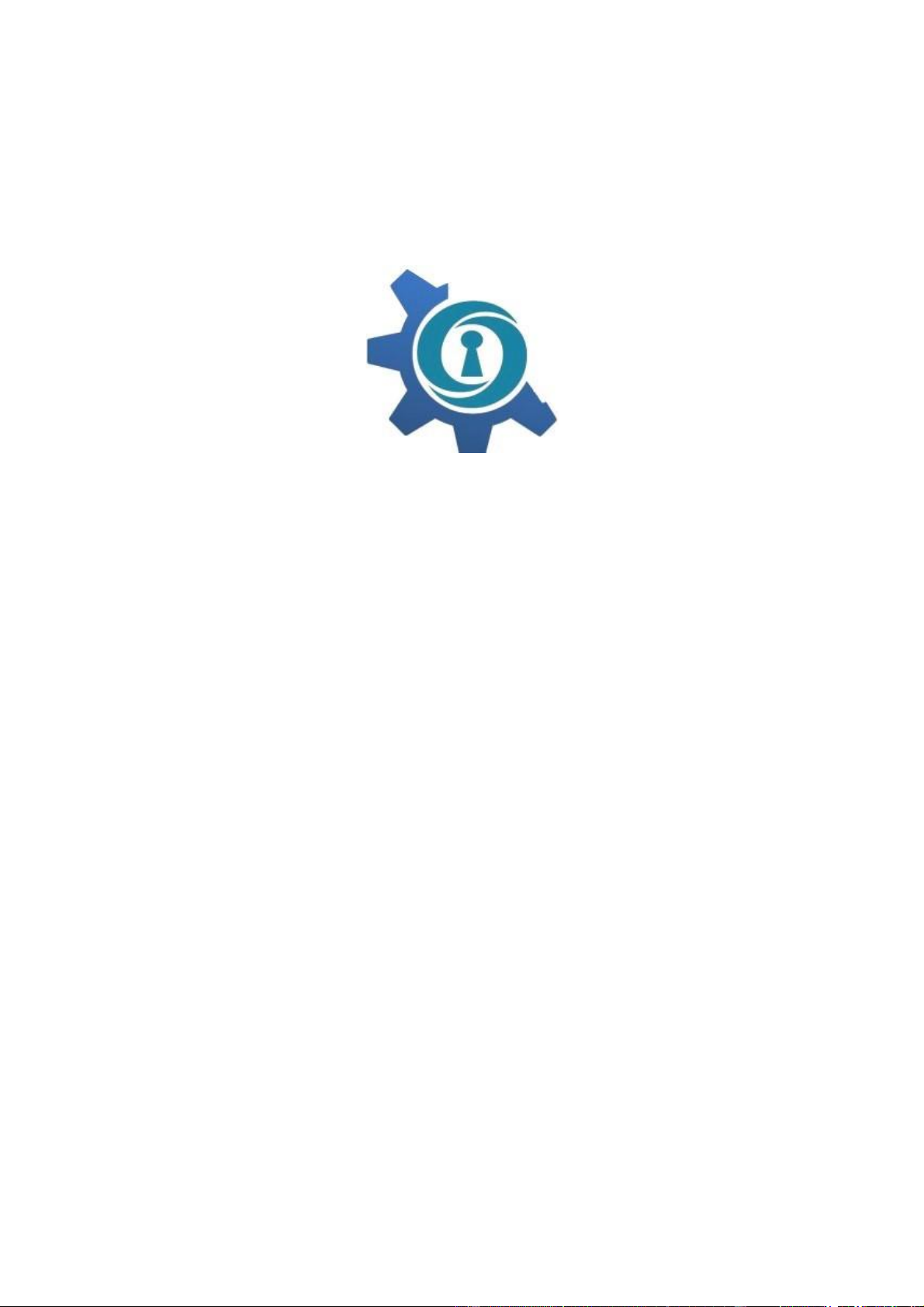
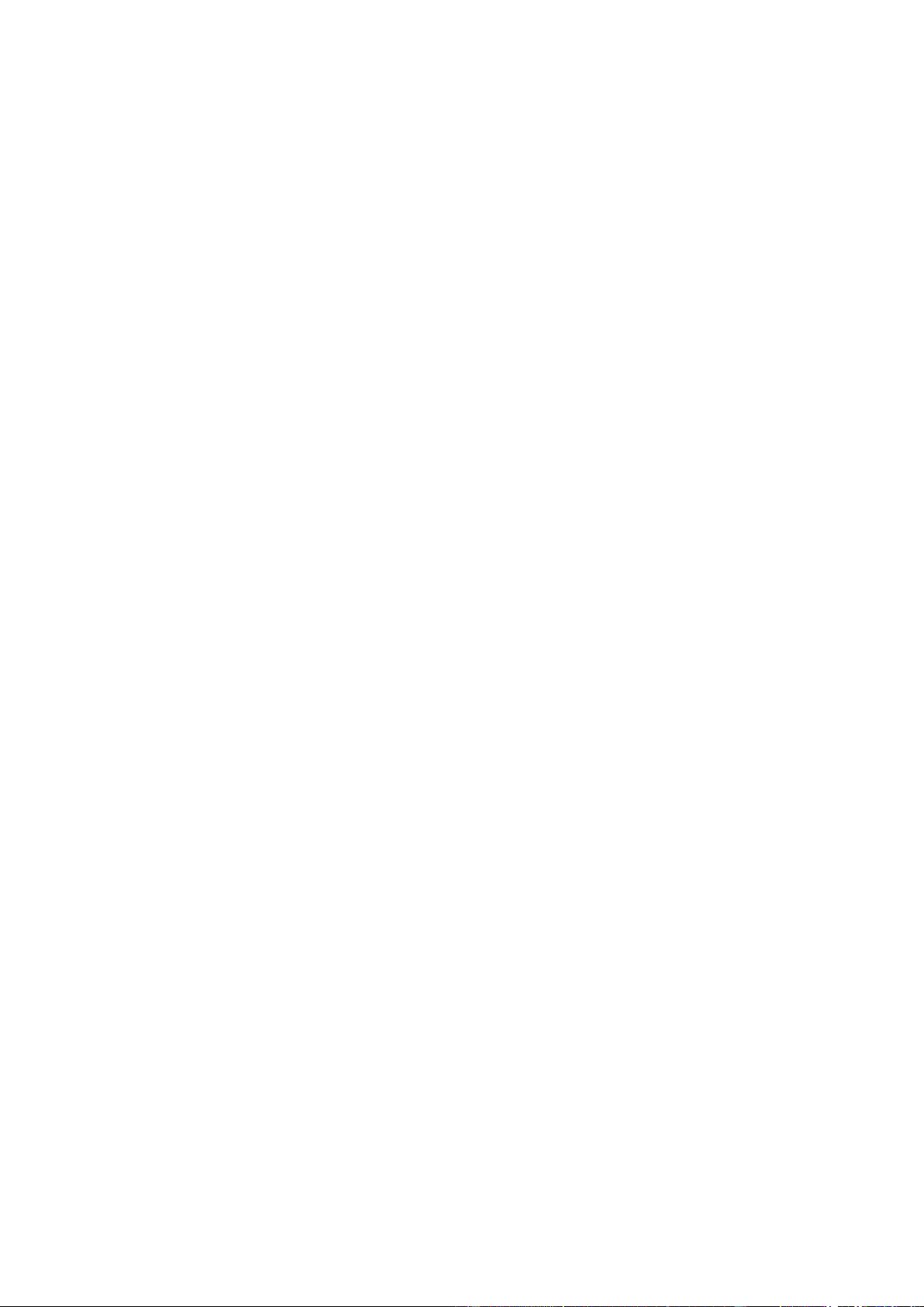
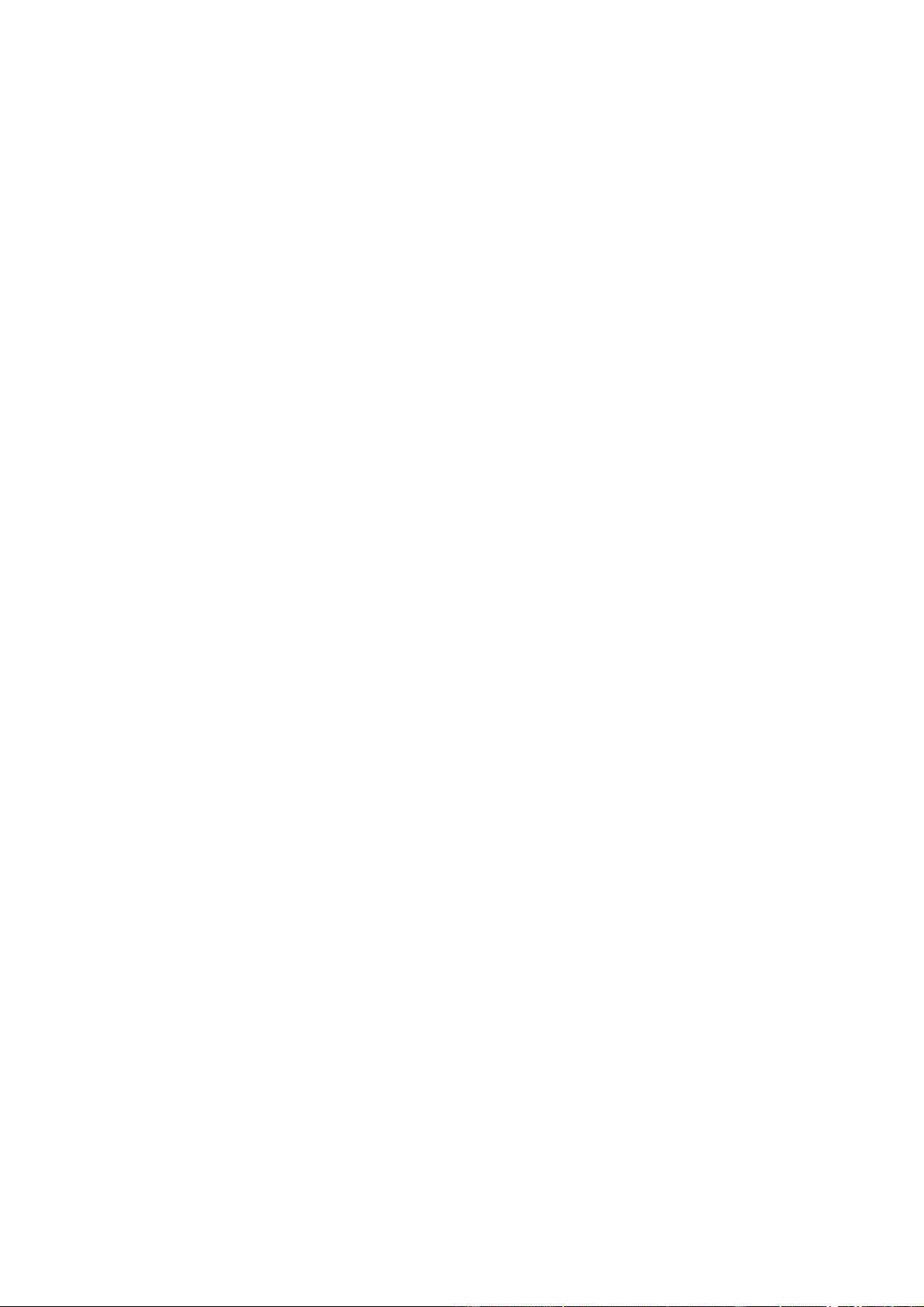
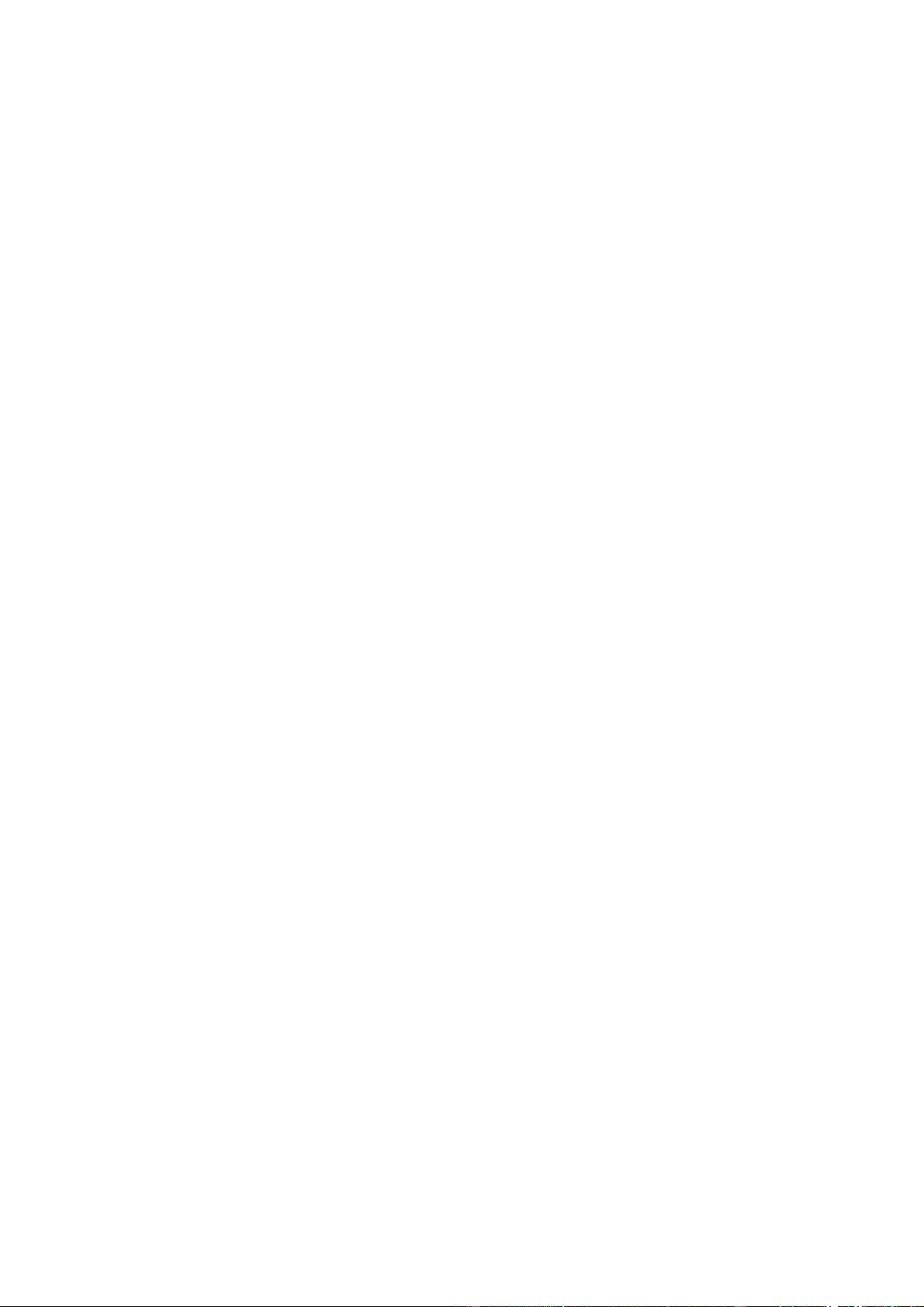
