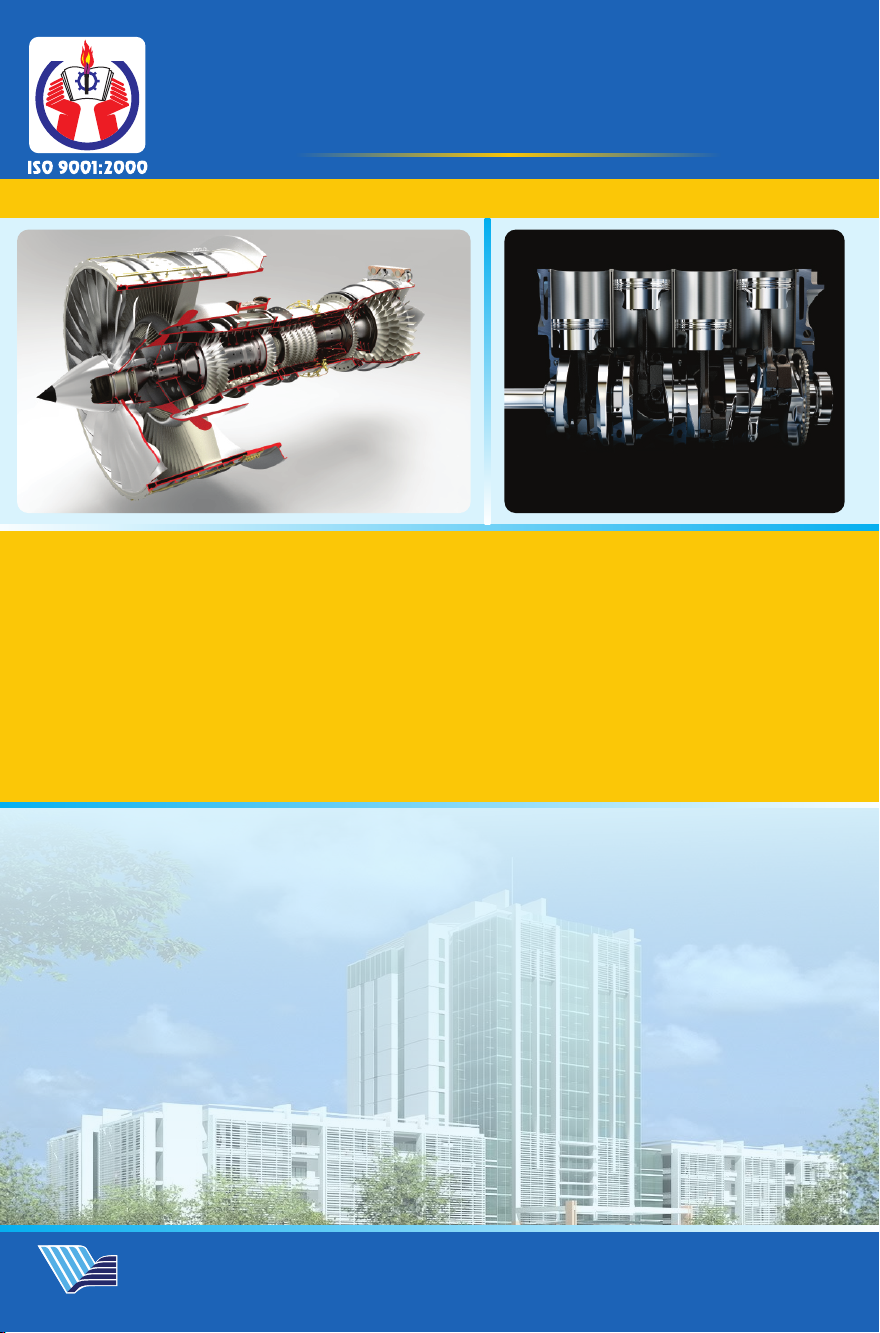
GIÁO TRÌNH
CÔNG NGHỆ
CHẾ TẠO MÁY
NHAØ XUAÁT BAÛN
ÑAÏI HOÏC QUOÁC GIA TP. HOÀ CHÍ MINH
PHAN MINH THANH - HỒ VIẾT BÌNH
BOÄ GIAÙO DUÏC VAØ ÑAØO TAÏO
TRÖÔØNG ÑAÏI HOÏC SÖ PHAÏM KYÕ THUAÄT THAØNH PHOÁ HOÀ CHÍ MINH
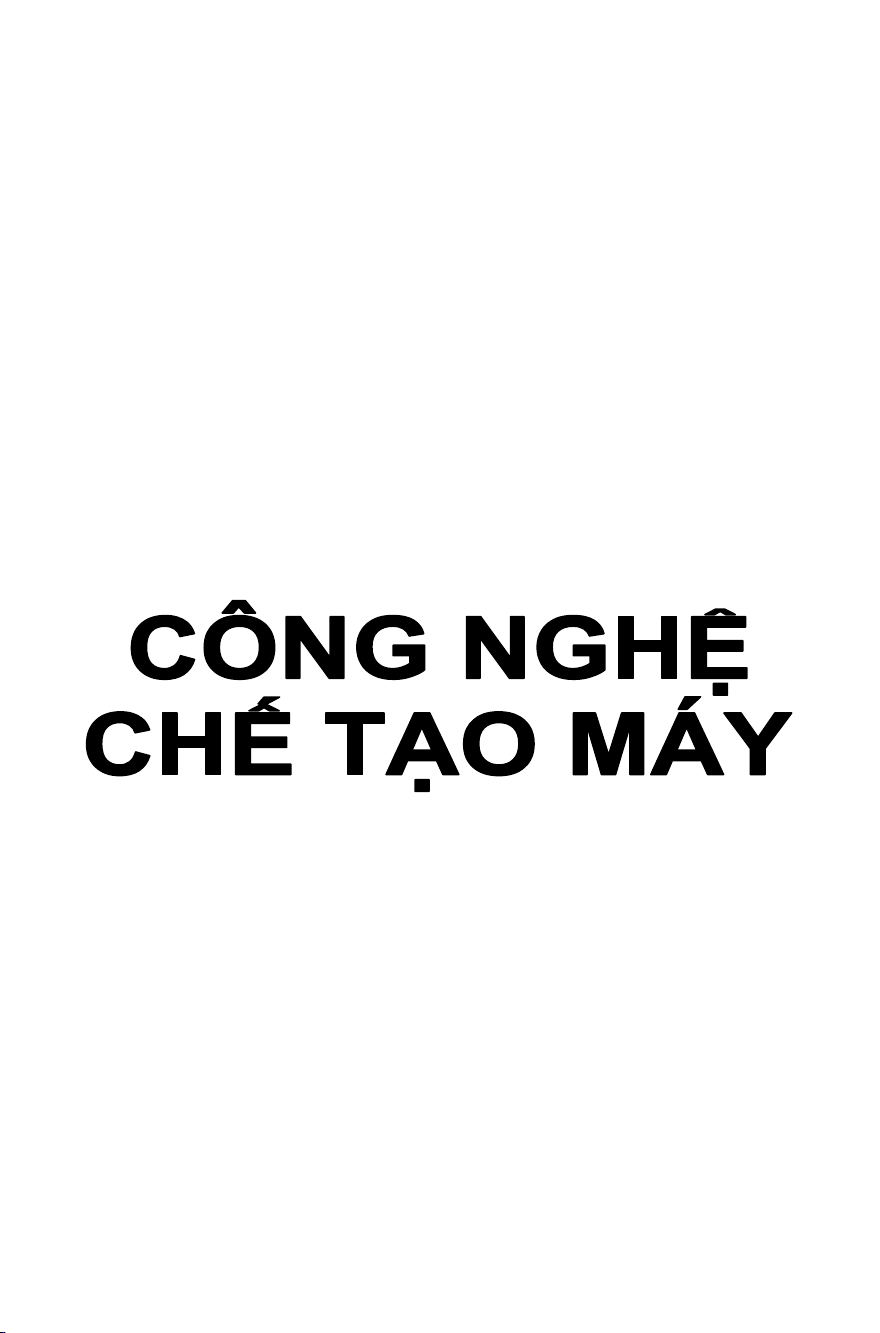
BỘ GIÁO DỤC VÀ ĐÀO TẠO
TRƯỜNG ĐẠI HỌC SƯ PHẠM KỸ THUẬT
THÀNH PHỐ HỒ CHÍ MINH
*******************
HỒ VIẾT BÌNH
PHAN MINH THANH
GIÁO TRÌNH
NHÀ XUẤT BẢN ĐẠI HỌC QUỐC GIA
THÀNH PHỐ HỒ CHÍ MINH
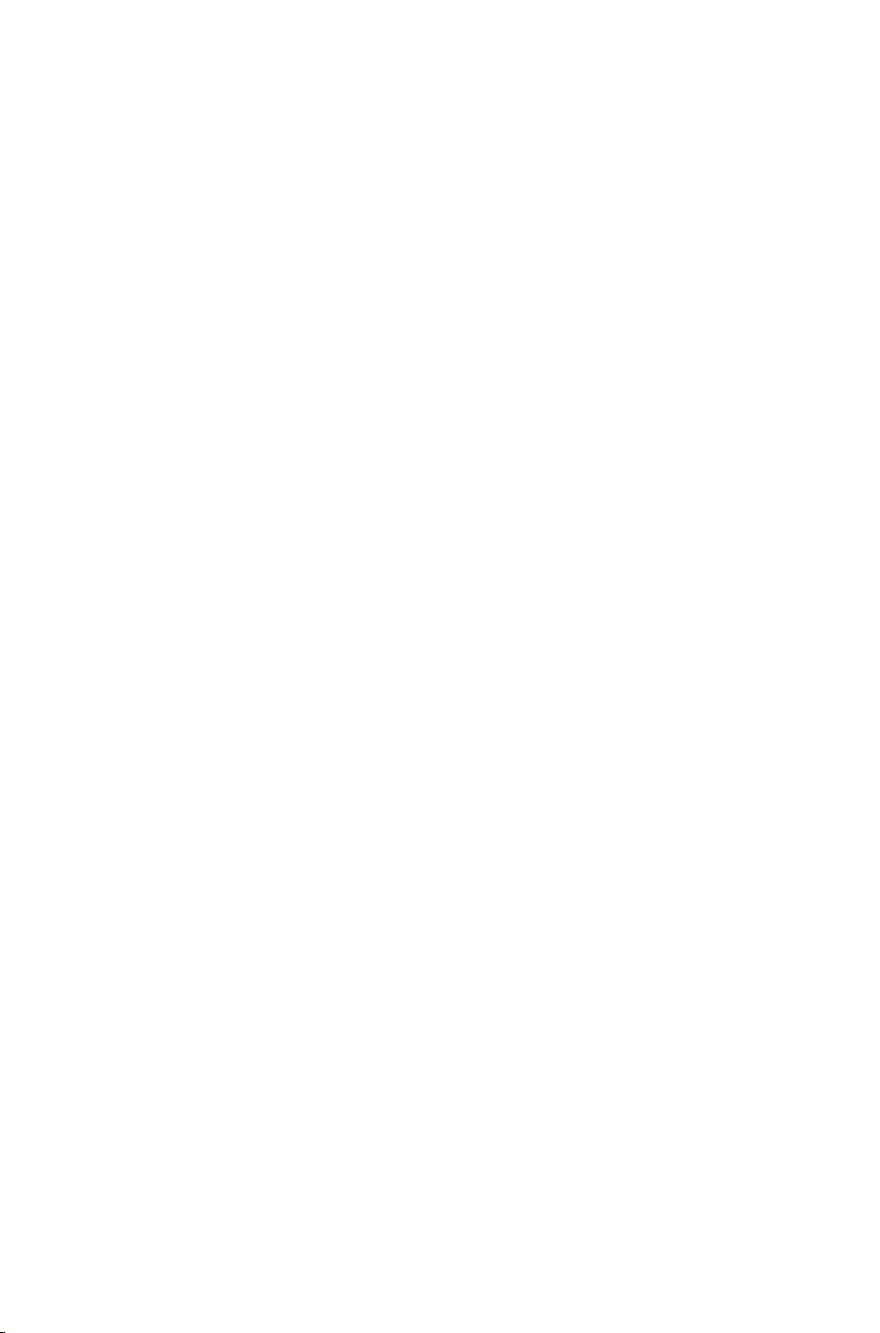
3
LỜI NÓI ĐẦU
Khối kiến thức thuộc nhóm công nghệ chế tạo máy được phân chia
thành hai giáo trình chính, đó là:
1 - CƠ SỞ CÔNG NGHỆ CHẾ TẠO MÁY là môn học cơ sở cho
tất cả các ngành cơ khí như: CKM, KCN, TKM, CKT, CKĐ, CĐT, CTĐ.
2- CÔNG NGHỆ CHẾ TẠO MÁY là môn học chuyên ngành cho
các ngành học: CKM, KCN. Nội dung của giáo trình này gồm các phần
chính: Thiết kế đồ gá, Thiết kế quá trình công nghệ, Công nghệ gia công
các chi tiết điển hình, Công nghệ lắp ráp các sản phẩm cơ khí.
Chương Thiết kế quá trình công nghệ có lồng ghép nội dung Tính
công nghệ trong kết cấu và Tính toán lượng dư. Đó là hai nội dung cần
có của công việc thiết kế quá trình công nghệ.
Chương Thiết kế đồ gá chủ yếu giới thiệu cơ sở thiết kế, còn các đồ
gá mẫu cũng như các chi tiết tiêu chuẩn được trình bày trong tài liệu “ĐỒ
GÁ GIA CÔNG CƠ KHÍ”. Chương này trình bày khá kỹ về cách tính sai
số chuẩn bằng phương pháp lập chuỗi, cách tính lực kẹp cần thiết để
chọn cơ cấu kẹp.
Để hoàn thành tập giáo trình này, ngoài sự cố gắng của các tác giả
còn có sự góp ý của đồng nghiệp và sự đóng góp tích cực của các sinh
viên làm luận án tốt nghiệp đã thực hiện tốt các bản vẽ làm cho giáo trình
sáng sủa, dễ đọc.
Các tác giả rất mong sự đóng góp ý kiến về nội dung sách của các
thầy cô đồng nghiệp và sinh viên.
Các tác giả
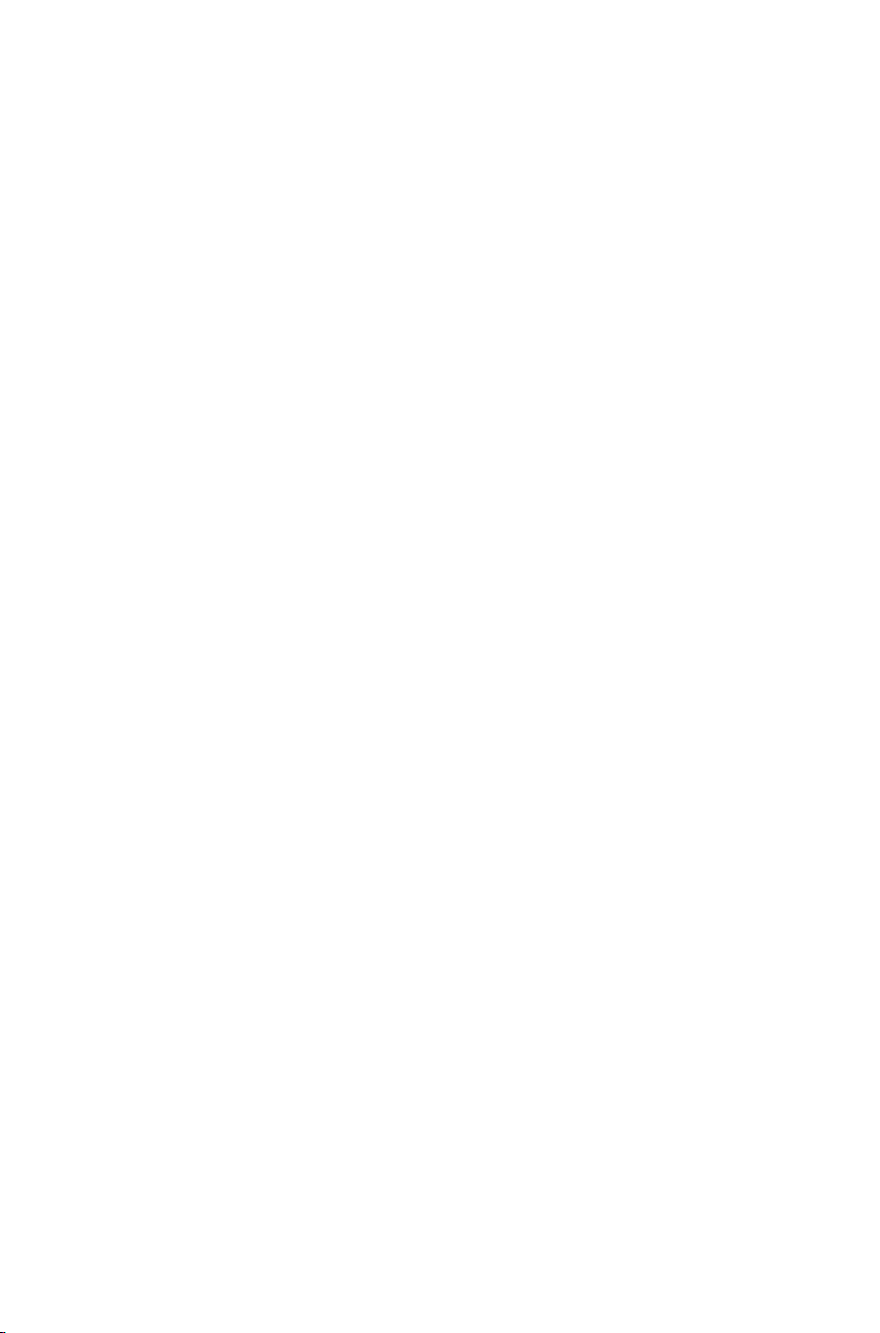
5
Chương 1
THIẾT KẾ QUY TRÌNH CÔNG NGHỆ
CHẾ TẠO CHI TIẾT MÁY
Mục tiêu :
- Trình bày được trình tự thiết kế quy trình công nghệ trên máy gia
công truyền thống và máy CNC.
- Thiết lập được quy trình công nghệ hợp lý khi gia công trên máy
truyền thống.
- Kiểm tra tính công nghệ trong kết cấu chi tiết máy từ đó đề xuất thay
đổi, cải tiến kết cấu chi tiết máy để việc chế tạo và lắp ráp thuận lợi nhất.
- Tra cứu và tính toán lượng dư gia công hợp lý nhằm giảm khối
lượng phôi và thời gian gia công.
1.1. PHƯƠNG PHÁP THIẾT KẾ QUY TRÌNH CÔNG NGHỆ GIA
CÔNG CƠ
Thiết kế quy trình công nghệ (QTCN) là một nội dung quan trọng
của công việc chuẩn bị sản xuất, nếu QTCN hợp lí phù hợp với điều kiện
sản xuất thì sẽ đạt năng suất, chất lượng và hiệu quả kinh tế cao. Vì vậy
cần tuân theo nội dung và trình tự thiết kế.
1.1.1. Các tài liệu ban đầu
Khi thiết kế QTCN cần phải có các tài liệu sau:
- Bản vẽ chi tiết với đầy đủ các hình chiếu, vật liệu, kích thước,
dung sai, độ bóng, độ cứng, các yêu cầu kỹ thuật về vị trí, hình dáng. Các
yêu cầu đặc biệt như cân bằng, tôi bề mặt hay thể tích …
- Sản lượng hàng năm, hoặc số lượng của một đợt sản xuất.
- Thời hạn thực hiện xong kế hoạch
- Điều kiện sản xuất (trang thiết bị...)
Khi thiết kế quy trình công nghệ, điều kiện thiết bị rất quan trọng,
có ba trường hợp đặt ra là:
+ Thiết kế quy trình công nghệ cho một nhà máy mới.
+ Thiết kế quy trình công nghệ cho một nhà máy có sẵn.
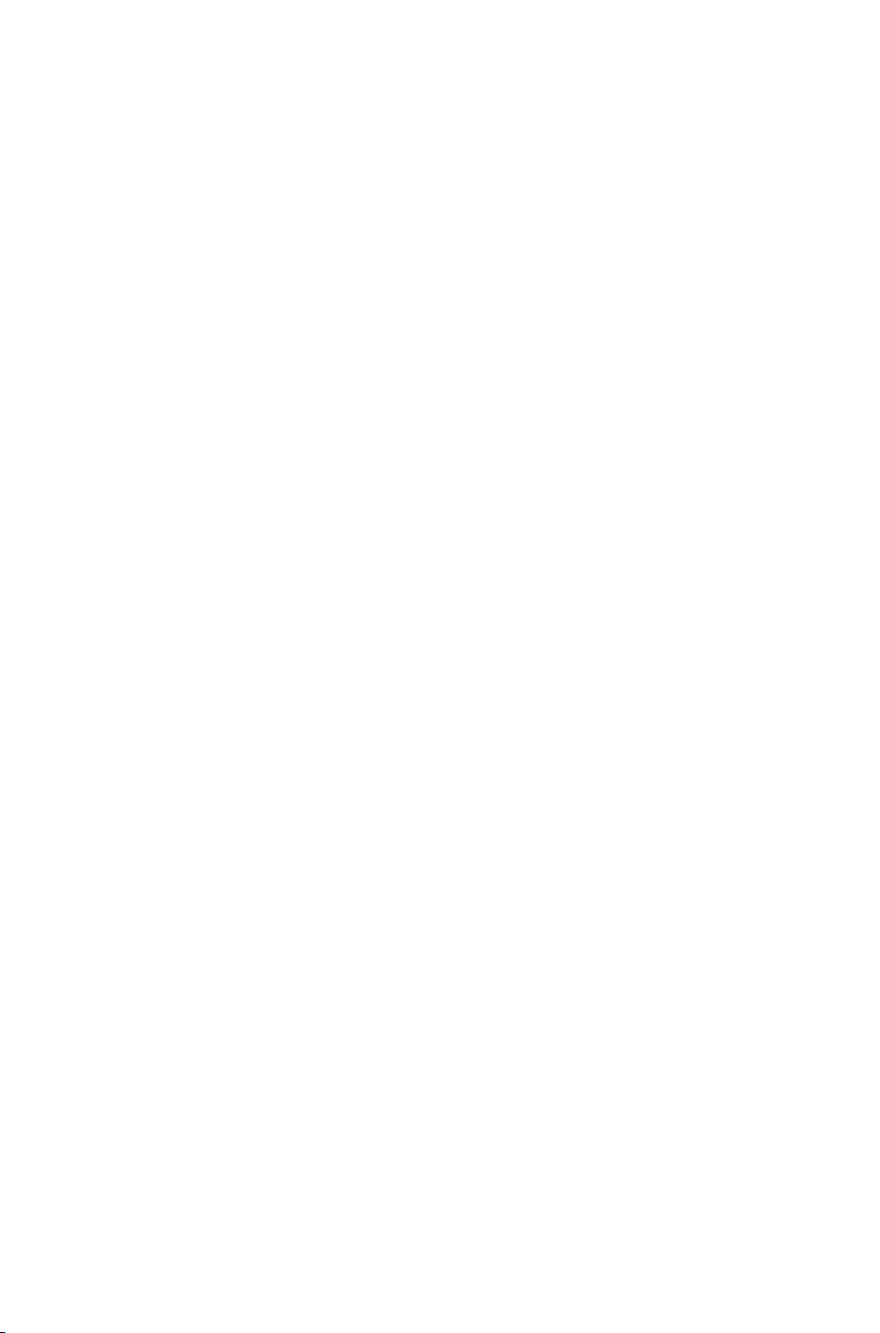
6
+ Thiết kế quy trình công nghệ cho một nhà máy có thêm phần mở
rộng sản xuất (nghĩa là đầu tư thêm cho nhà máy cũ).
Các tài liệu cần thiết để thiết kế quy trình công nghệ là các sổ tay
công nghệ, thuyết minh của các máy, các tiêu chuẩn về đồ gá, sổ tay
dụng cụ cắt, dụng cụ đo, sổ tay về dung sai, các sổ tay về định mức kỹ
thuật … Ngoài ra có thể cần đến máy vi tính và các phần mềm chuyên
dụng để tính và tra chế độ cắt, lượng dư gia công hay thiết lập trình tự gia
công (thực hiện các bản vẽ).
1.1.2. Trình tự thiết kế quy trình công nghệ
- Tìm hiểu chi tiết cần gia công: tìm hiểu điều kiện làm việc của chi
tiết, tính ổn định của sản phẩm trong nhu cầu sử dụng của xã hội. Nghiên
cứu các yêu cầu kỹ thuật, kết cấu của chi tiết xem tính công nghệ có phù
hợp với điều kiện sản xuất hay không?
- Xác định quy mô sản xuất và lựa chọn phương pháp tổ chức sản xuất.
- Chọn phôi và phương pháp tạo phôi.
- Xác định thứ tự các nguyên công. Cách gá đặt, chọn máy, dao.
- Chia nguyên công thành các bước công nghệ.
- Xác định lượng dư và dung sai cho từng bước công nghệ và lượng
dư tổng để quy định kích thước phôi.
- Xác định chế độ cắt gọt hợp lý.
- Chọn hoặc thiết kế đồ gá cho từng nguyên công
- Xác định bậc thợ cho từng nguyên công.
- Định mức thời gian và tính toán năng suất thực tế. So sánh các
phương án công nghệ.
Với trình tự vừa kể trên, có thể dựa vào các quy trình công nghệ
điển hình để giảm bớt khối lượng thiết kế. Với một chi tiết mới, không có
QTCN điển hình, chúng ta phải thực hiện đầy đủ các bước thiết kế đã
nêu. Sau đây là một số bước thiết kế chính.
1.1.3. Kiểm tra tính công nghệ trong kết cấu chi tiết máy
Tính công nghệ trong kết cấu nghĩa là hình dáng và kết cấu công
nghệ của chi tiết máy phải đơn giản, dễ chế tạo, dễ lắp ráp, giá thành rẻ
nhưng vẫn đảm bảo độ bền và chức năng làm việc.
1.1.3.1.
Cơ sở để đánh giá tính công nghệ trong kết cấu của chi tiết máy
- Tính công nghệ trong kết cấu chi tiết máy phụ thuộc vào quy mô
sản xuất.
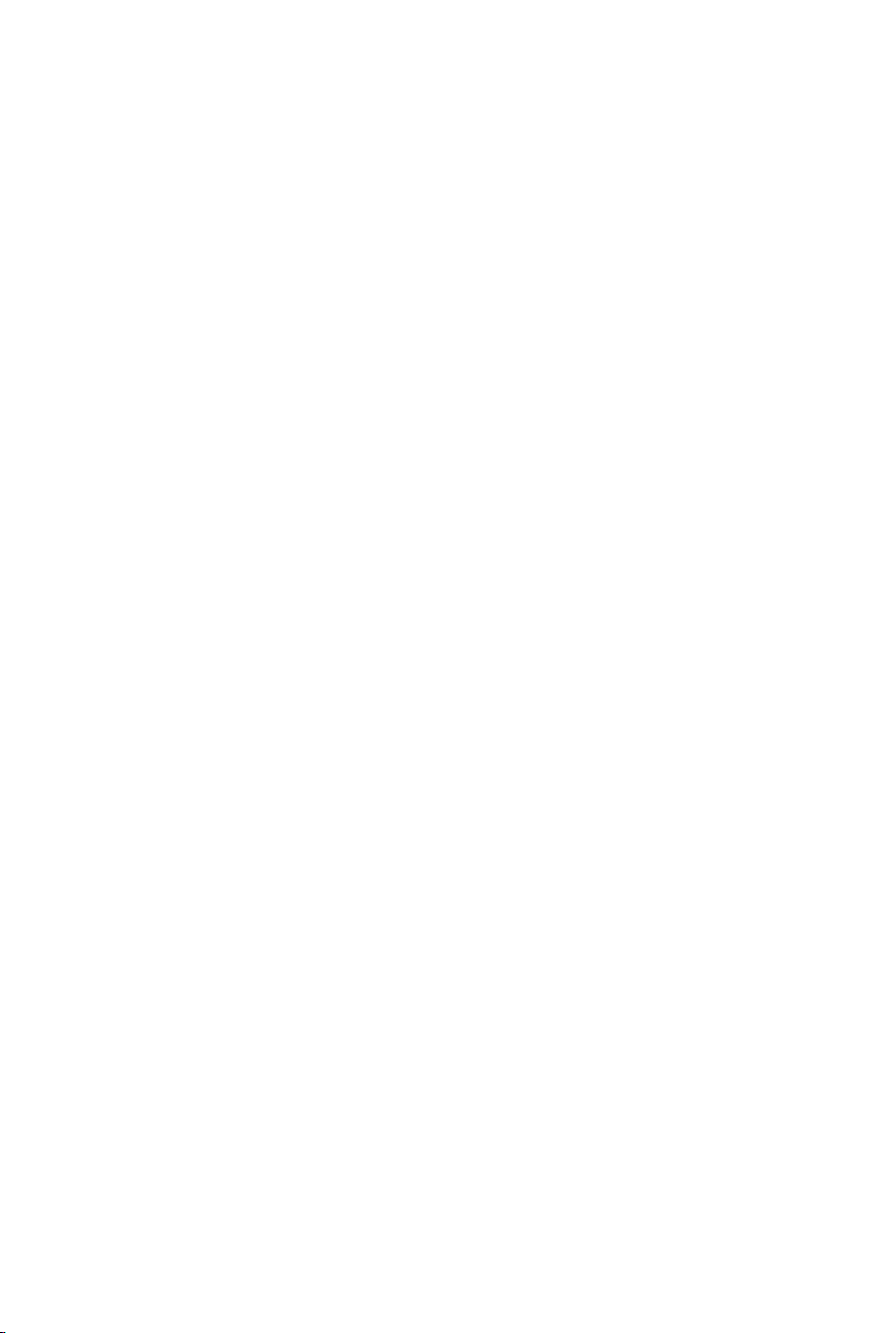
7
- Tính công nghệ trong kết cấu phải được nghiên cứu đồng bộ với
kết cấu tổng thể của sản phẩm cơ khí, không tính riêng từng phần tử kết
cấu, trên cơ sở đảm bảo chức năng và điều kiện làm việc của chi tiết.
- Tính công nghệ trong kết cấu phải được chú trọng triệt để trong
từng giai đoạn của quá trình chế tạo sản phẩm cơ khí ( tạo phôi, gia công
cơ, nhiệt luyện ).
- Tính công nghệ trong kết cấu phải phù hợp với điều kiện sản xuất
cụ thể.
1.1.3.2. Các chỉ tiêu đánh giá tính công nghệ trong kết cấu
a/ Trọng lượng kết cấu nhỏ nhất.
b/ Sử dụng vật liệu thống nhất, tiêu chuẩn, dễ tìm và rẻ.
c/ Quy định kích thước, dung sai và độ nhám bề mặt hợp lý.
d/ Sử dụng chi tiết máy và bề mặt chi tiết máy thống nhất, tiêu
chuẩn.
e/ Kết cấu hợp lý để gia công cơ khí và lắp ráp thuận tiện. Đặc biệt
đối với quá trình gia công cắt gọt phải bảo đảm các yêu cầu sau:
- Giảm lượng vật liệu cắt gọt bằng cách thiết kế phôi và các bề mặt
gia công hợp lý, xác định chính xác lượng dư gia công.
- Giảm quãng đường chạy dao khi cắt gọt.
- Đơn giản hóa kết cấu, đảm bảo tính kinh tế khi gia công và sử
dụng phôi liệu (ví dụ: tách một chi tiết phức tạp thành nhiều chi tiết đơn
giản để dễ gia công, tiết kiệm vật liệu).
- Tạo điều kiện sử dụng dao cắt thống nhất, tiêu chuẩn.
- Đảm bảo dao cắt làm việc thuận tiện, không bị va đập khi cắt.
- Đảm bảo chi tiết đủ cứng vững, tạo điều kiện cắt gọt với chế độ
cắt cao.
- Giảm phí tổn điều chỉnh thiết bị, trang bị công nghệ, giảm số lần
gá đặt chi tiết khi gia công.
- Phân biệt rõ ràng giữa bề mặt gia công và bề mặt không gia công
cũng như giữa các bề mặt ứng với các nguyên công khác nhau.
- Khi sử dụng thiết bị chuyên dùng phải chú ý đến đặc điểm riêng
về kết cấu để phù hợp với thiết bị gia công.
Sau đây là các ví dụ về phân tích tính công nghệ trong kết cấu của
chi tiết máy:
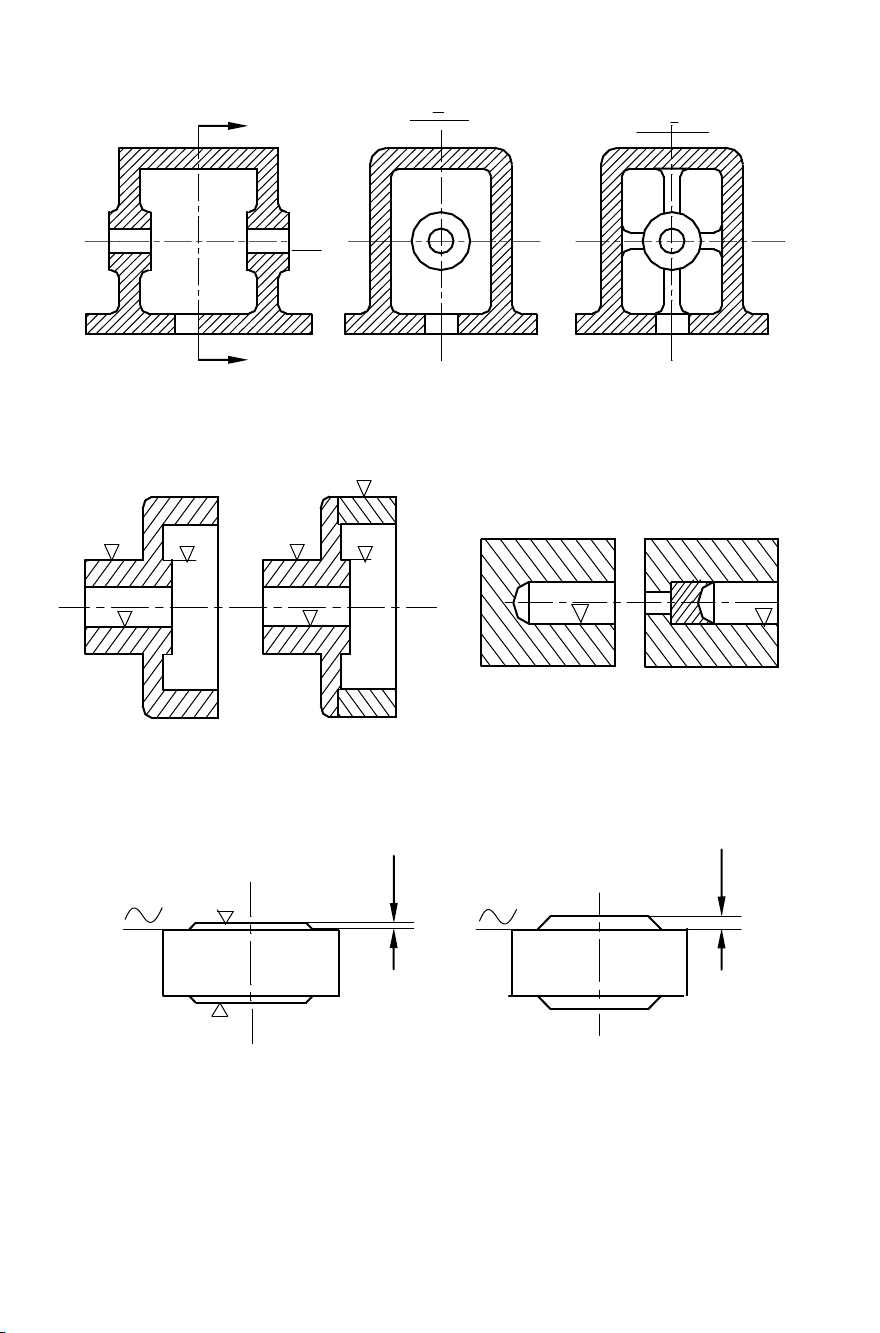
8
Hình 1.2: a) c) Chi tiết có kết cấu phức tạp khó gia công.
b) d) Kết cấu gồm hai chi tiết dễ gia công hơn.
a)
b)
c)
d)
A
A
A
b)
Hình 1.1: a) Chi tiết có thành mỏng kém cứng vững khi gia công lỗ.
b) Thêm gân trợ lực để tăng cứng vững.
A
A
a)
A
A
a)
Hình 1.3: a) Kết cấu chưa phân biệt rõ mặt gia công và mặt không gia công
b) Kết cấu hợp lí hơn
0,5
2
b)
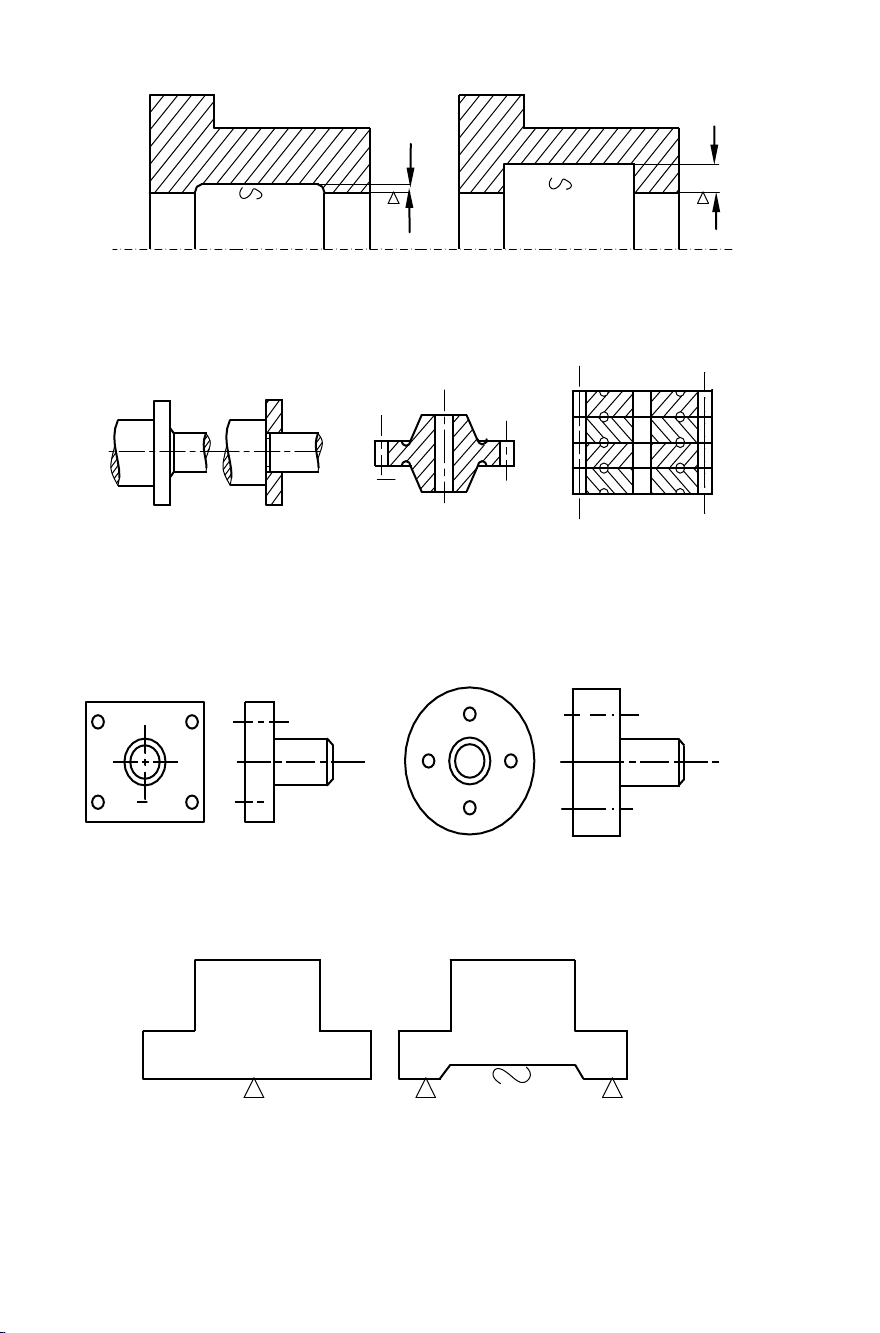
9
a)
b)
a) Kết cấu không phân biệt mặt gia công và mặt không gia công
b) Kết cấu đúng
5
2
Hình 1.6: a) Mặt bích vuông dễ gây va đập khi tiện mặt đầu.
b) Mặt bích tròn tránh được va đập khi tiện.
a)
b)
a)
c)
d)
Hình 1.5: a) Kết cấu hao phí vật liệu vì phải bỏ đi nhiều lượng dư.
b) Kết cấu gồm hai chi tiết ít hao phí vật liệu.
c) Kết cấu không gá đặt được nhiều phôi.
d) Kết cấu tạo điều kiện gá đặt nhiều phôi.
b)
a)
Hình 1.7: a) Kết cấu có diện tích gia công lớn, gây tốn kém khi cắt gọt.
b) Kết cấu giảm diện tích gia công cắt gọt.
b)
Hình 1.4
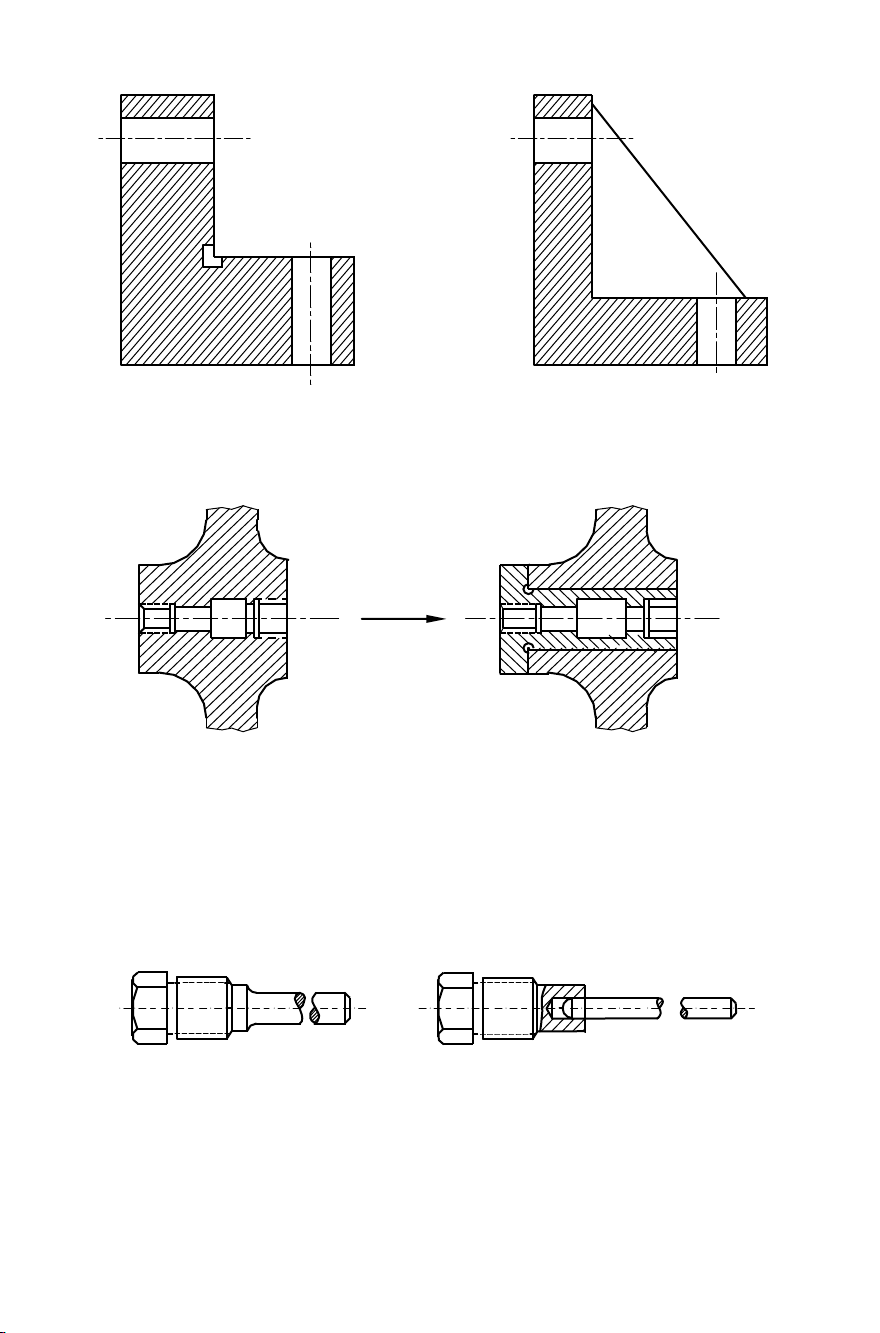
10
Hình 1.8: a) Ê ke tốn nhiều vật liệu.
b) Ê ke có gân chịu lực, thành mỏng, ít tốn vật liệu.
a)
b)
a)
b)
Hình 1.10
a) Kết cấu là một khối liền, khó chế tạo và không thuận lợi cho việc
sữa chữa.
b) Kết cấu hợp lý hơn, gồm hai chi tiết ráp lại, chế tạo đơn giản hơn .
a)
b)
Hình 1.9
a) Kết cấu gồm một khối liền (trên thân hộp) không sửa chữa được
b) Kết cấu thành hộp được lắp thêm bạc nên dễ sửa chữa, thay thế
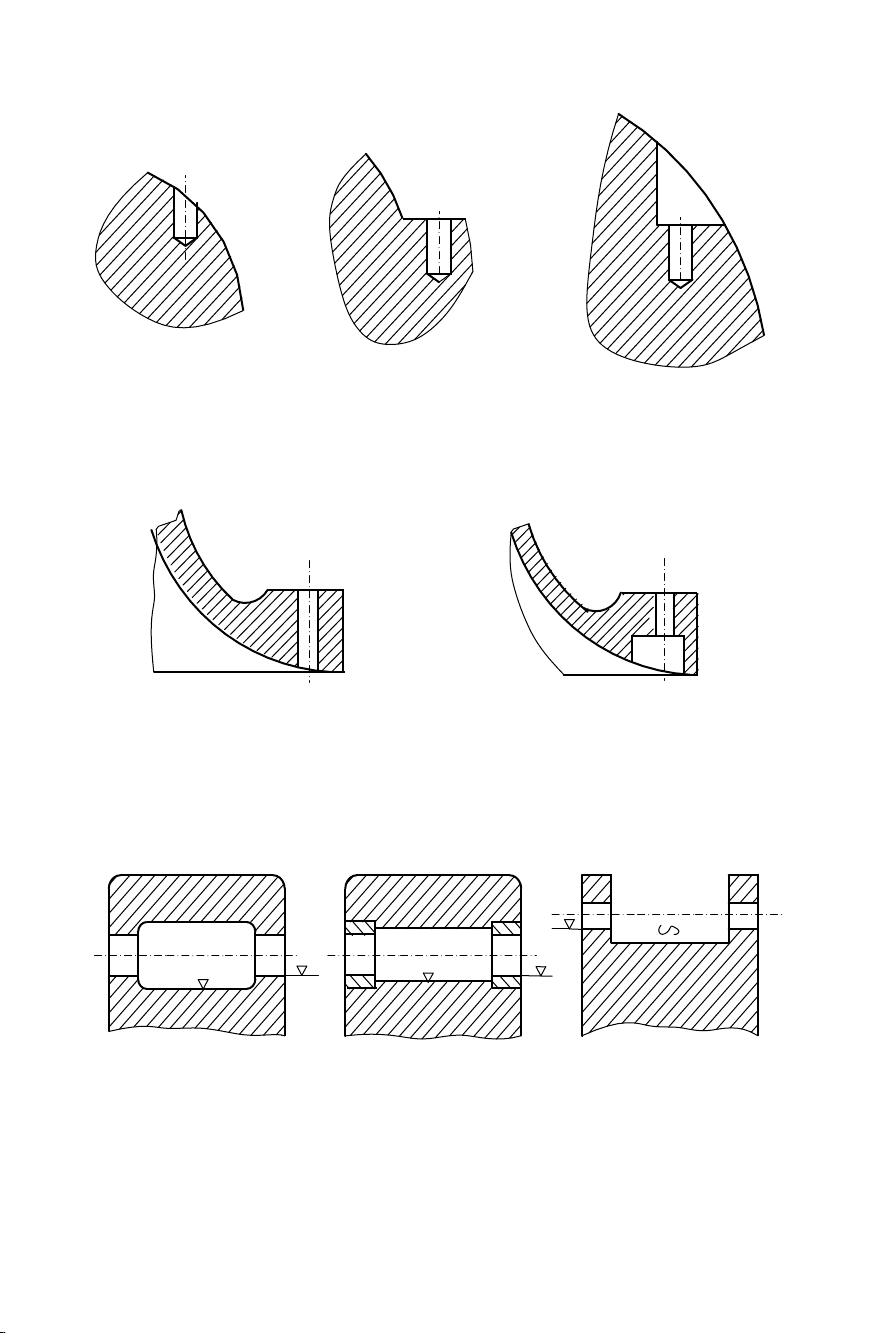
11
Hình 1.11: a) Kết cấu khó gia công, dễ gãy mũi khoan.
b) c) Kết cấu tạo điều kiện khoan lỗ an toàn.
a)
b)
c)
Hình 1.12
b)
a)
a) Kết cấu như vậy lỗ sẽ bị lay rộng và nghiêng khi khoan
b) Kết cấu hợp lý hơn
a)
b)
c)
Hình 1.13
a) Kết cấu khó chế tạo, không thuận lợi khi sử dụng .
b) Kết cấu có bạc, dễ chế tạo và sử dụng hơn .
c) Kết cấu đơn giản, dễ chế tạo và sửa chữa .
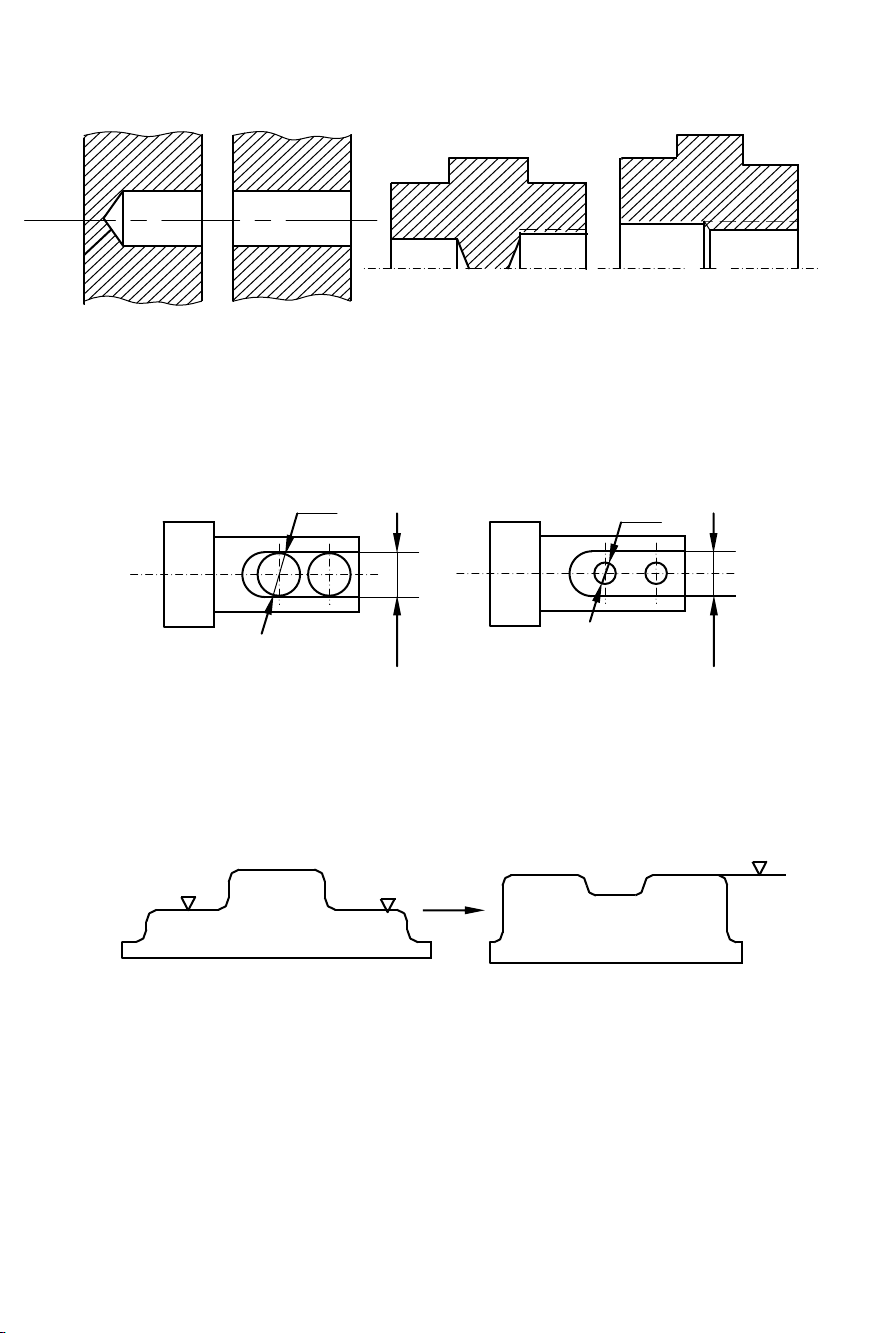
12
d)
c)
b)
a)
Hình 1.14
a) c) Kết cấu không có rãnh thoát dao nên dễ bị gãy, bể dao .
b) d) Kết cấu hợp lý hơn nên dễ chế tạo và lắp ráp hơn .
a)
b)
Hình 1.16
a) Kết cấu không tạo khả năng gia công cùng một đường chuyển dao.
b) Kết cấu hợp lí hơn
Hình 1.15
a) Đường kính mũi khoan bằng kích thước rãnh dễ gãy mũi khoan
b) Đường kính mũi khoan nhỏ hơn chiều rộng rãnh nên an toàn hơn
.
B
b)
D
B
a)
D
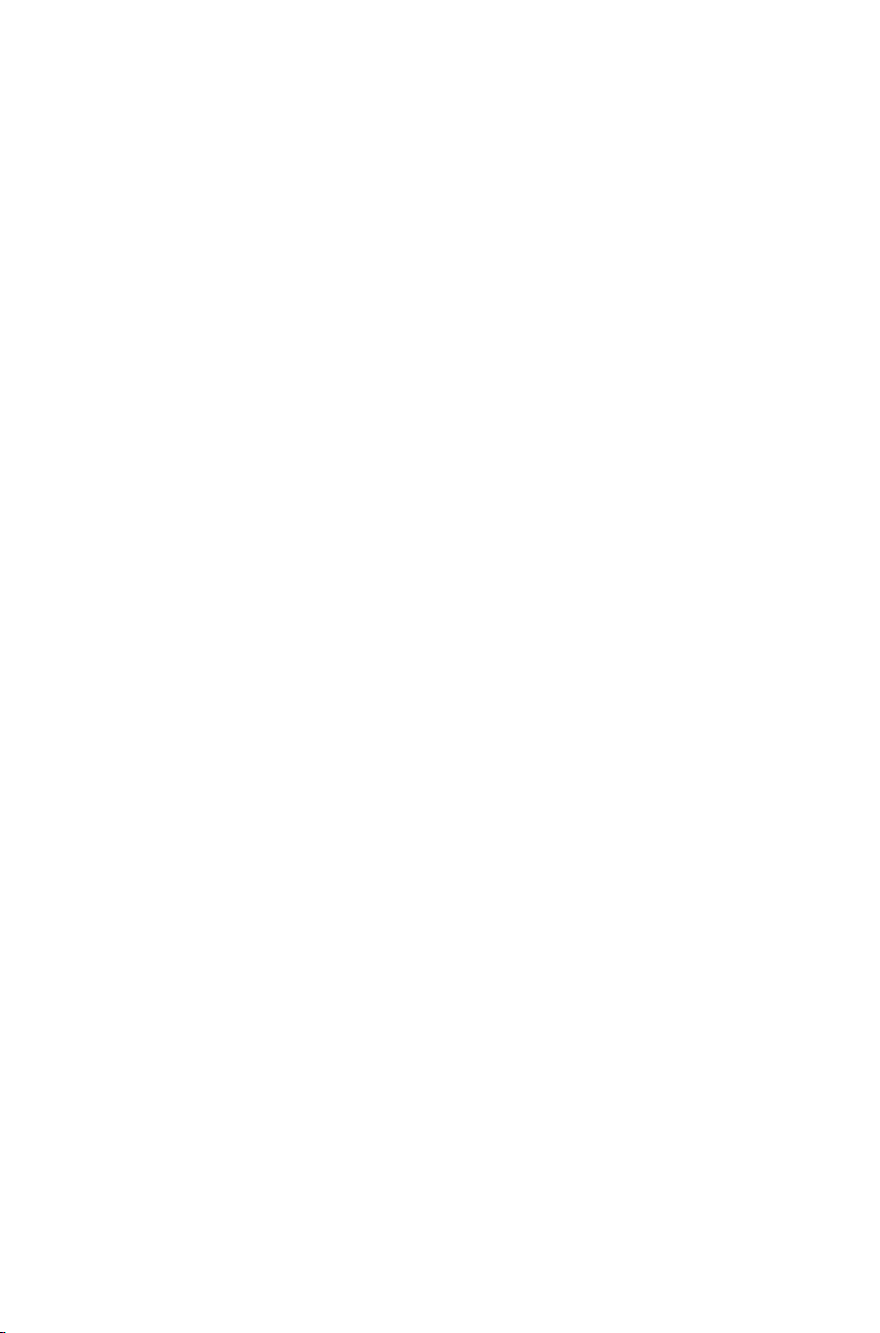
13
1.1.4. Xác định trình tự gia công hợp lí và thiết kế nguyên công
1.1.4.1. Xác định trình tự gia công hợp lí
Xác định trình tự gia công nghĩa là phân chia quá trình công nghệ
thành các nguyên công và bước. Mục đích chính là phải chọn được một
trình tự có chu kì gia công hoàn chỉnh một chi tiết là ngắn nhất, chất
lượng ổn định nhất, chi phí gia công thấp nhất, hiệu quả kinh tế cao.
Khi lập trình tự gia công cần căn cứ vào:
- Quá trình hình thành bề mặt gia công qua các giai đoạn gia công
thô, gia công tinh.
- Quá trình tạo độ cứng bề mặt bằng nhiệt luyện.
- Lí thuyết về chuẩn công nghệ và gá đặt khi gia công
- Điều kiện sản xuất cụ thể (thiết bị, trang bị công nghệ, bố trí mặt
bằng…).
Khi xác định thứ tự các nguyên công cần dựa vào quy trình công
nghệ điển hình của các chi tiết cơ bản như: trục, bạc, càng, hộp, bánh
răng …và tuân theo các chỉ dẫn sau:
1- Đầu tiên phải gia công các mặt làm chuẩn định vị (tốt nhất là
chuẩn tinh thống nhất).
Ở nguyên công đầu này, việc chọn chuẩn thô phải tuân thủ các
hướng dẫn ở chương chuẩn ở giáo trình Cơ sở công nghệ chế tạo máy.
2- Tiếp tục gia công các bề mặt làm chuẩn trên cơ sở đã có một bề
mặt làm chuẩn tinh, ví dụ ở nguyên công đầu tiên đã gia công được mặt
phẳng thì nguyên công thứ hai phải gia công được một hoặc hai lỗ để
phối hợp với mặt phẳng hạn chế 6 bậc tự do. Hoặc gia công tiếp hai mặt
phẳng để định vị thêm 3 bậc tự do nữa.
3- Các nguyên công tiếp theo cần chia ra: Những bề mặt cần độ
chính xác cao và những bề mặt cần độ chính xác thấp. Khi gia công các
bề mặt cần độ chính xác thấp, không ảnh hưởng gì đến các bề mặt có
chính xác cao thì nên gia công chúng sau. Ưu tiên gia công các bề mặt có
độ chính xác cao trước vì những bề mặt này dễ bị phế phẩm, lúc đó ta
chưa gia công các bề mặt có độ chính xác thấp.
Nếu việc gia công các bề mặt có độ chính xác thấp ảnh hưởng đến
các bề mặt có độ chính xác cao thì nên gia công chúng trước, và bề mặt
có độ chính xác cao nhất sẽ được gia công sau cùng (hai giai đoạn).
4- Nếu chi tiết hay bề mặt có qua nhiệt luyện thì nên chia ra hai giai
đoạn: trước và sau nhiệt luyện.
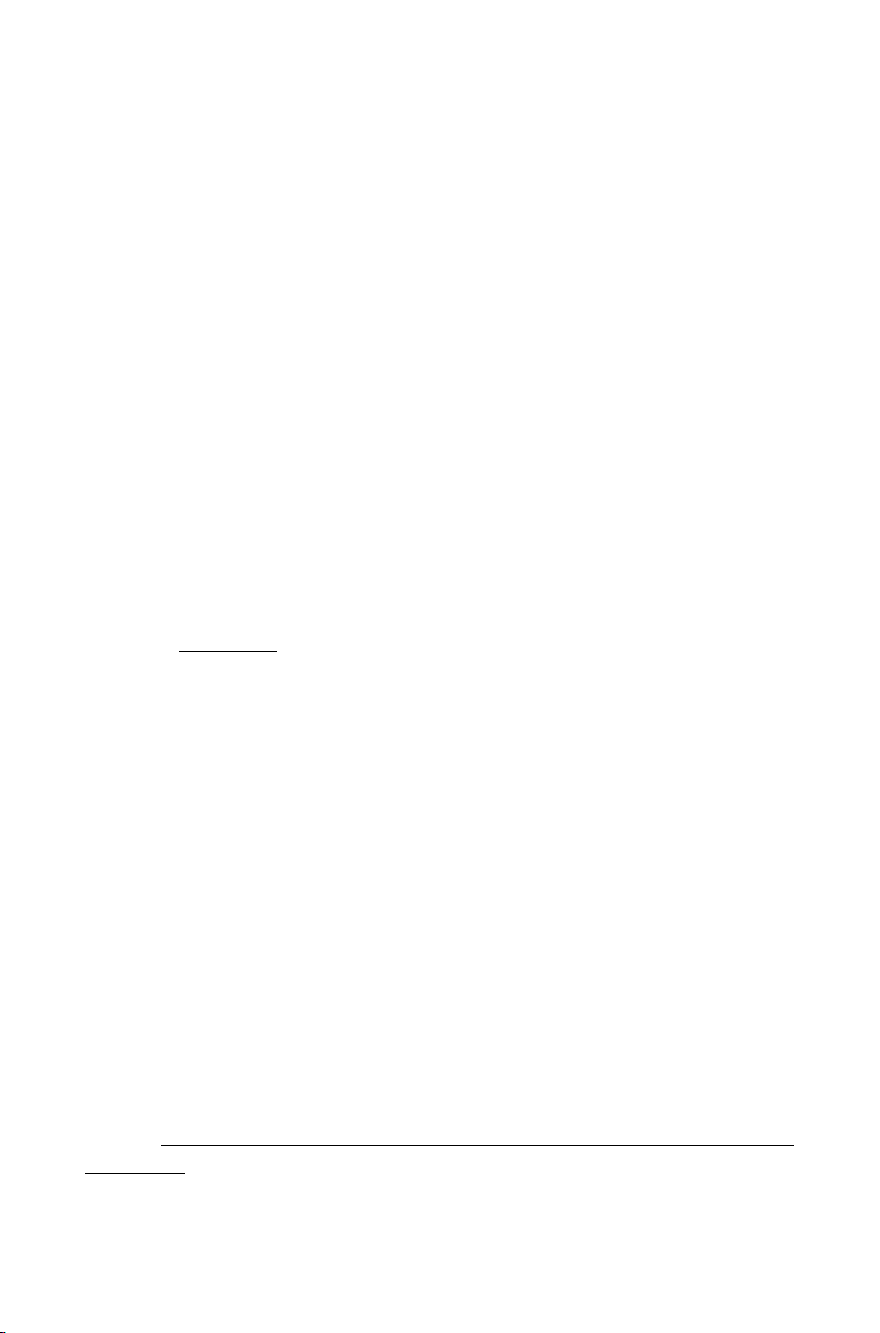
14
5- Những bề mặt có độ chính xác rất cao phải trải qua gia công lần
cuối như: mài nghiền, mài khôn, mài siêu tinh, đánh bóng thì nên tách giai
đoạn này riêng ra để dùng những thiết bị và môi trường gia công đặc biệt.
6- Cố gắng phân chia khối lượng gia công của từng nguyên công
đều nhau: nghĩa là thời gian nguyên công bằng nhau hay là bội số của
nhau để dễ bố trí máy theo sản xuất dây chuyền.
1.1.4.2. Thiết kế nguyên công
Thiết kế nguyên công nghĩa là thực hiện những công việc sau đối
với từng nguyên công:
- Chọn máy và dụng cụ cắt.
- Xác định chuẩn công nghệ, phương án gá đặt phôi, chọn đồ gá và
các trang thiết bị khác.
- Xác định chế độ cắt hợp lí.
- Định mức thời gian gia công.
- Xác định máy và nhân công (số lượng).
Sau đây phân tích cụ thể từng công việc:
a/ Chọn máy Phải tuân thủ các nguyên tắc tổng quát sau:
- Kiểu máy được chọn phải thực hiện được phương pháp gia công
đã xác định.
- Kích thước làm việc của máy phải đảm bảo quá trình gia công
thuận tiện, an toàn, tương ứng với kích thước trang bị, dụng cụ công nghệ
và hành trình cắt theo các phương và chiều khác nhau.
- Máy được chọn phải đảm bảo chất lượng gia công nghĩa là có độ
chính xác cao hơn độ chính xác của chi tiết gia công trên đó.
- Công suất máy phải phù hợp với công suất cắt gọt, nghĩa là không
nhỏ hơn và cũng không lớn hơn công suất cắt quá nhiều gây lãng phí .
- Nên chọn máy có năng suất cao, các phí tổn về thời gian chạy
không là ít nhất. Ưu tiên các máy bán tự động, tự động, điều khiển số…
- Ở dạng sản suất loạt nhỏ nên tập trung nguyên công trên một vài
máy để giảm chi phí vận chuyển và các chi phí khác trong sản xuất .
- Chú ý đến điều kiện sản xuất thực tế khi chọn máy.
b/ Xác định chuẩn công nghệ, phương án gá đặt, chọn trang bị
công nghệ
- Chuẩn công nghệ phải được xác định trên nguyên tắc 6 điểm đã
nêu ở chương Chuẩn ở giáo trình Cơ sở Công nghệ chế tạo máy.
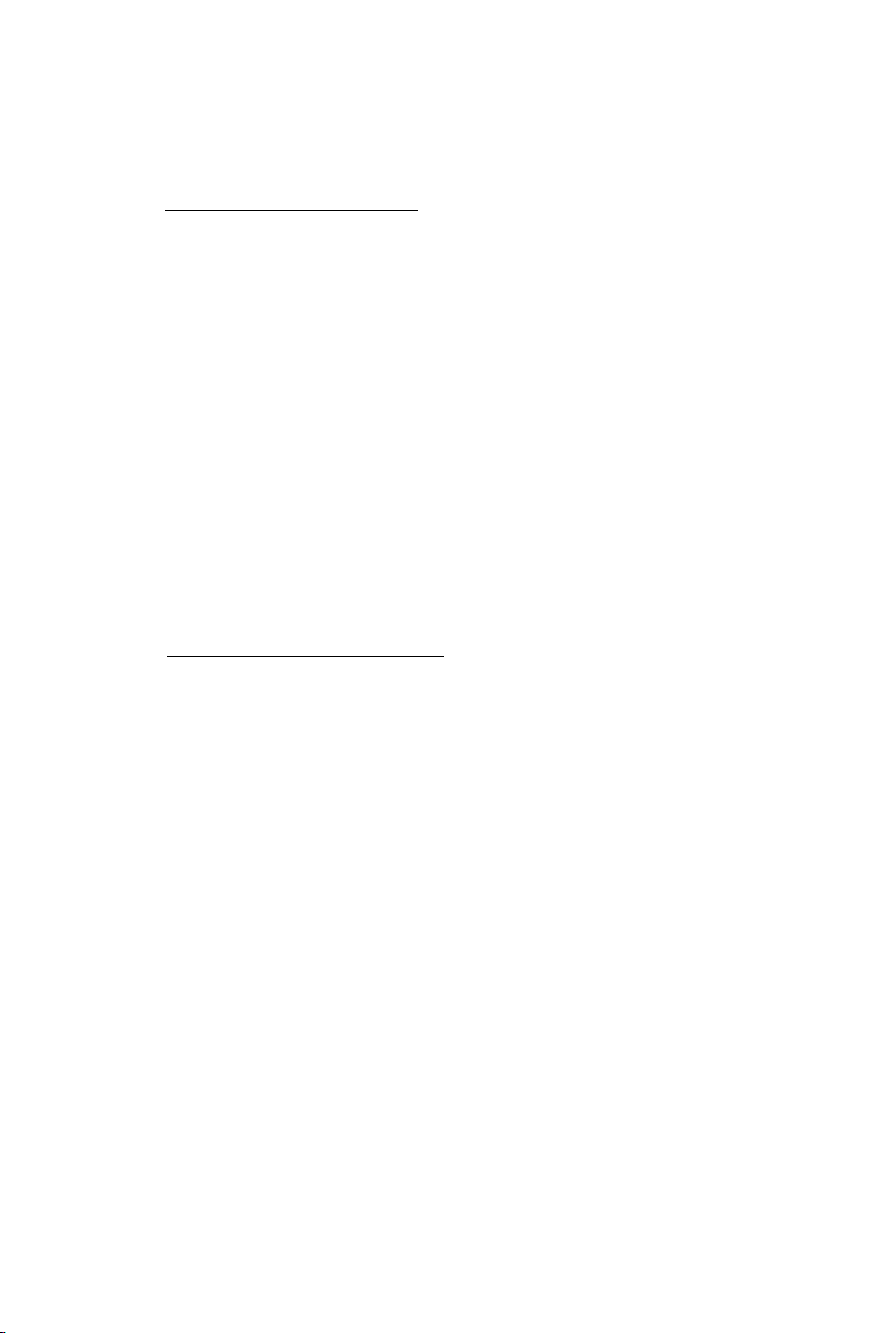
15
- Việc kẹp chặt tham khảo chương thiết kế đồ gá của giáo trình này.
- Sử dụng đồ gá chuyên dùng hoặc đồ gá tháo lắp nhanh trên máy
chuyên dùng.
c/ Xác định chế độ cắt hợp lí
Chế độ cắt (CĐC) ảnh hưởng trực tiếp đến năng suất và chất lượng
gia công.Vì thế khi chọn CĐC nên tham khảo chương Nguyên lý cắt
kim loại ở giáo trình Cơ sở Công nghệ chế tạo máy. Đặc biệt phải tối
ưu hóa chế độ cắt khi gia công.
Khi lựa chọn chế độ cắt nên tận dụng khả năng của dụng cụ cắt, nhất
là tuổi bền nhằm nâng cao năng suất cắt gọt ở những bước gia công thô.
Các giá trị tối ưu của CĐC hay các thông số công nghệ khác hiện
tại được xác định trước khi gia công (nghĩa là ngoài quá trình cắt), được
chỉnh sẵn trên máy theo những chỉ tiêu tối ưu khác nhau về kĩ thuật và
kinh tế. Nhưng trong quá trình cắt, do ảnh hưởng của các yếu tố ngẫu
nhiên mà các thông số công nghệ sẽ có giá trị thực tế sai lệch so với giá
trị tối ưu đã xác định. Vì vậy phương hướng chung là tối ưu hóa liên tục
các thông số công nghệ ngay trong quá trình cắt, nhằm đảm bảo các
thông số công nghệ luôn có giá trị tối ưu (giám sát quá trình cắt).
d/ Định mức thời gian gia công
Định mức thời gian gia công là xác định thời gian cần thiết để hoàn
thành nội dung công việc cho từng nguyên công và toàn bộ quá trình
công nghệ trong điều kiện sản xuất cụ thể nào đó.
Các thành phần thời gian thường được phân chia như sau:
T
o
- thời gian cơ bản, là thời gian máy làm việc, dụng cụ cắt trực
tiếp làm biến đổi hình dạng kích thước và tính chất cơ lí của chi tiết gia
công. Công thức tính toán thời gian này cho trong sổ tay: “Chế độ cắt
gia công cơ”.
T
p
- thời gian phụ, là thời gian do máy hoặc công nhân thao tác để
hoàn thành chu kì gia công. Ví dụ: thời gian chạy dao lùi ra, gá đặt và
tháo chi tiết, đo lường khi gia công …
T
nc
= T
0
+ T
p
là thời gian nguyên công, thời gian này chiếm tỉ lệ
lớn nhất.
T
pv
- thời gian phục vụ, nó bao gồm hai thành phần:
T
pvkt
- thời gian phuc vụ kĩ thuật như: đổi dụng cụ, sửa đá, mài dao,
bảo dưỡng máy.
T
pvtc
- thời gian phục vụ tổ chức như: tra dầu vào máy, quét dọn,
bàn giao ca, vận chuyển, chờ đợi…
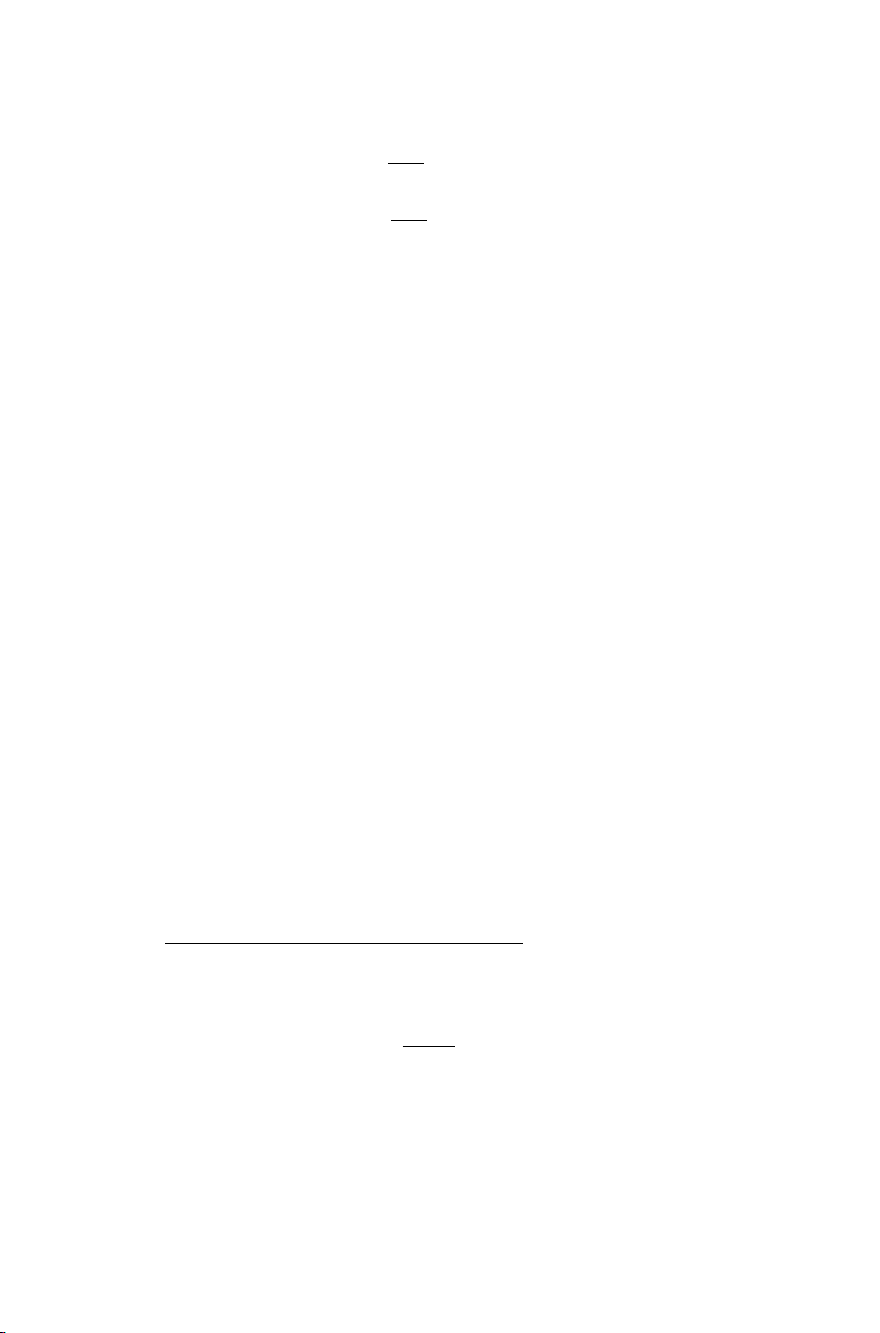
16
Như vậy: T
pv
= T
pvkt
+ T
pvtc
a,b: hệ số tỉ lệ thời gian tra ở các sổ tay công nghệ.
T
tn
– thời gian nghỉ ngơi tự nhiên theo nhu cầu của con người.
Tổ hợp các loại thời gian trên, ta được thời gian gia công từng chiếc là:
T
tc
= T
o
+ T
p
+ T
pv
+ T
tn
.
Khi gia công hàng loạt chi tiết cần phải điều chỉnh máy, ta có thêm
thời gian chuẩn bị kết thúc: T
cbkt
T
cbkt
bao gồm những công việc có liên quan đến việc chuẩn bị để
gia công một loạt chi tiết và thu dọn để kết thúc chúng, ví dụ: điều chỉnh
máy, thiết kế chế tạo đồ gá …Thời gian này không phụ thuộc vào số chi
tiết trong loạt (n). Số chi tiết trong loạt càng lớn thì thời gian từng chi tiết
trong loạt sẽ giảm xuống.
Như vậy: T
tc loạt
= T
tc
+ T
cbkt
/n
Để định mức thời gian, người ta thường dùng hai phương pháp:
Phương pháp bấm giờ: phương pháp này sát thực tế sản xuất, tương
đối chính xác vì thời gian cần thiết để gia công được phân tích thành từng
động tác tỉ mỉ và dùng đồng hồ theo dõi rồi ghi vào sổ tay. Độ chính xác
của phương pháp bấm giờ phụ thuộc vào số lần quan sát và điều kiện
thực hiện quá trình gia công, có khi phải vận dụng toán thống kê xác suất
để xử lí kết quả đo về thời gian gia công để có định mức lao động hợp lí.
Phương pháp kinh nghiệm: định mức theo kinh nghiệm thường
không chính xác nhưng nhanh, phù hợp với sản xuất nhỏ.
e/ Xác định số lượng máy và nhân công
Số lượng máy cần thiết cho một nguyên công được xác định theo
công thức:
Trong đó:
M – số máy tính toán cần thiết cho nguyên công.
T
m
– tổng giờ máy cần thiết để gia công hết sản lượng chi tiết
(giờ/năm).
100
a
TTT
popvkt
100
b
TTT
popvtc
mT
KT
M
M
m
.
.
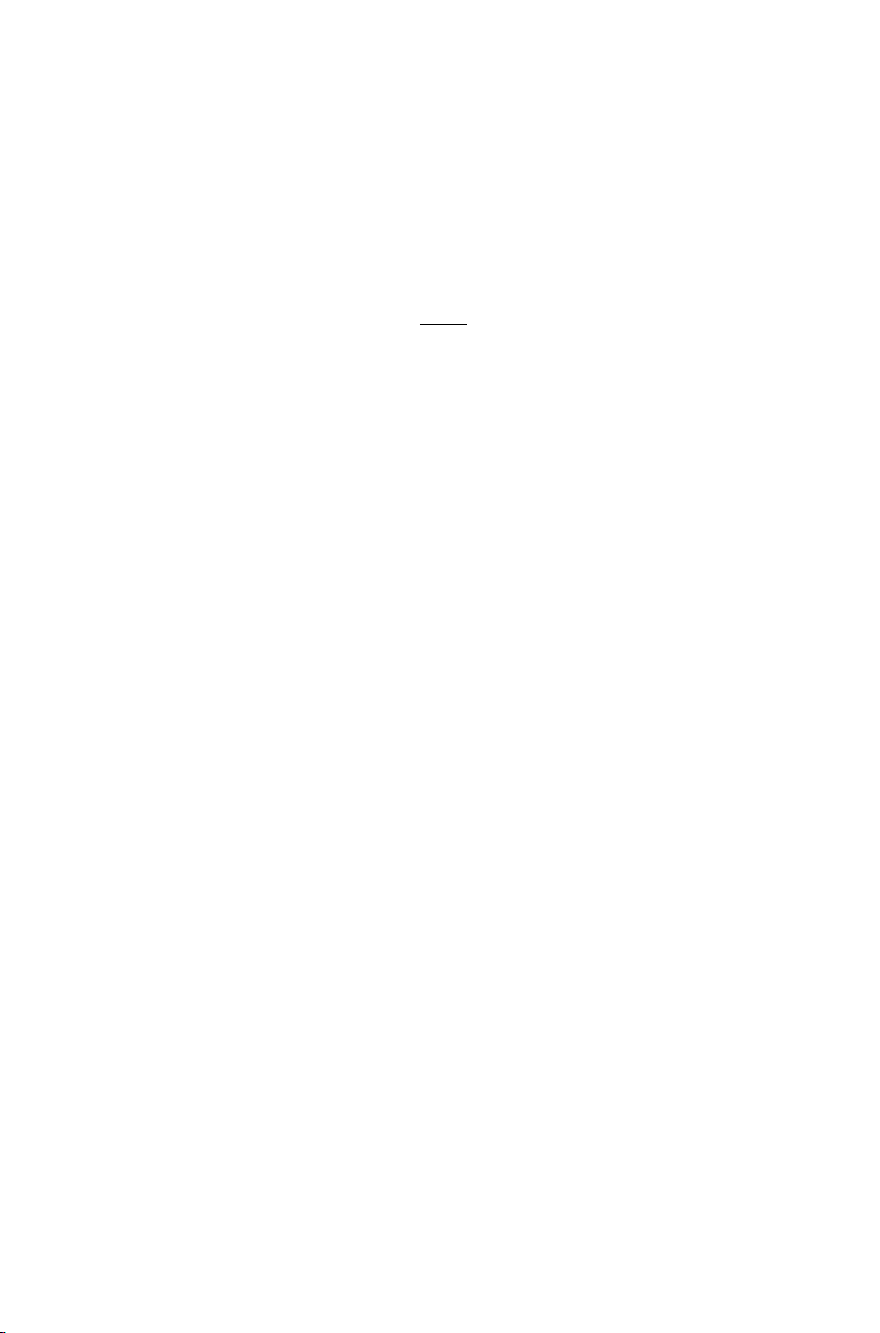
17
T
m
= T
tc loạt
.N (N là sản lượng hàng năm).
K – hệ số xét đến khả năng vượt định mức, tăng năng suất, thông
thường chọn K = 0,9 0,95.
T
M
– vốn thời gian làm việc thực tế của một máy theo chế độ một
ca sản xuất hàng ngày (T
M
có giá trị khoảng 2.200 giờ/năm):
m – số ca sản xuất hàng ngày (m = 1, 2 hoặc 3).
Số công nhân cần thiết cho nguyên công:
Trong đó:
T
n
– tổng giờ /người cần thiết cho cả sản lượng (giờ/năm)
Nguyên công gia công trên máy công cụ thì T
n
= T
m
.
T
c
– vốn thời gian làm việc của một công nhân làm việc một ca
(T
c
= 2000 giờ/năm)
1.1.5. Xác định lƣợng dƣ gia công hợp lý
1.1.5.1. Khái niệm và định nghĩa về lượng dư
a/ Khái niệm
Trong cơ khí chế tạo, tùy theo dạng sản xuất mà chi phí về vật liệu
có thể chiếm từ 30 % đến 60 % tổng chi phí chế tạo.
Xác định lượng dư gia công hợp lý về trị số và dung sai sẽ góp
phần làm giảm chi phí về vật liệu và đảm bảo hiệu quả kinh tế của quá
trình công nghệ vì:
- Lượng dư quá lớn sẽ tốn nguyên vật liệu, tiêu hao lao động, tiêu
tốn nhiều năng lượng điện, dụng cụ cắt, vận chuyển nặng … dẫn đến giá
thành tăng.
- Ngược lại, lượng dư quá nhỏ sẽ không đủ để hớt đi các sai lệch
của phôi do có hiện tượng in dập từ phôi qua chi tiết gia công. Hệ số in
dập giảm dần qua mỗi lần gia công, vì vậy để hoàn thành một bề mặt đạt
chất lượng phải trải qua nhiều bước gia công. Lượng dư phải đủ để thực
hiện các nguyên công cần thiết đó. Mặt khác lượng dư quá nhỏ có thể
xảy ra hiện tượng trượt giữa dao và chi tiết, dao sẽ bị mòn nhanh, bề mặt
gia công không đạt độ bóng yêu cầu.
b/ Định nghĩa
Lượng dư gia công cơ là lớp kim loại được hớt đi trong quá trình
gia công cơ khí.
c
n
T
KT
R
.
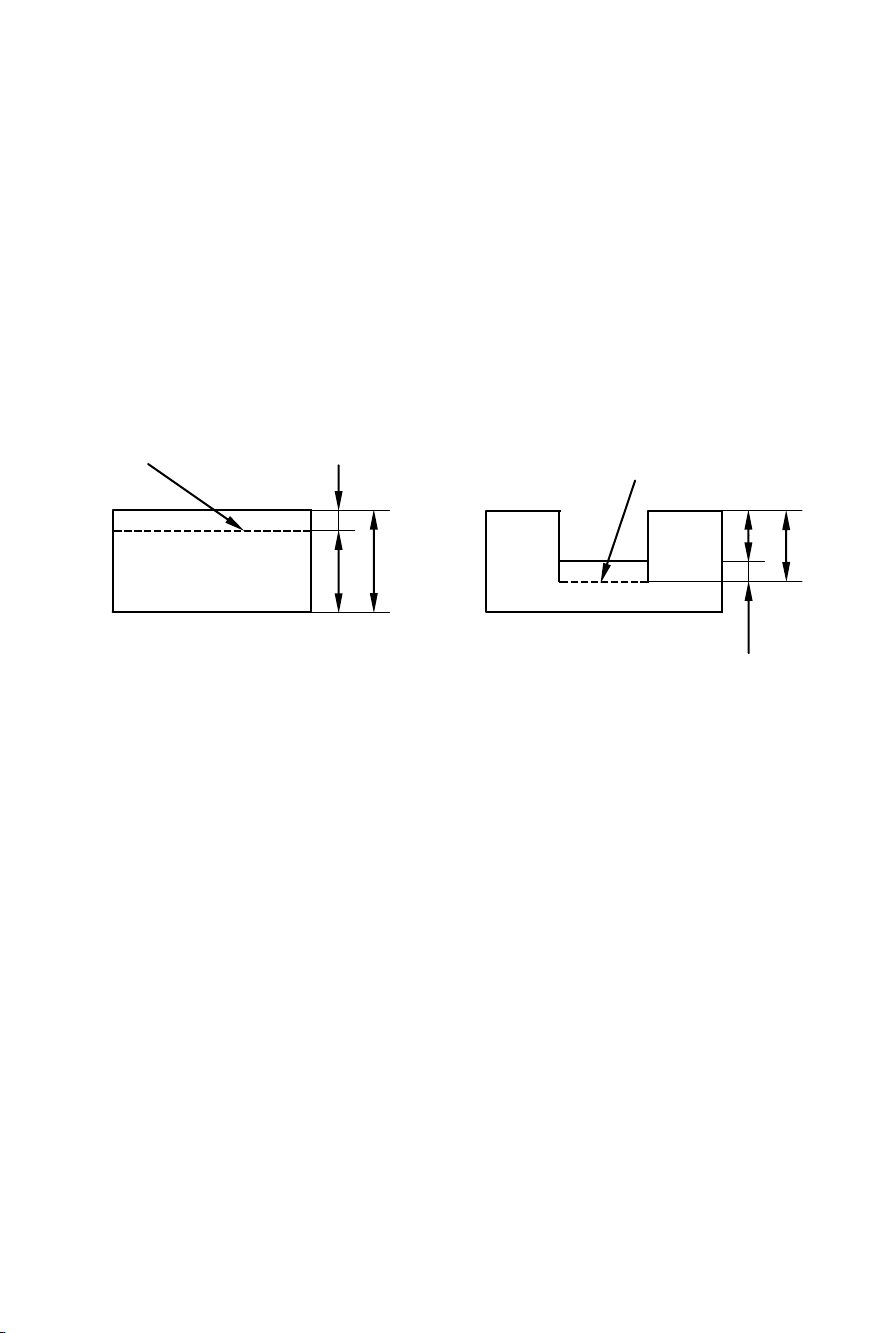
18
Để hoàn thành một bề mặt phải trải qua nhiều bước gia công nên có
hai khái niệm quan trọng là lượng dư tổng cộng và lượng dư trung gian.
- Lượng dư gia công tổng cộng (ký hiệu là Z
0
) là toàn bộ lớp kim
loại được hớt đi trong quá trình gia công qua tất cả các nguyên công hay
bước công nghệ.
- Lượng dư gia công trung gian (ký hiệu là Z
b
) là lớp kim loại được
hớt đi ở mỗi bước công nghệ hoặc mỗi nguyên công.
Quan hệ giữa Z
0
và Z
b
là:
n
bi
ZZ
1
0
(n là số nguyên công hay bước công nghệ)
Trên hình 1.17 thể hiện việc gia công ở nguyên công thứ i nào đó, ta có:
- Đối với mặt ngoài: Z
b
= a - b
- Đối với mặt trong: Z
b
= b - a
Trong đó:
b – là kích thước của bước (hay nguyên công) đang thực hiện.
a – là kích thước của bước (hay nguyên công) sát trước để lại.
Lượng dư tổng cộng được xác định như sau:
Đối với mặt ngoài: Z
o
= Kích thước phôi – Kích thước chi tiết =
n
bi
Z
1
Đối với mặt trong: Z
0
= Kích thước chi tiết – Kích thước phôi =
n
bi
Z
1
Khi xác định lượng dư cho các bề mặt đối xứng, ví dụ mặt trụ ta
thường tính 2Z
b
để tránh nhầm lẫn khi cộng với kích thước đường kính.
Trên hình 1.18, ta có:
Hình 1.17: Lượng dư gia công trung gian Z
b
b
a
Z
b
a) Mặt ngoài
Mặt gia công
b
a
b) Mặt trong
Mặt gia công
Z
b
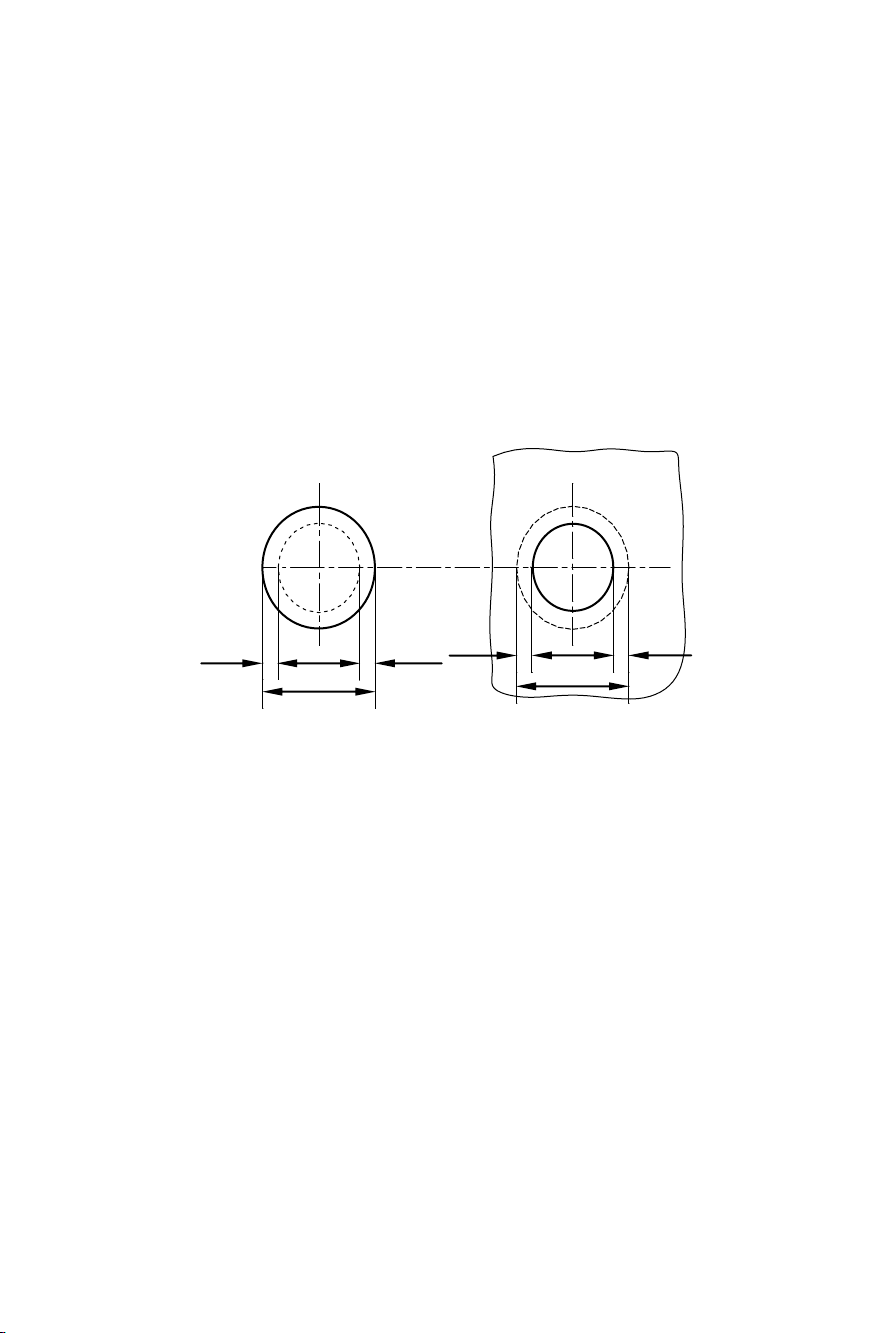
19
- Đối với mặt ngoài: 2Z
b
= d
a
- d
b
- Đối với mặt trong: 2Z
b
= d
b
- d
a
Trong đó: d
b
– Là kích thước đường kính đang thực hiện
d
a
– Là kích thước đường kính của nguyên công (hay
bước) sát trước để lại.
Lượng dư tổng cộng của bề mặt đối xứng sẽ là:
- Đối với mặt ngoài:
n
bi
ZZ
1
0
22
= d
phôi
– d
chi tiết
- Đối với mặt trong:
n
bi
ZZ
1
0
22
= d
chi tiết
– d
phôi
1.1.5.2. Các phương pháp xác định lượng dư gia công
Muốn xác định kích thước phôi phải xác định được lượng dư tổng,
sau đó cộng nó với kích thước chi tiết. Trong ngành cơ khí chế tạo máy
thường áp dụng hai phương pháp chính:
- Phương pháp tra bảng.
- Phương pháp tính toán.
Phương pháp tra bảng dựa vào cơ sở thống kê kinh nghiệm. Ở
phương pháp này lượng dư được tra trong các bảng của sổ tay công nghệ
chế tạo máy, hoặc các sổ tay tra cứu chuyên dùng thuộc các phân xưởng
sản xuất. Việc lập các bảng này dựa vào thống kê kinh nghiệm.
Ưu điểm của phương pháp này là nhanh, dễ thực hiện, nhưng
nhược điểm của nó là không xét đến điều kiện gia công cụ thể nên giá trị
Hình 1.18: Lượng dư
đối xứng
Z
b
b) Mặt trong
a) Mặt ngoài
d
b
Z
b
d
a
d
a
Z
b
Z
b
d
b
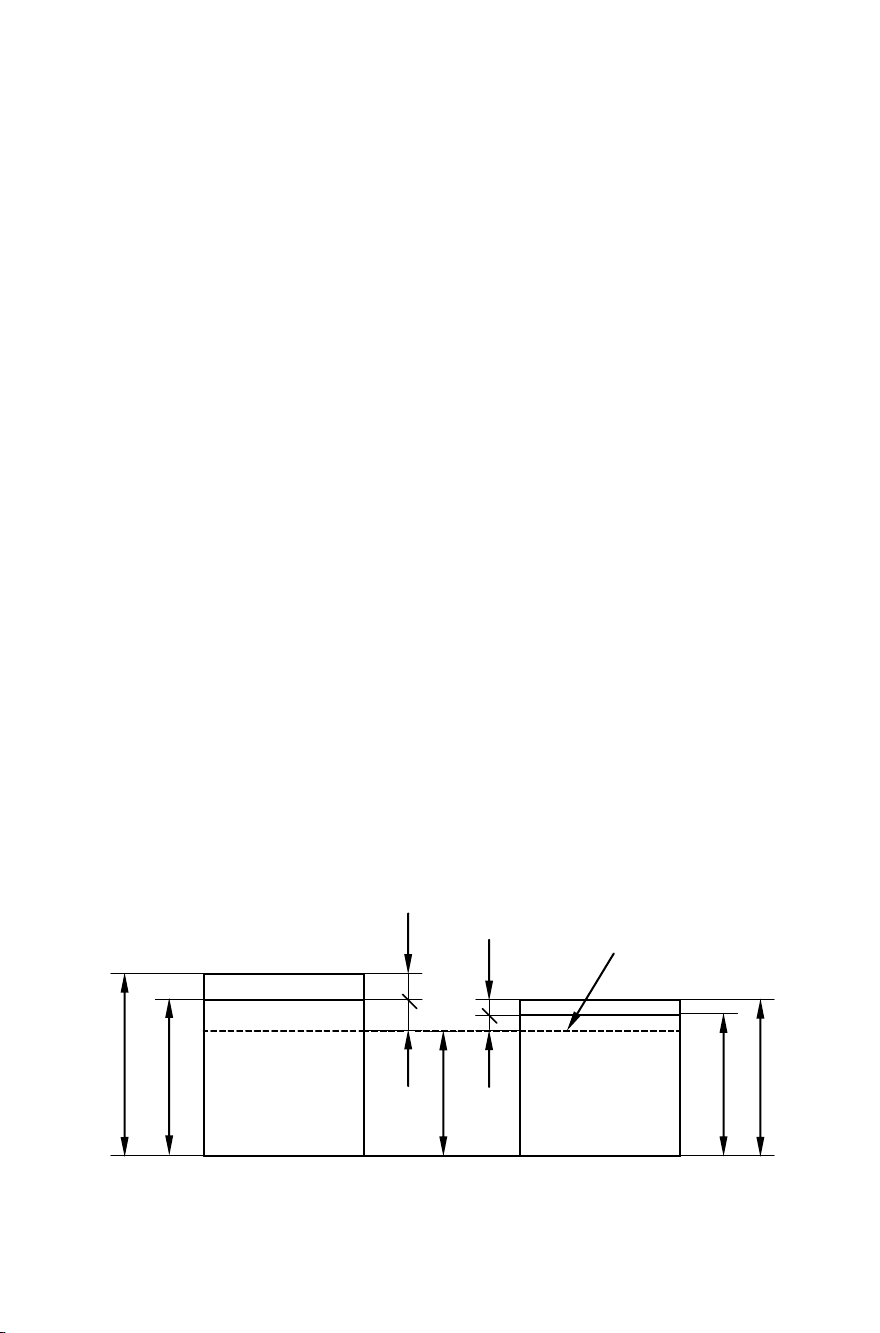
20
lượng dư thường lớn hơn giá trị cần thiết. Chỉ có một số bảng tra của
riêng phân xưởng hay nhà máy lập nên là phù hợp với điều kiện thực tế.
Phương pháp tính toán dựa trên việc phân tích và tổng hợp các yếu
tố tạo thành lớp kim loại cần phải hớt bỏ để có một chi tiết hoàn thiện.
Phương pháp này đưa lại hiệu quả kinh tế lớn nên có nhiều nhà khoa học
đã nghiên cứu và đưa ra phương pháp tính toán riêng. Sau đây, ta tìm
hiểu một trong những phương pháp tính lượng dư .
a/ Quan điểm về lượng dư của Kôvan
Khi gia công một loạt phôi cùng loại trên máy đã điều chỉnh sẳn; vì
kích thước phôi dao động trong giới hạn dung sai phôi nên lượng dư gia
công cũng sẽ dao động:
- Ở những phôi có kích thước a
min
Khi gia công xong sẽ có kích thước b
min
Lượng dư gia công cũng sẽ là Z
b min
- Ở những phôi có kích thước a
max
Khi gia công xong sẽ có kích thước b
max
Lượng dư gia công sẽ là Z
b max
Lượng dư thực khi gia công cả loạt sẽ dao động từ Z
b min
Z
b max
Vậy khi gia công mặt ngoài trên máy điều chỉnh sẵn như hình 1.19, ta có:
Z
b min
= a
min
- b
min
Z
b max
= a
max
- b
max
Còn mặt trong như hình 1.20:
Z
b min
= b
max
- a
max
Z
b max
= b
min
- a
min
Hình 1.19: Gia công mặt ngoài
Y
min
Z
b min
C
H
a
min
b
min
Y
max
b
max
a
max
Vị trí điều chỉnh dao
Z
bmax
b)
a)
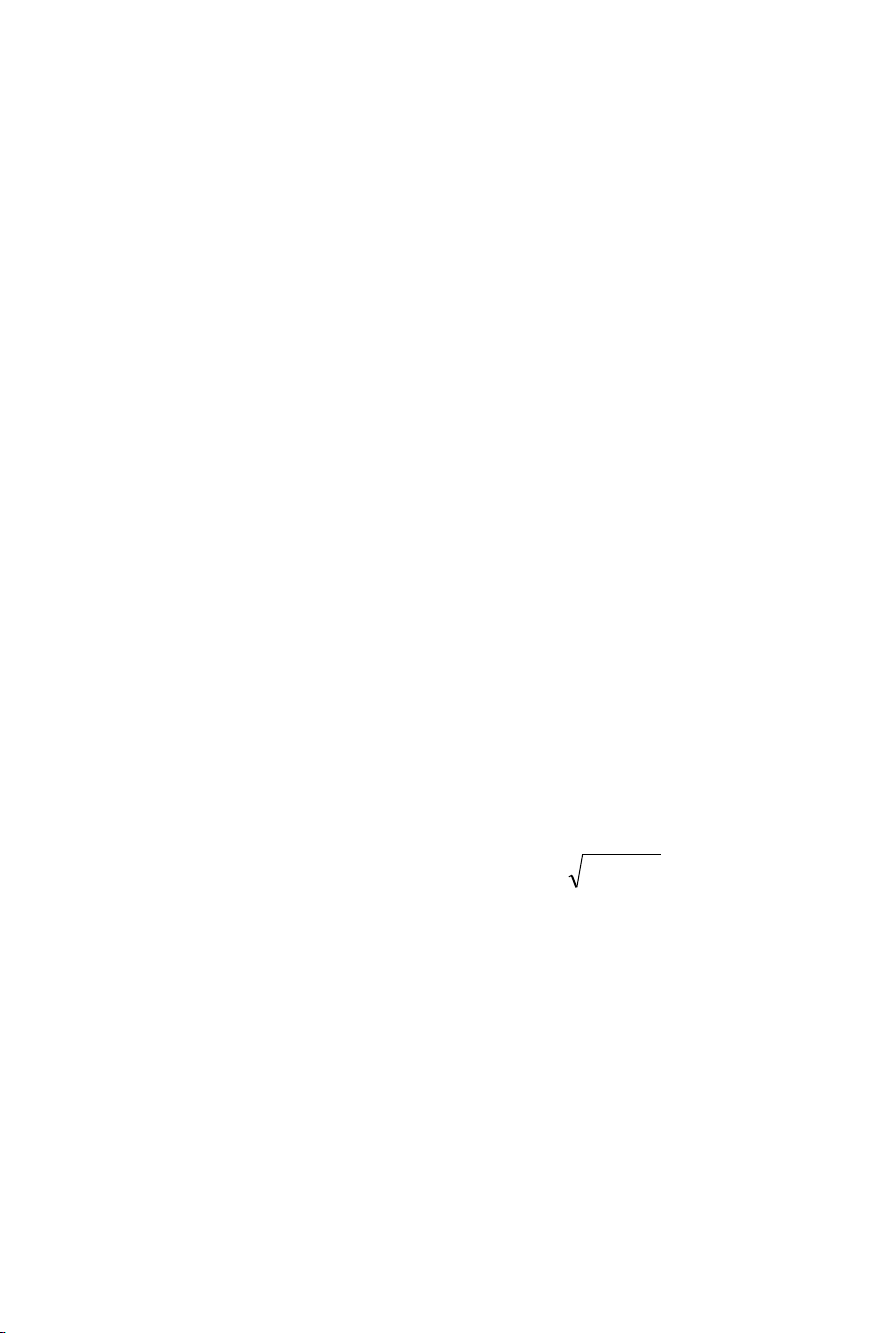
21
C
H
– Là kích thước điều chỉnh.
b –Kích thước đạt được ở nguyên công (hay bước) đang thực hiện.
a - Kích thước đạt được ở nguyên công (hay bước) sát trước.
Đối với mặt ngoài đối xứng:
2Z
b min
= D
a min
– D
b min
2Z
b max
= D
a max
– D
b max
Đối với mặt trong đối xứng:
2Z
b min
= D
b max
– D
a max
2Z
bmax
= D
b min
- D
a min
Giữa kích thước max và kích thước min sai lệch nhau một lượng là
, nên ta có:
z
= Z
b max
– Z
b min
=
a
-
b
Mặt đối xứng:
z
= 2Z
b max
– 2Z
b min
= D
a
- D
b
Các công thức trên đây dùng để tính kích thước trung gian của các
nguyên công (hay bước) khi đã biết lượng dư trung gian. Sau đây ta tìm
hiểu cách tính lượng dư trung gian theo phương pháp phân tích.
b) Công thức tính toán lượng dư trung gian theo Kôvan:
Đối với mặt phẳng: Z
b min
= ( R
za
+ T
a
) +
a
+
b
Đối với mặt đối xứng:
][22
22
min baazab
TRZ
Trong đó:
R
za
- Chiều cao trung bình lớp nhấp nhô bề mặt do nguyên
công hay bước sát trước để lại.
T
a
- Chiều sâu lớp hư hỏng bề mặt do nguyên công (hay
bước) sát trước để lại.
a
- Sai lệch về vị trí không gian do nguyên công hay bước
sát trước để lại. Ví dụ: độ không song song, độ cong vênh… Sai lệch này
tách khỏi sai lệch về hình dáng hình học như: độ côn, độ ô van.
b
- Sai số gá đặt do nguyên công đang thực hiện sinh ra. Sai
số này bao gồm sai số chuẩn và sai số kẹp chặt.
(1-1)
(1-2)
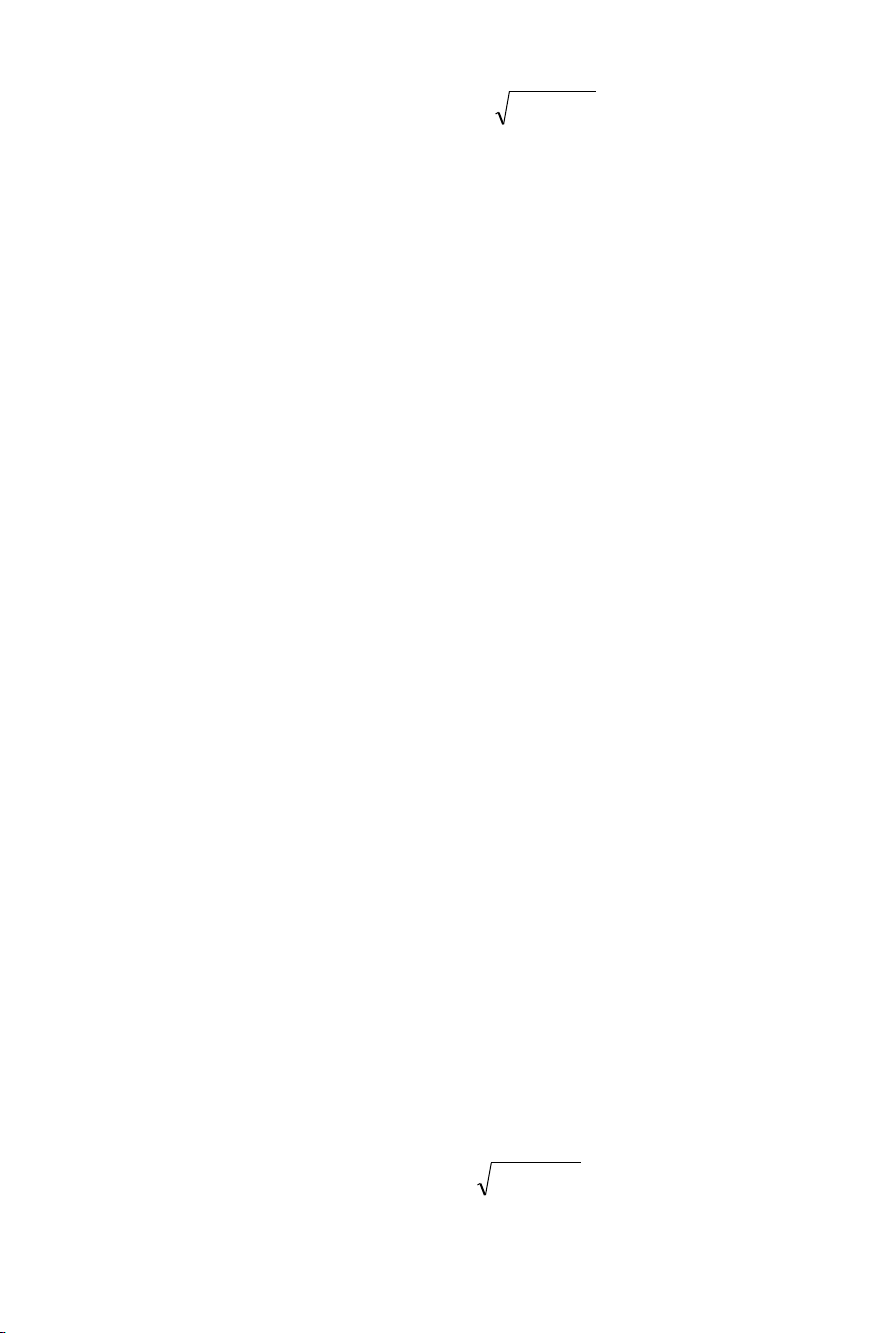
22
Hoặc :
][22
22
111min iiizii
TRZ
Ở đây: i- chỉ nguyên công đang thực hiện
i-1 - chỉ nguyên công kế trước
Các chú ý khi sử dụng công thức tính lượng dư:
- Sau nguyên công thứ nhất đối với các chi tiết làm bằng gang hay
kim loại màu, không còn T
a
trong công thức nữa. Sở dĩ như vậy vì lớp
kim loại hỏng tạo nên là do biến dạng dẻo mà đối với kim loại có độ hạt
thô như gang và kim loại màu thì hiện tượng đó không đáng kể.
- Sau nhiệt luyện mà đem mài, không tính T
a
trong công thức lượng
dư mài bởi vì T
a
là lớp kim loại được làm cứng do nhiệt luyện, đó là lớp
kim loại cần thiết khi sử dụng, lớp này có chiều sâu khá lớn.
- Một số nguyên công như: doa, chuốt lỗ, mài nghiền, mài vô
tâm… không khắc phục được sai số không gian và sai số gá đặt nên
không tính
a
và
b
vào công thức lượng dư. Như vậy:
2 Z
b min
= 2(R
za
+ T
a
)
- Có nhiều nguyên công chỉ nhằm mục đích nâng cao độ bóng bề
mặt như: đánh bóng, mài nghiền lần cuối, mài siêu tinh… công thức
lượng dư đối với mặt tròn xoay chỉ là:
2 Z
b min
= 2R
za
Các thành phần của lượng dư vừa kể trên phải tra bảng và tính toán.
R
za
- thường tra theo bảng về chỉ tiêu độ bóng bề mặt.
Ví dụ:
Phôi rèn dập : R
za
= 150 300 m; Phôi thép tiện thô: R
za
= 50 m
Phôi thép tiện tinh: R
za
= 25 m; Phay mặt đầu: R
za
= 100 m
T
a
- Trong nhiều trường hợp cho chung với R
za
:
Ví dụ: Phôi cán: R
za
+ T
a
= 300 m.
Phôi rèn tự do: R
za
+ T
a
= 2000 5000 m.
Phôi đúc cấp III: R
za
+ T
a
= 800 2000 m.
a
- Khi tính
a
cần xem xét hình dáng phôi và kích thước của nó.
Ví dụ: Trục phôi dập:
22
ctlka
lk
– độ lệch khuôn dập ;
ct
- độ cong của trục .
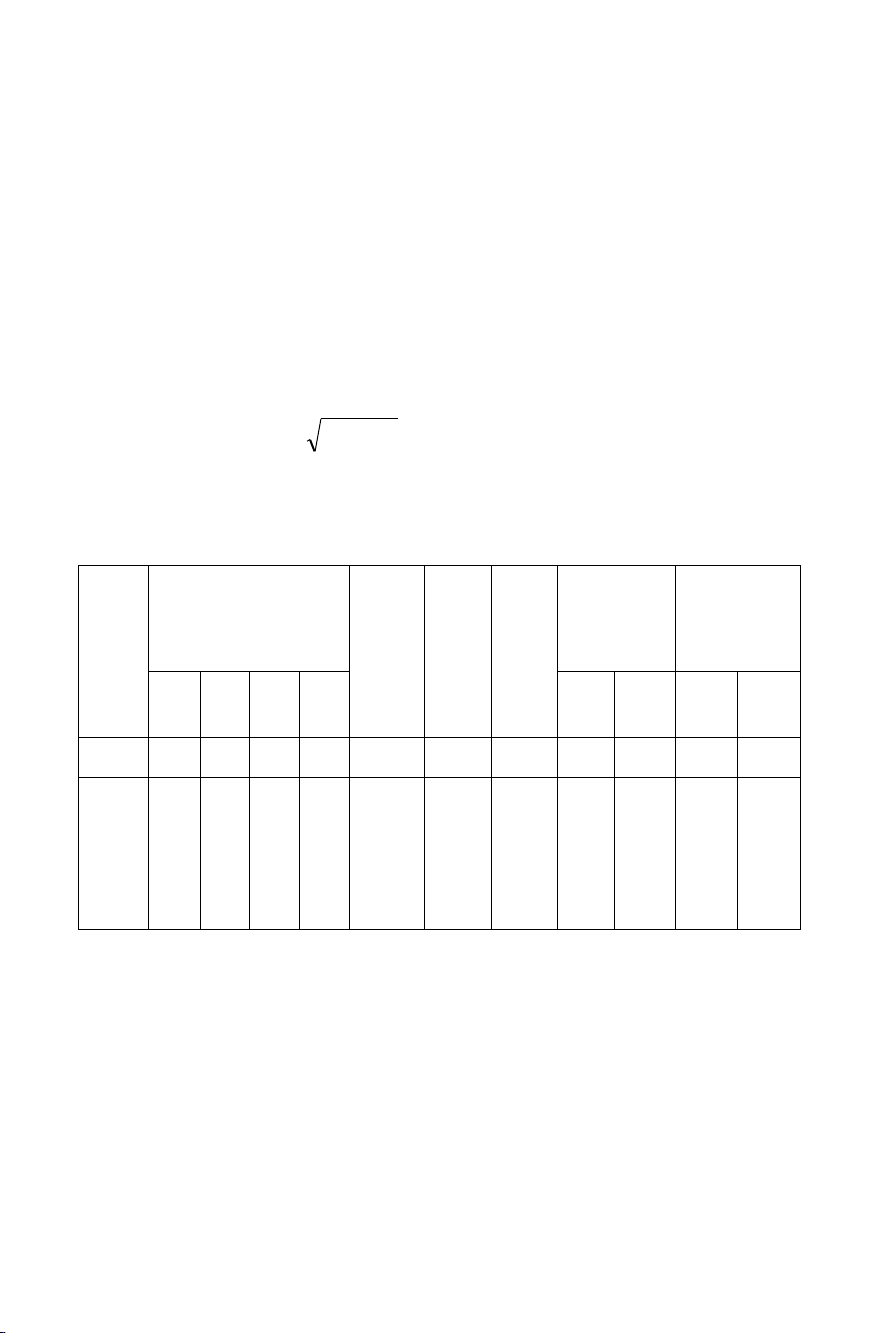
23
Cách tính
ct
như sau:
ct
=
c
. L
c
c
- độ cong đơn vị (m/mm);
L
c
- chiều dài tính toán (mm)
Sau mỗi bước ta phải tính sai lệch không gian còn lại
Thông thường :
còn lại
tính theo
ban đầu
.
Ví dụ : Sau tiện thô:
tiện thô
= 0,06
phôi
.
Sau tiện tinh :
tiện tinh
= 0,04
tiện thô
.
b
: thường tính theo công thức (đã học ở cơ sở công nghệ chế tạo máy).
22
kcb
(bỏ qua sai số đồ gá)
c) Trình tự tính lượng dư theo cách lập bảng
Để tính toán lượng dư theo cách lập bảng (do Kôvan đề ra) cho một
bề mặt nào đó, ta lập bảng gồm 12 cột sau:
Thứ
tự
các
bước
công
nghệ
Các yếu tố của lượng
dư (m)
Lượng
dư
tính
toán
Z
b min
(m)
Kích
thước
tính
toán
(mm)
Dung
sai
(m)
Kích thước
giới hạn
(mm)
Trị số giới
hạn của
lượng dư
(m)
R
za
T
a
a
b
max
Min
max
min
(1)
(2)
(3)
(4)
(5)
(6)
(7)
(8)
(9)
(10)
(11)
(12)
-Phôi
-Tiện
thô
-Tiện
tinh
Sau khi lập bảng, trình tự tiến hành như sau:
1 – Lập thứ tự các bước hay nguyên công ghi vào cột (1)
2 – Tra bảng các giá trị của R
z
và T của các bước công nghệ ghi
vào cột (2), (3)
3 – Tra và tính giá trị của ghi vào cột (4)
4 – Tính và ghi vào cột (5)
5 – Tra hoặc ước lượng giá trị dung sai ở từng bước công nghệ và
ghi vào cột (8), ở bước cuối cùng ghi theo trị số dung sai ghi trên bản vẽ,
các bước trung gian dung sai sẽ tăng dần cho đến dung sai phôi.
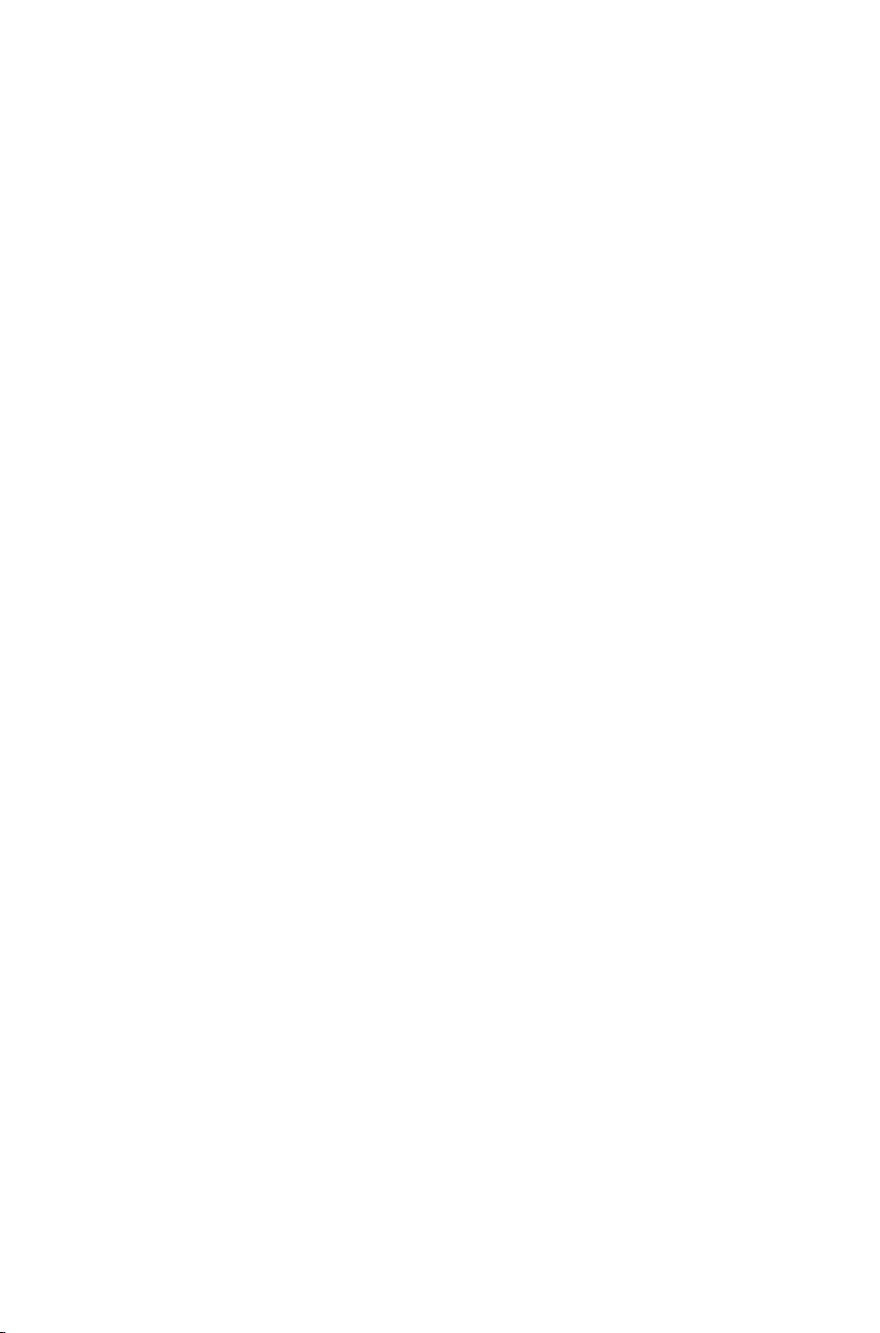
24
6 – Tính Z
bmin
theo công thức (1-1) và (1-2) rồi ghi vào cột (6).
