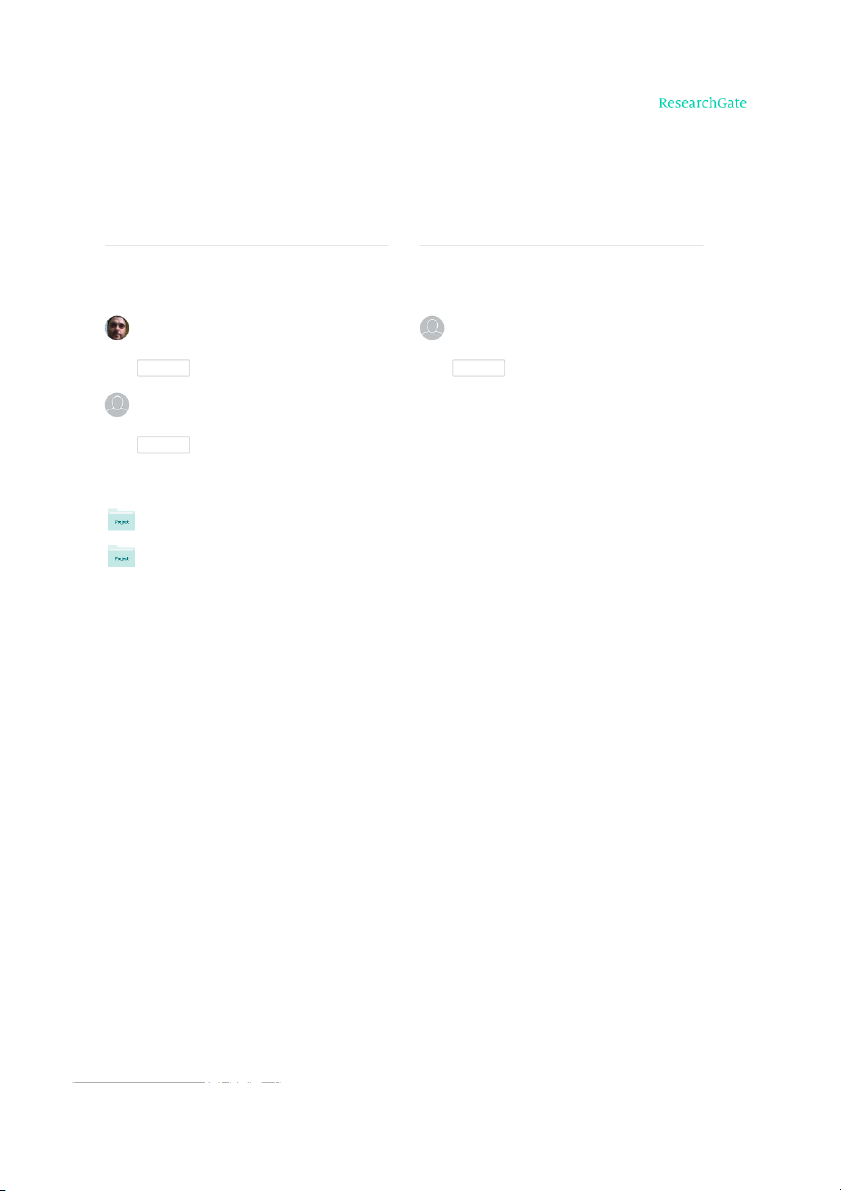

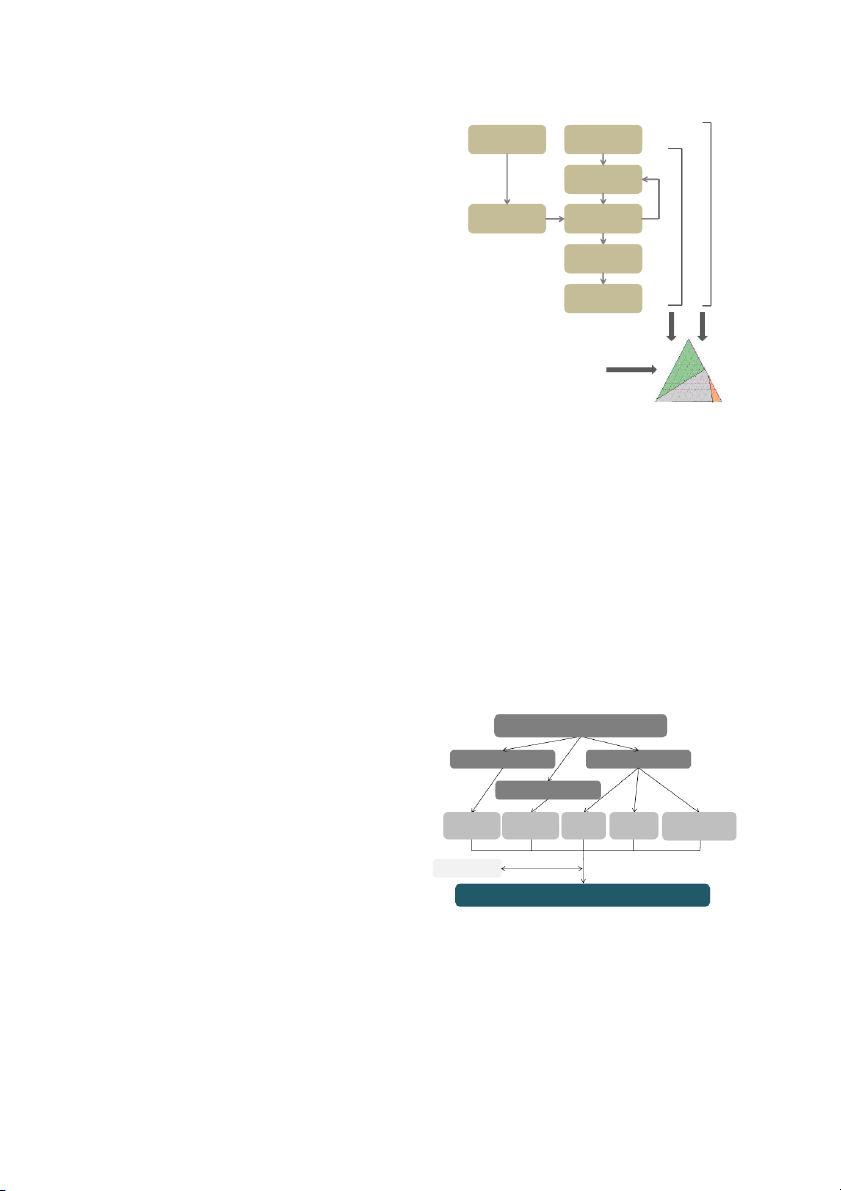
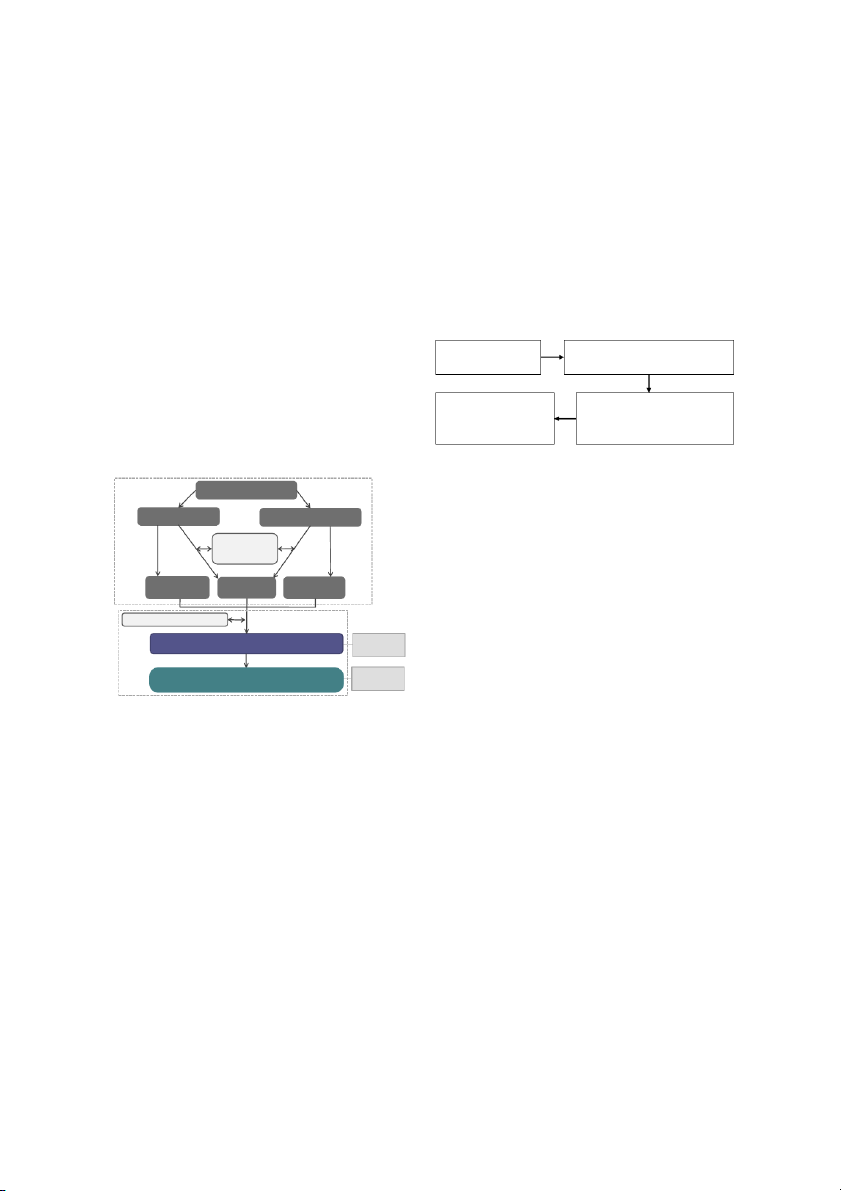
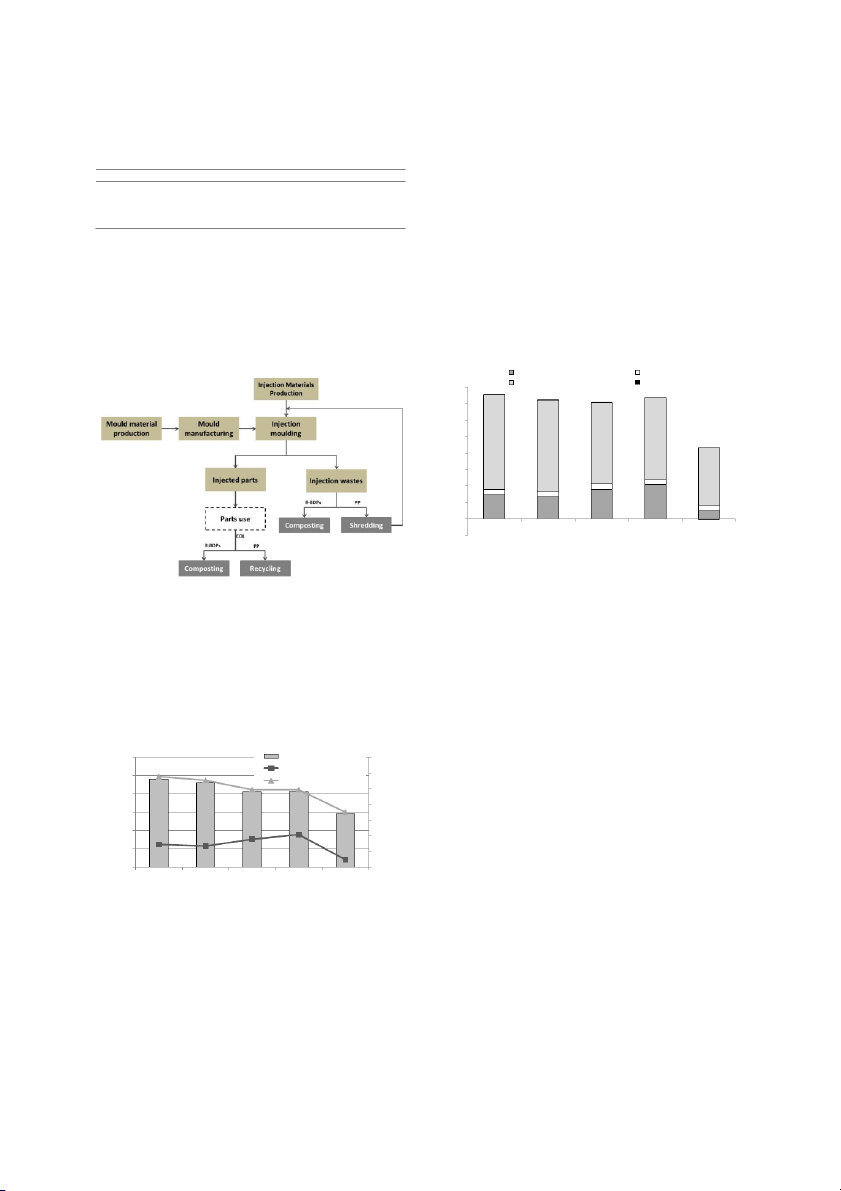
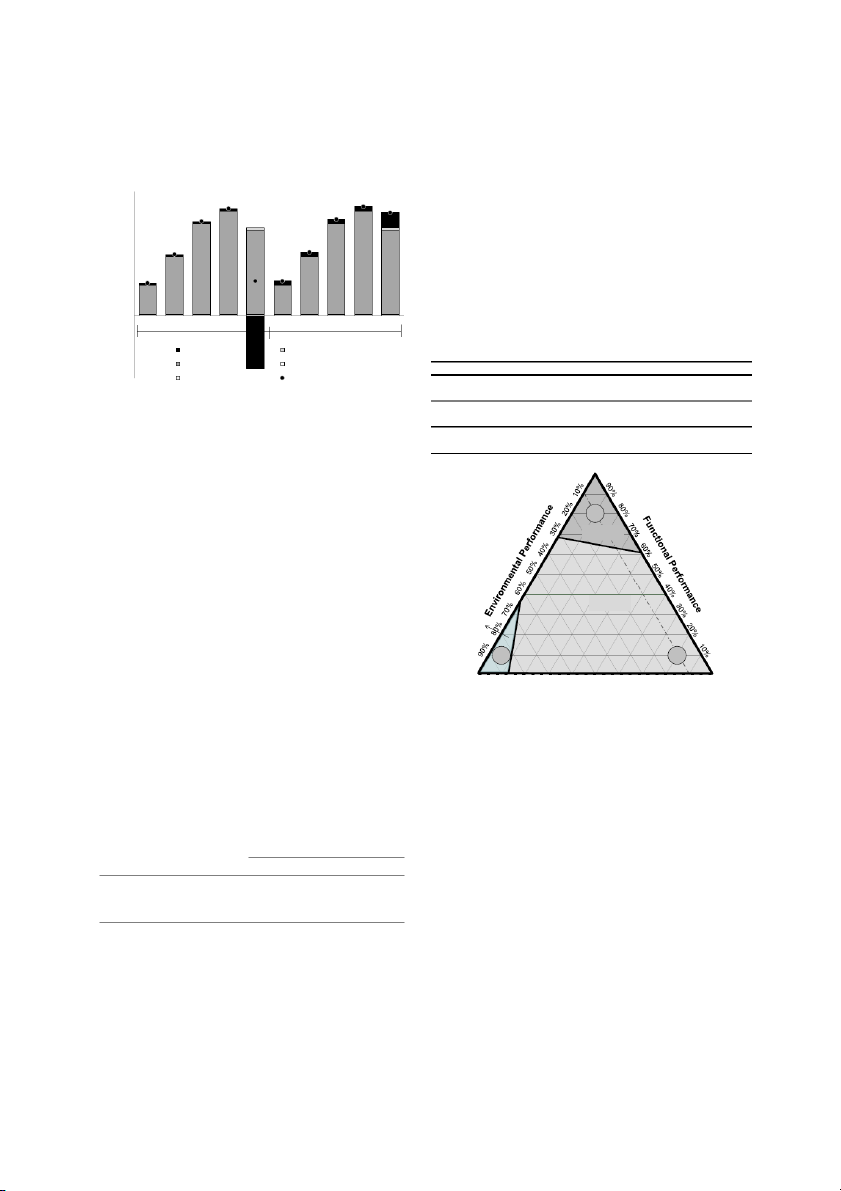
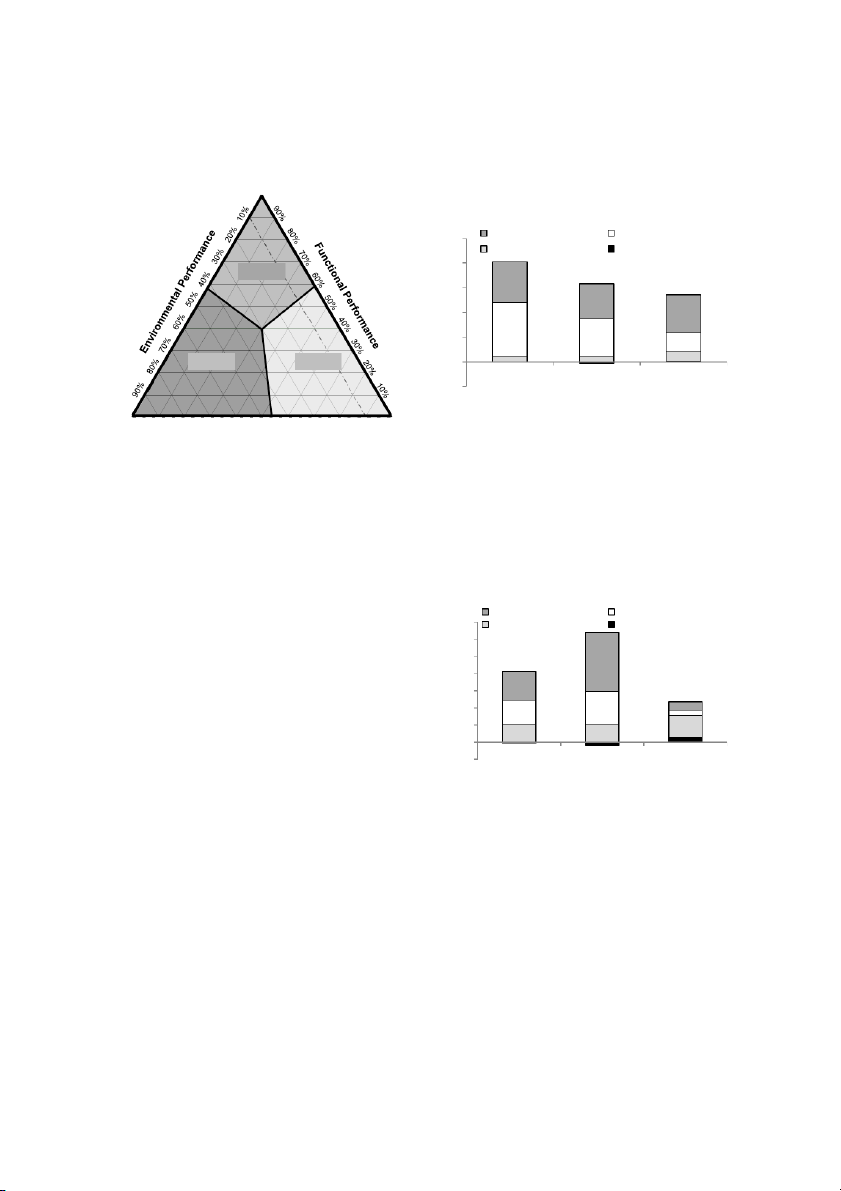
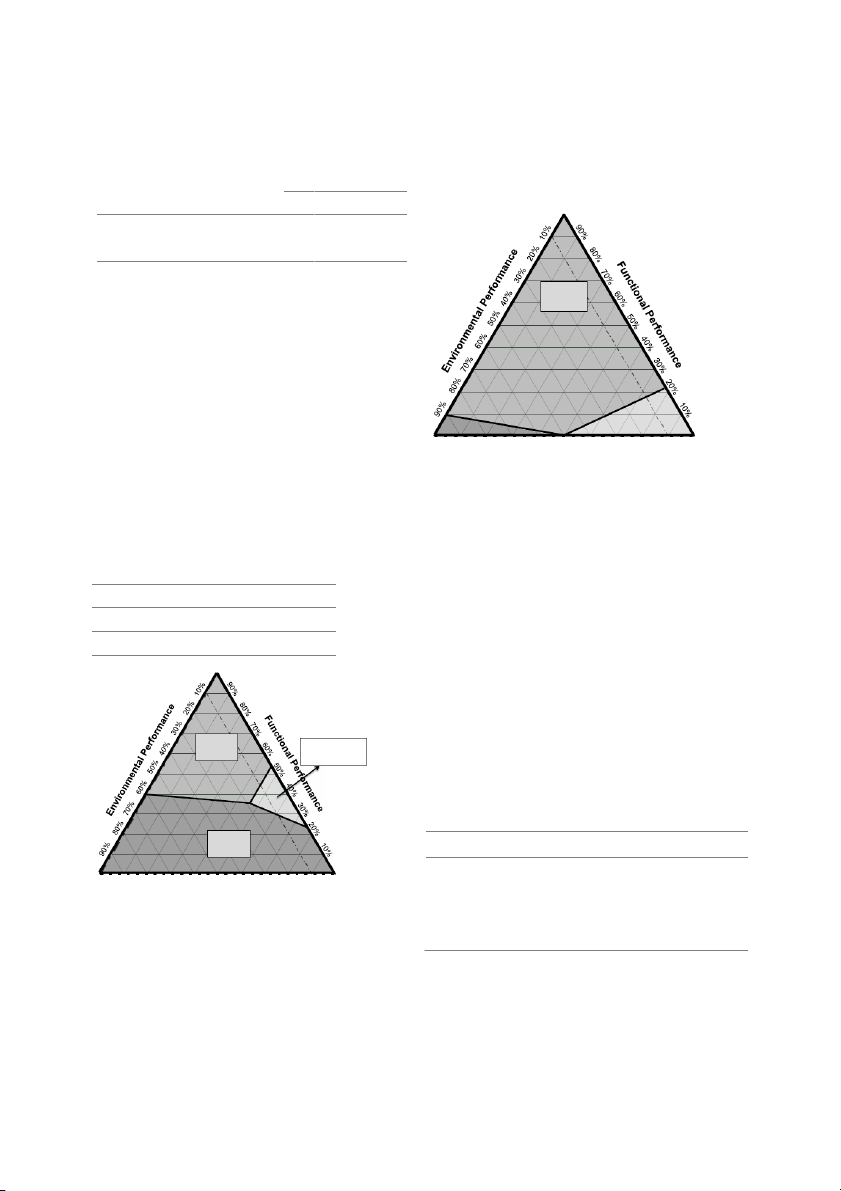
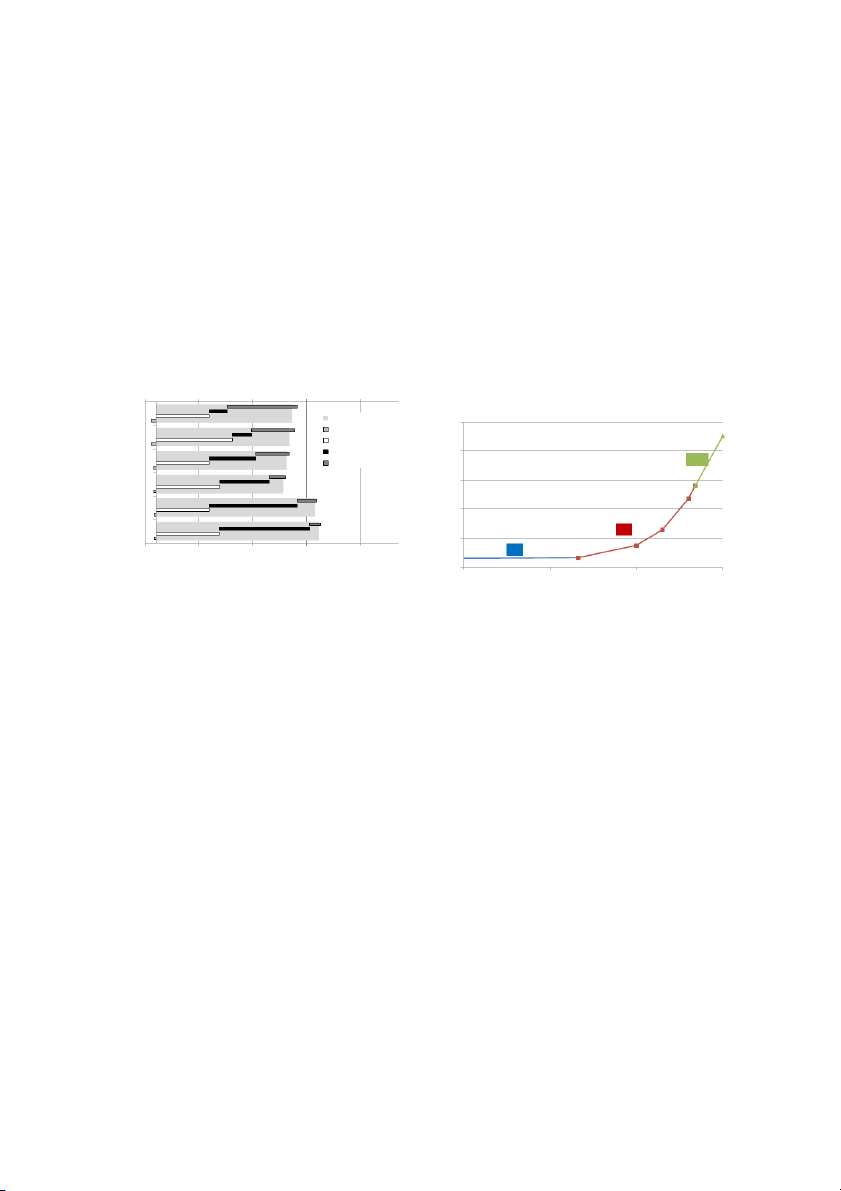
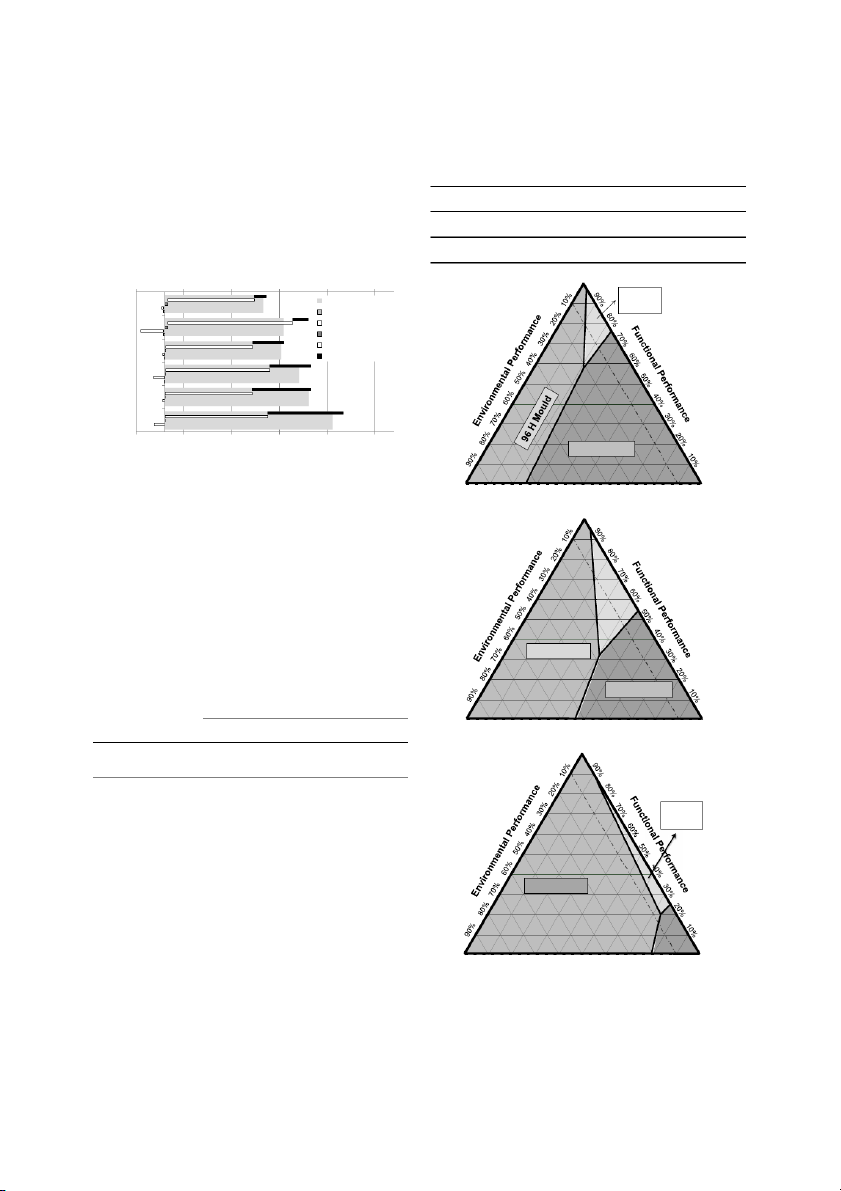
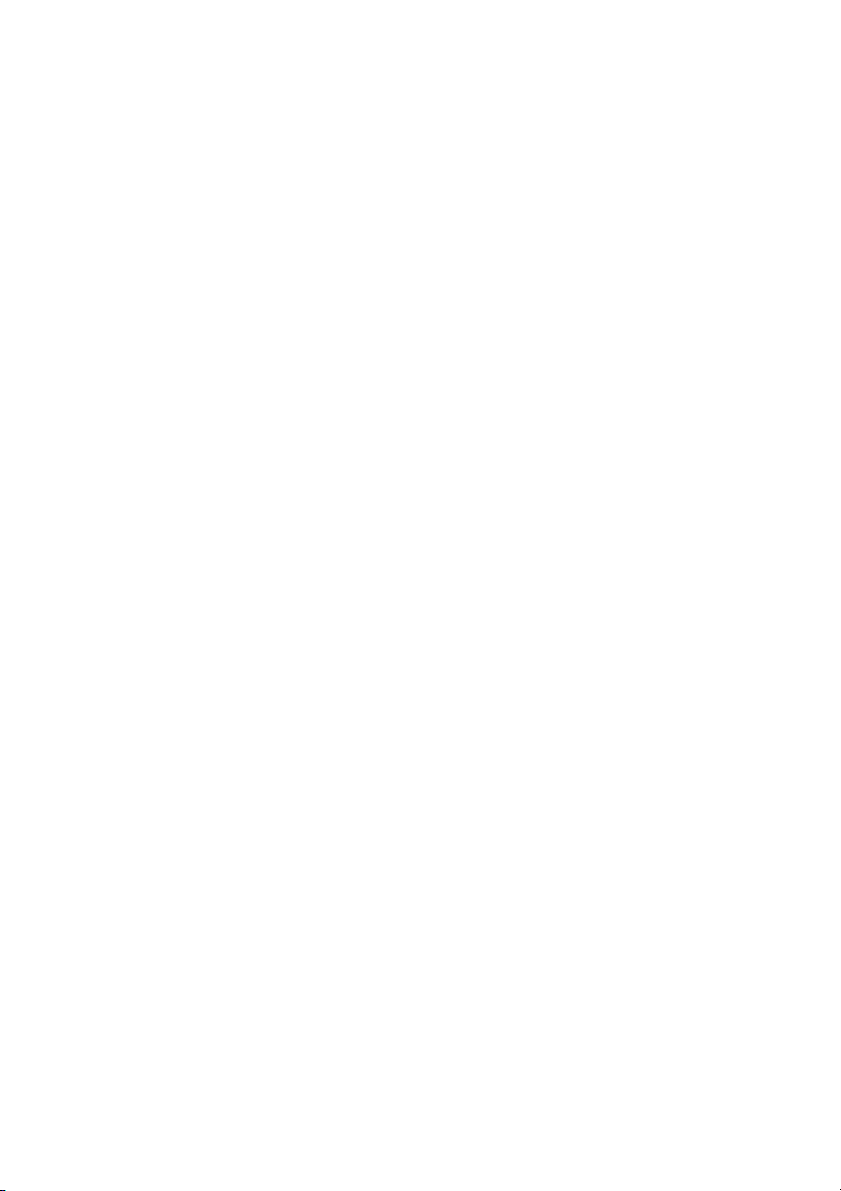
Preview text:
See discussions, stats, and author profiles for this publication at: https://www.researchgate.net/publication/236890510
Life Cycle Engineering: Modelling the Life Cycle Performance
Conference Paper · September 2012 CITATION READS 1 448 3 authors: Paulo Peças Ribeiro Ines
IDMEC, Instituto Superior Técnico, Universidade de Lisboa Technical University of Lisbon
134 PUBLICATIONS1,818 CITATIONS
62 PUBLICATIONS730 CITATIONS SEE PROFILE SEE PROFILE Elsa Henriques University of Lisbon
154 PUBLICATIONS2,274 CITATIONS SEE PROFILE
Some of the authors of this publication are also working on these related projects:
Railway wheels and axles View project
MAESTRI - Energy and resource management systems for improved efficiency in the process industries | a H2020-Project under the SPIRE-PPP Initiative: http://maestri- spire.eu/ View project
All content following this page was uploaded by Paulo Peças on 10 July 2018.
The user has requested enhancement of the downloaded file.
Life Cycle Engineering: Modelling the Life Cycle Performance
P. Peças, I. Ribeiro & E. Henriques
IDMEC, Instituto Superior Técnico, Av, Rovisco Pais 1049-001, Lisbon, Portugal.