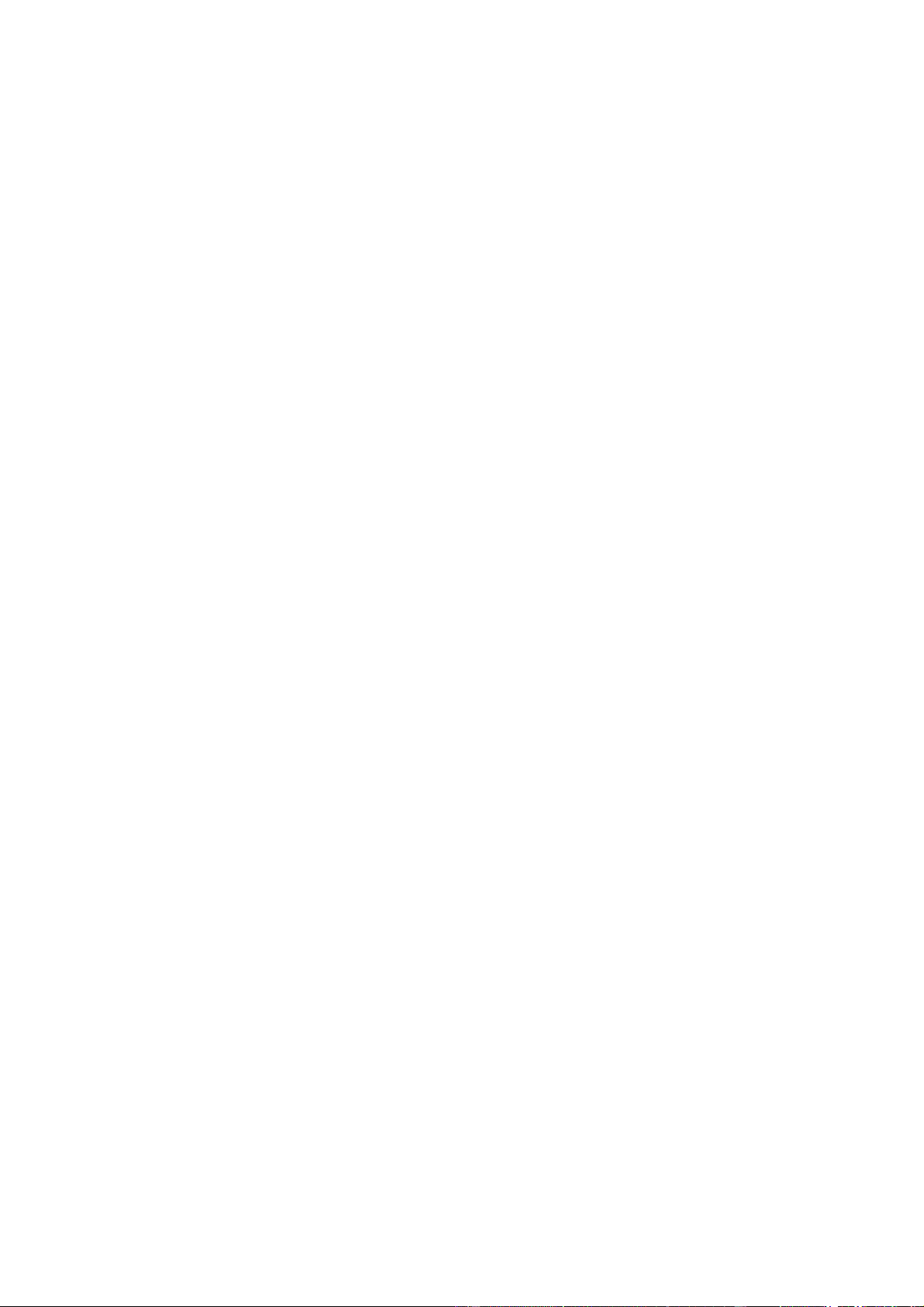
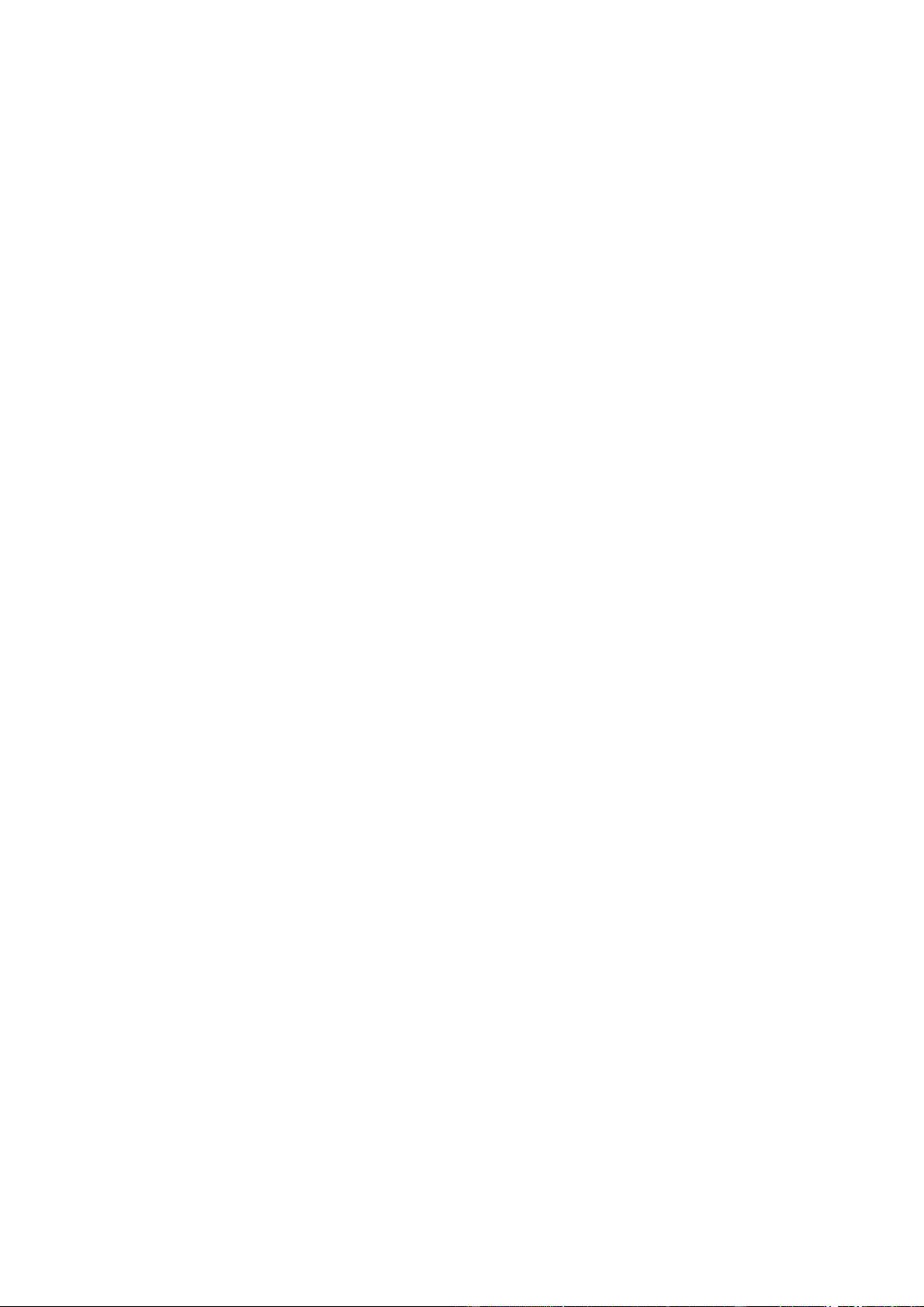
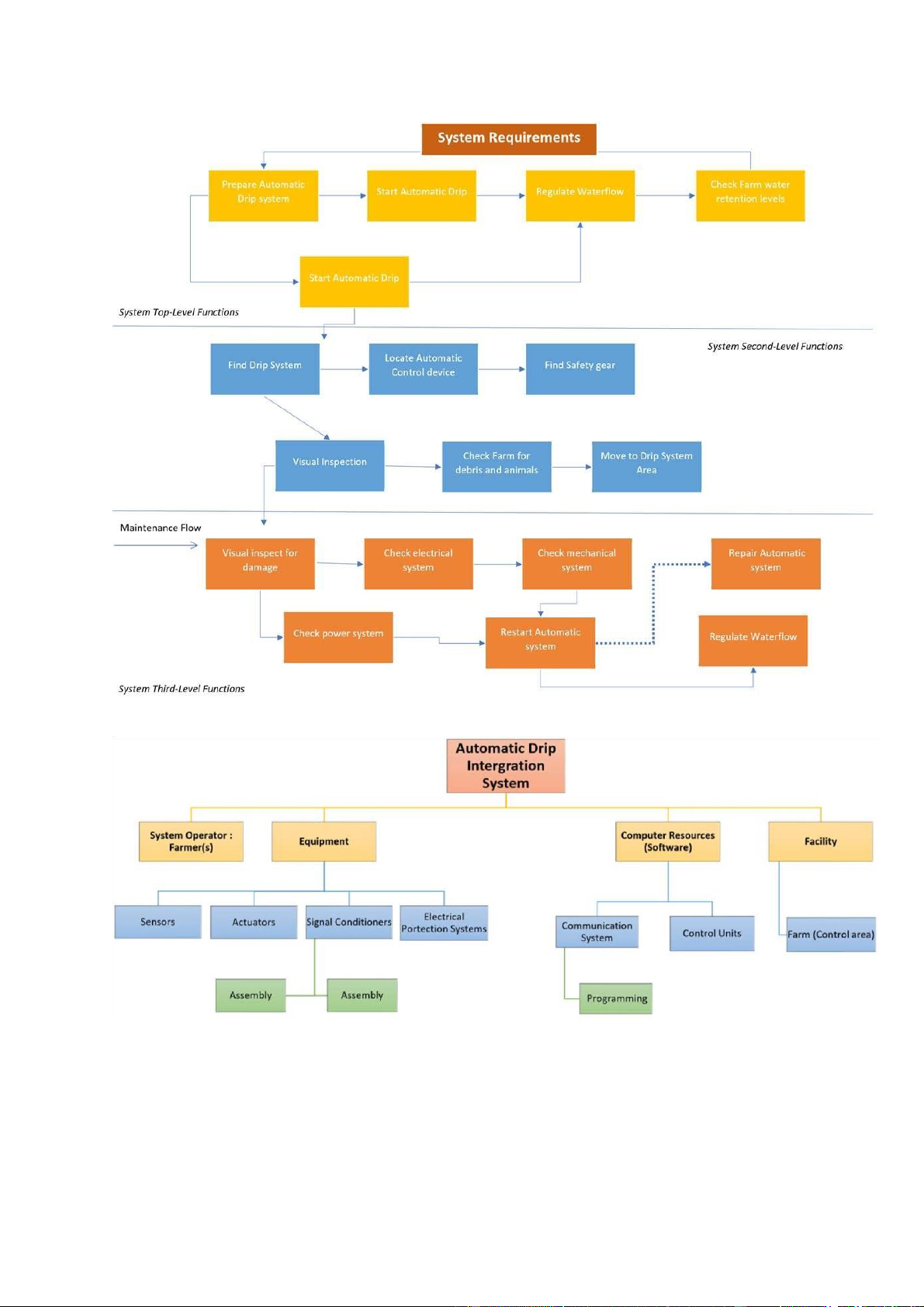
