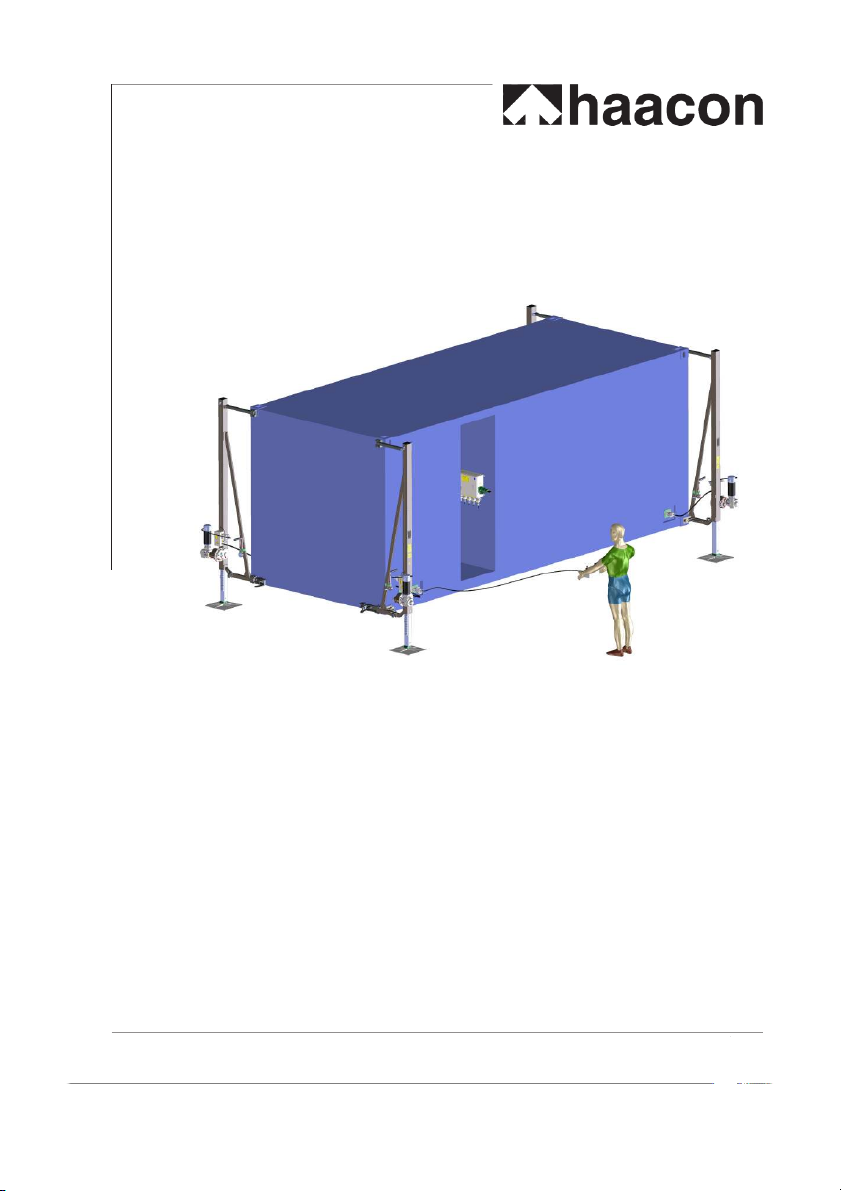
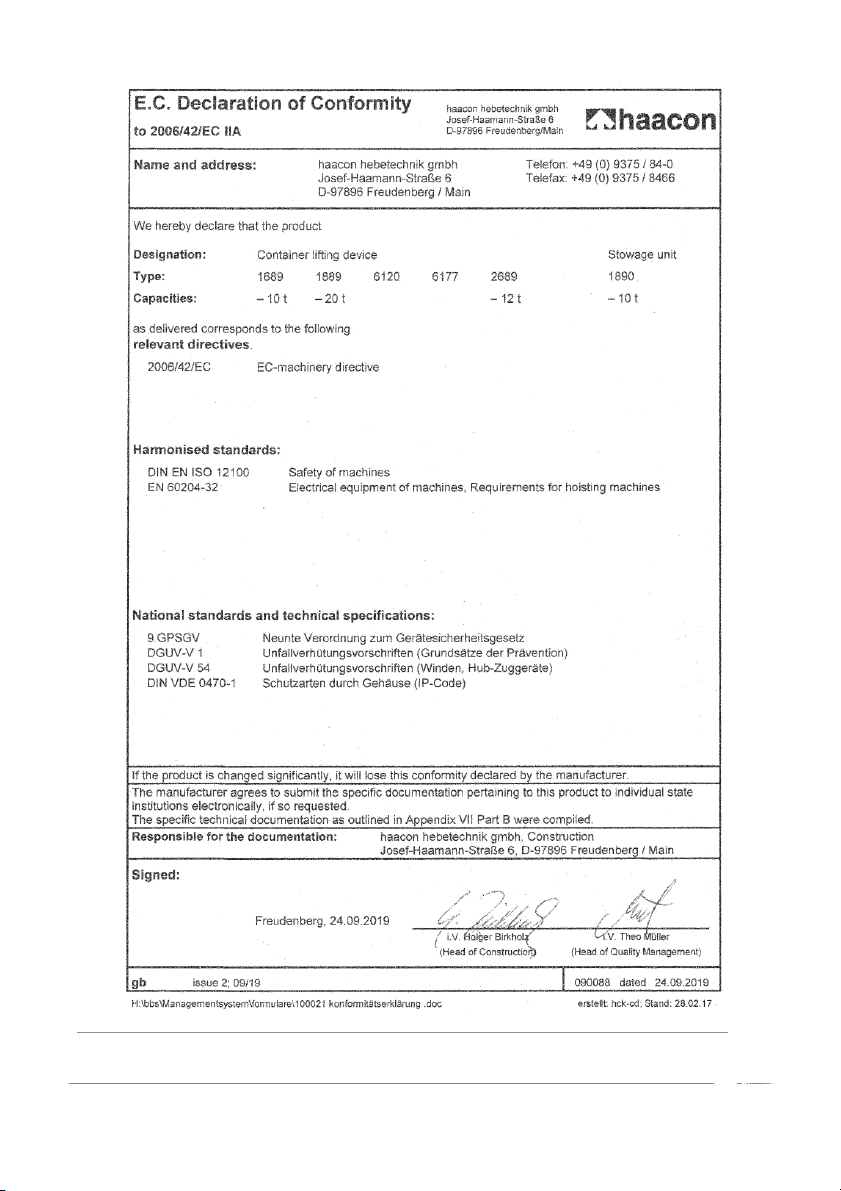
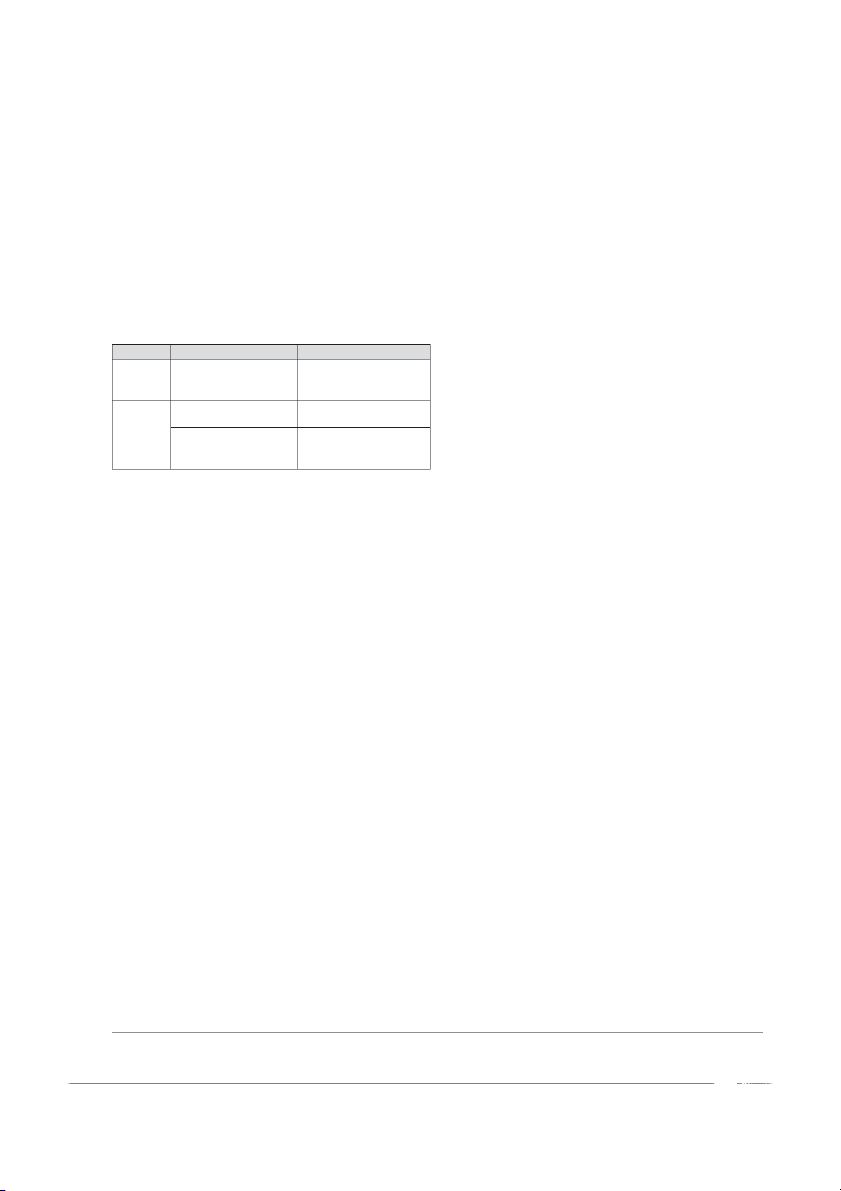
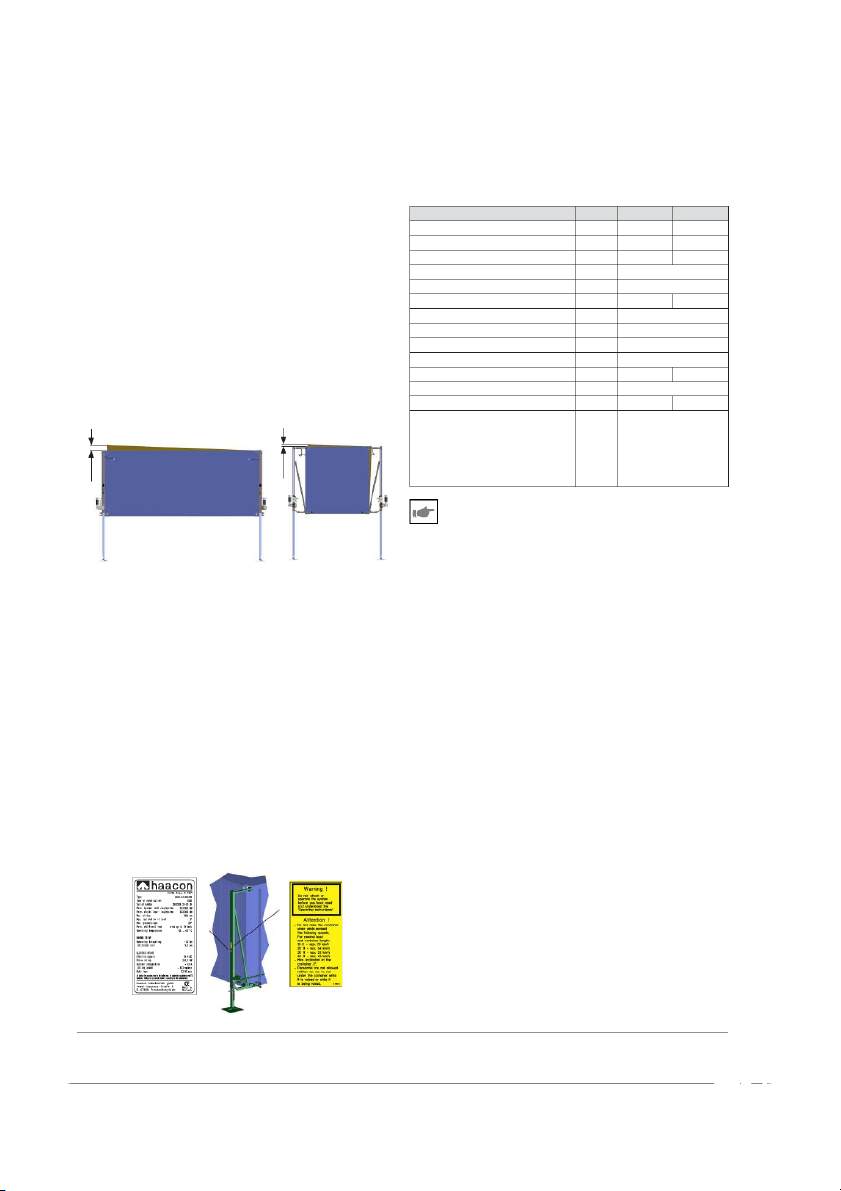
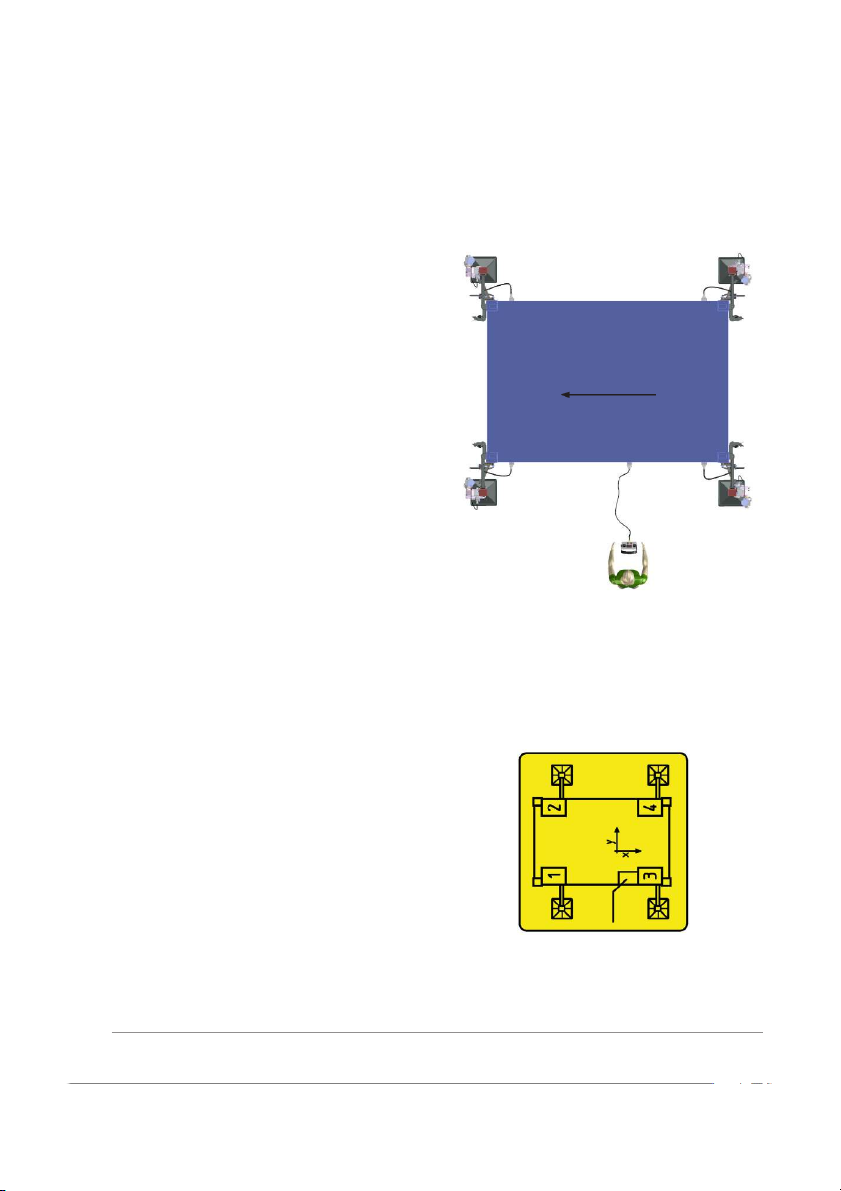
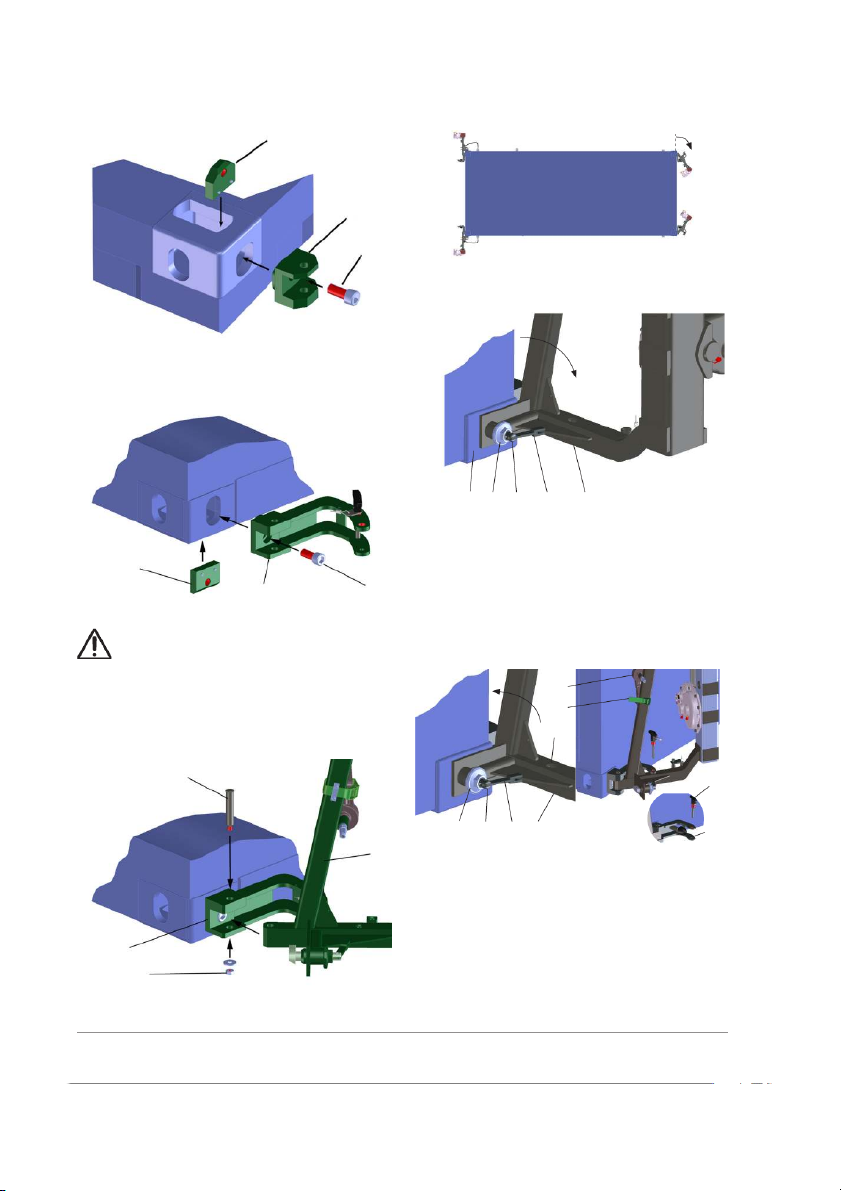
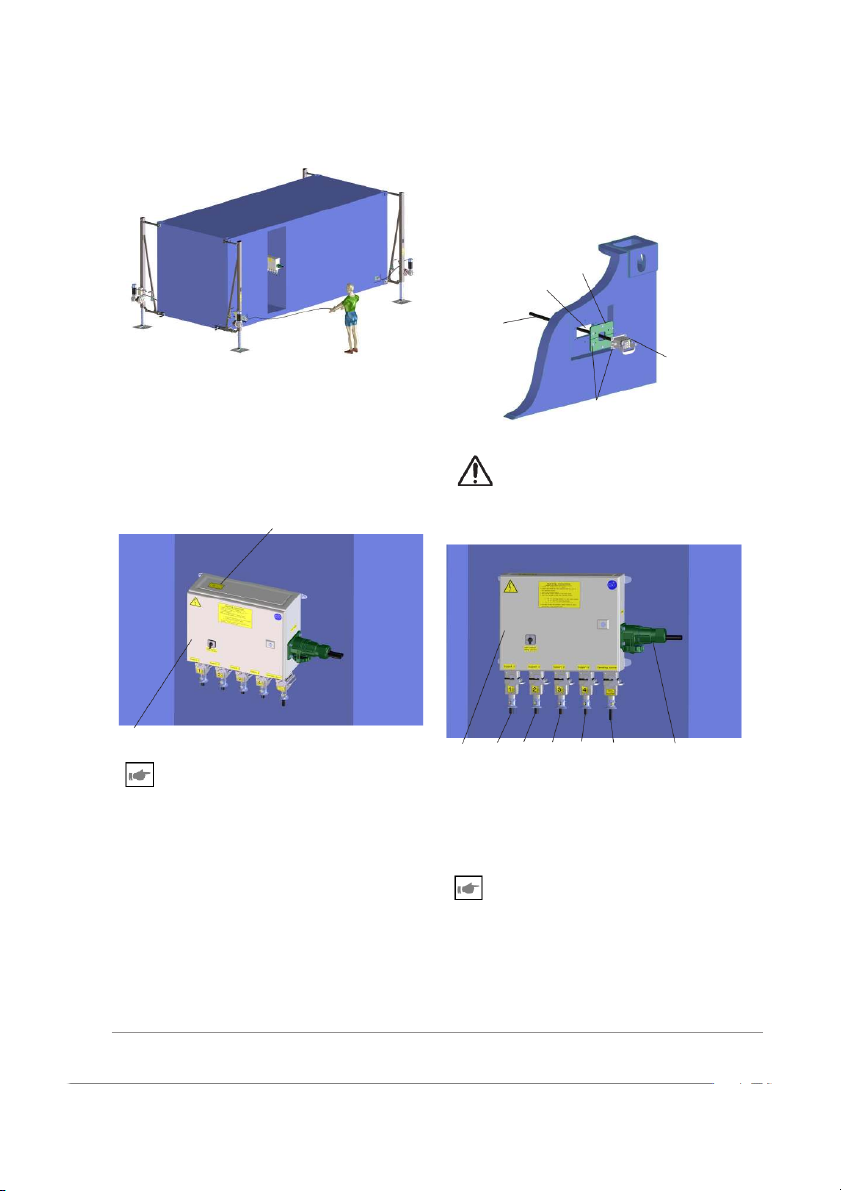
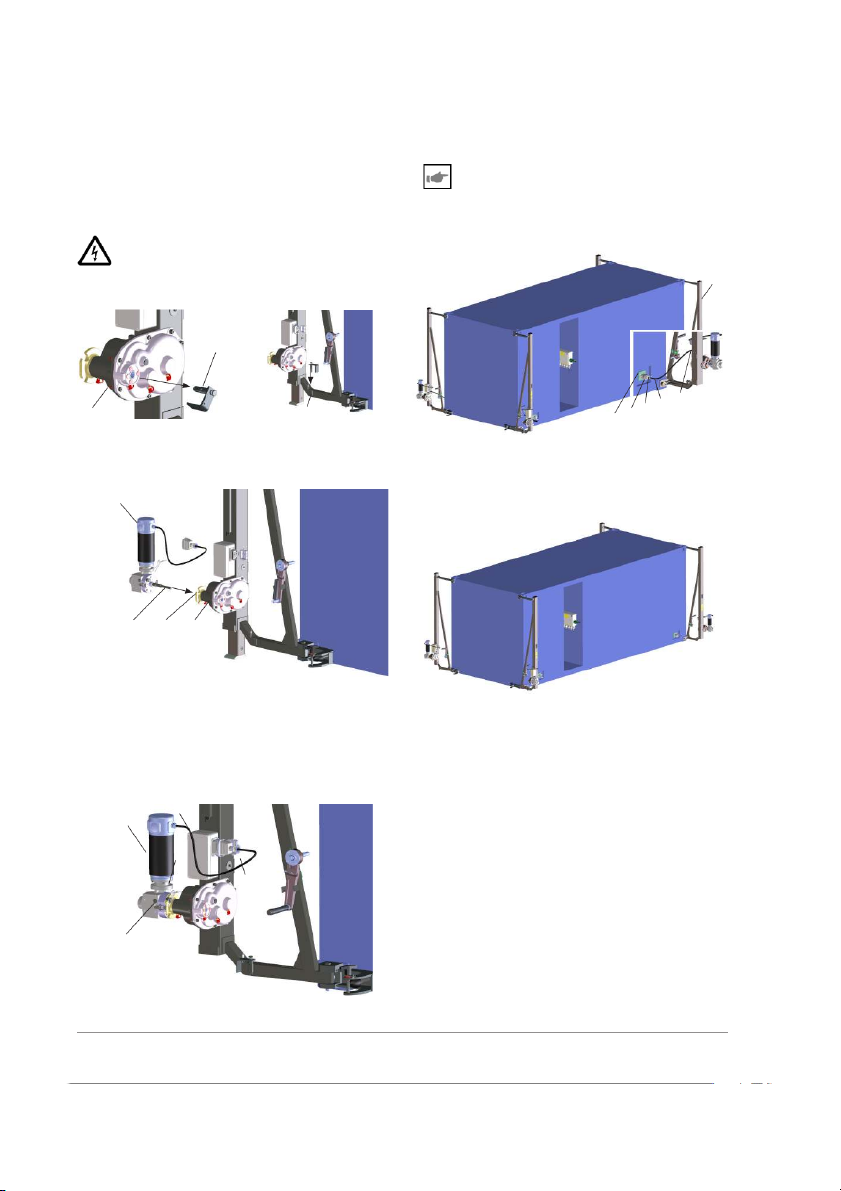
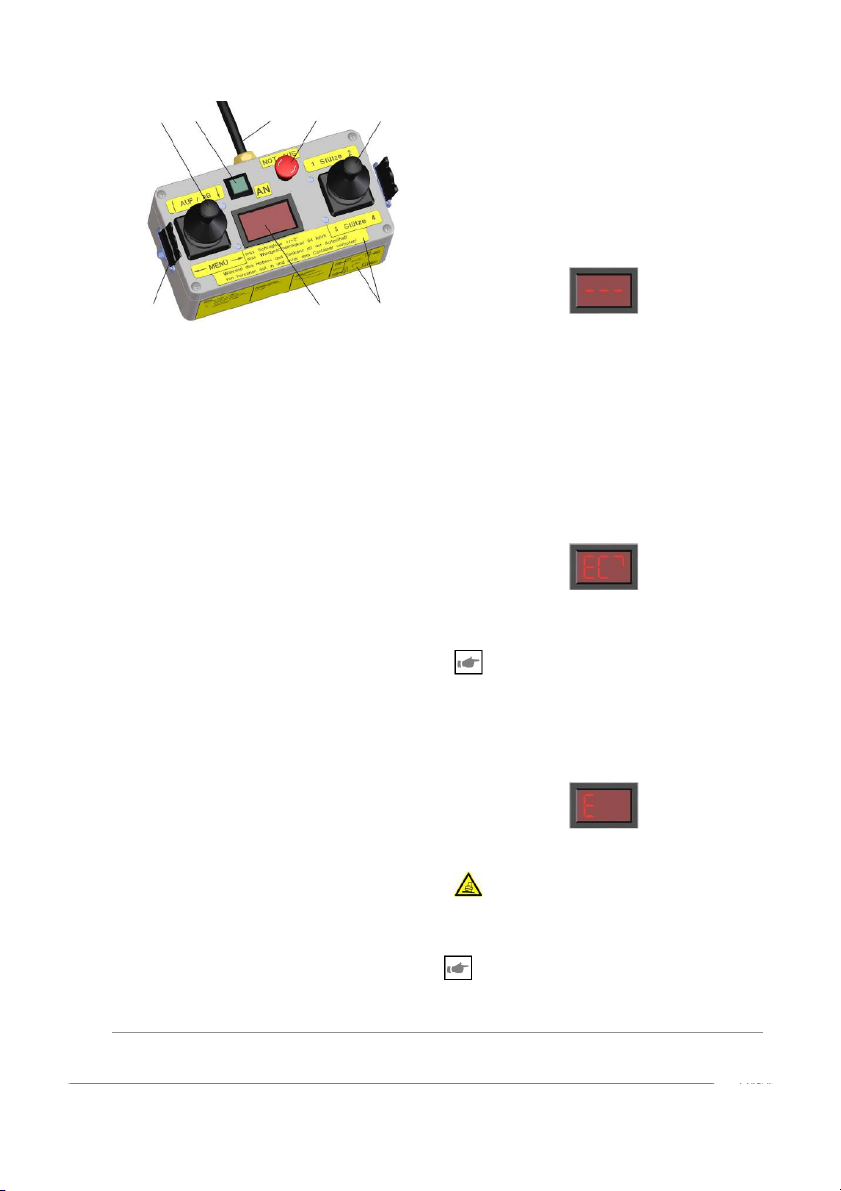
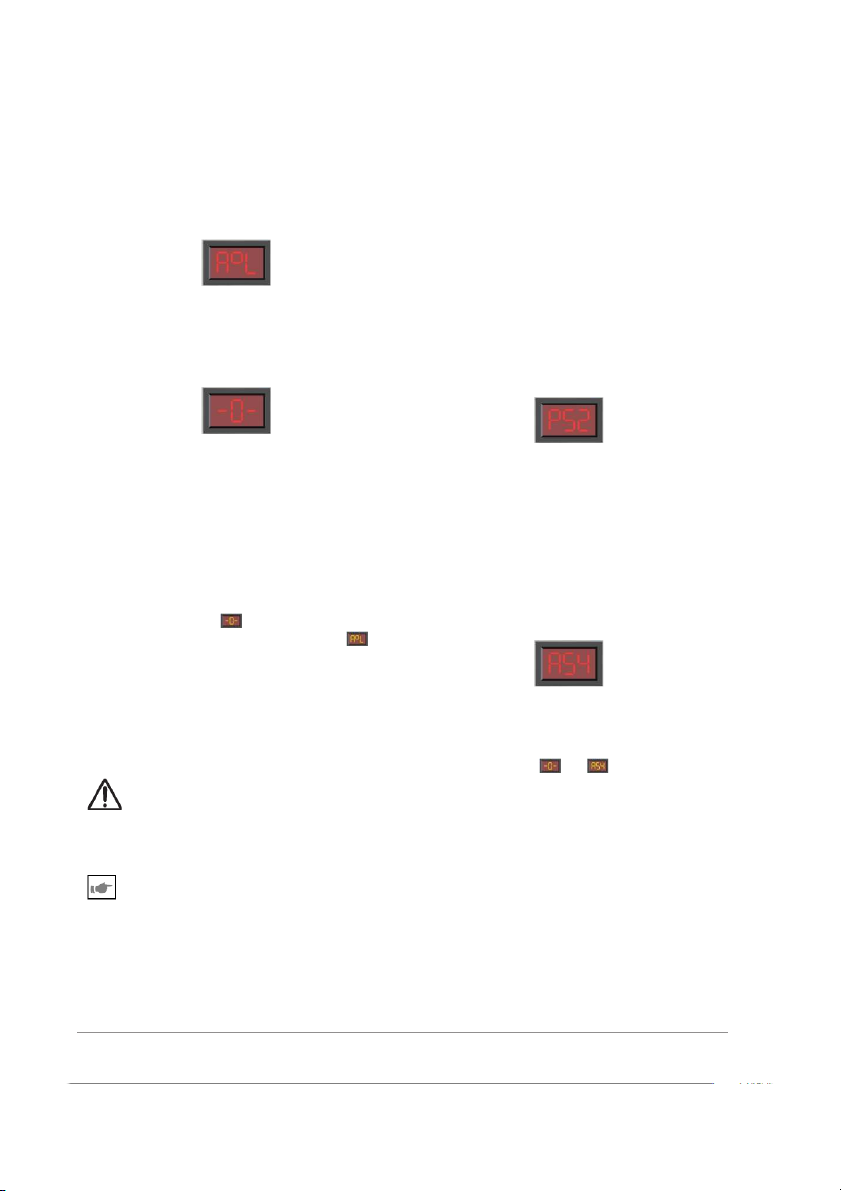
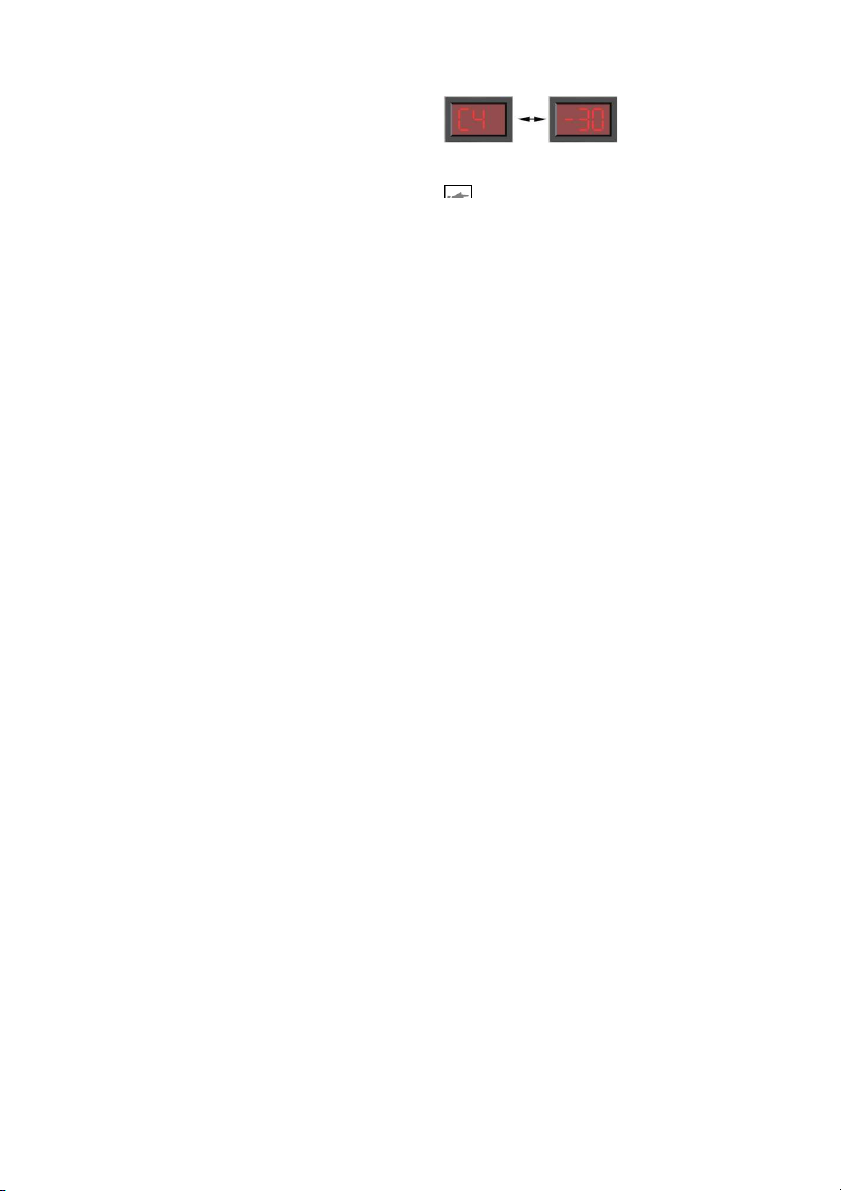
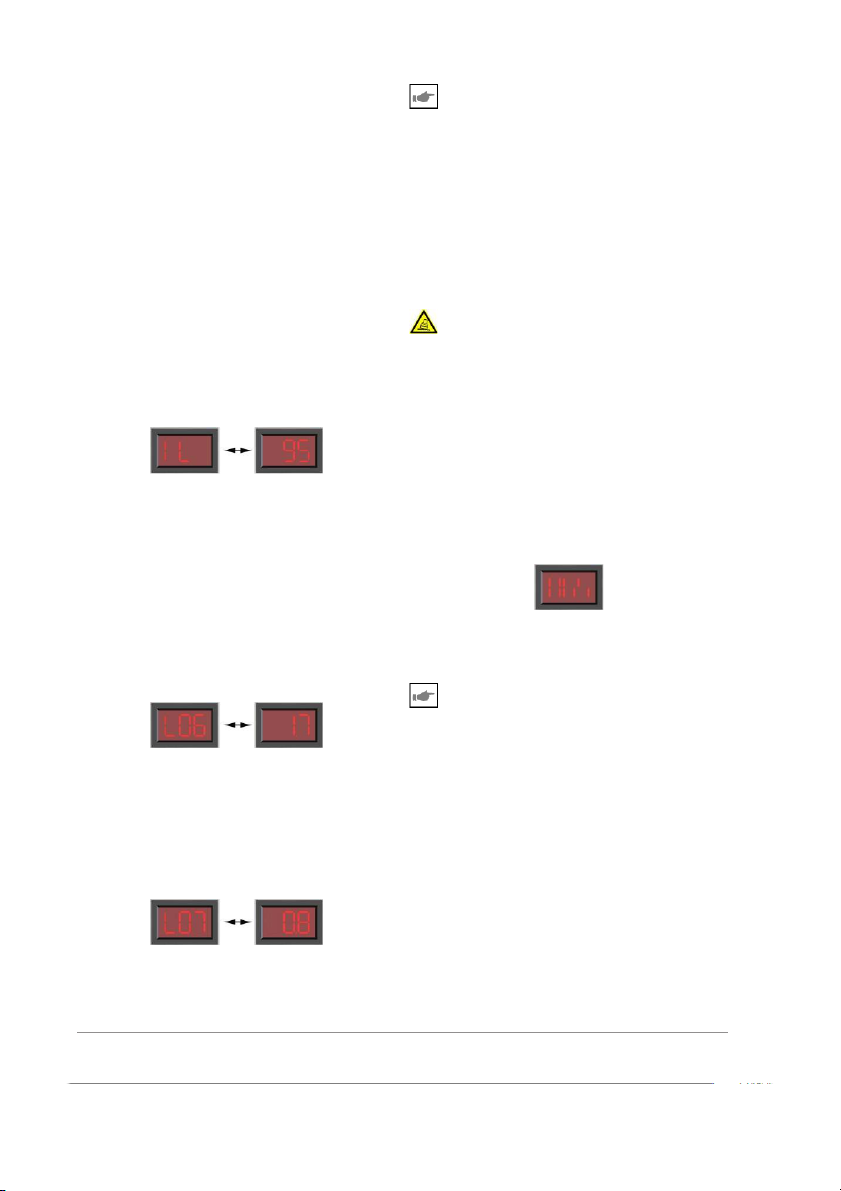
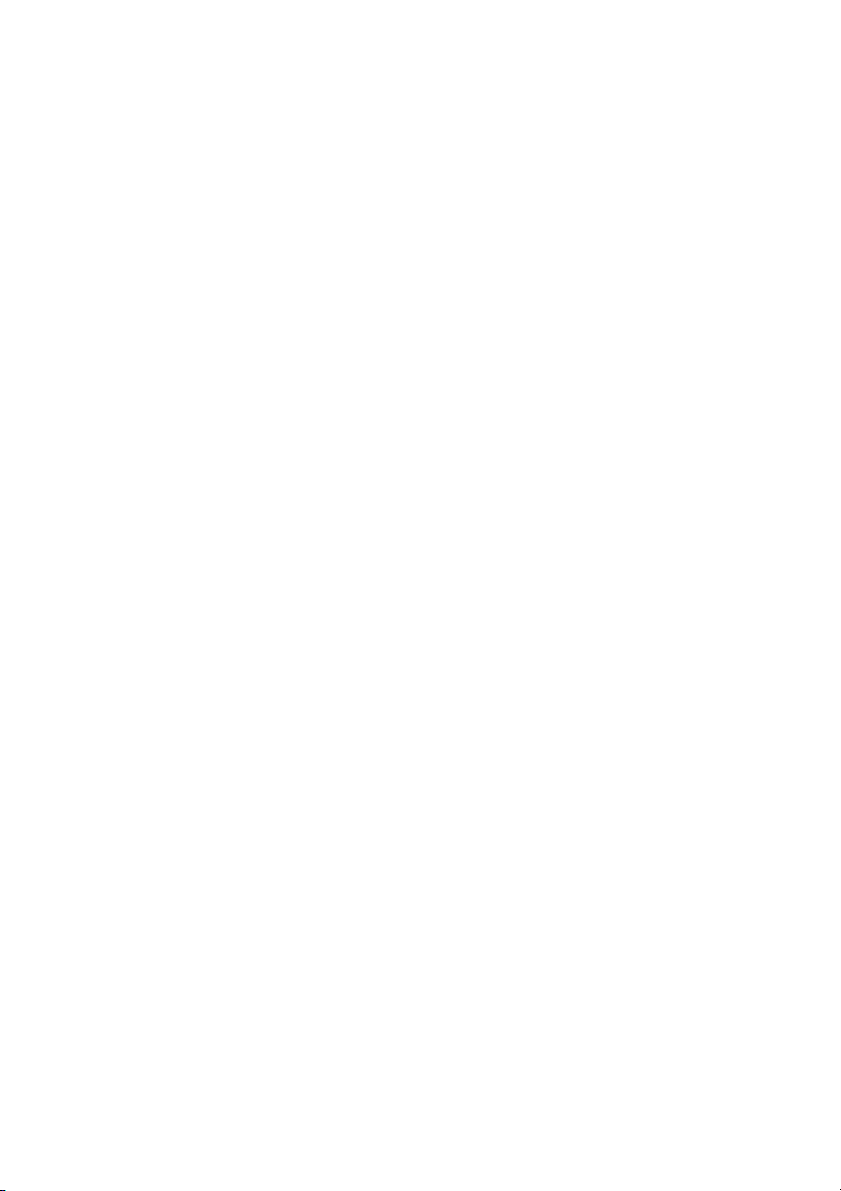
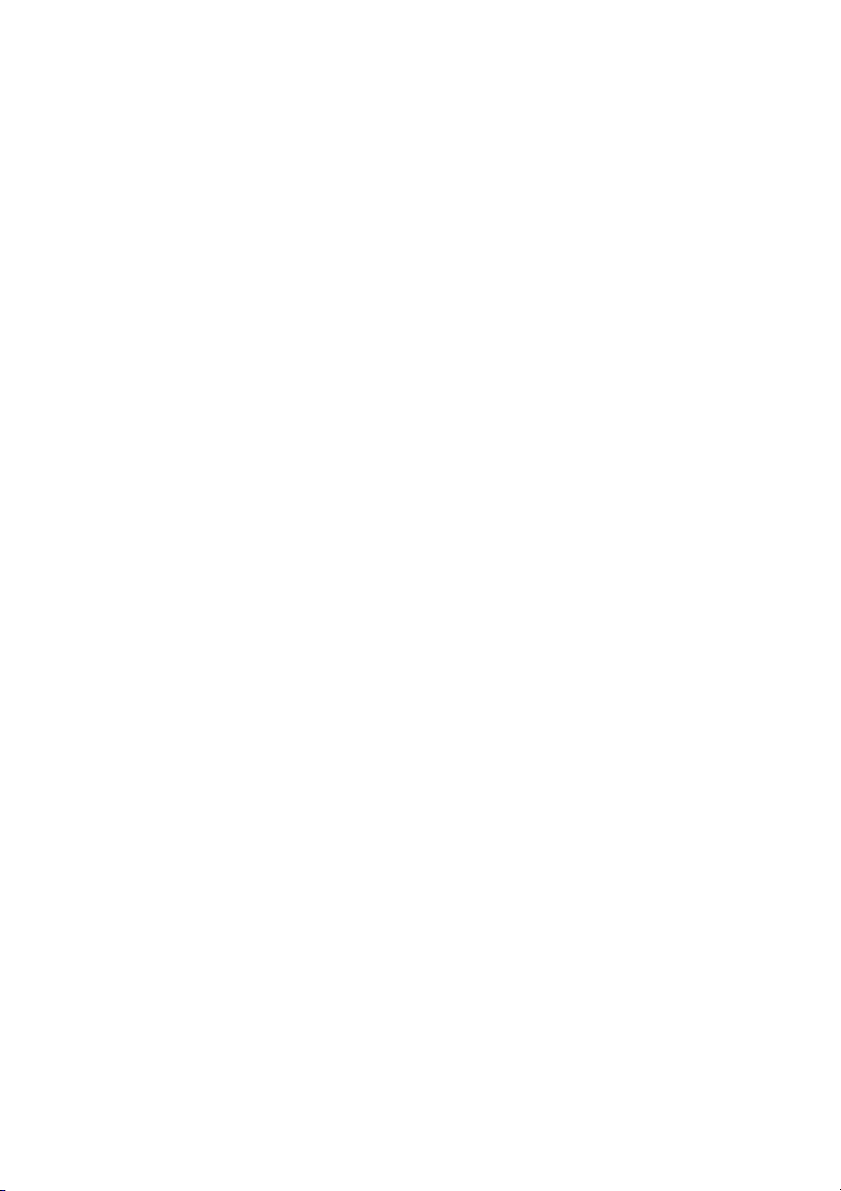
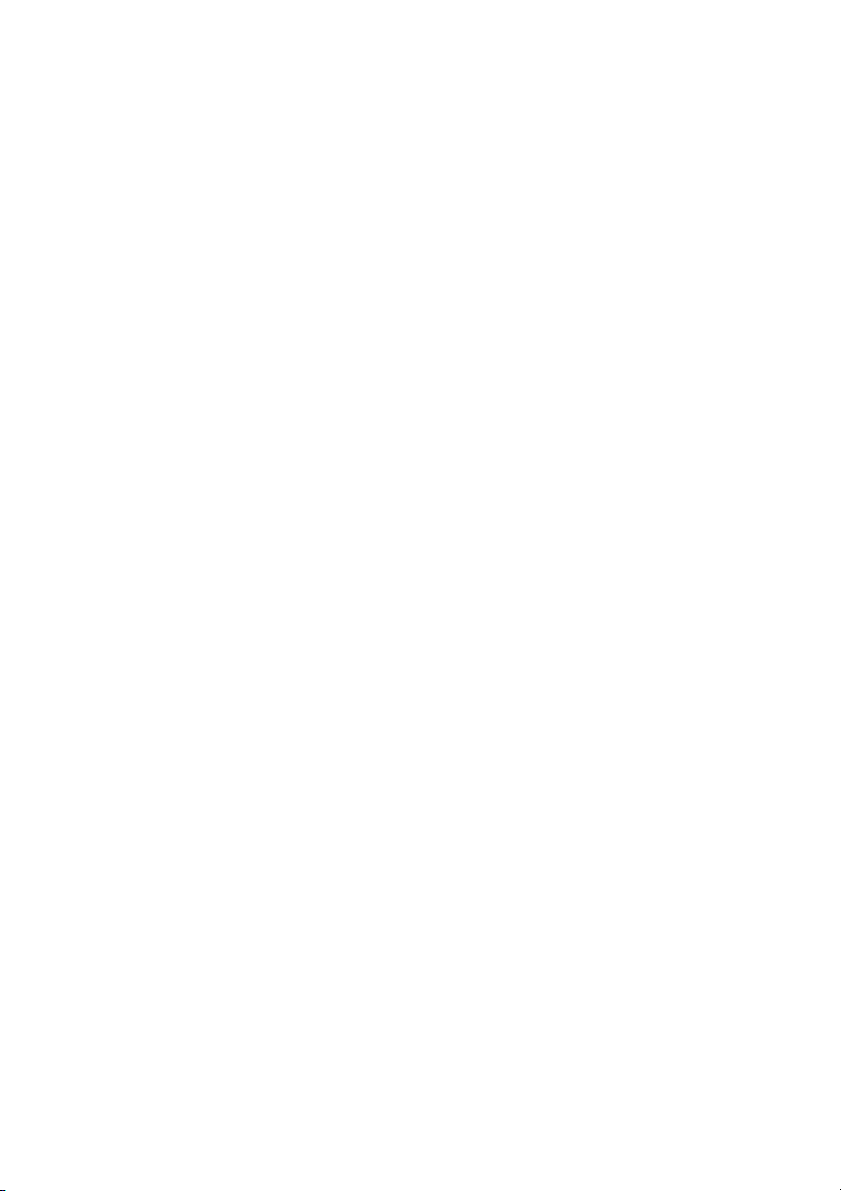
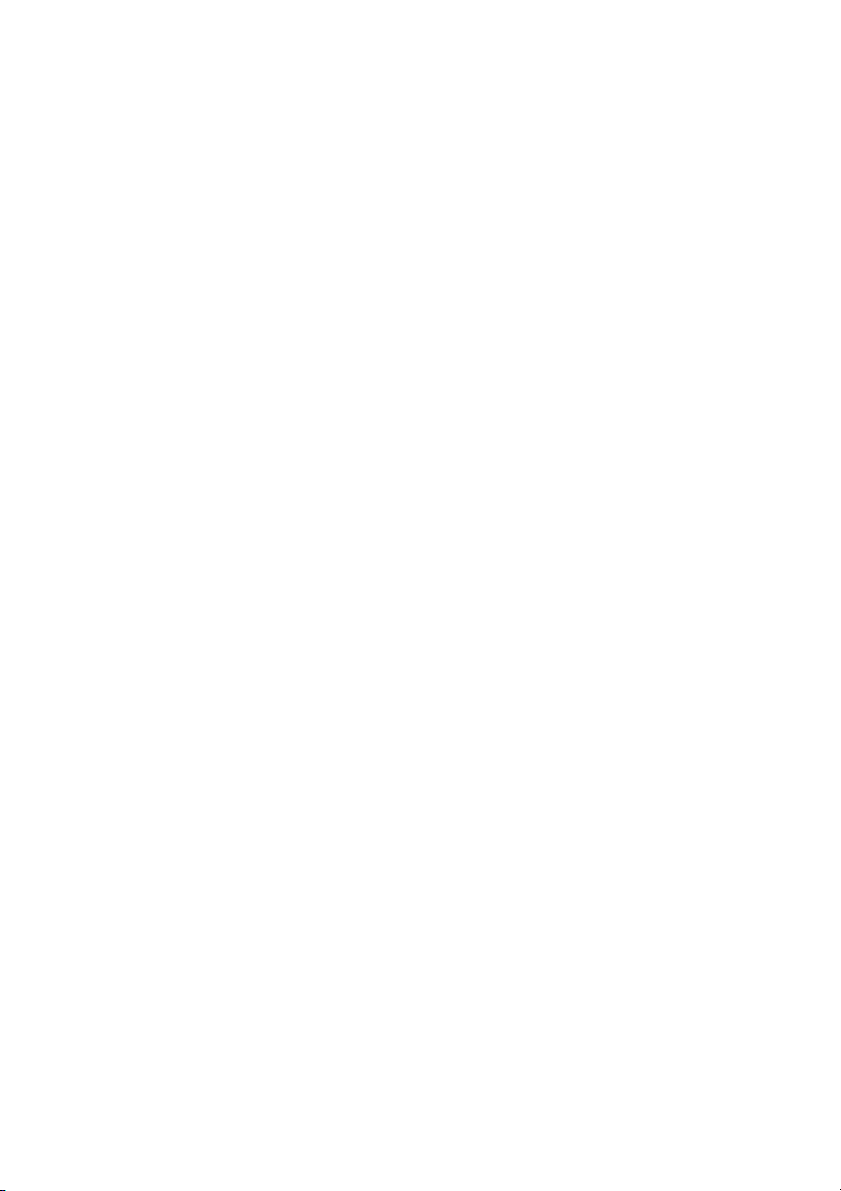
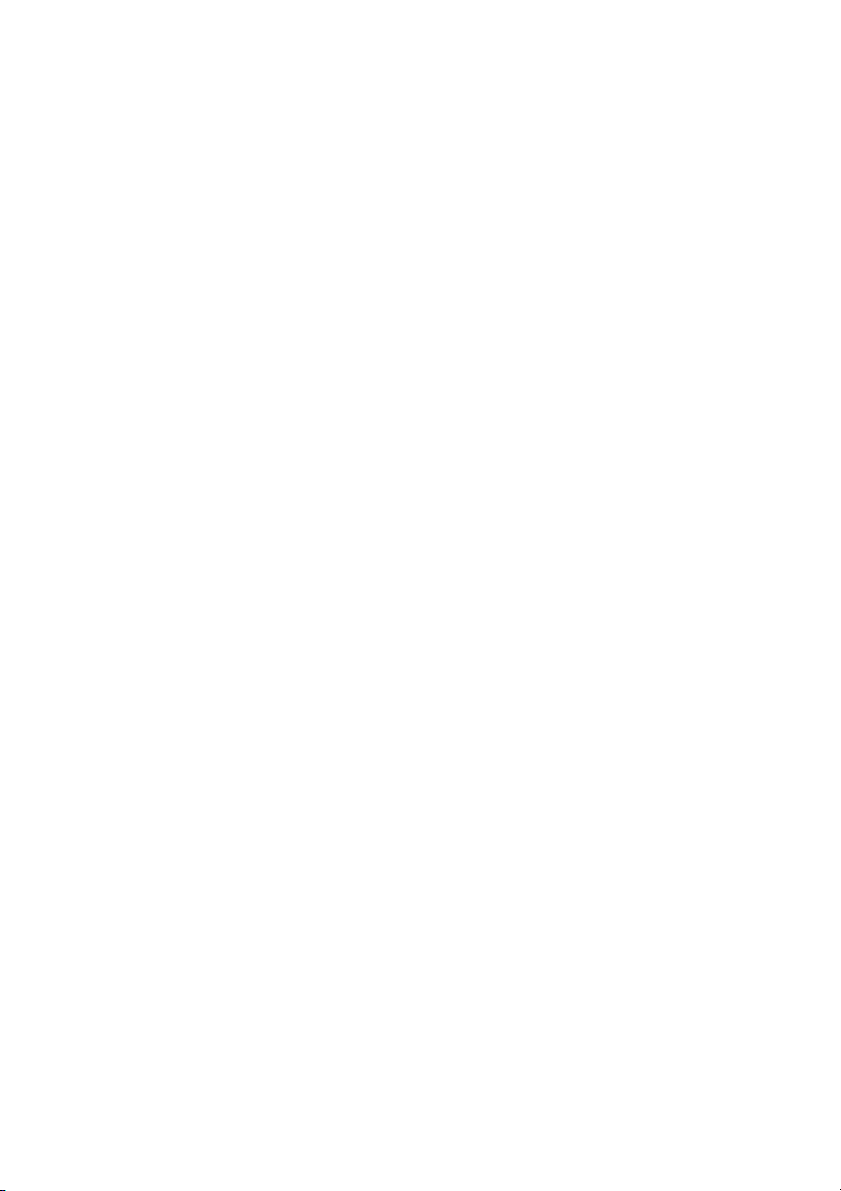
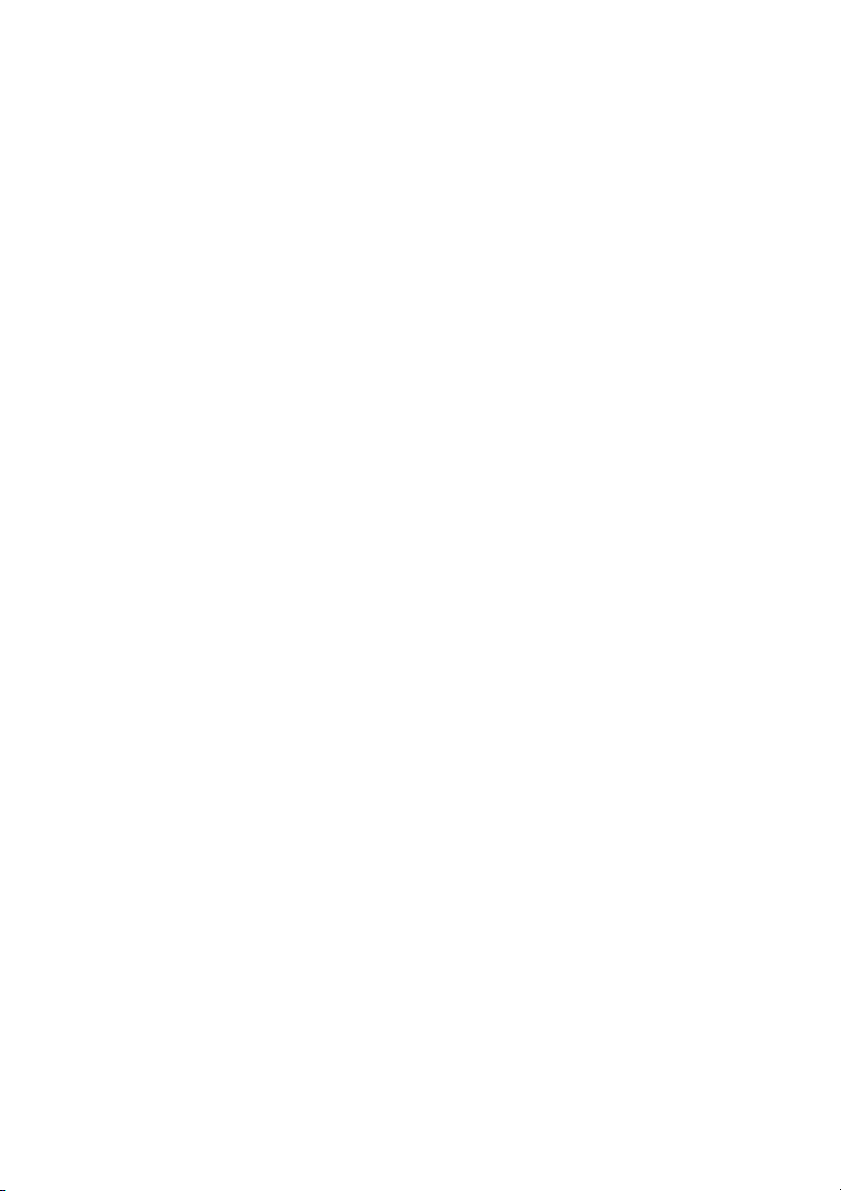
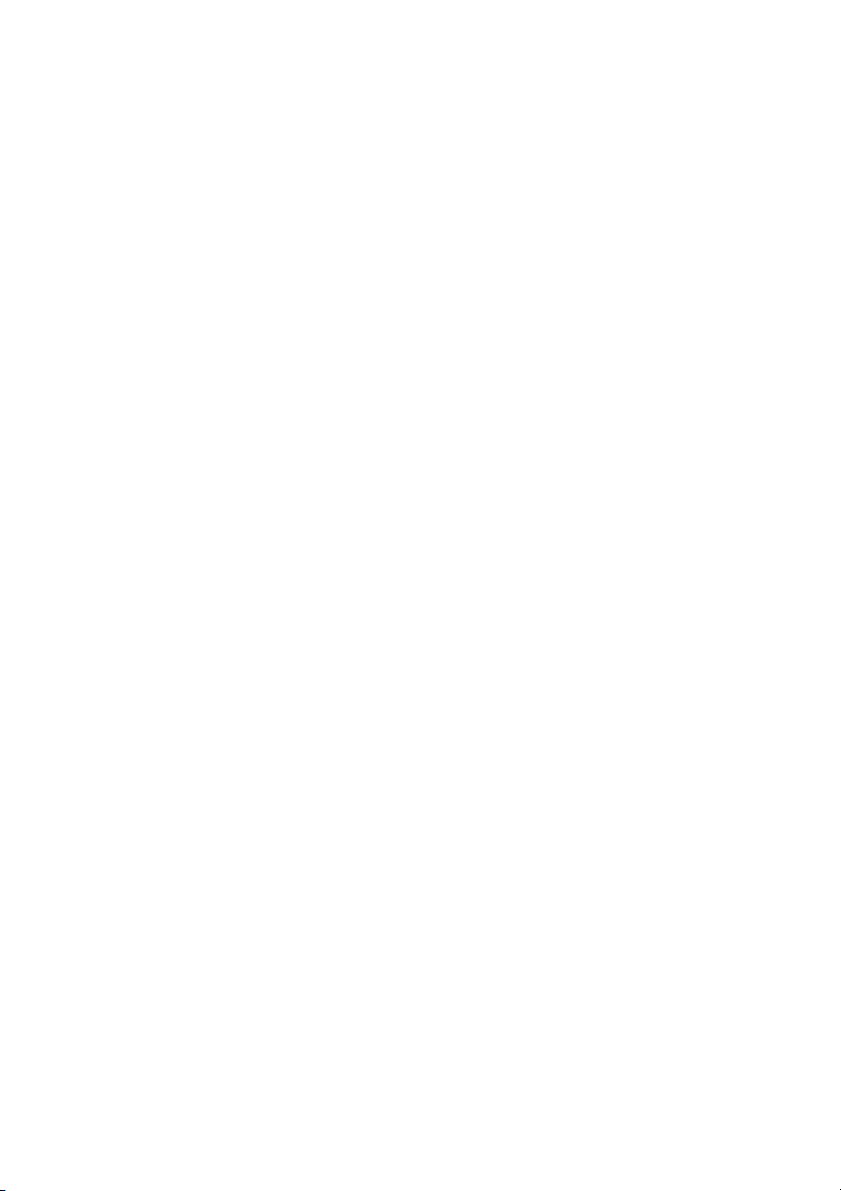
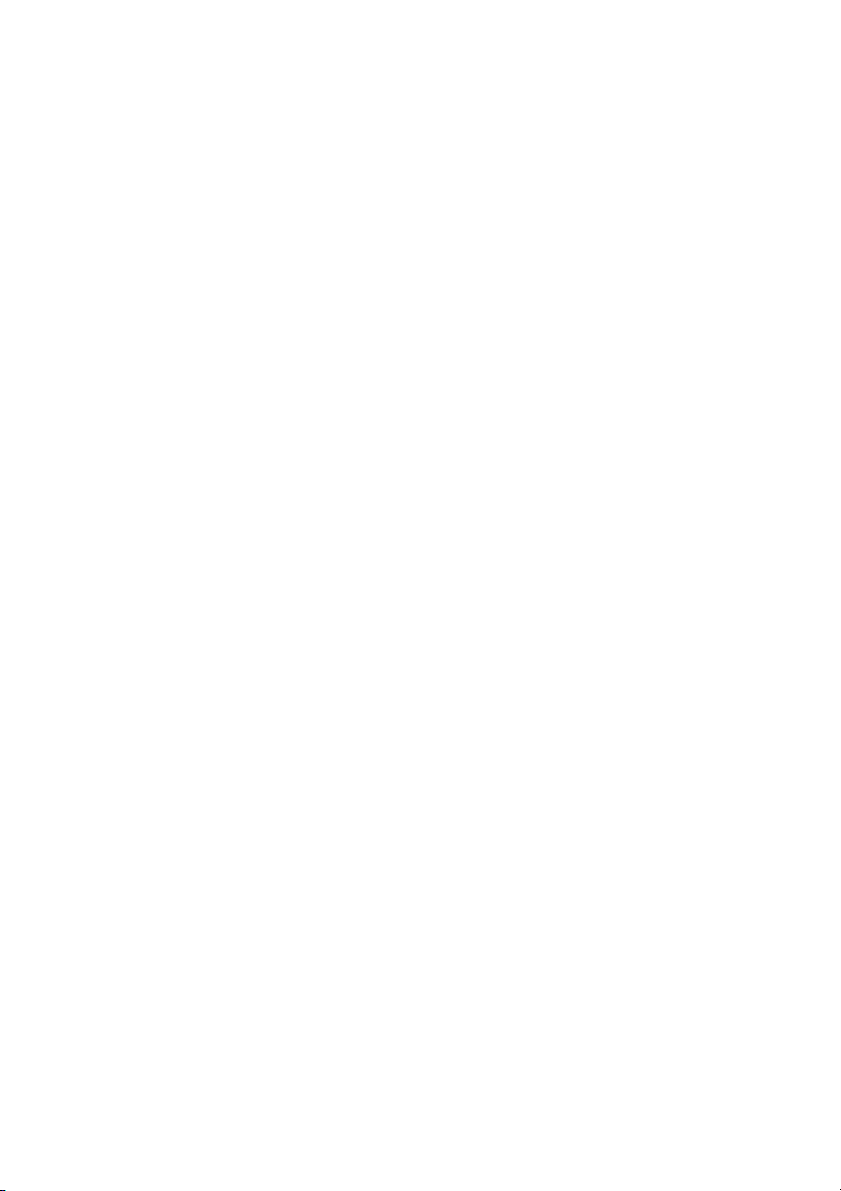
Preview text:
Operating manual (Translation) m o .c n o c a a .h In d e k ://lin ttp l h m o .c n o c a a .h g ://xin ttp l h Lifting device m o .c n o c a a .h
with electrical drive for automatic levelling k o o b e c 24 V-DC ://fa ttp h
– swings in against the front – y lo o n h c te g Type 1889.10 haacon hebetechnik gmbh liftin Josef-Haamann-Str. 6 in e D-97896 Freudenberg/Main c n te Tel: +49 (0) 93 75/84-0 e Fax: +49 (0) 93 75/84-66 p m e-mail: haacon@haacon.de o Internet: www.haacon.de C 094407_1052596_a_gb_hebvrr_s
haacon hebetechnik gmbh – Telefon +49 (0) 9375 - 84-0 . Fax +49 (0) 9375 - 8466 094407_1052596_a_gb_hebvrr_s
haacon hebetechnik gmbh – Telefon +49 (0) 9375 - 84-0 . Fax +49 (0) 9375 - 8466 2 Contents
