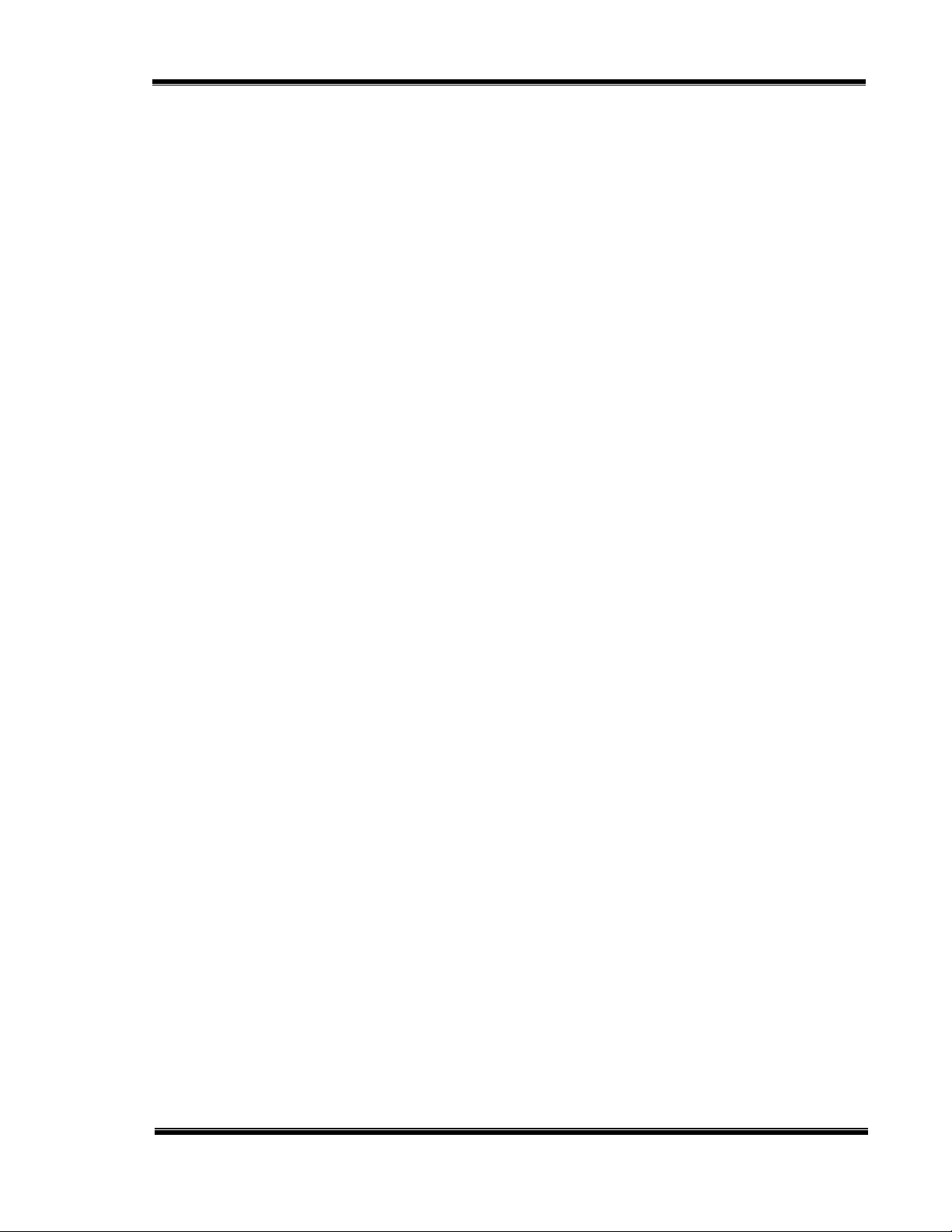
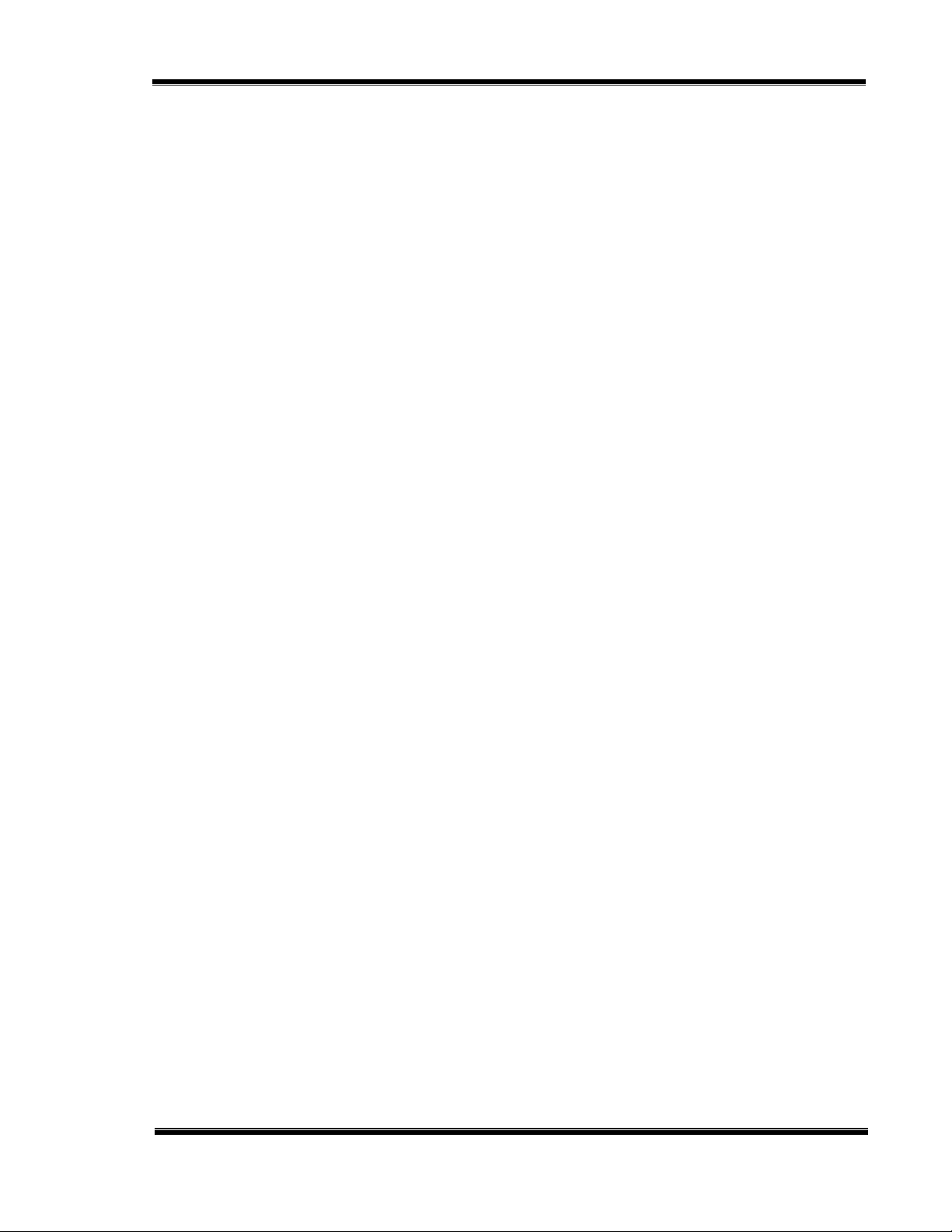
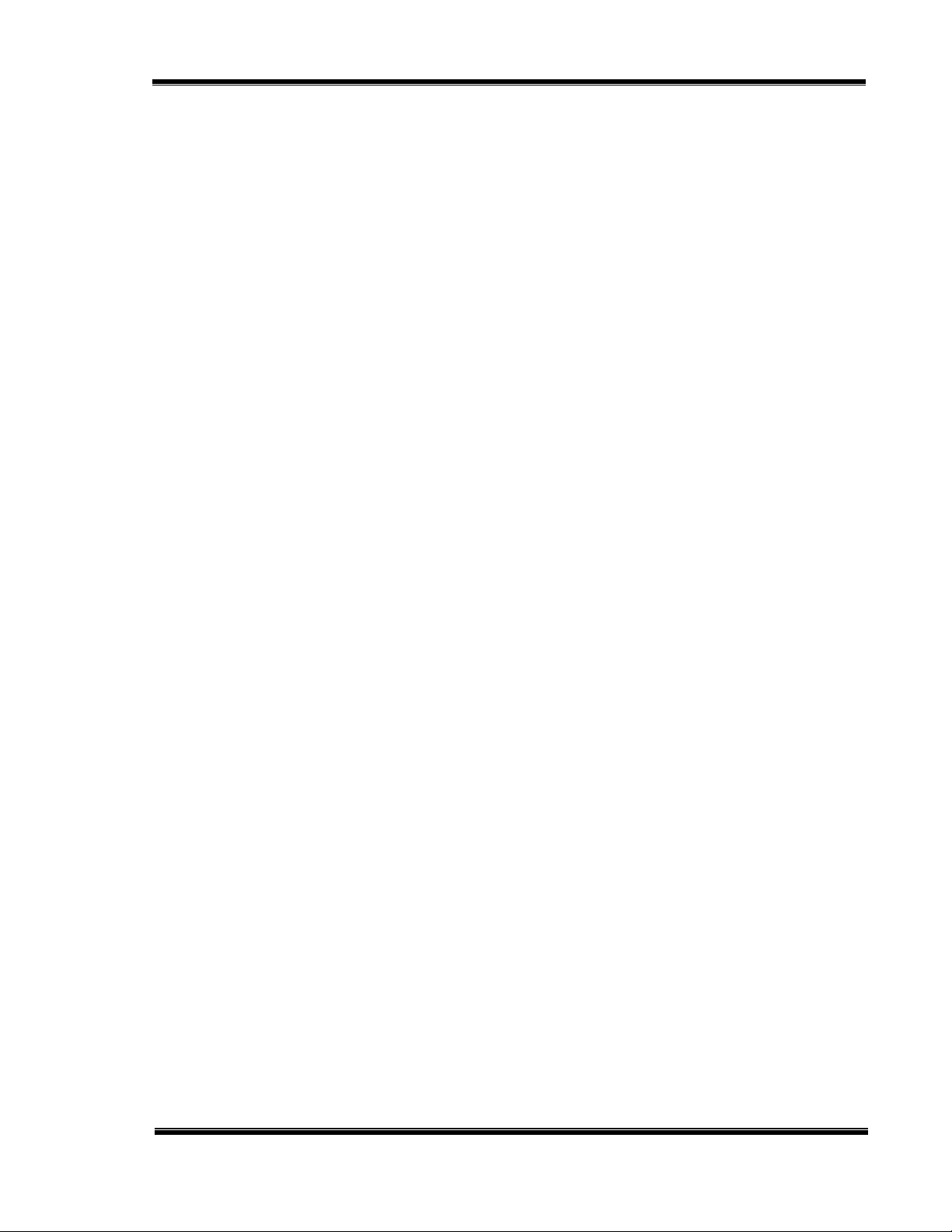
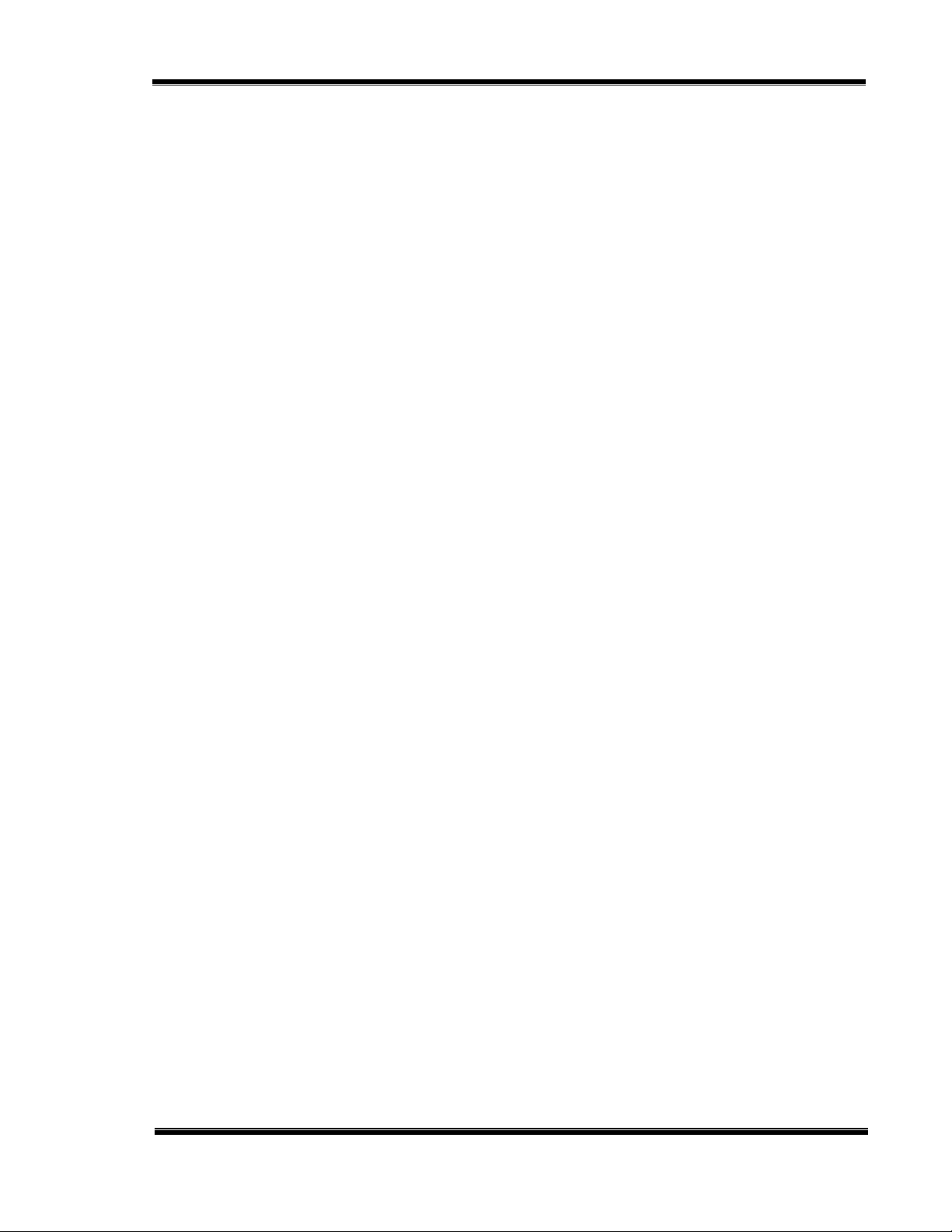
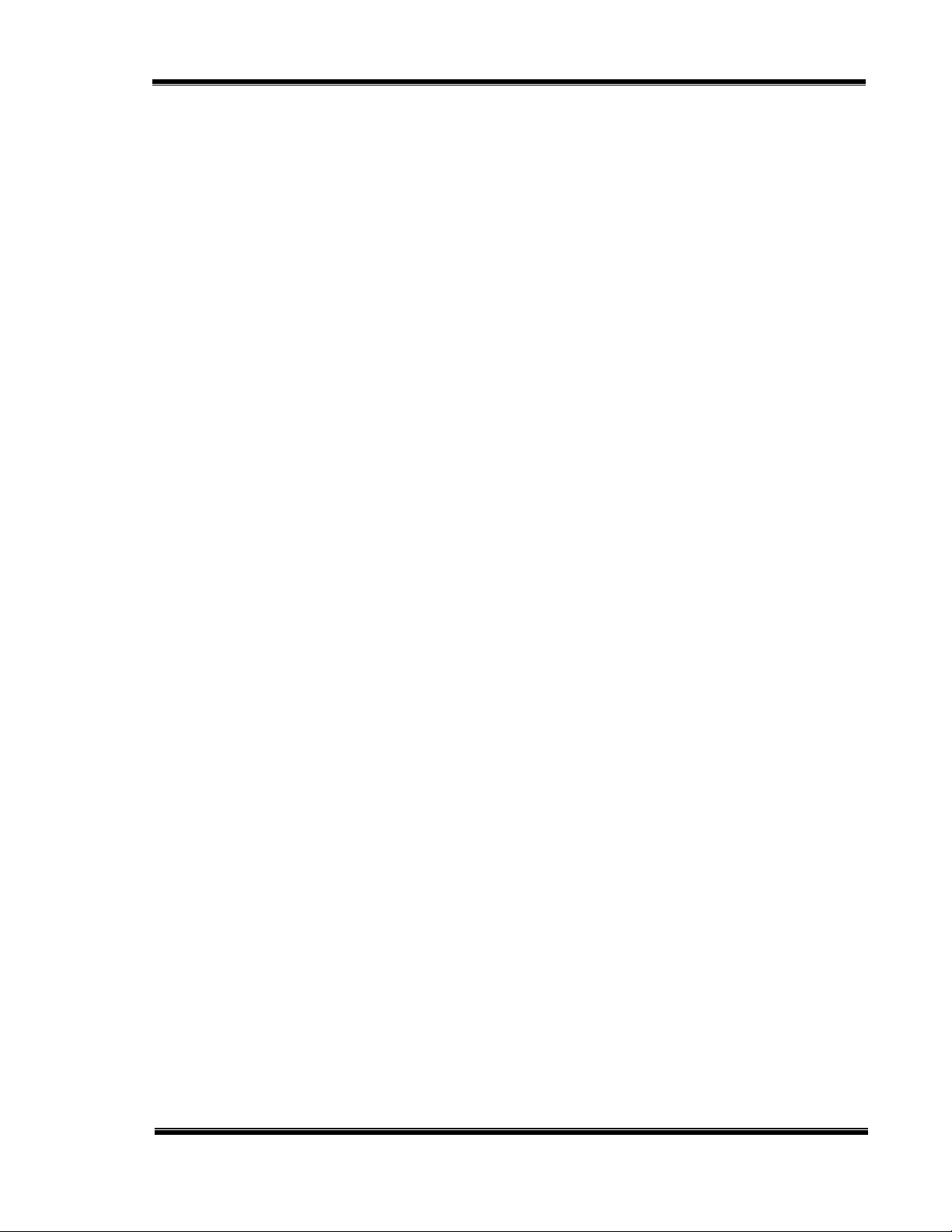
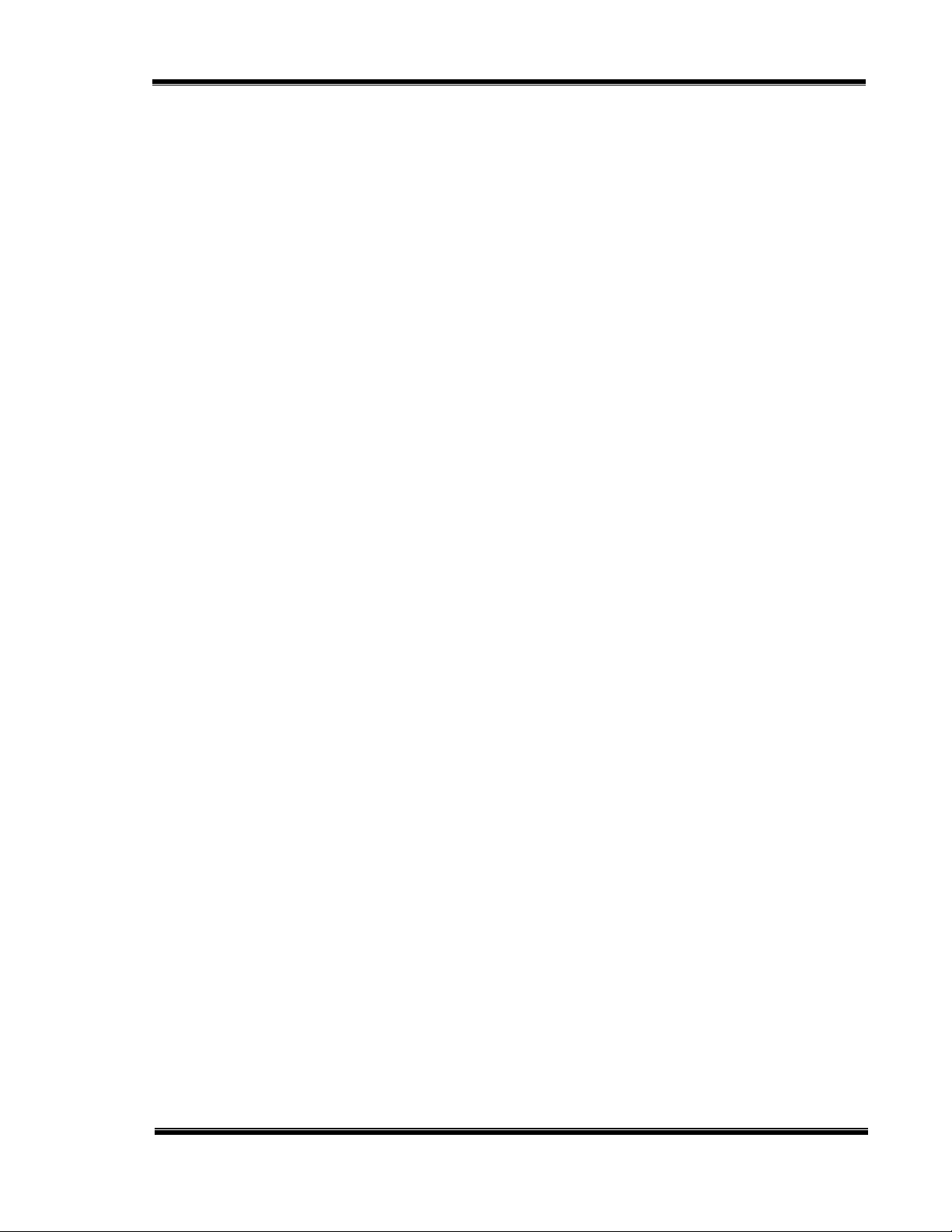
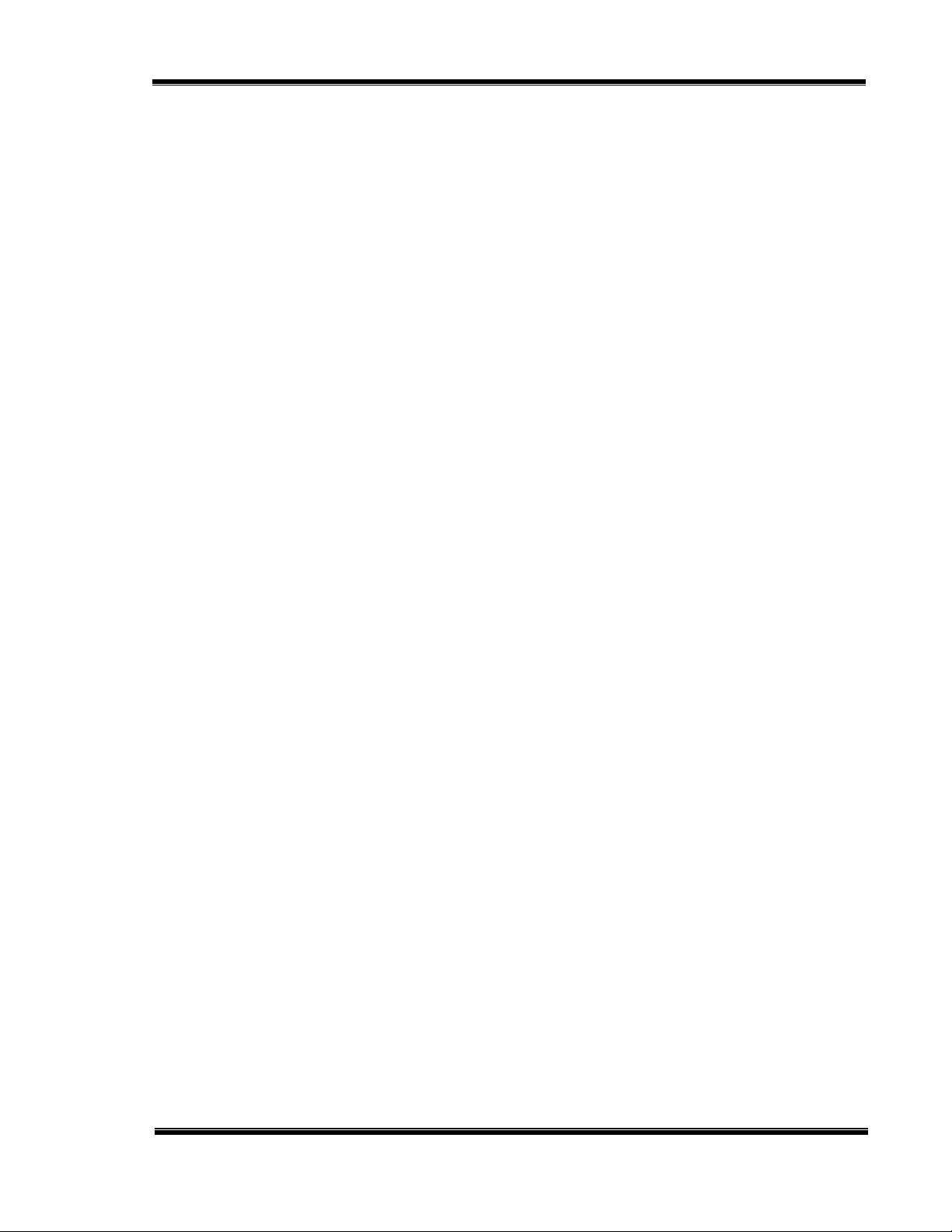
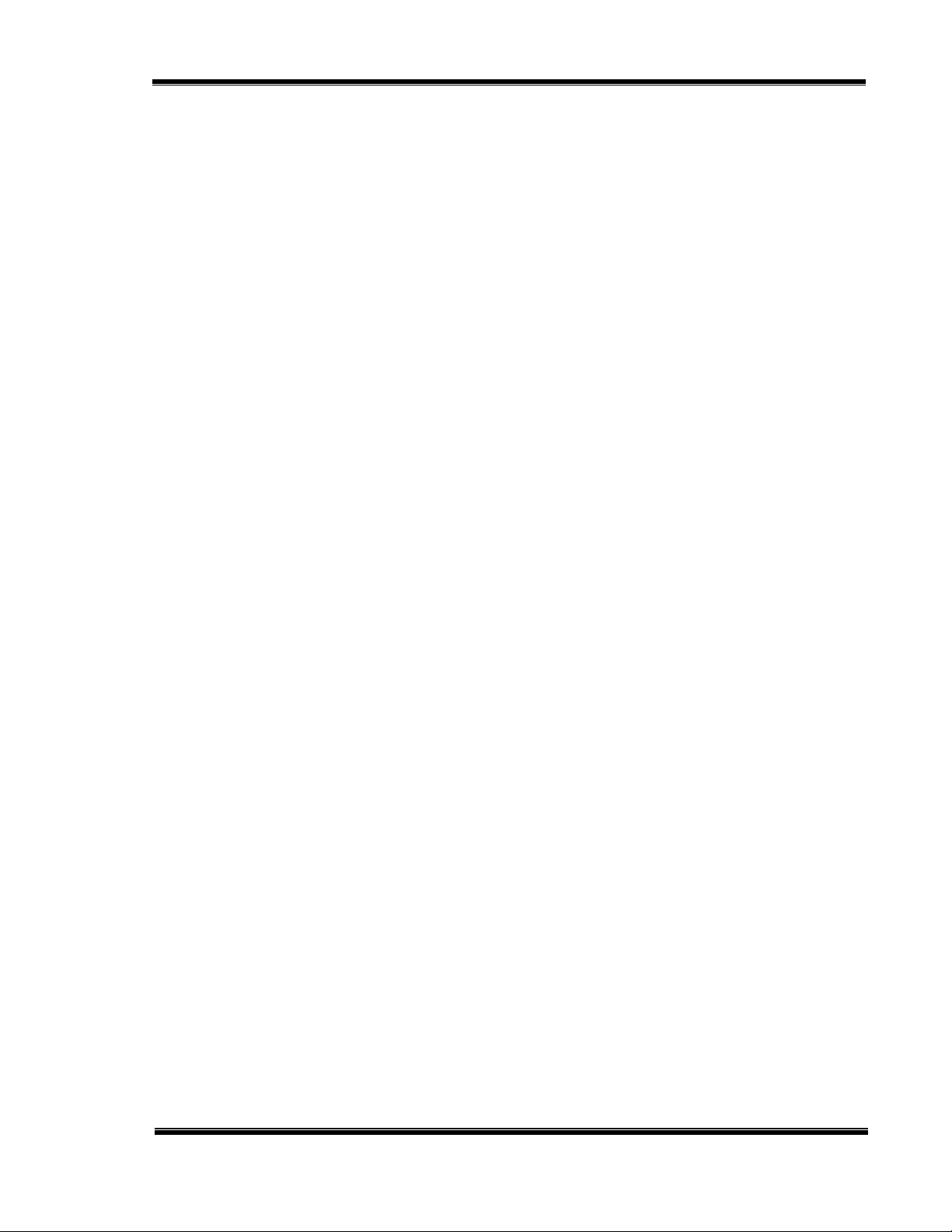
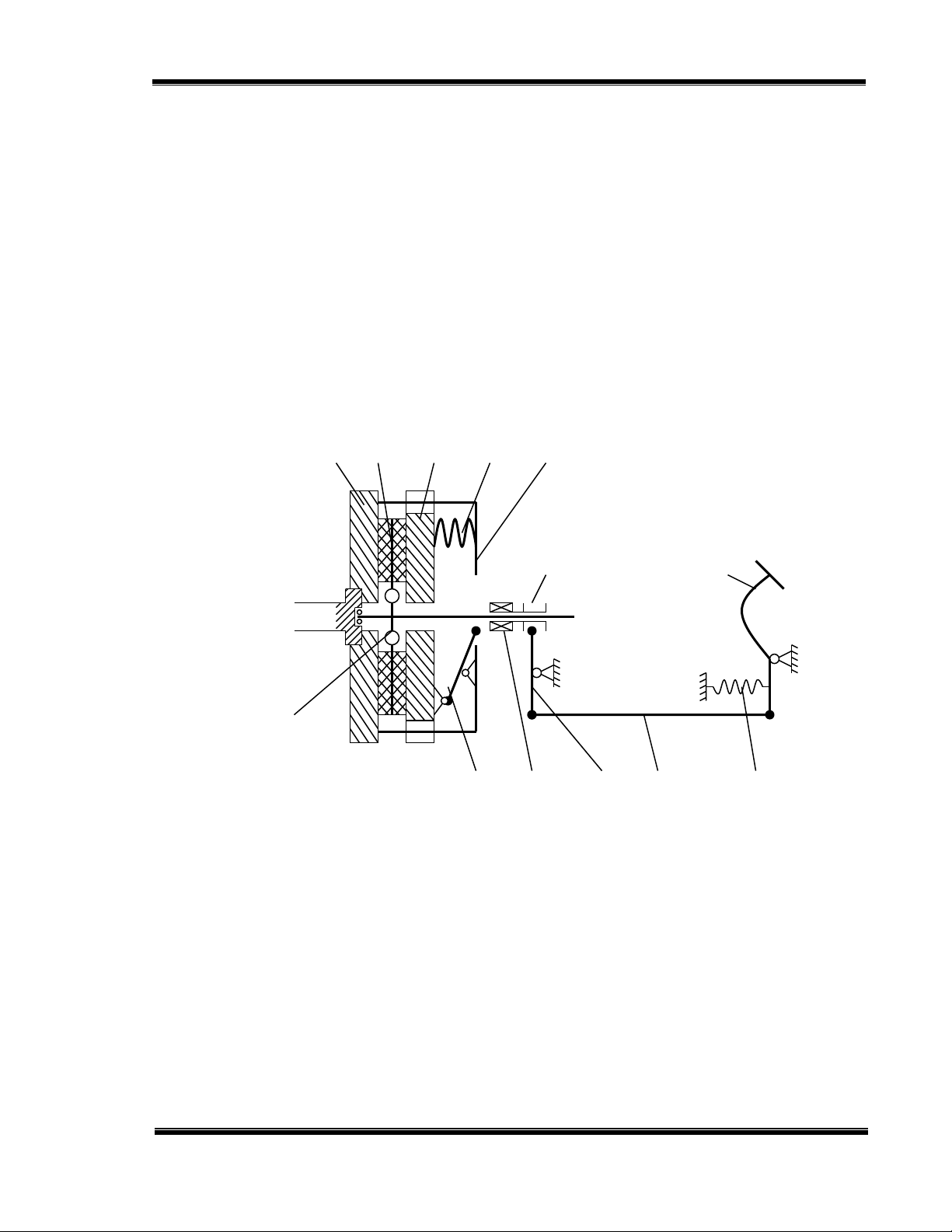
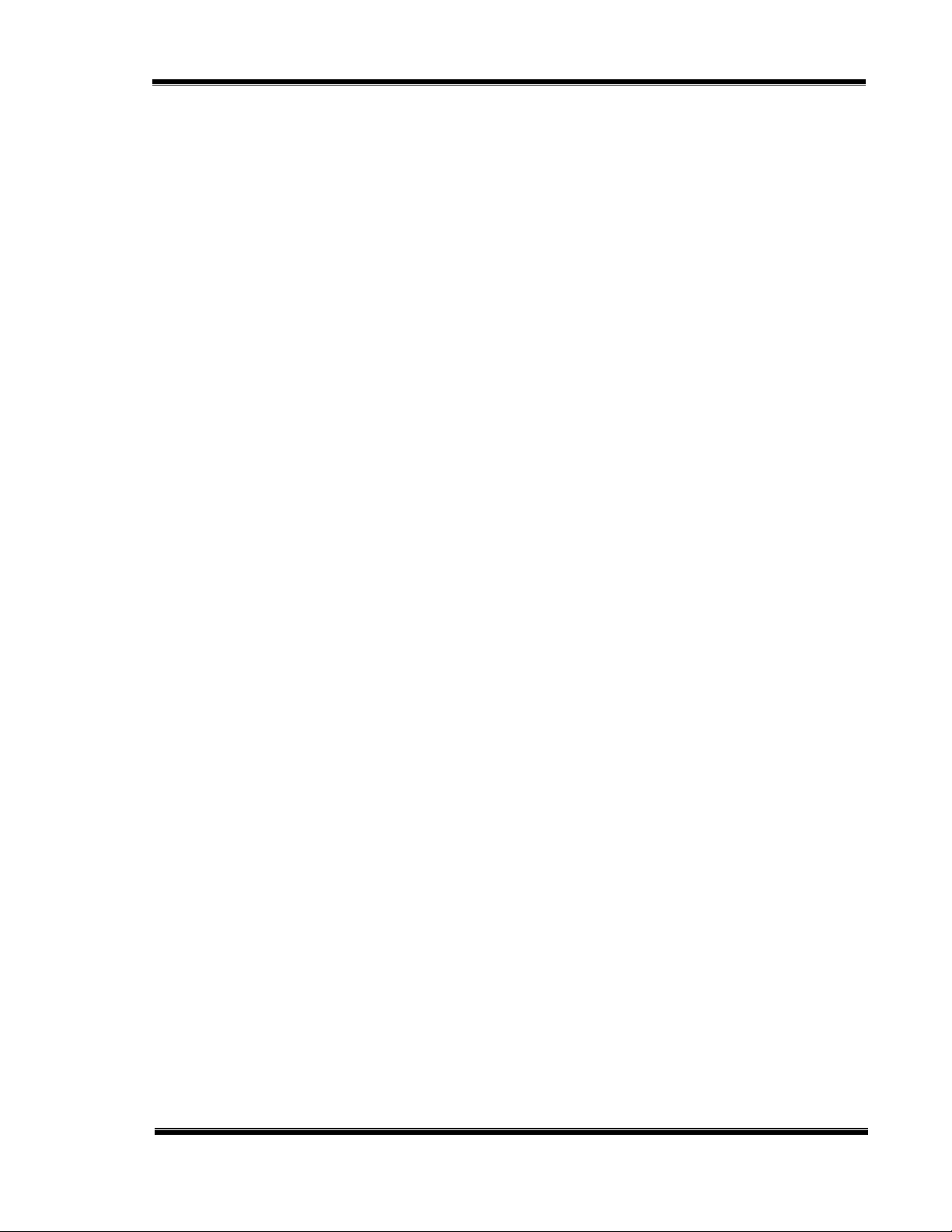
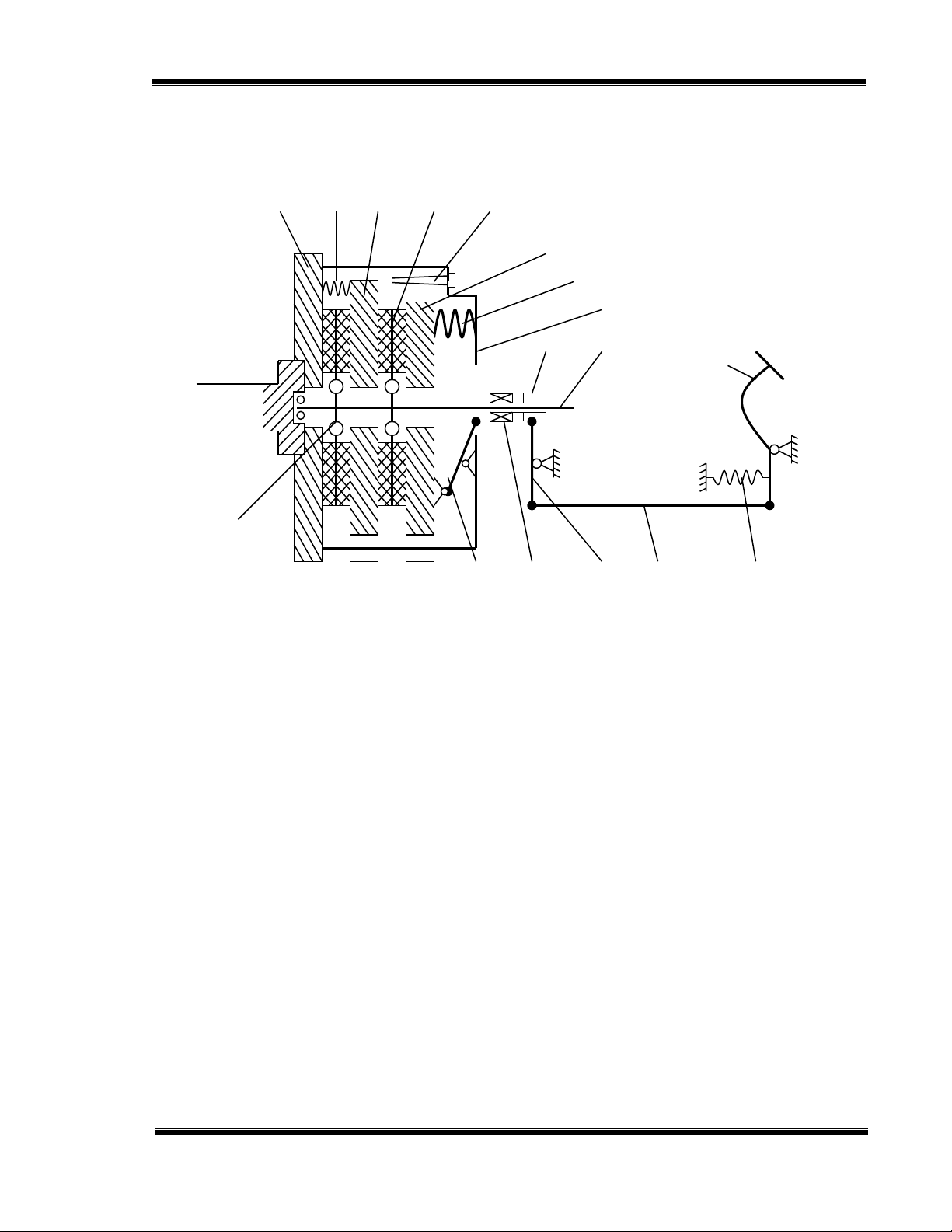
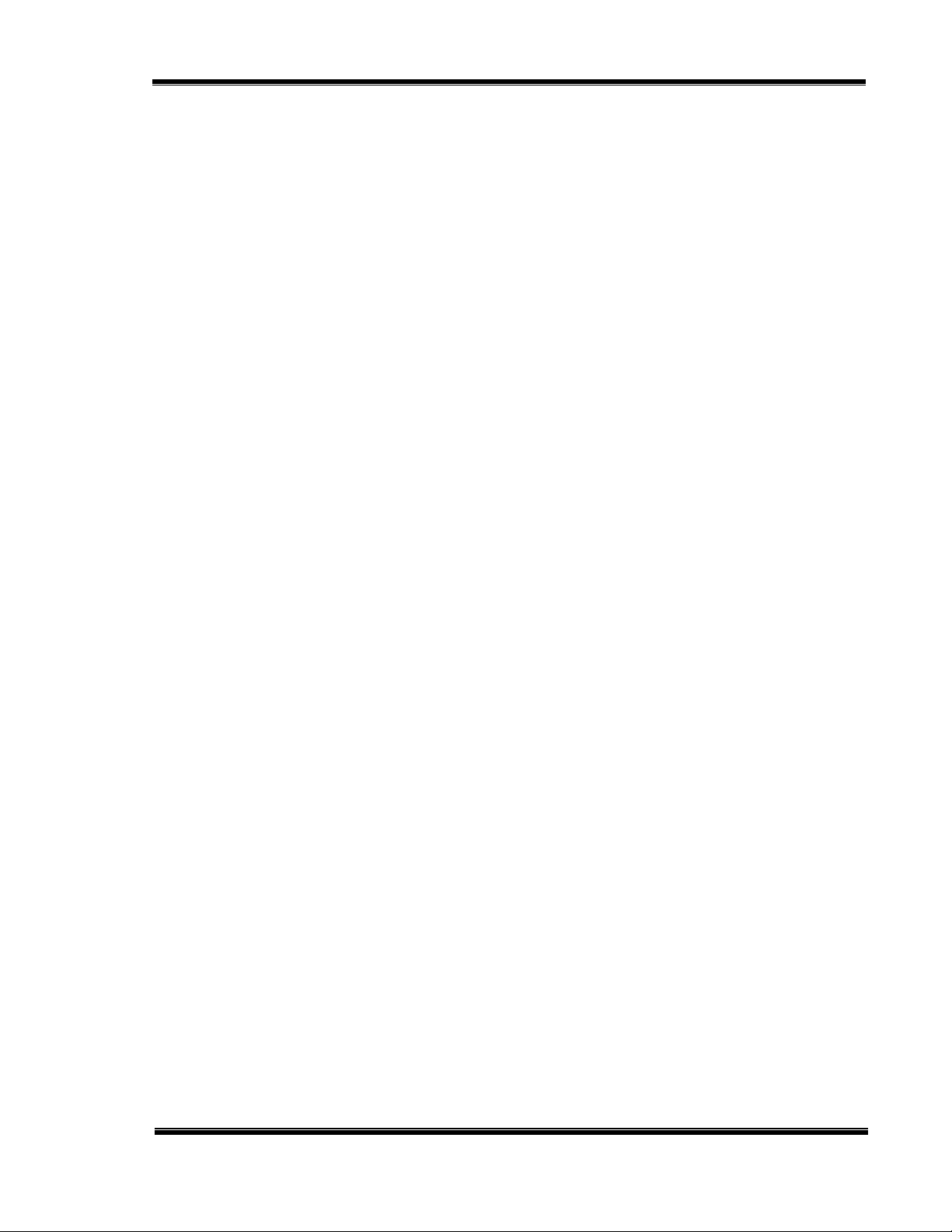
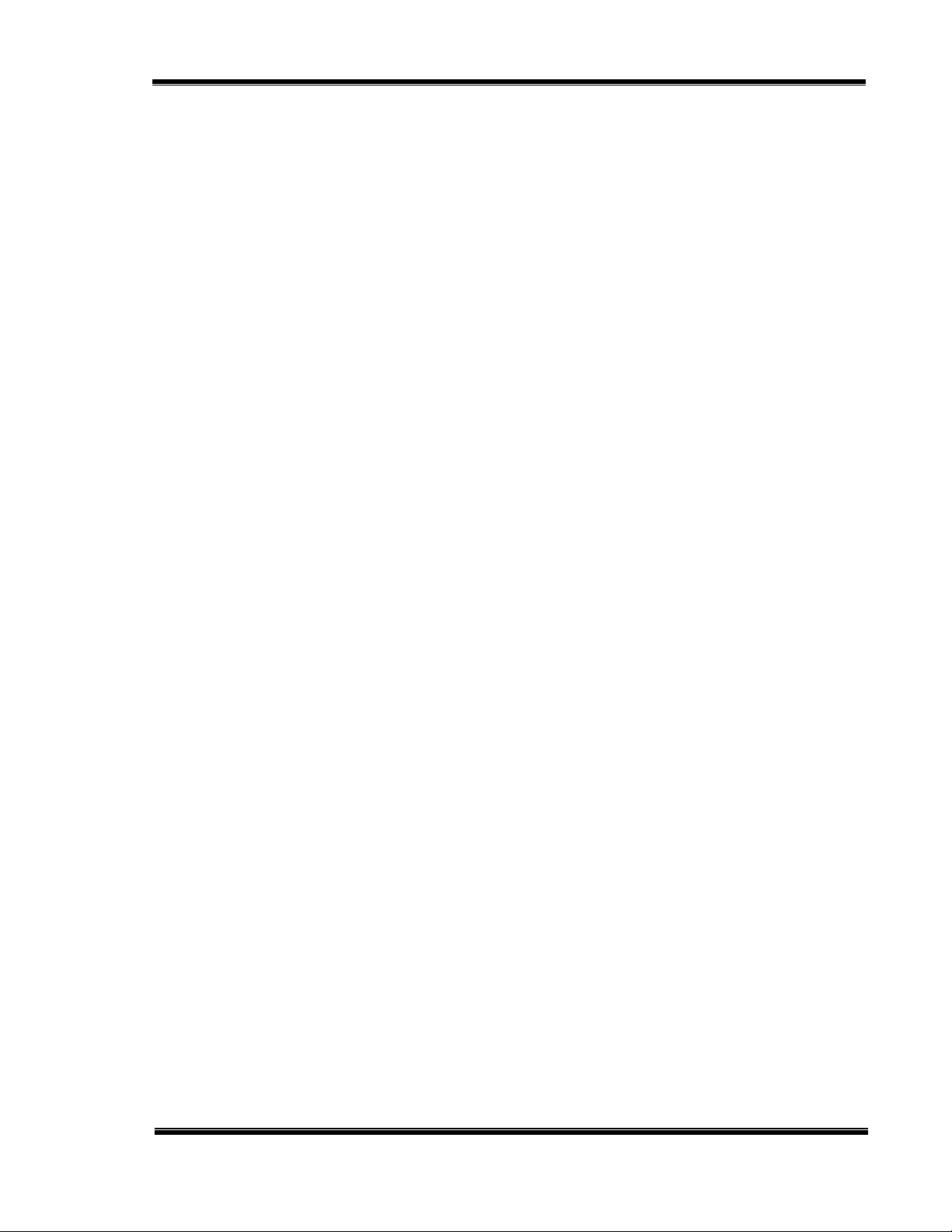
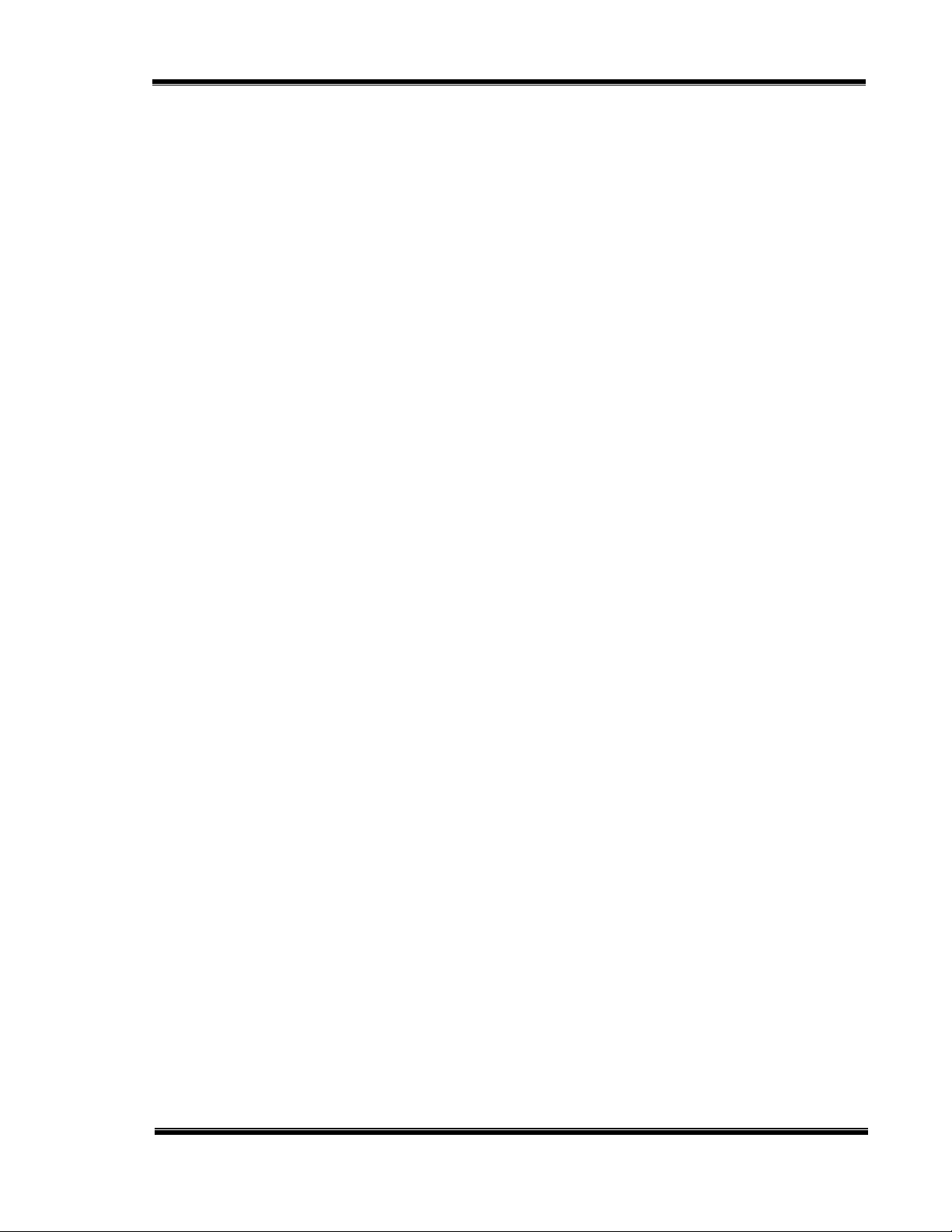
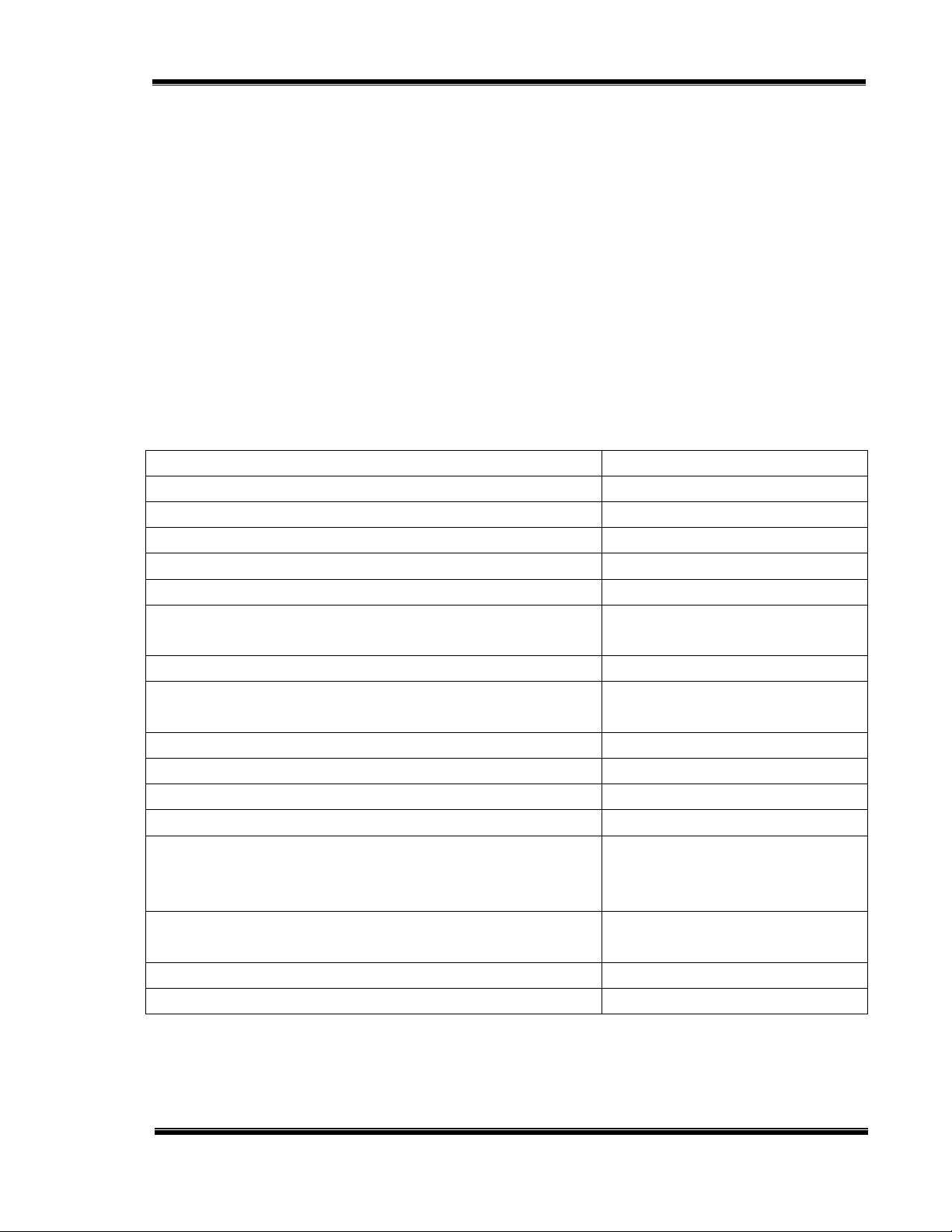
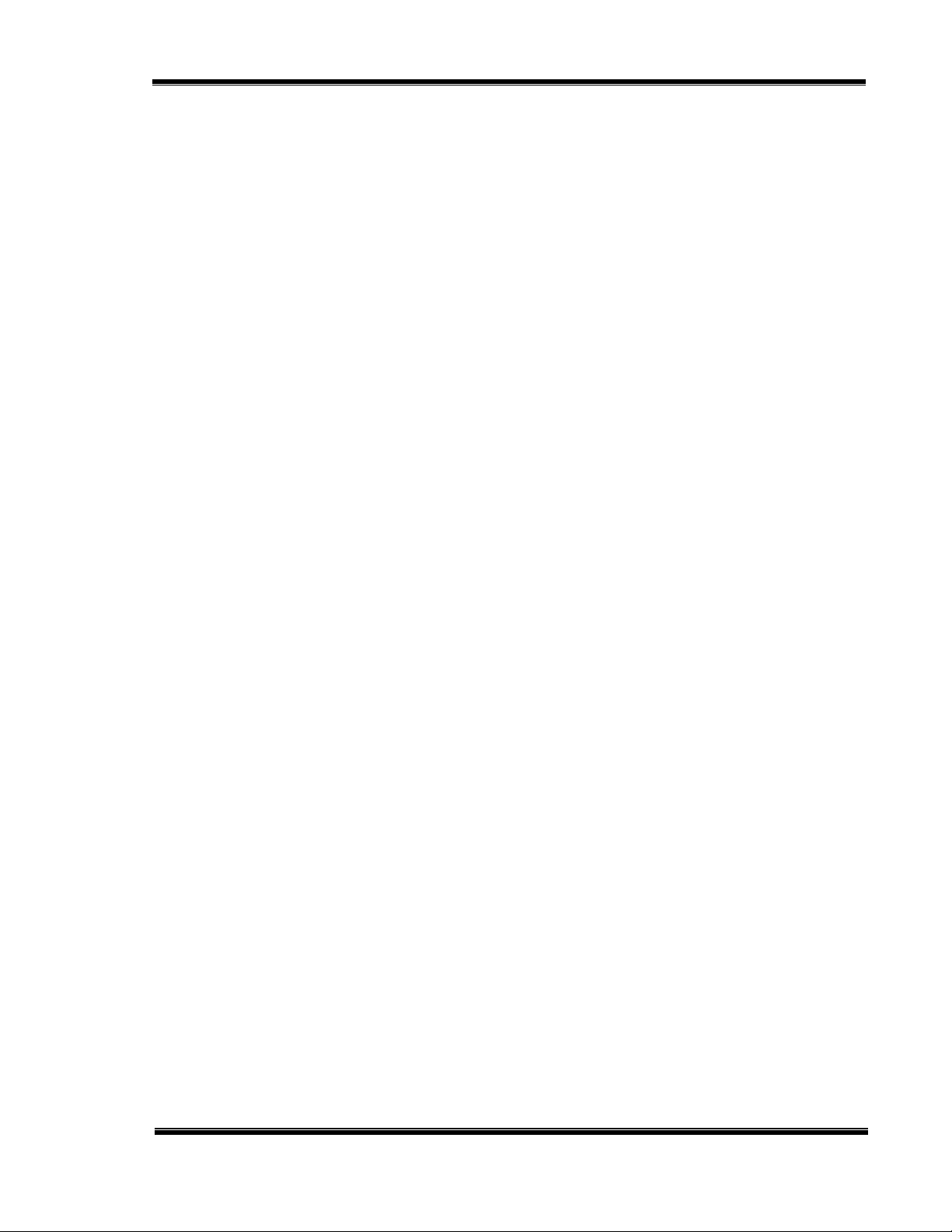
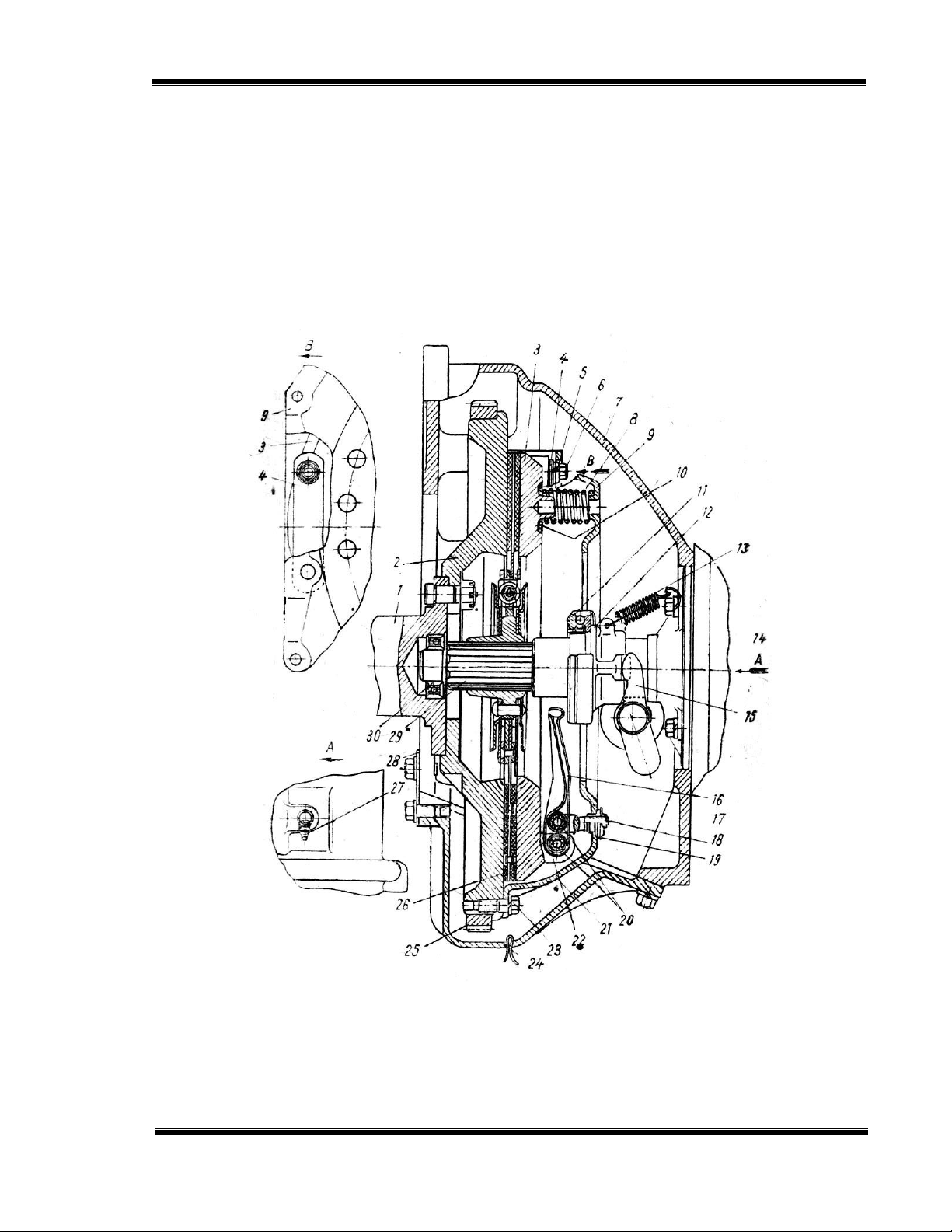
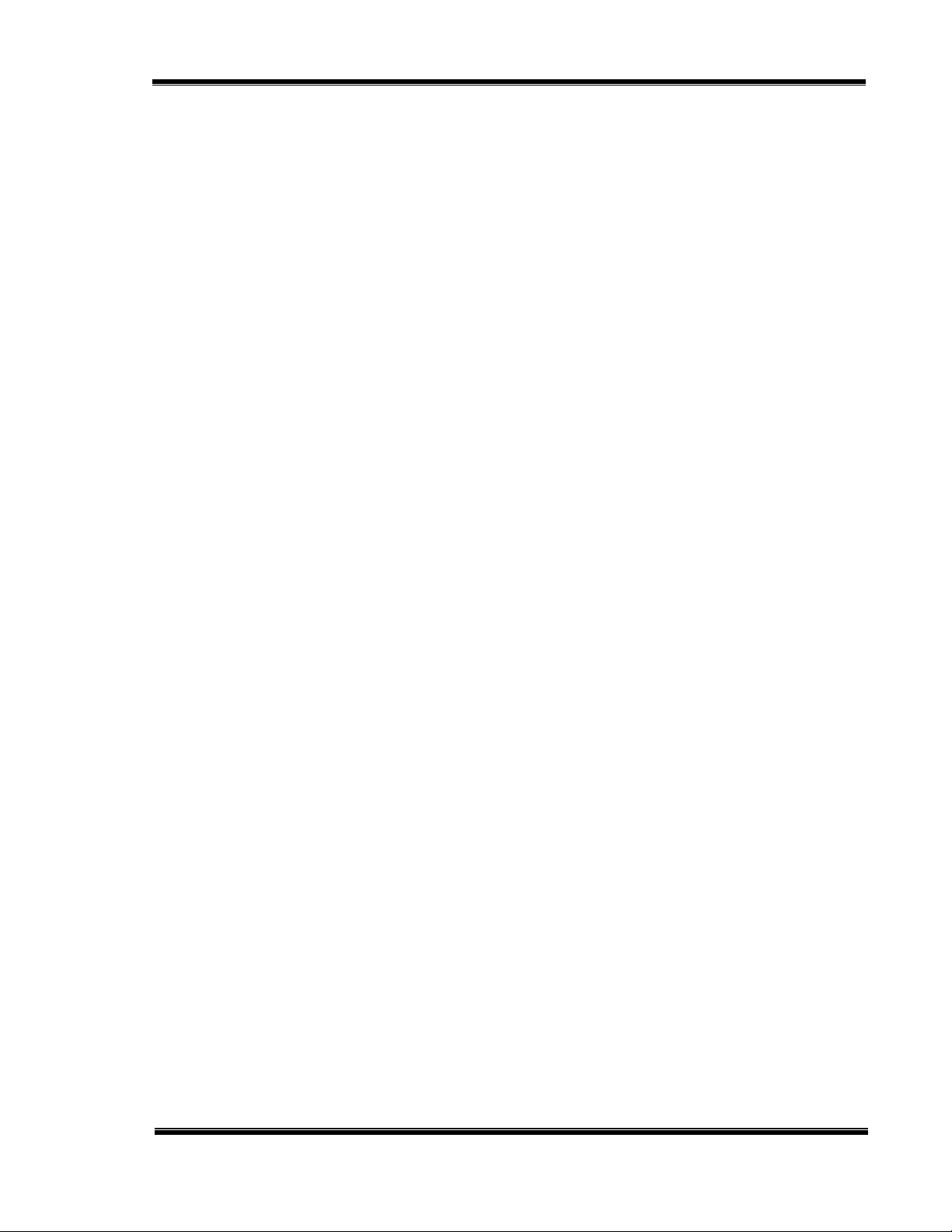
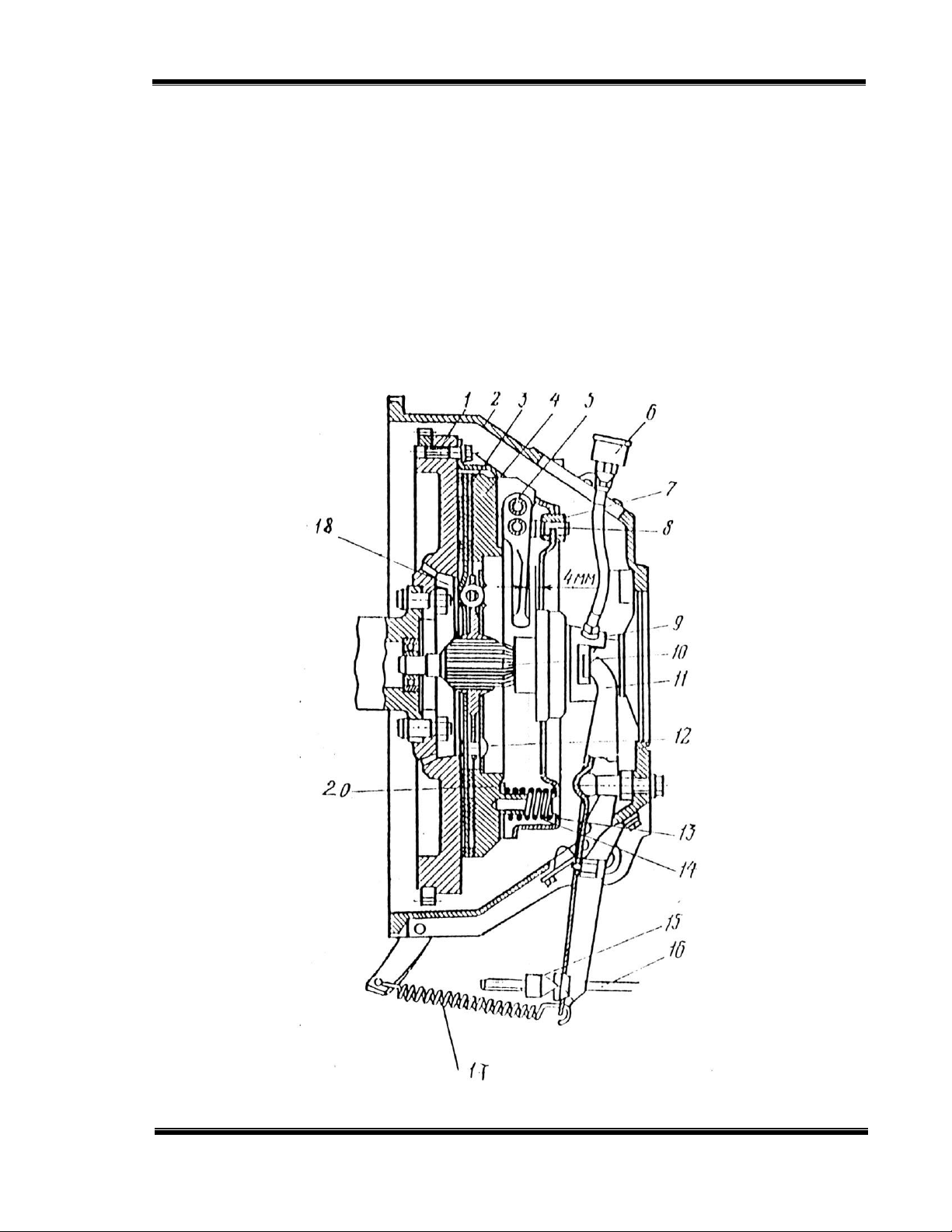
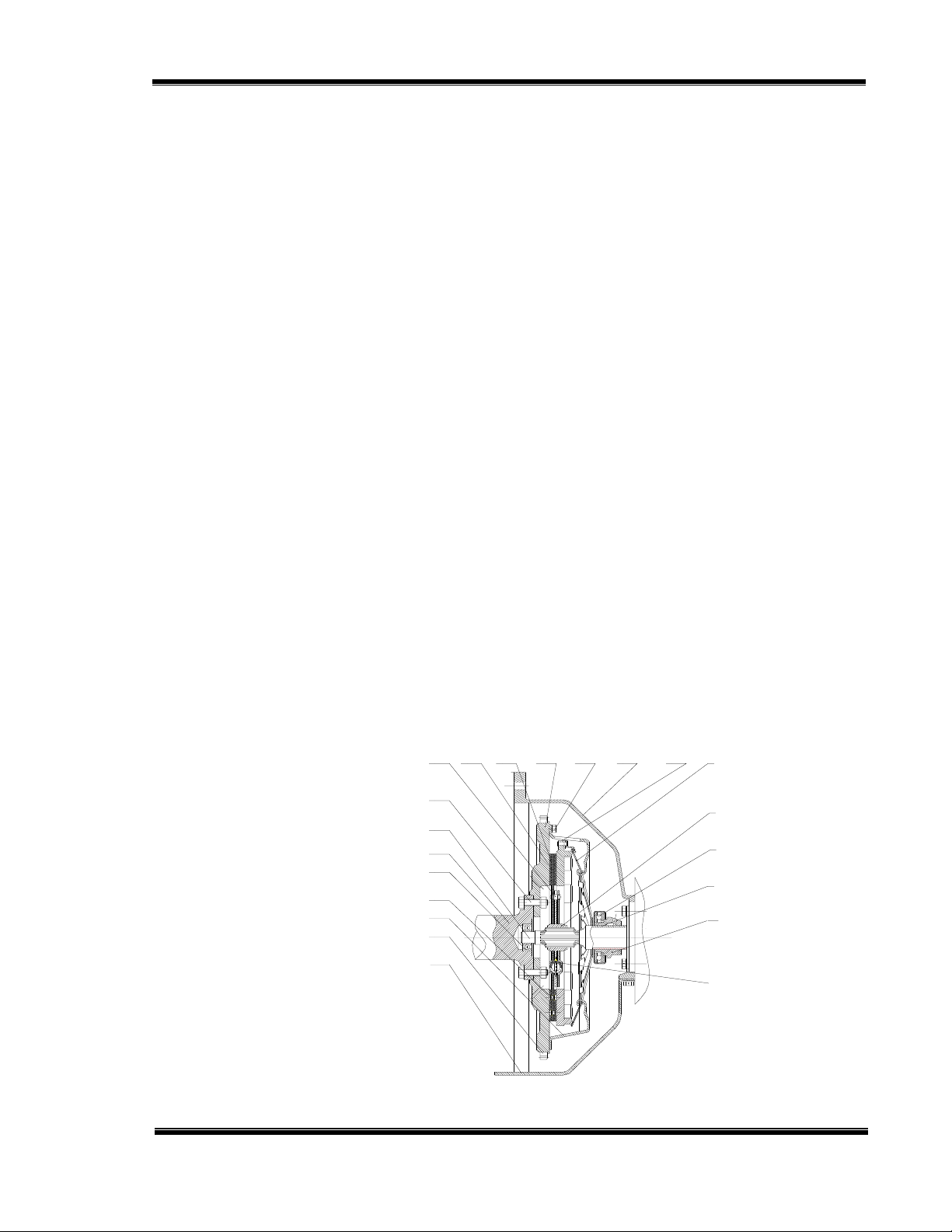
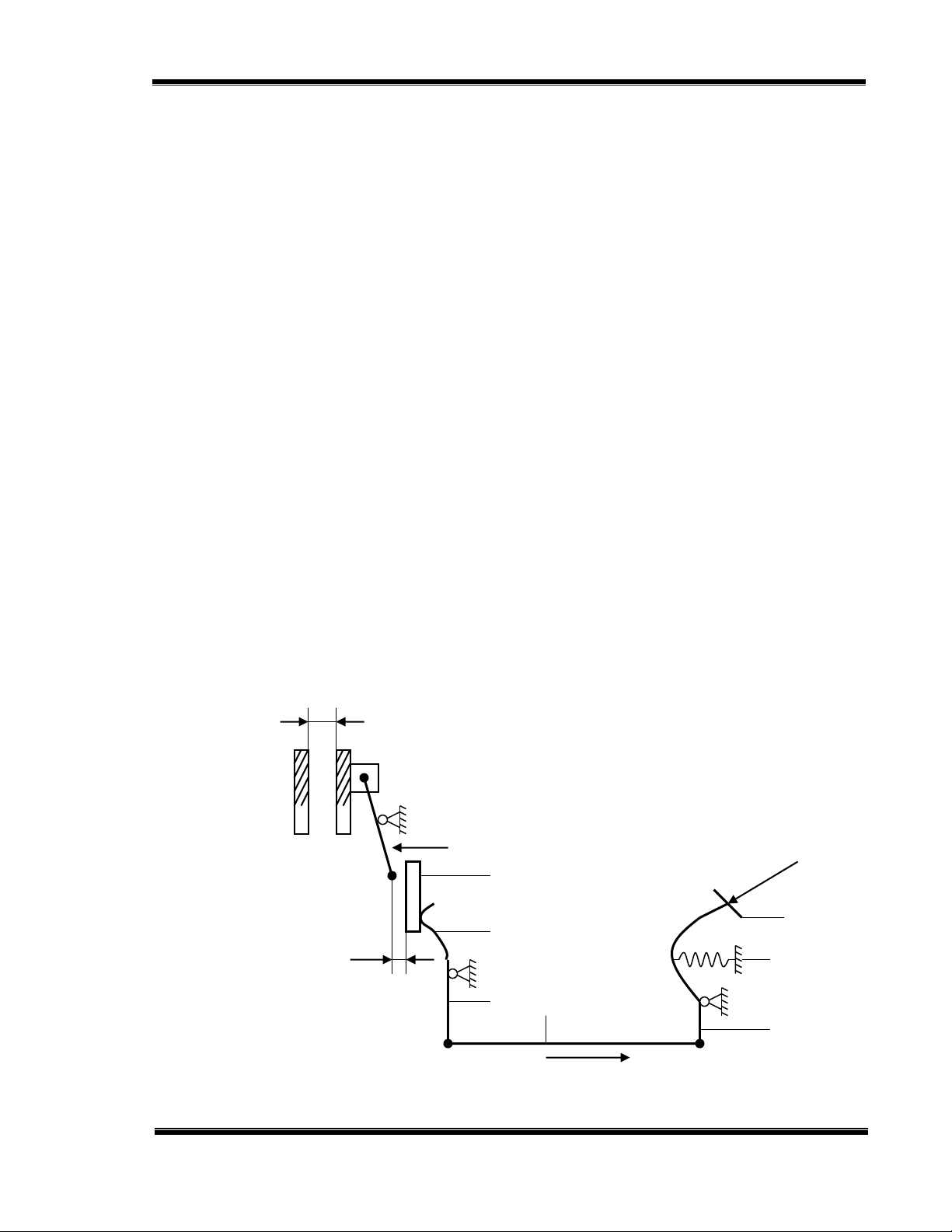
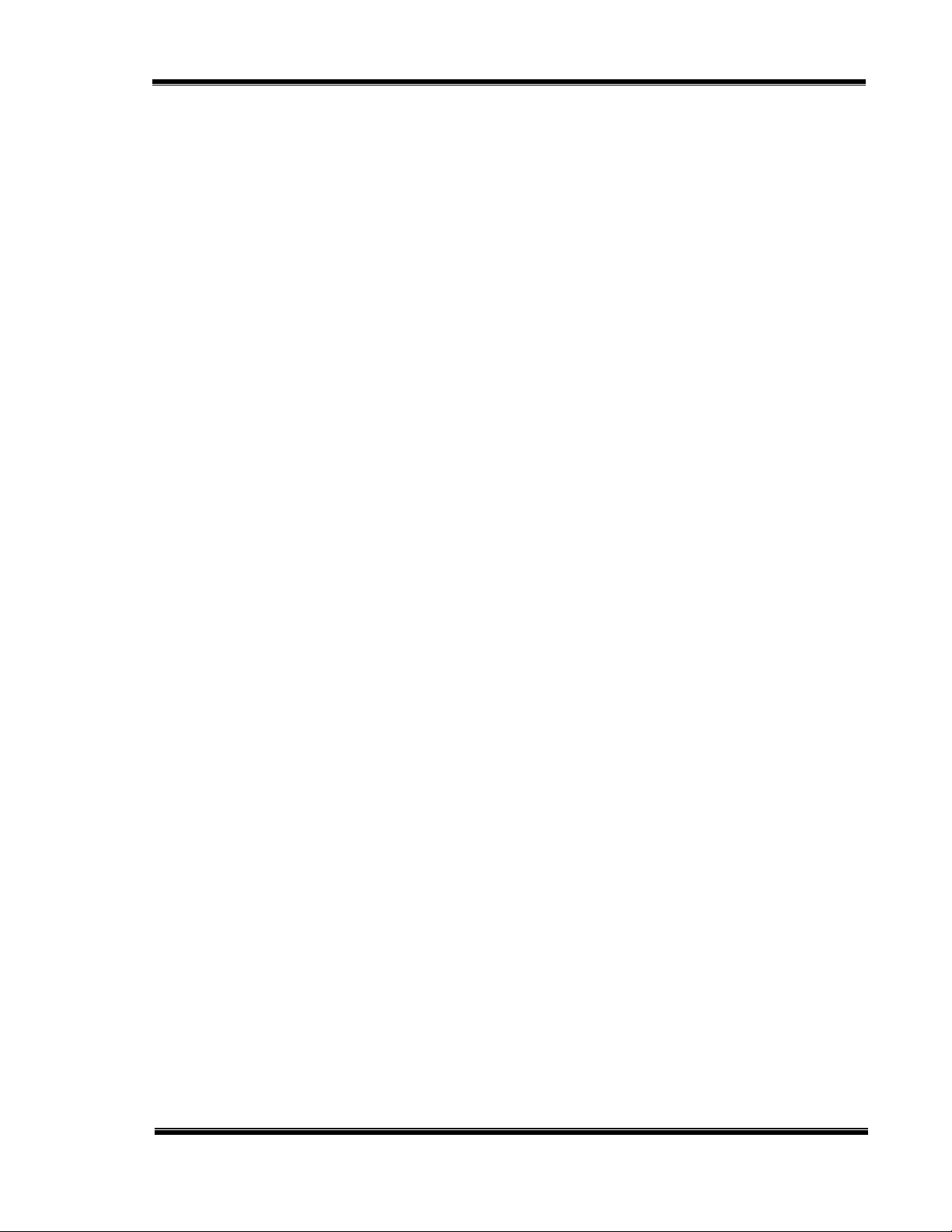
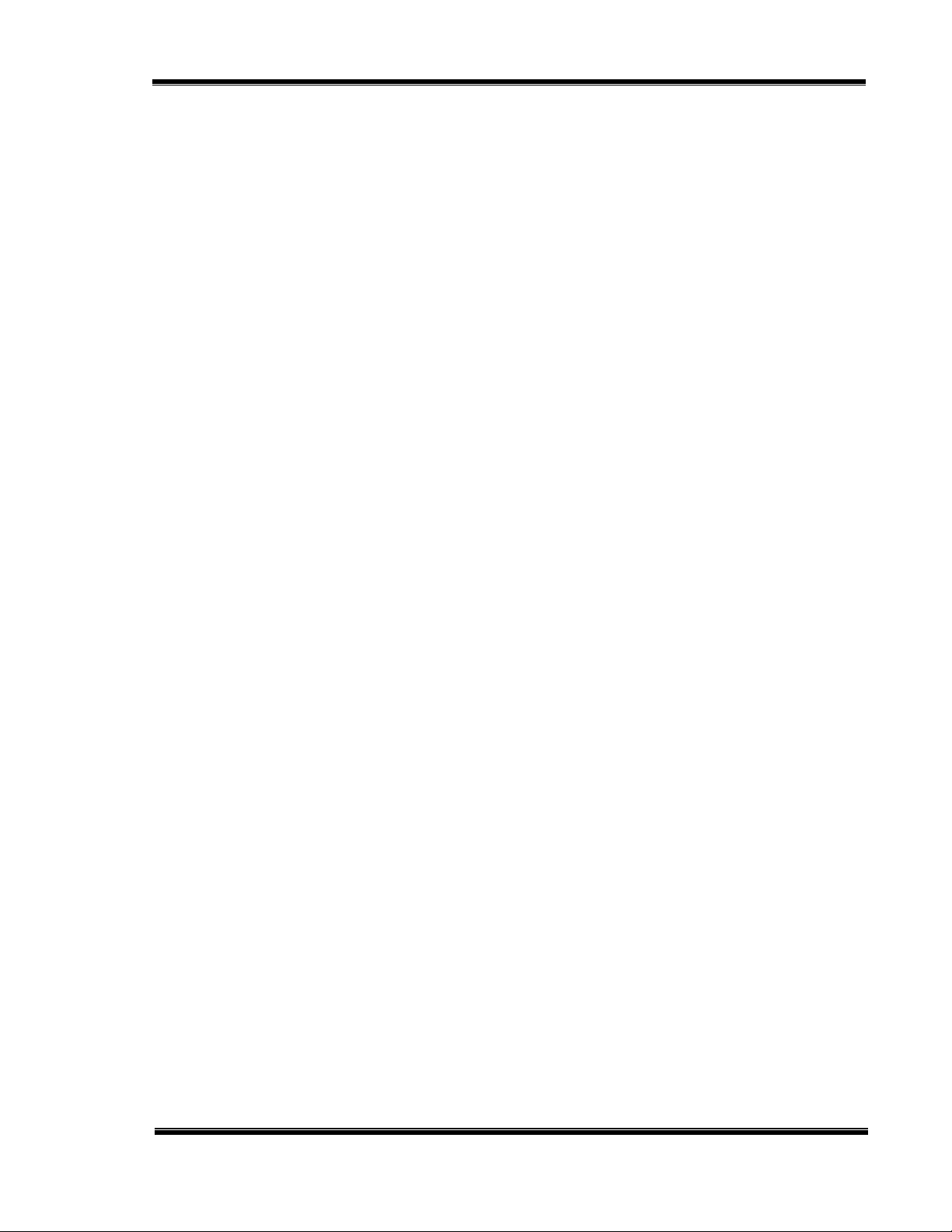
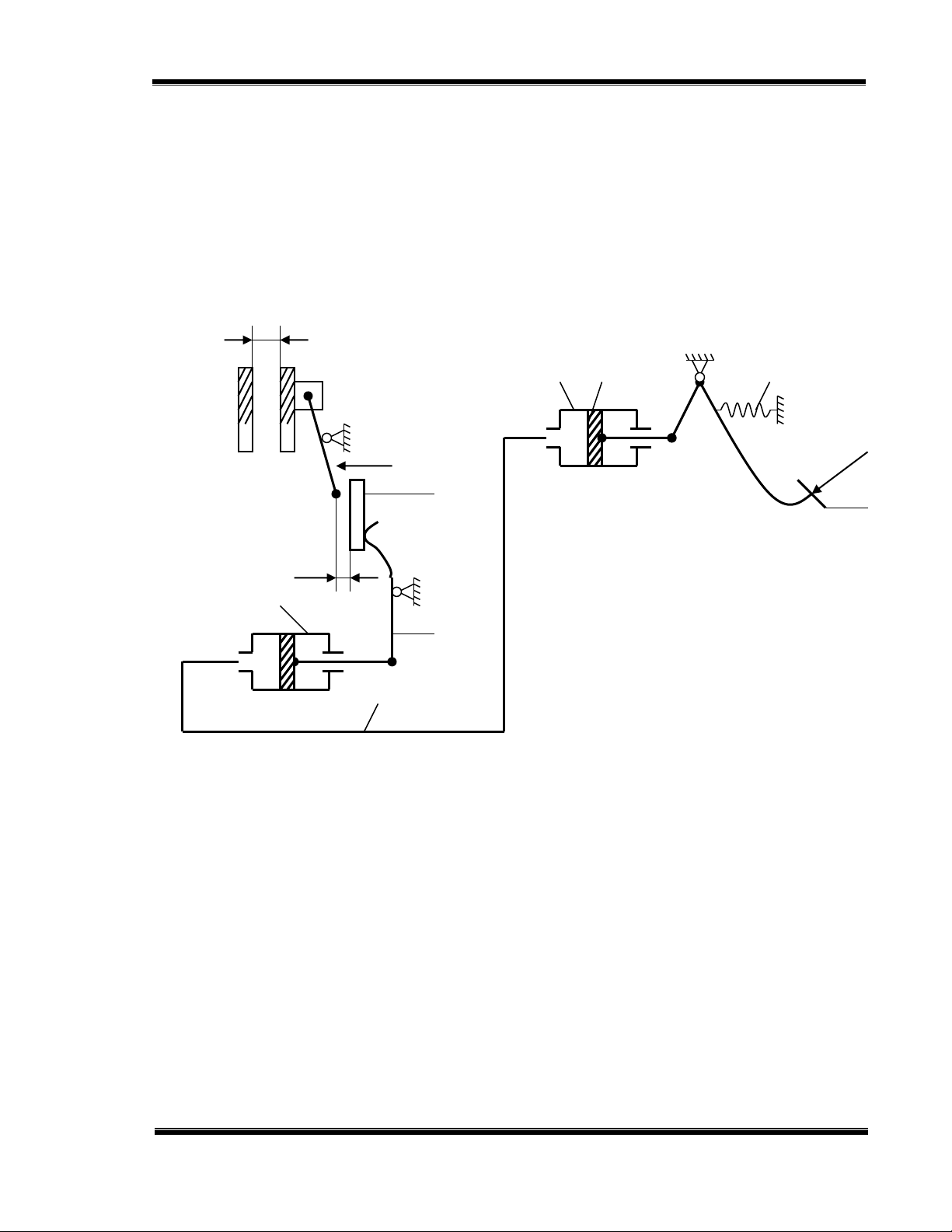
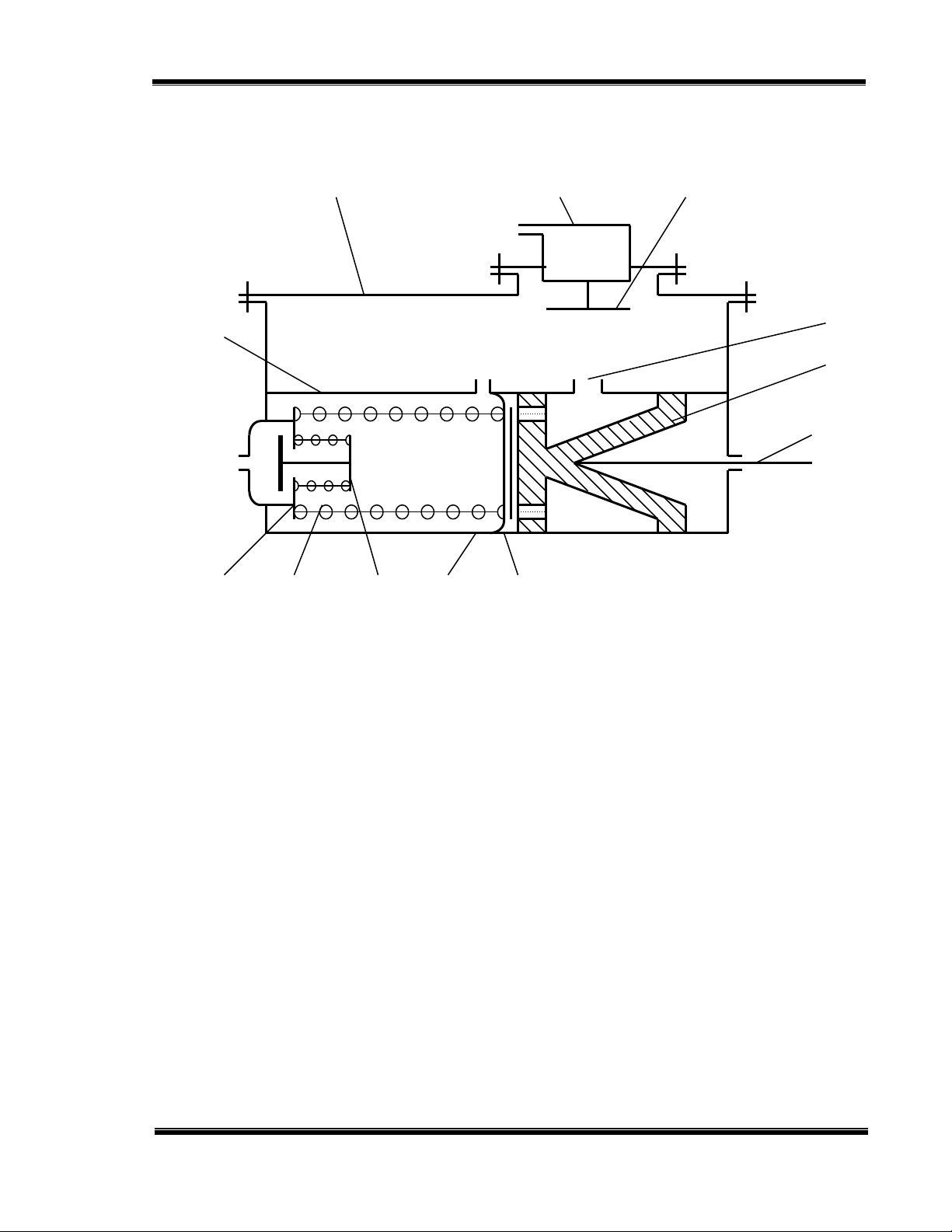
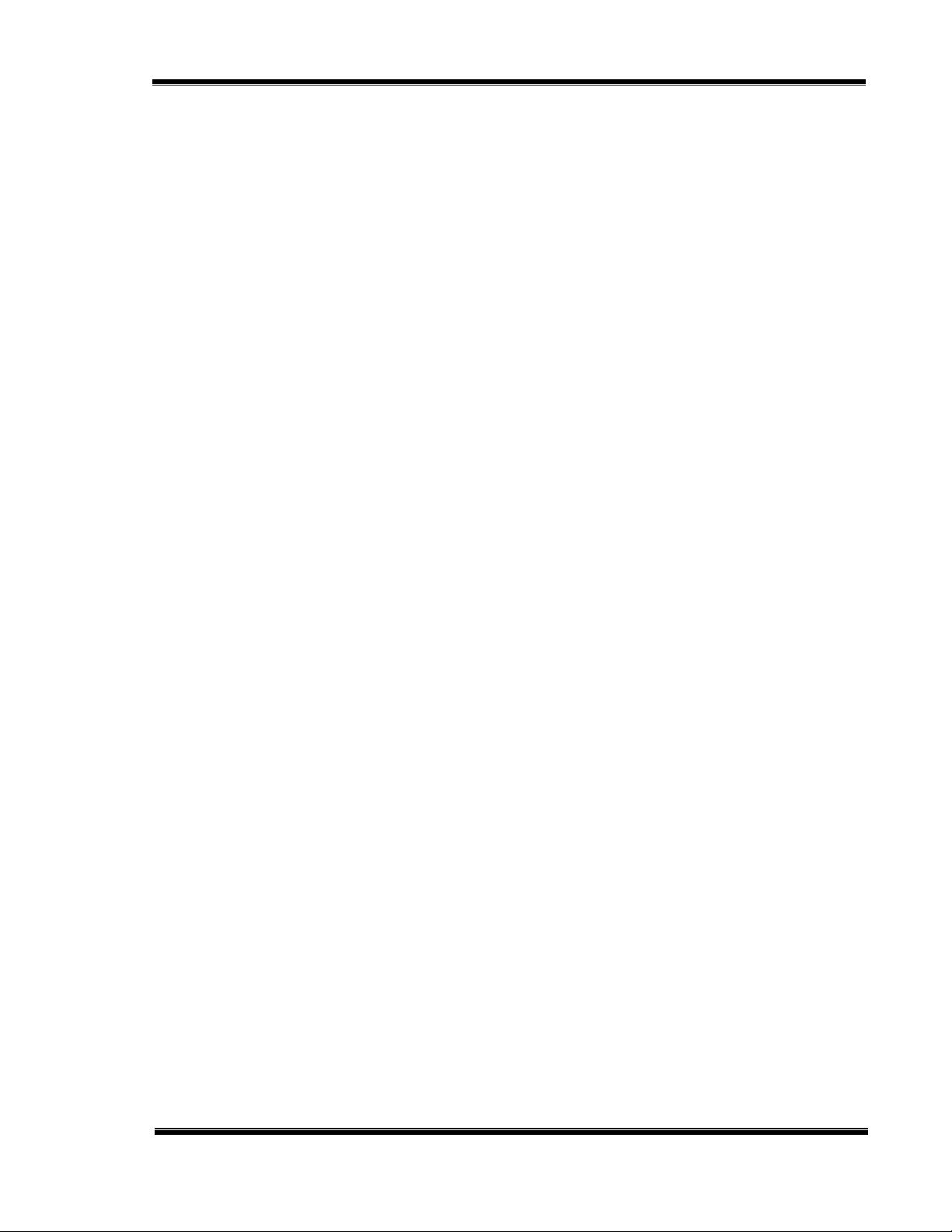
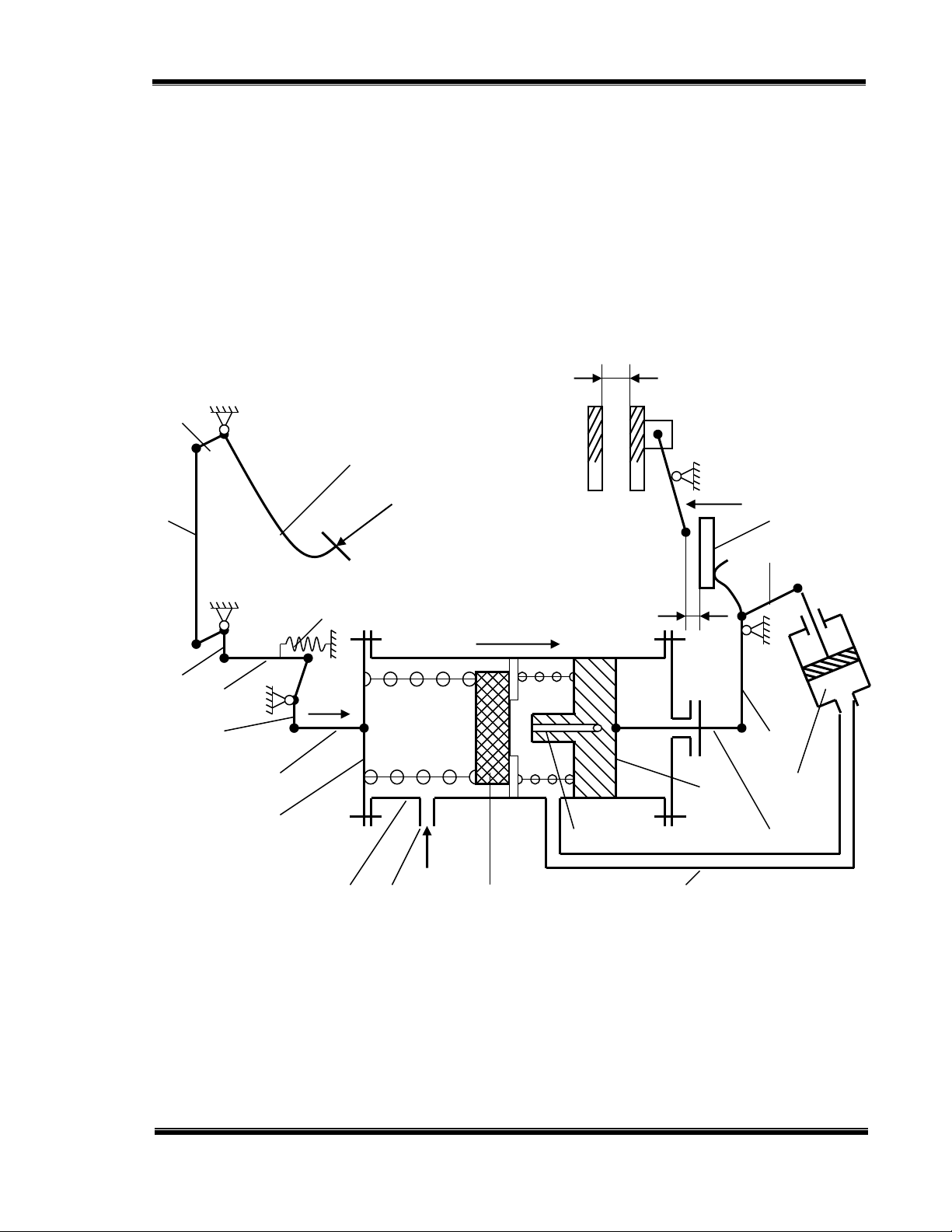
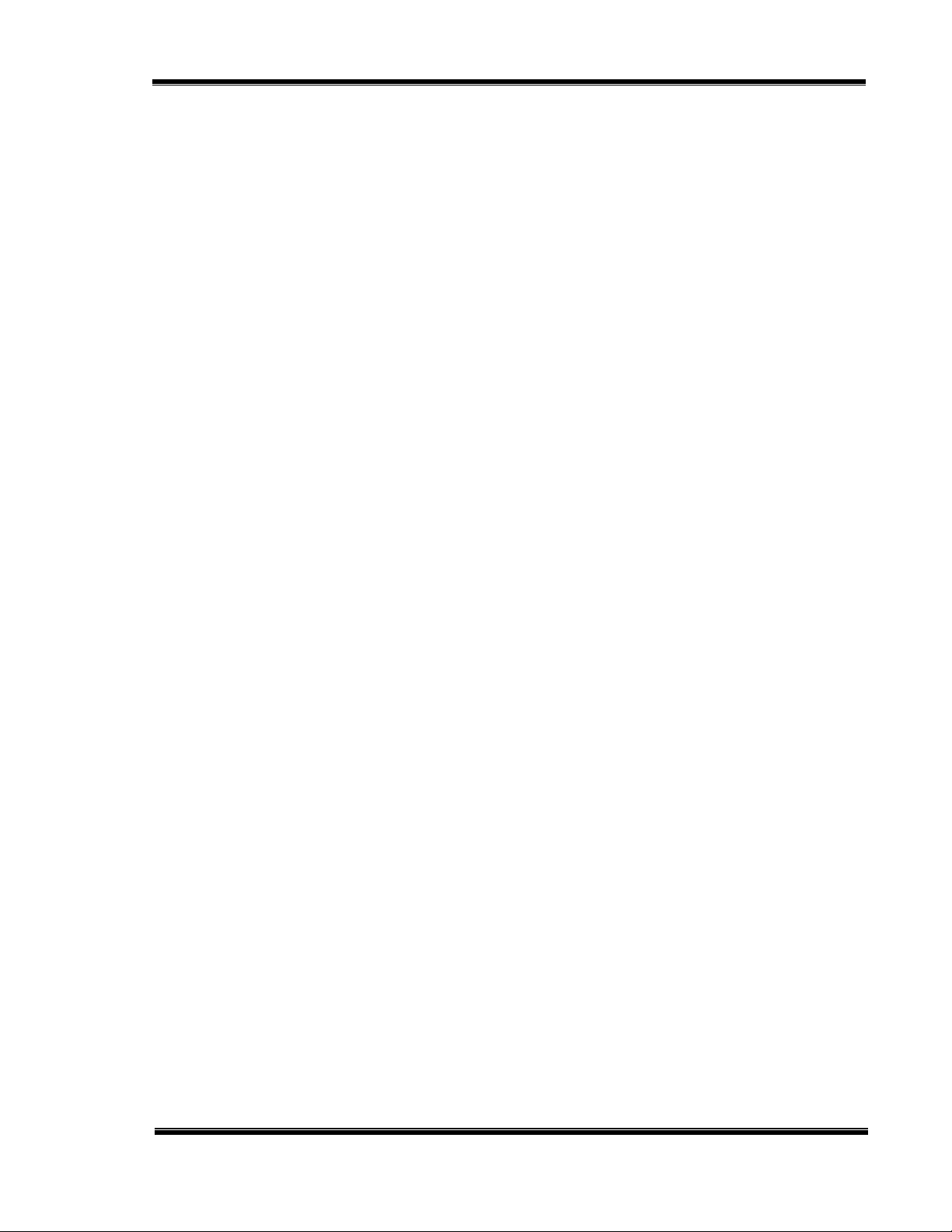
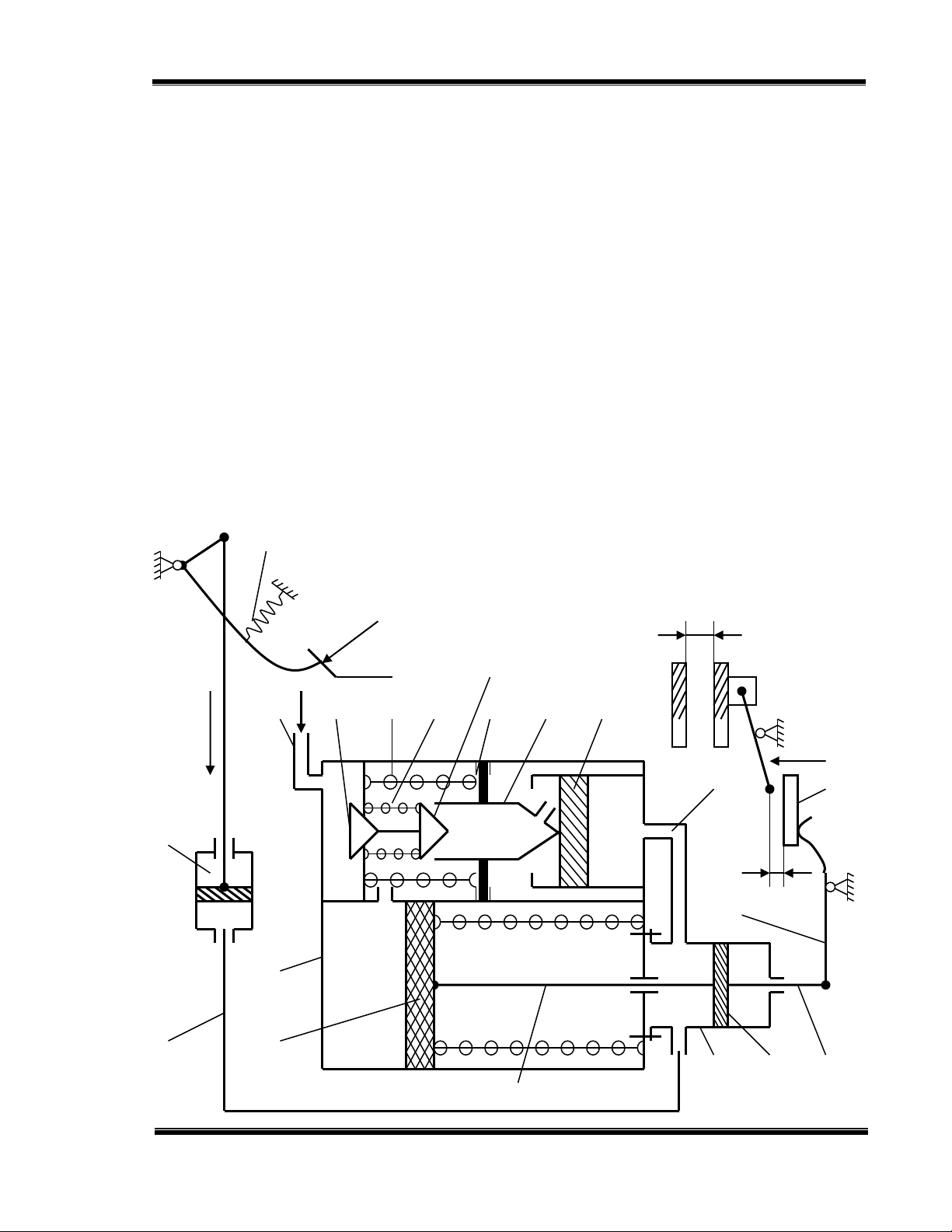
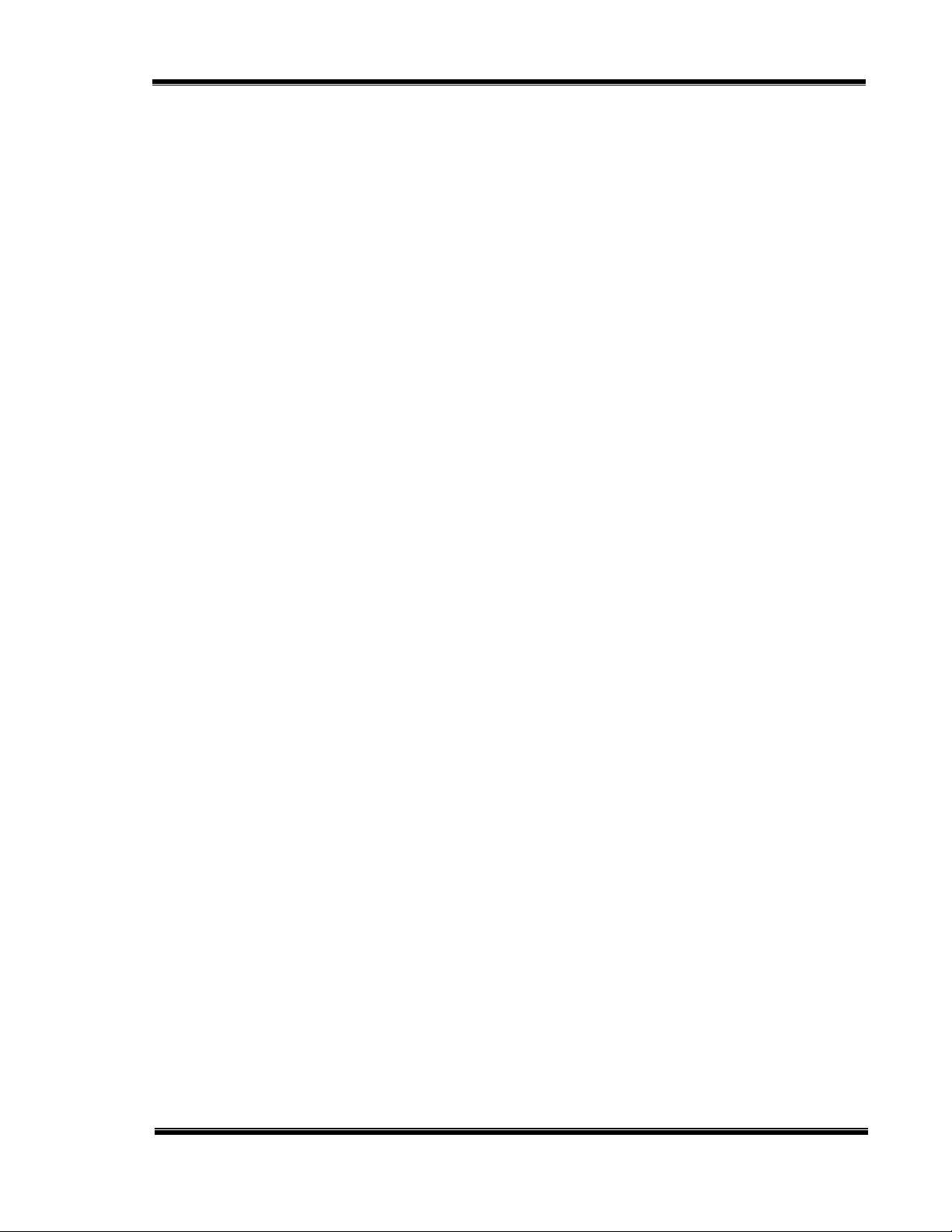
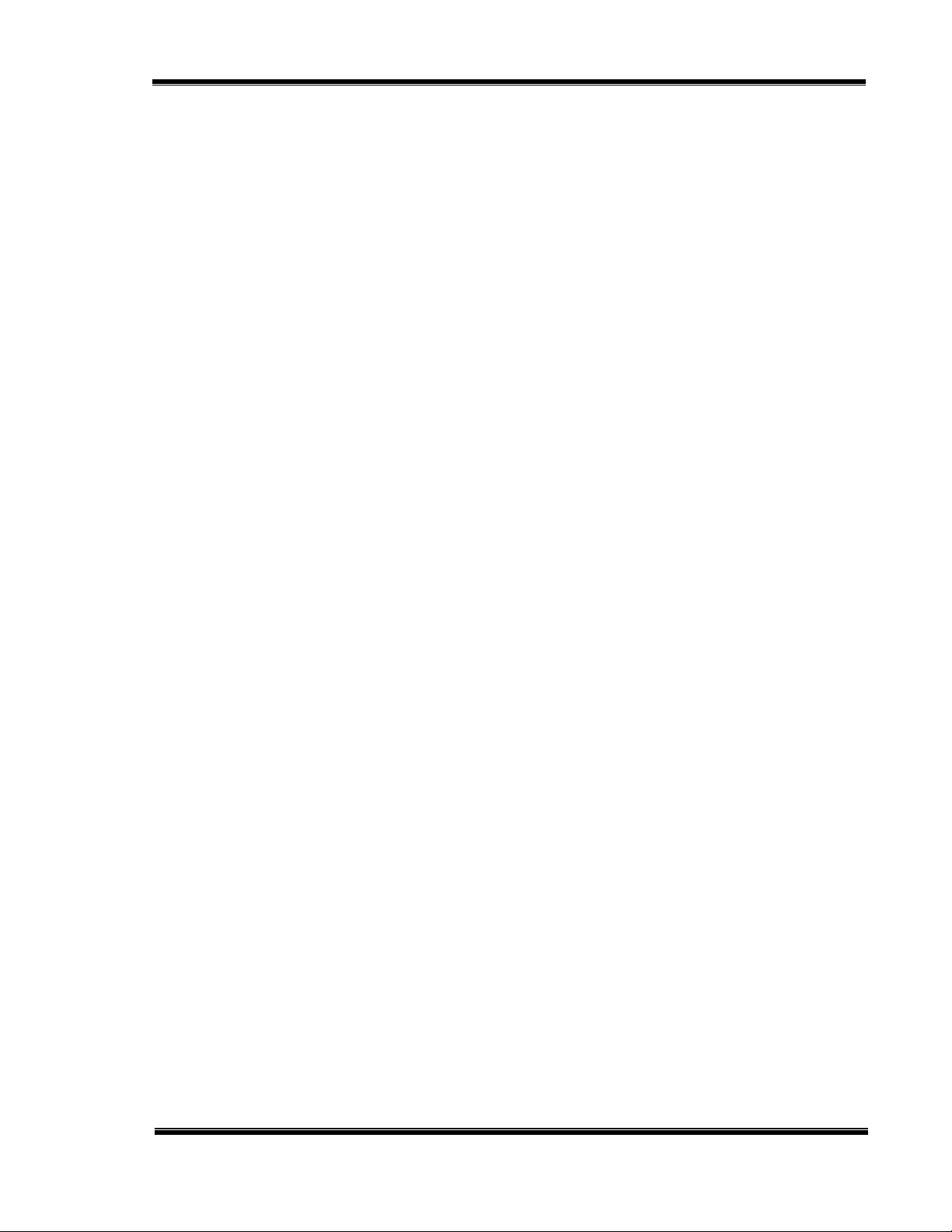
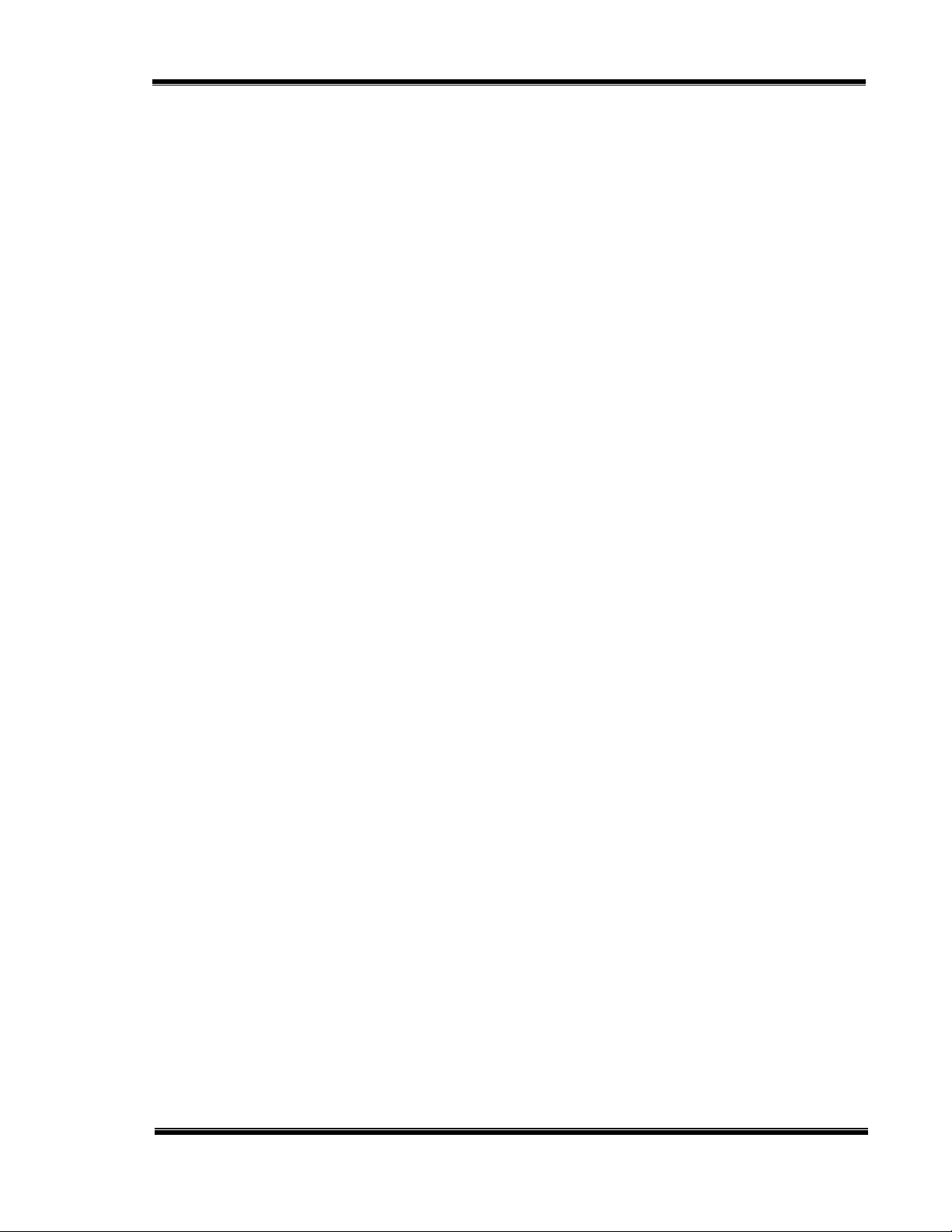
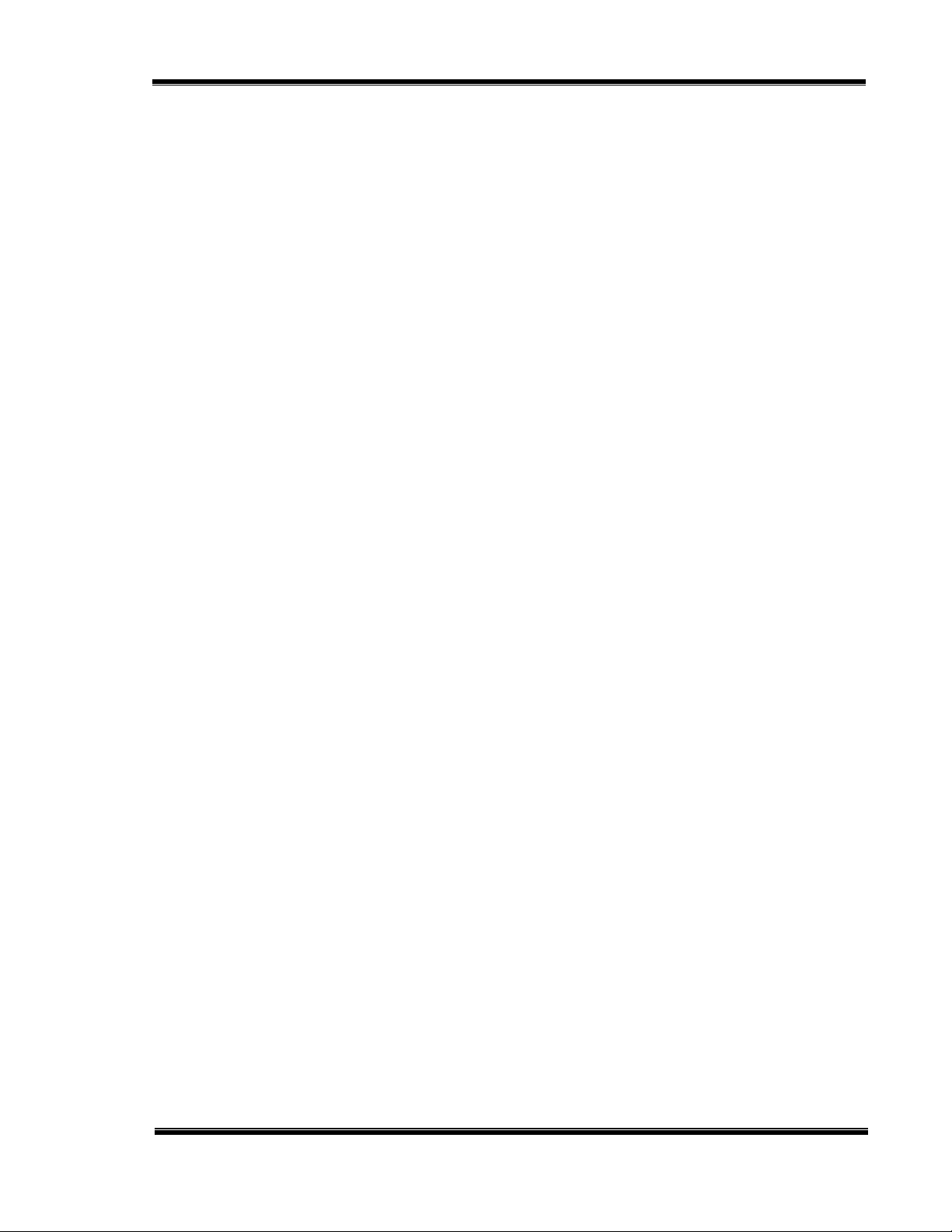
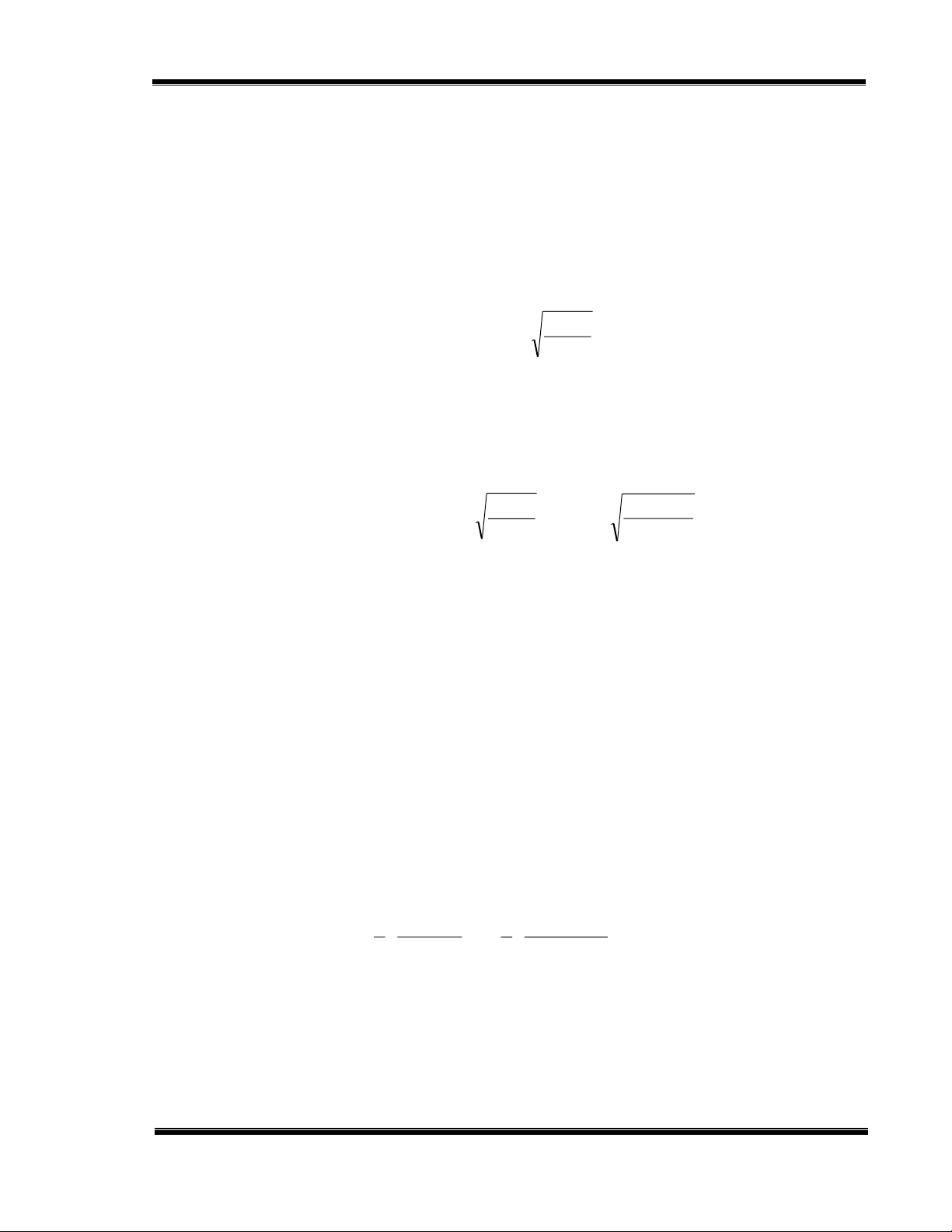
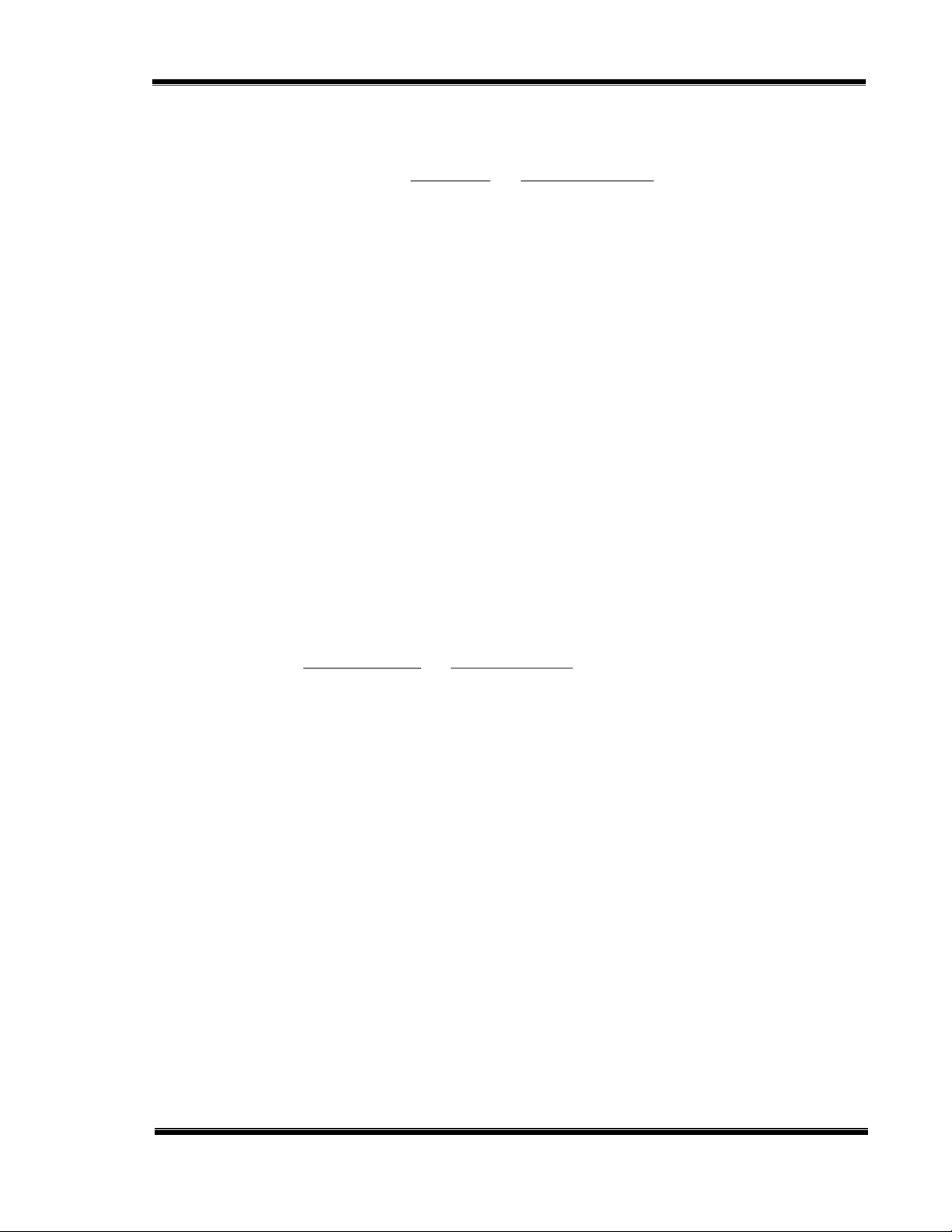
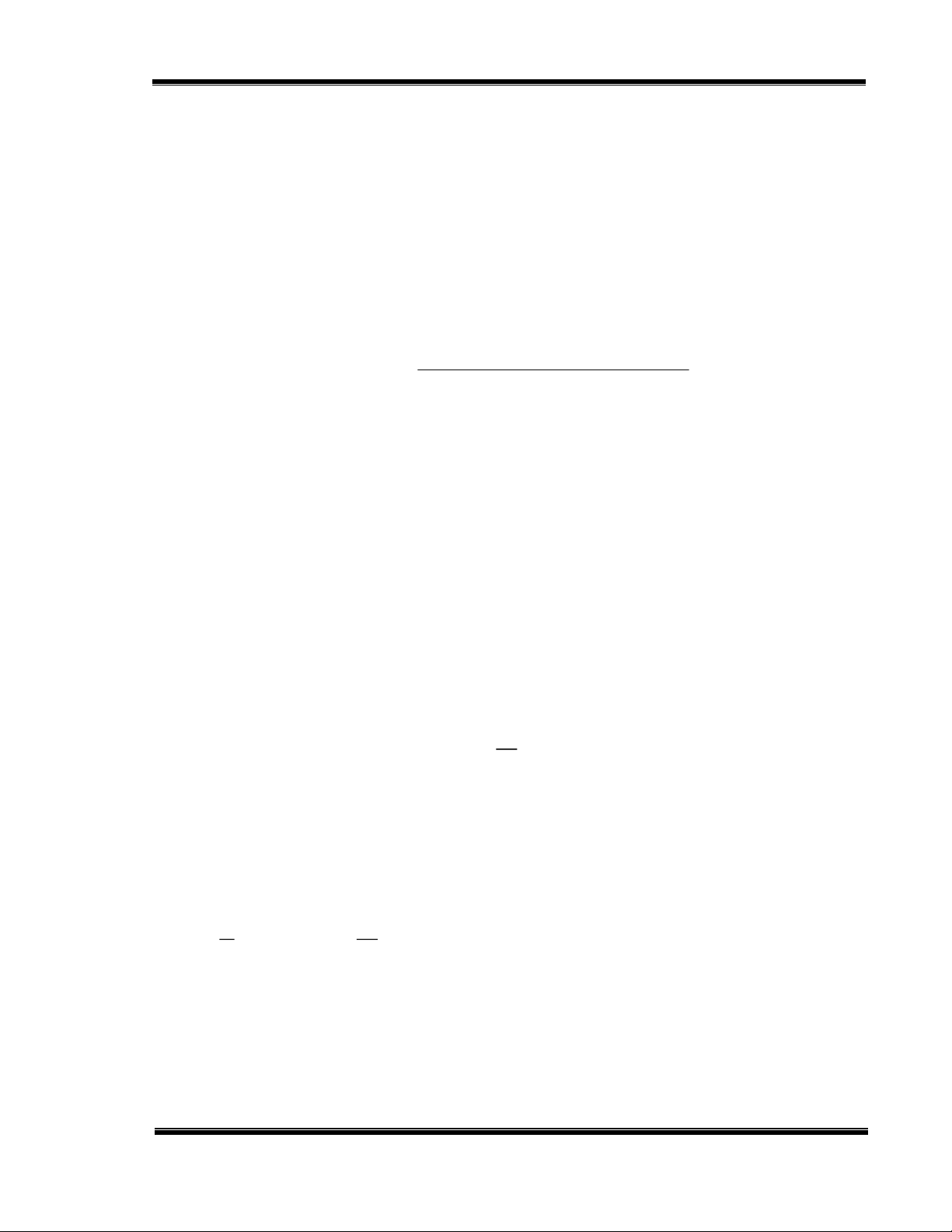
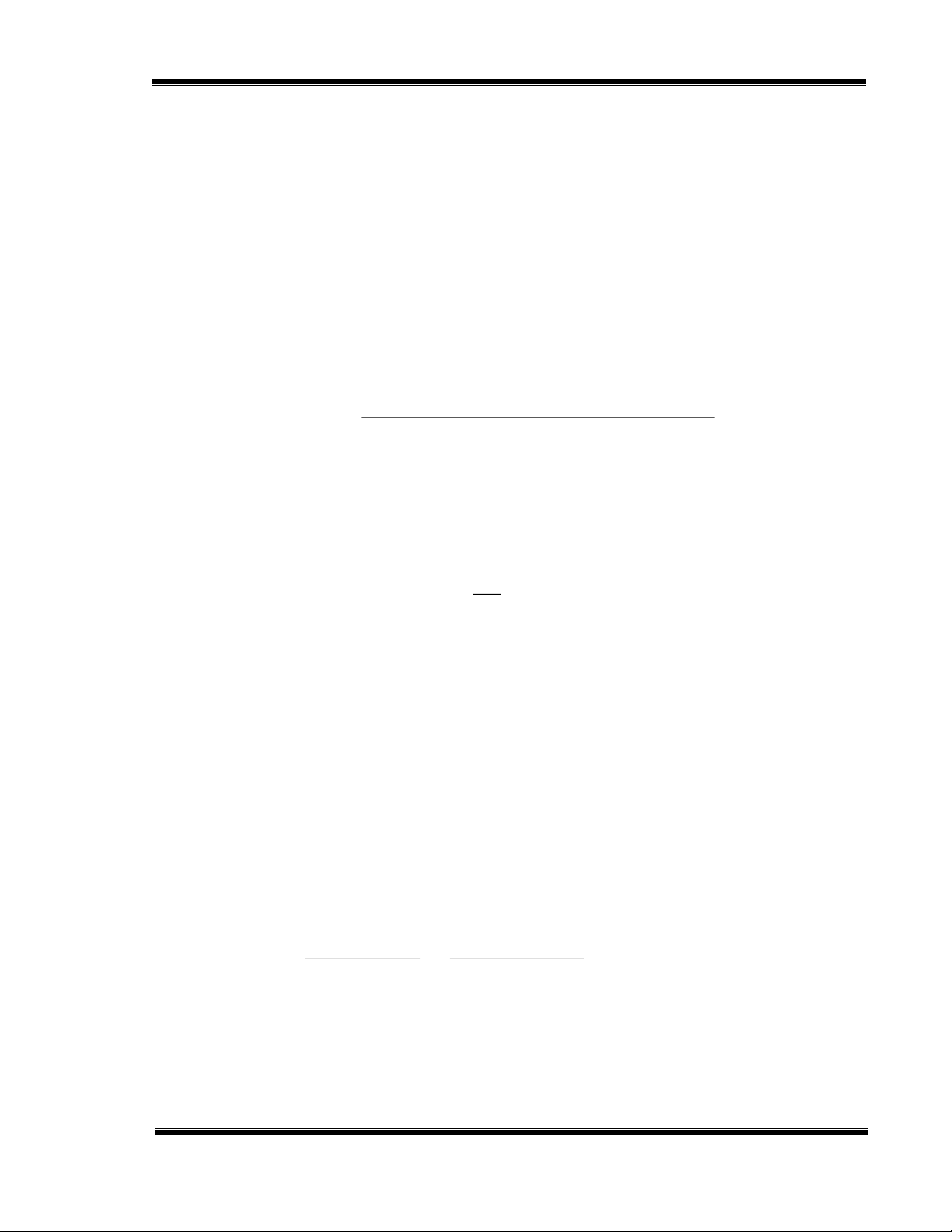
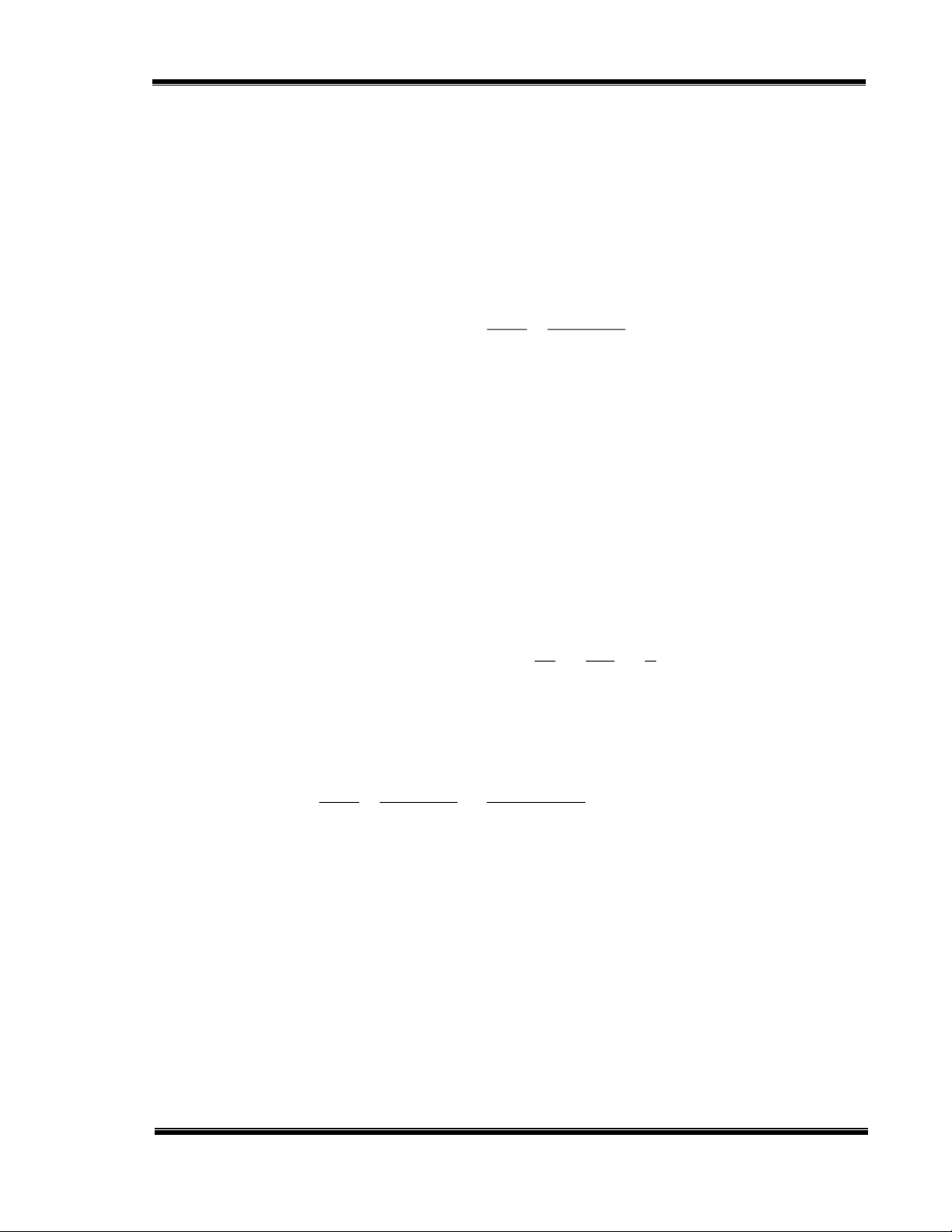
