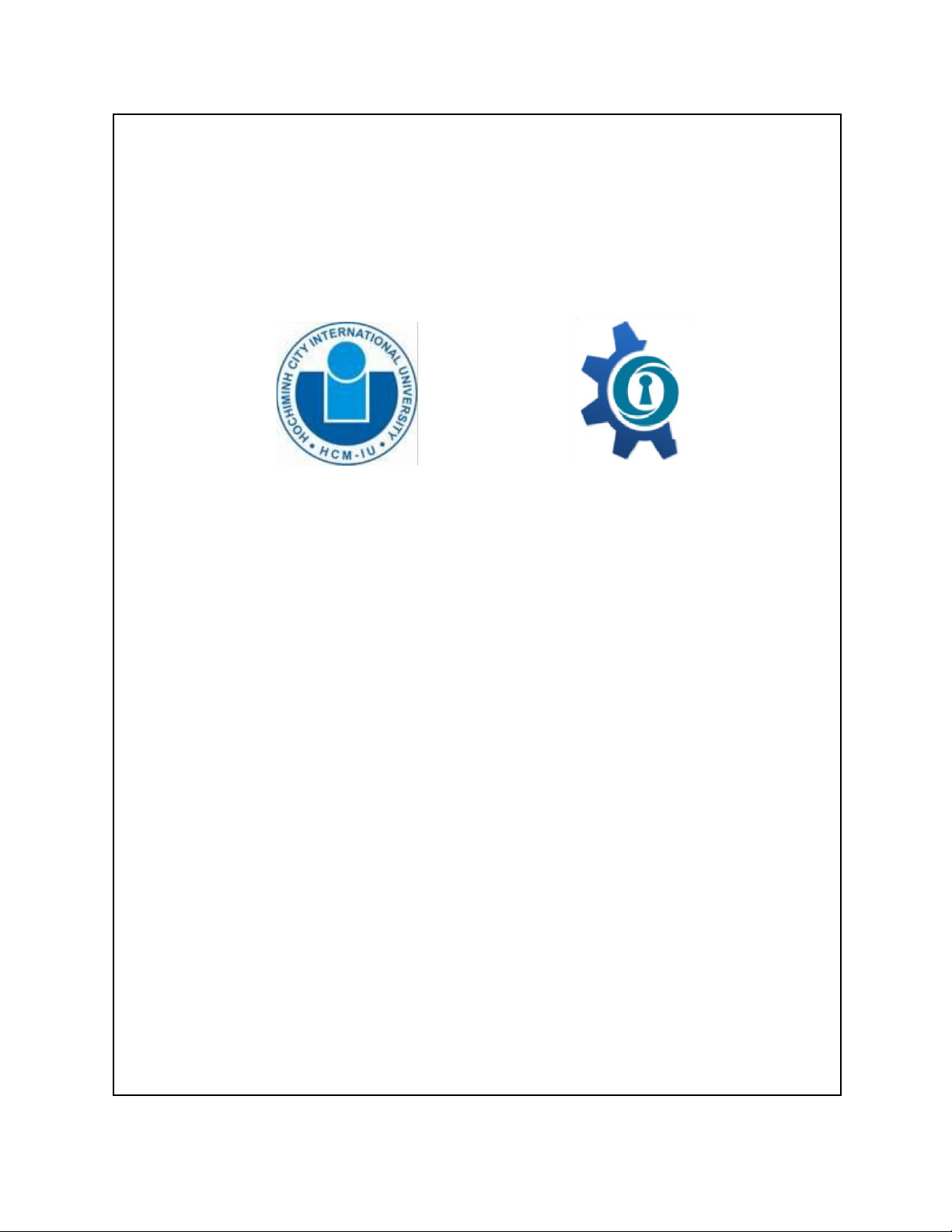
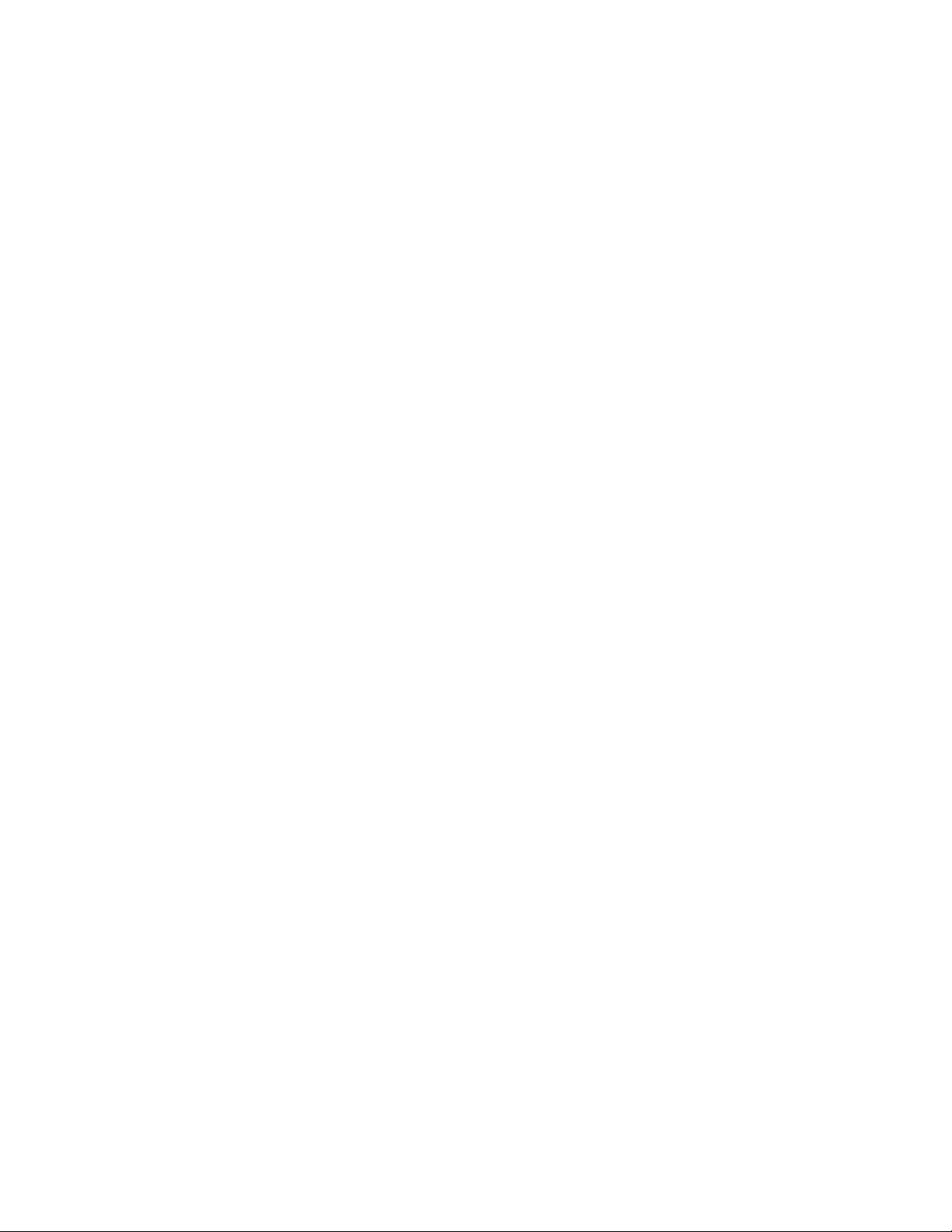
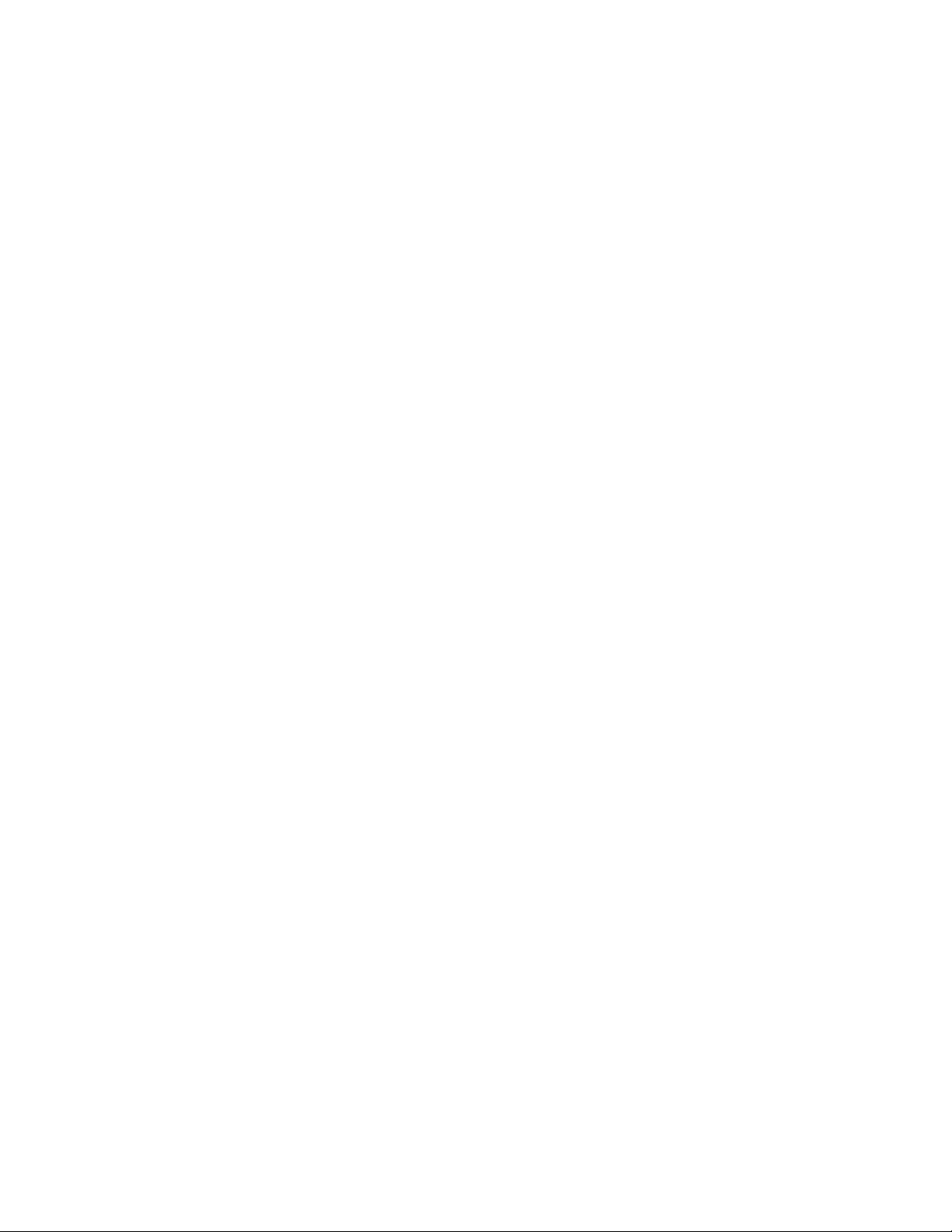
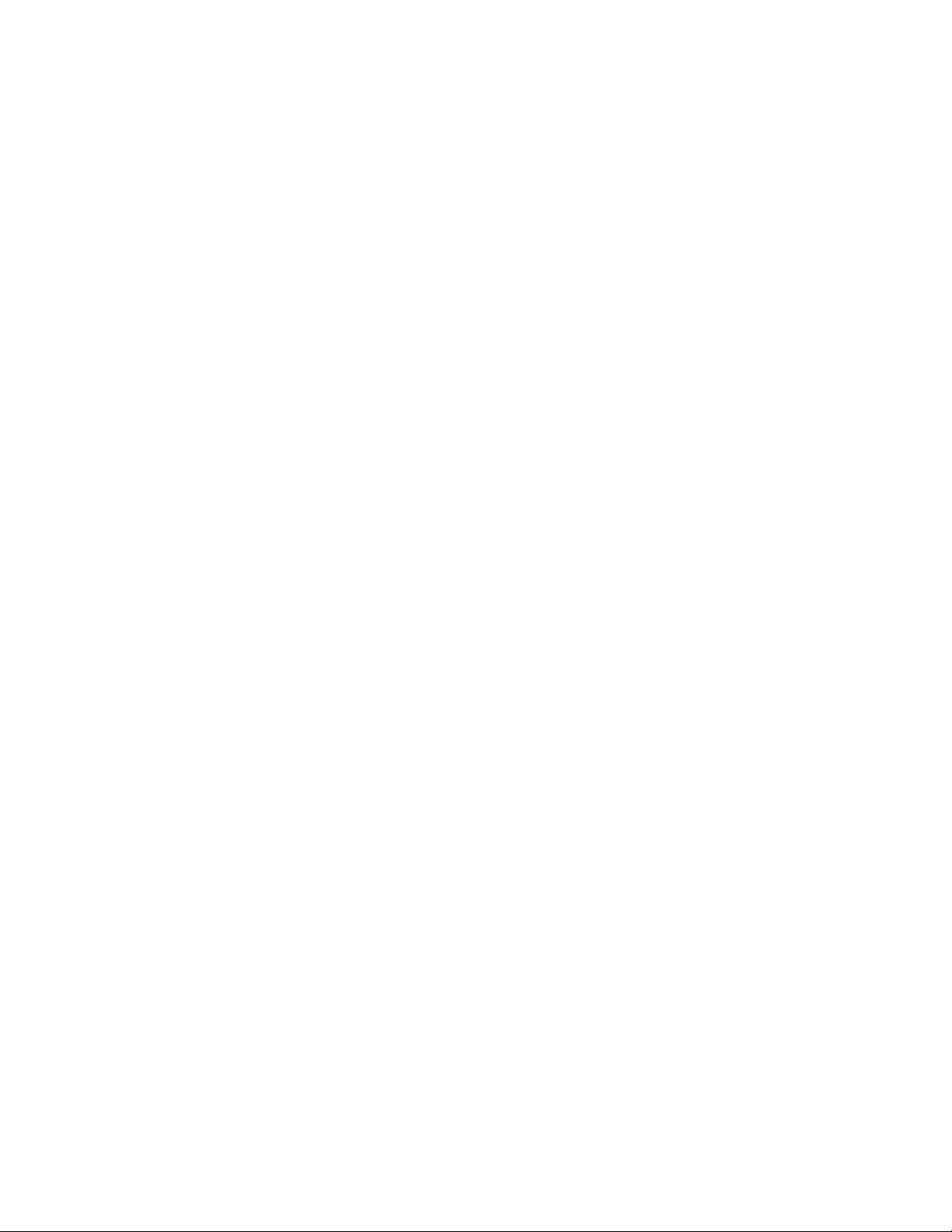
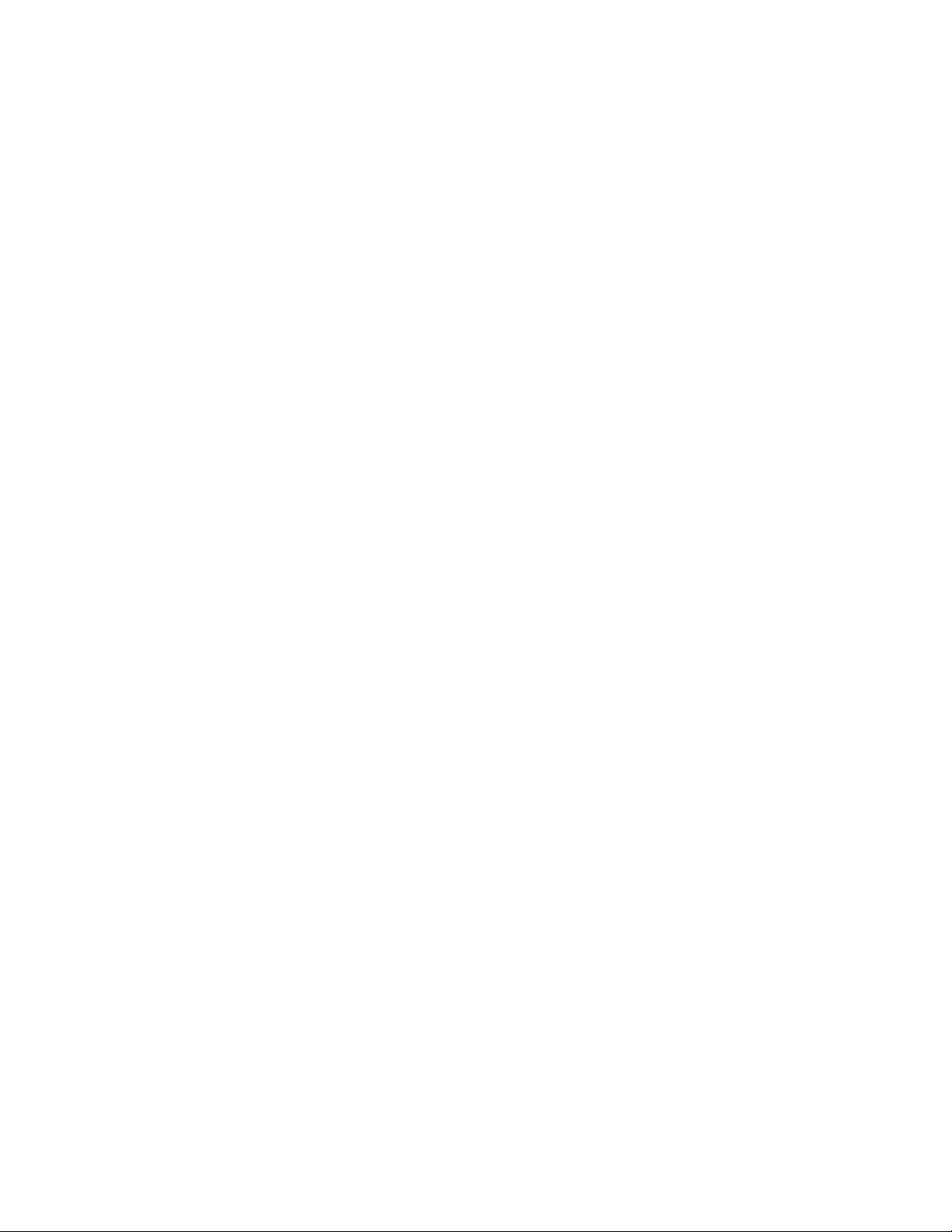
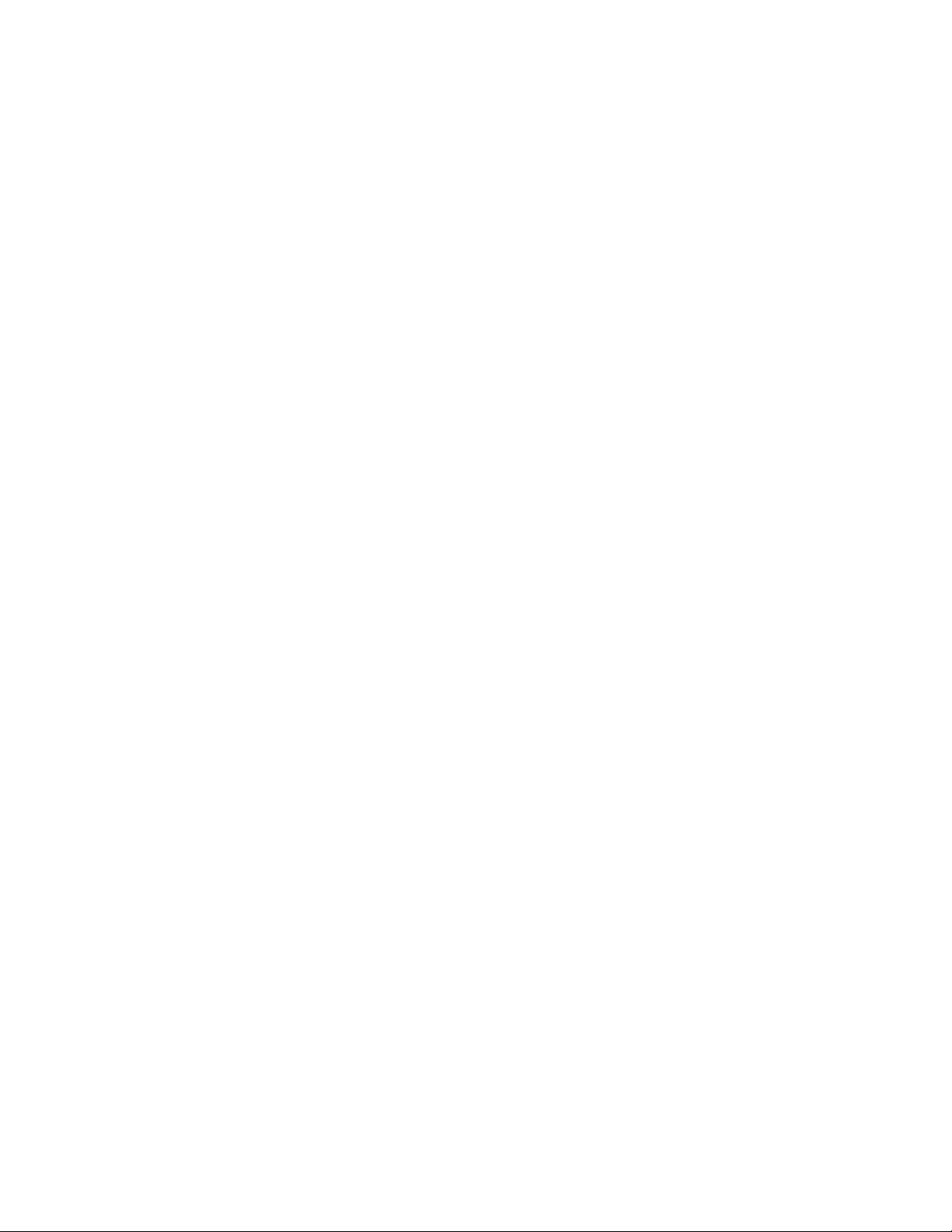
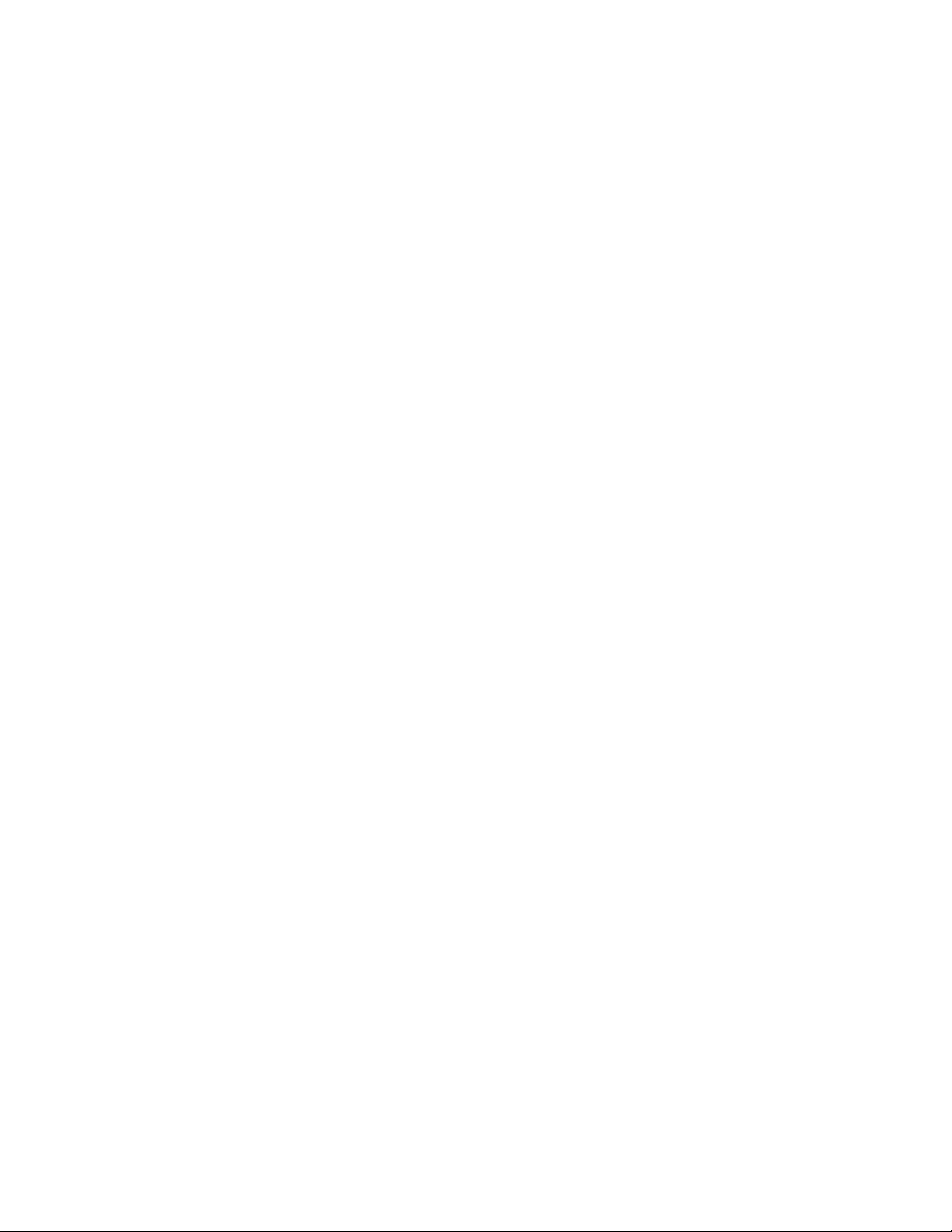
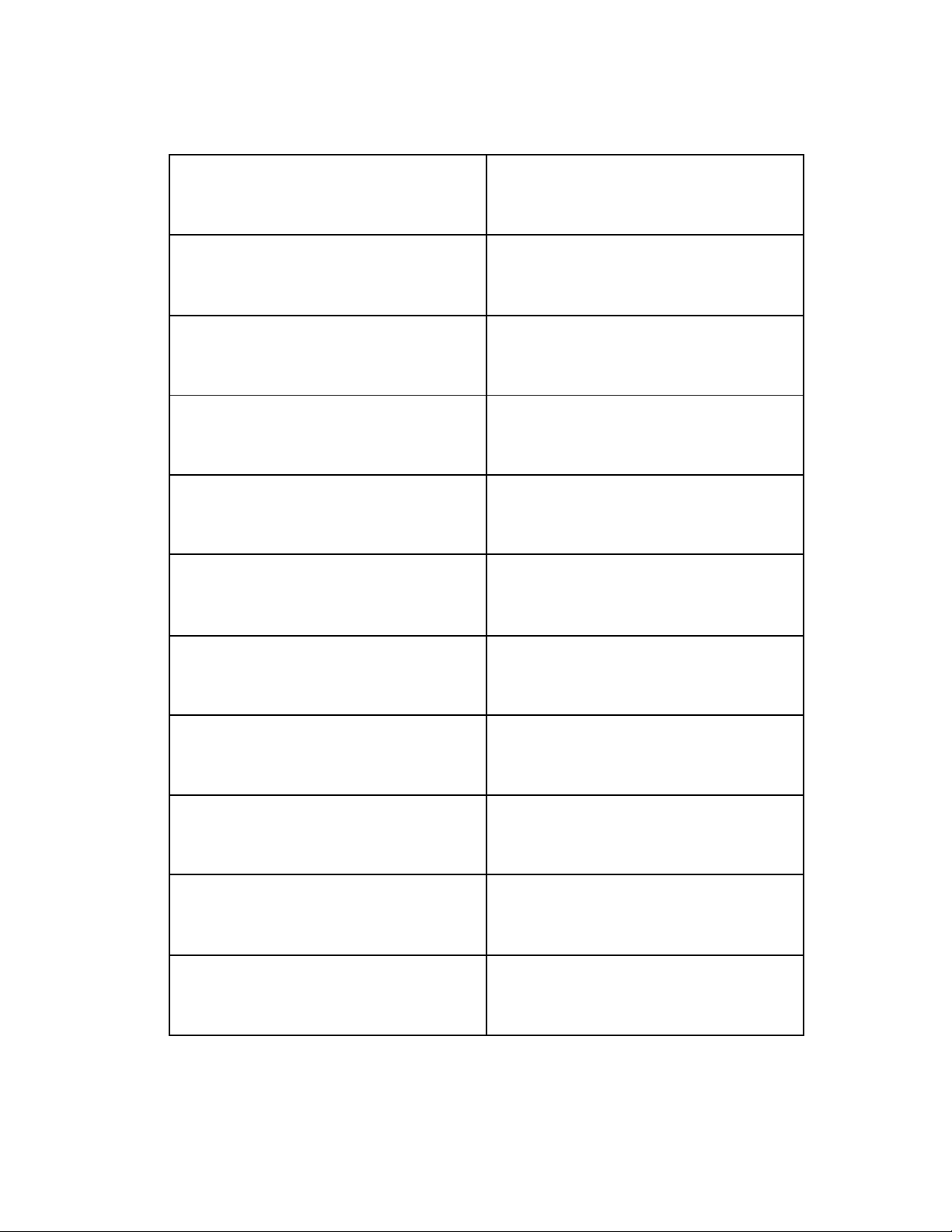
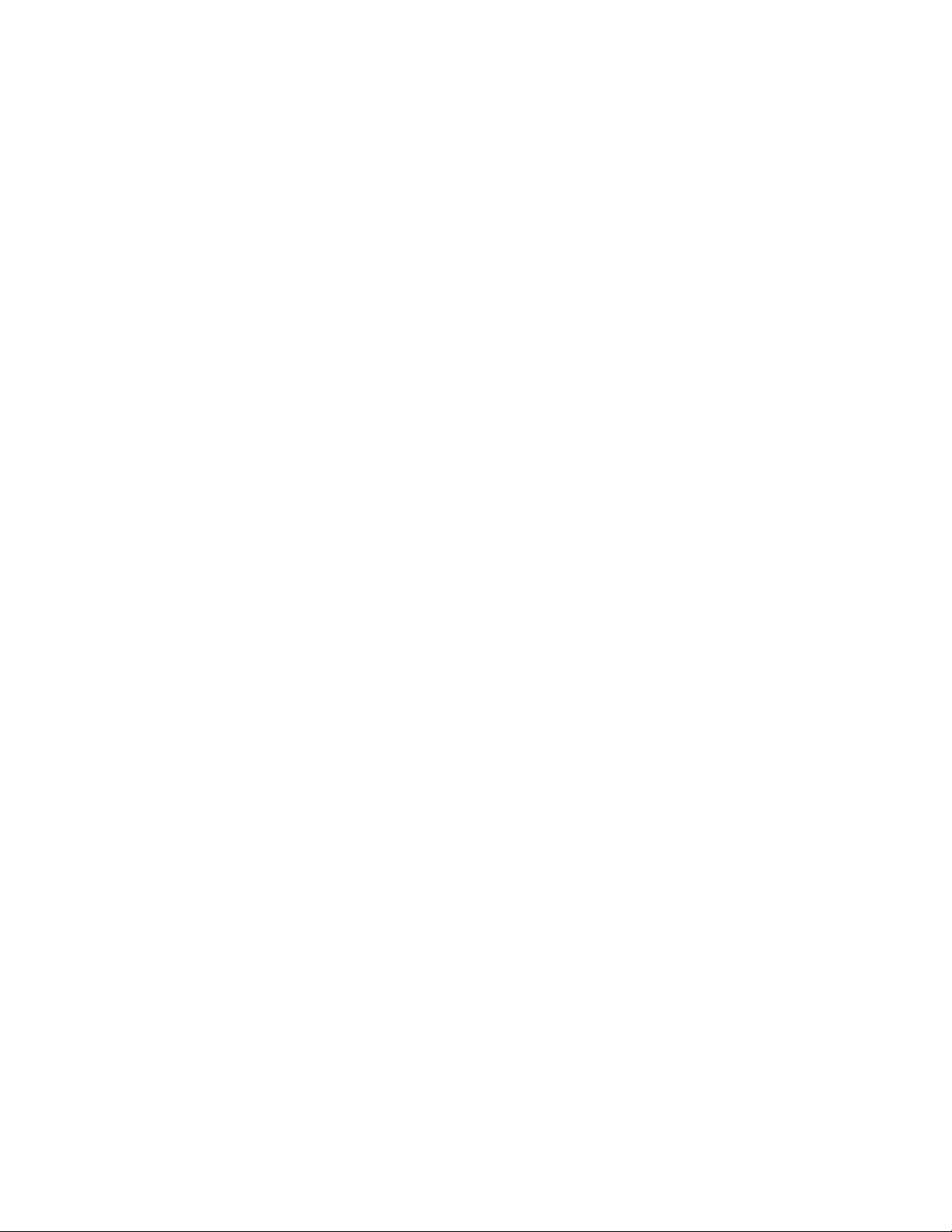
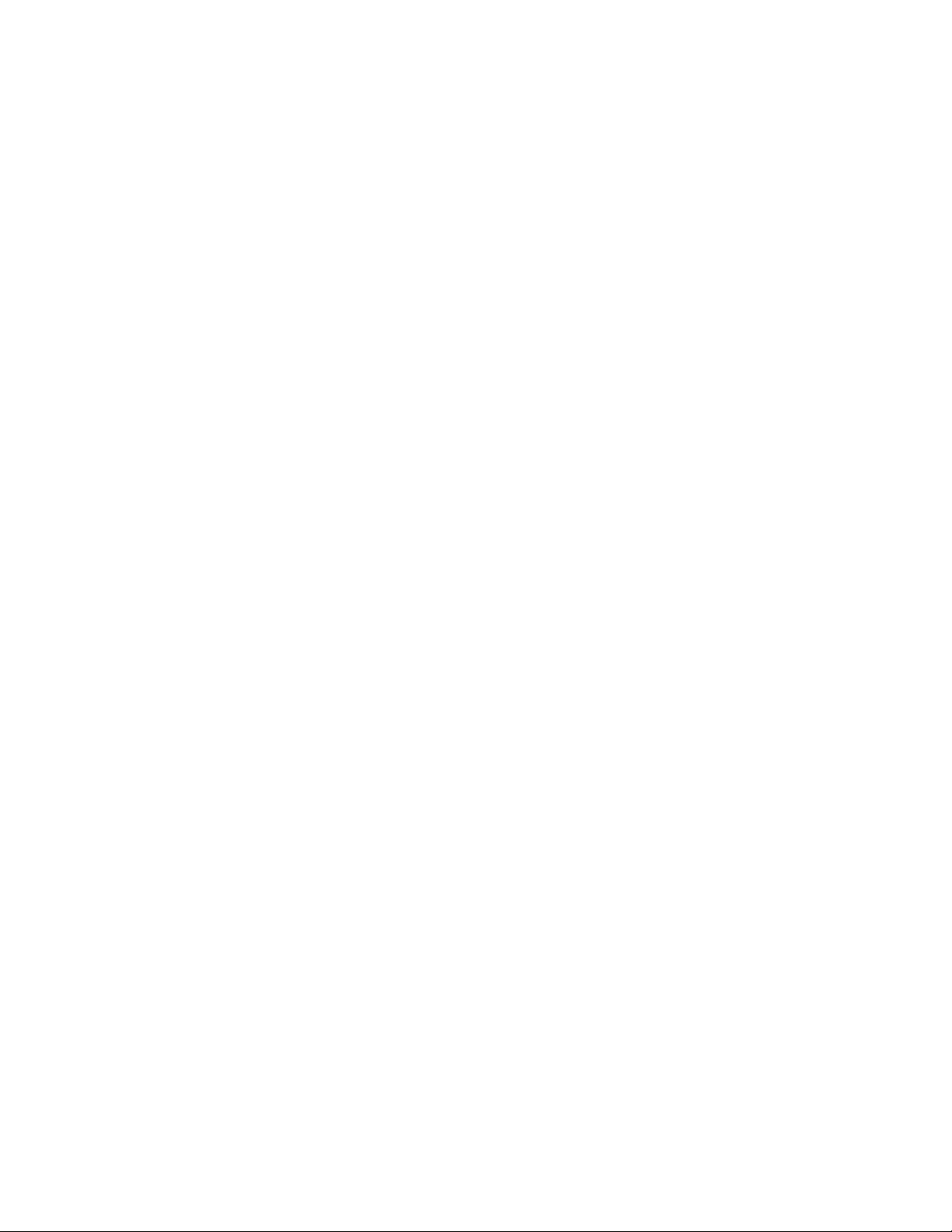
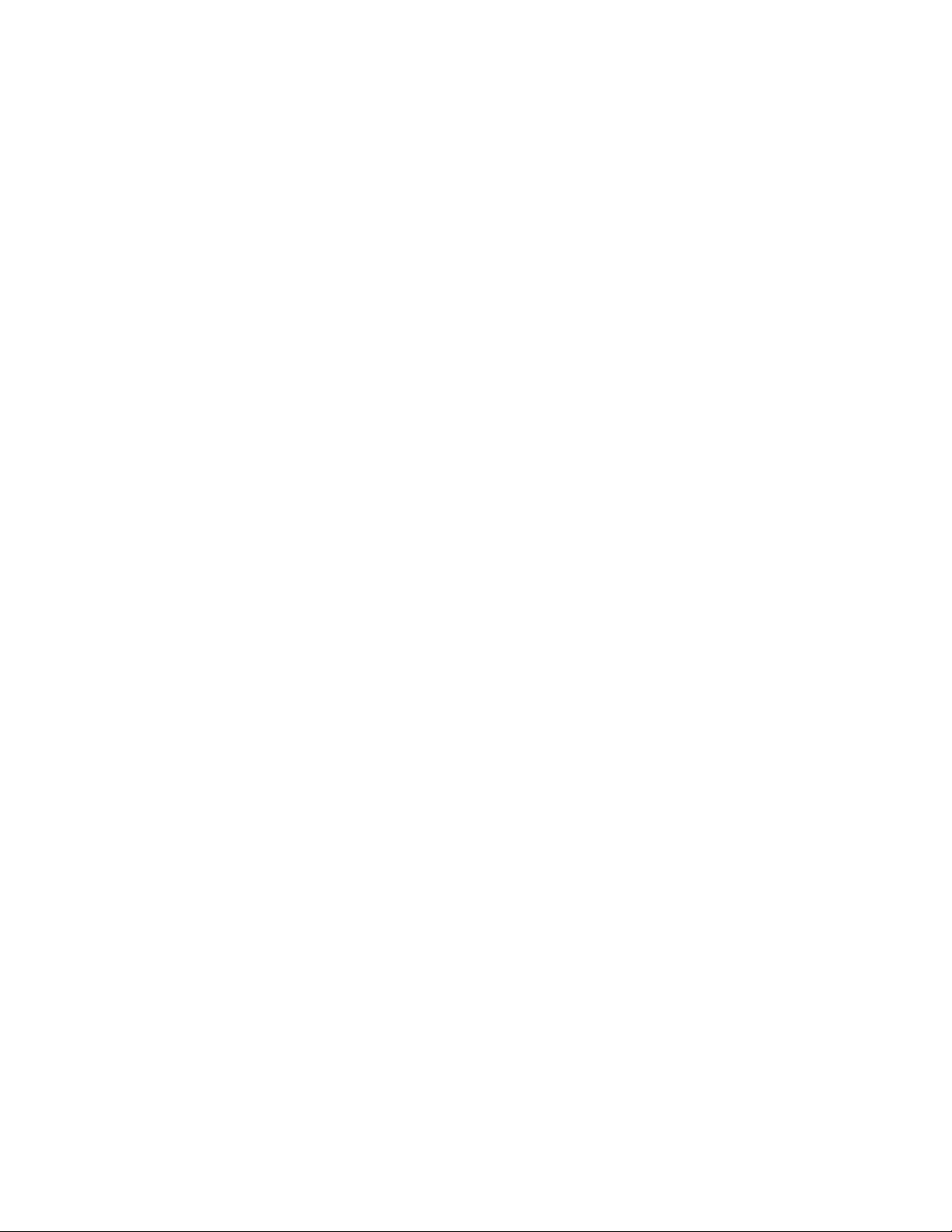
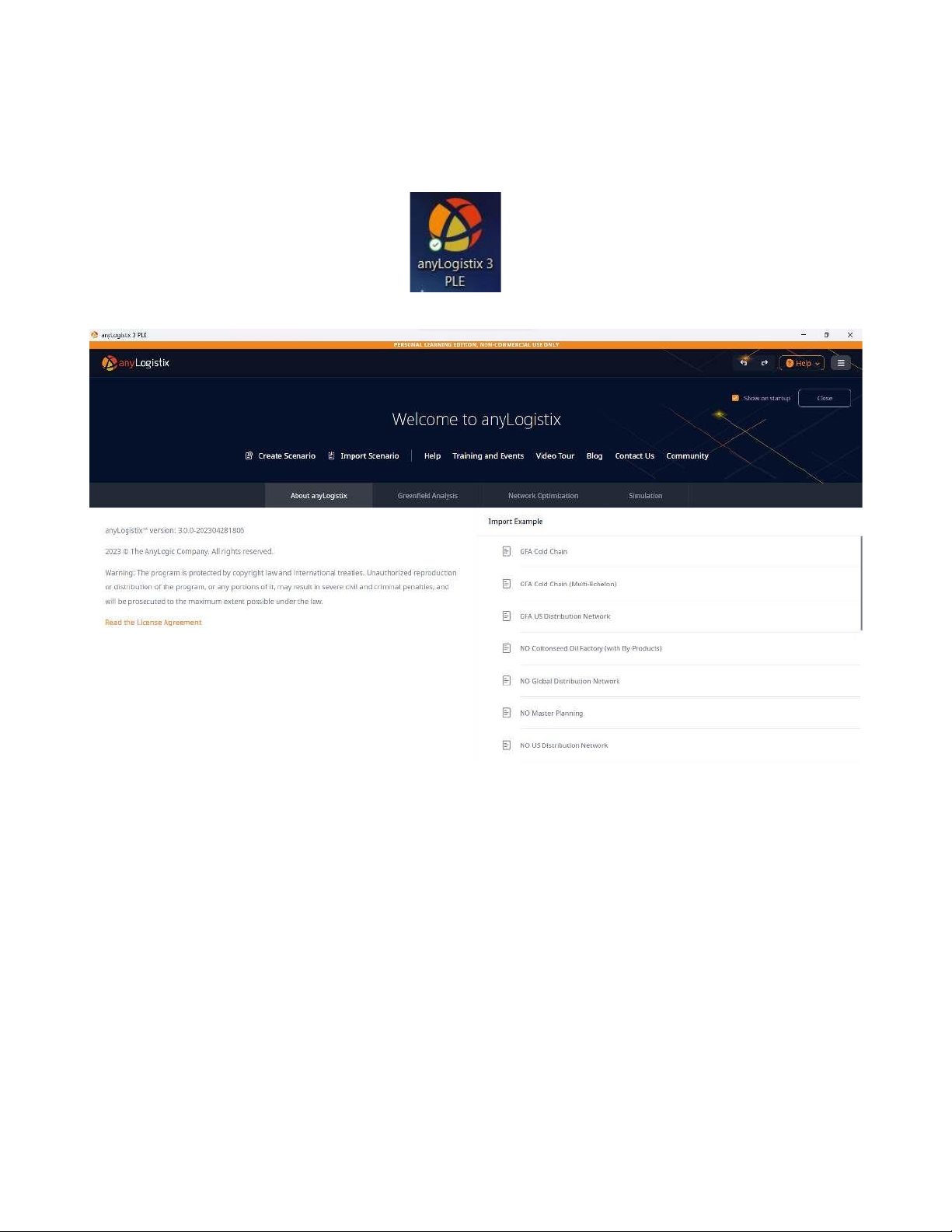