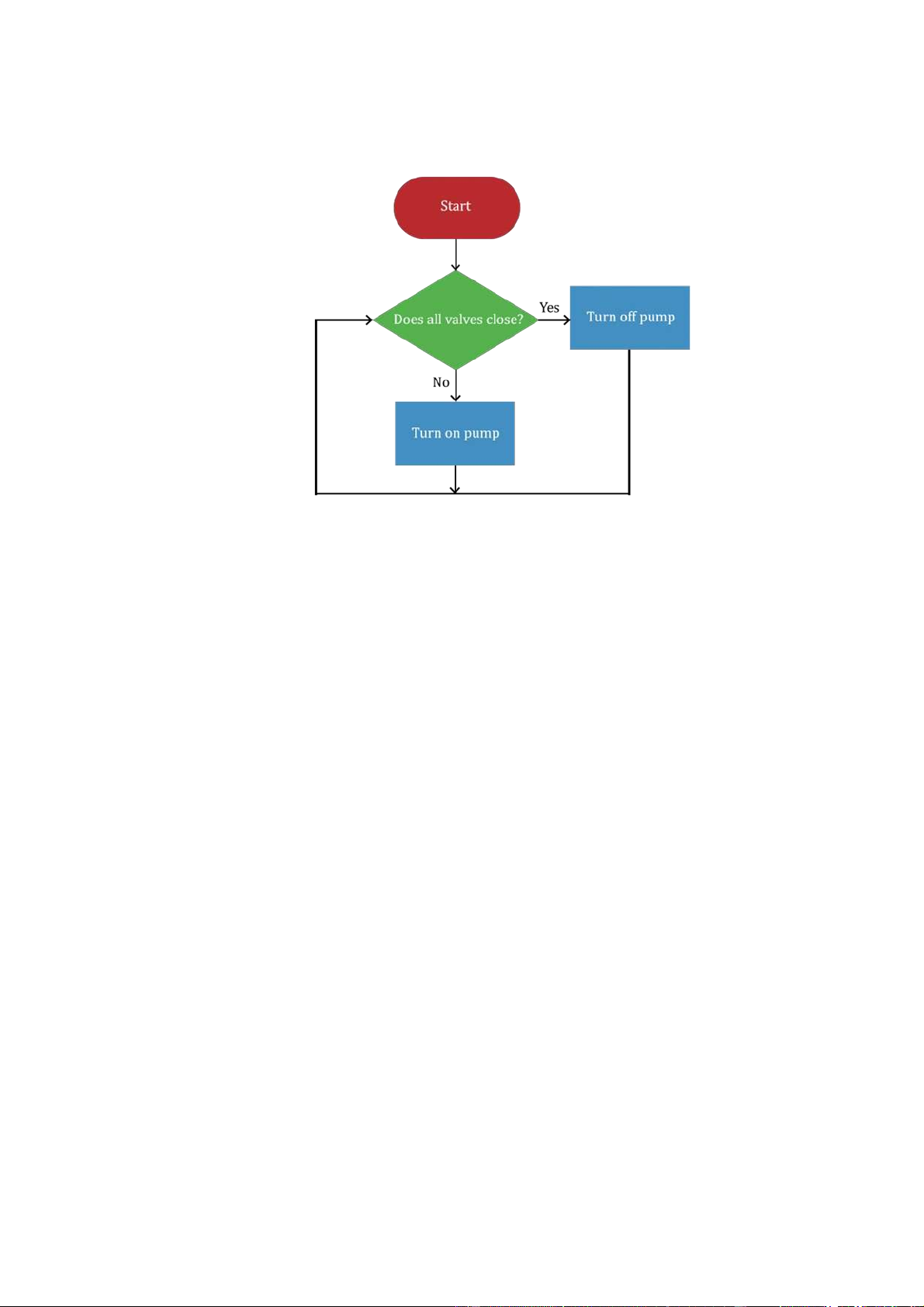
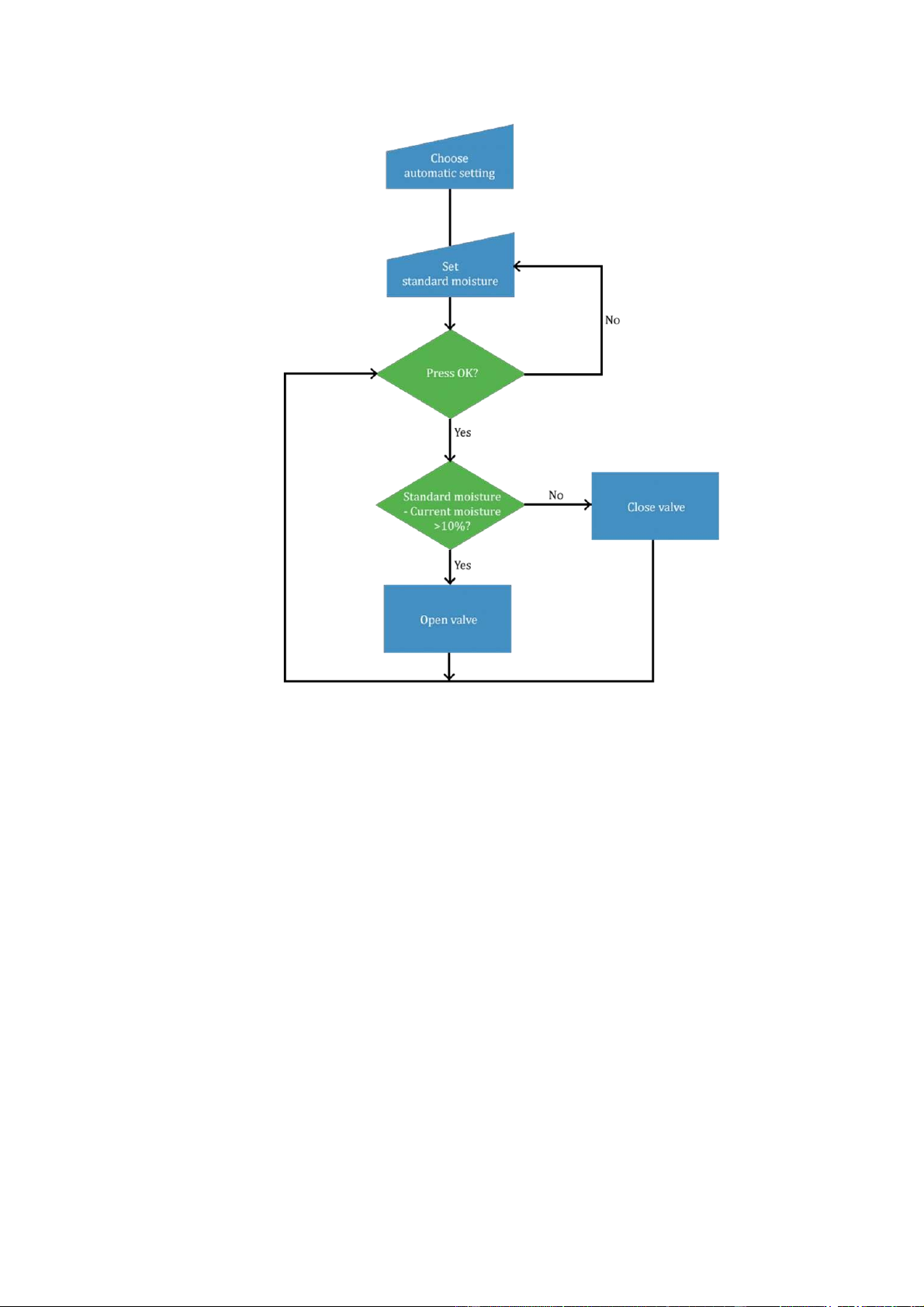
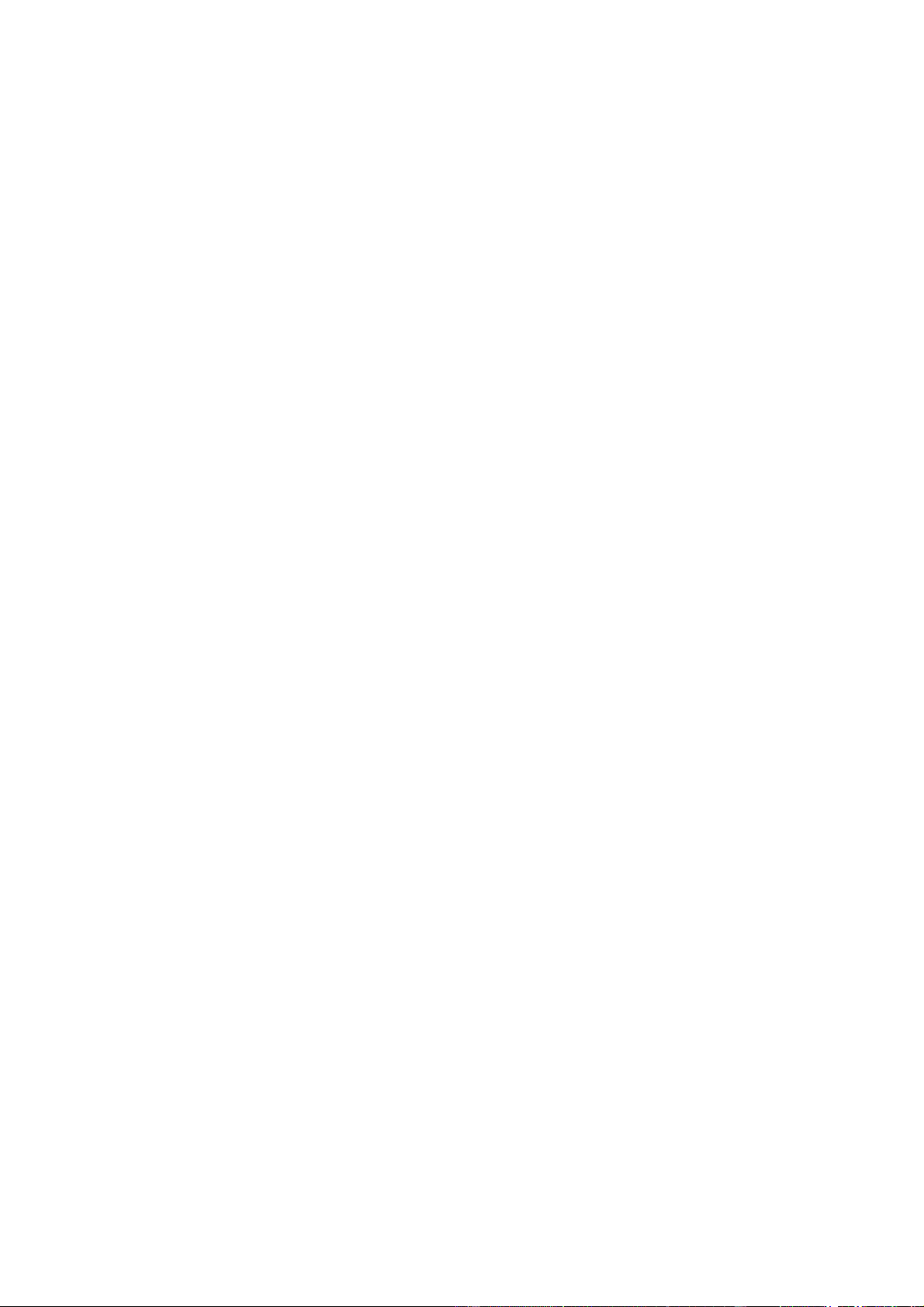
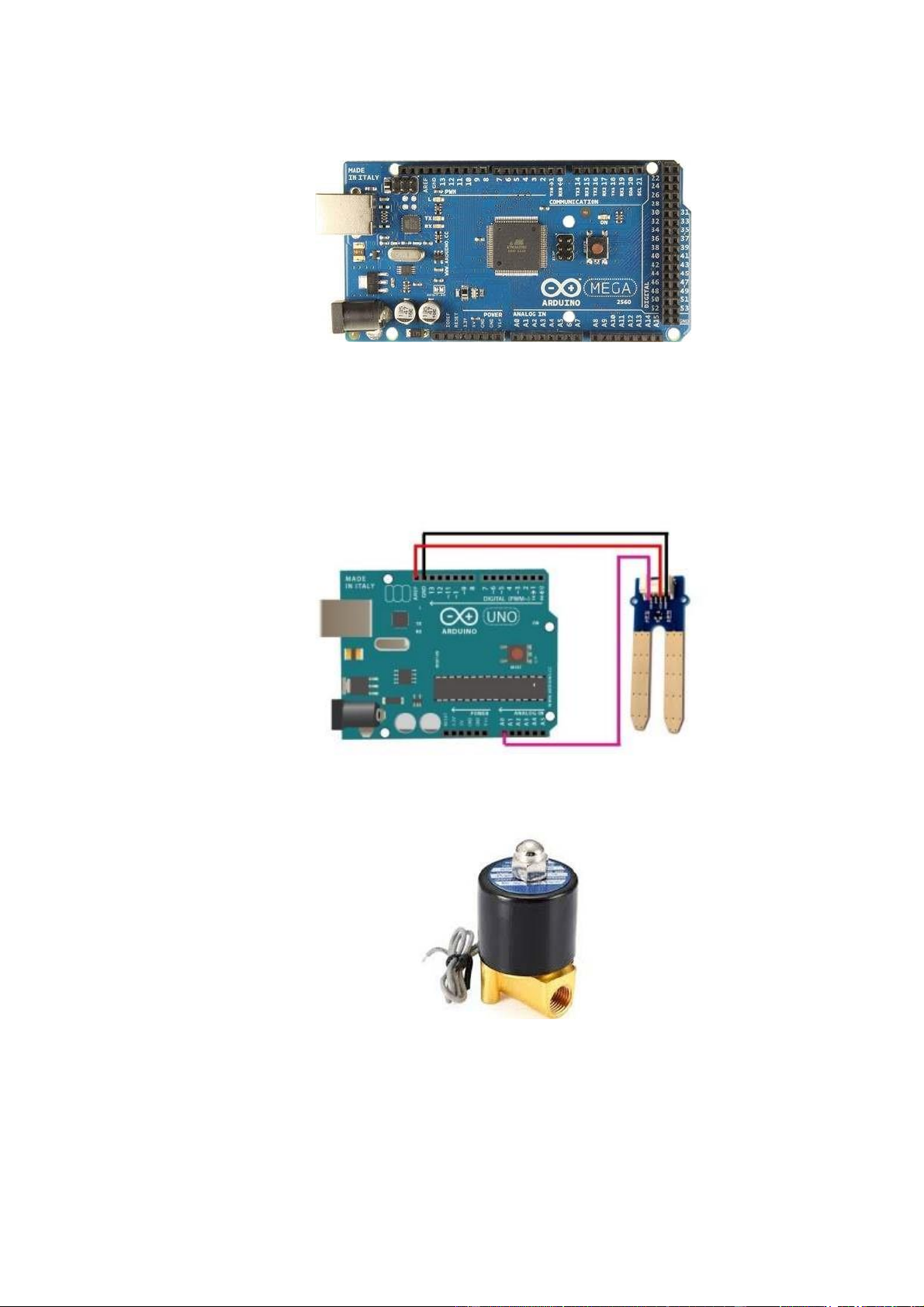
