
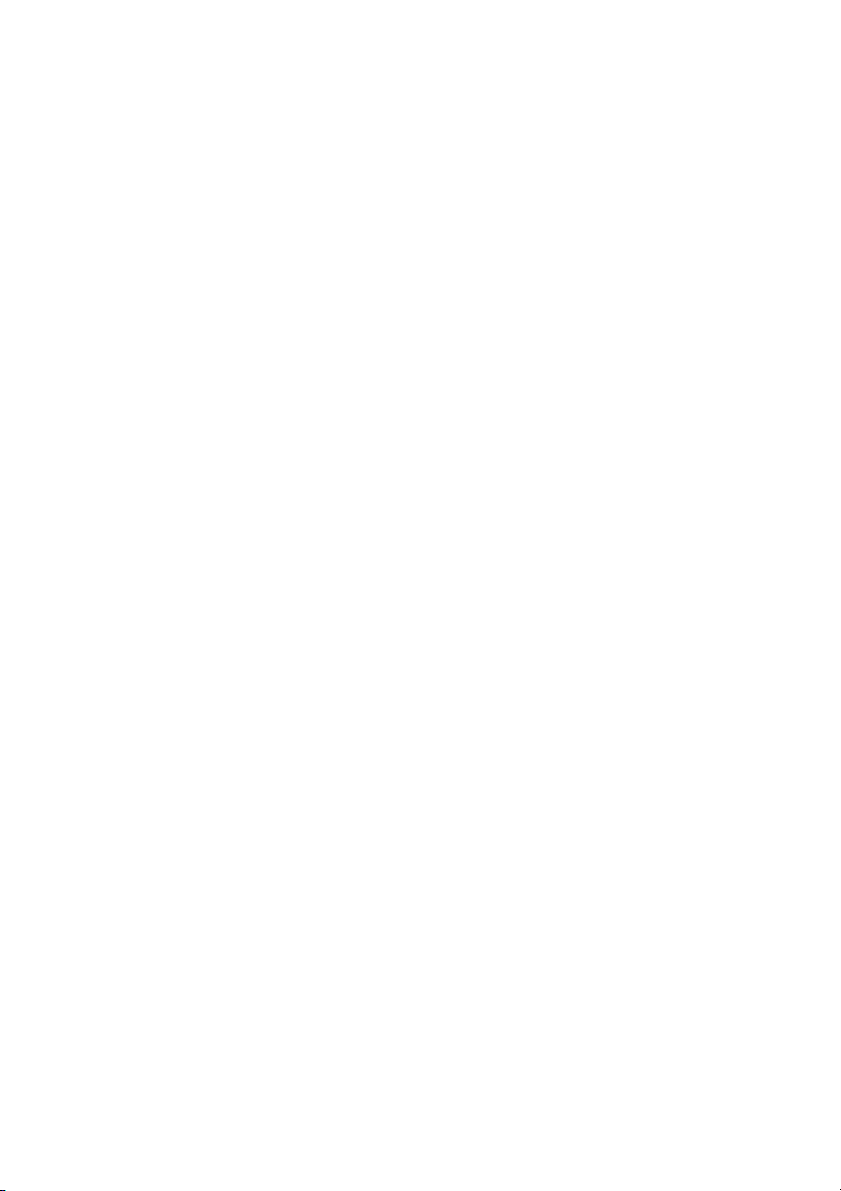
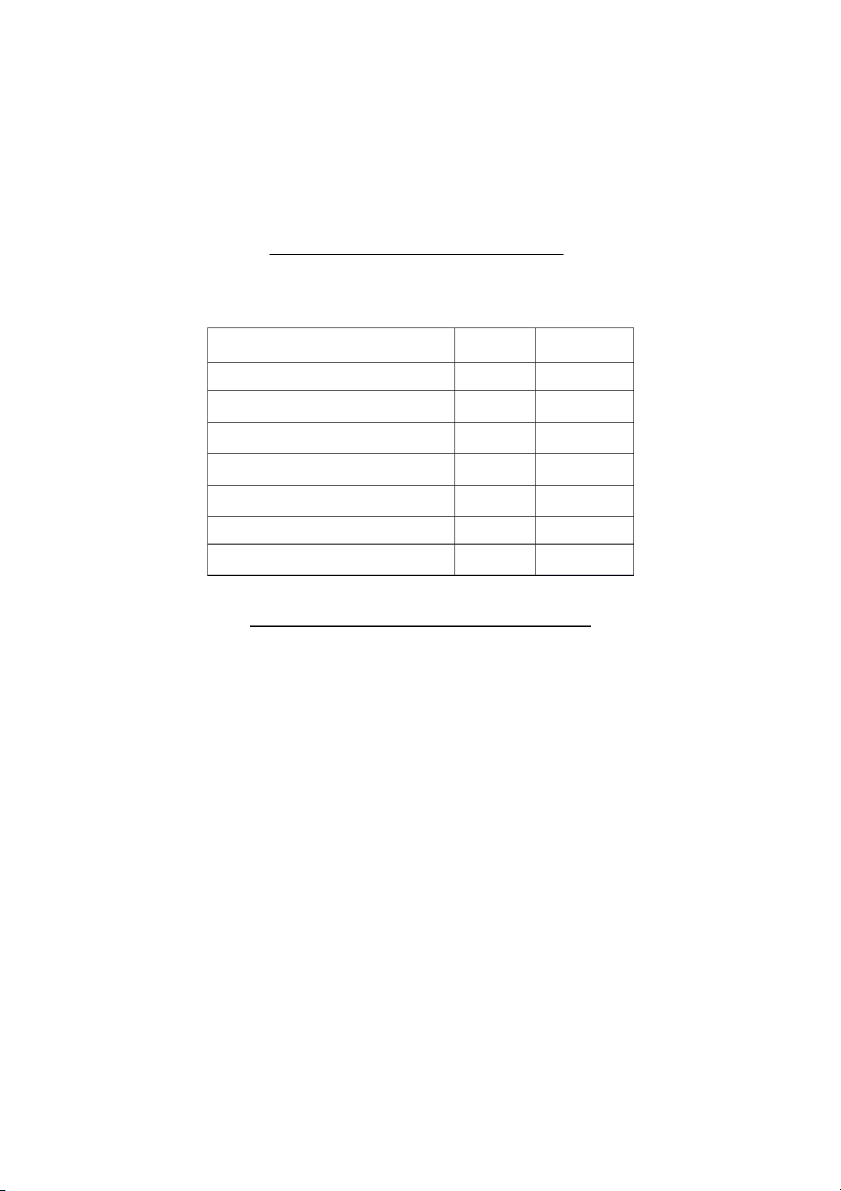
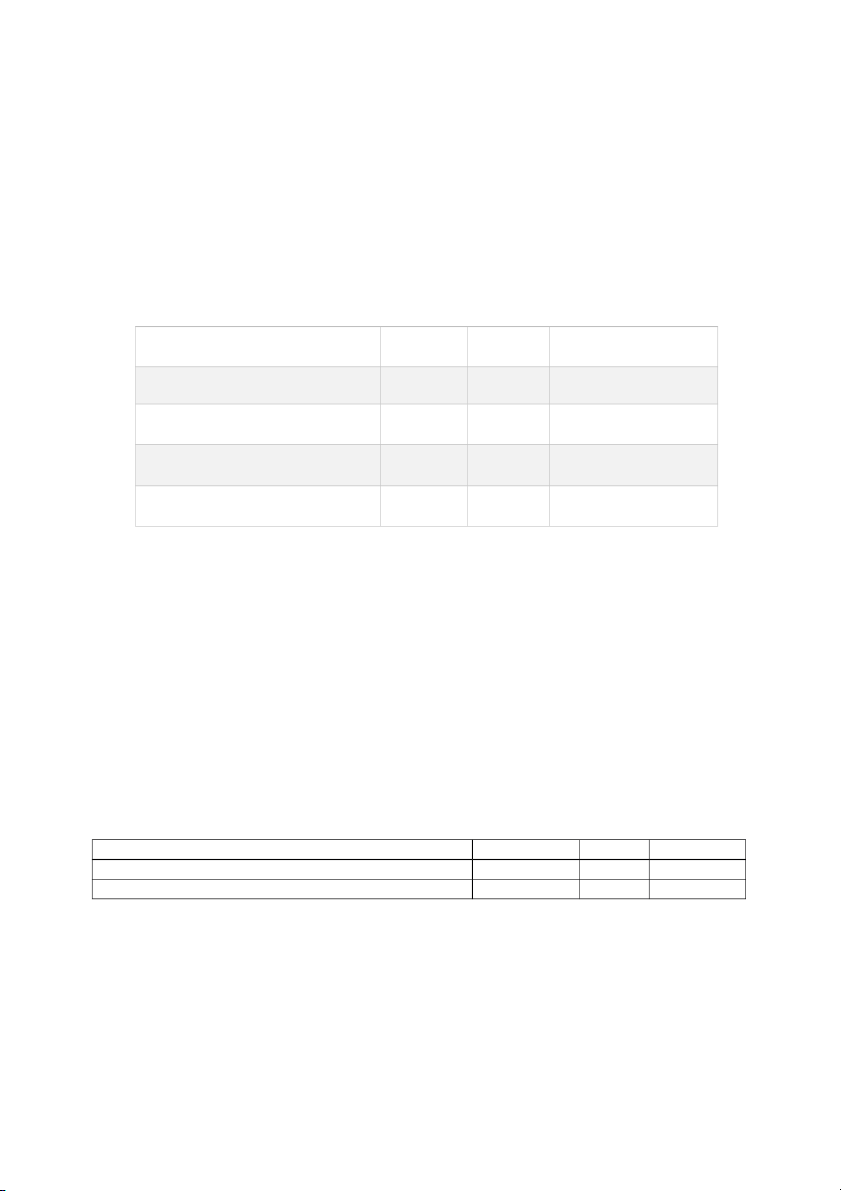
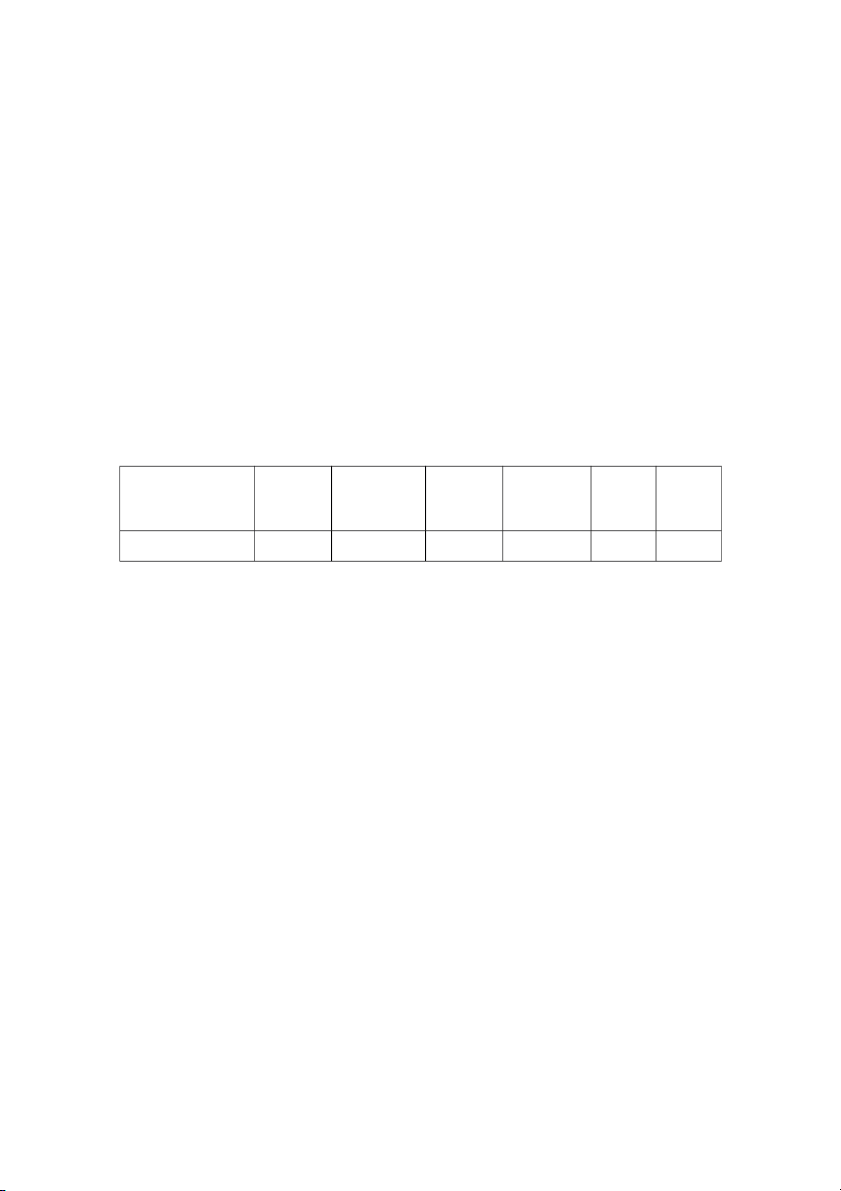
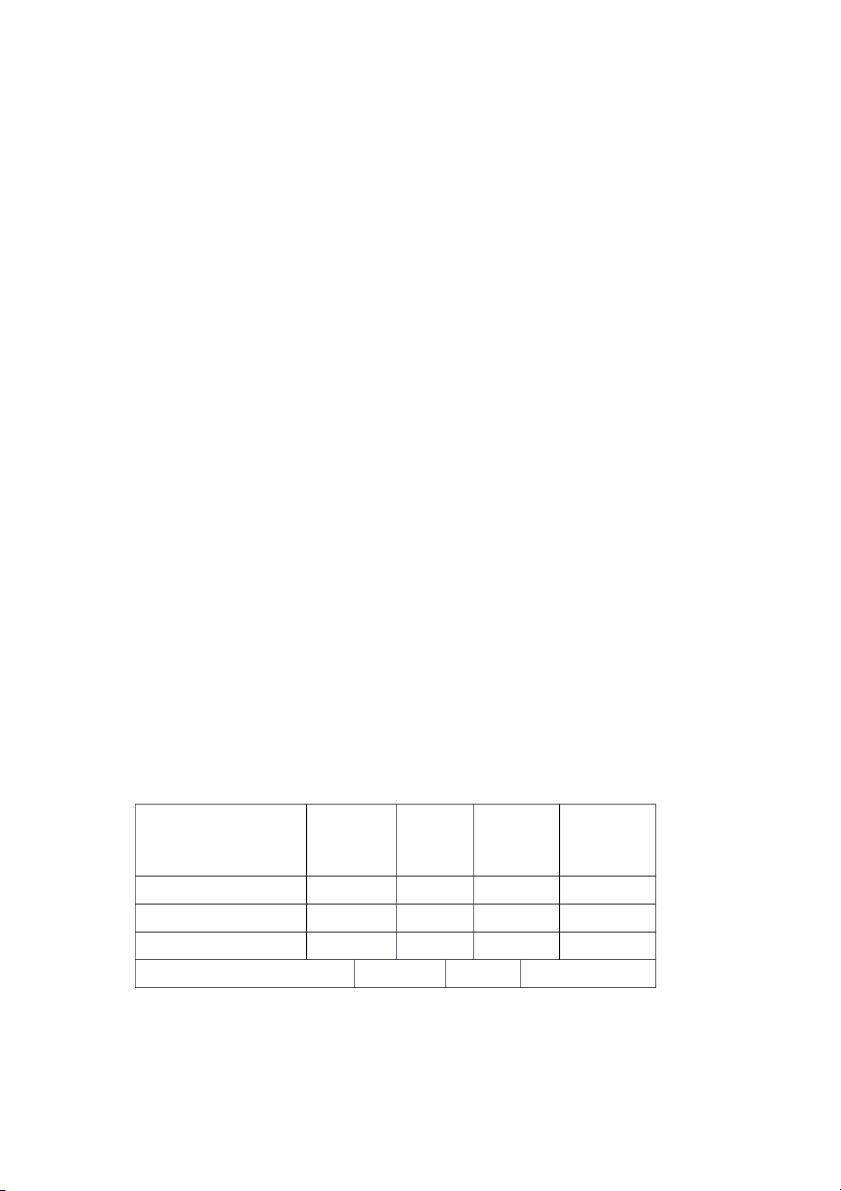
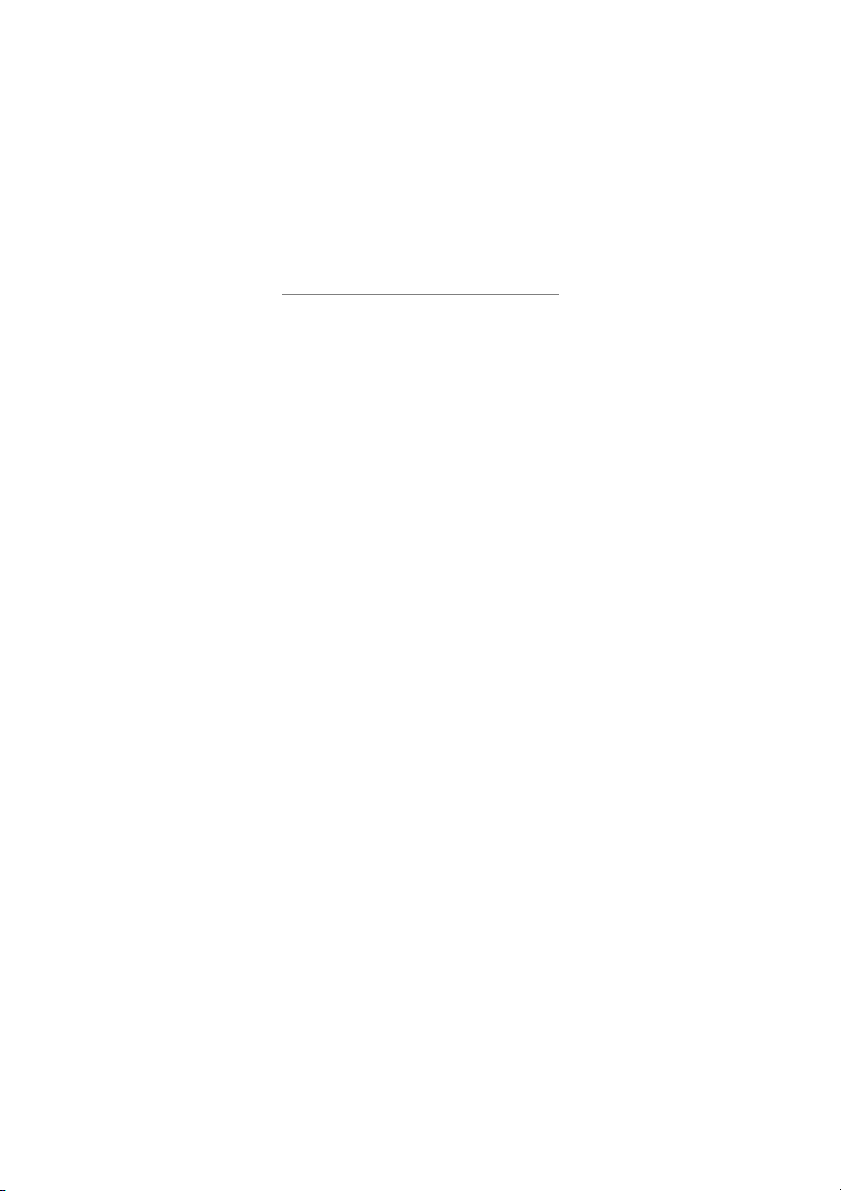
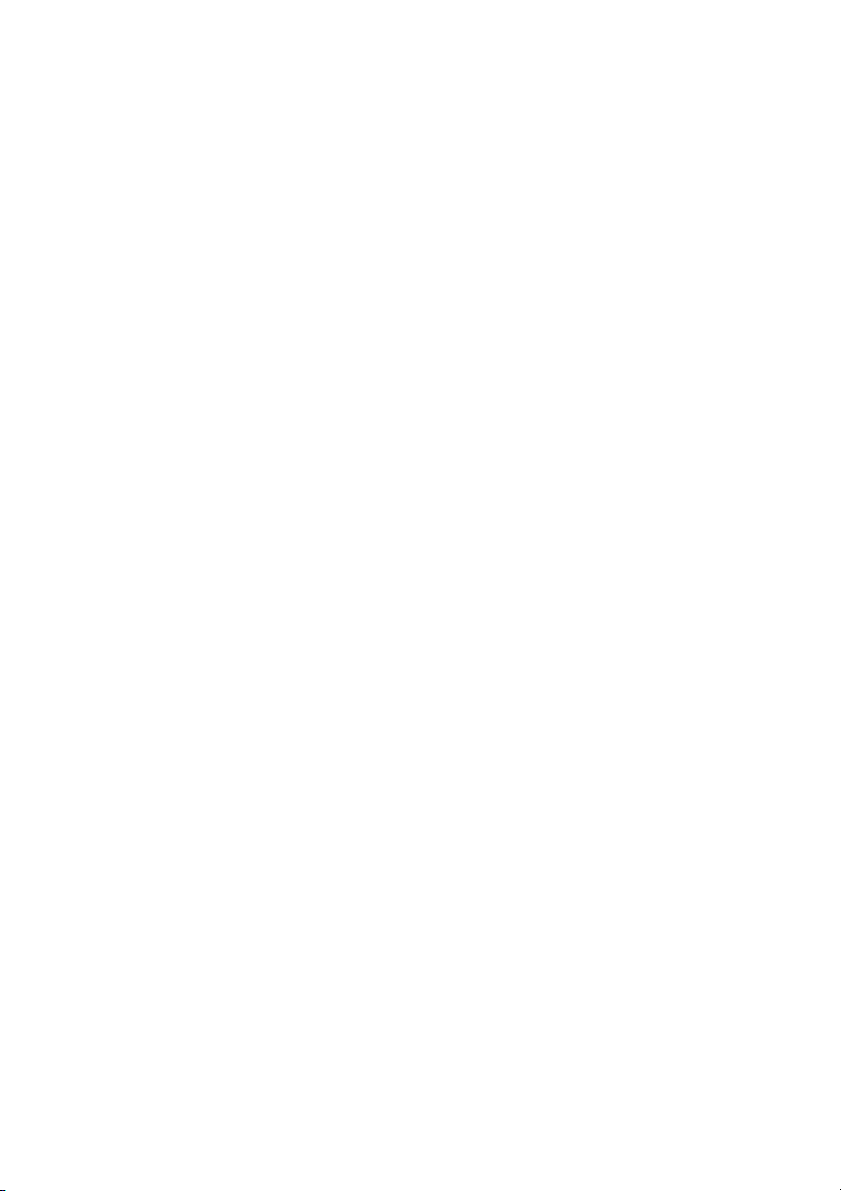
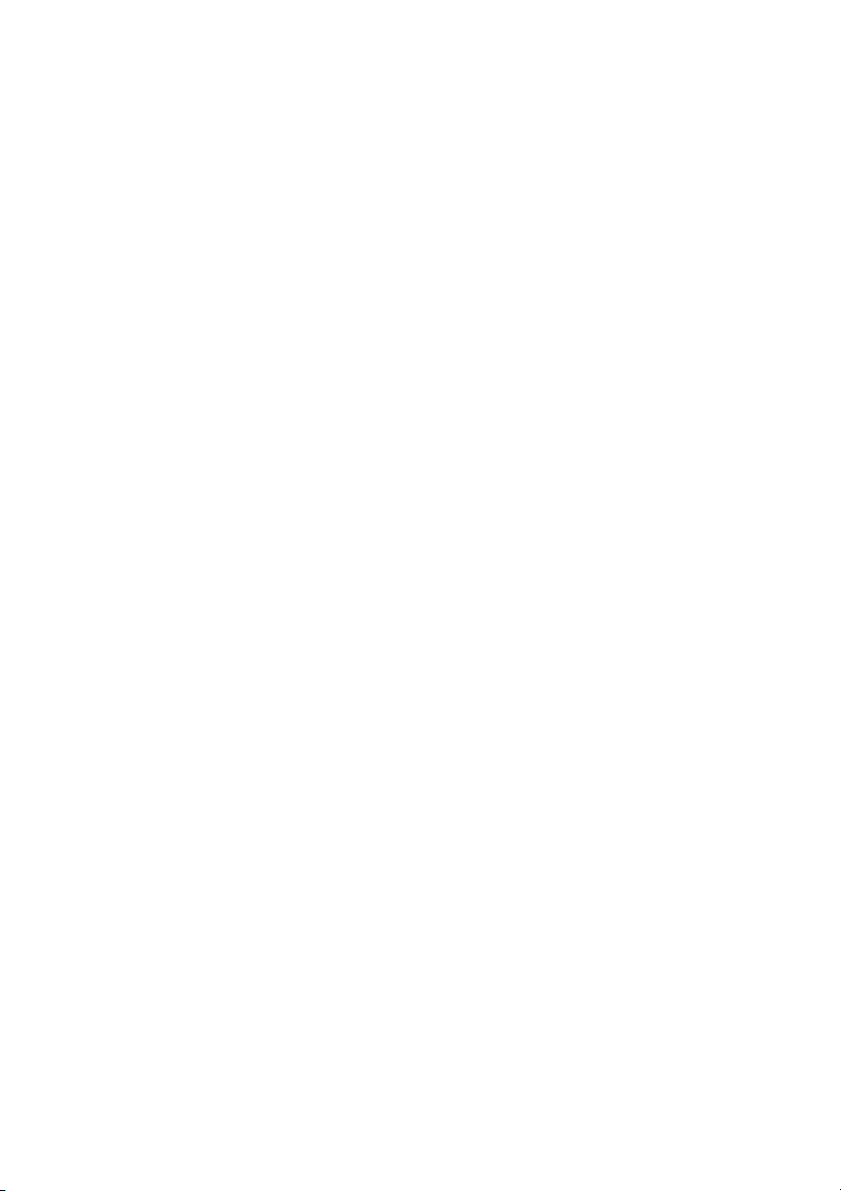
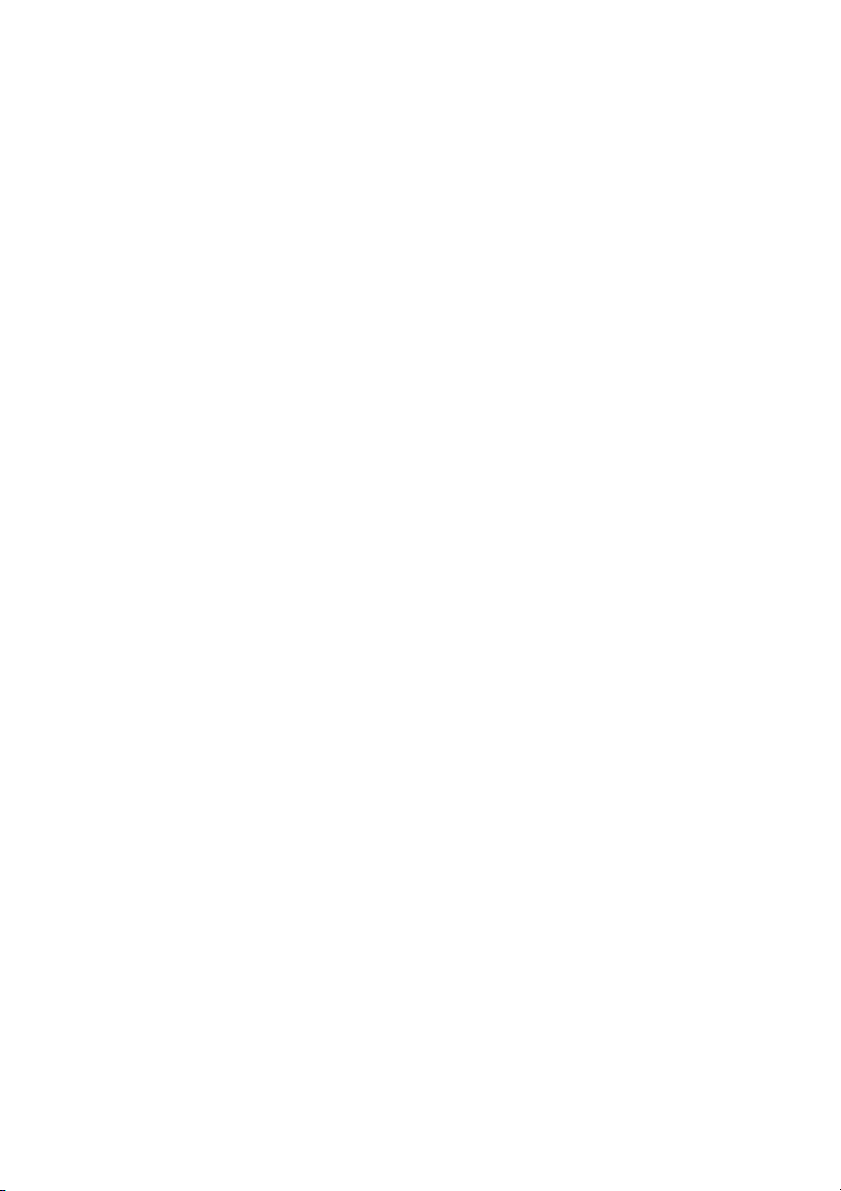
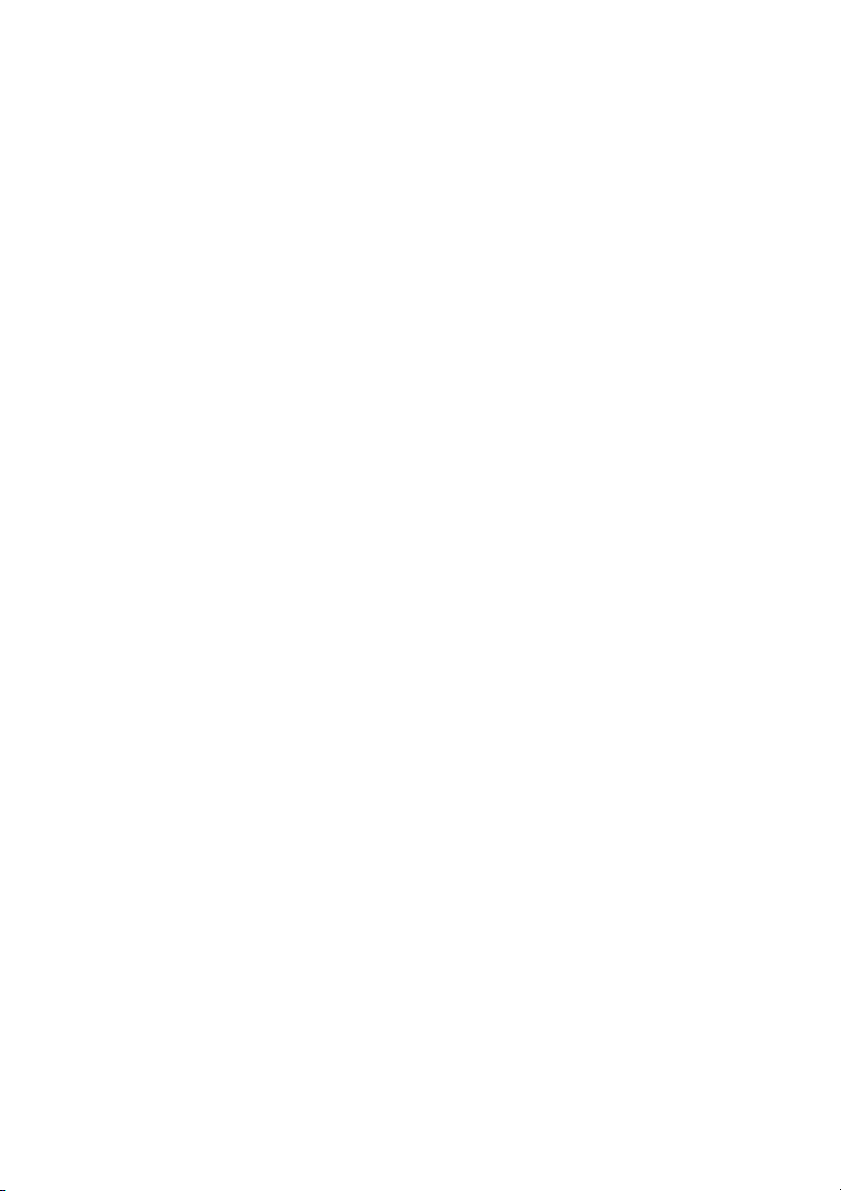
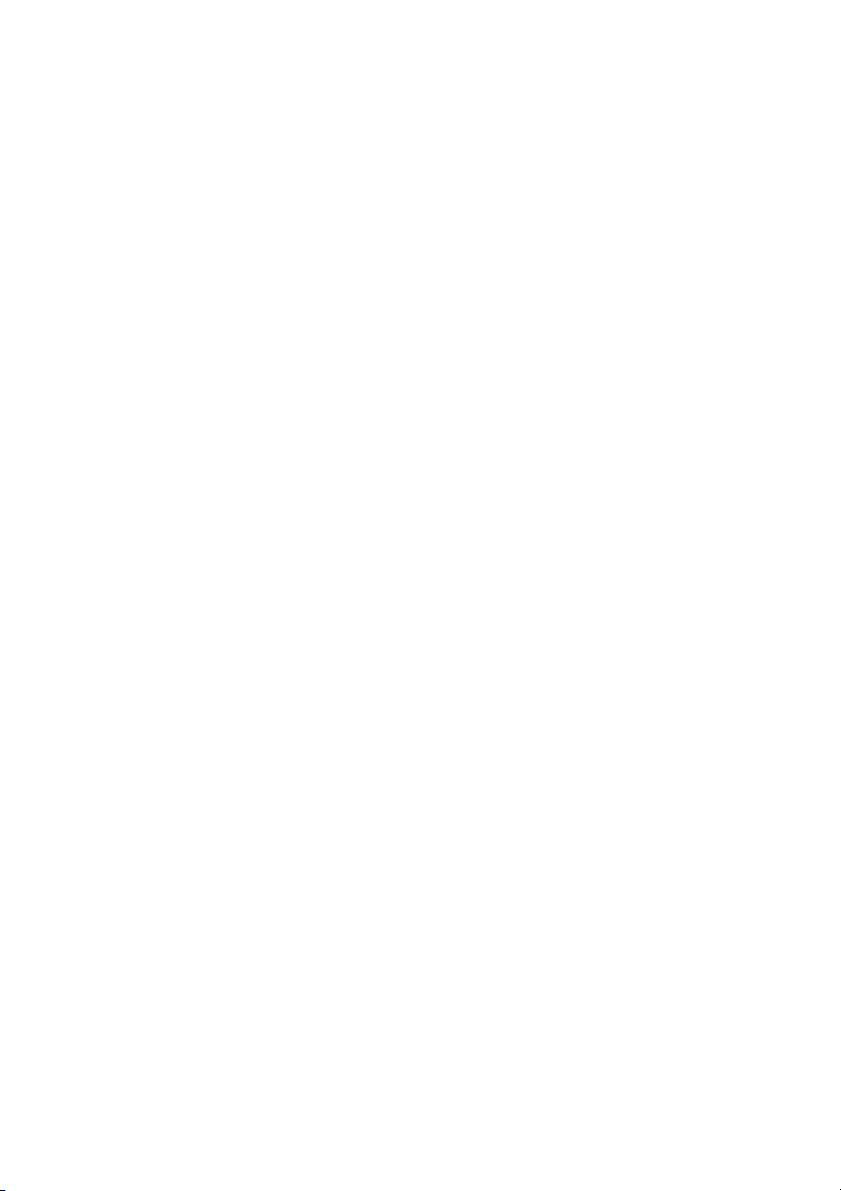
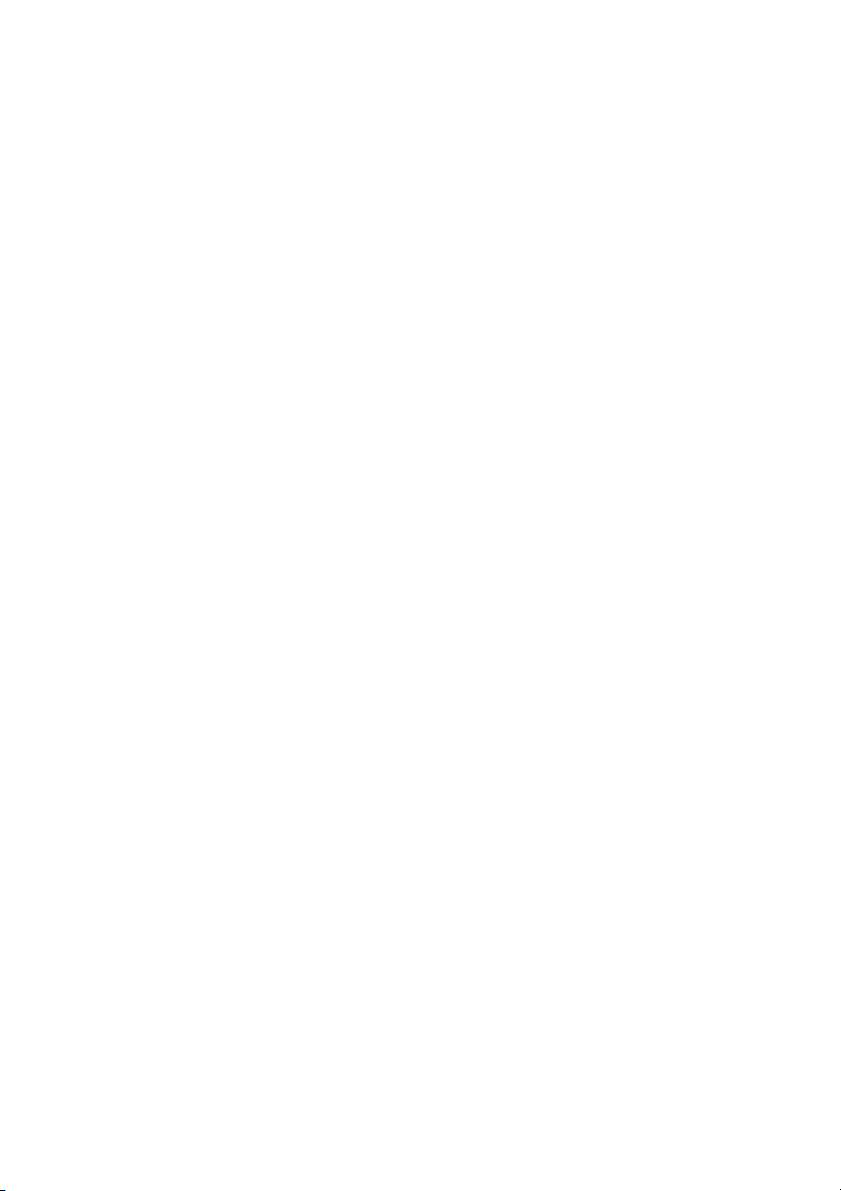
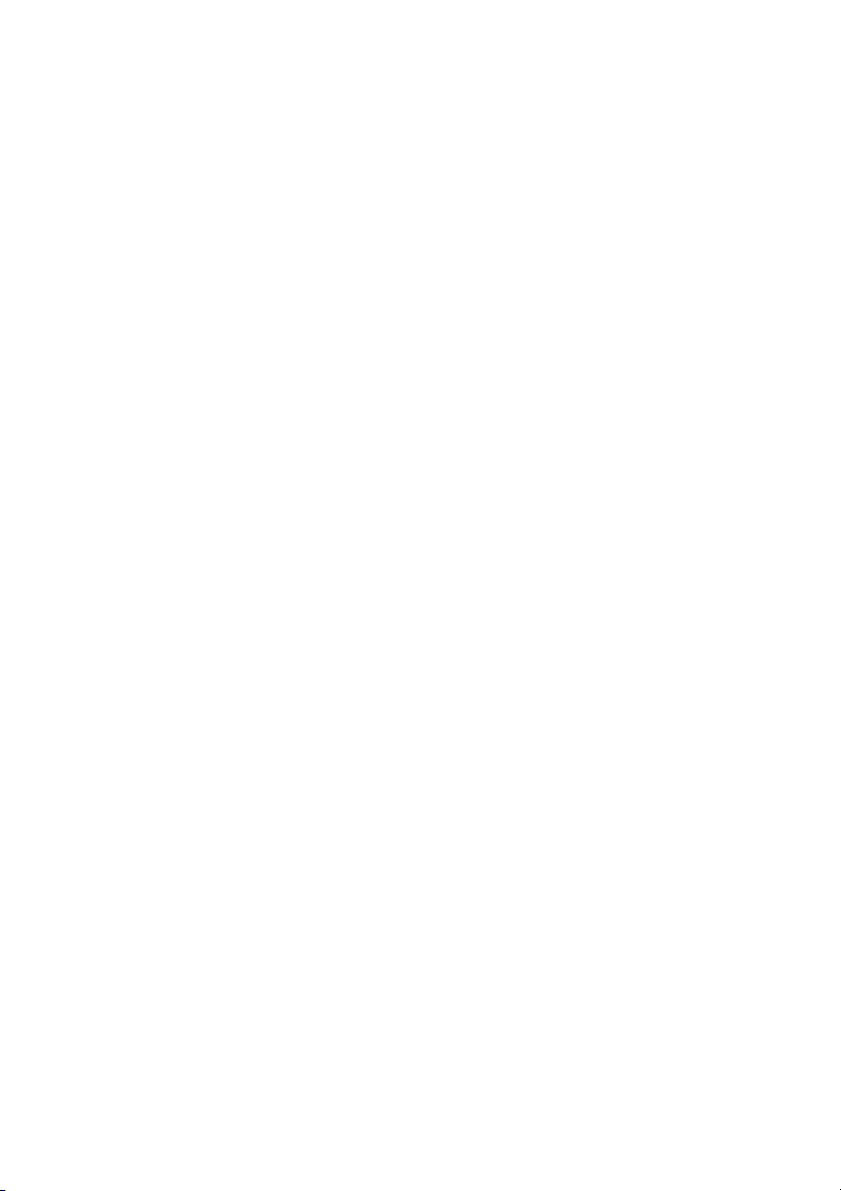
