
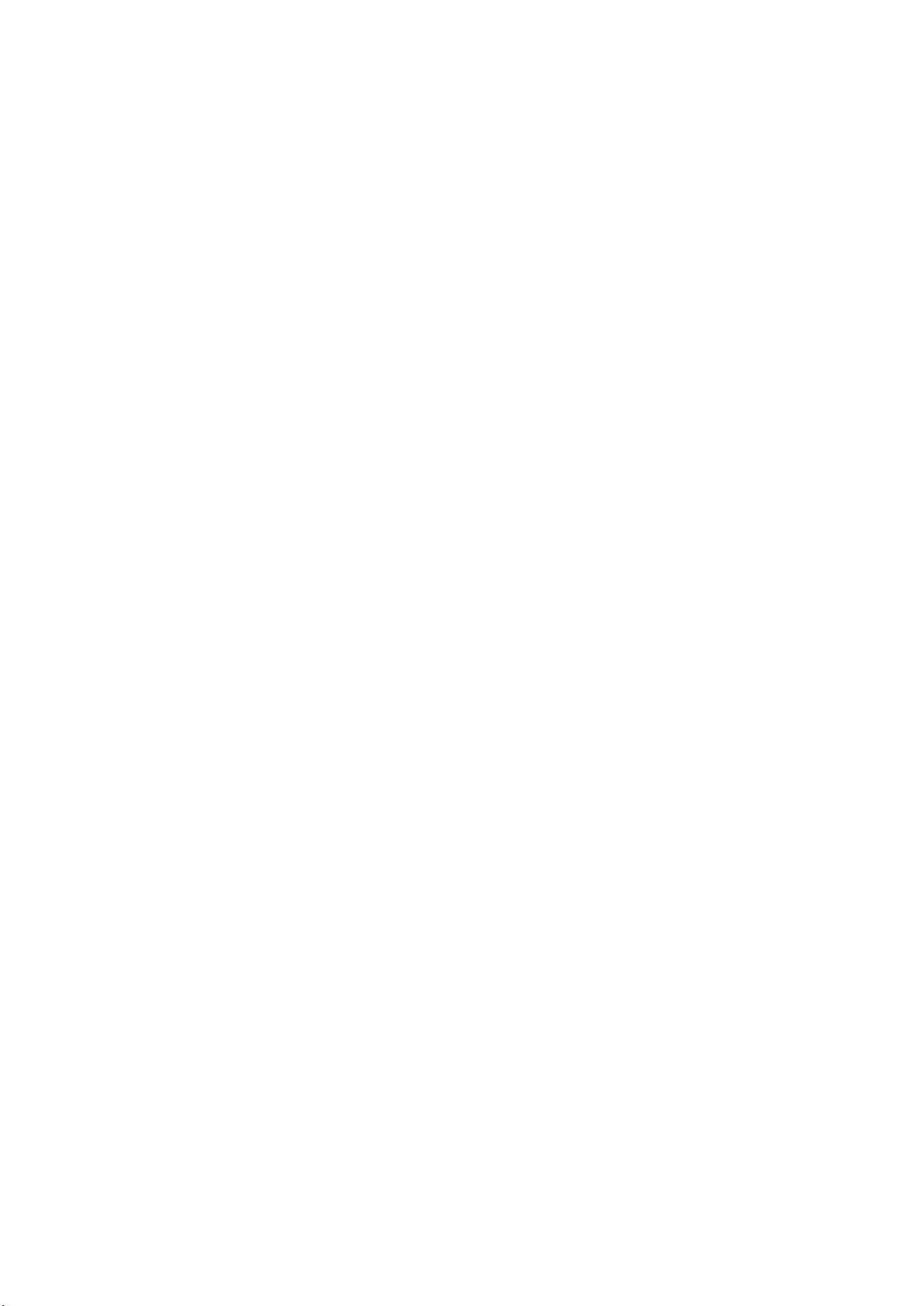
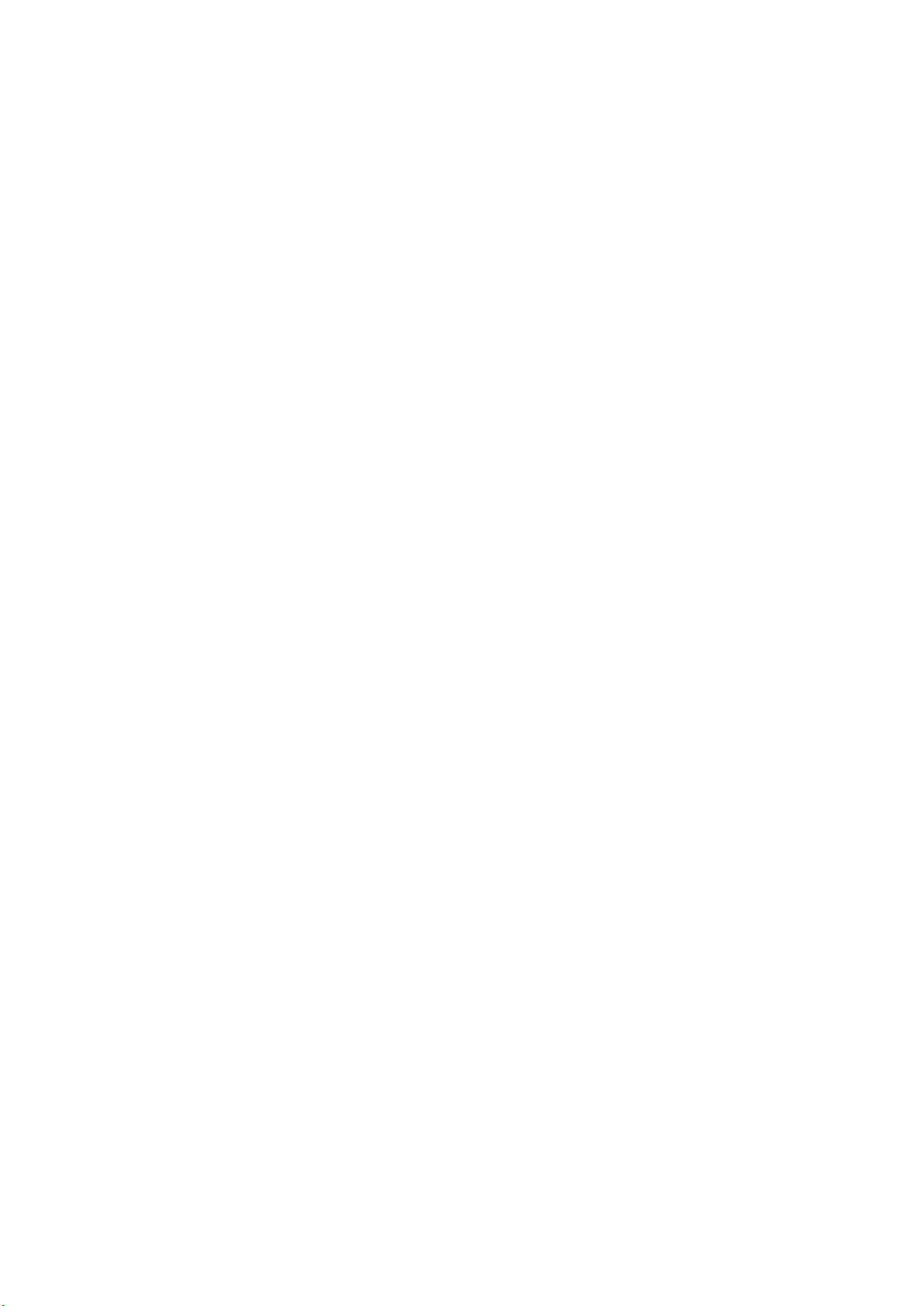
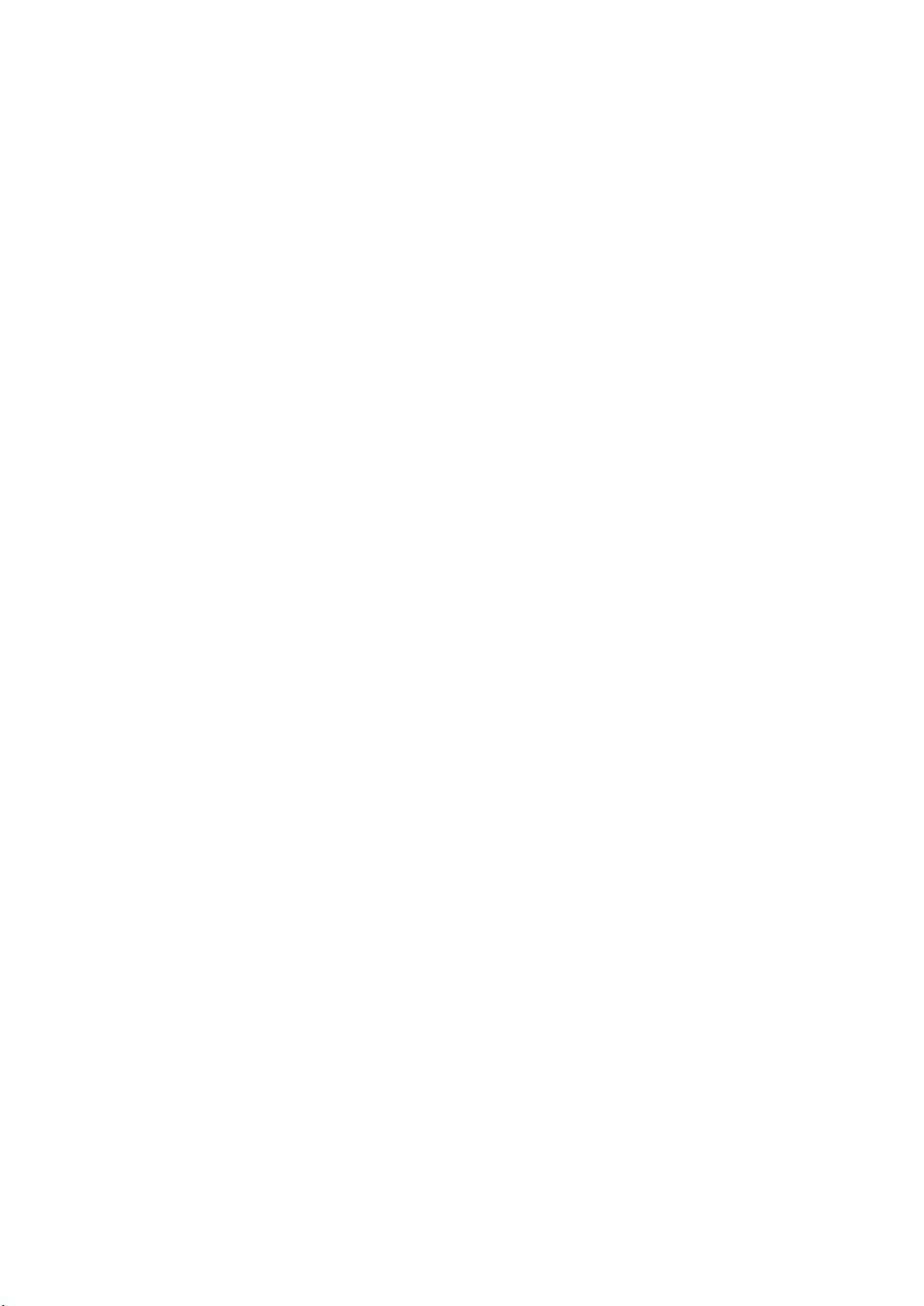
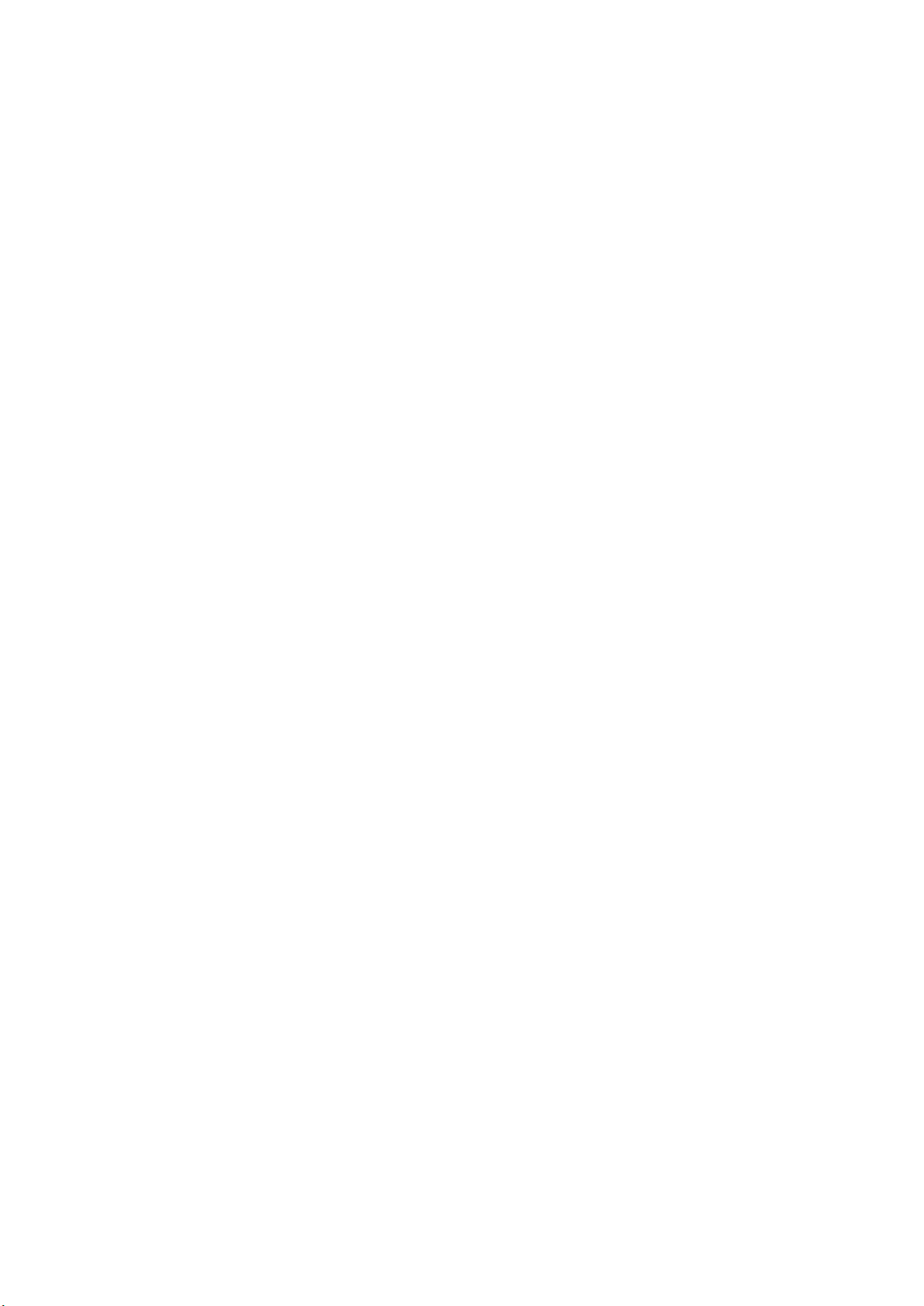
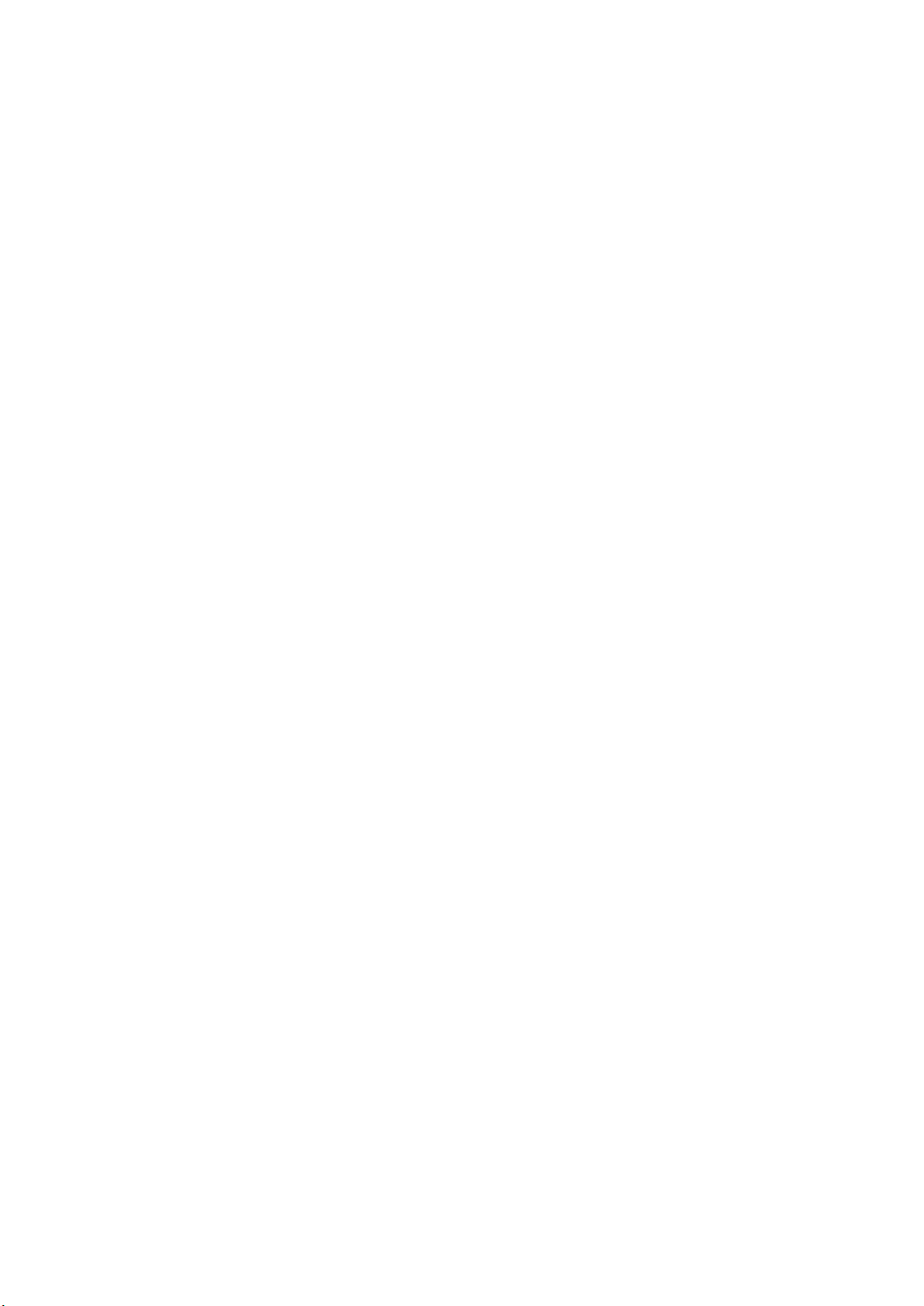
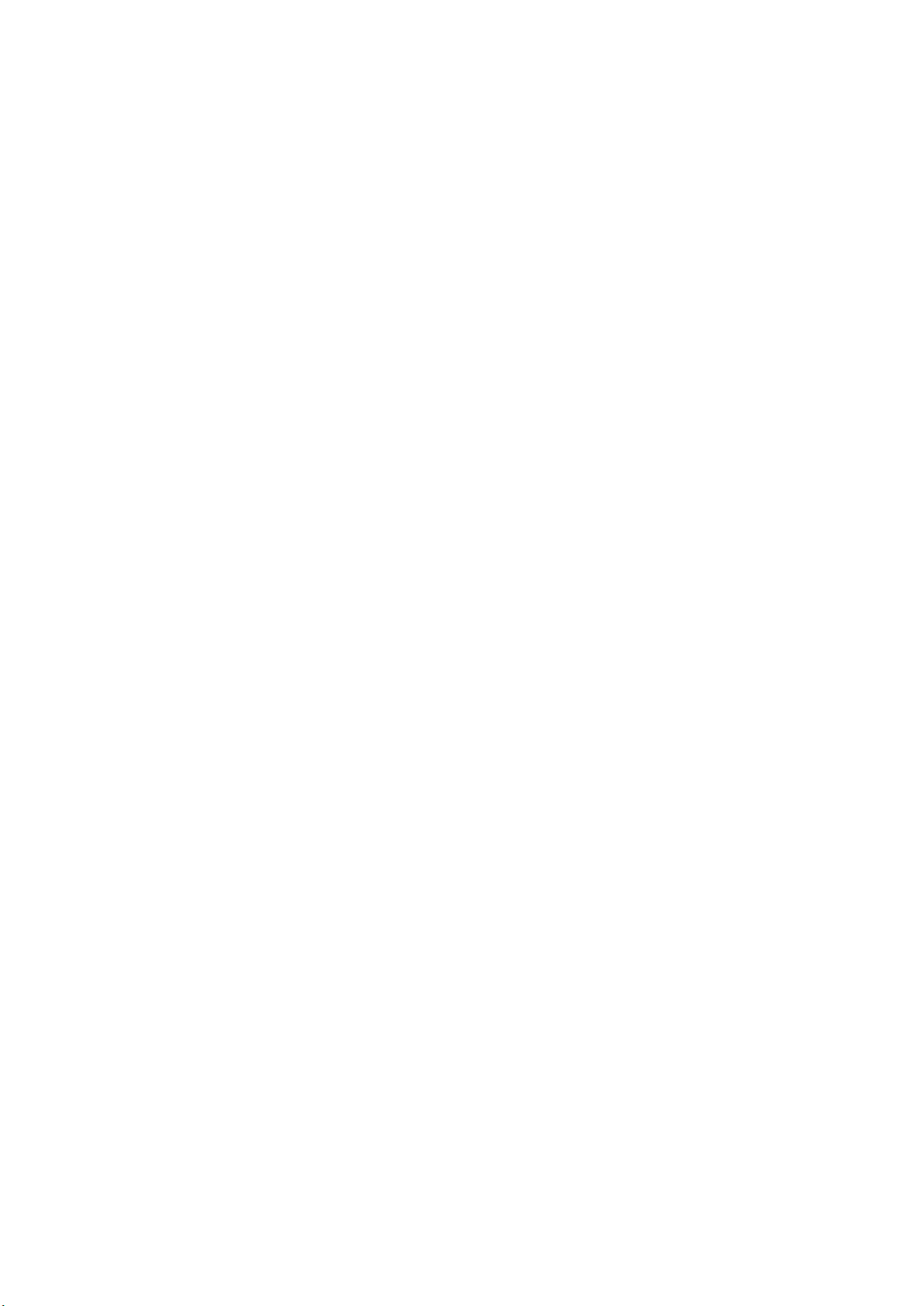
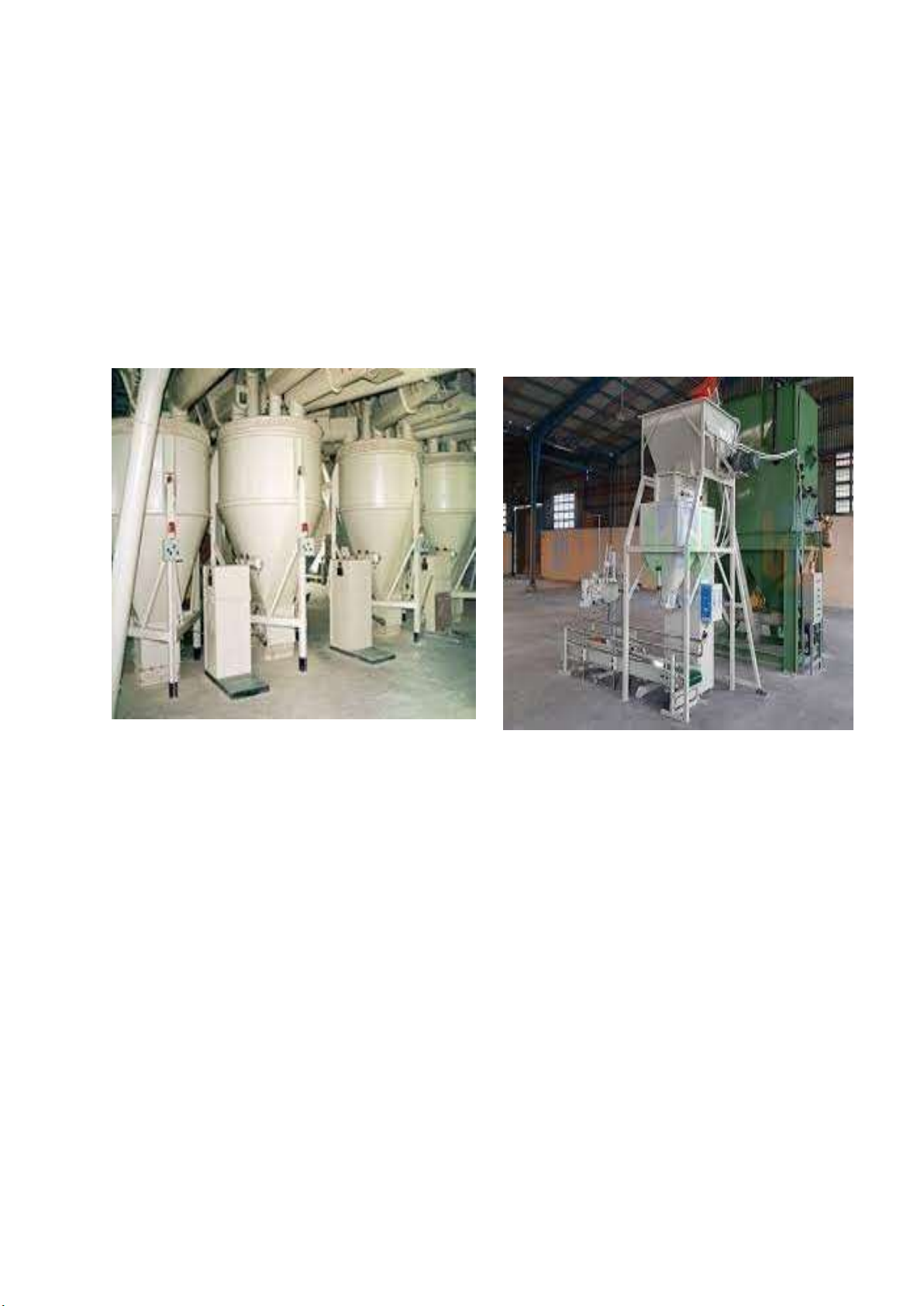
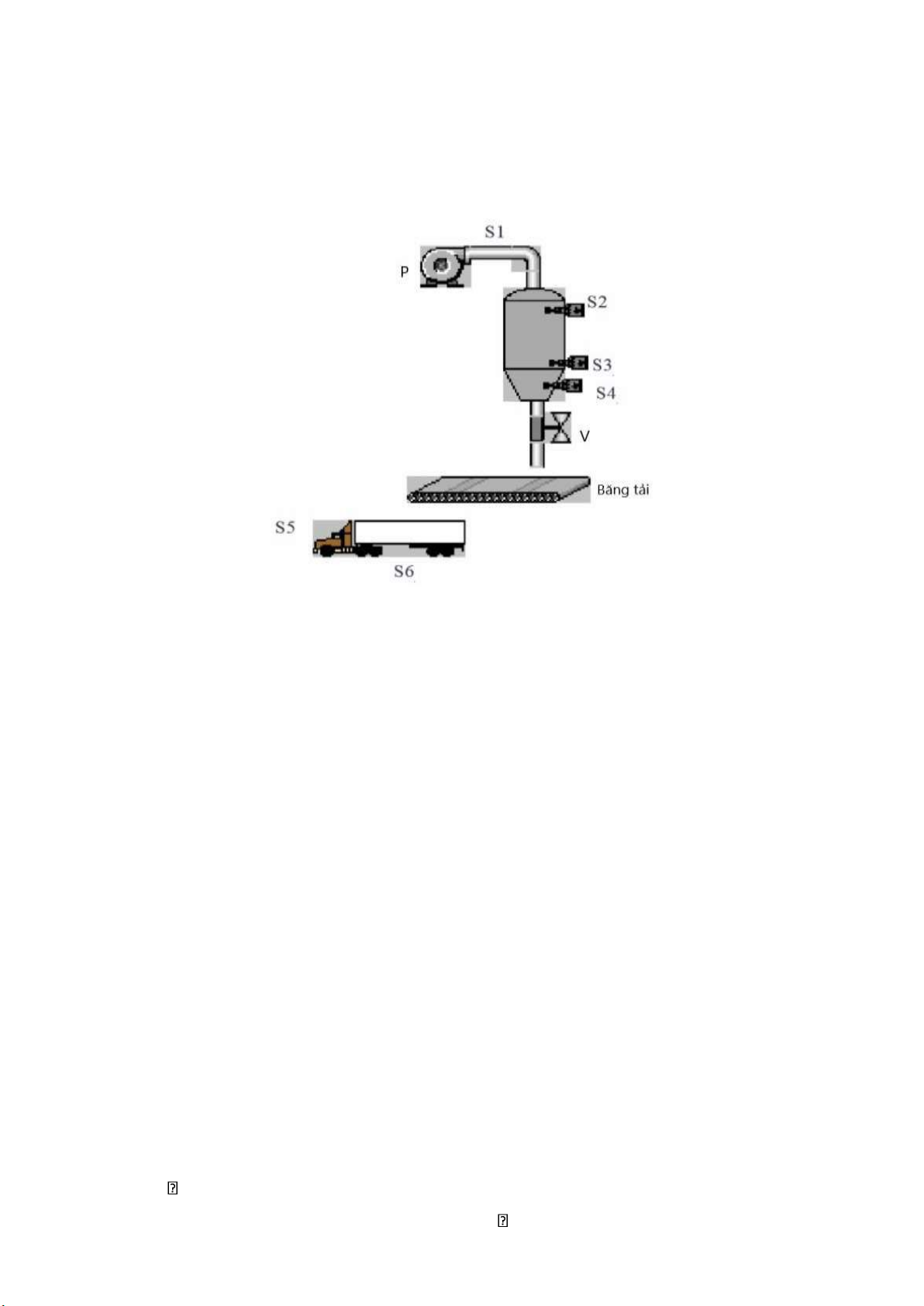
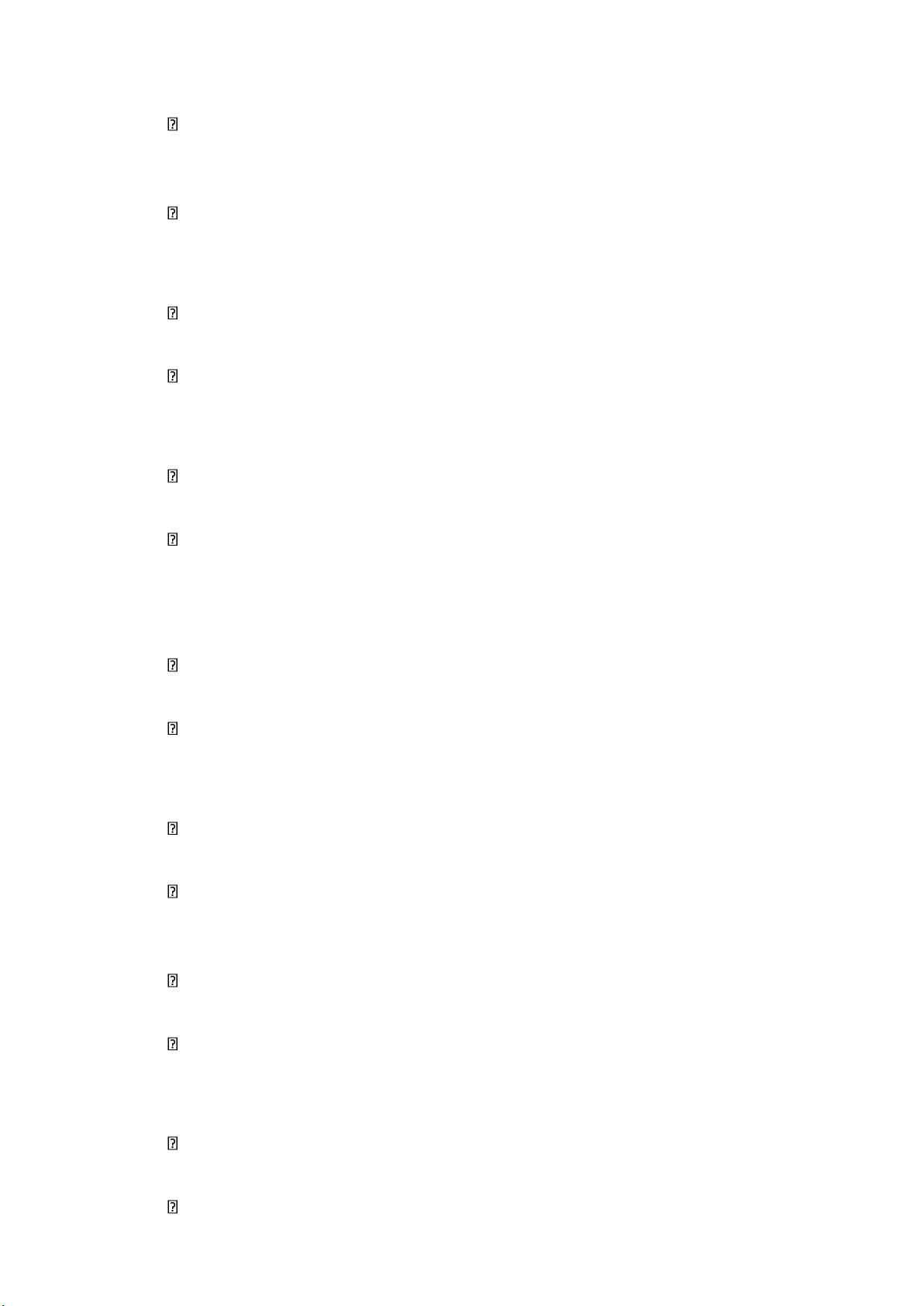
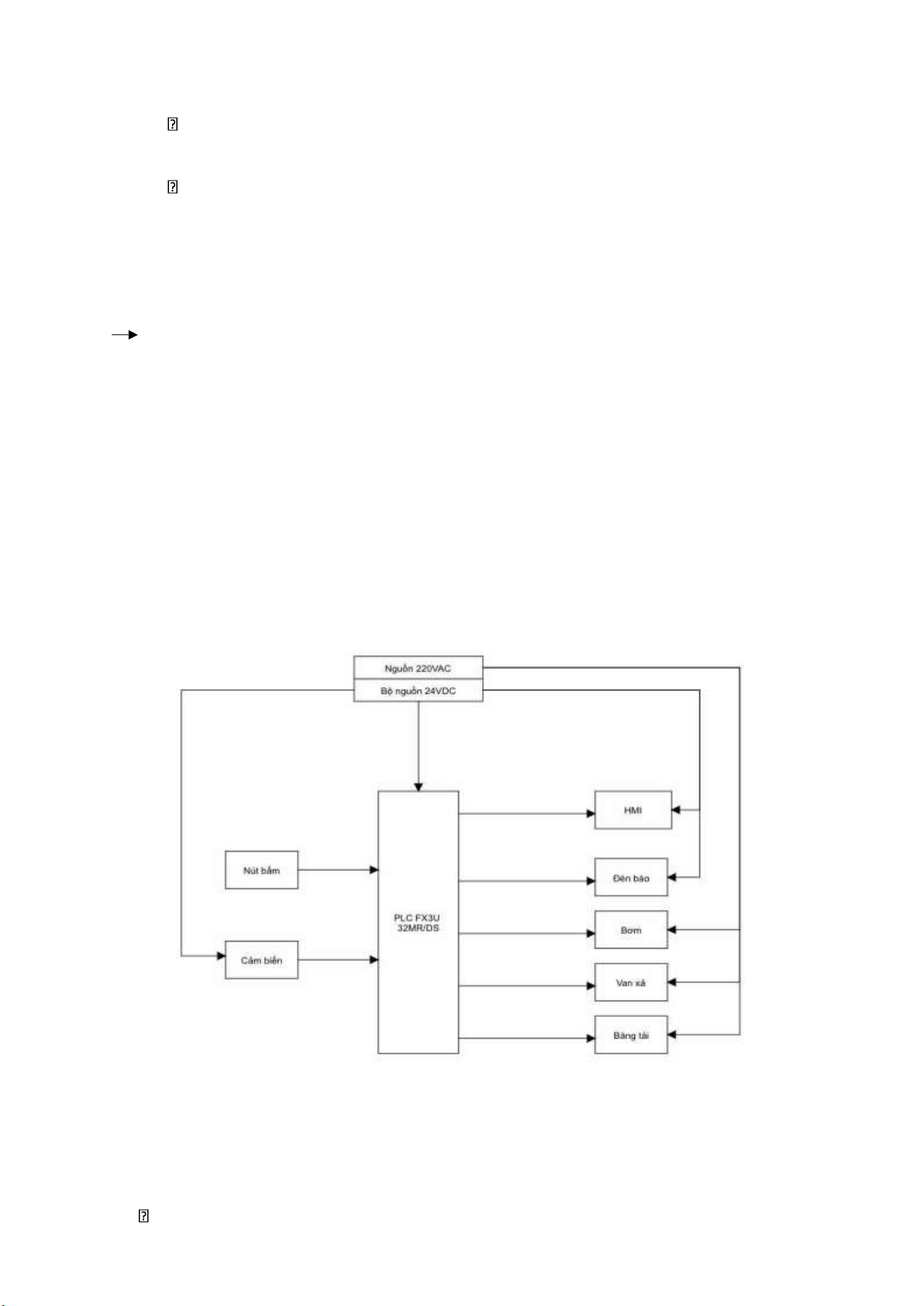
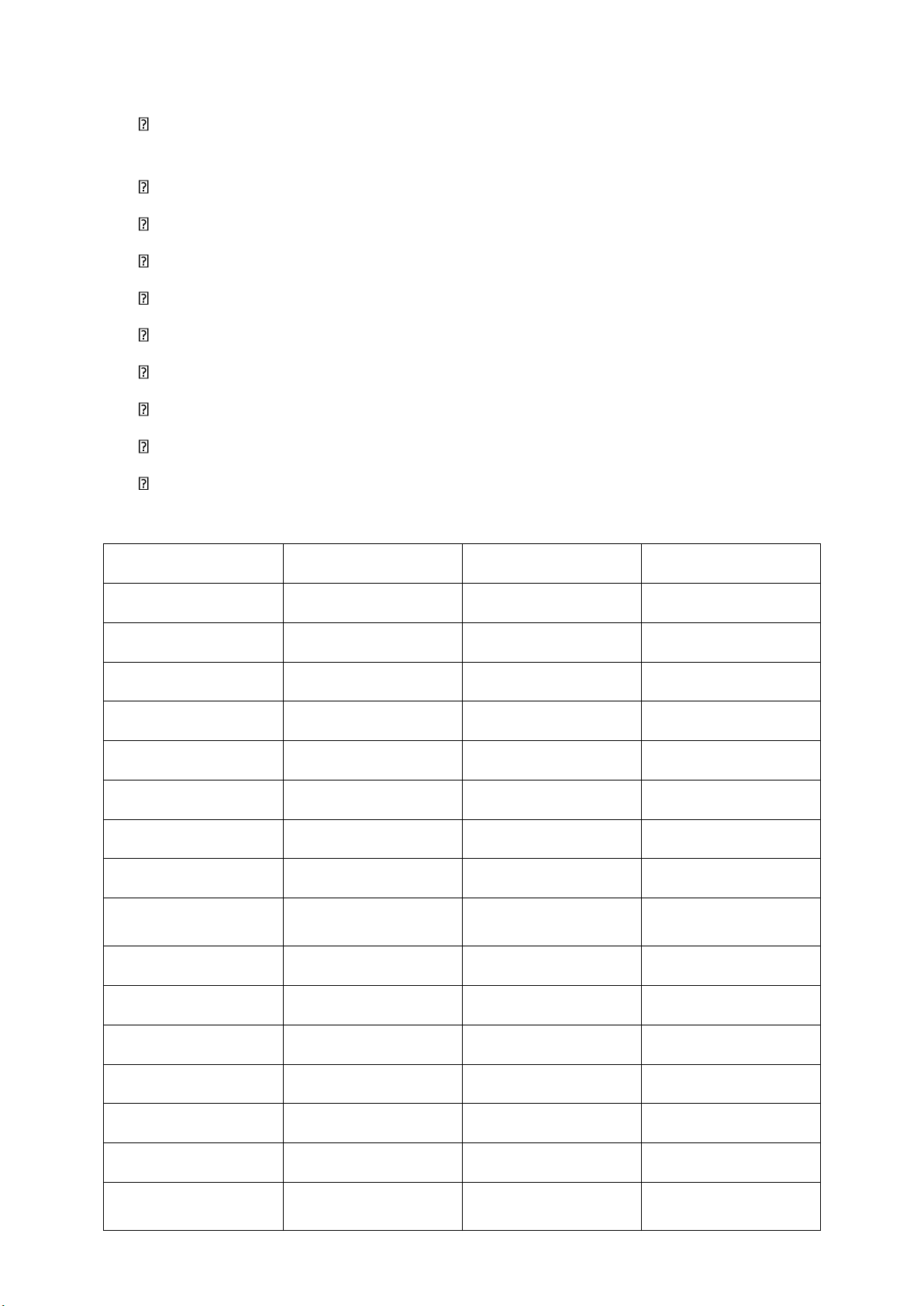
