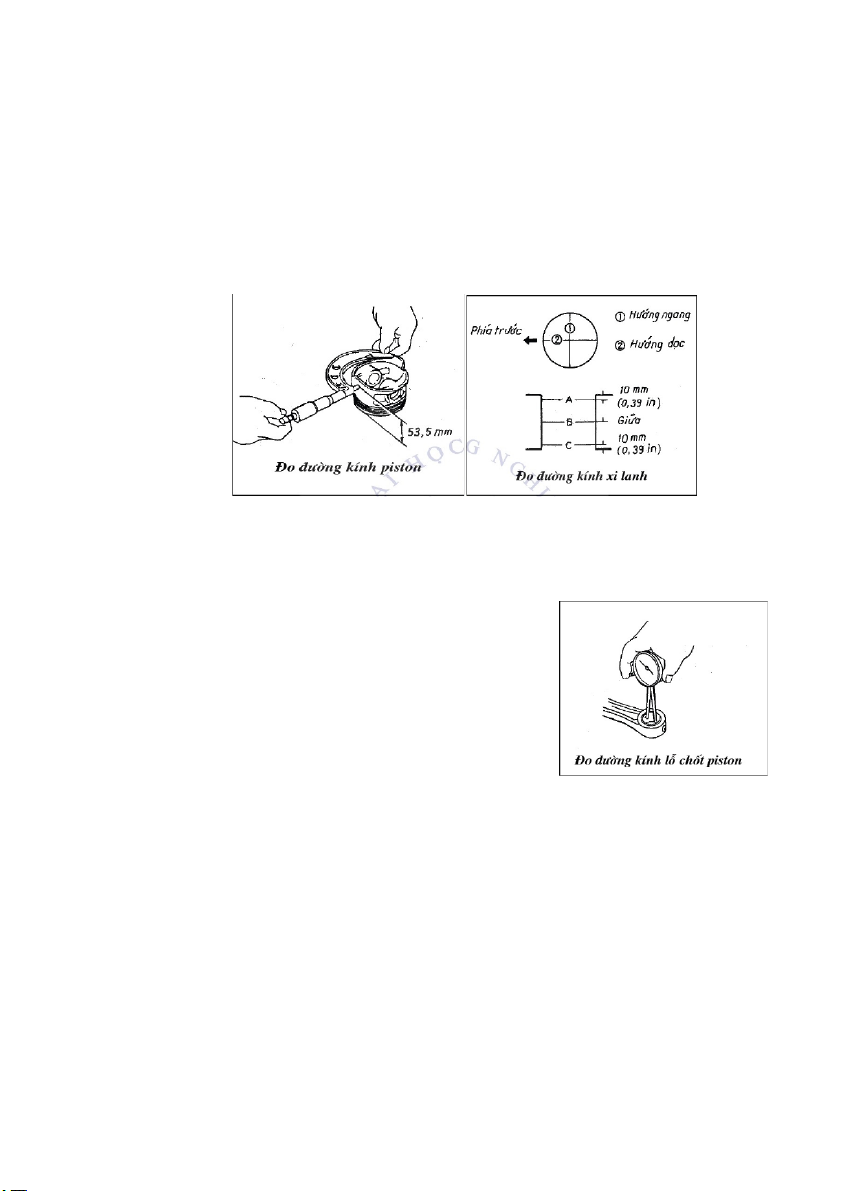
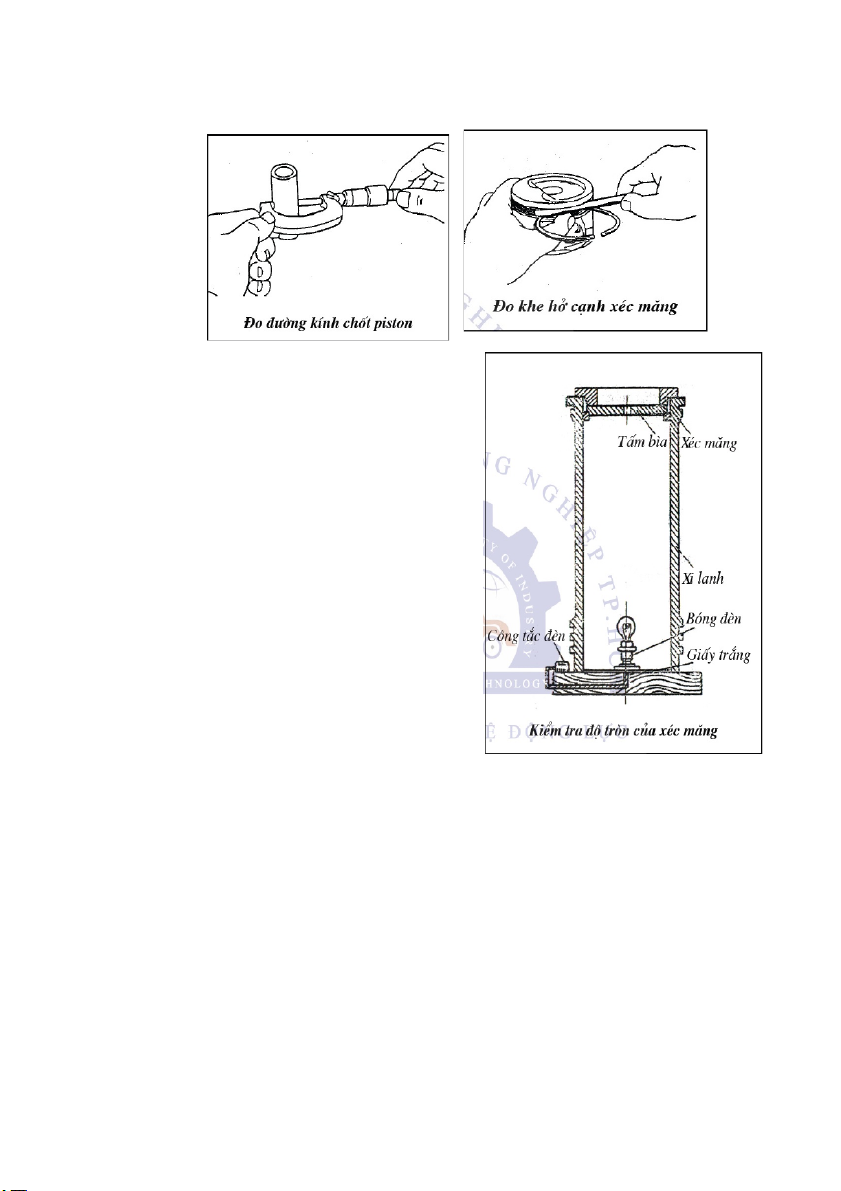
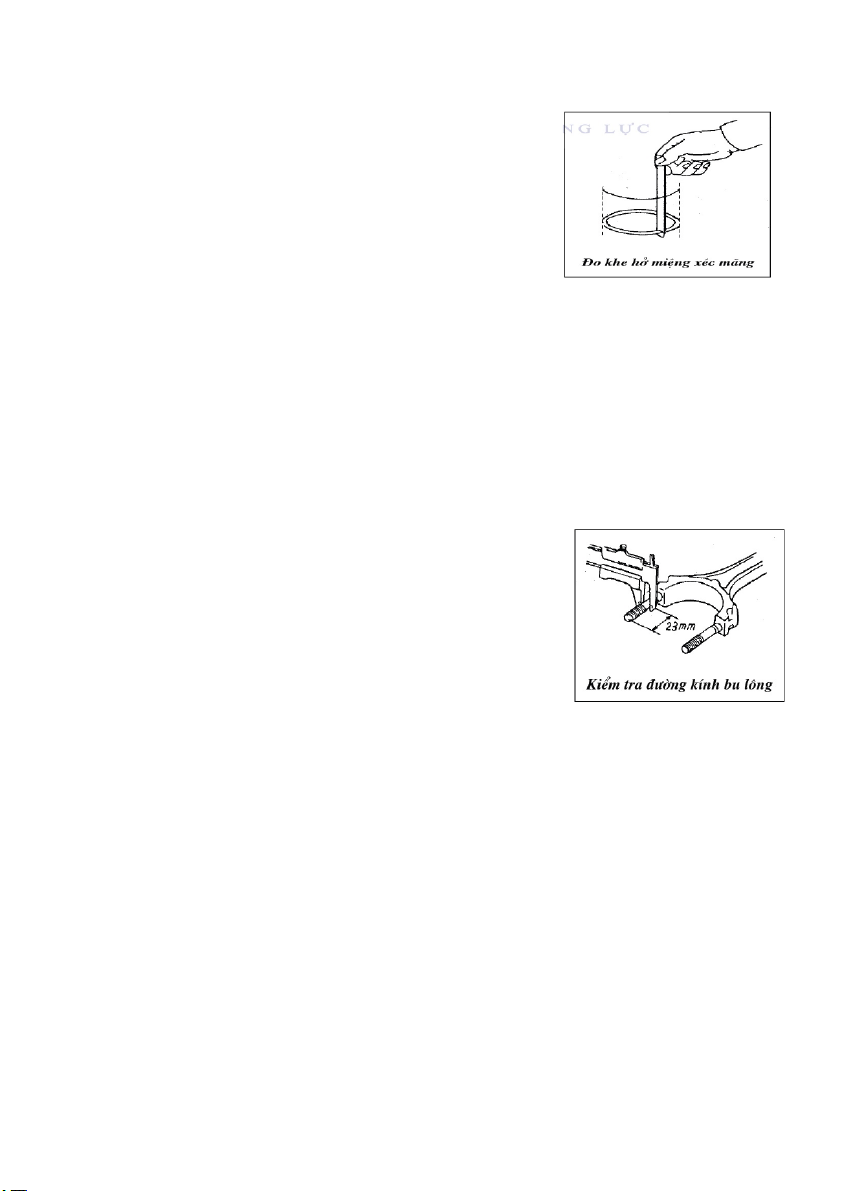
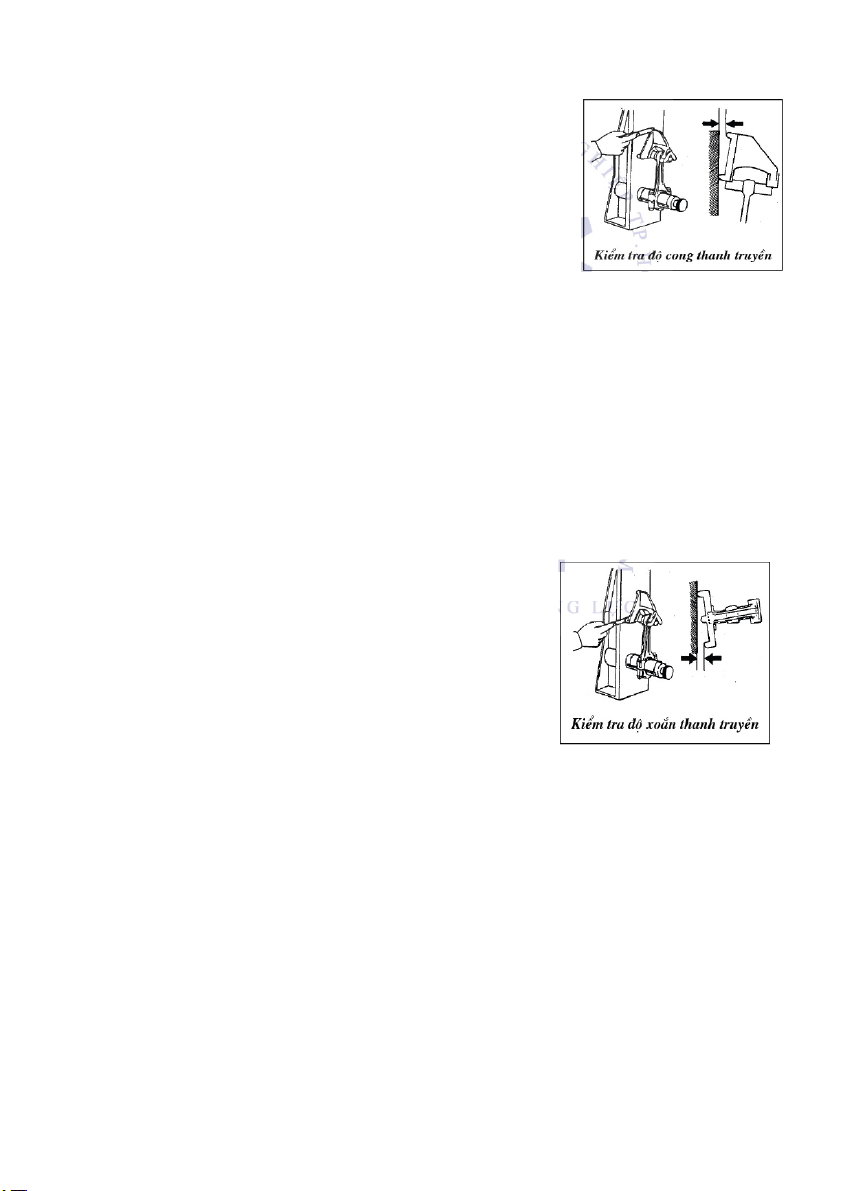
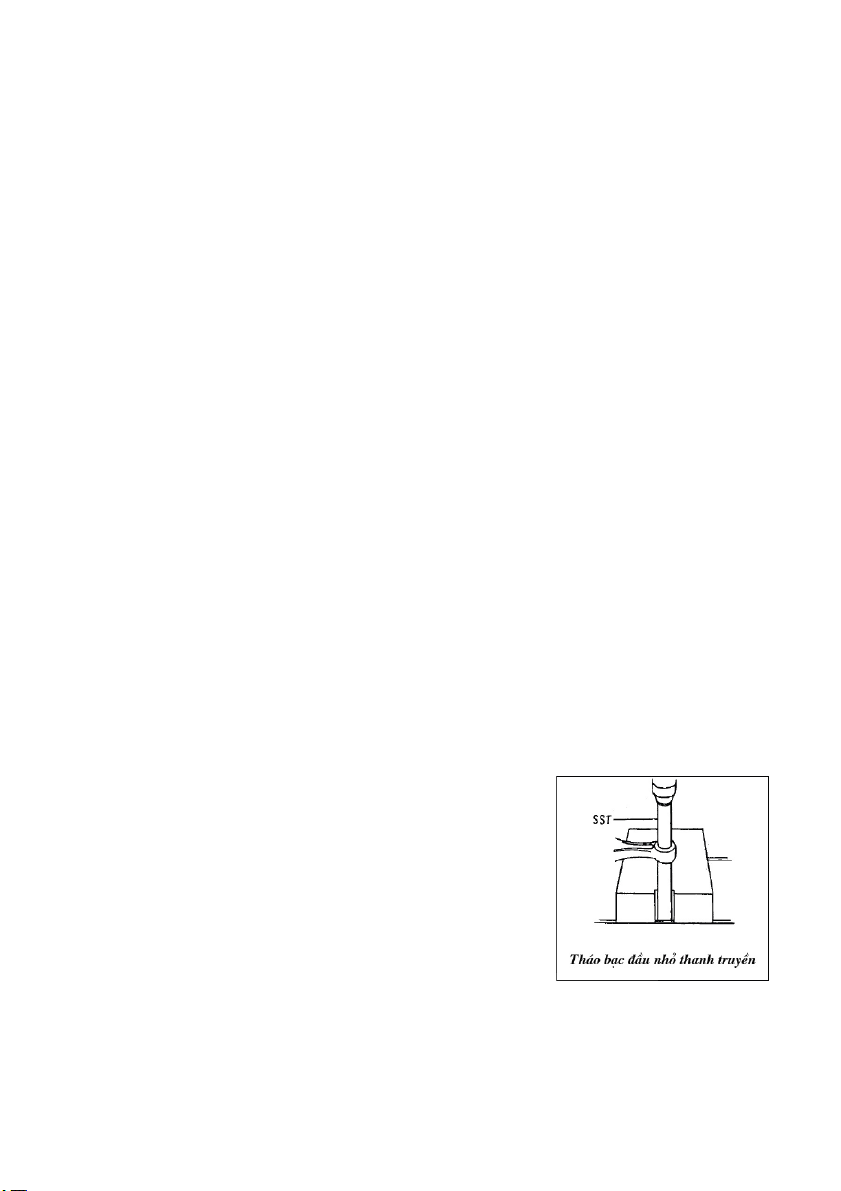
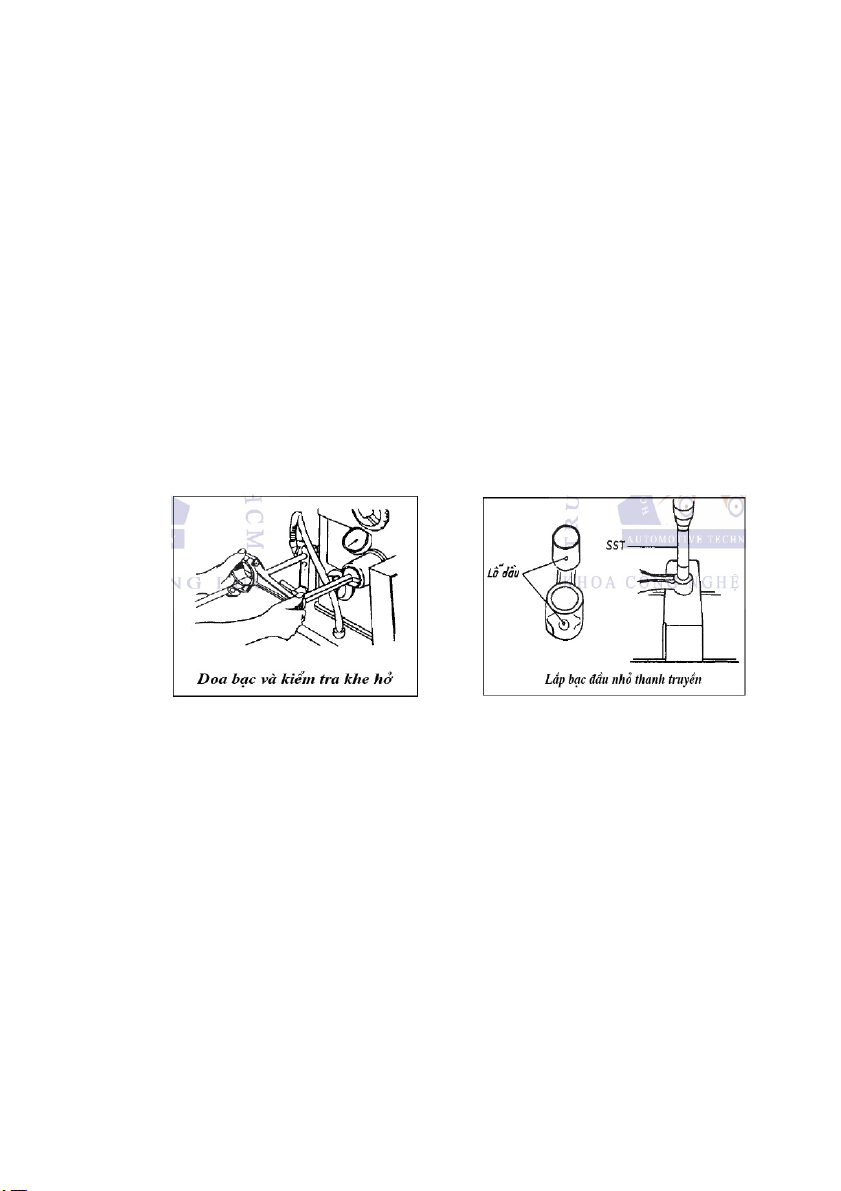
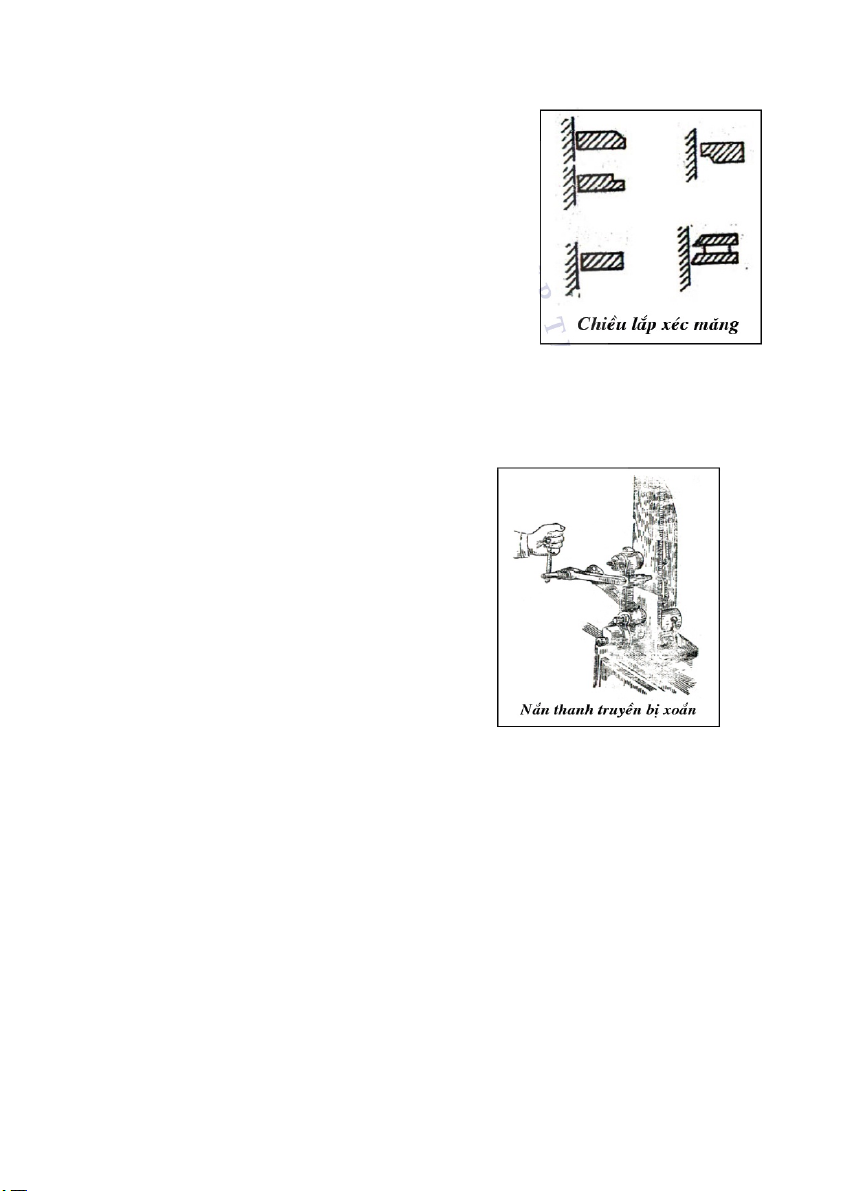
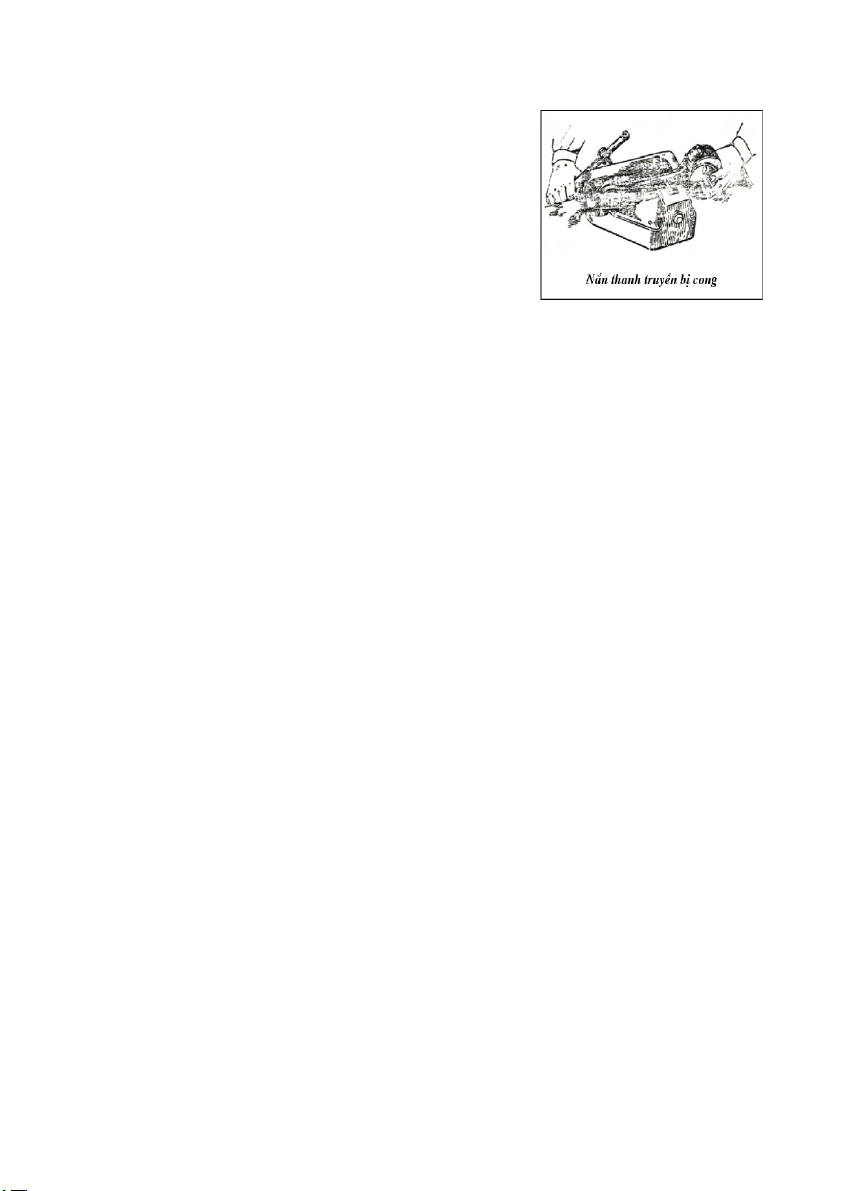
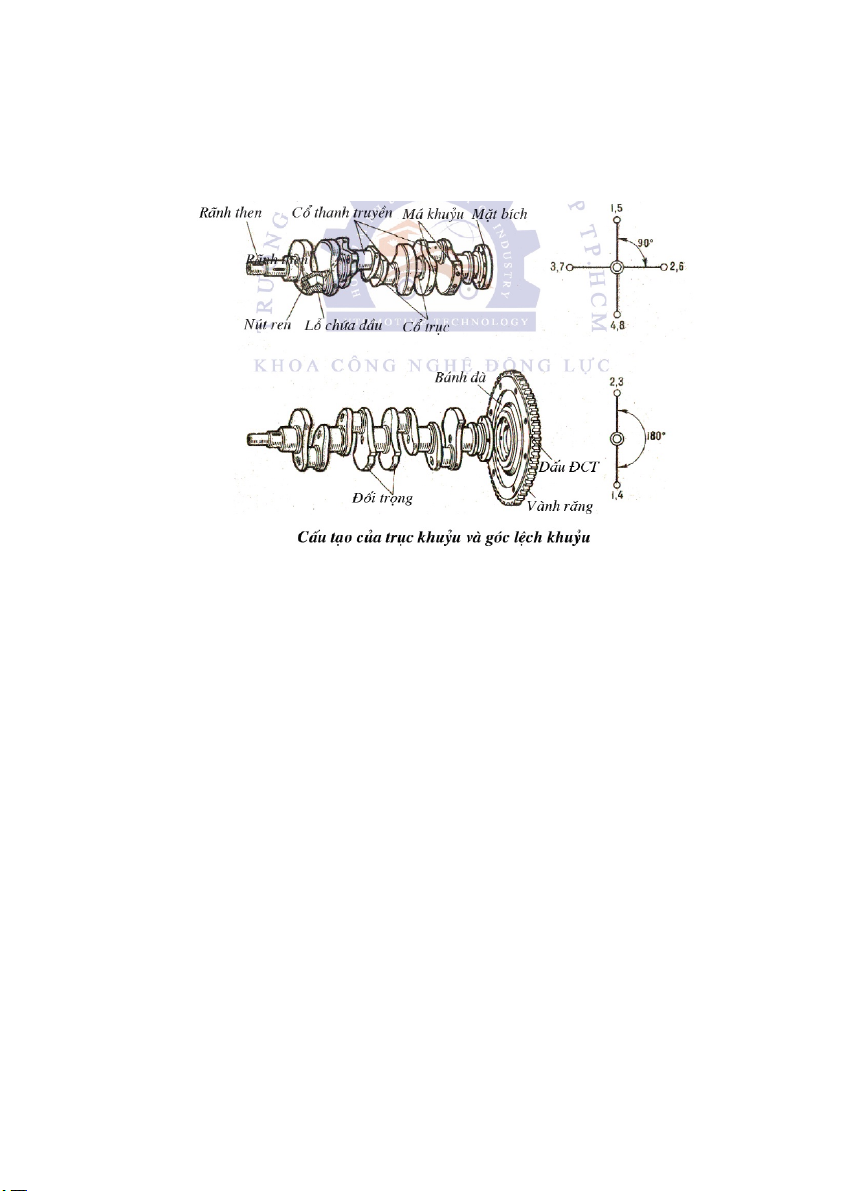
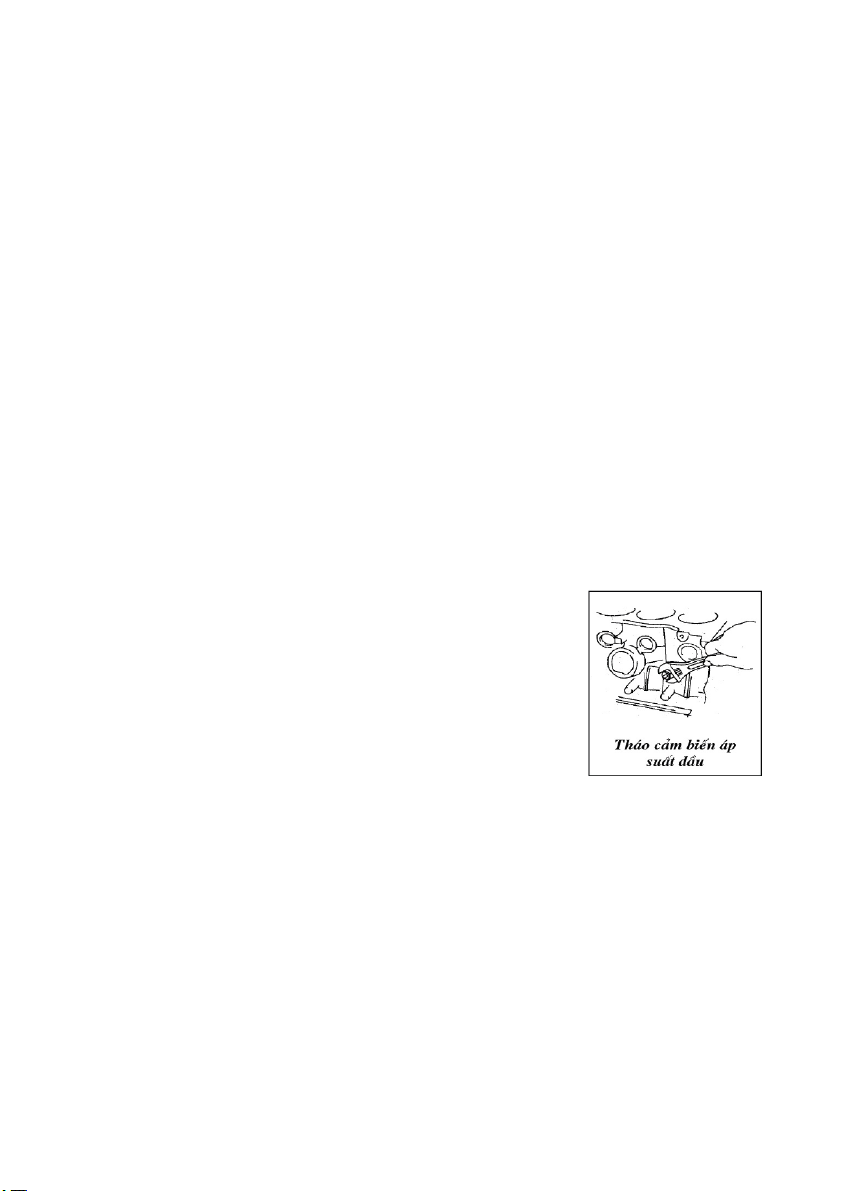
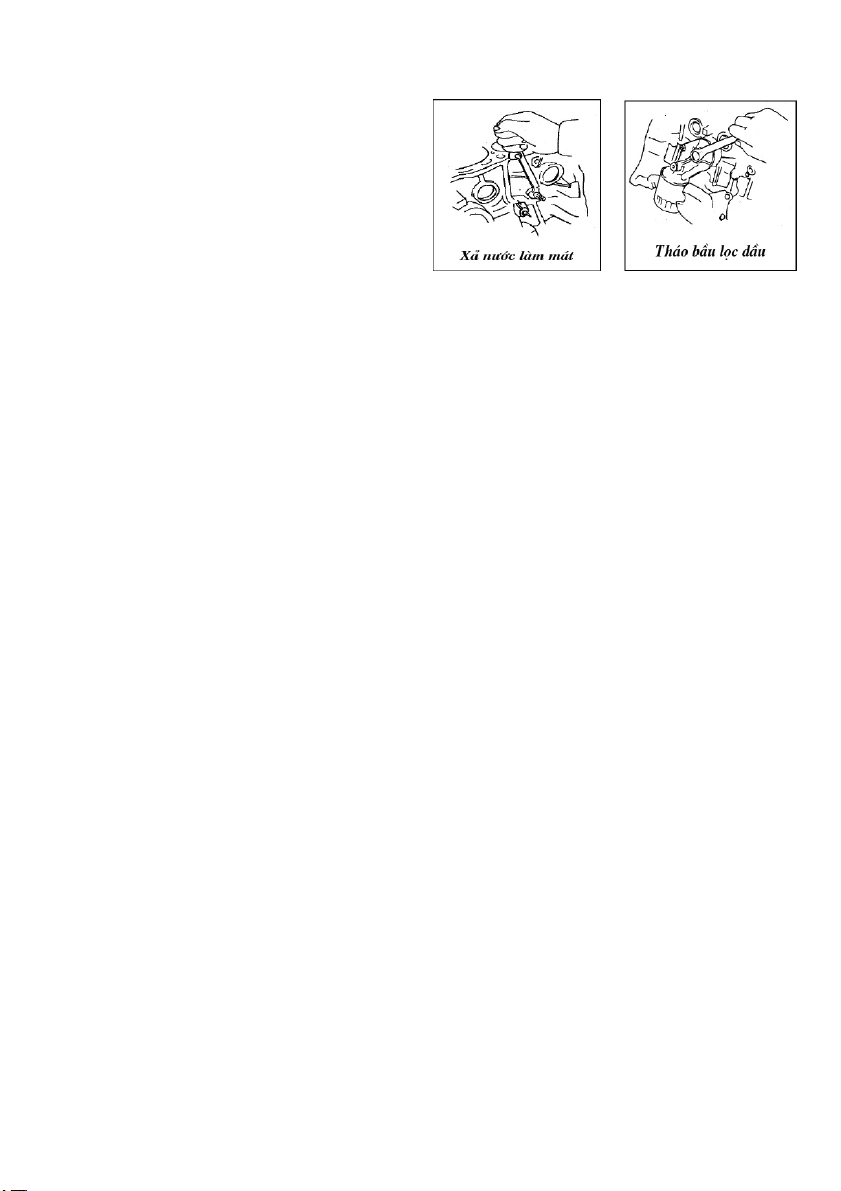
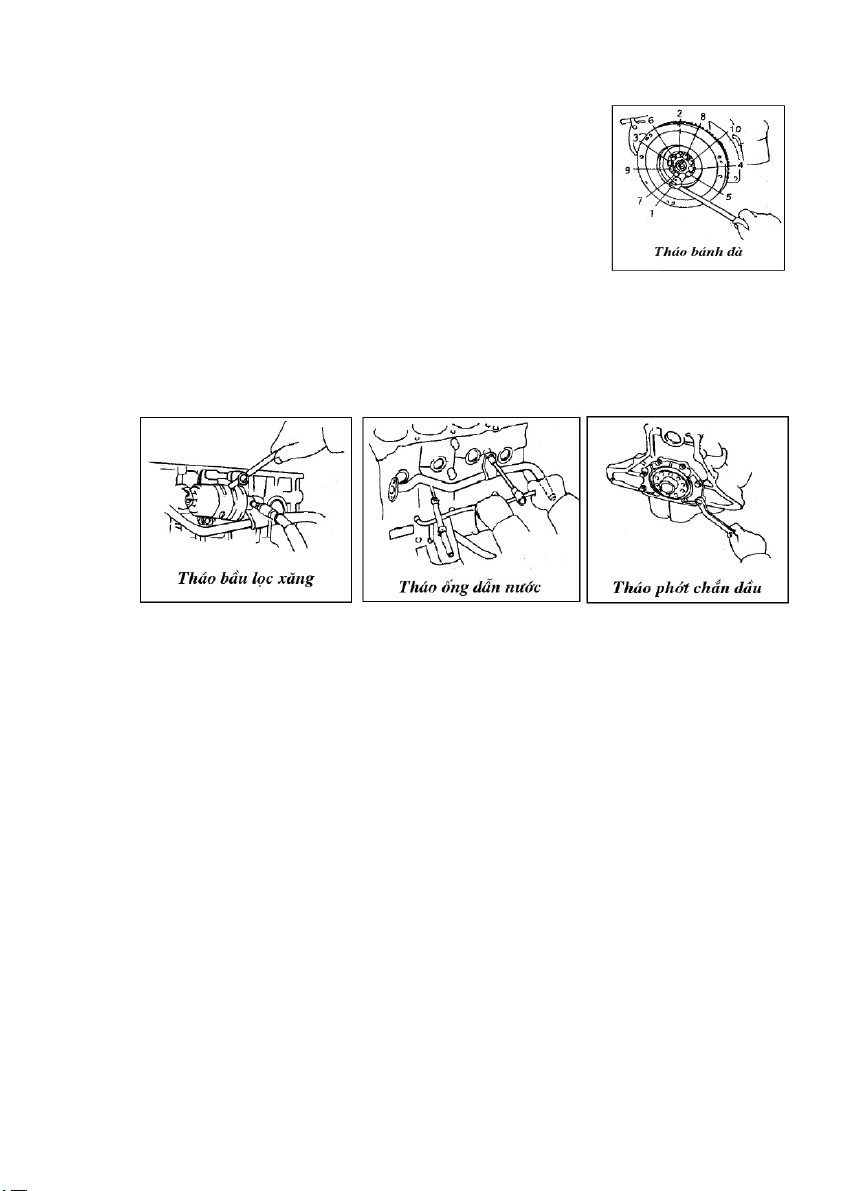
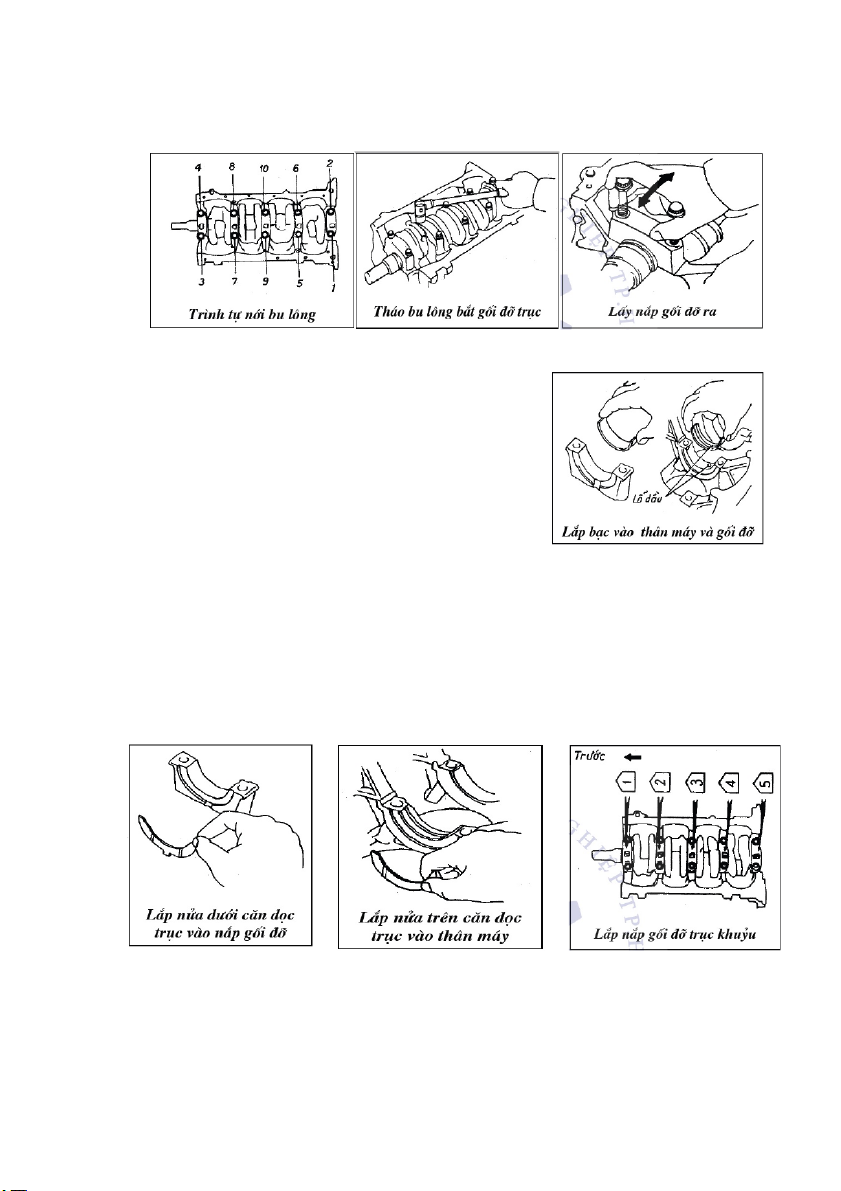
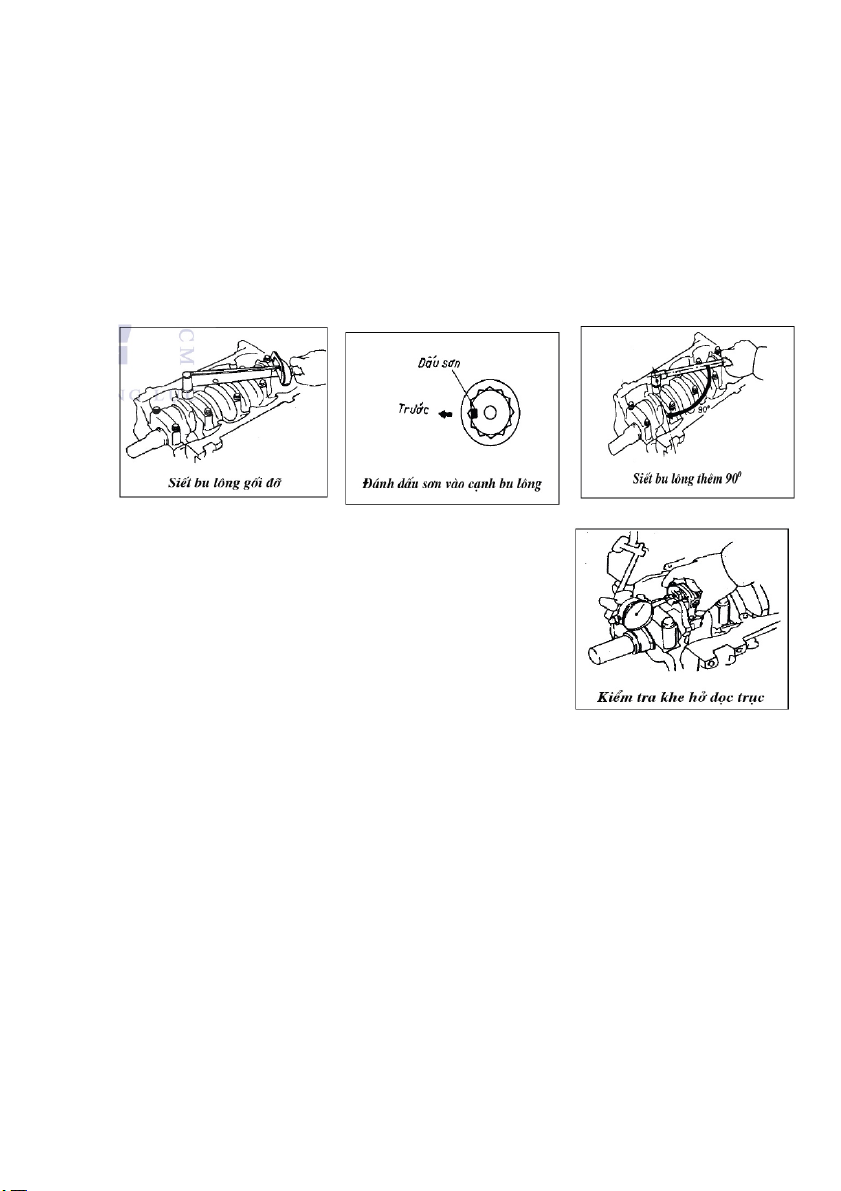
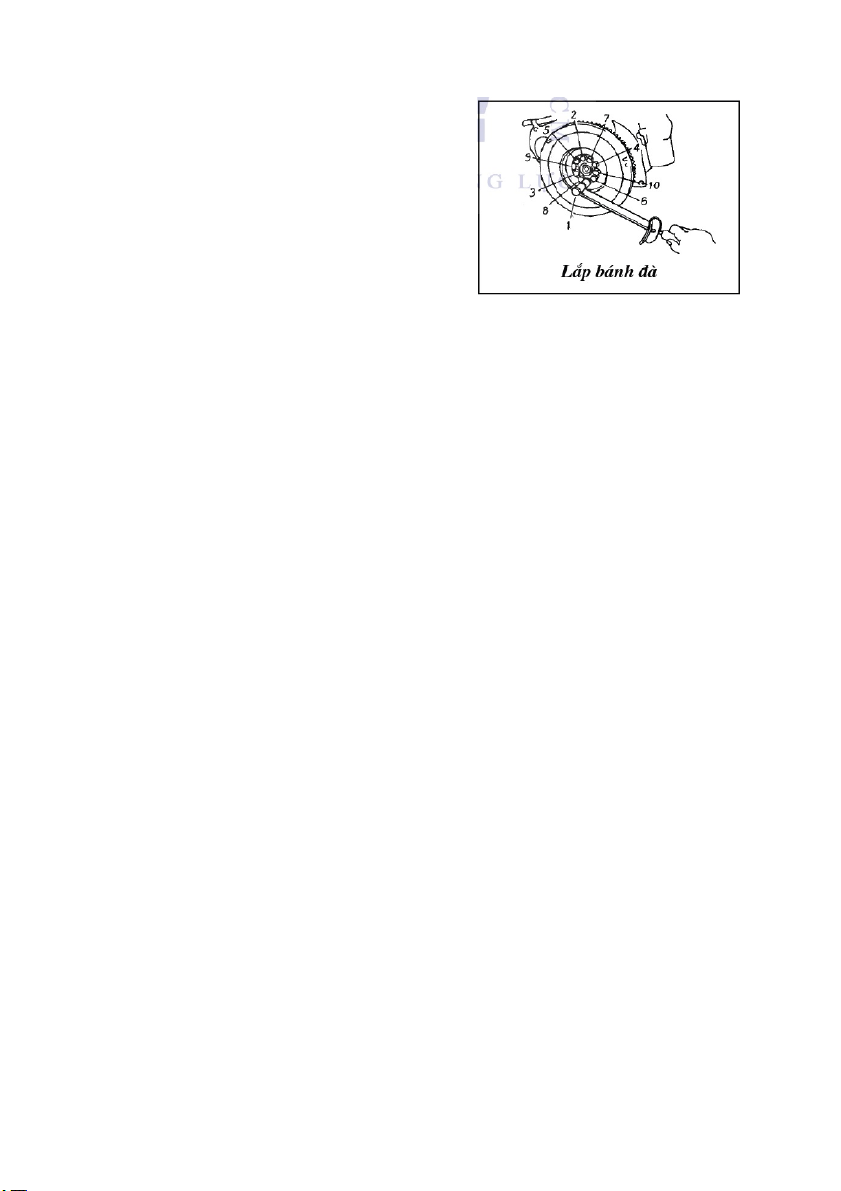
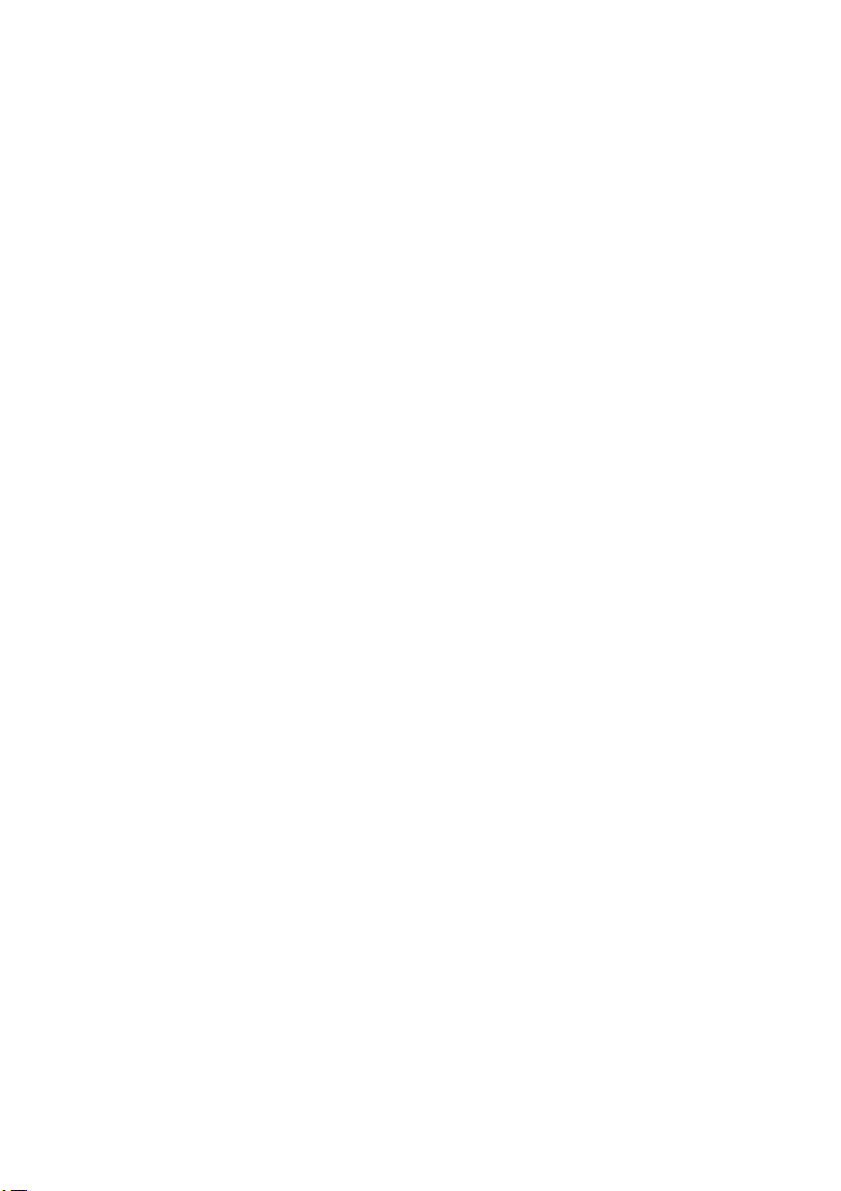
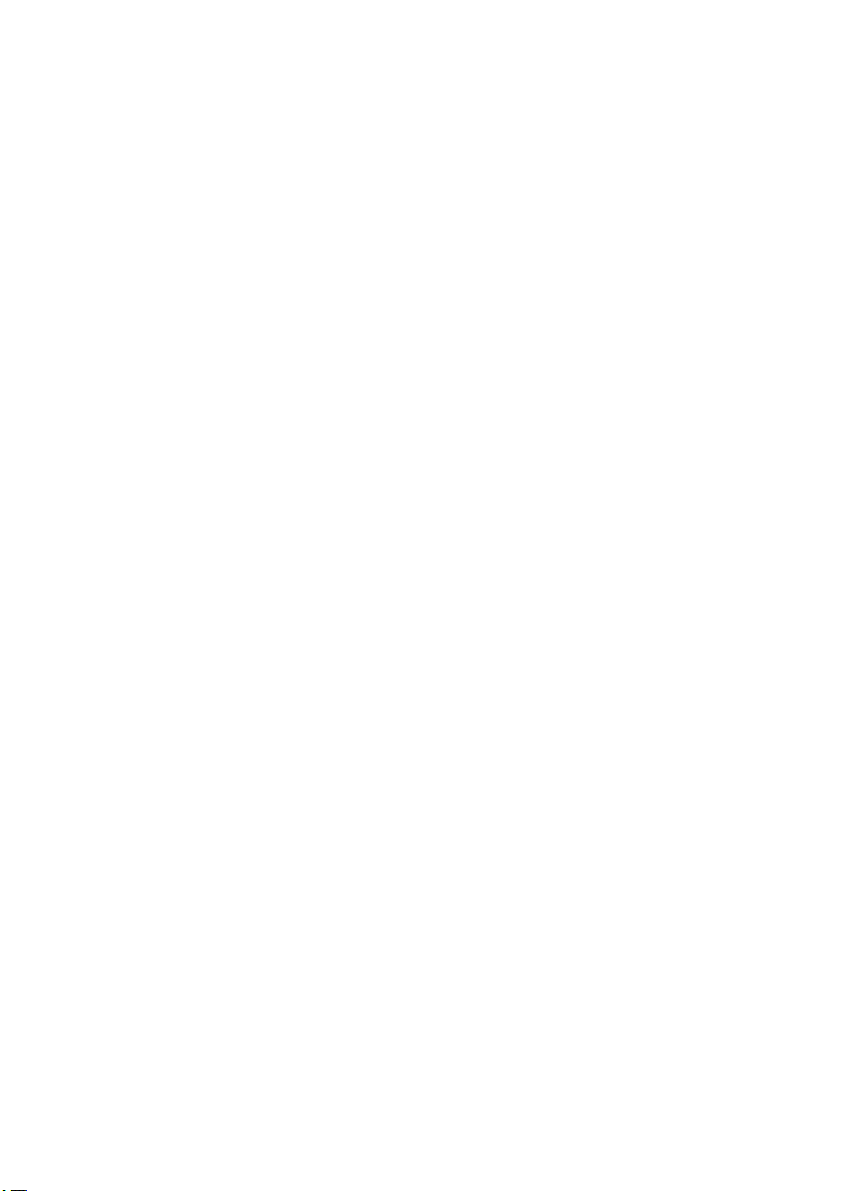
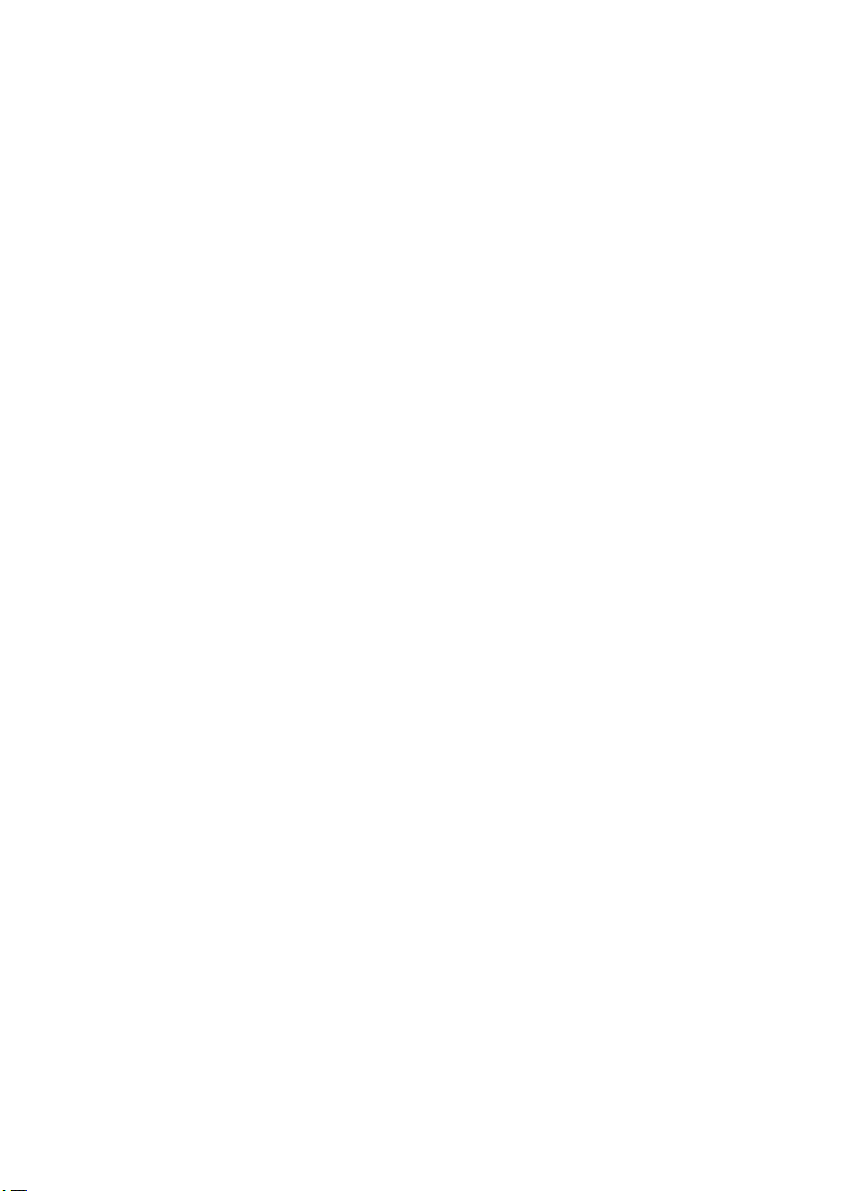
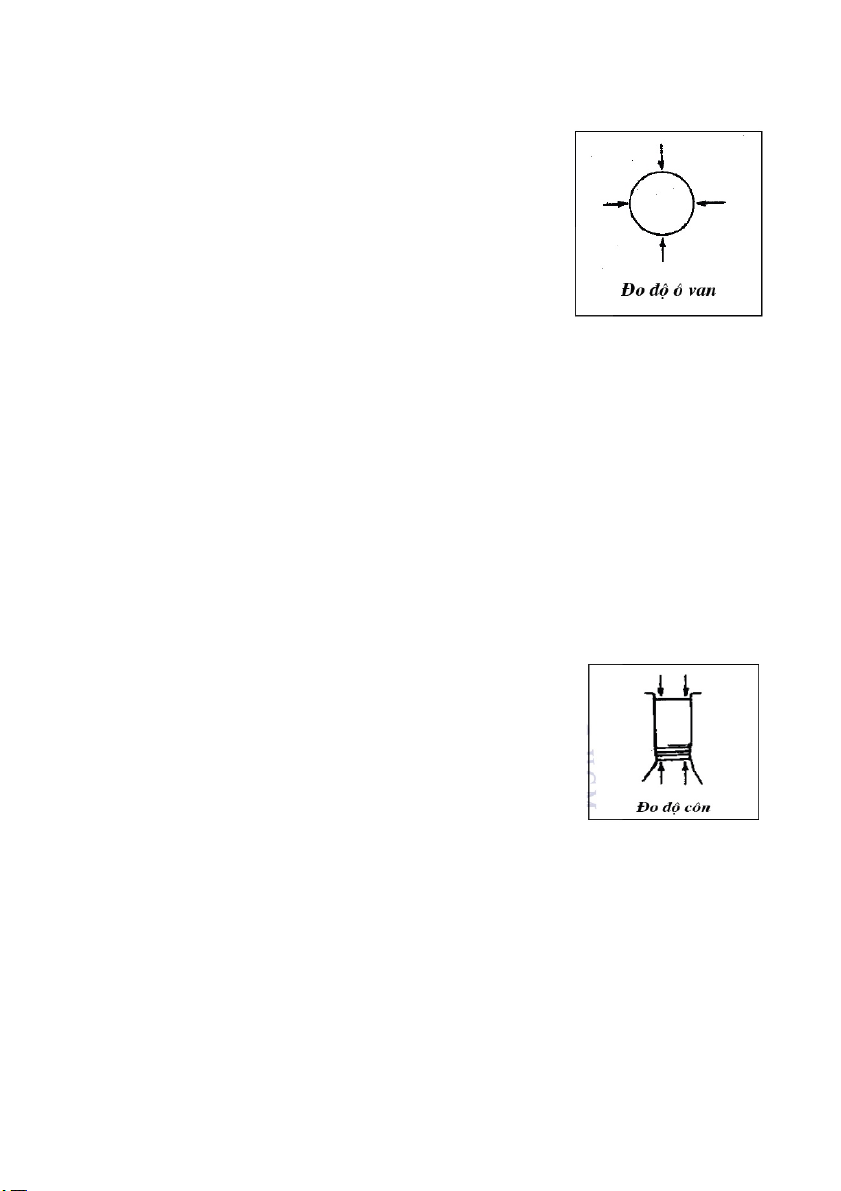
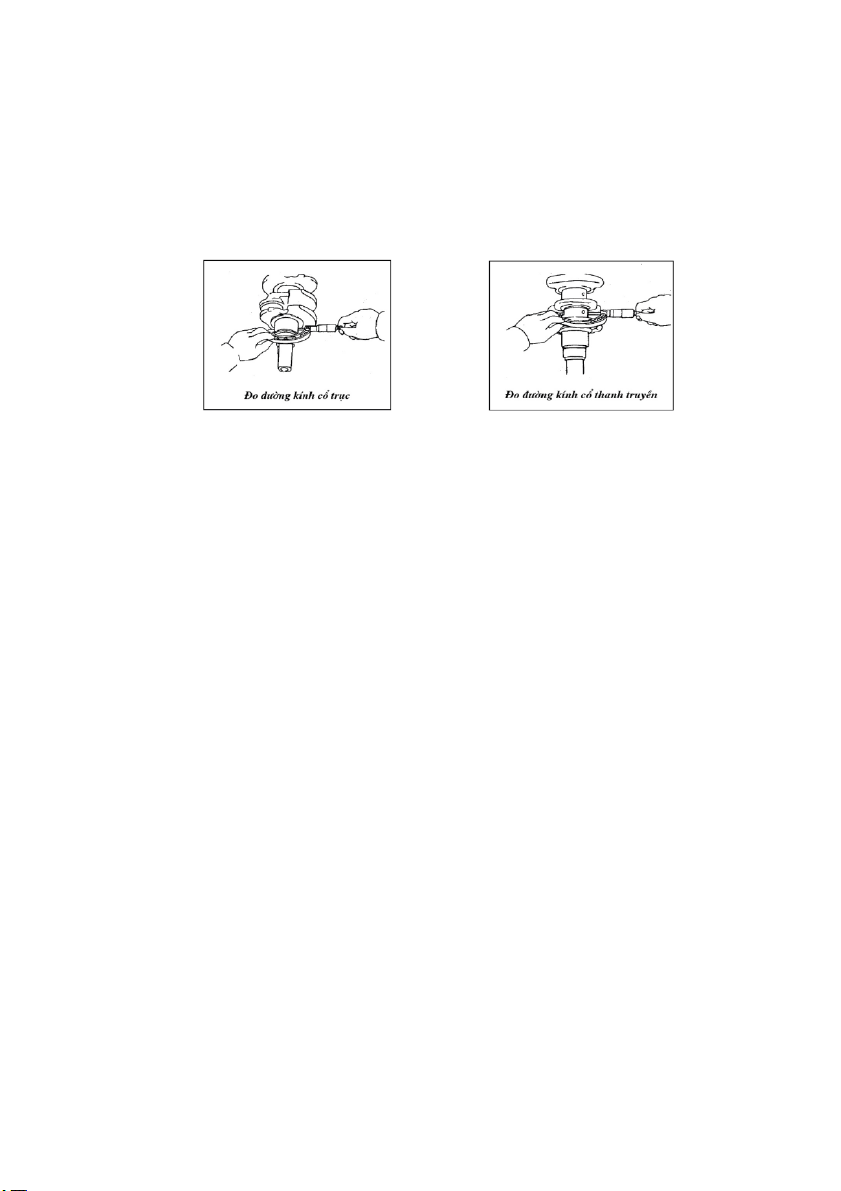
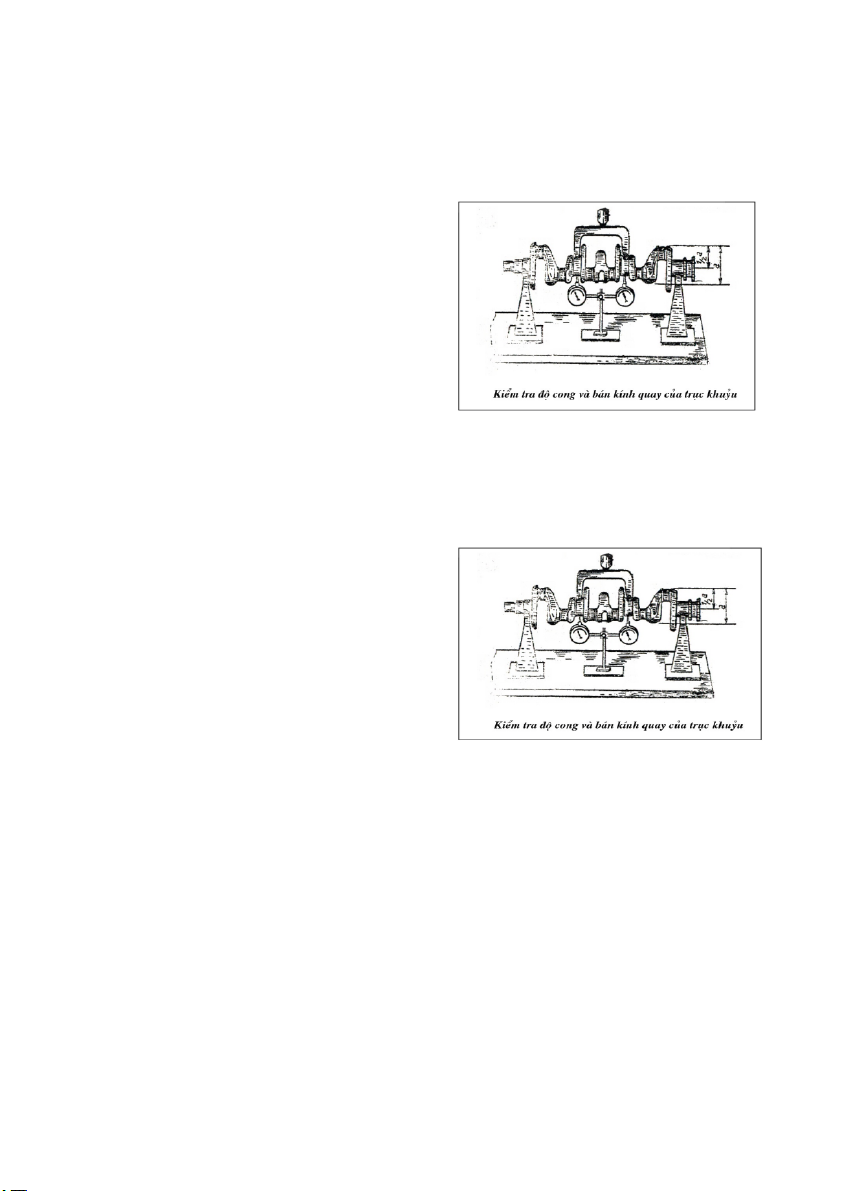
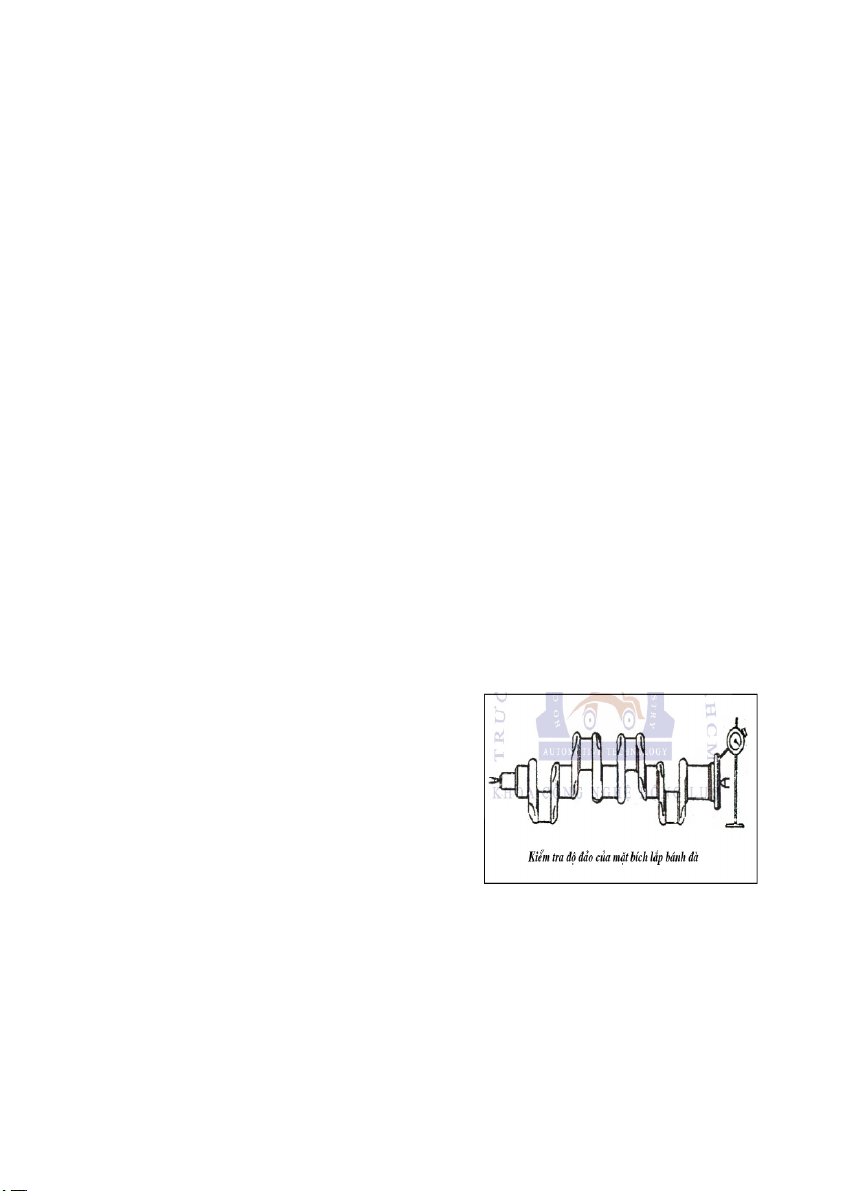
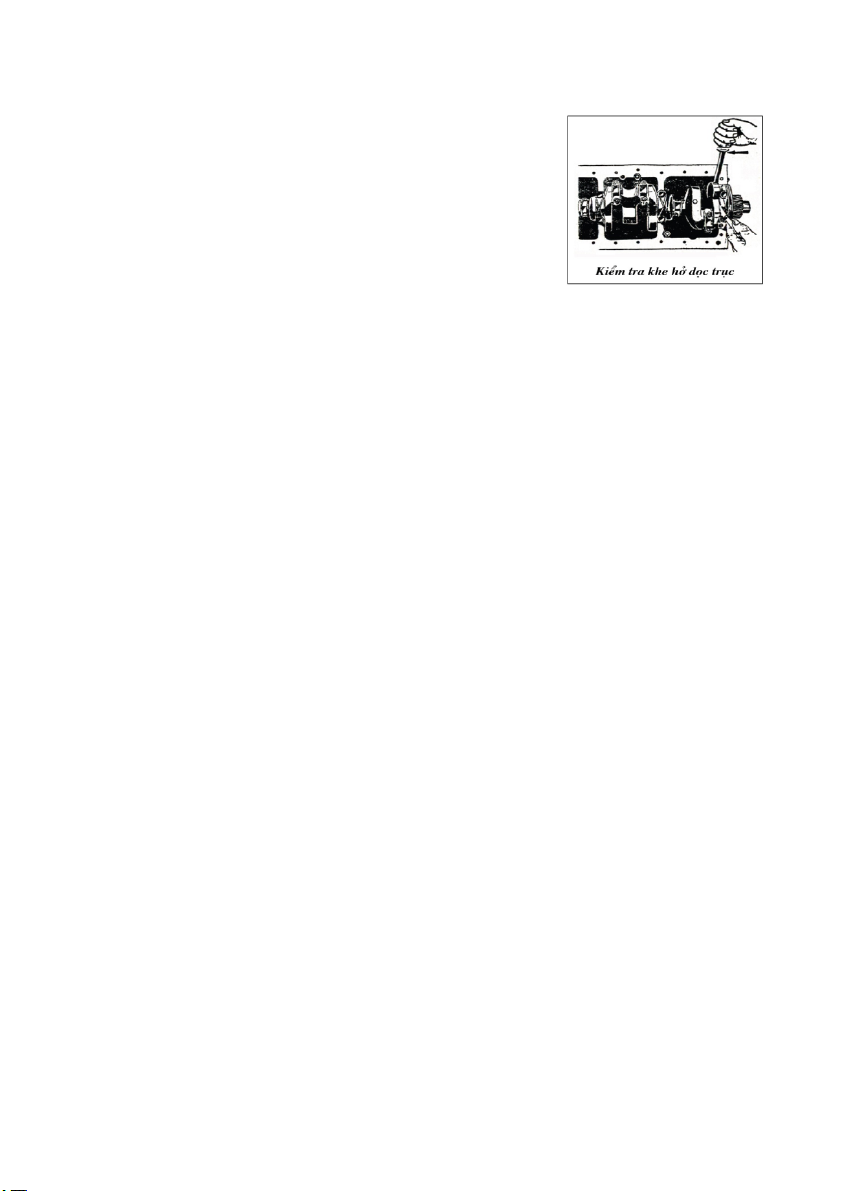
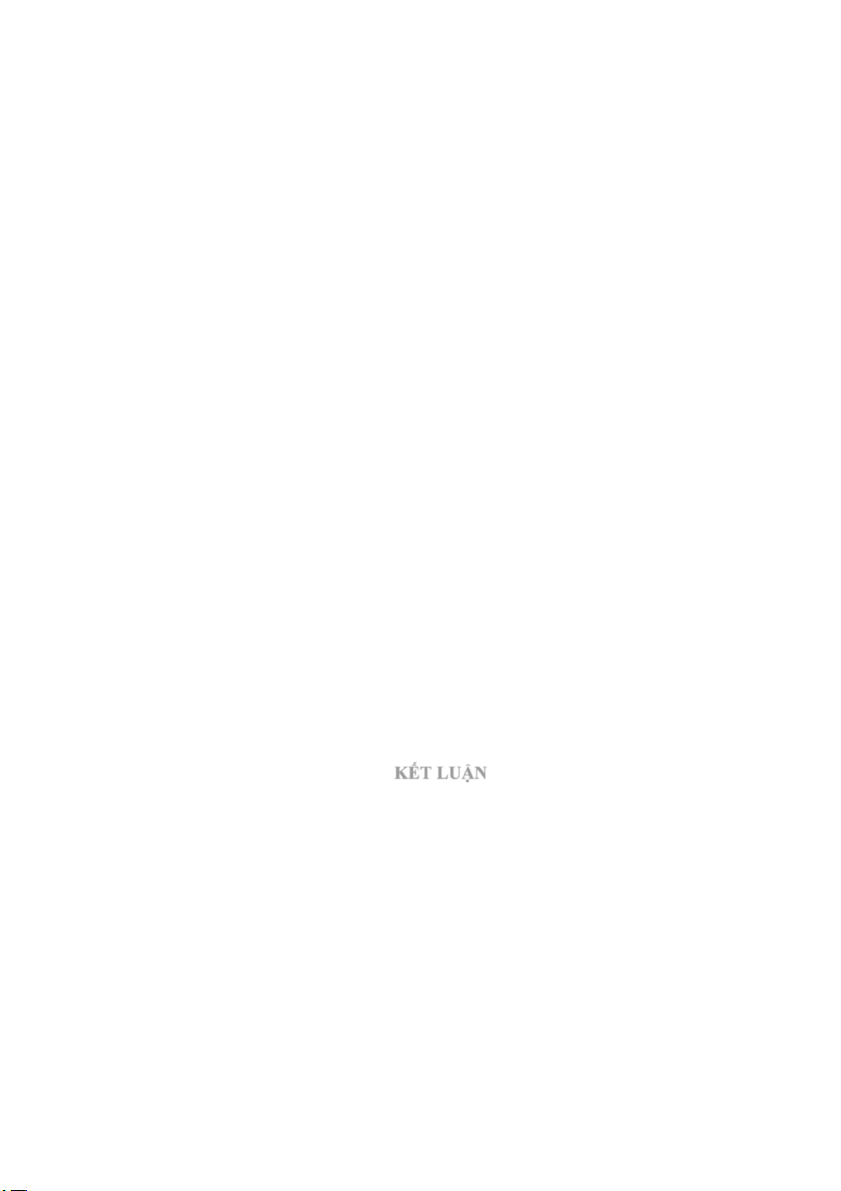
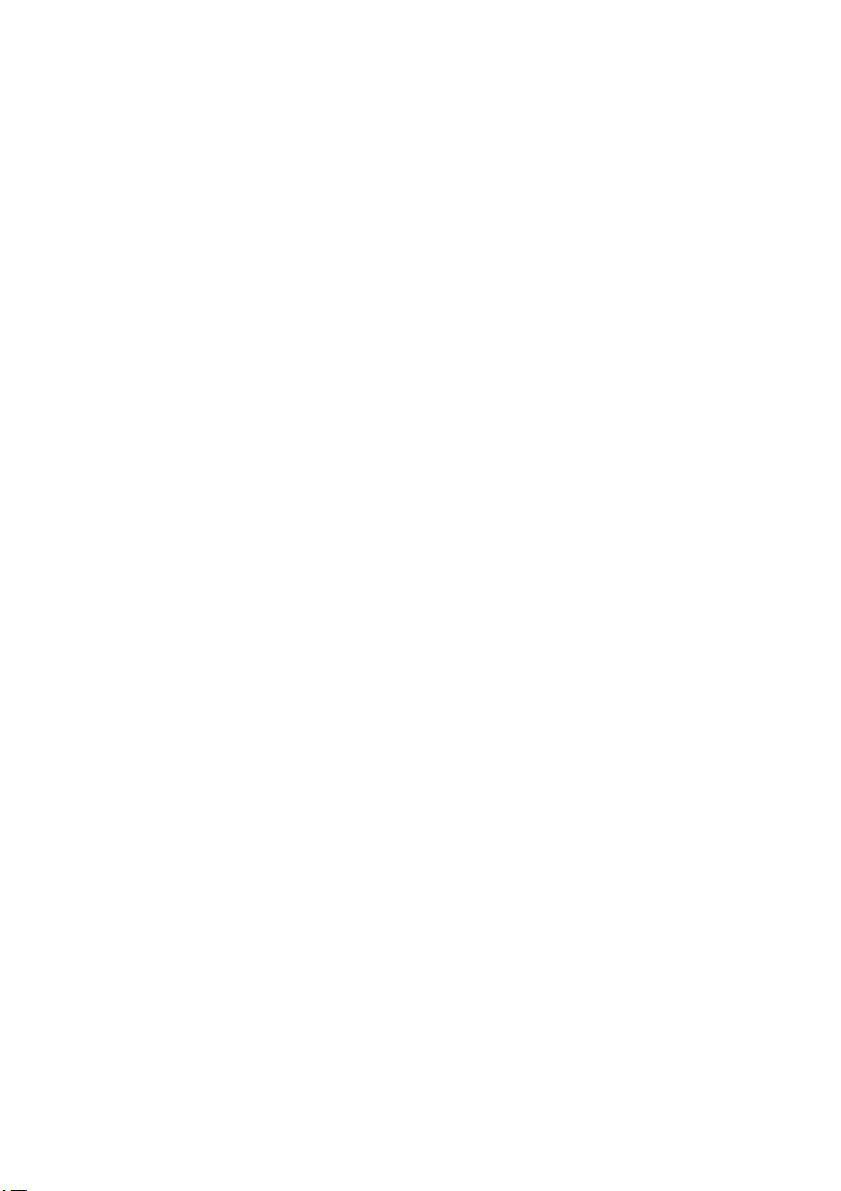
Preview text:
74 CHƯƠNG VI
THIẾT KẾ KỸ THUẬT VÀ TÍNH BỀN CÁC NHÓM VÀ CHI TIẾT CỦA CƠ CẤU 6.1. Nhóm piston
6.1.1. Các thông số ban đầu
Hình 6.1. Các thông số kết cấu của piston Thông số Kí hiệu Đường kính piston D 115 m m Chiều dày đỉnh piston δ (0,0 & 4 ÷ 0,12)D = &0,05.115 = 5,75 m m
Khoảng cách c từ đỉnh đến xécmăng thứ nhất c (0,6÷ 1,2)δ = 13,36.0,8 = 10,688&mm
Chiều dày s của phần đầu s
(0,06 ÷ 0,12)D=0,08.115 = 9,2 mm Chiều cao H của piston H
(0,5 ÷ 0,8)D=0,05.115 = 5,75m m Vị trí chốt piston H -h
(0,35&÷&0,45)D&=&
0.35.115=&40,25&mm& 74 75 Đường kính chốt piston dcp
(0.25&÷&0.35)D&=&
0,25.115&=&28,75&mm&
Đường kính bệ chốt piston db (1.3 ÷ 1.6)dcp = 1,3.28,75=37,37 m m
Đường kính lỗ trên chốt do
(0.6&÷&0.8)dcp&=&
0,6.28,75=&17,25&mm& Chiều dày phần thân s1
(0,02 ÷ 0,03)D =0.02,115= 2,3 mm Số séc-măng khí 4
Chiều dày hướng kính t của sec-măng khí t (1/25&÷&1/32)D& =1/25.115=&4,6&mm& Chiều cao a a 2,4&mm& Chiều dày rãnh séc-măng a1 ≥ a =& 2,5&mm& Số séc-măng dầu 4
Chiều dài phần thân piston L = H-h + dcp/2 +2,5 = !" 40,25+28,75/2+2,5=581,09 m m Chiều dài chốt piston lcp = 0,85.D = 0,85.115=97,75 m m
Khoảng cách giữa 2 bệ chốt b =0,3.D = 0,3.115=34,5 m m
Bảng 6.1. Các thông số kết cấu của piston (động cơ diesel)
6.1.2. Tính bền piston a) Đỉnh Piston
- Đỉnh piston chịu lực rất phức tạp, trạng thái ứng suất cũng rất phức tạp, - nó vừa chịu
tải trọng cơ học vừa chịu tải trọng nhiệt.
- Do đỉnh pit-tông chịu tải trọng phức tạp nên việc tính toán đỉnh pit-tông cũng chỉ tính