– Not to depose at wind speed over:
70 km/h for container length 10 ft.
1. User groups ...................................................................3
2. Safety instructions ..........................................................3
64 km/h for container length 20 ft.
3. Technical data ................................................................ 4
52 km/h for container length 30 ft.
4. General .........................................................................5
45 km/h for container length 40 ft.
5. Safety equipment ...........................................................5
6. Scope of supply .............................................................5
You must also ensure that if you wish to lift the maximum load the
7. Mounting of the lifting device ...........................................5
center of gravity of the load is positioned as cetral as possible
8. Mounting the e-drive ......................................................7 between the supports.
9. Electrical levelling drive ...................................................8
The length, width and height of the vehicle carrying the container
10. Commissioning ........................................................... 14
11. Operation ................................................................... 14
including the lifting device must be within the allowed dimensi-
12. Inspection .................................................................. 17 ons during transport.
13. Maintenance recommendation .................................... 17 Use exclusions
14. Disassembly, disposal ................................................. 17
– Not suitable for permanent operation and vibration stress.
15. Spare parts ................................................................ 17
16. Circuit diagrams .........................................................20
– Not approved for use in explosives areas / environments.
– Not suitable for aggressive environments. 1. USER GROUPS
– Not suitable for lifting hazardous loads. Duties Qualifications
– Not suitable for lifting liquid loads. Operator
Assembly, disassembly, Instruction by means of Organisational measures operation, visual the operating instruction;
– Ensure that these operating instructions are always at hand. inspection Authorised person
– Ensure that only suitably qualified and authorised personnel is Specialist Maintenance, repair Mechanic,
allowed to operate, sevice aund repair the lifting device. personnel Electrician where req. Inspection Authorised person acc.
– Ensure that this personnel is instructed at regular intervals in to TRBS 1203 (technical
all matters of industrial safety and environmental protection expert)
and that they are familiarwith the operating manual and the sa-
fety instructions contained there in. 2. SAFETY INSTRUCTIONS
– Ensure that all safety and warning notices on the lifting device
Specified normal operation
remain on the device and are kept in legible condition.
The lifting device type 1889 with automatic levelling is designed
– Check regulary the fully functional.