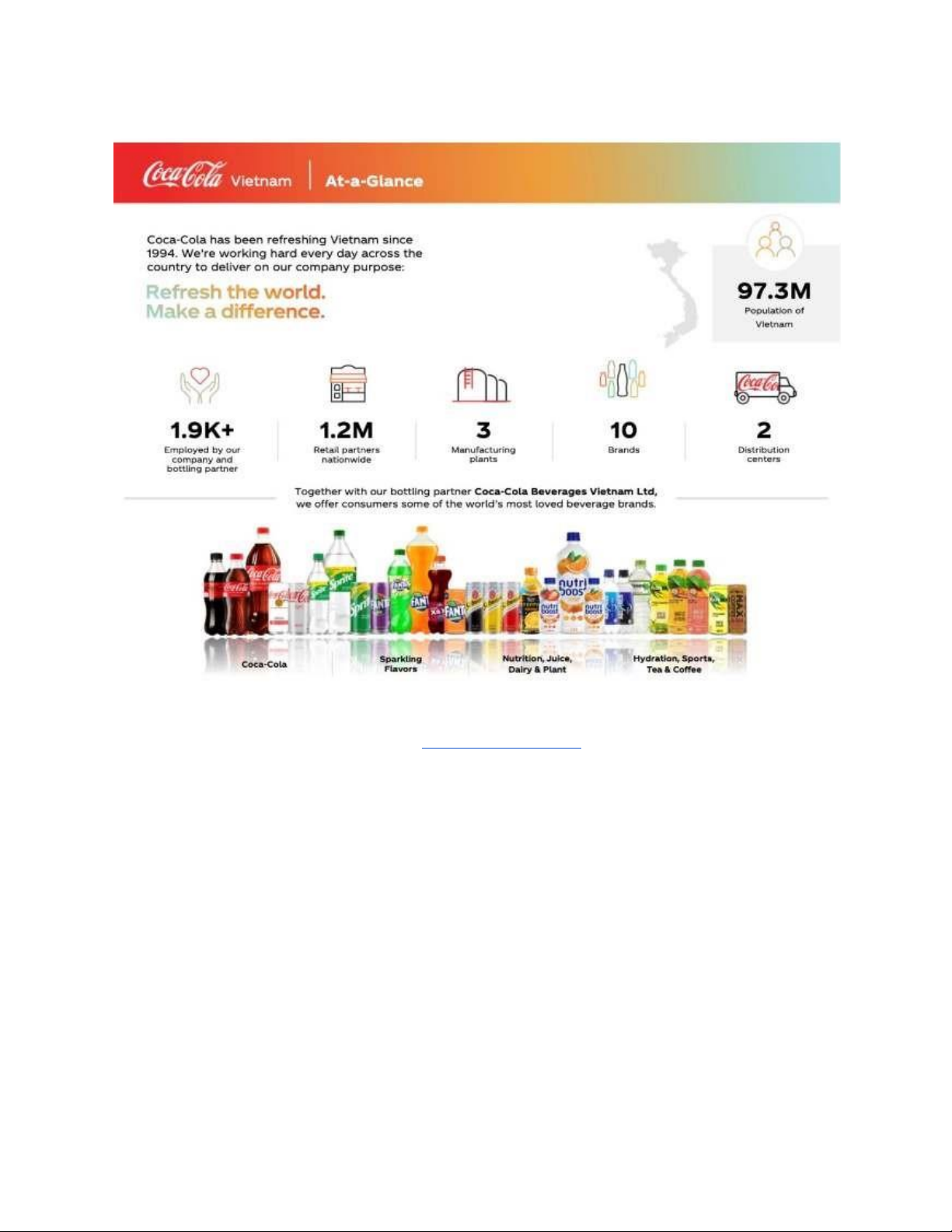
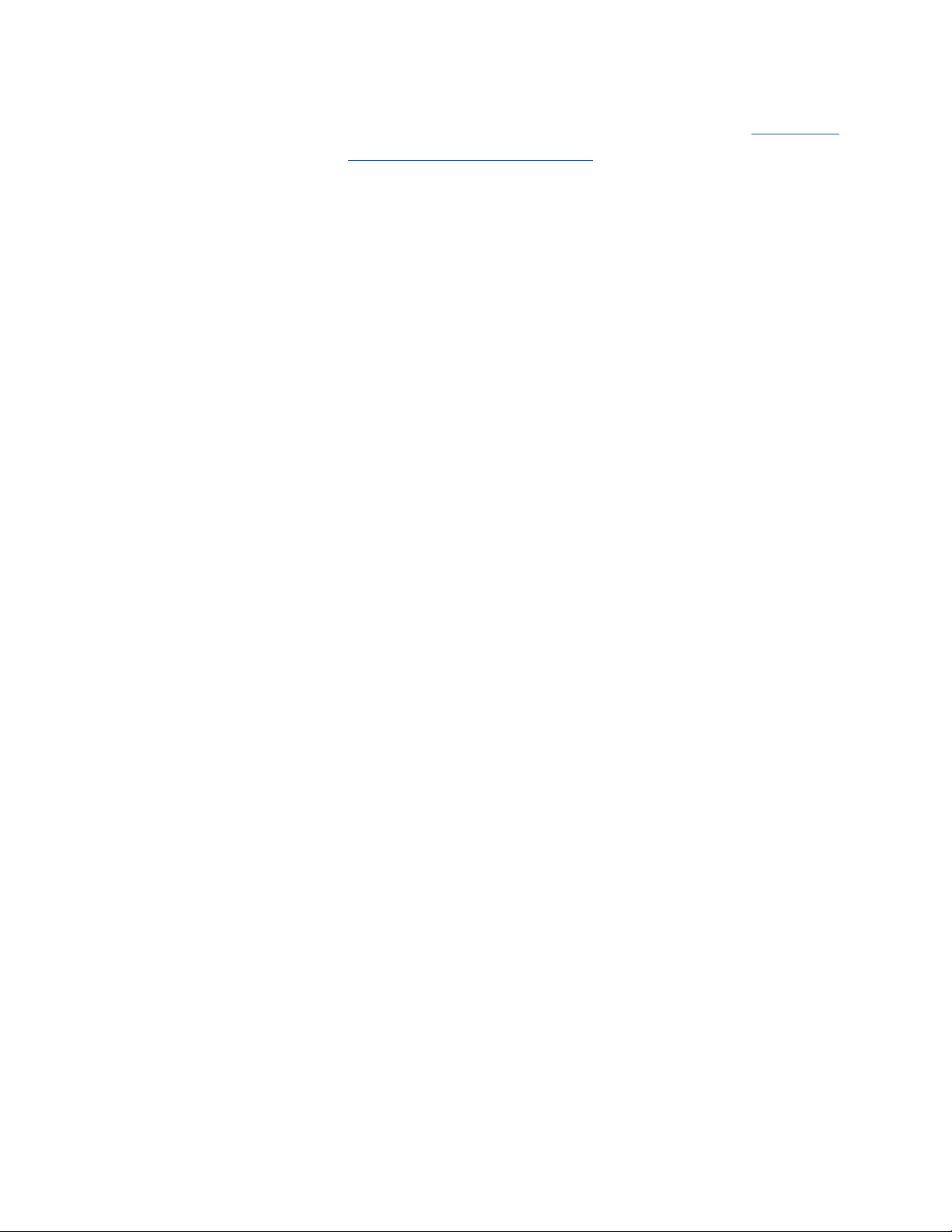
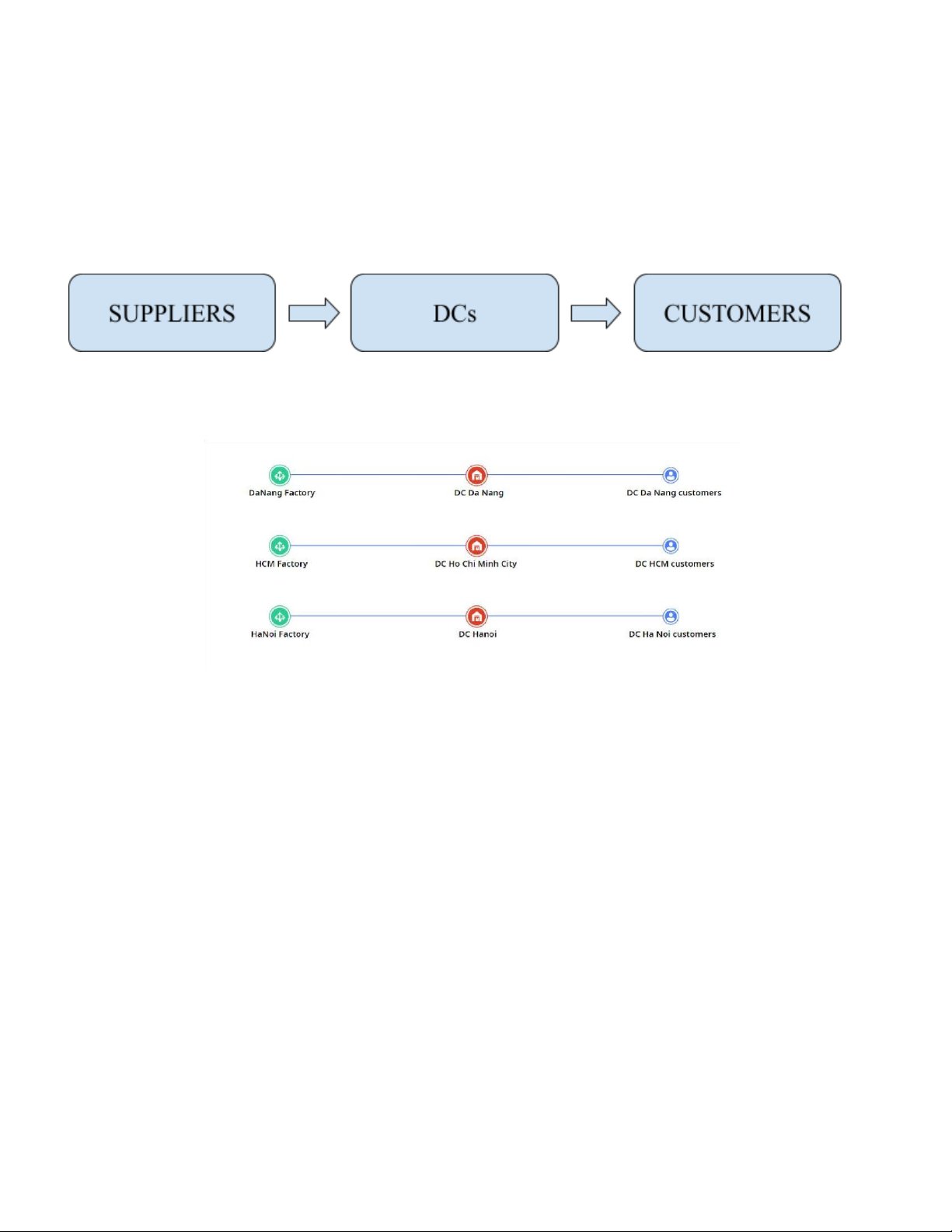
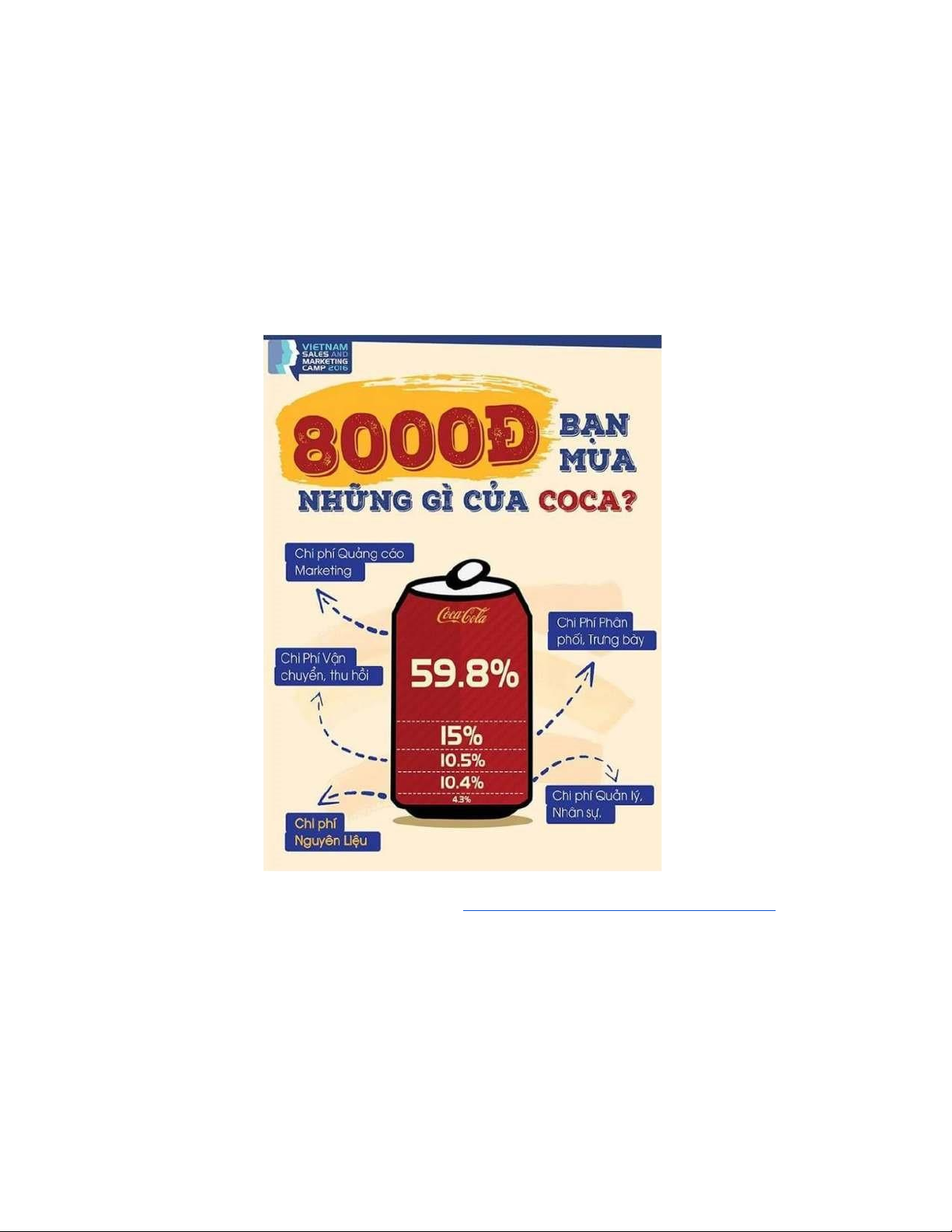
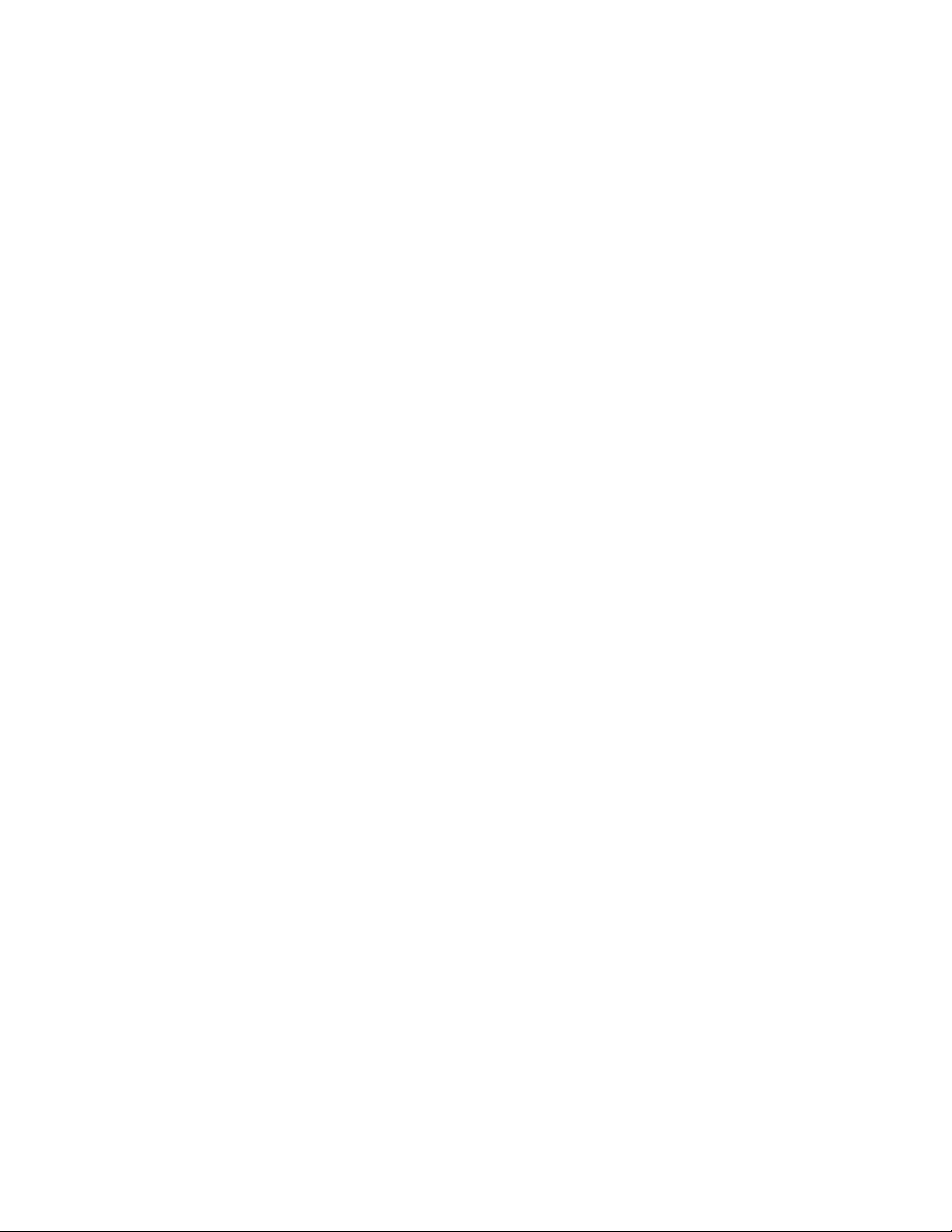
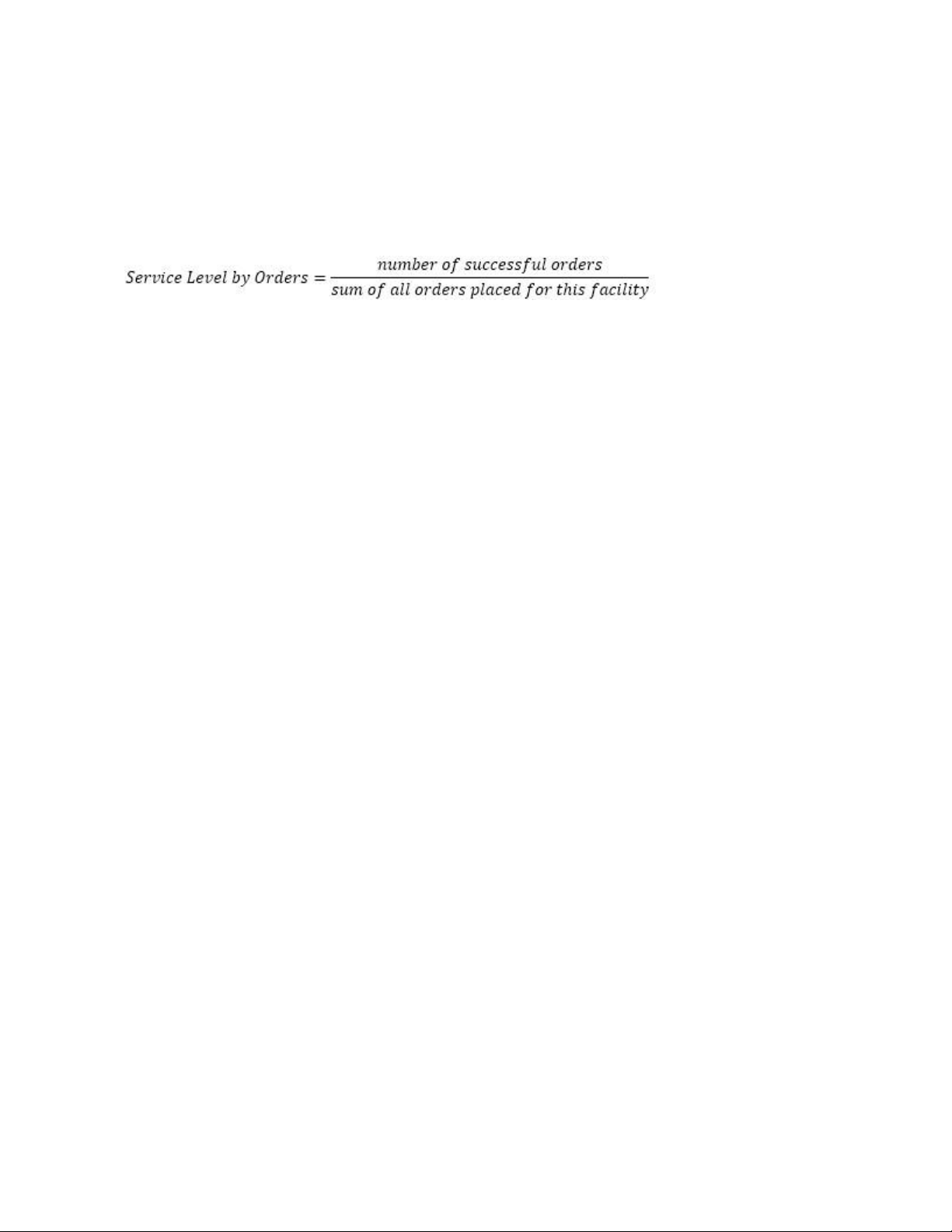
Preview text:
HO CHI MINH CITY INTERNATIONAL UNIVERSITY
SCHOOL OF INDUSTRIAL ENGINEERING & MANAGEMENT SUPPLY CHAIN RISK ASSESSMENT SIMULATION USING ANYLOGISTIX
Advisor: Assoc. Prof. Hồ Thị Thu Hòa Group 13 Ngô Trọng Đăng IELSIU22015 Hoàng Anh Khôi IELSIU22049 Lê Xuân Bảo Lộc