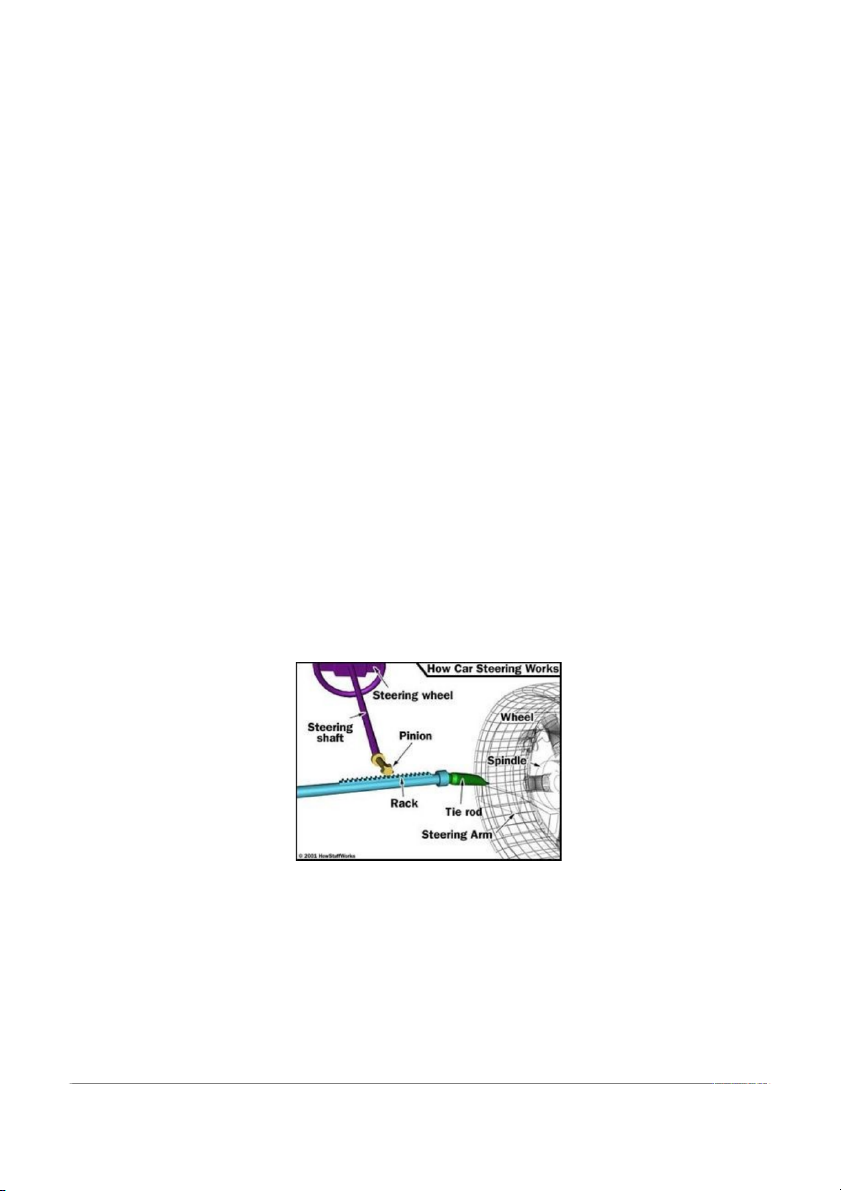
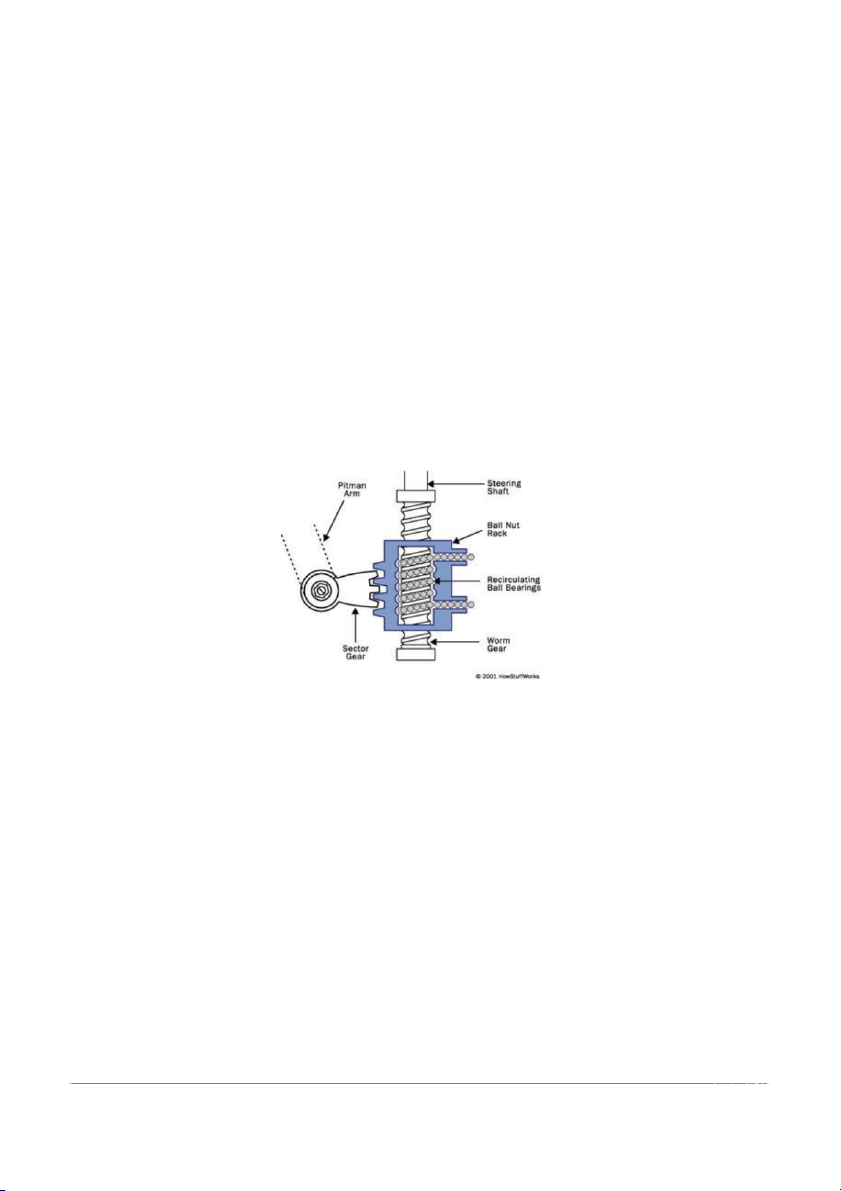
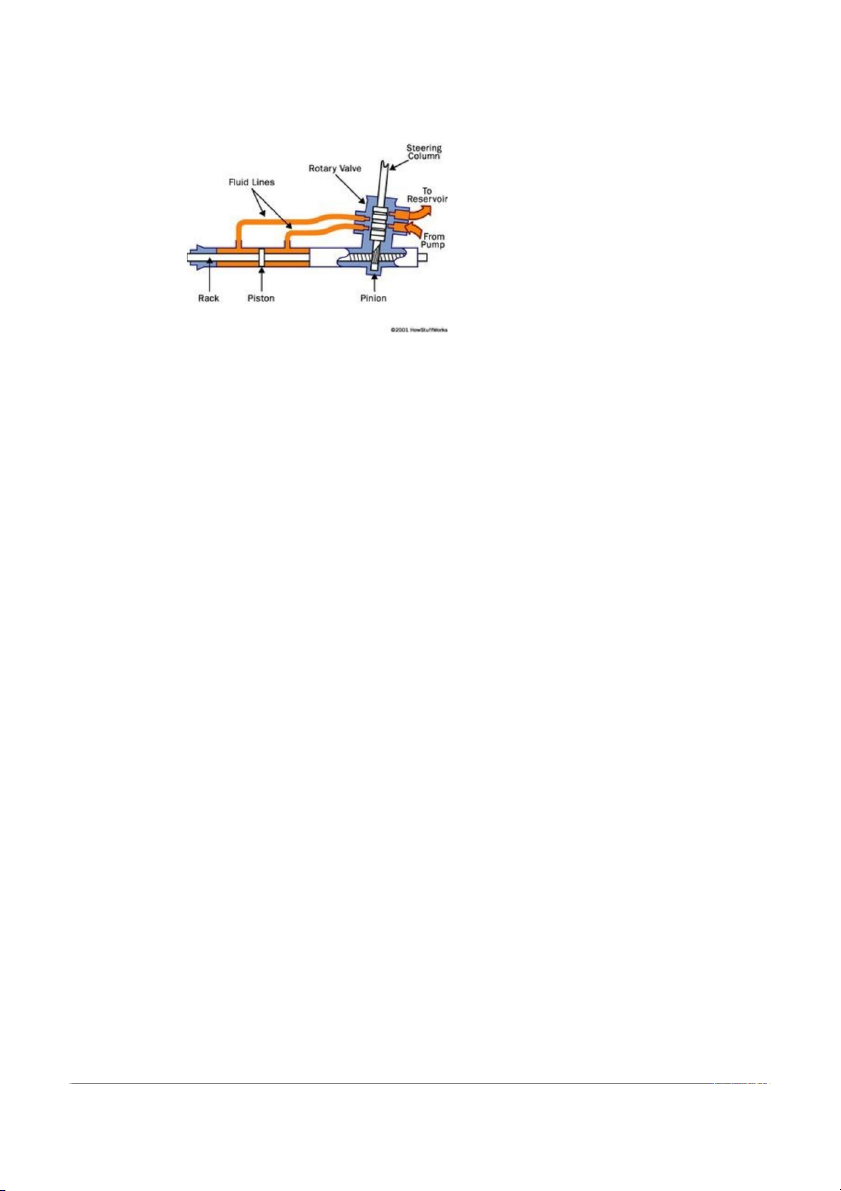
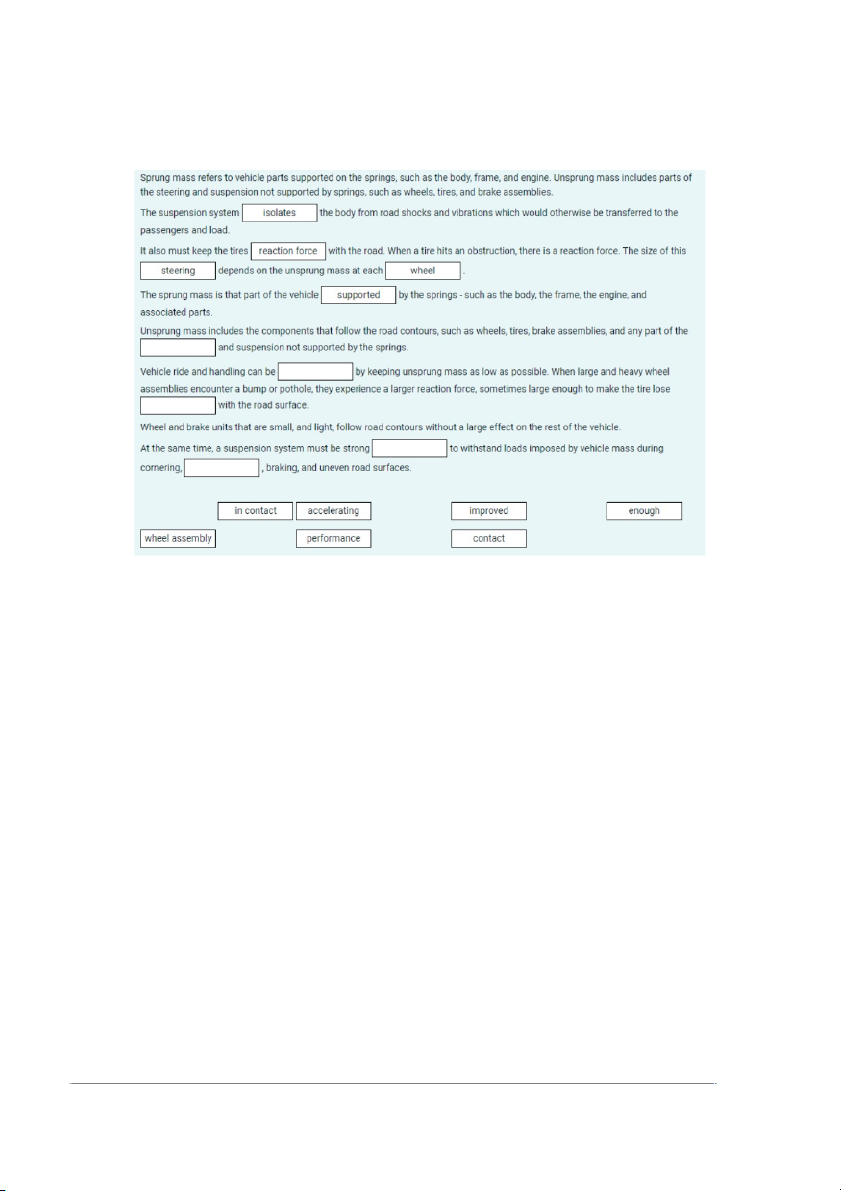
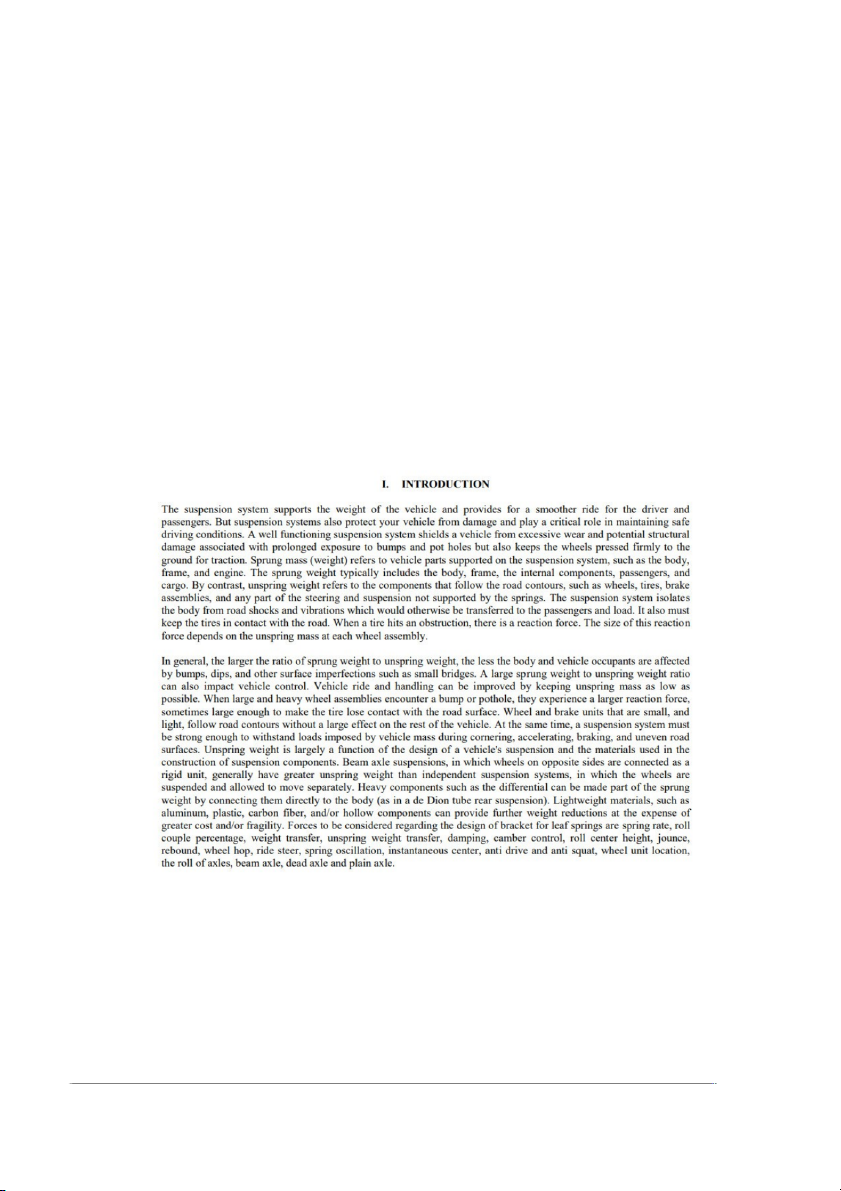
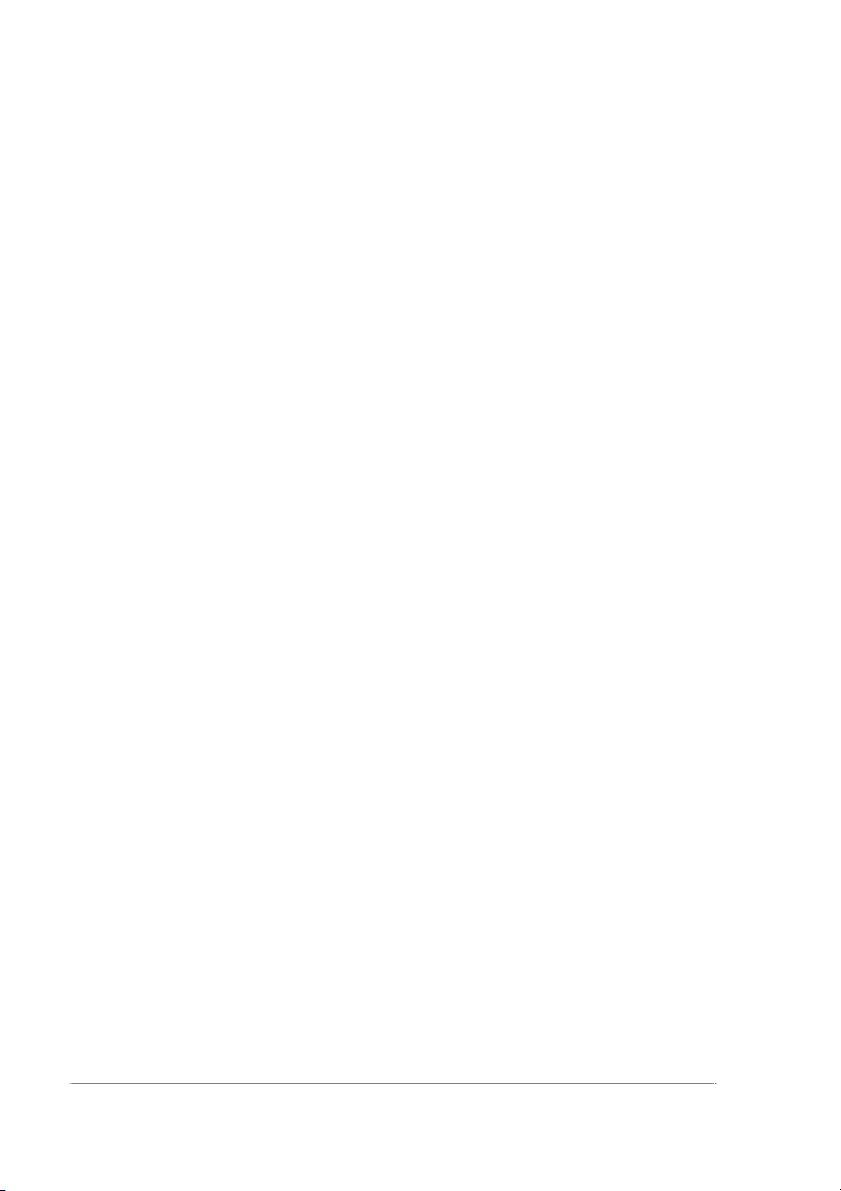
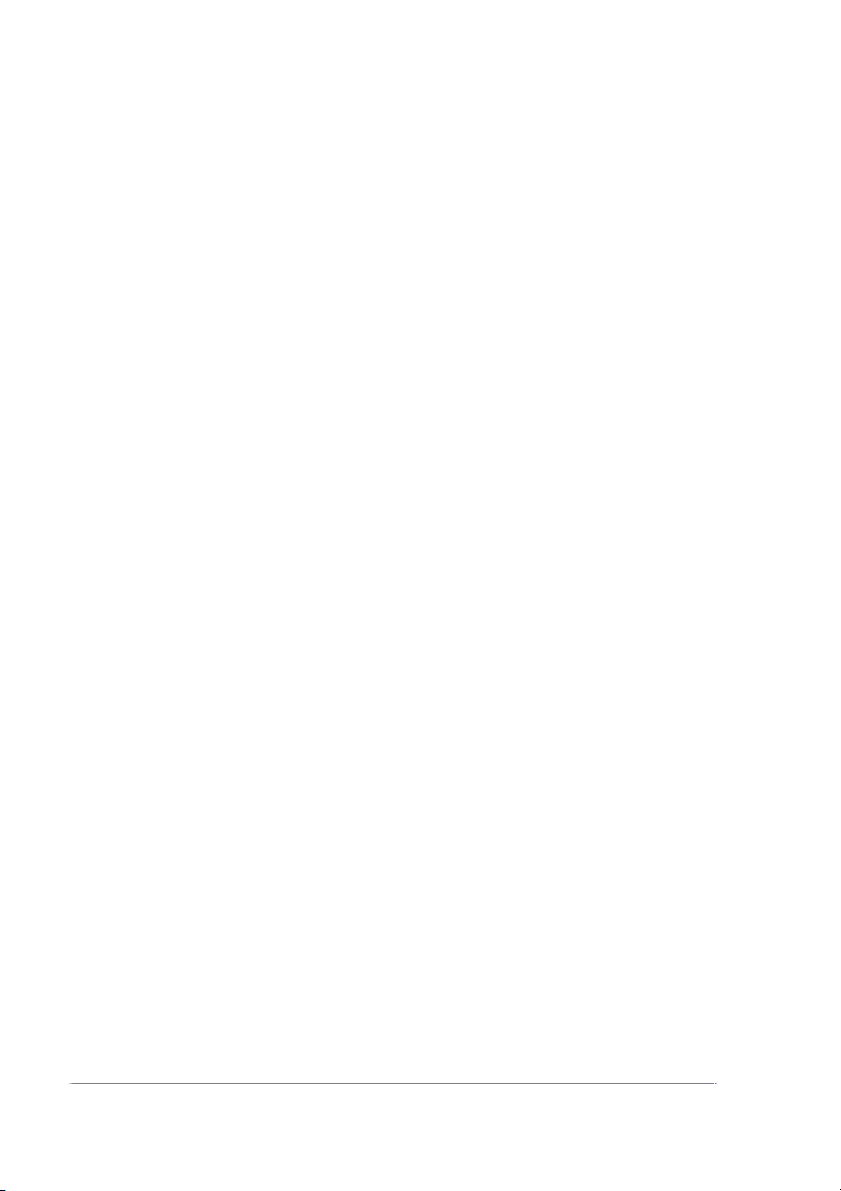
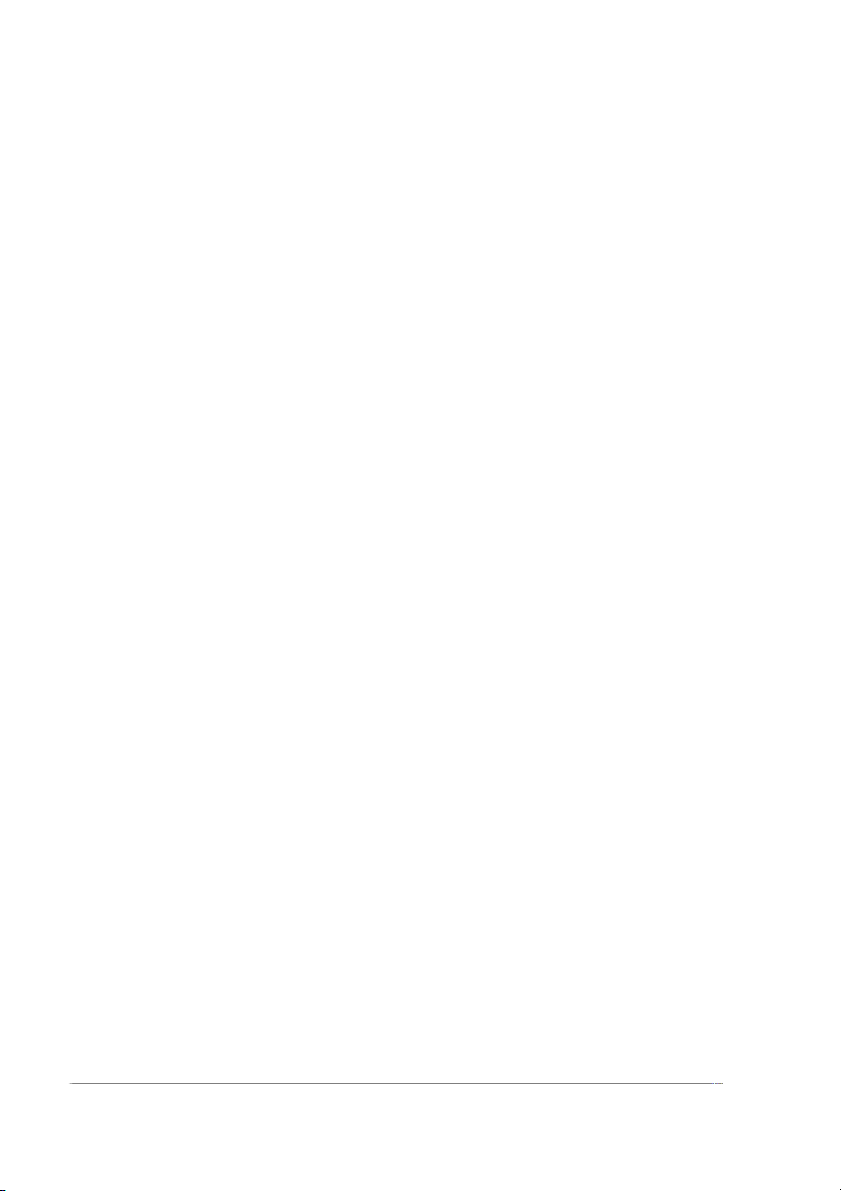
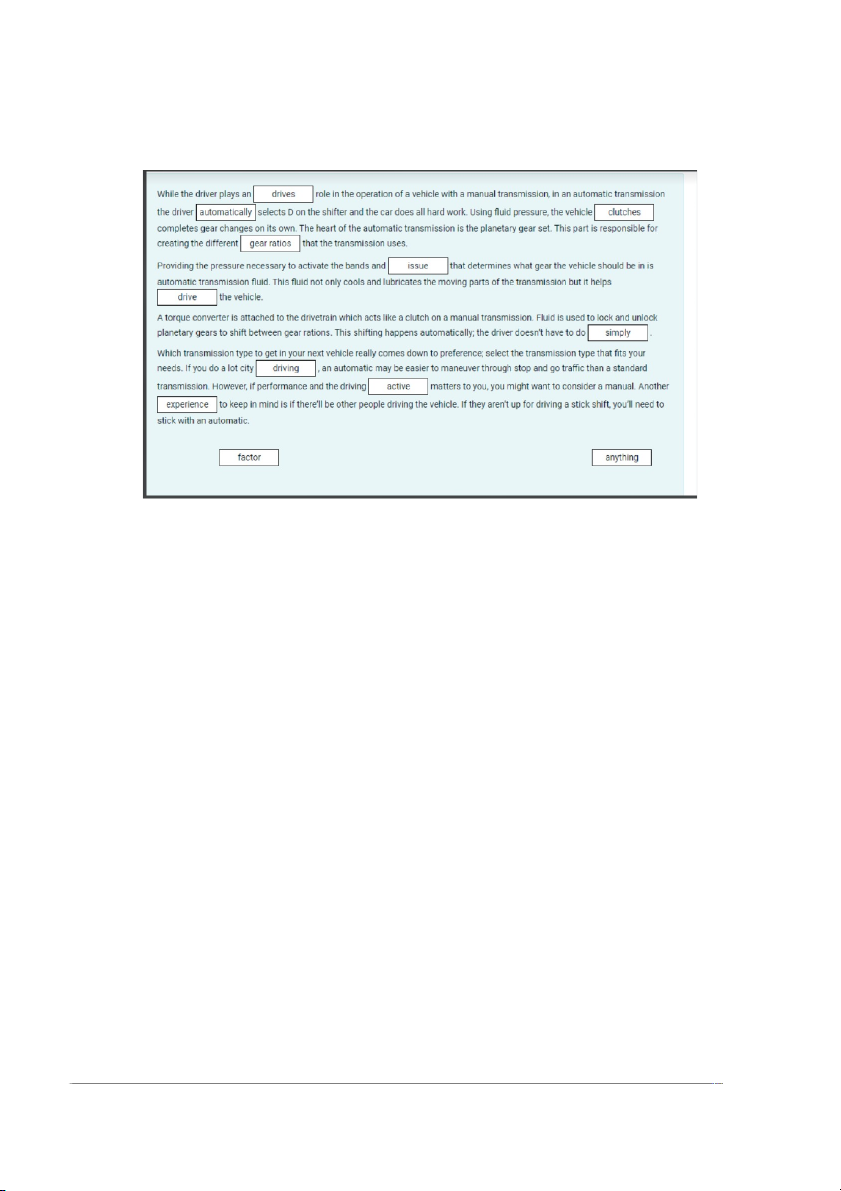
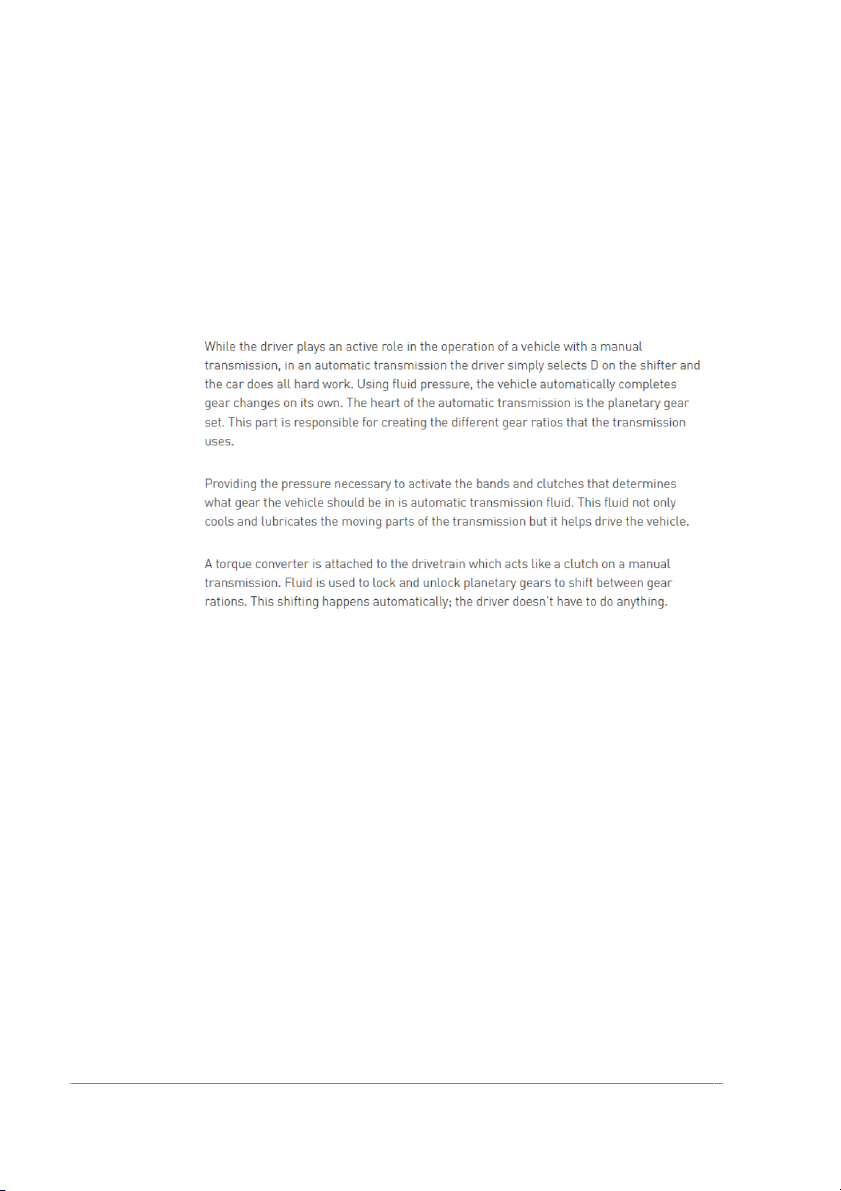
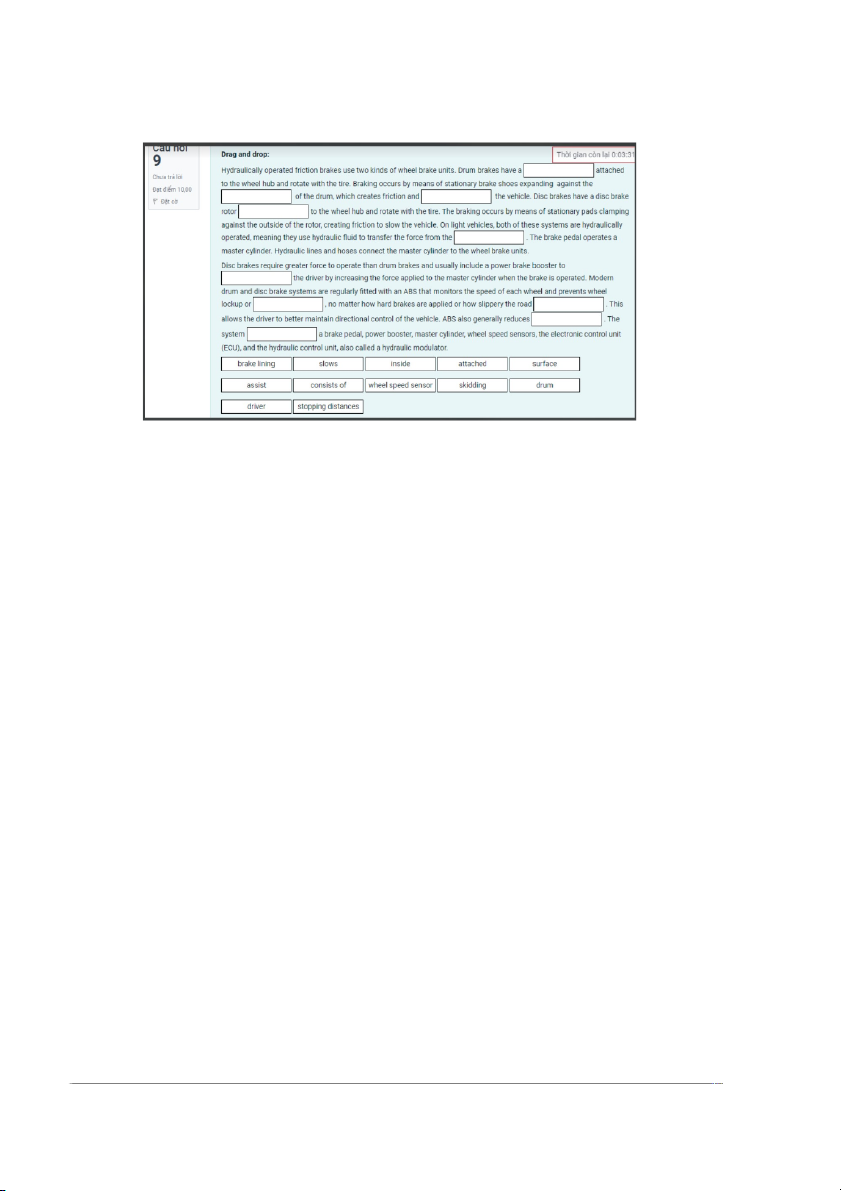
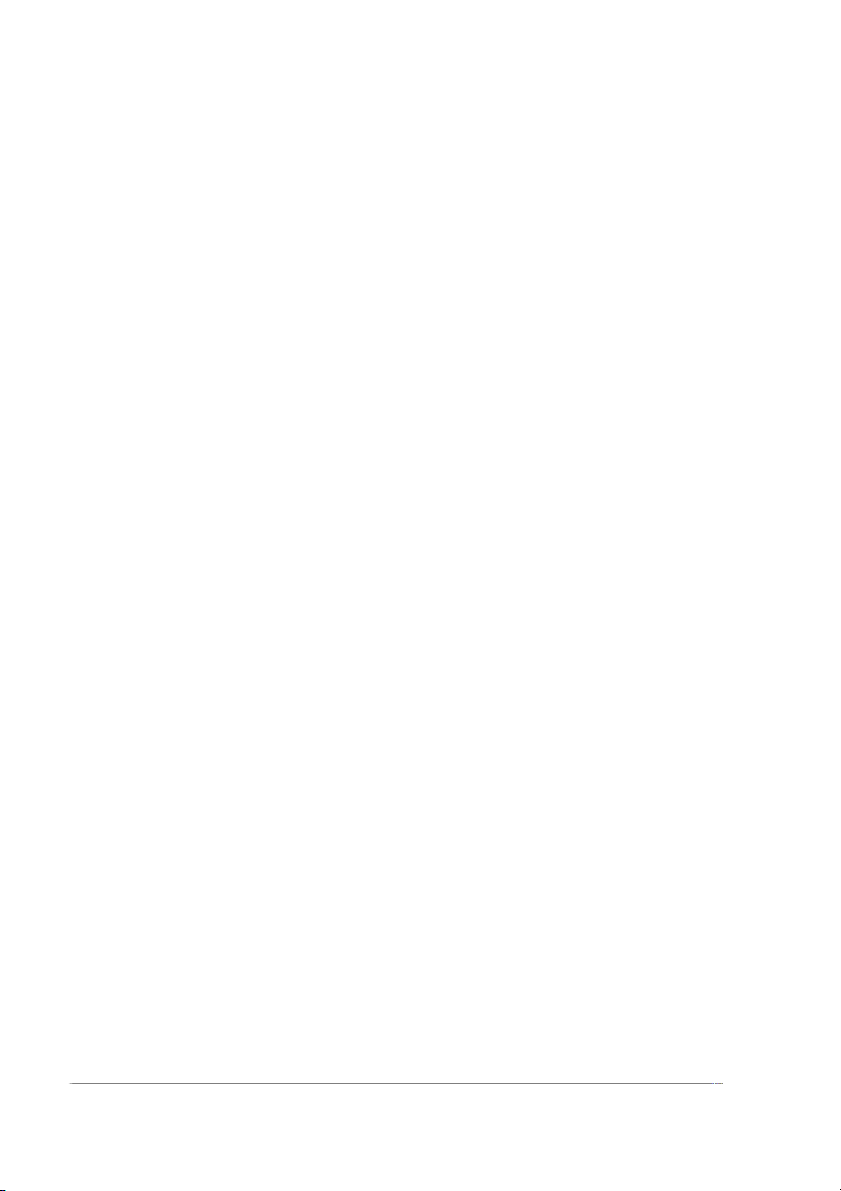
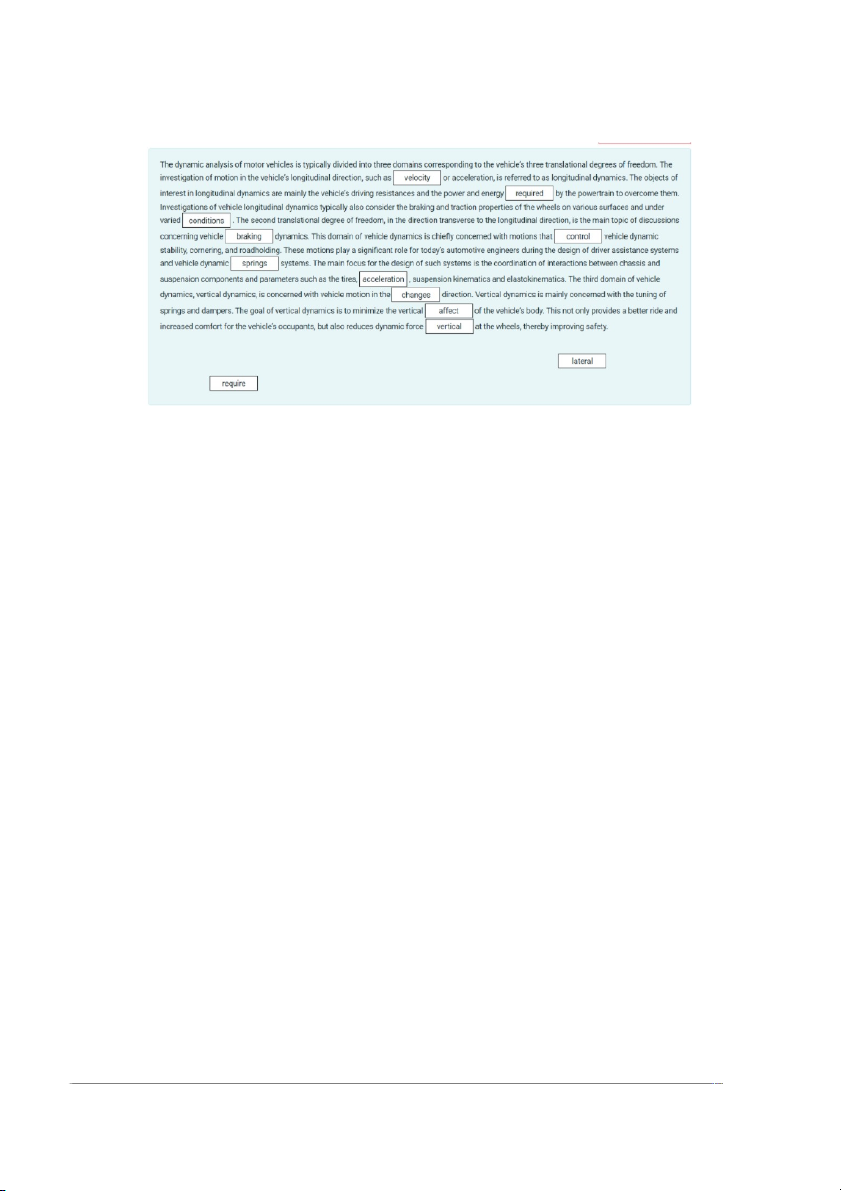
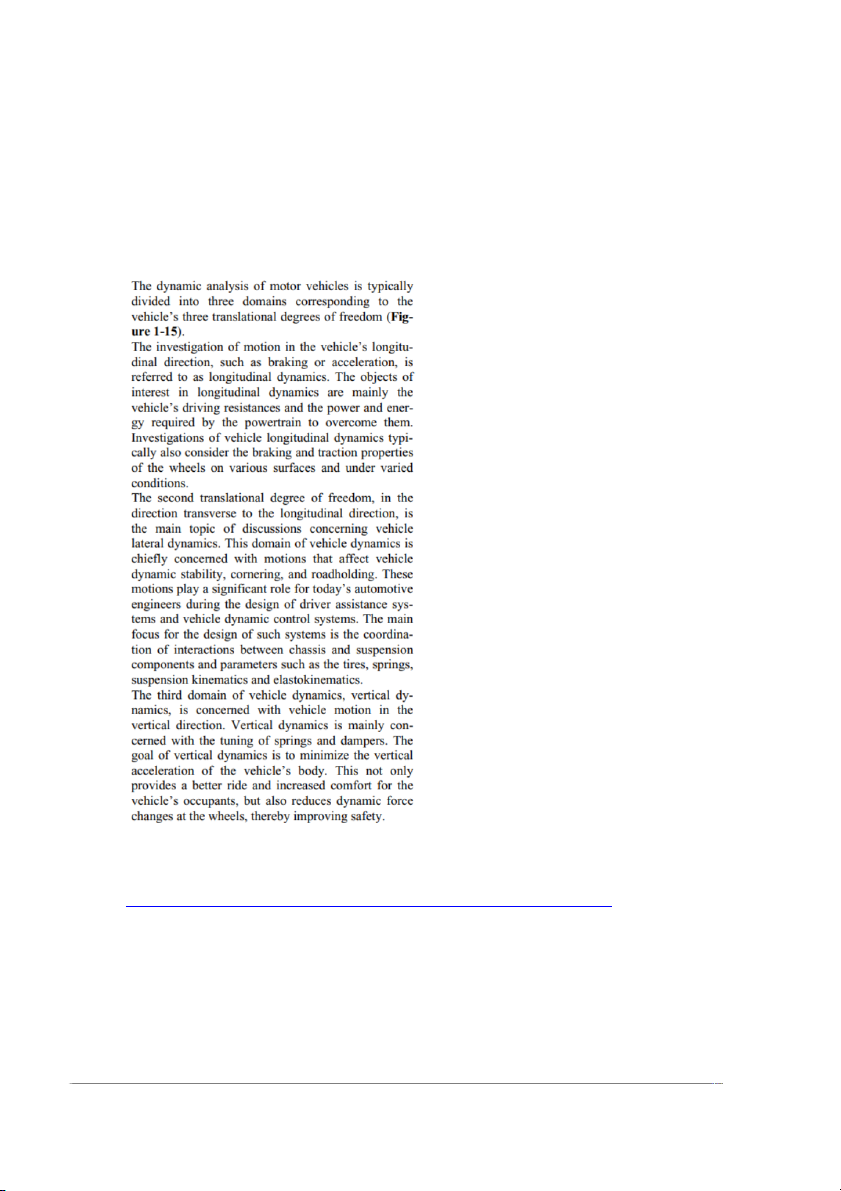
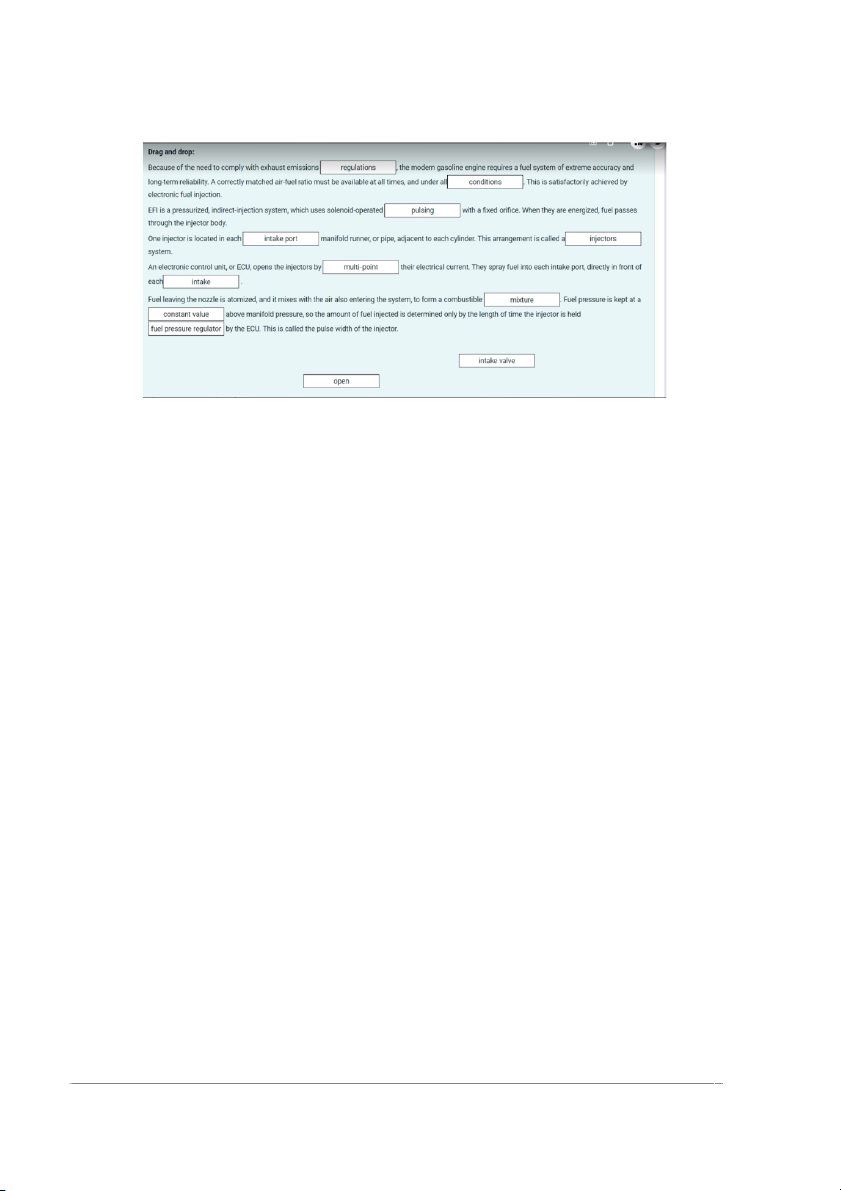

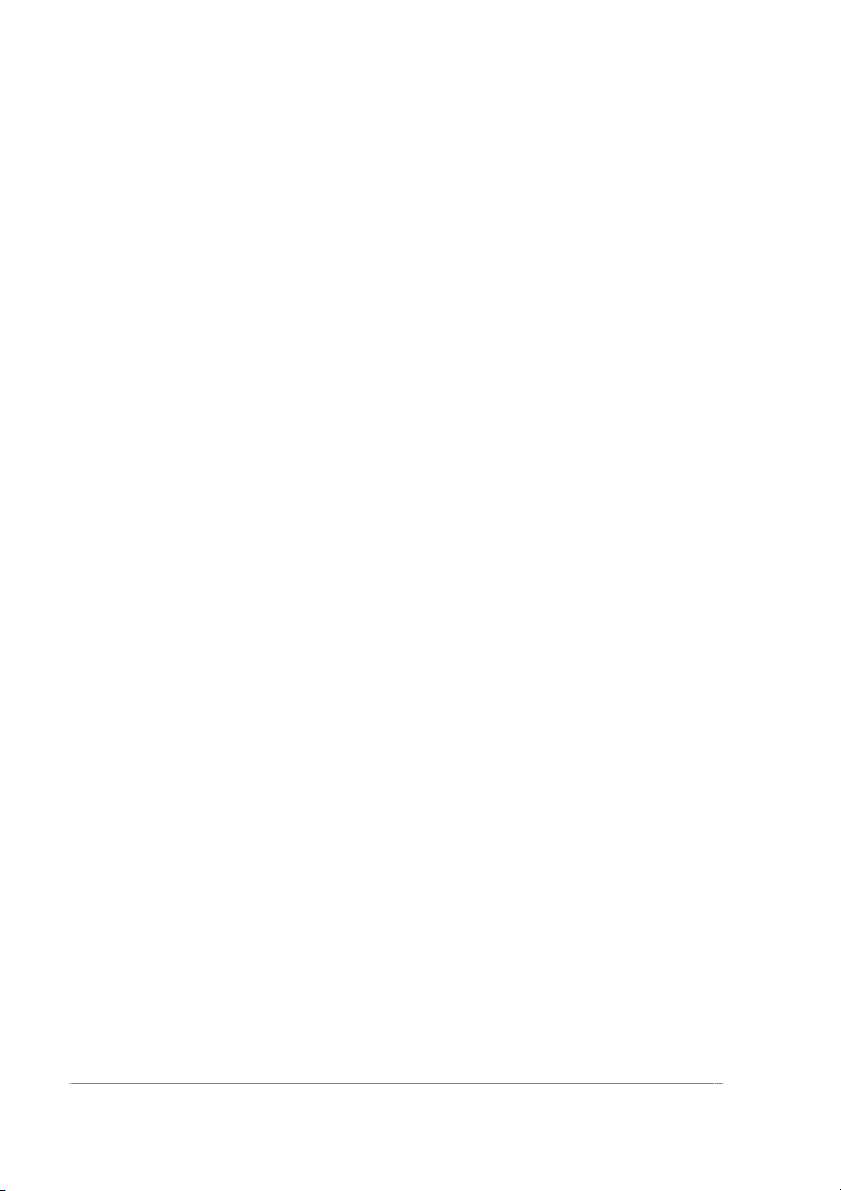
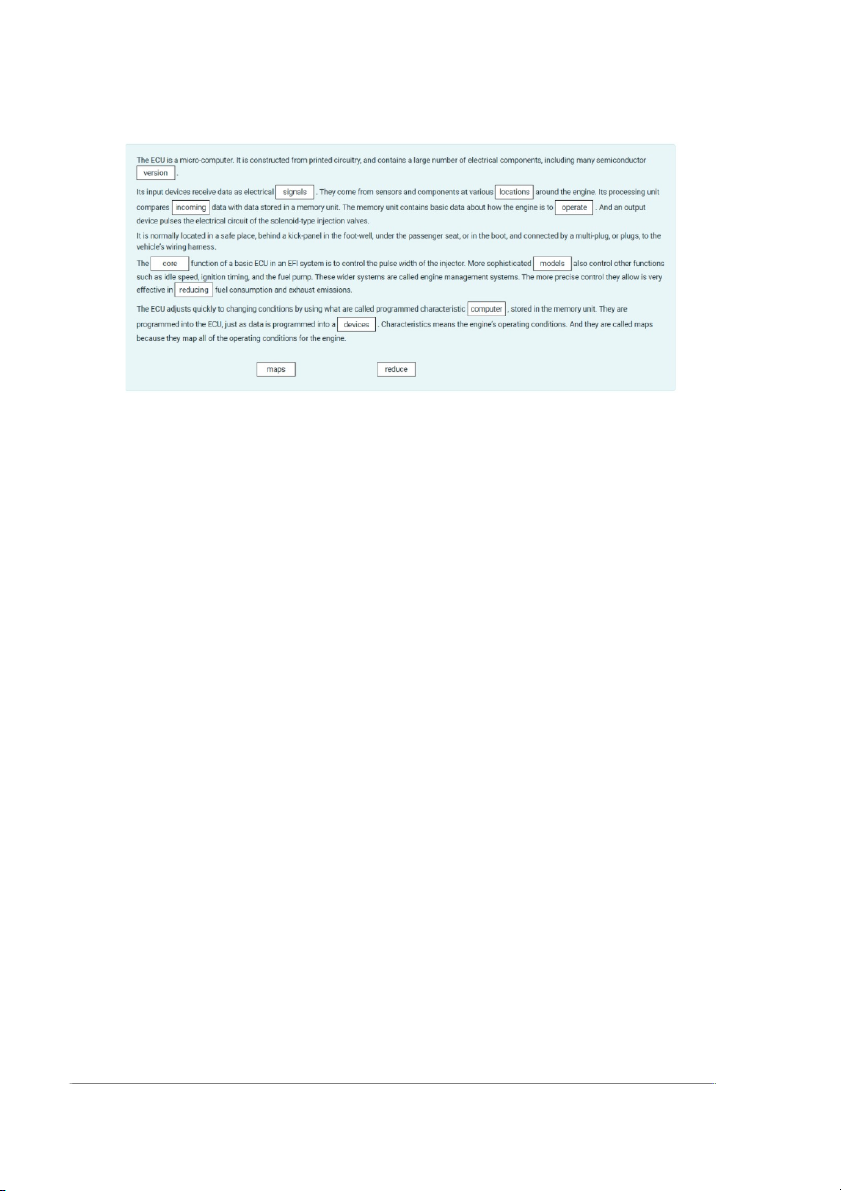
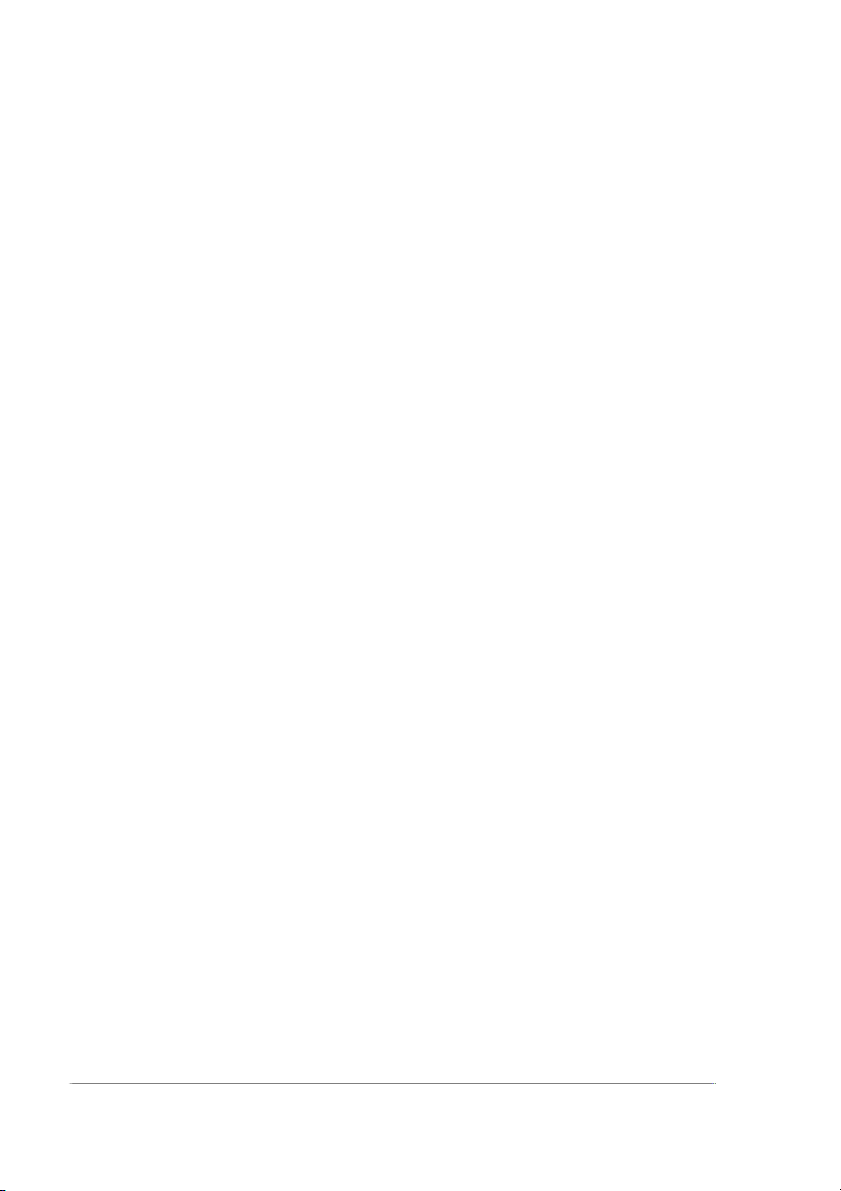
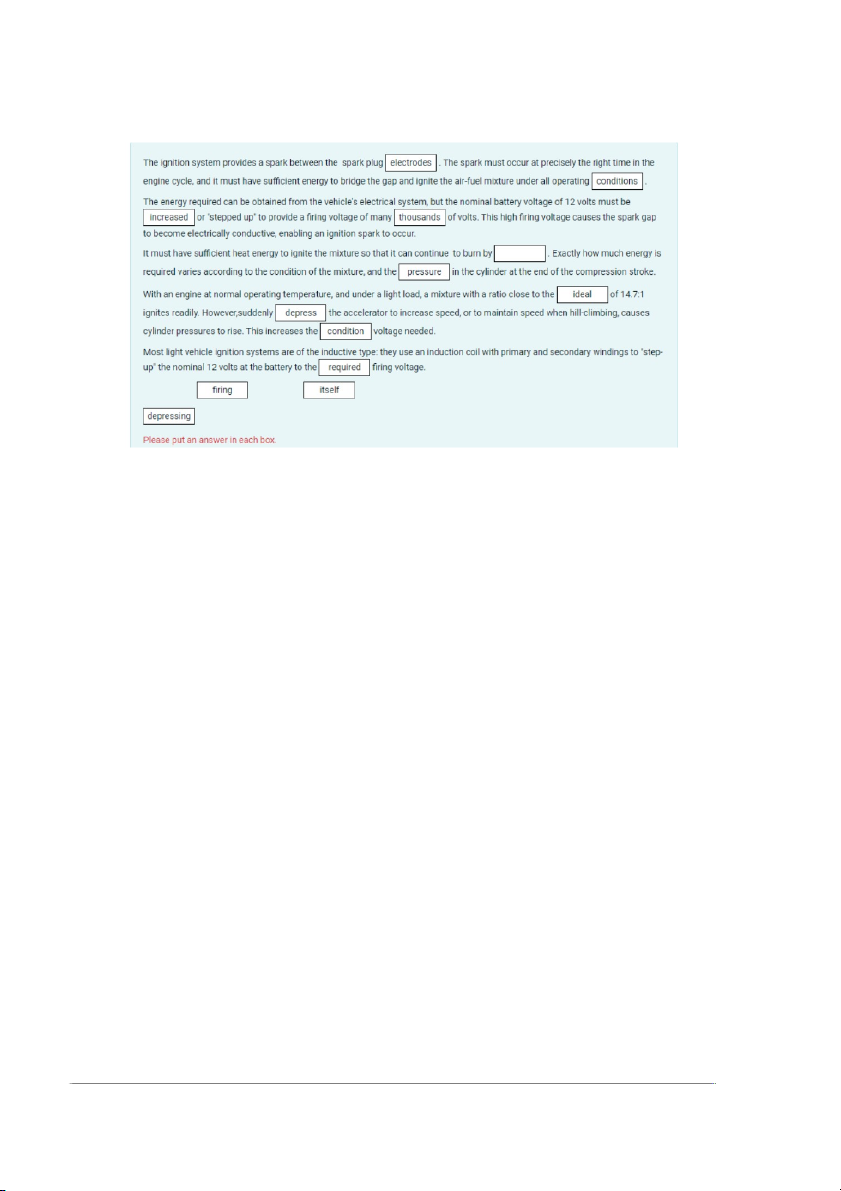
Preview text:
Bài 1
Rack And Pinion Steering System
The most common steering system, the rack and pinion gets its name
from the two gears it uses, the rack (the linear gear) and the pinion (circular
gear). This system is used in most of the cars and is usually not employed in
heavy-duty vehicles. Its working may appear complex but uses quite simple
