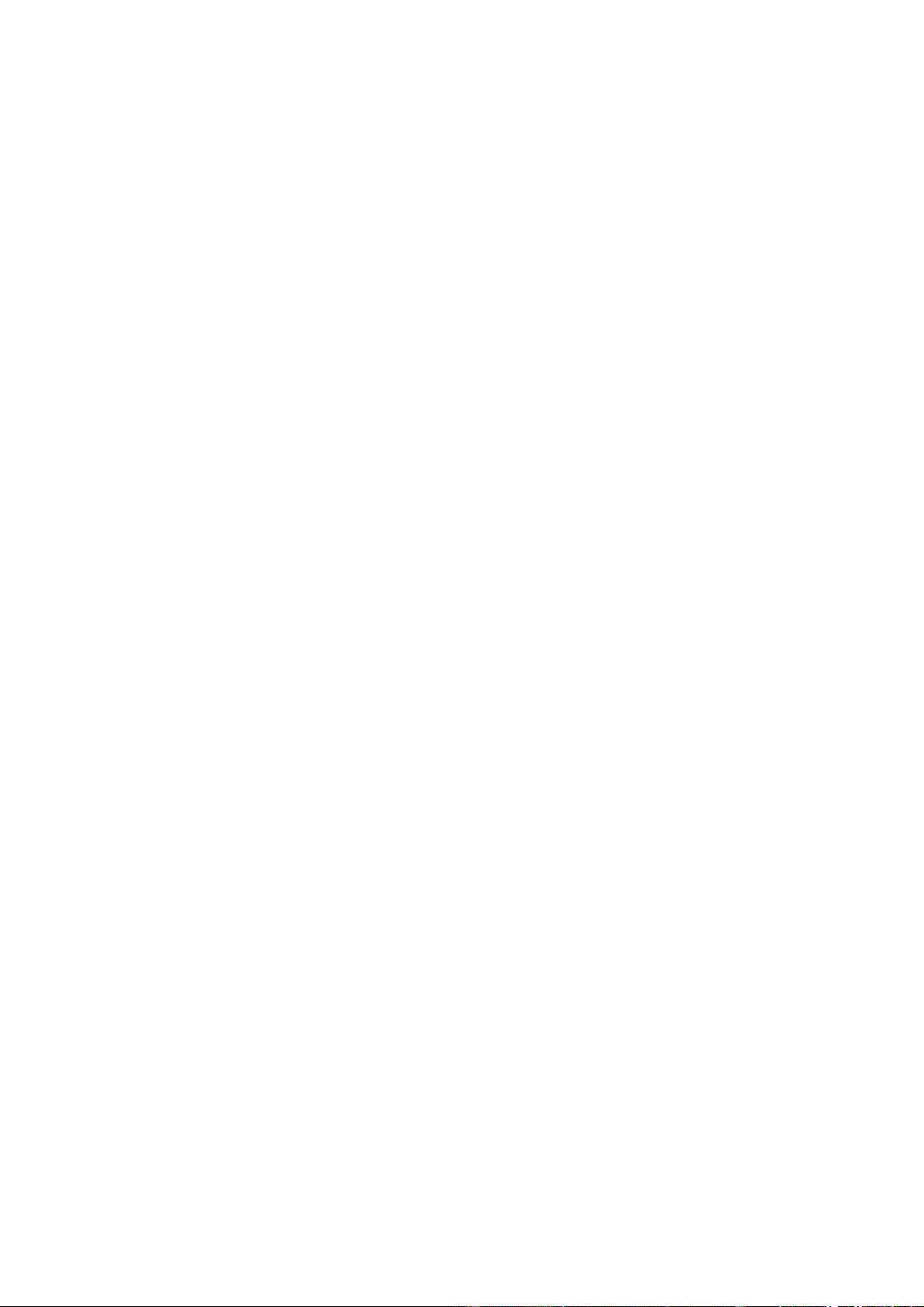
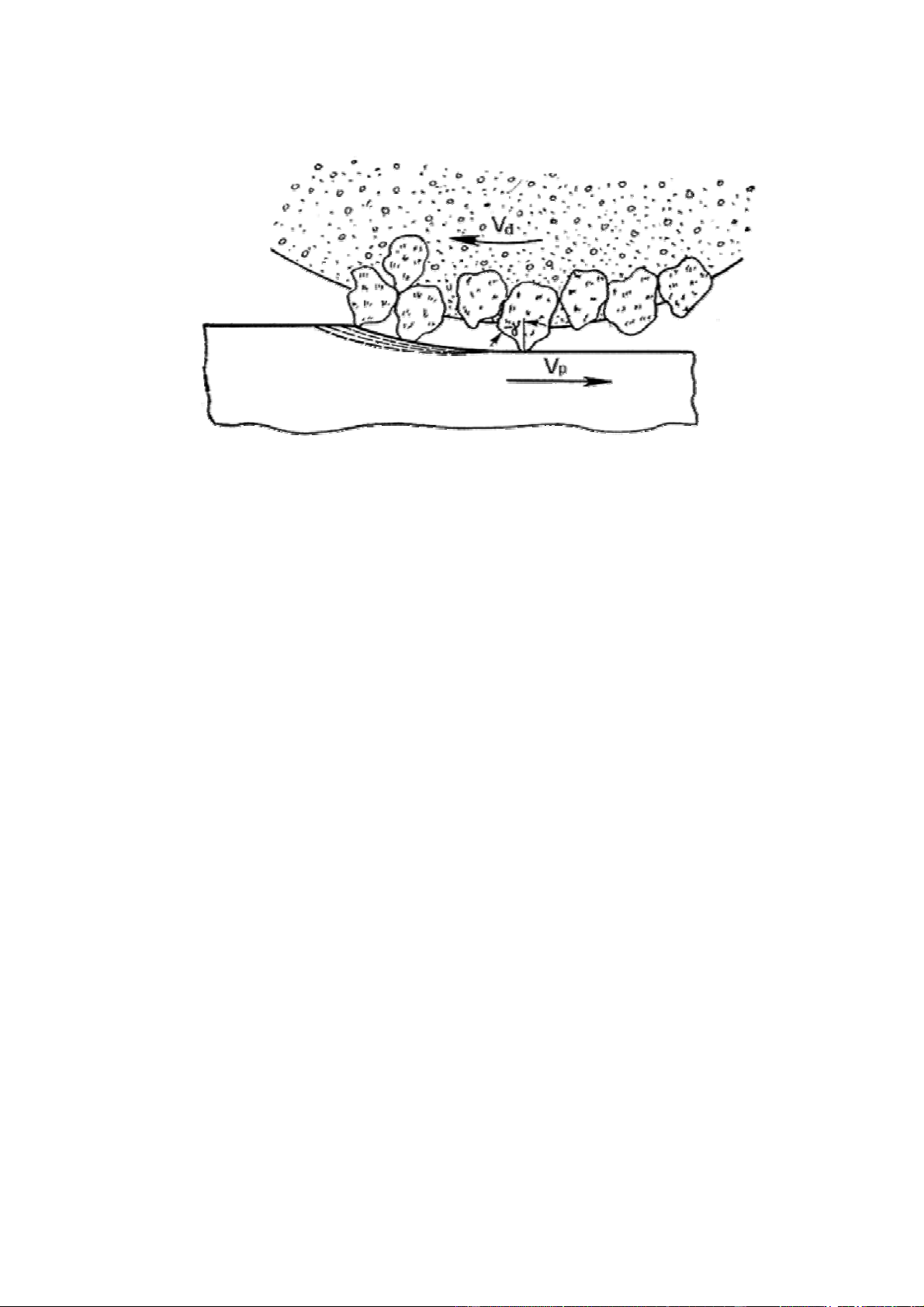
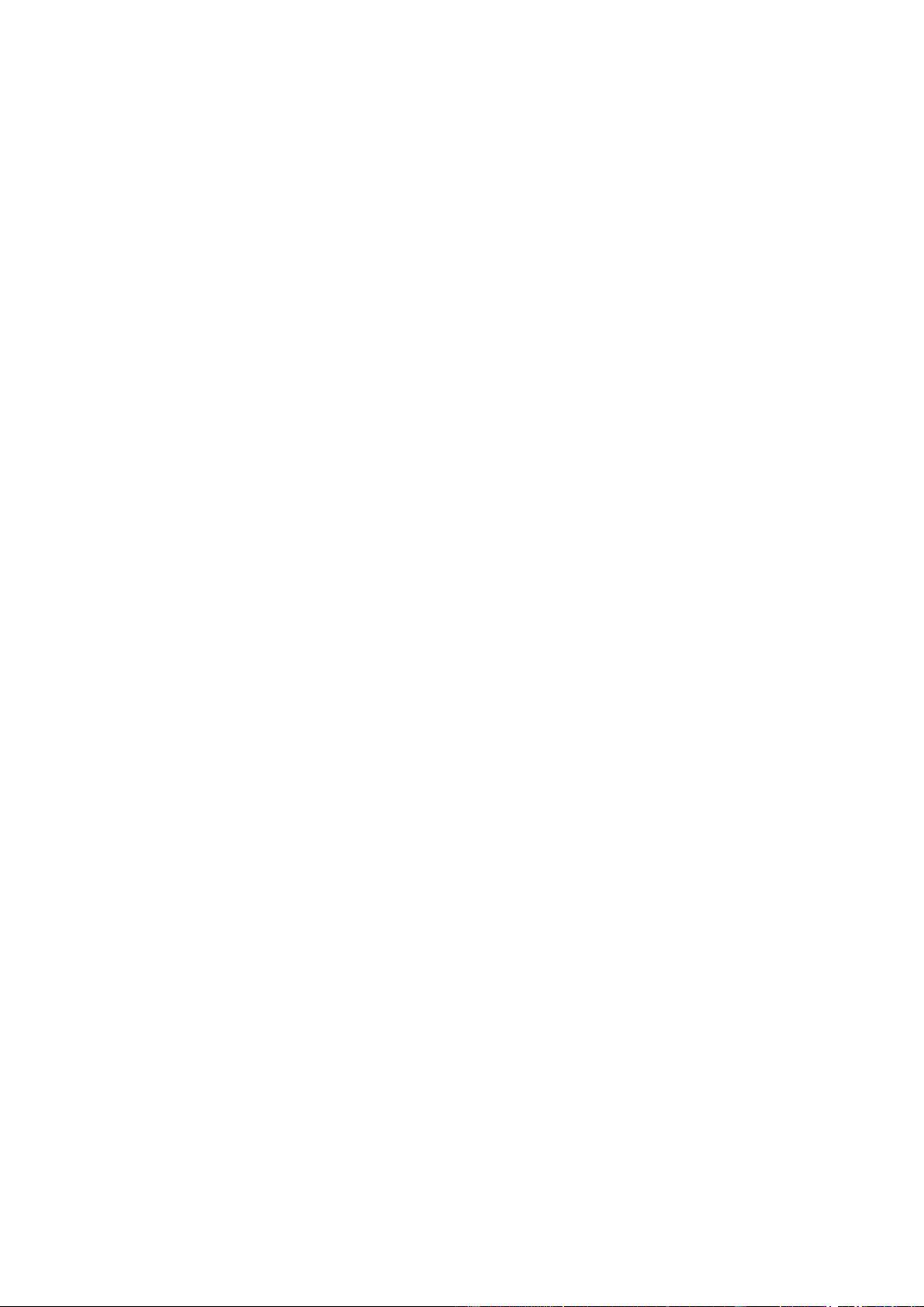
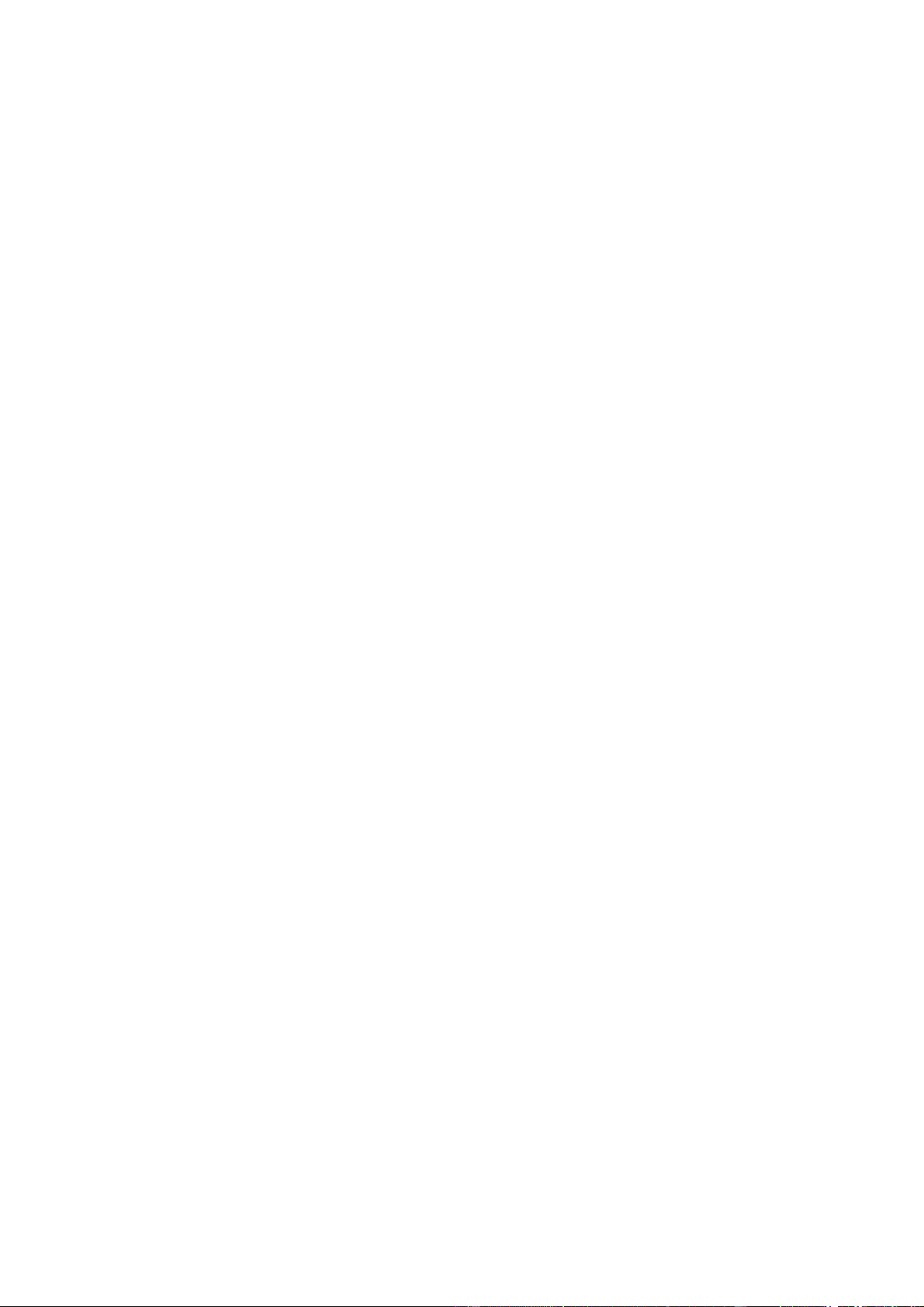
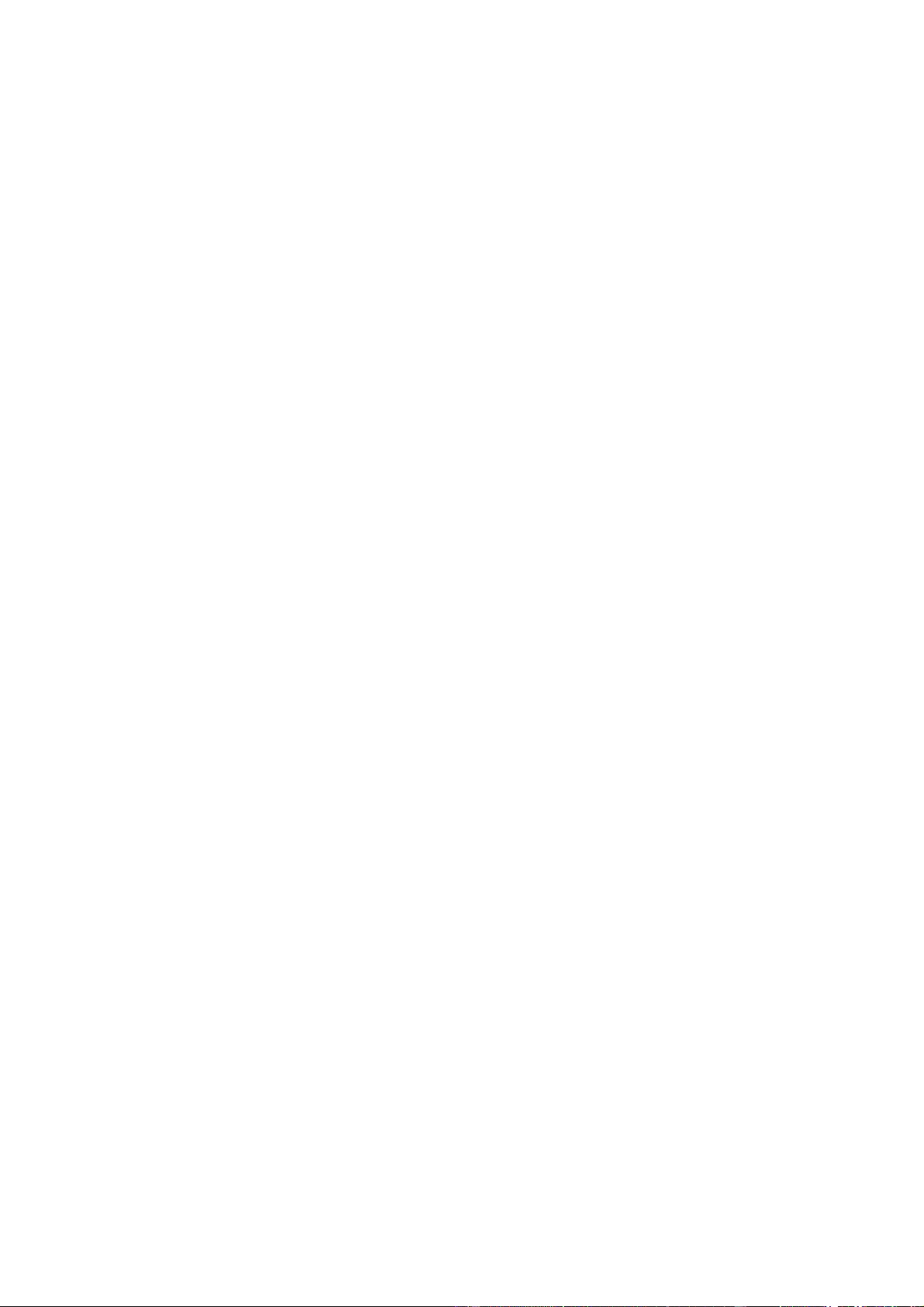
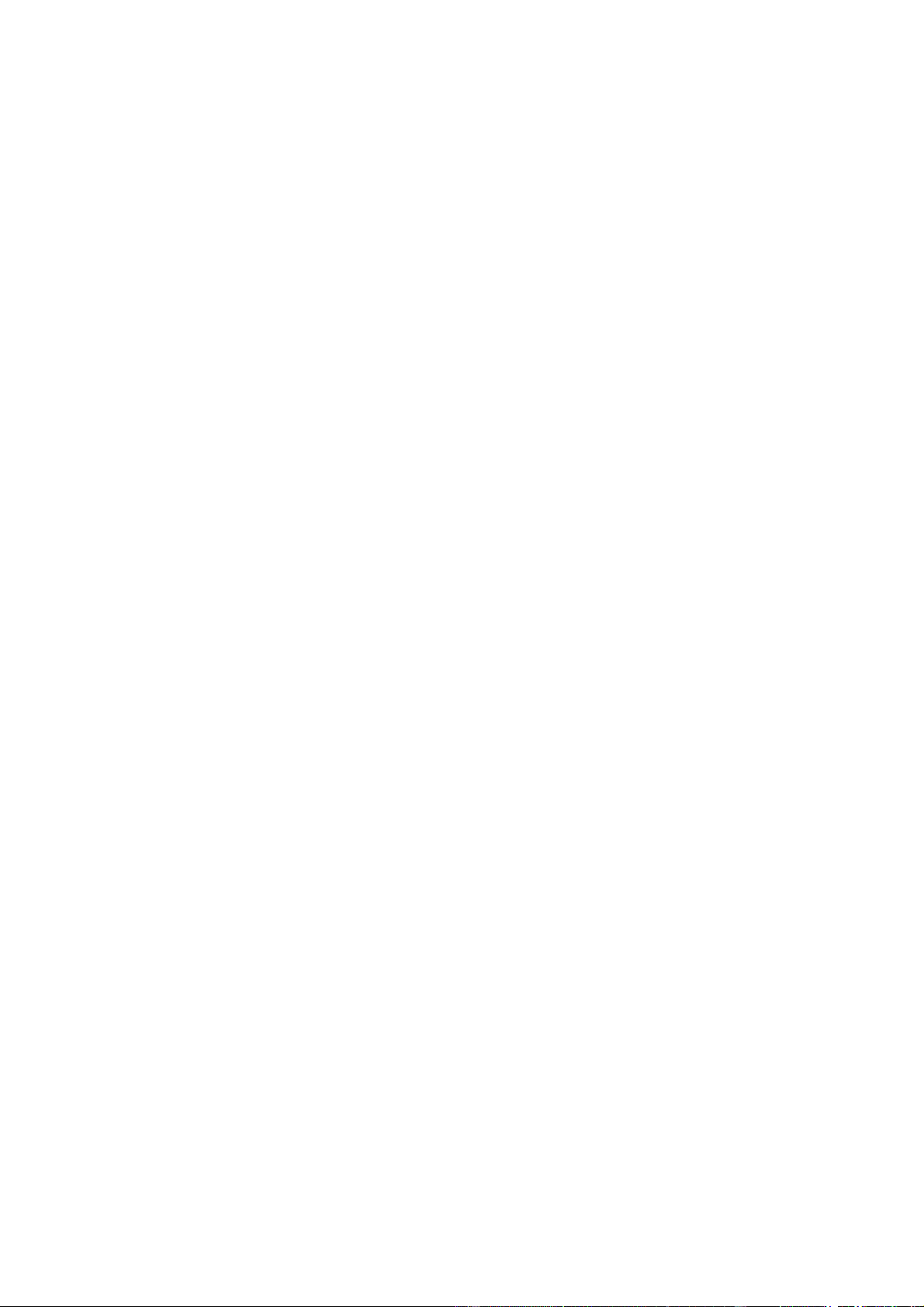

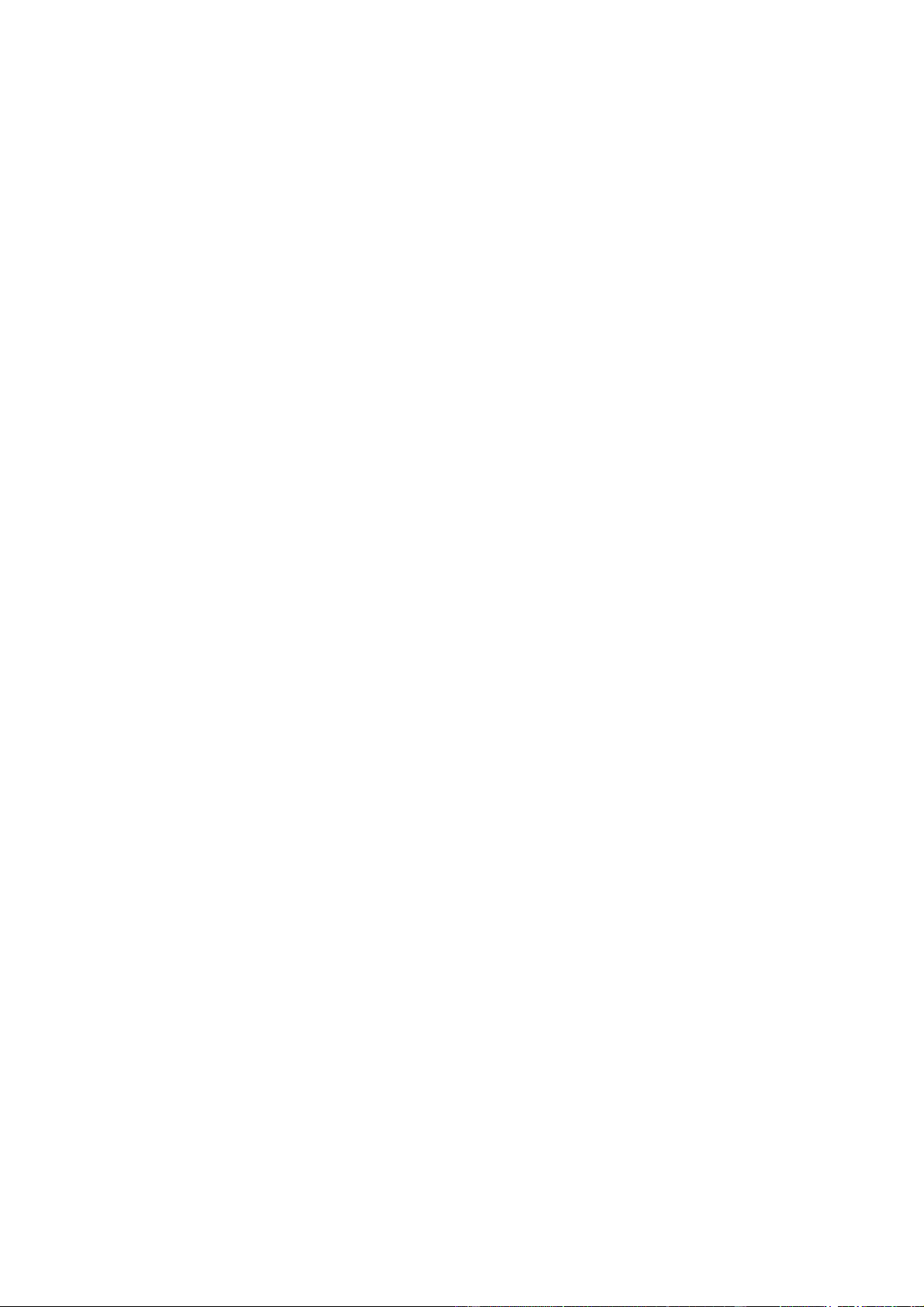
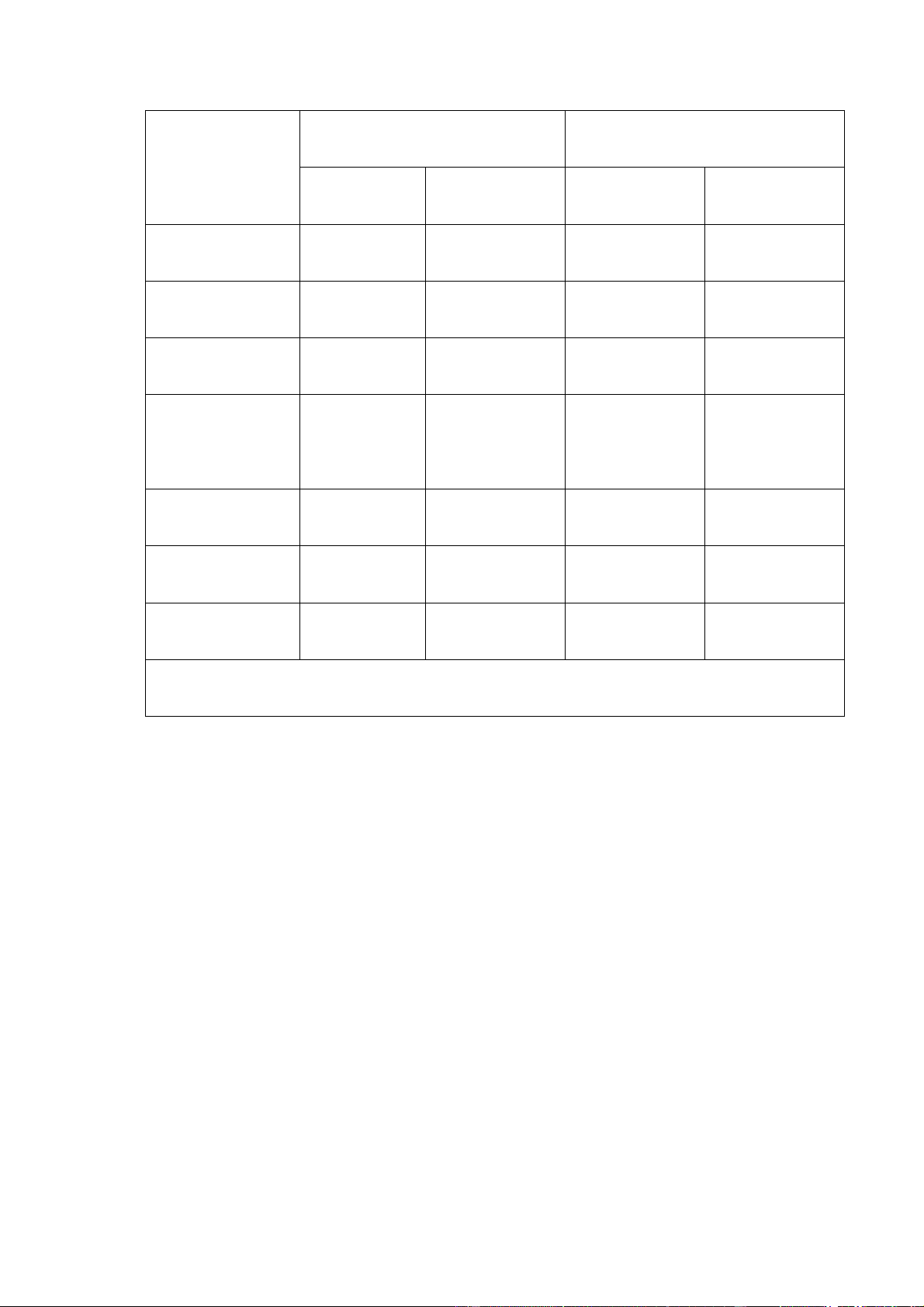
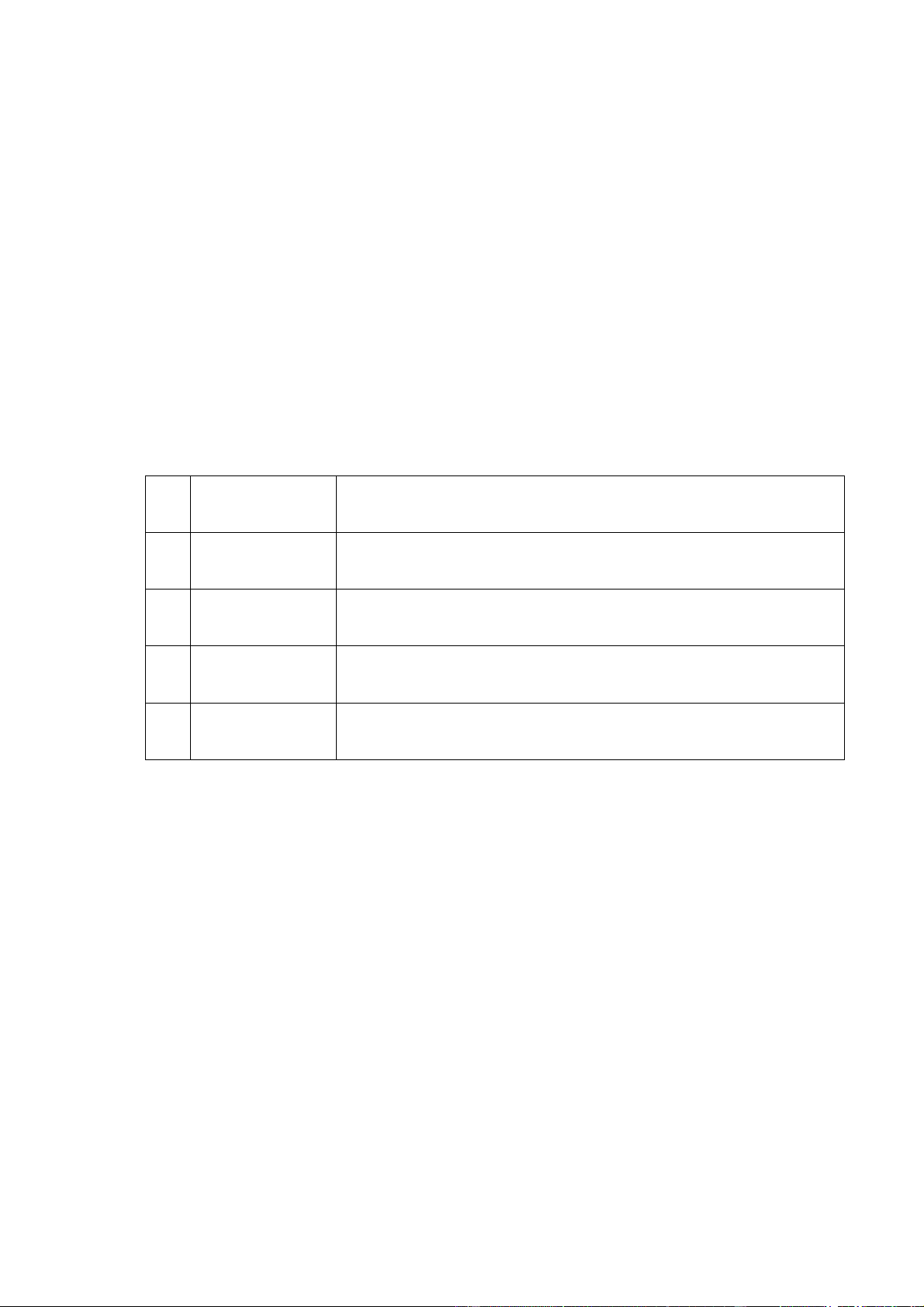
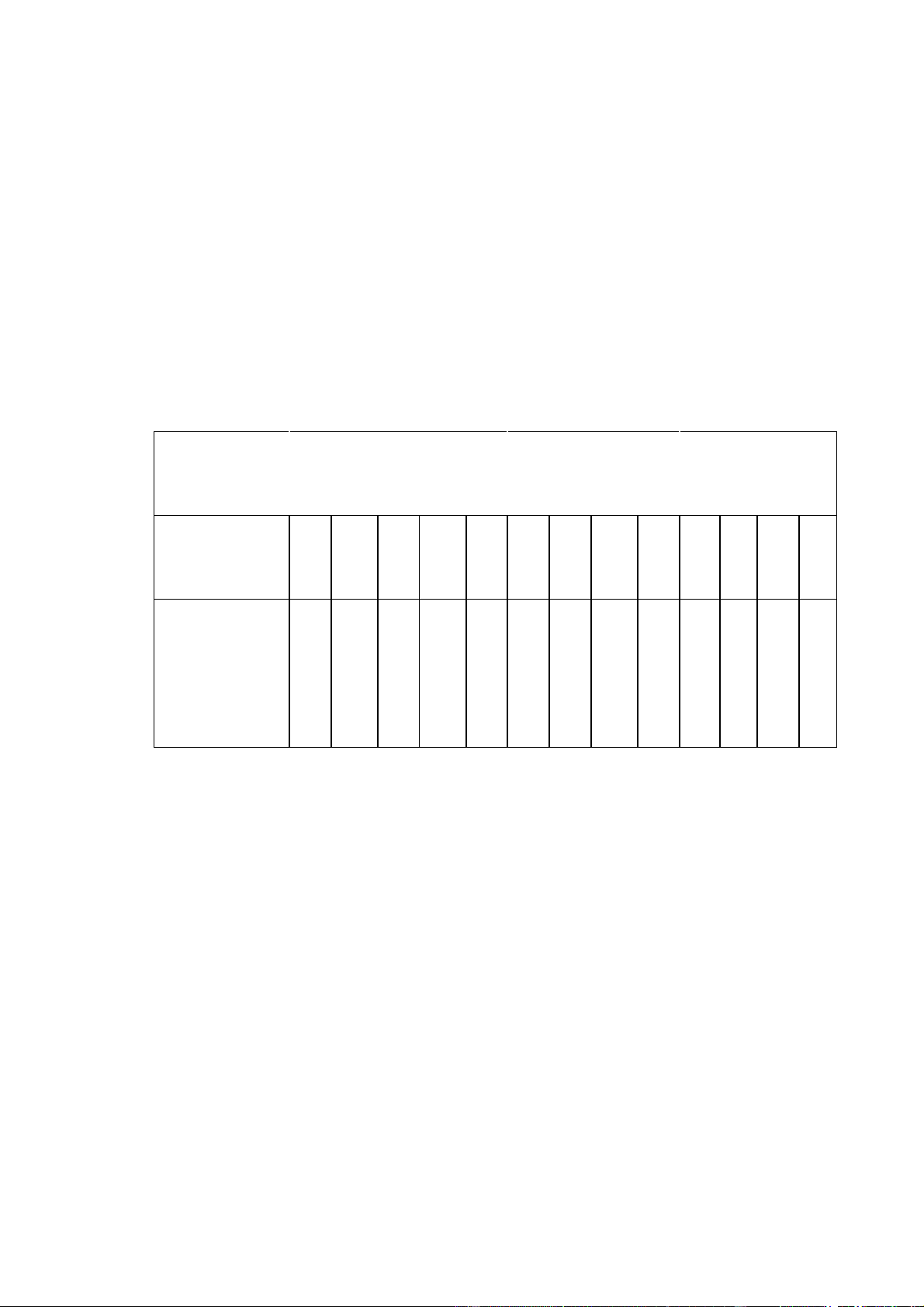
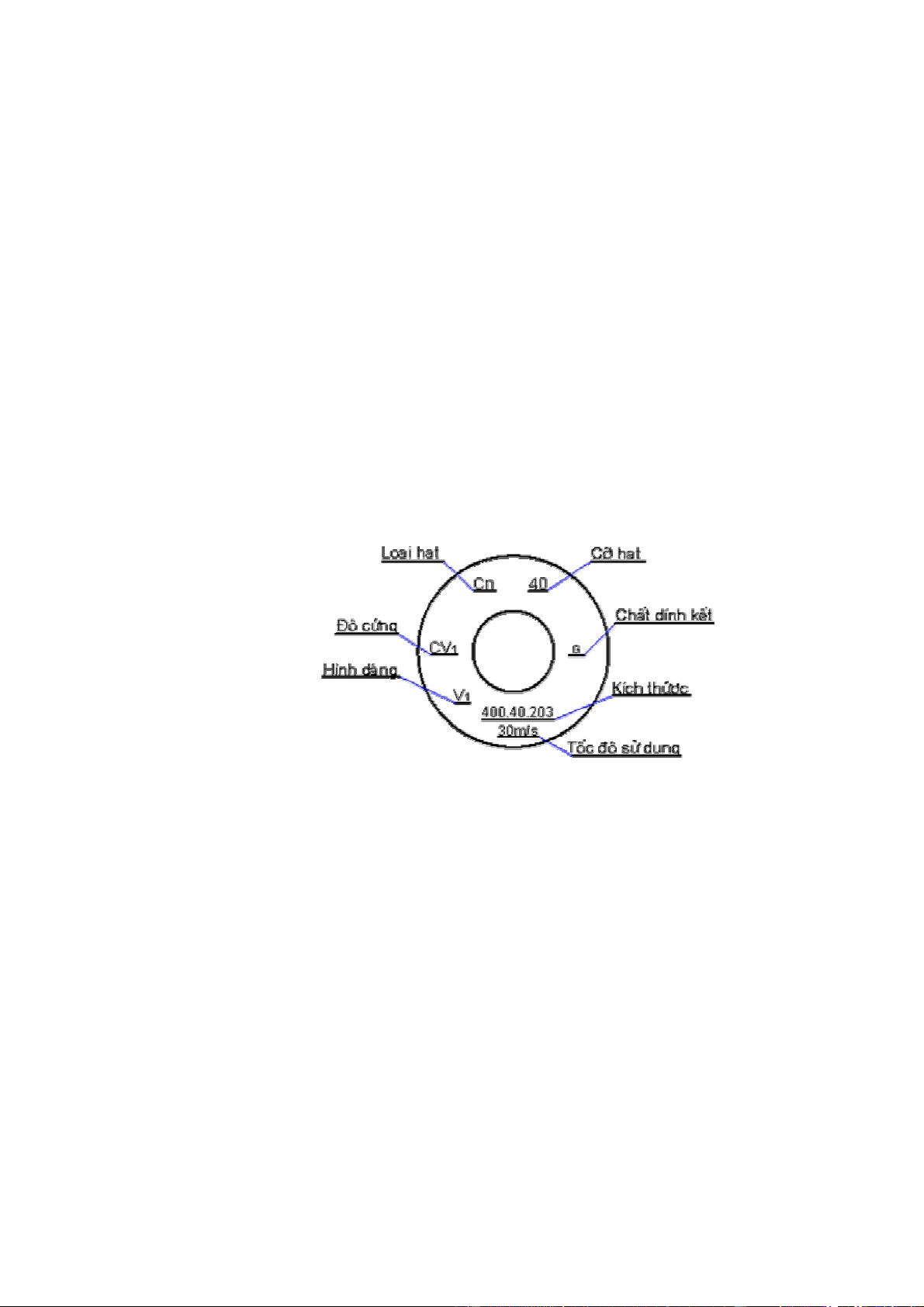
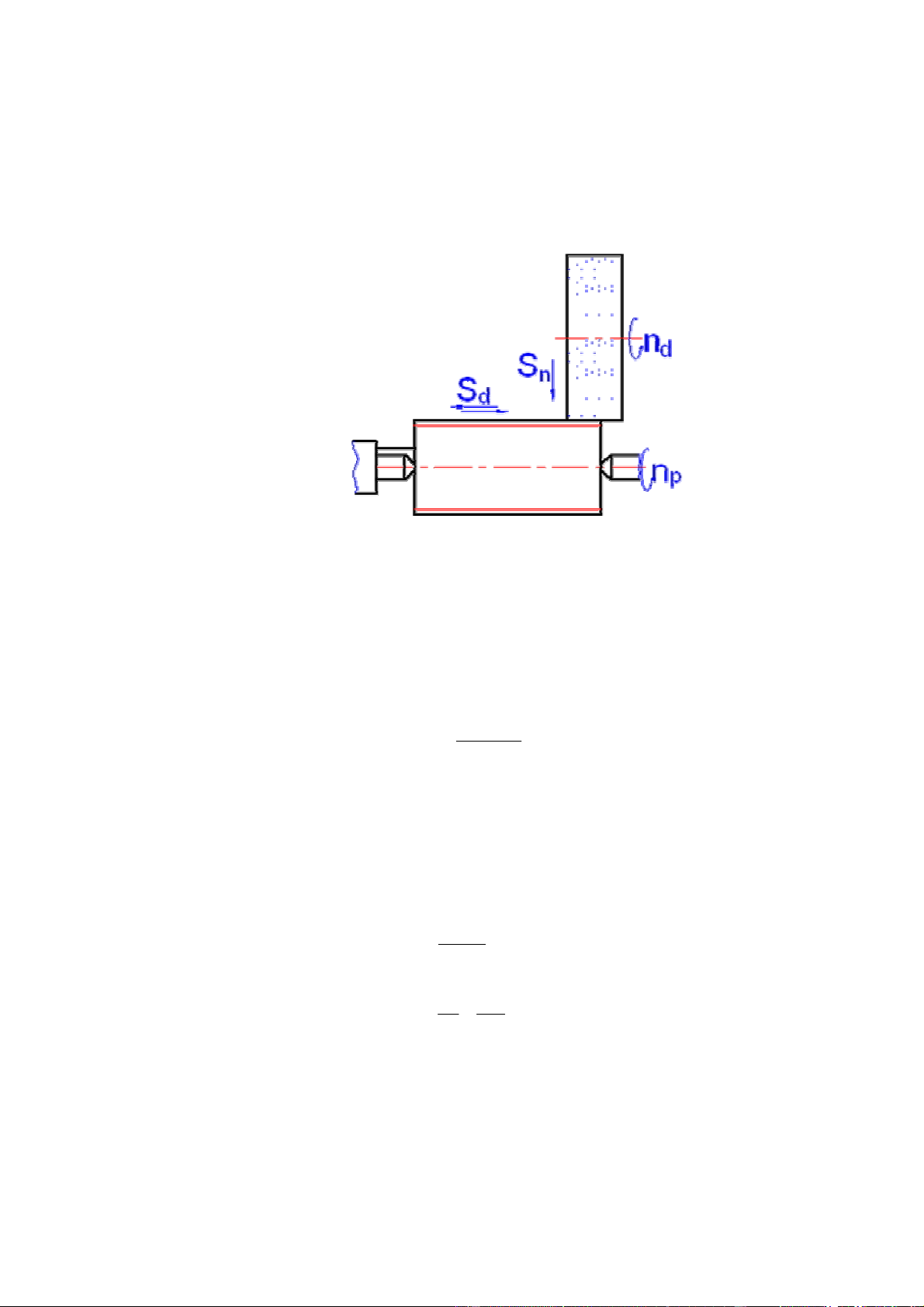
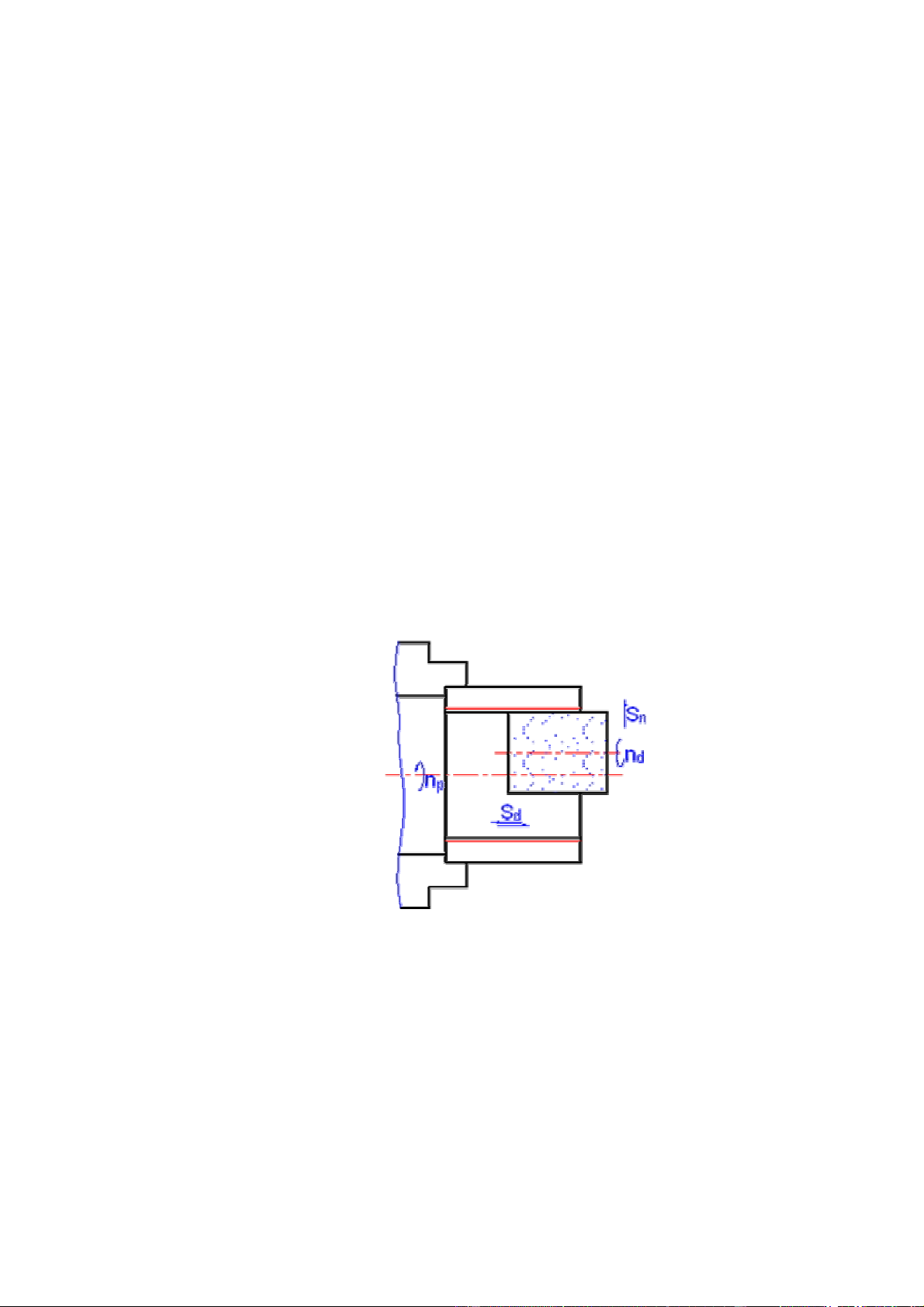
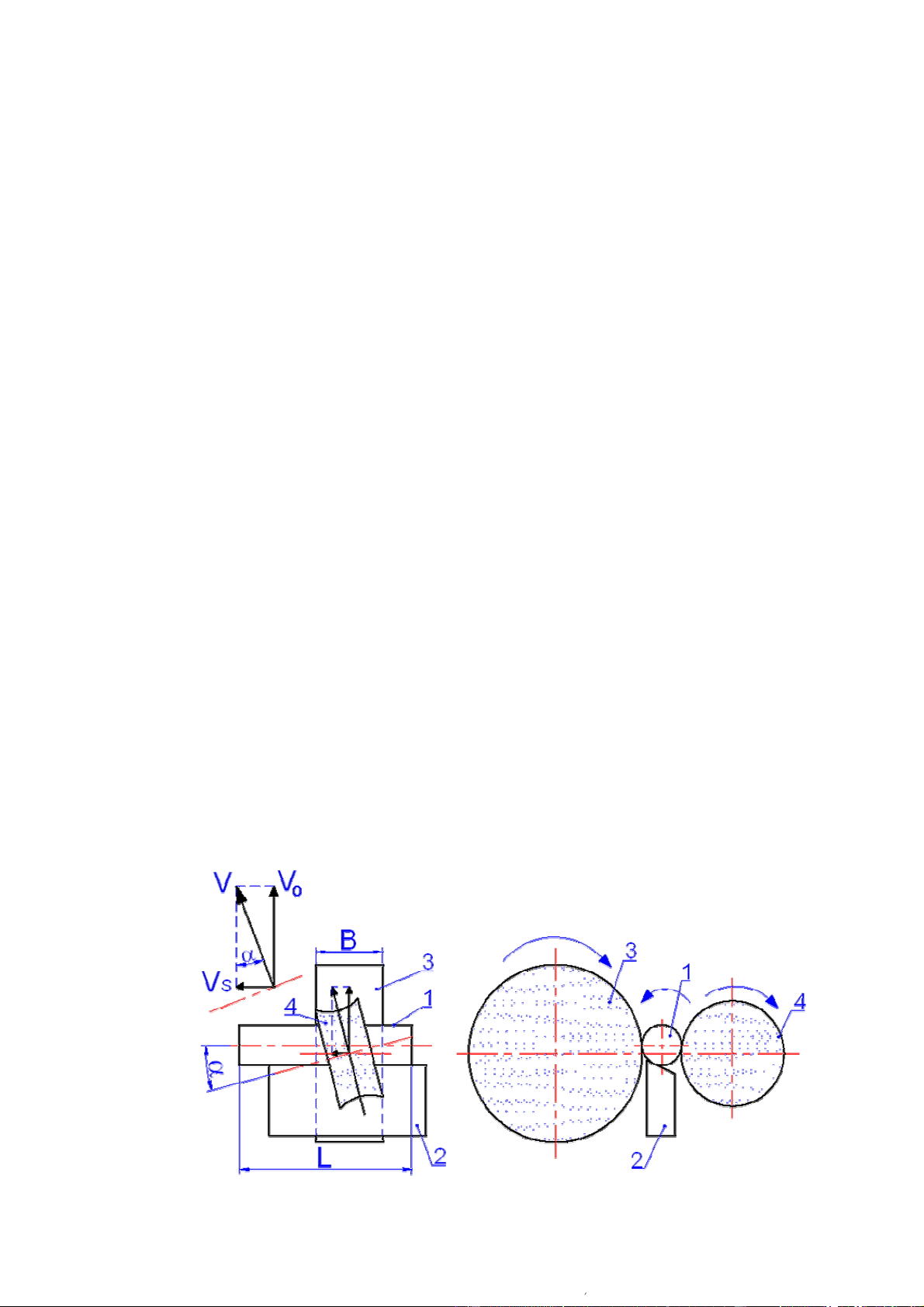
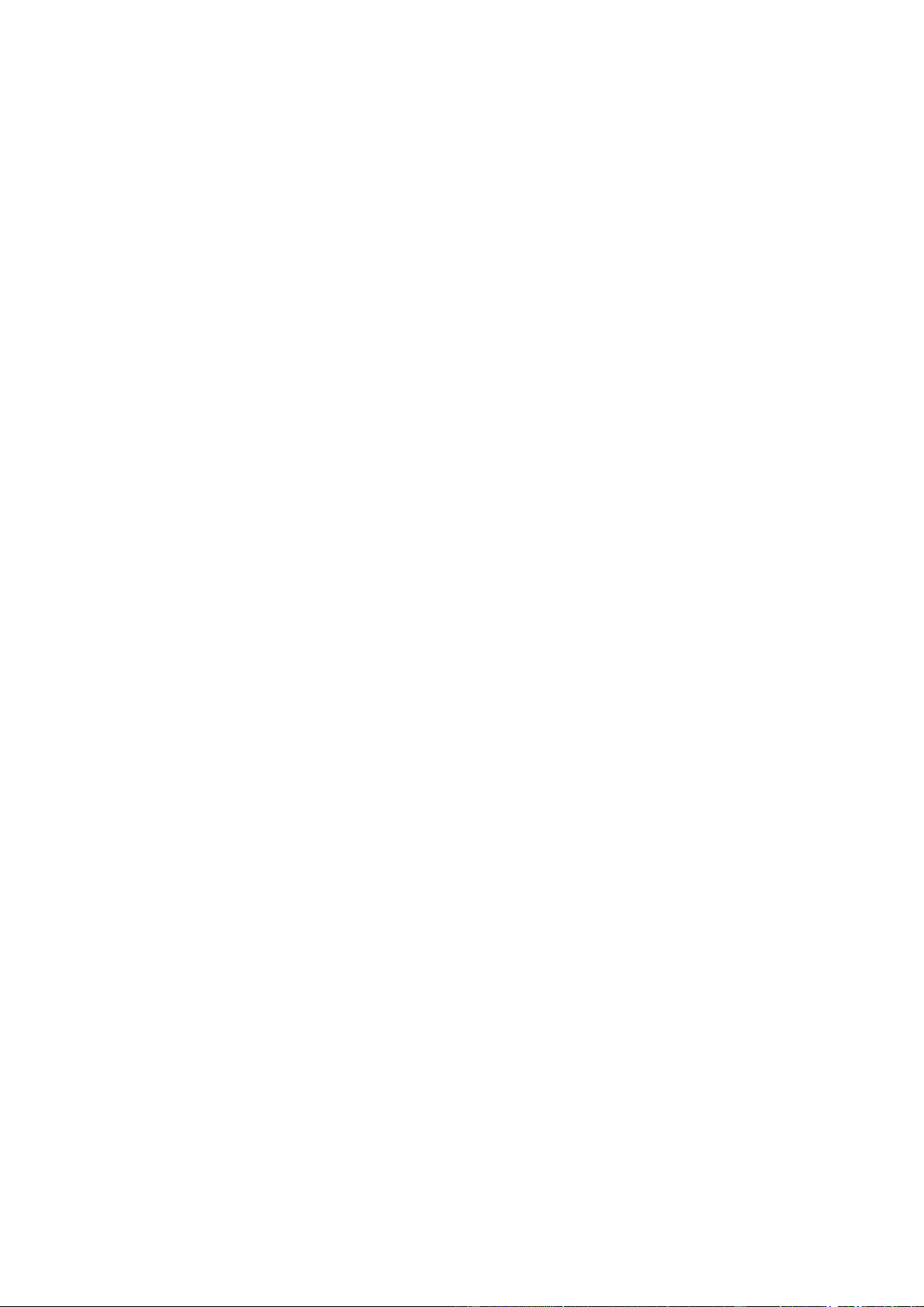
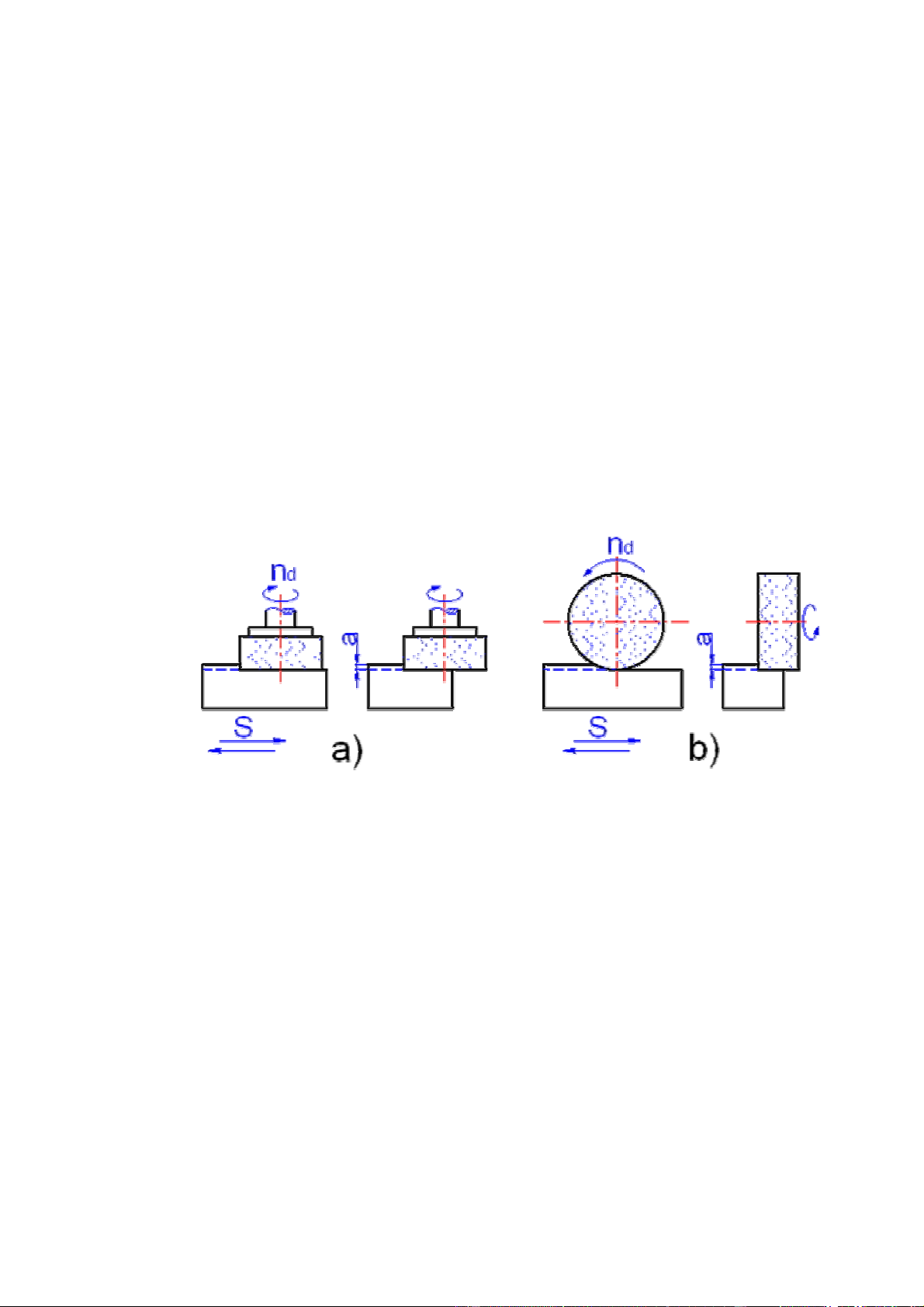
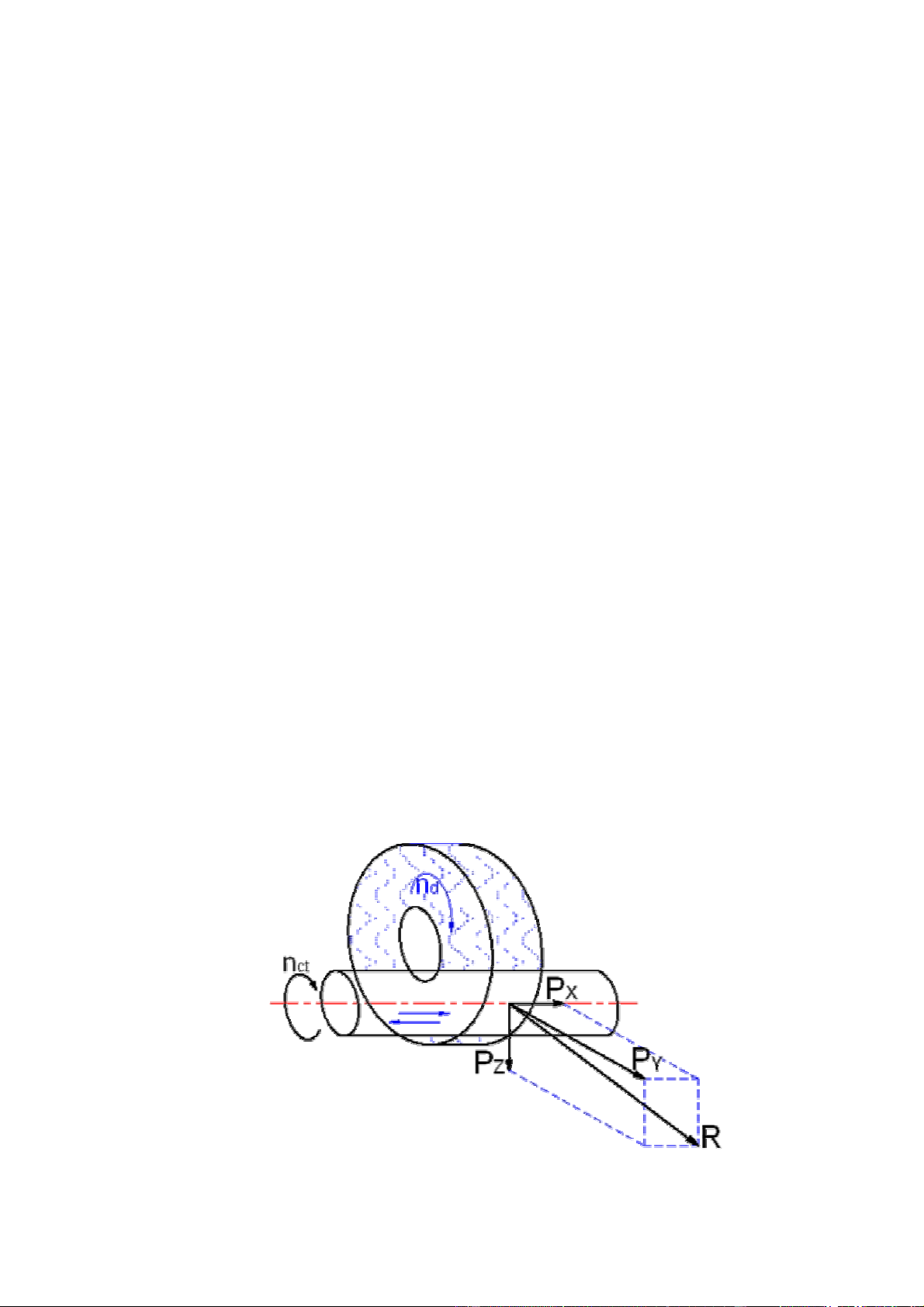
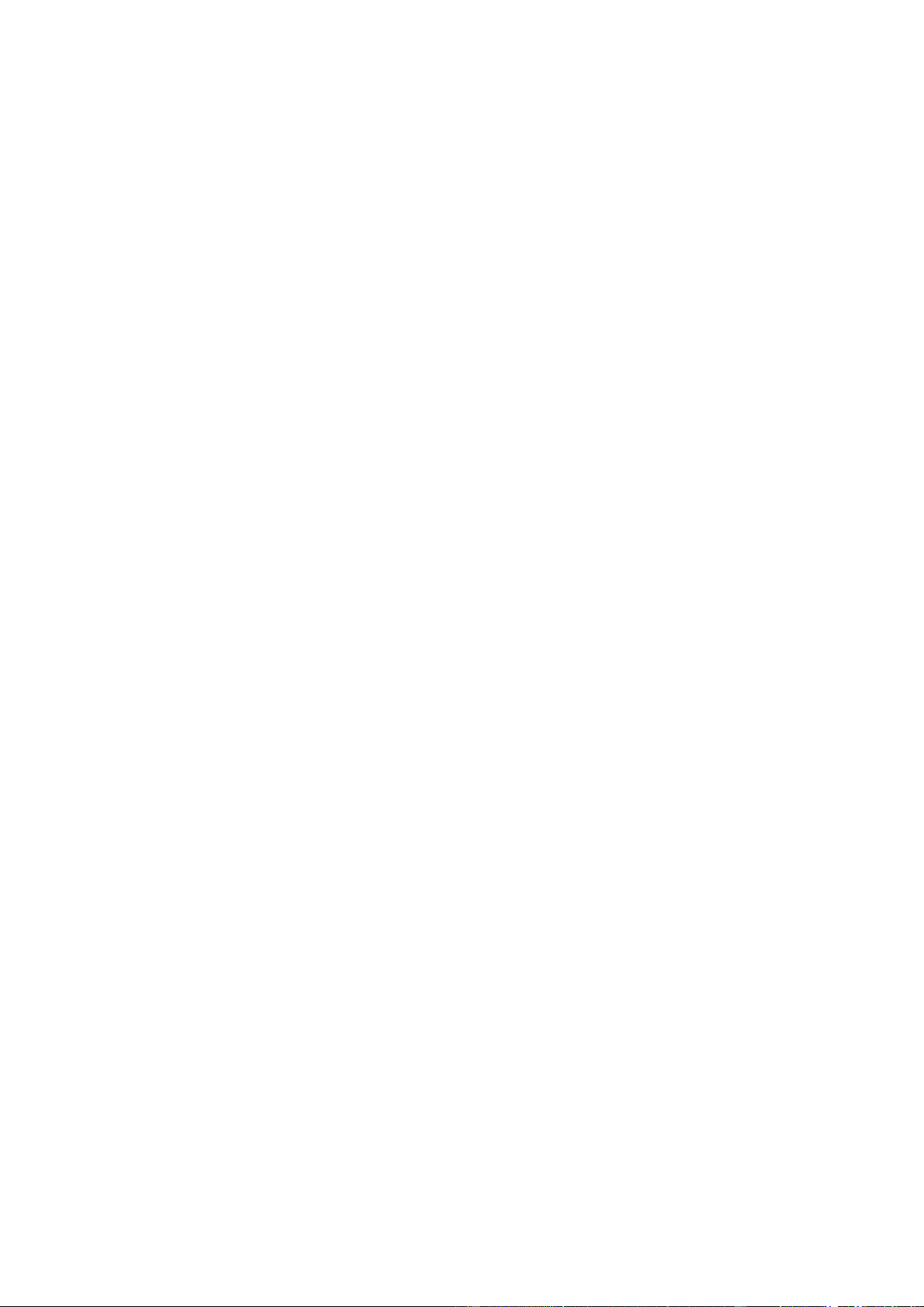

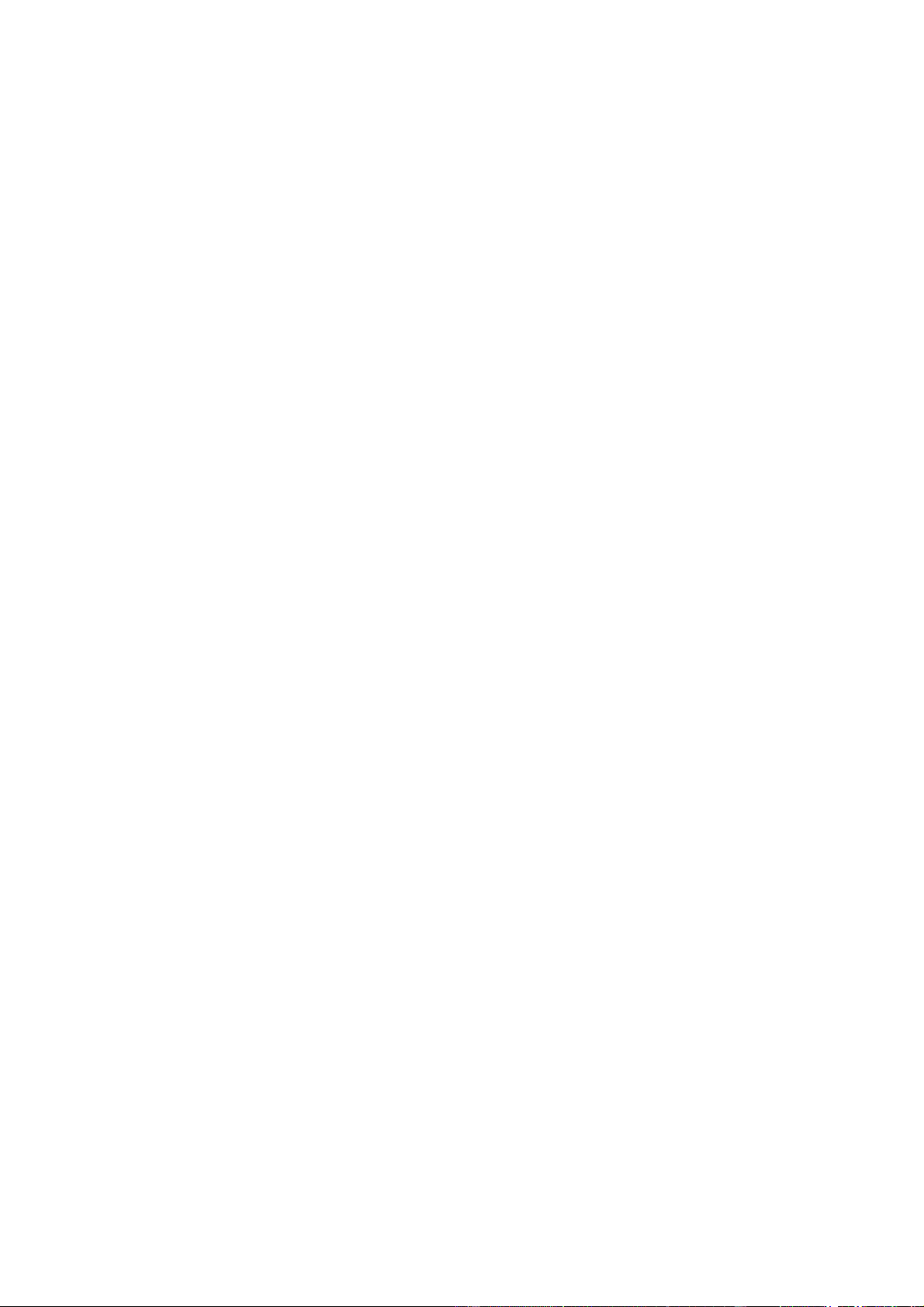
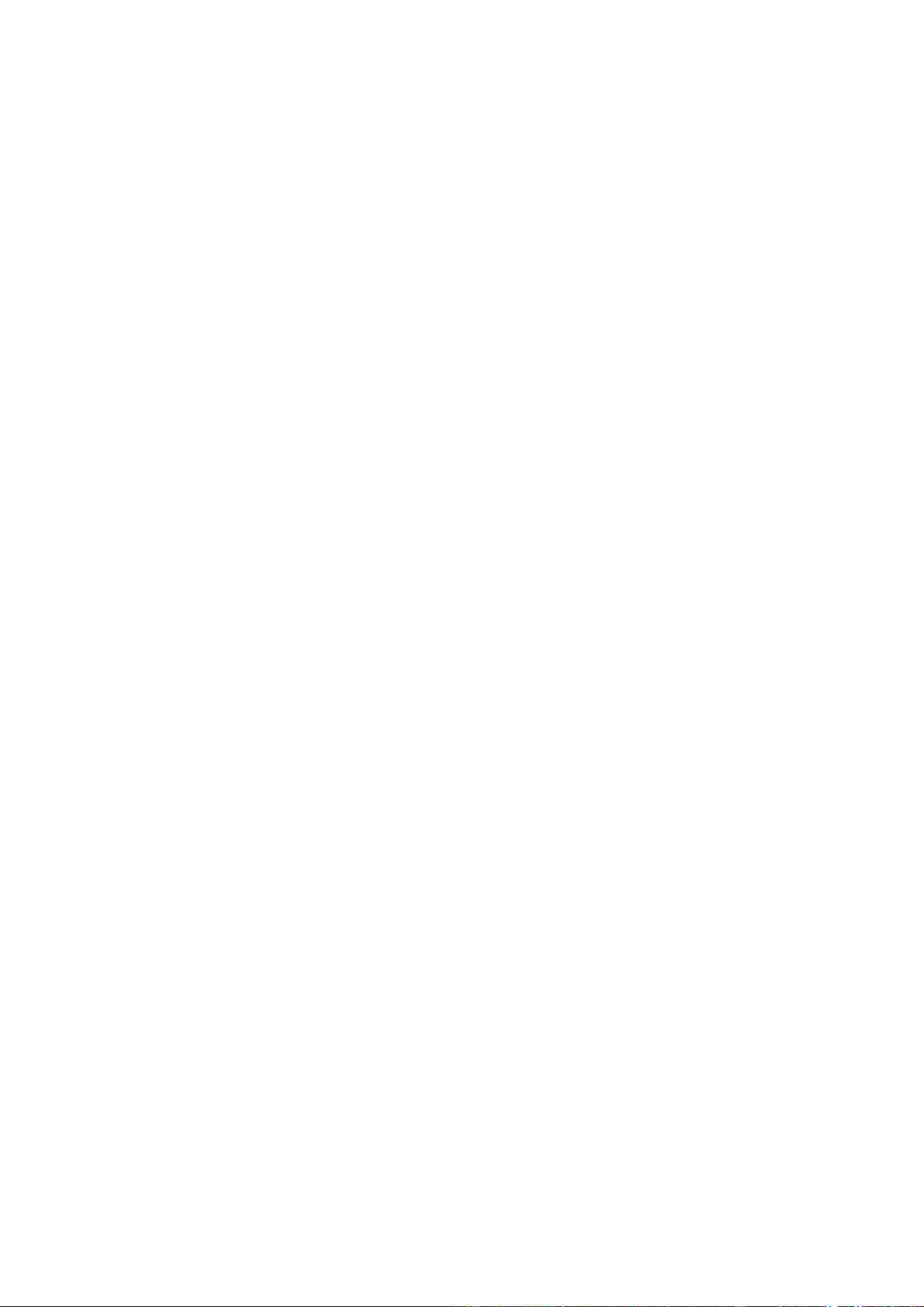
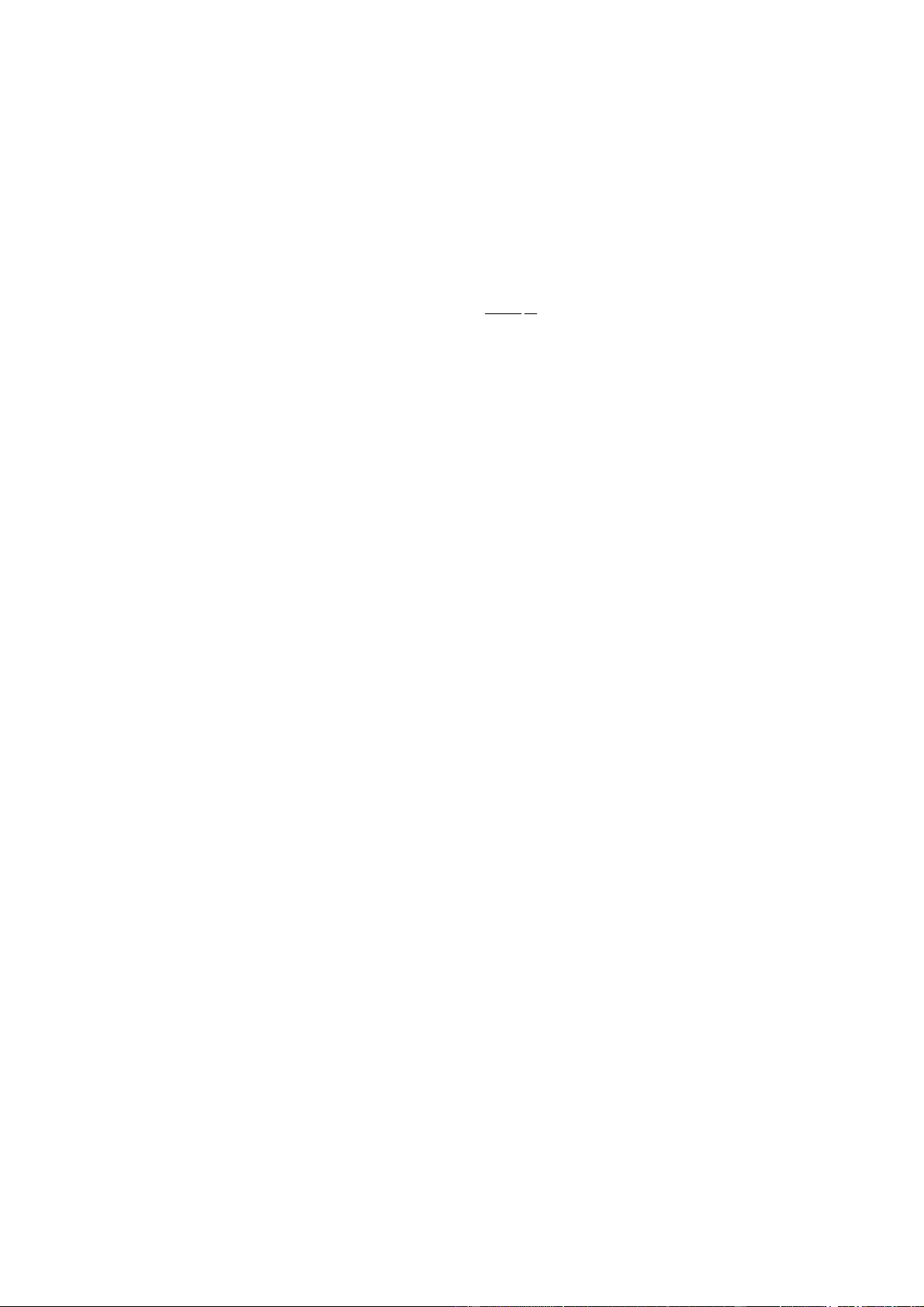
Preview text:
lOMoARcPSD|25518217 Chương 7 : Mài
1. ĐẶC ĐIỂM CỦA QUÁ TRÌNH MÀI
Mài là một trong những phương pháp gia công bằng cắt được sử
dụng rộng rãi và có lịch sử lâu đời nhất. Tuy nhiên phải đến thế kỷ thứ
19, khi xuất hiện máy mài và các loại vật liệu tổng hợp thì việc gia