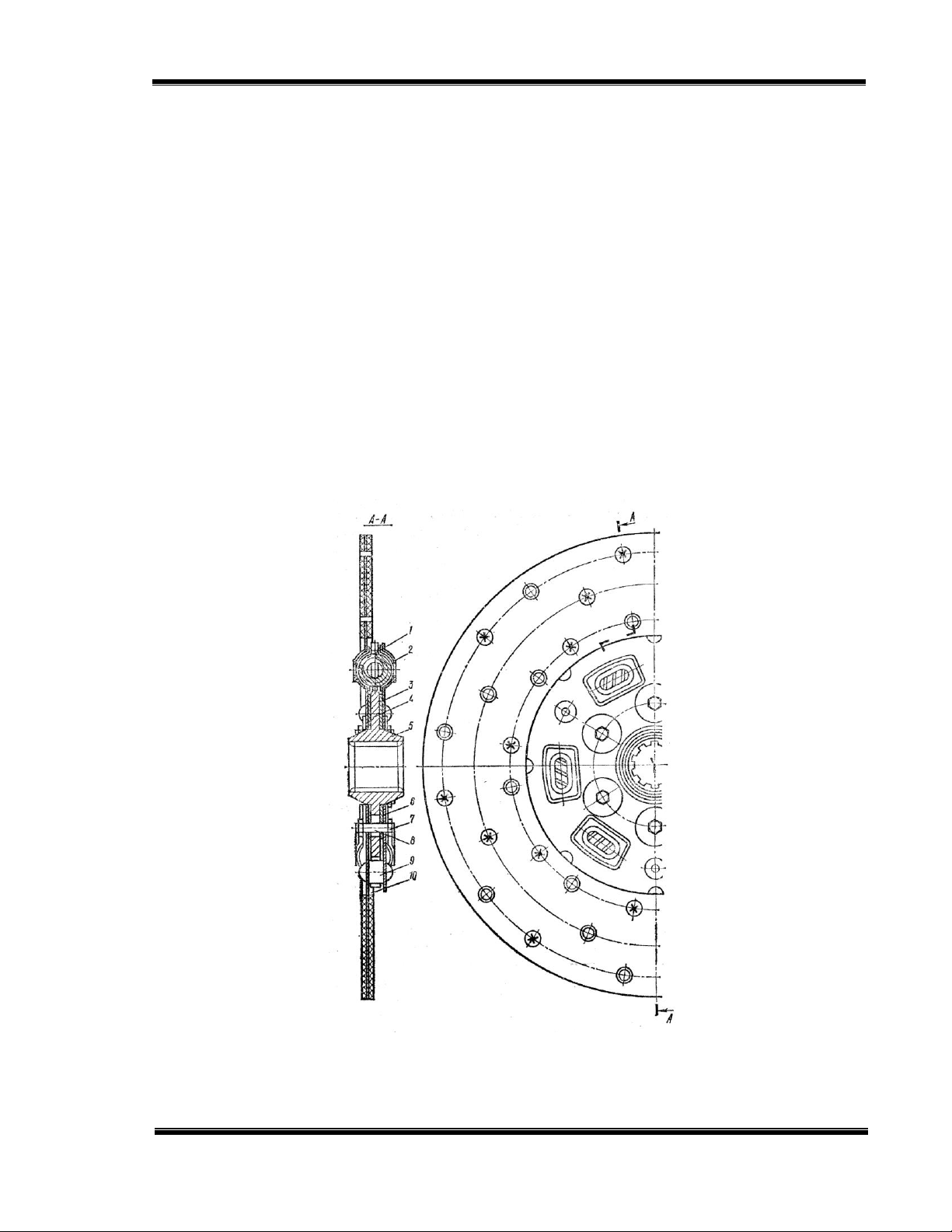
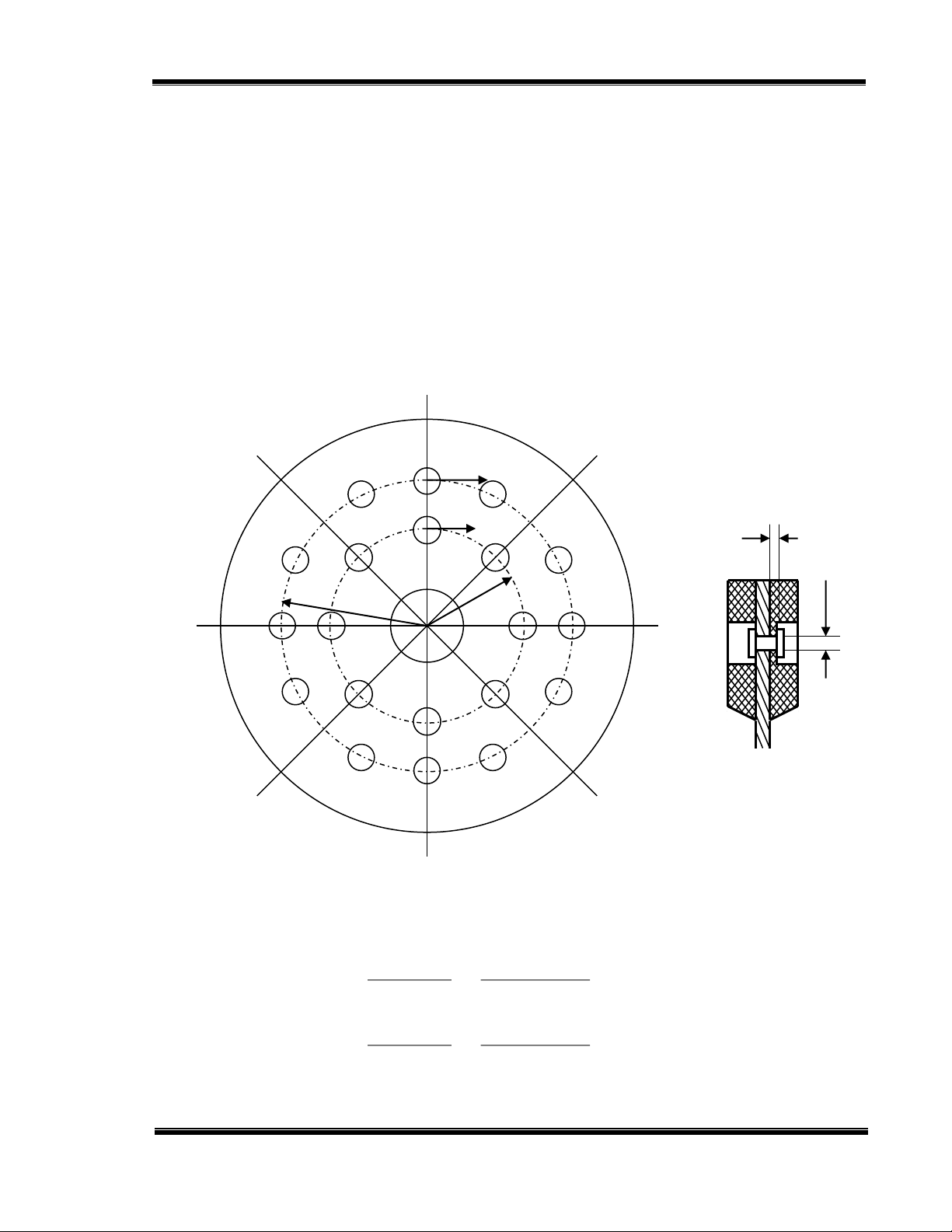
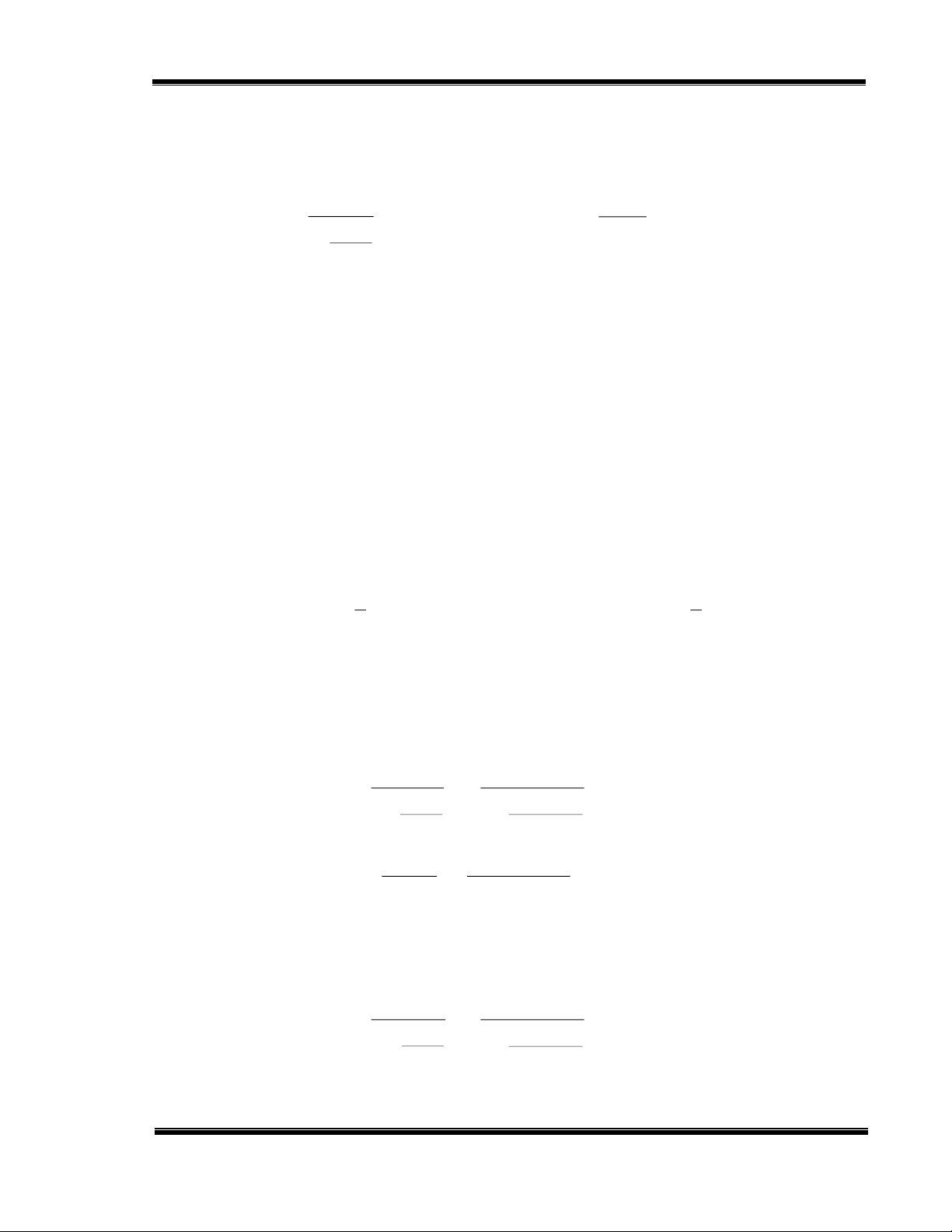
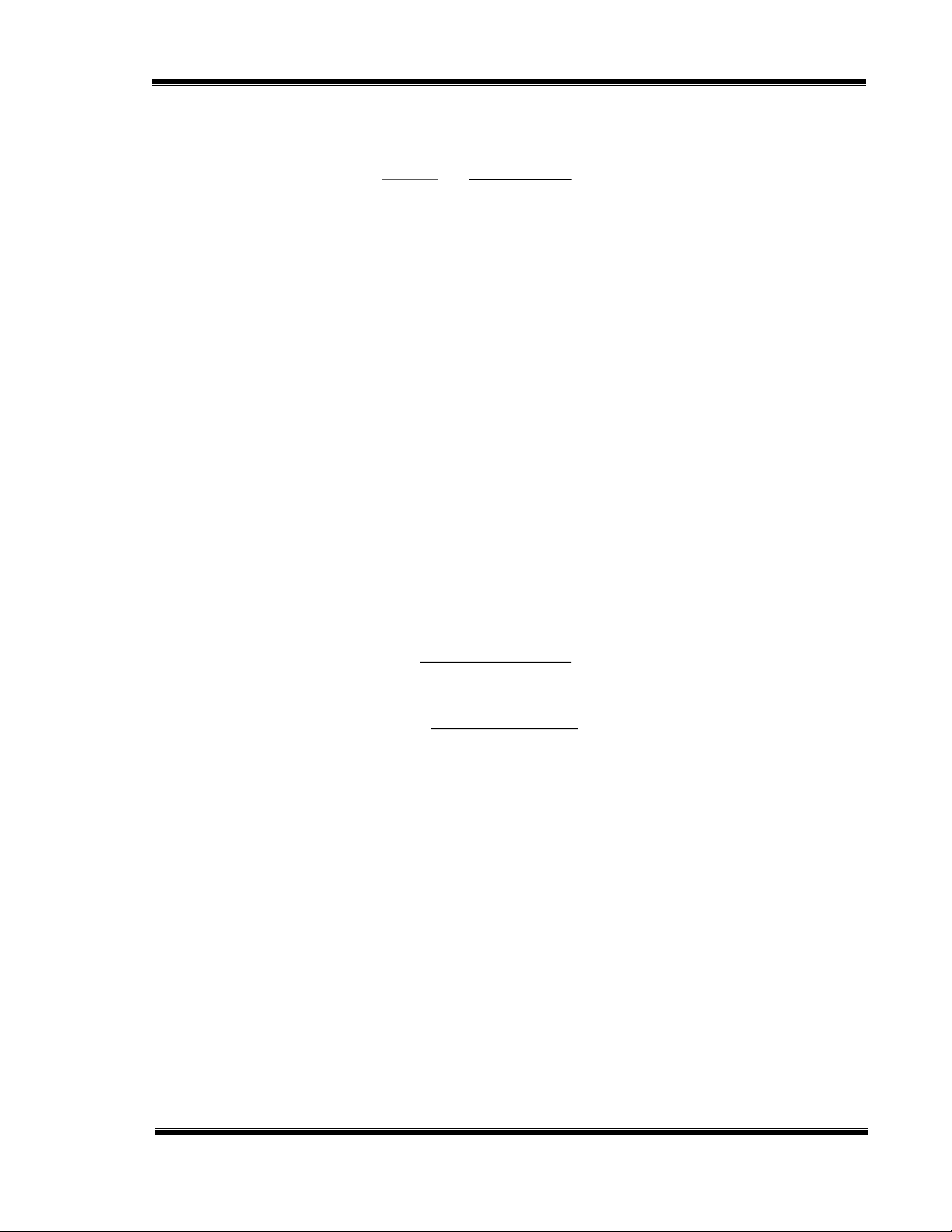
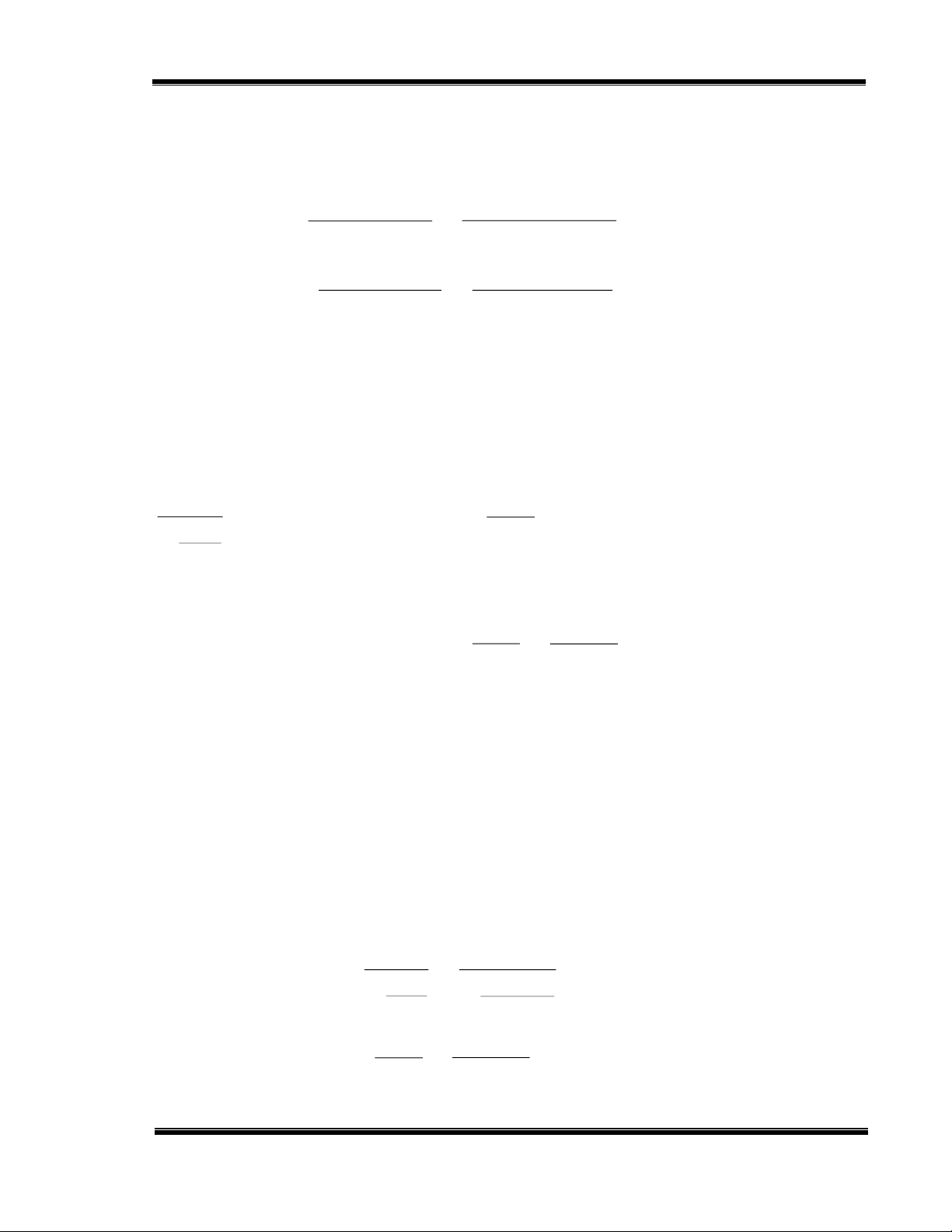
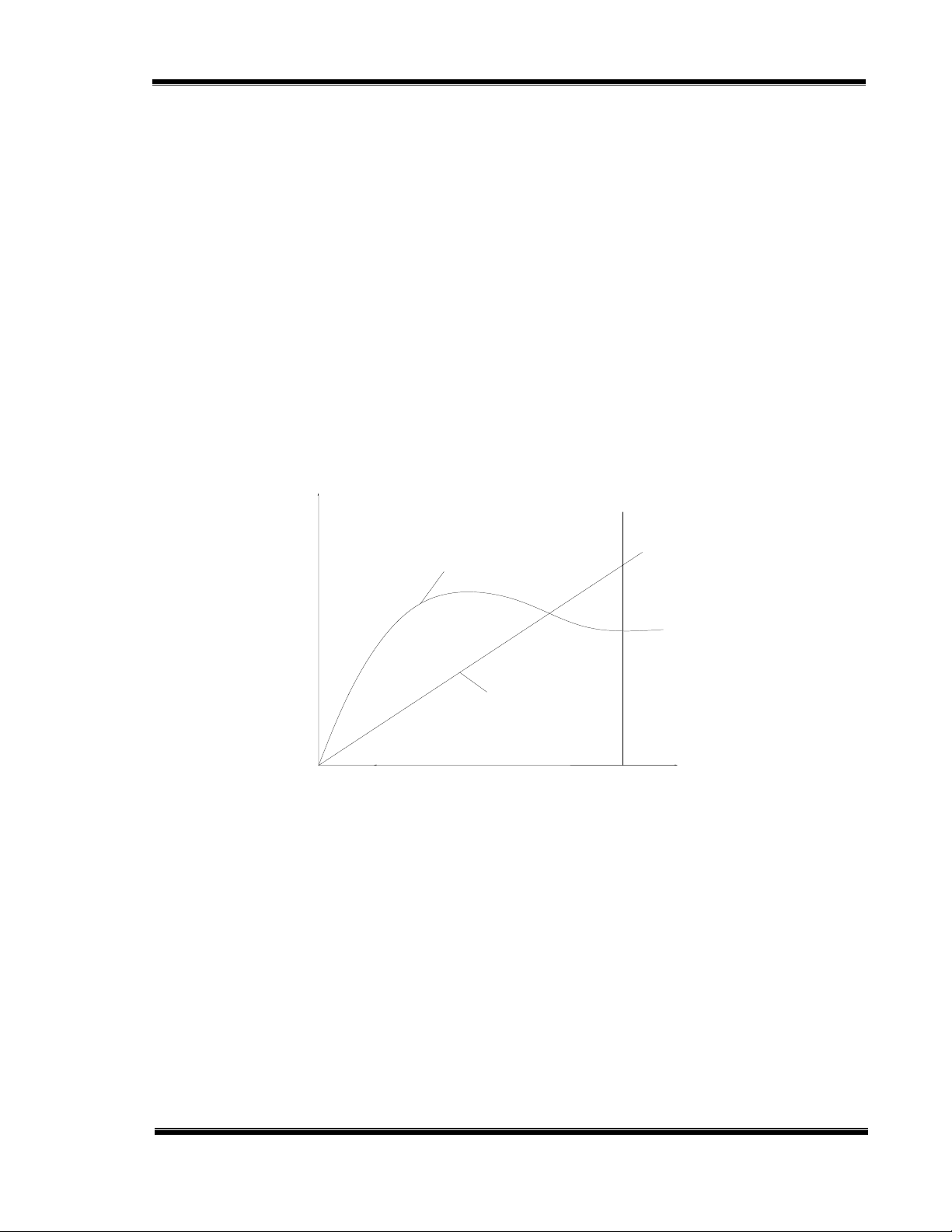

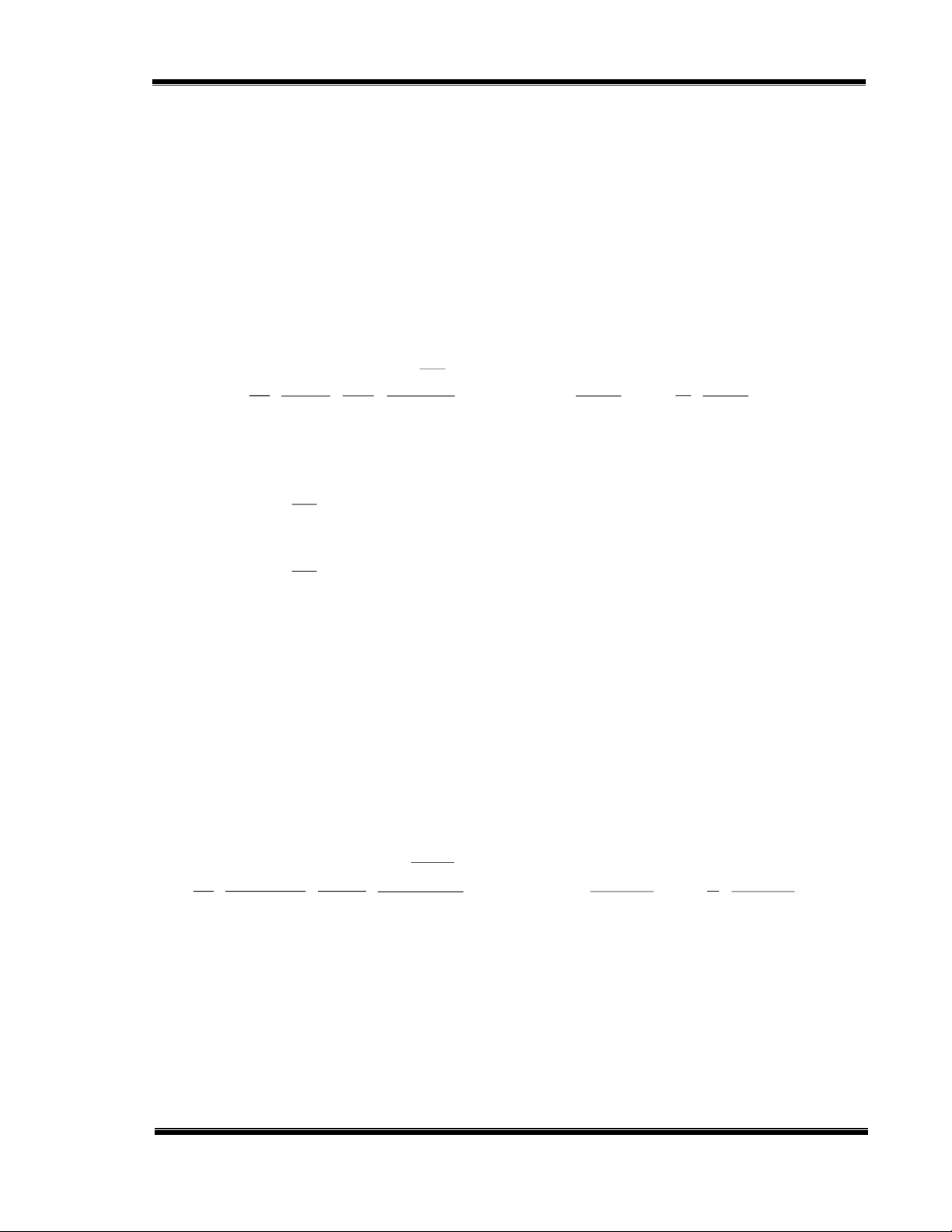
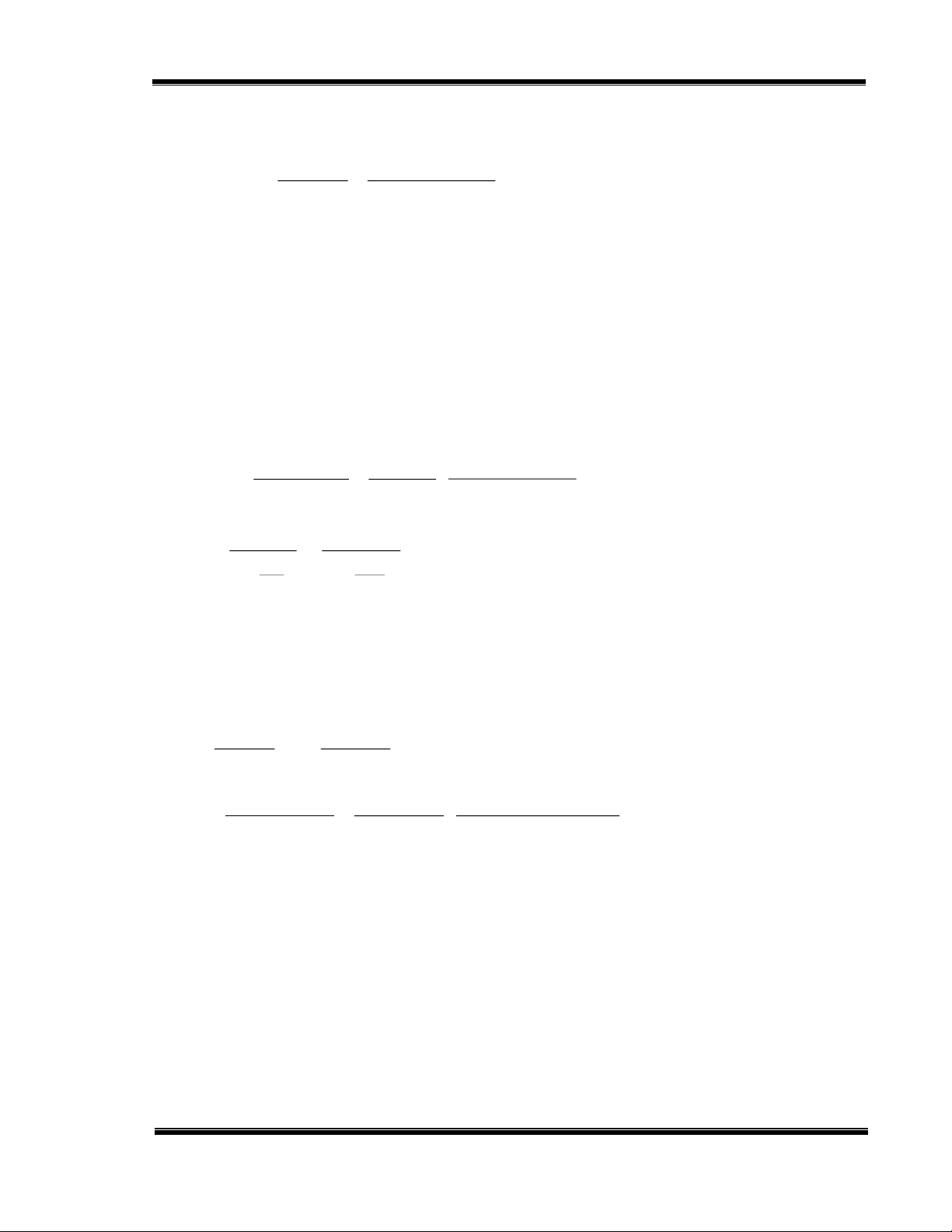
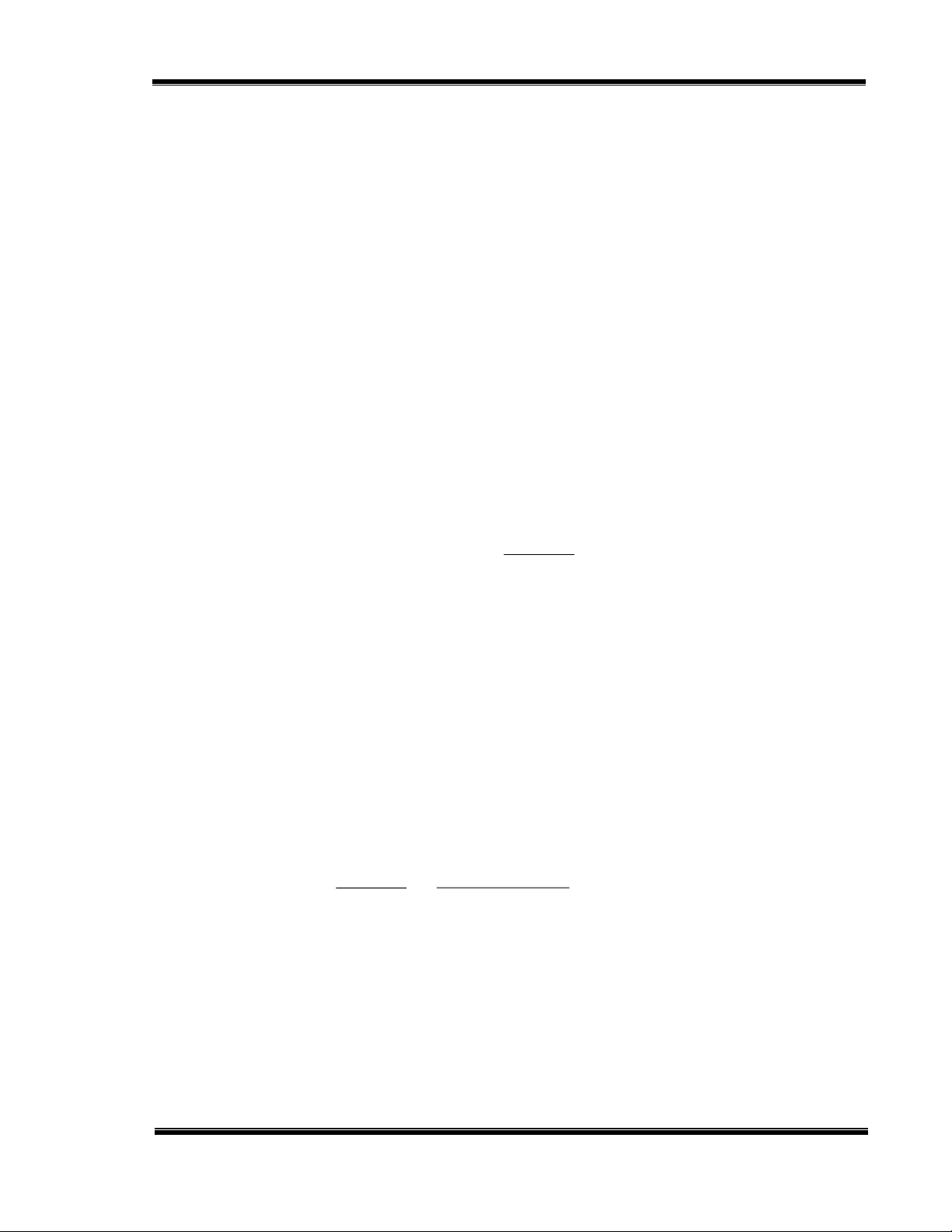
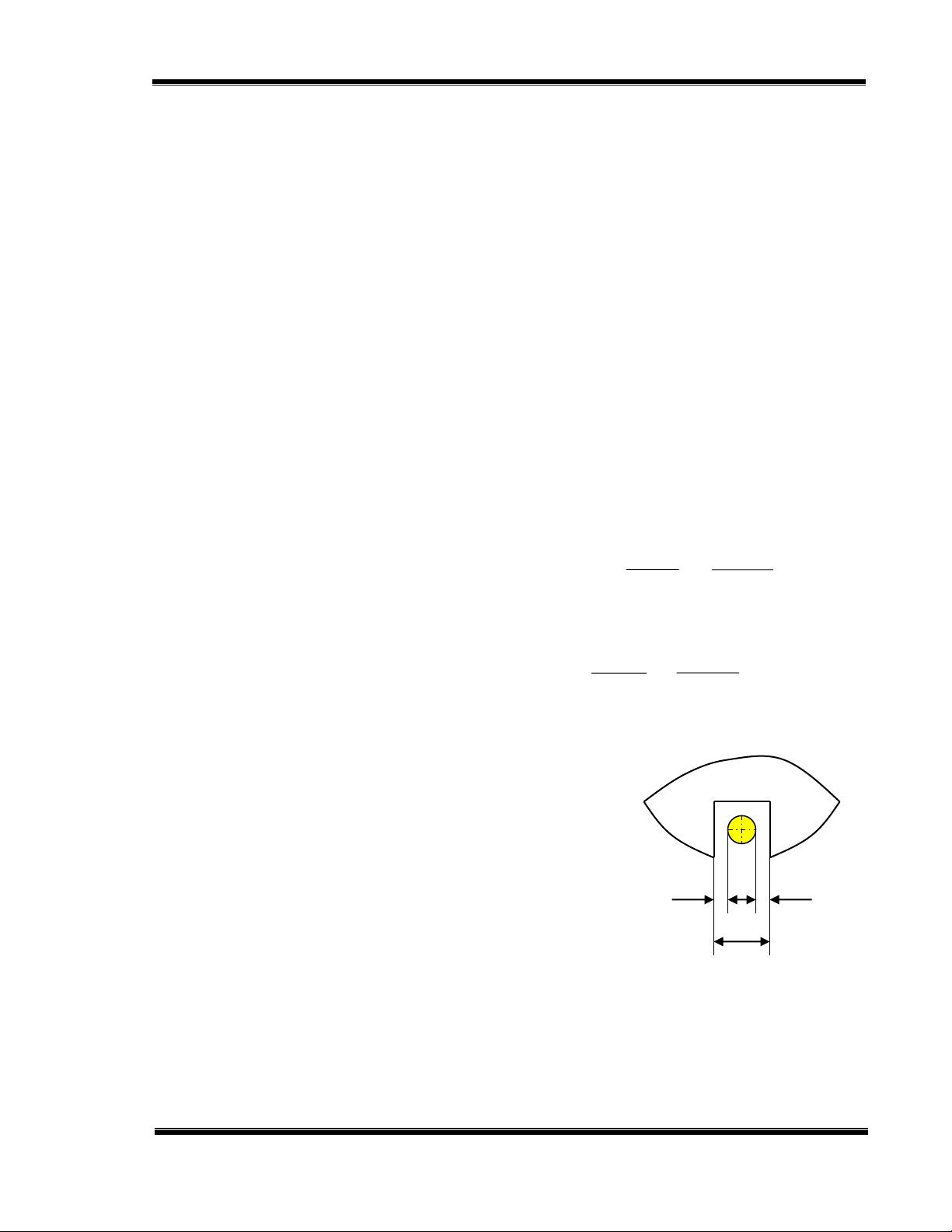
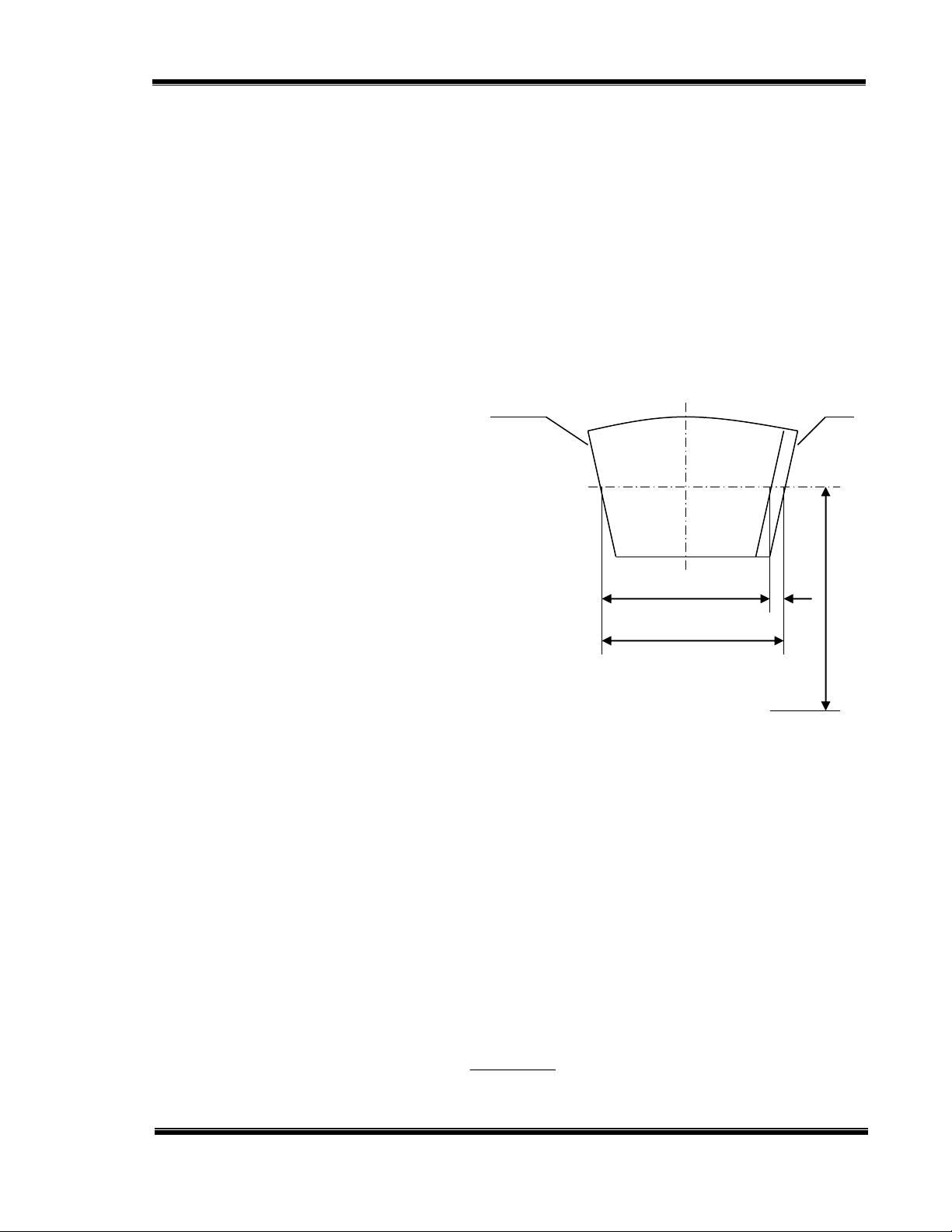
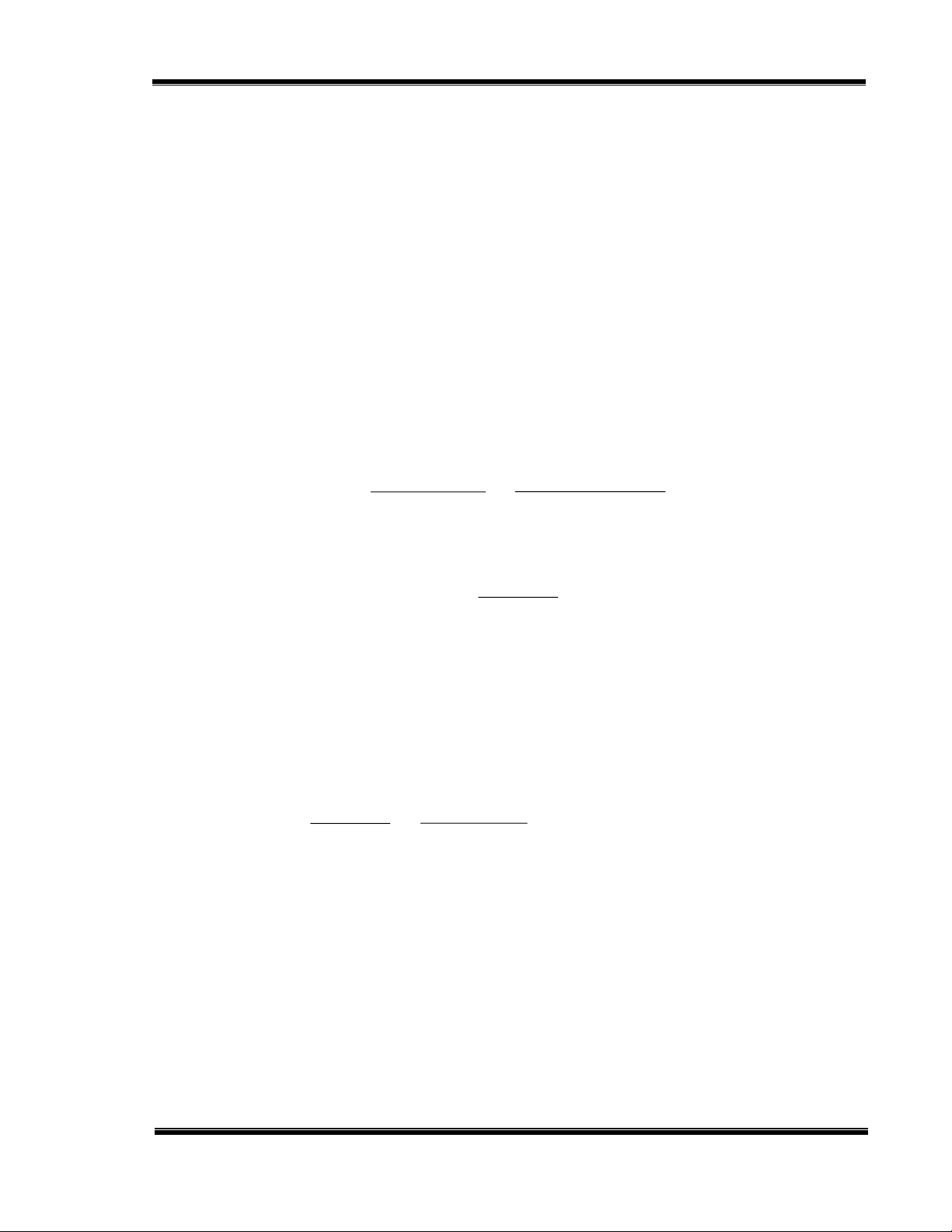
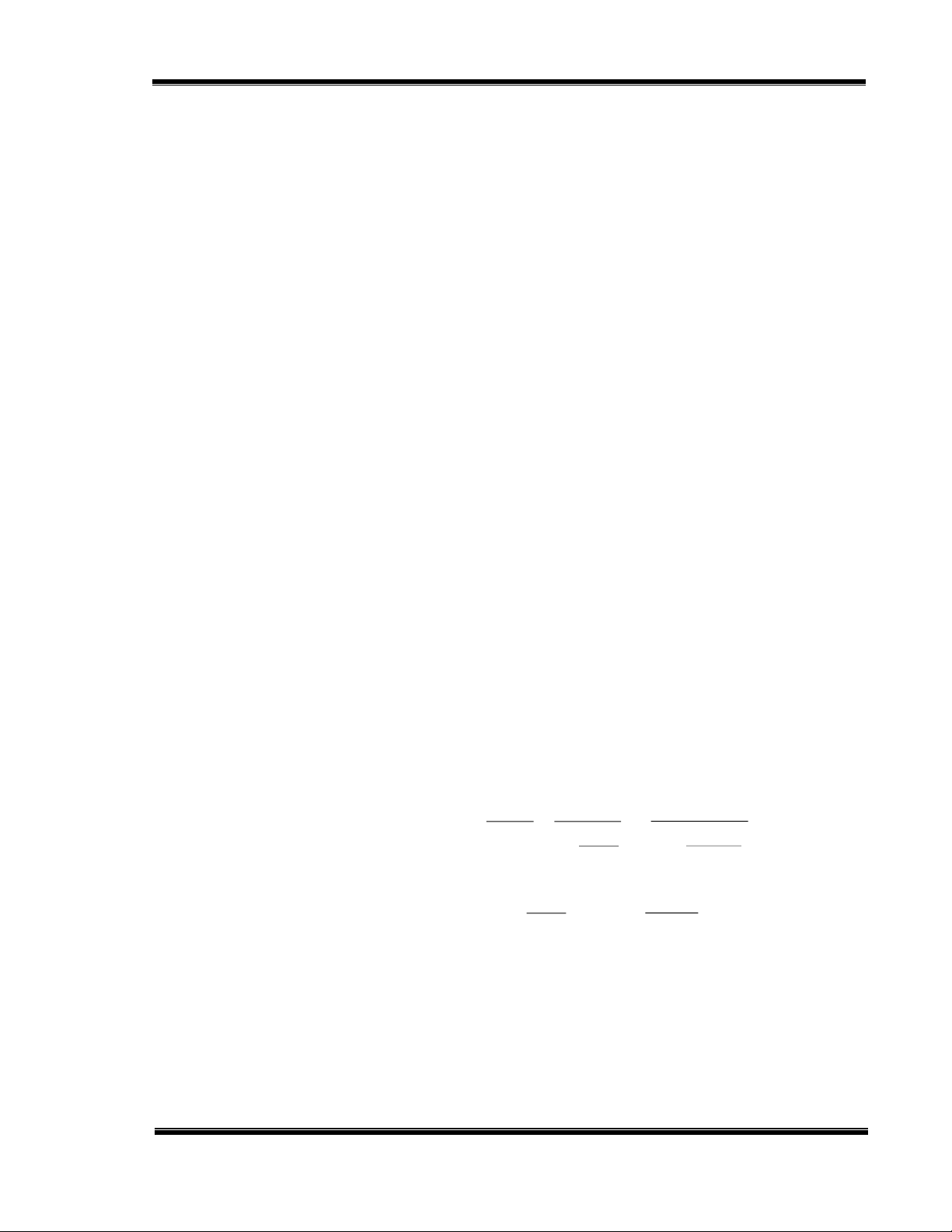
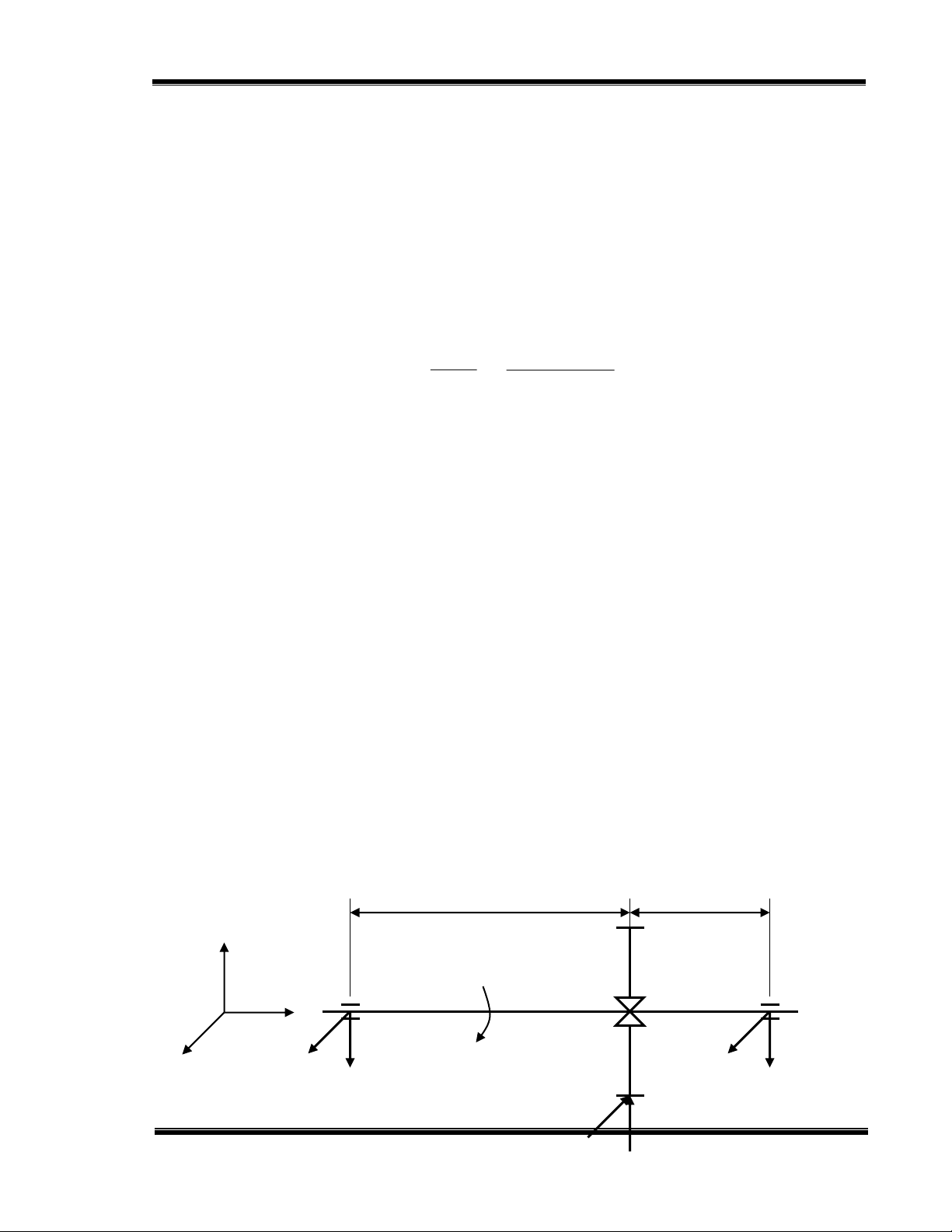
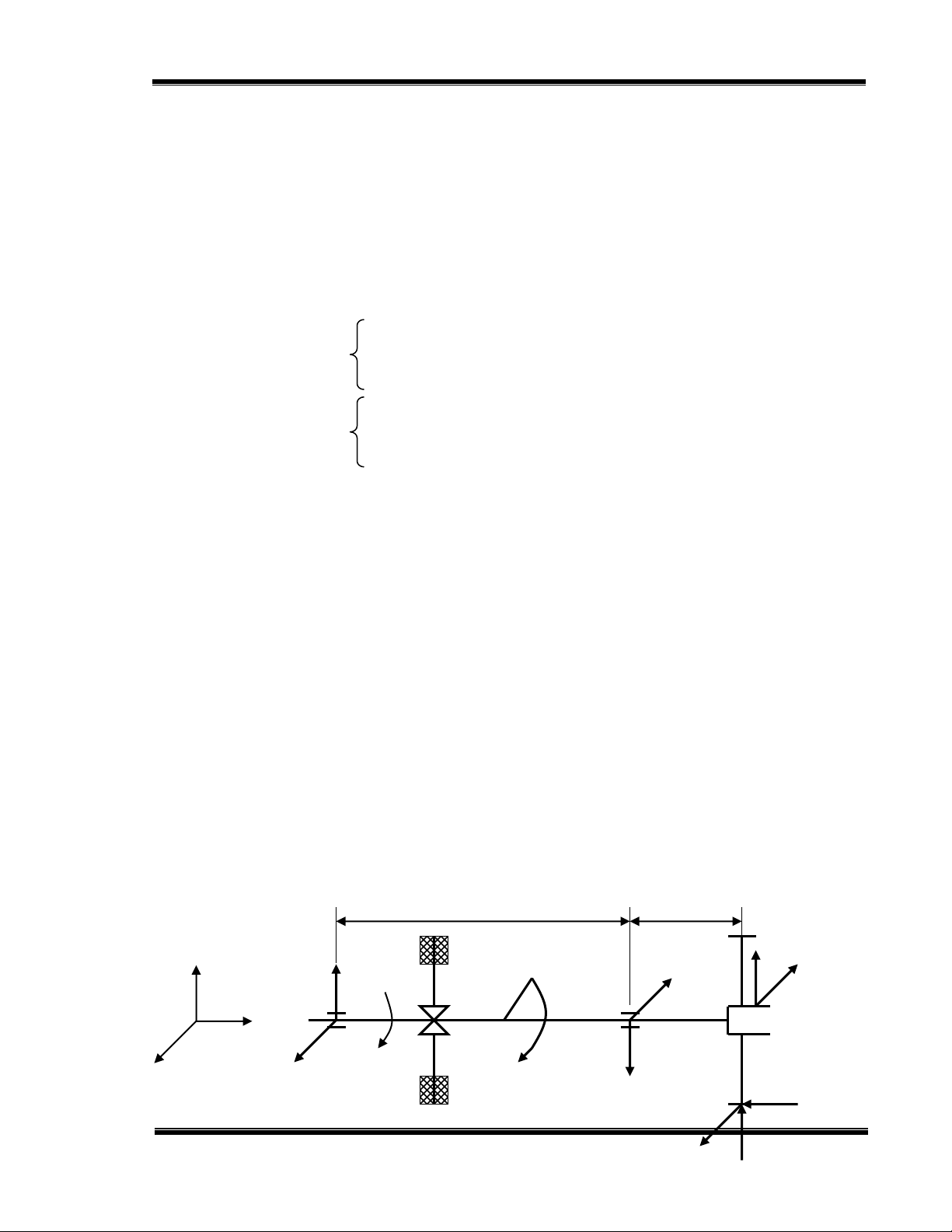
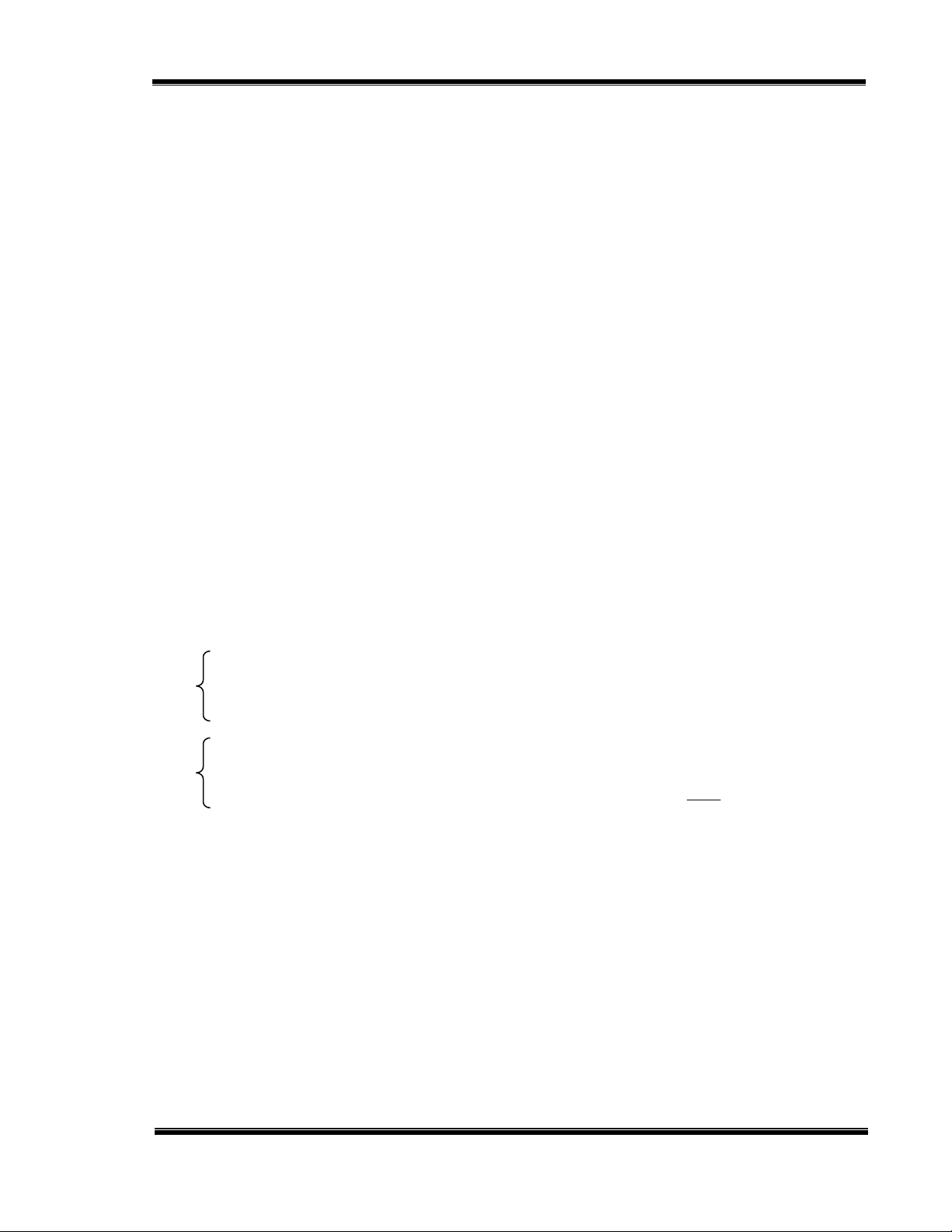
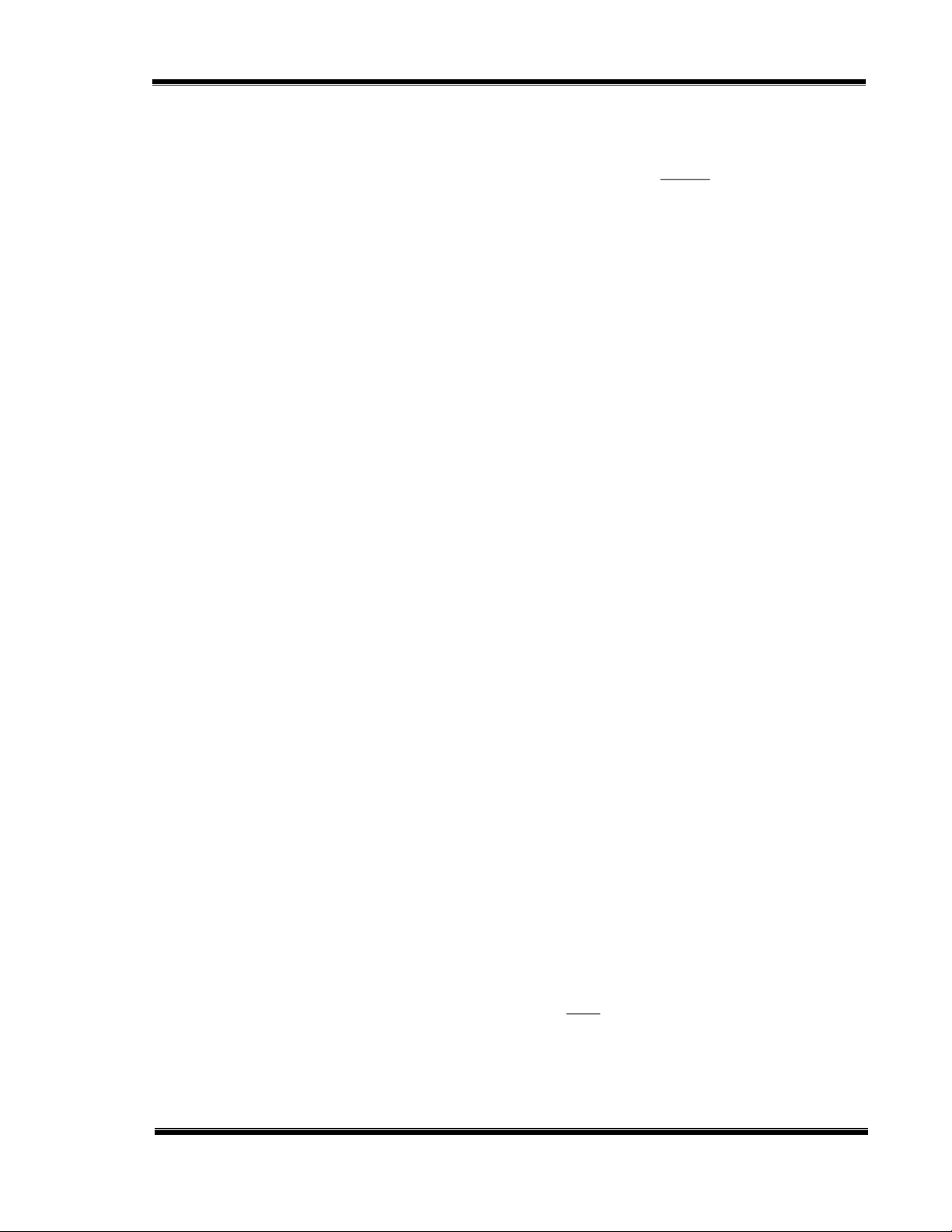
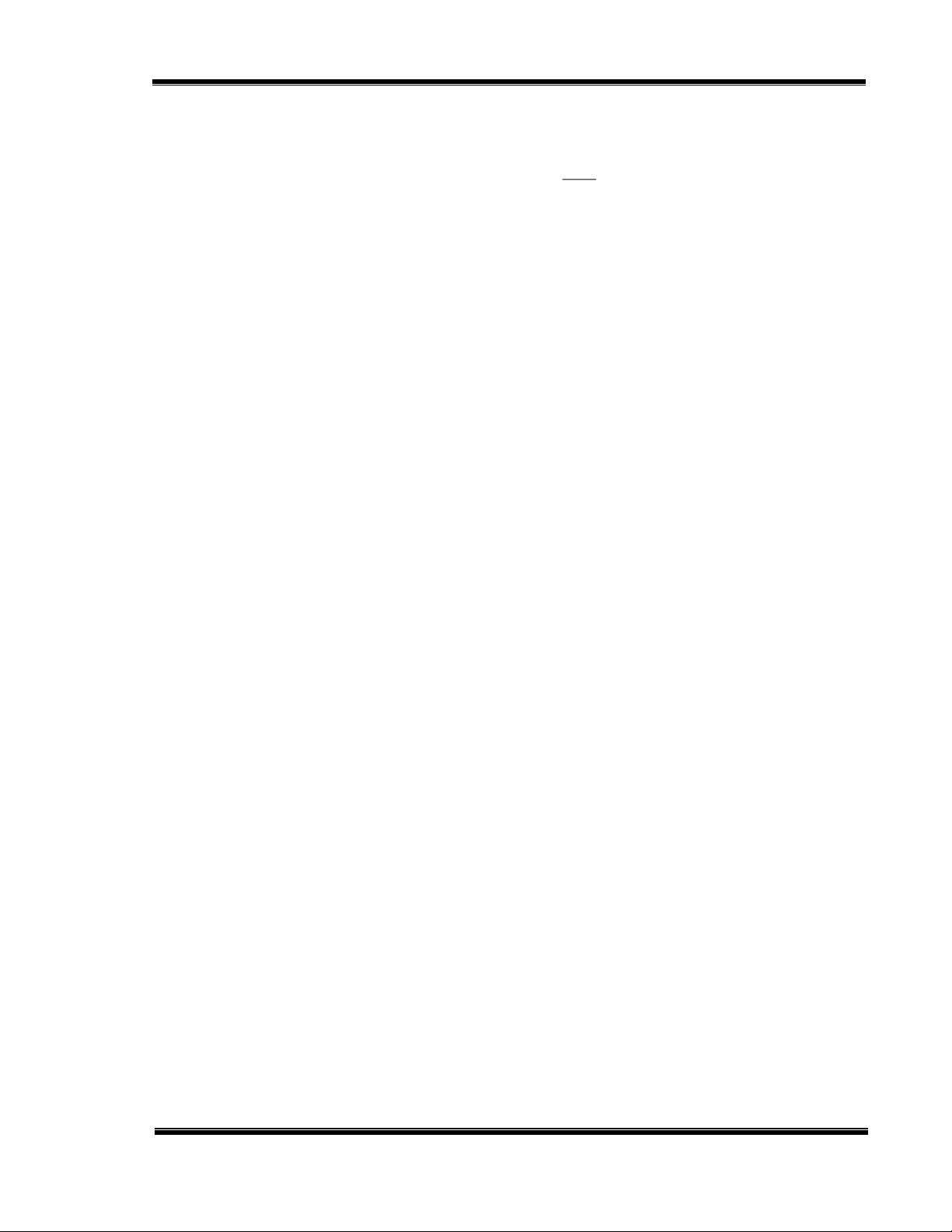
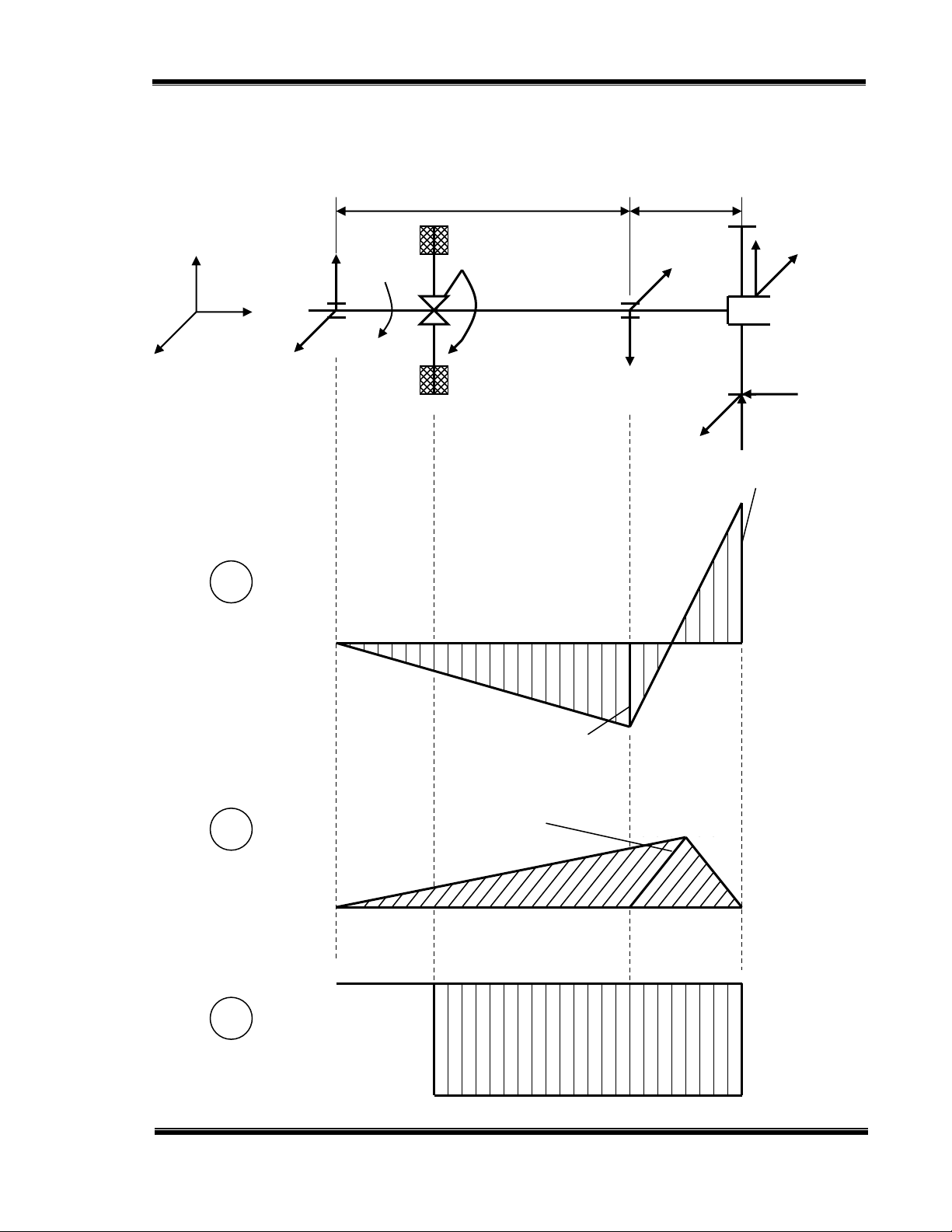
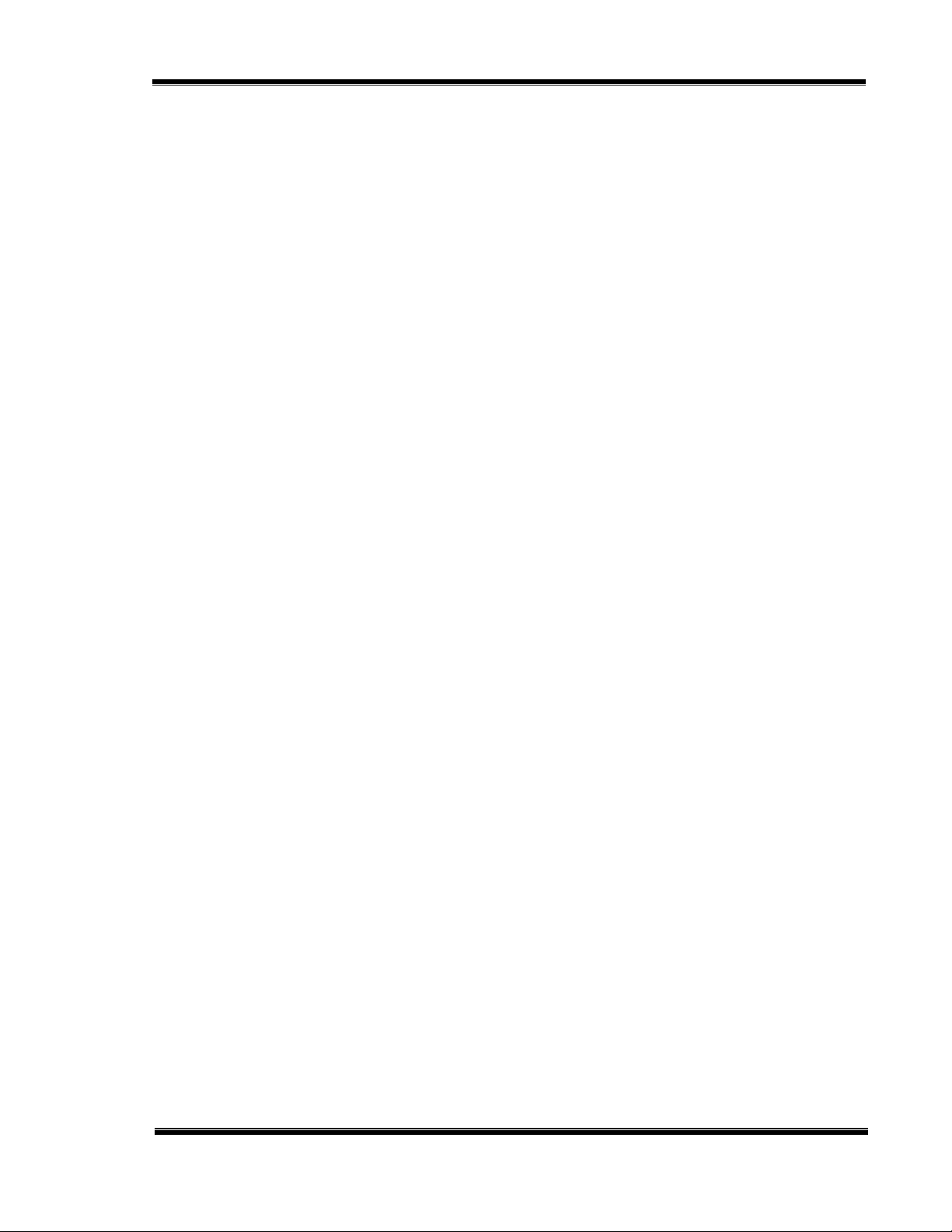
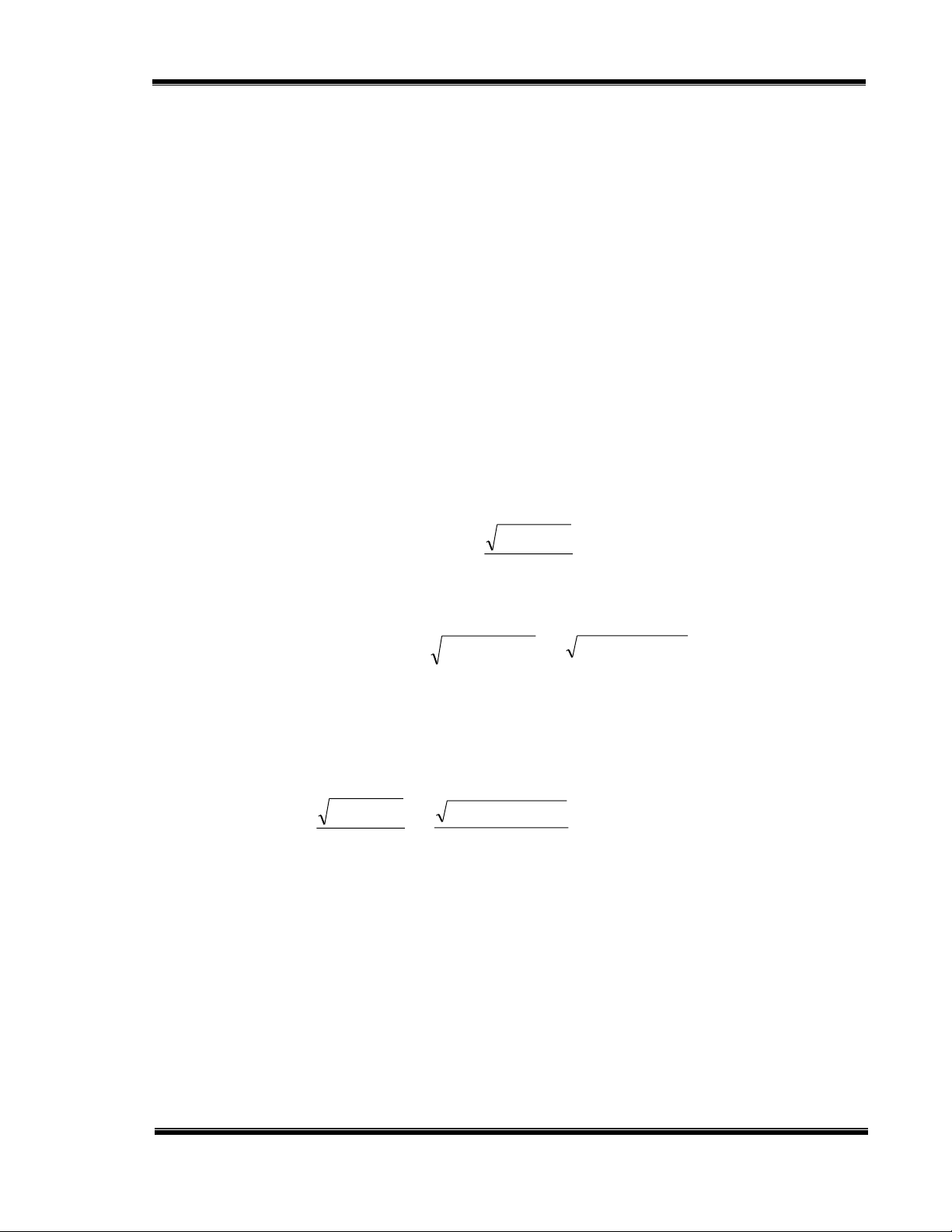
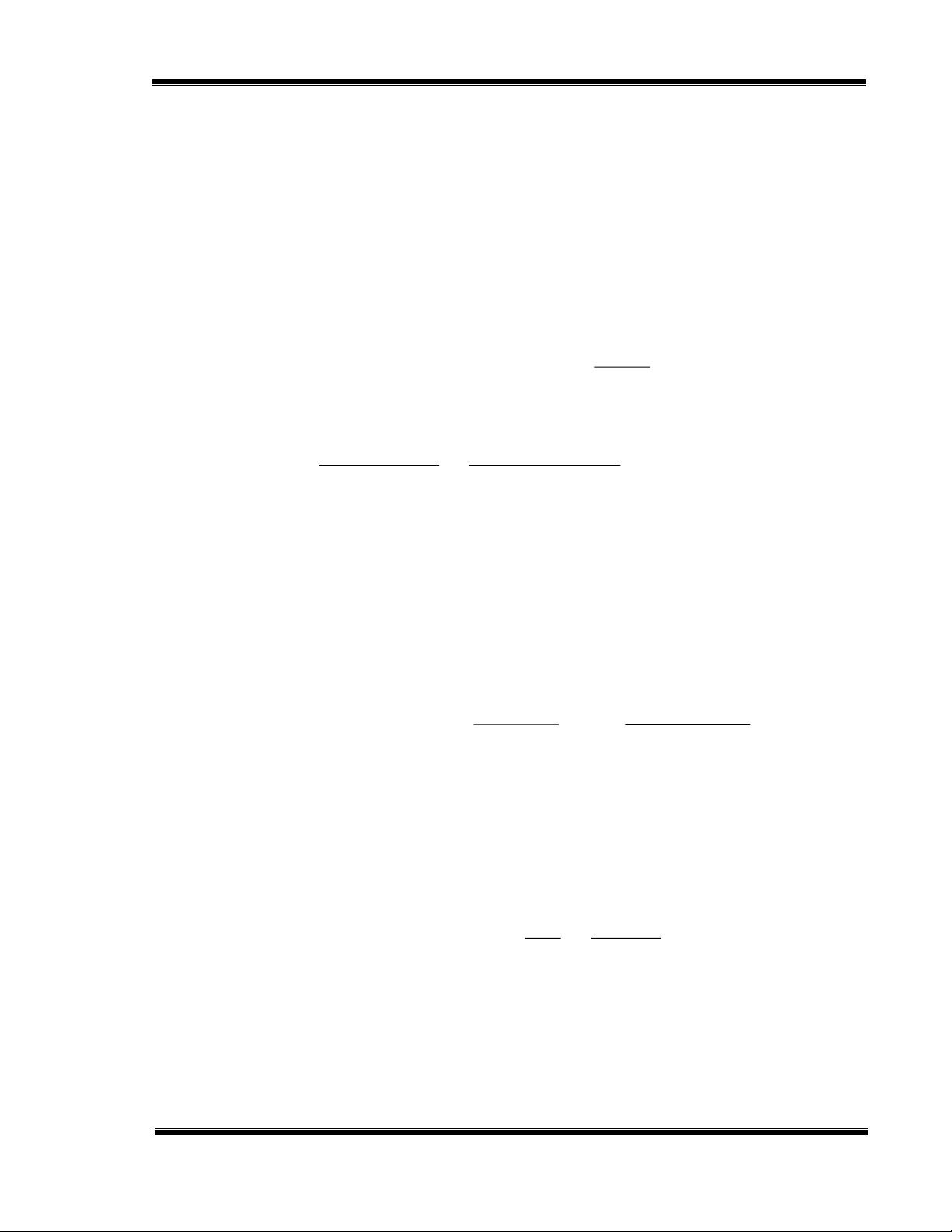
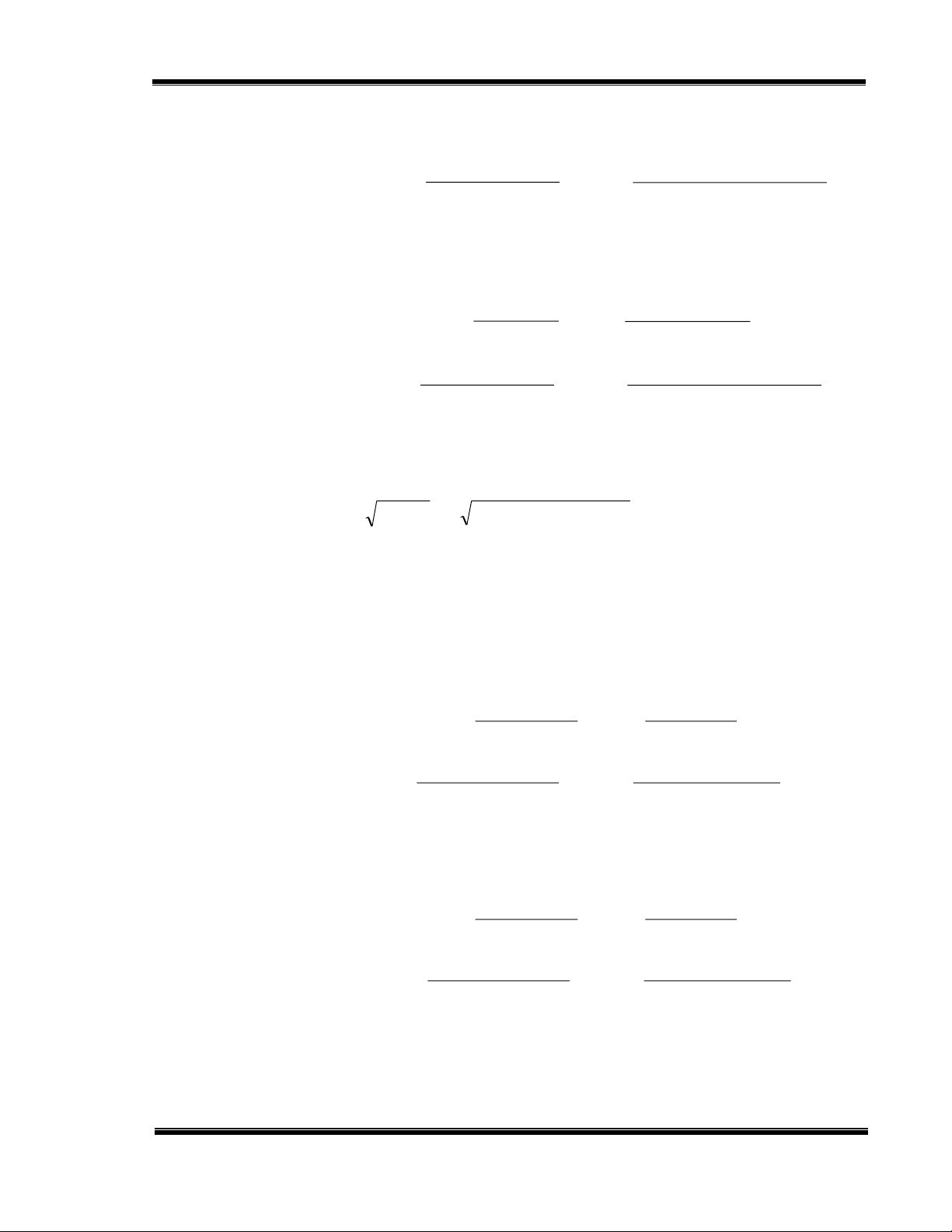
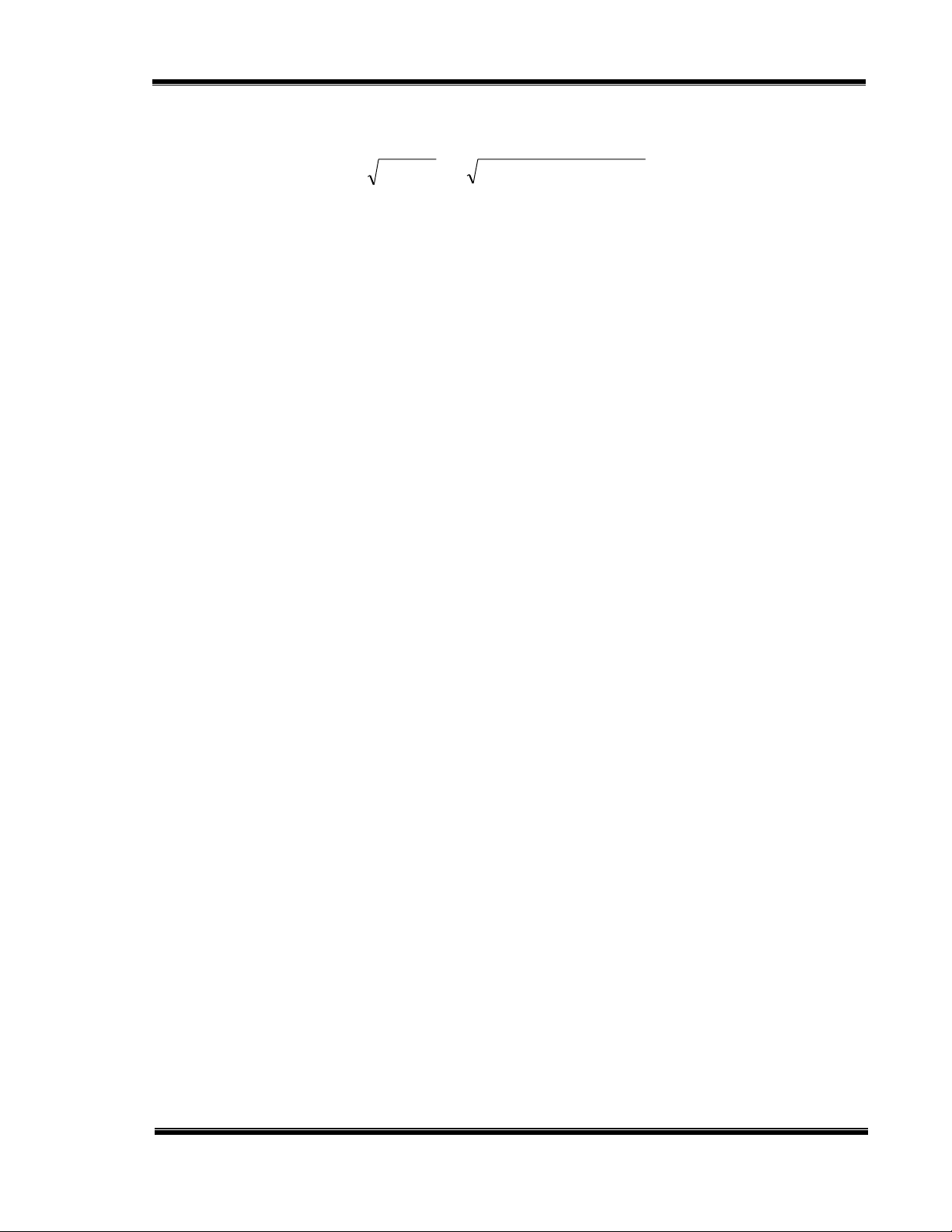
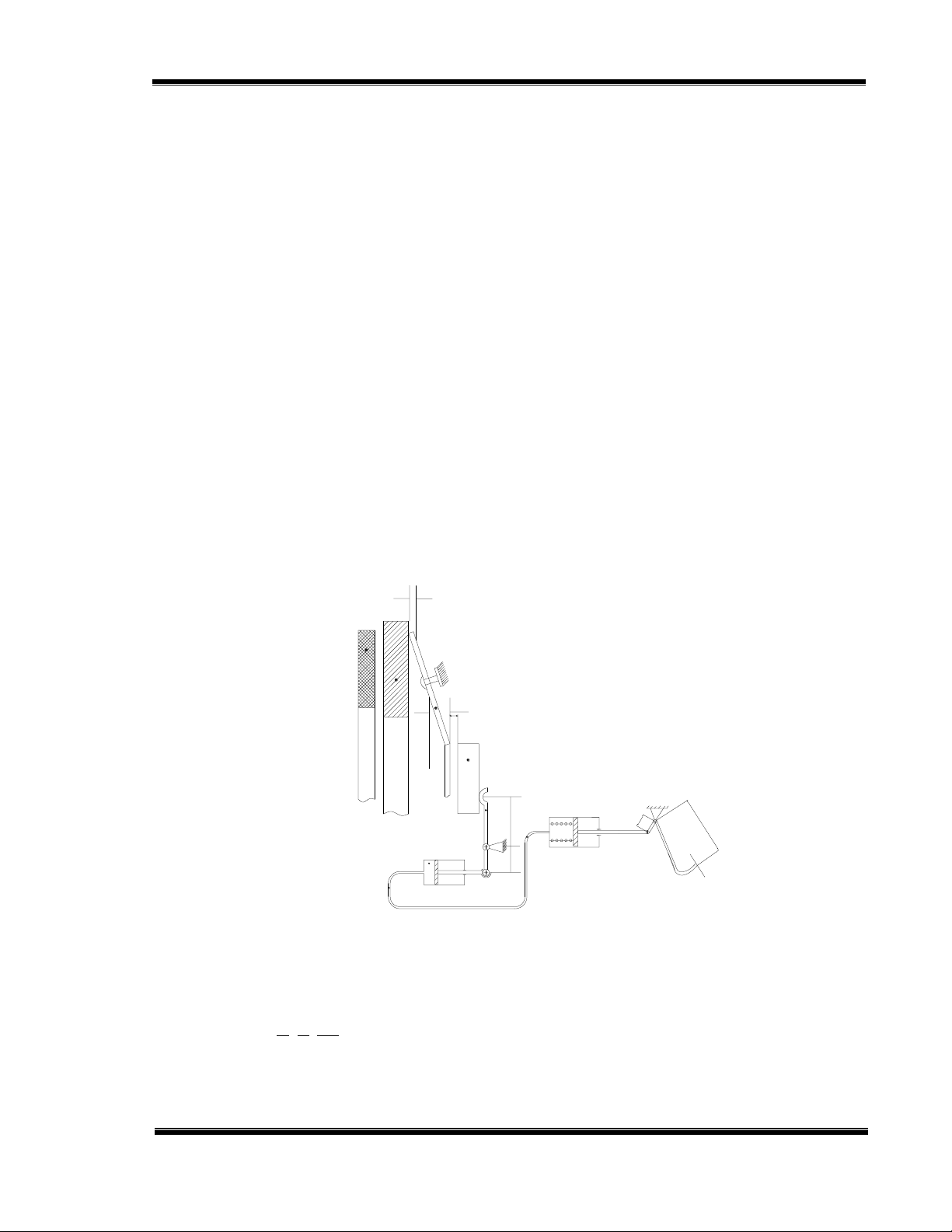
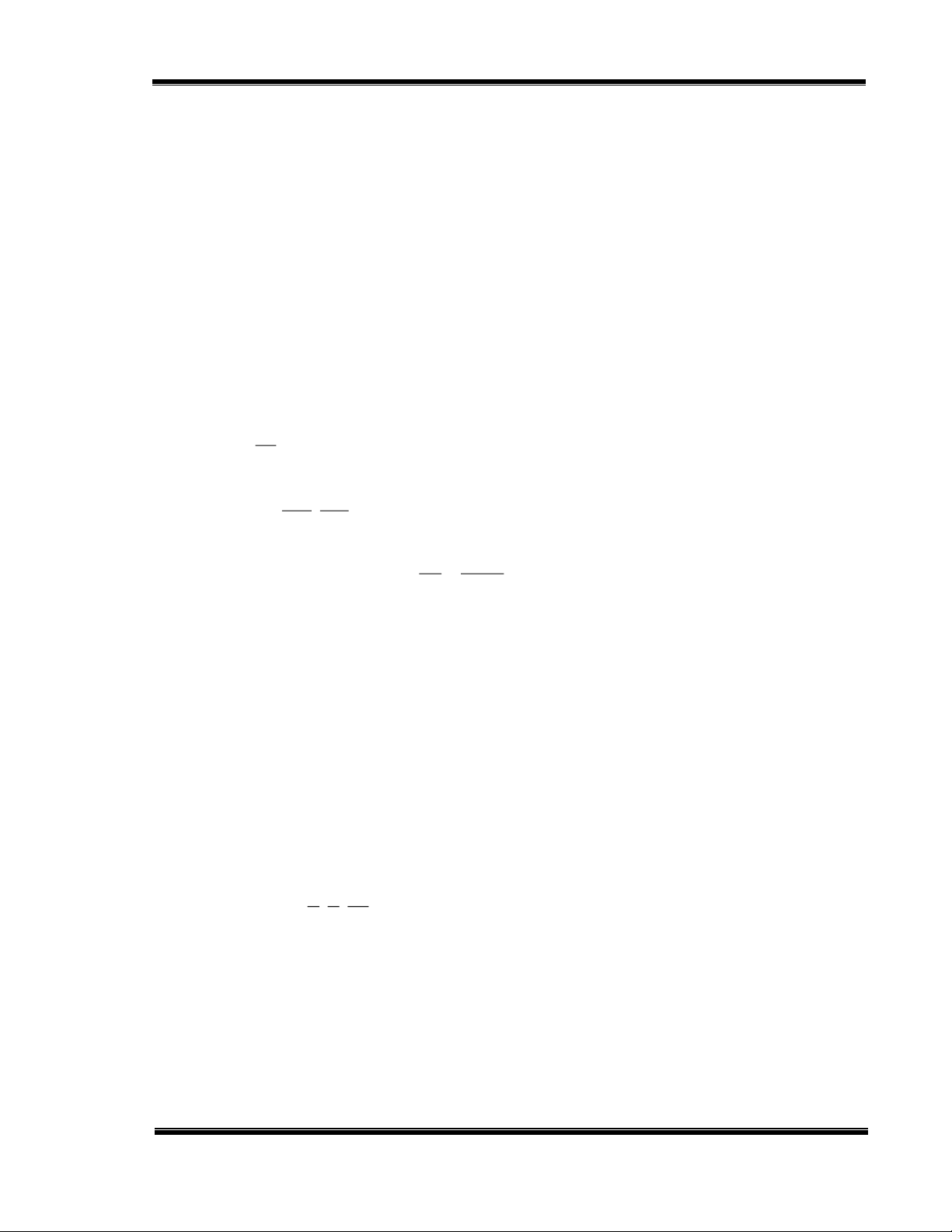
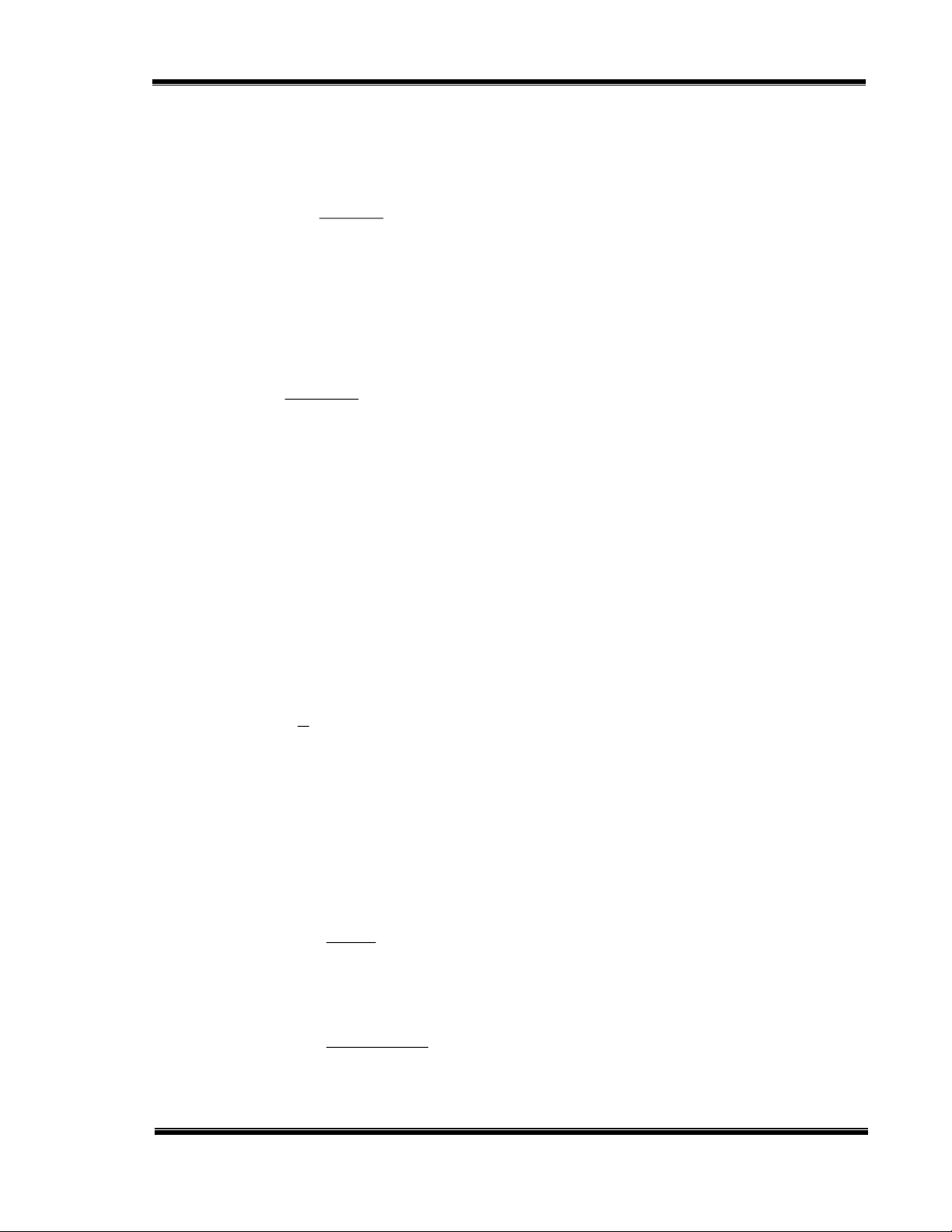
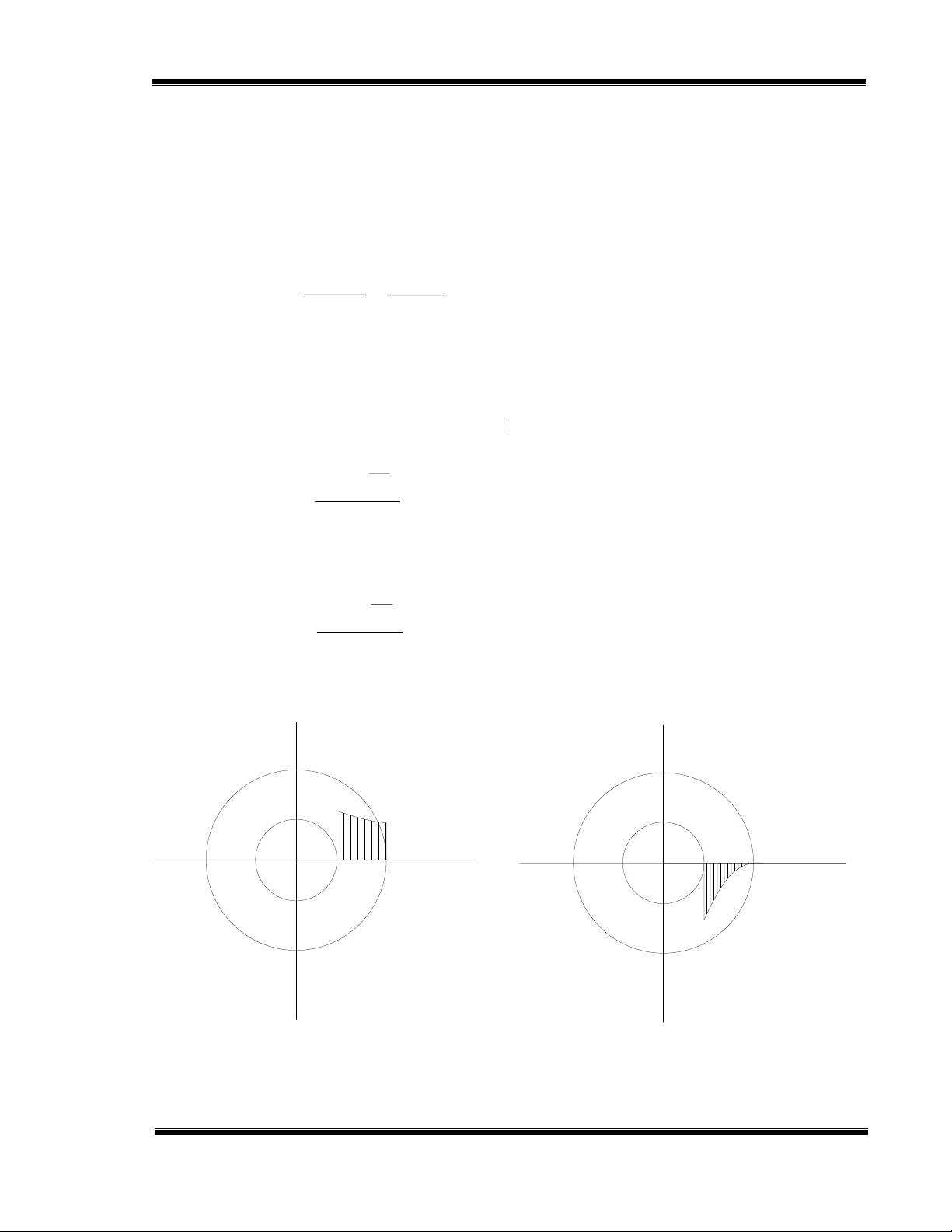
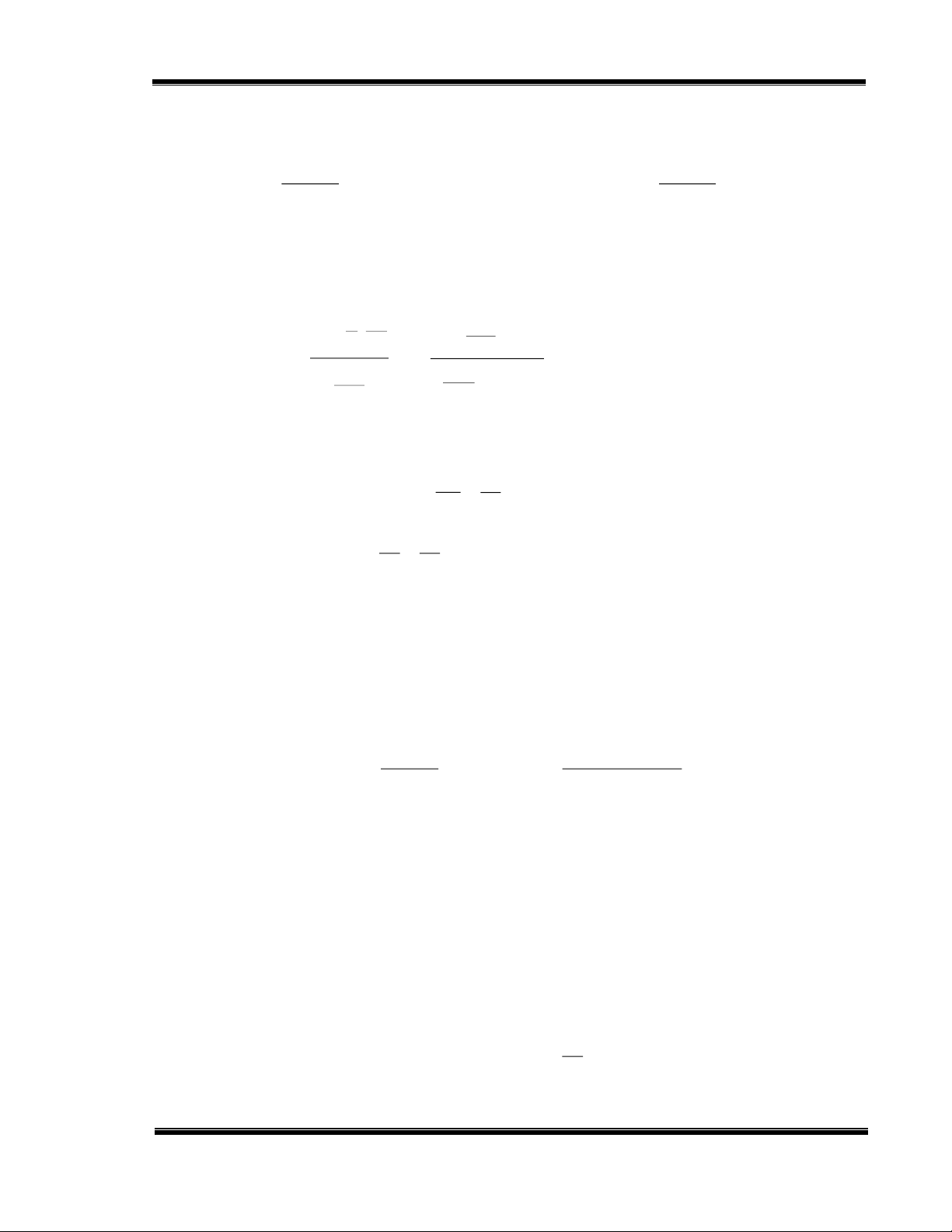
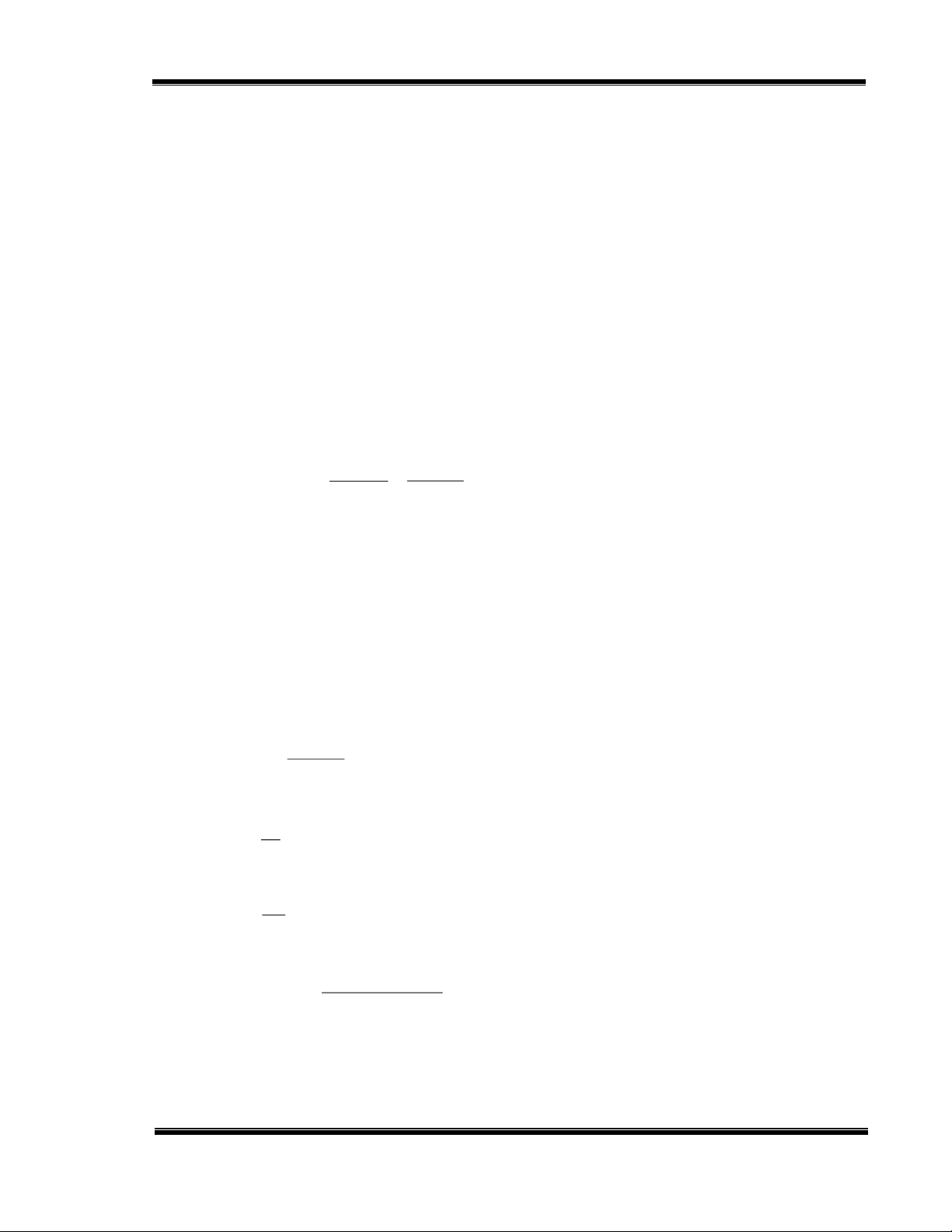
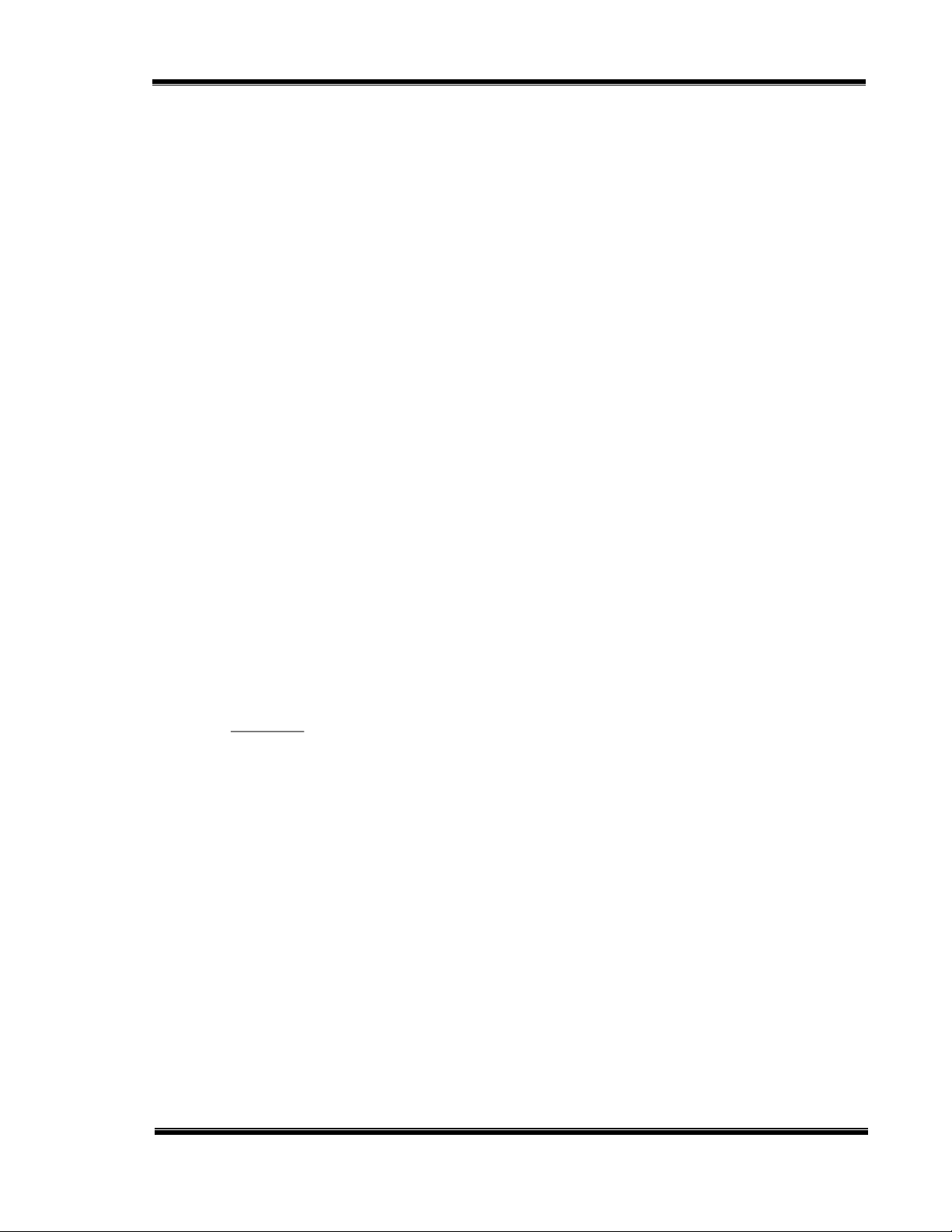
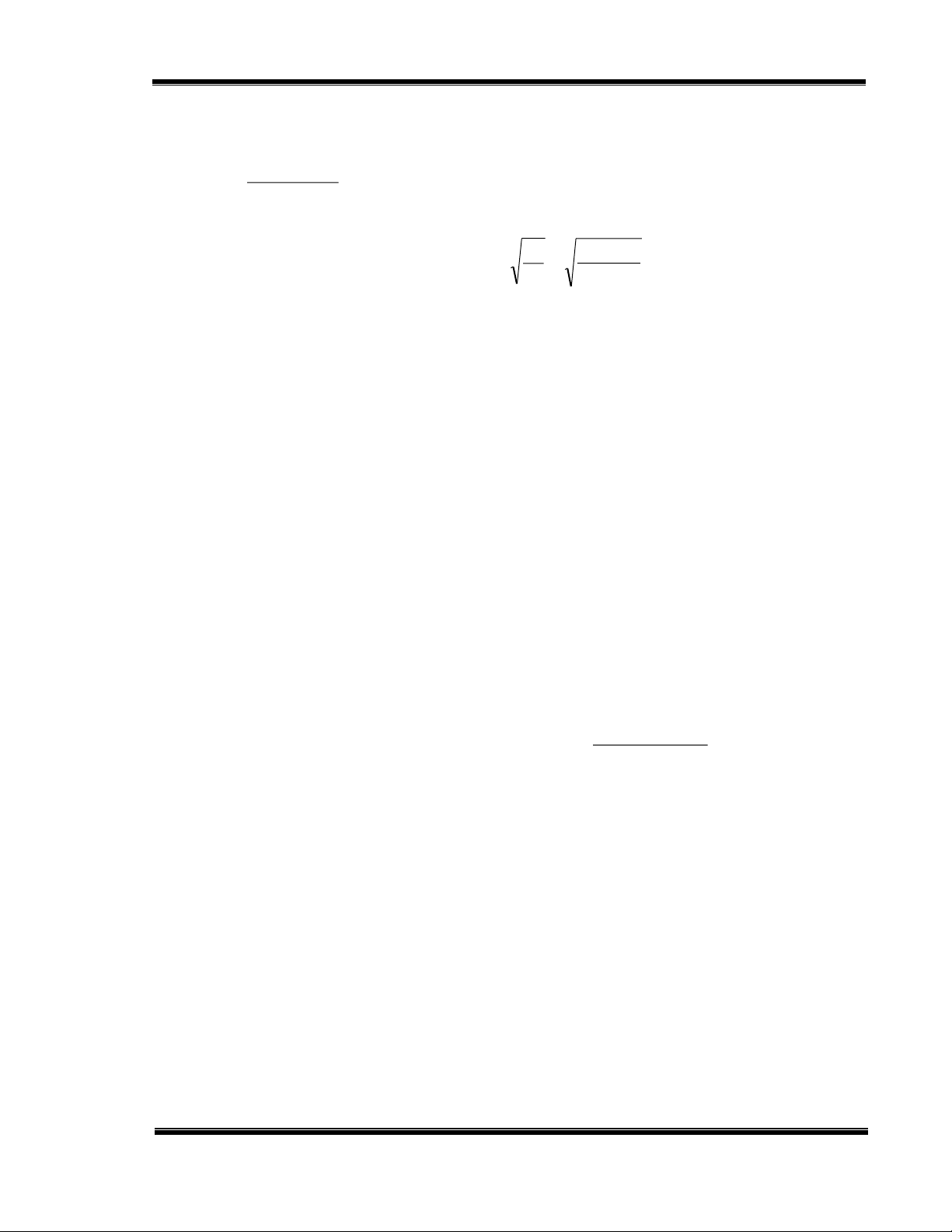
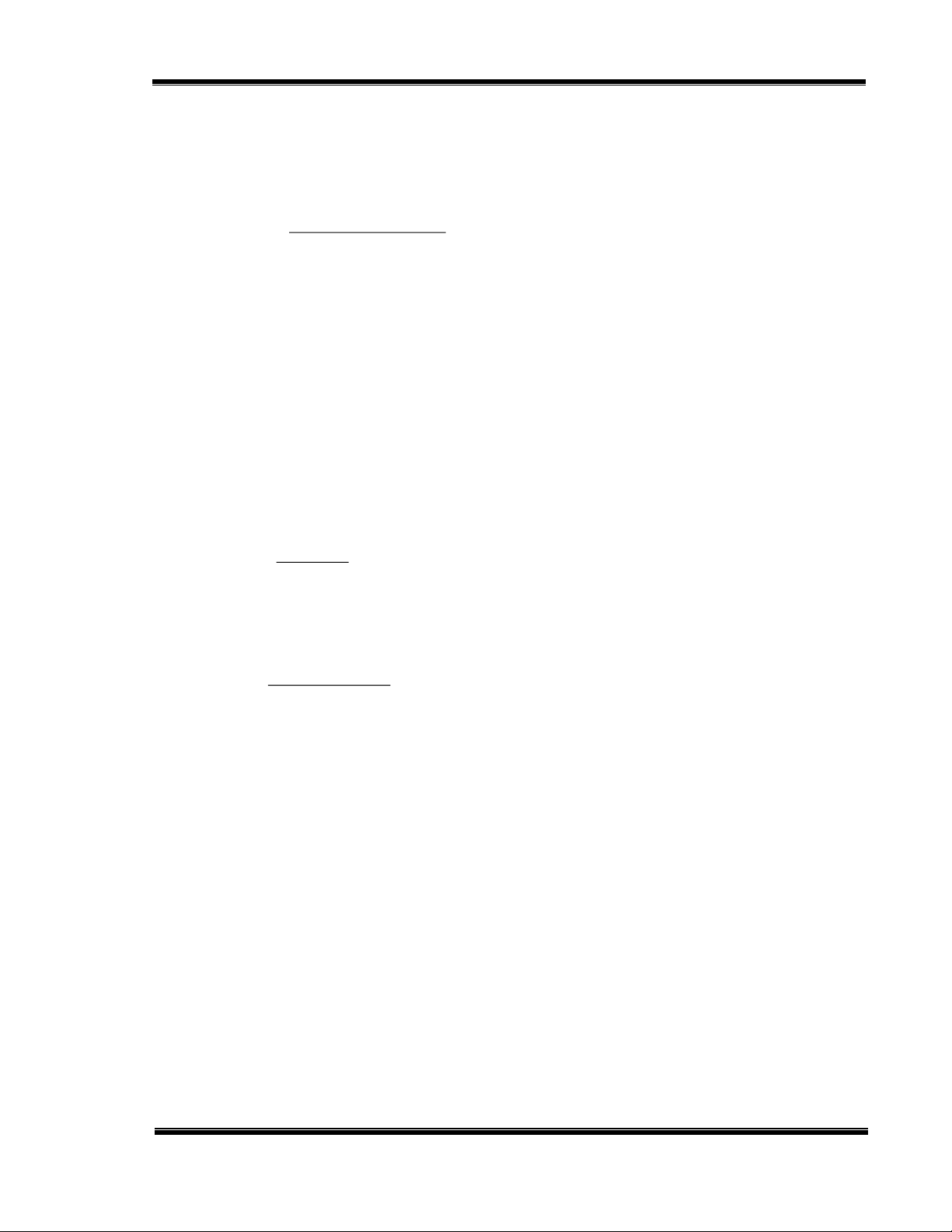
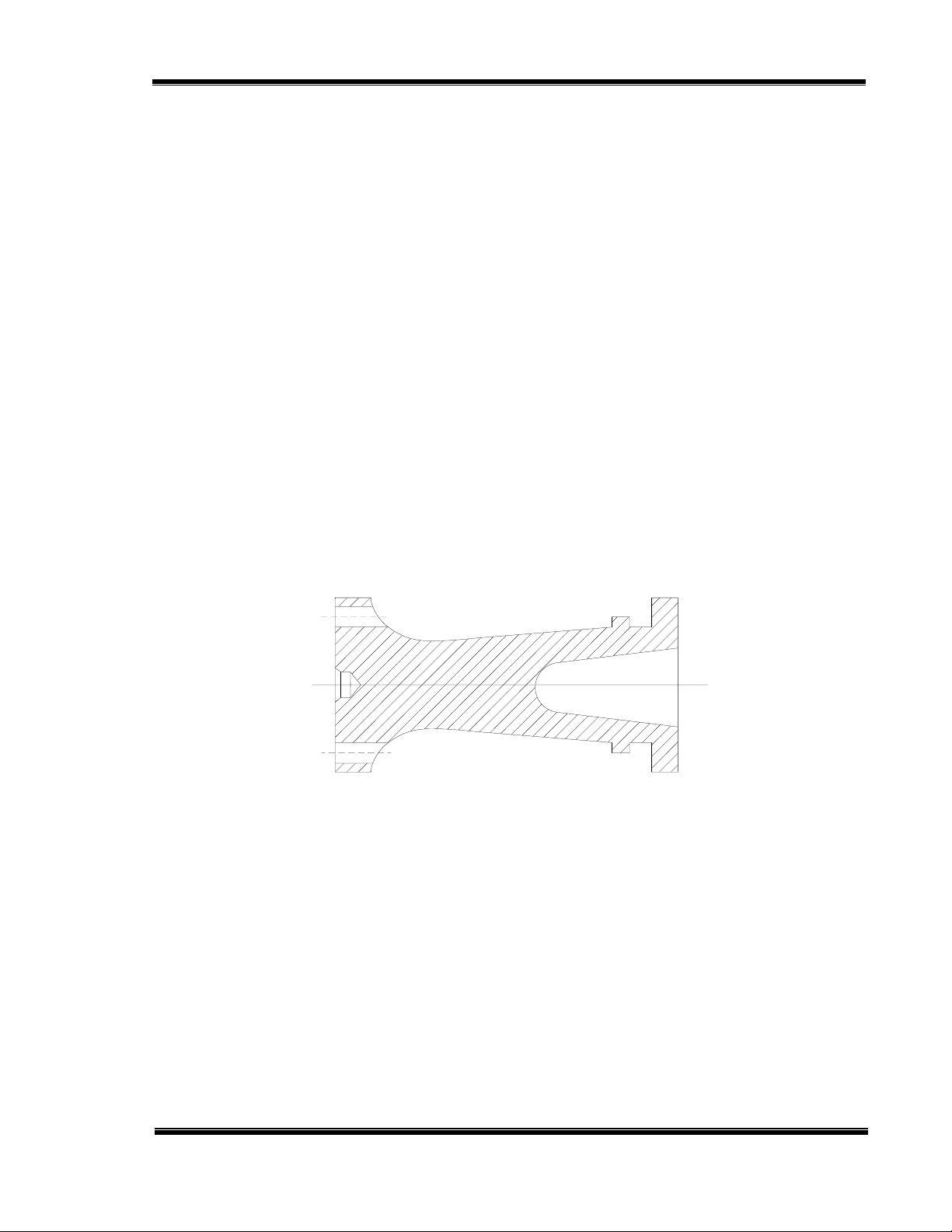
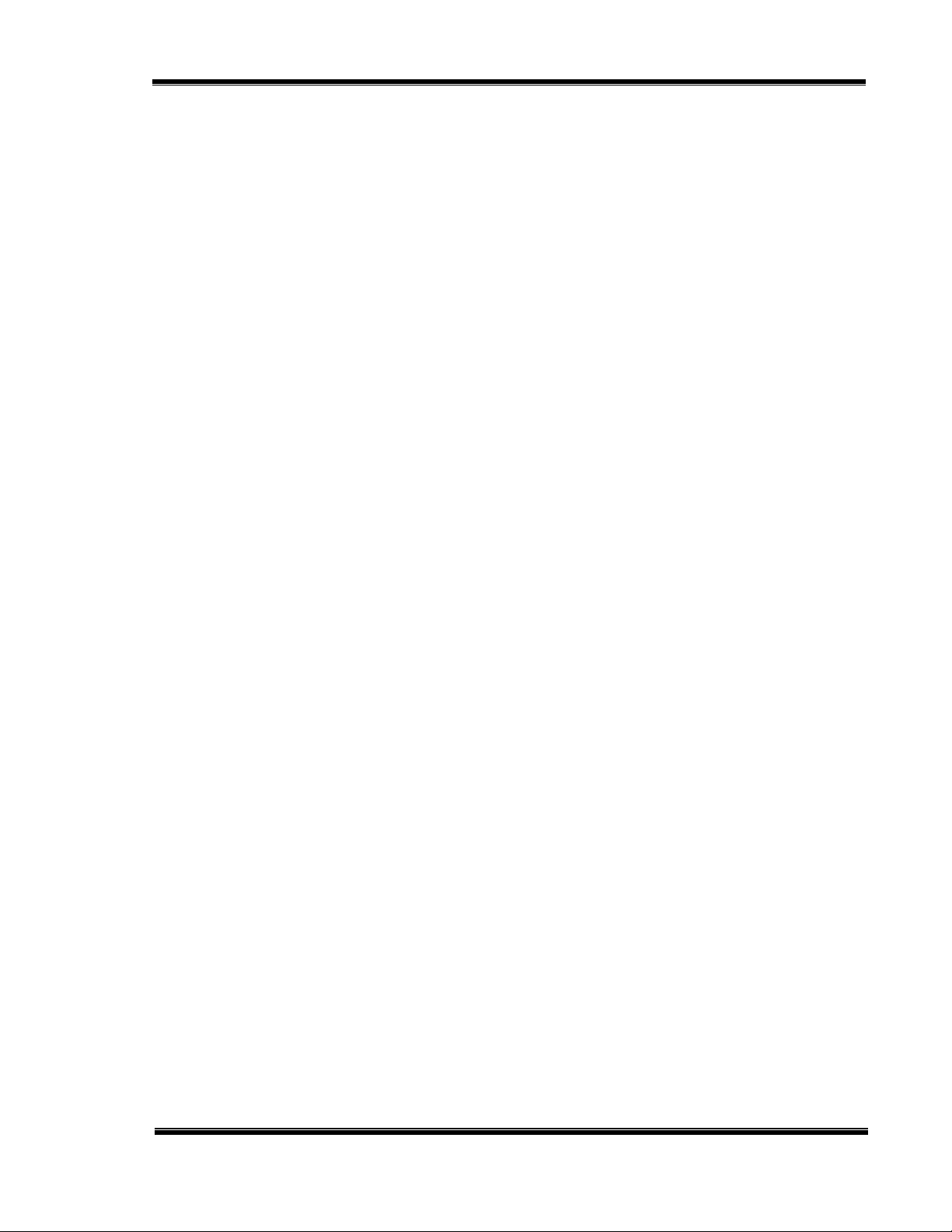
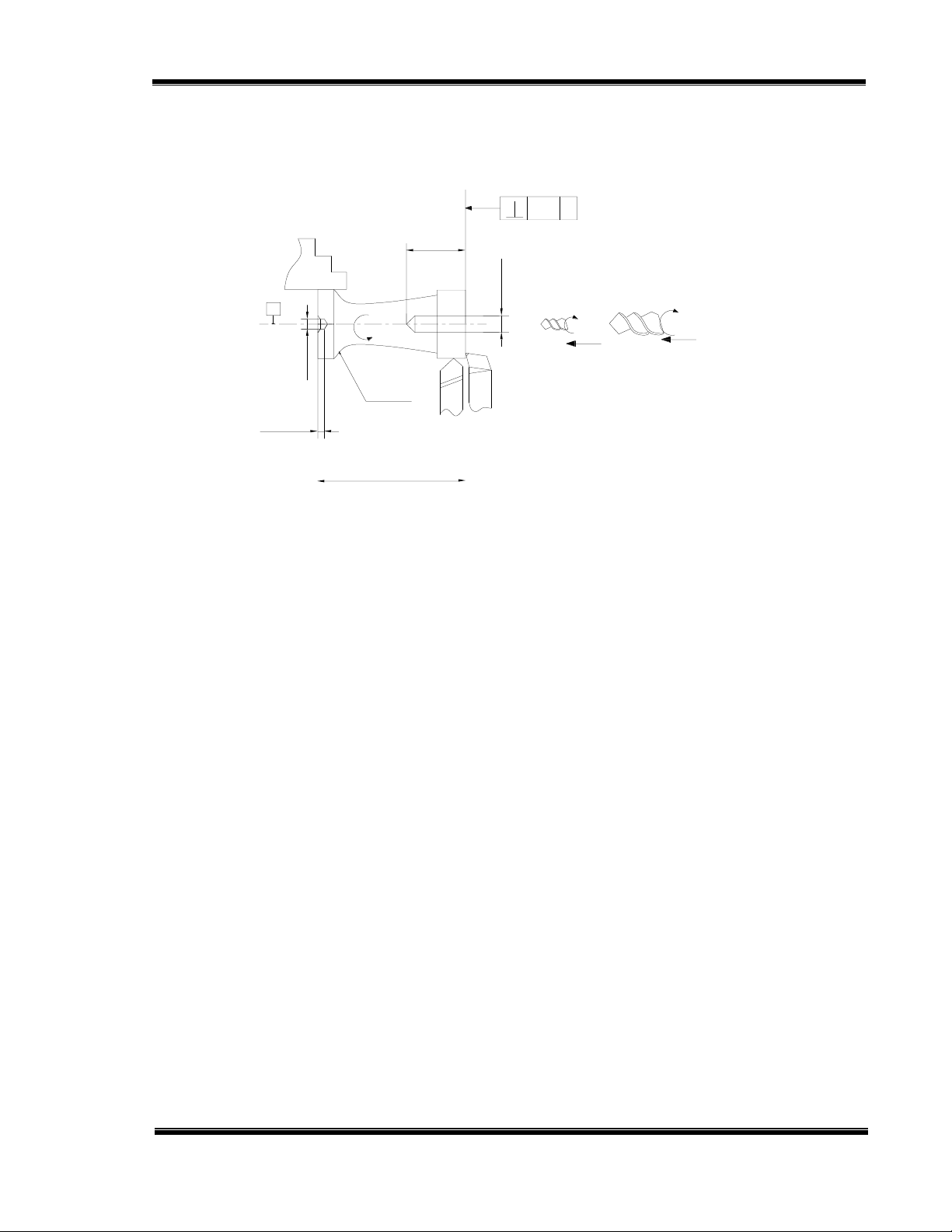
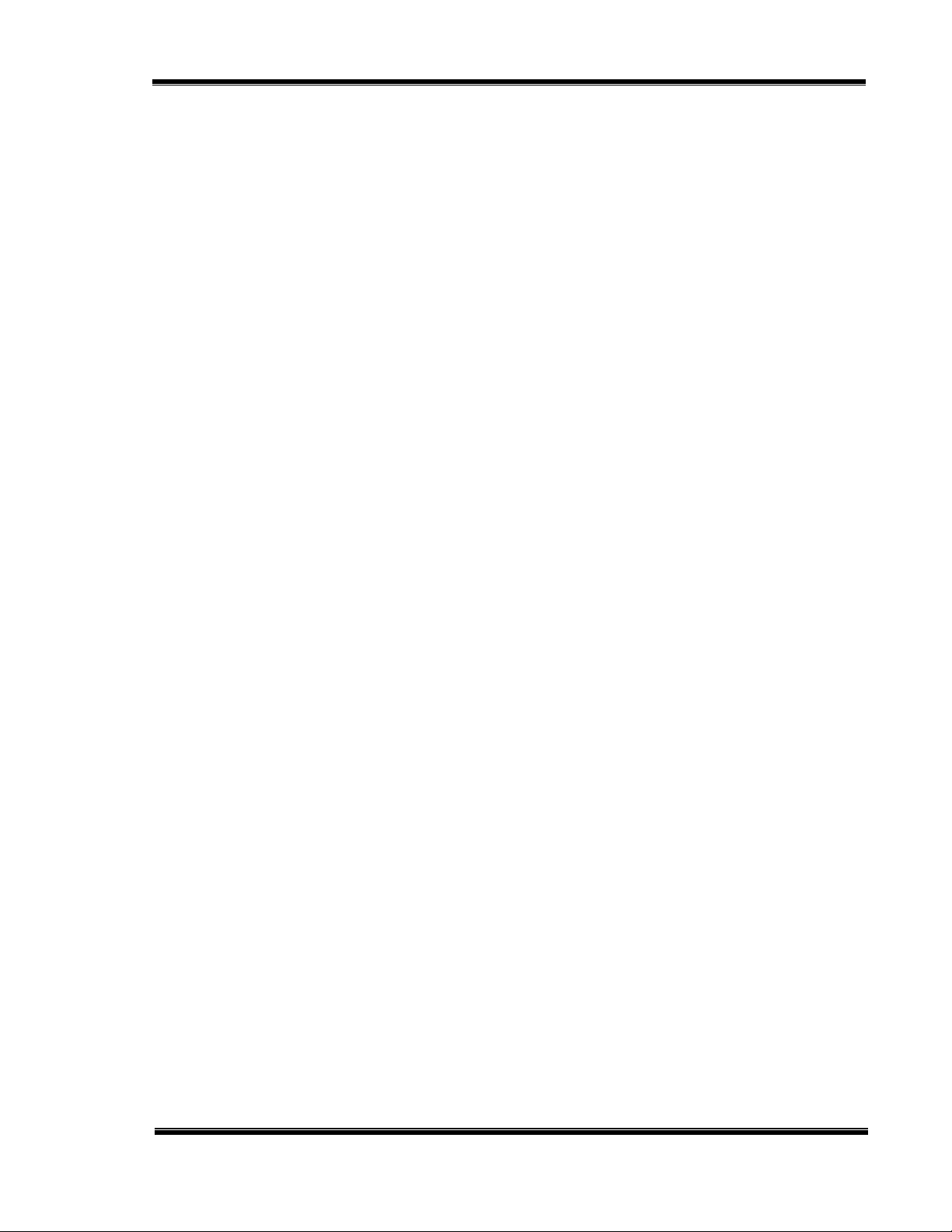
