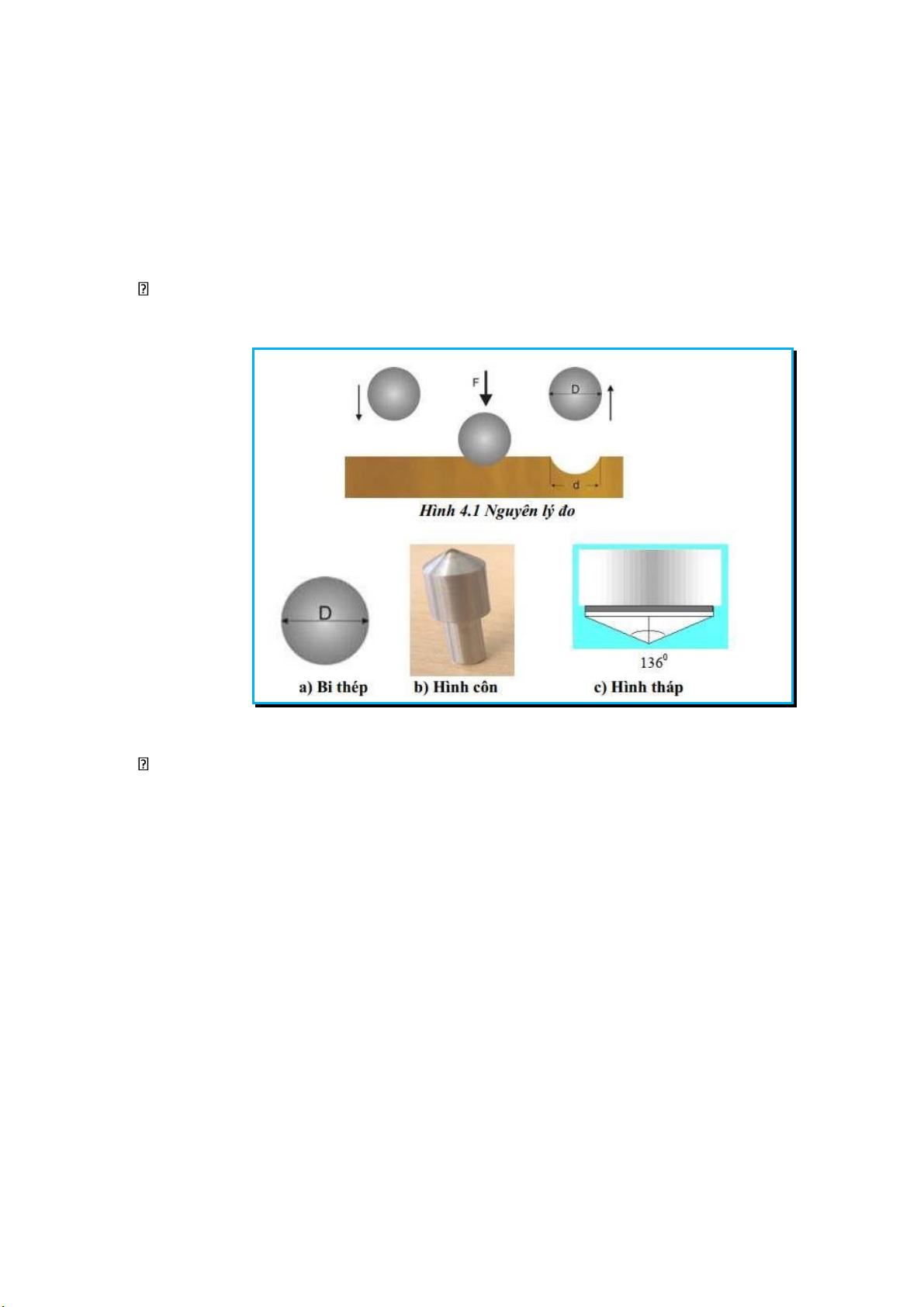
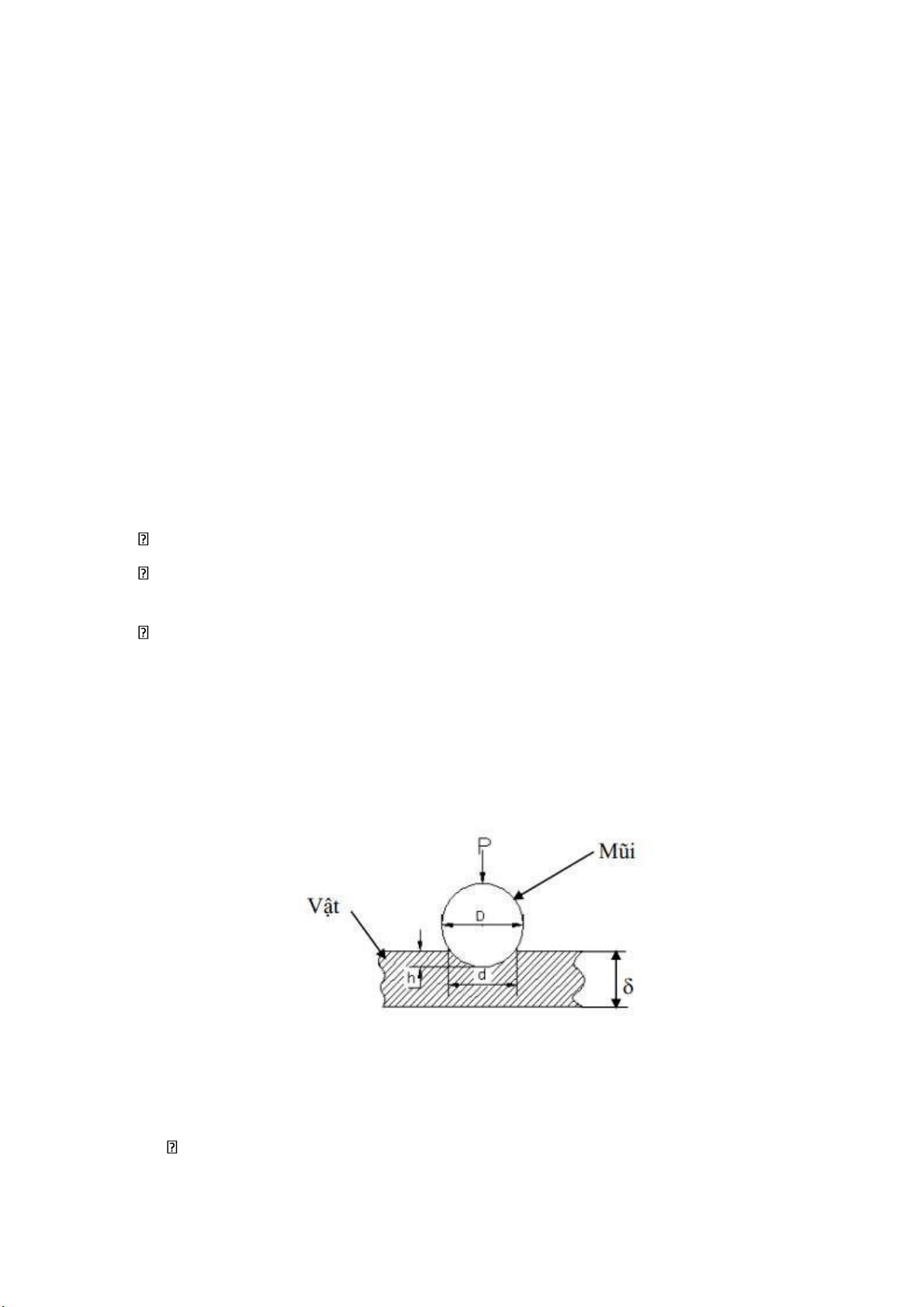
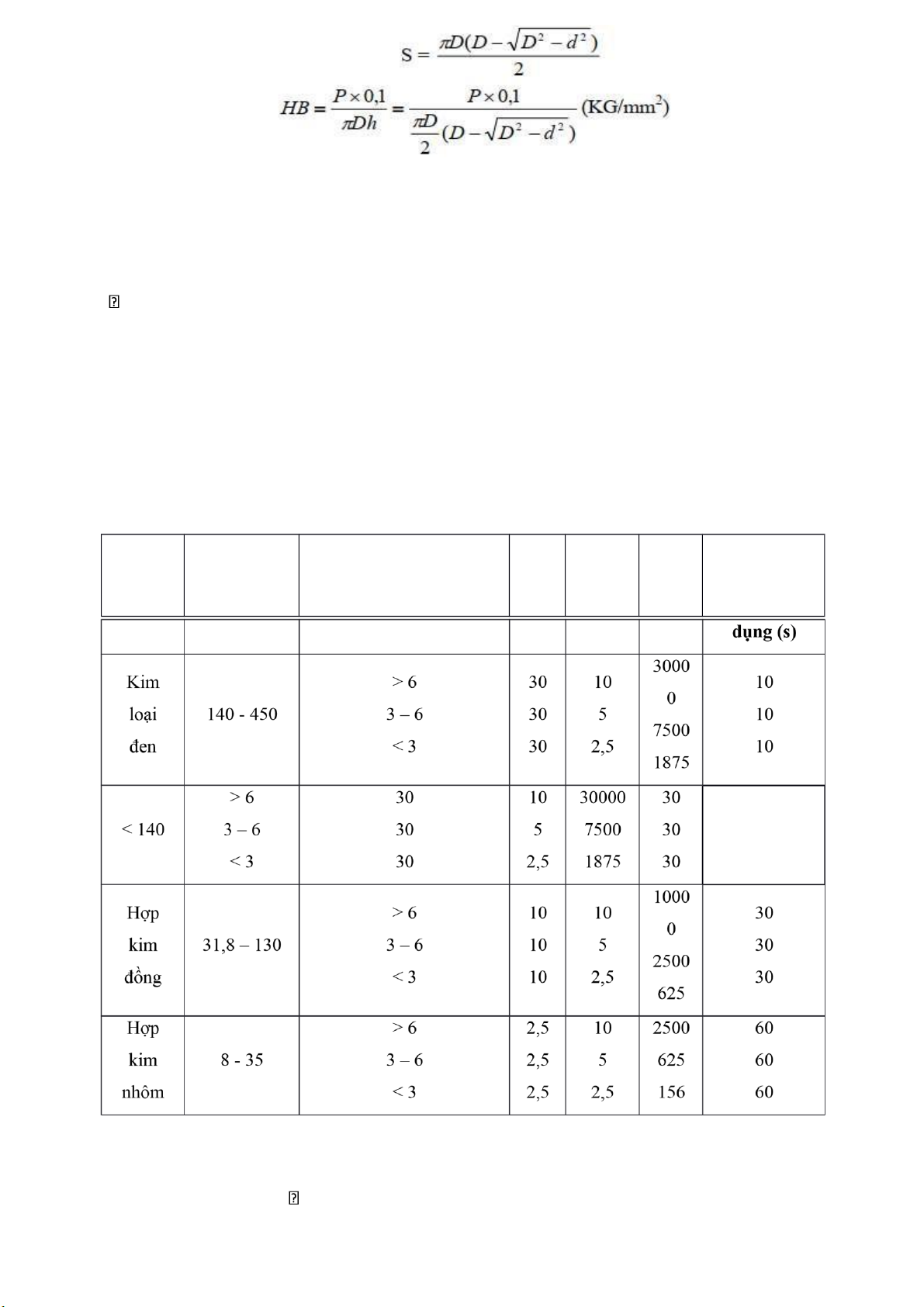