công bằng mài mới có những bước phát triển nhảy vọt.
Ngày nay, cùng với sự phát triển của ngành chế tạo máy, những
loại vật liệu có tính năng cơ học cao, khó gia công ngày càng được sử
dụng rộng rãi. Những đòi hỏi về độ chính xác và chất lượng gia công
ngày càng cao thì phạm vi sử dụng của mài ngày càng được mở rộng
nhanh chóng hơn bất kỳ dạng gia công nào khác.
Trong ngành chế tạo máy hiện đại, mài chiếm một tỷ lệ rất lớn,
máy mài chiếm khoảng 30% tổng số máy cắt kim loại. Trong ngành
chế tạo ổ bi, nguyên công mài chiếm khoảng 60% toàn bộ quy trình công nghệ.
Ngày nay, mài được dùng trong cả nguyên công thô vì cho năng
suất cao (do tốc độ cắt cao từ 60-80m/s hoặc cao hơn nữa). Khi gia
công tinh, mài đạt: độ nhẵn bề mặt cấp 7-8 và lớn hơn, độ chính xác kính thước cao cấp 6-7.
-Lượng dư gia công rất nhỏ, tốn ít vật liệu.
-Có thể mài thép đã tôi và các vật liệu siêu cứng…
Quá trình mài kim loại là quá trình cắt gọt của đá vào chi tiết tạo
ra rất nhiều phoi vụn do sự cắt và cào xước của các hạt mài vào vật
gia công. Do mài có những đặc điểm khác với các phương pháp gia công cắt gọt khác:
Downloaded by Van Le (mrl3v4n@gmail.com) lOMoARcPSD|25518217
Sơ đồ cắt của hạt mài.
+ Đá mài được coi là một loại dụng cụ cắt nhiều lưỡi, các lưỡi cắt
không giống nhau, mà sắp xếp lộn xộn trong chất dính kết.
+ Hình dạng hình học của mỗi hạt mài khác nhau, góc trước
thường < 00, do đó không thuận lợi cho quá trình thoát phoi và cắt
gọt. Vì vậy lực hướng kính Py khi mài rất lớn.
+ Tốc độ cắt khi mài rất lớn V=3050m/s, cùng một lúc, trong thời
gian ngắn tính bằng giây có nhiều hạt mài cùng tham gia vào cắt gọt
và tạo ra nhiều phoi vụn.
+ Độ cứng của hạt mài cao, do đó có thể cắt gọt được những loại
vật liệu cứng mà các loại dụng cụ cắt khắc, không cắt được như: thép
đã tôi, hợp kim cứng v.v…
+ Do có nhiều hạt mài cùng tham gia cắt gọt với < 00 tạo ra ma
sát rất lớn với vật liệu gia công gọi là hiện tượng “ cắt, cào xước” làm
chi tiết gia công bị nung nóng rất nhanh và nhiệt độ ở vùng mài lớn (từ 10000C – 15000C).
+ Lực mài tuy nhỏ nhưng diện tích tiếp xúc của đỉnh hạt mài với
bề mặt gia công rất nhỏ nên lực cắt đơn vị rất lớn.
Downloaded by Van Le (mrl3v4n@gmail.com) lOMoARcPSD|25518217