IELSIU22057 Vũ Đức Minh IELSIU22063 Ho Chi Minh City, Vietnam August, 2023 ABSTRACT
Increasingly competitive markets are making it imperative to manage logistics systems
more and more efficiently, especially in the area of risk assessment. Supply chain simulation is a tool for such a job.
Not only does it provide an insight into the mechanisms of a supply chain for the
uninitiated, it also allows for testing the resilience of a supply chain, utilising what-if scenarios
as representations of real-world situations.
Our project grew out of a number of files and data regarding Coca Cola Beverages
Vietnam, Ltd. and its supply chain. The goal of this report is to give readers an insight into the
processes of our project, while hopefully providing them with more knowledge on the
importance of forecasting, modelling, etc. to a supply chain manager.
The major of Logistic and Supply Chain Management project was designed to familiarise
ourselves with the skills needed in the industry. The project included a review of the system
requirements. The first section of the report covers the requirements for the major. The second
section includes the system requirement. Thirdly, this supply chain optimization approach could
further Coca-Cola VN’s ability to upscale its modern supply chain planning practices to the level
of the whole country’s network, increase its capacity, and gain deeper insight into logistics
investments. It is necessary to gain more knowledge on all fronts. Expansion and constant update
of knowledge on subjects such as supply chain operation, managerial decision-making is
essential to a supply chain manager. Additionally, anyLogistix PLE must be understood more in
depth to maximise utility and benefit. With that being said, a simulation engine with more
capabilities and functions is needed when it comes to more sophisticated representations of a supply chain. ACKNOWLEDGEMENTS
Many people have contributed to the success of our result. We would like to offer a special appreciation to them.
