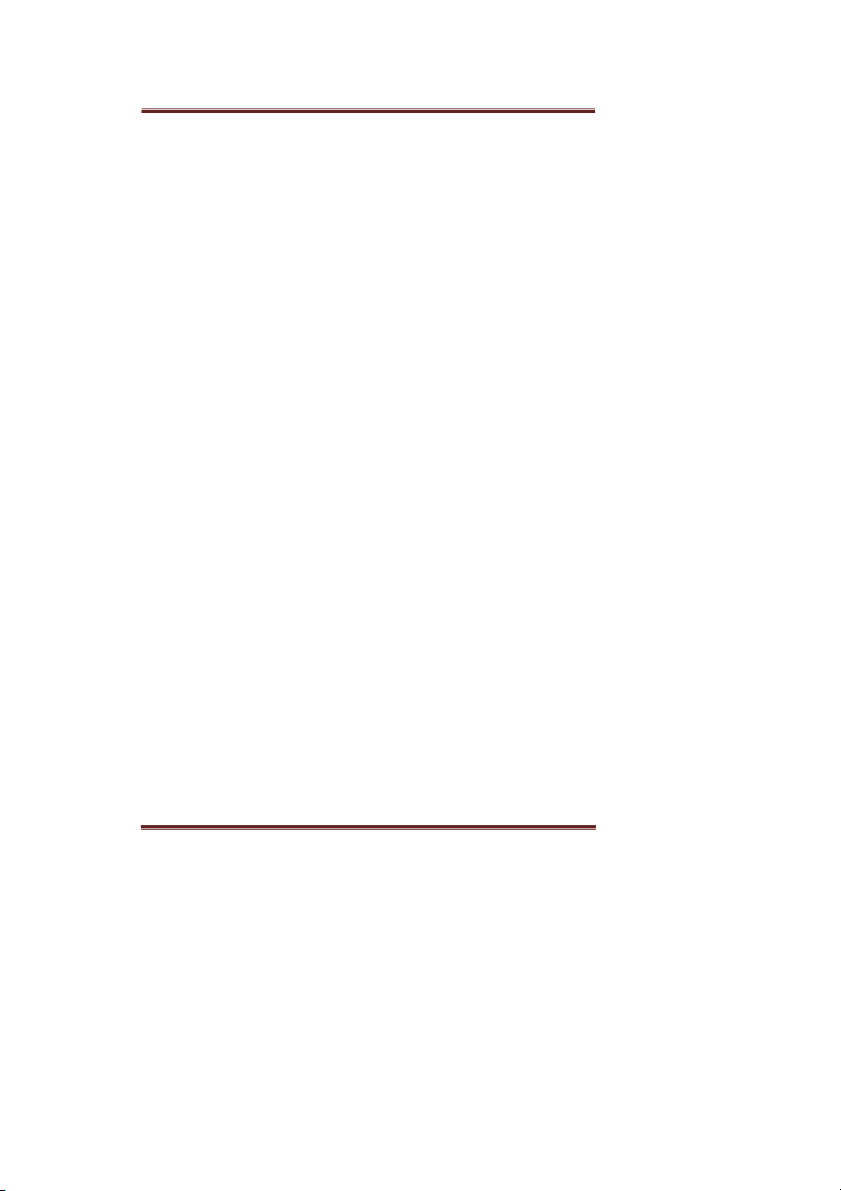
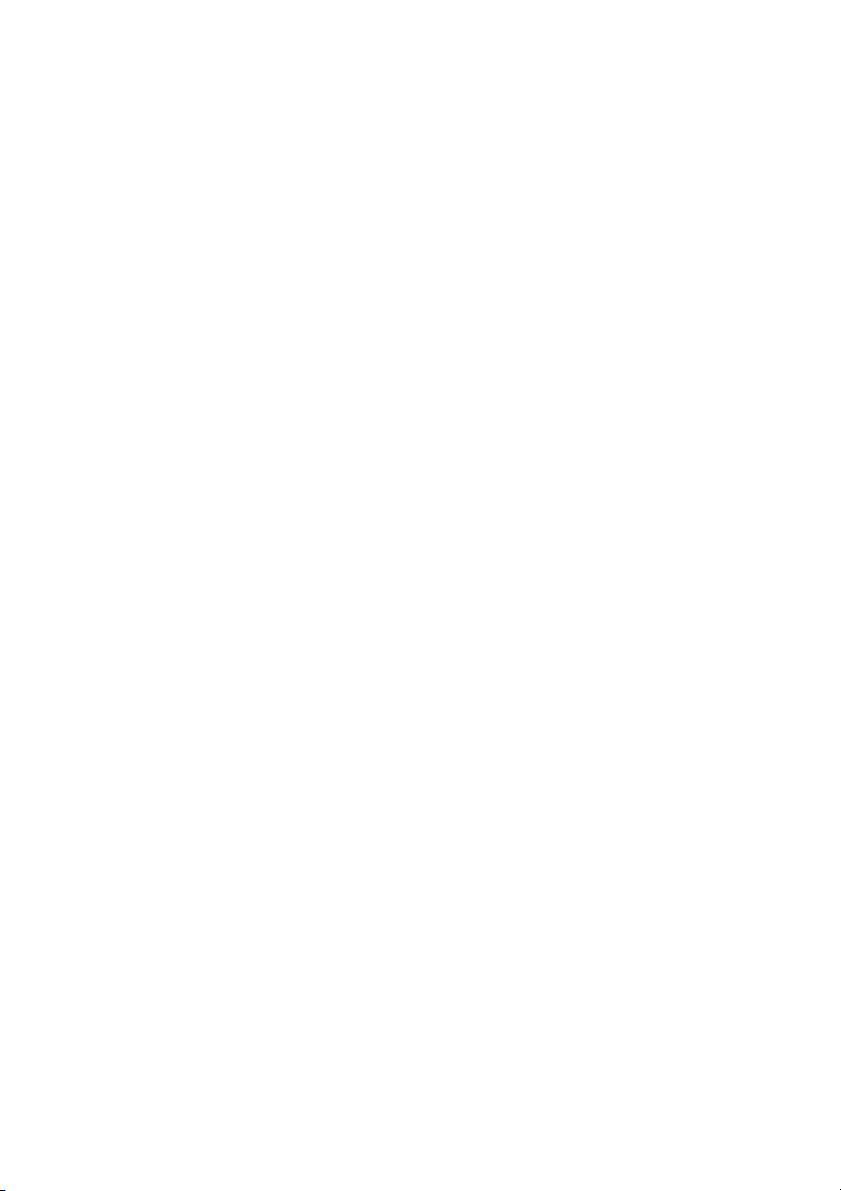
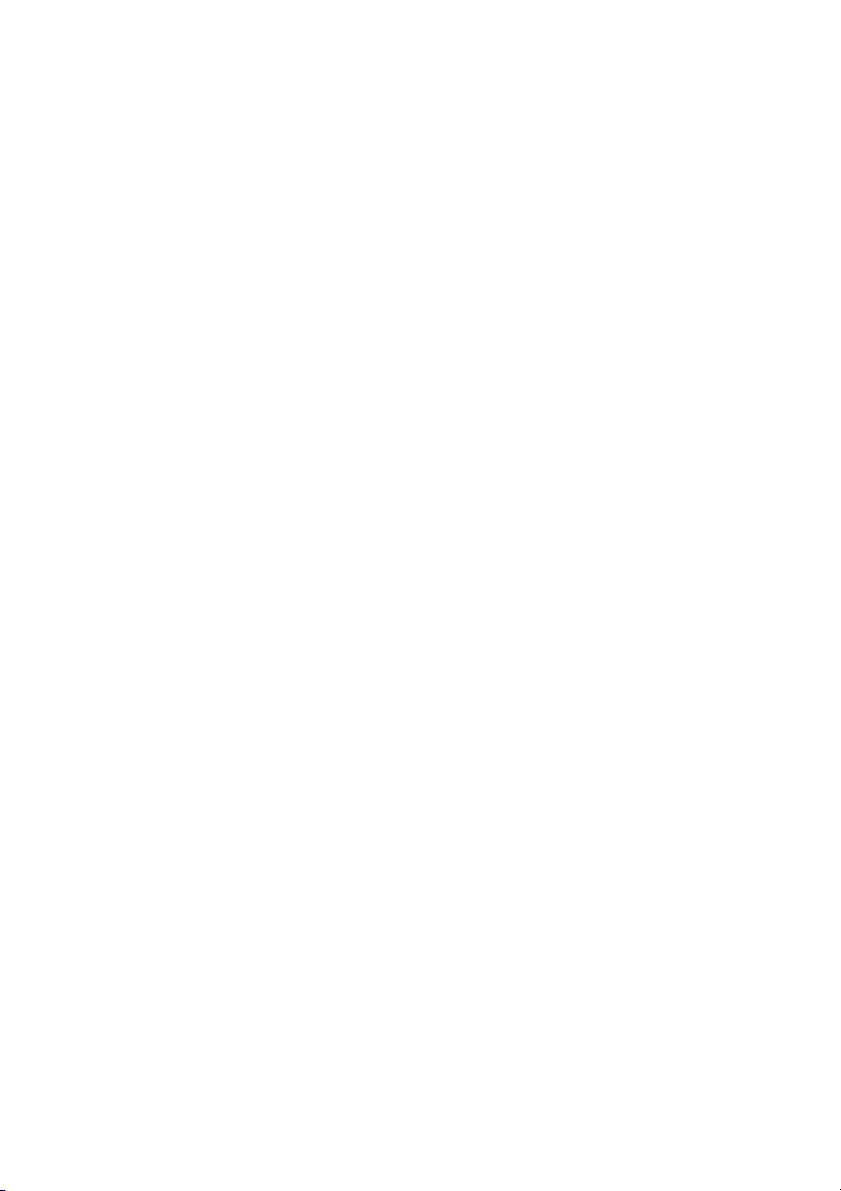
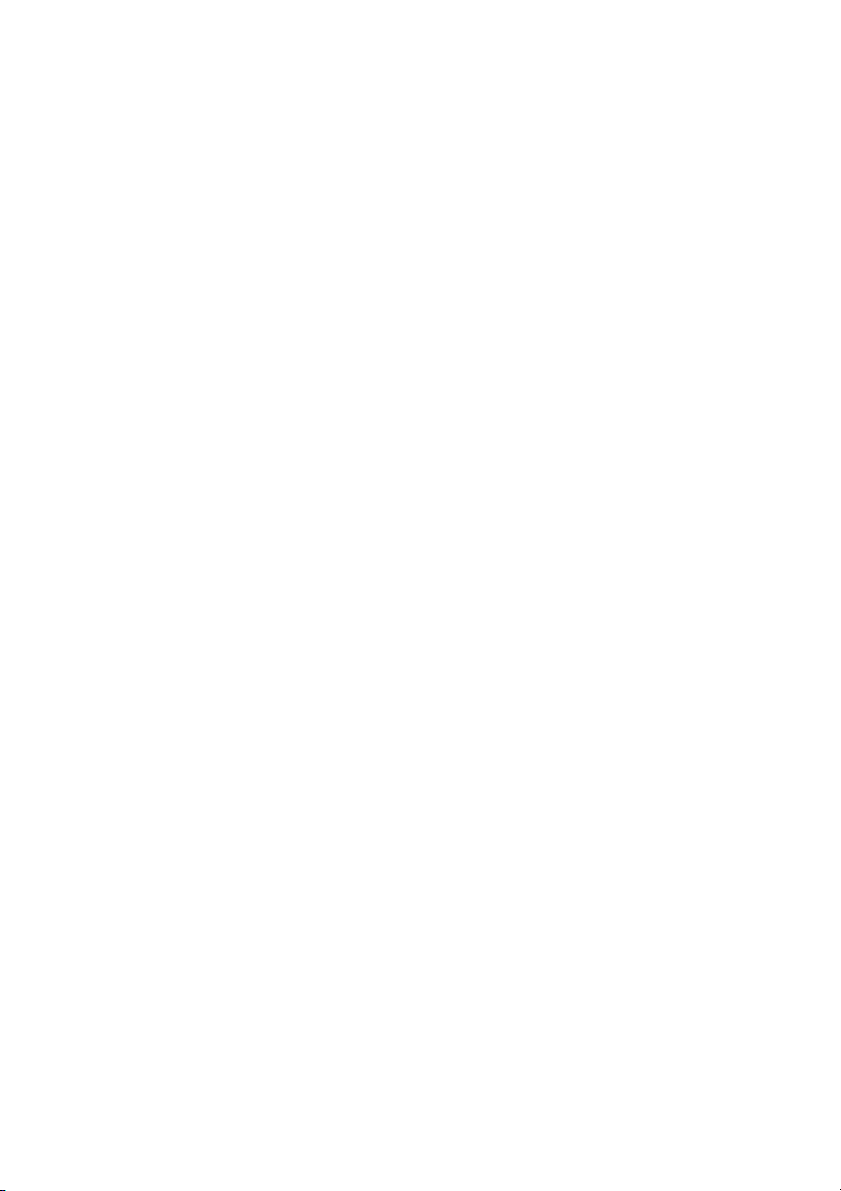
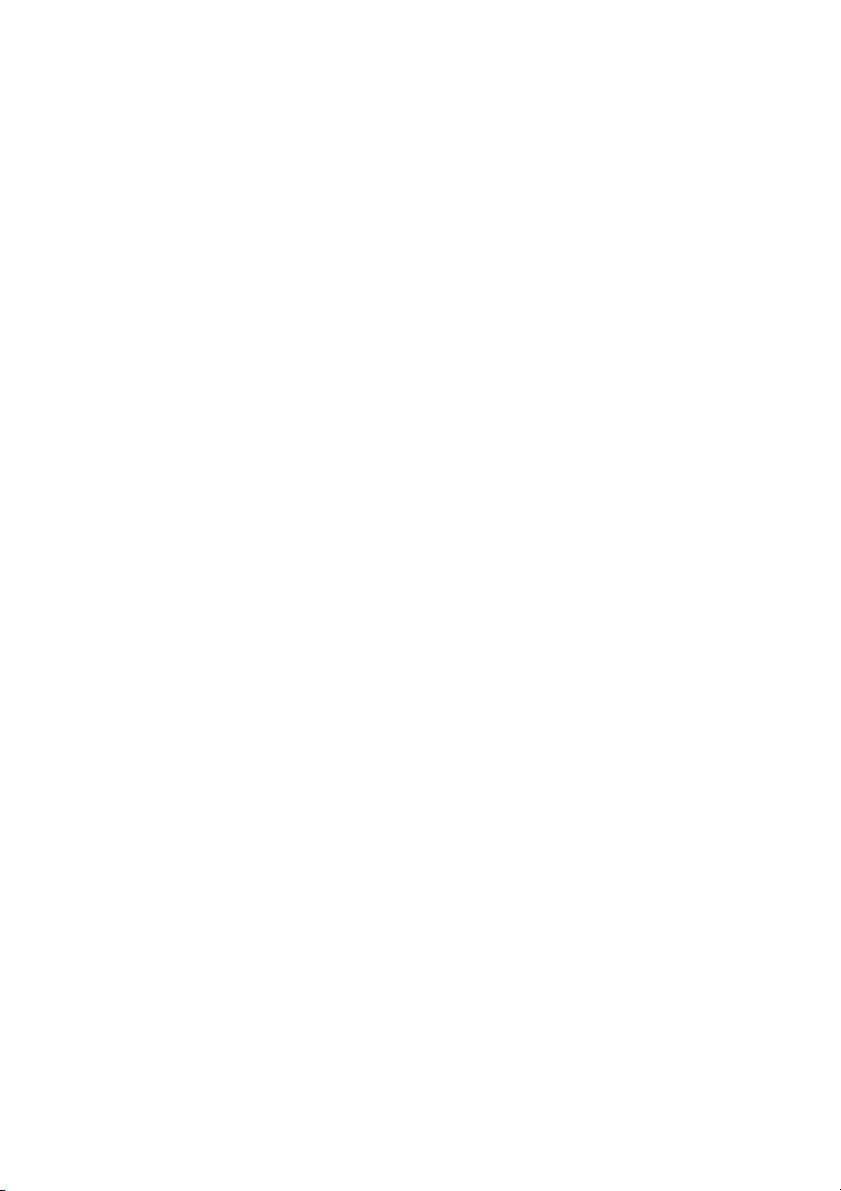
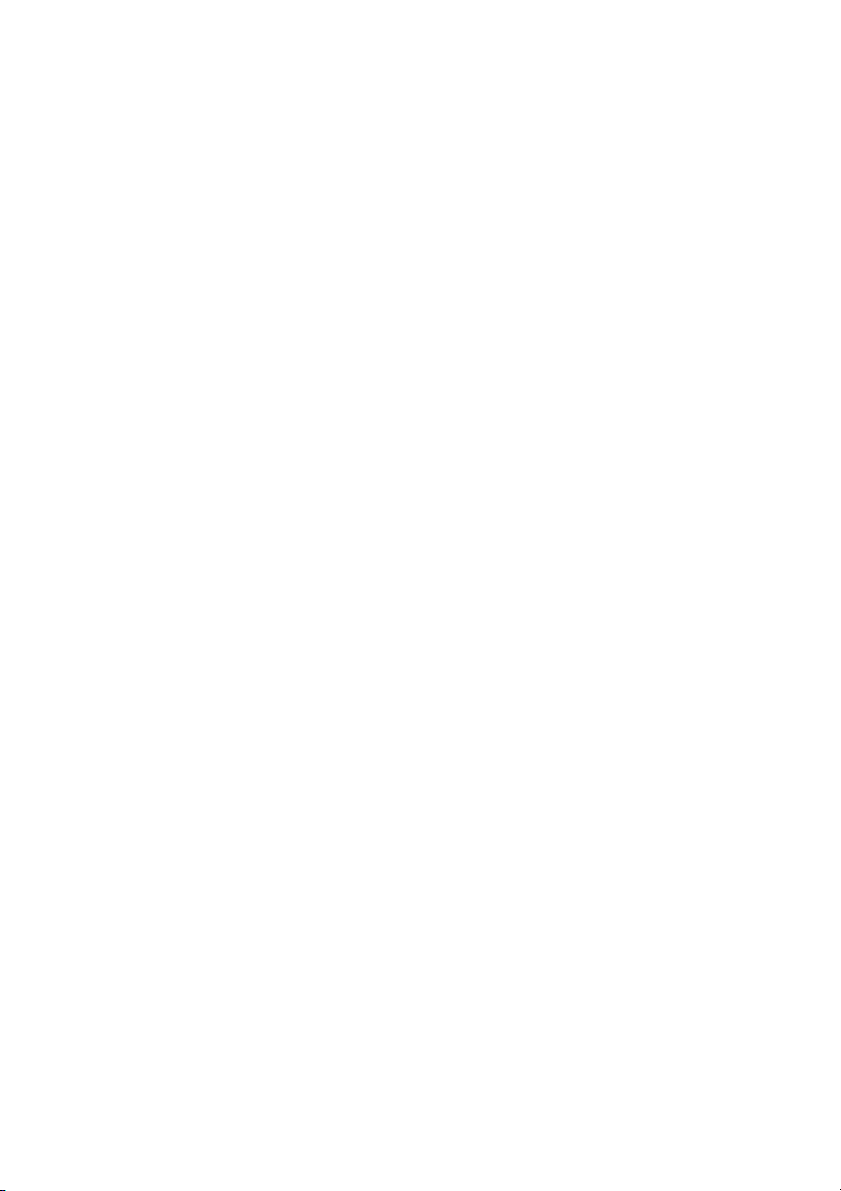
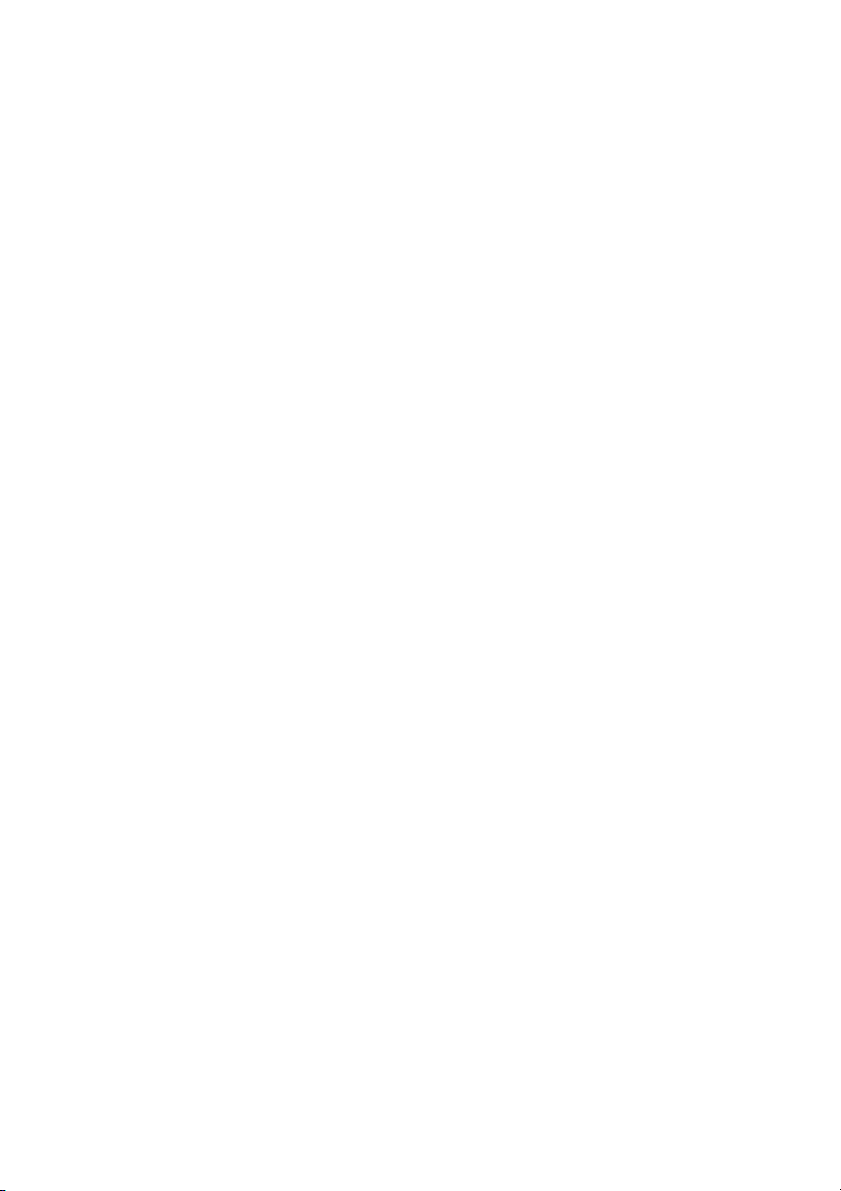
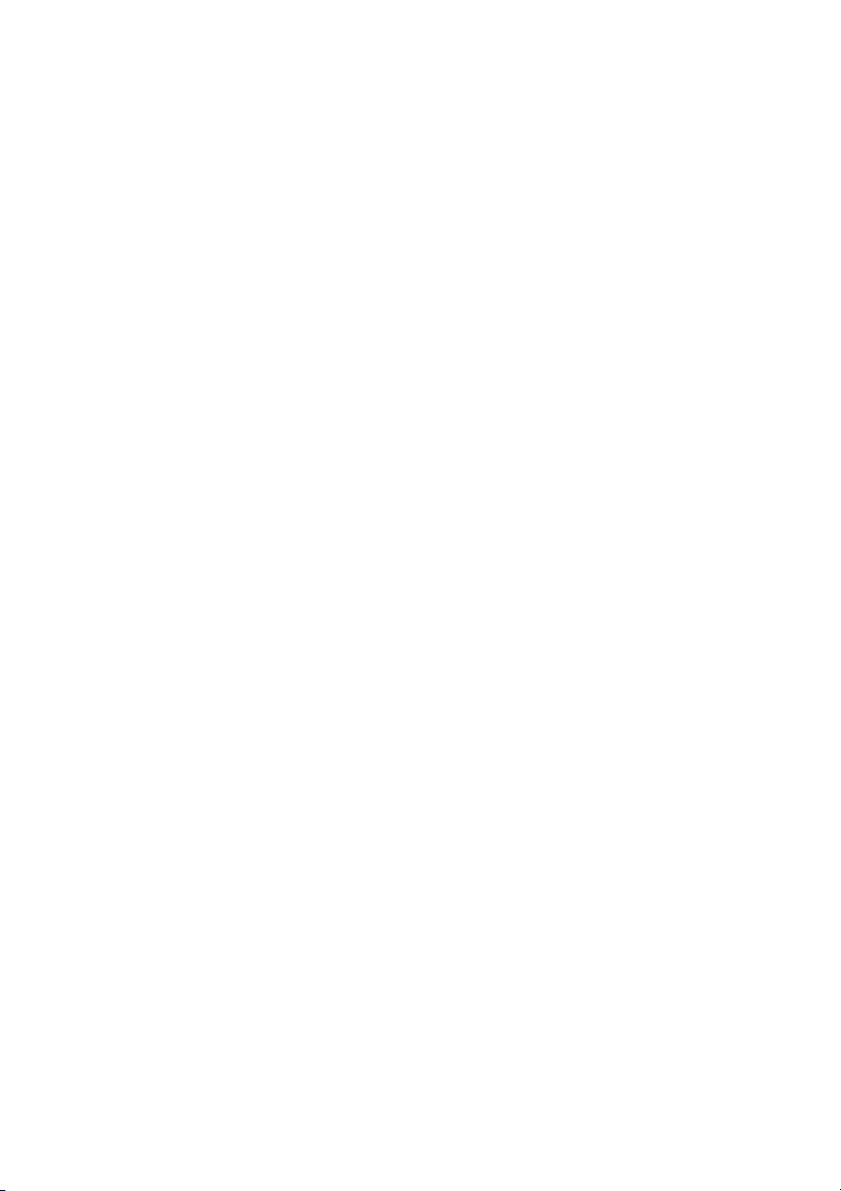
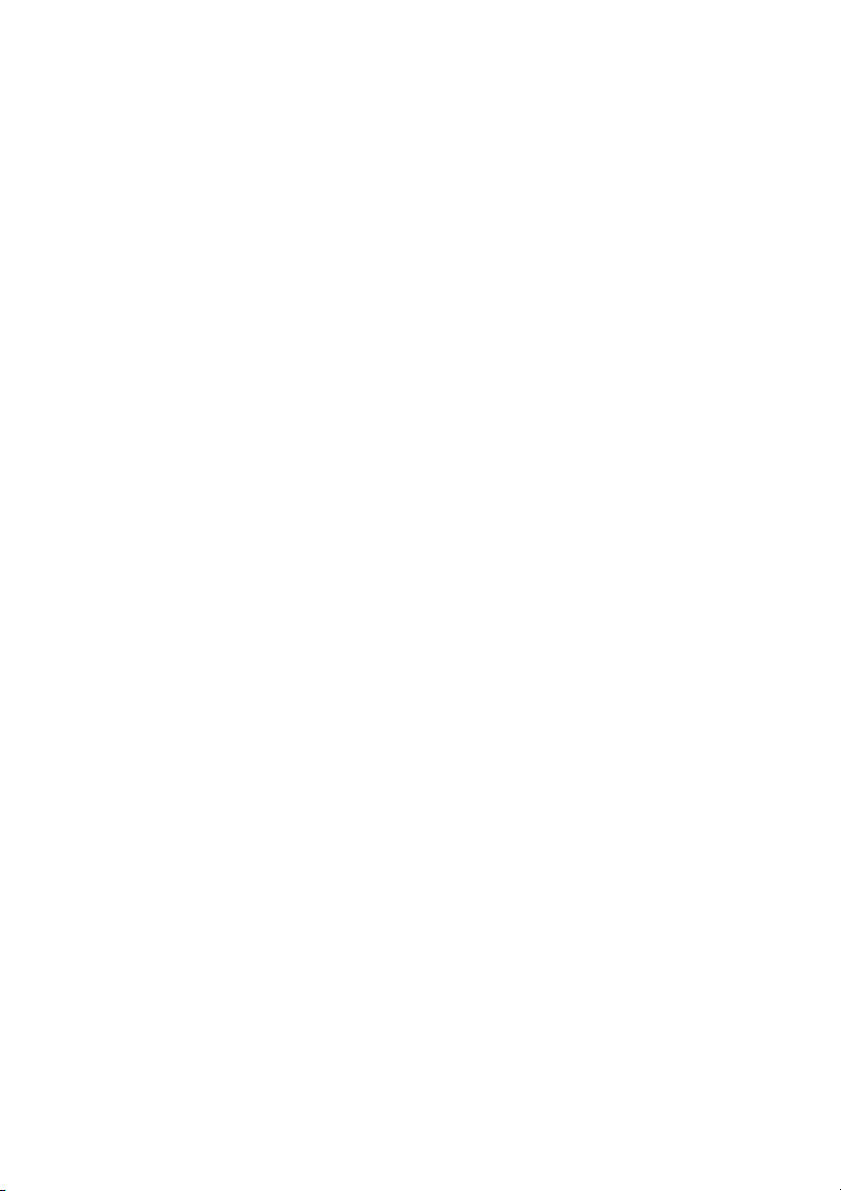
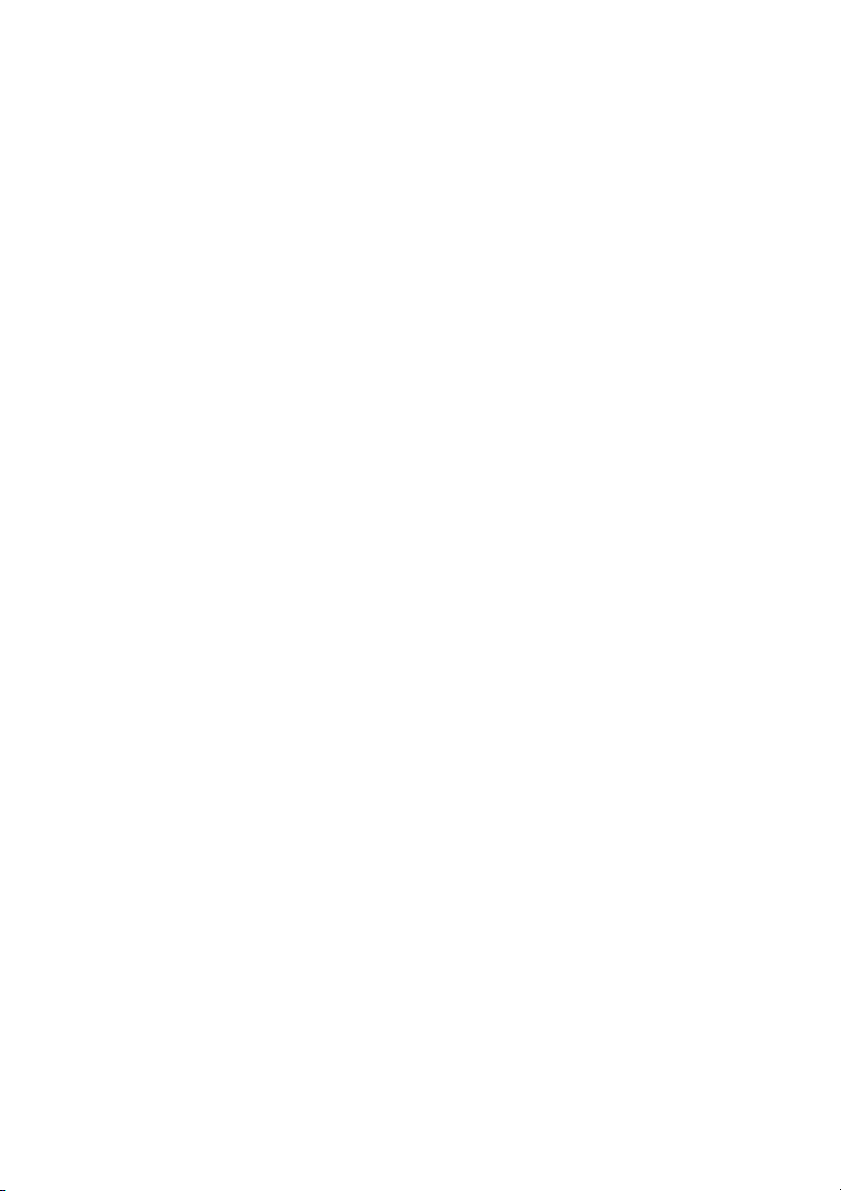
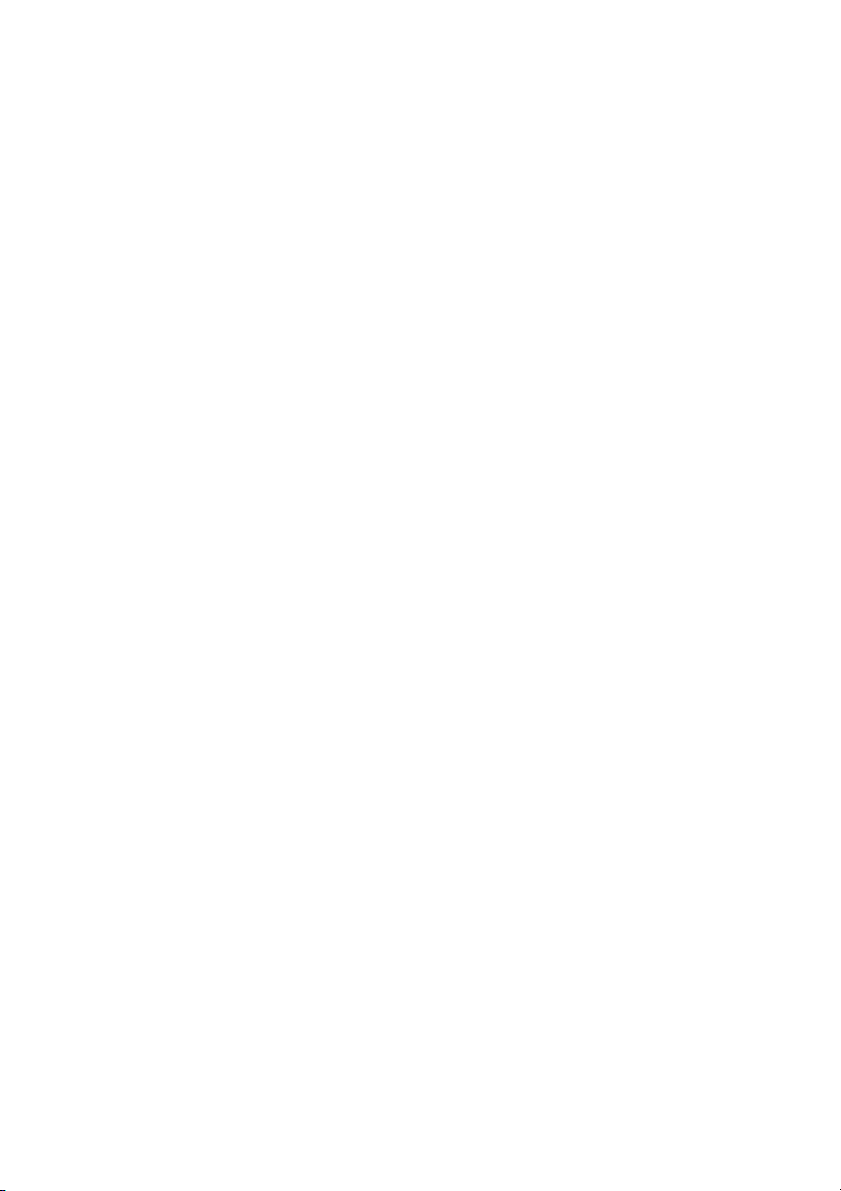
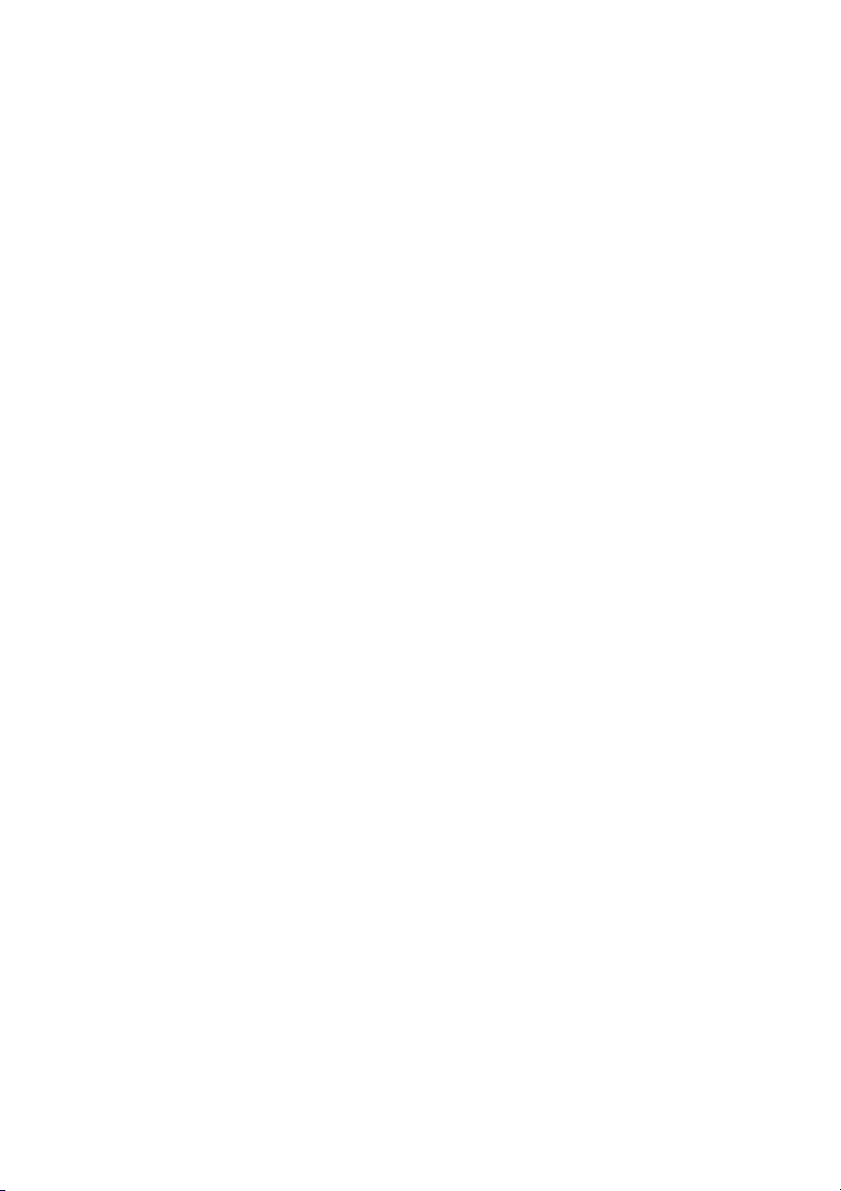
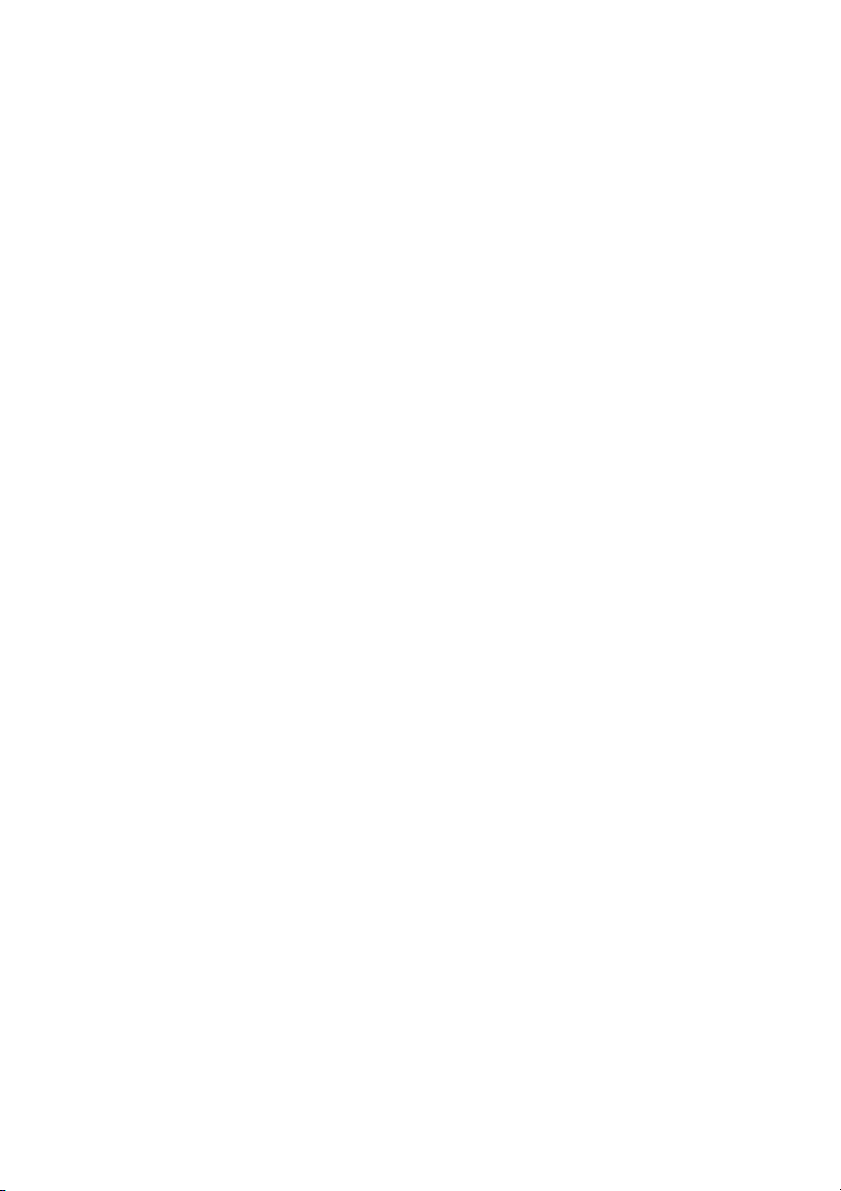
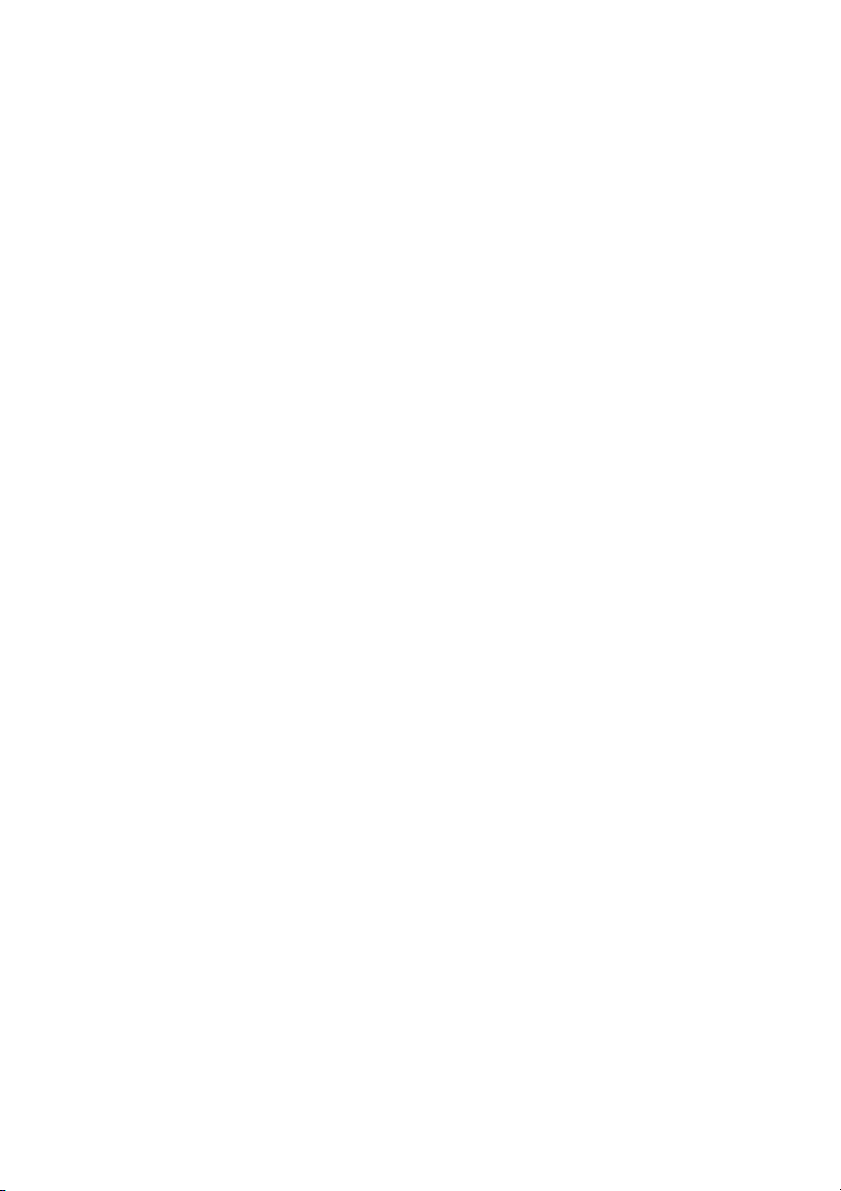
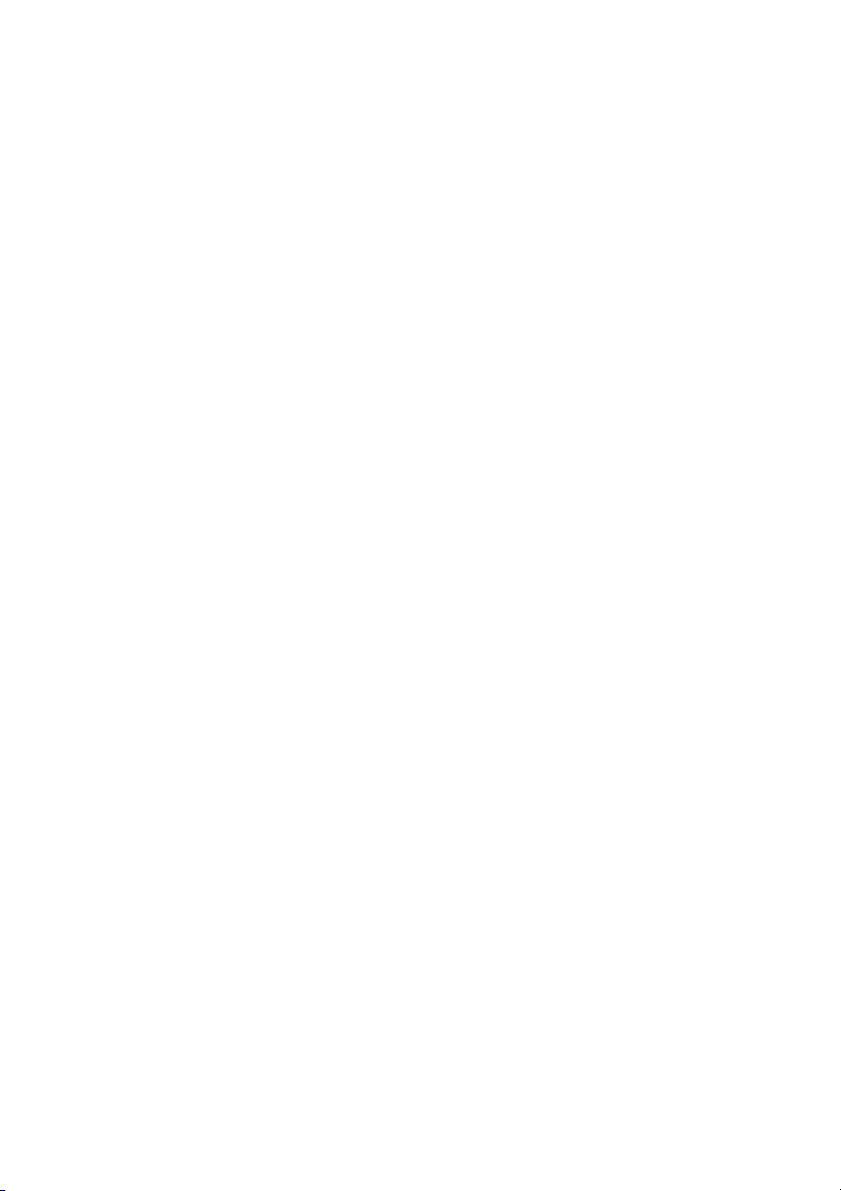
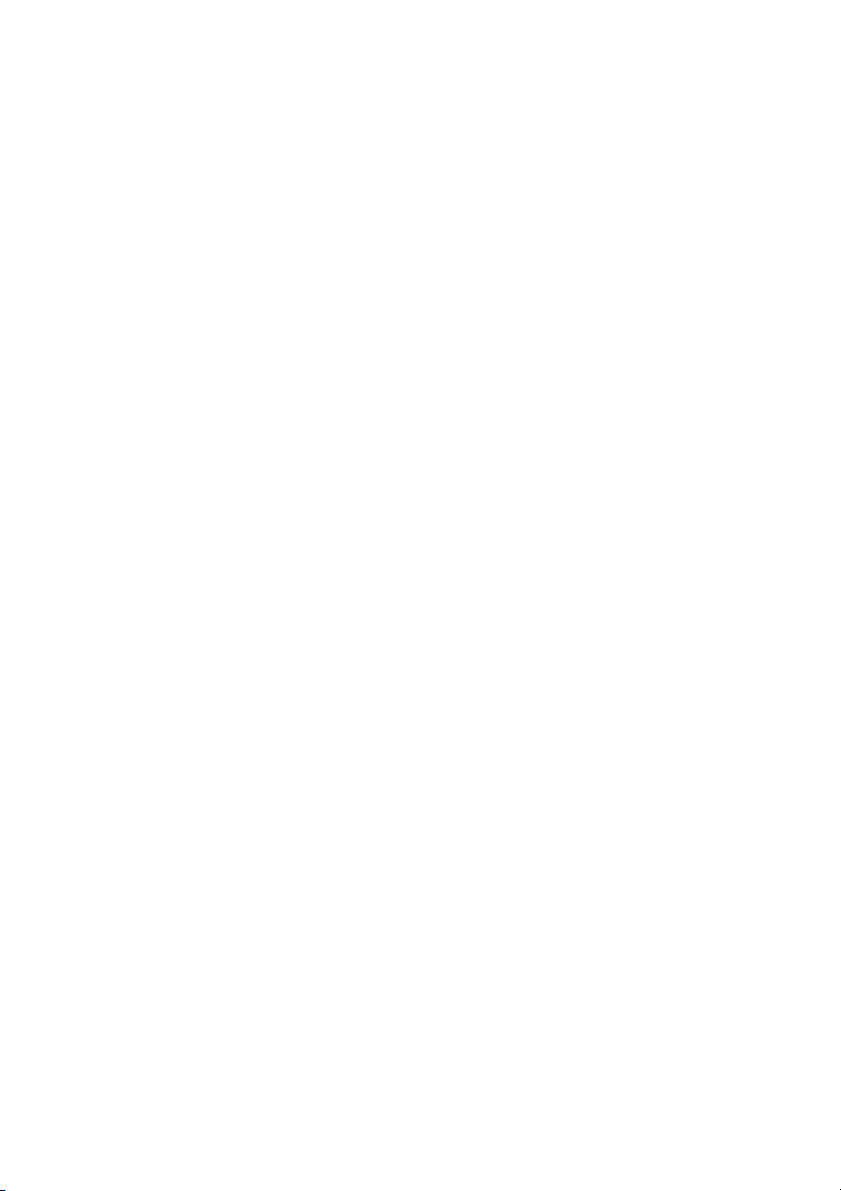
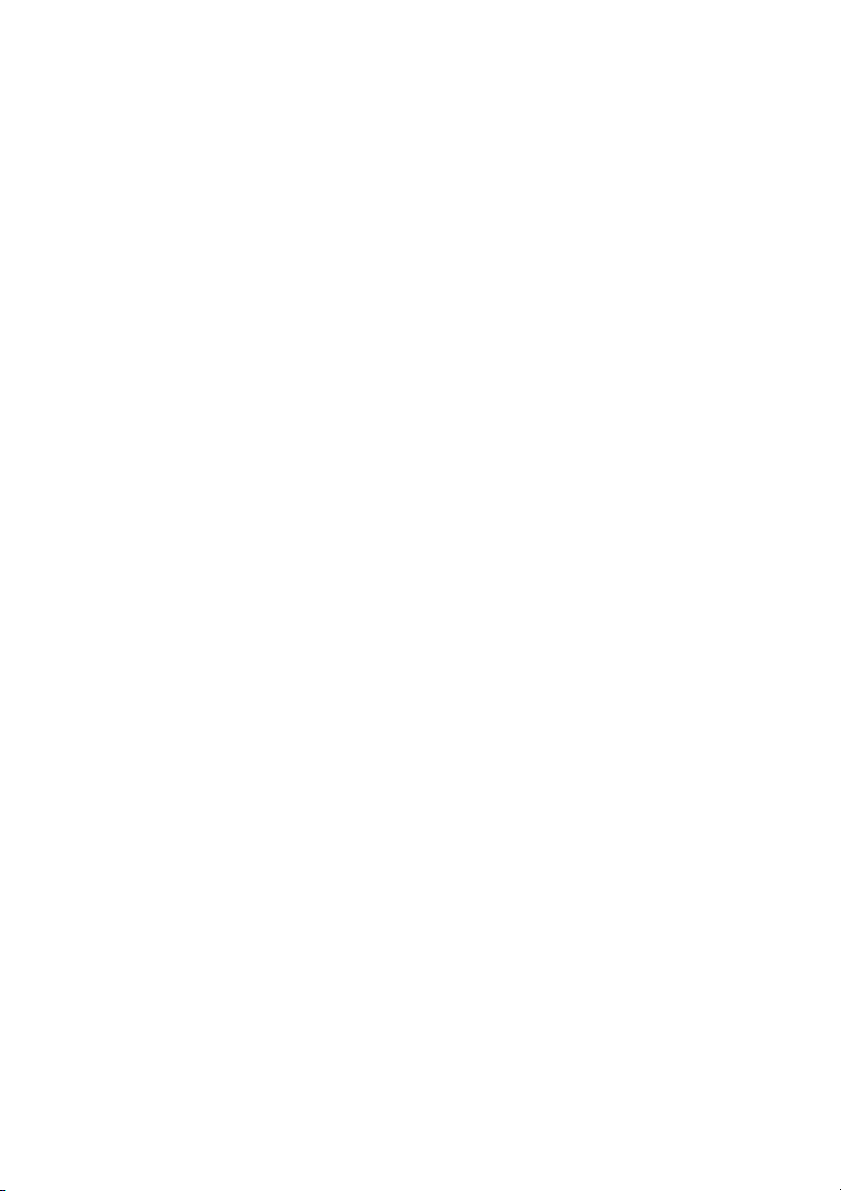
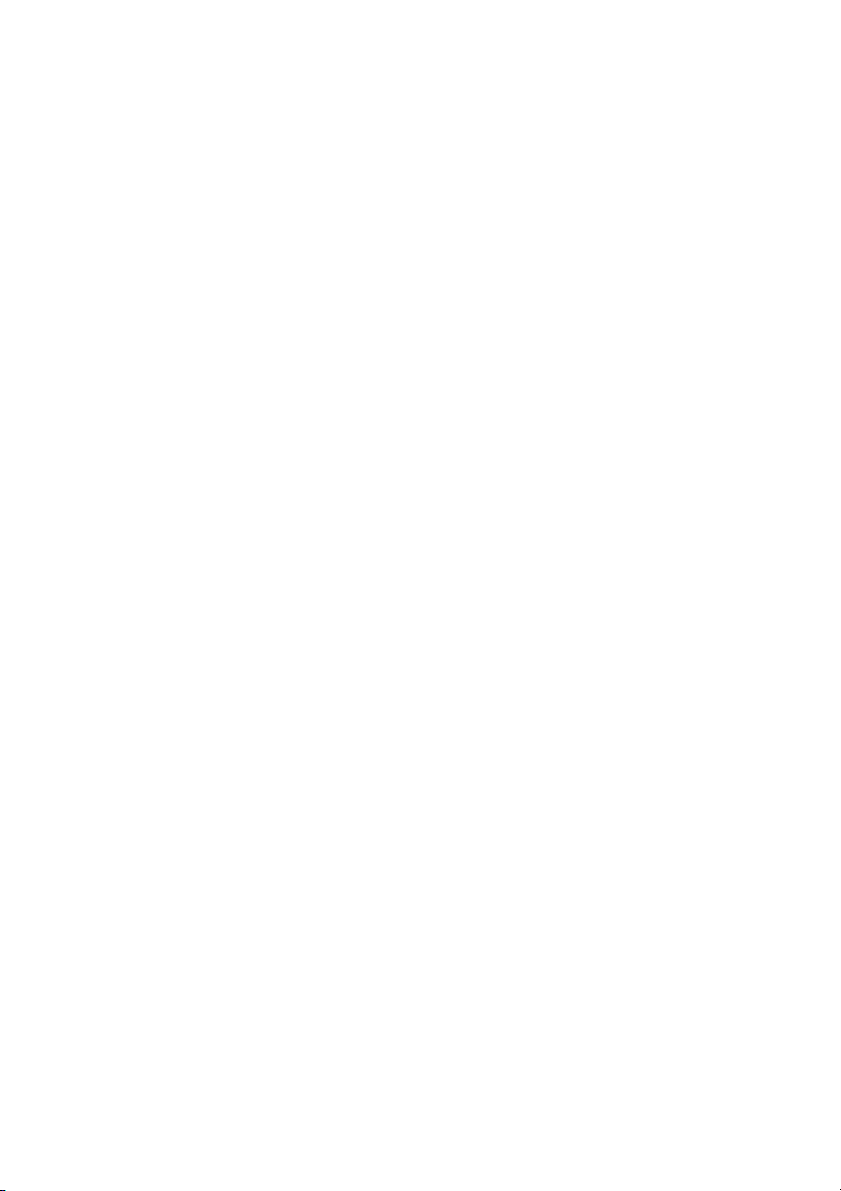
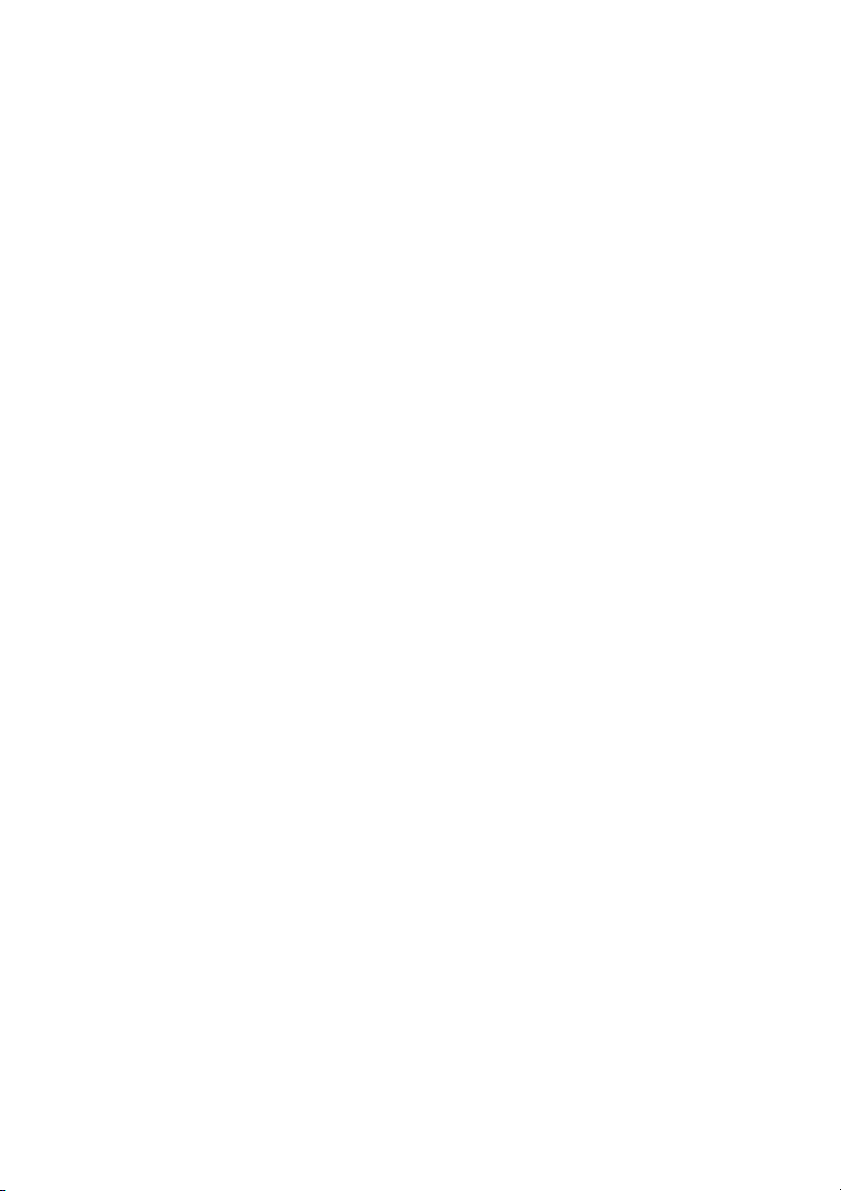
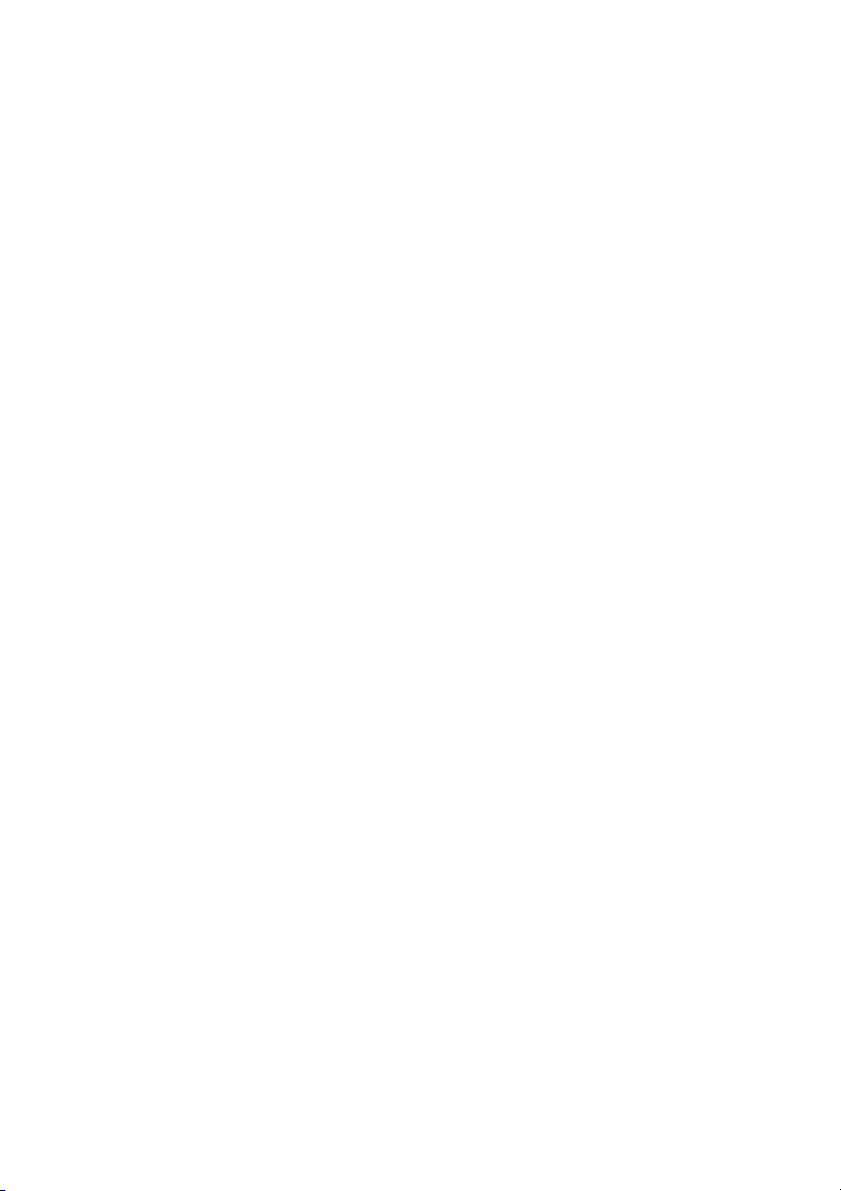
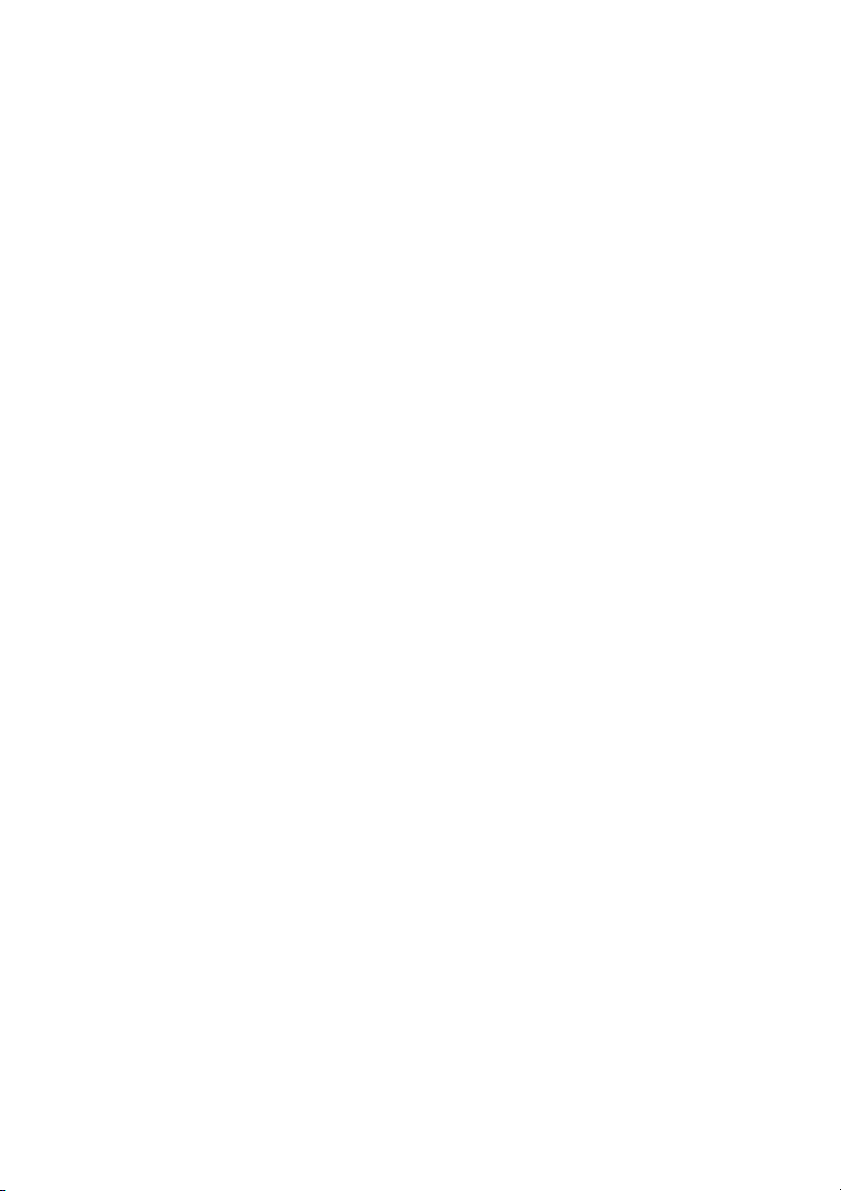
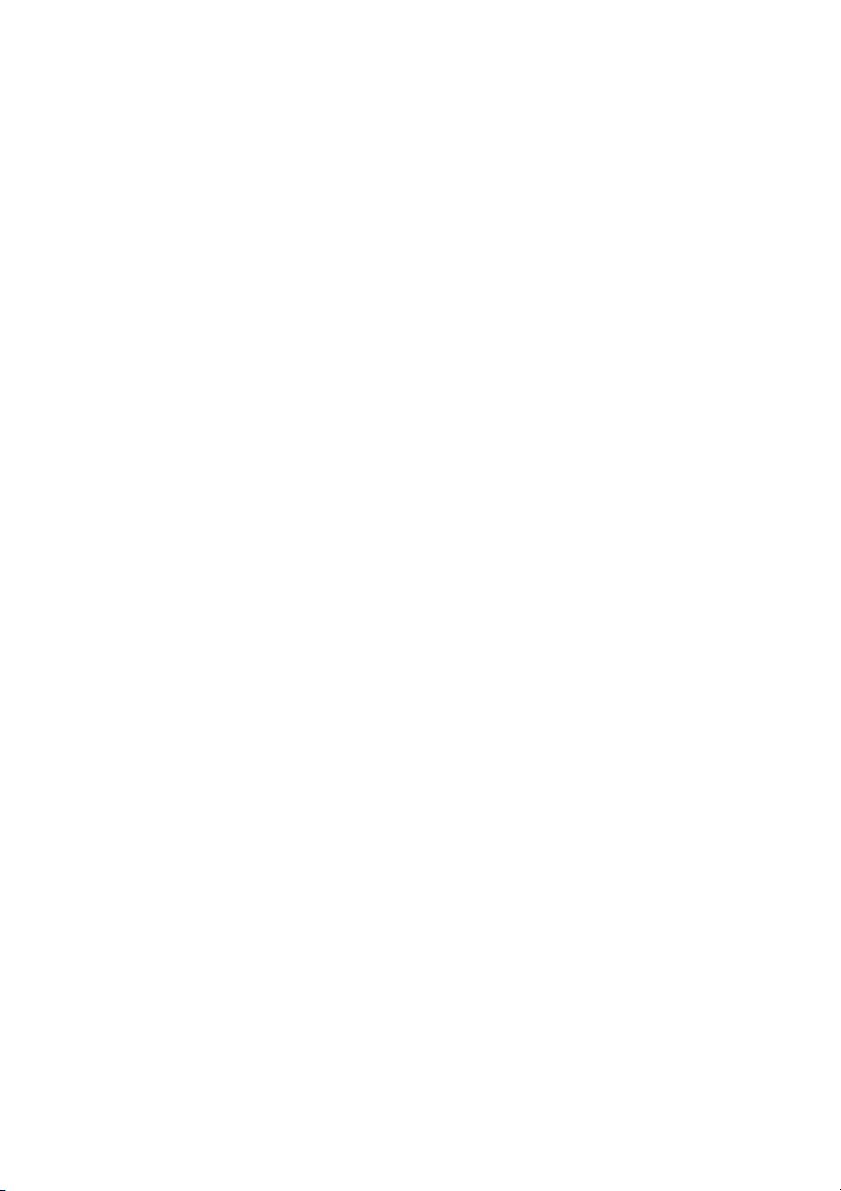
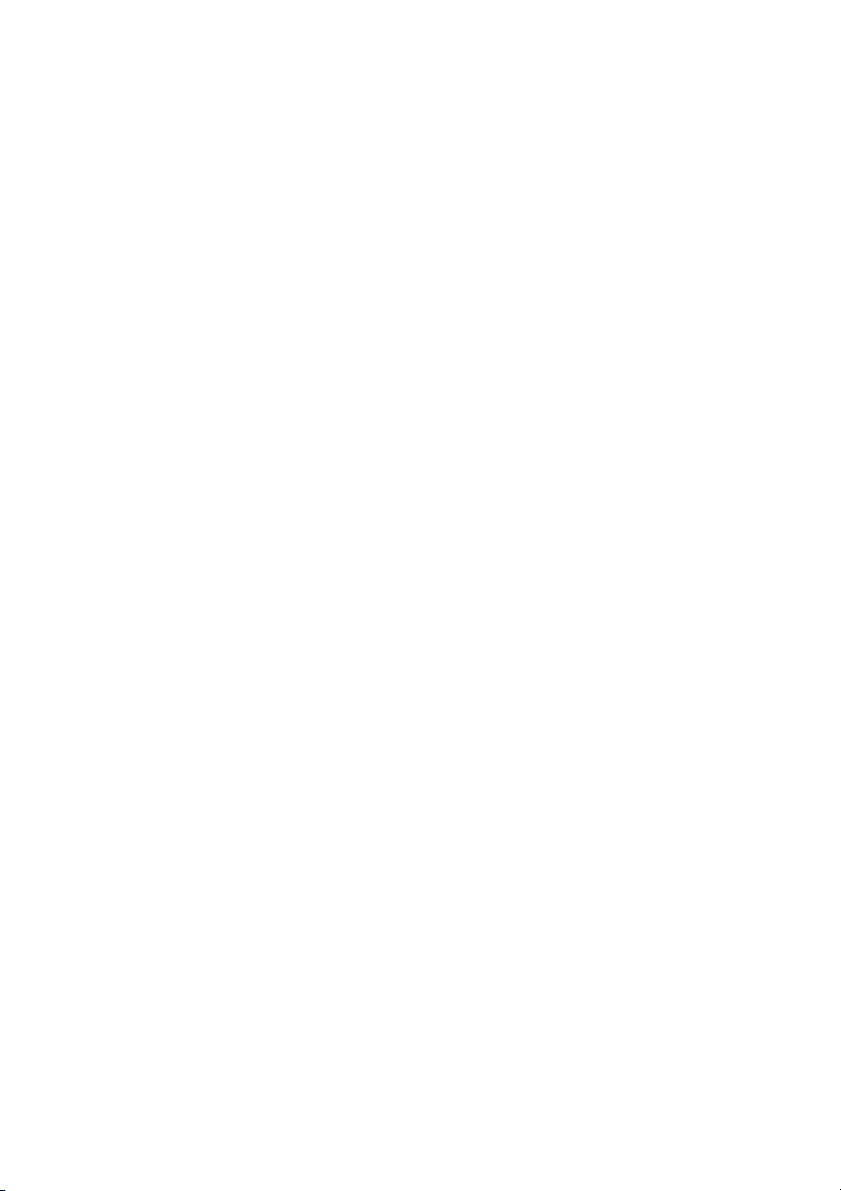
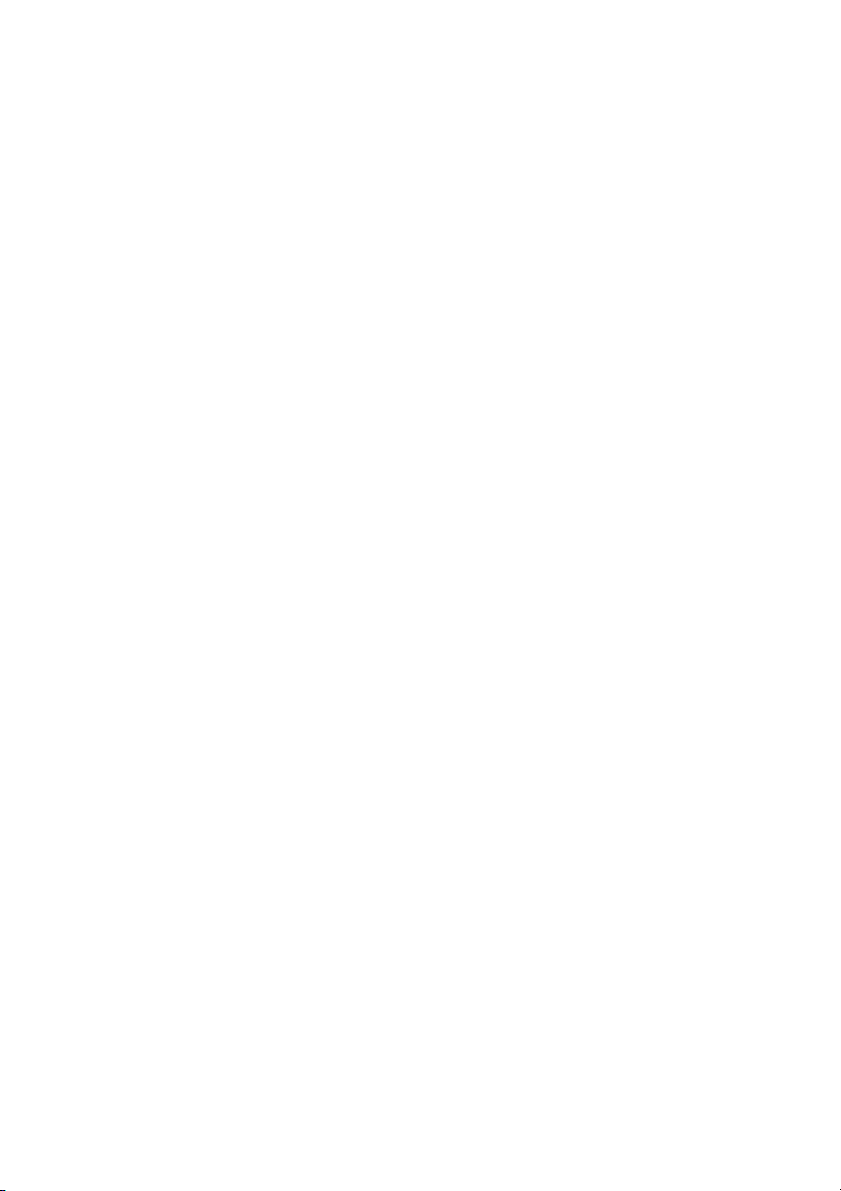
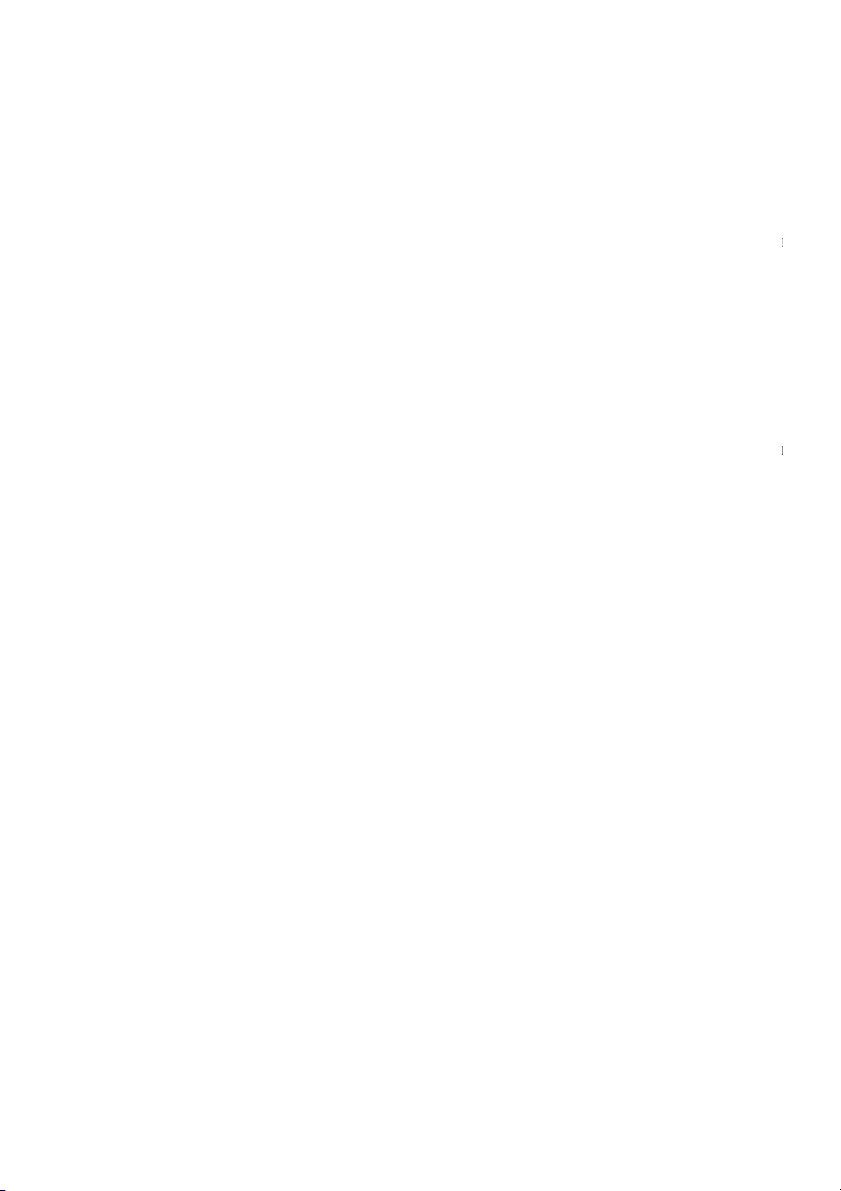

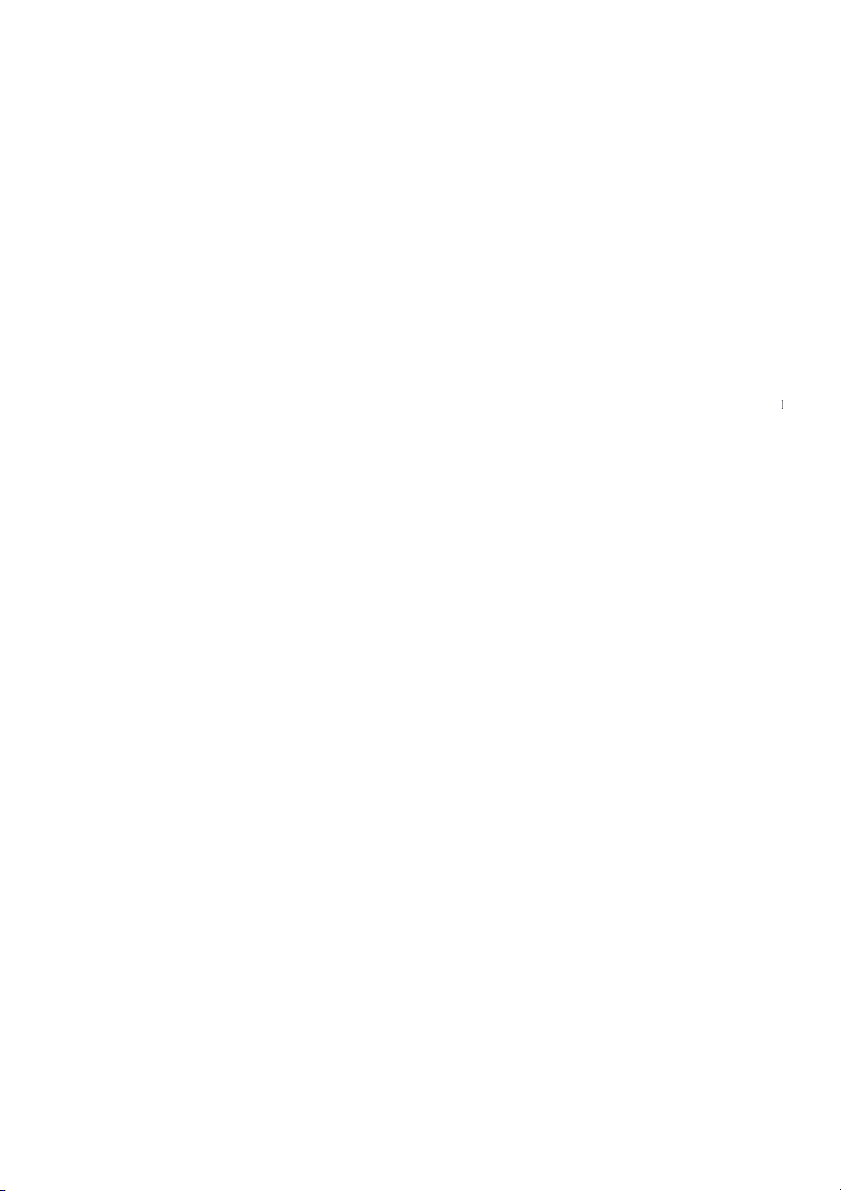
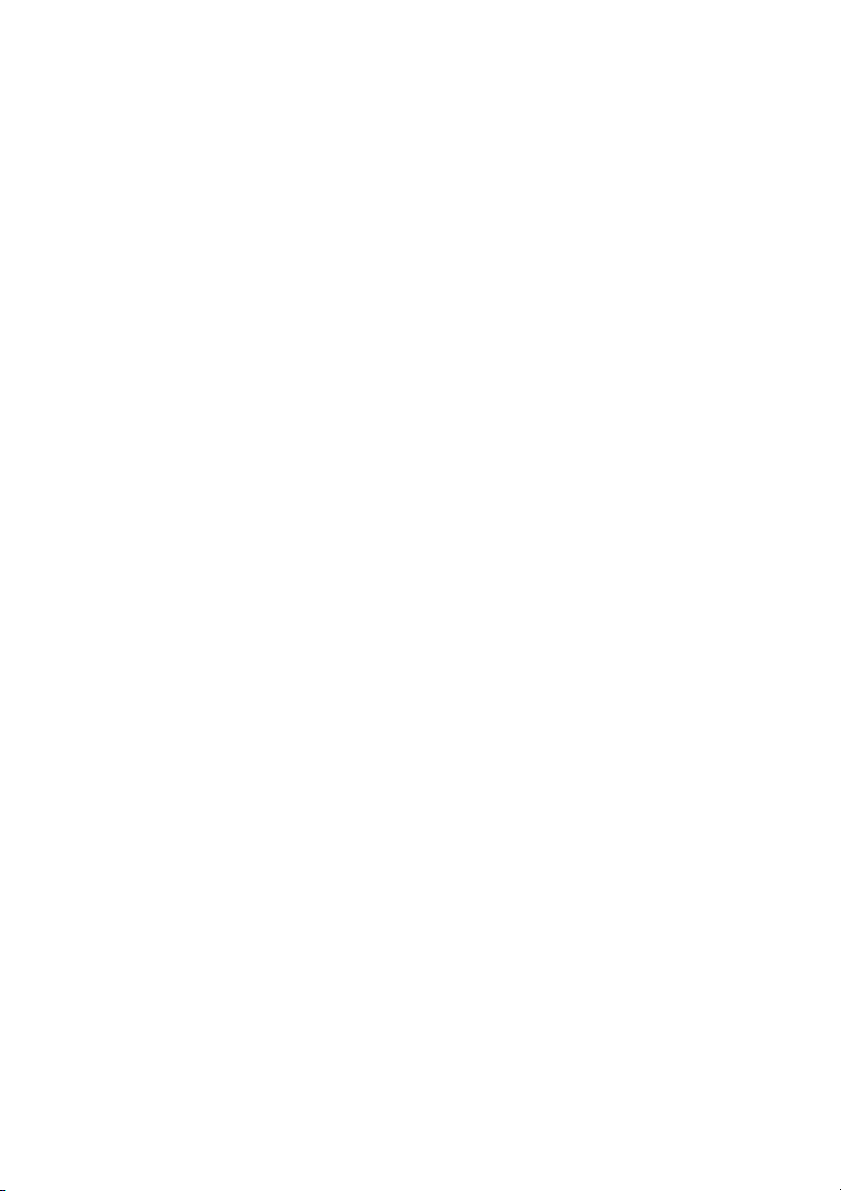
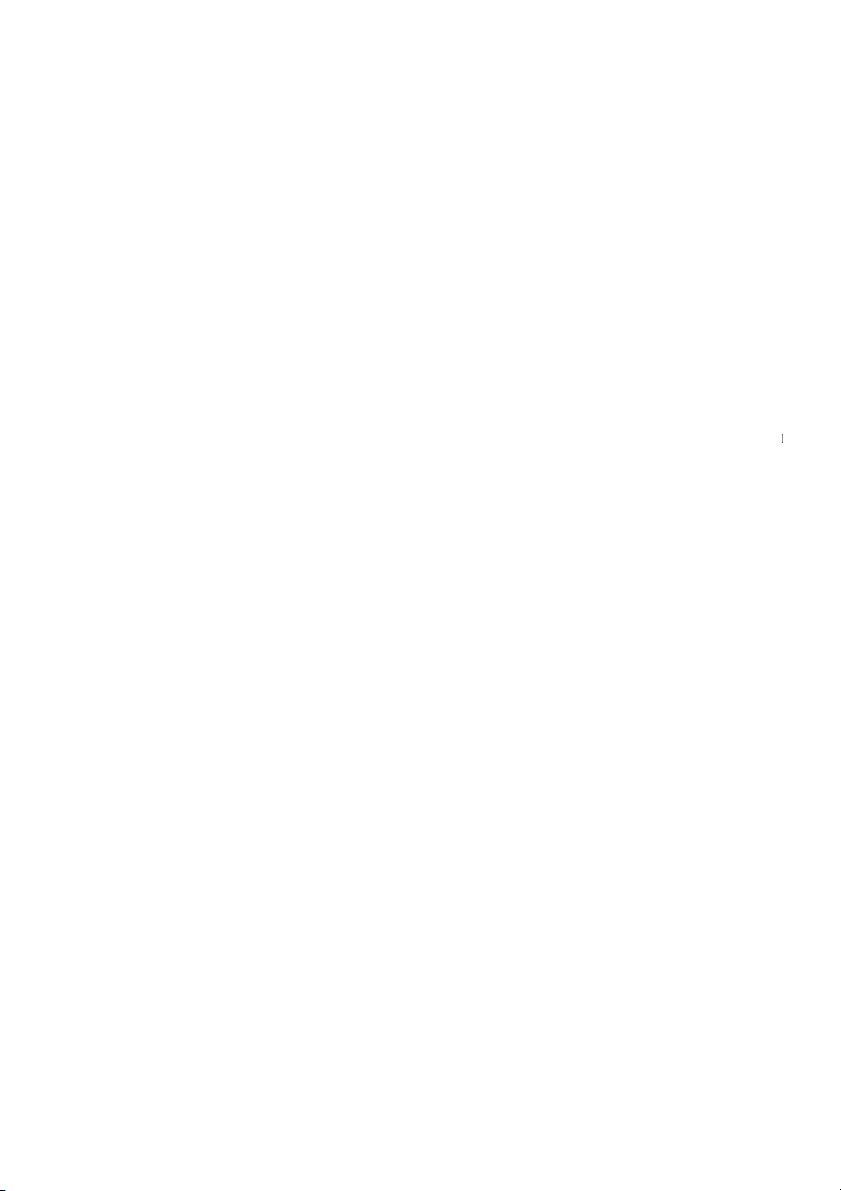
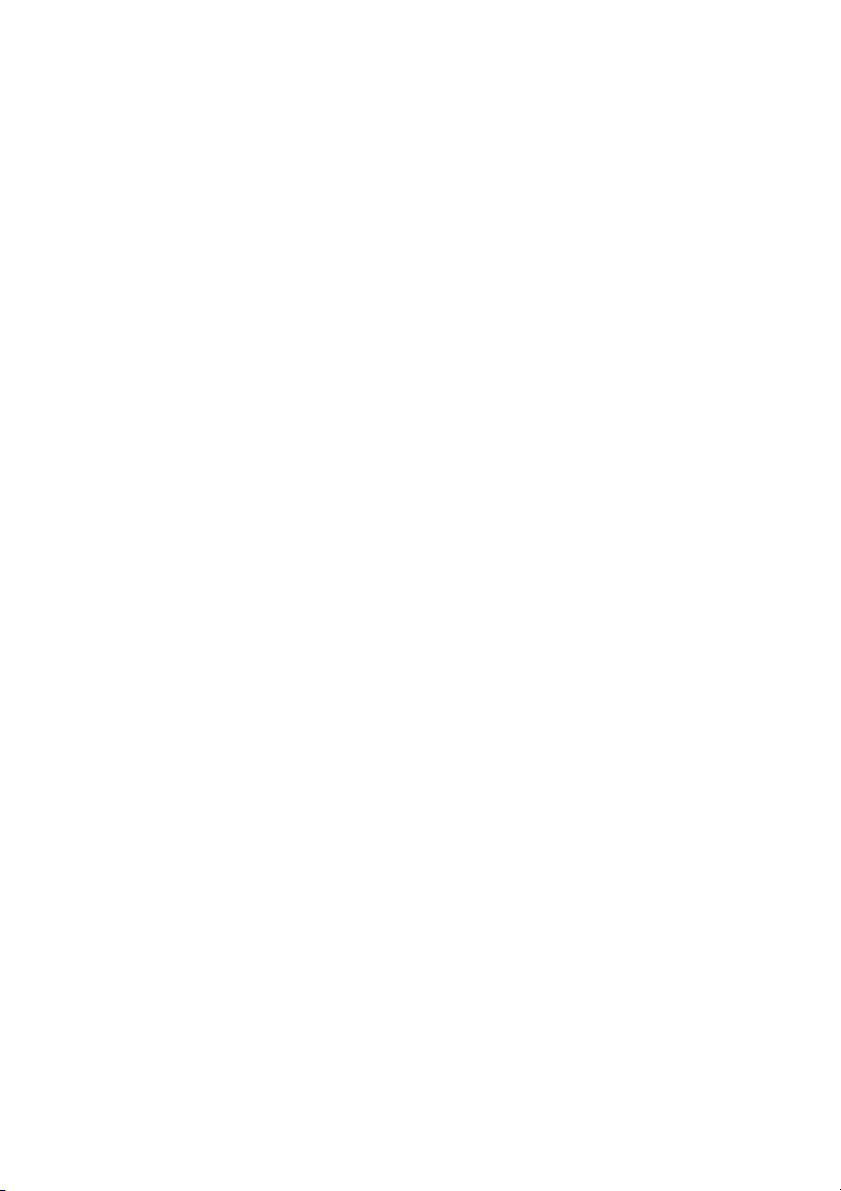
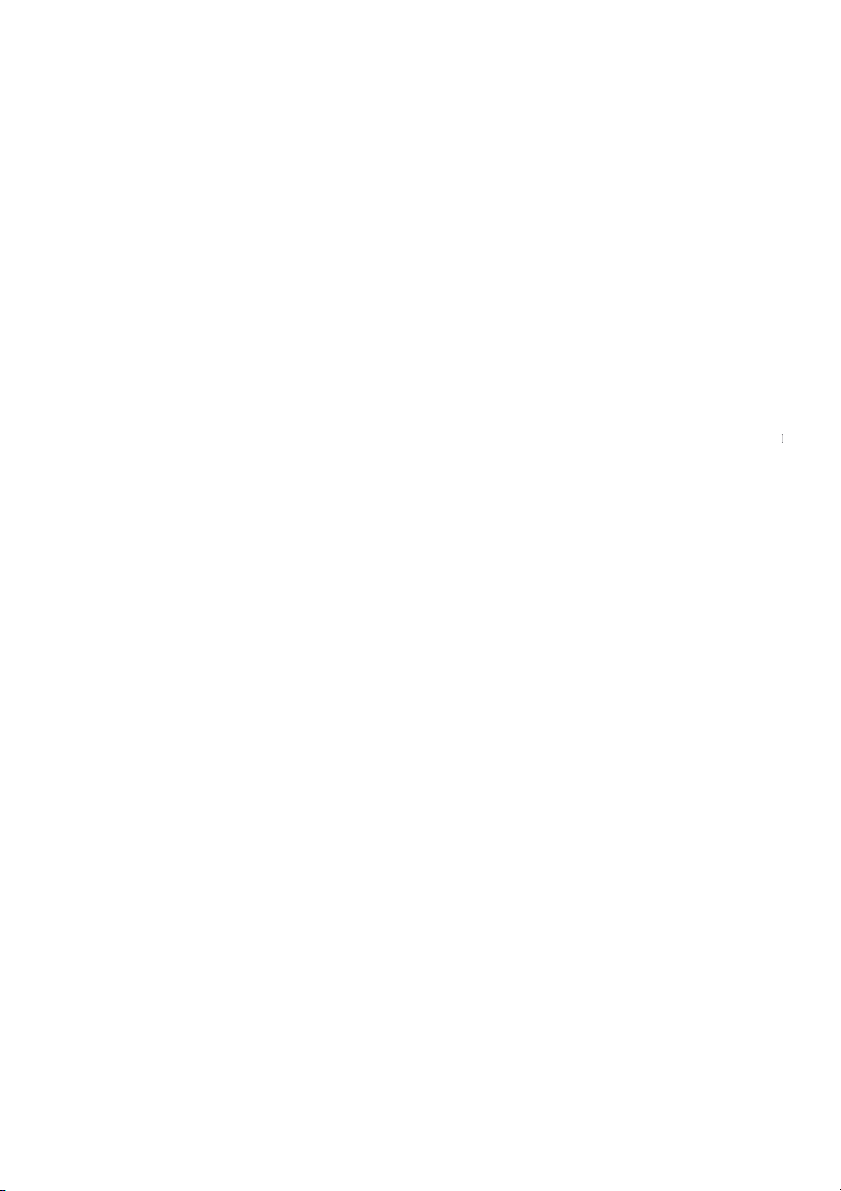
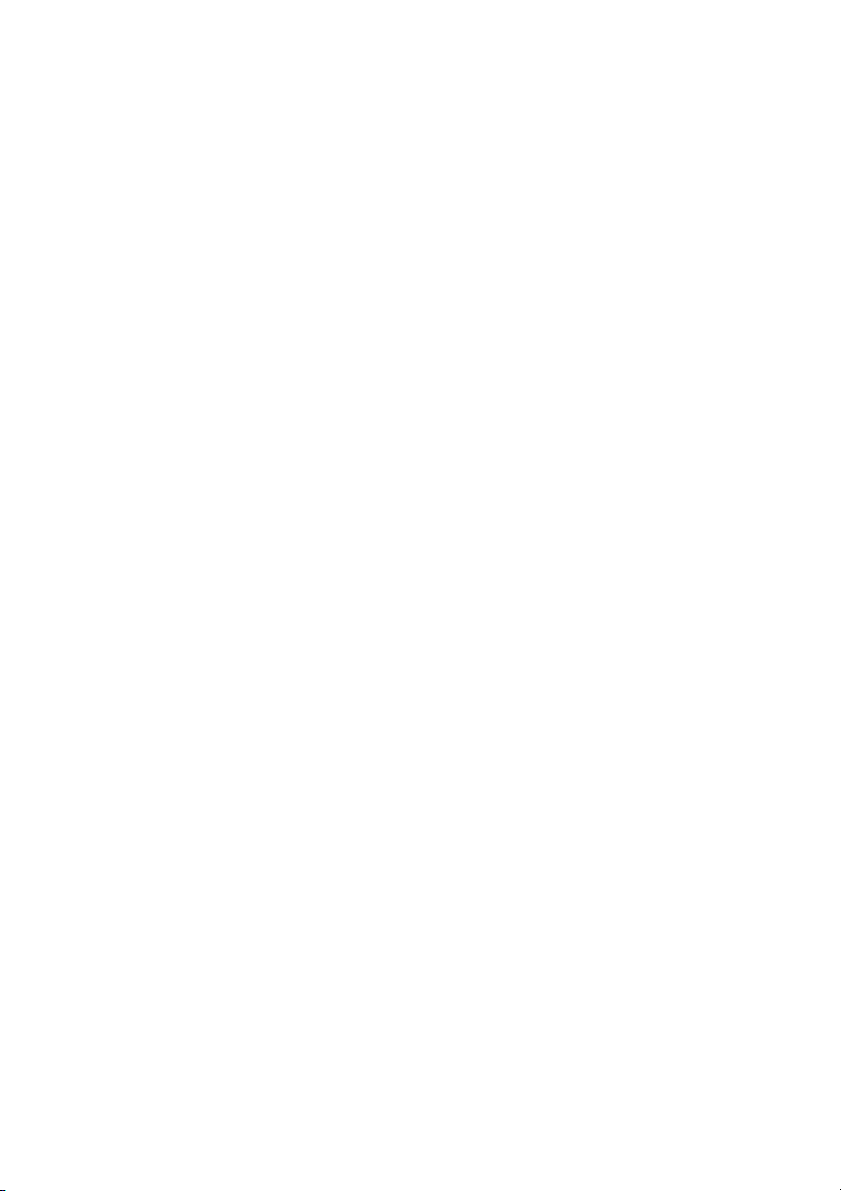
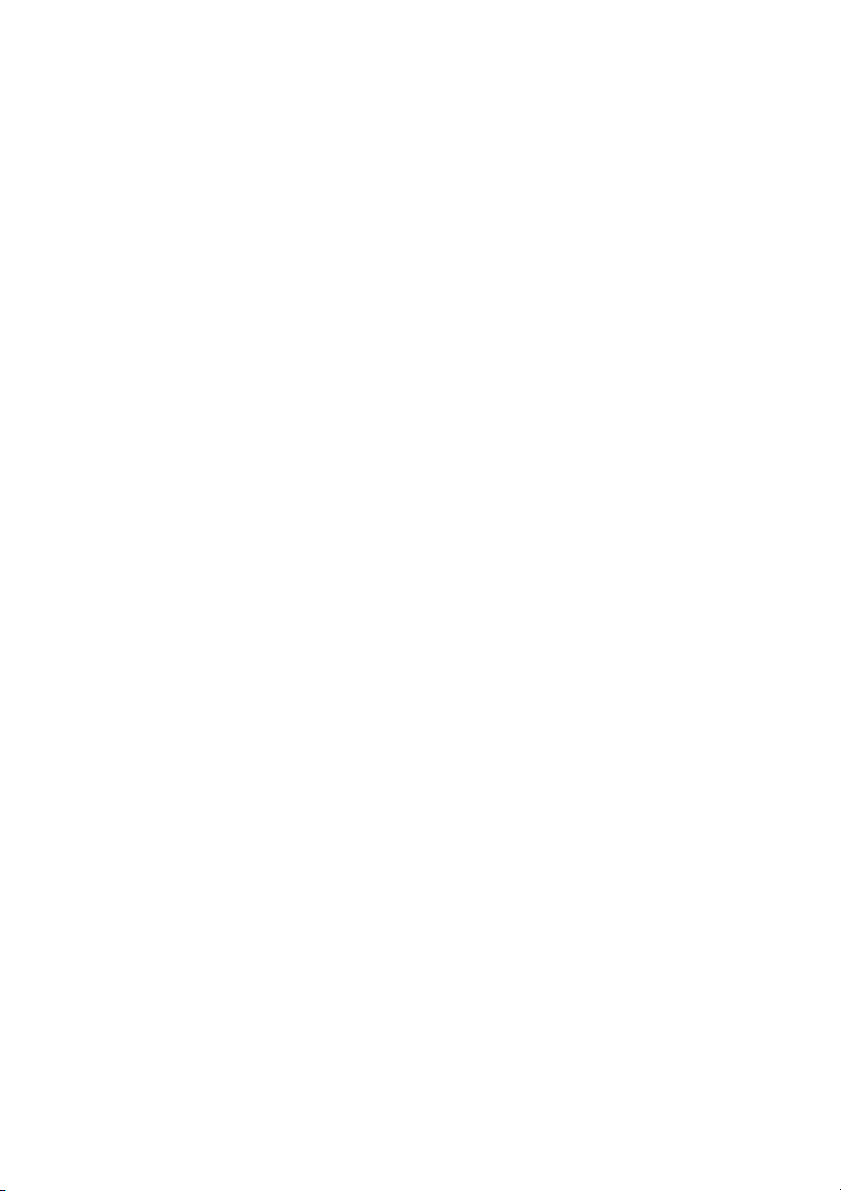
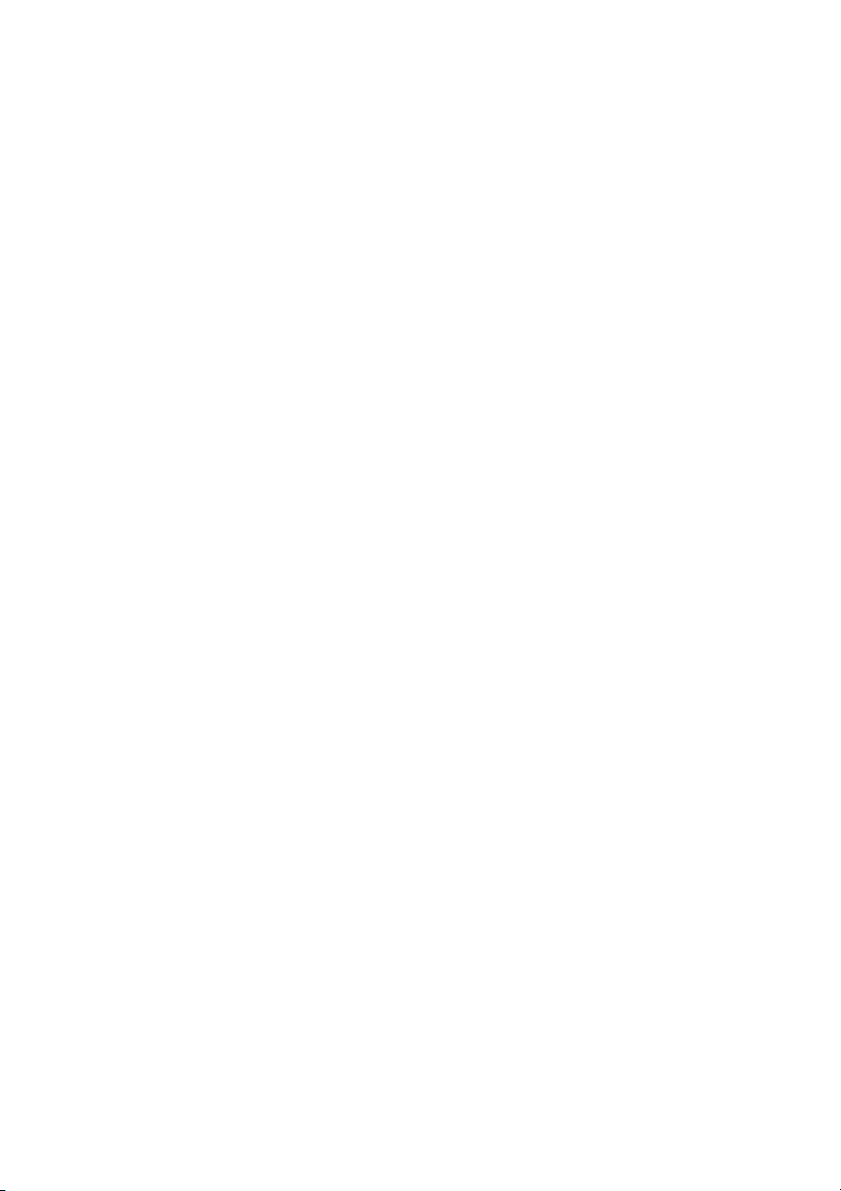
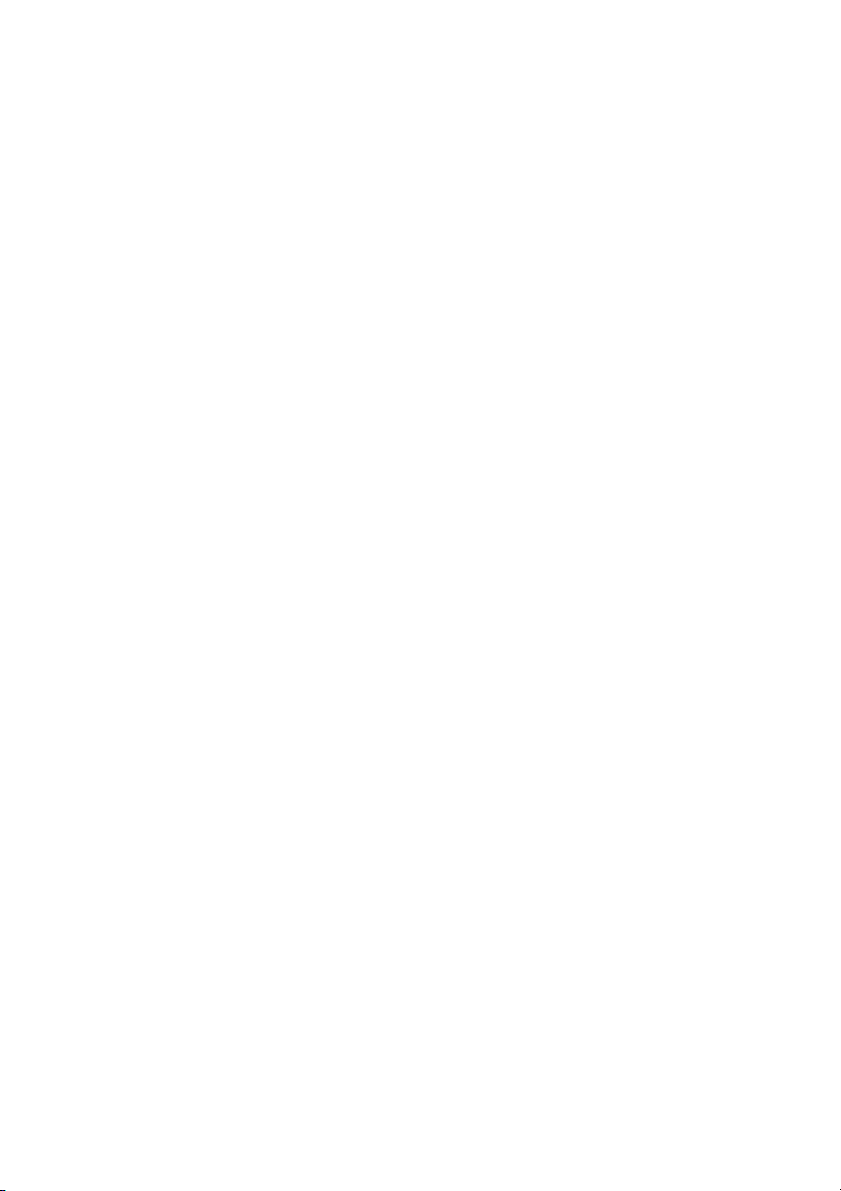
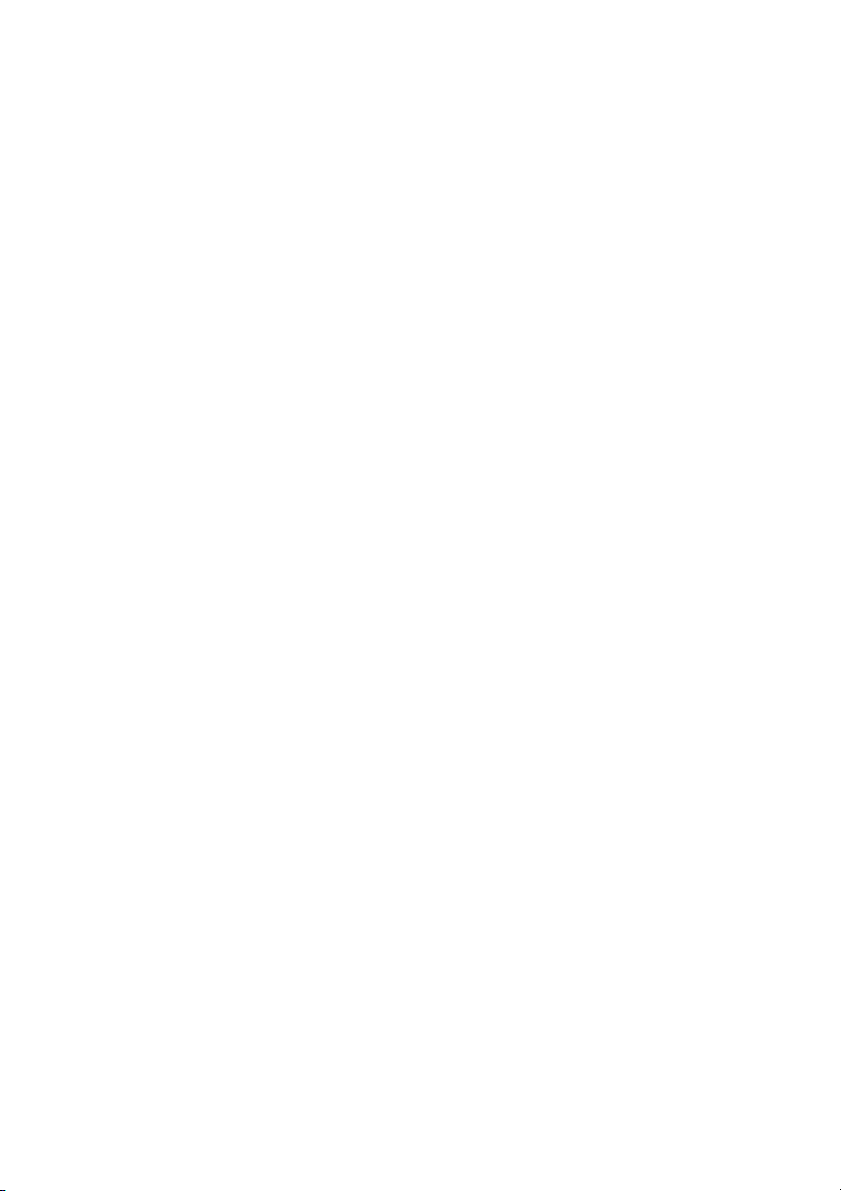
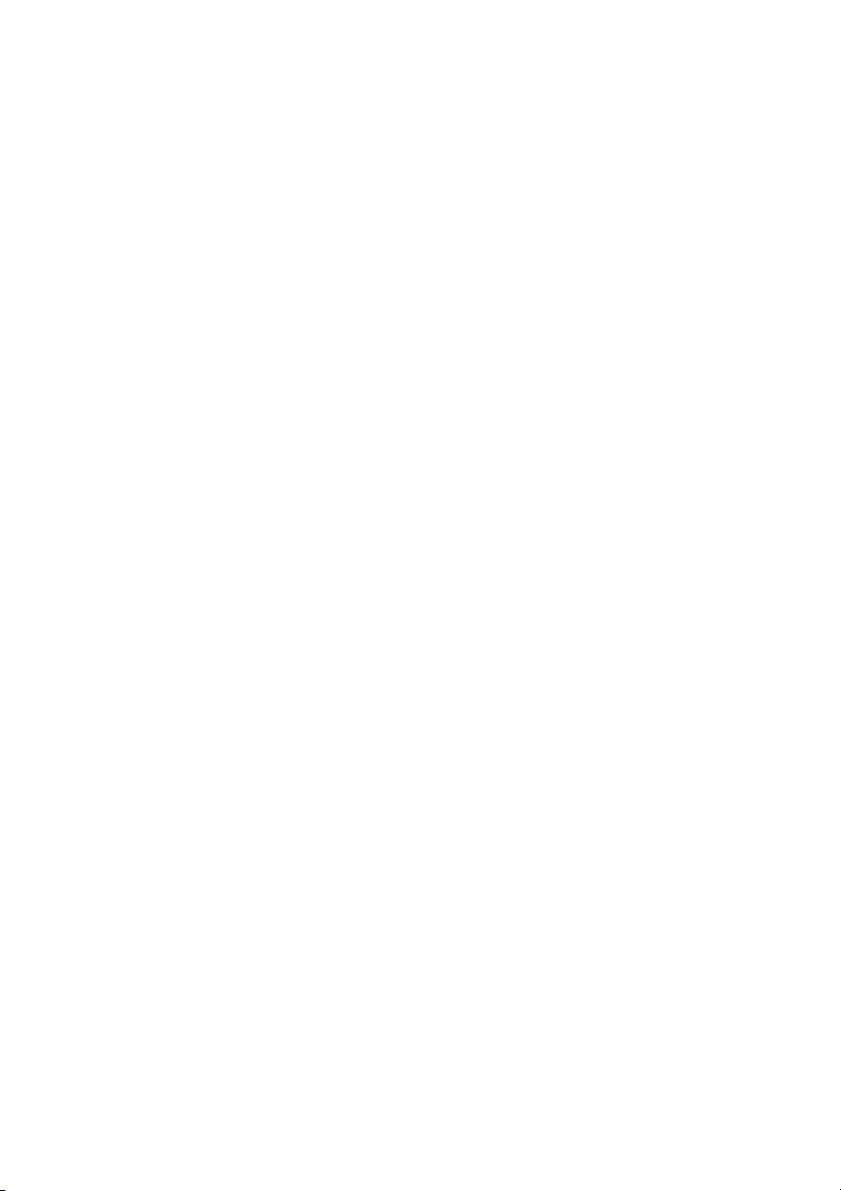
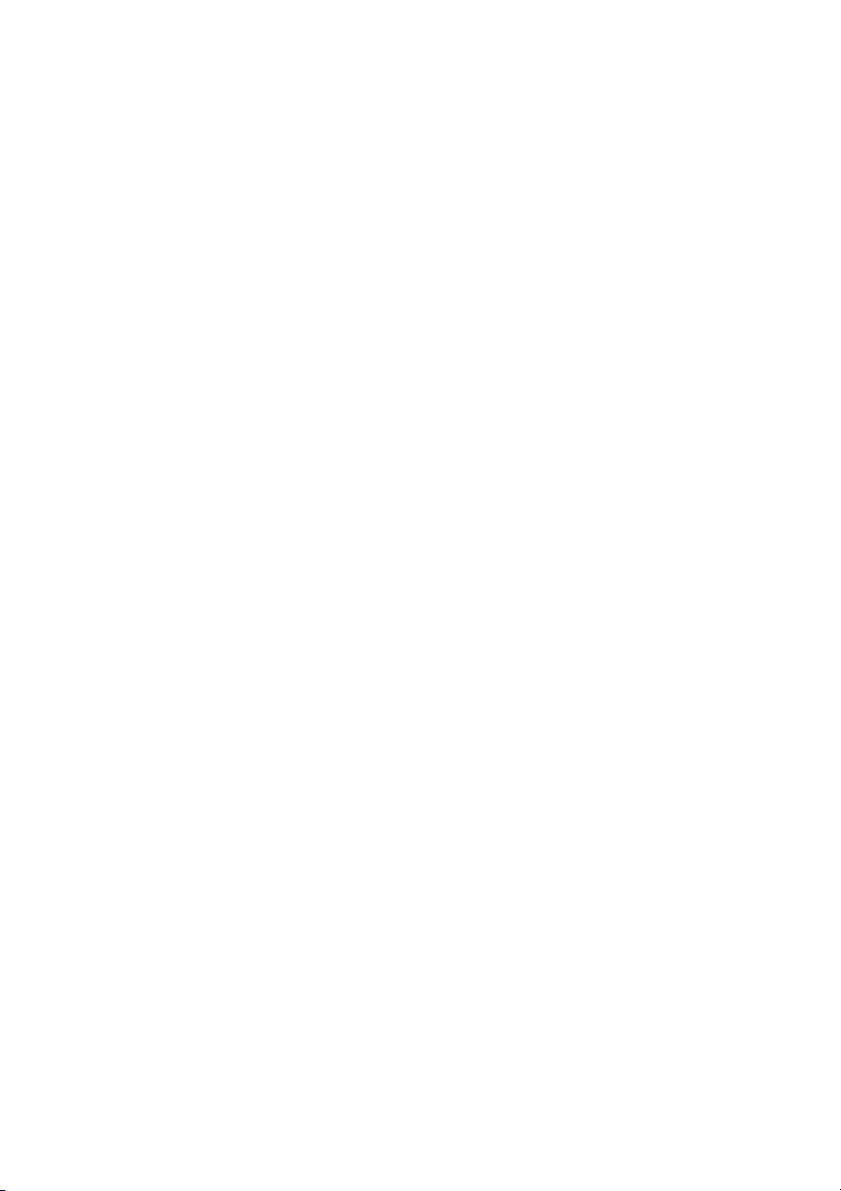
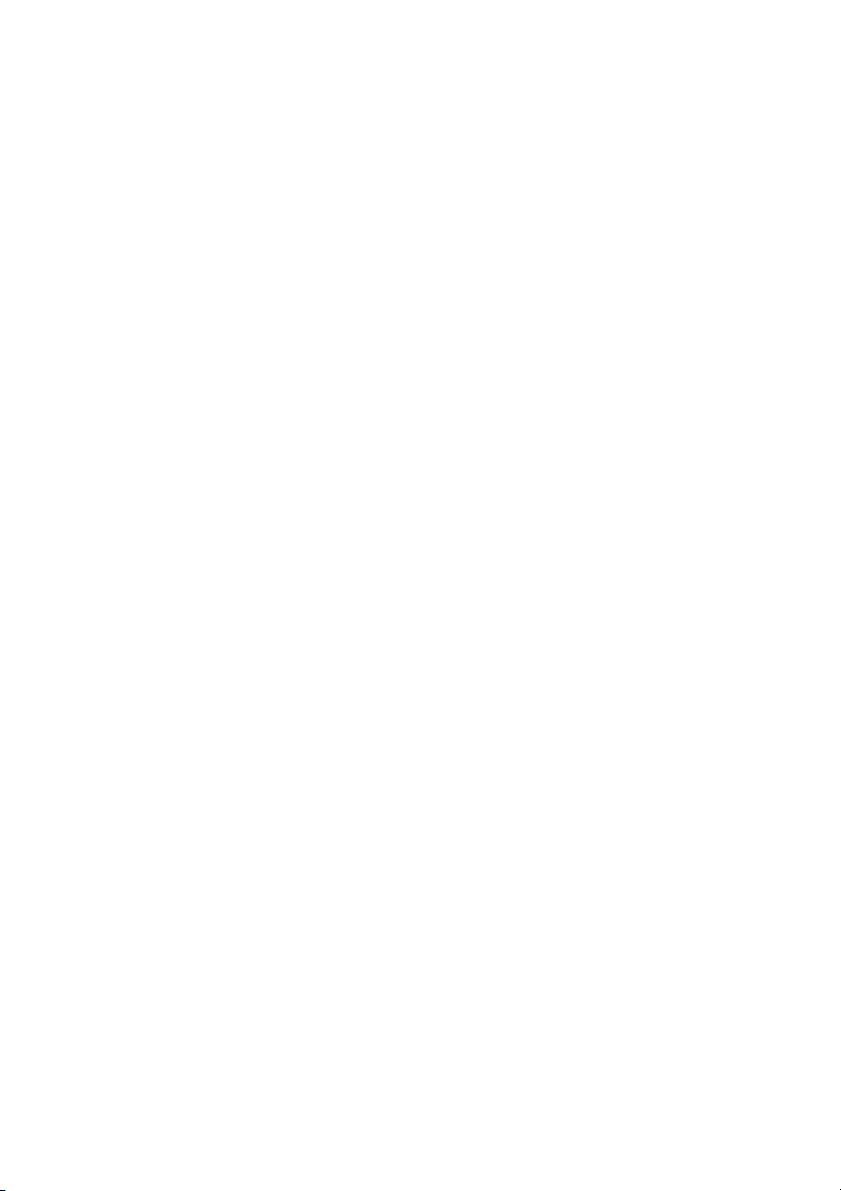
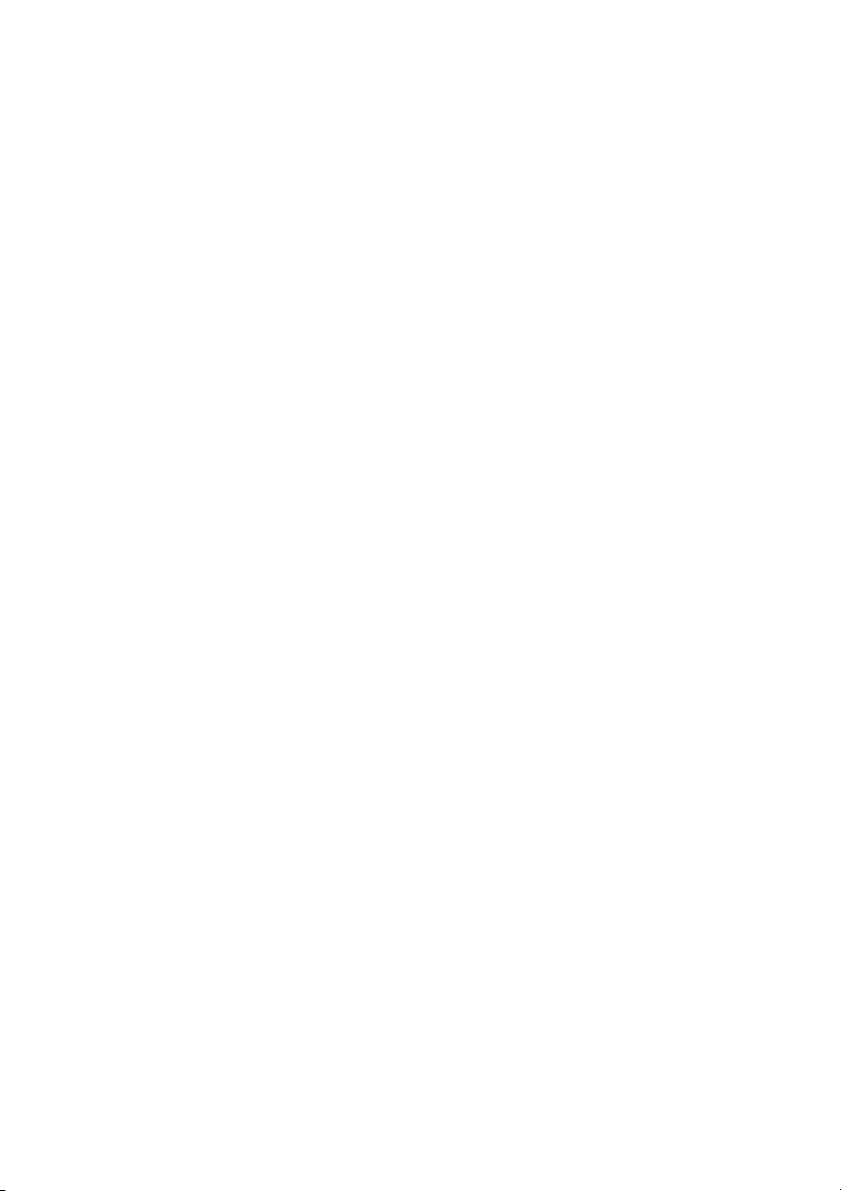
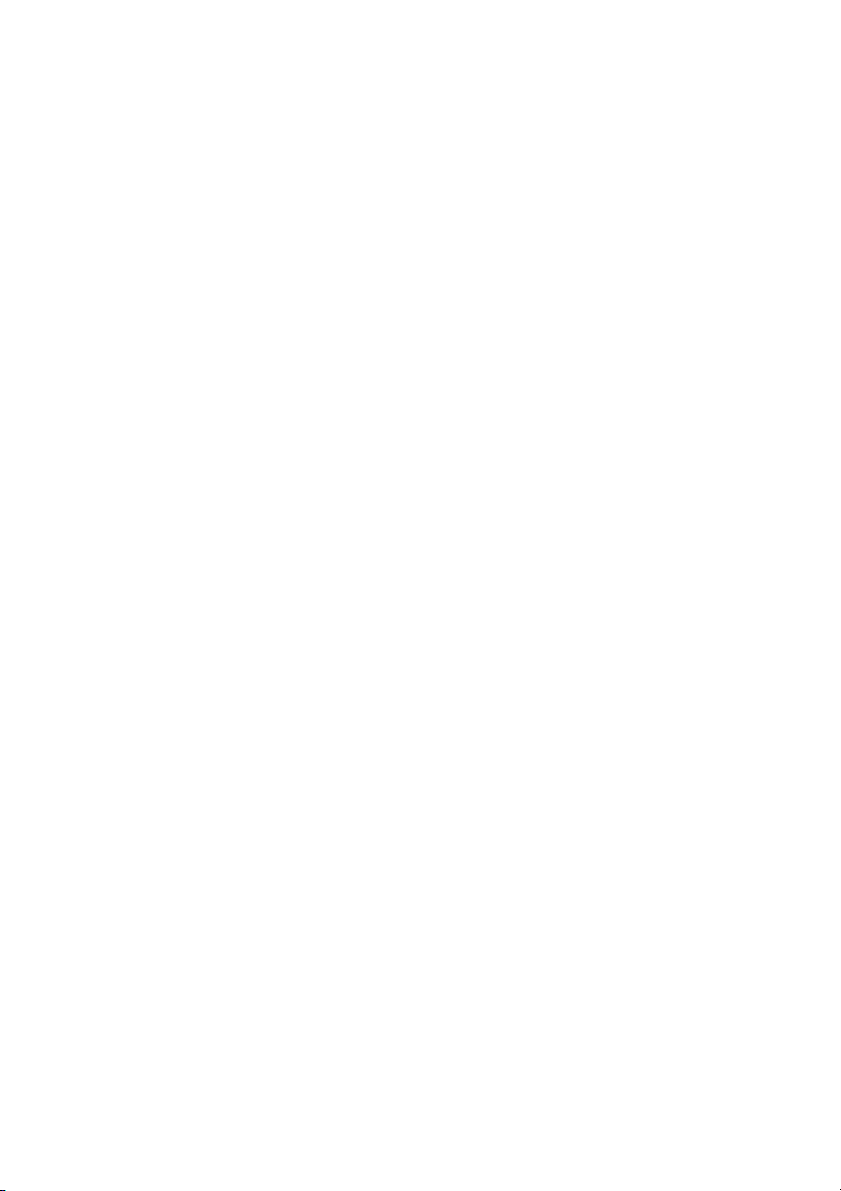
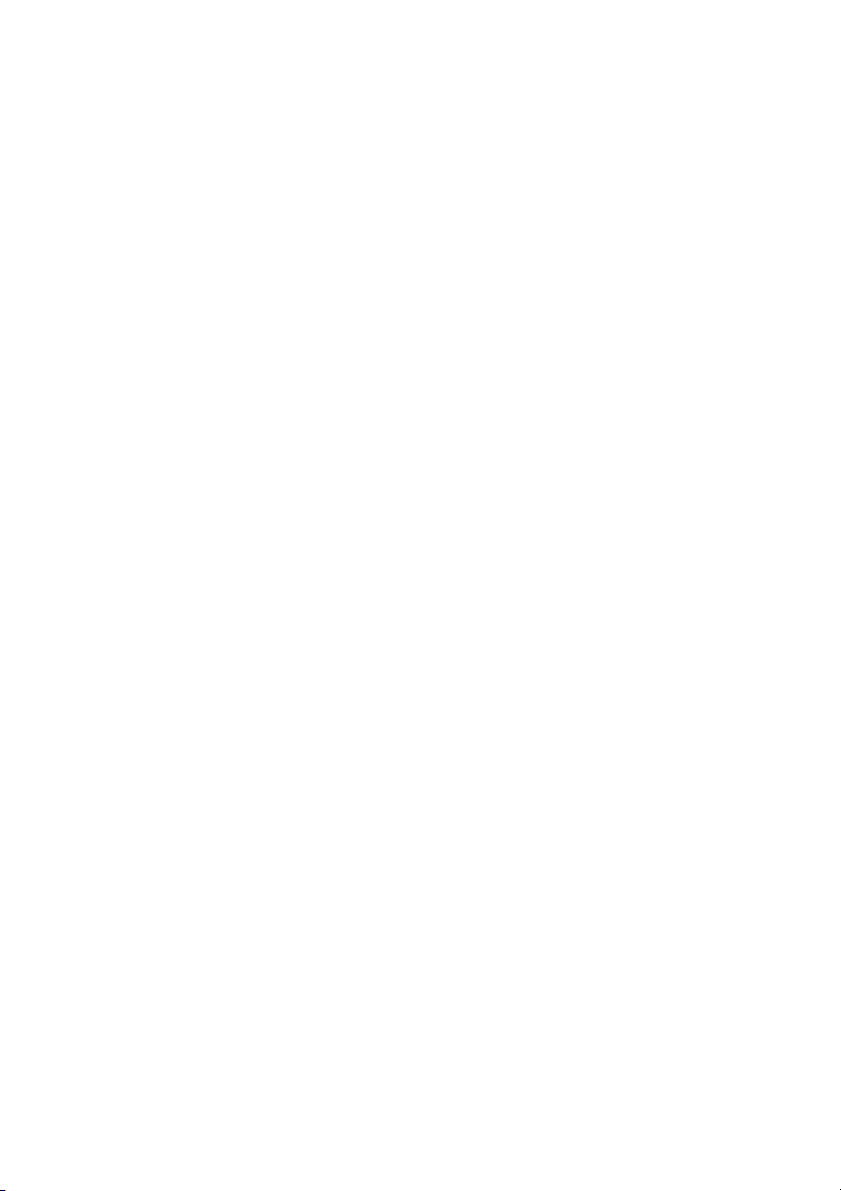
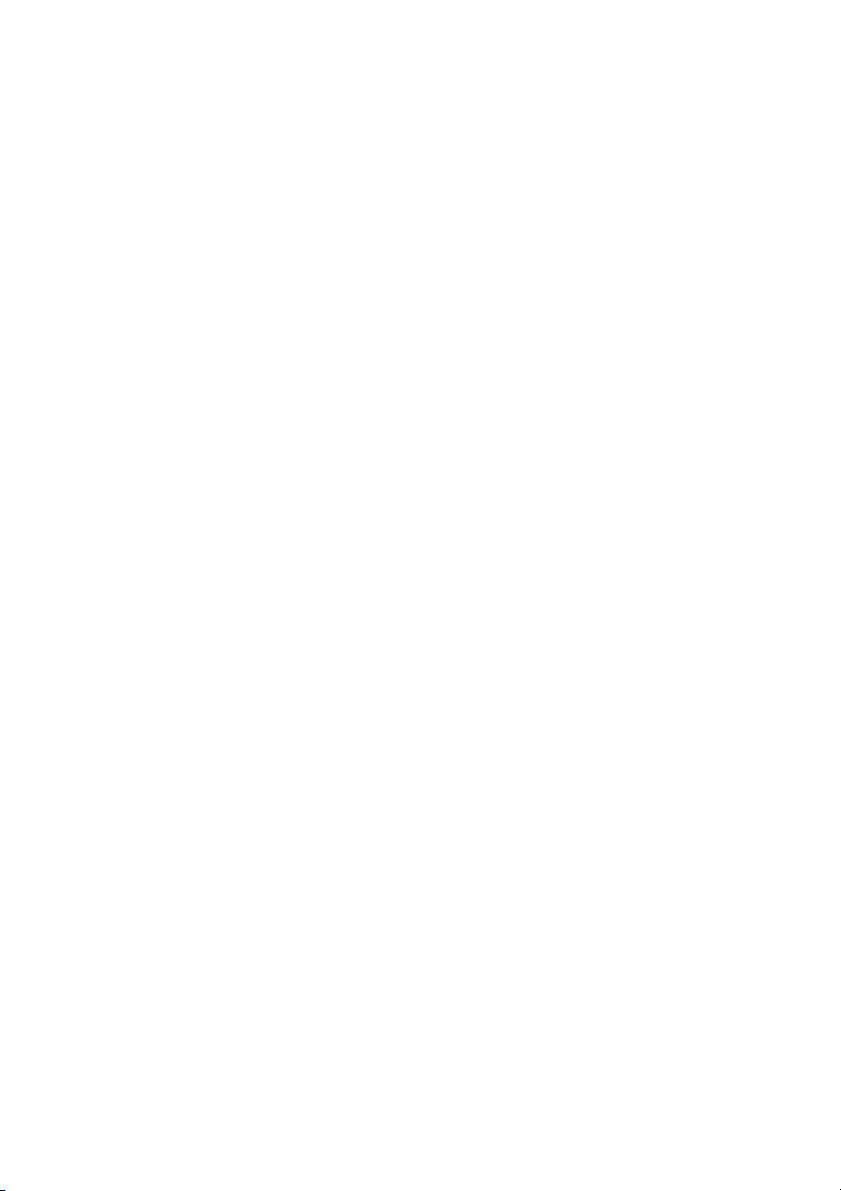
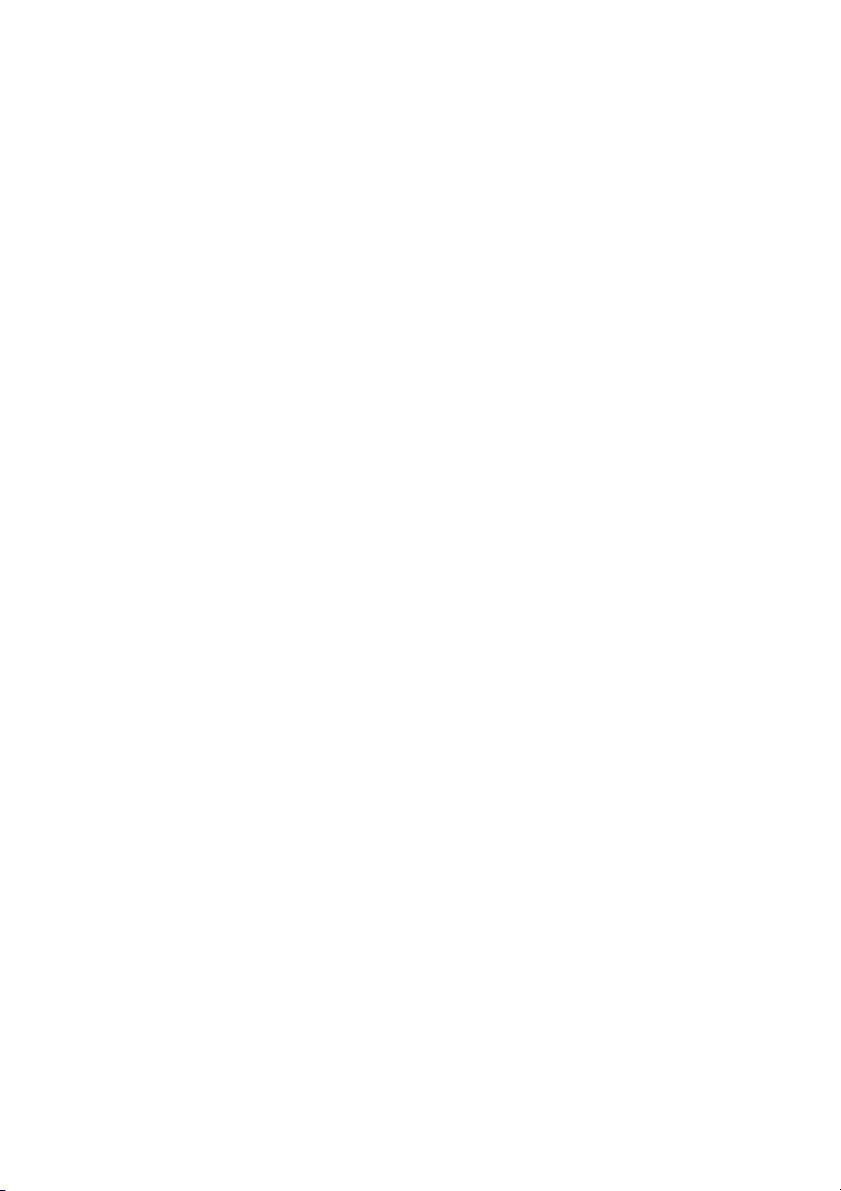
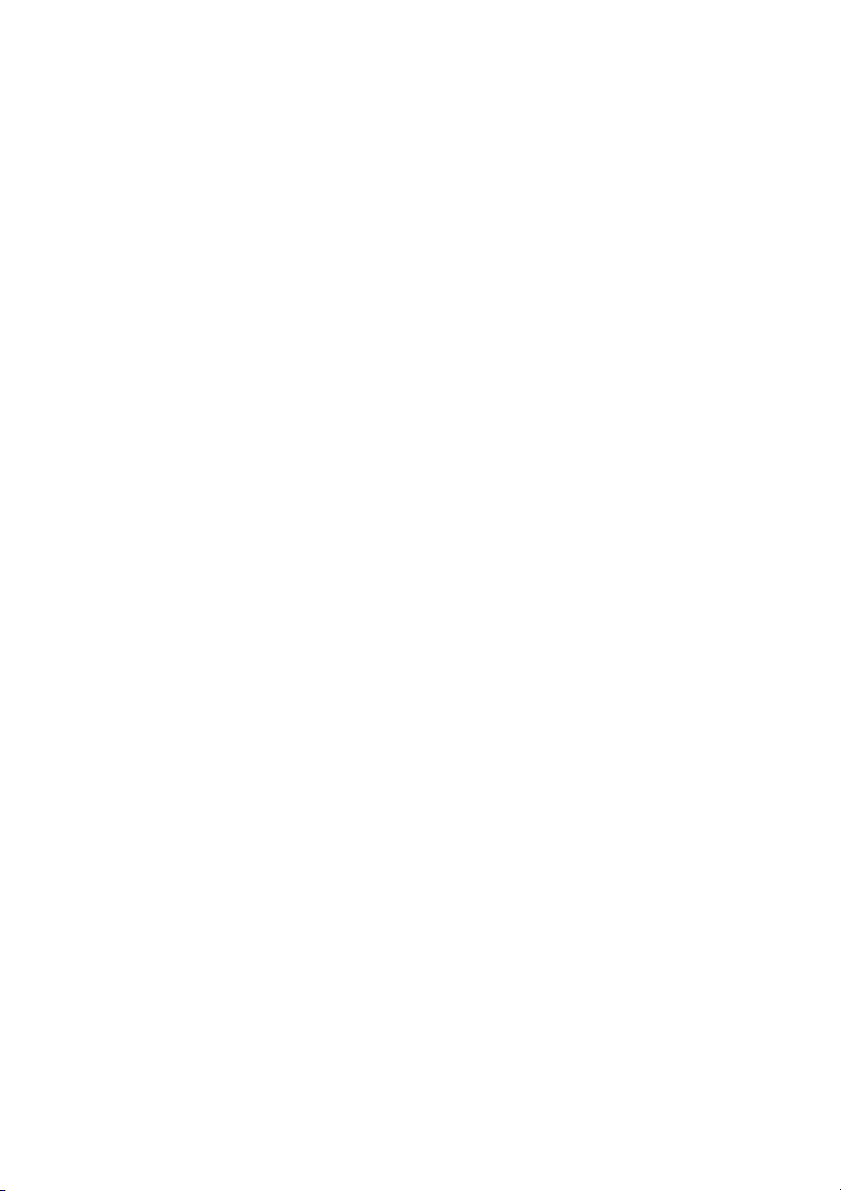
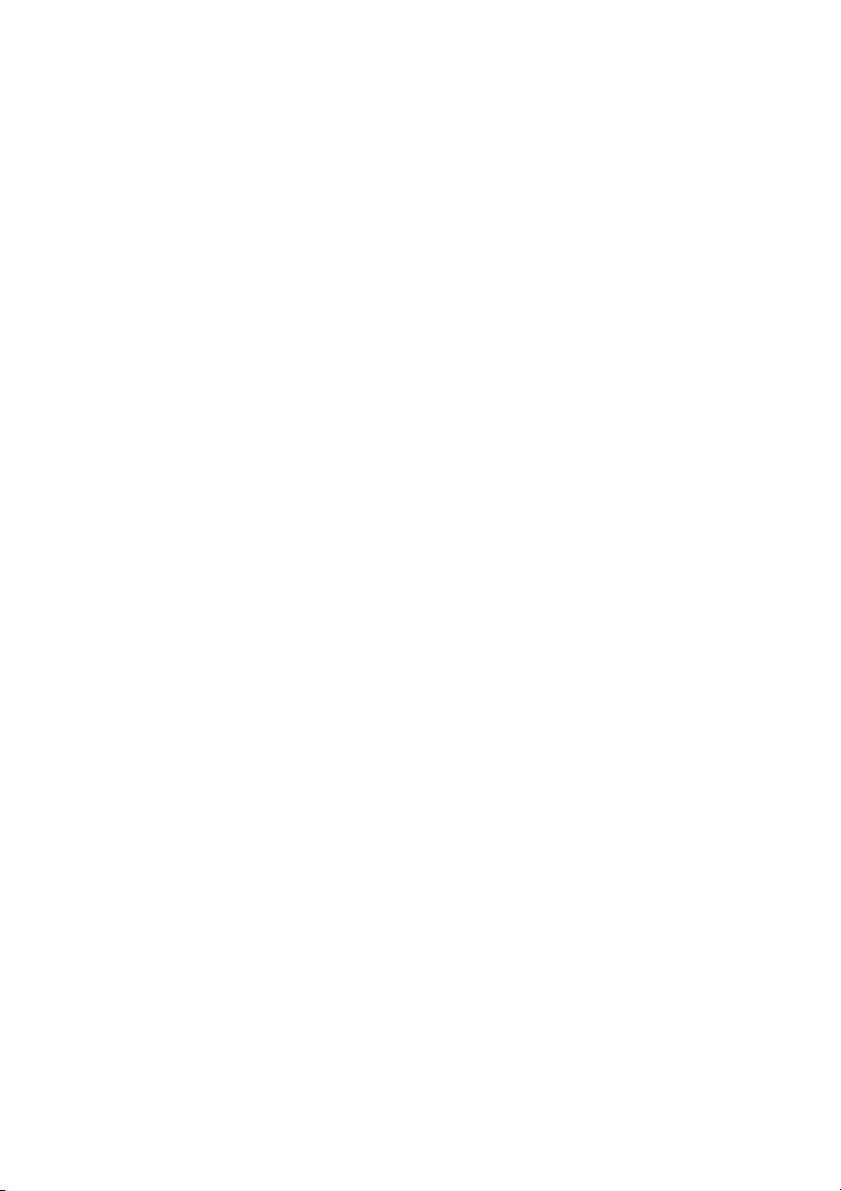
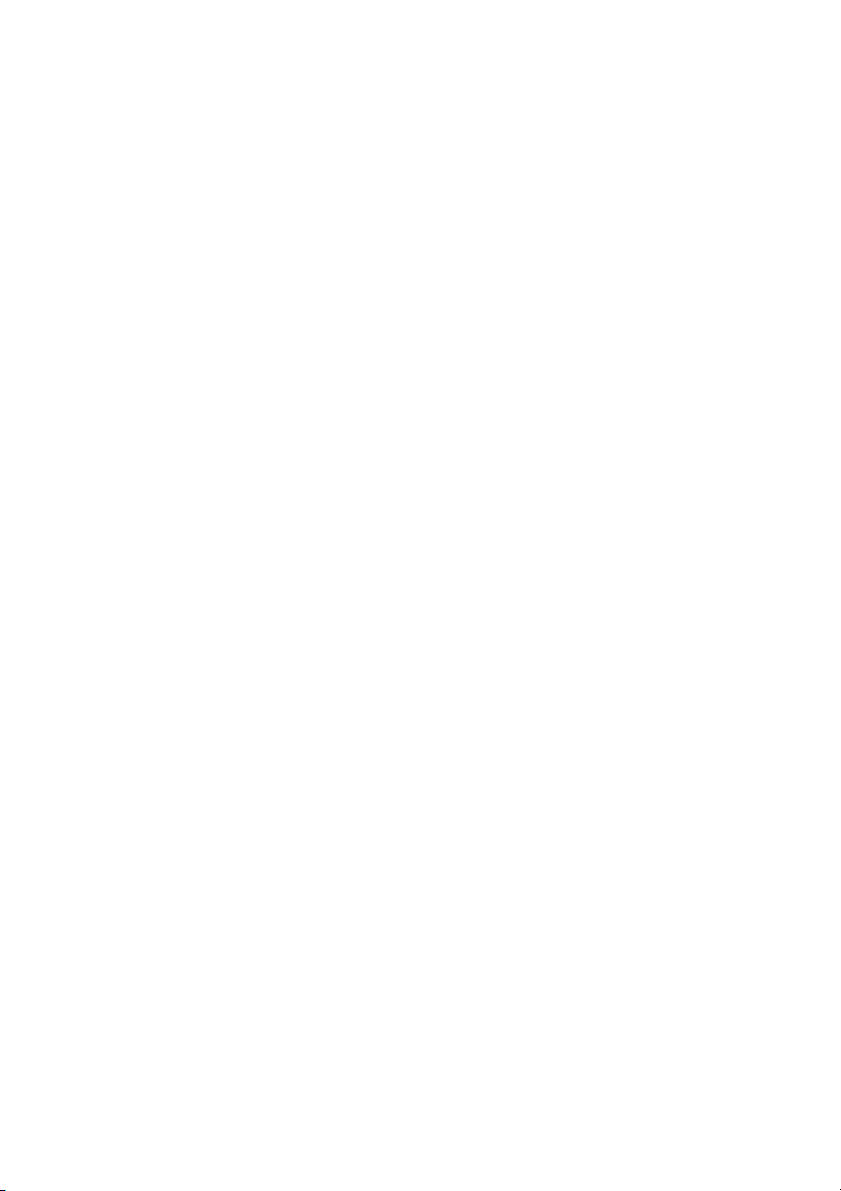
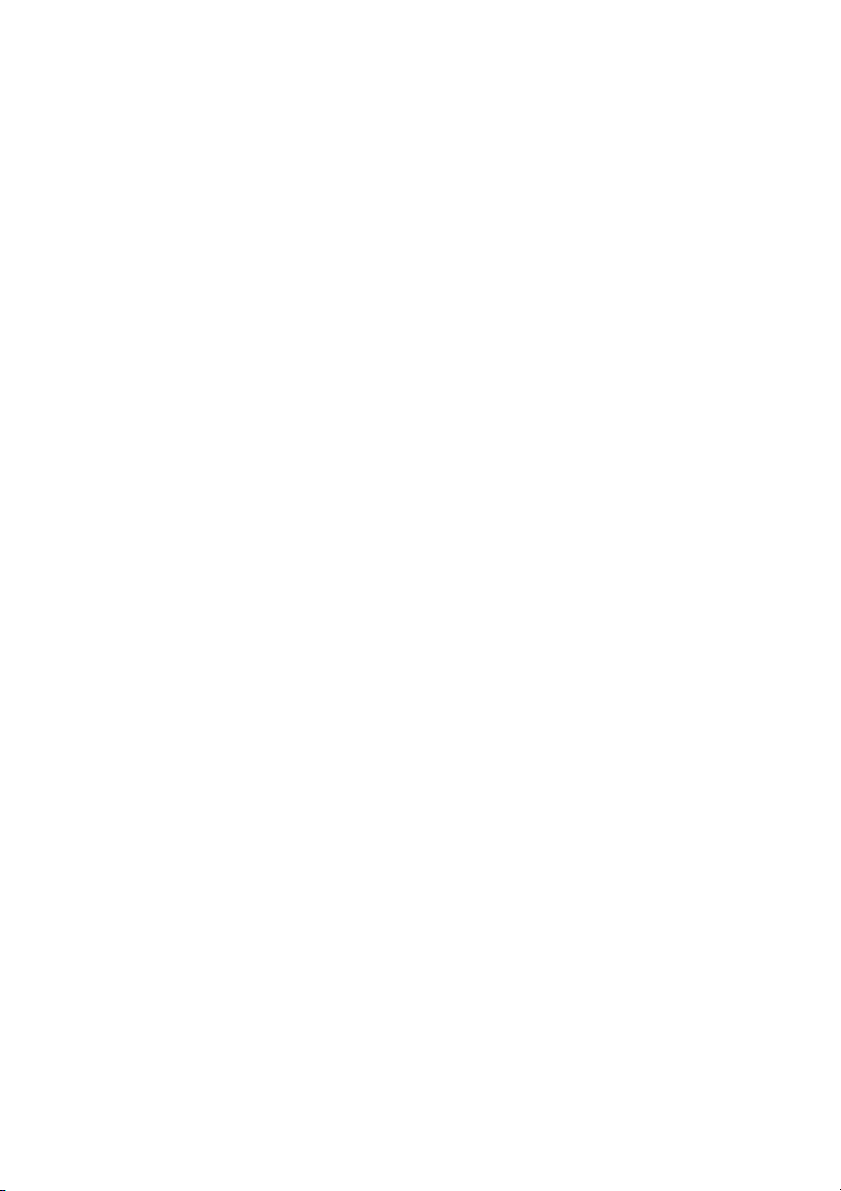
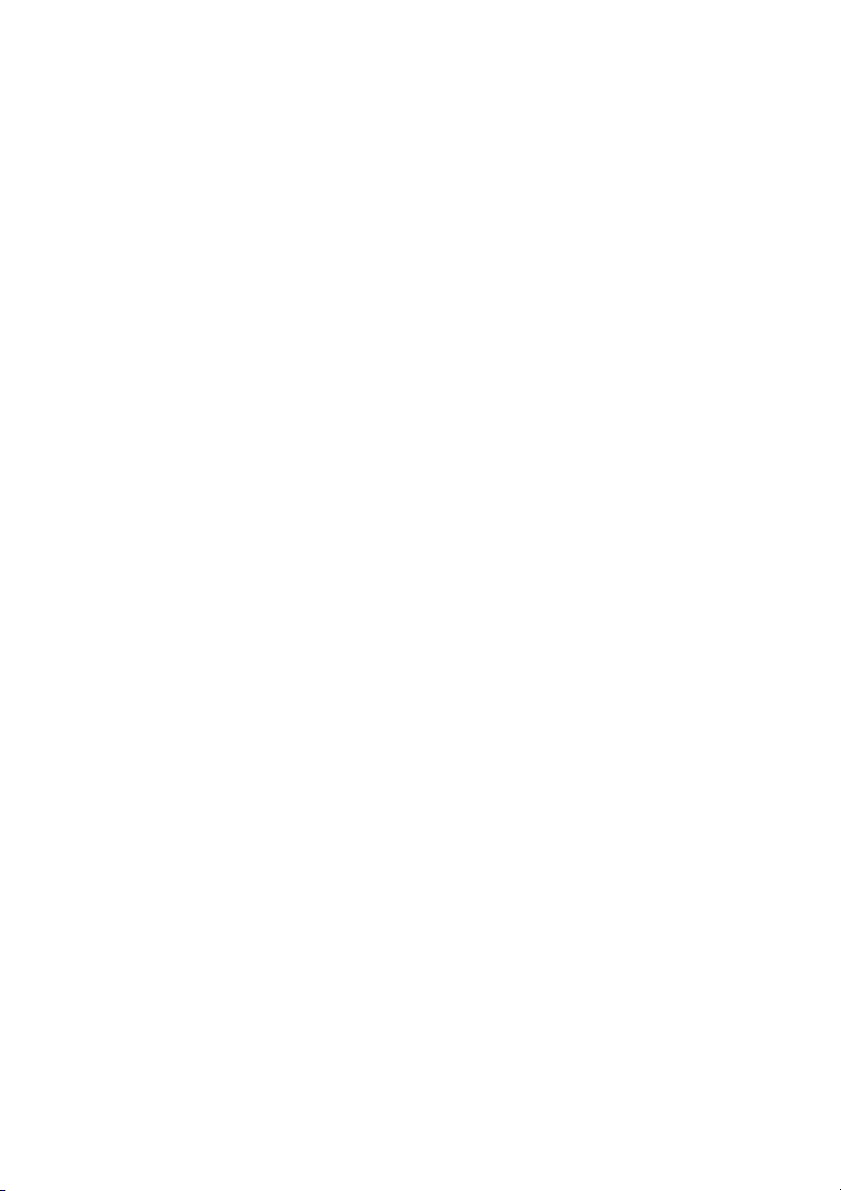
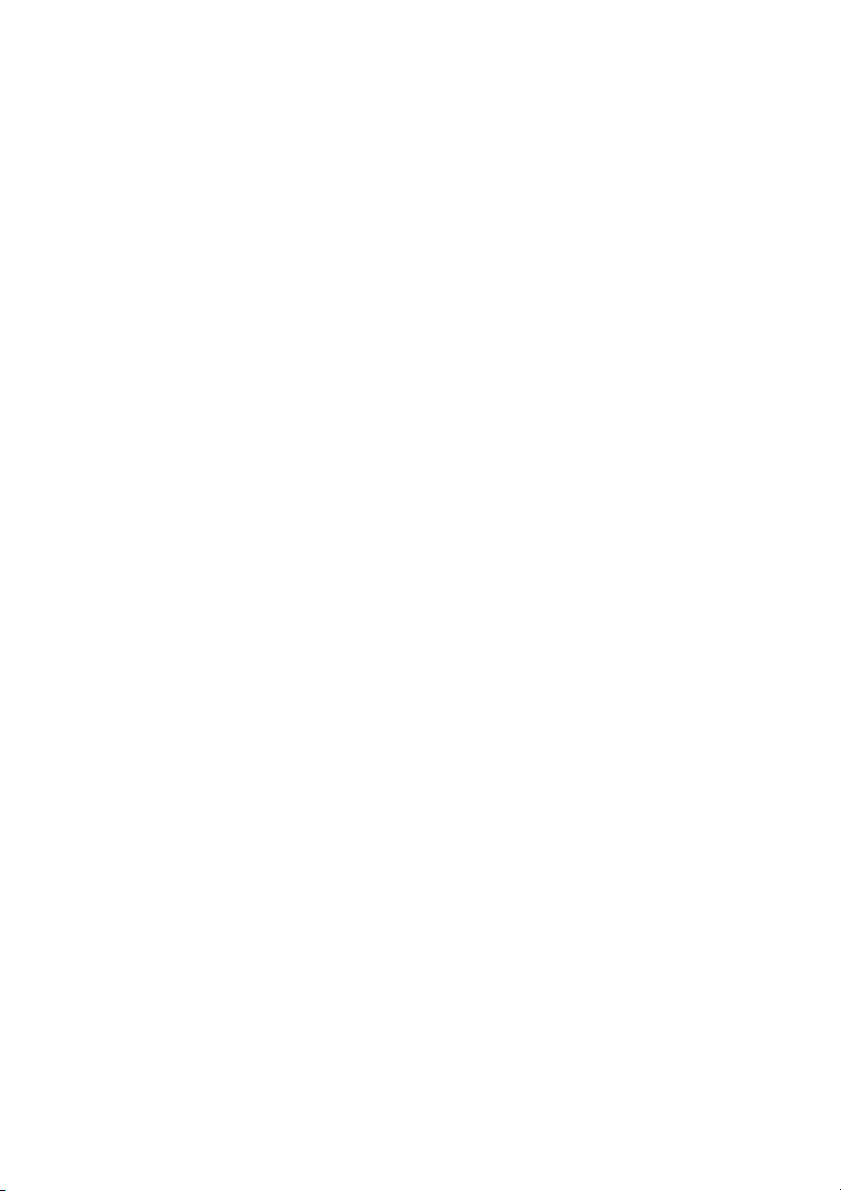
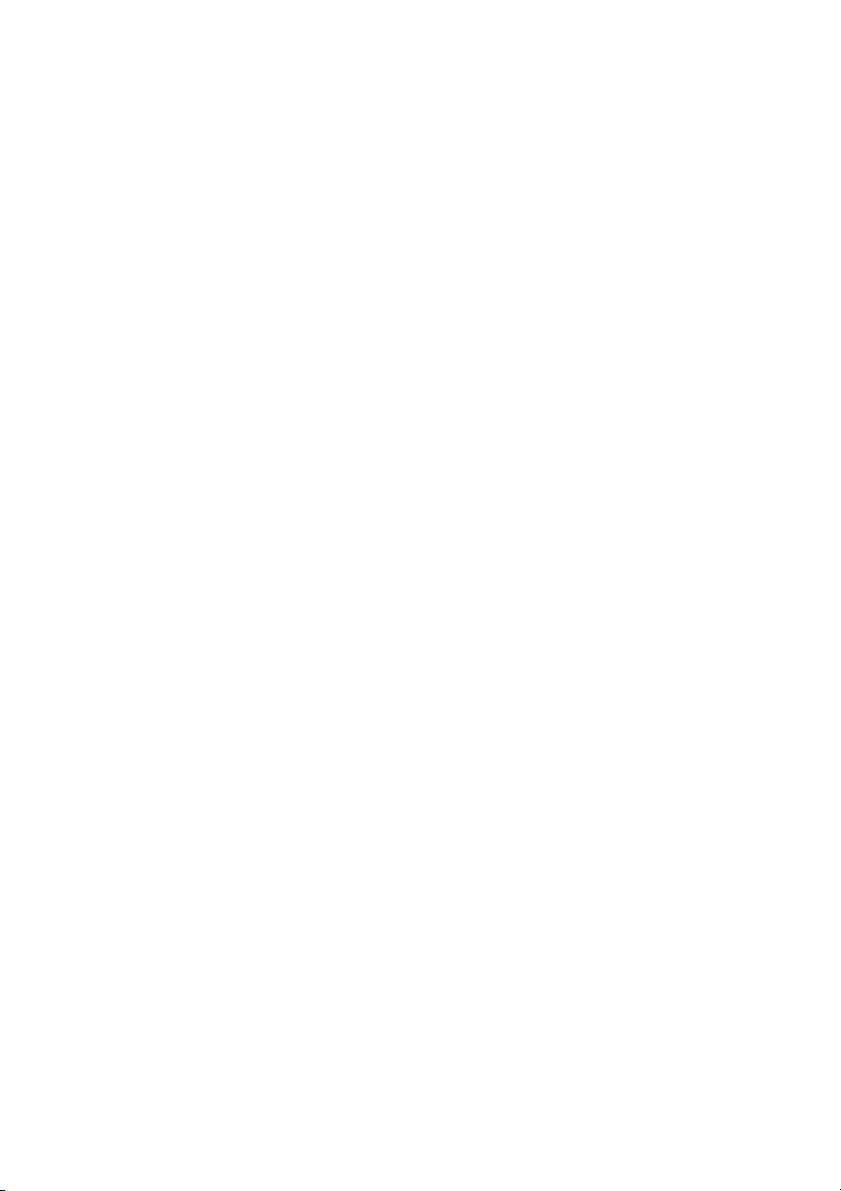
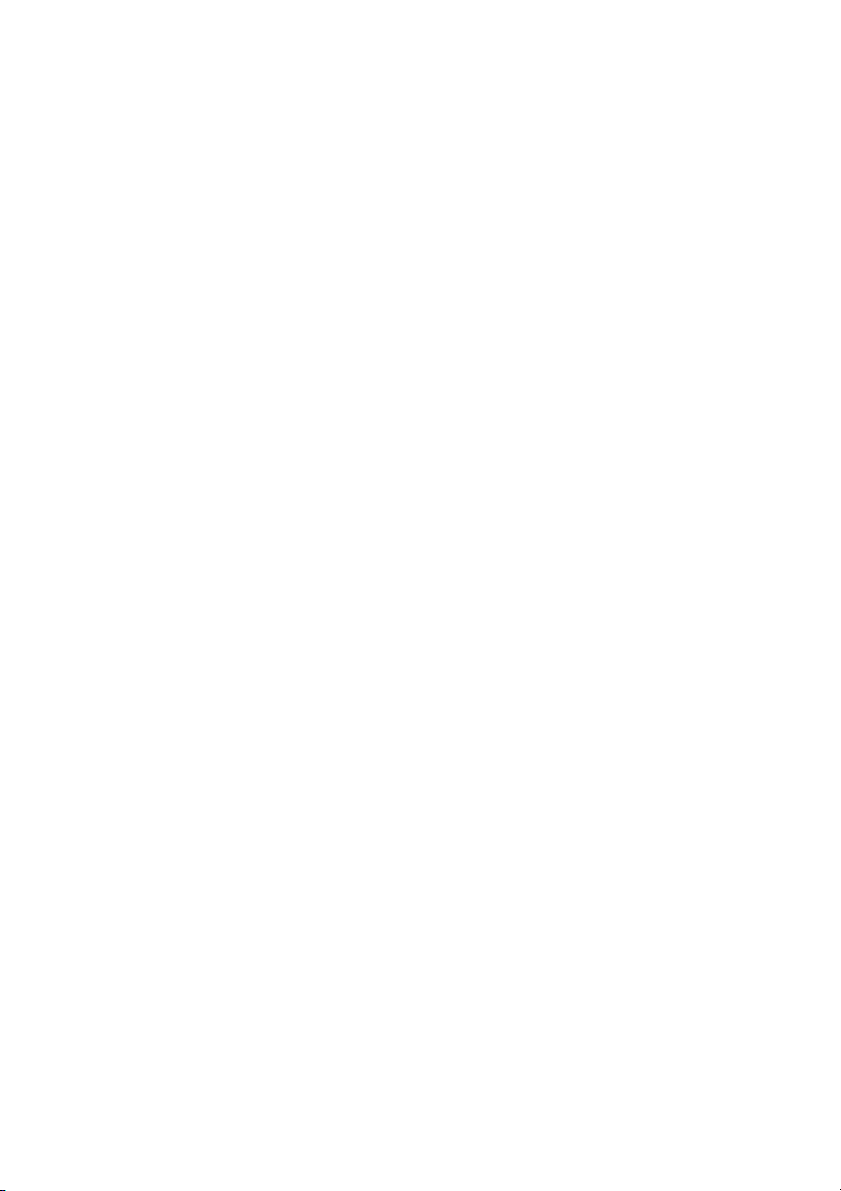
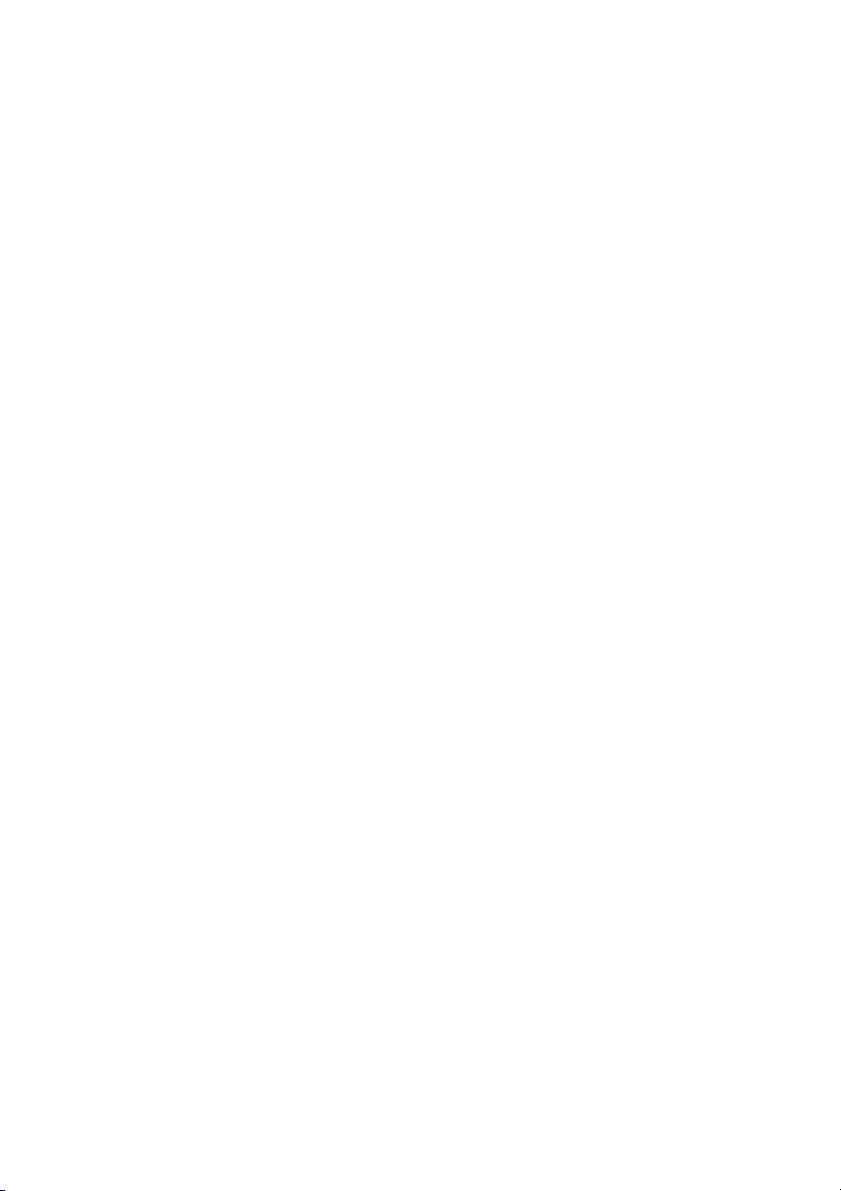
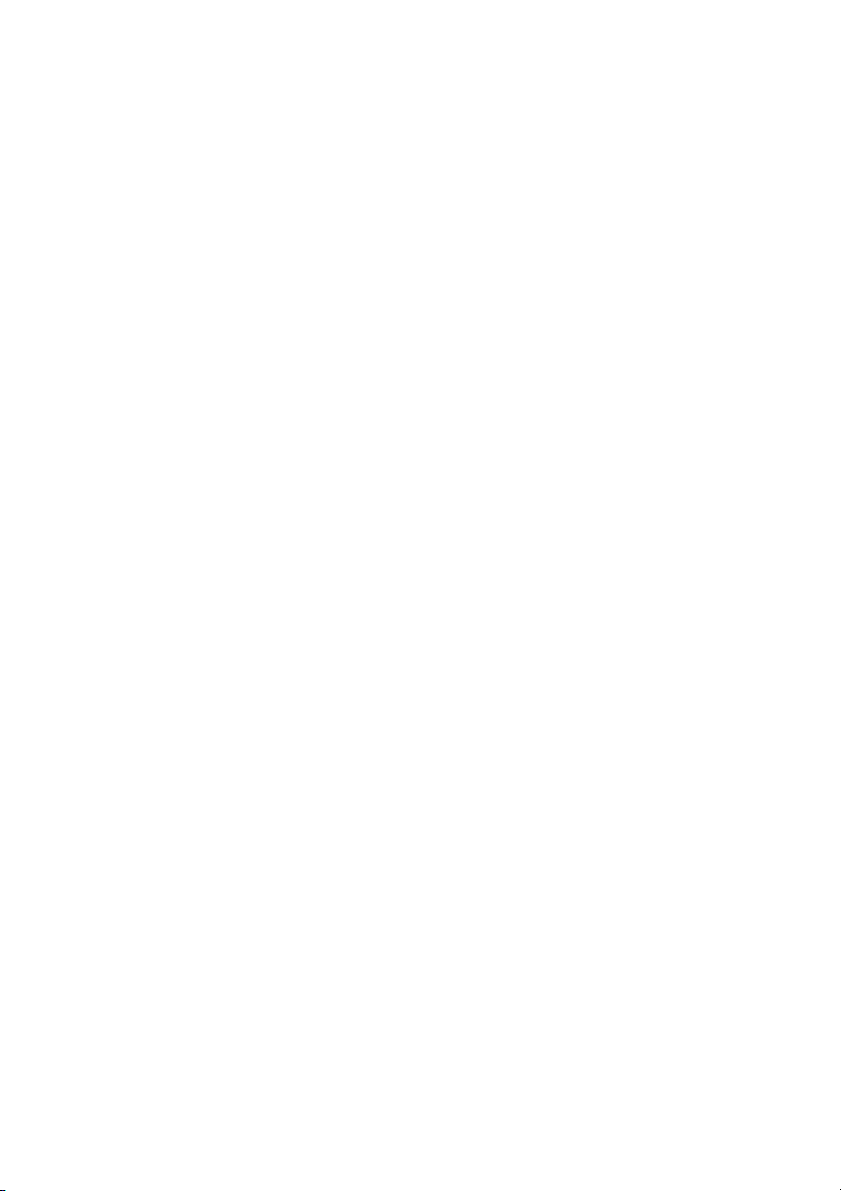
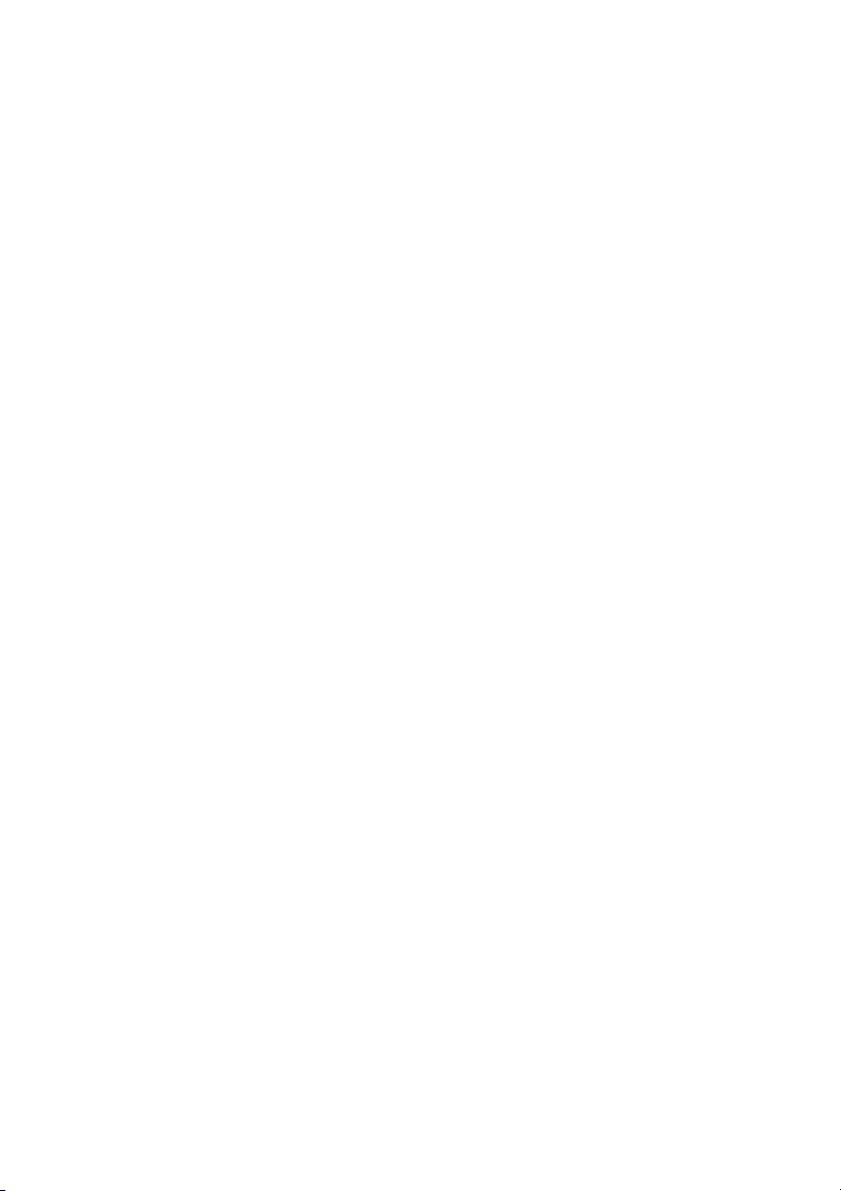
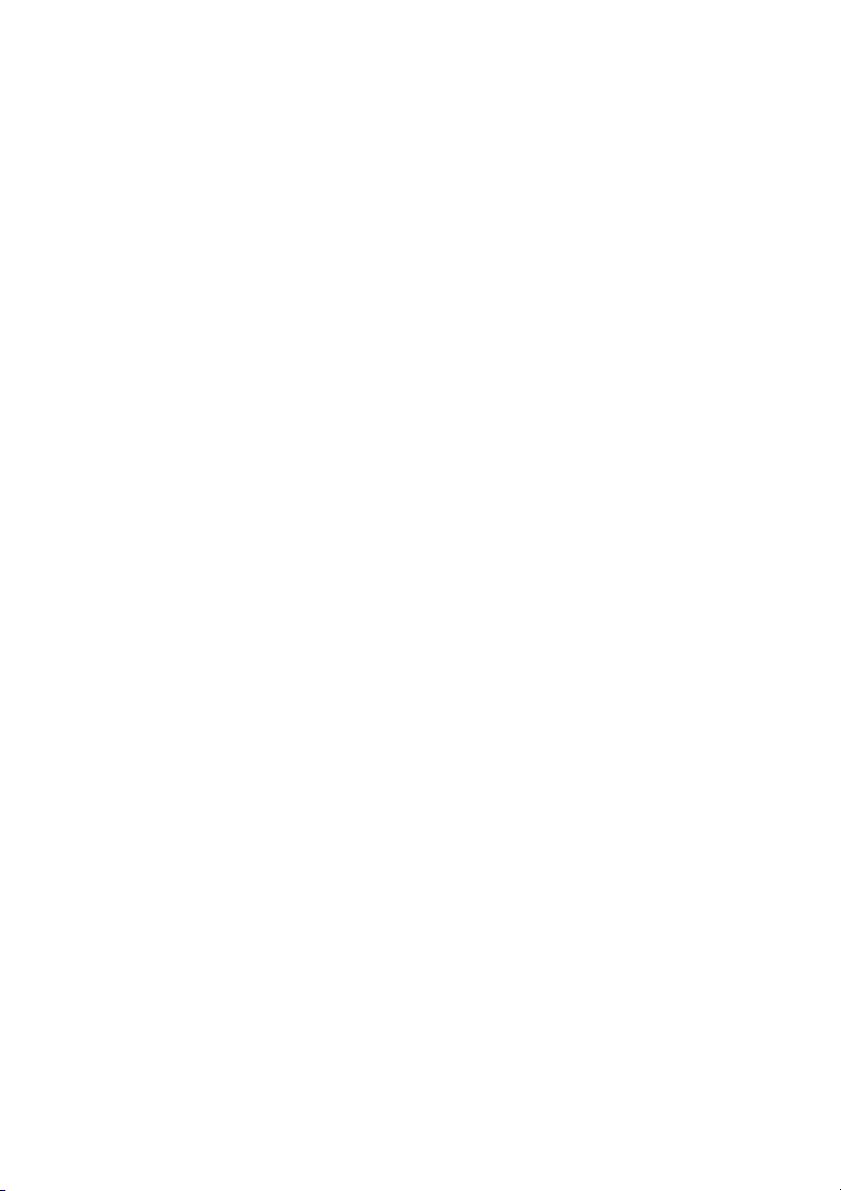
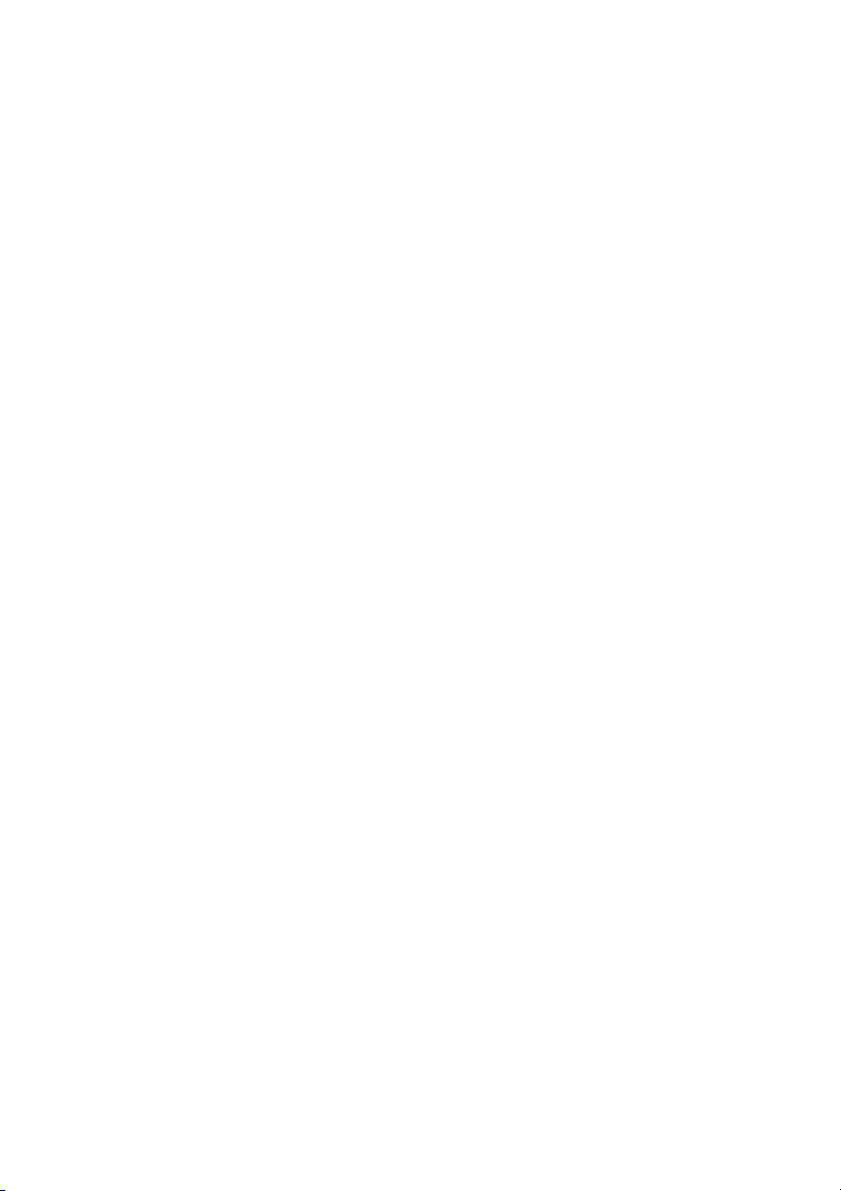
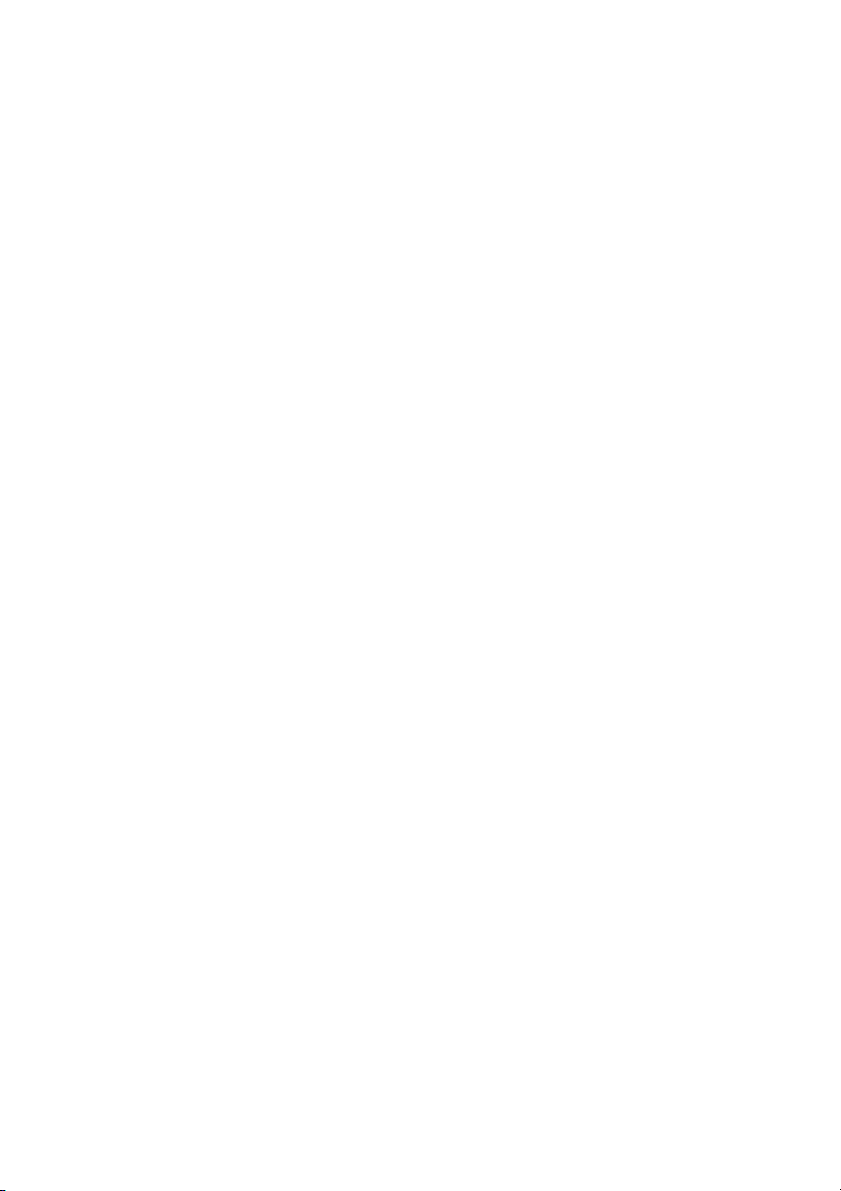
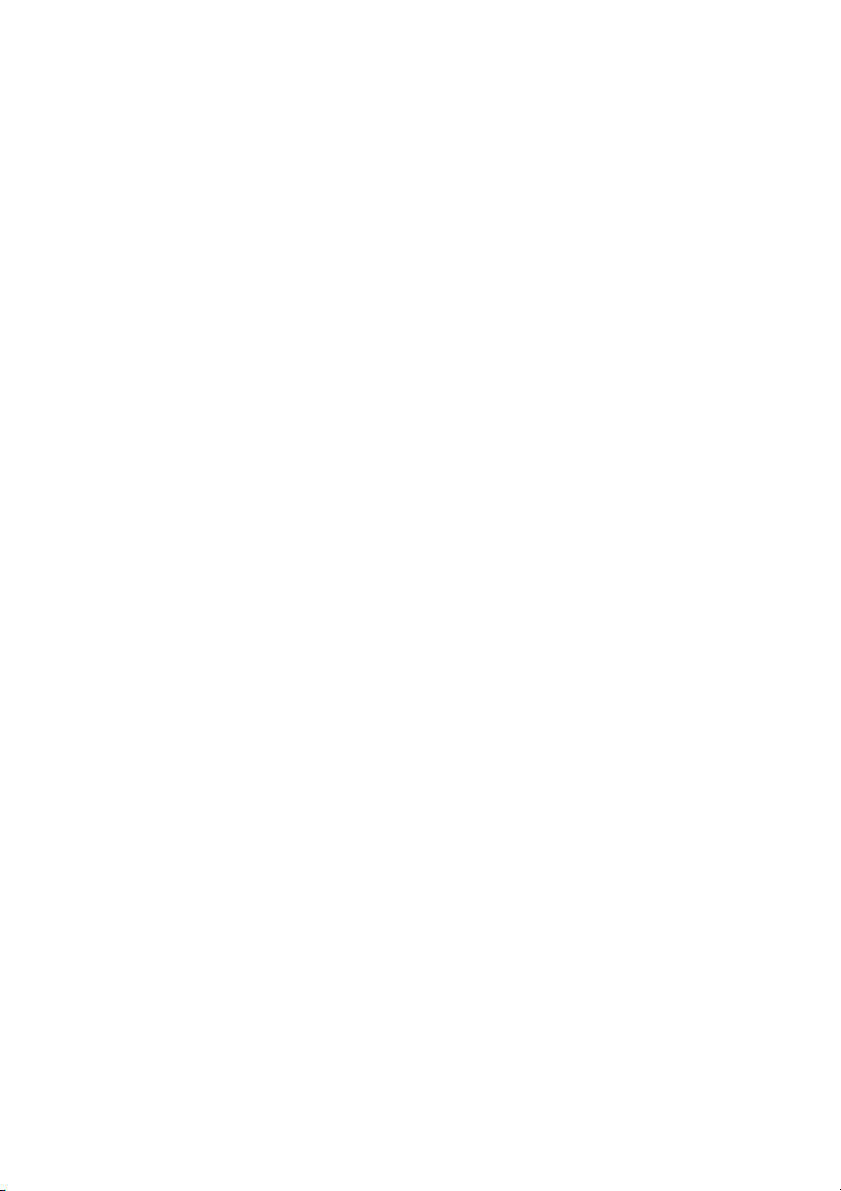
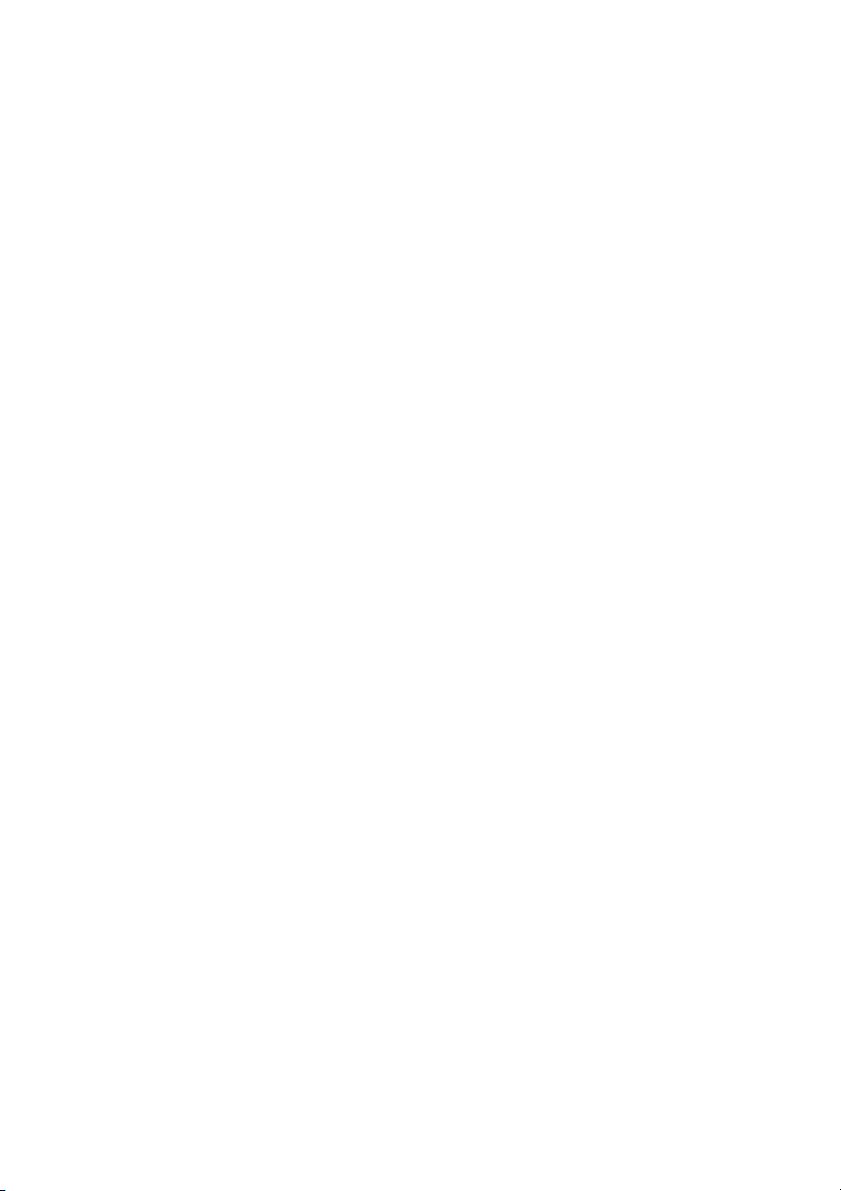
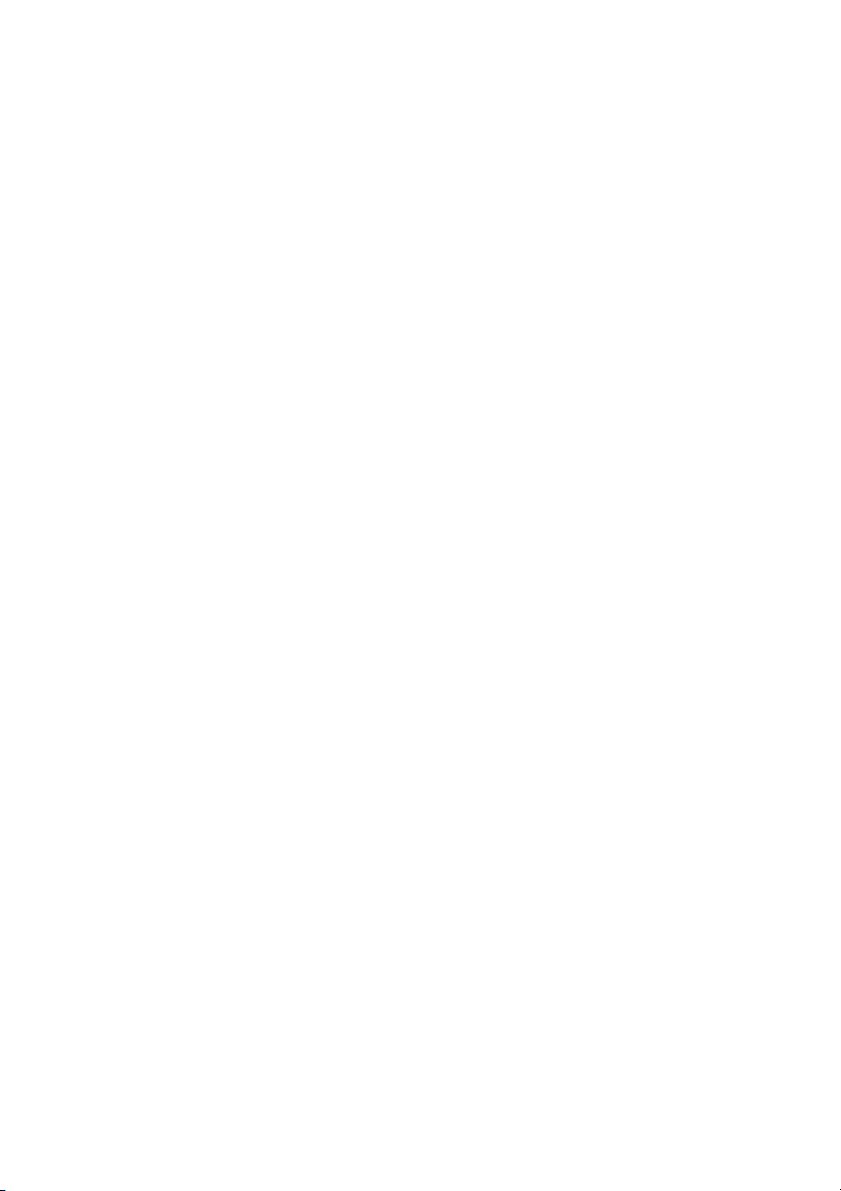
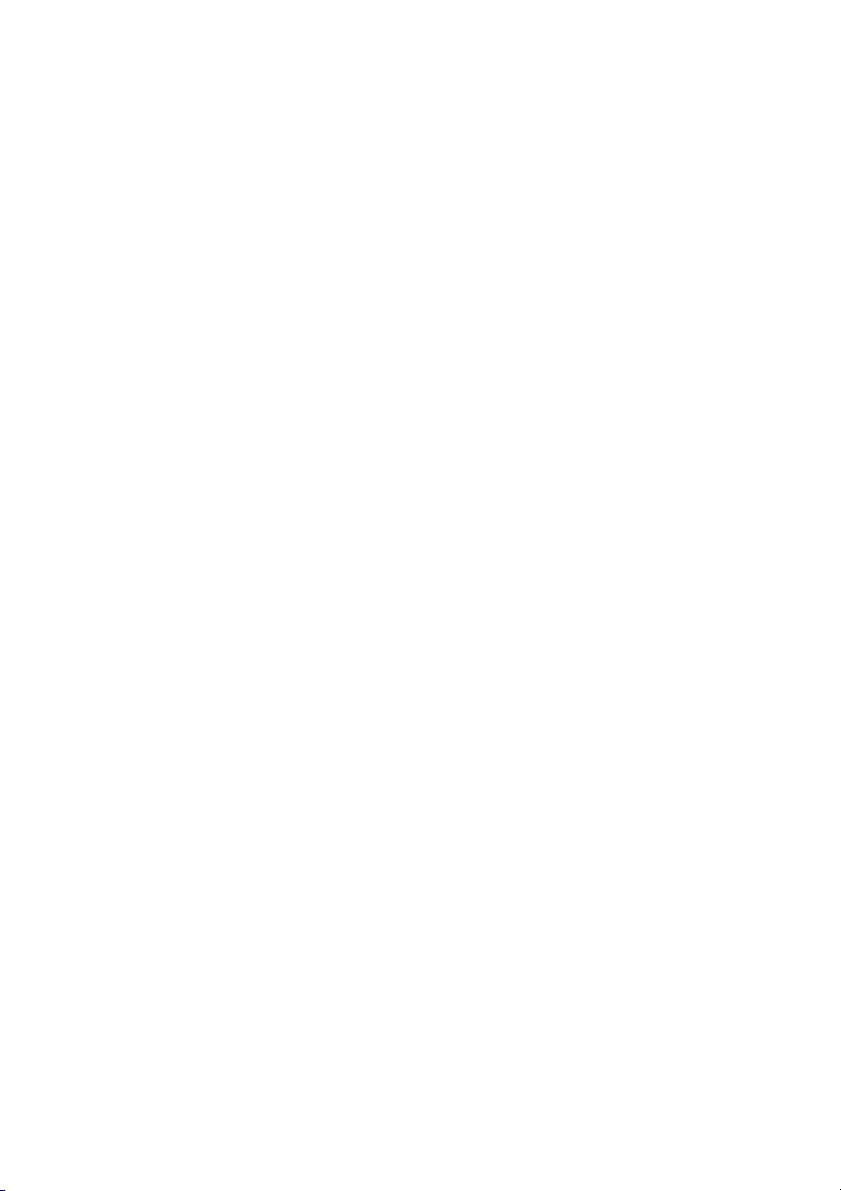
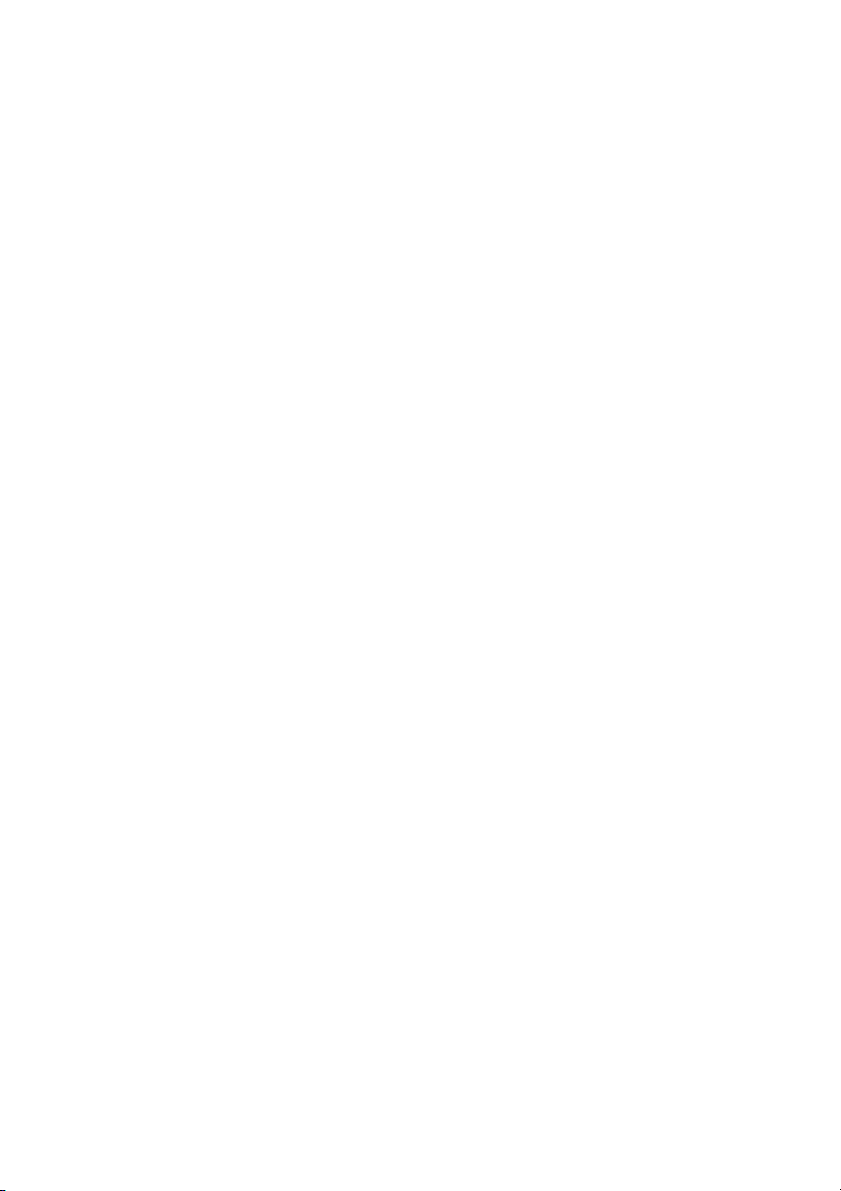
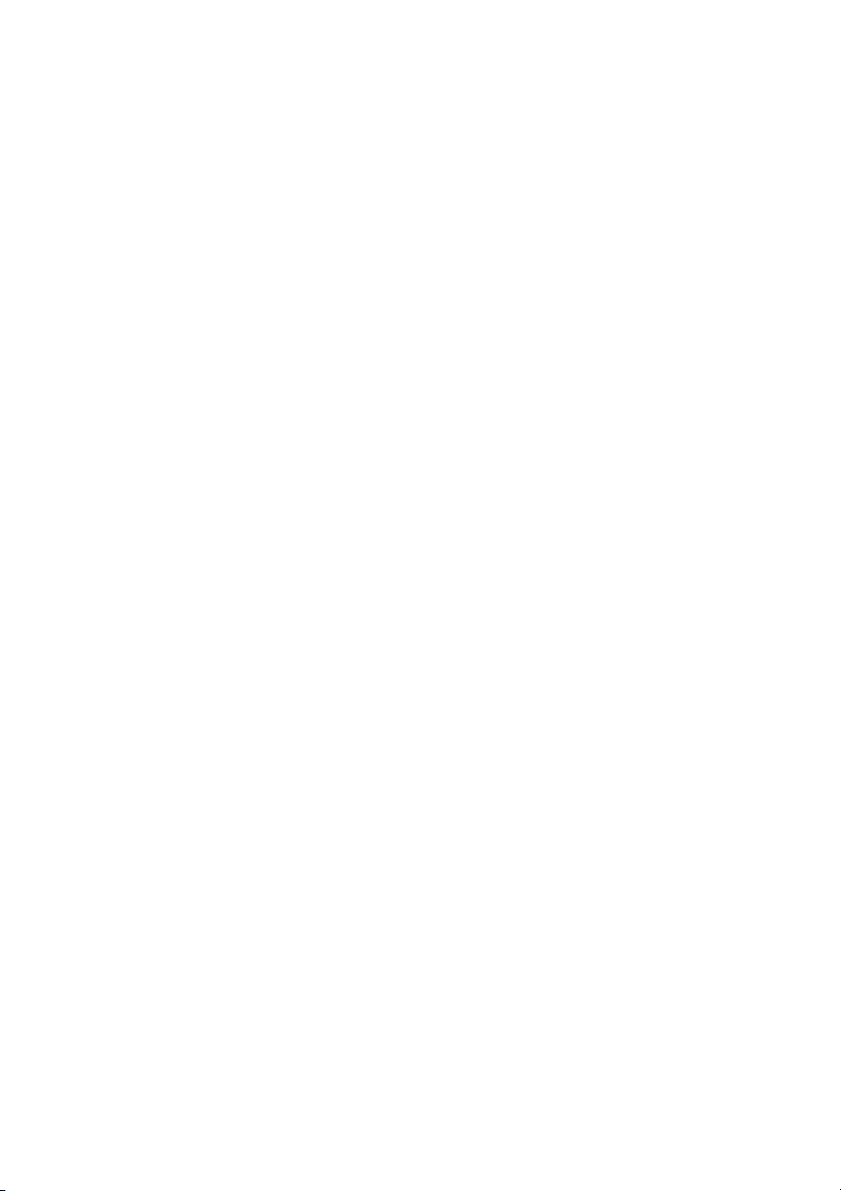
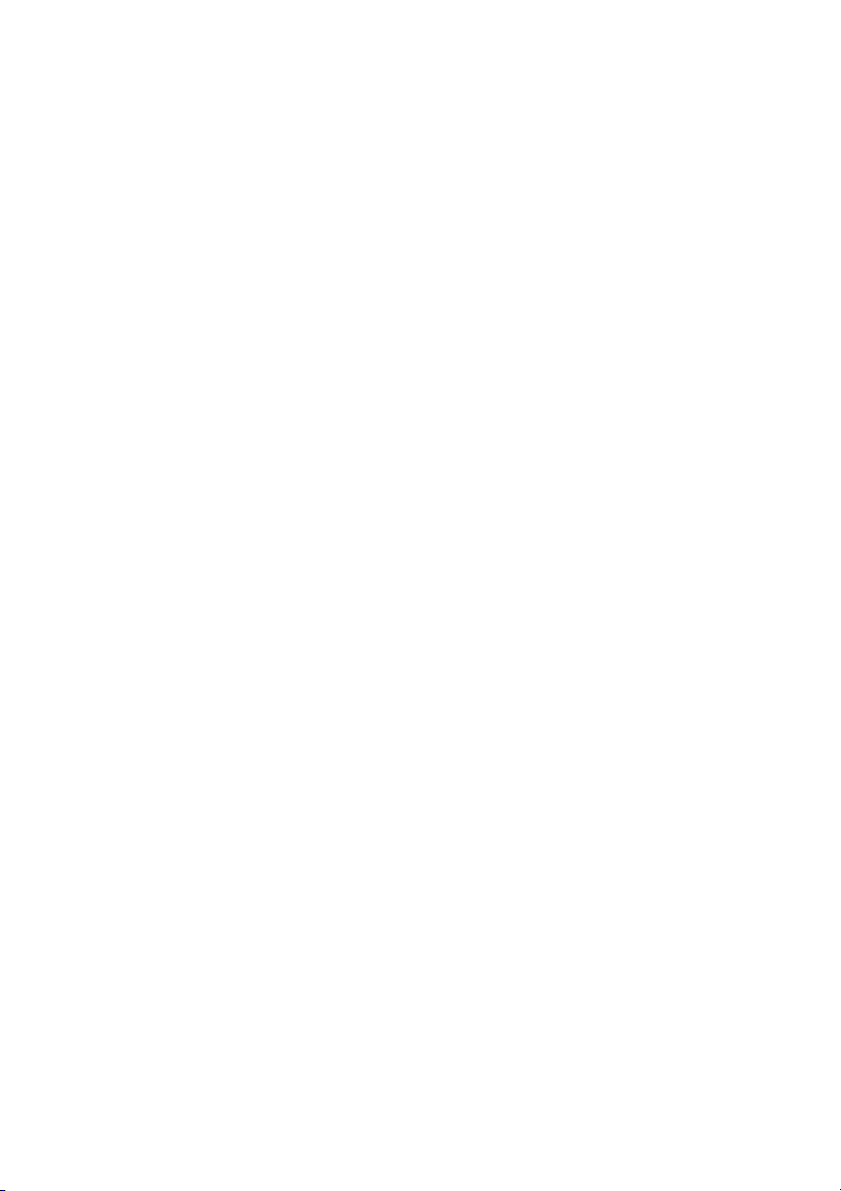
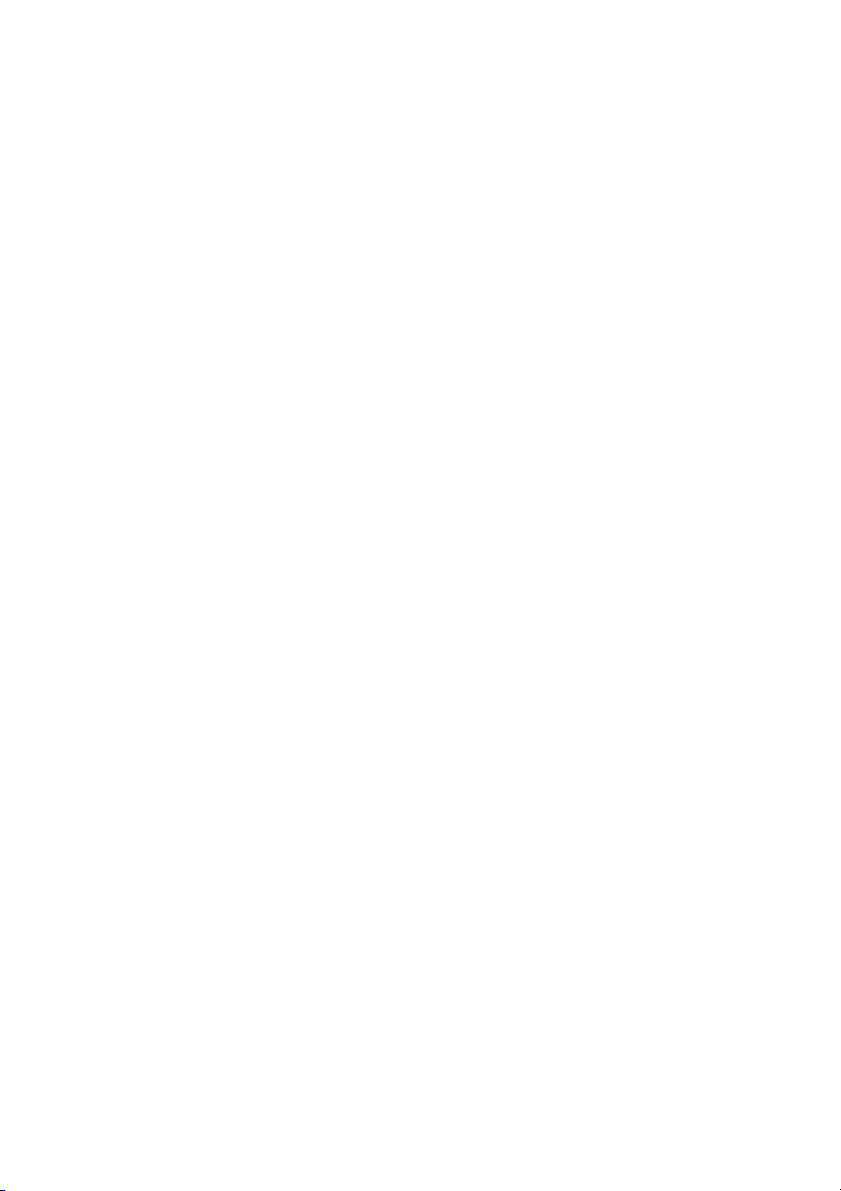
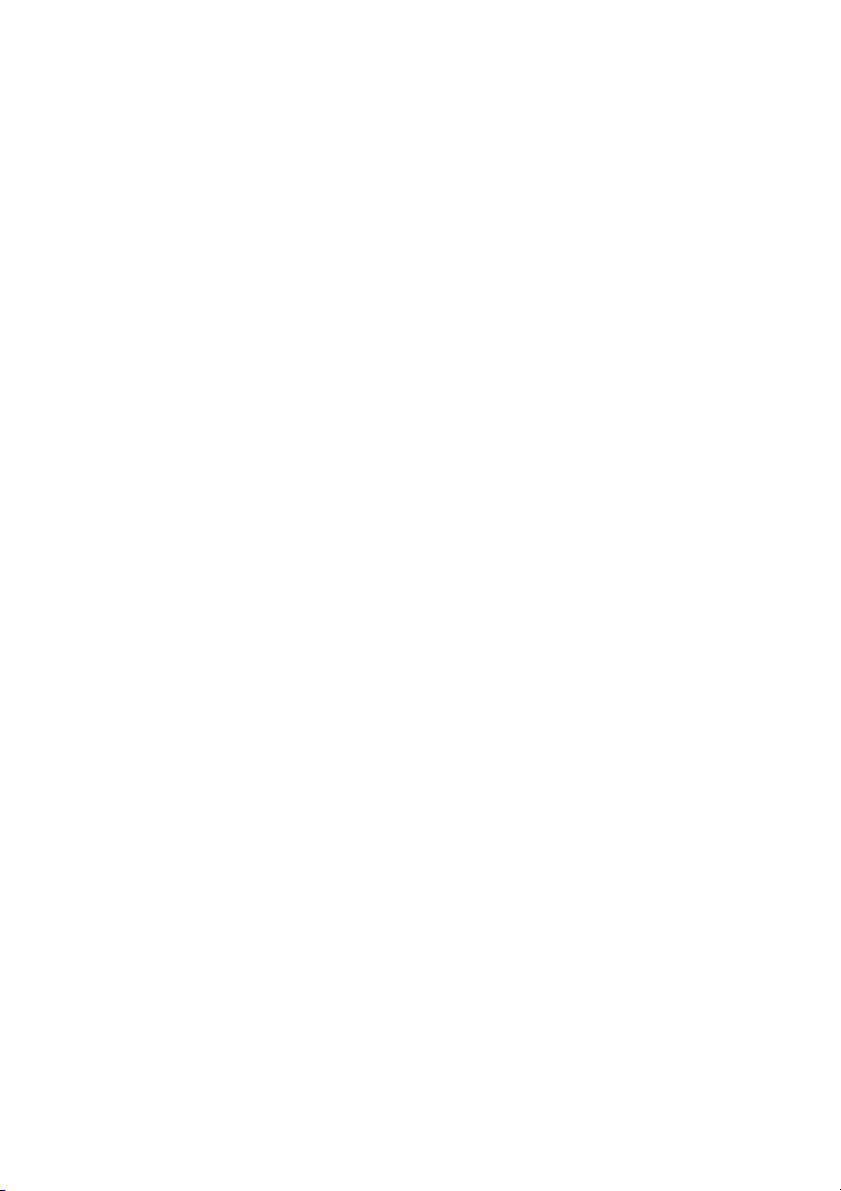
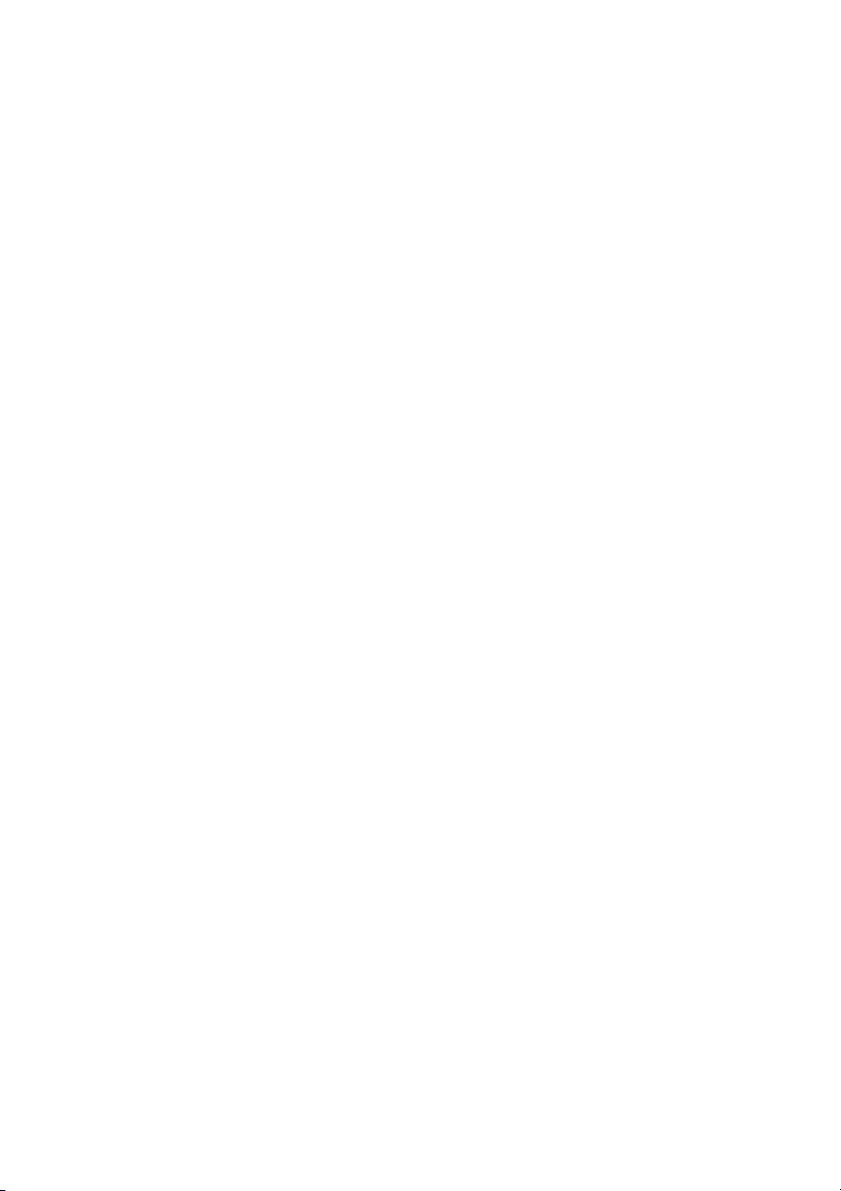
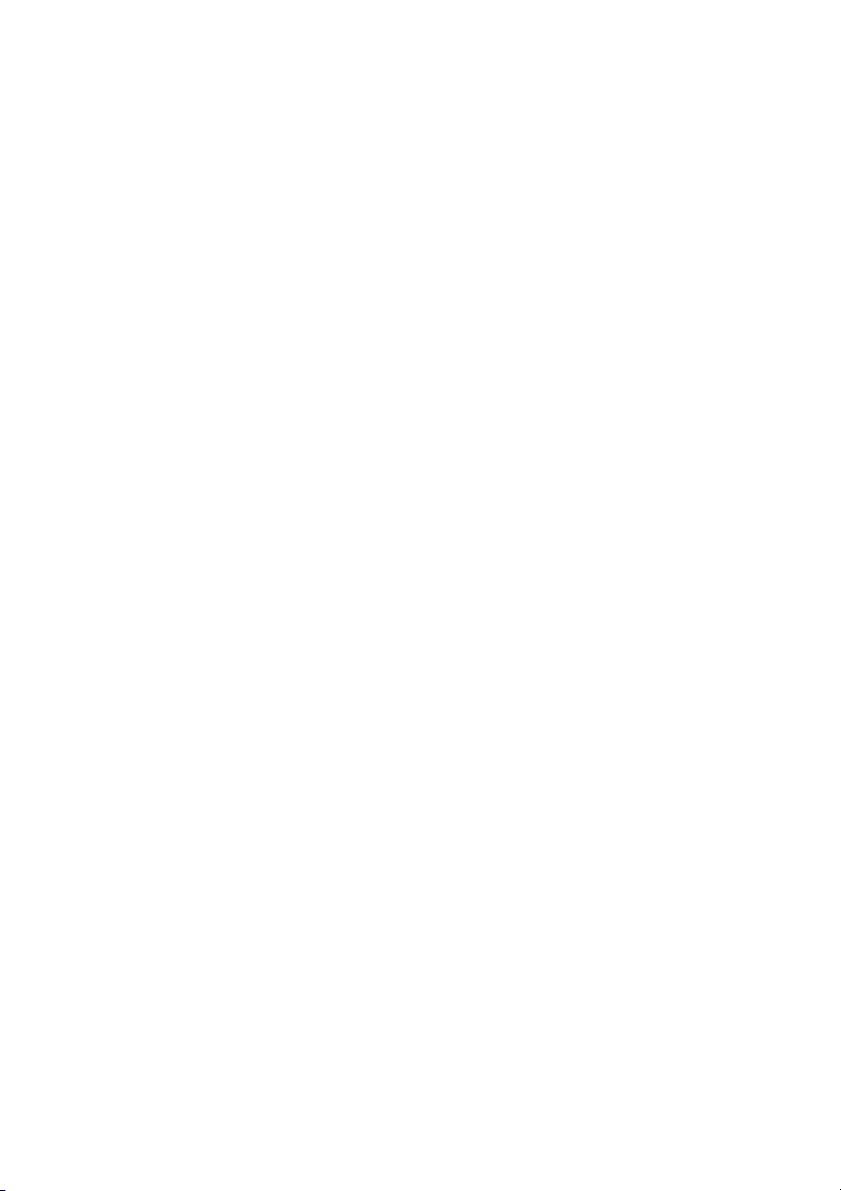
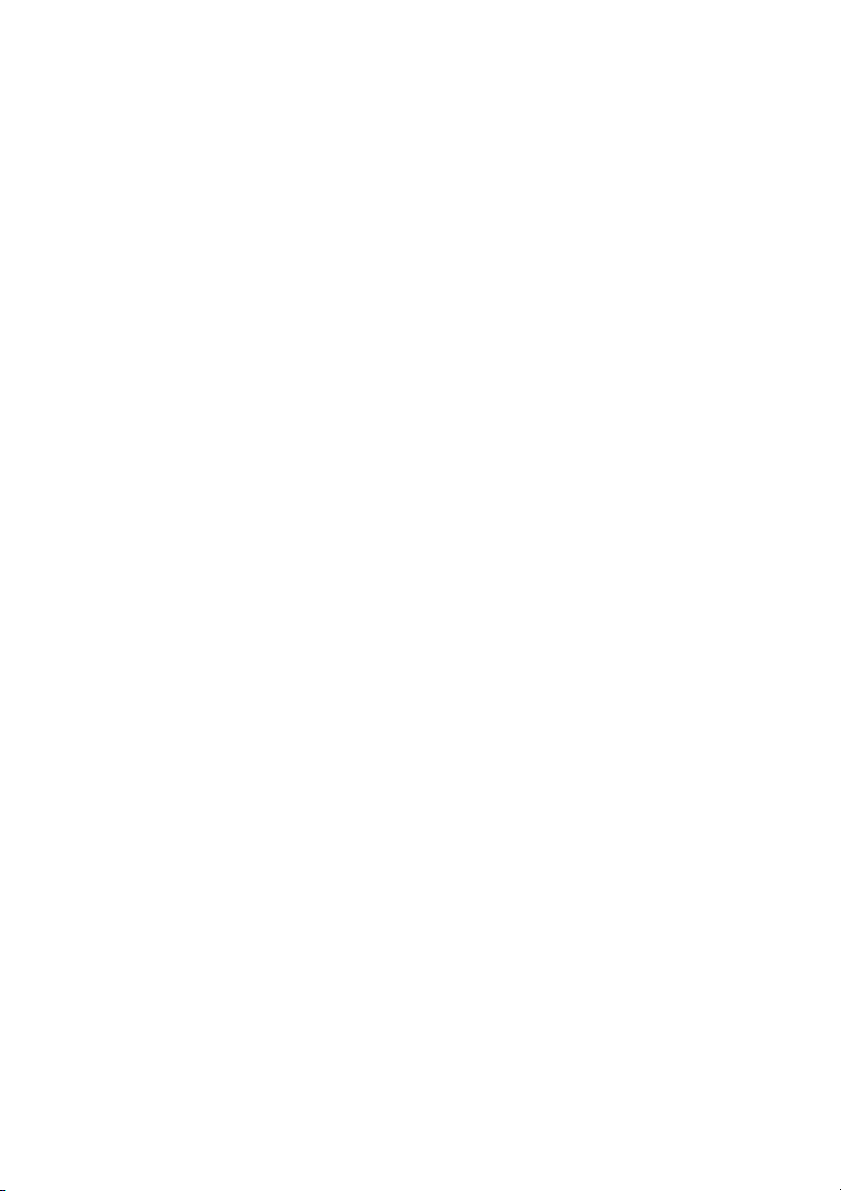
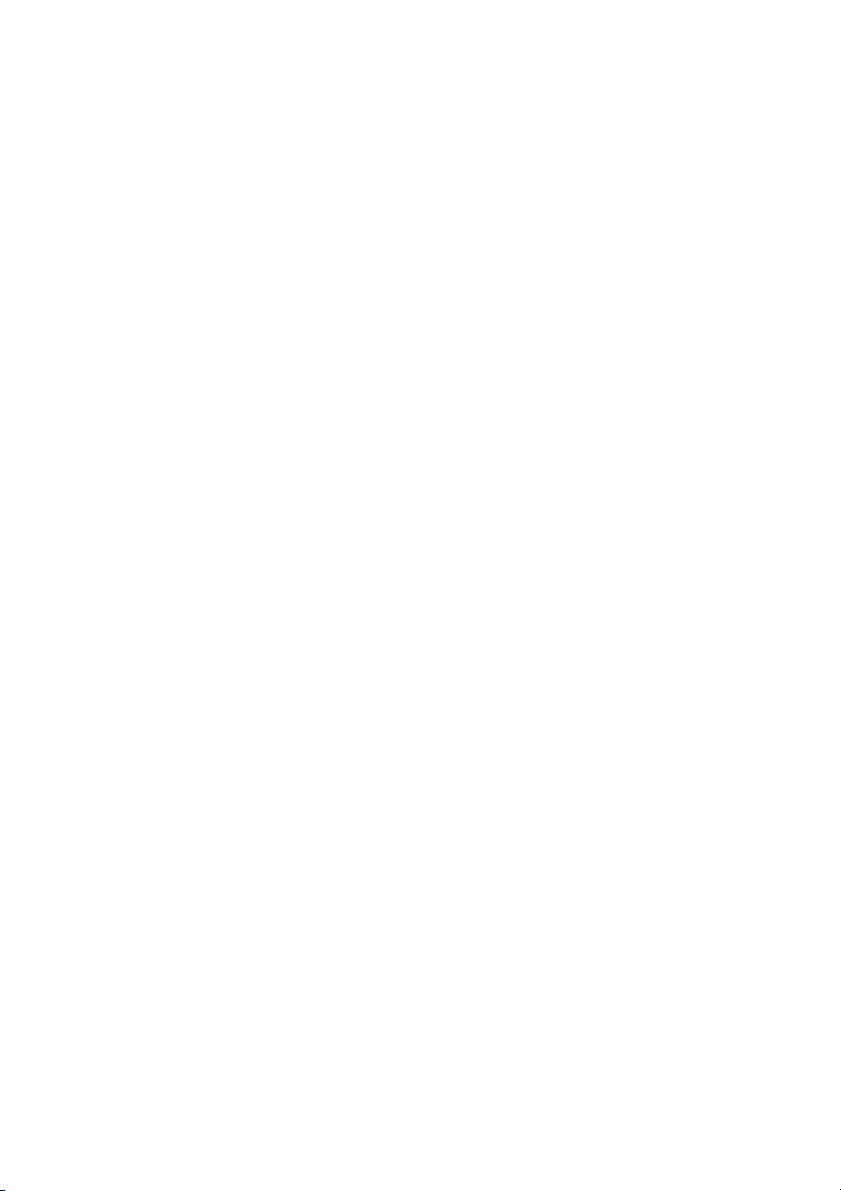
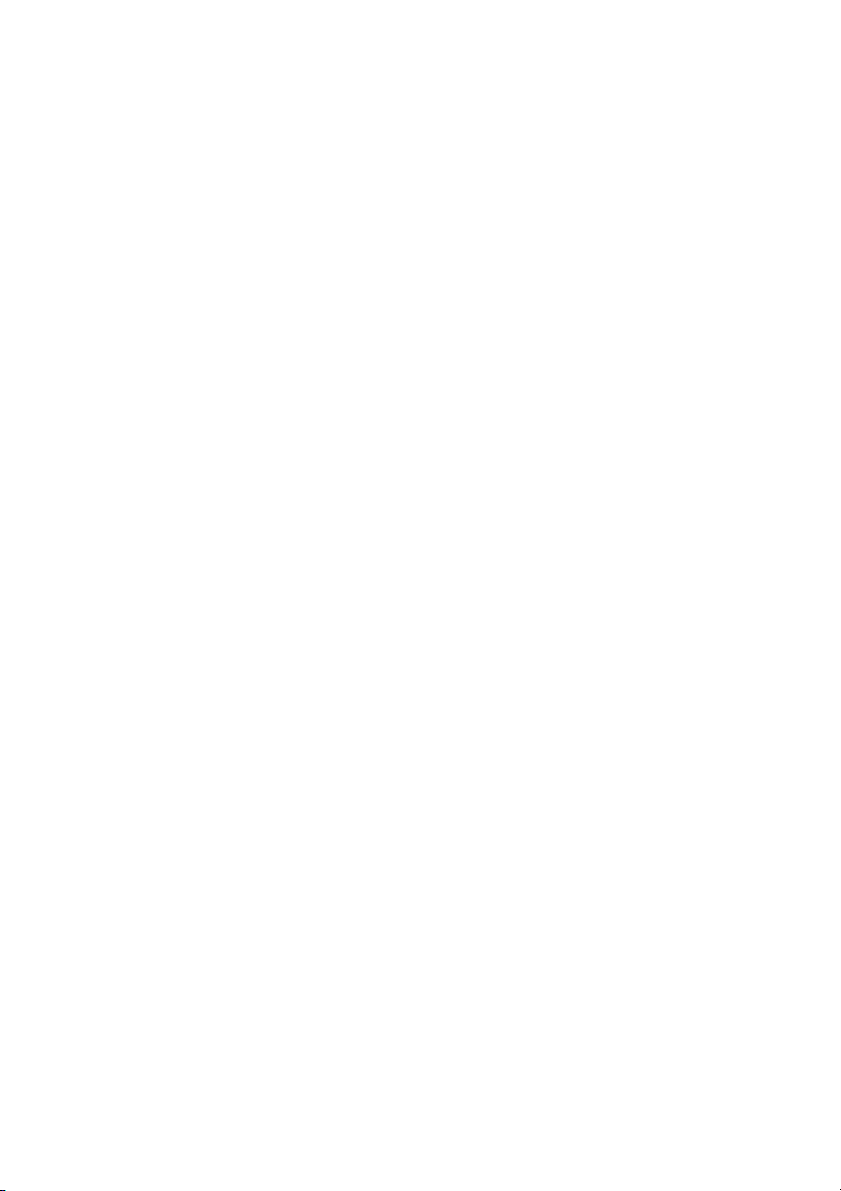