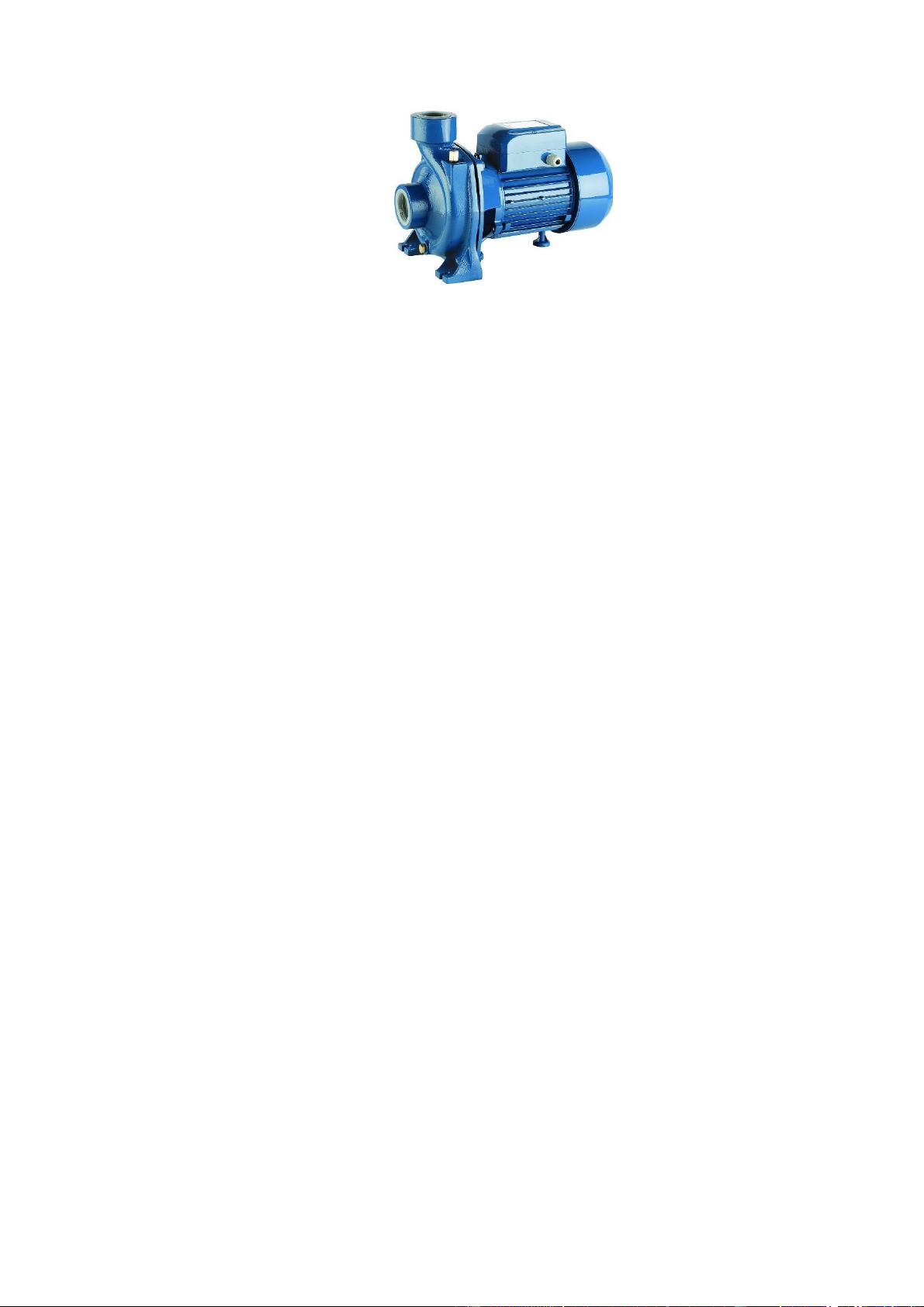
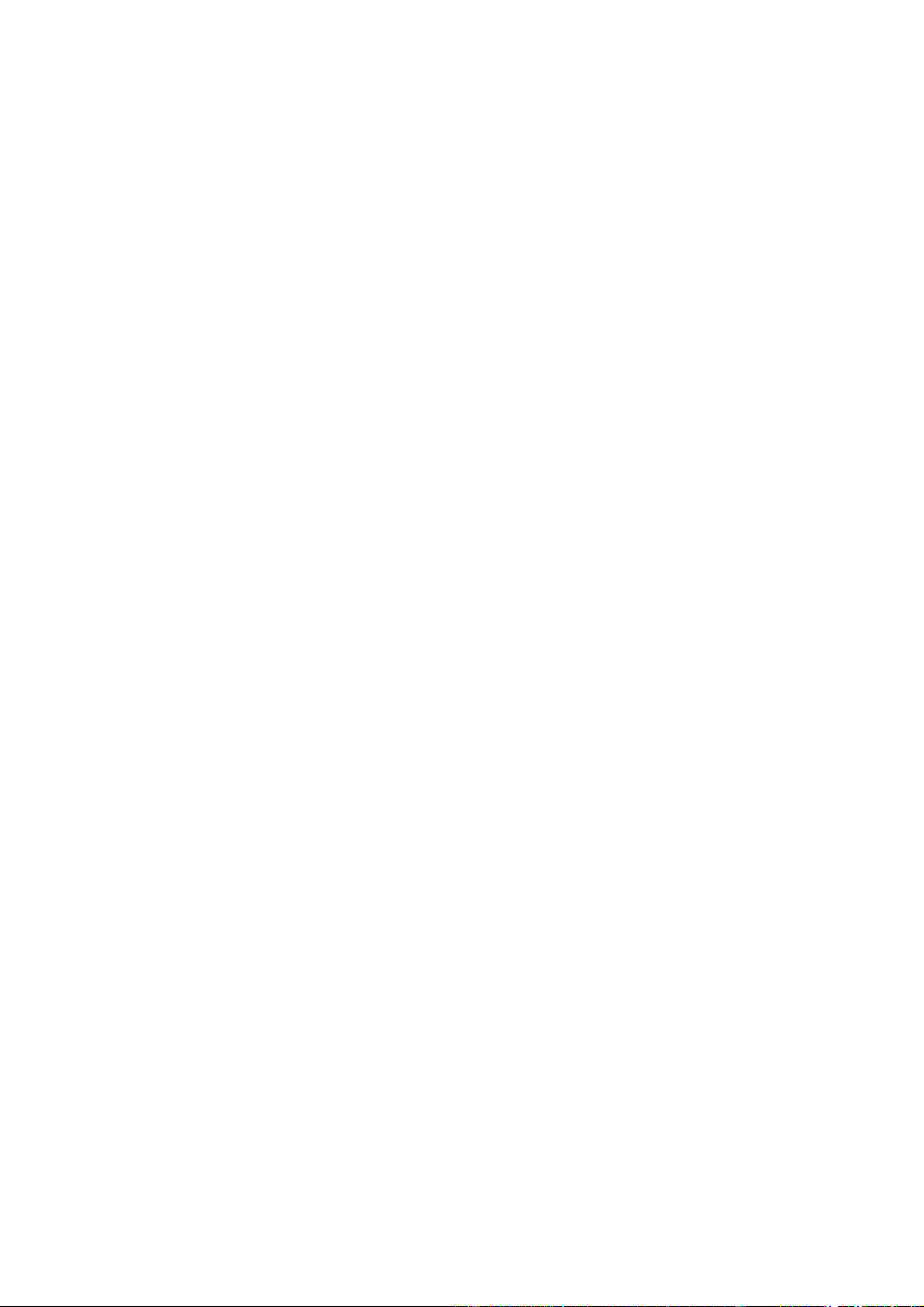
Preview text:
Department of Industrial & Systems Engineering
International University-VNU HCM
SYSTEM ENGINEERING PROJECT
AUTOMATED DRIP IRRIGATION SYSTEM 1. Vũ Bảo Trân IELSIU15109
2. Lê Phạm Nguyệt Thương BTBTIU15052 3. Josh Blackwell IE19EX001 4. Đặng Vân Thủy Cúc IELSIU16005 5. Huỳnh Ngọc Hải IELSIU17054 Table of Contents I.