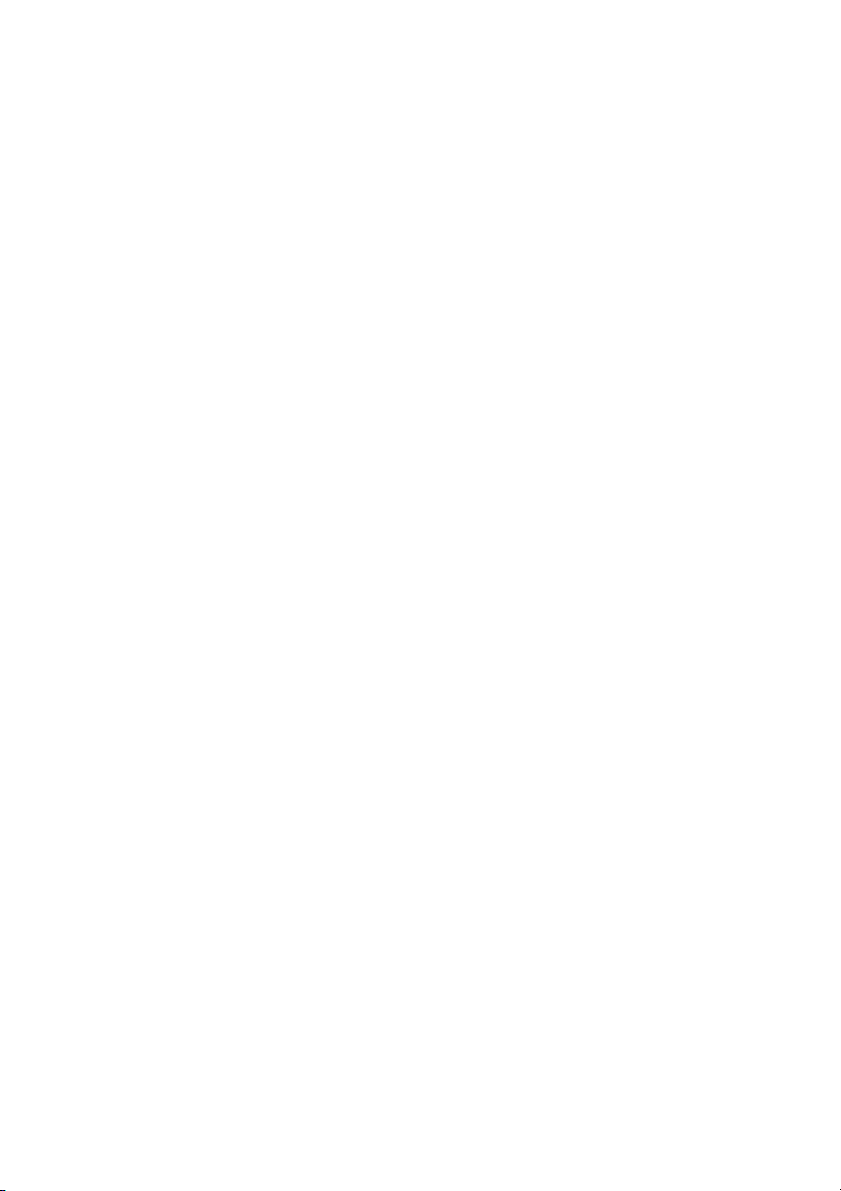
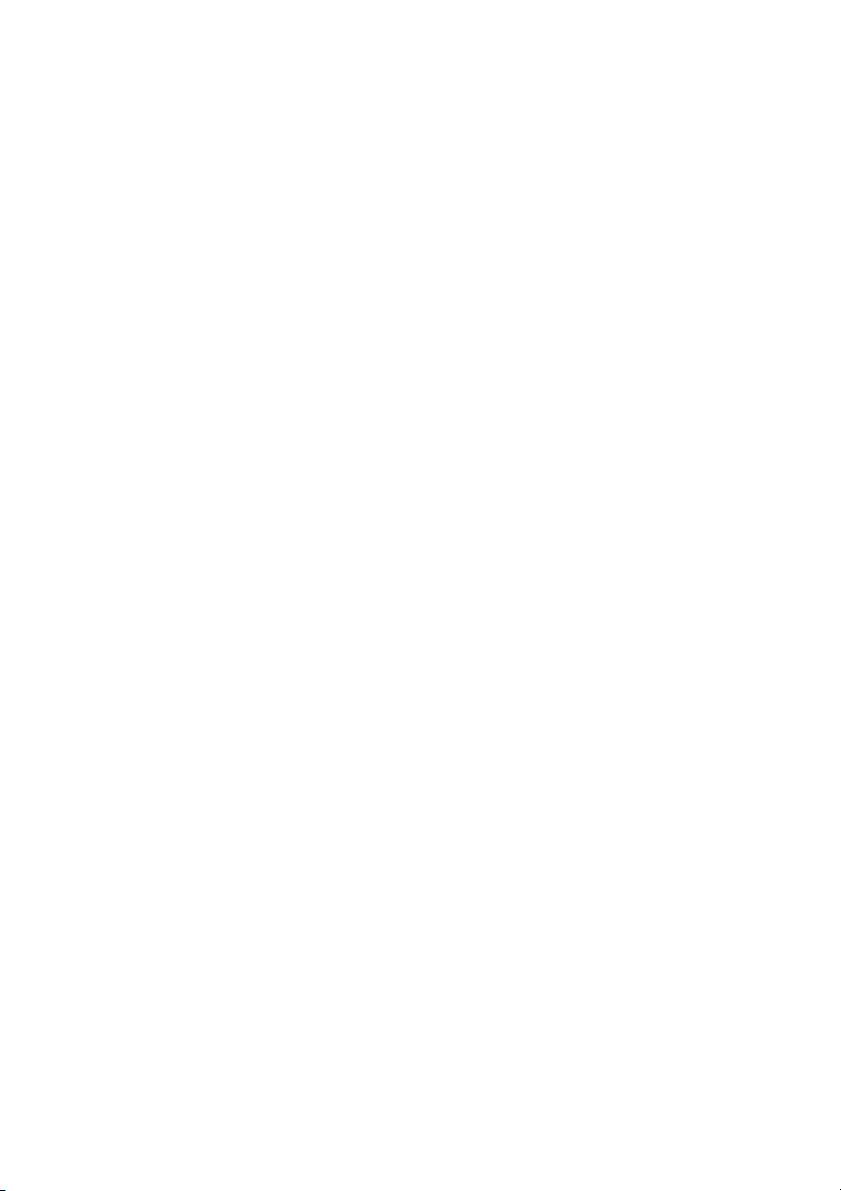
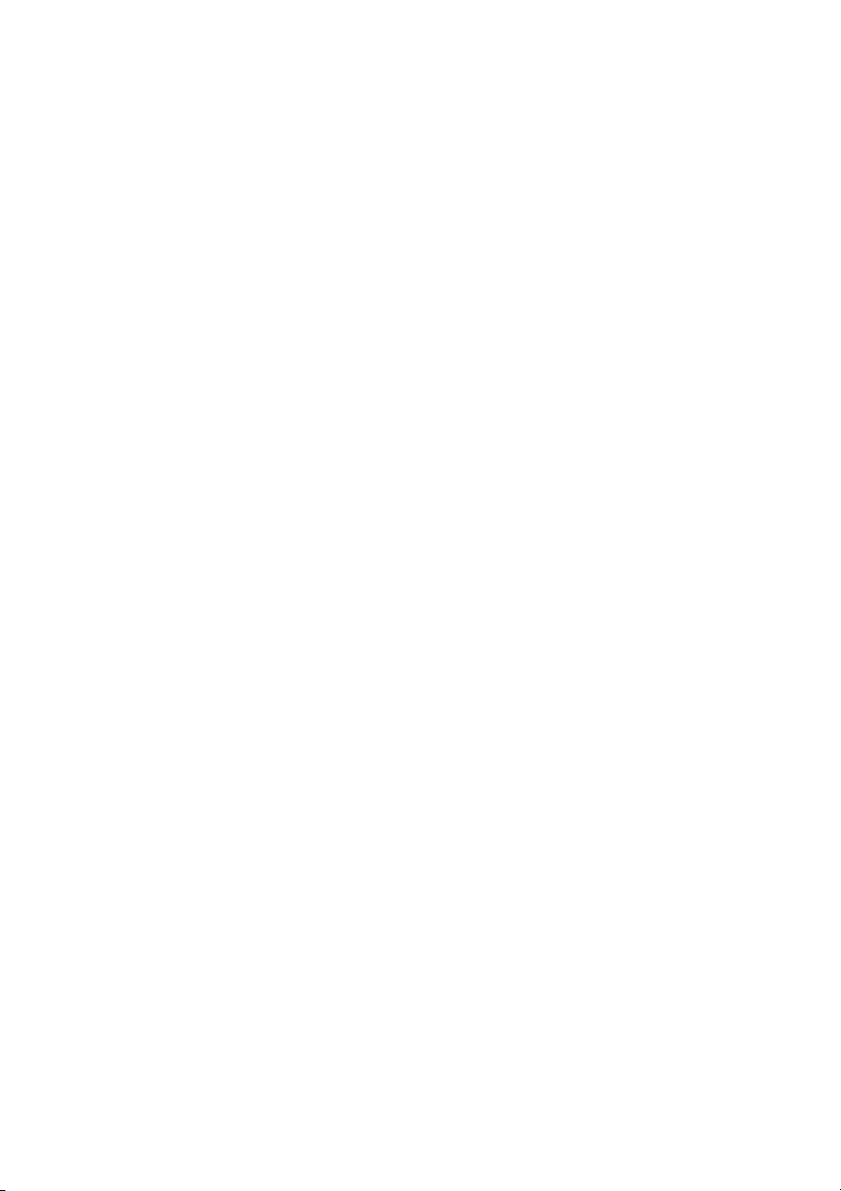
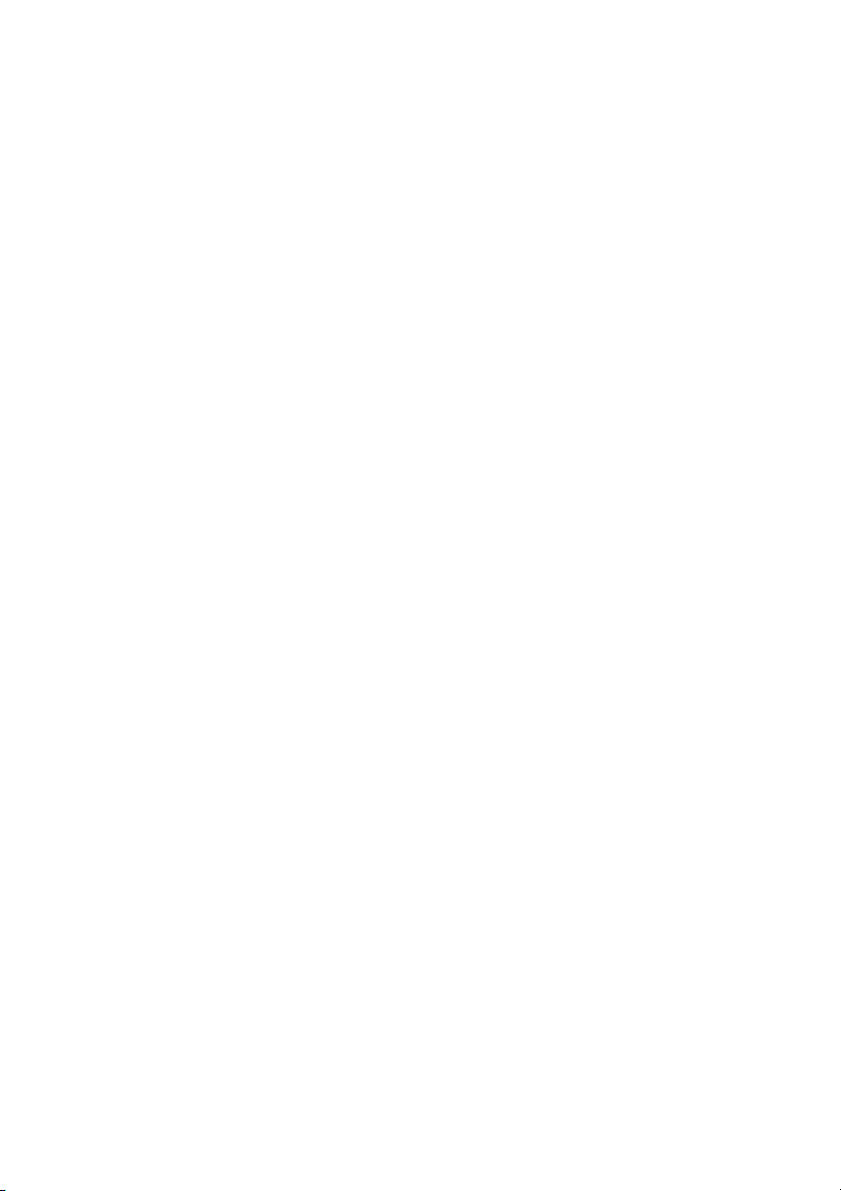
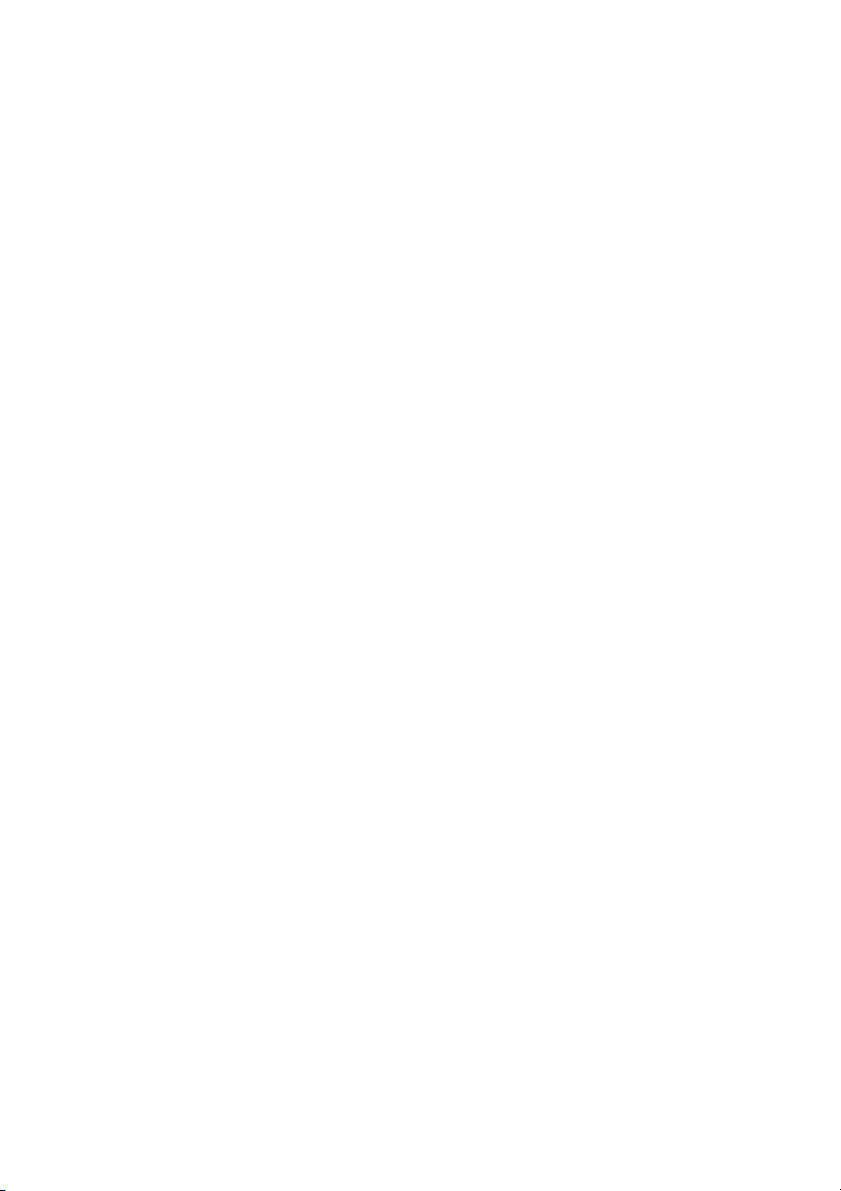
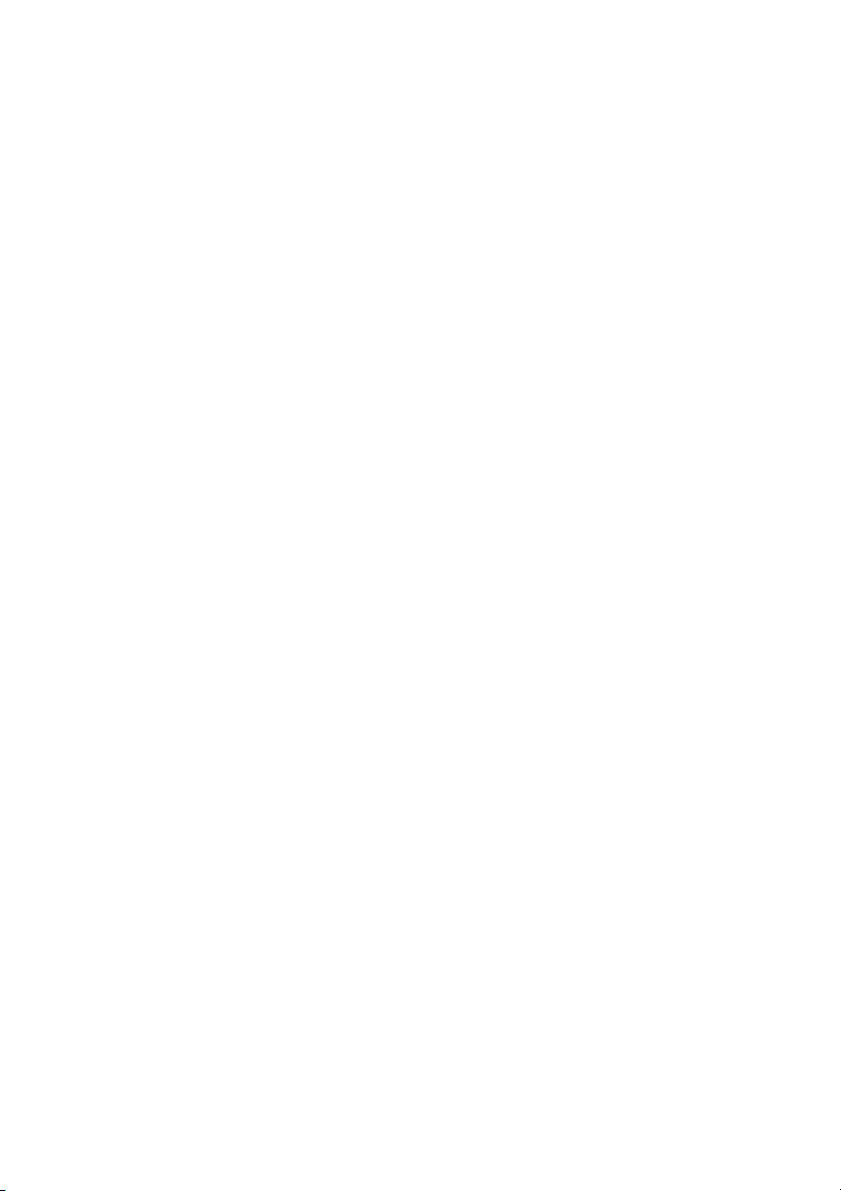
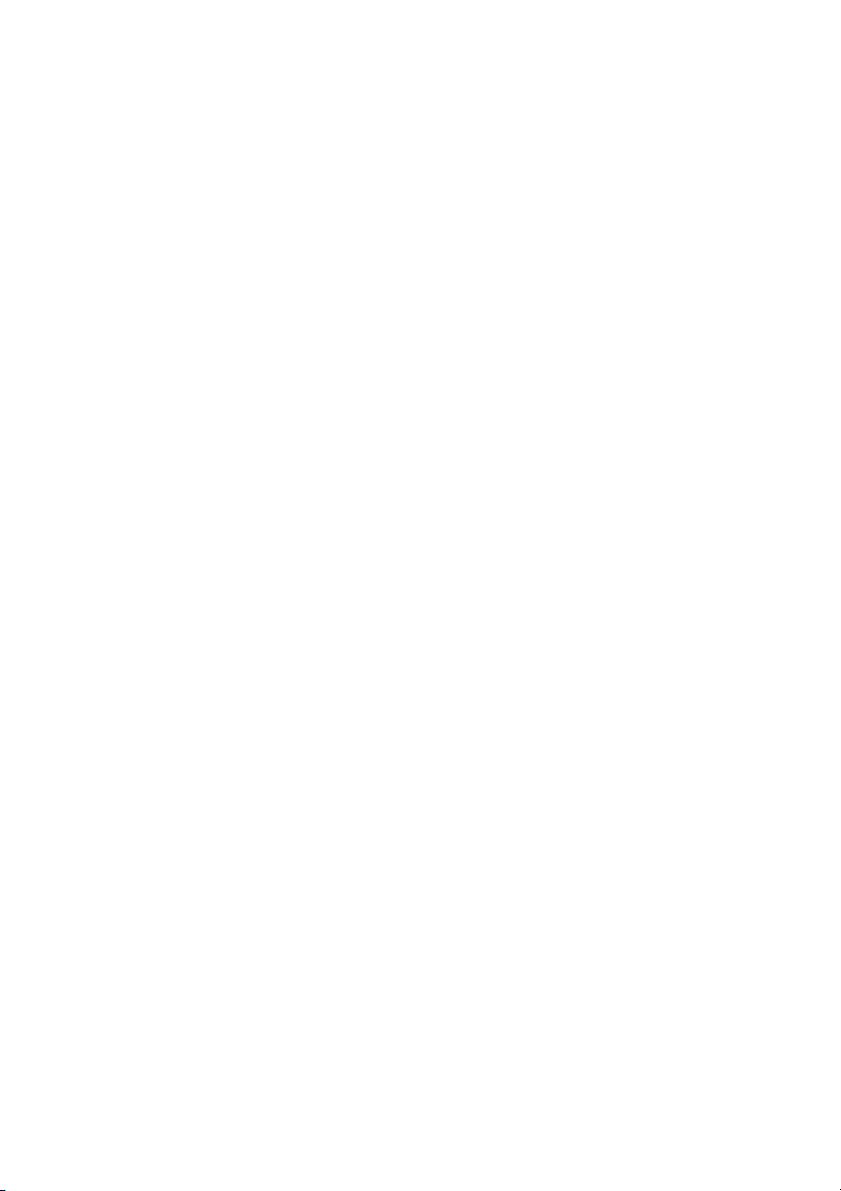
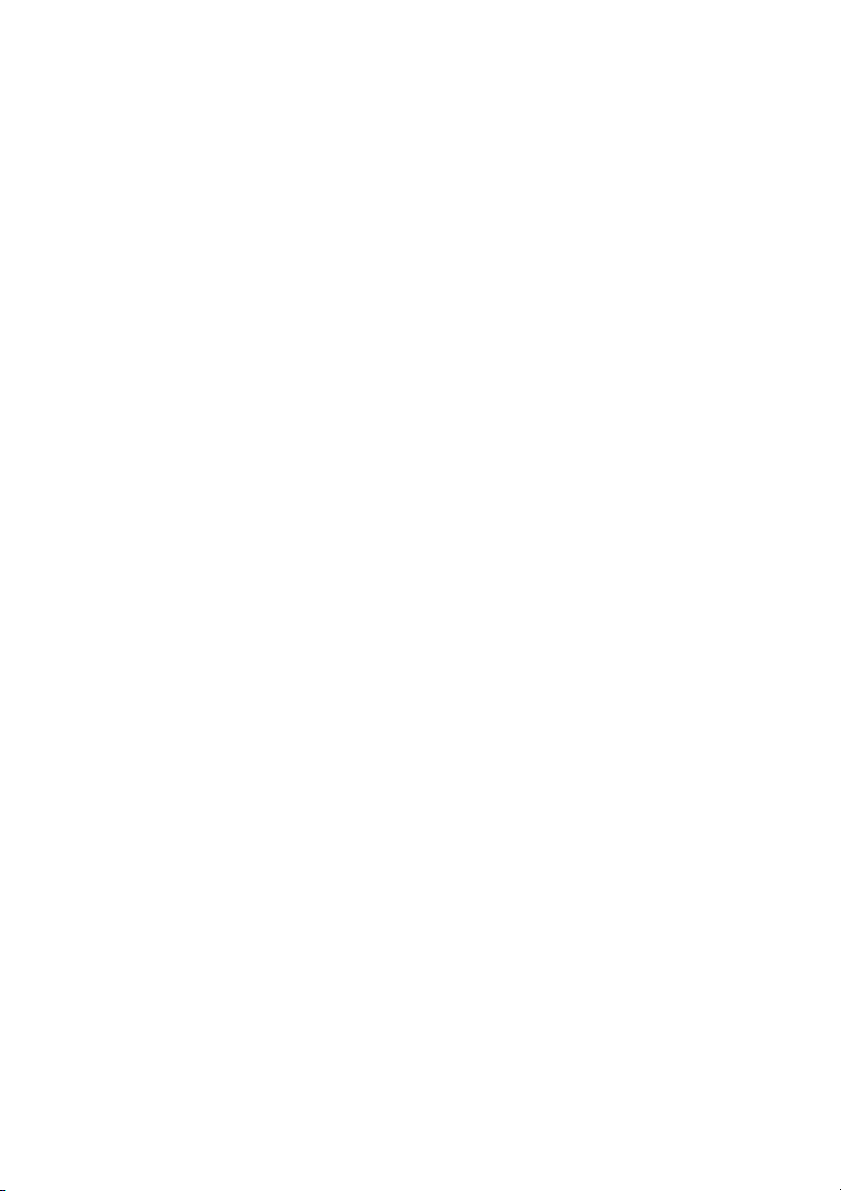
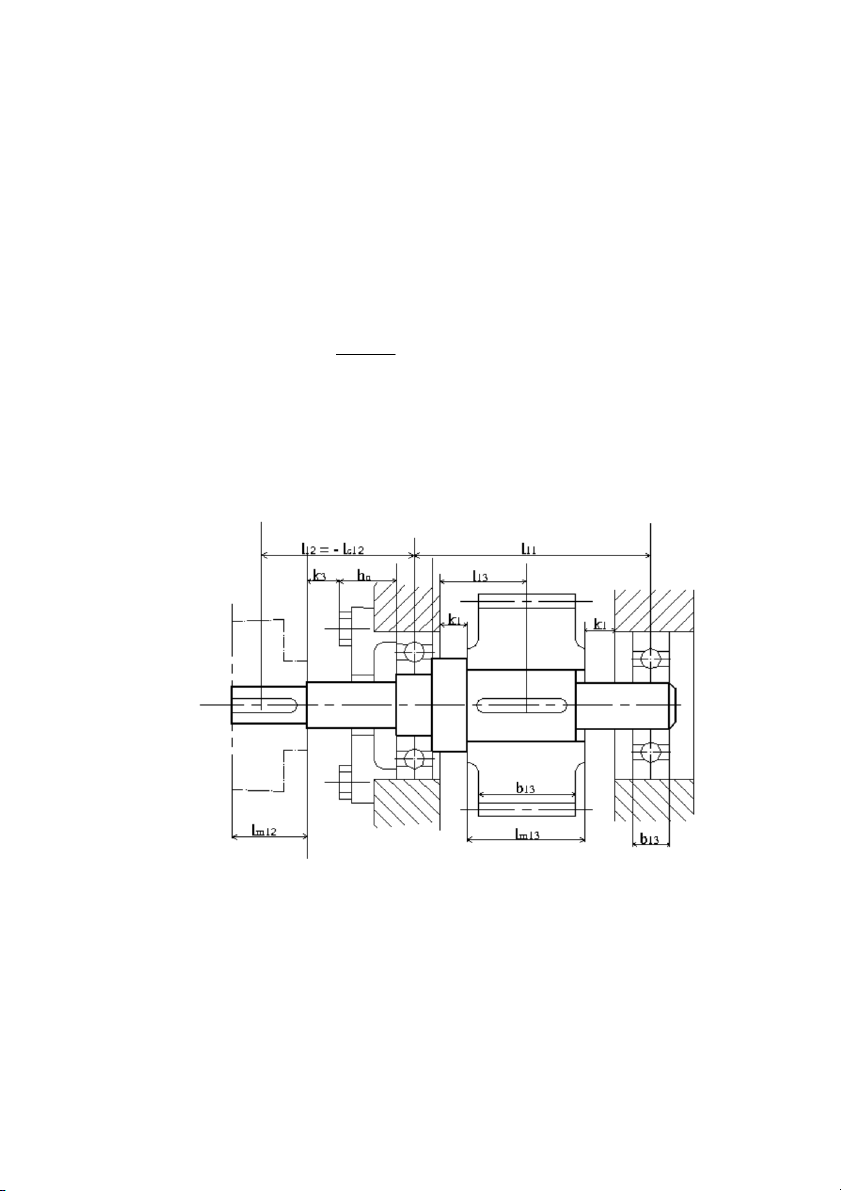
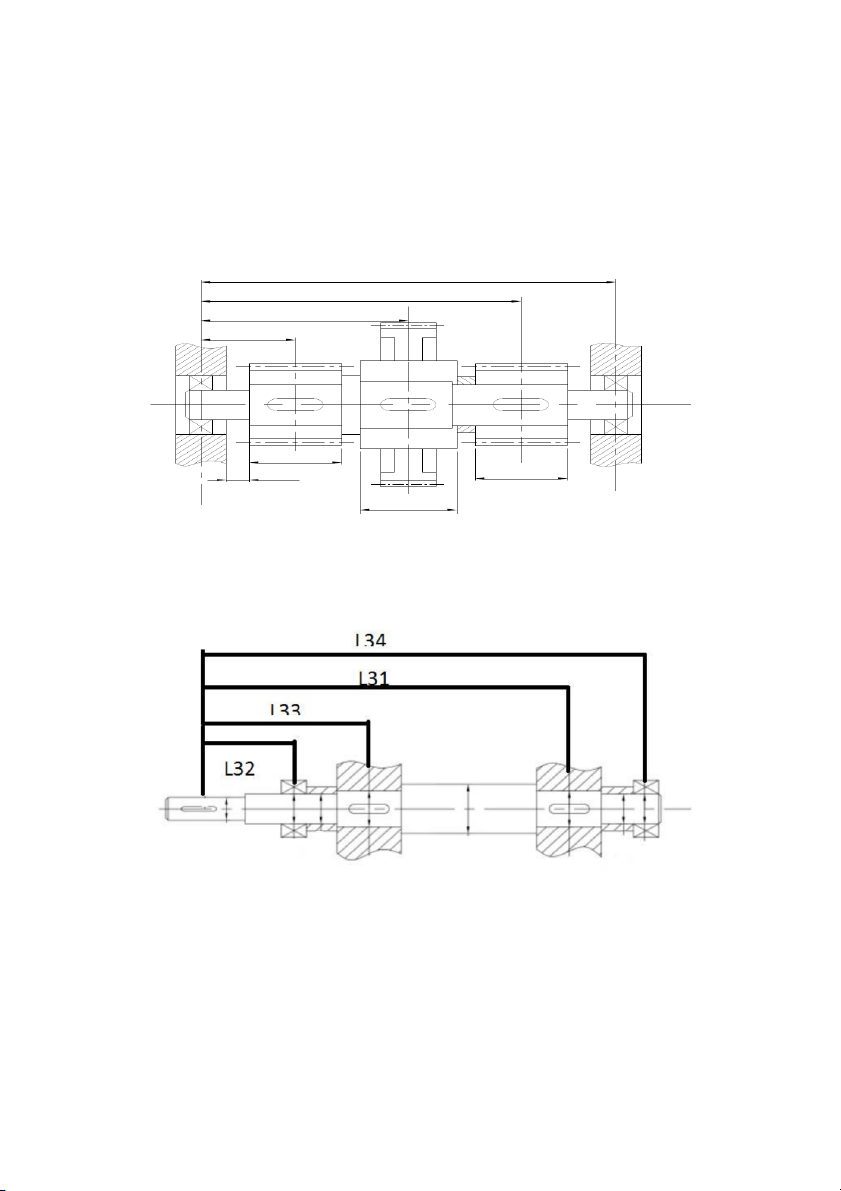
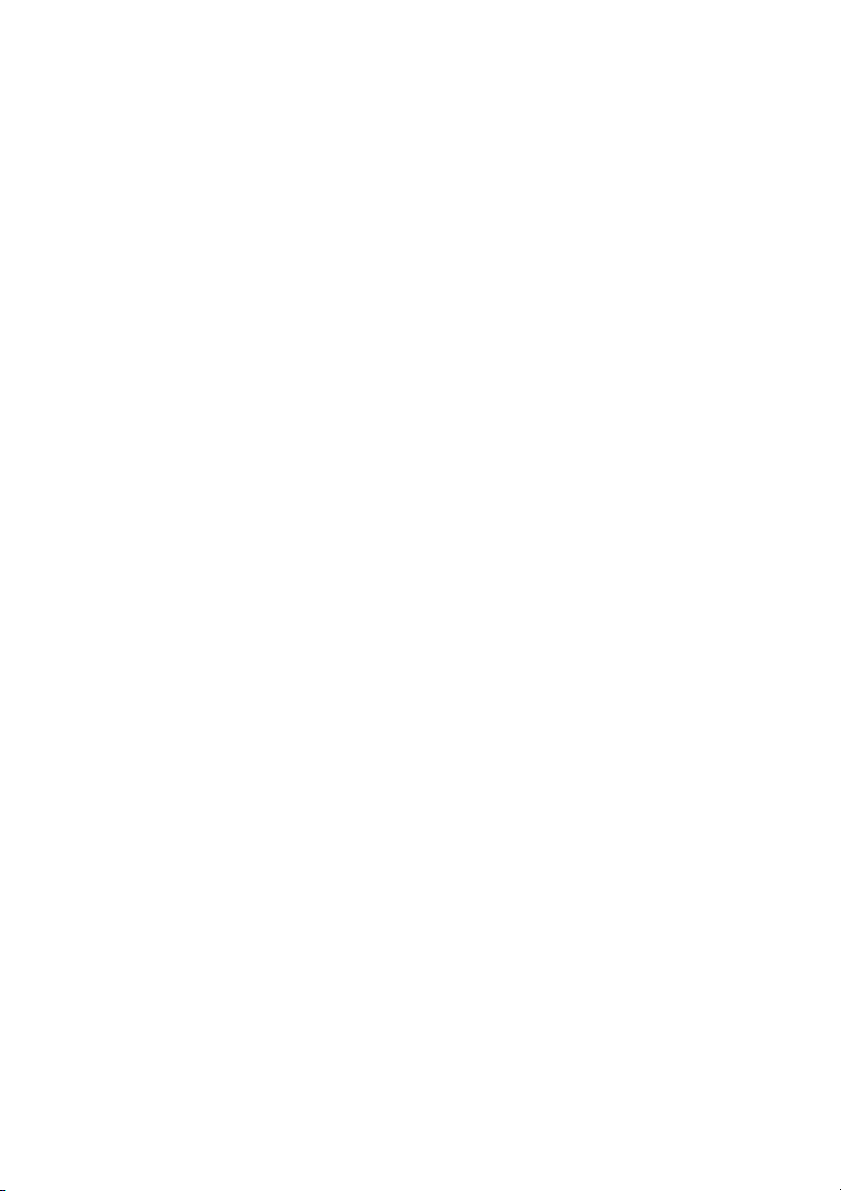
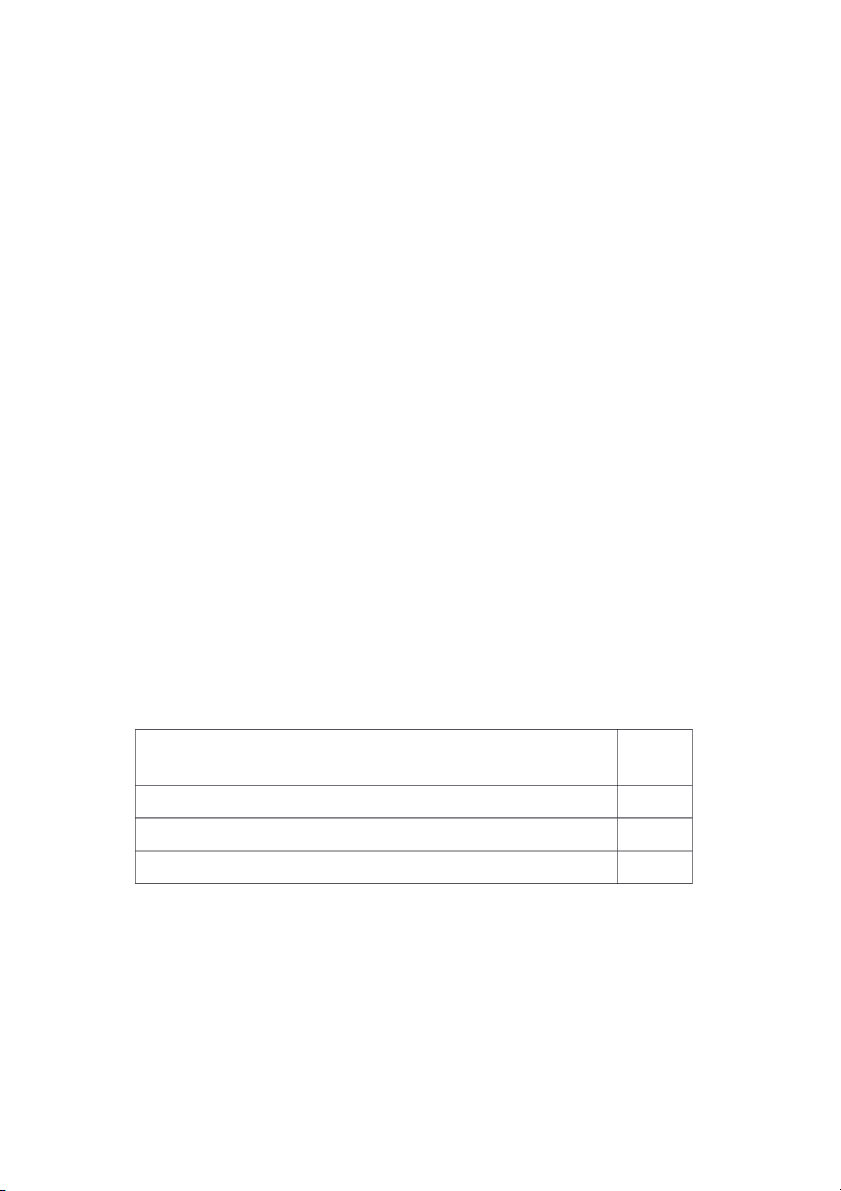
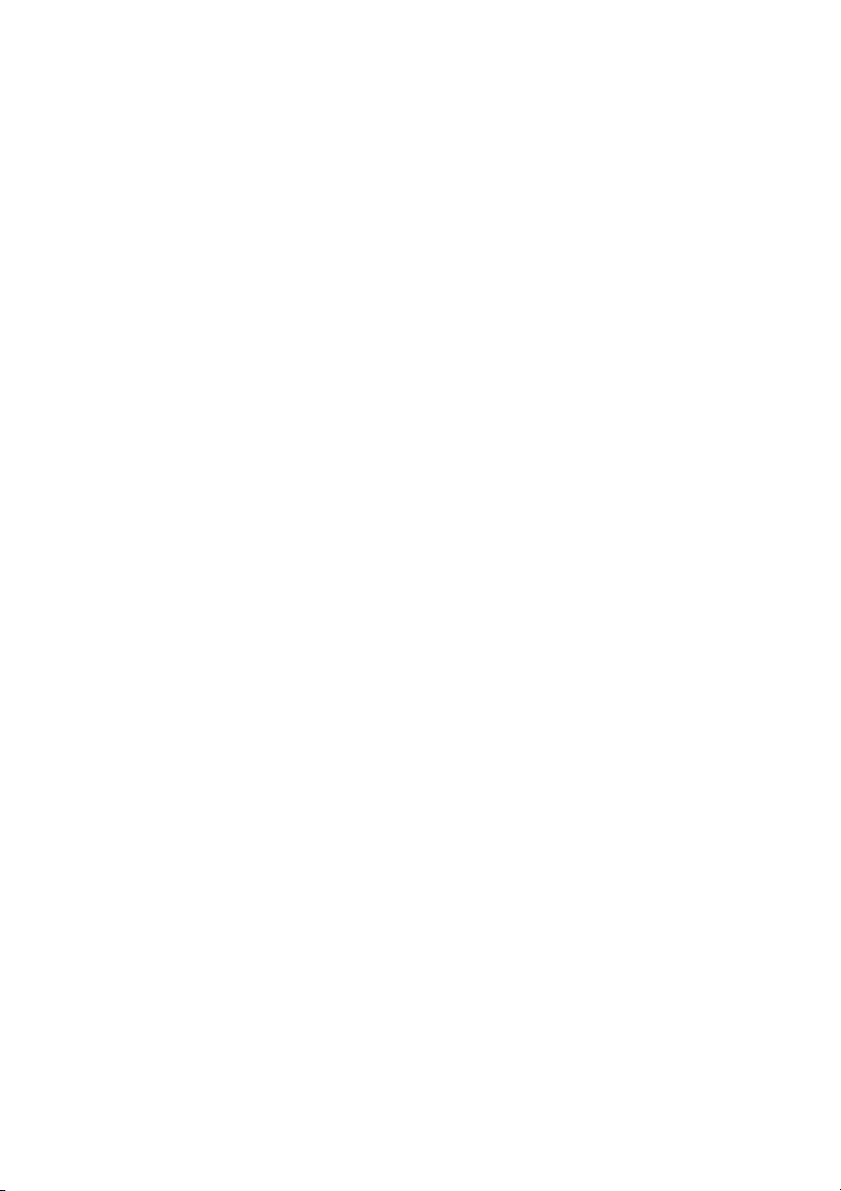