theo những phương pháp gần đúng, theo những giả thuyết nhất định.
- Phương pháp Back – công thức Back xây dựng trên các giả thuyết sau : 75 76
- Coi đỉnh pit-tông như một đĩa tròn, có chiều dày đồng đều đặt tự do trên hình trụ rỗng.
- Áp suất khí thể pz max = 9,52 MPa tác dụng lên đỉnh piston phân bố đều.
- Lực khí thể Pz max = pz max.Fp và phản lực của nó gây uốn đỉnh pit-tông. Xét ứng suất uốn ở tiết diện x-x.
- Trên nửa đỉnh pit-tông có các lực tác dụng sau đây: - Lực khí thể :
!!"#$ = #·$.&%·pzmax (MN) " " '
- Tác dụng lên trọng tâm của nửa hình tròn, cách trục x-x một đoạn: 2 D y . = 1 3 p
- Phản lực phân bố trên nửa đường tròn đường kính Di cũng có trị số bằng Pz
max/2, tác dụng trên trọng tâm của nửa đường tròn, cách trục x-x một đoạn: D1 y2 = p 76 77
- Do đó đỉnh chịu momen uốn: p p D 2.D zmax zmax 1 M y y u = .( - ) = .( - ) 2 1 2 2 p 3.p Coi D » D1 thì D 1 1 3 M p . . p .D u = z = max max 1 z (MN.m) 6p 24
- Modun chống uốn của đỉnh: D . 2 d 1 W = u 6
- Do đó ứng suất uốn đỉnh pit-tông: %
σu = pzmax. && = 9,52. )*% = 142,11 (MN/m2) '(% '.##% với :
D1 = D – 2t =115 – 2.4,6 = 105,8 mm
D2 = D1 – 2s =105,8 – 2.9,2 = 87,4 mm
→ Di =(D2+D)/2 = (87,4+115)/2= 101,2 (mm) -
Ứng suất cho phép đối với piston bằng gang đỉnh có gân: [su] = 25 ÷ 190 MN/m2
=> s <190 MN/m2 (thỏa) u b) Đầu piston
Tiết diện nguy hiểm nhất chịu kéo và chịu nén thường là tiết diện ngang x-x nằm phía
trên chốt chứa các lỗ thoát dầu bôi trơn từ rãnh xéc măng dầu.
• Ứng suất kéo: ( cuối hành trình thải, đầu hành trình nạp) * P * P s = jp = jp ≤ [ s ] = 10 (MPa) k k F p x 2 2 - x [D - D ] 1 2 4 Trong&đó:&
o Fx- x&-&diện&tích&tiết&diện&ngang&x-x&trừ&bớt&diện&tích&qua&đường&tâm&của&các&lỗ&
thoát&dầu&bôi&trơn,&𝑚".& 77 78
o 𝑃∗+,&=&mx-x.R.w2.(1-&l).10-6&
§ Bán&kính&quay&vòng&trục&khuỷu&R&=&40&(m)&
§ Thông&số&kết&cấu&l&=&0,25&
§ Vận&tốc&góc&của&trục&khuỷu&w&=&𝝅.𝟔𝟎𝟎𝟎&𝝅.𝟔𝟎𝟎𝟎=&628,31&(1/s)& 𝟑𝟎 𝟑𝟎
§ mx-x&=&(0,4÷0,6).mn&=&189,49&÷&284,24& (g).&chọn&mx-x&=&220&(g)&
Với mnp: khối lượng nhóm piston.
mp: khối lượng piston mp = 300,62 (g)
mx: khối lượng xécmăng mx = 46,42 (g)
mc: khối lượng chốt piston mc = 126,39 (g)
mnp = mp + mx + mc = 300,62 + 46,42 + 126,39 = 473,73 (g)
Vậy PjP = 0,22.0,04.628,312.(1 + 0,25).10-6 = 0,00434 (MN)
§ Diện tích tại tiết diện x-x: % % p F 2 2 #' #5* 6–65,5)8' ] x-x = [D - D ] = 2, .[5, = 2,658. 1 2 10:2 m2 ' 4 !∗ =>σ '( k = = 5,55'2' = 2,41 (MN/m ; 2 ) (thỏa: ≤ 10 MN/m2) $*$ #,)5 . " #5*+
• Ứng suất nén: ( đầu hành trình cháy dãn nở) σ *" ##*%
< = =!,"#$.$.&% = >, .$.5,
= 37,20&≤ 40 (MN/m2) (thỏa mãn) '.;$*$ '.",?* . ) #5*+ c)&Thân&piston&