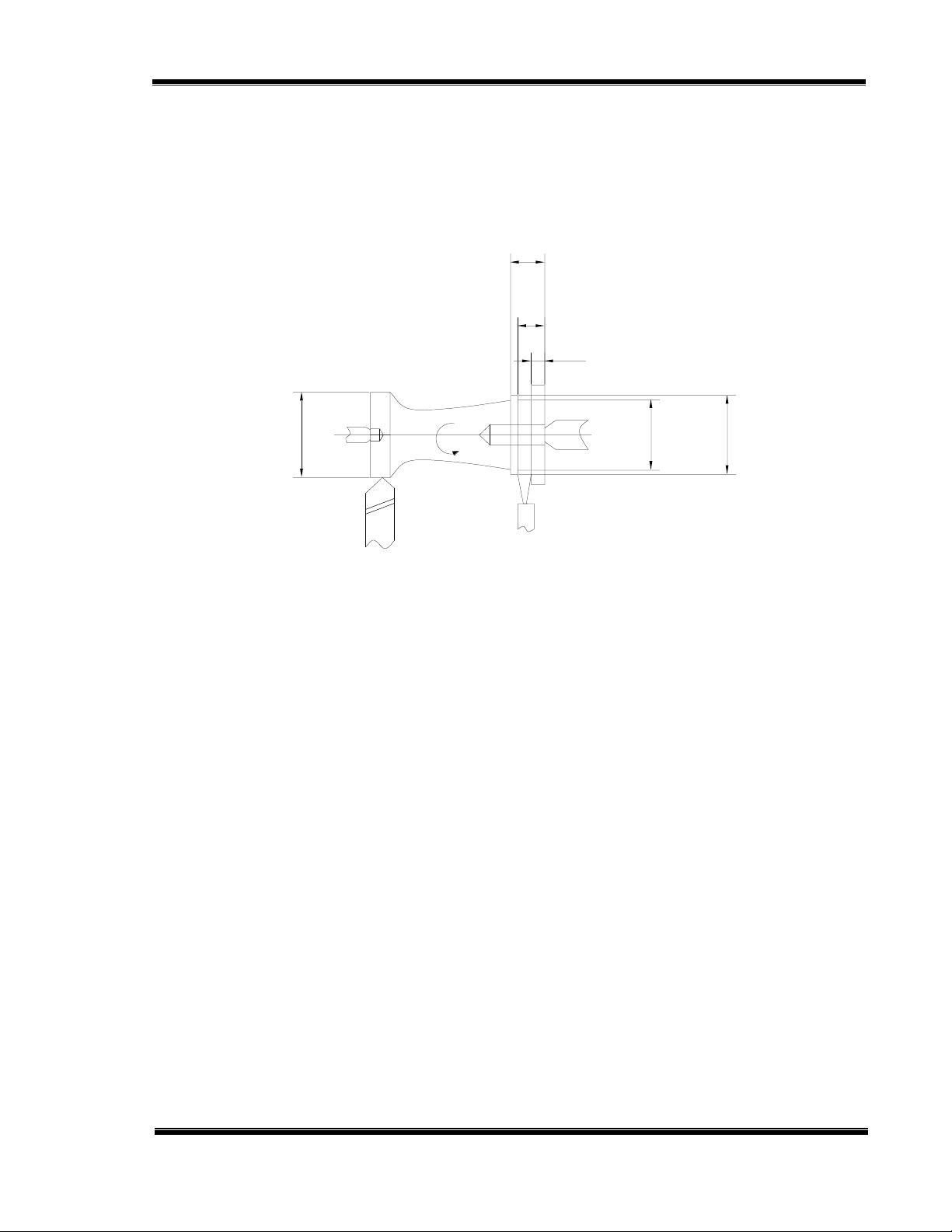
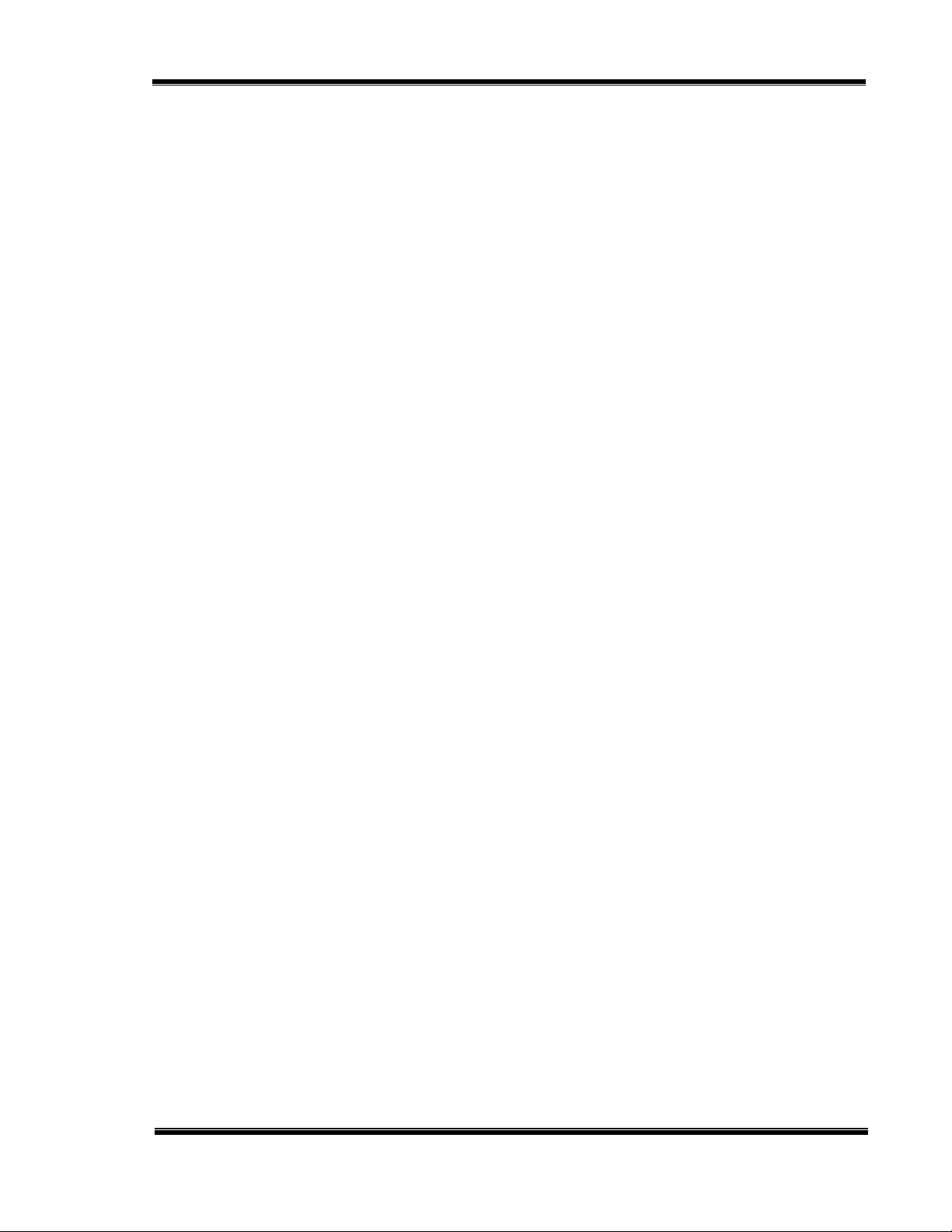
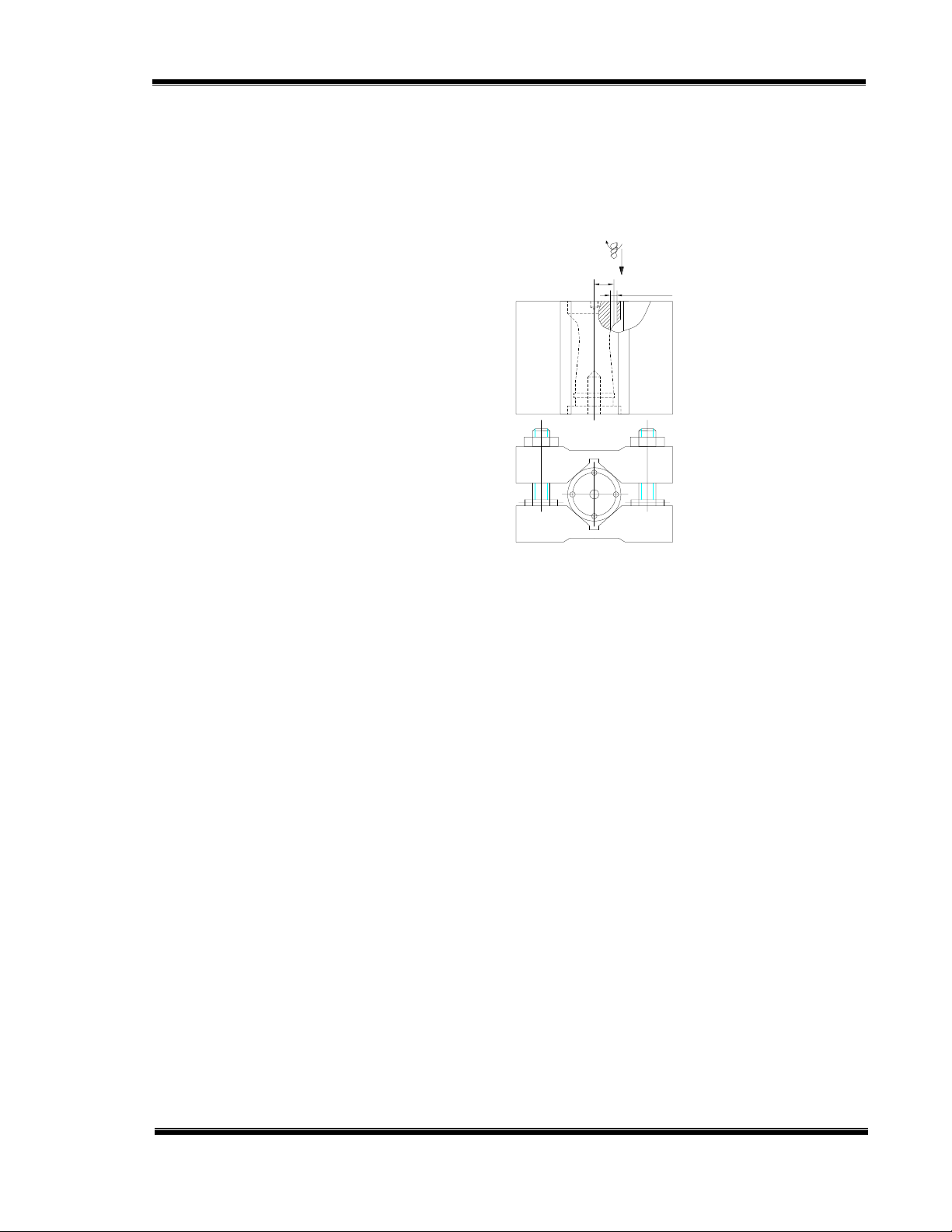
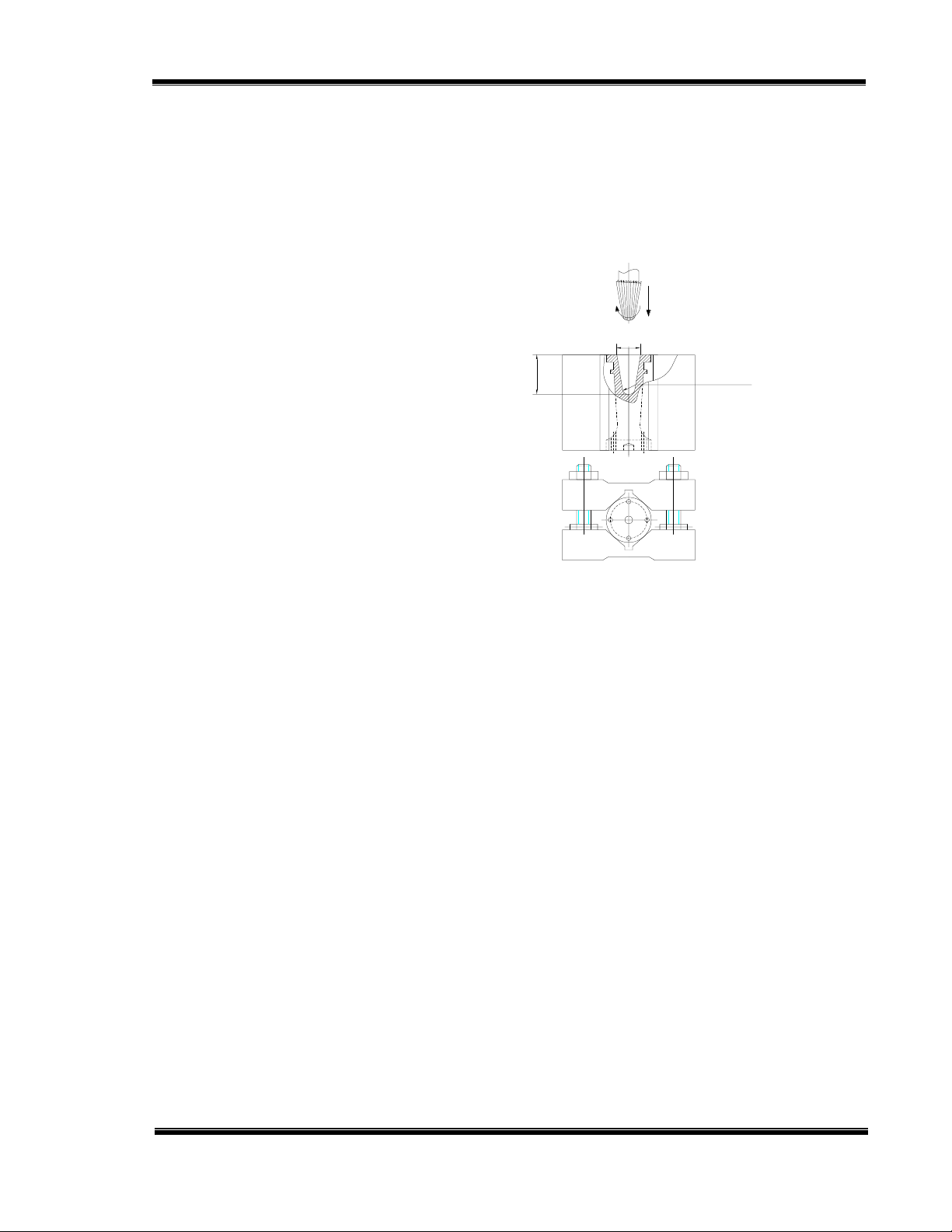
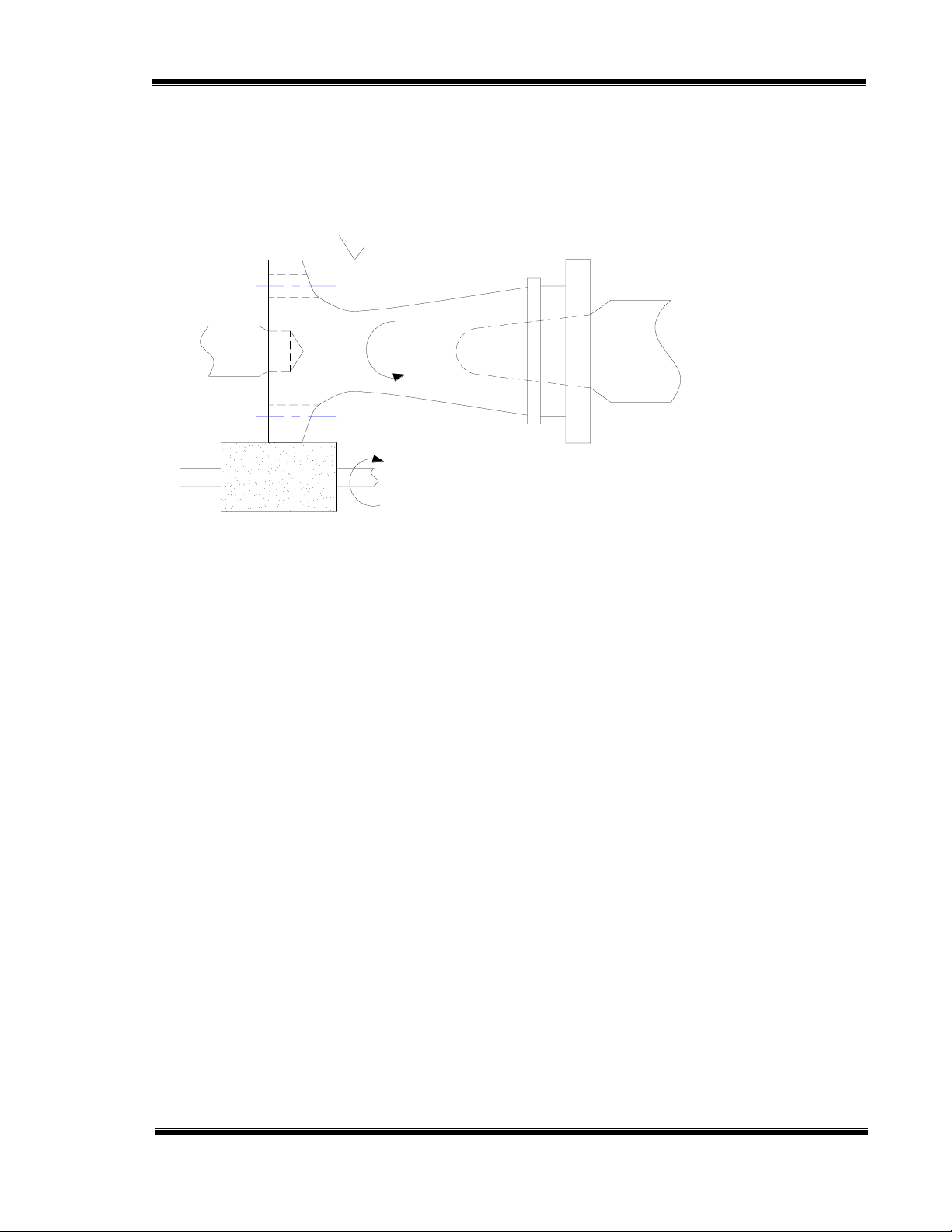
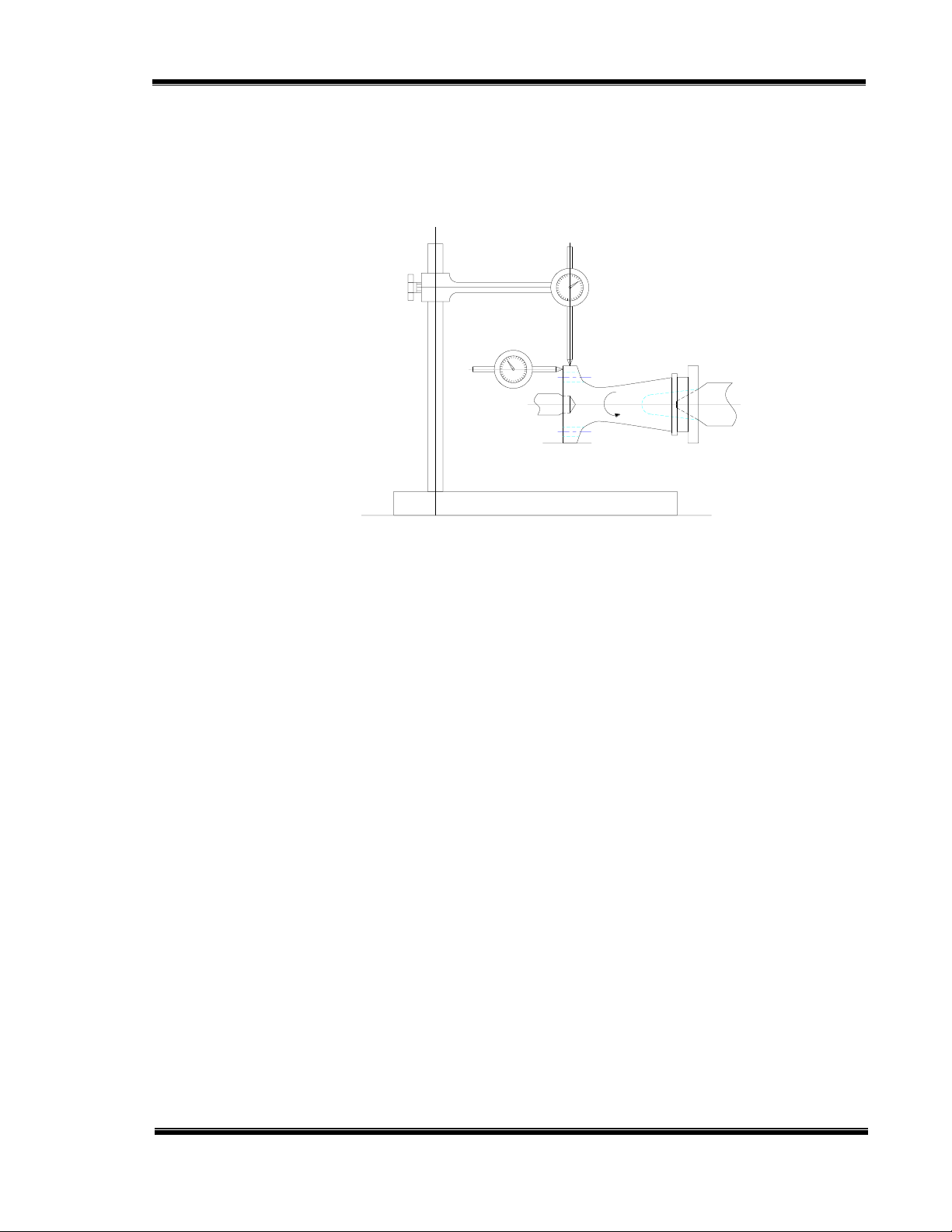
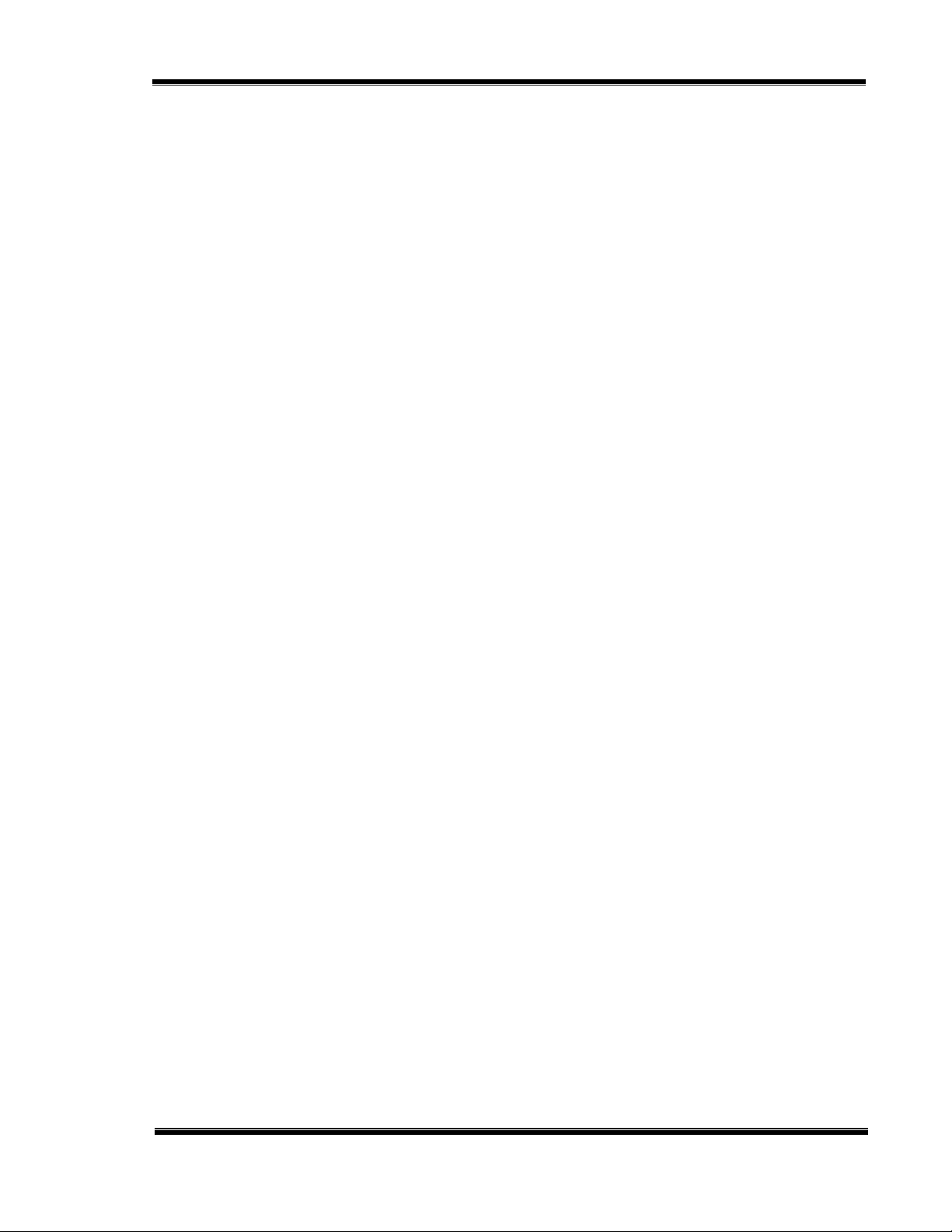
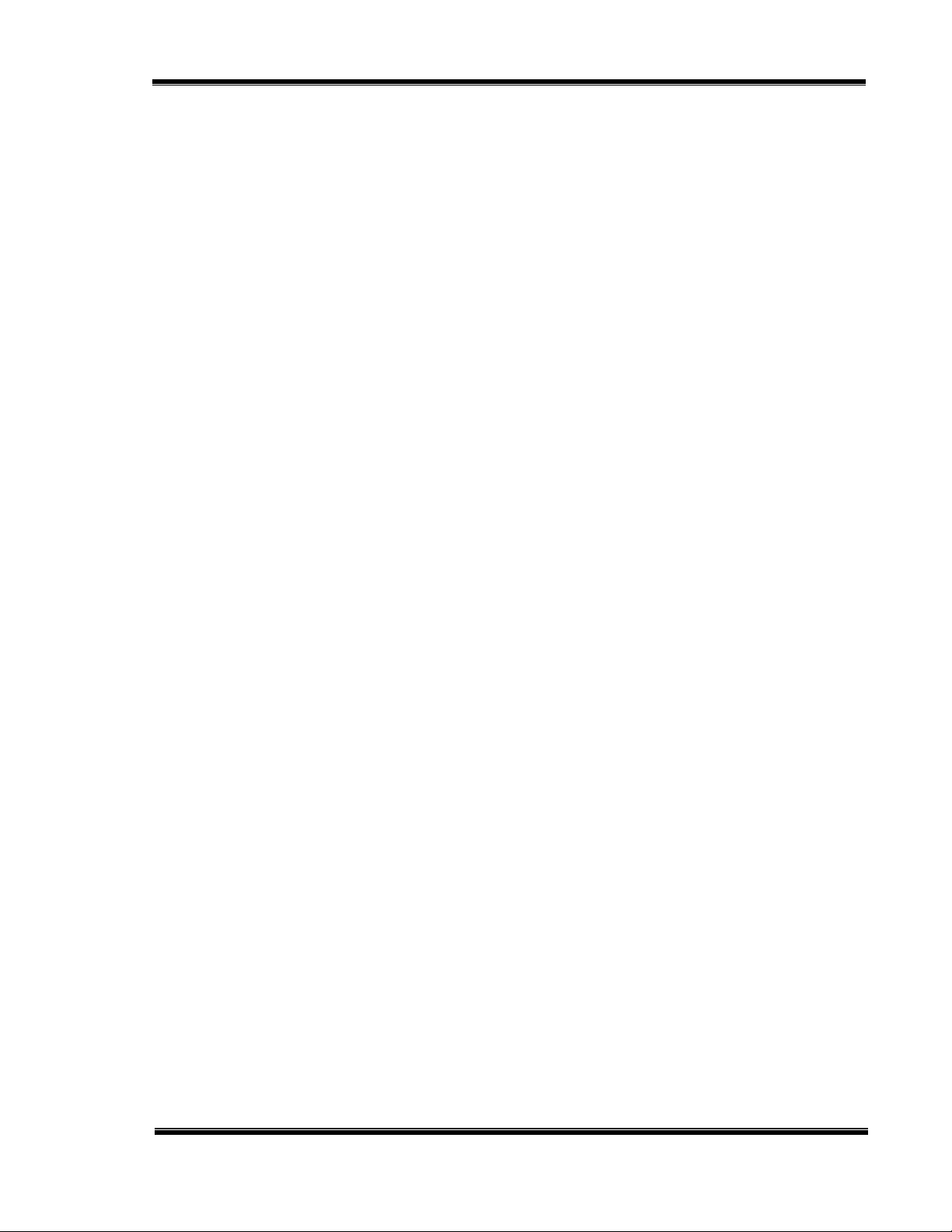
Preview text:
Lời Nói Đầu
Ôtô là phương tiện vận tải chủ yếu hiện nay và cả trong tương lai.Nó
đóng vai trũ hết sức quan trọng đối với đời sống con người và đối với sự phát
triển của mỗi quốc gia.Ôtô không chỉ là phương tiện chủ yếu để chuyên chở
hành khách ,hàng húa mà ngày nay cựng với sự phỏt triển tột bậc của cụng nghệ
ụtụ cũn là những tỏc phẩm nghệ thuật,thể hiện vẻ đẹp,sang trọng và sự hũan
mỹ.Ôtô là phương tiện chủ chốt trong ngành giao thông vận tải đang không
ngừng phát triển cả về quy mô và chất lượng để tạo điều kiện cho một nền kinh
tế phát triển,vỡ thế ở nước ta hiện nay Đảng và nhà nước đang rất chú trọng phát
triển ngành công nghiệp ôtô.
Về quan điểm phát triển :
- Công nghiệp ôtô là ngành Công nghiệp rất quan trọng cần được ưu tiên
phát triển để góp phần phục vụ có hiệu quả quá trình công nghiệp hóa, hiện đại
hóa và xây dựng tiềm lực an ninh, quốc phòng của đất nước.
- Phát triển nhanh ngành Công nghiệp ôtô trên cơ sở thị trường và hội
nhập với nền kinh tế thế giới ; lựa chọn các bước phát triển thích hợp, khuyến
khích chuyên môn hóa - hợp tác hóa nhằm phát huy lợi thế, tiềm năng của đất
nước ; đồng thời tích cực tham gia quá trình phân công lao động và hợp tác quốc