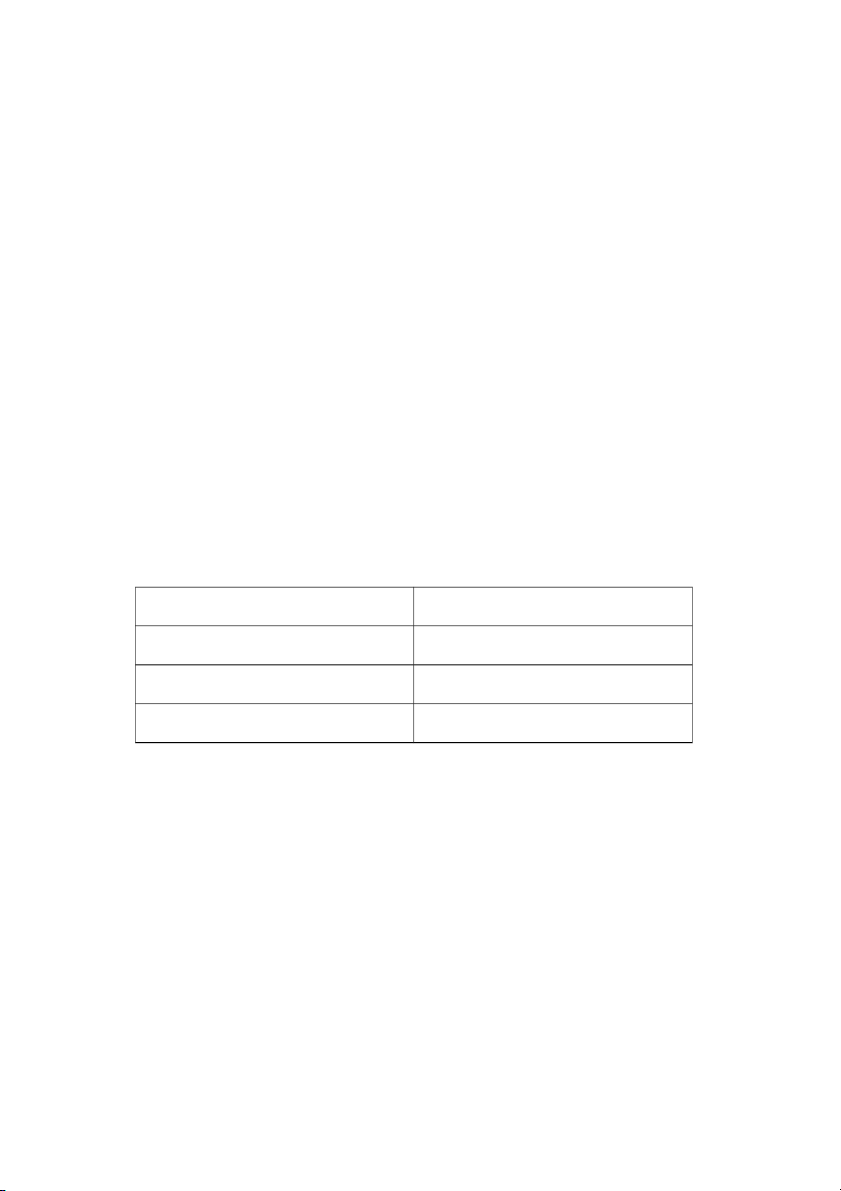
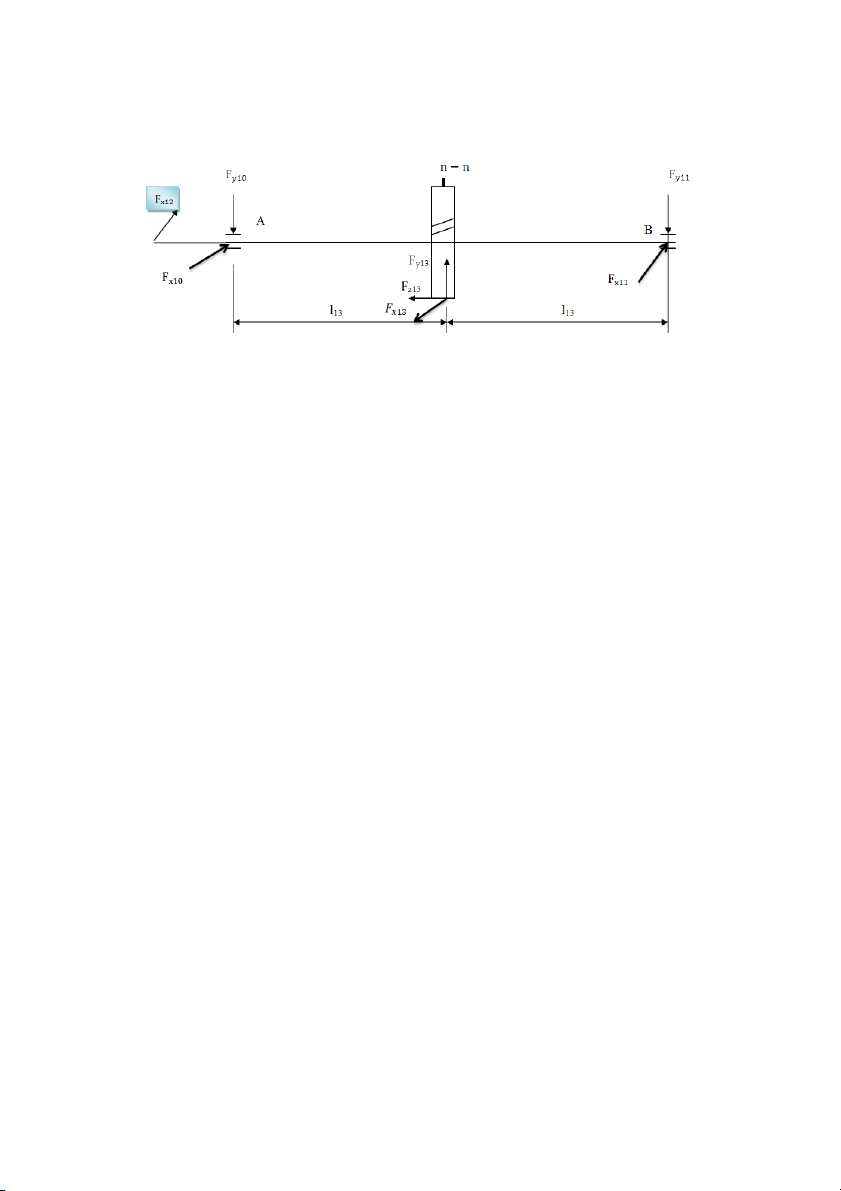
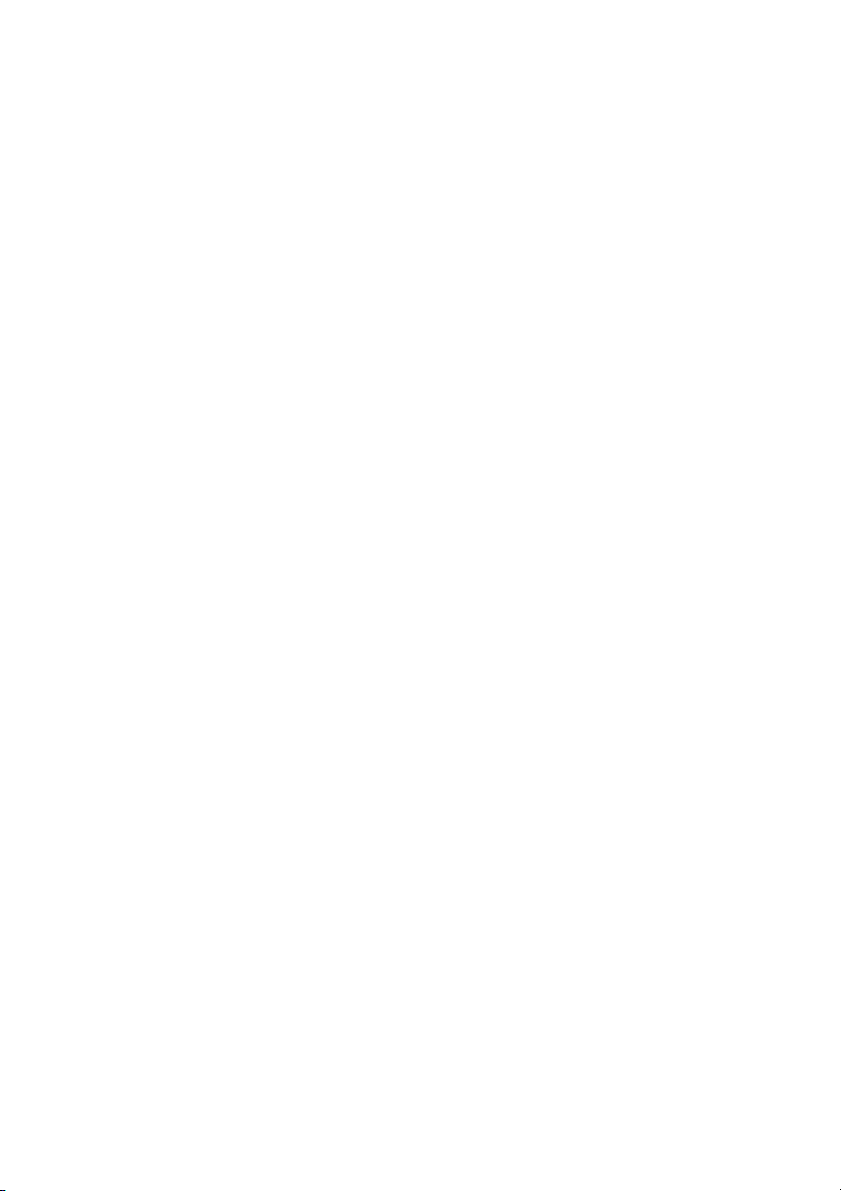
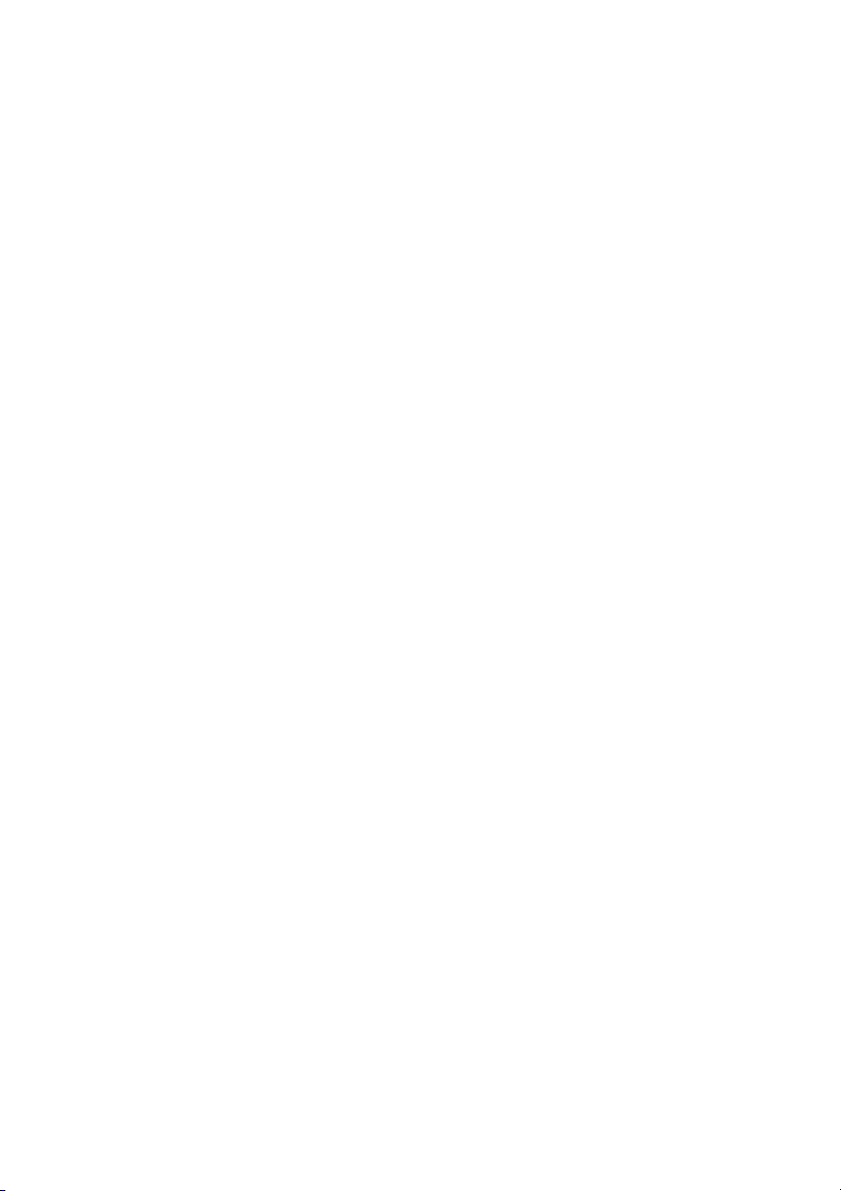
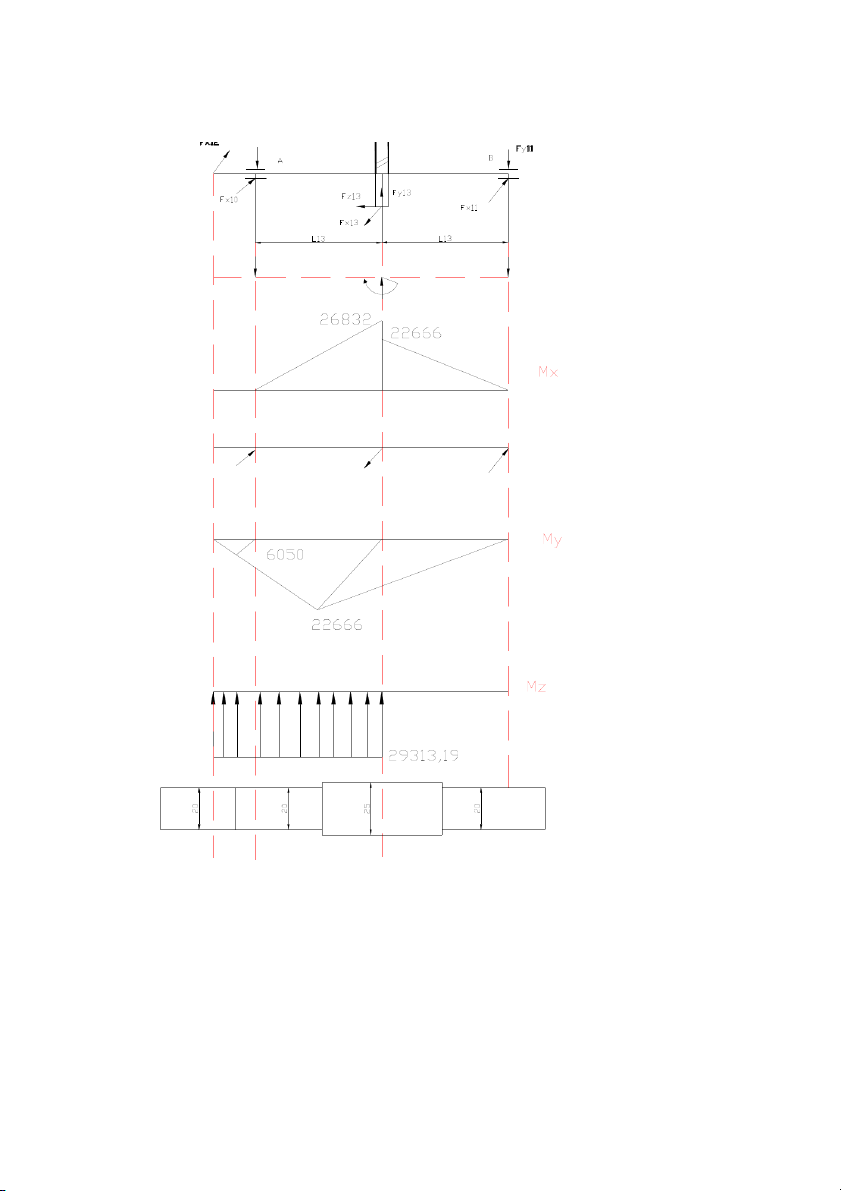
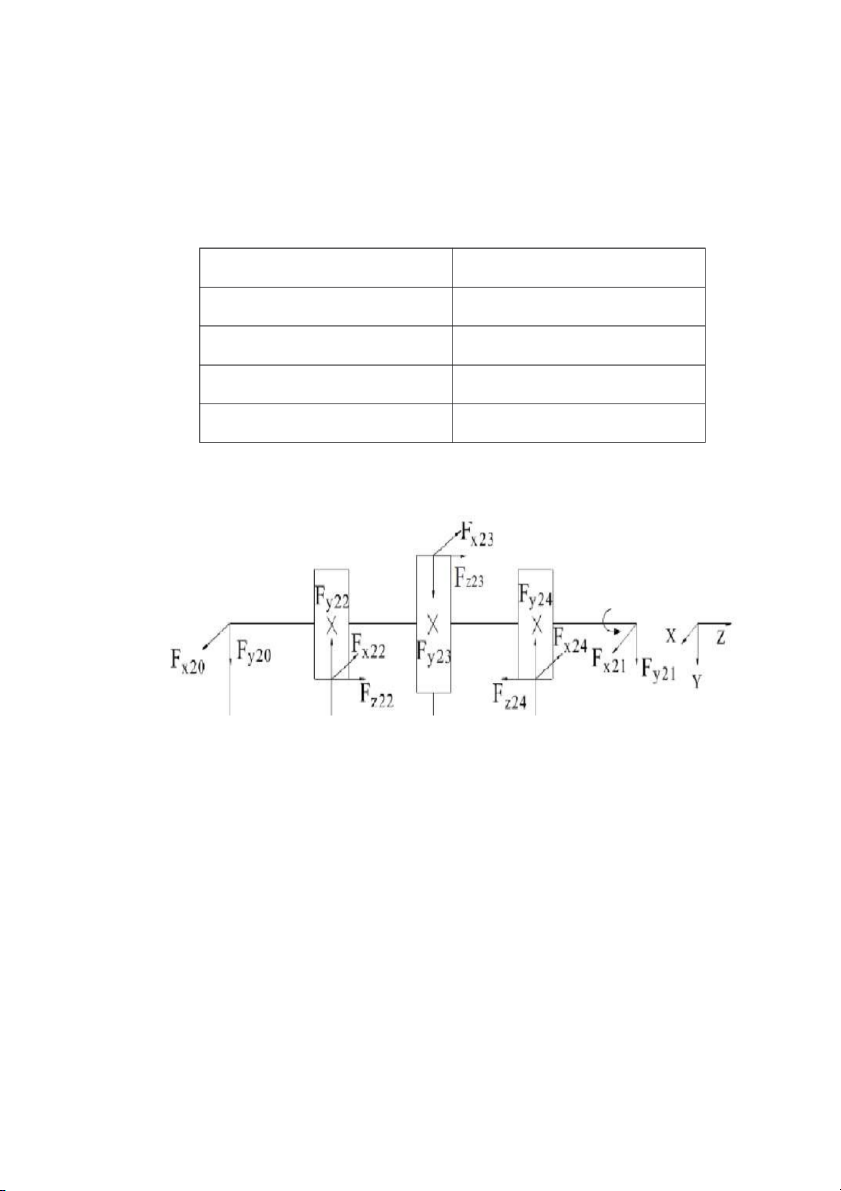
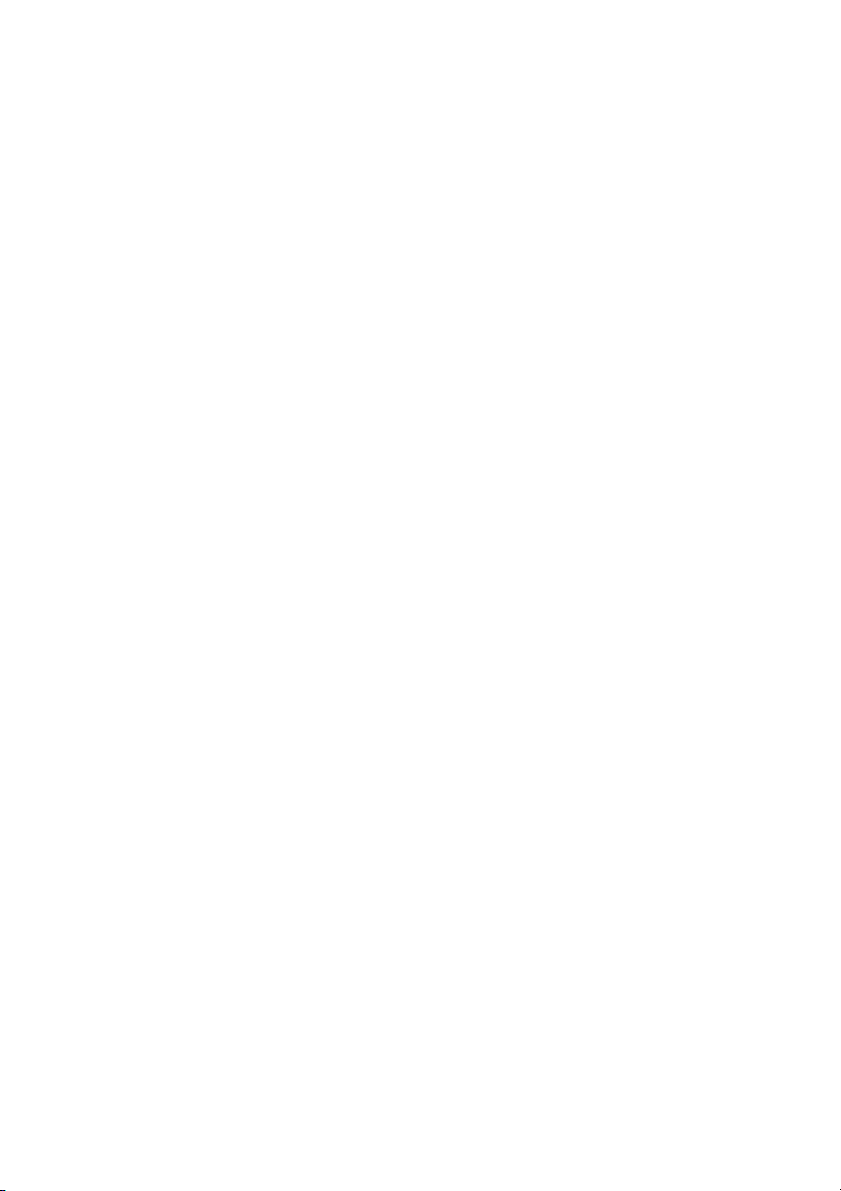
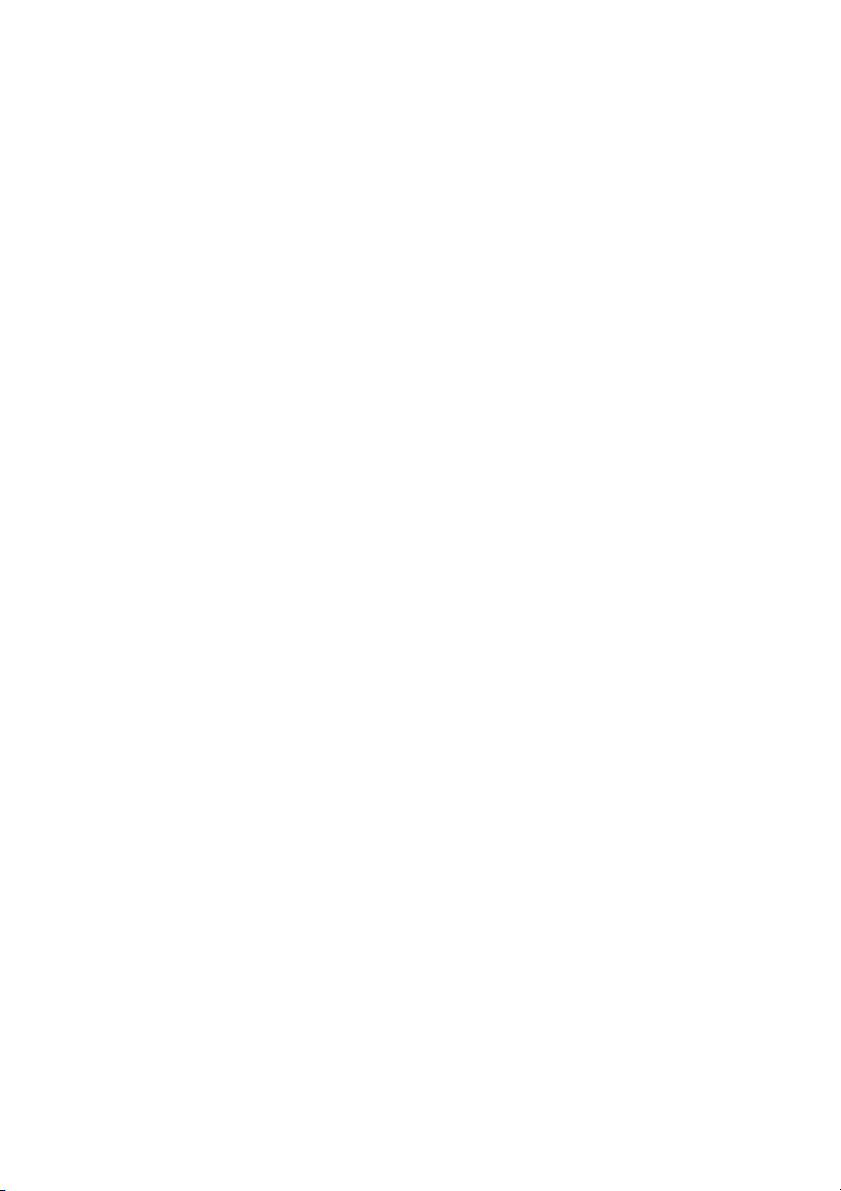
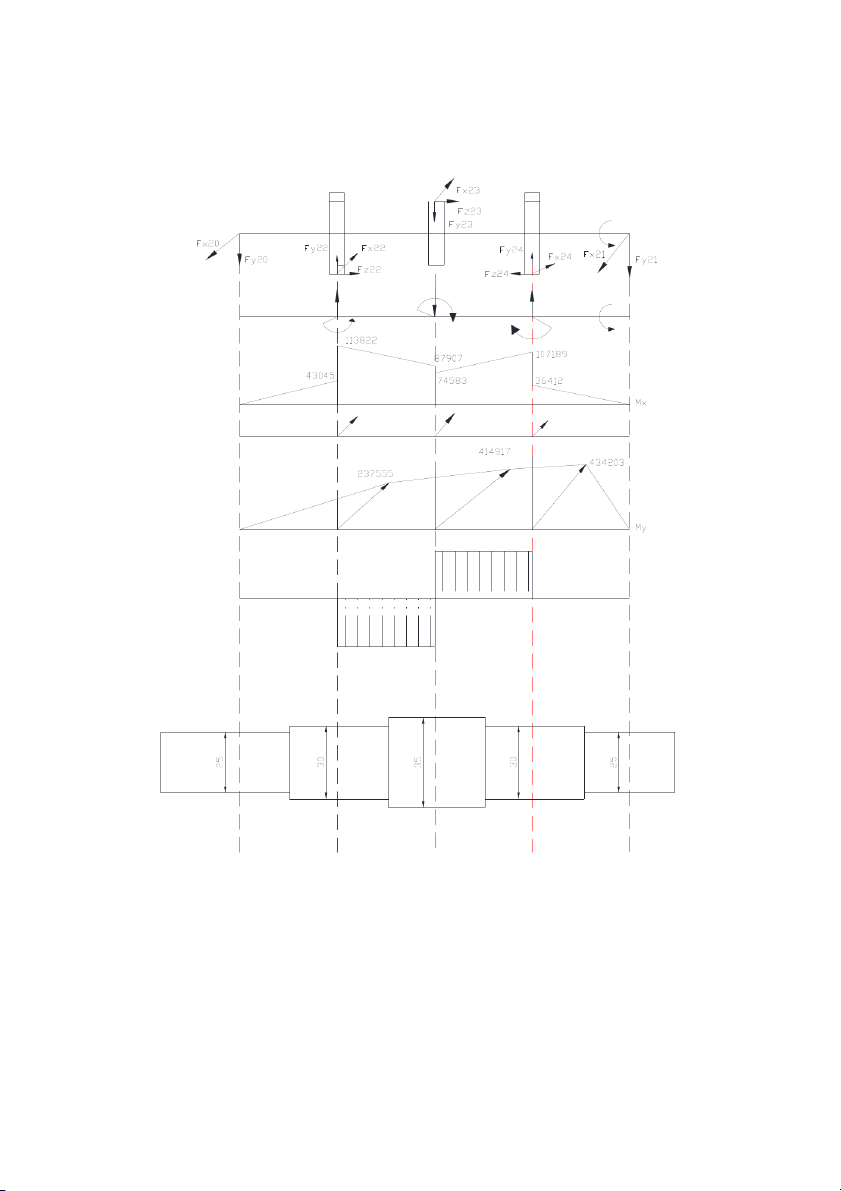
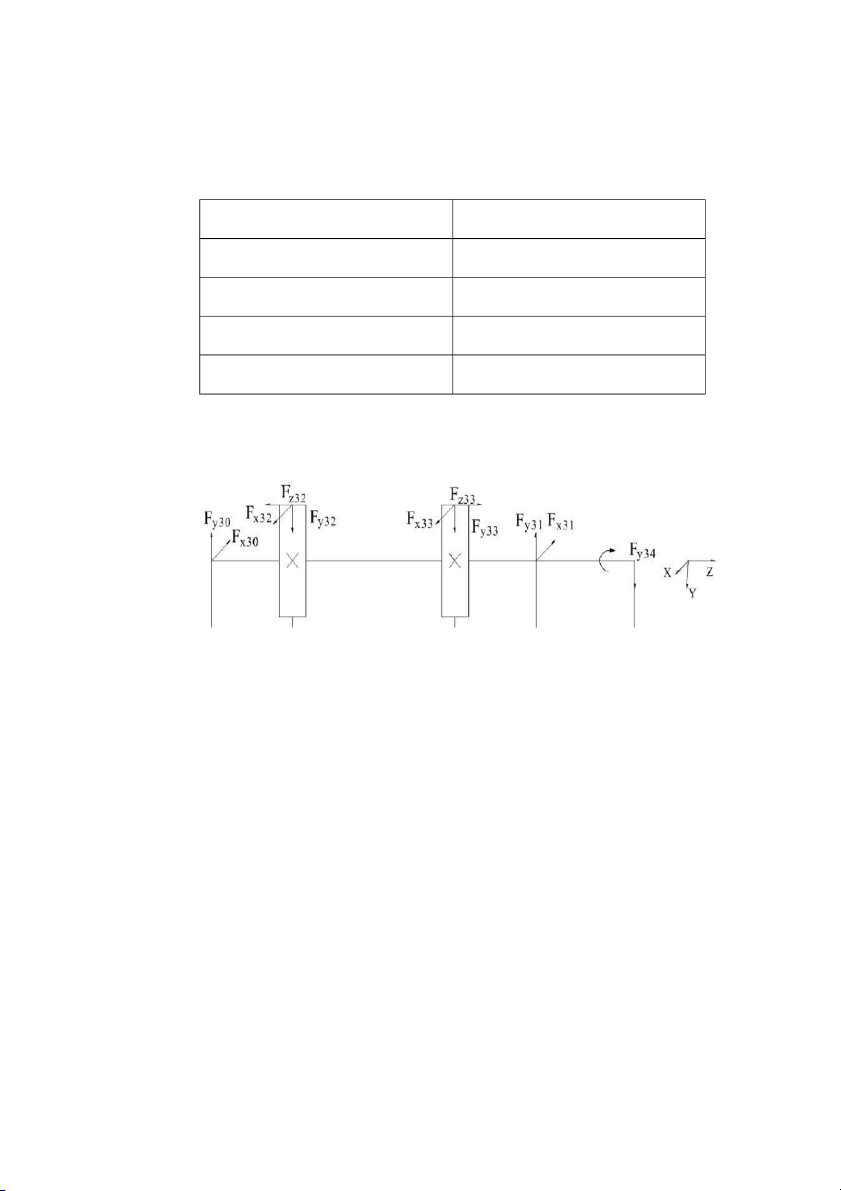
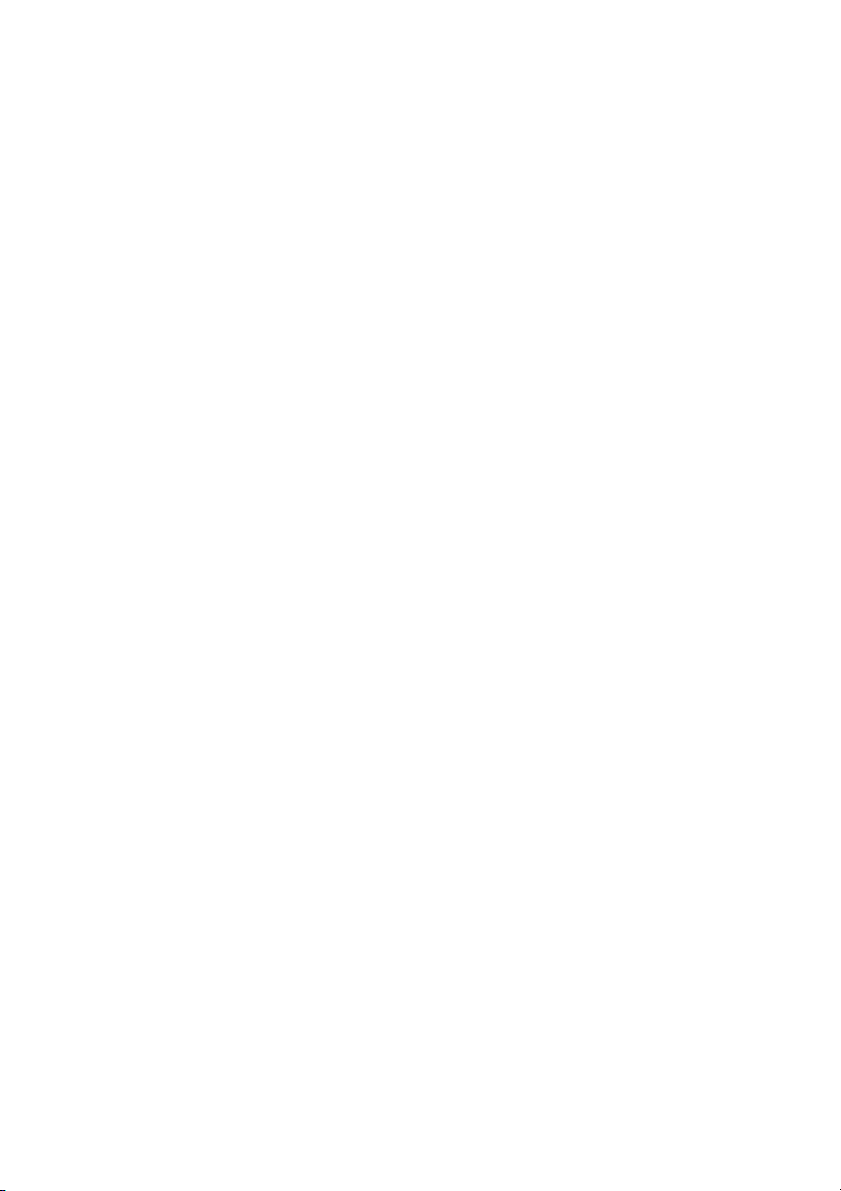
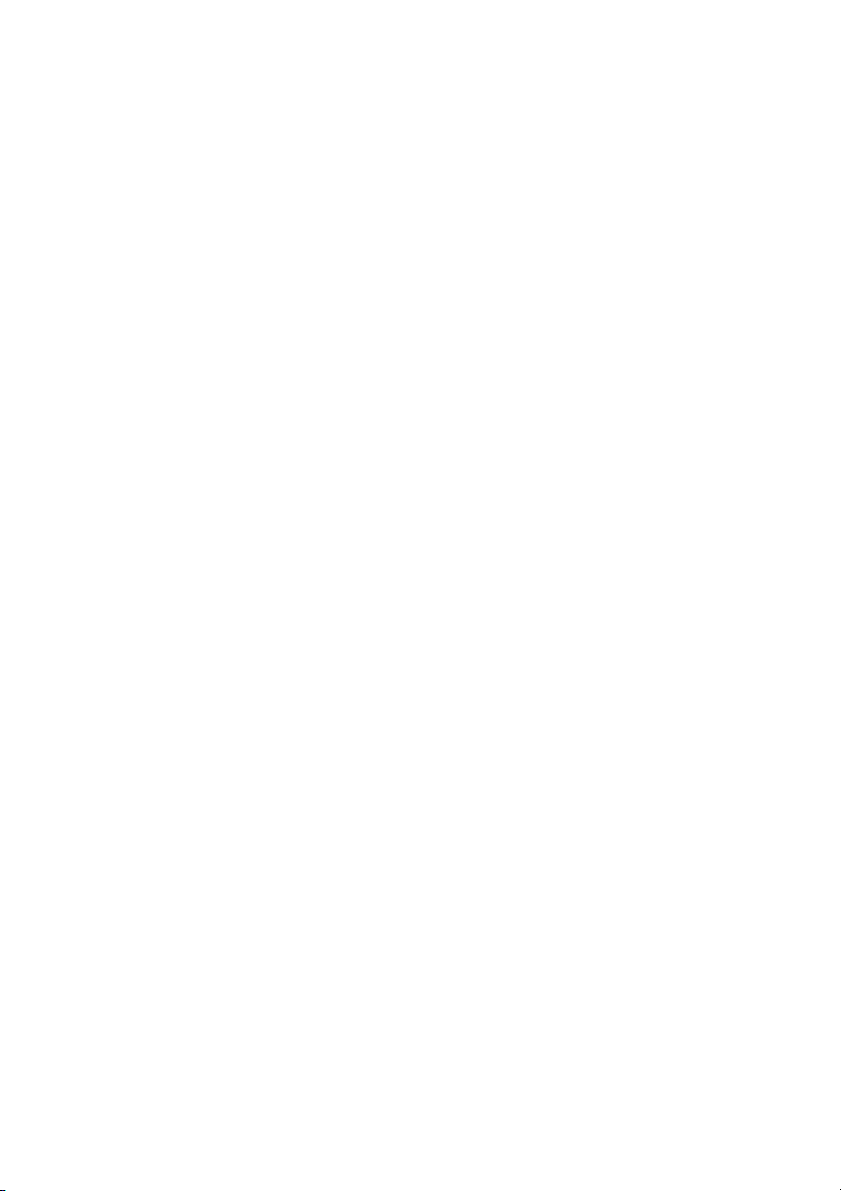
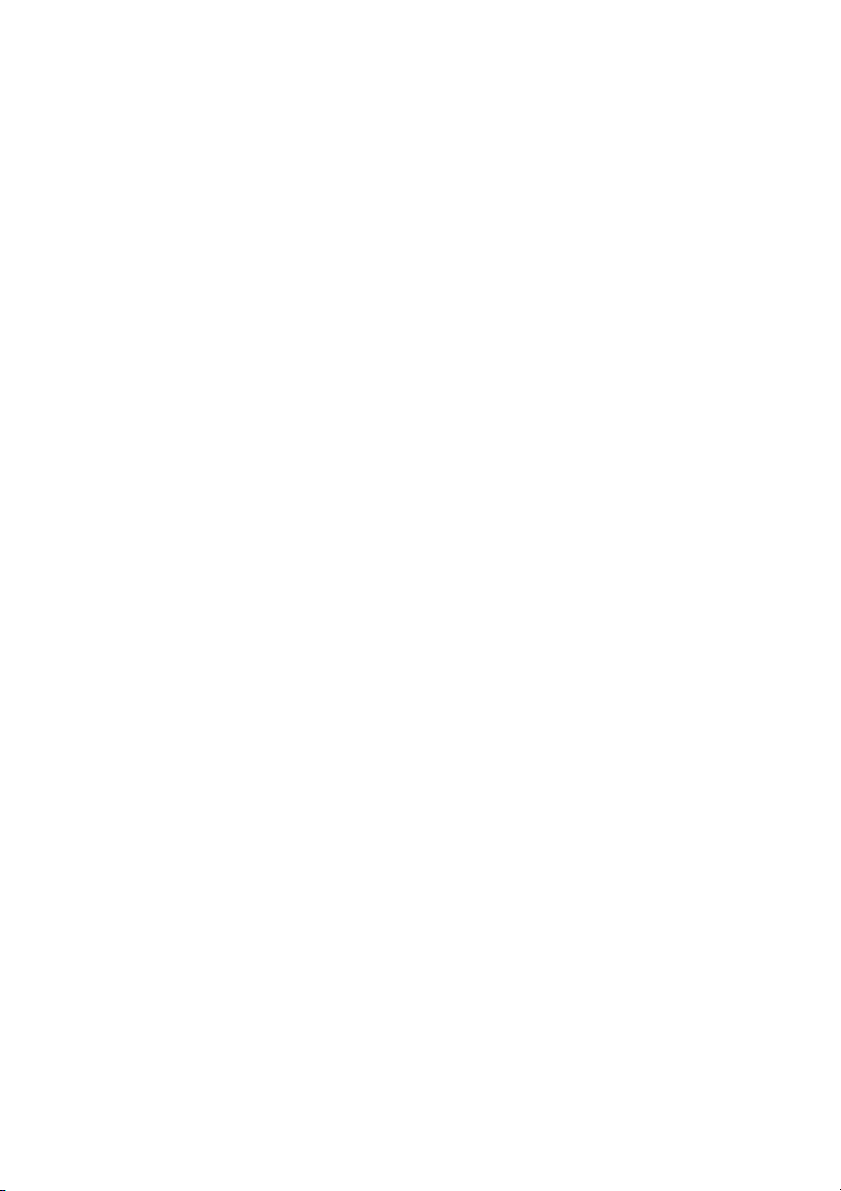