PROJECT OBJECTIVES AND APPROACH..........................................................................................1 1
Background....................................................................................................................................1 2
Problem statement........................................................................................................................1 3
Generation and analysis of alternatives.........................................................................................2 3.1
Alternative 1: Drip Irrigation..................................................................................................2 3.2
Alternative 2: Hydroponic Irrigation.......................................................................................2 3.3
Alternative 3: Automatic Drip Irrigation.................................................................................2 II.
REQUIREMENTS ANALYSIS AND CONCEPT OF OPERATIONS..........................................................3 1
Operational outcome:....................................................................................................................3 2
Key system performance requirement...........................................................................................3 3
Sources of Information..................................................................................................................3 4
Required input data.......................................................................................................................3
III. FUNCTIONAL ANALYSIS..............................................................................................................4 IV.
CONCEPTUAL DESIGN................................................................................................................5 V.
TEST PLAN......................................................................................................................................7 1
Uniformity Testing.........................................................................................................................7 2
Pump/Well Testing.........................................................................................................................7 3
Test Soil Moisture Sensor...............................................................................................................7
VI. SYSTEM SPECIFICATION..............................................................................................................8 1
Hardware tools..............................................................................................................................8 2
Software tool.................................................................................................................................9 VII.
CONCLUSION...........................................................................................................................10 I.
PROJECT OBJECTIVES AND APPROACH 1 Background
With more than 60% of the territory covered in desert, Israel is a drought-stricken country
that has managed to emerge as a major agricultural exporter and a leader in agricultural
technology thanks to the research and application of science in that field. In opposition to
Israel, notwithstanding the beginning as a major country in rice production, Vietnam still
needs a lot of innovation in agriculture. Accordingly, most Vietnam's agricultural products,
whose market share is often occupied by others, are not highly valued in the international
market. Facing the threat of the fiercely competitive market, Vietnamese agriculture
should apply high technology into production as an effective solution. However, at present,
most farmers still do not adapt to this method of production due to the cost, investment
and operating skills of machinery as well as technology which are really different from the
manual one. Moreover, the excessive cost of production leads to a sharp increase in
commodities cost which is several times higher than that of conventional products. In
addition, the safety of the product has not yet convinced customers resulting in the
unpopularity of high-technology farm products. The following condition raises the
question of how to create high-yield, easy-to-use, and cost-effective tools that are cheaper
than the current available one, especially two indispensable elements for cultivation: water and soil.
The absorption of water by plants is essential for various metabolic activities. Land plants
get their water supply from soil which serves as the source of water and minerals. It is
hypothesized that controlling the factors affecting the water uptake of plants does not
only help the plant grow best, but also saves the maximum amount of water compared to
the usual irrigation system as well as the amount of electricity operated by the pump. This
automatic irrigation system senses the moisture content of the soil and automatically
switches the pump when the power is on. A proper usage of irrigation system is very
important because the main reason is the shortage of land reserved water due to lack of
rain, unplanned use of water as a result large amounts of water goes waste. For this reason,
we use this automatic plant watering system, and this system is very useful in all climatic conditions. 2 Problem statement
Agriculture products supply chain in Vietnam is not sustainable, and one of the reasons is
the over reliance on rain fed agriculture. For nearly half of the year (from November to
April), the Southern Vietnam area experiences drought as the amount of rainfall received
cannot support crop growth. To guarantee the sustainable agriculture supply chain, proper
management of water resources is extremely necessary. This involves all deliberate
human actions aimed at designing models, such as automatic drip irrigation system to
ensure the availability, utilization of water for agricultural purposes. Also, the system is
expected to reduce the cost of irrigation. 1
In this project, our group aims to design an automatic irrigation system for 1002 garden
planting tomatoes. The objectives of this project are as follows:
a) To optimize water consumption, lower the watering bills
b) To reduce the number of workforce in the farm
c) To implement the automatic watering system based on soil moisturesensor.
3 Generation and analysis of alternatives
3.1 Alternative 1: Drip Irrigation
Method that allows optimum application of water and fertilizers in farming systems in
arid areas. The water applied directly infiltrates into the soil irrigating the root zone
influence through a piping system and emitters.
It is a type of micro-irrigation system that has the potential to save water and nutrients
by allowing water to drip slowly to the roots of plants, either from above the soil
surface or buried below the surface. The goal is to place water directly into the root
zone and minimize evaporation through a network of valves, pipes, tubing, and emitters.
3.2 Alternative 2: Hydroponic Irrigation
Irrigation system whereby crop roots receive a balanced nutrient solution dissolved in
water with all the chemical elements needed for plant growth, which can grow directly
on the mineral solution, or in an inert medium or substrate.
There are two points of view irrigation in hydroponics water system that provide the
frameworks, and foundation to make such systems work proficiently. One of these sees
the root zone as a store that must be refilled each time a certain level of exhaustion
has happened. The other perspective is to treat the complete framework as a conduit
of materials from a source to the root surface of the plants. In optimizing irrigation it
is important to understand both of these two aspects of the system.
3.3 Alternative 3: Automatic Drip Irrigation
Use of a device to operate irrigation structures so the change of flow of water from
one bay, or set of bays, to another can occur in the absence of the irrigator.
Sensing the moisture content of soil by a sensor and automatically turning on or off a
solenoid valve that supplies water to the farmland. This system supplies water as
needed by plant, thus optimizing plant growth and help conserve water and energy.
However, this is applicable for only large frames and have limited life because of
deterioration of the plastic component in a hot, arid climate when exposed to
ultraviolet light. Among the above alternatives, the most attractive approach is
automatic drip irrigation system. 2 II.
REQUIREMENTS ANALYSIS AND CONCEPT OF OPERATIONS
Automated drip irrigation has long been viewed as the advanced technology system
which is widely used nowadays in developed nations. There are four main parts that
farmers should be considered when installing the system. There are: -Operational outcomes
-Key system performance requirement -Sources of Information -Required Input data 1 Operational outcome:
First of all, low cost is one of the main reasons for the installation of Automated drip
irrigation which represents minimize the waste of water. In every system, the measure
tools must measure exactly the right amount of water which is needed by the typical type
of plants. The water must be not more or less because it will directly affect the growth of
the plant. If the water is more than the needed amount, the soil will be waterlogged and
it leads water to cut off the air supply for the root in the ground. This time, the drainage
system is required. If the water is less than the needed amount, the plant cannot grow.
The right amount of water also helps reduce disease and damage because plant foliage
stays dry. Furthermore, the fertilizer and pesticide can be supplied through the system
for the exact amount. Additionally, the system helps reduces the labor cost. It could save
lots of fixed and variable costs and reduce the headache of lacking labor. Lastly, one of
the factors that should be thinking about is power consumption. The utility cost and
installation cost must less than the saving cost that we could gain.