tế trong ngành Công nghiệp ôtô.
- Phát triển ngành Công nghiệp ôtô phải gắn kết với tổng thể phát triển
công nghiệp chung cả nước và các chiến lược phát triển các ngành liên quan đã
được phê duyệt, nhằm huy động và phát huy tối đa các nguồn lực của mọi thành
phần kinh tế, trong đó doanh nghiệp nhà nước giữ vai trò then chốt. 1
- Phát triển ngành Công nghiệp ôtô trên cơ sở tiếp thu công nghệ tiên tiến
của thế giới, kết hợp với việc đẩy mạnh hoạt động nghiên cứu - phát triển trong
nước và tận dụng có hiệu quả cơ sở vật chất, trang thiết bị hiện có, nhằm nhanh
chóng đáp ứng nhu cầu trong nước về các loại xe thông dụng với giá cả cạnh
tranh, tạo động lực thúc đẩy các ngành công nghiệp hỗ trợ trong nước phát triển
nhằm đẩy nhanh quá trình sản xuất linh kiện, phụ tùng trong nước.
- Phát triển ngành Công nghiệp ôtô phải phù hợp với chính sách tiêu dùng
của đất nước và phải bảo đảm đồng bộ với việc phát triển hệ thống hạ tầng giao
thông ; các yêu cầu về bảo vệ và cải thiện môi trường.
Về mục tiêu phát triển :
- Xây dựng và phát triển ngành Công nghiệp ôtô Việt Nam để đến năm
2020 trở thành một ngành Công nghiệp quan trọng của đất nước, có khả năng
đáp ứng ở mức cao nhất nhu cầu thị trường trong nước và tham gia vào thị
trường khu vực và thế giới.
Hệ thống ly hợp trên xe ôtô là một trong những cụm chi tiết chịu ảnh
hưởng lớn của điều kiện địa hình, môi trường khí hậu và nhiệt độ. Cụm ly hợp
lắp trên xe innova là loại ly hợp ma sát khô 1 đĩa thường đóng,có lò xo màng, có
hệ thống dẫn động cơ khí và có cường hóa khí nén.