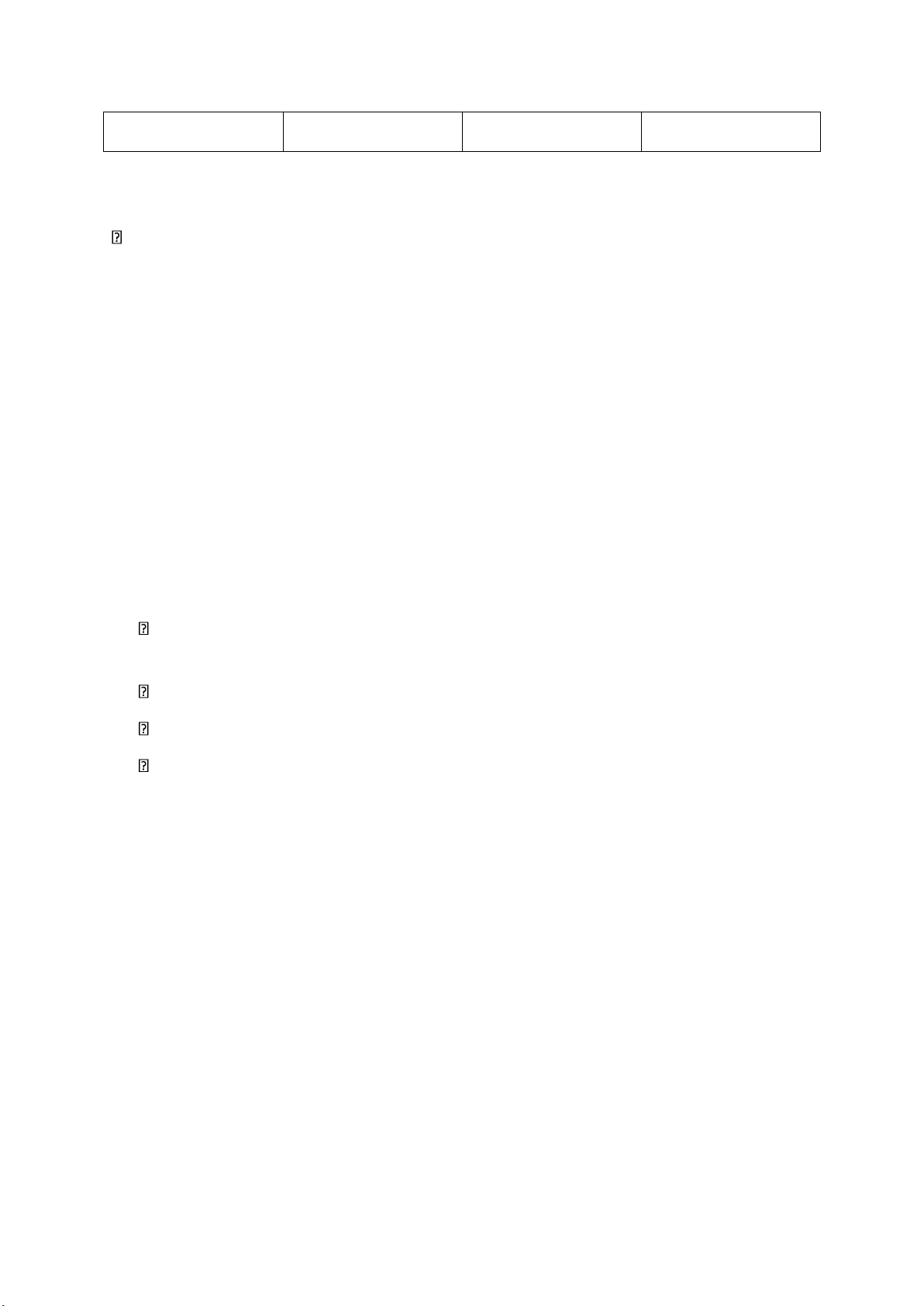
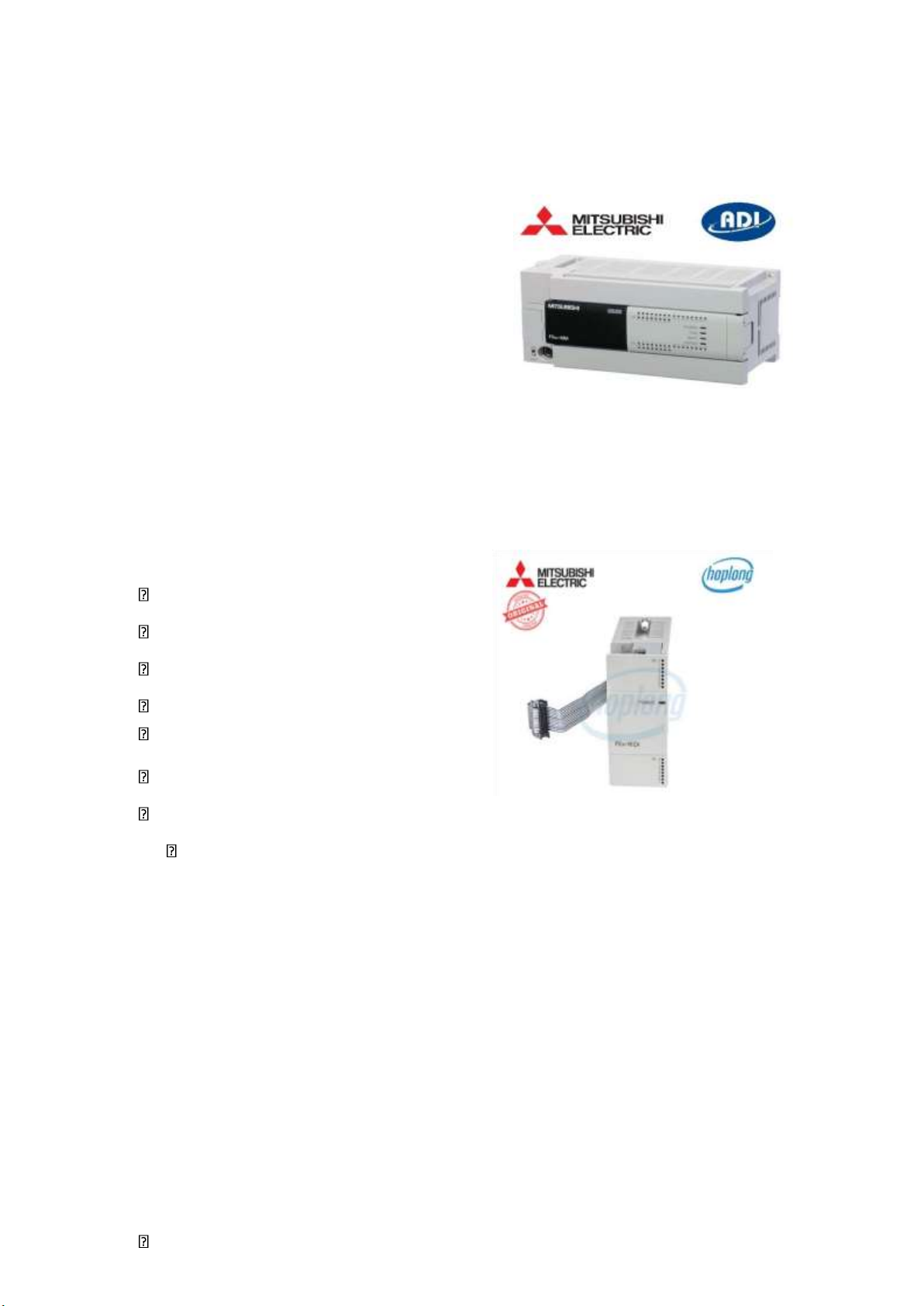
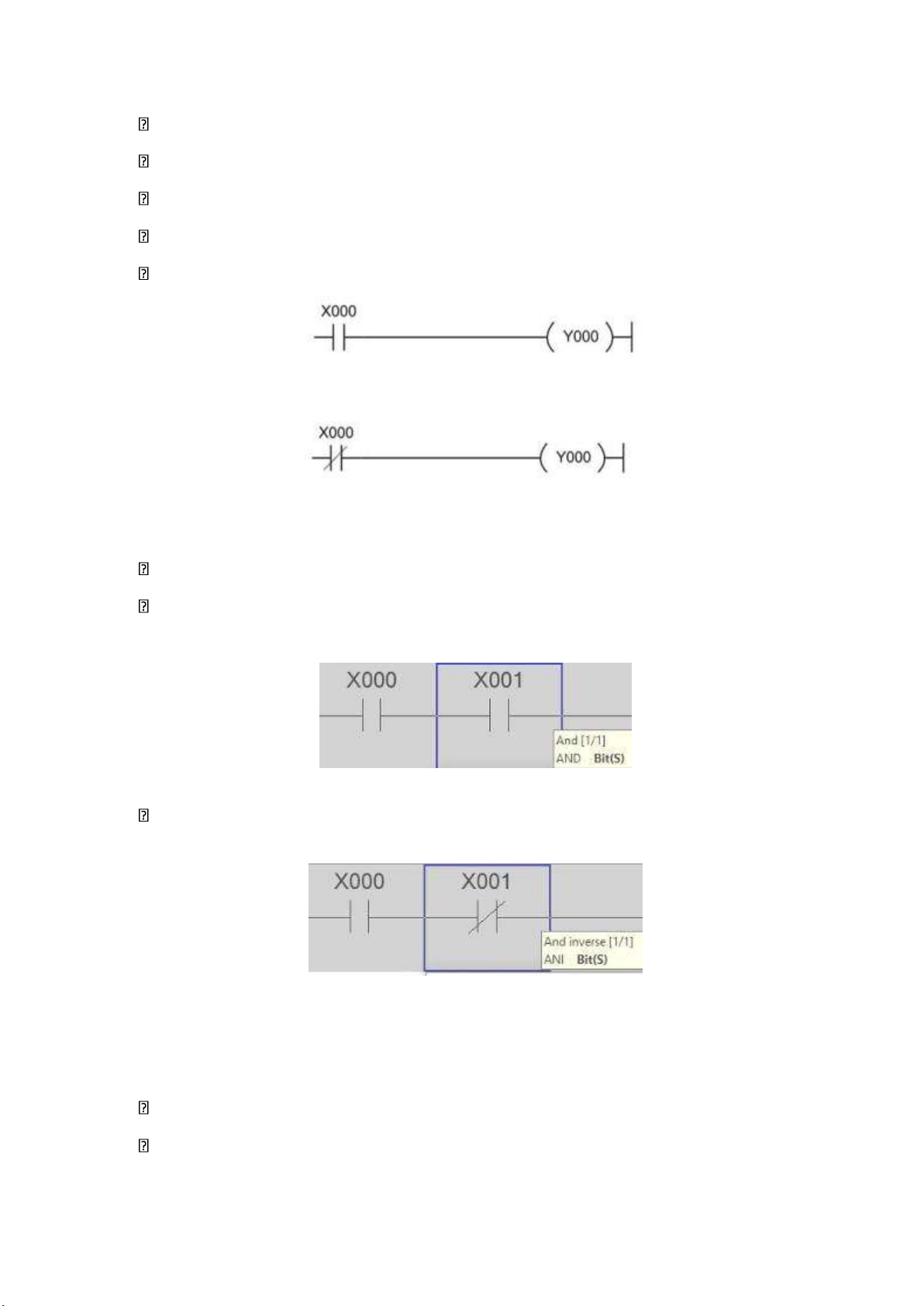
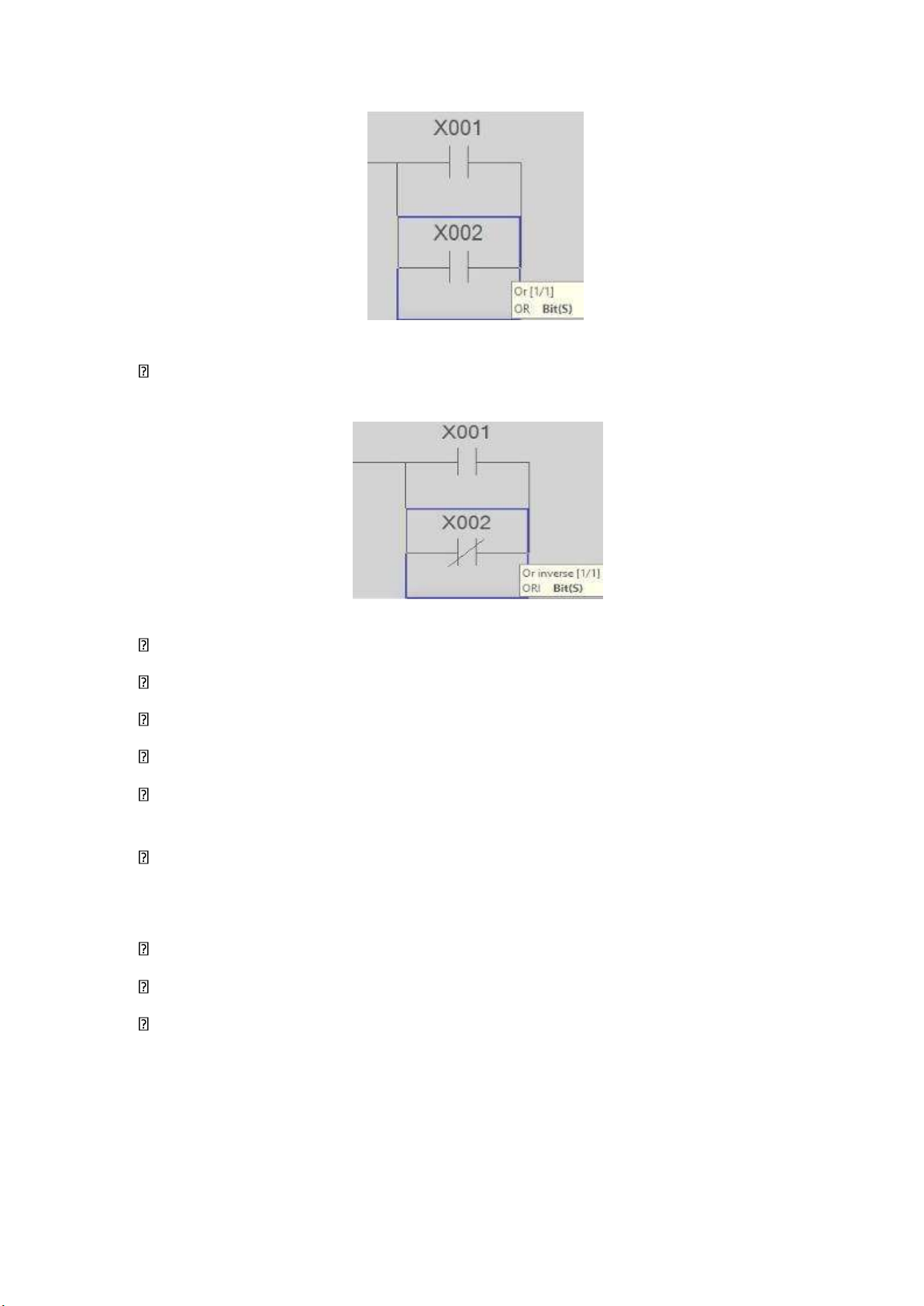
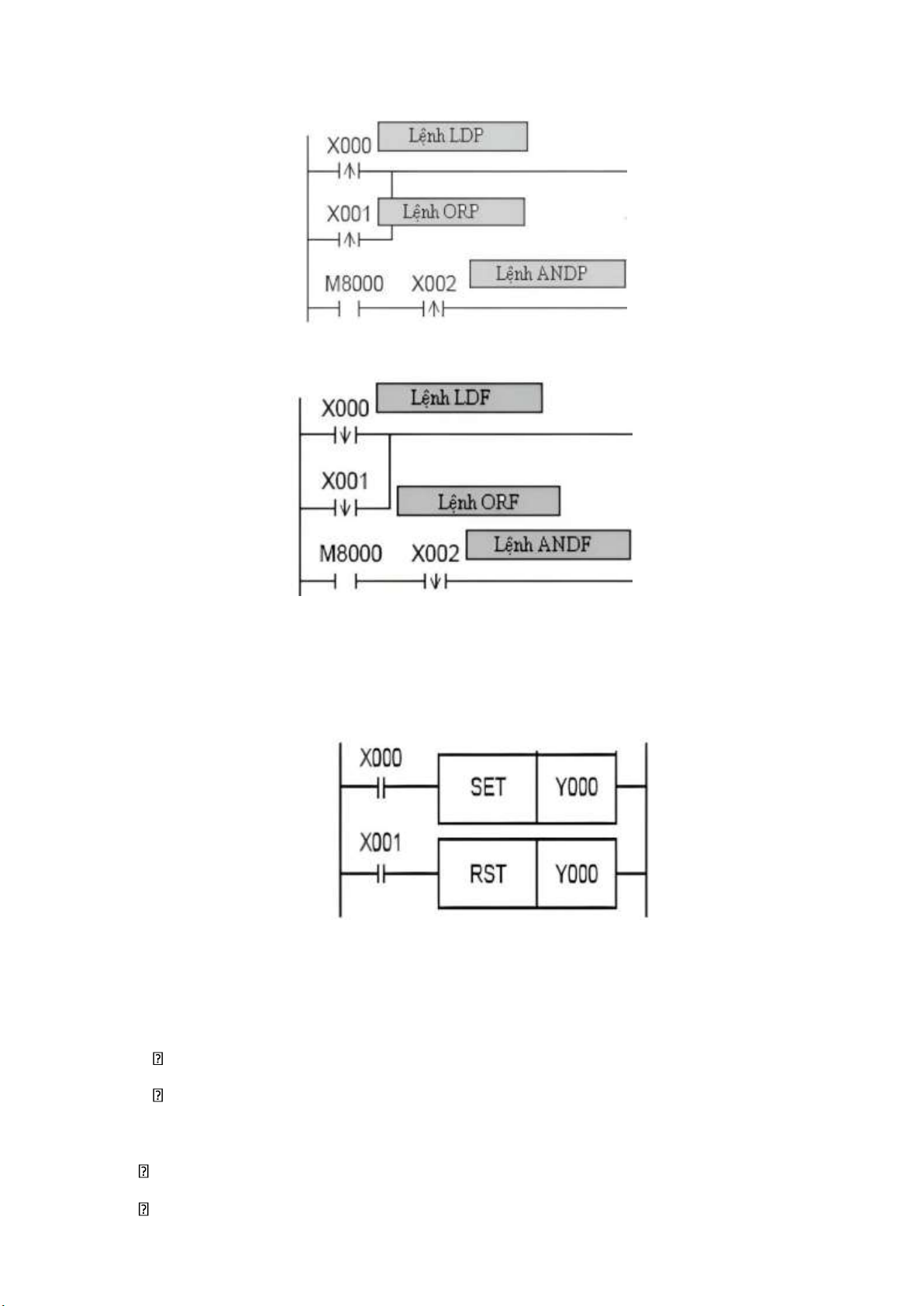
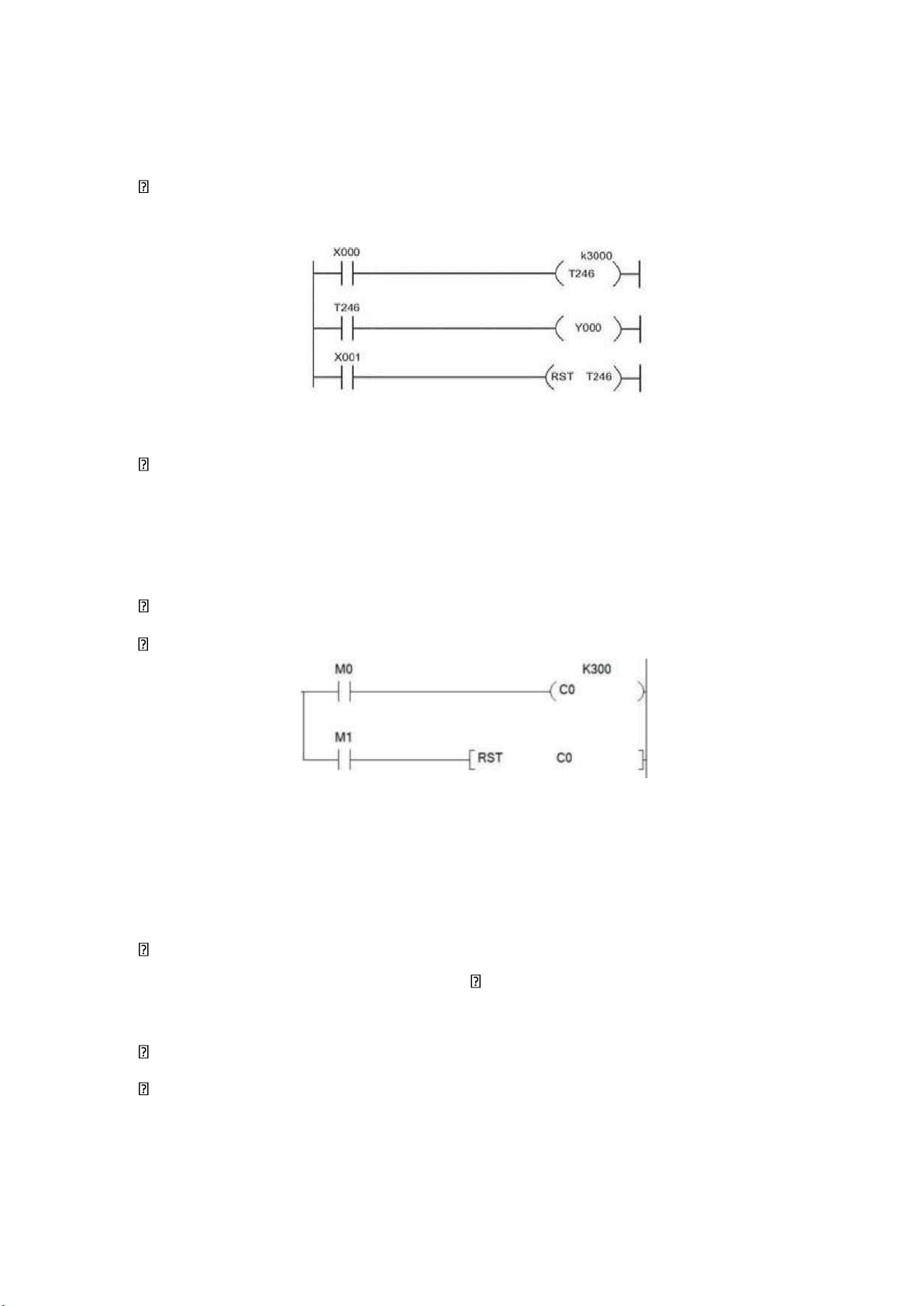
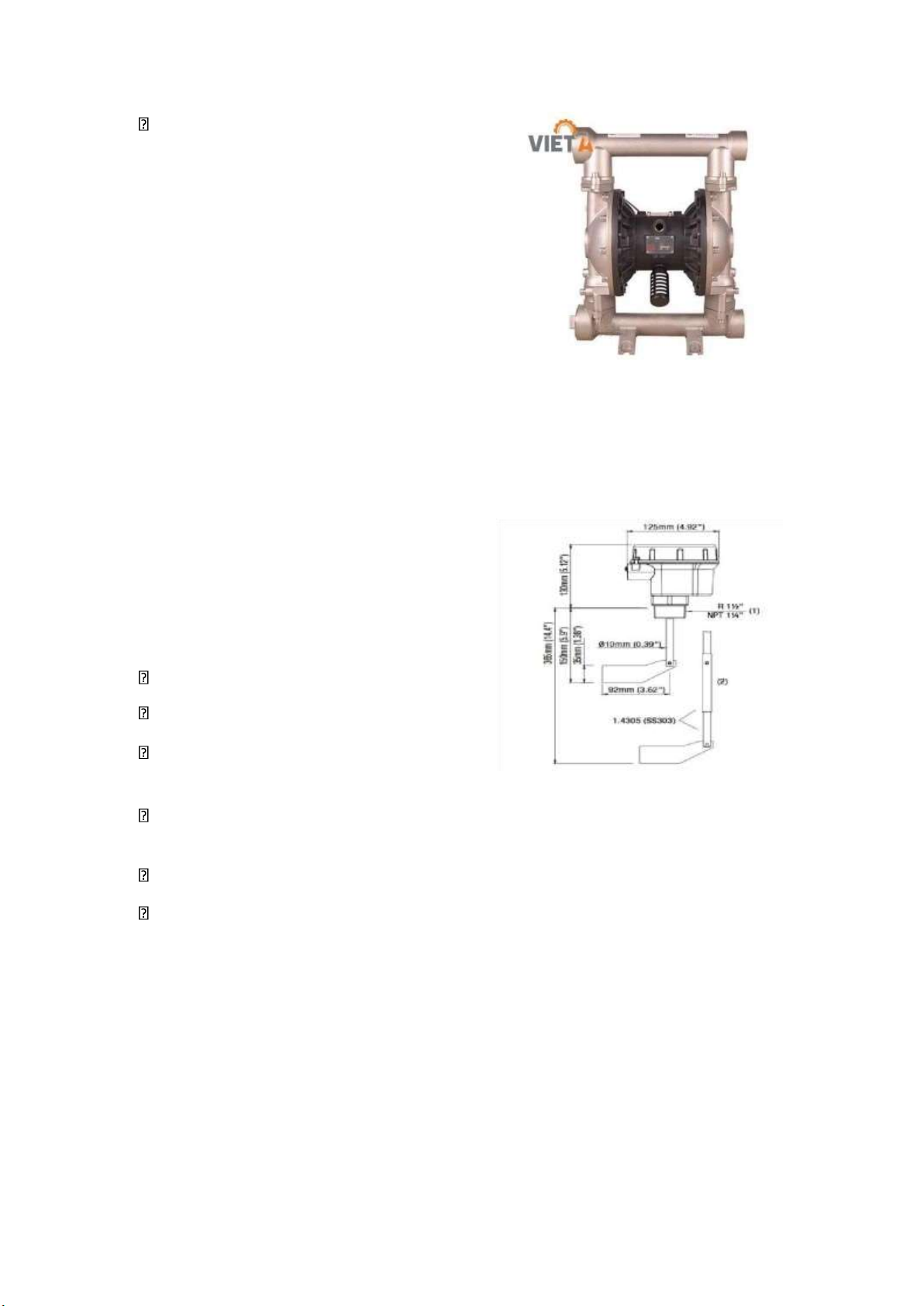
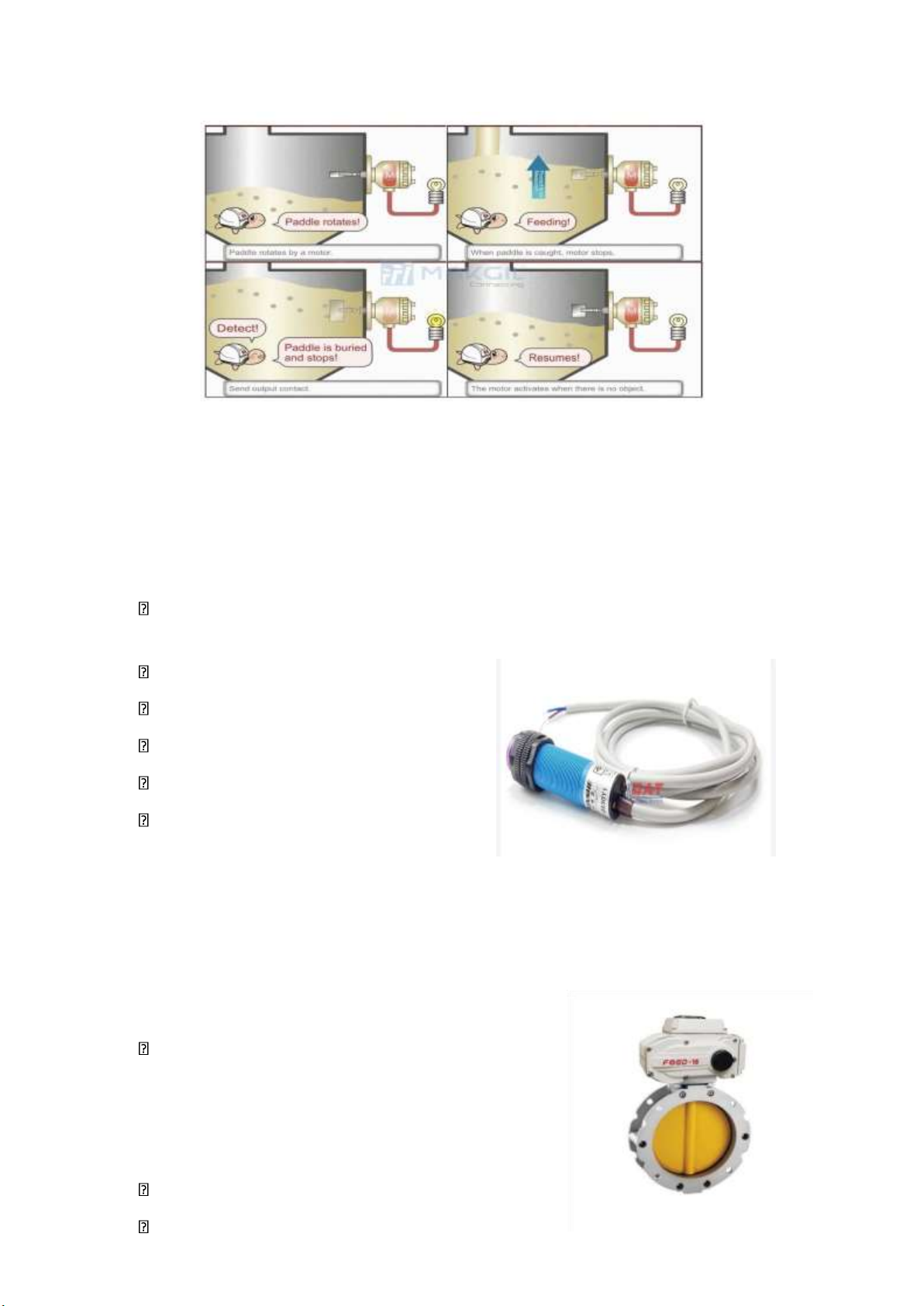
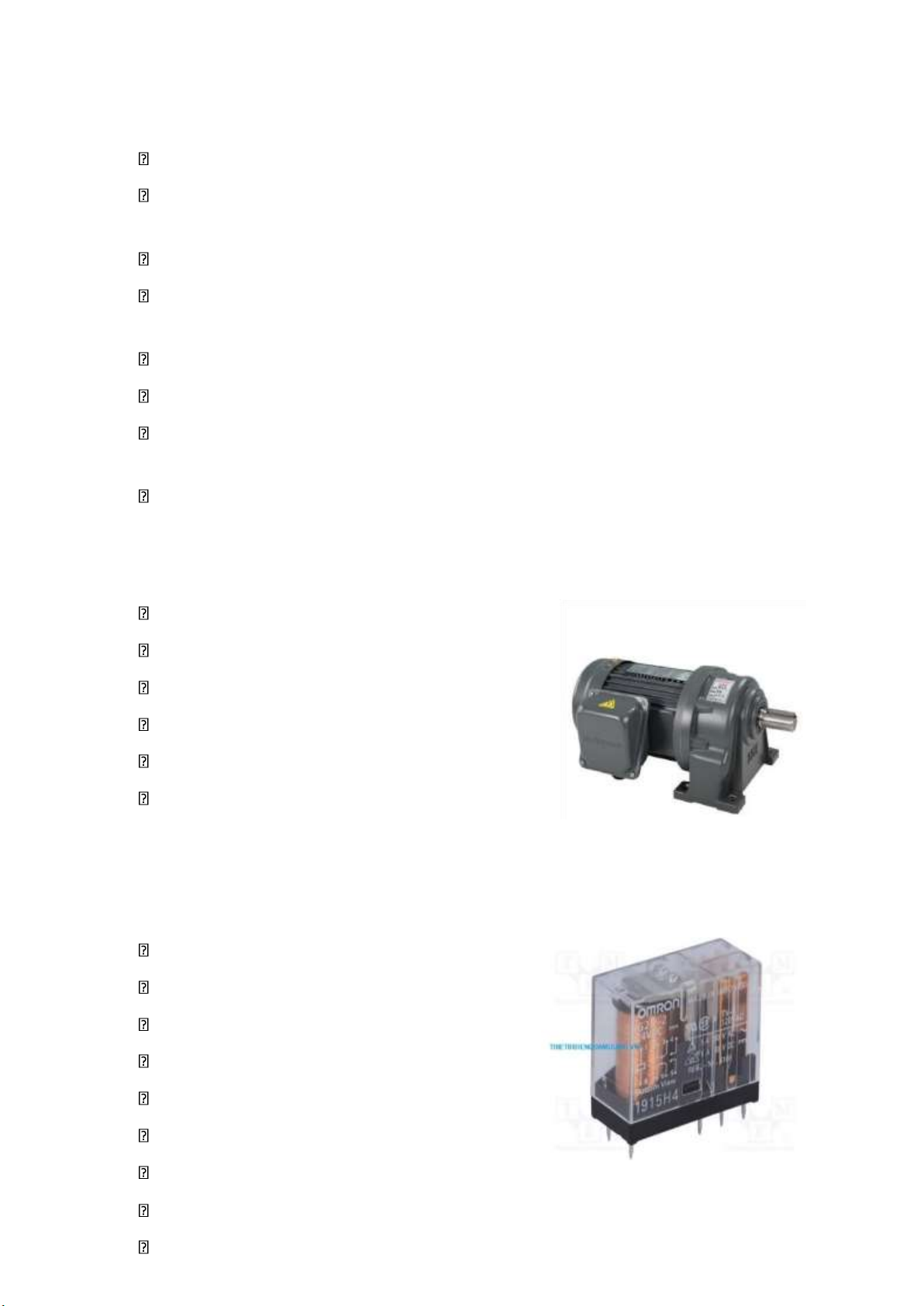
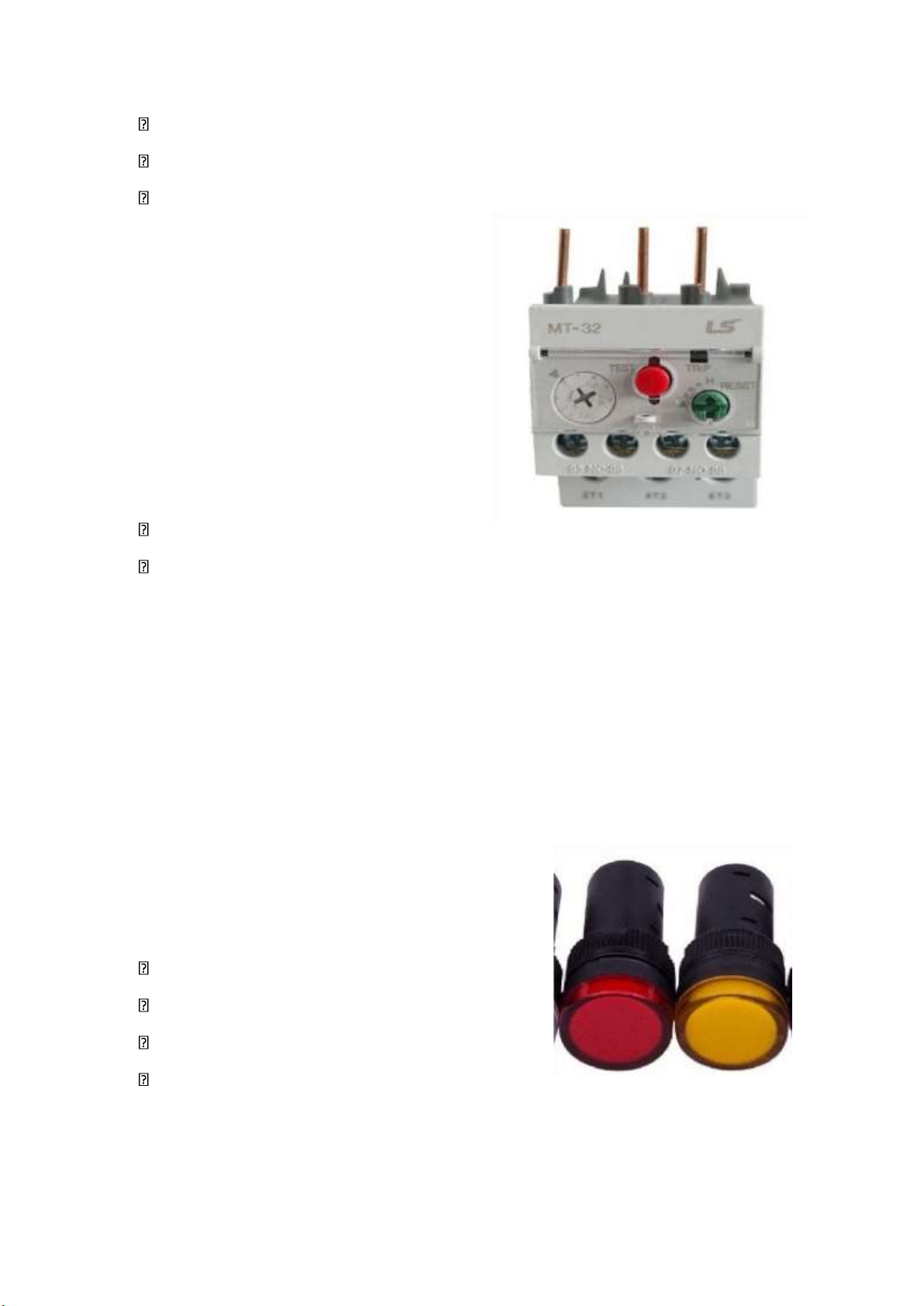