Khi tính cần lưu ý: Các yếu tố mang chỉ số a là của nguyên công
hay bước sát trước (như R
za
, T
a ,
a
), còn chỉ số mang chữ b là của nguyên
công hay bước đang thực hiện (
b
).
7 – Ghi các kích thước tính toán vào cột (7). Cách tính kích thuớc
tính toán như sau:
Đối với mặt ngoài: Ở nguyên công hay bước cuối cùng ghi kích
thước nhỏ nhất theo bản vẽ. Cộng kích thước này với lượng dư tính toán
ở cột (6) sẽ được kích thước tính toán của nguyên công hay bước sát
trước rồi ghi vào cột (7). Lần lượt làm như vậy cho đến khi được kích
thước của phôi.
Đối với mặt trong: Ở nguyên công hay bước cuối cùng ghi kích
thước lớn nhất theo bản vẽ. Lấy kích thước này trừ đi lượng dư tính toán
ở cột (6) sẽ được kích thước tính toán của nguyên công hay bước sát
trước ghi vào cột (7). Tiếp tục làm như vậy cho đến khi được kích thước
tính toán của phôi.
8 – Ghi kích thước giới hạn vào cột (9) và (10) như sau:
Đối với mặt ngoài: Lấy kích thước tính toán ở cột (7) đem quy
tròn rồi ghi vào cột (10). Cách quy tròn tùy theo hàng số có nghĩa của
dung sai nhưng tăng lên một đơn vị. Sau đó lấy kích thước ở cột (10)
cộng với dung sai ở cột (8) sẽ được kích thước ghi vào cột (9).
Đối với mặt trong: Lấy kích thước tính toán ở cột (7) đem quy
tròn rồi ghi vào cột (9). Cách quy tròn cũng lấy theo hàng số có nghĩa của
dung sai nhưng giảm đi một đơn vị. Sau đó lấy kích thước ở cột (9) trừ đi
dung sai ở cột (8) sẽ được kích thước ghi vào cột (10).
Việc tính toán ở bước này tiến hành theo hàng ngang.
9 – Tính trị số giới hạn của lượng dư để ghi vào cột (11) và (12):
Với mặt ngoài: Z
bmin
= a
min
- b
min
Z
bmax
= a
max
- b
max
a
min
, b
min
lấy ở cột (10); a
max
, b
max
lấy ở cột (9), Z
bmax
ghi vào cột
(11); còn Z
bmin
ghi vào cột (12).
Với mặt trong: Z
bmin
= b
max
- a
max
Z
bmax
= b
min
- a
min
Cách ghi cũng như mặt ngoài.
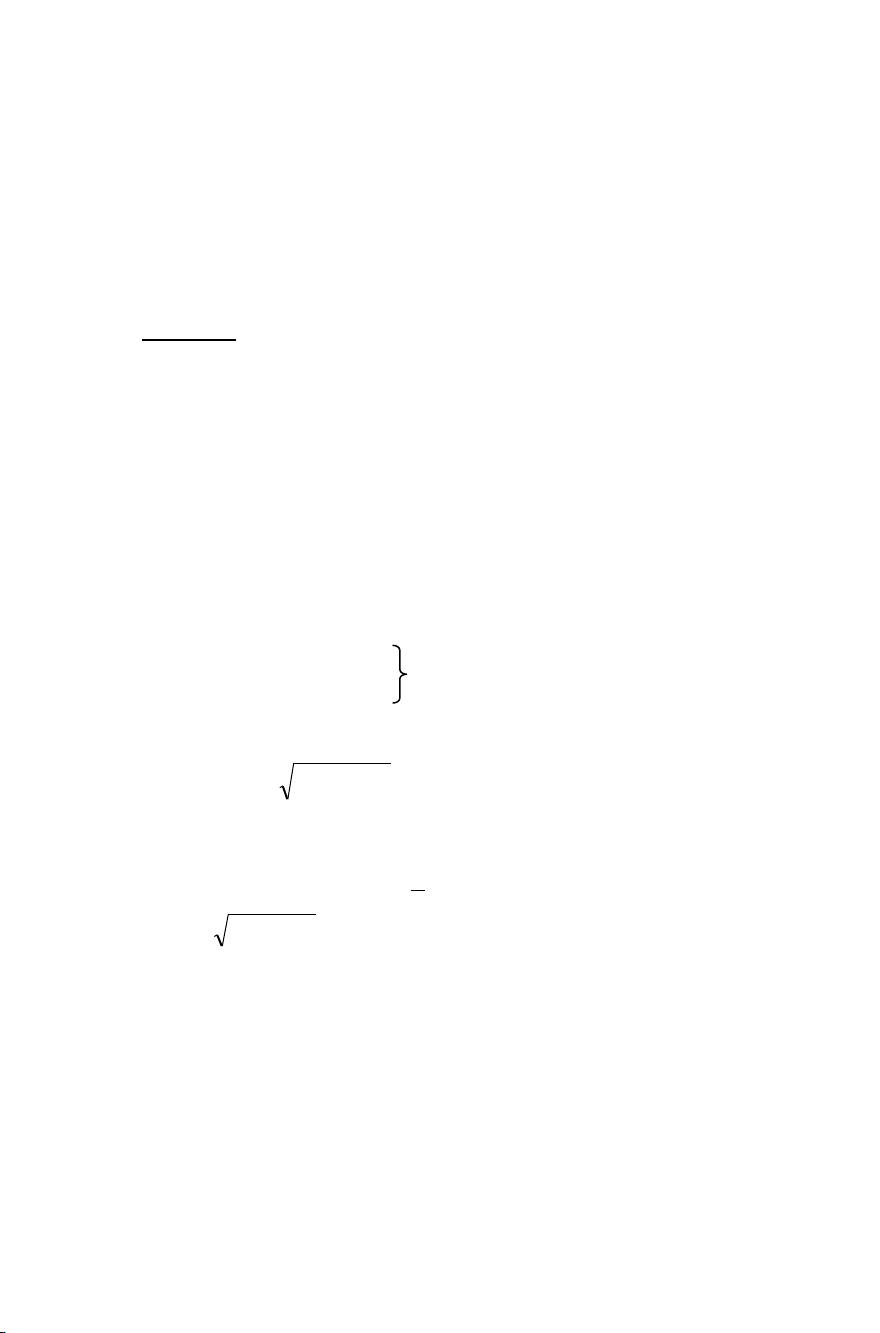
25
10 – Cộng tất cả các giá trị lượng dư ở cột (11) ta có lượng dư tổng
cộng Z
omax
; Cộng tất cả các giá trị lượng dư ở cột (12) ta có Z
omin .
11 – Kiểm tra lại mọi việc tính toán bằng các biểu thức:
Z
bmax
– Z
bmin
=
a
-
b
Và Z
omax
– Z
omin
=
phôi
-
chitiết
d) Ví dụ về tính lượng dư gia công:
Ví dụ 1: Gia công trục trơn: D = 350
-0,215
; L= 3000 mm; R
z
= 20;
VL: thép C: 200HB.
Chọn loại phôi: Phôi rèn tự do, dung sai phôi
ph
= 20 mm.
Gia công trên máy tiện: Gá đặt một đầu trên mâm 4 chấu và một
đầu chống tâm
1 - Để đạt R
z
= 20 cần qua hai bước: tiện thô và tiện tinh, như vậy ở
cột 1 ta ghi 3 dòng: phôi, tiện thô, tiện tinh.
2 - Ghi các giá trị R
za
và T
a
vào cột (2),(3):
Phôi: R
za
+T
a
=3000 ( theo sổ tay rèn dập hoặc sổ tay CNCTM tập 1)
Tiện thô: R
z
= 50 ,T = 50
Tiện tinh: R
z
= 20, T = 20
3 - Tính và ghi giá trị
a
vào cột (4)
Phôi:
22
ltcong
Với
cong
=
k
.L = 0,8.3 = 2,4mm (chiều dài L tính bằng mét)
Sai lệch do khoan tâm
lt
=
ph
4
1
= 0,25.20 = 5mm.
Tiện thô: = 0,06.5,55 = 0,333 mm = 333m.
Tiện tinh: = 0,04.333 =13,32m.
4 - Tính
b
và ghi vào cột (5).
Khi chi tiết gia công được gá đặt một đầu vào mâm 4 chấu, một
đầu chống tâm, thì sai số gá đặt
b
sẽ được xác định bằng phương pháp rà
gá trên mâm 4 chấu.
Khi tiện thô:
r
=1mm =1000m
mm55,554,2
22
theo chương “Độ chính xác gia công”
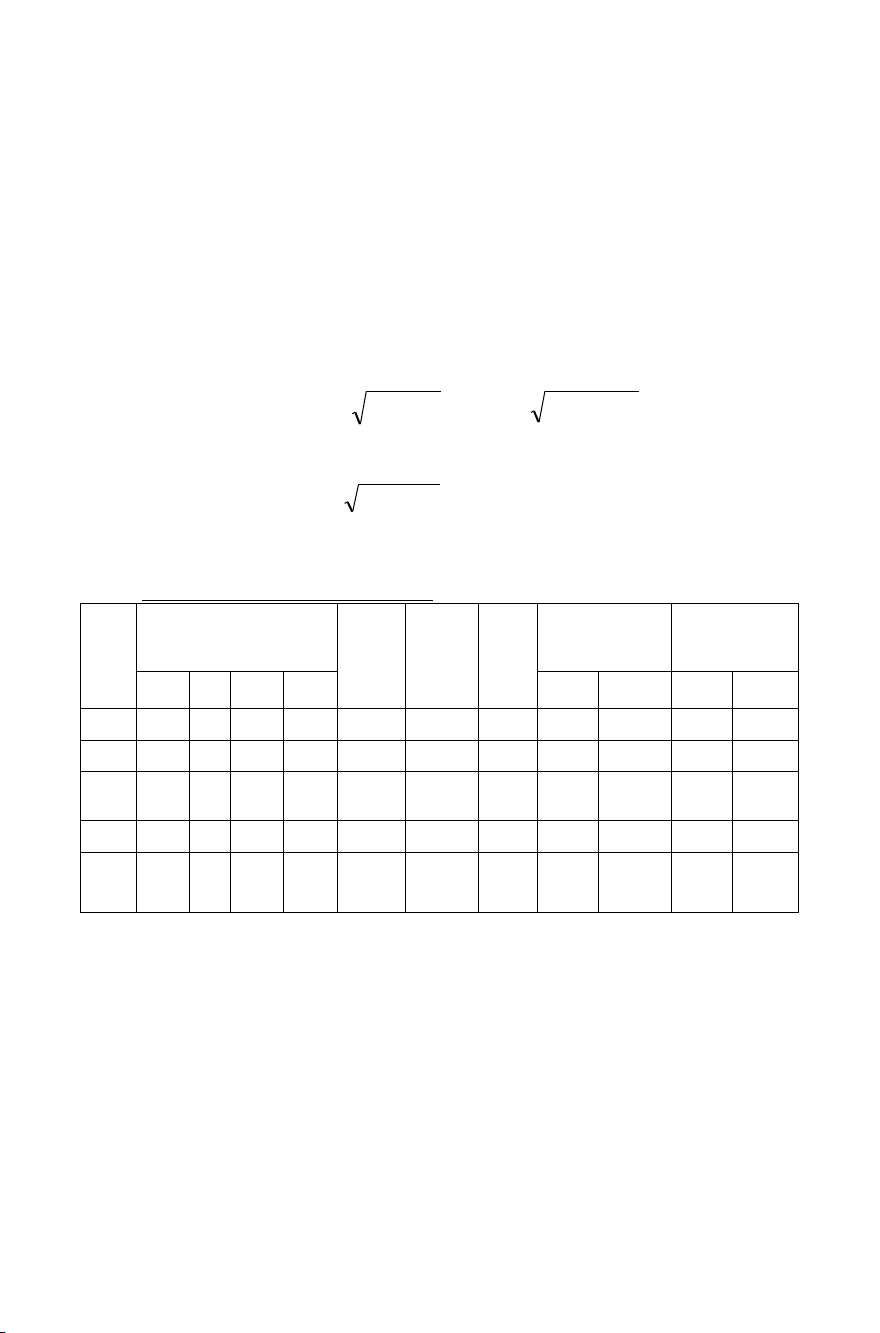
26
Khi tiện tinh:
r
= 0
5 - Ghi giá trị dung sai vào cột (8).
Ở bước tiện tinh = 215m (Theo bản vẽ chi tiết)
Ở bước tiện thô = 2350m (Chọn tăng lên).
Phôi: = 20000 m (Độ chính xác của phôi rèn tự do có đường
kính D = 350mm).
6 - Tính Z
bmin
rồi ghi vào cột (6).
Tiện thô:
Tiện tinh:
mmmZ
b
866,0866)03335050(22
2
min
Bắt đầu từ bước (7) thực hiện theo hướng dẫn và ghi vào bảng.
Bảng tính lượng dư
350
-0,215
Thứ
tự
gia
công
Các thành phần
lƣợng dƣ (m)
Lƣợng
dƣ
Z
bmin
(mm)
Kích
thƣớc
tính
toán
(mm)
Dung
sai
(mm)
Kích thƣớc giới
hạn (mm)
Trị số lƣợng
dƣ giới hạn
(mm)
Rz
T
max
min
max
min
(1)
(2)
(3)
(4)
(5)
(6)
(7)
(8)
(9)
(10)
(11)
(12)
Phôi
3000
5550
367,951
20,0
390,0
370,0
Thô
50
50
333
1000
17,3
350,651
2,350
353,0
350,65
37,0
19,350
Tinh
20
20
13,3
0
0,866
349,785
0,215
350,0
349,785
3,0
0,865
Tổng
40,0
20,215
Lượng dư tổng cộng: Z
0max
= 40,000mm.
Z
0min
= 20,215mm.
Kiểm tra lại:
Z
0max
–Z
0min
= 40,000 – 20,215 = 19,785 mm.
phôi
-
ct
= 20,000 - 0,215 = 19,785 mm.
Hai kết quả trên có giá trị như nhau, vậy việc tính toán đúng vì thỏa
mãn công thức: Z
0max
–Z
0min
=
phôi
-
ct
mmTRZ
baazab
3,17)155,53(2)(22
2222
min
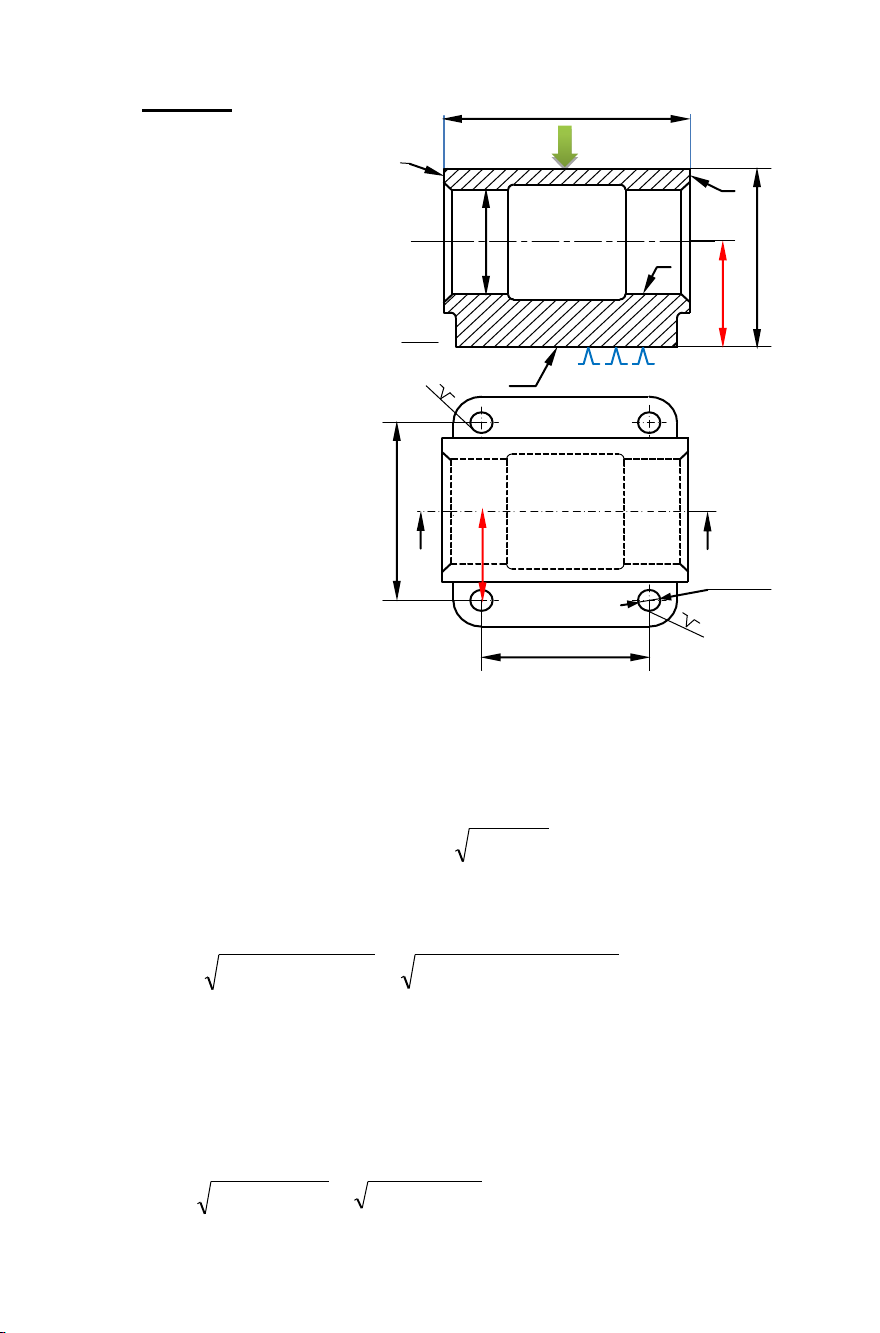
27
Ví dụ 2: Tính lượng
dư khi gia công lỗ
50
+0,05
. Độ chính xác của
phôi: cấp 1, khối lượng
phôi: 3,5kg, vật liệu phôi
gang xám (Hình 1.21).
Quy trình công
nghệ gồm hai nguyên
công (hai bước): tiện thô
và tiện tinh, chi tiết được
định vị mặt phẳng 2
(dùng hai phiến tì) và hai
lỗ 10 (chốt trụ và chốt
trám). Các mặt định vị đã
được gia công.
Để tiện cho việc tính
toán, ta lập bảng. Theo
bảng 2.11/trang 36HDTK
ĐA Công nghệ chế tạo
máy_GS.TS. Nguyễn Đắc
Lộc (chủ biên) [1] ta có
giá trị tra bảng là :
T + R
z
= 350 + 250 = 600 m. Sau bước thứ nhất, đối với gang có
thể loại trừ T, chỉ còn R
z
có giá trị 50m và 20 m (Tra bảng 3.5/71 [1] ).
Sai lệch không gian tổng cộng được xác định theo công thức sau:
22
vtcphôi
Giá trị cong vênh
c
của lỗ được tính theo cả hai phương hướng
kính và hướng trục:
Trong đó:
k
- độ cong vênh đơn vị, giá trị
k
tra bảng 3.7/75 [1],
còn l, d là chiều dài và đường kính lỗ.
vt
- sai lệch vị trí của bề mặt được tính lượng dư so với các bề mặt
làm chuẩn để gia công nó.
Giá trị
vt
được xác định theo công thức sau:
m
cbvt
640500400)()(
2222
mld
kkc
78100.7,050.7,0..
2222
(b)
80
Hình 1.21
(c)
70
100
50
+0,05
2 lỗ 14
A-A
A
2
2
3
A
4
1
82
W
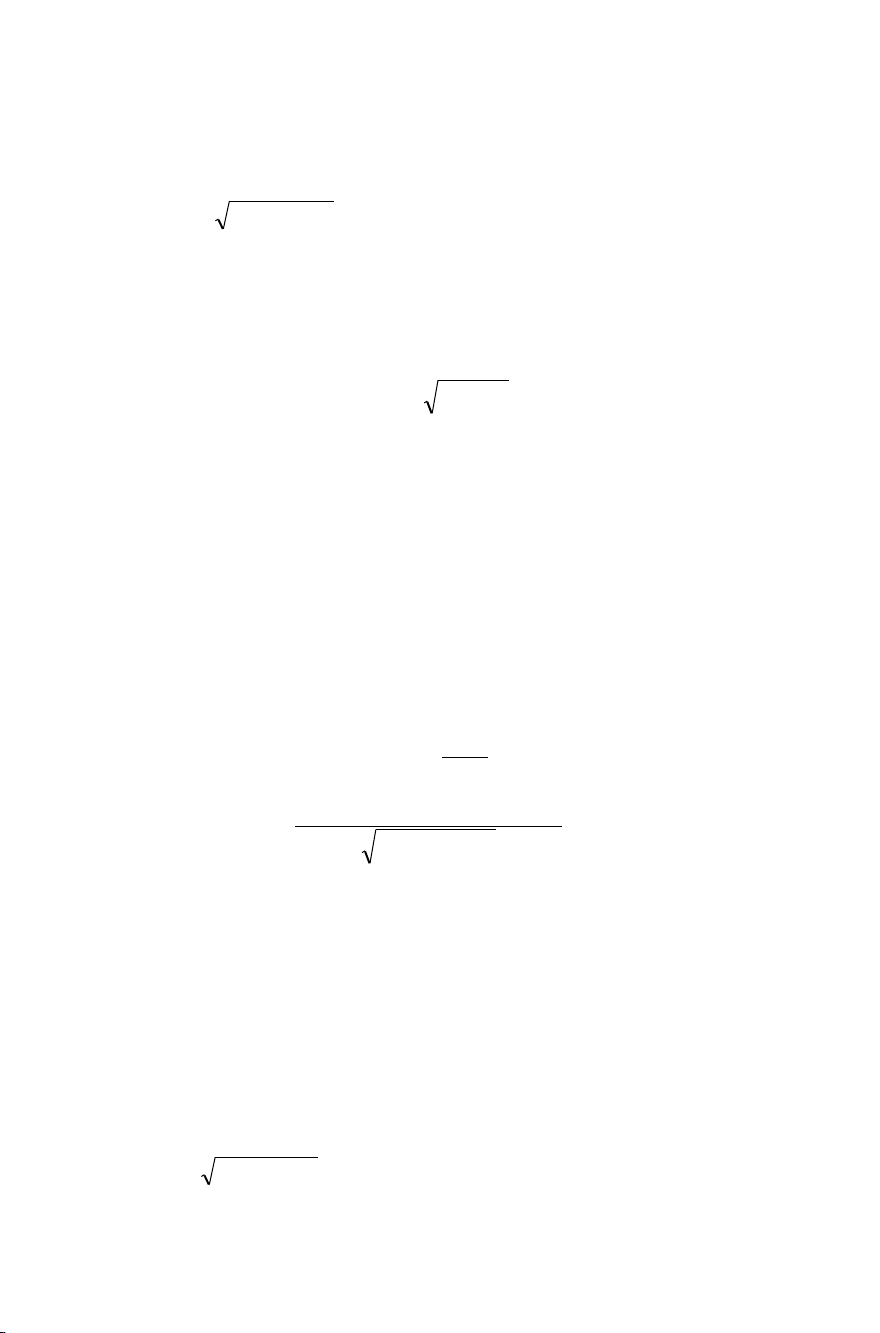
28
Ở đây:
b
,
c
là dung sai kích thước b, c của phôi. Nếu b, c có dung
sai là: 400m và 500m
Như vậy sai lệch không gian tổng cộng là:
m
phôi
64578640
22
Sai lệch không gian còn lại sau tiện thô là:
1
= 0,05.
phôi
= 0,05.645 = 32,25 m.
Sai số gá đặt khi tiện thô lỗ được xác định như sau:
22
kcgđ
Sai số chuẩn tính cho góc xoay của lỗ so với mặt chuẩn định vị
trong trường hợp này xuất hiện là do chi tiết bị xoay khi định vị vào hai
chốt mà hai chốt có khe hở với lỗ định vị.
2
max
=
c
+
l
+ 2
min
Ở đây:
l
- dung sai của lỗ định vị,
l
=16m = 0,016 mm.
c
- dung sai đường kính chốt,
c
=14m = 0,014mm.
min
là khe hở nhỏ nhất giữa lỗ và chốt,
min
=13m = 0,013 mm.
Góc xoay lớn nhất của chi tiết được xác định như sau:
Ở đây: H là khoảng cách giữa hai lỗ chuẩn.
Khi đó sai số chuẩn trên chiều dài lỗ gia công:
c
= L.tg
=100.0,0004 = 0,04 mm = 40
m.
Trong đó L là chiều dài lỗ gia công.
Sai số kẹp chặt
k
được tra trong bảng 3.14/90 [1]sổ tay CNCTM
tập 1,
k
=120m.
Vậy sai số gá đặt là:
m
gđ
12712040
22
Sai số gá đặt còn lại ở nguyên công tiện tinh là:
0004,0
8070
2/)2.013,0016,0014,0(
tan
22
H
max
tan
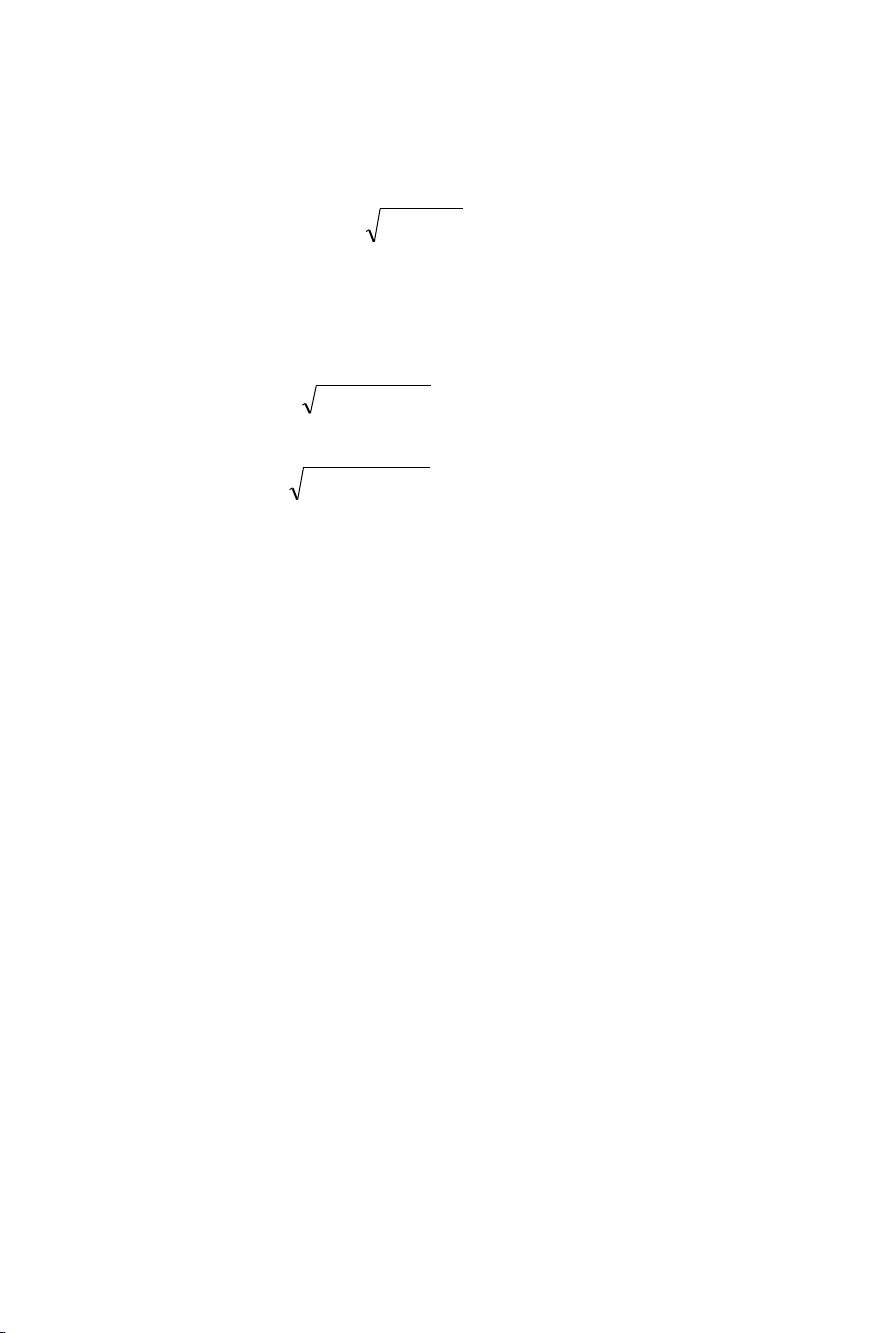
29
gđ2
= 0,05.
gđ
+
phđộ
= 6 m
Với :
phđộ
= 0 vì không có cơ cấu phân độ
Xác định lựợng dư nhỏ nhất theo công thức:
Với: i – nguyên công đang thực hiện
i – 1 – nguyên công kế trước
Lượng dư nhỏ nhất của tiện thô là:
mZ
2506)127640600(22
22
min
Lượng dư nhỏ nhất của tiện tinh là:
mZ
166)6)25,32(50(22
22
min
Cột kích thước tính toán được xác định như sau: Ta lấy kích thước
cuối cùng trừ đi lượng dư khi tiện tinh, ta sẽ được kích thước khi tiện thô,
sau đó lấy kích thước tiện thô trừ đi lượng dư tiện thô ta sẽ được kích
thước phôi.
d
t1
= 50,05 – 0,166 = 49,884 mm.
Kích thước phôi: d
tph
= 49,884 – 2,506 = 47,378 mm.
Dung sai của từng nguyên công :
Dung sai tiện tinh: = 50m( Lấy theo bản vẽ )
Dung sai tiện thô = 170m ( Theo khả năng tiện thô )
Dung sai phôi = 400m ( Tra bảng )
Cột kích thước giới hạn được xác định như sau: lấy kích thước tính
toán và làm tròn theo hằng số có nghĩa của dung sai ta được d
max
sau đó
lấy dung sai d
max
trừ dung sai d
min
.Vậy ta có:
Sau tiện tinh: d
max
= 50,05mm ; d
min
=50,05 – 0,05 =50 mm.
Sau tiện thô: d
max
= 49,884 mm ; d
min
= 49,884 –0,17 = 49,714 mm.
Kích thước của phôi :
d
max
= 47,378 mm ; d
min
=47,378–0,4 = 46,978 mm.
Cột lượng dư giới hạn được xác định như sau: Z
min
bằng hiệu giữa
hai kích thước lớn nhất của hai nguyên công kề nhau, Z
max
bằng hiệu giữa
hai kích thước nhỏ nhất của hai nguyên công kề nhau. Vậy ta có:
22
111min
22
iiiZii
TRZ
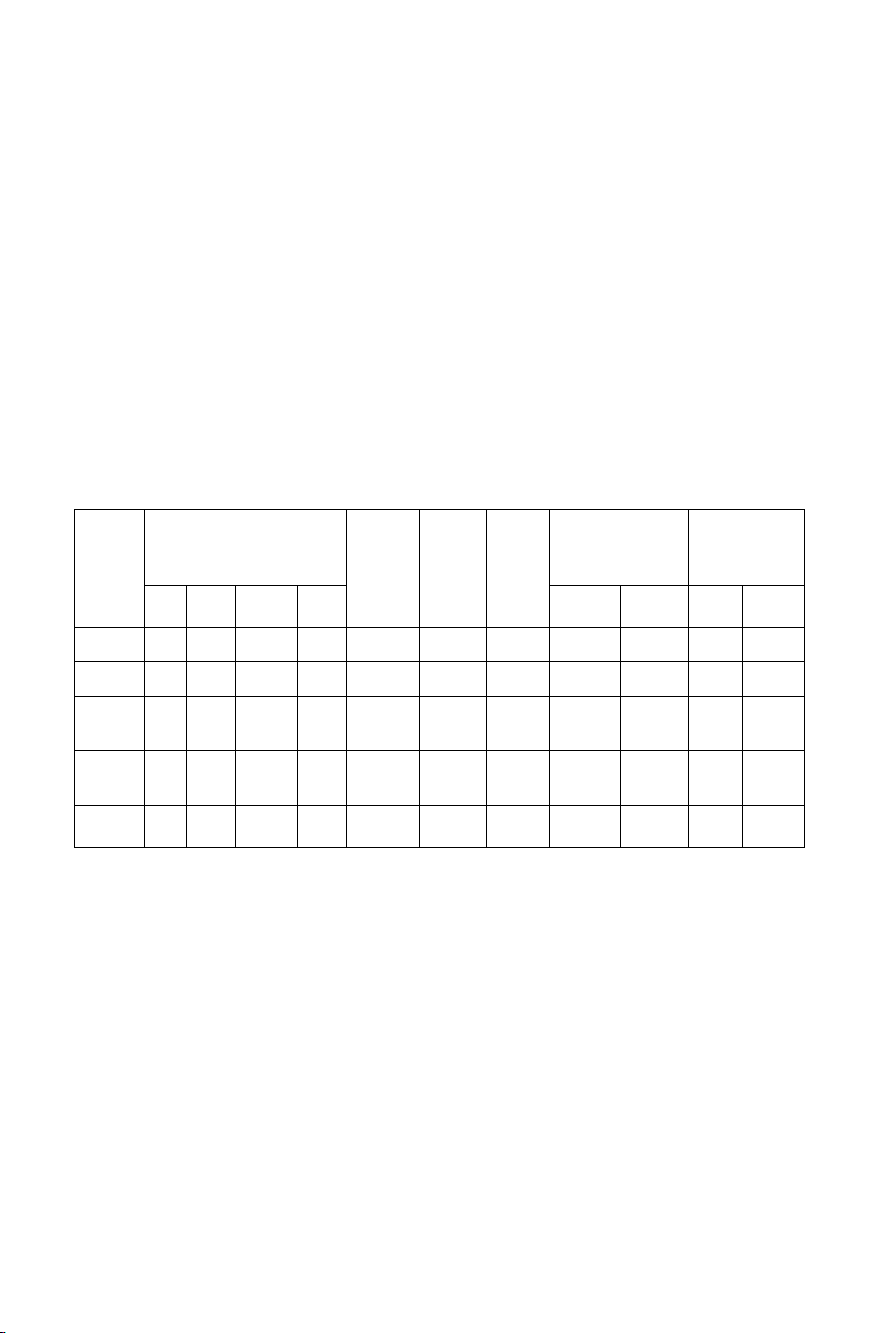
30
Khi tiện tinh:
2Z
min
= 50,05 – 49,884 = 0,166 mm =166 m.
2Z
max
= 50 – 49,714= 0,286 mm = 286m .
Khi tiện thô :
2Z
min
= 49,884 – 47,378 = 2,506mm = 2506 m.
2Z
max
= 49,714 – 46,978 = 2,736 mm = 2736m .
Tất cả các kết quả tính toán được ghi vào bảng tính lượng dư và
lượng dư tổng cộng được tính như sau:
2Z
0min
= 166 + 2506 = 2672m = 2,672 mm
2Z
0max
= 2810 +290 = 3100m = 3,1 mm
Bảng tính lượng dư lỗ
50
+0,05
Thứ tự
các
bƣớc
gia
công
Các thành phần lƣợng
dƣ (m)
Lƣợng
tính
toán
2Z
bmin
(m)
Kích
thƣớc
tính
toán
(mm)
Dung
sai
(m)
kích thƣớc giới
hạn (mm)
Trị số g/h
lƣợng dƣ
(mm)
Rz
T
max
min
max
min
(1)
(2)
(3)
(4)
(5)
(6)
(7)
(8)
(9)
(10)
(11)
(12)
Phôi
600
640
47,378
400
47,3
46,9
Tiện
thô
50
32,25
127
2506
49,884
170
49,880
49,71
2,81
2,580
Tiện
tinh
20
6
166
50,05
50
50,05
50,00
0,29
0,170
Tổng
3,10
2,75
Kiểm tra kết quả tính toán:
Sau tiện tinh:
2Z
max
– 2Z
min
= 290 – 170 = 120m;
1
-
2
= 170 –50 = 120 m.
Sau tiện thô:
2Z
max
- 2Z
min
= 2810 – 2580 = 230m ;
phôi
-
1
= 400 –170 = 230 m.
Hoặc: 2Z
0max
– 2Z
0min
= 3100 – 2750 = 350m.
phôi
-
2
= 400 –50 = 350 m.
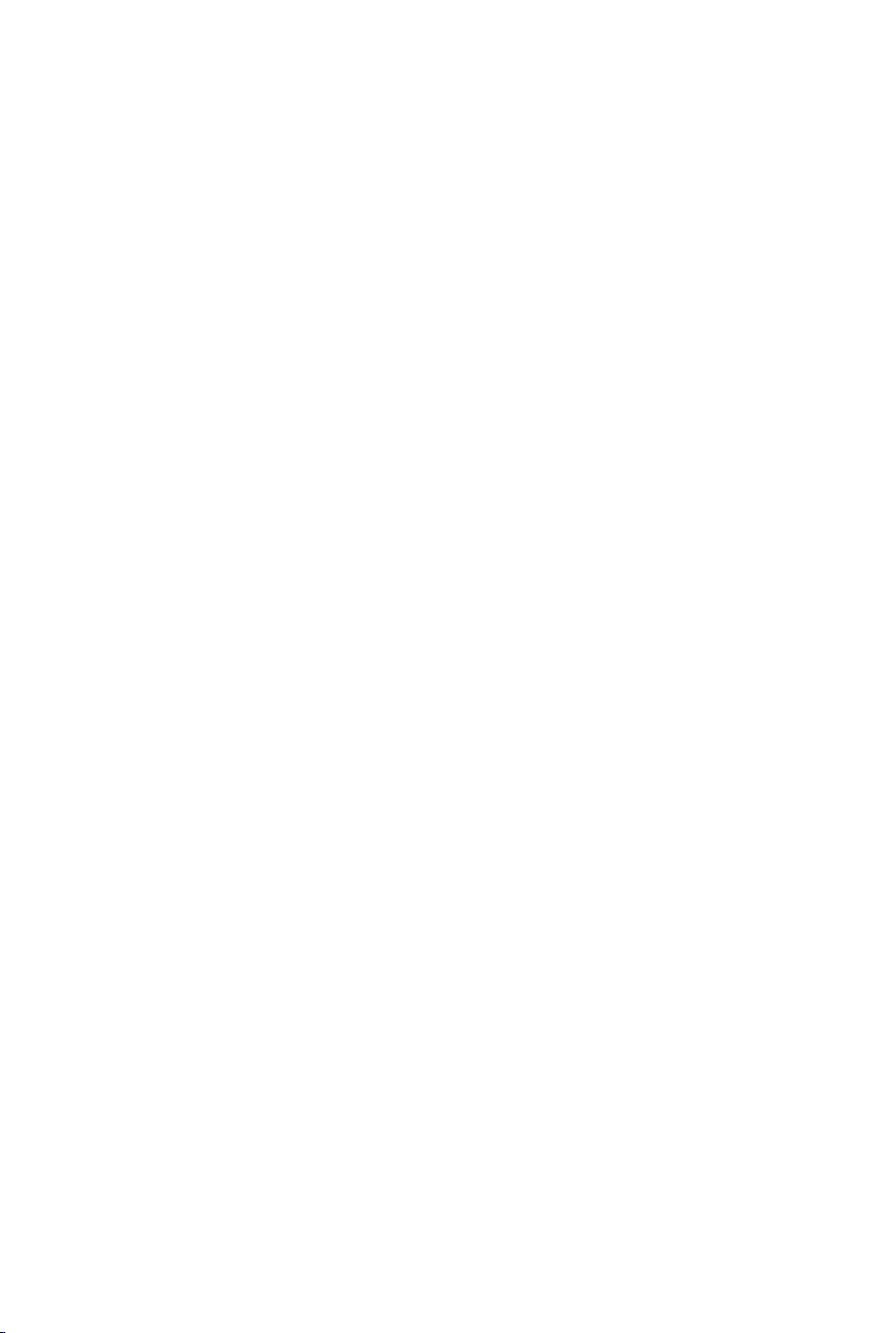
31
1.2. THIẾT KẾ QUY TRÌNH CÔNG NGHỆ GIA CÔNG TRÊN
MÁY CNC
Quy trình công nghệ gia công trên các máy CNC có những đặc
điểm sau:
-Tập trung nguyên công rất cao, nghĩa là một quy trình công nghệ
thường ít nguyên công nhưng mỗi nguyên công bao gồm rất nhiều bước.
- Các bước được chia thành các lớp cắt, mỗi lớp cắt được thực hiện
sau mỗi quỹ đạo dịch chuyển của dụng cụ cắt.
-Thành phần nhỏ nhất của quy trình công nghệ là các dịch chuyển
đơn giản và các điều khiển công nghệ do bộ điều khiển của máy cung
cấp. Các dịch chuyển đơn giản đó là các cung tròn, các đoạn thẳng hay
các đường cong khác.
Các dịch chuyển đơn giản được thực hiện bởi các cơ cấu máy nhờ
các lệnh điều khiển.
Lập quy trình công nghệ và viết chương trình điều khiển cho máy
CNC là một nhiệm vụ của chuẩn bị công nghệ.
Thiết kế quy trình công nghệ gia công trên máy CNC bao gồm ba
giai đoạn sau đây:
1.2.1. Lập tiến trình công nghệ
Tài liệu ban đầu là bản vẽ chi tiết và bản vẽ phôi. Những nhiệm vụ
của giai đoạn này là:
- Nghiên cứu phôi (kích cỡ, hình dáng, vật liệu, khả năng tạo chuẩn).
Phôi có thể còn thô và chưa được gia công cắt gọt (tấm, thanh, vật
đúc, vật rèn, …). Một số phôi có thể đã được gia công sơ bộ, chuyển đến
từ máy khác hoặc nguyên công khác.
Kích cỡ và hình dạng phôi quyết định việc xác định phương pháp
gá đặt.
Loại vật liệu phôi (thép, gang, hợp kim đồng, hợp kim nhôm, …)
quyết định đến sự lựa chọn dụng cụ cắt và chế độ gia công cắt gọt.
- Nghiên cứu tính công nghệ của chi tiết và tiêu chuẩn hóa các
thông số như chuẩn kích thước hoặc bán kính. Nếu cần thì phải hiệu
chỉnh lại bản vẽ phôi và bản vẽ chi tiết.
- Lập tiến trình gia công dựa vào hình dáng bề mặt và chọn máy
phù hợp.
- Chọn chuẩn công nghệ, phương pháp gá đặt và đồ gá
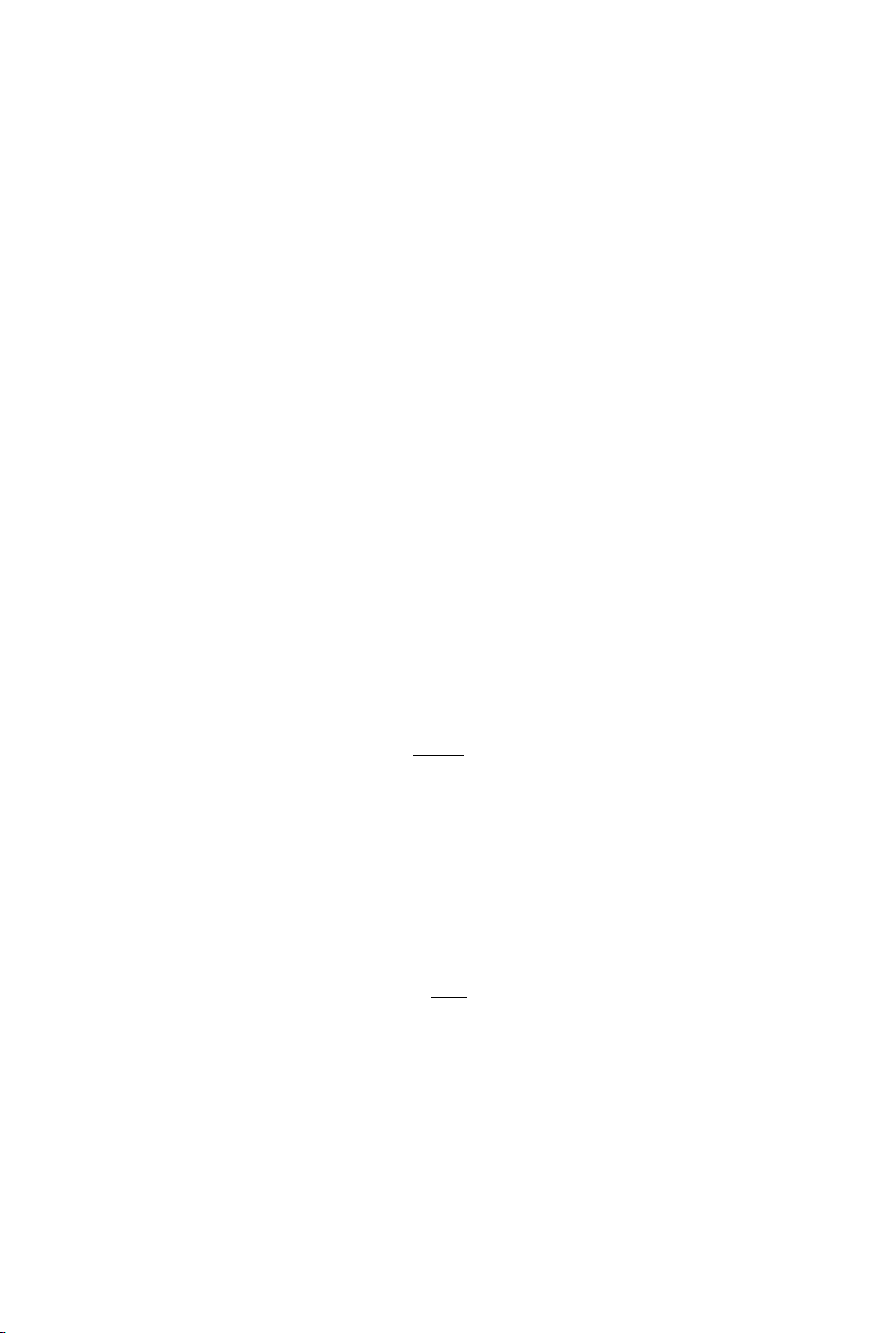
32
1.2.2. Thiết kế nguyên công
- Xác định nội dung nguyên công, chia nguyên công ra các bước và
các vị trí, cụ thể hóa phương pháp gá đặt chi tiết.
- Xác định lượng dư, dung sai cho từng bước công nghệ và lượng
dư tổng thể để quy định kích thước phôi.
- Xác định dụng cụ cắt và chọn chúng theo từng loại.
- Chia ra các lớp cắt, chọn chế độ cắt, chuẩn bị phương pháp điều
chỉnh máy và điều chỉnh dao.
1.2.3. Lập trình gia công
Giai đoạn này có các nhiệm vụ sau đây:
-Tính toán các quỹ đạo chuyển động của dao ngay sau khi xác định
tọa độ của các điểm.
- Lập trình và ghi vào bộ nhớ của máy CNC hoặc máy tính.
- Kiểm tra chương trình, sửa lỗi chương trình, chạy thử và gia công
thử chi tiết.
1.3. SO SÁNH CÁC PHƢƠNG ÁN CÔNG NGHỆ
Khi thiết kế các quá trình công nghệ phải so sánh các phương án
công nghệ khác nhau để tìm ra phương án tối ưu. Chỉ tiêu để đánh giá là
năng suất và giá thành.
Chỉ tiêu về năng suất.
Trong đó:
T
c
– thời gian của một ca sản xuất (giờ/ca).
T
tc
– thời gian từng chiếc ( phút/chiếc).
M
0
– số máy một công nhân vận hành.
Chỉ tiêu về giá thành:
Trong đó:
G –giá thành một sản phẩm.
N- sản lượng hàng năm.
K
sx
– chi phí sản xuất.
K
sx
= K
V
+ K
L
( + ) + K
M
+ K
D
+ K
G
[đồng/năm].
)/(.
.60
0
cactM
T
T
Q
tc
c
)/( cđ
N
K
G
sx
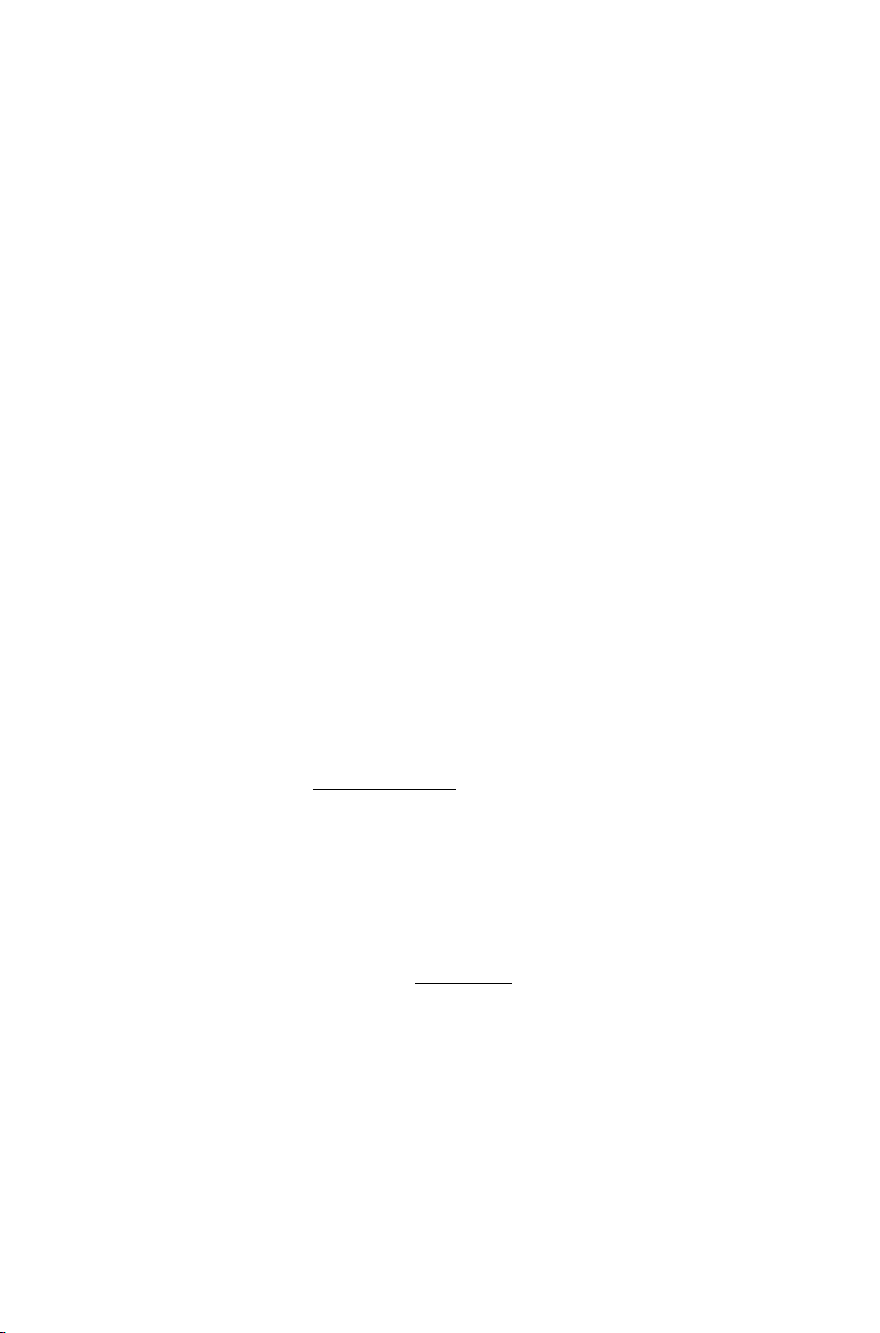
33
[đồng/chiếc]
Với: Kv – chi phí về vật liệu.
K
L
– Chi phí về lương cho công nhân sản xuất.
- Hệ số tiền thưởng, phụ cấp, bảo hiểm xã hội
(ví dụ: = 1,14 1,23)
- Hệ số chi phí quản lí, điều hành sản xuất
(ví dụ: = 1,5 4).
K
M
– Chi phí về máy.
K
D
–Chi phí về dụng cụ.
K
G
– Chi phí về trang bị công nghệ.
Giá thành gia công G được phân thành hai phần chính:
G = G1 + G2
G1 – Giá thành không phụ thuộc sản lượng N.
G2 –Giá thành phụ thuộc sản lượng N.
Đại lượng G1 được xác định theo chi phí vật liệu và chi phí lương
tính cho một chi tiết máy:
G1 = Kv + ( + )t
tc
.K
L
[đồng/chiếc] .
Đại lượng G2 được xác định theo chi phí về trang thiết bị, dụng cụ
công nghệ tính cho một chi tiết máy.
Khi so sánh các phương án công nghệ phải chú ý tới giá trị sản
lượng giới hạn (N
G
). Giá trị N
G
cho biết phạm vi ứng dụng kinh tế của
từng phương án. Ví dụ, khi so sánh hai phương án với giá thành gia công
là G
A
và G
B
ta có sản lượng giới hạn là:
Theo biểu đồ hình 1.22, nếu sản lượng thực tế N < N
G
thì chọn
phương án công nghệ A vì G
A
< G
B
, ngược lại nếu sản lượng thực tế lớn
hơn N
G
thì chọn phương án B vì G
B
< G
A
.
N
KKK
G
GDM
2
BA
AB
G
GG
GG
N
22
11
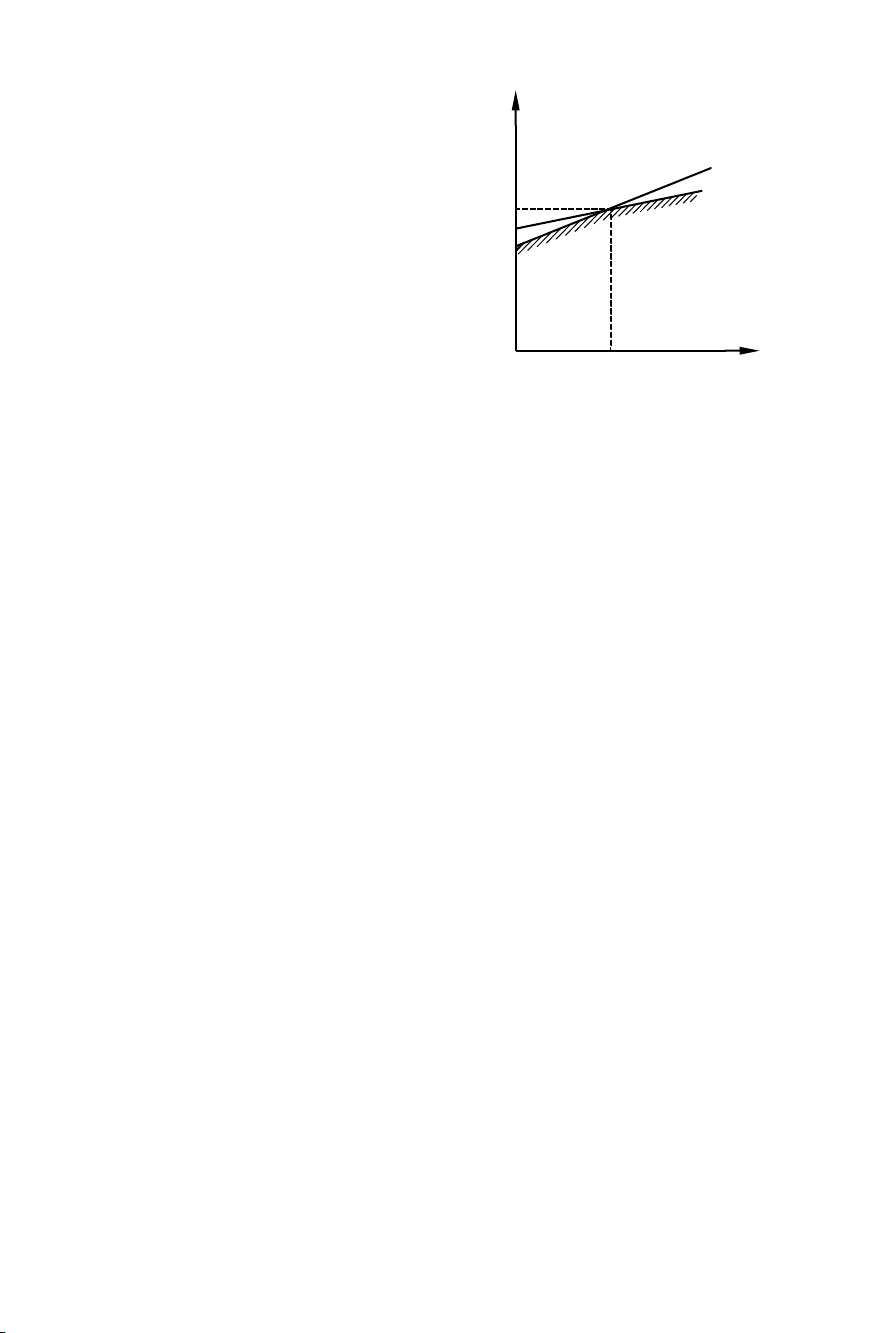
34
Khi so sánh các phương án công nghệ ta
thấy rõ phương án nào chi phí ít thì hiệu
quả kinh tế cao. Đặc biệt là phí tổn về
thời gian, vì phí tổn thời gian càng thấp
thì năng suất càng cao. Chính vì vậy các
biện pháp tăng năng suất, hạ giá thành ở
đây chính là các biện pháp giảm chi phí,
ở đây ta chú trọng tới chi phí về thời gian
vì nó liên quan tới công nghệ nhiều.
Sau đây là một số biện pháp chính
để giảm chi phí về thời gian.
Giảm thời gian cơ bản t
0
bằng cách:
- Tăng độ chính xác của phôi, xử lí nhiệt để cải thiện điều kiện cắt gọt.
- Cắt nhiều dao đồng thời để giảm hành trình chạy dao, xác định
hợp lí lượng ăn tới và vượt quá của dao.
- Chọn chế độ cắt cao khi gia công thô.
- Gia công đồng thời nhiều bề mặt bằng dụng cụ định hình hoặc
ghép nhiều dụng cụ cắt, sử dụng máy nhiều trục chính, lúc này t
0
t
0
.
Giảm thời gian phụ t
p
bằng cách:
- Giảm thời gian gá đặt chi tiết gia công bằng cách dùng đồ gá kẹp
nhanh (đồ gá khí nén, dầu ép, từ, điện cơ …).
- Thiết kế hệ thống kiểm tra tự động trong khi đang gia công để
giảm phí tổn về thời gian kiểm tra.
- Làm trùng thời gian phụ với thời gian cơ bản t
p
t
0
như dùng đồ
gá bàn quay để gá nhiều chi tiết hoặc vừa cắt vừa tháo lắp phôi, thực hiện
quá trình cắt khứ hồi, tiến hành cấp phôi và gá đặt phôi tự động. Sử dụng
nhiều dao, khi dao này lùi thì dao kia vào cắt…
- Giảm thời gian thay đổi và điều chỉnh dụng cụ cắt bằng cách dùng
dụng cụ cắt tổ hợp, dụng cụ chuyên dùng, sử dụng phương pháp tự động
điều chỉnh máy.
Trong quá trình định mức ta chưa kể đến các loại tổn thất khác
như: do bố trí chỗ làm việc thiếu hợp lí dẫn đến thao tác chậm bàn giao
ca kíp không đúng thời gian, cúp điện, cúp nước, thay đổi nhân sự bất
thường, trục trặc về thiết bị và công nghệ … Để tính đến những sự cố đó,
khi định mức có thể chọn thêm các hệ số khác.
N
G
G
A
G
B
O
N
G
Hình 1.22
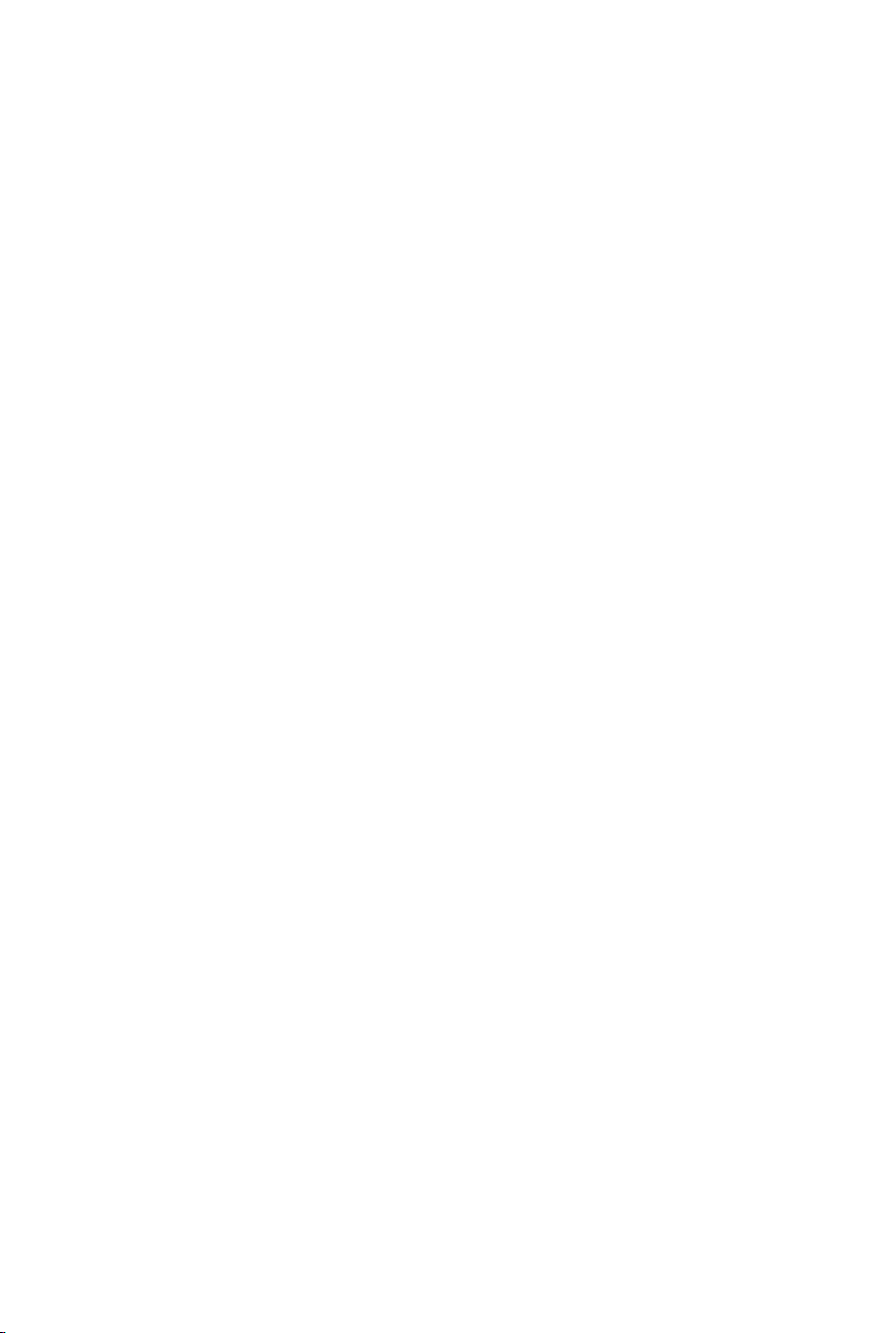
35
1.4. TIÊU CHUẨN HÓA QUÁ TRÌNH CÔNG NGHỆ
1.4.1. Khái niệm
Theo thống kê của nhiều nước có nền công nghiệp phát triển, có tới
75% sản phẩm của ngành chế tạo máy được sản xuất theo loạt vừa và
nhỏ. Vì vậy khi chuẩn bị kĩ thuật cho sản xuất, gồm chuẩn bị thiết kế kết
cấu và chuẩn bị công nghệ phải luôn luôn tìm biện pháp nâng cao tính
loạt cho một đơn vị nguyên công hoặc cho một quá trình công nghệ
nhằm đạt hiệu quả kinh tế khi gia công.
Biện pháp cơ bản để nâng cao tính loạt nhằm rút ngắn thời gian
chuẩn bị công nghệ là thống nhất hóa, tiến tới tiêu chuẩn hóa quá trình
công nghệ như:
- Công nghệ điển hình.
- Công nghệ nhóm.
- Công nghệ tổ hợp.
Tiêu chuẩn hóa quá trình công nghệ sẽ góp phần:
- Giải phóng cán bộ công nghệ khỏi những công việc tính toán,
trùng lặp nhiều tài liệu công nghệ.
- Giảm số lượng các trang bị công nghệ giống nhau.
- Đơn giản việc tính toán định mức về lao động và vật liệu.
- Giảm thời gian bố trí sản xuất.
Muốn tiêu chuẩn hóa quá trình công nghệ phải thống nhất hóa và
tiêu chuẩn hóa kết cấu của đối tượng sản xuất (chi tiết hoặc bộ phận máy)
bởi vì đối tượng sản xuất có kết cấu giống nhau sẽ có công nghệ giống
nhau. Để thống nhất hóa, tiêu chuẩn hóa kết cấu của đối tượng sản xuất
cần phải khảo sát và phân loại các chi tiết máy theo từng ngành và đặc
điểm công nghệ của chúng.
1.4.2. Công nghệ điển hình
Mục đích của điển hình hóa quá trình công nghệ là xây dựng một
quy trình công nghệ chung cho các đối tượng sản xuất (chi tiết, bộ phận,
sản phẩm) có kết cấu giống nhau.
Cơ sở của công nghệ điển hình là dựa vào việc phân loại chi tiết, bộ
phận máy … về mặt kết cấu và công nghệ, xác định hoặc lập nên các đối
tượng đại diện (điển hình) có đầy đủ các đặc trưng tiêu biểu của từng
kiểu. Nhờ vậy mà quá trình gia công chi tiết hoặc lắp ráp các bộ phận
cùng một kiểu nhất định được tiến hành theo những quy trình công nghệ
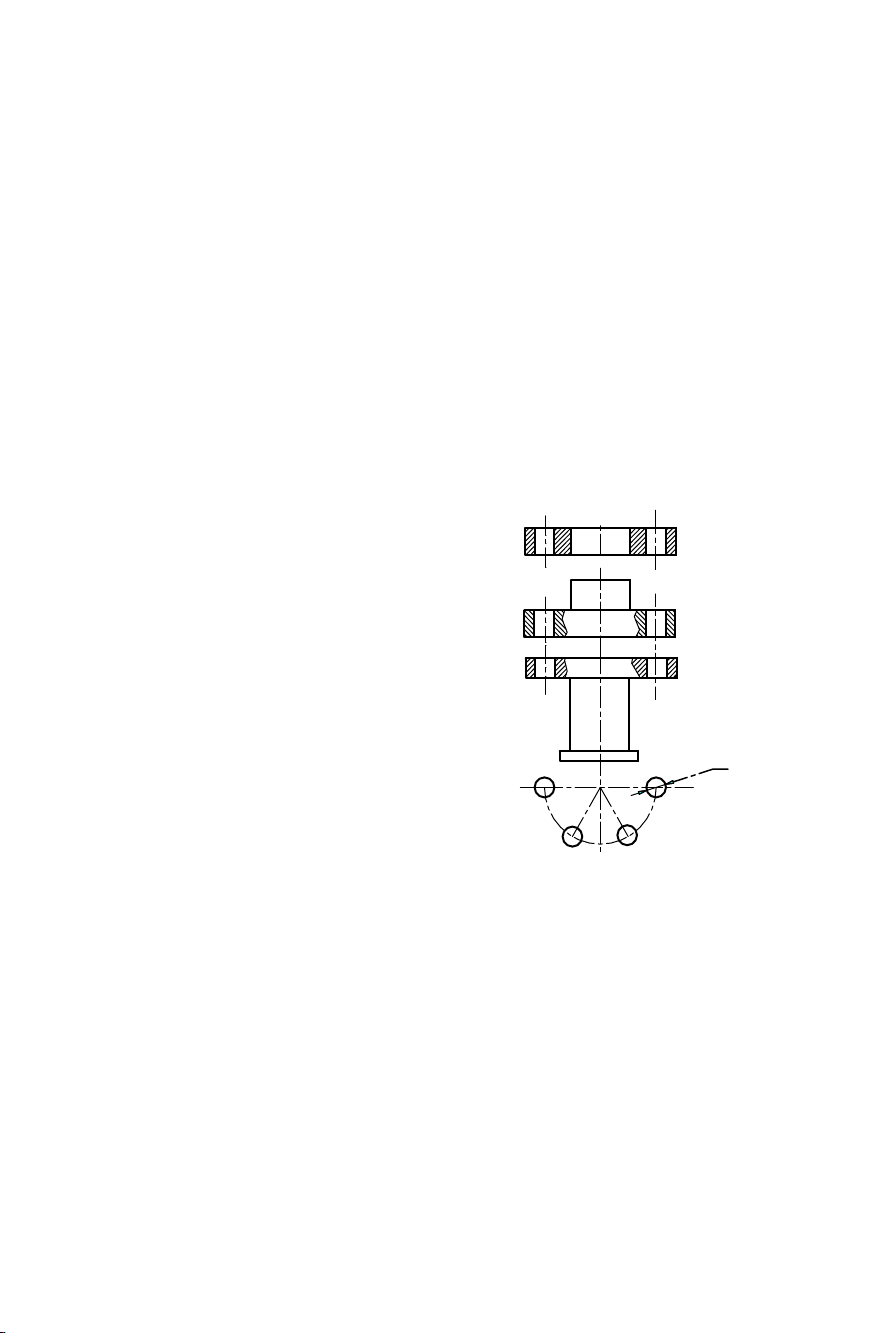
36
đã lập nên từ trước. Những quy trình này đã được thiết kế, kiểm nghiệm
đảm bảo các chỉ tiêu kinh tế kỹ thuật theo những điều kiện về trình độ
sản xuất nhất định.
Những nội dung cần thực hiện khi điển hình hóa quá trình công
nghệ là:
1 – Phân loại các chi tiết, bộ phận của sản phẩm thành các kiểu,
trong một kiểu thì các đối tượng phải giống nhau hầu như hoàn toàn về
kết cấu.
2 – Phân tích lựa chọn trong từng kiểu một đối tượng điển hình.
3 – Lập tiến trình công nghệ điển hình cho từng kiểu đối tượng,
dựa vào đối tượng điển hình đã chọn.
4 – Xác định trang thiết bị, dụng cụ, chế độ công nghệ cho từng
kiểu, ứng với tiến trình công nghệ điển hình.
1.4.3. Công nghệ nhóm
Cơ sở của công nghệ nhóm là
phân nhóm đối tượng sản xuất theo sự
giống nhau từng phần về kết cấu.Ví dụ
đối với chi tiết gia công là mức độ
giống nhau về một hoặc tập hợp một
vài bề mặt gia công như hình 1.23. Như
vậy cho phép gia công các chi tiết
trong cùng một nhóm ở nguyên công
giống nhau đó cùng trang thiết bị, dụng
cụ và trình tự công nghệ.
Khi gia công hệ lỗ 15 trên ba
chi tiết ở hình 1.23, có thể sử dụng
chung đồ gá, máy, chế độ công nghệ, dụng cụ cắt …Việc gia công như
vậy ta gọi là công nghệ nhóm. Công nghệ nhóm thường được thực hiện ở
từng nguyên công, cụ thể là trên từng máy, ví dụ: gia công nhóm trên
máy tiện, máy khoan, máy phay …
Như vậy qua việc phân nhóm, số lượng chi tiết gia công tính cho
một đơn vị trang thiết bị công nghệ sẽ tăng lên, hay còn gọi là tăng quy
mô sản xuất cho một thiết bị (tính loạt tăng). Điều đó sẽ mang lại hiệu
quả kinh tế cao.
Phạm vi của công nghệ nhóm tuy hẹp hơn công nghệ điển hình, vì
công nghệ nhóm chỉ bao gồm một số nguyên công chung ứng với một số
bề mặt gia công giống nhau của các chi tiết, nhưng công nghệ nhóm lại
Chi tiết 1
Chi tiết 3
Chi tiết 2
Hình 1.23
6lỗ 15
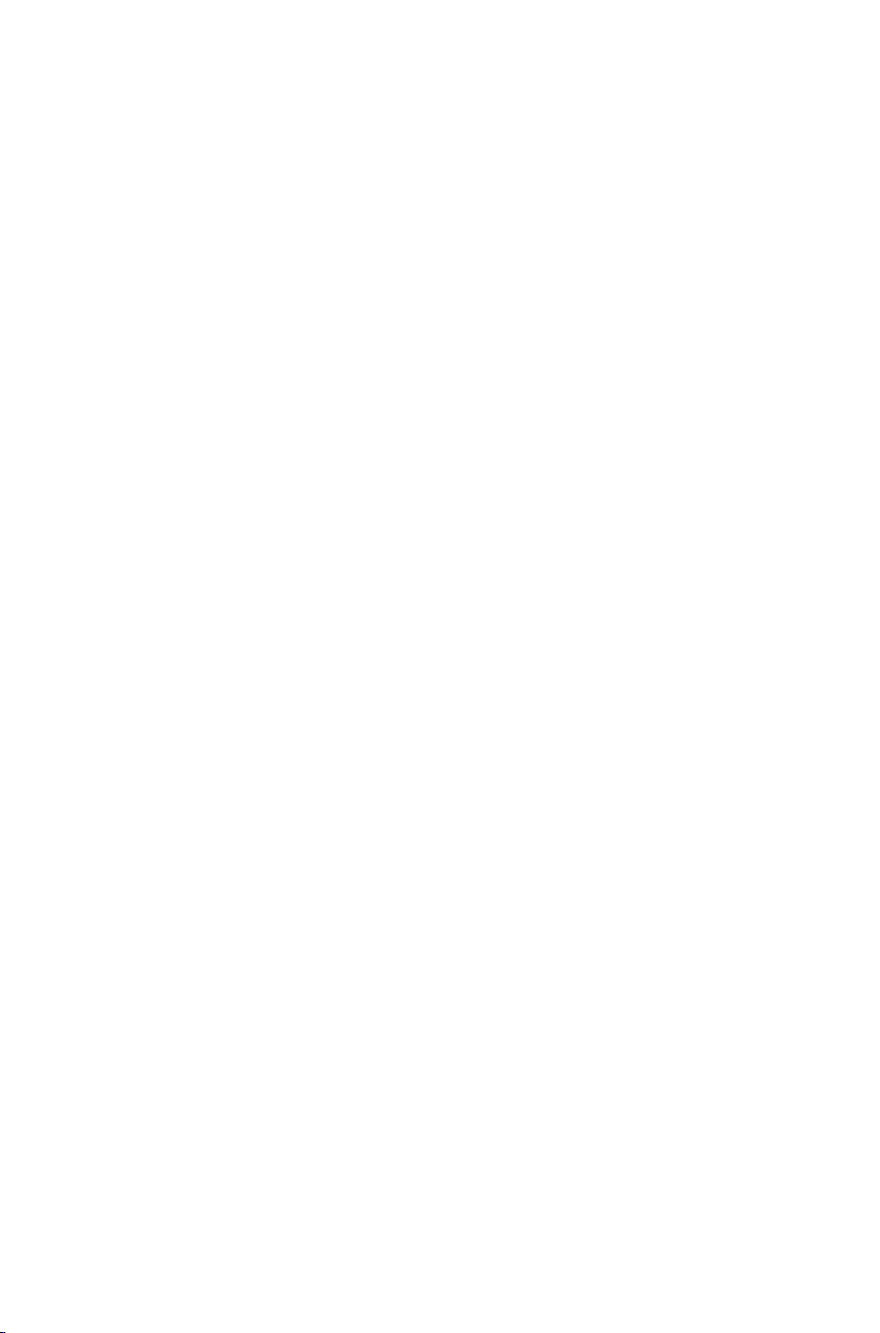
37
rất cụ thể, cho phép ứng dụng nhanh và đưa lại hiệu quả kinh tế cao ở
điều kiện sản xuất loạt nhỏ, đơn chiếc bởi vì ở công nghệ nhóm số lượng
chi tiết thuộc một nhóm có thể nhiều mặc dù kết cấu chung của các chi
tiết có khác nhau.
1.4.4. Công nghệ tổ hợp
Sản xuất theo dây chuyền trên cơ sở quá trình công nghệ tối ưu,
linh hoạt và tự động hóa trong quy mô sản xuất phổ biến là hàng loạt vừa
và nhỏ đặt ra vấn đề nghiên cứu công nghệ tổ hợp dựa trên việc kết hợp
các phương pháp thống nhất hóa, tiêu chuẩn hóa kết cấu của đối tượng
sản xuất, công nghệ điển hình và công nghệ nhóm nhằm khai thác tận
dụng những ưu điểm, hạn chế các nhược điểm của từng phương pháp
riêng biệt .
Những bước quan trọng trước hết cần phải thực hiện để có thể áp
dụng công nghệ tổ hợp là:
1- Phân loại và ghép nhóm đối tượng gia công (có thể xuất phát từ
loại hoặc kiểu) trong chủng loại đối tượng gia công có trong chương trình
sản xuất.
2- Xác định đối tượng đại diện (điển hình): xác định kiểu chi tiết
đại diện trong số kiểu chi tiết được gia công theo công nghệ tổ hợp trên
cơ sở độ phức tạp cao nhất về kết cấu và công nghệ.
3- Xác định số lượng quy đổi của từng kiểu chi tiết khác ra kiểu
điển hình bằng hệ số quy đổi. Hệ số quy đổi (tính gần đúng) là hệ số xét
đến sự khác nhau về kết cấu và công nghệ giữa kiểu đang xét và kiểu
điển hình. Sau đó tính tổng số lượng đã quy đổi ra kiểu điển hình của tất
cả các chi tiết được gia công tổ hợp.
4- Xác định phương án tổ hợp tối ưu về công nghệ (ví dụ đối với
các chi tiết chính xác của động cơ Diesel, bộ đôi chính xác cao, chi tiết
dạng trụ, các kiểu piston, xylanh, kim, đế với các cỡ D12, D20, W50,
C100 có thể có các phương án tổ hợp công nghệ như sau:
- Gia công tổ hợp các kiểu chi tiết piston, xylanh, kim, đế
- Gia công tổ hợp các loại chi tiết trục (piston, kim)
- Gia công tổ hợp các kiểu chi tiết bạc (lỗ): xylanh, đế
- Gia công tổ hợp từng kiểu chi tiết theo các cỡ (kiểu piston, kiểu
xylanh, kiểu đế gia công tổ hợp nhiều cỡ)
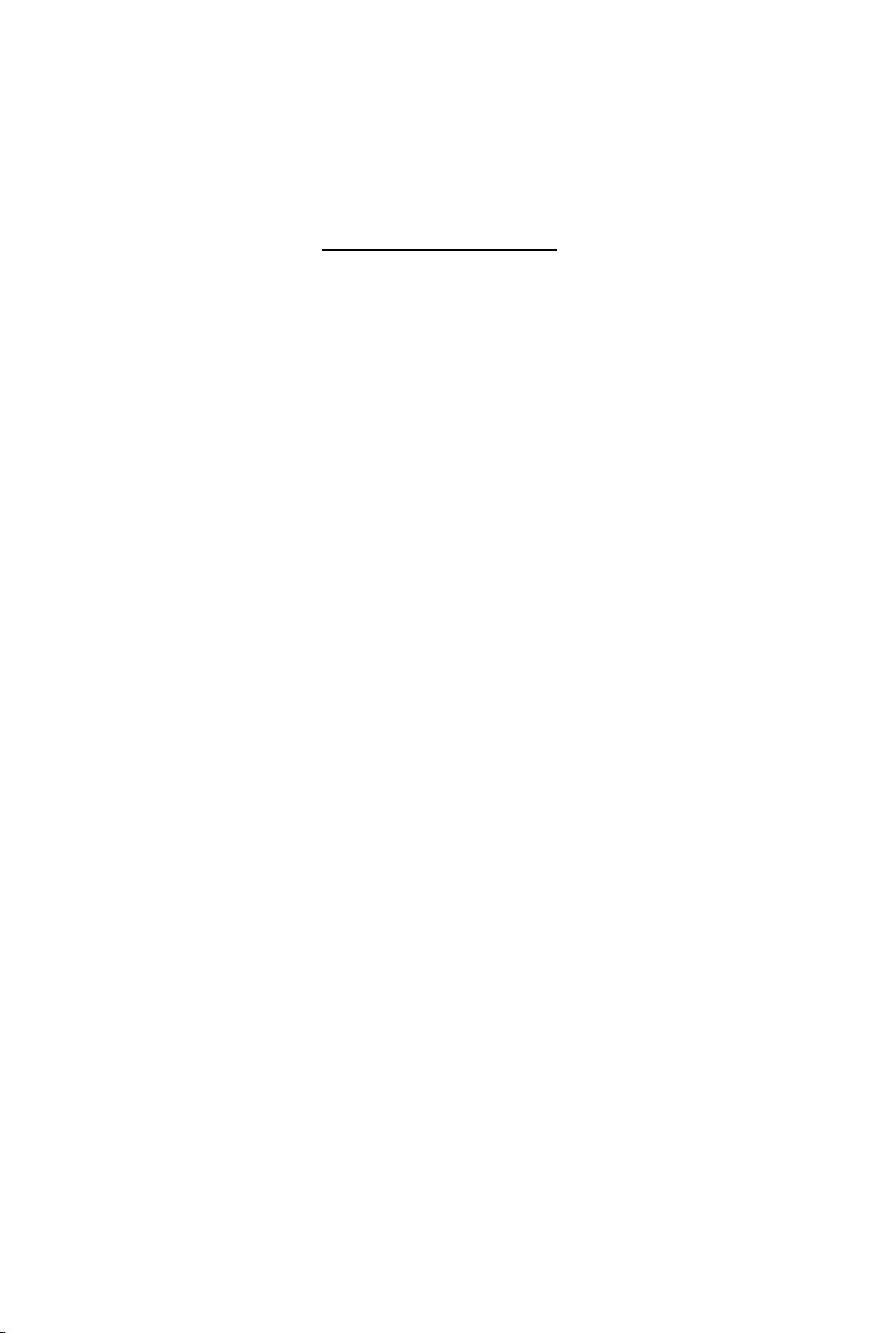
38
5- Thiết kế xây dựng quá trình công nghệ, nguyên công và dây
chuyền gia công theo phương án tổ hợp tối ưu về công nghệ, kể cả thiết
kế đồ gá điều chỉnh cho từng nguyên công.
CÂU HỎI ÔN TẬP
1. Phân biệt các thành phần của quy trình công nghệ gia công chi
tiết máy ? ( Cho ví dụ minh họa)
2. Trình bày trình tự thiết kế quy trình công nghệ hợp lý ?
3. Thế nào là phân tán hay tập trung nguyên công?
4. Sơ đồ gá đặt thể hiện những vấn đề gì?
5. Sơ đồ nguyên công thể hiện những vấn đề gì?
6. Trình bày nội dung của thiết kế nguyên công ?
7. Xác định lượng dư gia công bằng phương pháp tính toán (cách
lập bảng)?
8. Tính công nghệ trong kết cấu là gì? Các chỉ tiêu đánh giá tính
công nghệ trong kết cấu?
9. Thế nào là Công nghệ nhóm ? Cho ví dụ ?
10. Công nghệ điển hình là gì? Cho ví dụ ?
11. So sánh ưu nhược điểm của hai loại hình trên ?
12. Hãy cho biết thế nào là Tính loạt? Tại sao nói ứng dụng công nghệ
nhóm hoặc công nghệ điển hình để nâng cao tính loạt trong sản xuất cơ khí?
13. Tại sao phải ứng dụng công nghệ tổ hợp trong chế tạo cơ khí ?
14. So sánh các phương án công nghệ theo các tiêu chí nào?
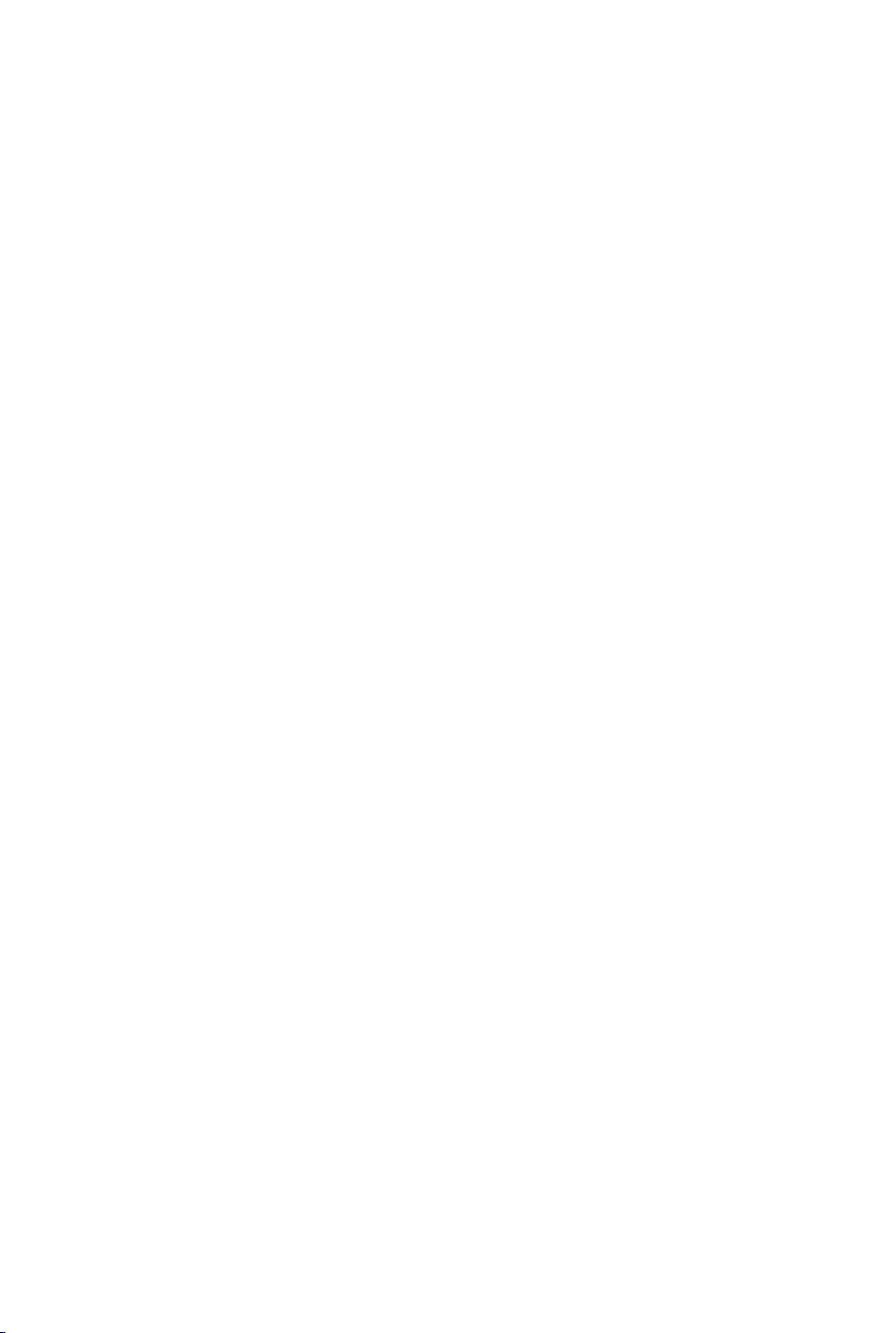
39
Chương 2
CÔNG NGHỆ GIA CÔNG CHI TIẾT ĐIỂN HÌNH
Mục tiêu:
1. Trình bày được quy trình công nghệ gia công chi tiết dạng hộp,
trục, càng, bạc với các nội dung:
+ Chọn chuẩn định vị để gia công
+ Trình tự gia công các bề mặt
+ Phương pháp gia công các bề mặt chính
+ Phương pháp đo lường, kiểm tra các yêu cầu kỹ thuật
2. Trình bày được quy trình công nghệ gia công bánh răng
+ Chuẩn định vị và quy trình công nghệ trước khi gia công răng
+ Các phương pháp gia công răng của bánh răng
+ Các phương pháp đo kiểm bánh răng sau khi gia công.
2.1. QUY TRÌNH CÔNG NGHỆ CHẾ TẠO CÁC CHI TIẾT DẠNG HỘP
Trong tất cả các loại máy móc từ máy công cụ, máy phát động lực,
máy thu hoạch trong nông nghiệp, máy chế biến nông sản, máy chế biến
gỗ, máy chế biến thủy hải sản v.v… đến các máy chuyên dùng đều có các
chi tiết dạng hộp. Hộp là loại chi tiết cơ sở quan trọng của một sản phẩm.
Hộp bao gồm những chi tiết có hình khối rỗng (xung quanh có thành
vách) thường làm nhiệm vụ của chi tiết cơ sở để lắp các đơn vị lắp (như
nhóm, cụm, bộ phận) của những chi tiết khác lên nó tạo thành một bộ
phận máy nhằm thực hiện một nhiệm vụ động học nào đó của toàn máy.
Có rất nhiều kiểu hộp và công dụng cũng khác nhau như hộp tốc độ,
hộp chạy dao, thân động cơ đốt trong, thân máy bơm v.v... Đặc điểm của
các chi tiết hộp là có nhiều vách, độ dày mỏng của các vách cũng khác
nhau, trong các vách có nhiều gân, có nhiều phần lồi lõm. Trên hộp có
nhiều mặt phải gia công với độ chính xác khác nhau và cũng có nhiều bề
mặt không phải gia công. Đặc biệt trên hộp thường có nhiều lỗ cần được
gia công chính xác để thực hiện các mối lắp ghép. Tùy công dụng mà các
lỗ trên hộp được chia ra:
- Lỗ chính xác: dùng để đỡ các đầu trục được gọi là lỗ chính.
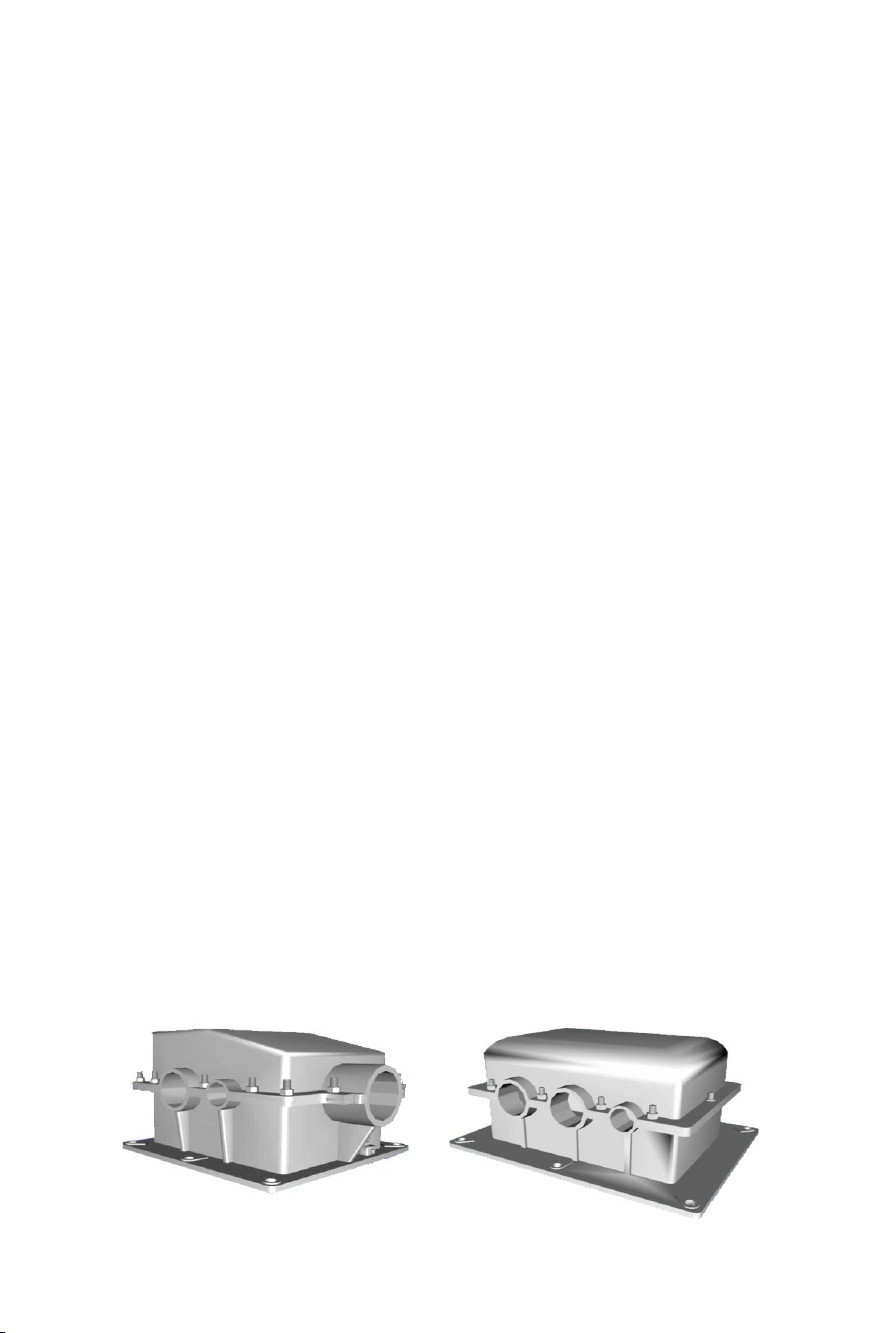
40
- Lỗ không chính xác: dùng để kẹp các bộ phận khác được gọi là lỗ phụ.
Trên hình 2.1 trình bày thân hộp giảm tốc là một trong những chi
tiết thuộc dạng hộp.
Nhìn chung chi tiết hộp là một chi tiết phức tạp, khó gia công, khi
chế tạo phải đảm bảo nhiều yêu cầu kỹ thuật khác nhau.
2.1.1. Những yêu cầu kỹ thuật chủ yếu chi tiết dạng hộp
Hộp có những bề mặt chính như các mặt đáy, mặt lỗ. Độ chính xác
của những bề mặt này có yêu cầu khá cao. Ngoài những bề mặt chính ra
trên hộp còn có những bề mặt phụ như các bề mặt đậy nắp, lỗ bắt bulông
v.v... những bề mặt này có độ chính xác không cao.
Những yêu cầu kỹ thuật cơ bản của hộp bao gồm:
- Độ không phẳng và độ không song song của các bề mặt chính
trong khoảng 0,050,1 mm trên toàn bộ chiều dài, độ nhám bề mặt của
chúng từ R
a
= 5 1,25 (57).
- Các lỗ có độ chính xác cấp 57 và độ nhám bề mặt R
a
=2,5 0,63,
đôi khi cần đạt R
a
= 0,32 0,16. Sai số hình dáng của các lỗ là 0,5 0,7
dung sai đường kính lỗ.
- Dung sai khoảng cách tâm giữa các lỗ phụ thuộc vào chức năng
của nó.
Nếu lỗ lắp trục bánh răng thì dung sai bằng 0,02 0,1 mm. Dung sai
độ không song song của các tâm lỗ bằng dung sai của khoảng cách tâm.
Độ không vuông góc của các tâm lỗ khi lắp bánh răng côn và trục vít là
0,02 0,06 mm.
- Dung sai độ không đồng tâm của các lỗ bằng ½ dung sai đường
kính lỗ nhỏ nhất.
- Độ không vuông góc giữa mặt đầu và tâm lỗ trong khoảng 0,01
0,05 mm trên 100 mm bán kính.
Hình 2.1a) Hình dáng dạng hộp
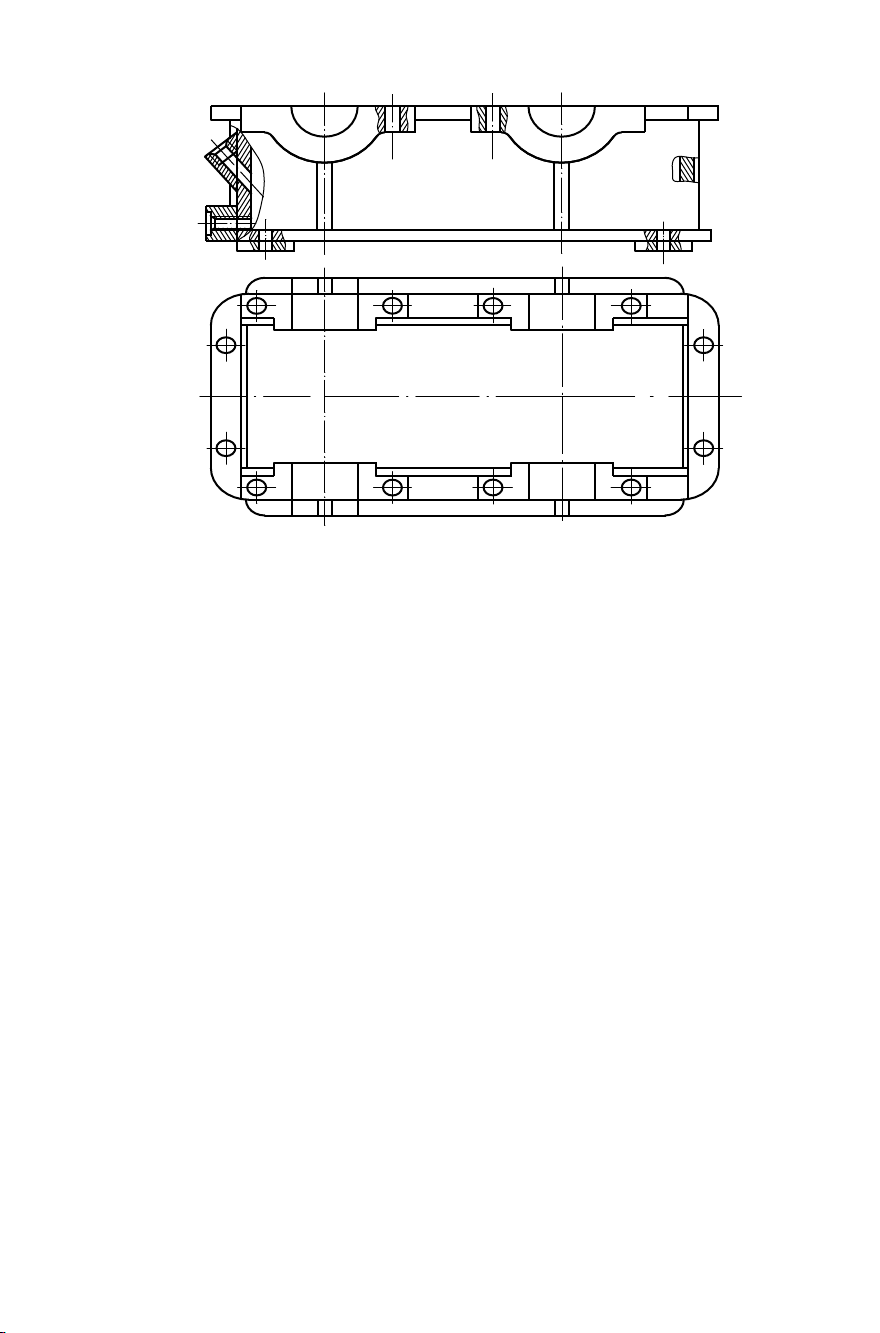
41
2.1.2. Tính công nghệ trong kết cấu của chi tiết dạng hộp
Tính công nghệ trong kết cấu của hộp không những ảnh hưởng đến
khối lượng lao động để chế tạo hộp, mà còn ảnh hưởng tới việc tiêu hao vật
liệu.Vì vậy ngay từ khi thiết kế phải chú ý đến kết cấu của chúng như:
- Hộp phải có đủ độ cứng vững để khi gia công không bị biến dạng
do lực cắt và có thể dùng chế độ cắt cao để đạt năng suất cao.
- Các bề mặt làm chuẩn phải có đủ diện tích nhất định, phải cho
phép thực hiện nhiều nguyên công khi dùng bề mặt đó làm chuẩn và phải
cho phép thực hiện quá trình gá đặt nhanh.
- Các bề mặt cần gia công của hộp không được có vấu lồi, lõm,
phải thuận lợi cho việc ăn dao, thoát dao. Kết cấu của các bề mặt phải tạo
điều kiện cho việc gia công đồng thời bằng nhiều dao.
- Các lỗ trên hộp nên có kết cấu đơn giản, không nên có rãnh hoặc có
dạng định hình, bề mặt lỗ không được đứt quãng. Các lỗ đồng tâm nên có
đường kính giảm dần từ ngoài vào trong. Các lỗ nên thông suốt và ngắn.
- Không nên bố trí các lỗ nghiêng so với mặt phẳng của các vách để
khi gia công tránh hiện tượng mũi khoan, khoét, doa bị ăn dao lệch hướng.
- Các lỗ kẹp chặt của hộp phải là các lỗ tiêu chuẩn.
Hình 2.1b) Kết cấu dạng hộp.
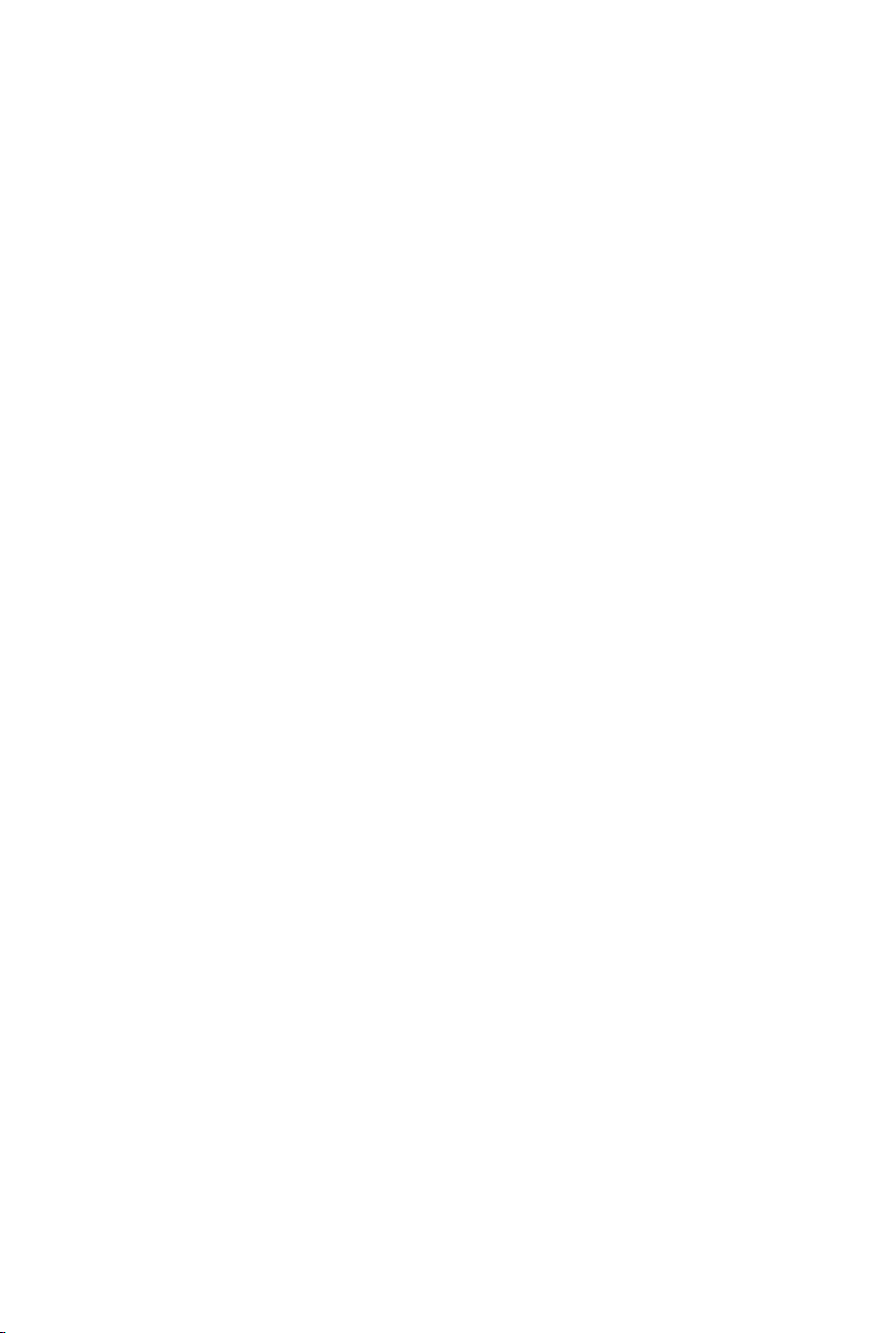
42
2.1.3 Vật liệu và phôi để chế tạo các chi tiết dạng hộp
Vật liệu để chế tạo các chi tiết dạng hộp thường dùng là gang xám,
thép đúc, hợp kim nhôm và những thép tấm hàn. Tùy theo điều kiện làm
việc, số lượng hộp và vật liệu mà phôi được chế tạo bằng nhiều cách
khác nhau.
- Phôi đúc bao gồm cả phôi gang, thép hoặc hợp kim nhôm là
những loại phôi phổ biến nhất để chế tạo các chi tiết dạng hộp. Chế tạo
phôi đúc thường dùng các phương pháp đúc sau:
+ Đúc gang trong khuôn cát, mẫu gỗ, làm khuôn bằng tay. Phương
pháp này cho độ chính xác thấp, lượng dư để gia công cắt gọt lớn, năng
suất thấp, đòi hỏi trình độ công nhân phải cao, thích hợp đối với dạng sản
xuất đơn chiếc và loạt nhỏ.
+ Dùng mẫu kim loại, khuôn cát, làm khuôn bằng máy, đạt độ
chính xác và năng suất cao, lượng dư cắt gọt nhỏ. Phương pháp này thích
hợp trong sản xuất hàng loạt và hàng khối.
+ Dùng phương pháp đúc trong khuôn vỏ mỏng phôi đúc đạt độ
chính xác 0,3 - 0,6 mm, tính chất cơ học tốt. Phương pháp này dùng
trong sản xuất hàng loạt lớn và hàng khối nhưng chỉ thích hợp cho các
chi tiết hộp cỡ nhỏ.
+ Đúc áp lực có thể tạo nên các chi tiết hộp cỡ nhỏ có hình thù
phức tạp.
Ở những chỗ gấp khúc của hộp cần phải có góc lượn, các hốc bên
trong cần được làm sạch, các mặt cạnh và đáy cần được làm sạch và
phẳng. Vật đúc ra không được có vết nứt, rỗ và các khuyết tật khác.
Chi tiết hộp đúc ra thường nguội không đều, gây ra biến dạng nhiệt
và ứng suất dư nên cần có biện pháp khử ứng suất dư trước khi gia công
cắt gọt.
- Phôi hàn được chế tạo từ thép tấm rồi hàn lại thành hộp. Loại phôi
này được dùng trong sản suất đơn chiếc và loạt nhỏ. Phôi hàn có hai kiểu:
+ Kiểu thô: hàn các tấm thép lại thành hộp, sau đó mới gia công.
+ Kiểu tinh: hàn các tấm thép đã được gia công sơ bộ các bề mặt cần
thiết thành hộp, sau đó mới gia công tinh lại.
Sử dụng phôi hàn sẽ rút ngắn được thời gian chuẩn bị phôi, đạt hiệu
quả kinh tế cao. Tuy nhiên dùng phôi hàn thường gặp khó khăn khi khử
ứng suất dư.
- Phôi dập được dùng đối với các chi tiết hộp nhỏ có hình thù
không phức tạp ở dạng sản xuất loạt lớn và hàng khối. Đối với thép có
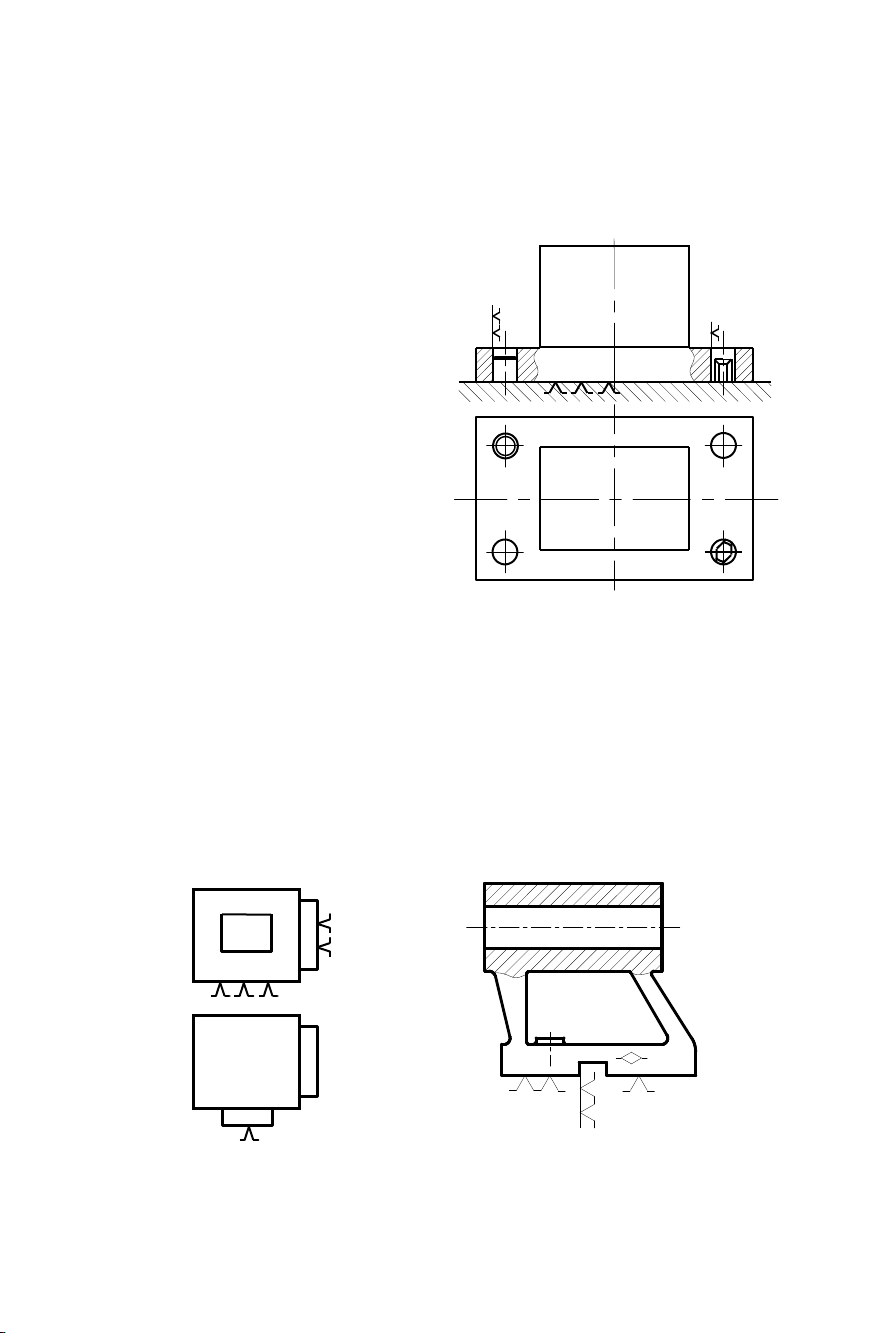
43
thể dập nóng còn đối với kim loại màu có thể dập nguội. Phương pháp
này tạo được cơ tính tốt và đạt năng suất cao.
2.1.4. Quy trình công nghệ gia công chi tiết hộp
2.1.4.1. Chuẩn định vị để gia công chi tiết hộp
Khối lượng gia công chi
tiết dạng hộp chủ yếu là tập
trung vào việc gia công các lỗ.
Muốn gia công nhiều lỗ trên
nhiều bề mặt khác nhau qua các
giai đoạn thô, tinh v.v... cần tạo
nên một chuẩn tinh thống nhất
cho chi tiết hộp. Chuẩn đó
thường là:
+ Mặt phẳng đáy cộng với
các lỗ vuông góc với mặt phẳng
đáy (Hình 2.2)
Hai lỗ chuẩn tinh phải
được gia công đạt đến độ chính
xác cấp 7 và có khoảng cách
chính xác đồng thời càng xa
nhau càng tốt.
Khi định vị chi tiết hộp trên đồ gá, mặt ngoài sẽ tiếp xúc với đồ
định vị mặt phẳng, hai lỗ sẽ được tiếp xúc với hai chốt (một chốt trụ và
một chốt trám). Như vậy chi tiết được định vị đủ 6 bậc tự do. Hai lỗ
chuẩn thường được dùng trong số các lỗ bulông trên đế của hộp.
+ Mặt phẳng đáy cộng với hai mặt bên (Hình 2.3)
Hình 2.4: Mặt đáy cộng với
rãnh trên mặt đáy
Hình 2.3: Mặt phẳng đáy
cộng với hai mặt bên
Hình 2.2: Mặt phẳng đáy cộng với
các lỗ vuông góc với mặt phẳng đáy
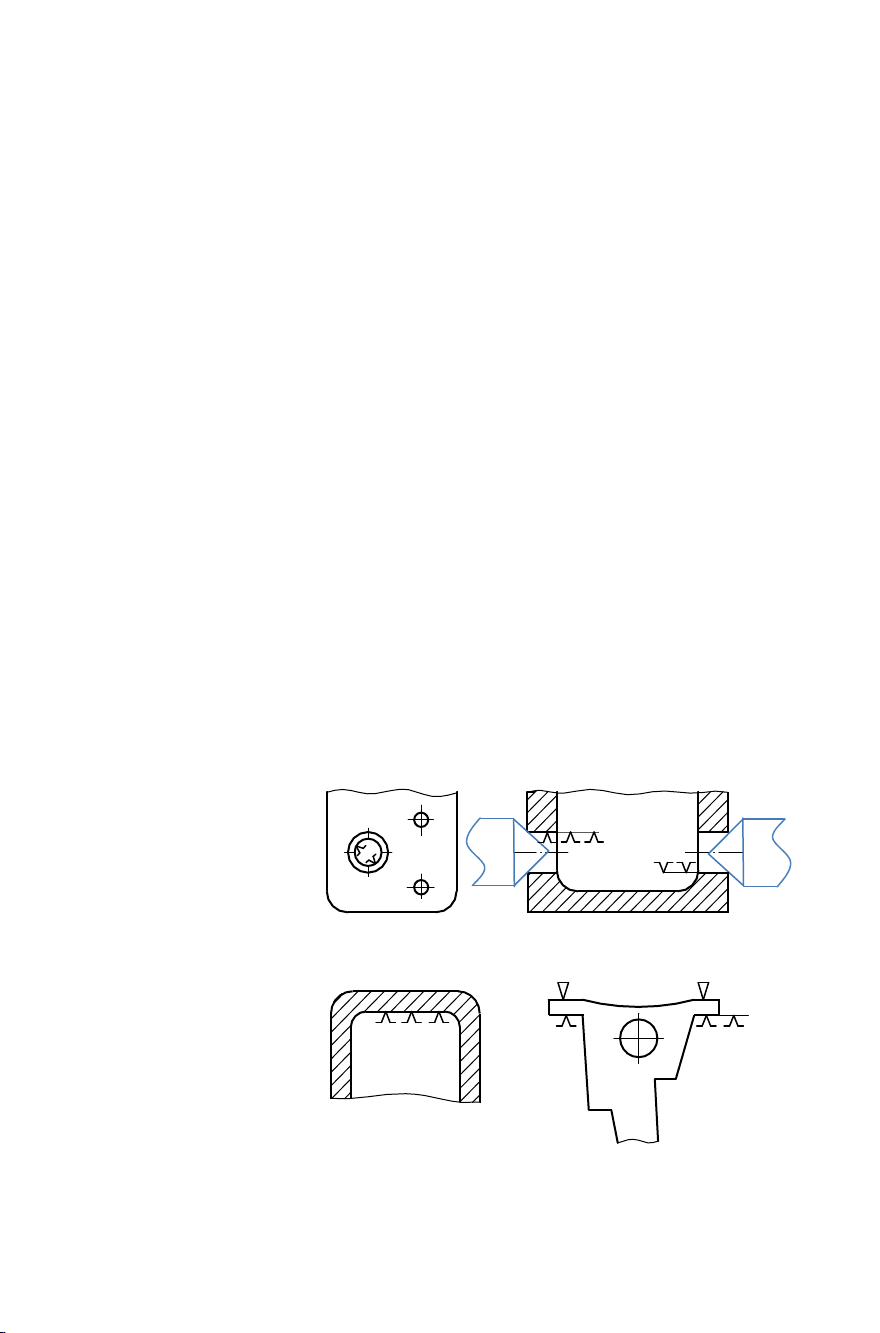
44
+ Mặt phẳng đáy cộng với rãnh trên mặt đáy (Hình 2.4)
+ Mặt phẳng bên cộng với các lỗ vuông góc với mặt phẳng bên.
Cần chú ý là không phải lúc nào cũng phải dùng hai trong số các lỗ
xỏ bulông đem gia công chính xác để làm chuẩn phụ, mà có thể căn cứ
vào kết cấu cụ thể của hộp như rãnh, sống trượt, mang cá, thậm chí cả lỗ
chính xác của hộp để khống chế các bậc tự do còn lại.
Sơ đồ gá đặt có tính chất điển hình như trên một mặt phẳng và hai
lỗ vuông góc với mặt phẳng đó) cho phép gá đặt chi tiết qua nhiều
nguyên công trên nhiều đồ gá, tránh được sai số tích lũy do việc thay đổi
chuẩn gây nên. Tạo được chuẩn tinh như thế, đồ gá cũng đơn giản đi
nhiều và tương tự nhau ở nhiều nguyên công.
Đối với chi tiết hộp, nguyên công đầu tiên phải là gia công tạo mặt
chuẩn (không kể nguyên công làm sạch và cắt đậu ngót, đậu rót của
phôi).
Việc chọn chuẩn thô cho nguyên công đầu tiên này hết sức quan
trọng vì nó ảnh hưởng đến lượng dư gia công cũng như độ chính xác ở
các nguyên công tiếp theo. Ở trường hợp này, có thể dùng những phương
án chọn chuẩn thô như sau (hình 2.5):
- Mặt thô của lỗ chính khống chế 5 bậc tự do (hình 2.5a). Dùng đồ
định vị là hai mũi chống tâm.
- Mặt thô không gia công ở bên trong khống chế 3 bậc tự do (hình
2.5b).
- Mặt trên ở
gờ vai khống chế 3
bậc tự do (hình
2.5c).
Trong các bề
mặt có thể làm
chuẩn thô nói trên,
quan trọng nhất là lỗ
chính vì nếu chọn
nó làm chuẩn thô thì
bảo đảm lượng dư
về sau cho bản thân
lỗ đều đặn, tạo điều
kiện cho việc gia
công lỗ dễ dàng. Khi
chọn chuẩn thô, nếu không chú ý đến mặt trong không gia công sẽ có thể
a)
b)
c)
Hình 2.5: Sơ đồ định vị khi chọn chuẩn thô
nguyên công đầu tiên.