Áp&suất&riêng&trên&bề&mặt&tiếp&xúc&với&mặt&gương&xylanh:&
qp = 𝑵𝒎𝒂𝒙 𝟎,𝟎𝟎𝟐𝟒 = 0,76 (MPa)
𝑫𝑳𝒕𝒉 𝟎,𝟎𝟗 . 𝟓 𝟎,𝟎𝟑𝟑𝟗
Trong&đó:&Lth -&chiều&dài&phần&dẫn&hướng&(phần&thân&piston),&m.&
& & & & & & & Nmax -&lực&ngang&lớn&nhất,&MN.&
Tính theo sự biến thiên của lực ngang N trên máy tính, ta xác định N max = 0.00244 MN 78 79
Động cơ có q = 0,6 ÷ 1,2 (MN/m2) => Thỏa mãn. p d) Bệ chốt
PG= &= m< ⋅ R ⋅ ω" ⋅ (1 + λ) ⋅ 10:?
&= 0,4737 ⋅ 0,535 ⋅ 628, 31" ⋅ (1 + 0,25) ⋅ 10:? = 9,35 ⋅ 10:2(MN) π ⋅ D" π ⋅ 0, 095" PH = 4 ⋅pH = 4 ⋅ 9,52 = 0,0675(MN) P → q H − PG= I &= 2⋅ dJ ⋅ l# 0,0675 − 9,35 ⋅ 10:2 &= 2 ⋅ 0,02 × 0,03 = 48,46(Mpa)
6.1.3. Tính toán bền chốt piston a) Ứng suất uốn
Nếu coi lực tác dụng phân bố theo sơ đồ sau:
Thì&ứng&suất&uốn&tính&như&sau:&coi&lực&Pz/2&tác&dụng&ở&điểm&cách&đầu&mút&chốt&
pit-tông&một&khoảng&2/3l1&(l1&chiều&dài&làm&việc&của&bệ&chốt),&ứng&suất&uốn&chốt&xác& định&như&sau:& & &
Hình&6.2.&Biểu&đồ&ứng&suất&uốn& †P & & σ
H − PG= ‡†lJ= + 2b − 1,5a‡ K = 1,2d2 ' J=(1 − α5) (MPa) Trong&đó&:&
- Đường&kính&ngoài&chốt&:&dcp&=&0,02m& d 0,55d α L J= 5 = d = = 0,55 M dJ=
- Chiều&dài&tiếp&xúc&với&bạc&đầu&nhỏ& a = l = 0, 024m d & 79 80
(0,0675 − 9,35. 10:2)(0,08075 + 2.0,0285 − 1,5.0,024) → σK = 1,2.0, 0282(1 − 0, 55') = 148(MPa)
Þ Thỏa&ứng&suất&cho&phép&của&piston&làm&bằng&hợp&kim& s [ ]Î150 ÷ 250 MPa u &
b) Ứng&suất&cắt&chốt& 𝟎, 𝟖𝟓 ⋅ †𝑷 𝟐) 𝝉 =
𝒛 − 𝑷𝒋𝒛‡⋅ (𝟏 + 𝜶𝒂 + 𝜶𝒂
𝒅𝒄𝒑 ×(𝟏 − 𝜶𝟎) 𝟐 = 𝟎,𝟖 ⋅ 𝟓U𝟎,𝟎𝟔𝟕 : 𝟓 𝟗,𝟑 . 𝟓 𝟏𝟎*𝟑
X⋅U𝟏Y𝟎,𝟓𝟓Y𝟎,𝟓𝟓X =61,19 (MPa) 𝟎,𝟎𝟎𝟑𝟑𝟐 × 𝟓 (𝟏:𝟎,𝟓𝟓) T
Þ hỏa&ứng&suất&cho&phép&của&piston&làm&bằng&hợp&kim: t Î [ ] 50 ÷ 70 MPa &
c) Tính&độ&biến&dạng&của&chốt&
Tiết&diện&giữa&của&chốt&có&độ&biến&dạng&lớn&nhất&và&được&xác&định&theo&biểu& thức&:& 0,09 †P 2 Δd H − PG=‡ 1 + α_ ]M^ = EI Ÿ ⋅ k J= 1 − α5 Trong&đó&:&
Mô&đun&đàn&hồi&đối&với&thép&:&E = 2 ⋅ 10*MPa&
k = 1,5 − 15(α5 − 0,4)" = 1,45
0,09 ⋅ (0,0675 − 9,35 ⋅ 10:2 ) 2 &→ Δd 1 + 0,55 :? ]M^ = 2 ⋅ 10* ⋅ 0,08075
Ÿ1− 0,55 ⋅1,45 =&19,2 (m)
mà:& 19,2 ⋅ 10:?( m) ≤ [Δd]M^ ] = 0,2 ⋅ dJ= = 0,2 ⋅ 0,03325 = 0,0067( m) ® Dd max thỏa.&
d) Ứng&suất&bến&dạng&
- Tại&điểm&1&trên&mặt&ngoài&(j&=&0o)&ứng&suất&kéo:& 80 81 P (2 + α 1 σ H − PG= _ )(1 + α_) # = I ⋅ ¤0,19 ⋅ J= ⋅ dJ= (1 − a_)" − (1− α_)¥⋅k (0,0675 − 9,35 ⋅ 10:2) (2 + 0,55) ⋅( 1 + 0,55) 1
&= 0,08075 ⋅0,03325 ⋅¤0,19⋅ (1 − 0,55)" − 0,45¥ ⋅1,45 &= 77,96(MPa)
- Tại&điểm&2&trên&mặt&ngoài&(j&=&0o)&ứng&suất&nén:& σ ! '(X (#Y"b5)(#Yb5) " = :U! :! ⋅¦0,19 ⋅ + # §⋅ k ` (#:b (#:b 4(⋅a4( 5)%b5 5) = :U5,5?8 : * >,2 ⋅ * #5*+
X ⋅¦0,19. ",#.#,**§¥ ⋅ 1,45 5,5)58 ⋅ * 5,522"* 5,'*%.5,** &= −174,38(MPa)