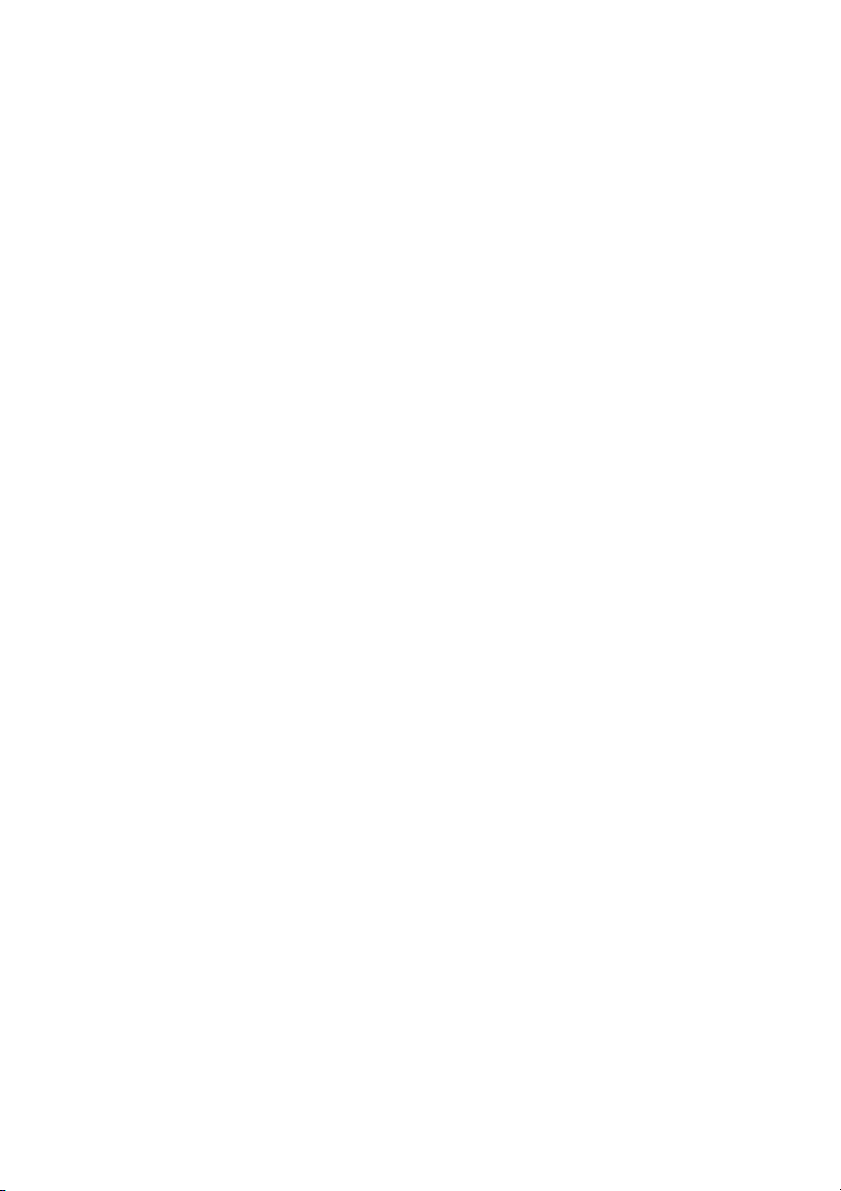
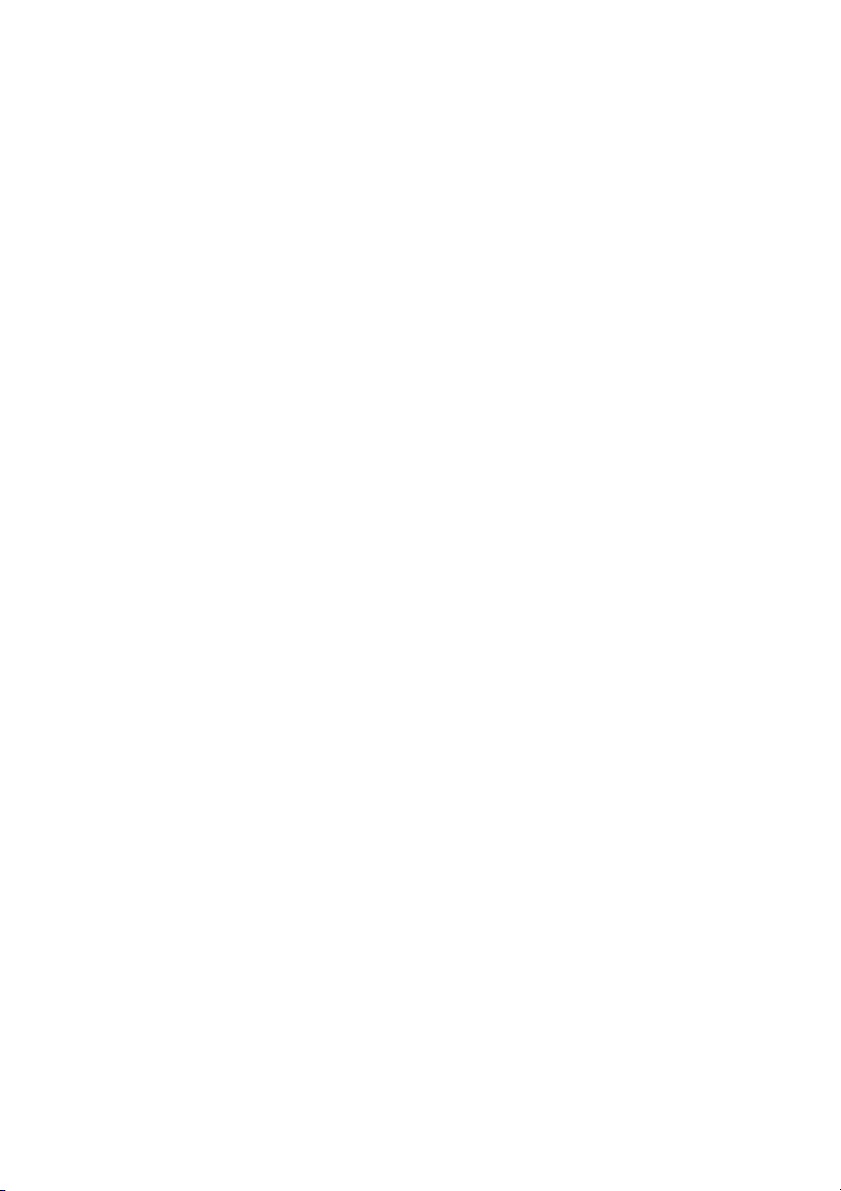
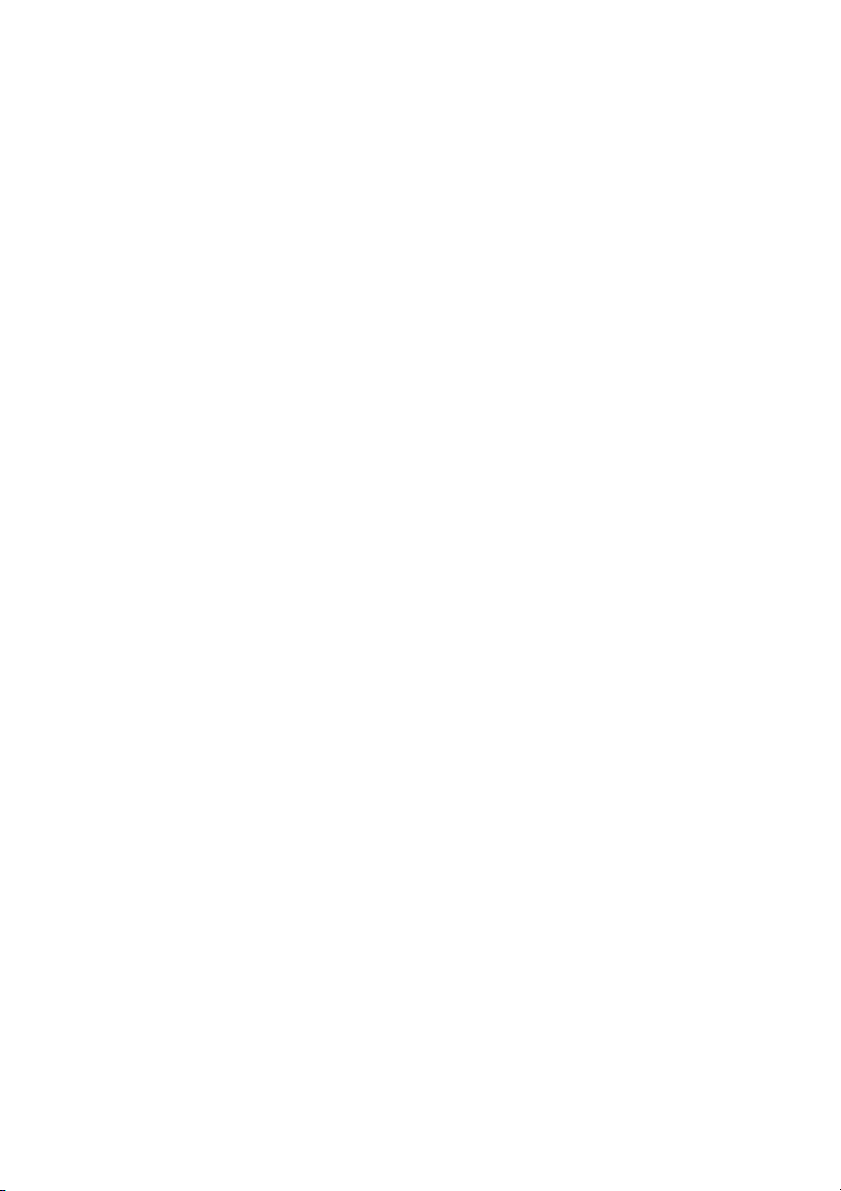
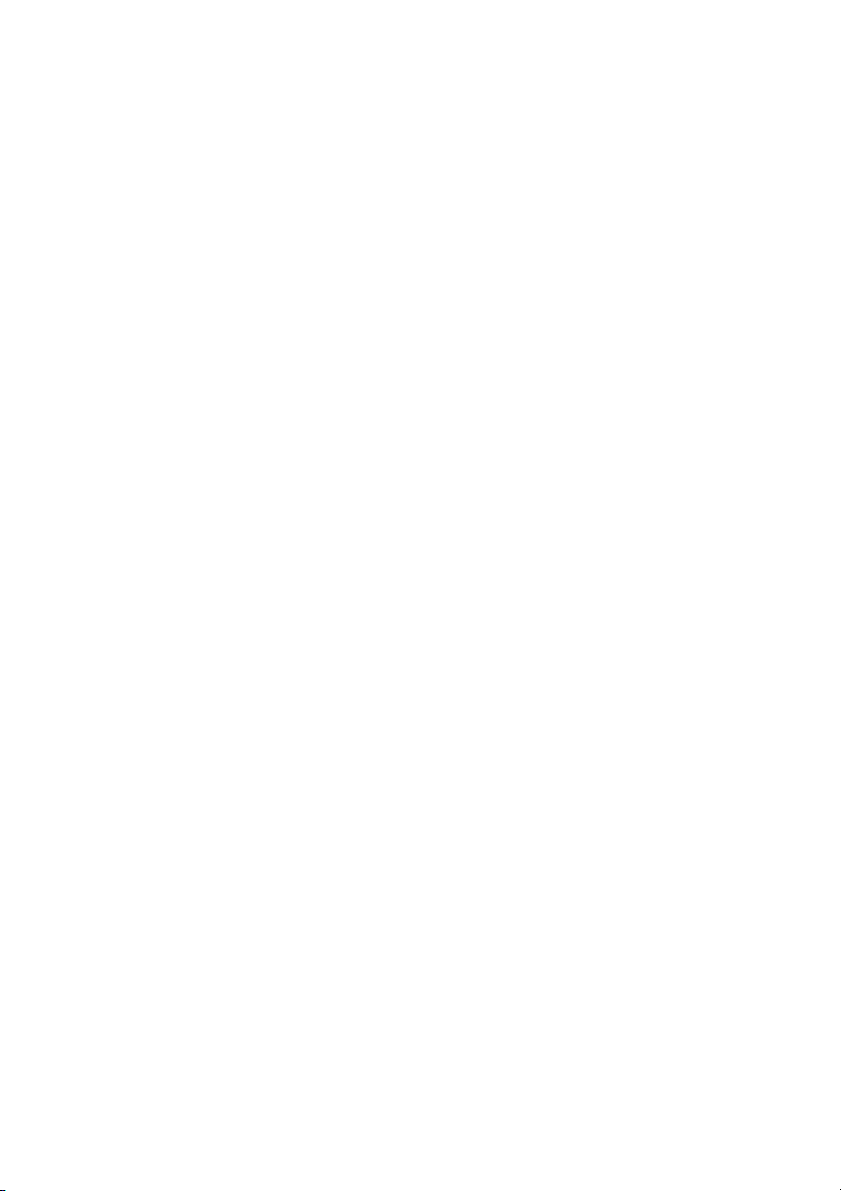
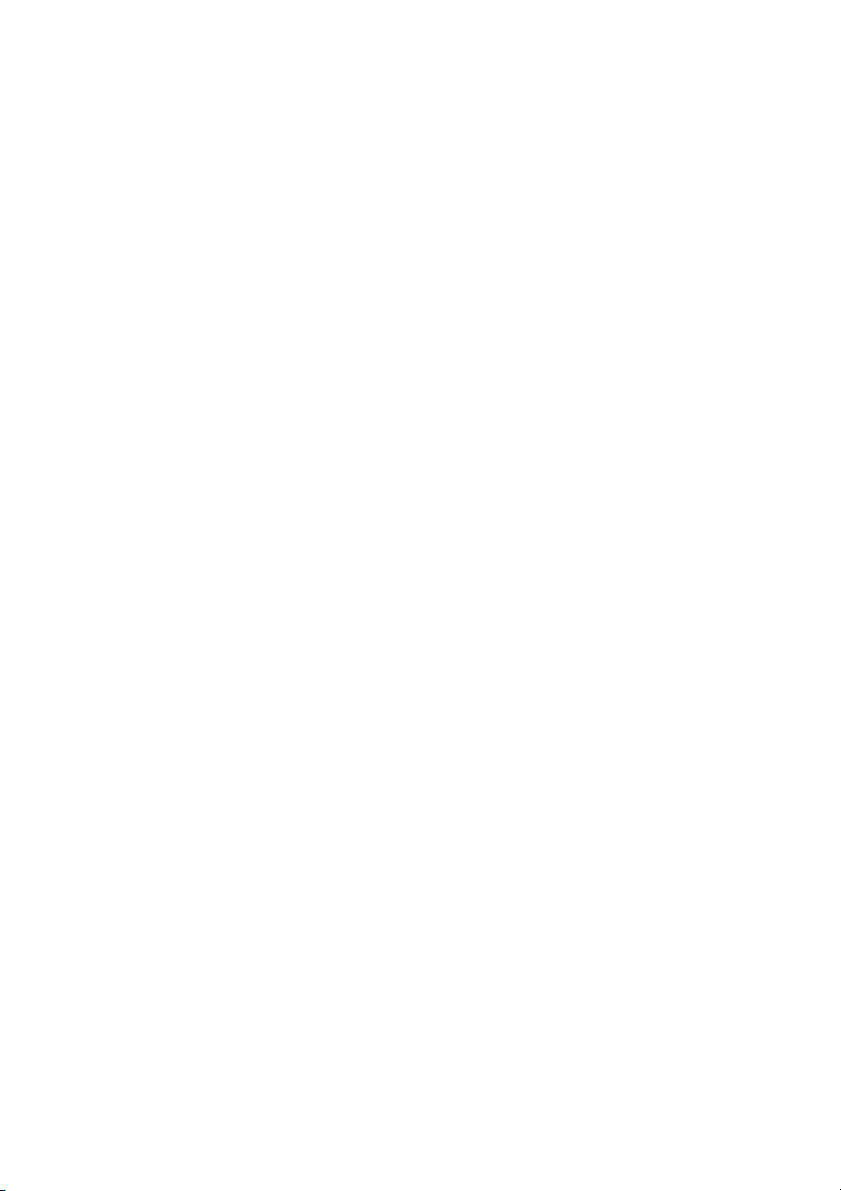
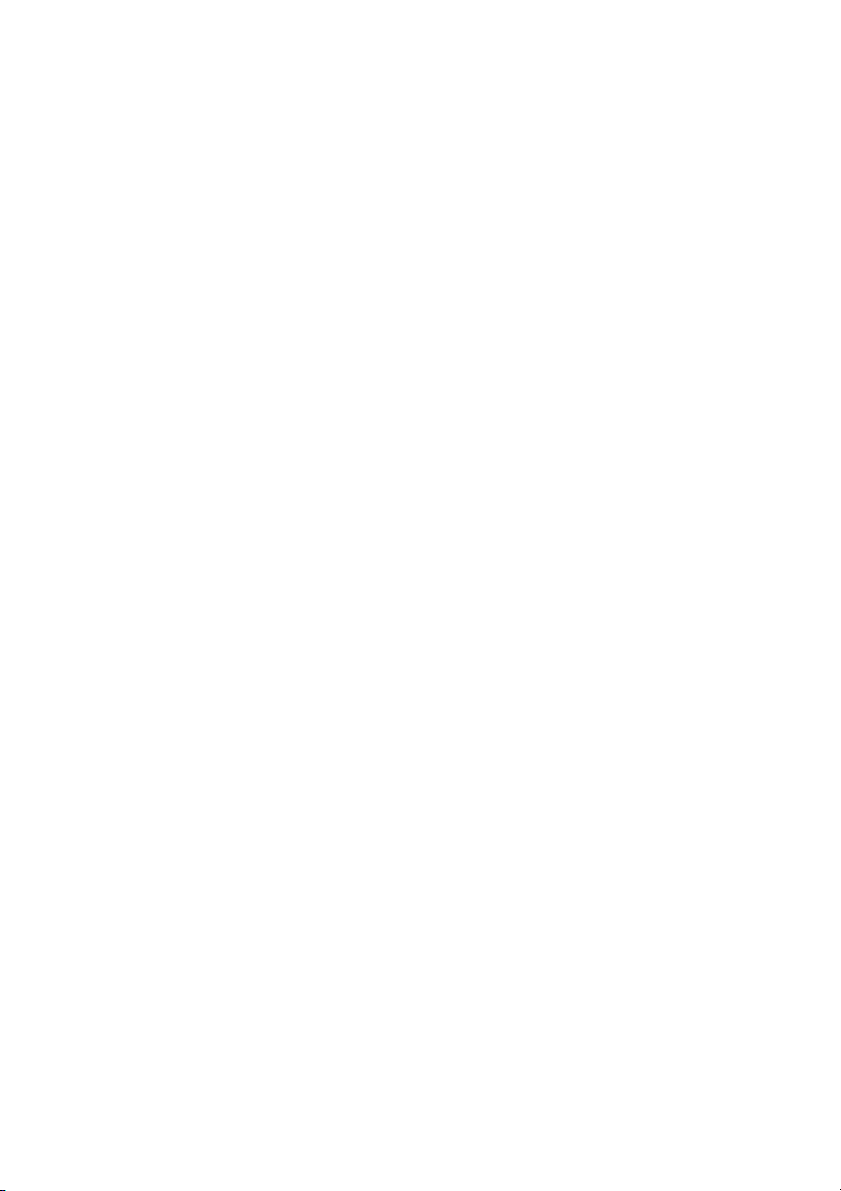
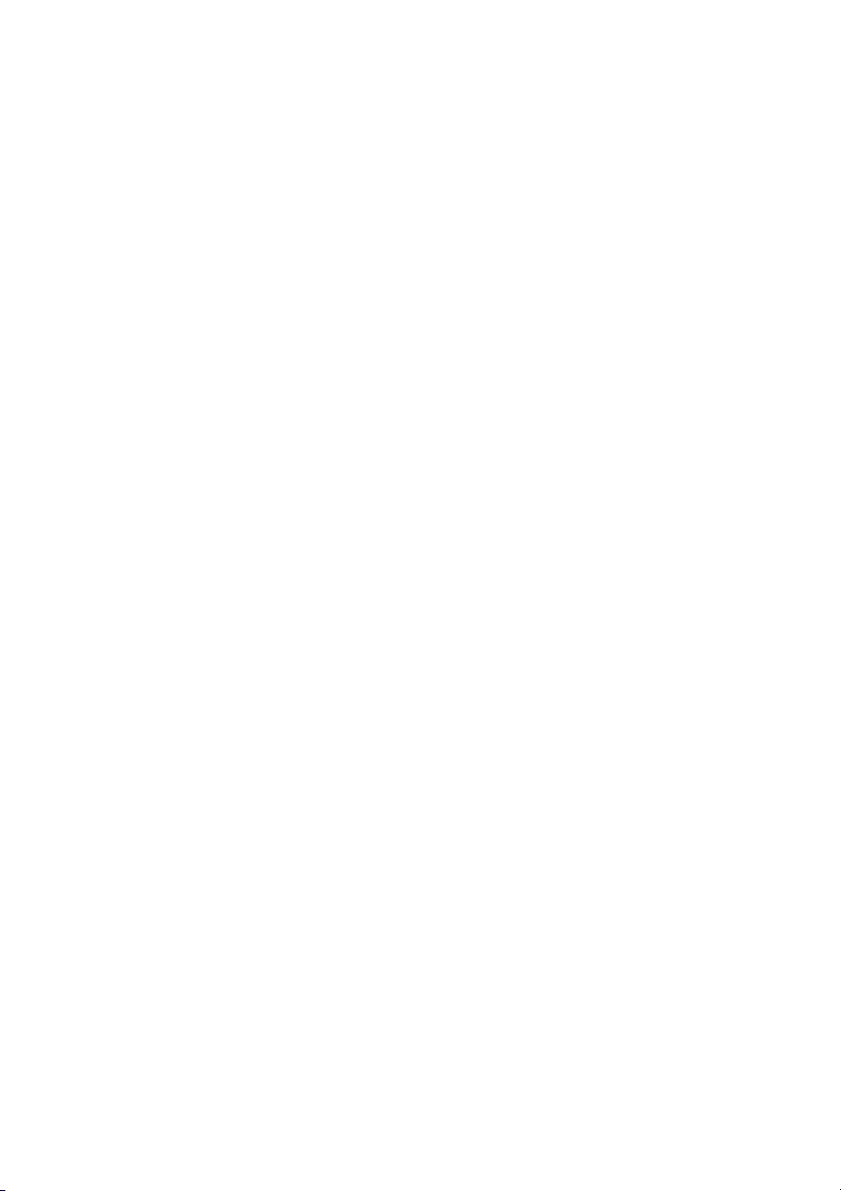
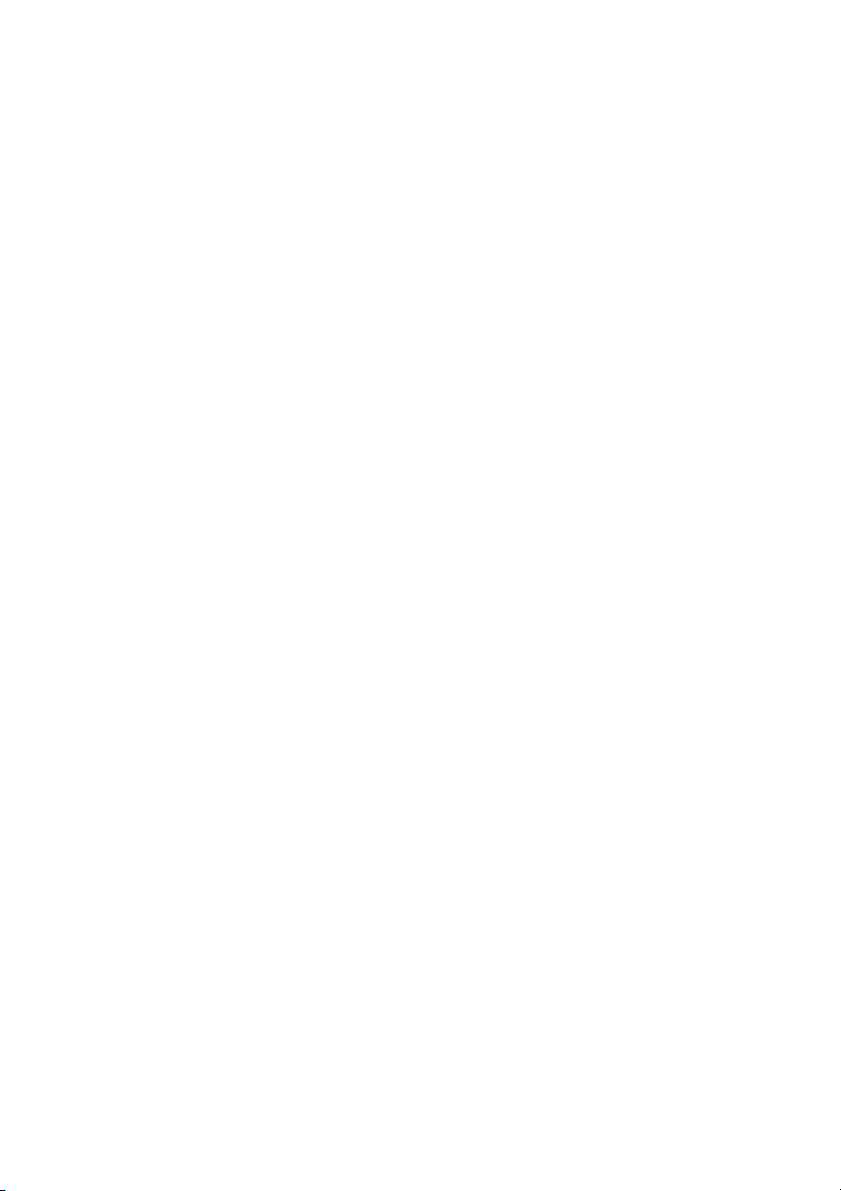
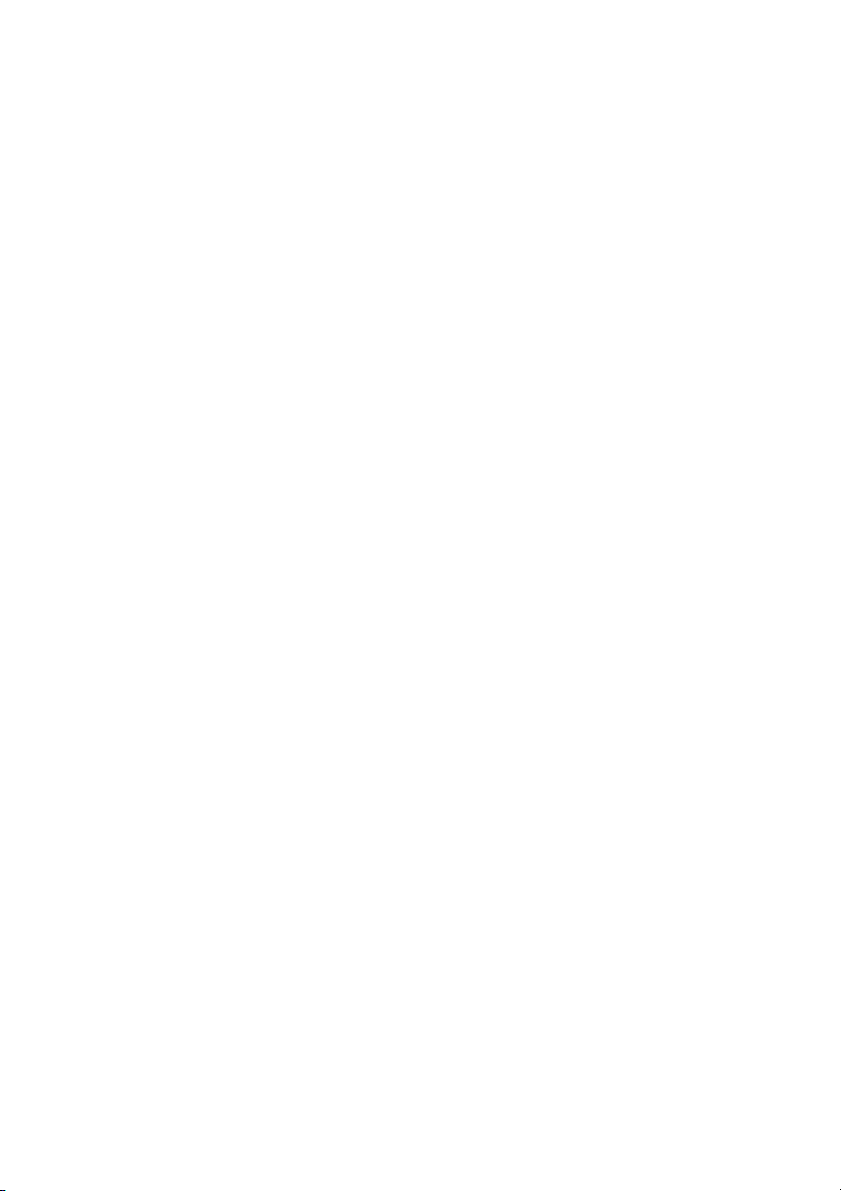
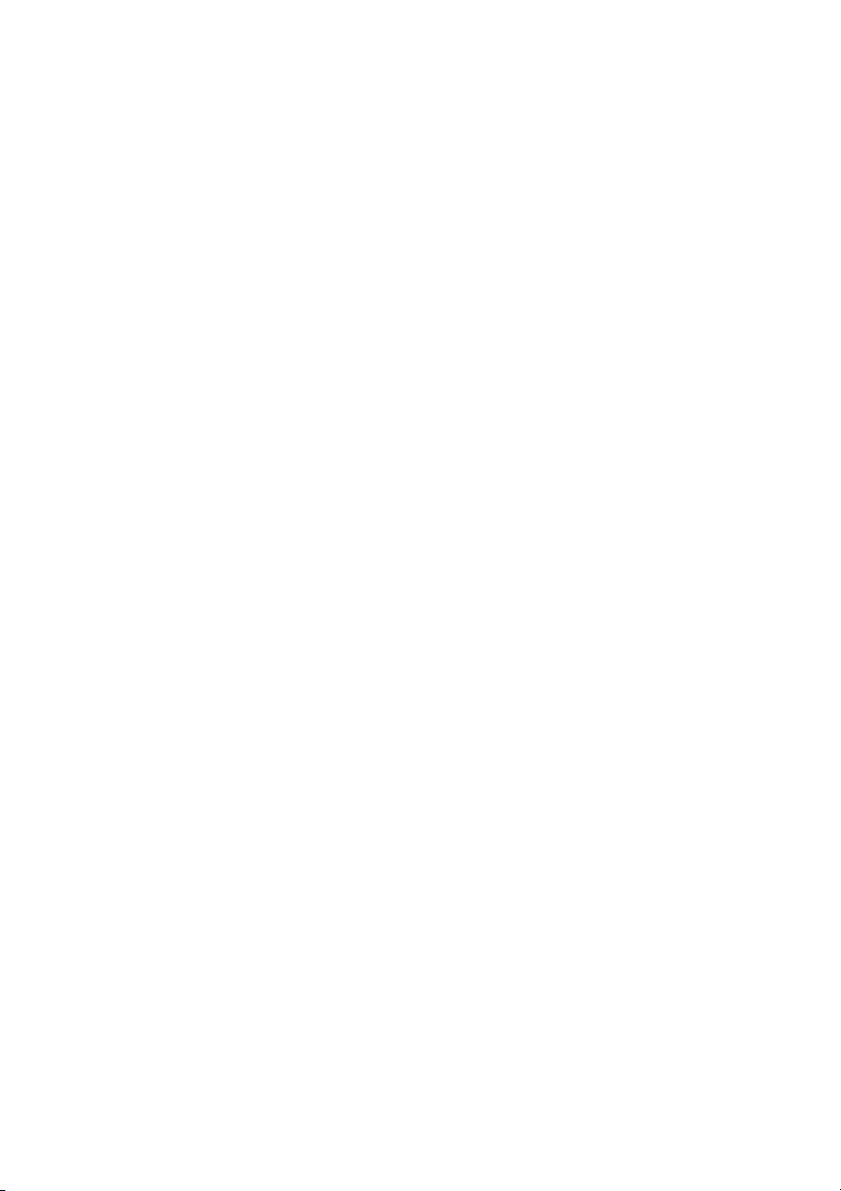
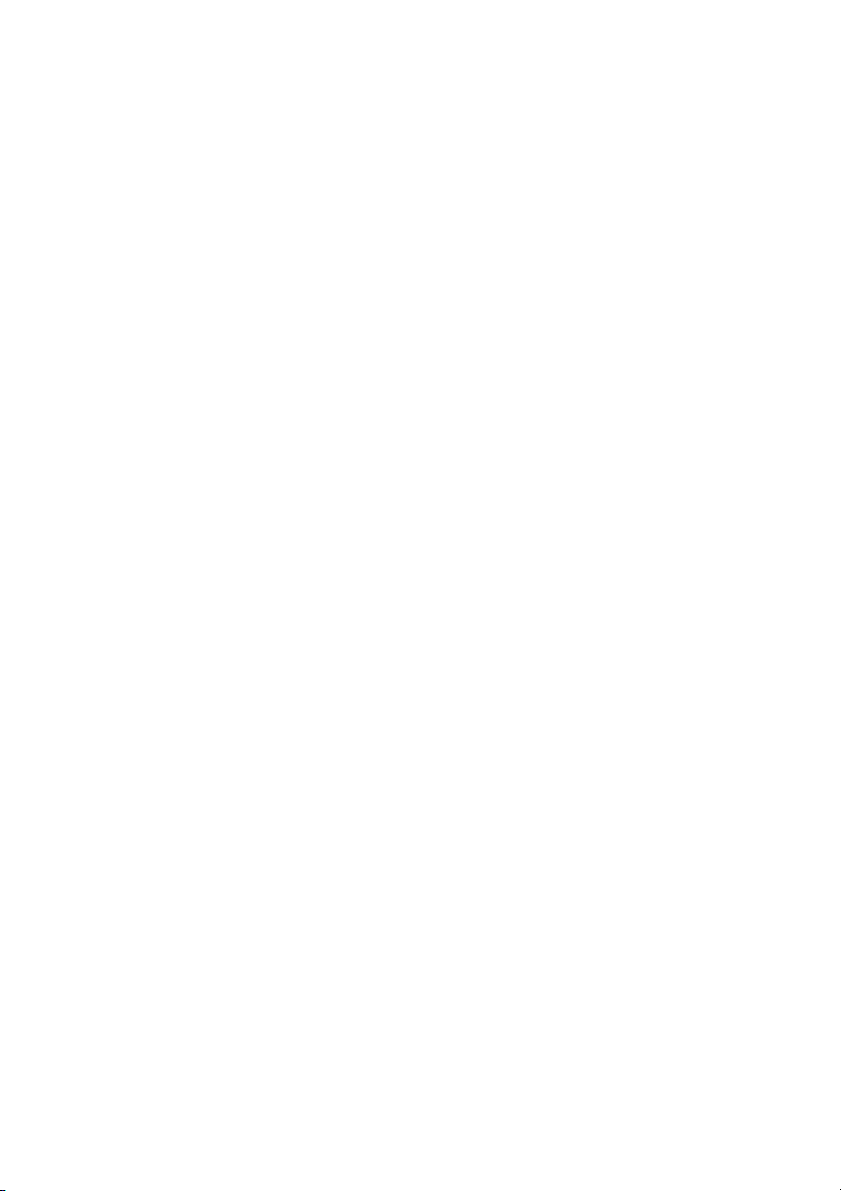
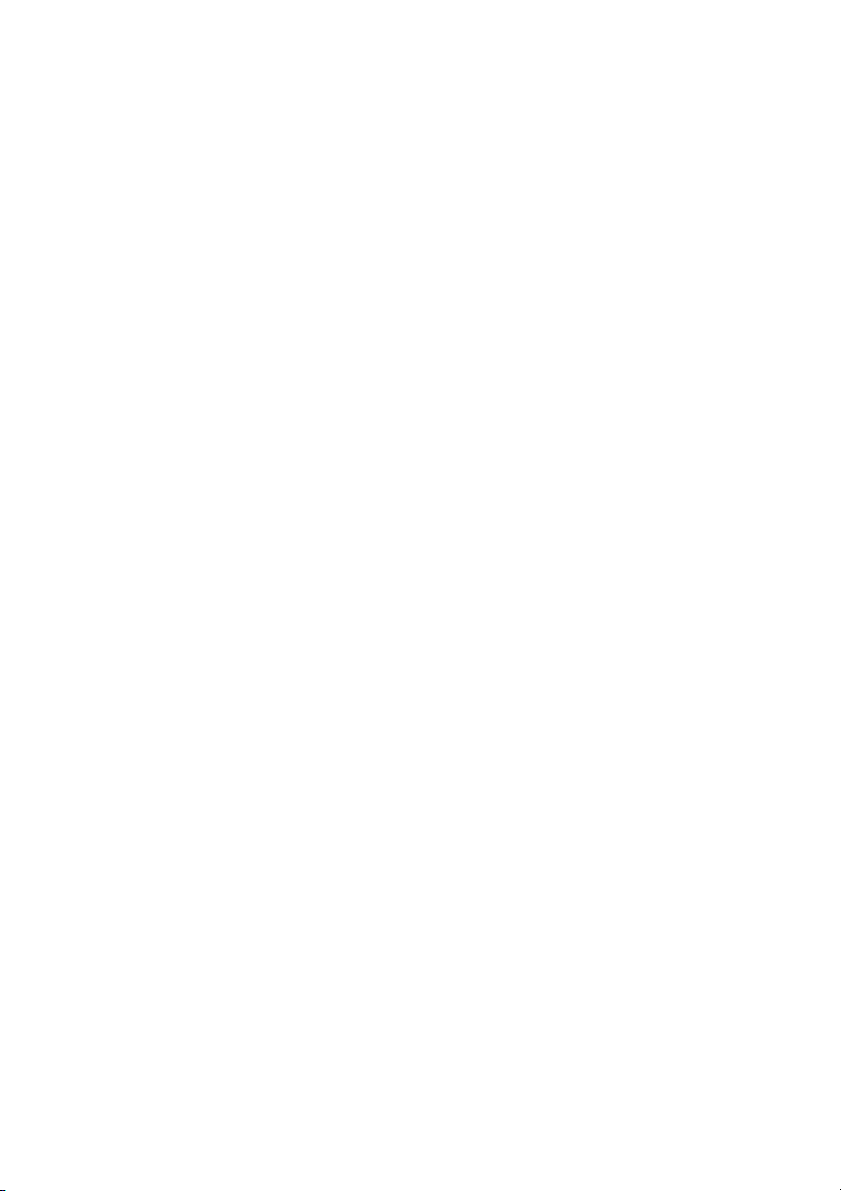
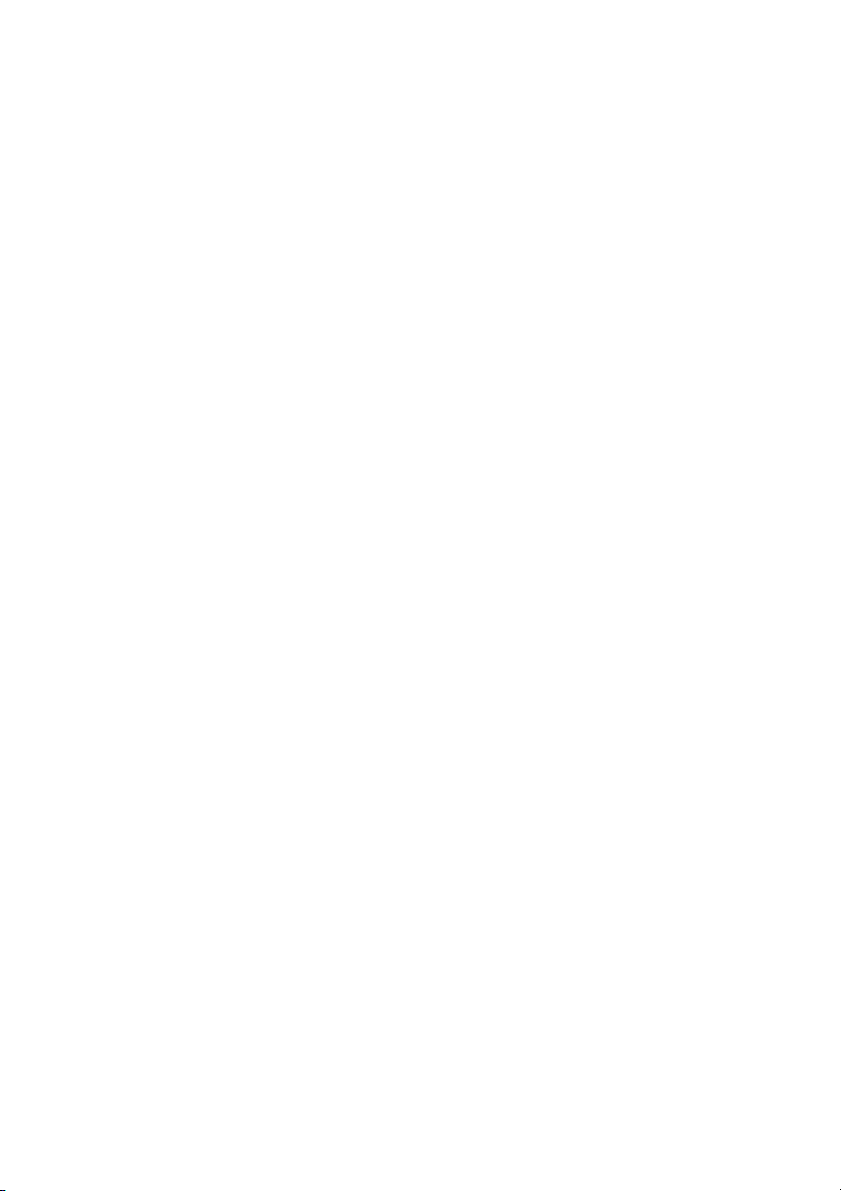
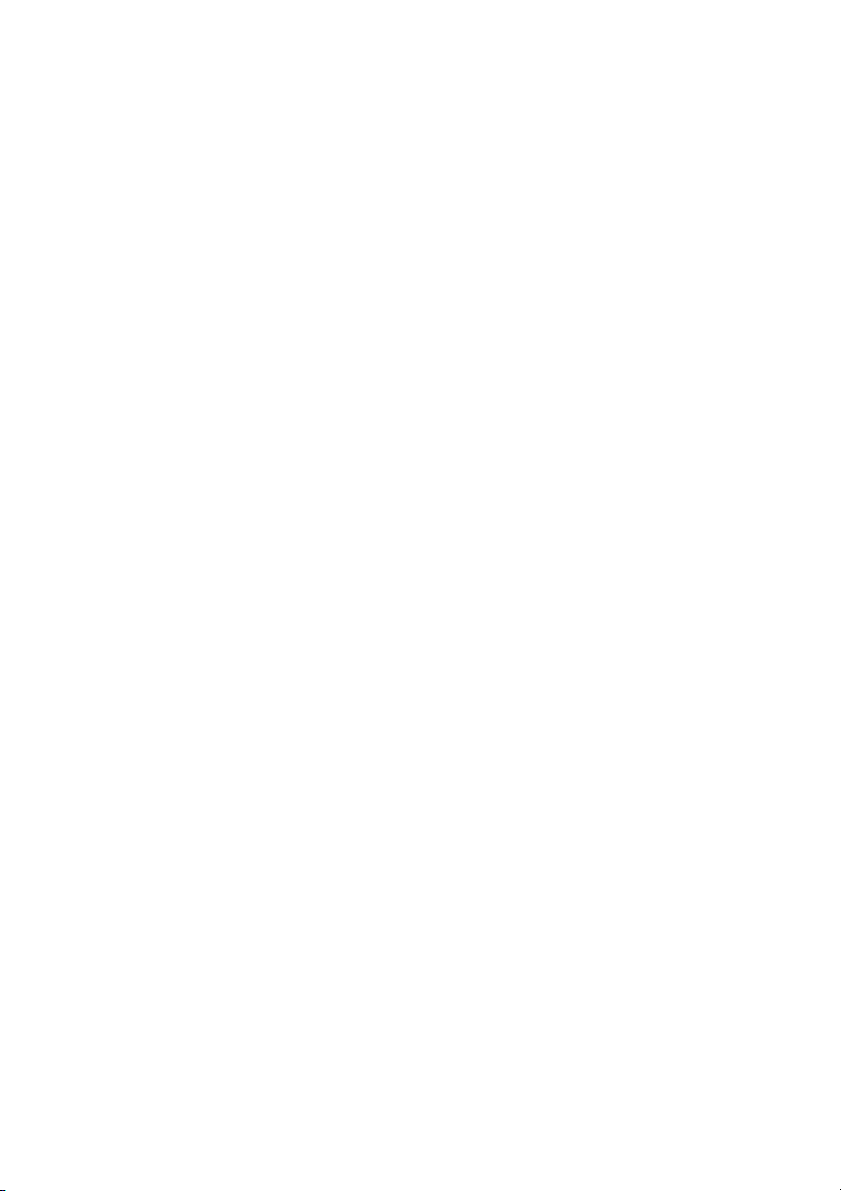
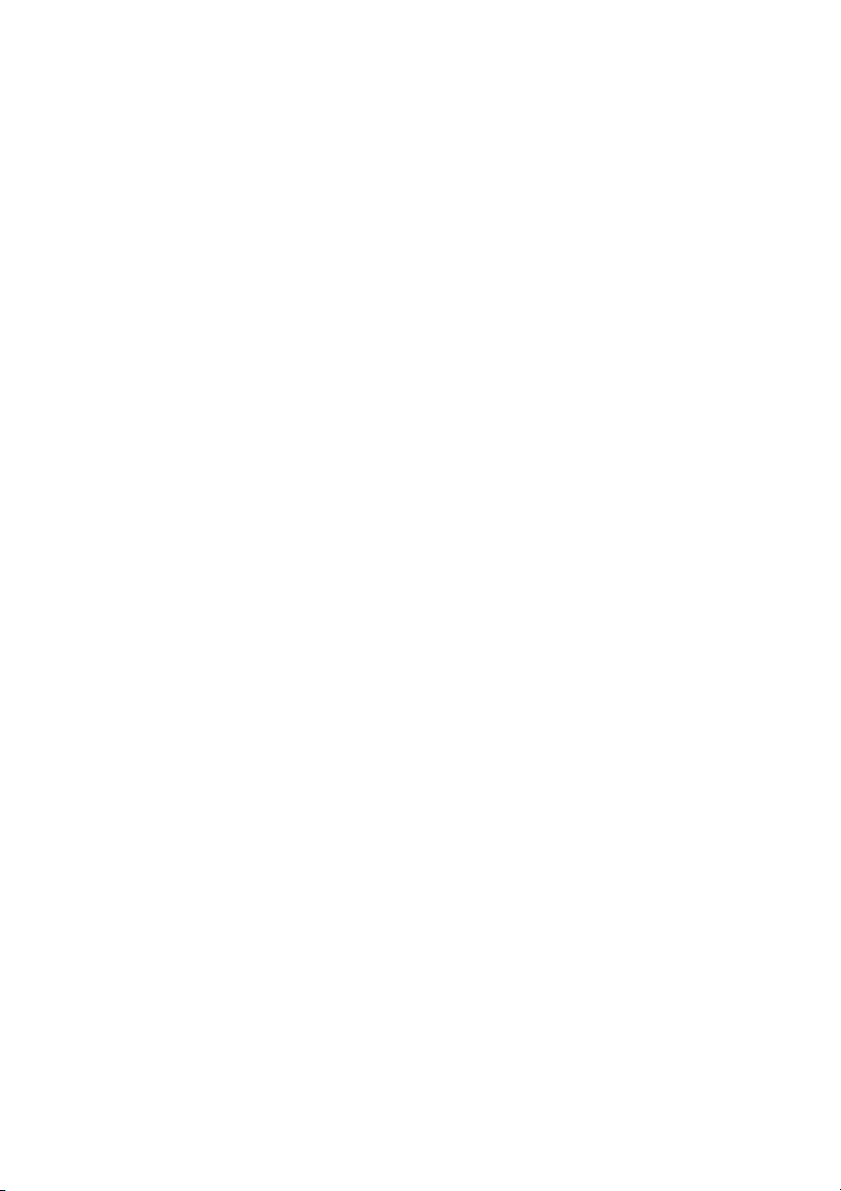
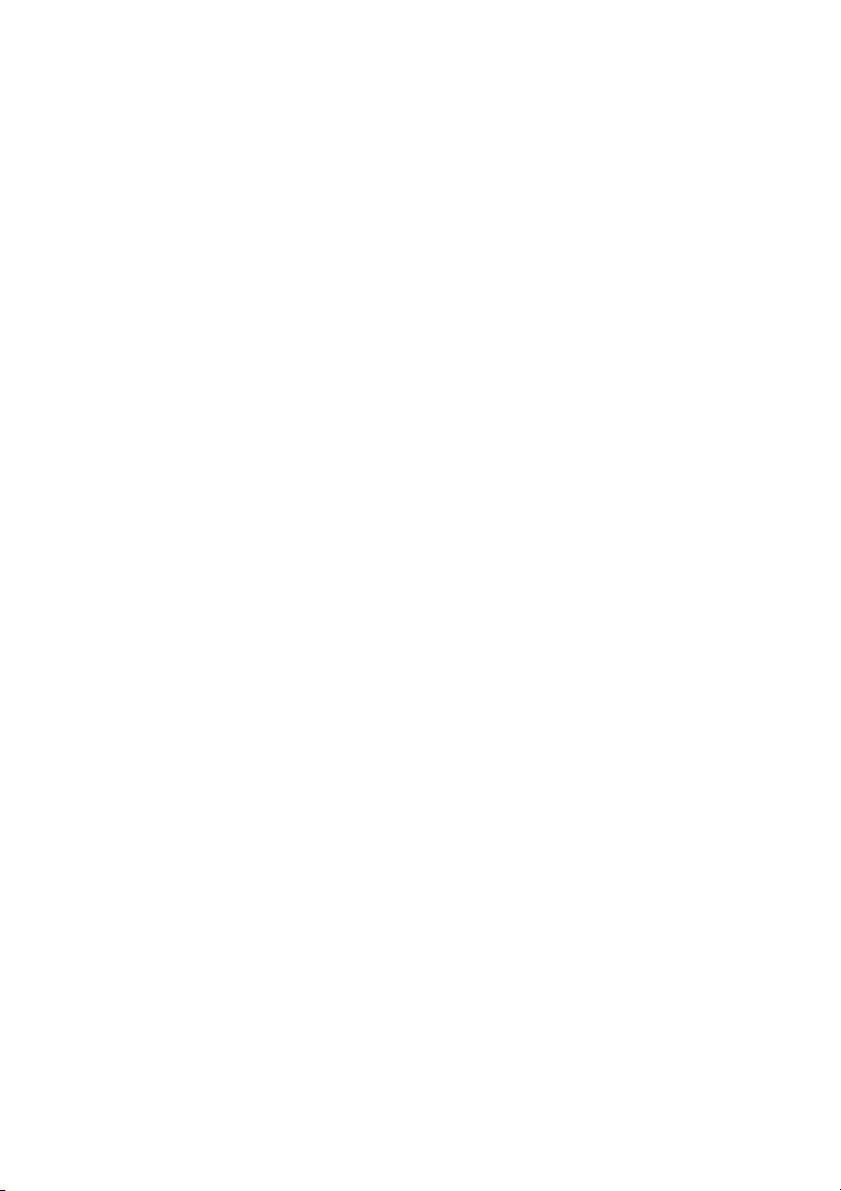
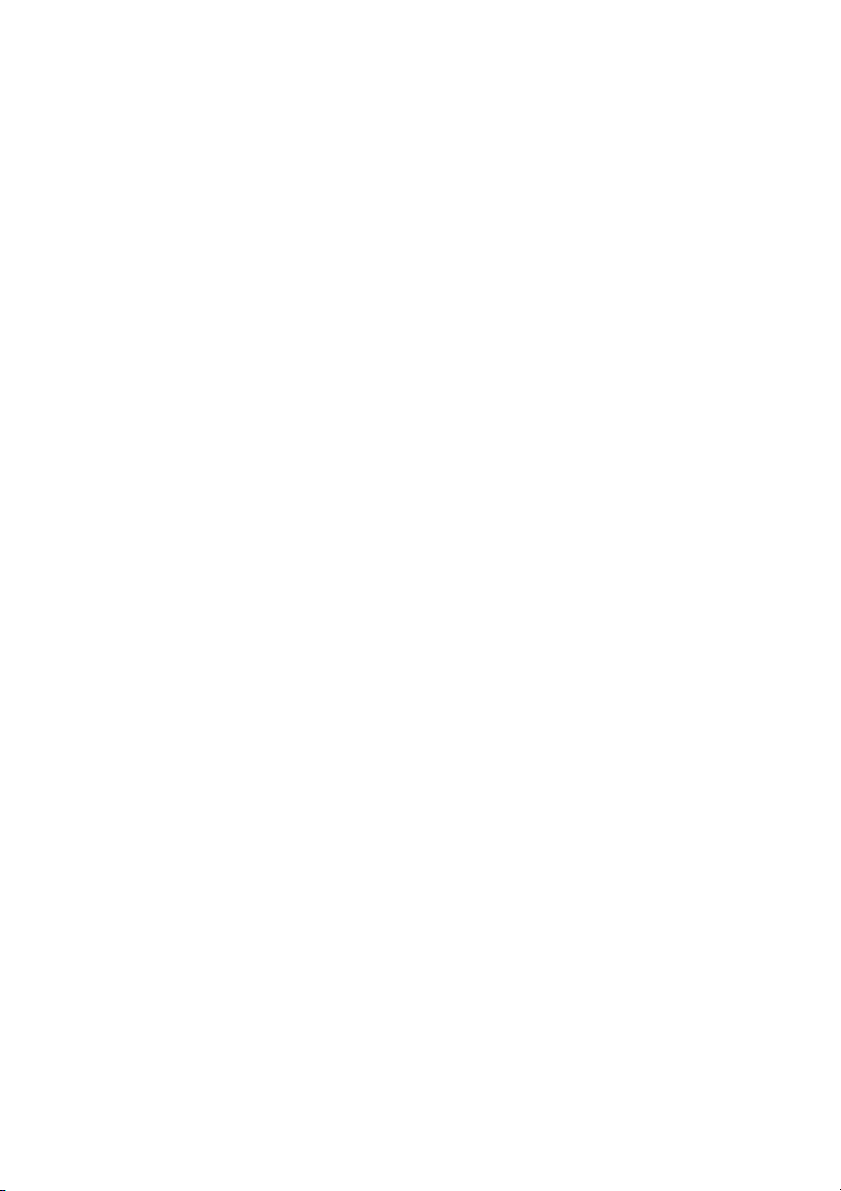
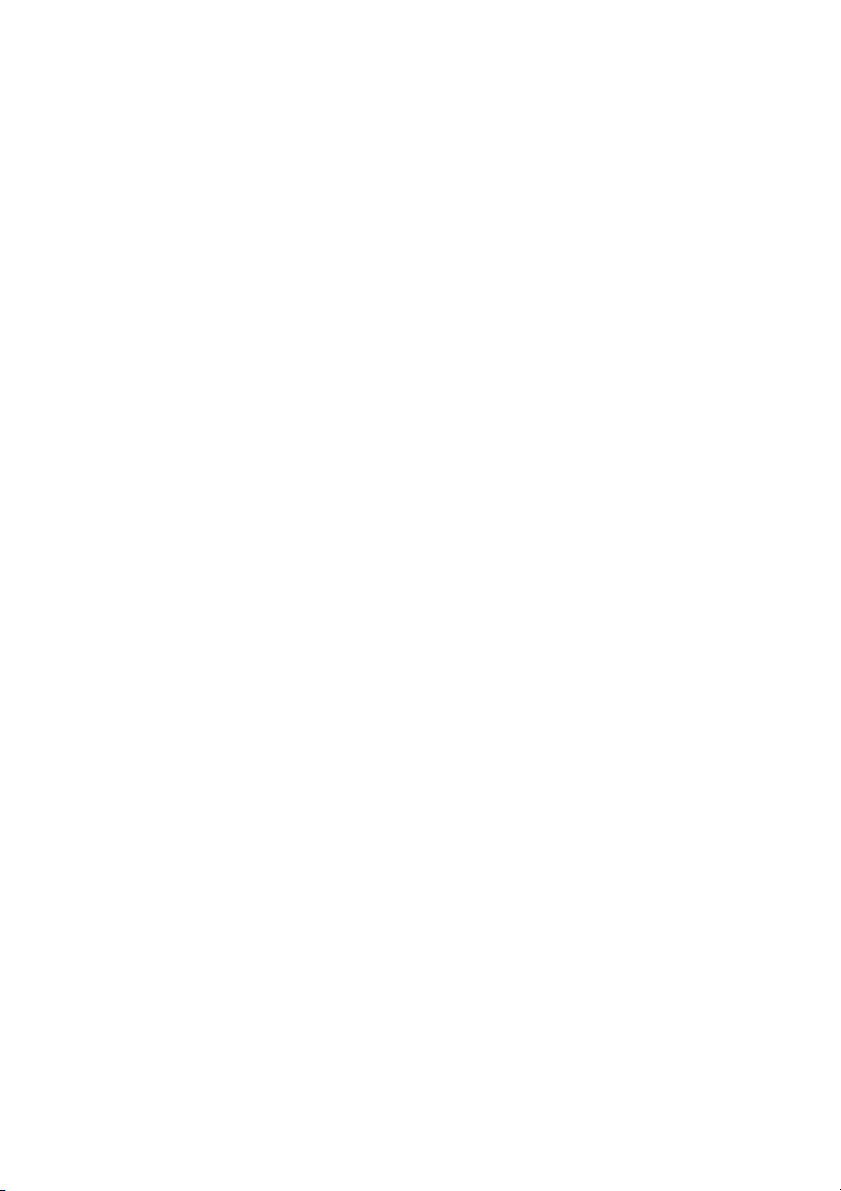
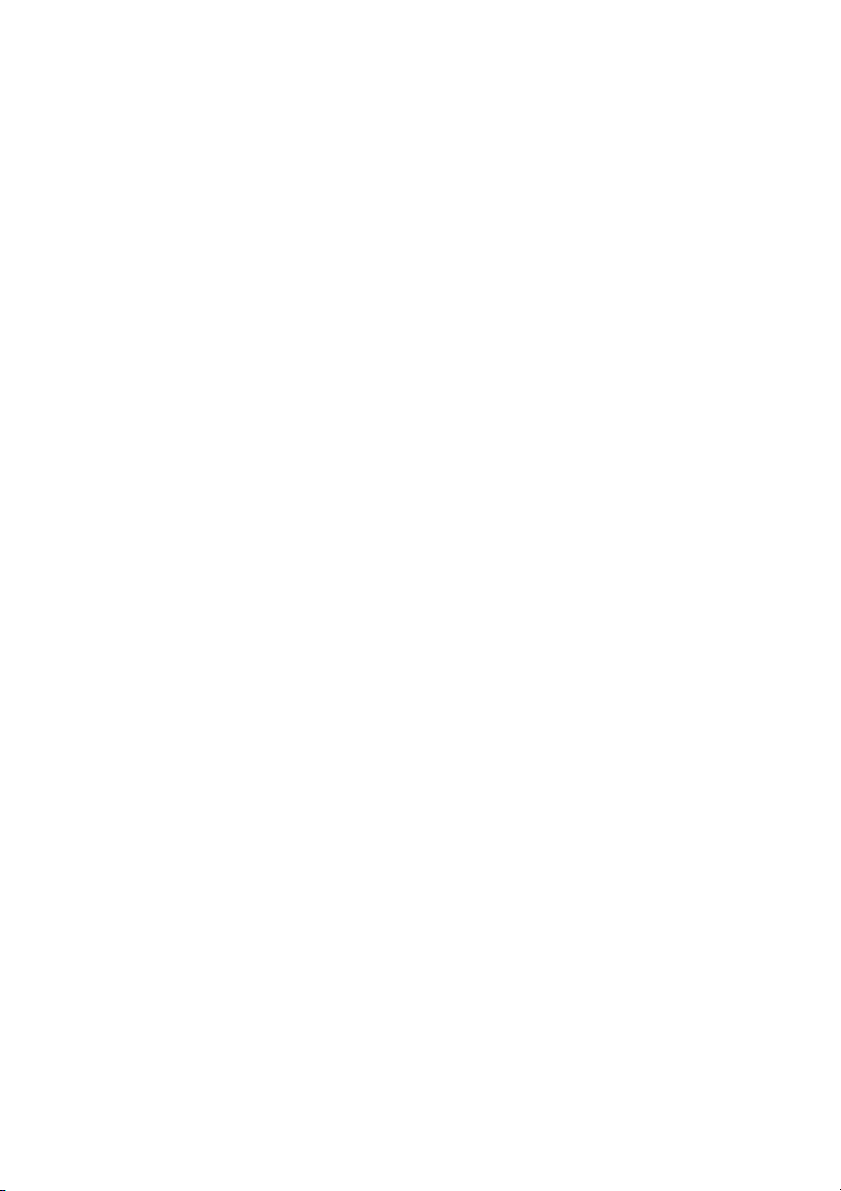
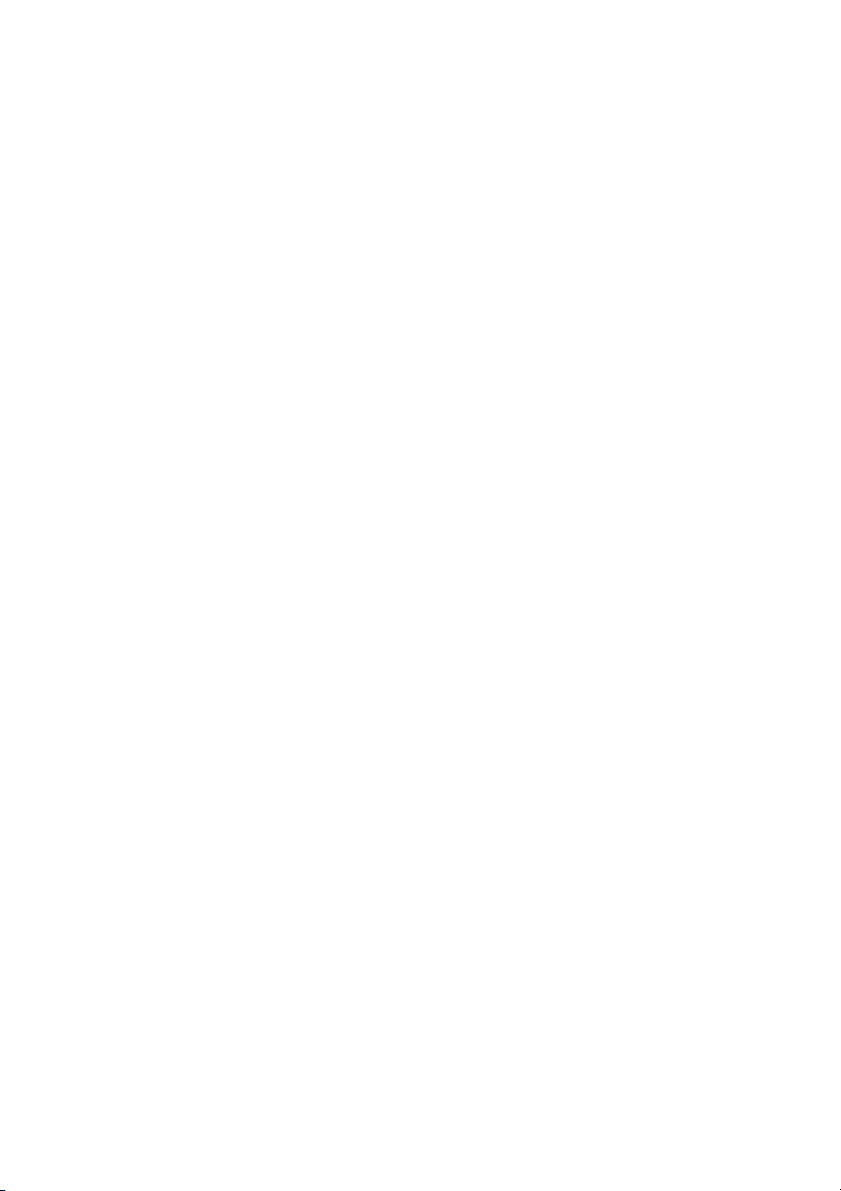
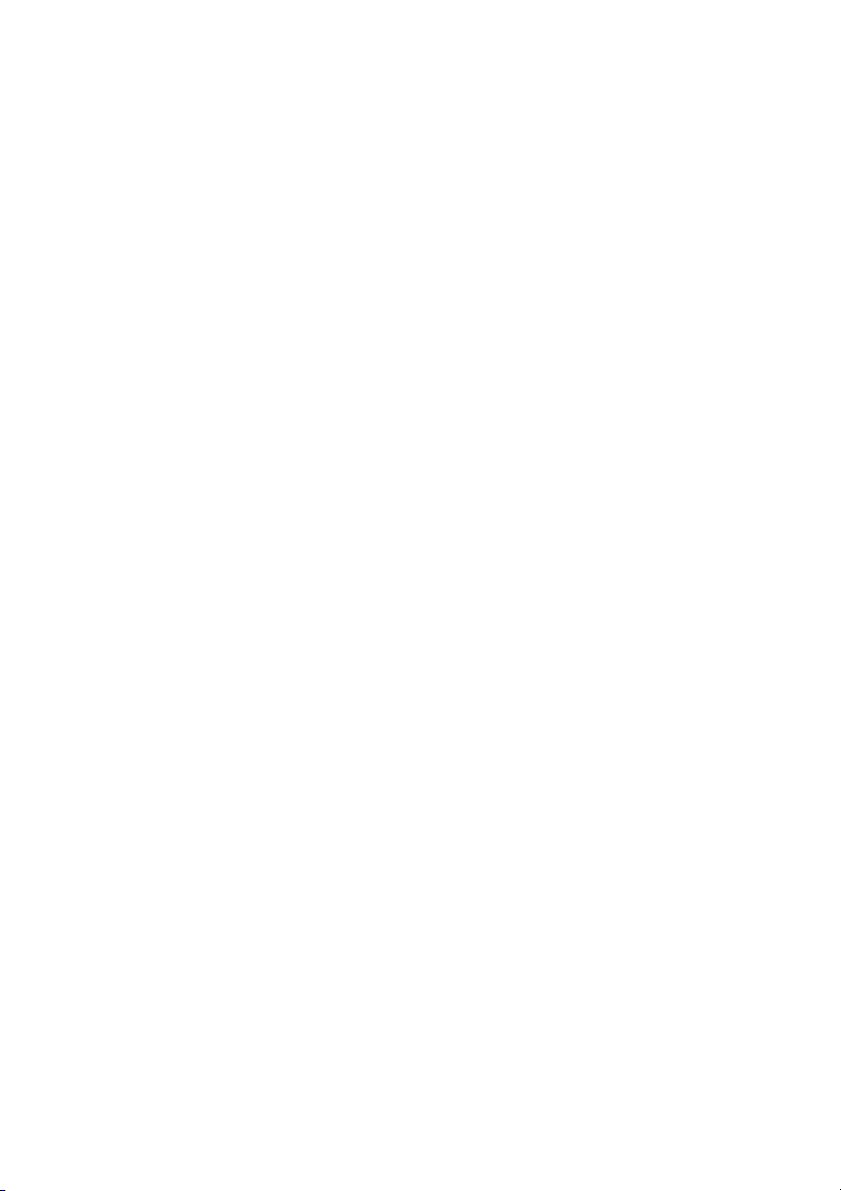
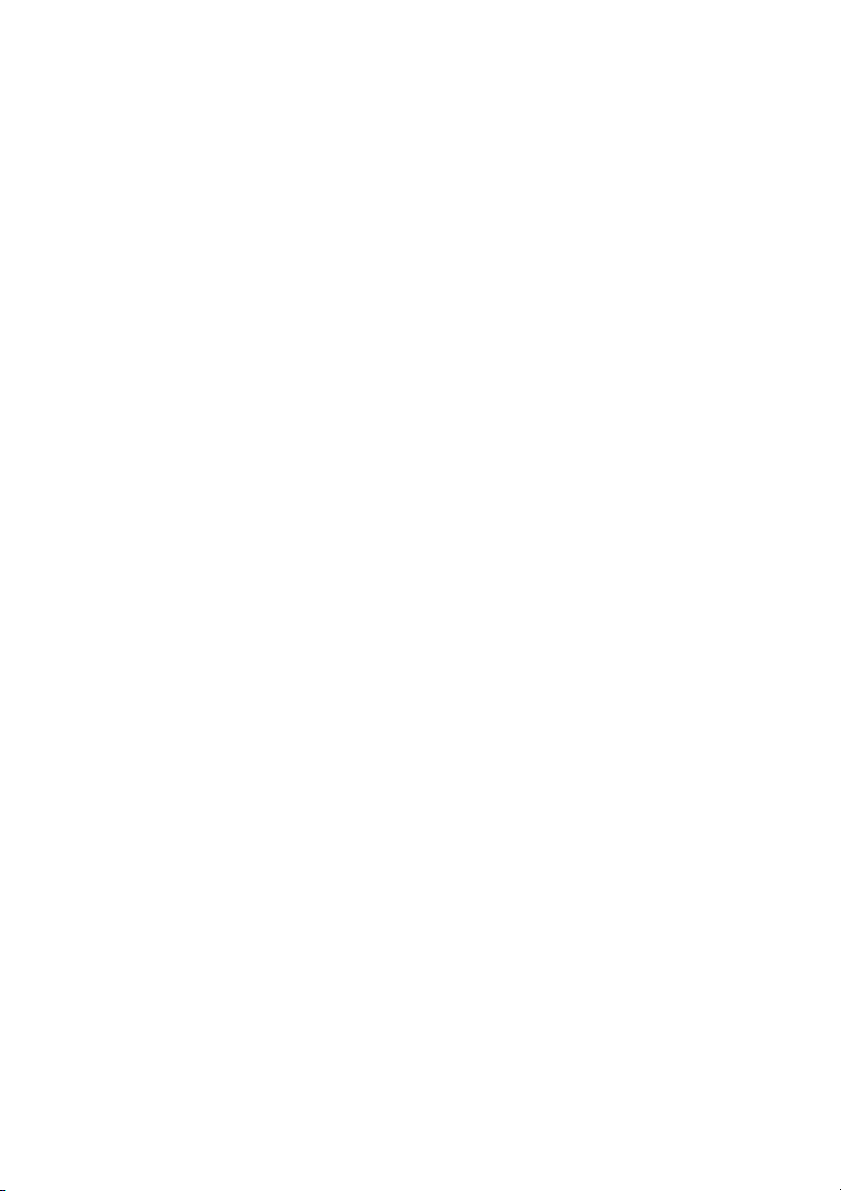
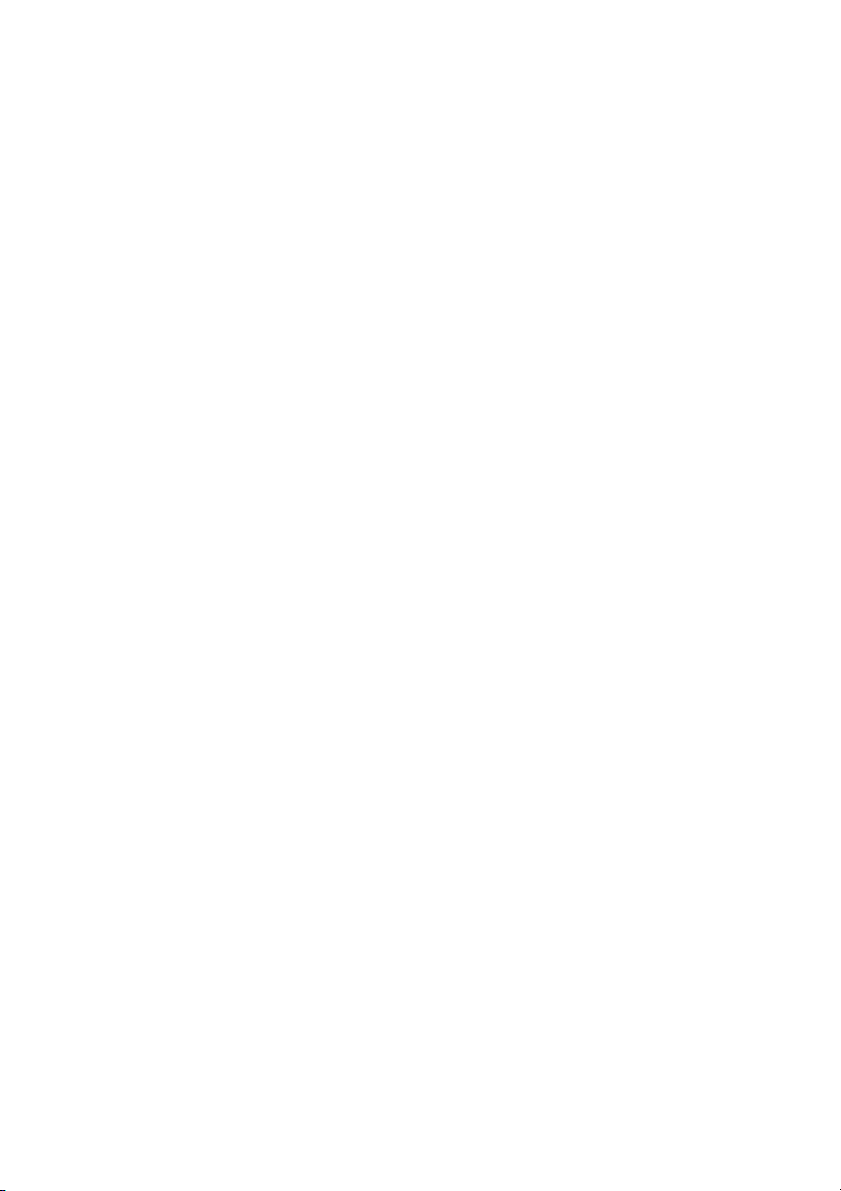
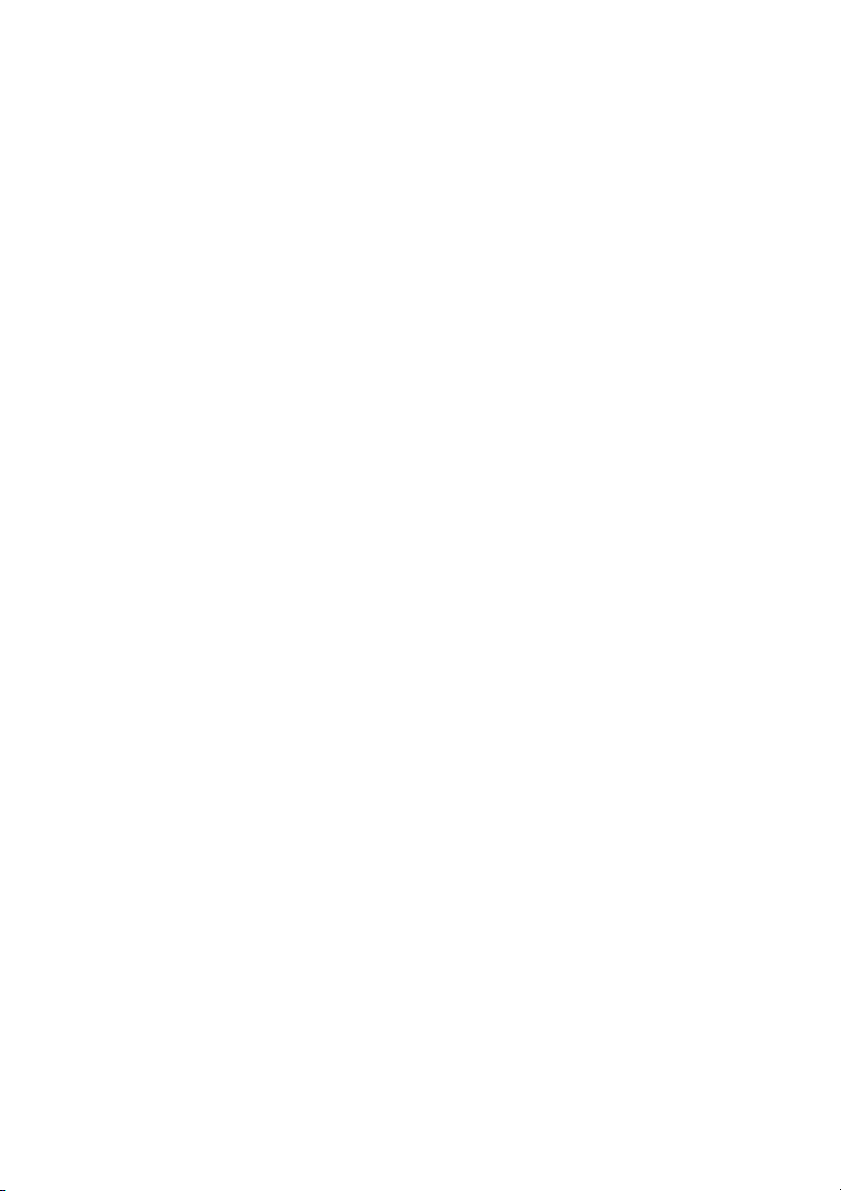
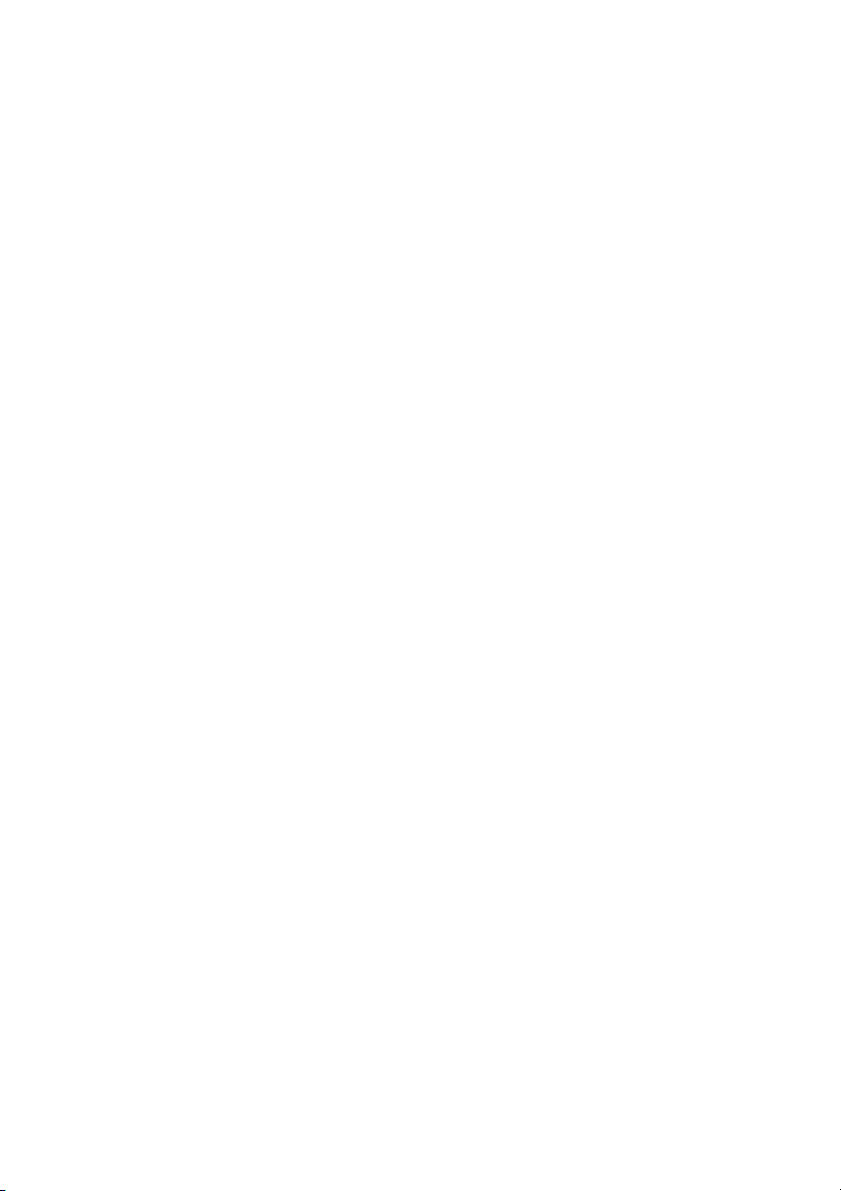
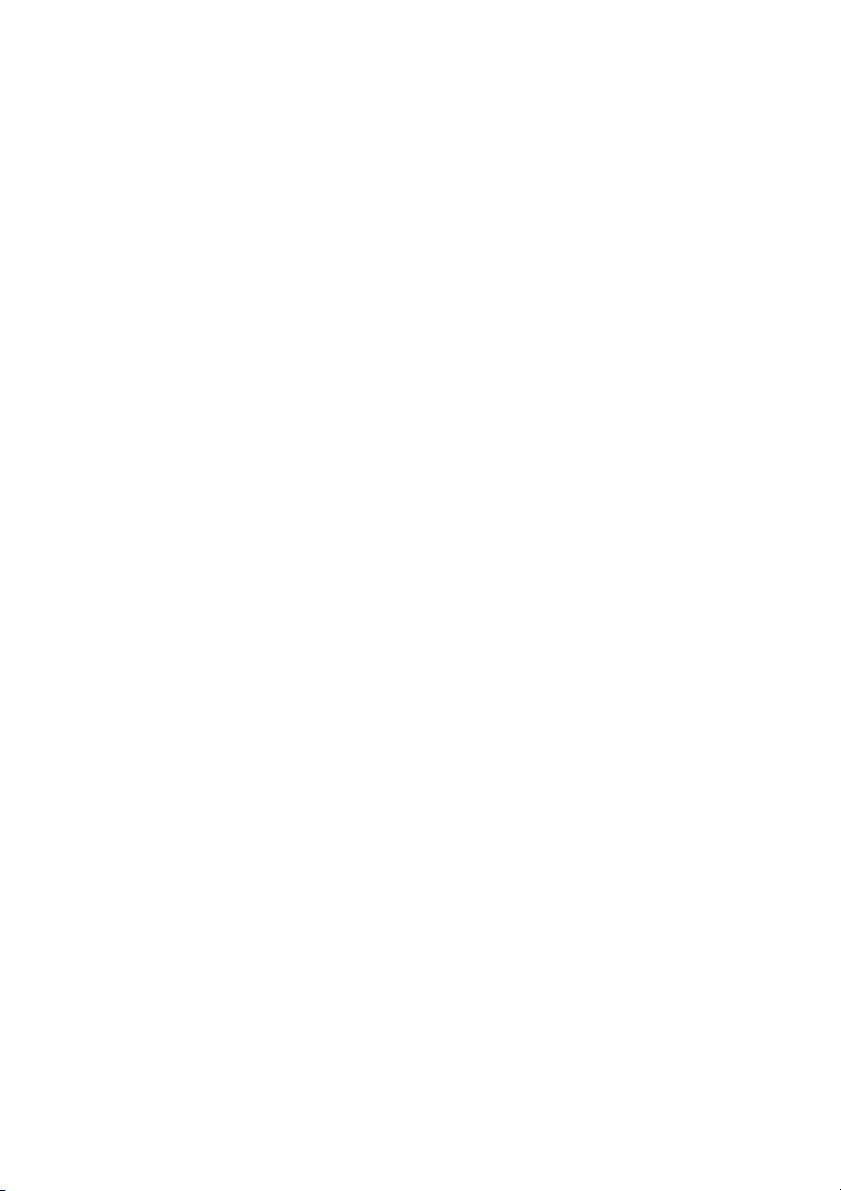
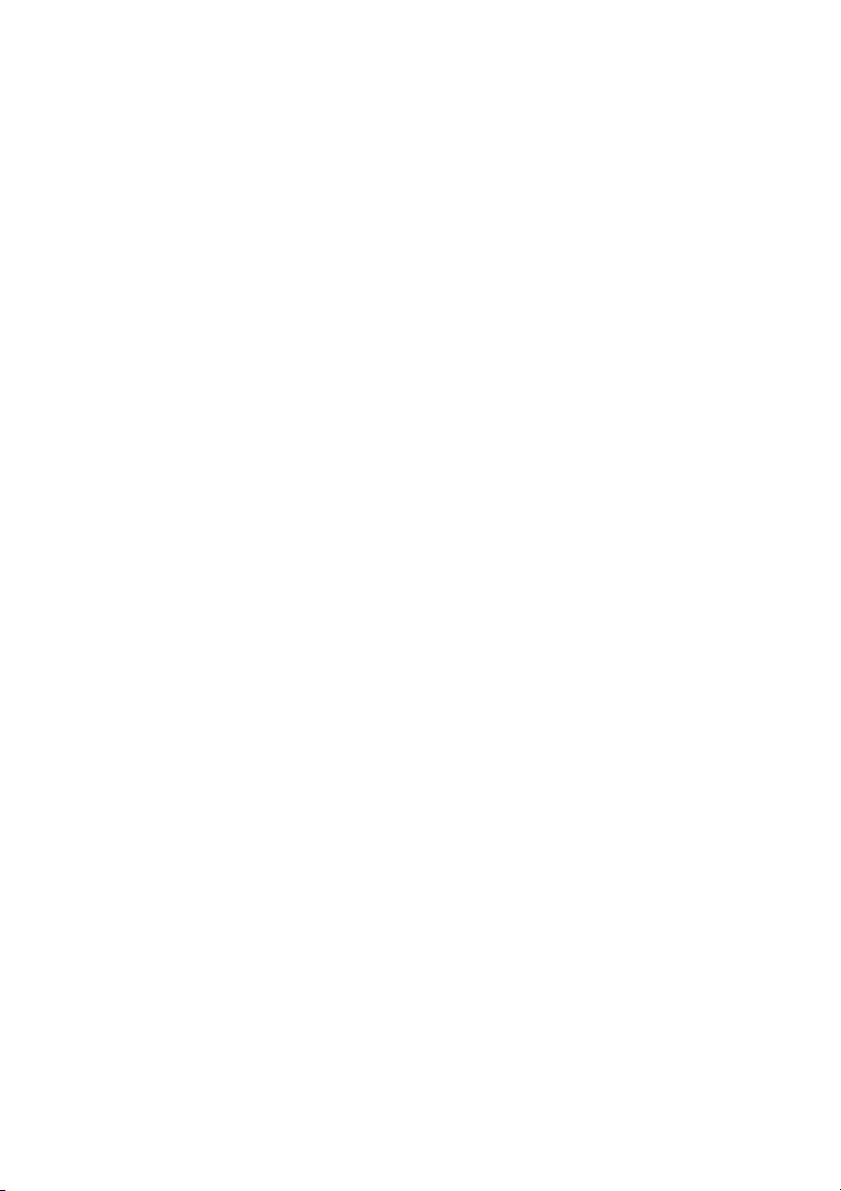
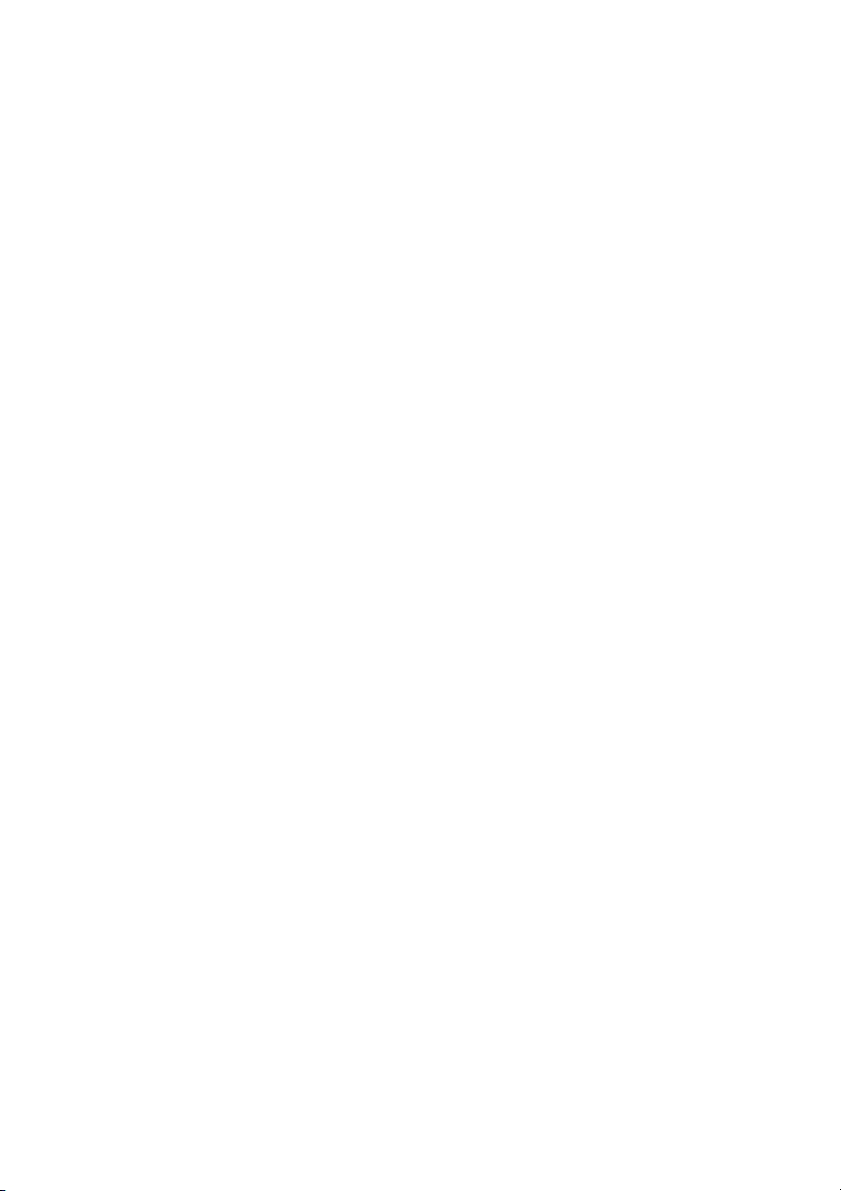
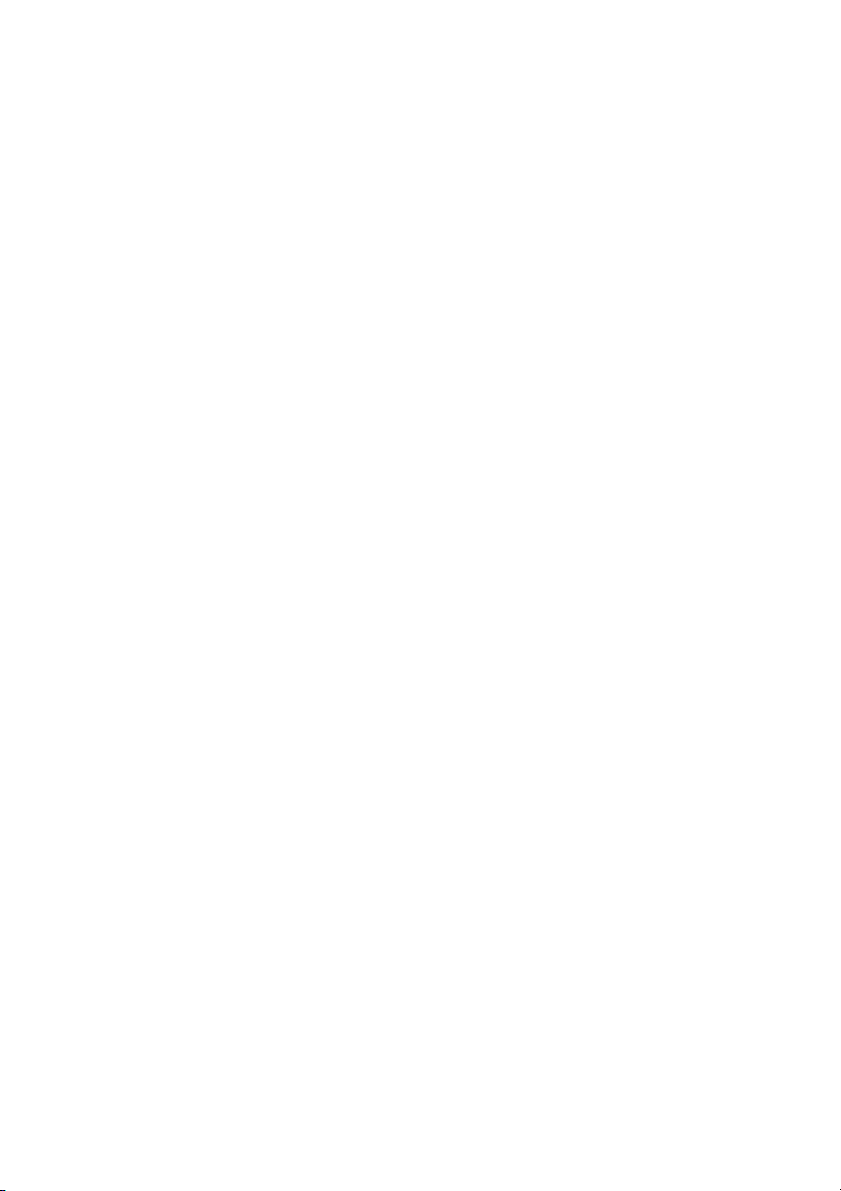
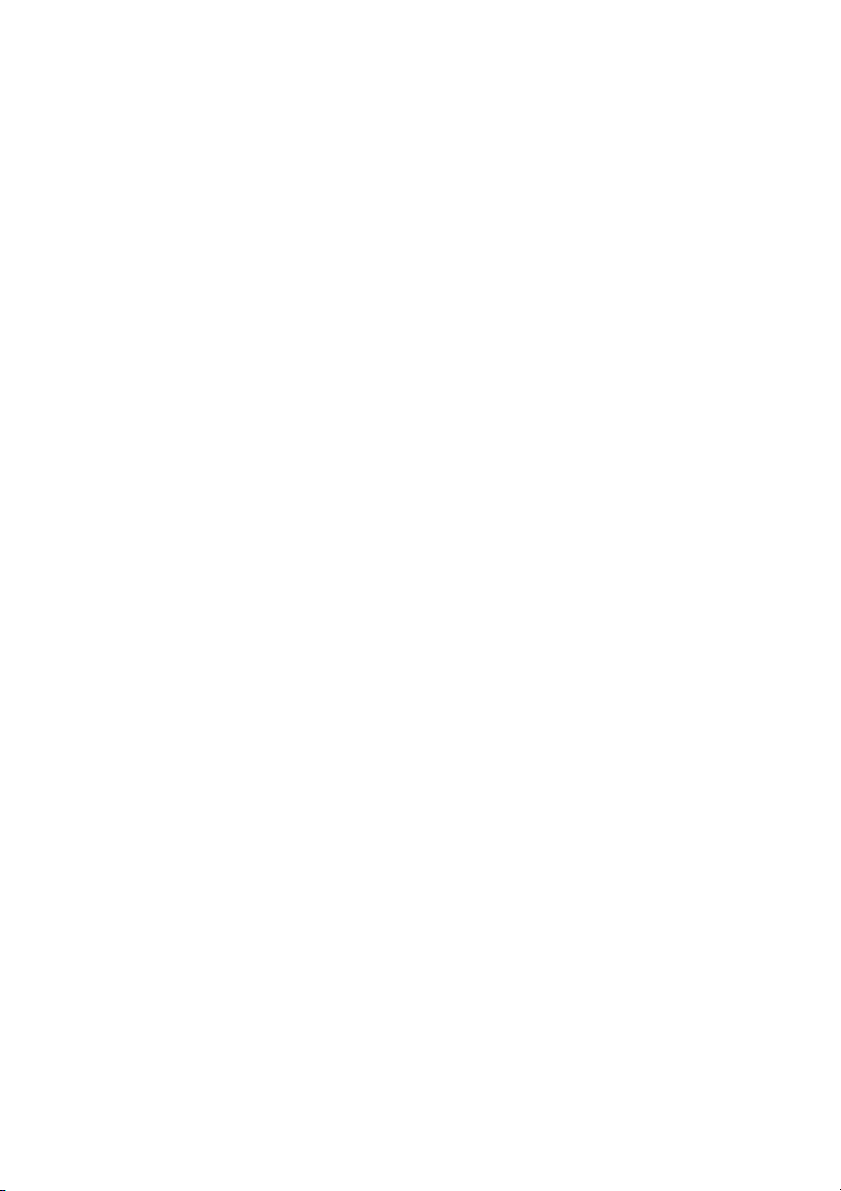
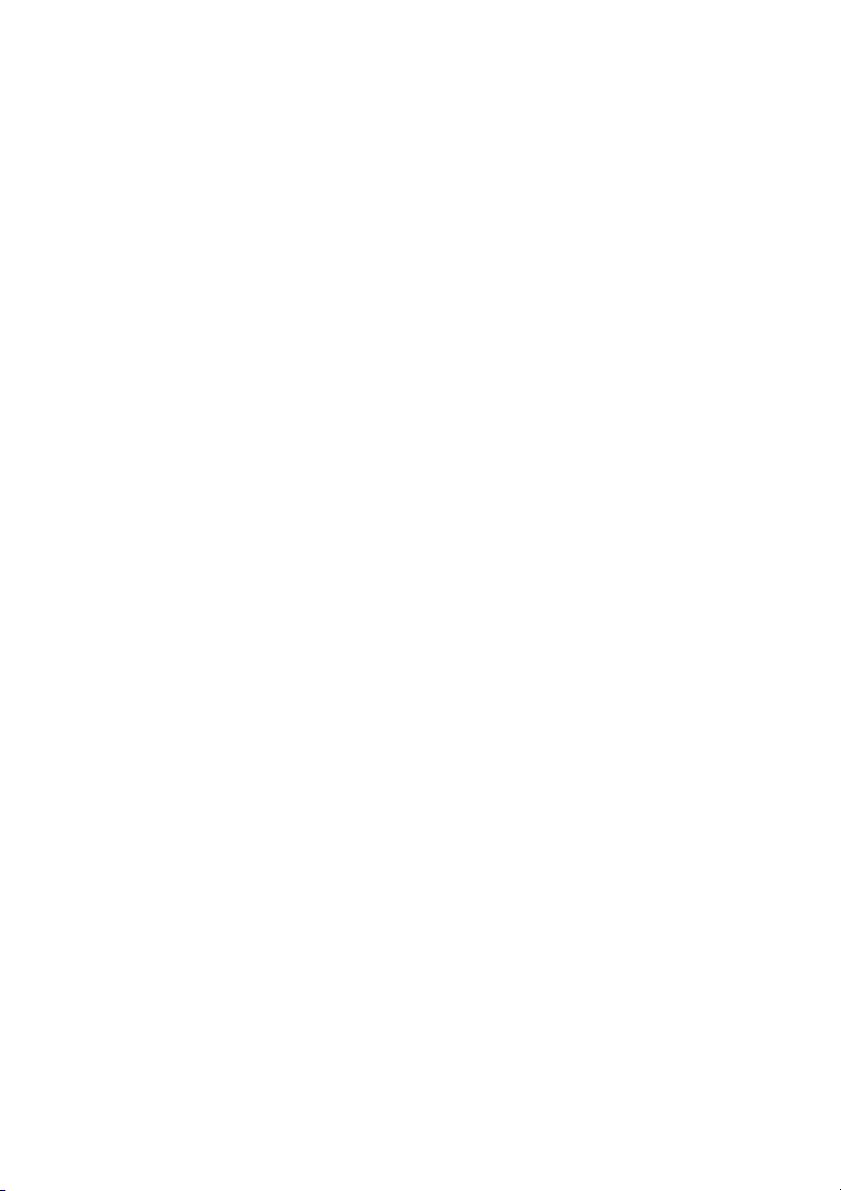
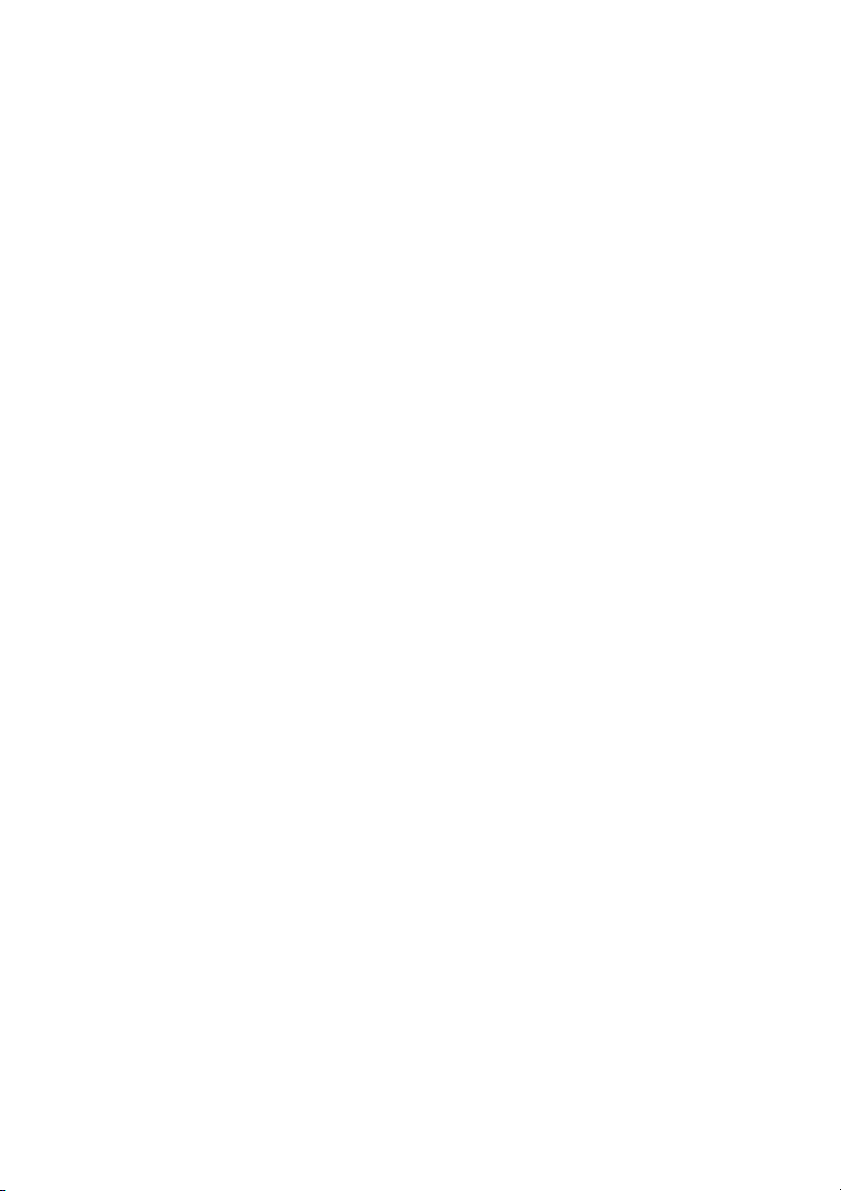
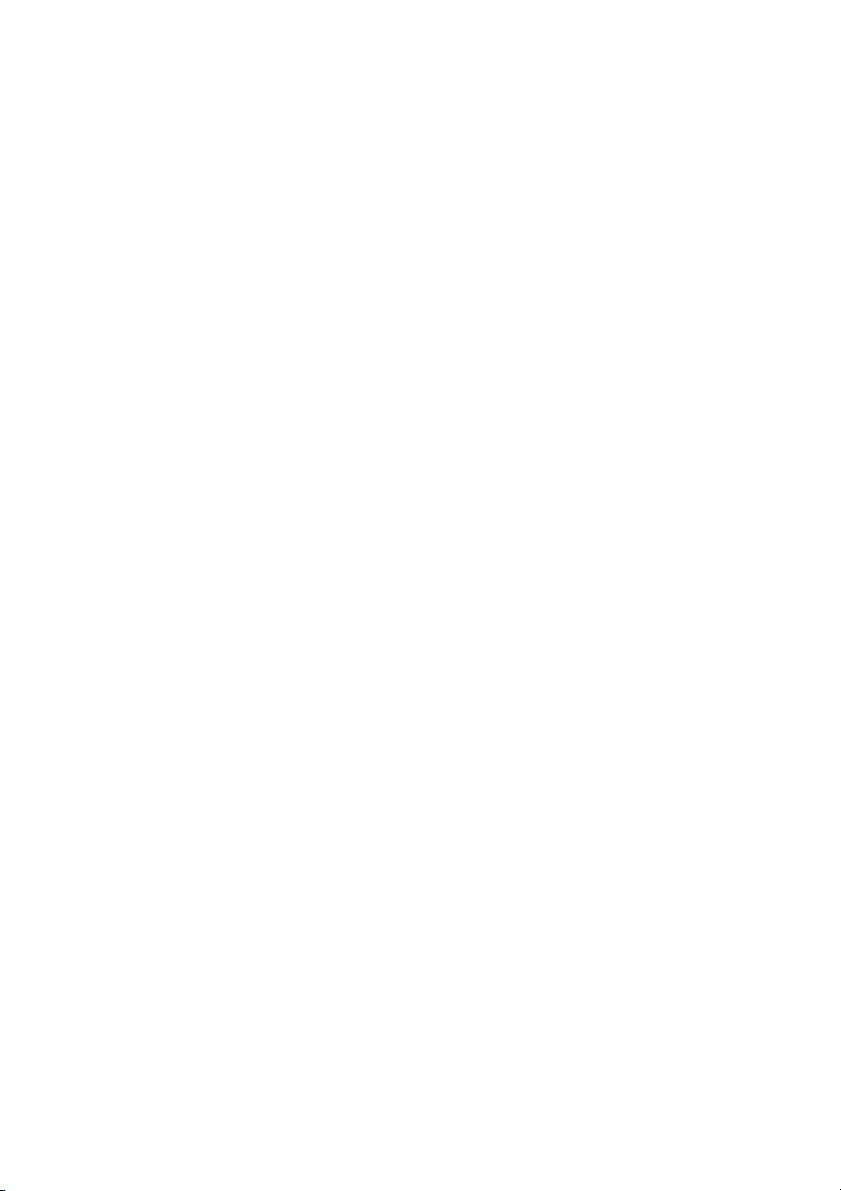
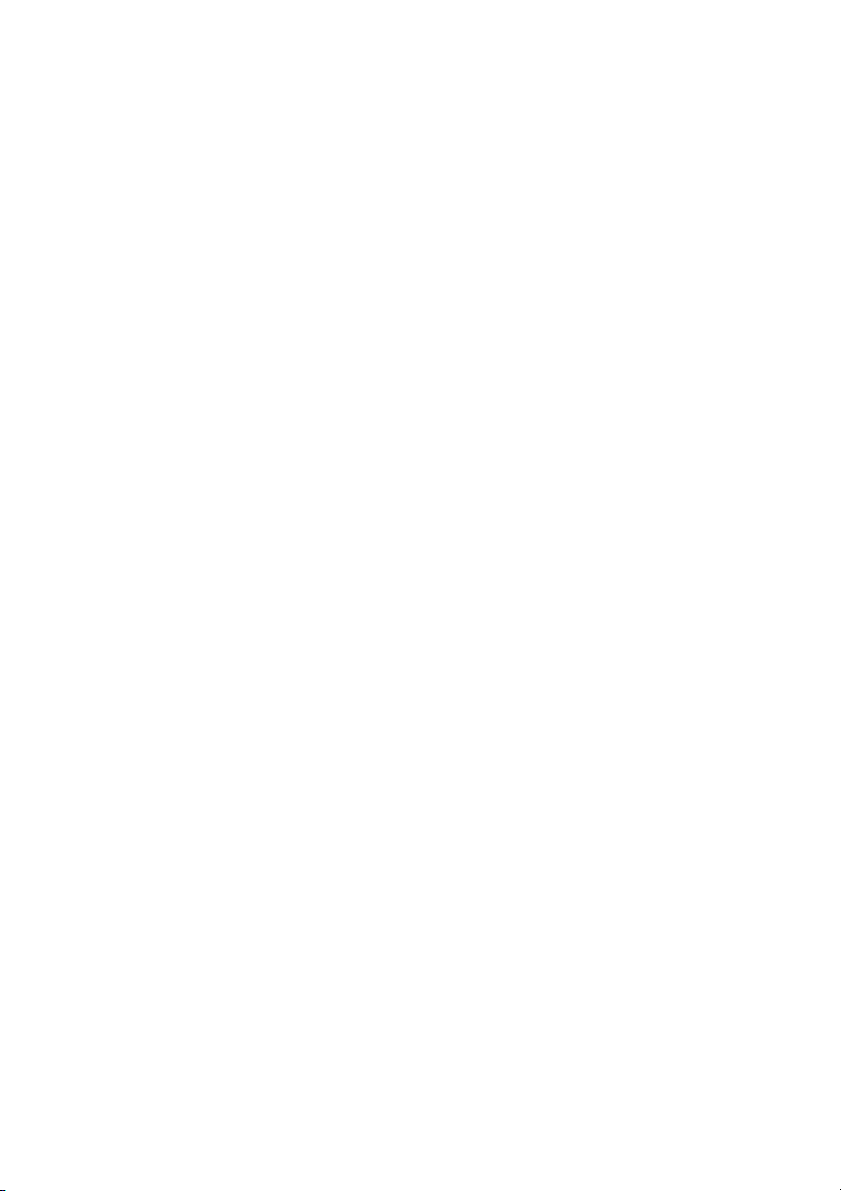
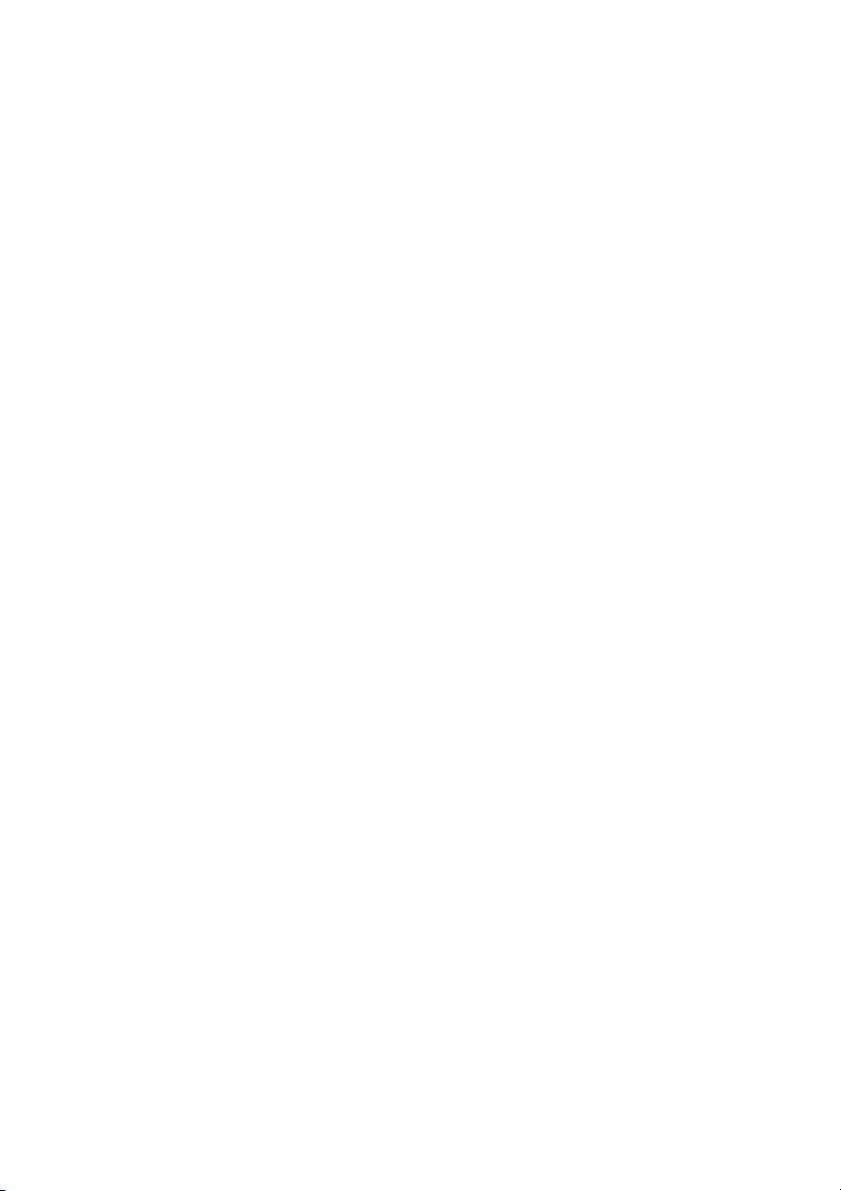
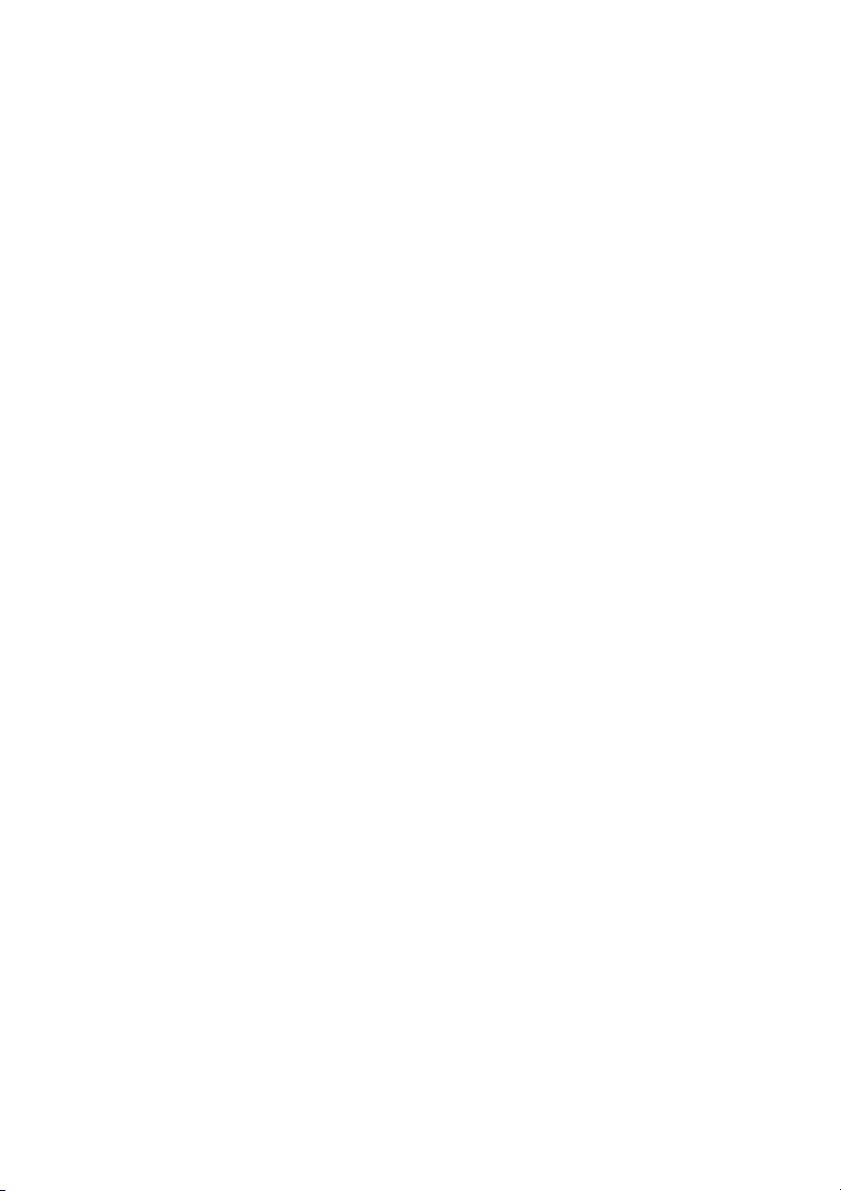
Preview text:
Đồ án tốt nghiệp chuyên ngành Công nghệ chế tạo cơ khí
Ý kiến của giáo viên hướng dẫn :
…………………………………………………………………………………………
……………………………………………………………………………………..…
Hà nội, ngày ….tháng ……năm 2018
Giáo viên hướng dẫn
T.S Trần Thị Vân Nga
Ý kiến của giáo viên đọc duyệt :
…………………………………………………………………………………………
……………………………………………………………………………………..…
Hà nội, ngày ….tháng ……năm 2018
Giáo viên đọc duyệt
……………………………………
Phê duyệt của Trưởng bộ môn đồng ý cho bảo vệ
Hà nội, ngày …...tháng ……năm 2018 Trưởng bộ môn
T.S Trần Thị Vân Nga
Lớp Công nghệ chế tạo cơ khí 55 1
Đồ án tốt nghiệp chuyên ngành Công nghệ chế tạo cơ khí
Lớp Công nghệ chế tạo cơ khí 55 2
Đồ án tốt nghiệp chuyên ngành Công nghệ chế tạo cơ khí MỤC LỤC
MỤC LỤC..................................................................................................................... 2
BẢNG KÊ DANH MỤC CÁC BẢNG BIỂU................................................................3
BẢNG KÊ DANH MỤC CÁC HÌNH VẼ.....................................................................4
LỜI NÓI ĐẦU............................................................................................................... 5
CHƯƠNG 1: PHÂN TÍCH ĐẶC ĐIỂM LÀM VIỆC CỦA CHI TIẾT VÀ CHỌN
PHƯƠNG PHÁP CHẾ TẠO PHÔI...............................................................................6
1.1. Phân tích đặc điểm làm việc và tính công nghệ trong kết cấu của chi tiết........6