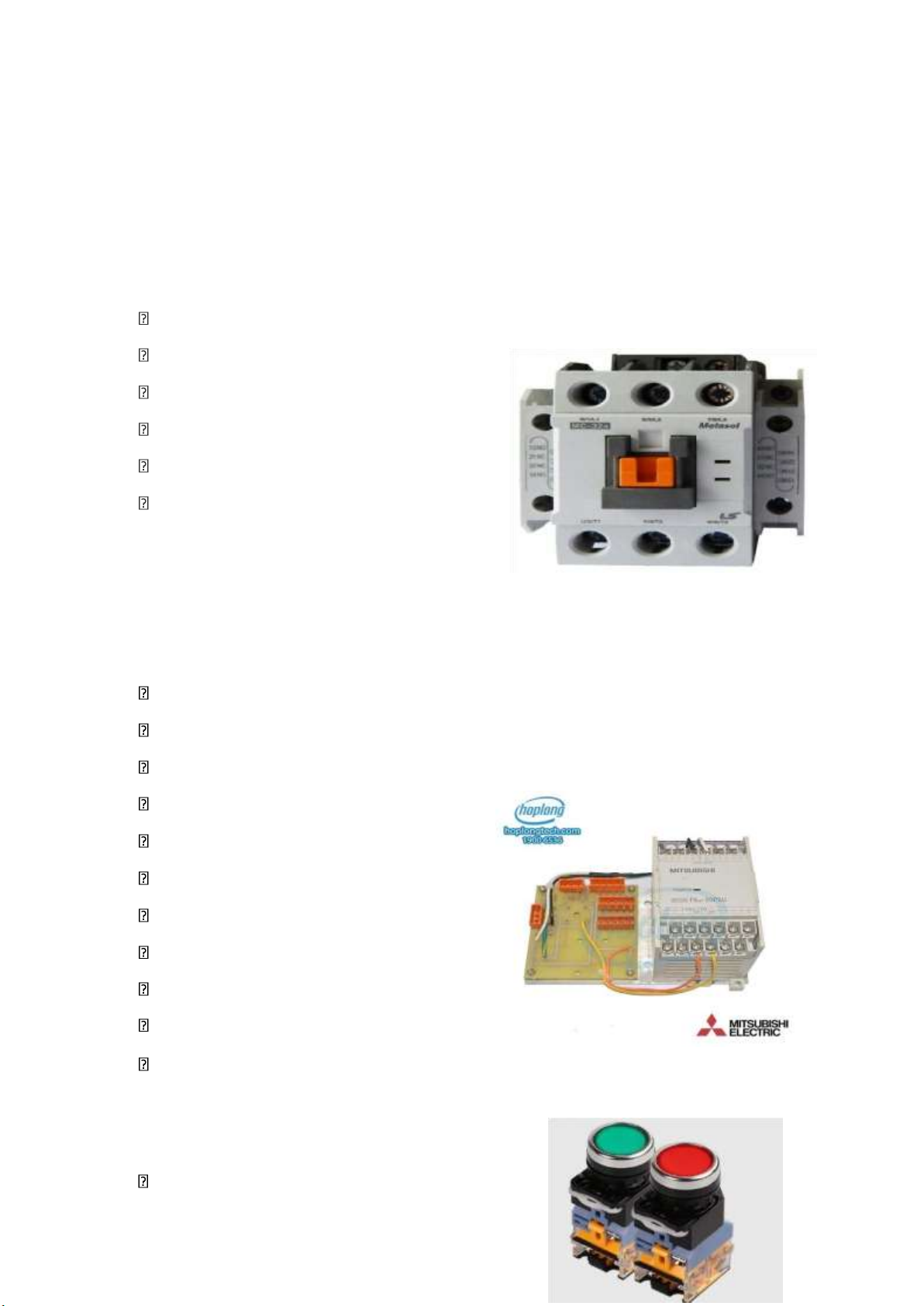
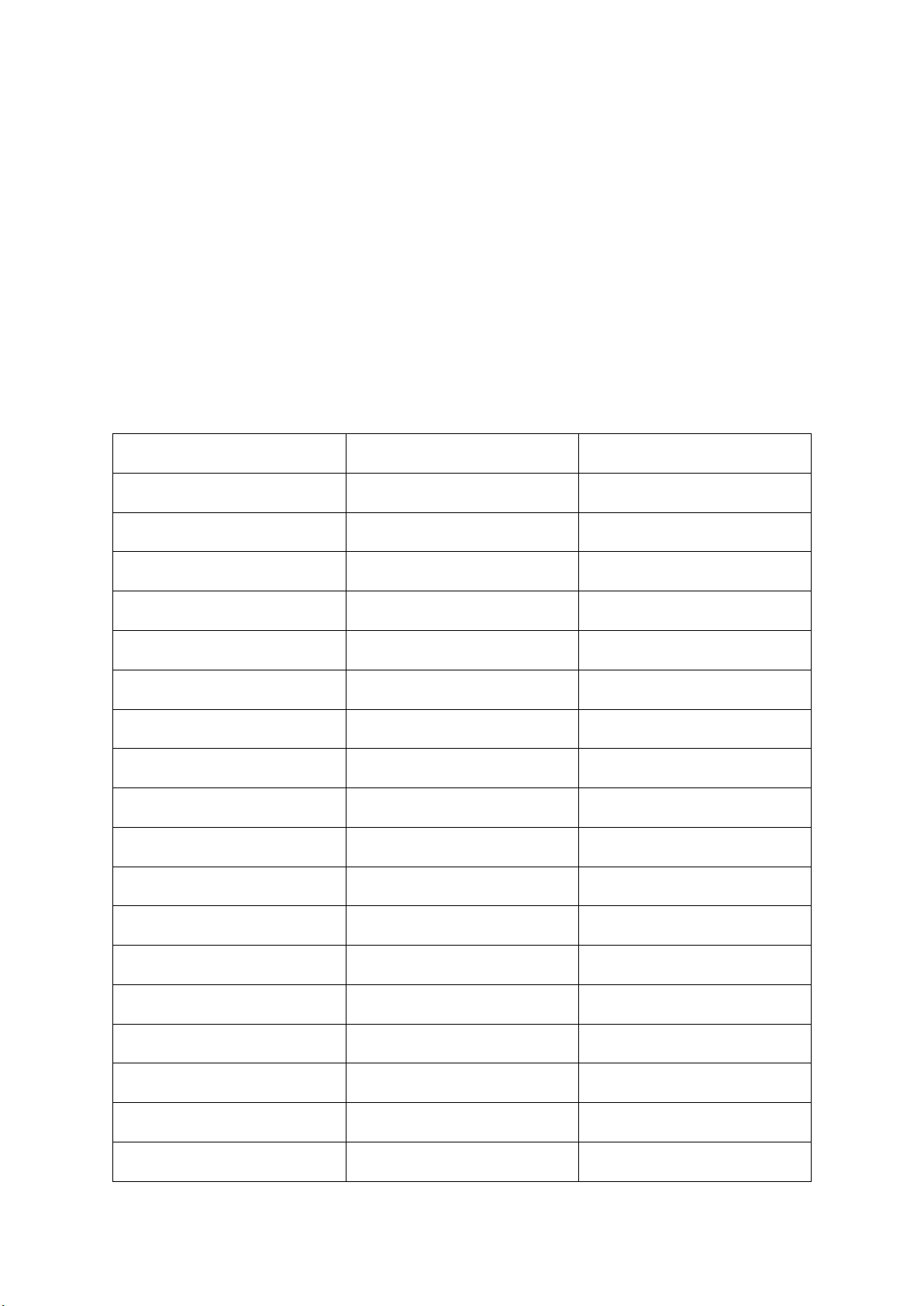
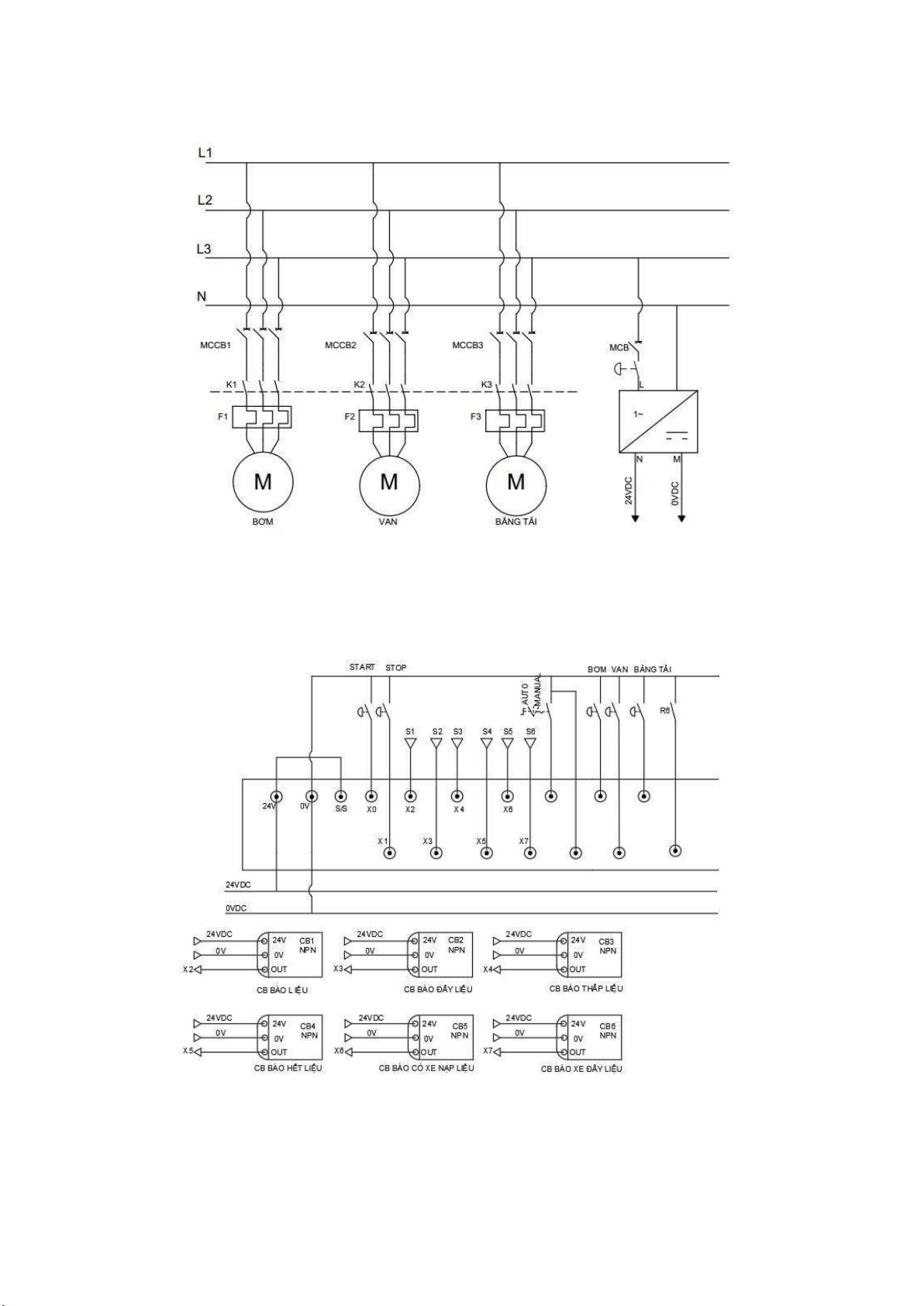
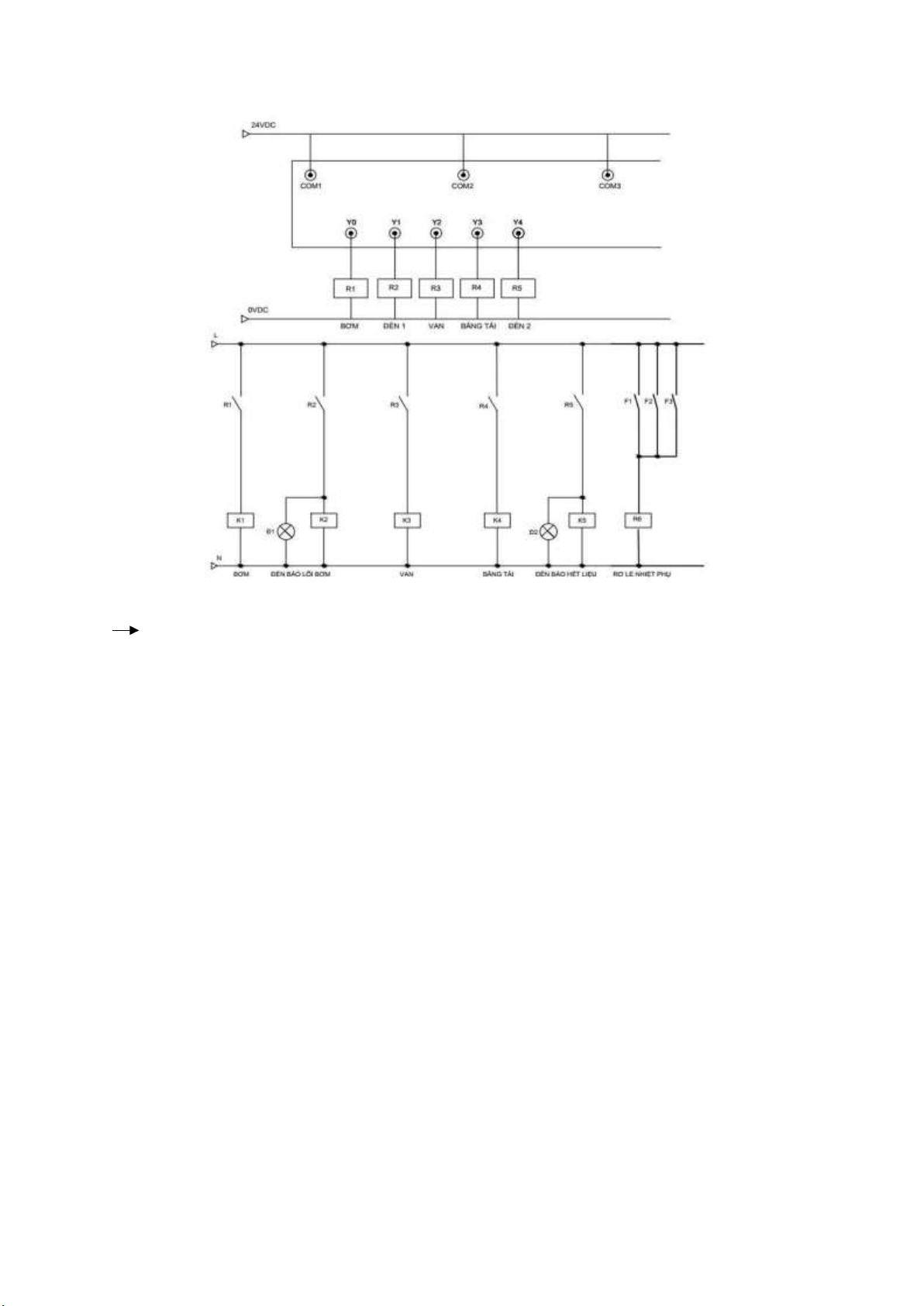
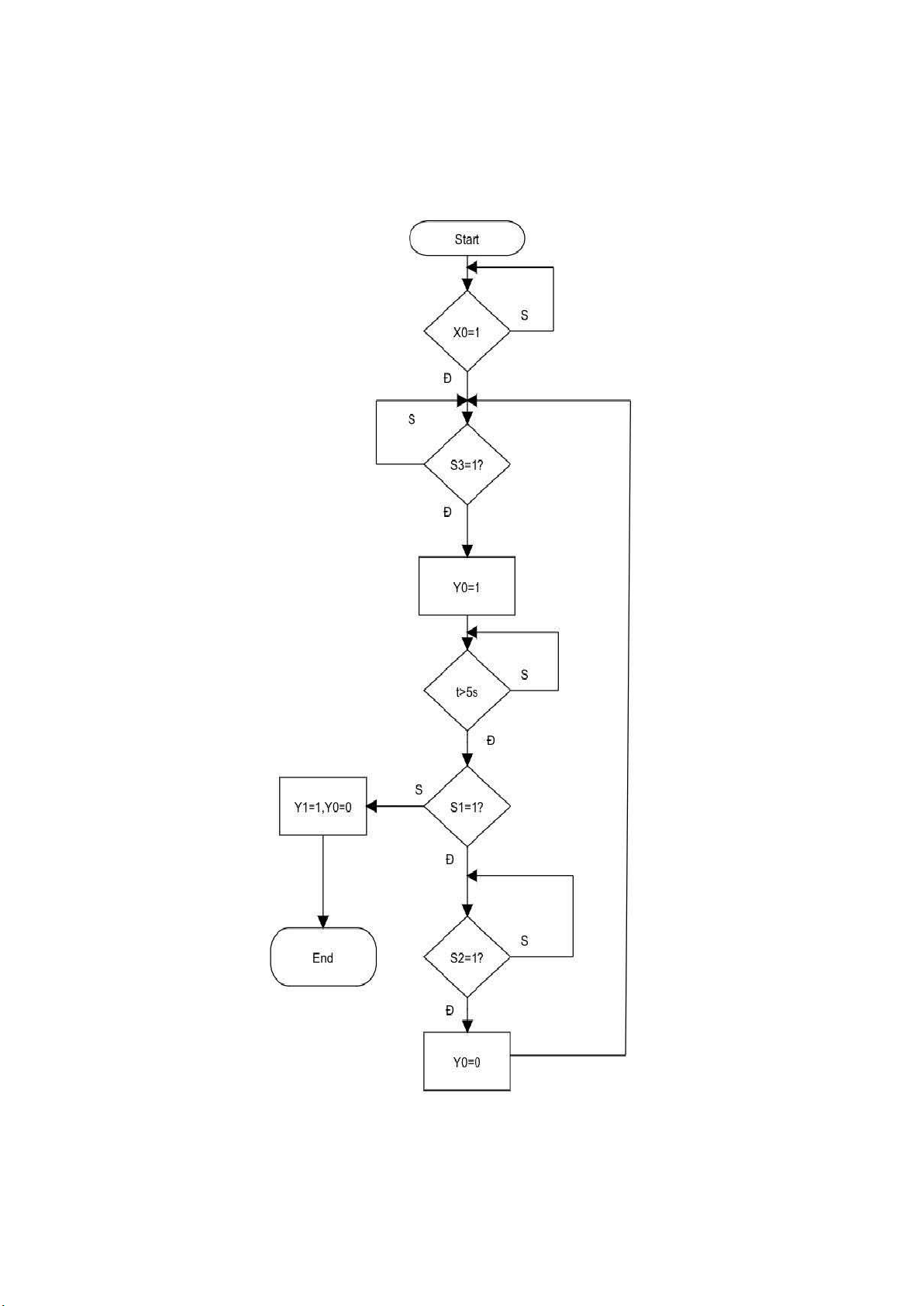
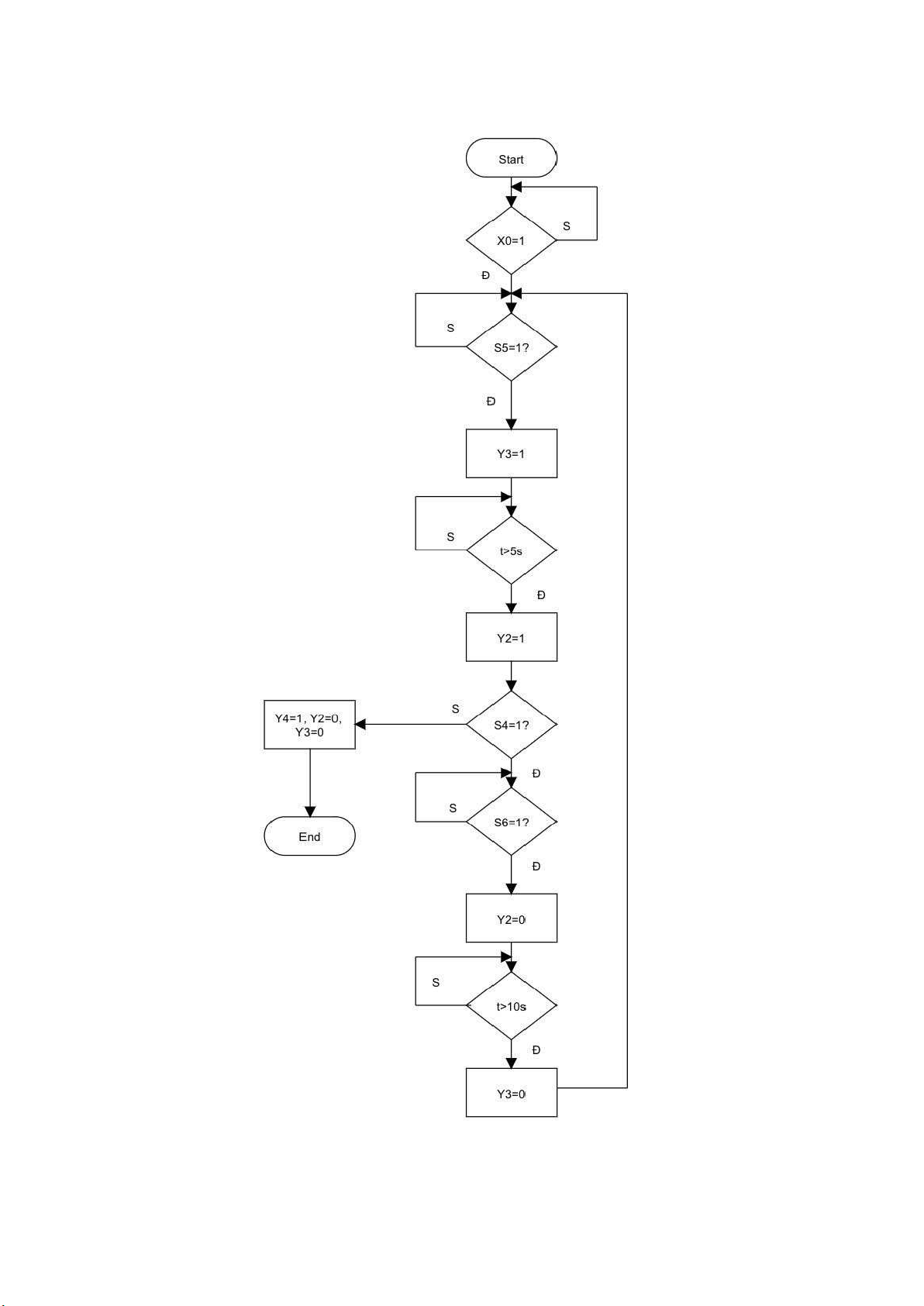
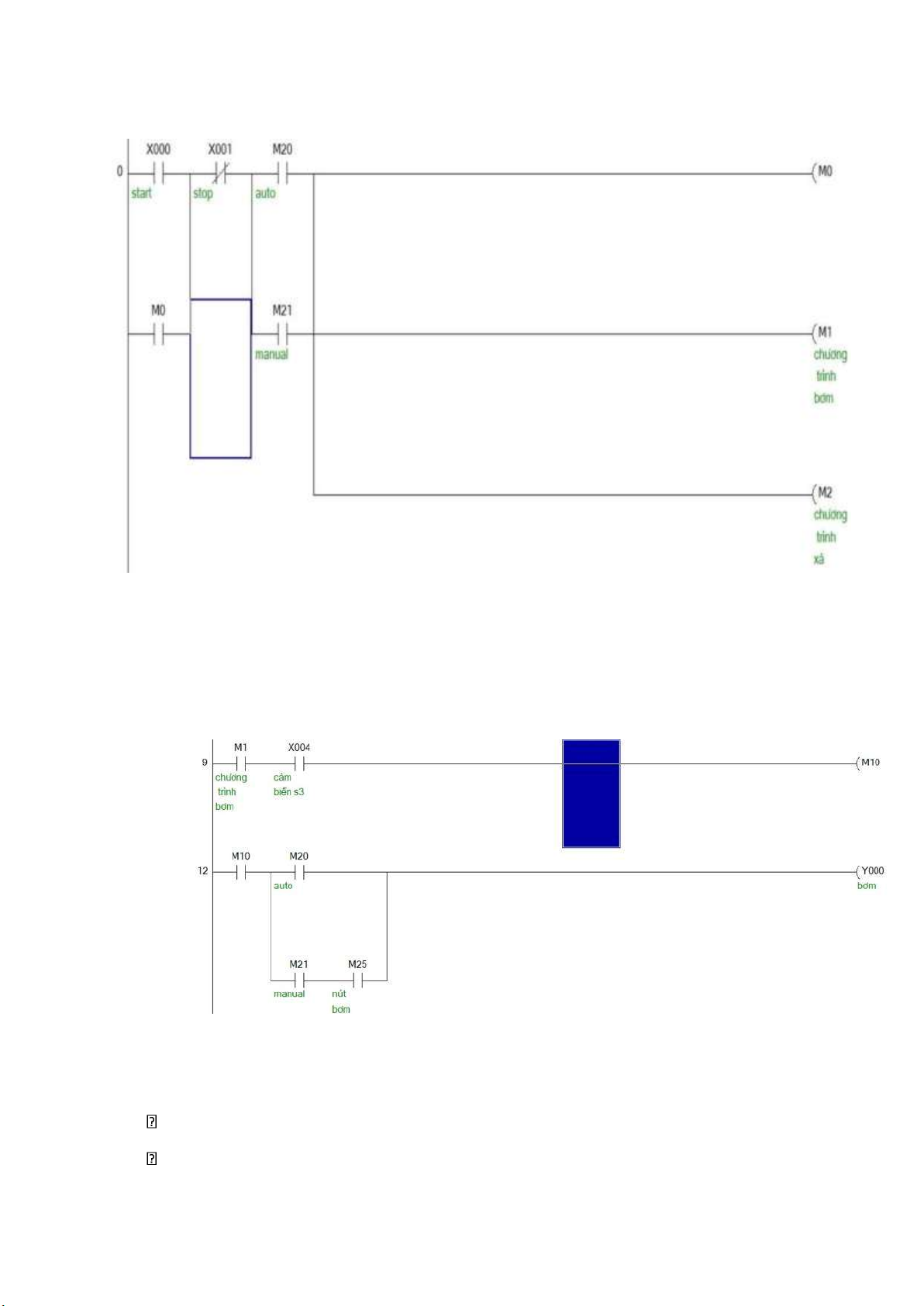
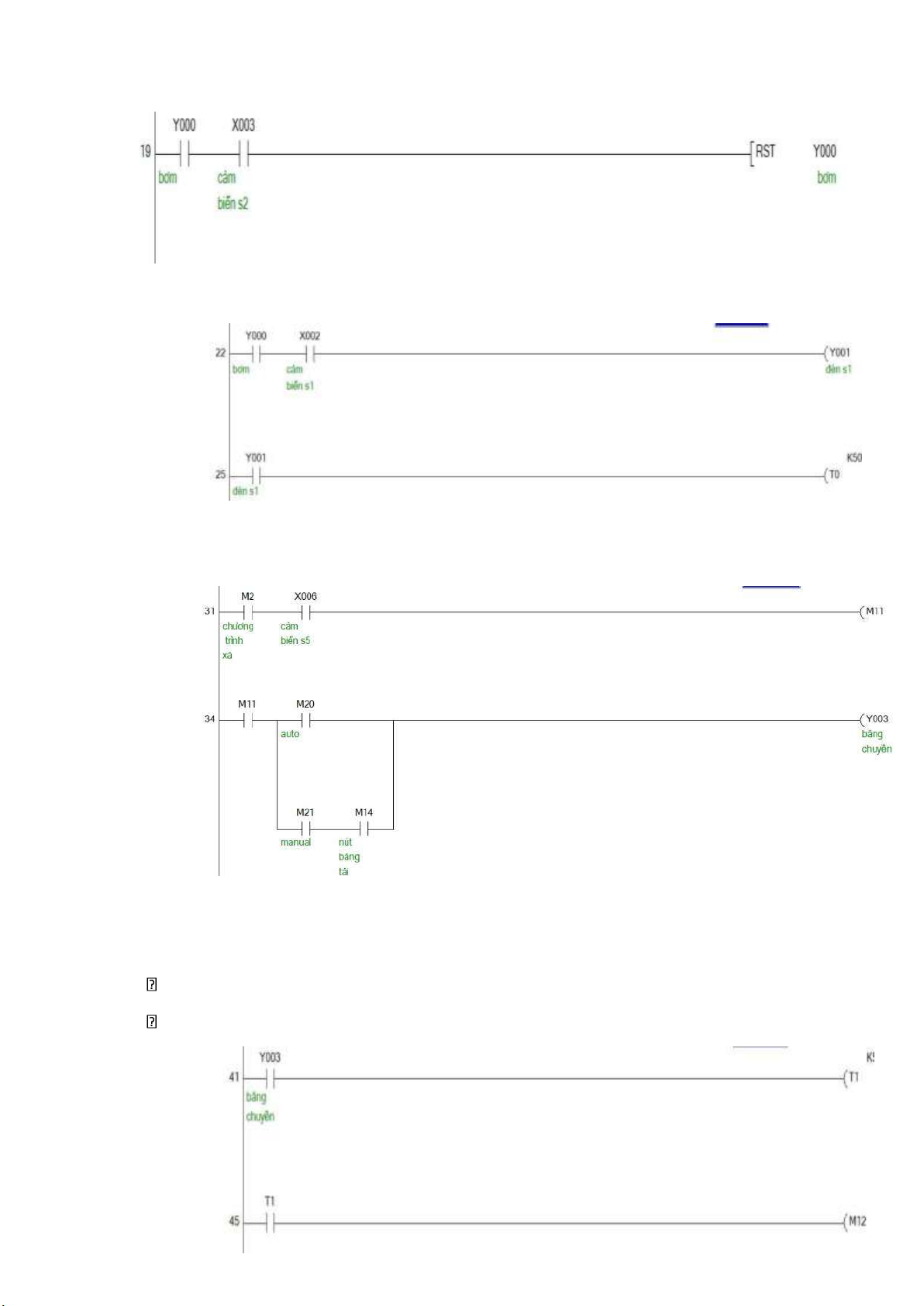
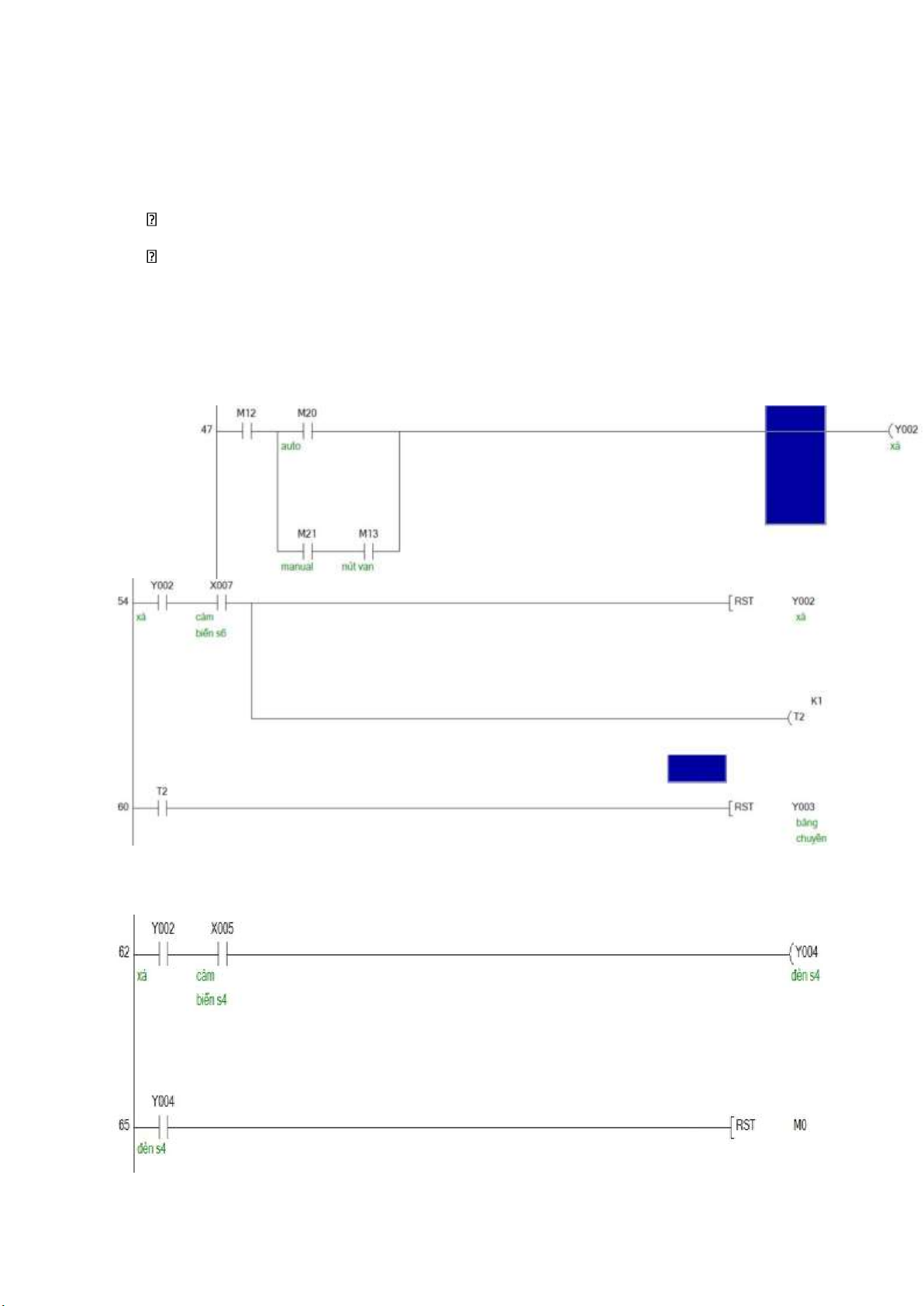
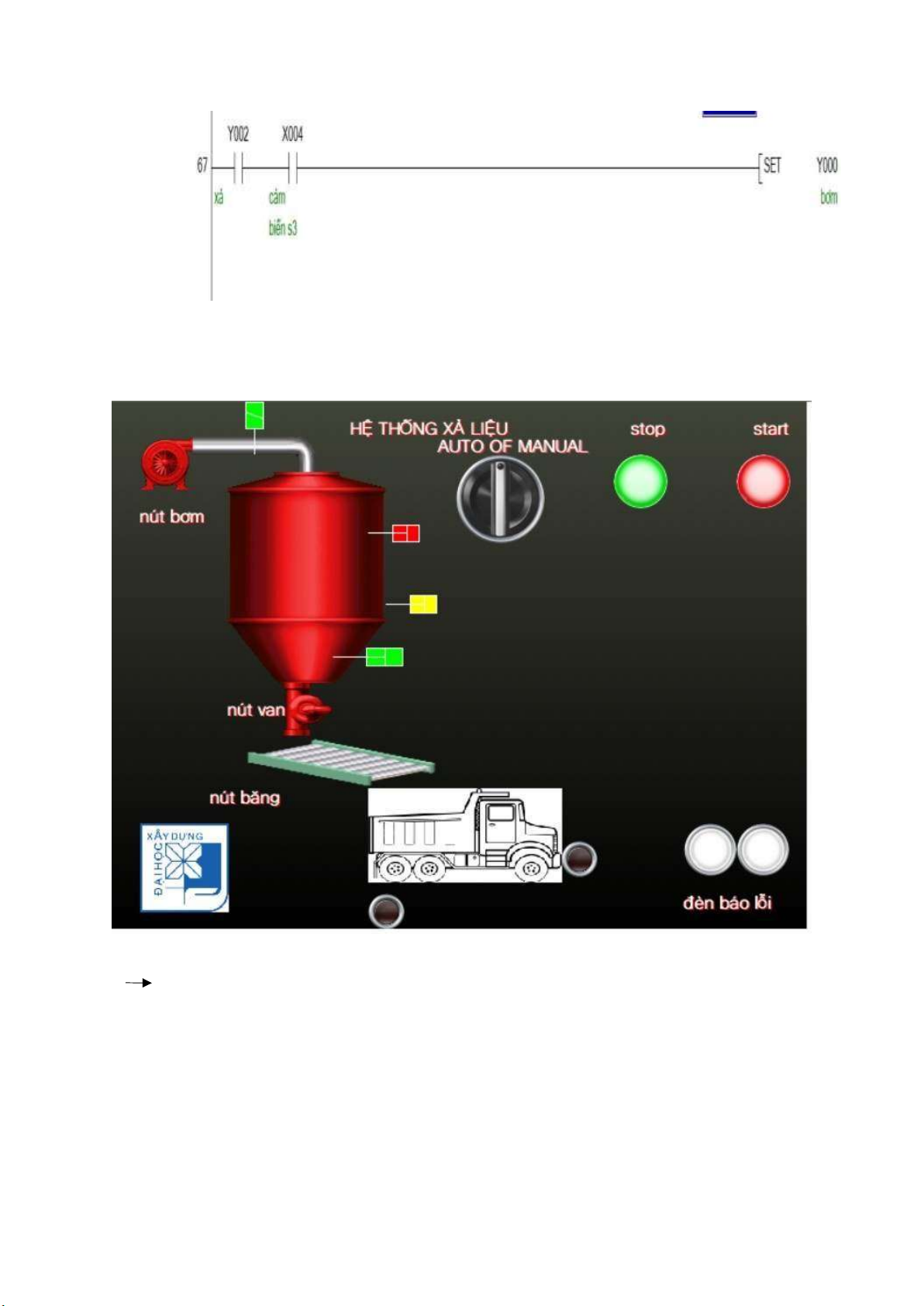
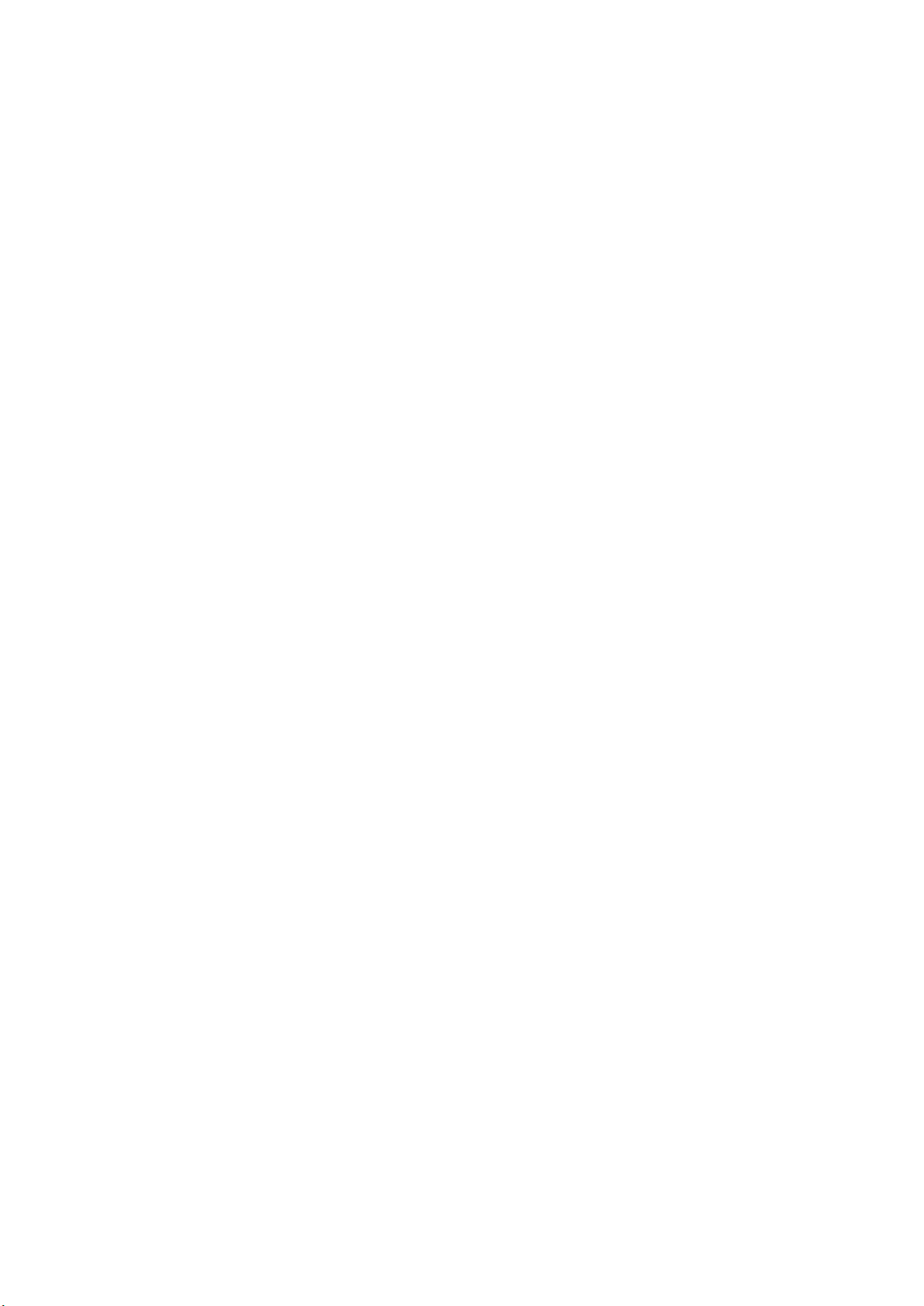