Assoc. Prof. Nguyen Van Hop, School Dean of Industrial Engineering and Management,
for organising this course. It has proven to be an amazing learning opportunity, where we get to
progress each in our own path, and along the way gain invaluable skills and knowledge.
Assoc. Prof. Dr. Ho Thi Thu Hoa, who has given us a better knowledge of our research
and given us some helpful advice to finish our work, has been our advisor, and our group cannot
thank her enough for her support and encouragement. We want to express our sincerest thanks
to our adviser for the learning opportunity she has given us.
In addition, we would not have been able to finish this assignment without the assistance
of our teaching assistants, Ms. Doan Thuy Nha, who assisted us with technical issues. Table Of Contents
ABSTRACT............................................................................................................................................
ACKNOWLEDGEMENTS..................................................................................................................
Table Of Contents..................................................................................................................................
List of figures..........................................................................................................................................
List of tables............................................................................................................................................
List of abbreviation................................................................................................................................
CHAPTER 1: INTRODUCTION ..................................................................................................... 1
1.1. System Requirements .............................................................................................................. 1
1.1.1. Rationale: ............................................................................................................................. 1
1.1.2. Problem statement ................................................................................................................ 1
1.2. Objectives ................................................................................................................................ 2
1.3. Scope ....................................................................................................................................... 2
1.4. Limitations .............................................................................................................................. 2
CHAPTER 2: SYSTEM DESCRIPTION ........................................................................................ 3
2.1 Background: ............................................................................................................................. 3
2.1.1 anyLogistix:........................................................................................................................... 3
2.1.2 Coca-Cola Beverages Vietnam Limited: ............................................................................... 5
2.2 Conceptual Design ................................................................................................................... 8
2.2.1: Idea ....................................................................................................................................... 8
2.2.1.1: General in-out ................................................................................................................... 8
2.2.2: Assumptions ....................................................................................................................... 10
2.3. anyLogistix model - Base case .............................................................................................. 12
2.3.1. Objectives ........................................................................................................................... 12
2.3.2. Input ................................................................................................................................... 12
2.3.2.1. Data inserted .................................................................................................................... 12
2.3.2.2. Processing ....................................................................................................................... 20
CHAPTER 3: EXPERIMENTAL DESIGN ................................................................................... 34
3.1: Risk background: .................................................................................................................. 34 3.2:
Cases.......................................................................................................................................43 .. 36
3.2.1: Case 1 ................................................................................................................................. 37
3.2.2: Case 2: ................................................................................................................................ 41
3.3: Comparisons...........................................................................................................................54
CHAPTER 4: CONCLUSION..........................................................................................................56
4.1. Advantages............................................................................................................................. 56
4.2. Disadvantages.........................................................................................................................56
4.3. Applications............................................................................................................................56 4.4.
Recommendation:...................................................................................................................56
REFERENCES...................................................................................................................................58
Appendix.............................................................................................................................................62 List of figures
Figure 2.1: Anylogistix icon.................................................................................................................. 5
Figure 2.2: Anylogistix app interface.................................................................................................... 5
Figure 2.3: General information on Coca-Cola Beverages Vietnam Limited Company.......................6
Figure 2.4: Coca-Cola VN attained sustainable development business in 2016 .................................. 7
Figure 2.5: Coca-Cola VN attained sustainable development business in 2022 .................................. 7
Figure 2.6: The flow of Coca - Cola products....................................................................................... 9
Figure 2.7: Simplified dítribution flow chart.........................................................................................9
Figure 2.8: Product flow chart considered in our project.................................................................... 10
Figure 2.9: Coca-Cola costs ................................................................................................................ 11
Figure 2.9: Coca Cola Hanoi Factory.................................................................................................. 12
Figure 2.10: Coca Cola Ho Chi Minh Factory.....................................................................................13
Figure 2.11: Coca Cola Da Nang Factory............................................................................................13
Figure 2.12: Coca Cola Hanoi DC.......................................................................................................14
Figure 2.13: Coca Cola Da Nang DC.................................................................................................. 14
Figure 2.14: Coca Cola Ho Chi Minh DC........................................................................................... 15
Figure 2.15: Shipping...........................................................................................................................16
Figure 2.16: Inventory policies............................................................................................................ 17
Figure 2.17: Paths................................................................................................................................ 18
Figure 2.18: Cost Calculation Parameters............................................................................................19
Figure 2.19: Facility expenses............................................................................................................. 19
Figure 2.20: Sourcing...........................................................................................................................20
Figure 2.21: Manage unit.....................................................................................................................20
Figure 2.22: Unit Conversion...............................................................................................................21
Figure 2.23: Demand generated proportional to population................................................................21
Figure 2.24: DCs and Factories............................................................................................................22
Figure 2.25: DC Da Nang customers group.........................................................................................23
Figure 2.26: DC HCM customers group..............................................................................................23
Figure 2.27: DC Ha Noi customers group........................................................................................... 23
Figure 2.28: Shipping...........................................................................................................................24
Figure 2.29: Sourcing...........................................................................................................................24
Figure 2.30: Cost Calculation Parameters............................................................................................25
Figure 2.31: Paths................................................................................................................................ 25
Figure 2.32: Facility expenses............................................................................................................. 26
Figure 2.33: Vehicle types....................................................................................................................26
Figure 2.34: Inventory policies............................................................................................................ 26
Figure 2.35: Simulation setting............................................................................................................27
Figure 2.36: Overall Paths................................................................................................................... 28
Figure 2.37: DC Danang Paths............................................................................................................ 28
Figure 2.38: DC HCM paths ...............................................................................................................28
Figure 2.39: DC Hanoi Paths............................................................................................................... 28
Figure 2.40: Profit and Loss dashboard............................................................................................... 29
Figure 2.41: Total cost for each DCs................................................................................................... 30
Figure 2.42: Service level by Orders................................................................................................... 30
Figure 2.43: Service level by Orders, Best-Mean-Worst line chart..................................................... 30
Figure 2.44: Demand Received (Dropped Order), per DC..................................................................31
Figure 2.45: Demand received (Dropped orders), aggregate...............................................................31
Figure 2.46: Demand received (Dropped Orders) line chart, 50-day periods......................................32
Figure 2.47: Demand Received (Dropped Orders) line chart, daily.................................................... 32
Figure 2.48: Available Inventory......................................................................................................... 33
Figure 2.49: Available inventory per DC (Green line - HCM DC, Blue line - Da Nang DC, Orange
line - Hanoi DC)...................................................................................................................................33
Figure 3.1: Events used in risk analysis case 1....................................................................................43
Figure 3.2: Experiment settings........................................................................................................... 43
Figure 3.3: Total Cost, aggregate - Case 1...........................................................................................43
Figure 3.4: Total Cost, per DC - Case 1...............................................................................................44
Figure 3.5: Revenue and Profit, per item - Case 1...............................................................................44
Figure 3.6: Revenue and Profit, aggregate - Case 1.............................................................................44
Figure 3.7: Service level by Orders, aggregate - Case 1......................................................................45
Figure 3.8: History by replication table, best-mean-worst Service level by Orders chart...................45
Figure 3.9: Events table case 1.............................................................................................................46
Figure 3.10: Events used in risk analysis case 2..................................................................................47
Figure 3.11: Total cost, aggregate - Case 2, Replication 9...................................................................48
Figure 3.12: Total cost, per DC - Case 2, Replication 9...................................................................... 48
Figure 3.13: Revenue, aggregate - Case 2, Replication 9....................................................................48
Figure 3.14: Revenue, aggregate - Case 2, Replication 9....................................................................49
Figure 3.15: Revenue, per item - Case 2, Replication 9...................................................................... 49
Figure 3.16: History by replication Profit, aggregate - Case , Replication 9.......................................49
Figure 3.17: Profit, aggregate - Case 2, Replication 9.........................................................................50
Figure 3.18: Profit, per item - Case 2, Replication 9........................................................................... 50
Figure 3.19: History by replication, best-mean-worst chart, Service level by Orders - Case 2...........51
Figure 3.20: Event table of Result Dashboard (replication 9)............................................................. 52
Figure A.1: Generating customers....................................................................................................... 56
Figure A.2: Demand generated proportional to population density.....................................................57
Figure A.3: Results of base case.......................................................................................................... 58
Figure A.4: Results of Case 1.............................................................................................................. 59
Figure A.5: Results of Case 2.............................................................................................................. 60
Figure A.6: Demand received (dropped products) of Case 1.............................................................. 60
Figure A.7: Bullwhip effect by product of Case 1...............................................................................61
Figure A.8: Demand received (dropped products) of Case 8.............................................................. 61
Figure A.9: Bullwhip effect by product of Case 2...............................................................................61
Figure A.10: Fulfilment received (Products On-time) Case 1.............................................................62
Figure A.11: Fulfilment received (Products On-time) Case 2............................................................. 62 List of tables
Table 2.1: Latitude and longitude of each Supplier and DC................................................................16
Table 3.1: Major risks suggest by Coca Cola company.......................................................................35
Table 3.2: Comparisons base case, case 1 and case 2.......................................................................... 53 List of abbreviation Distribution centres DCs Coca-Cola Beverages Vietnam Coca Cola VN Limited Fast Moving Consumer Goods FMCG anyLogistix Personal Learning anyLogistix PLE Edition version 3.0 Key performance indicator KPI COronaVIrus Disease of 2019 COVID-19 Pieces Pcs Ho Chi Minh HCM Geographic Information System GIS Full truck load FTL Less than truckload LTL lOMoARcPSD|47231818 CHAPTER 1: INTRODUCTION
1.1. System Requirements 1.1.1. Rationale:
As an attempt to familiarise ourselves with the knowledge and skills needed in our major of
Logistic and Supply Chain Management, this project was carried out.
According to Paul and Chowdhury (2020b) the challenge intensifies for manufacturers of high-
demand and indispensable goods such as toilet paper, hand sanitizer, food, drinks, face masks, etc. in
the context of the COVID-19 pandemic. In that situation, the demand for essential products skyrockets.
Simultaneously, another issue arises as the supply of raw materials experiences a significant decline,
due to lockdown and border restrictions, etc. This reduction is compounded by limitations in
production capacity, creating a complex web of challenges for these supply chains. Immediate and
effective action becomes crucial in such a situation. Manufacturers need to respond with adaptive
strategies to ensure the resilience of their supply chains. These strategies could include diversification
of sourcing for raw materials, alternative production methods, or collaborating with suppliers to secure priority access to materials.
This only goes to showcase the utter importance of risk management - the key to the survival
of a business, as it is only through careful planning and preparation could a supply chain stand a
chance against high impact risks.
Nowadays, simulation is evermore gaining in popularity, as society is advancing on the
technological front. Companies are increasingly gravitating toward the use of them, Coca-Cola being a prime example.
With these in mind, we have decided on doing risk assessment of Coca-Cola Beverages
Vietnam Limited’s supply chain using anyLogistix PLE.
1.1.2. Problem statement
In the world of Fast Moving Consumer Goods (FMCG), like Coca-Cola VN, a smooth supply
chain is vital for success. But this supply chain is exposed to many risks. If these risks aren't managed
well, they can cause problems not just with money, but also with how much people trust the company.