1.2. Chọn phương pháp chế tạo phôi.......................................................................9
CHƯƠNG 2: LẬP QUY TRÌNH CÔNG NGHỆ CHẾ TẠO CHI TIẾT......................15
2.1. Các bề mặt được gia công của chi tiết...............................................................15
2.2. Chọn chuẩn định vị...........................................................................................19
2.3. Thiết kế sơ đồ nguyên công..............................................................................22
2.4. Tính toán và chọn lượng dư gia công................................................................37
2.5. Các máy lựa chọn trong quy trình công nghệ....................................................46
2.6. Tính toán chế độ cắt..........................................................................................48
2.7. Bảng quy trình công nghệ.................................................................................88
CHƯƠNG 3: TÍNH TOÁN THIẾT KẾ ĐỒ GÁ CHO NGUYÊN CÔNG KHOAN,
KHOÉT, DOA LỖ 56...............................................................................................90
3.1. Thiết kế nguyên lý định vị và cấu tạo của đồ gá...............................................90
3.2. Tính toán lực kẹp chặt và tính toán đường kính bu lông...................................94
KẾT LUẬN...............................................................................................................103
TÀI LIỆU THAM KHẢO.........................................................................................104
BẢNG KÊ DANH MỤC CÁC BẢNG BIỂ
Lớp Công nghệ chế tạo cơ khí 55 3
Đồ án tốt nghiệp chuyên ngành Công nghệ chế tạo cơ khí
Bảng 2. 1: Bảng liệt kê các bề mặt được gia công.......................................................18
Bảng 2. 2: Bảng sơ đồ nguyên công.............................................................................24
Bảng 2. 3: Thông số công nghệ....................................................................................43
Bảng 2. 4: Tra lượng dư cho các bề mặt còn lại...........................................................44
Bảng 2. 5: Thông số chế độ cắt....................................................................................49
Bảng 2. 6: Thông số chế độ cắt....................................................................................51
Bảng 2. 7: Thông số chế độ cắt....................................................................................78
Bảng 2. 8: Thông số chế độ cắt....................................................................................79
Bảng 2. 9: Thông số dao..............................................................................................80
Bảng 2. 10: Thông số tính vận tốc...............................................................................81
Bảng 2. 11: Thông số tính Momen...............................................................................82