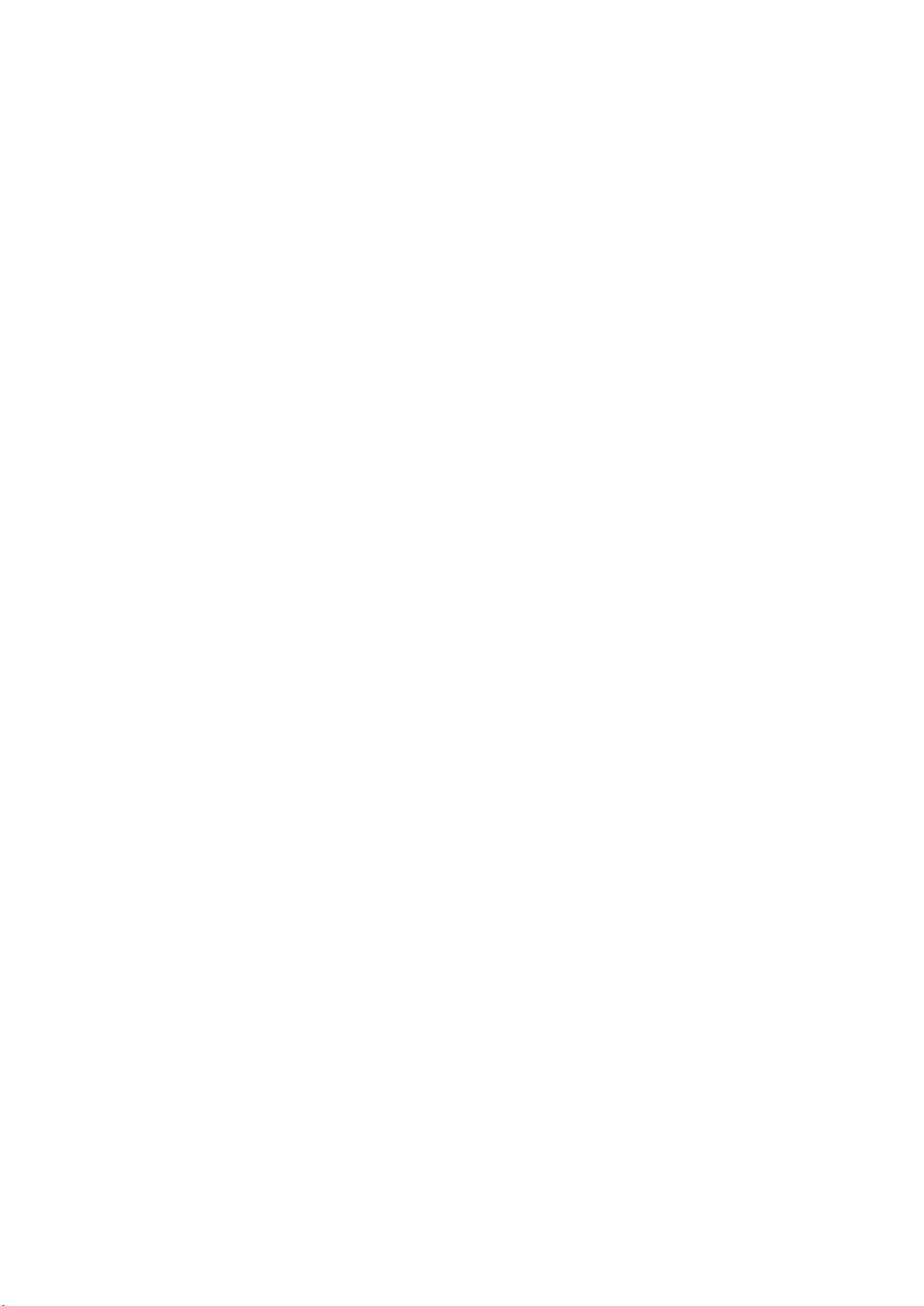
Preview text:
lOMoARcPSD| 38777299
TRƯỜNG ĐẠI HỌC XÂY DỰNG HÀ NỘI
BỘ MÔN ĐIỆN KỸ THUẬT ĐỒ ÁN MÔN HỌC
BỘ ĐIỀU KHIỂN KHẢ TRÌNH VÀ TỰ ĐỘNG HOÁ Tên đề tài
: Thiết kế hệ thống điều khiển xả liệu
Họ và tên sinh viên : Lớp : 66MEC1 MSSV :
Giảng viên hướng dẫn : Ths. Nguyễn Như Bách Hà Nội, 12-2023 lOMoARcPSD| 38777299
Trong thời kì hiện đại với sự phát triển nhanh chóng của khoa học kĩ thuật, cộng
nghiệp hoá hiện đại hoá ngày càng chiếm 1 vai trò, vị trí quan trọng trong đời sống xã
hội. Song song đó ngành tự động hoá cũng là 1 trong những ngành mới và đang phát
triển mạnh mẽ. Với nhu cầu tìm hiểu về hệ thống tự động hoá trong sản xuất và với kiến
thức học hỏi vốn có của sinh viên năm 3 trường Đại học Xây Dựng Hà Nội, nhóm em
được thầy giáo Th.S Nguyễn Như Bách giao cho đề tài “Thiết kế hệ thống điều khiển
xả liệu” để nghiên cứu và tìm hiểu. Đồ án sẽ tập trung vào phần chọn lựa thiết bị, vẽ sơ
đồ mạch đấu nối của hệ thống và thiết kế chương trình PLC điều khiển.
Trong thời gian tìm hiểu và làm đồ án nhóm em được thầy hướng dẫn rất nhiệt tình
và chu đáo.Việc hoàn thành đề tài này sẽ ko tránh khỏi những sai sót nên mong thầy
(cô) phê bình và đánh giá thêm để bọn em có thể rút được kinh nghiệm.
Chúng em xin trân thành cảm ơn!