The COVID-19 pandemic taught us how important it is to handle supply chain risks. FMCG
relies on getting products to people quickly. But things like natural disasters, transportation issues, or
even strikes can mess this up. When this happens, it's not just about losing money. It also damages the
company's reputation and relationships with customers and partners. (How The
COVID-19 Pandemic Has Changed Supply Chain Practices, 2022)
Because of the pandemic, companies like Coca-Cola VN have learned to be better prepared.
They look for possible risks, think about how bad they could be, and find ways to prevent or reduce 1 lOMoARcPSD|47231818
them. This could mean having backup suppliers, keeping extra products in storage, using technology
to track things, and being open with everyone involved.
Also, companies need to be able to change quickly when unexpected things happen. By using
technology and smart planning, they can make good choices even when things are uncertain. This
helps them keep going and keeps everyone's trust. 1.2. Objectives
We aim, with this report, to demonstrate a method to assess supply chain risks of Coca-Cola
VN by using the simulation function from anyLogistix. This approach aligns with the contemporary
practices in the field of logistics and supply chain management, allowing managers and students alike
to delve into the complexities of risk identification and mitigation strategies. Through this process,
we are not only identifying risks but also examining their potential impact under different conditions,
therefore anticipating challenges before they materialise. Simulation enables us to observe how supply
chain elements interplay, such as transportation routes, inventory levels, and demand fluctuations; as
well as potential vulnerabilities. Afterwards, we could propose some solutions which can be applied
to mitigate/control the risks. 1.3. Scope
In our project, we've replicated Coca-Cola VN's nationwide supply chain for 24-can cartons,
with particular focus on the distribution portion. Virtual customers, reflecting real ones across Vietnam,
drive demand based on population density. Our simulation factors in real-world dynamics like
distribution, and economic influences, offering insights into the supply-demand interplay.
The experiment is conducted over the course of a one-year duration within anyLogistix
PLE. This extensive time frame allows for an exploration of various scenarios and outcomes,
enabling us to extract valuable insights from the simulation. By simulating a year-long
timeframe, we are not only able to capture seasonal variations and potential long-term trends
but also thoroughly assess the resilience and adaptability of the supply chain under different conditions. 1.4. Limitations
First, this is our first time approaching a whole project, so we had trouble choosing the best
course of action to save time and manipulate the knowledge and information we have as much as possible.
Second, many factors have been ignored due to software and knowledge insufficiencies, and
some informed assumptions have been made. We focus our efforts on only the rudimentary
components of the supply chain, while making every other detail relevant and true to the best of our
ability. For example, the supply chain of Coca Cola VN is utterly complex. However, with the lOMoARcPSD|47231818
restrictions of anyLogistix PLE, we could consider only 3 suppliers, such that we have to diminish
the realistic supply chain to a more simple one, i.e., we had to overlook the raw material acquisition
and production phase. Also, representing Coca Cola factories as Factories in anyLogistix would
require extensive and unnecessary further configurations in the software, which we avoided by
representing them as Suppliers instead, for simplicity’s sake.
Last but not least, lack of data is one of the largest obstacles interrupting us from reaching the
most realistic supply chain and desired results. For example, the information about the number of coca
boxes consumed in each area in Viet Nam, so we have to generate them through the available function
in anyLogistix and we also do not have any data about them to confirm. Furthermore, we also do not
have any information about taxes and capacity of inventories to apply to our supply chain which is
the enormous shortcoming of this project.
These limitations mean that our project is highly experimental and exploratory. CHAPTER 2: SYSTEM DESCRIPTION 2.1 Background: 2.1.1 anyLogistix:
anyLogistix is the supply chain analytics software to design, optimise and analyse the supply
chain of a company by combining powerful analytical optimization together with innovative
simulation technologies, which is the application provided by the Anylogic company. The version we
were able to access for free was anyLogistix Personal Learning Edition version 3.0.
anyLogistix allows users to replicate a supply chain network and simulate its operations,
making allowances for the uncertainties and stochastics of the real world. In addition, simulation in
Anylogistix allows users to test multiple network or policy change scenarios to increase the supply
chain resilience and define contingency plans. With data reflecting the status of the supply chain can
be fed into the simulation model to create a supply chain digital twin. This enables quick and informed
decision-making when it is needed most - as a situation is developing. (anyLogistix.com website)
anyLogistix is used by many famous brands and factories in many aspects of industrial operations
such as Coca-Cola, Deloitte, and Houlihan Lokey, etc. because of its convenience and flexibility in
task management, which is not only risk assessing ability but also anyLogistix can run multiple tasks
like greenfield analysis, simulation, and network optimization. Specifically, the app can provide fast
generation of data input based on population, order demands or set up input manually.
Moreover, anyLogistix also provides numerous and accessible resources for users with its
variation of case studies, papers, textbooks, documentary, videos and even training courses. With the
ease of getting used to anyLogistix, this application can maintain the integrity of the business process
and enhance the current planning tools with a layer of strategic analytics. AnyLogistix can deal with
data from any platform because it can import data through an Excel spreadsheet or a database. 3 lOMoARcPSD|47231818
Databases are used to provide specialised data flow integrations with other supply chain management systems.
Here is a basic outlook of the application:
Figure 2.1: Anylogistix icon
Figure 2.2: Anylogistix app interface
After testing anyLogistix PLE, we find out that this free edition has some limitations such as
limited number of suppliers, shortage of outcome in flow chart expression, and tools are also limited
due to the free version, etc. Therefore, users can choose to apply the fee paying version to get fully
accessed, which the price is not suitable for individual users and students, or accept with some
drawbacks and limitations that this free edition provides to users. Even though, anyLogistix still
provides a lot of convenience and benefits to its customers. lOMoARcPSD|47231818
2.1.2 Coca-Cola Beverages Vietnam Limited:
Figure 2.3: General information on Coca-Cola Beverages Vietnam Limited Company (Coca-Cola Vietnam)
Despite being a late-comer in the Vietnam market, Coca-Cola VN’s prospects are great,
evidenced by its seventh consecutive year as a sustainable development business. (VnExpress, 2022)
The figure we get from their website shows some general information about Coca-Cola
Beverages Vietnam Limited Company in Vietnam which includes type of products, number of
factories, distribution centres. In this project, we only consider the normal Coca Cola 330ml type
product in the form of 24 pcs/cartons. 5 lOMoARcPSD|47231818
Figure 2.4: Coca-Cola VN attained sustainable development business in 2016 (Coca Cola
sustainable development 2016) lOMoARcPSD|47231818
Figure 2.5: Coca-Cola VN attained sustainable development business in 2022 (Coca Cola
sustainable development 2022)
Furthermore, the nationwide presence of Coca-Cola VN in Vietnam, with its extensive
distribution network and supply chain operations spanning across the country, effectively
justifies the relevance and practicality of conducting a supply chain simulation project for Coca- Cola in Vietnam. 7 lOMoARcPSD|47231818 2.2 Conceptual Design 2.2.1: Idea
2.2.1.1: General in-out
The actual supply chain of Coca-Cola in Vietnam is very complex. Refer to figure below.
Figure 2.6: The flow of Coca - Cola products (supply chain coca cola company) lOMoARcPSD|47231818
However, due to the constraints inherent to anyLogistix PLE listed above, our analysis
centred around the distribution segment of the supply chain. While our intent was to simulate
the entire supply chain, we acknowledge that software constraints made it difficult to include
other vital components such as raw material sourcing, production and backward logistics. This
particular scope specifies the movement of products from suppliers to distribution centres and ending at customers.
Figure 2.7: Simplified dítribution flow chart 2.1.1.2: Flow chart
Figure 2.8: Product flow chart considered in our project
The Coca-Cola supply chain is carefully designed for efficiency, especially from Factories to
Distribution Centers and then to Customers (Wholesalers, Retailers, and Consumers). We used the
AnyLogistix simulation app to focus on this part of the journey. The simulation showed how different
regions have different demands, helping us understand supply and demand better. While not covering
everything, our simulation helps us see how well things work and how different regions can be handled.
This can lead to even better simulations that match the real supply chain, helping us understand Coca-
Cola's distribution network better.
In anyLogistix PLE, we simulate the process of carrying 24-can Coca Cola boxes which are
produced in Ho Chi Minh, Da Nang and Ha Noi factories and carried to the customers. 3 suppliers are
equivalent to the 3 Coca Cola factories, because of the software limitations so that factories will be
considered as suppliers which provide finished products (a box of 24 cans) to their own Distribution
Centre (DC). Next, the DCs are Nguon Song Viet Limited Co. (453 Kim Nguu, Hai Ba Trung, Ha
Noi), Coca-Cola Distributor Thien Chan Hung (651 Nguyen Tat Thanh, Xuan Ha, Thanh 9 lOMoARcPSD|47231818
Khe, TP Da Nang) and Dang Khoi Distributor (59 Pham Ngoc Thach, Quan 3, TP HCM) (Yến, K,
2022). Lastly, the customers are generated by Anylogistix using Demand proportional to population density in each city. 2.2.2: Assumptions
We ignore raw material suppliers, since anyLogistix only allows 3 suppliers, which, in our case,
is insufficient. The price for raw materials are calculated in the cost for our products (with reference
to Vietnam Sales & Marketing Camp 2016).
Figure 2.9: Coca-Cola costs (Vietnam Sales and Marketing Camp 2016)
In our simulation, we use a Demand proportional to population density function to mimic Coca-
Cola VN's diverse customer base. This function adjusts based on the population density, giving us a
rough idea of customer demand, although an exact match is tough.
To make things manageable, we've simplified Coca-Cola VN's complex distribution network
by representing it with three main Distribution Centers (DCs) in each region.
We carefully assumed capacities of these Distribution Centers, considering the simulated
demand in each region. This capacity alignment reflects Distribution Centers' dynamic nature, lOMoARcPSD|47231818
showing how demand and capacity are connected. This connection aims to mirror reality as closely
as possible within the simulation.
While our simulation doesn't capture all of Coca-Cola VN's distribution complexities, it's an
inspired effort to mirror that complexity using anyLogistix. By combining dynamic demand modelling
and representative Distribution Centers, we aim to understand better how supply and demand interact
in Coca-Cola VN's distribution network. 11 lOMoARcPSD|47231818
2.3. anyLogistix model - Base case 2.3.1. Objectives
Running the simulations, we hope the results reflect our desired outcomes. The KPIs for the
Coca Cola VN project simulation are: Where:
products in the successful orders — the amount of products in the orders that were successfully fulfilled.
sum of products in all orders placed for this facility — here belong products from
both successful and unsuccessful orders.
Therefore, the service level must be as high as possible, we consider that the aggregate
service level above 80% is what we need to achieve in this project. Profit must be at least 25%
due to Revenue based on the assumption in 2.2.2 2.3.2. Input 2.3.2.1. Data inserted
The input we got for the simulation is a collection of information that we were able to gather
through our research process, plus some informed assumptions. Although there are still many
deviations from reality in our simulation.
The data is classified into two categories: real-life data and informed assumptions.
a. Real-life data ● Product: Name: Box/24pcs Unit: pcs
Selling Price: 185000 and Cost: 75000 (data from 2016, seen in figure 4)
Currency: VND ● Unit Conversion: Product: Box/24pcs
From 1 pcs to 0.013 m3 (Case and Pallet Spec Sheet, 2016) ● Locations:
Input directly “Latitude” and “Longitude” of Suppliers and DCs