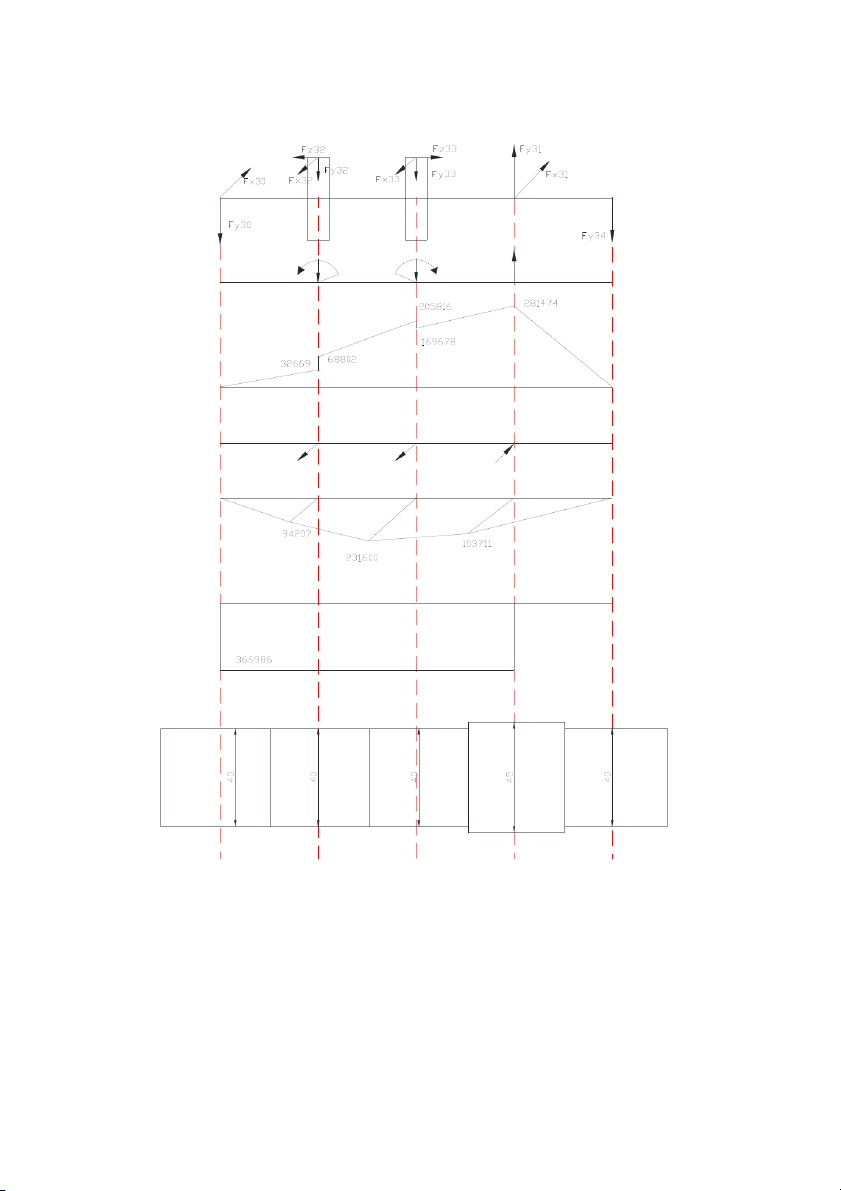
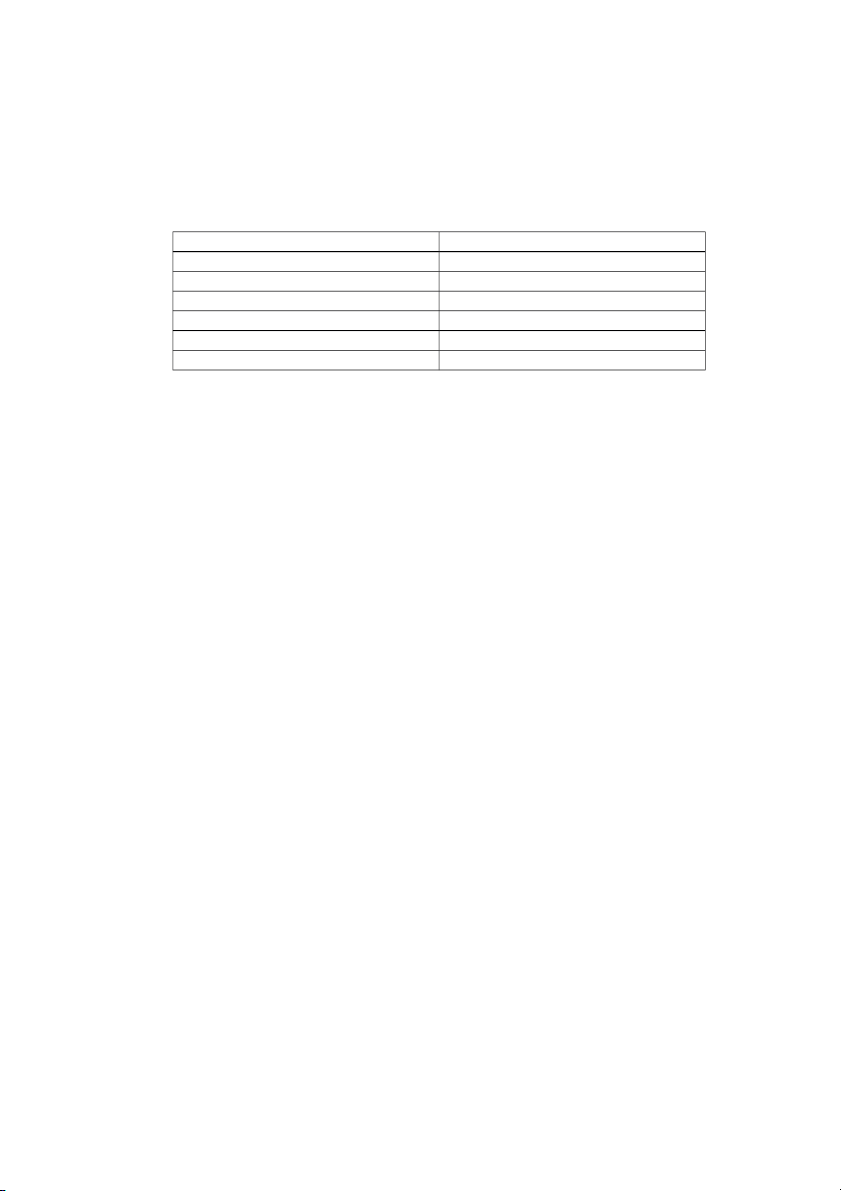

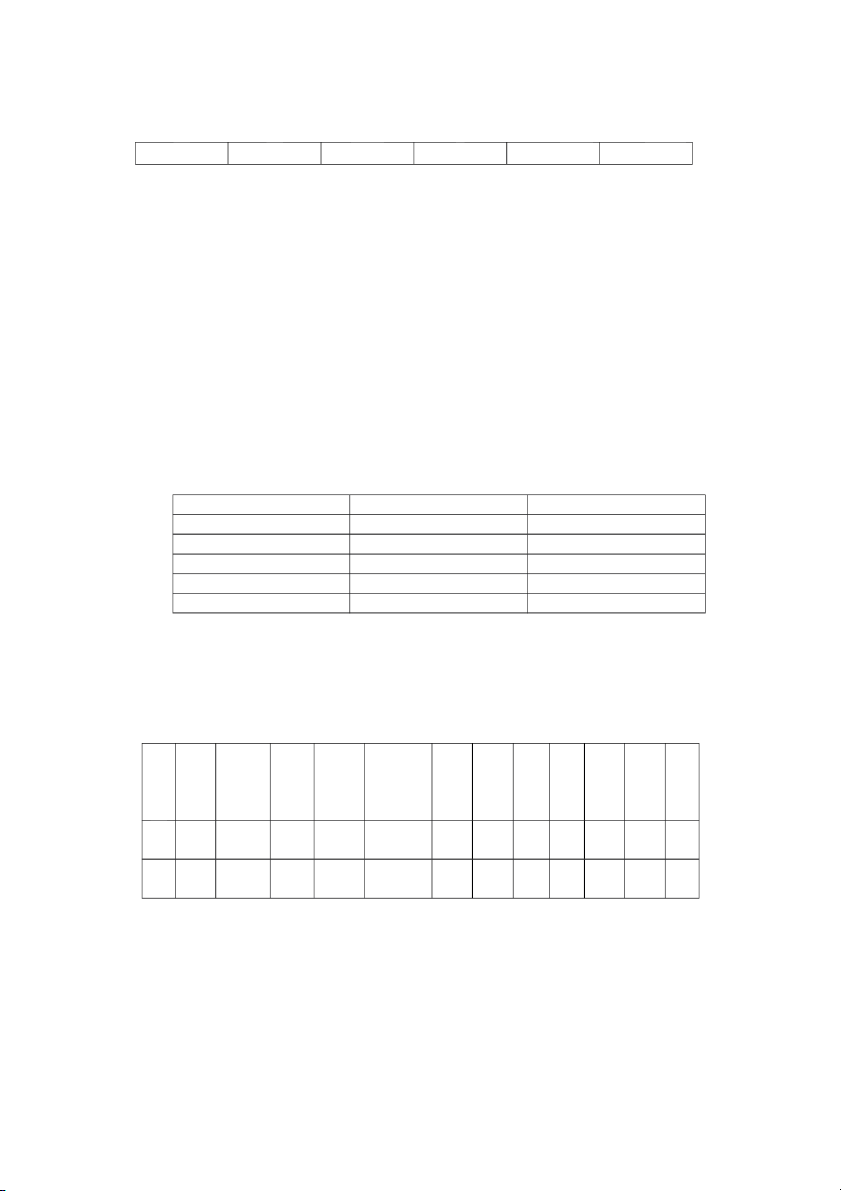
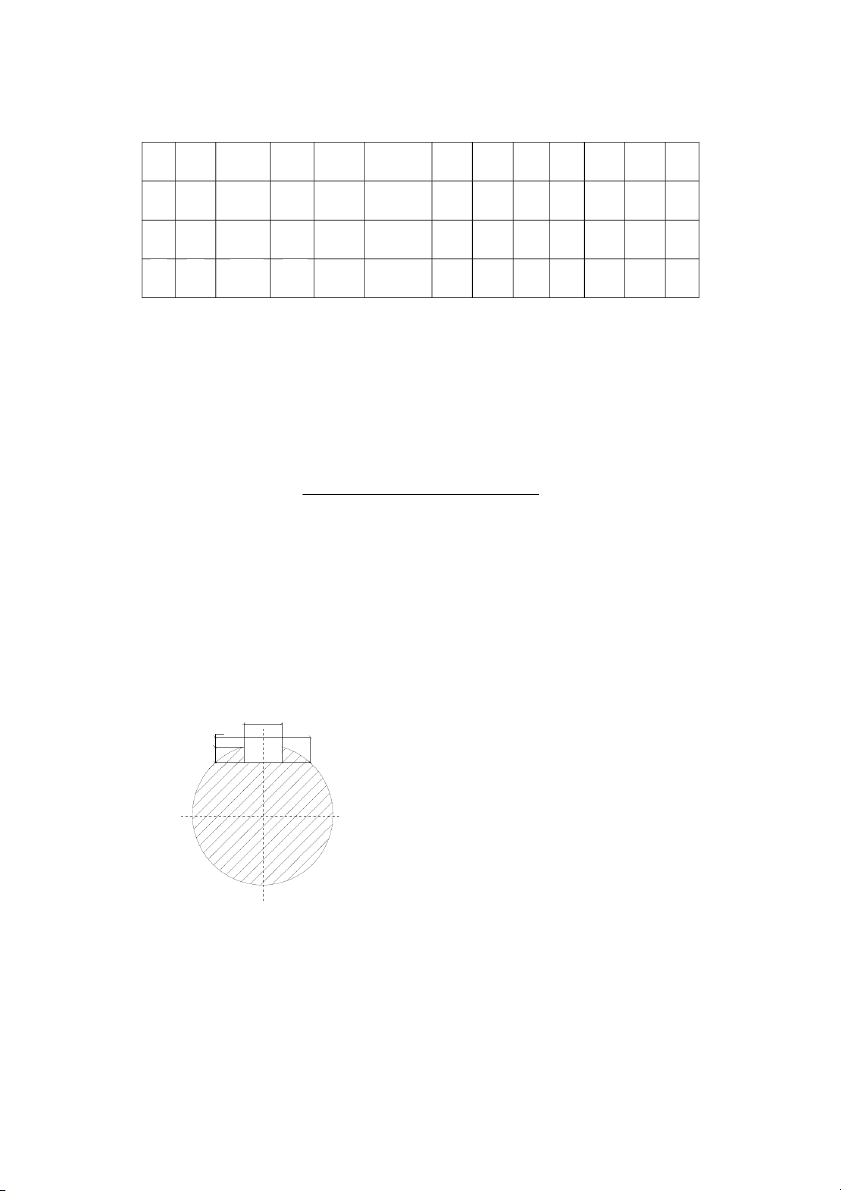
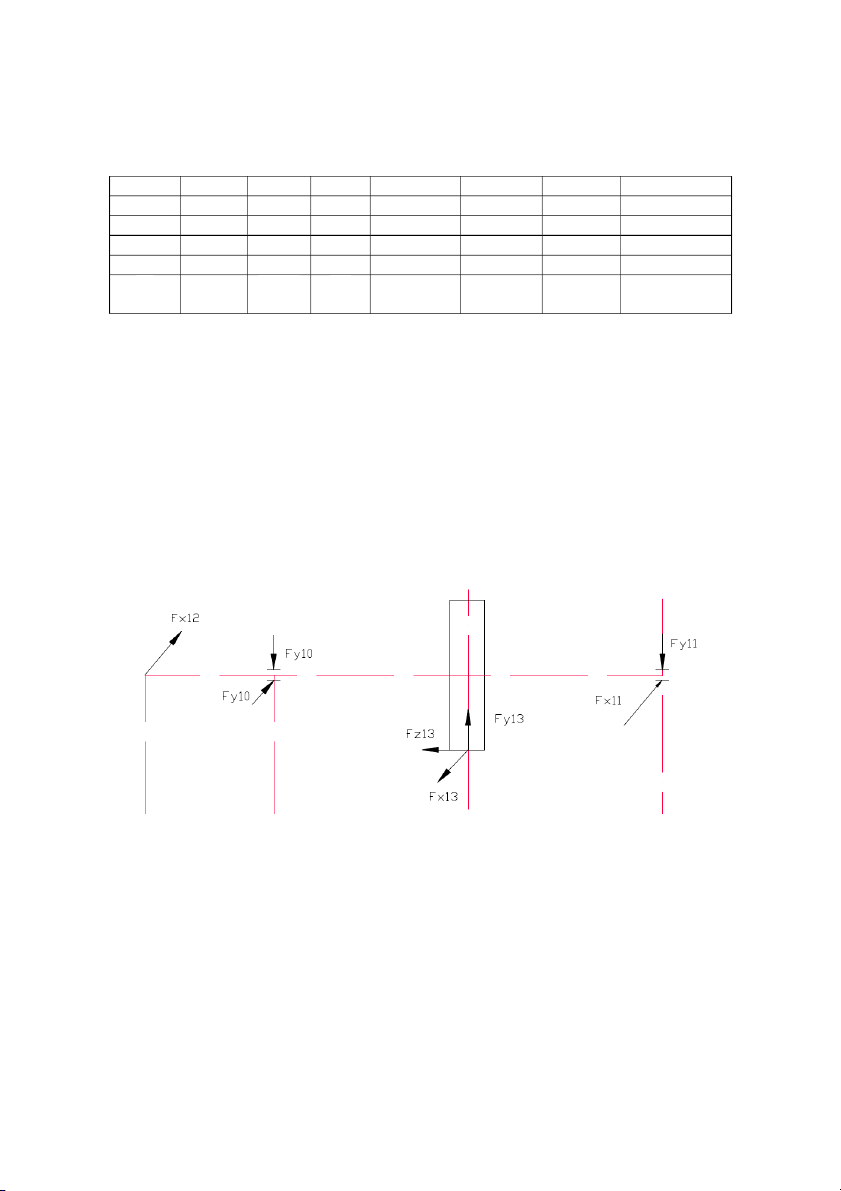
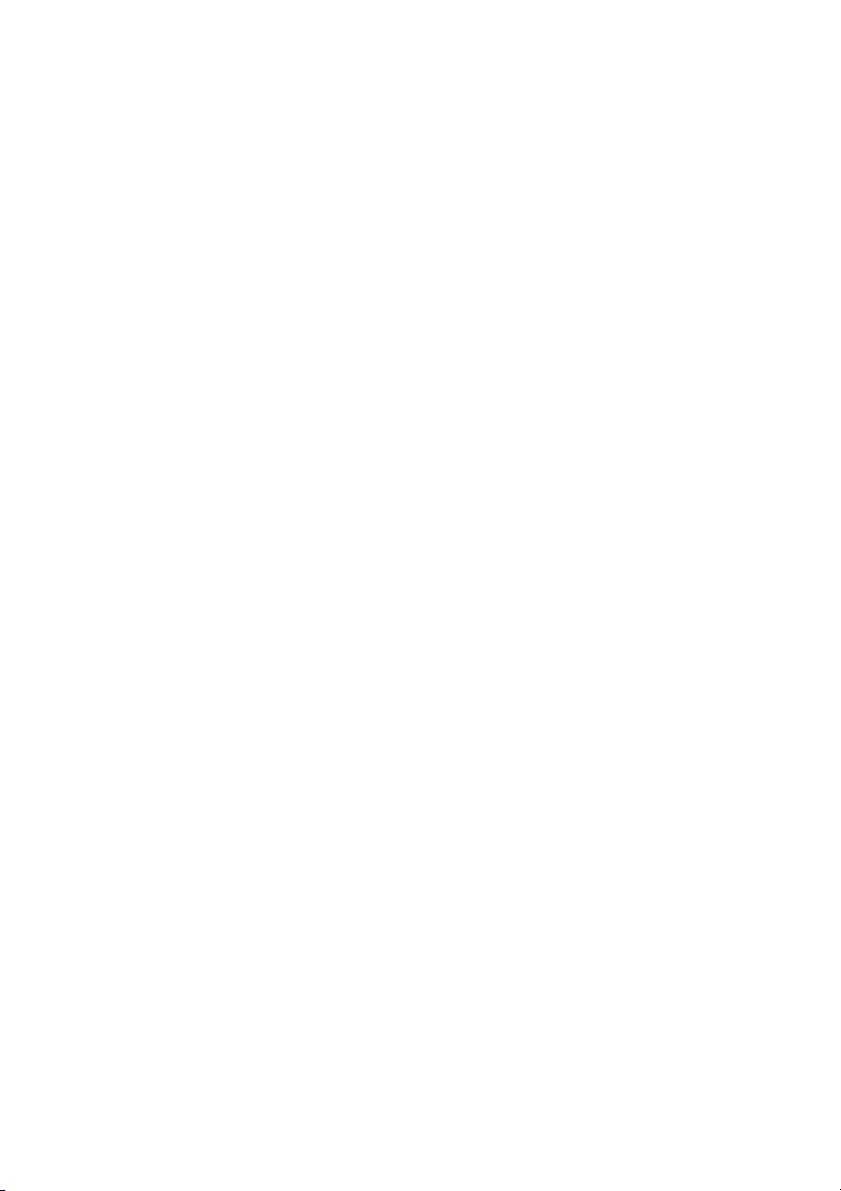
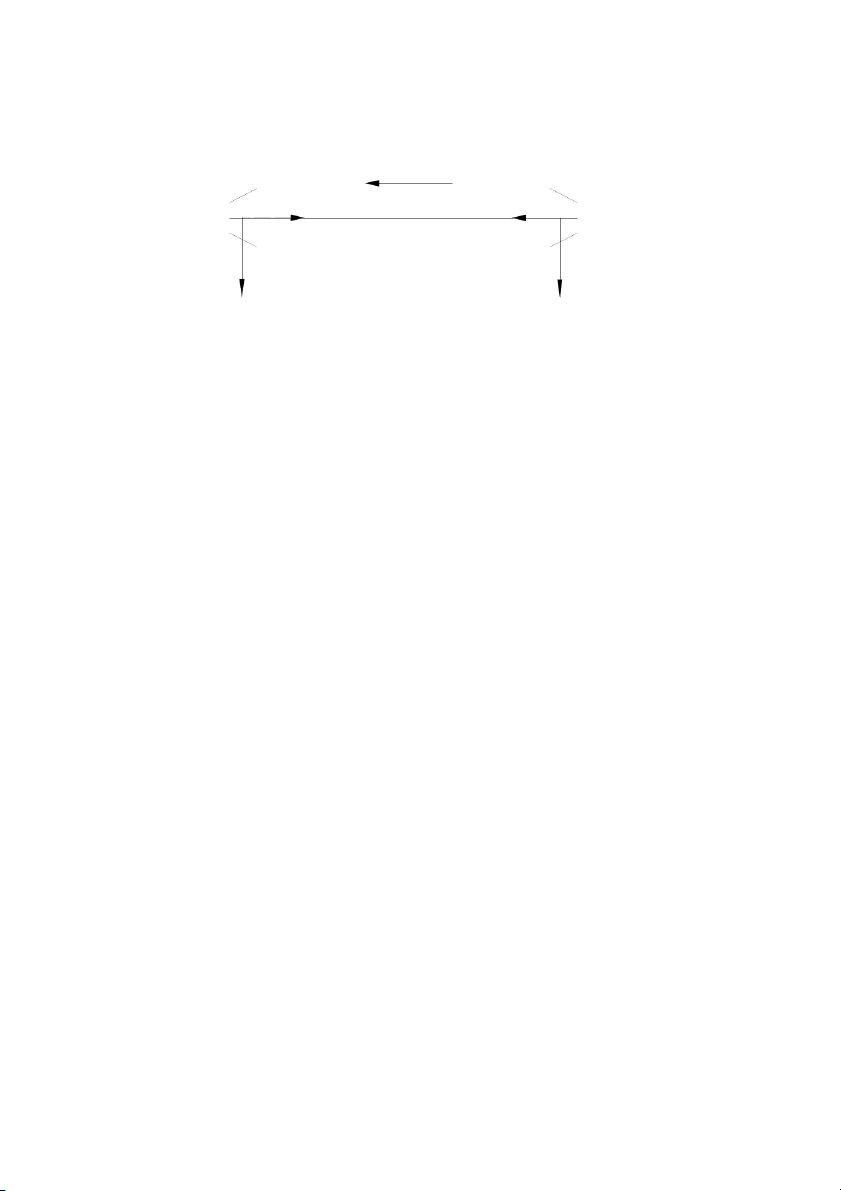
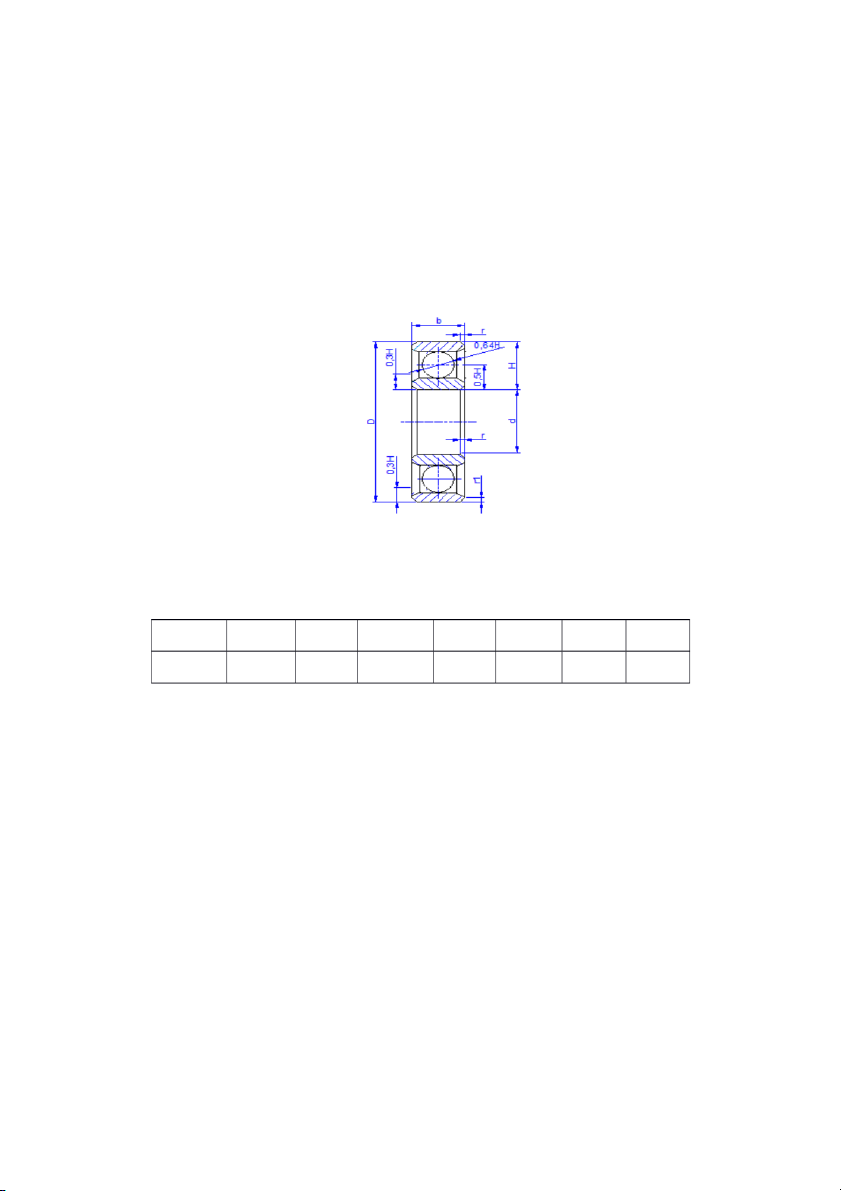
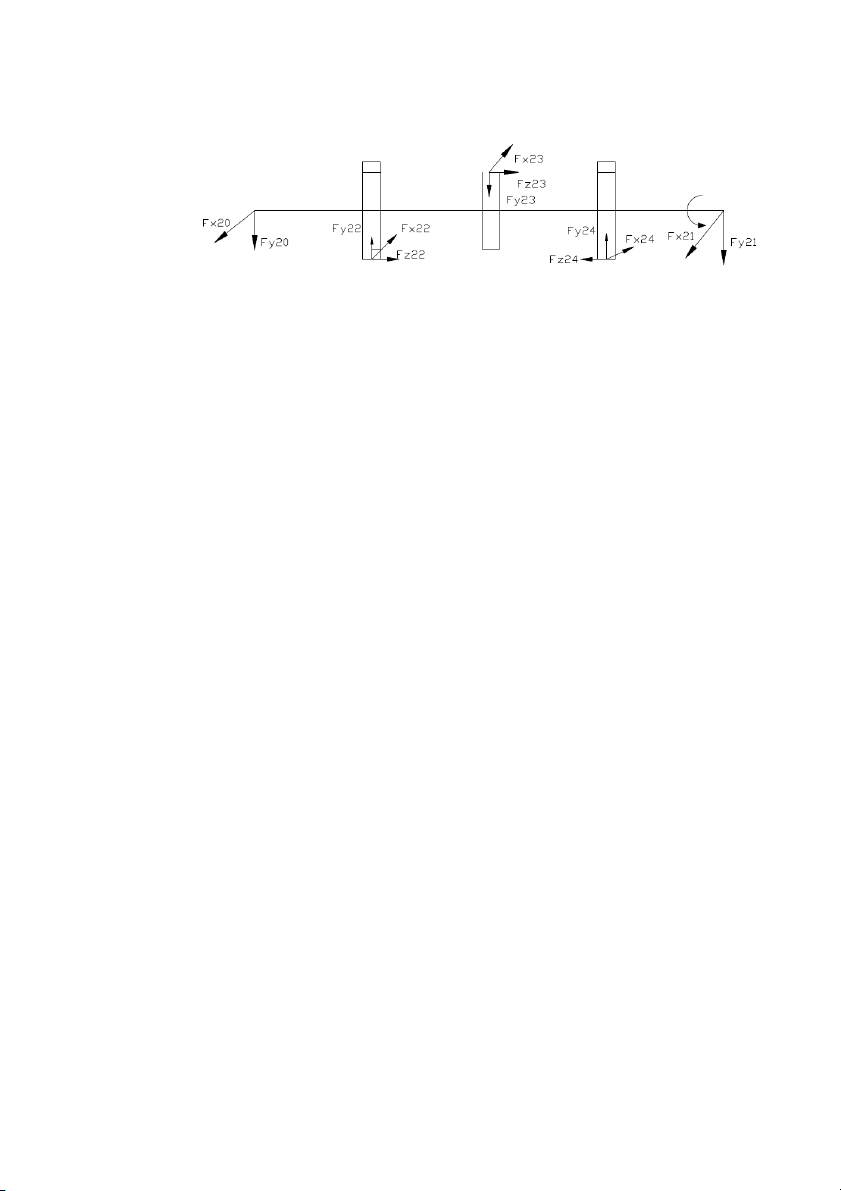
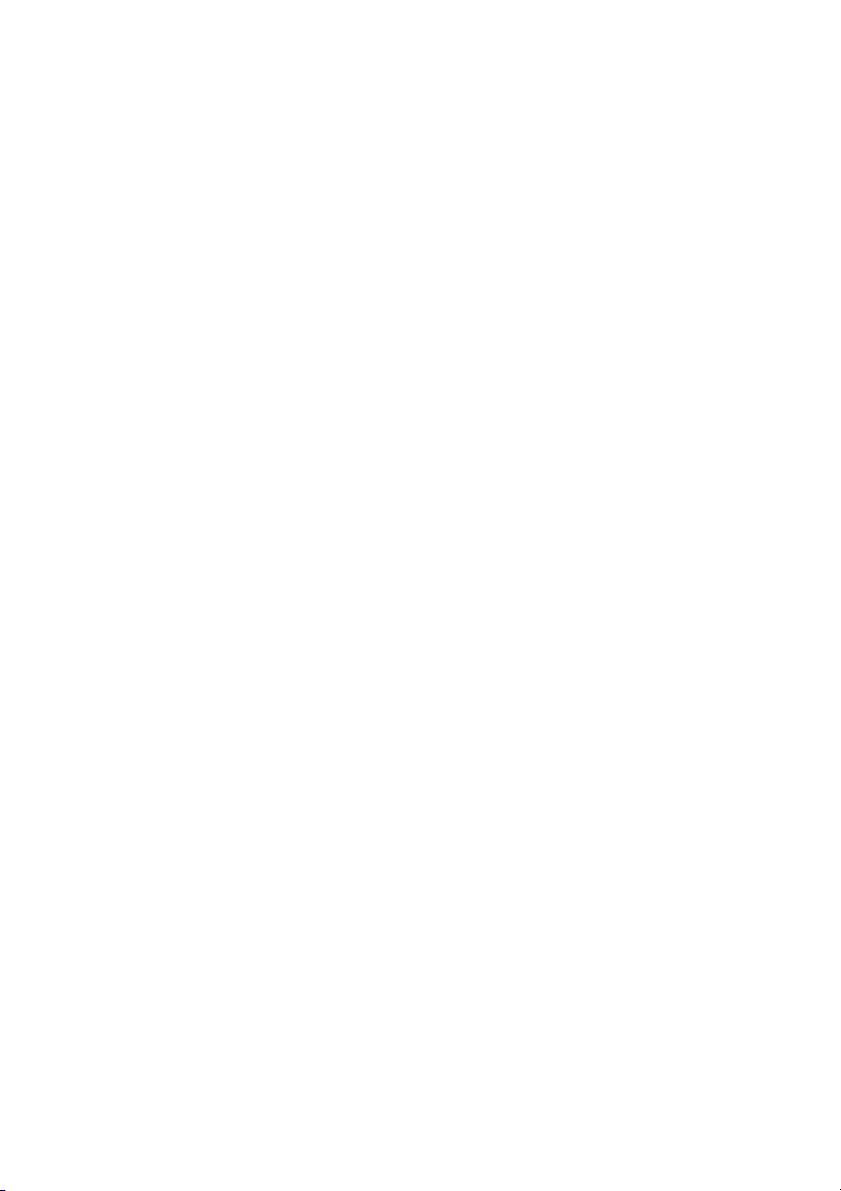
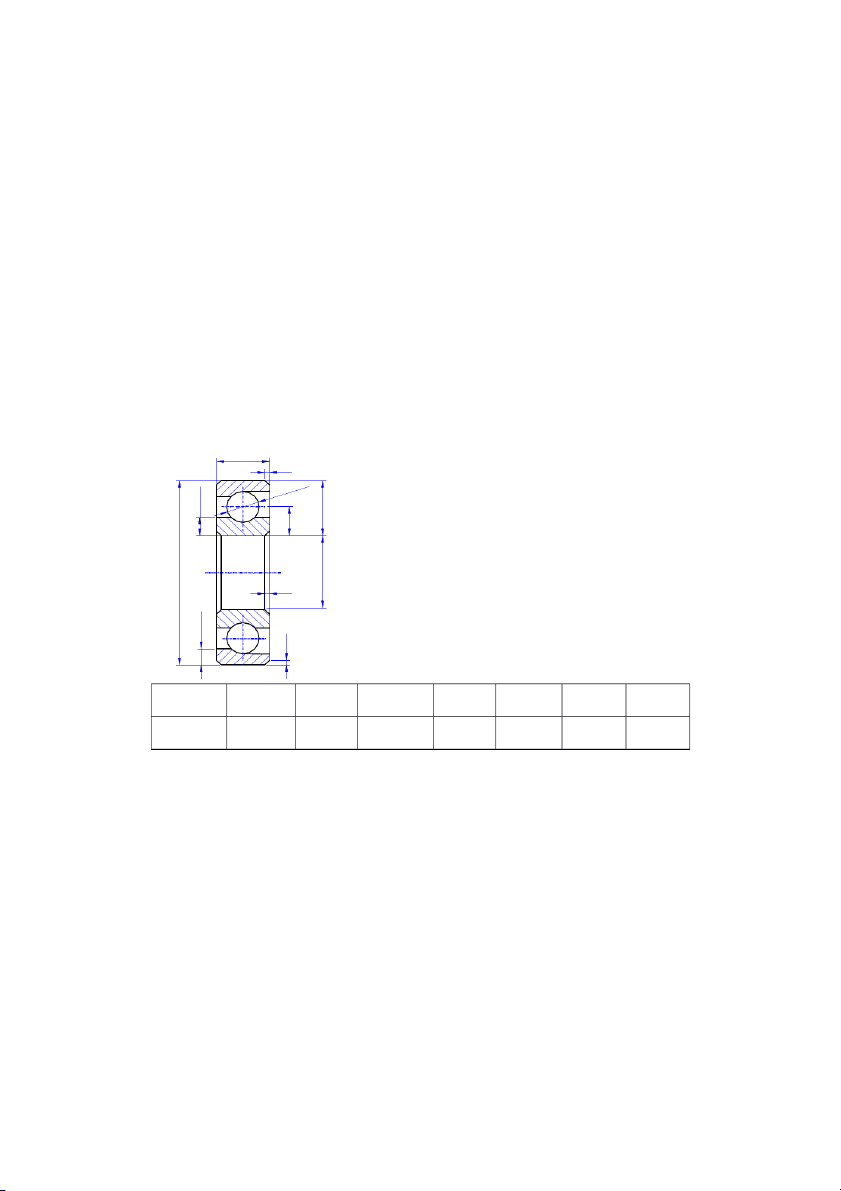
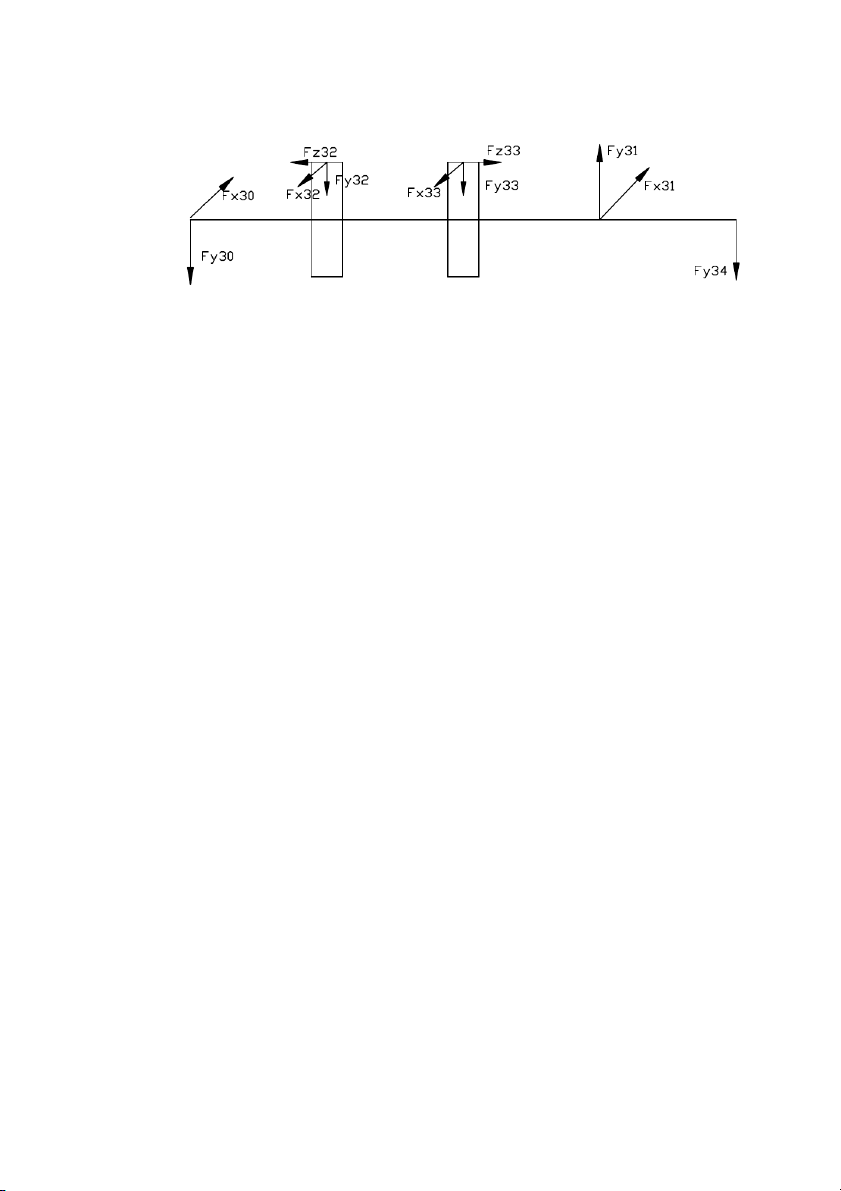
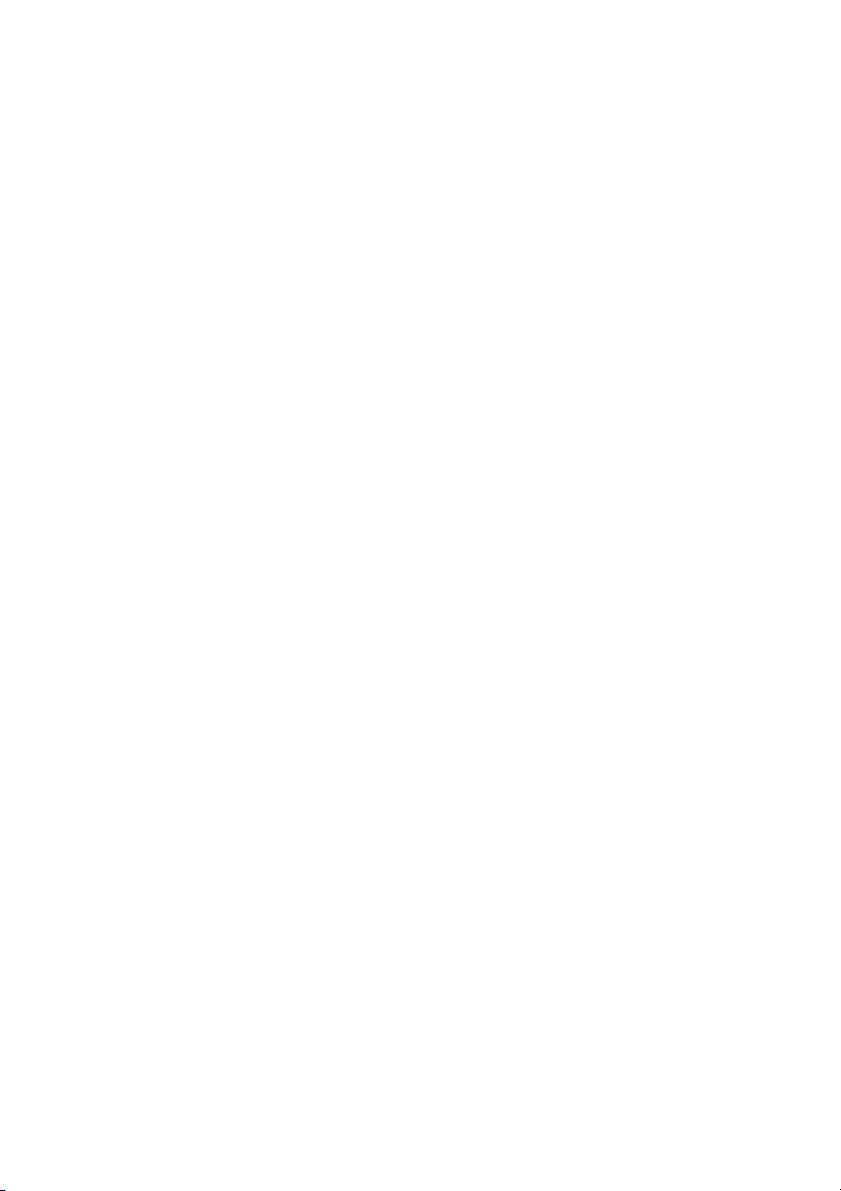