to move and position containers with a maximum gross weight of
– Check at regular intervals whether it is being used in safety and 10 or 20 tonnes. hazard conscious manner.
– Appropriate mounting on containers according to ISO 668 with
– Store clean, dry and protected.
corner fittings according to ISO 1161.
– Use only under normal lighting conditions!
At a variant connection consider the drawing in the annex!
– Operate the equipment in accordance with the information in
Installation, service and repair these operating instructions.
– Only by specialist personnel!
– Only use for the purpose for which it is designed.
– Only use original spare parts for repair.
– Only use to lift, lower and move horizontally.
– Do not modify or alter safety-relevant parts, this particularly
Only use for push loading freely movable loads.
applies to welding work at load-bearing parts.
– Only use when in perfect working order.
– Additional attachments must not impact safety.
– Only allow to be operated by instructed personnel.
– All planned modifications must be approved in writing by haa- con hebetechnik gmbh. Safety-conscious work
– The maintenance work set out in the operating manual
– First read the operating instructions.
– Always be conscious of safety and hazards when working.
(cleaning, lubrication, servicing, in-spection, etc.) must be completed on schedule.
– Observe lifting device and load during all movements.
– Immediately report any damage or defects to the person in
Further regulations to be observed charge.
– German Industrial Health and Safety Ordinance (BetrSichV).
