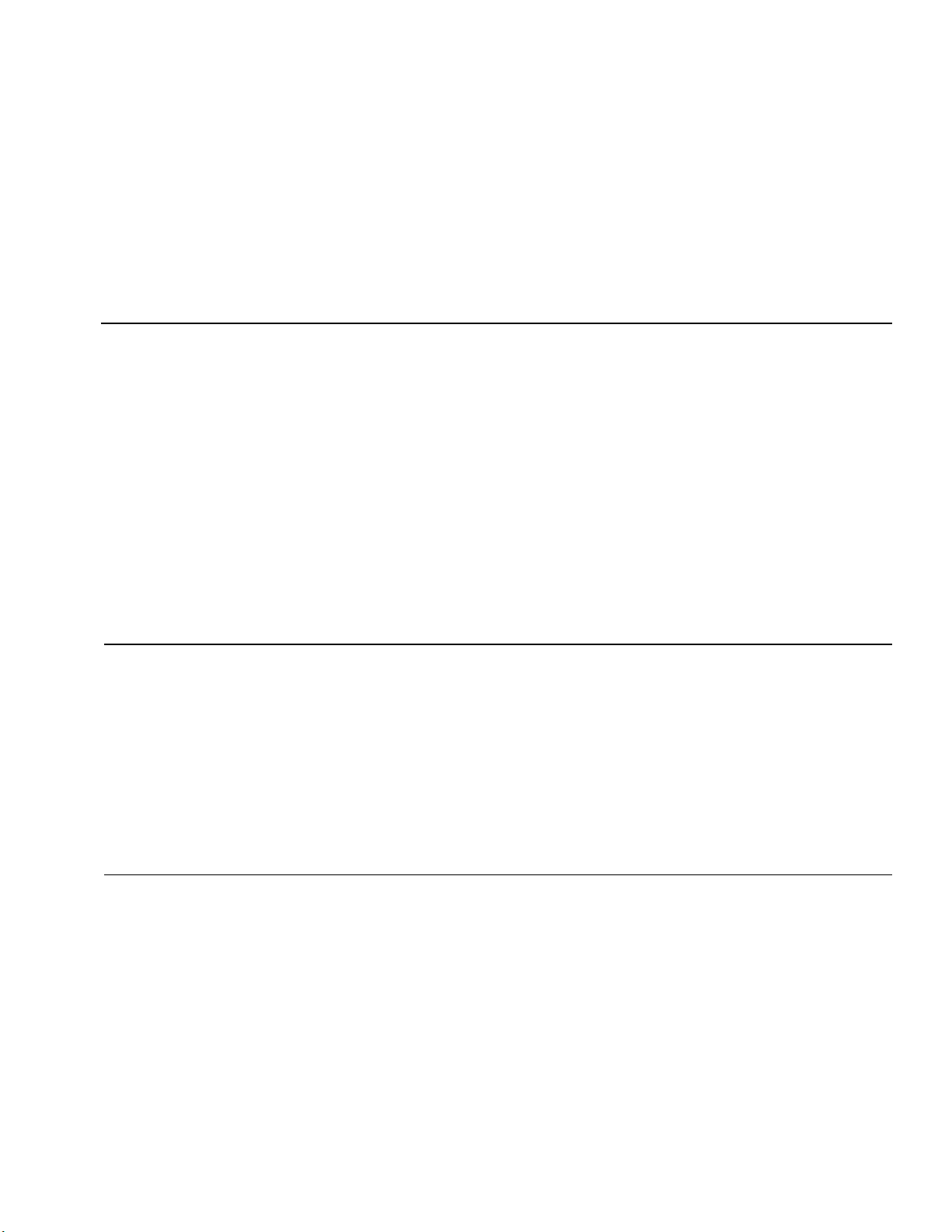
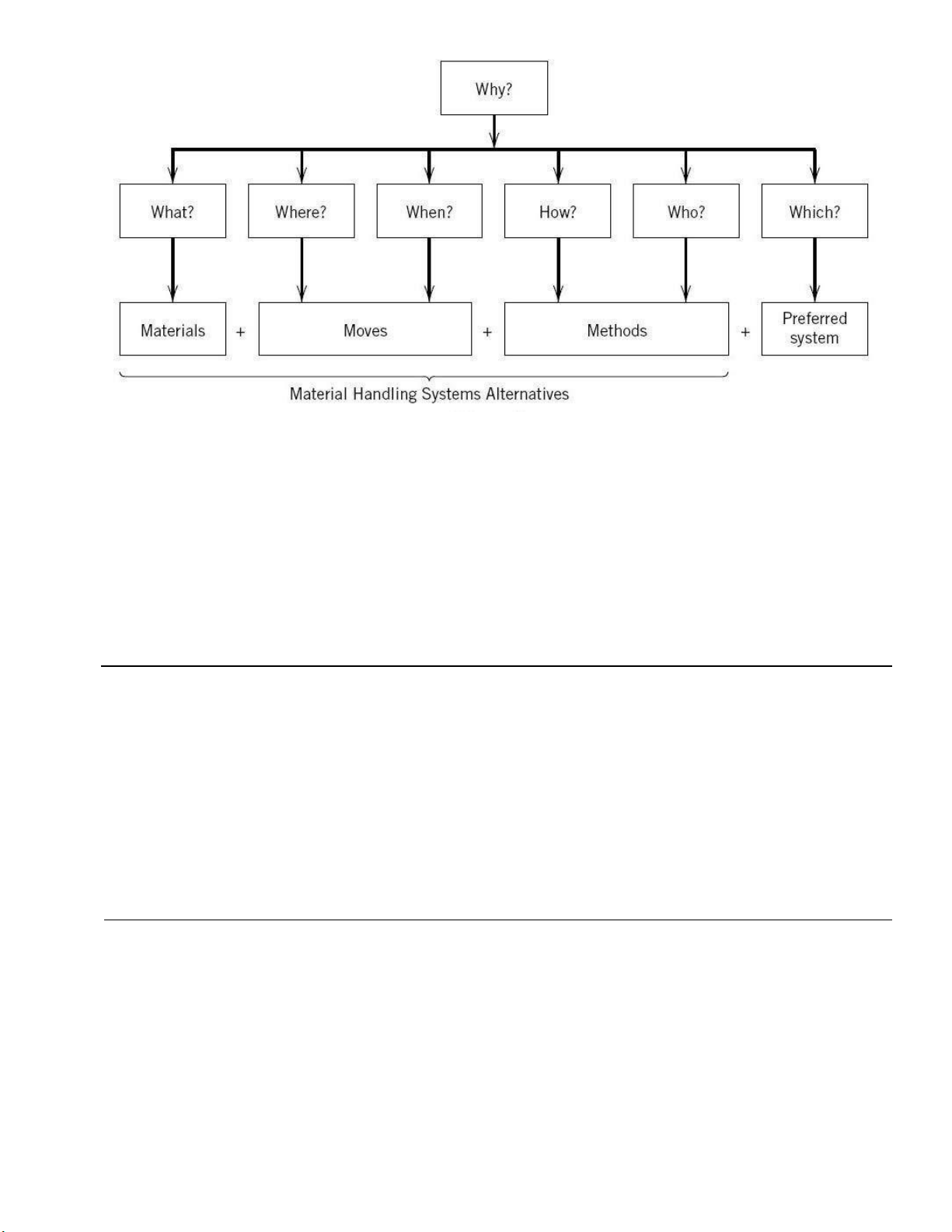
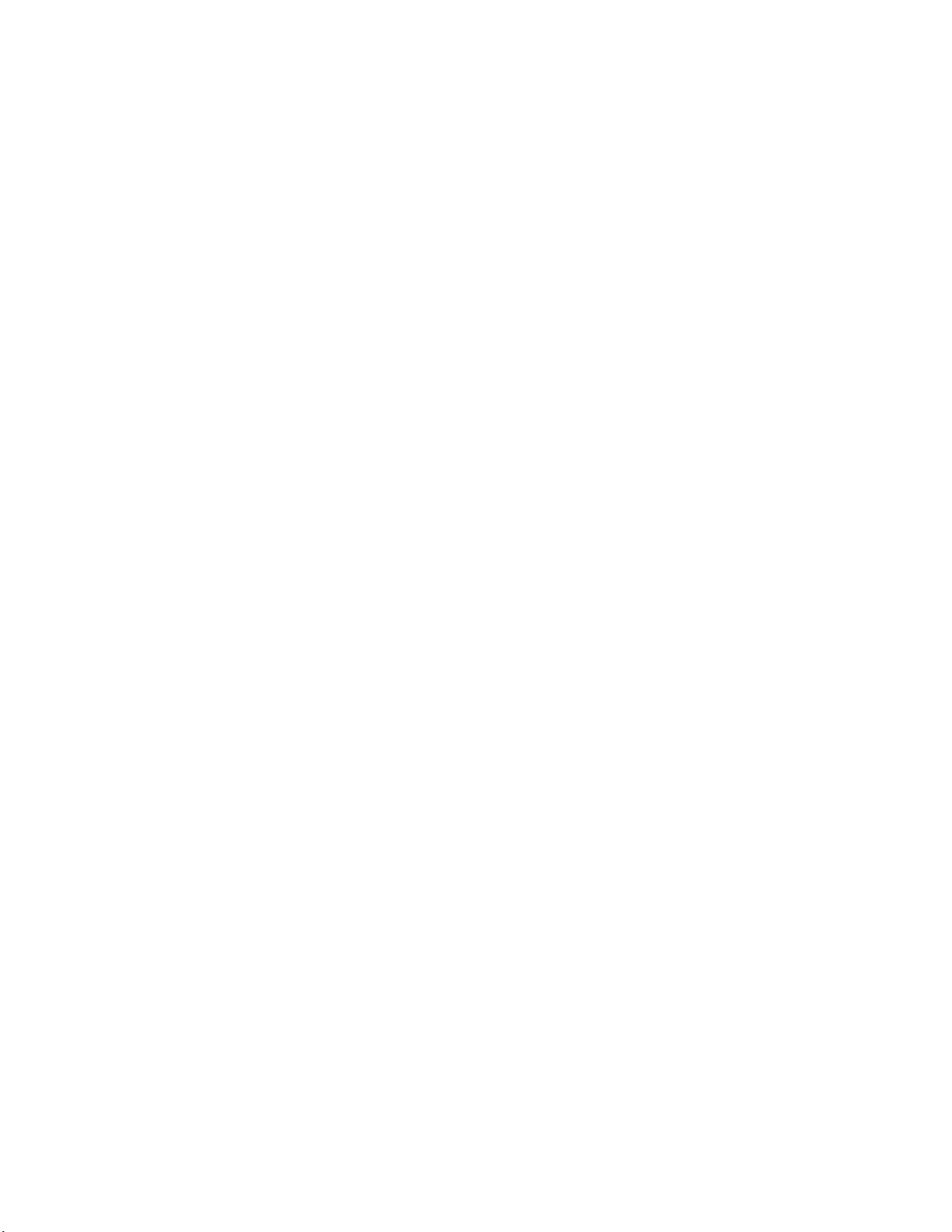
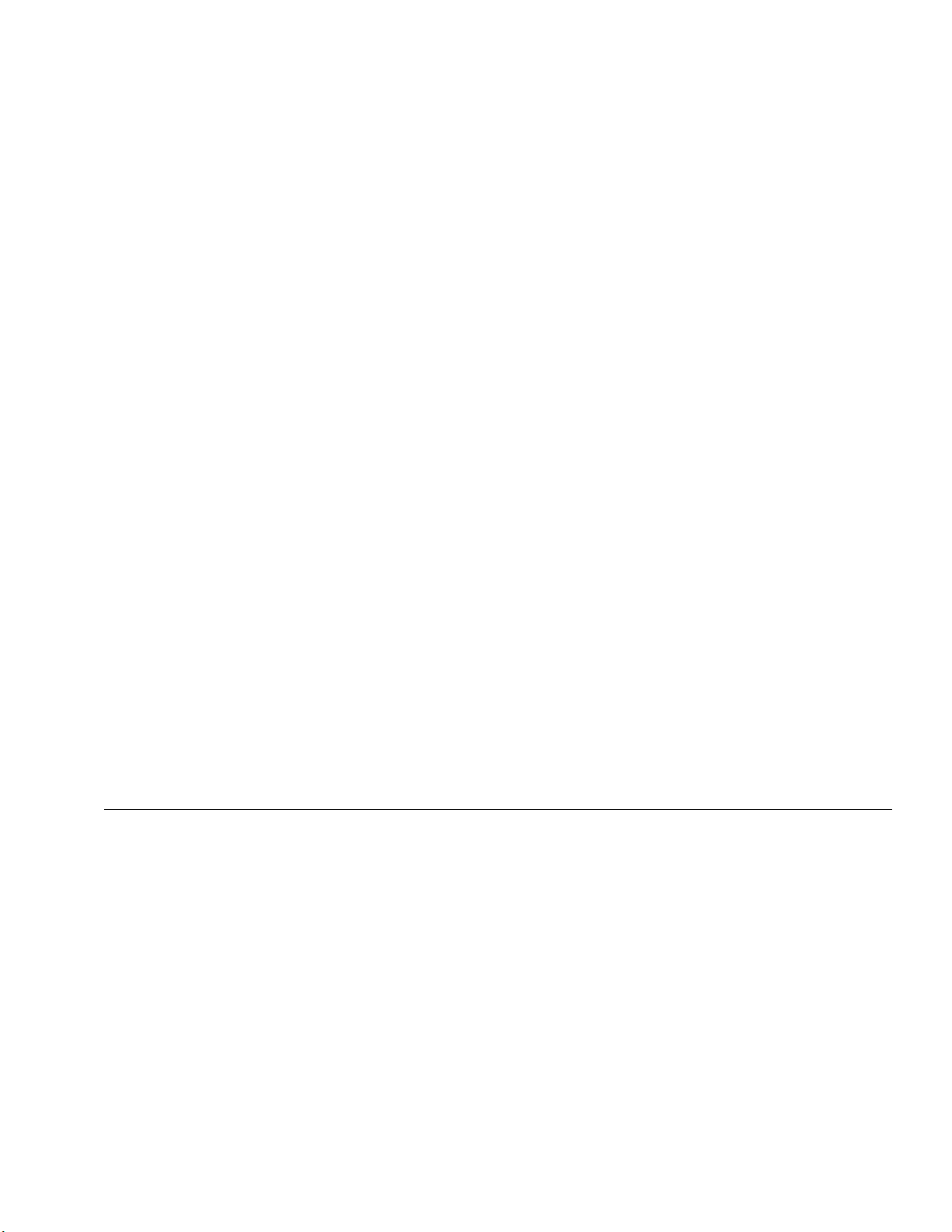
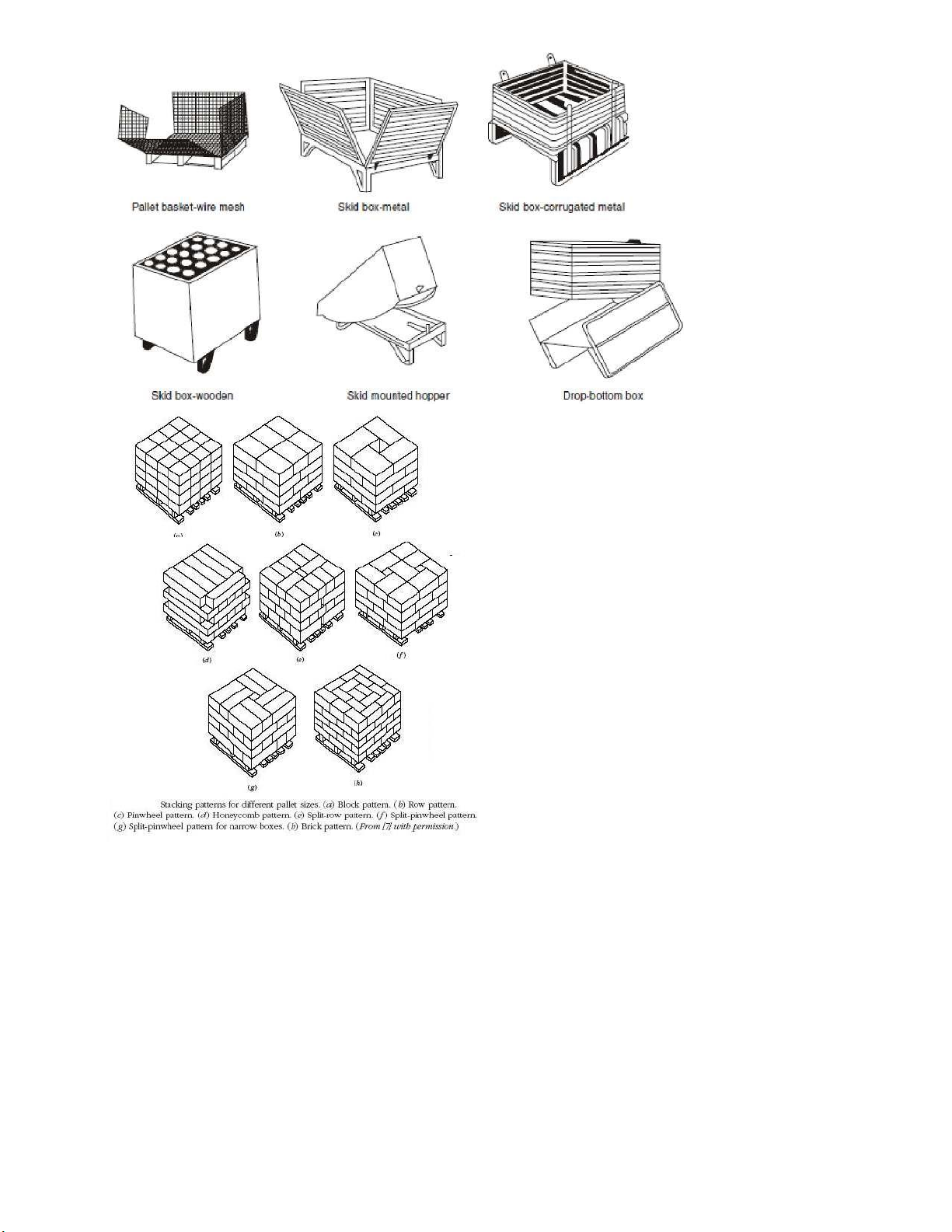
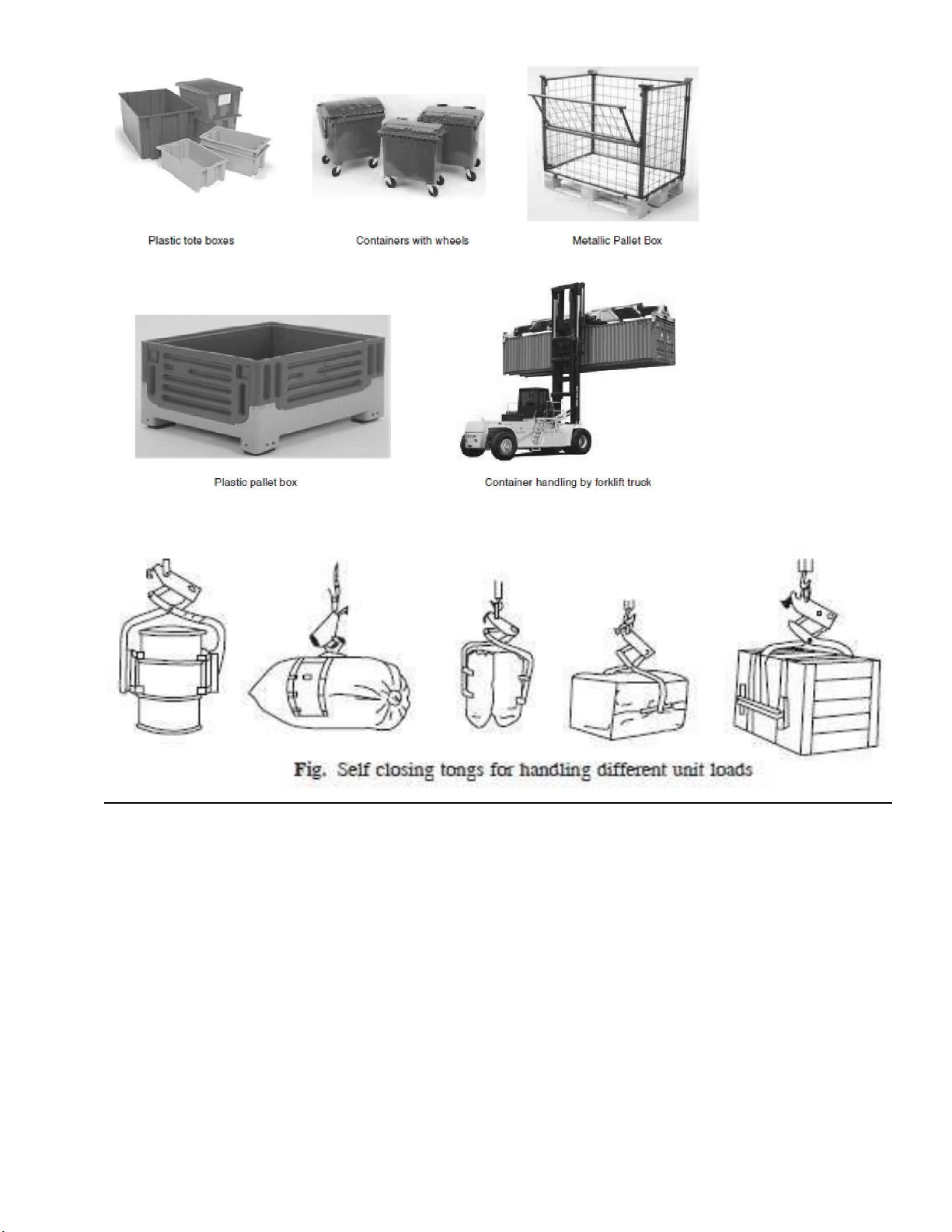
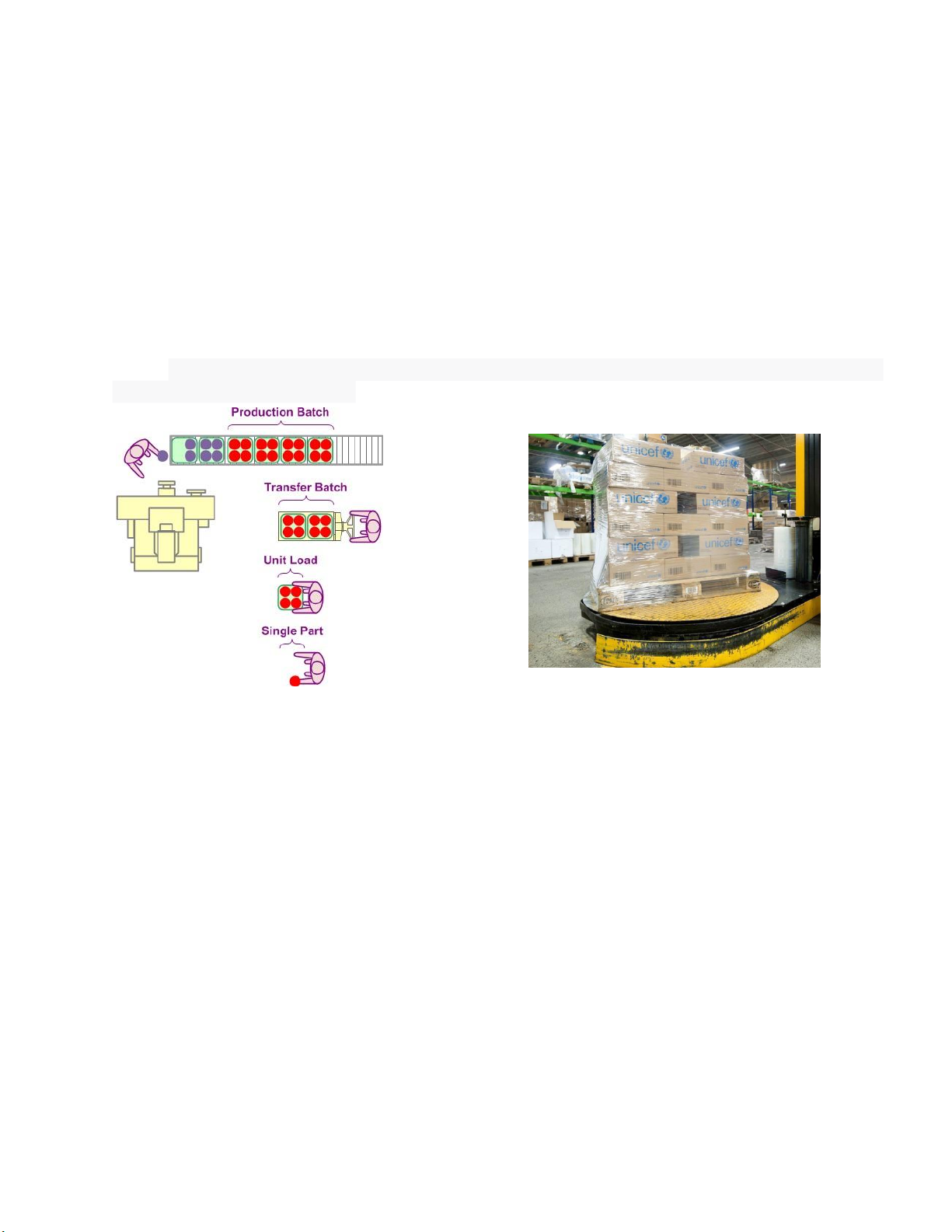
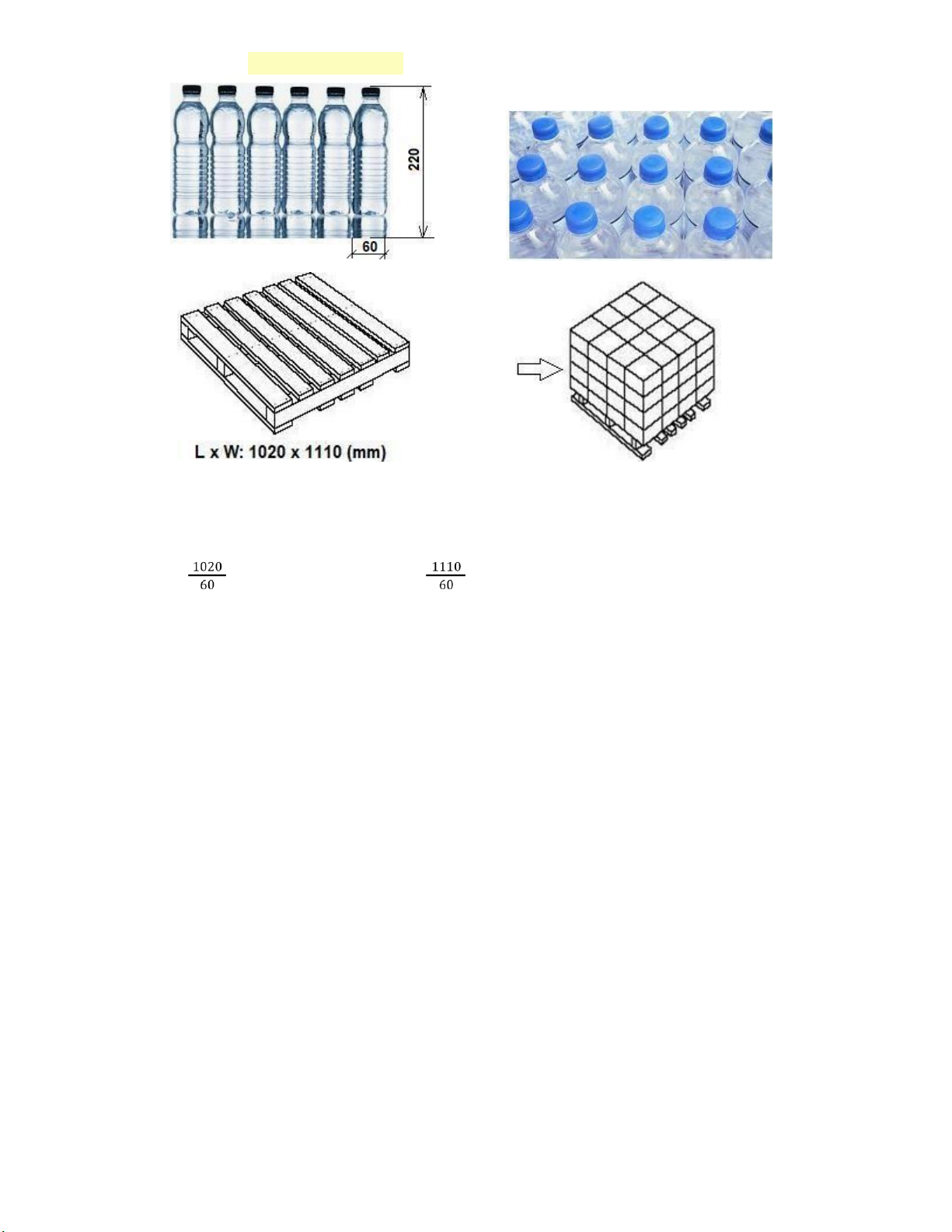
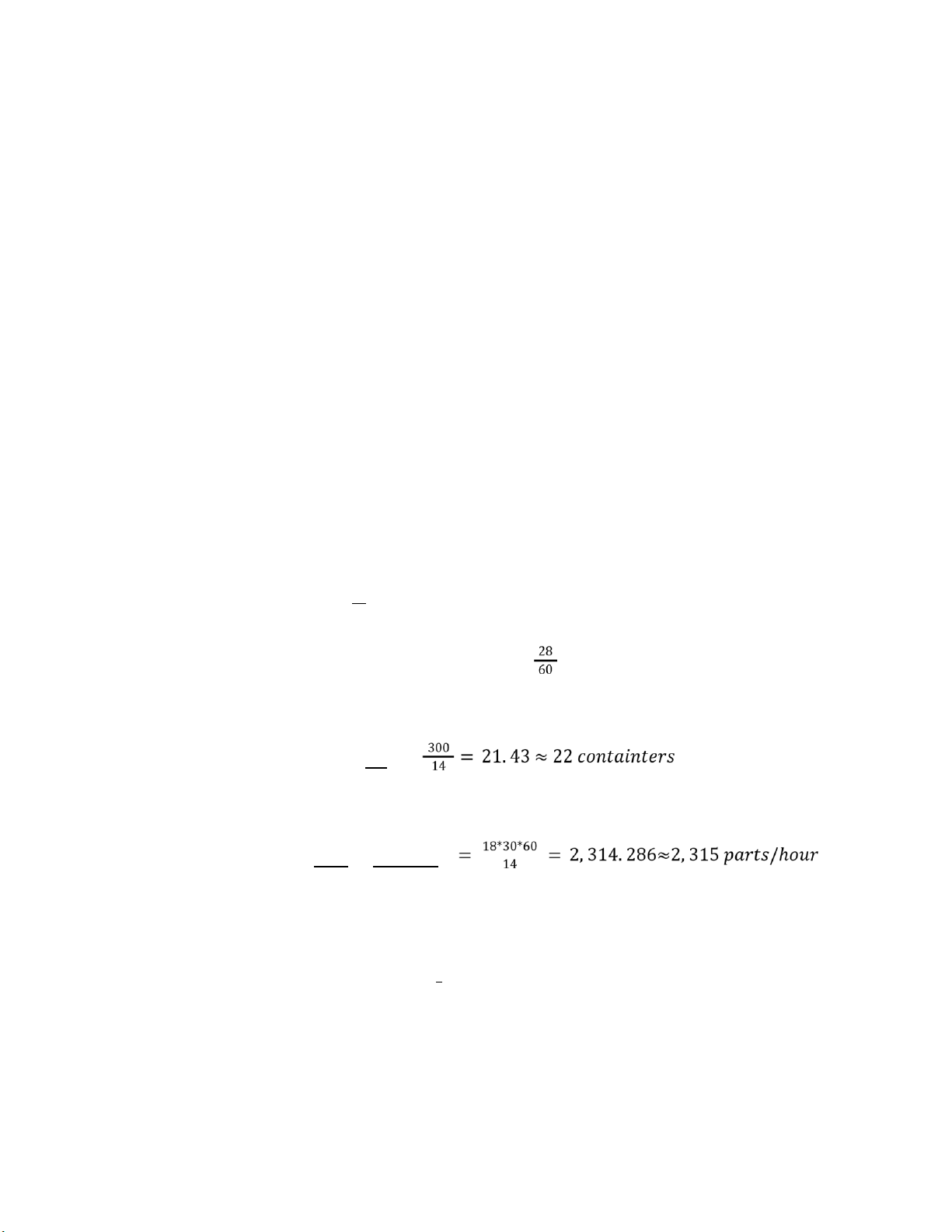
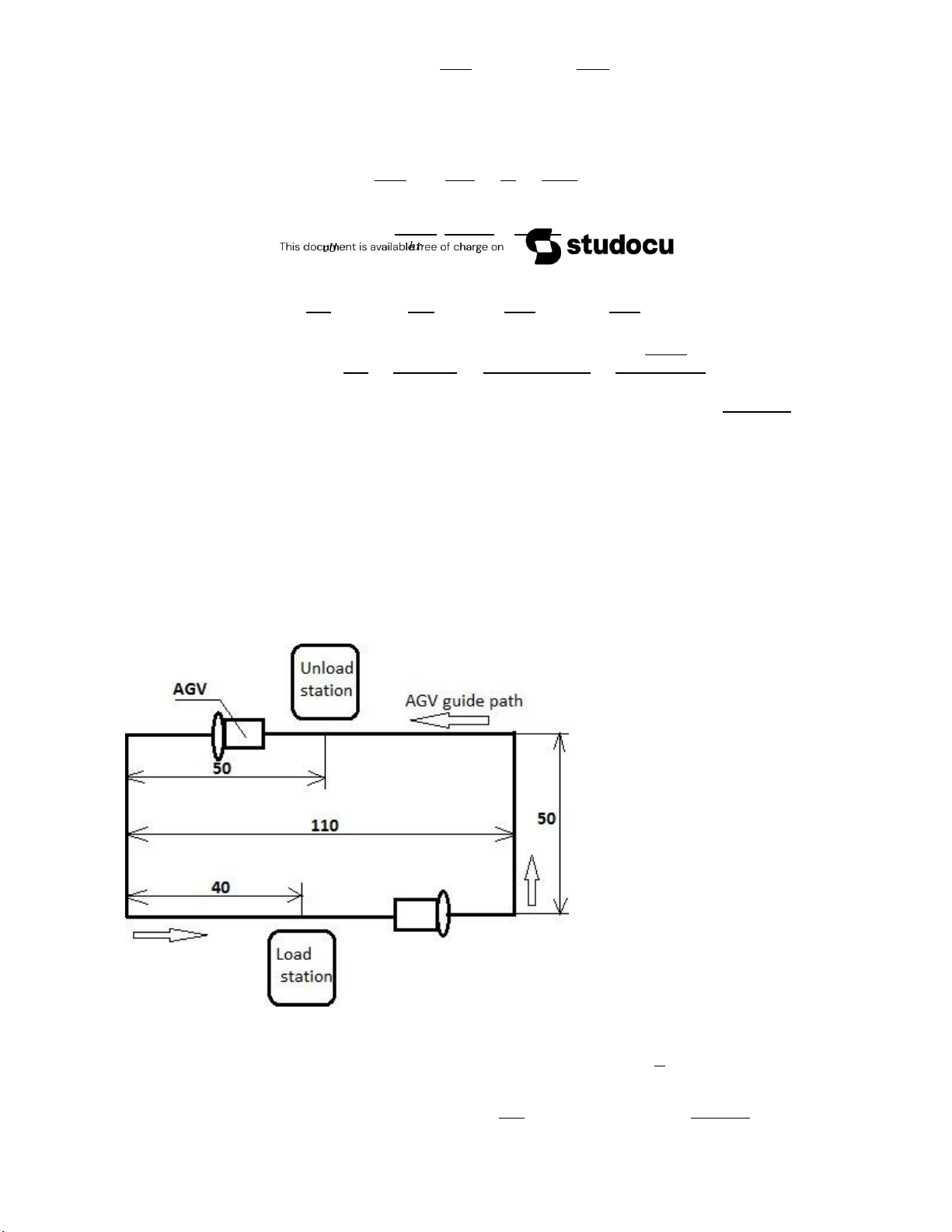
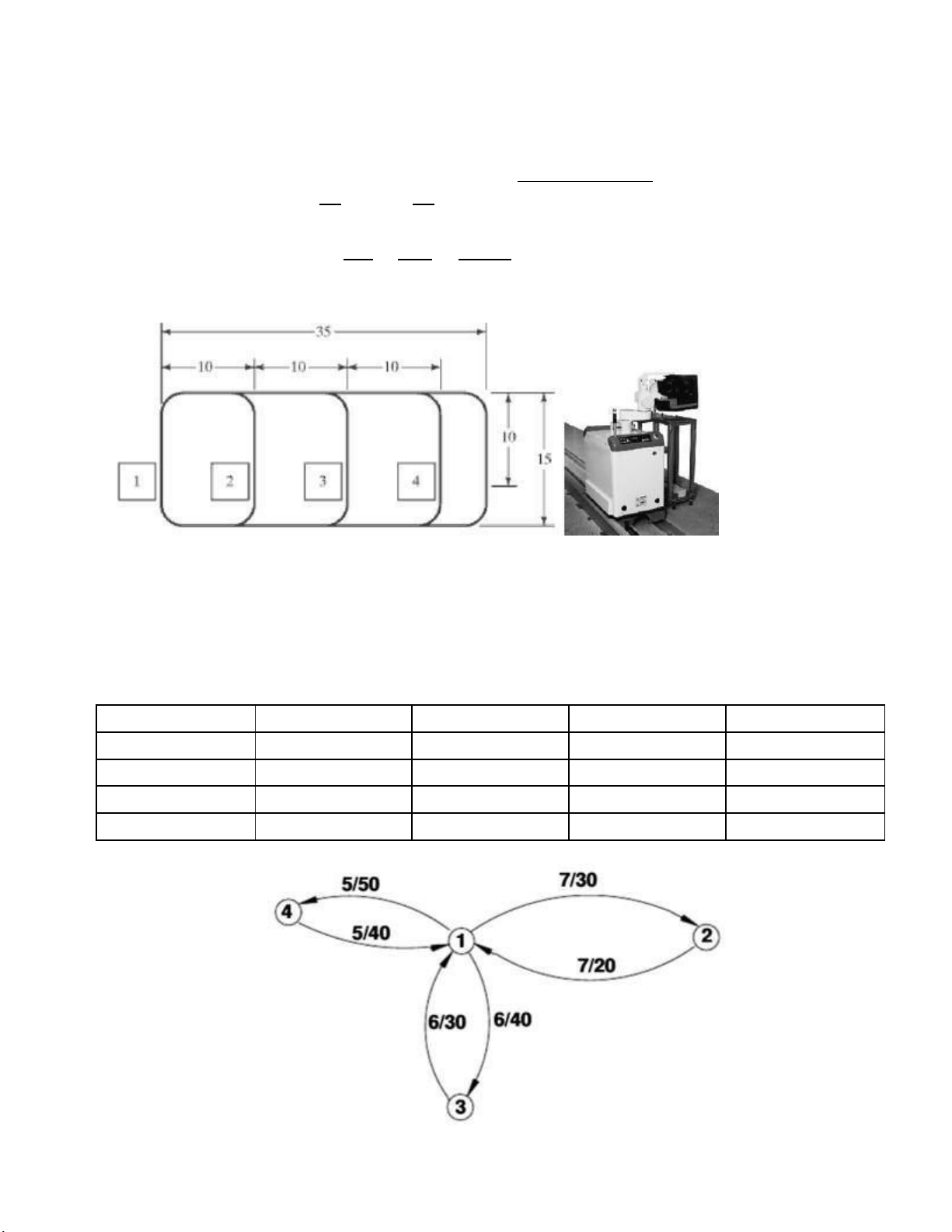
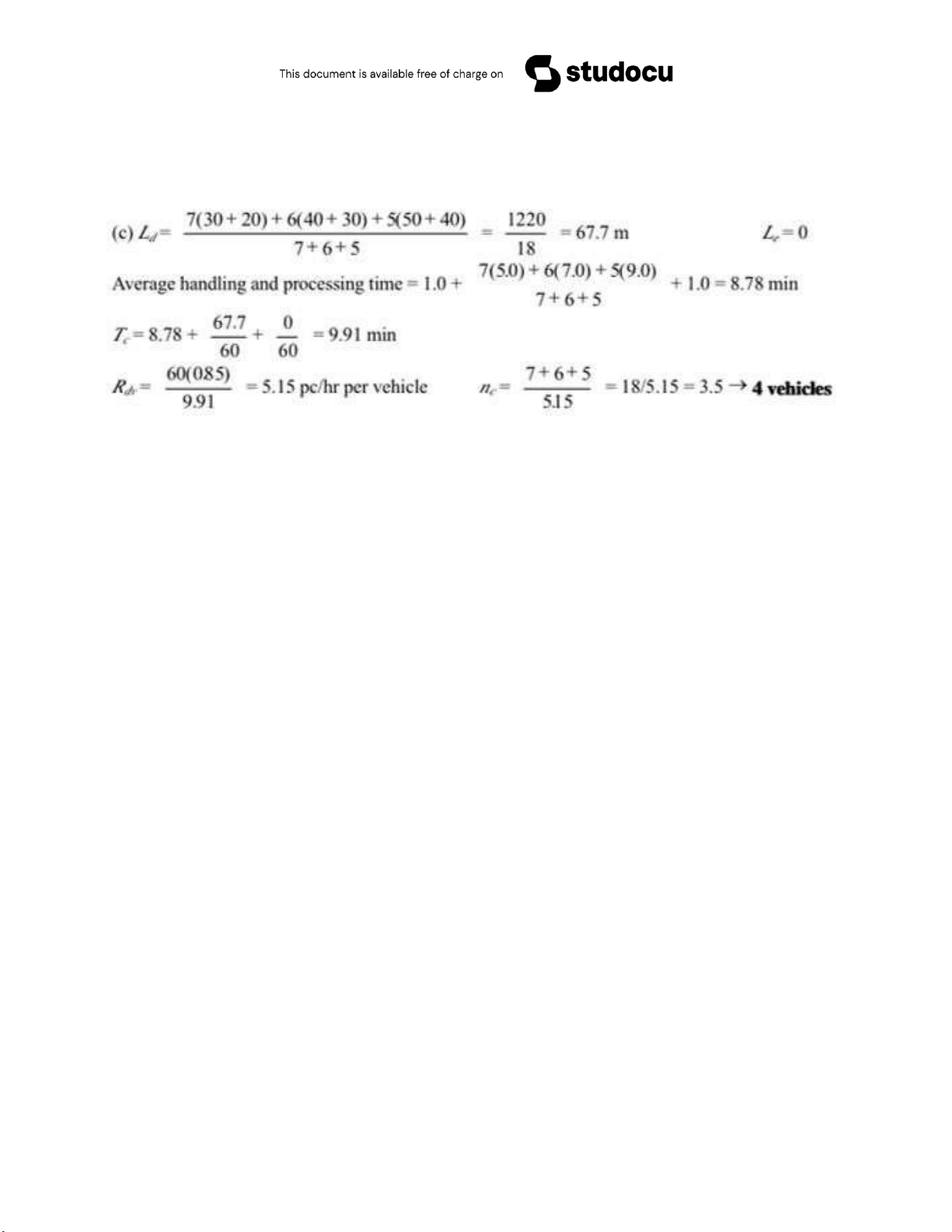
Preview text:
lOMoARcPSD|359 747 69 REVIEW 1
FOCUS 1) Chapter 1: Introduction to MHS
- Material Handling Definitions
●Compton’s Interactive Encyclopedia: “The movement of raw materials, semi-finished goods, and