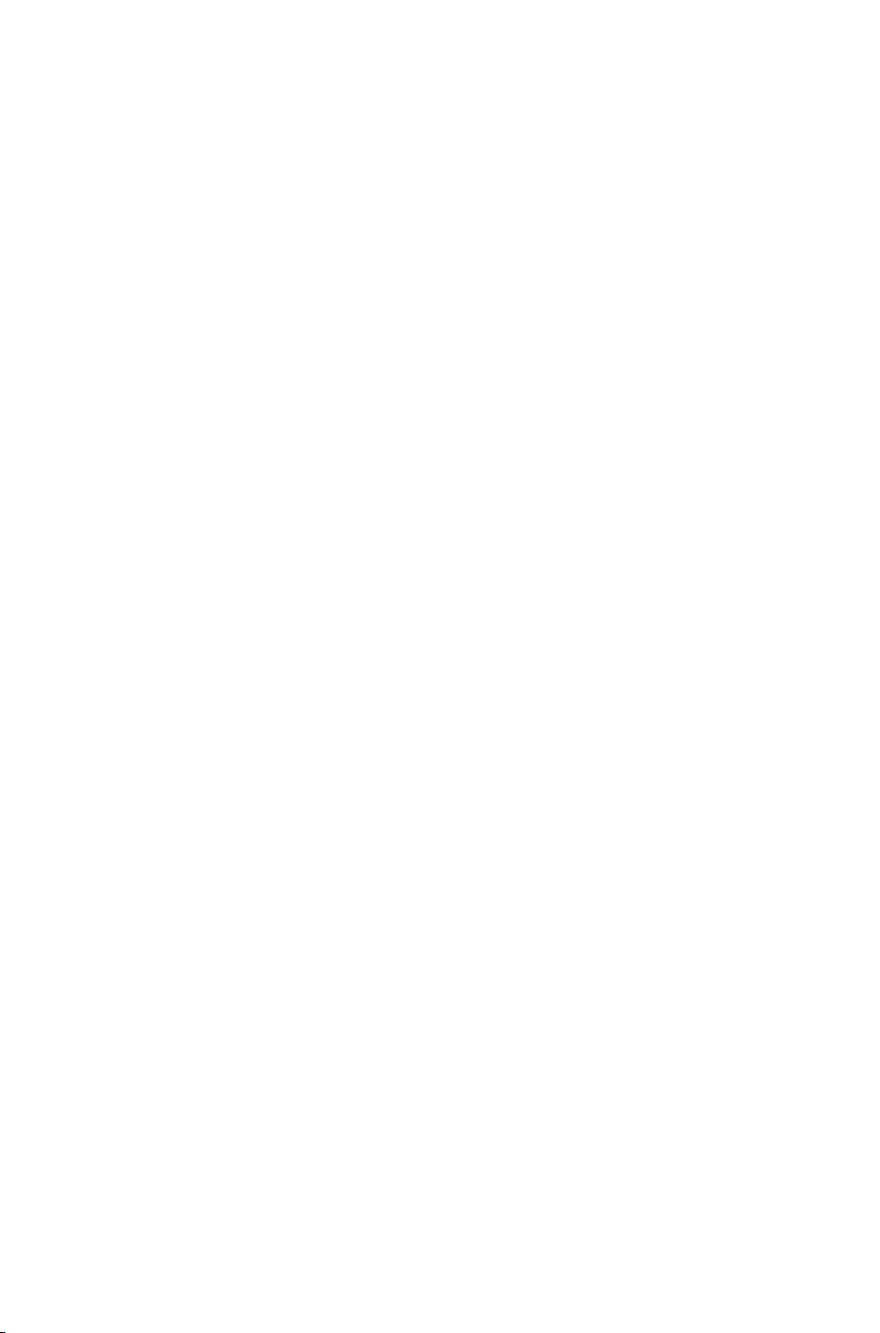
45
làm cho khe hở lắp ghép giữa nó với các bộ phận bên trong (như bánh
răng, tay gạt …) không đảm bảo.
Trong sản xuất hàng loạt nhỏ và đơn chiếc, do việc chế tạo phôi
kém chính xác và khi gia công không dùng đồ gá chuyên dùng, nên có
thể thực hiện nguyên tắc chọn chuẩn như trên bằng phương pháp lấy dấu.
Khi lấy dấu, có thể kết hợp chọn chuẩn thô này, đồng thời kiểm tra chuẩn
thô kia, chia lượng dư cho thỏa mãn các yêu cầu khác nhau, thậm chí tận
dụng được một số phôi, mà theo phương pháp tự động gá đặt thì không
hợp quy cách nữa. Tuy nhiên, việc lấy dấu có năng suất thấp và do đó giá
thành tăng, phương pháp này phù hợp với dạng sản xuất nhỏ.
2.1.4.2. Trình tự gia công các bề mặt chủ yếu của hộp
Quá trình công nghệ gia công các chi tiết dạng hộp bao gồm hai
giai đoạn chính:
- Gia công các bề mặt làm chuẩn tinh thống nhất (gồm ba trường
hợp cơ bản nêu trên).
- Dùng chuẩn định vị thống nhất để lần lượt gia công các mặt còn
lại như:
+ Gia công các mặt phẳng.
+ Gia công thô và bán tinh các lỗ lắp ghép.
+ Gia công các lỗ không chính xác dùng để kẹp chặt.
+ Gia công chính xác các lỗ lắp ghép.
+ Tổng kiểm tra.
2.1.5. Biện pháp thực hiện các nguyên công chính
2.1.5.1. Gia công mặt chuẩn
Nếu dùng máy vạn năng chia làm hai hoặc ba nguyên công: phay
mặt phẳng là một nguyên công và khoan, khoét, doa là một nguyên công.
Nếu dùng trên máy tổ hợp thì có thể thực hiện cùng một nguyên
công cho các trường hợp chọn chuẩn.
Ví dụ về việc gia công mặt phẳng đáy và hai lỗ vuông góc với mặt
phẳng đáy làm chuẩn:
- Gia công mặt phẳng đáy:
Dạng sản xuất nhỏ: Dùng máy phay hoặc máy bào vạn năng để gia
công. Trường hợp các hộp cỡ lớn có bề mặt chuẩn vuông hoặc gần tròn,
có thể gia công trên máy tiện đứng, còn hộp cỡ nhỏ thì ngoài phương
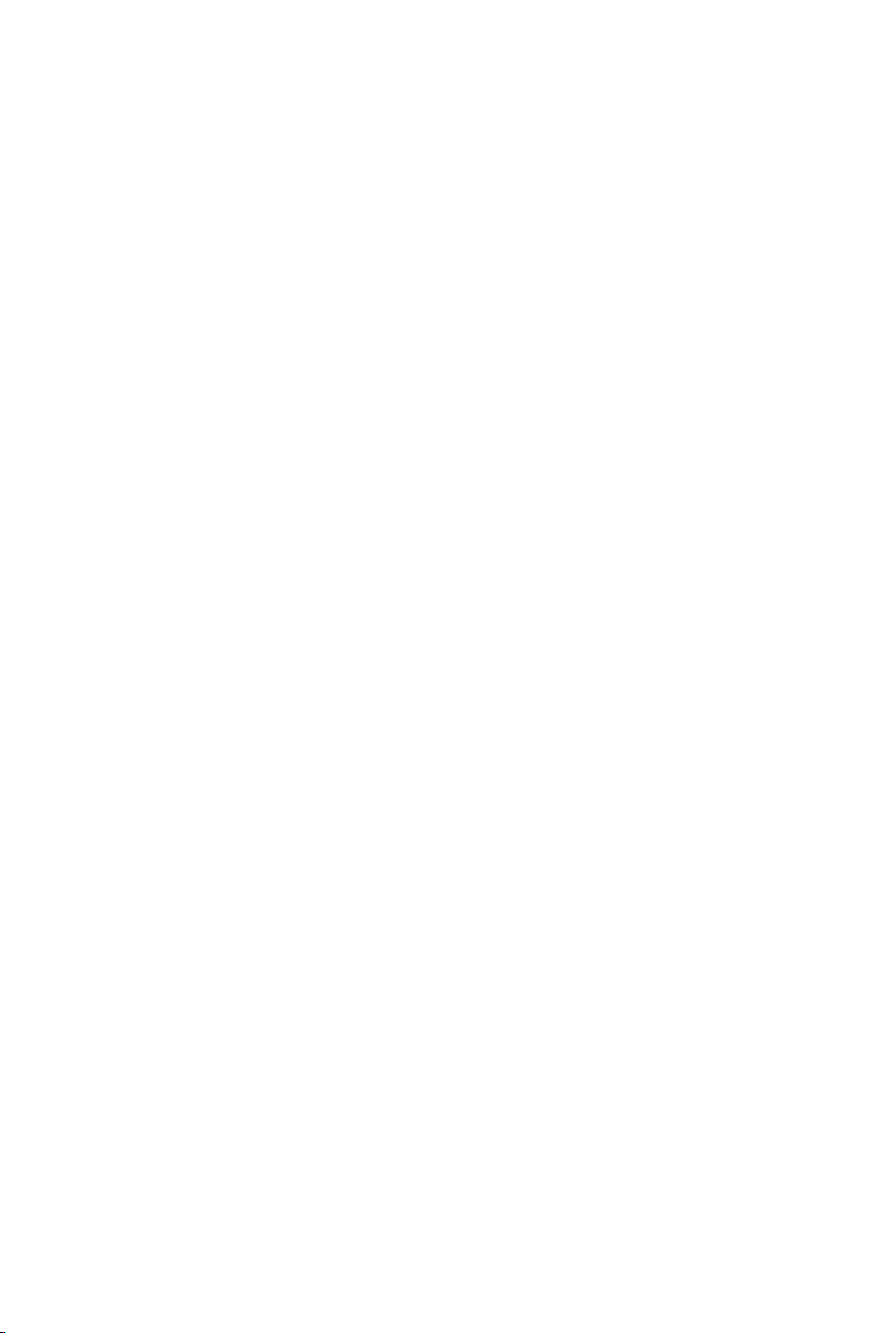
46
pháp bào và phay còn có thể gia công trên máy tiện vạn năng bằng cách
dùng mâm cặp bốn chấu để định vị hoặc dùng đồ gá chuyên dùng.
Trong dạng sản xuất hàng loạt lớn và hàng khối với hộp cỡ lớn
hoặc trung bình gia công mặt phẳng chuẩn được thực hiện trên máy nhiều
trục hoặc máy có bàn quay.Với các hộp cỡ nhỏ dùng phương pháp chuốt
mặt phẳng hoặc dùng máy tổ hợp hay máy chuyên dùng.
- Gia công hai lỗ chuẩn:
Nếu sản lượng nhỏ, có thể gia công bằng cách lấy dấu trước và
thực hiện trên máy khoan đứng. Với hộp lớn, việc gia công lỗ chuẩn có
thể tiến hành trên máy khoan cần.
Nếu sản xuất hàng loạt lớn hoặc hàng khối nên dùng máy nhiều
trục chuyên dùng. Cần chú ý rằng khi gia công hai lỗ chuẩn (hai lỗ định
vị) phải lần lượt tiến hành khoan, khoét, doa trong một lần gá và phải
dùng bạc dẫn hướng để đảm bảo đạt được độ nhám bề mặt và độ chính
xác của bản thân lỗ cũng như bảo đảm khoảng cách tâm hai lỗ nằm trong
phạm vi dung sai cho phép.
2.1.5.2. Gia công các mặt ngoài của hộp (mặt đầu các lỗ)
Gia công các mặt phẳng ngoài của hộp được tiến hành bằng các
phương pháp bào, phay, tiện, mài (trên máy tiện hoặc máy doa ngang).
Trong sản xuất đơn chiếc và hàng loạt nhỏ, thường sử dụng phương
pháp bào vì đơn giản và rẻ tiền. Năng suất của bào tuy thấp, nhưng cũng
có thể nâng cao được năng suất bằng cách gá nhiều chi tiết gia công cùng
một lúc.
Trong sản xuất hàng loạt vừa và lớn, gia công mặt ngoài có thể
dùng phương pháp phay. Với hộp cỡ nhỏ, có thể xếp nhiều chi tiết để gia
công cùng một lúc. Với hộp cỡ lớn, có thể tiến hành gia công trên máy
phay giường hoặc bào giường bảo đảm năng suất và đạt độ chính xác cao
như: độ không song song của các mặt 0,02 mm/1000 mm; độ không
phẳng 0,02 0,03 mm/1000 mm; độ không vuông góc 0,03 0,06
mm/500 mm.
Trong sản xuất hàng khối, đã và đang sử dụng rộng rãi phương
pháp phay liên tục trên máy phay có bàn quay và máy phay có tang trống
để gia công hai mặt phẳng song song cùng một lúc bằng hai dao.
Hình 2.6 thể hiện phương pháp gia công hai mặt song song bằng
máy phay hai trục chính hoặc máy một trục chính nhưng có bàn quay.
Ngoài ra, hiện nay còn sử dụng rộng rãi cả phương pháp chuốt để gia
công mặt phẳng của hộp.
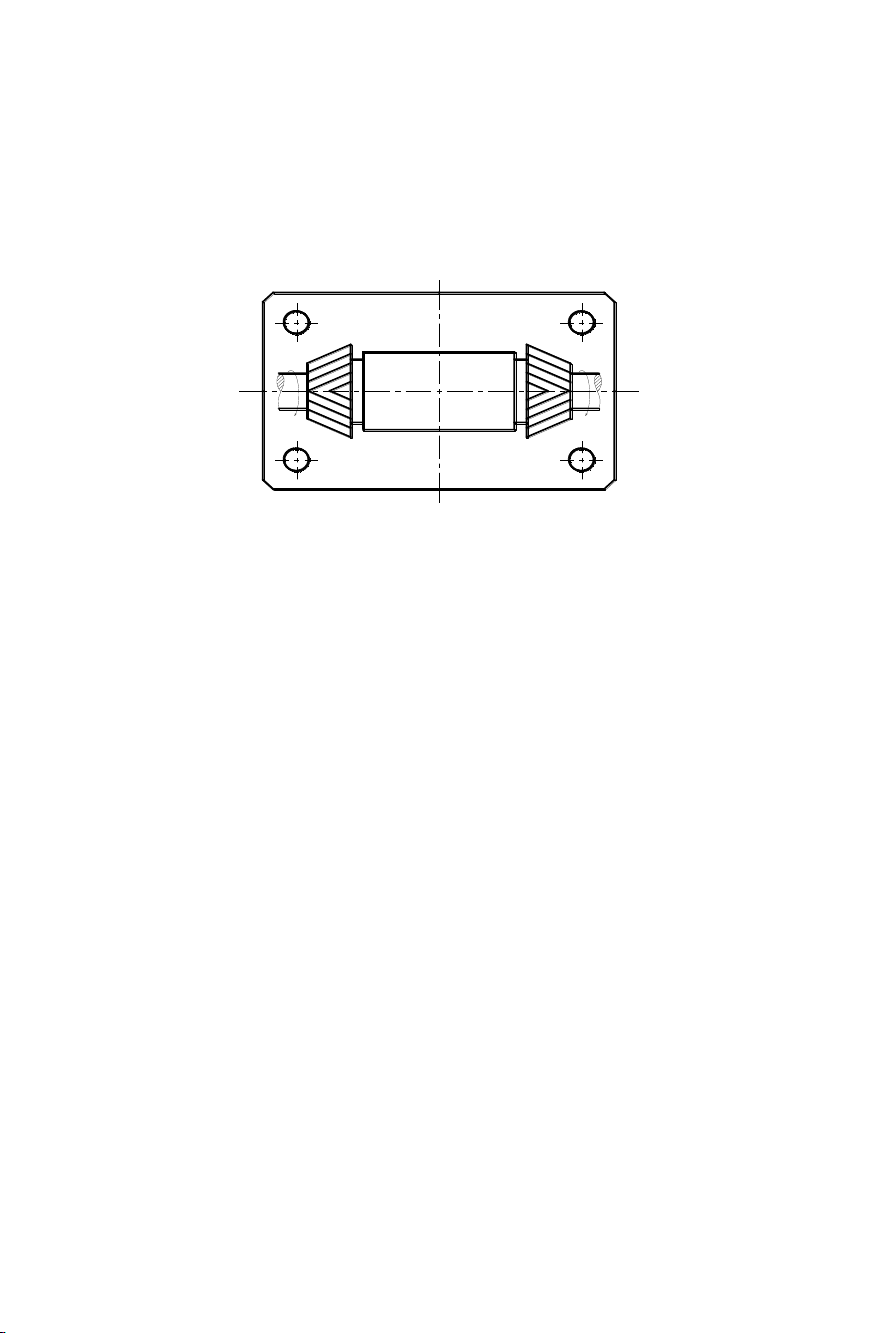
47
Những hộp có mặt ngoài và mặt trong tròn xoay được gia công trên
máy tiện đứng.
Trong nhiều trường hợp việc gia công mặt đầu các hộp chia thành
hai giai đoạn, gia công thô trên các máy vừa kể trên còn gia công tinh
được thực hiện trên máy doa ngang cùng với việc gia công các lỗ chính,
như vậy sẽ bảo đảm độ vuông góc cao giữa lỗ và mặt đầu.
Gia công tinh các mặt ngoài của hộp trong sản xuất hàng loạt lớn
và khối được thực hiện trên máy mài, còn trong sản xuất đơn chiếc và
loạt nhỏ thường dùng phương pháp cạo.
2.1.5.3. Gia công các lỗ chính (thường lỗ lắp ghép vòng bi)
Khi chế tạo các chi tiết dạng hộp, thời gian gia công các lỗ lắp ghép
chiếm một tỉ lệ khá lớn. Vì vậy, cần chọn phương pháp gia công hợp lý
để đảm bảo độ chính xác và tạo điều kiện nâng cao năng suất.
Biện pháp gia công các lỗ lắp ghép của hộp phụ thuộc vào sản
lượng của chi tiết. Có thể gia công trên máy doa ngang vạn năng, máy tổ
hợp nhiều trục chính. Trong một số trường hợp, có thể gia công trên dây
chuyền tự động và cũng có thể gia công lỗ hộp trên máy khoan đứng,
khoan cần, đôi khi còn có thể gia công trên máy tiện đứng hay máy tiện
thông thường. Dù gia công lỗ trên loại máy nào chăng nữa ta đều thấy:
- Đường kính các lỗ phụ thuộc cơ bản vào kích thước của dao (dao
định kích thước), hoặc phụ thuộc vào việc điều chỉnh kích thước của mũi
dao lắp trên trục dao.
- Độ chính xác về khoảng cách tâm, độ song song hay vuông góc
giữa đường tâm các lỗ với nhau cũng như các yêu cầu về vị trí khác của
lỗ được bảo đảm bằng hai phương pháp sau:
+ Gia công lỗ theo hệ thống bạc dẫn hướng trên đồ gá
Hình 2.6: Sơ đồ gia công mặt phẳng ngoài
của hộp trên máy phay hai trục chính
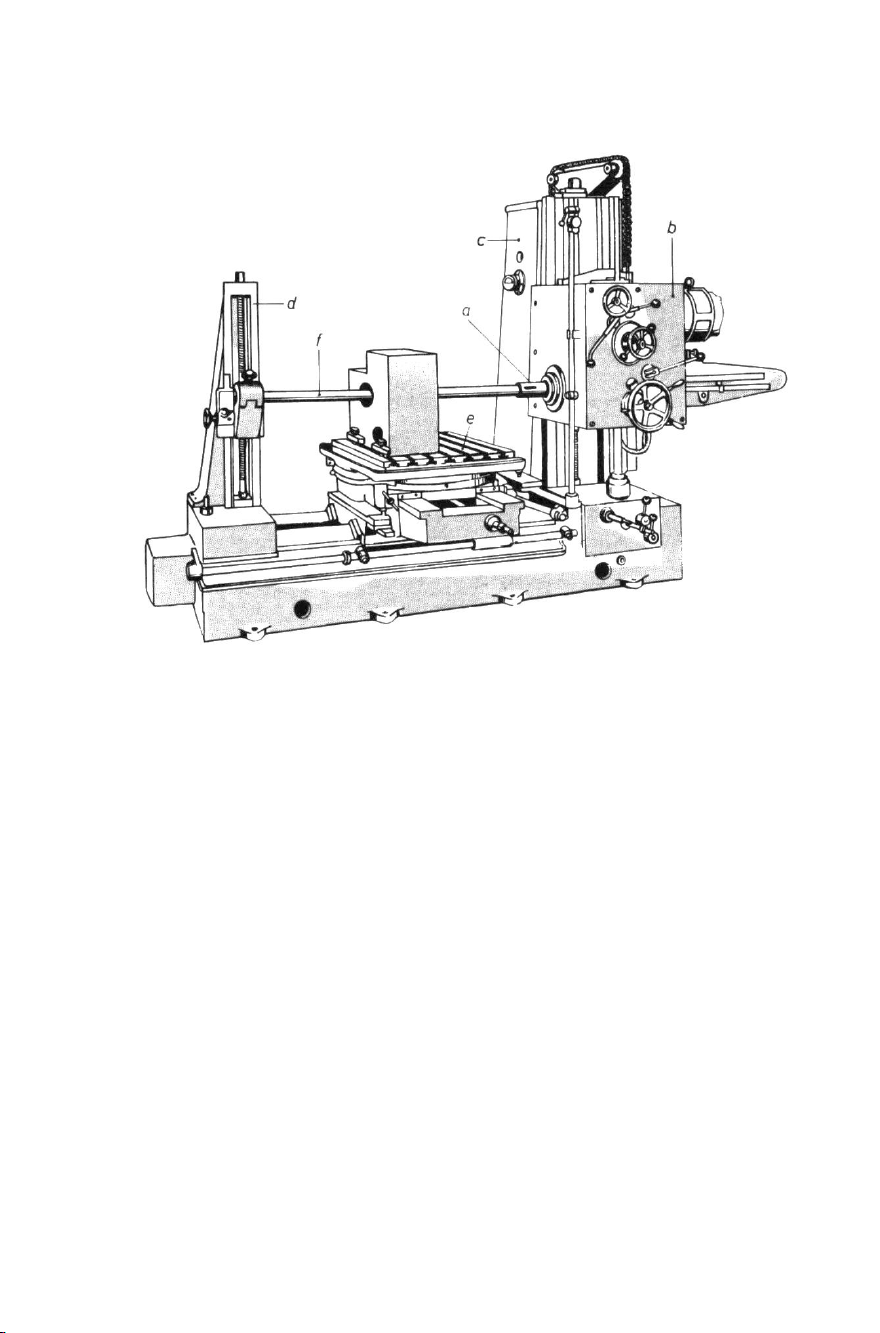
48
+ Gia công lỗ theo phương pháp xác định vị trí bằng tọa độ nhờ du
xích hay nhờ bộ nội suy trên máy CNC
Các phương pháp trên được thể hiện bằng những biện pháp cụ thể
thích hợp với từng dạng sản xuất.
Trong sản xuất hàng loạt lớn và hàng khối, các lỗ lắp ghép của hộp
được gia công trên máy doa, máy tổ hợp nhiều trục theo cách gia công
song song hoặc song song liên tục trên hai hoặc ba bề mặt của hộp. Khi
đó, vị trí của các lỗ được đảm bảo theo cách bố trí các trục chính trên
máy. Khi gia công trên máy tổ hợp (thường là máy CNC), nên chia thành
hai nguyên công thô và tinh hoàn thành trên hai máy của một đường dây,
hoặc chia làm hai bước hoàn thành tại hai vị trí của máy.
Đối với những lỗ của hộp có kích thước không lớn lắm có thể gia
công trên máy khoan đứng với đầu khoan nhiều trục và bạc dẫn hướng để
gia công các lỗ trên một bề mặt của hộp cùng một lúc, hoặc trên máy
khoan cần có dùng bạc dẫn hướng.
Trong sản xuất hàng loạt, các lỗ chính xác của hộp được gia công
trên máy doa ngang, doa đứng. Khi đó, kích thước lỗ do kích thước dao
quyết định, khoảng cách tâm các lỗ và độ song song giữa các lỗ được
đảm bảo nhờ sự dịch chuyển bàn máy và bằng vị trí các bạc dẫn hướng
Hình 2.7: Gia công mặt đầu và lỗ của hộp trên máy doa ngang
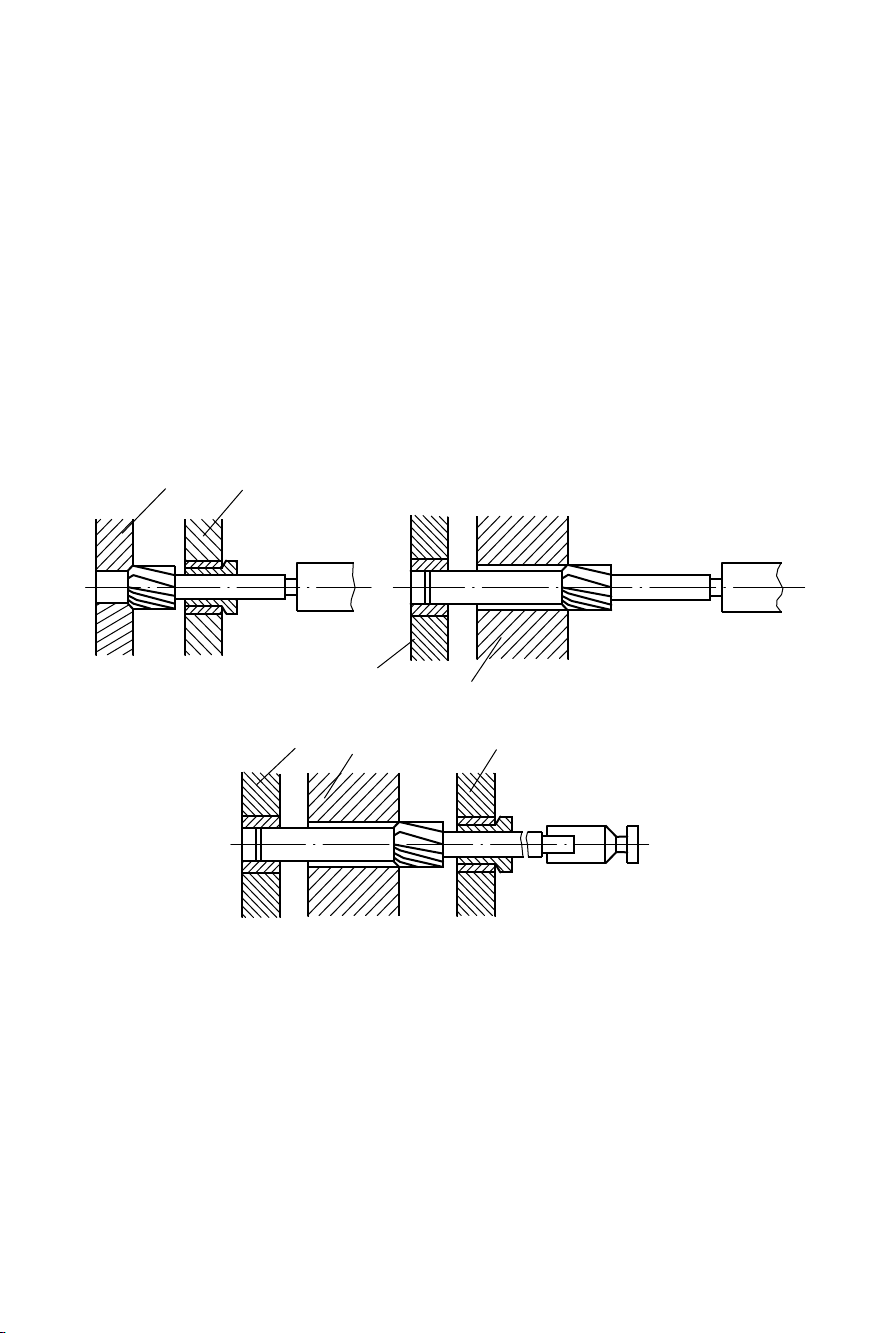
49
trục doa. Độ vuông góc giữa các lỗ được đảm bảo nhờ quay bàn máy
mang chi tiết so với trục doa.
Biện pháp kĩ thuật thực hiện phụ thuộc vào lỗ cần doa dài hay
ngắn, số lỗ trên một hàng lỗ, số hàng lỗ trên một bề mặt hộp và số bề mặt
hộp có lỗ cần gia công.
Nếu lỗ cần doa ngắn (không sâu), khi gia công cần dùng bạc định
hướng cho trục doa ở phía trước (hình 2.8a) hoặc ở phía sau lỗ gia công
(hình 2.8b). Khi lỗ hộp có chiều dài lớn phải định hướng trục doa cả phía
trước và phía sau (hình 2.8c).
Nếu có nhiều lỗ đồng trục trên một hàng, có thể thực hiện gia công
trên máy doa với biện pháp thích hợp. Để đảm bảo độ chính xác của hàng
lỗ, nên chia hai nguyên công thô và tinh.
Khi gia công thô
Trước tiên gia công lỗ ngoài cùng ở một phía của hộp bằng trục
dao công xôn. Sau đó gia công lỗ tiếp theo. Tiến hành gia công như vậy
đến khi xong một nửa số lỗ trên hàng lỗ đó. Sau đó quay bàn máy đi 180
o
a)
1
2
2
1
b)
2
1
2
c)
Hình 2.8: Sơ đồ định hướng dụng cụ khi doa lỗ chi tiết hộp.
a) Định hướng phía trước. b) Định hướng phía sau
c) Định hướng cả phía trước và sau.
1. Chi tiết gia công. 2. Đồ gá.
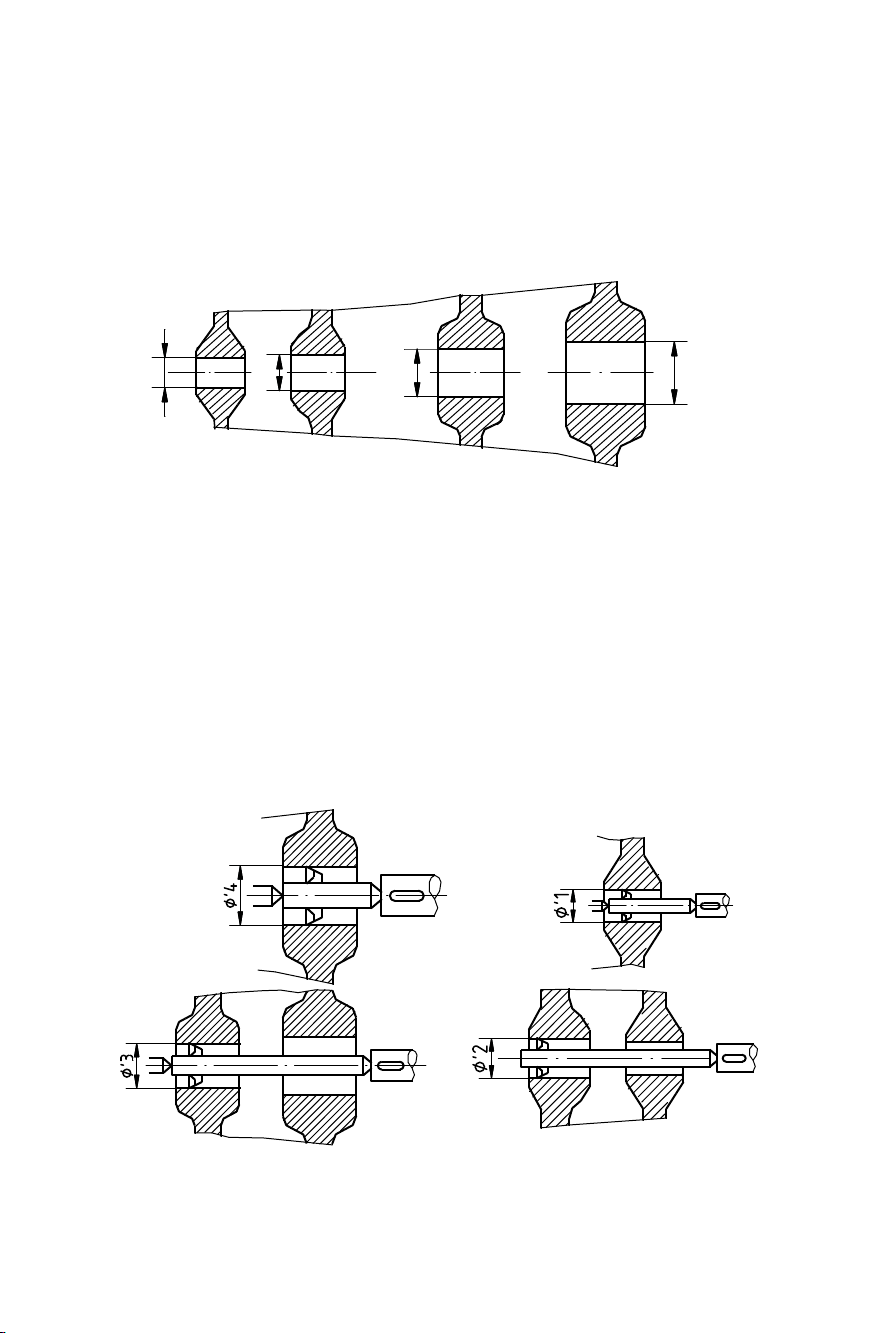
50
để gia công các lỗ ở phía đối diện của hộp với biện pháp như các lỗ ở
phía bên kia.
Làm như vậy, toàn bộ các lỗ trên một hàng lỗ đã được gia công thô.
Ví dụ, gia công một hàng 4 lỗ trên 4 vách khác nhau của hộp như hình 2.9.
Bốn lỗ này trên một hàng được bố trí nhỏ dần về một phía của hộp
với
1
<
2
<
3
<
4
Việc gia công thô được thực hiện theo sơ đồ hình 2.10 gồm các bước:
Bước 1: gia công lỗ
4
đạt ’
4
(hình 2.10a)
Bước 2: gia công lỗ
3
đạt ’
3
(hình 2.10b)
Sau đó quay bàn để quay chi tiết đi 180
o
và tiếp tục gia công.
Bước 3: gia công lỗ
1
đạt ’
1
(hình 2.10c)
Bước 4: gia công lỗ
2
đạt ’
2
(hình 2.10d)
Hình 2.10: Gia công thô các lỗ đồng trục.
a.
d
.
c
.
b
.
3
2
1
4
Hình 2.9: Sơ đồ các lỗ trên một hàng lỗ của hộp.
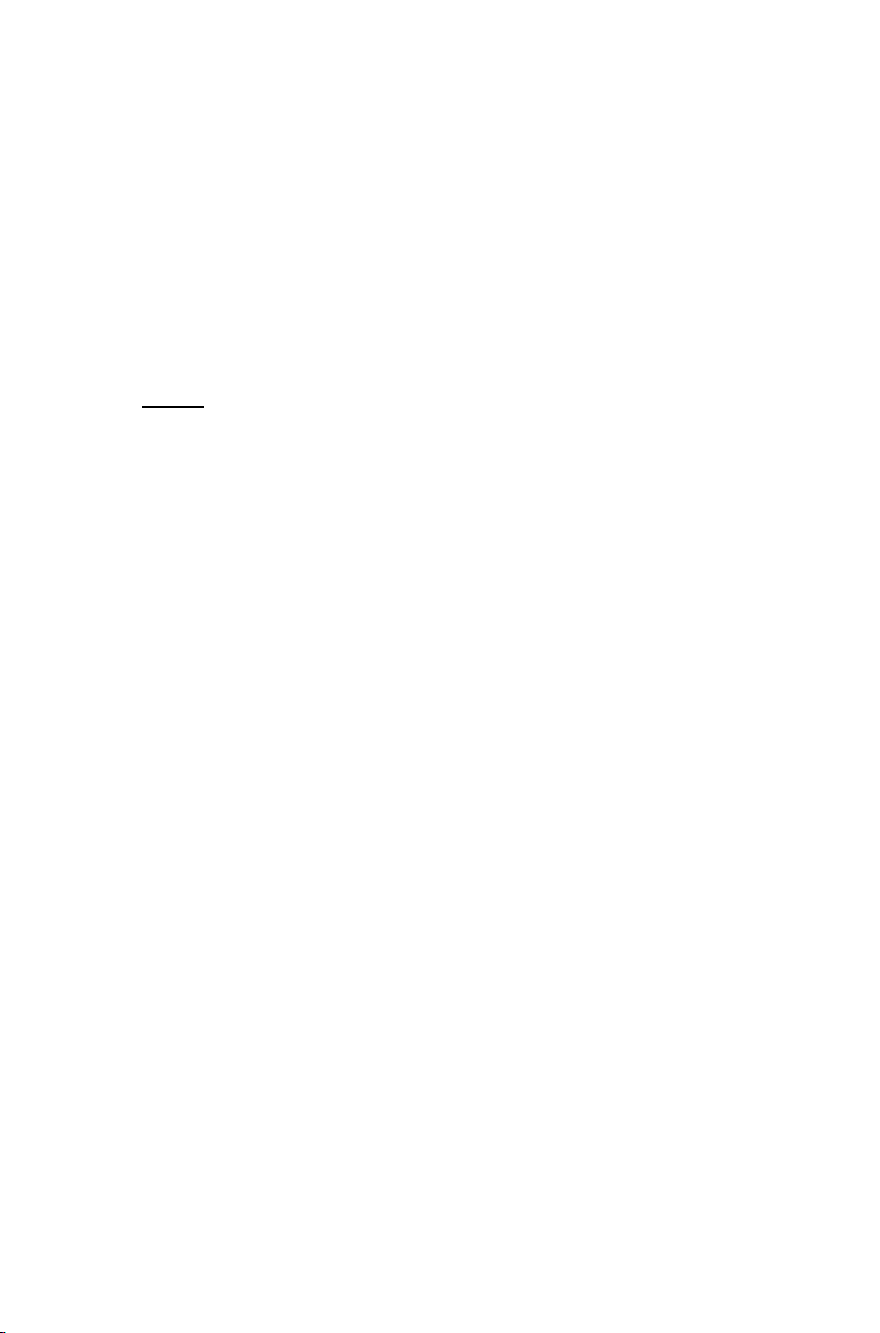
51
Khi gia công tinh
Việc gia công tinh các lỗ trên một hàng lỗ có thể tiến hành theo hai
phương án:
- Phương án thứ nhất: gia công liên tục các lỗ bằng cách sử dụng
các lỗ vừa gia công được để dẫn hướng dụng cụ cắt cho việc gia công các
lỗ tiếp theo.
- Phương án thứ hai: lần lượt gia công hai lỗ ngoài cùng của hai
mặt ngoài cùng đối diện của hộp, sau đó dùng hai lỗ này để dẫn hướng
dụng cụ cắt cho việc gia công các lỗ còn lại ở giữa.
Ví dụ: Gia công tinh các lỗ hộp trên hình 2.9 đã qua gia công thô ở
phần trên. Theo phương án thứ nhất, sơ đồ gia công được trình bày trên
hình 2.11 và gồm các bước:
Bước 1: gia công lỗ
4
(hình 2.11a)
Bước 2: dùng
4
dẫn trục dao gia công lỗ
3
(hình 2.11b)
Bước 3: dùng
3
dẫn trục dao gia công lỗ
2
(hình 2.11c)
Bước 4: dùng
2
dẫn trục dao gia công lỗ
1
(hình 2.11d)
Theo phương án thứ hai, sơ đồ gia công được trình bày trên hình
2.12, gồm các bước:
Bước 1: gia công lỗ
4
(hình 2.12a)
Sau đó quay bàn máy 180
o
tiếp tục gia công bước 2.
Bước 2: gia công lỗ
1
(hình 2.12b)
Bước 3: dùng
4
và
1
dẫn trục dao gia công các lỗ
3
,
2
đạt kích
thước yêu cầu (hình 2.12c).
Để gia công nhiều lỗ (hay nhiều hàng lỗ) trên một mặt hay nhiều
mặt của hộp, biện pháp công nghệ cũng tương tự như biện pháp gia công
một lỗ hoặc một hàng lỗ. Trong trường hợp ở mỗi mặt có thể có một số
nhóm lỗ giống nhau, có thể thực hiện theo các phương pháp sau:
Gia công hoàn chỉnh từng lỗ riêng biệt hoặc từng hàng lỗ riêng biệt
như đã được trình bày ở trên.
Với cùng một dao gia công để đạt một kích thước nào đó của tất cả
các lỗ giống nhau trên một bề mặt của hộp.
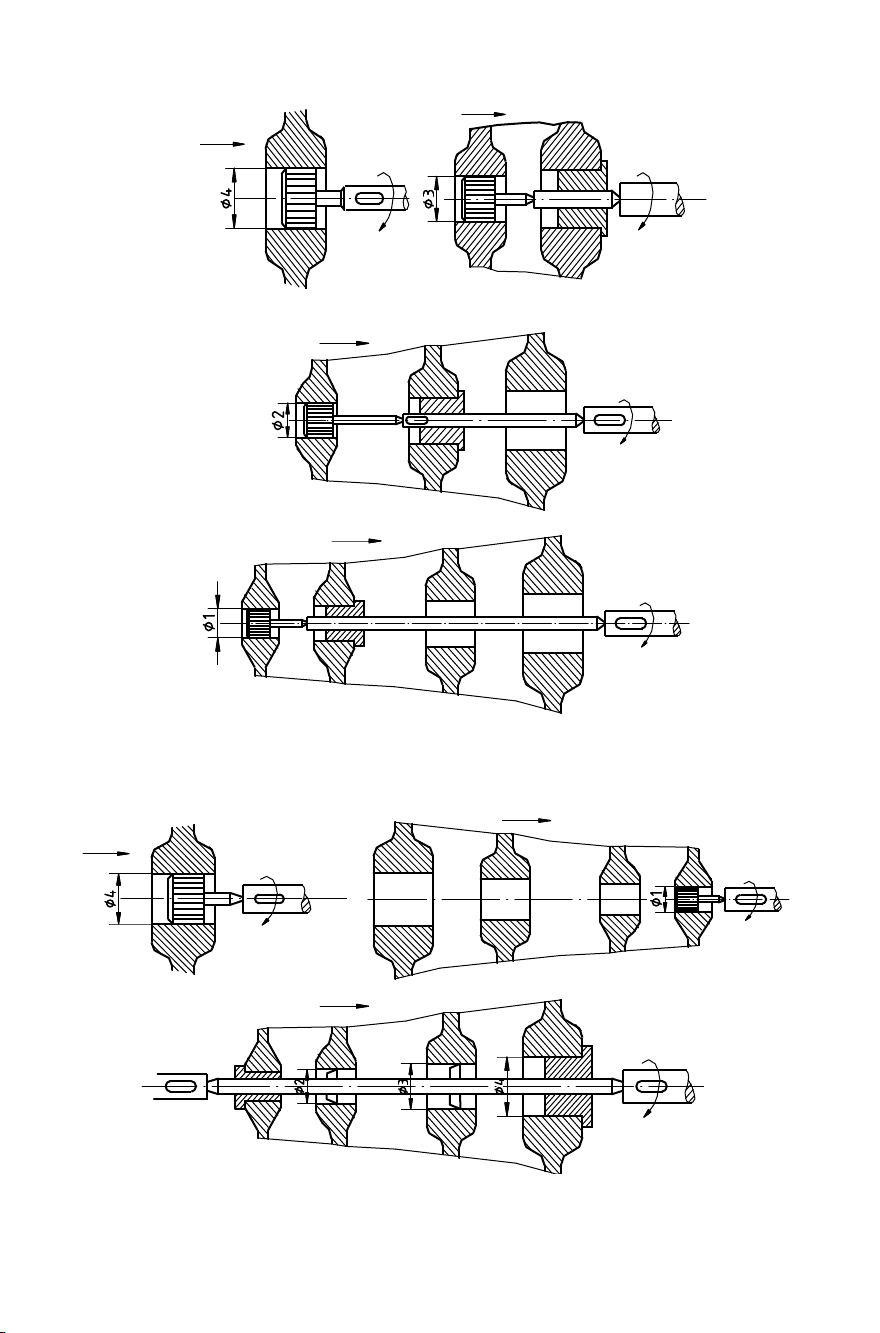
52
c)
d)
b)
a)
Hình 2.11: Sơ đồ doa các lỗ trên một hàng
theo phương án thứ nhất.
a)
b)
c)
Hình 2.12: Sơ đồ doa lỗ trên một hàng theo phương án thứ hai.
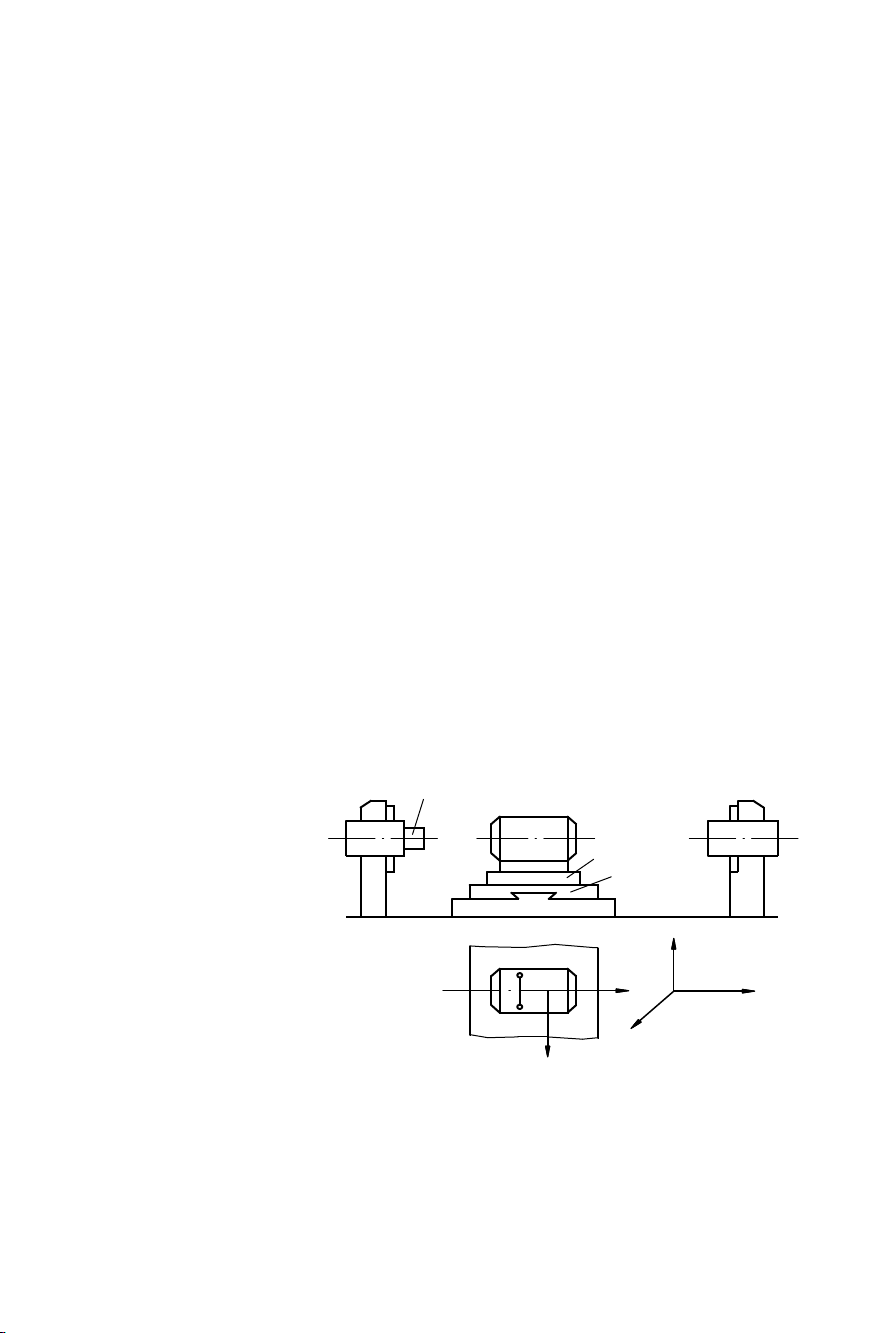
53
Để gia công các lỗ có kích thước khác ta tiến hành thay dao để gia
công tiếp. Cứ như vậy cho đến khi cả nhóm lỗ giống nhau được gia công
hoàn toàn. Tiếp đó tiến hành gia công nhóm lỗ khác trên mặt hộp. Cứ
như vậy cho đến khi tất cả các nhóm lỗ trên một bề mặt hộp được gia
công hoàn toàn. Sau đó, quay bàn mang chi tiết đi một góc nhất định để
gia công các lỗ trên mặt khác của hộp. Cứ làm như vậy cho đến khi toàn
bộ trên tất cả các bề mặt của hộp được gia công.
Dùng nhiều dao trên đầu doa nhiều trục để đồng thời gia công
nhiều lỗ có đường tâm song song.
Các phương án trên đây ngoài sự khác nhau về số lần thay dao, số
lần phân độ còn khác nhau về lượng dao thay thế, chế độ cắt, số vòng
quay của bàn máy.
Trong sản xuất loạt nhỏ và đơn chiếc, việc gia công lỗ hộp có thể
thực hiện trên máy khoan cần hoặc máy doa đứng, doa ngang không cần
bạc dẫn hướng cho dụng cụ cắt mà tiến hành bằng phương pháp rà gá
theo đường vạch dấu trên phôi. Thứ tự việc gia công lỗ hộp theo phương
pháp này như sau:
- Gá đặt và kiểm tra chi tiết hộp trên bàn máy sao cho đường tâm
của lỗ lấy dấu song song với đường tâm trục chính.
- Đưa đường tâm trục chính của máy trùng với tâm của lỗ đầu tiên
sẽ gia công.
- Tiến hành gia công.
- Dịch chuyển
bàn máy cùng với chi
tiết gia công theo
những khoảng cách
tâm đã cho tới khi trùng
với đường tâm của lỗ
cần doa tiếp theo.
- Gia công lỗ
tiếp theo
Việc gia công
lỗ của hộp bằng rà gá
theo dấu thể hiện như
trên hình 2.13. Chi
tiết gia công 3 được
định vị bằng mặt phẳng đáy trên mặt bàn máy 2. Trước khi đem lên máy
để gia công, chi tiết đã được vạch đường dấu aa vuông góc với đường
z
x
y
z
x
1
3
2
a
a
Hình 2.13: Sơ đồ rà gá hộp theo dấu để
gia công lỗ.
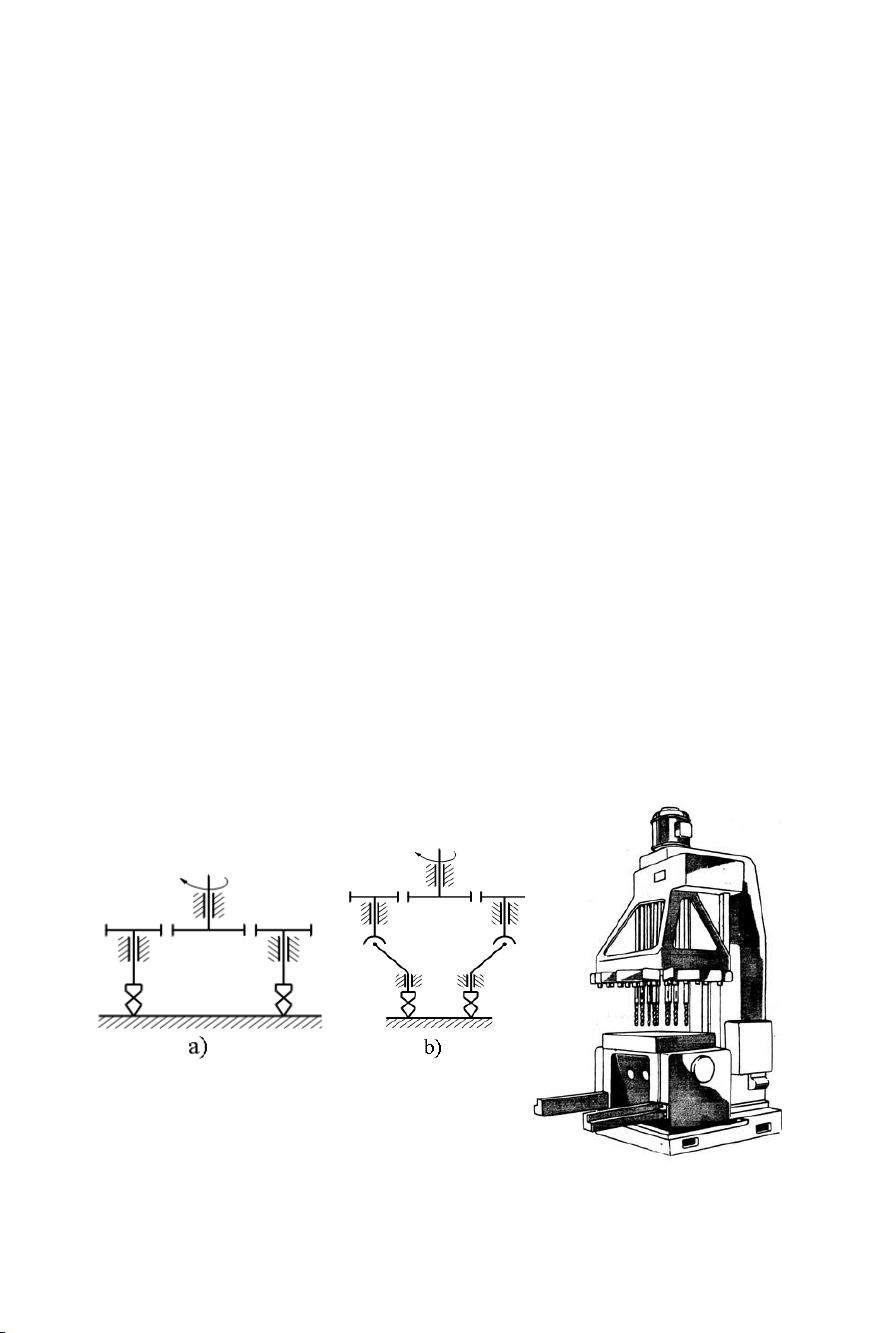
54
tâm lỗ cần gia công. Muốn cho tâm trục chính của máy song song với
tâm lỗ cần gia công, cần gắn mũi rà trên trục chính và cho chi tiết chuyển
động theo phương Z, xê dịch chi tiết sao cho đường vạch dấu aa trùng
mũi rà. Muốn đưa tâm lỗ gia công trùng tâm trục chính cần quay bàn
máy mang chi tiết dịch chuyển theo phương Z và dịch chuyển trục chính
(hoặc chi tiết) theo phương Y.
Ngoài ra, với chi tiết hộp cỡ nhỏ, có thể dùng đồ gá để gia công
trên các máy tiện vạn năng thông thường.
2.1.5.4. Gia công các lỗ kẹp chặt
Trong các chi tiết dạng hộp, ngoài những lỗ cơ bản, chính xác còn
có các lỗ dùng để kẹp chặt và các lỗ có ren. Đối với các lỗ có độ chính
xác cấp 12-10 và độ nhẵn bóng bề mặt với R
z
= 80-40 thì chỉ cần qua
khoan. Đối với lỗ có độ chính xác cấp10-9 và độ nhẵn bóng R
z
= 20, thì
sau khi khoan còn phải qua khoét, còn với lỗ phải qua khoan, khoét và
doa chỉ áp dụng khi độ chính xác lỗ cần đạt cấp 7-8. Việc gia công các lỗ
này cũng căn cứ vào sản lượng để chọn biện pháp gia công.
Khi sản lượng ít với mọi cỡ kích thước của hộp, các lỗ được gia
công trên máy khoan đứng hoặc khoan cần, khoảng cách tâm giữa các lỗ
được đảm bảo bằng cách lấy dấu hoặc nhờ các phiến dẫn, bạc dẫn khoan.
Đối với hộp quá lớn, có thể dùng máy khoan di động kẹp thẳng vào chi
tiết gia công hoặc cho máy khoan di động trên nền xưởng.
Trong sản xuất hàng loạt vừa, các lỗ kẹp chặt được gia công trên
máy khoan cần có lắp đầu rơvonve, trên đó có lắp nhiều dụng cụ gia công
khác theo thứ tự gia công. Làm như vậy sẽ giảm được thời gian tháo
lắp dụng cụ.
Trong sản xuất hàng loạt lớn và hàng khối với các chi tiết hộp cỡ
vừa, các lỗ được gia công trên máy tổ hợp hay máy khoan nhiều trục để
gia công nhiều lỗ cùng một lúc, có thể dùng đầu khoan nhiều trục định sẵn
c)
Hình 2.14: Sơ đồ nguyên lý đầu
khoan và máy khoan nhiều trục
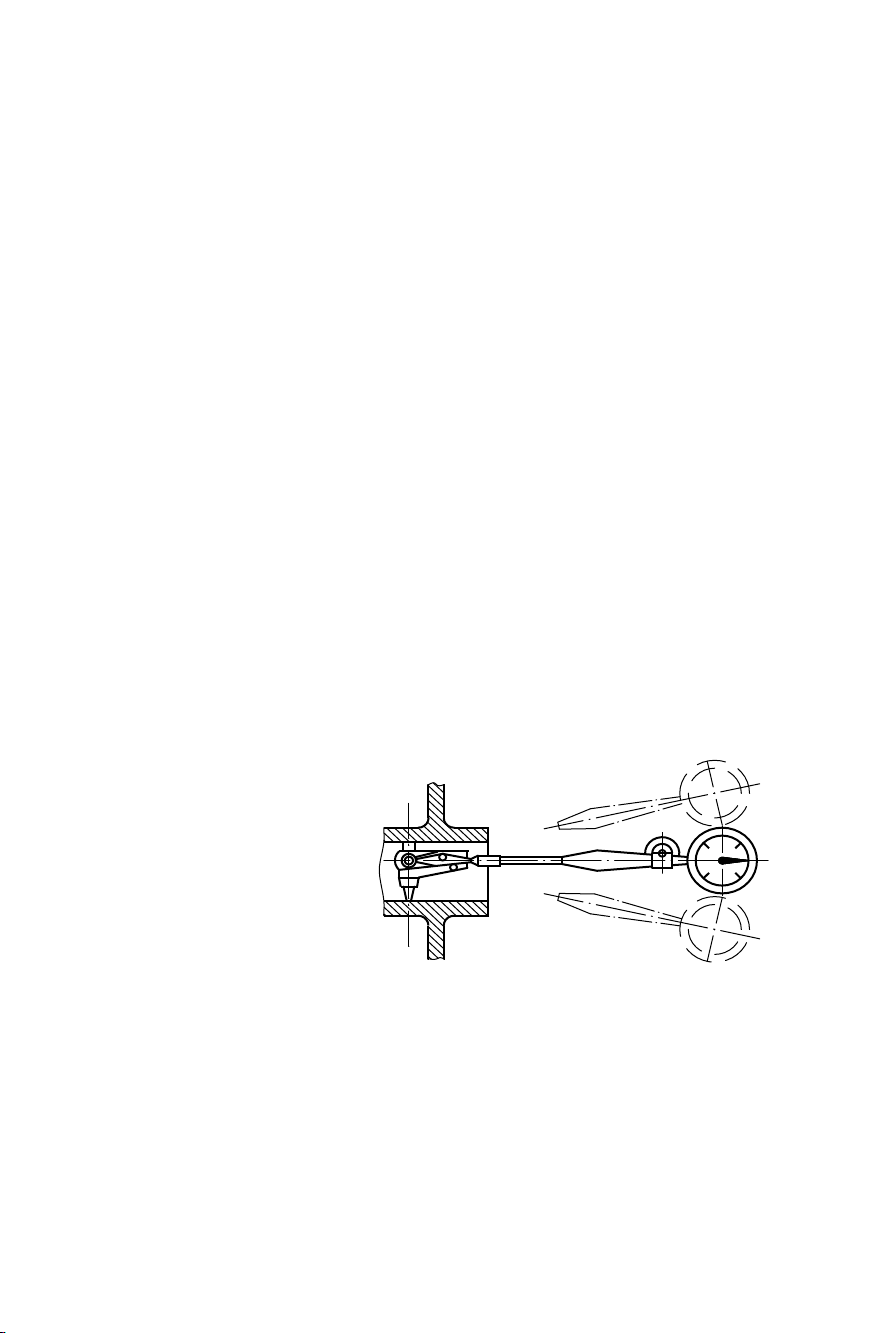
55
vị trí các trục (hình 2.14a) hoặc dùng đầu khoan nhiều trục thay đổi được
vị trí các trục nhờ khớp các đăng theo vị trí lỗ cần gia công (hình 2.14b).
Đối với các chi tiết cỡ nhỏ, nguyên công này được thực hiện trên
máy tổ hợp cùng với một số nguyên công khác.
Trong sản xuất hàng khối, các lỗ này còn có thể được gia công trên
các dây chuyền tự động. Với các lỗ có ren, khi gia công chúng còn phải
có thêm bước cắt ren. Tùy theo sản lượng, kết cấu và yêu cầu kĩ thuật
cũng như kích thước của ren mà chọn các phương pháp cắt ren cho hợp
lý như tarô tay hoặc tarô máy v.v…
2.1.5.5. Kiểm tra hộp
Trong quá trình chế tạo chi tiết dạng hộp, cần kiểm tra nhiều yêu
cầu kỹ thuật. Việc kiểm tra giữa các nguyên công được tiến hành sau khi
gia công các bề mặt quan trọng, có yêu cầu chính xác cao. Cuối giai đoạn
gia công phải có tổng kiểm tra các yếu tố đề ra trong yêu cầu kĩ thuật như
độ thẳng, độ phẳng của các mặt phẳng, độ song song, độ vuông góc, độ
đồng tâm và khoảng cách tâm giữa các lỗ v.v…
Độ thẳng của mặt phẳng nào đó được kiểm tra bằng cách dùng
thước hoặc đồng hồ so. Độ phẳng của các mặt phẳng hộp được kiểm tra
bằng nivô hoặc bằng đồng hồ so, hoặc bằng những bàn rà trên đó có bôi
lớp sơn đỏ để áp vào mặt cần kiểm tra. Độ phẳng được đánh giá bằng số
vết sơn trên một đơn vị diện tích. Với mặt phẳng của hộp quá lớn, có thể
kiểm tra độ phẳng bằng nguyên lý bình thông nhau.
Kích thước của
lỗ và hình dáng hình
học của lỗ chính xác
được kiểm tra bằng
thước cặp, ca líp, đồng
hồ so hoặc dụng cụ đo
lỗ có trang bị đồng hồ
so. Trên hình 2.15
trình bày sơ đồ kiểm
tra kích thước của lỗ bằng đồng hồ đo lỗ.
Hình dáng theo tiết diện ngang của lỗ như độ ô van, đa cạnh được
xác định bằng cách đo kích thước ở các vị trí khác nhau rồi so sánh kết
quả và rút ra kết luận.
Sai số hình dáng theo chiều dọc của lỗ như độ côn, độ tang trống
v.v… được xác định bằng cách kiểm tra đường kính lỗ ở các vị trí khác
nhau theo dọc trục.
Hình 2.15: Kiểm tra lỗ bằng đồng hồ đo lỗ
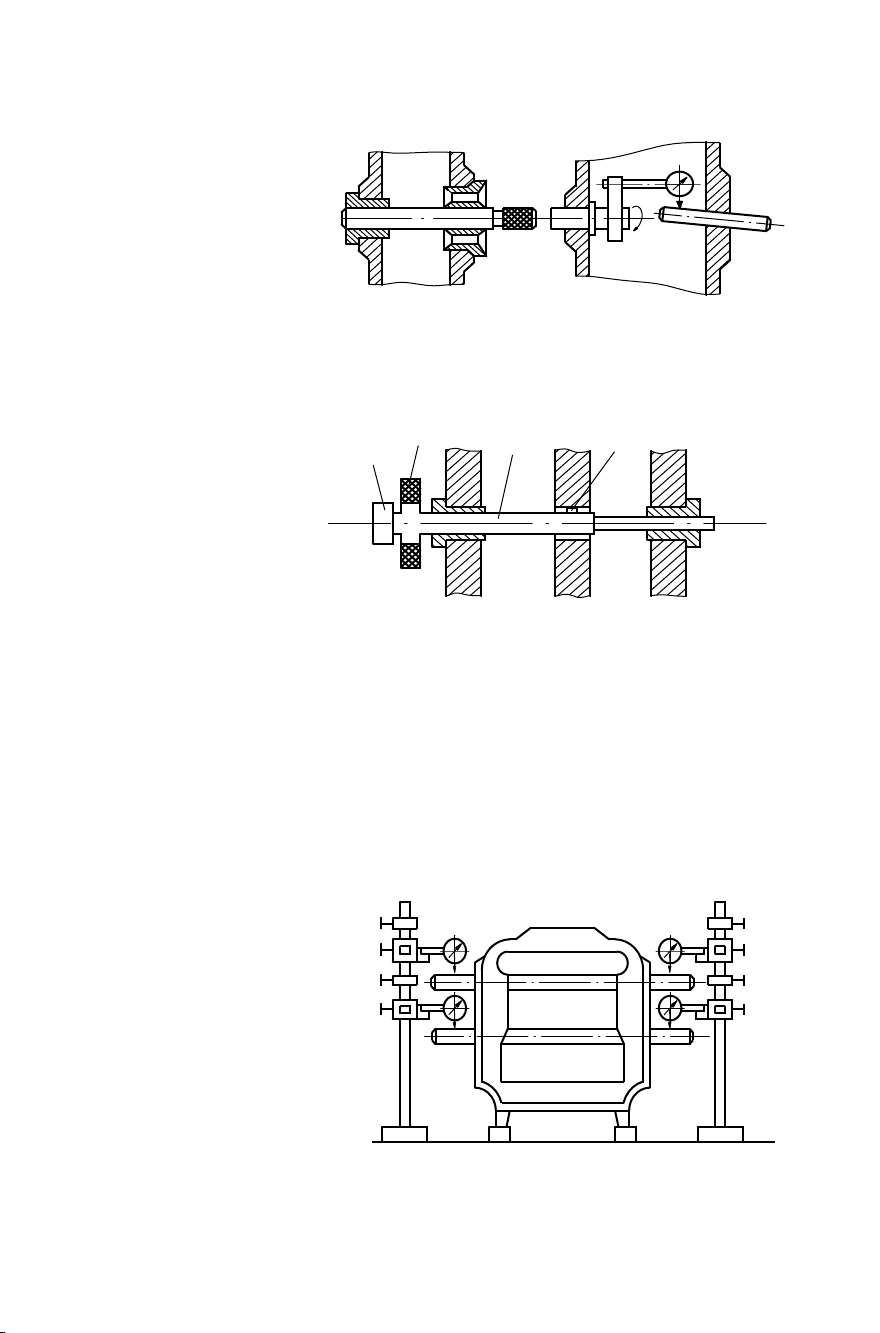
56
Kích thước chiều dài lỗ được xác định bằng thước cặp hoặc bằng ca líp.
Độ đồng tâm của
các lỗ cơ bản được xác
định bằng trục kiểm tra
(trục trơn hoặc trục
bậc). Với những lỗ quá
lớn, khi kiểm tra có thể
gá trục trong bạc (hình
2.16a). Để xác định cụ
thể độ đồng tâm của
hai lỗ có thể dùng trục
kiểm với đồng hồ so
(hình 2.16b).
Ngoài ra, để kiểm tra
độ đồng tâm còn có thể
dùng đồ gá chuyên
dùng. Trên hình 2.17
trình bày cách kiểm tra
độ đồng tâm của ba lỗ
trên ba vách khác nhau
của hộp.
Đồng hồ so 1 liên hệ với mũi đo 2 nhờ hệ thống tay đòn. Khi quay
tay quay 4 làm cho trục kiểm 3 (đã gá trong hai lỗ của hộp) quay. Nhờ
mũi đo 2 áp sát vào mặt lỗ và có liên hệ với đồng hồ so 1, có thể đọc
được độ lệch tâm của lỗ giữa so với hai lỗ hai bên.
Để kiểm tra độ đồng tâm còn có thể dùng phương pháp quang học
và các phương pháp khác nữa.
Khoảng cách tâm
và độ song song giữa
các lỗ được xác định
bằng thước cặp hoặc
đồng hồ so (hình 2.18).
Sơ đồ như trên chỉ
kiểm tra được độ không
song song của đường
tâm lỗ theo một phương
mà thôi.
a)
b)
Hình 2.16: Kiểm tra độ đồng tâm của các lỗ
a) Dùng trục kiểm gá trong bạc
b) Dùng trục kiểm với đồng hồ so
1
4
3
2
Hình 2.17: Sơ đồ kiểm tra độ đồng tâm
của ba lỗ trên ba vách hộp.
Hình 2.18: Kiểm tra khoảng cách tâm
giữa các lỗ và độ không song song của
đường tâm các lỗ.
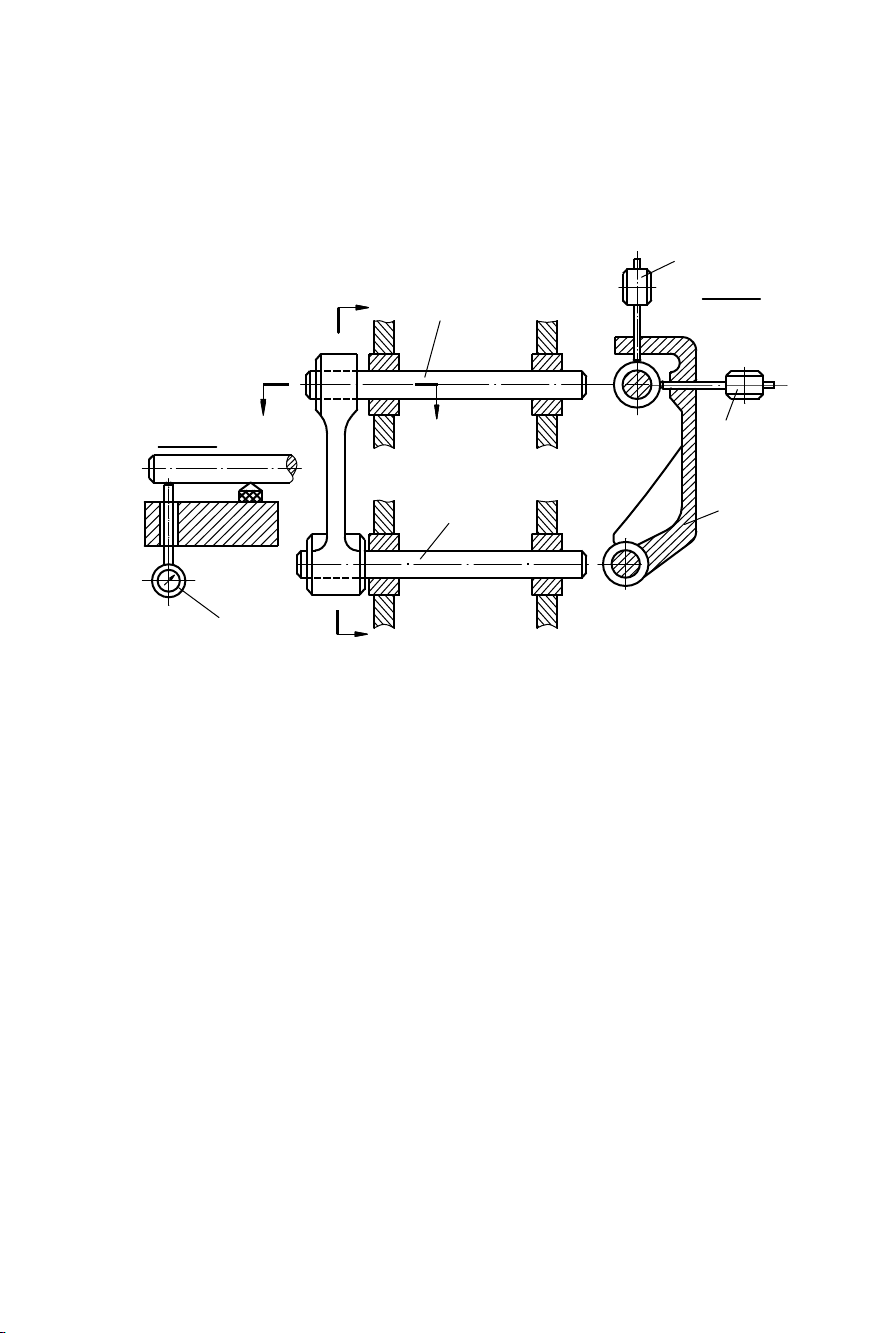
57
Để có thể kiểm tra độ không song song theo cả hai phương phải có đồ
gá chuyên dùng. Sơ đồ như vậy thể hiện trên hình 2.19. Lắp hai trục kiểm
vào hai lỗ cần kiểm, dùng bạc điều chỉnh cho không còn khe hở. Sau đó lắp
tay treo số 3 có mang đồng hồ 1, 2 vào trục 5, quay tay treo 3 cho mũi tì của
đồng hồ so 1 và 2 tì vào trục 4, tại đó chỉnh các đồng hồ so về vị trí 0.
Tháo tay treo ra và mang nó lắp vào phía đối diện của trục 4 và 5.
Tiến hành đo như trên sẽ có kết quả là:
Hiệu số chỉ trên đồng hồ 1 là sai số về độ không song song theo
phương thẳng đứng của hai lỗ trên chiều dài bằng khoảng cách giữa hai
đầu lắp tay treo. Hiệu số chỉ trên đồng hồ so số 2 cho biết sai số về độ
không song song theo phương nằm ngang của hai lỗ.
Trên tiết diện B-B biểu diễn cách đo sai số theo phương nằm
ngang. Trên bề dày của tay treo có một chốt tì cố định tì sát vào trục 4,
còn đầu kia là của đòn bẩy, qua đó báo đến đồng hồ so 2 và cho biết độ
không song song.
Khoảng cách từ tâm các lỗ đến các bề mặt hộp và độ không song
song giữa chúng, được xác định bằng đồng hồ so như trên hình 2.20.
Hình 2.19: Sơ đồ kiểm tra độ song song và khoảng cách tâm
các lỗ theo hai phương.
2
B
B - B
B
4
5
A
A
1
A - A
2
3
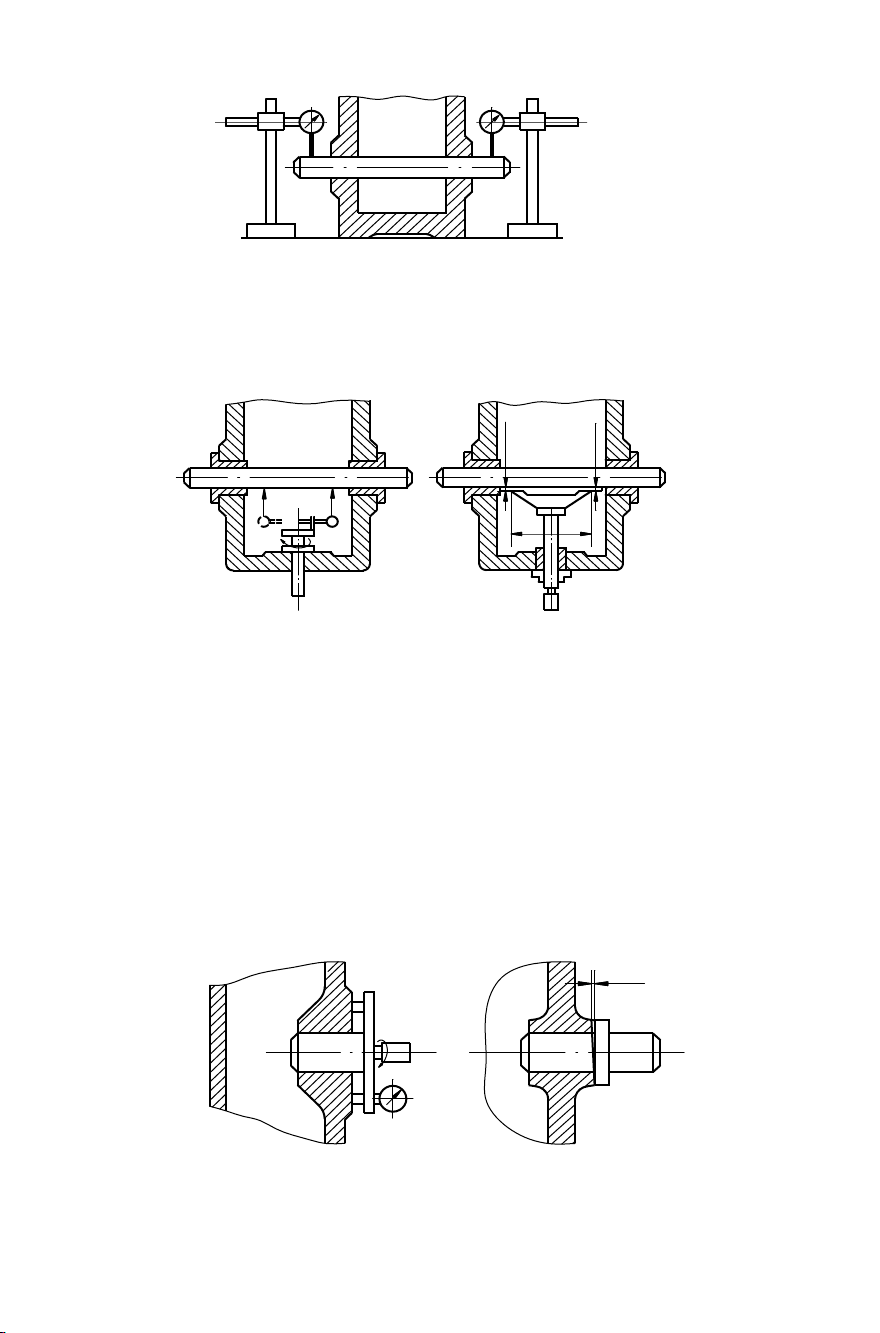
58
Độ vuông góc giữa tâm các lỗ được xác định bằng đồng hồ so hoặc
calip (hình 2.21).
Trong trường hợp dùng calip, cần xác định khe hở
1
và
2
. Độ
không vuông góc chính là hiệu giữa hai đại lượng này.
Độ vuông góc giữa tâm lỗ và mặt đầu được xác định bằng đồng hồ
so (hình 2.22a) hoặc bằng calip chuyên dùng (hình 2.22b).
Dưới đây là quy trình công nghệ chế tạo thân hộp giảm tốc độ đã
giới thiệu ở hình 2.1. Gia công hộp này gồm một số nguyên công chính
theo bảng 2.1
Hình 2.22: Kiểm tra độ vuông góc giữa tâm lỗ và mặt đầu
a) Bằng đồng hồ so; b) Bằng calip chuyên dùng
a)
b)
Hình 2.21: Kiểm tra độ vuông góc của hai lỗ
a) Dùng đồng hồ so; b)Dùng calip
1
2
L
b)
a)
Hình 2.20: Kiểm tra vị trí đường tâm lỗ
so với bề mặt cơ bản.
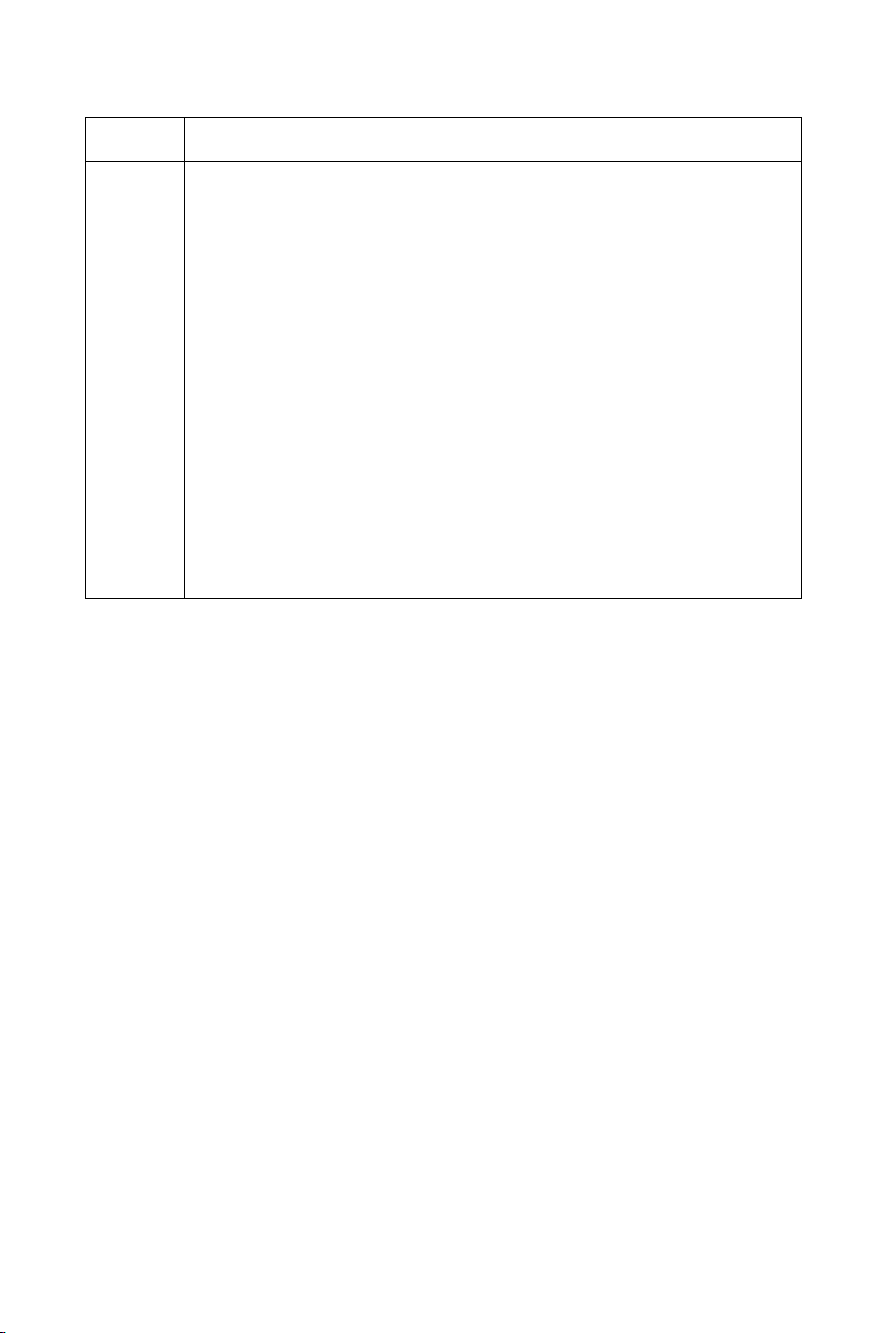
59
Bảng 2.1
Thứ tự
Nội dung nguyên công
1
2
3
4
5
6
7
8
9
10
11
Gia công mặt phẳng chuẩn của thân dưới.
Khoan và doa hai lỗ chuẩn vuông góc với mặt phẳng chuẩn.
Gia công thô mặt lắp ghép và mặt đầu các lỗ lắp ghép
Gia công tinh mặt lắp ghép và mặt đầu các lỗ lắp ghép
Gia công các lỗ trên mặt phẳng lắp ghép.
Gia công thô mặt lắp ghép của nắp trên.
Gia công lỗ trên mặt chuẩn của thân dưới.
Lắp hai nửa hộp và gia công hai lỗ côn định vị.
Doa thô và tinh các lỗ lắp ghép.
Gia công lại mặt đầu các lỗ lắp ghép.
Tổng kiểm tra.
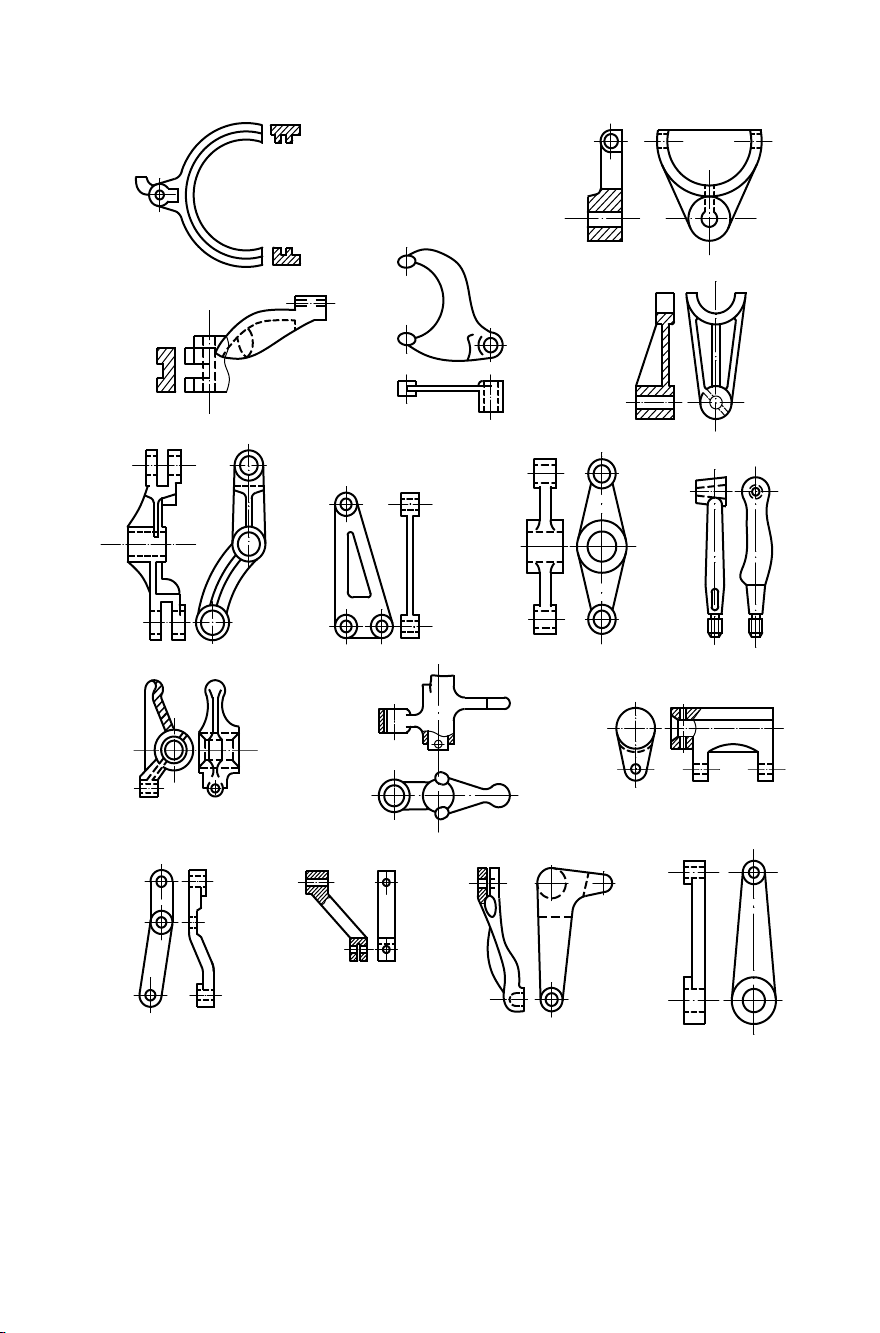
60
2.2. QUY TRÌNH CÔNG NGHỆ CHẾ TẠO CÁC CHI TIẾT DẠNG CÀNG
Càng là một loại chi tiết có một hoặc một số lỗ cơ bản mà tâm của
chúng song song với nhau hoặc tạo với nhau một góc nào đó.
Chi tiết dạng càng thường có chức năng biến chuyển động thẳng
của chi tiết này (piston của động cơ đốt trong chẳng hạn) thành chuyển
Hình 2.23: Các chi tiết dạng càng
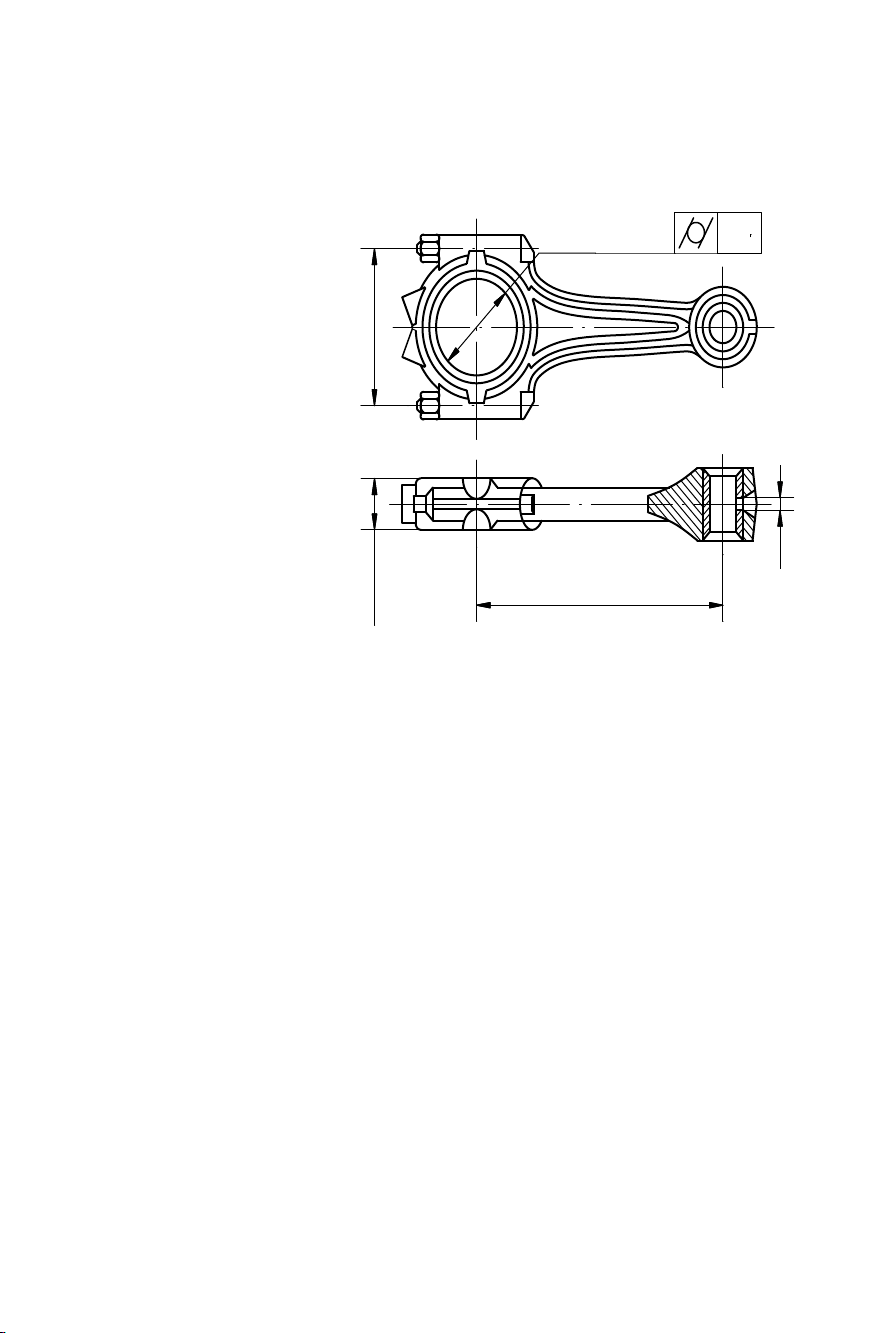
61
động quay của chi tiết khác (trục khuỷu) hoặc ngược lại. Ngoài ra, chi
tiết dạng càng còn dùng để đẩy bánh răng (khi cần thay đổi tỉ số truyền
trong các hộp tốc độ) và nhiều chức năng khác.
Trên chi tiết dạng
càng, ngoài những lỗ cơ
bản cần được gia công
chính xác, còn có
những lỗ dùng để kẹp
chặt, các rãnh then, các
mặt đầu của lỗ và
những bề mặt khác cần
được gia công.
Những dạng khác
nhau của chi tiết dạng
càng được trình bày trên
hình 2.23.
Trên hình 2.24 là
tay biên ở vị trí lắp
ghép trong động cơ đốt
trong. Đây là loại chi
tiết đặc trưng của các
chi tiết dạng càng.
2.2.1. Điều kiện kỹ thuật
Khi chế tạo các chi tiết dạng càng cần đảm bảo các yêu cầu kỹ
thuật sau:
- Kích thước các lỗ cơ bản được gia công với độ chính xác cấp 7
9; độ nhám bề mặt R
a
= 0,63 0,32.
- Độ không song song của các tâm lỗ cơ bản trong khoảng 0,03
0,05 mm trên 100 mm chiều dài.
- Độ không vuông góc của tâm lỗ so với mặt đầu trong khoảng 0,05
0,1 mm trên 100 mm bán kính.
- Độ không song song của các mặt đầu các lỗ cơ bản khác trong
khoảng 0,05 0,25 mm trên 100 mm bán kính mặt đầu.
- Các rãnh then được gia công đạt cấp chính xác 8 10 và độ nhám
R
z
= 40 10 hay R
a
=10 2,5.
- Các mặt làm việc của càng được nhiệt luyện đạt độ cứng 50 55 HRC.
Hình 2.24: Tay biên trong động cơ ôtô
0,08
69,5
185
82
29
+0.012
±0,1
-0,06
-0,13
±0,05
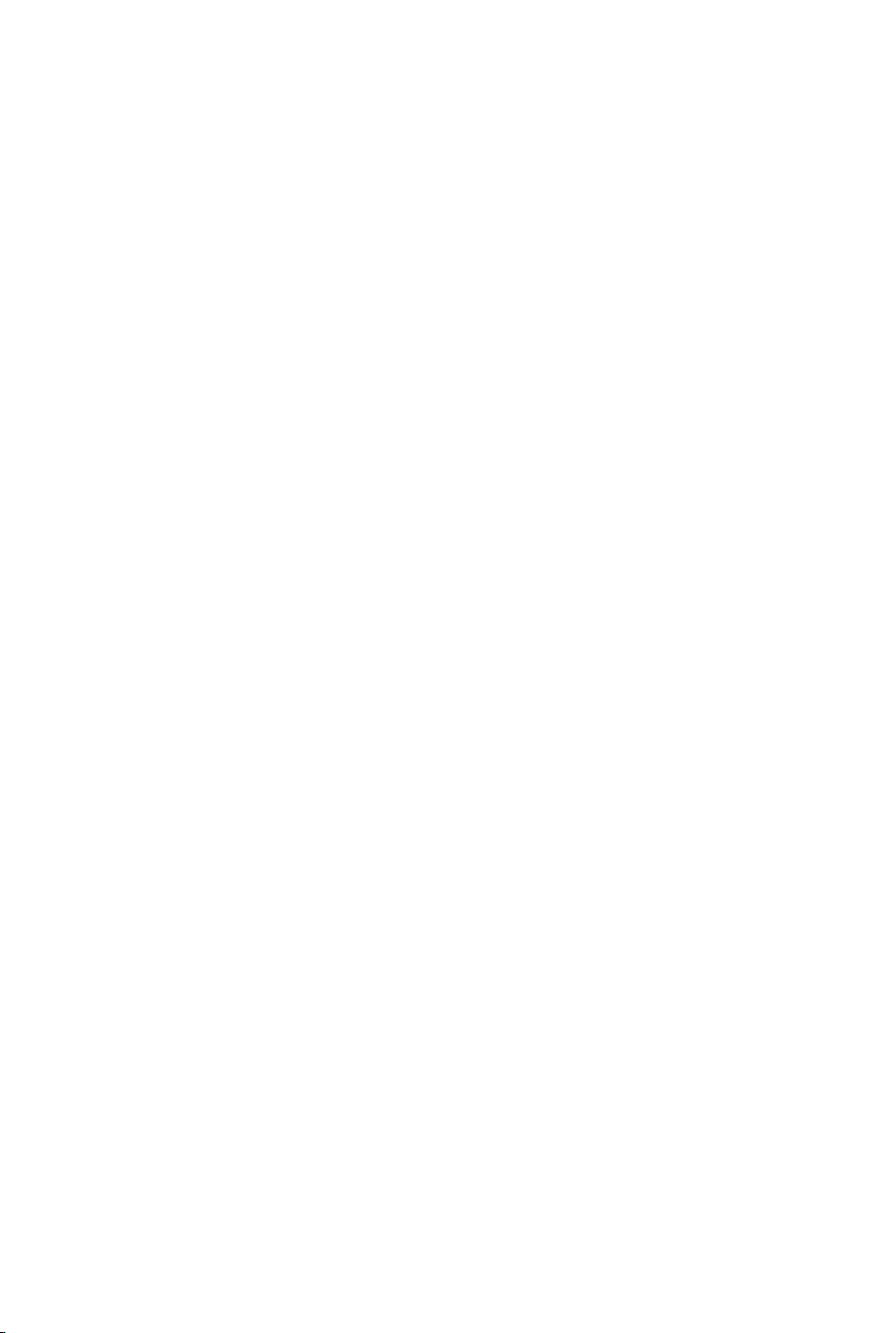
62
2.2.2. Vật liệu và phôi
Vật liệu dùng để chế tạo chi tiết dạng càng thông thường là thép
cacbon 20, 40, 45. Thép hợp kim 18CrNiMnA; 18Cr2Ni4A và 40CrMnA
có độ bền cao. Các loại gang xám GX12-28, GX 24-44 và gang rèn 37-
12, 4-35-10. Đôi khi càng được chế tạo từ kim loại màu.
Với những càng làm việc với tải trọng không lớn, có thể chọn vật
liệu là gang xám. Những càng có độ cứng vững thấp, làm việc có va đập
thì nên chọn vật liệu gang rèn. Còn những càng làm việc với tải trọng
lớn, để tăng độ bền nên dùng vật liệu là các loại thép có nhiệt luyện.
Các dạng phôi thường dùng chế tạo các chi tiết dạng càng là phôi
đúc như: gang, thép, kim loại mầu, phôi rèn, phôi dập.
Càng cỡ vừa và nhỏ nếu sản lượng ít, phôi được chế tạo bằng
phương pháp rèn tự do, nếu sản lượng lớn dùng phương pháp dập, sau đó
ép tinh trên máy ép để vừa tăng cơ tính vừa chống cong vênh cho càng.
Tùy theo kết cấu của càng mà có thể dập phôi từng đôi chi tiết một để
tăng năng suất. Phôi dập dùng thuận tiện cho các chi tiết càng có mặt đầu
lỗ lồi lên. Kết cấu phôi như vậy thì diện tích gia công sau này sẽ giảm.
Phôi đúc dùng cho càng bằng gang, kim loại mầu và cả bằng thép.
Tùy theo điều kiện sản xuất và sản lượng mà có thể đúc trong khuôn cát,
khuôn kim loại, khuôn mẫu chảy.
Càng loại lớn nếu sản lượng ít, chủ yếu là dùng phôi hàn, sản lượng
nhiều hơn thì kết hợp dùng hàn và dập tấm.
2.2.3. Tính công nghệ trong kết cấu của càng
Cũng như các dạng chi tiết khác, đối với chi tiết dạng càng tính
công nghệ có ý nghĩa quan trọng vì nó ảnh hưởng trực tiếp đến năng suất
và độ chính xác gia công.Vì vậy, khi thiết kế càng nên chú ý tới kết cấu
của nó như:
- Độ cứng vững của càng.
- Chiều dài của các lỗ cơ bản nên bằng nhau và các mặt đầu của
chúng cùng nằm trên hai mặt phẳng song song với nhau là tốt nhất.
- Kết cấu của càng nên đối xứng qua một mặt phẳng nào đó. Đối
với những càng có các lỗ vuông góc với nhau thì kết cấu phải thuận lợi
cho việc gia công các lỗ đó.
- Kết cấu của càng phải thuận lợi cho việc gia công nhiều chi tiết
cùng một lúc.
- Hình dáng của càng phải thuận lợi cho việc chọn chuẩn thô và
chuẩn tinh thống nhất.
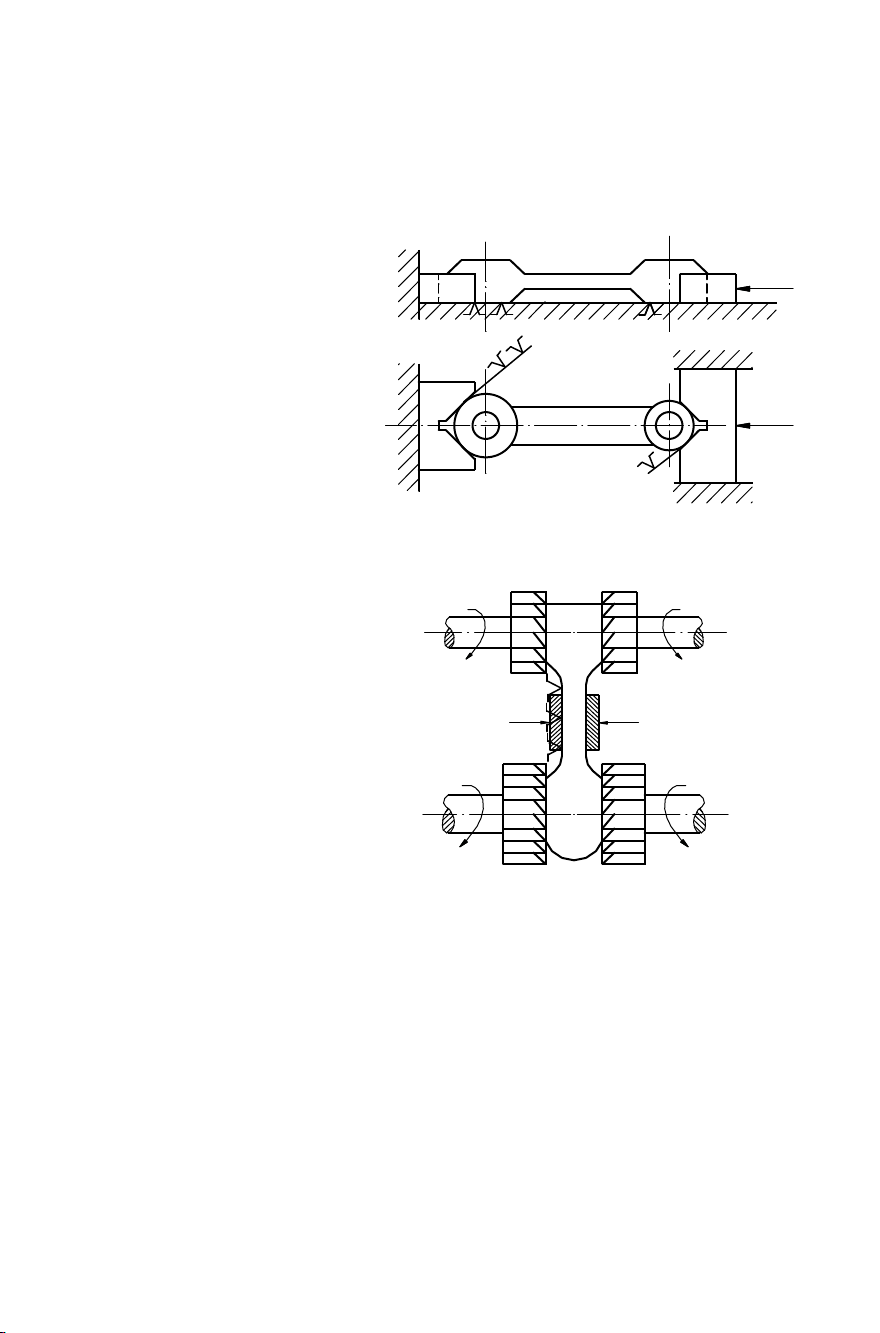
63
2.2.4. Quy trình công nghệ chế tạo các chi tiết dạng càng
2.2.4.1. Chuẩn định vị khi gia công
Khi định vị chi tiết càng để gia công, phải bảo đảm được vị trí tương
đối của các bề mặt với nhau, của các lỗ với nhau và độ vuông góc của các
lỗ với mặt đầu của nó.
Vì vậy chuẩn thô ban
đầu được chọn là vành tròn
ngoài của lỗ và một mặt
đầu của phôi, chọn chuẩn
như vậy để gia công mặt
đầu bên kia và gia công lỗ
cơ bản. Sơ đồ định vị chi
tiết càng để thực hiện việc
gia công này thể hiện trên
hình 2.25.
Theo phương pháp
này, chi tiết gia công được
định vị bằng mặt đầu phía
dưới, vành ngoài của lỗ cơ
bản bên trái được định vị
trên khối V cố định, vành
ngoài của lỗ cơ bản bên
phải được định vị bằng khối
V di động, lực kẹp W được
tác động qua khối V di
động này. Với cách định vị
này có thể dùng để gia công
mặt đầu bên kia và cũng
dùng để gia công lỗ cơ bản
của càng. Để bảo đảm độ
chính xác, việc gia công mặt đầu cần được thực hiện trước khi gia công
lỗ cơ bản.
Tuy nhiên, nếu chỉ với mục đích gia công mặt đầu của càng ở
nguyên công đầu tiên, có thể chọn phương án định vị vào phần thân càng
không gia công. Sơ đồ định vị như vậy thể hiện trên hình 2.26. Theo
phương pháp này, chi tiết càng thường định vị trên các đồ gá tự định tâm,
như vậy mặt đầu của càng sẽ đảm bảo đối xứng qua mặt phẳng đối xứng
của càng và có thể gia công bằng nhiều dao nên năng suất tăng.
Hình 2.25: Sơ đồ gá đặt khi gia công
mặt đầu và lỗ cơ bản của càng
W
W
W
W
Hình 2.26: Sơ đồ định vị để
gia công mặt đầu càng
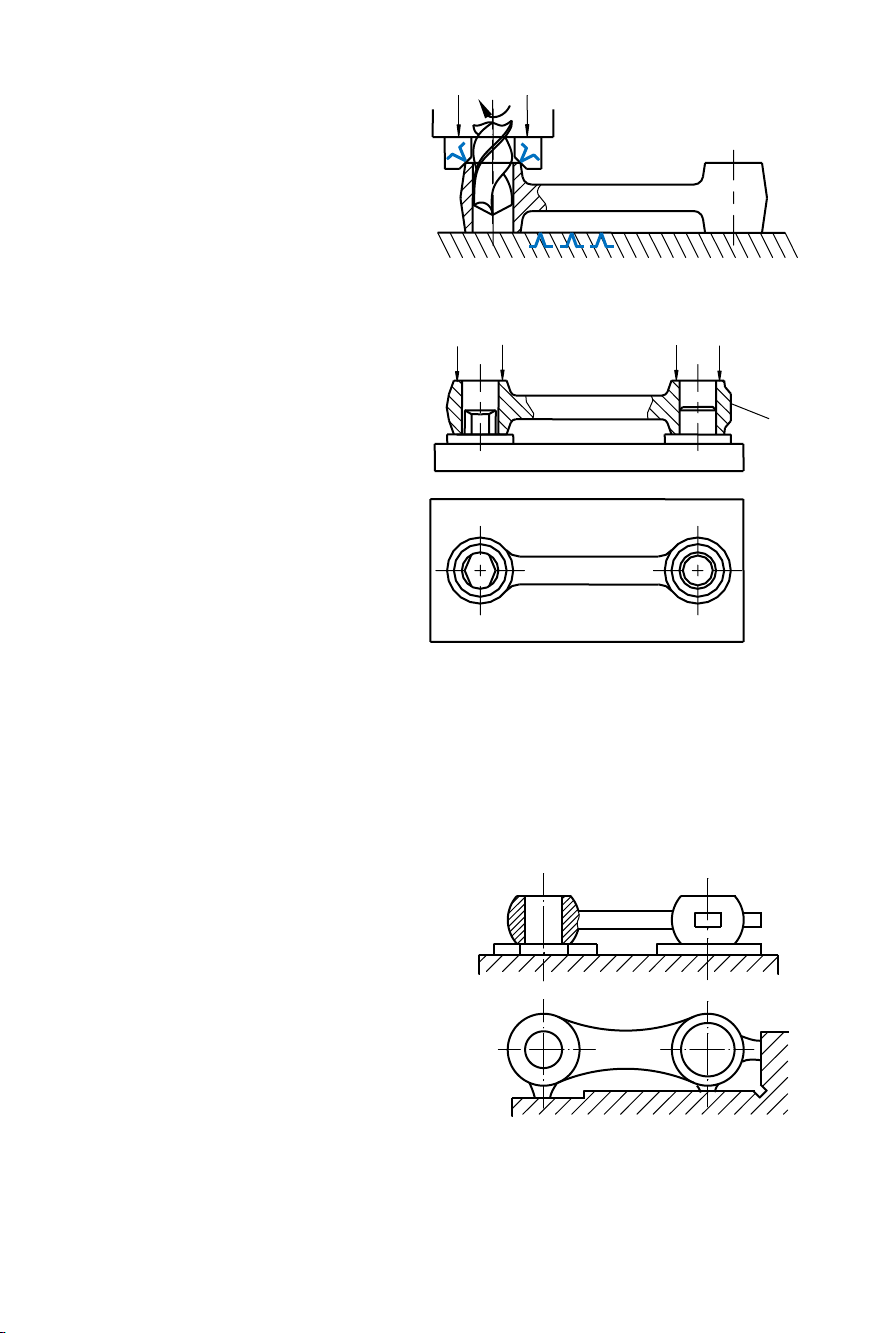
64
Để gia công lỗ cơ bản của
càng có thể dùng phương án
định vị như trên hình 2.25 đã
trình bày. Tuy nhiên, khi gia
công lỗ trái trước có thể dùng
chụp côn định vị vào mép trên
của vành ngoài như hình 2.27.
Sau khi có lỗ và mặt đầu
đã gia công, chọn chuẩn tinh
thống nhất là mặt đầu và hai lỗ
cơ bản để gia công các mặt còn
lại của càng. Trên hình 2.28 thể
hiện sơ đồ định vị khi dùng
chuẩn tinh thống nhất là mặt đầu
càng tì vào phiến tì khống chế
ba bậc tự do, một lỗ càng dùng
chốt trụ ngắn khống chế hai bậc
tự do và một lỗ càng dùng chốt
trám khống chế một bậc tự do.
Vị trí của các chốt định vị
tùy thuộc vào vị trí của bề mặt
cần gia công trên càng.
Khi dùng phương án định
vị như trên để gia công cần lưu ý một số vấn đề như:
- Nếu như các mặt đầu của càng không cùng một độ cao thì lấy mặt
đầu lớn làm định vị chính và phải dùng chốt tì phụ tì vào mặt đầu thấp để
tăng cứng vững khi gia công.
- Khi định vị bằng vành ngoài
của lỗ càng trên khối V thì sẽ có sai
số định vị bằng sự dịch chuyển tâm
của lỗ so với tâm vành ngoài khi
đường kính phôi vành ngoài thay đổi.
Để loại trừ sai số này có thể dùng các
cơ cấu V tự định tâm.
- Càng là loại chi tiết kém cứng
vững, để tránh biến dạng chi tiết khi
kẹp chặt thì điểm đặt của lực kẹp phải
đặt vào các điểm tì hay gần các điểm tì.
Ngoài phương án định vị như
trên để gia công càng, trong một số
Hình 2.29: Sơ đồ gá đặt khi
dùng chuẩn tinh thống nhất là
mặt đầu và ba vấu.
Hình 2.27: Sơ đồ gá đặt để gia
công lỗ cơ bản của càng
W
W
Hình 2.28: Sơ đồ định vị khi sử dụng
chuẩn tinh thống nhất
w
w
w
w
A
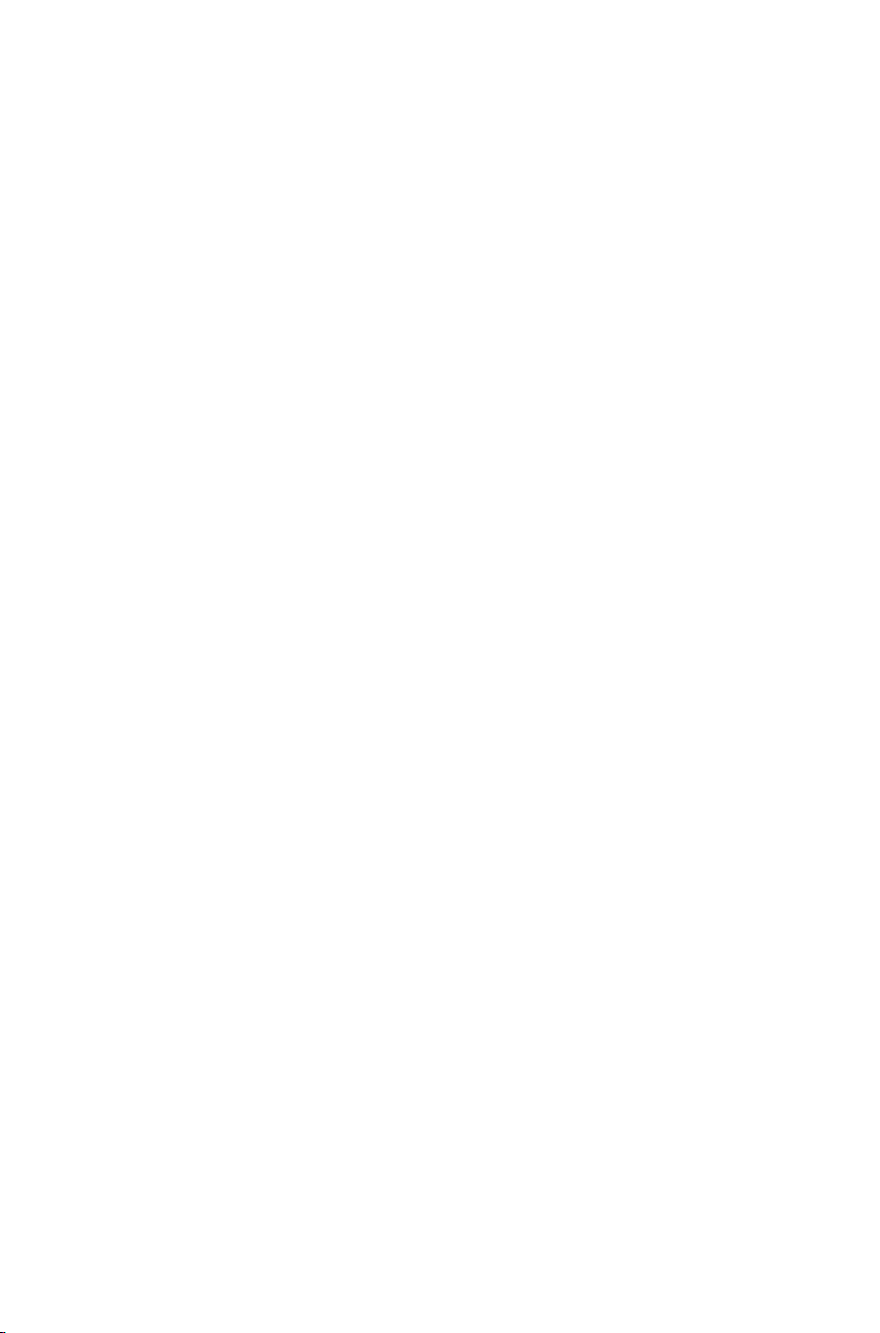
65
trường hợp có thể dùng chuẩn tinh thống nhất là mặt đầu và các vấu tì
phụ (đóng vai trò như chuẩn tinh phụ). Sơ đồ định vị như vậy thể hiện
trên hình 2.29.
Khi thực hiện theo phương án này, sau khi gia công xong mặt đầu
càng phải thực hiện gia công ba vấu trên vành ngoài ở hai đầu càng làm
chuẩn tinh phụ. Sau khi đã có mặt đầu và chuẩn tinh phụ, dựa vào đó để
làm chuẩn thống nhất gia công tất cả các mặt còn lại của càng.
2.2.4.2. Thứ tự các nguyên công gia công càng
Từ sự phân tích chuẩn trên đây, các nguyên công chủ yếu để gia
công càng bao gồm:
- Gia công mặt đầu.
- Gia công các vấu chuẩn phụ (nếu có).
- Gia công thô và tinh các lỗ cơ bản.
- Gia công các lỗ khác, các lỗ có ren.
- Cân bằng trọng lượng nếu cần.
- Kiểm tra.
2.2.5. Biện pháp thực hiện các nguyên công
2.2.5.1. Gia công mặt đầu
Như trên đã biết, mặt đầu của càng thường lồi lên có diện tích nhỏ rải
rác. Các mặt đầu này thường dùng làm chuẩn cho các nguyên công khác.
Tùy theo độ chính xác của phôi mà có thể gia công mặt đầu càng
bằng mài, chuốt, phay hoặc tiện. Phương pháp bào cũng gia công được
nhưng ít dùng vì mặt đầu nhỏ, rải rác nên năng suất thấp.
- Trong sản xuất hàng loạt lớn và hàng khối, nếu phôi có độ chính xác
cao thường gia công mặt đầu càng bằng mài hoặc chuốt. Bằng phương pháp
này vừa đạt được năng suất cao, vừa đạt được độ chính xác cao.
- Trong sản suất hàng loạt vừa và nhỏ, gia công mặt đầu càng bằng
phay hoặc tiện.
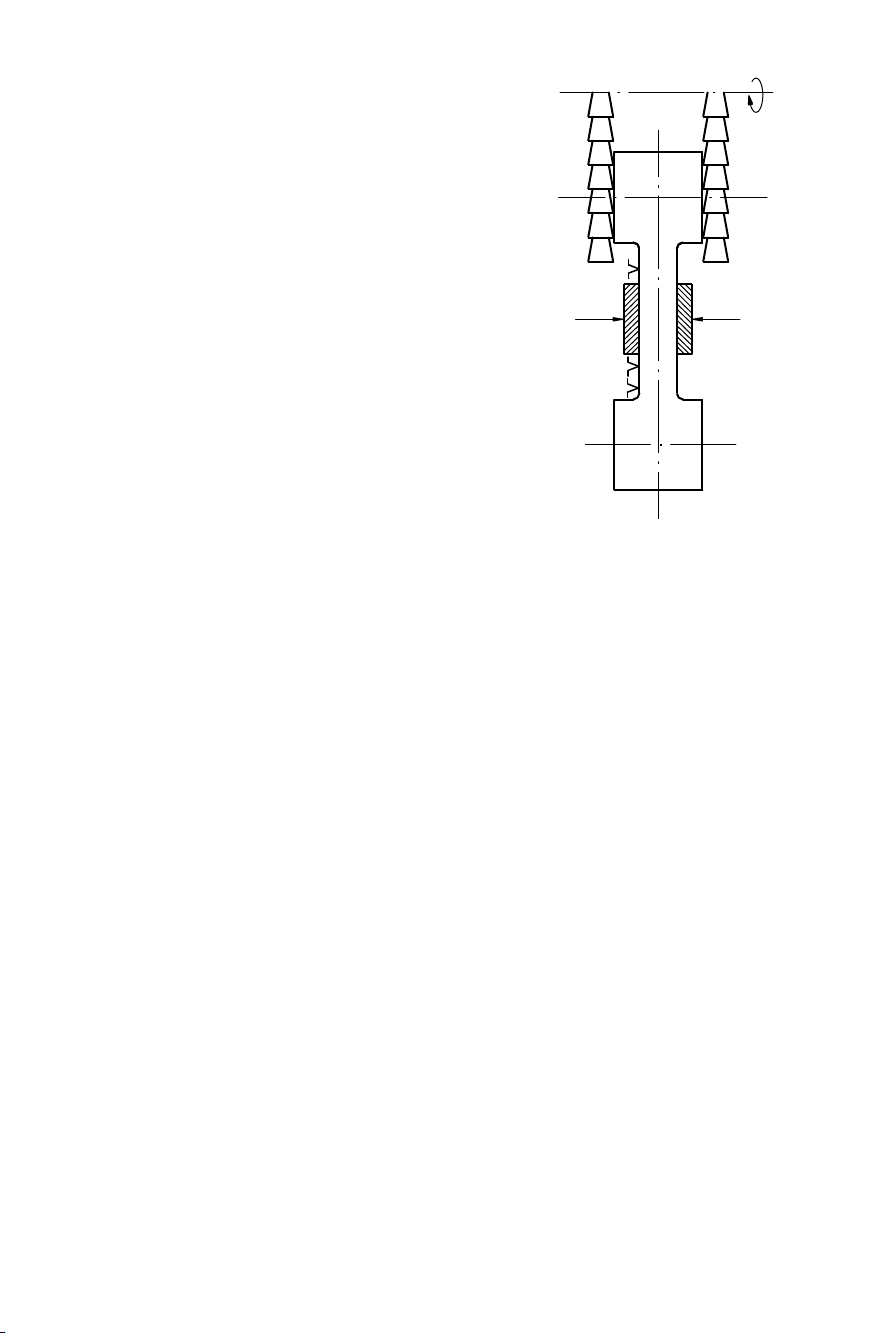
66
Tuy nhiên, nếu độ chính xác của phôi
quá thấp, thì ngay cả trong sản xuất hàng
loạt lớn và hàng khối vẫn áp dụng phương
pháp phay để gia công. Ngoài ra, việc chọn
phương pháp để gia công còn phụ thuộc
vào lượng dư gia công lớn hay nhỏ, hay nói
cách khác là phụ thuộc vào phương pháp
chế tạo phôi. Nếu như phôi rèn tự do trong
khuôn đơn giản sau đó lại được ép trên máy
ép, lượng dư gia công nhỏ thì có thể không
dùng phay được mà phải mài. Ngược lại
khi lượng dư gia công lớn thì dùng mài sẽ
không hợp lý mà phải phay.
Các mặt đầu của càng được gia công
từng phía lần lượt trên máy phay nằm
ngang hay thẳng đứng bằng một dao như
sơ đồ hình 2.25 hoặc cũng phay hai mặt
của mỗi đầu trên máy phay ngang bằng
một bộ hai dao phay đĩa ba mặt cắt. Lúc đó
gá đặt phôi trên các đồ định vị thích hợp và điều chỉnh các mặt tương đối
với dao nhờ các dụng cụ chuyên dùng. Trên hình 2.30 trình bày sơ đồ
định vị để gia công hai mặt đầu của biên trụ kim máy khâu bằng một bộ
hai dao phay đĩa ba mặt cắt trên máy phay nằm ngang. Theo sơ đồ này,
để đảm bảo hai mặt đầu đối xứng so với mặt phẳng giữa của biên, chi tiết
được định vị vào phần thân biên không gia công.
