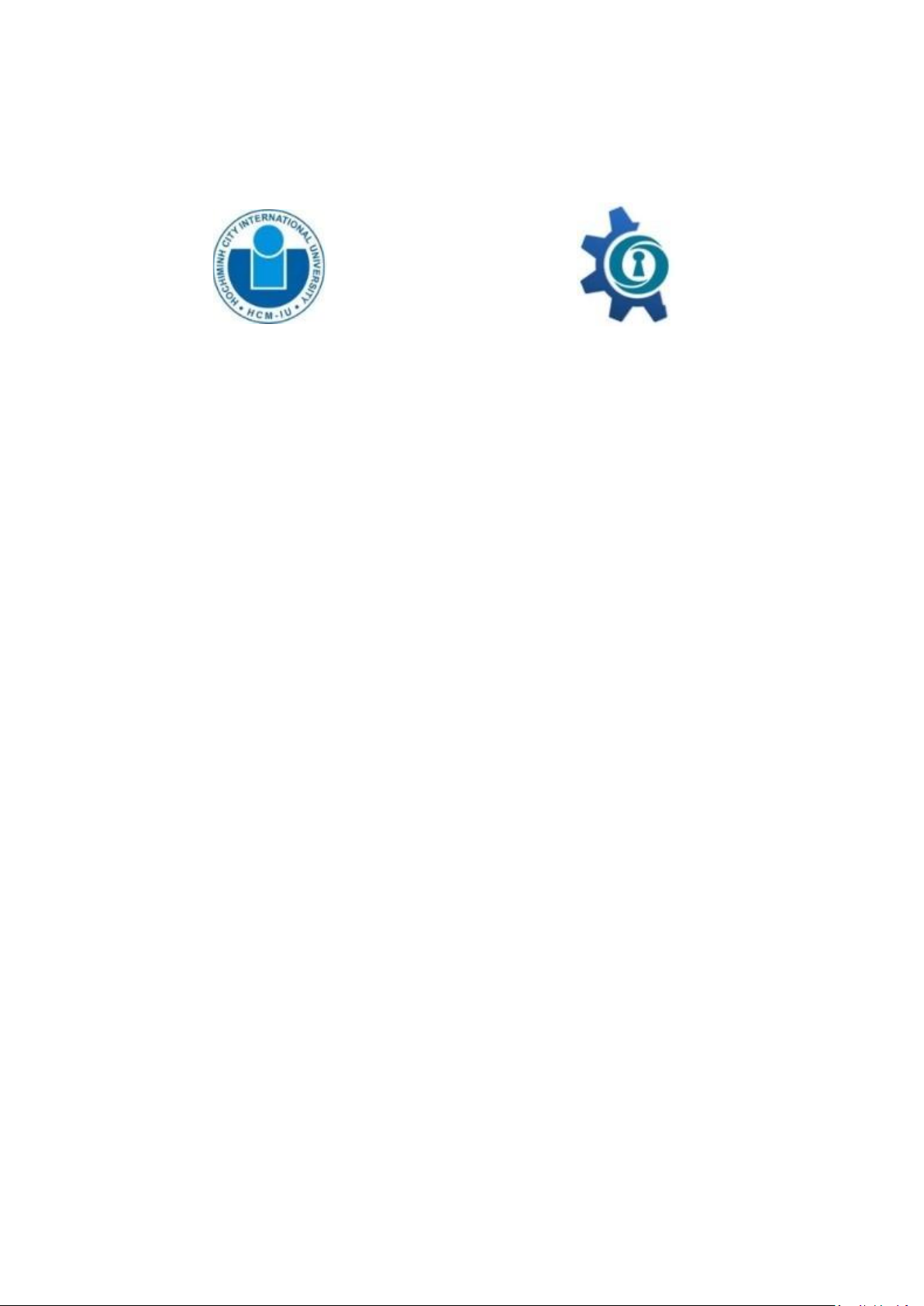
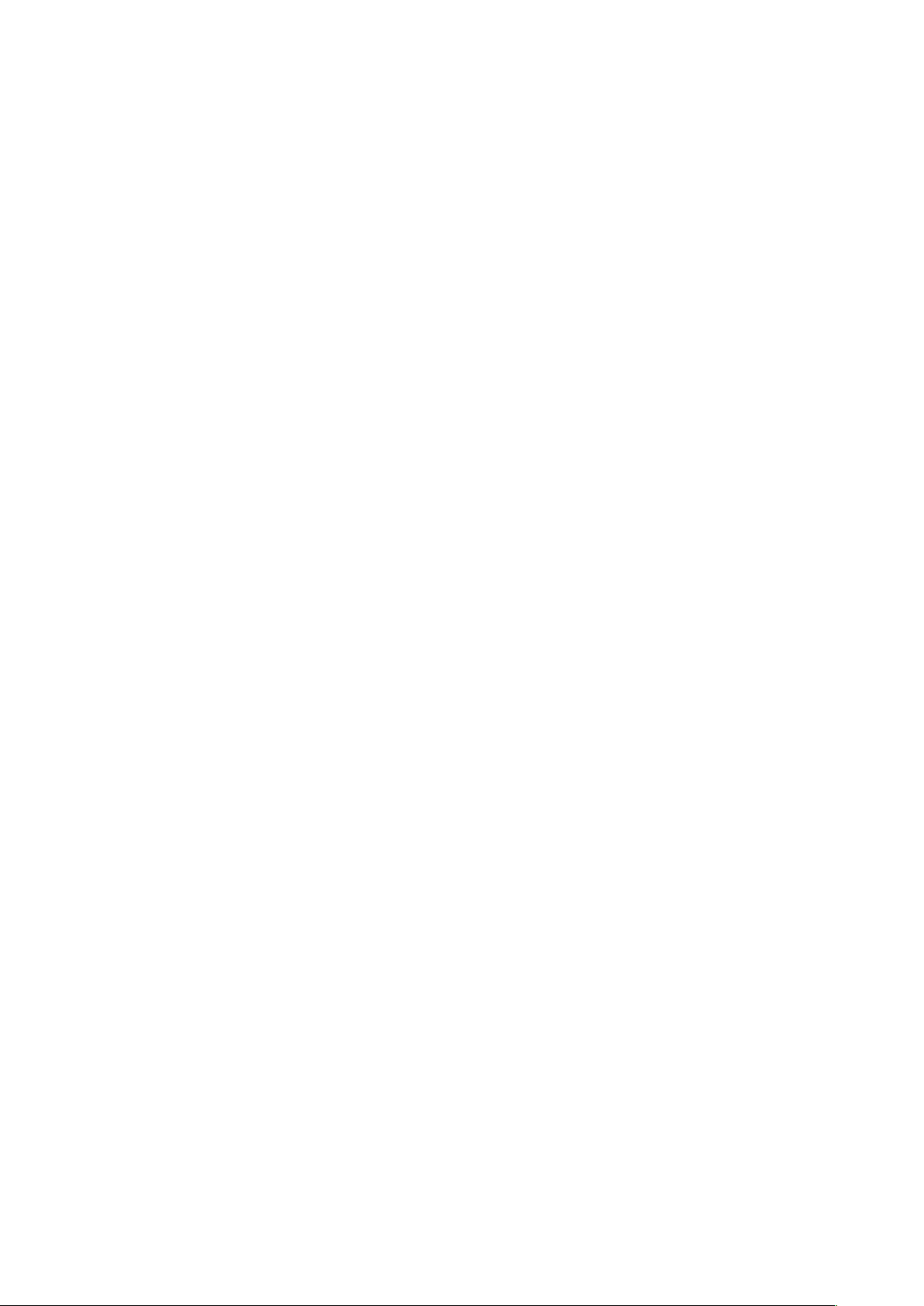
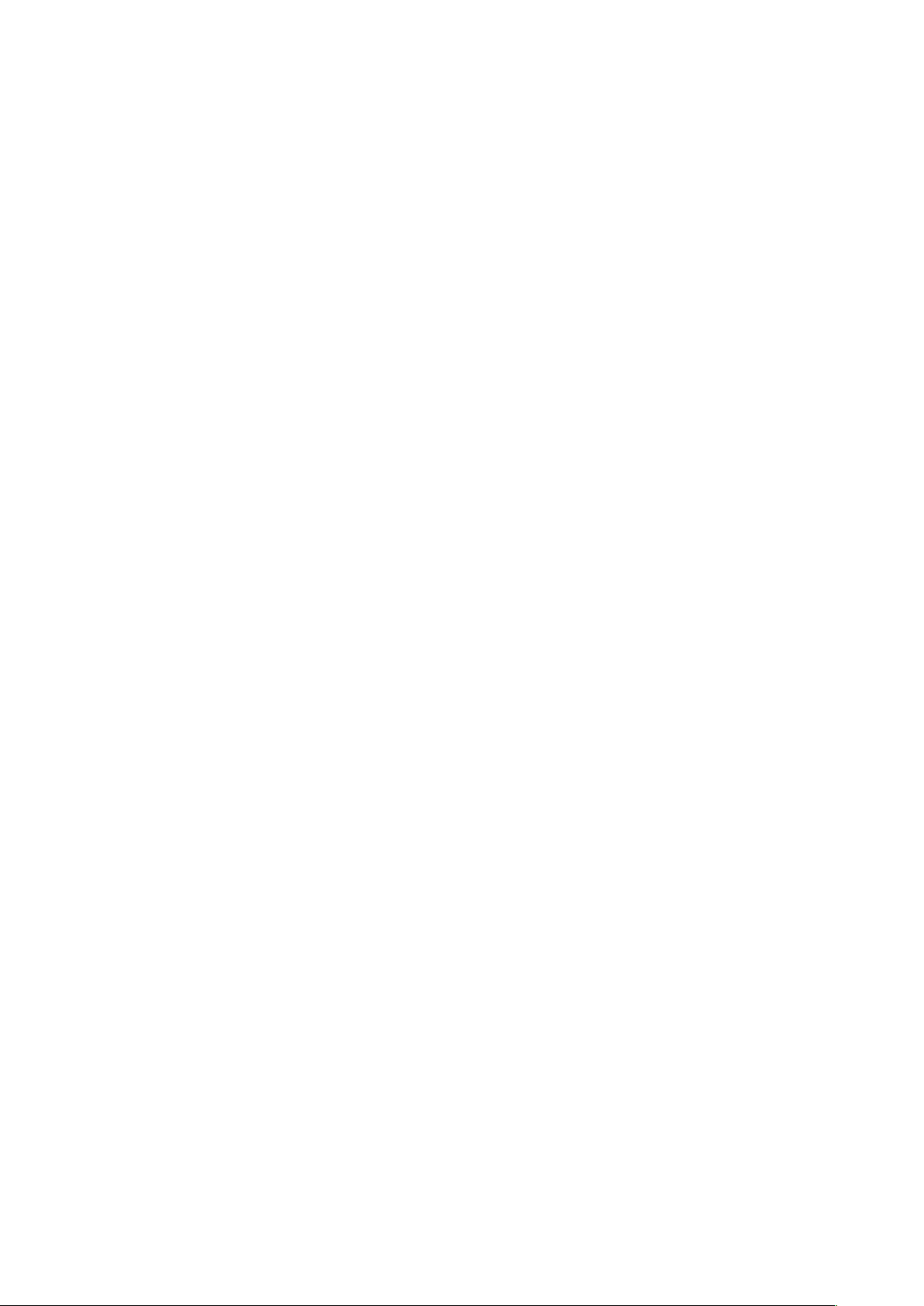
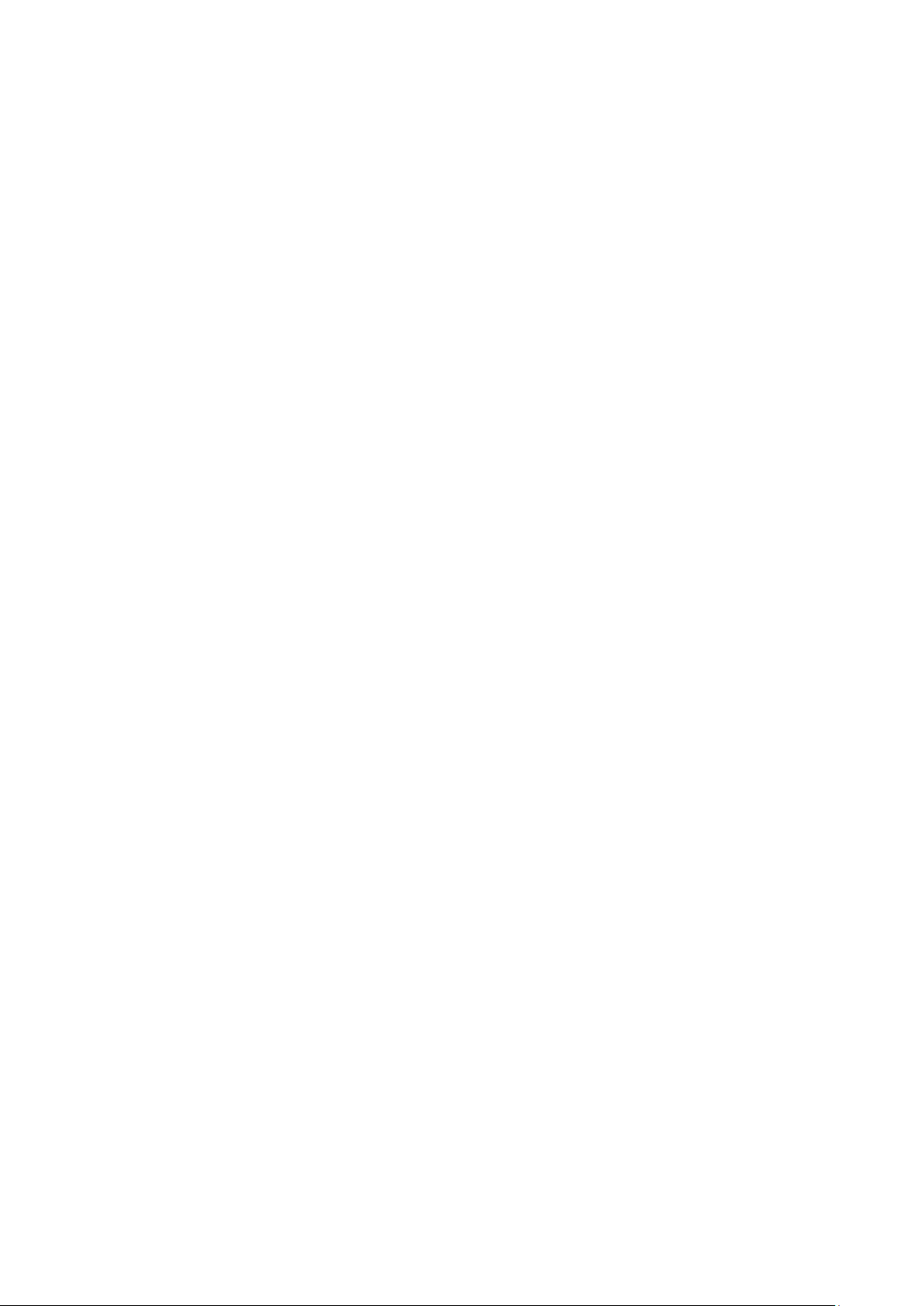
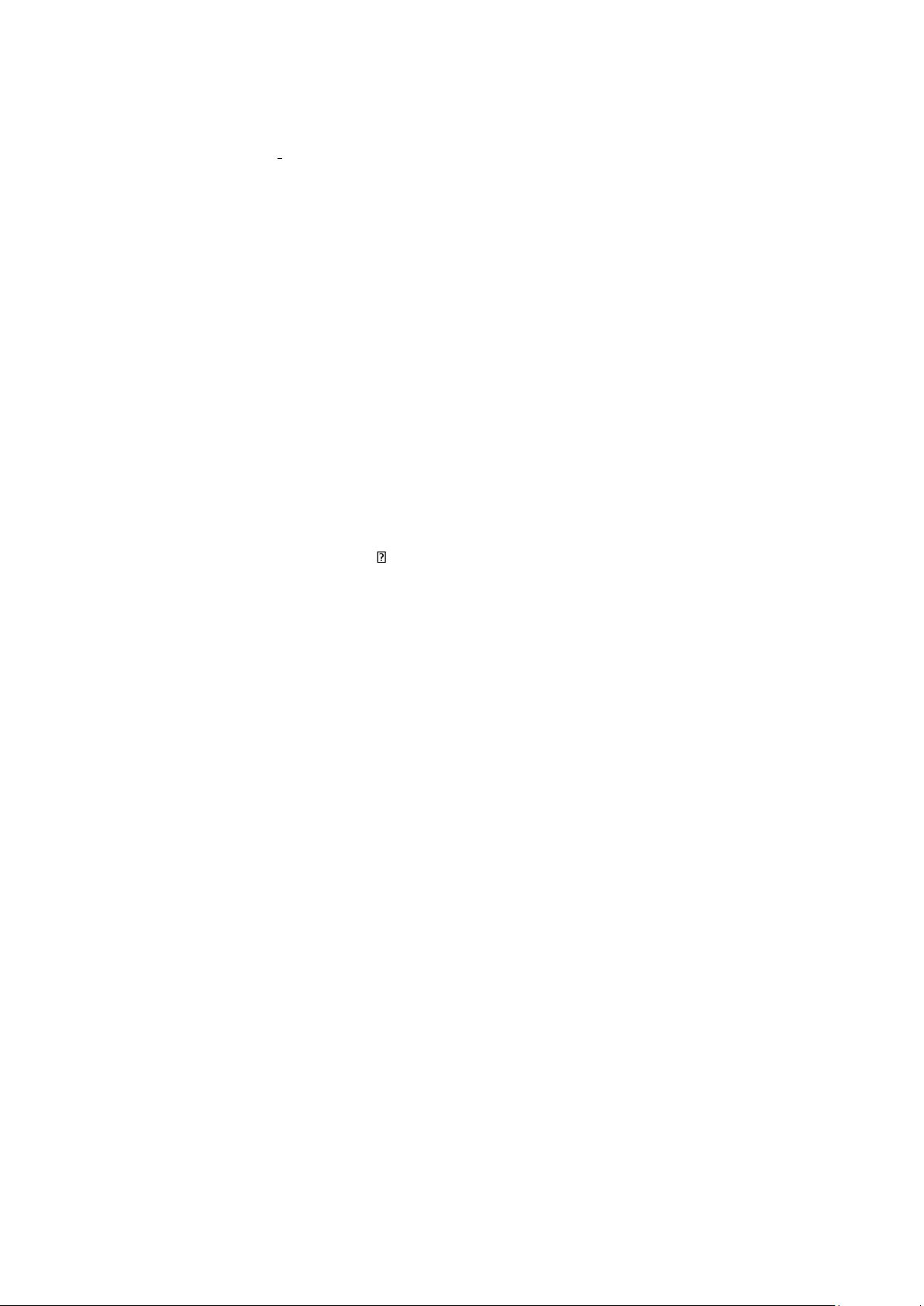
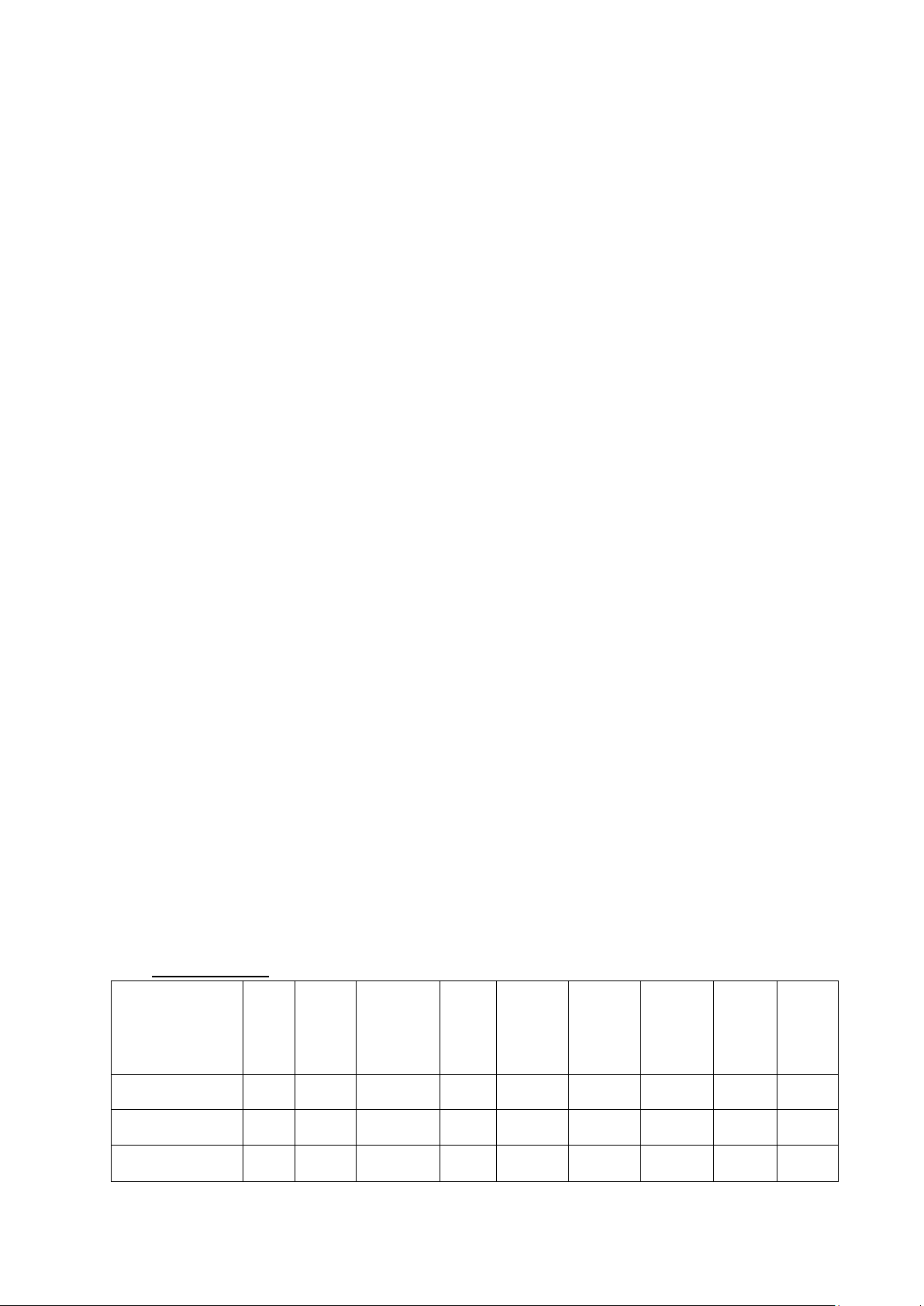
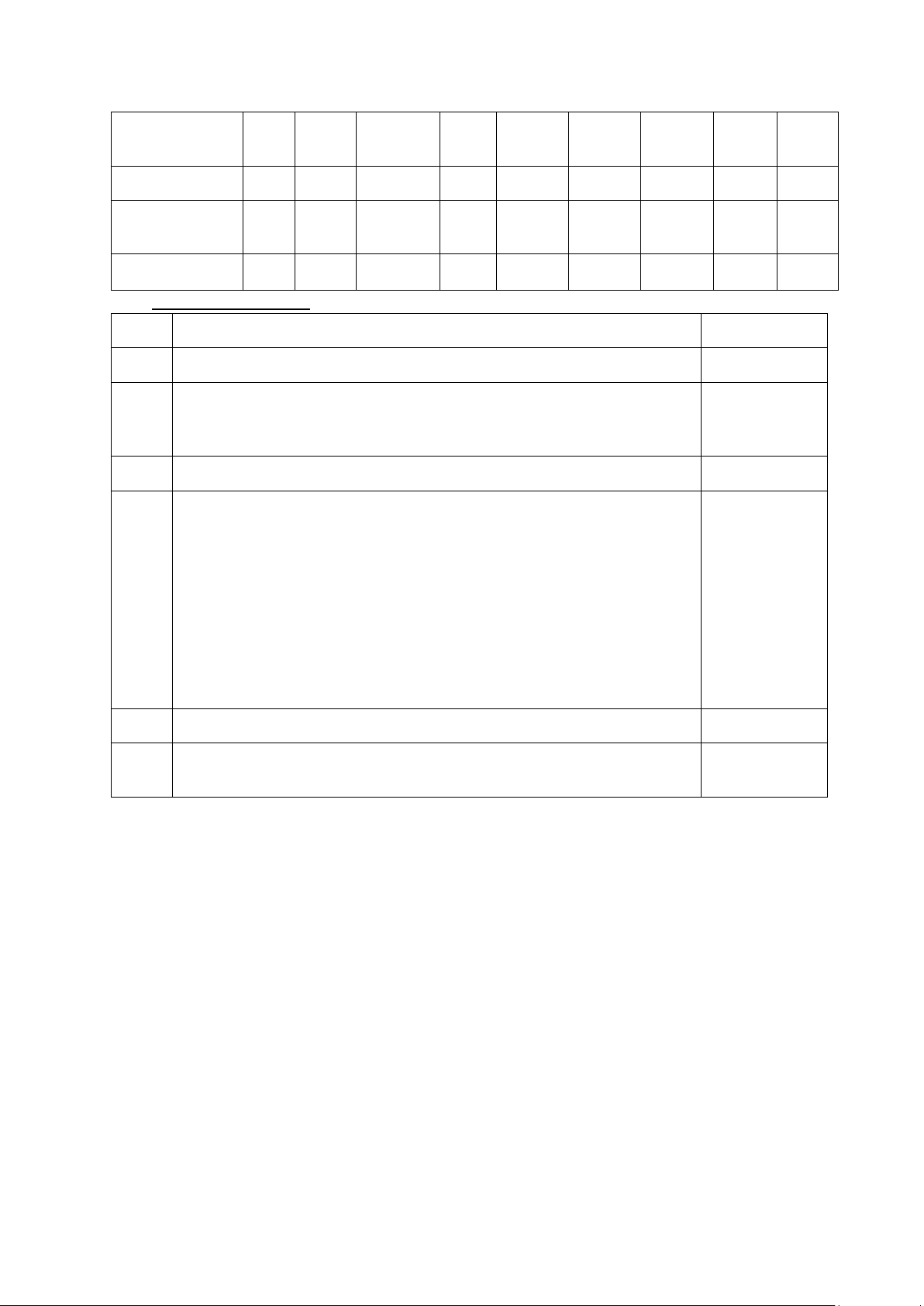
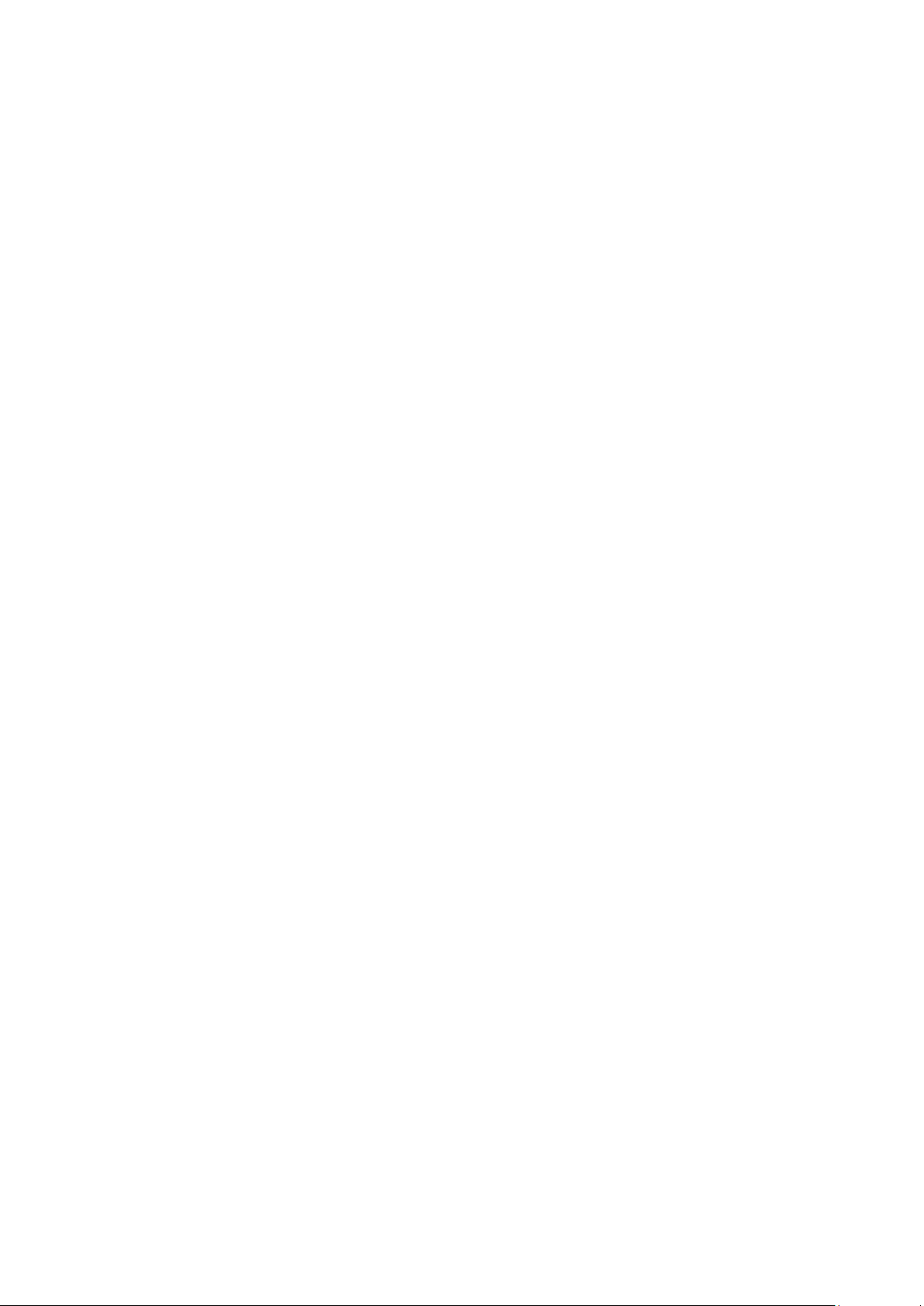
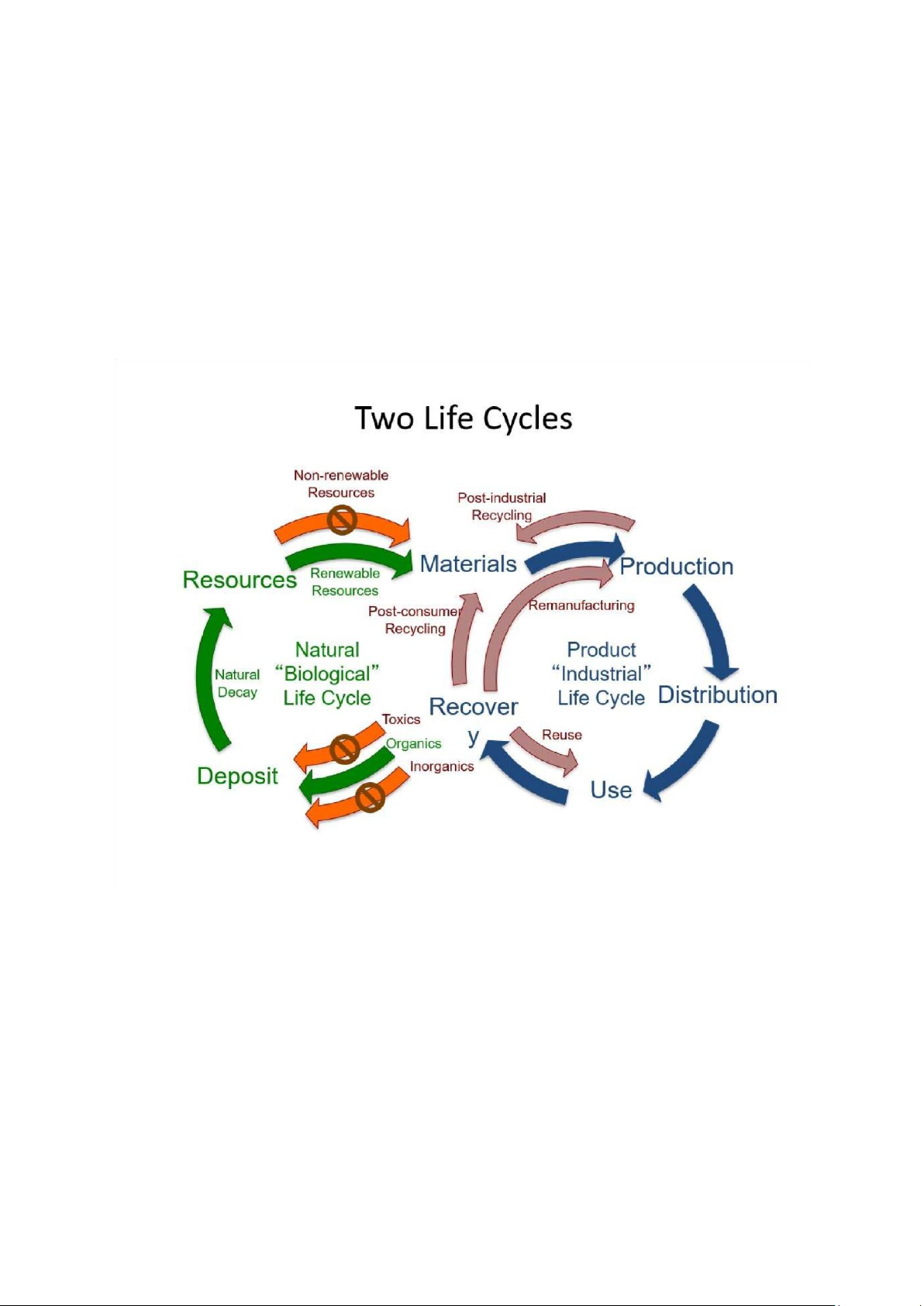
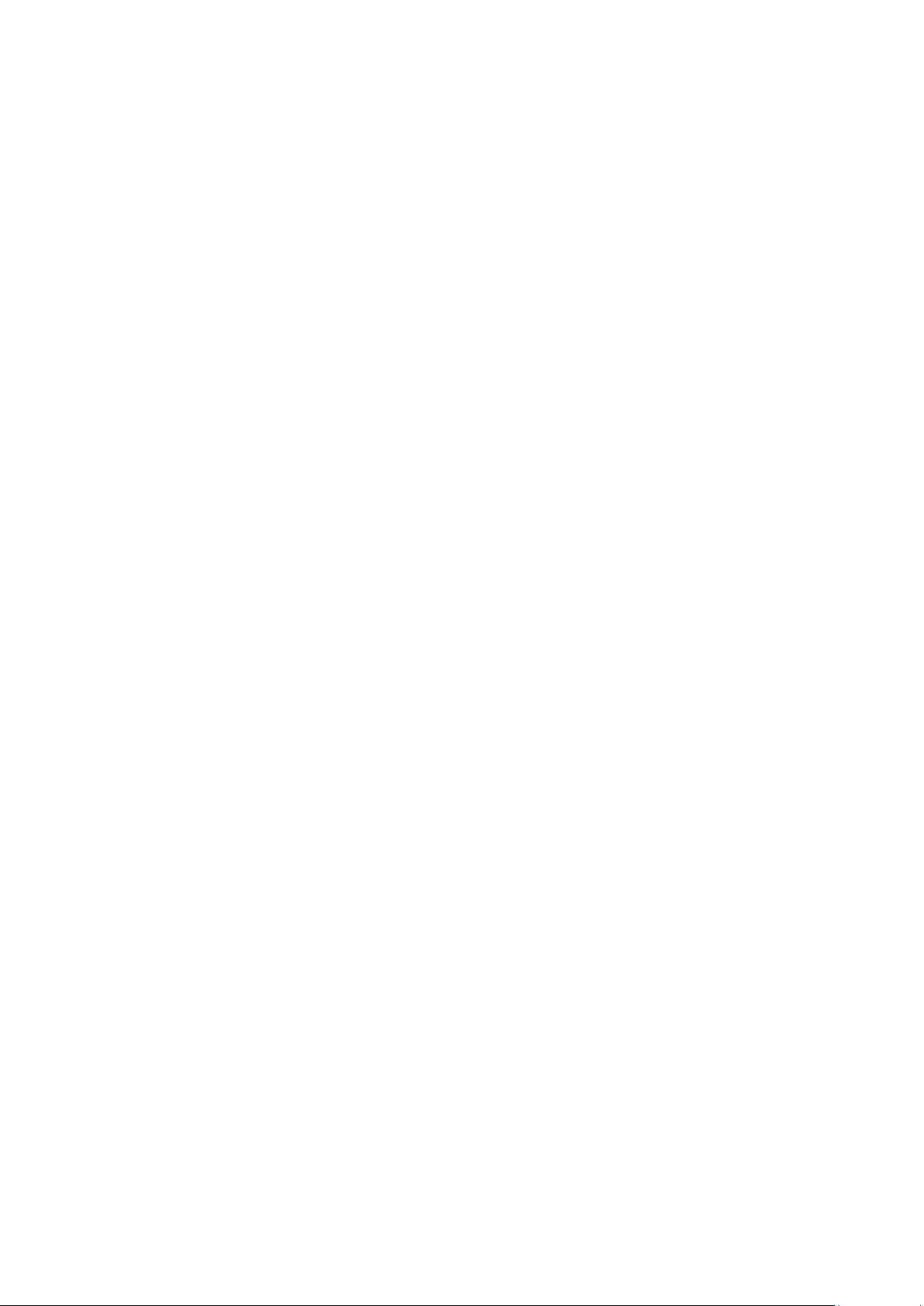
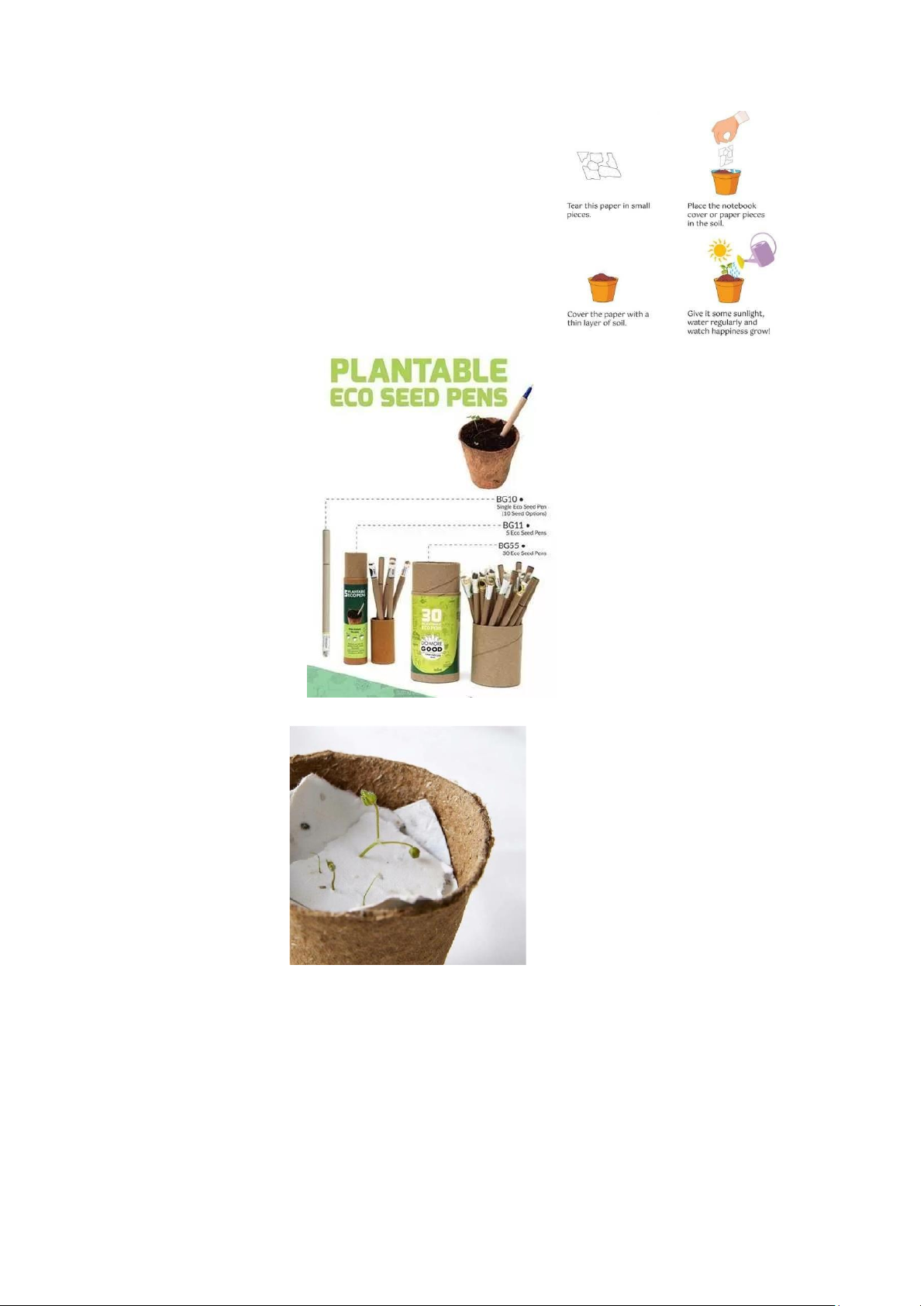
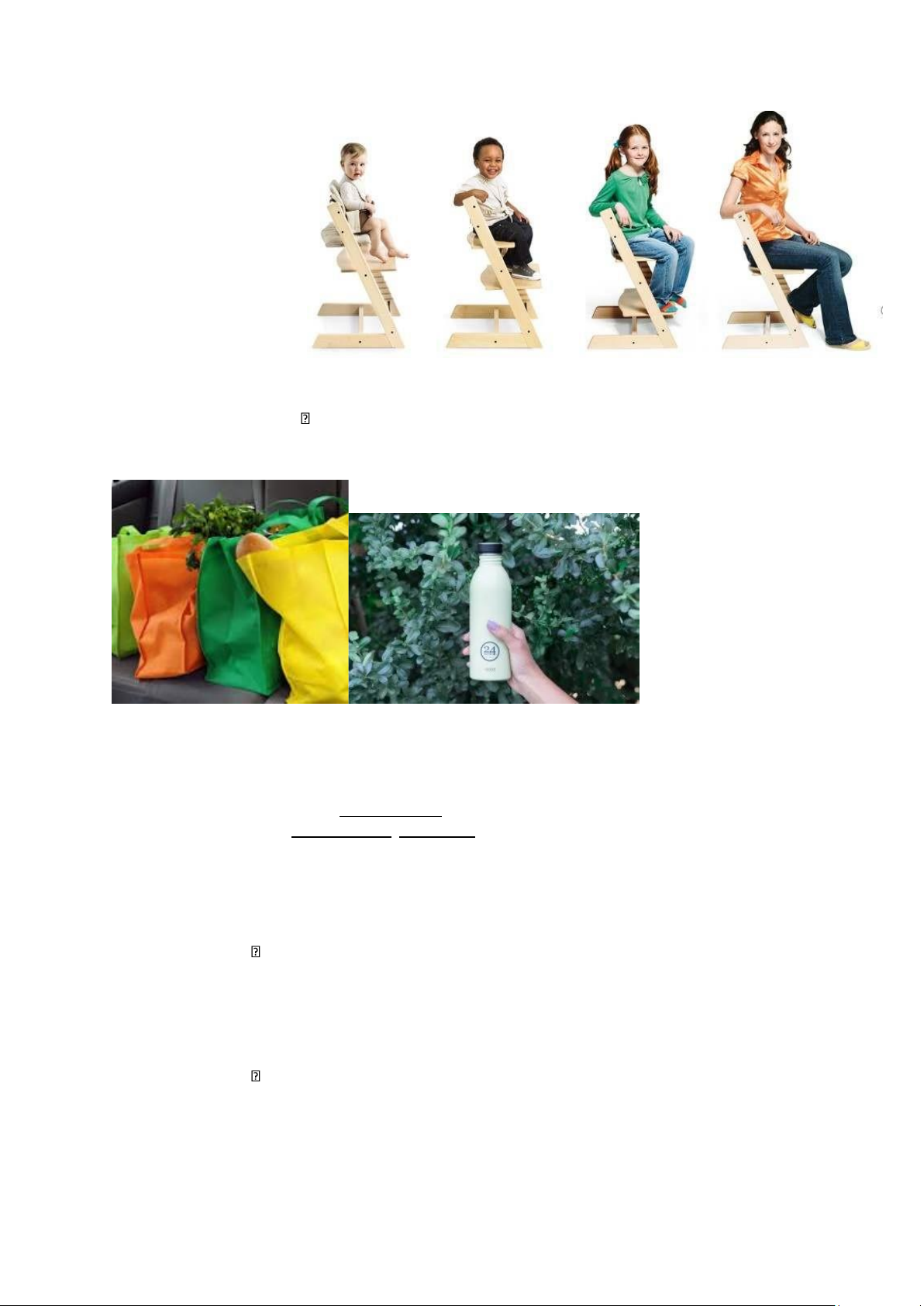
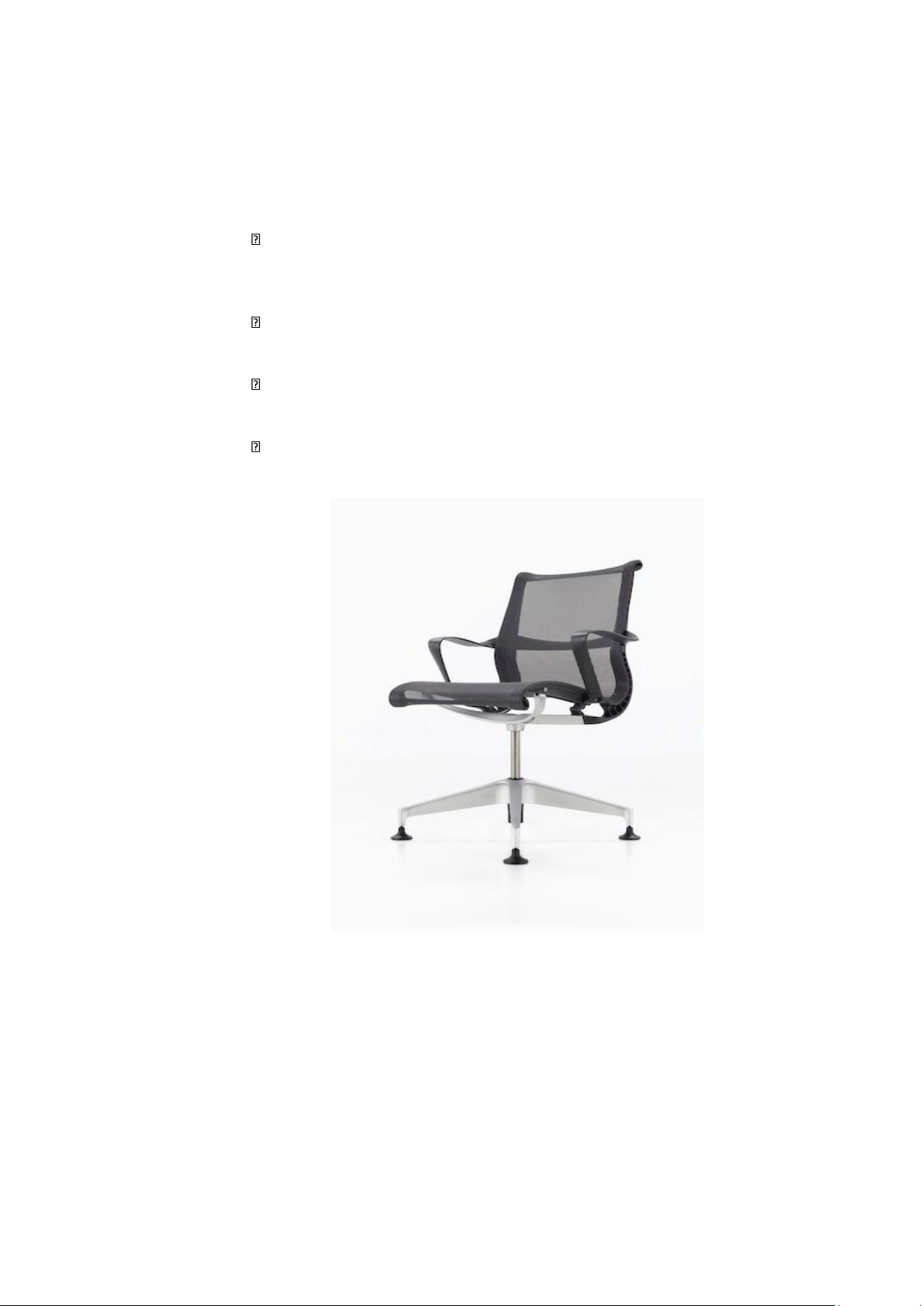
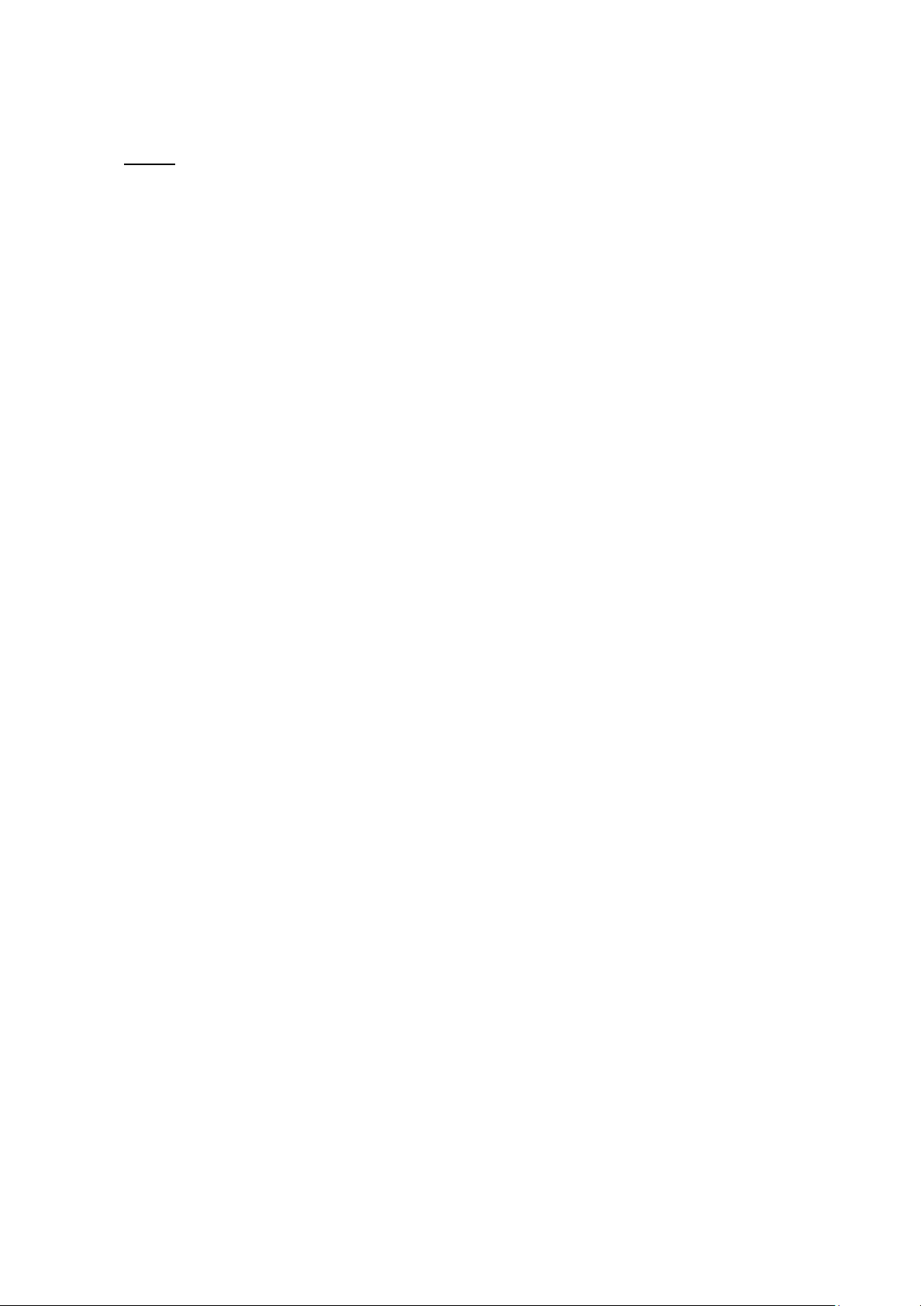
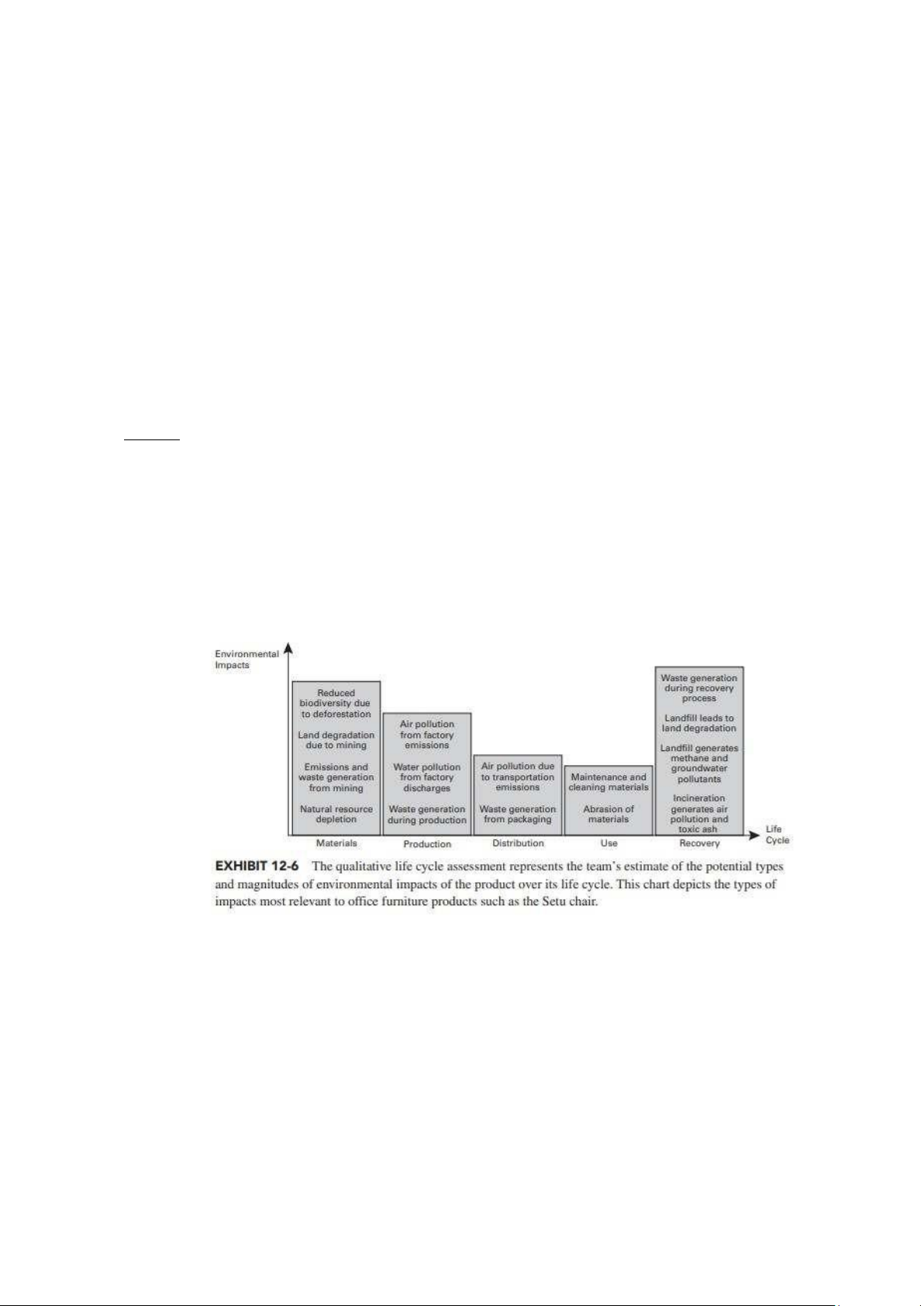
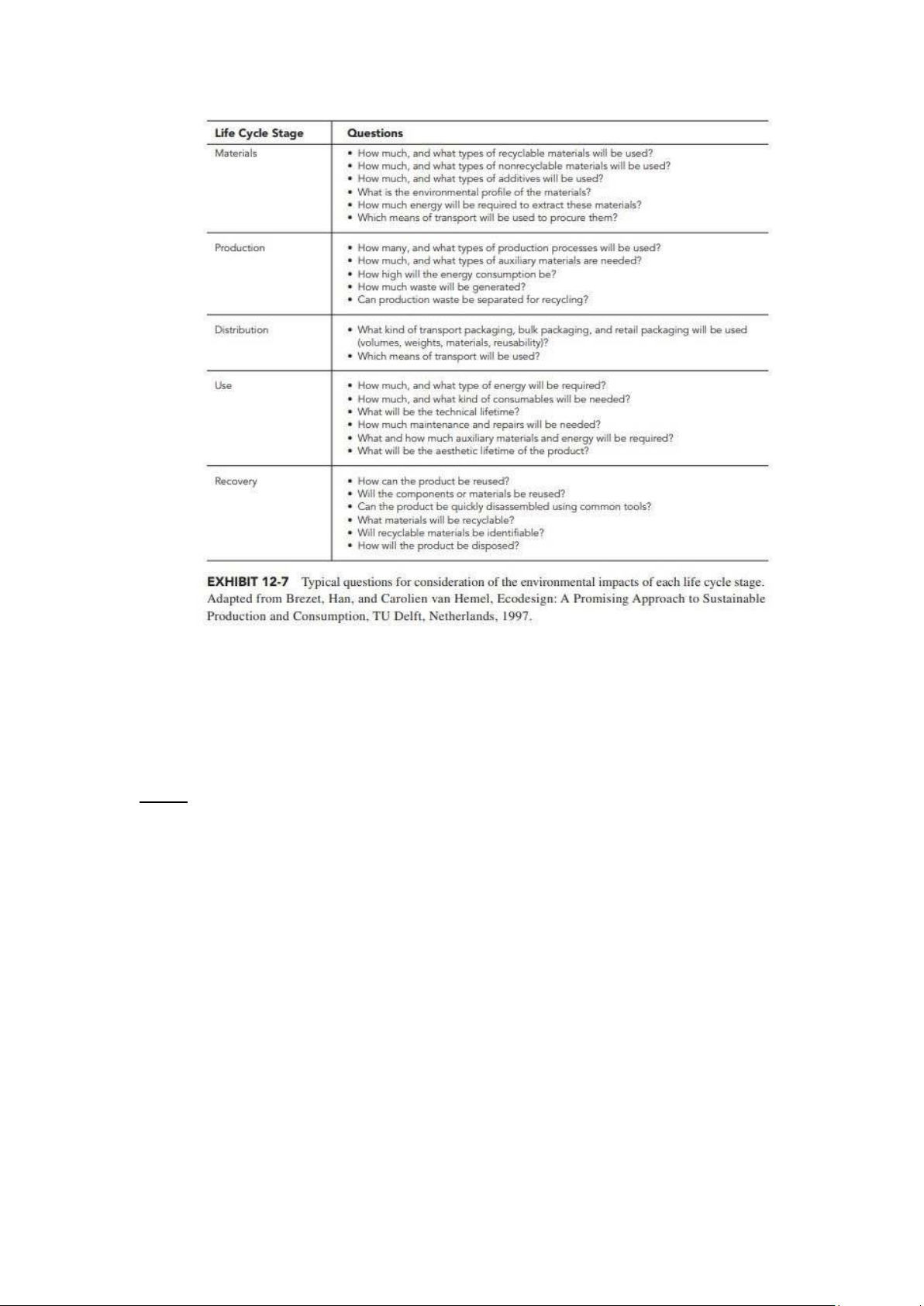
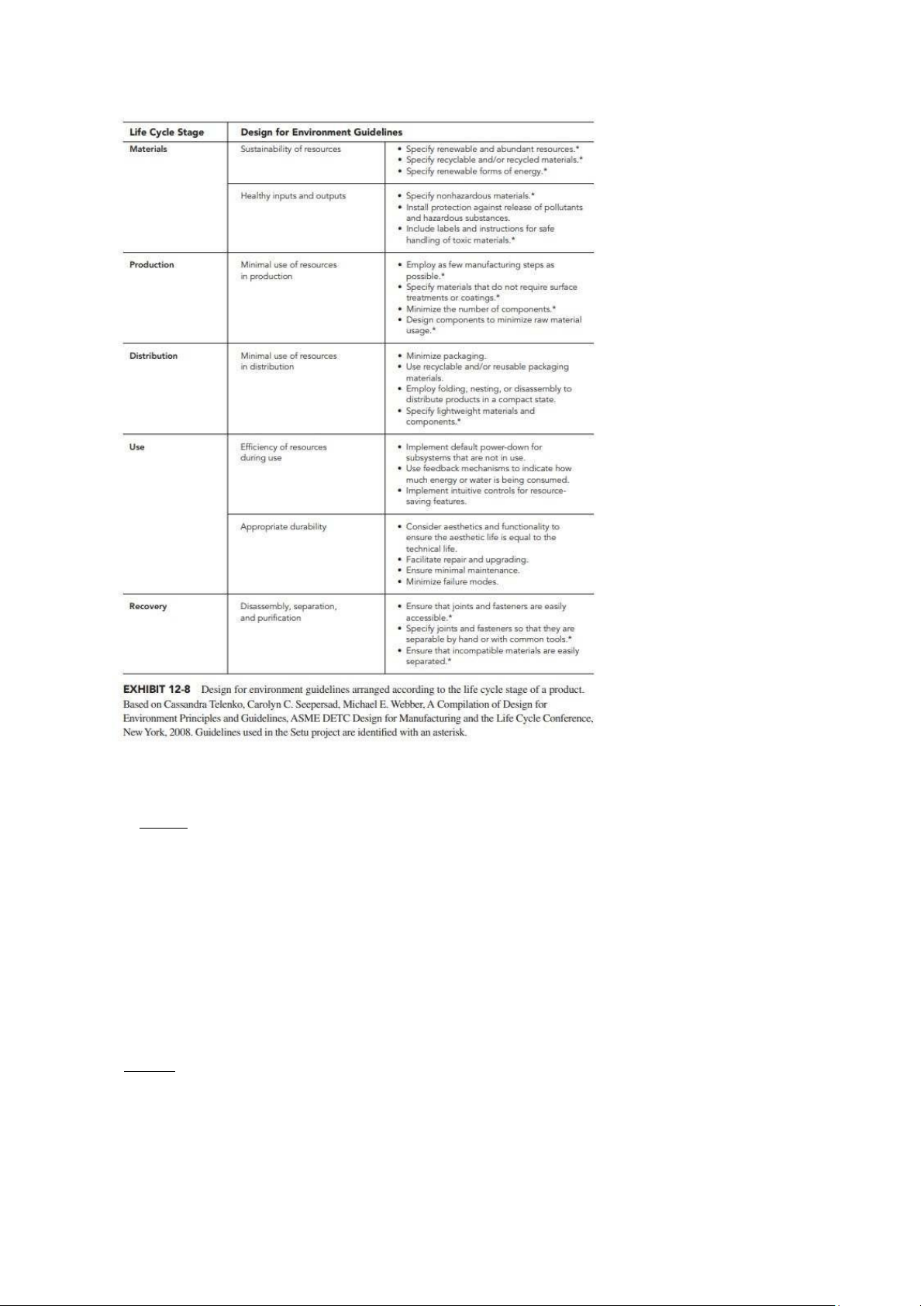
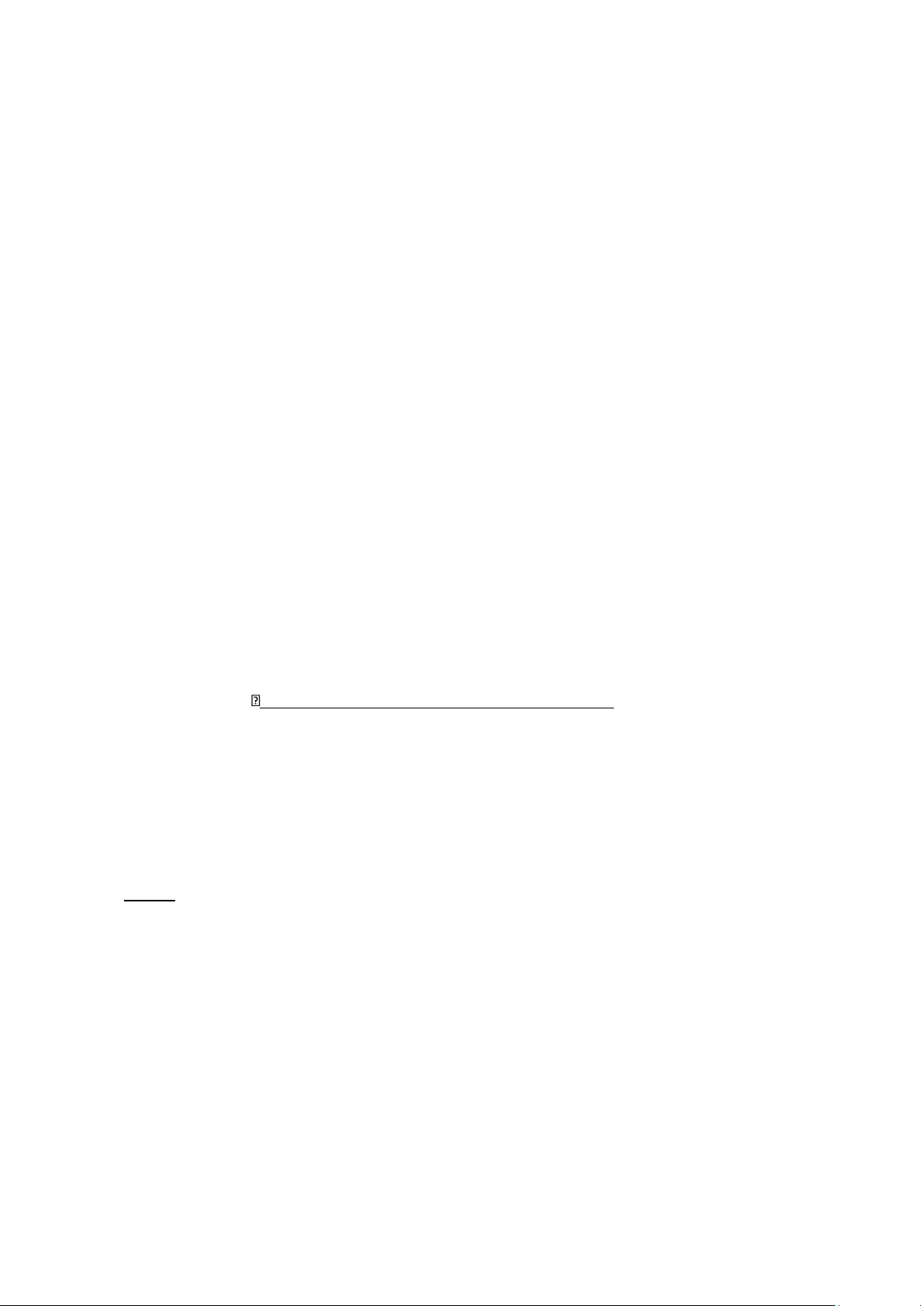
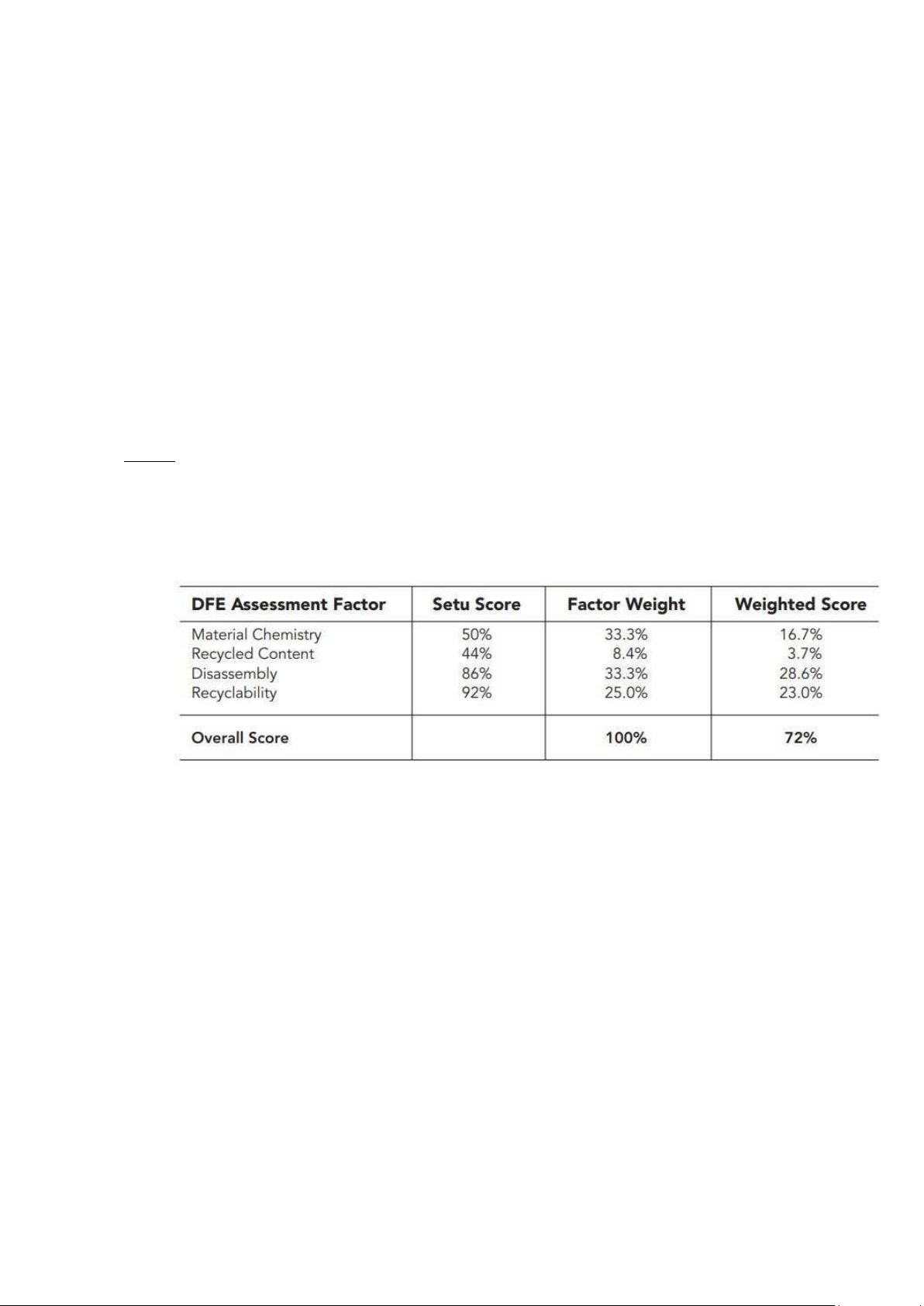