Việc nắm vững phương pháp tính toán thiết kế, quy trình vận hành, tháo
lắp điều chỉnh, bảo dưỡng các cấp và sửa chữa lớn ly hợp là một việc cần thiết.
Từ đó ta có thể nâng cao khả năng vận chuyển, giảm giá thành vận chuyển, tăng
tuổi thọ của xe, đồng thời giảm cường độ lao động cho người lái.
Trong quá trình làm đồ án, em hết sức cảm ơn sự giúp đỡ của thầy giáo
Phạm Vỵ, của các thầy cô giáo trong bộ môn Ôtô, cùng sự giúp đỡ của các bạn. 2
Với sự nỗ lực của bản thân, bản đồ án của em đã hoàn thành. Tuy nhiên do
trình độ và thời gian có hạn, kinh nghiệm thực tế còn thiếu, nên bản đồ án của
em chắc chắn sẽ còn nhiều thiếu sót. Em rất mong các thầy cô giáo cùng các bạn
đóng góp ý kiến, để bản đồ án của em được hoàn thiện hơn.
Em xin chân thành cảm ơn thầy giáo Nguyễn Trọng Hoan, các thầy cô
trong bộ môn Ôtô, cùng toàn thể các bạn, đã tận tình giúp đỡ em hoàn thành đồ án này.
Hà Nội, ngày 19 tháng 5 năm 2008 Sinh viên thiết kế Bùi Xuân Trường 3 CHƯƠNG I
TỔNG QUAN VỀ HỆ THỐNG LY HỢP TRÊN ÔTÔ
1. CÔNG DỤNG, PHÂN LOẠI VÀ YÊU CẦU CỦA LY HỢP
1.1. Công dụng ly hợp
Trong hệ thống truyền lực của ôtô, ly hợp là một trong những cụm chính, nó có công dụng là :
- Nối động cơ với hệ thống truyền lực khi ôtô di chuyển.
- Ngắt động cơ ra khỏi hệ thống truyền lực trong trường hợp ôtô khởi hành hoặc chuyển số.
- Đảm bảo là cơ cấu an toàn cho các chi tiết của hệ thống truyền lực không
bị quá tải như trong trường hợp phanh đột ngột và không nhả ly hợp.
Ở hệ thống truyền lực bằng cơ khí với hộp số có cấp, thì việc dùng ly hợp