– Repair equipment first before continuing work!
– Country-specific regulations.
– Do not leave the load suspended without supervision.
– German Accident prevention regulations (DGUV-V 54).
– Transport device protected against impacts and shocks, fal-
– Notice signs / identification plates. ling over or toppling.
The following are not allowed:
– Overload (–> technical data, type plate, payload plate) – Impacts, blows. – carriage persons.
– Remaining in or on the lifted load if it is lifted more than 400 mm from the ground.
Exception: When an additional safety device is used!
– people are not allowed to stand under the raised load without additional support.
– Exceed the maximum angle (–> entitled ‚Other instructions’). 094407_1052596_a_gb_hebvrr_s
haacon hebetechnik gmbh – Telefon +49 (0) 9375 - 84-0 . Fax +49 (0) 9375 - 8466 3 Other instructions
The content of the notice signs depends on type and design of Important!
the lifting device and its technical data.
1. Drive under the container with great care. Do not bump
All the safety signs and operating instruction signs on the lifting
anything with the truck since otherwise there is a danger that
device are to be kept clearly legible at all times. Replace dama- the hoist will buckle.
ged or illegible signs without delay.
Ask another person to guide you as you drive the truck 3. TECHNICAL DATA under the container! 24V-DC
2. People must not be allowed to stand in, on or under the con-
tainer during the lifting or lowering procedure. Lifting device type 1889.10 1889.20 Maximum load / set kN 100 200