+ Trong quá trình mài, đá mài có khả năng tự mài sắc nghĩa là
các hạt cùn bị bật ra khỏi chất dính kết và các hạt có đỉnh sắc ở lân
cận tham gia cắt. Hoặc hạt mài cùn bị vỡ tạo thành các lưỡi cắt sắc mới, tham gia cắt.
+ Do không thể thay đổi được vị trí và hình dạng hình học của hạt
mài trong đá mài nên việc điều khiển quá trình mài rất khó khăn.
+ Quá trình mài tạo cho bề mặt gia công một lớp cứng nguội,
phân bố không đều, chiều dày vào khoảng 2k và hình thành lên ứng
suất dư nếu giá trị ứng suất dư quá lớn, sẽ tạo ra vết nứt tế vi và làm
giảm độ bền của chi tiết, để khắc phục cần mài nghiền §2. ĐÁ MÀI
Đá mài là một vật thể xốp do hạt mài và chất dính kết cấu tạo
thành. Nói chung hạt mài của đá mài chỉ chiếm một thể tích bằng một
nửa thể tích của đá mài. Hạt mài đóng vai trò như những lưỡi cắt. Còn
chất dính kết làm nhiệm vụ liên kết các hạt mài lại thành viên đá mài
có hình dáng kích thước quy định. Đá mài được đặc trưng bởi các
thông số sau: Vật liệu hạt, cỡ hạt, độ cứng, chất dính kết, cấu trúc,
hình dáng kích thước của đá mài. 1, Vật liệu hạt mài a) Kim cương