PMI Conference 2012, Ghent, Belgium, September 13-14, p: 161-170
ABSTRACT: Nowadays, the products and process performance along its life cycle is a competitive issue for
the industrial development as well as a permanent challenge for the researchers. The plastic injection mould-
ing framework contains several characteristics implying the need to use wide spectrum modelling to assess
products and processes performance. In fact, the injection mould performance depends most of the time on the
design decision taken in the mould design phase. Its performance affects also the production phase of the plas-
tic part, which can influence the use phase of the product. Additionally, the plastic part material and design
has a direct influence on the mould design and mould manufacturing decisions. In this paper, a Life Cycle En-
gineering (LCE) framework to assess the performance of mould manufacturing and injection moulding alter-
natives is described. The LCE framework aims to support design decisions, integrating the performance of the
product/process in technological, environmental and economic dimensions throughout its duration. The ap-
proach proposed compares a set of alternatives and, through the aggregation of the three dimensions, identifies
the ‘‘best alternative domains’’. Some examples of the application of the approach are presented and dis-
cussed aiming to reveal the potential of the LCE approach in injection moulding framework. 1 INTRODUCTION
the life cycle stages. This is special important when
are involved new technologies or new materials
A plastic injection mould is designed to produce a
about what there are lack of knowledge and experi-
specific plastic part. Usually, the plastic part is only ence.
a small component in a more complex product, so its
In this study is proposed to use the Life Cycle
design must respect and fit the overall product de-
Engineering (LCE) framework to support the injec-
sign requirements. For the mould designer, the speci-
tion mould design phase. This framework contrib-
fications of the plastic part are considered invariant.
utes to a more informed decision-making process on
However, he/she is more or less free to deal with the
design features, materials and manufacturing pro-
mould design issues that have a deep impact in the
cesses. To illustrate the potential of the LCE frame-
moulding process. Therefore, in the mould design
work three case studies are described. In the next
phase attention must be given to the life cycle cost of
sections the general LCE approach is described as
the mould, its environmental impact and functional
well as the LCE framework proposed.
performance, rather than focus on the performance
of the plastics part in these dimensions. Furthermore,
it is important to evaluate the performance of the in- 2 LIFE CYCLE ENGINEERING
jection process, concerning the aspects that are in-
fluenced by the mould design decisions.
The LCE approach unlike most studies in the area of
The mould design, mould material, mould manu-
Life Cycle performance, besides including environ-
facturing and plastic part material & production rate
mental impacts, comprises also economical and
are all connected and affect each other in both direc-
functional performance analyses. Hence, it allows
tions. The selection of the mould design alternative
having an integrated view of the advantages and dis-
and/or the material of the plastic part must take into
advantages of selecting different design alternatives
account the effect of each change in the performance
regarding several dimensions of analysis.
of the several life cycle stages of the mould that in-
Jeswiet (2003) defined LCE as “Engineering ac-
cludes the injection moulding. So, design the mould
tivities which include: the application of technologi-
for the better life cycle performance is a challenging
cal and scientific principles to the design and manu-
but necessary task to assure competitiveness in all
facture of products, with the goal of protecting the
environment and conserving resources, while en-
couraging economic progress, keeping in mind the
need for sustainability, and at the same time optimiz- Mould material Raw Material A processing Acquisition C
ing the product life cycle and minimizing pollution L C –
and waste”. Being a general methodology connecting C n Plastics L o
several areas, it is necessary to use different methods Processing – ti a n
to evaluate the dimensions of analysis. It usually o lu ti a v
considers the life cycle of the product comprising the Mould Plastic Parts a E Production Manufacturing lu l
stages from material production till the product end- a v ta e n
of-life (Giudice et al. 2005) (Jeswiet et al. 2005). e ic m
The life cycle stages are analysed both in terms of Parts Use m n o
economic performance, through Life Cycle Cost n iro o v c n
(LCC) method, and in terms of environmental evalu- End of Life E E
ation, using Life Cycle Assessment (LCA). LCC ob-
jective is to cover the assessments of costs in all
steps of the product’s life cycle, including the costs
that are not normally expressed in the product mar- Functional
ket price (Krozer 2006), such as costs incurred dur- Assessment Selection
ing the usage and disposal. Regarding LCA, it is a Diagram
structured method to quantify potential environmen-
tal impacts of products or services over their full life
Figure 1: Overview of the Life Cycle Engineering framework.
cycle (Johansson et al. 2007) (Udo and Heijung
2007), being therefore a valuable tool to provide de-
The economic performance assessment is developed
signers with information on inputs, outputs and as-
according to LCC methodology. LCC is essentially
sociated environmental impacts of a defined system
an evaluation tool in the sense that it gets on to im-
(Warren and Weitz 1994). Regarding the functional
portant metrics for choosing the most cost-effective
dimension of analysis, the candidate alternatives ma-
solution from a series of alternatives (Krozer 2006).
terials are compared taking into consideration its in-
This methodology is integrated with the process-
trinsic characteristics, performances and its correla-
based cost models which regard cost as a function of
tions with the most important design features of the
technical factors (i.e. cycle time, downtime, reject
product. Finally, some authors propose a traditional
rate, equipment/tooling requirements, or the material
approach of analysing the three dimensions by at-
used). This type of models has been applied by re-
tributing weights to each dimension (Betz et al.
searchers to several processes within different
1998) (Saur et al. 2000). A different approach is
scopes, always with the intent to compare alterna-
proposed by the authors of this paper (Ribeiro et al. tives
– either in materials, processes or product ar-
2008, 2009). The three dimensions of analysis are
chitectures (Field et al. 2007; Johnson and Kirchain
aggregated in a single analysis framework. The re-
2009). The general proposed model with its general
sult is a more comprehensive view of the possible
inputs and structure is presented in Figure 2.
choices. The framework analysis space is a ternary
diagram, in which the performance dimensions are Process information
represented in each axis. With this framework, the
difficult task related to the materialization of the rel- Mass streams Production facilities
ative importance of the three dimensions into a set of
weights is overcome. The use of ternary diagrams to Energetic streams
support decisions is an innovative approach, which
has been applied in other industrial sectors (Ribeiro Resources Energy Machines Infrastructures Labour et al. 2008). consumed consumed and Tools and Overheads Costs Database 3 LCE FRAMEWORK TOTAL COST
The proposed LCE framework is illustrated in Figure
Figure 2: LCC model structure.
1, in which each life cycle stage is analysed both in
terms of economic and environmental performance.
The environmental performance is performed us-
Additionally the possible alternatives are analysed in
ing LCA, which is a structured method to quantify
terms of functionality. These three dimensions are
potential environmental impacts of products or ser-
aggregated in a single framework analysis, in which
vices over their full life cycle (Johansson et al. 2007)
depending on the importance given to each one, an
(Udo and Heijung 2007). Although LCA had
alternative appears as the best choice.
emerged in the early 1970s only in the 1990s a
standard terminology and methodology was estab-
sensibility of the results achieved to such weights are
lished (ISO 1997). Presently, LCA consists of four
the major drawbacks normally pointed to a global
steps: definition of the goal and scope of the study,
evaluation based on weights attribution. To over-
construction of the product life cycle model with all
come this disadvantage and have a clear view of the
environmental inflows and outflows (life cycle in-
possible “best alternative” correlated to its domain ventory stage
– LCI), evaluation of the environmen-
of weights, the global evaluation is performed
tal relevance of all the inflows and outflows (life cy-
through a ternary diagram, where each axis repre- cle impacts assessment stage – LCIA) and, finally,
sents one dimension of analysis. The diagram illus-
the interpretation of the results (Goedkoop et al.
trates not only the “best alternative” for a particular
2007). The LCA methodology is also integrated with
set of importance weights but also the domain of
process-based cost models. In fact, the mass, energy
weights for each “best alternative”.
and emissions determined for the cost computing are
The proposed framework is illustrated through
used as input on the LCA model, representing the
three case studies regarding the mould making and
LCI phase. For the LCIA phase, 11 environmental
injection moulding industries.