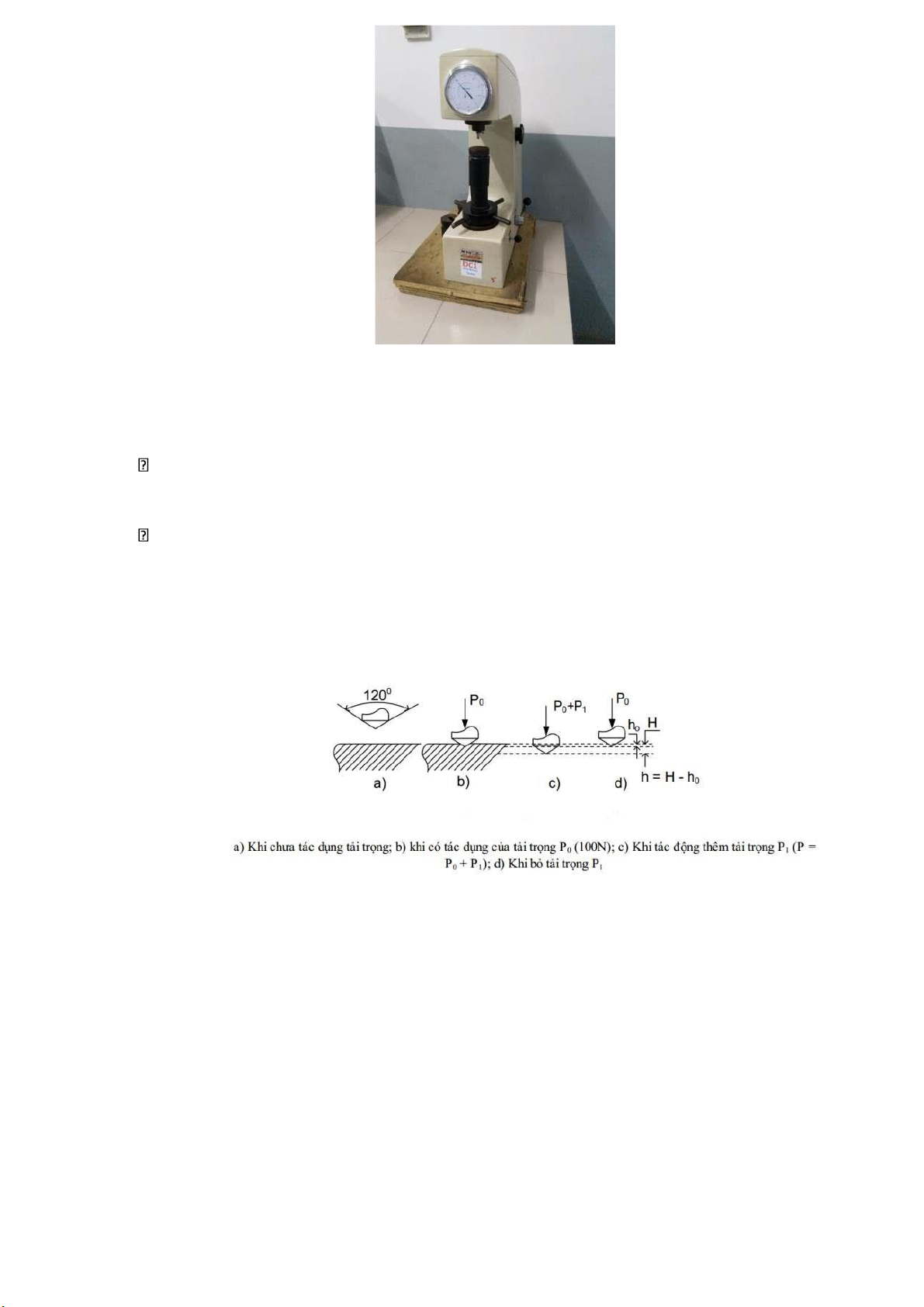
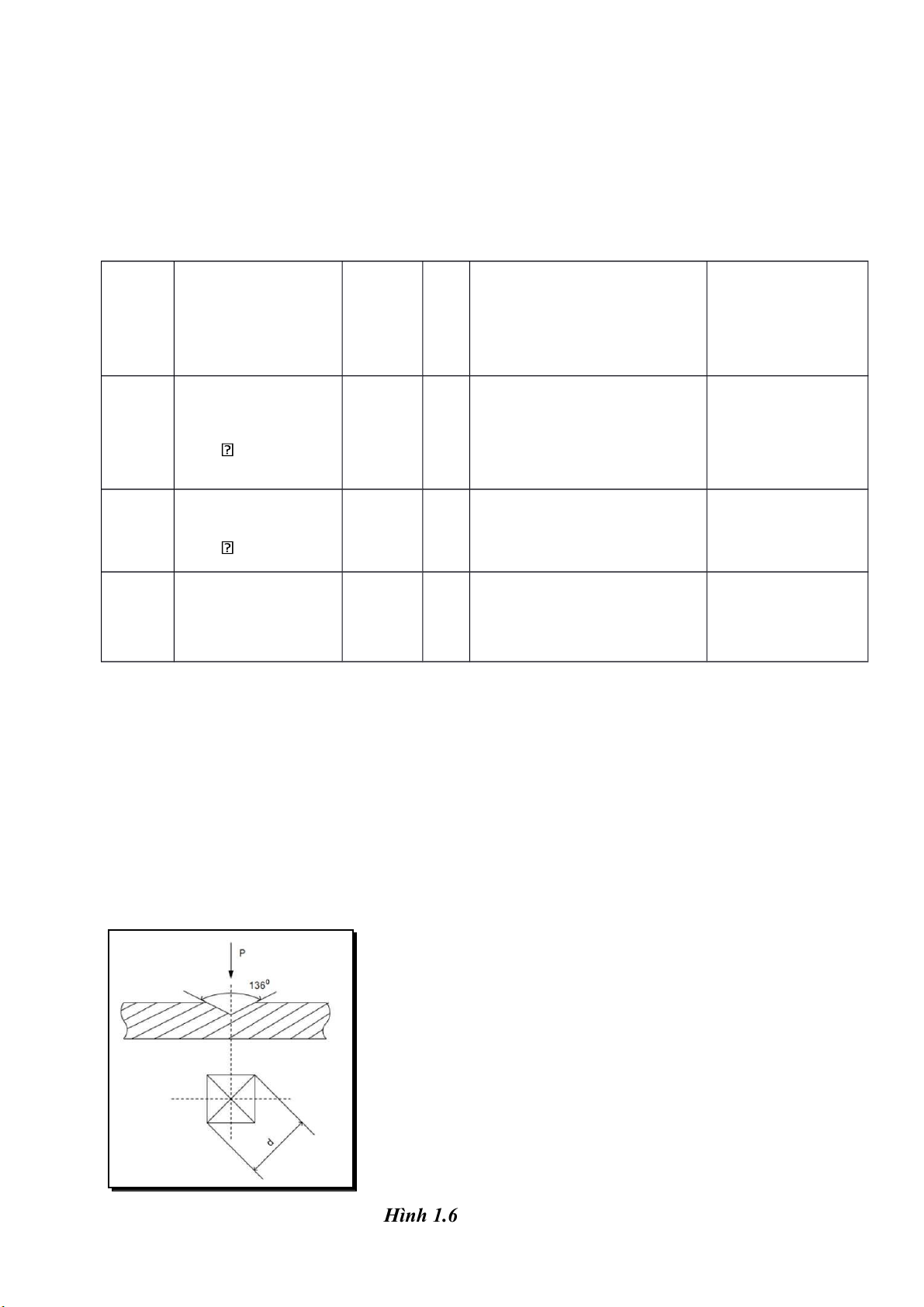
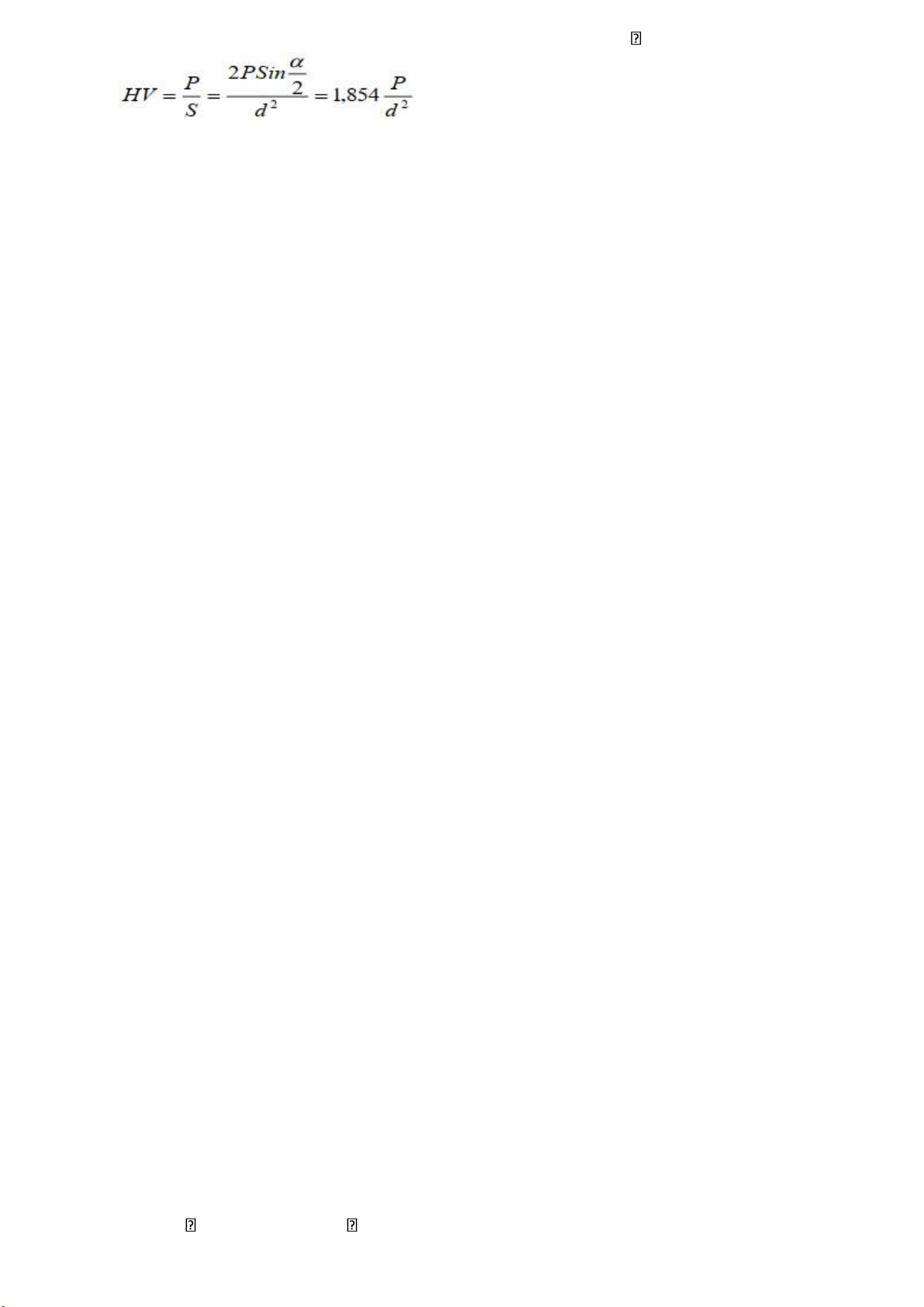