để tách tức thời động cơ ra khỏi hệ thống truyền lực sẽ làm giảm va đập giữa các
đầu răng, hoặc của khớp gài, làm cho quá trình đổi số được dễ dàng. Khi nối êm
dịu động cơ đang làm việc với hệ thống truyền lực (lúc này ly hợp có sự trượt)
làm cho mômen ở các bánh xe chủ động tăng lên từ từ. Do đó, xe khởi hành và tăng tốc êm.
Còn khi phanh xe đồng thời với việc tách động cơ ra khỏi hệ thống truyền
lực, sẽ làm cho động cơ hoạt động liên tục (không bị chết máy). Do đó, không
phải khởi động động cơ nhiều lần.
1.2. Phân loại ly hợp
Ly hợp trên ôtô thường được phân loại theo 4 cách : 4
+ Phân loại theo phương pháp truyền mômen.
+ Phân loại theo trạng thái làm việc của ly hợp.
+ Phân loại theo phương pháp phát sinh lực ép trên đĩa ép.
+ Phân loại theo phương pháp dẫn động ly hợp.
1.2.1. Phân loại theo phương pháp truyền mômen
Theo phương pháp truyền mômen từ trục khuỷu của động cơ đến hệ thống
truyền lực thì người ta chia ly hợp ra thành 4 loại sau :
Loại 1 : Ly hợp ma sát : là ly hợp truyền mômen xoắn bằng các bề mặt ma
sát, nó gồm các loại sau :
- Theo hình dáng bề mặt ma sát gồm có :
+ Ly hợp ma sát loại đĩa (một đĩa, hai đĩa hoặc nhiều đĩa).
+ Ly hợp ma sát loại hình nón.
+ Ly hợp ma sát loại hình trống.
Hiện nay, ly hợp ma sát loại đĩa được sử dụng rất rộng rãi, vì nó có kết cấu
đơn giản, dễ chế tạo và khối lượng phần bị động của ly hợp tương đối nhỏ. Còn
ly hợp ma sát loại hình nón và hình trống ít được sử dụng, vì phần bị động của ly
hợp có trọng lượng lớn sẽ gây ra tải trọng động lớn tác dụng lên các cụm và các
chi tiết của hệ thống truyền lực.