impact categories are considered, in the following
three areas: Human Health, Ecosystem Quality and Selection of n Requirement Weights by
Resources. The methodology aggregates all the requirements (i) pair-wise comparison – (W )
emissions and resources consumption from the life i
cycle into these impact categories and, afterwards,
weights the scores into a single value, called the Total Score of each Scoring of each alternative
“eco-indicator 99” (EI’99). The general proposed alternative j – j based on alternative
model is presented in Figure 3. Σ (Wi*Sij) performance – (S ) i:1 n ij
Figure 4: Basic methodology used for the functional assess-
LCI – Life Cycle Inventory
ment. More complex methods can be used. Process Information Mass Streams Energetic Streams 4 CASE STUDIES Emissions Data base
In this section are described three case studies cover-
ing three different ways of applying the proposed Resources Emissions Energy
LCE framework on alternative selection. The first Consumed Produced Consumed
case study is related with the selection or influence Impact Value System
of the plastic part material on the life cycle perfor-
mance. Four biodegradable materials are compared Human health Ecosystem Resources Impact
Environmental Impact Calculation categories
together with polypropylene. The second case study
is related with the selection of the mould design to
TOTAL ENVIRONMENTAL IMPACT EI ‘99
accomplish the same injected plastic part to be pro-
duced in small series. The mould manufacturing al-
LCIA – Life Cycle Impact Assessement
ternatives compared are: steel mould, aluminium Figure 3: L CA model structure.
mould and a spray-metal based mould. The third
case study regards the influence of mould design al-
Finally, the functional performance of the product
ternatives to inject a plastic peg. The number of
is performed using a multiple attribute decision
cavities and hot/cold runners are the alternative de-
method. The evaluation of the technical performance sign features.
of a product, tool or other equipment relies on the
know-how of professionals (and users) to choose the 4.1 Case study 1 I
– njection material selection
relevant technical attributes for the application (Fig.
4). Several decision making methods ca n be applied
The aim of this study is to compare four different bi-
on this kind of comparisons, such as graphic theory
odegradable polymers (BDPs), not only environmen-
and matrix approach and fuzzy multiple attribute de-
tally, but also in terms of economical and functional
cision-making methods (MADM) (Rao 2007). In
performances. Additionally, its performance it’s
common, all of them rely on the know-how and ex-
compared with a standard polymer: the Polypropyl-
pertise of professionals and users to determine the
ene (PP). The BDPs are all mixtures of PolyLacti-
relevant functional requirements for the application.
dAcid (PLA) and Starch STA, differing on the
Having the performance of the alternatives in the
amount used of these two components, as shown in
three dimensions is then proposed an integrated
Table 1. Although both components are composta-
mapping of its performance. The difficulty to attrib-
ble, the environmental burdens during the produc-
ute importance weights to the dimensions of analysis
tion of PLA are higher than in the STA case. How-
that closely reflect a corporation strategy, and the
ever, STA lacks in mechanical properties. Therefore,
by analysing a product life cycle using these differ-
there is trend of LCC reduction with the increasing
ent materials it is important to evaluate them based
of the PLA content. The better injection characteris- on a comprehensive approach.
tics of PLA compared with STA ones, allow the
BDPs with higher PLA content (90/10 and 80/20) to Table 1: BDPs description.
be injected with lower cycle times. The reduced pro- Material Manufacturer Trade name Composition 10/90 Cabopol Biomind C004 10%PLA+90%STA
duction time costs compensate the higher costs for 40/60 Rodenburg Biopol. Solanyl 35F 40%PLA+60%STA
the BDPs with higher PLA content (Fig. 7) . 80/20 Cabopol Biomind R006 80%PLA+20%STA 90/10
The higher costs of BDPs are caused by a higher Biotec Bioplast GS 2189 90%PLA+10%STA
cycle time and a higher material cost. Since the
The life cycle of plastic parts and the study
BDPs are beginning to be industrialized the optimi-
boundaries are described in Figure 5. Once this study
zation of the cycle time is not yet as strong as the
is only concerned with the plastic materials and not
one of PP. Additionally, the increase on the use of
with a particular product, the use phase won’t be an-
BDPs will contribute to its acquisition cost reduc-
alysed. Two opposite end-of-life (EOL) scenarios
tion. So, it’s expected in the near future the BDPs were considered:
will reduce significantly the LCC performance gap
Ideal: composting of BDPs and recycling of PP
to other widespread material like PP.
Flawed: depositing of BDPs and PP in landfill Materials acquisition Mould production Injection moulding End of Life 80 0.4% 0.5% 0.5% 0.5% 70 60 50 66.7% 76.0% ] 76.2% 69.5% € 40 ost [k 30 C 82.4% 4.7% 20 4.9% 4.6% 4.8% 10 19.0% 25.1% 28.1% 18.5% 8.2% 11.2% 0 -1.8% 10/90 40/60 80/20 90/10 PP -10
Alternative polymers BDPs and PP Figure 7: L
CC results and costs distribution for a production volume of 200,000 parts.
Figure 5: Plastic parts life cycle and study boundaries.
In the environmental performance assessment
of the BDPs and PP a cradle to grave approach is
Regarding the plastic parts manufacturing stage,
performed. The data previously collected for the in-
the process chosen is a very common one, injection
jected parts/samples and an annual average produc-
moulding. All parts were injected using the same in-
tion of 200,000 parts were considered. Taking into
jection mould; therefore in terms of polymers com-
consideration the system boundaries the results of
parison it won’t produce any changes. Still, its in-
the application of the LCA model are presented in
corporation will be reflected on the parts’ final costs
Figure 8 for the two EOL scenarios. and environmental impacts.
The impact of mould material and mould manu-
facturing are not significant. Also the EI of the injec- 60 Cycle time [sec] 70
tion moulding process (consumed energy) is also Raw material costs [€] 60 50 Injection costs [€]
very low. This fact is related with the production 50 ec] 40 ]€
volume that in fact is low for the injection moulding e [s 40 30
process. The most relevant cause of EI is the mass of 30 ost [k C 20
polymer used. The EI of the injected materials in- ycle tim 20 C
creases with the PLA content. The manufacturing 10 10
process of PLA is an energy consuming process 0 0 10/90 40/60 80/20 90/10 PP
causing it has a higher impact than PP. The influence Materials
of the EOL phase is mainly noticed for the PP since
Figure 6: Injection cycle time Vs. Injection and Raw material
in the Ideal EOL scenario this material is recycled. In costs for 200,000 parts.
the Flawed scenario the PP impact in landfill is
higher than the other materials.
The global results of the LCC model to each ma-
In summary the 10/90 BDP with the highest con-
terial life cycle phase are illustrated in Figure 6. The
tent in STA has the better environmental life cycle
LCC model was applied to an annual average pro-
performance on both EOL scenarios. The PP has a
duction volume of 200,000 units, distributed in
performance close to the 10/90 BDP in the Ideal
batches of 25,000 units. It’s possible to conclude that
EOL scenario mainly because the possibility of its
recycling. If the Flawed EOL scenario is considered
the EI of PP is equivalent to the 80/20 and 90/10
appearance. The better performance of PP in these
BDP. The 10/90 BDP confirms its best performance.
latter requirements is not enough to compensate its
Even though this scenario is not a recommended so-
worst performance in biodegradability, ranking it
cietal one it’s where the BDPs reveal its advantage
with the lowest functional assessment. of being biodegradable.
The assessment of the results achieved allows the
development of a global evaluation of the alterna- 2000 1723 1757 1659
tives. The outcomes of each individual dimension of 1519 1552
analysis (functional, economic and environmental 1500
performance) are adimensionalised (Table 3). It al- 988 1022
lows attributing weights to each dimension. The sum 1000
of the three dimensions weights must be 100% and 527 561 559
different combinations of weights might result in a 500 I'99 points
different “best alternatives”. E 0 10/90 40/60 80/20 90/10 PP P 10/90 40/60 80/20 90/10 PP
Tabela 3: Absolute and adimensionalized values for each per- Ideal EOL scenario Flawed EOL scenario
formance dimension assessment (200,000 parts produced and -500 End of Life Injection moulding Ideal EOL scenario). Injection materials Mould manufacturing 10/90 40/60 80/20 90/10 PP -1000 Mould material EI'99 TOTAL Value (k€) 76.5 73.1 71.4 74.4 42.8 LCC Adimens. 5.6 5.9 6.0 5.8 10.0
Figure 8: LCA final results for 200,000 unities produced for the Value (EI'99) 527 988 1519 1723 561
Ideal and for the Flawed EOL scenario. LCA Adimens. 10.0 5.3 3.5 3.1 9.4 Value 4.4 5.5 7.2 6.8 5.2 FA
In the LCE framework developed for this study, Adimens. 6.1 7.6 10.0 9.4 7.2
the functional assessment refers to functional re-
quirements and their contribution to the functional
performance of a typical application for the polymers
in comparison, over its life. Possible applications to C
biodegradable polymers are: daily use and disposa- 80/20
ble type of products, such as food or liquid contain-
ers, plastic bags or even hygiene products like tooth
brushes. Therefore, the selection of the requirements
for the polymers comparison should rely on the pol- PP
ymers’ physical properties but also on product users’ demands and expectations. 10/90
Having in mind the type of products in which
these polymers are intended to be used, the follow- B A
ing requirements to assess were selected: Lightness, 10% 20% 30% 40% 50% 60% 70% 80% 90%
Strength, Biodegradability and also Appearance. The Economical Performance
importance of each requirement was obtained by
Figure 9: Global evaluation for the Ideal EOL scenario. Points
pair-wised comparison having in mind the user sens-
(Econ.;Envi.;Func.): A (80%;10%10%); B (5%; 85%;10%); C
ing of a product made in these materials. Matching (10%;10%;80%).