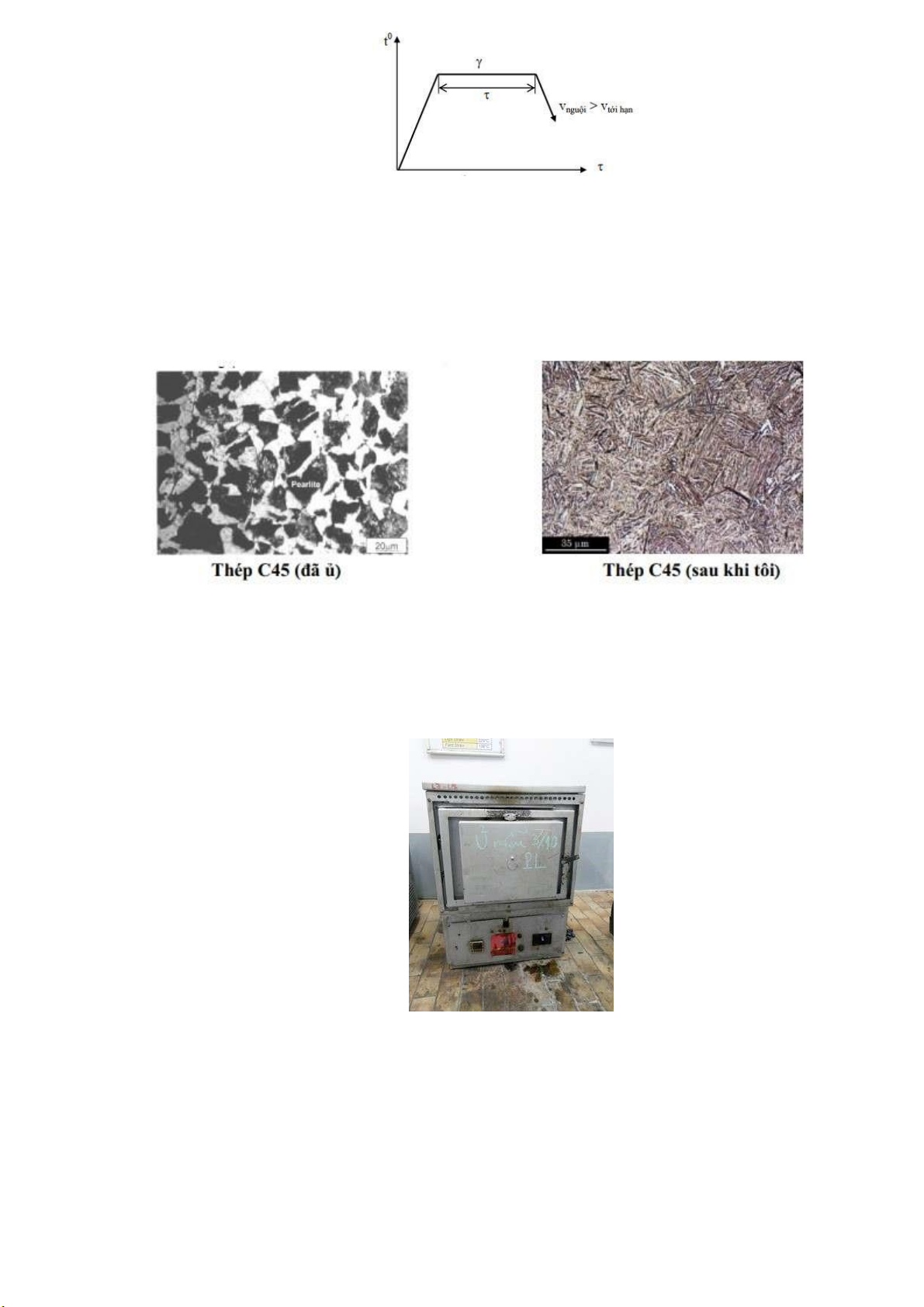
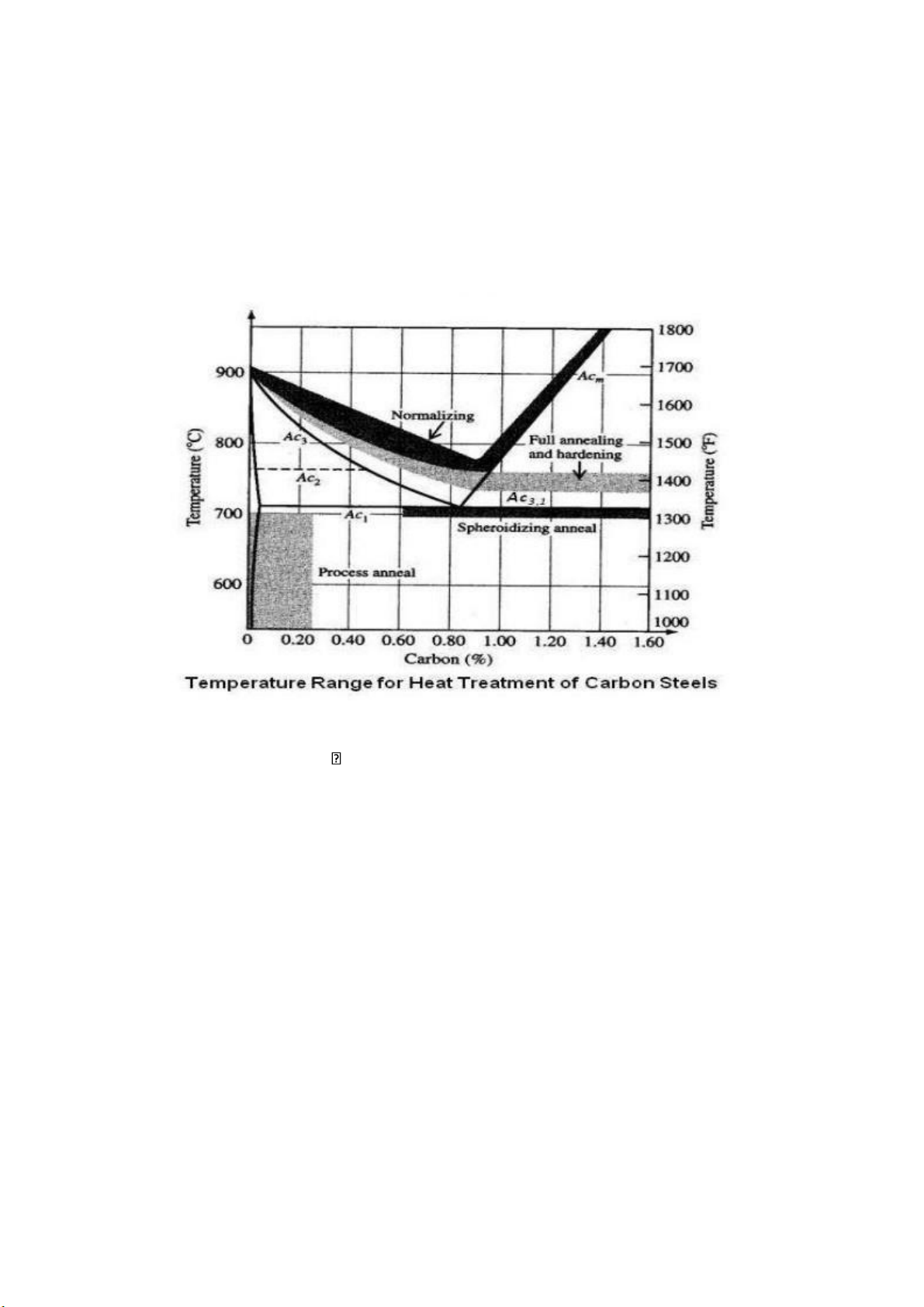