Bảng 2. 12: Thông số tính lực cắt................................................................................82
Bảng 2. 13: Thông số tính vận tốc...............................................................................83
Bảng 2. 14: Thông số tính Momen...............................................................................84
Bảng 2. 15: Thông số tính lực cắt................................................................................84
Bảng 2. 16: Thông số tính vận tốc...............................................................................85
Bảng 2. 17: Thông số tính vận tốc...............................................................................86
Bảng 2.18. Thông số chế độ cắt...................................................................................88
Bảng 2.19. Thông số tính lực.......................................................................................88
Bảng 2.20. Thông số chế độ cắt...................................................................................89
Bảng 2.21. Thông số chế độ cắt...................................................................................89
Bảng 2. 22: Bảng quy trình công nghệ......................................................................90Y
BẢNG KÊ DANH MỤC CÁC HÌNH VẼ.
Hình 1. 1: Bản vẽ chi tiết...............................................................................................8
Lớp Công nghệ chế tạo cơ khí 55 4
Đồ án tốt nghiệp chuyên ngành Công nghệ chế tạo cơ khí
Hình 1. 2: Bản vẽ lắp.....................................................................................................8
Hình 1. 3: Bản vẽ liệt kê các bề mặt cần gia công..........................................................9
Hình 2. 1: Chọn chuẩn tinh..........................................................................................19
Hình 2. 2: Chọn chuẩn thô...........................................................................................21
Hình 2. 3: Độ lệch tâm.................................................................................................37
Hình 2. 4: Bản vẽ phôi lồng.........................................................................................44
Hình 3. 1: Sơ đồ nguyên công 9...................................................................................90
Hình 3. 2: Bản vẽ đồ gá...............................................................................................93
Hình 3. 3: Sơ đồ momen lực........................................................................................95
Hình 3. 4: Sơ đồ momen lực TH1................................................................................96
Hình 3. 5: Sơ đồ momen lực TH2................................................................................98