- Tại&điểm&3&trên&mặt&trong&(j&=&90o)&ứng&suất&nén:& −†P ( σ H − PG=‡ 2 + α_)(1 + α_) 0,636 2 = l ⋅ ¤0,174 ⋅ J= ⋅ dJ= (1 − α_)" + (1− α_)¥ ⋅k −(0,0675 − 9,35 ⋅ 10:2) 2,55 ⋅ 1,55 0,636 &= 0,08075 ⋅ 0,03325
⋅ ¨0,174 ⋅ 0,45" + 0,45©⋅1,45 &= −151.04(MPa)
- Tại&điểm&4&trên&mặt&trong&(j&=&90o)&ứng&suất&kéo:& P (1 + 2α 0,636 α H − PG= _)(1 + α_) ' = l ⋅ ¤0,174 ⋅ − J= ⋅ dJ= (1 − α_)"α_ (1 − α_)¥ ⋅ k (0,0675 − 9,35 ⋅ 10:2) 2,1 ⋅ 1,55 0,636
&= 0,08075 ⋅0,03325 ⋅¨0,174 ⋅0,45" ⋅ 0,55 − 0,45 ©⋅1,45 &= 112,14(MPa)
® &Thỏa&đối&với&chốt&có&a = 0,4 ÷ 0,8 o &
& & & & & & & & & & & & & & & & &thì& és ù ë 60 170Mpa max û = ÷ &
e) Áp&suất&tiếp&xúc&với&(bạc)&đầu&nhỏ&thanh&truyền& 81 82 P (0,0675 − 9.35 ⋅ 10:2) q H − PG= a = l = , (MPa) ≤ [qI] J= ⋅ dJ= 0,08075 ⋅ 0,03325 = 21 66
Đối&với&chốt&lắp&tự&do:&[q ] = 20 ÷35(MP ) a d &
f) Tính&bền&séc&–&măng&
Tỉ&số:& & & & & & & & &𝑫& =&𝟏𝟏𝟓&=&38,3& 𝒕 𝟑
Độ&mở&:& 𝑨&=3& & 𝒕
&=>&A=&3.t&=&3.3&» &9(mm)&
Áp&suất&trung&bình&của&xéc&măng&lên&mặt&gương&xylanh&:& 𝟎,𝟏 . 𝟓 𝑬.𝑨 Ptb = 𝟏𝟓 𝟏𝟎𝟓 𝒕 = 𝟎, .𝟐,𝟐. .𝟑 = 3,43 (MPa) 𝑫f𝑫:𝟏g 𝟎,𝟎𝟗𝟓 𝟑 𝒕 𝒕 6f𝟎,𝟎𝟗𝟓g
𝟎,𝟎𝟎𝟑 𝟎,𝟎𝟎𝟑 Trong&đó&:&
-&Mô&đun&đàn&hồi&xéc&măng&thép&hợp&kim& 5
E = 2, 2.10 MPa&
-&A&là&khe&hở&miệng&xéc&măng&ở&trạng&thái&tự&do&m.&
Ứng&suất&uốn&làm&việc&sẽ&lớn&nhất&tại&tiết&diện&đối&xứng&I-I&(ứng&suất&kéo&bề&mặt& ngoài):&
𝟎, 𝟑𝟖𝟓 ⋅ 𝑨 ⋅ 𝑬 𝟎, 𝟑𝟖𝟓 ⋅ 𝟎, 𝟎𝟎𝟗 ⋅ 𝟐, 𝟐 ⋅ 𝟏𝟎𝟓 𝝈𝒖𝟏 = =
= 𝟏𝟕𝟕, 𝟓𝟓(𝑴𝑷𝒂) 𝑫 ⋅¶𝑫𝒕 − 𝟏¸
𝟎, 𝟏𝟏𝟓 ⋅ ¶𝟎, 𝟏𝟏𝟓 𝟎, 𝟎𝟎𝟑 − 𝟏¸
Ứng&suất&uốn&lớn&nhất&tại&bề&mặt&trong,&tiết&diện&đối&xứng&I-I&(ứng&suất&kéo&bề& mặt&trong)&:& 𝝈 g 𝟏𝟎𝟓 𝟏𝟏⋅𝟑)
𝒖𝟐 = 𝟒𝑬f𝟏:𝟎,𝟏𝟏𝑨 𝒕
= 𝟒⋅𝟐,𝟐⋅ ⋅(𝟏:𝟎, = 𝟐𝟎𝟖, 𝟐𝟐𝟒 (MPa) 𝒎𝑫f𝑫:𝟏,𝟒g
𝟐⋅𝟎,𝟏𝟏𝟓f𝟎,𝟏𝟏𝟓:𝟏,𝟒g 𝒕 𝒕
𝟎,𝟎𝟎𝟑 𝟎,𝟎𝟎𝟑
& & & & & & &Chọn&m=2.&
6.2. Nhóm thanh truyền
6.2.1. Các thông số ban đầu 82 83
Hình 6.2. Các thông số kết cấu của nhóm thanh truyền
6.2.1.1. Đầu nhỏ thanh truyền
Hình 6.3. Sơ đồ tính toán đầu nhỏ
Bảng 6.2. Các thông số kết cấu của đầu nhỏ thanh truyền 83 84 Thông số
Đường kính trong đầu nhỏ d# (1,1 ÷ 1,25)dJ= = 1,1.28,75 = 31,625&mm
Đường kính ngoài đầu nhỏ d " (1,25 ÷ 1,65)dJ= = 1,25.28,75 = 35,9375&mm
Đường kính trong bạc dI
d# − 2s = &28,75& − 2.9,2 = 10,35&mm Chiều dài đầu nhỏ l a
(0,28 ÷ 0,32)D= 0,28.115 = 32,2mm
Chiều dày bạc đầu nhỏ sb
(0,055 ÷ 0,085) dJ= = 0,055.28,75=1,581 mm Chiều dày đầu nhỏ sd (
d" − d#)/2 = (35,95 − 31,9)/2 = 2,025&mm
Khe hở giữa bạc lót đầu nhỏ thanh truyền với chốt Piston
∆ = (0,0004÷0,0015)dcp = (0,0004÷0,0015).28,75 = 8,87.10-3÷ 0,033 mm
6.2.1.2. Thân thanh truyền
- Thân thanh truyền có tiết diện chữ I được dùng phổ biến vì loại tiết diện này sử dụng vật
liệu rất hợp lí; do đó trọng lượng thanh truyền nhỏ mà độ cứng vững của thanh truyền lại lớn.
