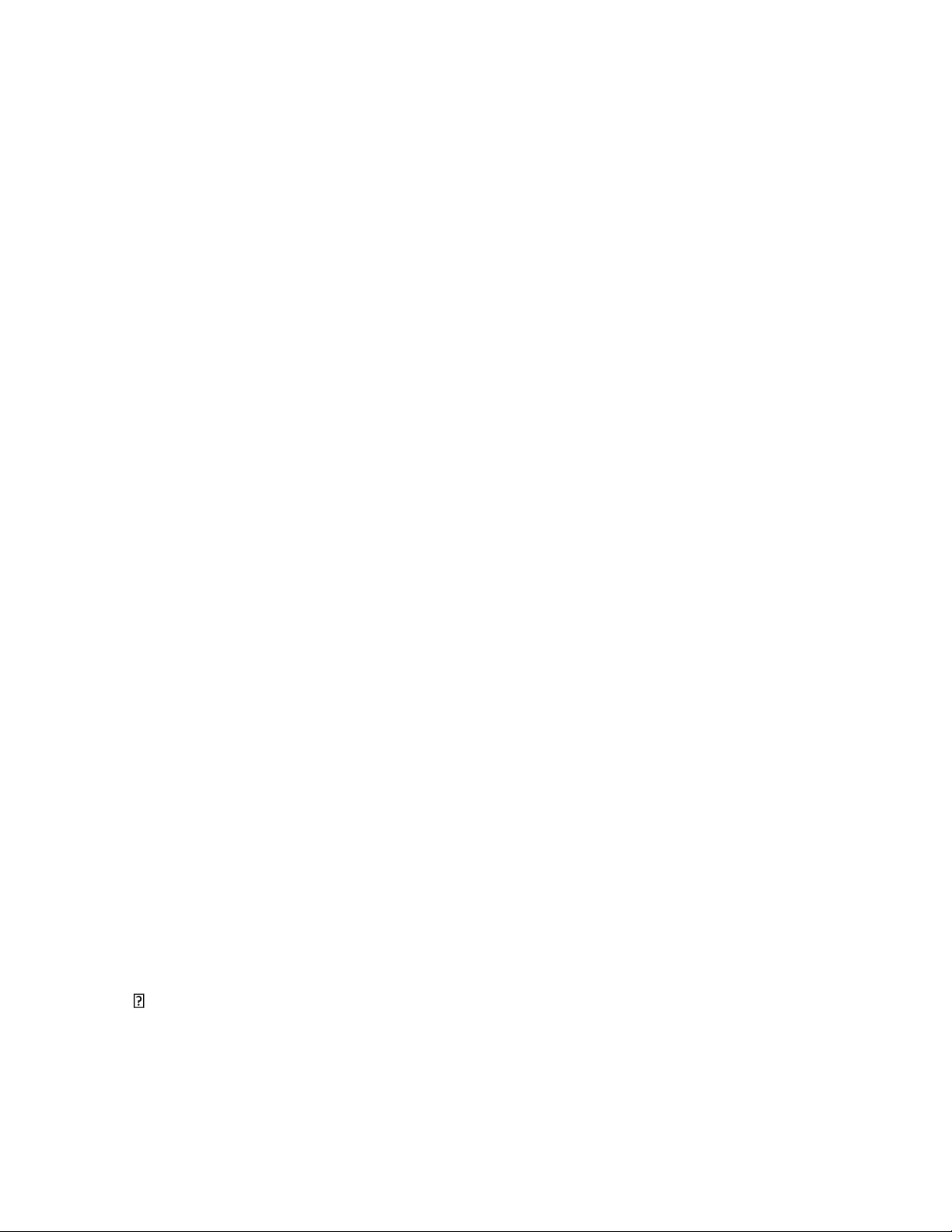
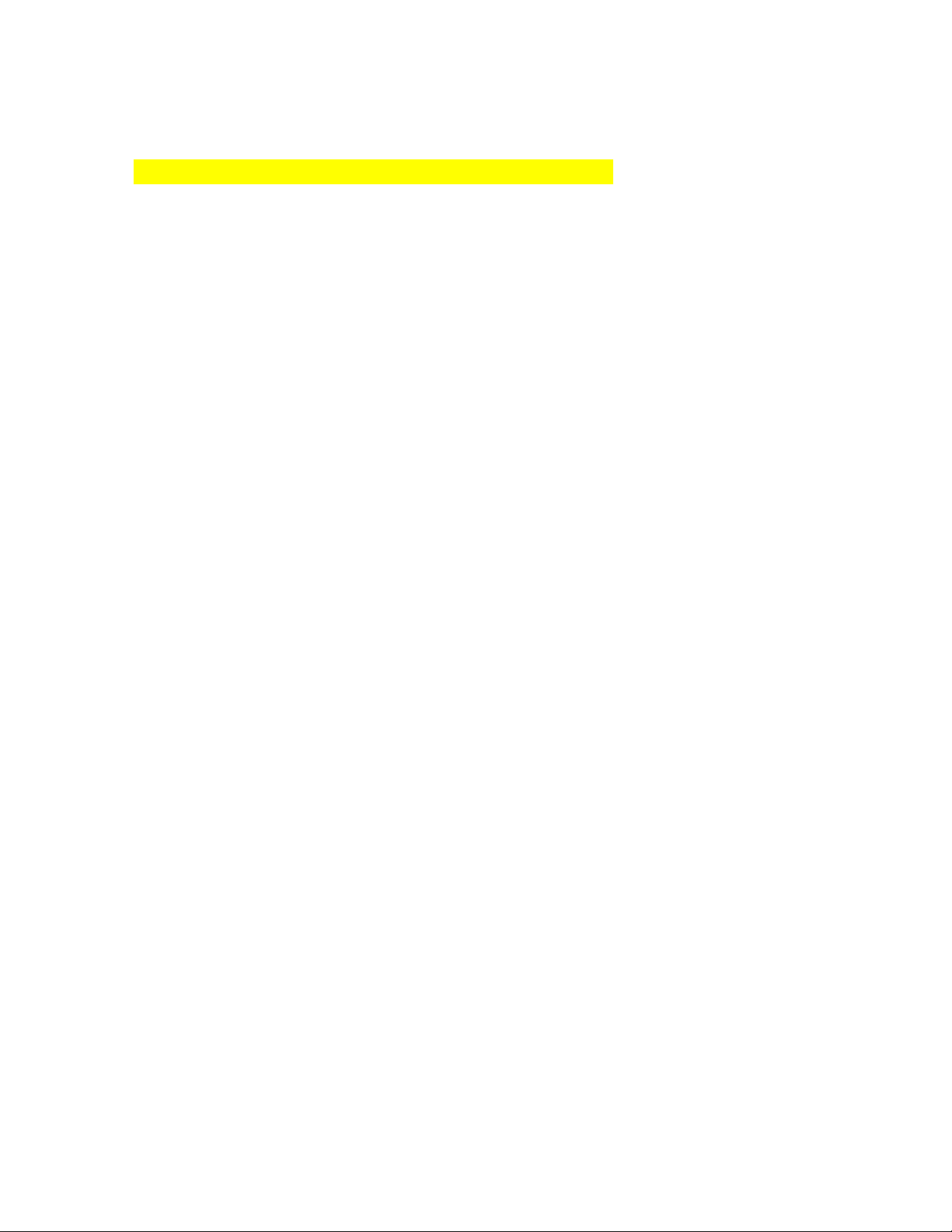
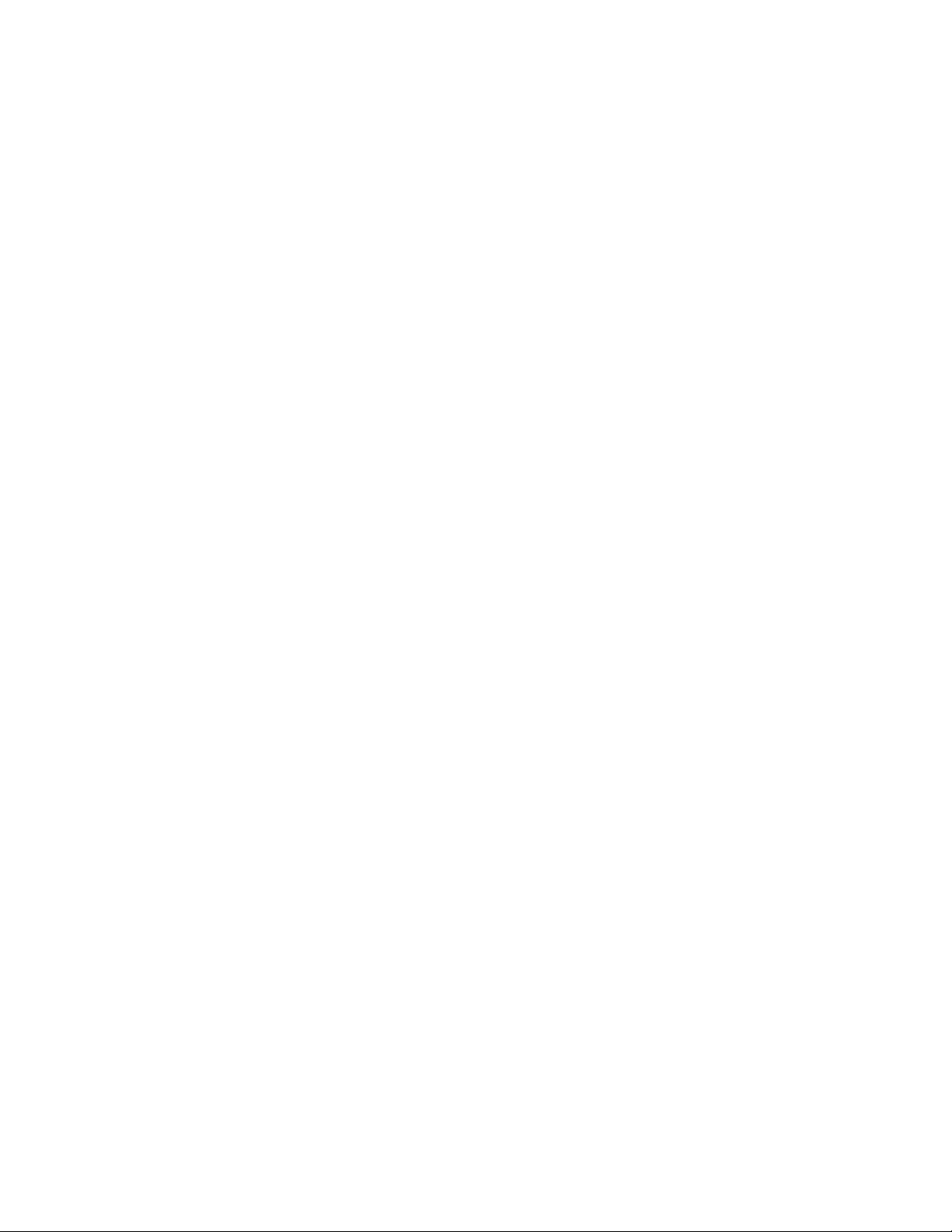
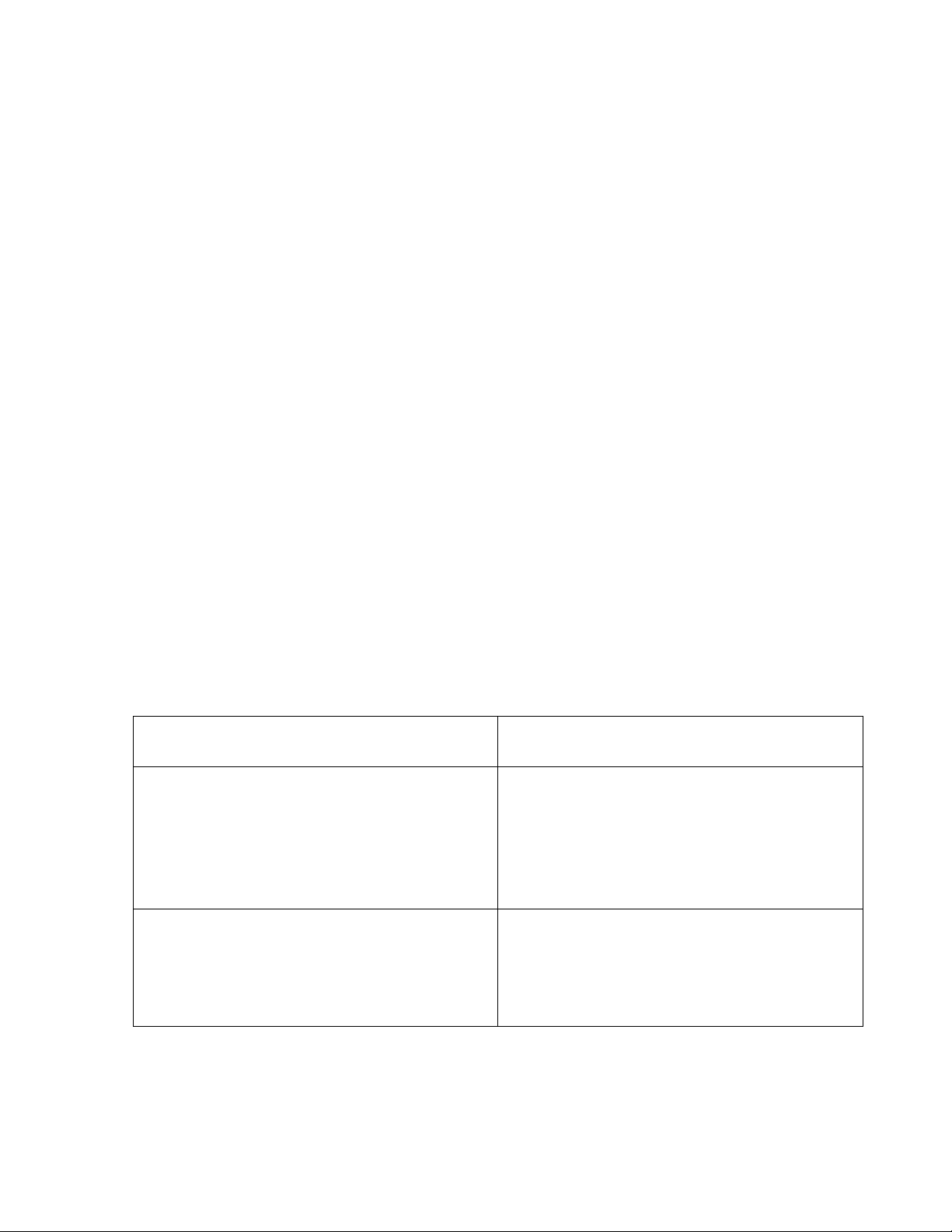
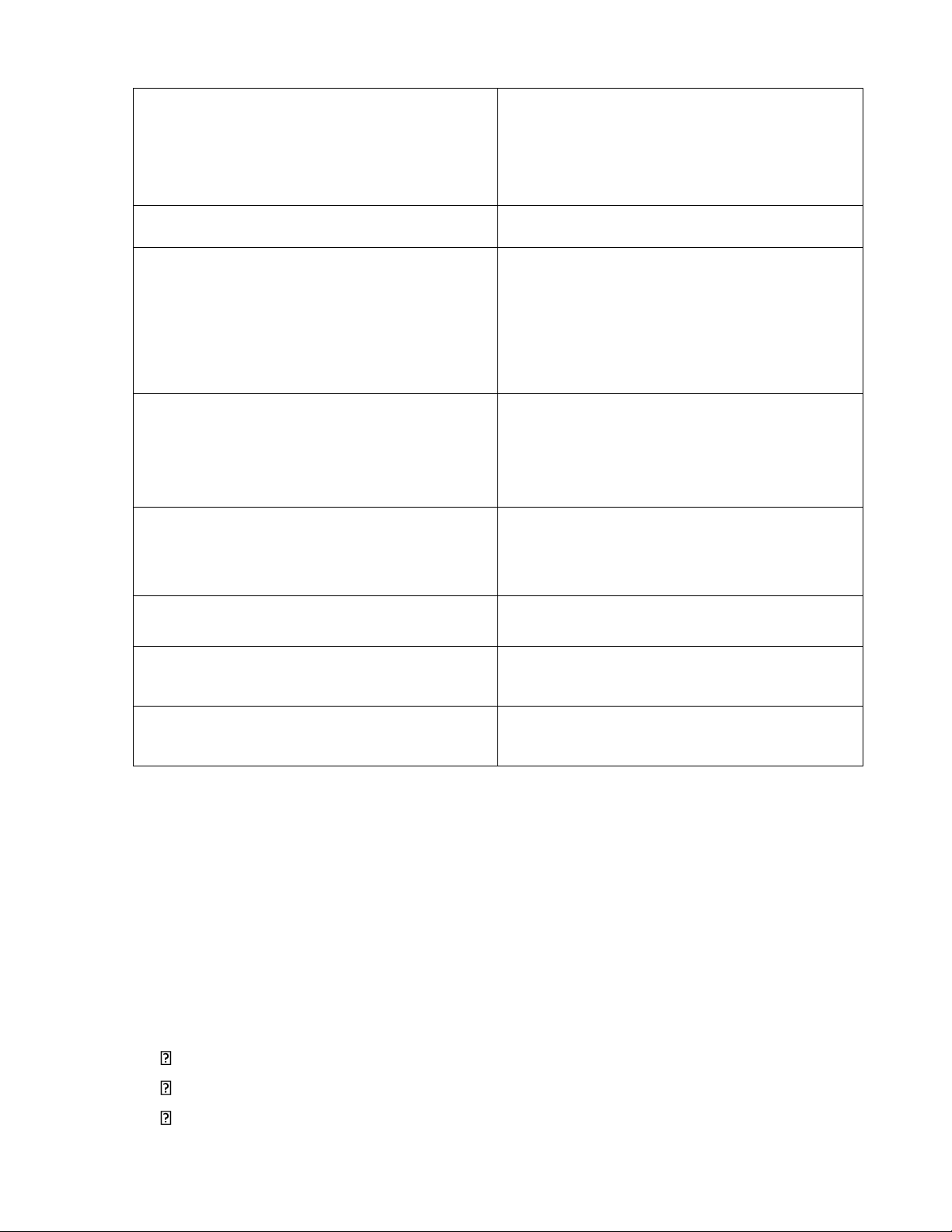
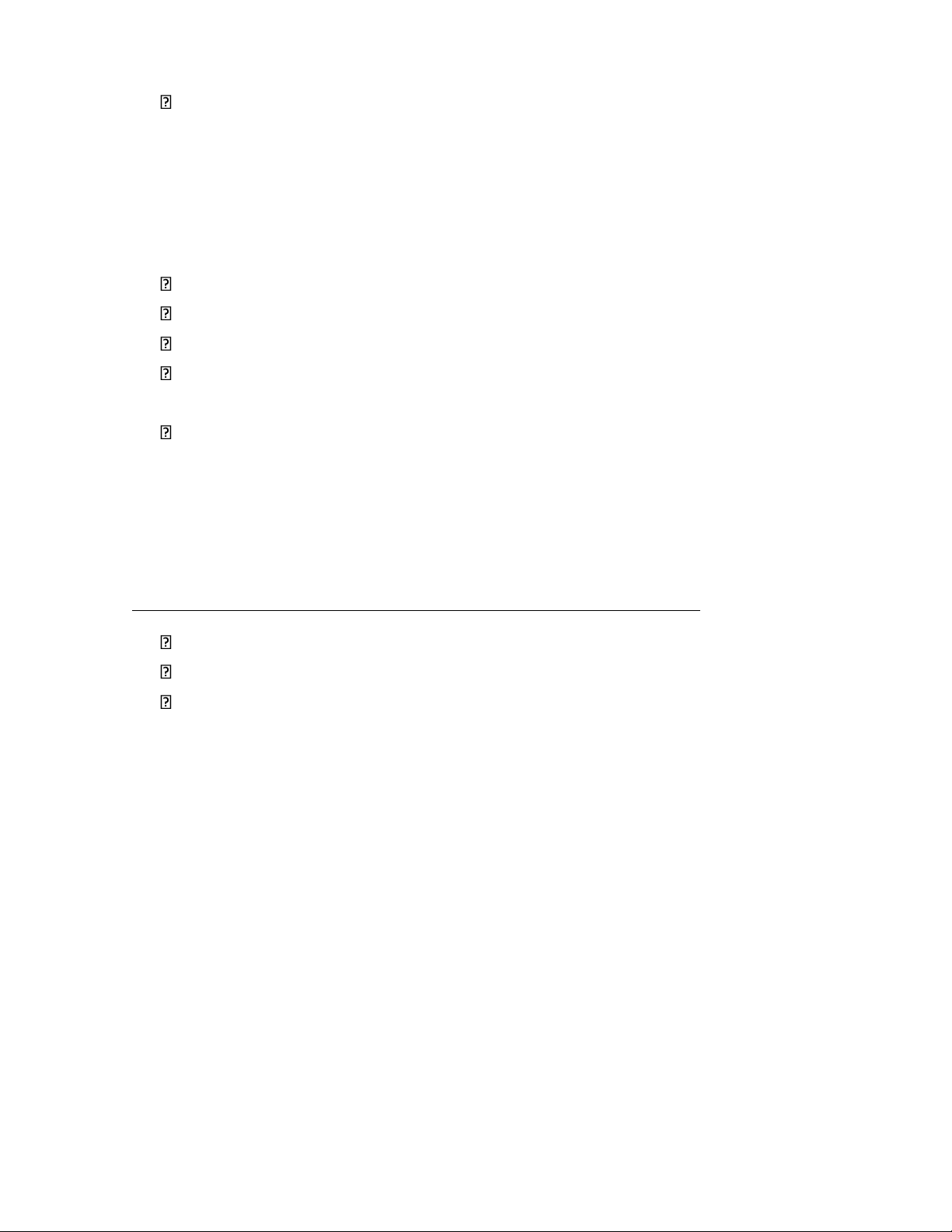
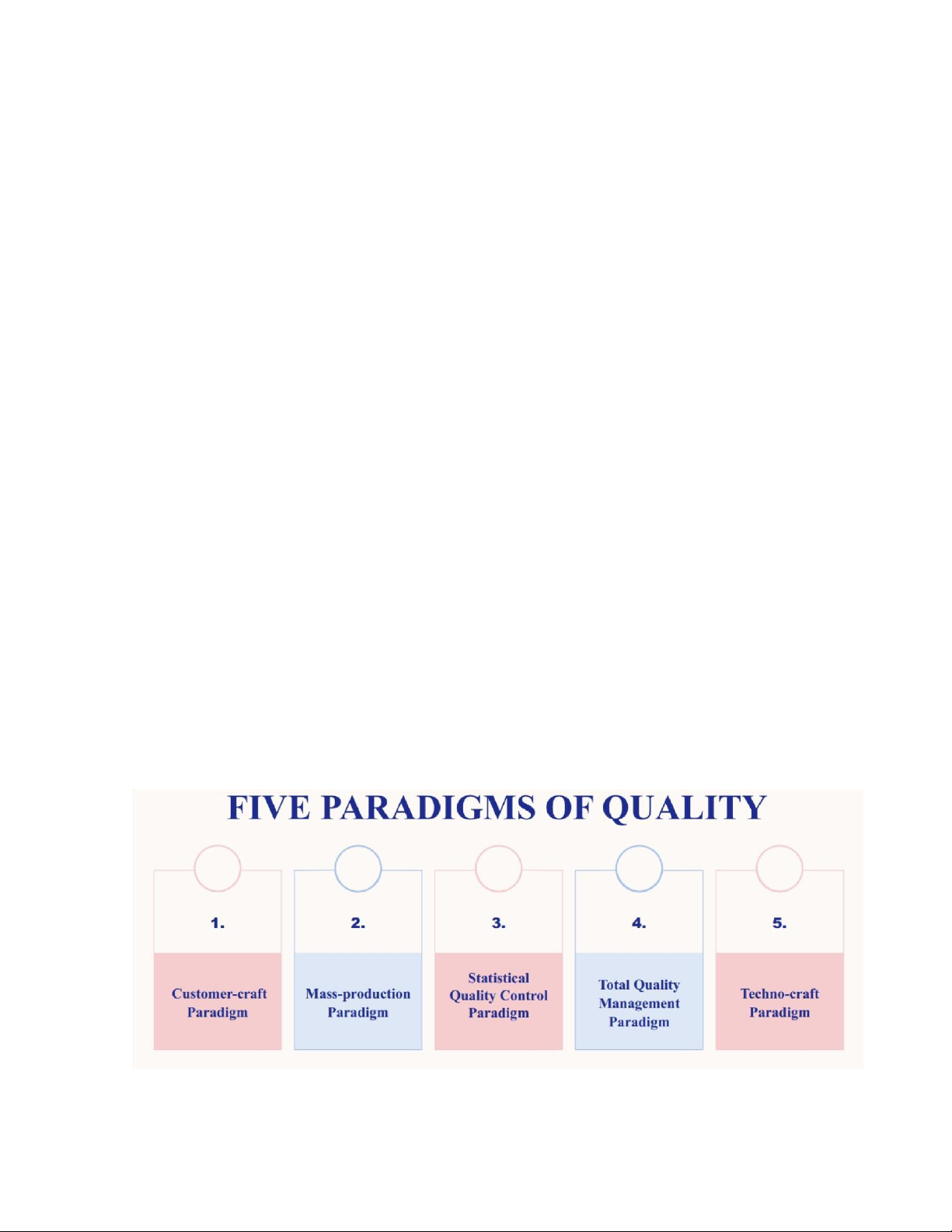
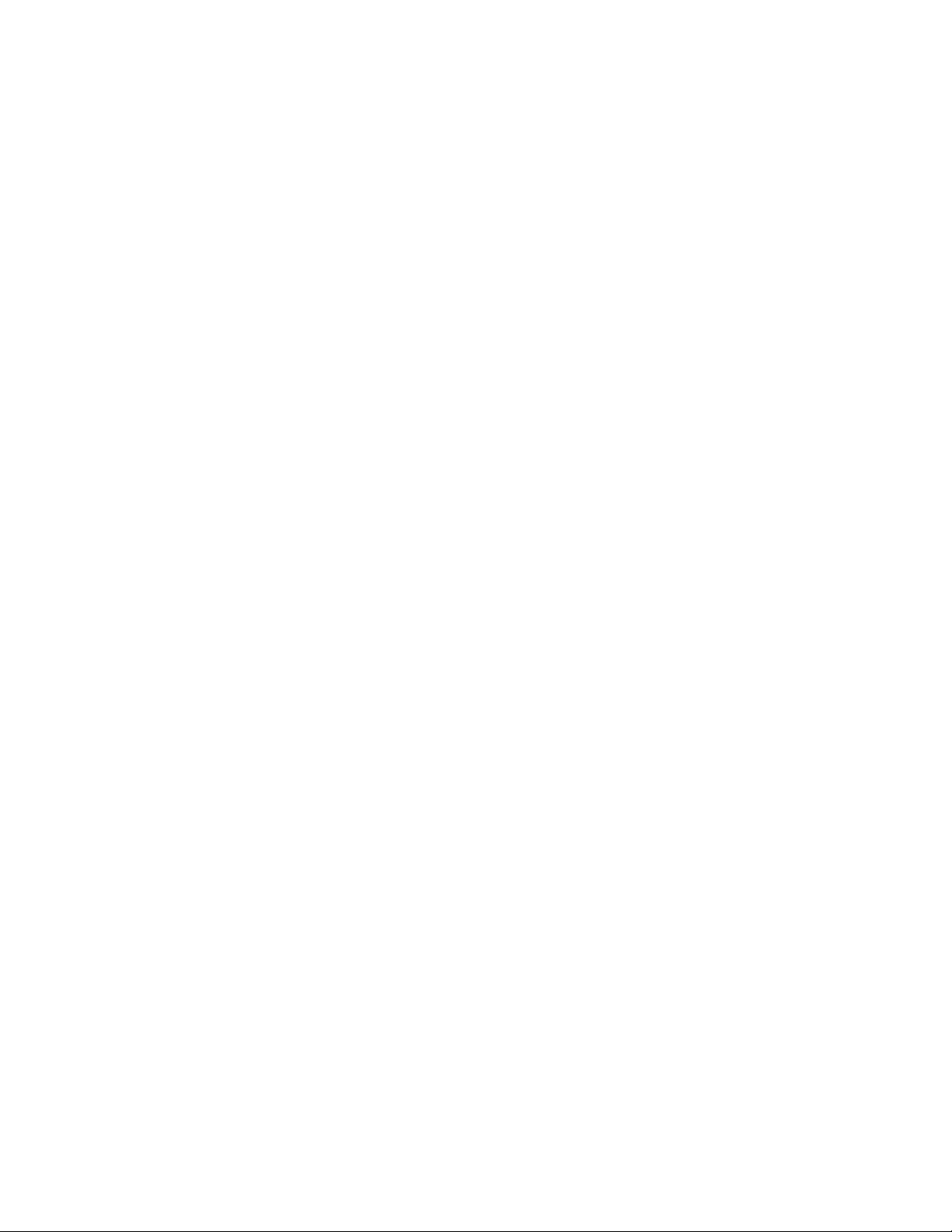
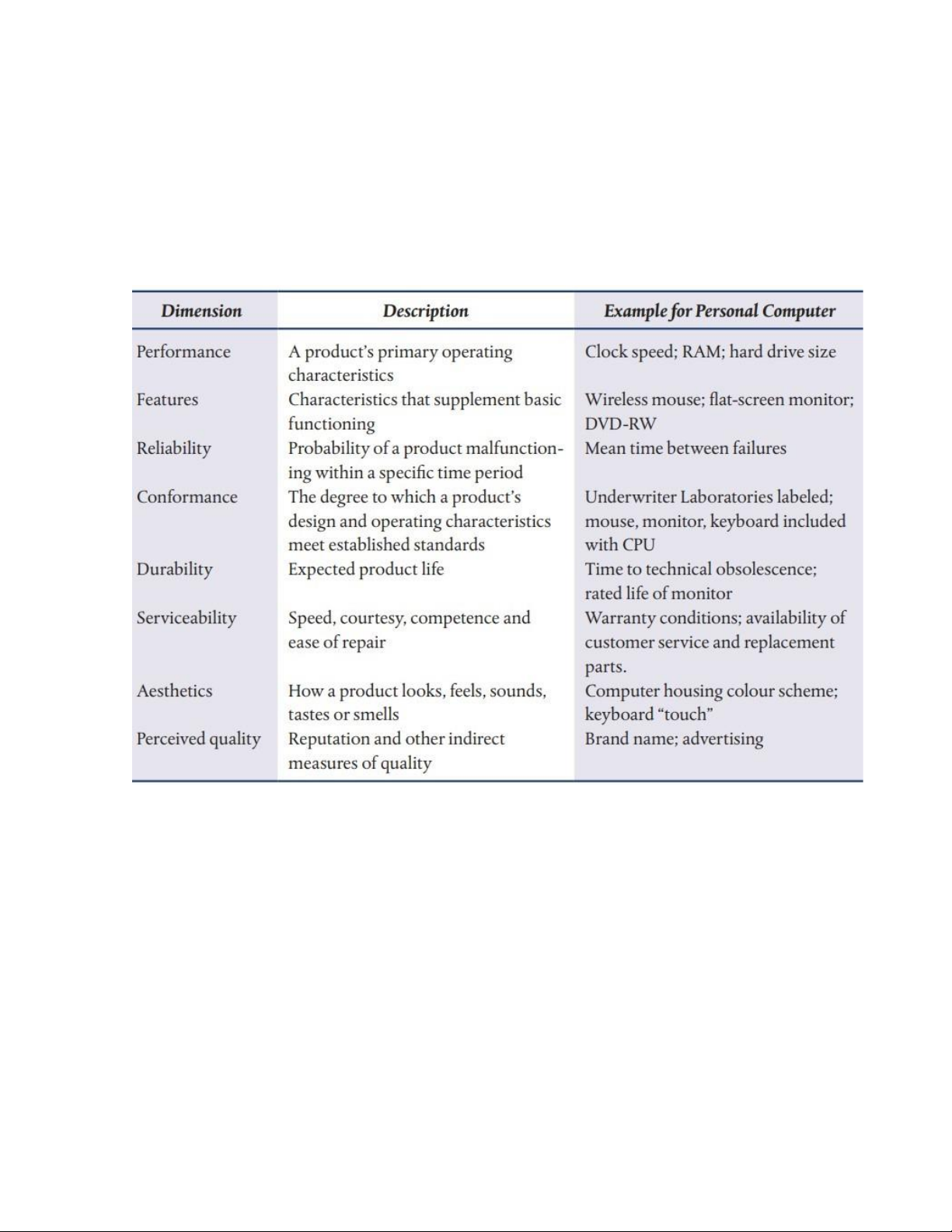


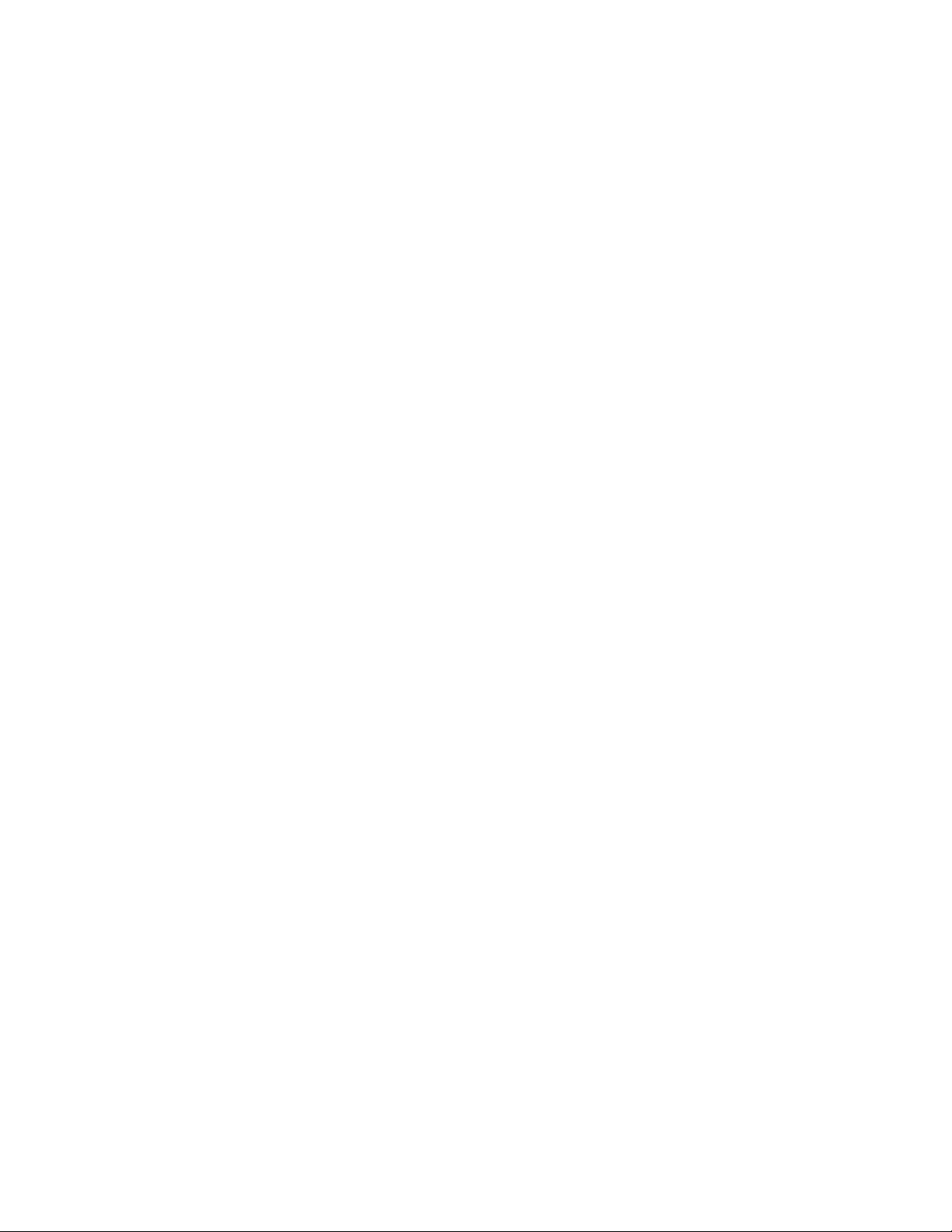
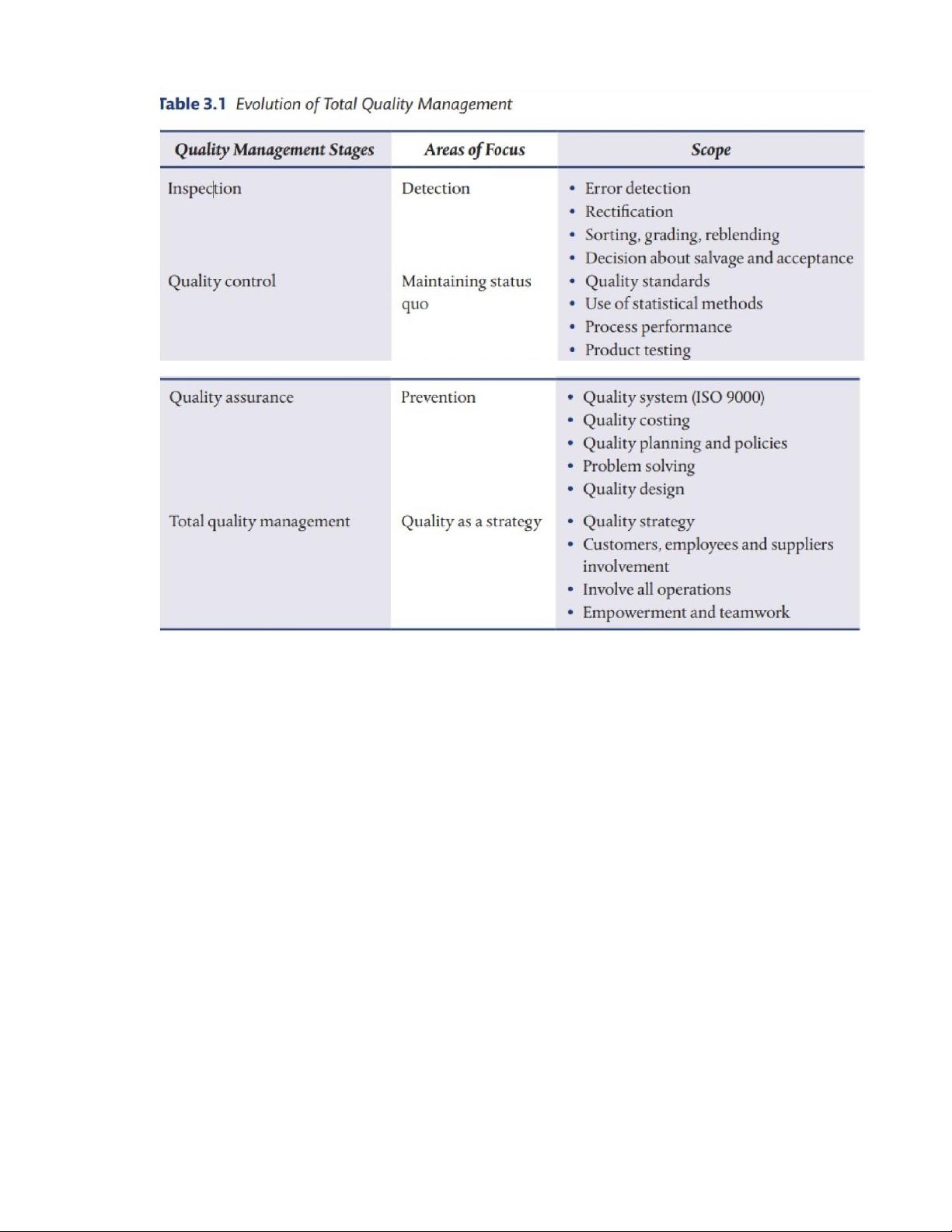
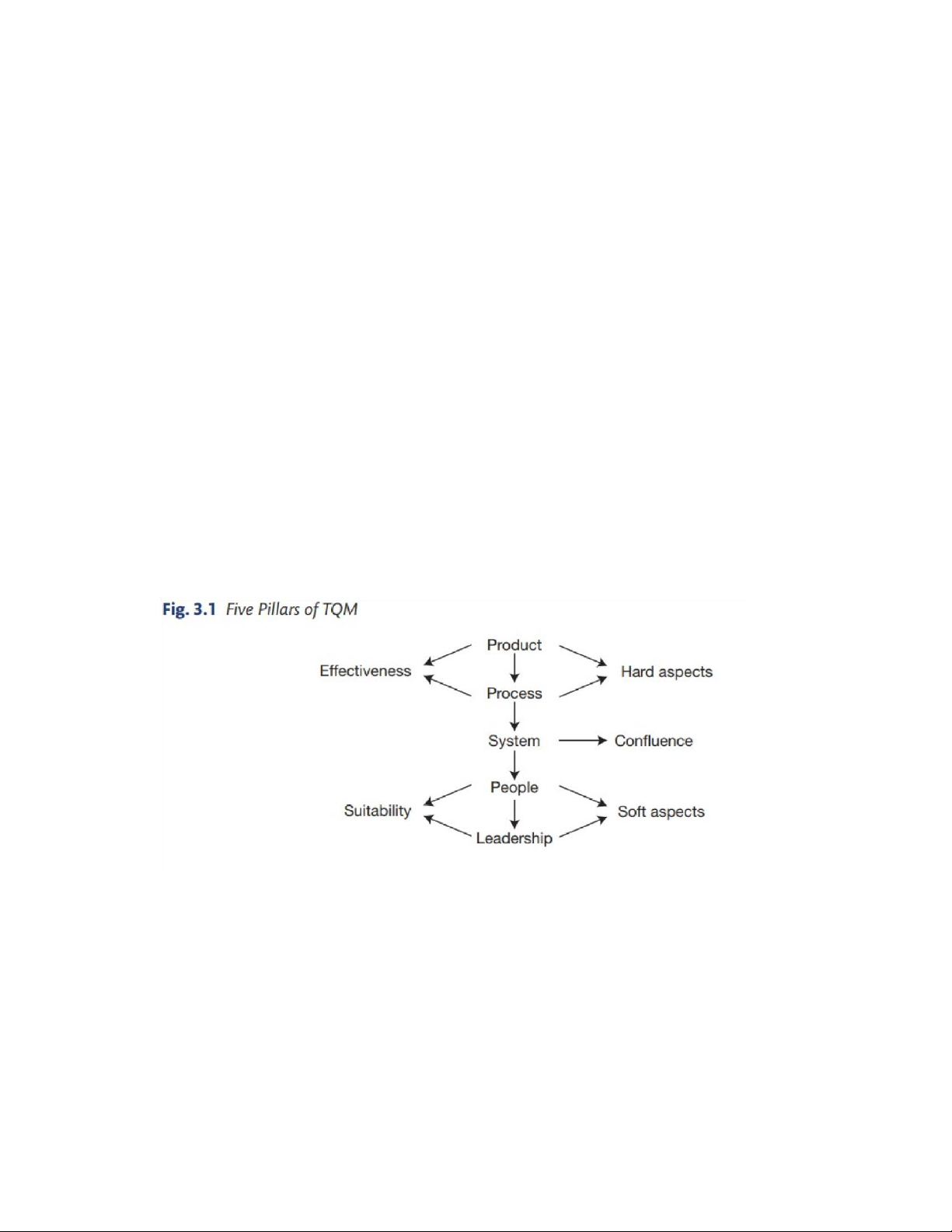
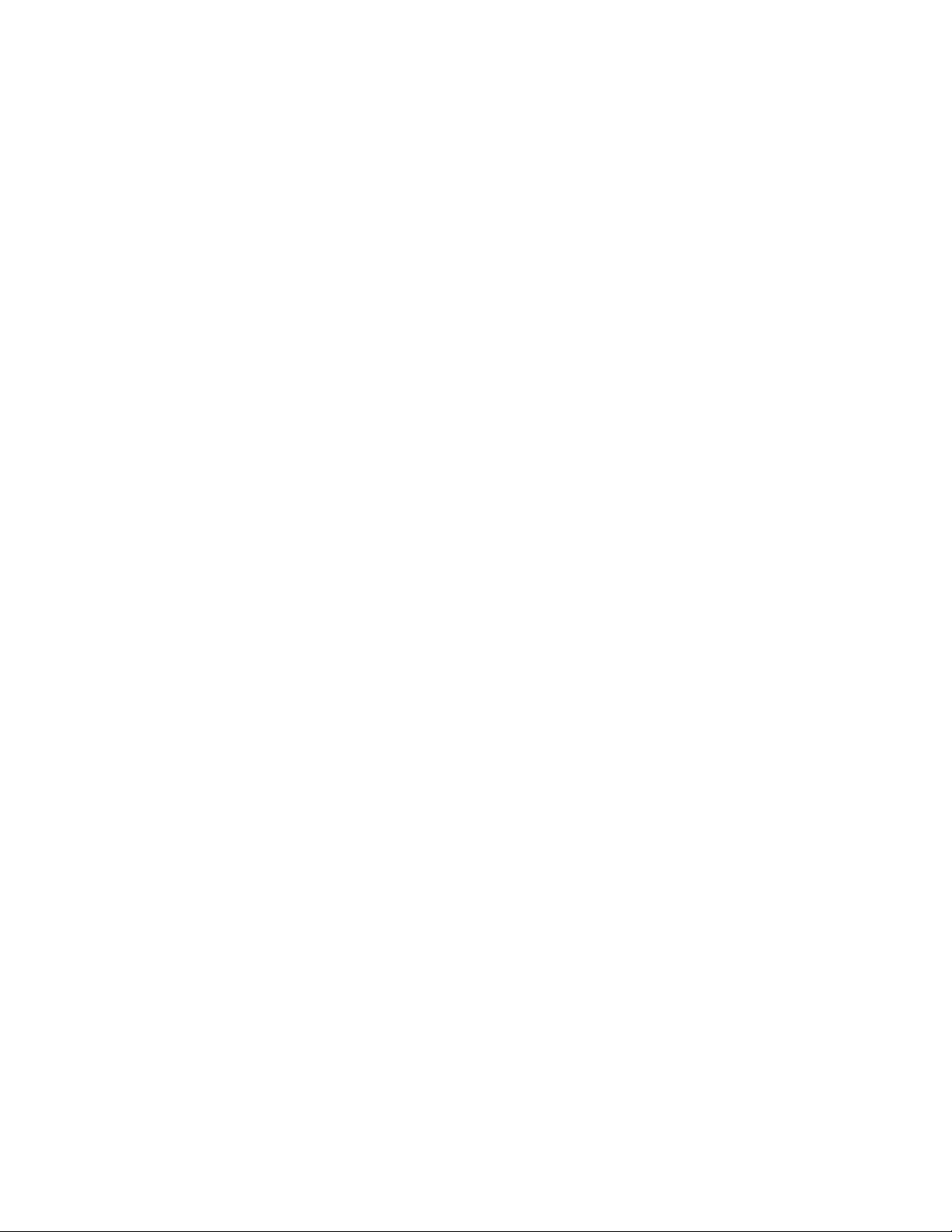
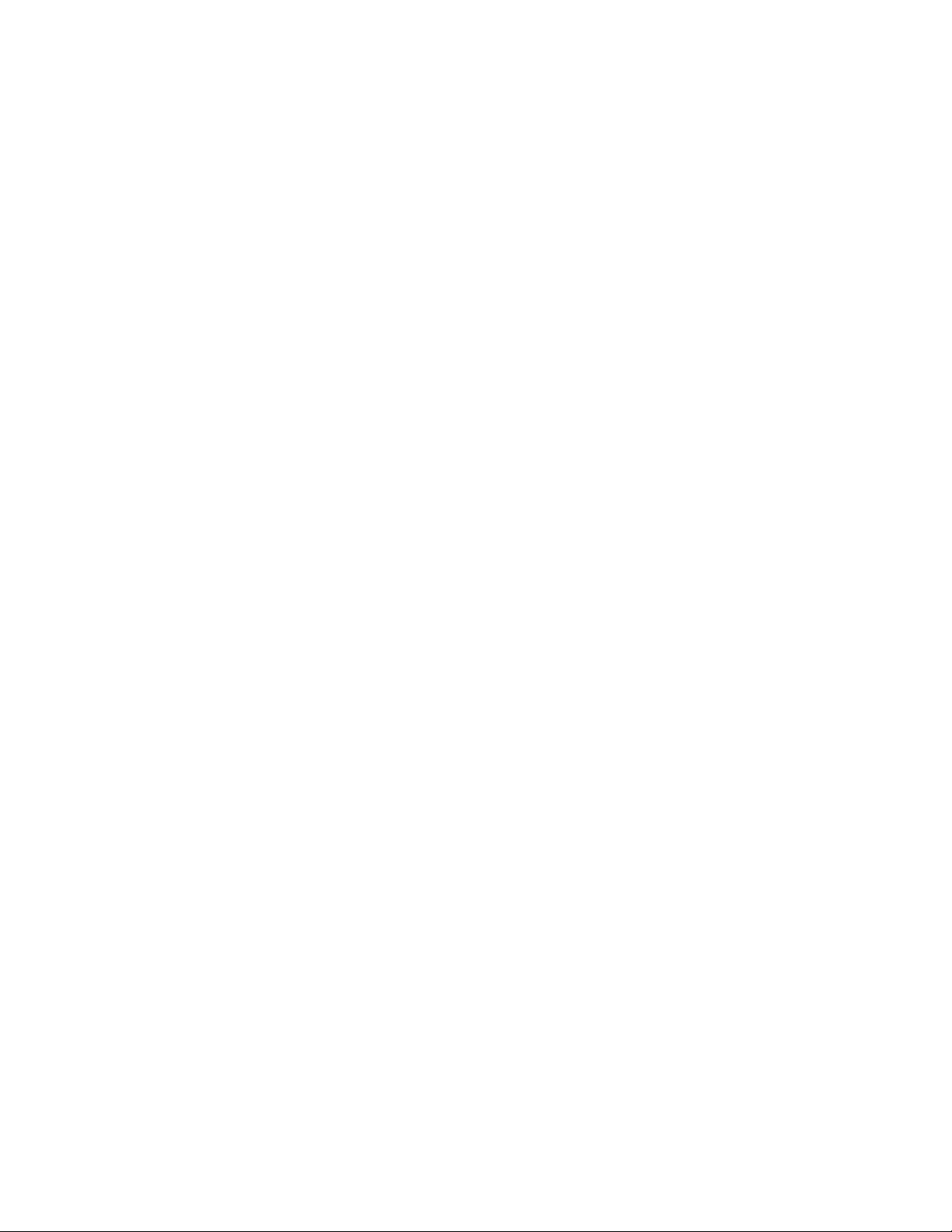
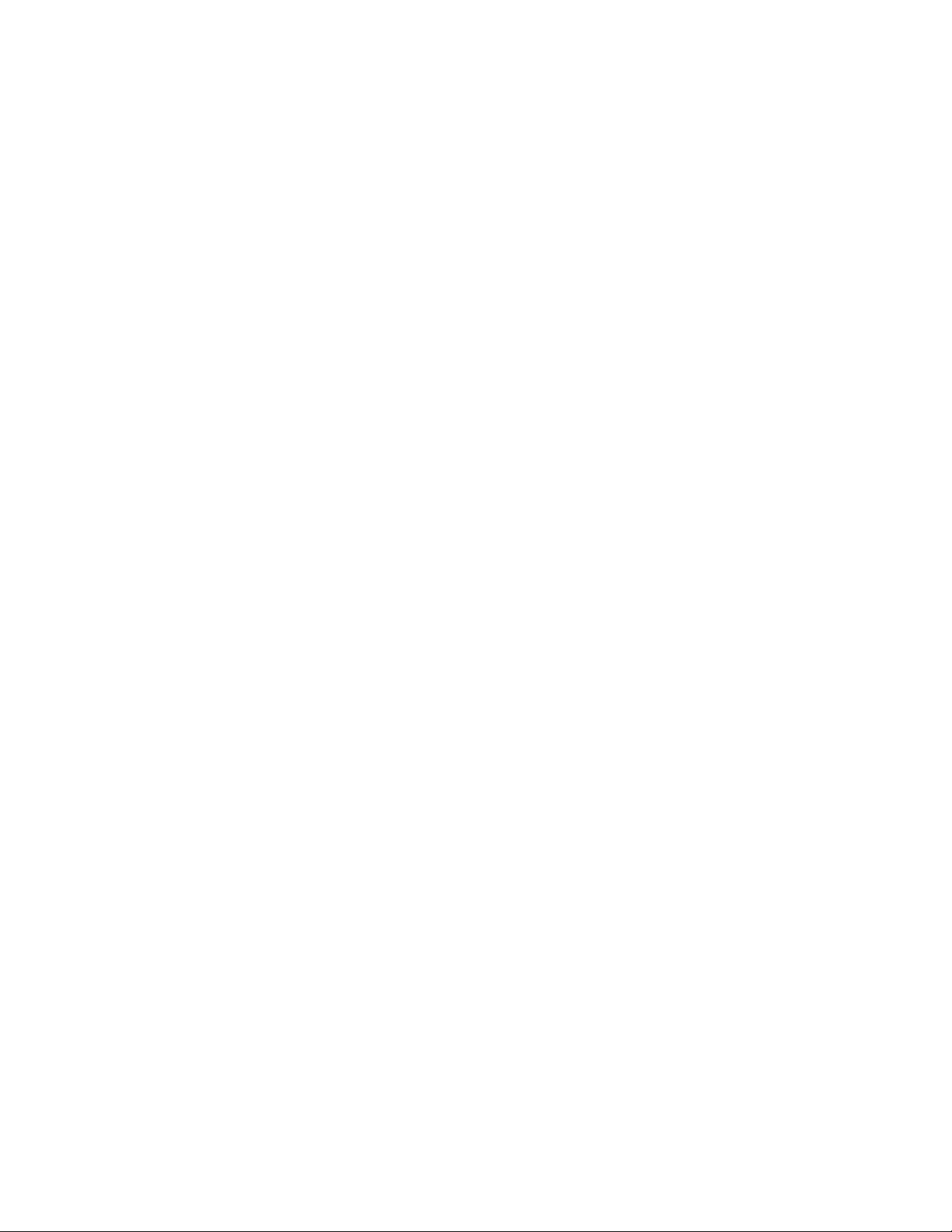
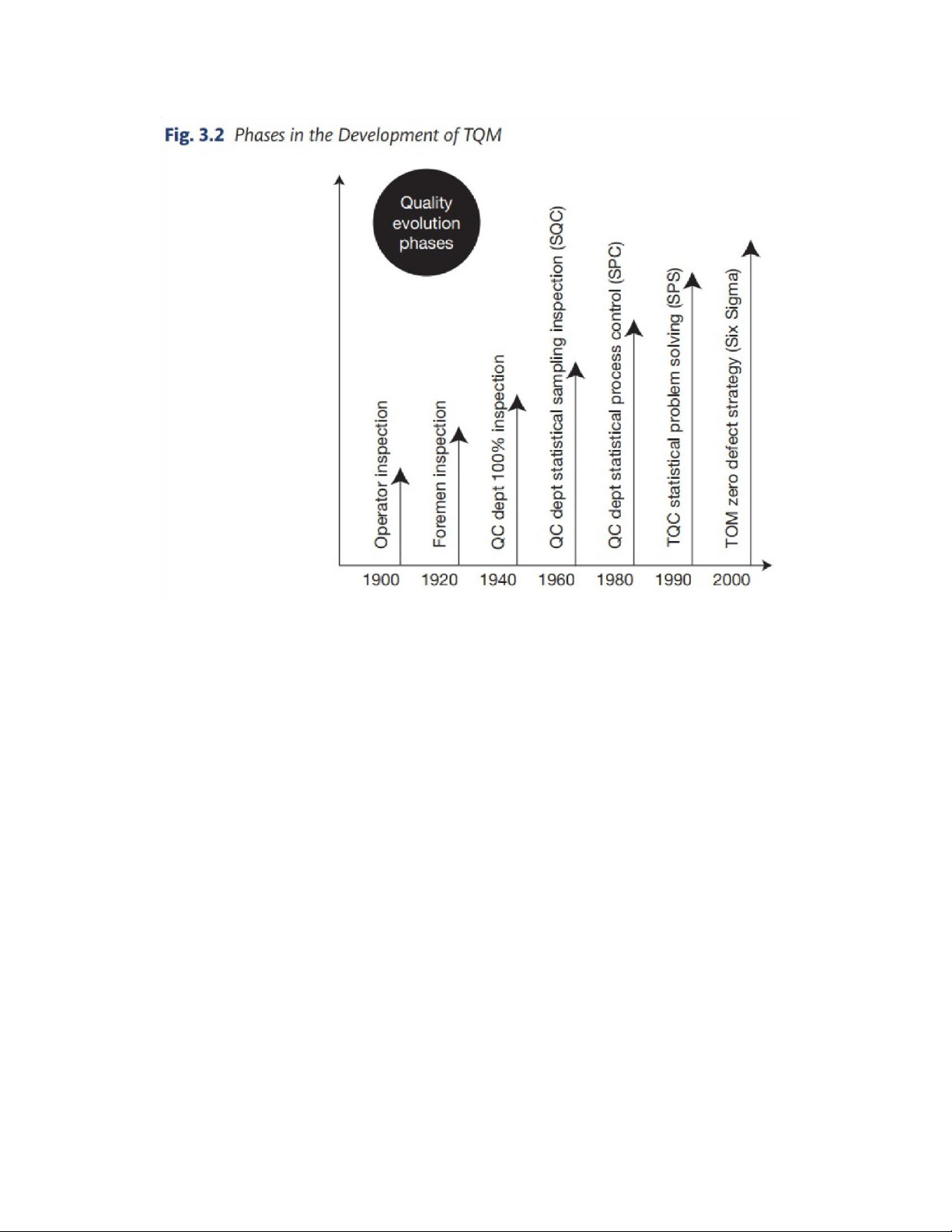
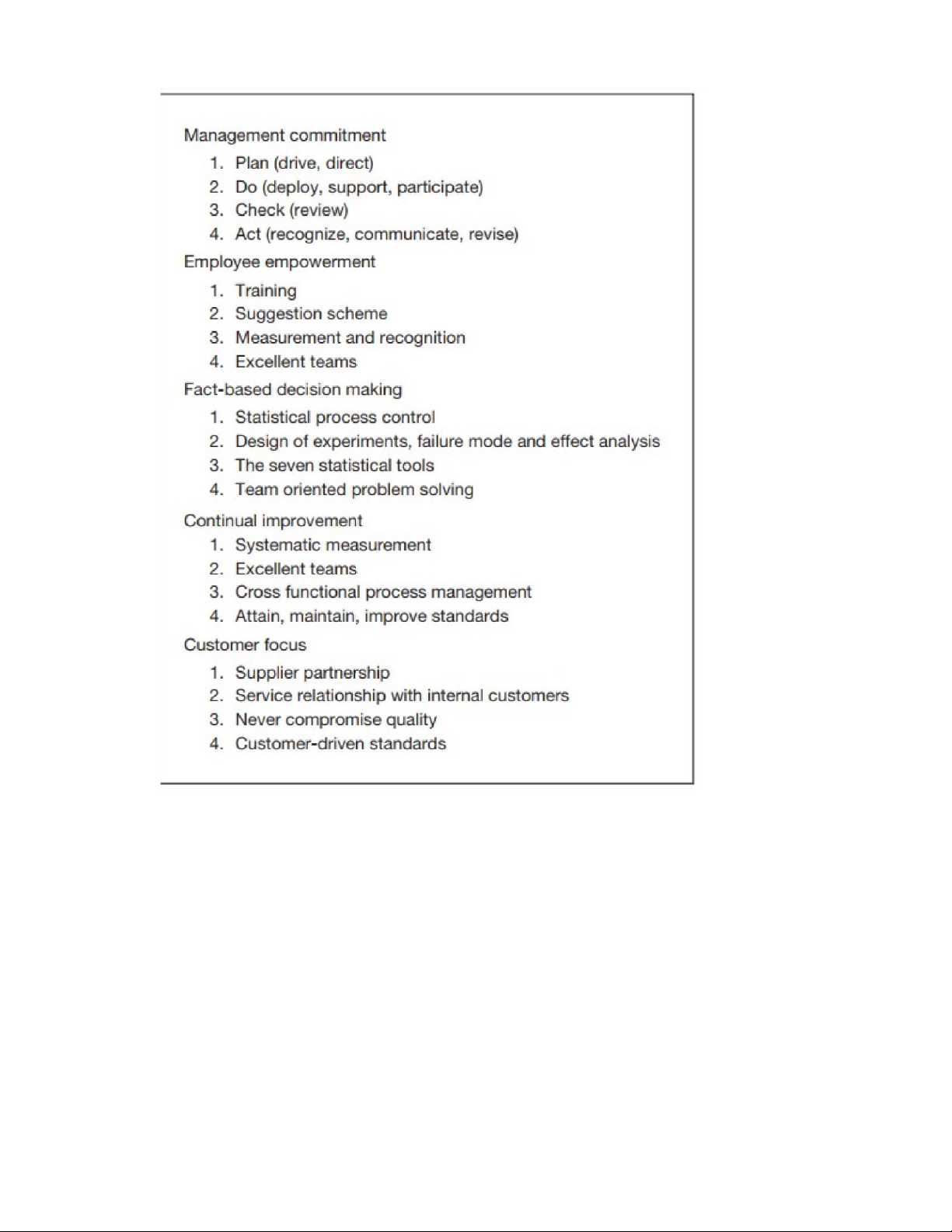
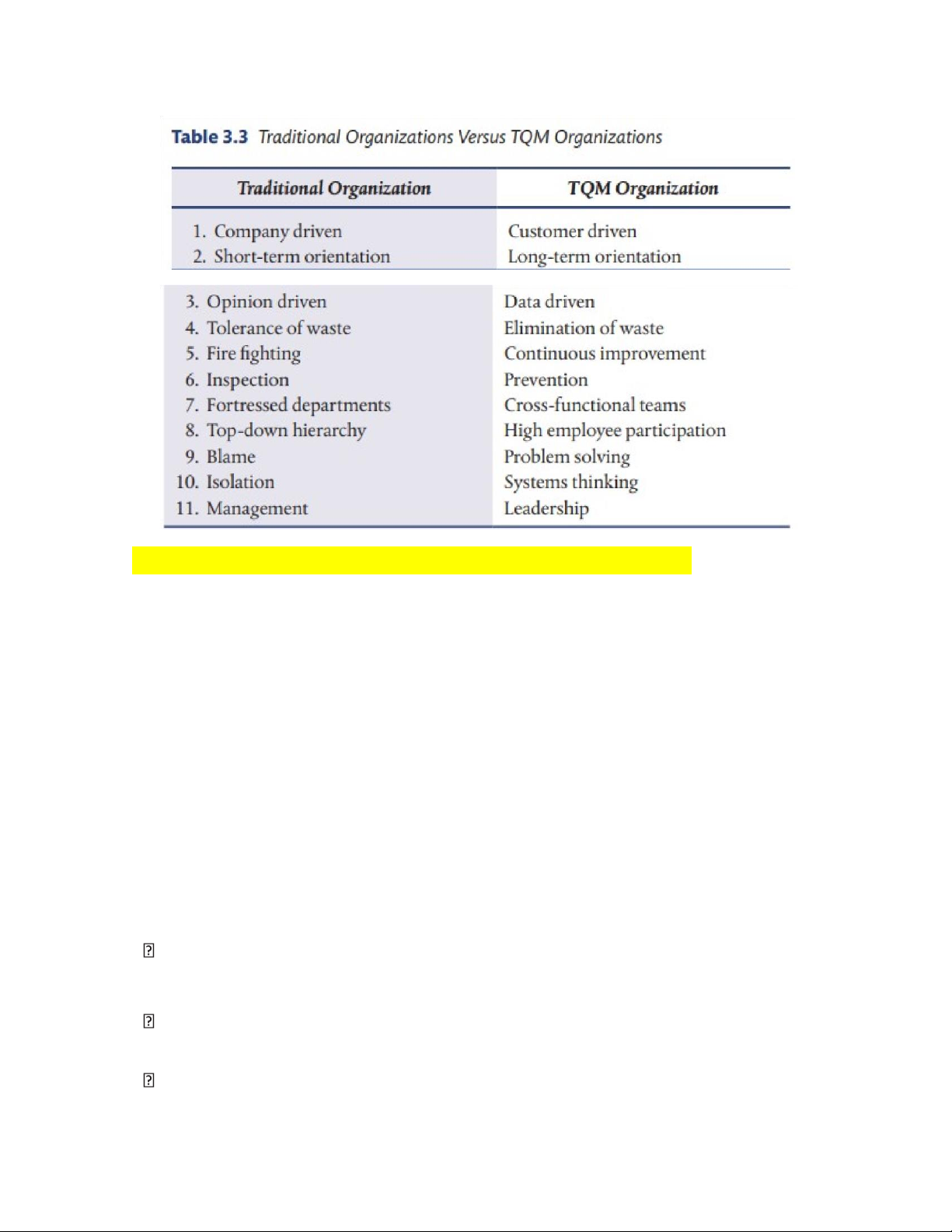
Preview text:
lOMoAR cPSD| 45349271 Table of Contents
CHAPTER 1: TOTAL QUALITY MANAGEMENT: AN OVERVIEW ........... 4
1. Define quality ........................................................................................................ 4
2. Why it is important to study matter ................................................................... 4
3. QUALITY CONTROL VS QUALITY ASSURANCE ..................................... 4
4. Discuss the three levels of quality ....................................................................... 5
5. What are the different types of quality? ............................................................ 6
6. List David Garvin’s five approaches to defining quality ................................. 7
7. Mention the five paradigms of quality ............................................................... 7
8. What are Garvin’s eight dimensions of product quality? ................................ 9
9. What are the SERVQUAL dimensions of service quality? ............................ 10
10. Differentiate between service quality and product quality .......................... 11
11. Differentiate between old quality and new quality ....................................... 11
12. What are the four categories of cost of poor quality? .................................. 11 CHAPTER 3: THE PHILOSOPHY OF TOTAL QUALITY
MANAGEMENT ................................................................................................... 12
1. Define TQM ........................................................................................................ 12