Hình 3. 6: Sơ đồ momen lực TH3..............................................................................100
Lớp Công nghệ chế tạo cơ khí 55 5
Đồ án tốt nghiệp chuyên ngành Công nghệ chế tạo cơ khí LỜI NÓI ĐẦU
Trong sự nghiệp công nghiệp hóa, hiện đại hóa đất nước, ngành cơ khí chế tạo
máy đóng vai trò quan trọng. Nó trực tiếp chế tạo ra máy móc phục vụ cho các ngành
nông nghiệp, công nghiệp, giao thông vận tải … Ngày nay, theo xu hướng phát triển
mạnh mẽ của nền kinh tế, cơ khí chế tạo máy đã và đang có những bước tiến đáng kể.
Nhiều sản phẩm cơ khí được tạo ra để thay thế dần hàng nhập ngoại góp phần chủ
động vật tư thiết bị cho sản xuất trong nước.
Trong quá trình chế tạo chi tiết máy, quá trình lập quy trình công nghệ chế tạo chi
tiết là giai đoạn chuẩn bị sản xuất và có vài trò quan trọng ảnh hưởng lớn đến chất
lượng sản phẩm. Chính vì vậy, kiến thức về lập quy trình công nghệ chế tạo chi tiết
máy là rất cần thiết đối với các kỹ sư công nghệ chế tạo.
Xuất phát từ đó, em thực hiện đề tài : “NGHIÊN CỨU LẬP QUY TRÌNH CÔNG
NGHỆ CHẾ TẠO CHI TIẾT VỎ BƠM 207.20, TÍNH TOÁN, THIẾT KẾ, LẬP QUY
TRÌNH LẮP RÁP ĐỒ GÁ KHOAN, KHOÉT DOA LỖ Φ56 ”.
Nội dung đồ án gồm 3 chương.
Chương 1: Phân tích chức năng làm việc của chi tiết.
Chương 2: Lập quy trình công nghệ gia công chi tiết thân vỏ bơm.
Chương 3: Tính toán, thiết kế đồ gá khoét, doa lỗ Φ56.
Em xin cảm ơn sự giúp đỡ, hướng dẫn tận tình của T.S Trần Thị Vân Nga và các
thầy cô trong bộ môn Công nghệ giao thông đã giúp em hoàn thành đồ án tốt nghiệp này.
Trong quá trình làm đề đề tài, do trình độ kiến thức, kinh nghiệm có hạn nên trong
nội dung trình bày không tránh khỏi những sai sót, mong nhận được sự góp ý của quý
thầy cô để bài làm được hoàn thiện hơn.
Em xin chân thành cảm ơn!
Ngày 14 tháng 12 năm 2018
Sinh viên thực hiện Nguyễn Thị Sinh
Lớp Công nghệ chế tạo cơ khí 55 6
Đồ án tốt nghiệp chuyên ngành Công nghệ chế tạo cơ khí
CHƯƠNG 1: PHÂN TÍCH ĐẶC ĐIỂM LÀM VIỆC CỦA CHI
TIẾT VÀ CHỌN PHƯƠNG PHÁP CHẾ TẠO PHÔI 1.1.
Phân tích đặc điểm làm việc và tính công nghệ trong kết cấu của chi tiết.
Qua bản vẽ chi tiết hình 1.1, bản vẽ lắp hình 1.2 và bản vẽ liệt kê các bề mặt cần gia công hình 1.3 ta thấy:
- Chi tiết gia công vỏ bơm là một bộ phận của bơm thủy lực hướng trục 207.20.
Vỏ bơm dùng để đỡ các chi tiết khác trong máy bơm, giúp các chi tiết khác của bơm làm việc ổn định.
- Chi tiết có thể xếp vào chi tiết dạng hộp, kết cấu gồm 2 lỗ để lắp nút bơm. Một
đầu là lỗ Φ100 để lắp trục chính của bơm với các ổ bi đỡ chặn. Một đầu để lắp với thân bơm dưới.
- Chi tiết có 2 bề mặt làm việc chính là bề mặt lỗ Φ100 có độ chính xác cao, cấp
7 nên khi gia công cần đảm bảo yêu cầu và bề mặt D nắp nút bơm.
- Chi tiết được làm bằng Gang xám GX 15-32 nên có độ cứng vững cao, không
bị biến dang trong quá trình gia công.
- Khi gia công các lỗ trên bề mặt 10 có các gân tăng cứng nên việc thoát dao và
ăn dao trở nên khó khăn hơn và các lỗ có dạng bậc nên khó khăn trong quá trình gia công.