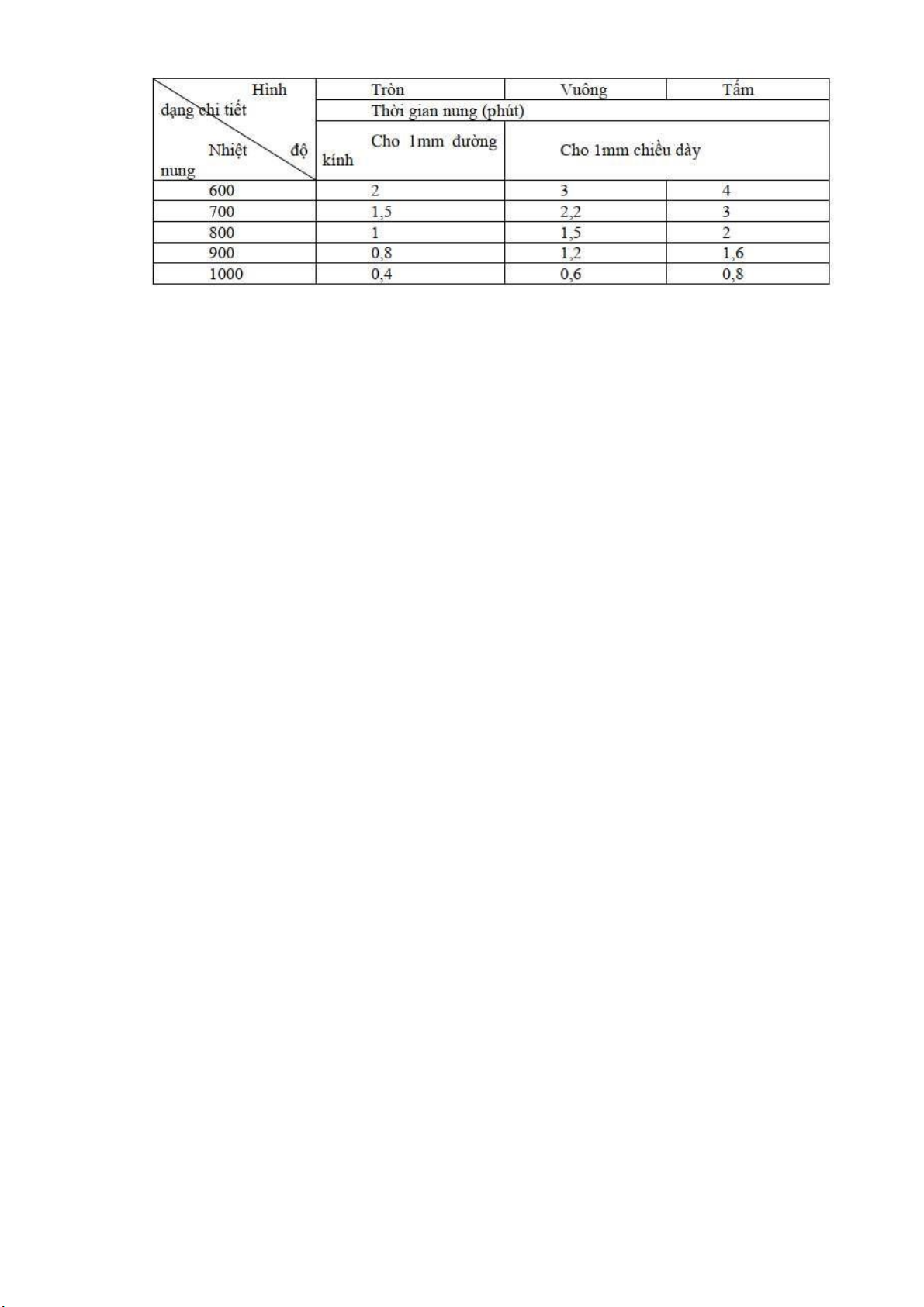
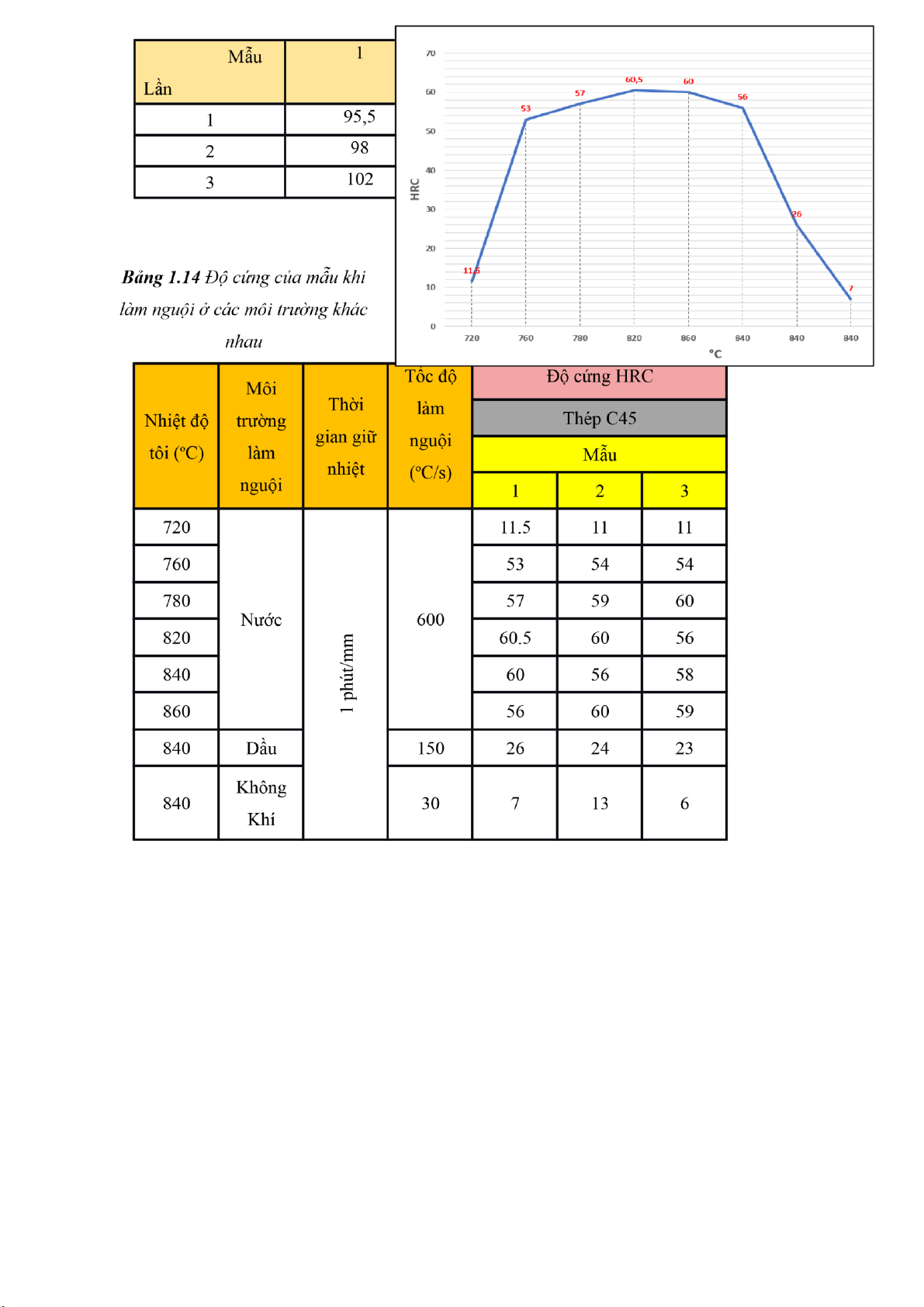
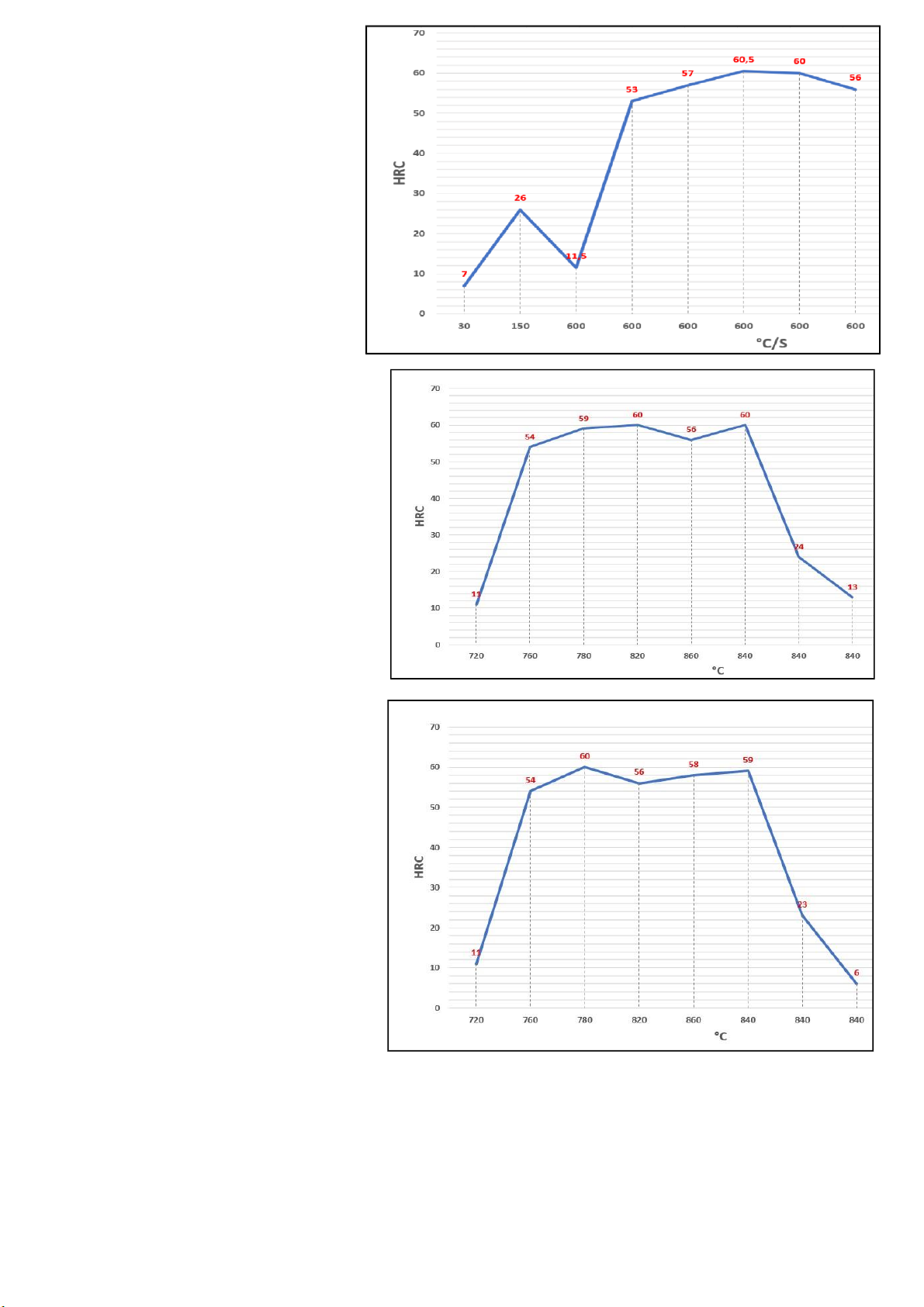