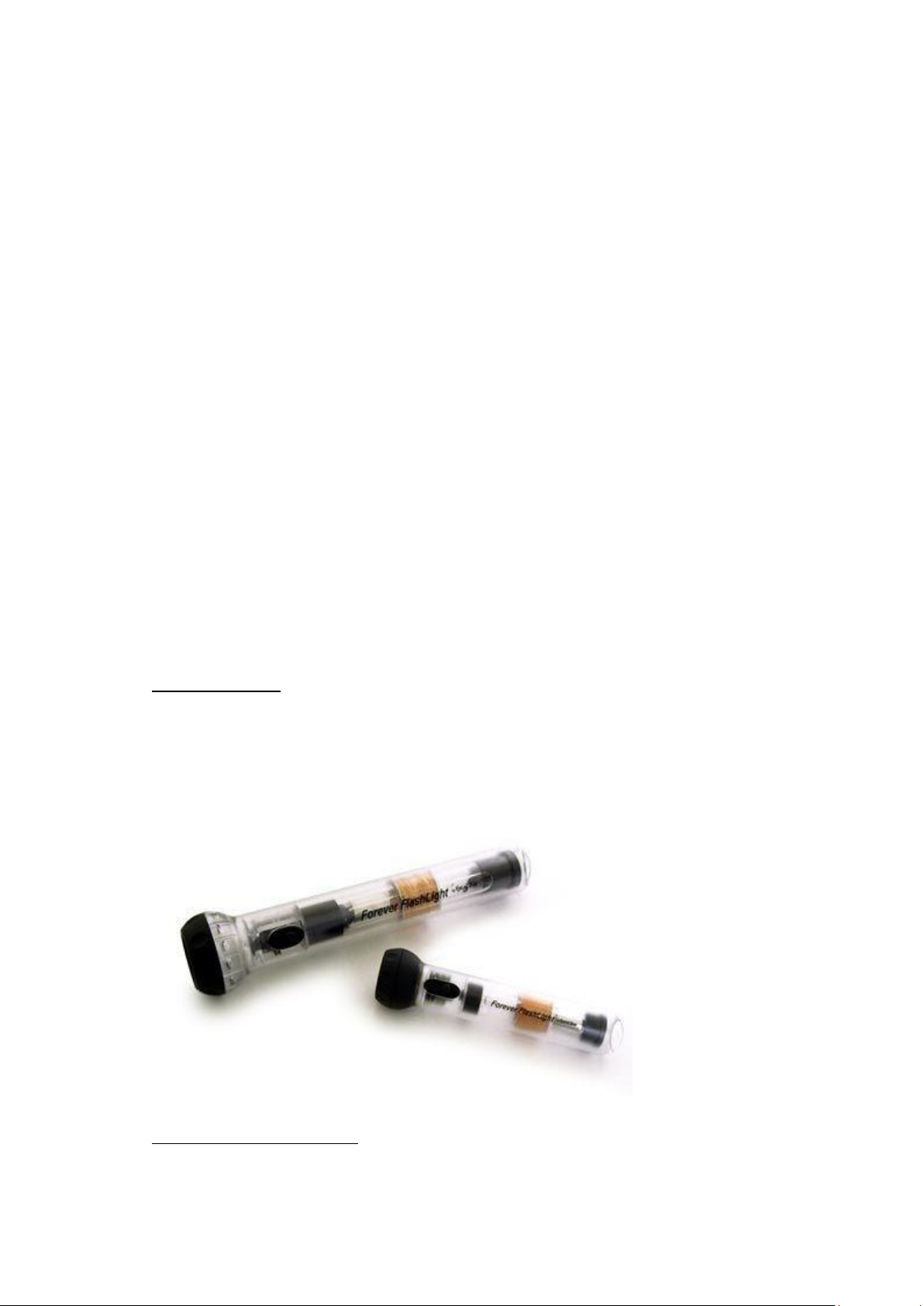
Preview text:
VIETNAM NATIONAL UNIVERSITY HCMC INTERNATIONAL UNIVERSITY
SCHOOL OF INDUSTRIAL ENGINEERING & MANAGEMENT PROJECT
Design For Environment Module code: IS034IU
Module name: Production Design and Development
Lecturer: Prof. TRẦN VĂN LÝ GROUP 3:
Phạm Hoàng Anh – IEIEIU22022
Trần Văn Hiếu – IEIEIU22079
Nguyễn Khành Huyền – IEIEIU22097
Hồ Văn Minh – IELSIU22354
Phạm Trần Hưng Phát – IELSIU22293
Hồ Thị Uyên Phương – IEIEIU22106
Nguyễn Hoàng Quân – IELSIU22254
Lê Thị Như Tâm – IEIEIU22068
Đào Minh Tấn – IEIEIU22083 Table of Contents
CHAPTER 1: INTRODUCTION................................................................5
1...........................................................................Objectives: 5 2.