physics. The steering wheel has a shaft attached to it and on the other end of the
shaft is the pinion. The pinion is positioned on top of the rack and moves when
the steering wheel is moved. The end of the rack has something called a tie rod.
The tie rods connect to the steering arm which in turn is connected to the wheel
hub. Onwards to the working of rack and pinion. When you rotate the steering
wheel the shaft rotates along with it. This in turn rotates the pinion which is on
top of the rack move linearly moving the tie rod. The tie rod connected to the
steering arm then causes the wheel to turn. The size of the pinion affects how
much turning you get. if the pinion is large in size it means that you'll be getting
more turn from less steering wheel rotation which will make it harder to control.
On the other hand, at smaller pinion means it'll be easier to control but you will
need multiple steering wheel turns to make the car comer.
Recirculating Ball Steering System
The recirculating ball steering system has two gears, the worm gear and
the sector gear. The steering wheel is connected to a threaded shaft which is
connected to a block. The worm gear is quite big and goes through the block
which is threaded in such a way it allows the worm gear inside. This block has
gear teeth outside of it to which the sector gear is connected. This sector gear is
then connected to the pitman arm while the pitman arm is attached to the tie rod.
There are ball bearings inside the block that fill the thread of the worm gear.
The working is simple just like rack and pinion.
When the steering wheel is rotated the shaft connected to the steering
rotates as well. The gear is bolted to not move up and down. This makes the
block and the worm gear rotate, The rotation makes the block move as it is not
held down by anything. The moving block then moves the sector gear which in
turn moves the pitman arm The thread of the worm gear is filled with ball
bearings which reduce Power-assisted rack and pinion friction and prevent the slop in gear.
The power steering adds some more parts to the rack and pinion system
which makes it easier to use, mainly the pump, pressure tubes, rotary control
valve, fluid lines and a hydraulic piston.
The job of the pump is to as you might have guessed, pump the fluid