3. People may stand on or in the raised container if it is no more Maximum load / support kN 50 100 than 400 mm off the ground. Weight / set kg ~ 720 ~ 920
4. The lifting device with a container must not be made to vibrate
Design height (for lift 1750 mm) mm > 2330 by means of crank impulses. Maximum lift mm 1750
5. The container may only be placed on solid ground by the lif- Lift / turn of crank mm 2,8 1,6 ting device. Maximum inclination of load ° 2 Power supply V 24
6. The area on which the container is placed or from which it is Rating W 4x355
lifted must be as flat as possible. Protection type - IP65
7. The maximum angle of 2° applies at the maximum load and Lift / minute mm ~120 ~100
at full lifting height (2° inclination corresponds to a height dif- Working temperature °C -33 ... +50
ference of approx. 210 mm in length an 85 mm in width for a
Ground pressure (50 kN/support) N/cm2 37,5 77 standard 20’ container). Maximum wind speed for container length 10 ft km/h 70 for container length 20 ft km/h 64 m m c for container length 30 ft km/h 52 c ,5 1 8 2 for container length 40 ft km/h 45
The technical data of customised versions of the lifting
device can deviate from here given defaults. The valid
information is shown on the enclosed overview drawing in the appendix. fig. 2-1
8. If the container‘s inclination is greater than 2°, a warning si-
gnal sounds and a flashing signal is shown on the display. In
this case, automatic operation must be ceased immediately. Additional measures:
– Load all 4 supports evenly.