Advantages and Disadvantages:...............................................5 a.
Advantages...........................................................................5
b. Disadvantages:......................................................................6 3.
Scopes and Limitations:..........................................................6 a.
Scopes:..................................................................................6
b. Limitations:............................................................................7
CHAPTER 2: PROGRESS.......................................................................8
1.................................................................... Job assignment: 8
2. Contents distribution:..............................................................8
CHAPTER 3: OVERVIEW.......................................................................9 I.
What is the Design for Environment?..........................................9 1.1
Introduction:..........................................................................9 1.2
The principles of Design for Environment:.............................9 1.3
Environmental Impact:........................................................10 1.4
Two life cycles:.....................................................................10 1.5
The examples of Design for Environment:............................12 II.
Case study: Herman Miller Setu Chair........................................13 2.1
What is Herman Miller?.......................................................13 2.2
Product Development Process and Application of DFE:............13 2.3
Description of the Setu Product:.........................................14 2.4
Conclusion:........................................................................15
III. The Design for Environment progress.......................................15 3.1
Step 1: Set the DfE Agenda: Drivers, Goals, and Team..........15 3.2
Step 2: Identify Potential Environmental Impacts...................16 3.3
Step 3: Select DfE Guidelines..............................................18 3.4
Step 4: Apply the DfE Guidelines to the Initial Product Design 18 3.5
Step 5: Assess the Environmental Impacts.............................19 3.6
Step 6: Refine the Product Design to the Reduce or Eliminate the Environmental
Impacts...............................................................20 3.7
Step 7: Reflect on the DfE Process and Results.....................20 IV. Four simple Design
for Environment Rules:...............................21
V. Example of Design for Environment:.........................................22
5.1 Forever Flashlight.............................................................22
5.2 Battery-Free Remote Control..............................................22
5.3 Toshiba’s GR-NF415GX Refrigerator.....................................23
5.4 Matsushita Alkaline Ion Water Purifier................................23
CHAPTER 4: RESULT..........................................................................24 1.