around when needed. The rotary control valve ensures that the movement of
fluid is only performed when the driver is actually steering the car. The
hydraulic piston moves around depending on which fluid line brings the high-
pressure fluid. This piston movement on the rack makes it easier for the driver
as it is applying most of the force necessary to steer the car. This concludes the
brief discussion on how a hydraulic power steering.
Link bài: https://bitly.com.vn/mru44t Bài 2 (đúng) Vocabulary: Keep in contact with Make contact with
Withstand /wɪðˈstænd/: to be strong enough, or not be changed by
something, or to oppose a person or thing successfully
Sprung mass refers to vehicle parts supported on the springs, such as the
body, frame, and engine. Unsprung mass includes parts of the steering and
suspension not supported by springs, such as wheels, tires, and brake assemblies.
The suspension system isolates the body from road shocks and vibrations
which would otherwise be transferred to the passengers and load.
It also must keep the tires in contact with the road. When a tire hits an
obstruction cản trở, there is a reaction force. The size of this reaction force
depends on the unsprung mass at each wheel assembly.
The sprung mass is that part of the vehicle supported by the springs - such
as the body, the frame, the engine, and associated parts.
Unsprung mass includes the components that follow the road contours,
such as wheels, tires, brake assemblies, and any part of the and steering
suspension not supported by the springs.
Vehicle ride and handling can be improved by keeping unsprung mass as
low as possible. When large and heavy wheel assemblies encounter a bump or
pothole, they experience a larger reaction force, sometimes large enough to
make the tire lose contact with the road surface.
Wheel and brake units that are small, and light, follow road contours
without a large effect on the rest of the vehicle. At the same time, a suspension
system must be strong enough to withstand loads imposed by vehicle mass
during cornering accelerating braking, and uneven road surfaces. wheel performance Bài 3 (đúng)
The antilock braking system controls braking force by controlling the
hydraulic pressure off the braking system, so that the wheel lock during braking.
Braking force and the tendency (Khuynh hướng) of the wheels to lock up