2. What are the four main stages in the development of TQM?........................ 12
3. List the five pillars of TQM ............................................................................... 14
4. Mention the eight key elements of TQM.......................................................... 14
5. What are the seven phases in the development of TQM? .............................. 18
7. Differentiate between a TQM organization and a traditional organization. 20
.................................................................................................................................. 20
9. Explain the TQMEX model .............................................................................. 20
10. Discuss the prerequisites of TQM ................................................................... 20
11. What are the steps for implementing a TQM programme? ........................ 21
Establish quality improvement teams ................................................................... 21
13. Explain the benefits of TQM with an example.............................................. 22
CHAPTER 4: LEADERSHIP AND TOTAL QUALITY MANAGEMENT .... 22
1. Define leadership ................................................................................................ 22 1 lOMoAR cPSD| 45349271
2. Explain five traits of a successful leader .......................................................... 22
3. Leadership functions ......................................................................................... 23
4. Discuss visionary leadership with an example/ Name the eight principles
ofvisionary leadership ............................................................................................ 24
5. Describe six natural levels of leadership .......................................................... 24
6. What do you mean by CSR? ............................................................................. 26
7. Explain the main components of CSR ............................................................. 26
9. Discuss CSR issues for various stakeholders ................................................... 27
10. Describe the benefits of CSR ........................................................................... 28