Presentation:........................................................................24 2.
Feedback on the teamwork progress...................................24
CHAPTER 5: CONCLUSION..................................................................25
CHAPTER 6: PEER ASSESSMENT.........................................................25
CHAPTER 7: REFERENCES..................................................................26 ACKNOWLEDGEMENT
During this period, we faced many challenges, but with the help of our TA and instructor, we
managed to overcome them and complete the project on time.
First and foremost, we would like to express our appreciation to Mr. Tran Van Ly and TA Van Hai for
their advice and support throughout the project. Without their help, the project might not have been completed.
Secondly, we want to show our gratitude to all the members of the group for their dedication to this
project. Thank you for contributing your knowledge and skills to the team and the project.
Finally, many thanks to everyone who participated in this project. This has been a valuable and
wonderful experience for us, providing us with knowledge and skills that will be immeasurable for our future endeavors. ABSTRACT
This report explores concept of Design for Environment (DFE). The chapter delves into the
environmental impacts of products throughout their life cycle, from material selection and
production to use and disposal. It highlights the growing importance of DFE in today's world and
outlines a structured process for integrating environmental considerations into product
development. The report examines the key steps involved in DFE, including setting goals, identifying
environmental impacts, selecting DFE guidelines, and applying them during the design phase. It
explores the concept of life cycle assessment and its role in understanding a product's environmental
footprint. Additionally, the report may touch upon a specific case study presented in the chapter,
showcasing the practical application of DFE principles.
In conclusion, the report emphasizes the significance of DFE in creating sustainable products. By
incorporating environmental considerations throughout the development process, designers can
minimize a product's environmental impact and contribute to a more sustainable future.
CHAPTER 1: INTRODUCTION 1. Objectives:
Product life cycle involves various environmental impacts, including extracting and
processing raw materials; during manufacturing; assembly, and distribution; packaging, use,
and maintenance. Environmentally benign products are products that comply with
environmental regulations and may have significant features that reduce environmental
impact. The ideal environmentally benign product is one that not only would be
environmentally neutral to make and use but also would reverse whatever substandard
conditions exist in its use environment. The ideal environmentally benign product would also
end its life cycle by becoming a useful input for another product instead of creating waste.
Design for Environment (DfE) tools, methods, and strategies have, therefore, become an
important set of activities for product development organizations. This chapter presents a
method for DFE, using the Herman Miller Setu chair as an example to illustrate the
successful application of the DFE process.
2. Advantages and Disadvantages: a. Advantages:
• Environmental Benefits o Reduced Pollution and Waste: By minimizing the
use of hazardous materials and designing for recyclability, DfE can significantly reduce pollution and waste.
o Reduced Pollution and Waste: By minimizing the use of hazardous
materials and designing for recyclability, DfE can significantly reduce pollution and waste.
o Reduced Pollution and Waste: By minimizing the use of hazardous
materials and designing for recyclability, DfE can significantly reduce pollution and waste. • Economic Benefits
o Cost Savings: EfÏcient use of materials and energy can lower production
costs. Additionally, products designed for longevity and easy disassembly
can reduce costs related to disposal and recycling.
o Market Differentiation: Environmentally friendly products can appeal to
environmentally conscious consumers, potentially increasing market share.
o Regulatory Compliance: Proactively designing products to meet current
and future environmental regulations can prevent costly redesigns and
penalties. Social Benefits
o Health and Safety: Reducing the use of toxic substances can improve
health and safety for workers and consumers. o Corporate Image:
Companies that prioritize environmental considerations can enhance
their reputation and brand loyalty. • Innovation
o Driving Innovation: DfE can stimulate innovation by encouraging the
development of new materials, technologies, and processes that have lower environmental impacts. b. Disadvantages:
• Increased Costs and Complexity o Initial Costs: Implementing DfE practices
can require significant upfront investment in research, development, and new
technologies. o Complexity in Design: Balancing environmental considerations
with functionality, cost, and aesthetics can add complexity to the design process.
• Limited Supplier and Material Options o Material Availability:
Environmentally friendly materials may be less readily available or more
expensive than conventional alternatives.
o Supply Chain Constraints: Sourcing sustainable materials can complicate
supply chains, especially if suppliers do not adhere to similar environmental standards.
• Market and Consumer Challenges o Market Readiness: Some consumers may
be unwilling to pay a premium for environmentally friendly products, limiting market penetration.
o Perceived Value: The benefits of DfE may not always be immediately
visible to consumers, making it harder to justify higher prices.
• Technical Challenges o Performance Trade-offs: Environmentally friendly
materials and processes may sometimes result in performance trade-offs, such
as reduced durability or functionality.
o Technological Limitations: Current technology may not always support
the environmental goals, requiring further innovation and development.
• Regulatory and Standards Uncertainty o Changing Regulations: Keeping up
with evolving environmental regulations and standards can be challenging and
may require frequent adjustments in design and production processes.
3. Scopes and Limitations: a. Scopes:
• Product Lifecycle Stages: DfE considers all stages of a product's lifecycle,
including raw material extraction, manufacturing, distribution, use, and end-of- life management.
• Material Selection: Focuses on selecting materials that are renewable,
recyclable, and have minimal environmental impact.
• Energy EfÏciency: Emphasizes designing products that consume less energy during production and use.
• Waste Minimization: Aims to reduce waste generation through better design,
manufacturing processes, and end-of-life strategies like recycling and composting.
• Product Design: Encourages modular design, ease of disassembly, and use of
standard components to facilitate repair, upgrade, and recycling.
• Corporate Strategy: Involves integrating environmental considerations into
corporate strategies and decision-making processes. b. Limitations:
• Economic Constraints: The initial costs for implementing DfE can be high, making it
challenging for small and medium-sized enterprises (SMEs) to adopt these practices.
• Technological Barriers: Existing technology may not always support the
environmental goals of DfE, requiring further research and development.
• Market Acceptance: Consumer willingness to pay a premium for environmentally
friendly products can be limited, affecting market adoption.
• Regulatory Uncertainty: Constantly changing environmental regulations can make it
difÏcult for companies to maintain compliance without frequent adjustments to their processes and products.
• Supply Chain Issues: Sourcing sustainable materials can complicate supply chains
and may limit the availability of necessary components.
• Performance Trade-offs: In some cases, environmentally friendly materials and
processes may lead to reduced product performance, which can affect consumer
satisfaction and market competitiveness. CHAPTER 2: PROGRESS 1. Job assignment: Task Nh Min Uyên Văn Hoàn Hoàn Khán h Hưn Văn ư h Tấn Phươn g Hiế u g g Huyề n g Phát Min h Tâm Quân Anh Content x x x x x x x x x PowerPoint x Q&A x x x x x x x Presentatio n x x x x x x x x Report x x x x x x x x x Check report x Submit x
2. Contents distribution: Part Outline In charge 1 Introduction Như Tâm 2
What is DfE? (Introduction, Environmental impacts, Two life cycles) Như Tâm, Hoàng Quân 3
Case study: Herman Miller Setu chair Hoàng Anh 4
The DfE progress (Introduction, Step 1, Step 2, Step 3, Step 4, Step 5, Step Hoàng 6, Step 7) Anh, Khánh Huyền, Hưng Phát, Văn Minh, Uyên Phương, Văn Hiếu, Minh Tấn 5 Simple DfE rules Văn Hiếu 6
Example of DfE innovation Hoàng Quân CHAPTER 3: OVERVIEW I.
What is the Design for Environment? 1. Introduction:
• Every product has environmental impacts. Design for the
Environment (DfE) attempts to reduce the impact of product
design upon the environment of a product or service. It takes into
account the whole life cycle — going beyond just the use of recycled
materials or proper packaging or disposal.
• Effective DfE practices, maintain or improve product quality and
cost, while reducing environmental impacts. The DfE approach
includes five aspects that follow the life cycle of a product and
enables companies to be more environmentally friendly in their work.
• DfE expands the traditional manufacturer’s focus on the
production and distribution of its products to a closed-loop life
cycle, optimizes the relationship and interaction of the economic
system and the environmental system, and strives to produce sustainable development.
2. The principles of Design for Environment:
• Use cleaner materials and processes: Opts for materials and
manufacturing methods that have a lower environmental footprint,
such as eco-friendly materials and renewable energy sources.
• Reduce material use: Design products with efÏciency in mind,
minimizing waste and excess material. Lightweight designs and
modular components can help achieve this goal.
• Save energy: Prioritize energy-efÏcient processes during production,
use, and disposal. Consider energysaving technologies and practices.
• Facilitate recycling: Design products that are easy to disassemble
and recycle. Use recyclable materials and promote circular economy practices.
• Ensure long life and functionality: Create durable products that
withstand wear and tear, reducing the need for frequent replacements.
• EfÏcient distribution: Optimize transportation and distribution
systems to minimize energy consumption and emissions.
• Facilitate clean consumption: Designing products and systems that
minimize environmental impact and promote sustainability.
3. Environmental Impact:
Every product may have a number of environmental impacts over its life
cycle. The following list explains some of the environmental impacts deriving
from the manufacturing sector (adapted from Lewis and Gertsakis, 2001):
• Global warming: is a result of emissions of carbon dioxide (CO2),
methane (CH4), chlorofluorocarbons (CFCs), black carbon particles,
and nitrogen oxides (NOx) from industrial processes and products.
• Resource depletion: Many of the raw materials used for production,
such as iron ore, gas, oil, and coal, are nonrenewable and supplies are limited.
• Solid waste: Products may generate solid waste throughout their life
cycle. Some of this waste is recycled, but most is disposed in
incinerators or landfills. Incinerators generate air pollution and toxic
ash (which goes into landfills). Landfills may also create
concentrations of toxic substances, generate methane gas (CH4),
and release groundwater pollutants.
• Water pollution: The most common sources of water pollution are
discharges from industrial processes, which may include heavy
metals, fertilizers, solvents, oils, synthetic substances, acids, and
suspended solids. Waterborne pollutants may affect ground water,
drinking water, and fragile ecosystems.
• Air pollution: Sources of air pollution include emissions from
factories, power generating plants, incinerators, residential and
commercial buildings, and motor vehicles. Typical pollutants include
CO2, NOx, sulfur dioxide (SO2), ozone (O3), and volatile organic compounds (VOCs).
• Land degradation: Land degradation concerns the adverse effects
that raw material extraction and production, such as mining,
farming, and forestry, have on the environment. The effects include
reduced soil fertility, soil erosion, salinity of land and water, and deforestation.
• Biodiversity: Biodiversity concerns the variety of plant and animal
species, and is affected by land clearing for urban development,
mining, and other industrial activities.
• Ozone depletion: The ozone layer protects the earth against the
harmful effects of the sun’s radiation. It is degraded by reactions
with nitric acid (created by the burning of fossil fuels) and chlorine compounds (such as CFCs). 4. Two life cycles: •
Life cycle thinking is the basis of DFE. This helps to expand the traditional manufacturer’s
concern with the production and distribution of its products to comprise a closed-loop
system relating the product life cycle to the natural life cycle, both of which are illustrated in this picture. •
The product life cycle begins with the extraction and processing of raw materials from
natural resources, followed by production, distribution, and use of the product. Finally,
at the end of the product’s useful life, there are several recovery options—
remanufacturing or reuse of components, recycling of materials, or disposal through
incineration or deposit in a landfill. The natural life cycle represents the growth and
decay of organic materials in a continuous loop. The two life cycles intersect, as shown in
the diagram, with the use of natural materials in industrial products and with the
reintegration of organic materials back into the natural cycle. •
While most product life cycles take place over a few months or years, the natural cycle
spans a wider range of time periods. Most organic materials (plant- and animal-based)
can decay relatively quickly and become nutrients for new growth of similar materials.
However, other natural materials (such as minerals), are created on a much longer time
scale, and so are considered to be nonrenewable natural resources; therefore,
depositing most mineral-based industrial materials into landfills does not readily re-
create similar industrial materials for perhaps thousands of years (and often creating
unnatural concentrations of certain harmful wastes). Each of the product life cycle stages
may consume energy and other resources and may generate emissions and waste, all of
which have environmental impacts. From this life cycle perspective, to reach conditions
of environmental sustainability, the materials in products must be balanced in a
sustainable, closed-loop system. •
This gives rise to three challenges of product design to reach sustainability, which are
also represented in the life cycle diagram of this picture: o Eliminate the use of
nonrenewable natural resources (including nonrenewable sources of energy). o
Eliminate disposal of synthetic and inorganic materials that do not decay quickly.
o Eliminate the creation of toxic wastes that are not part of natural life cycles
5. The examples of Design for Environment:
• Plantable seed recycled paper/pen/pencil is a type of biodegradable
products made from 100% recycled fibers. It’s embedded with seeds,
such as wildflowers, herbs, or vegetables. After using, plant this product
in soil, the seeds germinate and grow, while the paper itself naturally composts away.