Với sơ đồ định vị đó, khi gia công các càng lớn như thế, để nâng
cao năng suất có thể dùng máy phay nhiều trục, gia công được cả bốn
mặt đầu cùng một lúc như trên hình 2.26.
Để tăng năng suất khi phay, có thể dùng đồ gá gia công nhiều chi
tiết cùng một lúc (trên bàn máy đặt hai đồ gá giống nhau) và tiến hành
gia công theo kiểu chạy dao đi lại (hình 2.31) hoặc các đồ gá đó được đặt
lên một bàn quay (hình 2.32).
Hình 2.30: Sơ đồ định vị để
gia công mặt đầu của tay
biên máy khâu.
w
w
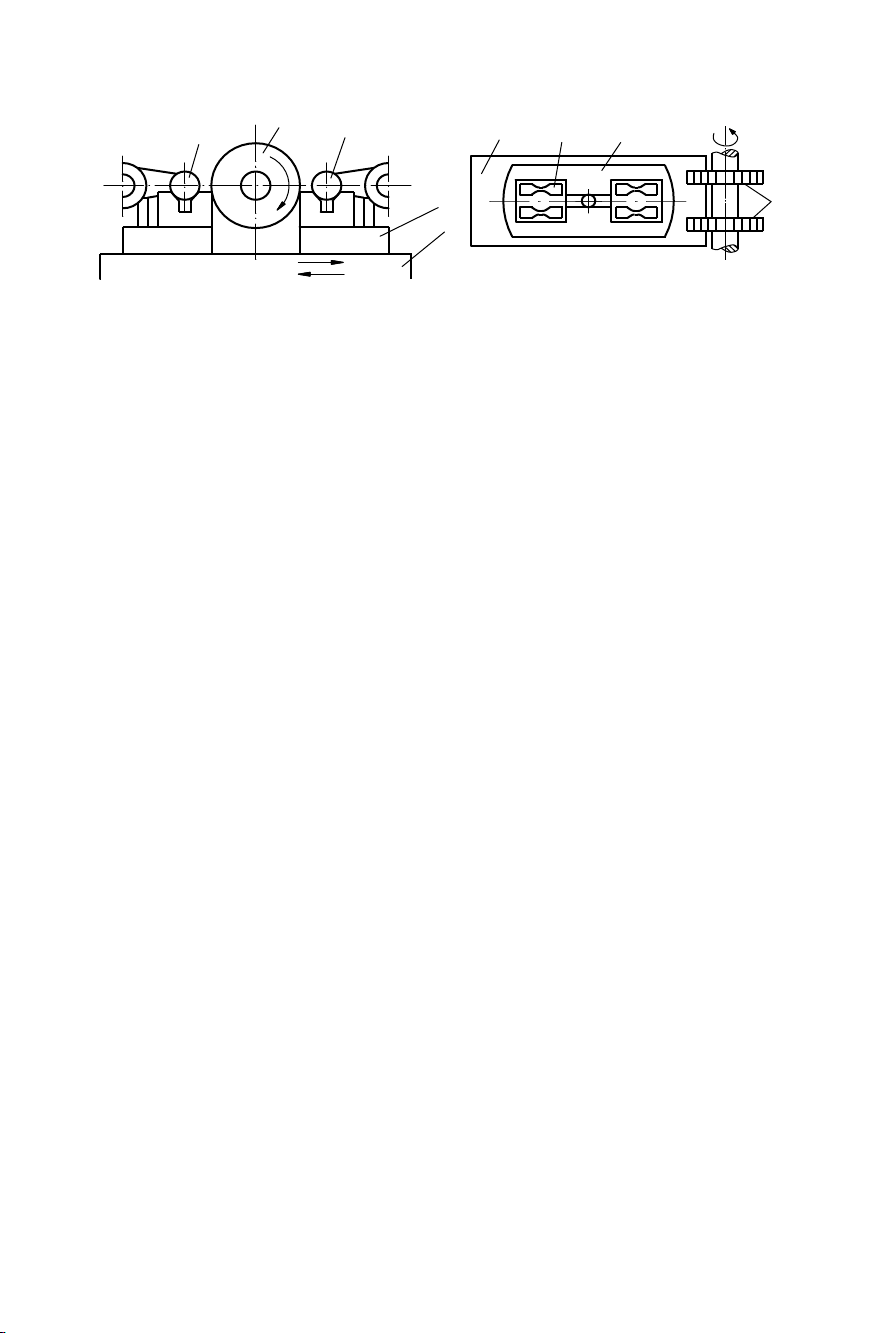
67
Lúc này việc gá đặt phôi lên đồ gá được tiến hành theo chu kỳ,
nghĩa là trong khi đang cắt gọt chi tiết trên đồ gá thứ nhất thì tiến hành gá
lắp phôi mới lên đồ gá thứ hai.
Mặt đầu của càng cũng có thể gia công bằng phương pháp chuốt.
Khi chuốt, mặt đầu được gia công riêng từng đầu. Gia công xong đầu lớn
rồi mới gia công đầu nhỏ. Máy được dùng là máy chuốt một vị trí hoặc
nhiều vị trí. Sau khi gia công xong, độ song song mặt đầu có thể đạt tới
0,1 mm.
Trong một số trường hợp yêu cầu độ chính xác cao, sau khi phay
hoặc chuốt, mặt đầu càng còn phải qua mài trên máy mài phẳng hay máy
mài phẳng có bàn quay. Mài các mặt đầu cùng một lúc nếu bề dày bằng
nhau, mài xong một phía lật lại mài phía kia. Trường hợp bề dày khác
nhau thì mài đầu lớn riêng, đầu nhỏ riêng. Cũng có thể thực hiện mài trên
máy mài chuyên dùng để gia công cả hai phía cùng một lúc.
2.2.5.2. Gia công thô và tinh các lỗ cơ bản trên càng
Các lỗ cơ bản của càng có yêu cầu chính xác bản thân cao vì nó lắp
ghép với chi tiết khác. Nó cũng có yêu cầu chính xác về vị trí tương quan
như độ vuông góc với mặt đầu, độ song song của đường tâm các lỗ. Tùy
theo sản lượng và điều kiện sản xuất mà có biện pháp gia công thích hợp.
- Trong sản xuất nhỏ, sản lượng ít với mọi cỡ của càng lỗ cơ bản
được gia công trên máy khoan đứng, khoan cần hoặc trên máy tiện, máy
doa ngang bằng phương pháp lấy dấu và rà gá.
- Trong sản xuất hàng loạt, sản lượng nhiều hơn, các lỗ cơ bản của
càng được gia công trên máy khoan đứng, khoan cần hoặc máy khoan có
đầu rơvônve bằng phương pháp tự động lấy kích thước nhờ bạc lắp trên
phiến dẫn.
2
1
2
3
4
Hình 2.31: Sơ đồ kiểu chạy dao
đi lại
1. Dao phay; 2.Chi tiết gia công
3. Đồ gá; 4. Bàn máy
4
2
3
1
Hình 2.32: Sơ đồ gá đặt trên
bàn quay
1.Dao; 2. Chi tiết gia công
3. Bàn quay; 4. Bàn máy
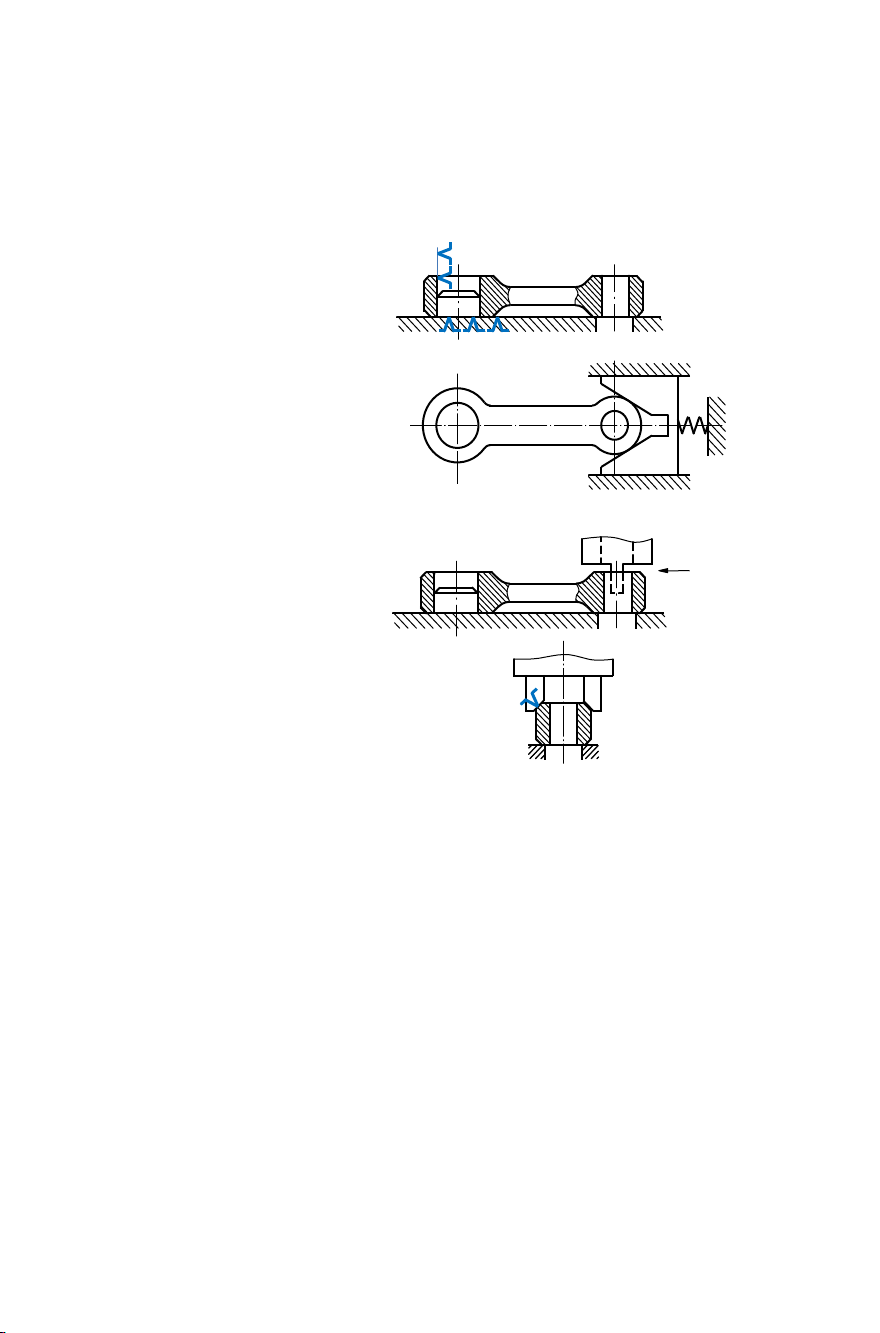
68
Biện pháp thực hiện có những phương án sau:
Phương án thứ nhất:
Gia công một lỗ, sau đó dùng lỗ này làm chuẩn định vị cùng với
mặt đầu để gia công các lỗ tiếp theo. Theo phương án này chi tiết được
định vị bằng mặt đầu và
vành ngoài của mặt đầu
(hình 2.25) hoặc bằng mặt
đầu và mép trên của vành
ngoài (hình 2.27).
Vì chỉ gia công một lỗ
nên chỉ cần khống chế 5 bậc
tự do, bậc tự do xoay quanh
tâm lỗ cần gia công không
ảnh hưởng đến độ chính xác
cần đạt. Lỗ được gia công
qua ba bước: khoan, khoét,
doa. Cũng có thể thay khoét
và doa bằng phương pháp
chuốt hoặc thay doa bằng
nong lỗ.
Sau khi đã gia công
được một lỗ, tiến hành gia
công các lỗ tiếp theo. Lúc
này chi tiết được định vị
bằng mặt đầu, mặt lỗ vừa
gia công xong và một mặt
nào đó trên thân càng hạn
chế nốt bậc tự do xoay. Để
hạn chế bậc tự do xoay này
có thể dùng khối V tùy động
tì vào vành ngoài của một đầu càng.
Sơ đồ gá đặt này thể hiện trên hình 2.33.
Theo phương án này khoảng cách tâm của các lỗ được đảm bảo
nhờ độ chính xác khoảng cách của tâm chốt định vị và tấm bạc dẫn cho
lỗ tiếp theo. Gia công các lỗ tiếp theo cũng phải tuân thủ theo ba bước
như đối với lỗ đầu tiên.
Phương án thứ hai:
Gia công lần lượt tất cả các lỗ sau một lần định vị. Theo phương án
này, chi tiết gia công phải được định vị đủ 6 bậc tự do: mặt đầu khống
b)
a)
Hình 2.33: Sơ đồ định vị để gia
công lỗ tiếp theo của càng
a) Dùng khối V di động chống xoay
b) Dùng vấu côn chống xoay.
A
A
Nhìn theo
A
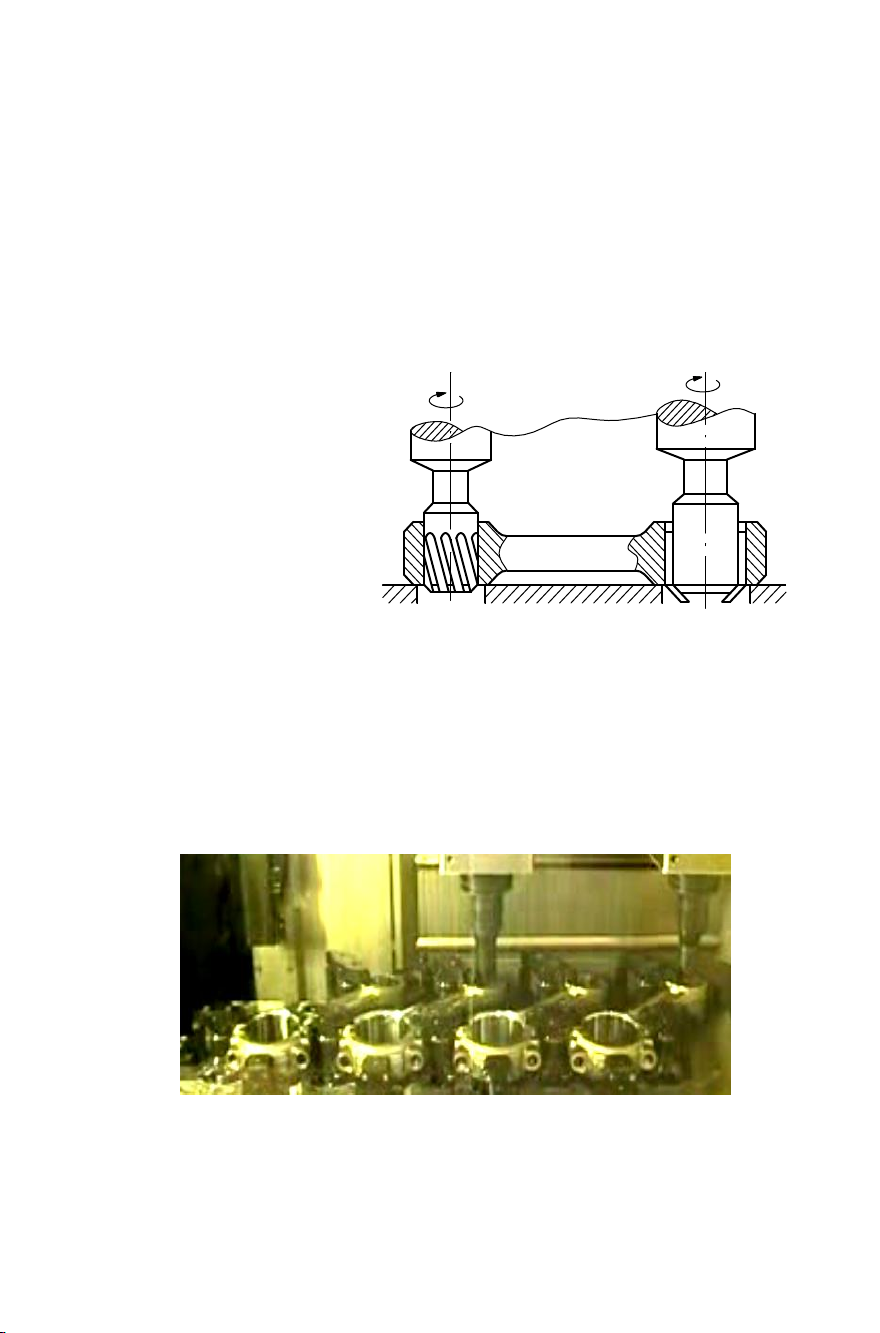
69
chế 3 bậc tự do; khối V tì vào vành ngoài khống chế 2 bậc tự do; khối V
tùy động tì vành ngoài khống chế 1 bậc tự do (hình 2.25). Vị trí và
khoảng cách giữa các lỗ do vị trí các bạc dẫn lắp trên phiến dẫn quyết
định. Gia công lần lượt các lỗ theo các bước khoan, khoét, doa trên máy
khoan cần bằng cách di chuyển đầu khoan, đồ gá cố định hoặc trên máy
khoan đứng bằng cách di chuyển đồ gá.
- Trong sản xuất hàng khối, gia công các lỗ cơ bản được tiến hành
trên máy khoan nhiều trục hoặc máy tổ hợp nhiều trục chính. Dùng máy
tổ hợp có thể đạt hiệu quả kinh tế cao vì nó có khả năng gia công song
song hoặc song song liên tục
tất cả các lỗ trong một lần
gá. Trên đó, nếu dùng dụng
cụ tổ hợp có thể xén được cả
mặt đầu của lỗ. Theo
phương án này, độ chính xác
về vị trí các lỗ bảo đảm tốt,
độ song song giữa các lỗ và
khoảng cách giữa các lỗ
cũng đạt được tốt hơn các
phương pháp trên. Hình 2.34
trình bày sơ đồ gia công hai
lỗ biên cùng một lúc.
Nếu lỗ có đường kính lớn hơn 30 mm, khi tạo phôi đã có lỗ sẵn, thì
trình tự sẽ là tiện rộng (hay khoét), gia công tinh với một số lỗ cần lắp
bạc đồng thì sau khi gia công tinh lỗ rồi mới đóng bạc vào, sau đó lại
phải gia công tinh lại bạc đồng.
2.2.5.3. Gia công các lỗ có ren, lỗ để kẹp chặt
Hình 2.34a) Sơ đồ gia công hai lỗ biên
cùng một lúc.
Hình 2.34b) Gia công hai lỗ trên máy CNC
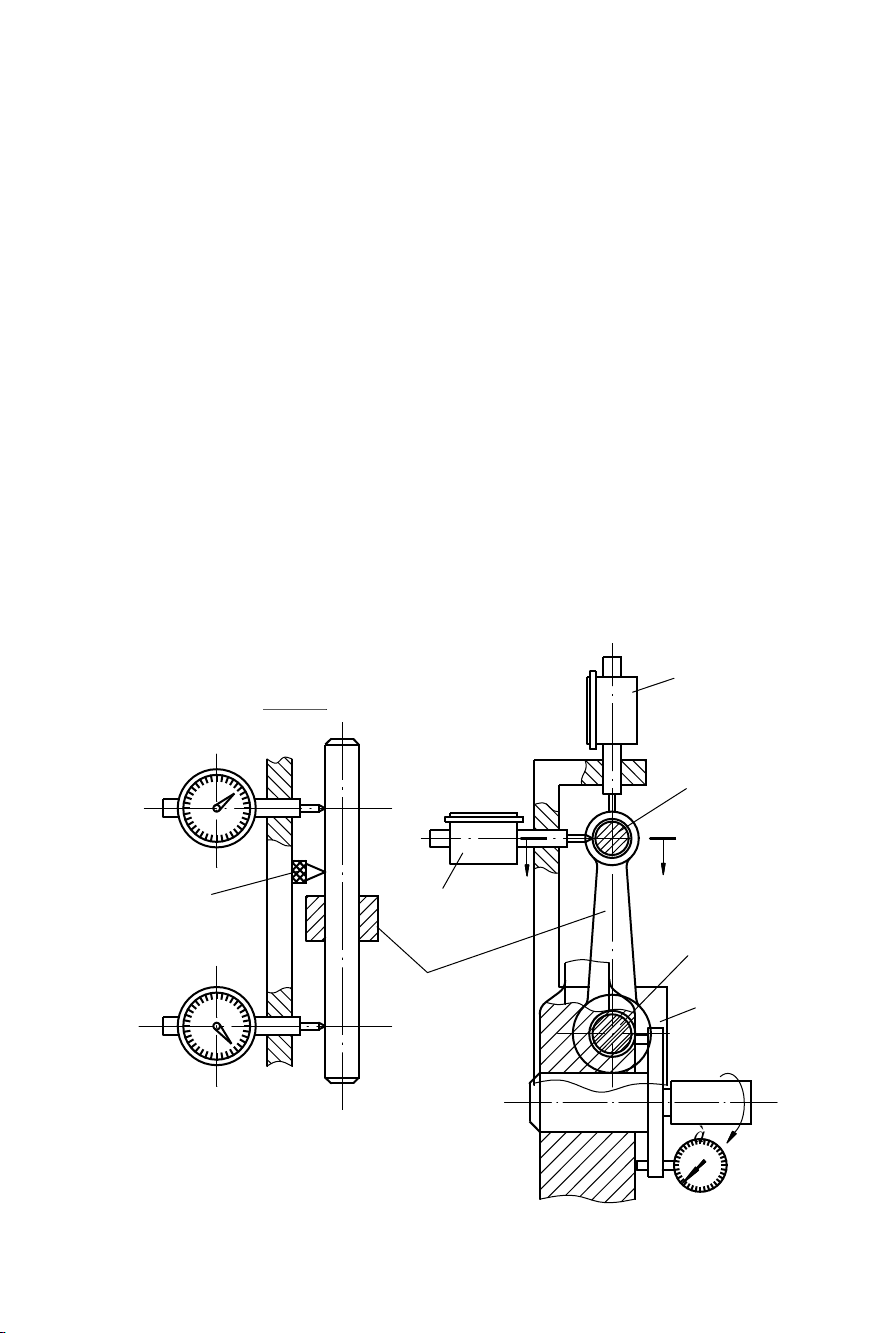
70
Thông thường các lỗ này có yêu cầu độ chính xác không cao,
thường là cấp 10. Trường hợp dùng để định vị đúng vị trí giữa càng với
một bộ phận khác, các lỗ này phải gia công đạt cấp chính xác 7. Ví dụ
như lỗ định vị giữa thân biên và nắp biên. Việc gia công các lỗ này
thường được tiến hành sau khi gia công các mặt đầu và một hoặc các lỗ
cơ bản (sơ đồ định vị có thể như hình 2.28). Đối với các lỗ có yêu cầu độ
chính xác không cao thì dùng phương pháp khoan. Còn những lỗ có yêu
cầu chính xác phải khoan, khoét, doa. Tùy theo sản lượng mà trên cơ sở
của sơ đồ định vị thiết kế các đồ gá, các thiết bị có năng suất phù hợp.
2.2.5.4. Kiểm tra các chi tiết dạng càng
Đối với các chi tiết dạng càng, ngoài việc kiểm tra đường kính lỗ
và bề dầy của các đầu càng còn phải kiểm tra khoảng cách của tâm các lỗ
cơ bản, độ vuông góc giữa mặt đầu và đường tâm lỗ, độ không song song
giữa các tâm lỗ.
- Đường kính các lỗ cơ bản được kiểm tra bằng thước cặp, calíp
hoặc đồng hồ đo lỗ.
- Độ không song song giữa các đường tâm lỗ được kiểm tra bằng
đồng hồ so với đồ gá như hình 2.35.
Lắp càng kiểm tra 6 lên
chốt định vị 2 qua lỗ thứ nhất.
Hình 2.35: Sơ đồ kiểm tra độ không song song hai lỗ càng
A
A
1
2
3
4
5
6
7
II
I
A - A
Hình 2.36: Sơ đồ kiểm tra độ vuông
góc của lỗ và mặt đầu càng
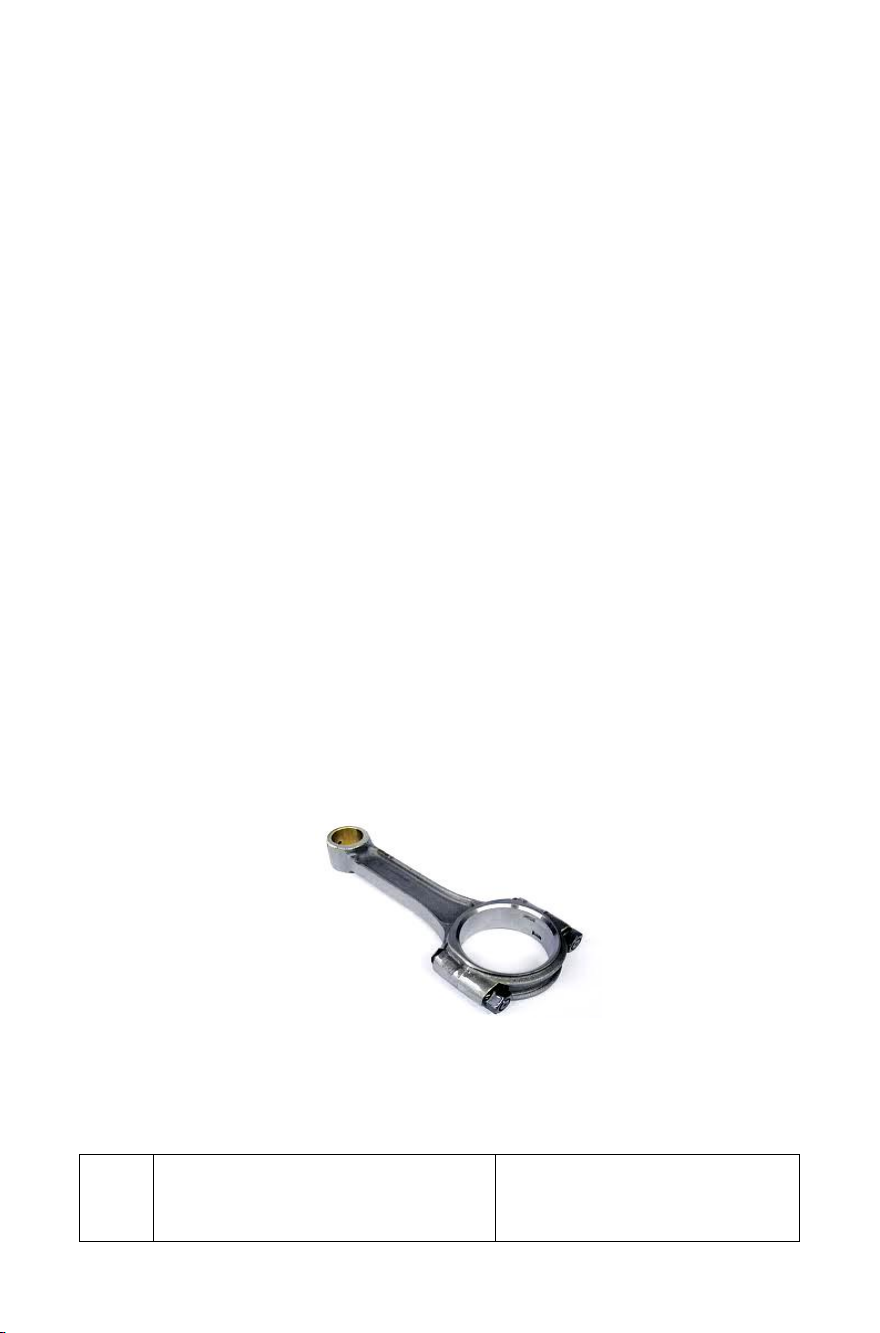
71
Chốt 2 được cố định trên thân 1 (cũng có thể đặt lên hai khối V). Lồng
trục kiểm 3 vào lỗ thứ hai của càng. Quay càng quanh chốt định vị 2 cho
đến khi trục kiểm 3 chạm vào cữ tỳ 7. Hiệu số của hai đồng hồ 4 và 5 ở
hai vị trí I, II biểu hiện độ không song song của hai lỗ càng theo hai
phương đứng và ngang. Đo khoảng cách giữa chốt định vị và trục kiểm
tra biết khoảng cách hai lỗ.
Vị trí đường tâm các lỗ dưới một góc được kiểm tra bằng đồ gá
chuyên dùng. Độ vuông góc giữa lỗ và mặt đầu của càng được kiểm tra
bằng đồ gá chuyên dùng và đồng hồ so.
Sơ đồ kiểm tra được trình bày trên hình 2.36.
Lắp trục tâm vào lỗ của càng, quay trục tâm một vòng. Số chỉ độ
chênh của đồng hồ so cho biết độ không vuông góc với bán kính từ mũi tì
của đồng hồ so với tâm quay.
Tùy theo sản lượng và độ chính xác yêu cầu mà thiết kế đồ gá
chuyên dùng hay sử dụng một số thiết bị kiểm tra vạn năng có độ chính
xác phù hợp.
2.2.6. Quy trình công nghệ gia công biên
Biên của động cơ đốt trong (hình 2.24) là một trong những chi tiết
điển hình của càng, nó có yêu cầu kỹ thuật cao, lại có hình dáng kém
cứng vững, đồng thời trong quá trình chế tạo phải lắp với nắp biên.
Sau đây, giới thiệu quy trình công nghệ gia công biên động cơ ô tô
vận tải hình 2.24b. Quy trình được trình bày ở bảng 2.2.
Bảng 2.2: Quy trình công nghệ chế tạo biên động cơ ôtô
Thứ tự
nguyên
công
Tên nguyên công
Máy
Hình 2.24b

72
1
Mài sơ bộ hai mặt đầu
Máy mài phẳng có bàn quay tự động,
kẹp bằng điện từ
2
Khoan, khoét lỗ đầu nhỏ
Máy khoan đứng nhiều trục
3
Chuốt lỗ đầu nhỏ
Máy chuốt đứng
4
Chuốt mặt bán nguyệt và mặt lắp ghép với
nắp biên
Máy chuốt đứng
5
Chuốt mặt nắp đầu bulông
Máy chuốt đứng
6
Gia công thô lỗ lắp bulông
Máy phay, khoan, tổ hợp hai phía
7
Khoan những lỗ nhỏ ở đầu to và vát mép
Máy tổ hợp 3 trục
8
Mài mặt nắp
Máy mài phẳng có bàn quay 2 trục
9
Lắp nắp biên và thân biên
Bàn nguội
10
Khoan, doa lỗ bulông
Máy khoan đứng nhiều trục
11
Mài mặt đầu cả hai bên
Máy mài phẳng bàn nam châm quay
12
Khoét và doa lỗ đầu to
Máy khoan đứng nhiều trục
13
Ép bạc vào lỗ nhỏ
Máy ép
14
Sửa bạc sau khi ép
Máy khoan đứng hoặc máy ép
15
Mài hoặc tiện kim cương lỗ đầu to
Máy mài lỗ hoặc máy doa kim cương
16
Mài khôn lỗ đầu to
Máy khôn đứng
17
Kiểm tra
Các dụng cụ và trang bị thích hợp
2.3. QUY TRÌNH CÔNG NGHỆ GIA CÔNG CÁC CHI TIẾT
DẠNG TRỤC
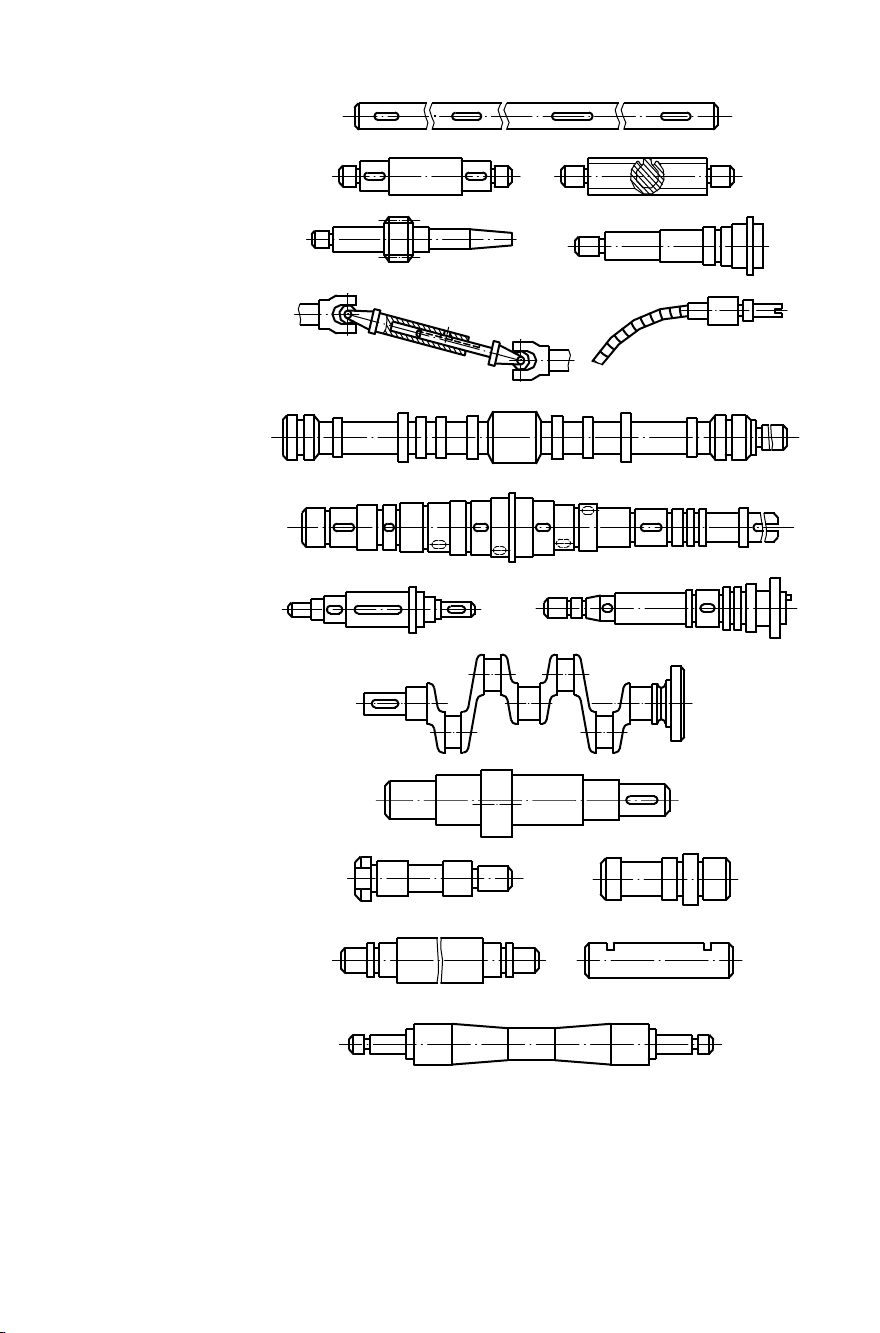
73
Các chi tiết
dạng trục là loại
chi tiết được
dùng rất phổ
biến trong ngành
chế tạo máy.
Chúng có bề mặt
cơ bản cần gia
công là mặt tròn
xoay ngoài. Mặt
này thường dùng
làm mặt lắp ghép
(hình 2.37). Tùy
theo kết cấu mà
có thể chia các
chi tiết dạng trục
ra các loại sau:
-Trục trơn:
trên suốt chiều
dài của trục chỉ
có một kích
thước đường
kính d. Khi L/d<
4: trục trơn ngắn;
L/d = 410: trục
trơn thường; L/d
>10: trục trơn
dài.
- Trục bậc:
trên suốt chiều
dài L của trục có
một số kích
thước đường
kính khác nhau.
Trên trục bậc có
thể còn có rãnh
then hoặc then
hoa, hoặc có ren.
- Trục rỗng: loại trục rỗng giữa có tác dụng giảm trọng lượng và
cũng có thể làm mặt lắp ghép.
Hình 2.37: Các chi tiết dạng trục
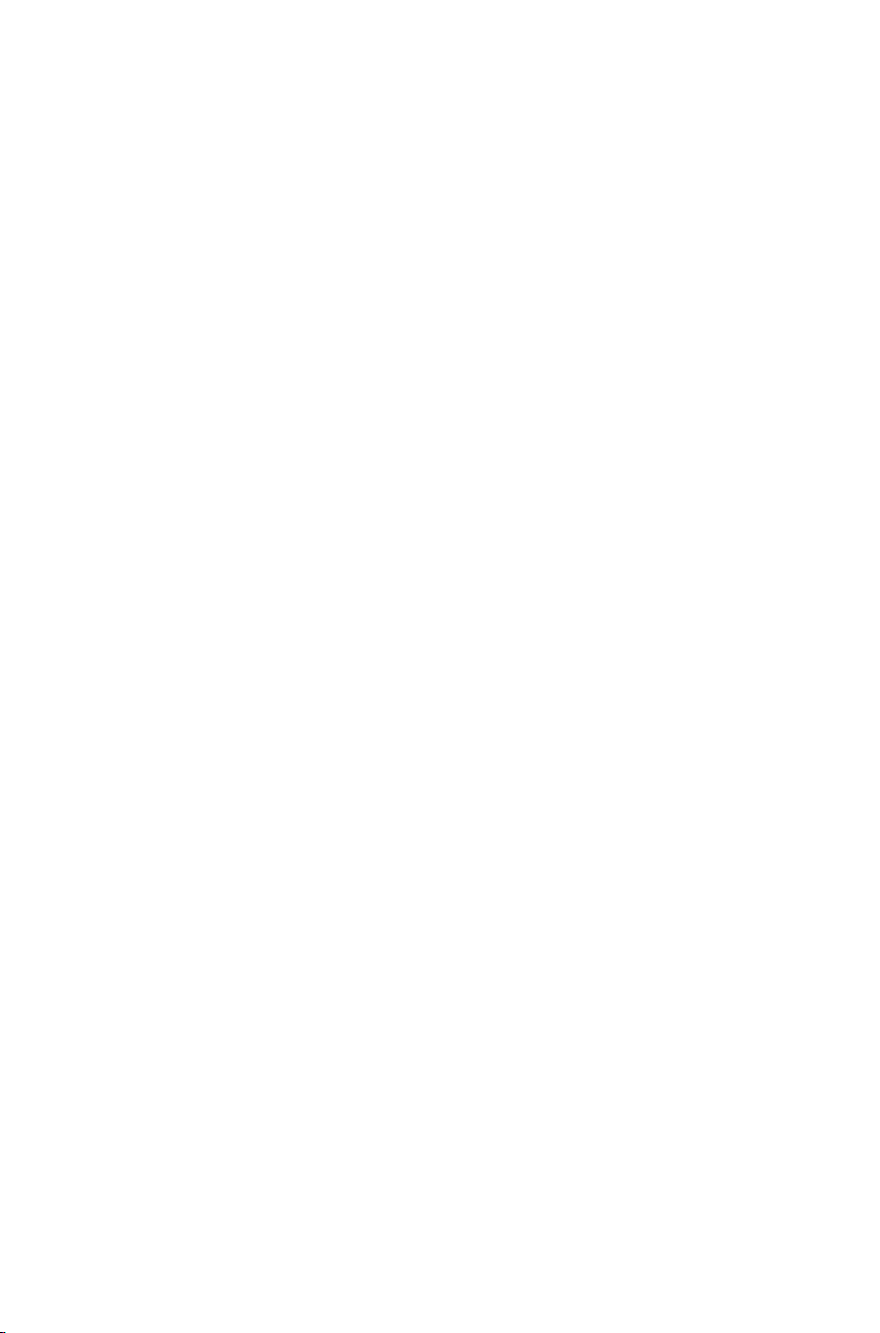
74
- Trục răng: loại trục mà trên đó có bánh răng liền trục.
- Trục lệch tâm là loại trục có những cổ trục không cùng nằm trên
một đường tâm như trục khuỷu.
2.3.1. Điều kiện kỹ thuật chi tiết dạng trục
Khi chế tạo các chi tiết dạng trục cần bảo đảm các điều kiện kỹ
thuật sau:
- Kích thước đường kính các cổ lắp ghép yêu cầu cấp chính xác
710, trong một số trường hợp cần đạt cấp 5.
- Độ chính xác về hình dáng hình học như độ côn, độ ô van của các
trục nằm trong giới hạn 0,250,5 dung sai đường kính cổ trục.
- Bảo đảm dung sai chiều dài mỗi bậc trục trong khoảng 0,050,2 mm.
- Độ đảo của các cổ trục lắp ghép không vượt quá 0,010,03 mm.
- Độ không song song của các rãnh then hay then hoa đối với tâm
trục không vượt quá 0,01 mm trên 100mm chiều dài.
- Độ nhám của các cổ trục lắp ghép đạt R
a
= 1,251,16, của các
mặt đầu R
z
= 4020 và bề mặt không lắp ghép R
z
= 8040.
Về tính chất cơ lý của bề mặt trục như độ cứng bề mặt, độ thấm tôi
tùy từng trường hợp cụ thể mà đặt điều kiện kỹ thuật.
Ngoài ra đối với một số trục làm việc với tốc độ cao còn có yêu cầu
cân bằng tĩnh và cân bằng động.
2.3.2. Vật liệu và phôi chế tạo trục
Vật liệu để chế tạo các chi tiết dạng trục bao gồm thép cacbon như
thép 35, 40, 45; thép hợp kim như thép crôm, crôm-niken; 40X; 40; 50
v.v… Các chi tiết trục máy cán, trục khuỷu có thể chế tạo bằng gang có
độ bền cao.
Việc chọn phôi để chế tạo trục phụ thuộc vào hình dáng, kết cấu và
sản lượng của loại trục đó. Ví dụ với trục trơn thì tốt nhất là dùng phôi
thanh. Với trục bậc có đường kính chênh nhau không lớn lắm thường
dùng phôi cán nóng.
Trên máy tiện tự động nên dùng phôi cán nguội hoặc đã mài vô tâm.
Trong sản xuất nhỏ và đơn chiếc, phôi của trục được chế tạo bằng
cách rèn tự do hoặc rèn tự do trong khuôn đơn giản, đôi khi có thể dùng
phôi cán nóng. Phôi của trục lớn được chế tạo bằng cách rèn tự do hoặc
hàn ghép từng phần lại.
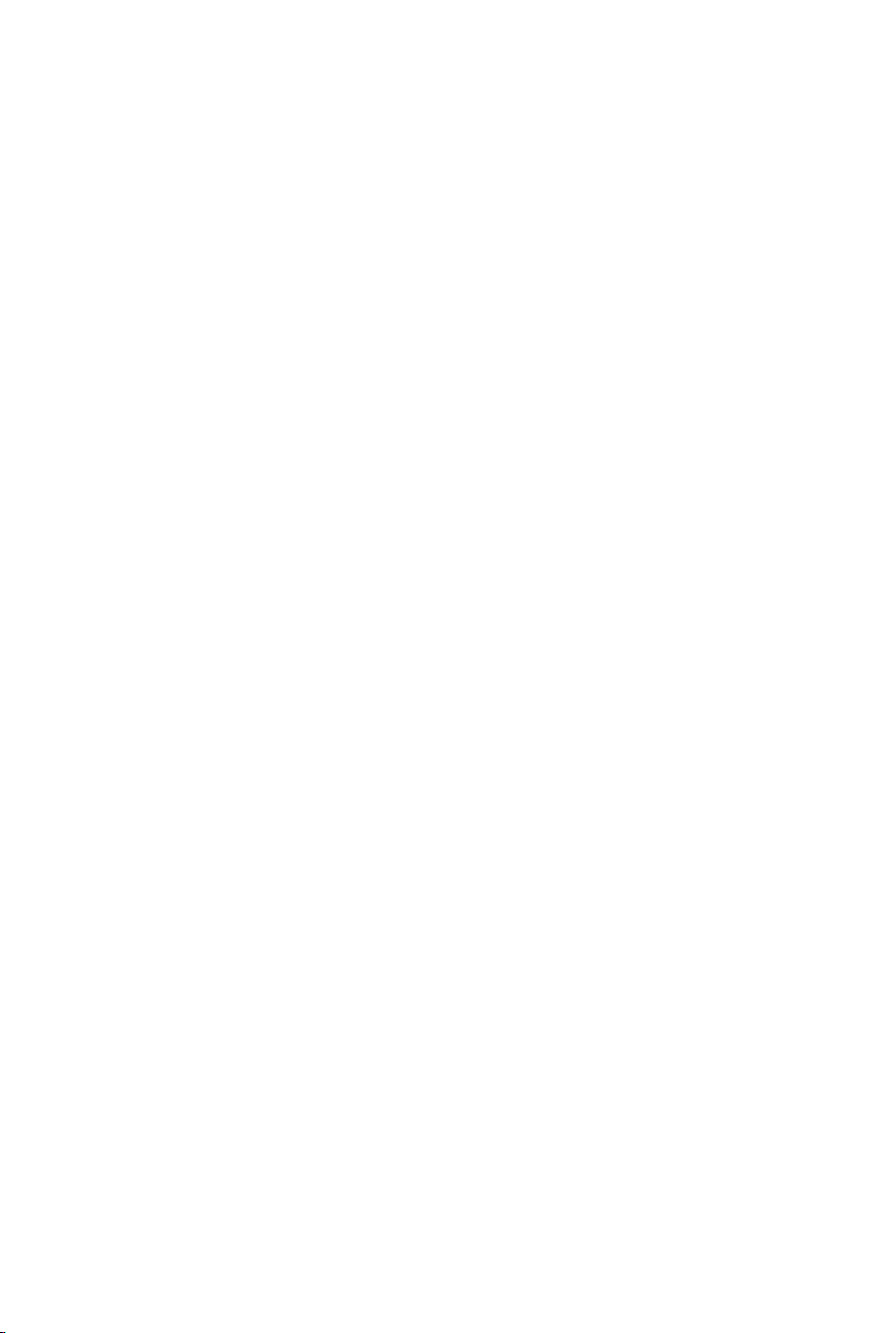
75
Trong sản xuất hàng loạt lớn và hàng khối, phôi của trục được chế
tạo bằng dập nóng trên máy dập hoặc ép trên máy ép, với trục bậc có thể
rèn trên máy rèn ngang và cũng có thể được chế tạo bằng phương pháp
đúc.
Phôi trục bằng gang có độ bền cao được chế tạo bằng phương pháp
đúc. Phôi đúc cho phép giảm lượng dư và khối lượng gia công trong quá
trình chế tạo.
Thông thường trước khi gia công, việc gia công chuẩn bị phôi được
tiến hành ở phân xưởng chuẩn bị phôi. Nếu là phôi thanh thì quá trình
chuẩn bị phôi bao gồm các bước nắn thẳng, cắt đứt phôi thành từng đoạn,
gia công lỗ tâm. Còn nếu là phôi rèn, phôi dập, phôi đúc thì các ba via,
đậu ngót, đậu rót được làm sạch trước khi đem gia công cơ. Đôi khi việc
gia công các chuẩn tinh phụ cũng được thực hiện tại phân xưởng chuẩn
bị phôi.
2.3.3. Tính công nghệ trong kết cấu của trục
Khi thiết kế chi tiết dạng trục cần phải chú ý đến các vấn đề sau:
- Các bề mặt trên trục có khả năng gia công được bằng các dao
thông thường.
- Đường kính các cổ trục nên giảm dần về hai đầu.
- Giảm đường kính trục đến mức có thể mà vẫn bảo đảm mọi chức
năng làm việc của nó.
- Nghiên cứu khả năng thay rãnh then kín bằng rãnh then hở để
nâng cao năng suất gia công.
- Nghiên cứu khả năng gia công trục trên các máy thủy lực.
- Xem xét đến độ cứng vững của trục khi gia công. Trong những
trường hợp gia công đồng thời bằng nhiều dao thì tỉ số L/D phải nhỏ hơn
10.
Một vấn đề nữa cũng cần chú ý là quy trình công nghệ chế tạo trục
trơn khác hẳn trục bậc về tính đơn giản và tính kinh tế, vì vậy cần nghiên
cứu khả năng thay trục bậc bằng trục trơn.
Trong nhiều trường hợp nên dùng trục rỗng để giảm khối lượng vật
liệu nhưng vẫn bảo đảm độ bền.
2.3.4. Quy trình công nghệ chế tạo các chi tiết dạng trục
2.3.4.1. Chuẩn định vị

76
Đối với các chi tiết dạng trục yêu cầu về độ đồng tâm giữa các cổ
trục là rất quan trọng. Để đảm bảo yêu cầu này, khi gia công trục cần
phải dùng chuẩn tinh thống nhất.
Chuẩn thống nhất khi gia công các chi tiết dạng trục thường là:
- Hai lỗ tâm côn hoặc hai mép lỗ trụ ở hai đầu của trục
- Một lỗ tâm kết hợp với một mặt trụ, hoặc hai mặt trụ.
Có thể dùng mũi tâm thường như hình 2.38a. Đối với trục rỗng,
dùng mũi tâm có khía nhám như hình 2.38b. Dùng lỗ tâm làm chuẩn có
thể gia công tất cả các mặt ngoài, phay rãnh then, then hoa, ren trên trục.
Khi dùng hai lỗ tâm làm chuẩn và định vị trên hai mũi tâm để gia công
mặt ngoài, sẽ không có sai số chuẩn cho kích thước đường kính các cổ
trục vì lúc đó chuẩn định vị trùng với chuẩn đo lường (chuẩn đó chính là
tâm quay). Nhưng sẽ có sai số chuẩn theo hướng trục nếu như mũi tâm
bên trái là mũi tâm cứng khi gia công các bậc trục theo phương pháp điều
chỉnh sẵn dao đạt kích thước.
Nguyên nhân là
do trong quá trình chế
tạo hai lỗ tâm ở nguyên
công trước có sai số về
chiều sâu của lỗ tâm,
trong khi đó mũi dao
được điều chỉnh cách
mũi tâm bên trái một
kích thước không đổi.
Điều đó dẫn đến kích
thước từ mũi dao đến mặt đầu bên trái của trục (kích thước chiều dài một
bậc trục, kích thước b sẽ thay đổi nếu lỗ tâm côn của trục sâu, nông khác
nhau (hình 2.39).
a)
b)
Hình 2.38: Sơ đồ định vị trục bằng hai lỗ tâm trên hai mũi tâm
a. Hai mũi tâm thường. b. Hai mũi tâm có khía nhám.
Hình 2.39: Sơ đồ định vị trên hai mũi tâm
A =
const
C =
const
a
b
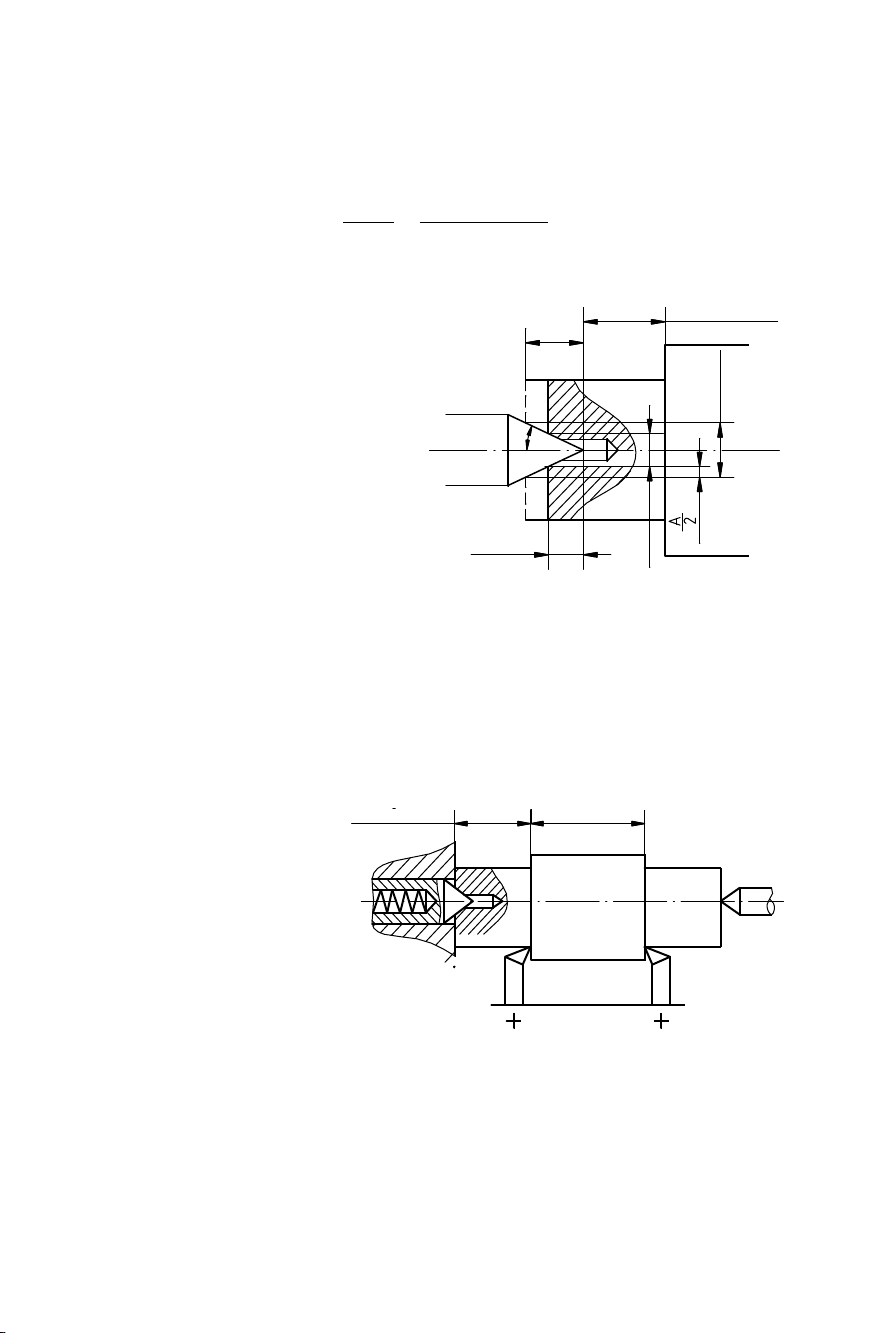
77
Có thể tính toán được sai số chuẩn theo chiều trục
c
(b), sai số này
dẫn đến sai số kích thước của bậc trục b. Khi phôi có lỗ tâm sâu nhất D
Amax
sẽ tạo ra b
2
, khi phôi có lỗ tâm nông nhất D
Amin
sẽ tạo ra b
1
(hình 2.40).
tg
DD
tg
A
bbb
AA
b
c
22
minmax
12)(
Trong đó:
A
- dung sai đường kính
phần côn của lỗ tâm,
- góc ở đỉnh côn của lỗ
tâm (60
o
, 75
o
).
Sai số chuẩn theo chiều
trục ảnh hưởng đến dung sai kích
thước cần đảm bảo theo chiều
trục trên các bậc trục mà chuẩn
đo lường là mặt đầu.
Để khắc phục sai số này,
dùng chốt tì vào mặt đầu và mũi
tâm tùy động (mũi tâm có lò xo
đẩy). Sơ đồ định vị trục trên mũi
tâm tùy động được trình bày trên
hình 2.41.
Nếu chuẩn đo lường khi gia công bậc trục không phải là mặt đầu mà
là một yếu tố khác của
phôi, thì sai số chuẩn
được xác định bằng dung
sai kích thước liên quan
giữa mặt đầu và chuẩn đo
lường.
Khi dùng hai tâm
làm chuẩn thì phải dùng
tốc kẹp vào mặt ngoài ở
phía đầu trục bên trái để
truyền mômen xoắn. Có
thể dùng loại tốc thẳng
(khi mài) hoặc tốc cong (khi tiện). Khi dùng phương pháp gia công nhiều
dao, đối với trục dài có thể truyền mômen xoắn từ cả hai đầu trục.
Có thể dùng mũi tâm cứng (không quay cùng chi tiết) phía ụ động
khi số vòng quay của chi tiết gia công nhỏ, còn nếu số vòng quay chi tiết
Hình 2.40: Sơ đồ tính toán sai
số chẩn
c
(b) theo chiều trục khi
định vị trên hai mũi tâm.
C = const
b
D
2
Amax
Amin
D
b
1
α
Hình 2.41: Sơ đồ định vị trục trên
mũi tâm tùy động.
b = const
a = const
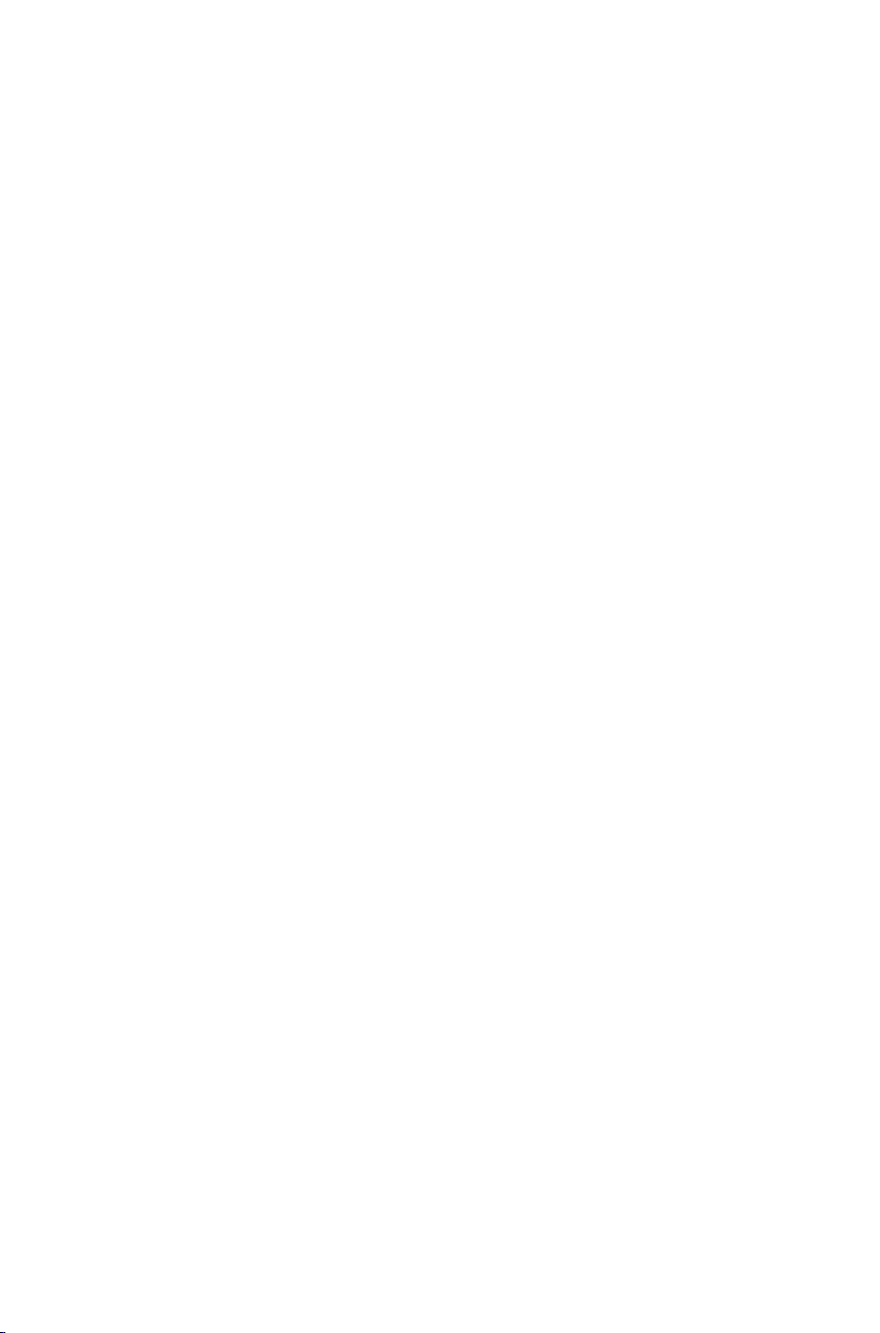
78
lớn hơn 500 vòng/phút, ma sát lớn, nhiệt độ cao làm cho dầu mỡ ở lỗ tâm
chảy ra ngoài, mũi tâm chóng mòn hoặc cháy gây nên sai lệch hình dáng
cho chi tiết, lúc này phải dùng mũi tâm sau quay cùng với chi tiết. Khi
gia công những trục có độ cứng vững kém phải thêm tì phụ như luynet
(khi tiện) và các chốt tì phụ (khi phay).
- Ngoài hai lỗ tâm cũng có thể lấy chuẩn là mặt ngoài của trục để
gia công các mặt ngoài của bậc trục khác; gia công các rãnh then, then
hoa, mặt đầu cũng như các mặt khác trên trục. Biện pháp thực hiện có thể
là cặp trên mâm cặp 3 chấu, 4 chấu, ống kẹp, mâm tự kẹp hoặc gá trên
khối V tùy theo bề mặt gia công là tròn xoay hay bề mặt có một vị trí
tương quan so với đường tâm trục. Định vị như vậy sẽ có sai số chuẩn
hướng kính và hướng trục.
- Đối với các trục rỗng, khi gia công tinh mặt ngoài, chi tiết được
định vị bằng mặt trong lỗ đã gia công để đảm bảo độ đồng tâm giữa mặt
trong và mặt ngoài.
- Ngoài ra, để gia công trục có thể dùng chuẩn phối hợp cả mặt
ngoài và lỗ tâm. Khi đó trục được cặp vào mâm cặp hoặc ống kẹp ở một
đầu và ở đầu kia lỗ tâm được chống trên mũi tâm.
Trên cơ sở của việc chọn chuẩn định vị cho các chi tiết dạng trục,
cần có biện pháp công nghệ và thứ tự gia công các bề mặt thích hợp với
kết cấu của từng loại trục.
2.3.4.2. Thứ tự các nguyên công và biện pháp công nghệ
A. Thứ tự gia công các bề mặt
Thứ tự gia công các bề mặt trục trơn và trục bậc cũng có thể coi là
đại diện cho các chi tiết dạng trục. Việc lập trình tự gia công các bề mặt
và chọn thiết bị cho các chi tiết dạng trục phụ thuộc vào các yếu tố cơ
bản như hình dáng, kích thước, độ cứng vững, yêu cầu độ chính xác đạt
được cũng như sản lượng hàng năm.
Khi chế tạo các trục trơn và trục bậc có thể chia ra các giai đoạn
chính sau:
a. Gia công chuẩn bị
- Cắt đứt phôi theo kích thước chiều dài hoặc bội số của chiều dài
trên máy nhiều trục hoặc máy cắt đứt tự động chuyên dùng, máy cưa,
cũng có thể cắt đứt trên máy tiện.
- Khỏa hai mặt đầu và khoan hai lỗ tâm. Nếu trục dài phải dùng
luynet thì cần phải có nguyên công gia công cổ đỡ.
b. Gia công trước nhiệt luyện
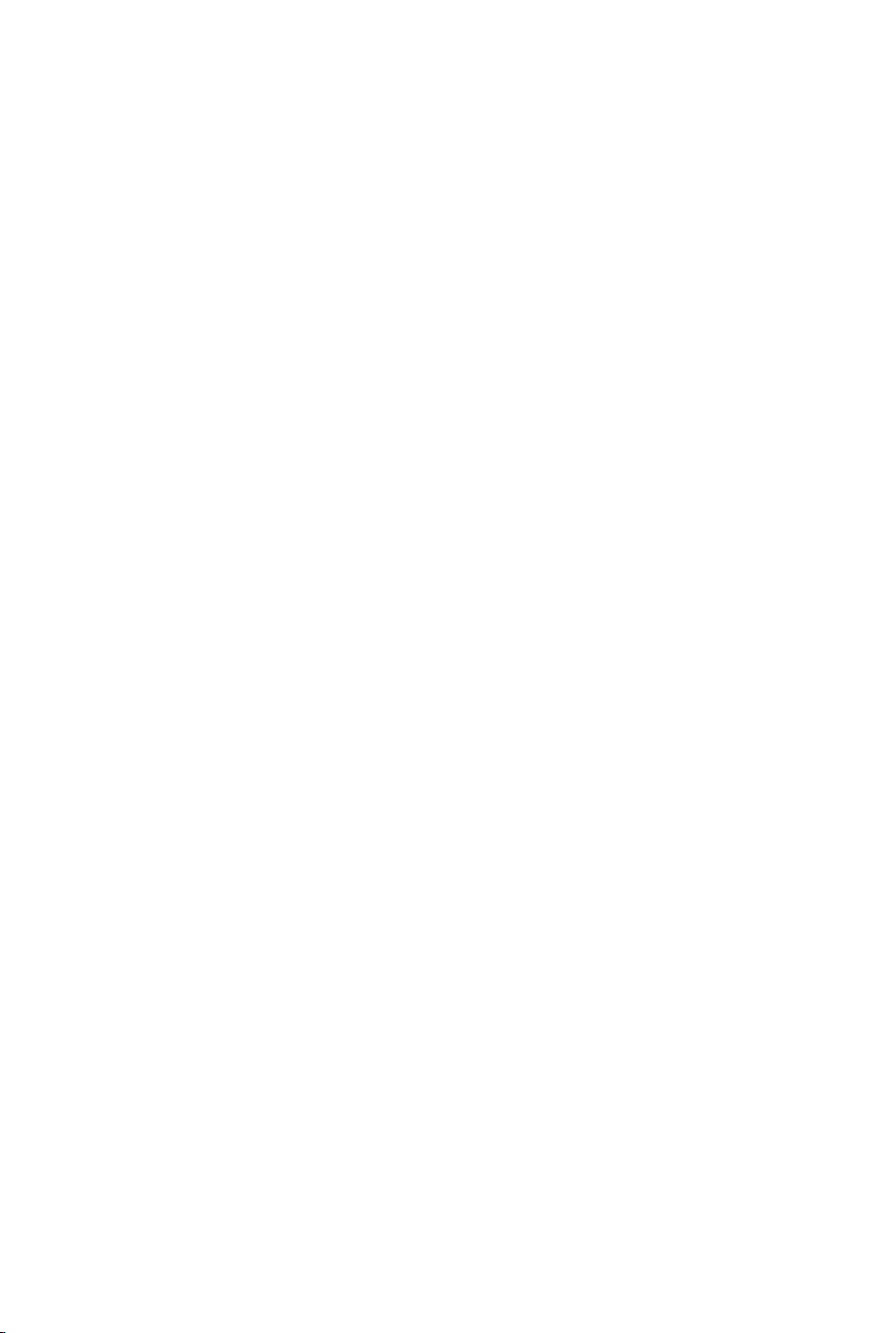
79
- Tiện thô và bán tinh các mặt trụ trên máy tiện (thường dùng hai
lần gá để gia công hai đầu).
- Mài thô các mặt trụ. Nếu là trục rỗng thì sau khi tiện thô và bán
tinh phải khoan và doa lỗ rồi mới gia công tinh mặt ngoài.
- Mài thô một số cổ trục để đỡ chi tiết khi phay.
- Nắn thẳng trục có < 100 và L/D > 10.
- Gia công các mặt định hình, rãnh then, rãnh chốt, răng trên trục.
- Gia công các lỗ vuông góc hoặc làm thành một góc với đường
tâm trục, gia công các mặt có ren, mặt không quan trọng.
c. Nhiệt luyện
d. Nắn thẳng sau khi nhiệt luyện để khắc phục biến dạng.
e. Gia công tinh sau khi nhiệt luyện
- Mài thô và tinh các cổ trục.
- Mài thô và tinh các mặt định hình (nếu có).
- Đánh bóng.
- Tổng kiểm tra.
B. Biện pháp thực hiện các nguyên công chính
a. Khỏa mặt đầu và khoan lỗ tâm:
Khi chế tạo các trục có chiều dài L>120mm từ phôi dập hoặc phôi
thanh thì hai lỗ tâm được dùng làm chuẩn định vị. Sau khi cắt đứt phôi
thì khỏa mặt đầu và khoan lỗ tâm phải được thực hiện tiếp theo ngay.
Công việc này được thực hiện theo các phương pháp sau:
Trong sản xuất đơn chiếc và loạt nhỏ thường phay hai mặt đầu của
trục, sau đó lấy dấu rồi khoan lỗ tâm theo dấu. Cũng có thể gá trục lên mâm
cặp, tiện mặt đầu, khoan tâm, sau đó đổi đầu để gia công phía còn lại.
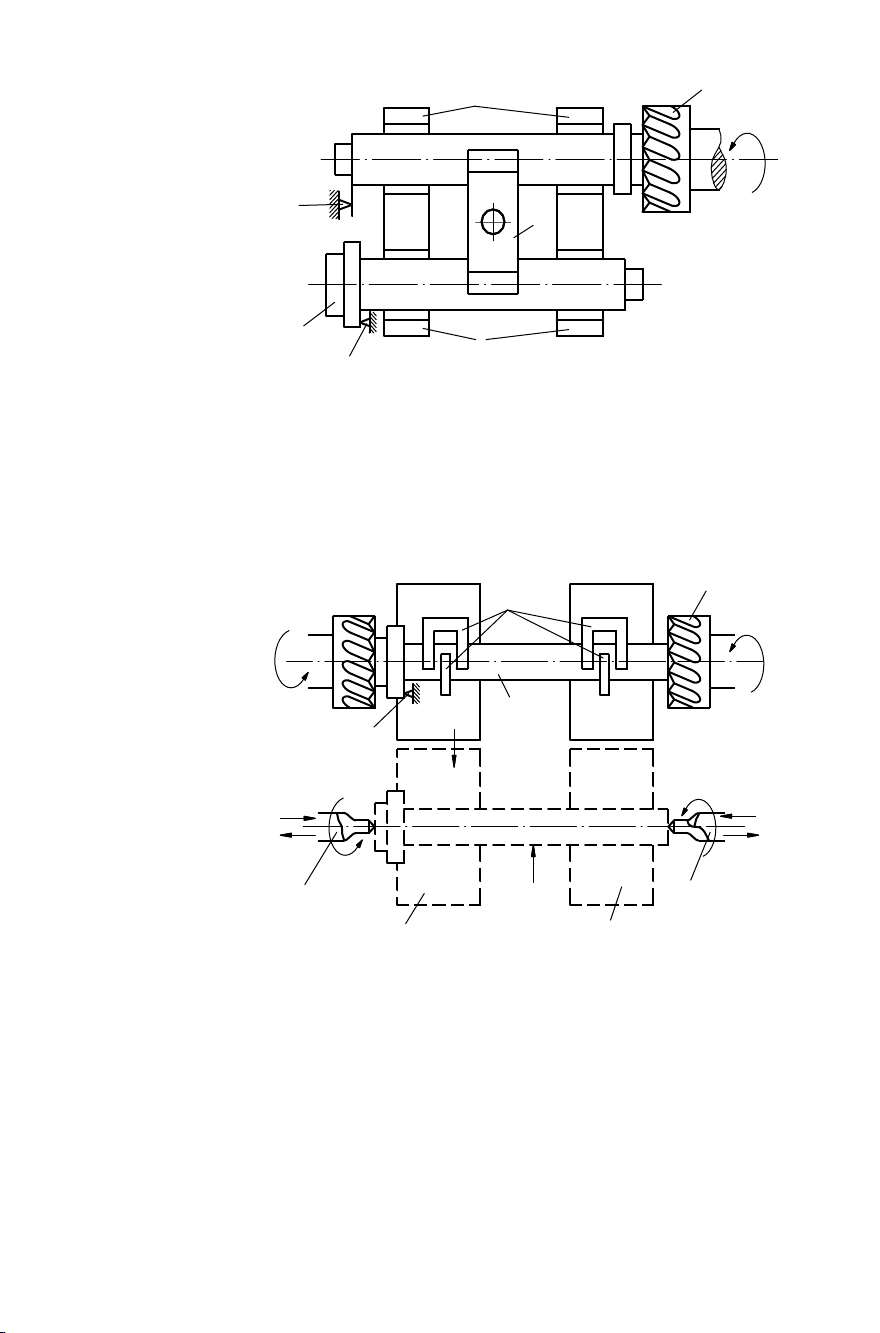
80
Trong sản
xuất hàng loạt
lớn và hàng
khối, việc khỏa
mặt đầu và
khoan lỗ tâm
được thực hiện
theo một trong
ba cách như sau:
Cách 1:
Phay mặt đầu
trên máy phay
có tang quay,
sau đó khoan lỗ
tâm trên máy
khoan hai phía.
Cách 2:
Phay mặt đầu
trên máy phay
nằm ngang và
gia công lỗ
tâm trên máy
chuyên dùng.
Hình 2.42 là
sơ đồ gia công
mặt đầu của
trục trên máy
phay nằm
ngang trong
dạng sản xuất
hàng loạt. Sau
mỗi lần
chuyển dao tại
vị trí II lấy ra
được một trục
gia công xong
cả hai đầu,
trục ở vị trí I được chuyển sang vị trí II để cắt đầu thứ hai, còn trong vị trí
I phôi mới được đặt vào để cắt đầu thứ nhất.
5
Hình 2.43: Sơ đồ gia công đồng thời mặt đầu và lỗ
tâm trụ trên máy chuyên dùng.
1) xe dao; 2) các khối V định vị và kẹp chặt; 3) chi tiết gia
công; 4) chốt tì; 5) dao phay; 6) mũi khoan tâm.
2
A
1
3
4
5
A
2
B
1
B
2
B
1
B
2
6
6
1
1
1
3
4
4
2
1
I
II
Hình 2.42: Sơ đồ gia công mặt đầu trục trên
máy phay ngang.
1) Khối V định vị 2) Khối V kẹp chặt
3) Chi tiết gia công 4) Chốt tì 5) Dao phay.
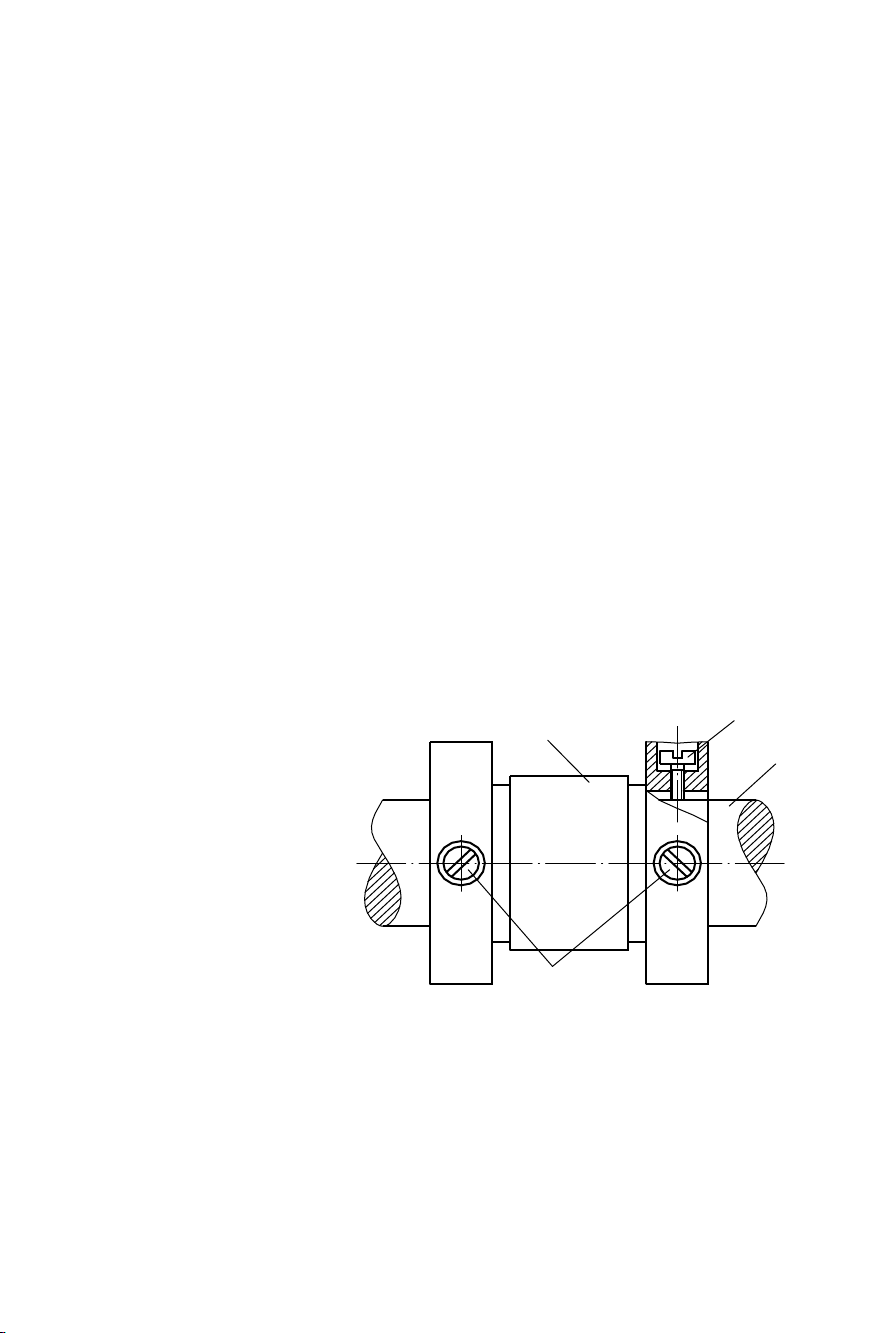
81
Theo hai cách trên đây việc khỏa mặt, khoan tâm được chia thành
hai nguyên công.
Cách thứ ba: là trên một nguyên công đồng thời phay mặt đầu và
khoan lỗ tâm ở cả hai phía trên máy chuyên dùng. Cách này dùng trong
dạng sản xuất hàng loạt lớn và hàng khối. Sơ đồ gia công theo cách này
được trình bày trên hình 2.43 (máy vạt mặt khoan tâm chuyên dùng).
Chi tiết gia công được định vị trên khối V, chuyển động dọc trục
được không chế bằng chốt tì áp vào mặt đầu của bậc trục. Để phay xong
cả hai mặt đầu bằng hai dao, bàn máy mang vật dịch chuyển A
1
rồi dừng
lại ở vị trí khoan tâm, lúc này các trục chính mang mũi khoan tâm thực
hiện chuyển động quay và B
1
để cùng khoan tâm ở cả hai đầu. Sau khi
làm xong, trục chính thực hiện dịch ra B
2
, bàn máy thực hiện chuyển
động A
2
để về vị trí tháo chi tiết và gá phôi mới. Máy dạng này là chuyên
dùng, bán tự động kí hiệu MP76M. Bàn máy kiểu tang trống có ba vị trí:
- Vị trí I dùng để gá và tháo phôi.
- Vị trí II thực hiện phay mặt đầu.
- Vị trí III thực hiện khoan tâm với mũi khoan chuyên dùng.
Mỗi vị trí được xác định bằng cách quay bàn máy đi 120
o
.
b. Tiện thô và tinh mặt trụ của các bậc trục
Công việc tiện thô
và tinh được thực hiện
trên một trong các loại
máy như: máy tiện vạn
năng thông thường, máy
tiện có trang bị bàn dao
chép hình thủy lực, máy
bán tự động chép hình
thủy lực, máy tiện một
trục nhiều dao.
Chọn loại máy nào
để gia công phụ thuộc vào
điều kiện sản xuất và sản
lượng của chi tiết.
Trong sản xuất nhỏ
và đơn chiếc, với phôi trục từ cán hoặc rèn tự do tùy theo hình dáng bên
ngoài và kích thước của trục cũng như tỉ lệ giữa các đường kính lớn, nhỏ
mà tiến hành tiện liên tục các bậc trên máy tiện vạn năng. Khi đó việc gia
1
Hình 2.44: Ống điều chỉnh để định vị phôi
vào luynet.
1) Chi tiết gia công 2) Cổ ống để tựa vào
luynet 3) Vít điều chỉnh (vít đầu chìm).
3
3
2
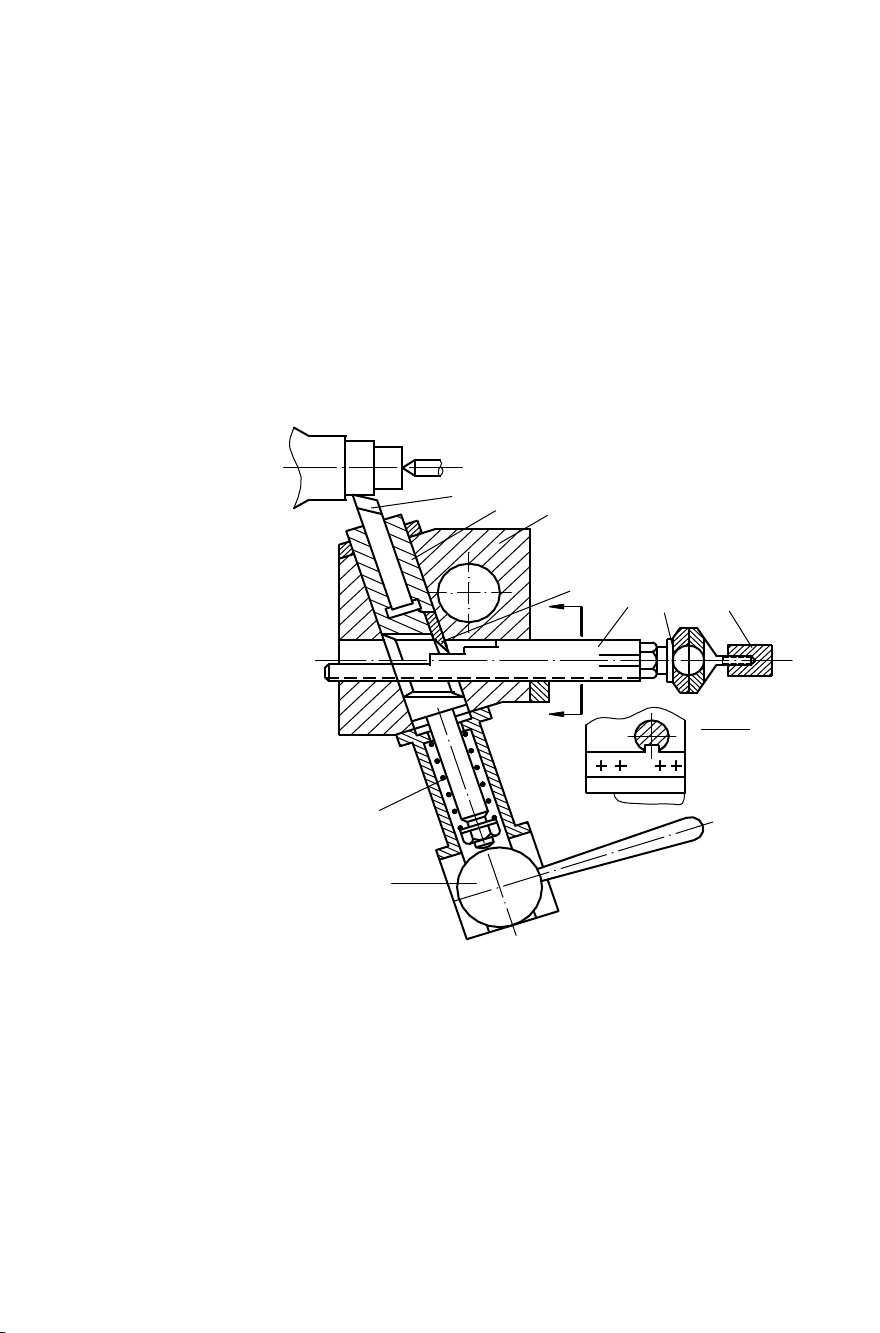
82
công lỗ tâm trên các trục lớn được làm theo dấu. Nếu thực hiện trên máy
tiện thì trục được kẹp một đầu vào mâm cặp, còn đầu kia đỡ vào luynet.
Muốn thực hiện định vị như vậy trước tiên phải gia công cổ đỡ luynet.
Việc đỡ luynet còn dùng như một tì phụ để tăng cứng vững khi gia công
trục có L/D lớn. Tuy nhiên đối với trục có đường kính nhỏ hơn 200 mm,
để không phải gia công cổ đỡ luynet, đôi khi dùng ống điều chỉnh chuyên
dùng. Ống được kẹp lên cổ không gia công và mặt ngoài ống được định
vị trong luynet. Để tâm của ống trùng với chi tiết gia công phải điều
chỉnh các vít đầu chìm 3. Kết cấu ống điều chỉnh này được trình bày trên
hình 2.44.
Để tạo thành các bậc trục có thể cắt theo lớp, theo đoạn hoặc hỗn hợp
bằng phương pháp
tiện. Nếu sản
lượng nhiều hơn
một chút, có thể
thực hiện cắt dần
từng bậc trên nhiều
máy khác nhau.
Trong sản
xuất hàng loạt
nhỏ, mặt trụ ngoài
của trục được gia
công trên máy tiện
thông thường có
trang bị thêm các
thiết bị chép hình
thủy lực. Trên
hình 2.45 trình
bày một đồ gá tiện
chép hình trên
máy tiện vạn năng
với cơ cấu chép
hình bằng cơ khí.
Nhờ có lò
xo 9 luôn đẩy vào
cán con trượt 2,
do đó đẩy con trượt 2 xuống dưới, làm cho mũi tì 4 luôn tì sát vào mặt
định hình của dưỡng 5. Khi cho bàn dao chạy về trái dao 1 được gá trên
con trượt 2 sẽ cắt ra được các bậc của trục phù hợp với bậc trên dưỡng 5.
Khi cắt hết chiều dài các bậc trục, mũi dò bị tụt xuống phần thấp trên
Hình 2.45: Đồ gá tiện chép hình trục bậc.
1) Dao cắt; 2 ) Con trượt; 3) Vỏ đồ gá; 4) Mũi tì được
kẹp chặt vào con trượt; 5) Dưỡng chép hình; 6) Khớp
bản lề; 7) Đai ốc điều chỉnh; 8) Bánh lệch tâm;
9) Lò xo.
9
8
A-A
7
6
5
4
3
2
1
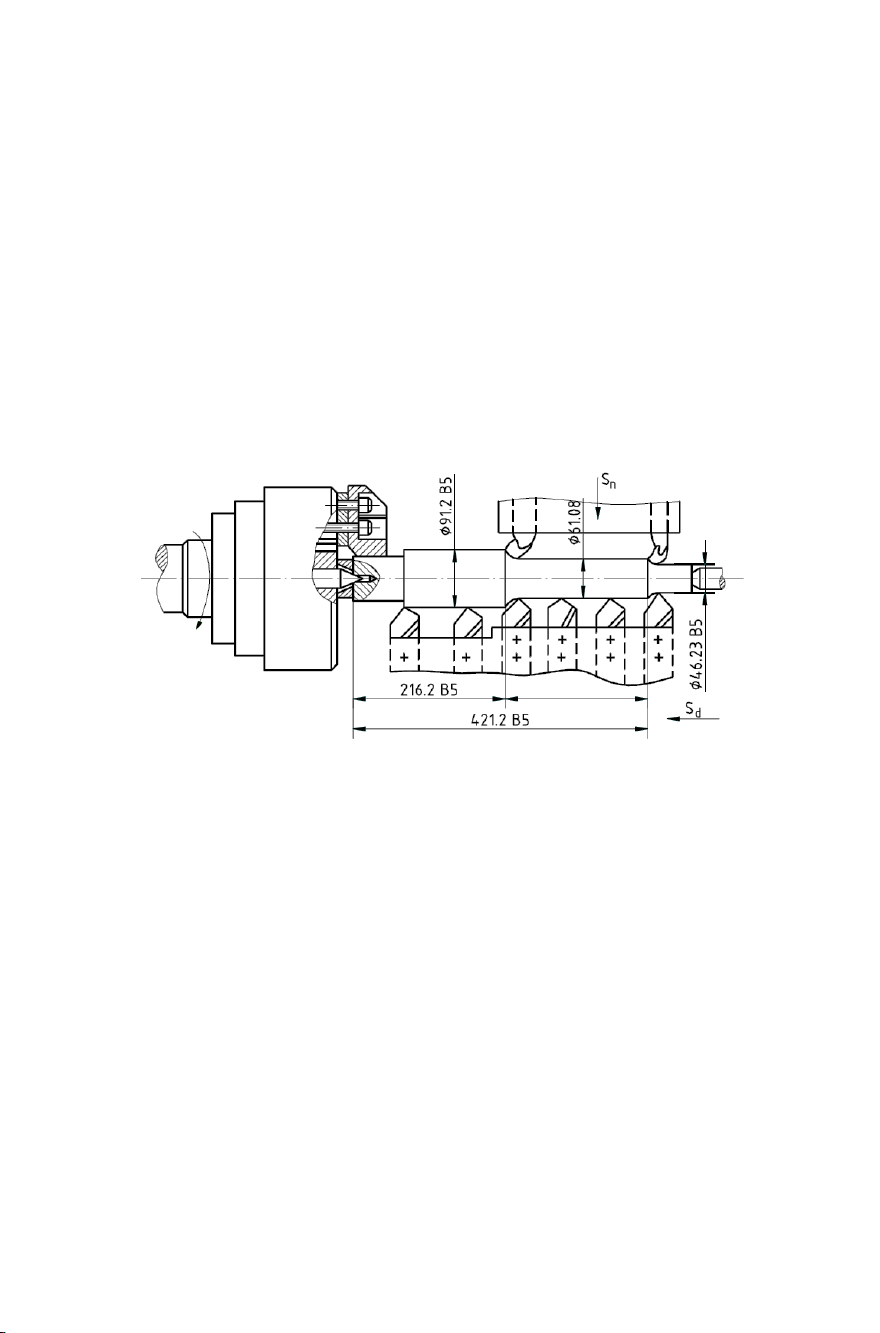
83
dưỡng, lò xo đẩy cả con trượt có mang dao xuống dưới, dao được rút ra
khỏi phôi. Muốn đưa mũi dò về vị trí ban đầu phải tháo chi tiết rồi quay
bánh lệch tâm để đẩy con trượt cùng mũi dò lên trên và chạy bàn dao về
phía phải êcu điều chỉnh 7 và khớp bản lề 6 để điều chỉnh vị trí chiều dọc
bậc trục cần gia công.
Thời gian gia công từng chiếc trên máy tiện có trang bị bàn dao
chép hình thủy lực rút ngắn từ 2,5 - 3 lần so với khi gia công trên máy
tiện thường, thời gian chuẩn bị và kết thúc cũng nhỏ.
Trong sản xuất hàng loạt lớn và hàng khối, việc gia công các mặt
trụ của trục được tiến hành trên máy bán tự động một trục nhiều dao hoặc
nhiều trục nhiều dao. Sơ đồ gia công trục bậc trên máy bán tự động được
trình bày trong hình 2-46.
Khi sử dụng phương pháp tiện nhiều dao sẽ có một loạt nhân tố phụ
ảnh hưởng đến độ chính xác gia công như:
- Sai số do vị trí của một vài con dao điều chỉnh không chính xác.
- Các dao mòn không đều nhau.
- Biến dạng đàn hồi của hệ thống công nghệ thay đổi. Vì vậy trên
máy tiện bán tự động một trục, nhiều dao chỉ có thể đạt chính xác cấp 9-
10 khi tiện thô và cấp 7-8 khi tiện tinh. Khi dùng nhiều dao gia công trên
máy bán tự động, nhiều trục thẳng đứng có thể đạt độ chính xác cấp 7-8
sau một vài bước.
Tiện nhiều dao trên bất kỳ kiểu máy nào cũng đều có ưu điểm hơn
tiện một dao là giảm được thời gian gia công cơ bản. Việc bố trí dao có
thể thực hiện theo nhiều cách:
Hình 2.46: Sơ đồ tiện trục bậc trên máy bán tự động
nhiều dao, một trục chính
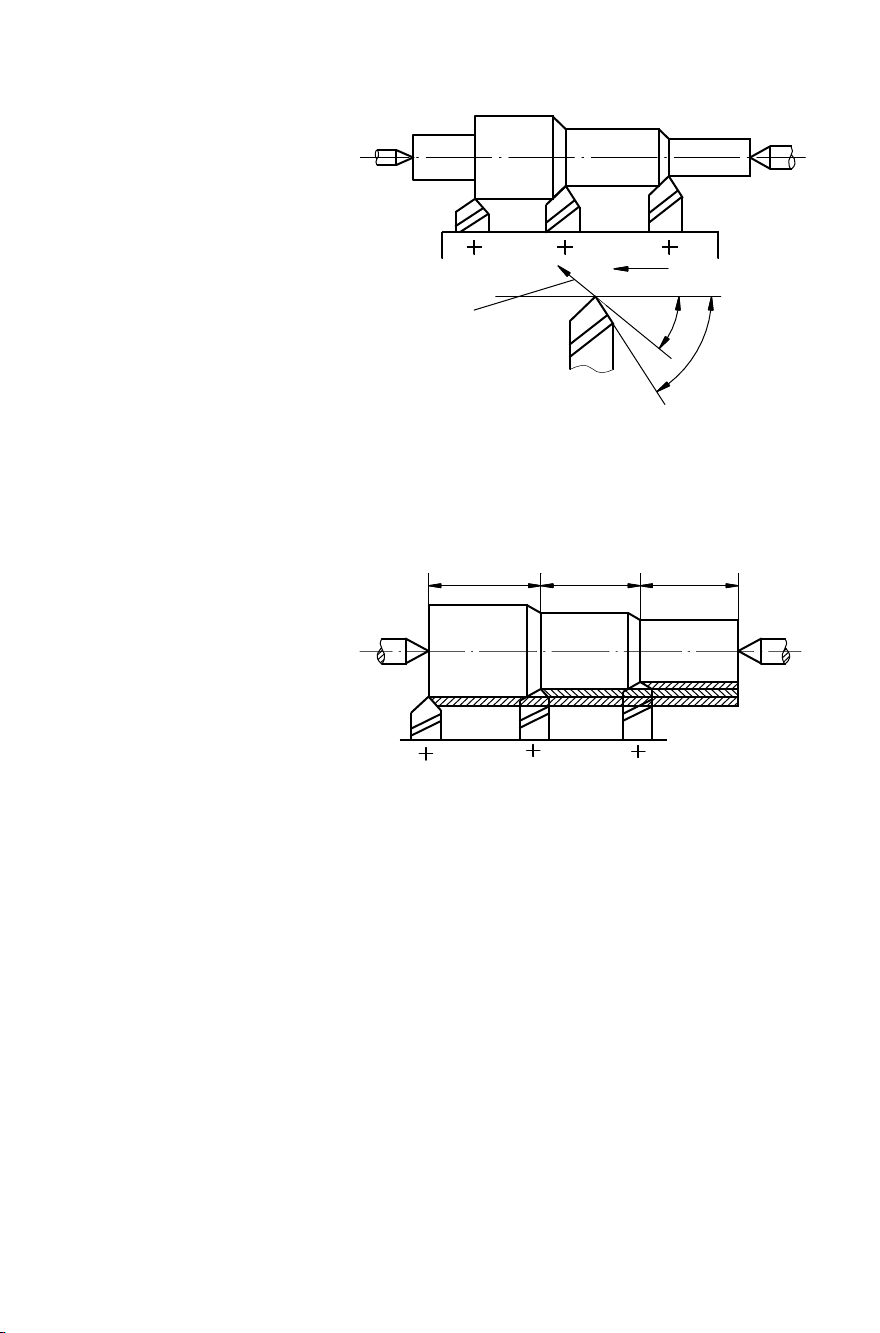
84
+ Chia đoạn theo chiều dài từng bậc trục.
Theo cách này, trừ
dao thứ nhất ăn vào mặt
đầu, còn tất cả các dao
khác trước khi ăn dọc phải
ăn vào chi tiết. Khi ăn vào
không cho phép ăn theo
hướng kính mà phải
nghiêng đi một góc (hình
2.47), trong đó <
1
.
+Chia theo lượng dư:
Theo cách này, tất
cả các dao được gá theo
đường kính xác định và
cách nhau những đoạn
bằng chiều dài các bậc,
dao nào cắt lượng dư của
dao đó (hình 2.48).
Hành trình chạy dao
dọc lớn và bị hạn chế bởi
ụ sau. Phương pháp này
thường dùng để tiện các
trục có các bậc nhỏ dần về
một phía, chiều dài của
từng bậc ngắn, lượng dư
nhỏ. Số lượng dao được
dùng bị hạn chế bởi độ cứng vững của chi tiết gia công, công suất máy và
cấu tạo của giá dao.
Trong sản xuất hàng loạt lớn và hàng khối để gia công mặt trụ của
trục còn dùng cả máy bán tự động chép hình thủy lực. Sơ đồ tiện trục bậc
trên máy tiện bán tự động chép hình thủy lực được trình bày trên hình
2.49. Trên máy có hai bàn dao: bàn dao dọc với một dao luôn liên hệ với
dưỡng chép hình thông qua cơ cấu thủy lực và mũi dò để tiện ra biên
dạng của trục, còn bàn dao ngang để tiện ra các gờ, vai trục.
Hình 2.47: Sơ đồ bố trí dao và ăn dao
vào khi tiện nhiều dao bằng cách chia
đoạn theo chiều dài từng bậc.
S
1
θ
Hướng ăn dao
Hình 2.48: Sơ đồ bố trí dao khi tiện
nhiều dao bằng cách chia theo lượng dư.
L
3
L
2
L
1
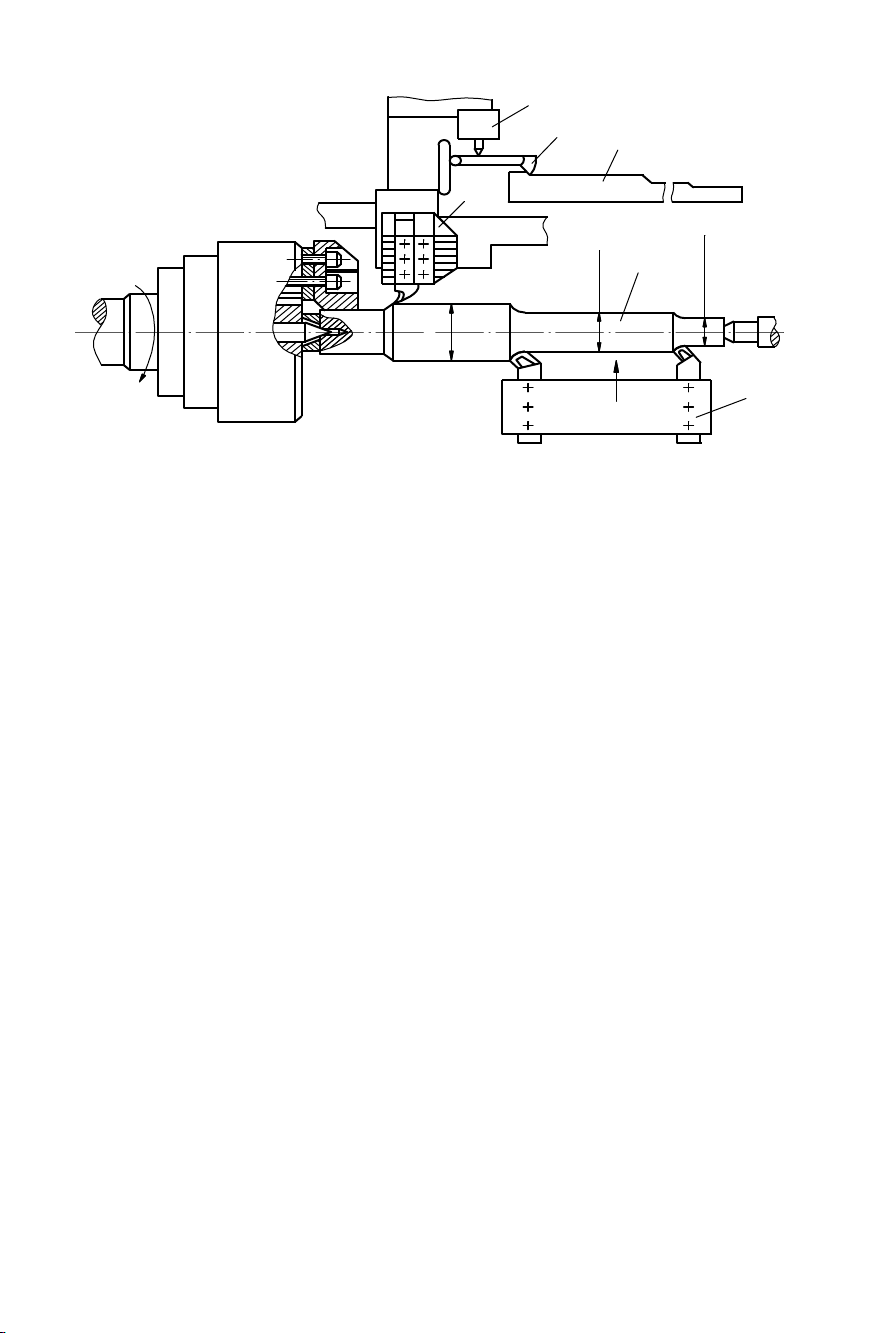
85
Dùng máy tiện bán tự động chép hình thủy lực sẽ có một loạt các
ưu điểm so với tiện nhiều dao như:
+ Thời gian để điều chỉnh và điều chỉnh lại máy tiện bán tự động
chép hình thủy lực giảm đi theo số lượng dao trong giá dao, đơn giản
việc gá lắp mẫu, đơn giản sơ đồ điều chỉnh. Thời gian điều chỉnh giảm đi
23 lần so với dùng nhiều dao.
+ Năng suất gia công cao vì có thể cắt ở tốc độ cắt cao nếu công
suất máy cho phép.
+ Tiện chép hình thủy lực dùng thuận lợi đối với các trục kém cứng
vững, dùng để tiện tinh các trục dài có yêu cầu độ nhẵn bóng bề mặt cao
mà không thể dùng phương pháp điều chỉnh cắt nhiều dao được.
c. Mài thô và tinh các cổ trục
Mài thô cổ trục thường được hoàn thành theo nguyên công mài thô
và mài tinh. Khi mài có thể thực hiện trên máy mài tròn ngoài với tiến
dao dọc hoặc tiến dao ngang. Với các trục bậc ngắn và trục trơn có thể
mài trên máy mài vô tâm. Khi mài trên máy mài tròn ngoài, thường trục
được định vị bằng hai lỗ tâm trên hai mũi tâm. Trước nguyên công mài
tinh phải sửa lỗ tâm để loại trừ những sai hỏng do bề mặt lỗ tâm bị ôxy
hóa hoặc bị cháy trong quá trình nhiệt luyện. Khi mài trên máy mài vô
tâm thì mặt gia công chính là mặt định vị.
Hình 2.49: Sơ đồ bố trí dao trên máy tiện bán tự
động chép hình thủy lực.
1) Dưỡng chép hình; 2) Mũi dò; 3) Cơ cấu thủy lực;
4) Bàn dao dọc; 5) Bàn dao ngang; 6) Chi tiết gia công.
45,23 B4
60 B4
90 C4
S
n
6
5
4
2
3
1
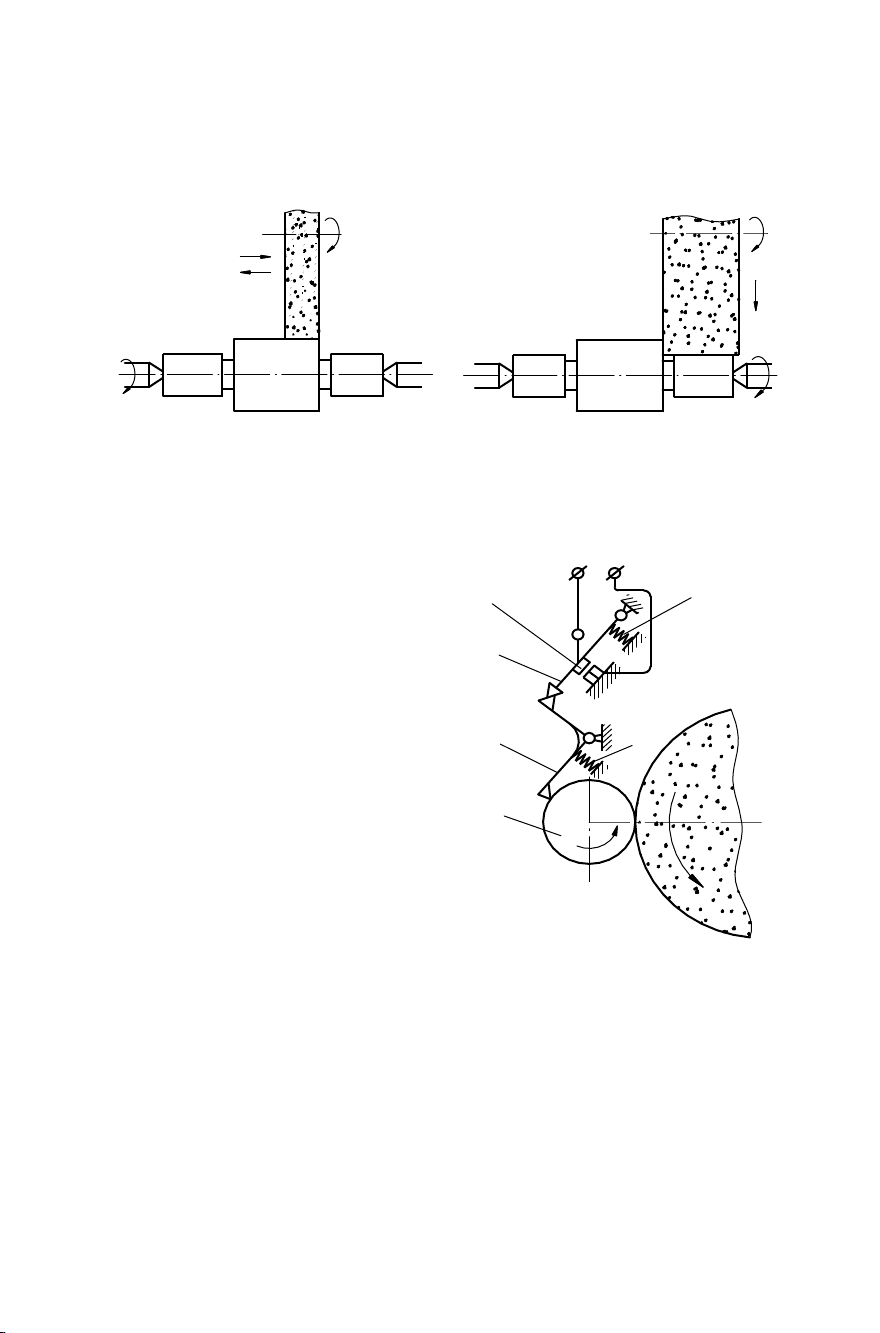
86
- Mài tiến dao dọc khi chiều dài l > 80mm. Trường hợp này được
dùng khá phổ biến khi mài trục. Lượng chạy dao dọc được tính bằng
mm/vòng chi tiết. Trị số của nó phụ thuộc vào độ nhám bề mặt yêu cầu
và đường kính chi tiết (hình 2.50a).
- Mài tiến dao ngang khi chiều dài l < 80 mm. Trường hợp này
không tiến dao dọc mà chỉ có tiến
dao ngang và áp dụng khi chiều
dài trên đoạn gia công nhỏ hơn bề
rộng của đá mài hoặc khi gia công
các mặt định hình tròn xoay (hình
2.50b).
Ở nguyên công mài, do thời
gian phụ để kiểm tra chi tiết là lớn,
vì vậy để nâng cao năng suất, khi
mài thường dùng các thiết bị kiểm
tra ngay trong quá trình gia công.
Trên hình 2.51 trình bày sơ
đồ cơ cấu kiểm tra một điểm tiếp
xúc với tiếp điểm rơi. Tay đòn 2
dưới tác dụng của lò xo 6 luôn tiếp
xúc với trục gia công 1.
d. Gia công các mặt định hình
Các mặt định hình trên trục bao gồm các mặt có ren, bánh răng,
then hoa, rãnh then, các mặt lệch tâm v.v… Để gia công các mặt này phải
có biện pháp kỹ thuật thích hợp.
* Gia công mặt có ren trên trục
Trên trục thường có ren theo chiều trục và ren trên các lỗ được bố
trí dưới một góc nào đó so với đường tâm trục.
6
4
5
3
2
1
Hình 2.51: Sơ đồ cơ cấu kiểm tra
kích thước trục trong quá trình mài.
Hình 2.50: Sơ đồ mài mặt trụ ngoài của trục trên máy mài tròn ngoài.
a) Tiến dao dọc; b) Tiến dao ngang.
a)
b)
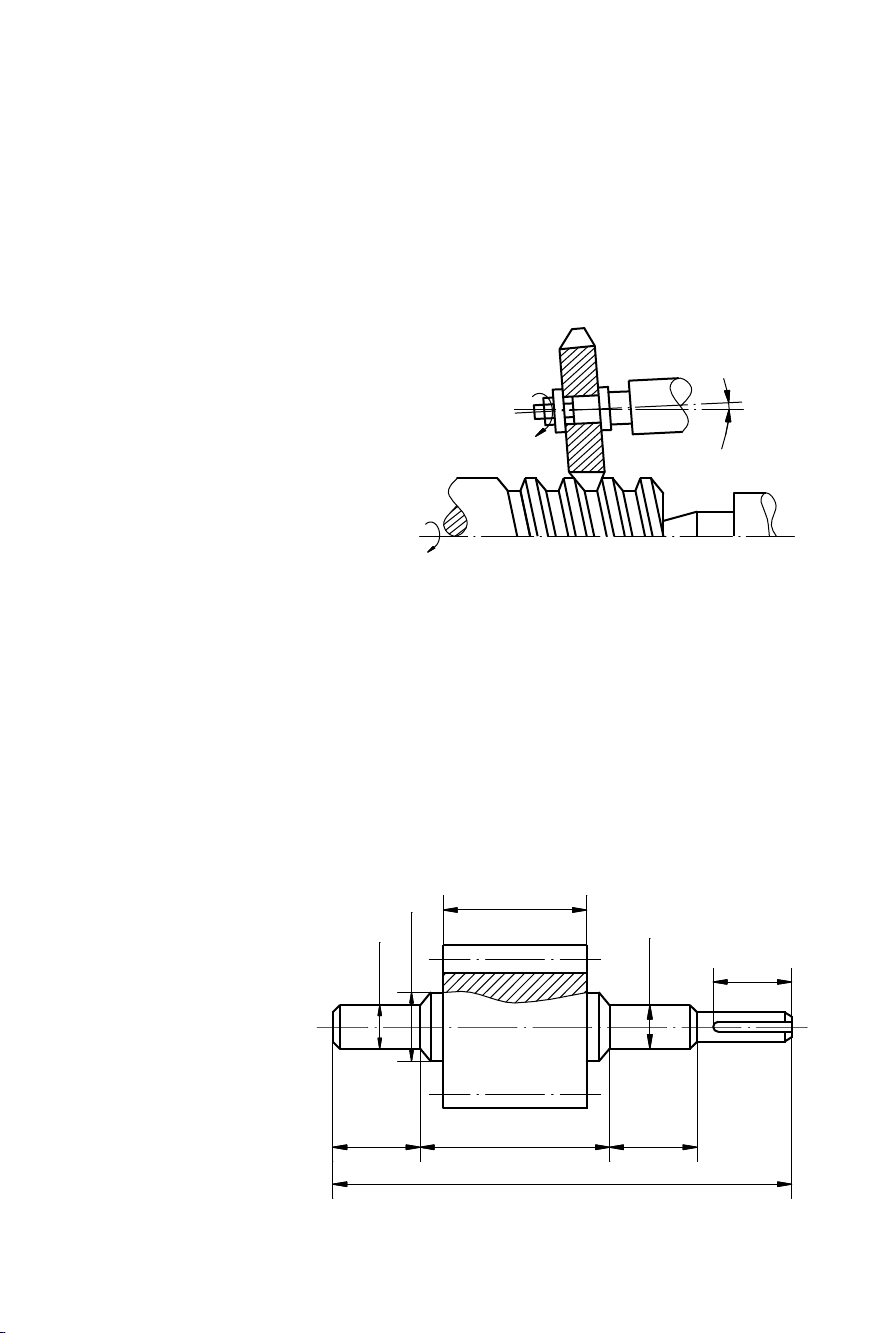
87
- Gia công ren theo chiều trục:
Thường có hai loại ren: kẹp chặt và truyền lực.
+ Ren kẹp chặt có dạng hình tam giác, khoảng chiều dài ren ngắn.
Với mọi cỡ của trục ren này thường được gia công trên máy tiện.
Nếu sản lượng ít, dùng dao tiện ren một lưỡi hoặc bàn ren. Sản
lượng nhiều dùng dao tiện ren hình răng lược. Trong sản xuất hàng
khối, ren này được cắt bằng đầu cắt ren hoặc dùng phương pháp cắt
ren cao tốc.
+ Ren truyền lực có dạng
hình thang hoặc hình vuông. Khi
sản lượng ít, ren này thường được
gia công trên máy tiện vạn năng.
Sản lượng nhiều, có thể dùng
phương pháp phay ren. Để đảm
bảo độ đồng tâm giữa ren và trục,
chi tiết gia công thường được
định vị bằng hai lỗ tâm trên hai
mũi tâm. Trên hình 2.52 trình bày
sơ đồ phay ren trên trục bằng dao
phay đĩa. Tuy nhiên để phay ren còn có thể dùng dao phay ngón.
- Gia công ren trên các lỗ làm thành một góc với trục.
Loại lỗ ren này thường dùng để bắt bulông kẹp chặt các chi tiết
khác với trục. Các lỗ ren này thường được cắt bằng tarô trên máy tiện,
máy khoan, máy bán tự động và tự động. Kiểu máy phụ thuộc vào sản
lượng và hình dáng chi tiết. Nếu sản lượng ít còn có thể cắt bằng tarô
thực hiện bằng tay
trên bàn nguội.
Gia công
răng trên trục
Ở một số loại
trục có kết cấu răng
của bánh răng liền
trục. Trên hình 2.53
trình bày một loại
trục răng có kích
thước khá lớn.
Quy trình công
nghệ chế tạo loại trục
Hình 2.52: Sơ đồ phay ren trên
trục bằng dao phay đĩa
Hình 2.53: Kết cấu một lọai trục có bánh răng
180
+0,5
250
180
L
130
300
625
300
1600

88
có bánh răng này cũng tuân theo trình tự đối với loại trục trơn, trục bậc
khác. Chỉ có khác là cần có thêm nguyên công gia công răng của bánh
răng. Răng trên trục có thể là răng thẳng, răng nghiêng, răng côn hay có
dạng khác. Việc gia công các loại răng này có thể thực hiện bằng phương
pháp định hình hay bao hình tùy theo dạng sản xuất và điều kiện sản
xuất. Các phương pháp gia công răng sẽ được trình bày trong mục “Gia
công bánh răng”.
* Gia công rãnh then và then hoa
Rãnh then thường được gia công trên máy phay. Có thể dùng dao
phay ngón thực hiện trên máy phay đứng và dao phay đĩa thực hiện trên
máy phay ngang.
Khi gia công rãnh then trục được định vị bằng cổ trục trên khối V
hoặc cũng có thể dùng lỗ tâm làm chuẩn, gá đặt phải đảm bảo đường sinh
của trục song song với hướng chạy dao. Trên hình 2.54 trình bày sơ đồ
định vị trục trên khối V để gia công rãnh then, thực hiện trên máy phay
ngang bằng dao phay đĩa.
Mặt then hoa trên trục thường gia công bằng phương pháp phay,
ngoài ra còn có thể bằng phương pháp bào, chuốt hoặc cán nguội. Với
then hoa chính xác, còn phải gia công tinh bằng phương pháp mài. Phay
then hoa có thể thực hiện bằng một hoặc hai lần tùy theo sản lượng và
đường kính trục.
Trong sản xuất hàng loạt, phay then hoa được thực hiện qua hai
lần, đầu tiên phay mặt bên, sau đó phay đường kính (hình 2.55b,c). Cũng
có thể thực hiện phay một lần bằng dao phay định hình (hình 2.55a).
Cách thực hiện này phải có dụng cụ phân độ đi kèm với cơ cấu định vị để
thực hiện lần lượt các then trên trục then hoa.
Trong sản xuất hàng loạt lớn thực hiện bằng dao phay lăn trên máy
phay lăn chuyên dùng. Các then được hình thành đồng thời nhờ bao hình,
không cần có cơ cấu phân độ (hình 2.56).
Đối với những trục có đường kính d < 6080mm chỉ cần phay một
lần, các trục lớn hơn phải chia ra phay thô và phay tinh. Với những trục
cần nhiệt luyện, sau khi nhiệt luyện muốn loại trừ các sai lệch không
Hình 2.54: Sơ đồ định vi trên khối V để gia công rãnh then
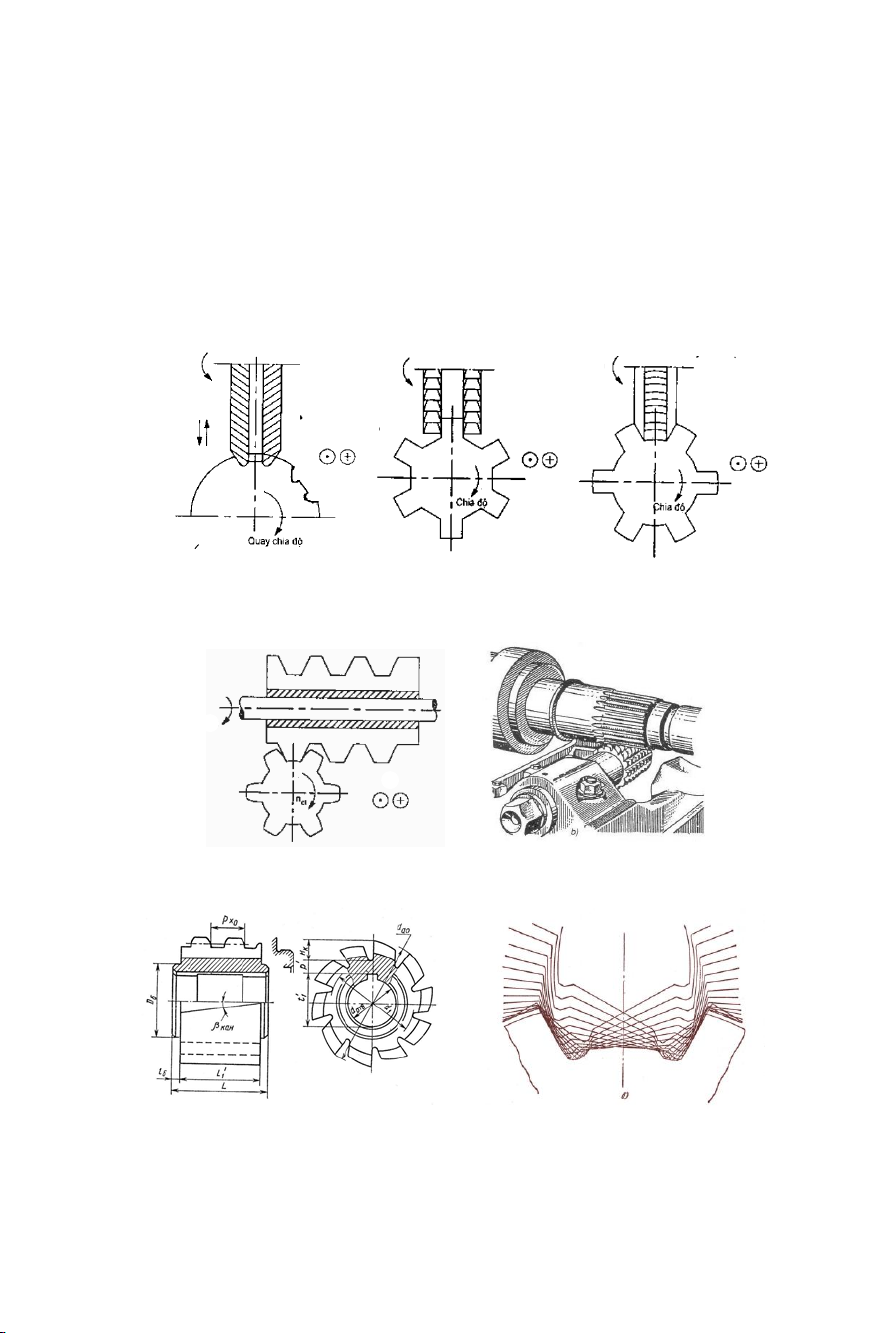
89
gian, đảm bảo độ nhám bề mặt và độ chính xác, cần có nguyên công cắt
tinh, thường là mài.
Để có biện pháp đúng đắn trong việc gia công trục then hoa, còn
cần xem xét điều kiện kỹ thuật của trục then hoa, định tâm theo mặt trong
hay theo mặt ngoài.
Nếu then hoa định tâm theo mặt ngoài thì việc gia công qua các
bước sau:
+ Phay then hoa bằng phương pháp định hình hoặc bao hình
+ Mài mặt cạnh then hoa và mặt trụ ngoài sau khi nhiệt luyện.