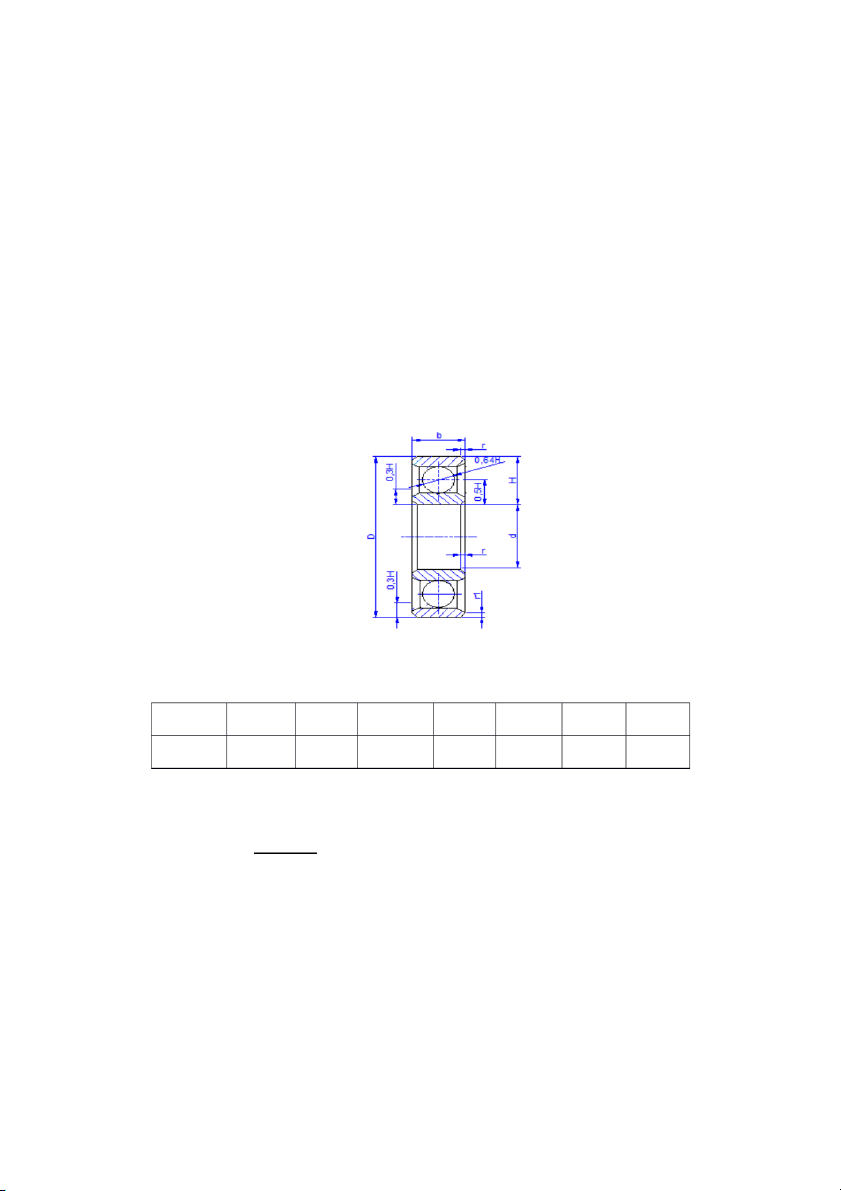
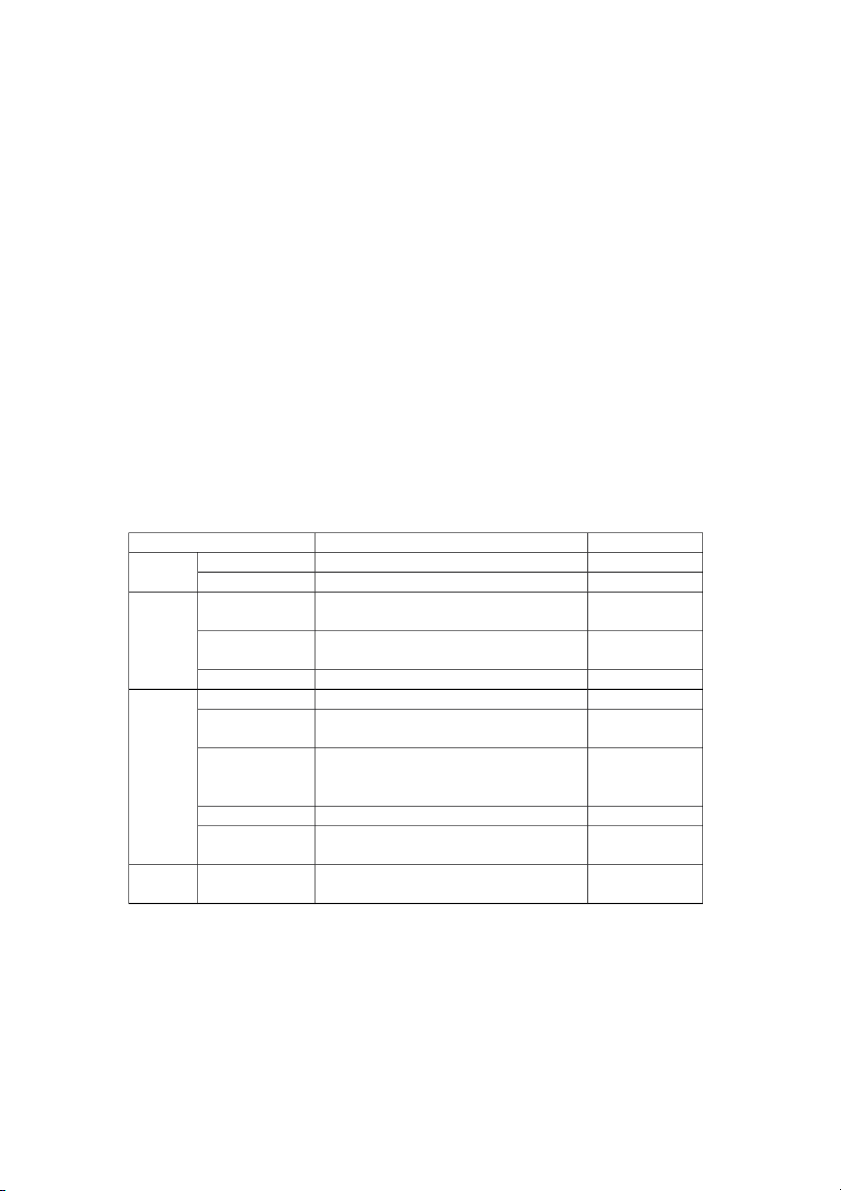
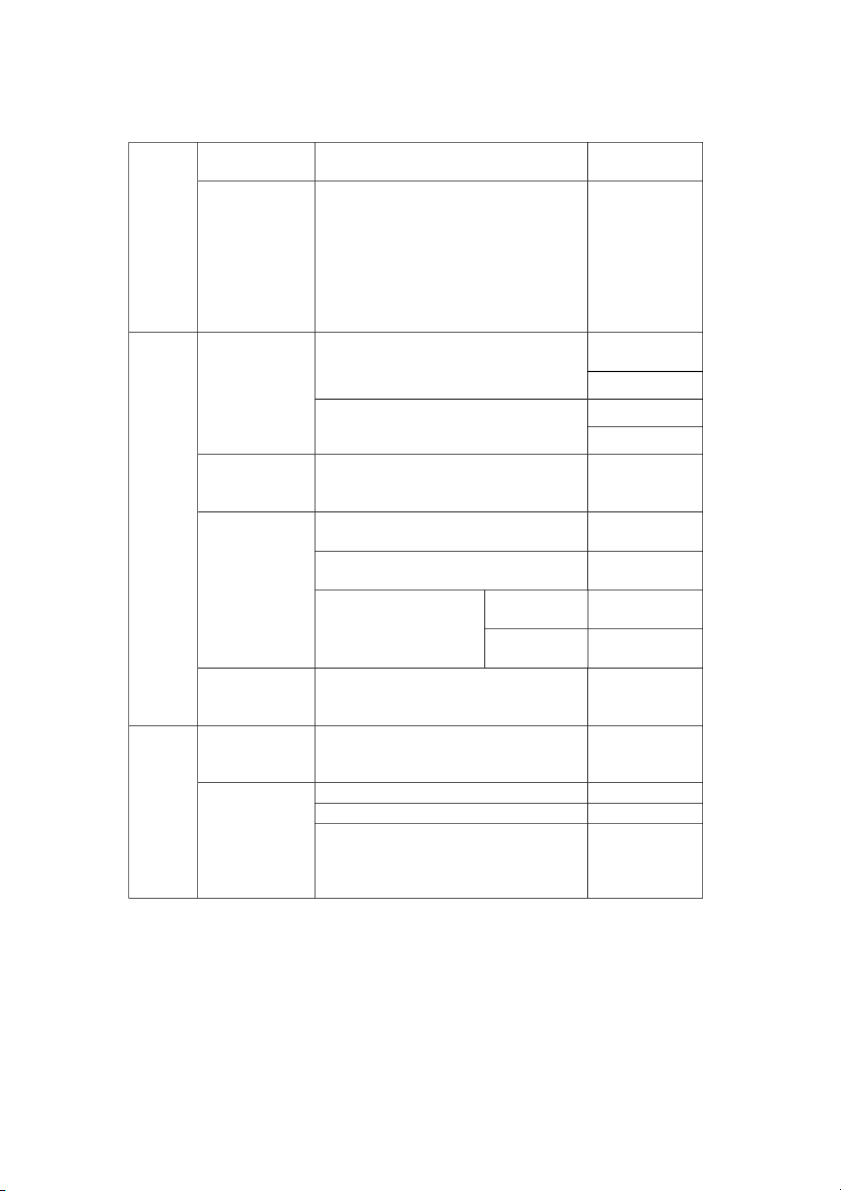
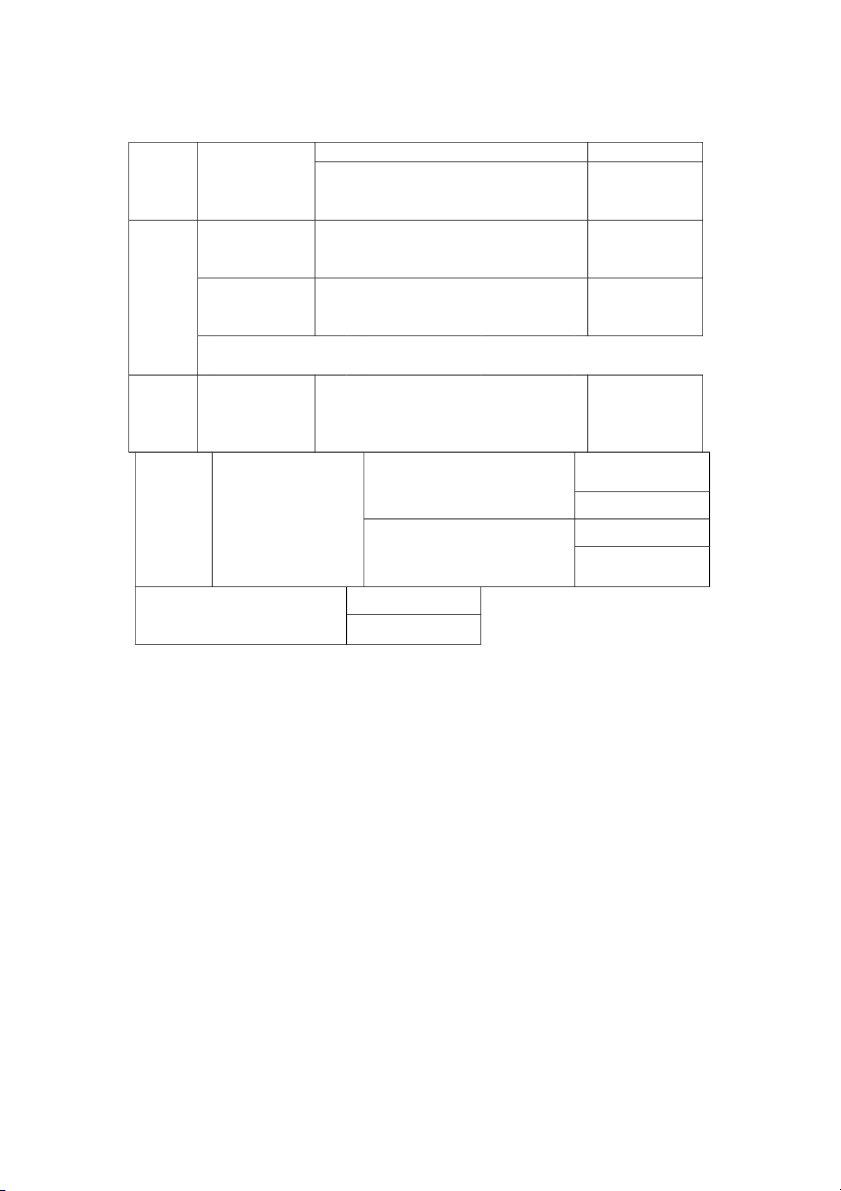
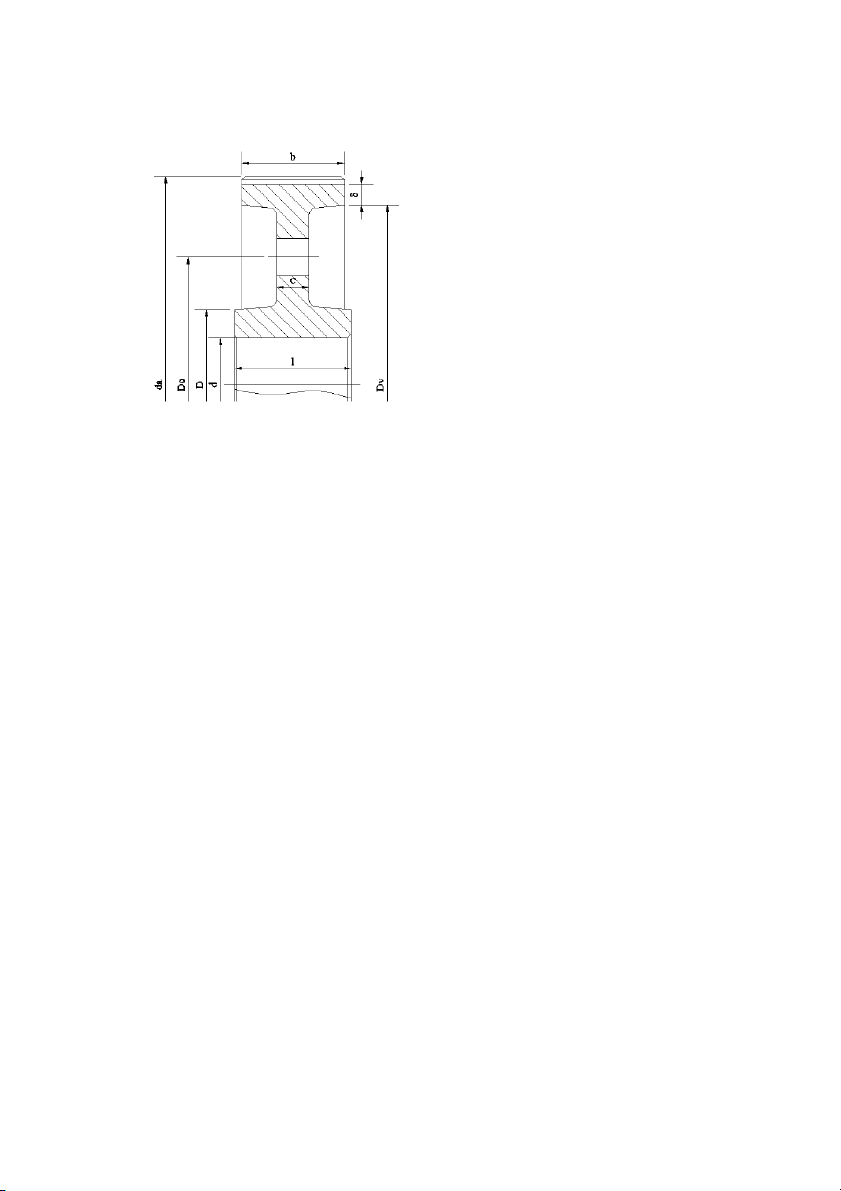
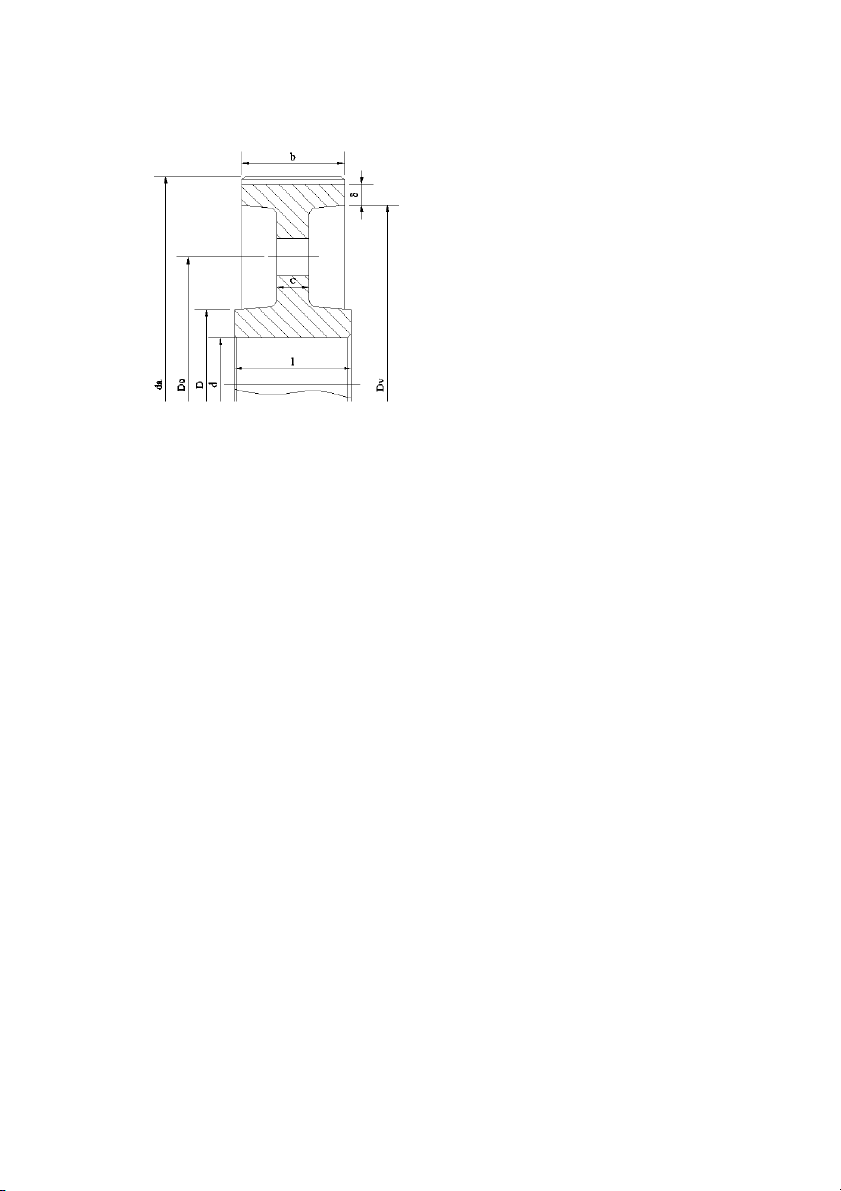
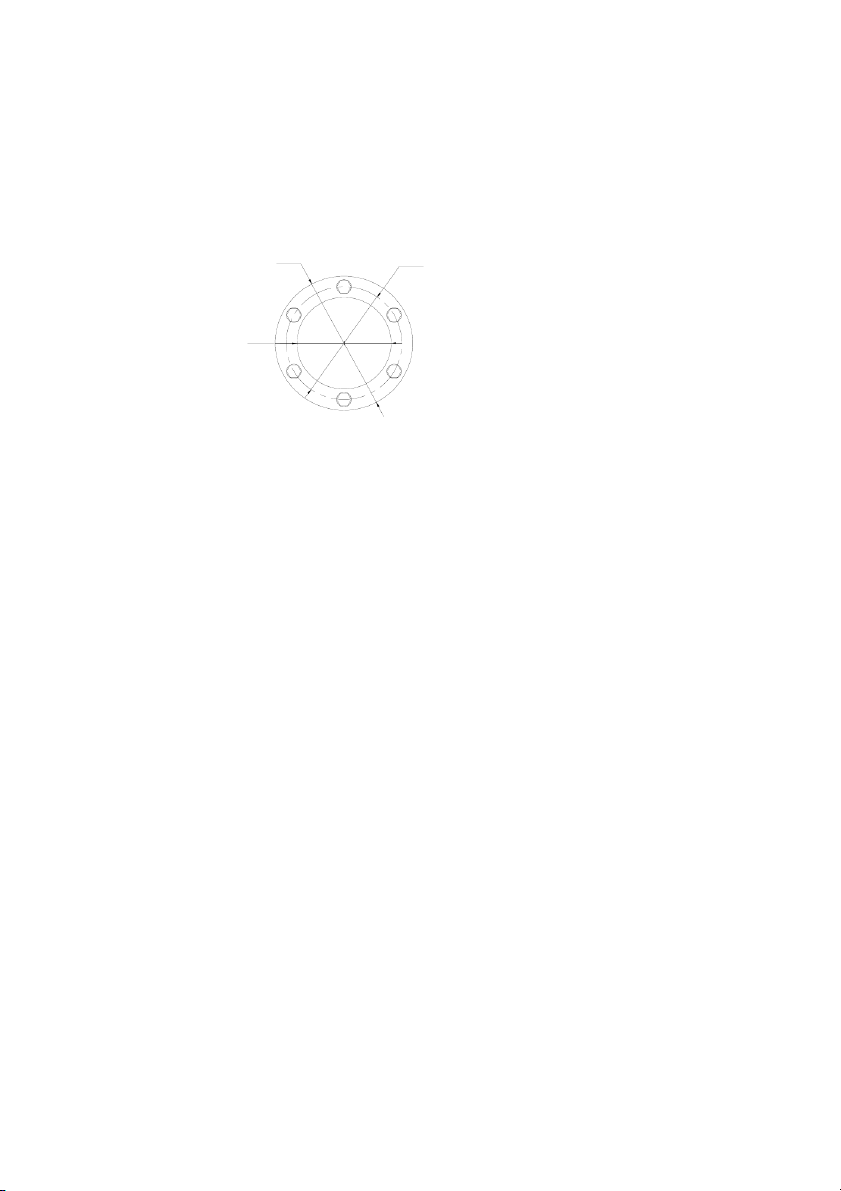
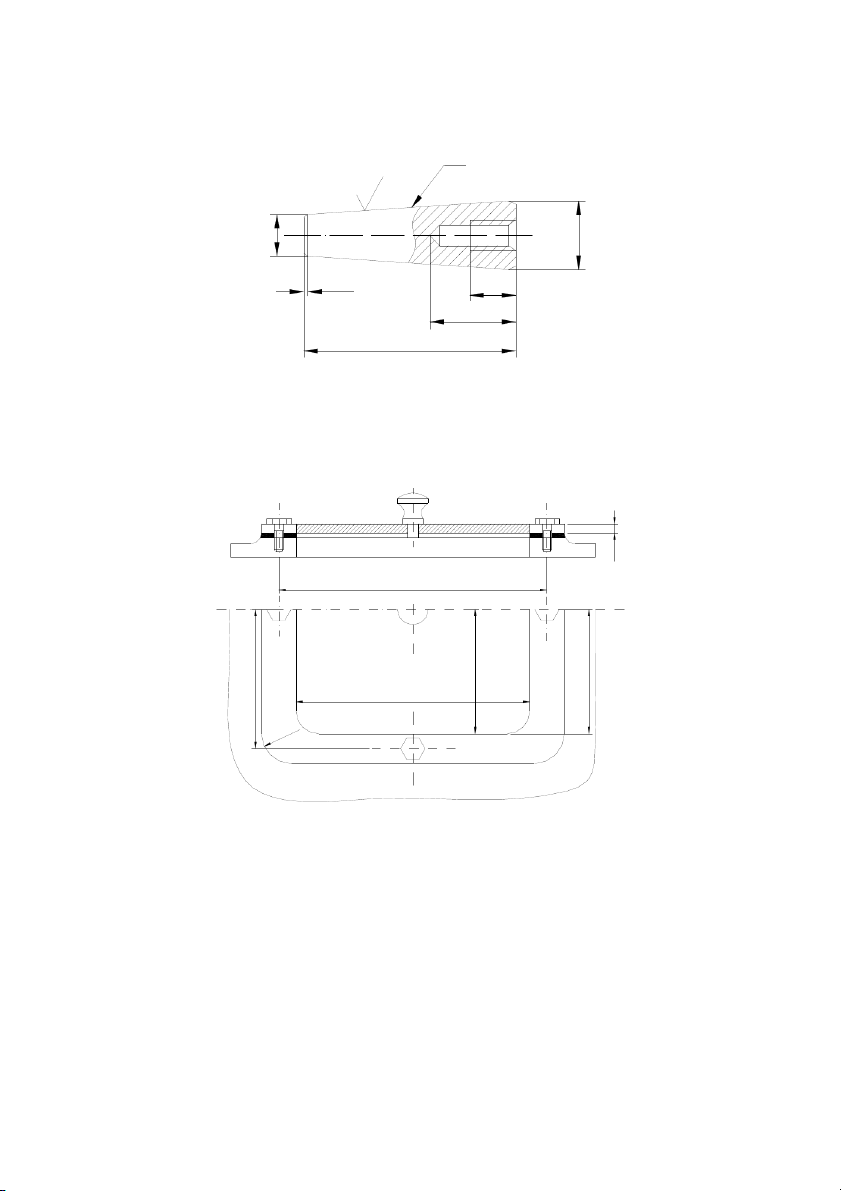
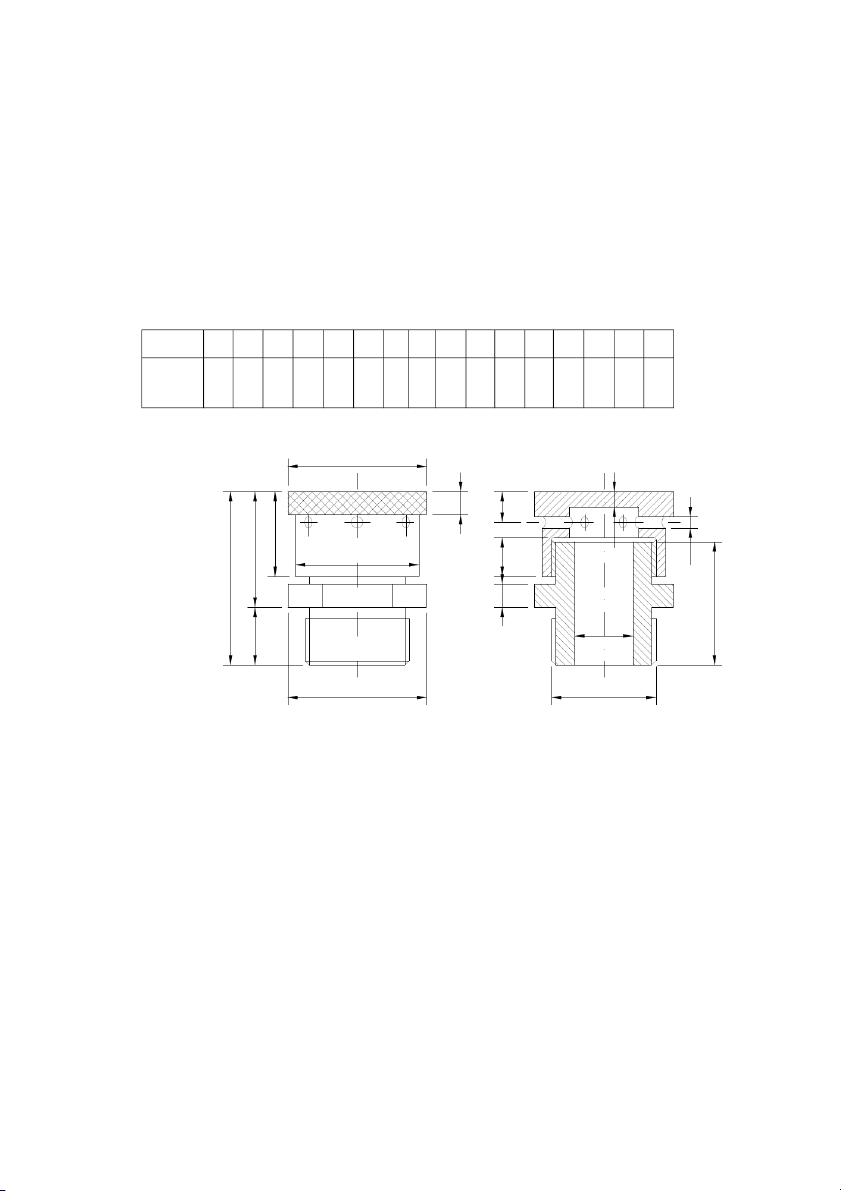
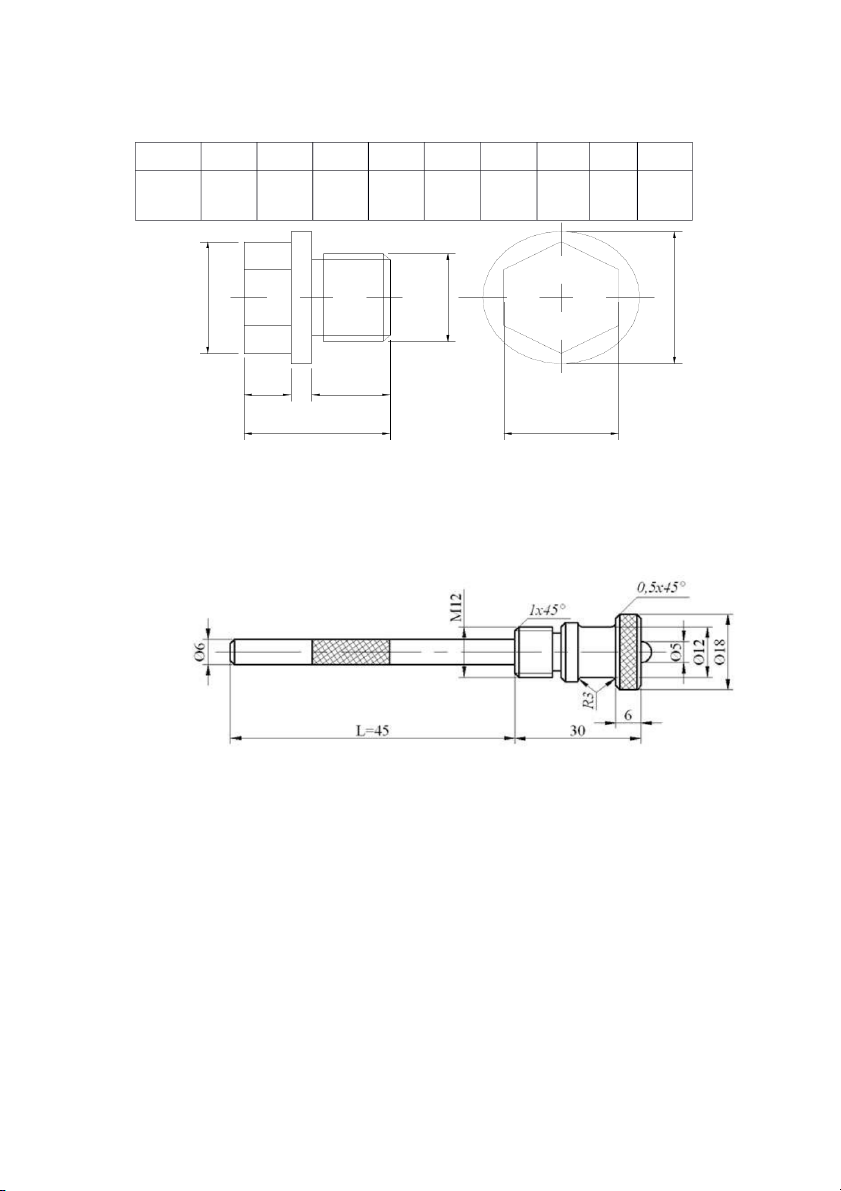
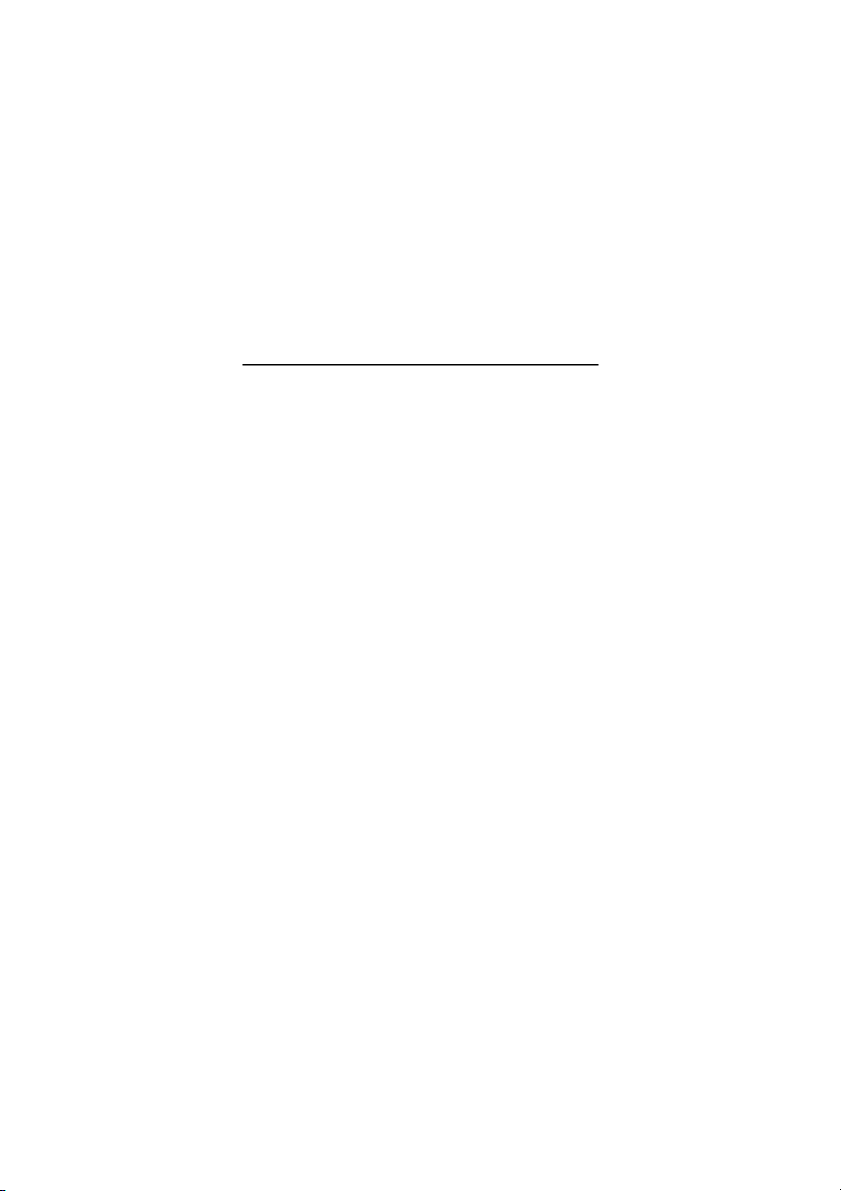
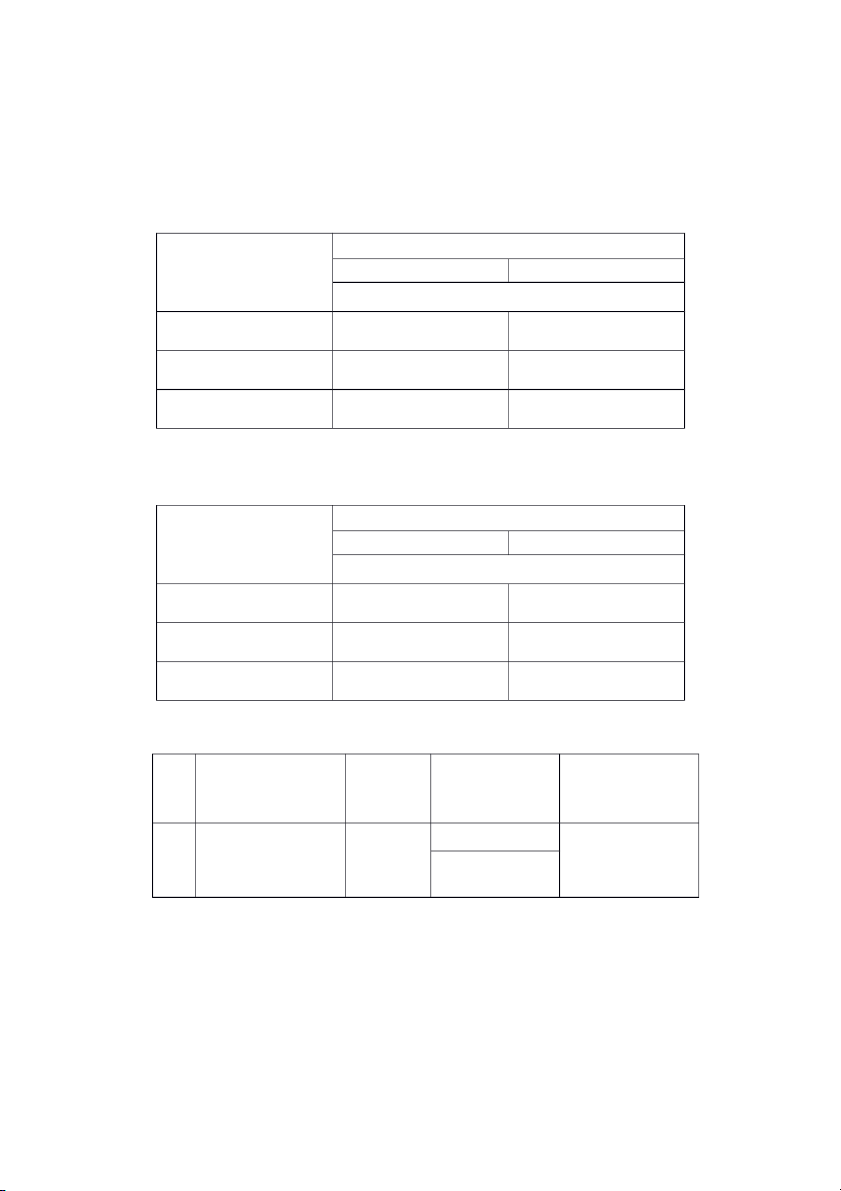
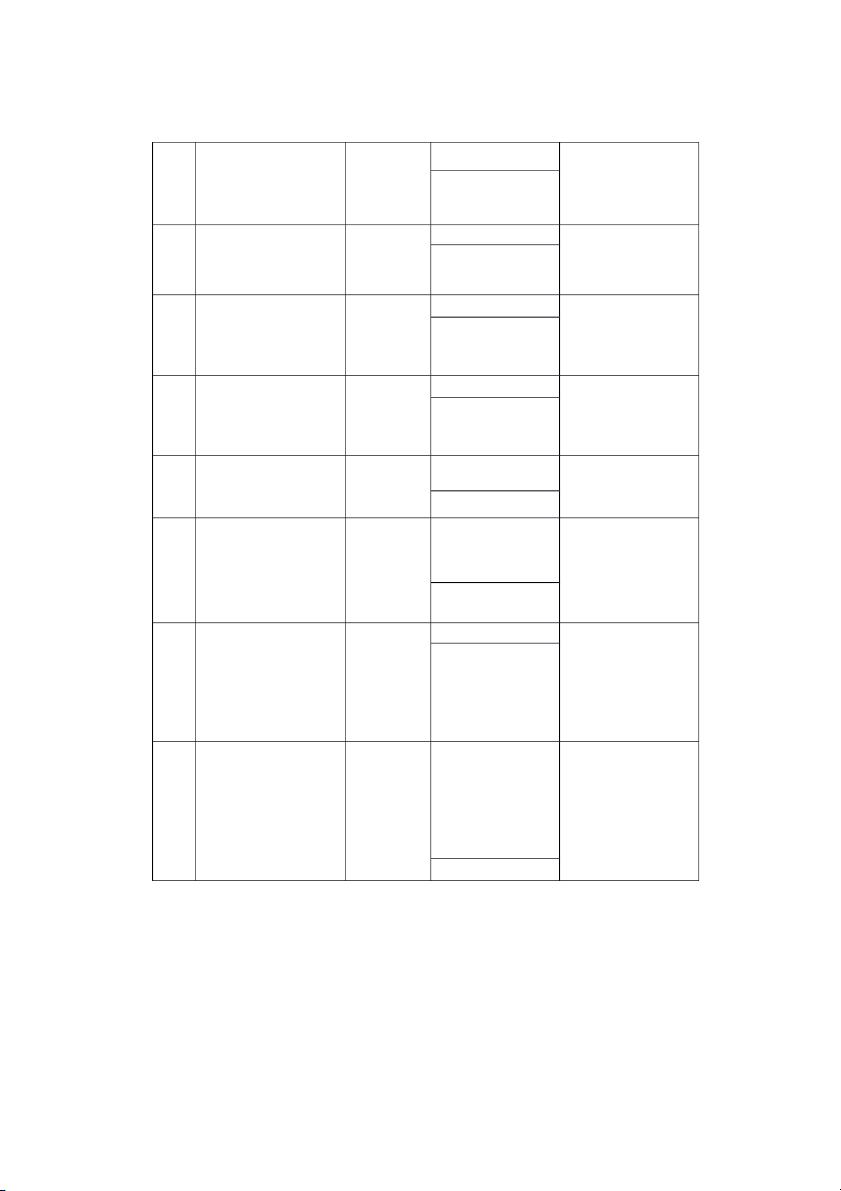