these weights with the materials properties using the
MADM it’s possible to compute the materials func-
In the Figure 9 is illustrated the mapping of the tional performance (Table 2) .
alternative materials for the Ideal EOL scenario. In
this scenario the PP has the best performance in eco-
Table 2: Functional dimension assessment (S
nomic dimension. The difference to the BDPs in this ij: 1-lowest; 10-
highest performance based on materials properties).
dimension is higher than to the 10/90 in the envi- Score of each alternative (S
ronmental dimension and to the 80/20 in the func- i ) j
tional dimension. So, the PP domain is wide only Requirements Weigth (Wi) 10/90 40/60 80/20 90/10 PP Lightness 9% 1 3 8 5 10
loosing when high importance (weight) is given to Strength 43% 1 5 10 9 7
environmental dimension (point B) or to functional Biodegradability 38% 10 7 4 4 1
dimension (point C). Depending on the strategic de- Appearance 10% 1 4 7 9 10 Total 4.4 5.5 7.2 6.8 5.2
sign aim the weight of each dimension is set accord-
ingly resulting in a point/zone of material selection.
The material with lower STA (10/90) presents the
The flexibility of the process-based models used
best results for biodegradability but is the worst in
allow for sensitivity analysis. Changings in produc-
the other requirements. The 80/20 and 90/10 materi-
tion volume, batch volume, materials cost, cycle
als present the best results, namely due to its better
time, etc. will affect the best alternative mapping. To
ranking in strength and high ranking in lightness and
illustrate this is presented in Figure 10 the diagram
for the Flawed EOL scenario. In this case the relative
for the SMT mould since the mould materials are not
better performance of the 10/90 BDP to PP increases
recyclable but its influence in the overall cost is very
its domain. The result is a clear presence of the three
low. The longer machining time of the steel mould is
materials in the “best alternative” diagram whose se-
the cause for its worst economic performance. The
lection depends on the weights given to each per-
low injection moulding cycle time allowed by this formance dimension.
mould cavity has no effect in the context of very small series. 10 Materials acquisition Mould production Injection moulding End of Life 8 80/20 41% 6 ]€ 46% 4 57% ost [k 53% C 2 48% 27% 6% 10/90 PP 8% 1% 15% 0 -0,3% -1,7% Steel Aluminium SMT -2 Material of the Mould cavity
Figure 11: LCC results and costs distribution for a production 10% 20% 30% 40% 50% 60% 70% 80% 90% volume of 200 parts injected. Economical Performance
Figure 10: Global evaluation for the Flawed EOL scenario.
For the same plastic production volume context
the SMT also reveal the lowest EI (Fig. 12). The
manual-based operations of mould production and 4.2 Case Study 2 M
– ould material alternatives
the type of materials used contribute to a reduced EI
In this case study the LCE framework is proposed to
of the SMT mould. Nevertheless the EI of the injec-
support the selection of mould material alternatives
tion moulding phase mould is higher than the others
solutions in the mould design phase. The example
even for low production volume. The EI of the EOL
comprises the comparison between three mould
phase is positive as the others are negative because
types. They differ essentially in the cavity material
the SMT mould cavity becomes a non-recyclable
used: one is made in aluminium, other in steel and composite.
other is a mould produced through a rapid tooling Materials acquisition Mould production 350
technique – spray metal shell backfilled with resin Injection moulding End of Life
and aluminium powder (SMT mould). It is assumed 300
that the mould structure is the same (all in steel) and 250 55%
the injected part has the same geometry, material and 200
quality features. There are some differences in the 41% 150
cycle time, namely for the SMT mould caused by the 100 '99 [points] 34% 31% 21% 13%
lower thermal conductivity of the resin-based cavity. EI 50 55%
The scope of the study is to compare the perfor- 26% 17% 11% 0
mance on very low production volume (below 2,000 -1,5% -3,2% -50 Steel Aluminium SMT
parts), so it’s assumed the need for one aluminium Material of the Mould cavity
and one steel mould. Each SMT mould can inject up
Figure 12: LCA final results for 200 unities produced.
to 200 parts. Therefore there is the need to produce
one SMT mould cavity for each 200 parts injected.
The cost and EI of the plastic material was not con-
The functional dimension is assessed by three re-
sidered since are the same for all the alternatives.
quirements related with the reliability and complexi-
But the energy consumption impact in costs and EI
ty of the technologies necessary to produce the
of the injection moulding phase was included since
mould in each alternative (Table 4). The SMT mould
it’s different among the mould material alternatives.
requires more manufacturing steps with non-
The SMT mould has the best life cycle perfor-
common technologies in a mould maker shop-floor,
mance on the economic dimension for the produc-
so a lower score is given. Nevertheless, the process
tion of 200 parts (Fig. 11). The main reasons rely on
is faster and more flexibility in terms of obtaining
its lower material acquisition and mould production
the final cavity to inject parts. The fourth require-
costs. In the context of very small production series
ment is related with the mould performance in the
the worst performance of the SMT mould in the in-
injection phase. The uncertainty of the behaviour of
jection moulding phase doesn’t affect significantly
the SMT mould in the injection phase is the cause
its economic performance. The EOL costs are higher
for its worse score in this requirement. In summary,
the mould with the steel cavity has the better func-
cle costs, then the aluminium mould is the best
tional performance and the SMT mould the worst.
choice and similarly, if very high importance is giv-
en to environmental issues, the SMT mould is the
Table 4: Functional dimension assessment (Sij: 1-lowest; 10-
“best mould”. Regarding even higher production
highest performance based on moulds cavities characteristics).
volumes, the steel mould is the best choice for al-
Score of each alternative (Si )j
most all weights combinations. Weigth Steel Aluminium SMT Requirements (Wi)
Mould prod. technology reliability 17% 10 7 1
Number of mould production steps 14% 10 8 1
Time to plastic part production 22% 1 5 10 Mould capability in injection 47% 10 7 1 Total 8.02 6.7 3.0 Steel
The ternary diagram developed with the results mould
regarding a production volume of 200 parts (Table
5) is illustrated in Figure 13, in which the three
moulds appear as a possible solution. In fact the
SMT mould achieves the best performance in the
environmental and in the economic dimensions. The
steel mould has highest the score in the functional
analysis. So, its domain is clear if more than 50% Aluminium
importance is given to the technical performance. SMT mould mould
Nevertheless, the good performance of the alumini- 10% 20% 30% 40% 50% 60% 70% 80% 90%
um mould in the economic dimension allow to be Economical Performance
the best choice when a weight between 50% to 80%
Figure 14: Global evaluation regarding the production volume
is given to costs and lower than 20% is given to EI
of 2,000 parts (10 SMT moulds cavities are required).
where the aluminium mould has it worst perfor- mance. 4.3 Case Study 3 M
– ould design alternatives
Tabela 5: Absolute and adimensionalised values for each per-
The third case study is about comparing the life cy-
formance dimension assessment (200 parts produced).
cle performance of different mould design alterna- Steel Aluminium SMT Value (€) 8060 6219 5437
tives on the production of a propylene cloth peg (2 LCC Adimens. 6.7 8.7 10.0
parts per peg). The design characteristics under study LCA Value (EI'99) 203 310 118
are the number of mould cavities and the type of Adimens. 5.8 3.8 10.0
runners – cold and hot (Table 6). Value 8.2 6.7 3.0 FA Adimens. 10.0 8.4 3.7
Before analysing the results of the LCE frame-
work application to this case study is important to
clarify the analysis boundaries. The cloth peg use
phase economic and environmental impacts were not
considered. But the injection moulding impacts and
the required volume of plastic material were both Steel Aluminium
considered. In this case study the use of different mould mould
types of runners will cause different volume of con-
sumed and recycled plastic material affecting the
materials acquisition phase and the EOL phase.