are affected by a combination of factors such as the friction coefficient of the
road surface and the difference between the vehicle speed and the road wheel
speed. The ABS prevents the road wheels from locking up during heavy braking
by controlling the vehicle's brake system hydraulic pressure.
During normal braking, as the rotational speed of the wheel falls, no
electric current flows from the ECU to the hydraulic unit. The solenoid valve is
not energized. The brake master cylinder hydraulic pressure is applied to the
brake unit, and the ABS is not involved. However, even though the ABS is
passive during normal braking, its control module is constantly monitoring for
rapid deceleration of any of the wheels.
If a wheel-speed sensor signals severe wheel deceleration - which means
the wheel is likely to lock up - the ECU sends a current to the hydraulic unit.
This energizes the solenoid valve. The action of the valve isolates the brake
circuit from the master cylinder. This stops the braking pressure at that wheel
from rising, and keeps it constant.
If the sensors signal the wheel is still decelerating too rapidly, the ECU
sends a larger current to the hydraulic unit. The armature moves even further
and opens the valve. It opens a passage from the brake circuit. Brake fluid is
sent from the brake circuit back to the master cylinder. Pressure in the brake
caliper circuit is reduced so that the wheel is braked less heavily.
If the wheel sensors indicate that lowering the brake pressure is letting
the wheel accelerate again, the ECU stops sending current to the hydraulic unit
and de energizes the solenoid valve. This lets the pressure increase, so that the wheel is again decelerated.
This cycle signals itself about four to six times per second It is normal in
an ABS for the valves in the hydraulic control unit to keep changing position as
they change (modulate điều chỉnh) the brake pressure that's being increased
(applied). These changes in position may cause rapid pulsations to be felt through the brake pedal. solenoid decelerated
link bài: https://bitly.com.vn/tmb3vt Bài 4 dung
In a conventional four-wheel drive vehicle, propeller shafts ( drive
shaft) connect a transfer case at the rear of the transmission to final drive units on both front and rear axles.