Hình 2.57: Dao phay lăn then hoa và quỹ đạo dao
Hình 2.55: Phay định hình
b)
a)
c)
n
n
n
S
d
S
d
S
d
S
Hình 2.56: Phay bao hình
S
d
n
d
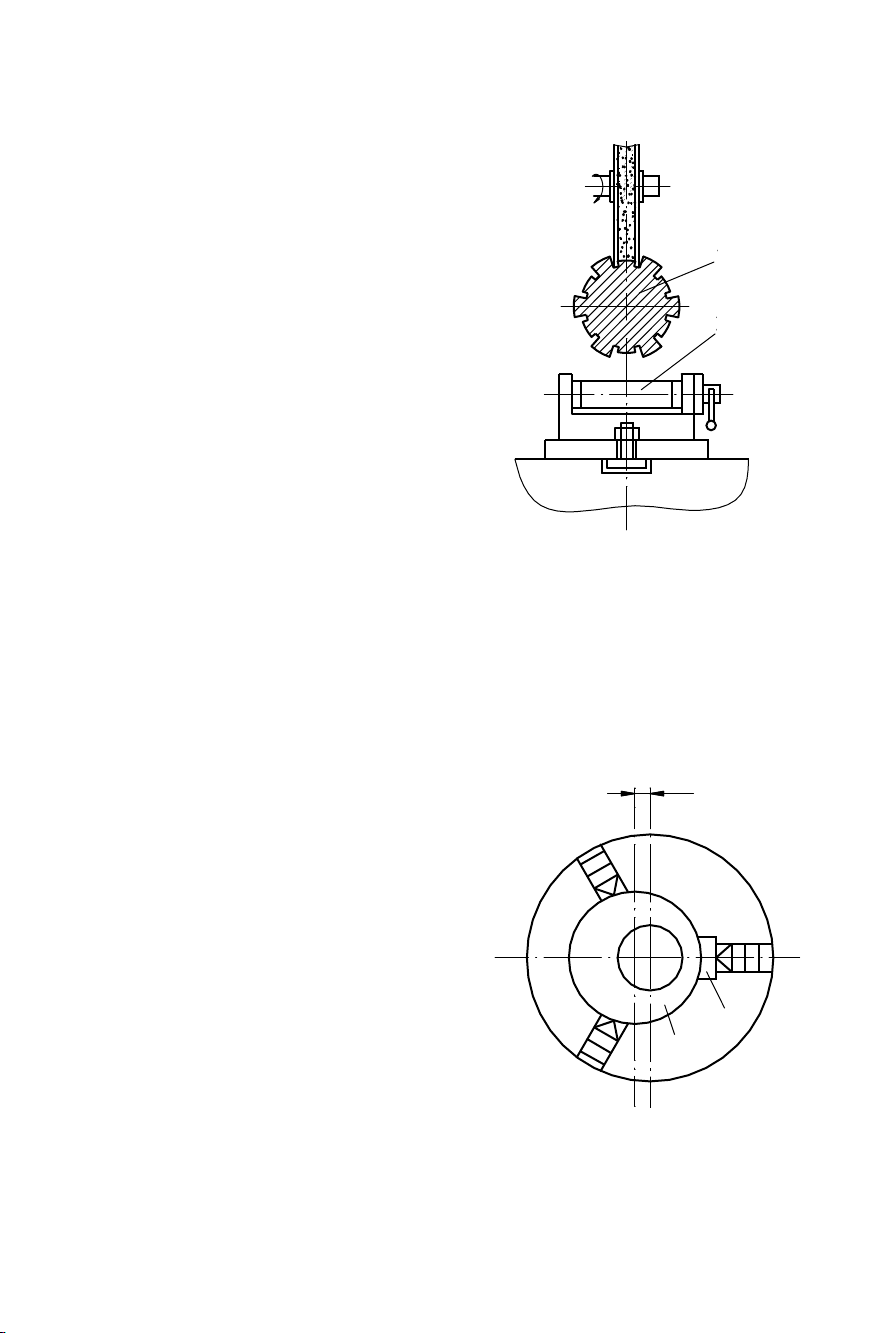
90
Nếu then hoa không cần nhiệt luyện thì tiến hành phay then hoa sau
khi mài tinh mặt tròn ngoài.
Then hoa định tâm theo mặt
trong được gia công qua các bước sau:
+ Phay then hoa (có để lượng
dư cho mài).
+ Phay rãnh thoát đá mài cho
trường hợp mài mặt trụ trong.
+ Mài tinh mặt cạnh và mặt trụ
trong bằng đá mài định hình.
Để mài tinh trục then hoa, chi
tiết gia công được định vị trên hai mũi
tâm cứng, ngoài ra còn phải khống chế
vị trí góc của then hoa. Trên hình 2.58
trình bày sơ đồ định vị khi mài rãnh
then hoa. Trong trường hợp này, vị trí
góc của trục được xác định bằng cơ
cấu 2. Với phương pháp này chỉ mài
được từng rãnh một nên năng suất
không cao.
Ngoài phương pháp phay then hoa thông dụng như đã trình bày ở
trên, người ta còn có thể dùng phương
pháp bào. Để nâng cao năng suất khi
bào, dùng biện pháp gia công bằng
nhiều dao định hình thực hiện cùng một
lúc.
Cũng có thể thực hiện chuốt then
hoa. Với phương pháp chuốt năng suất
cao hơn phay nhiều lần. Phương pháp
cán nguội bằng các con lăn định hình
cũng được sử dụng, với phương pháp
này tạo được trục then hoa có độ bền
xoắn cao hơn then hoa gia công bằng
phương pháp phay.
* Gia công các mặt lệch tâm
Ở một số chi tiết dạng trục, trên
một bậc nào đó có bề mặt không tròn
xoay mà là dạng cam, ví dụ như trục
Hình 2.58: Sơ đồ mài răng then
hoa bằng đá tròn định hình
1.Trục then hoa được định vị trên
mũi tâm cứng.
2.Cơ cấu định vị góc xoay
1
2
Hình 2.59: Sơ đồ gá để gia
công mặt lệch tâm trên trục
1. Chi tiết gia công.
2. Miếng điệm.
2
1
e
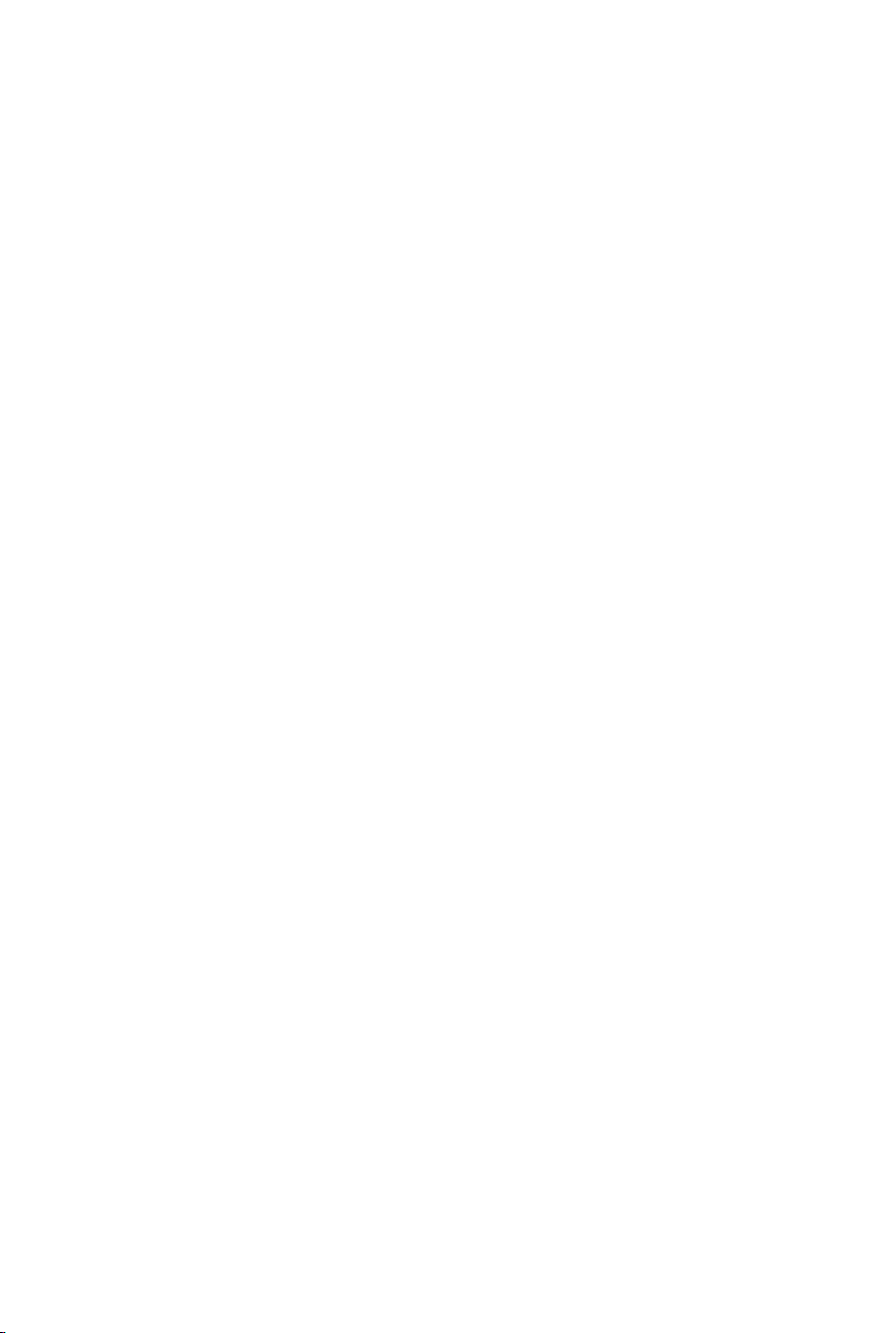
91
cam trong động cơ ôtô, có loại trục có nhiều bậc nhưng các bậc không
cùng trên một đường tâm, ví dụ như trục khuỷu của động cơ ôtô, máy
kéo. Những mặt lệch tâm này phải có biện pháp gia công thích hợp mới
tạo nên hình dạng bề mặt cũng như độ chính xác kích thước của chúng.
Có những tài liệu chuyên sâu viết về công nghệ chế tạo trục cam, trục
khuỷu là loại trục đặc biệt. Ở đây chỉ trình bày biện pháp để gia công mặt
cam cũng như mặt lệch tâm trên chi tiết dạng trục nói chung.
Gia công mặt lệch tâm tròn xoay
Để gia công những mặt lệch tâm tròn xoay, nghĩa là bậc trục có
tâm lệch so với tâm trục một khoảng e nào đó, có thể dùng phương pháp
tiện trên mâm cặp ba chấu bằng cách gá lệch chi tiết đi một đoạn nhờ bề
dày của miếng căn đệm thích hợp. Để thay miếng căn đệm có thể dùng
bạc lệch tâm trung gian giữa trục và các chấu của mâm cặp. Cũng có thể
dùng phương pháp rà gá thực hiện trên mâm cặp bốn chấu.
Các phương pháp nêu trên chỉ dùng cho những trục ngắn và khoảng
lệch tâm không lớn lắm, vì nó phụ thuộc vào kích thước của mâm cặp
(khoảng chạy của các chấu cặp). Cách gá đặt như trên có thể dùng cả cho
tiện cũng như mài.
Khi gia công những mặt lệch tâm trên các trục dài như các mặt cam
trên trục cam, chi tiết gia công được định vị trên các cổ trục đã qua mài
thô hoặc bằng hai lỗ tâm. Với sản xuất đơn chiếc và loạt nhỏ, gia công
mặt cam được thực hiện trên máy tiện vạn năng với đồ gá chép hình.
Trong sản xuất lớn, tiện các mặt cam được tiến hành trên máy tiện bán tự
động chép hình. Nguyên lý cắt các mặt cam và định hình trên trục có thể
thực hiện theo hai phương pháp:
+ Phương pháp thứ nhất: giá dao không lắc lư trong quá trình cắt.
Sơ đồ cắt của phương pháp này giống như phương pháp tiện chép
hình thông thường. Do đặc điểm của cam là có lượng nâng khác nhau
nên trong quá trình cắt, góc sau của dao sẽ thay đổi dẫn đến mặt sau của
dao cà vào mặt chi tiết gia công. Để cắt được, góc sau của dao phải lớn,
thường = 40
0
45
0
vượt quá cả phạm vi góc sau cho phép của dao.
Phương pháp này chỉ dùng để cắt cam có lượng nâng K < 60mm.
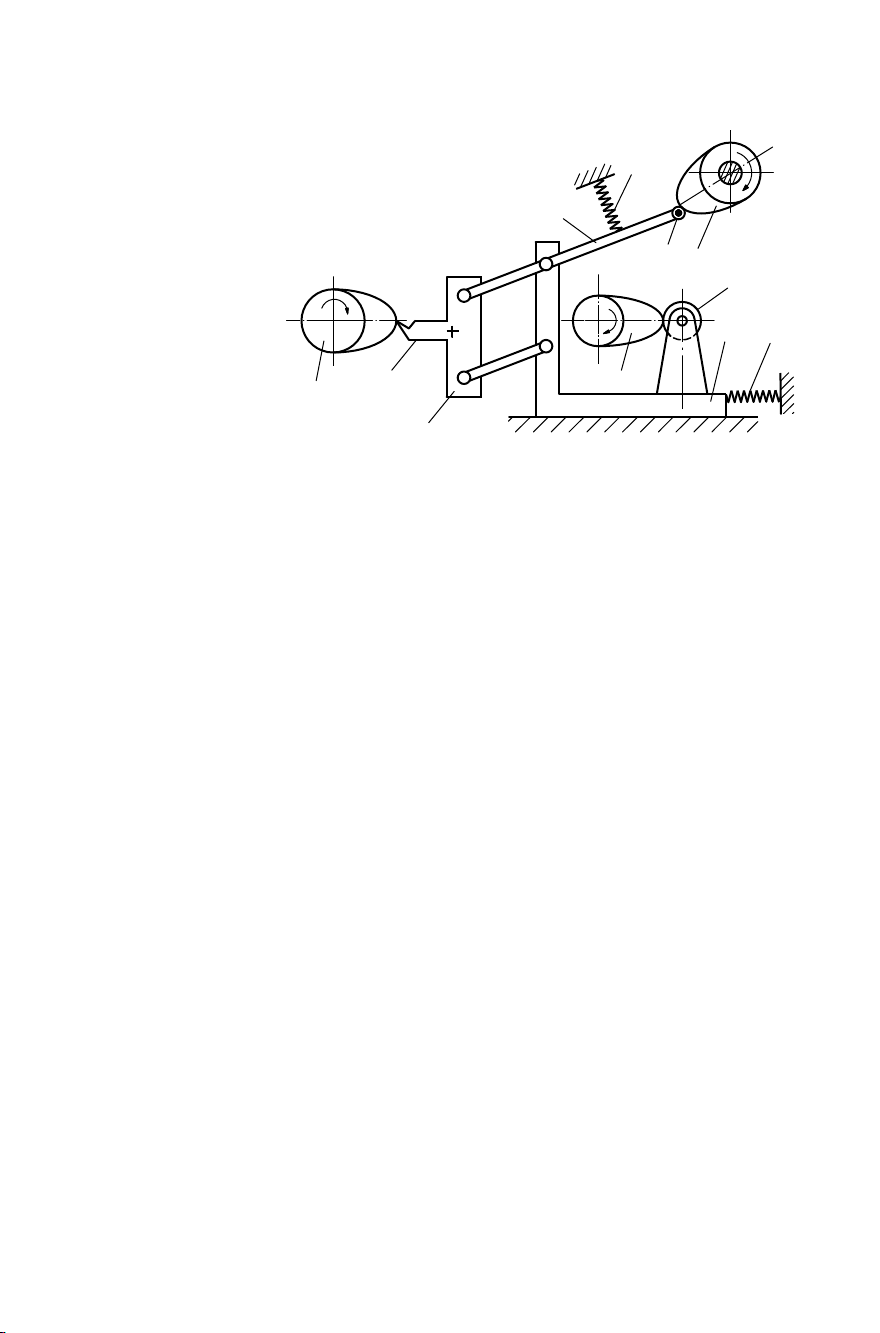
92
+ Phương pháp thứ hai: giá dao lắc lư.
Theo phương
pháp này, ngoài
việc chép hình
thông thường còn
cần tạo nên cho
dao trong quá trình
cắt một sự thay đổi
để phù hợp với
lượng nâng thay
đổi của cam, đảm
bảo góc sau của
dao luôn là hằng
số. Sơ đồ cắt theo
nguyên lý này
được trình bày trên
hình 2.60.
Dao 1 được lắp trên đài gá dao 2 của xe dao. Bàn dao 9 mang đài
gá dao luôn ép chặt vào cam mẫu 3 nhờ lò xo 7 thông qua con lăn 10.
Khi cam 3 quay, do lượng nâng của cam thay đổi, dao 1 cùng đài gá dao
2 và bàn dao 9 ra vào cắt vật gia công 8 có biên dạng phù hợp với biên
dạng phù hợp với biên dạng của cam 3. Trong khi đó, cam 4 cũng quay
đồng bộ với cam 3 và vật gia công 8. Lò xo 5 làm việc ở trạng thái kéo
cần lắc 11 làm cho con lăn 6 luôn tiếp xúc với cam 4. Khi cam 4 quay, do
lượng nâng thay đổi, thông qua cần lắc 11 làm cho đài đá dao 2 lắc lư tạo
nên góc sau luôn là hằng số mặc dù số lượng nâng của cam chi tiết gia
công 8 thay đổi.
Theo phương pháp này biên dạng của trục cam mẫu 3 phải đặc biệt
lớn hơn cam cần gia công để bù trừ vào phần dao lắc lư.
Mài những mặt lệch tâm và mặt cam trên trục có thể thực hiện trên
máy mài tròn ngoài với đồ gá chuyên dùng. Nguyên tắc của những dạng
gia công này là chép hình với cam mẫu có hình dạng ngoài giống như
hình dạng của chi tiết cần gia công.
Hình 2.60: Sơ đồ nguyên lý cắt mặt cam
trên trục bằng phương pháp tiện chép hình
có giá dao lắc lư
6
11
8
10
9
7
5
4
3
2
1
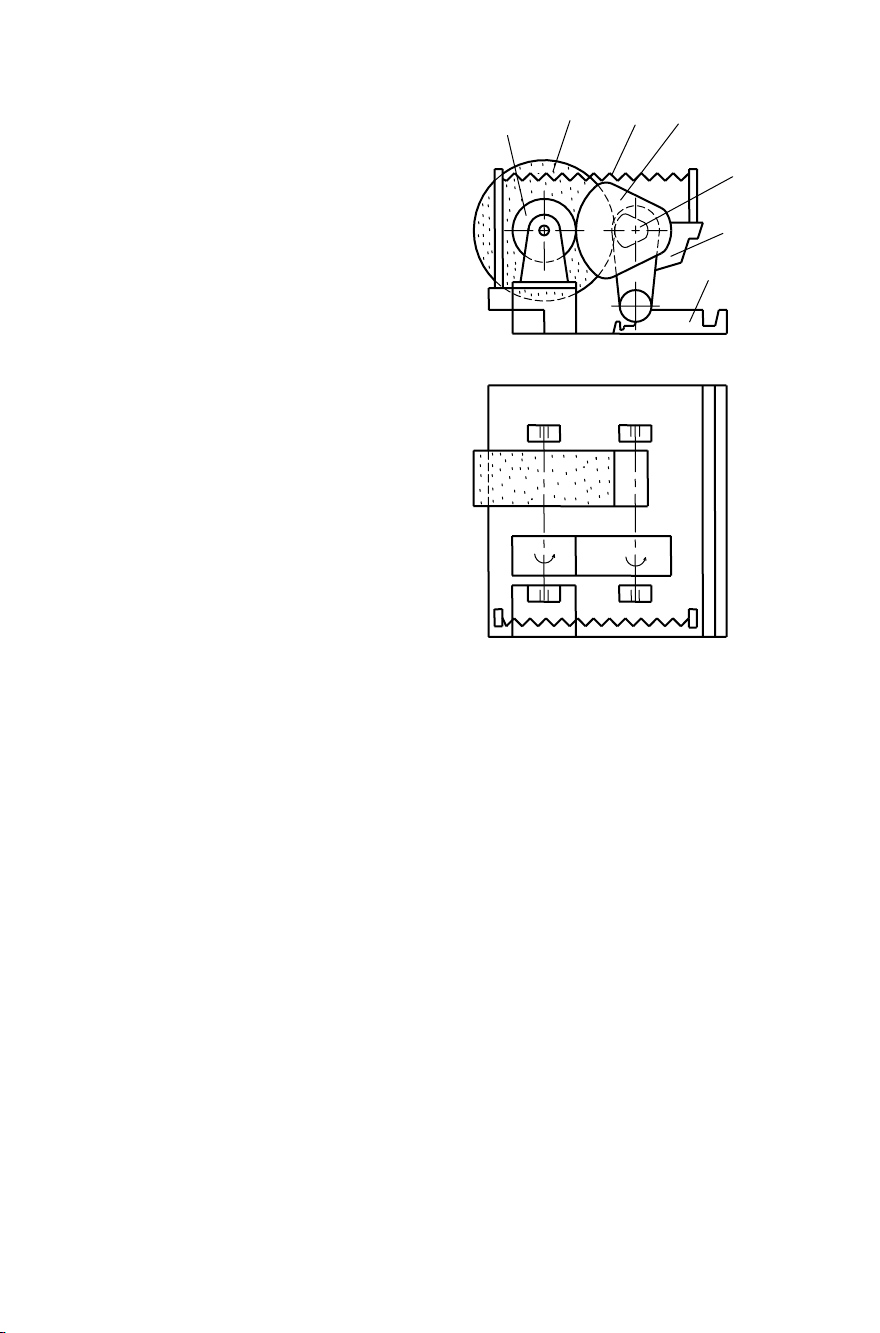
93
Tỉ lệ giữa cam mẫu và
kích thước của chi tiết có thể
lớn hơn, nhỏ hơn hoặc bằng
một. Trên hình 2.61 là sơ đồ
cơ cấu chép hình của đồ gá
mài mặt cam trên máy mài
tròn ngoài.
Trục gia công và cam
mẫu lắp cùng trục và được
lắc trên hai mũi tâm chuyển
động quay của cam mẫu 4 và
con lăn 7 với lò xo 5 làm cho
chuyển động lắc được thực
hiện tạo ra hình dạng của mặt
cam theo hình dạng của cam
mẫu.
Chi tiết gia công được
định vị trên hai mũi tâm,
ngoài ra còn phải khống chế
góc xoay để đảm bào vị trí
góc của các cam trên trục. Để
nâng cao độ chính xác về
hình dáng của chi tiết gia
công, tốc độ quay của chi tiết
nên chọn trong phạm vi
v = 58 m/ph, khi mài tinh
nên chọn v = 23 m/ph.
Gia công các bậc trục lệch tâm (trục khuỷu).
Trong các chi tiết dạng trục thường có loại trục mà các bậc của
chúng không đồng tâm, đó là loại trục khuỷu của động cơ biến chuyển
động thẳng thành chuyển động quay. Ta coi trục khuỷu là loại trục đặc
biệt có tâm bậc trục không trùng với tâm quay của trục. Gọi những bậc
trục trùng với tâm quay của trục là cổ chính và các bậc trục lệch tâm,
được lắp với lỗ tay biên là cổ biên.
Khi gia công cổ biên của trục khuỷu có hai cách gá:
+ Cách thứ nhất: gá lệch cổ chính để đưa tâm cổ biên về tâm quay
của trục chính. Muốn vậy, phải gá tâm cổ chính lệch khỏi tâm trục chính
một đoạn bằng khoảng cách giữa hai tâm của cổ biên và cổ chính.
Hình 2.61: Sơ đồ mài chép hình mặt cam
trên máy mài tròn ngoài
1. Bàn máy
2. Giá lắc để lắp chi tiết
3. Chi tiết; 4. Cam mẫu
5. Lò xo; 6. Đá mài
7. Con lăn tì.
n
n
1
2
3
4
5
6
7
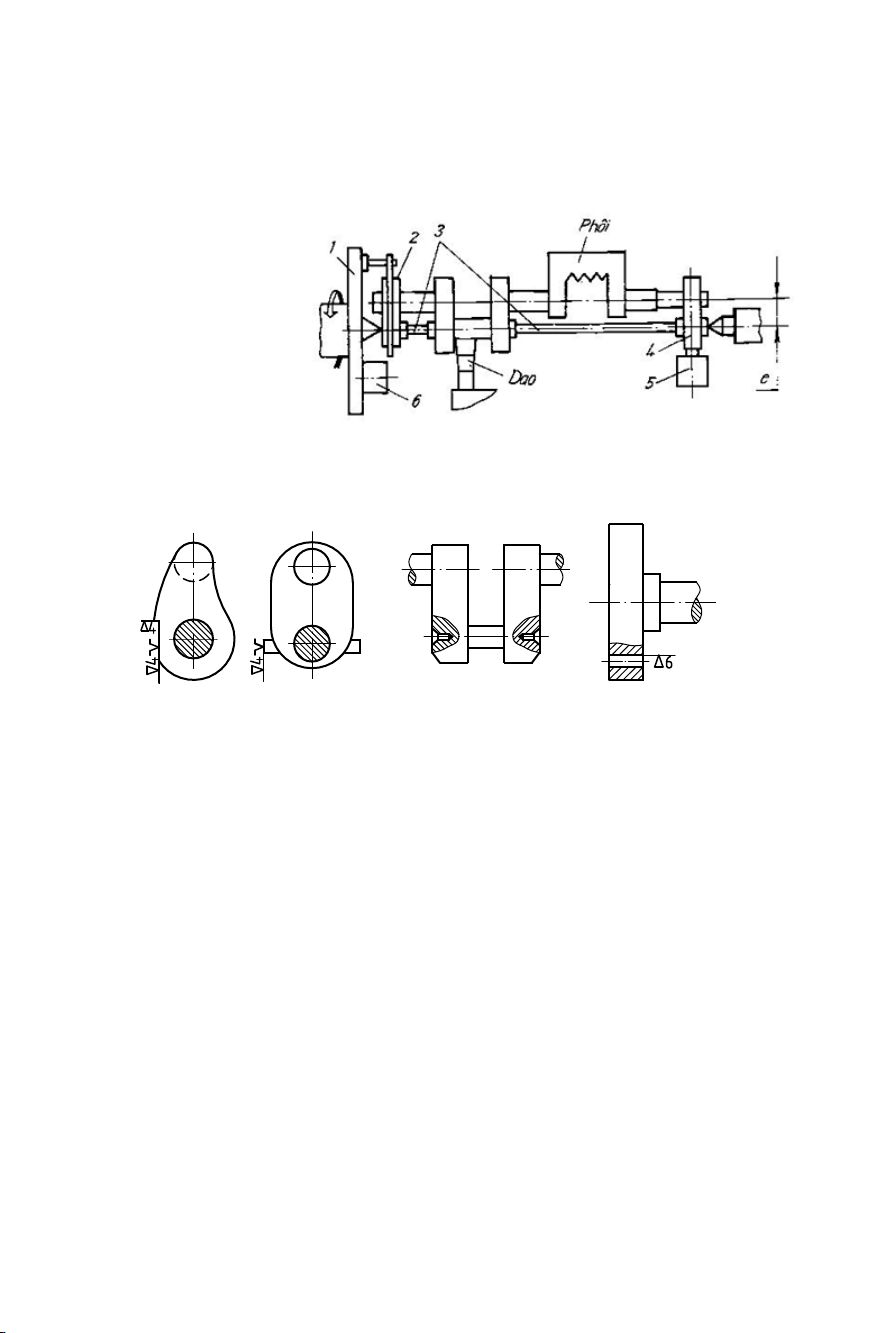
94
Nhưng muốn đưa tâm cổ biên về đúng tâm quay của trục chính máy,
ngoài việc đánh lệch cổ chính còn phải định vị góc xoay (hình 2.62).
Trong sản xuất đơn chiếc, loạt nhỏ việc khống chế góc xoay có thể
thực hiện bằng cách rà đúng trước khi kẹp chặt. Trong sản xuất hàng loạt,
thường hay dùng một
điểm tì nữa trên
khuỷu để khống chế
góc xoay đó. Điểm tì
này thường là mặt
vát trên vai má
khuỷu(hình 2.63a,b),
hoặc lỗ tâm khoan
trên má khuỷu (hình
2.63c), hoặc lợi dụng
một lỗ nhỏ ở mặt đầu bích của trục khuỷu (hình 2.63d).
+ Cách thứ hai: trục khuỷu quay quanh tâm cổ chính. Dao được gá
trên hai trục khuỷu mẫu quay đồng bộ với trục khuỷu gia công (hình
2.64). Cách gá này được thực hiện trên những máy chuyên dùng.
Dao cắt được lắp trên xe dao gắn liền với hai trục khuỷu mẫu đặt
song song với trục khuỷu cần gia công, quay cùng chiều và đồng bộ với
trục khuỷu cần gia công. Khi chúng quay, mũi dao vạch lên quỹ đạo II
còn tâm của cổ biên có quỹ đạo I.
Như vậy, khi trục khuỷu quay hết một vòng, dao cũng cắt hết chu
vi cổ biên. Bằng phương pháp này, tất cả các cổ biên có thể được gia
công cùng một lúc nếu mỗi cổ biên lắp một xe dao.
Nói chung khi gia công cổ biên, chọn chế độ cắt thấp hơn khi gia
công cổ chính. Do lực cắt và lực kẹp chiều trục của mũi tâm trục khuỷu
dễ bị uốn (hình 2.65a) cần chống uốn bằng đai kẹp (hình 2.65b) hoặc
bulông kiểu kích (hình 9.65c) để giữ chi tiết không bị biến dạng trong
quá trình gia công.
Hình 2.63: Điểm tì chống xoay khi tiện cổ biên
a)
b)
c)
d)
Hình 2.62: Sơ đồ định vị khi tiện cổ
biên
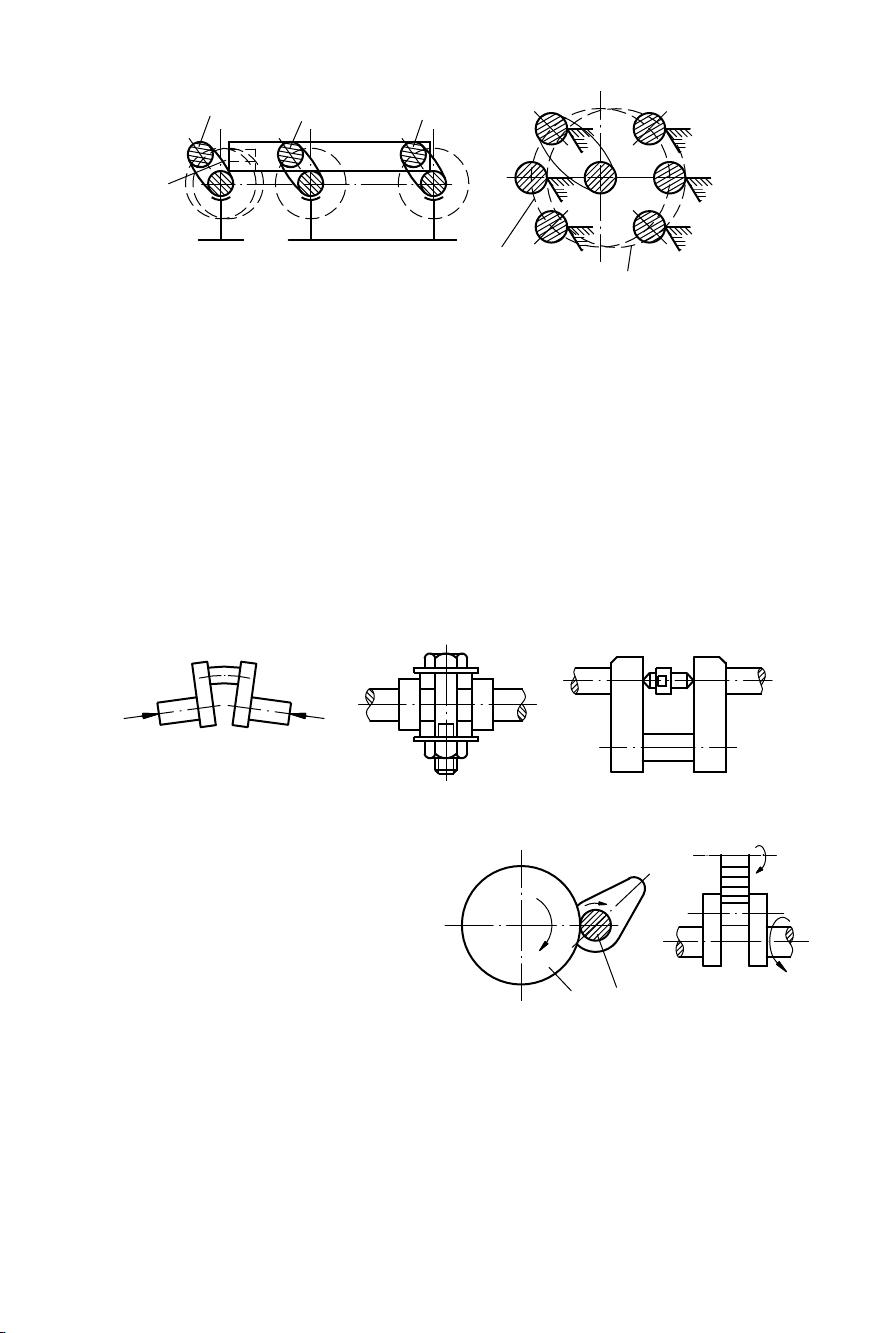
95
Ngoài ra còn có thể gia công cổ biên bằng phương pháp phay trên
máy chuyên dùng với dao phay đĩa đường kính = 4501100 mm, răng
chắp hợp kim cứng (hình 2.66a).
Hiện nay việc gia công trục khuỷu được thực hiện trên trung tâm
gia công CNC (hình 2.66b) theo nguyên tắc tập trung nguyên công. Cổ
khuỷu được phay bằng dao phay mặt đầu (hình 2.66c).
Khi gia công tinh cổ biên
thường dùng phương pháp mài trên
máy mài trục khuỷu chuyên dùng
hoặc trên máy mài tròn ngoài với
đồ gá thích hợp. Cách gá đặt giống
như khi tiện. Mỗi lần định vị khi
mài có thể gia công được các cổ
biên cùng đường tâm. Sau khi mài
được các cổ biên cùng đường tâm
lại phải phân độ đi một góc thích
hợp để gia công các cổ biên cùng
đường tâm khác. Khi mài do đá mài tiến dao ngang nên lực cắt lớn, để
tránh biến dạng tại vị trí đối diện với đá phải dùng các vấu tì đỡ vào cổ
biên (hình 2.67). Biện pháp này cũng cần thiết khi mài các cổ trục.
Hình 2.65: Sự biến dạng của trục khuỷu và biện pháp chống uốn
a)
c)
b)
Hình 2.64: Sơ đồ tiện cổ biên bằng cách gá dao trên hai
trục khuỷu mẫu
1. Trục khuỷu gia công; 2,3. Trục khuỷu mẫu; 4. Dao cắt
I. Quỹ đạo chuyển động của tâm cổ biên.
II. Quỹ đạo chuyển động của mũi dao.
I
II
2
3
4
1
Hình 2.66a) Sơ đồ phay cổ biên
1. Dao; 2. Trục khuỷu.
2
1
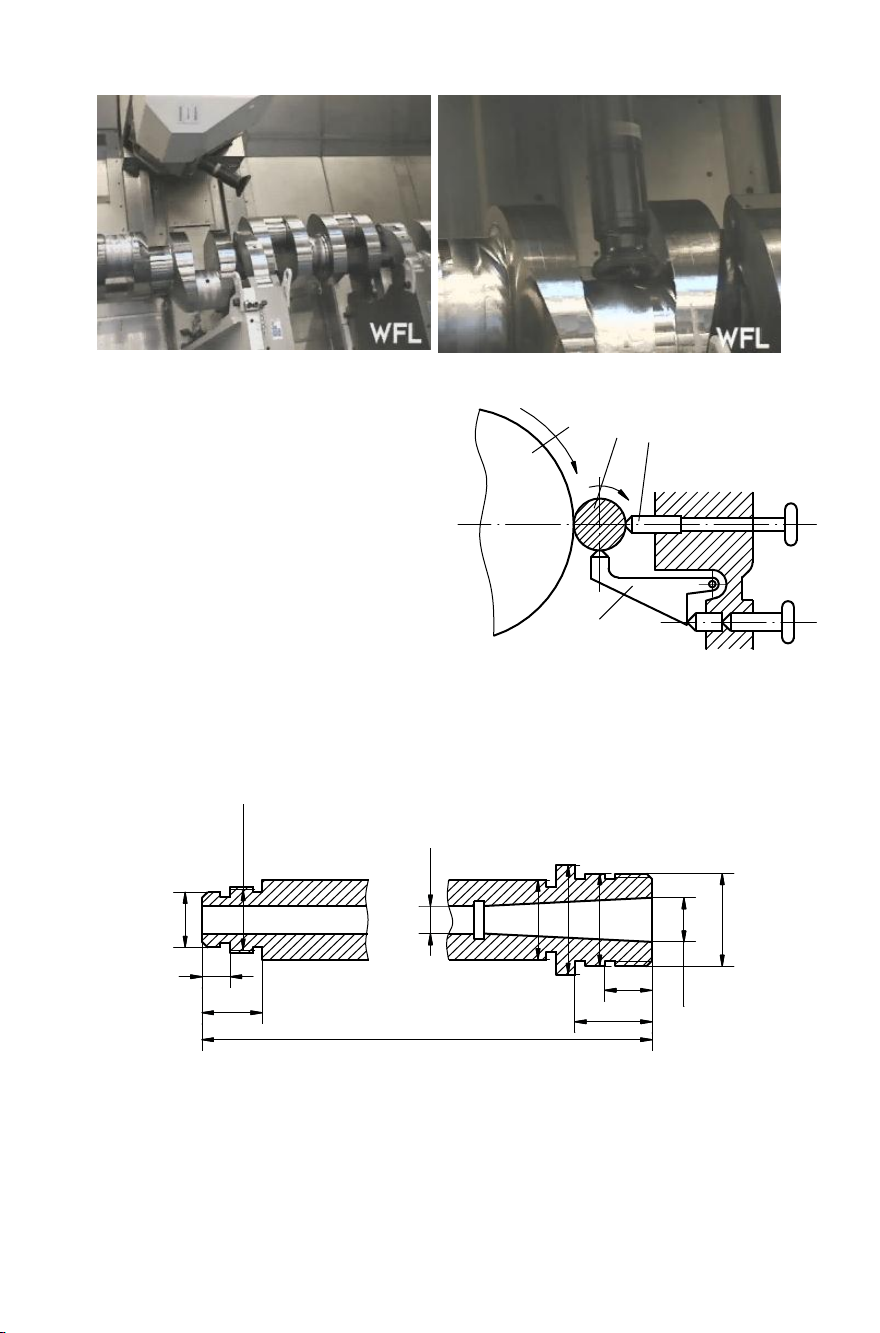
96
e. Gia công các lỗ chính
xác dọc trục
Ở một số loại trục như các
trục chính của máy cắt, và một
vài chi tiết khác như nòng súng,
thường có lỗ rỗng bên trong và
trên đó có những bề mặt côn
hoặc trụ đòi hỏi độ chính xác về
kích thước cũng như độ đồng tâm
so với mặt ngoài của trục. Trên
hình 2.68 trình bày kết cấu của
một loại trục chính của máy cắt
kim loại.
Có thể quan niệm loại trục này cũng chỉ là một dạng trục bậc có lỗ
rỗng bên trong. Vì vậy chỉ cần đề ra biện pháp gia công các lỗ chính xác
bên trong sao cho đồng tâm với mặt ngoài của trục.
Tùy theo dạng của phôi mà ta có biện pháp gia công thích hợp.
Hình 2.67: Sơ đồ bố trí vấu tì tăng
cứng vững khi mài cổ biên
1. Đá mài; 2. Chi tiết;
3,4. Các vấu tì của luynet.
4
3
2
1
Hình 2.68: Kết cấu trục chính của máy 1615, 1615M
44,4
M68x6
70C
88
70C
35
M52x1,5
48H
20
40
35
58
79
6
´
b)
c)
Hình 2.66b,c) Gia công trục khuỷu trên trung tâm CNC
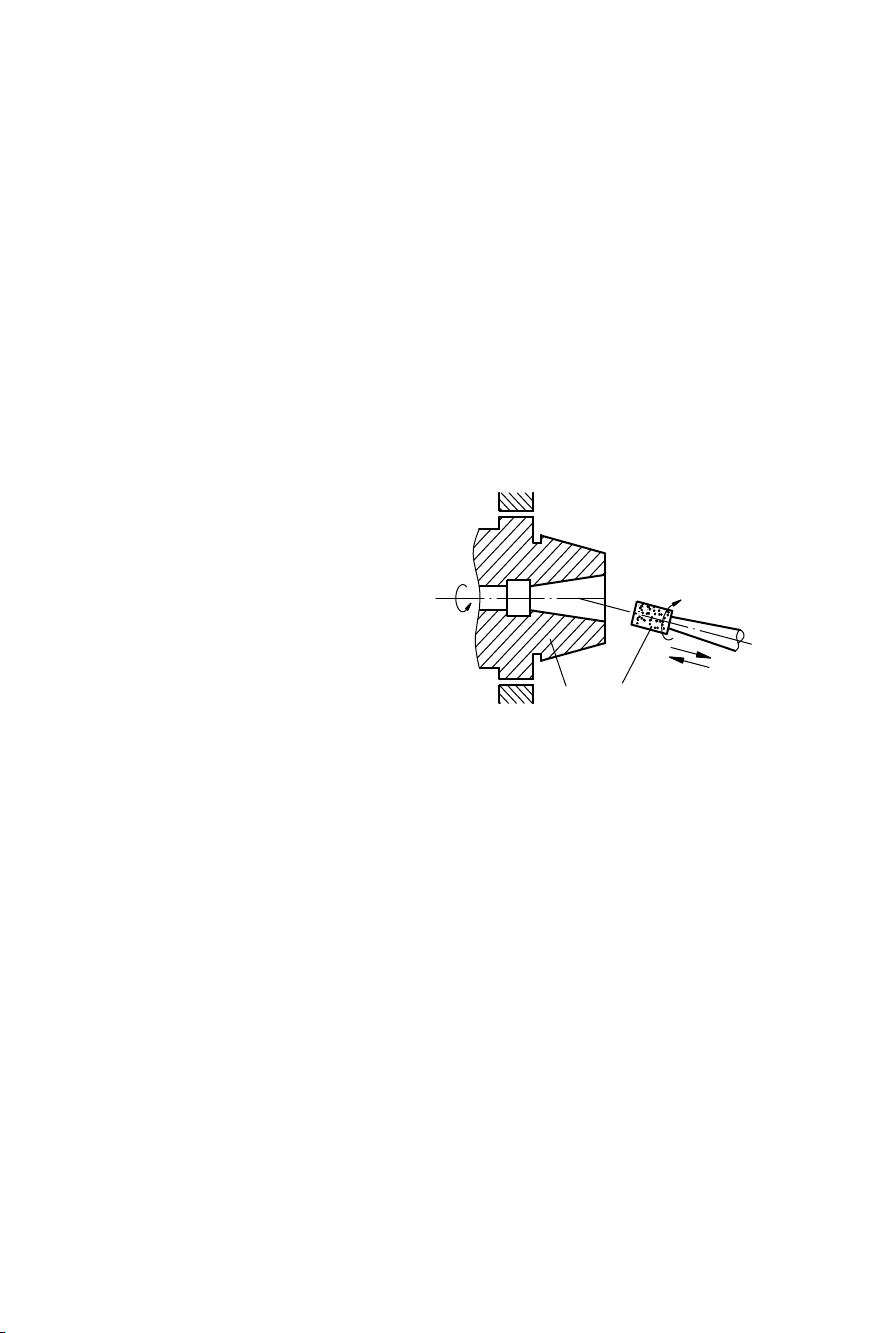
97
- Nếu phôi đặc từ thép cán, rèn hoặc dập thì sau khi tiện thô
được các bậc ngoài của trục, tiến hành gia công thô mặt lỗ bằng khoan
(với lỗ có 1 5d – khoan ruột gà; có 1 > 5d – mũi khoan sâu đặc biệt;
có d = 75100 mm – khoan vòng để lấy lõi). Sau đó gia công tinh lỗ
bằng khoét, doa hoặc tiện trong.
Sau khi có lỗ đã gia công tinh, dùng lỗ định vị để gia công tinh mặt ngoài.
- Nếu phôi đúc đã có lỗ sẵn thì dùng chính ngay lỗ thô đó làm
chuẩn (định vị trên hai mũi tâm khía nhám) để gia công thô các bậc ngoài
của trục. Sau đó dùng mặt ngoài tinh định vị để gia công lỗ. Khi gia công
lỗ bậc cần chú ý: Nếu lỗ có 1 5d dùng các trục doa thường, còn khi 1 >
5d thì dùng dao tiện trong có lắp các dao để đồng thời gia công các bậc.
Sau đó dùng lỗ làm chuẩn tinh (thường là hai lỗ côn ở hai đầu trục) để
gia công tinh mặt ngoài của trục. Đối với chi tiết trục chính của máy cắt
kim loại, phần lỗ côn ở đầu
trục chính yêu cầu có độ côn
chính xác, độ bóng bề mặt
và độ đồng tâm cao hơn so
với các cổ trục. Vì vậy, sau
khi đã có mặt ngoài tinh phải
dùng cổ trục ngoài định vị
(thậm chí phải rà theo mặt
ngoài thật chính xác và dùng
trục côn mẫu để thử) để mài
lỗ côn. Sơ đồ mài được trình
bày trên hình 2.69.
Ngoài chuyển động quay đá mài còn có chuyển động chạy dao
nghiêng một góc (bằng nửa góc côn cần mài), so với tâm chi tiết. Muốn
bảo đảm độ nhẵn bóng cao hơn thì sau khi mài có thể mài nghiền, sau khi
nghiền được rửa sạch.
f. Khoan lỗ vuông góc với đường tâm trục
Để khoan lỗ thường dùng máy khoan. Kiểu máy và cách định vị
phụ thuộc vào hình dạng trục và công dụng của lỗ. Nói chung chi tiết gia
công được định vị trên hai khối V. Để hạn chế bậc tự do chiều trục có thể
lấy gờ của trục làm điểm tì. Cũng có thể định vị trục trên hai mũi tâm
cứng. Trong trường hợp này, tùy theo vị trí và đường kính lỗ cần khoan
mà có thể thêm tì phụ để tăng độ cứng vững khi gia công.
Trong thực tế, có những lỗ xiên một góc so với đường tâm trục.
Khi gia công những lỗ này, việc định vị không khác so với lỗ vuông góc
Hình 2.69: Sơ đồ mài lỗ côn trên trục rỗng
1. Trục gia công; 2. Đá mài.
2
1
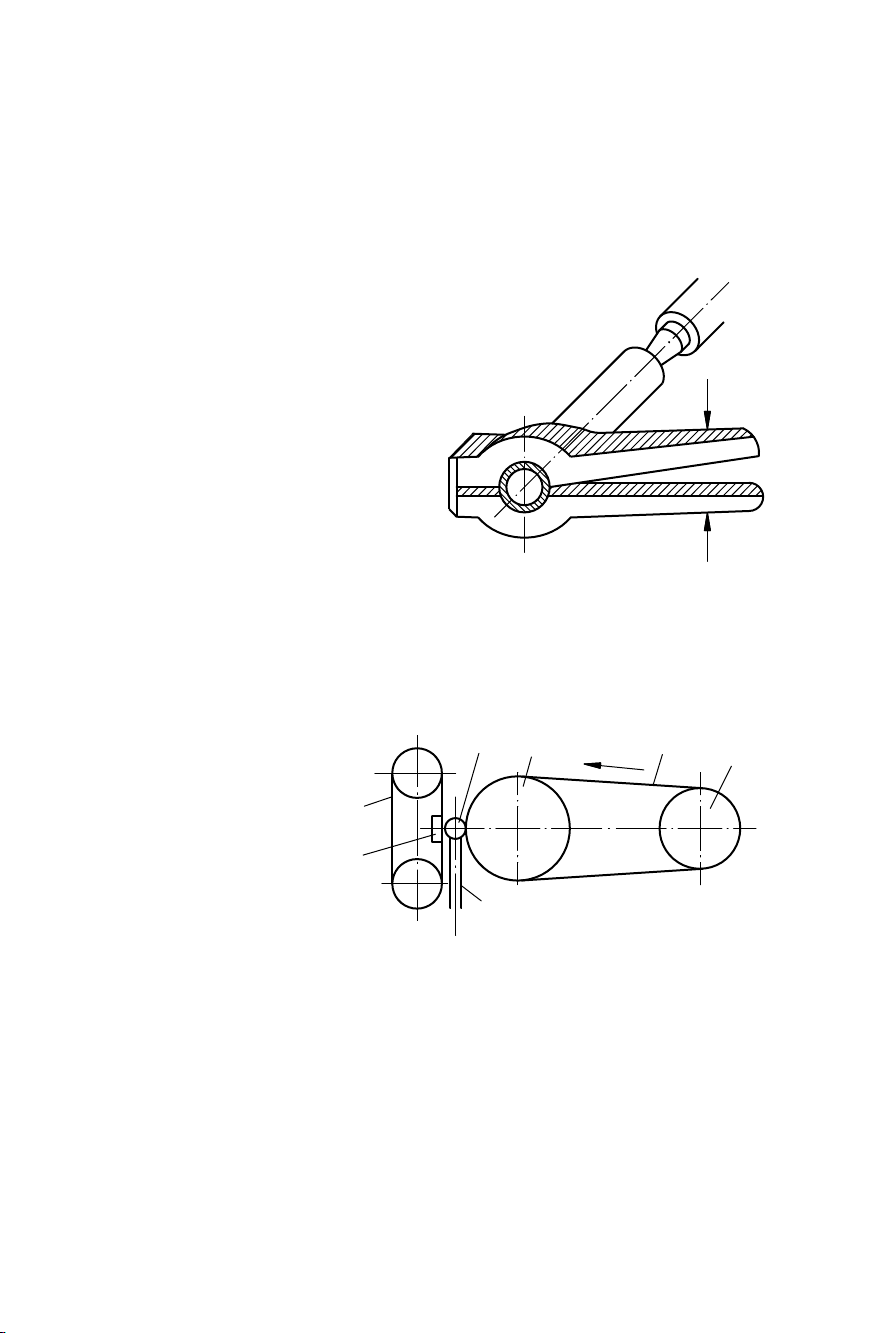
98
trục, chỉ có điều là phải điều chỉnh đồ định vị sao cho lỗ cần gia công phù
hợp với hướng chạy dao của mũi khoan.
g. Gia công tinh lần cuối
Đối với các trục có độ chính xác thông thường, chỉ cần mài tinh là
đủ. Song đối với một số loại trục chính xác cao như trục chính của các
loại máy cắt, trục khuỷu, sau khi mài tinh các cổ trục, phải qua gia công
tinh lần cuối bằng cách
đánh bóng hoặc mài khôn
hoặc mài siêu tinh xác.
Cách thực hiện các
nguyên công này đã được
trình bày kỹ trong bài “Đặc
trưng các phương pháp gia
công bằng cắt gọt”.
Đánh bóng bằng vải
có trát bột mài hạt nhỏ và
dầu nhờn là phương pháp
thủ công dùng trong sản
xuất đơn chiếc. Có thể dùng
đai gỗ kẹp vào cổ trục, ở
phía trong có vành da bôi
bột mài như trên
hình 2.70.
Áp lực và
chuyển động chạy
dao do tay người
thực hiện, chuyển
động quay của chi
tiết nhờ máy vạn
năng.
Để tăng năng
xuất có thể đánh
bóng trục trên máy
đánh bóng chuyên
dùng. Trên hình 2.71 trình bày sơ đồ nguyên lý của máy đánh bóng
không tâm bằng đai mài.
Việc gia công thực hiện bởi đai mài 1 lắp trên hai con lăn 2 và 3.
Chi tiết gia công 6 được đặt trên thanh đỡ 7 và quay nhờ đai dẫn 4. Để
gia công được, phải tạo ra áp lực nhờ miếng tì 5.
Hình 2.71: Sơ đồ nguyên lý máy đánh bóng
không tâm
1. Đai mài; 2,3. Con lăn; 4. Đai mài dẫn; 5.
Miếng tì; 6. Chi tiết gia công; 7. Thanh đỡ
7
3
1
4
5
2
6
Hình 2.70: Sơ đồ đánh bóng
trục bằng tay
P
P
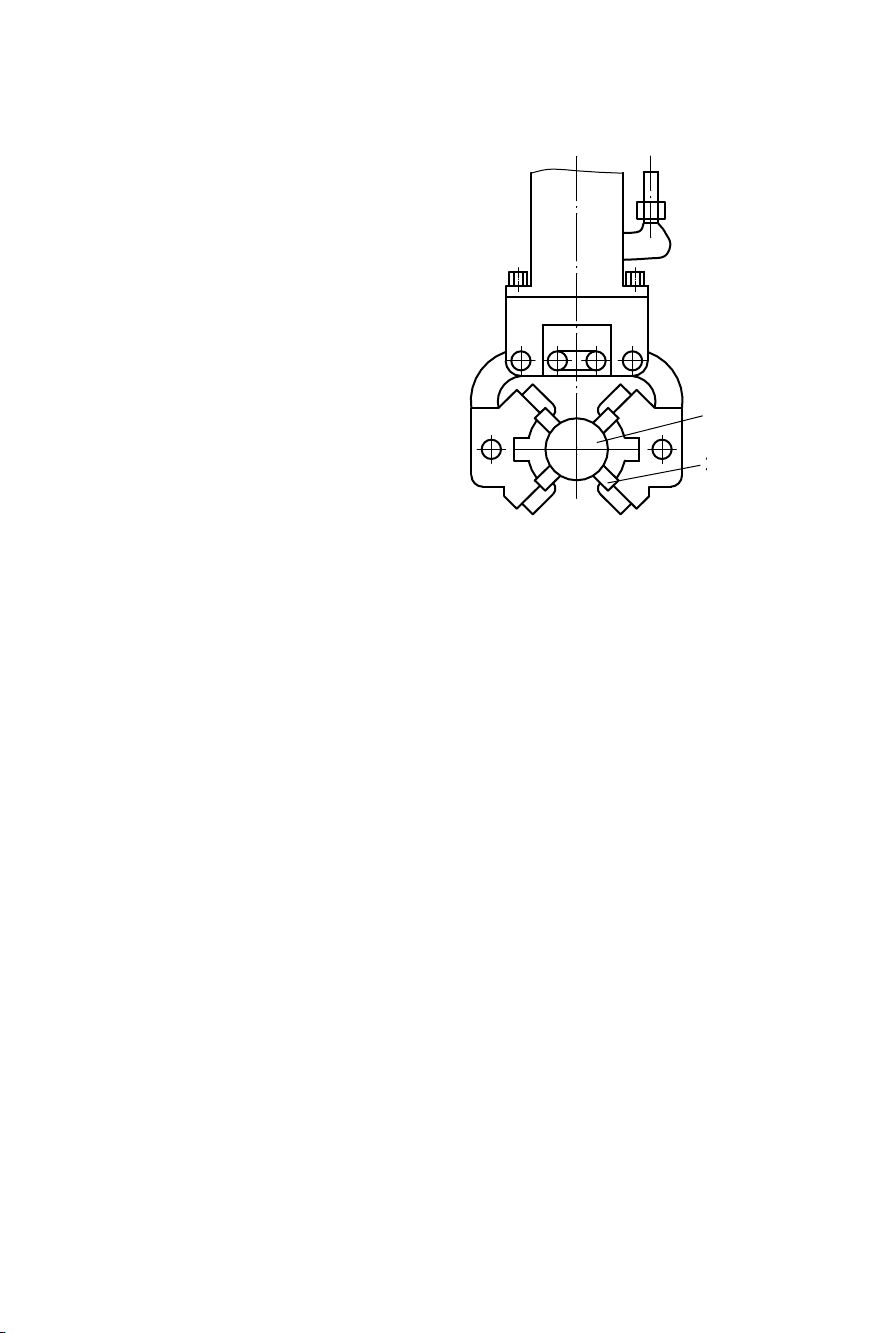
99
Muốn có năng suất cao hơn , có thể thay việc đánh bóng bằng mài
khôn trục. Trên h
ình 2.72 trình bày sơ đồ nguyên lý một đầu khôn để gia
công trục.
Đầu mài khôn được
nối tùy động với máy và
chuyển động dọc đi lại. Chi
tiết được gá vào mũi tâm
và quay tròn. Muốn có chất
lượng bề mặt cao, cũng có
thể dùng phương pháp mài
siêu tinh xác. Quá trình cắt
cũng dùng những thanh đá
như mài khôn nhưng có
thêm một chuyển động lắc
(dao động dọc trục). Nhờ
chuyển động này, các vết
mài xóa lên nhau nên đạt
độ nhám bề mặt cao.
2.3.5. Kiểm tra trục
Đối với các chi tiết dạng trục thường phải kiểm tra kích thước, độ
nhám bề mặt, hình dáng hình học bề mặt.
- Kiểm tra kích thước bao gồm kích thước đường kính và chiều dài
các bậc trục, kích thước then, then hoa và ren trên trục v.v… khi dung sai
các kích thước này lớn hơn 0,02mm có thể dùng thước cặp. Khi dung sai
kích thước nhỏ hơn 0,02mm có thể dùng panme, calip, đồng hồ so. Nếu
yêu cầu chính xác cao, dùng dụng cụ quang học. Trong sản xuất lớn dùng
đồ gá chuyên dùng để kiểm tra.
- Kiểm tra hình dạng hình học của các cổ trục được thực hiện nhờ
đồng hồ so. Chi tiết kiểm ra được gá trên hai mũi tâm của máy tiện hay
đồ gá chuyên dùng. Kiểm tra ở một tiết diện đánh giá được độ ô van, đa
cạnh. Kiểm tra ở nhiều tiết diện dọc trục suy ra độ côn.
- Kiểm tra vị trí tương quan giữa các bề mặt bao gồm:
+ Kiểm ta độ dao động giữa các cổ trục được thực hiện bằng cách
đặt trục lên khối V, còn đầu đo của đồng hồ thì tì vào cổ trục cần đo.
Hiệu số giữa hai chỉ số lớn nhất và nhỏ nhất trên đồng hồ khi quay trục đi
một vòng xác định trị số dao động đó.
Hình 2.72: Sơ đồ đầu khôn để khôn cổ trục
1. Chi tiết gia công;
2. Thanh đá trên đầu khôn.
1
2
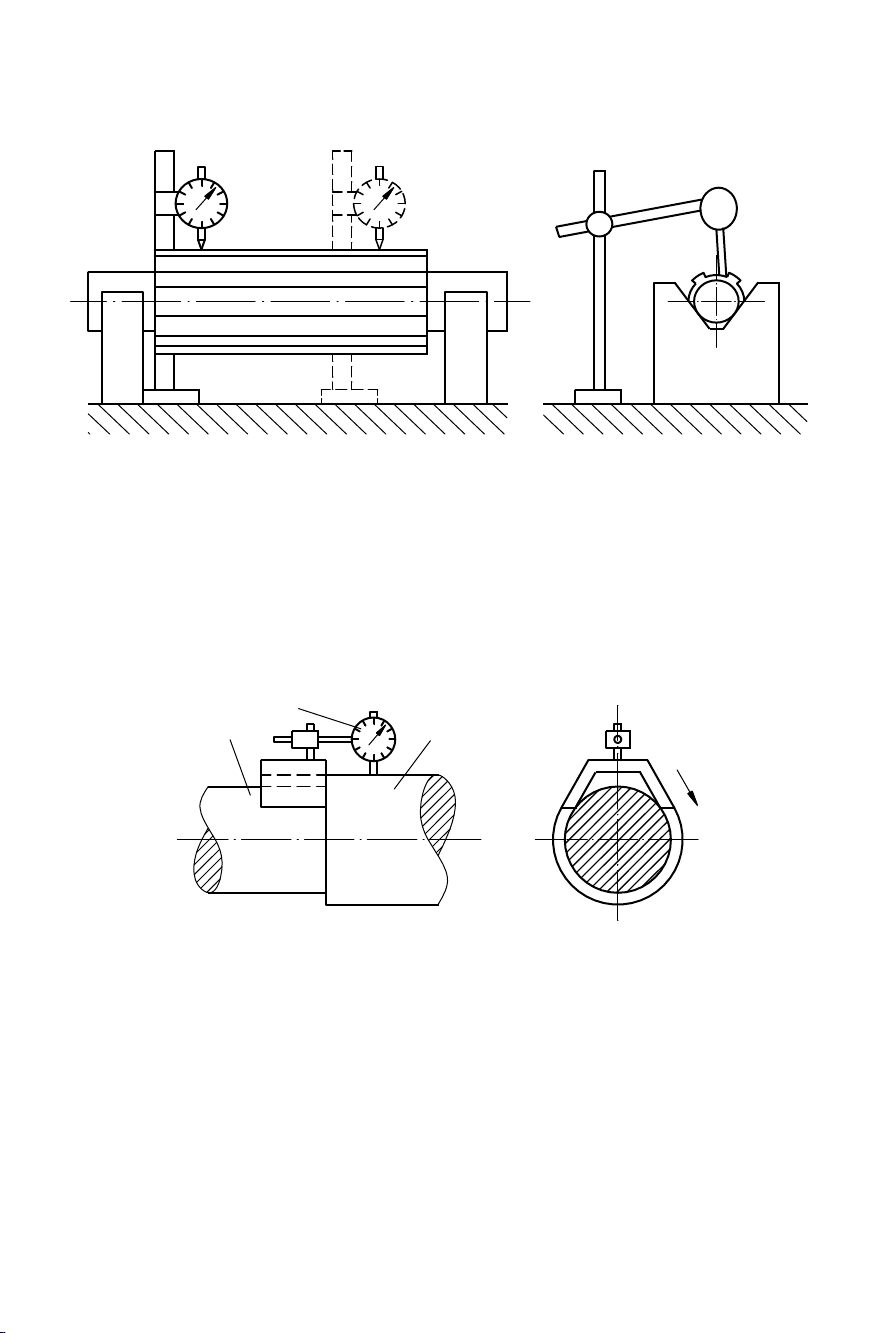
100
+ Độ song song của các then, then hoa (đỉnh, chân và mặt bên) với
đường tâm của các cổ đỡ được xác định nhờ đồng hồ đo ở hai vị trí (hình 2.73).
Với sơ đồ này cũng có thể kiểm tra được độ dao động giữa đỉnh và
chân của then hoa.
+ Kiểm tra độ đồng tâm của các cổ trục nhờ đồ gá mang đồng hồ so
quay quanh một bậc trục trong khi đó mũi tì của đồng hồ tì vào bậc trục
cần kiểm tra (hình 2.74).
2.4. QUY TRÌNH CÔNG NGHỆ GIA CÔNG CÁC CHI TIẾT
DẠNG BẠC
Bạc là chi tiết được dùng rộng rãi trong ngành chế tạo máy. Đó là
những chi tiết hình ống tròn, thành mỏng, mặt đầu có vai hoặc không có
vai, mặt trong có thể trụ hoặc côn; bạc có thể nguyên hoặc xẻ rãnh, mặt
Hình 2.73: Sơ đồ kiểm tra độ song song của then
hoa với đường tâm trục
Hình 2.74: Sơ đồ kiểm tra độ đồng tâm giữa hai cổ trục
1.Cổ trục đo; 2. Cổ trục chuẩn; 3. Đồng hồ so
2
3
1
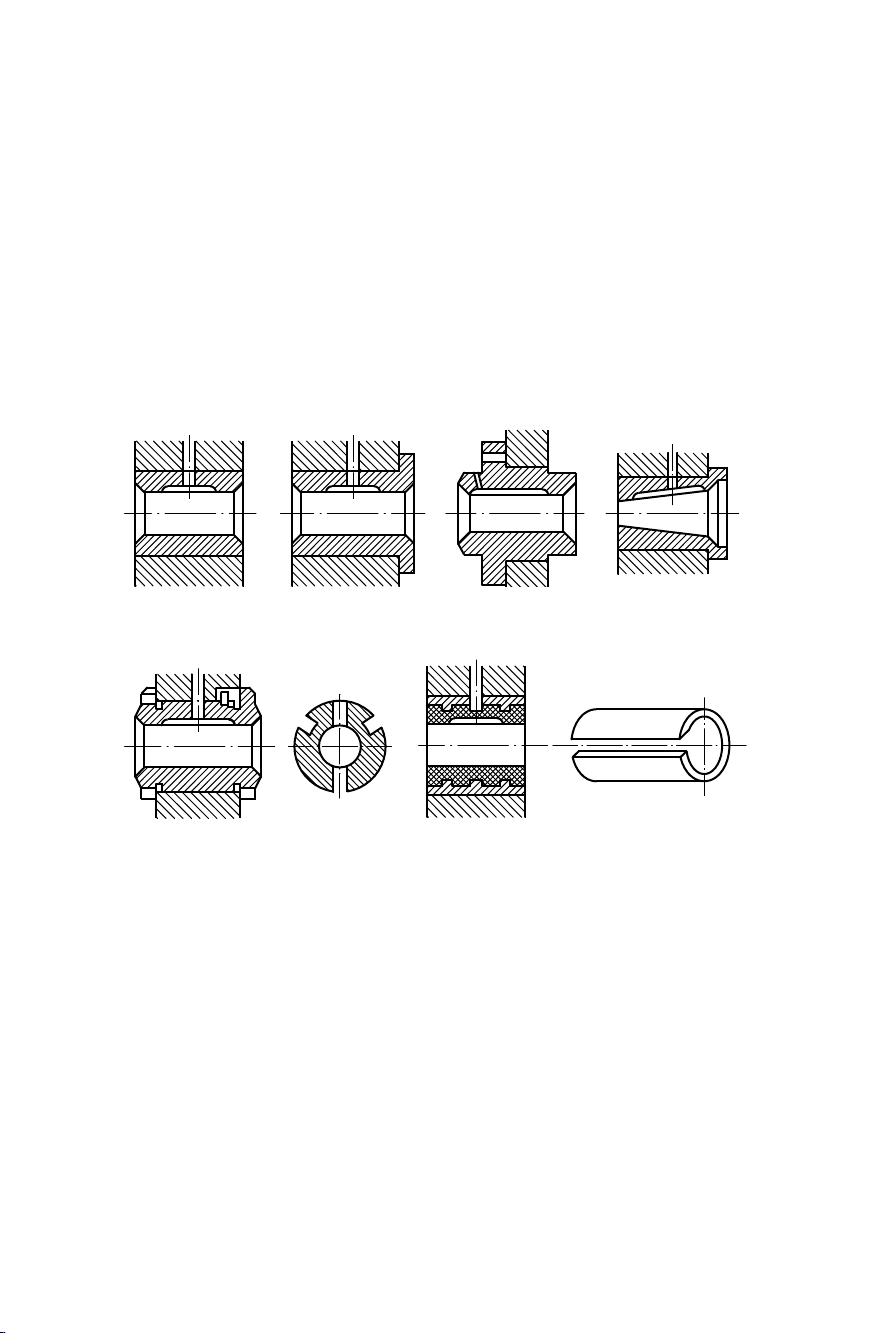
101
làm việc của bạc có rãnh dầu, trên bạc có lỗ ngang để tra dầu. Trên hình
2.75 trình bày kết cấu của các loại bạc khác nhau.
Về mặt kết cấu có thể chia các chi tiết dạng bạc ra các loại như sau:
- Loại bạc trơn không có gờ (hình 2.75a).
- Loại bạc có gờ hoặc mặt bích (hình 2.75b, c).
- Loại bạc có lỗ hình côn (hình 2.75d).
- Loại bạc có xẻ rãnh (hình 2.75đ).
- Loại bạc có lát thêm lớp hợp kim chống mòn (hình 2.75e).
- Loại bạc mỏng có xẻ rãnh (hình 2.75g).
Nếu dựa vào máy cắt để gia công các nguyên công chính của bạc,
có thể chia bạc ra làm 6 nhóm theo kích thước đường kính gồm: dưới 25;
2532; 3240; 4050;5065;65100mm.
Đặc trưng quan trọng về kích thước của bạc là tỉ số giữa chiều dài
và đường kính ngoài lớn nhất của chi tiết, tỉ số đó là: 0,5 3,5.
2.4.1. Điều kiện kỹ thuật
Khi chế tạo chi tiết dạng bạc, yêu cầu kỹ thuật quan trọng nhất là
độ đồng tâm giữa mặt ngoài và mặt lỗ, cũng như độ vuông góc giữa mặt
đầu và đường tâm. Cụ thể là phải đảm bảo các điều kiện như sau:
- Đường kính mặt ngoài của bạc đạt cấp chính xác 710.
Hình 2.75: Các dạng kết cấu của bạc
a)
b)
c)
d)
đ)
g)
e)
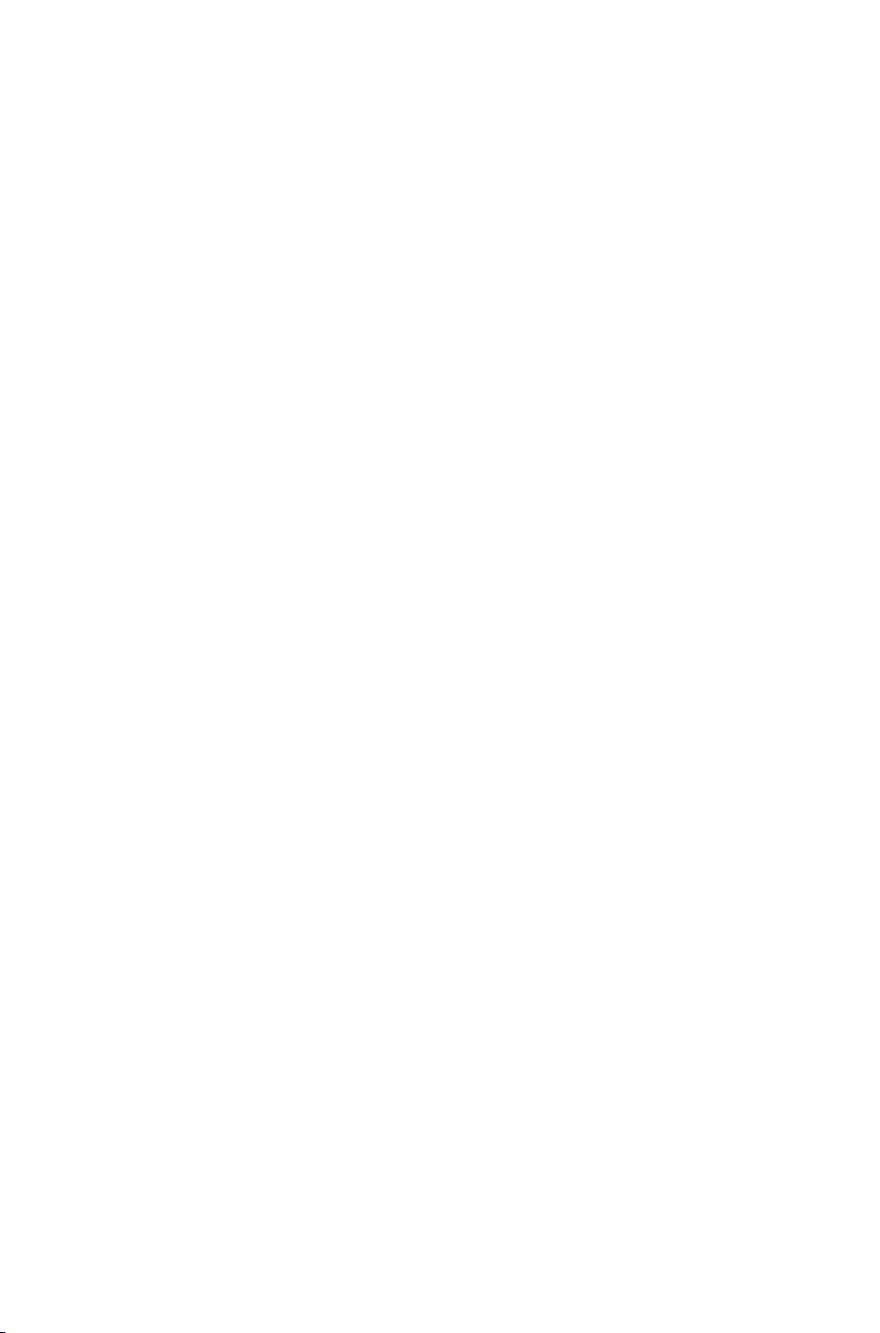
102
- Đường kính lỗ đạt cấp chính xác 7, đôi khi cấp 10, đối với các lỗ
bạc cần lắp ghép chính xác có thể yêu cầu cấp 5.
- Độ dày thành bạc cho phép sai lệch trong khoảng 0,030,15mm.
- Độ đồng tâm giữa mặt ngoài và mặt lỗ bạc tùy từng điều kiện
làm việc của bạc mà quy định cụ thể, thông thường độ không đồng tâm
này lớn hơn 0,015mm.
- Độ không vuông góc giữa mặt đầu và đường tâm lỗ nằm trong
khoảng (0,10,2mm)/100mm bán kính. Với loại bạc chịu tải trọng theo
chiều trục thì độ không vuông góc này từ (0,020,03)/100mm bán kính.
- Độ nhám bề mặt thường cho:
+ Với bề mặt ngoài cần đạt R
a
=2,5.
+ Với bề mặt lỗ tùy theo yêu cầu mà cho: R
a
=2,50,63, đôi khi
R
a
=0,32.
+ Với mặt đầu R
z
=4010; R
a
=2,5.
2.4.2. Vật liệu và phôi
Vật liệu thường dùng để chế tạo các chi tiết dạng bạc là thép, đồng
thau, đồng đỏ, gang và các hợp kim đặc biệt khác. Ngoài ra còn dùng
chất dẻo và gốm sứ để chế tạo một số bạc đặc biệt.
Việc chọn phôi để chế tạo các chi tiết dạng bạc phụ thuộc vào điều
kiện làm việc, hình dạng và sản lượng của nó, cụ thể là:
Với bạc có đường kính lỗ nhỏ hơn 20mm thường dùng thép thanh
định hình và thép thanh cán nóng hoặc phôi đúc đặc (không có lỗ sẵn).
Với bạc có đường kính lỗ lớn hơn 20mm thường dùng các phôi ống hoặc
phôi đúc có lỗ sẵn. Trong trường hợp đó, tùy theo sản lượng và yêu cầu
kỹ thuật cũng như điều kiện sản xuất mà có thể đúc trong khuôn cát (làm
khuôn bằng máy) hoặc có thể đúc trong khuôn kim loại, đúc li tâm hay
đúc áp lực.
Những bạc có thành mỏng và xẻ rãnh thường làm bằng đồng thau
hoặc đồng đỏ, cũng có thể dùng các tấm kim loại cuốn lại.
Với những bạc bằng vật liệu sứ hoặc chất dẻo thường được làm
bằng cách ép và sau đó thiêu kết. Những phôi ép và đúc áp lực đều có thể
tạo sẵn được các lỗ có đường kính nhỏ tới 3mm hoặc nhỏ hơn nữa.
2.4.3. Tính công nghệ trong kết cấu của bạc
Cũng như các chi tiết dạng khác, tính công nghệ trong kết cấu của
bạc có ý nghĩa quan trọng đối với việc gia công để đạt các yêu cầu kỹ
thuật cần thiết.
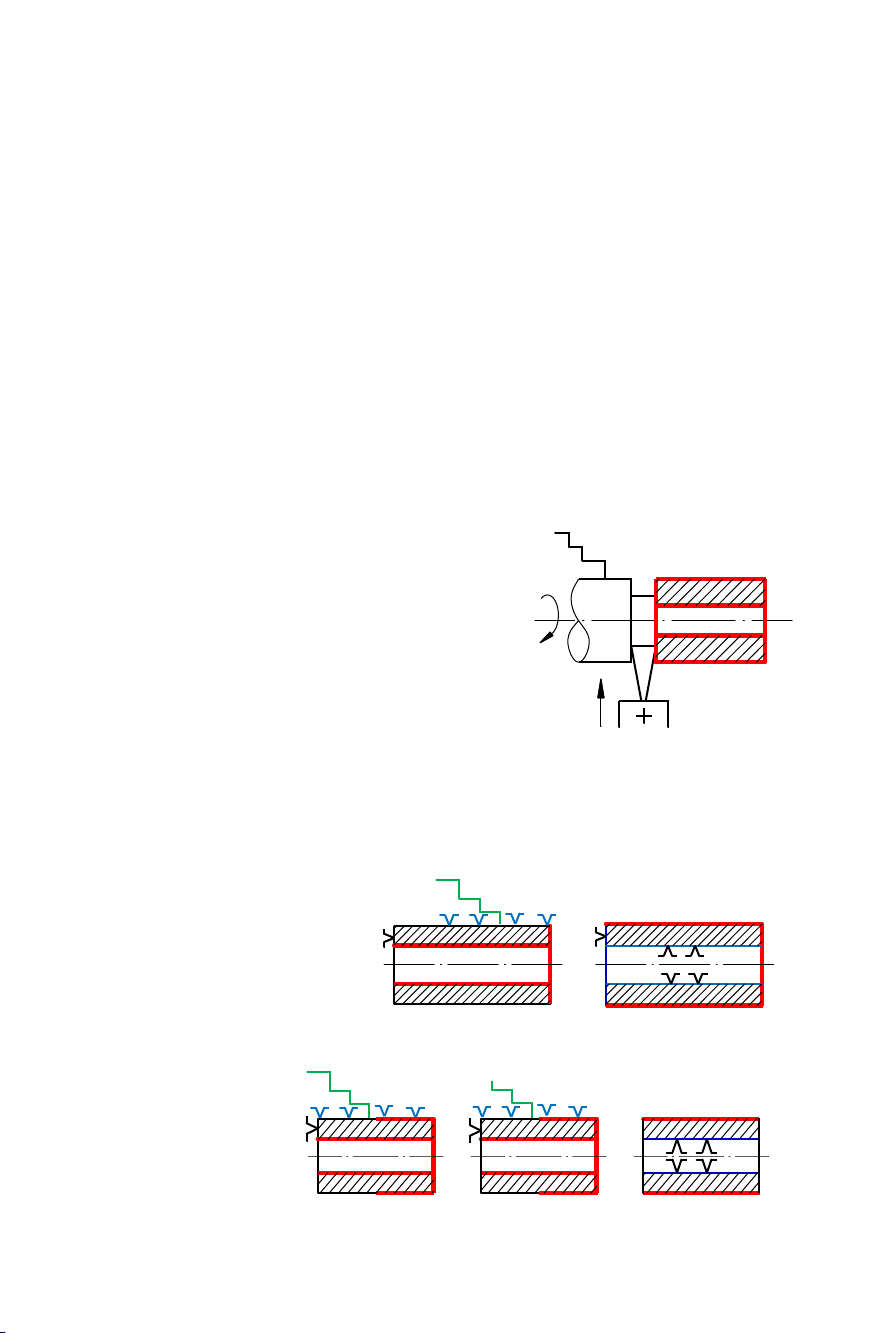
103
Trước hết cần chú ý đến đặc trưng quan trọng đối với bạc là tỉ số
giữa chiều dài và đường kính ngoài lớn nhất của chi tiết. Tỉ số đó phải
nằm trong giới hạn 0,53,5.
Tiếp đến phải chú ý đến kích thước lỗ của bạc bởi vì cùng một
đường kính gia công lỗ bao giờ cũng khó hơn gia công trục.
Bề dày của thành bạc cũng không nên mỏng quá để tránh biến dạng
khi gia công và nhiệt luyện.
2.4.4. Quy trình công nghệ khi gia công bạc
2.4.4.1. Chuẩn định vị khi gia công các mặt chính của bạc
Khi gia công bạc cần phải đảm bảo hai điều kiện kỹ thuật cơ bản
của bạc là độ đồng tâm giữa mặt ngoài và mặt lỗ, độ vuông góc giữa
đường tâm lỗ và mặt đầu của bạc. Các bề mặt này là những mặt chính
của bạc.
Hai điều kiện kỹ thuật trên đây có thể giải quyết bằng một trong
các phương pháp sau:
- Gia công cả mặt ngoài, lỗ và mặt đầu
trong cùng một lần gá (hình 2.76).
Phương án gia công tất cả các mặt
chính trong một lần gá có thể thực hiện khi
chế tạo các bạc bằng phôi thanh hoặc phôi
ống với việc cắt đứt ở bước cuối cùng. Đối
với các phôi đúc từng chiếc, muốn gia công
tất cả các mặt chính sau một lần gá, cần phải
tạo nên các vấu lồi dài thêm để làm chuẩn,
điều đó sẽ tăng phế liệu và giảm hệ số sử
dụng vật liệu. Phương pháp này được dùng trong sản xuất đơn chiếc.
- Gia công tất cả các
mặt chính sau hai lần gá
đặt hoặc là sau hai nguyên
công trong đó có một lần
định vị vào lỗ để gia công
tinh mặt ngoài (hình 2.77).
- Gia công
tất cả các mặt
chính sau ba lần gá
đặt hoặc là sau ba
nguyên công trong
đó có một lần định
Hình 2.76: Gia công các
mặt chính của bạc trong
cùng một lần gá.
Hình 2.78: Gia công các mặt chính sau ba lần gá
Hình 2.77: Gia công các mặt chính của bạc
sau hai lần gá.
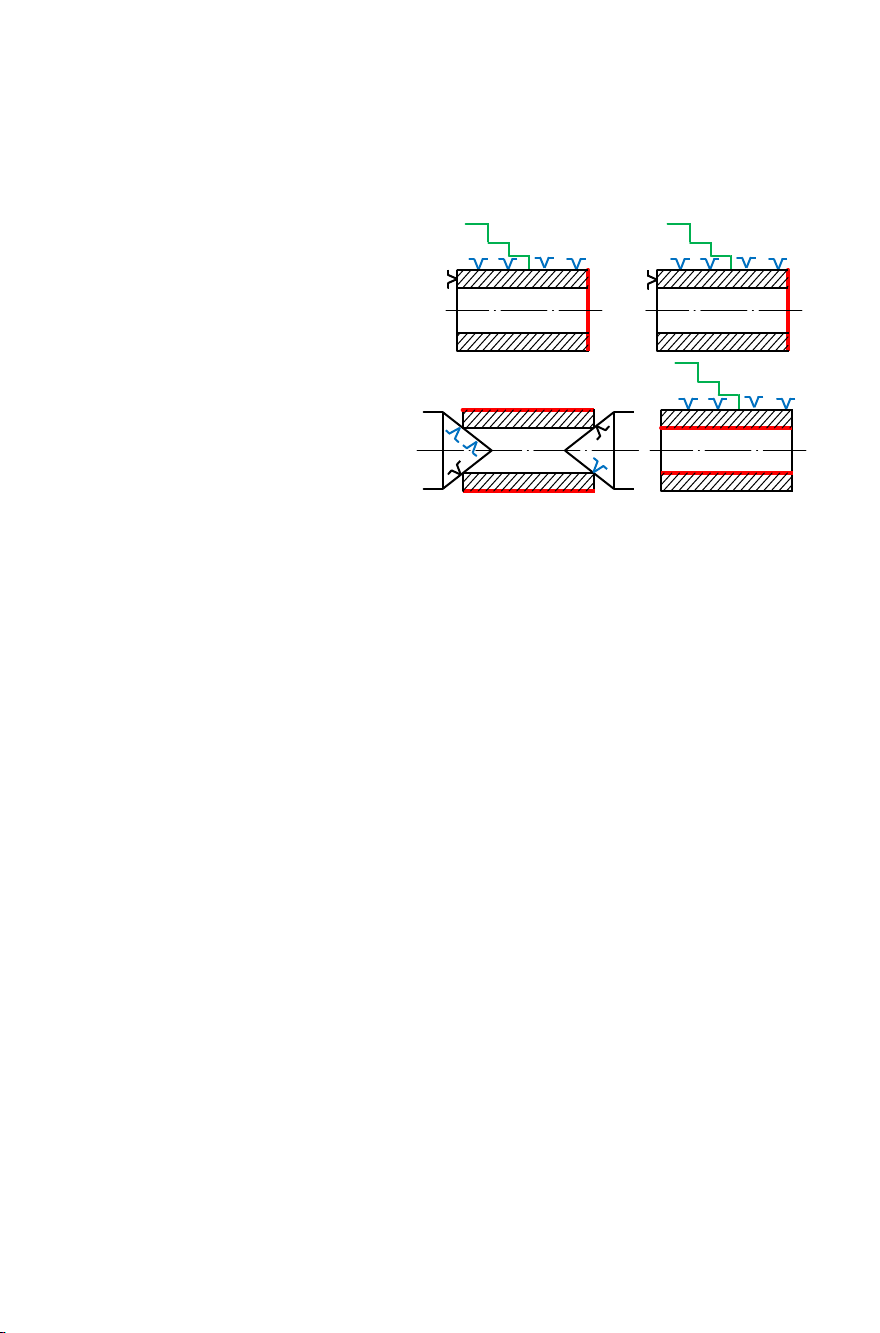
104
vị vào lỗ để gia công tinh mặt ngoài (hình2.78).
- Gia công tất cả các mặt chính sau bốn lần gá đặt hay là sau bốn
nguyên công trong đó có một lần định vị vào mặt ngoài để gia công tinh
lỗ (hình 2.79).
Nếu như có kết cấu mũi
tâm thích hợp thì có thể thực
hiện gia công hai mặt đầu cùng
lần gá với gia công mặt ngoài.
Từ các phương pháp giải quyết
độ đồng tâm ở trên, ta thấy rằng
việc định vị vào mặt lỗ bạc để
gia công mặt ngoài có ưu điểm
hơn so với định vị vào mặt
ngoài để gia công lỗ vì nếu định
vị bằng mặt lỗ, có thể dùng trục
gá đàn hồi thì sai số gá đặt hoặc
không có (nếu dùng chống tâm)
hoặc có trị số rất nhỏ (nếu kẹp chặt trục gá đàn hồi đó lên mâm cặp).
Ngoài ra khi dùng lỗ tâm làm chuẩn để gia công mặt ngoài thì độ lệch
tâm giữa lỗ và mặt ngoài được loại bỏ.
Để gia công các mặt tiếp theo của bạc thì có thể chọn mặt trong và
mặt đầu hoặc mặt ngoài và mặt đầu của bạc làm chuẩn tùy theo kết cấu
và vị trí của mặt cần gia công.
2.4.4.2. Trình tự gia công các bề mặt
Khi lập trình tự gia công các bề mặt và chọn thiết bị cần dựa vào
hình dáng của phôi và sản lượng của chúng. Tuy nhiên trình tự gia công
các bề mặt của bạc thường như sau:
- Gia công các mặt chính của bạc.
- Khoan các lỗ phụ.
- Gia công các mặt định hình.
- Nhiệt luyện.
- Gia công tinh các lỗ, các mặt ngoài.
- Đánh bóng các mặt yêu cầu có độ bóng cao.
- Kiểm tra.
Hình 2.79: Gia công các mặt chính
sau bốn lần gá
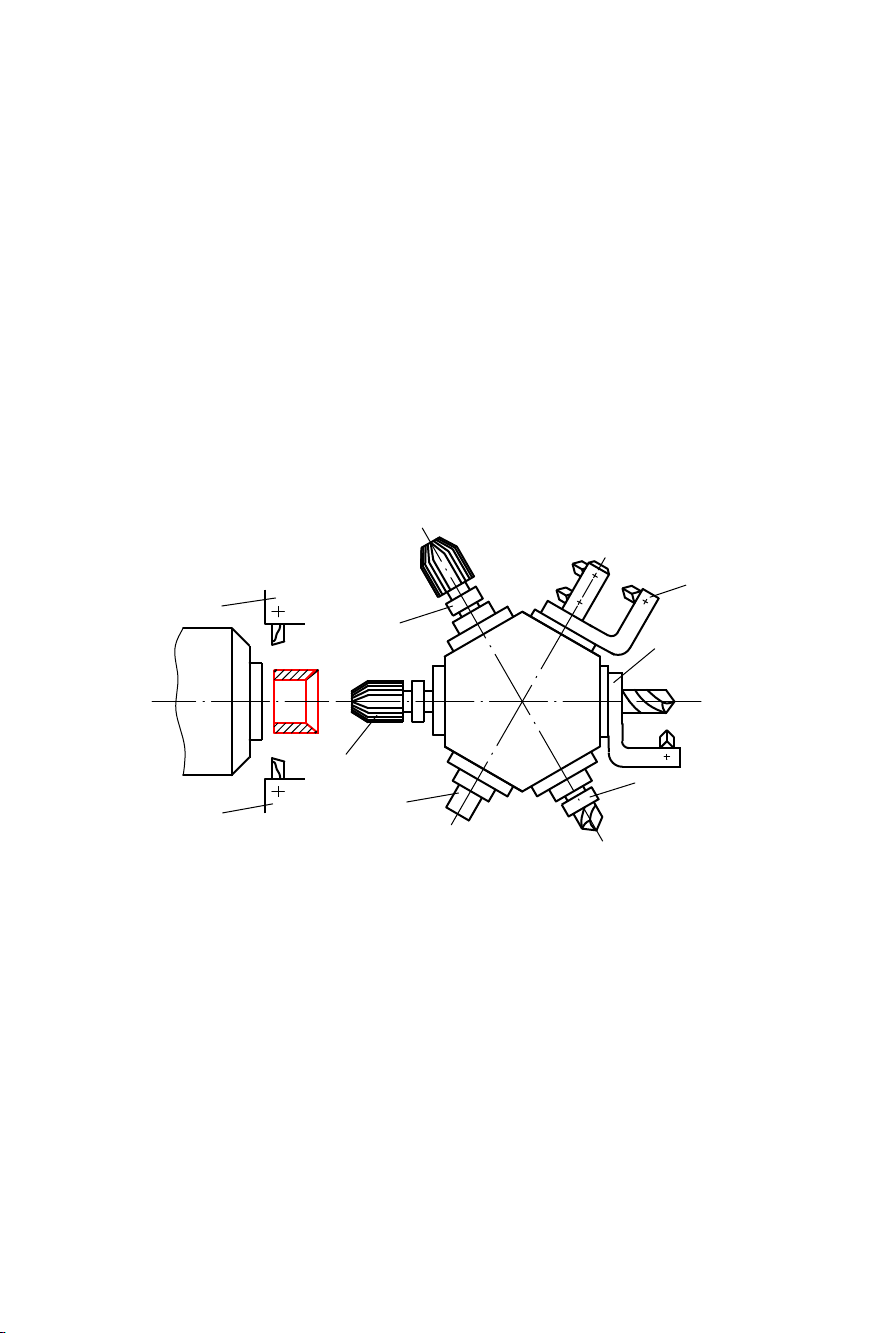
105
2.4.5. Biện pháp thực hiện các nguyên công
2.4.5.1. Gia công mặt chính của bạc
Biện pháp kỹ thuật gia công mặt chính của bạc (mặt ngoài, mặt trong
và mặt đầu) phụ thuộc rất nhiều vào dạng phôi và sản lượng của bạc.
a. Các bạc chế tạo từ phôi thanh
- Nếu sản lượng ít có thể tiến hành gia công trên máy tiện vạn năng
trong một lần gá qua các bước: xén đầu, khoan mồi, khoan lỗ, tiện trong,
tiện ngoài, cắt đứt.
- Nếu sản lượng lớn, việc gia công các mặt chính của bạc được
thực hiện trên máy rơvonve tự động một trục hoặc nhiều trục trong một
lần gá qua các bước: xén mặt đầu, đẩy thanh tới cỡ tì, khoan lỗ, tiện mặt
tròn ngoài, vát mép, doa thô, doa tinh và cắt đứt.
Sơ đồ gia công các mặt chính của bạc trên máy Rơvonve thể hiện
trên hình 2.80.
b. Chế tạo bạc từ phôi ống
Biện pháp gia công các mặt chính của bạc từ phôi ống cũng cơ bản
giống như đối với bạc chế tạo từ phôi thanh, nhưng phải thay nguyên
công khoan lỗ bằng khoét và doa lỗ.
c. Chế tạo bạc từ phôi đúc hoặc rèn từng chiếc
- Nếu sản lượng ít với chi tiết cỡ lớn và vừa thì thực hiện gia công
trên máy tiện cụt, tiện đứng; với chi tiết cỡ nhỏ có thể gia công mặt chính
trên máy tiện vạn năng thông thường.
- Nếu sản lượng nhiều với chi tiết cỡ nhỏ và vừa, gia công các mặt
chính thực hiện trên máy tiện một trục nhiều dao hay máy tiện nhiều trục
nhiều dao.
Hình 2.80: Sơ đồ gia công các mặt chính của bạc từ phôi
thanh trên máy Rơvonve
6
5
4
3
2
8
7
1
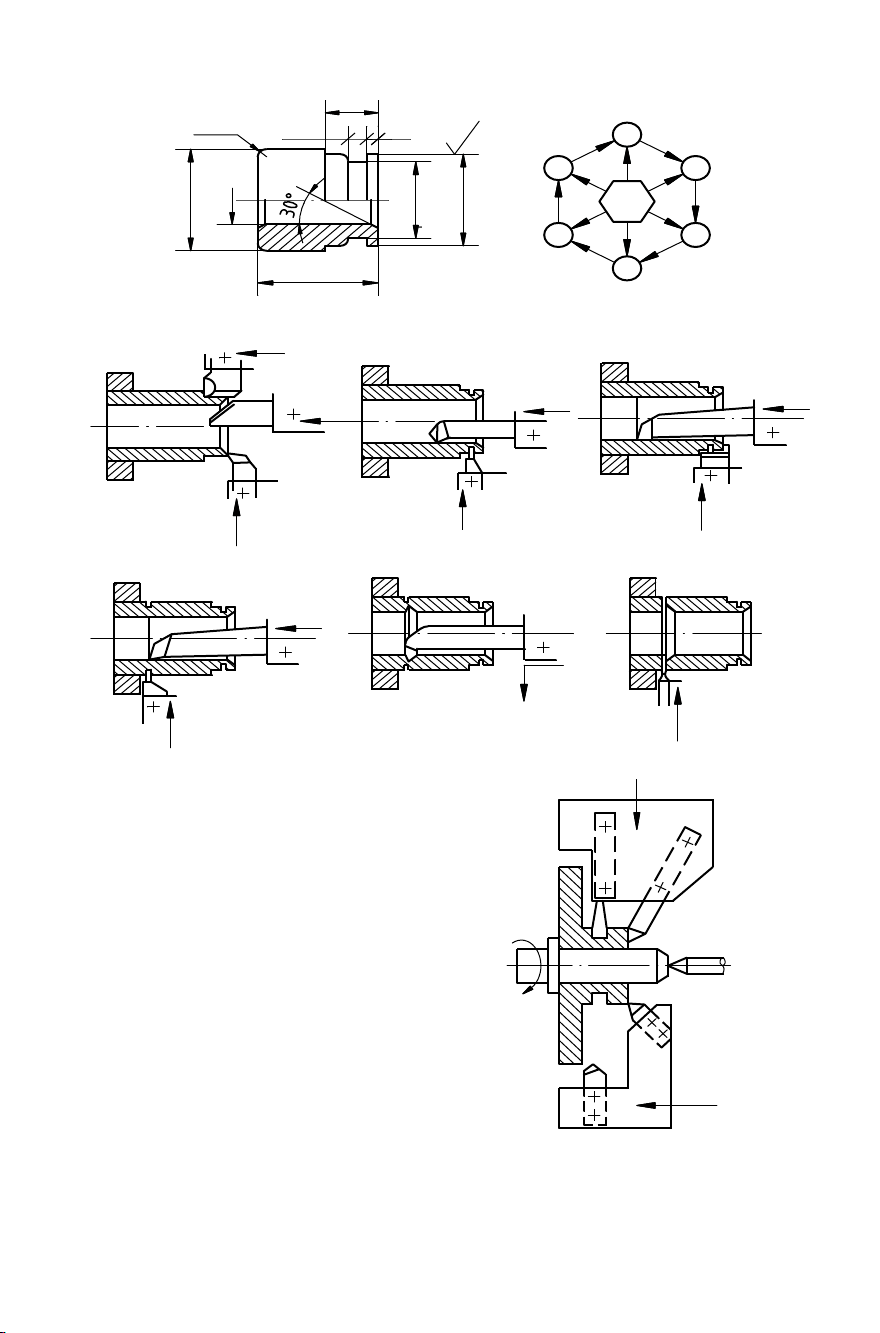
106
Trên hình 2.82 thể hiện sơ đồ
tiện tinh mặt ngoài của bạc trên máy
tiện bán tự động một trục nhiều dao.
Trên loại máy này, các dao gia công
đường kính ngoài được bố trí ở bàn
dao trước, các dao gia công rãnh và
vát mép được bố trí ở bàn dao sau.
Bàn dao trước chạy dọc, bàn dao sau
chạy ngang thực hiện đồng thời.
Việc gia công các lỗ bạc, trước
nguyên công tiện tinh mặt ngoài
thường dùng tiến trình công nghệ
như sau:
- Khoét rộng lỗ bạc và vát mép
lỗ trên máy khoan đứng, khi đó dùng
Hình 2.82: Sơ đồ tiện tinh
mặt ngoài của bạc trên máy
bán tự động nhiều dao.
Hình 2.81: Sơ đồ gia công bạc trên máy tiện nhiều dao
I
IV
II
V
III
VI
a) Cấu tạo bạc
3,2
4
16
4,5
R12
26
-0,1
31,4
-
0,1
31,5
+0
,1
26,1
+0
,1
36,4
-
0,1
b) Các vị trí gia công
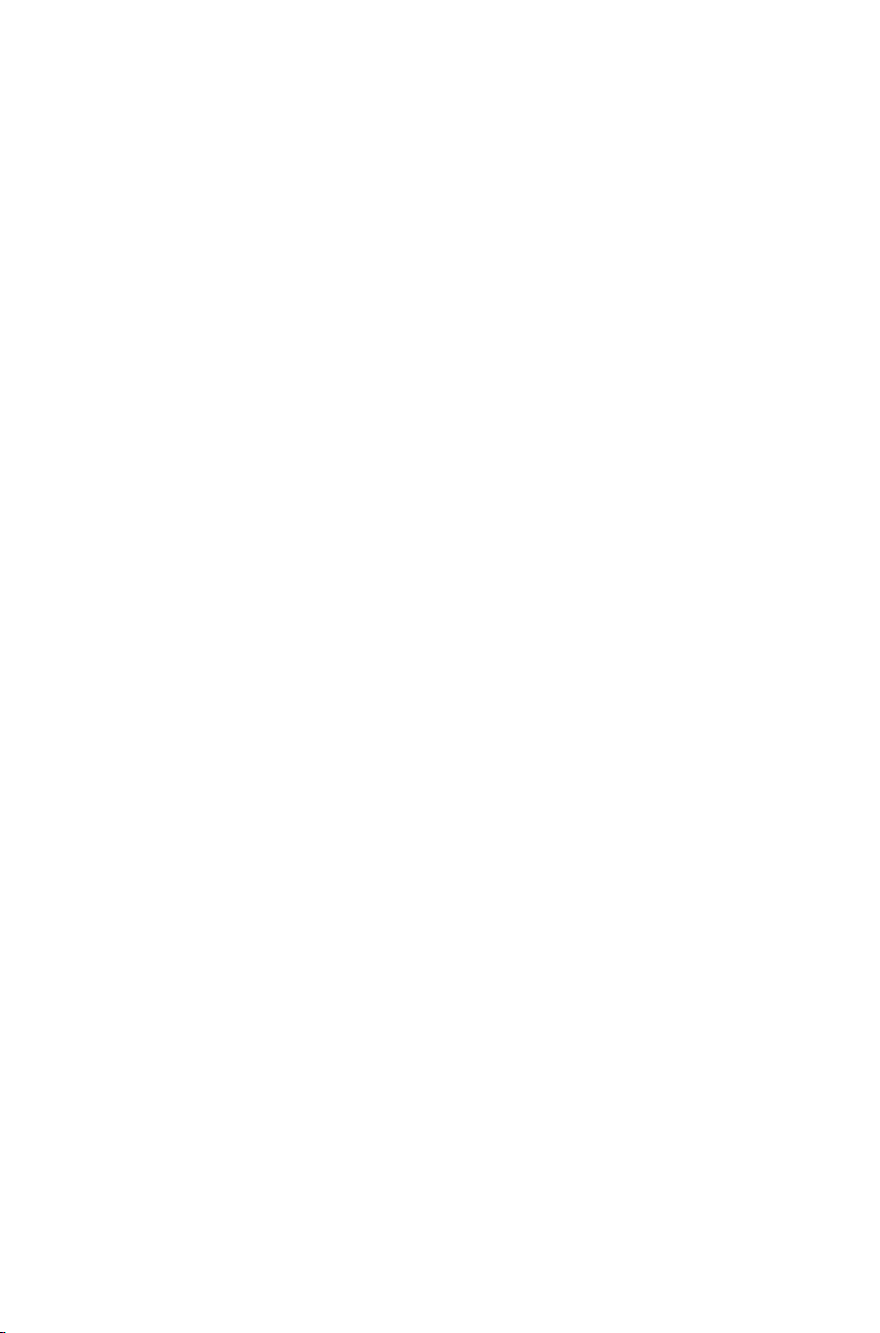
107
mặt ngoài và mặt đầu làm chuẩn định vị và kẹp chặt bằng mâm cặp.
- Gia công tinh lỗ có thể thực hiện trên máy chuốt nằm ngang. Ở
nguyên công này cần dùng đồ gá chuốt có chỏm cầu tự lựa để có thể định
vị vào mặt đầu chưa được gia công. Đôi khi thực hiện gia công tinh lỗ
bằng phương pháp lăn ép.
Đối với các loại bạc có thành mỏng, kém cứng vững để gia công
các mặt chính việc định vị không có gì khác đối với các loại bạc nói
chung đã trình bày ở trên, nhưng lực kẹp chặt phải là hướng trục để tránh
gây biến dạng hướng kính trong và sau khi gia công.
Để gia công các mặt chính của loại bạc có kết cấu đặc biệt cần phải
có biện pháp thích hợp. Ví dụ như:
+ Những bạc có lỗ côn thường được khoét và doa bằng các dao
hình côn. Những bạc côn có xẻ rãnh khi sản lượng lớn, gia công mặt côn
nhờ cơ cấu chép hình, khi sản xuất nhỏ, đơn chiếc, việc gia công lỗ côn
bằng cách xoay bàn dao trên máy tiện thông thường.
+ Những bạc có một lớp hợp kim chống mòn (bạc hai lớp) thì sau
khi gia công tinh lỗ, tiến hành đúc (hoặc ép) lớp hợp kim trên mặt lỗ, rồi
phải gia công tinh lại lớp hợp kim.
+ Những bạc mỏng đàn hồi có xẻ rãnh phải có biện pháp đặt vào
khe rãnh một miếng đệm và gắn cứng vào đó bằng một lớp kim loại dễ
chảy, sau đó gia công tinh lỗ, lớp kim loại này sẽ được hớt đi ở nguyên
công cuối cùng.
+ Những bạc bằng kim loại – sứ có nền sắt hoặc đồng, có biện pháp
thích hợp cho từng loại. Khi gia công bạc kim loại – sứ nền sắt phải dùng
dao hợp kim cứng BK8. Muốn tăng tính chống ma sát của các loại bạc
xốp này sau khi thiêu kết, phải ngâm trong dầu máy bay ở nhiệt độ
100120
o
C, với thời gian thích hợp tùy theo bề dày thành bạc.
+ Các bạc bằng chất dẻo có thể chế tạo từ phôi thanh, phôi ống
hoặc phôi ép rời từng chiếc. Khi chế tạo, việc gia công cắt gọt cũng
tương tự như bạc bằng kim loại.
2.4.5.2. Gia công các lỗ phụ
Các lỗ phụ trên bạc thường là các lỗ để tra dầu, lỗ có ren để kẹp
chặt với các chi tiết khác. Để gia công các lỗ bạc này, bạc được định vị
bằng mặt ngoài và mặt đầu hoặc mặt trong và mặt đầu.
- Nếu sản lượng ít, lỗ được khoan trên máy khoan đứng với đồ gá
có bạc dẫn hoặc khoan theo dấu.
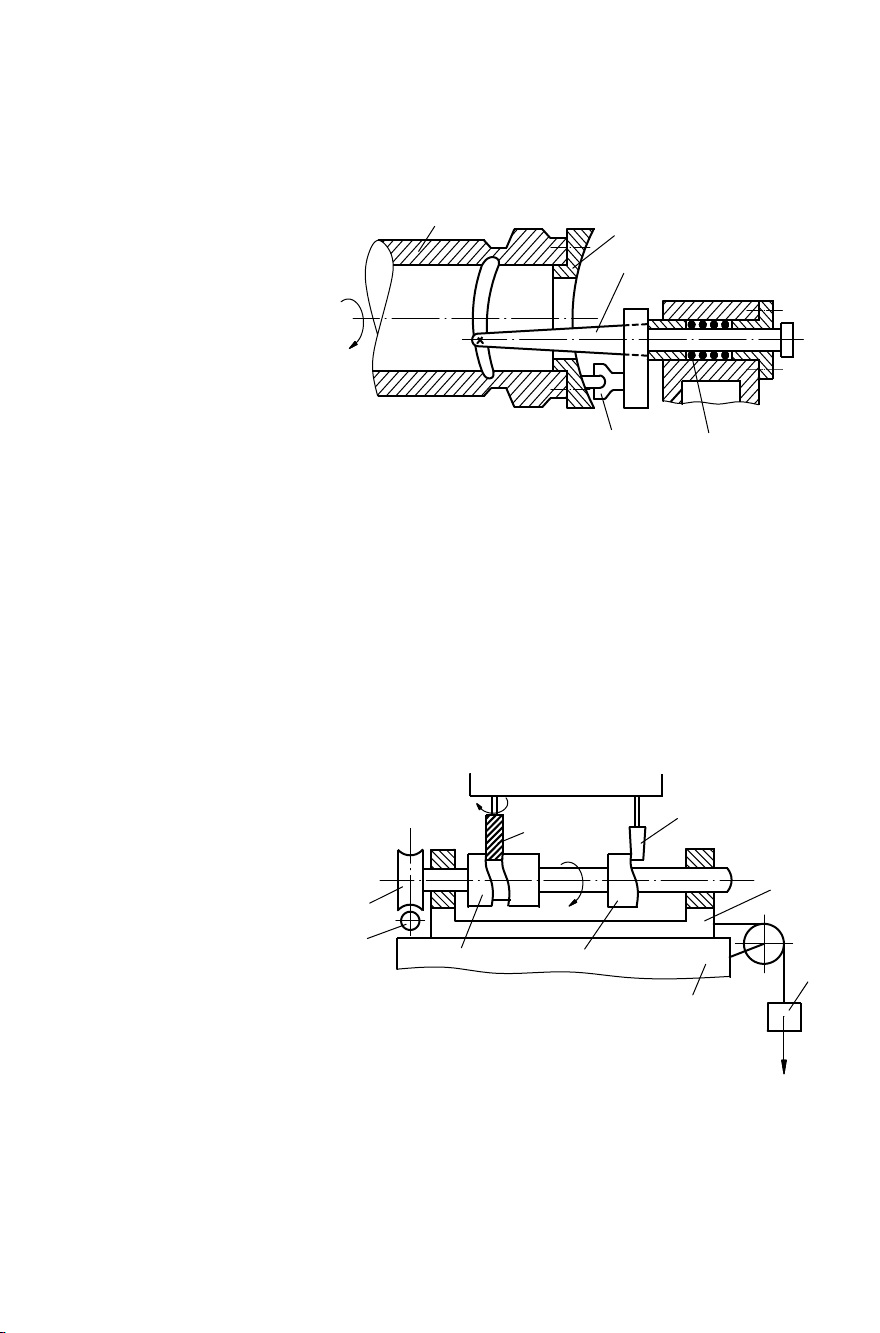
108
- Nếu sản lượng nhiều có thể dùng máy khoan có đầu rơvonve hoặc
đầu khoan nhiều trục để gia công tất cả các lỗ cùng một lúc. Với chi tiết
cỡ vừa, có thể gia công trên máy tổ hợp.
2.4.5.3. Gia công thô và tinh các mặt định hình trong và ngoài
Những mặt định
hình này bao gồm các
rãnh then, rãnh dầu, răng
khía và rãnh then trong.
- Các rãnh then:
nếu sản xuất nhỏ, đơn
chiếc rãnh then được
gia công trên máy xọc,
nếu sản xuất loạt lớn
then được gia công trên
máy chuốt.
- Rãnh then mặt
ngoài được gia công bằng dao phay ngón trên máy phay đứng hoặc dao
phay đĩa trên máy phay ngang như đối với chi tiết dạng trục
- Các rãnh dầu hoặc mặt định hình ở mặt trong của bạc thường
được gia công bằng phương pháp tiện chép hình. Trên 2.83 trình bày sơ
đồ nguyên lý đồ gá tiện chép hình rãnh dầu ở mặt lỗ của bạc.
Dưỡng chép hình 2 có biên dạng mặt đầu thích hợp với rãnh cần
gia công, dưỡng 2
được gá vào chi tiết
gia công 1. Khi trục
chính quay sẽ mang
chi tiết cùng với dưỡng
quay theo. Do mặt đầu
của dưỡng lồi, lõm nên
nó đẩy con lăn 4 cùng
với bộ phận gá dao và
dao 3 ra, vào, do đó
dao cắt ra được hình
dạng rãnh yêu cầu. Lò
xo 5 có tác dụng đẩy
con lăn luôn tiếp xúc
với dưỡng.
Với rãnh định
hình trên mặt ngoài của bạc như rãnh cam thùng thì có thể gia công bằng
Hình 2.83: Sơ đồ nguyên lý đồ gá tiện chép
hình rãnh dầu trong lỗ của bạc.
1. Chi tiết gia công; 2. Dưỡng chép hình;
3. Dao cắt; 4. Con lăn; 5. Lò xo.
3
2
4
5
1
Hình 2.84:Sơ đồ nguyên lý đồ gá phay chép hình
rãnh trên mặt ngoài của bạc.
1. Chi tiết gia công; 2. Dưỡng chép hình; 3. Con
lăn; 4. Dao phay ngón; 5. Đối trọng; 6,7. Bộ truyền
trục vít – bánh vít; 8. Thân đồ gá; 9. Bàn máy.
4
3
6
7
8
2
9
5
1
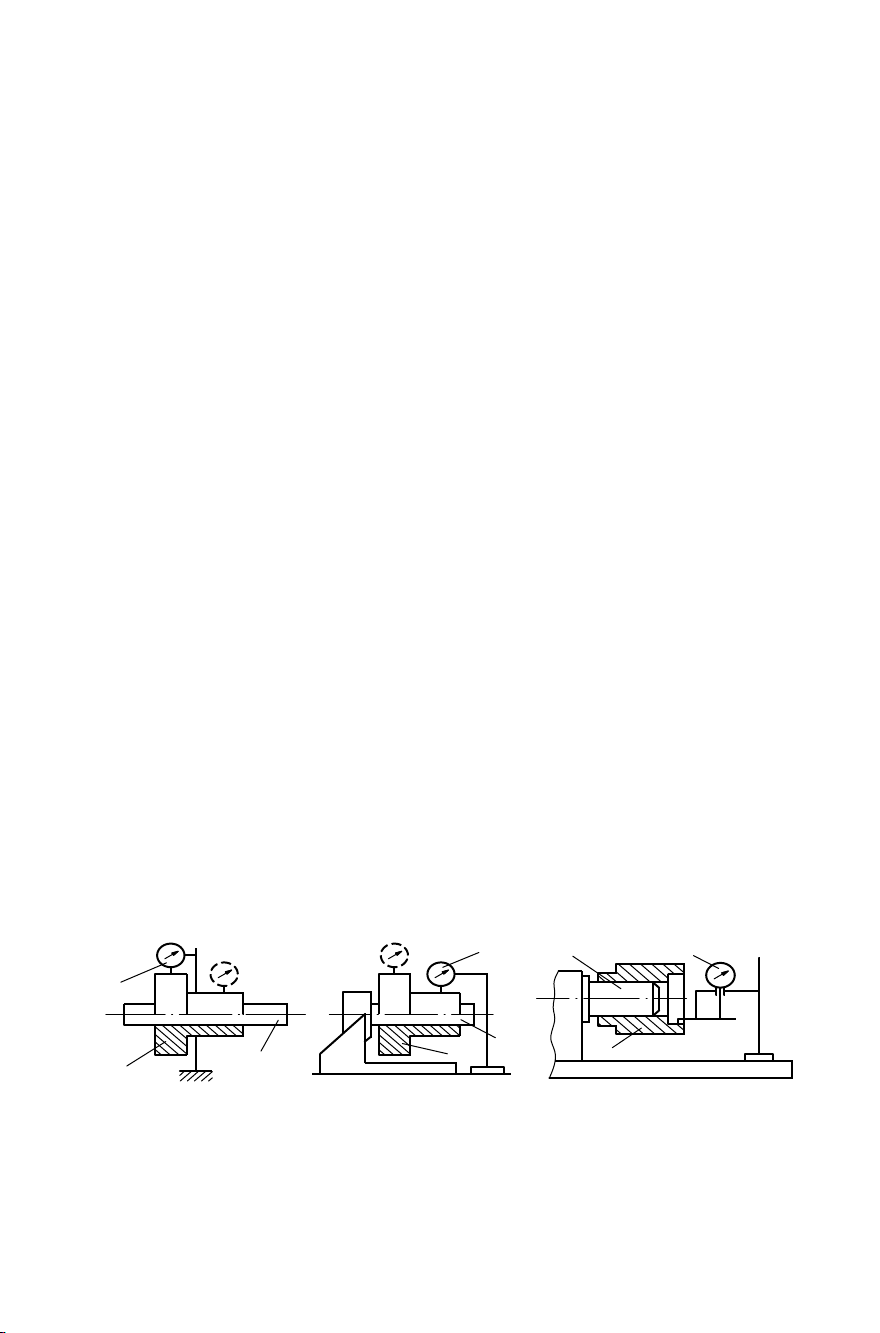
109
phương pháp tiện chép hình hoặc phay chép hình. Trên hình 2.84 trình
bày sơ đồ nguyên lý đồ gá phay chép hình rãnh trên mặt ngoài của bạc.
Chi tiết gia công 1 và dưỡng chép hình 2 được lắp đồng trục và
được quay đồng bộ nhờ bộ truyền trục vít bánh vít 6,7. Đối trọng 5 luôn
luôn kéo thân gá 8 với toàn bộ đồ gá về phía phải để cho con lăn tiếp xúc
với cam mặt đầu 2, do đó dao cắt 4 cắt được rãnh phù hợp với biên dạng
mặt đầu cam.
- Răng khía trên bạc hay bánh răng liền bạc được gia công bằng các
phương pháp phay, bào, phay lăn, xọc (được trình bày ở phần Gia công
bánh răng).
2.4.5.4. Gia công sau nhiệt luyện
Các bề mặt chính xác của bạc sau khi nhiệt luyện cần phải gia công
tinh (thường là các mặt trong của bạc, cũng có khi là mặt ngoài). Để đảm
bảo độ đồng tâm của các bề mặt, cần lấy mặt nọ làm định vị để gia công
mặt kia.
Các bề mặt gia công tinh thường thực hiện trên máy mài. Đối với
chi tiết có đường kính lớn, khó gia công trên máy mài thì phải dùng loại
dao hợp kim cứng hoặc kim cương để tiện mỏng trên máy tiện cụt, tiện
đứng với các đồ gá thích hợp. Nếu bề mặt bạc cần độ nhẵn bóng và chính
xác cao hơn, thì có thể dùng phương pháp mài khôn hoặc mài nghiền để
gia công tinh lần cuối.
2.4.5.5. Kiểm tra bạc
Khi gia công các chi tiết dạng bạc thường phải kiểm tra các yếu tố
về kích thước bản thân như đường kính ngoài, đường kính lỗ, chiều dài
bạc, chiều dầy thành bạc, độ nhám bề mặt v.v…
Trong dạng sản xuất đơn chiếc và loạt nhỏ thường dùng các dụng cụ
đo vạn năng để đo các kích thước và các mẫu để so sánh độ nhám bề mặt.
Còn trong sản xuất loạt lớn có thể dùng các dụng cụ kiểm chuyên dùng.
Hình 2.85: Sơ đồ kiểm tra độ đồng tâm giữa các bề mặt.
a,b. Độ đồng tâm giữa mặt trong và ngoài.
c. Độ đồng tâm của hai lỗ bậc.
1. Chi tiết kiểm tra ; 2. Trục tâm ; 3. Đồng hồ so.
b)
a)
3
2
1
3
2
1
3
2
1
c)
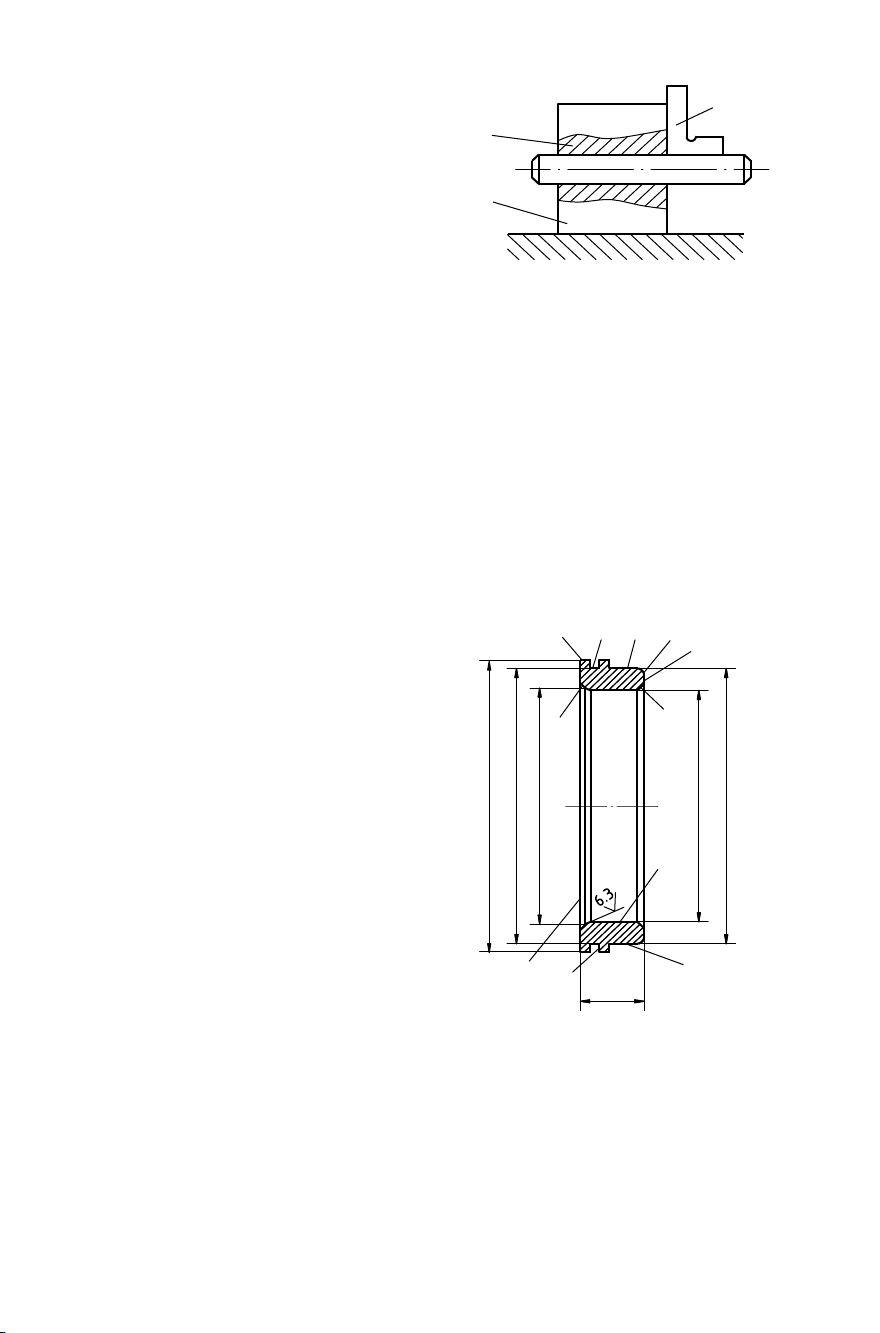
110
Đối với các yếu tố về vị trí
tương quan như độ đồng tâm
giữa mặt lỗ và mặt đầu tốt nhất là
dùng một số đồng hồ so và đồ gá
kiểm tra giống như sơ đồ kiểm
các bậc trên trục bậc. Trên hình
2.85 trình bày một số sơ đồ kiểm
tra vị trí tương quan giữa các mặt
trên bạc.
Độ vuông góc giữa mặt
đầu và đường tâm lỗ bạc có thể
kiểm tra bằng đồng hồ so hoặc
thước đo góc. Trên hình 2.86 trình bày sơ đồ kiểm tra độ vuông góc giữa
đường tâm lỗ và mặt đầu bằng thước đo góc.