• Stokke Tripp Trapp Chair: Peter Opsvik (for Stokke,
1972) designed the award-winning Tripp Trapp chair to grow with the child, increasing the
effective lifetime of the chair.
Usable bag or bottle (stainless- steel water bottle) are eco-friendly
alternative to single-use plastic bags, designed for multiple uses and reducing plastic waste. II.
Case study: Herman Miller Setu Chair.
1. What is Herman Miller?
MillerKnoll, Inc., doing business as Herman Miller, is an American company that
produces ofÏce furniture, equipment, and home furnishings.
Today, in addition to our classic pieces and new designs for the home, Herman Miller
is a recognized innovator in contemporary interior furnishings, work chairs,
healthcare solutions, and technologies and services.
2. Product Development Process and Application of DFE:
Furthermore, the majority of ofÏce chairs currently in use are manufactured
using materials and processes that are harmful to the environment. Recent
studies have indicated that many chairs in ofÏce environments, where
individuals often sit for periods ranging from a few minutes to a few hours,
not only lack comfort but are also improperly adjusted, leading to
dissatisfaction and negatively impacting work productivity.
Recognizing this situation, Herman Miller designed the Setu chair in
collaboration with Studio 7.5 - a design firm based in Germany. He applied
the steps of the DFE process to create the Setu chair. From selecting
environmentally friendly materials to designing cost-effective and recyclable
components, each step was executed to optimize product performance and
minimize environmental impact. This partnership combined expertise in
design and a deep understanding of market needs, resulting in a product
that addresses comfort and environmental concerns.
3. Description of the Setu Product:
In June 2009, Herman Miller, Inc., unveiled the Setu multipurpose chair,
featured in Figure 1, designed for settings where people occupy seats for
brief periods, such as conference rooms, temporary workstations, and collaborative spaces.
Named after the Hindi word for bridge, Setu aimed to set new standards in
simplicity, adaptability, and comfort for multipurpose seating, with a strong
focus on environmental friendliness.
The core innovation of the Setu chair lies in its ingeniously engineered flexible
spine, composed of two polypropylenebased materials. This spine serves as
the foundation for achieving optimal comfort for a diverse range of users.
By embracing simplicity and innovation, Setu redefines the standards for
multipurpose seating, setting a new benchmark for comfort, adaptability,
and environmental consciousness.
Figure 1. Herman Miller launched the Setu chair in June 2009. The spine of the Setu
chair is a combination of two polypropylene materials precisely engineered to flex
and support as the user moves in the chair. (Courtesy of Herman Miller, Inc.) 4. Conclusion:
The Setu chair by Herman Miller is a prime example of applying the DFE process to
create an environmentally friendly product that meets market demand. It not only
showcases Herman Miller's commitment to environmental protection but also
serves as inspiration for other businesses in the ofÏce furniture manufacturing industry. III.
The Design for Environment progress
1. Step 1 : Set the DfE Agenda: Drivers, Goals, and Team
The DFE process begins as early as the product planning phase with setting the
DFE agenda. This step consists of 3 activities: Identifying the internal and external
drivers of DFE, Setting the environmental goals for the product, and Setting up the
DFE team. By setting the DFE agenda, the organization can identify a clear and
actionable path toward environmentally friendly product design.
a. Identify the Internal and External Drivers of DFE •
The planning phase of DFE begins with a discussion of the reasons why the
organization wishes to address the environmental performance of its products. •
It’s useful to document both the internal and external drivers of DFE. •
Since many changes in technology, regulation, experience, stakeholders, and
competition affect capability and challenges. So the list here may evolve over time: •
Internal drivers are the DFE objectives within the organization.Typical internal drivers
of DFE are: Product quality, Public image, Cost reduction, Operational safety,
Employee motivation, Ethical responsibility, Consumer behavior. •
External drivers of DFE typically include: Environmental legislation, Market demand,
Competition, Trade organizations, Suppliers, Social pressures. b. Set goals •
This is a very important activity in the product planning phase. •
Setting the environmental goals for each product development project. •
Many organizations have established a strategy that includes longterm environmental goals. •
These goals define how the organization complies with environment regulations and
how it reduces environmental impacts of products, services, and operation. •
The more understanding which periods of the life cycle have a big influence on the
environment the more appropriate goals the organizations can achieve. Here is the
table based on the understanding of the life cycle stage. •
Herman Miller understands that the primary environmental impacts of their ofÏce
furniture products are in the materials, production, and recovery stages. For the Setu
chair, Herman Miller aimed to use exclusively materials with low environmental
impact, facilitate product disassembly, and enable recycling. c. Set up the DFE team •
DFE requires participation by many functional experts on the product development project. •
The typical composition of a DFE team consists of: o A DFE leader. o An
environmental chemistry and materials expert. o A manufacturing engineer. o A
representative from the purchasing and supply chain organization. •
The DFE team composition depends on the organization and needs of the specific
project, and may also include: o Marketing professionals. o Outside consultants. o Suppliers. o Other experts. •
Herman Miller created their DFE team in 1999 to work with the designers and
engineers on every product development project to review material chemistry,
disassembly, recyclability, incoming and outgoing packaging, energy sources and
uses, and waste generation. o The DFE team is involved as early as possible to
ensure that DFE considerations are taken into account right from the start.
o By working closely with each product development team, the DFE team
provides the tools and knowledge for making environmentally sound design decisions.
2. Step 2: Identify Potential Environmental Impacts
DFE prioritizes identifying potential environmental impacts across a product's entire
lifecycle during the concept development phase. This allows early consideration of
environmental factors even when specific data (materials, energy use, emissions, waste)
is scarce, preventing detailed impact assessment. However, existing product data can
prove valuable when redesigning products (refer to life cycle assessment methods in step 5).
A chart (Exhibit 12-6) helps assess environmental impact throughout a product's lifecycle
(e.g., materials, production, use, disposal)
This tool, inspired by existing frameworks like the LiDS Wheel and EcoDesign Web, helps
identify which lifecycle stages pose the greatest environmental concern.
Teams creating the chart ask key questions (detailed in Exhibit 12-7) about potential
environmental impact at each lifecycle stage.
The chart uses bar height to visually represent the team's judgment on the severity of
environmental impact at each stage.
This helps prioritize Design for Environment (DFE) efforts by highlighting which lifecycle
stages have the biggest impact for a specific product category (e.g., focus on material
selection for ofÏce furniture).
3. Step 3 : Select DfE Guidelines
Early design choices can be environmentally friendly using DFE guidelines. These guidelines (like
Exhibit 12-8) match a product's lifecycle stages (step 2) and offer specific tips for each stage
(materials, production) to reduce environmental impact. Choosing them during concept
development helps throughout design, with many focusing on material selection for its big environmental effect.
For the Setup project, the DFE experts provided the product development team with several
guidelines. These guidelines are identified with an asterisk in Exhibit 12-8.
4. Step 4 : Apply the DfE Guidelines to the Initial Product Design
The next step is to apply the DFE Guidelines to the Initial Product Design. Do this with
aim to be lightweight to reduce materials use and transportation impacts and to ease
the disassembly of the Setu to facilitate recycling.
This has the result of: o Created a design for the chair that eliminates the need
for an under-seat tilt mechanism and can save weight by up to 20 pounds (9 kg).
o Arranging joints in an accessible manner. o Confirming that parts can be
detached manually or using standard equipment. o It has 4 types: Safest,
Low Hazard, Uncertain, High Hazard
5. Step 5 : Assess the Environmental Impacts
The next step is to assess, to the extent possible, the environmental impacts of the
product over its entire life cycle. To do so with precision requires a detailed
understanding of how the product is to be produced, distributed, used over its
lifetime, and recycled or disposed at the end of its useful life.
This assessment is generally done on the basis of the detailed bill of materials
(BOM), including sources of energy, component material specifications, suppliers,
transportation modes, waste streams, recycling methods, and disposal means.
Several quantitative life cycle assessment (LCA) tools are available to conduct such
an environmental assessment. These tools range in price and complexity and would
be selected based on the types of materials and processes involved, and the
precision required of the analysis.
LCA requires a significant amount of time, training, and data. Many LCA analyses are
comparative and provide a basis for considering the environmental performance of
product design alternatives. Commercial LCA software is becoming widely used in
product design and supporting data are available for common materials, production
processes, transport methods, energy generation processes, and disposal scenarios.
Herman Miller uses their own proprietary DFE assessment tool, developed for them
by MBDC. The DFE tool consists of a spreadsheet interface and the materials
database using the color coding described above. The tool considers four factors for
each component in the product:
• Material chemistry - fraction of the materials by weight that are the
safest possible in terms of human toxicity and environmental concerns
• Recycled content - fraction of the materials by weight that are post-
industrial or post-consumer recycled content
• Disassembly - fraction of the materials by weight that can be readily disassembled
• Recyclability - fraction of the materials by weight that are
recyclable Once the initial Setu design was established, the chair
was divided into modules, with different teams assigned to develop
each module. As each team designed their module, the DFE team
assessed the design using the DFE tool.
Compare the environmental impacts to DFE goals: This step compares the
environmental impacts of the evolving design to the DFE goals established in
the planning phase. If several design options were created in the detail
design phase, they may now be compared to judge which one has the
lowest environmental impacts. Unless the product development team is
very experienced in DFE, the design will generally have much room for
improvement. Usually several DFE iterations are required before the team is
satisfied that the product is as good as it should be from a DFE perspective
6. Step 6 : Refine the Product Design to the Reduce or Eliminate the Environmental Impacts
The objective of this step and subsequent DFE iterations is to reduce or eliminate any
significant environmental impacts through a redesign.
• After production begins, the redesign of DFE can continue for ongoing
improvement. We can use four stages of continuous improvement to refine the
product design: Plan -> Do -> Check > Act. We repeat until the environmental
impacts have been reduced to an acceptable level and the environmental
performance fits the DFE goals.
• We can take the Herman Miller chair for example. The Setu team found a way to
co-mold the spine using two different polypropylene materials that are
compatible with recycling without separation. The inner and outer rails of the
spine are made of a polypropylene-and-glass composite, while the connecting
spokes use a more flexible polypropylene-and-rubber composite. The base was
uncoated and unpolished, with no finishing labor and no harmful toxins, it is
durable and has a lower environmental impact than traditionally finished chair
bases, this method is called “minimal design”. All of this was made After multiple design iterations.
• In product design, every choice we make comes with its own set of
consequences. We must be prepared to acknowledge and accept the trade-offs
that are inherent in the decision-making process.
• In the development of Setu, the team had to make a tough decision regarding
the materials for the chair's arms. They wanted to avoid using PVC, but using
only olefinic materials like polypropylene was not feasible due to concerns about
durability and fatigue failure. As a result, they chose to mold the arms from
nylon and then over-mold them with a thermoplastic elastomer. However,
because these materials are not chemically compatible for recycling, this
decision limited the chair’s overall recyclability.
7. Step 7 : Reflect on the DfE Process and Results
New project as with every aspect of the product development process, the final activity is to ask:
• How well did we execute the DFE process?
• How can our DFE process be improved?
• What DFE improvements can be made on derivative and future products?
Table. Herman Miller’s DFE assessment tool considers four factors and computes a weighted
overall score of 72% for the Setu chair.
• A perfect product from a DFE perspective is a goal that may take years to achieve.
• Effective DFE requires a product development team that strives for continuous improvement.
• The DFE team may be able to further develop the Setu chair to reduce some of the known impacts.
Successful DFE implementation resulted in negative environmental impacts, especially
in material chemistry and recycled content use.
DFE Results: Highlight the outcomes of implementing DFE practices. This could include:
• Reduction in environmental impacts (e.g., energy use, greenhouse gas emissions, waste generation)
• Improved resource efÏciency (e.g., reduced material usage, optimized energy consumption)
• Compliance with environmental regulations and standards
• Enhanced product performance or marketability due to environmental attributes
• Cost savings through efÏciency gains or waste reduction
• Positive impacts on brand reputation and customer perception
DFE Process Improvement
• Utilized LCA software to monitor DFE results and refine products.
• Planned to integrate "carbon footprint" into DFE tool.
• Carbon footprint refers to greenhouse gas emissions caused by a product.
• Consideration of carbon footprint influences material choices. IV.
Four simple Design for Environment Rules:
When designing products, it's vital to prioritize their environmental impact. Hence, adhere to these four simple rules:
Design products and processes with industrial materials that can be recycled continually with no
loss in performance, thereby creating new industrial materials.
Design products and processes with natural materials that can be fully returned to the earth’s
natural cycles, thereby creating new natural materials.
Design products and processes that do not produce unnatural, toxic materials that cannot be
safely processed by either natural or industrial cycles.
Design products and processes with clean, renewable sources of energy, rather than fossil fuels. V.
Example of Design for Environment: 1. Forever Flashlight •
Forever Flashlight: Shake-powered, eliminates batteries and bulbs. •
Generates power: User shakes the flashlight. •
Shake duration: 15-30 seconds provides 5 minutes of light. •
LED bulb: Long-lasting and efÏcient. •
Eco-friendly: Reduces battery waste. •
Always prepared: Never be caught in the dark.
2. Battery-Free Remote Control •
Company: Volvo Car Corp. and Delft University of Technology