finished articles through various stages of production and warehousing is called Materials Handling”.
●Material Handling is concerned with the movement, storage, and control of materials in a process.
●Material Handling and logistics are expensive operations which comprise of 10% to 80% of the product cost.
●Materials handling comprises 20% to 35% of the cost of a manufactured product, more often than not;
and for agricultural products and foodstuffs, they may sometimes be much higher.
●Material handling is defined by the Materials Handling Institute (www.mhia.org) as the movement,
storage, control, and protection of materials and products throughout the process of their manufacture,
distribution, consumption, and disposal.
The five commonly recognized aspects of material handling are:
* Motion. Parts, materials, and finished products that must be moved from one location to another should
be moved in an efficient manner and at minimum cost
* Time. Materials must be where they are needed at the moment, they are needed
* Place. Materials must be in the proper location and positioned for use
* Quantity. The rate of demand varies between the steps of processing operations. Materials must be
continually delivered to, or removed from, operations in the correct weights, volumes, or numbers of items required.
* Space. Storage space, and its efficient utilization, is a key factor in the overall cost of an operation or process •
Material handling is the art and science of moving, storing, protecting, and controlling material
– Moving: Required to create time and place utility. The value of having the material at the
right time and the right place.
– Storing: Provides a buffer between operations, facilitates the efficient use of people and machines.
– Protecting: Includes the packaging, packing against damage and theft.
– Controlling: Physical: Orientation, sequence and space between material.
Status: Real-time awareness of the location, amount, destination, origin, ownership, and schedule of material
- Material Handling system Equation
Materials + Moves + Methods = Preferred system lOMoARcPSD|359 747 69
- Materials Handling Equation
A simple but useful way of planning and designing a materials handling problem is described