11. Define SQM ....................................................................................................... 30
12. What is a vision, mission, value statement? ................................................... 30
13. Explain the five phases of SQM ...................................................................... 30
14. Explain balanced scorecard/ Name the four perspectives of a balanced
scorecard/ Benefit ................................................................................................... 31
16. Define quality culture. 5 stages of quality culture ........................................ 32
19. Forces for change ............................................................................................. 33
21. Describe the six approaches to deal with resistance to change .................... 35
1. Which are the two main approaches to quality control? ............................... 36
2. Variability ........................................................................................................... 37
3. Describe SPC ...................................................................................................... 38
4. Describe probability ........................................................................................... 38
5. What are the different types of probability distributions? ............................ 38
6. five parameters used to investigate measurement system analysis ............... 38
7. What is process capability? ............................................................................... 38
8. Discuss process capability studies ..................................................................... 38
10. Two widely used process capability indices ................................................... 39
11. What is sampling? ............................................................................................ 40
12. What is a good sampling plan? ....................................................................... 40
13. The advantages of sampling inspections ........................................................ 40
14. What are the two ways in which inspection is carried out? ......................... 41 2 lOMoAR cPSD| 45349271
15. Name the two broad classification of sampling methods ............................. 41
16. What is acceptance sampling? What are the reasons for acceptance
sampling? ................................................................................................................ 42
17. Name the three types of acceptance sampling plans ..................................... 42
18. What is an OC curve? How can we make an acceptance sampling plan
stricter? ................................................................................................................... 43
19. Name the quality indices for acceptance sampling ....................................... 43
20. What is an ideal OC curve? Explain the producer’s and consumer’s risk. 43
.................................................................................................................................. 43
21. Define quality assurance .................................................................................. 44
22. What is a quality policy? ................................................................................. 45
23. Explain the meaning of a quality manual ...................................................... 45 3 lOMoAR cPSD| 45349271
CHAPTER 5: STATISTICAL CONCEPTS IN QUALITY MANAGEMENT36
CHAPTER 1: TOTAL QUALITY MANAGEMENT: AN OVERVIEW 1. Define quality.
Quality is about meeting the needs and expectations of customers Customer-driven
(Definitions of Quality)
• Value for price paid: Quality is defined in terms of the utility of the product
or service for the price paid.
• Support services: Quality is defined in terms of the support provided after the
product or service is purchased.
• Psychological criteria: A way of defining quality that focuses on judgemental
evaluations of what constitutes product or service excellence.
2. Why it is important to study matter. IMPORTANCE OF QUALITY - Meet customer expectations
- Increase reputation and image
- Meets or exceeds industry standards - Effective cost management
3. QUALITY CONTROL VS QUALITY ASSURANCE Quality control Quality assurance
It’s a set of activities for ensuring quality It’s a set of activities for ensuring quality
in products. The activities focus on in processes by which products are
identifying defects in the actual developed. produced.
It aims to identify and correct defects in It aims to prevent defects with a focus