- Các lỗ bề mặt D không thể gia công xuyên suốt được do bị vướng bề mặt 6 .
Nên khi thực hiện gia công lỗ bề mặt D sau khi gia công xong 1 lỗ ta phải đổi
đầu để gia công lỗ còn lại.
- Vỏ bơm là một chi tiết dạng hộp, kết cấu của chi tiết gồm 1 đầu là lỗ để lắp với
trục chính và các ổ bi đỡ chặn. Một đầu còn lại là có các lỗ lắp ghép để lắp ghép với thân sau của bơm.
- Bên cạnh là 2 lỗ, mặt đầu 2 lỗ có các lỗ để lắp với chi tiết nút bơm đường dầu vào và đường dầu ra.
- Chi tiết có các gân tăng cứng để tăng độ cứng vững cho chi tiết.
Lớp Công nghệ chế tạo cơ khí 55 7
Đồ án tốt nghiệp chuyên ngành Công nghệ chế tạo cơ khí
Lớp Công nghệ chế tạo cơ khí 55 8
Đồ án tốt nghiệp chuyên ngành Công nghệ chế tạo cơ khí
Hình 1. 1: Bản vẽ chi tiết
Hình 1. 2: Bản vẽ lắp
Lớp Công nghệ chế tạo cơ khí 55 9
Đồ án tốt nghiệp chuyên ngành Công nghệ chế tạo cơ khí
Lớp Công nghệ chế tạo cơ khí 55 10
Đồ án tốt nghiệp chuyên ngành Công nghệ chế tạo cơ khí
Hình 1. 3: Bản vẽ liệt kê các bề mặt cần gia công
Lớp Công nghệ chế tạo cơ khí 55 11
Đồ án tốt nghiệp chuyên ngành Công nghệ chế tạo cơ khí 1.2.
Chọn phương pháp chế tạo phôi
Căn cứ vào kết cấu của chi tiết được thể hiện trên bản vẽ chi tiết (hình 1.1) và vật liệu chế
tạo chi tiết là gang xám GX15-32, ta thấy phương pháp đúc là phương pháp phù hợp để
chế tạo chi tiết. Đúc có nhiều phương pháp, cần căn cứ vào đặc điểm của các phương
pháp để chọn phương pháp đúc thích hợp.
1.2.1. Các phương pháp đúc
a) Đúc trong khuôn cát: được dung khá phổ biến vì nó đơn giản, rẻ tiền nhưng khuôn
chỉ dùng một lần, độ bóng chính xác thấp. Ngày nay người ta còn dung phương
pháp đúc đặc biệt như: Đúc trong khuôn kim loại, đúc áp lực, đúc ly tâm, đúc trong
khuôn mẫu chảy, đúc liên tục… nhằm nâng cao độ bóng, độ chính xác và nâng cao năng suất. - Ưu điểm :
+ Đúc có thể đúc nhiều loại vật liệu khác nhau, thường là gang, thép, kim loại màu, và
hợp kim của chúng. Khối lượng từ vài gam đến hang tấn.
+ Chế tạo được vật đúc có hình dạng, kết cấu phức tạp như thân máy công cụ, vỏ động cơ,
tượng…mà các phương pháp khác chế tạo khó khăn hoặc không chế tạo được.
+ Độ chính xác về hình dáng, kích thước và độ bóng có thể đạt khá cao nếu dung phương pháp đúc đặc biệt.
+ Có thể đúc nhiều lớp kim loại khác nhautrong một vật đúc hoặc cơ tính mặt ngoài và
bên trong vật đúc khác nhau.
+ Đúc có khả năng cơ khí hóa và tự động hóa.
+ Vốn đầu tư ít, tính chất sản xuất linh hoạt, năng suất tương đối cao cho nên giá thành
vật đúc tương đối rẻ. - Nhược điểm:
Lớp Công nghệ chế tạo cơ khí 55 12
Đồ án tốt nghiệp chuyên ngành Công nghệ chế tạo cơ khí
+ Tốn kim loại cho hệ thống rót, đậu hơi, đậu ngót. Ví dụ như: nhôm, hợp kim nhôm
lượng kim loại hao phí đến 25% so với vật đúc.
+ Đúc dễ gây ra khuyết tật như thiếu hụt, rỗ khí, cháy cát … làm cho chế độ phế phẩm có khi khá cao.
+ Đúc trong khuôn cát và làm khuôn bằng tay thì độ chính xác, độ bóng và năng suốt thấp.