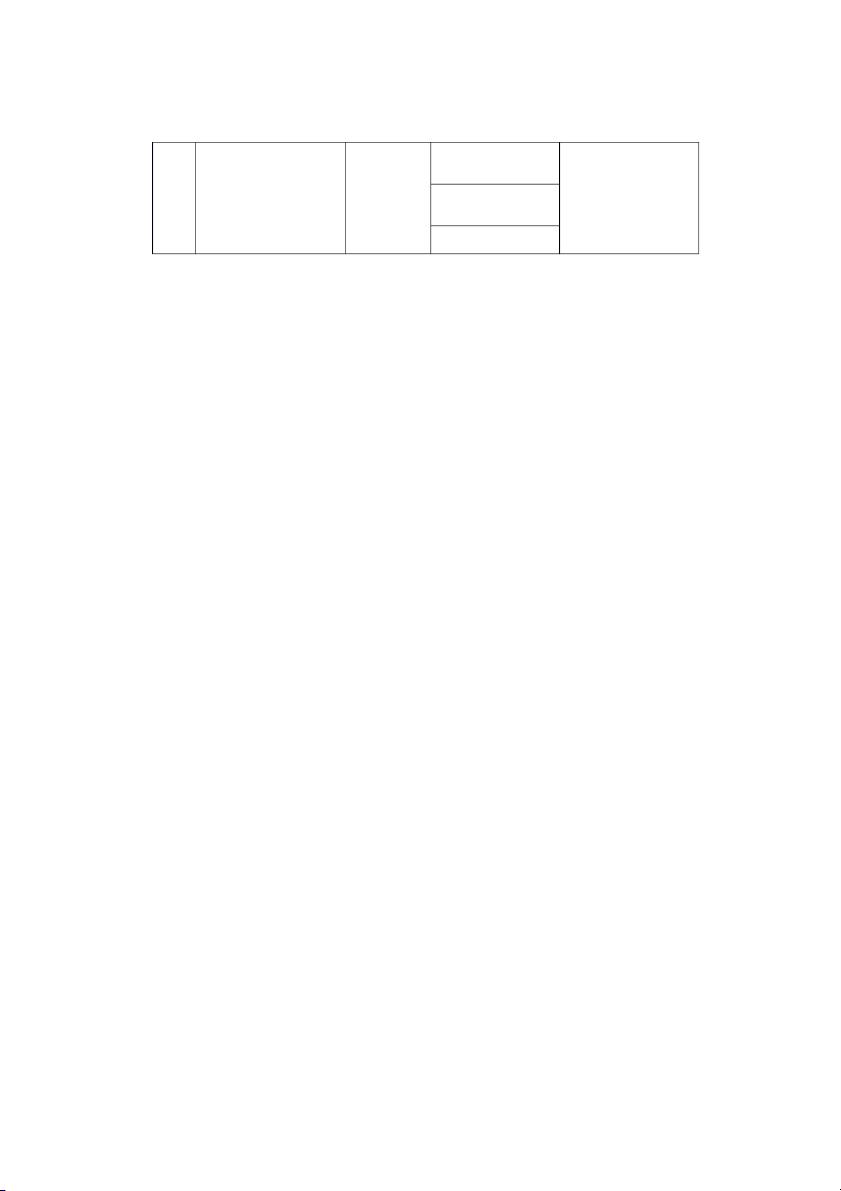
Preview text:
Trường đại học giao thông vận tải Khoa: Cơ khí
Bộ môn :Thiết kế máy
THIẾT KẾ MÔN HỌC CHI TIẾT MÁY Đề số:1 –Phương án 6
THIẾT KẾ TRẠM DẪN ĐỘNG BĂNG TẢI
Họ và tên : Trần Hoàng Đức Mã sinh viên : 171303145
Lớp : Công nghệ chế tạo cơ khí K58
Giáo viên hướng dẫn : Bùi Vũ Hùng Lời nói đầu
Trong nền kinh tế hiện nay ngành công nghiệp phát triền mạnh.Công nghiệp
hóa hiện đại hóa nền kinh tế.Trong đó ngành cơ khí được xem là ngành chủ lực của nền công nghiệp.