- Theo vật liệu chế tạo bề mặt ma sát gồm có : + Thép với gang. + Thép với thép.
+ Thép với phêrađô hoặc phêrađô đồng. + Gang với phêrađô.
+ Thép với phêrađô cao su.
- Theo đặc điểm của môi trường ma sát gồm có : 5 + Ma sát khô.
+ Ma sát ướt (các bề mặt ma sát được ngâm trong dầu).
Ưu điểm của ly hợp ma sát là : kết cấu đơn giản, dễ chế tạo.
Nhược điểm của ly hợp ma sát là : các bề mặt ma sát nhanh mòn do hiện
tượng trượt tương đối với nhau trong quá trình đóng ly hợp, các chi tiết trong ly
hợp bị nung nóng do nhiệt tạo bởi một phần công ma sát.
Tuy nhiên ly hợp ma sát vẫn được sử dụng phổ biến ở các ôtô hiện nay do
những ưu điểm của nó.
Loại 2 : Ly hợp thủy lực : là ly hợp truyền mômen xoắn bằng năng lượng
của chất lỏng (thường là dầu).
Ưu điểm của ly hợp thủy lực là : làm việc bền lâu, giảm được tải trọng
động tác dụng lên hệ thống truyền lực và dễ tự động hóa quá trình điều khiển xe.
Nhược điểm của ly hợp thủy lực là : chế tạo khó, giá thành cao, hiệu suất
truyền lực nhỏ do hiện tượng trượt.
Loại ly hợp thủy lực ít được sử dụng trên ôtô, hiện tại mới được sử dụng ở
một số loại xe ôtô du lịch, ôtô vận tải hạng nặng và một vài ôtô quân sự.
Loại 3 : Ly hợp điện từ : là ly hợp truyền mômen xoắn nhờ tác dụng của từ
trường nam châm điện. Loại này ít được sử dụng trên xe ôtô.
Loại 4 : Ly hợp liên hợp : là ly hợp truyền mômen xoắn bằng cách kết hợp
hai trong các loại kể trên (ví dụ như ly hợp thủy cơ). Loại này ít được sử dụng trên xe ôtô.
1.2.2. Phân loại theo trạng thái làm việc của ly hợp
Theo trạng thái làm việc của ly hợp thì người ta chia ly hợp ra thành 2 loại sau :
Ly hợp thường đóng : loại này được sử dụng hầu hết trên các ôtô hiện nay. 6
Ly hợp thường mở : loại này được sử dụng ở một số máy kéo bánh hơi
như C - 100 , C - 80 , MTZ2 ...
1.2.3. Phân loại theo phương pháp phát sinh lực ép trên đĩa ép
Theo phương pháp phát sinh lực ép trên đĩa ép ngoài thì người ta chia ra các loại ly hợp sau :
Loại 1 : Ly hợp lò xo : là ly hợp dùng lực lò xo tạo lực nén lên đĩa ép, nó gồm các loại sau :
- Lò xo đặt xung quanh : các lò xo được bố trí đều trên một vòng tròn và
có thể đặt một hoặc hai hàng.
- Lò xo trung tâm (dùng lò xo côn).
Theo đặc điểm kết cấu của lò xo có thể dùng lò xo trụ, lò xo đĩa, lò xo côn.
Trong các loại trên thì ly hợp dùng lò xo trụ bố trí xung quanh được áp
dụng khá phổ biến trên các ôtô hiện nay, vì nó có ưu điểm kết cấu gọn nhẹ, tạo
được lực ép lớn theo yêu cầu và làm việc tin cậy.
Loại 2 : Ly hợp điện từ : lực ép là lực điện từ.
Loại 3 : Ly hợp ly tâm : là loại ly hợp sử dụng lực ly tâm để tạo lực ép
đóng và mở ly hợp. Loại này ít được sử dụng trên các ôtô quân sự.
Loại 4 : Ly hợp nửa ly tâm : là loại ly hợp dùng lực ép sinh ra ngoài lực ép
của lò xo còn có lực ly tâm của trọng khối phụ ép thêm vào. Loại này có kết cấu
phức tạp nên chỉ sử dụng ở một số ôtô du lịch như ZIN-110, POBEDA...
1.2.4. Phân loại theo phương pháp dẫn động ly hợp
Theo phương pháp dẫn động ly hợp thì người ta chia ly hợp ra thành 2 loại sau :
Loại 1 : Ly hợp điều khiển tự động.
Loại 2 : Ly hợp điều khiển cưỡng bức. 7
Để điều khiển ly hợp thì người lái phải tác động một lực cần thiết lên hệ
thống dẫn động ly hợp. Loại này được sử dụng hầu hết trên các ôtô dùng ly hợp
loại đĩa ma sát ở trạng thái luôn đóng.
Theo đặc điểm kết cấu, nguyên lý làm việc của hệ thống dẫn động ly hợp
thì người ta lại chia ra thành 3 loại sau :
- Dẫn động bằng cơ khí.
- Dẫn động bằng thủy lực và cơ khí kết hợp.
- Dẫn động bằng trợ lực : có thể bằng trợ lực cơ khí (dùng lò xo), trợ lực
bằng khí nén hoặc trợ lực bằng thủy lực. Nhờ có trợ lực mà người lái điều khiển
ly hợp dễ dàng, nhẹ nhàng hơn.
1.3. Yêu cầu ly hợp
Ly hợp là một trong những hệ thống chủ yếu của ôtô, khi làm việc ly hợp
phải đảm bảo được các yêu cầu sau :
- Truyền hết mômen của động cơ mà không bị trượt ở bất kỳ điều kiện sử
dụng nào. Muốn vậy thì mômen ma sát của ly hợp phải lớn hơn mômen cực đại
của động cơ (có nghĩa là hệ số dự trữ mômen của ly hợp phải lớn hơn 1).
- Đóng ly hợp phải êm dịu, để giảm tải trọng va đập sinh ra trong các răng
của hộp số khi khởi hành ôtô và khi sang số lúc ôtô đang chuyển động.
- Mở ly hợp phải dứt khoát và nhanh chóng, tách động cơ ra khỏi hệ thống
truyền lực trong thời gian ngắn (vì mở không dứt khoát sẽ làm cho khó gài số được êm dịu).
- Mômen quán tính phần bị động của ly hợp phải nhỏ để giảm lực va đập
lên bánh răng khi khởi hành và sang số.
- Điều khiển dễ dàng, lực tác dụng lên bàn đạp nhỏ.
- Các bề mặt ma sát phải thoát nhiệt tốt. 8
- Kết cấu ly hợp phải đơn giản, dễ điều chỉnh và chăm sóc, tuổi thọ cao.
Ly hợp làm nhiệm vụ bộ phận an toàn để tránh quá tải cho hệ thống truyền lực.
Tất cả những yêu cầu trên, đều được đề cập đến trong quá trình chọn vật
liệu, thiết kế và tính toán các chi tiết của ly hợp.
2. CẤU TẠO VÀ NGUYÊN LÝ LÀM VIỆC CỦA LY HỢP LOẠI ĐĨA MA SÁT KHÔ
2.1. Sơ đồ cấu tạo của ly hợp loại đĩa ma sát khô 1 2 3 4 5 6 7 13 12 11 10 9 8
Hình 1.1. Sơ đồ cấu tạo ly hợp ma sát khô một đĩa 1 - bánh đà ; 2 - đĩa ma sát ; 3 - đĩa ép 4 - lò xo ép ; 5 - vỏ ly hợp ; 6 - bạc mở 7 - bàn đạp ;
8 - lò xo hồi vị bàn đạp 9 - đòn kéo ; 10 - càng mở ; 11 - bi "T" 12 - đòn mở ; 13 - lò xo giảm chấn. 9 10 1 2 3 4 6 5 7 8 9 10 11 17 16 15 14 13 12
Hình 1.2. Sơ đồ cấu tạo ly hợp ma sát khô hai đĩa 1 - bánh đà ;
2 - lò xo đĩa ép trung gian
3 - đĩa ép trung gian ; 4 - đĩa ma sát ; 5 - đĩa ép ngoài
6 - bulông hạn chế ; 7 - lò xo ép ; 8 - vỏ ly hợp 9 - bạc mở ; 10 - trục ly hợp ; 11 - bàn đạp
12 - lò xo hồi vị bàn đạp ly hợp ; 13 - thanh kéo 14 - càng mở ; 15 - bi "T" ; 16 - đòn mở 17 - lò xo giảm chấn.
2.2. Cấu tạo chung của ly hợp loại đĩa ma sát khô
Đối với hệ thống ly hợp, về mặt cấu tạo thì người ta chia thành 2 bộ phận :
- Cơ cấu ly hợp : là bộ phận thực hiện việc nối và ngắt truyền động từ
động cơ đến hệ thống truyền lực. 11
- Dẫn động ly hợp : là bộ phận thực hiện việc điều khiển đóng mở ly hợp.
Trong phần này, ta xét cấu tạo của cơ cấu ly hợp, nó gồm 3 phần chính :
bánh đà, đĩa ma sát và đĩa ép.
- Nhóm các chi tiết chủ động gồm bánh đà, vỏ ly hợp, đĩa ép, đòn mở và
các lò xo ép. Khi ly hợp mở hoàn toàn thì các chi tiết thuộc nhóm chủ động sẽ quay cùng bánh đà.
- Nhóm các chi tiết bị động gồm đĩa ma sát, trục ly hợp. Khi ly hợp mở
hoàn toàn các chi tiết thuộc nhóm bị động sẽ đứng yên.
Theo sơ đồ cấu tạo hình 1.1.a : vỏ ly hợp 5 được bắt cố định với bánh đà 1
bằng các bulông, đĩa ép 3 có thể dịch chuyển tịnh tiến trong vỏ và có bộ phận
truyền mômen từ vỏ 5 vào đĩa ép. Các chi tiết bánh đà 1, đĩa ép 3, lò xo ép 4, vỏ
ly hợp 5 được gọi là phần chủ động của ly hợp và chi tiết đĩa ma sát 2 được gọi
là phần bị động của ly hợp. Các chi tiết còn lại thuộc bộ phận dẫn động ly hợp.
Đối với một số ôtô vận tải khi cần phải truyền mômen lớn người ta sử
dụng ly hợp ma sát khô hai đĩa bị động. So với ly hợp ma sát khô một đĩa bị
động thì ly hợp ma sát khô hai đĩa bị động có những ưu nhược điểm sau :
+ Nếu cùng một kích thước đĩa bị động và cùng một lực ép như nhau thì ly
hợp hai đĩa truyền được mômen lớn hơn ly hợp một đĩa.
+ Nếu phải truyền một mômen như nhau thì ly hợp hai đĩa có kích thước
nhỏ gọn hơn ly hợp một đĩa.
+ Ly hợp hai đĩa khi đóng êm dịu hơn nhưng khi mở lại kém dứt khoát hơn ly hợp một đĩa.
+ Ly hợp hai đĩa có kết cấu phức tạp hơn ly hợp một đĩa.
Theo sơ đồ cấu tạo hình 1.1.b : cũng bao gồm các bộ phận và các chi tiết
cơ bản như đối với ly hợp một đĩa. Điểm khác biệt là ở ly hợp hai đĩa có hai đĩa 12
ma sát 4 cùng liên kết then hoa với trục ly hợp 10. Vì có hai đĩa ma sát nên ngoài
đĩa ép 5 còn có thêm đĩa ép trung gian 3. Ở ly hợp hai đĩa phải bố trí cơ cấu
truyền mômen từ vỏ hoặc bánh đà sang đĩa ép và cả đĩa ép trung gian. Vì nhược
điểm của ly hợp hai đĩa là mở không dứt khoát nên ở những loại ly hợp này thì
người ta phải bố trí cơ cấu để tạo điều kiện cho ly hợp khi mở được dứt khoát.
Trên hình 1.1.b thì cơ cấu này được thực hiện bởi lò xo đĩa ép trung gian 2 và bu
lông điều chỉnh 6. Khi mở ly hợp thì lò xo 2 sẽ đẩy đĩa ép trung gian 3 tách khỏi
đĩa ma sát bên trong và khi đĩa ép trung gian chạm vào đầu bu lông điều chỉnh 6
thì dừng lại nên đĩa ma sát bên ngoài cũng được tự do.
- Bộ phận dẫn động điều khiển ly hợp gồm : bàn đạp ly hợp, đòn dẫn
động, càng mở ly hợp, đòn mở ly hợp và bạc mở ly hợp. Ngoài ra, tùy theo từng
loại ly hợp mà có thể thêm các bộ phận dẫn động bằng thủy lực, bằng khí nén
như các xilanh chính và xilanh công tác.
2.3. Nguyên lý làm việc của ly hợp loại đĩa ma sát khô
Nguyên lý làm việc theo hình 1.1 :
Trạng thái đóng ly hợp : ở trạng thái này lò xo 4 một đầu tựa vào vỏ 5, đầu
còn lại tì vào đĩa ép 3 tạo lực ép để ép chặt đĩa bị động 2 với bánh đà 1 làm cho
phần chủ động và phần bị động tạo thành một khối cứng. Khi này mômen từ
động cơ được truyền từ phần chủ động sang phần bị động của ly hợp thông qua
các bề mặt ma sát của đĩa bị động 2 với đĩa ép 3 và lò xo ép 4. Tiếp đó mômen
được truyền vào xương đĩa bị động qua bộ giảm chấn 13 đến moayơ rồi truyền
vào trục ly hợp. Lúc này giữa bi "T" 11 và đầu đòn mở 12 có một khe hở từ 3-4
mm tương ứng với hành trình tự do của bàn đạp ly hợp từ 30-40 mm.
Trạng thái mở ly hợp : khi cần ngắt truyền động từ động cơ tới trục sơ cấp
của hộp số người lái tác dụng một lực vào bàn đạp 7 thông qua đòn kéo 9 và 13
càng mở 10, bạc mở 6 mang bi "T" 11 sẽ dịch chuyển sang trái. Sau khi khắc
phục hết khe hở bi "T" 11 sẽ tì vào đầu đòn mở 12. Nhờ có khớp bản lề của đòn
mở liên kết với vỏ 5 nên đầu kia của đòn mở 12 sẽ kéo đĩa ép 3 nén lò xo 4 lại để
dịch chuyển sang phải. Khi này các bề mặt ma sát giữa bộ phận chủ động và bị
động của ly hợp được tách ra và ngắt sự truyền động từ động cơ tới trục sơ cấp của hộp số.
Nguyên lý làm việc theo hình 1.2 :
Trạng thái đóng ly hợp : ở trạng thái này các lò xo ép 7 một đầu tựa vào
vỏ ly hợp 8, đầu còn lại tì vào đĩa ép 5 tạo lực ép để ép chặt toàn bộ các đĩa ma
sát 4 và đĩa ép trung gian 3 với bánh đà 1 làm cho phần chủ động và phần bị
động tạo thành một khối cứng. Khi này mômen từ động cơ được truyền từ phần
chủ động sang phần bị động của ly hợp thông qua các bề mặt ma sát của các đĩa
ma sát 4 và đĩa ép trung gian 3 với đĩa ép 5 và lò xo ép 7. Tiếp đó mômen được
truyền vào xương đĩa bị động qua bộ giảm chấn 17 đến moayơ rồi truyền vào
trục ly hợp. Lúc này giữa bi "T" 15 và đầu đòn mở 16 có một khe hở từ 3-4 mm
tương ứng với hành trình tự do của bàn đạp ly hợp từ 30-40 mm.
Trạng thái mở ly hợp : khi cần ngắt truyền động từ động cơ tới trục sơ cấp
của hộp số thì người lái tác dụng một lực vào bàn đạp 11 thông qua đòn kéo 13
và kéo càng mở 14, bạc mở 9 mang bi "T" 15 sẽ dịch chuyển sang trái. Sau khi
khắc phục hết khe hở bi "T" 15 sẽ tì vào đầu đòn mở 16. Nhờ có khớp bản lề của
đòn mở liên kết với vỏ 8 nên đầu kia của đòn mở 16 sẽ kéo đĩa ép 5 nén lò xo 7
lại để dịch chuyển sang phải tạo khe hở giữa các đĩa ma sát với các đĩa ép, đĩa ép
trung gian và bánh đà. Khi này các bề mặt ma sát giữa bộ phận chủ động và bị
động của ly hợp được tách ra và ngắt sự truyền động từ động cơ tới trục sơ cấp của hộp số. 14
Ngoài các trạng thái làm việc trên, thì ly hợp còn xuất hiện trạng thái trượt
tương đối giữa các bề mặt ma sát của ly hợp. Hiện tượng này thường xuất hiện
khi đóng ly hợp (xảy ra trong thời gian ngắn) hoặc khi gặp quá tải (phanh đột
ngột mà không nhả ly hợp). CHƯƠNG II
LỰA CHỌN PHƯƠNG ÁN THIẾT KẾ
1. CÁC THÔNG SỐ THAM KHẢO CỦA XE ÔTÔ INNOVA Thông số innova
- Kích thước bao [dài x rộng x cao] (mm) 4555 x 1770 x 1745
- Chiều rộng cơ sở [trước và sau] (mm) 1510 x 1510 - Chiều dài cơ sở (mm) 2750
- Trọng lượng bản thân (KG) 1530
- Trọng lượng toàn bộ xe (KG) 2170
- Tốc độ cực đại (km/h) 200 4 xilanh thẳng hàng, 16 - Động cơ van, cam kép với VVT-i
- Công suất cực đại, ở 5600 vg/ph (ml) 134
- Mômen xoắn cực đại, ở 4000 vg/ph (kG.m) 18,6
1 đĩa,ma sát khô,dẫn động - Ly hợp
thủy lực có trợ lực chân không I : 4,12
- Tỉ số truyền của hộp số lùi : 4,12
- Tỉ số truyền của truyền lực chính 4,53 - Kích thước lốp 195/70/R14T 15
2. LỰA CHỌN KẾT CẤU CỤM LY HỢP
2.1.Kết cấu ly hợp 1 đĩa ma sát
2.1.1. Kết cấu ly hợp lắp trên xe ZIN-130
Ly hợp lắp trên xe ZIN-130 là ly hợp một đĩa ma sát khô (hình 2.1).
- Đĩa ép 3 bị ép bởi lò xo ép 8 bố trí xung quanh vỏ ly hợp 9. Vỏ ly hợp
được lắp ghép với bánh đà 2 nhờ các bulông 23. Đĩa ép 3 và vỏ ly hợp 9 liên kết
với nhau bằng lò xo lá 4, mỗi lò xo lá có một đầu được tán cố định với vỏ ly hợp
bằng các đinh tán và đầu còn lại được lắp cố định với đĩa ép 3 bằng các bulông.
Do đó, đã tạo nên sự liên kết cứng giữa đĩa ép với vỏ ly hợp (vỏ trong) theo
phương pháp tuyến để đảm bảo truyền được mômen xoắn, đồng thời đảm bảo
được sự di chuyển dọc trục của đĩa ép khi mở và đóng ly hợp.
- Đĩa bị động của ly hợp trên xe ZIN-130 :
Xương đĩa bị động được chế tạo bằng thép và có xẻ rãnh. Đĩa ma sát được
lắp ghép với xương đĩa bằng các đinh tán. Bộ giảm chấn gồm 8 lò xo giảm chấn
đặt xung quanh cách đều nhau cùng tấm ma sát. Xương đĩa được ghép chặt với
moayơ đĩa bị động bằng các đinh tán. Đinh tán được chế tạo bằng thép.
- Đòn mở ly hợp 16 (hình 2.1) : gồm có 4 chiếc và được chế tạo bằng thép.
Mỗi đòn mở thì đầu ngoài liên kết khớp bản lề với đĩa ép 3 qua các ổ bi kim.
Phần giữa đòn liên kết bản lề với càng nối qua ổ bi kim. Càng nối gối tựa lên vỏ
ly hợp bằng đai ốc hình chỏm cầu. Các đai ốc này bị ép vào vỏ ly hợp bằng đệm
đàn hồi, mỗi đệm đàn hồi này được cố định vào vỏ ly hợp bằng hai bu lông nhỏ. 16
Nhờ có mối liên kết như vậy mà càng nối có thể chuyển động xoay để tạo ra tâm
quay thay đổi ở giữa đòn mở ly hợp, cần thiết cho sự di chuyển của đĩa ép khi
mở và đóng ly hợp. Đai ốc chỏm cầu còn có tác dụng điều chỉnh đầu đòn mở để
các đòn mở cùng nằm trong mặt phẳng song song với mặt phẳng của đĩa ép.
Hình 2.Ly hợp lắp trên xe ZIN-130
1. Trục khuỷu ; 2. Bánh đà ; 3. Đĩa ép ; 4. Tấm thép truyền lực ; 5. Bao của lò xo
6. Bulông bắt chặt lò xo ; 7. Cácte bộ ly hợp ; 8. Lò xo ép ; 9. Vỏ trong ly hợp ; 17
10. Đệm cách nhiệt ; 11. Bi “T” ; 12. Khớp nối ; 13. Lò xo trả về khớp nối ; 14.
Bạc dẫn hướng của khớp nối ; 15. Càng mở ly hợp ; 16. Đòn mở ; 18. Êcu điều
chỉnh ; 19. Đế tựa của bulông điều chỉnh ; 20. Chốt ; 21. Nắp của cácte ly hợp ;
23. Bulông bắt chặt vỏ ly hợp ; 24. Chốt chẻ ; 25. Vành răng bánh đà ; 26. Đĩa
ma sát ; 27. Vú mỡ ; 28. Nút ; 29. Trục ly hợp ; 30. Ổ bi trước của trục ly hợp.
- Bạc mở ly hợp gồm có ổ bi tỳ 11 và bạc trượt (hình 2.1). Trong ổ bi tỳ có
đủ lượng mỡ dự trữ để bôi trơn trong suốt quá trình sử dụng mà không cần bổ
xung thêm (chỉ thay thế và bổ xung khi ly hợp được tháo để sửa chữa lớn).
- Lò xo hồi vị bạc mở ly hợp 13 dùng để giữ bạc mở luôn có khe hở với
đầu đòn mở, đảm bảo cho ly hợp luôn đóng hoàn toàn và khi đóng ly hợp thì bạc
mở nhanh chóng tách khỏi đầu đòn mở.
2.1.2. Kết cấu ly hợp lắp trên xe AZ-53
Ly hợp lắp trên xe AZ-53 là ly hợp một đĩa ma sát khô (hình 2.2).
- Bộ phận chủ động của ly hợp : Bánh đà 1 bắt với vỏ trong ly hợp 13, vỏ
trong quay cùng với bánh đà. Vỏ 13 có khoang để giữ các lò xo ép 14 hình trụ
đặt xung quanh. Đĩa ép được chế tạo bằng gang, mặt ngoài có các vấu lồi để giữ các lò xo ép.
- Bộ phận bị động của ly hợp : Đĩa ma sát 3 có hai tấm ma sát làm bằng
vật liệu có hệ số ma sát cao, được ghép với nhau qua xương đĩa bằng các đinh
tán. Xương đĩa được chế tạo bằng thép và trên có các xẻ rãnh. Đĩa ma sát được
ghép với moayơ đĩa bị động bằng các đinh tán bằng thép. Moayơ đĩa bị động
được chế tạo bằng thép và có thể di trượt trên trục ly hợp 10 nhờ các then hoa.
Bộ phận giảm chấn gồm có 6 lò xo giảm chấn 18, đặt xung quanh và cách đều
nhau. Tấm ma sát được ghép với xương đĩa bằng các đinh tán. Lò xo giảm chấn
được đặt trong các lỗ của đĩa bị động và tấm đỡ. 18
- Hệ thống dẫn động điều khiển ly hợp : Ly hợp được dẫn động điều khiển
bằng cơ khí. Đòn mở ly hợp 5 được chế tạo bằng thép, đầu trên đòn mở liên kết
bản lề với đĩa ép qua các ổ bi kim, giữa đòn liên kết bản lề với càng nối 8 thông
qua ổ bi kim. Khe hở giữa đầu đòn mở và bạc mở là = 4 mm. Điều chỉnh đòn
mở ta dùng đai ốc 7. Bạc mở ly hợp gồm có ổ bi tỳ và bạc trượt 9. Trên bạc trượt có lắp ống bơm mỡ 6. 19
Hình 2.2 Ly hợp lắp trên xe AZ-53
1. Bánh đà ; 2. Vỏ ngoài ly hợp ; 3. Đĩa ma sát ; 4. Đĩa ép ; 5. Đòn mở ly hợp ; 6.
Ống bơm mỡ ; 7. Đai ốc điều chỉnh ; 8. Càng nối ; 9. Bạc trượt ; 10. Trục ly hợp
; 11. Càng mở ly hợp ; 12. Đinh tán nối các tấm đĩa ; 13. Vỏ trong ly hợp ; 14.
Lò xo ép ; 15. Đai ốc điều chỉnh ; 16. Thanh kéo ; 17. Lò xo hồi vị càng mở ly
hợp ; 18. Lò xo giảm chấn ; 19. Xương đĩa ; 20. Đế cách nhiệt lò xo ép.
2.1.3Ly hợp lắp trên xe innova
- Phần chủ động : gồm các chi tiết lắp ghép trưc tiếp hoặc gián tiếp với bánh đà
của động cơ và có cùng tốc độ quay với bánh đà.Trên hỡnh 2.3 phần chủ động
gồm: bánh đà, đĩa ép,vỏ ly hợp,lũ xo màng(lũ xo ộp)
- Phần bị động gồm các chi tiết lắp ghép trực tiếp hoặc gián tiếp với trục bị động
của ly hợp và có cùng tốc độ với trục bị động của ly hợp.Trên hỡnh2.3 phần bị
động gồm: trục bị động,đĩa bị động.Trục bị động thường là trục sơ cấp của hộp số
- Phần dẫn động điều khiển ly hợp gồm các chi tiết điều khiển ly hợp,chúng gồm
cả các chi tiết nằm trong phần chủ động như đũn mở ( đồng thời là lũ xo màng),
bạc mở và cỏc chi tiết điều khiển bạc mở
- Bộ phận tạo lực ộp gồm: giỏ tựa ( vỏ ly hợp ) , lũ xo ộp, đĩa ép 9 10 11 12 13 14 15 16 8 17 7 6 18 5 19 4 3 20 2 1 21 20
Hỡnh 2.3.Ly hợp lắp trờn xe innov
Trờn hỡnh 2.3 cú : 1.nắp dưới; 2.bánh đà; 3.vỏ trong ly hợp; 4.đinh tán đĩa ma
sát; 5.ổ bi; 6.trục khuỷu; 7.trục sơ cấp; 8.đai ốc; 9.đinh tán moayơ; 10.xương đĩa;
11.tấm ma sát; 12.đĩa ép; 13.bulông; 14.vỏ ly hợp; 15.đinh tán; 16.lũ xo màng;
17.moayơ; 18.biT; 19.bạc lót; 20.ống gài; 21.lũ xo giảm chấn. 2.2Kết luận
Qua các kết cấu ly hợp đó nờu ở trờn ta chọn phương án 3 – ly hợp lắp trên xe
innnova làm cơ sở để thiết kế tính toán cụm ly hợp cho xe 7 chỗ.
3. LỰA CHỌN PHƯƠNG ÁN DẪN ĐỘNG ĐIỀU KHIỂN LY HỢP
3.1. Phương án 1 : Dẫn động ly hợp bằng cơ khí.
Đây là hệ thống dẫn động điều khiển ly hợp bằng các đòn, khớp nối và
được lắp theo nguyên lý đòn bẩy. Loại dẫn động điều khiển ly hợp đơn thuần
này có kết cấu đơn giản, dễ chế tạo và có độ tin cậy làm việc cao. Hệ thống dẫn
động này được sử dụng phổ biến ở các ôtô quân sự như xe ZIN-130, ZIN-131, ...
Nhược điểm cơ bản của hệ thống dẫn động này là : yêu cầu lực tác động
của người lái nên bàn đạp ly hợp phải lớn, nhất là đối với loại xe ôtô hạng nặng. 1 Qbđ 8 2 6 O2 3 5 4 O1 21
Hình 3.1. Sơ đồ hệ thống dẫn động ly hợp bằng cơ khí 1. Bạc mở ; 2. Càng mở ly hợp 3. Cần ngắt ly hợp ;
4. Cần của trục bàn đạp ly hợp 5. Thanh kéo của ly hợp ; 6. Lò xo hồi vị 8. Bàn đạp ly hợp Nguyên lý làm việc :
Khi người lái tác dụng một lực Q lên bàn đạp ly hợp 8 sẽ làm cho cần của
trục bàn đạp ly hợp 4 quay quanh tâm O1 kéo thanh kéo của ly hợp 5 dịch
chuyển sang phải (theo chiều mũi tên). Làm cho cần ngắt ly hợp 3 và càng mở ly
hợp 2 quay quanh O2 . Càng mở gạt bạc mở 1 sang trái (theo chiều mũi tên) tác
động vào đầu đòn mở của ly hợp, kéo đĩa ép tách ra khỏi đĩa ma sát.
Khi người lái nhả bàn đạp 8 thì dưới tác dụng của lò xo hồi vị 6, bàn đạp
trở về vị trí ban đầu duy trì khe hở giữa bạc mở với đầu đòn mở. Nhờ có các lò
xo ép để ép đĩa ép tiếp xúc với đĩa ma sát, ly hợp được đóng lại.
Hành trình toàn bộ của bàn đạp ly hợp thường từ 130 150 mm. Trong
quá trình làm việc, do hiện tượng trượt tương đối giữa các bề mặt ma sát, nên đĩa
ma sát thường bị mòn, do đó hành trình tự do của bàn đạp ly hợp bị giảm xuống.
Khi các bề mặt ma sát mòn tới mức nào đó thì hành trình tự do của ly hợp giảm
tới mức tối đa, sẽ không tạo được cảm giác cho người lái nữa, đồng thời gây hiện
tượng tự ngắt ly hợp. Trong trường hợp khác, khi hành trình tự do của bàn đạp ly
hợp quá lớn, làm cho người lái đạp bàn đạp hết hành trình toàn bộ mà ly hợp vẫn
chưa mở hoàn toàn, cũng tạo hiện tượng trượt tương đối giữa các bề mặt ma sát,
sẽ gây mòn các bề mặt ma sát một cách nhanh chóng.
Trong cả hai trường hợp nêu trên đều không có lợi, vì vậy phải điều chỉnh
hành trình tự do của bàn đạp ly hợp trong một miền cho phép. 22
Ưu điểm : Kết cấu đơn giản, dễ chế tạo, có độ tin cậy làm việc cao, dễ tháo lắp và sửa chữa.
Nhược điểm : Kết cấu phụ thuộc vào vị trí đặt ly hợp. Yêu cầu lực của
người lái tác dụng lên bàn đạp lớn. Hiệu suất truyền lực không cao. 23
3.2. Phương án 2 : Dẫn động ly hợp bằng thủy lực.
Đây là hệ thống dẫn động điều khiển ly hợp bằng cách dùng áp lực của
chất lỏng (dầu) trong các xilanh chính và xilanh công tác. 3 4 2 Qbđ 8 1 6 O 7 5
Hình 3.2.1.Sơ đồ hệ thống dẫn động ly hợp bằng thủy lực 1. Bàn đạp ly hợp ; 2. Lò xo hồi vị 3. Xilanh chính ; 4. Piston xilanh chính
5. Đường ống dẫn dầu ; 6. Xilanh công tác 7. Càng mở ly hợp ; 8. Bạc mở ly hợp 24 2 3 4 a 1 C b 5 E 6 D 12 11 10 9 8 7
Hình 3.2.2 Sơ đồ cấu tạo xilanh chính của dẫn động ly hợp bằng thủy lực 1. Xilanh ; 2. Bình chứa dầu ; 3. Nút đổ dầu vào 4. Tấm chắn dầu ; 5. Piston ; 6. Cần piston 7. Lá thép mỏng hình sao ; 8. Phớt làm kín 9. Lò xo hồi vị piston ; 10. Van một chiều 11. Lò xo van một chiều ; 12. Van hồi dầu a. Lỗ cung cấp dầu b. Lỗ điều hòa Nguyên lý làm việc :
Khi người lái tác dụng một lực Q lên bàn đạp ly hợp 1, nhờ thanh đẩy, đẩy
piston 4 của xilanh chính 3 sang trái, bịt lỗ bù dầu b, làm dầu trong khoang D bị
nén lại. Khi áp lực dầu trong khoang D thắng lực ép của lò xo van một chiều 11
ở van một chiều 10 thì van một chiều mở ra. Lúc này dầu từ khoang D theo 25
đường ống dẫn dầu 5 vào xilanh công tác 6 đẩy piston sang phải, làm cho càng
mở ly hợp 7 quay quanh O, đồng thời đẩy bạc mở 8 sang trái (theo chiều mũi
tên). Bạc mở tác động nên đầu dưới của đòn mở ly hợp tách đĩa ép ra khỏi bề
mặt ma sát. Ly hợp được mở.
Khi người thả bàn đạp ly hợp 1 thì dưới tác dụng của lò xo hồi vị 2 và lò
xo ép làm các piston của xilanh chính và xilanh công tác từ từ trở về vị trí ban
đầu. Lúc này dầu từ xilanh công tác 6 theo đường ống dẫn dầu 5 qua van hồi dầu 12 vào khoang D.
Khi người lái nhả nhanh bàn đạp ly hợp 1, thì do sức cản của đường ống
và sức cản của van hồi dầu 12 làm cho dầu từ xilanh công tác 6 không kịp về
điền đầy vào khoang D. Vì thế tạo ra độ chân không ở khoang D, nên dầu từ
khoang C qua lỗ cung cấp dầu a vào khoang E, rồi sau đó dầu qua lỗ nhỏ ở mặt
đầu piston ép phớt cao su 8 để lọt sang bổ sung dầu cho khoang D (tránh hiện
tượng lọt khí vào khoang D, khi khoang D có độ chân không). Khi dầu đã khắc
phục được sức cản của đường ống và van hồi dầu 12 để trở về khoang D, thì
lượng dầu dư từ khoang D theo lỗ bù dầu b trở về khoang C, đảm bảo cho ly hợp đóng hoàn toàn.
Lỗ bù dầu b còn có tác dụng điều hòa dầu khi nhiệt độ cao. Lúc nhiệt độ
cao dầu trong khoang D nở ra, làm áp suất dầu tăng lên, dầu qua lỗ bù dầu b về
khoang C. Vì thế khắc phục được hiện tượng tự mở ly hợp.
Ưu điểm : Kết cấu gọn, việc bố trí hệ thống dẫn động thủy lực đơn giản và
thuận tiện. Có thể đảm bảo việc đóng ly hợp êm dịu hơn so với hệ thống dẫn
động ly hợp bằng cơ khí. Ống dẫn dầu không có biến dạng lớn, nên hệ thống dẫn
động thủy lực có độ cứng cao. Đồng thời hệ thống dẫn động bằng thủy lực có thể
dùng đóng mở hai ly hợp. 26
Nhược điểm : Loại hệ thống dẫn động bằng thủy lực không phù hợp với
những xe có máy nén khí. Yêu cầu hệ thống dẫn động ly hợp bằng thủy lực cần có độ chính xác cao.
3.3. Phương án 3 : Dẫn động ly hợp bằng cơ khí có cường hóa khí nén.
Đây là hệ thống dẫn động điều khiển ly hợp bằng các thanh đòn, khớp nối.
Đồng thời kết hợp với lực đẩy của khí nén. 2 O1 1 3 Qbđ 19 18 6 O2 O4 4 5 O3 7 A B 16 8 14 17 9 a 15 10 11 12 13
Hình 3.3. Sơ đồ hệ thống dẫn động ly hợp bằng cơ khí có cường hóa khí nén 1. Bàn đạp ly hợp ; 3 ; 5. Thanh kéo
2 ; 4 ; 7 ; 8 ; 18. Đòn dẫn động ; 6. Lò xo hồi vị
9. Mặt bích của xilanh phân phối ; 10. Thân van phân phối 27
11. Đường dẫn khí nén vào ; 12. Phớt van phân phối 13. Đường dẫn khí nén ; 14. Piston van phân phối 15. Cần piston ; 16. Càng mở ly hợp 17. Xilanh công tác ; 19. Bạc mở ly hợp Nguyên lý làm việc :
Khi người lái tác dụng một lực Q lên bàn đạp ly hợp 1, làm cho đòn dẫn
động 2 quay quanh O1 , thông qua thanh kéo 3 làm đòn 4 quay quanh O2 và qua
thanh kéo 5 làm đòn dẫn động 7 quay quanh O3 . Nhờ có đòn dẫn động 8 cùng
với mặt bích của xilanh phân phối 9 và đẩy thân van phân phối 10 sang phải
(theo chiều mũi tên). Khi mặt phải của thân van phân phối chạm vào đai ốc hạn
chế hành trình nắp trên cần piston 15 thì làm cho càng mở ly hợp 16 quay quanh
O4 và đẩy bạc mở ly hợp 19 sang trái (theo chiều mũi tên). Ly hợp được mở.
Đồng thời với việc khi nắp bên phải của thân van phân phối tỳ vào đai ốc
hạn chế hành trình của cần piston 15 thì đầu piston van phân phối 14 cũng tỳ vào
phớt van 12 và làm van 12 mở ra. Khí nén lúc này từ khoang A qua van 12 vào
khoang B, rồi theo đường dẫn khí nén 13 vào xilanh 17 và đẩy xilanh lực dịch
chuyển làm đòn dẫn động 18 quay quanh O4 . Kết hợp với càng mở ly hợp 16
quay và đẩy bạc mở ly hợp 19 sang trái. Ly hợp được mở.
Khi người lái thôi tác dụng vào bàn đạp ly hợp 1 thì dưới tác dụng của lò
xo hồi vị 6 kéo bàn đạp trở về vị trí ban đầu. Đồng thời thông qua đòn dẫn động
8 kéo thân van phân phối 10 sang trái, khi mặt đầu bên phải của piston 14 chạm
vào mặt bích bên phải của thân van thì piston 14 được đẩy sang trái, làm càng
mở ly hợp 16 quay và đẩy bạc mở ly hợp 19 sang phải. Cùng lúc đó, dưới tác
dụng của lò xo hồi vị phớt van phân phối 12 và đẩy van này đóng kín cửa van.
Khí nén từ xilanh lực 17 theo đường dẫn khí nén 13 vào khoang B và qua đường 28
thông với khí trời a ở thân piston 14 ra ngoài. Lúc này ly hợp ở trạng thái đóng hoàn toàn.
Ưu điểm : Hệ thống dẫn động làm việc tin cậy, khi cường hóa khí nén
hỏng thì hệ thống dẫn động cơ khí vẫn có thể điều khiển ly hợp được.
Nhược điểm : Khi cường hóa hỏng thì lực bàn đạp lớn. Loại hệ thống dẫn
động này phù hợp với những xe có máy nén khí.
3.4. Phương án 4 : Dẫn động ly hợp bằng thủy lực có cường hóa khí nén.
Đây là hệ thống dẫn động điều khiển ly hợp bằng các thanh đòn và áp lực
của dầu trong các xilanh lực. Đồng thời kết hợp với áp lực của khí nén lấy từ các máy nén khí. 2 O1 Qbđ 1 17 19 18 20 21 16 15 14 13 12 3 A O2 11 5 B 4 6 8 9 10 29 7
Hình 3.4. Sơ đồ hệ thống dẫn động ly hợp bằng thủy lực có cường hóa khí nén 1. Bàn đạp ly hợp ; 2. Lò xo hồi vị 3. Xilanh chính ;
4 ; 13. Đường ống dẫn dầu 5. Xilanh công tác ; 6. Piston xilanh 7. Cần piston ; 8. Xilanh thủy lực 9. Piston xilanh thủy lực ;
10. Cần piston xilanh thủy lực 11. Càng mở ly hợp ; 12. Bạc mở ly hợp 14. Piston xilanh mở van ; 15. Cốc van phân phối 16. Màng ngăn ; 17. Van xả 18. Van nạp ;
19. Đường ống dẫn khí nén Nguyên lý làm việc :
Khi người lái tác dụng một lực Q lên bàn đạp ly hợp 1, làm cho tay đòn
bàn đạp quay quanh O1 và đẩy cần piston của xilanh chính 3 đi xuống (theo
chiều mũi tên). Dầu từ xilanh chính 3 được piston nén lại và theo đường ống dẫn
dầu 4 vào xilanh thủy lực 8. Áp lực dầu tác dụng vào mặt piston xilanh thủy lực
9 và đẩy nó cùng cần piston 10 sang phải. Làm cho càng mở ly hợp 11 quay
quanh O2 và đẩy bạc mở ly hợp 12 sang trái (theo chiều mũi tên). Ly hợp được mở.
Đồng thời dầu có áp suất theo đường ống dẫn dầu 13 tác dụng lên piston
xilanh mở van 14 thì đẩy piston 14 cùng cốc van 15 và màng ngăn 16 sang trái.
Đóng van xả 17 lại và van nạp 18 được mở ra. Khí nén từ máy nén khí theo
đường ống dẫn khí nén 19 qua van nạp 18 vào khoang A, rồi theo lỗ thông xuống
khoang B và đẩy piston xilanh 6 cùng cần piston 7 sang phải. Kết hợp với lực 30
đẩy của áp lực dầu, đẩy piston xilanh thủy lực 9 cùng cần piston 10 làm cho càng
mở ly hợp 11 quay quanh O2 và đẩy bạc mở ly hợp 12 sang trái. Ly hợp được mở.
Khi người lái thôi tác dụng vào bàn đạp ly hợp 1 thì dưới tác dụng của lò
xo hồi vị 2 kéo bàn đạp trở về vị trí ban đầu. Piston của xilanh chính 3 dịch
chuyển lên phía trên và dầu từ xilanh công tác trở về xilanh chính. Đồng thời van
xả 17 mở, van nạp 18 đóng lại. Khí nén từ khoang B qua lỗ thông sang khoang A
và qua van xả 17 rồi theo lỗ trên cốc van phân phối 15 thông với khí trời ra
ngoài. Ly hợp đóng hoàn toàn.
Ưu điểm : Hệ thống dẫn động làm việc tin cậy, khi cường hóa khí nén
hỏng thì hệ thống dẫn động bằng thủy lực vẫn hoạt động bình thường. Lực của
người lái tác dụng vào bàn đạp ly hợp nhỏ. Hành trình toàn bộ của bàn đạp
không lớn. Loại hệ thống dẫn động này thì đảm bảo được yêu cầu đóng ly hợp
êm dịu, mở dứt khoát và dùng phù hợp với những xe có máy nén khí.
Nhược điểm : Kết cấu phức tạp, bảo dưỡng, điều chỉnh sửa chữa khó khăn
và yêu cầu độ chính xác của hệ thống dẫn động cao. NHẬN XÉT :
Qua phân tích, tìm hiểu kết cấu, nguyên lý hoạt động, xem xét ưu
điểm và nhược điểm của từng phương án dẫn động điều khiển ly hợp, ta thấy
Phương án 2 : Dẫn động ly hợp bằng thủy lực có trợ lực chân không phù hợp
với việc thiết kế hệ thống ly hợp cho xe ôtô 7 chỗ trên cơ sở xe innova.
Phương án này đảm bảo nguyên tắc :
- Lực bàn đạp phải đủ lớn để có cảm giác mở ly hợp.
- Sử dụng phải chắc chắn nhẹ nhàng. 31
- Dễ chăm sóc, bảo dưỡng và sửa chữa. 32 CHƯƠNG III
NỘI DUNG THIẾT KẾ TÍNH TOÁN
1. XÁC ĐỊNH MÔMEN MA SÁT CỦA LY HỢP
Ly hợp cần được thiết kế sao cho nó phải truyền được hết mômen của
động cơ và đồng thời bảo vệ được cho hệ thống truyền lực khỏi bị quá tải. Với
hai yêu cầu như vậy mômen ma sát của ly hợp được tính theo công thức : Mc = . Me max
Trong đó : Me max - mômen xoắn cực đại của động cơ.
- hệ số dự trữ của ly hợp.
Hệ số phải lớn hơn 1 để đảm bảo truyền hết mômen của động cơ trong
mọi trường hợp. Tuy nhiên hệ số cũng không được chọn lớn quá để tránh tăng
kích thước đĩa bị động và tránh cho hệ thống truyền lực bị quá tải. Hệ số được chọn theo thực nghiệm.
Tra bảng 1 Sách hướng dẫn "Thiết kế hệ thống ly hợp của ôtô", ta xác định
hệ số dự trữ của ly hợp : Với ôtô con : = 1,3 1,75 → Ta chọn = 1,5
Vậy mômen ma sát của ly hợp :
Mc = . Me max = 1,5 . 18,6= 27,9kGm = 273,7 Nm
2. XÁC ĐỊNH KÍCH THƯỚC CƠ BẢN CỦA LY HỢP
2.1. Xác định bán kính ma sát trung bình của đĩa bị động
Mômen ma sát của ly hợp được xác định theo công thức :
Mc = . Me max = . P . Rtb . i
Trong đó : - hệ số ma sát. 33
P - tổng lực ép lên các đĩa ma sát (kG).
i - số đôi bề mặt ma sát.
Rtb - bán kính ma sát trung bình (cm).
Tính sơ bộ đường kính ngoài của đĩa ma sát theo công thức kinh nghiệm : M D emax 2 = 2 R2 = 3,16 C
Trong đó : Me max - mômen cực đại của động cơ, tính theo Nm.
D2 - đường kính ngoài của đĩa ma sát, tính theo cm. C - hệ số kinh nghiệm. Với ôtô con → C = 4,7 M 18,6.9,81 → D emax 2 = 2 R2 = 3,16 = 3,16 = 20cm =200 mm C 4,7
So sánh đường kính ngoài của đĩa ma sát với đường kính bánh đà động cơ
lấy theo xe tham khảo : Dbđ = 365 mm (đường kính trong lòng) thì ta thấy rằng
D2 = 200 mm < Dbđ = 365 mm Vậy ta chọn D2 =220mm
→ Bán kính ngoài của đĩa ma sát : R2 = 110 mm
Bán kính trong của đĩa ma sát được tính theo bán kính ngoài :
R1 = (0,53 0,75) R2 = (0,53 0,75) . 110 = (58,3 82,5) mm →
chọn trị số R1: R1 = 70 mm
Bán kính ma sát trung bình được tính theo công thức : 2 3 R − 3 R 2 3 110 − 3 70 R 2 1 tb = = = 90 mm 2 2 2 2 3 R − R 3 110 − 70 2 1
2.2. Xác định số lượng đĩa bị động Chọn i = 2,ta có:
Số đôi bề mặt ma sát được tính theo công thức : 34 M M i = c = c P R 2 Σ 2 R b [q] tb tb
Trong đó : Mc - mômen ma sát của ly hợp. Mc = 27,9 kGm
b - bề rộng tấm ma sát gắn trên đĩa bị động.
b = R2 - R1 = 110 - 70= 40 mm = 4 cm
[q] - áp lực riêng cho phép trên bề mặt ma sát.
Tra bảng 3 Sách hướng dẫn "Thiết kế hệ thống ly hợp của ôtô", với
nguyên liệu làm các bề mặt là thép với phêrađô → ta chọn hệ số ma sát : = 0,3
Tra bảng 3 Sách hướng dẫn "Thiết kế hệ thống ly hợp của ôtô", ta xác định áp lực riêng cho phép : [q] = 100 250 kN/m2 → Ta chọn [q] = 250 kN/m2 = 2,5 kG/cm2
=>Kiểm tra áp suất trên bề mặt ma sát theo công thức : M 100 . 9 , 27 q = c = = 2,28kG/cm2 2 R2 b i 9 . 14 , 3 . 2 2 . 4 . 2 . 3 , 0 tb
Vậy q = 2,28 kG/cm2 < [q] = 2,5 kG/cm2
Bề mặt ma sát bảo đảm đủ độ bền cho phép.
3. XÁC ĐỊNH CÔNG TRƯỢT SINH RA TRONG QUÁ TRÌNH ĐÓNG LY HỢP
Khi đóng ly hợp có thể xảy ra hai trường hợp :
- Đóng ly hợp đột ngột tức là để động cơ làm việc ở số vòng quay cao rồi
đột ngột thả bàn đạp ly hợp. Trường hợp này không tốt nên phải tránh.
- Đóng ly hợp một cách êm dịu : Người lái thả từ từ bàn đạp ly hợp khi xe
khởi động tại chỗ sẽ làm tăng thời gian đóng ly hợp và do đó sẽ tăng công trượt 35
sinh ra trong quá trình đóng ly hợp. Trong sử dụng thường sử dụng phương pháp
này nên ta tính công trượt sinh ra trong trường hợp này.
3.1. Xác định công trượt của ly hợp khi khởi động tại chỗ
Phương pháp này sử dụng công thức tính theo kinh nghiệm của Viện HAHM. 6 , 5 G M (n /10 ) 0 2 2 r L = e max o b
i i i ( 95 , 0 M
i − G r ) o h f e max t b Trong đó :
L - công trượt của ly hợp khi khởi động tại chỗ (KGm).
G - trọng lượng toàn bộ của ôtô. G = 2170 kG
Me max - mômen xoắn cực đại của động cơ. Me max = 18,6 kGm
no - số vòng quay của động cơ khi khởi động ôtô tại chỗ. Chọn
no = 0,75 ne max = 0,75 . 4000 = 3000 vg/ph
Với ne max là số vòng quay cực đại của động cơ. r
: Bán kính làm việc của lốp: với cỡ lốp 195/70/R14T b d = = + r .r .( B , 25 ). 4 b 0 2
: hệ số biến dạng của lốp, chọn loại lốp áp suất thấp; =0,935. d 14 r = .( + B) = 9 , 0 3 .( 5 +195/ , 25 , 25 ). 4 4 = 34 ( 9 ) mm = 3 , 0 4 ( 9 ). m b 2 2
it - tỉ số truyền của hệ thống truyền lực. it = io . ih . if = 18,664
io - tỉ số truyền của truyền lực chính. io = 4,53 36
ih - tỉ số truyền của hộp số chính. ih = ih1 = 4,12
if - tỉ số truyền của hộp số phụ. if = 1
- hệ số cản tổng cộng của đường. = f + tg f - hệ số cản lăn. ;
- góc dốc của đường.
Khi tính toán ta có thể chọn = 0,16
Vậy công trượt của ly hợp khi khởi động tại chỗ : 6 , 5 2170 9 , 27 3 ( 000/10 ) 0 2 3 , 0 482 L = = 4945 KGm 6 , 18 64 ( 95 , 0 9 , 27 6 , 18 64 − 2170 3 , 0 48 ) 16 , 0
3.2. Xác định công trượt riêng
Để đánh giá độ hao mòn của đĩa ma sát, ta phải xác định công trượt riêng theo công thức sau : L lo = [lo] (KGm/cm2) F i
Trong đó : lo - công trượt riêng.
L - công trượt của ly hợp (KGm).
F - diện tích bề mặt ma sát của đĩa bị động (cm2).
i - số đôi bề mặt ma sát. i = 2
[lo] - công trượt riêng cho phép.
Tra bảng 4 Sách hướng dẫn "Thiết kế hệ thống ly hợp của ôtô", ta xác định
công trượt riêng cho phép :
Với ôtô du lịch → [lo] = 10 12 KGm/cm2 L 4945 lo = = = 10,94 KGm/cm2 < [l o] (R2 − R2 ) i 14 , 3 11 ( 2 − 72 ) 2 2 1
Vậy công trượt riêng thỏa mãn điều kiện cho phép.