– Align container so that it is horizontal. In order to slacken
off the bending stress in the gear rack tubes, release the
supports individually in mode ‚E‘.
– Observe the degree of bending in the gear rack tubes. They must remain even.
– If the container‘s angle of tilt exceeds 4° in either the X or Y
axis, then the system will shut down and an error message is shown on the display.
9. Do not operate the lifting device in stormy conditions.
Technical information at the lifting device
In order to prevent accidents and damage, notice signs are af-
fixed to the lifting device and the instructions there on must be followed: fig. 2-2 094407_1052596_a_gb_hebvrr_s
haacon hebetechnik gmbh – Telefon +49 (0) 9375 - 84-0 . Fax +49 (0) 9375 - 8466 4 4. GENERAL
7. MOUNTING OF THE LIFTING DEVICE
The lifting device type 1889 is designed to move and position
The lifting device has to be installed in the ISO corners of the
containers with a maximum gross weight of 10 or 20 tonnes.
container to be lifted. The position of the upper arm has to be ad-
It consists of four rack supports with spur gears, dispenser
apted thereby to the existing container height. With the assembly
housing and gear motor. The main control unit can be fastened in
of the lifting device must be paid attention to the fact that two
or on the container. Motors and support plates can be removed
mirror-image supports are mounted on every container side. On from the supports.
this process, the gearboxes of the respective supports must lie
During transport the lifting device is swung in against the front
at the container turned away side of the support. In order to the
of the container and locked and secured with pins. The support
right positions of the lifting supports please take notice of the positioning plan below.
plates and cranks are stowed separately. A locking device that
can be inserted into the crank drive prevents the gear rack mo- ving downwards. support 2 resp. 3 support 1 resp. 4
The lifting device type 1889 has a self inhibiting spur gear, which
holds the load securely in any height (you must nevertheless
comply with the safety instructions).
The rack supports form a stable unit with the container. The large
support plates means that the device can be used anywhere in
the open air where there is firm ground.
Generally, the gear rack supports are mutually driven and level- driving direction
led by means of the controller. However, each of the supports
can also be shifted manually by switching over to manual con-
trol. The lifting mechanism is moved by means of four electric
motors. The system can be operated with four inserted cranks in case of emergency.
This operating manual applies to the swinging lifting devices for
containers type 1889 for shelters and containers with ISO-corner support 1 support 2
fittings at the top and bottom. Alternatively haacon has several
modified versions in its product range, for example lifting devices
that are permanently mounted, removable lifting device and lif-
ting devices for containers without ISO corners, etc.
This gear rack support complies with DGUV-V 54 and the EC Ma- chine Directive 2006/42/EEC. 5. SAFETY EQUIPMENT fig. 7-1
The mechanical and electrical components for each support are
protected against overloading by means of a safety coupling.
The number of the each support is shown nearby the gear
Each of the gear rack supports are equipped with inductive pro-
box. Also the last character of the serial number is equal to the
ximity switches to monitor the end positions. Once these are re- number of the support.
ached, the gear sections and motor are protected by means of a
When attaching the individual components in the sequence de-
safety coupling. However, it is nevertheless imperative to subse-
scribed, observe the correct arrangement of the support numbe-
quently check all of the parts affected by the flux of force.
ring. (fig. 7-2). The positioning of the main control unit can vary
Dimension the supporting structure at least for 150 % of the depending on customer wishes. maximum load. 6. SCOPE OF SUPPLY
1 set lifting device type 1889 consists of:
– 4 gear rack supports each with its own motor control housing – 4 screw-on upper arms r - e – 4 supporting plates w in ie ta v
– 4 fixed or removable gear motors n p o c - to
– 1 main control unit with control cable and handheld control unit
– 4 ratchet cranks (emergency operation)
– 1 Open-ended spanner, 30 mm l tro x n o
The following accessories are optionally available: o b c – mounting winch – ergo crank fig. 7-2 – transport box 094407_1052596_a_gb_hebvrr_s
haacon hebetechnik gmbh – Telefon +49 (0) 9375 - 84-0 . Fax +49 (0) 9375 - 8466 5
1. Insert the clamp plate (1) into the top corner fitting, place the 4. Operating position
mounting (2) with a suitable contour against the corner fitting
Swivel the rack support (1) into a position perpendicular
and secure it with a pan head crew (3).
to the long side of the container. 1 n n itio itio s s o o p g rt p o 2 tin p ra s e n p ra O T 3
Insert the locking bolts (2) into the corner fitting of the container
(3), turn through 90° and tighten in place with the nut (4). Pivot safety lever (5) into place. fig. 7-3
2. Insert the clamp plate (1) into the bottom corner fitting, place
the mounting (2) with a suitable contour against the corner
fitting and secure it with a pan head screw (3). 3 4 2 5 1 fig. 7-6 5. Positioning for transport 1
Unlatch the safety lever (1), loosen the nut (2) and turn
the locking bolt (3) by 90°. Swivel the rack support (4) in until 2 3
the locking hole (5) in the bottom support aligns with the fig. 7-4
pinning position of the bottom hanger (6). Screw the threaded
locking bolt (7) into the bottom hanger (6) and tighten hand-
Before finally tightening the pan head screws (3)
tight. Stow the crank (8) on the rack support and fasten in
(fastening torque of pan head screw app. 250 Nm)
place with a tie-down strap (9).
ensure that the mountings are perfectly horizontal and
that the lower surface of mounting touches the corner 8 fitting. 9
3. Fit one support (1) with its top and bottom arm into each cor-
ner fitting (2). Push in both the bolts (3) at both the top and 5
bottom and secure them with washer and hex nut (4). 3 7 2 3 1 4 6 1 fig. 7-7
The dismantling of the lifting device happens in backwards order. 2 4 fig. 7-5 094407_1052596_a_gb_hebvrr_s
haacon hebetechnik gmbh – Telefon +49 (0) 9375 - 84-0 . Fax +49 (0) 9375 - 8466 6
8. MOUNTING THE E-DRIVE
2. Feed the control lines (1) through the designated openings
An electric drive especially designed for the lifting device saves
(2) in the in load-bearing recesses of the supports. Ensure
time and staff. This electric drive is optionally available for every
correct assignment. The length of the control lines (1) is mat-
type of the lifting device in the common operating voltages.
ched to the position of the levelling control system. Once the
control cables (1) have been fed through, feed past the moun-
ting plates (3) from top and bottom (4), and screw in place on
the wall of the container; seal in place if necessary. Fasten the
connection box (5) for the control lines (1) with screws (4) to the mounting plates (3). 3 2 1 5 fig. 8-1 Mounting 4
1. Fasten the levelling control unit (1) at the connection points
provided on the container. These connection points must be fig. 8-3
torsionally robust. In doing so, ensure that the incline sensor
Incorrectly fastened connections between the sup-
(located inside the levelling control unit) is correctly positio-
ports and the levelling control system will cause mal-
ned relative to the respective support positions per informati-
functions to the automatic levelling system. on plate (2), fig. 7-2.
3. Ensure that the control lines (1) are correctly assigned to the 2 levelling control system (2). 1 fig. 8-2 2 1/A 1/B 1/C 1/D E F
The screw-on surface of the levelling control unit must fig. 8-4
be as parallel as possible with the main axis of the con-
A … Control line for support 1
tainer. If the incline sensor is installed askew, this will
B … Control line for support 2 impair the commissioning.
C … Control line for support 3
D … Control line for support 4
E … Connection for control unit F … Power connection
Do not apply force. The control lines (1) can only be
connected to their associated sockets due to a coding system. 094407_1052596_a_gb_hebvrr_s
haacon hebetechnik gmbh – Telefon +49 (0) 9375 - 84-0 . Fax +49 (0) 9375 - 8466 7
Safety Instructions Electrical Equipment
7. Connect the attached support (1) to the levelling control unit.
Disconnect from the power supply when working on the electrical
To do so, plug the connection cable (2) into the receptacle equipment.
of the control line (3), which is already routed and fitted
Only permit authorised specialists to work on the electrical
inside. Then lock in place with the safety bar (4). Repeat this
equipment. And electrical specialist is a person with suitable trai-
procedure at all four supports.
ning and experience, as well as knowledge of the relevant regu-
The connection cable (2) must have some excess
lations, who is able to recognize risks and avoid dangers, caused by electricity.
length between the cable fastening (5) and the plug (6)
Always keep control cabinets closed.
to enable the support (1) to pivot. Never: Work on live parts.
4. Pull the run-off protection (1) out of the support gear unit (2) 1
and store it in the holder provided (3). 1 5 2 6 2 3 4 3 fig. 8-5 fig. 8-6
5. Attach gear motors to all supports. Feed the drive shaft (1) of
the gear motor (2) on the ratchet disc side (3) into the support
gear unit (4) and attach to the ratchet disc (3). fig. 8-9 2
9. The e-drives are now fitted. 1 3 4 fig. 8-7
6. Secure the gear motor (1) to prevent it coming away during fig. 8-10
the lifting process by plugging the spring clip (2) into the stop
bolts. If the gear motors are to remain on the lifting device
9. ELECTRICAL LEVELLING DRIVE
for an extended period of time, fasten them in place with
The mobile manual control unit enables easy and manageable
clamping fasteners (3). Connect the connection cable (4) of
operation of the system. All functions are activated by means of
the gear motor with the dispenser housing (5) of the support joysticks. and secure. Electrical components 5
The lifting equipment with automatic levelling system is equip- 1 ped with: 2
4 Electric motors of 500 W each at 160 V-DC for driving the supports 4
1 central levelling control system
with PWM-controllers (pulse width modulation) for speed re- gulation 1 sensor box with inclinometer 3 1 manual control unit 8 proximity switches for end position monitoring 4 proximity switches fig. 8-8 for ground contact sensing
All electrical components have protection class IP54 or better. 094407_1052596_a_gb_hebvrr_s
haacon hebetechnik gmbh – Telefon +49 (0) 9375 - 84-0 . Fax +49 (0) 9375 - 8466 8
Description of control unit Modes - standard operation
The levelling control system is operated in various modes which 7 4 1 5 8
can be selected for standard operation after the control system
is switched on by means of the control unit. The following modes
can be selected by means of horizontal movement of the left- hand joystick: – Standby
Once the system is switched on with the ‚ON‘ button, the level-
ling control system activates within 20 s. The process is indi-
cated in the status display. Once the process is complete, the
status display indicates standby. Display: 2 6 3 System standby
The impact-resistant aluminium control unit is connected to the – Mode: ‚E‘
levelling control system by means of a control cable (1). The
Establish ground contact or lift
shoulder belt (2) is designed to enable fatigue-free operation.
This mode serves to make contact with the ground and forms
Signs (3) provide an overview of the control modes and functions
the basis for all additional modes. for the following controls:
Moving the right-hand joystick enables selection of the sup- – On switch (4)
ports to be moved. In the centre position, all of the supports
Pressing the ‚ON‘ switch causes the system to be switched on.
are moved simultaneously, otherwise the selected supports are moved.
The on switch illuminates green if the control cable to the le-
Moving the left-hand joystick vertically up causes the unloa-
velling control system is correctly plugged, the „EMERGENCY-
ded supports to be extended until they make contact with the
STOP“ switch is unlocked and the levelling control system is in
ground. Once the specified load has been achieved, the re- switch position ‚1‘.
spective support switches off. The status display signalises that
– Off switch / EMERGENCY-STOP (5)
ground contact has been made for all four corners separately.