- Tiết diện ngang thân thanh truyền có dạng chữ I, được chế tạo theo phương pháp rèn khuôn. 84 85
Hình 6.4. Sơ đồ tính toán thân thanh truyền
Bảng 6.3. Các thông số kết cấu của thân thanh truyền
Thông số thân thanh truyền Chiều dài thanh truyền L 154 mm H 25,25 mm h 0,668H = 16,67 mm B 0,75H = 18,94 mm b/2 0,292H = 7,37 mm t 0,166H = 4,192 mm
6.2.1.3. Đầu to thanh truyền 85 86
Đầu to thanh truyền là đầu lắp thanh truyền với cổ khuỷu. Kích thước đầu to thanh
truyền phụ thuộc vào đường kính và chiều dài cổ khuỷu.
Bảng 6.4. Các thông số kết cấu của đầu to thanh truyền
Thông số đầu to thanh truyền
Đường kính chốt khuỷu dck (0,56÷ 0,75)D = 53,2 mm
Khoảng cách tâm bu lông c (1,3 ÷ 1,75)dck = 69,16 mm Chiều dài đầu to lđt (0,45÷ 0,95)dck = 26,6 mm
Chiều dày bạc lót mỏng db (0,03÷ 0,05)dck = 1,596 mm Chiều rộng bạc lb 63,154 mm Chiều dày nắp dn 4 mm Chiều rộng nắp l db n = lb+ =67,154 mm
6.2.1.4. Bu lông thanh truyền
Bu lông thanh truyền là chi tiết nhỏ nhưng rất quan trọng. Vì khi bu lông thanh truyền
bị đứt, động cơ sẽ bị hư hỏng nặng và có thể gây tai nạn lao động đối với người điều khiển, vận hành.
+ Thiết kế bu lông thanh truyền chỉ chịu lực kéo, tránh các lực cắt, kéo, uốn.
+ Tăng sức bền, chống mỏi cho bu lông thanh truyền bằng cách bố trí góc lượn tại
những chổ thay đổi kích thước đường kính, dùng loại đai ốc chịu lực kéo để giảm ứng suất
trên các mối ren, cần siết đúng lực và siết đúng kỹ thuật.
Hình 6.5. Kích thước bulông thanh truyền 86 87
Bảng 6.5. Các thông số kết cấu của bulông thanh truyền
Thông số bulông thanh truyền Giá trị
Số bulông cho mỗi thanh truyền z 2 dbl 16 mm dmin (do) 14 mm dtb 13 mm
6.2.2.&Tính&bền&đầu&nhỏ&thanh&truyền&
Đầu&nhỏ&mỏng& æ d 32,114 ö 2 ç = =1, 4455 <1,5 ÷ d 22, 217 è 1 ø & 𝑑 45,73 Ÿ& "
&= &1,25& < &1,5 𝑑 & = # 36,58
6.2.2.1. Khi chịu kéo (ĐCT ở cuối thải, đầu nạp) d 45,73 + 36,58 ρ = # + d" 4 = mm 4 = 20,58 ρ# = 12,469 mm P 9,35. 10:2 p = G= 2ρ = 2.0,0206 = 0,227(MPa)
- Coi đầu nhỏ là 1 dầm cong đối xứng ngàm tại tiết diện C-C về mỗi phía như hình vẽ trên vói góc ngàm g : H 25,25 ,
γ = 90∘ + arccos& 2 + ρ# 2 + 12 469 5 r = 90∘ + arccos& = 118, 39 " + ρ# 16,057 + 12,469
- Cắt dầm cong tại tiết diện đối xứng A-A và thay bằng lực kéo và mômen uốn tương ứng NA và MA :
NA = Pj(0,572 – 0,0008 γ) = 9,35.10-3.(0,572 – 0,0008.118,39) = 4,46.10-3 MN
MA = Pj ρ(0,00033γ – 0,0297)
= 9,35.10-3.0,02085.(0,00033.118,39 – 0,0297) = 1,83.10-6 MNm.
- Hệ số ảnh hưởng việc lắp bạc lót vào đầu nhỏ thanh truyền 87 88 E F d d c = = ",".#5=."' , 2 2> = 0,694 E F E F ",".#5=."' , 2 2 Y > #,".#5=.#> , ? *8 + d d b b Trong đó:
Môđun đàn hồi vật liệu đầu nhỏ, chọn: Ed = 2,2.105 MPa đối với thép.
Môđun đàn hồi vật liệu bạc, chọn: Eb = 1,2.105 MPa đối với đồng thau.
Fd = (d2-d1)ld = (45,73-36,58)´ 26,6 = 243,39 mm2
Fb = (d1-d0)ld = (36,58 – 29,19)´ 26,6 = 196,57 mm2 - Tại tiết diện C-C:
Mjc = MA + NA ρ(1 – cos γ) – 0,5Pjρ(sin γ – cos γ)
= 1,83.10-6 + 4,46.10-3.0,02058.(1- cos118,39)
– 0,5.9,35.10-3.0,02058.(sin118,39 – cos118,39) = 6,9.10-6 MNm
Njc = NA cos γ + 0,5Pj(sin γ – cos γ)
= 4,46.10-3.cos118,39 + 0,5.9,35.10-3.(sin118,39 – cos118,39) = 4,21.10-3 MN
- Ứng suất kéo của mặt ngoài đầu nhỏ : 1 σ 5 6ρ + s < '( = 2M() s(2ρ + s)+ χN() l s* 1 &= 5 6.0,02058 + 0,0046 2 ⋅ 6,9 ⋅ 10+, ⋅ +- 0,004 .
6 (2.0,02058 + 0,0046) + 0,694 ⋅ 4,21 ⋅ 10 <0,0266.0,0046 = 92,5 (MPa)
- Ứng suất kéo của mặt trong đầu nhỏ : 1 σ 5 6ρ − s < !( = −2M + χN () s(2ρ − s) () l s * 1 &= 5 6 ⋅ 0,02058 − 0,0046 −2 ⋅ 6,9 ⋅ 10 +, +-
0,0046 ⋅ (2 ⋅ 0,02058 − 0,0046) + 0,694.4,21 ⋅ 10 <0,0266 ⋅ 0,0046 &= −55,845&(MPa)
6.2.2.2. Khi chịu nén (ở ĐCT, đầu hành trình dãn nở)
- Lực nén tác dụng lên đầu nhỏ thanh truyền
Pn = Pz - Pj = 0,0675 – 9,35.10-3 = 0,05815 MN
Tra đồ thị hình 5.9 tài liệu [1]:
k> = 0,07 → NA = 8,686.10-5 (MN) !? 88 89 l> = 0,015 → N -7 A = 4,945.10 (MN) !?m
Tại tiết diện nguy hiểm C-C:
- Mnc = MA +Naρ(1 – cosγ) - P<ρ ¶no
" $ $
= 1,83.10-6 + 8,686.10-6.0,02058.(1-cos118,39)-1,196.10-3 .¶no<##),2>− "
& & ",#?>. sin118,39 − # cos118,39¸ = -2,14.10-6 (MNm). $ $
- Ncn = NA.cosγ +χ.Pn¶no<6p − psinγ − # cosγ¸ " $ $
= 4,46.10-3.cos118.39 + 0,694.0,05815.¶no<##),2>− ",#?>. sin118,39 − " $ # .cos118,39¸ $ = - 1,47.10-3 MN
- Ứng suất nén của mặt ngoài đầu nhỏ : σ ?mYn nZ = ¦2M&+ χN n(" 6 m Y6n) `@q = ¦2.2, 14:?. ?.5,5"5* Y ) 5,55'? &+ &0,694.1, 47.10:2 § . # 5,55' . ? (".5,5"5* Y ) 5,55'?) 5,5"? . ? 5,55'? = -29,62 MN/m2
- Ứng suất nén của mặt trong đầu nhỏ : Σ ?m:n tZ = ¦−2M&+ χN n(" 6 m :6n) `@q = ¦2.2, 14:?. ?.5,5"5* Y ) 5,55'? &+ &0,694.1, 47.10:2 § . # 5,55' . ? (".5,5"5* Y ) 5,55'?) 5,5"? . ? 5,55'? = 16,38 MN/m2
6.2.2.3. Ứng suất biến dạng của đầu nhỏ thanh truyền:
- Độ giãn nở khi đầu nhỏ thanh truyền chịu nhiệt D = (a -a ) o t d t b
= (1,8-1).10-5 . 370.0,03658= 0,0108 mm 1 Trong đó: a = a = 5 1.10- (vật liệu thép) b tt
Ngoài ra độ dôi lắp ráp ta chọn theo mối lắp (H7/k6) D = 0, 01 m 5 m 89 90
- Tổng độ dôi D + D gây áp suất lên bề mặt lắp ghép: t D + D P = t 2 2 2 2 æd + d d +db ö 2 1 1 ç + µ µ ÷ 2 2 2 2 + d - d d - ç d 2 1 1 b ÷ d1 + ç E E ÷ ç d b ÷ è ø = 5,5# Y * 5,5#5) = 19,28 MN/m2 2?,*). % % % r A=,B+ C+D,=E Y5," 6 ? Y6 +D,=E%CGA,=EY5,"?s A=,B+%*+D,=E% +D,=E%*GA,=E% %,%.GH= ,,, G,%.GH=
6.2.2.4. Ứng suất biến dạng do p gây nên được tính theo công thức Lame
- Ứng suất trên mặt ngoài đầu nhỏ thanh truyền: 2d" 2.36,58" σ # t< = P , /m" d" " = 19,28 " " = 68 51MN " − d# 45,73 − 36,58
- Ứng suất trên mặt trong: d" + d" 45,73" + 36,58" σ " # tL = P , . /m" d" " = 19 28 " " = 87 79MN " − d# 45,73 − 36,58
6.2.2.5. Hệ số an toàn của đầu nhỏ thanh truyền
- Ứng suất cực đại của chu trình là:
σ]M^ = σ- Ứng suất cực tiểu của chu trình: σ]o< = σ
- Hệ số an toàn của đầu nhỏ thanh truyền: 2σ
& & & & & & & & & &n :# u = σ2.250
= 92,5+ 29,62 + 0.1.(92,5 −29,62 + 2.68,51 = 3,518. Trong đó: + Ch ọn y s = 0,1
+ Đối với thép cacbon: s = 180÷ 250MPa s = 250MPa - 1 nên chọn -1 90 91
6.2.2.6. Độ biến dạng của đầu nhỏ theo hướng kính d 8P
8 ⋅ 9,35 ⋅ 10:2 ⋅ 20, 582 ⋅ 10:> ⋅ (118∘ − 90∘)" δ = Gρ2(γ − 90∘)" 10)EJ =
10) ⋅ 2,1 ⋅ 10* ⋅ 2,353 ⋅ 10:#5 = 1.034.10-7 mm
Moment tiết diện dọc của đầu nhỏ: 3 3 l s 0, 024.0, 0049 d 1 - 0 4 J = = = 2,353.10 (m ) 12 12 d [d < ]= 0,02÷ 0,03m m thỏa bền.
6.2.3. Tính toán bền thân thanh truyền (động cơ cao tốc)
- Lực tác dụng tác dụng khi thanh truyền chịu nén và uốn dọc tại tiết diện trung bình
khi piston ở vị trí ĐCT:
P∑ = Pz –( mnp + mttl)Rω ( 1+λ).10-6
= 0,0675 – (0,4737 + 0,171).0,04.628,312 .(1 + 0,25).10-6 = 0,0548 MN Với mtt1 = 0,171 (kg)
- Ứng suất tổng theo CT Nave-Rankin: σx = !∑ k .1,1= 297,95 MPa ; x = 5,5*') "5",2#2.#5*D JK ! σ ∑ y = k .1,1= 297,95 MPa ; y = 5,5*') "5",2#2.#5*D JK Trong đó : chọn k k x » y » 1,1
Diện tích trung bình ngang thân: 2 F BH bh mm tb = -
= 17, 773.22, 22 -12, 976.14,843 = 202, 313
- Tại vị trí ĐCT của piston ở cuối hành trình thải, đầu hành trình nạp, lực quán tính
gây ra ứng suất kéo tiết diện trung bình: ! σ 'G k = k ·1,1 = -69,05 MPa ; x = :5,5#"8 "5",2#2.#5*D JK
Pj1 = -(mnp + mtt1)Rω(λ+1).10-6
= - (0,4737 + 0,171).0,04.628,312.(1+0,25).10-6 = -0,0127 MN
- Hệ số an toàn tại tiết diện trung bình của thân: 91 92 nσx = "u*G (u^6:6uv)Y6wL(u^6:6uv) = "."*5 = 1,239 ("> , 8 > 6 * Y6? , > 5 ) * Y65,#.(">8,> 6 * Y6?>,5*)
6.2.4. Tính toán bền đầu to thanh truyền
- Tổng lực kéo ở đầu to thanh truyền:
Pj∑ = Pj + PxM = ÈmG(1 + λ) + (my − m<ÉRω. 10:?
= ( 0,644.(1+0,25) + (0,398 +0)).0,04.628,31.10-6 = 0,0189 MN
(bỏ qua khối lượng đầu to mn = 0)
- Moment và lực pháp tuyến tại mặt cắt A-A: c
ÊMz = P{| 2(0,0127 + 0,00083γ_ )& Nz = P{|(0,522 + 0,003γ_) ∘ :*
ËMz = 0,0189 5,5?>#?(0,0127 + 0, 00083.40 ) = 2,99. 10 Nm " N ∘
z = 0,0189(0,522 + 0, 003.40 ) = 0,0121&MN
- Ứng suất tổng cộng lớn nhất tại bề mặt ngoài mặt cắt A-A: N },~ . ~ •€•‚ €,€•}• >YQ> σ OP R „,ƒ.•€•… > •,ƒ . ~ •€•ƒ! ∑ = = = 187,404 MPa #YSK },• . † •€••• S "! @ „,‚‡ . • •€••€ } $ % &',")*⋅*} Với : !W ˆ ˆ # = = ⋅ 10,- = 1,79 ⋅ 10,' m. & &
Moment quán tính tiết diện nắp: l 2 67,154 ⋅ 42 J <δ< :#5 a = 12 = 12 ⋅ 10:#" = 3,581 ⋅ 10 m'
Moment quán tính tiết diện bạc: l 2 0,063154 ⋅ 0,00162 J IδI :## I = 12 = 12 = 2,16.10 m'
Diên tích tiết diện A-A: F 2
A = ln. δ< + lb. δ< = 0,067154.0,004+0,063154.0,001596 = 3,694.10-4 m Vậy s < s = ÷ MPa S [ S ] (150 200) thỏa bền.
6.2.5. Tính toán bền bu-lông thanh truyền 92 93
- Lực kéo trên mỗi bu-long. P 0,0189 P {| :2
I = z = 2 = 9,45 ⋅ 10 MN ∣ - Lực xiết bulông: P :2
z = (2 ÷ 4)PI = 18,9 ⋅ 10 MN Chọn c = 0,1 5 Vậy tổng lực kéo là: P :2
IL = Pz + χPI = (18,9 + 0,15 ⋅ 9,45) ⋅ 10:2 = 20,32 ⋅ 10 MN - Ứng suất kéo : 4P 4 ⋅ 20,32 ⋅ 10:2 σ IL v = πd" = ]o< π ⋅ 0, 015" = 132&MPa - Ứng suất xoắn: τ ,>⋅ *+⋅5,5#2 ^ = !>aJK = #) #5 = 22,39&MPa 'a+H '.5,5#'+ - Ứng suất tổng: σ = Îσ" " + 4. , " = , I v + 4τ^" = Ï132 22 39 139 39MPa Vậy s <[s = ÷ S S ] (120 180 ) thỏa bền.
6.3. Nhóm trục khuỷu
6.3.1. Các thông số ban đầu 93 94 & &
Hình 6.6.&Các thông số kết cấu của trục khuỷu& Thông số trục khuỷu Giá trị
Đường kính cổ trục khuỷu dct (0,65 ÷ 0,8)D = 61,75 mm
Chiều dài cổ trục khuỷu lct (0,5÷0,6)dct = 30,875 mm
Đường kính chốt khuỷu dck (0,56÷0,75)D = 53,2 mm
Chiều dài chốt khuỷu lck (0,45÷0,6) dck = 31,92 mm
Chiều rộng má khuỷu hmk (1÷1,25)D = 99,75 mm Chiều dày má khuỷu bmk (0,2÷0,22)D = 19 mm 94 95
Bán kính góc lượn của má khuỷu rmk (0,06÷0,08) dck = 3,192 mm
Bán kính quay của má khuỷu rmk 19,3 mm
Bán kính quay của đối trọng rdt 19,3 mm Độ trùng điệp e
= (dck + dct)/2 – R = 17,465 mm
Khoảng cách từ tâm cổ đến tiết diện nguy hiểm r = (dct - ε)/2 = 22,143 mm l' = l' = lct/2 + bmk + lck/2 50,398 mm a = bmk/2 + lck/2 25,46 mm b = b' = b' = bmk /2 + lct/2 24,938 mm lo =l + l' 100,796 mm c = c' = c' 20,819 mm
Bảng 6.6. Các thông số kết cấu của trục khuỷu
6.3.2. Tính bền trục khuỷu
Tính sức bền theo cách phân đoạn, ta chia trục khuỷu ra làm nhiều đoạn, mỗi đoạn ứng
với mỗi khuỷu, chiều dài mỗi đoạn bằng khoảng cách giữa 2 tâm điểm của ổ trục và coi
mỗi đoạn như 1 dầm tĩnh định đặt trên 2 gối tựa. Khi cắt đoạn trục khuỷu, ta giả thiết rằng:
khuỷu trục là 1 dầm có độ cứng vững tuyệt đối.
Khi tính bền thường tính cho trục nào nguy hiểm nhất tức là khuỷu mà trên đó tải trọng có giá trị lớn nhất. 95 96
Hình 6.7. Sơ đồ lực và momen tác dụng lên trục khuỷu P
- Lực quán tính ly tâm của má khuỷu r1 P
- Lực quán tính ly tâm của đối khuỷu r 2
Z’, Z’’ - Phản lực pháp tuyến trên các gối trục bên trái và bên phải
T’, T’’ - Phản lực tiếp tuyến trên các gối trục bên trái và bên phải
6.3.2.1. Trong trường hợp khởi động
Hình 6.8. Sơ đồ lực trường hợp khởi động
- Giả thiết trục khuỷu ở vị trí điểm chết trên (a = 0)
- Lực tác dụng lên trục khuỷu sẽ là :
Z0 = Z = Pzmax.Fp = 9,52.0,00473 = 0,045 MN T = 0
- Các phản lực xác định theo công thức sau :
Z' = Z' = `M.Z = *5,2>)·0,045 = 0,0225 MN `H #55,8>?
v Tính sức bền của chốt khuỷu :
- Moment uốn chốt khuỷu:
Mu = Z'.l' = 0,0225.0,0504 = 1,134 .10-3 MNm
- Ứng suất uốn chốt khuỷu là : σ #2' #5 u = lP = 6#, 6. :2 = 76,725 MN/m2 ‰P #,'8 . ) #5*= Với môđun chống uốn: 96 97 Wu = $ d3 .0,05323 = 1,478.10-5 m3 2" ck = $ 2"
v Tính sức bền má khuỷu :
- Lực pháp tuyến Z gây ra ứng suất uốn tại tiết diện A-A của má khuỷu
- Ứng suất uốn má khuỷu bằng : M M σ 5""* 5"'> u = lP = ?.Š .I = ?.5, .5, = 93,35 MN/m2 ‰P$ ‹.I% 5,5>>8 . * 5,5#>%
- Ứng suất nén má khuỷu : σn = Š = 5,5'* = 11,87 MN/m2 "I‹ ".5,5# . > 5,5>>8*
- Ứng suất tổng cộng :
σ∑ = σu + σn = 93,35 + 11,87 = 105,22 MN/m2
v Tính sức bền của cổ trục khuỷu :
- Ứng suất uốn cổ trục khuỷu : M M σ 5""* 5"'> u = Š .I 5, .5, = 24,23 MN/m2 ‰P ",2# . " #5*= Với môđun chống uốn: Wu = $ d3 .0,061753 = 2,312.10-5 MN/m2 2" ct = $ 2"
6.3.2.2. Trường hợp trục khuỷu chịu lực Zmax
- Lực tác dụng xác định theo công thức sau :
Z0 = Zmax – ( C1+ C2 )= Pzmax – Rω2 ÈmG(1 + λ)&+&mJv6 +&myÉ
= 0,0675 – 0,04. 628,312 [0,511. (1 + 0,25) + 0,253& + &0,3196].10-6 = 0,066 MN
C là lực quán tính ly tâm của chốt khuỷu: 2 6 C m Rw .10- = 1 ck 1
C là lực quán tính ly tâm của khối lượng thanh truyền quy về tâm chốt khuỷu: 2 2 C m Rw .10- = B 6 2 97 98
Hình 6.9. Sơ đồ tính toán trục khuỷu
- Lực quán tính ly tâm của má khuỷu và đối trọng :
Pr1 = mmkρmkω2 = 0,362 . 0,0193.628,312.10-6 = 1,305.10-3 MN
Pr2 = mdtρdtω2 = 0,354 . 0,0193.628,312.10-6 = 1,28.10-3 MN
- Phản lực tác dụng lên các gối trục : Z' = Z' =ŠH – pr1 + pr2 "
= 5,5'* - 1,305.10-3 +1,28.10-3 = 2,246.10-3 MN "
v Xác định khuỷu nguy hiểm: -
Mặt khác khi tính toán sức bền của một khuỷu nào đó của trục khuỷu động
cơ nhiều xylanh, ngoài lực Zmax ra, khuỷu đó còn chịu moment xoắn do các khuỷu phía
trước nó truyền đến vì vậy khuỷu chịu lực và moment lớn nhất sẽ là khuỷu nguy hiểm
nhất, dựa vào đồ thị T=f(α) với góc lệch công tác 180 j = o ct ta có bảng giá trị sau: α 0 180 360 540 T (MN) 0 7.0791.10-19 8.325.10-19 2.70373.10-18
Thứ tự làm việc của động cơ là 1-3-4-2: Khuỷu α 98 99 0 180 360 540 1 0 7.07914E-19 8.32549E-19 2.70373E-18 2 7.07914E-19 8.32549E-19 2.70373E-18 0 3 2.70373E-18 0 7.07914E-19 8.32549E-19 4 8.32549E-19 2.70373E-18 0 7.07914E-19 ∑Ti- 1.54046E- 1 0 18 4.24419E-18 2.70373E-18
- Dựa vào bảng trên ta thấy khuỷu thứ 4 chịu lực (∑Ti-1)max do đó cần phải tính bền cho khuỷu này.
v Tính bền chốt khuỷu :
- Ứng suất uốn chốt khuỷu : M M M *+ *+ σ TG T% "'? #5*+ 5"'> 25* #5 .5,5"**:#,").#5 .5,5"# u = lP = Š .I Y= .M:= .J = ", . .5, Y#, . ‰P ‰P #,'8 . ) #5*= = 24,56 MN/m
- Ứng suất xoắn chốt khuỷu : M τ ""' #5*GE 5' &*G k= lU = ∑• .Ž = ', . .5, = 0,571.10-14 MN/m2 ‰ ".‰ ".#,'8 . ) #5*= U P
- Ứng suất tổng của ứng suất uốn và ứng suất xoắn : σ " " :#')"
∑ = ÏσK" & + & 4τv = Ï24,56 + &4. (0,571.10 & = 24,56 MN/m2
v Tính sức bền cổ trục khuỷu :
Tính ở chỗ chuyển tiếp giữa cổ trục và má khuỷu (nơi nguy hiểm nhất)
- Ứng suất uốn cổ trục : M M σ "'? #5*+ 5"'> u = lP = Š .I = ", . .5, = 2,42 MN/m2 ‰P ‰P ",2# . " #5*=
- Ứng suất xoắn cổ trục : 99 100 τ M ""' #5*GE 5' &*G k = lU = ∑• .Ž = ', . .5, = 3,65.10-15 MN/m2 ‰ ".‰ U P ".",2# . " # : 5 =6
- Ứng suất tổng cộng khi chịu uốn và xoắn : σ " " ( :#*)"
∑ = ÏσK & + & 4τv = Ï 2,42" + &4. 3,65.10 & = 2,42 MN/m2
v Tính sức bền má khuỷu :
Trong quá trình làm việc má khuỷu chịu uốn và nén trên trục x-x và y-y
- Ứng suất nén trên má khuỷu : M σ T% "'? #5*+ ") #5*+ u = Š .= = ", . 6:6#, . = 0,521 MN/m2 I.‹ 5,5# . > 5,5>>8*
- Ứng suất uốn trong mặt phẳng vuông góc với mặt phẳng khuỷu trục(uốn quanh y-y). V σ• M ""' #5*GE 5' &*G K = lP = lU = ∑• .Ž = ', . .5, = 5,39.10-15 MN/m2 ‰V ‰V K.W% H,HGX.H,HXXB=% P P D D
- Ứng suất uốn trong mặt phẳng khuỷu trục (uốn quanh trục x-x). σ^ $ M M *+ T% "'? #5*+ 5"'> ") #5 .(5,5"**:5,5"5 ) ) K = lP = Š .I Y! (M:J) = ", . .5, Y#, . ‰$ K.W% H,HGX.H,HXXB=% P D D = 1,946 MN/m2.