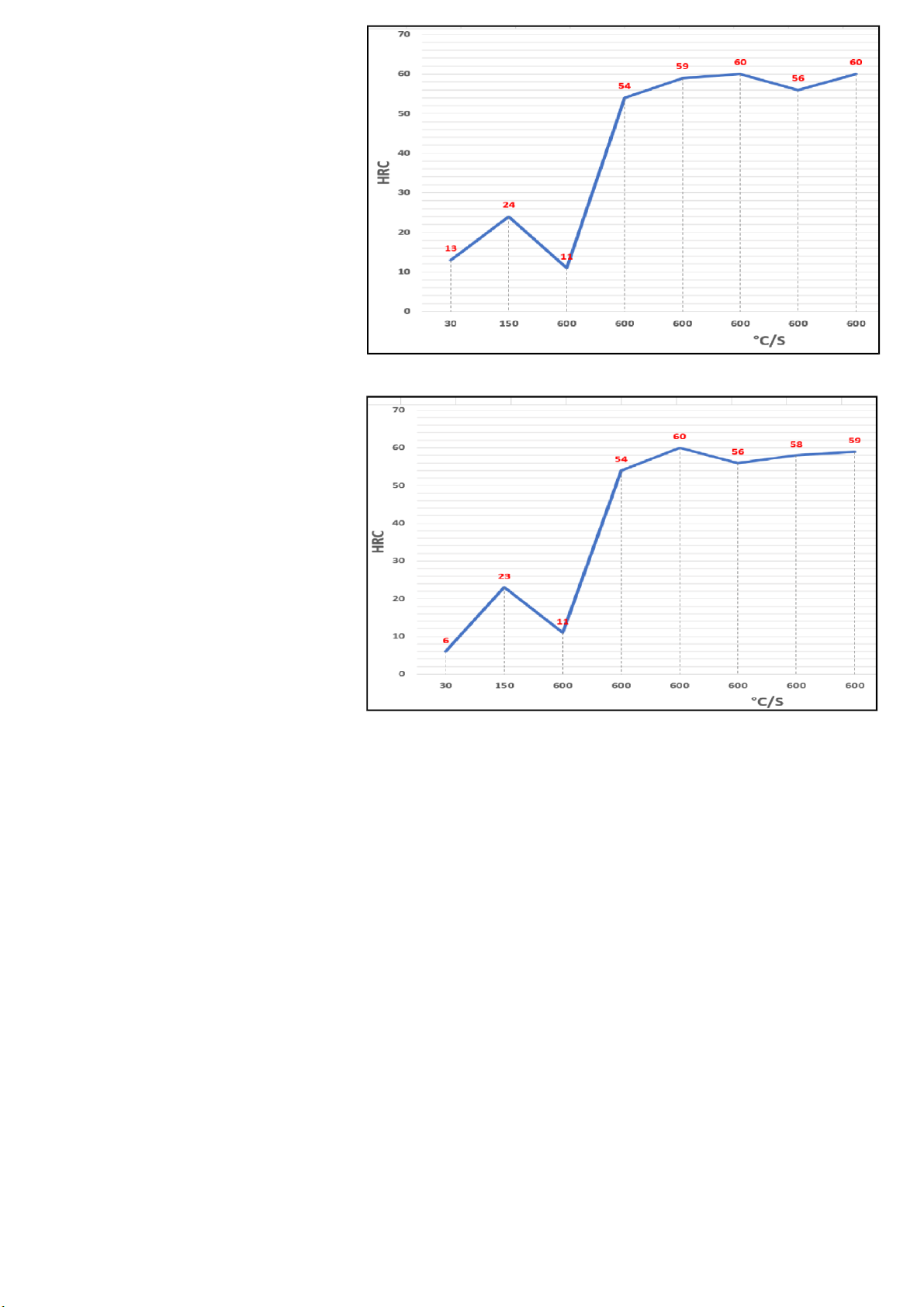
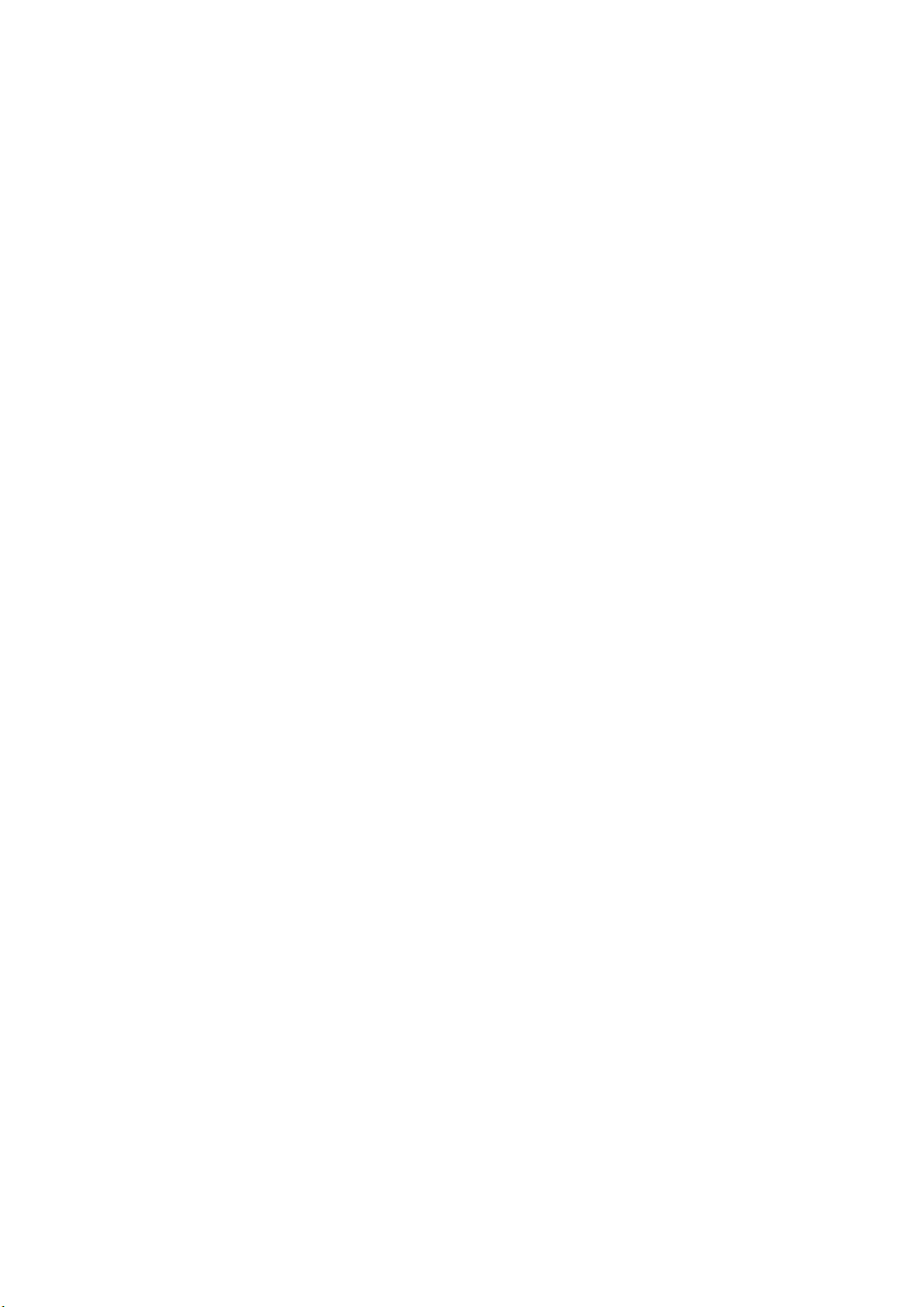
Preview text:
PHẦN 1: GIỚI THIỆU CÁC PHƯƠNG PHÁP ĐO ĐỘ CỨNG
I. MỤC TIÊU MÔN HỌC.
- Nắm vững nguyên lý đo độ cứng theo các phương pháp Brinell, Rockwell và Vicker.