Đối với sinh ngành cơ khí sau khi ra trường được trang bị đầy đủ kiến thức
để góp phần vào xây dựng nền kinh tế nước nhà ngày càng phát triển mạnh.Nhất là
ngành công nghiệp, trong xu thế công nghiệp hóa hiện đại hóa như hiện nay.
Đối với em là sinh viên khoa cơ khí trường Đại Học Giao Thông Vận Tải.
Được sự tận tình chỉ bảo của các thầy cô giáo trong khoa, cung cấp cho em nhiều
kiến thức để khi ra trường có thể áp dụng vào công việc thực tiễn góp một phần
vào sự phát triển của nền công nghiệp nước ta. 1
Trong quá trình học tập tại trường, em được nghiên cứu nhiều môn học, từ lý
thuyết đến thực hành.Trong đó có môn ‘Đồ Án Chi Tiết Máy’.Là một môn quan
trọng của ngành cơ khí mà mỗi sinh viên cơ khí ai cũng phải làm.
Đối với riêng cá nhân em, khi nhận được đề tài đồ án chi tiết máy:
“THIẾT KẾ TRẠM DẪN ĐỘNG BĂNG TẢI”. Còn gặp rất nhiều khó
khăn bước đầu nhưng được sự tận tình chỉ bảo của các thầy cô trong khoa, giúp em
tự tin hơn để hoàn thành đồ án một cách tốt nhất.Trong đó có thầy Bùi Vũ Hùng là
giáo viên hướng dẫn cho em làm đồ án chi tiết máy. Được sự hướng dẫn tận tình
của thầy đã giúp em có được vốn kiến thức để hoàn thành đồ án một cách tốt nhất.
Qua thời gian làm việc cùng thầy em thấy kiến thức chuyên ngành cơ khí
của mình được cải thiện lên rất nhiều.
Tuy nhiên đây là lần đầu được tính toán thiết kế nên vẫn còn những điểm
thiếu sót, em mong được sự giúp đỡ và góp ý của các thầy cô để kiến thức của em
được cải thiện tốt hơn.
Em xin chân thành cảm ơn sự tận tình giúp đỡ của thầy Bùi Vũ Hùng để em
được hoàn thành tốt môn học này. Sinh viên thực hiện Trần Hoàng Đức Mục lục :
Phần I: Tính toán chọn động cơ và Phân phối tỷ số truyền
Phần II: Tính toán thiết kế bộ truyền bánh răng nghiêng
Phần III: Tính toán thiết kế bộ truyền xích
Phần IV: Tính toán thiết kế trục
Phần V: Thiết kế ổ lăn
Phần VI:Thiết kế vỏ hộp giảm tốc Phần VII: Dung sai 2
[TL1]. Tính toán hệ dẫn động cơ khí tập 1 – PGS.TS –Trịnh Chất – Lê Văn Uyển
[TL2]. Tính toán hệ dẫn động cơ khí tập 2 – PGS.TS –Trịnh Chất – Lê Văn Uyển
Các số liệu phục vụ cho công việc thiết kế :
*Chế độ làm việc : mỗi ngày làm việc 2 ca , mỗi ca 4 giờ ,làm việc 280 ngày, tải trọng va đập nhẹ. Phương án 6 Thứ nguyên Lực vòng trên băng tải 400 kG Vận tốc băng tải 0,9 m/s Đường kính trong D 320 mm Chiều rộng băng tải B 380 mm Thời hạn phục vụ 6 Năm Chiều cao tâm băng 300 mm
Sai số vận tốc cho phép 4 %
Phần I: Chọn động cơ và phân phối tỷ số truyền I. Chọn động cơ
1. Để chọn động cơ ta tiến hành theo các bước sau :
Tính công suất cần thiết của động cơ
Xác định sơ bộ số vòng quay đồng bộ của động cơ
Dựa vào công suất và số vòng quay đồng bộ kết hợp với các yêu
cầu về quá tải , mômen mở máy và phương pháp lắp đặt động cơ
để chọn kích thước động cơ phù hợp với yêu cầu thiết k
- Từ đồ thị ta tính được :
Công suất tính toán ứng với M trên đồ thị (M,t) : 3
- Công suất quá tải khi mở máy :
- Công suất tương đương tính theo công thức 2.13 [TL1]
- Hiệu suất chung của bộ truyền : Tra theo bảng 2.3 [TL1]: Tên gọi Kí hiệu Giá trị Số lượng Hiệu suất khớp nối 0,99 1 Hiệu suất 1 cặp ổ lăn 0,99 4
Hiệu suất 1 cặp bánh răng 0,97 3
Hiệu suất bộ truyền xích 0,92 1
Hiệu suất của toàn bộ hệ thống :
Công suất cần thiết trên trục động cơ: -
2. Theo công thức 2.16 trang 21 [TL1] .
3. Xác định sơ bộ số vòng quay đồng bộ.
- Tỷ số truyền ut của hệ thống dẫn động : ut = uHGT .uxích
- Theo bảng 2.4 , tỷ số truyền nên dùng cho các bộ truyền trong hệ: Tên gọi Kí hiệu Giá trị Số Lượng
Tỉ số truyền sơ bộ của bộ truyền bánh răng trụ 8…40 1
Tỉ số truyền sơ bộ của bộ truyền xích 2…5 1 4 ut = 3.8= 24 Số vòng quay sơ bộ
nsb = nlv. utsb = 53,71. 24 = 1289,04 (vòng/phút)
Chọn số vòng quay đồng bộ của động cơ .
4. Động cơ được chọn dựa vào bảng P1.1 đến bảng P1.7 và phải thỏa mãn điều kiện sau: Mà : Kí hiệu động cơ DK51-4 4,5 1440 0,85 2 1,4 84 II.
Phân phối tỷ số truyền .
- Tỉ số truyền ut của hệ thống :
Theo bảng 3.1 [TL1] cho kết quả phân phối tỷ số truyền cho các cấp bánh răng
trong hộp giảm tốc 2 cấp bánh răng trụ phân đôi thỏa mãn đồng thời 3 chỉ tiêu :
khối lượng nhỏ nhất , mô men quán tính thu gọn nhất và thể tích bánh nhúng trong dầu ít nhất . Chọn uHGT = 14 :
- Tính lại theo ui trong hộp giảm tốc : 5 Tóm lại : III.
Xác định mômen và số vòng quay các trục .
- Số vòng quay các trục : nđc = 1440 (vòng/phút) (vòng/phút) (vòng/phút) (vòng/phút)
- Công suất làm việc trên các trục : Plv = 3,6 (KW) P3 = (KW) P2 = (KW) P1 = (KW)
Mômen xoắn trên các trục : T 6 6
3 = 9,55.10 .= 9,55.10 . = 366986,09 (Nmm) T 6 6
2 = 9,55.10 .= 9,55.10 . = 126257,37 (Nmm) T 6 6
1 = 9,55.10 .= 9,55.10 . = 29313,19 (Nmm) T 6 6
dc = 9,55.10 .= 9,55.10 . = 29843,75 (Nmm)
Từ các kết quả trên ta có bảng phân phối tỉ số truyền như sau Trục Động cơ I II III Thông số Công suất P (KW) 4,5 4,42 4,24 3,95 Số vòng quay n (v/p) 1440 1440 320,71 102,79 6 Mômen xoắn T (Nmm) 29843,75 29313,19 126257,37 366986,09 Tỉ số truyền u 1 4,49 3,12
Trên đây là phần thiết kế chọn động cơ và phân phối tỉ số truyền của bài toán.
Phần II : Thiết kế bộ truyền bánh răng
Số giờ làm việc ở các chế độ (phục vụ 6 năm ) : + t1=6.280.2.1= 3360 h + t2=6.280.2.2= 6720 h + t3=6.280.2.1= 3360 h I)
Thiết kế bộ truyền bánh răng trụ răng nghiêng .
1. Vật liệu chế tạo .
- Do không có yêu cầu đặc biệt và theo quan điểm thống nhất thiết kế ,ở đây
chọn vật liệu 2 cấp bánh răng như nhau :
*Bánh nhỏ : Thép 45 tôi cải thiện : độ cứng HB=241-285 ( tra theo bảng 6.1 [TL1]) .
*Bánh lớn : Thép 45 tôi cải thiện : Độ cứng HB=192-240 ( tra theo bảng 3.2b [TL1]) .
2. Ứng suất cho phép . + Theo bảng 6.2 [TL1] : 7
Chọn độ rắn bánh nhỏ HB1= 245 , bánh lớn HB2= 230, khi đó : + Theo 6.5 [TL1] :
- Theo công thức 6.7 [TL1] : Vì : Vì
+ Theo 6.1 sơ bộ xác định được :
SH= 1,1 tạm thời lấy ZR.ZV.KXH=1 :
+Với cấp nhanh và cấp chậm sử dụng răng nghiêng , do đó theo 6.12 sách [TL1] :
+ Theo công thức 6.4 [TL1] :
- Đối với tất cả các loại thép Vì Vì
+ Tạm thời lấy do đó theo 6.2 [TL1] :
với bộ truyền quay 1 chiều ( thì được : 8
+ Ứng suất quá tải cho phép theo 6.13 và 3.14 :
3) Xác định thông số cơ bản của bộ truyền . * Tính cấp nhanh .
a) Khoảng cách trục sơ bộ : theo công thức 6.15 [TL1]
+ Theo bảng 6.6 [TL1] chọn
+ Theo bảng 6.5 [TL1] chọn
+ Theo 6.16 [TL1] do cặp bánh răng ăn khớp ngoài
+ Theo bảng 6.7 [TL1] chọn sơ đồ 3
Thay số được ( do ăn khớp ngoài nên mang dấu “+”) : Chọn .
b) Xác định các thông số ăn khớp . - Xác định môđun m .
+ Theo công thức 6.17 [TL1] : -> Lấy m = 2 mm 9
- Xác định số răng , góc nghiêng và hệ số dịch chỉnh :
+ Chọn sơ bộ góc nghiêng [TL1]
+ Số răng bánh nhỏ theo công thức 6.19 trang 99 [TL1] : Lấy Z1= 18 + Số răng bánh lớn Lấy Z2= 81
+ Tổng số răng của 2 bánh :
+ Khoảng cách trục thực : Làm tròn
+ Vậy tỉ số truyền thực : + Tính lại góc nghiêng :
+ Chiều rộng vành răng :
+ Hệ số trùng khớp dọc:
- Xác định hệ số dịch chỉnh:
+ Góc ăn khớp ( công thức 6.27 [TL1] ) : 10
c) Kiểm nghiệm răng theo sắc bền tiếp xúc . - Theo bảng 6.5 [TL1] : - Theo 6.35 [TL1] : Với :
- Do đó theo 6.34 [TL1] : - Theo 6.37 [TL1] : Trong đó theo 6.38b [TL1] :
- Đường kính vòng lăn bánh nhỏ bảng 6.15b [TL1] :
- Theo công thức 6.40 [TL1] :
n1: số vòng quay của bánh chủ động , theo bảng 6.14 [TL1] . ( theo bảng 6.14 [TL1] )
- Theo 6.42 [TL1] sách tính toán thiết kế hệ dẫn động cơ khí : Theo bảng 6.15 [TL1] : Theo bảng 6.16 [TL1] :
- Do đó theo trang 107 [TL1] :
- Theo công thức 6.39 [TL1] :
- Thay các giá trị vừa tính được vào 6.33 ( trang 105 [TL1] ) : 11
- Xác định chính xác ứng suất tiếp xúc cho phép :
+ Theo công thức 6.1 ( trang 91 [TL1] ) :
Kết luận : Không thỏa mãn điều kiện độ bền tiếp xúc .
Phương pháp sửa : chọn bw = 46
- Hệ số trùng khớp dọc : - Theo 6.37 [TL1] :
- Do đó theo trang 107 [TL1] :
- Thay các giá trị vừa tính được vào 6.33 ( trang 105 [TL1] ) :
- Xác định chính xác ứng suất tiếp xúc cho phép :
+ Theo công thức 6.1 ( trang 91 [TL1] ) :
Kết luận : thỏa mãn điều kiện độ bền tiếp xúc .
d) Kiểm nghiệm răng về sức bền uốn
+ Theo bảng 6.7 trang 33 [TL1] : chọn
+ Theo bảng 3.17 trang 42 [TL1] : chọn 12 Theo bảng 3.17a [TL1] : Theo bảng 3.17b [TL1] : Do đó : Vậy
+ Số răng tương đương bánh nhỏ :
+ Số răng tương đương bánh lớn : +
+ Hệ số dạng răng tra bảng 6.18 sách [TL1] : hệ số dịch chỉnh Bánh nhỏ : YF1= 3,9 Bánh lớn : YF2= 3,6
+ Kiểm nghiệm ứng suất uốn :
- Xác định chính xác ứng suất uốn cho phép : Với m= 2 13 Có :
Kết luận : thỏa mãn độ bền uốn .
g) Các thông số và kích thước bộ truyền . + Khoảng cách trục : + Mô đun pháp : m=2 mm
+ Chiều rộng vành răng : + Tỉ số truyền : + Góc nghiêng của răng : + Số răng bánh răng : + Hệ số dịch chỉnh :
Theo các công thức trong bảng 6.11 sách tính toán thiết kế hệ dẫn động cơ khí, tính được : Đường kính vòng chia : Đường kính đỉnh rang : Đường kính đáy răng : 14
h) Tinh lực tác dụng lên các trục + Lực vòng : + Lực hướng tâm : + Lực dọc trục : Tính cấp chậm .
a) Khoảng cách trục sơ bộ : theo công thức 6.15 trang 96 [TL1] :
+ Theo bảng 6.6 trang 97 [TL1] chọn
+ Theo bảng 6.5 trang 96 [TL1] chọn
+ Theo 6.16 trang 97 [TL1] do cặp bánh răng ăn khớp ngoài
+ Theo bảng 6.7 trang 98 [TL1] chọn sơ đồ 3 :
Thay số được ( do ăn khớp ngoài nên mang dấu “+”) : Chọn .
b) Xác định các thông số ăn khớp . - Xác định môđun m :
+ Theo công thức 6.17 [TL1] : 15 -> Lấy m = 2 mm
- Xác định số răng , góc nghiêng và hệ số dịch chỉnh .
+ Chọn sơ bộ góc nghiêng :
+ Số răng bánh nhỏ theo công thức 6.19 [TL1] : Lấy Z1= 28 + Số răng bánh lớn : Lấy Z2= 89
+ Tổng số răng của 2 bánh :
+ Khoảng cách trục thực :
+ Vậy tỉ số truyền thực : + Tính lại góc nghiêng :
+ Chiều rộng vành răng :
+ Hệ số trùng khớp dọc :
- Xác định hệ số dịch chỉnh :
+ Góc ăn khớp ( công thức 6.27 [TL1] ) : 16
c) Kiểm nghiệm răng theo sắc bền tiếp xúc . - Theo bảng 6.5 [TL1] : - Theo 6.35 [TL1] : Với :
- Do đó theo 6.34 [TL1] : - Theo 6.37 [TL1] : Trong đó theo 6.38b [TL1] :
- Đường kính vòng lăn bánh nhỏ bảng 3.13 trang 40 [TL1] :
- Theo công thức 6.40 [TL1] :
n2: số vòng quay của bánh bị động ,theo bảng 6.13 [TL1] . ( theo bảng 6.14 [TL1] ) - Theo 6.42 [TL1] :
Theo bảng 6.15 trang 44 [TL1] :
Theo bảng 6.16 trang 44 [TL1] :
- Do đó theo 6.41 [TL1] : - Theo 6.39 [TL1] : 17
- Thay các giá trị vừa tính được vào 6.1 [TL1] :
- Xác định chính xác ứng suất tiếp xúc cho phép :
+ Theo công thức 3.10 ( trang 27 [TL1] ) :
Kết luận: Thỏa mãn điều kiện độ bền tiếp xúc
d) Kiểm nghiệm răng về sức bền uốn .
+ Theo bảng 6.7 [TL1] chọn
+ Theo bảng 6.14 [TL1] chọn Theo bảng 6.15 [TL1] Theo bảng 6.16 [TL1] Do đó: Vậy
+ Số răng tương đương bánh nhỏ :
+ Số răng tương đương bánh lớn : 18
+ Hệ số dạng răng tra bảng : 6.18 [TL1] hệ số dịch chỉnh Bánh nhỏ : YF1= 3,9 Bánh lớn : YF2= 3,6
+ Kiểm nghiệm ứng suất uốn :
- Xác định chính xác ứng suất uốn cho phép : Với m= 2 Có:
Kết luận : thỏa mãn độ bền uốn .
g) Các thông số và kích thước bộ truyền . + Khoảng cách trục : + Mô đun pháp : m=2 mm
+ Chiều rộng vành răng : + Tỉ số truyền : 19 + Góc nghiêng của răng : + Số răng bánh răng : + Hệ số dịch chỉnh :
Theo các công thức trong bảng 6.11 [TL1] , tính được : Đường kính vòng chia :
Đường kính đỉnh răng : Đường kính đáy răng :
h) Tinh lực tác dụng lên các trục . + Lực vòng : + Lực hướng tâm : + Lực dọc trục :
Phần III : Thiết kế bộ truyền xích
1. Chọn loại xích .
- Vì tải trọng nhỏ , vận tốc thấp, dùng xích con lăn 20
2. Xác định các thông số của xích và bộ truyền .
- Theo bảng 5.4 [TL1] : với , chọn số răng đĩa nhỏ , do đó số răng đĩa lớn
- Tính hệ số điều kiện sử dụng công thức 5.4 [TL1] : trong đó :
+ Hệ số số răng đĩa dẫn :
+ Hệ số vòng quay đĩa dẫn :
+ Công suất tính toán ( công thức 5.3 [TL1]) :
+ Tra bảng 5.5 [TL1]với chọn được xích ống con lăn 1 dãy có bước p =25,4
mm, diện tích bản lề F=179,74 mm2, có công suất cho phép [ .Với loại xích này
theo bảng 5.2 tìm được kích thước chủ yếu của xích , tải trọng phá hủy Q= 56,7
kN, khối lượng 1 mét xích q=2,6 kg
3. Định khoảng cách trục a và số mắt xích X .
- Khoảng cách trục a = 40p = 40.25,4 = 1016 mm
- Tính số mắt xích ( công thức 5.12 [TL1]) : 21
- Lấy số mắt xích chẵn x=120 , tính lại khoảng cách trục theo công thức :
- Để xích không chịu lực căng quá lớn , giảm a một lượng bằng :
- Kiểm nghiểm số lần va đập trong 1 giây ( công thức 5.14 [TL1]) :
- Theo bảng 5.9 [TL1], số lần va đập cho phép trong 1s [i] = 30
Cho nên điều kiện : được thỏa mãn .
4. Tính kiểm nghiệm xích về độ bền . - Theo 5.15 [TL1] :
Q= 56,7 kN , khối lượng 1 mét xích q=2,6 kg Trong đó : Do đó :
- Theo bảng 5.10 [TL1] với n= 200 vg/ph , [s]=8,2
Vậy s> [s] : bộ truyền xích đảm bảo độ bền .
5. Đường kính đĩa xích .
- Theo công thức 5.17 và bảng 13.4 [TL1] : 22
6. Tính lực tác dụng lên trục .
- Theo công thức 6.15 [TL1] :
Trong đó : đối với bộ truyền nghiêng 1 góc nhỏ hơn 40o ( bộ truyền nằm ngang) , kx=1,15
Phần IV: Thiết Kế Trục I.
Chọn vật liệu chế tạo trục .
- Chọn thép C45 tôi thường hóa có ứng suất bền Chọn Sơ đồ : Trục 1 : 23 Trục 2 : l21 l24 l23 l22 lm22 lm24 k1 lm23 Trục 3 : 24 II.
Tính chọn khớp nối .
- Thông số đầu vào : Mômen cần truyền
Đường kính trục động cơ:
1. Chọn khớp nối .
- Ta sử dụng khớp nối vòng đàn hồi để nối trục :
- Chọn khớp nối theo điều kiện : Trong đó : Do vậy :
Tra bảng 16.10a [TL3] với điều kiện :
Tra bảng 16.10b [TL3] với ta được :
2. Kiểm nghiệm khớp nối .
- Ta kiểm nghiệm theo 2 điều kiện :
a. Điều kiện sức bền dập của vòng đàn hồi . .
b. Điều kiện bền của chốt . Với . 25 III.
Tính đường kính sơ bộ các trục ( công thức 7.2 [TL1] )
- Trục I là trục vào của hộp giảm tốc với ( ; n1= 1440vg/ph) :
- Trục II là trục trung gian của hộp giảm tốc với ( ;n2= 320,71 vg/ph) :
- Trục III là trục ra của hộp giảm tốc với ( ; n3= 102,79 vg/ph ) : I.
Xác định khoảng cách giữa các gối đỡ và điểm đặt lực .
- Chiều dài trục cũng như khoảng cách giữa các gối đỡ và các điểm đặt lực phụ
thuộc vào sơ đồ động, chiều dài mayơ của các chi tiết quay , chiều rộng ổ ,
khe hở cần thiết và các yếu tố khác.
- Để chuẩn bị cho bước tính gần đúng trong ba chỉ số dI, dII ,dIII , để chọn loại ổ
bi đỡ cỡ trung bình tra bảng 10.2 [TL1] có được chiều rộng của ổ lăn cần lắp
là : (Chọn ổ bi đỡ 1 dãy )
- Theo bảng (10.3) chọn :
Khoảng cách từ mặt cạnh của chi tiết quay đến thành trong của hộp k1 = 10
hay khoảng cách giữa các chi tiết quay
Khoảng cách từ mặt cạnh ổ đến thành trong của hộp giảm tốc k2 = 10
Khoảng cách từ mặt cạnh của chi tiết quay đến nắp ổ k3 = 15
Chiều cao nắp ổ và đầu bu lông hn = 18 26
- Chiều dài mayơ bánh răng nghiêng trên trục I. Xác định theo công thức (10.10 [TL1] ) :
- Chiều dài mayơ bánh răng trụ răng nghiêng trên trục II. Xác định theo công thức (10.10 [TL1] ) :
- Chiều dài mayơ bánh răng trụ răng nghiêng trên trục III. Xác định theo công thức (10.10 [TL1] ) :
- Chiều dài mayơ nửa khớp nối trục vòng đàn hồi .Xác định theo công thức (10.10 [TL1] ) :
- Khoảng cách lki trên trục thứ k từ gối đỡ A đến chi tiết quay thứ i + Trục I : k + Trục II : 27
l23 = l22 + 0,5.(lm22 + lm23) + k1 =48,5 + 0,5(36 +36) + 10 = 94,5 mm l24 = 2.l23 - l22 = 140,5 mm l21 = 2.l23 = 2.93,5= 189 mm + Trục III :
- Khoảng công-xôn trên trục III :
lc34 = 0,5.(lm34 + b03) + K3 + hn = 0,5(54+25)+15+18 = 72,5 mm. II. Tính gần đúng trục . a. Trục I .
- Ta có thông số tính toán cho trục I :
- Sơ đồ phân tích lực của trục I : 28
Tính phản lực ở các gối A và B :
- Lực từ khớp nối tác dụng lên trục I :
Theo phương ox : tra bảng 15.10 [TL2] ta có + Lực vòng + Lực hướng tâm : + Lực dọc trục :
- Trong mặt phẳng Oyz ta có phản lực các gối tựa :
Xét phương trình mômen tại điểm A theo phương y :
Xét phương trình cân bằng lực theo phương y : 29
- Trong mặt phẳng Oxz ta có phản lực các gối tựa :
Xét phương trình mômen tại điểm A theo phương x :
Xét phương trình cân bằng lực theo phương x :
Phản lực tại 2 gối A và B tính được cụ thể là :
Mômen uốn tổng và mômen uốn tương đương tại các tiết diện trên chiều dài trục. a.Mômen uốn tổng : - - -
b.Mômen uốn tương đương : - - - - -
c.Đường kính trục ở tiết diện này : 30
Biểu đồ mômen trục 31 32 b. Trục II .
- Ta có thông số tính toán cho trục II :
Tính phản lực ở các gối đỡ :
- Sơ đồ phân tích lực của trục II :
+ Đối với bánh bị dẫn 3 :
+ Đối với bánh răng dẫn 2,4b: 33
- Trong mặt phẳng Oyz ta có phản lực các gối tựa :
Xét phương trình cân bằng mômen tại điểm C theo phương y :
Xét phương trình cân bằng lực theo phương y :
- Trong mặt phẳng Oxz ta có phản lực các gối tựa :
Xét phương trình mômen tại điểm C theo phương x :
Xét phương trình cân bằng lực theo phương x:
Phản lực tại 2 gối C và D tính được cụ thể là:
Mômen uốn tổng và mômen uốn tương đương tại các tiết diện trên chiều dài trục. a. Mômen uốn tổng: - - - 34 -
b. `Mômen uốn tương đương : - - - = - -
c. Đường kính trục ở tiết diện này : : 35
Biểu đồ mômen của trục II 63128,69 63128,69 36 a. Trục III .