the finished product and is a reactive on the process used to make the product. process.
It’s a proactive quality process. 4 lOMoAR cPSD| 45349271
The goal is to idenfify defects after a The goal is to improve development and
product is developed and before it’s test processes so that defects don’t arise released.
when the product is being developed
Finding and eliminating sources of It establishes a good quality quality problems through
tools management system and conducts equipment so that
customer’s assessment of its adequacy and periodic
requirements are continually met.
conformance audits of the operations of the system
The activities or techniques used to Prevention of quality problems through
achieve and maintain the product planned and systematic activities
quality, process, and service.
including documentation is done.
It’s usually the responsibility of a All team members involved in
specific team that tests the product for developing the product are responsible defects. for quality assurance. It is a corrective tool It is a managerial tool
Statistical quality control (SQC) is a part Statistical process control is a part of of quality control quality assurance
Validation/Software testing is an Verification is an example of quality example of quality control assurance
4. Discuss the three levels of quality.
Viewing organization from three levels helps clarify roles and responsibilities for
quality management, requiring total involvement of all employees in a committed organization.
1. Organizational level
Quality concerns at this level involve meeting external customer requirements,
requiring regular customer inputs and top managers to focus on organizational level.
The following questions are designed to help define at this level.
What products and services meet your expectations?
What products and services do not meet your expectations?
What are the products or services that you need but are not receiving? 5 lOMoAR cPSD| 45349271
Are you receiving products or services that you do not need? 2. Process Level
Organizational units like marketing, design, product development,boperations,
finance, purchasing, and billing can optimize activitiesbunder their control,
potentially sub-optimizing the entire organization.
What products or services are the most important to external customers?