Trên đây là những khái niệm cơ bản về công nghệ chế tạo bạc nói
chung. Trong một số ngành chế tạo máy, thường phải chế tạo một số loại
bạc có sản lượng lớn. Các bạc này được chế tạo theo những dây chuyền
công nghệ chuyên dùng.
Sau đây là một ví dụ về
quy trình công nghệ chế tạo một
loại bạc của máy khai thác than
K52 (Liên Xô cũ). Kết cấu của
chi tiết được giới thiệu trên hình
2.87. Chi tiết chế tạo từ vật liệu
thép hợp kim 30CrMnTi với
phôi ống cắt rời từng chiếc.
Quy trình công nghệ chế
tạo bạc nói trên bao gồm các
nguyên công sau đây:
- Tiện thô mặt đầu 1, mặt
ngoài 4 và lỗ chi tiết 9, chi tiết
được định vị ở mặt 5 (đã gia
công sơ bộ) và được kẹp chặt
trên mâm cặp ba chấu của máy tiện.
- Thấm cacbon với độ sâu 0,9-1,3mm.
- Tiện tinh mặt đầu 7, 10 và vát mép các mặt 6, 8.
- Tiện bán tinh các mặt 1, 4, 9 (định vị và kẹp chặt như nguyên
công đầu).
Hình 2.86: Sơ đồ kiểm tra độ vuông
góc giữa lỗ và mặt đầu.
1. Chi tiết kiểm tra ; 2. Trục tâm;
3. Thước góc
3
2
1
Hình 2.87: Bạc máy khai thác than K52
173
185
197
-
0,15
3
4
5
6
8
7
43
-0,2
9
1
0
1
1
2
1
170H7
190U7
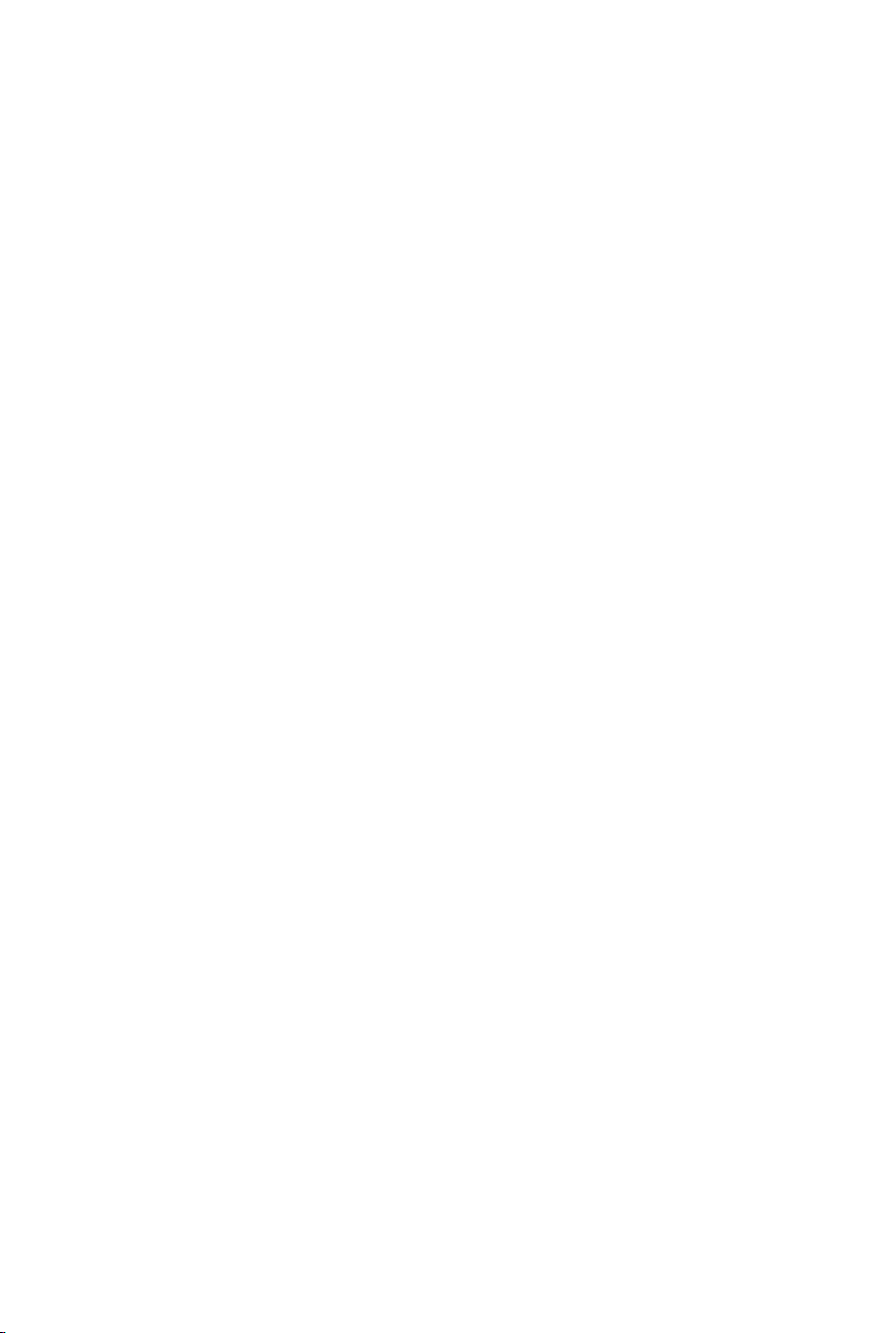
111
- Tiện tinh các mặt 1,9, 4, 10, 11, 3, 2. Chi tiết được định vị ở các
mặt 5,7 và kẹp chặt ở mặt 5.
- Nhiệt luyện đạt độ cứng 60HRC.
- Mài mặt đầu 7 trên máy mài phẳng. Chi tiết được định vị ở mặt 1
và kẹp chặt bằng bàn từ.
- Mài mặt 5 và 10 trên máy mài tròn ngoài, chi tiết được định vị ở
lỗ 9 trên trục gá.
- Đánh bóng bề mặt ngoài đạt R
a
=5-0,65. Chi tiết được định vị như
nguyên công mài tròn ngoài.
Trong quy trình công nghệ trên đây đã thể hiện được độ đồng tâm
giữa mặt lỗ và mặt ngoài bằng cách gia công chính xác lỗ 170H7, sau
đó lấy lỗ làm chuẩn để gia công mặt ngoài.
2.5. GIA CÔNG BÁNH RĂNG
Bánh răng, bánh vít là những chi tiết dùng để truyền lực và chuyển
động mà ta thường thấy trong nhiều loại máy khác nhau. Với sự phát
triển của ngành chế tạo máy và với yêu cầu của sửa chữa thay thế, các
loại chi tiết này ngày càng được sản xuất nhiều hơn. Ở nhiều nước, người
ta đã xây dựng nhà máy, phân xưởng chuyên sản xuất bánh răng, bánh vít
với trình độ cơ khí hóa và tự động cao.
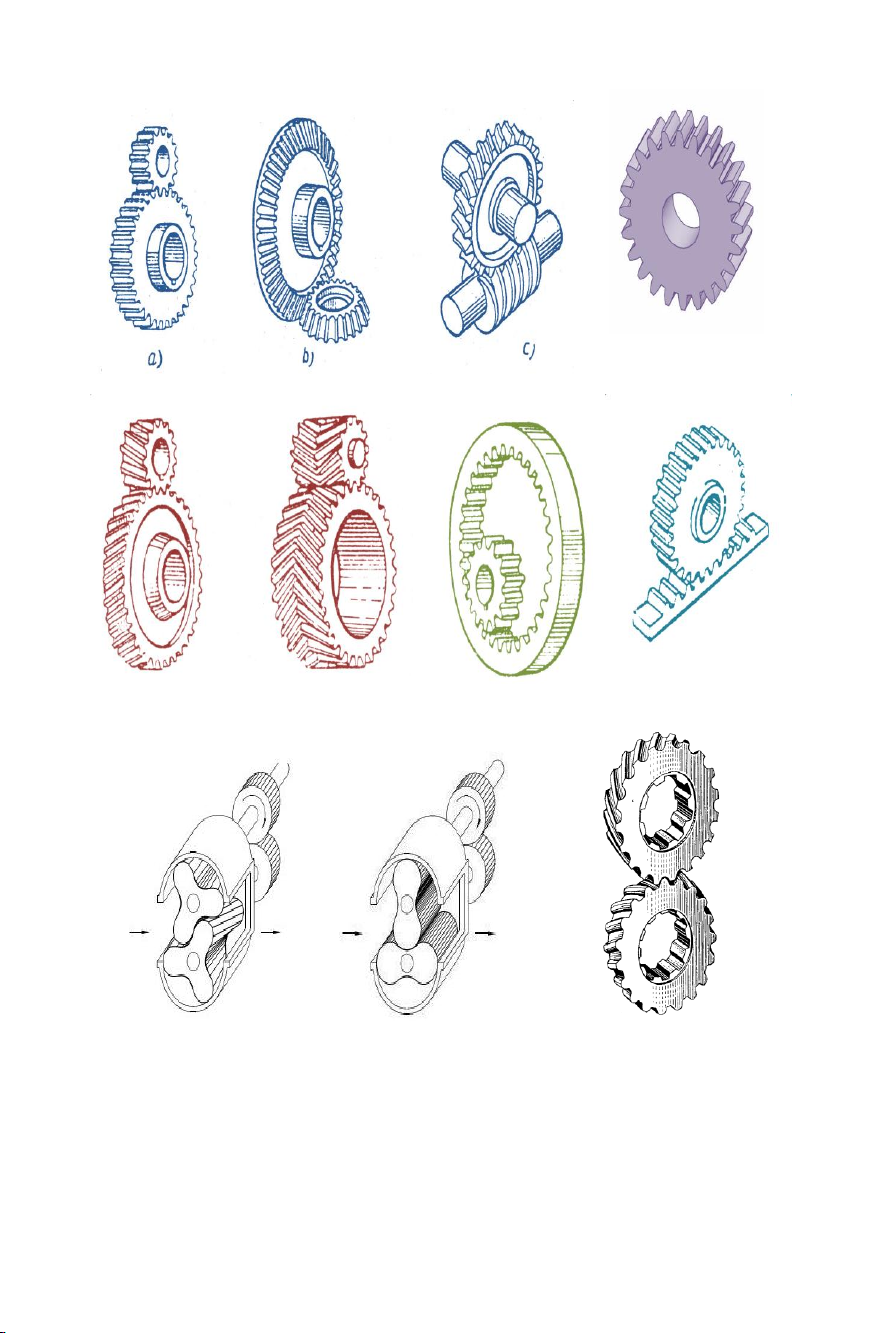
112
Trong những năm gần đây, việc chế tạo bánh răng đã đạt được
nhiều thành tựu mới trong việc nâng cao năng suất và chất lượng gia
công khi gia công trên các máy tổ hợp CNC.
d)
i)
k)
h)
e)
Hình 2.88: Các bộ truyền bánh răng
m) Bánh răng số 8
răng Cycloid
l) Bánh răng tam giác
n) Bánh răng Novikov
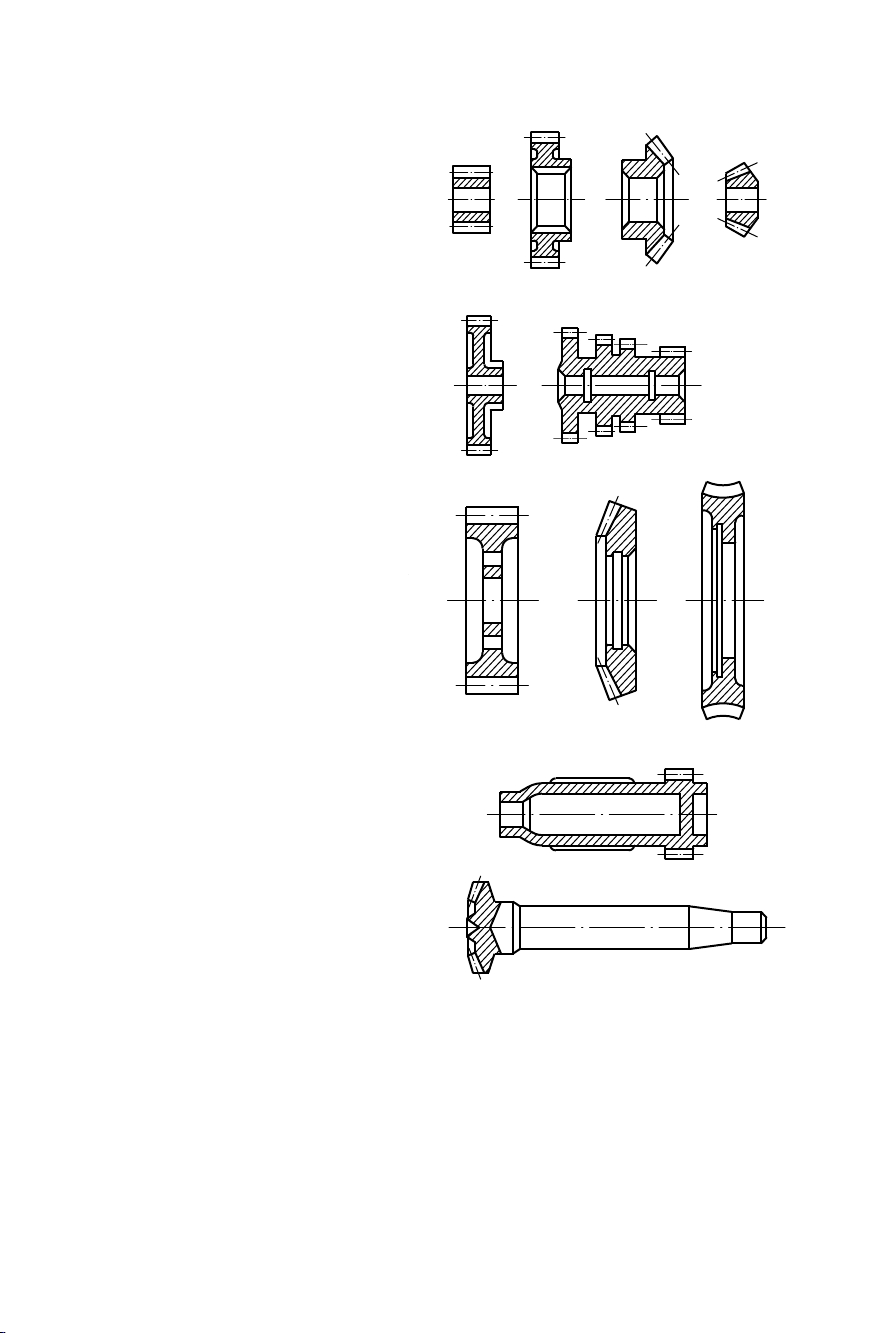
113
2.5.1. Phân loại và độ chính xác bánh răng
2.5.1.1. Phân loại
Bánh răng được chia
làm ba loại:
- Bánh răng trụ (răng
thẳng và răng nghiêng).
- Bánh răng côn (răng
thẳng và răng xoắn).
- Bánh vít.
Dựa theo đặc tính công
nghệ, bánh răng được chia
làm các loại sau đây:
Bánh răng trụ và răng
côn không có mayơ và có
mayơ, lỗ trơn và lỗ then hoa
(hình 2.89a).
Bánh răng bậc lỗ trơn
và lỗ then hoa (hình 2.89b).
Bánh răng trụ, bánh
răng côn và bánh vít dạng đĩa
(hình 2.89c).
Trục răng trụ và trục
răng côn (hình 2.89d).
2.5.1.2. Độ chính xác
bánh răng
Độ chính xác của bánh
răng được đánh gia theo tiêu
chuẩn nhà nước TCVN.
Theo tiêu chuẩn này, bánh
răng được chia thành 12 cấp
chính xác, ký hiệu theo thứ tự bằng các con số 1, 2, 3, 4, 5, 6, 7, 8, 9, 10, 11,
12. Trong đó cấp chính xác 1 là cao nhất,và cấp chính xác 12 là thấp nhất.
Trong tiêu chuẩn không ghi dung sai của các cấp 1, 2 và 12, trong
thực tế thường chỉ dùng các cấp chính xác 3 đến 11.
Hình 2.89: Các loại bánh răng.
a)
b)
c)
d)
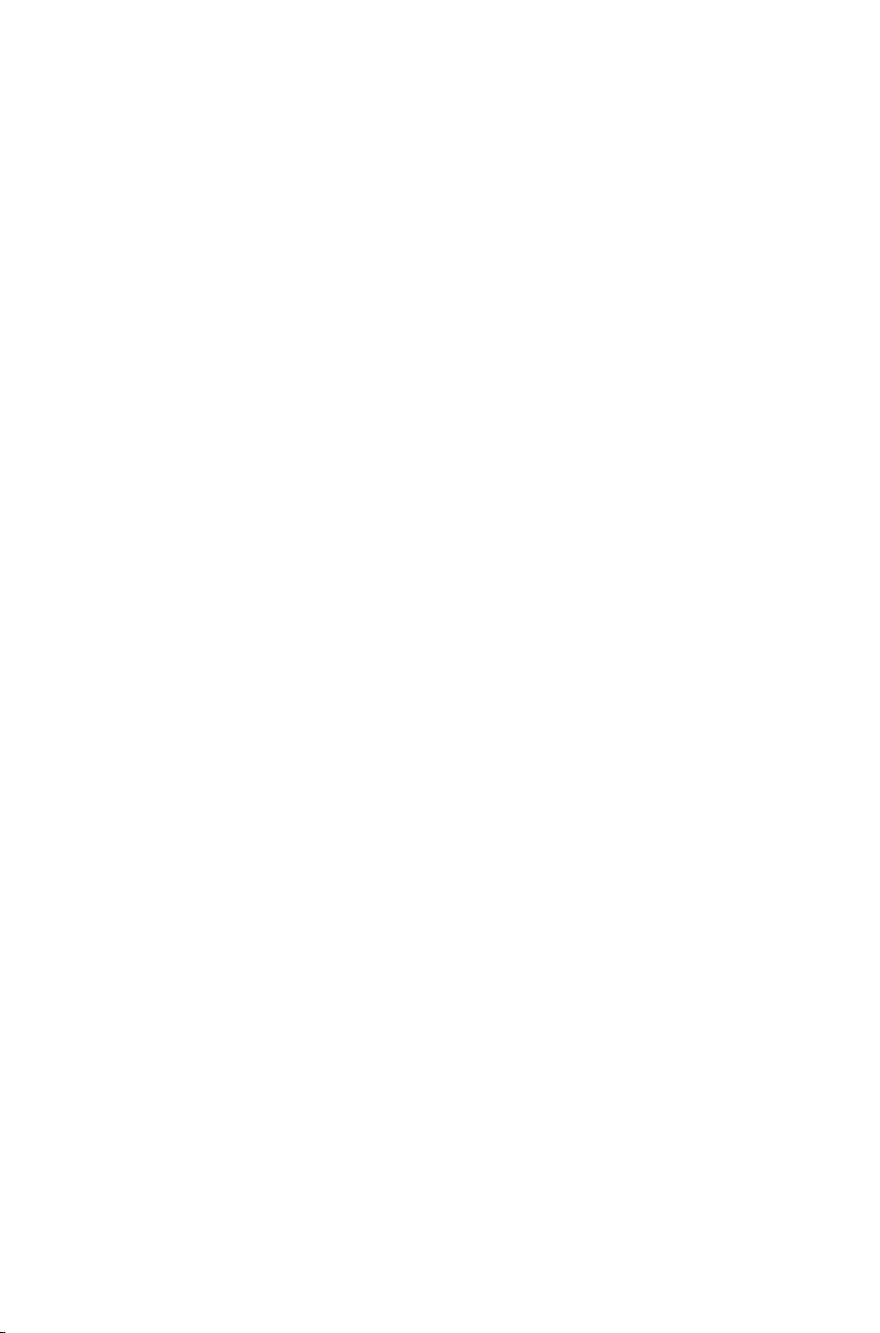
114
Đối với mỗi cấp chính xác, tiêu chuẩn còn nêu ra các chỉ tiêu để
đánh giá độ chính xác của bánh răng. Những chỉ tiêu đó là:
a. Độ chính xác truyền động: Độ chính xác này được đánh giá bằng
sai số góc quay của bánh răng sau một vòng. Sai số này xuất hiện là do sai
số của hệ thống công nghệ. Ngoài ra, độ chính xác truyền động còn được
đánh giá bằng sai số bước vòng và sai lệch khoảng pháp tuyến chung.
b. Độ ổn định khi làm việc: Độ ổn định khi làm việc ảnh hưởng
trực tiếp đến độ ồn khi làm việc và tuổi thọ của bánh răng, độ ổn định khi
làm việc được đánh giá và bằng sai số chu kỳ ( là giá trị trung bình của
sai số truyền động bằng tỉ số giữa sai lệch lớn nhất và số răng của bánh
răng). Độ ổn định khi làm việc được đánh giá bằng sai lệch bước cơ sở.
c. Độ chính xác tiếp xúc: Độ chính xác tiếp xúc được đánh giá bằng
vết tiếp xúc của prôfin răng theo chiều dài, chiều cao và được biểu diễn
bằng %.
d. Độ chính xác khe hở cạnh răng: Chỉ tiêu này quy định bốn loại
khe hở cạnh răng:
- Khe hở bằng 0.
- Khe hở nhỏ.
- Khe hở trung bình.
- Khe hở lớn.
Khoảng cách tâm giữa hai bánh răng ăn khớp với nhau càng lớn
(tức là bánh răng càng lớn) thì khe hở cạnh răng càng lớn.
2.5.2. Vật liệu và phôi bánh răng
2.5.2.1. Vật liệu
Việc chọn vật liệu để chế tạo bánh răng phụ thuộc vào điều kiện
làm việc của chúng. Các bánh răng truyền lực thường được chế tạo bằng
thép hợp kim crôm (15Cr, 15CrA, 20CrA, 40Cr, 45Cr); crôm-niken và
crôm-môlipđen (40CrNi, 35CrMoA, 18CrMnTi). Các bánh răng chịu tải
trung bình và nhỏ được chế tạo bằng thép cacbon như thép 45 và gang.
Ngoài ra còn dùng vải ép, da ép để chế tạo bánh răng làm việc không có
tiếng ồn. Những bánh răng này ăn khớp với bánh răng thép hoặc gang.
Gần đây, người ta còn dùng chất dẻo để chế tạo bánh răng. So với
bánh răng bằng thép thì bánh răng chất dẻo có độ bền thấp hơn, nhưng nó
lại có khả năng làm việc với tốc độ cao mà không gây tiếng ồn.
2.5.2.2. Phôi bánh răng
Trong sản xuất lớn, phôi chế tạo bánh răng thép thường là phôi rèn.
Còn trong sản xuất nhỏ, đơn chiếc, người ta thường dùng phôi thanh, vì
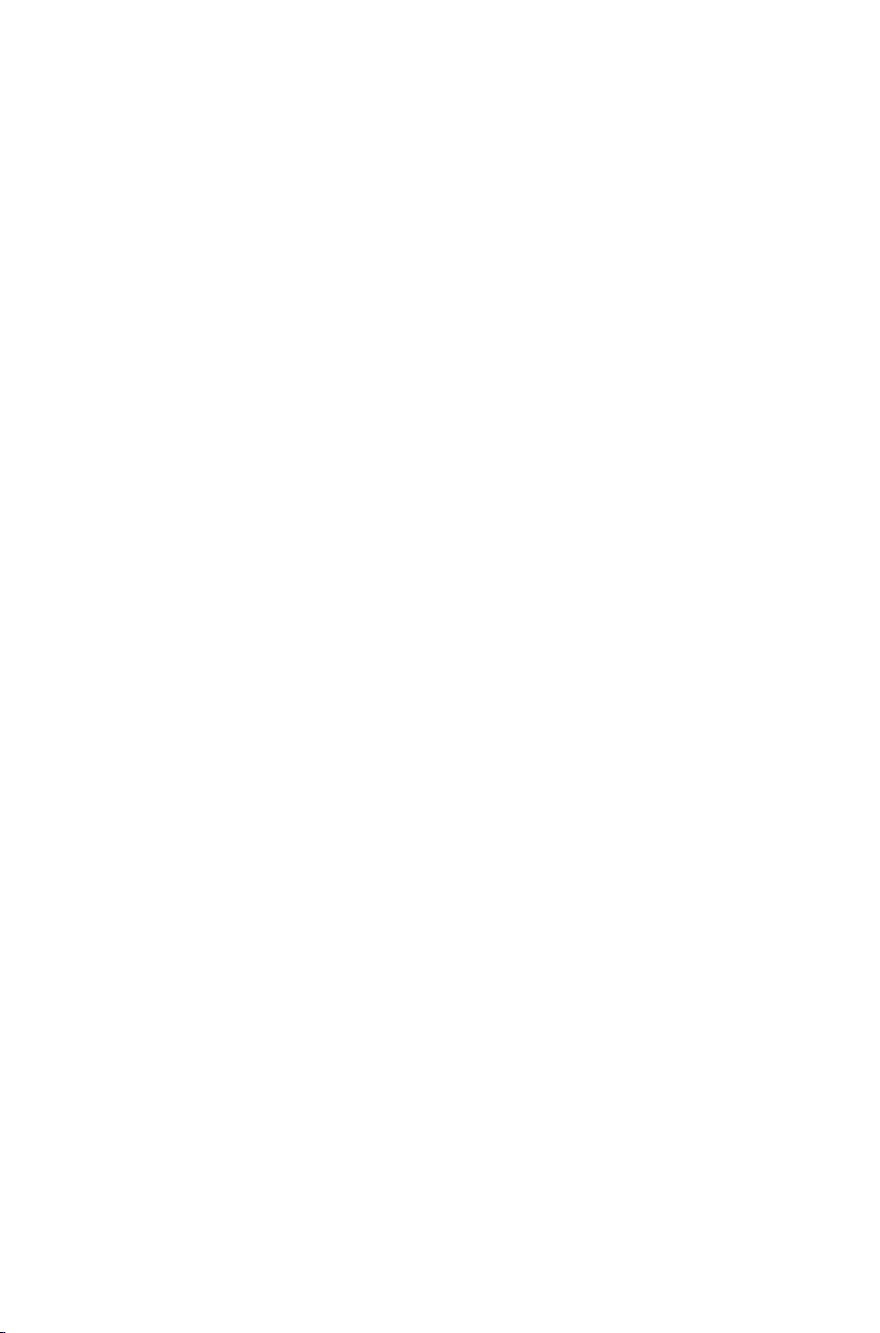
115
khi ấy phôi rèn lại không kinh tế. Sở dĩ như vậy vì dùng thép thanh phải
cắt gọt nhiều, tốn vật liệu, tốn công lại không đạt được cơ tính cao,
không phù hợp với sản xuất lớn. Những bánh răng, bánh vít làm bằng
gang hoặc có khi bằng thép mà có kích thước quá lớn nên dùng phương
pháp đúc để chế tạo phôi.
Trong những trường hợp bánh răng, bánh vít có đường kính lỗ lớn
hơn 25 mm và chiều dài lỗ nhỏ hơn hai lần đường kính thì người ta tạo lỗ
khi rèn hoặc đúc.
Trong những năm gần đây, người ta bắt đầu chế tạo bánh răng bằng
kim loại bột thiêu kết. Như vậy bánh răng không cần phải gia công cơ.
Phôi chính là kim loại bột.
2.5.3. Yêu cầu kỹ thuật và nhiệt luyện bánh răng
2.5.3.1. Yêu cầu kỹ thuật
Ngoài các yêu cầu về độ chính xác ăn khớp và truyền động, khi chế
tạo bánh răng cần bảo đảm những yêu cầu kỹ thuật sau đây:
Độ không đồng tâm giữa mặt lỗ và đường tròn cơ sở nằm trong
khoảng 0,05 0,1 mm.
Độ không vuông giữa mặt đầu và tâm lỗ (hoặc trục) nằm trong
khoảng 0,01 0,015 mm trên 100 mm đường kính.
Mặt lỗ và các cổ trục của trục răng gia công đạt chính xác cấp 7.
Độ nhám của các bề mặt trên đạt R
a
= 1,25 0,63.
Các bề mặt kết cấu khác được gia công đạt cấp chính xác 8, 9,10;
Độ nhám R
a
= 10 2,5 hay R
z
= 40 10.
Sau khi nhiệt luyện đạt độ cứng 55 60 HRC, độ sâu khi thấm
cacbon là 12 mm.
Độ cứng các bề mặt không gia công thường đạt 180 280 HB.
2.5.3.2. Nhiệt luyện bánh răng
Do yêu cầu làm việc, răng phải có độ cứng và độ bền cần thiết, không
cho phép có vết nứt, vết cháy, biến dạng do nhiệt phải bé, cơ tính phải ổn
định trong quá trình làm việc. Muốn đạt được những yêu cầu trên, cần
phải có chế độ nhiệt luyện thích hợp.
Đối với các loại thép ít cacbon (kể cả thép hợp kim) sau khi cắt
răng phải thấm cacbon.
Với các bánh răng có yêu cầu tính chịu mòn cao phải thấm nitơ.
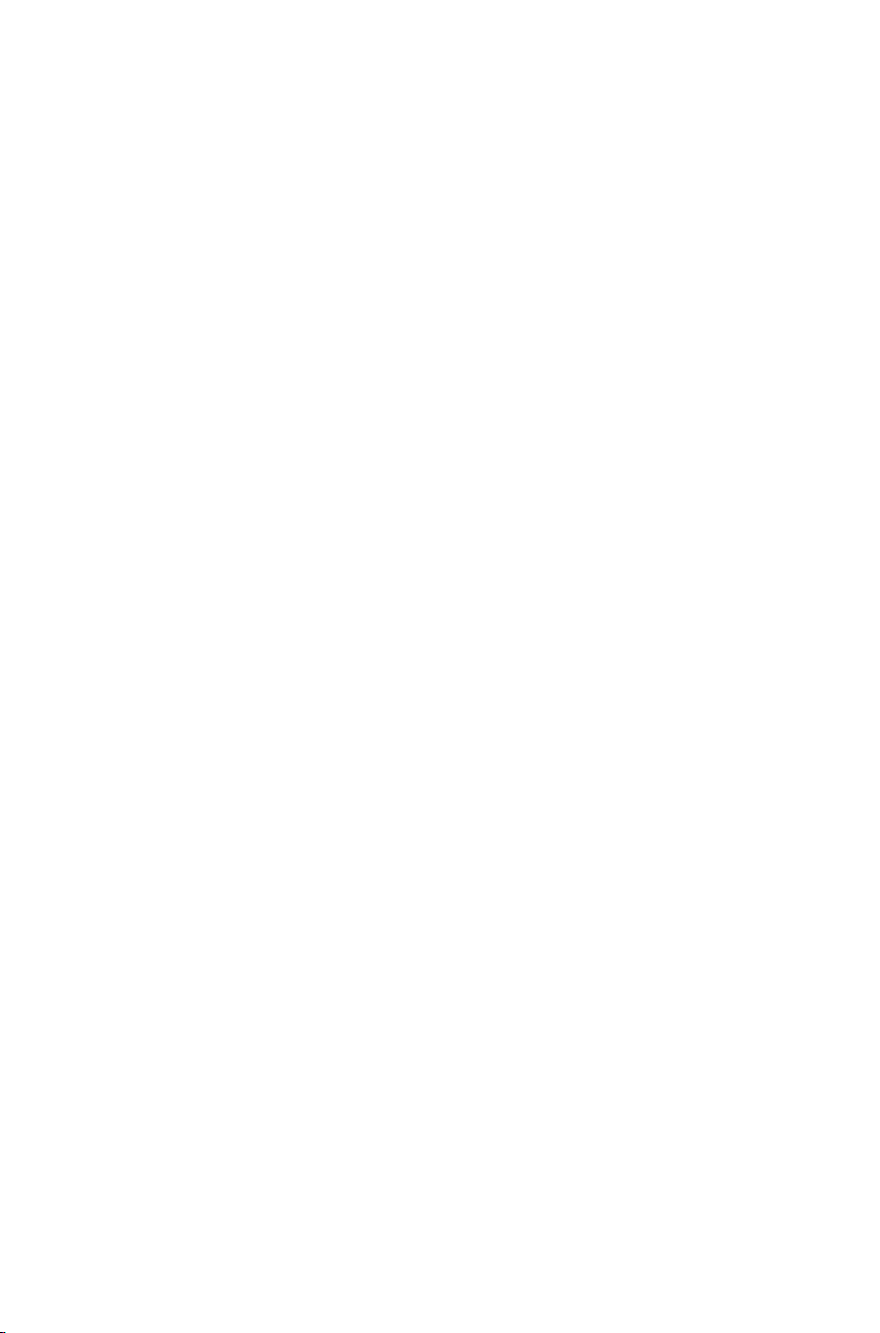
116
Trước khi gia công phôi, bánh răng thường được thường hóa hoặc
tôi cải thiện để tăng cơ tính cắt gọt. Độ cứng cần đạt là 220280 HB.
Sau khi cắt răng, bánh răng được được nhiệt luyện bằng nhiều
phương pháp khác nhau. Đối với các bánh răng môđun và kích thước nhỏ
thường được tôi thể tích, còn bánh răng có môđun lớn và kích thước lớn
thường được tôi bằng dòng điện tần số cao.
Phương pháp tôi bằng dòng điện có tần số cao thường có nhiều ưu
điểm như dễ điều chỉnh độ sâu lớp thấm tôi, biến dạng bé, độ bóng bề
mặt không giảm nhiều. Tuy nhiên vốn đầu tư vào thiết bị cao, mỗi vòng
răng phải có vòng nung khác nhau nên không thích hợp với sản xuất nhỏ,
đơn chiếc.
2.5.4. Chuẩn định vị và quy trình công nghệ trước khi gia công răng
2.5.4.1. Chuẩn định vị
Tùy theo kết cấu, sản lượng và độ chính xác yêu cầu mà ta chọn
chuẩn cho thích hợp. Về cơ bản chọn chuẩn giống khi gia công chi tiết
dạng bạc.
Khi gia công bánh răng có lỗ, dù là bánh răng trụ, bánh răng côn,
bánh vít, chuẩn tinh thống nhất là mặt lỗ. mặt lỗ cũng chính là chuẩn tinh
chính vì nó được dùng khi lắp ráp. Do vậy khi gia công phôi, người ta
chú ý đến gia công lỗ. Ngoài lỗ ra cần chọn thêm mặt đầu làm chuẩn.
Trong trường hợp đó, lỗ và mặt đầu phải gia công trong một lần gá để
đảm bảo độ vuông góc giữa mặt đầu và tâm lỗ.
Trong sản xuất đơn chiếc và hàng loạt nhỏ, ở nguyên công đầu tiên
nên chọn các bề mặt làm chuẩn thô là một mặt đầu và mặt ngoài của
bánh răng.
Sau khi nhiệt luyện, trong những trường hợp cần mài lại lỗ, người
ta phải dùng vành răng để định vị bằng vòng lăn. Như vậy trong những
trường hợp gia công bánh răng có lỗ, chuẩn định vị có thể là tất cả các bề
mặt.
Đối với các loại trục răng, chuẩn lắp ráp là bề mặt cổ trục, vì vậy
phôi của loại bánh răng này được gia công như các trục bậc và chuẩn
định vị có thể là mặt đầu, cổ trục và hai lỗ tâm.
2.5.4.2. Quy trình công nghệ trước khi gia công răng
Quy trình công nghệ gia công phôi trước khi cắt răng bao gồm các
nguyên công sau đây:
- Gia công thô lỗ.
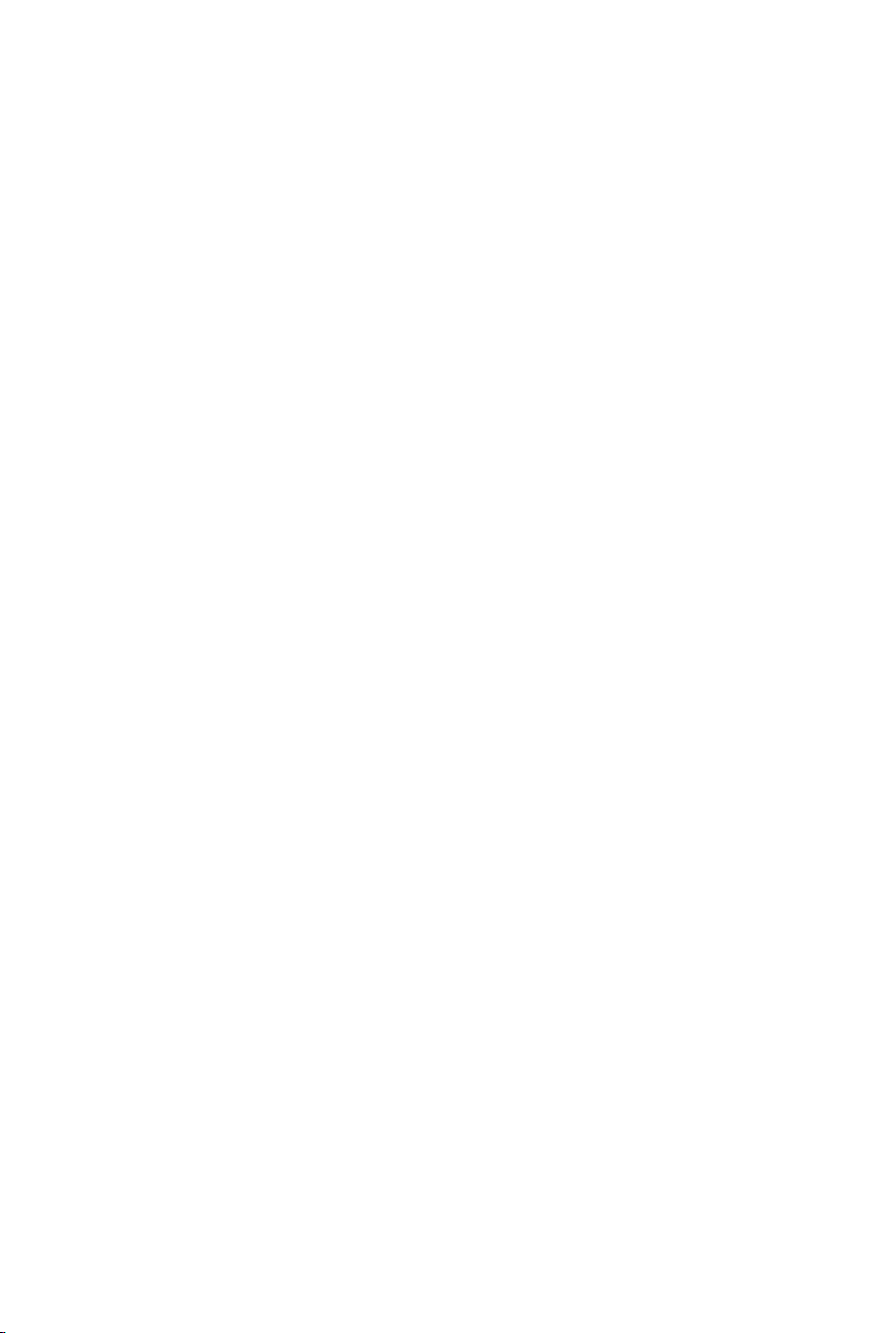
117
- Gia công tinh lỗ.
- Gia công thô mặt ngoài.
- Gia công tinh mặt ngoài.
. Trong những trường hợp cần thiết còn thêm các nguyên công như
khoan lỗ, phay rãnh then, then hoa trên trục răng hoặc ren v.v…
Khi sản lượng nhỏ, bánh răng thường được gia công trên máy tiện.
Lỗ của các bánh răng đòi hỏi phải có độ chính xác cao nên cần phải doa.
Trong sản xuất hàng loạt lớn, hàng khối có thể dùng phương pháp
chuốt để gia công lỗ (kể cả lỗ có rãnh then hoặc then hoa). Trong trường
hợp này, trước khi chuốt thường khoan hoặc khoét lỗ trên máy khoan
đứng. Các nguyên công khác chỉ được gia công sau khi chuốt lỗ, bởi vì
khi chuốt lỗ có thể đạt được độ chính xác đường kính lỗ khá cao, nhưng
độ chính xác về vị trí tương quan của tâm lỗ đối với mặt khác lại thấp.
Trong sản xuất đơn chiếc và hàng loạt nhỏ, các nguyên công được
thực hiện trên các máy tiện và các máy rơvônve. Còn trong sản xuất hàng
loạt lớn và hàng khối, các nguyên công đó được thực hiện trên máy tiện
bán tự động hoặc trên dây chuyền tự động.
Các bánh răng có đường kính lớn hơn 500 mm thường được gia
công trên các máy tiện đứng.
Với mọi dạng sản xuất có thể dùng máy tiện CNC, đặc biệt có
những máy tổ hợp CNC vừa tiện vừa phay lăn răng.
2.5.5. Các phương pháp gia công răng của bánh răng
2.5.5.1. Gia công răng của bánh răng trụ
Bánh răng cần có độ bền và tuổi thọ cao để trong quá trình làm việc
không gây ồn và có hiệu suất tốt. Điều đó đòi hỏi sự chú ý thích đáng vào
phương pháp gia công răng của các bánh răng.
Chúng ta có thể phân chia thành phương pháp gia công bánh răng từ
một số quan điểm lớn.
Về nguyên lý tạo răng có thể phân chia thành hai phương pháp gia
công răng.
Phương pháp định hình (hay phân độ). Bằng phương pháp này
chúng ta cắt từng rãnh răng, sau đó phân độ một góc 360
0
/z cho đến rãnh
răng cuối cùng bằng dụng cụ cắt có lưỡi dạng rãnh răng.
Phương pháp bao hình (hay phương pháp lăn). Với phương pháp
này dụng cụ được lăn tương đối trên vành của bánh răng gia công và khi
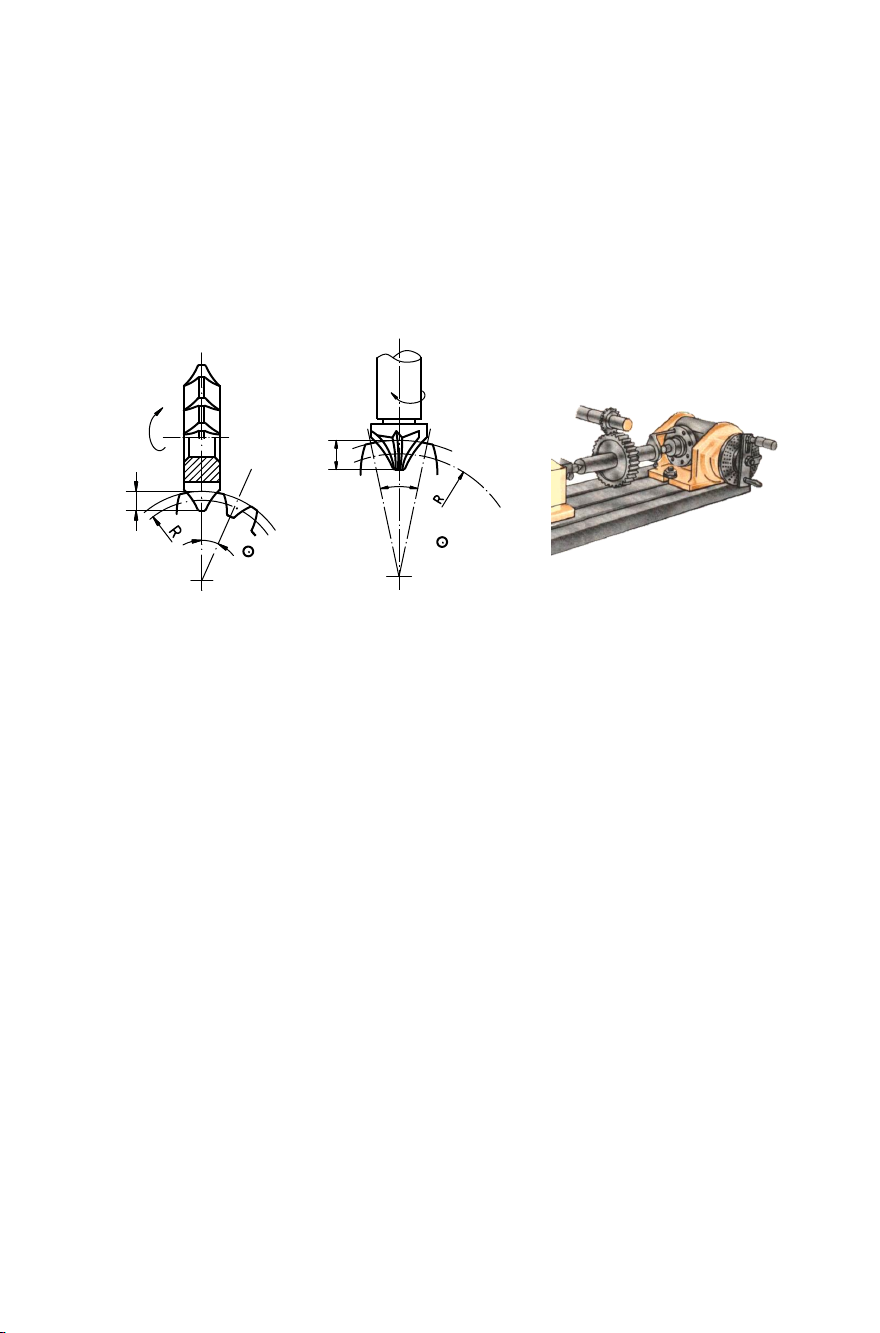
118
đó các lưỡi cắt của dụng cụ dần dần chiếm các vị trí trên bánh răng mà
đường bao của chúng là prôfin thân khai của bánh răng gia công .
Theo phương pháp gia công, có thể thực hiện gia công răng bằng
phay, xọc, mài và bằng các phương pháp gia công tinh khác
A. Các phương pháp cắt răng theo nguyên lý định
hình
a. Phương pháp phay định hình
Phay răng bằng phương pháp định hình được tiến hành bằng dao phay
định hình mà prôfin của nó phù hợp với prôfin của rãnh răng. Dao phay là
dao phay đĩa môđun (hình 2.91a) hoặc dao phay ngón môđun (hình 2.91b).
Sau khi phay xong một rãnh răng, vật được quay đi một bước với góc
a = 360
0
/z (z là số răng của bánh răng gia công) và rãnh răng tiếp theo lại
được phay.
Phương pháp này được sử dụng nhiều khi dùng máy phay vạn năng có
trang bị dụng cụ chia độ. Khi gia công vật được gá vào ụ phân độ đặt trên
bàn máy (hình 2.91c) và được điều chỉnh ở độ cao sao cho rãnh răng có
chiều sâu theo yêu cầu.
Khi phay bánh răng trụ răng thẳng dao và vật có có vị trí tương đối
như trên hình 2.91a và hình 2.91b. Để cắt hết chiều dày của bánh răng, bàn
máy mang ụ phân độ cùng với chi tiết phải thực hiện chạy dao dọc theo
hướng răng.
Khi phay bánh răng trụ răng xoắn, bánh răng được điều chỉnh bằng
cách quay bàn máy đi một góc phù hợp với góc nghiêng của răng. Để tạo
được răng xoắn cần thực hiện đồng bộ chạy dao của bàn và chuyển động
quay của đầu chia độ.
Hình 2.91: Gia công bánh răng trụ bằng dao phay mô đun
b) Dao ngón
h
o
a) Dao đĩa
h
o
c) Sơ đồ gá đặt khi phay
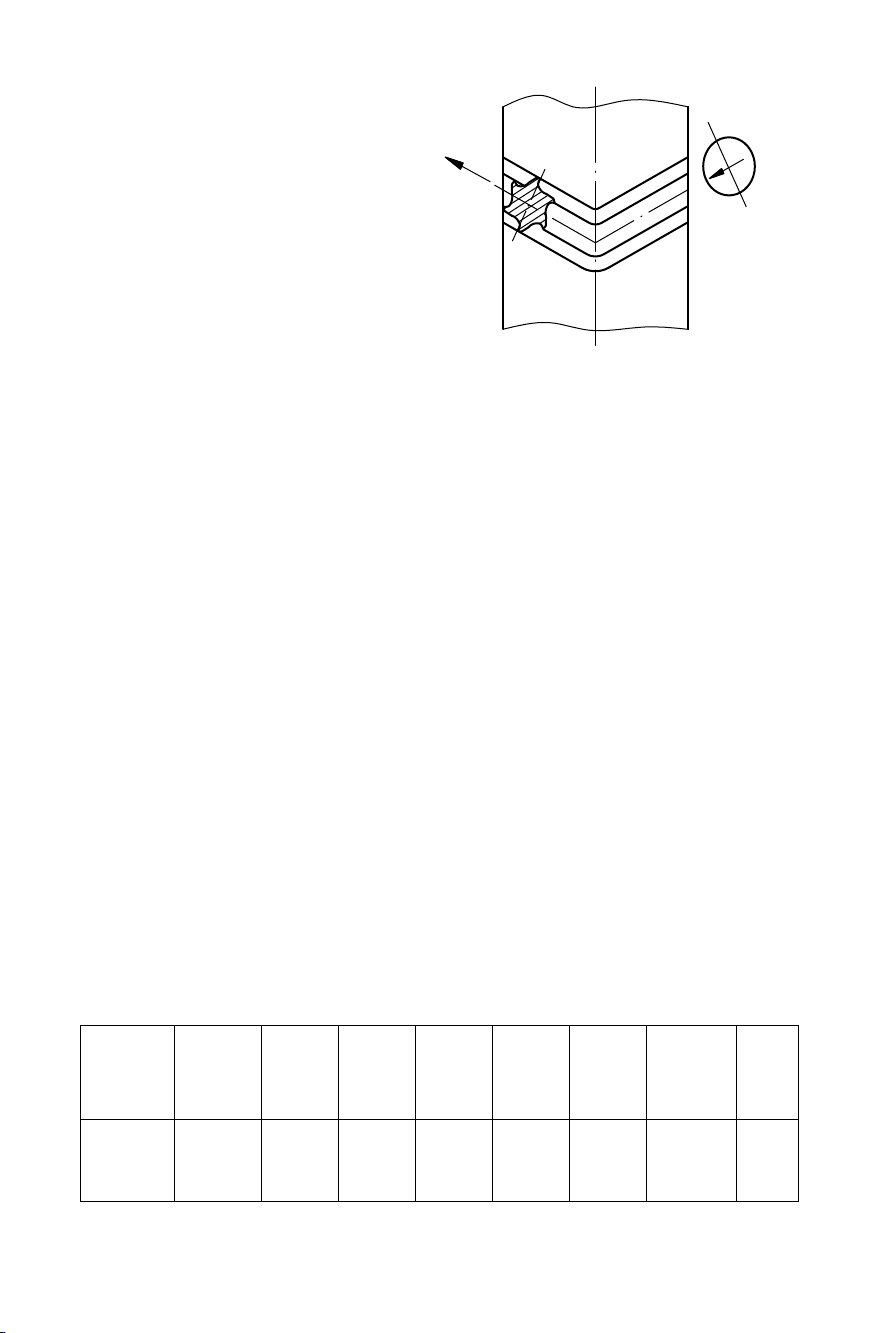
119
Với phương pháp này còn
có thể sản xuất được bánh răng
trụ răng hình chữ V (hình 2.92).
Bánh răng trụ răng chữ V
được phay bằng dao phay ngón
trên máy phay vạn năng tương tự
như bánh răng trụ răng nghiêng
nhưng phải làm hai lần, hoặc
cũng có thể gia công trên máy
bán tự động chuyên dùng.
Phương pháp gia công định
hình này được dùng trong các nhà
máy nhỏ hoặc nhà máy sửa chữa, ở
đó số lượng bánh răng cần phay không nhiều và răng của chúng không cần
chính xác cao. Phương pháp này được dùng khi sản xuất bánh răng có
đường kính và môđun lớn mà phương pháp khác không thực hiện được.
Tuy nhiên phương pháp định hình đạt được độ chính xác thấp và có
khó khăn trong việc điều chỉnh chính xác vị trí tương đối giữa dao và vật.
Với phương pháp này răng của dao phải có dạng rãnh răng của bánh răng.
Thế nhưng dạng rãnh răng của một bánh răng thay đổi theo môđun
và số răng. Về mặt lý thuyết, để có dạng răng chính xác ứng với một
môđun và một số răng cần có một dụng cụ cắt riêng, như vậy số dao phải
chế tạo rất nhiều.
Để đảm bảo tính kinh tế, dao phay định hình phải sản xuất theo một
bộ 8; 15 hoặc 26 con với cùng môđun và góc ăn khớp. Mỗi dao dùng để
sản xuất một bánh răng trong phạm vi số răng nhất định. Trong phạm vi
số răng đó chỉ có duy nhất một số răng đúng biên dạng còn các số răng
còn lại phải chịu sai số về biên dạng.
Ví dụ trong một bộ dao có 8 dao đảm nhận việc gia công các số
răng như sau (bảng 2.3):
Bảng 2.3
Dao
phay số
1
2
3
4
5
6
7
8
Cho
tổng số
răng
12 – 13
14 – 16
17 – 20
21 – 25
26 –34
35 – 54
55 – 134
134
Hình 2.92: Phay bánh răng trụ răng
hình chữ V bằng dao phay ngón.
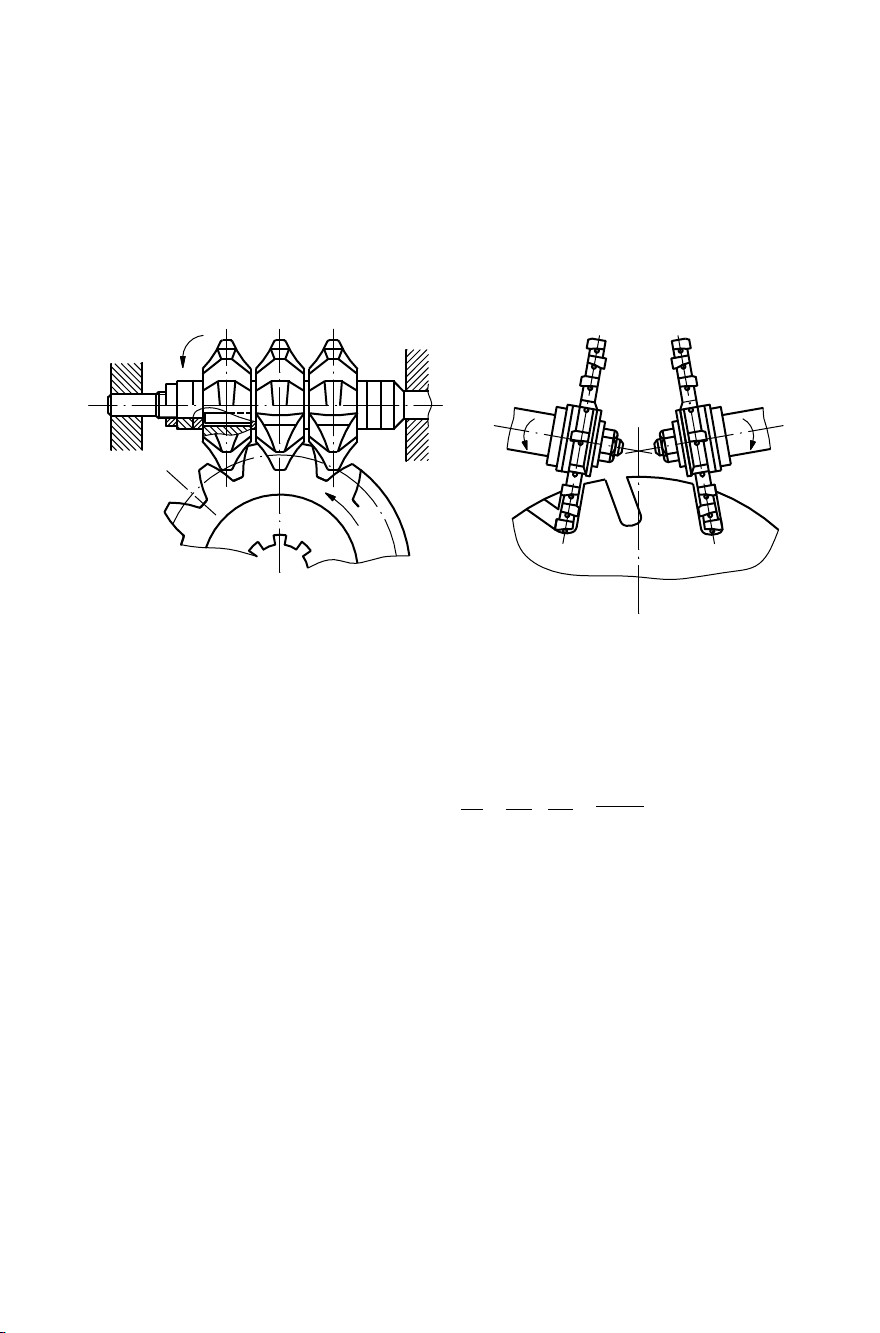
120
Vì vậy, bánh răng được sản xuất bằng phương pháp phay định hình
chỉ đạt cấp chính xác 78 và được dùng cho bộ truyền động có tốc độ
thấp, không lớn hơn 5 m/s.
Tuy nhiên trong sản xuất hàng loạt lớn và hàng khối, đối với những
bánh răng có môđun lớn, phương pháp này dùng để gia công phá (giảm
bớt lượng dư cho gia công tinh). Trong trường hợp này không cần chế
tạo môđun có biến dạng thân khai mà chỉ cần chế tạo dao có dạng cung
tròn. Có thể cắt theo sơ đồ như hình 2.93.
Thời gian cơ bản khi phay bánh răng trụ răng thẳng bằng dao phay
đĩa môđun trên máy phay có cơ cấu chia độ tự động được xác định theo
công thức sau:
m
iz
m
iz
SS
lllT oO
..
.11
21
21
(phút)
Ở đây: l
o
- chiều dài của răng (mm)
l
1
- chiều dài đoạn ăn dao (mm)
l
2
- chiều dài đoạn thoát dao (mm)
S
1
- lượng chạy dao phút của hành trình cắt (mm)
S
2
- đoạn dài dịch chuyển của chi tiết tính theo phút của
hành trình chạy nhanh (mm)
z – số răng của chi tiết
i - số lần cắt
m - môđun bánh răng
- thời gian quay phân độ một răng
Hình 2.93: Cắt răng thô bằng dao phay
đĩa.
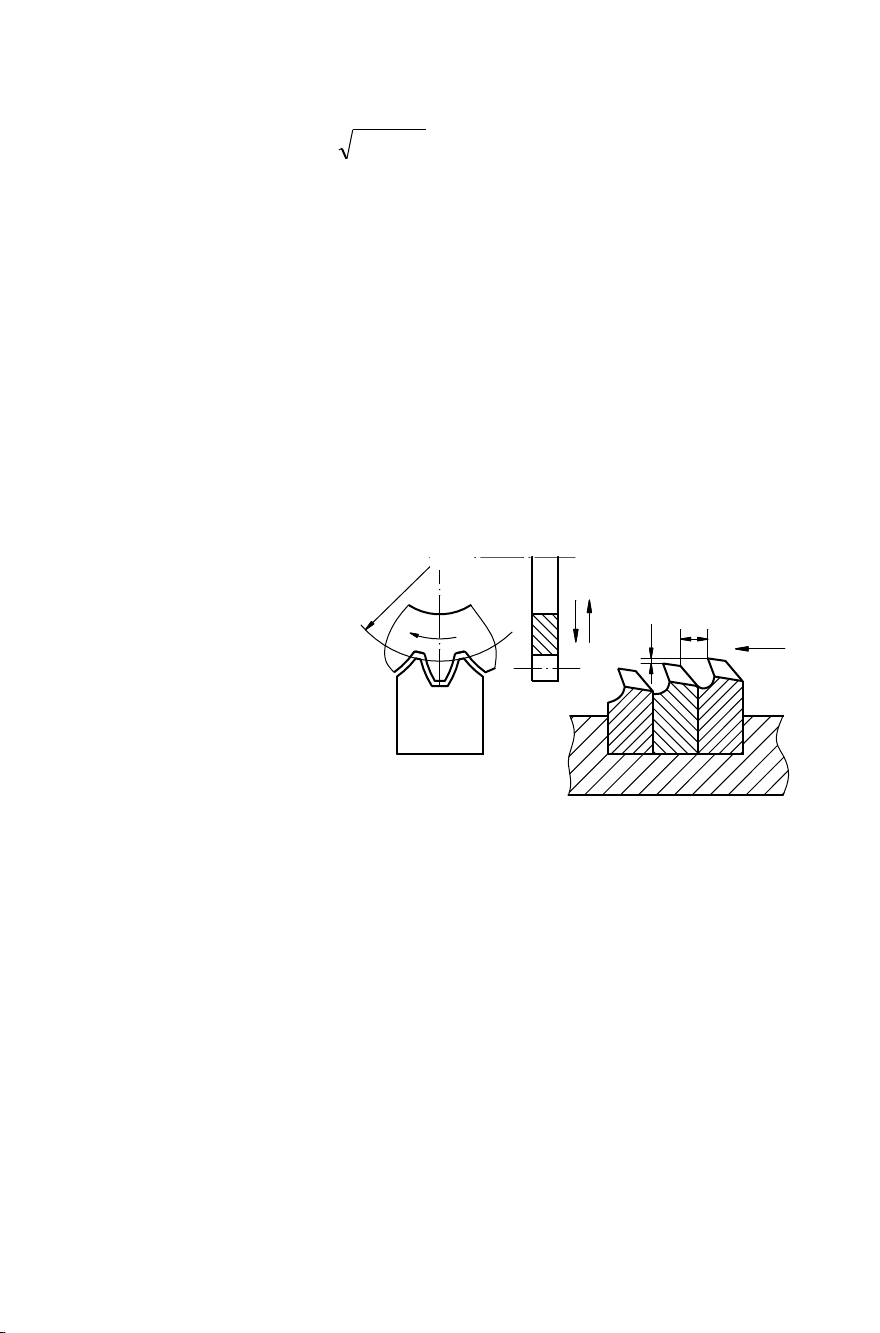
121
Chiều dài đoạn ăn dao l
1
được tính theo công thức:
)21(1 tDtl
(mm).
Ở đây: t - chiều sâu rãnh răng (mm)
D - đường kính dao phay (mm).
Lượng chạy dao phút S
1
được xác định như sau:
S
1
= S
z
. z . n
Ở đây: S
z
- lượng chạy dao răng (mm)
n - số vòng quay của dao trong một phút.
Cắt răng theo phương pháp định hình còn có thể dùng phương pháp
xọc, nhưng năng suất thấp nên ít dùng.
b. Phương pháp chuốt định hình
Chuốt định hình là
phương pháp cho năng
suất và độ chính xác cao.
Phương pháp này được sử
dụng trong sản xuất hàng
loạt lớn và hàng khối.
Theo phương pháp này,
dao chuốt có prôfin giống
prôfin của rãnh răng. Hình
2.94 là sơ đồ gia công
bằng phương pháp chuốt,
có thể chuốt một rãnh
hoặc nhiều rãnh cùng một
lúc. Sau mỗi hành trình của dao, một hoặc một số rãnh răng được gia
công, bánh răng được quay đi một góc nhờ cơ cấu phân độ.
Phương pháp chuốt toàn bộ các rãnh cùng một lúc rất ít được dùng
vì kết cấu của dao rất phức tạp, khả năng thoát phôi kém, lực cắt lớn.
Dụng cụ là một bộ dao định hình với từng nấc được lắp vào đầu
chuốt, lượng nâng của mỗi một lưỡi cắt phụ thuộc vào chiều dày lớp phoi
được cắt S
z
, loại vật liệu bánh răng và tốc độ cắt V. Lượng nâng này
được chọn như đối với dao chuốt thông thường. Lớp vật liệu phải cắt đi
được phân chia theo tổng số lớn các lưỡi cắt của dụng cụ, do vậy mà tuổi
thọ và tuổi bền của dao lớn. Song chi phí cho dụng cụ là rất lớn, nên
chuốt chỉ dùng cho sản xuất lớn, cho những bánh răng có môđun lớn và
cho bánh răng không gia công nhiệt và không mài.
Hình 2.94: Chuốt răng bánh răng.
Sz
t
v
S
n
D
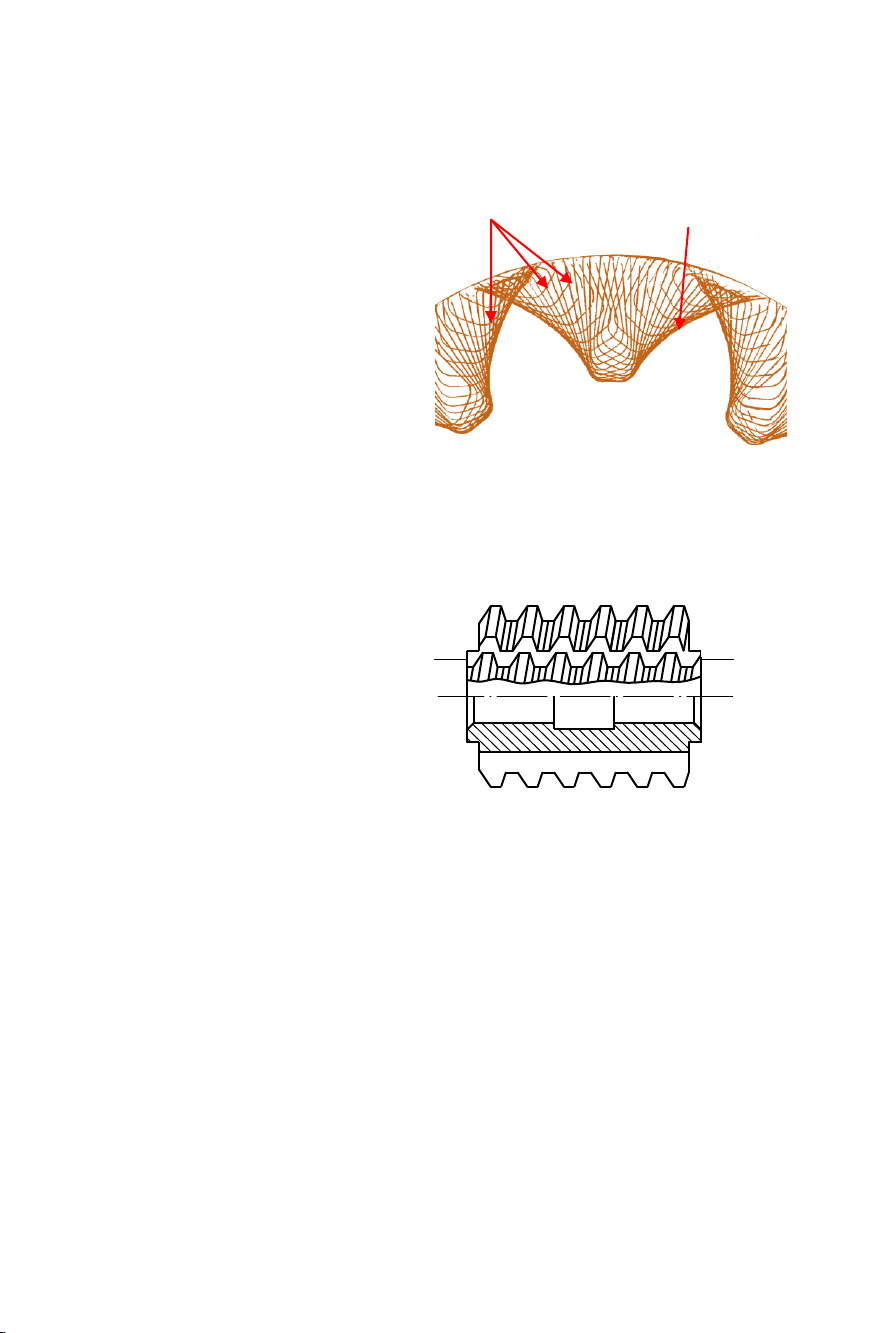
122
B. Các phương pháp cắt răng theo nguyên lý bao hình
Các phương pháp này
được tiến hành theo nguyên lý
ăn khớp của hai bánh răng
hoặc bánh răng và thanh răng,
trong đó một là dụng cụ cắt
còn một là chi tiết gia công.
Có nhiều phương pháp
cắt răng theo nguyên lý bao
hình.
a. Phay lăn răng
Phay răng bằng phương
pháp lăn bao hình là phương
pháp sản xuất bánh răng phổ
biến nhất, cho năng suất cao và
độ chính xác tốt, dụng cụ là
dao phay lăn (hình 2.95b), nó
có dạng trục vít thân khai mà
prôfin của nó ở mặt pháp tuyến
N-N là thanh răng cơ bản.
Với loại dao phay này có
thể gia công được răng của
bánh răng và răng của bánh vít.
Phay răng bằng phương
pháp phay lăn được tiến hành
trên máy chuyên dùng, trên đó
dao với bánh răng gia công
thực hiện sự ăn khớp của bộ truyền trục vít. Sự ăn dao của dao phay lăn là
liên tục, tất cả các răng của bánh răng được gia công đồng thời, nên máy
không cần thiết bị đổi chiều phức tạp, cũng không cần thiết bị chia độ do
đó tất cả thời gian phục vụ có liên quan đến công việc đó bị loại trừ.
Sự ăn khớp của dao phay lăn và bánh răng gia công phải đảm bảo
cho bước răng của cặp ăn khớp ở mặt phẳng pháp tuyến t
n
= . m; góc
ăn khớp của cả cặp trong mặt phẳng pháp tuyến = 20
0
; tỷ lệ tốc độ góc
bằng tỷ lệ số vòng quay của cả cặp và ngược với tỷ lệ số răng của chúng,
nghĩa là:
b) Dao phay lăn trục vít.
Hình 2.95
N
N
a) Các vị trí của lưỡi cắt trên
bánh răng gia công bằng
phương pháp bao hình.
Biên dạng thân
khai
Các vị trí của
lưỡi cắt
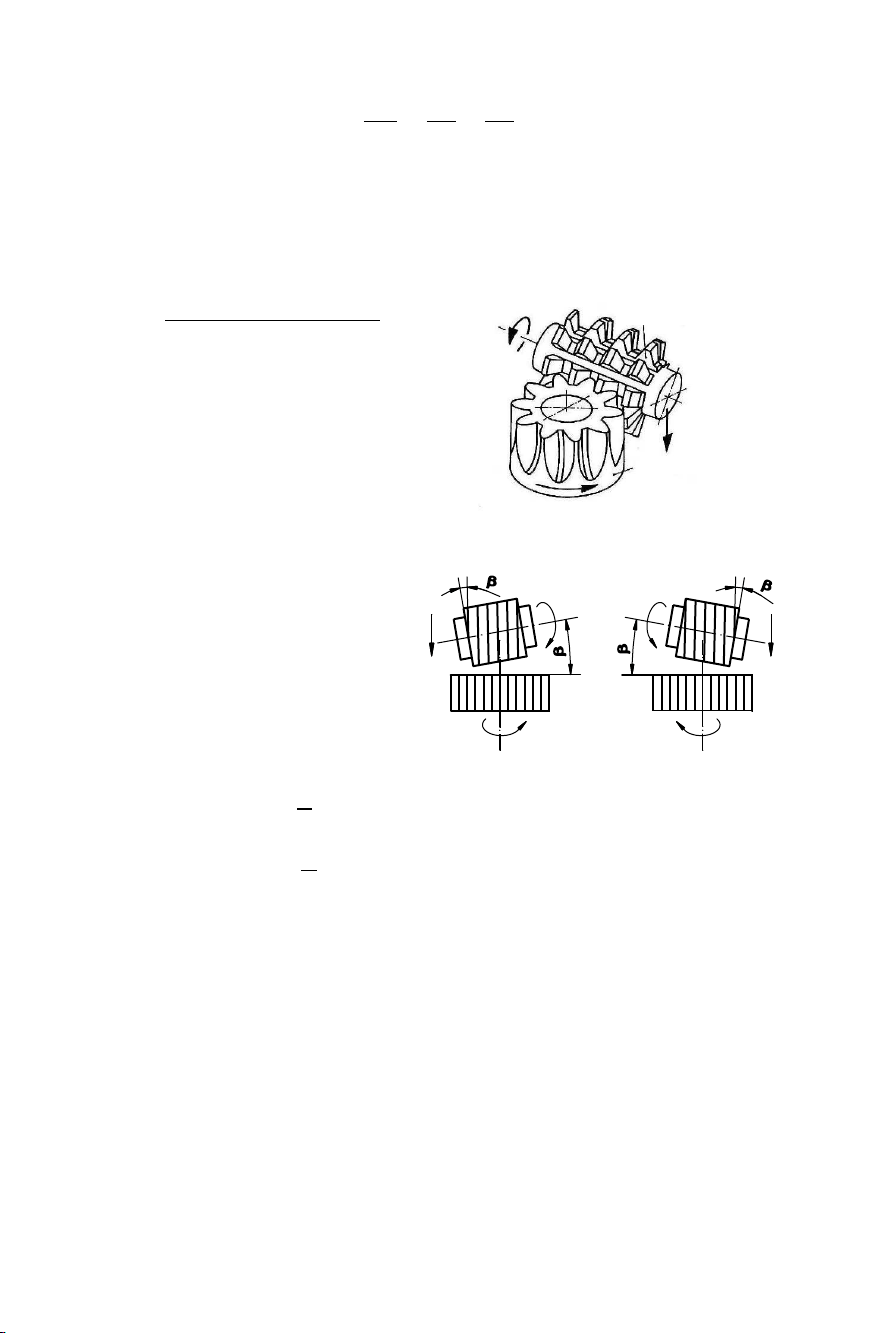
123
d
c
c
d
c
d
z
z
n
n
Ở đây:
d
, n
d
, z
d
- tốc độ góc, số vòng quay, số răng (số đầu mối) của dao.
c
, n
c
, z
c
- tốc độ góc, số vòng quay, số răng của bánh răng.
* Phay lăn răng thẳng
Khi gia công, chuyển
động bao hình được dựa trên
nguyên lý ăn khớp giữa dao
và phôi, đó là các chuyển
động quay của dao và phôi,
đồng thời dao phay lăn còn có
chuyển động tịnh tiến dọc trục
của phôi nhằm cắt hết chiều
dày của bánh răng. Trước khi
cắt, dao còn có chuyển động
hướng kính sao cho vòng lăn
của dao tiếp xúc với vòng lăn
của phôi, điều này cũng nhằm
đạt được chiều sâu của rãnh
răng. Sơ đồ cắt thể hiện trên
hình 2.96.
Khi phôi quay
z
1
vòng,
dao phay phải quay
k
1
vòng
(z: số răng của bánh răng cần
cắt; k: số đầu mối của dao).
Khi phay bánh răng thẳng, trục của dao phay phải đặt nghiêng so
với trục của vật gia công một góc đúng bằng góc nâng của đường xoắn
vít trên trục chia của dao. Dao phay đưọc gá theo hướng nghiêng phải
hay trái tùy theo hướng nghiêng của răng dao (hình 2.97). Mối liên hệ
giữa vòng quay của dao phay lăn và bánh răng gia công được thực hiện
nhờ các các bộ truyền cơ khí hoặc phối hợp giữa hai động cơ theo
phương pháp điều khiển số (máy phay lăn răng CNC).
Lượng chạy dao của dao phay lăn theo phương dọc trục của phôi
sau một vòng quay của phôi phụ thuộc vào tốc độ cắt của dao phay lăn.
Hình 2.97: Sơ đồ bố trí dao khi phay
lăn thẳng
a) Gá dao nghiêng hướng phải
b) Gá dao nghiêng hướng trái
v
v
n
c
a)
n
c
b)
S
S
Hình 2.96: Sơ đồ phay lăn răng.
Dao phay
Bánh
răng
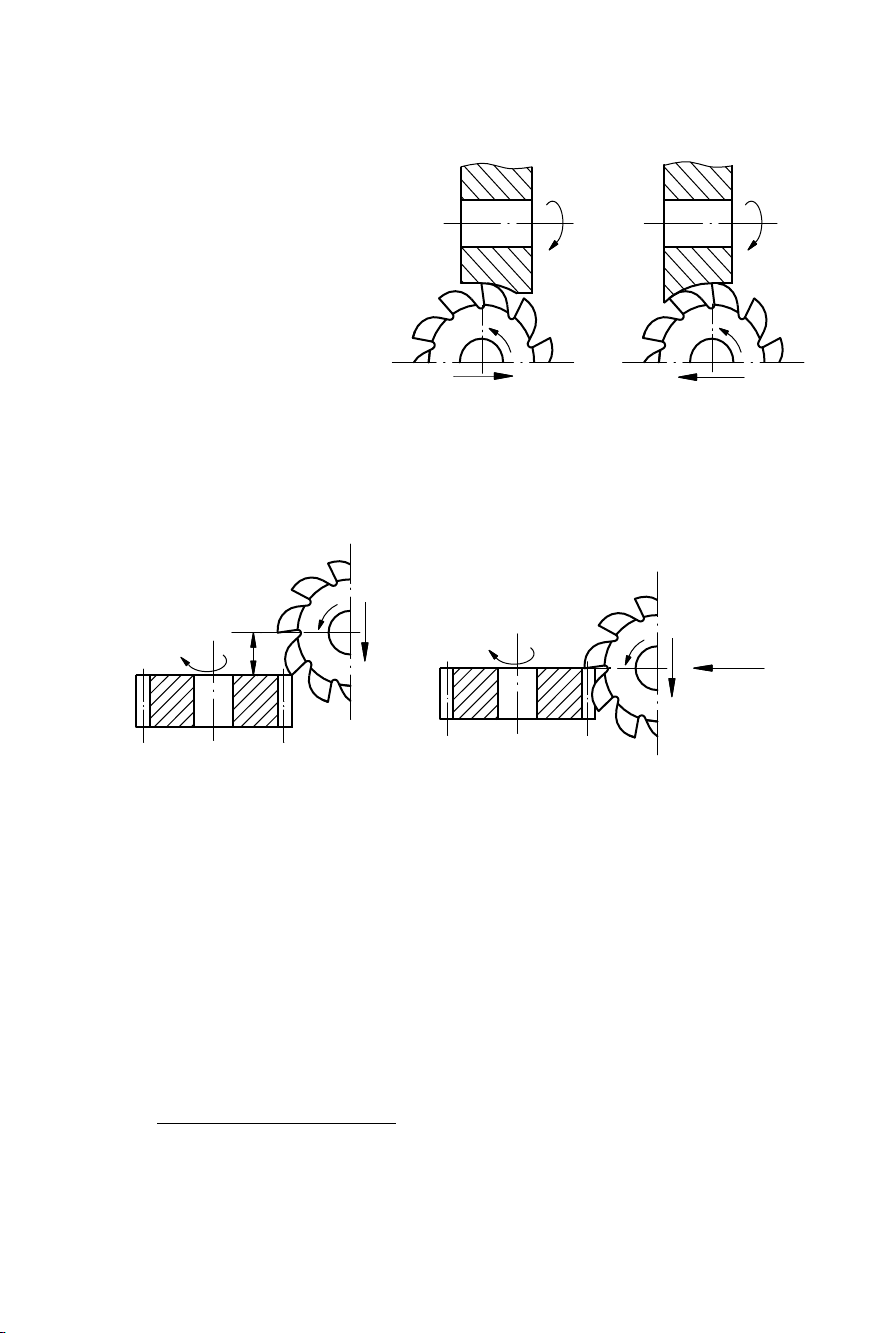
124
Nếu bánh răng có môđun nhỏ thì phay bằng một lần cắt, bánh răng
có mođun lớn thì phải phay bằng một số lần cắt.
Cho đến nay phần lớn
các máy phay lăn răng đều
làm việc bằng phương pháp
phay nghịch (hình 2.98b) vì
cắt êm, ít gây va đập; ít làm
gẫy và vỡ dao. Những máy
phay lăn mới được cải biến
cho phương pháp phay thuận
(hình 2.98a), ở máy phay này
dao có vị trí đầu tiên là ở
dưới vật và chạy dao từ dưới
lên. Với phương pháp này
cho phép nâng cao tốc độ cắt
lên 20 40% và lượng chạy dao lên 80%.
Các dao phay có đường kính lớn hơn, bảo đảm hiệu quả cắt lớn
hơn, chất lượng bề mặt răng tốt hơn và có độ chính xác cao hơn.
Khi cắt có thể tiến dao theo hướng trục (hình 2.99a) hoặc ban đầu
tiến dao theo hướng kính sau đó mới tiến dao theo hướng trục bánh răng
(hình 2.99b).
Theo cách thứ hai có thể rút gắn hành trình cắt một đoạn bằng l
(hình 2.99b) chính là đoạn ăn tới hay chuẩn bị cắt của dao.
* Phay lăn răng nghiêng
Bánh răng nghiêng được phay bằng phương pháp phay lăn tương
tự như bánh răng với răng thẳng. Nhưng để đảm bảo cho đoạn xoắn vít
Hình 2.98: Sơ đồ cắt khi phay lăn răng.
a) Phay thuận; b) Phay nghịch
a)
b)
n
d
n
c
S
S
1
b)
a)
l
n
c
n
d
S
Hình 2.99: Các phương pháp tiến dao
a) Hướng trục; b) Hướng kính và hướng trục
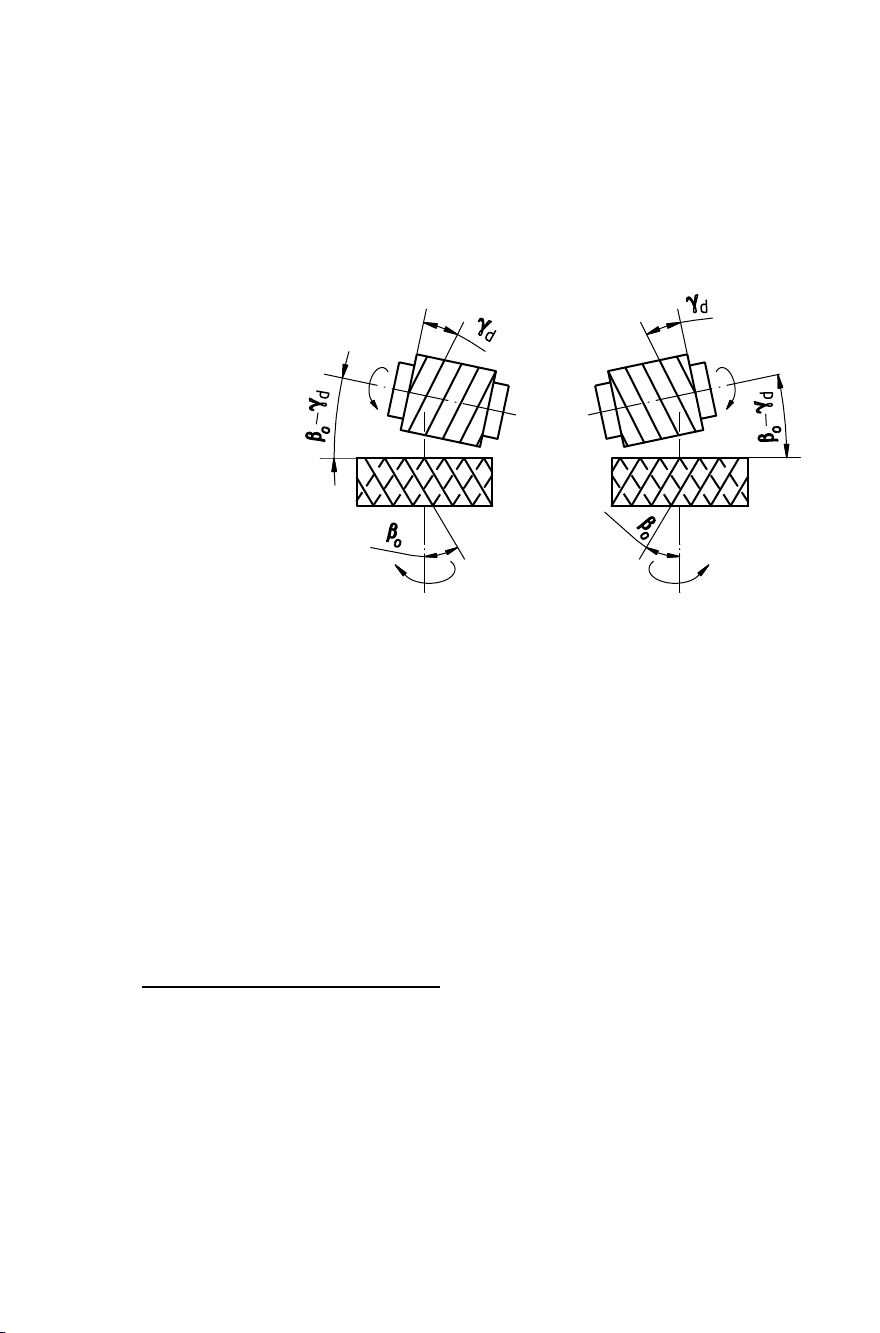
125
của dao ở vùng cắt trùng với phương răng chi tiết cần gia công, phải gá
trục dao làm với mặt đầu chi tiết một góc sao cho thỏa mãn:
=
o
d
Trong đó:
o
- góc nghiêng trên vòng chia của răng bánh răng gia công.
d
– góc nâng ở vòng chia của dao.
Trong công
thức này dấu (-)
được dùng khi
dao và chi tiết
cùng chiều
nghiêng (hình
2.100). Dấu (+)
dùng khi dao và
chi tiết ngược
chiều nghiêng.
Cũng có thể
vẽ sơ đồ gá dao
phay lăn lúc phay
răng nghiêng khi
dao và chi tiết
ngược chiều
nghiêng tương tự
như hình vẽ 2.100.
Vì hướng chạy dao S
d
song song với trục của bánh răng nên khi
phay bánh răng nghiêng phôi phải có chuyển động quay bổ sung để
hướng của răng dao lăn trùng với hướng răng gia công. Chuyển động này
được thực hiện nhờ bộ truyền dẫn vi sai đã được thiết kế trong xích
truyền động của máy.
* Chế độ cắt khi phay lăn răng
Khi phay lăn răng, cả răng thẳng và răng nghiêng phải chọn chế độ
cắt thích hợp để đảm bảo yêu cầu của sản phẩm.
- Tốc độ cắt khi lăn răng phụ thuộc vào nhiều yếu tố như môđun,
vật liệu gia công, chế độ nhiệt luyện, vật liệu và tuổi thọ của dao, độ
chính xác yêu cầu của chi tiết, độ cứng vững của hệ thống công nghệ,
chất lượng và phương pháp làm lạnh. Với dao lăn bằng thép gió dùng
trên máy phay lăn thông thường, để cắt thép thì tốc độ cắt v chọn trong
Hình 2.100: Sơ đồ gá dao phay lăn khi phay răng
nghiêng.
a) Bánh răng nghiêng trái, dao xoắn trái.
b) Bánh răng nghiêng phải, dao xoắn phải.
n
d
n
c
a)
n
d
n
c
b)
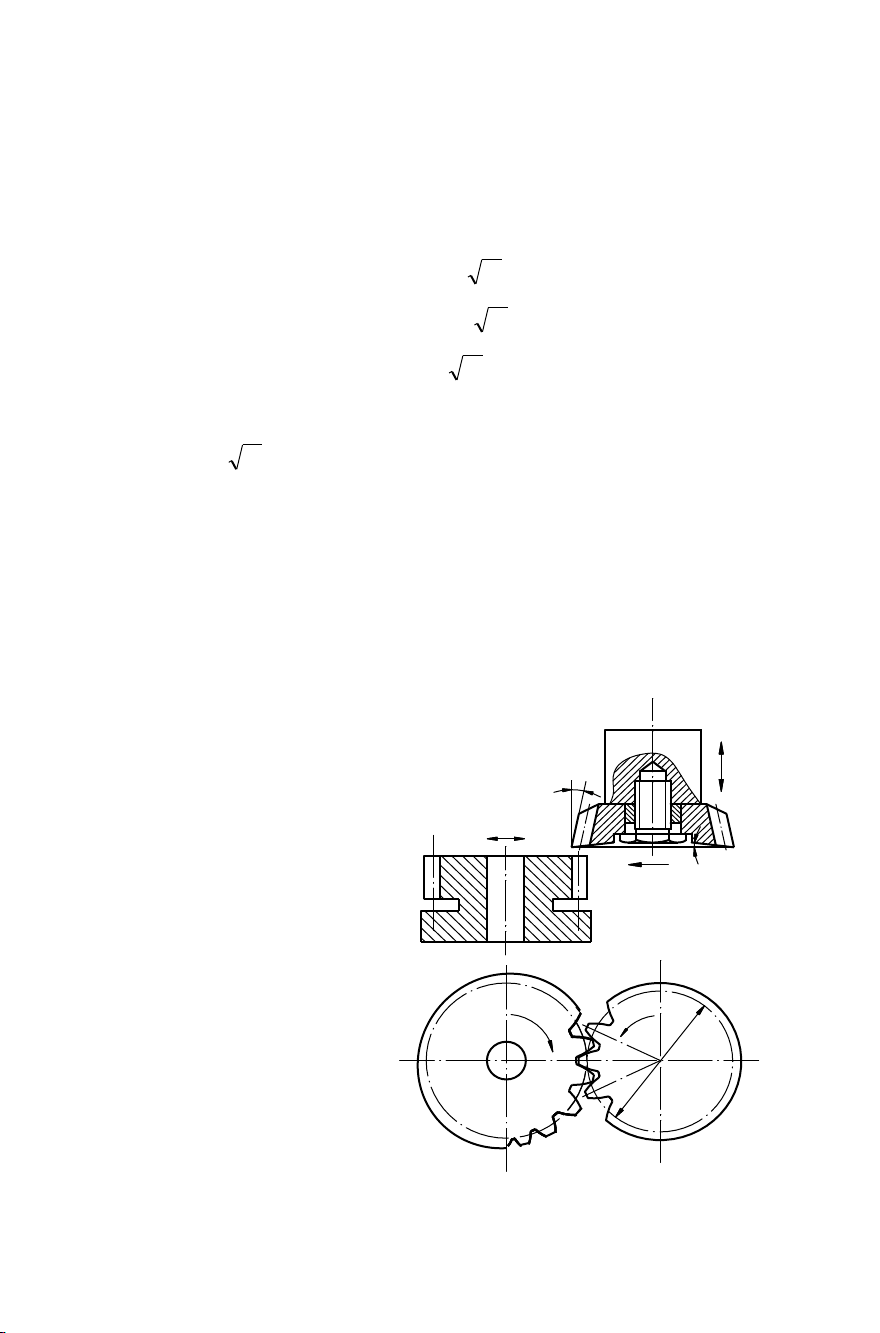
126
khoảng 15 30 m/phút. Với dao bằng hợp kim cứng cho phép tăng tốc độ
cắt lên 60 70 m/phút hoặc cao hơn.
- Lượng chạy dao: lượng chạy dao dọc trục bánh răng có ảnh
hưởng đến độ nhấp nhô bề mặt, do vậy khi phay thô nên chọn S = 1 2
mm/vòng phôi, khi phay tinh chọn 0,6 1,3 mm/vòng phôi
Lượng dư gia công thô Sh = 0,4
m
Lượng dư cho mài răng Sb = 0,2
m
Độ cao chiều cao răng h = 0,1
m
Với m 1,75
h = 0,2
m
với m 2 - 24
Nhìn chung phương pháp lăn răng có nhiều ưu điểm lớn như: tính
vạn năng cao, năng suất cao hơn phương pháp khác như xọc răng (sẽ
được trình bày ở phần sau nhất là khi gia công bánh răng mô đun lớn).
Tuy nhiên phương pháp này cũng có một số nhược điểm là dao phức tạp,
khó chế tạo và đòi hỏi khoảng thoát dao lớn.
b. Xọc răng
Xọc răng bao hình có
thể thực hiện bằng dao
dạng bánh răng (hình
chậu) hay dao dạng thanh
răng (hình lược) trên
máy xọc bao hình.
Xọc răng bằng dao
dạng bánh răng
Với phương pháp
này có thể tạo bánh răng
thẳng, bánh răng
nghiêng, bánh nhiều bậc
mà khoảng cách giữa các
bậc nhỏ và đặc biệt để
sản xuất bánh răng ăn
khớp trong. Về bản chất,
dụng cụ là một bánh răng
mà mặt đầu được tạo
thành mặt trước còn các
Hình 2.101: Xọc răng bằng dao xọc răng.
αH
S
1
S
v
n
d
n
c
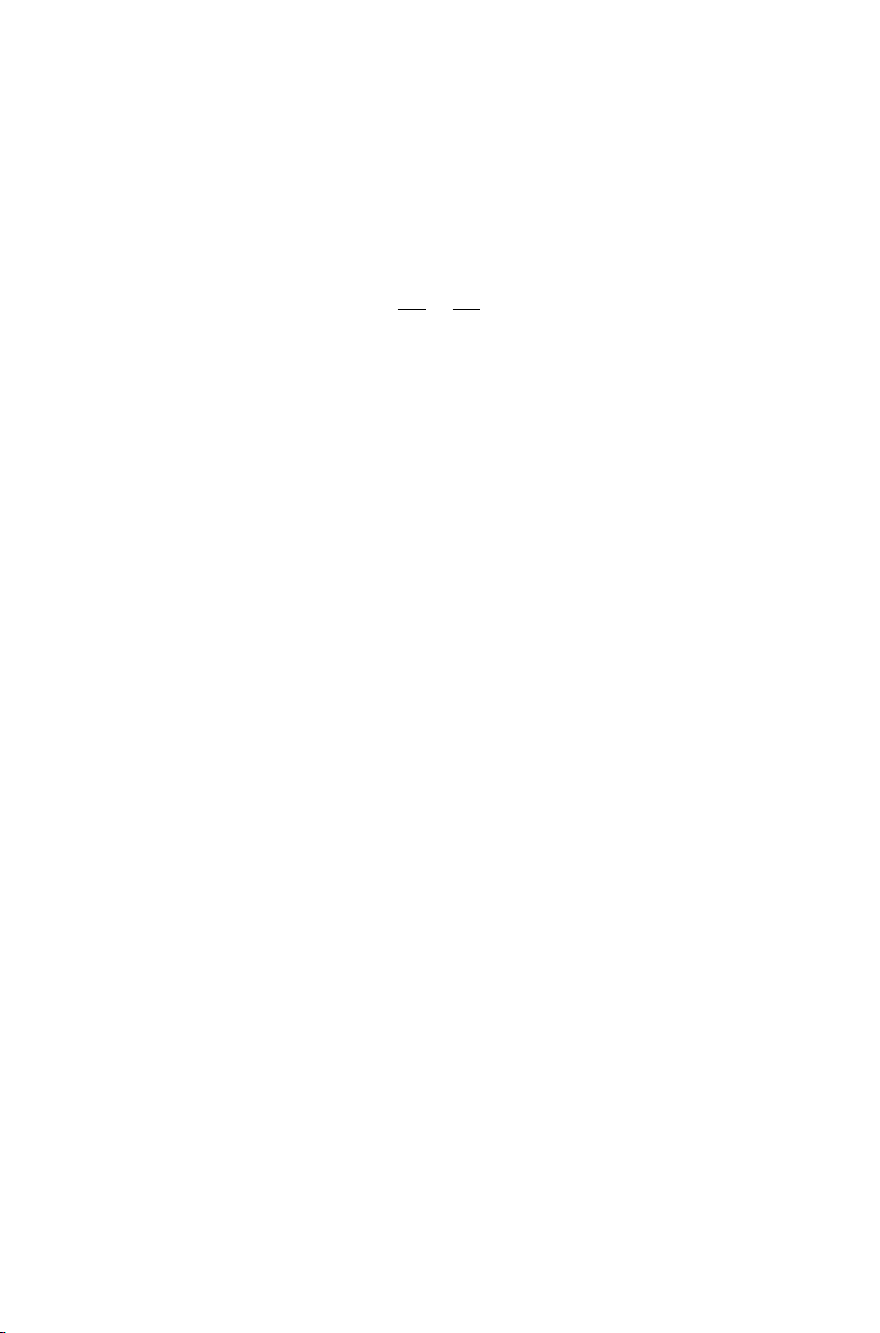
127
mặt bên tạo thành các mặt sau của lưỡi cắt. Trong quá trình gia công,
dụng cụ chuyển động cắt theo hướng dọc trục của bánh răng và cùng với
vật có chuyển động quay cưỡng bức (hình 2.101).
Khoảng cách trục của dụng cụ và chi tiết gia công bằng đúng
khoảng cách tâm của cặp bánh răng tương tự ăn khớp không có khe hở.
Tốc độ vòng của dao và chi tiết phải tuân theo tỷ số:
c
d
d
c
z
z
n
n
Ở đây:
n
c
, n
d
- số vòng quay của chi tiết và dao xọc.
z
c
, z
d
- số răng của chi tiết và dao.
Xọc răng bằng dao xọc dạng bánh răng là dựa trên nguyên tắc
chuyển động tương hỗ giữa dao và vật. Dao xọc và vật gia công được
quay cưỡng bức xung quanh trục của chúng theo hướng ngược nhau (khi
gia công bánh răng ăn khớp ngoài) và cùng hướng (khi gia công bánh
răng ăn khớp trong).
Dao thực hiện chuyển động đi lại v là chuyển động thẳng (khi gia
công bánh răng thẳng), là chuyển động xoắn (khi gia công bánh răng
nghiêng). Khi hành trình của dao theo hướng xuống dưới là thực hiện
tách phôi và khi chuyển động trở lại là hành trình chạy không.
Lúc này vật gia công được dịch ra S
1
khỏi sự ăn khớp - gọi là
nhường dao để tránh phá hủy dao và tránh chà xát mặt đã gia công với
dao làm cho chất lượng gia công bề mặt bị xấu đi. Công việc này được
thực hiện bởi cam E trên sơ đồ máy xọc răng hình 2.102.
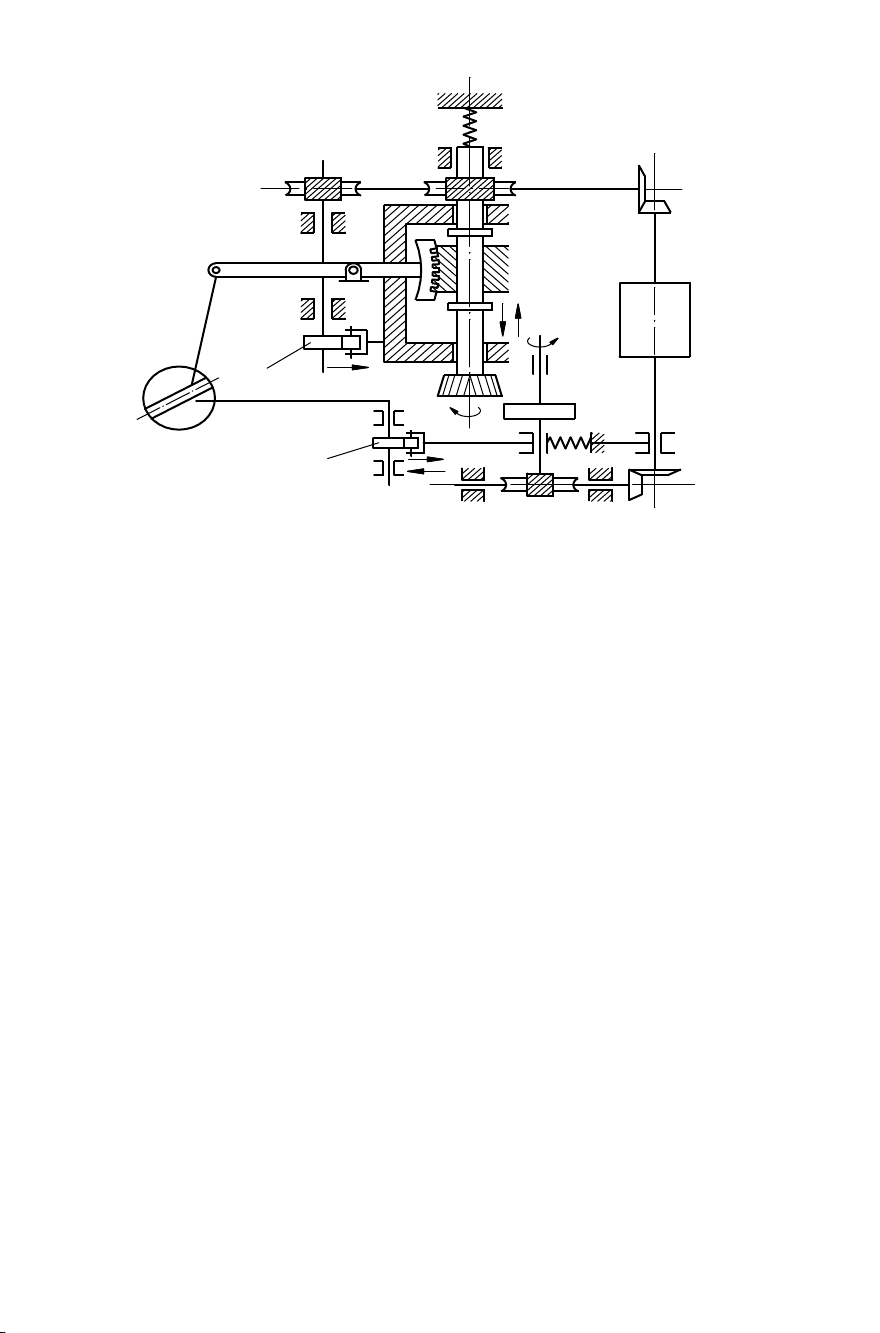
128
Khi gia công không thể ngay một lúc cắt hết chiều sâu rãnh răng
bánh răng được, mà phải từ từ tiến dao hướng kính. Khi tiến dao chi tiết
quay một cung tương ứng với thời gian tiến dao, rồi sau đó lại quay thêm
ít ra là một vòng nữa để dao cắt hết chiều cao răng của cả vòng răng, việc
đó được thực hiện nhờ cam trên máy (cam G trên hình 2.102).
Tùy theo môđun (m) của bánh răng gia công mà có kết cấu cam 1
lần, 2 lần hoặc 3 lần tiến dao. Đối với bánh răng có m = 1 - 2 dùng cam
một lần tiến dao, còn những bánh răng có m = 2,25 cắt bằng cam 2 lần
tiến dao và nếu m = 4 phải dùng cam 3 lần tiến dao.
Khi xọc răng phải chọn tốc độ cắt hợp lý. Tốc độ cắt chịu ảnh
hưởng của nhiều yếu tố như vật liệu gia công, yêu cầu kỹ thuật, điều kiện
cắt. Có thể tính tốc độ cắt theo số hành trình kép của đầu xọc trong một
phút. Các máy xọc răng thông thường có số hành trình kép trong một
phút từ 400 1000.
Hiện nay đang phát triển loại máy xọc răng kỹ thuật số (CNC).
Xọc răng là một phương pháp cắt răng có thể đạt được độ chính
xác tương đối tốt vì dao dễ chế tạo chính xác. Trong nhiều trường hợp,
nó là phương pháp duy nhất có thể gia công được sản phẩm, ví dụ như
gia công răng bậc mà khoảng cách các bậc nhỏ, bánh răng chữ nhân,
bánh răng trong. Trong trường hợp cắt bánh răng trong, chỉ có thể cắt
được khi:
Hình 2.102: Sơ đồ động máy xọc răng bằng dao xọc bánh răng.
v
n
c
n
d
G
S
E
S
1
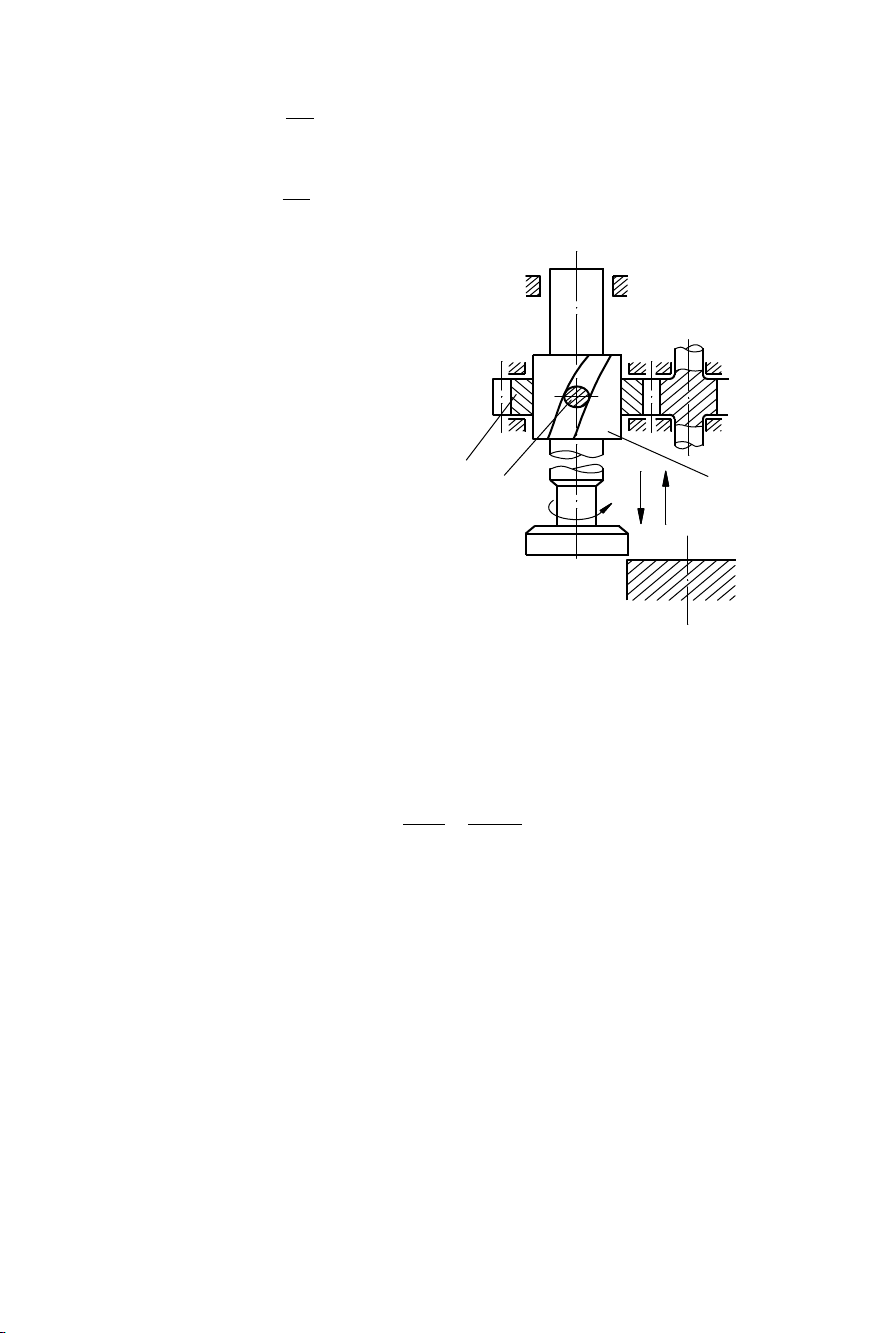
129
2
d
c
z
z
khi góc áp lực
o
o
20
3
d
c
z
z
khi góc áp lực
o
o
15
Nếu không thỏa mãn điều
kiện này sẽ xảy ra cắt lẹm đỉnh
răng.
Thông thường dùng
phương pháp xọc răng để gia
công bánh răng thẳng. Tuy
nhiên cũng có thể xọc được
bánh răng nghiêng khi dao có
răng nghiêng cùng với bạc dẫn
nghiêng tương ứng (hình
2.103).
Xọc răng có nhược điểm
là năng xuất không cao, khi cắt
răng nghiêng dao khó chế tạo
và đòi hỏi dao cũng như bạc
dẫn chuyên dùng.
Thời gian cơ bản khi xọc
răng được tính:
nS
zm
nS
h
T
v
o
.
..
.
1
Ở đây:
h - chiều cao răng (mm),
m - môđun bánh răng (mm),
z - số răng bánh răng gia công,
S
1
- lượng chạy dao hướng kính, mm/hành trình kép,
n - số hành trình kép trong một phút,
S
v
- lượng chạy dao vòng của dao xọc, mm/hành trình kép.
Hình 2.103: Sơ đồ khi xọc răng
bánh răng nghiêng.
1 – Bạc dẫn;
2 – Bánh răng;
3 – Rãnh dẫn nghiêng.
2
3
1
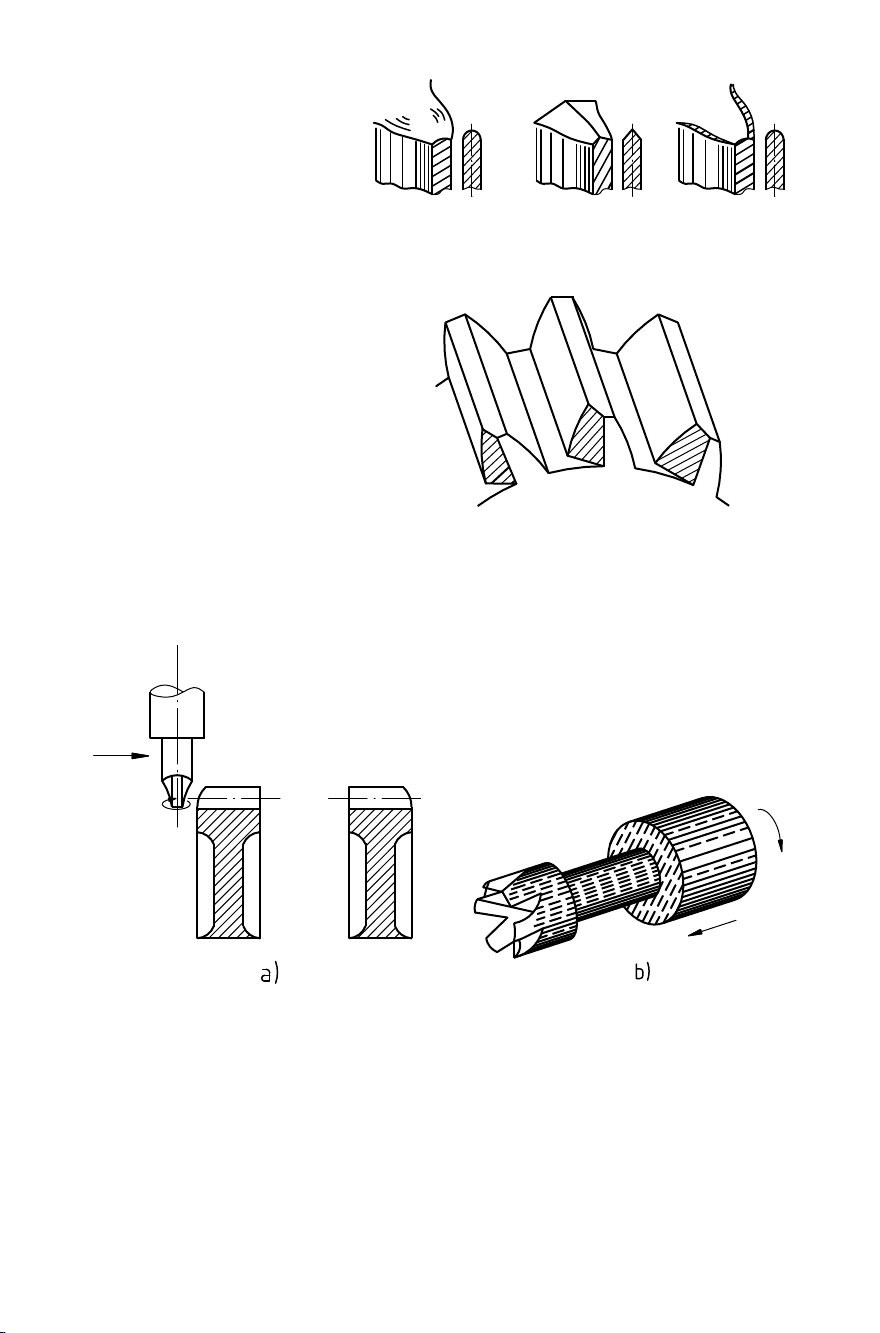
130
C. Vê, vát đầu răng
Ở những bánh răng
cần di trượt để thay đổi tỷ
số truyền đầu răng thường
được vê tròn hay vát nhọn,
vát cạnh cho dễ ra vào khớp
(hình 2.104).
Vát tròn (hình
2.104a) dùng khi bánh răng
vừa quay vừa di trượt.
Vát nhọn (hình
2.104b) dùng khi bánh răng
không quay mà di trượt.
Vát cạnh (hình
2.104c) dùng khi bánh răng
quay tốc độ thấp mà di
trượt.
Cũng có khi bánh răng chỉ cần vát một bên (hình 2.105) với điều
kiện truyền động chỉ một chiều.
Có thể thực hiện nguyên công này bằng dũa tay khi sản xuất đơn
chiếc. Để đạt được năng suất và độ chính xác cao việc vê vát đầu răng
được thực hiện trên máy chuyên dùng vê tròn bằng dao phay ngón định
Hình 2.105: Dạng vát đầu răng khi ra
vào khớp một chiều.
Hình 2.104: Các dạng đầu răng.
c)
b)
a)
Hìmh 2.106: Sơ đồ vê đầu răng.
a) Bằng dao phay ngón định hình
b) Bằng dao phay chuyên dùng.
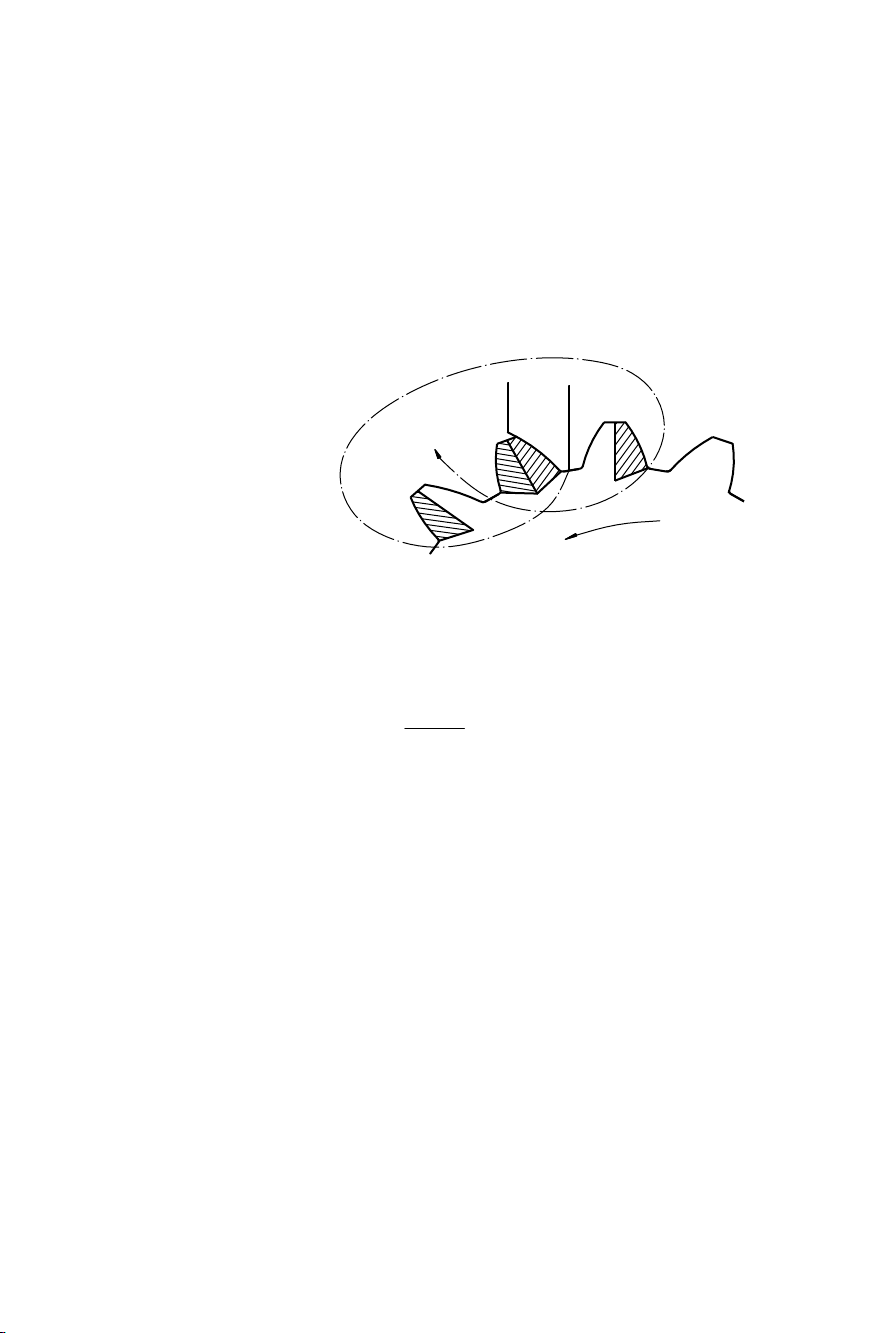
131
hình (hình 2.106a). Trong quá trình cắt, dao có chuyển động quay theo một
cung tròn 180
o
, cắt từ cạnh bên này sang cạnh bên kia của một đầu răng,
còn bánh răng đứng yên. Cắt xong một răng, dao được nâng lên, bánh răng
thực hiện chuyển động phân độ 1/Z. Sau khi phân độ xong, dao trở về vị trí
làm việc để cắt răng tiếp theo. Thời gian cắt một răng mất 13 giây.
Phương pháp này cắt không liên tục nên năng suất vẫn chưa cao.
Để nâng cao năng suất, có thể cắt liên tục bằng dao phay định hình
chuyên dùng (hình 2.106b), khi cắt cả dao và chi tiết đều chuyển động, giữa
hai chuyển động này có xích truyền động cưỡng bức (hình 2.107). Quỹ đạo
tương đối của dao so với
chi tiết là một đường
Epixicloid. Đầu răng gia
công được vát nhọn chứ
không tròn.
Thời gian gia
công một mặt đầu của
bánh răng (vê tròn tất
cả các răng) được xác
định:
Ở đây: t - thời gian gia công một răng.
- thời gian bánh răng quay được một răng và thời gian dao tiến
vào, lùi ra.
z - số răng của bánh răng.
Hiện nay việc gia công bánh răng trụ trước nhiệt luyện có thể được
hoàn thành trên một máy tổ hợp gồm nhiều bước khác nhau như:
- Tiện thô và tinh mặt ngoài, vát mép ngoài
- Khoan, tiện thô và tinh lỗ, vát mép lỗ
- Khoan lỗ hướng tâm hoặc lỗ xiên, ta rô ren, cắt rãnh
- Phay bao hình biên dạng răng, vê đầu răng
- Cắt đứt và vận chuyển bánh răng ra ngoài.
Hình 2.107: Sơ đồ chuyển động khi vát
nhọn đầu răng
Dao
z
t
T .
60
0
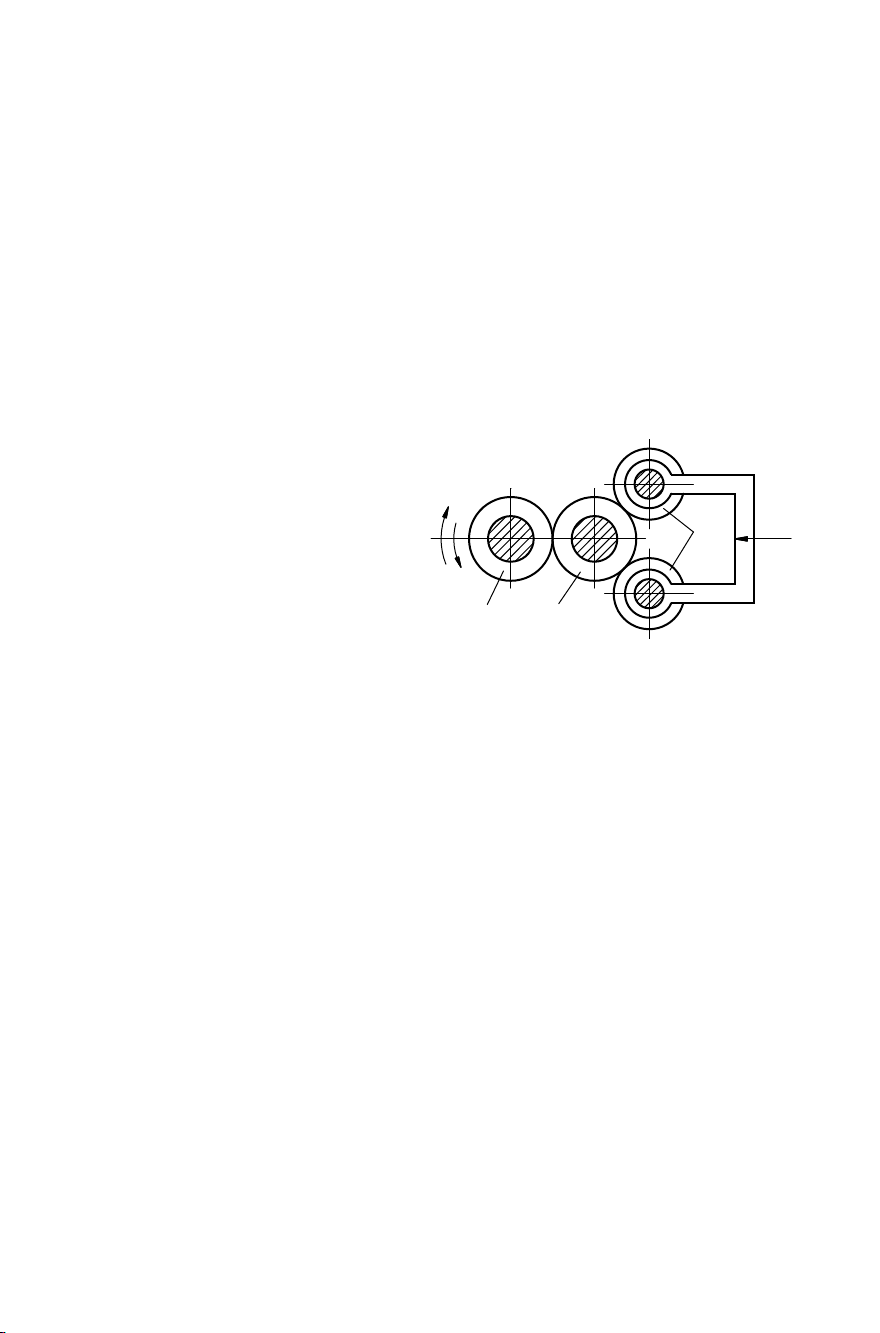
132
D. Các phương pháp gia công tinh bánh răng trụ
Có thể chia các phương pháp gia công tinh bánh răng ra làm hai loại:
- Loại thứ nhất: gia công không có phôi như phương pháp chạy rà
bánh răng.