- Ứng suất uốn tổng khi má khuỷu chịu nén và chịu uốn : σ • ^ -15 2
∑ = σn + σK + σK = 11,87+5,39.10 +1,946 = 13,816 MN/m
6.3.2.3. Trường hợp khuỷu trục chịu lực tiếp tuyến lớn nhất (Tmax)
Ø Vị trí tính toán là tại α α
= Tmax (xác định trên đồ thị) α (độ) 463 643 103 283 T (MN)
0.006199643 -0.000620033 0.003857512 -0.001067604
Ta xác định các trị số của T ở các góc quay α: Tmax = 0,006199643 MN ở α = 463 độ. Ø Bảng tính (åTi-1)max : 100 101 khuỷu 463 643 103 283 1 0.006199643 -0.000620033 0.003857512 -0.001067604 2 -0.000620033 0.003857512 -0.001067604 0.006199643 3 -0.001067604 0.006199643 -0.000620033 0.003857512 4 0.003857512 -0.001067604 0.006199643 -0.000620033 ∑Ti-1 0 0.003237479 0.002169875 -0.001067604
Dựa vào bảng trên ta thấy khuỷu thứ 3 chịu lực (∑Ti-1)max do đó cần phải tính toán
sức bền của khuỷu trục này.
Căn cứ vào bảng số liệu ta thấy khuỷu thứ 3 là nguy hiểm nhất :
với : Zo = Z (a=138o) = -5.33872.10-5 MN
Z' = Z' = ŠH – P + P = :*.22)8 ."# : 5 * - 1,305.10-3+1,28.10-3 " r1 r2 " = -5,17.10-5 KN
T' = T' = 5,55?#>> = 0,00309 MN "
v Tính sức bền chốt khuỷu :
- Ứng suất uốn trong mặt phẳng khuỷu trục : σ^ $ M M TG.M:!T%.J K = lP = Š .` Y! ‰P$ ‰P$ = :*,# .8#5*=.5,5*5 6 ' Y#,25 . * #5*+.5,5"* . * #," . ) #5*+.5,5"5) = -0,176 MN/m2 #,'8 . ) #5*=
- Ứng suất uốn trong mặt phẳng vuông góc với mặt phẳng khuỷu trục: V σ^ 5525> 5*5' K = lP = ••.`•= 5, .5, = 10,54 MN/m2 ‰PV ‰PV #,'8 . ) #5*=
- Ứng suất uốn tổng cộng : σ •‡" )" + , " = 10,54 MN/m2 u = Î(σK
^ )" &+ †σK & = Ï(−0,176 10 54
- Ứng suất xoắn chốt khuỷu : 101 102 τ M &*G k = lU = (å • Y•).Ž ‰ ",‰ U P = (65,552" 6 ' Y65,5?#> ). > 5,5' = 12,77 MN/m2 ".#,'8 . ) #5*=
- Ứng suất uốn tổng hợp khi chịu uốn và xoắn : σ " " " "
∑ = Ï σK& + & 4τv = Ï10,54 + 4.12,77 = 27,63 MN/m2
v Tính sức bền của má khuỷu :
- Ứng suất uốn do Z’’ gây ra : σ #8 #5*= 5"'> uz = lP$ = ŠMMIMM = :*, . .5, = -0,215 MN/m2 ‰ W.K% H,HXXD.H,HGX% P D D
- Ứng suất uốn do lực quán tính ly tâm Pr2 gây ra : σ T% ") #5*+.(5,5*5 : ' 5,5"5 ) ) ur = lPT = ! (M:J)= #, . = 6,031 MN/m2 ‰P W.K% H,HXXD.H,HGX% D D
- Ứng suất uốn do lực tiếp tuyến T gây ra : MM σ 5525> 5"# uT = • .x = 5, .5, = 2,07 MN/m2 K.W% H,HGX.H,HXXD% D D
Với r = 0,021m là khoảng cách từ tâm cổ trục khuỷu đến tiết diện nguy hiểm của má khuỷu.
- Ứng suất uốn do moment xoắn M’’k gây ra : MM σ 552"' 55?#>> 5' &*G uM = lU = (å • Y•).Ž=(65, 6Y65, ).5,= 12,02 MN/m2 K.W% K.W% H,HGX.H,HXXD% D D D " Mk (0,04896 +0,0164).0,0386 2 s uM = = 1 = 34 MN/m 2 2 . b h 0,0155.0,0855 6 6
- Ứng suất xoắn má khuỷu do lực tiếp tuyến T’’ gây ra : Mk τ = k Wk
Do tiết diện chịu xoắn của má khuỷu có dạng hình chữ nhật nên khi chịu xoắn, ứng
suất xoắn của các điểm trên tiết diện hình chữ nhật đều khác nhau 102 103
Hình 6.10. Sơ đồ mặt cắt má khuỷu
ü Ở điểm 1, 2, 3, 4 có τ 0 = k ü Ở điểm I, II có τ τ = k kmax ü Ở điểm III, IV có τ τ = k kmin
- Ứng suất xoắn được xác định theo công thức sau : MM MM τ 552# 5"'> kmax = • .I = 5, 6.5, = 2,86 MN/m2 ‘ % G.‹.I 5,8 . * 5,5>> . ? 5,5#>%
τkmin = g2. τkmax = 0,215.2,86 = 0,615 MN/m2
Trong đó : g1 = 0,75 và g2 = 0,215 là hệ số ứng suất phụ thuộc vào hệ số h/b=5,5
- Ứng suất nén má khuỷu : MM σ T% #8 #5*= ") #5*+ n = Š :! = :*, . :6#, . 6 = -0,704 MN/m2 ‹.I 5,5>> . ? 5,5#>
- Do ứng suất tác dụng lên má khuỷu rất phức tạp nên ta phải lập bảng xét dấu các ứng suất tác dụng : 2 2 σ (å å = σ) + 4τ (MN/m2) k
Ø Bảng xét dấu ứng suất tác dụng lên má khuỷu: Ứng suất 1 2 3 4 I II III IV n
0,704 0,704 0,704 0,704 0,704 0,704 0,704 0,704 103 104 uz
0.215 -0,215 0,215 -0,215 0,215 -0,215 0 0 ur
6,031 6,031 6,031 6,031 6,031 6,031 6,031 6,031 uT 2,07 2,07 -2,07 -2,07 0 0 2,07 -2,07 uM -11,12 -11,12 11,12 11.12 0 0 -11,12 11,12 Ss -2,1 -2,53 16 15,57 6,95 6,52 -2,315 15,79 0 0 0 0 2,86 2,86 0,615 0.615 2,1 2,53 16 15,57 8,63 8,67 2,8 15,78
6.3.2.4. Trường hợp khuỷu trục chịu lực å Tmax
Ø Bảng xác định khuỷu trục nguy hiểm : α (độ) 675 135 315 495 ∑T (MN) 0.016400883 0.016296188 0.016362171 0.016304733
Ta xác định các trị số của T ở các góc quay α: ∑Tmax = 0,016400883 MN ở α = 675 độ Ø Bảng tính (åTi-1)max khuỷu 675 135 315 495 1
0.016400883 0.016296188 0.016362171 0.016304733 2
0.016296188 0.016362171 0.016304733 0.016400883 3
0.016304733 0.016400883 0.016296188 0.016362171 4
0.016362171 0.016304733 0.016400883 0.016296188 ∑Ti-1
0 0.032658359 0.048963092 0.016304733
Ta thấy (åTi-1)max = 0.048963092MN/m2 tại khuỷu trục thứ 4, nên khuỷu trục này là
nguy hiểm nhất và cần phải tính toán.
Với : Zo = Z (a=675o) = – 0,003248 MN Z' = Z' = ŠH – P
–65,552"') −1,305.10:2 + 1,28.10:2= -1,65.10-3 " r1 + Pr2 = " KN
∑T' = ∑T' = ∑•]M 6^ = 5,5#?' = 8,2.10-3 MN " "
v Tính sức bền chốt khuỷu :
- Ứng suất uốn trong mặt phẳng khuỷu trục: 104 105 M^ Z• ⋅ l• + P σ^ K x#. a − Px#. c K = W K^ = WK^ = :#,? .*#5*+.5,5*5 Y ' #,25 . * #5*+.5,5"* : * #," . ) #5*+.5,5"5) = −1,802&MN/m" 6#,'8 . ) #5*=
- Ứng suất uốn trong mặt phẳng vuông góc với mặt phẳng khuỷu trục: V
& & &σ•K = lP = |•M.`M = ),".#5*+.5,5*5' = 27,96 MN/m" ‰V ‰V 6#,'8 . ) #5*= P P
- Ứng suất uốn tổng cộng: σ • " u = Î(σK
^)" &+ †σK‡"& = Ï(−1,802)" + 27,96 = 28,02 MN/m"
- Ứng suất xoắn chốt khuỷu: M• †∑ & T τ v G:# + ΣT‡ R v = W = & v WK = (5.5')> 6 ? Y5,5#? ). ' 5,5' = 155,73 MN/m" ",2# . " #5*=
- Ứng suất uốn tổng hợp khi chịu uốn và xoắn: σ " " " " = 312,72
∑ = ÏσK & + & 4τv = Ï28,02 + 4.155,73 MN/m"
v Tính sức bền của cổ trục khuỷu :
- Ứng suất uốn do lực pháp tuyến Z’ gây ra: σ^ $ ?* #5*+ 5"'> K = lP = ŠMM⋅IMM = :#, . .5, = -1,78 MN/m" ‰$ ‰ ",2# . " #5*= P P$
- Ứng suất do lực tiếp tuyến T’ gây ra: V σ• #5*+ 5"'> K = lP = |•MM.`MM = ),". .5, = 8,83 MN/m" ‰V ‰ ",2# . " #5*= P P
- Ứng suất uốn tổng cộng: σ ^ •
u = Î(σK)" & + †σK‡"& = Ï(−1,78)" + 8.83" = 9,01 MN/m" - Ứng suất xoắn: 105 106 M•• †∑& T τ v G:# + ΣT‡R v = W = & v 2WK = (5.5')> 6 ? Y5,5#? ). ' 5,5' = 56,31 MN/m" ".",2# . " #5*=
- Ứng suất uốn tổng hợp khi chịu uốn và xoắn: σ " " " = 112,98
∑ = ÏσK & + & 4τv = Ï9,01" + 4.56,31 MN/m"
v Tính sức bền của má khuỷu
- Ứng suất uốn do Z’ gây ra: σ ?* #5*+.5,5"'> " u z= lP! = ŠMMIMM = :#, . = −&6,81&MN/m ‰ W.K% H,HXXE.H,HGX% P D D
- Ứng suất uốn do lực quán tính ly tâm Pr2 gây ra: σ T% ") #5*+.(5,5*5 : ' 5,5"5 ) ) ur = lPT= ! (M:J) = #, . = 6,031 MN/m2 ‰ % P W.K% H,HXXD.H,HGX D D
- Ứng suất uốn do lực tiếp tuyến T gây ra: MM σ #5*+ 5"# uT = |• .x = ),". .5, = 5,48 MN/m2 K.W% H,HGX.H,HXXD% D D
Với r = 0,021m là khoảng cách từ tâm cổ trục khuỷu đến tiết diện nguy hiểm của má khuỷu.
- Ứng suất uốn do moment xoắn M”k gây ra: MM σ 5')>? 5#?' 5' &*G uM = lU = (å • Y•).Ž=(65. 6Y65, ).5,= 83,22 MN/m2 K.W% K.W% H,HGX.H,HXXD% D D D
- Ứng suất xoắn má khuỷu do lực tiếp tuyến T” gây ra: MM MM τ #5*+ 5"'> kmax = |• .I &= & |•MM.IMM = ),". 6.5, = 17,04 MN/m ‰ W.K% H,HXXD.H,HGX% U + +
Do tiết diện chịu xoắn của má khuỷu có dạng hình chữ nhật nên khi chịu xoắn, ứng
suất xoắn của các điểm trên tiết diện hình chữ nhật đều khác nhau.
ü Ở điểm 1, 2, 3, 4 có τ = 0 k ü Ở điểm I, II có τ τ = k kmax 106 107 ü Ở điểm III, IV có τ τ = k kmin
- Ứng suất xoắn được xác định theo công thức sau : MM MM τ #5*+ 5"'> kmax = |• .I = ),". 6.5, = 7,57 MN/m2 ‘ % G.‹.I 5,8 . * 5,5>> . ? 5,5#>%
τkmin = g2. τkmax = 0,215.7,57 = 1,628 MN/m2
Trong đó: g1 = 0,75 và g2 = 0,215 là hệ số ứng suất phụ thuộc vào hệ số h/b=5,5
- Ứng suất nén má khuỷu : MM σ T% ?* #5*+ ") #5*+ n = Š :! = :#, . :6#, . 6 = -1,55 MN/m2 ‹.I 5,5>> . ? 5,5#>
Ø Do ứng suất tác dụng lên má khuỷu rất phức tạp nên ta phải lập bảng xét dấu các ứng suất tác dụng. 2 2 σå (å = σ) + 4τ (MN/m2) k
Ø Bảng xét dấu ứng suất tác dụng lên má khuỷu: Ứng suất 1 2 3 4 I II III IV sn 1,55 1,55 1,55 1,55 1,55 1,55 1,55 1,55 suz 6,81 -6,81 6,81 -6,81 6,81 -6,81 0 0 sur 6,031 6,031 6,031 6,031 6,031 6,031 6,031 6,031 suT 5,48 5,48 -5,48 -5,48 0 0 5,48 -5,48 suM -83,22 -83,22 83,22 83,22 0 0 -83,22 83,22 Ss -63,34 -76,97 92,13 78,5 14,39 0,77 -70,46 85,32 t k 0 0 0 0 12.16 12.16 2.61 2.61 så 63,34 76,97 92,13 78,5 18,84 12,18 70,5 85,36
à Ta thấy tất cả các ứng suất tính toán tác dụng lên khuỷu trục đều nằm trong khoảng
cho phép, vì vậy trục khuỷu này đủ bền.
6.3.2.5. Tính bền trục khuỷu khi xét đến ảnh hưởng của phụ tải động
- Trong thực tế sử dụng trục khuỷu thường bị gãy ở các phần nối tiếp
với cổ trục, chốt khuỷu, má khuỷu hoặc gãy ngang vị trí có rãnh khoan dầu.
Nghiên cứu các hiện tượng hỏng này, ta thấy tuyệt đại đa số đều mang tính 107 108
chất hư hỏng do chịu tải trọng thay đổi và va đập (tải trọng động). Như vậy
khi tính bền trục khuỷu trên cơ sở tính bền bằng phương pháp phân đoạn
cần xét đến ảnh hưởng của tải trọng động với các vùng chịu ứng suất tập trung.
- Tính toán sức bền của trục khuỷu khi xét đến phụ tải động chủ yếu là
tính hệ số an toàn của các phần của khuỷu trục khi chịu uốn và xoắn.
Với vật liệu là thép cacbon ta có thể chọn: s 340 / 2 = MN m t 280 / = MN m - ;2 1 1-
Khi tính hệ số an toàn cho cổ khuỷu và chốt khuỷu, tỷ số của hệ số ứng suất tập trung
K so với hệ số kích thước ta có thể chọn: k k s = t = 2,5 e e s t
Hệ số y được xác định theo [3] – Bảng 2.9 – trang 43 sách thiết kế máy Þy y s = 0, 2; t = 0, 1
v Hệ số an toàn của cổ trục khuỷu :
- Trong quá trình làm việc cổ trục khuỷu chịu ứng suất uốn và ứng suất xoắn.
- Nói chung ứng suất uốn thường có giá trị nhỏ, do đó khi tính toán trục với hệ số an toàn ta có thể bỏ qua.
- Khi tính toán hệ số an toàn của cổ trục khuỷu ta chỉ xét đến mômen xoắn. τ "#$ 55?" 5' max = l"#$ = • .Ž = 5, .5, = 10,73 MN/m2 ‰ ‰ ",2# . " #5*= U U τ 55*) 5' "&? min = l"&? = • .Ž = :5, .5, = -10,04 MN/m2 ‰ ‰ ",2# . " #5*= U U τ "#$ , Y , "&? a = ’ 6:6’ = #5 82 #5 5' = 10,39 MN/m2 " "
Với: Tmax, Tmin được xác định trong bảng kết quả tính toán động học:
Tmax = 0,0062 MN; Tmin = -0,0058MN; R =0,04 m
n’ = ’*G =& ")5 = 10,78 UY 6.’ ",*6.# , 5 2 6 > Z # Y
Do đó hệ số an toàn của cổ trục khuỷu khi chịu xoắn: 108 109 n = > = ÷ t [nt ] 2,5 4
Như vậy cổ khuỷu đủ bền.
v Hệ số an toàn của chốt khuỷu :
- Trong quá trình làm việc,tương tự như cổ khuỷu, chốt khuỷu cũng
chịu tác động đồng thời của ứng suất nén và uốn. Các ứng suất này đều
có ảnh hưởng rất lớn đến sức bền trục khuỷu. Do đó trong quá trình tính
toán ta phải tính riêng hệ số an toàn chịu uốn và hệ số an toàn chịu xoắn.
Tương tự: Tmax = 0,0062 MN; Tmin =-0,0058MN; R =0,0386 m
- Hệ số an toàn của chốt khuỷu khi bị xoắn:
- Căn cứ vào đồ thị T S
= f (a )ta lập bảng để tính M a chi theo góc . M T T T R = ch ( S + i - - ' 1 )
Ø Từ đó ta xác định được các giá trị: Moment Mmax Mmin Khuỷu 1 0.000119626 -0.000111825 2 7.84257.10-5 -0.000153025 3 0.000244564 1.31136.10-5 4 0.000203364 -2.80865.10-5
Vì trục thứ 3 chịu lực lớn nhất nên ta tính bền cho trục thứ 3: τ "#$ max = l"#$ = •
.Ž = 5,555"'*?' = 10,62 MN/m2 ‰ ‰ ",2# . " #5*= U U τ 2##2? #5*= "&? min = l"&? = • .Ž = #. . = 0,57 MN/m2 ‰ ‰ ",2# . " #5*= U U τ "#$ , Y5, "&? a = ’ 6:6’ = #5 ?" *8 = 5,6 MN/m2 " "
- Hệ số an toàn khi xoắn: n’ = ’*G =& ")5 = 20 UY 6.’ ",*6.*,?6 Z # Y
- Hệ số an toàn của chốt khuỷu khi bị uốn: 109 110
Vì đường tâm dẫn dầu theo phương nằm trong mặt phẳng chứa khuỷu nên moment tác
dụng trên mặt phẳng chứa đường tâm dẫn dầu chính là: Mo = -MZ Với M Z l P a P c = + - z ' ' r 1 r 2 Lập bảng tính toán M a 5 z theo góc
ta tìm được: Momax = 43,78.10- MNm M 5 omin = 27,55.10- - MNm 5 43, 78.10- σ l5"#$ max = = 29,62 MN/m2 ‰ = P #,'8 . ) #5*= 5 -27,55.10- σ l5"&$ max = = -18,64 MN/m2 ‰ = P #,'8 . ) #5*= σ "#$ , Y , "&? a = u 6:6u = "> ?" #) ?' = 24,13 MN/m2 " " σ "#$ , : , "&? a = u 6Y6u = "> ?" #) ?' = 5,49 MN/m2 " "
- Hệ số an toàn khi uốn là: nu = u*G =& 2'5 = 5,83 UL6.u ",*6." , ' # 6 2 :65,".# , 5 5 6 * Z #YwL.u" L
- Hệ số an toàn tổng hợp: n = “<%Y<% ”*,)2%Y"5% L Y
v Hệ số an toàn của má khuỷu : -
Má khuỷu chịu ứng suất rất phức tạp: uốn, xoắn, kéo, nén
nhưng thành phần ứng suất uốn và xoắn ảnh hưởng nhiều nhất nên ta kể
đến thành phần này trong tính toán. Khi tính hệ số an toàn thường tính
toán đối vời tiết diện cắt nang má và tiếp tiến với một cổ trục khuỷu. -
Hệ số an toàn uốn của má khuỷu bên trái và bên phải: Ta xem
trục khuỷu hoàn toàn đối xứng nên chi cần kiểm tra một má khuỷu bên trái.