What processes produce those products and services?
What are the key inputs to the process?
Which processes have the most significant effect on the organization’s
customer- driven performance standards?
Who are my internal customers and what are their needs
3. The performer or job level or the task design level
At the performer level, output standards should align with organizational and
process-level quality and customer service requirements, requiring employees to
understand and adhere to these standards.
To define quality at the job level, one must ask questions such as:
What is required by customers, both internal and external?
How can the requirements be measured?
What is the specific standard for each measure?
5. What are the different types of quality?
Types of quality are recognized to ensure consistent production of goods and services at reasonable costs. 1) Quality of Design
- Quality of the design is the quality which producer and supplier is intended to offer to customer.
- The quality of design is determined by conducting market research to identify
product characteristics that equate to customer satisfaction.
2) Quality of Conformance
- Quality of conformance is the level product actually produced and delivered
through the production or service process of the organization as per the specification design. 6 lOMoAR cPSD| 45349271
- Quality of conformance is the ability of a company and its suppliers to produce
products with predictable dependability and uniformity at a given cost, based on design quality requirements.
3) Quality of Performance
Quality of performance is the process of organizing manufacturing to ensure product
quality adheres to specifications.
6. List David Garvin’s five approaches to defining quality.
GARVIN’S APPROACHES TO DEFINING QUALITY
1) The Transcendent Approach:A product or service possesses excellence based
on its subjective relationship to some standard.
2) The Product-based Approach:Quality is the degree to which a product
possesses a specified set of attributes necessary to fulfill a stated purpose.”
3) The User-based Approach:Quality is the degree to which a product or service
satisfies the user’s needs, wants, or preferences.
4) The Manufacturing-based Approach: This approach seeks to objectively