by the materials handling equation: If Materials Handling is necessary, then MATERIALS + MOVES
= METHODS. This is represented by the Fig. 2.1.1 below, as adopted from Apple(3). The planning starts
with the question ‘‘why’’ at all the contemplated materials handling is needed? If the necessity is clearly
established then only a new handling system is to be considered. Next question is ‘‘what’’ type of
materials to be moved to ‘‘where’’ and ‘‘when’’ ? Answer to this question leads to the method to be
deployed i.e. ‘‘How’’ and by ‘‘whom’’ (manpower/operator) the materials handling will be effected. In
effect, the equation emphasizes the necessity of carefully analyzing both the MATERIALS to be handled
and MOVES to be made before selecting the METHODS. - Objectives of MHS
1. Minimize cost of material handling.
2. Minimize delays and interruptions by making available the materials at the point of use at rightquantity and at right time.
3. Increase the productive capacity of the production facilities by effective utilization of capacity andenhancing productivity.
4. Safety in material handling through improvement in working condition.
5. Maximum utilization of material handling equipment.
6. Prevention of damages to materials.
7. Lower investment in process inventory - Selection of MH Equipment
Selection of Material Handling equipment is an important decision as it affects both cost and efficiency
of handling system. The following factors are to be taken into account while selecting material handling equipment.