Là một trong 3 dạng thù hình của các bon (than đá, graphit, kim cương).
Do việc khai thác kim cương thiên nhiên gặp nhiều khó khăn nên
trong kỹ thuật ngày nay chủ yếu dùng kim cương nhân tạo, nhận được
từ việc nén graphit dưới áp suất lớn p=100.000atm ở nhiệt độ 20000C – 27000C.
Downloaded by Van Le (mrl3v4n@gmail.com) lOMoARcPSD|25518217
Đặc điểm nổi bật của kim cương là:
- Có độ cứng tế vi rất cao HV=105 N/mm2
- Có bán kính cong của hạt mài nhỏ = 1,1- 3,3mm
- Hệ số dẫn nhiệt rất cao (lớn hơn 14 lần so với cacbitsilic và gần
45 lần so với corun điện)
Vì vậy, khi mài bằng kim cương nhiệt độ mài thấp, chất lượng chi
tiết gia công cao. Dùng để sửa đá mài, các nguyên công tinh có yêu
cầu độ nhẵn bề mặt từ cấp 9 – 14, để mài nghiền, mài siêu tinh xác,
mài các loại vật liệu siêu cứng (hợp kim cứng, sứ …).
b) Coranh đông nâu, ký hiệu Cn (theo tiêu chuẩn Nga : Corun điện
thường ký hiệu: 12A, 13A, 14A, 15A v à 16A ). Nhận được từ quá trình
nấu chảy bôxit hay glinôden trong lò điện ở nhiệt độ cao ( 2000-
20500). Thành phần chủ yếu là Al203, có dải màu sắc từ hồng đến nâu
thẫm, tuỳ thuộc vào hàm lượng của ôxit nhôm. Hiện nay, đang sản