measure the degree to which a product or service complies with predetermined specifications.
5) The Value-based Approach: This approach assesses quality in terms of costs
and benefits: the more benefits outweigh costs, the more a product or service
increases in value. Products or services with higher value enjoy higher quality
7. Mention the five paradigms of quality. 1. Customer-craft Paradigm 7 lOMoAR cPSD| 45349271
The product is created or services are rendered exactly in the manner desired by the
customer. Hence, the focus on the product/service and their performance is relative to the demand.
Ex: bank loans, coffee shops, furniture supplier, etc. 2. Mass-production Paradigm
- This paradigm developed post mechanization.
- Focuses on speed of production without direct customer involvement ( Even
though the product is defined with the customer in mind).
- Product performance is relatively low and rework and waste generation are evident.
- Delivery times are often low due to sales from available inventory. -
Service organizations in this model are labor intensive.
Ex: Readymade buildings for commercial enterprises.
3. Statistical Quality Control Paradigm
This is similar to the mass production paradigm except that the emphasis here is more
on the process. Applied together with mechanized production, the statistical process
control results in low scrap and rework and low cost of production. Products are
designed and built, and statistical techniques are used after which customers are acquired.
Ex: automobile parts, electronic components, etc.
4. Total Quality Management Paradigm
- The focus here is on the customer and the supplier.
- Product lines here are the same as in the case of the mass production paradigm.
However, the customer is a part of the product definition, creation and
performance evaluation phases.
- Employee involvement and empowerment, customer-focus, continuous
improvement, top management commitment, training, teamwork are its key tenets.
- The result is a high quality product, low cost, fast delivery and substantially
reduced opportunities for rework and low generation of scrap 5. Techno-craft Paradigm
- A new frontier of quality that seeks to employ the custom-craft paradigm in
performance while reducing delivery time. 8 lOMoAR cPSD| 45349271
- Requires a high level of product process flexibility.