- Loại thứ hai: gia công có cắt phôi như phương pháp mài răng, cà
răng, mài nghiền răng, mài khôn răng.
a. Chạy rà bánh răng
Phương pháp chạy rà bánh răng được thực hiện khi bánh răng gia
công ăn khớp với một hoặc ba bánh răng mẫu đã tôi cứng nên có độ cứng
và chính xác cao hơn. Trong quá trình gia công, nhờ có áp lực của bánh
răng mẫu tác dụng lên bánh răng
gia công mà bề mặt răng của nó
được là phẳng và được nén, nên
sau khi chạy rà độ cứng và độ
chính xác được nâng lên. Sơ đồ
chạy rà bánh răng bằng ba mẫu
thể hiện trên hình 2.108.
Bánh răng gia công 1 quay
do bánh mẫu 2 tác động và truyền
chuyển động cho hai bánh mẫu 3.
Để chạy rà đều cần phải quay
theo hai chiều với số vòng quay
giống nhau từ 3 25 vòng/phút. Áp lực P chọn 5 10 atm. Thời gian
chạy rà 10 30 phút với bánh răng có m = 2 5.
Phương pháp này thường dùng để gia công bánh răng không cần
nhiệt luyện, khi chạy rà có thể bôi dầu hoặc chạy rà khô.
b. Cà răng
Cà răng là phương pháp gia công tinh bánh răng cho những bánh
răng không cứng lắm như các bánh răng không tôi, hoặc sau khi ủ trước
khi tôi.
Bánh răng trước khi cà phải được chế tạo chính xác hơn so với
bánh răng đem mài. Lượng dư cho cà lớn nhất là 0,15mm cho một răng.
Bằng phương pháp cà răng có thể gia công được bánh răng thẳng, răng
nghiêng, răng trong hoặc ngoài.
Dụng cụ để cà răng là loại bánh răng hoặc thanh răng đã được tôi
cứng, cho ăn khớp không khe hở với bánh răng gia công. Trên bề mặt
răng của dụng cụ được xẻ các rãnh để tạo ra các cạnh sắc làm lưỡi cắt.
Hình 2.108: Sơ đồ chạy rà bánh
răng trụ bằng 3 bánh mẫu.
2
1
3
P
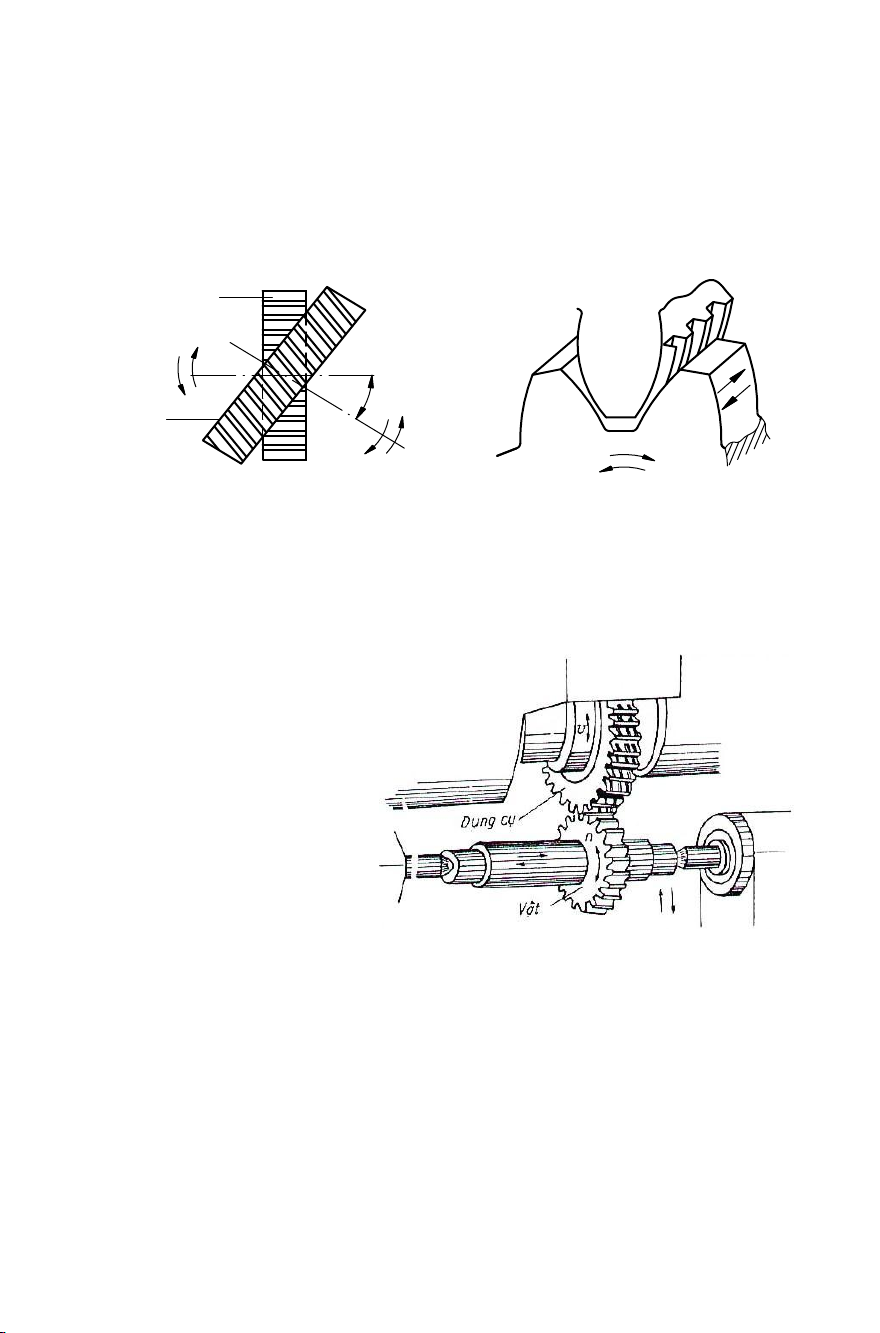
133
Hình 2.09 trình bày sơ đồ gia công và cấu tạo của bánh cà. Quá trình cắt
gọt xảy ra khi bánh cà trượt và lăn trên mặt răng của bánh răng gia công.
Lớp phôi cà đi rất mỏng từ 0,001 0,005 mm.
Cà răng để sửa đi những sai số về hình dáng và nâng cao độ nhẵn
bóng bề mặt răng, độ nhám có thể đạt R
a
= 0,63 0,16. Có thể gia công
các bánh có đường kính từ 6 1200 mm với môđun từ 0,1 12 mm.
Dụng cụ cà răng dạng
bánh răng được sử dụng phổ
biến hơn vì nó có thể cà
được những bánh răng có
kích thước bất kì, cả bánh
răng trong và bánh răng
ngoài. Với phương pháp này
có thể sửa được sai số của
bước răng. Sơ đồ cà răng
bằng bánh cà hình dĩa được
trình bày trên hình 2.109a
và có thể thấy rõ hơn ở trên
hình 2.110.
Để tạo sự cắt gọt tốt cho bánh cà, trục của dao cà và trục của vật gia
công phải đặt chéo nhau một góc = 5 15
o
. Nhờ vậy hiện tượng trượt
tương đối không chỉ xảy ra theo biên dạng mà theo cả hướng răng. Chính
thành phần vận tốc trượt theo hướng răng làm cho các lưỡi cắt tạo nên bởi
các rãnh thoát phôi cạo lên bề mặt răng chi tiết tách ra một lớp phôi mỏng.
Khi gia công, chỉ có dao nhận được chuyển động quay từ động cơ,
còn chi tiết quay theo dao trên hai mũi tâm. Để cà được cả hai phía của
răng, chuyển động quay của bánh cà phải được đổi chiều thuận nghịch.
Hình 2.110: Cà răng bằng
bánh cà hình đĩa.
Hình 2.109: Sơ đồ cà răng (a); Cấu tạo của răng dao cà (b).
1. Bánh cà; 2. Chi tiết gia công.
a)
b)
1
2
1
2
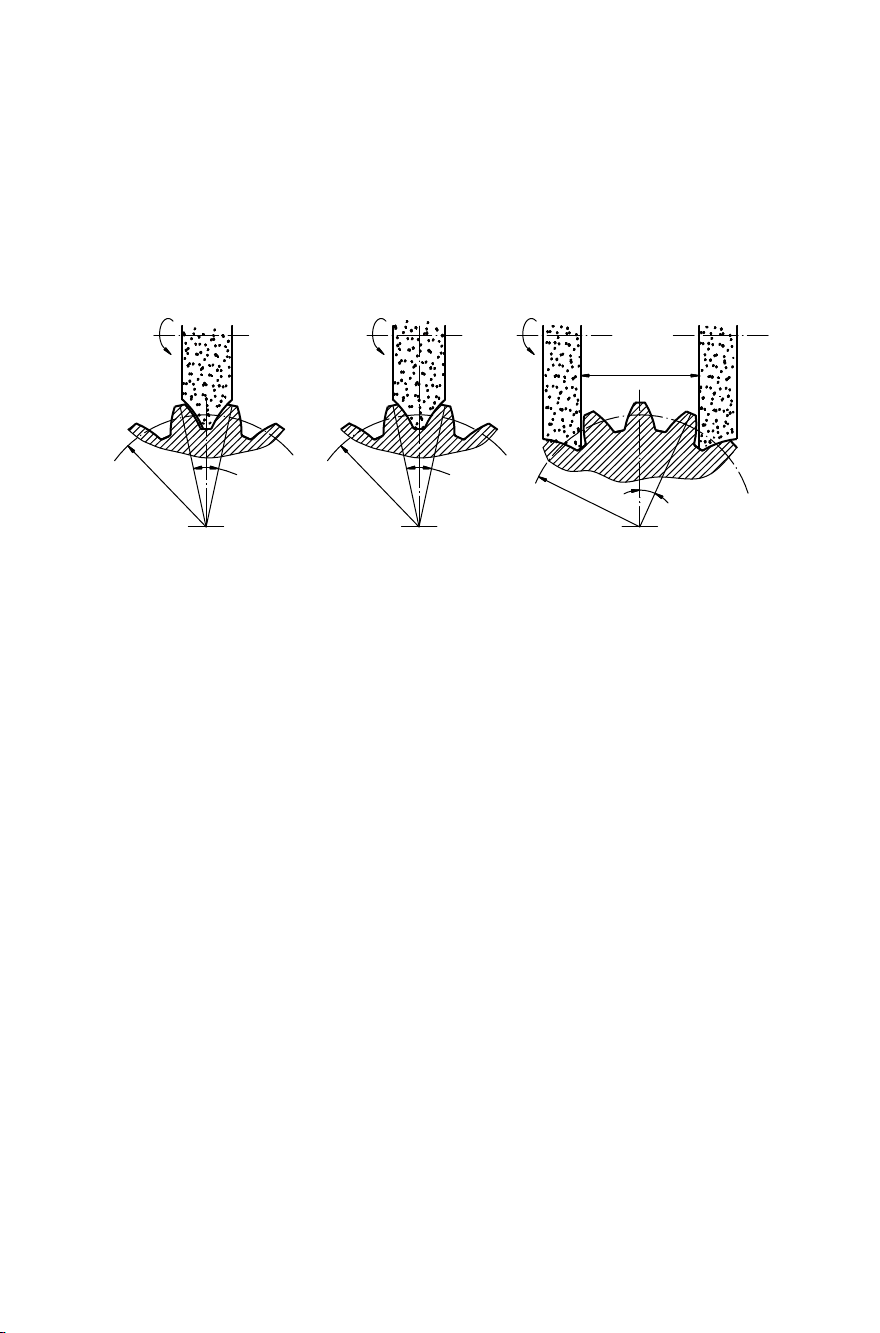
134
Ngoài ra, các chi tiết còn có chuyển động chạy dao S để cắt hết chiều dài
rãnh răng và sau mỗi hành trình có chuyển động tịnh tiến thẳng đứng đến
bánh cà để lấy chiều sâu cắt.
c. Mài răng bánh răng
Mài răng bánh răng là phương pháp gia công tinh bánh răng trước
hoặc sau nhiệt luyện, có khả năng đạt độ chính xác cao từ cấp 4 6, độ
nhẵn bóng bề mặt răng đạt từ R
a
= 1,25 0,32.
Phương pháp mài răng thường được dùng để gia công những dụng
cụ để cắt răng, những bánh răng mẫu, những bánh răng trong những máy
có yêu cầu kỹ thuật cao. Máy mài bánh răng có cấu tạo phức tạp năng
suất thấp, giá thành chế tạo cao, vì vậy mài răng chỉ dùng trong sản xuất
hàng khối và hàng loạt lớn. Mài răng được thực hiện theo hai nguyên lý:
định hình và bao hình.
* Mài răng theo phương pháp định hình
Khi mài răng theo phương pháp định hình, prôfin đá mài có dạng
của rãnh răng cần gia công. Trong quá trình gia công, đá mài thực hiện
chuyển động cắt quay tròn, ngoài ra đá còn chuyển động dọc theo trục
của bánh răng để cắt hết chiều dầy răng.
Sử dụng đầu phân độ để mài các rãnh khác nhau của bánh răng.
Phương pháp này cũng tương tự như phay bằng dao phay môđun định
hình. Sơ đồ gia công thể hiện trên hình 2.111 có thể mài mỗi lần một mặt
bên răng hoặc cả hai mặt bên răng cùng một lúc bằng một hoặc hai đá.
Với phương pháp mài cả hai mặt bên của răng bằng một đá mài thì
dạng prôfin đá phụ thuộc vào môđun, vào tổng số răng và góc ăn khớp.
Phương pháp mài hai mặt bên của răng bằng hai đá cho độ chính
xác cao hơn và hiệu quả hơn. Hai đá mài được bố trí cách nhau một
Hình 2.111: Sơ đồ mài răng bằng đá mài định hình.
a. Mài định hình một mặt bên của răng.
b. Mài định hình hai mặt bên của răng bằng 1 đá.
c. Mài định hình hai mặt bên của răng bằng 2 đá.
a)
c)
L
R
R
R
v
v
v
b)
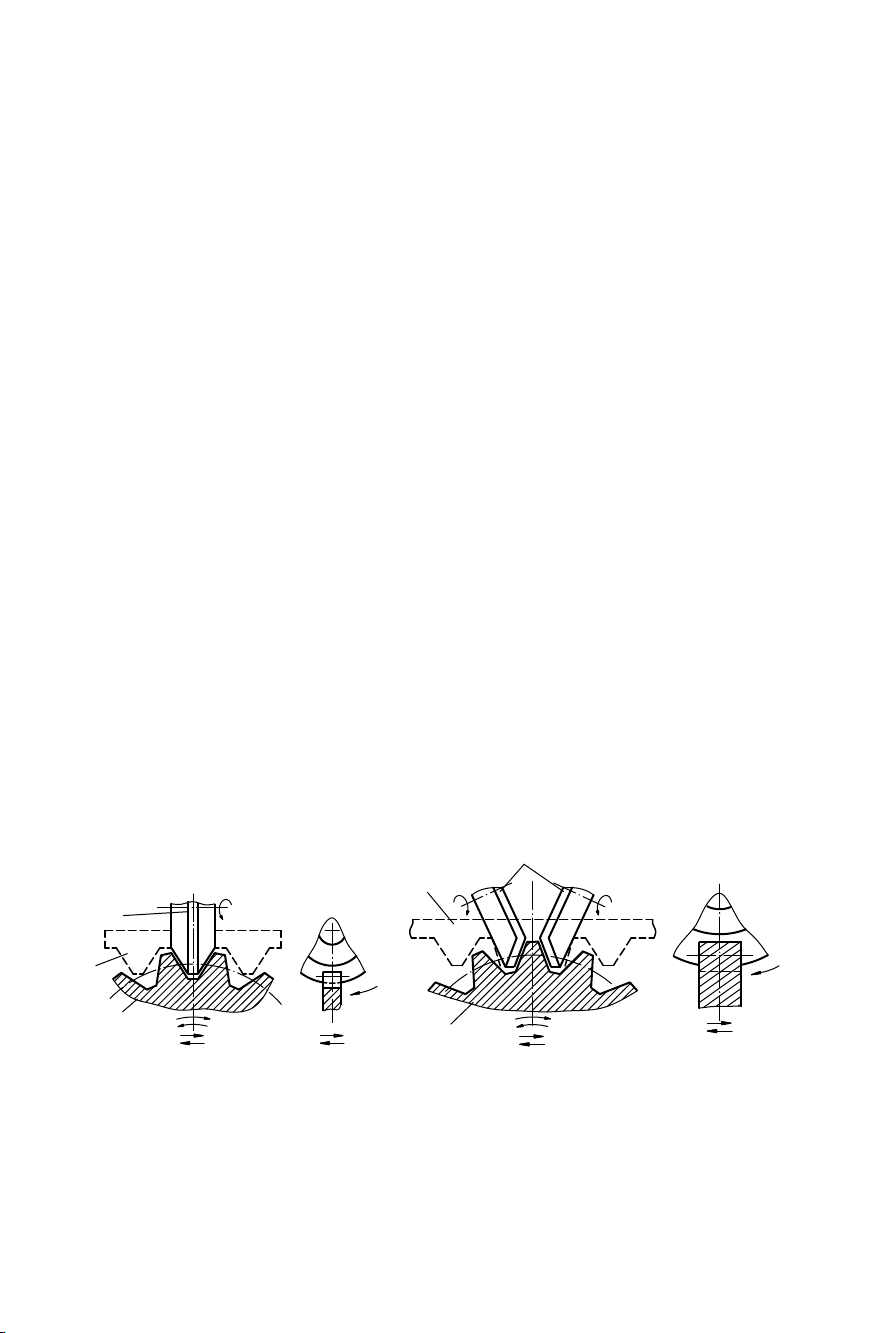
135
khoảng L, giá trị này phụ thuộc vào tổng số răng. Mỗi một đá mài một
mặt bên của răng và như thế dễ dàng loại trừ độ không chính xác xuất
hiện khi phay răng.
Khi mài định hình, tất cả những sai số hình dạng của đá từ ban đầu
cũng như bị mài mòn trong quá trình mài sẽ trực tiếp gây ra sai số cho
vật mài. Vì vậy, đá mài cần được sửa chính xác theo dưỡng. Ở những
máy mài hiện đại có trang bị những bộ phận sửa đá tự động theo chu kỳ
mài. Khi mài xong một răng, đá lùi xa còn vật gia công được phân độ
sang răng khác, đưa mũi kim cương vào sửa đá theo dưỡng.
Khi mài định hình thường dùng tốc độ quay của đá v = 30 35m/s,
tốc độc tiến của đá v
t
= 8 16m/ph. Lượng dư mài là 0,2 0,3mm và chia
làm 3, 4 bước.
Ưu điểm của phương pháp mài định hình là có thể gia công được
bánh răng ngoài và răng trong, nhưng nhược điểm là phải có nhiều dưỡng
chép hình, đĩa phân độ, điều chỉnh máy tương đối phức tạp, độ chính xác
và năng suất không cao.
* Mài bánh răng theo phương pháp bao hình
Mài răng theo phương pháp bao hình đạt độ chính xác cao hơn và
ứng dụng rộng rãi hơn so với mài định hình. Gia công theo phương pháp
này dựa theo nguyên lý ăn khớp của thanh răng với bánh răng mà thanh
răng có cùng môđun và góc ăn khớp với bánh răng gia công. Khi mài
theo phương pháp này thường dùng các loại đá như sau:
Mài bánh răng bằng đá có prôfin hình thang của một răng thanh
răng. Mặt làm việc của đá hình côn. Đá mài tiếp xúc với bánh răng gia
công chỉ ở một điểm (hình 2.112a).
Hình 2.112: Mài răng bằng đá mài có prôfin hình thang của một
răng thanh răng.
a. Mài bằng một đá có prôfin hình thang của một răng thanh răng
b. Mài bằng hai đá đĩa đặt nghiêng một góc sao cho hai mặt
côn của hai đá tạo ra prôfin hình thang.
v
2
1
3
2
1
3
S
d
v
b)
v
1
2
S
d
3
2
1
a)
3
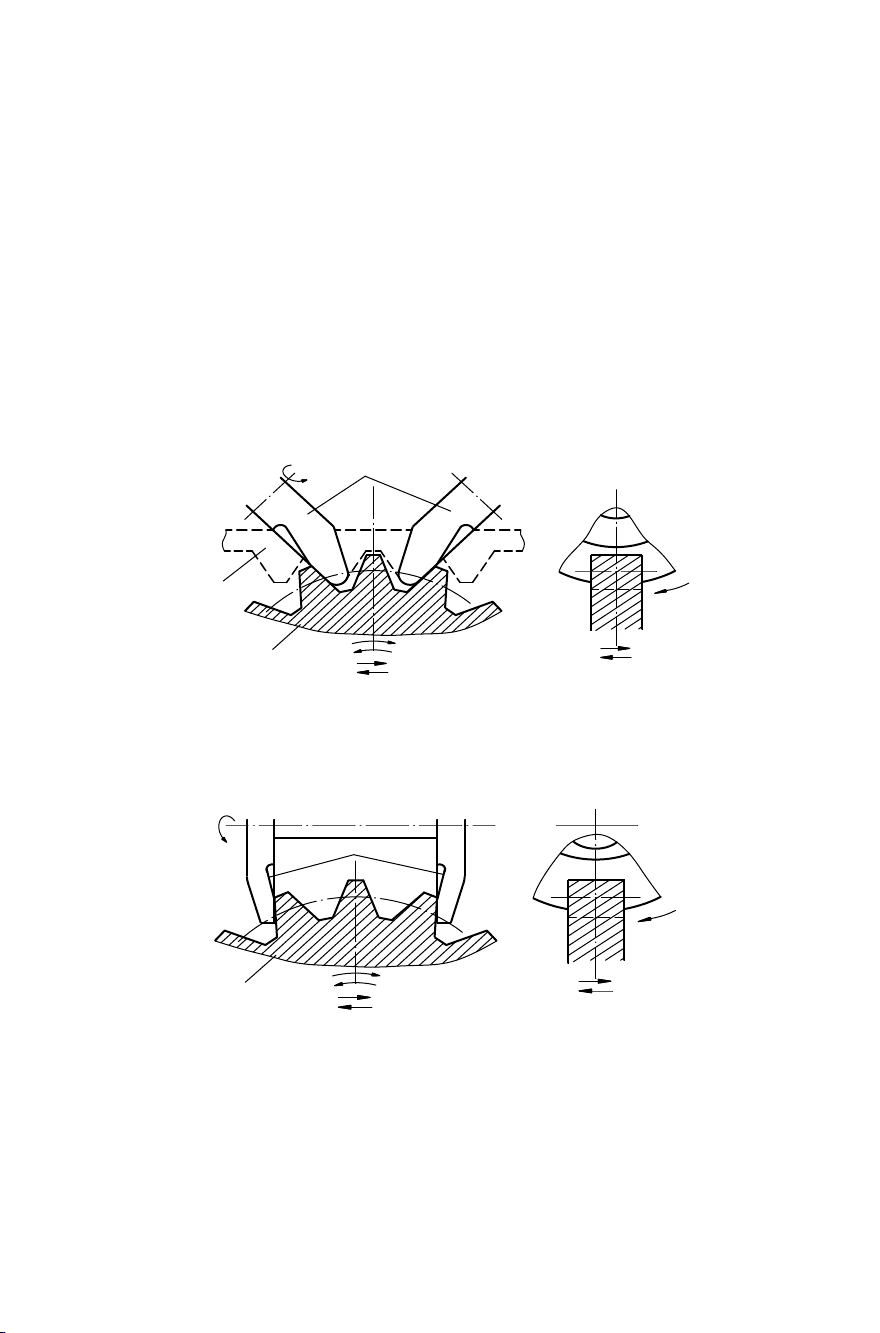
136
Theo phương pháp này, cũng có thể mài bằng một đá có prôfin
hình thang của một thanh răng (hình 2.112a) và cũng có thể dùng hai đá
đĩa đặt nghiêng một góc sao cho hai mặt côn của hai đá tạo ra prôfin hình
thang một thanh răng (hình 2.112b).
Mài răng bằng hai đá mài hình đĩa đặt một góc bằng góc ăn khớp
sao cho đá tạo ra với mặt bên của răng một thanh răng tưởng tượng mà
bánh răng gia công được lăn theo thanh răng này. Đá có mặt côn và vì
thế chỉ mài được bằng mép của mặt đầu. Mặt làm việc của đá là mặt
phẳng nên tiếp xúc giữa đá và mặt răng bánh răng là tiếp xúc đường. Sơ
đồ gia công thể hiện trên hình 2.113.
Mài răng bằng hai đá hình đĩa với trục quay vuông góc với trục
bánh răng gia công. Sơ đồ gia công thể hiện trên hình 2.114.
Phương pháp này nhanh hơn đáng kể so với phương pháp trước.
Mài răng bằng phương pháp bao hình bằng đá mài hình côn và hình
đĩa bằng các sơ đồ trình bày ở trên đều theo nguyên lý sau: đá mài 1 có
Hình 2.113: Mài răng bằng hai đá đĩa
nghiêng một góc bằng góc ăn khớp.
1
v
v
S
d
3
3
2
2
1
Hình 2.114: Mài răng bằng hai đá đĩa có
trục quay vuông góc với trục bánh răng gia
công.
v
v
S
d
1
2
3
1
3
1
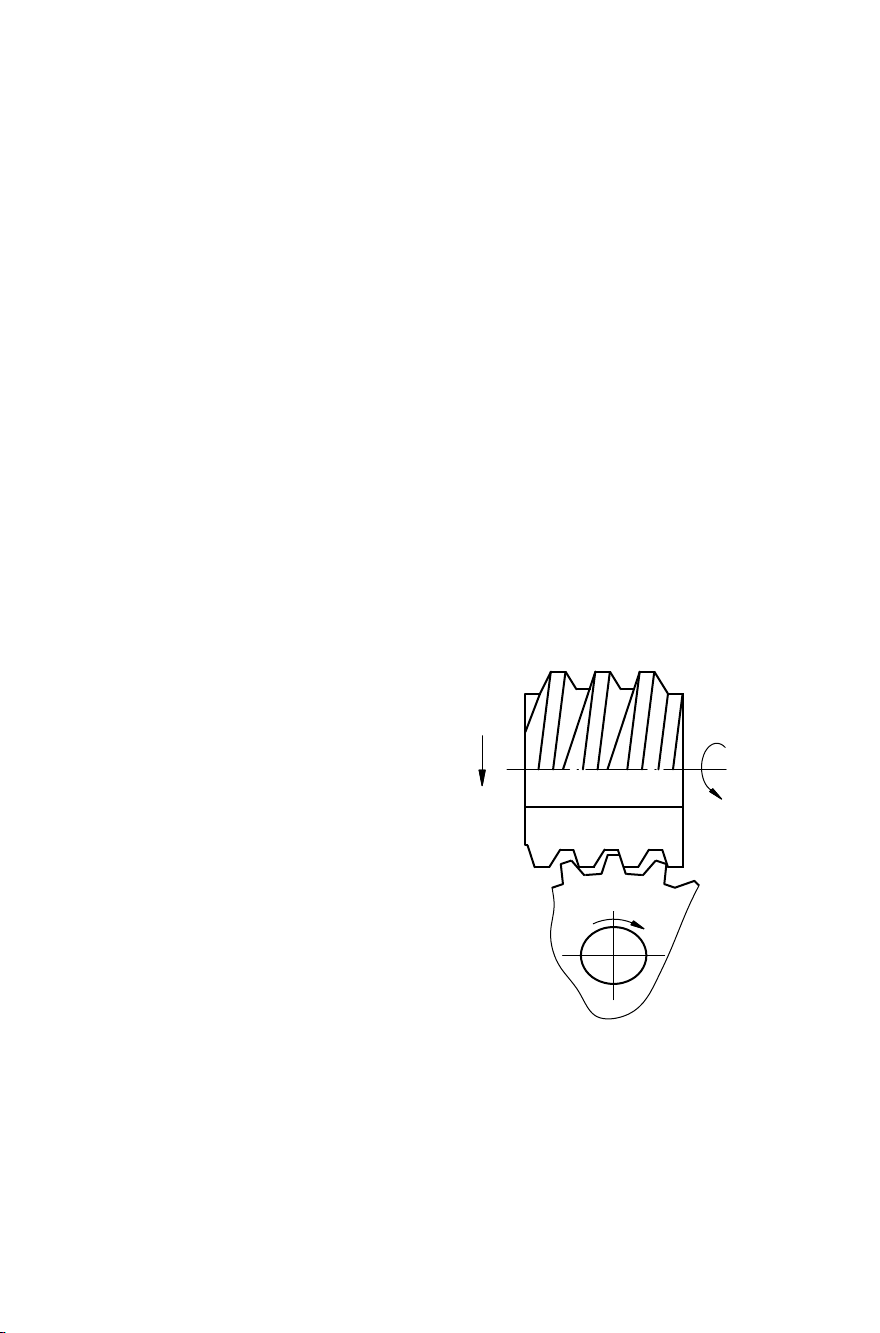
137
bề mặt làm việc như là răng của thanh răng 2 ăn khớp với bánh răng gia
công 3.
Khi gia công bằng phương pháp bao hình cần có các chuyển động
sau: chuyển động quay của đá mài với tốc độ v
đ
; chuyển động đi lại tịnh
tiến của bánh răng gia công hay ụ đá mài theo hướng vuông góc với trục
bánh răng (chuyển động 1) phù hợp với sự quay của bánh răng (chuyển
động 2); chuyển dịch tương đối của đá dọc theo răng bánh răng (chuyển
động 3) – đó là chạy dao dọc S
đ
; sự quay của bánh răng đi một bước sau
khi kết thúc gia công một răng.
Do đá mài chỉ là một răng của thanh răng nên mỗi lần chỉ bao hình
được một răng hoặc một rãnh răng, đồng thời cần có bộ phận phân độ từ
răng này qua răng khác.
* Mài răng bằng đá mài dạng trục vít
Dạng đá này dùng mài bánh răng hình trụ thân khai có năng suất
cao hơn các phương pháp mài khác do quá trình gia công liên tục và
đồng thời trên một số răng. Phương pháp này có thể gia công bánh răng
trụ răng nghiêng. Đá mài được chế tạo theo dạng trục vít có một hoặc hai
đầu mối, đường kính đá khoảng 300 400 mm. Sơ đồ gia công được thể
hiện trên hình 2.115. Các chuyển động trong quá trình gia công bao gồm:
Chuyển động quay của
bánh răng gia công xung quanh
trục của nó (chuyển động III);
chuyển động của đá xung quanh
trục của nó (chuyển động I),
chuyển động này tạo nên chuyển
động cắt gọt với tốc độ 22 –
32mm/s. Các chuyển động I và
III tạo thành các chuyển động
bao hình như phay lăn răng.
Ngoài ra còn có chuyển động của
đá dọc theo trục hoặc theo hướng
của răng (nếu là răng nghiêng) để
mài hết chiều dày của răng với
tốc độ dịch chuyển 0,3 – 3
mm/một vòng bánh răng.
Chuyển động hướng kính II với trị số 0,01 0,08 mm để mài hết
chiều sâu của răng. Gia công bằng phương pháp này có thể đạt độ chính
xác cấp 4 5, độ nhẵn bóng R
a
= 1,25 0,16.
Hình 2.115: Sơ đồ mài răng
bằng đá mài trục vít.
I
II
III
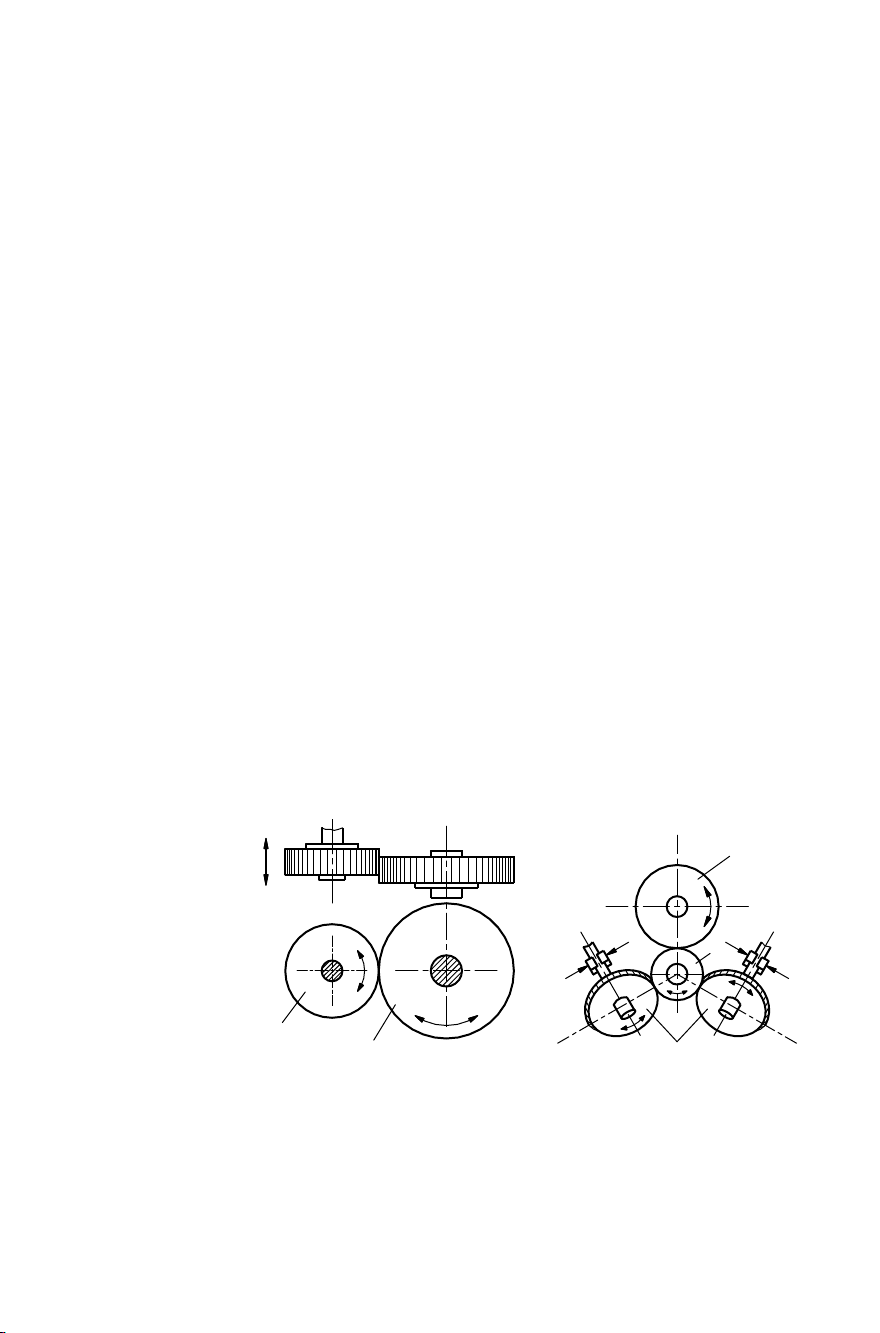
138
Thời gian gia công rất ngắn, khoảng 0,2 0,3 phút cho một răng.
Khi mài bánh răng có môđun nhỏ hơn 1, có thể mài một lần. Với bánh
răng có môđun lớn hơn, có thể phải mài bằng bán tinh và mài tinh.
Trước và sau khi mài cần kiểm tra và sửa đá nếu cần.
d. Mài nghiền bánh răng
Mài nghiền bánh răng là một phương pháp gia công tinh sau nhiệt
luyện để nâng cao độ nhẵn bóng bề mặt răng có thể đạt R
a
= 0,63 – 0,32
hiệu chỉnh được những sai số chung về dạng răng, bước và độ đảo,
những biến dạng sau khi nhiệt luyện, làm sạch các ôxyt, các vết lồi lõm,
do đó khi làm việc sẽ giảm bớt tiếng ồn. Tuy nhiên máy nghiền không
thể hiệu chỉnh được sai số lớn và năng suất gia công thấp.
Máy nghiền được sử dụng trong những trường hợp bánh răng có
yêu cầu cao về độ chính xác như các bánh răng trong ô tô.
Bản chất của phương pháp nghiền răng là cho bánh răng gia công
quay ăn khớp với một hoặc ba bánh răng bằng gang đóng vai trò dụng cụ
nghiền, trên bề mặt răng của chúng có bôi bột nghiền, có hai phương
pháp mài nghiền răng:
- Phương pháp thứ nhất: trục của bánh răng gia công song song
với trục của bánh nghiền (hình 2.116a).
- Phương pháp thứ hai: trục của bánh răng gia công nghiêng một
góc với trục của bánh nghiền (hình 2.116b).
Đối với phương pháp thứ nhất, bánh răng gia công 1 là bánh chủ
động truyền chuyển động cho bánh nghiền 2.
Để có thể
nghiền được cả
hai mặt bên của
răng cần phải
có chuyển động
quay theo hai
chiều thuận
nghịch. Ngoài
ra có chuyển
động dao dọc
trục để mài hết
chiều dày răng.
Ở phương pháp thứ hai, bánh răng gia công 1 ăn khớp với ba bánh
nghiền, trong đó có hai bánh số 2 có răng nghiêng còn bánh số 3 có răng
1
a)
2
b)
2
3
1
Hình 2.116: Sơ đồ mài nghiền bánh răng.

139
thẳng. Vì vậy, trục của bánh 3 song song với bánh răng gia công, còn trục
của hai bánh số 2 nghiêng so với bánh răng gia công một góc và góc này
có có thể điều chỉnh được. Hai bánh dẫn có số vòng quay n = 150 300
vg/ph, bánh răng gia công có chuyển động tịnh tiến dọc theo trục từ 40 –
200 hành trình kép trong một phút.
Gia công theo phương pháp
thứ hai có năng suất và độ chính
xác cao hơn phương pháp thứ nhất,
vì trong quá trình ăn khớp khi
nghiền, bánh răng gia công tiếp
xúc với bánh nghiền theo vết 3
(hình 2.117). Chính vì vậy mà sau
khi nghiền sự tiếp xúc của bánh
răng gia công và các bánh nghiền
được đều khắp và tốt hơn.
Biện pháp thực hiện các phương pháp nghiền trên có hai cách:
- Nghiền
không có khe hở: khi
sự ăn khớp giữa
bánh răng gia công
và bánh nghiền
không có khe hở
(hình 2.118 b).
Trong trường
hợp này cả hai bên
sườn của răng đều
được mài nghiền
đồng thời, có thể
hiệu chỉnh sai số chung về bước răng và làm bóng bề mặt răng.
- Nghiền có khe hở (hình 2.118 a).
Trong trường hợp này, mỗi mặt bên của răng được gia công riêng.
Khi mài nghiền phải tạo ra một áp lực lên mặt răng từ 5–7 kg/cm
2
.
Bánh nghiền được chế tạo từ gang hạt mịn có độ cứng 180 – 120HB như
gang xám 21 – 40; gang xám15 – 32. Chiều rộng của bánh nghiền cần
lớn hơn chiều rộng bánh răng gia công 4 10 mm. Lượng dư mài nghiền
răng một phía không lớn hơn 0,02 – 0,05 mm. Thời gian mài nghiền một
phía của răng cần 0,53 phút. Một bánh nghiền có thể gia công được 500
1000 bánh răng sau đó phải đem đi tiện lại.
1
2
3
Hình 2.117: Vết nghiền trên bánh
răng gia công.
1
2
2
1
a)
b)
Hình 2.118: Sơ đồ biện pháp nghiền
a. Nghiền có khe hở.
b. Nghiền không co khe hở.
1. Bánh nghiền; 2. Bánh răng gia công.

140
2.5.5.2. Các phương pháp gia công răng bánh răng côn
Gia công bánh răng côn thuộc loại công việc khó trong sản xuất.
Bánh răng côn có các loại răng thẳng, răng nghiêng và răng xoắn (hình
2.119). Riêng loại răng xoắn (hay răng cong) lại chia ra: răng cong cung
tròn, răng cong thân khai và răng cong Epixicloid.
Chiều cao răng của các loại bánh răng trên có thể đều hoặc thay đổi
tùy theo tính năng của chúng (hình 2.120).
Tùy theo yêu cầu và thiết kế của từng loại máy, các loại bánh răng
côn có thể ở dạng đĩa có lỗ hoặc liền trục. Để đạt hiệu quả kinh tế phải có
phương pháp gia công thích hợp với mỗi loại.
A. Gia công bánh răng côn thẳng
Răng của bánh côn thắng được gia công bằng phương bào, phay
hoặc chuốt. Mặt bên của răng được hình thành bằng định hình hoặc bao
hình. Phương pháp bao hình cho độ chính xác tốt hơn và được tiến hành
theo bao hình phân độ hay bao hình liên tục.
a)
b)
c)
Hình 2.119: Các loại bánh răng côn
a. Răng thẳng, b. Răng nghiêng, c. Răng cong.
a)
b)
o
Hình 2.120: Các dạng chiều cao của bánh răng côn.
a. chiều cao răng đều. b. chiều cao răng thay
đổi.
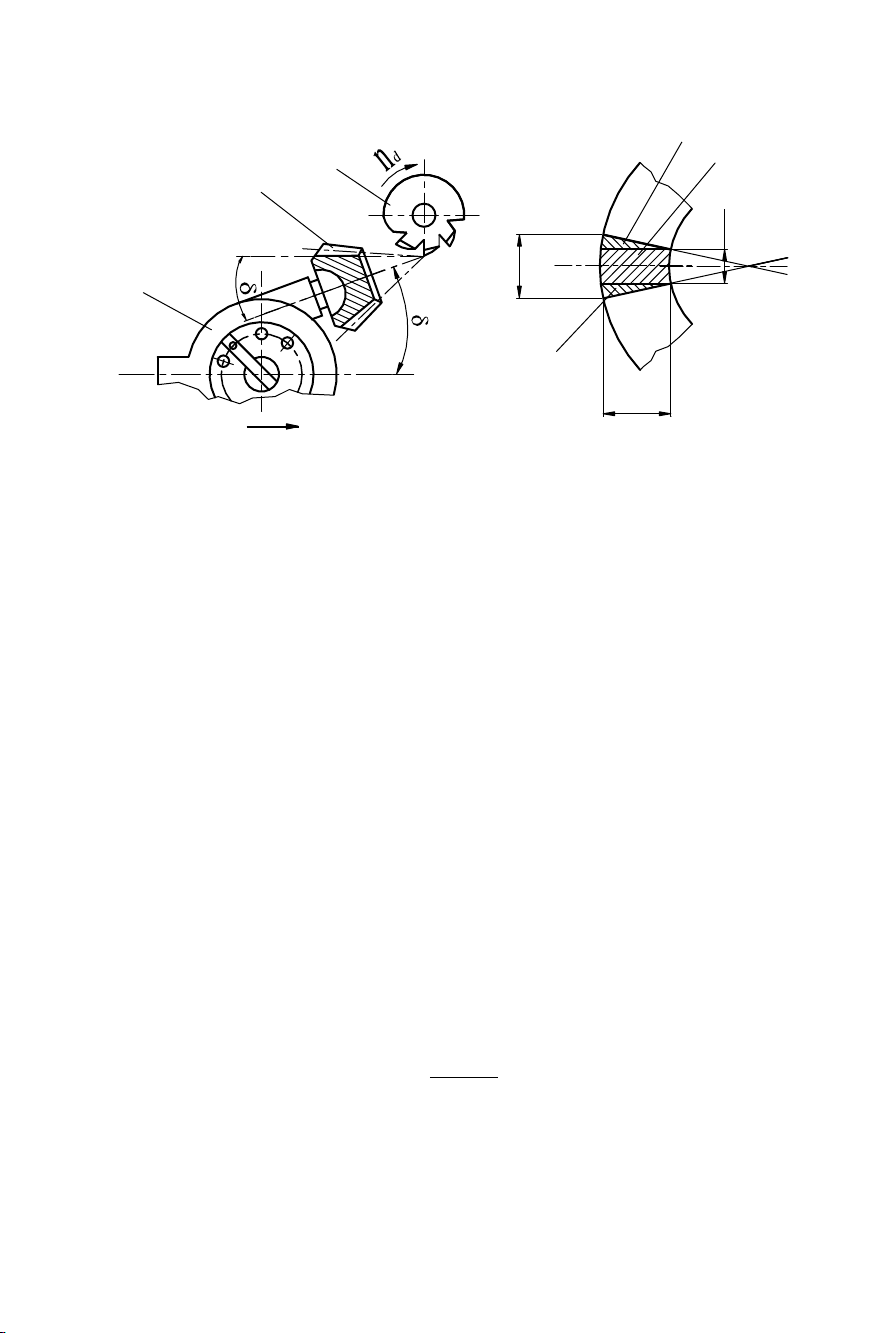
141
1. Gia công răng bằng phương pháp định hình
Bánh côn răng thẳng và răng nghiêng được phay bằng dao phay
định hình với phương pháp phân độ, thực hiện trên máy phay vạn năng
có ụ phân độ.
Dụng cụ là dao phay định hình đĩa hay ngón. Bánh răng gia công
được gá vào ụ chia độ và nghiêng đi một góc hình 2.121a phù hợp với
góc côn ở chân răng . Mỗi một rãnh răng được phay qua ba bước, thể
hiện trên hình 2.121b.
- Bước 1: phay phần vật liệu 1 của rãnh, chiều rộng của phần này
tối đa bằng chiều rộng đầu nhỏ của rãnh răng.
- Bước 2: quay bánh răng đi một góc về một phía, sau đó phay
phần vật liệu 2 trên rãnh răng.
- Bước 3: quay bánh răng đi đi một góc về phía ngược lại, sau
đó quay phần vật liệu 3 trên rãnh răng.
Góc nghiêng của trục ụ chia độ chích xác căn cứ vào góc côn
chân răng cho trên bản vẽ. Góc xoay của bánh răng (hình 2.121b) suy
ra từ tính toán hình học theo hình vẽ:
;
2
21
L
bb
tg
Trong đó: b
1
– chiều rộng rãnh răng ở phía đầu to được đo trên cát
tuyến của côn chia (mm).
b
2
– chiều rộng rãnh răng ở phía đầu nhỏ được đo trên cát tuyến
của côn chia (mm).
Hình 2.121: Phay răng bánh răng côn bằng dao định hình.
b)
b2
L
3
b1
1
2
a)
Ụ chia độ
Dao
Vật
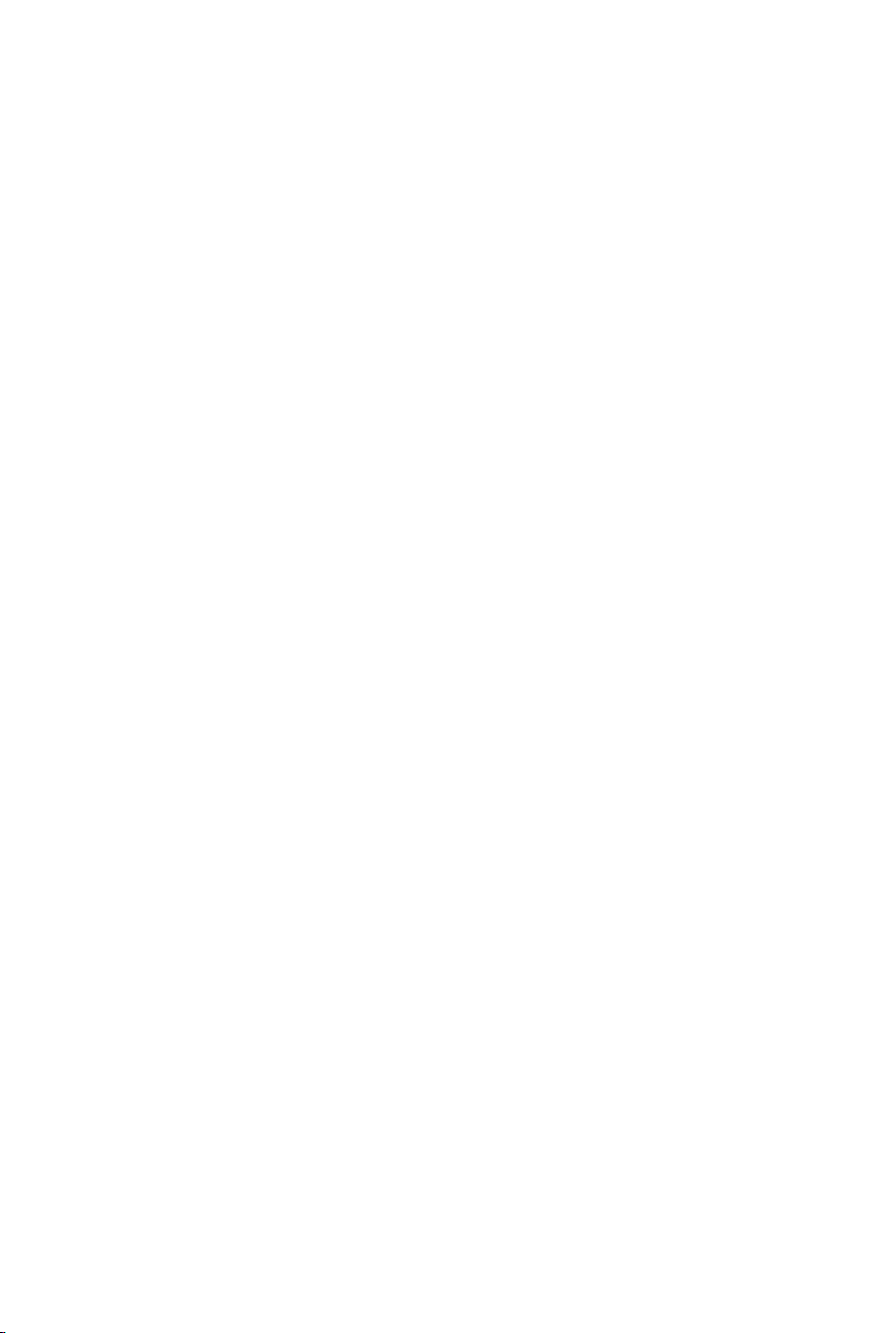
142
L – chiều dài răng.
Phương pháp này được sử dụng để sản xuất bánh răng côn có độ
chính xác không yêu cầu cao và để sản xuất bánh răng có môđun lớn.
2. Gia công răng bằng phương pháp bao hình
Trong các phương pháp gia công răng chỉ có phương pháp bao hình
mới có thể tạo được những dạng răng chính xác. Điều này đúng cho cả
bánh răng trụ và bánh răng côn.
Phương pháp bao hình gia công bánh răng có côn xuất phát điểm
tương tự như ở bánh răng trụ, ở đó răng được tạo nên bởi sự lăn của trụ
chia bánh răng theo mặt phẳng chia của thanh răng, còn ở bánh răng côn
thì răng được tạo nên bởi sự lăn của côn chia bánh răng theo mặt phẳng
chia của bánh dẹt sinh. Bánh dẹt sinh này được coi như là bánh côn với
góc đỉnh của côn chia là 180
o
.
Prôfin răng được tạo nên bằng sự lăn tương đối của dụng cụ và
bánh răng gia công. Dụng cụ là một hoặc hai dao có lưỡi cắt dạng hình
thang. Dụng cụ thực hiện chuyển động đến đỉnh đi lại theo hướng côn
chia của bánh răng.
Dụng cụ lại được gá trên một đầu dao mà đầu dao này phải thực
hiện chuyển động ăn khớp với bánh răng gia công. Hiện nay tồn tại một
số phương pháp gia công theo nguyên lý nêu trên.
a. Phay bao hình bánh răng côn
Bằng phương pháp phay bao hình này có thể nâng cao được năng
suất gia công bánh răng côn. Dao phay có đường kính lớn, dạng răng
chắp, mặt bên của chúng là cạnh của hình thang giống dạng răng của
thanh răng hình 2.122.
Trục chính của dao phay đĩa được đặt trên mặt đầu của một bàn
trượt quay mà số vòng quay n
đ
của nó liên hệ với số vòng quay n
c
của
bánh răng, tạo nên chuyển động lăn giữa lưỡi cắt của dụng cụ và mặt bên
của bánh răng côn. Khi đường kính của dao phay đĩa lớn hơn nhiều so
với chiều rộng vành của bánh răng gia công, dao có thể chỉ cần chuyển
động cắt v, nếu như chiều rộng vành răng lớn hơn 20 mm thì dao, ngoài
chuyển động cắt v còn phải chạy dao dọc s.
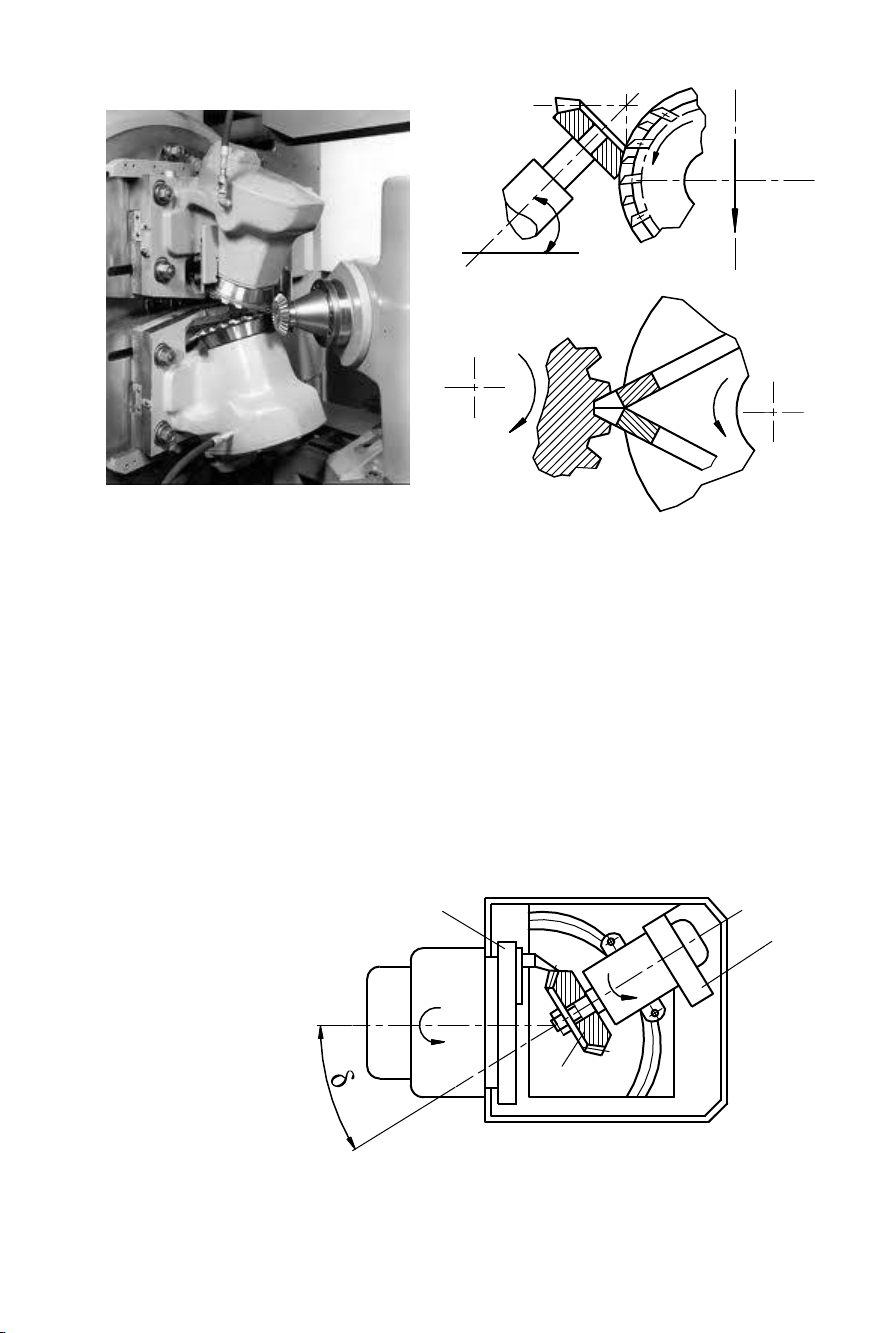
143
Sau khi phay xong một rãnh, bàn quay có mang dao phay đĩa được
quay đến vị trí ban đầu, vật gia công được quay đi một bước bằng dụng
cụ chia độ và chu trình làm việc được lặp lại.
Gia công bằng phương pháp này tăng năng suất 3 – 7 lần và thời
gian giảm 40% so với các phương pháp lăn thông thường khác. Các máy
chuyên dùng như 5P23 của Liên Xô, ZFTK của Đức, No104 và 114 của
Mỹ thực hiện gia công bánh răng côn theo nguyên lý này.
b. Bào bao hình bánh răng côn
Ở những bánh
răng côn có môđun
lớn hơn 15 mm
thường được bào theo
dưỡng chép hình. Còn
những bánh răng có
môđun nhỏ có thể
được tiến hành bằng
phương pháp bào bao
hình. Khi bào theo
nguyên lý bao hình
trên máy “Harbeck”
hoặc “Gleason” hoặc
“Bilgram Reinecker”
3
1
2
nd
nc
Hình 2.123: Bào bao hình bánh răng côn.
1. Trục chính. 2. Bánh răng gia công. 3. Đầu dao.
v
S
nd
nc
Hình 2.122: Phay răng bánh răng
côn bằng hai dao phay đĩa.
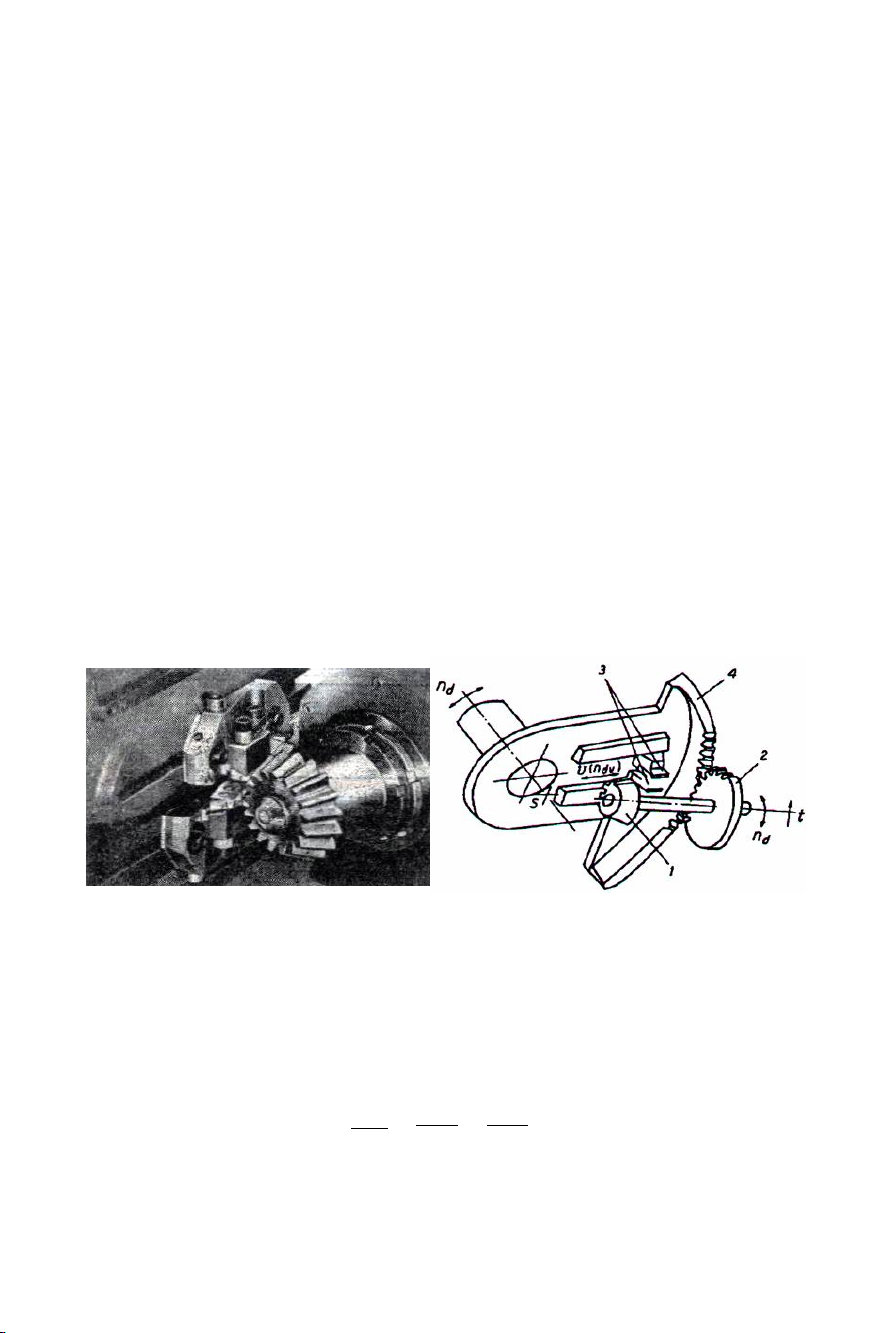
144
một hoặc hai dao có dạng hình thang được gá trên rãnh của đầu dao quay.
Dao thực hiện chuyển động cắt đi lại v theo hướng đến đỉnh bánh răng côn
và trùng với đường côn chân răng, đồng thời được quay với đầu dao xung
quanh trục của nó với số vòng quay n
d
. Bánh răng côn gia công được gá
trên trục chính của máy mà trục chính này được điều chỉnh ở vị trí phù hợp
với góc đỉnh của bánh răng gia công. Nhờ chuyển động quay ăn khớp của
đầu dao n
d
và vật gia công n
c
, các lưỡi cắt của dao tạo nên mặt bên của
răng gia công bằng các lát cắt bao ở dạng thân khai. Sơ đồ gia công bánh
răng côn răng thẳng bằng bào bao hình thể hiện trên hình 2.123.
Có thể bào bằng một hoặc hai dao cùng một lúc. Nếu bào bằng hai
dao thì một dao cắt mặt bên phải và một dao cắt mặt bên trái của răng.
Hai dao đi lại ngược chiều nhau. Sau khi cắt xong một đầu răng, vật và
dao trở lại vị trí ban đầu, vật được quay đi một bước nhờ dụng cụ chia độ
và chu trình gia công được lặp lại. Với sơ đồ trên hình 2.123 đã có thể
hình dung ra những chuyển động cần thiết cho phương pháp bào bánh
răng côn bằng bao hình.
Để hiểu rõ hơn nguyên lý này có thể tham khảo thêm hình 2.124
trên đó thể hiện rõ kết cấu của bào bao hình. Các lưỡi cắt của hai dao bào
3 có dạng như mặt bên của răng bánh dẹt sinh kéo dài (vành răng 4) của
giá dao lắc lư (lắc lư cả hai phía).
Nhờ bánh răng 2 và 4 quay ăn khớp nhau, mà trên trục của 2 có gá
bánh răng gia công 1 (cả hai bánh này có cùng một côn chia nên chuyển
động lăn không trượt của côn chia bánh răng gia công với bánh dẹt sinh
có tỉ số truyền:
2.1
2.12.1
Z
Z
n
n d
dd
Ở đây: n
1.2
và
1.2
– số vòng quay và tốc độ góc của vật gia công
(bánh nhỏ 1 và bánh lăn 2).
Hình 2.124: Kết cấu đầu dao và sự liên
hệ của nó với trục chính mang phôi.
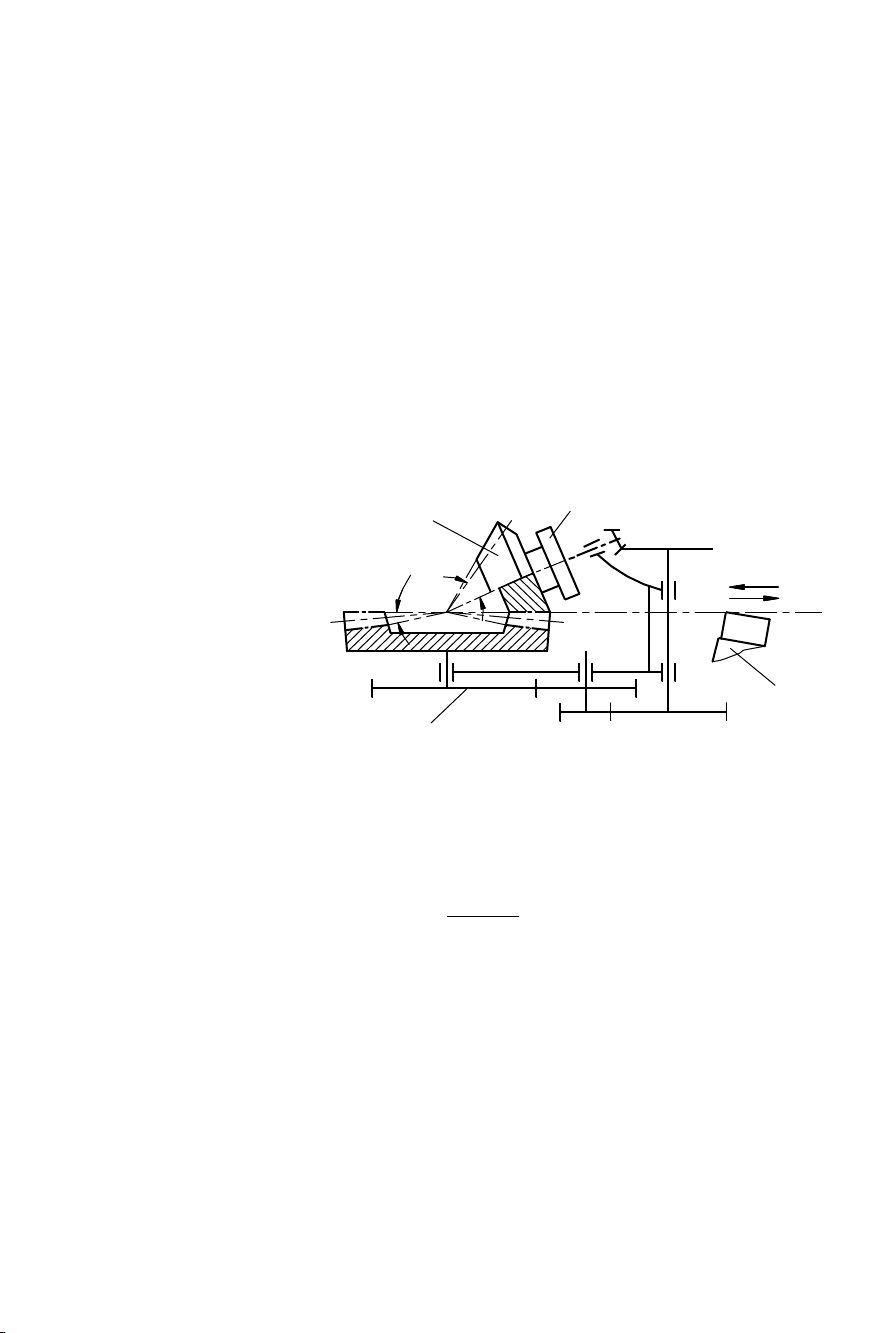
145
n
d
,
d
– số vòng quay và tốc độ góc của bánh dẹt sinh.
Z
d
; Z
1.2
– số răng của bánh dẹt sinh và vật gia công.
Cả hai dao động chuyển động theo hướng từ chân răng đến đỉnh S
với tốc độ cắt v. Sau khi gia công xong một rãnh răng, bánh răng 2 được
quay đi một bước t và rãnh răng tiếp theo được gia công, như vậy bánh
răng được gia công xong sau một vòng quay. Trước khi ngừng hành trình
cắt, dao được ngửa ra để lưỡi cắt không cà vào mặt bên của răng.
Các máy bào bánh côn răng thẳng theo kiểu cũ đã dựa trên nguyên
lý nói trên. Nhưng theo nguyên lý đó, cần thiết phải có một số lớn bánh
răng thay thế 2 theo góc đỉnh côn chân răng, đồng thời có một sai số
prôfin răng do khe hở không tránh khỏi giữa răng của bánh lăn và bánh
dẹt sinh. Vì vậy ở các máy kiểu mới, người ta dùng hệ thống bánh răng
thay thế của cơ cấu như sơ đồ trên hình 2.125.
Chuyển động
ăn khớp bao hình của
bánh răng gia công 1
và dao được thực
hiện thông qua các
bánh răng Z
a
, Z
b
qua
các bánh răng thay
thế Z
f
, Z
e1
, Z
e2
, Z
c
đến bánh răng dẹt
sinh tưởng tượng Z
d
(số vòng quay n
d
) mà
đại diện cho nó là
đầu dao với bàn xe
dao 3. Do đó số vòng quay của vật gia công n
1.2
được cho bởi công thức:
2.1
2.1
2.1
sin
cos
d
nn
Ở đây:
1.2
– góc chân răng bánh dẹt sinh.
c1.2
– góc côn chia bánh răng gia công.
n
d
– số vòng quay bánh dẹt sinh.
Thời gian cắt một răng phụ thuộc vào vật liệu gia công, môđun và
lượng dư gia công. Số lần cắt phụ thuộc vào môđun và lượng dư gia công.
B. Gia công bánh côn răng cong
Bánh côn răng cong được dùng nhiều vì khả năng truyền động lớn,
truyền động êm, ít ồn, hệ số trùng khớp cao, có thể đạt được tỉ số truyền
Bánh lăn thay thế
Ze2
Zf
c1.2
1.2
V(ndv)
3
Đầu chia
1(z1.2)
Zc
Ze1
Zb
Za
s
Zn(nd)
Hình 2.125: Bào răng côn bao hình với
nguyên tắc mới.
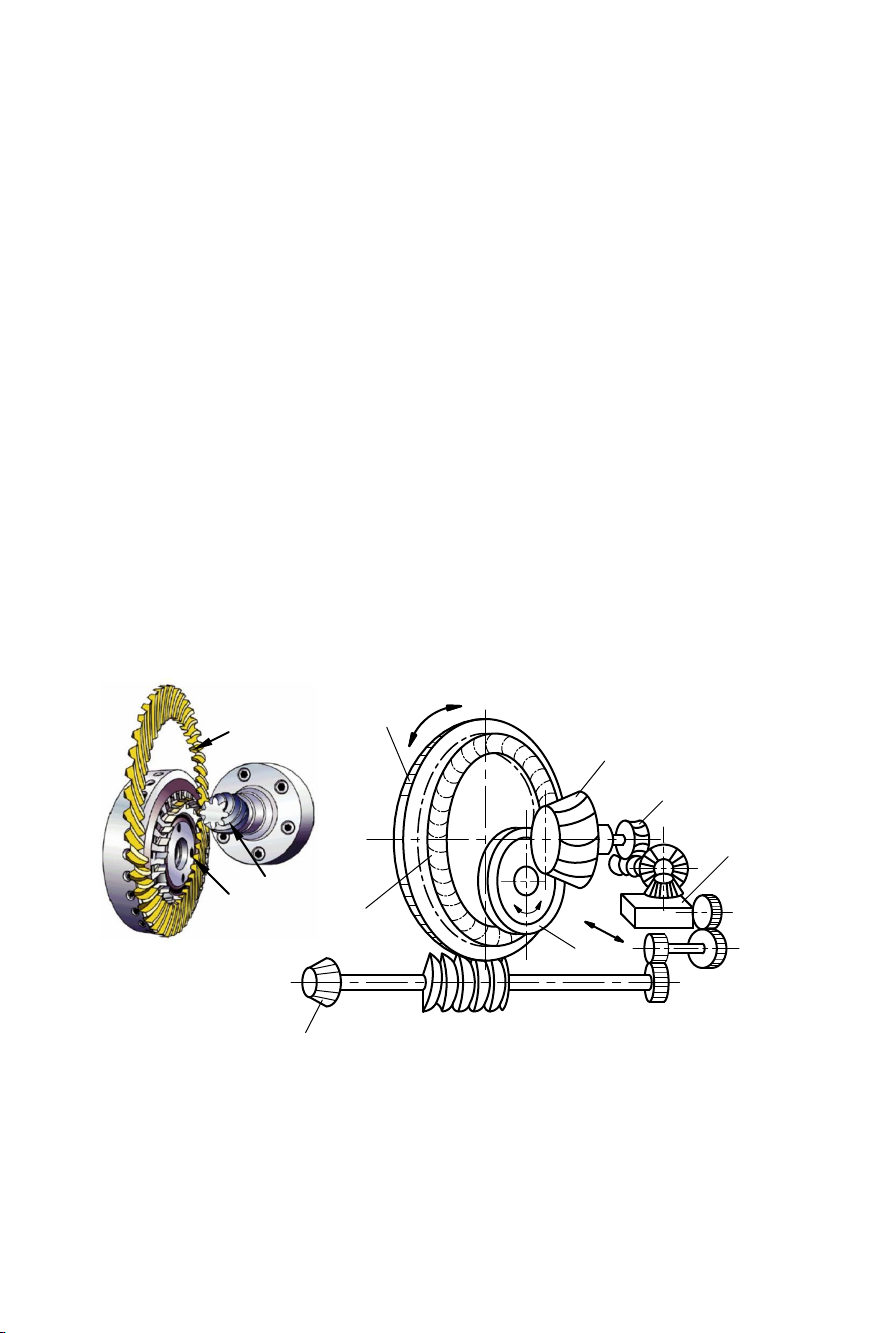
146
lớn với không gian tương đối bé. Tuy vậy lực chiều trục của truyền động
bánh côn răng cong thường lớn hơn so với bánh côn răng thẳng.
Về mặt chế tạo, đòi hỏi phải có thiết bị phức tạp chuyên dùng,
nhưng do có thể cắt được liên tục nên năng suất đạt được cao hơn so với
gia công gia công bánh côn răng thẳng. Nói chung, bánh côn răng cong
không thể mài được trừ loại bánh côn răng cung tròn.
Căn cứ vào đường cong hướng răng trên mặt nón chia của bánh dẹt
sinh có thể chia bánh côn răng cong làm ba loại:
- Răng cung tròn, còn gọi là răng thuộc hệ “Gleason”. Loại này
thường có chiều cao răng thay đổi.
- Răng cung epixycloid, còn gọi là răng thuộc hệ “Mam – mano”,
loại này thường có chiều cao răng không thay đổi.
- Răng cung thân khai, còn gọi là răng thuộc hệ “Klin – Gelnberg”.
Mỗi loại răng như trên sẽ có phương pháp gia công thích hợp. Sau
đây trình bày phương pháp gia công bánh côn răng cung tròn.
Loại bánh côn có răng cung tròn được được gia công trên máy
Gleason bằng phương pháp bao hình với đầu dao phay quay. Nguyên tắc
làm việc của máy xuất phát từ sự ăn khớp (hay lăn) giữa bánh dẹt sinh Z
d
với bánh răng gia công 1 (hình 2.126).
Đầu chia
b)
Truyền dẫn từ động cơ
2
1
O
1
d
1
c
1
b
1
a
1
3
S
k
v
Z
d
n
d
SS
d
Hình 2.126: Phay bánh côn răng cung tròn trên máy "Gleason"
a) Nguyên lý phay bằng đầu dao theo phương pháp bao hình
b) Sơ đồ nguyên tắc làm việc của máy
1. Bánh răng gia công; 2. Đĩa gá lắc lư
3. Đầu dao phay; Z
d
bánh dẹt sinh tưởng tượng
a)
Z
d
3
1
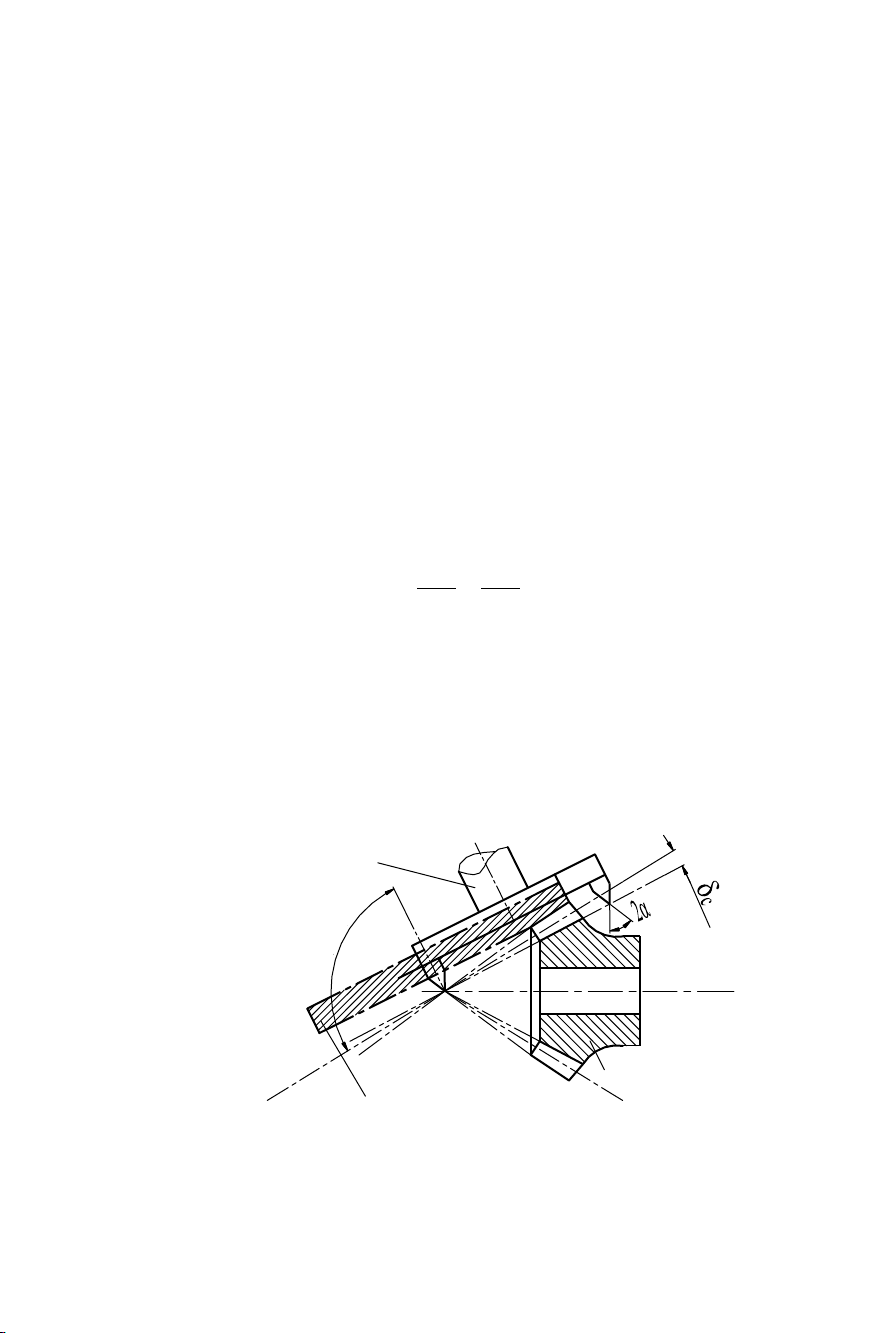
147
Bánh dẹt sinh Z
d
được thay thế bằng đĩa gá lắc lư 2, mà trên đó
được lắp đầu dao phay có tâm quay nằm trên và lệch so với tâm của đĩa
gá. Trên đầu dao phay có các dao có dạng hình thang, thông thường
chúng được bố trí một lưỡi cắt phía ngoài, một lưỡi cắt trong liên tiếp
nhau. Khi điều chỉnh máy để gia công phải để sao cho đỉnh nón chia của
bánh răng gia công cùng với đỉnh của bánh dẹt sinh (hình 2.126), mặt
phẳng đầu răng của dao tiếp xúc với mặt nón chân răng.
Theo nguyên lý này, đầu dao phay 3 quay với tốc độ cắt v(nd), tốc
độ này không bị ràng buộc với các chuyển động làm việc khác của máy.
Trước lúc bắt đầu làm việc vật được dịch chuyển hướng kính S
k
để lấy
chiều sâu rãnh răng. Ngoài chuyển động quay quanh trục của mình, đầu
dao phay còn được quay quanh cùng với đĩa gá thực hiện chuyển động ăn
khớp của bánh dẹt sinh Z
d
với bánh răng gia công 1 được gá trên trục
chính của máy. Chuyển động lắc lư của đĩa gá n
d
(
d
) (tức chuyển động
ăn khớp của bánh dẹt sinh) với chuyển động của bánh răng n
c
(
1.2
) phải
thỏa mãn tỷ số truyền:
2.1
2.1
2.1
Z
Z
i
d
d
d
Ở đây:
d
– tốc độ góc của đĩa gá.
1.2
– tốc độ góc của bánh răng gia công.
Z
d
– số răng của bánh dẹt sinh.
Z
1.2
– số răng của bánh răng gia công.
Bộ truyền được điều chỉnh bằng các bánh răng thay thế (a
1
; b
1
; c
1
,
d
1
) ở giữa lực
truyền lắc lư và
trục chính O
1
.
Vì lưỡi cắt của
dao tạo nên
giống như răng
của bánh dẹt
sinh nên nó tạo
thành mặt cong
phía bên ngoài
và phía bên
trong của một
rãnh răng bánh
răng gia công.
Bánh dẹt sinh
Đầu dao
s s
d
Bánh răng gia công
Hình 2.127: Sơ đồ điều chỉnh dao và vật gia công.
90
o
-
c
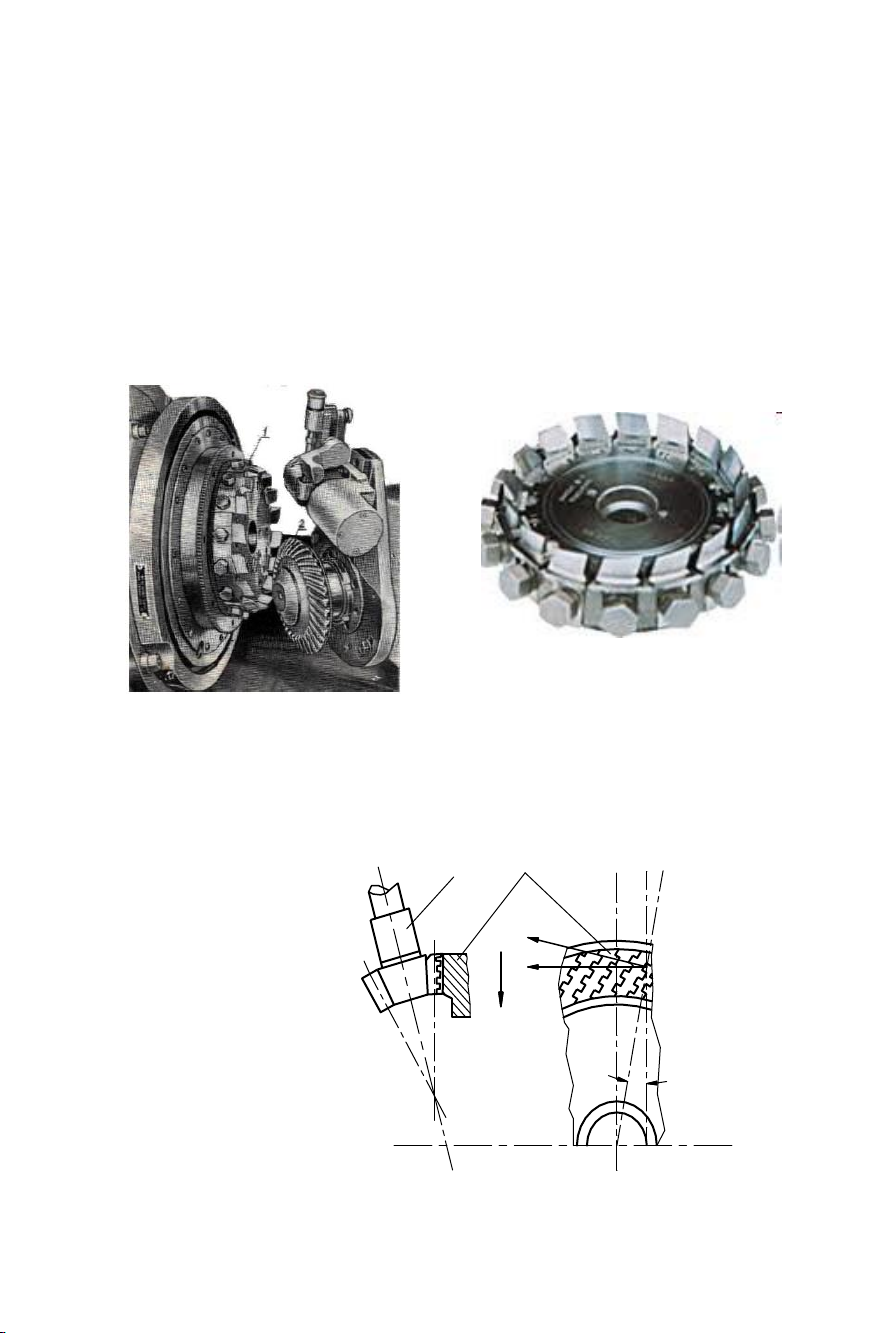
148
Để ăn khớp đúng, cần thiết phải điều chỉnh sao cho đỉnh côn chia của
bánh được phay S trùng với tâm của bánh dẹt S
d
và phải sao cho mặt
phẳng đỉnh của mũi dao tiếp xúc với mặt côn chân răng của bánh răng
gia công (hình 2.127).
Từng khe răng được phay dần dần và sau khi phay xong một rãnh
răng, đầu phay ra khỏi vị trí ăn khớp với bánh răng gia công. Để phay
rãnh răng tiếp theo, đĩa gá với đầu dao phay và vật gia công được quay
trở về vị trí ban đầu và vật gia công được quay phân độ thêm một bước.
Sau đó, chu trình gia công được lặp lại.
C. Gia công tinh bánh răng côn
a. Cà bánh răng côn
Cà bánh răng côn
nhằm nâng cao độ nhẵn
bóng bề mặt và độ
chính xác của răng, khôi
phục sự ăn khớp tốt của
răng. Khi cà răng côn,
răng cong, bánh răng
phẳng răng cong được
dùng làm bánh cà. Sơ
đồ gia công được trình
bầy trên hình 2.129.
Trục quay của
bánh cà 1 không trùng
với đỉnh côn của bánh
2
1
v
v
Ou
Q
O
v
Hình 2.129: Sơ đồ cà bánh răng côn răng cong.
1. Bánh cà. 2. Bánh răng gia công.
Hình 2.128: Máy và dao khi phay bánh côn cung tròn
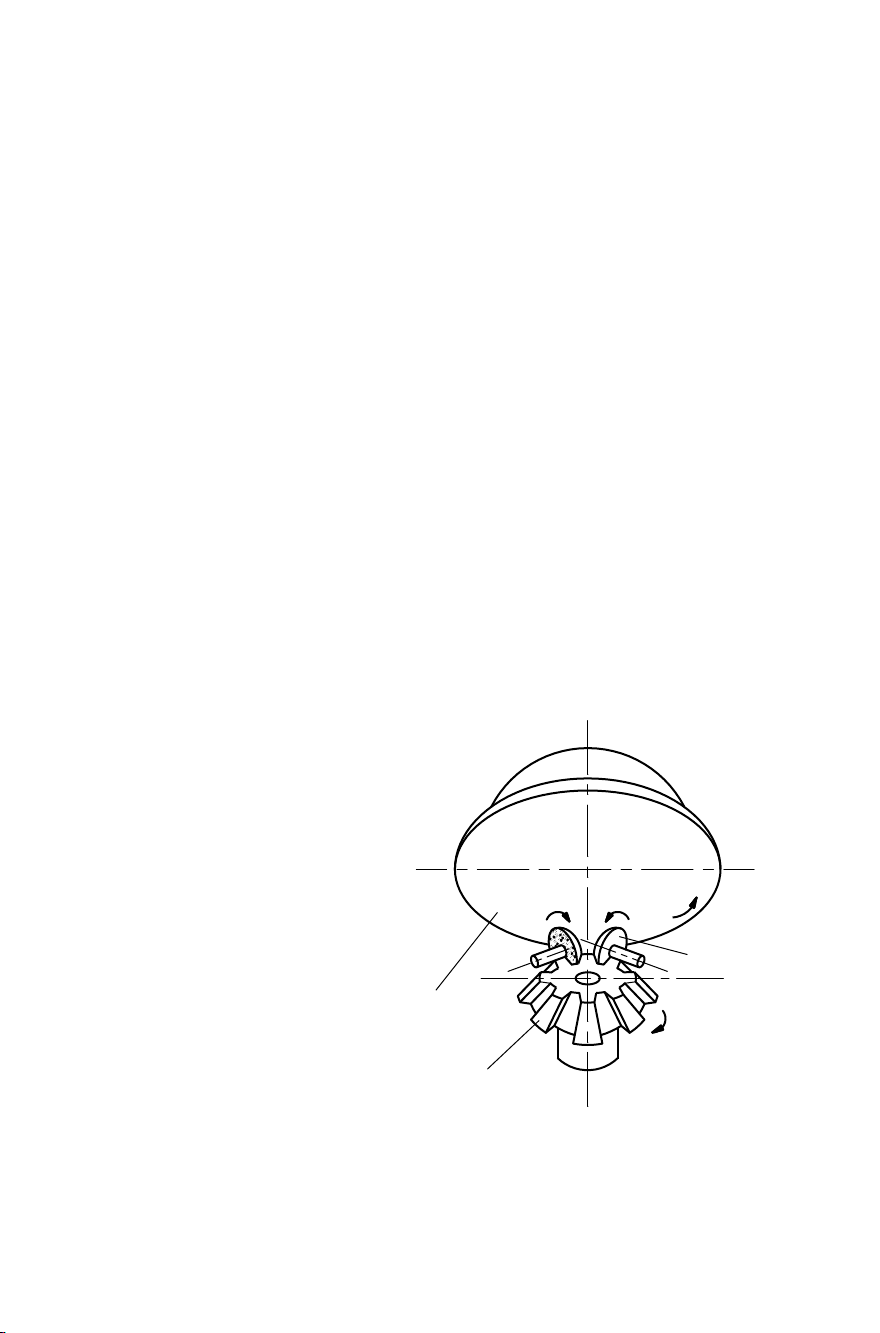
149
răng gia công 2, do đó khi chúng ăn khớp với nhau trong quá trình gia
công tạo nên sự không trùng hướng của tốc độ bánh cà v
u
và tốc độ của
bánh răng gia công v. Vì vậy, sinh ra tốc độ trượt v
c
dọc theo răng của
bánh răng gia công. Tốc độ trượt này thực hiện chuyển động cắt của dao
vào mặt răng của bánh răng gia công.
Quá trình cắt xẩy ra liên tục khi bánh cà và bánh răng gia công ăn
khớp nhau và quay không đảo chiều. Bánh cà là bánh chủ động, bánh
răng gia công chuyển động theo và có liên quan đến chuyển động dao
hướng kính.
Tốc độ cắt khi cà răng côn chọn từ 15 – 20m/ph. Sai số bước vòng
của răng sau khi cà đạt 0,02 đến 0,05 mm. Vết tiếp xúc đạt 80 - 100% theo
chiều cao răng, còn theo chiều dọc răng đạt 70 - 90%. Điều chỉnh vị trí và
trị số tiếp xúc thực hiện bằng cách thay đổi vị trí của bánh răng gia công
đối với bánh cà, góc của dạng răng, bán kính cong của răng bánh cà.
So với các phương pháp gia công khác, phương pháp cà răng bánh
côn còn có ưu điểm là năng suất cao, tăng được độ nhẵn bóng bề mặt, độ
chính xác về hình dạng của bánh gia công, thiết bị gia công đơn giản và
rẻ tiền. Phương pháp này phù hợp với sản xuất hàng loạt lớn và cho
những bánh răng có yêu cầu kỹ thuật không cao lắm.
b. Mài răng bánh côn
Mài răng bánh côn là một phương pháp gia công tinh dùng cho
những bánh răng có yêu
cầu cao về độ chính xác và
độ nhẵn bóng bề mặt răng.
Do công nghệ mài và thiết
bị gia công phức tạp, năng
suất thấp nên chỉ sử dụng
phương pháp này khi
những phương pháp khác
không thực hiện được. Các
bánh răng côn được mài
thường dùng làm những
bánh mẫu, bánh kiểm,
hoặc là những dụng cụ cắt
gọt như bánh cà, bánh
nghiền, thường dùng trong
các bộ truyền của máy có
độ chính xác cao, làm việc
với tốc độ lớn.
3
1
II
I
Hình 2.130: Sơ đồ mài bánh răng côn răng
thẳng bằng hai đá dĩa.
1. Đá mài, 2. Bánh răng gia công,
3. Mâm lắc.
2
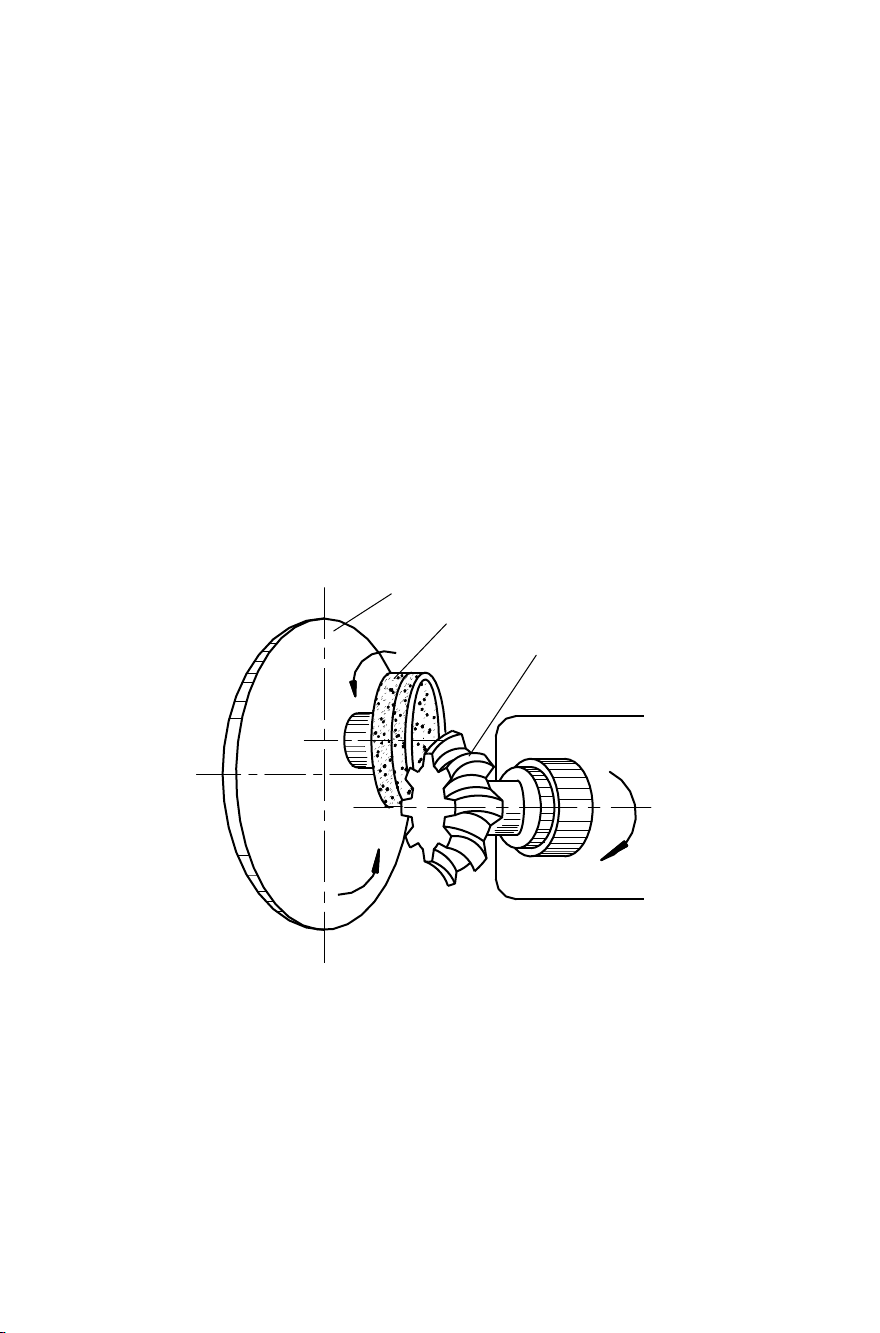
150
Khi mài bánh răng côn răng thẳng dùng một hay hai đá đĩa phẳng
hoặc côn, thực hiện mài theo phương pháp bao hình. Sơ đồ mài bánh
răng côn thẳng được trình bày trên hình 2.130.
Đá mài 1 đặt vào con trượt trên mâm lắc 3 của máy. Trong quá
trình cắt đá quay tròn và con trượt mang đá đi lại theo hướng đường
thẳng côn chỉa của bánh răng côn. Khi đó, mâm lắc mang đá có chuyển
động quay I thích ứng với chuyển động quay II của bánh răng gia công 2.
Sau khi mài xong một răng, bánh răng 2 quay phân độ để gia công rãnh
tiếp theo.
Tốc độ của đá mài từ 25 - 30m/s. Độ nhẵn bóng bề mặt sau khi mài
có thể đạt R
a
= 0,63 - 0,32. Lượng dư của mỗi phía có thể chọn từ 0.07 -
0,12mm và hành trình mài từ 4 - 10 lần.
Mài bánh côn răng cong: Khi mài loại bánh côn răng cong dùng đá
mài hình chậu (hình bát) có đường sinh trụ, bề mặt làm việc của đá được sửa
côn và thực hiện mài bao hình. Sơ đồ mài được trình bày như hình 2.131.
Đá mài 2 thực hiện chuyển động quay I quanh trục của nó. Trục của
đá này được lắp trên mâm quay 1 và mâm quay này lại thực hiện chuyển
động quay II quanh trục của mâm và khác với trục của đá. Chuyển động
của mâm phải phù hợp với chuyển động quay III của bánh răng gia công.
Nhờ có các chuyển động trên đá sẽ gia công được một rãnh răng. Sau khi
gia công xong một rãnh, phải thực hiện chuyển động phân độ cho bánh
III
II
2
1
I
3
Hình 2.131: Sơ đồ mài bánh răng côn răng cong bằng đá chậu.
1. Mâm quay, 2. Đá mài, 3. Bánh răng gia công.
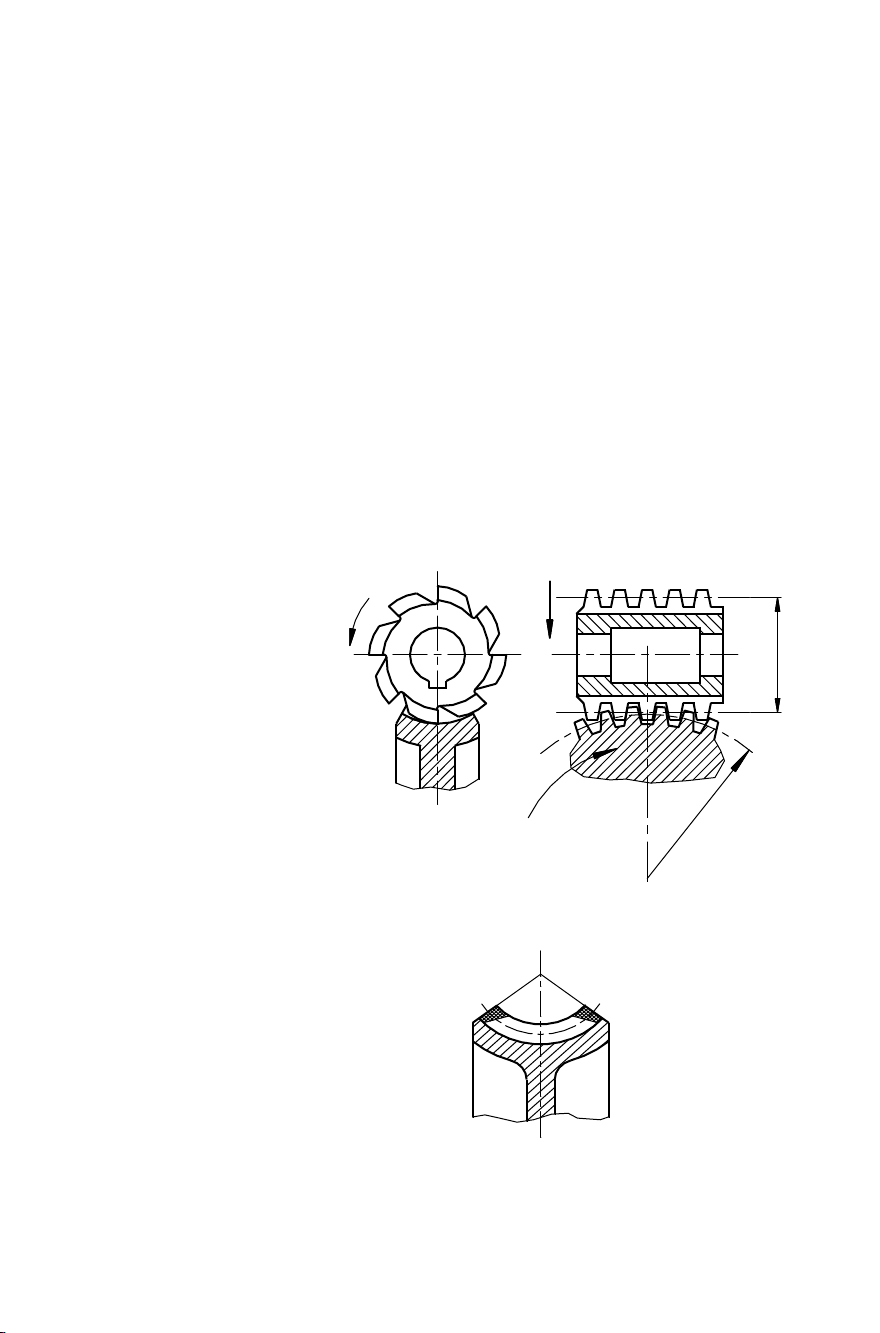
151
răng gia công rãnh răng tiếp theo. Phương pháp này được dùng để mài
những bánh răng chính xác trong hàng loạt và hàng khối.
2.5.5.3. Gia công bánh vít
Khi gia công bánh vít, dụng cụ cắt trong mọi trường hợp sẽ đều
đóng vai trò trục vít ăn khớp với bánh vít được cắt. Về mặt kết cấu, dụng
cụ cắt dạng vít phải hoàn toàn giống trục vít sẽ ăn khớp với bánh vít gia
công khi làm việc, chỉ có khác là đường kính ngoài của dao lớn hơn
đường kính ngoài của trục vít ăn khớp với bánh vít một lượng bằng khe
hở hướng kính. Gia công bánh vít được thực hiện trên máy phay lăn răng
thông thường hoặc trên máy phay ngang. Hiện nay tồn tại một số phương
pháp gia công bánh vít sau:
a. Gia công bánh vít bằng phay lăn
Khi gia công bánh vít bằng dao phay lăn, có thể có hai phương
pháp tiến dao: tiến dao hướng kính và tiến dao tiếp tuyến.
*Phương pháp tiến dao hướng kính
Khi thực hiện
phương pháp này, cần
gá đặt sao cho đường
kính của dao phay lăn
nằm trong mặt phẳng
đối xứng của bánh vít.
Sơ đồ gia công được
trình bày trên hình
2.132.
Khi cắt gọt, dao
thực hiện chuyển động
quay tròn, chi tiết quay
tròn. Hai chuyển động
này theo một tỉ số truyền
xác định. Chuyển động
chạy dao hướng kính
được dao (hoặc chi tiết)
thực hiện cho đến khi
dao có vị trí tương ứng
vị trí của trục vít ăn khớp
với bánh vít. Lượng tiến
dao hướng kính S = 0,55
- 1mm trong một vòng
D
n
n
k
R
S
v
Hình 2.132: Lăn răng bánh vít bằng phương
pháp tiến dao hướng kính.
Hình 2.133: Dạng bánh vít bị cắt lẹm khi gia
công bằng tiến dao hướng kính.
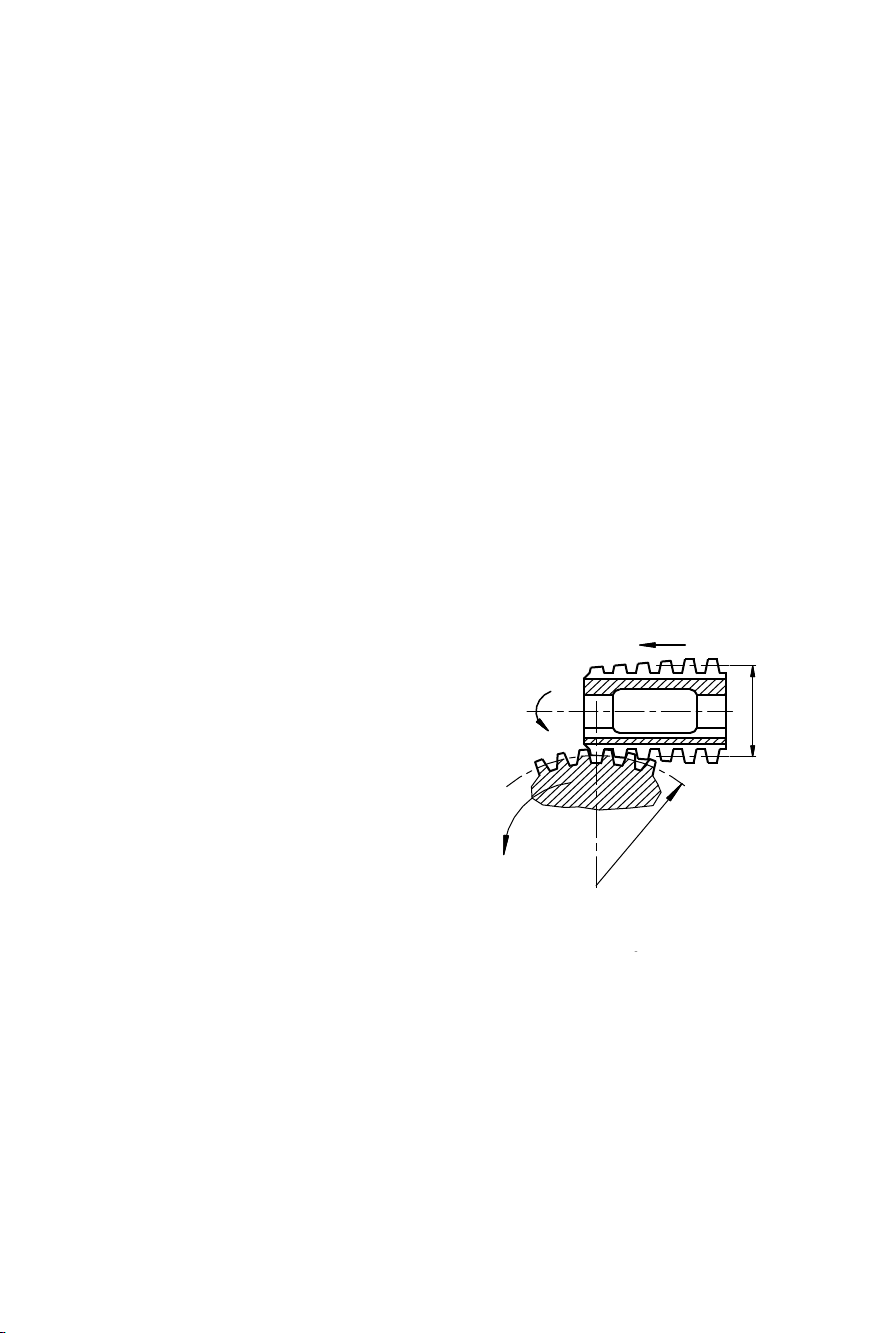
152
quay của chi tiết. Sau khi cắt hết chiều sâu răng, chi tiết phải quay thêm 1-2
vòng nữa để nâng cao độ chính xác của răng.
Phương pháp này cho phép đạt năng suất cao vì hành trình tiến dao
ngắn, nhưng có nhược điểm là do góc nghiêng ở đỉnh chi tiết không
giống góc xoắn của dao nên sinh ra hiện tượng cắt lẹm (hình 2.133). Do
vậy khi góc nâng của trục vít lớn hơn 6
0
- 8
0
thì không cho phép dùng
phương pháp này để gia công lần cuối. Trong thực tế khi không có dao
phay lăn bánh vít, có thể dùng dao phay lăn bánh răng để gia công bánh
vít. Trong trường hợp đó, bánh vít được gia công sẽ có sai số lớn (dao
phay lăn răng có đường kính càng lớn so với trục vít thì sai số gia công
càng lớn). Dao phay lăn bánh vít thường có góc hớt lưng bé hơn dao
phay lăn bánh răng. Sở dĩ phải làm như vậy để khi mài mặt trước, chiều
dày của răng biến đổi chậm, giảm bớt sự phân tán kích thước của loại
bánh vít được gia công, nâng cao tính lắp lẫn của sản phẩm chế tạo ra.
Khi gia công bánh vít bằng phương pháp này, ngoài hiện tượng bị
cắt lẹm, do độ nhám bề mặt răng cũng không được cao. Để khắc phục
hiện tượng đó, có thể dùng phương pháp tiến dao tiếp tuyến.
*Phương pháp tiến dao tiếp tuyến
Khi gia công bánh vít bằng
phương pháp lăn tiến dao theo
hướng tiếp tuyến, đường tâm của
dao lăn được gá đặt cách đường tâm
của chi tiết một khoảng đúng bằng
khoảng cách giữa tâm bánh vít và
trục vít. Sơ đồ gia công thể hiện
trên hình 2.134. Khi cắt, dao quay
tròn và tiến thẳng theo hướng tiếp
tuyến với vòng lăn của bánh vít,
còn chi tiết chỉ thực hiện chuyển
động quay bao hình.
Về kết cấu, dao phay lăn gồm hai phần: phần đầu hình côn để sau
khi cắt chiều sâu cắt không tăng quá đột ngột, phần sau hình trụ để cắt
tinh. Góc côn thường 10
0
- 15
0
.
Số vòng quay của dao và chi tiết chẳng những phải phù hợp với tỉ
số truyền của cặp bánh vít - trục vít yêu cầu, mà chi tiết còn có thêm
chuyển động vi sai để bù lại lượng tiến dao theo hướng tiếp tuyến.
Phương pháp này để gia công bánh vít có m = 3 - 12 mm. Lượng tiến dao
tiếp tuyến S = 1,1 - 1,6 mm trong một vòng quay chi tiết.
n
k
D
n
R
S
Hình 2.134: Lăn răng bánh vít
bằng phương pháp tiến dao tiếp
tuyến.
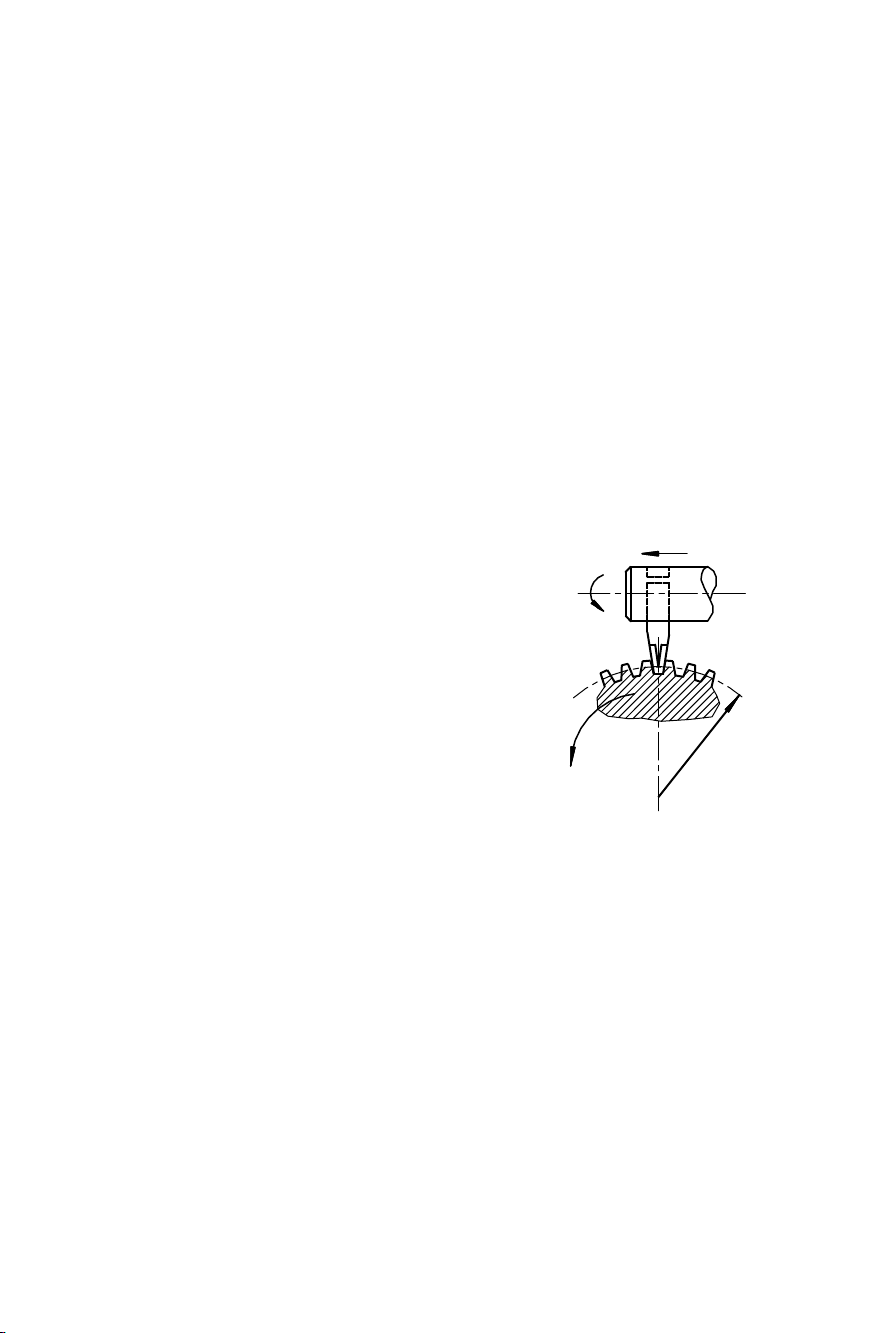
153
Nói chung, phương pháp này có năng suất thấp nhưng cũng hay
được dùng trong sản xuất vì dễ điều chỉnh khoảng cách tâm, độ bóng mặt
răng cao không có hiện tượng cắt lẹm. Theo phương pháp này có thể cắt
bằng hai lần chuyển dao. Lần đầu đảm nhiệm khoảng cách 6/7 lượng dư
tổng cộng và lần thứ hai cắt đúng kích thước.
*Phương pháp vừa tiến dao hướng kính vừa tiến dao tiếp tuyến
Phương pháp gia công phối hợp cả hai cách tiến dao khác nhau khắc
phục được nhược điểm của hai phương pháp trên. Theo phương pháp này,
ban đầu cắt thô bằng cách tiến dao hướng kính sẽ đạt được năng suất cao,
sau khi đạt được khoảng cách tâm của cặp ăn khớp trục vít - bánh vít, thì
bắt đầu tiến dao theo hướng tiếp tuyến để sửa đúng bề mặt gia công. Như
vậy chỉ cần dao phay lăn hình trụ, khoảng chạy dao dọc theo hướng tiếp
tuyến chỉ cần 1,5 bước là đủ.
b. Gia công bánh vít bằng dao phay một lưỡi
Gia công bánh vít theo phương pháp
này được dùng khi không có dao phay lăn
chuyên dùng trong điều kiện sản xuất nhỏ.
Sơ đồ gia công được thể hiện trên hình
2.135. Lưỡi dao được gắn trên trục dao
quay tạo thành dao phay lăn một lưỡi.
Biên dạng và kích thước của lưỡi dao phải
giống hệt như một lưỡi dao phay lăn
tương ứng.
Khi cắt dao có chuyển động quay
tròn, chi tiết có chuyển động quay tròn.
Hai chuyển động quay này phải theo một
tỉ số truyền giống như bánh vít gia công
xong ăn khớp với trục vít. Để lăn tròn hết sườn răng còn phải có chuyển
động chạy dao theo hướng tiếp tuyến (hoặc hướng kính).
Ngoài ra, chi tiết phải có chuyển động quay thêm tương ứng. Nếu
chạy dao theo hướng tiếp tuyến, thì trục dao được gá sao cho đường tâm
của nó cách đường tâm của chi tiết một khoảng cách đúng bằng khoảng
cách giữa trục vít và bánh vít khi làm việc.
Theo phương pháp này, số lưỡi cắt chỉ là 1, nên muốn có độ nhám bề
mặt răng thấp, thì lượng chạy dao phải bé vì vậy năng suất gia công thấp.
n
c
R
S
Hình 2.135: Gia công bánh vít
bằng dao phay một lưỡi.
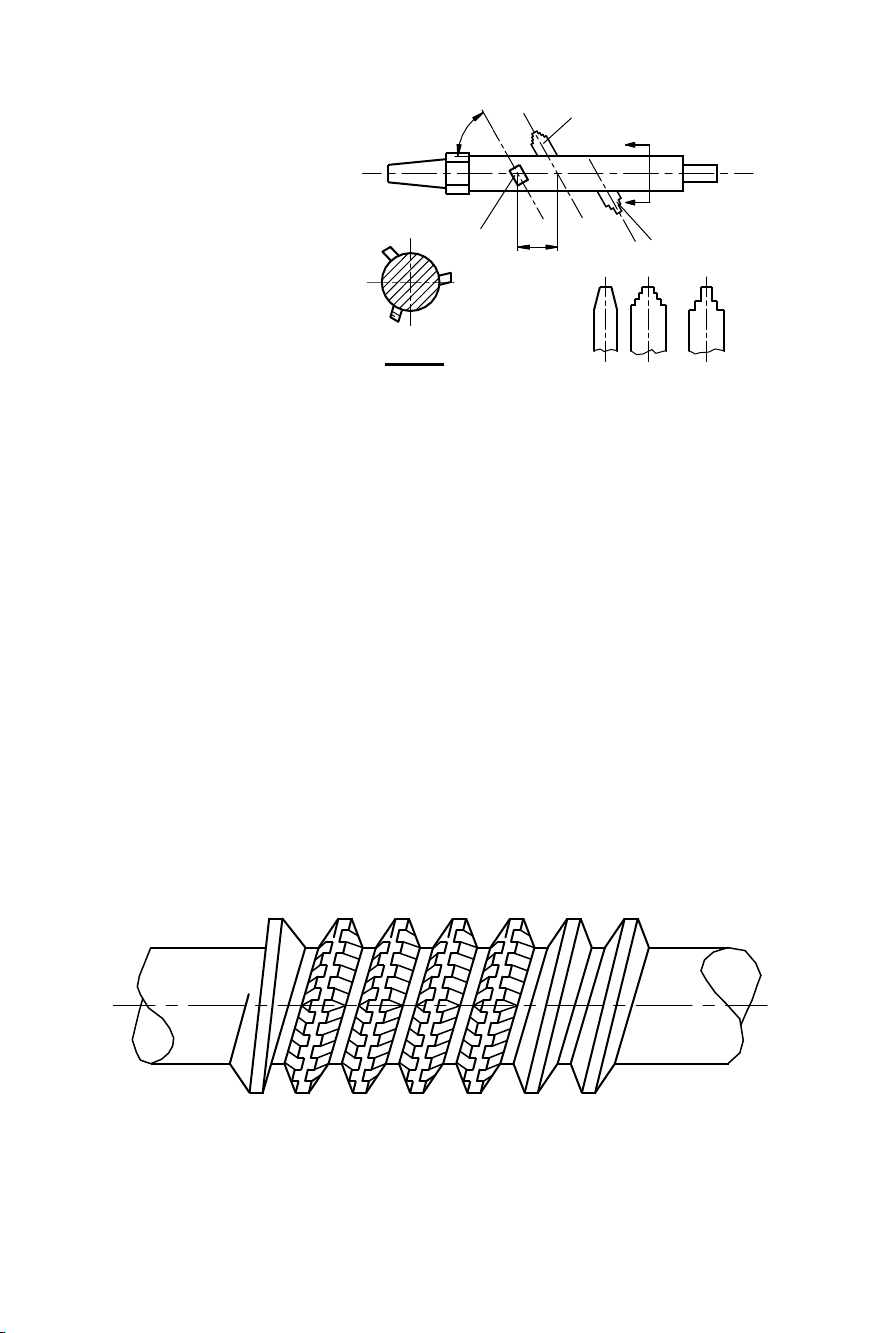
154
Để nâng cao
năng suất và độ bóng
bề mặt răng, có thể lắp
hai hoặc ba dao trên
một trục dao. Các dao
này được lắp trên cùng
một đường xoắn bằng
đường xoắn của trục
vít ăn khớp với bánh
vít cần gia công ()
(hình 2.136). Các dao
trước cắt thô, dao sau
cùng cắt tinh. Các dao
trước có thể làm thành
bậc thang không cần
có biên dạng chính xác.
c. Gia công tinh bánh vít
Để gia công tinh bánh vít, có thể dùng phương pháp cà. Dao cà có
dạng trục vít và trên mặt xoắn vít có nhiều rãnh bé (hình 2.137).