1. Properties of the material
Whether it is solid, liquid or gas, and in what size, shape and weight it is to be moved, are important
considerations and can already lead to a preliminary elimination from the range of available equipment
under review. Similarly, if a material is fragile, corrosive or toxic this will imply that certain handling
methods and containers will be preferable to others
2. Layout and characteristics of the building
Another restricting factor is the availability of space for handling. lOMoARcPSD|359 747 69
Low-level ceiling may preclude the use of hoists or cranes, and the presence of supporting columns in
awkward places can limit the size of the material-handling equipment. If the building is multistoried,
chutes or ramps for industrial trucks may be used. Layout itself will indicate the type of production
operation (continuous, intermittent, fixed position or group) and can indicate some items of equipment that
will be more suitable than others. Floor capacity also helps in selecting the best material handling
equipment. 3. Production flow
If the flow is fairly constant between two fixed positions that are not likely to change, fixed equipment
such as conveyors or chutes can be successfully used. If, on the other hand, the flow is not constant and the direction
changes occasionally from one point to another because several products are being produced
simultaneously, moving equipment such as trucks would be preferable 4. Cost considerations
The above factors can help to narrow the range of suitable equipment, while costing can help in taking a
final decision. Several cost elements need to be taken into consideration when comparisons are made
between various items of equipment that are all capable of handling the same load.
Initial investment and operating and maintenance costs are the major cost to be considered. By
calculating and comparing the total cost for each of the items of equipment under consideration, a more
rational decision can be reached on the most appropriate choice 5. Nature of operations
Selection of equipment also depends on nature of operations like whether handling is temporary or
permanent, whether the flow is continuous or intermittent and material flow pattern-vertical or horizontal. 6. Engineering factors
Selection of equipment also depends on engineering factors like door and ceiling dimensions, floor space,
floor conditions and structural strength. 7. Equipment reliability
Reliability of the equipment and supplier reputation and the after-sale service also plays an important
role in selecting material handling equipment *Equipment*
• Balance between the production problem, the capabilities of the equipment available, and the human element involved
• Objective is to arrive at the lowest cost per unit of material handled • Depends on:
◦Material to be moved ◦Movement ◦Storage ◦Costs
◦Equipment factors: adaptability, flexibility, load capacity, power, speed, space requirements,
supervision required, ease of maintenance, environment • Conveyors:
◦Large capacity over considerable distance
◦Materials or parts can be added ◦Permanent position
◦Various packages, individual items, bulk material • Trucks: ◦Delivery in batches ◦Flexibility ◦Portable power supply ◦Load usually on a pallet • Cranes: ◦Lifting heavy pieces lOMoARcPSD|359 747 69 ◦Limited mobility ◦Very expensive ◦Foundation requirements 2) Chapter 2: Unit Load - Unit load Design
7 steps to design a unit load: - Unit load concept applicable? - Select the unit load type -
Identify most remote source of load -
Determine farthest practicable destination for load - Establish unit load size -
Determine unit load configuration -
Determine how to build unit load Unit load design involves determining
1. Type, size, weight, and configuration of the load
2. Equipment and method used to handle the load
3. Methods of forming (or building) and breaking down the load.
Determination of the load size
• Size (volume and weight) of the unit load has major impact on the specification and operation of the material handling
• The Optimal Unit Load is the quantity where the system idle time, WIP and transportation cost are minimized. Larger unit load: + fewer moves
- bigger and heavier equipment - wider aisles
- higher floor load capacities
- increased work-in-process inventorySmaller unit load:
+ reduced work-in-process inventory
+ simple material handling methods (i.e., push carts)
+ reduced completion time (How??) - more moves
- increased material handling time - Pallet loading Problem
• The relationship between the container and the pallet • The objectives:
◦to maximize the use of space ◦to maximize load stability lOMoARcPSD|359 747 69 lOMoARcPSD|359 747 69
• Different types of tongs are used in conjunction with crane for lifting and moving many types of unit loads - Principles of MH ( slide Chapter 2.1) 3) Chapter 4: Conveyor
- Characteristics of Conveyors
The main characteristics of conveyors for purposes of classification are the type of traction and the
loadcarrying elements. A distinction is made between conveyors with belt, chain, and cable drive
elements an d conveyors without a drive element (gravitational, inertial, and screw conveyors).
These are gravity or powered equipment commonly used for moving bulk or unit load continuously or
intermittently, uni-directionally from one point to another over fixed path, where the primary function is
conveying of the material by the help of movement of some parts/components of the equipment. The
equipment as a whole does not move.
- Conveyor Analysis: (chap 4)
4) Chapter 5: AGV (in slide dùm- năn nỉ :”<)
- Typical navigation systems for AGV - AGV Analysis lOMoARcPSD|359 747 69 EXAMPLES/QUESTIONS
1) What is Systems Principle of Materials Handling? Please suggest few examples of MHS?
Material movement and storage activities should be fully integrated to form a coordinated, operational
system which spans receiving, inspection, storage, production, assembly, packaging, unitizing, order
selection, shipping, transportation and the handling of returns.
2) What are general characteristics of belt conveyors? (i)
Belt conveyors operate in one vertical plane, horizontally or with an inclination (up or down)
depending on the frictional property of the load conveyed. (ii)
For changing direction of the materials being conveyed, in the horizontal plane, more than one belt conveyors are needed. (iii)
Conveying capacity of a conveyor can be controlled by changing belt speed. (iv)
Belt conveyors are generally employed for continuous flow of materials. (v) Metal/special
belts can carry hot, abrasive or reactive materials. 3)
which can contain multiple part s
Production batch can be split into a smaller transfer batch containing several unit loads, each of lOMoARcPSD|359 747 69
What is Unit load? Design the unit load của the drinking water bottles to place it on the pallet as shown.
• Unit load – amount of material that can be moved as a single mass between two locations
• A unit load is one or more boxes secured to a pallet or skid so that boxes can be handled by
mechanical means Reference Solution:
Using 4-way pallet with given size (LxW: 1020x1110 mm) Side 1020:
= 17 𝑏𝑜𝑡𝑡𝑙𝑒𝑠; Side 1110:
= 18. 5~18 𝑏𝑜𝑡𝑡𝑙𝑒𝑠
⇨ A batch of bottles will contains 17 * 18 = 306 𝑏𝑜𝑡𝑡𝑙𝑒𝑠 and is arranged in block pattern to maximize the use of space.
Due to the height of a bottle (220 mm), we can have 5 batches in a pallet unit load with total 1,100mm
which is nearly closed to the in-reach height of a person. The estimated blank space we can have:
{[1. 02 * 1. 11 * 0. 22] − Π * 0. 03[ 2 * 306 * 0. 22]} * 5 = 0. 2937𝑚3 4) Typical Navigation systems for AGV, Applications: Given data
(warehouse, workshop,…layout); Choose navigation system for AGV. • Laser triangulation • Inertial • Magnetic tape • Magnetic grid • Natural feature • Wire • Optical
With given data is only layout of warehouse, workshop,…, Natural Feature Navigation system is the best
option in this case. Due to the fact that AGV will move around the layout without any marks, lines, or grids
on the floor, they move based on reference images, and camera or laser to record features during setup and
sense features during navigation.
5) AGVs Design: How do you design AGVs?
*AGV can be designed based on below features: - Stopping Accuracy:
Automatic load transfer- High accuracy
Manual load transfer- Low accuracy lOMoARcPSD|359 747 69
Unit load transporters are used for systems requiring high accuracy.
Feedback system can be used to provide stopping accuracy Depends
on the requirement/application.
- Facility: Environmental compatibility, elevator, sensors, etc facilities must be considered while designing AGVS.
- Safety features: Emergency buttons, object detection for collision avoidance, warning signals, must be built into the system. - Maintenance:
Preventive maintenance intervals should be specified.
Routine and repair maintenance including lubrication, checking systems electrical/electronic parts . Service manual.
Maintenance facilities: Vehicle jack stands, Low-level power indicators.
*However, there are many issues must be considered before designing system for an AGVS: Selection of guidepath and vehicle
Guidepath layout / Flow path design Number of vehicles
There are several other issues regarding timing of AGVs, dispatching rules, routes, etc. Also, there must
be interaction between design and operational issues for system design.