- The requirement is to integrate machine (computer), men and automation.
- Each unit is designed and built on the basis of customer requirements. -
Examples: in the software and apparel industries.
8. What are Garvin’s eight dimensions of product quality?
A quality product is a product that meets the expectations of the customers. The eight
dimensions of quality help producers to meet these expectations.
Performance: refers to the basic requirements that a product or service must meet to
satisfy the customer’s needs.
Features: refers to the additional capabilities or characteristics that a product or services may have.
Realiability: refers to the ability of a product or service to perform consistently and dependably over time. 9 lOMoAR cPSD| 45349271
Conformance: refers to the degree to which a product or service meets establiched standards and specifications.
Durability: refers to the ability of a producr or service to withstand normal wear and
tear and continue to perform over time. Serviceability:
Aesthetic: refers to the visual and sensory appeal of a product or service.
Perceived quality: refers to the customer’s overall i,pression of the quality of a product or service.
9. What are the SERVQUAL dimensions of service quality? 10 lOMoAR cPSD| 45349271
10.Differentiate between service quality and product quality.
11.Differentiate between old quality and new quality.
The difference between old and new quality lies in the fact that the old is the work of
craftsmen, wheares the new os the work of a system.
12.What are the four categories of cost of poor quality?
Cost of poor quality (COPQ): the cost associated with providing poor quality
products or services. There are 4 categories: internal failure costs, external failure
costs, appraisal costs amd prevention costs. 11 lOMoAR cPSD| 45349271
Cost of Quality = Cost of Conformance + Cost of Non-conformance
Prevention costs: are incurred to prevent or avoid quality problems: These costs are
associated woth the design, implementation, and maintenance of the quality management system.
Appraisal costs: are associated with measuring and monitoring activities related to
quality. These costs are associated with the suppliers’ and customers’ evaluation of
purchased materails, processes, products, and services to ensure that they conform to specifications Failure cost
Internal failure costs: are incurred to remedy defects discovered before the product
or service is delivered to the customer. These costs occur when the results of work
fail to reach design quality standards and are detected befor they are transferred to the customer.
External failure costs: are incurred to remedt defects discoverd by customers. These
costs occur when products or services that fail to reach design quality standards are
not detected until after transfer to customer.
CHAPTER 3: THE PHILOSOPHY OF TOTAL QUALITY MANAGEMENT 1. Define TQM.
TQM is an integrated effort designed to improve quality performance at every level of the organization.
Total: Quality involves everyone and all the activities performed in the company.
Quality: Conformance to the requirements (meeting customer requirements).
Management: Quality can and must be managed.
A core definition of Total Quality Management (TQM) describes a management
approach to long–term success through customer satisfaction.
2. What are the four main stages in the development of TQM?
The four stages identified in the evolution of TQM are: Inspection; Quality
Control; Quality Assurance; TQM. 12 lOMoAR cPSD| 45349271
TQM will force change in culture, processes and practice. These changes will be
more easily facilitated and sustained if there is a formal management system in place.
Quality Control was introduced to detect and fix problems along the production
line to prevent the production of faulty products. Statistical theory played an important role in this area.
Statistical Quality Control (SQC) is the term used to describe the set of
statistical tools used by quality professionals. SQC is used to analyze the quality problems and solve them.
Quality assurance is a component of quality management and is ‘focused on
providing confidence that quality requirements will be fulfilled. TQM •
Emphasis is placed on the target and achieving the target as soon aspossible. •
The system is simple and straight-forward. 13 lOMoAR cPSD| 45349271 •
Information delivery is accurate. •
The process is considered after the goal has been established.
Downside: Employees stop actively thinking of and implementing process
improvement – they don’t want to risk making a mistake or creating delays.
TQC (total quality control)
Emphasis is placed on the process and continuous process improvement. •
Total participation is required. Employees are encouraged to generate ideasand implement them. •
It is flexible – processes and methods can be easily changed. •
The target is not absolute - good for a changing market.
Downside: Sometimes the end result is very different from the original target
employees tend to lose sight of the goal because they are too focused on the process.
3. List the five pillars of TQM.
4. Mention the eight key elements of TQM
To be successful in implementation of TQM there are eight key elements. These eight
key elements of TQM are: ethics, integrity, trust, leadership, teamwork, training,
communication and recognition.
The term TQM has been coined to describe a philosophy that makes quality the
driving force behind leadership, design, planning and improvement initiatives. For
this, the organization needs to concentrate on eight key elements—ethics, integrity,
trust, leadership, teamwork, training, communication and recognition as shown in 14 lOMoAR cPSD| 45349271
Figure 3.4. These elements can be divided into the following four groups—
foundation, building bricks, binding mortar and roof. I. Foundation:
It includes ethics, integrity and trust.
TQM is built on a foundation of ethics, integrity and trust. It fosters
openness, fairness and sincerity and encourages the involvement of
everyone in the organization. This is the key to unlocking the ultimate
potential of TQM. Though these three elements coexist, each offers
something unique to the TQM concept.
1. Ethics: It is a combination of written and unwritten codes of principles and
values that govern decisions and actions within a company. In the business
world, an organization’s culture sets standards for determining the difference
between good and bad decision making and behaviour. Business ethics boils
down to knowing the difference between right and wrong and choosing to do
what is right. It describes the actions of individuals within an organization, as
well as those of the organization as a whole.
2. Integrity: It is the consistency of actions, values, methods, measures, principles,
expectations and outcomes. As a holistic concept, it judges the quality of a
system in terms of its ability to achieve its own goals. Integrity may be seen as
the quality of having a sense of honesty and truthfulness in regard to the
motivation for one’s actions.
3. Trust: Trust builds a cooperative environment essential for TQM. Trust is a
byproduct of integrity and ethical conduct. It is a relationship based on reliance.
Trust fosters everybody’s participation and allows empowerment that
encourages pride of ownership and commitment. Trust fosters individual
risktaking for continuous improvement and is essential to ensure customer satisfaction.
II. Building Bricks: It includes leadership, teamwork and training. Leadership,
teamwork and training are the building bricks of TQM. Leadership in TQM
requires the manager to provide an inspiring vision, make strategic
decisions and instill values that guide subordinates. Teamwork offers
continuous improvement in processes and operations. The teams may be
quality improvement teams or excellence teams, problemsolving teams or
natural work teams. Training is very important for employees to be highly productive. 15 lOMoAR cPSD| 45349271
4. Leadership: It is the most important element in TQM. Leadership is about
raising the aspirations of followers and enthusing people with a desire to reach
the goals. A good leader creates a vision, passionately owns it and relentlessly
drives it till completion. Total quality management initiatives have to be
introduced and led by the top management.
5. Teamwork: There are some well-established links between the use of work
teams and the development of total quality management programmes. There are,
however, a great variety of teams that are used in conjunction with the
philosophy of TQM and there is seemingly no settled or dominant combination
of team types that are used. The attributes of teams that are used in conjunction
with TQM may vary greatly. Teams may be temporary, adhoc or permanent,
they may be functional or cross-functional, voluntary or compulsory, have
members with multiple skills or complementary skills, and may have a limited
scope of responsibility or they may exercise considerable autonomy and selfdirection.
TQM organizations mainly adopt three types of teams: a.
Problem-solving teams: These are temporary and formed to solve
certainproblems, identify and overcome causes of those problems. They generally
last from one week to three months. b.
Quality improvement teams: These are temporary teams with the purpose
ofdealing with specific problems that often recur. These teams are set up for a
period of three to twelve months. c.
Natural work teams: These teams consist of small groups of skilled
workerswho share tasks and responsibilities. These teams use concepts such as
employee involvement teams, self-managing teams and quality circles.
6. Training: Training is essential for all the employees to be highly productive. All
the employees will need to be trained in interpersonal skills, ability to function
in teams, problem solving, decision making, job performance and improvement,
business economics and technical skills. Employees are trained by supervisors
of each department so that they can become effective employees of the company.
Bird’s-eye view: Total quality is a description of the attitude, culture and
organization of a company that strives to provide customers with products and
services that satisfy their needs. 16 lOMoAR cPSD| 45349271
III. Binding Mortar: It includes communication. Communication binds
everything together, starting from the foundation and going up to the roof.
Communication is the vital link between all the TQM elements and must
be prevalent in an organization in order for TQM to work the way it should.
The channels of communication need to be credible and easily interpreted
for all members of the organization.
6. Communication: It acts as a link between all the elements of an organization.
For communication to be effective, the receiver must interpret the message in
the way the sender intended. The different types of communication are downward communication, upward communication and lateral communication.
Downward communication: This is a dominant form of communication in an
organization. Presentations and discussions are two examples of this form of
communication. The supervisors are able to make the employees clearly understand TQM using this.
Upward communication: The lower-level employees are able to offer
suggestions on the effects of TQM to the upper management using upward
communication. Supervisors must listen effectively and incorporate the insights
and constructive criticism offered by the employees in correcting the situations
that arise through the use of TQM. This creates a level of trust between
supervisors and employees. This is also similar to empowering communication,
where supervisors listen to others.
Lateral communication: This type of communication is important because it
breaks down barriers between departments. It also allows a more professional
dealing with customers and suppliers.
IV. Roof: It includes recognition. Recognition is the last and final element of
TQM. There can be a huge change in self-esteem, productivity and quality
when the contributors are recognized. This recognition brings greater
internal customer satisfaction, which in turn leads to external customer
satisfaction in the organization.
8. Recognition: Recognition should be provided for both suggestions and
achievements, for both teams and individuals. The most important
responsibility on a supervisor is that of according recognition to the employees under him. 17 lOMoAR cPSD| 45349271
5. What are the seven phases in the development of TQM?
6. Mention the key principles of TQM.
People at all levels are the essence of an organization and their full involvement
enables their abilities to be used for the organization’s benefit.
The process approach is a management strategy. When managers use a process
approach, it means that they manage and control the processes that make up their organizations. 18 lOMoAR cPSD| 45349271 19 lOMoAR cPSD| 45349271
7. Differentiate between a TQM organization and a traditional organization.
8. Differentiate between conventional quality and total quality.
9. Explain the TQMEX model.
The TQMEX Model advocates an integrated approach in order to support the
transition to systems management, which is an ongoing process of continuous
improvement that begins when the company commits itself to managing by
quality. The model illuminates the elements that help us to understand the TQM
philosophy and its implementation company-wide. It is necessary to develop a
conceptual model in order to have a systematic approach to TQM. TQMEX model
is a sequence of steps arranged logically to serve as a guideline for the
implementation of a process in order to achieve the ultimate goal.
10. Discuss the prerequisites of TQM.
The following points should be kept in mind while implementing TQM:
Top management must be able to overcome the obstacles, most of which will
emanate from the management itself.
It must be understood that TQM cannot be accomplished with the participation of
only a few. All employees in the organization must pursue this end.
Resources, i.e. people, time, money and effort, must be dedicated over a long period of time. 20