- Làm quen và biết cách sử dụng các máy đo độ cứng thông dụng.
II. CƠ SỞ LÝ THUYẾT.
1. Đặc điểm và các phương pháp đo độ cứng:
Độ cứng là khả năng chống lại biến dạng dẻo cục bộ của kim loại, dưới tác dụng của tải
trọng thông qua mũi đâm.
Hình 1.0 - Hình dạng mũi đâm
Độ cứng là một đặc trưng cơ tính quan trọng của vật liệu. Nó có thể dễ dàng đo được
thông qua các thiết bị đo mà không cần phải phá hủy mẫu.
Phương pháp đo độ cứng có ưu điểm:
a) Từ giá trị độ cứng đo được, có thể suy ra độ bền của kim loại dẻo. Vì độ cứng là sự
chống lại biến dạng dẻo cục bộ, còn độ bền là sự chống diến dạng dẻo toàn bộ. Từ giá
trị độ cứng Brinell, ta có thể gián tiếp tính được độ bền.
b) Đo độ cứng đơn giản, thời gian ngắn (từ vài giây đến vài phút). Mẫu thử không phải
chuẩn bị đặc biệt. Không phá hủy mẫu khi thử.
c) Có thể đo được chitiết rất lớn hoặc rất nhỏ, rất dày hoặc rất mỏng (các lớp mạ, thấm…)
Tùy theo tác dụng của mũi đâm lên bề mặt mẫu, mà người ta chia ra làm nhiều phương
pháp đo độ cứng khác nhau: -
Phương pháp đâm: dùng 1 tải trọng xác định đặt lên mũi đâm (hình côn, hình tháp, hình
cầu..) có độ cứng rất cao (kim cương, hợp kim cứng, thép tôi..) để mũi đâm tác dụng lên bề
mặt mẫu, gây ra biến dạng tại vị trí đâm. Sau đó, căn cứ cào diện tích hoặc chiều sâu vết lõm
ứng với tải trọng tác dụng mà tính ra số đo của độ cứng. Phương pháp này được dùng phổ biến nhất. -
Phương pháp nảy lại: dùng để đo độ biến dạng đàn hồi bằng cách thả viên bi từ độcao
xác định lên bề mặt vật liệu. Sau đó, căn cứ vào chiều cao trước và sau khi thả bi mà tính ra số đo độ cứng. -
Phương pháp đo độ xước: là phương pháp đo khả năng chống lại phá hoại bề mặt của
vật liệu. Nội dung của phương pháp này là vừa ấn mũi kim cương lên bề mặt mẫu, vừa kéo
cho mũi kim cương chuyển động với tốc độ xác định, để tạo thành vết xước. Căn cứ vào lực
ấn, chiều sâu, chiều rộng vết xước mà tính ra số đo độ cứng.
2. Các phương pháp đo độ cứng.
2.1 Phương pháp đo độ cứng Brinell (HB).
Mũi đâm là bi thép (Hình 1.0 a), có các đường kính sau: D = 2,5; 5; 10 (mm)
Tải trọng tương ứng là P = 1875; 7500; 30000 (N); P có thể đo bằng kilogram lực (KG).
Mối quan hệ giữa P và D:
Nguyên lý đo của phương pháp: Ấn viên bi bằng thép đã tôi cứng lên bề mặt mẫu, dưới tác
dụng của tải trọng tương ứng với đường kính bi đã định trước. Trên mặt mẫu sẽ có vết lõm
hình chỏm cầu. Gọi P (N) là tải trọng tác dụng, S (mm2) là diện tích vết lõm, số đo Brinen
được tính bằng công thức sau: (KG/mm2) [P : N]
Hình 1.1 - Kích thước mũi đâm và vật mẫu
Nếu gọi D là đường kính viên bi; chiều sâu vết lõm là h. Ta có: S = Dh
Tuy nhiên việc đo đường kính d của vết lõm lại dễ dàng hơn nhiều so với độ sâu h nên diện
tích chỏm cầu có thể tính bằng công thức:
Đối với thép và gang thường dùng P = 3000kG, D = 10mm
Để xác định độ cứng HB cần phải đo được đường kính vết lõm và dùng công thức trên để
tính (song có thể dùng bảng tính sẵn để tra bảng – Bảng 1.2)
Điều kiện đo độ cứng Brinell
+ Chiều dày mẫu thí nghiệm không nhỏ hơn 10 lần chiều sâu của vết lõm.
+ Bề mặt mẫu thử phải sạch, phẳng, không có khuyết tật.
+ Chiều rộng, dài của mẫu và khoảng cách giữa 2 vết đo phải lớn hơn 2D.
+ Thời gian tác động cũng ảnh hưởng đến kết quả đo. Thông thường thời gian này có thể tra theo bảng 1.2
Bảng 1.2 Điều kiện sử dụng thang đo độ cứng Brinell Độ cứng
Chiều dày bé nhất P/D D(mm Vật liệu Thời gian P(N) HB ( mm ) 2 ) tác
Phạm vi sử dụng: Phương pháp Brinell chỉ đo được những vật liệu mềm, kim loại màu
(đồng, nhôm, niken…), hợp kim màu, thép sau khi ủ, các loại gang graphite. Không đo được
những vật liệu mỏng ( < 10h).
Hình 1.3 - Máy độ cứng Brinell
2.2 Phương pháp đo độ cứng Rockwell (HRA; HRB; HRC).
Mũi đâm bi thép, kim cương (hoặc hợp kim cứng) hình côn (Hình 1.0 b), có góc đỉnh là
1200, hoặc bi thép, có đường kính d ==1,588 mm.
Ở phương pháp này qui định: Mũi đâm đi xuống 0,002mm thì độ cứng giảm 1 đơn vị.
Khoảng cách giữ 2 vết lõm hoặc giữa vết lõm với cạnh mẫu không nhỏ hơn 1,5mm khi
dùng mũi kim cương, 4mm khi dùng mũi bi thép. Mỗi mẫu đo 3 lần rồi lấy trung bình cộng.
Hình 1.4 Phương pháp đo độ cứng Rockwell
Tùy theo dạng mũi đâm và tải trọng ta chia ra các thang sau đây:
- Độ cứng Rockwell C – mũi kim cương, tải trọng 1500N – HRC.
- Độ cứng Rockwell A – mũi kim cương, tải trọng 600N – HRA.
- Độ cứng Rockwell B – mũi bi ∅1,588mm, tải trọng 1000N – HRB.
Số đo độ cứng Rockwell được xác định:
Trong đó: K là hằng số ứng với từng mũi đâm.
h là chiều sâu vết lõm (mm).
0,002mm là giá trị 1 vạch của đồng hồ so.
Bảng 1.5 - Giới hạn đo của các thang Rockwell Than Tải Giới Hạn đo cho g Loại mũi đâm trọng kk Phạm vi sử dụng phép đo P(N)
Vật liệu rất cứng (Thép Kim cương – nón 10 HRA 600 hợp kim, hợp kim cứng, 70 ÷ 85 = 1200 0 WC, TiC… Kim cương – nón 10
Vật liệu cứng tôi (Thép HRC 1500 20 ÷ 67 = 1200 0 sau Martensite) Bi thép 13
Gần như HB, vật liệu dày, HRB 1000 25 100 d=1,588mm 0 mỏng.
2.3 Phương pháp đo độ cứng Vicker.
Phương pháp Vicker về nguyên lý đo giống như phương pháp Brinell nhưng thay bi thép
bằng mũi kim cương hình tháp (Hình 1.0 c), có góc giữa hai mặt bên là 1360. Tải trọng sử
dụng P = (50 ÷ 1500)N, phụ thuộc chiều dày mẫu đo.