6) A 300-ft long roller conveyor operates at a velocity = 30 ft/min and is used to move parts in containers
between load and unload stations. Each container holds 18 parts. One worker at the load station is able
to load parts into containers and place the containers onto the conveyor in 28 sec. It takes 20 sec to
unload at the unload station. Determine:
𝐿𝑑 = 300𝑓𝑡; 𝑣𝑐 = 30 𝑓𝑡 𝑚𝑖𝑛
; 𝑛𝑝 = 18 𝑝𝑎𝑟𝑡𝑠∕𝑐𝑜𝑛𝑡𝑎𝑖𝑛𝑒𝑟 = π𝑟2; 𝑇𝐿 = 28 𝑠𝑒𝑐; 𝑇𝑈 = 20 𝑠𝑒𝑐
(a) center-to-center distance between containers, 𝑠 = 𝑣 * 𝑇 = 30 *= 14 𝑓𝑡 𝑐 𝑐 𝐿
(b) number of containers on the conveyor at one time, and 𝐿 𝑛𝑐 = 𝑠𝑑𝑐 = (c) hourly flow rate of parts. 𝑛 𝑣 𝑅𝑓 = 𝑠𝑝𝐶𝑐
(d) By how much must conveyor speed be increased in order to increase flow rate to 3,500 parts/hr?
Increasing 𝑣 would have not effect towards increasing 𝑅 in this problem. The loading rate, set by 𝑇 = 28 𝑠𝑒𝑐, 𝑐 𝑓 𝐿
is what limits the flow rate in this system. 𝑅𝑓 ≤ 𝑇1𝐿
7) Five forklift trucks are used to deliver pallet loads of parts between work cells in a factory. Average
travel distance loaded is 500 ft and the travel distance empty is estimated to be the same. The trucks are
driven at an average speed of 2.5 miles/hr when loaded and 3.5 miles/hr when empty. Terminal time per
delivery averages 2.0 min (load = 1,.0 min and unload = 1.0 min). If the traffic factor is assumed to be
0.95, availability= 90%, and worker efficiency = 0.85, what is the maximum hourly delivery rate of the five trucks? lOMoARcPSD|359 747 69
𝐿𝑑 = 𝐿𝑒 = 500𝑓𝑡; 𝑣𝑐𝐿 = 2. 5 𝑚𝑖𝑙𝑒𝑠ℎ𝑟 ; 𝑣𝑐𝑈 = 3. 5 𝑚𝑖𝑙𝑒𝑠ℎ𝑟 ; 𝑇𝐿 = 𝑇𝑈 = 1 𝑚𝑖𝑛
𝐹 = 0. 95; 𝐴 = 0. 9; 𝐸𝑤 = 0. 85 𝑇
𝑣= 2. 5 𝑚𝑖𝑙𝑒𝑠 ( ) ℎ𝑟
5280𝑚𝑖𝑙𝑒𝑓𝑡 * 601ℎ𝑜𝑢𝑟𝑚𝑖𝑛 = 220𝑓𝑡/𝑚𝑖𝑛 𝑐𝐿 𝑚𝑖𝑙𝑒 𝑠 𝑐 𝑈 ℎ 𝑟
𝑣 = 3. 5 ( 5280𝑚𝑖𝑙𝑒𝑓𝑡 * 601ℎ𝑜𝑢𝑚𝑖𝑛𝑟 ) = 308𝑓𝑡/𝑚𝑖𝑛 𝐿𝑑 𝐿𝑒 500 500 𝑇𝑐 = 𝑇𝐿 + 𝑣𝑐𝐿 + 𝑇𝑈 + 𝑣𝑐𝑈 = 1 + 220 + 1 + 308 = 5. 896 𝑚𝑖𝑛 𝐴𝑇 60𝐴𝐹𝑇𝐸𝑤 60*0.9*0.95*0.85
7.396 𝑑𝑒𝑙𝑖𝑣𝑒𝑟𝑖𝑒𝑠ℎ𝑜𝑢𝑟 𝑅𝑑𝑣 = 𝑇𝑐 = 𝑇𝑐 = 5.896 = 𝑣𝑒ℎ𝑖𝑐𝑙𝑒
→𝑀𝑎𝑥𝑖𝑚𝑢𝑚 ℎ𝑜𝑢𝑟𝑙𝑦 𝑟𝑎𝑡𝑒 𝑜𝑓 𝑡ℎ𝑒 𝑓𝑖𝑣𝑒 𝑡𝑟𝑢𝑐𝑘𝑠 = 5 * 𝑅𝑑𝑣 = 36. 98 𝑑𝑒𝑙𝑖𝑣𝑒𝑟𝑖𝑒𝑠ℎ𝑜𝑢𝑟
8) Consider the AGVs layout in figure. Vehicles travel counterclockwise around the loop to deliver loads
from the load station to the unload station. Loading time = 70 min and unloading time = 0.5 min. The
following performance parameters are given: - Vehicle velocity: 50m/min - Availability: 0.95 - Traffic factor: 0.90 - Worker efficiency: 1.0 -
The total of 40 deliveries/hour must be completed by the AGVs
𝑇𝐿 = 70 𝑚𝑖𝑛; 𝑇𝑈 = 0. 5 𝑚𝑖𝑛; 𝑣𝑐 = 50 𝑚𝑖𝑛𝑚
𝐴𝑇 = 60 * 0. 95 * 0. 9 * 1 = 51. 3 ℎ𝑜𝑢𝑟𝑚𝑖𝑛 𝑝𝑒𝑟 𝑣𝑒ℎ𝑖𝑐𝑙𝑒; 𝑅𝑓 = 40 𝑑𝑒𝑙𝑖𝑣𝑒𝑟𝑖𝑒𝑠ℎ𝑜𝑢𝑟 Determine:
a) Travel distances loaded and empty lOMoARcPSD|359 747 69 𝐿 = 50 + 70 + 60 = 180 𝑚 𝑑
𝐿 = 50 + 50 + 40 = 140 𝑚 𝑒 b) Ideal delivery cycle time 𝐿𝑑 𝐿𝑒 180 140 𝑇𝐶 = 𝑇𝐿 + 𝑣𝑐 + 𝑇𝑈 + 𝑣𝑐 = 70 + 50
+ 0. 5 + 50 = 76. 9 𝑚𝑖𝑛
c) Number of vehicles required to satisfy the delivery demand?𝑊𝐿 𝑅 𝑇 𝑓 𝑐 40*76.9 𝑛𝑐 = 𝐴𝑇 = 𝐴𝑇 = 51.3
= 59. 96≈60 𝑣𝑒ℎ𝑖𝑐𝑙𝑒𝑠
9) A flexible manufacturing system (FMS) is being planned. It has a ladder layout as pictured in
Figure. It uses a rail guided vehicle (RGV) system to move parts between stations in the layout.
All workparts are loaded into the system at station 1, moved to one of three processing stations (2, 3, or
4), and then brought back to station 1 for unloading. Once loaded onto its RGV, each workpart stays
onboard the vehicle throughout its time in the FMS. Load and unload times at station 1 are each 1.0 min.
Processing times are: 5.0 min at station 2; 7.0 min at station 3; and 9.0 min at station 4.
Hourly production of parts through the system is: 7 parts through station 2; 6 parts through station 3 and; 5 parts through station 4.
(a) Develop the from-to Chart for trips and distances; From/To 1 2 3 4 1 0 7/30 6/40 5/50 2 7/20 0 - - 3 6/30 - 0 - 4 5/40 - - 0
(b) Develop the network diagram. lOMoARcPSD|359 747 69
(c) Determine the number of rail guided vehicles that are needed to meet the requirements of the flexible
manufacturing system, if vehicle speed = 60 m/min and the anticipated traffic factor = 0.85.
Assume reliability = 100%. 𝐹 = 0. 85; 𝑣 = 60 𝑚∕ 𝑇 𝑐
Document Outline
- REVIEW 1
- FOCUS 1) Chapter 1: Introduction to MHS
- 1. Properties of the material
- 2. Layout and characteristics of the building
- 4. Cost considerations
- 5. Nature of operations
- 6. Engineering factors
- 7. Equipment reliability
- 2) Chapter 2: Unit Load
- Determination of the load size
- 3) Chapter 4: Conveyor
- 4) Chapter 5: AGV (in slide dùm- năn nỉ :”<)
- EXAMPLES/QUESTIONS