Table 6 – Designation of the design alternatives SMT Ref. Mould design type Cycle Mass/cycle mould Time (s) (g/cycle) 16H 16 cavities, hot runners 16.3 47.9 10% 20% 30% 40% 50% 60% 70% 80% 90% 16C 16 cavities, cold runners 20.9 56.4 Economical Performance 32H 32 cavities, hot runners 17.1 95.9
Figure 13: Global evaluation regarding the production volume 32C 32 cavities, cold runners 22.8 114.4 of 200 parts. 96H 96 cavities, hot runners 19.5 287.6 96C 96 cavities, cold runners 25.4 414.0
Considering the scenario of the production of
2,000 parts (Fig.14) the steel mould is the best
The LCC of the cloths peg was assessed through a
choice if more the 22% of importance is given to the
process-based cost model in order to allow posterior
technical performance of the mould. Bellow this
sensitivity analysis related with the impacts of
value, if very high importance is given to the life cy-
changes in design, materials, manufacturing process-
es, production volume, etc. The material cost is un-
alternatives with the evolution of the production
derstanding from a manufacturing point of view
volume. The LCC model takes into account for each
meaning that it takes in all the material mass re-
production volume the technological modifications
quired for the injection process multiplied by the its
required in the production system, namely it selects
commercial specific price. The plastic material re-
the most adequate injection machine for each pro-
quired for the injection process but not included in
duction volume, the related resources required, etc.
the final product (plastic waste in the mould feeding
For high production volumes (more than 4.81
system) can be reused in the injection process. Nev-
MPegs) the pegs bodies injected in 96 cavities
ertheless, for quality reasons a limit of 10% of mate- moulds with hot-r nner u s achieves the lower LCC. It
rial recycling was allowed for each injection. The
means that the lower cycle times allow lower injec-
remaining material was considered to be sold or in-
tion moulding costs that together with lower material
corporated in other products as recycled plastic. Re- consumption (hot-r nner u s) compensates the higher
garding the EOL, the mould was considered to be
cost of the mould (constant in the range of produc-
sent to recycling and so sold as scrap alloy steel.
tion volumes considered). For lower volumes, until
Finally all costs were gathered and the total LCC
around 211.6 kPegs, the 32C alternative is the best
of each alternative was computed (Fig. 15) for a pro-
one, due mainly to the increasing importance of the
duction volume of 4x106 cloths pegs (4 Mpegs) in-
mould cost for the cloths peg life cycle cost. For
volving the injection of 8x106 body parts.
lower production volumes the mould productivity -10 40 90 140 190
largely reduces its impact and the LCC value be-
comes essentially driven by the mould cost. 96H 127 TOTAL LCC 25 Recycling 96C 124 esign Plastic Material Injection Moulding 20 32H 122 ) 96H ould D Mould U M 32C 15 118 4 808 480 Pegs ost (k lternative M 16H 148 10 A ycle C C 16C 32C 152 ife L 5 16C -10 40 90 140 190 Life Cycle Cost (kMU) 211 589 Pegs 0
Figure 15: LCC of the mould design alternatives for 4Mpeg 10000 100000 1000000 10000000
(Mould includes mould production and material cost). Production Volume (# pegs)
Figure 16: Best (lowest LCC) alternatives for different produc-
For this level of production volume the im- tion volumes.
portance of the plastic material costs is high for all
the alternatives. But the effect of the production vol-
In order to evaluate the environmental perfor-
ume in the injection moulding costs is only evident
mance of the different alternatives the LCA model
for the mould alternatives with lower cavities per
was applied (Fig. 17). Beside other study boundaries
mould (16). For the moulds of 96 cavities the injec-
mentioned, the used cloths pegs were considered to
tion moulding costs are really low. Nevertheless the
be deposited in landfill since there is no recycling
very high costs of these moulds increase its overall
framework; the plastic material required for the in-
LCC costs. The moulds with 32 cavities have a bal-
jection process but not included in the product
anced performance achieving the best economic life
(waste) was considered to be recycled, in the com-
cycle performance: the mould is slightly more ex-
pensive than the one with 16 cavities but efficient
pany or by any recycling framework.
enough to avoid high injection moulding costs. The
From the LCA model results is possible to ob-
EOL costs are not significant in every alternative.
serve the extremely reduced EI of the mould. The
The effect on the type of runners used is visible in
plastic material has the major slice of impact mainly
increasing the amount of material required in the
in alternatives with 96 and 32 cavities. In fact, as ob-
case of cold runners and in the increasing of the served for the costs, the E I of plastic material varies
mould cost in the case of hot runners. For the in a relative strict range.
moulds with 96 and 32 cavities the use of cold run-
The alternatives with lower environmental per-
ners allow for a lower LCC but the opposite happen
formance are the ones that use cold runners, due to
for the mould with 16 cavities. Nevertheless the
the extra material required for the feeding channels
number of cavities has a higher impact on the eco-
and the limit of 10% of recycled material in the in-
nomic performance than the type of runners.
jection process. It must be noticed that since this
Taking advantage of the use of process-based cost
wasted material was considered for recycling, there
models the build-up of sensitivity analysis is possi-
is a recovering of impacts for the alternatives using
ble. In Figure 16 is presented the best mould design
cold runners (negative impact figures). This fact mo-
tivates a relative balance of the overall impact of the
use of cold runner decrease the overall performance
consumed materials, which results in a higher im- in the functional dimension.
portance of the impact of the injection moulding
process (energy consumption) in the alternatives
Table 8: Absolute and adimensionalised values for each per-
ranking. Therefore, alternatives with lower cycle
formance dimension assessment (4 Mpegs produced).
time per part have a lower environmental impact. 16H 16C 32H 32C 96H 96C Value (MU)
147995 151500 121652 118326 126733 124229
The alternatives with cold runner moulds present LCC Adimens. 8.0 7.8 9.7 10.0 9.3 9.5
always higher impact than the similar ones with hot Value (EI'99) 15109 17584 12210 14077 10308 12466 LCA
runners, due to higher impact of injection moulding Adimens. 6.8 5.9 8.4 7.3 10.0 8.3 and material consumption. Value 4.55 4.3 4.95 5.5 6.7 6.45 FA Adimens. 6.8 6.4 7.4 8.2 10.0 9.6 -3000 2000 7000 12000 17000 22000 96 C 96H 10308 TOTAL LCIA Mould Mould Recycling (-) 96C Plastic Recycling (-) 12466 Mould lternative Plastic Material 32H 12210 Injection Moulding esign A 32C 14077 ould D 16H 15109 M 16C 17584 -3000 2000 7000 12000 17000 22000 Life Cycle Impact - EI'99 (Pt) 32 C Mould Figure 17:
LCIA of the mould design alternatives for 4 Mpegs. 10% 20% 30% 40% 50% 60% 70% 80% 90%
For the functional analysis dimension the re- Economical Performance
quirements selected are related with the moulds pro- a)
duction and its performance in injection moulding
(Table 7). The number of cavities and the use of hot
runners increase the mould complexity. The effect of
this complexity is only partially reflected in the pro-
duction cost accounting of the LCC model. In this 96 C
dimension are essentially reflected the non-tangible Mould
effects of increasing the number of production steps
and the components to integrate in the mould and the
subsequent increasing of the potential of mistakes. 96 H Mould
Table 7: Functional dimension assessment (Sij: 1-lowest; 10- 32 C Mould
highest performance based on moulds cavities characteristics).
Score of each alternative (Si )j Weigth 10% 20% 30% 40% 50% 60% 70% 80% 90% Requirements 16H 16C 32H 32C 96H 96C (W Economical Performance i) b) Mould complexity 35% 10 9 6 5 2 1 Mould reliability 25% 1 3 5 7 8 10 Mould capability 40% 2 1 4 5 10 9 Total 4.55 4.3 4.95 5.5 6.7 6.45
The same approach was followed for the perfor- 96 C Mould
mance of the moulds in the injection moulding. The
use of higher number of cavities will reduce the
number of cycles, so the need for maintenance is
lower for the same number of injected parts. The use 96 H Mould
of hot runners improves the injection process capa-
bility since it’s easier to control the process. Also the
decreasing of the number of cycles with the number 32 C
of cavities affects the performance in this require- Mould
ment. Both mould reliability and capability were not 10% 20% 30% 40% 50% 60% 70% 80% 90%
considered in the LCC model used. Economical Performance c)
The 96H mould is the one with better perfor-
Figure 18: Ternary selection diagrams representing the “best”
mance in the functional dimensions followed closely
solutions map for different production volumes: a) 0.5 MPegs;
by the 96C mould. The number of cavities and the b) 2 Mpegs and c) 4 MPegs .