3.3. Kiểm tra theo nhiệt độ các chi tiết 37
Công trượt sinh nhiệt làm nung nóng các chi tiết như đĩa ép, đĩa ép trung
gian ở ly hợp 2 đĩa, lò xo, ...
Do đó phải kiểm tra nhiệt độ của các chi tiết, bằng cách xác định độ tăng
nhiệt độ theo công thức : .L .L T = = [T] c m 427 c G t t Trong đó :
L - công trượt sinh ra khi ly hợp bị trượt (KGm).
c - tỉ nhiệt của chi tiết bị nung nóng.
Với thép và gang c = 0,115 kcal/kG oC
mt - khối lượng chi tiết bị nung nóng(đĩa ép) (kG), mt=6kg
Gt - trọng lượng chi tiết bị nung nóng (kG).
- hệ số xác định phần công trượt dùng nung nóng chi tiết cần tính. 1 1 1
Với đĩa ép ngoài → = = = 2n 2 1 2
[T] - độ tăng nhiệt độ cho phép của chi tiết.
Với ôtô không có kéo rơmoóc : [T] = 8 oC 10 oC .L .L 5 , 0 4945 T = = = = 8,39 oC < [T] c m 427 c G 427 115 , 0 6 t t
Vậy đĩa ép thỏa mãn độ tăng nhiệt độ cho phép.
- Khi đĩa ép ngoài bị nung nóng thì lò xo ép cũng bị nung nóng nhưng có
độ tăng nhiệt độ còn nhỏ hơn độ tăng nhiệt độ của đĩa ép ngoài (do có đệm cách
nhiệt). Do vậy, ta không cần kiểm tra nhiệt độ của lò xo ép. 38
4. TÍNH TOÁN SỨC BỀN MỘT SỐ CHI TIẾT CHỦ YẾU CỦA LY HỢP
4.1. Tính sức bền đĩa bị động
Để giảm kích thước của ly hợp, khi ly hợp làm việc trong điều kiện ma sát
khô thì chọn vật liệu có hệ số ma sát cao. Vật liệu của tấm ma sát thường chọn là
loại phêrađô. Đĩa bị động gồm các tấm ma sát và xương đĩa. Xương đĩa thường
chế tạo bằng thép cacbon trung bình và cao. → Ta chọn thép 50
Chiều dày xương đĩa thường chọn từ (1,5 2,0) mm. Ta chọn x = 2 mm
Chiều dày tấm ma sát thường chọn từ (3 5) mm. Ta chọn = 4,5 mm
Hình 3.12. Cấu tạo đĩa bị động của xe 39
Tấm ma sát được gắn với xương đĩa bị động bằng đinh tán. Vật liệu của
đinh tán được chế tạo bằng đồng, có đường kính d = 4 mm. Đinh tán được bố trí
trên đĩa theo hai dãy tương ứng với các bán kính như sau :
Vòng trong : r1 = 8,5 cm = 85 mm
Vòng ngoài : r2 = 10 cm = 100 mm F2 F1 l r2 r1 d
Hình 3.13. Sơ đồ phân bố lực trên đinh tán
Lực tác dụng lên mỗi dãy đinh tán được xác định theo công thức : M r 6 , 18 100 5 , 8 F emax 1 1 = = = 46 kG 2 ( 2 2 r + r ) 2 5 , 8 ( 2 +102 ) 1 2 M r 6 , 18 10010 F emax 2 2 = = = 54 kG 2 ( 2 2 r + r ) 2 5 , 8 ( 2 + 102 ) 1 2 40
Đinh tán được kiểm tra theo ứng suất cắt và ứng suất chèn dập. F F c = [ [ c] ; cd = cd] (kG/cm2) d2 n l d n 4
Trong đó : c - ứng suất cắt của đinh tán ở từng dãy.
cd - ứng suất chèn dập của đinh tán ở từng dãy.
F - lực tác dụng lên đinh tán ở từng dãy.
n - số lượng đinh tán ở mỗi dãy. Vòng trong n1 = 12 đinh Vòng ngoài n2 = 12 đinh
d - đường kính đinh tán. d = 4 mm
l - chiều dài bị chèn dập của đinh tán. 1 1
l = chiều dày tấm ma sát. Ta có l = . 4,5 = 2,25 mm 2 2
[c] - ứng suất cắt cho phép của đinh tán. [c] = 100 kG/cm2
[cd] - ứng suất chèn dập cho phép của đinh tán. [cd] = 250 kG/cm2
Ứng suất cắt và ứng suất chèn dập đối với đinh tán ở vòng trong : F 46 1 c1 = = = 30,52 kG/cm2 < [ c] d2 14 , 3 , 0 42 n 12 1 4 4 F 46 1 cd1 = = = 42,59 kG/cm2 < [cd] n l d 12 , 0 225 , 0 4 1
Vậy các đinh tán đảm bảo độ bền cho phép.
Ứng suất cắt và ứng suất chèn dập đối với đinh tán ở vòng ngoài : F 54 2 c2 = = = 35,82 kG/cm2 < [ c] d2 14 , 3 , 0 42 n 12 2 4 4 41 F 54 2 cd2 = = = 50 kG/cm2 < [cd] n l d 12 , 0 225 , 0 4 2
Vậy các đinh tán đảm bảo độ bền cho phép.
4.2. Tính sức bền moayơ đĩa bị động
Chiều dài của moayơ đĩa bị động được chọn tương đối lớn để giảm độ đảo
của đĩa bị động. Moayơ được ghép với xương đĩa bị động bằng đinh tán và lắp
với trục ly hợp bằng then hoa.
Chiều dài moayơ thường chọn bằng đường kính ngoài của then hoa trục ly
hợp. Khi điều kiện làm việc nặng nhọc thì chọn L = 1,4 D (D là đường kính
ngoài của then hoa trục ly hợp).
Khi làm việc then hoa của moayơ chịu ứng suất chèn dập và ứng suất cắt
được xác định theo công thức : 4 M emax c = [c]
z z L b (D + d) 1 2 8 M emax cd = [cd] z z L (D2 − d2 ) 1 2
Trong đó : Me max - mômen cực đại của động cơ. Me max = 18,6 kGm
z - số then hoa của một moayơ. z = 10 L - chiều dài moayơ. L = 3 cm
D - đường kính ngoài của then hoa. D = 3,5 cm
d - đường kính trong của then hoa. d = 2,8 cm
b - bề rộng của một then hoa. b = 4 mm = 0,4 cm
Các thông số trên được chọn theo xe tham khảo.
Với vật liệu chế tạo moayơ là thép 40X thì ứng suất cho phép của moayơ là 42 [c] = 100 kG/cm2 ; [cd] = 200 kG/cm2 4 M 4 , 18 6 100 emax c = = = 98,4 kG/cm2 < [c] z L b (D + d) 10 3 , 0 4 5 , 3 ( + ) 8 , 2 8 M 8 , 18 6 100 emax cd = = = 123,94 kG/cm2 < [cd] z L (D2 − d2 ) 10 3 5 , 3 ( 2 − 8 , 2 2 )
Vậy moayơ đảm bảo độ bền cho phép.
Đinh tán nối moayơ với xương đĩa bị động thường làm bằng thép có đường kính d = (6 10) mm → Ta chọn d = 6 mm
Đinh tán được kiểm tra theo ứng suất cắt và ứng suất chèn dập c = F F [ [ c] ; cd = cd] (kG/cm2) d2 n l d n 4
Trong đó : F - lực tác dụng lên đinh tán. M 6 , 18 100 F = emax = = 186 kG 2 r 2 5
Với r - bán kính đặt đinh tán. r = 5 cm = 50 mm
n - số lượng đinh tán ở một moayơ. n = 4 đinh
d - đường kính đinh tán. d = 6 mm = 0,6 cm
l - chiều dài bị chèn dập của đinh tán. l = 0,4 cm
Vật liệu chế tạo đinh tán là thép 30 thì ứng suất cho phép của đinh tán là [c] = 300 kG/cm2 ; [cd] = 800 kG/cm2
Ứng suất cắt và ứng suất chèn dập đối với đinh tán ở moayơ : F 186 c = = = 164,54 kG/cm2 < [ c] d2 14 , 3 , 0 62 n 4 4 4 F 186 cd = = = 193,75 kG/cm2 < [cd] n l d 4 , 0 4 , 0 6 43
Vậy đinh tán đảm bảo độ bền cho phép.
4.3. Tính lũ xo màng
Xét quan hệ biên dạng và lực ép l? c nén lò xo màng lò xo tr? biên d?ng 44
Khi tỏc dụng lực vào lũ xo màng thỡ ban đầu cần 1 lực lớn hơn lực tác
dụng vào lũ xo trụ cho cựng 1 biến dạng, sau đó khi biến dạng tăng lên thỡ lũ xo
màng đảm bảo cho lực điều khiển người lái nhẹ đi.
Ta tớnh toỏn lũ xo màng. Dc Da Di Pn L2 L1 P De
Lực ép cần sinh ra để ép đĩa ép khi đóng ly hợp : M 273,7 P l = = =6082 (N) .R i. 0,25.0,092 . TB
Dựa trên cơ sở xe tham khảo và các yêu cầu trong việc lựa chọn,thiết kế lũ
xo màng ta chọn cỏc kớch thươc cơ bản sau:
D : Đường kính ngoài lũ xo màng D e e = 2 1 0 m m 45 : Đường kính trong D D i i = 7 0 m m
Chiều dày lũ xo màng ä= 2,5mm
Số thanh phân bố đều lên màng Z= 12
Lực tổng hợp P được thể hiện thông qua số kết cấu như sau: 1 L 2 .E .l n K 1- K l 1- K F= . . 1 . n .[ä2 + (h – l 1 1 1 1. .( h - . ))] 3 2 1- 2 D 2 (1- K ) 1- K 2 1- K P e 2 2 2 Trong đó : D K a 1= = 0,76 ( Da= 160mm) D e D K c 2= = 0,79 ( Dc= 166mm) D e
Môđun đàn hồi E = 2.105 ( N/mm2 )
Chiều cao h = ä.2,2= 2,5.2,2= 5,5(m)
(hệ số 2,2 đảm bảo vùng lực ép không đổi rộng và không lật lũ xo).
Dịch chuyển của đĩa tại điểm đặt lực ép l1= 2,2mm µ : hệ số µ P P= 0,26 Do vậy : 1 L 2 n 3,14.2.10 5 2,5.2 76 , 0 1- 0,76 2 1- 0,76 F= . . . .[2,52+(5,5–2. .(5,5- . ))] 3 2 1- , 0 26 2 210 2 (1- 79 , 0 ) 1- 79 , 0 2 1- 79 , 0 F= 6424(N)
So sánh ta thấy : F> P= 6082(N).Lực ép lớn hơn dẫn đến hệ số â
tăng lên.Ta tính lại hệ số â.
Ta có : Ml= â.Memax=µ.P.i.Rtb nên : 46 .P i.R 0,25.608 2 2 . . 0,09 = tb = =1,5. M 81 , 9 . 6 , 18 e max
Kết quả này nằm trong vùng cho phép của â(â=1,3-1,75)
Do vậy kích thước của lũ xo đạt tiêu chuẩn.
Lũ xo đĩa được tính bền bằng cách xác định ứng suất tại điểm chịu
tải nhất là tâm của phần tử đàn hồi giữa các thành mở với vũng đặc của hỡnh nún. Ứng suất được tính: 2FnDa E (D − Da) 2 2 + ó= + . 2 (Di + Da) 1 ( 2 2 − ) 2Da p De- Da - 210 160 Với D = = =184(mm) De 210 ln ln Da 160
Và =2h/(De-Da)= 2.5,5/(210-160)=0,2
ä độ biểu diễn của lũ xo màng, ä a a= %.ä = 4%.2,5 = 0,1(mm)
Fn lực cần tác dụng để ngắt ly hợp. De- Dc 21 - 0 166 Fn= P . = 6 . 082=4787(N) Dc − Di 166 − 70 5 2 2 − + Vậy 2.1911.160 2.10 1 ( 84 16 ) 0 , 0 2 1 , 0 ó= + . 5 , 2 2 (70 + ) 160 1 ( 2 , 0 262 − ) 1 . 2 60 = 9,14.108(N/m2)
Vật liệu chế tạo lũ xo màng là thộp 60T ứng suất giới hạn [ó]=14. 108(N/m2)
Vậy lũ xo màng đủ bền. 47
4.4. Tính toán lò xo giảm chấn của ly hợp
Lò xo giảm chấn được đặt ở đĩa bị động để tránh hiện tượng cộng hưởng ở
tần số cao của dao động xoắn do sự thay đổi mômen của động cơ và của hệ
thống truyền lực. Đồng thời đảm bảo truyền mômen một cách êm dịu từ đĩa bị
động đến moayơ trục ly hợp.
Mômen cực đại có khả năng ép lò xo giảm chấn được xác định sau : G r M b b max = i i i o h1 f
Trong đó : Gb - trọng lượng bám của ôtô (kG). → Gb = 2170.9,81= 21287 kG
- hệ số bám của đường, với đường tốt lấy = 0,8
rb - bán kính làm việc trung bình của bánh xe. rb = 0,349 m
io - tỉ số truyền của truyền lực chính. io = 4,53
ih1 - tỉ số truyền của hộp số ở số truyền 1. ih1 = 4,12
if - tỉ số truyền của hộp số phụ ở số truyền thấp. if = 1 G r 27287 8 , 0 349 , 0 M b b max = = = 318,46 kGm i i i 53 , 4 12 , 4 1 o h1 f
Mômen quay mà giảm chấn có thể truyền được bằng tổng mômen quay
của các lực lò xo giảm chấn và mômen ma sát.
Mmax = M1 + M2 = P1 . R1 . Z1 + P2 . R2 . Z2 Trong đó : 48
M1 - Mômen quay của các lực lò xo giảm chấn dùng để dập tắt dao động
cộng hưởng ở tần số cao.
M2 - Mômen ma sát dùng để dập tắt dao động cộng hưởng ở tần số thấp.
Thường lấy M2 = 25% Mmax = 25% . 31846 = 7961,5 kGcm →
M1 = Mmax - M2 = 31846 -7961,5 = 23884,5 kGcm
R1 - bán kính đặt lò xo giảm chấn. → Ta chọn R1 = 40 mm
Z1 - số lượng lò xo giảm chấn đặt trên moayơ. → Ta chọn Z1 = 4
R2 - bán kính trung bình đặt các vòng ma sát. → Ta chọn R2 = 65 mm
Z2 - số lượng vòng ma sát (số đôi cặp ma sát). → Ta chọn Z2 = 4
- hệ số ma sát giữa vòng ma sát và đĩa bị động. M 238845 , P 1
1 - lực ép của một lò xo giảm chấn. → P1 = = = 1492,8 R Z 4 4 1 1 kG M , 2802 75 P 2
2 - lực tác dụng lên vòng ma sát. → P2 = = = 107,8 kG R Z 5 , 6 4 2 2
Khi chưa truyền mômen quay, thanh tựa nối các đĩa sẽ có khe hở 1 , 2
tới các thành bên của moayơ.
Theo sơ đồ hình 3.16 ta có :
1 - khe hở đặc trưng cho biến dạng giới hạn
của lò xo khi truyền mômen từ động cơ. 1 d 2
2 - khe hở đặc trưng cho biến dạng giới hạn
của lò xo khi truyền mômen bám từ bánh xe. B
Độ cứng tối thiểu của lò xo giảm chấn (hay gọi là mômen quay tác dụng
lên đĩa bị động để xoay đĩa đi 1o so với moayơ).
Độ cứng được xác định theo công thức : 49 S = 17,4 . R 2 1 . K . Z1 (kGcm)
Trong đó : K - độ cứng của một lò xo (kG/cm). K = 1,3 kG/cm
Z1 = 6 - số lượng lò xo giảm chấn đặt trên một moayơ. S = 17,4 . R 2
1 . K . Z1 = 17,4 . 42 . 1,3 . 4 = 1447,68 kGcm
Các cửa sổ đặt lò xo của moayơ có kích thước chiều dài là A phải nhỏ hơn
chiều dài tự do của lò xo một ít, lò xo luôn ở trạng thái căng ban đầu,
thường chọn A = (25 27) mm Cửa sổ moayơ Cửa sổ ở tấm đệm → Ta chọn A = 25 mm
Khi chuyển mômen quay từ động cơ và
từ bánh xe qua bộ phận giảm chấn giống nhau
thì cửa sổ ở moayơ và ở đĩa bị động có chiều dài như nhau. A a
Ở các giảm chấn có độ cứng khác nhau, A1 R1
chiều dài cửa sổ moayơ phải bé hơn so với
cửa sổ ở đĩa một đoạn a = A1 - A
Thường a = (1,4 1,6) mm
Cạnh bên cửa sổ làm nghiêng 1 góc (1 1,5o) → Ta chọn 1,5o
Đường kính thanh tựa chọn d = (10 12) mm đặt trong kích thước lỗ B. → Ta chọn d = 12 mm
Kích thước lỗ B được xác định theo khe hở 1 , 2 . Các trị số 1 , 2 chọn
trong khoảng từ (2,5 4) mm. → Ta chọn 1 = 2 = 3,5 mm
Vậy kích thước đặt lỗ thanh tựa là :
B = d + 1 + 2 = 12 + 3,5 + 3,5 = 19 mm
Ứng suất xoắn của lò xo được xác định theo công thức : 8 P D k = 1 [] (kG/cm2) 3 d 50 Trong đó :
D' - đường kính trung bình của vòng lò xo, thường chọn D' = (14 19) mm → Ta chọn D' = 16 mm
d' - đường kính dây lò xo, thường chọn d' = (3 4) mm. Chọn d' = 4 mm
P1 - lực cực đại tác dụng lên một lò xo giảm chấn (kG).
Vật liệu chế tạo lò xo giảm chấn là thép 65, có ứng suất xoắn cho phép là
[] = (6500 8000) kG/cm2 → Ta chọn [] = 6500 kG/cm2 [ ] 6500 Pmax = P1 = = 1944 kG 8 d 3 D k 8 14 , 3 , 0 43 , 1 6 3 , 1
Số vòng làm việc của lò xo được xác định theo công thức : 4 G d no = 3 6 , 1 P D 1
Trong đó : G - môđun đàn hồi dịch chuyển. G = 8 . 105 kG/cm2
- độ biến dạng của lò xo giảm chấn từ vị trí chưa làm việc
đến vị trí làm việc, thường chọn = (2,5 4) mm → Ta chọn = 3 mm 4 G d 5 4 3 8 10 , 0 4 no = = = 4,82 vòng 5 vòng 3 6 , 1 P D 3 6 , 1 1944 6 , 1 1
Chiều dài làm việc của vòng lò xo được tính theo công thức (ứng với khe
hở giữa các vòng lò xo bằng không) : l1 = no . d = 5 . 4 = 20 m
Chiều dài của vòng lò xo ở trạng thái tự do :
l2 = l1 + + 0,5 d = 20 + 3 + 0,5 . 4 = 25 mm 51
4.5. Tính sức bền trục ly hợp
Trục ly hợp vừa là trục sơ cấp hộp số, đầu cuối của trục có cặp bánh răng
nghiêng luôn ăn khớp. Đầu trước của trục lắp ổ bi và đặt trong khoang của bánh
đà, đầu sau lắp ổ bi trên thành vỏ hộp số.
a. Chế độ tính toán trục ly hợp : Ta dùng mômen truyền từ động cơ xuống trục
ly hợp để tính toán, Me max = 18,6 kGm. Vì mômen truyền từ bánh xe chủ động
lên trục ly hợp (theo điều kiện bám) lớn hơn mômen truyền từ động cơ xuống trục ly hợp.
b. Tính các lực tác dụng lên cặp bánh răng luôn ăn khớp :
Các thông số của bánh răng nghiêng luôn ăn khớp :
- Đường kính đỉnh răng da = 126,05 mm - Đường kính vòng chia d = 111,72 mm - Đường kính chân răng df = 104,34 mm - Môđun pháp tuyến mn = 4,25 mm - Số răng Z = 25 - Góc nghiêng của răng
= 25o ; góc ăn khớp = 20o - Bề rộng vành răng B = 33,55 mm 2 M 2 M 2 6 , 18 1000 Tính lực vòng : P t emax = v1 = = = 332 N Z m m , 4 25 s Z n 25 co s o cos18 tg o tg20 Tính lực hướng tâm : Pr1 = Pv1 . = 332 . =127 N co s o cos18 Tính lực dọc trục :
Pa1 = Pv1 . tg = 332. tg18o =108 N
c. Tính các lực tác dụng lên cặp bánh răng gài số 1 : 52
Trục thứ cấp hộp số có đầu trục dưới được lắp ổ lăn và đặt vào khoang của
bánh răng luôn ăn khớp. Do vậy mà trục ly hợp cũng chịu một phần lực tác dụng
do trục thứ cấp gây ra (ta tính cho tay số 1).
Mômen tính toán trục thứ cấp ở tay số 1 : M 1
t = Me max . ih1 = 18,6 . 4,12 = 76,63 N 2 M 1 2 63 , 76 1000 Tính lực vòng : P t v2 = = = 601 N Z m 51 5
Trong đó : Z - số răng của bánh răng gài số 1. Z = 51 m - môđun pháp tuyến. m = 5 Tính lực hướng tâm :
Pr2 = Pv2 . tg = 601 . tg20o = 219 N Tính lực dọc trục : Pa2 = 0
(bánh răng trụ răng thẳng).
d. Tính các phản lực tác dụng lên trục ở vị trí lắp ổ lăn :
Tính các phản lực tại 2 gối đỡ trên trục thứ cấp hộp số : l3 = 308 l4 = 107 y 0 (3) (4) (5) z n3 x Fx23 Fy23 Fx25 Fy25 53 Fv2 Fr2
Xét mặt phẳng (xOz) và mặt phẳng (yOz). Giả sử các phản lực có chiều
như hình vẽ. Ta có hệ phương trình sau : Fx = Fx23 - Pv2 + Fx25 = 0
M3 (Fx) = Pv2 . l3 - Fx25 . (l3 + l4) = 0 Fy = Fy23 - Pr2 + Fy25 = 0
M3 (Fy) = Pr2 . l3 - Fy25 . (l3 + l4) = 0 Fx = Fx23 + Fx25 = 601
M3 (Fx) = 601. 308 - Fx25 . (308 + 107) = 185108 - Fx25 . 415 = 0 Fx25 = 446 N Fx23 = 601 - 446 = 155 N Fy = Fy23 + Fy25 = 219
M3 (Fy) = 219 . 308 - Fy25 . (308 + 107) = 67452 - Fy25 . 415 = 0 Fy25 = 163 N Fy23 = 219 - 163 =56 N
Các phản lực đều dương nên chiều của các phản lực theo giả thiết là đúng.
Tính các phản lực tại hai gối đỡ 0 và 1 trên trục ly hợp : l1 = 305 l2 = 41 Fy13 y Fy10 Fx11 Fx13 O z (0) n1 (2) Mz (1) (3) x Fx10 54 Fy11 Pa1 Pv1 Pr1
Nhận xét : Nếu ta gọi hai lực do trục thứ cấp tác dụng lên trục ly hợp tại vị
trí có bánh răng nghiêng là Fx13 và Fy13 . Hai lực này có giá trị tuyệt đối bằng hai
lực Fx23 và Fy23 trên trục thứ cấp, có điểm đặt vào bánh nghiêng luôn ăn khớp, có
phương chiều ngược với Fx23 và Fy23 .
Như vậy ta có : Fx13 = Fx23 = 155 N Fy13 = Fy23 = 56 N
Ta có thể coi đường tác dụng lực của hai lực Fx13 và Fy13 cùng nằm trong
mặt phẳng chứa đường tác dụng lực của Pv1 và Pr1 .
Xét mặt phẳng (xOz) và mặt phẳng (yOz). Giả sử các phản lực có chiều
như hình vẽ. Ta có hệ phương trình sau :
Fx = Fx10 - Fx11 + Pv1 - Fx13 = 0
Mo (Fx) = Fx11 . l1 - Pv1 . (l1 + l2) + Fx13 . (l1 + l2) = 0
Fy = Fy10 - Fy11 + Pr1 + Fy13 = 0 dw M a
o (Fy) = Fy11 . l1 - Pr1 . (l1 + l2) - Fy13 . (l1 + l2) + Pa1 = 0 2
Fx = Fx10 - Fx11 = Fx13 - Pv1 = 155 - 332 = - 177
Mo (Fx) = Fx11 . 305 - 332. (305 + 41) + 155 . (305 + 41) = 0
= Fx11 . 305 - 114872 + 53630 = 0 Fx11 = 201 N Fx10 = 201 - 177 = 24 N
Fy = Fy10 - Fy11 = - Pr1 - Fy13 = - 127 - 56 = - 183 55 , 111 72
Mo (Fy) = Fy11 . 305 - 127 . 346 - 56 . 346 + 108 . = 0 2
= Fy11 . 305 - 43942 - 19376 + 6033 = 0 Fy11 = 188N Fy10 = - 183 + 188 = 5 N
Các phản lực đều dương nên chiều của các phản lực theo giả thiết là đúng.
e. Tính các mômen trên trục ly hợp và vẽ biểu đồ mômen :
Ta đặt trục ly hợp trong hệ trục (Oxyz).
Như vậy trục ly hợp chịu uốn theo phương Ox và Oy, xoắn quanh Oz.
Mặt cắt A-A giữ lại bên trái : Mx = Mx - Fy10 . l1 = 0
Mx = Fy10 . l1 = 5 . 305 = 1525 Nmm My = My + Fx10 . l1 = 0
My = - Fx10 . l1 = - 24 . 305 = - 7320 Nmm
Mặt cắt B-B giữ lại bên trái :
Mx = Mx - Fy10 . (l1 + l2) + Fy11 . l2 = 0
Mx = Fy10 . (l1 + l2) - Fy11 . l2 =
= 5 . (305 + 41) - 188 . 41 = - 5978 Nmm
My = My + Fx10 . (l1 + l2) - Fx11 . l2 = 0
My = - Fx10 . (l1 + l2) + Fx11 . l2 =
= - 24 . (305 + 41) + 201 . 41 = -63 Nmm
Mặt cắt A-A giữ lại bên phải : dw M a
x = Mx - Fy13 . l2 - Pr1 . l2 + Pa1 = 0 2 56 dw M a
x = Fy13 . l2 + Pr1 . l2 - Pa1 = 2
= 56 . 41 + 127 . 41 - 108 . 55,86 = 1470 Nmm
My = My - Fx13 . l2 + Pv1 . l2 = 0
My = Fx13 . l2 - Pv1 . l2 = 155 . 41 - 332. 41 = - 7257 Nmm Mz = Mz - Pv1 . ra = 0
Mz = Pv1 . ra = 332 . 55,86 = 18546 Nmm
Vẽ biểu đồ mômen uốn và mômen xoắn. 57 l1 = 305 l2 = 41 Fy13 y Fy10 Fx11 Fx13 O z 2 (0) n1 Mz (1) (3) x Fx10 Fy11 Pa1 Pv1 Pr1 5978 Nmm Mx 1470 Nmm 7257 Nmm My Mz 18546 Nmm 58 59
f. Tính sức bền trục ly hợp :
Trục ly hợp được chế tạo bằng thép 40X, có ứng suất cho phép :
[th] = 500 700 kG/cm2 ; [c] = 300 kG/cm2 ; [cd] = 250 kG/cm2
Từ biểu đồ mômen, ta thấy rằng các vị trí trên trục ly hợp có tiết diện nguy hiểm cần được kiểm tra :
Tiết diện (11) lắp ổ lăn trên trục (kiểm tra theo bền uốn).
Tiết diện (12) lắp moayơ đĩa bị động (kiểm tra độ chèn dập then).
Tiết diện (13) có bánh răng luôn ăn khớp (tính độ võng góc xoay).
+ Tính bền trục ly hợp theo độ bền uốn và xoắn tại vị trí (11) : 2 2 M + M Ta có : u x th = [] (kG/cm2) 3 0,1 d
Trong đó : Mu - mômen uốn tác dụng lên trục ly hợp. M 2 2 u = 2 M + M = 2 1470 + 7257 =7404 Nmm x11 y11
Mx - mômen xoắn tác dụng lên trục ly hợp. Mx = Mz = 18546 Nmm
d - đường kính trục tại tiết diện nguy hiểm. d = 35 mm 2 2 M + M 2 2 7404 + 18546 u x th = = = 1,48 kG/mm2 = 148kG/cm2 3 0,1 d 3 1 , 0 35
Vậy th = 148 kG/cm2 < [] = 500 kG/cm2
Trục ly hợp đảm bảo độ bền uốn và xoắn tại vị trí (11).
+ Tính bền trục ly hợp tại vị trí có then hoa :
Các thông số cơ bản của then hoa được chọn theo xe tham khảo.
Đường kính đỉnh của then hoa : da = 35 mm
Đường kính chân của then hoa : df = 28 mm 60
Đường kính vòng chia của then hoa : d = 30 mm Bề rộng của then hoa : B = 4 mm Chiều cao của then hoa : h = 4 mm
Số lượng của then hoa : z = 10 Chiều dài của moayơ : l = 30 mm d + d
Đường kính trung bình của then hoa : d a f tb = = 31,5 mm 2
Tính ứng suất chèn dập của then hoa : 2 M 2 6 , 18 100 emax cd = = = 131 kG/cm2 < [cd] 0,75 z h l d 75 , 0 10 , 0 4 3 15 , 3 tb
Vậy cd = 131 kG/cm2 < [cd] = 250 kG/cm2
Then hoa của trục ly hợp đảm bảo độ bền chèn dập.
+ Tính bền trục theo độ cứng vững (tại vị trí bánh răng luôn ăn khớp) :
Tính độ võng của trục ly hợp :
Độ võng của trục trong mặt phẳng (yOz) : l 2 (l + l ) r l (2l + 3l ) f 2 1 2 a 2 1 2 đ = (Pr1 + Fy13) . - Pa1 . 3EJ 6EJ Trong đó :
ra - bán kính vòng lăn của bánh răng luôn ăn khớp.
E - môđun đàn hồi của vật liệu. E = 2 . 104 kG/mm2
J - mômen quán tính của tiết diện trục. d4 . 14 , 3 624 J = = = 724964 mm2 64 64
Với d = 62 mm - đường kính của trục tại vị trí
có bánh răng luôn ăn khớp. 61 12 4 305 ( + 4 ) 1 5 86 , 5 41 (2 + 305 3 41) fđ = (466 + 263) . - 395 . = 3 2 4 10 724964 6 2 4 10 724964 = 0,00212 mm
Độ võng của trục trong mặt phẳng (xOz) : l 2 (l + l ) r l (2l + 3l ) f 2 1 2 a 2 1 2 n = (Pr1 + Fx13) . - Pa1 . 3EJ 6EJ 12 4 305 ( + 4 ) 1 5 86 , 5 41 (2 + 305 3 41) fn = (127+ 155) . - 108 . = 3 2 4 10 724964 6 2 4 10 724964 = 0,00828 mm
Độ võng tổng hợp trong hai mặt phẳng (xOz) và (yOz) : f = 2 2 f + f = 2 2 00212 , 0 + , 0 00828 = 0,0085 mm d n
Vậy f = 0,0085 mm < [f] = 0,1 mm
Độ võng của trục ly hợp đạt yêu cầu cho phép.
Tính góc xoay của trục tại vị trí có bánh răng luôn ăn khớp :
Góc xoay của trục trong mặt phẳng (yOz) : l (2l + l 3 ) r (l + 3l ) 2 1 2 a 1 2 đ = (Pr1 + Fy13) . - Pa1 . 6EJ EJ 3 1 4 (2 305 + 3 4 ) 1 5 86 , 5 (30 + 5 3 41) đ = (127 + 56) . - 108 . = 6 2 4 10 724964 3 2 4 10 724964 = 0,000035 rad
Góc xoay của trục trong mặt phẳng (xOz) : l (2l + l 3 ) r (l + 3l ) 2 1 2 a 1 2 n = (Pr1 + Fx13) . - Pa1 . 6EJ EJ 3 1 4 (2 305 + 3 4 ) 1 5 86 , 5 (30 + 5 3 41) đ = (127 + 155) . - 108 . = 6 2 4 10 724964 3 2 4 10 724964 = 0,00019 rad
Góc xoay tổng hợp trong hai mặt phẳng (xOz) và (yOz) : 62 = 2 2 + = 2 2 0 , 0 00035 + 0 , 0 0019 = 0,00019 rad d n
Vậy = 0,00019 rad < [] = 0,001 rad
Góc xoay của trục ly hợp đạt yêu cầu cho phép. CHƯƠNG IV
THIẾT KẾ TÍNH TOÁN HỆ DẪN ĐỘNG LY HỢP 63
THIẾT KẾ TÍNH TOÁN HỆ DẪN ĐỘNG THỦY LỰC
CÓ TRỢ LỰC CHÂN KHÔNG.
I.XÁC ĐỊNH LỰC VÀ HÀNH TRèNH CỦA BÀN ĐẠP KHI KHÔNG CÓ TRỢ LỰC Sơ đồ dẫn động l1 l2 d b a c 2 a c d i 2 dd= . . 1 b d d1 64 Ta có: a = 360mm b = 50mm c = 180mm d = 50mm
( khảo sát xe tham khảo) 2 d 2 = 0,852 2 d1 360 180 idd= 2 . 85 , 0 . =18,72 50 50 F 4787 Vậy lực bàn đạp : Q n bd= = =256(N) i 18,72 dd
• Xác định hành trỡnh bàn đạp
Hành trỡnh bàn đạp được xác định theo công thức: St= Slv+ S0 Trong đó :
St : là hành trỡnh tổng( toàn bộ) của bàn đạp ly hợp
S : là hành trỡnh tự do của bàn đạp để khắc phục khe hở o So được tính: 2 a c d S 2 = o= . . . i . 2 dd b d d1
ä: khe hở giữa bi mở và đầu nhỏ của lũ xo, chọn : ä= 3mm S0= 3.18,72=56,16
S : là hành trỡnh làm việc của bàn đạp để khắc phục khe hở giữa các bề lv mặt ma sát , Slv= idd.L2 65
Hành trỡnh của đầu nhỏ lũ xo đĩa D - D l c i 2= l 1 D − D e c
Trong đó : l1 là hành trỡnh làm việc của đầu to lũ xo đĩa để mở ly hợp, chọn l1= 2mm 16 - 6 70 l2= 2. = 4,36(mm) 210− 166
Slv= 18,72.4,36 =81,6(mm)
Suy ra S = 81,6 + 56,16 = 138(mm).Hành trỡnh này nằm trong giới hạn cho t phộp [St]= 150mm
II.THIẾT KẾ DẪN ĐỘNG THỦY LỰC
1.Thiết kế tính toán xilanh công tác
a.Xác định kích thước
Hành trỡnh làm việc của piston cụng tỏc S2 được xác định : c S2=S . 1 d
Trong đó hành trỡnh của bi mở S1
S1= l2+ ä =4,36 + 3 = 7,36(mm) S2= 7,36.180/50 =26,5(mm)
Ta xác định được thể tích dầu trong xi lanh công tác: S d 2 V 2 2 2 = 4
d = 22 mm( giữ nguyên đường kính xi lanh công tác) 2 22 . 14 , 3 2 26,5. V2 = = 10068(mm3) 4 66
Chọn chiều dày ống t =4mm
b.Kiểm tra bền xilanh công tác
Đường kính ngoài: D2= d2+ 2t = 22+2.4 = 30(mm) D + d 30+ 22 R 2 2 tb= = = 13(mm) 4 4
Nhận thấy t > 0,1Rtb2 nên ta kiểm tra bền xy lanh công tác theo ứng suất sinh ra trên ống dây: Ứng suất hướng tâm: 2 2 b P 1 a − 2 r är= 2 2 b − a 2 2 b P 1 a + 2 r ä0= 2 2 b − a A B A B P 67 2 a + 2 b 2 a 2 P P 2 2 2 a − b a − 2 b Trong đó: P: áp suất trong ống: a d 2 360 2 Q . . 2 bđ . 256 . 85 , 0 b d 21 P = 50 = =3,05.106(N/m2) 2 d 14 , 3 2 2 . , 0 022 4 4
r :khoảng cách từ điểm xét đến đường tâm ống D 30 b: bán kính ngoài b = 2 = = 15mm 2 2 d 22 a: bán kính a = 2 = = 11 mm 2 2
Từ biểu đồ mômen ta thấy rằng điểm nguy hiểm nằm ở mép trong A của ống .
Theo thuyết bền ứng suất lớn nhất a2 + b2 0 , 0 112 6 + 0 , 0 152 A = A = A = p +1 = 10 . 05 , 3 +1 =8,9.106(N/ m2) td r 2 2 2 2 b − a 0 , 0 15 − 0 , 0 11
Vật liệu chế tạo xylanh là gang CY24-42 có [ó]= 2,4. 107(N/ m2). So sánh A
< [ó], do vậy xylanh công tác đủ bền td
2.Tính toán thiết kế xylanh chính
* Xác định các kích thước 2 d
Hành trỡnh xylanh chớnh : S 2 3= S2. = 26,5.0,852=19,14(mm) 2 d1 68
Thể tích dầu thực tế trong xylanh chính fải lớn hơn tính toán một ít do
hiệu suất dẫn động dầu <1.
Nên thể tích dầu là V3= V2.1,1= 10068.1,1=11074,8(mm3)
Đường kính trong d =26mm,chiều dày t=4mm 1
*Kiểm tra độ bền xylanh chính
Đường kính ngoài: D1=d1+ 2t= 26 + 2.4= 34(mm) D + d 34+ 26 R 1 1 tb= = =15(mm) 4 4
Nhận thấy t<0,1Rtb nên ta kiểm tra bền xylanh chính theo ứng suất sinh ra trên ống dày.
Tương tự như kiểm tra xylanh chính
Ứng suất lớn nhất là mép trong (A) của ống a2 + b2 A = p +1 song ở đây td 2 2 b − a d a = 1 = 13(mm) 2 D b = 1 = 17(mm) 2 0 , 0 172 + 0 , 0 132 => A = 05 , 3 +1 =9,87. 106(N/ m2) td 2 2 0 , 0 17 − 0 , 0 13
Vậy xylanh chính đủ bền. 69
III.THIẾT KẾ BỘ TRỢ LỰC CHÂN KHÔNG
1.Xác định lực mà bộ cường hóa phải thực hiện
Ta đó cú khi khụng cường hóa lực tác động bàn đạp Qbđk= 256(N)
Đề giảm bớt sức lao động của người lái ta lắp thêm bộ trợ lực tác động lên bàn
đạp ta chọn là : Qbđc= 70(N).Ta bố trí cường hóa ngay trước xylanh chính về phía
bàn đạp khi đó ta xác định được lực mà bộ cường hóa phải sinh ra :
Qc=( Qbđk- Qbđc)a/b = ( 256-70).360/50=1339(N)
Vậy bộ cường hóa chân không phải sinh ra 1 lực là 1339(N) và ta chọn lực để
mở van cường hóa là Qm= 30N.
2. Xác định thiết diện màng sinh lực và hành trỡnh màng sinh lực Q + P S = c max P Trong đó: Qc= 1339(N)
Pmax là lực lớn nhất tỏc dụng lờn lũ xo,chọn Pmax= 15%Qc
S: tiết diện màng sinh lực
P: độ chênh áp suất trước và sau màng sinh lực
Chọn P= 5. 104(N/m2) ứng với chế độ làm việc không tải của động cơ. Vậy ta có : 70 1339 + 201 S= = 30797(mm2) 05 , 0 S 4 4.30797
=>đường kính màng sinh lực = = =210(mm) m 14 , 3
Hành trỡnh màng sinh lực Sm= S3=19,14(mm) Lấy Sm= 20(mm)
3.Tớnh lũ xo hồi vị màng sinh lực
Khi bộ cường hóa sinh hết lực của mỡnh thỡ lỳc đó lũ xo hồi vị chịu tải
lớn nhất. Để xác định được kích thước lũ xo hồi vị ta chọn tải trọng lớn nhất tác dụng lên nó là: Pmax= 15%Qc= 15%.1339=201(N)
Lực lũ xo ghộp ban đầu Pbđ= 7%.Qc=94(N) 4 .G.d
Xác định số vũng làm việc của lũ xo; no= 803 (P − P ) max bđ
: độ biến dạng của lũ xo từ vị trớ chưa làm việc đến vị trí làm việc =Sm= 20(mm)
G: modun đàn hồi dịch chuyển G = 8.1010N/m2)
d: đường kính dày làm lũ xo,chọn d = 3(mm)
D: đường kính trung bỡnh của lũ xo giảm chấn 71 Chọn D = 34(mm) . 02 , 0 2 4 8.10 .0,003 Vậy n =4,5 vũng o= 803 034 , 0 . 2 (201− ) 94
Số vũng toàn bộ của lũ xo : n = n + 1 = 5,5 vũng o
Giả thiết khe hở cực tiểu giữa cỏc vũng lũ xo này khi mở hết ly hợp là
ä= 1,5mm.Nờn chiều dài tự nhiờn của lũ xo là :
l = nd + äd + Sm= 5,5.3 + 1,5.4,5 + 20 = 44(mm)
Lũ xo được kiểm bền theo ứng suất xoắn P 8 k . D . = max 3 d .
Trong đó k là hệ số ảnh hưởng k = 1,13 13 , 1 . 034 , 0 . 201 . 8 => = = 3,4.108(N/m2) 3 003 , 0 . 14 , 3
Vật liệu chế tạo lũ xo là thộp 60T có ứng suất cho phép là [ ]=7.
108(N/m2) nờn lũ xo đủ bền. 72 CHƯƠNG V
QUY TRÌNH CÔNG NGHỆ GIA CÔNG CHI TIẾT
CHI TIẾT: PISTON CHÍNH
I.NHIỆM VỤ VÀ KẾT CẤU 1.Kết cấu piston
2.Chức năng và điều kiện làm việc của piston
Piston nhận lực từ ty đẩy xy lanh chính,piston nén dầu tạo áp suất cao.Như
vậy yêu cầu piston có độ kín khít cao với xylanh.Yêu cầu bề mặt làm việc của
piston có độ bong cao nhằm giảm ma sát với xylanh.Do đó giảm sự mũn của
piston và xy lanh,tăng độ tin cậy khi làm việc.
3.Yêu cầu kỹ thuật đối với piston
a.Vật liệu chế tạo : nhôm hợp kim
b.Đạt độ bóng và dung sai như ghi trên bản vẽ. 73
c.Các kích thước không ghi dung sai thỡ lấy bằng dung sai của mỏy tạo ra kớch thước đó.
d.Dung sai độ đồng trục của mặt trụ làm việc là 0,15mm.
e.Nhiệt luyện đạt độ cứng 50HRC.
II.PHÂN TÍCH TÍNH CÔNG NGHỆ VÀ CHỌN CHUẨN GIA CÔNG 1.Tính công nghệ.
Chi tiết piston có tính công nghệ,điều kiện kĩ thuật có thể gia công được
kết cấu của piston phù hợp với điều kiện làm việc,công nghệ lắp ráp đơn giản,khi
chọn chuẩn và gá đặt chi tiết khi gia công.
2.Chọn chuẩn công nghệ.
Do yêu cầu của độ đồng tâm cao và độ ô van nhỏ.Ta chọn mặt cắt ngoài
làm chuẩn thô để gia công piston.Tiếp đó gia công 2 lỗ tâm và lấy 2 lỗ tâm làm
chuẩn tinh để gia công các kích thước khác của piston.
3.Phương pháp chế tạo phôi.
Dựa vào đặc điểm tính chất và hỡnh dạng của chi tiết ( piston ) gia
cụng, ta chọn phương pháp chế tạo phôi là phương pháp đúc ly tâm với đường
kính phôi đúc ø33, lượng dư gia công cơ khí d
= 5mm… Vật liệu bằng nhôm
hợp kim.Phần kích thước của mặt côn sau khi đúc xong không fải gia công lại.
4.Phương pháp gia công chi tiết.
Do phương pháp gia công không phức tạp,với số lượng ít nên ta gia
công chi tiêt trên máy thông dụng và đồ gá vạn năng sẵn có để gia công chi
tiết,như vậy việc gia công chi tiết thuộc loại đơn chiếc. 5.Đồ gá.
Ta dùng đồ gá vạn năng để gia công chi tiết,làm như vậy để hạ giá thành sản phẩm.
III.CÁC NGUYÊN CÔNG GIA CÔNG CHI TIẾT
1.Nguyên công 1: khỏa mặt tiện thô, khoan 2 lỗ tâm 74 0,2 b 21 b n 2 n n1 s s2 1 R10 54±0,3
Tiện thô mặt ngoài và khỏa hai mặt đầu Khoan 2 lỗ tâm : a.Bước 1:
Tiện thô mặt ngoài dầu(A) đạt ø30mm
Thực hiện trên máy tiện T614 Dao P9( thép gió)
Lượng chạy dao S = 0,25mm/vũng Chiều sâu cắt t = 1mm
Tốc độ máy n = 1380 vũng/phỳt b.Bước 2 :
Khỏa 2 mặt đầu đạt I = 49mm
Thực hiện trên máy T614 Dao P9( thép gió )
Lượng chạy dao S = 0,25 mm/vũng
Chiều sâu cắt t = 1,15mm
Tốc độ máy n = 1380 vũng/phỳt c.Bước 3 :
Khoan lỗ tâm (A) ø4mm,chiều sâu lỗ I = 2,5mm
Thực hiện trên máy T614 Dao mũi khoan ø5
Lượng chạy dao S = 0,14 mm/vũng 75 Chiều sâu cắt t = 0,2mm
Tốc độ máy n = 1380 vũng/phỳt d.Bước 4 :
Khoan lỗ tâm đầu (B) ø6mm,chiều sâu lỗ I = 21mm
Thực hiện trên máy T614 Dao P9( thép gió )
Lượng chạy dao S = 0,14 mm/vũng Chiều sâu cắt t = 0,2mm
Tốc độ máy n = 1380 vũng/phỳt. 76
2.Nguyờn cụng 2 : Tiện tinh,hạ bậc và tiện rónh lắp phớt. 10 8 4 1, ±062 n a.Bước 1 :
Tiện tinh mặt ngoài đạt ø26+0,5 Chống tu vào 2 lỗ tâm.
Thực hiện trên máy tiện T614 Dao DTP9 1250
Lượng chạy dao S = 0,25mm/vũng Chiều sâu cắt t = 0,5mm
Tốc độ máy n = 1380vũng/phỳt b.Bước 2
Hạ bậc đầu (B) đạt ø26mm
Thực hiện trên máy tiện T614 Dao DTP9 1250
Lượng chạy dao S = 0,25mm/vũng Chiều sâu cắt t = 0,5mm
Tốc độ máy n = 1380vũng/phút 77 c.Bước 3 :
Tiện rónh lắp phớt đạt ø19±0,1
Thực hiện trên máy tiện T614 Dao DTP9 1250
Lượng chạy dao S = 0,25mm/vũng Chiều sâu cắt t = 0,3mm
Tốc độ máy n = 1380vũng/phỳt. 78
3.Nguyên công 3 : khoan 4 lỗ ø2,5 ở đầu. 1 n s1 10
Dùng định vị kẹp chữ vê (V)
Xác định tâm của 4 lỗ
Thực hiện trên máy khoan A2-952
Dùng dao định hỡnh chỏm cầu
Lượng chạy dao S = 0,14mm/vũng Chiều sâu cắt t = 0,2mm
Tốc độ máy n = 980 vũng/phỳt. 79
4. Nguyên công 4 : Doa lỗ đặt ty đẩy . S n 2, ±02 r3,8±0,2 2
Dùng định vị kẹp chữ vê (V)
Xác định tâm của 4 lỗ
Thực hiện trên máy khoan A2-952 Dao mũi khoan ø2
Lượng chạy dao S = 0,14mm/vũng Chiều sâu cắt t = 0,5mm
Tốc độ máy n = 980vũng/phỳt 80
5.Nguyờn cụng 5 : Mài trũn mặt ngoài theo chiều dài của piston. 3,2 n n1 Mài tinh đạt ø26±0,1
Thực hiện trên máy mài 3 −12 Dùng đá mài 1k450-125
Tốc độ máy n =450vũng/phỳt 1
Tốc độ máy n = 2250 vũng/phỳt 2
Lượng chạy dao S = 1,14mm/vũng
Chiều sâu cắt t = 0,06 mm. 81
6.Nguyên công 6 : kiểm tra. n
Kiểm tra kích thước bằng thước cặp
Kiểm tra độ vuông góc,độ trũn, độ đồng trục bằng đồng hồ kiểm.
Kiểm tra độ nhám bằng thiết bị quang học.
TÀI LIỆU THAM KHẢO 82
1. Hướng dẫn đồ án môn học
“Thiết kế hệ thống ly hợp của Ôtô - Máy kéo”
Lê Thị Vàng - Hà Nội 1992
2. Tập bài giảng “Thiết kế tính toán Ôtô”
PGS. TS. Nguyễn Trọng Hoan - Hà Nội 2003
3. Bài giảng “Cấu tạo Ôtô”
Phạm Vỵ , Dương Ngọc Khánh - Hà Nội 2004
4. Sổ tay Ôtô
Bộ giao thông vận tải Liên Xô
Viện nghiên cứu khoa học vận tải ôtô
Nhà xuất bản công nhân kỹ thuật - Hà Nội 1984
5. Bản vẽ kết cấu ly hợp Ôtô - Máy kéo
Người soạn : Nguyễn Hữu Cẩn - Xuất bản 1966
6. Sổ tay “Công nghệ chế tạo máy” - 3 tập
GS. TS. Nguyễn Đắc Lộc , PGS. TS. Lê Văn Tiến
PGS. TS. Ninh Đức Tốn , PGS. TS. Trần Xuân Việt
Nhà xuất bản khoa học và kỹ thuật - Hà Nội 2003
7. Atlas Đồ gá
PGS. TS. Trần Văn Địch - Hà Nội 2003
8.Sức bền vật liệu tập 1,2
Chủ biên Lê Quang Minh-Nguyễn Văn Vượng
Nhà xuất bản giáo dục 2000.
9.Cấu tạo gầm xe con
Tác giả Nguyễn Khắc Trai
Nhà xuất bản khoa học và kỹ thuật - Hà Nội 2003. KẾT LUẬN 83
Sau thời gian làm đồ án, được sự h ướng dẫn tận tình của thầy
Nguyễn Trọng Hoan cũng như sự giúp đỡ của các thầy giáo khác
trong bộ môn, em đã hoàn thành những yêu cầu và nhiệm vụ của Đồ
án tốt nghiệp.
Trong đồ án này em đã thiết kế hệ thống ly hợp theo mẫu xe
tham khảo INNOVA với hệ dẫn động thủy lực có trợ lực chân không.
Do thời gian có hạn và vốn kiến thức còn hạn chế nên đồ án tốt
nghiệp không thể tránh khỏi những thiếu sót, em mong các thầy giáo
chỉ bảo để sửa chữa, rút kinh nghiệm để khi ra tr ường trở thành một
kỹ sư có trình độ vững vàng hơn.
Một lần nữa em xin chân thành cảm ơn sự h ớng dẫn tận tình
của thầy Nguyễn Trọng Hoan cùng sự giúp đỡ tận tình của các thầy giáo khác trong bộ môn! 84