Hà Nội, ngày 28 tháng 11 năm 2023 Sinh viên thiết kế lOMoARcPSD| 38777299 MỤC LỤC
DANH MỤC HÌNH VẼ...............................................................................................i
DANH MỤC BẢNG BIỂU.........................................................................................ii
CHƯƠNG 1. TÌM HIỂU CÔNG NGHỆ..................................................................................1
1. Giới thiệu sơ qua về hệ thống điều khiển xả liệu .............................................................1
1.1. Lịch sử hình thành và phát triển ..................................................................................1
1.2. Phân loại hệ thống điều khiển xả liệu (dạng bột) ........................................................2
2. Cấu tạo của hệ thống xả liệu ..............................................................................................3
3. Nguyên lí hoạt động ............................................................................................................4
4. Yêu cầu an toàn hệ thống ...................................................................................................4
CHƯƠNG 2: LỰA CHỌN PHẦN CỨNG, PHẦN MỀM ......................................................6
1. Sơ đồ khối hệ thống điều khiển xả liệu..............................................................................6
2. Lựa chọn PLC cho hệ thống điều khiển xả liệu tự động .................................................7
2.1 PLC ..................................................................................................................................8
2.2 Modul mở rộng ...............................................................................................................9
2.3 Ngôn ngữ lập trình .........................................................................................................9
3. Lựa chọn thiết bị cho hệ thống xả liệu ............................................................................13
3.1 Động cơ bơm nhiên liệu ...............................................................................................13
3.2 Cảm biến mức ...............................................................................................................14
3.3 Cảm biến hồng ngoại ...................................................................................................15
3.4 Van xả ...........................................................................................................................15
3.5 Động cơ băng truyền ....................................................................................................16
3.6 Rơ le trung gian ............................................................................................................16
3.7 Đèn báo .........................................................................................................................17
3.8 Contactor .......................................................................................................................17
3.9 Bộ nguồn .......................................................................................................................18
3.10 Nút bấm .......................................................................................................................18
4. Xây dựng sơ đồ mạch lực và mạch đấu nối ....................................................................19
4.1 Phân chia cổng I/O .......................................................................................................19
4.1 Mạch lực .......................................................................................................................20
4.2 Mạch đấu nối ................................................................................................................20
CHƯƠNG 3: XÂY DỰNG CHƯƠNG TRÌNH .....................................................................22 lOMoARcPSD| 38777299
1. Lưu đồ thuật toán ..............................................................................................................22
2. Chương trình .....................................................................................................................24
3. Mô phỏng HMI Mitsubishi ...............................................................................................27
KẾT LUẬN ...............................................................................................................................28
HƯỚNG PHÁT TRIỂN ...........................................................................................................28
TÀI LIỆU THAM KHẢO........................................................................................34 lOMoAR cPSD| 38777299 DANH MỤC HÌNH VẼ
Hình 2.1 Sơ đồ khối hệ thống điều khiển xả liệu.......................................................8
Hình 2.27 Sơ đồ mạch lực.........................................................................................22
Hình 2.28 Sơ đồ đầu nối INPUT PLC......................................................................23
Hình 2.29 Sơ đồ đấu nối OUTPUT PLC.................................................................23
Hình 3.1 Lưu đồ thuật toán bơm liệu vào tank.......................................................25 Hình
3.2 Lưu đồ thuật toán xả liệu..........................................................................26DANH ii lOMoARcPSD| 38777299
CHƯƠNG 1. TÌM HIỂU CÔNG NGHỆ
1. Giới thiệu sơ qua về hệ thống điều khiển xả liệu
Hệ thống xả liệu là một phần quan trọng của nhiều quá trình công nghiệp và ứng
dụng khác nhau. Hệ thống này được sử dụng để kiểm soát việc xả ra hoặc phân phối
các chất lỏng, khí, hoặc chất rắn từ một nguồn tới một đích. Dưới đây là một số thông
tin cơ bản về hệ thống xả liệu
• Mục tiêu của hệ thống xả liệu: Mục tiêu chính của hệ thống xả liệu là kiểm soát
luồng chất lỏng, khí, hoặc chất rắn để đáp ứng yêu cầu cụ thể của quá trình,
chẳng hạn như điều khiển nồng độ, áp suất, lưu lượng, hoặc nhiệt độ.
• Các thành phần chính: Hệ thống xả liệu thường bao gồm bộ điều khiển (có thể
là PLC, máy tính, hoặc vi xử lý), cảm biến để theo dõi trạng thái của chất lỏng
hoặc khí, cơ cấu van và bơm để kiểm soát luồng chất, cũng như các ống dẫn và thiết bị liên quan.
• Loại hệ thống xả liệu: Có nhiều loại hệ thống xả liệu, bao gồm hệ thống xả
lỏng, xả khí, xả chất rắn, và hệ thống xả tự động hóa trong nhiều lĩnh vực khác
nhau, như trong công nghiệp hóa chất, nước và nước thải, sản xuất thực phẩm,
và nhiều ứng dụng khác.
• Ứng dụng: Hệ thống xả liệu được sử dụng để điều khiển quá trình sản xuất, làm
mát và sưởi ấm, kiểm soát áp suất, kiểm soát môi trường, và thực hiện nhiều
chức năng quan trọng khác trong công nghiệp và các lĩnh vực khác.
• Điều khiển: Để kiểm soát hệ thống xả liệu, các thuật toán điều khiển, như PID
(Proportional-Integral-Derivative), được sử dụng để điều chỉnh van và bơm dựa
trên thông tin từ các cảm biến.
1.1. Lịch sử hình thành và phát triển
Hệ thống xả liệu đã phát triển và được ứng dụng trong nhiều lĩnh vực khác
nhau trong suốt nhiều thế kỷ.
• Thế kỷ 18 và 19: Sự phát triển của công nghiệp và máy móc trong thế kỷ 18
đã tạo ra nhu cầu kiểm soát và điều khiển các quy trình sản xuất. Trong thời
kỳ này, người ta sử dụng các thiết bị cơ học và thủ công để kiểm soát luồng
chất lỏng, khí, và nhiệt độ.
• Thế kỷ 20: Sự phát triển của công nghệ điện tử và điện tử số đã tạo ra cơ hội
cho sự tự động hóa và điều khiển tự động. Điều này đã dẫn đến việc xuất
hiện các bộ điều khiển tự động và các hệ thống điều khiển xả liệu phức tạp
hơn. Các máy tính, vi xử lý, và các thuật toán điều khiển thông minh đã trở
thành một phần quan trọng của hệ thống này.
• Giữa thế kỷ 20 và đầu thế kỷ 21: Sự phát triển của công nghệ điều khiển và
vi xử lý đã làm cho hệ thống điều khiển xả liệu trở nên hiệu quả hơn và có lOMoARcPSD| 38777299
khả năng tích hợp với các quy trình phức tạp. Các thuật toán điều khiển tiến
bộ như PID (Proportional-Integral-Derivative) đã trở thành phổ biến trong
các ứng dụng điều khiển xả liệu.
• Hiện đại: Trong thời đại hiện đại, sự phát triển của công nghệ thông tin,
mạng, và trí tuệ nhân tạo đã làm cho hệ thống điều khiển xả liệu trở nên
thông minh hơn và khả năng giao tiếp với các hệ thống khác. Các hệ thống
điều khiển xả liệu ngày nay có khả năng tự động dự đoán và điều chỉnh để
đáp ứng yêu cầu cụ thể.
• Ứng dụng rộng rãi: Hệ thống điều khiển xả liệu đã trở thành một phần quan
trọng của nhiều ngành công nghiệp, bao gồm công nghiệp hóa chất, công
nghiệp dầu khí, sản xuất thực phẩm, y tế, và nhiều lĩnh vực khác.
Lịch sử hình thành của hệ thống điều khiển xả liệu điều bắt nguồn từ nhu
cầu trong quá trình sản xuất và quản lý quy trình. Sự phát triển của công nghệ
và kiến thức trong lĩnh vực này đã giúp tạo ra các hệ thống điều khiển ngày
càng thông minh và hiệu quả.
1.2. Phân loại hệ thống điều khiển xả liệu (dạng bột)
Hệ thống điều khiển xả liệu dạng bột thường được phân loại dựa trên nhiều
yếu tố khác nhau, bao gồm quy trình sản xuất, loại bột, kích thước hạt, và mục
tiêu kiểm soát. Dưới đây là một số phân loại phổ biến:
1.2.1. Theo cách xả bột
• Xả bột liên tục: Hệ thống xả bột liên tục thường được sử dụng trong các quy
trình sản xuất liên tục như sản xuất giấy, sản xuất thức ăn cho động vật, vv.
• Xả bột rải đợt: Trong hệ thống này, bột được xả từng đợt hoặc lần, thích hợp
cho các quy trình sản xuất pha lẻ, thay đổi thường xuyên.
1.2.2. Theo loại bột
• Bột khô: Đây là loại bột không chứa nhiều nước và thường có kết cấu tương đối đồng nhất.
• Bột ẩm hoặc bột dạng bùn: Loại này chứa nhiều nước hơn và có thể có kết cấu khác nhau.
1.2.3. Theo kích thước hạt
• Bột có kích thước hạt đồng nhất: Đây là loại bột với kích thước hạt đồng đều.
Hệ thống điều khiển cho loại này thường đơn giản hơn.
• Bột có kích thước hạt không đồng nhất: Bột có kích thước hạt không đồng nhất
yêu cầu kiểm soát chính xác hơn trong việc xả và xử lý.
1.2.4. Theo mục tiêu kiểm soát
• Kiểm soát lưu lượng (Flow control): Mục tiêu chính của hệ thống này là duy trì
lưu lượng xả bột ở một mức nhất định. lOMoARcPSD| 38777299
• Kiểm soát tỷ lệ hỗn hợp (Ratio control): Trong trường hợp bạn cần kết hợp
nhiều loại bột hoặc hỗn hợp, hệ thống này kiểm soát tỷ lệ của từng thành phần.
• Kiểm soát áp suất hoặc nhiệt độ (Pressure or temperature control): Trong một
số trường hợp, kiểm soát áp suất hoặc nhiệt độ có thể quan trọng để đảm bảo sự
ổn định của quá trình xả bột.
Phân loại cụ thể của hệ thống điều khiển xả bột sẽ phụ thuộc vào yếu tố cụ
thể của quy trình sản xuất và yêu cầu của ứng dụng. Các hệ thống điều khiển
này có thể sử dụng các cảm biến, van, bơm, và bộ điều khiển để duy trì hiệu
suất và chất lượng sản phẩm trong quá trình xả bột.
Hình 1.1 Hệ thống xả liệu
2. Cấu tạo của hệ thống xả liệu
• Bơm: Thường được sử dụng để tạo áp suất và đẩy chất lỏng từ tank đến điểm
sử dụng. Có nhiều loại bơm như bơm trục đứng, bơm trục ngang, bơm ly tâm, bơm pistonz
• Cảm biến: Được sử dụng để theo dõi và điều chỉnh thông số của hệ thống, như
lưu lượng chất lỏng, áp suất, nhiệt độ, mức độ trong tank, v.v. Có nhiều loại
cảm biến như cảm biến áp suất, cảm biến lưu lượng, cảm biến mức, cảm biến nhiệt độ,...
• Băng tải: là một thiết bị truyền tải sản phẩm, nguyên vật liệu,... giúp di chuyển
từ vị trí này sang vị trí khác với tốc độ nhanh, hiệu quả và chính xác.
• Tank: Là nơi chứa chất lỏng trước khi được bơm và cung cấp đến các điểm sử
dụng. Tank có thể có kích thước và công suất khác nhau tùy thuộc vào yêu cầu sử dụng.
• Van: Được sử dụng để điều khiển lưu lượng chất lỏng thông qua hệ thống xả
liệu. Có nhiều loại van như van cửa, van bi, van cầu, van bướm, v.v. Van có thể
hoạt động thủ công hoặc tự động. Các thành phần này hoạt động cùng nhau để lOMoARcPSD| 38777299
đảm bảo việc cung cấp chất lỏng từ tank đến các điểm sử dụng một cách hiệu quả và chính xác.
3. Nguyên lí hoạt động
Hình 1.2 Hệ thống xả liệu (mô hình)
Khi ấn START hệ thống bắt đầu hoạt động
Tank chưa có liệu, bơm P bắt đầu bơm nhiên liệu đến vị trí của cảm biến S2
thì dừng bơm. Trong quá trình bơm, nếu sau 5s khởi động bơm, cảm biến S1
không phát hiện có liệu chảy vào tank thì lập tức dừng bơm và báo sự cố máy bơm ra ngoài.
Cảm biến S5 báo có xe vào nạp liệu thì mở băng tải chạy sau 5s thì mở van V để xả liệu
Cảm biến S6 báo xe đã được bơm đầy liệu thì đóng van xả liệu và sau 10s đóng băng tải
Trong quá trình, nếu cảm biến S3 báo mức liệu thấp thì bơm P khởi động để
bơm nhiên liệu vào tank đến vị trí S2.
Khi cảm biến S4 báo hết nhiên liệu thì không cho phép xả liệu, dừng toàn
bộ chương trình và báo sự cố ra ngoài.
Nhấn STOP để dừng hệ thống.
4. Yêu cầu an toàn hệ thống
Để đảm bảo an toàn cho các thiết bị trong hệ thống xả liệu dạng bột khi gặp sự cố hỏng hóc:
• Khi động cơ gặp sự cố
Ngay lập tức dừng động cơ và ngưng cung cấp nhiên liệu đến động cơ để
ngăn chặn nguy cơ cháy nổ lan rộng. Khi xảy bơm gặp sự cố lOMoAR cPSD| 38777299
Ngay lập tức dừng hoạt động của bơm để ngăn chặn nguy cơ lan rộng và cắt
nguồn điện hoặc nguồn cung cấp nhiên liệu đến bơm để đảm bảo an toàn
trong quá trình xảy ra sự cố.
Thiết bị phải được cách ly khỏi nguồn điện và hệ thống xả phải được tắt để
tránh hư hỏng hoặc rò rỉ thêm
• Khi xảy ra trường hợp không đóng được van
Thiết bị phải được trang bị thiết bị dừng khẩn cấp để có thể kích hoạt nhanh
chóng và dễ dàng trong trường hợp khẩn cấp
Thiết bị phải có van an toàn hoặc van giảm áp có khả năng giải phóng áp
suất hoặc vật liệu dư thừa trong hệ thống xả
• Khi xảy ra trường hợp cảm biến hồng ngoại hỏng
Thiết bị phải có cảm biến dự phòng hoặc bộ điều khiển thủ công có thể phát
hiện và điều chỉnh lưu lượng và áp suất của vật liệu trong hệ thống.
Thiết bị phải có hệ thống báo động có thể cảnh báo cho người vận hành và
những công nhân khác về bất kỳ trục trặc hoặc bất thường nào trong hệ thống.
• Khi xảy ra trường hợp băng truyền bị kẹt
Thiết bị phải được trang bị thiết bị dừng khẩn cấp và hệ thống báo động để
có thể kích hoạt nhanh chóng và dễ dàng
Nhanh chóng ngắt nguồn điện để tạm dừng việc bơm, xả hệ thống và tiến hành sửa chữa lỗi
• Khi xảy ra sự cố quá tải
Ngắt nguồn điện và dừng hệ thống xả liệu để tránh gây hư hại thêm cho thiết bị.
Kiểm tra nguyên nhân gây quá tải, có thể do dây dẫn không đủ tải, dùng
nhiều thiết bị trên một ổ cắm, chọn aptomat có công suất thấp, hoặc do lỗi của thiết bị.
Sửa chữa hoặc thay thế các thiết bị bị hỏng hoặc không phù hợp, có thể cần
sử dụng các thiết bị đo ampe kìm để kiểm tra quá tải.
Sử dụng các thiết bị bảo vệ quá tải như relay nhiệt, cầu chì, rơle, để ngắt mạch khi có sự cố
• Khi xuất hiện ngắn mạch
Tắt ngay nguồn điện để tránh gây hư hại thêm cho thiết bị và ngăn chặn nguy cơ cháy nổ.
Kiểm tra nguyên nhân gây ngắn mạch, có thể do dây dẫn bị rò rỉ, bị đứt, bị
chập, hoặc do lỗi của thiết bị. lOMoARcPSD| 38777299
Sửa chữa hoặc thay thế các thiết bị bị hỏng hoặc không phù hợp, có thể cần
sử dụng các thiết bị đo ampe kìm để kiểm tra.
Sử dụng các thiết bị bảo vệ quá tải như relay nhiệt, cầu chì, rơle, để ngắt mạch khi có sự cố.
An toàn là quan trọng nhất. Việc ứng phó với sự cố trong hệ thống điều
khiển xả liệu cần sự cẩn trọng và nhanh nhẹn, luôn chuẩn bị sẵn sàng đối phó
với các tình huống khẩn cấp tránh các thiệt hại không mong muốn.
Sau khi kết thúc chương 1 thì chúng ta phần nào hiểu rõ hơn về hệ thống điều
khiển xả liệu. Chương 1 đã cung cấp kiến thức tổng quan, bằng những thông
tin cơ bản, lịch sử hình thành của hệ thống xả liệu. Ngoài ra còn có cả cấu tạo,
phận loại hệ thống, nguyên lí hoạt động với yêu cầu an toàn.
Chương tiếp theo chúng ta sẽ đi sâu hơn, tìm hiểu kĩ hơn về phân tích hệ
thống điều khiển xả liệu và các yếu tố quan trọng liên quan. Nhiệm vụ chính
chương sau là trình bày cấu trúc và hoạt động của hệ thống, bao gồm sơ đồ đấu
nối các thiết bị cũng như lựa chọn thiết bị PLC phù hợp.
CHƯƠNG 2: LỰA CHỌN PHẦN CỨNG, PHẦN MỀM
1. Sơ đồ khối hệ thống điều khiển xả liệu
Hình 2.1 Sơ đồ khối hệ thống điều khiển xả liệu
Hệ thống điều khển xả liệu bao gồm các thiết bị chính:
Bộ điều khiển PLC: lập trình để thực hiện một loạt trình tự các sự kiện lOMoARcPSD| 38777299
Bơm nhiên liệu: được sử dụng để tạo áp suất đẩy nhiên liệu từ tank đến điểm sử dụng Các cảm biến S1: báo liệu vào tank S2: báo tank đầy liệu S3: báo tank thấp liệu S4: báo tank hết liệu
S5: báo có xe vào nạp liệu S6: báo xe đầy liệu
Van xả: điều khiển lưu lượng tốc độ xả của nhiên liệu
Băng truyền: truyền tải nhiên liệu, sản phẩm một cách tự động
2. Lựa chọn PLC cho hệ thống điều khiển xả liệu tự động Tên gọi Tín hiệu Chức năng Nút START DI Khởi động hệ thống Nút STOP DI Dừng hệ thống Cảm biến S1 DI Báo có liệu vào tank Cảm biến S2 DI Báo tank đầy liệu Cảm biến S3 DI Báo tank thấp liệu Cảm biến S4 DI Báo tank hết liệu Cảm biến S5 DI Báo có xe nạp liệu Cảm biến S6 DI Báo xe đầy liệu Nút Auto/Manual DI Chuyển đổi trạng thái Auto và Manual Nút Bơm DI Đóng mở bơm Nút Van DI Đóng mở van Nút băng tải DI Đóng mở băng tải Bơm DO Cấp liệu vào tank Đèn 1 DO Báo lỗi bơm Van DO Xả liệu ra băng tải Băng tải DO Vận chuyển liệu vào xe lOMoARcPSD| 38777299 Đèn 2 DO Báo tank hết liệu
Bảng 2.1 I/O và chức năng từng bộ phận Kết luận: DI = 12; DO = 5
Lựa chọn PLC FX3U 32MR/DS 2.1 PLC
Bộ điều khiển lập trình PLC (programmable Logic Controller) là bộ điều
khiển logic lập trình được hay còn tên gọi khác là bộ điều khiển tuần tự.
PLC FX3U 32MR/DS là thế hệ sản phẩm đời thứ ba của bộ điều khiển lập
trình PLC FX thương hiệu Mitsubishi. Với nhiều ưu điểm và các tính năng nổi
bật, bộ lập trình PLC FX3U 32MR/DS đã mang lại nhiều thành công trong công nghiệp. 2.1.1 Ưu điểm
Mitsubishi là thương hiệu Nhật Bản với chất lượng hàng đầu được các chuyên
gia, kỹ sư trong ngành đánh giá cao về chất lượng cũng như công nghệ bên trong
thiết bị điện công nghiệp đến từ Mitsubishi. Và bộ điều khiển lập trình PLC
FX3U 32MR/DS cũng không ngoại lệ:
Thiết kế nhỏ gọn: các công nghệ hiện đại về kỹ thuật điều khiển lập trình, các
link kiện, vi xử lý được sắp xếp gọn gàng trong bộ khung nhỏ gọn.
Tốc độ xử lý nhanh, hiệu suất cao, tính năng mở rộng tốt.
Bộ nhớ lớn, dễ dàng ghi vào/đọc từ bộ nhớ.
Tuổi thọ cao, tiết kiệm được chi phí bảo hành sửa chữa đáng kể.
Mitsubishi luôn biết cách làm hài lòng các khách hàng của mình bằng những
dòng thiết bị điện cao cấp, bộ điều khiển lập trình PLC FX3U 32MR/DS mang
đến những giải pháp vô cùng thông minh về công nghệ điều khiển cũng như các
giải pháp tiết kiệm năng lượng hiệu quả, tiết kiệm không gian cho tủ điện của bạn ,… 2.1.2 Tính năng
Bộ điều khiển lập trình PLC FX3U 32MR/DS Mitsubishi cho phép người vận
hành thực hiện linh hoạt các hoạt động điều khiển như: điều khiển tốc độ động
cơ, thời gian hoạt động của tải,… Cung cấp đầy đủ các tính năng của mạch rơ le,
PLC FX3U 32MR/DS có thể điều S chứa được những chương trình điều khiển phức tạp.
Kết nối dễ dàng với các thiết khác: máy tính,…
Mỗi lệnh của chương trình sẽ có một vị trí riêng trong bộ nhớ.
Có thể mở rộng truyền thông qua cổng USB.