σ•M = (Z]M^ − Z]o< ). `MM ¶ IM + #¸ "`H ‰"&? ; 110 111
= ( 0,0213+0,0113).#.Ó 5,5"'> + # Ô ' H,HXXE.H,HGX% 5,5>> . ) 5,5#> D = 38,1 MN/m2 -
Do hệ số y nhỏ nên thường bỏ qua ảnh hưởng của ứng suất s
bình quân s . Do đó hệ số an toàn khi má khuỷu chịu uốn . m nu = u*G =& 2'5 = 5,64 UL6.u ",*6." , ' # 6 2 Z # L -
Hệ số an toàn của má khi chịu xoắn:
Mkmax = b•.Tmax. `MM = 0,0249.0,0062. # = 7,72.10-5 MNm `H "
Mkmin = b•.Tmin.`MM = 0,0249.(-0,0058).# = -7,2.10-5 MNm `H " W 5>>? 5#>% 3 k = ‹.I% = 5, .5, = 5,99.10-6 m ? ? -
Biên độ ứng suất xoắn: τ [,"#$ 8" #5*= [,"&? a = l 6:6l = (8, Y8,"). = 12,45 MN/m2 ".‰ 6 v ".*,> . > #5*D -
Hệ số an toàn khi chịu xoắn:
n’ = ’*G =& ")5 = 8,9 UY 6.’ ",*6.# , " ' 6 * Z # Y -
Hệ số an toàn tổng hợp: n = = 4,79 “<%Y<% ”*,?'%Y),>% L Y -
Hệ số an toàn của má khuỷu thường nằm trong khoảng 1.3 ÷ 2.5
Như vậy má khuỷu đủ bền và có độ cứng vững lớn.
v Kết luận : Sau khi kiểm tra bền trục khuỷu theo phương pháp phân đoạn và hệ số
an toàn, ta thấy điều kiện bền trục khuỷu đạt yêu cầu về độ bền và độ cứng vững. 111 112 CHƯƠNG VII
QUY TRÌNH THÁO, LẮP, ĐIỀU CHỈNH, BẢO DƯỠNG VÀ SỬA CHỮA CƠ
CẤU KT THANH TRUYỀN
7.1. Tháo lắp nhóm pit-tông, séc-măng, thanh truyền
7.1.1. Tháo nhóm piston, xéc măng và thanh truyền ra
khỏi động cơ
a) Tháo rời các cụm trên động cơ
1. Xả dầu và nước làm mát ra khỏi động cơ.
2. Tháo động cơ ra khỏi xe và đưa động cơ lên giá tháo lắp. 3. Tháo nắp máy. 4. Tháo đáy dầu.
5. Quay trục khuỷu cho piston của máy cần tháo xuống ĐCD.
6. Quan sát nhận biết các dấu trên piston và thanh truyền.
- Dấu thứ tự của piston và thanh truyền trên động cơ.
- Dấu chỉ chiều lắp piston và thanh truyền.
- Nếu trên piston không có dấu phải đánh dấu trước khi tháo.
7. Dùng dụng cụ chuyên dùng làm sạch gờ xi lanh.
8. Tháo bu lông thanh truyền, lấy nắp đầu to và nửa bạc ra.
9. Dùng cán búa hoặc chày đồng đẩy cụm piston, xéc măng,
thanh truyền ra khỏi động cơ.
- Dùng đoạn ống nhựa mềm bịt đầu bu lông thanh truyền để tránh làm xớc xi lanh.
- Không dùng búa để đóng vào thanh truyền hoặc bạc.
10. Gá bạc và nửa đầu to thanh truyền thành bộ, tránh nhầm lẫn.
11. Tiếp tục tháo các nhóm piston, xéc măng, thanh truyền còn lại. 112 113
b) Tháo rời các chi tiết của nhóm piston, xéc măng, thanh truyền
1. Kẹp thanh truyền lên ê tô.
- Phải đệm lót vào thân thanh truyền để tránh hhỏng
2. Dùng kìm chuyên dùng tháo các xéc măng khí ra.
- Tháo lần lượt các xéc măng từ phía trên xuống.
- Sắp xếp các xéc măng theo thứ tự.
- Không dùng tay để tháo xéc măng, tránh làm gãy xéc măng. 3. Tháo xéc măng dầu ra.
- Sắp xếp xéc măng thành từng bộ, không để lẫn các xéc măng.
4. Dùng kìm chuyên dùng tháo vòng hãm chốt pit-tông .
5. Gia nhiệt cho piston trong nước sôi đến 800C .
6. Kẹp pit-tông lên giá đỡ, dùng thanh đồng và búa nhựa tháo chốt pit-tông, tách rời pit- tông và thanh truyền ra.
7. Dùng chổi lông rửa sạch các chi tiết trong dung dịch làm sạch.
8. Sắp xếp các chi tiết theo thứ tự thành từng bộ, không để lẫn các chi tiết. 113 114
7.1.2. Lắp nhóm piston xéc măng, thanh truyền
a) Lắp pit-tông vào thanh truyền
1. Lắp vòng hãm mới vào một bên lỗ chốt pit-tông .
- Ướm vòng hãm vào rãnh trên piston sao cho đầu vòng hãm trùng với lỗ trên bệ chốt pit-tông .
- Dùng kìm chuyên dùng lắp vòng hãm vào rãnh, đảm bảo chắc chắn.
2. Hâm nóng pit-tông trong nước sôi đến 800 C.
3. Quan sát và quay piston cho dấu chỉ chiều lắp trùng với dấu của thanh truyền. 114 115
4. Dùng ngón tay đẩy chốt pit-tông vào bệ chốt.
5. Lắp vòng hãm thứ hai vào.
b) Lắp xéc măng vào piston 1. Lắp xéc măng dầu. - Lắp vòng đàn hồi. - Lắp hai vòng đỡ.
2. Lắp các xéc măng khí theo thứ tự từ dưới lên trên sao cho đúng chiều (mặt có dấu quay lên trên).
3. Nhỏ một ít dầu bôi trơn vào rãnh séc măng, không nhỏ quá nhiều, chia đều.
- Không để các miệng séc- măng thẳng hàng.
- Không để các miệng séc-măng trùng lỗ piston.
c) Lắp nhóm pit-tông, séc măng, thanh truyền vào động cơ 115 116
1. Lắp bạc lót vào thanh truyền và nắp đầu to thanh truyền.
2. Bôi một lớp dầu bôi trơn vào bề mặt bạc lót.
3. Lắp nửa bạc có lỗ dầu vào thân thanh truyền.
- Bạc phải nằm đúng vị trí, vấu hãm chống xoay phải tốt đảm bảo chắc chắn.
- Lỗ dầu phải trùng với lỗ trên thân thanh truyền.
4. Lắp đoạn ống mềm vào đầu bu lông thanh truyền để tránh làm xước cổ biên và xi lanh.
5. Bôi dầu bôi trơn vào xy lanh và cổ biên.
6. Dùng dụng cụ chuyên dùng để bó xéc măng cho ôm khít vào pit-tông .
7. Dùng chày gỗ hoặc cán búa gõ nhẹ vào đỉnh piston cho
cụm pit-tông, séc măng và thanh truyền vào xy lanh theo
đúng thứ tự từng máy.
Chú ý: Phải đúng chiều lắp quy định trên đỉnh pit-tông.
8. Quan sát dấu thứ tự và chiều lắp nắp đầu to thanh truyền, chọn đầu to và lắp vào thân
thanh truyền (dấu trên đầu to thanh truyền quay về phía đầu máy). 116 117
9. Lắp đai ốc bắt thanh truyền và siết chặt theo mô men quy định . -
Bôi một lớp dầu mỏng lên phần ren của bu lông. -
Dùng tay vặn đai ốc vào cho đến khi thấy chặt. -
Dùng khẩu siết ốc cho đều và đủ mô men quy định. Chú ý:
ü Phải siết ốc thanh truyền thành nhiều bước.
ü Siết đều hai đai ốc và đúng mô men.
ü Sau mỗi lần siết ốc cần quay thử trục khuỷu để kiểm tra tình trạng mối ghép.
ü Nếu trục khuỷu quay không trơn đều thì phải tháo ra kiểm tra và sử lý ngay.
ü Nếu có bu lông nào gãy hoặc biến dạng thì phải thay.
ü Đai ốc bị cháy ren cũng thay Chú ý: Phải siết ốc thanh truyền thành nhiều bước
ü Siết đều hai đai ốc và đúng mô men.
ü Sau mỗi lần siết ốc cần quay thử trục khuỷu để kiểm tra tình trạng mối ghép.
ü Nếu trục khuỷu quay không trơn đều thì phải tháo ra kiểm tra và sử lý ngay.
10. Dùng sơn đánh dấu cạnh phía trước của đai ốc.
11. Siết đai ốc thêm 900 nữa.
12. Kiểm tra sao cho các dấu sơn đều quay về một bên .
13. Kiểm tra sao cho trục khuỷu quay trơn.
Nếu trục khuỷu quay nặng hoặc không trơn đều thì phải tháo ra kiểm tra và xử lý.
7.2. Kiểm tra tình trạng kỹ thuật nhóm piston, séc-măng, thanh truyền
Ø Củng cố thao tác tháo lắp nhóm piston, séc măng, thanh truyền.
Ø Thực hiện được các công việc kiểm tra và đánh giá chính xác tình trạng kỹ thuật của các chi tiết.
Ø Sử dụng hợp lý các dụng cụ và thiết bị chuyên dùng. 117 118
Ø Tổ chức nơi làm việc gọn gàng, sạch sẽ, đảm bảo an toàn.
7.2.1. Kiểm tra kỹ thuật piston a) Làm sạch piston:
- Dùng dao cạo làm sạch muội than bám trên đỉnh piston.
- Dùng dụng cụ chuyên dùng làm sạch muội than trong rãnh lắp séc măng .
- Dùng bàn chải lông và chất tẩy rửa làm sạch toàn bộ piston rồi thổi sạch bằng khí nén.
b) Kiểm tra vết xước, nứt, vỡ piston:
- Quan sát trên toàn bộ piston để phát hiện các vết nứt, vỡ, xước, cháy
rỗ trên bề mặt dẫn hướng. -
Kiểm tra độ côn, độ ô van của piston:
- Kiểm tra độ côn : Dùng pan me đo ngoài đo đờng kính pit-tông trên
phần dẫn hướng vuông góc với đường tâm lỗ chốt ở 2 vị trí đầu và cuối
phần dẫn hướng. Hiệu số giữa 2 lần đo là độ côn của pit-tông. Nếu độ côn
lớn hơn mức cho phép phải thay pit-tông.
- Kiểm tra độ ô van : Dùng panme đo ngoài đo đường kính pit-tông ở 2
vị trí vuông góc với nhau trên cùng một tiết diện ngang của phần dẫn
hướng . Hiệu số giữa 2 lần đo là độ ô van của pit-tông . Độ ô van lớn hơn
quy định phải thay pit-tông. -
Kiểm tra khe hở giữa pit-tông và xi lanh:
Dùng căn lá để kiểm tra khe hở pit-tông và xy lanh: Ta đo pit-tông đã tháo hết sécmăng
vào trong xy lanh, dùng căn lá có chiều dày thích hợp (dài 200m rộng 13mm) vào khe hở
giữa pit-tông và xy lanh. Sau đó dùng lực kế móc vào căn lá và kéo căn lá ra.
- Với lực kéo từ 2 - 3 kg, nếu căn lá tuột ra khỏi pit-tông và xy lanh thì
chiều dầy của căn lá chính là khe hở giữa pit-tông và xy lanh, khe hở này
không được vượt quá 0,15 mm.(khe hở tiêu chuẩn là 0,03 - 0,08 mm). 118 119
- Dùng pan me đo đường kính piston theo hướng vuông góc với đường tâm lỗ chốt pit-tông.
- Dùng pam me đo trong hoặc đồng hồ so đo trong đo đường kính của
xi lanh theo hướng vuông góc với đường tâm trục khuỷu tại các vị trí A, B, C. -
Tính khe hở giữa pit-tông và xi lanh. -
Nếu khe hở lớn quá quy định thì phải thay piston hoặc doa xy lanh và thay pit-tông
theo kích thước sửa chữa.
7.2.2. Kiểm tra kỹ thuật chốt piston
a) Kiểm tra bề mặt chốt piston
- Dùng mắt quan sát bề mặt làm việc của chốt xem có
vết xước, cháy rỗ không. - Nếu có vết xước, rỗ, vết mòn
thì phải thay chốt piston. 119 120
- Kiểm tra khe hở giữa chốt piston và bạc lót:
- Dùng panme đo ngoài để đo đường kính chốt pit-tông .
- Dùng đồng hồ so đo trong để đo đường kính lỗ chốt pit-tông .
- Tính khe hở giữa chốt pit-tông và lỗ chốt
Khe hở tối đa cho phép: 0,015 mm
- Nếu khe hở lớn quá giới hạn cho phép thì
phải thay bạc đầu nhỏ thanh truyền
7.2.3. Kiểm tra kỹ thuật xéc măng a) Kiểm tra khe hở cạnh
1. Lắp xéc măng vào rãnh pit-tông và xoay tròn
séc măng trong rãnh pit-tông. séc măng phải xoay
nhẹ nhàng trong rãnh pit-tông.
2. Chọn căn lá có chiều dầy thích hợp đo khe hở giữa séc măng và rãnh pit-tông.
ü Khe hở tiêu chuẩn 0,03 – 0,08 mm
ü Khe hở tối đa cho phép 0,20 mm. -
Kiểm tra khe hở miệng séc măng: 120 121
3. Tháo séc măng cần kiểm tra ra khỏi pit-tông . Đặt séc
măng vào trong xy lanh, dùng pit-tông đẩy cho séc măng nằm
phẳng trong xy lanh đúng vị trí quy định.
4. Chọn căn lá có chiều dầy thích hợp đo miệng séc măng,
khe hở miệng séc măng chính là chiều dầy của căn lá đã chọn.
ü Khe hở tiêu chuẩn: séc măng khí 0,15 – 0,25 mm.
ü Séc măng dầu 0,13 – 0,38 mm.
ü Khe hở tối đa cho phép: séc măng khí 1,20 mm. ü Séc măng dầu 0,98 mm. - Kiểm tra khe hở lưng:
4. Dùng thước đo độ sâu để đo độ sâu của rãnh lắp séc măng, dùng pan me để đo chiều
rộng của séc măng, hiệu số kích thước đo được chính là khe hở lưng xéc măng. Khe hở quy định 0,20 - 0,35 mm. -
Kiểm tra độ tròn của séc măng (độ lọt ánh sáng):
5. Đặt séc măng vào trong xy lanh, dùng pit-tông đẩy xéc
măng cho phẳng, đặt 1 bóng đèn điện ở phía dưới xilanh, phía
trên xéc măng đặt 1 tấm bìa có đường kính nhỏ hơn đường
kính xi lanh nhưng lớn hơn đường kính trong của séc măng.
Quan sát mức độ lọt ánh sáng qua khe hở giữa lưng séc măng
và thành xy lanh. Một séc măng không được có quá 2 chỗ lọt ánh sáng, chiều dài mỗi cung
tròn không quá 300 tổng chiều dài của các cung lọt ánh sáng không quá 600 với khe hở
cung lọt là 0,03 mm. Nếu khe hở nhỏ hơn 0,015 mm thì chiều dài cung lọt ánh sáng cho
phép có thể lên tới 1200.
7.2.4. Kiểm tra kỹ thuật thanh truyền
a) Kiểm tra bu lông thanh truyền
1. Dùng mắt để quan sát xem bu-lông, đai ốc có bị chờn cháy ren hay không . 121 122
2. Dùng panme đo đường kính thân bu-lông.
3. Đường kính tối thiểu không nhỏ hơn đờng kính tiêu chuẩn 0,20 – 0,35 mm.
4. Nếu đường kính nhỏ hơn mức tối thiểu thì thay bu lông mới. -
Kiểm tra các lỗ dẫn dầu trên thân thanh truyền xem có bị tắc không:
5. Nếu các lỗ dẫn dầu bị tắc thì phải thông rửa sạch cặn bẩn rồi dùng không khí nén thổi sạch. -
Kiểm tra khe hở giữa bạc đầu to thanh truyền và cổ trục khuỷu:
6. Dùng phương pháp kẹp chì để kiểm tra khe hở bạc đầu to thanh truyền với cổ trục
khuỷu. Khe hở tiêu chuẩn từ 0,03 – 0,07 mm. Khe hở tối đa 0,11 – 0,16 mm. Nếu khe hở
lớn hơn mức tối đa thì thay bạc đầu to thanh truyền hoặc sửa chữa cổ trục thanh truyền và thay bạc mới.
- Kiểm tra độ cong của thanh truyền:
7. Dùng thiết bị chuyên dùng để kiểm tra độ cong của thanh truyền
8. Độ cong tối đa cho phép 0,05 trên chiều dài 100 mm
9. Nếu độ cong lớn quá mức tối đa thì phải thay thanh
truyền hoặc dùng dụng cụ chuyên dùng để nắn lại.
- Kiểm tra độ xoắn của thanh truyền:
10. Dùng dụng cụ chuyên dùng để kiểm tra độ xoắn (độ vặn).
11. Độ xoắn tối đa cho phép 0,15 trên chiều dài 100 mm.
12. Nếu độ xoắn lớn hơn mức tối đa cho phép thì phải thay thanh truyền.
7.3 Sửa chữa nhóm pit-tông, séc-măng, thanh truyền
Ø Nắm được một số thông của các chi tiết trong nhóm piston, séc măng, thanh truyền. 122 123
Ø Bảo dưỡng và sửa chữa được các hư hỏng của các chi tiết đảm bảo các yêu cầu kỹ thuật.
Ø Sử dụng thành thạo các thiết bị chuyên dùng vào công việc sửa chữa.
Ø Tổ chức nơi làm việc gọn gàng, sạch sẽ, đảm bảo an toàn.
7.3.1 Sửa chữa piston
- Khi piston hỏng hoặc doa xi lanh thì phải thay piston mới. Khi thay piston mới phải
thay cả bộ piston. Piston mới cần đạt các yêu cầu sau:
- Phải chọn đúng loại piston của nhà sản xuất, không dùng piston khác loại có kích thước tương đương.
- Trọng lượng các piston phải bằng nhau. Với những piston có đường kính từ 100 mm
trở lên, trọng lượng giữa các piston cho phép sai lệch không quá 15 gam, piston có
đường kính nhỏ hơn 100 mm sai lệch cho phép không quá 9 gam.
- Đối với các động cơ ô tô hiện nay không cho phép thay thế từng piston riêng lẻ:
• Đối với pit-tông có vết nứt nhỏ không ảnh hởng tới sự làm việc bình thờng
của động cơ thì có thể cho phép khoan chặn hai đầu vết nứt một bằng một lỗ nhỏ để
tránh vết nứt phát triển.
• Trên bề mặt làm việc của piston có vết xước nhẹ thì dùng giấy ráp mịn và dầu
đánh bóng rồi dùng lại.
7.3.2. Sửa chữa chốt píttông
Trong quá trình làm việc chốt pit-tông chủ yếu bị mòn do chịu tải trọng xung kích và
điều kiện bôi trơn kém. Khi chốt pit-tông bị mòn sẽ gây ra
tiếng gõ khi động cơ làm việc. Khi đó cần phải thay chốt pit-
tông mới và bạc đầu nhỏ thanh truyền theo kích thớc sửa
chữa tăng lớn quy định:0,05; 0,075; 0,10; 0,125 mm ...
Các yêu cầu khi thay chốt piston:
- Chốt pit-tông phải đúng loại và đúng kích thớc sửa chữa quy định. 123 124
- Độ côn và độ ô van phải nhỏ hơn 0,003 mm.
- Trọng lượng của các chốt pit-tông không đợc chênh lệch quá 8 gam.
ü Thay chốt pit-tông và bạc đầu nhỏ thanh truyền.
ü Tháo bạc đầu nhỏ thanh truyền.
1. Tháo bạc đầu nhỏ thanh truyền ra bằng dụng cụ chuyên dùng.
2. Chọn chốt pit-tông và bạc mới cho phù hợp.
3. Lắp bạc mới vào đầu nhỏ thanh truyền bằng dụng cụ chuyên dùng.
Chú ý: Lỗ dầu trên bạc phải trùng với lỗ dầu trên thanh truyền.
4. Doa lỗ bạc đầu nhỏ thanh truyền và kiểm tra độ khít của bạc với chốt pit-tông.
- Doa và mài bóng lỗ bạc đầu nhỏ thanh truyền và kiểm tra khe hở giữa bạc và chốt pit- tông. - Kiểm tra độ khít của
bạc với chốt pit-tông ở nhiệt độ bình thường bôi dầu máy lên chốt và dùng
tay đẩy chốt vào lỗ bạc đầu nhỏ thanh truyền. 124 125
7.3.3. Sửa chữa séc măng -
Séc măng là chi tiết nhanh
mòn do điều kiện làm việc chịu nhiệt độ
cao, bôi trơn kém. Khi séc măng bị mòn,
gãy phải thay séc măng mới. Khi chọn
lắp và thay séc măng mới phải căn cứ
vào kích thước sửa chữa của xy lanh để
chọn séc măng cho phù hợp. Séc măng
mới phải đảm bảo các yêu cầu sau: -
Séc măng phải đúng kích thước sửa chữa và đúng chủng loại. -
Khe hở miệng từ 0,15 - 0,25 mm. Nếu khe hở miệng không
đúng phải chọn lại séc măng.
Không dũa miệng xéc măng.
- Khe hở cạnh 0,015 – 0,02 mm. Nếu khe hở cạnh quá nhỏ thì bôi một ít bột rà xupáp
lên tấm kính rồi mài mỏng séc măng đến khi khe hở cạnh đạt tiêu chuẩn.
- Khe hở lưng 0,20 mm. Nếu khe hở lưng không đúng phải chọn séc măng khác.
- Độ lọt ánh sáng đúng quy định, độ lọt ánh sáng không đạt yêu cầu thì chọn séc măng khác.
- Các séc măng phải lắp đúng chiều các mép vát.
7.3.4. Sửa chữa thanh truyền 125 126
1. Thông rửa các lỗ phun dầu, đường
dầu trên thân thanh truyền.
2. Các bu-lông, đai ốc bị chờn cháy ren thì phải thay mới.
3. Sửa chữa thanh truyền bị cong: -
Khi thanh truyền bị cong thì
thay thanh truyền mới hoặc có thể nắn
thanh truyền trên thiết bị chuyên dùng. Nếu không có thiết bị chuyên dùng
thì có thể nắn thanh truyền trên ê tô. Tuy nhiên, sau một thời gian sử dụng
thanh truyền có thể bị cong trở lại do còn ứng suất.
4. Sửa chữa thanh truyền bị xoắn -
Khi thanh truyền bị xoắn thì phải thay thanh truyền. -
Có thể nắn thanh truyền bằng thiết bị chuyên dùng nhng chỉ sử
dụng tạm thời vì sau một thời gian sử dụng thanh truyền lại bị xoắn trở lại do ứng suất gây nên.
7.4. Tháo lắp nhóm trục khuỷu, bánh đà
Ø Củng cố kiến thức về nhiệm vụ, cấu tạo của thanh truyền.
Ø Hiểu đợc trình tự và thực hiện được công việc tháo lắp trục khuỷu - bánh đà đúng
qui trình đảm bảo yêu cầu kỹ thuật.
Ø Hiểu đợc các đặc điểm cấu tạo của các loại trục khuỷu.
Ø Tổ chức nơi làm việc gọn gàng, sạch sẽ, khoa học đảm bảo an toàn cho ngời và thiết bị.
7.4.1. Nhiệm vụ, cấu tạo của trục khuỷu a) Nhiệm vụ:
- Trục khuỷu là chi tiết rất quan trọng của động cơ. Nó tiếp nhận lực từ
pit-tông truyền qua chốt pit-tông và thanh truyền, biến lực đó thành mô 126 127
men quay rồi truyền ra ngoài qua bánh đà. Đồng thời nó tiếp nhận lực
quán tính truyền ngược lại pit-tông ở các kỳ nạp, nén và xả. -
Cấu tạo của trục khuỷu:
- Trong quá trình làm việc trục khuỷu chịu tải trọng lớn và thay đổi theo
chu kỳ với ứng suất khá lớn và chịu mài mòn. Do trục khuỷu có hình dạng
khá phức tạp nên nó thường được đúc bằng thép hoặc bằng gang có chất
lợng cao (gang cầu). Trục khuỷu gồm các bộ phận sau: •
Đầu trục khuỷu: Dùng để lắp các chi tiết của cơ cấu dẫn
động bánh răng, puly. Đầu trục khuỷu thường có lỗ ren lắp ốc khởi
động động cơ bằng tay quay hoặc bu lông hãm. •
Cổ trục khuỷu: được đặt vào các ổ đỡ trong thân máy,
nó đỡ toàn bộ trục khuỷu. Giữa cổ trục và thân máy có bạc lót. •
Cổ thanh truyền (cổ biên): là vị trí lắp ghép với đầu to
thanh truyền. Giữa cổ thanh truyền và đầu to thanh truyền có bạc
lót. Ở động cơ nhiều xy lanh, các cổ thanh truyền đợc bố trí lệch 127 128
nhau một góc nhất định tuỳ theo số xy lanh và kiểu động cơ: động
cơ thẳng hàng, động cơ chữ V. Góc này gọi là góc lệch khuỷu.
- Trong cổ trục và cổ thanh truyền có khoan các lỗ dẫn dầu bôi trơn. ở
một số trục khuỷu, cổ thanh truyền đợc làm rỗng để giảm nhẹ trọng lợng
của cổ thanh truyền đồng thời lọc một phần cặn bẩn trong dầu bôi trơn,
hai đầu lỗ có nút ren bịt kín •
Má khuỷu : Là bộ phận nối giữa cổ trục và cổ thanh truyền . •
Đối trọng : dùng để cân bằng lực quán tính ly tâm của
cổ thanh truyền và đầu to thanh truyền gây nên đảm bảo cho động
cơ không bị rung khi làm việc. •
Đuôi trục khuỷu : Có mặt bích lắp bánh đà và để lắp phớt
chắn dầu. Trong đuôi trục khuỷu có lỗ lắp vòng bi đỡ trục sơ cấp của hộp số.