4 Key system performance requirement
The critical consideration is the stable of the system. The system must maintain the same
performance level all the time. If there are lots of fluctuations, the systems will need more
monitor and improvement. Furthermore, environmental intervention is one the factors
that makes the destruction of the harvest. It makes the price of production increasing.
Hence, the key requirement for the system prevents any external factors. The other
important point is the ease of using for the domestic user. The content of the software of
the system must clear and understand easily. 5 Sources of Information
Data is an essential factor in monitoring the system. Data information could be found in
varied sources. However, the user has to select the appropriate data that is suitable for
their system and farm. The wrong using information may lead to damage and increasing costs. 6 Required input data
Depending on the type of growing plants, information about the type of plants, soil
moisture, humidity and maintenance factors should take into account. Due to the fact 3
that each plant will have typical environmental conditions for growing and disease that it
may suffer. The more right input data the more profit that people could earn. In the future,
automated drip irrigation systems will develop the special sensors which helps a farmer
decide automated the right amount of water based on the soil moisture. and feedback data at every hour. III. FUNCTIONAL ANALYSIS
The figure below shows the functional breakdown of our Automated Drip Integration
System into components. We broke our system down into elements, hence obtaining the Functional Allocation. 4
In general, the Automated Dip Irrigation system is divided as below IV. CONCEPTUAL DESIGN
Drip irrigation is a type of micro-irrigation system that helps to save water and nutrients
by allowing water to drip slowly to the roots of plants, either from above the soil surface
or buried below the surface. Its purpose brings water directly into the root zone and 5
minimize evaporation. Drip irrigation systems distribute water through a network of valves, pipes, tubing, and outlets.
Figure 3. Relationship between valves and pump
Based on that definition, we design our system to comply with the requirements, and
automate the process with the use of a microcontroller board – Arduino Mega 2560. The
model is set to control 3 different, independent areas that need watering, each of which
is controlled by a solenoid valve to let water pass through the tube or not.
A pump is utilized in the model to allow water to flow throughout the garden. However,
to save power and to prevent tubes from heavily pressurized, pump can only be turned
on when at least a valve is opened (see Figure 3).
In addition, to prove the efficiency of the model, user is provided a prediction of the
change in soil moisture according to the time interval. By experimenting, the model should
follow a conversion between time unit (second) and change in soil moisture (%), so that
manual input is closely related to the purpose of users. It may become easier and more
convenient when the model is automated, that is, no such manual input is required. That
leads to the use of sensors to measure soil moisture and responses of valves to the values derived from sensors. 6
Figure 4. Valve’s response to soil moisture sensor
In Figure 4, Standard moisture is a preset and Current moisture is the value immediately
measured by a sensor. It sends analog signal to the controller, where it is translated to
percentage for comparison with Standard moisture. A difference larger than 10% will
cause the valve to open (only if Standard moisture is larger than the other one). Otherwise,
it remains closed. The loop is repeated constantly and is sensitive to any change in soil
moisture. In other words, this automatic operation facilitates a stable soil moisture range without the hands of human. 7 V. TEST PLAN 1 Uniformity Testing
Uniformity testing is a troubleshooting procedure to check that the water distributed by
the irrigation system is being applied uniformly to the field within practical limitations.
The test procedure only measures the amount of water applied to the soil surface and is
not intended to indicate the amount of water that infiltrated the soil into the root zone.
Evaporation, runoff and leaching could all affect the amount of water available to plants
in the root zone. A low coefficient of uniformity could lead to plant stress and disease
issues because of a water deficit or too much water in different sections of the field
despite the average application rate being acceptable. The goal for the coefficient of
uniformity is greater than 90%. This test functions as low cost insurance to determine if
the nozzles and sprinklers are applying water evenly. The test will take 1 or 2 people about
4 hours to complete depending on the size of the field. It is recommended that a
uniformity test be performed every 3-5 years depending on usage and water quality. 7 Pump/Well Testing
Pump testing is typically done in an open discharge method where the pump is
disconnected from the irrigation system and a flow meter, pressure indicator a valve is
installed on the pump output. The pump is started and the valve partially closed until the
design system pressure is reached. The system is allowed to run for a period of time,
generally 15 minutes, and then the valve is opened and closed to obtain enough points
to draw a pressure/flow curve. The static water level should be recorded as well as the
water level at each flow point 8 Test Soil Moisture Sensor
Purpose of soil moisture sensor testing is to test the sensor values and its functionality.
The environment used to test are a glass of water and Arduino IDE. The testing procedure
includes opening the serial monitor in Arduino IDE and see the sensor value for the dry
condition. The second step is opening the serial monitor in Arduino IDE and see the
sensor value for the dry condition. Lastly, immersing the soil moisture sensor into a glass
of water and see for the wet condition in the serial monitor in Arduino IDE too. Expected
Result would be the soil moisture sensor is light up in the controller when it is switched
on, and it can show the lower and upper boundaries of the sensor value in dry and wet conditions. VI. SYSTEM SPECIFICATION 1 Hardware tools
Hardware that are used are listed in the table below, followed by quick descriptions of
how they are applied in the model.
• Arduino Mega 2560: is an open-source operating system that relies on easy-to-
use hardware. It is a microprocessor board, designed to build applications that
interact with each other or with the environment. It has 54 digital input/output 8
pins, 19 analog inputs, 4 UARTs, a 16 MHz crystal oscillator, an USB connection, a
power jack, an ICSP header and a reset button.
• Moisture Sensor: The soil moisture sensor comprises of two tests that are
utilized to the degree the volumetric substance of water. The two tests permit the
current to pass through the soil, which gives the resistance esteem to the degree
the dampness esteem. When there is water in the soil there will be less
resistance and the soil will handle more power. But if the soil is dry it conduct
power weekly and needs less power and more resistance.
• Electric Valve is controlled by electric current with the effect of electromagnetic
force. They are used to close, open, distribute, mix water with nutrients.
• Pump is used in this project to pump the water needed for irrigation from the
main water tank through pipes. The pump is selected for this project should has
good advantages. Such as, it has a lightweight. Also, it has a small size, so it is
easy to install and replace it. Furthermore, it must has an enough efficiency to pump water for irrigation. 9 9 Software tool
We used App inventor to develop mobile application to control the system from the far
distance. There are different IDE’s that permit a versatile application to be modified. For
this venture, we chose to utilize the Massachusetts Established of Technology’s (MIT) App
Innovator, which is a web-based IDE that permits clients to make android apps on a
browser. App Creator was created by MIT in participation with Google to supply an
environment where applications can be created with ease, permitting clients to move
from being customers of innovation to getting to be makers of it.
And we use Arduino to code the program to manage all the system. Arduino is an open-
source gadgets stage based on easy-to-use equipment and computer program. Arduino
sheets are able to examined inputs - light on a sensor, a finger on a button, or a Twitter
message - and turn it into an yield - actuating an engine, turning on an Driven, distributing
something online. You can tell your board what to do by sending a set of enlightening to
the microcontroller on the board. To do so you utilize the Arduino programming dialect
(based on Wiring), and the Arduino Computer program (IDE), on Processing and other open-source software. 10 VII. CONCLUSION
Automatic irrigation saves up to 60% of water compared to manual irrigation. This helps
to cut down on water bills significantly each month. Significant human resource savings
compared to manual irrigation. The system is fixed, ensuring long life for equipment used in irrigation.
Regarding the model, the microcontroller-based drip irrigation proves to be a real time
feedback control system which monitors and controls all the activities of drip irrigation
system efficiently. The present proposal is a model to modernize to the agriculture
industries at a mass scale with optimum expenditure. The system helps to eliminate the
stress of manual irrigation and irrigation control while at the same time conserving the
available water supply. Improving irrigation efficiency can contribute greatly to reducing
production costs of agricultural products, thereby making the industry to be more
competitive and sustainable. The model has successfully run after many times improving
and repairing. However, it remains an experimental prototype with inherent limitations.
Although using moisture sensor in automatic drip irrigation system by moisture sensor is
simple method of measurement, which delivers the results immediately and offers
accurate results. The measured values depend on properties of various living condition
of plants and moisture sensors provide less accuracy in sandy soils due to large particles
and they are required to be calibrated for each soil types. 11