+ Khó kiểm tra khuyết tật trong vật đúc.
b) Đúc trong khuôn kim loại :
Đúc trong kim loại là rót kim loại lỏng vào khuôn bằng kim loại. - Ưu điểm:
+ Khuôn kim loại có thể dung được nhiều lần ( vài tram đến hang vạn lần) tùy thuộc vào kim loại vật đúc.
+ Vật đúc có độ chính xác cao (cấp 6, 7) và độ bóng bề mặt cao (vì độ chính xác và độ bóng của long khuôn cao).
+ Tổ chức kim loại mịn nhỏ (do nguội nhanh) nén cơ tính tốt. - Nhược điểm:
+ Giá thành chế tạo khuôn đắt nên chỉ dung trong sản xuất hàng loạt lớn và hàng khối.
+ Độ dẫn nhiêt của khuôn lớn nên giảm khả năng điền đầy của kim loại, do đó khó đúc
vật phức tạp và vật có thành mỏng.
+ Độ dẫn nhiệt của khuôn lớn nên đúc gang dễ bị hóa trắng.
+ Khuôn và lõi bằng kim loại nên không có tính lún, ngăn cản sự co của kim loại làm cho vật đúc dễ bị nứt.
Lớp Công nghệ chế tạo cơ khí 55 13
Đồ án tốt nghiệp chuyên ngành Công nghệ chế tạo cơ khí c) Đúc ly tâm
Đúc ly tâm là rót kim loại lỏng vào khuôn quay, nhờ lực ly tâm mà kim loại lỏng phân bố
đều theo bề mặt bên trong của khuôn hoặc điền đầy lòng khuôn để tạo thành vật đúc. - Ưu điểm:
+ Đúc được chi tiết tròn xoay rỗng mà không cần dùng lõi ( tiết kiệm vật liệu và công làm lõi).
+ Không cần hệ thống rót, đầu ngót nên tiết kiệm kim loại vật đúc.
+ Do tác dụng của lực ly tâm nên kim loại điền đầy khuôn tốt, đúc được vật thành mỏng,
vật có đường gân, hình nổi mỏng.
+ Vật đúc sạch do tạp chất, xỉ và phi kim loại nhẹ có lực ly tâm bé nên không bị lẫn vào vật đúc.
+ Tổ chức kim loại mịn chặt, không bị rỗ co, rỗ khí do đông đặc dưới tác dụng của lực ly tâm. - Nhược điểm:
+ Thích ứng vật đúc tròn xoay.
+ Khuôn cần độ bền cao (vì chịu hiệt độ cao, chịu tác dụng của lực ly tâm, sức ép của kim
loại mỏng lên thành khuôn).
+ Khó nhận đường kính lỗ bên trong vật đúc chính xác (vì khó xác định lượng kim loại rót vào khuôn chính xác).
+ Bề mặt trong vật đúc có chất lượng kém vì chứa tạp chất, xỉ.
+ Khuôn quay tốc độ cao phải cân bằng và kín.
+ Vật đúc dễ bị thiên tích (Vì trọng lượng riêng của các nguyên tố kim loại khác nhau cho
nên lực ly tâm khác nhau).
Lớp Công nghệ chế tạo cơ khí 55 14
Đồ án tốt nghiệp chuyên ngành Công nghệ chế tạo cơ khí d) Đúc liên tục
Là phương pháp đúc mà kim loại lỏng được rót liên tục vào khuôn và xung quanh được làm nguội cưỡng bức. - Ưu điểm:
+ Do vật đúc ra liên tục nên có thể tránh được rỗ co, rỗ khí, xỉ… Không cần phải cắt bỏ
các đầu thừa của sản phẩm do co ngót, không phải đặt các đậu ngót.
+ Giảm được nguyên công cắt đầu phôi.
+ Cơ tính cao, chất lượng vật đúc tốt.
+ Ứng dụng để đúc ống, đúc thỏi các loại: vuông, tròn, tấm.
+ Cho phép cơ khí hóa và tự động hóa. - Nhược điểm:
+ Không đúc được các vật phức tạp.
+ Do tốc độ nguội lớn nên gang dễ bị biến trắng
+ Kim loại dễ bị mắc treo ở trong khuôn. e) Đúc dưới áp lực.
Đúc dưới áp lực là phương pháp đúc trong kim loại mà quá trình điền đầy khuôn và
kết tinh bị cưỡng bức bởi một áp lực. - Ưu điểm:
+ Có tất cả các đặc điểm của đúc trong khuôn kim loại như vật đúc có độ bóng, độ chính xác cao.
+ Đúc được những vật đúc có thành mỏng và phức tạp.
Lớp Công nghệ chế tạo cơ khí 55 15
Đồ án tốt nghiệp chuyên ngành Công nghệ chế tạo cơ khí
+ Vật đúc nguội nhanh nên cơ tính cao. + Năng suất cao.
+ Cơ tính tốt do tổ chức kim loại mịn chặt hơn, ít khuyết tật.
+ Đúc dưới áp lực dùng để chế tạo các chi tiết phức tạp nh3: van dầu khí, vỏ bơm
xăng dầu, nắp buồng ép. - Nhược điểm:
+ Hình dáng vật đúc không được quá phức tạp.
+ Khuôn làm việc dưới áp suất của dòng chảy kim loại rất lớn nên khuôn mau mòn và chống bị hỏng.
+ Phải sấy khuôn trước khi rót kim loại.
f) Đúc trong khuôn mẫu chảy.
Là phương pháp sử dụng nhiều trong ngành RADIO để chế tạo các chi tiết phức tạp
mà có khối lượng nhỏ từ vài gam trở nên. Người ta sử dụng bộ mẫu được làm từ vật
liệu dễ chảy, khi rót kim loại lỏng vào khuôn, mẫu sẽ chảy ra tạo ra lòng khuôn để điền đầy kim loại. - Ưu điểm:
+ Hòm khuôn không tháo rời, mẫu được chế tạo liền thành một khối nên không cần phải lắp ráp.
+ Mẫu được chế tạo từ vật liệu dễ nóng chảy.
+ Khi nung nóng mẫu sẽ chảy ra và tạo nên lòng khuôn vì vậy mỗi mẫu chỉ dùng để
chế tạo một sản phẩm.
+ Do không phải làm khuôn rời, không phải lắp ráp khuông khi đúc nên độ chính xác
cao, không có các chất bẩn rơi vào lòng khuôn.
Lớp Công nghệ chế tạo cơ khí 55 16
Đồ án tốt nghiệp chuyên ngành Công nghệ chế tạo cơ khí
+ Thời gian chế tạo nhanh.
+ Ứng dụng để chế tạo các loại chi tiết: Đúc dao phay, dao chuốt, các loại bánh rang,
líp xe đạp, đĩa xe moto, các phụ tùng máy nổ. - Nhược điểm:
+ Chu trình sản xuất dài.
+ Chỉ chế tạo những vật đúc nhỏ. (m<1,5kg) + Giảm giá thành.
Lớp Công nghệ chế tạo cơ khí 55 17
Đồ án tốt nghiệp chuyên ngành Công nghệ chế tạo cơ khí
1.2.2 Lựa chọn phương pháp chế tạo phôi. Căn cứ vào:
- Yêu cầu của đề bài dạng sản xuất là dạng sản xuất hàng loạt nhỏ.
- Đặc điểm của các phương pháp đúc
Em chọn phương pháp đúc trong khuôn cát để chế tạo phôi vì :
- Phương pháp này có ưu điểm: Đơn giản, dễ cơ khí tự động hóa, vốn đầu tư không
nhiều linh hoạt trong sản xuất, nên phù hợp với loại hình sản xuất nhỏ.
- Đúc được các chi tiết có hình đáng phức tạp mà các phương pháp khác không làm
được, nên phù hợp với kết cấu của chi tiết.
Lớp Công nghệ chế tạo cơ khí 55 18
Đồ án tốt nghiệp chuyên ngành Công nghệ chế tạo cơ khí
CHƯƠNG 2: LẬP QUY TRÌNH CÔNG NGHỆ CHẾ TẠO CHI TIẾT
2.1. Các bề mặt được gia công của chi tiết
Các bề mặt gia công của chi tiết được thể hiện trên hình 1.3 và liệt kê ở bảng 2.2.
Bảng 2. 1: Bảng liệt kê các bề mặt được gia công Stt Tên bề mặt Đặc điểm bề mặt Độ nhám Độ Các giai đoạn chính cần gia công để xác đạt được yêu cầu 1 Bề mặt 1 Bề mặt trụ tròn Rz40 11-13 Tiện thô, tiện tinh 2 Bề mặt 2 Bề mặt trụ tròn Ra2,5 7 Tiện thô,tiện tinh 3 Bề mặt 3
Bề mặt phẳng biên dạng Rz80 13 Tiện thô tròn 4 Bề mặt 4
Bề mặt đầu của trụ tròn Ra2,5 7 Tiện thô,tiện tinh 5 Bề mặt 5
Bề mặt đầu trụ trong của Ra2,5 7 Tiện thô,tiện lỗ tinh. 6 Bề mặt 6 Ra2,5 7 Tiện thô,tiện tinh 7 Bề mặt 7 Bề mặt phẳng Ra2,5 10-11 Phay thô
Lớp Công nghệ chế tạo cơ khí 55 19
Đồ án tốt nghiệp chuyên ngành Công nghệ chế tạo cơ khí 8 Bề mặt 8 Bề mặt lỗ Rz20 9 Khoan 9 Bề mặt 9 Mặt phẳng đáy chi tiết Rz80 13 Phay thô 10 Bề mặt E Bề mặt làm việc chính Rz5 6-7 Tiện thô, tiện
của chi tiết do đó bề mặt tinh, mài thô,
này phải chịu được mài mài tinh, mòn cao trong quá tình làm việc của bơm 11 Bề mặt E.1
Bề mặt đầu nghiêng 30º Rz40 11-13 Tiện thô, tiện tinh 12 Bề mặt E.2
Bề mặt đẩu rãnh nghiêng Rz40 11-13 Tiện thô, tiện 30º tinh 13 Bề mặt E.3 Bề mặt rãnh Rz40 11-13 Tiện thô, tiện tinh 13 Bề mặt D Bề mặt làm việc chính Ra2,5 7 Khoét thô,
của chi tiết do đó bề mặt khoét tinh,doa
này phải chịu được mài thô, doa tinh mòn cao trong quá tình làm việc của bơm 14 Bề mặt D.1
Bề mặt đầu nghiêng 20º Rz20 9 Khoan vát mép 15 Bề mặt 3 Bề mặt phẳng để khoan Rz80 Khoan, taroren các lỗ M16 16 Bề mặt 7 Bề mặt phẳng để khoan Ra2,5 Khoan , taroren các lỗ M8 17 Bề mặt 10
Bề mặt phẳng để khoan Rz80 13 Phay thô
Lớp Công nghệ chế tạo cơ khí 55 20
Đồ án tốt nghiệp chuyên ngành Công nghệ chế tạo cơ khí các lỗ ϕ 8 18 Bề 11.1 Bề mặt lỗ ϕ 8 Rz40 13 Khoan 19
Bề mặt Bề mặt lỗ ϕ 8 Ra1,25 14 Khoan 11.2 20 Bề mặt 12 Bề mặt phẳng Rz80 13 Phay thô 21 Mặt T Bề mặt phẳng Rz80 13 Phay, khoan lỗ 22
Bề mặt 1.1 Bề mặt đầu nghiêng 30º Rz80 13 Tiện vát mép
2.2. Chọn chuẩn định vị
2.2.1.Yêu cầu và nguyên tắc chung khi chọn chuẩn:
Chọn chuẩn là công việc rất quan trọng trong quá trình thiết kế, vì vậy phải thỏa mãn các yêu cầu sau:
+ Chọn chuẩn phải đảm bảo yêu cầu kỹ thuật gia công.
+ Chọn chuẩn sao cho năng suất cao và giá thành chi tiết hạ.
Nguyên tắc chung khi chọn chuẩn:
+ Chọn chuẩn phải tuân theo nguyên tắc 6 điểm khi định vị để khống chế hết số bậc tự do
cần thiết một cách hợp lý nhất. Tránh các hiện tượng định vị thiết số bậc tự do cần thiết
hoặc hiện tượng siêu định vị.
+ Chọn chuẩn sao cho lực cắt, lực kẹp không làm cho chi tiết gia công, đồ gá gia công bị
biến dạng, cong vênh đồng thời lực kẹp nhỏ để giảm được sức lao động của công nhân.
+ Chọn chuẩn sao cho kết cấu đồ gá đơn giản, gọn nhẹ và sự dụng thuận tiện, thích hợp
cho các hình thức sản xuất.
Lớp Công nghệ chế tạo cơ khí 55 21
Đồ án tốt nghiệp chuyên ngành Công nghệ chế tạo cơ khí 2.2.2. Chọn chuẩn tinh:
Nguyên tắc chọn chuẩn tinh:
+ Cố gắng chọn chuẩn tinh là chuẩn tinh chính.
+ Chọn chuẩn tinh sao cho có tính trung chuẩn càng cao càng tốt, như vật sẽ đảm bảo
được sai số gá đặt là nhỏ nhất.
+ Chọn chuẩn sao cho chi tiết có độ cứng vững cao nhất dưới tác dụng của lực cắt và lực kẹp chặt.
+ Chọn chuẩn sao cho kết cấu đồ gá đơn giản và thuận tiện khi sử dụng.
Chọn chuẩn tinh là chuẩn tinh thống nhất cho một hay nhiều lần gá đặt trong toàn bộ quá
tình gá đặt gia công chi tiết. Như vậy, sẽ giảm bớt được sai số do thay đổi chuẩn và gá đặt,
giảm bớt được số chủng loại đồ gá.
Với các yêu cầu và nguyên tắc chọn chuẩn nêu trên, chọn bề mặt 9, lỗ 8A, 8B làm chuẩn
tinh để gia công chi tiết. Vì chọn hai bề mặt này làm chuẩn sẽ đảm bảo nguyên tắc chọn
chuẩn tinh thống nhất. Có thể dùng hai bề mặt này có thể làm chuẩn để gia công hầu hết
các bề mặt của chi tiết.
Lớp Công nghệ chế tạo cơ khí 55 22
Đồ án tốt nghiệp chuyên ngành Công nghệ chế tạo cơ khí
Hình 2. 1: Chọn chuẩn tinh 2.2.3.Chọn chuẩn thô:
Yêu cầu khi chọn chuẩn thô:
+ Đảm bảo độ chính xác về mặt vị trí tương quan giữa các bề mặt gia công với bề mặt không gia công.
+ Phân bố đều lượng dư gia công cho các bề mặt sẽ gia công.
Các nguyên tắc để chọn chuẩn thô:
+ Theo một phương kích thước nhất định nếu trên chi tiết gia công có một bề mặt không
gia công thì nên chọn bề mặt đó làm chuẩn thô.
+ Theo một phương kích thước nhất định nếu chi tiết co s2 hay nhiều bề mặt gia công thì
ta nên chọn bề mặt nào đòi hỏi độ chính xác về vị trí tương quan so với các bề mặt gia công làm chuẩn thô.
+ Theo phương kích thước nhất định, nếu trên chi tiet có các bề mặt đều phải gia công thì
nên chọn bề mặt nào có lượng dư gia công nhỏ và đồng đều làm chuẩn thô.
Lớp Công nghệ chế tạo cơ khí 55 23
Đồ án tốt nghiệp chuyên ngành Công nghệ chế tạo cơ khí
+ Ứng với một bậc tự do cần thiết thì chuẩn thô chỉ được chọn và sử dụng không quá 1
lần trong cả quy trình công nghệ. Nếu vi phạm lời khuyên này thì gọi là vi phạm chuẩn
thô. Nếu phạm chuẩn thô thì sẽ làm cho sai số về vị trí tương quan giữa các mặt gia công với nhau rất lớn.
Dựa vào các yêu cầu và nguyên tắc chọn chuẩn thô trên và kết cấu của chi tiết ta chọn bề
mặt D làm chuẩn thô của chi tiết để gia công bề mặt 9 làm chuẩn tinh. Vì khi chọn bề mặt
D làm chuẩn thô sẽ đảm bảo lượng dư sẽ được phân bố đủ cho bề mặt gia công.
Hình 2. 2: Chọn chuẩn thô
2.3. Thiết kế sơ đồ nguyên công
Sơ đồ nguyên công:
Theo trình tự gia công, yêu cầu chất lượng bề mặt của chi tiết gia công và điều kiện kỹ
thuật làm việc của chi tiết ta chọn máy gia công và dụng cụ cắt theo bảng 2.3.
Lớp Công nghệ chế tạo cơ khí 55 24
Đồ án tốt nghiệp chuyên ngành Công nghệ chế tạo cơ kh
Bảng 2. 2: Bảng sơ đồ nguyên công STT
Tên nguyên công và sơ đồ gá đặt Định vị và kẹp chặt
Chọn máy và dụng cụ cắt 1 NC1: Phay bề mặt 9
Định vị: Chi tiết được định vị 5 Máy phay đứng 6H12
bậc tự do. Hai lỗ chốt trụ ngắn Sơ đồ gia công:
Dao phay mặt đầu gắn mảnh h
định vị 4 bậc tự do, 1 chốt tì kim BK6 có kích th
vào mặt vuông góc định vị 1 100x50x32, ω = 25 - 35º bậc tự do.
Kẹp chặt: Chi tiết được kẹp chặt nhờ đai ốc 2 NC2: Khoan lỗ 2 lỗ 8A, 8B
Định vị: Lỗ khoan được lấy Máy khoan cần 2A55
dấu và khi khoan rà theo lỗ đã Mũi khoan ruột già hợp k
lấy dấu. Dùng mặt 3 để định vị cứng. Thông só mũi khoan D 3 bậc tự do. 8mm, L = 100mm, l = 50mm.
Kẹp chặt: Chi tiết được kẹp chặt bằng đai ốc
Lớp Công nghệ chế tạo cơ khí 55 25
Đồ án tốt nghiệp chuyên ngành Công nghệ chế tạo cơ khí 3
NC3: Tiện thô mặt trụ ngoài
Định vị: Chi tiết được định vị 6 Máy tiện 1K62
bậc tự do. Phiến tì tì vào mặt 9 Bước 1: Tiện bề mặt 1
Dao tiện gắn mảnh hợp kim
định vị 3 bậc tự do, chốt trám cứng BK6. Thông số dao: H = Bước 2: Tiện bề mặt 2
và chốt trụ ngắn định vị 3 bậc 20 mm, B = 16 mm, L = 120mm,
Bước 3: Tiện bề mặt 3 tự do. m = 6 mm, a = 16 mm, r = 1mm.
Kẹp chặt: Chi tiết được kẹp Bước 4: Tiện bề mặt 4
Thông số dao tiện mặt đầu:H =
chặt bằng trục dài tỳ vào bề
Bước5: Tiện vát mép bề mặt 1.1 16 mm, B = 12 mm, L = 100 mặt D mm, m = 7 mm, a = 10 mm, r = 1 mm.
Lớp Công nghệ chế tạo cơ khí 55 26
Đồ án tốt nghiệp chuyên ngành Công nghệ chế tạo cơ kh 4
NC4: Tiện tinh mặt trụ ngoài
Định vị: Chi tiết được định vị 6 Máy tiện 1K62
bậc tự do. Phiến tì tì vào mặt 9 Bước 1: Tiện bề mặt 1
Dao tiện gắn mảnh hợp k
định vị 3 bậc tự do, chốt trám cứng BK6. Thông số dao: H Bước 2: Tiện bề mặt 2
và chốt trụ ngắn định vị 3 bậc 20 mm, B = 16 mm, L = 120m Bước 3: Tiện bề mặt 4 tự do. m = 6 mm, a = 16 mm, r = 1m
Kẹp chặt: Chi tiết được kẹp
Bước 4: Tiện bề mặt 1.1
Thông số dao tiện mặt đầu:H
chặt bằng trục dài tỳ vào bề 16 mm, B = 12 mm, L = mặt D mm, m = 7 mm, a = 10 mm, 1 mm.
Lớp Công nghệ chế tạo cơ khí 55 27
Đồ án tốt nghiệp chuyên ngành Công nghệ chế tạo cơ khí 5 NC5: Tiện thô lỗ Φ100K7
Định vị: Chi tiết được định vị 6 Máy tiện 1K62
bậc tự do. Phiến tì tì vào mặt 9 Bước 1: Tiện bề mặt E
Dao tiện gắn mảnh hợp kim
định vị 3 bậc tự do, chốt trám cứng BK6. Thông số dao: H =
Bước 2: Tiện rãnh bề mặt E.3
và chốt trụ ngắn định vị 3 bậc 20 mm, B = 16 mm, L = 120mm,
Bước 3: Tiện vát mép bề mặt E.1 tự do. m = 6 mm, a = 16 mm, r = 1mm.
Kẹp chặt: Chi tiết được kẹp
Bước 4: Tiện vát mép bề mặt E2.
Thông số dao tiện mặt đầu:H =
chặt bằng trục dàitỳ vào bề mặt Bước 5: Tiện bề mặt 6 16 mm, B = 12 mm, L = 100 D mm, m = 7 mm, a = 10 mm, r = Bước 6: Tiện bề mặt 5 1 mm.
Lớp Công nghệ chế tạo cơ khí 55 28
Đồ án tốt nghiệp chuyên ngành Công nghệ chế tạo cơ kh 6 NC6: Tiện tinh lỗ Φ100K7
Định vị: Chi tiết được định vị 6 Máy tiện 1K62
bậc tự do. Phiến tì tì vào mặt 9 Bước 1: Tiện bề mặt E
Dao tiện gắn mảnh hợp k
định vị 3 bậc tự do, chốt trám cứng BK6. Thông số dao: H
Bước 2: Tiện rãnh bề mặt E.3
và chốt trụ ngắn định vị 3 bậc 20 mm, B = 16 mm, L = 120m
Bước 3: Tiện vát mép bề mặt E.1 tự do. m = 6 mm, a = 16 mm, r = 1m
Kẹp chặt: Chi tiết được kẹp
Bước 4: Tiện vát mép bề mặt E2.
Thông số dao tiện mặt đầu:H
chặt bằng trục dài tỳ vào bề 16 mm, B = 12 mm, L = Bước 5: Tiện bề mặt 6 mặt D mm, m = 7 mm, a = 10 mm,
Lớp Công nghệ chế tạo cơ khí 55 29
Đồ án tốt nghiệp chuyên ngành Công nghệ chế tạo cơ khí Bước 6: Tiện bề mặt 5 1 mm. 7 NC7: Phay bề mặt 7
Định vị: Chi tiết được định vị 6 Máy phay đứng 6H12
bậc tự do. Phiến tì tì vào mặt 9 Bước 1: Phay bề mặt 92
Dao phay mặt đầu gắn mảnh hợp
định vị 3 bậc tự do, chốt trám kim BK6 có kích thước Bước 2: Đổi đầu
và chốt trụ ngắn định vị 3 bậc 100x50x32
tự do. Và chốt tỳ tăng độ cứng vũng cho chi tiết.
Lớp Công nghệ chế tạo cơ khí 55 30
Đồ án tốt nghiệp chuyên ngành Công nghệ chế tạo cơ kh
Kẹp chặt: Chi tiết được kẹp chặt bằng đai ốc 8 NC8: Phay bề mặt T
Định vị: Chi tiết được định vị 6 Máy phay đứng 6H12
bậc tự do. Phiến tì tì vào mặt 9 Dao phay mặt đầu gắn mảnh h
định vị 3 bậc tự do, chốt trám kim BK6 có kích th
và chốt trụ ngắn định vị 3 bậc 100x32x32, ω = 25 - 35º
tự do. Và chốt tỳ tăng độ cứng vững cho chi tiết.
Kẹp chặt: Chi tiết được kẹp
chặt bằng trục dài ép vào 2 lỗ
Lớp Công nghệ chế tạo cơ khí 55 31
Đồ án tốt nghiệp chuyên ngành Công nghệ chế tạo cơ khí bên. 9 NC9: Khoét, doa bề mặt D
Định vị: Chi tiết được định vị 6 Máy khoan cần 2A55
bậc tự do. Phiến tì tì vào mặt 9
Bước 1: Khoét thô lỗ đạt 48
Thông số mũi khoét rộng: D =
định vị 3 bậc tự do, chốt trám 53 mm và D = 55,71 mm, L =
Bước 2: Khoét tinh lỗ đạt 55.71
và chốt trụ ngắn định vị 3 bậc 180 mm, l = 85 mm, d = 22 mm. tự do.
Bước 3: Doa thô lỗ đạt 55,91 Thông số mũi doa: D =
Kẹp chặt: Chi tiết được kẹp
Bước 4: Doa tinh lỗ đạt 56. 55,91mm và D = 56 mm, L = chặt bằng đai ốc Bước 5: Vát mép lỗ 140 mm, l = 40 mm.
Bước 6: Đổi đầu và thực hiện bước 1 đến bước 5.
Lớp Công nghệ chế tạo cơ khí 55 32
Đồ án tốt nghiệp chuyên ngành Công nghệ chế tạo cơ kh 10
NC10: Khoan lỗ trên bề mặt 7
Định vị: Chi tiết được định vị 6 Máy khoan cần 2A55
bậc tự do. Phiến tì tì vào mặt 9 Bước 1: Khoan lỗ
Mũi khoan bằng hợp kim cứ
định vị 3 bậc tự do, chốt trám Thông số mũi khoan rộng: D Bước 2: Taroren
và chốt trụ ngắn định vị 3 bậc mm, L = 70 mm, l = 80 mm.
tự do. Và chốt tỳ tăng độ cứng Bước 3: Đổi đầu vững cho chi tiết
Kẹp chặt: Chi tiết được kẹp
Lớp Công nghệ chế tạo cơ khí 55 33
Đồ án tốt nghiệp chuyên ngành Công nghệ chế tạo cơ khí chặt bằng đai ốc. 11 NC11: Khoan lỗ
Định vị: Chi tiết được định vị 6 Máy khoan cần 2A55
bậc tự do. Phiến tì tì vào mặt 9
Bước 1: Khoan lỗ trên bề mặt 3
Mũi khoan bằng hợp kim cứng.
định vị 3 bậc tự do, chốt trám Thông số mũi khoan: D = 14 Bước 2: Taroren
và chốt trụ ngắn định vị 3 bậc mm, L = 100 mm, l = 50 mm. tự do.
Thông số dao: mũi khoan: D = 8
Kẹp chặt: Chi tiết được kẹp mm, L = 100 mm, l = 50 mm.
chặt bằng trục dài tỳ vào bề mặt D
Lớp Công nghệ chế tạo cơ khí 55 34
Đồ án tốt nghiệp chuyên ngành Công nghệ chế tạo cơ kh
Bước 3: Khoan lỗ trên bề mặt 10 Bước 4: Taroren
Lớp Công nghệ chế tạo cơ khí 55 35
Đồ án tốt nghiệp chuyên ngành Công nghệ chế tạo cơ khí 12
NC12: Khoan lỗ trên bề mặt T
Định vị: Chi tiết được định vị 6 Máy khoan cần 2A55
bậc tự do. Phiến tì tì vào mặt 9 Mũi khoan bằng hợp kim cứng.
định vị 3 bậc tự do, chốt trám Thông số mũi khoan: D = 2 mm,
và chốt trụ ngắn định vị 3 bậc L = 50 mm, l = 20 mm.
tự do. Và chốt tỳ tăng độ cứng vững cho chi tiết
Kẹp chặt: Chi tiết được kẹp
chặt bằng trục dài tỳ vào bề mặt D
Lớp Công nghệ chế tạo cơ khí 55 36
Đồ án tốt nghiệp chuyên ngành Công nghệ chế tạo cơ kh 13 NC13: Mài lỗ 100K7
Định vị: Chi tiết được định vị 6 Máy mài tròn trong 3A227,
bậc tự do. Phiến tì tì vào mặt 9 mài ΠΠ prophin thẳng, với Bước 1: Mài thô
định vị 3 bậc tự do, chốt trám thông số đá mài: D = 32 mm Bước 2: Mài tinh
và chốt trụ ngắn định vị 3 bậc = 3mm, d = 6mm. Vật liệu tự do. mài 2A, độ hạt 50.
Kẹp chặt: Chi tiết được kẹp
chặt bằng trục dài tỳ vào bề mặt D
Lớp Công nghệ chế tạo cơ khí 55 37
Đồ án tốt nghiệp chuyên ngành Công nghệ chế tạo cơ khí 14 NC14: Kiểm tra
Sử dụng các dụng cụ đo: Thước kẹp, pame..
Lớp Công nghệ chế tạo cơ khí 55 38
Đồ án tốt nghiệp chuyên ngành Công nghệ chế tạo cơ khí
2.4. Tính toán và chọn lượng dư gia công
2.4.1. Tính toán lượng dư cho bề mặt 100K7 10
Bề mặt 100K7 có độ chính xác cấp 7. 100K7 = 100 25
Để đạt được độ chính xác cấp 7 thì ta chọn phương pháp đúc cấp chính xác II gồm các
bước gia công: Tiện thô, tiện tinh, mài thô, mài tinh. 2Z 2(R T )
Công thức tính lượng dư: b min za z a b
Theo bảng 10.[2] ta có giá trị Rz, Tl bằng 600 µm (250 µm + 350). 2 2
Sai số không gian của lỗ đúc sẵn: ph cv
lt (bảng 1.23. Tài liệu [2] Trong đó ρ l
cv - sai số do độ cong vênh ( . cv cv trong đó Δcv = 1,2 - độ cong vênh trên
1mm chiều dài ; l – chiều dài lỗ, l = 117 (mm);
ρcv = 1,2.117 = 140 (µm)
Lớp Công nghệ chế tạo cơ khí 55 39
Đồ án tốt nghiệp chuyên ngành Công nghệ chế tạo cơ khí
ρlt - độ lệch tâm của lỗ do thao đúc có vị trí sai lệch so với vị trí yêu cầu.
Hình 2. 3: Độ lệch tâm
Do ta chọn bề mặt 9 là chuẩn tinh thống nhất và định vị them bằng 2 lỗ 8A, 8B để gia
công bề mặt E. Nên độ lệch tâm của lỗ bằng lượng dư gia công của bề mặt 9. Khi đó ta có: ρlt = 0,1 (mm) 2 2 2 2 Ta có ph cv lt 140 100 172 (µm)
Sai lệch còn lại sau nguyên công tiện thô: 0,06. 0,06.172 10( m) 1 a
Sai lệch còn lại sau nguyên công tiện tinh:
Lớp Công nghệ chế tạo cơ khí 55 40
Đồ án tốt nghiệp chuyên ngành Công nghệ chế tạo cơ khí 0,05. 0,05.10 0, 45( m) 2 a
Sai lệch còn lại sau nguyên công mài thô: 0,4 0,4.0,45 0,18( ) m 3 a
Sai lệch còn lại sau nguyên công mài thô: 0,2 0, 2.0,18 0,036( ) m 4 a
Sai số gá đặt khi định vị theo 2 lỗ và gia công mặt trên: 2 2 d g c kc
Sai số kẹp chặt được xác định theo bảng 24.[4] ε = 120 ( k µm)
Sai số chuẩn trên chiều dài gia công lỗ c A B min Trong đó:
δA là dung sai của lỗ định vị, δA = 90 (µm)
δB là dung sai của đường kính chốt, δA = 14 (µm)
ρmin là khe hở nhỏ nhất giữa lỗ và chốt, ρmin = 13 (µm) 90 14 13 117 c A B min (µm) 2 2 2 2 117 120 167 Ta có: gd c kc
Sai số gá đặt sau nguyên công tiện tinh là: 0,05. 0,05.167 8 gd1 gd (µm)
Lớp Công nghệ chế tạo cơ khí 55 41
Đồ án tốt nghiệp chuyên ngành Công nghệ chế tạo cơ khí
Sai số gá đặt sau nguyên công mài thô là: 0,04. 0,04.8 0,32 gd2 gd3 (µm)
Sai số gá đặt sau nguyên công mài tinh là: 0,02. 0,02.0,32 0,0064 gd 2 gd 3 (µm)
Lượng dư nhỏ nhất của tiện thô là : 2 2 2 2 2Z 2(R T ) 2. 600 140 167 2.818( m) 1min 1 1 d g
Lượng dư nhỏ nhất của tiện tinh là: 2 2 2 2 2Z 2(R T ) 2. 50 10 8 2.63( ) m 3min 3 3 gd1
Lượng dư nhỏ nhất của mài thô là: 2 2 2 2 2Z 2(R T ) 2. 25 0, 45 0,32 2.26( m) 4min 4 4 gd2
Lượng dư nhỏ nhất của mài tinh là: 2 2 2 2 2Z 2(R T ) 2. 15 0,18 0,0064 2.15( ) m 5min 5 5 gd3
Xác định kích thước trong quá trình gia công: Mài thô: d = d 3
+0,5= 100,01 + 0,2 = 100,21 (mm) 4
Tiện tinh: d2 = d3 +0,4 = 100,21+ 0,12= 100,33 (mm)
Tiện thô: d1 = d2 +1,2 = 100,33 + 0,4 = 100,73 (mm)
Phôi: d = d + = 100,73 + 3 = 103,73 (mm) 1
Lớp Công nghệ chế tạo cơ khí 55 42
Đồ án tốt nghiệp chuyên ngành Công nghệ chế tạo cơ khí
Xác định kích thước giới hạn:
Tra bảng 1.[8] ta có dung sai của nguyên công mài tinh δ = 0,035 (mm) 4
d4max = d4min + δ4 = 100,03 + 0,035 = 100,07 (mm)
Tra bảng 1.[8] ta có dung sai của nguyên công mài thô δ3 = 0,054 (mm)
d3max = d3min + δ3 = 100,53 + 0,054 = 100,58 (mm)
Tra bảng 1.[8] ta có dung sai của nguyên công tiện tinh δ2 = 0,14 (mm)
d2max = d2min + δ2 = 100,93+ 0,14 = 101,1 (mm)
Tra bảng 1.[8] ta có dung sai của nguyên công tiện thô δ4 = 0,35 (mm)
d1max = d1min + δ1 = 102,13 + 0,35 = 102,5 (mm)
Tra bảng 1.[8] ta có dung sai của phôi δp = 0,87 (mm)
dmax = dmin + δp = 103,73+ 0,87 = 104,6 (mm)
Xác định lượng dư giới hạn:
+ Zi max: Hiệu kích thước giới hạn lớn nhất.
+ Zi min: Hiệu kích thước giới hạn nhỏ nhất.
Lớp Công nghệ chế tạo cơ khí 55 43
Đồ án tốt nghiệp chuyên ngành Công nghệ chế tạo cơ khí
Bảng 2. 3: Thông số công nghệ Bước công Các yếu tố (µm) Lượng Kích Dung Kích thước giới Lượng dư giới nghệ dư tính thước tính sai δ hạn (mm) hạn (µm) toán toán dmin (µm) Rza Ta ρa εgd dmin dmax 2Zimin 2Zimax 2Zi min Phôi 600 172 0 - 103,73 870 103,7 104,6 - - Tiện thô 50 - 10 167 818 100,73 350 100,7 102,5 1600 2100 Tiện tinh 25 - 0,45 8 63 100,33 140 100,3 101,1 1200 1400 Mài thô 15 - 0,18 0,32 26 100,21 54 100,2 100,58 400 520 Mài tinh 5 - 0,036 0,006 15 100,01 35 100,01 100,05 500 530 Tổng cộng 3700 4500
Lớp Công nghệ chế tạo cơ khí 55 44
Đồ án tốt nghiệp chuyên ngành Công nghệ chế tạo cơ khí
2.4.2. Tra lượng dư cho các bề mặt còn lại
Bảng 2. 4: Tra lượng dư cho các bề mặt còn lại STT Tên bề mặt Tra lượng dư (mm) Tài liệu tham khảo 1 Bề mặt 1 6 Bảng 3-95.[5] 2 Bề mặt 2 5 Bảng 3-95.[5] 3 Bề mặt 3 5 Bảng 3-95.[5] 4 Bề mặt 4 5 Bảng 3-95.[5] 5 Bề mặt 5 4 Bảng 3-95.[5] 6 Bề mặt 6 4 Bảng 3-95.[5] 7 Bề mặt 7 4 Bảng 3-95.[5] 8 Bề mặt 9 4 Bảng 3-95.[5] 9 Bề mặt D 8 Bảng 1.33.[2] 2.4.3. Bản vẽ phôi lồng
Căn cứ vào lượng dư gia công tính toán và tra bảng, có thể xây dựng bản vẽ lồng phôi như hình 2.4
Lớp Công nghệ chế tạo cơ khí 55 45
Đồ án tốt nghiệp chuyên ngành Công nghệ chế tạo cơ khí
Hình 2. 4: Bản vẽ phôi lồng
Lớp Công nghệ chế tạo cơ khí 55 46
Đồ án tốt nghiệp chuyên ngành Công nghệ chế tạo cơ khí
2.5. Các máy lựa chọn trong quy trình công nghệ Theo tài liệu [1] ta có:
2.5.1. Máy tiện 1K62 có các thông số như sau:
+) Chiều cao tâm 200 mm, khoảng cách giữa 2 tâm đến 1400 mm.
+) Công suất động cơ: N = 10kW.
+) Hiệu suất máy: n = 0.75.
+) Đường kính lỗ suốt trục chính 45mm – Côn mooc: N0 = 5.
+) Lực cho phép của cơ cấu chạy dao Px = 360 KG.
+) Số vòng quay trục chính (v/ph):
12.5; 16; 20; 25; 31.5; 40; 50; 63; 80; 100; 125; 160; 200; 250; 315; 400; 500; 630; 800; 1000; 1250; 1600; 2000.
+) Lượng tiến dọc (mm/v):
0.07; 0.014; 0.084; 0.097; 0.11; 0.12; 0.13; 0.14; 0.15; 0.17; 0.195; 0.21; 0.23; 0.26; 0.28;
0.30; 0.34; 0.39; 0.43; 0.47; 0.52; 0.57; 0.61; 0.70; 0.78; 0.95; 1.04; 1.14; 1.21; 1.4; 1.56;
1.74; 1.9; 2.08; 2.28; 2.42; 2.8; 3.12; 3.48; 3.8; 4.16.
+) Lượng tiến ngang (mm/v):
0.035; 0.037; 0.042; 0.048; 0.055; 0.06; 0.065; 0.07; 0.074; 0.084; 0.097; 0.11; 0.12; 0.13;
0.14; 0.15; 0.17; 0.195; 0.21; 0.23; 0.26; 0.28; 0.3; 0.34; 0.39; 0.43; 0.47; 0.52; 0.57; 0.6;
0.7; 0.78; 0.87; 0.95; 1.04; 1.14; 1.21; 1.4; 1.56; 1.74; 1.9; 2.08.
2.5.2. Máy mài tròn trong 35250 có các thông số kỹ thuật chính:
+) Đường kính gia công lớn nhất của lỗ mài là 200 mm.
Lớp Công nghệ chế tạo cơ khí 55 47
Đồ án tốt nghiệp chuyên ngành Công nghệ chế tạo cơ khí
+) Công suất động cơ trục chính đá mài 5kW
+) Hiệu suất máy η = 0,9.
+) Giới hạn số vòng quay của phôi trong một phút( điều chỉnh vô cấp ): 80-800
+) Giới hạn tốc độ tiến dọc ụ mài điều chỉnh vô cấp m/ph: 0,3-10
+) Bước tiến ngang của đá mài tròn mm/htk: 0,0025 – 0,005 – 0,0075 – 0,010 – 0,01250 –
0,03 – 0,06 – 0,09 – 0,120 – 0,15-
+) Giới hạn số vòng quay đá mài tròn trong một phút,v/ph: 4500 - 5000
2.5.3. Máy phay đứng 6H12 với các thông số cơ bản:
+) Bề mặt làm việc của bàn: 320 x 1250 mm .2
+) Công suất động cơ: 7kW.
+) Hiệu suất máy η: 0,75.
+) Số vòng quay trục chính: 30-47,5-60-75-95-120-151-190-240-302-381-480-605-762- 960-1210-1500v/ph.
+) Bước tiến của bàn: 30-47,5-60-75-95-120-151-190-240-302-381-480-605-762-960- 1210-1500 mm/ph.
+) Lực lớn nhất cho phép theo cơ cấu tiến của máy: 1500KG.
5.2.4. Máy khoan cần 2A55 với các thông số cơ bản:
+) Đường kính gia công lớn nhất: 50 mm.
+) Côn mooc trục chính: N = 5. 0
+) Công suất đầu khoan: 4,5kW.
+) Công suất nâng xà ngang: 1,7kW.
Lớp Công nghệ chế tạo cơ khí 55 48
Đồ án tốt nghiệp chuyên ngành Công nghệ chế tạo cơ khí
+) Số vòng quay trục chính: 30-37,5-47,5-60-75-95-118-150-190-235-300-375-475-600- 753-950-1180-1500-1700 mm/ph.
+) Bước tiến 1 vòng quay trục chính: 0,05-0,07-0,1-0,2-0,28-0,4-0,56-0,79-1,15-1,54-2,2 mm/v.
+) Momen xoắn lớn nhất: 75KGm.
+) Lực dọc trục lớn nhất 2000KG.
2.6. Tính toán chế độ cắt
2.6.1. Tính chế độ cắt cho nguyên công 1 phay bề mặt 9
a) Chọn máy: Để phay mặt đầu ta chọn máy phay đứng 6H12 của Nga tra bảng 9-38 [1]
b) Chọn dao: Để phay mặt đầu ta dùng dao phay mặt đầu răng chắp mảnh hợp kim cứng. BK6
Các thông số: - Đường kính dao: D = 100 (mm), B = 50 (mm), d = 32 (mm) Bảng 4 -95. [5] - Số răng: Z= 10
Thông số của dao tra ở bảng 4-94 trang 376 [5] c) Tra chế độ cắt Chiều sâu cắt: 2 (mm)
Lượng chạy dao răng: SZ = 0,16 (mm/răng).
Lượng chạy dao vòng: S=Sz.Z= 0,18.10 =1,6 mm/vòng.
Tốc độ cắt V (m/phút) được tính theo công thức: C . q D V V .k T .
m t .xS .yB .u P v Z Z
Lớp Công nghệ chế tạo cơ khí 55 49
Đồ án tốt nghiệp chuyên ngành Công nghệ chế tạo cơ khí
Các hệ số CV, m,p, u, x, y, q được tra ở bảng 5.39.[6] ta có:
Bảng 2. 5: Thông số chế độ cắt Cv qv xv yv Uv pv mv 445 0,2 0,15 0,35 0,2 0 0,32 .
Chu kỳ bền trung bình của dao phay tra ở bảng 5.40 ta có T=180 (phút)
Hệ số điều chỉnh chung cho tốc độ cắt Kv phụ thuộc vào điều kiện cụ thể k k .k .k V MV nv uv .
+) kMV : Hệ số phụ thuộc vào chất lượng của bề mặt gia công cho trong bảng 5-1-> 5-4.[6] ta có kMV=1. +) k k
uv : Hệ số phụ thuộc vào vật liệu dụng cụ cắt uv = 1 tra bảng 5-7.[6] +) k k
nv : Hệ số phụ thuộc vào trạng thái bề mặt phôi 0,8 nv .tra bảng 5-6.[6] Vậy kv=1.1.0,8 = 0,8 Vậy V= 132,85 m/phút. 1000.V 1000.132,85 n 423,01
Số vòng quay trục chính: .D 3,14.100 vòng/phút.
Chọn số vòng quay theo máy ta có: n = 475 vòng/phút. . n .D 475.3,14.100 V 149,15 t 1000 1000 m/phút.
Lượng chạy dao phút và lượng chạy dao thực tế theo máy:
Lớp Công nghệ chế tạo cơ khí 55 50
Đồ án tốt nghiệp chuyên ngành Công nghệ chế tạo cơ khí
Sm = SZ bảng . Z . n = 0,16.10.475 = 760 mm/ph
Theo máy chọn Sm = 750 mm/ph. Vậy: 750 S 0,16 Zthuc 10.475 mm răng C . x p t . y p S . u p B .Z p z P .K z q p Lực cắt P p D . p n z: Tra bảng 3-5. [1] ta có:
Bảng 2. 6: Thông số chế độ cắt Cp xp yp up ωp qp 54,5 0,9 0,74 1 0 1 Theo bảng 12-1.[1] ta có: 0,3 0,3 65 b K K 0,96 p mp 75 75 0,9 0,74 1 54,5.2 .0,16 .50 .10 P 131,02
Thay vào công thức ta có: z 1 0 100 .475 KG P V z . 131,02.132,85 N 2,84 Công suất cắt: 60.102 60.102 kW
2.6.2. Tính chế độ cắt cho nguyên công 2 khoan 2 lỗ 8A, 8B Khoan lỗ 8
Chọn máy: Để khoan 2 lỗ 8A, 8B ta chọn máy khoan cần 2A55
Lớp Công nghệ chế tạo cơ khí 55 51
Đồ án tốt nghiệp chuyên ngành Công nghệ chế tạo cơ khí
Chọn dao: Để khoan 2 lỗ ta dùng mũi khoan bằng hợp kim cứng và gắn mảnh hợp kim cứng BK8 Các thông số Chiều sâu cắt t = 4 (mm)
Lượng chạy dao: tra bảng 5-94 [6] chọn S = 0,18mm/vòng.
Tra theo máy ta được: S = 0,1 mm/vòng.
Tốc độ cắt tra bảng 5-95[6] ta có Vb=57m/phút.
Tính vận tốc cắt V=Vb.kv Với Vb=57 m/phút, k = 0,8 v
Ta có V= 57.0,8 = 45,6 m/phút Số vòng quay trục chính: 1000.V 1000.45,6 n 1815,28 .D 3,14.8 vòng/phút
Chọn theo máy 1700 vòng/phút . n .D 1700.3,14.8 V 42,7
Tính lại vận tốc cắt: 1000 1000 vòng/phút Công suất cắt: N = Nb.Kv
Tra bảng 5-96 [6]ta có: N = 1,1 kW; Kv = 0,8 Suy ra: N = 0,08 kW
Lớp Công nghệ chế tạo cơ khí 55 52
Đồ án tốt nghiệp chuyên ngành Công nghệ chế tạo cơ khí
2.6.3. Tính toán chế độ cắt cho nguyên công tiện 3 tiện thô các bề mặt trụ ngoài, tiện
mặt đầu và tiện vát mép.
a) Chọn máy: Máy tiện 1K62
b) Chọn dao: Dao tiện ngoài gắn mảnh hợp kim cứng BK6
- Có các thông số chính như sau:H=16 mm; B=10 mm; L=100 mm; m=4 mm; a=10 mm; r= 1 mm.
Bước 1: Tiện bề mặt 1
Chiều sâu cắt: t = 1,3 mm.
Số lần chạy dao: 2 lần.
Lượng chạy dao: S= 0,6 mm/vòng (bảng 2-1.[2]).
Tra lại theo máy ta có: S = 0,57 mm/vòng Cv V Tốc độ cắt: m T . x t . y S .kv
Tra bảng 1-1.[1] ta có: C = 292; x = 0,15 ; y = 0,2 ; m = 0,2 v
Chu kì bền trung bình của dao: T= 60 phút
kv: Hệ số điều chỉnh chung cho tốc độ cắt phụ thuộc vào các điều kiện cụ thể. kv= kmv.k .k nv .k uv φv.krv
kmv: Hệ số phụ thuộc vào chất liệu của vật liệu gia công. Chọn kmv = 1
knv: Hệ số phụ thuộc vào trạng thái bề mặt phôi. Chọn knv = 0,8
Lớp Công nghệ chế tạo cơ khí 55 53
Đồ án tốt nghiệp chuyên ngành Công nghệ chế tạo cơ khí
kuv: Hệ số phụ thuộc vào vật liệu dụng cụ cắt. Chọn k = 1 uv
kφv: Hệ số phụ thuộc vào góc cắt chính. Chọn kφv = 1 Ta có k = 1.0,8.1.1 = 0,8 v 292 V .0,8 110,81 0,2 0,15 0,2 60 .1,3 .0,57 (m/phút) 1000.V 1000.110,81 n 282,7
Tốc độ của trục chính: .D 3,14.124,8 (vòng/phút)
Chọn tốc độ quay theo máy ta có: n= 250 (vòng/phút) .D.n 3,14.124,8.250 V 97,96 Vậy 1000 1000 (m/phút) P 10.C . Pxz t . nz V . yPz S .k Lực cắt P z pz pz z: Tra bảng 2-19.[2] ta có:
Cpz = 92 ; x = 1 ; y = 0,75 ; n =0 Tra bảng 15-1.[1] ta có
kp: Hệ số chỉnh cho lực cắt: kpz =kmp.kφp.krp.kλp
Tra bảng 5-9, 5-23.[6] ta có:
Chọn krp = 0,87 ; chọn kλp = 1 ; chọn kφp = 0,89, kγp = 1
kp = kmp.kφp.krp = 1.0,87.0,89.1=0,77
Lớp Công nghệ chế tạo cơ khí 55 54
Đồ án tốt nghiệp chuyên ngành Công nghệ chế tạo cơ khí y x pz pz n 0,75 1 0 P
10.C .S .t .V z .k
10.92.0,57 .1,3 .97,96 .0,77 604,12 z pz p z (N) Lực tiếp tuyếnPx: Tra bảng 2-19.[2] ta có:
Cpx= 46 ; x = 1 ; y = 0,4 ; n =0 Tra bảng 15-1.[1] ta có
kpx: Hệ số chỉnh cho lực cắt: k =k px rp.kφp.krp.kλp
Tra bảng 5-9, 5-23.[6] ta có:
Chọn krp = 1 ; chọn kλpy = 1 ; chọn kφpy = 01,17, kγp = 1,
kpx= kmp.kφp.krp = 1.1,17.1.1= 1,17 y x px px n 0,4 1 0 P
C .S .t .V x.k
46.0,57 .1, 3 .97,96 .1,17 55,87 x px p x (KG) P C . x n y Py t . y V . Py S .k Lực hướng kính: y Py py Tra bảng 2-19.[2] ta có:
Cpy= 54 ; x = 0,9 ; y = 0,75 ; n =0
kp: Hệ số chỉnh cho lực cắt: kp=krp.kφp.krp.kλp
Tra bảng 5-9, 5-23.[6] ta có:
Chọn krp = 0,66 ; chọn kλpy = 1 ; chọn kφpy = 0,5, kγp = 1, kp = 0,66.0,5.1.1 = 0,33 x n y Py Py 0,9 0 0,75 P
C .t .V .S .k
54.1,3 .97, 96 .0,57 .0,33 14,8 y Py py (KG)
Lớp Công nghệ chế tạo cơ khí 55 55
Đồ án tốt nghiệp chuyên ngành Công nghệ chế tạo cơ khí P .V 604,12.97,96 z N 9,67 Công suất cắt: 60.102 60.102 (kW)
Bước 2: Tiện bề mặt 2
Chiều sâu cắt: t = 1,1 mm.
Số lần chạy dao: 2 lần.
Lượng chạy dao: S= 0,57 mm/vòng (bảng 2-1.[2]). Cv V Tốc độ cắt: m T . x t . y S .kv
Tra bảng 1-1.[1] ta có: C = 292; x = 0,15 ; y = 0,2 ; m = 0,2 v
Chu kì bền trung bình của dao: T= 60 phút
kv: Hệ số điều chỉnh chung cho tốc độ cắt phụ thuộc vào các điều kiện cụ thể. kv= kmv.k .k nv .k uv φv.krv
kmv: Hệ số phụ thuộc vào chất liệu của vật liệu gia công. Chọn kmv = 1
knv: Hệ số phụ thuộc vào trạng thái bề mặt phôi. Chọn k = 0,8 nv
kuv: Hệ số phụ thuộc vào vật liệu dụng cụ cắt. Chọn k = 1 uv
kφv: Hệ số phụ thuộc vào góc cắt chính. Chọn kφv = 1 Ta có k = 1.0,8.1.1 = 0,8 v
Lớp Công nghệ chế tạo cơ khí 55 56
Đồ án tốt nghiệp chuyên ngành Công nghệ chế tạo cơ khí 292 V .0,8 113,62 0,2 0,15 0,2 60 .1,1 .0,57 (m/phút) 1000.V 1000.113,62 n 288
Tốc độ của trục chính: .D 3,14.125,6 (vòng/phút)
Chọn tốc độ quay theo máy ta có: n= 250 (vòng/phút) .D.n 3,14.125, 6.250 V 98,6 Vậy 1000 1000 (m/phút) P 10.C . Pxz t . nz V . yPz S .k Lực cắt P z pz pz z: Tra bảng 2-19.[2] ta có:
Cpz = 92 ; x = 1 ; y = 0,75 ; n =0 Tra bảng 15-1.[1] ta có
kp: Hệ số chỉnh cho lực cắt: kpz =kmp.kφp.krp.kλp
Tra bảng 5-9, 5-23.[6] ta có:
Chọn krp = 0,87 ; chọn kλp = 1 ; chọn kφp = 0,89, kγp = 1
kp = kmp.kφp.krp = 1.0,87.0,89.1=0,77 y x pz pz n 0,75 1 0 P
10.C .S .t .V z .k
10.92.0,57 .1,1 .98,6 .0,77 511,18 z pz p z (N) Lực tiếp tuyếnPx: Tra bảng 2-19.[2] ta có:
Cpx= 46 ; x = 1 ; y = 0,4 ; n =0 Tra bảng 15-1.[1] ta có
Lớp Công nghệ chế tạo cơ khí 55 57
Đồ án tốt nghiệp chuyên ngành Công nghệ chế tạo cơ khí
kpx: Hệ số chỉnh cho lực cắt: k =k px rp.kφp.krp.kλp
Tra bảng 5-9, 5-23.[6] ta có:
Chọn krp = 1 ; chọn kλpy = 1 ; chọn kφpy = 01,17, kγp = 1,
kpx= kmp.kφp.krp = 1.1,17.1.1= 1,17 y x px px n 0,4 1 0 P
C .S .t .V x .k
46.0,57 .1,1 .98, 6 .1,17 47.28 x px p x (KG) P C . Pxy t . yn V . Pyy S .k Lực hướng kính: y Py py Tra bảng 2-19.[2] ta có:
Cpy= 54 ; x = 0,9 ; y = 0,75 ; n =0
kp: Hệ số chỉnh cho lực cắt: k =k p rp.kφp.krp.kλp
Tra bảng 5-9, 5-23.[6] ta có:
Chọn krp = 0,66 ; chọn kλpy = 1 ; chọn kφpy = 0,5, kγp = 1, kp = 0,66.0,5.1.1 = 0,33 xPy n yPy 0,9 0 0,75 P
C .t .V .S .k
54.1,1 .98, 6 .0,57 .0,33 12,74 y Py py (KG) P .V 511,18.98,6 z N 8, 23 Công suất cắt: 60.102 60.102 (kW)
Bước 3: Tiện bề mặt 3 Chiều sâu cắt: t = 1 mm.
Số lần chạy dao: 5 lần.
Lượng chạy dao: S= 0,57 mm/vòng (bảng 2-1.[2]).
Lớp Công nghệ chế tạo cơ khí 55 58
Đồ án tốt nghiệp chuyên ngành Công nghệ chế tạo cơ khí Cv V Tốc độ cắt: m T . x t . y S .kv
Tra bảng 1-1.[1] ta có: C = 292; x = 0,15 ; y = 0,2 ; m = 0,2 v
Chu kì bền trung bình của dao: T= 60 phút
kv: Hệ số điều chỉnh chung cho tốc độ cắt phụ thuộc vào các điều kiện cụ thể. kv= kmv.k .k nv .k uv φv.krv
kmv: Hệ số phụ thuộc vào chất liệu của vật liệu gia công. Chọn kmv = 1
knv: Hệ số phụ thuộc vào trạng thái bề mặt phôi. Chọn knv = 0,8
kuv: Hệ số phụ thuộc vào vật liệu dụng cụ cắt. Chọn kuv = 1
kφv: Hệ số phụ thuộc vào góc cắt chính. Chọn kφv = 1 Ta có k = 1.0,8.1.1 = 0,8 v 292 V .0,8 115,25 0,2 0,15 0,2 60 .1 .0,57 (m/phút) 1000.V 1000.115, 25 n 193,18
Tốc độ của trục chính: .D 3,14.190 (vòng/phút)
Chọn tốc độ quay theo máy ta có: n= 160 (vòng/phút)
Lớp Công nghệ chế tạo cơ khí 55 59
Đồ án tốt nghiệp chuyên ngành Công nghệ chế tạo cơ khí .D.n 3,14.190.160 V 95,45 Vậy 1000 1000 (m/phút) P 10.C . Pxz t . nz V . yPz S .k Lực cắt P z pz pz z: Tra bảng 2-19.[2] ta có:
Cpz = 92 ; x = 1 ; y = 0,75 ; n =0 Tra bảng 15-1.[1] ta có
kp: Hệ số chỉnh cho lực cắt: kpz =kmp.kφp.krp.kλp
Tra bảng 5-9, 5-23.[6] ta có:
Chọn krp = 0,87 ; chọn kλp = 1 ; chọn kφp = 0,89, kγp = 1
kp = kmp.kφp.krp = 1.0,87.0,89.1=0,77 p y z p x z z n 0,75 1 0 P
10.C .S .t .V .k
10.92.0,57 .1 .95,45 .0,77 464,71 z pz p z (N) Lực tiếp tuyếnP : x Tra bảng 2-19.[2] ta có:
Cpx= 46 ; x = 1 ; y = 0,4 ; n =0 Tra bảng 15-1.[1] ta có
kpx: Hệ số chỉnh cho lực cắt: k =k px rp.kφp.krp.kλp
Tra bảng 5-9, 5-23.[6] ta có:
Chọn krp = 1 ; chọn kλpy = 1 ; chọn kφpy = 01,17, kγp = 1,
kpx= kmp.kφp.krp = 1.1,17.1.1= 1,17
Lớp Công nghệ chế tạo cơ khí 55 60
Đồ án tốt nghiệp chuyên ngành Công nghệ chế tạo cơ khí y x px px n 0,4 1 0 P
C .S .t .V x.k 46.0,57 .1 .95, 45 .1,17 42,98 x px p x (KG) P C . x n y Py t . y V . Py S .k Lực hướng kính: y Py py Tra bảng 2-19.[2] ta có:
Cpy= 54 ; x = 0,9 ; y = 0,75 ; n =0
kp: Hệ số chỉnh cho lực cắt: kp=krp.kφp.krp.kλp
Tra bảng 5-9, 5-23.[6] ta có:
Chọn krp = 0,66 ; chọn kλpy = 1 ; chọn kφpy = 0,5, kγp = 1, kp = 0,66.0,5.1.1 = 0,33 x y Py n Py 0,9 0 0,75 P
C .t .V .S .k 54.1 .95,45 .0,57 .0,33 11,69 y Py py (KG) P .V 464,71.95,45 z N 7,17 Công suất cắt: 60.102 60.102 (kW)
Bước 4: Tiện bề mặt 4
Chế độ cắt của bước 4 này giống bước 2 của nguyên công 3: Sử dụng chế độ cắt của bước 2
Bước 5: Tiện vát mép.
Chế độ cắt của bước 5 này giống bước 1 của nguyên công 3: Sử dụng chế độ cắt của bước 1 của nguyên công 3.
2.6.4. Tính toán chế độ cắt cho nguyên công tiện 4 tiện tinh các bề mặt trụ ngoài và tiện mặt đầu
a) Chọn máy: Máy tiện 1K62
Lớp Công nghệ chế tạo cơ khí 55 61
Đồ án tốt nghiệp chuyên ngành Công nghệ chế tạo cơ khí
b) Chọn dao: Dao tiện ngoài gắn mảnh hợp kim cứng BK6
- Có các thông số chính như sau:H=16 mm; B=10 mm; L=100 mm; m=4 mm; a=10 mm; r= 1 mm.
Bước 1: Tiện bề mặt 1
Chiều sâu cắt: t = 0,2 mm.
Số lần chạy dao: 2 lần.
Lượng chạy dao: S= 0,31 mm/vòng (bảng 2-1.[2]).