2.1.3 Thông số cơ bản
Điện áp hoạt động: 24VAC. Số đầu I/O: 32 lOMoARcPSD| 38777299 Kiểu đầu ra: Relay Số đầu ra: 16 Số đầu vào: 16
Kiểu đầu vào: Sink/Source Kiểu lắp đặt: DIN Rail
Bộ nhớ chương trình: 64000 Steps
Công suất tiêu thụ: 25W/30 VA
Giao diện lập trình: Computer, HMI
Kiểu kết nối: USB, RS232C, RS485
Hình 2.2 PLC FX3U 32MR/DS Mitsubishi
Cáp kết nối: FX-USB-AW, USB-SC09, USB-SC09-FX
Dòng điện đầu ra: 800mA
Trọng lượng; 0.6 kg
2.2 Modul mở rộng
Modul mở rộng FX2N-16EX-ES/UL Mitsubishi Thông số kỹ thuật:
Mã sản phẩm: FX2N-16EX-ES/UL Dòng: MELSEC-F Loại hình; FX2N
Các điểm I/O chiếm dụng trên PLC:16
Đầu vào kỹ thuật số tích hợp: 16
Điện áp hoạt động: 24VDC
Đấu dây: Terminal Hình 2.3 Modul mở rộng FX2N-16EX-ES/UL Thương hiệu Mitsubishi
2.3 Ngôn ngữ lập trình
Ngôn ngữ lập trình của PLC FX3U là điều khiển bằng ngôn ngữ LD (ladder
diagram), SFC (Sequential Function Chart) và ST (Structured Text). Ngôn ngữ
chính sử dụng nhiều nhất là LD.
LD (Ladder diagram) là một ngôn ngữ lập trình đồ họa được sử dụng phổ
biến cho việc lập trình các hệ thống điều khiển PLC. Nó dựa trên các giả thiết
và nguyên tắc từ các mạch điện điều khiển truyền thống sử dụng các rơle và các
phép toán logic để điều khiển các thiết bị và quy trình. Ưu điểm là dễ thực hiện,
dễ hiểu, dễ khắc phục sự cố, hỗ trợ ghi chú và chỉnh sửa thuận tiện. Nhưng ngôn
ngữ lập trình LD lại được tiêu chuẩn hóa rất nhiều và không mang lại tính linh hoạt hoàn toàn.
Một số tập lệnh của PLC FX3U theo ngôn ngữ lập trình LD: Lệnh Load và Load Inverse lOMoARcPSD| 38777299
Load (LD): Nhiệm vụ là khởi tạo lại công tắc NO.
Load inverse (LDI) : Nhiệm vụ là khởi tạo lại công tắc NC. Lệnh OUT Điều khiển cuộn dây.
Nhiều lệnh OUT có thể nối song song với nhau.
Hình 2.4 Lệnh LD và OUT
Hình 2.5 Lệnh LDI và OUT Lệnh AND và AND INVERSE
AND: Dùng để nối tiếp nhiều công tắc NO, có thể nối tiếp nhiều công tắc cùng một lúc. Hình 2.6 Lệnh AND
ANI (AND INVERSE): Nối tiếp nhiều công tắc NC, có thể nối tiếp nhiều công tắc cùng một lúc. Hình 2.7 Lệnh ANI Lệnh OR, OR INVERSE
OR: Dùng để nối song song các công tắc NO, tối đa là 10 nhánh nối song song cho một cuộn dây. lOMoARcPSD| 38777299 Hình 2.8 Lệnh OR
ORI (OR INVERSE): Nối song song các công tắc NC, tối đa là 10 nhánh nối
song song cho một cuộn dây. Hình 2.9 Lệnh ORI
Lệnh Load Pulse and Load Trailing pulse.
LDP (Load Pulse): hoạt động khi có xung chuyển từ OFF sang ON
LDF (Load Falling Pulse): hoạt động khi có xung chuyển từ ON sang OFF
Lệnh And Pulse, And Trailing Pulse
Lệnh ANDP (And Pulse) hoạt động khi có xung chuyển từ trạng thái OFF sang ON.
Lệnh ANDF (And Falling Pulse) hoạt động khi có xung chuyển từ trạng thái ON sang OFF.
Lệnh ANDP và ANDF dược sử dùng tương tự như lệnh AND và ANI.
Lệnh OR Pulse ,OR Trailling Pulse
ORP (OR Pulse) hoạt động khi có xung chuyển từ trạng thái OFF sang ON.
ORF (OR Falling Pulse) hoạt động khi có xung chuyển từ trạng thái ON sang OFF.
• Lệnh ORP và ORF được dùng tương tự như lệnh AND và ADNI. lOMoARcPSD| 38777299
Hình 2.10 Lệnh LDP, ORP và ANDP
Hình 2.11 Lệnh LDF, ORF và ANDF • Lệnh Set và RST
Đặc điểm: SET và RST có thể dùng cho cùng một thiết bị bao nhiêu lần tùy ý.
Tuy nhiên trạng thái tác động lại là trạng thái cuối cùng.
Hình 2.12 Lệnh SET và RST • Lệnh Timer, Counter
Dạng chung OUT và RST của Timer và Counter :
OUT: Chức năng điều khiển cuộn dây bộ định thời hoặc bộ đếm
RST: Đặt lại giá trị tác động cho bộ đếm hoặc bộ định thời Hoạt động
của bộ định thì và bộ đếm : Bộ định thì (Timer)
Các bộ định thì hoạt động dựa trên phương pháp đếm các xung clock. Ngõ ra
của Timer sẽ được kích hoạt khi giá trị đếm được đạt đến giá trị hằng số K nhất lOMoARcPSD| 38777299
định. Khoảng thời gian trôi qua sẽ được tính bằng công thức: giá trị đếm được
nhân với độ phân giải của Timer.
Timer 10 ms đếm giá trị 100 thì khi đó khoảng thời gian trôi qua đều được tính
như sau: 100 x 10ms = 100 x 0.01s = 1s
Hình 2.13 Lệnh Timer
Khoảng thời gian định thì được đặt trực tiếp thông qua hằng số K, hoặc được
đăt gián tiếp qua thanh ghi dữ liệu D. Thông thường dùng thanh ghi dữ liệu
được chốt để đảm bảo không bị mất dữ liệu khi mất điện. Tuy nhiên nếu điện
áp của nguồn , điện áp của pin bị giảm quá mức thì thời gian định thì có thể bị sai. Bộ đếm (Counter)
Khi dùng Counter hằng số K sẽ xác định số cần đếm.
Hình 2.14 Lệnh Counter
3. Lựa chọn thiết bị cho hệ thống xả liệu
3.1 Động cơ bơm nhiên liệu
Máy bơm bột Parma YC-CH50/Alu-Buna N
Lưu lượng bơm lớn, được làm từ hợp kim dày chịu lực tốt, phù hợp với việc
bơm yêu cầu nhanh, giá thành hợp lí. Lưu lượng bơm: 25m3/h, 416 lít/phút
Đường kính ống hút – xả: 70mm Cột áp: 70m lOMoARcPSD| 38777299 Nguồn cấp: 220V
Không cần sử dụng phớt cơ khí hay
các bộ phận làm kín tương tự để ngăn ròrỉ.
Có khả năng tự mồi, áp suất và lưu lượng
bơm đa dạng. Chạy khô an toàn mà
không hề sinh nhiệt hoặc gây hỏng hóc.
Bơm được nhiều loại hóa chất nguy
hiểm, hóa chất dễ cháy nổ, độc hại.
Hình 2.15 Bơm bột Parma YC-CH50
3.2 Cảm biến mức
Cảm biến báo mức chất rắn dạng xoay VELT-RPS-M
Được sử dụng rộng rãi cho chất
rắn, có thể lắp đặt tại nhiều vị trí trong
thùng chứa, tuổi thọ cao, nguyên lý
hoạt động đơn giản, chính xác, nhanh
chóng, giá cả hợp lí, cài đặt bảo trì đơn giản. Nguồn cấp: 24VDC
Nhiệt độ làm việc: -20oC đến 80oC
Áp suất hoạt động: Áp suất môi trường A.T.M
Kết nối: ½ PF Hình 2.16 Cấu tạo của cảm biến mức dạng xoay Cấp bảo vệ: IP65
Tín hiệu ngõ ra: Tiếp điểm relay NO và NC Nguyên lí hoạt động:
• Khi cánh Khuấy không tiếp xúc với vật liệu sẽ xoay chậm theo một vận tốc cố định.
• Khi có vật liệu tiếp xúc, cánh khuấy bị chặn lại, lò xo bên trong cảm biến căng
ra kéo motor tách khỏi nguồn cấp, cảm biến sẽ xuất tín hiệu ngõ ra, điều khiển
thiết bị được kết nối. lOMoARcPSD| 38777299
Hình 2.17 Hình ảnh mô tả nguyên lí hoạt động của cảm biến mức chất rắn dạng xoay
3.3 Cảm biến hồng ngoại
Cảm biến vật cản hồng ngoại E3F-DS30C4
Được sử dụng để xác định khoảng cách tới vật cản bằng cách phát tia hồng
ngoại và nhận lại tia phản xạ từ vật cản. Cảm biến này có độ phản hồi nhanh và
ít nhiễu do sử dụng mắt nhận và phát tia hồng ngoại theo tần số riêng biệt
Xác định có xe vào nhập liệu, phản hồi nhanh, động chính xác cao, giá thanh rẻ. Nguồn cấp: 24 VDC
Khoảng cách phát hiện: 1.2 - 1.5m Dòng kích ngõ: 200mA NPN
Hoạt động tốt trong môi trường bụi và ngoài trời
Hình 2.18 Hình ảnh cảm biến hồng ngoại E3F-DS30Y1 3.4 Van xả
Van bướm bột điều khiển điện
Ưu điểm của Van bướm điều khiển bằng điện:
Van được điều khiển bởi dòng điện nên việc
đóng/mở van trở nên rất thuận tiện, linh hoạt,
tự động hóa cao. Có thể kết nối với tủ điều
khiển PLC để đóng/mở và giám sát từ xa giúp
giảm chi phí nhân công vận hành.
Kiểu kết nối: wafer, lug, bích, clamp… Nguồn cấp: 220V lOMoARcPSD| 38777299
Hình 2.19 Van bướm tự động
Có thể lắp cho các đường ống kích thước lớn (Lên đến hơn 2000mm).
Van được làm từ nhiều chất liệu khác nhau như: gang, thép, thép không gỉ…
nên có thể phù hợp với nhiều môi trường khác nhau.
Khi mất điện đột xuất có thể đóng/mở van bằng tay quay thông thường….
Van có thể cài đặt trạng thái: thường mở hoặc thường đóng tùy theo nhu cầu của ứng dụng.
Có thể lắp đặt, bão dưỡng và thay thế dễ dàng.
Van hoạt động không gây ra tiếng ồn.
Khi van đóng/mở xong sẽ tự động ngắt điện (không bị ngâm điện) nhờ vào công tắc hành trình.
Van có thiết kế nhỏ gọn vì vậy có thể lắp đặt được ở nhiều vị trí khác nhau.
3.5 Động cơ băng truyền Model GH32-750W-120S Công suất: 3kW
Tốc độ motor: ~ 1420 Vòng/phút
Điện áp ngõ vào: 3 Pha 220V / 380V
Tỷ số truyền (ratio): 1/120
Kháng nước kháng bụi: IP44
Hiệu suất động cơ: IE2
Hình 2.20 Động cơ băng truyền
3.6 Rơ le trung gian
Rơ le trung gian OMRON G2R-2 24V 5A 8 chân 2 cặp tiếp điểm - A1H12
Điện áp kích coil: 24 VDC Tiếp điểm: DPDT Cách gắn: Tháo lắp
Dòng điện chuyển mạch: 5A
Điện áp chuyển mạch max AC: 250 VAC
Điện áp chuyển mạch max DC: 30 VDC
Chiều cao: 41.7mm Hình 2.21 Rơ le trung gian Chiều sâu: 13mm
Công suất max AC: 1.25 kVA lOMoARcPSD| 38777299 Chiều dài: 29mm Series: G2R Số cực: 2 Rơ le nhiệt LS MT-32
Rơ le nhiệt LS là thiết bị điện hỗ
trợ dùng bảo vệ động cơ và mạch điện
tránh khỏi sự cố quá tải, vói cấu tạo
với lưỡng kim nhiệt ở 3 cực. Khi phát
hiện xảy ra sự cố sẽ tự động ngắt
mạch điện để bảo vệ tải, quá trình để
thực hiện cần thời gian từ vài giây
cho đến vài phút tác động. Ngoài ra,
rơ le nhiệt không tự ngắt khi có hiện tượng ngắn mạch. Dòng điện: 32A
Dải điều chỉnh: 4 – 6A
Hình 2.22 Relay nhiệt 3.7 Đèn báo
• Đỏ để báo sự cố bơm • Vàng báo hết liệu Thông số kỹ thuật: Đèn Led PLC 8.5W 2P G24d-3 Điện áp: 220VAC Công suất: 8.5W Tuổi thọ: 30000 giờ
Hình 2.23 Hình ảnh đèn báo PLC 3.8 Contactor
Contactor là thiết bị trung gian dùng để đóng – ngắt mạch điện. Contactor
đóng vai trò như một công tắc thông thường, nhưng nó được kích hoạt bằng
điện. Ứng dụng dùng một dòng điện nhỏ để điều khiển một dòng điện có công lOMoARcPSD| 38777299
suất lớn; thông qua nút nhấn (bằng tay) hoặc cảm biến đóng ngắt tự động kích hoạt
Contactor LS MC-32a 380V 32A 15kW 2NC+2NO
Khởi đông từ LS được làm từ các vật liệu có độ bền cao, có khả năng hoạt ̣
động và chống chịu trong môi trường khắc nghiệt, nhiệt độ thấp nhất -5 độ C
và cao nhất tới 40 độ C. Khởi đông từ LS có thể lắp đặt trên DIN rail 35mm ̣
hoặc bắt vít. Mặt che của thiết bị được trang bị khả năng chống bụi. Dòng điện: 32A
Điện áp điều khiển: 220V Công suất: 15kW Tiếp điểm: 2NO + 2NC Cấp bảo vệ: IP20 Tiêu chuẩn: CCC, IEC, UL Hình 2.24 Contactor
3.9 Bộ nguồn Bộ nguồn 24VDC Input: 110-265VAC, 50-60Hz
Điện áp vào nhỏ nhất: 90VAC Output: 24VDC Công suất: 35W Dòng định mức: 5A Dòng bảo vệ: 1.25A Dòng tải max: 7A
Cách ly chống nhiễu: 3kVAC
Nhiệt độ làm việc: -20 đến 70oC
Độ ẩm 30-90% Hình 2.25 Bộ nguồn PLC 24VDC 3.10 Nút bấm
Công tắc nhấn nhả On/Off Kích thước: Φ20 lOMoARcPSD| 38777299 Hình 2.26 Nút bấm
4. Xây dựng sơ đồ mạch lực và mạch đấu nối
4.1 Phân chia cổng I/O Tên gọi Cổng Nút START X0 Nút STOP X1 Cảm biến S1 X2 Cảm biến S2 X3 Cảm biến S3 X4 Cảm biến S4 X5 Cảm biến S5 X6 Cảm biến S6 X7 Auto M20 Manual M21 Nút Bơm M25 Nút Van M13 Nút Băng tải M14 Bơm Y0 Đèn 1 Y1 Van Y2 Băng tải Y3 Đèn 2 Y4
Bảng 2.2 Phân chia cổng PLC lOMoARcPSD| 38777299
4.1 Mạch lực
Hình 2.27 Sơ đồ mạch lực
4.2 Mạch đấu nối
Hình 2.28 Sơ đồ đấu nối INPUT PLC lOMoARcPSD| 38777299
Hình 2.29 Sơ đồ đấu nối OUTPUT PLC
Tất cả những gì đã được trình bày trong chương này là một bước quan trọng
để hiểu rõ về hệ thống điều khiển xả liệu và các yếu tố quan trọng liên quan đến
nó. Nó giúp người đọc biết được sâu hơn về cấu trúc của hệ thống trong mạch đấu
nối, sự lựa chọn kỹ lưỡng các thiết bị của PLC, cũng như các tập lệnh và thiết bị
quan trọng để tạo nên một hệ thống hoạt động hiệu quả.
Chương cuối cùng sẽ tập trung vào xây dựng chương trình điều khiển để
đáp ứng được nhu cầu và đem lại hiệu suất tối ưu nhất. lOMoARcPSD| 38777299
CHƯƠNG 3: XÂY DỰNG CHƯƠNG TRÌNH
1. Lưu đồ thuật toán
Hình 3.1 Lưu đồ thuật toán bơm liệu vào tank lOMoARcPSD| 38777299
Hình 3.2 Lưu đồ thuật toán xả liệu lOMoARcPSD| 38777299 2. Chương trình
Khi bắt đầu chương trình ta cấp nguồn cho hệ thống X0=1 vì là X0 là nút
nhấn start để duy trình dòng điện nên ta dùng M0.
Để kết thúc chương trình ta có X1; M20, M21 lần lượt là chế độ làm việc auto và manual.
Khi hệ thống xả liệu làm việc phân ra hai chức năng chính là bơm liệu và xả liệu M1, M2
Khi chế độ bơm làm việc cảm biến S3 (cảm biến báo tank hết liệu) nhận
tín hiệu mạch cấp nguồn cho biến trung gian M10 M10=1 lúc đó có hai chế độ:
Auto M20=1 bơm hoạt động =>Y0=1
Manual M21=1, bấm nút bơm M25=1 bơm hoạt động =>Y0=1 lOMoARcPSD| 38777299
Khi bơm hoạt động Y0=1 bơm liệu vào tank đến S2 (Tank đầy liệu) S2=1 lúc đó bơm tắt Y0=0
Trong khi bơm hoạt động Y0=1 cảm biến S1=1 (cảm biến báo không có
liệu qua đường ống) nhận tiến hiệu lúc đó báo lỗi qua đèn Y1=1. Báo đèn
Y1 xong sau 5s T0=1 tắt chương trình Quá trình xả liệu:
M2 biến xả liệu khi cảm biến S5=1 (cảm biến báo xe vào vị trí) nhận tín hiệu mạch M11=1
Khi biến trung gian M11=1 có hai chế độ làm việc:
Auto M20=1 => băng chuyền hoạt động Y3=1
Manual M21=1; bấm nút băng tải M14=1 => băng tải hoạt động Y3=1 lOMoARcPSD| 38777299
Khi băng tải hoạt động Y3=1 sau 5s T1=1 T1=1 =>biến M12=1
M12=1 có hai chế độ làm việc:
Auto M20=1 => van hoạt động Y2=1
Manual M21=1, nhấn nút van xả M13=1 => van hoạt động Y2=1
Van xả hoạt động xả liệu đến khi S6 nhận được tín hiệu S6=1 (cảm biến xe
đầy liệu) lúc đó tắt van xả Y2=0, sau 10s T2=1 => tắt băng chuyền Y3=0
Khi trong quá trình xả liệu cảm biến báo tank cạn liệu nhận tín hiệu S4=1
=> đèn báo lỗi Y4=1 => sau đó tắt chương trình lOMoARcPSD| 38777299
Trong quá trình xả liệu tank hết liệu nhận được tín hiệu S3=1 => bơm hoạt
động và tiếp tục chương trình đến khi kết thúc.
3. Mô phỏng HMI Mitsubishi
Hình 3.3 Hệ thống xả liệu qua mô phỏng HMI
Kết thúc chương cuối đã cho chúng ta thấy được cách xây dựng chương
trình trong hệ thông điều khiển xả liệu vô cùng phức tạp. Từ việc xây dựng lưu
đồ thuật toán bằng những thông số I/O rồi chạy chương trình để điều khiển
bằng tay, tự động qua phần mềm GX Works 2. Qua đó giúp chúng ta nhận ra
sự quan trọng của việc triển khai chương trình một cách chính xác và hiệu quả
trong hệ thống điều khiển xả liệu. lOMoARcPSD| 38777299 KẾT LUẬN
Qua chương trình điều khiển hệ thống xả liệu giúp chúng em thêm kiến
thức, kinh nghiệm để xây dựng một hệ thống một cách hoàn chỉnh hoạt động
một cách chính xác và hiệu quả. Ba chương trong đồ án đã cung cấp khái quạt
về các bước hoàn thành một dự án về hệ thống xả liệu tự động hóa
Tất cả những thông tin trên cho biết tổng thể về quá trình xây dựng hệ
thống điều khiển xả liệu. Qua đó áp dụng và hiệ thực đã nhận ra vai trò quan
trọng của việc lựa chọn thiết bị, PLC, và việc triển khai chương trình một cách chính xác.
Tóm lại, chúng ta cần phải hiểu rõ kiến thức cơ bản và không ngừng học
hỏi cái mới để cho thể xây dựng những hệ thống điều khiển hiệu quả và tiên
tiến.Nhóm em cũng mong dự án này sẽ là động lực để chúng em phát triển hơn
trong lĩnh vực điều khiển và tự động hóa. HƯỚNG PHÁT TRIỂN
Đề tài mới chỉ dừng lại ở việc thiết kế hệ thống điều khiển xả liệu nên chưa phản ánh
hết khả năng của hệ thống. Cho nên để hệ thống có thể phát triển hơn thì nhóm em xin
được phép đề xuất một vài phương án như cải tiến như sau:
• Bổ sung thêm hệ thống báo nếu s6 bị hỏng
• Bổ sung hệ thêm bơm phụ nếu bơm chính hỏng
• Bổ sung thêm hệ thống cảnh cáo cần bảo hành các thiết bị
TÀI LIỆU THAM KHẢO lOMoAR cPSD| 38777299
MITSUBISHI_FX3U-Users-Manual---Hardware-Edition.
Schneider-Catalog: Contacor and Protection Relays.
GOT2000 User’s Manual HMI Mitsubishi. GOT2000 Catalogue.