Độ cứng Vicker được xác định:
Trong đó: P tải trọng (N hay KG) Hình 1.6
Phương pháp đo độ cứng Vicker
S là diện tích bề mặt vết lõm (mm2)
Để thuận tiện, người ta có thể tính S thông qua đường chéo d và = 136 3. Công dụng.
3.1. Ưu điểm các phương pháp đo độ cứng:
- Độ cứng là sự chống lại biến dạng dẻo cục bộ còn độ bền là sự chống lại biếndạng dẻo
toàn bộ. Nên có thể thông qua tính độ cứng để suy ra độ bền của kim loại.
- Đo độ cứng tương đối đơn giản, tốn ít thời gian (trên dưới 1 phút/1 mũi đo) - Có thể đo
được các chi tiết dày hoặc mỏng.
- Biết được khả năng làm việc của chi tiết.
3.2. Độ cứng thông dụng của các chi tiết như sau:
- Độ cứng phù hợp nhất cho cắt gọt: (160 ÷ 180) HB
- Các chi tiết lò xo, khuôn dập nóng: (40 ÷ 45) HRC
- Các bánh răng chịu tải trọng nhỏ, vận tốc chậm (các loại máy công cụ): (52÷58) HRC.-
Mọi bánh răng chịu tải trọng lớn, vận tốc cao; mọi dụng cụ cắt gọt; các khuôn dập nguội;
các ổ lăn; các đĩa ma sát, và những chi tiết khác bị mài mòn tương tự… độ cứng lớn hơn (60 ÷ 62) HRC. PHẦN 2: TÔI THÉP .
I. MỤC ĐÍCH YÊU CẦU
- Nắm được quá trình tôi thép: cách chọn nhiệt độ tôi, thời gian nung và môi trường làm nguội.
- Xác định được mối quan hệ của tốc độ làm nguội tức môi trường làm nguội đến độcứng của thép.
II. CƠ SỞ LÝ THUYẾT.
2.1. Định nghĩa: Tôi là một phương pháp nhiệt luyện gồm có nung nóng chi tiết hoặc thép đến
trạng thái , giữ nhiệt thời gian và làm nguội nhanh Vnguội ≥ Vtới hạn.
Hình 1.8 Phương pháp đo độ cứng Vicker
+ Tốc độ nguội tới hạn là tốc độ nguội nhỏ nhất mà chi tiết chuyển biến hoàn toàn thành Maxtensit (Mt).
+ Thép khác nhau có tốc độ nguội tới hạn khác nhau.
+ Vnguội: Tốc độ nguội của môi trường nguội.
Hình 1.9 Phương pháp đo độ cứng Vicker
2.2. Chọn nhiệt độ tôi:
Nhiệt độ tôi ảnh hưởng trực tiếp đến cơ tính của thép sau khi tôi. Để tôi thép cacbon, có thể
dựa vào giản đồ trạng thái sắt - cacbon và %C để chọn nhiệt độ tôi.
Hình 1.10 - Lò nhiệt luyện
• Đối với thép trước cùng tích và thép cùng tích (%C ≤ 0,8%)
Chọn nhiệt độ tôi cao hơn A , nghĩa là nung nóng thép đến trạng thái hoàn toàn Austenite. C3
Phương pháp này gọi là tôi hoàn toàn. t0tôi = AC3 + (30 ÷ 50)0C
Trong khoảng 0,1 ÷ 0,8%C điểm AC3 của thép giảm xuống. Nung nóng chậm AC3 = A3.
• Đối với thép sau cùng tích (0,8% < %C ≤ 2,14%)
Nhiệt độ tôi cao hơn A , nhưng thấp hơn Accm, nghĩa là nung lên trạng thái không hoàn C1
toàn austenite. Tổ chức nung để tôi là + C . Đây là phương pháp tôi không hoàn toàn. eII t0tôi = AC1 + (30 ÷ 50)0C
Thép sau cùng tích nhiệt độ tôi giống nhau. Nung nóng chậm A , khoảng C1 = A1
(760÷780)0C, không phụ thuộc vào thành phần cacbon.
• Có thể xác định AC3 và AC1 bằng cách dựa vào giản đồ trạng thái Fe-C hoặc tra sổ
tay nhiệt luyện.
Hình 1.11 – Khoảng nhiệt độ nhiệt luyện của thép cacbon
2.3. Thời gian giữ nhiệt : Phụ thuộc vào nhiều yếu tố:
- Khoảng nhiệt độ nung. - Môi trường nung. - Kích thước chi tiết. - Hình dạng chi tiết.
- Cách sắp xếp các chi tiết.
Kinh nghiệm: tính theo chiều dày nhỏ nhất ở tiết diện lớn nhất, hoặc tra theo bảng sau:
Bảng 1.12 Bảng thời gian nung của các mẫu
Môi trường nguội cần có khả năng làm nguội lớn hơn tốc độ nguội tới hạn để thép đạt
độ cứng tốt. Nếu tốc độ nguội nhỏ hơn tốc độ nguội tới hạn thì độ cứng sẽ bị suy giảm.
Một số môi trường nguội thường dùng: nước nóng (40 ÷ 60)0C, nước thường (25 ÷ 30)0C,
nước lạnh (5 ÷ 15)0C, dung dịch NaOH hoặc NaCl, dầu nhớt, không khí, muối nóng chảy, emusi: dầu + nước.
Thông thường đối với thép cacbon chọn môi trường nguội là nước; đối với thép hợp
kim môi trường nguội là dầu nhớt. Chọn vận tốc nguội:
Vnguội = Vtới hạn + (30 ÷ 50)0C
III. QUY TRÌNH THÍ NGHIỆM TÔI THÉP.
- Mỗi nhóm nhận một mẫu phôi thép C45, mài nhẵn 1 mặt và mặt còn lại mài bằng để đo độ cứng.
- Thiết lập nhiệt độ lò nhiệt luyện ở nhiệt độ theo từng nhóm như bản - Cho mẫu vào lò nhiệt
luyện sau khi đạt nhiệt độ yêu cầu thì tắt lò.
- Đợi sau 10 phút lấy mẫu ra khỏi lò:
+ 6 mẫu bỏ vào xô nước. + 1 mẫu vào xô dầu.
+ Làm nguội ngoài không khí.
- Lấy các mẫu đem mài xơ bộ để loại lớp oxit bám trên mặt của mẫu rồi đem đi đo độcứng HB.
IV. KẾT QUẢ THÍ NGHIỆM.
Bảng 1.13 Độ cứng của mẫu trước khi tôi [đã thường hóa] (Đo HB)
Đồ thị quan hệ nhiệt độ tối và độ cứng sau tôi: Mẫu 1 Mẫu 2 Mẫu 3
Đồ thị quan hệ tốc độ nguội và
độ cứng sau tôi: Mẫu 1 Mẫu 2 Mẫu 3 V. NHẬN XÉT.
- Với cùng nhiệt độ nung (840oC) và nung trong 10’,
khi ta làm nguội ở các môi trường khác nhau thì độ cứng của mẫu khác nhau, tăng hoặc giảm.
Làm nguội ở môi trường dầu có độ cứng cao hơn làm nguội trong không khí.
- Đối với làm nguội trong môi trường không khí, độ cứng của mẫu thay đổi không đángkể (từ 23 lên 26)
- Đối với các môi trường còn lại, độ cứng của mẫu tang theo thứ tự tăng dần là: không khí, dầu, và nước.
- Đối với làm nguội trong môi trường nước, độ cứng của mẫu thay đổi không đángkể (từ 56 lên 60,5)
- Khi làm nguội trong môi trường dầu (720oC) và nước (840oC) ở , độ cứng của hai mẫu này
xấp xỉ bằng nhau (11 và 13). Do đó trong thực tế, người ta dung phương pháp làm nguội
trong nước để thu được tổ chức cần thiết thay vì làm nguội trong dầu.
- Trong quá trình làm nguội nhanh (trong nước) với tốc độ cao hơn tốc độ tới hạn vth : ostenit
sẽ chuyển biến thành mactenxit.
- Trong quá trình làm nguội vừa ( trong dầu) với tốc độ nguội khoảng 150oC/s. Pha ostenit sẽ
chuyển biến thành bainit.
- Trong quá trình làm nguội đủ chậm (cùng lò, không khí), ostenit sẽ chuyển biếnlại thành peclit.