Tra theo máy ta có: S = 0,3m/vòng Cv V Tốc độ cắt: m T . x t . y S .kv
Tra bảng 1-1.[1] ta có: C = 292; x = 0,15 ; y = 0,2 ; m = 0,2 v
Chu kì bền trung bình của dao: T= 60 phút
kv: Hệ số điều chỉnh chung cho tốc độ cắt phụ thuộc vào các điều kiện cụ thể. kv= kmv.k .k nv .k uv φv.krv
kmv: Hệ số phụ thuộc vào chất liệu của vật liệu gia công. Chọn kmv = 1
knv: Hệ số phụ thuộc vào trạng thái bề mặt phôi. Chọn k = 0,8 nv
kuv: Hệ số phụ thuộc vào vật liệu dụng cụ cắt. Chọn k = 1 uv
kφv: Hệ số phụ thuộc vào góc cắt chính.
Lớp Công nghệ chế tạo cơ khí 55 62
Đồ án tốt nghiệp chuyên ngành Công nghệ chế tạo cơ khí Chọn kφv = 1 Ta có k = 1.0,8.1.1 = 0,8 v 292 V .0,8 208,53 0,2 0,15 0,2 60 .0,2 .0,3 (m/phút) 1000.V 1000.208,53 n 535, 57
Tốc độ của trục chính: .D 3,14.124 (vòng/phút)
Chọn tốc độ quay theo máy ta có: n= 500 (vòng/phút) . . D n 3,14.124.500 V 194,68 Vậy 1000 1000 (m/phút) P 10.C . Pxz t . nz V . yPz S .k Lực cắt P z pz pz z: Tra bảng 2-19.[2] ta có:
Cpz = 92 ; x = 1 ; y = 0,75 ; n =0 Tra bảng 15-1.[1] ta có
kp: Hệ số chỉnh cho lực cắt: kpz =kmp.kφp.krp.kλp
Tra bảng 5-9, 5-23.[6] ta có:
Chọn krp = 0,87 ; chọn kλp = 1 ; chọn kφp = 0,89, kγp = 1
kp = kmp.kφp.krp = 1.0,87.0,89.1=0,77 ypz xpz n 0,75 1 0 P
10.C .S .t .V z .k
10.92.0,3 .0, 2 .194,68 .0,77 57, 43 z pz p z (N) Lực tiếp tuyến P : x Tra bảng 2-19.[2] ta có:
Lớp Công nghệ chế tạo cơ khí 55 63
Đồ án tốt nghiệp chuyên ngành Công nghệ chế tạo cơ khí
Cpx= 46 ; x = 1 ; y = 0,4 ; n =0 Tra bảng 15-1.[1] ta có
kpx: Hệ số chỉnh cho lực cắt: kpx =krp.kφp.krp.kλp
Tra bảng 5-9, 5-23.[6] ta có:
Chọn krp = 1 ; chọn kλpy = 1 ; chọn kφpy = 01,17, kγp = 1,
kpx= kmp.kφp.krp = 1.1,17.1.1= 1,17 y x px px n 0,4 1 0 P
C .S .t .V x .k 46.0,3 .0,2 .194,68 .1,17 6,65 x px p x (KG) P C . x n y Py t . y V . Py S .k Lực hướng kính: y Py py Tra bảng 2-19.[2] ta có:
Cpy= 54 ; x = 0,9 ; y = 0,75 ; n =0
kp: Hệ số chỉnh cho lực cắt: k =k p rp.kφp.krp.kλp
Tra bảng 5-9, 5-23.[6] ta có:
Chọn krp = 0,66 ; chọn kλpy = 1 ; chọn kφpy = 0,5, kγp = 1, kp = 0,66.0,5.1.1 = 0,33 x n y Py Py 0,9 0 0,75 P
C .t .V .S .k
54.0,2 .194, 68 .0,3 .0,33 1, 7 y Py py (KG) P .V 57, 43.194,68 z N 1,83 Công suất cắt: 60.102 60.102 (kW)
Lớp Công nghệ chế tạo cơ khí 55 64
Đồ án tốt nghiệp chuyên ngành Công nghệ chế tạo cơ khí
Bước 2: Tiện bề mặt 2
Chiều sâu cắt: t = 0,3 mm.
Số lần chạy dao: 1 lần.
Lượng chạy dao: S= 0,21 mm/vòng (bảng 2-1.[2]). Cv V Tốc độ cắt: m T . x t . y S .kv
Tra bảng 1-1.[1] ta có: C = 292; x = 0,15 ; y = 0,2 ; m = 0,2 v
Chu kì bền trung bình của dao: T= 60 phút
kv: Hệ số điều chỉnh chung cho tốc độ cắt phụ thuộc vào các điều kiện cụ thể. kv= kmv.k .k nv .k uv φv.krv
kmv: Hệ số phụ thuộc vào chất liệu của vật liệu gia công. Chọn kmv = 1
knv: Hệ số phụ thuộc vào trạng thái bề mặt phôi. Chọn knv = 0,8
kuv: Hệ số phụ thuộc vào vật liệu dụng cụ cắt. Chọn kuv = 1
kφv: Hệ số phụ thuộc vào góc cắt chính. Chọn kφv = 1 Ta có k = 1.0,8.1.1 = 0,8 v 292 V .0,8 210,73 0,2 0,15 0,2 60 .0,3 .0,21 (m/phút)
Lớp Công nghệ chế tạo cơ khí 55 65
Đồ án tốt nghiệp chuyên ngành Công nghệ chế tạo cơ khí 1000.V 1000.210,73 n 536.9
Tốc độ của trục chính: .D 3,14.125 (vòng/phút)
Chọn tốc độ quay theo máy ta có: n= 500 (vòng/phút) . . D n 3,14.125.500 V 196, 25 Vậy 1000 1000 (m/phút) P 10.C . Pxz t . nz V . yPz S .k Lực cắt P z pz pz z: Tra bảng 2-19.[2] ta có:
Cpz = 92 ; x = 1 ; y = 0,75 ; n =0 Tra bảng 15-1.[1] ta có
kp: Hệ số chỉnh cho lực cắt: kpz =kmp.kφp.krp.kλp
Tra bảng 5-9, 5-23.[6] ta có:
Chọn krp = 0,87 ; chọn kλp = 1 ; chọn kφp = 0,89, kγp = 1
kp = kmp.kφp.krp = 1.0,87.0,89.1=0,77 y x pz pz n 0,75 1 0 P
10.C .S .t .V z .k
10.92.0, 21 .0,3 .196,25 .0,77 65,93 z pz p z (N) Lực tiếp tuyếnP : x Tra bảng 2-19.[2] ta có:
Cpx= 46 ; x = 1 ; y = 0,4 ; n =0 Tra bảng 15-1.[1] ta có
kpx: Hệ số chỉnh cho lực cắt: k =k px rp.kφp.krp.kλp
Tra bảng 5-9, 5-23.[6] ta có:
Lớp Công nghệ chế tạo cơ khí 55 66
Đồ án tốt nghiệp chuyên ngành Công nghệ chế tạo cơ khí
Chọn krp = 1 ; chọn kλpy = 1 ; chọn kφpy = 01,17, kγp = 1,
kpx= kmp.kφp.krp = 1.1,17.1.1= 1,17 y x px px n 0,4 1 0 P
C .S .t .V x.k
46.0, 21 .0,3 .196, 25 .1,17 8,65 x px p x (KG) P C . x n y Py t . y V . Py S .k Lực hướng kính: y Py py Tra bảng 2-19.[2] ta có:
Cpy= 54 ; x = 0,9 ; y = 0,75 ; n =0
kp: Hệ số chỉnh cho lực cắt: kp=krp.kφp.krp.kλp
Tra bảng 5-9, 5-23.[6] ta có:
Chọn krp = 0,66 ; chọn kλpy = 1 ; chọn kφpy = 0,5, kγp = 1, kp = 0,66.0,5.1.1 = 0,33 x n y Py Py 0,9 0 0,75 P
C .t .V .S .k
54.0,3 .196,25 .0,21 .0,33 1,87 y Py py (KG) P.V 65,93.196,25 z N 2,11 Công suất cắt: 60.102 60.102 (kW)
Bước 3: Tiện bề mặt 4
Chế độ cắt của bước 3 này giống bước 2 của nguyên công 4: Sử dụng chế độ cắt của bước 2.
Bước 4: Tiện bề mặt 1.1
Chế độ cắt của bước 4 này giống bước 1 của nguyên công 4: Sử dụng chế độ cắt của bước 1.
Lớp Công nghệ chế tạo cơ khí 55 67
Đồ án tốt nghiệp chuyên ngành Công nghệ chế tạo cơ khí
2.6.5 Tính toán chế độ cắt cho nguyên công 5 tiện thô lỗ
100K7, tiện vát mép và tiện mặt đầu.
a) Chọn máy: Máy tiện 1K62
b) Chọn dao: Dao tiện ngoài gắn mảnh hợp kim cứng BK6
- Có các thông số chính như sau:H=16 mm; B=10 mm; L=100 mm; m=4 mm; a=10 mm; r= 1 mm.
Bước 1: Tiện bề mặt E Chiều sâu cắt: t = 1 mm.
Số lần chạy dao: 2 lần.
Lượng chạy dao: S= 0,25 mm/vòng (bảng 2-3.[2]).
Chọn theo máy ta có: S = 0,23 mm/vòng Cv V Tốc độ cắt: m T . x t . y S .kv
Tra bảng 1-1.[1] ta có: C = 292; x = 0,15 ; y = 0,2 ; m = 0,2 v
Chu kì bền trung bình của dao: T= 60 phút
kv: Hệ số điều chỉnh chung cho tốc độ cắt phụ thuộc vào các điều kiện cụ thể. kv= kmv.k .k nv .k uv φv.krv
kmv: Hệ số phụ thuộc vào chất liệu của vật liệu gia công. Chọn kmv = 1
knv: Hệ số phụ thuộc vào trạng thái bề mặt phôi. Chọn k = 0,8 nv
Lớp Công nghệ chế tạo cơ khí 55 68
Đồ án tốt nghiệp chuyên ngành Công nghệ chế tạo cơ khí
kuv: Hệ số phụ thuộc vào vật liệu dụng cụ cắt. Chọn kuv = 1
kφv: Hệ số phụ thuộc vào góc cắt chính. Chọn kφv = 1 Ta có k = 1.0,8.1.1 = 0,8 v 292 V .0,8 138,19 0,2 0,15 0,2 60 .1 .0,23 (m/phút) 1000.V 1000.138,19 n 437,9
Tốc độ của trục chính: .D 3,14.100,5 (vòng/phút)
Chọn tốc độ quay theo máy ta có: n= 400 (vòng/phút) . . D n 3,14.100,5.400 V 126, 22 Vậy 1000 1000 (m/phút) P 10.C . Pxz t . nz V . yPz S .k Lực cắt P z pz pz z: Tra bảng 2-19.[2] ta có:
Cpz = 92 ; x = 1 ; y = 0,75 ; n =0 Tra bảng 15-1.[1] ta có
kp: Hệ số chỉnh cho lực cắt: kpz =kmp.kφp.krp.kλp
Tra bảng 5-9, 5-23.[6] ta có:
Chọn krp = 0,87 ; chọn kλp = 1 ; chọn kφp = 0,89, kγp = 1
kp = kmp.kφp.krp = 1.0,87.0,89.1=0,77
Lớp Công nghệ chế tạo cơ khí 55 69
Đồ án tốt nghiệp chuyên ngành Công nghệ chế tạo cơ khí y x pz pz n 0,75 1 0 P
10.C .S .t .V z .k
10.92.0,23 .1 .126, 22 .0,77 235,27 z pz p z (N) Lực tiếp tuyếnP : x Tra bảng 2-19.[2] ta có:
Cpx= 46 ; x = 1 ; y = 0,4 ; n =0 Tra bảng 15-1.[1] ta có
kpx: Hệ số chỉnh cho lực cắt: k =k px rp.kφp.krp.kλp
Tra bảng 5-9, 5-23.[6] ta có:
Chọn krp = 1 ; chọn kλpy = 1 ; chọn kφpy = 01,17, kγp = 1,
kpx= kmp.kφp.krp = 1.1,17.1.1= 1,17 y x px px n 0,4 1 0 P
C .S .t .V x .k
46.0, 23 .1.126, 22 .1,17 29,89 x px p x (KG) P C . x n y Py t . y V . Py S .k Lực hướng kính: y Py py Tra bảng 2-19.[2] ta có:
Cpy= 54 ; x = 0,9 ; y = 0,75 ; n =0
kp: Hệ số chỉnh cho lực cắt: k =k p rp.kφp.krp.kλp
Tra bảng 5-9, 5-23.[6] ta có:
Chọn krp = 0,66 ; chọn kλpy = 1 ; chọn kφpy = 0,5, kγp = 1, kp = 0,66.0,5.1.1 = 0,33 x n y Py Py 0,9 0 0,75 P
C .t .V .S .k
54.1 .126, 22 .0, 23 .0,33 5,92 y Py py (KG)
Lớp Công nghệ chế tạo cơ khí 55 70
Đồ án tốt nghiệp chuyên ngành Công nghệ chế tạo cơ khí P.V 235, 27.126,22 z N 4,85 Công suất cắt: 60.102 60.102 (kW)
Bước 2: Tiện bề mặt E.3
Chiều sâu cắt: t = 1,3 mm.
Số lần chạy dao: 1 lần.
Lượng chạy dao: S= 0,3 mm/vòng (bảng 5-72.[6]).
Tra theo máy ta có: S = 0,3 mm/vòng Cv V Tốc độ cắt: m T . x t . y S .kv
Tra bảng 1-1.[1] ta có: C = 292; x = 0,15 ; y = 0,2 ; m = 0,2 v
Chu kì bền trung bình của dao: T= 120 phút
kv: Hệ số điều chỉnh chung cho tốc độ cắt phụ thuộc vào các điều kiện cụ thể. kv= kmv.k .k nv .k uv φv.krv
kmv: Hệ số phụ thuộc vào chất liệu của vật liệu gia công. Chọn kmv = 1
knv: Hệ số phụ thuộc vào trạng thái bề mặt phôi. Chọn knv = 0,8
kuv: Hệ số phụ thuộc vào vật liệu dụng cụ cắt. Chọn kuv = 1
kφv: Hệ số phụ thuộc vào góc cắt chính. Chọn kφv = 1
Lớp Công nghệ chế tạo cơ khí 55 71
Đồ án tốt nghiệp chuyên ngành Công nghệ chế tạo cơ khí Ta có k = 1.0,8.1.1 = 0,8 v 292 V .0,8 101,13 0,2 0,15 0,2 180 .1,3 .0,3 (m/phút) 1000.V 1000.101,3 n 314, 43
Tốc độ của trục chính: .D 3,14.102,6 (vòng/phút)
Chọn tốc độ quay theo máy ta có: n= 250 (vòng/phút) .D.n 3,14.102,6.250 V 80,54 Vậy 1000 1000 (m/phút) P 10.C . Pxz t . nz V . yPz S .k Lực cắt P z pz pz z: Tra bảng 2-19.[2] ta có:
Cpz = 92 ; x = 1 ; y = 0,75 ; n =0 Tra bảng 15-1.[1] ta có
kp: Hệ số chỉnh cho lực cắt: kpz =kmp.kφp.krp.kλp
Tra bảng 5-9, 5-23.[6] ta có:
Chọn krp = 0,87 ; chọn kλp = 1 ; chọn kφp = 0,89, kγp = 1
kp = kmp.kφp.krp = 1.0,87.0,89.1=0,77 y x pz pz n 0,75 1 0 P
10.C .S .t .V z .k
10.92.0,3 .1,3 .80,54 .0, 77 373,3 z pz p z (N) Lực tiếp tuyếnP : x Tra bảng 2-19.[2] ta có:
Cpx= 46 ; x = 1 ; y = 0,4 ; n =0
Lớp Công nghệ chế tạo cơ khí 55 72
Đồ án tốt nghiệp chuyên ngành Công nghệ chế tạo cơ khí Tra bảng 15-1.[1] ta có
kpx: Hệ số chỉnh cho lực cắt: k =k px rp.kφp.krp.kλp
Tra bảng 5-9, 5-23.[6] ta có:
Chọn krp = 1 ; chọn kλpy = 1 ; chọn kφpy = 01,17, kγp = 1,
kpx= kmp.kφp.krp = 1.1,17.1.1= 1,17 y x px px n 0,4 1 0 P
C .S .t .V x.k 46.0,3 .1,3 .80,54 .1,17 43,22 x px p x (KG) P C . x n y Py t . y V . Py S .k Lực hướng kính: y Py py Tra bảng 2-19.[2] ta có:
Cpy= 54 ; x = 0,9 ; y = 0,75 ; n =0
kp: Hệ số chỉnh cho lực cắt: kp=krp.kφp.krp.kλp
Tra bảng 5-9, 5-23.[6] ta có:
Chọn krp = 0,66 ; chọn kλpy = 1 ; chọn kφpy = 0,5, kγp = 1, kp = 0,66.0,5.1.1 = 0,33 x n y Py Py 0,9 0 0,75 P
C .t .V .S .k 54.1,3 .80,54 .0,3 .0,33 9,15 y Py py (KG) P .V 373,3.80,54 z N 4,9 Công suất cắt: 60.102 60.102 (kW)
Bước 3: Tiện vát mép bề mặt E.1
Chế độ cắt của bước 3 này giống với bước 1 của nguyên công 5: Sử dụng chế độ cắt của bước 1 nguyên công 5.
Bước 4: Tiện bề mép bề mặt E.2
Lớp Công nghệ chế tạo cơ khí 55 73
Đồ án tốt nghiệp chuyên ngành Công nghệ chế tạo cơ khí
Chế độ cắt của bước 4 này giống với bước 1 của nguyên công 5: Sử dụng chế độ cắt của bước 1 nguyên công 5.
Bước 5: Tiện bề mặt 5
Chế độ cắt của bước 5 này giống với bước 1 của nguyên công 5: Sử dụng chế độ cắt của bước 1 nguyên công 5.
Bước 6: Tiện bề mặt 6
Chế độ cắt của bước 6 này giống với bước 1 của nguyên công 5: Sử dụng chế độ cắt của bước 1 nguyên công 5.
2.6.6 Tính toán chế độ cắt cho nguyên công 6 tiện tinh lỗ
100K7, tiện vát mép và tiện mặt đầu.
a) Chọn máy: Máy tiện 1K62
b) Chọn dao: Dao tiện ngoài gắn mảnh hợp kim cứng BK6
- Có các thông số chính như sau:H=16 mm; B=10 mm; L=100 mm; m=4 mm; a=10 mm; r= 1 mm.
Bước 1: Tiện bề mặt E
Chiều sâu cắt: t = 0,2 mm.
Số lần chạy dao: 1 lần.
Lượng chạy dao: S= 0,11 mm/vòng (bảng 2-4.[2]). Cv V Tốc độ cắt: m T . x t . y S .kv
Tra bảng 1-1.[1] ta có: C = 292; x = 0,15 ; y = 0,2 ; m = 0,2 v
Chu kì bền trung bình của dao: T= 60 phút
Lớp Công nghệ chế tạo cơ khí 55 74
Đồ án tốt nghiệp chuyên ngành Công nghệ chế tạo cơ khí
kv: Hệ số điều chỉnh chung cho tốc độ cắt phụ thuộc vào các điều kiện cụ thể. kv= kmv.k .k nv .k uv φv.krv
kmv: Hệ số phụ thuộc vào chất liệu của vật liệu gia công. Chọn kmv = 1
knv: Hệ số phụ thuộc vào trạng thái bề mặt phôi. Chọn knv = 0,8
kuv: Hệ số phụ thuộc vào vật liệu dụng cụ cắt. Chọn kuv = 1
kφv: Hệ số phụ thuộc vào góc cắt chính. Chọn kφv = 1 Ta có k = 1.0,8.1.1 = 0,8 v 292 V .0,8 203,89 0,2 0,15 0,2 60 .0,2 .0,11 (m/phút) 1000.V 1000.203,89 n 648, 68
Tốc độ của trục chính: .D 3,14.100,1 (vòng/phút)
Chọn tốc độ quay theo máy ta có: n= 630 (vòng/phút) .D.n 3,14.100,1.630 V 198,01 Vậy 1000 1000 (m/phút) P 10.C . Pxz t . nz V . yPz S .k Lực cắt P z pz pz z: Tra bảng 2-19.[2] ta có:
Lớp Công nghệ chế tạo cơ khí 55 75
Đồ án tốt nghiệp chuyên ngành Công nghệ chế tạo cơ khí
Cpz = 92 ; x = 1 ; y = 0,75 ; n =0 Tra bảng 15-1.[1] ta có
kp: Hệ số chỉnh cho lực cắt: kpz =kmp.kφp.krp.kλp
Tra bảng 5-9, 5-23.[6] ta có:
Chọn krp = 0,87 ; chọn kλp = 1 ; chọn kφp = 0,89, kγp = 1
kp = kmp.kφp.krp = 1.0,87.0,89.1=0,77 p y z p x z n 0,75 1 0 P
10.C .S .t .V z .k
10.92.0,11 .0, 2 .198,01 .0,77 27,06 z pz p z (N) Lực tiếp tuyếnP : x Tra bảng 2-19.[2] ta có:
Cpx= 46 ; x = 1 ; y = 0,4 ; n =0 Tra bảng 15-1.[1] ta có
kpx: Hệ số chỉnh cho lực cắt: k =k px rp.kφp.krp.kλp
Tra bảng 5-9, 5-23.[6] ta có:
Chọn krp = 1 ; chọn kλpy = 1 ; chọn kφpy = 01,17, kγp = 1,
kpx= kmp.kφp.krp = 1.1,17.1.1= 1,17 p y x p x x n 0,4 1 0 P
C .S .t .V x .k
46.0,11 .0, 2 .198, 01 .1,17 4, 45 x px p x (KG) P C . x n y Py t . y V . Py S .k Lực hướng kính: y Py py Tra bảng 2-19.[2] ta có:
Cpy= 54 ; x = 0,9 ; y = 0,75 ; n =0
Lớp Công nghệ chế tạo cơ khí 55 76
Đồ án tốt nghiệp chuyên ngành Công nghệ chế tạo cơ khí
kp: Hệ số chỉnh cho lực cắt: kp=krp.kφp.krp.kλp
Tra bảng 5-9, 5-23.[6] ta có:
Chọn krp = 0,66 ; chọn kλpy = 1 ; chọn kφpy = 0,5, kγp = 1, kp = 0,66.0,5.1.1 = 0,33 x n y Py Py 0,9 0 0,75 P
C .t .V .S .k
54.0, 2 .198,01 .0,11 .0,33 0,8 y Py py (KG) P.V 27,06.198,01 z N 0,87 Công suất cắt: 60.102 60.102 (kW)
Bước 2: Tiện bề mặt E.3
Chiều sâu cắt: t = 0,2 mm.
Số lần chạy dao: 1 lần.
Lượng chạy dao: S= 0,085 mm/vòng (bảng 2-7.[2]).
Tra theo máy ta được: S =0,084 mm/vòng Cv V Tốc độ cắt: m T . x t . y S .kv
Tra bảng 1-1.[1] ta có: C = 292; x = 0,15 ; y = 0,2 ; m = 0,2 v
Chu kì bền trung bình của dao: T= 180 phút
kv: Hệ số điều chỉnh chung cho tốc độ cắt phụ thuộc vào các điều kiện cụ thể. kv= kmv.k .k nv .k uv φv.krv
kmv: Hệ số phụ thuộc vào chất liệu của vật liệu gia công. Chọn kmv = 1
Lớp Công nghệ chế tạo cơ khí 55 77
Đồ án tốt nghiệp chuyên ngành Công nghệ chế tạo cơ khí
knv: Hệ số phụ thuộc vào trạng thái bề mặt phôi. Chọn k = 0,8 nv
kuv: Hệ số phụ thuộc vào vật liệu dụng cụ cắt. Chọn k = 1 uv
kφv: Hệ số phụ thuộc vào góc cắt chính. Chọn kφv = 1 Ta có k = 1.0,8.1.1 = 0,8 v 292 V .0,8 172,74 0,2 0,15 0,2 180 .0,2 .0,084 (m/phút) 1000.V 1000.172,74 n 534
Tốc độ của trục chính: .D 3,14.103 (vòng/phút)
Chọn tốc độ quay theo máy ta có: n= 500 (vòng/phút) . . D n 3,14.103.500 V 161, 71 Vậy 1000 1000 (m/phút) P 10.C . Pxz t . nz V . yPz S .k Lực cắt P z pz pz z: Tra bảng 2-19.[2] ta có:
Cpz = 92 ; x = 1 ; y = 0,75 ; n =0 Tra bảng 15-1.[1] ta có
kp: Hệ số chỉnh cho lực cắt: kpz =kmp.kφp.krp.kλp
Tra bảng 5-9, 5-23.[6] ta có:
Lớp Công nghệ chế tạo cơ khí 55 78
Đồ án tốt nghiệp chuyên ngành Công nghệ chế tạo cơ khí
Chọn krp = 0,87 ; chọn kλp = 1 ; chọn kφp = 0,89, kγp = 1
kp = kmp.kφp.krp = 1.0,87.0,89.1=0,77 y x pz pz n 0,75 1 0 P
10.C .S .t .V z .k
10.92.0,084 .0, 2 .161,71 .0,77 22,1 z pz p z (N) Lực tiếp tuyếnPx: Tra bảng 2-19.[2] ta có:
Cpx= 46 ; x = 1 ; y = 0,4 ; n =0 Tra bảng 15-1.[1] ta có
kpx: Hệ số chỉnh cho lực cắt: k =k px rp.kφp.krp.kλp
Tra bảng 5-9, 5-23.[6] ta có:
Chọn krp = 1 ; chọn kλpy = 1 ; chọn kφpy = 01,17, kγp = 1,
kpx= kmp.kφp.krp = 1.1,17.1.1= 1,17 y x px px n 0,4 1 0 P
C .S .t .V x.k
46.0,084 .0,2 .161, 71 .1,17 3,99 x px p x (KG) P C . Pxy t . ny V . Pyy S .k Lực hướng kính: y Py py Tra bảng 2-19.[2] ta có:
Cpy= 54 ; x = 0,9 ; y = 0,75 ; n =0
kp: Hệ số chỉnh cho lực cắt: kp=krp.kφp.krp.kλp
Tra bảng 5-9, 5-23.[6] ta có:
Chọn krp = 0,66 ; chọn kλpy = 1 ; chọn kφpy = 0,5, kγp = 1, kp = 0,66.0,5.1.1 = 0,33
Lớp Công nghệ chế tạo cơ khí 55 79
Đồ án tốt nghiệp chuyên ngành Công nghệ chế tạo cơ khí x y Py n Py 0,9 0 0,75 P
C .t .V .S .k
54.0,2 .161, 71 .0,084 .0,33 0,65 y Py py (KG) P .V 22,1.161, 71 z N 0,58 Công suất cắt: 60.102 60.102 (kW)
Bước 3: Tiện vát mép bề mặt E.1
Chế độ cắt của bước 3 này giống với bước 1 của nguyên công 6: Sử dụng chế độ cắt của bước 2 nguyên công 6.
Bước 4: Tiện bề mép bề mặt E.2
Chế độ cắt của bước 4 này giống với bước 1 của nguyên công 6: Sử dụng chế độ cắt của bước 2 nguyên công 6.
Bước 5: Tiện bề mặt 5
Chế độ cắt của bước 5 này giống với bước 1 của nguyên công 6: Sử dụng chế độ cắt của bước 1 nguyên công 6.
Bước 6: Tiện bề mặt 6
Chế độ cắt của bước 5 này giống với bước 1 của nguyên công 6: Sử dụng chế độ
cắt của bước 1 nguyên công 6.
2.6.7 Tính toán chế độ cắt cho nguyên công 7 phay thô bề mặt 7
a) Chọn máy: Để phay mặt đầu ta chọn máy phay đứng 6H12 của Nga tra bảng 9-38 [7]
b) Chọn dao: Để phay mặt đầu ta dùng dao phay mặt đầu răng chắp mảnh hợp kim cứng. BK6
Các thông số: - Đường kính dao: D = 100 (mm), B = 50 (mm), d = 32 (mm) Bảng 4-95 [5] - Số răng: Z= 10
Lớp Công nghệ chế tạo cơ khí 55 80
Đồ án tốt nghiệp chuyên ngành Công nghệ chế tạo cơ khí
Thông số của dao tra ở bảng 4-94 trang 376 [5] c) Tra chế độ cắt Chiều sâu cắt: 2 (mm)
Lượng chạy dao răng: SZ = 0,16 (mm/răng).
Lượng chạy dao vòng: S=Sz.Z= 0,18.10 =1,6 mm/vòng.
Tốc độ cắt V (m/phút) được tính theo công thức: C . q D V V .k T .
m t .xS .yB .u P v Z Z
Các hệ số CV, m,p, u, x, y, q được tra ở bảng 5.39.[6] ta có:
Bảng 2. 7: Thông số chế độ cắt Cv qv xv yv Uv pv mv 445 0,2 0,15 0,35 0,2 0 0,32
Chu kỳ bền trung bình của dao phay tra ở bảng 5.40 ta có T=180 (phút)
Hệ số điều chỉnh chung cho tốc độ cắt Kv phụ thuộc vào điều kiện cụ thể k k .k .k V MV nv uv .
+) kMV : Hệ số phụ thuộc vào chất lượng của bề mặt gia công cho trong bảng 5-1-> 5-4.[6] ta có kMV=1. +) k k
uv : Hệ số phụ thuộc vào vật liệu dụng cụ cắt uv = 1 tra bảng 5-7.[6] +) k k
nv : Hệ số phụ thuộc vào trạng thái bề mặt phôi 0,8 nv .tra bảng 5-6.[6] Vậy k =1.1.0,8 = 0,8 v
Lớp Công nghệ chế tạo cơ khí 55 81
Đồ án tốt nghiệp chuyên ngành Công nghệ chế tạo cơ khí Vậy V= 132,85 m/phút. 1000.V 1000.132,85 n 423,01
Số vòng quay trục chính: .D 3,14.100 vòng/phút.
Chọn số vòng quay theo máy ta có: n = 475 vòng/phút. . n .D 475.3,14.100 V 149,15 t 1000 1000 m/phút.
Lượng chạy dao phút và lượng chạy dao thực tế theo máy:
Sm = SZ bảng . Z . n = 0,16.10.475 = 760 mm/ph
Theo máy chọn Sm = 750 mm/ph. Vậy: 750 SZthuc 0,16 10.475 mm răng C t S B Z
p . x p . y p z . u p . P .K z q p Lực cắt P p D . p n z: Tra bảng 3-5. [1] ta có:
Bảng 2. 8: Thông số chế độ cắt Cp xp yp up ωp qp 54,5 0,9 0,74 1 0 1 Theo bảng 12-1.[1] ta có: 0,3 0,3 b 65 K K 0,96 p mp 75 75
Lớp Công nghệ chế tạo cơ khí 55 82
Đồ án tốt nghiệp chuyên ngành Công nghệ chế tạo cơ khí 0,9 0,74 1 54,5.2 .0,16 .50 .10 P 131,02 z
Thay vào công thức ta có: 1 0 100 .475 KG P .V 131, 02.132,85 z N 2,84 Công suất cắt: 60.102 60.102 kW
2.6.8. Tính chế độ cắt cho nguyên công 8 phay bề mặt T
a) Chọn máy: Để phay mặt đầu ta chọn máy phay đứng 6H12 của Nga tra bảng 9-38 [7]
b) Chọn dao: Để phay mặt đầu ta dùng dao phay mặt đầu răng chắp mảnh hợp kim cứng. BK6
Các thông số: - Đường kính dao: D = 100 (mm), B = 50 (mm), d = 32 (mm) Bảng 4-95 [5] - Số răng: Z= 10
Thông số của dao tra ở bảng 4-94 trang 376 [5]
c) Tra chế độ cắt: tra bảng 5-125.[6] Chiều sâu cắt: 2 (mm)
Lượng chạy dao răng: SZ = 0,19 (mm/răng). tra bảng 5-125.[6]
Lượng chạy dao vòng: S=Sz.Z= 0,19.10 =1,9 mm/vòng.
Tốc độ V = 180 tra bảng 5-127.[6] Công suất N = 1,84 kW
2.6.9. Tính toán chế độ cắt cho nguyên công 9 khoét, doa và vát mép bề mặt D
Chọn máy: Để khoét, doa lỗ 56 ta chọn máy khoan cần 2A55
Lớp Công nghệ chế tạo cơ khí 55 83
Đồ án tốt nghiệp chuyên ngành Công nghệ chế tạo cơ khí
Chọn dao: Để khoét 2 lỗ ta dùng mũi khoét đuôi côn răng chắp, hợp kim cứng BK8. Các thông số dao: (mm)
Bảng 2. 9: Thông số dao Đường kính danh L l (mm) Số côn mooc Số răng z nghĩa D (mm) (mm) Khoét thô 53 180 85 Khoét tinh 55,71 180 85 Doa thô 55,91 140 40 4 4 Doa tinh 56 140 40 4 4
Bước 1: Khoét thô lỗ đạt Φ53 D d 53 48 t 2,5 Chiều sâu cắt 2 2 (mm).
Lượng chạy dao S = 0,9 mm/vòng tra bảng 2-.3.[2]
Tra theo máy ta được S = 0,79 mm/vòng C . q D v V .k m x y v Vận tốc khi khoét: T .t .S m/phút Theo bảng 5-29.[6] ta có:
Bảng 2. 10: Thông số tính vận tốc Cv q x y mv 105 0,4 0,15 0,45 0,4
Theo bảng 5-1.[6] ta có: KMV = 1 ; bảng 5-31.[6] ta có: Klv = 1
Lớp Công nghệ chế tạo cơ khí 55 84
Đồ án tốt nghiệp chuyên ngành Công nghệ chế tạo cơ khí
bảng 5-5.[6] ta có: K = 0,8; bảng 5-6.[6] ta có: K nv uv = 0,83
Ta có Kv = 1.0,83.1.0,8 = 0,66
Tra bảng 5-30.[6] ta được T = 80 ph 0,4 105.53 V .0,66 56,96 0,4 0,15 0,45 Thay vào ta được: 80 .2,5 .0,79 m/phút Số vòng quay: 1000.V 1000.56,96 n 324, 26 .D 3,14.53 v/ph Theo máy lấy: n = 300 v/ph Momen khi khoét thô: M x q y x = 10.CM.t . D .S .kp (Nm)
Tra bảng 5-9.[6] ta đc kp = 1 Theo bảng 5-32.[6] ta có:
Bảng 2. 11: Thông số tính Momen CM q x y 0,196 0,85 0,8 0,7 Ta có M 0,8 x = 10.0,196.2,5 .53 .0,79 0,85 0,7.1 = 101,06 (Nm) Lực chiều trục P: P = 10.C q y p.t .D x . S .k (N) p
Tra bảng 5-9.[6] ta đc kp = 1
Lớp Công nghệ chế tạo cơ khí 55 85
Đồ án tốt nghiệp chuyên ngành Công nghệ chế tạo cơ khí Theo bảng 3-52.[6] ta có:
Bảng 2. 12: Thông số tính lực cắt Cp q x y 46 - 1 0,4
Ta có: P = 10.46.2,51.530. 0,79 .1 = 1046,5 (N) 0,4 Công suất cắt: 101,06.300 N 3,1 9750 (kW)
So với máy thì đảm bảo làm việc an toàn.
Bước 2: Khoét tinh lỗ đạt Φ55,71 D d 55,71 53 t 1,355 Chiều sâu cắt 2 2 (mm).
Lượng chạy dao S = 0,9 mm/vòng tra bảng 2-.3.[2]
Tra theo máy ta được S = 0,79 mm/vòng C . q D v V .k m x y v Vận tốc khi khoét: T .t .S m/phút Theo bảng 5-29.[6] ta có:
Bảng 2. 13: Thông số tính vận tốc Cv q x y mv 105 0,4 0,15 0,45 0,4
Lớp Công nghệ chế tạo cơ khí 55 86
Đồ án tốt nghiệp chuyên ngành Công nghệ chế tạo cơ khí
Theo bảng 5-1.[6] ta có: KMV = 1 ; bảng 5-31.[6] ta có: Klv = 1
bảng 5-5.[6] ta có: K = 0,8; bảng 5-6.[6] ta có: K nv uv = 0,83
Ta có Kv = 1.0,83.1.0,8 = 0,66
Tra bảng 5-30.[6] ta được T = 80 ph 0,4 105.55, 71 V .0,66 63, 7 0,4 0,15 0,45 Thay vào ta được: 80 .1,355 .0,79 m/phút Số vòng quay: 1000.V 1000.63, 7 n 364,14 .D 3,14.55, 71 v/ph Theo máy lấy: n = 300 v/ph Momen khi khoét tinh: M x q y x = 10.CM.t . D .S .kp (Nm)
Tra bảng 5-9.[6] ta đc kp = 1 Theo bảng 5-32.[6] ta có:
Bảng 2. 14: Thông số tính Momen CM q x y 0,196 0,85 0,8 0,7 Ta có M 0,8 0,7 x = 10.0,196.1,355 .55,71 .0,79 0,85 .1 = 64,59 (Nm) Lực chiều trục P: P = 10.C x q y p.t .D . S .kp (N)
Lớp Công nghệ chế tạo cơ khí 55 87
Đồ án tốt nghiệp chuyên ngành Công nghệ chế tạo cơ khí
Tra bảng 5-9.[6] ta đc kp = 1 Theo bảng 3-52.[6] ta có:
Bảng 2. 15: Thông số tính lực cắt Cp q x y 46 - 1 0,4
Ta có: P = 10.46.1,3551.55,710. 0,79 .1 = 567,21 (N) 0,4 Công suất cắt: 64,59.300 N 1,98 9750 (kW)
So với máy thì đảm bảo làm việc an toàn.
Bước 3: Doa thô lỗ đạt 55,91 D d 55,91 55,71 t 0,1 Chiều sâu cắt 2 2 mm
Lượng chạy dao S = 2,38 mm/vòng
Theo máy chọn S = 2,2 mm/vòng C . q D v V .k m x y v Vận tốc khi doa : T .t .S m/phút Theo bảng 5-29.[6] ta có:
Bảng 2. 16: Thông số tính vận tốc Cv q x y m
Lớp Công nghệ chế tạo cơ khí 55 88
Đồ án tốt nghiệp chuyên ngành Công nghệ chế tạo cơ khí 109 0,2 0 0,5 0,45
Theo bảng 5-1.[6] ta có: KMV = 1 ; bảng 5-31.[6] ta có: Klv = 1
bảng 5-5.[6] ta có: K = 0,8; bảng 5-6.[6] ta có: K nv uv = 0,83
Ta có: K = 1.0,83.1.0,8 = 0,66 v
Tra bảng 5-30.[6] ta được T = 180 ph 0,2 109.55,91 V .0,66 10,9 0,45 0 0,45 Thay vào ta được: 180 .0,1 .2, 2 m/phút Số vòng quay: 1000.V 1000.10,9 n 62,08 .D 3,14.55,91 v/ph Theo máy lấy: n = 60 v/ph
Momen xoắn khi doa nhỏ có thể bỏ qua.
Bước 4: Doa tinh lỗ đạt 56 D d 56 55,91 t 0,045 Chiều sâu cắt 2 2 mm
Lượng chạy dao S = 2,38 mm/vòng
Theo máy chọn S = 2,2 mm/vòng C . q D v V .k m x y v Vận tốc khi doa : T .t .S m/phút Theo bảng 5-29.[6] ta có:
Lớp Công nghệ chế tạo cơ khí 55 89
Đồ án tốt nghiệp chuyên ngành Công nghệ chế tạo cơ khí
Bảng 2. 17: Thông số tính vận tốc Cv q x y m 109 0,2 0 0,5 0,45
Theo bảng 5-1.[6] ta có: KMV = 1 ; bảng 5-31.[6] ta có: Klv = 1
bảng 5-5.[6] ta có: K = 0,8; bảng 5-6.[6] ta có: K nv uv = 0,83
Ta có: Kv = 1.0,83.1.0,8 = 0,66
Tra bảng 5-30.[6] ta được T = 180 ph 0,2 109.56 V .0,66 10,91 0,45 0 0,45 Thay vào ta được: 180 .0,045 .2, 2 m/phút Số vòng quay: 1000.V 1000.10,91 n 62,04 .D 3,14.56 v/ph Theo máy lấy: n = 60 v/ph
Momen xoắn khi doa nhỏ có thể bỏ qua.
2.6.10. Tính toán chế độ cắt cho nguyên công 10
Chế độ cắt của nguyên công 10 này giống với chế độ cắt của nguyên công 2 nên sử dụng
chế độ cắt của nguyên công 2. Thực hiện taroren bằng tay.
2.6.11. Tính toán chế độ cắt cho nguyên công 11
Bước 1: Khoan lỗ trên bề mặt 3 Khoan lỗ 14
Lớp Công nghệ chế tạo cơ khí 55 90
Đồ án tốt nghiệp chuyên ngành Công nghệ chế tạo cơ khí
Chọn dao: Để khoan lỗ ta dùng mũi khoan bằng hợp kim cứng và gắn mảnh hợp kim cứng BK8 D 14 t 7 Chiều sâu cắt 2 2 (mm)
Lượng chạy dao: tra bảng 5-94 [6] chọn S =0,22mm/vòng. Tra theo máy ta được = 0,2mm/vòng.
Tốc độ cắt tra bảng 5-95[6] ta có V = 64 (m/phút). b
Tính vận tốc cắt V=Vb.kv Với Vb= 64 m/phút, k = 0,8 v Ta có: V= 64.0,8 = 51,2 (m/phút) Số vòng quay trục chính: 1000.V 1000.51,2 n 1164,6 .D 3,14.14 (vòng/phút)
Chọn theo máy 950 vòng/phút . n .D 950.3,14.14 V 41,76
Tính lại vận tốc cắt: 1000 1000 vòng/phút Công suất cắt: N = Nb.Kv
Tra bảng 5-96 [6] ta có: N = 1,9 kW; Kv = 0,8 Suy ra: N = 1,52 kW
Bước 3: Khoan lỗ trên bề mặt 10
Sử dụng chế độ cắt của nguyên công 2
Lớp Công nghệ chế tạo cơ khí 55 91
Đồ án tốt nghiệp chuyên ngành Công nghệ chế tạo cơ khí
2.6.12. Tính toán chế độ cắt cho nguyên công 12
Khoan các lỗ trên bề mặt T
Dùng khoan tay để khoan các lỗ trên bề mặt T
2.6.13. Tính toán chế độ cắt cho nguyên công 13 Bước 1: Mài thô Số lần mài: 1 lần
Dùng mặt chu vi đá mài với bước tiến ngang: N C . r V . y S . q d .tx N ph p Tra bảng 5-56.[6] ta có:
Bảng 2.18. Thông số chế độ cắt CN r x y q z 0,81 0,55 1 0,7 0,3 1
Tra bảng 5-55.[6] ta được:
Bảng 2.19. Thông số tính lực Vđm Vphôi t S Sp (m/s) (m/phôi) mm mm/phôi mm/vòng 20 4 0,03 0,5 - Thay vào ta được:
Lớp Công nghệ chế tạo cơ khí 55 92
Đồ án tốt nghiệp chuyên ngành Công nghệ chế tạo cơ khí r y q x 0,55 0,7 0,3 1
N C .V .S .d .t 0,81.4 .0,5 .100,06 .0,03 0, 07 N ph p (kW) Bước 1: Mài tinh Số lần mài: 1 lần
Dùng mặt chu vi đá mài với bước tiến ngang: N C . r V . y S . q d .t x N ph p Tra bảng 5-56.[6] ta có:
Bảng 2.20. Thông số chế độ cắt CN r x y q z 0,81 0,55 1 0,7 0,3 1
Tra bảng 5-55.[6] ta được:
Bảng 2.21. Thông số chế độ cắt Vđm Vphôi t S Sp (m/s) (m/phôi) mm mm/phôi mm/vòng 20 4 0,02 0,5 - Thay vào ta được: r y q x 0,55 0,7 0,3 1
N C .V .S .d .t 0,81.4 .0,5 .100 .0,02 0,047 N ph p (kW)
2.7. Bảng quy trình công nghệ
Căn cứ vào kết quả tính toán chế độ cắt đã tính toán ở mục 2.6 ta có bảng quy trình công nghệ:
Lớp Công nghệ chế tạo cơ khí 55 93
Đồ án tốt nghiệp chuyên ngành Công nghệ chế tạo cơ khí
Lớp Công nghệ chế tạo cơ khí 55 94
Đồ án tốt nghiệp chuyên ngành Công nghệ chế tạo cơ khí
Bảng 2. 22: Bảng quy trình công nghệ
Lớp Công nghệ chế tạo cơ khí 55 95
Đồ án tốt nghiệp chuyên ngành Công nghệ chế tạo cơ khí
CHƯƠNG 3: TÍNH TOÁN THIẾT KẾ ĐỒ GÁ CHO NGUYÊN
CÔNG KHOAN, KHOÉT, DOA LỖ 56
3.1. Thiết kế nguyên lý định vị và cấu tạo của đồ gá. 3.1.1 Sơ đồ nguyên công
Hình 3. 1: Sơ đồ nguyên công 9
Định vị: Chi tiết được định vị 6 bậc tự do. Mặt đáy của chi tiết tỳ vào phiến tỳ định vị 3
bậc, mặt 7 tỳ vào chốt tỳ định vị 1 bậc, dùng chốt trám định vị 2 bậc tự do còn lại.
Kẹp chặt: Chi tiết được kẹp chặt nhờ bu lông.
Lớp Công nghệ chế tạo cơ khí 55 96
Đồ án tốt nghiệp chuyên ngành Công nghệ chế tạo cơ khí
3.1.2. Cấu tạo của đồ gá và nguyên lý làm việc.
Đồ gá thiết kế như hình 3.2 Nguyên lý làm việc
Chi tiết gia công 1 được định vị trên phiến tỳ 12 khống chế 3 bậc tự do, 2 chốt trụ ngắn
19 khống chế 3 bậc tự do và cụm chốt tỳ 7 khống chế 1 bậc tự do giúp tăng độ cứng vũng
cho chi tiết. Chi tiết được kẹp chặt nhờ trục khi xiết đai ốc 9 lắp trên vòng đệm 10.
Khi khoét thô lỗ đạt 53 xong, nới đai ốc 9 để thay bạc thay nhanh 15 tiến hành khoét tinh lỗ đạt 55,71.
Sau đó nới vít 5 để thay bạc thay nhanh 1 tiến hành doa thô lỗ đạt Φ55,91.Khi doa thô lỗ
đạt 55,91 xong, nới đai ốc 5 để thay bạc thay nhanh 1 tiến hành doa tinh lỗ 56
Sau khi khoét, doa xong lỗ thứ nhất tiến hành nới lỏng đai ốc 22 kéo chốt phân độ 21
xuống dưới dùng tay đòn lắp vào chốt xoay phiến tỳ 12 để tiếp tục gia công đầu lỗ bên kia
theo trình tự tương tự như trên.
Khi khoét, doa xong nới lỏng đai ốc 9 và chốt trụ ngắn 19 và lấy chi tiết ra.
Hình 3. 2: Cấu tạo đồ gá
Lớp Công nghệ chế tạo cơ khí 55 97
Đồ án tốt nghiệp chuyên ngành Công nghệ chế tạo cơ khí
3.2. Tính toán lực kẹp chặt và tính toán đường kính bu lông
3.2.1. Tính toán lực kẹp chặt Sơ đồ momen lực:
Hình 3. 3: Sơ đồ momen lực
Chi tiết chịu các lực tác dụng:
Mc – Momen xoắn trên mũi khoét do lực cắt gây ra (Nm) Pc - Lực dọc trục (N)
W – Lực kẹp chặt chi tiết (N)
Lớp Công nghệ chế tạo cơ khí 55 98
Đồ án tốt nghiệp chuyên ngành Công nghệ chế tạo cơ khí
F1 – Lực ma sát do vòng đệm gây ra (N)
F2 – Lực ma sát do phiến tỳ định vị gây ra (N)
Chú ý: Bỏ qua trọng lực bản thân của chi tiết, bỏ qua ma sát tại chốt trám.
Lực cắt P có khả năng gây cho vật gia công dịch chuyển theo phương dọc trục. Lực kẹp
chặt Q vuông góc với lực cắt P sẽ gây ra các lực ma sát F1, F2 trên bề mặt kẹp chặt và bề
mặt định vị. Các lực ma sát này chống lại lực cắt P gây ra cho chi tiết gia công. Dưới tác
dụng của mô men xoắn Mc do lực cắt gây ra và lực dọc trục P chi tiết có xu hướng bị trượt
và bị lật tại điểm A, trượt khỏi điểm B.
TH1: Chi tiết có xu hướng bị trượt
Hình 3. 4: Sơ đồ momen lực TH1
Lớp Công nghệ chế tạo cơ khí 55 99
Đồ án tốt nghiệp chuyên ngành Công nghệ chế tạo cơ khí
Và ta có phương trình cân bằng chống trượt: F1 + F2 ≥ k.Pc . k P W= f f 1 2 (2) Trong đó:
Pc – lực cắt. Pc = 1046,5 N
f1 là hệ số ma sát giữa chi tiết và vòng đệm kẹp chặt. Chọn f1 = 0,1 theo tài liệu [7]
f2 là hệ số ma sát giữa chi tiết và vòng đệm kẹp chặt. Chọn f2 = 0,2 theo tài liệu [7] k - là hệ số an toàn k = k0.k1.k .k 2 .k 3 .k 4 5.
Với k – hệ số an toàn chung cho mọi trường hợp k 0 0 = 1,5
k1 – hệ số tính đến trạng thái của bề mặt gia công phôi đã qua cắt gọt. Chọn k = 1 1,2.
k2 – Hệ số tính đến sự tăng lực cắt do lưỡi cắt bị mòn trong quá trình gia công. Chọn k2 = 1.
k3 - hệ số kể đến sự tăng lực cắt khi gia công trên bề mặt không liên tục. chọn k = 1,2. 3
k4 – hệ số kể đến sự thay đổi của lực kẹp chặt phụ thuộc vào cơ cấu truyền dẫn lực trên đồ gá. Chọn k= 1,3.
k5 – hệ số tính đến khả năng xuất hiện mô men gây xoay vật gia công. Chọn k5 = 1. Suy ra: k = 1,5.1,2.1.1,2.1,3.1 = 2,81 . k P 2,81.1046,5 W= c 14703,32 f f 0,1 0,1
Thay vào phương trình (2) ta có: 1 2 (N)
Lớp Công nghệ chế tạo cơ khí 55 100
Đồ án tốt nghiệp chuyên ngành Công nghệ chế tạo cơ khí
TH2: Chi tiết có xu hướng bị lật tại điểm A
Hình 3. 5: Sơ đồ momen lực TH2
Và ta có phương trình cân bằng chống trượt: k.Pc.l1 = W.l2 k.P .l1 W= c l Suy ra: 2 (2) Trong đó:
Pc – lực cắt khi khoét thô. Pc = 1046,5 N
l1- là khoảng cách từ tâm đến điểm A
l2- là khoảng cách từ tâm đến điểm đặt lực W
f1 là hệ số ma sát giữa chi tiết và vòng đệm kẹp chặt. Chọn f1 = 0,1 theo tài liệu [9]
Lớp Công nghệ chế tạo cơ khí 55 101
Đồ án tốt nghiệp chuyên ngành Công nghệ chế tạo cơ khí
f2 là hệ số ma sát giữa chi tiết và vòng đệm kẹp chặt. Chọn f2 = 0,2 theo tài liệu.[9] k - là hệ số an toàn k = k0.k1.k .k 2 .k 3 .k 4 5.
Với k – hệ số an toàn chung cho mọi trường hợp k 0 0 = 1,5
k1 – hệ số tính đến trạng thái của bề mặt gia công phôi đã qua cắt gọt. Chọn k = 1 1,2.
k2 – Hệ số tính đến sự tăng lực cắt do lưỡi cắt bị mòn trong quá trình gia công. Chọn k2 = 1.
k3 - hệ số kể đến sự tăng lực cắt khi gia công trên bề mặt không liên tục. chọn k = 1,2. 3
k4 – hệ số kể đến sự thay đổi của lực kẹp chặt phụ thuộc vào cơ cấu truyền dẫn lực trên đồ gá. Chọn k= 1,3.
k5 – hệ số tính đến khả năng xuất hiện mô men gây xoay vật gia công. Chọn k5 = 1. Suy ra: k = 1,5.1,2.1.1,2.1,3.1 = 2,81 k.P .l 2,81.1046,5.50 c 1 W= 1176,26 l 125
Thay vào phương trình (2) ta có: 2 (N)
Lớp Công nghệ chế tạo cơ khí 55 102
Đồ án tốt nghiệp chuyên ngành Công nghệ chế tạo cơ khí
TH3: Chi tiết bị lật tại diểm B
Hình 3. 6: Sơ đồ momen lực TH3 Ta có phương trình: k.Pz.l4 = W.l3
Lớp Công nghệ chế tạo cơ khí 55 103
Đồ án tốt nghiệp chuyên ngành Công nghệ chế tạo cơ khí k.P .l4 W= z l Suy ra: 3 (3) Trong đó: 2.M 2.101,06 c P 3,81 z P D 53 z – lực cắt. N
l3- là khoảng cách từ tâm đến điểm A, l3 = 125 mm
l4- là khoảng cách từ tâm đến điểm đặt lực M , l 0 = 76mm 4
f1 là hệ số ma sát giữa chi tiết và vòng đệm kẹp chặt. Chọn f1 = 0,1 theo tài liệu [9]
f2 là hệ số ma sát giữa chi tiết và vòng đệm kẹp chặt. Chọn f2 = 0,2 theo tài liệu [9] k - là hệ số an toàn k = k0.k1.k .k 2 .k 3 .k 4 5.
Với k – hệ số an toàn chung cho mọi trường hợp k 0 0 = 1,5
k1 – hệ số tính đến trạng thái của bề mặt gia công phôi đã qua cắt gọt. Chọn k = 1 1,2.
k2 – Hệ số tính đến sự tăng lực cắt do lưỡi cắt bị mòn trong quá trình gia công. Chọn k2 = 1.
k3 - hệ số kể đến sự tăng lực cắt khi gia công trên bề mặt không liên tục. chọn k = 1,2. 3
k4 – hệ số kể đến sự thay đổi của lực kẹp chặt phụ thuộc vào cơ cấu truyền dẫn lực trên đồ gá. Chọn k= 1,3.
k5 – hệ số tính đến khả năng xuất hiện mô men gây xoay vật gia công. Chọn k5 = 1. Suy ra: k = 1,5.1,2.1.1,2.1,3.1 = 2,81
Lớp Công nghệ chế tạo cơ khí 55 104
Đồ án tốt nghiệp chuyên ngành Công nghệ chế tạo cơ khí k.P .l 2,81.3,81.76 z 4 W= 6,51 l 125
Thay vào chương trình (3) ta được: 3 (N)
KL: Qua 3 TH ta thấy để chi tiết không bị lật tại các điểm và không bị trượt thì W = 14703,32 (N)
3.2.2. Tính lực kẹp chặt bu lông Ta có W = [W] Trong đó:
W - là lực kẹp cần thiết của bu lông đảm bảo điều kiện kẹp chặt vật. Ta có công thức: 2 W [W] 0,5.d . tb K Trong đó:
dtb – Đường kính trung bình của ren.
[σK] – Giới hạn bền của vật liệu làm bu lông.
Từ công thức trên ta xác định được kích thước bu lông thỏa mãn cả 2 điều kiện với chiều dài tay đòn tiêu chuẩn: L ≈14.dtb W dtb 0,5. K Ta có σ 2 2
K = 12 kG/mm = 117,72 N/mm tra theo tài liệu [9]t tra sách chế tạo máy. Vật liệu C45 thường hóa. W 14703,32 d 15,8 tb 0,5. 0,5.117,72 K mm
Lớp Công nghệ chế tạo cơ khí 55 105
Đồ án tốt nghiệp chuyên ngành Công nghệ chế tạo cơ khí
Để đảm bảo tính công nghệ và tính thẩm mỹ cho đồ gá từ đó ta chọn đai ốc có đường kính d = 36 mm.
Lớp Công nghệ chế tạo cơ khí 55 106
Đồ án tốt nghiệp chuyên ngành Công nghệ chế tạo cơ khí KẾT LUẬN
Sau khi hoàn thành đồ án tốt nghiệp với đề tài:“NGHIÊN CỨU LẬP QUY TRÌNH CÔNG
NGHỆ CHẾ TẠO CHI TIẾT VỎ BƠM 207.20 TÍNH TOÁN, THIẾT KẾ ĐỒ GÁ KHOAN,
KHOÉT, DOA LỖ Φ56”, em đã đạt được những kết quả như sau:
- Thiết lập được các bản vẽ: bản vẽ chi tiết, bản vẽ lắp, bản vẽ quy trình công nghệ,
bản vẽ đồ gá, bản vẽ tách đồ gá.
- Qua đó nắm được đặc điểm, cấu tạo nguyên lý hoạt động của chi tiết.
- Lập quy trình công nghệ chế tạo chi tiết vỏ bơm: xác định trình tự gia công, tính
toán chế độ cắt, tính toán và tra lượng dư gia công.
- Tính toán, thiết kế, lập quy trình lắp ráp đồ gá khoan, khoét, doa lỗ Φ56.
Qua thực hiện đề tài đã giúp chúng em hệ thống hóa được các kiến thức đã được đào
tạo trong quá trình học đại học, biết cách sử dụng, tra cứu tài liệu, hoàn thiện kỹ năng vẽ
2D, lập bản vẽ kỹ thuật trên phần mền Autocad, thiết lập bản vẽ 3D… Đây cũng sẽ là
những kiến thức cần thiết cho chúng em sau ra trường và công tác trong lĩnh vực công nghệ chế tạo cơ khí.
Lớp Công nghệ chế tạo cơ khí 55 107
Đồ án tốt nghiệp chuyên ngành Công nghệ chế tạo cơ khí TÀI LIỆU THAM KHẢO
[1]. Nguyễn Ngọc Đào, Trần Thế San, Hồ Viết Bình, (2006), Chế độ cắt gia công cơ khí; NXB Đà Nẵng.
[2]. PGS.TS Trần Văn Địch, ThS Lưu Văn Nhang, ThS Nguyễn Thanh Mai, (2002), Sổ
tay gia công cơ, NXB Khoa học và kỹ thuật.
[3]. PGS.TS Trần Văn Địch, (2002), Sổ tay và Atlas đồ gá, NXB Khoa học và kỹ thuật.
[4]. PGS.TS Trần Văn Địch, (2005), Thiết kế đồ án Công nghệ chế tạo máy, NXB Khoa học và kỹ thuật.
[5]. PGS.TS Nguyễn Đắc Lộc, PGS.TS Lê Văn Tiến, PGS.TS Ninh Đức Tốn, TS Trần
Xuân Việt, (2000), Sổ tay Công nghệ chế tạo máy tập 1, NXB Khoa học và kỹ thuật.
[6]. PGS.TS Nguyễn Đắc Lộc, PGS.TS Lê Văn Tiến, PGS.TS Ninh Đức Tốn, TS Trần
Xuân Việt, (2000), Sổ tay Công nghệ chế tạo máy tập 2; NXB Khoa học và kỹ thuật.
[7]. PGS.TS Nguyễn Đắc Lộc, PGS.TS Lê Văn Tiến, PGS.TS Ninh Đức Tốn, TS Trần
Xuân Việt, (2000), Sổ tay Công nghệ chế tạo máy tập 3; NXB Khoa học và kỹ thuật.
[8]. Ninh Đức Tốn, (2012), Dung sai và lắp ghép, NXB Giáo dục Việt Nam.
[9]. Trương Nguyễn Trung, Trương Phương Anh, (2012), Kỹ thuật chế tạo máy, NXB Giao thông vận tải.
Lớp Công nghệ chế tạo cơ khí 55 108