xuất các loại corun điện thường với hàm lượng Al203 từ 8995%. Còn
lại là các tạp chất có dạng Fe203, Si02, Ti02… Độ cứng tế vi: 20.50023.000N/mm2.
Thường để mài vật liệu dẻo và bền chặt: thép đã tôi, thép đúc, thép cán v.v…
c) Coranh đông trắng, ký hiệu Ct (theo tiêu chuẩn Nga: Corun
điện trắng ký hiệu 22A, 23A, 24A, 25A). Nhận được từ quá trình nấu
chảy Al203 trong lò hồ quang, hạt có màu trắng, màu xám trắng hoặc
màu hồng tươi. Hàm lượng ôxyt nhôm chiếm khoảng 9799%. Độ
cứng tế vi: 21.00023.500N/mm2.
Coranh đông trắng có độ cứng cao hơn nhưng lại giòn hơn nên
độ bền thấp hơn Coranh đông nâu. Tính năng cắt của Coranh đông
Downloaded by Van Le (mrl3v4n@gmail.com) lOMoARcPSD|25518217
trắng cao hơn khoảng 3040% so với Coranh đông nâu. Khả năng tự mài sắc tốt hơn.
Dùng thay cho loại thường khi yêu cầu bề mặt gia công có độ
nhẵn cao hơn và hệ số sinh nhiệt thấp. Thường dùng để gia công các
loại thép gió và thép dụng cụ đã tôi.
d) Các bít silíc (Cacborum): Thu được do kết quả tác động tương
hỗ giữa Si02 và C trong lò điện trở, hàm lượng SiC khoảng 9799% và
một lượng rất nhỏ khoáng sản khác.