Vehicles with part-time four wheel drive are designed for optional off
road use. Four wheel drive can be selected for abnormal ( Bất thường) surfaces
and disconnected for normal road surfaces. In this application, the engine and
transmission are mounted longitudinally at the front. Propeller shafts connect a
transfer case, which is attached to the rear of the transmission, to final drive
units on both front and rear axles. The beam type axle housings enclose the
crown wheel and pinion and differential gears, and the offset propeller shafts
mean the drive is connected through short and long axle shafts to the driving
wheels. Steering is catered for by mounting the front wheel hubs on large ball
swivels, attached to the ends of the axle housing. Universal joints are
incorporated in the front axle shafts. The transfer case lets the driver select
either two-wheel-drive or four-wheel-drive in high range, or four-wheel drive in
low range. A neutral position allows an accessory, such as a cable winch, to be
driven from use. power transmitted gear on the transmission output shaft. When
four wheel drive is engaged, the front and rear propeller shafts are locked
together and driven at the a same speed. Drive is transmitted to front and rear
final drive units simultaneously. take-off selected Vocabulary:
The drive shaft (also called propeller shaft or prop shaft) : a component of the
drive train in a vehicle, with the purpose of delivering torque from the
transmission to the differential, which then transmits this torque to the wheels in order to move the vehicle. Bài 5 Đúng
While the driver plays an active role in the operation of a vehicle with a manual
transmission, in an automatic transmission the driver simply selects D on the
shifter and the car does all hard work. Using fluid pressure, the vehicle
automatically completes gear changes on its own. The heart of the automatic
transmission is the planetary gear set. This part is responsible for creating the
different gear ratios that the transmission uses.
Providing the pressure necessary to activate the bands and clutches that
determines what gear the vehicle should be in is automatic transmission fluid.
This fluid not only cools and lubricates the moving parts of the transmission but it helps drive the vehicle.
A torque converter is attached to the drivetrain which acts like a clutch on a
manual transmission. Fluid is used to lock and unlock planetary gears to shift
between gear rations. This shifting happens automatically, the driver doesn't have to do anything
Which transmission type to get in your next vehicle really comes down to
preference; select the transmission type that fits your needs. If you do a lot city
driving, an automatic may be easier to maneuver through stop and go traffic
than a standard transmission. However, if performance and the driving
experience matters to you, you might want to consider a manual. Another Factor
to keep in mind is if there'll be other people driving the vehicle. If they aren't up
for driving a stick shift, you'll need to stick with an automatic. drives issue link bài: Bài 6 đúng
Hydraulically operated friction brakes use two kinds of wheel brake units. Drum
brakes have a drum attached to the wheel hub and rotate with the tire. Braking
occurs by means of stationary brake shoes expanding agains the inside of the
drum, which creates friction and slows.the vehicle. Disc brakes have a disc
brake rotor attached to the wheel hub and rotate with the tire. The braking
occurs by means of stationary pads clamping against the outside of the rotor,
creating friction to slow the vehicle. On light vehicles, both of these systems are
hydraulically operated, meaning they use hydraulic fluid to transfer the force
from the brake lining .The brake pedal operates a master cylinder. Hydraulic
lines and hoses connect the master cylinder to the wheel brake units. Disc
brakes require greater force to operate than drum brakes and usually include a
power brake booster to assist the driver by increasing the force applied to the
master cylinder when the brake is operated. Modern drum and disc brake
systems are regularly fitted with an ABS that monitors the speed of each wheel
and prevents wheel lockup or skidding, no matter how hard brakes are applied
or how slippery the road surface .This allows the driver to better maintain
directional control of the vehicle. ABS also generally reduces stopping
distances.The system consists of a brake pedal, power booster, master cylinder,
wheel speed sensors, the electronic control unit (ECU), and the hydraulic
control unit, also called a hydraulic modulator. driver wheel speed sensor drum Bài 7.1 (đúng)
The dynamic analysis of motor vehicles is typically divided into three
domains corresponding to the vehicle's three translational degrees of freedom.
The investigation of motion in the vehicle's longitudinal direction, such as
braking or acceleration, is referred to as longitudinal dynamics. The objects of
interest in longitudinal dynamics are mainly the vehicle's driving resistances
and the power and energy required by the powertrain to overcome them.
Investigations of vehicle longitudinal dynamics typically also consider the
braking and traction properties of the wheels on various surfaces and under varied conditions.
The second translational degree of freedom, in the direction transverse to
the longitudinal direction, is the main topic of discussions concerning vehicle
Lateral dynamics. This domain of vehicle dynamics is chiefly concerned with
motions that affect vehicle dynamic stability, cornering, and road holding.
These motions play a significant role for today's automotive engineers during
the design of driver assistance systems and vehicle dynamic control systems.
The main focus for the design of such systems is the coordination of
interactions between chassis and suspension components and parameters such as
the tires, springs, suspension kinematics and elastokinematics.
The third domain of vehicle dynamics, vertical dynamics, is concerned
with vehicle motion in the vertical direction. Vertical dynamics is mainly
concerned with the tuning of springs and dampers. The goal of vertical
dynamics is to minimize the vertical acceleration of the vehicle's body. This not
only provides a better ride and increased comfort for the vehicle's occupants,
but also reduces dynamic force changes at the wheels, thereby improving safety. require velocity Tracnghiem:
https://123docz.net/document/4607098-tieng-anh-chuyen-nganh.htm Bài 7 (đúng)
Drag and drop: Because of the need to comply with exhaust emissions
regulations (quy định) , the modern gasoline engine requires a fuel system of
extreme accuracy and long-term reliability. A correctly matched air-fuel ratio
must be available at all times, and under all conditions. This is satisfactorily
achieved by electronic fuel injection. EFI is a pressurized, indirect-injection
system, which uses solenoid-operated injectors (kim phun hoạt động bằng điện
từ) with a fixed orifice. When they are energized, fuel passes through the
injector body. One injector is located in each intake port manifold runner, or
pipe, adjacent (liền kề) to each cylinder. This arrangement is called a multi-
point system. An electronic control unit, or ECU, opens the injectors by pulsing
their electrical current. They spray fuel into each intake port, directly in front of each intake valve.
Fuel leaving the nozzle is atomized, and it mixes with the air also entering the
system, to form a combustible mixture. Fuel pressure is kept at a constant value
above manifold pressure, so the amount of fuel injected is determined only by
the length of time the injector is held fuel pressure regulator by the ECU. This is
called the pulse width of the injector. intake open Bài 8 (đúng)
Drag and Drop: Air cooled engines with multi cylinders, especially under a
bonnet, must have some form of fan cooling and ducting. This is to make sure
all cylinders are cooled evenly. The cylinders and cylinder heads are finned.
Hotter areas, such as near the exhaust ports on the cylinders, have bigger fins.
Fan blown air is directed by a metal cowling so it stays close to the finned
areas. Air flow is controller by a thermostatically controlled flap. When the
engine is warming up, the flap is closed to restrict the movement of air. When
the engine reaches its operating temperature, the flap opens and allows the air to
flow over the engine. The large cooling fan is driven from the engine by a belt .
This belt must not be allowed to slip or break, because serious damage will
occur. Regular servicing is important.
The main parts of a water cooling system are as follows: water jacket, water
pump, thermostat, radiator, cooling fan. Water cooled engines work by
surrounding the hot areas inside the engine with a water jacket. The water takes
on heat from the engine and, as it circulates through the radiator, gives it off to
the atmosphere. The heat concentrates around the top of the engine, so a water
pump is needed to ensure proper circulation. When the thermostat is open, the
water pump circulates water through the radiator and around the engine. When
the thermostat is closed, water circulates only round the engine and not through
the radiator. Forcing water around the engine prevents vapour pockets forming
in very hot areas. Water circulation is assisted by the thermo-siphon action as
the water is heated, it rises and moves to the top of the radiator. This pushes
down on the colder water underneath, which moves into the engine. This water is heated, rises and so on. controlled water pump
link bài: https://bitly.com.vn/pqwsl5 Bài 9 dung
The ECU is a micro-computer. It is constructed from printed circuitry, and
contains a large number of electrical components, including many
semiconductor (chất bán dẫn) devices.
Its input devices receive data as electrical signals. They come from sensors and
components at various locations around the engine. Its processing unit compares
incoming data with data stored in a memory unit. The memory unit contains
basic data about how the engine is to operate . And an output device pulses the
electrical circuit of the solenoid-type injection valves. It is normally located in a
safe place, behind a kick-panel in the foot-well Choã ñeå chaân., under the
passenger seat, or in the boot (Ngaên ñaët aéc quy), and connected by a
multi-plug, or plugs, to the vehicle's wiring harness (Buoái (boù) daây
ñieän). The core function of a basic ECU in an EFI system is to control the
pulse width (độ rộng xung) of the injector. More sophisticated models also
control other functions such as idle speed, ignition timing, and the fuel pump.
These wider systems are called engine management systems. The more precise
control they allow is very effective in reducing fuel consumption and exhaust emissions.
The ECU adjusts quickly to changing conditions by using what are called
programmed characteristic version, stored in the memory unit. They are
programmed into the ECU, just as data is programmed into a computer.
Characteristics means the engine's operating conditions. And they are called
maps because they map all of the operating conditions for the engine. Maps reduce Bài 10 dungs
The ignition system provides a spark between the spark plug electrodes. The
spark must occur at precisely the right time in the engine cycle, and it must have
sufficient energy to bridge the gap and ignite the air-fuel mixture under all
operating conditions. The energy required can be obtained from the vehicle's
electrical system, but the nominal battery voltage of 12 volts must be increased
or "stepped up" to provide a firing voltage of many thousands of volts. This
high firing voltage causes the spark gap to become electrically conductive,
enabling an ignition spark to occur. It must have sufficient heat energy to ignite
the mixture so that it can continue to burn by itself Exactly how much energy is
required varies according to the condition of the mixture, and the pressure in the
cylinder at the end of the compression stroke.
With an engine at normal operating temperature, and under a light load, a
mixture with a ratio close to the ideal of 14.7:1 ignites readily. However,
suddenly depressing the accelerator to increase speed, or to maintain speed
when hill-climbing, causes cylinder pressures to rise. This increases the firing voltage needed.
Most light vehicle ignition systems are of the inductive type: they use an
induction coil with primary and secondary windings to "stepup" the nominal 12
volts at the battery to the required firing voltage.