Pressing the ‚EMERGENCY-STOP‘ switch causes the system Display:
to be switched off. The button locks down when it is pressed
and the on switch illumination goes off. It is only possible to
switch on the system again after releasing the lock. In order to
do so, turn the mushroom knob in the direction of the arrow. Mode ‚E‘ – Status display (6)
Supports 1, 2 and 3 – ground contact made
A three-digit digital display provides information about the se-
Support 4 – no ground contact
lected mode, switch status of the proximity switches and basic
adjustment of the levelling control system.
The first field of the status display signalises the mode.
The following fields represent the supports 1 to 4 corre-
– Joystick for primary control (7)
sponding to the selection options of the right-hand joy-
The left-hand joystick serves to control the main functions of stick.
the lifting equipment. Moving the joystick in the horizontal di-
rection (right-left) enables selection of the various modes and
Moving the left-hand joystick vertically downwards causes the
configuration of the basic settings. Movement in vertical direc-
supports to be retracted. Once the limit position has been rea-
tion (forward and back) serves to start the lifting or lowering
ched - ‚supports retracted‘, the respective support switches off.
movement within the selected mode. Display:
– Joystick for secondary control (8)
The right-hand joystick serves to change the parameters of the
selected basic settings and enables selection of the supports
in lifting / lowering mode, insofar as this is allowed by the se- Mode ‚E‘
lected mode. Diagonal movement selects individual supports
Supports 1, 2, 3 and 4 – no ground contact
and horizontal / vertical movement moves pairs of supports for
the drive. When the joystick is in the central position, all four
CAUTION! Hazardous operation! Do not use this
supports are controlled simultaneously.
mode to lower the container. Due to the lack of monito-
ring offered by this mode and the possibility to control
the supports individually, there is a risk of causing the container to topple!
A warning signal sounds and the status display flashes as
a warning when the supports are retracted in this mode
due to the risk involved. Once all of the supports reach
their limit positions - ‚supports retracted‘, these warnings are cancelled. 094407_1052596_a_gb_hebvrr_s
haacon hebetechnik gmbh – Telefon +49 (0) 9375 - 84-0 . Fax +49 (0) 9375 - 8466 9 – Mode: ’A°L’
Modes - extended operation
Alignment / movement in home state
Additional modes are integrated into the levelling control system
This mode serves to enable alignment and movement of the
for special situations such as maintenance, testing, loading, etc.
container after ground contact has been established.
In order to enter the extended selection menu, the right-hand
Moving the left-hand joystick vertically causes the container
joystick must be pointed outwards (in the direction of supports
to be lifted up or lowered. The container is moved during a pe-
2 + 4) when the on switch is actuated. The following modes can
riod of 60 seconds, parallel to the initial position, in order that
be selected by means of horizontal movement of the left-hand
possible jamming, e.g. within the load receptacle of a carrier joystick: vehicle is avoided. – Mode: ’PS’ Display: Memory programming
In certain application situations it is necessary to store the in-
clination of the container, in order to be able to return to the
same angle at a subsequent time. Moving the left-hand joy- Mode ‚A°L‘
stick vertically causes the current position of the container to
be stored in the non-volatile memory. Up to four different po-
Subsequently the container is levelled to an accuracy of 0°
sitions can be stored. The last digit of the display indicates the
± 0.15° in the transverse as well as the longitudinal direction.
number of the selected memory space. The memory space
Once the position has been achieved, this will be signalised on
can be selected by means of moving the right-hand joystick the display. vertically. Display: Display: Mode ‚A°L‘ Mode ’PS’ Container levelled Memory space no. 2 (Total deviation <0.15°) – Mode: ’AS’
Once the container has been successfully levelled, it is pos- Alignment / move to memory
sible to carry out levelled lifting or lowering. A continuous re-
This mode serves to lift or lower the container while maintai-
ference/actual comparison of the container level across both
ning a previously stored position. Prerequisite for this
the X and Y axes is carried out during the process together with
mode is that ground contact has already been made.
corresponding drive control. In order to avoid unnecessary
Moving the right-hand joystick vertically enables the desired
control processes and thereby a slowing of the lifting speed,
memory space to be selected. Moving the left-hand joystick
the permissible deviation during lifting and lowering operations
vertically causes the container to be aligned to the stored po-
is increased to 0.4°. If there is a total deviation of less than
sition and subsequently lifted or lowered. 0.15°, the display indicates
. In the event of a total deviation Display:
between 0.15° and 0.4°, the display changes over to .
The levelling control system monitors the ground contact pro-
cesses and automatically restores the state in the event of
loss. If this cannot be achieved within the specified duration (2
seconds), then an error message is generated and the system Mode ’AS’ Memory space no. 4
shuts down. In the event that more than one ground contact
is lost (container topples diagonally), the system shuts down
The characteristics described for ’A°L’ mode apply to operation
immediately. In this case, ground contact must be manually
in this mode in terms of safety and control. The status display
restored by the operator by means of mode ‚E‘. view changes between and ,depending on the total Hazardous operation! deviation.
The max. permissible inclination for the container is
2°. Slightly increased angles of inclination are possible
at low heights or reduced loads. The operator of the
lifting equipment is responsible for determining and utilising these values.
If the container is more than 2° from zero position in eit-
her the X or Y axis at the start of the lifting or lowering
process, a warning signal sounds and a warning lamp
flashes on the status display. The permissible working
range of the controller extends to a maximum inclinati-
on of ±4° across both axes. Electrical operation is not
possible outside of this range. 094407_1052596_a_gb_hebvrr_s
haacon hebetechnik gmbh – Telefon +49 (0) 9375 - 84-0 . Fax +49 (0) 9375 - 8466 10 – Mode: ’HA’ ’C4’ temperature Manual mode
This mode serves to lift or lower the container manually, there-
by excluding the automatic position control system. Also in this
case, prerequisite for this mode is that ground contact has al-
Temperature display for the electronic components in the swit-
ready been made. The left-hand joystick serves to enable the ching cabinet. Example: -30°C
container to be lifted or lowered. The right-hand joystick then
In the event of temperatures under - 32°C, you must wait
enables the position of the container to be varied by means of
for the heating period to elapse before starting up the
selecting the individual support (pairs).
system. In order to do so, remove the electrical drives Display:
from the support legs and allow them to operate briefly
without a load. Due to their dissipated power, the electro-
nic components will increase the temperature in the swit-
ching cabinet. At temperatures under - 32°C, the tempe- Mode ’HA’
rature flashes on the display and operation is blocked. Hazardous operation! ’U5’ control voltage
The max. permissible inclination for the container is 2°.
Slightly increased angles of inclination are possible at
low heights or reduced loads. The operator of the lifting
equipment is responsible for determining and utilising
Displays the current control voltage. Example: 14.7 V. these values.
An error message is displayed if the control voltage is un-
The visual and acoustic warnings in the event of inclina- der 12V.
tions >2°, as well as the ground contact monitor are ac-
’L6’ inclination in the direction of the X-axis.
tive. The levelling control system enables a maximum in-
clination of 3,8° in manual mode and can continue to
operate while maintaining this position, if required. – Mode: ’SA’
Displays the current inclination of the container in the direction of Status query
This mode serves to query the status of the system. The status
the X-axis (in the direction of travel). Example: 1,2°.
display screen first shows the information ID code and after a ’L7’ inclination in the direction of the Y-axis
short time it changes over to the respective value. Moving the
left-hand joystick vertically enables the following information to be selected:
’O1’ limit position up - ’supports extended’
Displays the current inclination of the container in the direction of
the Y-axis (transversely to the direction of travel). Example: -2,0°.
The reference point for displaying the current inclination
in either of the axes is support no. 1. If this is raised above
The first field of the value display signalises the mode. The fol-
the other supports, the displayed angle is positive.
lowing fields represent the supports 1 to 4 corresponding to ’A8’ Motor efficiency
the selection options of the right-hand joystick. Example: Sup-
ports 1 and 4 are fully extended.
’U2’ limit position down - ’supports retracted’
Displays the current specified maximum value in % with which
the motors are operated (–> chapter ’Setting-up mode’). Exa- mple: 100 %.
Display analogue to limit position up - ’supports extended’. Ex-
ample: Supports 1 and 3 are fully retracted. ’E3’ ground contact
Display analogue to limit position up - ’supports extended’. Ex-
ample: Supports 1, 2 and 3 have ground contact. 094407_1052596_a_gb_hebvrr_s
haacon hebetechnik gmbh – Telefon +49 (0) 9375 - 84-0 . Fax +49 (0) 9375 - 8466 11 Modes - setting-up mode
If the position offset for levelled containers amounts to
Various basic settings must be configured in order to commis-
more than ± 2°, then the sensor box must be realigned, as
sion the system or after significant modifications to the system
the permissible inclination during lifting / lowering will
or its power supply. In order to do so, the levelling control sys-
otherwise exceed the measuring range of the inclination
tem has an integrated additional selection menu available. This sensor.
menu can be activated by pressing the on switch with both joy-
To exit the selection menu, press both joysticks simultaneously
sticks pointing inwards. The following configuration options can
inwards once more. The configured power limit and the current
be selected by means of horizontal movement of the left-hand
position offset for the sensors will be transferred into into the joystick:
levelling control system‘s non-volatile memory. The stored po-
– Configuration option: ’IL’
sition offset serves as a reference value for subsequent control Maximum motor efficiency
processes. For this reason, the container must be in a levelled
Changing this option enables a proportional configuration of position when the menu is exited. If necessary, the inclination of
the maximum motor efficiency to be configured. Among other the container must be corrected using the hand cranks and sui-
things, this is required if the power supply required for en- table measuring instruments.
suring trouble-free operation of the system cannot be made
CAUTION! Risk of toppling! The container must be in a
available. The configurable range is between 53 % and 100 %.
levelled position when the menu is exited.
The configured value can be changed by means of vertically
moving the left-hand joystick. The output of the motors will
Once the menu has been exited, all of the previously described
be restricted if the value is lowered. As a result of this, the lift
modes will be released and can be selected by means of moving
speed and the overall power consumption of the system will
the left-hand joystick horizontally. However, during lifting and lo- be reduced.
wering operation, the status display switches over to a special
screen which indicates the current load of each motor. In doing Display:
so, the screen is subdivided into 3 fields comprising four vertical
markers each. The vertical markers represent the supports 1 to 4
corresponding to the selection options of the right-hand joystick.
A depiction of the marker in the left field means that the motor is Configuration option ’IL’
currently controlling the respective support. The markers in the Max. motor efficiency at 95 %
centre field indicate that the respective motor is currently being
– Configuration option: ‚L06‘
operated at minimum 50% capacity. If the markers in the right
Absolute position offset in X direction
field are active, then the associated motor is running at full load.
Displays the absolute deviation of the position sensor in the di- Display:
rection of the X-axis (in the direction of travel). It is not possible
to change this value by means of the level control system. The
value shown is merely for informational / display purposes and
is important insofar as it is transferred to the non-volatile me-
Special display for setting-up mode
mory when the selection menu is exited, where it is used as a
reference value for the levelled container and for subsequent
Supports 1 to 4 are being controlled
position control. Changing the displayed value is only possible
Supports 1, 3 and 4 are running at min. 50% load
by means of manually changing the inclination of the container.
Supports 1 and 4 are under full load Display:
The visual and acoustic warnings in the event of inclina-
tions >2°, as well as the ground contact monitor are active.
In order to exit setting-up mode and to return to standard mode
or extended mode, switch the levelling control system off and Configuration option ‚L06‘ back on again.
Absolute position offset in X direction 1.7°
– Configuration option: ‚L07‘
Absolute position offset in Y direction
Displays the absolute deviation of the position sensor in the
direction of the Y-axis (transversely to the direction of travel).
The characteristics of this configuration option are analogous
to those described for ‚L06‘. Display: Configuration option ‚L07‘
Absolute position offset in Y direction 0.8° 094407_1052596_a_gb_hebvrr_s
haacon hebetechnik gmbh – Telefon +49 (0) 9375 - 84-0 . Fax +49 (0) 9375 - 8466 12