Đặc tính quan trọng của các bit silíc là độ cứng cao, có góc nhọn,
dòn và dễ bị vỡ thành các tinh thể nhỏ. Mặt của hạt nhẵn, khó dính
vào chất liên kết, do đó hao phí đá nhiều hơn, tuỳ theo thành phần tạp
chất mà có màu xanh hoặc màu đen. Nó được chia làm 2 loại cơ bản:
*) Cácbít silic đen, ký hiệu Sđ: (theo tiêu chuẩn Nga: Cacborum
đen, ký hiệu ). Cácbit silic đen là loại vật liệu tinh dạng SiC, trong đó
có khoảng 9798% SiC. Độ cứng tế vi: 2800030000N/mm2.
Cácbit silic đen có độ bền cao, độ cứng cao, độ bền nhiệt cao
(khoảng 20500C) khả năng tự mài sắc tốt và tính năng cắt tốt. Nhược
điểm là hơi giòn, nên đá mài với chất dính kết Cácbit silic đen thường
được dùng để mài vật liệu có độ bền thấp như đồng thanh mềm, đồng
thau, gang trắng, gang xám, nhôm và vật liệu phi kim.
*) Cacbit silic xanh ký hiệu Sx: (theo tiêu chuẩn Nga: Cácbarun
xanh ký hiệu K3). Cácbit silic xanh là loại vật liệu kết tinh dạng SiC, có
khoảng 9899% SiC. Độ cứng tế vi: 2900032000N/mm2. Tính tự mài
sác cao hơn, tính năng cắt cao hơn cácbit silic đen khoảng 20%.
Nhược điểm là giòn, độ bền thấp hơn cacbit silic đen và thấp hơn cả
Coranh đông trắng, giá thành đắt hơn cácbit silic đen.
Downloaded by Van Le (mrl3v4n@gmail.com) lOMoARcPSD|25518217
Dùng để gia công vật liệu cứng (sứ và hợp kim cứng…) hiện
dùng các ký hiệu 63C và 64C.
e) Cácbit Bo, ký hiệu B4C: Nhận được trong lò điện hồ quang do
kết quả tác dụng tương hỗ giữa Bo và cốc dầu mỏ ít tro ở nhiệt độ
2000-23500. Trong thành phần của B4C có đến 74% B và gần 1,5%C
tự do. Cácbit Bo có độ cứng rất cao: 3700043000N/mm2. Do đó, nó
có tính năng cắt gọt tốt, dung để gia công thép hợp kim, hợp kim cứng
và các loại vật liệu khó gia công. 2. Chất dính kết
Khi chế tạo đá mài, hạt mài kết hợp với nhau nhờ chất dính kết
giữa chúng ( vật liệu hạt mài và vật liệu dính kết, được trộn lẫn với
nhau, đóng khuôn, nung, gia công cơ và thử 100% trước khi đem sử
dụng. Gồm các loại chất dính kết sau:
- Chất dính kết vô cơ: Kêramic, Silic cát…
- Chất dính kết hữu cơ: Bakelit, vunganit…
- Chất dính kết kim loại
a) Chất dính kết gốm, ký hiệu G (theo tiêu chuẩn Nga: Kêramic ký hiệu K).
Chế tạo từ đất sét chịu lửa, fenspat, thạch anh và một số chất
khác. Dụng cụ chế tạo từ chất dính kết gốm có độ bền, độ chịu nhiệt
và độ cứng cao, nhưng trở lên dòn cứng hơn, ngoài ra nó chịu được
tác dụng hoá học của nhiều chất khác.
Đó là chất dính kết vô cơ được sử dụng rộng rãi nhất. Hiện nay
có tới 70% đá mài được chế tạo từ chất dính kết này. Đá mài bằng
chất dính kết G có thể đạt được Vc=65m/s. Nhược điểm của chất dính
kết gốm là giòn nên không dung để chế tạo đá mài có chiều dày nhỏ
và chịu tải trọng va đập.
Downloaded by Van Le (mrl3v4n@gmail.com) lOMoARcPSD|25518217
Chất dính kết gốm được chia thành hai nhóm: Nóng chảy (thuỷ
tinh) và thiêu kết (dạng sứ). Loại nóng chảy dùng cho đá mài có vật
liệu hạt là Coranh đông. Loại thiêu kết dùng cho vật liệu hạt là cacbit silic.
b) Chất dính kết bakêlit, ký hiệu B (theo tiêu chuẩn Nga: Bakêlit ký
hiệu ). Đó là chất kết dính hữu cơ cũng được dùng phổ biến, Bakêlit
là loại nhựa tổng hợp được chế tạo từ axít cacbônic và phóc ma lin.
Ưu điểm của chất dính kết này là: độ bền cao, độ đàn hồi lớn,
chịu được va đập tốt, nhiệt sinh ra ít khi mài. Do đó cho phép cắt với
tốc độ cao khoảng 60m/s.
Nhược điểm cơ bản của chất dính kết Bakêlit là kém bền vững về
phương điện hoá, nhiệt. Nó bị phá huỷ bởi dung dịch kiềm có độ
PH8. Độ bền cơ học và lực giữ hạt mài giảm nhanh ở nhiệt độ
2000C. Vì vậy chỉ được phép làm việc khi có tưới dung dịch trơn nguội
với độ kiềm nhỏ hơn 1.5%.
Đá mài dùng chất dính kết Bakêlit được sử dụng rộng rãi ở tốc độ
cao để mài rãnh, mài sắc dao đã tôi, mài bề mặt định hình, mài tarô, bàn ren, mũi doa…
Do bakêlit có tính đàn hồi cao nên có thể dùng để chế tạo đĩa mài với chiều dày 0,18mm.
c) Chất dính kết Vunkanit, ký hiệu V (theo tiêu chuẩn Nga:
Vunkanit ký hiệu B). Đó là chất dính kết hữu cơ được chế tạo bằng
cách lưu hoá cao su đã được làm mềm bằng benzen với lưu huỳnh.
Bao gồm 70% cao su và 30% lưu huỳnh.
Đá mài chế tạo bằng chất dính kết Vunkanit có độ bền mòn cao,
thường dùng làm đá dẫn của các máy mài vô tâm.
Downloaded by Van Le (mrl3v4n@gmail.com) lOMoARcPSD|25518217
Do có độ đàn hồi tốt nên được dùng để chế tạo đĩa mài có chiều
dày từ 0.30.5mm với đường kính từ 150200mm.
Đá mài vunkanit cho phép dùng với tốc độ rất cao có thể tới
75m/s. Thường dùng để cắt đứt, mài rãnh, mài rãnh then, mài định
hình chính xác lần cuối.
Nhược điểm của đá mài vunkanit là độ xốp thấp và chịu nhiệt
kém. ở nhiệt độ 1500C đá bắt đầu bị mềm. Khi nhiệt độ lớn hơn 2000C
đá dễ bị cháy. Vì vậy khi cắt, buộc phải tưới dung dịch trơn nguội.
3. Độ cứng của đá mài.
Độ cứng của đá mài là khả năng chống lại sự bứt hạt mài ra khỏi
bề mặt làm việc của đá dưới tác dụng của ngoại lực và nhiệt cắt ( là
khả năng chất dính kết chống bật hạt mài khỏi bề mặt đá dưới tác
dụng của ngoại lực và nhiệt cắt).
Độ cứng của hạt mài và độ cứng của đá mài là hai khái niệm
hoàn toàn khác nhau. Cùng một loại vật liệu hạt mài có thể chế tạo
thành đá mài cứng hoặc đá mài mềm. Đá mài mềm là loại đá có khả
năng chống lại sự bứt hạt mài ra khỏi bề mặt đá rất yếu, tức là dễ bứt
hạt mài ra khỏi đá. Còn đá mài cứng thì khó bứt hạt mài ra khỏi bề mặt đá.
Độ cứng của đá mài được chia thành 7 nhóm và 16 cấp (bảng dưới).
Độ cứng đá mài phụ thuộc vào số lượng, chất lượng chất dính
kết, dạng vật liệu hạt mài, quy trình công nghệ chế tạo v.v…
Độ cứng của đá mài được phân làm nhiều cấp khác nhau và cho trong bảng sau:
Downloaded by Van Le (mrl3v4n@gmail.com) lOMoARcPSD|25518217 Độ cứng của Ký hiệu Cấp độ cứng đá mài Nga Việt Nga Việt Mềm M M M1, M2, M3 M1, M2, M3 Mềm vừa CM MV CM1, CM2 MV1, MV2 Trung bình C TB C1, C2 TB1, TB2 Cứng vừa CT CV CT1, CT2, CV1, CV2, CT3 CV3 Cứng T C T1, T2 C1, C2 Rất cứng BT RC BT1, BT2 RC1, RC2 Đặc biệt cứng T ĐC T1, T2 ĐC1, ĐC2
Chú thích: Độ cứng tăng theo chiều tăng của chỉ số cấp độ cứng
Độ cứng đá mài ảnh hưởng đến năng xuất và chất lượng của sản
phẩm mài. Nếu chọn độ cứng quá thấp, ảnh hưởng đến khả năng cắt
gọt của đá, hao phí đá nhiều, ngược lại chọn độ cứng quá cao dễ gây ra cháy bề mặt mài.
Nguyên tắc chung khi chọn độ cứng đá mài:
Khi gia công vật liệu cứng chọn đá mềm và ngược lại khi gia công
vật liệu mềm chọn đá cứng, vật liệu rất mềm và dẻo như đồng,
nhôm…nên dung đá mài mềm.
Do vật liệu cứng hạt mài dễ bị mòn, cần dung đá mềm để tăng
khả năng tự mài sắc, còn khi gia công vật liệu mềm, hạt mài ít bị cùn,
tăng độ cứng để tăng tuổi bền của đá.
Downloaded by Van Le (mrl3v4n@gmail.com) lOMoARcPSD|25518217
Khi gia công thô nên chọn đá cứng hơn để tăng năng xuất, khi gia
công các bề mặt định hình nên chọn đá có độ cứng trung bình để vừa
đảm bảo được hình dạng bề mặt gia công, vừa đảm bảo năng xuất.
4. Độ hạt của đá mài.
Được biều thị bằng kích thước thực tế của hạt mài. Tính năng cắt
của đá phụ thuộc vào kích thước của hạt. Khi mài thô, dùng hạt mài
có kích thước lớn. Khi mài tinh dùng cỡ hạt nhỏ. Khi gia công vật liệu
mềm và dẻo, để giảm hiện tượng nhét phoi và lỗ của bề mặt đá mài,
nên dùng cỡ hạt lớn. Hạt mài được phân thành 4 nhóm (bảng): TT Nhóm Độ hạt 1 Hạt mài
200, 160, 125, 100, 80, 63, 50, 40, 32, 25, 20, 16. 2 Bột mài 12, 10, 8, 6, 5, 4, 3 3 Bột m ịn M63, M50, M40, M28, M20, M14 4 Bột cực mịn M10, M7, M5, M3, M2, M1
Nhóm 1và 2 mỗi đơn vị ứng với 0.01mm
Nhóm 3 và 4 mỗi đơn vị ứng với 0.001mm
Ngoài ra kích thước của hạt còn phải tăng trong những trường hợp sau:
- Dùng đá bằng chất Bakêlit, B để thay cho chất dính kết K.
- Tăng số vòng quay của đá.
- Tăng cung tiếp xúc giữa đá mài và chi tiết gia công.
- Mài vật liệu có độ dẻo cao.
5. Cấu trúc của đá mài.
Downloaded by Van Le (mrl3v4n@gmail.com) lOMoARcPSD|25518217
Cấu trúc của đá mài thể hiện ở tỷ lệ phần trăm của thể tích hạt
mài, thể tích chất dính kết, thể tích khoảng trống trong đá mài. Các tỷ
lệ thể tích đó quyết định độ chặt (hay độ xốp) của đá mài. Cấu trúc đá
mài được chia làm 13 cấp, đánh số từ cấp 012. Số cấp cấu trúc càng
cao, khoảng cách giữa các hạt mài càng lớn, do đó đá mài càng xốp
nghĩa là số lượng hạt mài càng giảm và khoảng trống càng tăng.
Phân loại cấu trúc đá mài và tỷ lệ phần trăm hạt mài trong mỗi
cấp được cho trong bảng sau: Loại cấu trúc Chặt Trung bình Xốp Cấp cấu trúc 0 1 2 3 4 5 6 7 8 9 10 11 12
Số % hạt mài 62 60 58 56 54 52 50 48 46 44 42 40 38 trong thể tích đá mài
Đá có cấu trúc xốp dùng để mài cao tốc rất tốt vì phoi ít bị nhét
vào đá, ma sát giảm nên có thể mài với chiều sâu cắt lớn, sửa đá ít
hơn và tăng năng suất cao hơn. Thực nghiệm cho thấy, đá mài càng
xốp, bề mặt gia công càng ít bị cháy hơn.
Nếu đá mài càng mềm, nên chọn cấu trúc càng xốp để phoi ít bị nhét vào bề mặt đá.
Để tạo độ xốp cho đá, khi chế tạo đá mài người ta trộn thêm các
chất phụ như mùn cưa, than vụn, graphit…Khi thiêu kết, các chất phụ
sẽ cháy và tạo ra các khoảng trống.
Downloaded by Van Le (mrl3v4n@gmail.com) lOMoARcPSD|25518217
6. Hình dáng của đá mài.
Hình dáng của đá mài được quy định theo tiêu chuẩn và được
phân loại như sau: Đối với viên mài có các loại từ V1 đến V20. Đối với
đầu mài có các loại từ Đ1 đến Đ7. Với thỏi mài có: T1đến T6, với
miếng mài có: M1 đến M6.