7.4.2. Nhiệm vụ và cấu tạo của bánh đà a) Nhiệm vụ
- Bánh đà có tác dụng bảo đảm sự làm việc
đều đặn của động cơ, làm cho pit-tông chuyển
động qua các điểm chết. Trong quá trình cháy
giãn nở sinh công, bánh đà tích trữ năng lợng
để cung cấp cho các quá trình nạp, nén và thải,
do đó động cơ quay được đều hơn. Bánh đà còn là nơi lắp bộ phận truyền
công suất của động cơ ra ngoài. b) Cấu tạo: 128 129 - Bánh đà là một đĩa kim loại tròn, có khối
lợng lớn, được cân bằng động chính xác. Trên vành ngoài bánh đà có
lắp vành răng để khởi
động động cơ. Bánh đà được lắp vào mặt bích ở đuôi trục khuỷu bằng các
bu lông. Vật liệu chế tạo bánh đà thường là gang xám, gang biến tính. Đối
với động cơ có số vòng quay cao và truyền mô men lớn thì bánh đà được
đúc hoặc giập bằng thép ít cácbon. Vành răng khởi động được chế tạo
bằng thép và qua nhiệt luyện. Trên một số bánh đà có dấu xác định ĐCT của piston máy số 1.
7.4.3. Tháo lắp trục khuỷu - bánh đà a) Trình tự tháo 1. Xả nớc làm mát. 2. Xả dầu bôi trơn.
3. Tháo các bộ phận liên quan giữa động cơ và ô tô: Bơm diesel, bầu lọc diesel, máy
khởi động, máy phát điện, ống nước làm mát, ống hút, ống xả.....
4. Tháo bầu lọc dầu bôi trơn. 5. Tháo bu lông chân máy.
6. Đưa động cơ ra ngoài, đặt trên giá đỡ động cơ.
7. Tháo hộp số, ly hợp ra khỏi động cơ. 8. Tháo bánh đà. 129 130
- Nới lỏng đều các bu lông
- Tháo rời các bu lông, để lại hai bu lông đối xứng
- Đỡ bánh đà và tháo hai bu lông còn lại, lấy bánh đà ra khỏi động cơ.
- Tháo tấm vách sau của động cơ.
Chú ý: Nới đều bu-lông và đúng thứ tự hình vẽ .
9. Tháo nắp máy, đáy dầu.
10. Tháo phao lọc dầu và đường dầu ngang
11. Tháo cụm pit-tông, thanh truyền, xéc măng ra khỏi động cơ.
12. Lật ngửa của động cơ.
13.Tháo nắp gối đỡ trục khuỷu.
- Kiểm tra dấu trên nắp gối đỡ. Nắp gối đỡ phải có dấu chỉ thứ tự và chiều lắp. Nếu
không có dấu phải đánh dấu trớc khi tháo
- Nới lỏng dần các bu lông bắt gối đỡ theo ba giai đoạn và đúng trình tự.
- Nắm chặt bu lông gối đỡ, lắc nắp gối đỡ và lấy gối đỡ cùng nửa bạc dưới ra
- Lấy căn dọc trục ra (chỉ cổ trục ở giữa).
Chú ý: Giữ bạc nằm trong nắp gối đỡ, không để rơi bạc ra ngoài
Sắp xếp các nắp gối đỡ theo thứ tự
13. Nhấc trục khuỷu ra ngoài và đặt lên giá đỡ
Chú ý: Giữ nửa bạc trên nằm trong thân máy, không để bạc rơi ra ngoài 130 131
14. Gá nắp gối đỡ vào thân máy để tránh bạc không bị rơi ra.
b) Lắp trục khuỷu, bánh đà
1. Lắp bạc lót cổ trục vào thân máy và nắp gối đỡ.
Chú ý: Lắp nửa bạc có lỗ dẫn dầu vào thân máy.
2. Lắp nửa căn dọc trục vào thân máy, chú ý chiều có rãnh dầu quay ra ngoài.
3. Đặt trục khuỷu vào thân máy.
4. Lắp nửa căn dọc trục vào nắp gối đỡ sao cho các rãnh dầu quay ra ngoài.
5. Lắp các nắp gối đỡ trục khuỷu.
- Quan sát dấu thứ tự và chiều lắp nắp gối đỡ.
- Lắp các nắp gối đỡ vào sâo cho đúng thứ tự và chiều.
6. Bắt các bu-lông giữ gối đỡ trục. 131 132
- Bôi một lớp dầu bôi trơn lên bề mặt ren của bu-lông.
- Vặn các bu-lông vào bằng tay cho đến khi nặng tay.
- Dùng khẩu vặn chặt các bu-lông vào thành ba bước theo thứ tự quy định.
- Dùng sơn đánh dấu cạnh trước của bu-lông.
- Lần lợt siết thêm các bu lông vào 900 nữa sao cho các dấu sơn quay về cùng một phía.
- Quay thử trục để kiểm tra. Trục phải quay được nhẹ nhàng không bị kẹt hoặc nặng.
7. Kiểm tra khe hở dọc trục của trục khuỷu. Khe hở phải
trong giới hạn quy định.
- Khe hở quy định: 0,02 – 0,22 mm.
- Khe hở tối đa cho phép: 0,30 mm.
- Nếu khe hở lớn quá giới hạn tối đa phải thay căn dọc trục khác.
8. Lắp phớt chắn dầu phía sau..
- Bôi một lớp keo làm kín lên mặt giá đỡ phớt chắn dầu.
- Bắt chặt giá đỡ phớt chắn dầu.
9. Lắp giá đỡ máy phát điện. 132 133
10. Lắp đường ống dẫn nớc. 11. Lắp bầu lọc diesel.
12. Lắp cảm biến đo áp suất dầu.
- Làm sạch bề mặt ren của cảm biến.
- Bôi một lớp keo lên bề mặt ren.
- Lắp cảm biến vào thân máy .
13. Lắp nút xả nước làm mát động cơ.
- Làm sạch bề mặt ren của nút xả nớc.
- Bôi một lớp keo lên bề mặt ren.
- Lắp nút xả nớc vào thân máy. 14. Lắp bầu lọc dầu. - Thay vòng đệm mới.
- Bôi một lớp keo làm kín vào đệm.
- Lắp bầu lọc cùng giá đỡ vào thân máy.
15. Lắp cụm pit-tông, thanh truyền, séc măng vào động cơ.
16. Lắp phao lọc dầu và đường dầu ngang.
17. Lắp nắp máy, đáy dầu. 18. Lắp tấm vách sau. 19. Lắp bánh đà.
- Bôi một lớp keo lên hai hoặc ba vòng ren của bu-lông .
- Đa bánh đà vào đuôi trục khuỷu sao cho đúng vị trí định vị.
- Bắt chặt các bu lông bánh đà. 20. Lắp hộp số 21. Lắp chân máy 133 134
7.5. Kiểm tra - Sửa chữa nhóm trục khuỷu, bánh đà
Ø Biết được những hư hỏng của trục khuỷu, bánh đà và nguyên nhân gây ra.
Ø Thực hiện được các công việc kiểm tra và đánh giá đúng tình trạng kỹ thuật của trục khuỷu, bánh đà.
Ø Nắm đợc các phương pháp sửa chữa trục khuỷu, bánh đà. Tính toán đợc kích thước
sửa chữa trục khuỷu theo các kích thớc thực tế.
Ø Thực hiện công việc chính xác, tổ chức nơi làm việc gọn gàng, sạch sẽ, đảm bảo an toàn.
7.5.1. Những hư hỏng của trục khuỷu, bánh đà và nguyên nhân gây ra:
- Những hư hỏng thường gặp trong quá trình làm việc của trục khuỷu
là: cổ trục bị mòn, bị rạn nứt; trục bị cong hoặc xoắn; bề mặt cổ trục bị
xước, rỗ; trục khuỷu bị gãy; rãnh then, lỗ ren, lỗ bu lông bắt bánh đà bị biến dạng….
a) Cổ trục, cổ thanh truyền bị mòn
- Khi động cơ làm việc, do tác dụng của áp lực khí cháy trong xy lanh
làm cho bề mặt cổ trục và cổ thanh truyền bị mòn. Cổ trục và cổ thanh
truyền thường bị mòn không đều. Khi trục khuỷu quay, lực ly tâm do đầu
to thanh truyền sinh ra làm cho thanh truyền có xu hướng rời khỏi cổ thanh
truyền và thường xuyên ép vào bề mặt phía trong (gần đường tâm trục
khuỷu). Do tác dụng lâu dài của lực ly tâm nên bề mặt phía trong cổ trục
thanh truyền bị mòn nhiều hơn phía ngoài. Tương tự như vậy, ở cổ trục
chính thì mặt gần kề cổ trục thanh truyền bị mòn nhiều.
- Mặt khác, dầu bôi trơn dới tác dụng của lực ly tâm làm cho các tạp
chất cứng có trọng lượng lớn văng ra tập trung về một đầu cổ trục gây
mòn côn cho cổ trục thanh truyền
- Cổ trục thanh truyền thường mòn nhanh hơn cổ chính, lượng mòn của
cổ trục thanh truyền thường gấp 2 lần lượng mòn ở cổ chính. Trong các 134 135
cổ chính, lượng mòn giữa các cổ cũng không đều nhau, cổ chính gần bánh
đà mòn nhiều hơn các cổ khác.
- Sự mài mòn cổ trục và cổ thanh truyền làm bán kính quay của trục
khuỷu tăng lên dẫn đến làm tăng tỷ số nén, các chi tiết trong nhóm pit-
tông, thanh truyền, séc măng bị mòn nhanh và ảnh hưởng không tốt đến
quá trình làm việc của động cơ. Đồng thời khe hở lắp ghép giữa các chi
tiết tăng lên làm điều kiện bôi trơn kém đi, áp lực dầu bôi trơn giảm, sự
mài mòn các chi tiết tăng lên.
b) Trục khuỷu bị cong và xoắn
Nguyên nhân gây ra biến dạng cong và xoắn trục khuỷu chủ yếu do:
- Khe hở của gối đỡ và cổ trục quá lớn, trong khi làm việc có sự va vấp
trong quá trình làm việc chịu mô men xoắn quá lớn, gối đỡ bị cháy làm
trục khuỷu quay khó khăn.
- Khe hở gối đỡ và cổ trục quá nhỏ hoặc mô men xiết ốc cổ trục không
đều, xiết ốc không đúng trình tự quy định.
- Động cơ tăng ga đột ngột làm trục khuỷu chịu ứng suất quá lớn gây
biến dạng đột ngột làm trục khuỷu bị xoắn hoặc cong. Ngoài ra sự làm
việc của động cơ không ổn định, trục khuỷu chịu lực không đều, các vị trí
của các chi tiết trong cơ cấu khuỷu trục thanh truyền không đúng cũng có
thể làm cho trục khuỷu bị cong, xoắn.
c) Trục khuỷu bị rạn nứt, gãy
- Trong quá trình làm việc, trục khuỷu có thể bị rạn nứt. Vết nứt thường
xảy ra ở phần tiếp giáp giữa cổ trục, cổ thanh truyền và má khuỷu (vai
trục). Có nhiều nguyên nhân làm trục khuỷu bị rạn nứt .
- Bán kính góc lợn giữa má khuỷu với cổ trục, cổ thanh truyền không
đúng gây ra ứng suất tập trung . 135 136
- Khe hở giữa gối đỡ và cổ trục quá lớn gây ra va đập theo chu kỳ tạo
nên ứng suất thay đổi gây ra rạn nứt. Vết nứt xuất hiện sẽ phát triển nhanh và gây gãy trục khuỷu.
d) Bề mặt của cổ trục, cổ thanh truyền, gối đỡ bị xước, cháy
- Ngoài hư hỏng do mòn, trục khuỷu thường hư hỏng do cổ trục, cổ
thanh truyền bị xước, cháy rỗ. Nguyên nhân gây xước, cháy rỗ do:
- Điều kiện và chất lượng dầu bôi trơn kém, trong dầu có nhiều tạp chất
như bụi bẩn, có lẫn hạt mài hoặc bị rò rỉ nước vào hệ thống bôi trơn, đường
dầu bôi trơn bị tắc…
- Khe hở giữa bạc và cổ trục, cổ thanh truyền quá nhỏ, trong quá trình
làm việc sinh nhiệt làm cháy rỗ bề mặt cổ trục.
- Lắp ráp không đúng, lỗ dầu trên bạc không trùng với đường dầu trên
thân máy làm cho dầu bôi trơn không vào bề mặt cổ trục, cổ thanh truyền.
e) Vành răng khởi động bị mòn, sứt mẻ
- Vành răng khởi động thường bị mòn, bị sứt mẻ các răng do làm việc
lâu ngày, do va đập giữa các răng trong quá trình khởi động động cơ. Khi
vành răng khởi động bị mòn, sứt mẻ làm cho quá trình vào khớp của các
bánh răng gặp khó khăn, có tiếng kêu khi khởi động.
f) Bề mặt làm việc của bánh đà bị mòn, xước, cháy
- Bề mặt tiếp xúc với ly hợp thường bị mòn, xước, cháy do ly hợp trượt
trong quá trình đóng mở ly hợp hoặc do đĩa ma sát quá mòn, đĩa ép bị vỡ
hay lò xo ép bị hỏng…..
- Khi bề mặt làm việc của bánh đà bị mòn, xước, cháy sẽ làm giảm ma
sát giữa đĩa ma sát và bánh đà làm tăng sự trượt của ly hợp.
g) Bánh đà bị rạn nứt 136 137
- Trong quá trình làm việc, bánh đà có thể bị nứt, vỡ do quá tải hoặc do
có khuyết tật khi chế tạo
7.5.2. Kiểm tra, sửa chữa trục khuỷu
a) Kiểm tra trục khuỷu bị xước, cháy rỗ, rạn nứt: v Kiểm tra:
- Quan sát toàn bộ trục khuỷu phát hiện các
vết xước, cháy rỗ, rạn nứt. v Sửa chữa:
- Nếu trục khuỷu có vết rạn nứt thì phải thay trục khuỷu mới.
- Nếu trên bề mặt trục khuỷu có vết cháy rỗ, vết xước nhẹ thì dùng vải
ráp mịn bôi một lớp dầu bôi trơn hoặc dùng đá dầu mài bóng cổ trục và cổ
thanh truyền Nếu có vết cháy rỗ, xước sâu thì phải mài trục khuỷu trên
máy mài chuyên dùng có cơ cấu dịch tâm.
b) Kiểm tra độ mòn cổ trục và cổ thanh truyền:
- Dùng pan me đo ngoài để kiểm tra độ mòn côn, mòn ô van của cổ trục và cổ thanh truyền
1. Kiểm tra độ mòn ô van: •
Đo kích thước cổ trục và cổ thanh
truyền ở hai vị trí vuông góc nhau trên cùng
một mặt cắt ngang . Độ ô van của cổ trục và
cổ thanh truyền được xác định bằng hiệu số của hai lần đo.
Chú ý: Không đo sát vào lỗ dầu bôi trơn
Độ ô van cho phép: 0,05 mm
2. Kiểm tra độ mòn côn: 137 138 •
Đo kích thước cổ trục và cổ thanh truyền ở hai vị trí trên cùng
một mặt cắt dọc (phía trong và ngoài của cổ thanh truyền là vị trí mòn
nhiều nhất). Độ mòn côn là hiệu số giữa hai lần đo
Chú ý: Vị trí đo cách má khuỷu 8 – 10 mm, không đo sát má khuỷu
Độ mòn côn cho phép: 0,05 mm. 3. Sửa chữa: •
Nếu độ ô van và độ côn vượt quá giới hạn cho phép phải sửa
chữa trục khuỷu bằng cách mài cổ trục, cổ thanh truyền theo kích thước
sửa chữa quy định (theo cốt sửa chữa). Mỗi cốt sửa chữa, đờng kính
cổ trục và cổ thanh truyền giảm 0,25 mm. •
Khi mài trục khuỷu tiến hành trên thiết bị chuyên dùng là máy
mài có cơ cấu dịch tâm. Trước khi mài phải xác định bán khính góc
lợn và sửa đá theo bán kính góc lượn đó. Sau khi mài cổ trục và cổ
thanh truyền cần đánh bóng để đạt độ bóng theo yêu cầu. Độ bóng phải đạt Ä9 - Ä10 •
Sau khi mài cổ trục và cổ thanh truyền phải thay các bạc lót
theo kích thớc sửa chữa tương ứng và cạo rà bạc để đảm bảo sự tiếp xúc tốt.
§ Diện tích tiếp xúc sau khi cạo bạc: 75%
§ Vết tếp xúc phân bố đều trên toàn bộ bề mặt bạc
Chú ý: Tuỳ vào độ mòn và tình trạng kỹ thuật thực tế của cổ trục và cổ thanh truyền mà
sửa chữa toàn bộ hoặc chỉ sửa chữa cổ thanh truyền hay cổ trục nhưng không sửa chữa 138 139
riêng lẻ từng cổ trục hay từng cổ thanh truyền. Tất cả các cổ trục hoặc cổ thanh truyền phải
sửa chữa theo cùng kích thớc để đảm bảo sự cân bằng động -
Kiểm tra độ cong, độ xoắn của trục khuỷu: 1. Kiểm tra độ cong của trục khuỷu: • Đặt khuỷu lên hai
gối đỡ (hoặc lắp lên mũi
chống tâm), cho mũi tiếp
xúc của đồng hồ so tiếp
xúc với cổ trục ở giữa,
quay trục khuỷu đi một vòng đồng thời quan sát sự dao động của kim
đồng hồ trong một phạm vi nào đó. Lấy trị số đó trừ đi độ ô van của
cổ trục ta sẽ được độ cong của trục khuỷu. Độ cong cho phép: 0,03 – 0,05 mm 2. Kiểm tra độ xoắn của trục khuỷu: • Lắp trục khuỷu
lên giá đỡ, cho cổ thanh
truyền nằm ở vị trí nằm ngang, dùng thước đo
chiều cao đo khoảng cách
từ các cổ trục thanh truyền có cùng đường tâm đến mặt bàn máy, độ
chênh lệch của hai khoảng cách đo được là độ xoắn của trục khuỷu.
Độ xoắn cho phép < 0,10mm. •
Nếu độ cong, độ xoắn của trục khuỷu vượt quá giới hạn cho
phép thì phải sửa chữa. 3. Sửa chữa: 139 140 •
Nếu trục khuỷu xoắn quá giới hạn cho phép thì phải thay trục khuỷu mới. •
Nếu trục khuỷu bị cong thì nắn trục khuỷu trên máy ép thuỷ lực
20 tấn theo phương pháp nắn nguội: •
Đặt trục khuỷu lên hai giá chữ V, xoay đúng chiều cong của
trục khuỷu rồi cố định trục khuỷu lại. Tác dụng một lực vào cổ trục ở
giữa theo chiều ngược với chiều cong của trục khuỷu. Để tránh làm
hỏng cổ trục cần đặt tấm đồng đệm lót vào cổ trục. Phía dưới cổ trục
đặt đồng hồ so để theo dõi độ biến dạng của trục khuỷu và khống chế
lực tác dụng. Nếu trục khuỷu bị cong nhiều quá thì phải tiến hành nắn
nhiều lần để tránh làm trục khuỷu biến dạng quá nhiều gây nứt gãy trục. -
Kiểm tra bán kính quay của trục khuỷu:
- Dùng thước đo chiều cao đo khoảng cách giữa vị trí cao nhất và thấp
nhất của cổ trục thanh truyền (khoảng cách a), sau đó chia đôi khoảng
cách đo được chính là bán kính quay của trục khuỷu (1/2a). Bán kính quay
ở các cổ trục thanh truyền không được chênh lệch quá 0,15 mm. -
Kiểm tra độ đảo của mặt bích lắp bánh đà:
- Đưa trục khuỷu lên giá đỡ
chữ V hoặc hai mũi chống tâm
của máy tiện, cho đầu tiếp xúc
của đồng hồ so tiếp xúc với mép
ngoài của mặt bích, quay trục
khuỷu một vòng đồng thời quan
sát sự dao động của kim đồng
hồ. Khoảng dao động của kim đồng hồ so chính là độ đảo của mặt bích
lắp bánh đà. Độ vênh cho phép < 0,10 mm. 140 141 -
Kiểm tra khe hở giữa cổ trục, cổ thanh truyền và bạc lót:
- Dùng phương pháp kẹp chì để kiểm trau.
Chú ý: Khi kiểm tra phải xiết ốc đúng mô men quy định.
Không được quay trục khuỷu trong quá trình kiểm tra. -
Kiểm tra khe hở hớng trục của trục khuỷu:
- Lắp trục khuỷu vào thân máy, xiết ốc đủ lực.
- Dùng đòn bẩy đẩy trục về phía sau.
- Đặt căn lá vào khe hở giữa căn dọc trục phía trớc và má khuỷu. Chiều
dày của căn lá chính là khe hở dọc trục của trục khuỷu. Khe hở tối đa cho phép: 0,30 mm.
- Nếu khe hở lớn quá quy định thì phải thay căn dọc trục có chiều dày lớn hơn.
7.5.3. Kiểm tra, sửa chữa bánh đà
a. Kiểm tra bánh đà bị mòn, xước, cháy bề mặt tiếp xúc với đĩa ma sát
- Quan sát trên toàn bộ bề mặt bánh đà để phát hiện vết mòn, vết xước,
cháy hoặc các vết nứt vỡ.
- Nếu bánh đà bị nứt vỡ thì thay bánh đà mới.
- Nếu vành răng khởi động quá mòn thì phải thay vành răng mới. Nếu
trên vành răng có quá 3 răng bị sứt mẻ cũng phải thay vành răng mới.
- Khi bề mặt làm việc của bánh đà bị mòn, xước, cháy thì phải mài lại
trên máy mài phẳng hoặc đưa lên máy tiện để tiện láng hết vết mòn, xớc, cháy.
- Sau khi mài, bề mặt làm việc phải đạt độ bóng Ä6 - Ä7
b. Kiểm tra độ đảo của bánh đà 141 142
- Dùng thước phẳng và căn lá để kiểm tra độ không phẳng của bề mặt làm việc.
- Dùng mũi chống tâm và đồng hồ so để kiểm tra độ đảo của bánh đà:
- Lắp bánh đà vào trục khuỷu rồi kiểm tra độ đảo của bánh đà giống như
phần kiểm tra độ đảo của mặt bích lắp bánh đà.
Độ đảo cho phép < 0,05 mm.
Chú ý: Phải kiểm tra và sửa chữa độ đảo của mặt bích lắp bánh đà trước khikiểm tra độ đảo của bánh đà.
c. Kiểm tra các lỗ ren trên bánh đà
- Quan sát các lỗ ren trên bánh đà, nếu các lỗ ren bị hư hỏng thì phải sửa
chữa bằng cách khoan rỗng lỗ, dùng tarô làm lại ren mới rồi thay các bu
lông tương ứng với lỗ ren mới.
- Sau khi sửa chữa bánh đà, độ không cân bằng động của bánh đà không lớn hơn 25 gam.
- Bề mặt làm việc của bánh đà phải vuông góc với đường tâm của trục
khuỷu, độ không vuông góc < 0,15 mm.
- Không thay bánh đà của động cơ này sang động cơ khác khi chưa kiểm tra cân bằng động. KẾT LUẬN
Môn học kết cấu tính toán động cơ đốt trong của ô tô giúp em hiểu rõ hơn nguyên lí hoạt
đông, cấu tạo, … của dộng cơ như thế nào. Cũng như qua bài đồ án tính toán động cơ đốt
trong này cũng cho em biết rỗ về các thông số trạng thái, kích thước, thông số kỹ thuật của
các bộ phận trong động cơ. Và giới hạn làm việc của các bộ phân, khi nào thì ta cần bảo
hành hoặc thay thế, tải trọng và trọng tải giới hạn của động cơ nó như thế nào… 142 143
Trên thế giới nói chung và ở Việt Nam nói chung ngành ô tô đang phát triển mạnh do
nhu cầu di chuyển của con người nó càng tăng lên. Vì thế nên động cơ ô tô, ô tô giữ vai trò
rất quan trọng trong nền phát triển của đất nước…
Em xin chân thành cảm ơn! 143