- Ta có thông số tính toán cho trục III :
- Sơ đồ phân tích lực của trục III :
Tính phản lực tại các gối :
- Lực từ đĩa xích tác dụng lên trục :
- Lực từ bánh răng bị dẫn 2,3 tác dụng lên trục : + Lực vòng : + Lực hướng tâm : + Lực dọc trục :
- Trong mặt phẳng Oyz ta có phản lực các gối tựa :
Xét phương trình cân bằng mômen tại điểm E theo phương y: 37
Xét phương trình cân bằng lực theo phương y:
- Trong mặt phẳng Oxz ta có phản lực các gối tựa :
Xét phương trình cân bằng mômen tại điểm E theo phương x:
Xét phương trình cân bằng lực theo phương x:
Phản lực tại 2 gối E và F tính được cụ thể là:
Mômen uốn tổng và mômen uốn tương đương tại các tiết diện trên chiều dài trục. a. Mômen uốn tổng : - - - 38
b. `Mômen uốn tương đương :
c. Đường kính trục ở tiết diện này: 39
Biểu đồ mômen của trục III 40 41 : VI.
Kiểm nghiệm trục về độ bền mỏi . 1. Hệ số an toàn .
[S]: Hệ số an toàn cho phép
: Hệ số an toàn chỉ xét riêng ứng suất pháp tại tiết diện j
: Hệ số an toàn chỉ xét riêng đến ứng suất tiếp tại tiết diện j Trong đó :
Theo bảng 10.7 [TL2] ta được
2. Các trục của hộp giảm tốc đều quay, ứng suất tiếp thay đổi theo chu kỳ đối
xứng. Do đó theo công thức (10.22 ) :
Với Mj theo công thức (10.15) : 42
- Vì trục I quay 1 chiều, ứng suất xoắn thay đổi theo chu kỳ mạch động. Do đó theo công thức 10.23 :
3. Xác định hệ số an toàn tại các tiết diện nguy hiểm .
- Dựa vào kết cấu và biểu đồ mômen trục , ta thấy các tiết diện nguy hiểm cần
được kiểm tra về độ bền mỏi.
Trục I: Tiết diện 10 lắp ổ lăn và tiết diện 13 lắp bánh răng
Trục II: Tiết diện 22 và 23 lắp bánh răng
Trục III: Tiết diện tại 32 và 33 lắp bánh răng.Tiết diện 31 lắp ổ lăn. 4. Chọn lắp ghép .
- Các ổ lăn lắp ghép trên trục theo kiểu k6, lắp đĩa xích , nối trục , bánh răng
theo kiểu k6 kết hợp lắp then Với :
Kết hợp với tra bảng 7.3b [TL1] :
- Kích thước của then (theo bảng 9.1[TL1]), trị số momen cản uốn và mômen
cản xoắn (theo bảng 10.6 [TL1] ) ứng với các tiết diện trục như sau: Tiết diện Đường b x h kính trục, mm 10 20 6x6 3,5 642 1427 13 25 8x7 4 1251 2785 22 30 10x8 5 2130 4781 23 35 10x8 5 3566 7775 32 40 14x9 5,5 7611 16557 43 33 40 12x8 5 5364 11647
5. Xác định hệ số và đối với các tiết diện nguy hiểm theo công thức 10.25 và 10.26 [TL1] .
- Các trục gia công trên máy tiện , tại các tiết diện nguy hiểm yêu cầu đặt , theo
bảng 10.8 hệ số tập trung ứng suất do trạng thái bề mặt :
- Không dùng các phương pháp tăng bền bề mặt nên do đó hệ số tăng
- Theo bảng 7.5c [TL1] , khi dùng dao phay ngón hệ số tập trung ứng suất tại rãnh then là :
- Theo bảng 10.10[TL1] ta có các thông số sau d10=20 =0,92 =0,89 d13=25 =0,89 =0,8 d22=30 =0,88 =0,81 d23=35 =0,85 =0,78 d31=45 =0,81 =0,76 d33=40 =0,85 =0,78
- Kết quả tính được ghi ra bảng sau Ti d σaj ết (m di m) ện 10 20 642 142 29313,1 10, 10, 1,9 1,7 16, 9,3 8, 7 9 36 27 7 9 02 7 96 25 125 27 940 4873 75,14 8,7 2,0 1,9 2,1 10, 2,1 25 1 85 05 4 4 3 8 4 95 0 44 22 30 213
478 1471 63128,6 69, 6,6 2,0 1,9 2,1 14, 2, 0 1 89 9 1 6 6 2 66 1 23 35 356
777 1763 63128,6 49, 4,0 2,1 2,0 2,8 23, 2, 6 5 89 9 46 6 3 3 1 01 79 31 45 7611
165 3645 366986, 47, 11, 2,2 2,0 3,3 8,1 3, 57 08 09 89 08 3 9 3 9 08 33 40 5364
116 2263 366986, 42, 15, 2,1 2,0 3,8 5,9 3, 47 51 09 2 75 3 3 6 3 24 - Với: *Kết luận :
- Ta thấy các tiết diện nguy hiểm trên đều đảm bảo an toàn về độ bền mỏi
PHẦN V: Tính toán then và ổ lăn I. Then
- Với các tiết diện dùng mối ghép then ta tiến hành kiểm nghiệm mối ghép về độ bền dập
- Theo công thức (9.1 và 9.2) [TL2] Với
- Tính và chọn theo tính chất ta có chiều dài then được cho trong bảng 9.1[TL2] b t2 h t 1 45
- Ta có bảng kiểm nghiệm then như sau: d(mm) lt (mm) b x h t1 T (N.m) Then 20 27 6x6 3,5 29313,19 43,43 18,09 Then bằng 30 40,5 10x8 5 63128,69 34,64 10,39 Then bằng 35 47,25 10x8 5 63128,69 25,45 7,63 Then bằng 45 60,75 14x9 5,5 76,71 19,18 Then bằng 40 54 12x11 5,5 61,18 28,32 Then bằng cao
- Theo bảng 7.12 và 7.13 [TL1] với tải trọng va đập nhẹ , dạng lắp cố định
Vậy các mối ghép then đều đảm bảo độ bền dập và độ bền cắt II. Ổ lăn 1. Chọn ổ lăn
- Các trục có lực dọc trục tác dụng nên ta chọn ổ bi đỡ- chặn
2. Chọn cấp chính xác ổ lăn
- Chọn cấp chính xác 0 có độ đảo hướng tâm 20 và giá thành tương đối 1 3. Trục I
- Tải trọng hướng tâm tác dụng lên ổ A
- Tải trọng hướng tâm tác dụng lên ổ B 46
Ta thấy FrA < FrB ta xét tỷ số :
Nên dùng ổ bi đỡ chặn tra bảng ta chọn ổ bi đỡ 1 dãy kí hiệu (305 cỡ trung )
với đường kính trong d= 25 mm, đường kính ngoài D= 72 mm, chiều rộng
B= 17 mm, khả năng tải động C= 17,6 kN, khả năng tải tĩnh C0= 11,6 kN
b. Kiểm nghiệm khả năng tải động của ổ
Đối với hộp giảm tốc, chọn cấp chính xác 0, với độ đảo hướng tâm 20µm(Tr213 - [2])
Tính kiểm nghiệm khả năng tải động của ổ.
- Khả năng tải động của ổ thoả mãn điều kiện[2] :
Trong đó: Q- tải trọng động quy ước (kN)
L- tuổi thọ tính bằng triệu vòng quay.
m- bậc đường cong mỏi khi thử về ổ lăn, với ổ bi m = 3
- Gọi Lh là tuổi thọ của ổ lăn tính bằng giờ thì: L = Lh60n.10-6
(Với n là số vòng quay của ổ (v/ph). Lh tuổi thọ của ổ tính bằng giờ, đối với hộp giảm tốc thì L 3 h = (10…25).10 giờ) Chọn Lh = 12.giờ
L= 12. 103.60.1440.10-6 = 1036,8 (triệu vòng)
Xác định tải trọng quy ước Q, theo công thức[2] :
Với ổ bi đỡ chặn : Q = ( X.V.Fr + Y.Fa).Kt.Kd Trong đó :
+ V - hệ số ảnh hưởng của vòng nào khi quay, V = 1(vòng trong quay)
+ X,Y - hệ số tải trọng hướng tâm và dọc trục.
+ Kt - hệ số kể đến ảnh hưởng của nhiệt độ, do nhiệt độ của hộp giảm tốc < 105C nên Kt = 1.
+ Kd - hệ số kể đến đặc tính của tải trọng. Theo bảng 11.3 – Tr 215[2], ta có Kd = 1.
+ Fa, Fr - tải trọng dọc trục và tải trọng hướng tâm, kN
- Xác định lực dọc trục Fa : 47 Fa Fs1 Fs2 Fr1 Fr2 -
Dưới tác dụng của các lực hướng kính, các ổ sẽ xuất hiện các lực dọc trục phụ
FsA ;FsB : Fs = e.Fr (e - hệ số)
Với : i = 1, Fa = 229,76 = 0,23 kN . Ta có iFa/Co = 0,23/9,17 = 0,029
Tra bảng 11.4 – Tr 216 [2], ta có e = 0,34.
Do đó, lực dọc trục phụ:
FsA = e.FrA = 0,34.743,05 = 252,64 (N)
FsB = e.FrB = 0,34.885,07 = 300,92 (N)
Tổng lực dọc trục tác dụng lên ổ :
FaA = FsB + Fa1 = 300,92 + 229,76 = 530,68(N)
FaB = FsA - Fa1 = 252,64 – 229,76 = 22,88 (N)
Vậy FaA = max( FaA; FsA )= 530,68(N)
FaB = max ( FaB; FsB )= 300,92 (N) - Tìm X,Y xét tỷ số:
Tra bảng 11.4 – Tr216 [2], ta được : XA = 0,45 ; YA = 1,62 XB = 1 ; YB = 0 - Tải trọng quy ước Q:
QA = (0,45.1.743,05 + 1,62. 530,92).1.1 = 1194,46 N ≈ 1,19 kN
QB = (1.1.885,07 + 0. 300,29 ).1.1 = 885,07 N ≈ 0,89 kN
Khả năng tải động của ổ A và B :
Vậy, ổ đã chọn thoả mãn khả năng tải động.
d. Kiểm nghiệm khả năng tải tĩnh.
-Để tránh biến dạng dư hoặc dính bề mặt tiếp xúc thì ổ được chọn cần
thoả mãn điều kiện sau [2]:
Trong đó : C0 - khả năng tải tĩnh của ổ,kN
Qt - tải trọng tĩnh quy ước,kN
-Tải trọng quy ước được xác định theo công thức : Qt = X0.Fr + Y0.Fa 48
Với X0, Y0 - hệ số tải trọng hướng tâm và dọc trục.
Tra bảng 11.6 –Tr221 [2], ta có : X0 = 0,5 ; Y0 = 0,47.
+ QtA = 0,5.743,05 + 0,47.530,92 = 621,06 N = 0,621 kN < FrA=0,743 kN QtA = FrA=0,743 kN
+ QtB = 0,5.885,07 + 0,47. 300,92 = 583,97 N = 0,584 kN < FrB=0,885 kN QtB = FrB=0,885 kN -Qt < C0 = 11,6 kN
Vậy, ổ đã chọn thoả mãn khả năng tải tĩnh.
Kết cấu ổ lăn trục I :
Bảng thông số ổ bi đỡ - chặn trục I: Kí hiệu ổ d,mm D,mm b=T,mm r,mm r1,mm C,KN C0,KN 305 25 62 17 2 1,0 17,6 11,6 4. Trục II a. Chọn ổ lăn 49
Tổng lực dọc trục : Fa = Fa3 – Fa2 = 1118,29 – 229,76 = 888,53(N) ≈ 0,888 kN
Tải trọng hướng tâm tác dụng lên ổ C
Tải trọng hướng tâm tác dụng lên ổ D
Ta thấy FrC > FrD ta xét tỷ số :
Nên dùng ổ bi đỡ chặn tra bảng ta chọn ổ bi đỡ chặn kí hiệu (46306 cỡ trung
hẹp ) với đường kính trong d= 30 mm, đường kính ngoài D= 72 mm, chiều
rộng B= 19 mm, khả năng tải động C= 25,6 kN, khả năng tải tĩnh C0= 18,17 kN
b. Kiểm nghiệm khả năng tải động của ổ
Đối với hộp giảm tốc, chọn cấp chính xác 0, với độ đảo hướng tâm 20µm(Tr213 - [2])
Tính kiểm nghiệm khả năng tải động của ổ.
- Khả năng tải động của ổ thoả mãn điều kiện[2] :
Trong đó: Q- tải trọng động quy ước (kN)
L- tuổi thọ tính bằng triệu vòng quay.
m- bậc đường cong mỏi khi thử về ổ lăn, với ổ bi m = 3
- Gọi Lh là tuổi thọ của ổ lăn tính bằng giờ thì: L = Lh60n.10-6 50
(Với n là số vòng quay của ổ (v/ph). Lh tuổi thọ của ổ tính bằng giờ, đối với hộp giảm tốc thì L 3 h = (10…25).10 giờ) Chọn Lh = 12.giờ
L= 12. 103.60.320,71.10-6 = 230,91 (triệu vòng)
Xác định tải trọng quy ước Q, theo công thức[2] :
Với ổ bi đỡ chặn : Q = ( X.V.Fr + Y.Fa).Kt.Kd Trong đó :
+ V - hệ số ảnh hưởng của vòng nào khi quay, V = 1(vòng trong quay)
+ X,Y - hệ số tải trọng hướng tâm và dọc trục.
+ Kt - hệ số kể đến ảnh hưởng của nhiệt độ, do nhiệt độ của hộp giảm tốc < 105C nên Kt = 1.
+ Kd - hệ số kể đến đặc tính của tải trọng. Theo bảng 11.3 – Tr 215[2], ta có Kd = 1.
+ Fa, Fr - tải trọng dọc trục và tải trọng hướng tâm, kN
- Xác định lực dọc trục Fa :
Dưới tác dụng của các lực hướng kính, các ổ sẽ xuất hiện các lực dọc trục phụ
FsA ;FsB : Fs = e.Fr (e - hệ số)
Với : i = 1, Fa = 0,888kN . Ta có iFa/Co = 0,888/18,17 = 0,048
Tra bảng 11.4 – Tr 216 [2], ta có e = 0,35.
Do đó, lực dọc trục phụ:
FsC = e.FrC = 0,35.2801,44 = 980,5 (N)
FsD = e.FrD = 0,35.2793,23 = 977,63 (N)
Tổng lực dọc trục tác dụng lên ổ :
FaC = FsD + Fa1 = 977,63 + 888,53 = 1866,16(N)
FaD = FsC - Fa1 = 980,5– 888,53 = 91,97 (N)
Vậy FaC = max( FaC; FsC )= 1866,16 (N)
FaD = max ( FaD; FsD )= 977,63 (N) - Tìm X,Y xét tỷ số:
Tra bảng 11.4 – Tr216 [2], ta được : XA = 0,45 ; YA = 1,62 XB = 1 ; YB = 0 - Tải trọng quy ước Q:
QA = (0,45.1.2801,44 + 1,62. 1866,16)1.1 = 3883,83 N ≈ 3,88 kN
QB = (1.1.2793,23 + 0. 977,63 ).1.1 = 2793,23 N ≈ 2,79 kN
Khả năng tải động của ổ A và B :
Vậy, ổ đã chọn thoả mãn khả năng tải động. 51
d. Kiểm nghiệm khả năng tải tĩnh.
-Để tránh biến dạng dư hoặc dính bề mặt tiếp xúc thì ổ được chọn cần
thoả mãn điều kiện sau [2]:
Trong đó : C0 - khả năng tải tĩnh của ổ,kN
Qt - tải trọng tĩnh quy ước,kN
-Tải trọng quy ước được xác định theo công thức : Qt = X0.Fr + Y0.Fa
Với X0, Y0 - hệ số tải trọng hướng tâm và dọc trục.
Tra bảng 11.6 –Tr221 [2], ta có : X0 = 0,5 ; Y0 = 0,47.
+ QtA = 0,5.2801,44 + 0,47.1866,16 = 1860 N = 1,86 kN < FrA= 2,8 kN QtA = FrA= 2,8 kN
+ QtB = 0,5.2793,23 + 0,47. 977,63 = 1856 N = 1,86 kN < FrB=2,79 kN QtB = FrB=2,79 kN -Qt < C0 = 18,17 kN
Vậy, ổ đã chọn thoả mãn khả năng tải tĩnh. Kết cấu trục 2 : b r 0,64H 0,3H H 0,5H D d r 0,3H r1 Kí hiệu ổ d,mm D,mm b=T,mm r,mm r1,mm C,KN C0,KN 46306 30 72 19 2 1,0 25,6 18,17 5. Trục III a. Chọn ổ lăn 52
Tải trọng hướng tâm tác dụng lên ổ E
Tải trọng hướng tâm tác dụng lên ổ F
Ta thấy FrE < FrF ta xét tỷ số :
Nên dùng ổ bi đỡ 1 dãy tra bảng ta chọn ổ bi đỡ chặn dãy kí hiệu (308 cỡ
trung) với đường kính trong d=40 mm , đường kính ngoài D=90 mm , chiều
rộng B= 23 mm, khả năng tải động C=31,9 kN, khả năng tải tĩnh C0=21,7 kN
b. Kiểm nghiệm khả năng tải động của ổ
Đối với hộp giảm tốc, chọn cấp chính xác 0, với độ đảo hướng tâm 20µm(Tr213 - [2])
Tính kiểm nghiệm khả năng tải động của ổ.
- Khả năng tải động của ổ thoả mãn điều kiện[2] :
Trong đó: Q- tải trọng động quy ước (kN)
L- tuổi thọ tính bằng triệu vòng quay.
m- bậc đường cong mỏi khi thử về ổ lăn, với ổ bi m = 3
- Gọi Lh là tuổi thọ của ổ lăn tính bằng giờ thì: L = Lh60n.10-6
(Với n là số vòng quay của ổ (v/ph). Lh tuổi thọ của ổ tính bằng giờ, đối với hộp giảm tốc thì L 3 h = (10…25).10 giờ) 53 Chọn Lh = 12.giờ
L= 12. 103.60.102,79.10-6 = 74 (triệu vòng)
Xác định tải trọng quy ước Q, theo công thức[2] :
Với ổ bi đỡ chặn : Q = ( X.V.Fr + Y.Fa).Kt.Kd Trong đó :
+ V - hệ số ảnh hưởng của vòng nào khi quay, V = 1(vòng trong quay)
+ X,Y - hệ số tải trọng hướng tâm và dọc trục.
+ Kt - hệ số kể đến ảnh hưởng của nhiệt độ, do nhiệt độ của hộp giảm tốc < 105C nên Kt = 1.
+ Kd - hệ số kể đến đặc tính của tải trọng. Theo bảng 11.3 – Tr 215[2], ta có Kd = 1.
+ Fa, Fr - tải trọng dọc trục và tải trọng hướng tâm, kN
- Xác định lực dọc trục Fa :
Dưới tác dụng của các lực hướng kính, các ổ sẽ xuất hiện các lực dọc trục phụ
FsA ;FsB : Fs = e.Fr (e - hệ số)
Với : i = 1, Fa = 1,118 kN . Ta có iFa/Co = 1,118/30,7 = 0,036
Tra bảng 11.4 – Tr 216 [2], ta có e = 0,35.
Do đó, lực dọc trục phụ:
FsE = e.FrE = 0,35.2107 = 737,45 (N)
FsF = e.FrF = 0,35.6485 = 2269,75 (N)
Tổng lực dọc trục tác dụng lên ổ : Fa = F E
sF + Fa1 = 2269,75 + 1118,29 = 3388,04 (N)
FaF = FsE - Fa1 = 737,45– 1118,29 = -380,84 (N)
Vậy FaE = max( FaE; FsE ) = 3388,04 (N)
FaF = max ( FaF; FsF ) = 2269,75 (N) - Tìm X,Y xét tỷ số:
Tra bảng 11.4 – Tr216 [2], ta được : XA = 0,45 ; YA = 1,62 XB = 1 ; YB = 0 - Tải trọng quy ước Q:
QA = (0,45.1.2107 + 1,62. 1118,29)1.1 = 2759,78 N ≈ 2,76 kN
QB = (1.1.6485 + 0. 1118,29 ).1.1 = 6485 N ≈ 6,49 kN
Khả năng tải động của ổ A và B :
Vậy, ổ đã chọn thoả mãn khả năng tải động.
d. Kiểm nghiệm khả năng tải tĩnh. 54
-Để tránh biến dạng dư hoặc dính bề mặt tiếp xúc thì ổ được chọn cần
thoả mãn điều kiện sau [2]:
Trong đó : C0 - khả năng tải tĩnh của ổ,kN
Qt - tải trọng tĩnh quy ước,kN
-Tải trọng quy ước được xác định theo công thức : Qt = X0.Fr + Y0.Fa
Với X0, Y0 - hệ số tải trọng hướng tâm và dọc trục.
Tra bảng 11.6 –Tr221 [2], ta có : X0 = 0,5 ; Y0 = 0,47.
+ QtA = 0,5.2107 + 0,47.1118,29 = 1579 N = 1,58 kN < FrA= 2,1 kN QtA = FrA= 2,1 kN
+ QtB = 0,5.6485 + 0,47. 1118,29 = 3768 N = 3,77 kN < FrB=6,49 kN QtB = FrB = 6,49 kN -Qt < C0 = 21,7 kN
Vậy, ổ đã chọn thoả mãn khả năng tải tĩnh.
Kết cấu ổ lăn trục III:
Bảng thông sôố ổ bi đỡ 1 dãy trụ c III: Kí hiệu ổ d,mm D,mm b=T,mm r,mm r1,mm C,KN C0,KN 308 40 90 23 2,5 1,0 31,9 21,7
Phần VI: Tính toán vỏ hộp và các chi tiết khác 55
5.1. CÁC KÍCH THƯỚC CƠ BẢN CỦA VỎ HỘP GIẢM TỐC
Vỏ hộp giảm tốc
Công dụng: Đảm bảo vị trí tương đối giữa các chi tiết và bộ phận máy, tiếp
nhận tải trọng do các chi tiết lắp trên vỏ truyền đến, đựng dầu bôi trơn bảo
vệ các chi tiết máy tránh bụi bặm.
Thành phần bao gồm: thành hộp, gân, mặt bích, gối đỡ…
Chi tiết cơ bản: độ cứng cao, khối lượng nhỏ.
Vật liệu làm vỏ: gang xám GX15-32
Phương pháp gia công: đúc
a. Chọn bề mặt lắp ghép và thân
- Bề mặt lắp ghép của vỏ hộp (phần trên của vỏ là nắp, phần dưới là thân)
thường đi qua đường tâm các trục
- Bề mặt lắp ghép song song với trục đế
b. Xác định các kích thước cơ bản của vỏ hộp
Dựa vào bảng 18.1Tr85[2] ta có bảng các kích thước cơ bản của vỏ hộp Tên gọi Biểu thức tính toán Giá trị Chiều Thân hộp: dày Nắp hộp: Gân Chiều dày gân: tang e cứng Chiều cao gân: h Độ dốc Khoảng Đường Bu lông nền: kính Bu lông cạnh ổ: Bu lông ghép mặt bích thân và nắp: Vít ghép nắp ổ: Vít ghép nắp của thăm Mặt Chiều dày mặt bích bích thân: 56 ghép Chiều dày mặt nắp và bích nắp: thân Bề rộng mặt bích:
Với K2: bề rộng mặt ghép bu lông cạnh ổ Với Chọn K2=36 mm Kích Bề rộng mặt thước ghép bu lông gối trục cạnh ổ: Tâm bu lông cạnh ổ: Trục I Bề rộng mặt Trục II ghép bu lông cạnh ổ: Khoảng cách từ tâm bu lông đến mép lỗ: Chiều dày khi không có phản hồi: Chiều dày khi có phần lồi: Khoảng cách
xác định theo đường kính dao khoét từ tâm bu lông đến mép lỗ:
Mặt đế Bề rộng mặt đế hộp hộp: Chiều dày khi có phần lồi: Giữa bánh răng
(phụ thuộc loại hộp giảm tốc) và thành hộp Giữa bánh răng và đáy hộp 57 Giữa mặt bên các bánh răng 4 với nhau
L, B – Chiều dài và chiều rộng của hộp Khe hở Từ đáy hộp giữa đến vị trí mức các chi dầu cao nhất tiết Từ đáy hộp h (0,75 2)h 10mm min 1 1 đến vị trí mức dầu thấp nhất Số 4 lượng
L, B – Chiều dài và chiều rộng của bu lông hộp nền Z Kích Đường kình ngoài Trục I:
thước gối và tâm lỗ vít trục Tra bảng 18.2[2] Trục II: Tra bảng 18.2[2] Trục II: 1.1 4.2. KẾT CẤU BÁNH RĂNG
- Kết cấu bánh răng 2 cặp 1 58 b = 46 d = 35 da2 = 167,64 df2 = 158,64
c =(0,2÷0,3).bw= (0,2÷0,3).46=9,2÷13,8= 12
Dv = df2 - 2. = 158,64-2.7 = 144,64
D = (1,5÷1,8).d=(1,5÷1,8).35= 52,5÷63 = 60
Do = (Dv-D)/2 +D = (144,64-60)/2+60=102,32
- Kết cấu bánh răng 2 cặp 2,3 59 b = 54 d = 40 da2 = 209 df2 = 200
c =(0,2÷0,3).bw= (0,2÷0,3).54=10,8÷16,2= 14
Dv = df2 - 2. = 200-2.7 = 186
D = (1,5÷1,8).d=(1,5÷1,8).40= 60÷72= 70
Do = (Dv-D)/2 +D = (184-70)/2+70=127 1.2 4.3. KẾT CẤU NẮP Ổ
Các kích thước đường kính tâm lỗ vít (D) và đường kính ngoài của bích (D) của các nắp ổ:
- Với nắp ổ 1: =52 mm,D2=64 mm, D3=79 mm, d4 = M8 60
- Với nắp ổ 2: = 72 mm, D2=85 mm, D3=100 mm, d4 = M8
- Với nắp ổ 3: = 90 mm, D2=102 mm, D3=120 mm, d4 = M8 D3 D2 D4 I. Các chi tiết khác 1. Chốt định vị
Mặt ghép giữa nắp và thân nằm trong mặt phẳng chứa đường tâm các trục. Lỗ trụ
lắp ở trên nắp và thân hộp được gia công đồng thời.Để đảm bảo vị trí tương đối của
nắp và thân trước và sau khi gia công cũng như khi lắp ghép, dùng 2 chốt định vị.
Nhờ có chốt định vị , khi xiết bulông không làm biến dạng vòng ngoài của ổ (do sai
lệch vị trí tương đối của nắp và thân), do đó loại trừ được môt số nguyên nhân làm cho ổ chóng bị hỏng
Ta dùng chốt định vị hình côn có ren trong vì dễ tháo lắp chốt
tra bảng 18-4c, [II] ta chọn :d=8 ;do=M5 ;l1=9 ;l2=12 ;c=1,2 c1=0,7 ;l=25...65 lấy l=40
Hình dạng và kích thước chốt định vị hình côn ren trong 61 1 : 50 3,2 d 1d c x 45 l1 l2 l 2. Cửa thăm.
- Để kiểm tra, quan sát các tiết máy trong hộp khi lắp ghép và để đổ dầu vào
hộp , trên đỉnh hộp có làm cửa thăm, cửa thăm được đậy bằng nắp trên nắp có lỗ thông hơi. 4 C /2 /2 B /2 1 B K A R
Hình 13. Kích thước cửa thăm. 62
- Tra bảng 18 – 5 trang 92 [TL2],chọn cửa thăm sau: A = 100 (mm), B = 75
(mm), A1 = 150 (mm), B1 = 100 (mm), C = 125 (mm), K = 87 (mm), R =
12(mm).Vít bắt cửa thăm: M8 22, với số lượng là 4 chiếc.
3. Nút thông hơi.
- Khi làm việc, nhiệt độ trong hộp tăng lên. Để giảm áp suất và điều hoà
không khí bên trong và bên ngoài hộp, dùng nút thông hơi, kích thước nút
thông hơi chọn theo bảng18 – 6 trang 93 [TL2], chọn nút thông hơi có kích thước cơ bản sau: A B C D E G H I K L M N O P Q R S M27 1 3 3 3 15 45 36 32 6 4 10 8 22 6 32 18 2 5 0 6 2 G O M N K C P L 3 6 lç E I H D B R A
Hình 3. Hình dạng và kích thước nút thông hơi. 4. Nút tháo dầu.
- Sau một thời gian làm việc dầu bôi trơn chứa trong hộp bị bẩn (do bụi bặm
và do các hạt mài), hoặc bị biến chất, do đó cần phải thay dầu mới. Để tháo
dầu cũ, ở đáy hộp có lỗ tháo dầu, lỗ này được bịt kín bằng nút tháo dầu khi
hộp giảm tốc làm việc, kích thước nút tháo dầu chọn theo bảng 18 – 7 trang
93 [TL3], chọn kí hiệu nút là: M20 2 có các kích thước sau: - 63 d b m f L c q D S D0 M20 15 9 3 28 2,5 17,8 30 22 25,4 2 0 D d D m b L S
Hình 4. Hình dạng và kích thước nút tháo dầu trụ. 5. Que thăm dầu
- Để kiểm tra mức dầu ta dùng que thăm dầu hình 18_11c và kích thước như hình 18_11d [TL2]. II.
Phương pháp bôi trơn 1. Bôi trơn ổ lăn
+ Do ổ lăn làm việc lâu dài , tốc độ thấp nhiệt độ làm việc <150 nên ta bôi trơn bằng mỡ
+ Ta dùng vòng phớt để che kín ổ lăn
2. Bôi trơn hộp giảm tốc 64
+ Do vận tốc vòng <12m/s nên ta bôi trơn bằng phương pháp ngâm dầu.
Chiều sâu ngâm dầu từ Với h là chiều cao chân răng
+ Chọn độ nhớt của dầu:
Theo Bảng 18-11[TL2]: Chọn độ nhớt của dầu của nhớt ở là + Chọn loại dầu:
Bảng 18-13 [TL2] : Dùng dầu ôtô,máy kéo AK-15. Phần VII: CHỌN CẤP
CHÍNH XÁC, LẮP GH É P 1/ Chọn cấp chính xác Chọn cấp chínhnh xác 9 2/ Chọn kiểu lắp
- Ưu tiên sử dụng hệ thống lỗ vỡ khi đó có thể tiết kiệm được chi phớ gia
cụng nhờ giảm bớt được số lượng dụng cụ cắt và dụng cụ kiểm tra khi gia lỗ.
- Khi lắp phối hợp trờn bản vẽ lắp nắp ổ lăn lờn vỏ H7/d11; lắp bạc chặn giữa
bánh răng và ổ lăn F8/k6; lắp bánh răng lên trục H7/k6.
- Để thuận tiện khi lắp ổ lăn ta chọn kiểu lắp ổ lăn lên trục k6; kiểu lắp ổ lăn
lên vỏ hộp H7, cho cả ba cặp ổ.
- Sai lệch giới hạn của kích thước then theo chiều rộng b h9
- Sai lệch giới hạn của rónh then trờn trục , ghép có độ hở H9 3/ Dung sai
Để lắp ghép vũng trong lờn trục và vũng ngoài lờn vỏ, người ta sử dụng các
miền dung sai tiêu chuẩn của trục và lỗ theo TCVN 2245-7 phối hợp với các miền
dung sai của cácc vũng ổ. 65 Ta có
Miền dung sai và sai lệch giới hạn của lỗ với cỏc kiểu lắp ưu tiên Miền dung sai Kích thước H7 H8 mm Sai lệch giới hạn +25 +64 Trên 30 đến 50 0 +25 +30 +76 Trên 50đến 90 0 +30 +35 Trên 90 đến 120 0
Miền dung sai và sai lệch giới hạn của trục với các kiểu lắp ưu tiên Miền dung sai Kích thước K6 D11 mm Sai lệch giới hạn +18 Trên 30 đến 50 +12 +30 -100 Trên 50đến 80 +2 -290 +25 Trờn 80 đến 120 -120 +3 -340
Bảng tra dung sai lắp ghép Tên mối ghép Kiểu lắp STT Sai lệch giới hạn Ghi chú của lỗ và trục Bánh răng nghiêng + 21 m 1 30 Bánh răng lớn cấp + 15 m 22,24 trục I nhanh với trục I + 2 m 66 + 25 m Bán Bánh răng nghiêng 2 35 h răng nhỏ cấp + 18 m 23 và trục II chậm với trục II + 2 m + 25 m Bánh răng nghiêng 3 40 + 18 m Bánh răng lớn cấp 33 và trục III chậm với trục III + 2 m + 18 m 4 Khớp nối và I 20 +12 m + 1 m +25 m 5 Đĩa xích và trục III 40 +18 m +2 m Then (lắp khớp nối) - 30 m 6 6 và trục I bxh=6x6 - 30 m Then (lắp bánh răng -36 m 7 10 22,24) và trục II bxh=8x7 -36 m -36 m bxh=8x7 Then (lắp bánh răng 8 10 -36 m 23) và trục II -36 m Then (lắp bánh rang 9 nghiêng 32) và trục 12 bxh=10x8 III -36 m 67 -36 m Then (lắp đĩa xích) 10 14 -36 m bxh=8x7 và trục III -36 m
- Mối ghép giữa bánh răng và trục với yêu cầu không tháo lắp thường
xuyên,khả năng định tâm đảm bảo, không di trượt dọc trục nên ta dùng
kiểu lắp . Còn đối với mối ghép bạc và trục độ đồng tâm yêu cầu
không cao nên ta dùng kiểu lắp .
- Mối ghép then và trục ta dùng mối ghép trung gian , còn đối với mối
ghép giữa lỗ hộp và nắp thì ta dùng mối ghép lỏng chẳng hạn . H7 ứng vs đường kính <80mm.
- Mối ghép giữa ổ và trục thì lắp theo hệ thống lỗ ta chọn kiểu lắp k6,
còn mối ghép giữa vòng ngoài ổ và lỗ hộp ta dùng mối ghép . 68