Để tiện cho việc chọn đá, trên mặt đầu của đá mài được ghi các
thông số kỹ thuật của đá mài. Ví dụ: Cn40CV1G V1-400x40x203 30m/s
Downloaded by Van Le (mrl3v4n@gmail.com) lOMoARcPSD|25518217
3. CÁC PHƯƠNG PHÁP MÀI THÔNG DỤNG 1. Mài tròn ngoài.
Sơ đồ cắt khi mài tròn ngoài
Quá trình mài tròn ngoài có bốn chuyển động cắt:
-Chuyển động quay tròn của đá là chuyển động cắt chính. Tốc độ
cắt của đá mài được tính bằng: .DK.nK V , m/s. K 100 . 0 60
Thường lấy: Vk=18 50m/s
-Chuyển động quay tròn các chi tiết gia công với tốc độ tính theo công thức: .D.n V , m/phút 1000 Thường lấy: 1 1 V ( ).V K 40 100
-Chuyển động tịnh tiến đảo chiều của đá dọc theo trục chi tiết gia
công. Đó là chuyển động chạy dao hướng trục với lượng chạy dao bằng:
Downloaded by Van Le (mrl3v4n@gmail.com) lOMoARcPSD|25518217 St = (0,3 0,6)B
-Chuyển động chạy dao hướng kính St. Đó chính là chiều sâu
ăn dao ứng với mỗi lần chạy dao. Thường lượng chạy dao
hướng kính khi mài rất nhỏ, khoảng. St = 0.0050.025 mm
ở đây: DK - Đường kính của đá mài, mm
nK - Số vòng quay của đá mài trong một phút, vg/ph D - Đường kính phôi, mm
N - Số vòng quay của phôi trong một phút, vg/ph
B - Chiều rộng của đá mài, mm
2. Mài tròn trong (mài lỗ).
Sơ đồ cắt khi mài tròn trong
Mài lỗ cũng có bốn chuyển động cắt như mài tròn ngoài.
Chuyển động quay tròn của đá là chuyển động cắt chính, với tốc độ cắt Vđ = 1830m/s.
Tốc độ cắt của mài lỗ thường nhỏ hơn so với mài tròn ngoài
vì khi mài lỗ, đường kính đá mài bị khống chế bởi đường kính lỗ
Downloaded by Van Le (mrl3v4n@gmail.com) lOMoARcPSD|25518217
phôi. Để vừa đảm bảo năng suất cắt, vừa đảm bảo chất lượng bề
mặt gia công, thường chọn đường kính đá mài lỗ bằng Dk =
(0,60,8)D. Trong đó D là đường kính lỗ phôi. Mặt khác số vòng
quay của đá cũng bị giới hạn bởi số vòng quay của trục chính máy mài.
Chi tiết quay ngược chiều với đá mài, thường lấy số vòng
quay của chi tiết lớn hơn so với trường hợp mài tròn ngoài, lượng
chạy dao hướng kính lấy nhỏ hơn so với mài tròn ngoài. Còn
lượng chạy dao hướng kính được lấy bằng: St = (0,20,8)B Trong đó:
B - chiểu rộng của đá mài, mm
Khi mài tròn trong chi tiết lớn, nặng: chi tiết đứng yên, còn đá
mài vừa quay tròn quanh trục của nó vừa quay hành tinh theo bề
mặt lỗ phôi, đồng thời thực hiện các chuyển động chạy dao
hướng trục và hướng kính. 3. Mài vô tâm.
Downloaded by Van Le (mrl3v4n@gmail.com) lOMoARcPSD|25518217 Sơ đồ mài vô tâm
Mài vô tâm là phương pháp mài cho hiệu quả kinh tế cao vì
giảm bớt đựơc thời gian kẹp chặt và định tâm chi tiết, yêu cầu tay
nghề của công nhân không cao, ít phế phẩm và dễ tự động hoá.
Mài vô tâm được dùng để mài tròn ngoài và trong, cho chất
lượng bề mặt gia công cao. Có thể thực hiện 2 phương pháp
chạy dao: Mài chạy dao dọc và mài chạy dao ngang. Phương
pháp thứ nhất dùng để mài các chi tiết dai không có bậc, phương
pháp thứ hai dùng để mài các chi tiết có bậc, các chi tiết có chiểu
dài bằng hoặc gần bằng chiều rộng của đá.
Khi mài vô tâm ngoài chạy dao dọc, chi tiết 1 được đặt tự do
trên phiến tỳ 2, đá mài 3 và đá dẫn 4. Phiến tỳ đặt song song với
trục đá mài, mặt vát của nó ép chi tiết tiếp xúc với đá dẫn để nhận
chuyển động do đá dẫn tạo nên. Trục đá dẫn được gá nghiêng so
với trục chi tiết một góc = 1050 để truyền cho chi tiết chuyển
động quay tròn và chuyển động chạy dao dọc trục. Do vậy giữa
bề mặt đá dẫn và chi tiết có tiếp xúc điểm. Để tránh hiện tượng
trượt, bề mặt đá dẫn được chế tạo theo dạng hypecbôlôit tròng
xoay có đường sinh là đường thẳng.
Đá dẫn được chế tạo bằng chất dính kết Vunkanít có đàn tính
cao để tạo ra áp lực tiếp xúc giữa đá dẫn với chi tiết. Đồng thời
tận lượng độ bền mòn cao của đá Vunkanit nhằm tăng chất
lượng của bề mặt gia công.
Đá dẫn có độ hạt chọn trong khoảng 1610. Tốc độ đã dẫn
chọn nhỏ để tăng hệ số ma sát nhằm tăng lực ma sát giữa đá dẫn với chi tiết.
Downloaded by Van Le (mrl3v4n@gmail.com) lOMoARcPSD|25518217
Tâm chi tiết đặt cao hơn tâm đá mài một lượng h tra trong sổ
tay (phụ thuộc vào đường kính chi tiết). Nếu gá chi tiết không
đúng sẽ nhận được bề mặt gia công không tròn, có dạng ô van hoặc đa giác.
Có thể lấy h = (0,5 1)R.
Trong đó: R – bán kính của chi tiết, nhưng h không vượt quá 1015mm. 4. Mài phẳng.
Có hai phương pháp mài phẳng:
-Dùng mặt đầu của đá để mài, gọi là mài mặt hoặc mài xoa.
-Dùng chu vi của đá để mài gọi là mài lăn.
Phương pháp mài xoa có diện tích tiếp xúc giữa mặt đầu của
đá với bề mặt gia công lớn nên cho năng suất cắt cao. Nhưng
chất lượng bề mặt gia công thấp vì điều kiện làm nguội khó khăn.
Nhiệt mài phát sinh lớn, dễ gây ra biến dạng nhiệt trong quá
trính mài. Khắc phục bằng cách gá nghiêng trục đá một góc
khoảng 1020 để giảm diện tích tiếp xúc giữa đá với bề mặt gia
công, đồng thời đưa dung dịch trơn nguội tới vùng cắt dễ hơn.
Downloaded by Van Le (mrl3v4n@gmail.com) lOMoARcPSD|25518217
Phương pháp này thường dùng để mài những chi tiết có độ chính
xác thấp và bề rộng mài nhỏ.
Phương pháp mài lăn có diện tích tiếp xúc giữa chu vi đá với
bề mặt gia công nhỏ hơn nên năng suất cắt thấp hơn. Nhưng dễ
làm nguội và cho chất lượng bề mặt gia công cao. Phương pháp
này thường dùng để mài những chi tiết có bề rộng lớn và yêu cầu chính xác cao.
Mài phẳng cũng có bốn chuyển động cắt như mài tròn ngoài:
Đá mài thực hiện chuyển động cắt chính là chuyển động quay
tròn quanh trục của nó. Sau mỗi hành trình của bàn máy, đá mài
thực hiện chuyển động ăn dao để cắt hết lượng dư. Chi tiết kẹp
trên bàn máy thực hiện chuyển động chạy dao dọc là chuyển
động tịnh tiến hoặc quay tròn theo bàn máy, tuỳ thuộc vào kiểu
máy mài sử dụng. Để cắt hết chiều rộng của chi tiết, đá mài thực
hiện chuyển động chạy dao ngang.
4- LỰC VÀ CÔNG SUẤT CẮT KHI MÀI
Downloaded by Van Le (mrl3v4n@gmail.com) lOMoARcPSD|25518217
Khi mài, lực cắt cũng phân thành ba thành phần lực: Px, Py, Pz.
Do lượng dư khi mài nhỏ nên thành phần lực tiếp tuyến Pz và
đặc biệt là lực chiểu trục Px rất nhỏ.
Do các hạt mài phân bố bất hợp lý, góc trước tại các đỉnh
hạt mài thường có trị số âm. Nên tạo ra lực hướng kính Py rất lớn
so với các thành phần lực khác. Thông thường:
Py = (1 3)Pz; Px = (0,05 0,07)Pz.
Lực tiếp tuyến Pz được tính theo công thức sau: Pz = Cpz. V0,7. S0,7. t0,6, N Trong đó:
V - tốc độ của chi tiết gia công, m/ph
St - lượng chạy dao dọc, mm/vg.
t - chiều sâu cắt, mm/htk.
CpZ - hệ số phụ thuộc vào vật liệu gia công.
Khi mài thép đã tôi, lấy: Cpz=22
Khi mài thép chưa tôi, lấy: Cpz=21 Khi mài gang, lấy: Cpz=20
Mặc dù lực cắt Pz nhỏ nhưng do tốc độ cắt của đá mài rất
lớn, nên công suất cắt khi mài rất lớn và được tính theo công thức sau: N = C 0,5 0.55 N. Vk . St . t0.5, KW
Trong đó: Vk - tốc độ cắt của đá mài, m/s
Downloaded by Van Le (mrl3v4n@gmail.com) lOMoARcPSD|25518217
CN - hệ số phụ thuộc vào loại đá mài, tra trong sổ tay.
Công suất của động cơ điện làm quay đá mài được tính bằng: z P .V.K N , KW dc 3 60 1 . 0 .1
Công suất của động cơ điện làm quay chi tiết gia công: P .V .K z k N , KW dc 1000.2 Trong đó:
1 và 2 - hiệu suất truyền động từ động cơ điện đến đá mài và chi tiết gia công.
K - hệ số an toàn, bào đảm cho mày làm việc ổn định.
Thường lấy: K = 1,2 1,5.
5 - SỰ MÀI MÒN VÀ TUỔI BỀN CỦA ĐÁ MÀI
Trong quá trình mài, hạt mài bị mòn và mất khả năng cắt. Tốc
độ quay của chi tiết, lượng chạy dao, chiều sâu mài ứng với
t0,005mm, độ cứng của vật liệu gia công đều càng lớn, độ hạt
càng lớn, tốc độ quay của đá càng nhỏ thì lực tác dụng lên mỗi
hạt mài riêng biệt sẽ càng lớn làm cho độ mòn đỉnh hạt mài càng
lớn. Đặc biệt hạt mài càng bị mòn nhiều khi chiều sâu mài
t0,005mm vì khi đó xẩy ra sự trượt rất lớn giữa hạt mài với bề mặt gia công.
Downloaded by Van Le (mrl3v4n@gmail.com) lOMoARcPSD|25518217
Ngoài độ mòn của đỉnh hạt mài, khi các hố rỗng giữa các hạt
mài bị bít kín bởi các bụi phoi, các mảnh hạt và chất dính kết sinh
ra khi mòn cũng làm giảm khả năng cắt của đá mài.
Khi gia công thô, nếu thấy xuất hiện chấn động, bề mặt gia
công bị gằn. Khi gia công tính thấy xuất hiện các vệt sáng gợn
sóng trên bề mặt gia công hoặc thấy độ nhẵn bề mặt gia công
giảm thì cần phải tiến hành sửa đá vì đá bị mòn. Có thể sửa đá
bằng đầu kim cương hoặc bằng đá mài khác cứng hơn, sửa đá
ngoài việc làm mất các hạt bị cùn còn tạo ra hình dáng hình học
chính xác cho đá mài đã bị sai lêch do sự mòn không đều.
Đá mài chủ yếu để gia công tinh nên tiêu chuẩn mài mòn của
đá là tiêu chuẩn mài mòn công nghệ và được tra trong sổ tay.
Khoảng thời gian cắt liên tục của đá mài giữa hai lần sửa đá
gọi là tuổi bền của đá mài. Tuổi bền của đá mài thường lấy bằng
T=10 16ph và phụ thuộc vào kiểu mài.
Khi mài tròn ngoài, lấy: T= 30 40ph
Khi mài lỗ, mài định hình, lấy: T= 10ph
Khi mài vô tâm, lấy: T= 30 60ph.
6 - CHỌN CHẾ ĐỘ CẮT KHI MÀI
1- Chọn đá mài: tuỳ theo điều kiện mài, yêu cầu gia công, vật
liệu gia công mà chọn vật liệu mài, cỡ hạt, chất dính kết, cấu trúc
đá mài, độ cứng và hình dạng kích thước đá mài, tốc độ tiếp
tuyến lớn nhất cho phép của đá mài. Chọn trong các sổ tay vể mài.
Downloaded by Van Le (mrl3v4n@gmail.com) lOMoARcPSD|25518217
2- chọn chiểu sâu cắt: phụ thuộc vào kiểu mài và yêu cấu gia công:
-Mài tròn ngoài: khi mài thô, chọn: t = 0,01 0,25mm
khi mài tính, chọn: t = 0,005 0,075mm
-Mài lỗ: khi mài thô, chọn: t = 0,005 0,03mm
khi mài tinh, chọn: t = 0,002 0,01mm
-Mài vô tâm: Khi mài thô, chọn: t = 0,02 0,2mm
khi mài tinh, chọn: t = 0,0025 0,01mm
-Mài phẳng: khi mài thô, chọn: t = 0,015 0,15mm
khi mài tinh, chọn: t = 0,005 0,015mm
Chiều sâu cắt khi mài có thể tra trong sổ tay.
3- Chọn lượng chạy dao dọc
Lượng chạy dao dọc được tính sau một vòng quay của chi
tiết khi mài tròn hoặc sau một hành trình kép của bàn máy khi mài phẳng.
Thường lấy: St = (0,3 0,6)B
Trong đó: B- chiều rộng của đá mài
Lượng chạy dao dọc có thể tra trong các sổ tay.
4- Chọn tốc độ cắt khi mài
Tốc độ cắt của đá mài được chọn theo sổ tay, phụ thuộc vào
độ bền của đá mài, độ cứng vững và công suất của máy mài.
Theo tốc độ cắt đã chọn, cần được hiệu chỉnh theo số vòng quay thiết kế của máy mài.
Downloaded by Van Le (mrl3v4n@gmail.com) lOMoARcPSD|25518217
Số vòng quay của chi tiết gia công được chọn theo sổ tay
phụ thuộc vào vật liệu gia công, tính chất gia công và độ cứng của đá mài. 5- Tính thời gian máy. L h T , ph 0 .K n.S1 t Trong đó:
L- chiều dài của chi tiết gia công khi mài tròn hoặc chiều rộng
của chi tiết khi mài phẳng, mm
n- số vòng quay của chi tiết trong một phút hoặc số hành
trình kép của bàn máy trong 1 phút.
St- lượng chạy dao dọc sau một vòng quay của chi tiết hoặc
sau một hành trình kép của bàn máy.
h- lượng dư gia công, mm.
t- chiều sâu mài tinh sau một lần chuyển dao, mm/htk.
K- hệ số tính đến việc quay dao thêm máy lần cuối để tăng độ nhẵn bề mặt.
Thường lấy: K = 1,4 2,5.
Downloaded by Van Le (mrl3v4n@gmail.com)