Nhờ những rãnh này mà hình thành các lưỡi cắt với mặt trước cà
mặt sau. Dạng của lưỡi cắt có góc sau = 0
0
, chiều rộng mặt sau 0,2 -
0,5mm, góc trước = 6
0
-7
0
. Khi mài dao cà không được mài mặt trước
mà mài mặt sau vì mặt ấy mới đại diện cho mặt xoắn làm việc của trục
vít và nó có ảnh hưởng trực tiếp đến độ chính xác của bánh vít được gia
công. Khi mài dao cà này phải mài trong cùng một điều kiện (cùng một
lần điều chỉnh máy) với trục vít sẽ ăn khớp với bánh vít được gia công,
có như vậy mới đảm bảo độ chính xác của bộ truyền. Lượng dư để cho cà
bánh vít thường vào khoảng 0,15 mm - 0,25mm.
Có hai cách cà: cà cưỡng bức và cà tự do. Cả hai cách đều có thể
thực hiện trên máy lăn răng.
t
A-A
3
1
2
3
2
1
A
A
Hình 2.136: Sơ đồ trục dao và các lưỡi cắt của
từng dao khi gia công bánh vít bằng dao phay
với ba lưỡi cắt.
Hình 2.137: Dạng dao dùng để cà bánh răng.
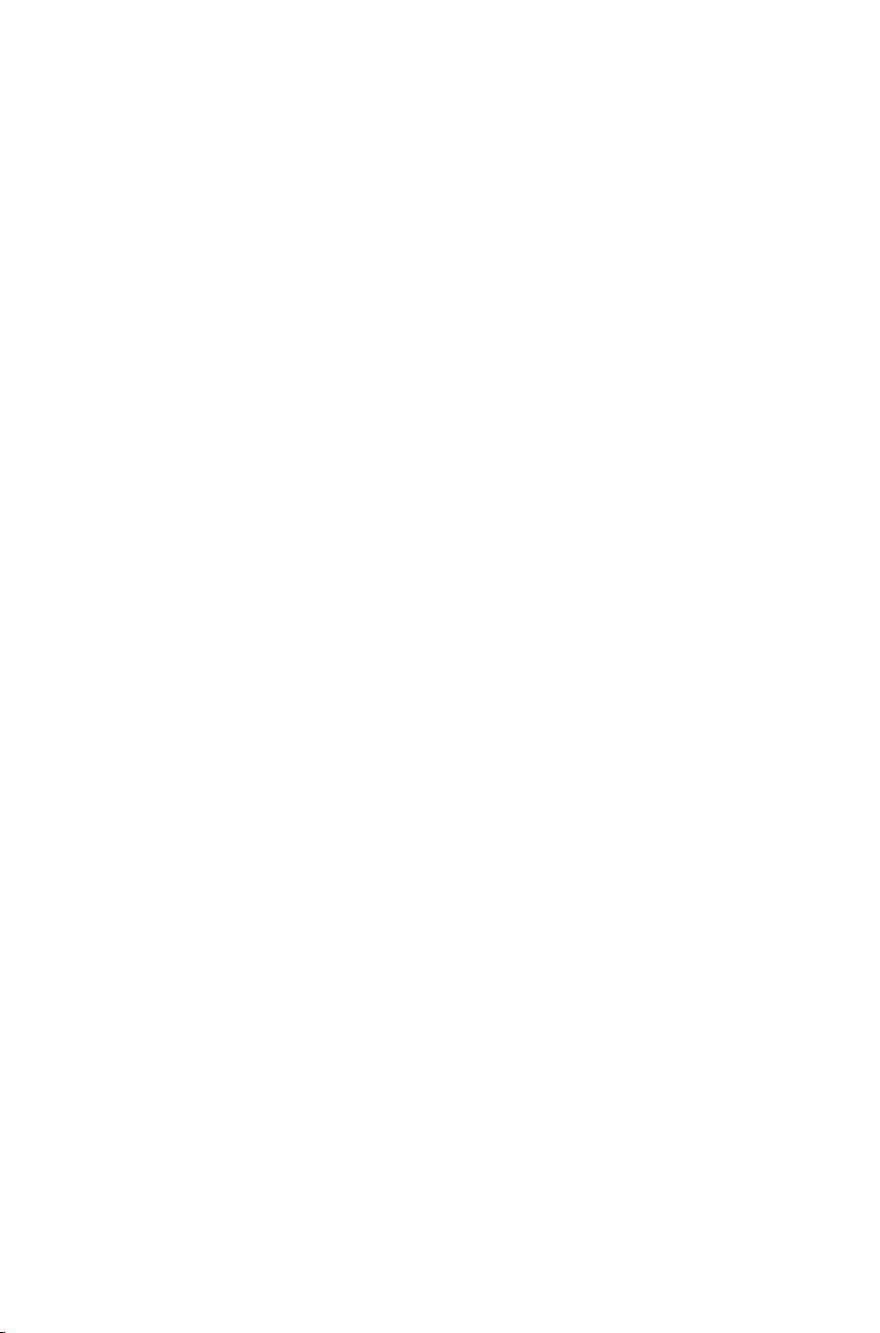
155
Cà tự do là phương pháp cà khi giữa dao và chi tiết gia công không
có xích truyền động cưỡng bức. Chi tiết có thể quay tự do theo chuyển
động quay của dao. Với cách cà như vậy, độ chính xác của chi tiết gia
công chỉ phụ thuộc vào độ chính xác của dao và một phần phụ thuộc vào
độ chính xác chi tiết trước khi cà. Phương pháp này có thể nâng cao độ
bóng, độ chính xác biên dạng và giảm bớt sai số bước răng.
Cà cưỡng bức là phương pháp cà khi chi tiết không được quay tự
do mà giữa sự quay của dao và chi tiết gia công bị chi phối bởi xích
truyền động cưỡng bức. Như vậy độ chính xác của chi tiết gia công phụ
thuộc vào độ chính xác của xích nói trên.
Ngoài phương pháp cà để gia công tinh bánh vít, những năm gần
đây còn phát triển phương pháp mài cà còn gọi là mài khôn bánh vít.
Theo phương pháp này, dụng cụ là đá mài có dạng trục vít sẽ ăn
khớp với bánh vít gia công. Khi gia công các chuyển động của đá mài và
chi tiết giống như khi cà. Theo phương pháp này, năng suất và chất lượng
đều tốt.
2.5.6. Kiểm tra bánh răng
Tùy theo điều kiện sử dụng và nhiệm vụ chính của bánh răng khi
làm việc, người ta có thể kiểm tra bánh răng theo các yêu cầu sau đây:
Độ chính xác động học
Độ chính xác động học được kiểm tra khi bánh răng có yêu cầu
truyền động chính xác như các bánh răng trong máy đo, máy gia công
chính xác, đầu phân độ.
Độ chính xác động học bao gồm các chỉ tiêu sau đây:
- Sai số động học.
- Sai số tích lũy bước vòng.
- Độ đảo vòng chia.
- Sai lệch chiều dài khoảng pháp tuyến chung.
- Sai lệch khoảng cách tâm khi bánh răng quay một vòng.
Độ ổn định khi làm việc
Độ ổn định khi làm việc được kiểm tra khi bánh răng làm việc ở
tốc độ cao và nó bao gồm các chỉ tiêu sau đây:
- Sai số chu kì.
- Sai số bước cơ sở.
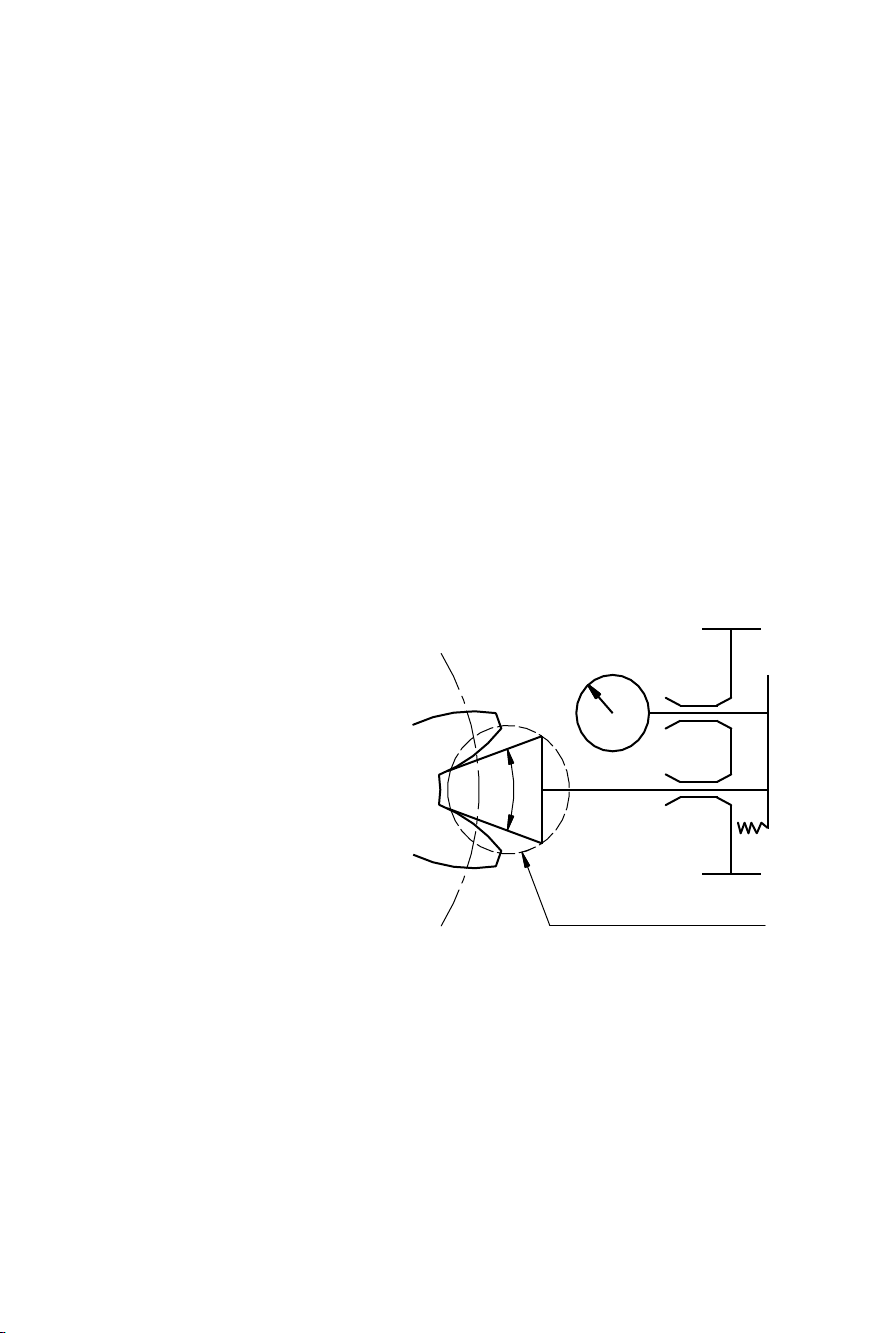
156
- Sai số bước vòng.
- Sai số prôfin.
- Sai lệch khoảng cách tâm khi quay đi một răng.
Độ chính xác tiếp xúc
Độ chính xác tiếp xúc được kiểm tra khi bánh răng làm việc với
trọng tải lớn. Nó bao gồm chỉ tiêu sau đây:
- Diện tích tiếp xúc.
- Sai lệch phương của răng.
Khe hở mặt bên
Khe hở mặt bên được kiểm tra khi bánh răng làm việc cả hai chiều.
Như vậy, chúng ta thấy có rất nhiều chỉ tiêu của bánh răng cần phải
kiểm tra. Sau đây, chúng ta chỉ nghiên cứu một số phương pháp kiểm tra
chỉ tiêu cơ bản của bánh răng trụ.
2.5.6.1. Kiểm tra độ đảo vòng chia
Để kiểm tra thông số này,
người ta dùng đồng hồ so và
con lăn hình côn (hình 2.138).
Con lăn có góc côn 40
0
,
đường kính ở đỉnh của hình
côn thường lấy bằng 1,5
môđun của bánh răng. Con lăn
được thả cho tiếp xúc với hai
mặt răng, lúc đó kim đồng hồ
chỉ một giá trị. Nếu ta lần lượt
cho con lăn tiếp xúc với tất cả
các rãnh răng, ta sẽ thấy đồng
hồ chỉ một giá trị lớn nhất và
nhỏ nhất (hiệu của chúng
chính là độ đảo vòng chia).
Khi kiểm tra, dụng cụ có hai chân tì lên hai đầu răng (cùng phía)
gắn đường kính chia. Đồng hồ so chỉ các giá trị khác nhau khi ta kiểm tra
các bước khác nhau.
Sai số các vòng là hiệu giữa hai bước nào đó trên một đường tròn
của bánh răng.
40
o
Hình 2.138: Kiểm tra độ đảo vòng chia
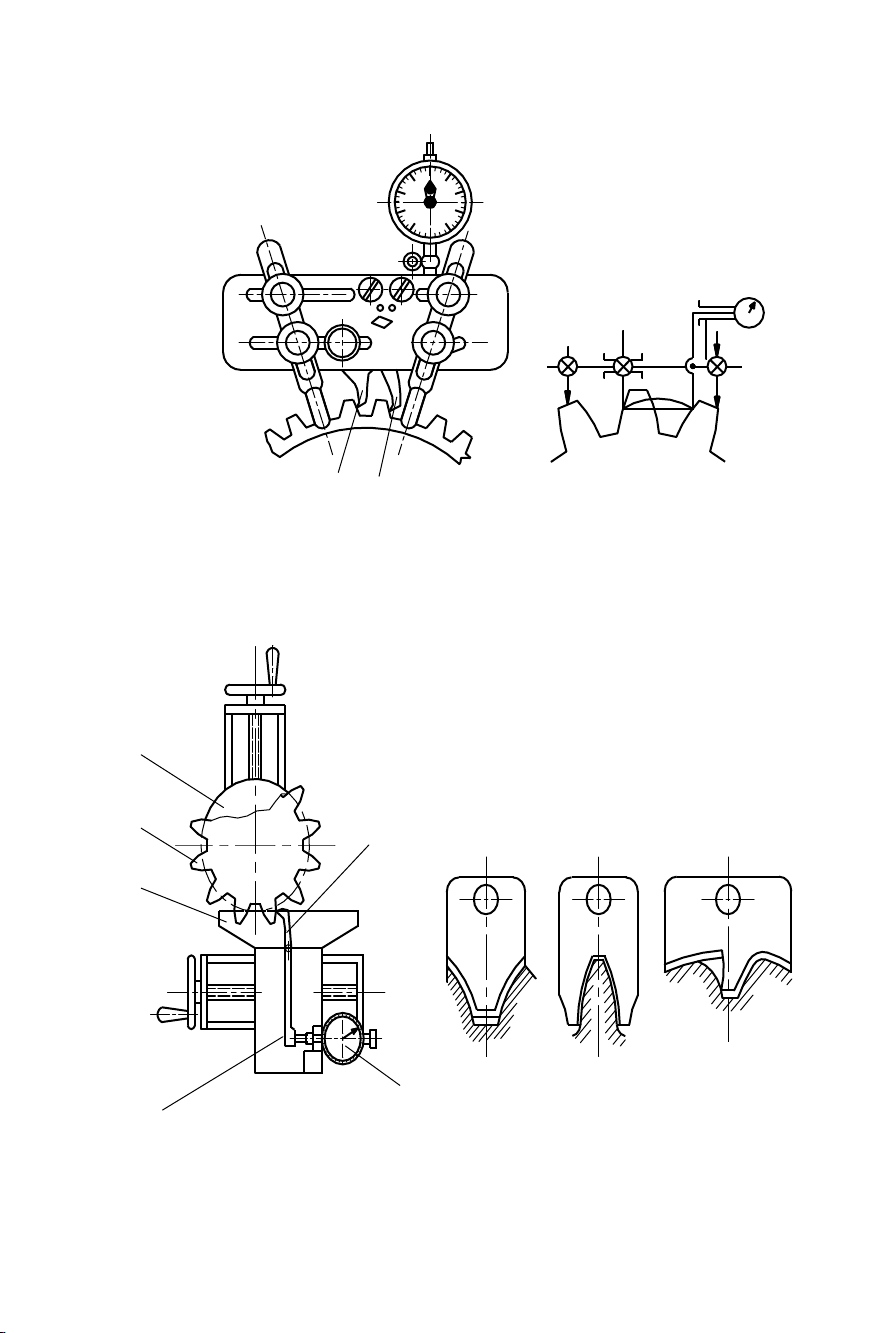
157
2.5.6.2. Kiểm tra sai lệch prôfin
Sai lệch prôfin răng được kiểm tra bằng máy chuyên dùng MN3
(hình 2.140).
1
2
a)
2
1
b)
m3-15
0.005mm
Hình 2.139: Sơ đồ kiểm tra bước vòng.
a. Dụng cụ đo bước vòng. b. Sơ đồ kiểm tra.
3
2
1
4
5
a)
b)
Hình 2.140: Kiểm tra sai lệch prôfin.
6
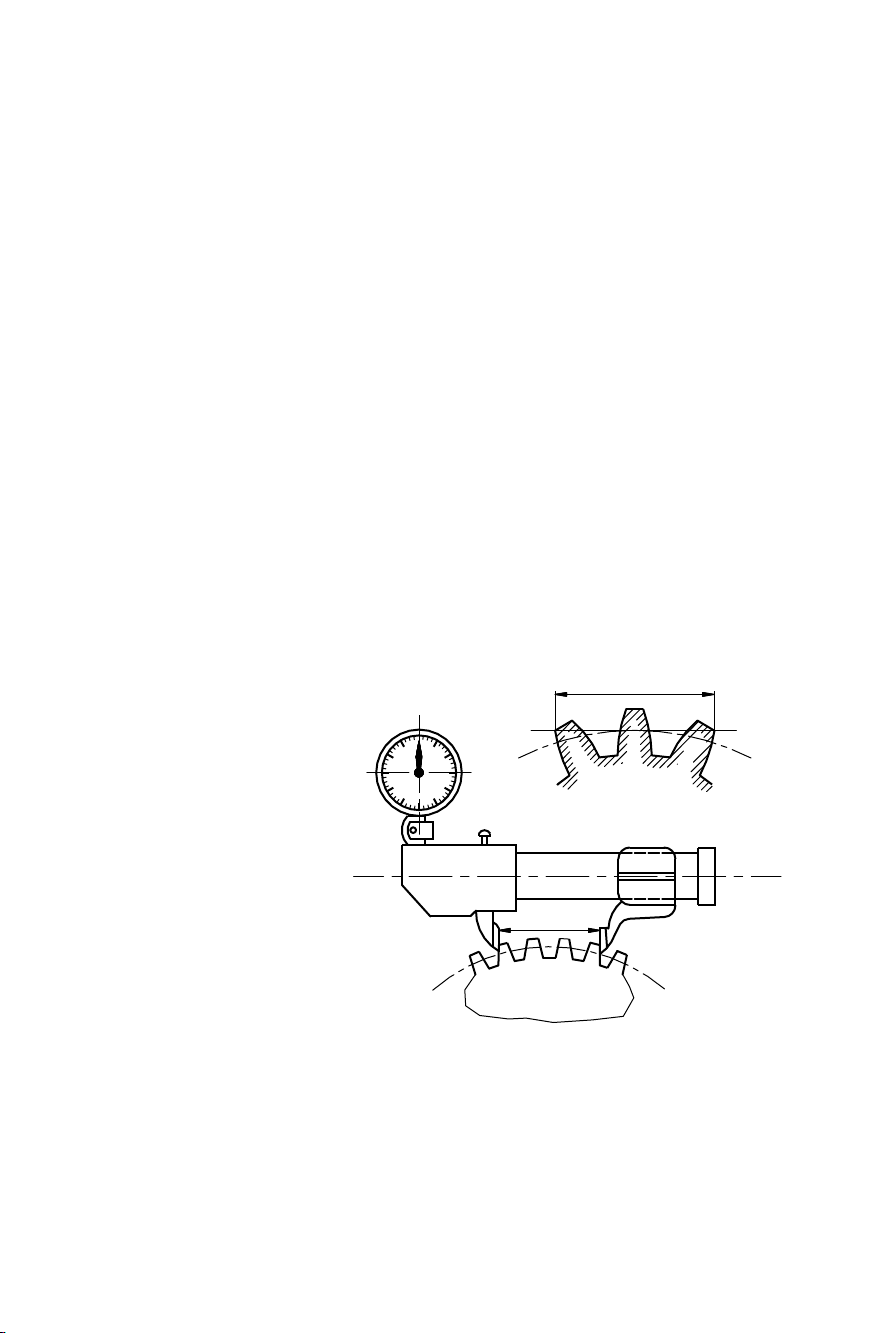
158
Bánh răng kiểm tra 2 lắp cứng trên đĩa 3 (đĩa 3 có đường kính bằng
đường kính cơ sở của bánh răng). Thước 1 tiếp xúc với đĩa 3, đầu đo tiếp
xúc với prôfin. Khi ta quay bánh răng 2, nếu prôfin răng có sai số thì đầu
đo 4 (có đầu 6 tì vào đầu đo của đồng hồ 5) sẽ làm cho kim của đồng hồ
dịch chuyển. Nếu prôfin không có sai số, kim đồng hồ đứng tại chỗ.
Ngoài máy đo prôfin chuyên dùng, trong thực tế, người ta còn dùng
các dưỡng để xác định sai số prôfin (hình 2.140b).
2.5.6.3. Kiểm tra sai lệch khoảng pháp tuyến chung
Chiều dài khoảng pháp tuyến chung L là khoảng cách giữa hai
điểm a – b trên hai mặt prôfin khác nhau.
Trên hình 2.141 là một loại thước đo khoảng cách các pháp tuyến
chung (chiều dài L). Sai lệch khoảng pháp tuyến cho phép đánh giá sai số
động học của bánh răng.
2.5.6.4. Kiểm tra vết tiếp xúc
Vết tiếp xúc có thể kiểm tra sau khi các bánh răng ăn khớp với
nhau đã lắp vào vị trí hoặc trên máy chạy rà.
2.5.6.5. Kiểm tra tổng hợp ăn khớp hai bên
Phương pháp
kiểm tra tổng hợp ăn
khớp hai bên phản ảnh
các sai số theo phương
hướng kính sau một
vòng quay hay sau một
răng như: sai số prôfin,
độ đảo vành răng, sai số
bề dày của răng …
Trong sản xuất lớn, đó
là một phương pháp
kiểm tra không thể
thiếu được.
Hình 2.142 là sơ
đồ nguyên lý của máy
kiểm tra theo phương
pháp. Ở đây bánh răng cần kiểm tra 1 và bảng mẫu 2 được lắp trên hai
bên trượt 3 và 4. Bàn trượt 3 có thể di trượt khi quay vít 5, còn bàn trượt
4 bị lò xo luôn luôn ép cho bánh răng ăn khớp với bánh răng 1.
L
b
a
L
Hình 2.141: Kiểm tra sai lệch khoảng pháp
tuyến chung.
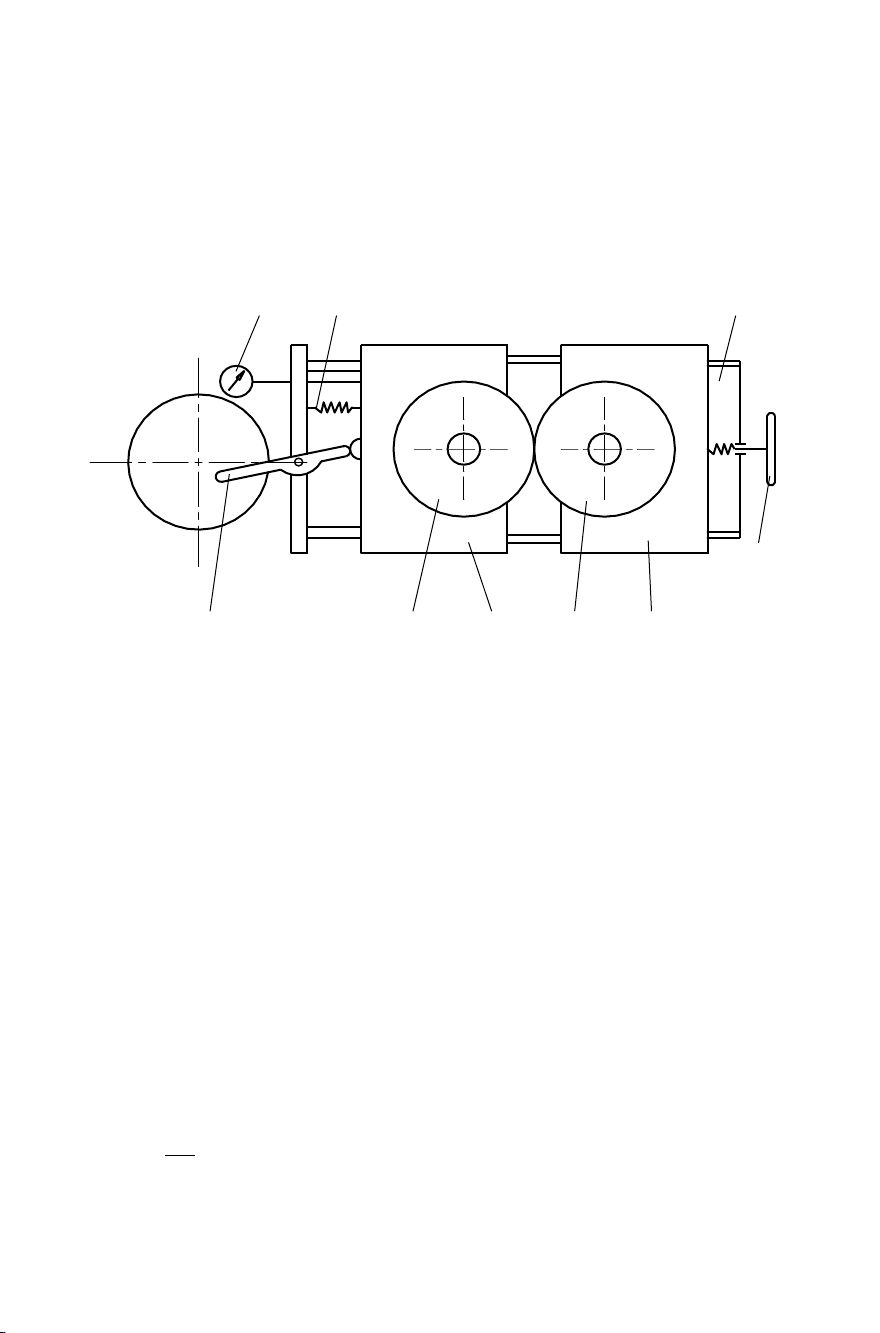
159
Trong quá trình ăn khớp nếu bánh răng 1 có sai số, bàn trượt 4 sẽ
dịch chuyển theo phương hướng kính. Lượng dịch chuyển đó được chỉ
thị trên đồng hồ 7 hoặc được ghi thành đồ thị nhờ cơ cấu 8. Trong quá
trình kiểm tra, bàn trượt 3 cố định, nó chỉ di chuyển khi cần thay đổi
khoảng cách tâm giữa hai trục gá để kiểm tra các bánh răng có kích thước
khác nhau. Kết quả kiểm tra theo phương pháp này cho phép ta đánh giá
các chỉ tiêu sau đây:
- Dao động khoảng cách tâm khi quay một vòng dùng để đánh giá
chỉ tiêu học.
- Dao động khoảng cách tâm quay 1 răng dùng để đánh giá độ ổn
định khi làm việc do sai số bước cơ sở, sai số prôfin gây ra.
2.5.6.6. Kiểm tra sai số tích lũy bước vòng
Sai số tích lũy bước vòng là sai số lớn nhất về sự phân bố của hai
prôfin răng cùng phía trên một đường tròn của bánh răng.
Sai số tích lũy bước vòng được xác định bằng các dụng cụ đo
chuyên dùng. Hình 2.143 là sơ đồ kiểm tra đơn giản nhất.
Máy đo bao gồm một đĩa chia 3, chốt định vị 2. Chi tiết kiểm tra 1
được lắp cứng trên trục của đĩa chia 3. Mỏ đo 4 tì vào đầu đo 5 của đồng
hồ so. Ở vị trí như trên sơ đồ, ta điều chỉnh cho kim đồng hồ có chỉ số 0.
Sau đó ta rút chốt định vị 2, dùng tay quay đĩa chia 3 và chi tiết 1 đi một
góc =
Z
2
lúc đó mỏ đo tì 4 vào prôfin của răng bên cạnh.
8
2
4
1
3
5
7
6
9
Hình 2.142: Sơ đồ kiểm tra tổng hợp ăn khớp hai bên.
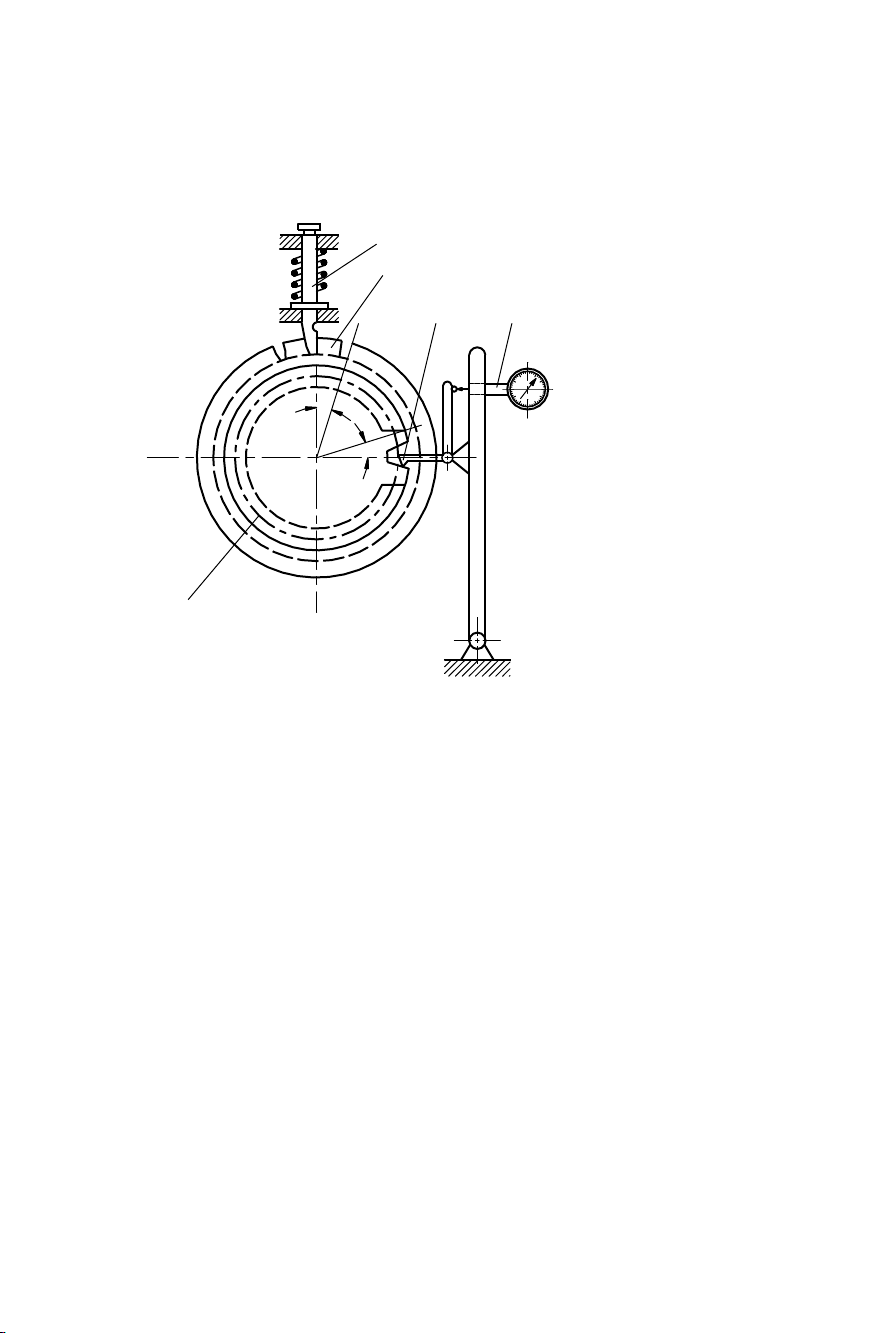
160
Làm như vậy đối với tất cả các răng, ta sẽ có nhiều giá trị khác
nhau của đồng hồ so.
Sai số tích lũy bước vòng là hiệu đại số giữa hai giá trị lớn nhất và
nhỏ nhất của chỉ số đồng hồ.
2.5.6.7. Kiểm tra bánh răng bằng máy CMM (Coordinate
Measuring Machine)
Máy đo tọa độ CMM là tên gọi chung của các thiết bị vạn năng có
thể thực hiện việc đo các thông số hình học theo phương pháp tọa độ.
Thông số cần đo được tính từ các tọa độ điểm đo so với gốc tọa độ của
máy. Các loại máy này còn được gọi là máy quét hình vì chúng còn được
dùng để quét hình dáng của vật thể. Có hai loại máy đo tọa độ thông
dụng là máy đo bằng tay (đầu đo được dẫn động bằng tay) và máy đo
CNC (đầu đo được điều khiển tự động bằng chương trình số).
Các máy đo tọa độ CMM hoạt động theo nguyên lý dịch chuyển
một đầu dò để xác định tọa độ các điểm trên bề mặt của vật thể. Máy đo
tọa độ thường theo cả ba phương chuyển vị X, Y, Z. Bàn đo được làm
bằng đá granít, đầu đo được gắn trên giá lắp trên thân trượt theo phương
Z, khi đầu đo được điều chỉnh đến một điểm đo nào đó thì đầu đọc sẽ cho
ta biết ba tọa độ X, Y, Z tương ứng với độ chính xác cao, có thể lên đến
0,1 m . Máy CMM thường thiết kế với bốn phần chính:
- Thân máy
2
3
4
5
1
Hình 2.143: Kiểm tra sai số tích lũy bước vòng.
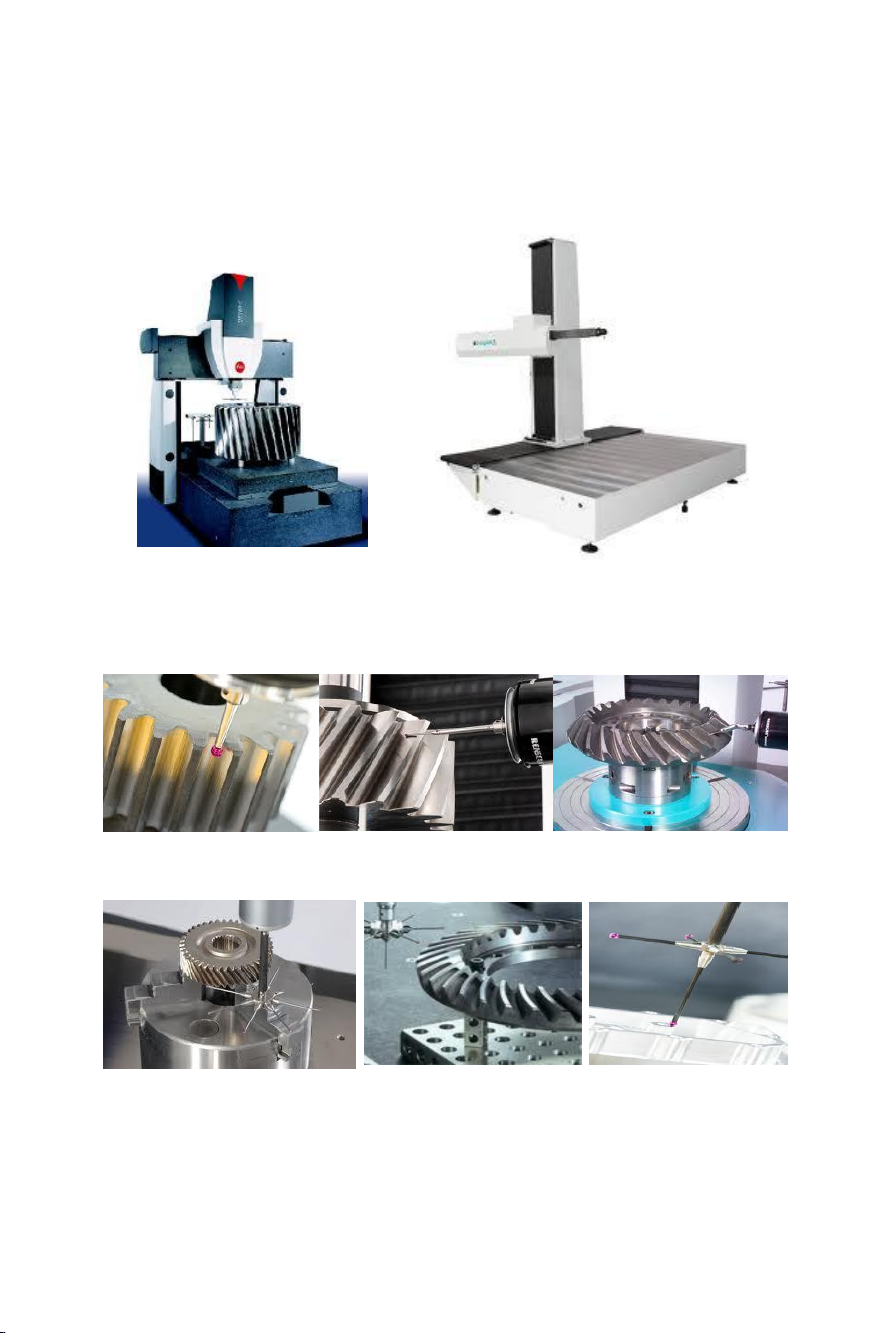
161
- Đầu dò
- Hệ thống điều khiển hoặc máy tính.
- Phần mềm đo.
Hình 2.144: Máy đo tọa độ ba chiều CMM
a) Loại hai trụ
b) Loại một trụ
Hình 2.145: Kiểm tra biên dạng răng
Hình 2.46: Kiểm tra bước vòng
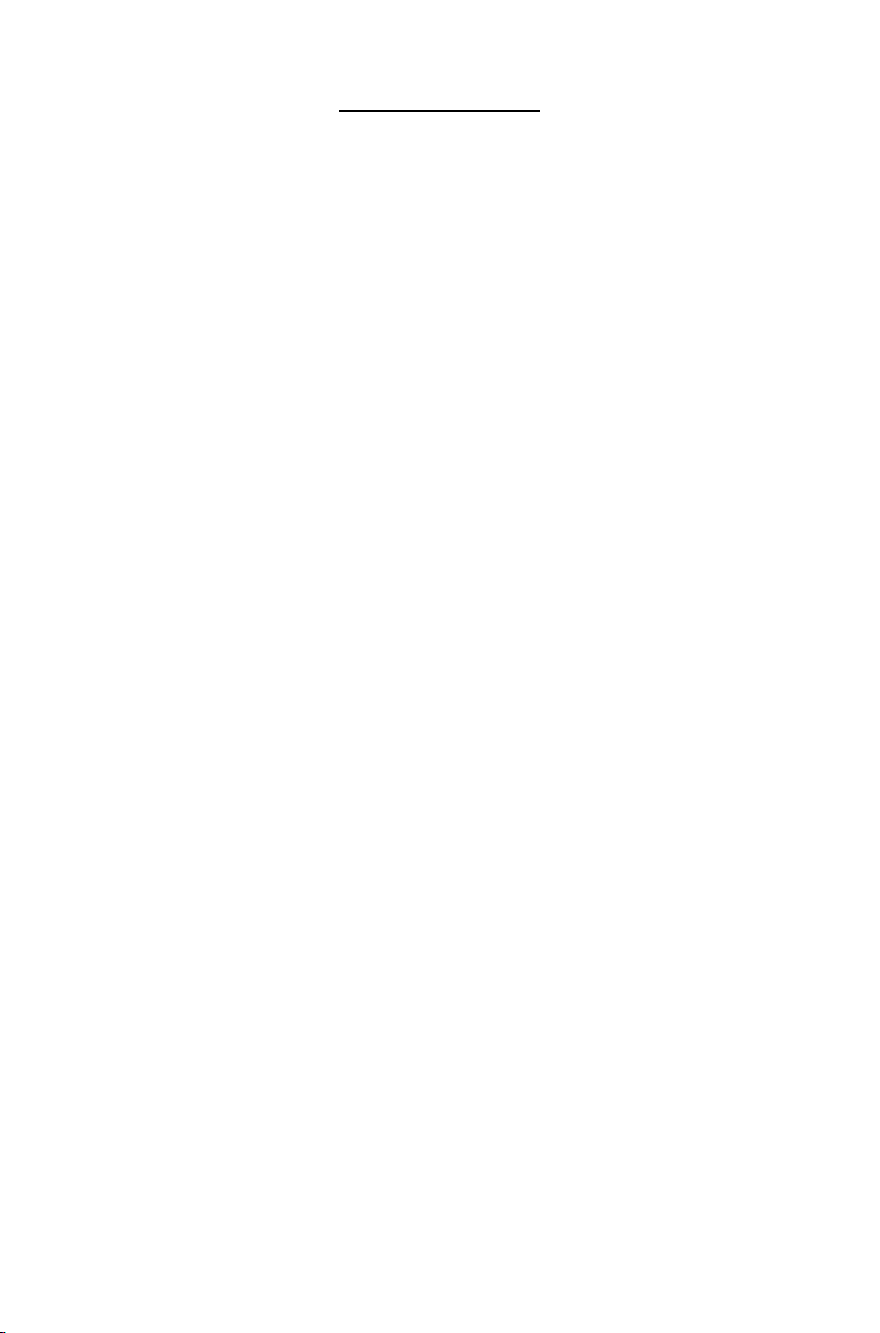
162
CÂU HỎI ÔN TẬP
1. Trình bày những yêu cầu kỹ thuật chủ yếu của chi tiết dạng hộp ?
2. Nêu tính công nghệ trong kết cấu của chi tiết dạng hộp ?
3. Chuẩn định vị để gia công chi tiết hộp gồm những dạng nào ? Cho
ví dụ minh họa.
4. Hãy nêu trình tự gia công các bề mặt chủ yếu của hộp ?
5. Trình bày biện pháp thực hiện nguyên công gia công măt chuẩn ?
Cho ví dụ minh họa.
6. Biện pháp gia công các lỗ lắp ghép phụ thuộc vào điều kiện nào ?
Đặc điểm chung của phương pháp gia công lỗ lắp ghép trên các loại máy
là gì ?
7. Trình bày phương pháp kiểm tra độ chính xác kích thước, kiểm tra
vị trí tương quan của chi tiết hộp (như độ song song, độ đồng tâm, độ
vuông góc…)?
8. Điều kiện kỹ thuật cần thiết khi chế tạo chi tiết càng ?
9. Cho biết vật liệu và phôi chế tạo càng ?
10. Trình bày tính công nghệ trong kết cấu của càng ?
11. Hãy cho biết các phương án định vị càng khi gia công mặt đầu và
lỗ cơ bản ?
12. Nêu thứ tự các nguyên công gia công càng ?
13. Gia công mặt đầu để tăng năng suất ta có thể áp dụng các biện
pháp nào ?
14. Có mấy phương án gia công các lỗ cơ bản của càng ? Cho biết ưu
nhược điểm của từng phương án đó ?
15. Nêu phương pháp kiểm tra kích thước và vị trí tương quan của
càng ?
16. Hãy nêu điều kiện kỹ thuật chi tiết dạng trục ? Yêu cầu về vị trí
tương quan nào được xem là quan trọng nhất ?
17. Trình bày tính công nghệ trong kết cấu của trục ? Tại sao đường
kính của các cổ trục nên giảm dần về hai phía ?
18. Thông thường khi gia công trục thì chuẩn tinh thống nhất được
dùng là ?
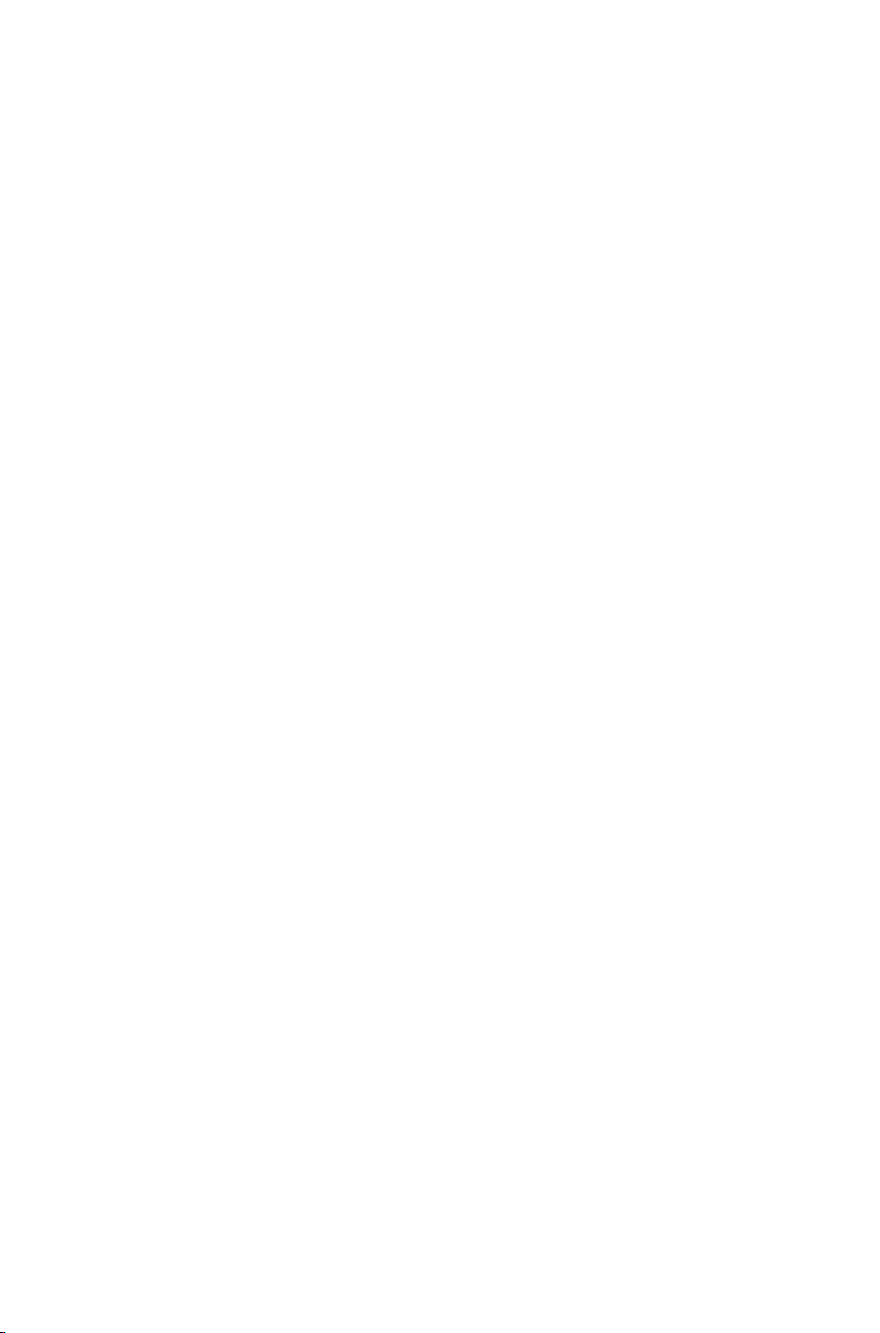
163
19. Khi định vị trên hai mũi tâm để gia công mặt ngoài trục thì có xảy
ra sai số chuẩn không ? Nếu có thì ảnh hưởng đến kích thước nào và biện
pháp khắc phục ( ví dụ minh họa ) ?
20. Hãy nêu cụ thể thứ tự gia công các bề mặt trục ?
21. Nêu các biện pháp thực hiện nguyên công khỏa mặt đầu và khoan
lỗ tâm
22. Tại sao có trường hợp trục liền răng ? Có ưu nhược điểm gì so với
trục và bánh răng lắp ghép ?
23. Các phương pháp gia công rãnh then hoa ?
24. Phương pháp gia công mặt lệch tậm tròn xoay ? Phương pháp gia
công cam không tròn?
25. Khi gia công cổ biên của trục khuỷu có mấy cách gá ? Hãy trình
bày các cách đó ? Phương pháp mới để gia công trục khuỷu?
26. Biện pháp nào để chống uốn do lực cắt và lực kẹp chiều trục mũi
tâm? Hình minh họa ?
27. Phương pháp kiểm tra kích thước, hình dạng hình học và vị trí
tương quan giữa các bề mặt của trục ?
28. Điều kiện kỹ thuật của bạc là gì ?
29. Cho biết vật liệu và phôi chế tạo bạc ?
30. Trình bày tính công nghệ trong kết cấu của bạc ?
31. Cho biết các phương pháp chọn chuẩn định vị để gia công nhằm
đạt độ đồng tâm của chi tiết BẠC
32. Các rãnh dầu hoặc mặt định hình ở trong bạc được gia công bằng
phương pháp gì ?
33. Phương pháp kiểm tra kích thước, hình dạng hình học và vị trí
tương quan giữa các bề mặt của bạc ?
34. Bánh răng , bánh vít là những chi tiết máy dùng để làm gì ? Phân
loại theo hình dạng và theo đặc tính ?
35. Cho biết vật liệu và phôi bánh răng ?
36. Yêu cầu kỹ thuật khi gia công bánh răng?
37. Trình bày công nghệ nhiệt luyện bánh răng ?
38. Trình bày quy trình công nghệ trước khi gia công bánh răng ?
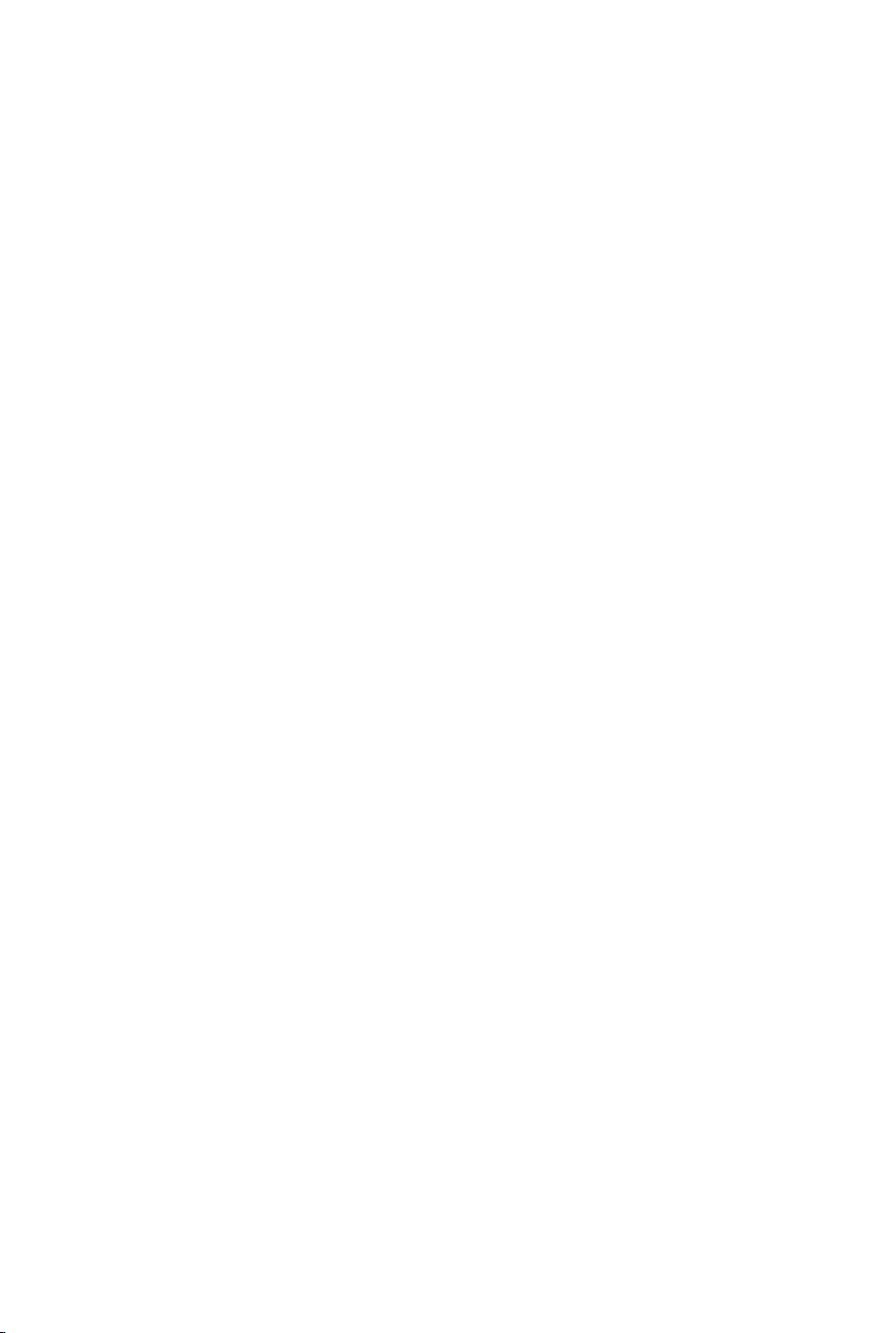
164
39. Về nguyên lý tạo răng có thể chia thành mấy phương pháp gia
công răng ? Hãy nêu cách thực hiện chúng ?
40. Phay răng bằng phương pháp định hình được tiến hành như thế
nào ? Cho biết ưu nhược điểm của phương pháp này ? Vẽ hình gia công
bánh răng trụ bằng dao phay modul
41. Trình bày phương pháp chuốt bao hình bánh răng ? Hình minh họa
42. Trình bày nguyên lý bao hình khi phay lăn răng thẳng ? Vẽ hình
minh họa.
43. Trình bày nguyên lý bao hình khi phay lăn răng nghiêng ? Vẽ hình
minh họa.
44. Hãy trình bày nguyên lý chuyển động bao hình gia công bánh răng
theo phương pháp xọc răng bằng dao dạng bánh răng ? Vẽ hình minh họa.
45. Mục đích của việc vê, vát đầu răng là gì ? Áp dụng có các loại
bánh răng nào ? Biện pháp thực hiện việc vê, vát đầu răng?
46. Phương pháp gia công tinh bánh răng được chia hai loại gì ?
47. Trình bày phương pháp chạy rà bánh răng ?
48. Trình bày phương pháp cà răng bánh răng ?
49. Trình bày phương pháp mài răng theo phương pháp định hình ?
Cho biết ưu nhược điểm của phương pháp này ?
50. Trình bày phương pháp mài răng theo phương pháp bao hình ?
Cho biết ưu nhược điểm của phương pháp này ?
51. Trình bày phương pháp mài răng bằng đá mài dạng trục vít ?Cho
biết ưu nhược điểm của phương pháp này ?
52. Trình bày công nghệ gia công bánh răng côn thẳng dạng phay răng
theo phương pháp định hình ?
53. Trình bày công nghệ gia công bánh răng côn thẳng dạng phay răng
theo phương pháp bao hình ?
54. Bánh răng côn cung được ứng dụng trong kỹ thuật như thế nào ?
Phân loại ?
55. Trình bày nguyên lý gia công côn răng cung tròn ?
56. Trình bày phương pháp cà bánh răng côn ? So với các phương
pháp khác thì phương pháp này có ưu nhược điểm gì ?
57. Trình bày phương pháp mài bánh răng côn ? So với các phương
pháp khác thì phương pháp này có ưu nhược điểm gì ?
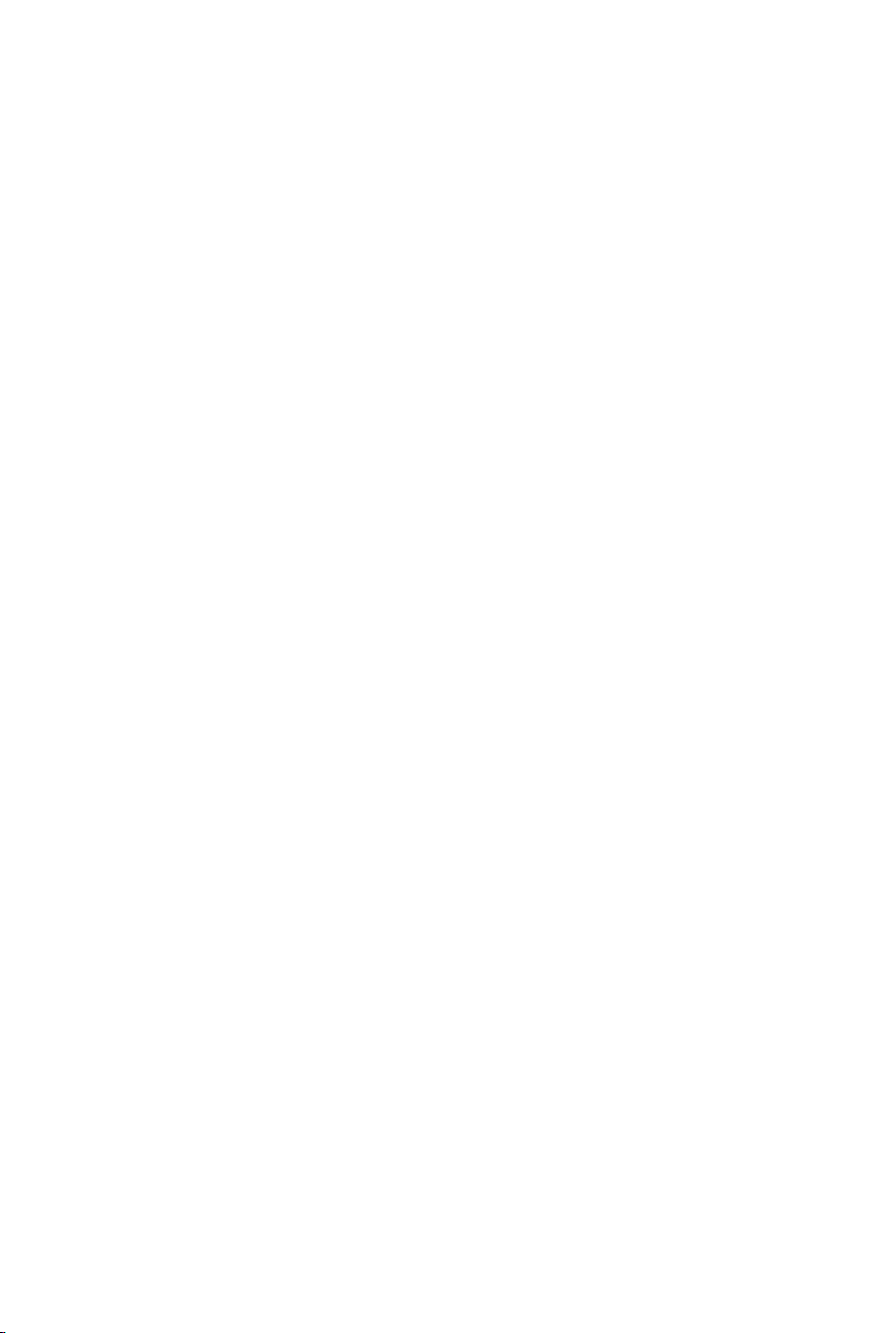
165
58. So sánh nguyên lý, ưu nhược điểm của phương pháp tiến dao
hướng kính và tiến dao tiếp tuyến khi gia công bánh vít bằng phay lăn ?
Phương pháp tổng hợp đã giải quyết được vấn đề gì ?
59. Trình bày phương pháp gia công trục vít bằng dao phay ?
60. Trình bày phương pháp gia công tinh bánh vít bằng phương pháp
cà và mài khôn bánh vít ?
61. Hãy nêu các yêu cầu kiểm tra bánh răng về độ chính xác động học,
độ ổn định làm việc, độ chính xác tiếp xúc, khe hở mặt bên?
62. Hãy nêu rõ phương pháp kiểm tra độ đảo vòng chia, kiểm tra sai
lệch profin, kiểm tra sai lệch khoảng pháp tuyến chung, kiểm tra vết tiếp
xúc, kiểm tra tổng hợp ăn khớp hai bên, kiểm tra sai số tích lũy bước
vòng ?
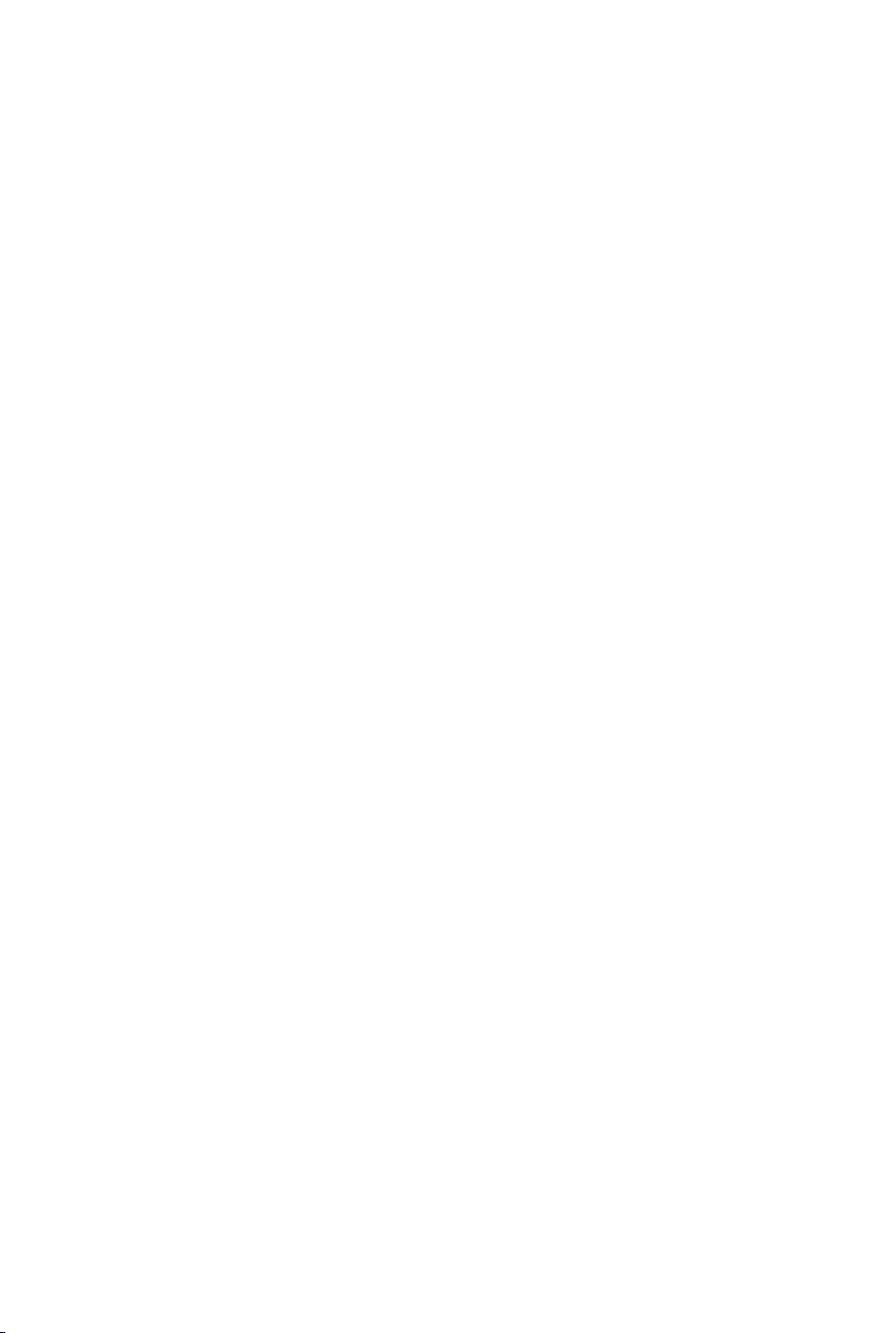
166
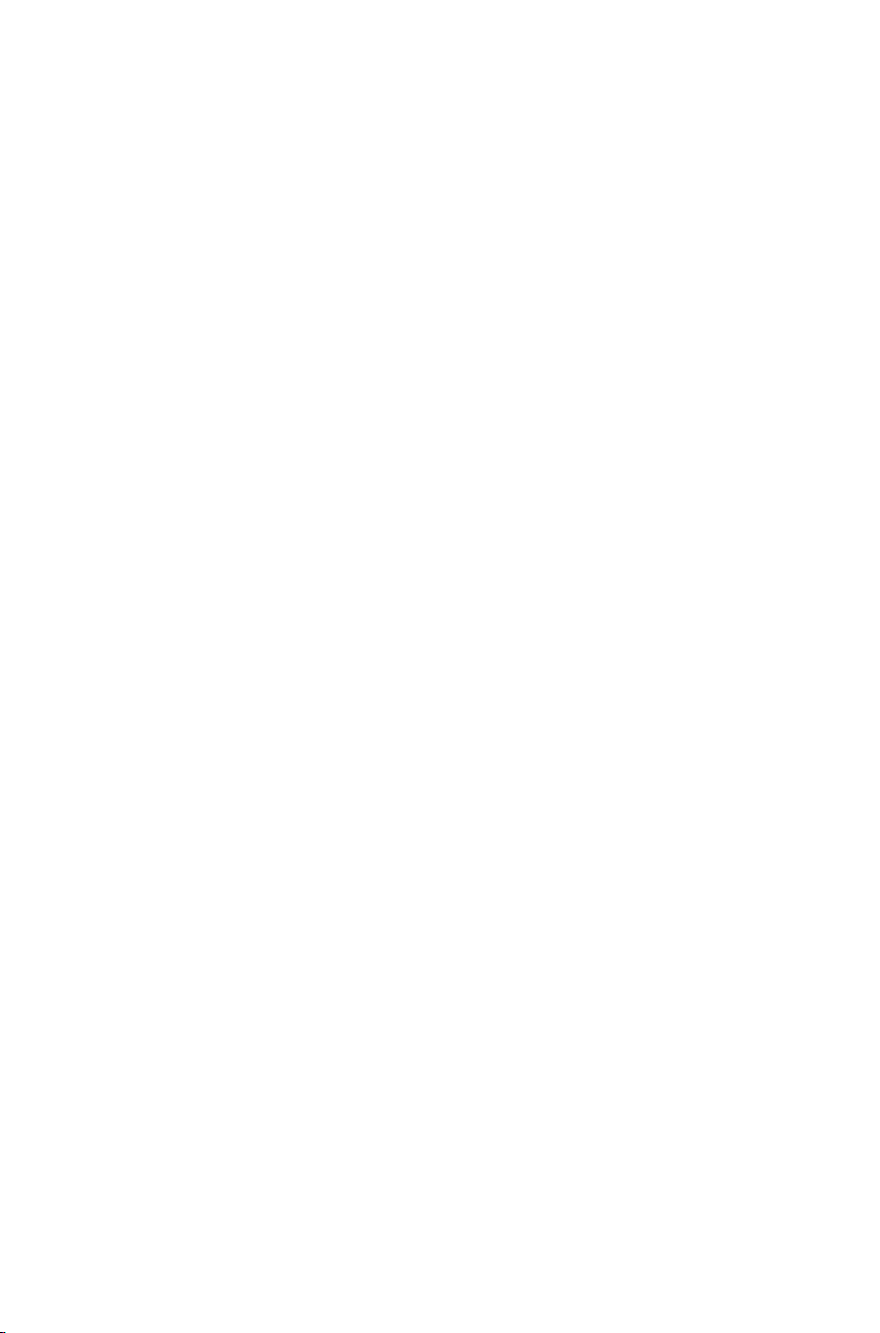
167
Chƣơng 3
THIẾT KẾ ĐỒ GÁ
Mục tiêu:
- Phân biệt các loại đồ gá, trình bày được phương pháp thiết kế đồ gá
chuyên dùng.
- Tính toán sai số do gá đặt gây ra từ đó xác định được sai số chế tạo
đồ gá.
- Phân tích và tính toán được lực kẹp cần thiết(W
ct
) và lực kẹp do cơ
cấu kẹp tạo(W) ra để lựa chọn cơ cấu kẹp.
- Áp dụng các loại cơ cấu định vị, các loại cơ cấu kẹp chặt và các
cơ cấu khác để thiết kế đồ gá..
3.1. KHÁI NIỆM CHUNG VỀ ĐỒ GÁ
3.1.1. Khái niệm về trang bị công nghệ
Trong quá trình sản xuất của ngành cơ khí chế tạo máy, toàn bộ các
phụ tùng kèm theo máy gia công để giúp cho máy đó thực hiện có hiệu
quả quá trình công nghệ gia công các chi tiết máy đều được gọi là các
trang bị công nghệ.
Như vậy trang bị công nghệ nói chung bao gồm các loại đồ gá trên
máy cắt, đồ gá lắp ráp, đồ gá đo lường, các dụng cụ cắt, các dụng cụ phụ,
các cơ cấu cấp phôi, tháo phôi, các loại khuôn đúc, rèn, dập, ép...
Việc thiết kế toàn bộ các trang thiết bị công nghệ để sản xuất một
sản phẩm có thể chiếm tới 80 ÷ 90% khối lượng lao động trong công tác
chuẩn bị sản xuất. Giá thành chế tạo trang bị công nghệ chiếm tới 15 ÷
20% giá thành các thiết bị. Do đó muốn đạt được hiệu quả kinh tế cao, thì
việc nghiên cứu các phương pháp thiết kế chế tạo các trang bị cho sản
xuất là điều rất cần thiết.
3.1.2. Khái niệm về đồ gá
Đồ gá là một loại trang bị công nghệ dùng để gá đặt chi tiết khi gia
công (đồ gá gia công), khi lắp ráp hoặc khi đo lường các yếu tố hình học.
Nhiệm vụ của đồ gá là định vị, kẹp chặt chi tiết và một số nhiệm vụ khác.
Khi trang bị đồ gá cho sản xuất cần chú ý mấy điểm sau:
- Đối với sản xuất hàng khối và hàng loạt lớn nên dùng các đồ gá
hiện đại, chuyên dùng và thao tác nhanh hơn so với đồ gá dùng trong sản
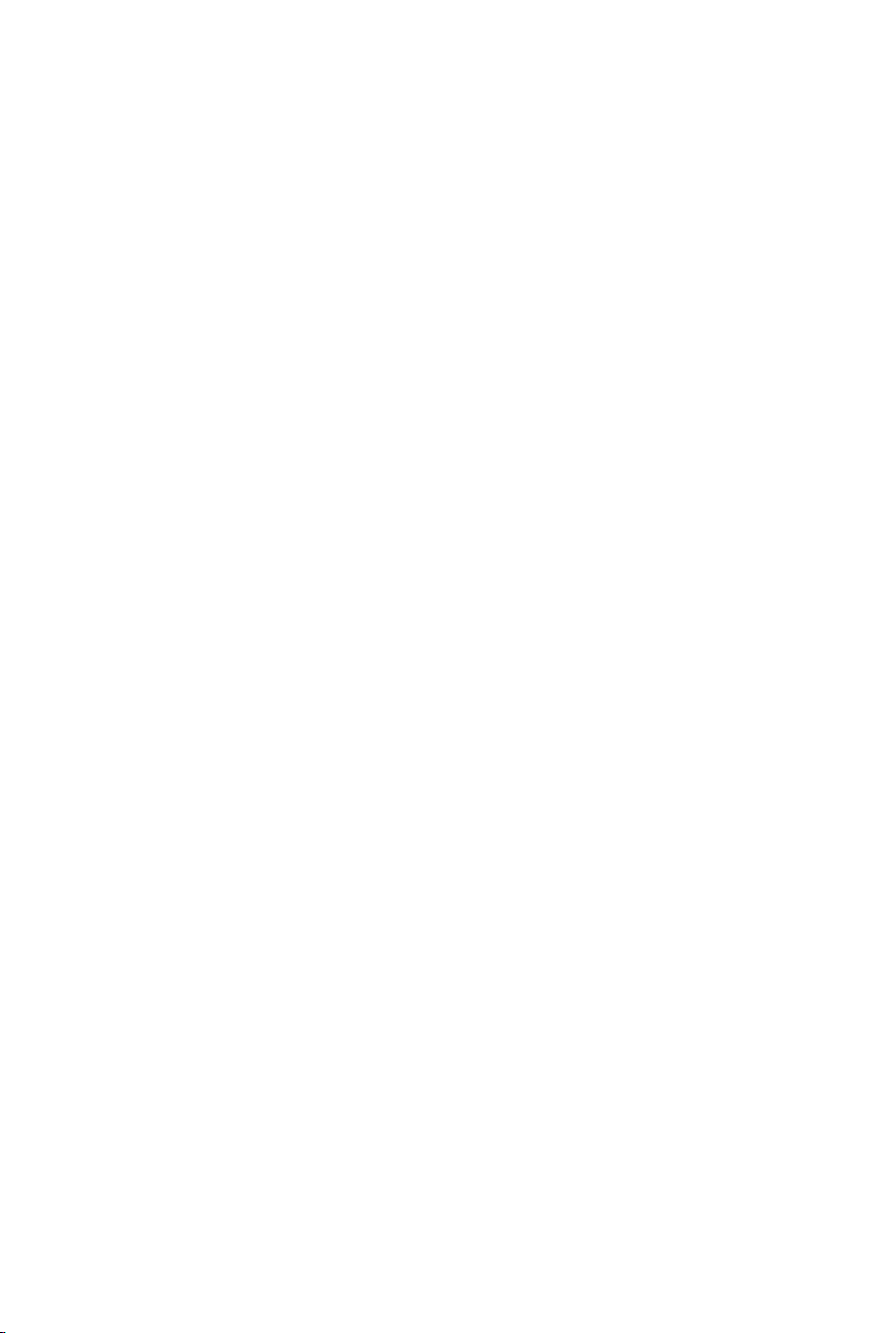
168
xuất hàng loạt bé và vừa. Tuy vậy các trang thiết bị đắt tiền này sẽ được
hoàn vốn nhanh chóng từ lợi nhuận khi chế tạo chi tiết gia công thu được.
- Đối với sản xuất hàng loạt bé và vừa phải tìm các phương pháp
kéo dài thời gian sử dụng đồ gá trong tình trạng các chi tiết gia công tồn
tại tương đối ngắn trong sản xuất. Phương pháp cơ bản để giải quyết vấn
đề đó là các đồ gá hay các bộ phận của đồ gá phải được sử dụng lặp đi
lặp lại khi gia công các chi tiết khác nhau, tức là phải có khả năng điều
chỉnh được. Các vấn đề đó giải quyết bằng cách tiêu chuẩn hóa các loại
đồ gá hoặc các bộ phận tạo thành đồ gá trên cơ sở phân loại các chi tiết
và các bộ phận chủ yếu của đồ gá và điển hình hóa quá trình công nghệ
chế tạo chúng.
3.1.3. Cấu tạo tổng quát của đồ gá
Đồ gá được cấu tạo bởi các bộ phận chính sau đây:
Bộ phận định vị.
Bộ phận kẹp chặt và các cơ cấu truyền lực.
Các cơ cấu hướng dẫn dụng cụ cắt như: phiến dẫn, bạc dẫn, then
dẫn, dưỡng so dao...
Các cơ cấu quay và phân độ.
Thân đồ gá và đế đồ gá để lắp ráp các bộ phận trên tạo thành một
bộ đồ gá hoàn chỉnh.
Cơ cấu định vị và kẹp chặt đồ gá vào máy cắt kim loại.
3.1.4. Tác dụng của đồ gá
Nâng cao năng suất và độ chính xác gia công vì vị trí của chi tiết
so với máy, dao được xác định bằng các đồ định vị, không phải rà gá mất
nhiều thời gian. Độ chính xác gia công được đảm bảo nhờ phương án
chọn chuẩn, độ chính xác của đồ gá và đặc biệt là không phụ thuộc vào
tay nghề công nhân. Vị trí của dao so với đồ định vị (quyết định kích
thước gia công) đã được điều chỉnh sẵn.
Mở rộng khả năng công nghệ của thiết bị: nhờ đồ gá mà một số
máy có thể đảm nhận công việc của máy khác chủng loại, ví dụ: có thể
mài trên máy tiện, có thể tiện trên máy phay hoặc phay trên máy tiện...
Đồ gá giúp cho việc gia công nguyên công khó mà nếu không có
đồ gá thì không thể gia công được, ví dụ: khoan lỗ nghiêng trên mặt trụ.
Đồ gá phân độ để phay bánh răng, gia công chép hình...
Giảm nhẹ sự căng thẳng và cải thiện điều kiện làm việc của công
nhân, không cần sử dụng thợ bậc cao.
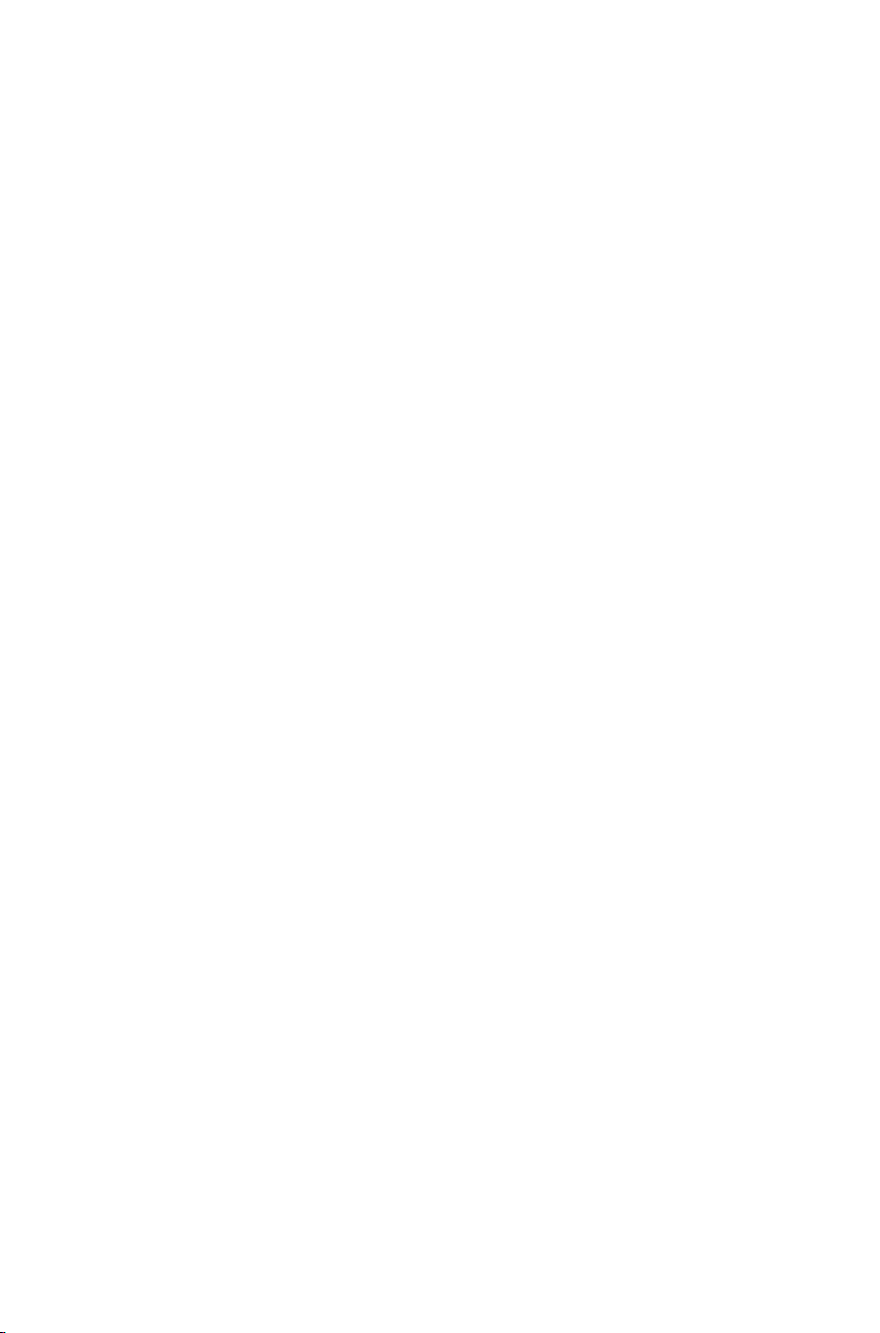
169
Nhờ những tác dụng trên mà việc sử dụng đồ gá đúng loại, đúng
lúc sẽ mang lại hiệu quả kinh tế cao.
3.1.5. Yêu cầu đối với đồ gá
Đồ gá trên máy cắt kim loại phải có những yêu cầu sau:
Kết cấu phải phù hợp với dạng sản xuất, ví dụ trong sản xuất lớn
nên dùng đồ gá chuyên dùng có kết cấu đơn giản, trong sản xuất nhỏ nên
dùng đồ gá vạn năng nhưng có thể điều chỉnh được... Tuy nhiên trong
mọi trường hợp, hiệu quả kinh tế vẫn là chỉ tiêu để lựa chọn phương án
kết cấu cho đồ gá.
Đảm bảo được độ chính xác gia công đã cho. Sai số khi gia công
chi tiết trên đồ gá phụ thuộc vào nhiều yếu tố trong đó có đồ gá. Người
thiết kế đồ gá phải hiểu được sai số nào của đồ gá sẽ ảnh hưởng đến sai
số gia công chi tiết. Cần khống chế các sai số của đồ gá và các sai số có
liên quan ở một mức nào đó để đảm bảo sai số cho phép của chi tiết gia
công.
Nếu đồ gá quay khi gia công cần cân bằng đồ gá để tránh rung
động ảnh hưởng đến chất lượng gia công.
Sử dụng thuận tiện và an toàn khi làm việc. Để sử dụng thuận
tiện, đồ gá phải đảm bảo việc gá đặt và tháo chi tiết gia công nhanh, dễ
dàng, tay gạt kẹp chặt dễ thao tác, dễ dàng làm sạch phoi trên đồ gá và gá
đặt đồ gá trên máy phải đơn giản.
An toàn lao động là một chỉ tiêu quan trọng đối với đồ gá đặc
biệt là đồ gá quay cùng với trục chính máy trong quá trình làm việc như
trên máy tiện, máy mài tròn... các đồ gá này không nên có phần lồi nhô ra
lớn và khi làm việc cần có bộ phận che chắn bảo vệ.
3.1.6. Phân loại đồ gá
3.1.6.1. Phân loại theo nhóm máy
- Đồ gá trên máy tiện, máy tiện rơvonve.
- Đồ gá trên máy phay.
- Đồ gá trên máy bào.
- Đồ gá trên máy mài.
- Đồ gá trên máy khoan.
- Đồ gá trên máy doa.
- Đồ gá trên máy chuốt.
- Đồ gá trên máy gia công bánh răng.
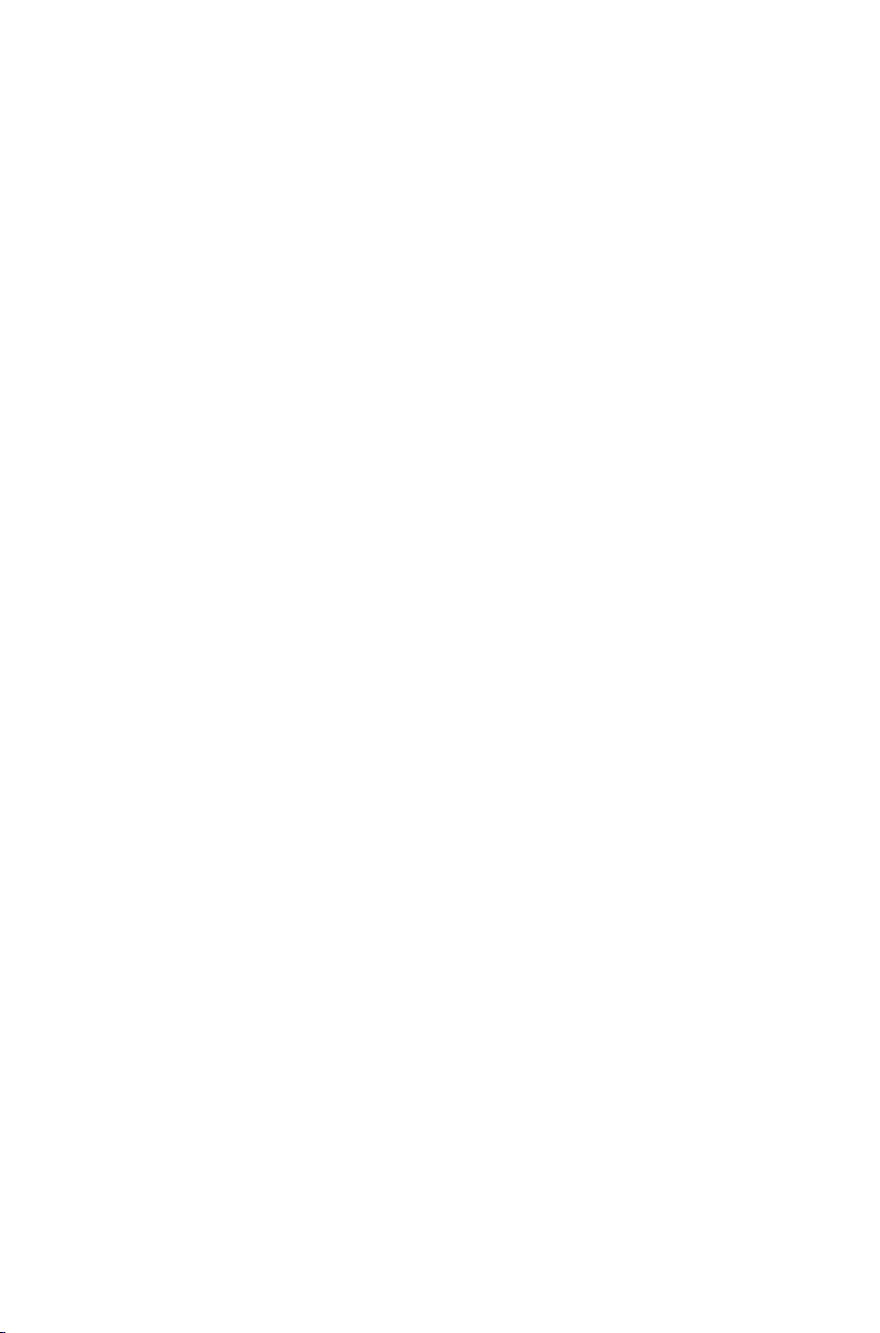
170
3.1.6.2. Phân loại theo mức độ chuyên môn hóa
Đồ gá vạn năng thông dụng
Đồ gá vạn năng thông dụng còn có thể gọi là đồ gá vạn năng không
điều chỉnh. Khi sử dụng đồ gá vạn năng thông dụng không cần phải lắp
bổ sung thêm các chi tiết và bộ phận khác vào đồ gá. Loại đồ gá này
được dùng để định vị và kẹp chặt các chi tiết có kích thước và hình dáng
khác nhau trong sản xuất đơn chiếc và hàng loạt nhỏ. Các đồ gá vạn năng
thông dụng thường được chế tạo như loại thiết bị phụ kèm theo máy của
các nhà máy chế tạo máy công cụ. Ví dụ như: mâm cặp vạn năng, êtô vạn
năng, đầu phân độ vạn năng
Đồ gá vạn năng điều chỉnh
Đồ gá này gồm có bộ phận cố định và bộ phận thay đổi. Bộ phận
cố định là phần cơ sở dùng cho mọi chi tiết gia công khác nhau. Bộ phận
thay đổi là những chi tiết của đồ gá được sử dụng tùy theo hình dạng và
kích thước của chi tiết gia công. Ví dụ như các loại êtô khí nén dùng để
phay, có má êtô thay đổi còn đế êtô là phần cố định.
Đồ gá chuyên môn hóa điều chỉnh
Đồ gá này dùng để định vị và kẹp chặt một nhóm các chi tiết có
kích thước, có kết cấu công nghệ gần như nhau, phương pháp gia công và
đặc tính của các bề mặt định vị tương tự nhau.
Đồ gá chuyên môn hóa điều chỉnh gồm hai bộ phận: bộ phận vạn
năng và bộ phận thay thế. Bộ phận vạn năng thường không đổi và bao
gồm: thân đồ gá, truyền dẫn..., bộ phận thay thế gồm các chi tiết thay thế
được chế tạo thích hợp với hình dáng và kích thước của nhóm chi tiết gia
công trên đồ gá.
Trên đồ gá chuyên môn hóa, điều chỉnh có thể điều chỉnh các chi
tiết định vị để gá đặt các chi tiết cùng kiểu nhưng có kích thước khác
nhau. Việc sử dụng các chi tiết thay thế sẽ mở rộng khả năng công nghệ
của đồ gá, giảm được số lượng các đồ gá chuyên dùng, do đó rút ngắn
được thời gian chuẩn bị sản xuất khi chuyển sang sản xuất loại sản phẩm
mới. Đồ gá chuyên môn hóa điều chỉnh được dùng phổ biến trong sản
xuất hàng loạt và hàng loạt lớn.
Đồ gá chuyên dùng
Loại đồ gá này chỉ thực hiện được một nguyên công của một chi tiết
cụ thể nào đó. Khi thay đổi đối tượng sản xuất, loại này không dùng được.
Đồ gá chuyên dùng có ưu điểm là với một lần điều chỉnh máy có
thể gia công tất cả các chi tiết trong lô sản phẩm đạt độ chính xác đã cho.
Do đó có thể nâng cao năng suất lao động, giảm thời gian phụ và sức lao
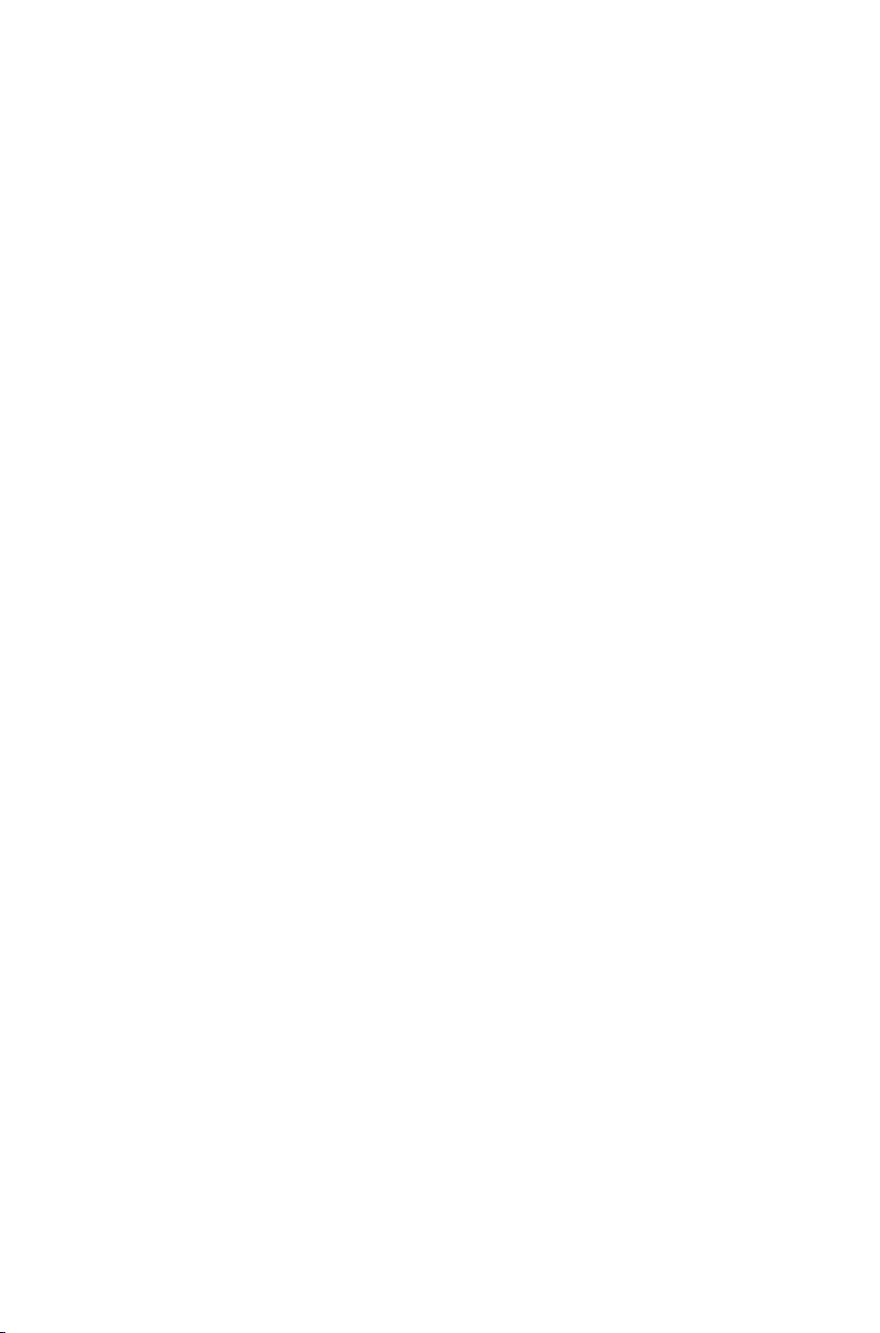
171
động của công nhân. Ưu điểm này càng thể hiện rõ trong sản xuất hàng
loạt lớn và hàng khối.
Tuy nhiên trong sản xuất đơn chiếc và hàng loạt nhỏ, sử dụng đồ gá
chuyên dùng sẽ không kinh tế vì chi phí cho thiết kế chế tạo đồ gá làm cho
giá thành sản phẩm cao, không rút ngắn được thời gian chuẩn bị sản xuất.
Đồ gá tổ hợp
Đồ gá tổ hợp là đồ gá được tổ hợp lại từ những chi tiết và bộ phận
tiêu chuẩn hóa đã được chế tạo sẵn và được dùng lại nhiều lần để gá đặt
được nhiều loại chi tiết khác nhau. Đồ gá này được dùng trong tất cả các
dạng sản xuất. So với các đồ gá vạn năng và đồ gá chuyên dùng, sử dụng
đồ gá tổ hợp có hiệu quả kinh tế rất cao bởi vì chi phí về thiết kế và chế
tạo đồ gá loại này cho một sản phẩm cụ thể nào đó thấp, rút ngắn được
thời gian chuẩn bị sản xuất khi chuyển sang sản xuất loạt sản phẩm mới.
3.2. PHƢƠNG PHÁP THIẾT KẾ ĐỒ GÁ
3.2.1. Phƣơng hƣớng chung
Ngày nay, sản phẩm cơ khí rất đa dạng và thay đổi mẫu mã liên
tục. Trong sản xuất tồn tại nhiều loại hình khác nhau như: sản xuất hàng
loạt lớn, loạt vừa, loạt nhỏ và đơn chiếc, trong đó sản xuất loạt nhỏ chiếm
tỷ lệ khá lớn. Hơn nữa máy CNC giúp thực hiện các chức năng phân độ,
tạo hình phức tạp…nên đồ gá trên các máy này thường đơn giản hơn đồ
gá trên các máy điều khiển cơ. Để đáp ứng với mọi loại hình sản xuất, đồ
gá cần định hướng phát triển như sau:
Tiêu chuẩn hóa kết cấu của từng chi tiết, từng cụm chi tiết để có
thể dễ dàng lắp thành đồ gá.
Dùng các phương tiện tác dụng nhanh như: dầu ép, khí nén, điện
từ, điện cơ, chân không...
Tự động hóa khâu gá đặt để nâng cao năng suất và phù hợp với
các thiết bị tự động
Có thể sử dụng đồ gá điều chỉnh để gia công nhóm nhằm nâng
cao tính hàng loạt trong sản xuất.
Sản xuất hàng loạt lớn thì yêu cầu chính là năng suất vì vậy cần
cơ khí hóa và tự động hóa đồ gá nhằm nâng cao năng suất đồng thời nâng
cao độ chính xác gia công. Ở đây sử dụng rộng rãi các phương tiện tác
dụng nhanh: đồ gá nhiều vị trí, phân độ và kẹp chặt tự động...
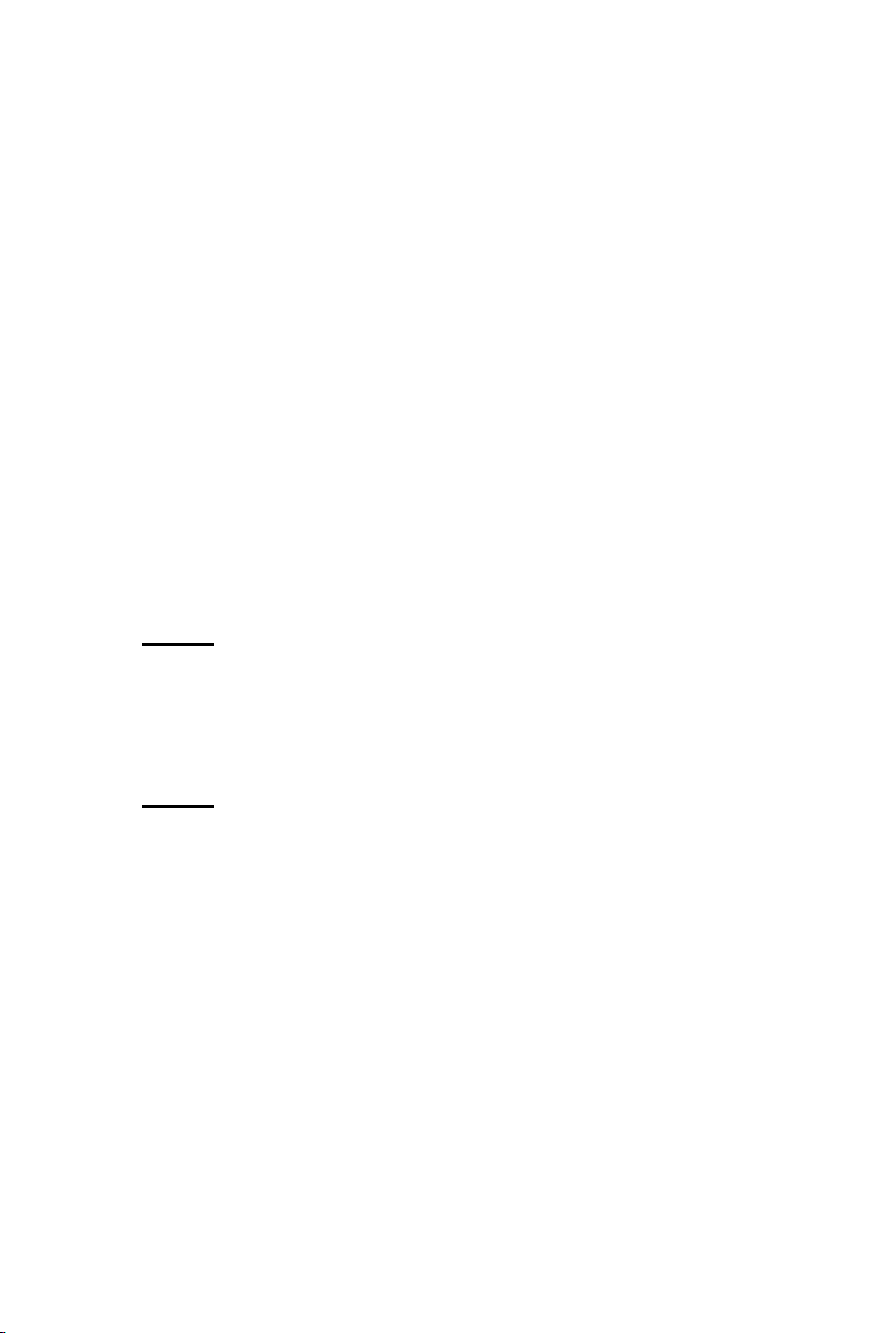
172
Sản xuất loạt vừa cũng cần cơ khí hóa và bán tự động đồ gá, sử
dụng cơ cấu tác động nhanh.
Sản xuất nhỏ cần sử dụng loại đồ gá tháo lắp nhanh trên cơ sở
các chi tiết và bộ phận tiêu chuẩn hóa. Đồng thời cơ khí hóa việc kẹp
chặt để giảm nhẹ sức lao động của công nhân.
3.2.2. Tài liệu ban đầu để thiết kế đồ gá
Bản vẽ chi tiết gia công với đầy đủ kích thước, và các điều kiện
kỹ thuật.
Sơ đồ nguyên công đang thiết kế đồ gá với kích thước, dung sai,
độ bóng và phương án định vị, kẹp chặt.
Bảng thiết bị, các bước gia công, chế độ cắt s,v,t...
Sản lượng hàng năm ( chiếc/năm)
Các sổ tay công nghệ, sổ tay tiêu chuẩn đồ gá.
3.2.3. Phƣơng pháp và trình tự thiết kế đồ gá
Khi thiết kế đồ gá phải trải qua bốn bước cơ bản sau:
Bước 1: Thiết kế nguyên lý
Dựa trên phương án định vị và kẹp chặt đã có ở sơ đồ công nghệ.
Người thiết kế vẽ phác sơ đồ nguyên lý của đồ gá như: đồ định vị, đồ kẹp
chặt, cơ cấu dẫn hướng, sơ bộ về thân đồ gá, bộ phận định vị đồ gá vào
máy... thể hiện ở một vài hình chiếu.
Bước 2: Thiết kế kết cấu cụ thể ( bản vẽ lắp )
Sau khi tham khảo các chi tiết tiêu chuẩn, bộ phận tiêu chuẩn,
người thiết kế tiến hành vẽ bản vẽ lắp. Các chi tiết trong đồ gá hầu hết là
chọn, riêng cơ cấu kẹp chặt phải tính toán sức bền.
Bản vẽ này thường theo tỷ lệ 1/2, 1/1 hoặc 2/1. Trên bản vẽ ghi đầy
đủ chế độ lắp ghép cho các mối lắp quan trọng. Đánh số thứ tự, đặt tên và
chọn vật liệu cho từng chi tiết, ghi những yêu cầu kỹ thuật quan trọng
như: độ vuông góc, độ song song, độ đồng tâm.
Số hình chiếu của bản vẽ có thể là một, hai, hay ba sao cho thể hiện
hết các chi tiết của đồ gá, thường vẽ hình chiếu ở vị trí gia công trước
tiên, rồi vẽ tiếp các hình chiếu khác.
Một số kích thước cần ghi cụ thể là:
- Kích thước Cao x Dài x Rộng nhất của đồ gá.
- Khoảng cách giữa đồ định vị và đồ dẫn hướng.
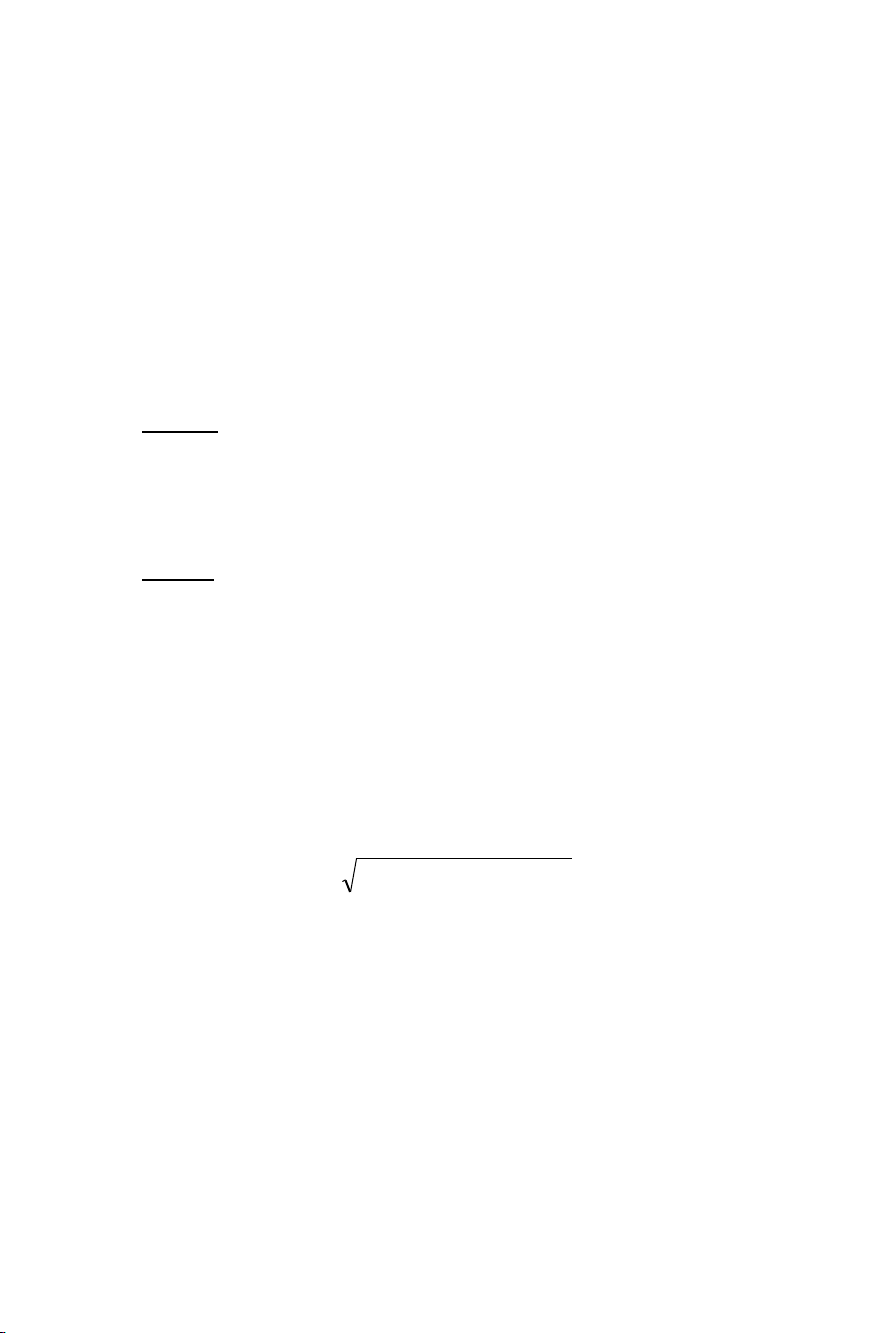
173
- Bề dày miếng căn.
Những kích thước thẳng không có dung sai của vật gia công thì
kích thước tương ứng của đồ gá có dung sai là 0,1 mm, còn kích thước
góc tương ứng lấy dung sai là 10
0
.
Những kích thước của chi tiết gia công có dung sai thì kích thước
tương ứng của đồ gá có dung sai bằng
1
/
2
1
/
3
dung sai của kích thước chi
tiết gia công (hoặc phải tính sai số chuẩn, sẽ trình bày ở chương này).
Khi thực hiện bản vẽ này cần theo nguyên tắc từ trong ra ngoài,
nghĩa là vẽ chi tiết trước, rồi đến cơ cấu định vị, đến cơ cấu kẹp, đến thân
đồ gá, rồi cơ cấu dẫn hướng...
Bước 3: Vẽ tách chi tiết, từ bản vẽ lắp ta vẽ tách chi tiết thành
những bản vẽ riêng, mỗi chi tiết thường thể hiện trên một khổ A4, những
chi tiết tiêu chuẩn thì có thể không cần vẽ. Những chi tiết không tiêu
chuẩn phải vẽ đầy đủ các hình chiếu, ghi đầy đủ kích thước, nếu chi tiết
nào không vẽ tách được, chứng tỏ bản vẽ lắp còn thiếu.
Bước 4: Hiệu chỉnh bản vẽ lắp
Trên cơ sở các bản vẽ chi tiết, hiệu chỉnh lại bản vẽ lắp cho chính
xác, cả về kích thước lẫn vị trí tương quan.
Khi đem cho phân xưởng chế tạo, cần đem các bản vẽ chi tiết kèm
theo bản vẽ lắp để người công nghệ tham khảo khi gia công và dùng khi
lắp ráp đồ gá.
3.2.4. Những tính toán cần thiết khi thiết kế đồ gá
3.2.4.1. Tính sai số chế tạo đồ gá
Xuất phát từ công thức:
Trong đó:
c –
sai số do chọn chuẩn
k
- sai số do kẹp chặt
ct
– sai số chế tạo đồ gá
m
– sai số do mòn đồ gá
đc
- sai số điều chỉnh đồ gá
Theo thống kê kinh nghiệm nên chọn sai số gá đặt [
gđ
] =
1
/
3
dung
sai kích thước cần gia công. Từ đó ta có công thức tính sai số chế tạo cho
phép của đồ gá:
22222
đcmctkcgđ
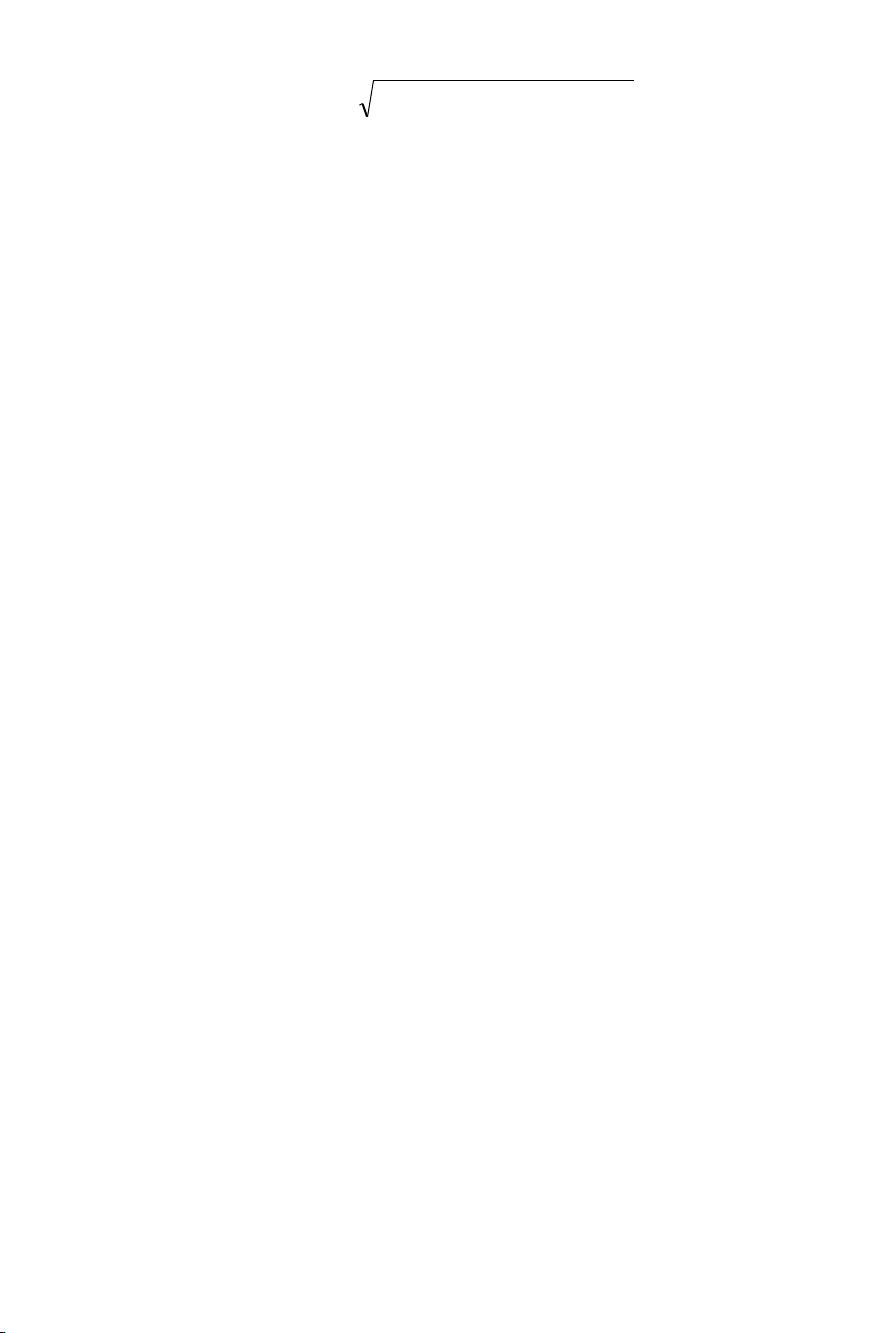
174
Sai số chế tạo cho phép dùng để ghi dung sai cho các kích thước
của đồ gá ảnh hưởng đến trực tiếp đến kích thước gia công.
3.2.4.2. Tính toán lực kẹp cần thiết
Để chọn cơ cấu kẹp có khả năng chống lại lực cắt và các ngoại lực
khác làm thay đổi vị trí chi tiết đã định vị cần phải tính W
ct
dựa trên sơ
đồ gá đặt.
3.2.4.3. Tính lực kẹp do cơ cấu kẹp tạo ra
Cơ cấu kẹp phải tạo ra được
=
ct
.Trong các công thức tính lực
kẹp do cơ cấu kẹp tạo ra, ta thay
=
ct
từ đó rút ra các thông số cần thiết
của cơ cấu kẹp.
3.2.4.4. Chọn và tính toán sức bền của các cơ cấu chịu lực
Các cơ cấu này thường là đòn kẹp, bulông, cần píttông …
3.3. CHUẨN VÀ SAI SỐ CHUẨN
3.3.1. Chuẩn
3.3.1.1. Định nghĩa
Chuẩn là tập hợp các điểm, đường hoặc bề mặt mà người ta căn cứ
vào đó để xác định vị trí các điểm, đường hoặc bề mặt khác của bản thân
chi tiết đó hoặc của các chi tiết khác trong quá trình thiết kế, gia công,
đo lường, lắp ráp …
3.3.1.2. Phân loại chuẩn
Thường phân chia chuẩn thành hai loại: chuẩn thiết kế và chuẩn
công nghệ.
a. Chuẩn thiết kế
Chuẩn thiết kế là chuẩn dùng trong quá trình thiết kế nghĩa là tập
hợp những bề mặt, đường, điểm mà người ta căn cứ vào đó để xác định
vị trí của các bề mặt, đường, điểm của bản thân chi tiết đó hoặc của
những chi tiết khác trong quá trình thiết kế.
Chuẩn thiết kế có thể là chuẩn thực hoặc chuẩn ảo.
b. Chuẩn công nghệ
Người ta chia chuẩn công nghệ làm bốn loại:
- Chuẩn định vị (chuẩn gia công ).
)(][][
22222
đcmkcgđct
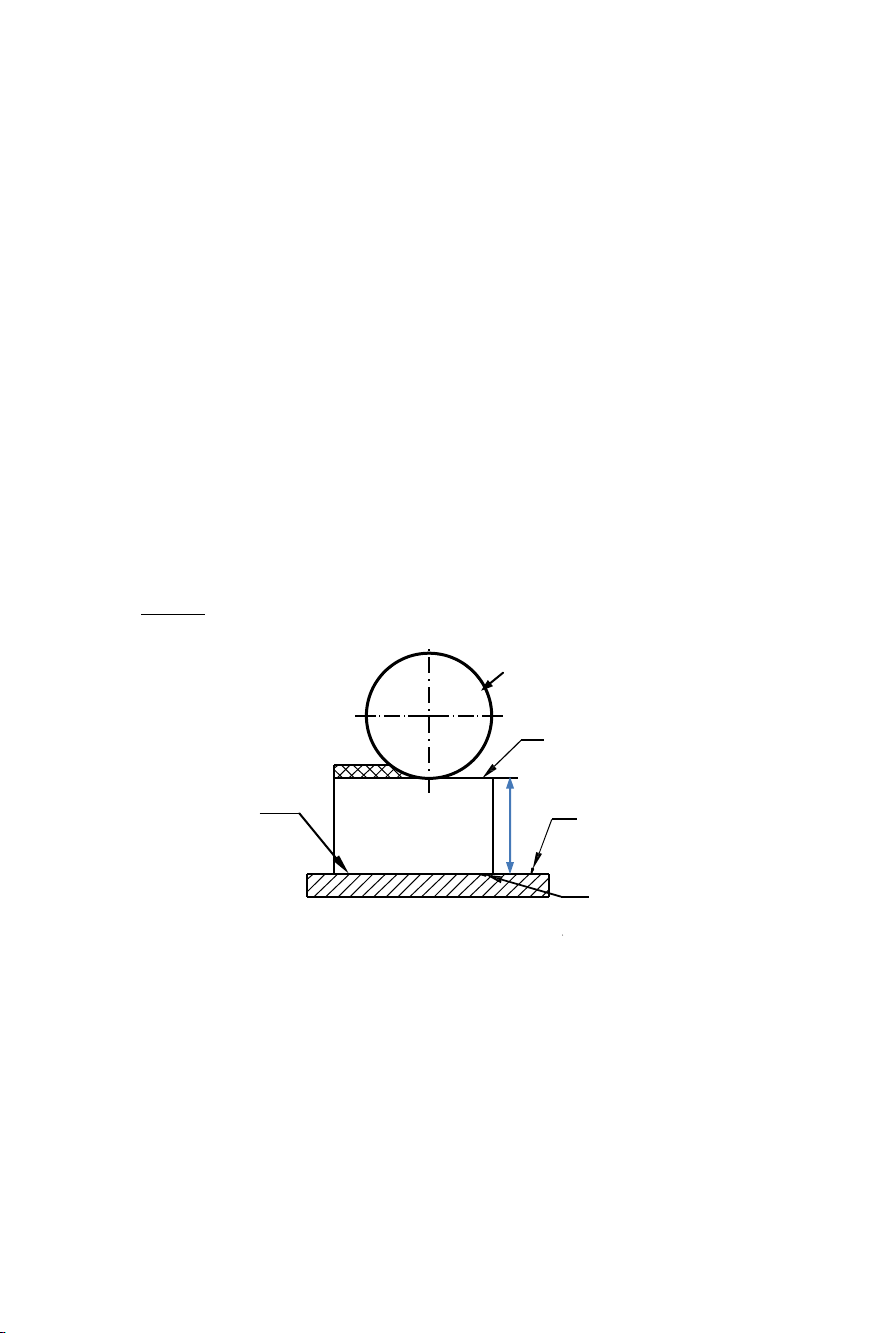
175
- Chuẩn đo lường (có thể trùng gốc kích thước công nghệ).
- Chuẩn điều chỉnh.
- Chuẩn lắp ráp.
Chuẩn định vị
Chuẩn định vị là tập hợp những điểm, đường hoặc bề mặt có thực
trên chi tiết gia công dùng để xác định vị trí chi tiết khi gia công, đôi lúc
có thể dùng điểm hay đường đại diện.
Chuẩn đo lường
Chuẩn đo lường là bề mặt có thực trên chi tiết hoặc một phần của
bề mặt đó mà ta lấy làm gốc để đo vị trí của bề mặt gia công.
Chuẩn điều chỉnh
Chuẩn điều chỉnh là bề mặt có thực trên đồ gá hay máy dùng để điều
chỉnh dụng cụ cắt (xác định vị trí của dụng cụ cắt so với chuẩn định vị ).
Một số ví dụ phân biệt các loại chuẩn
Ví dụ 1:
Trong ví dụ 1, ta nhận thấy: chuẩn định vị, gốc kích thước và
chuẩn điều chỉnh trùng nhau, mặc dù chúng có thể nằm trên chi tiết
hay trên đồ gá.
Dụng cụ cắt
H
Mặt gia công
Chuẩn điều chỉnh
( trên đồ gá )
Chuẩn định vị (trên
chi tiết)
Gốc kích thước
(trên chi tiết)
Hình 3.1: Sơ đồ phay mặt phẳng
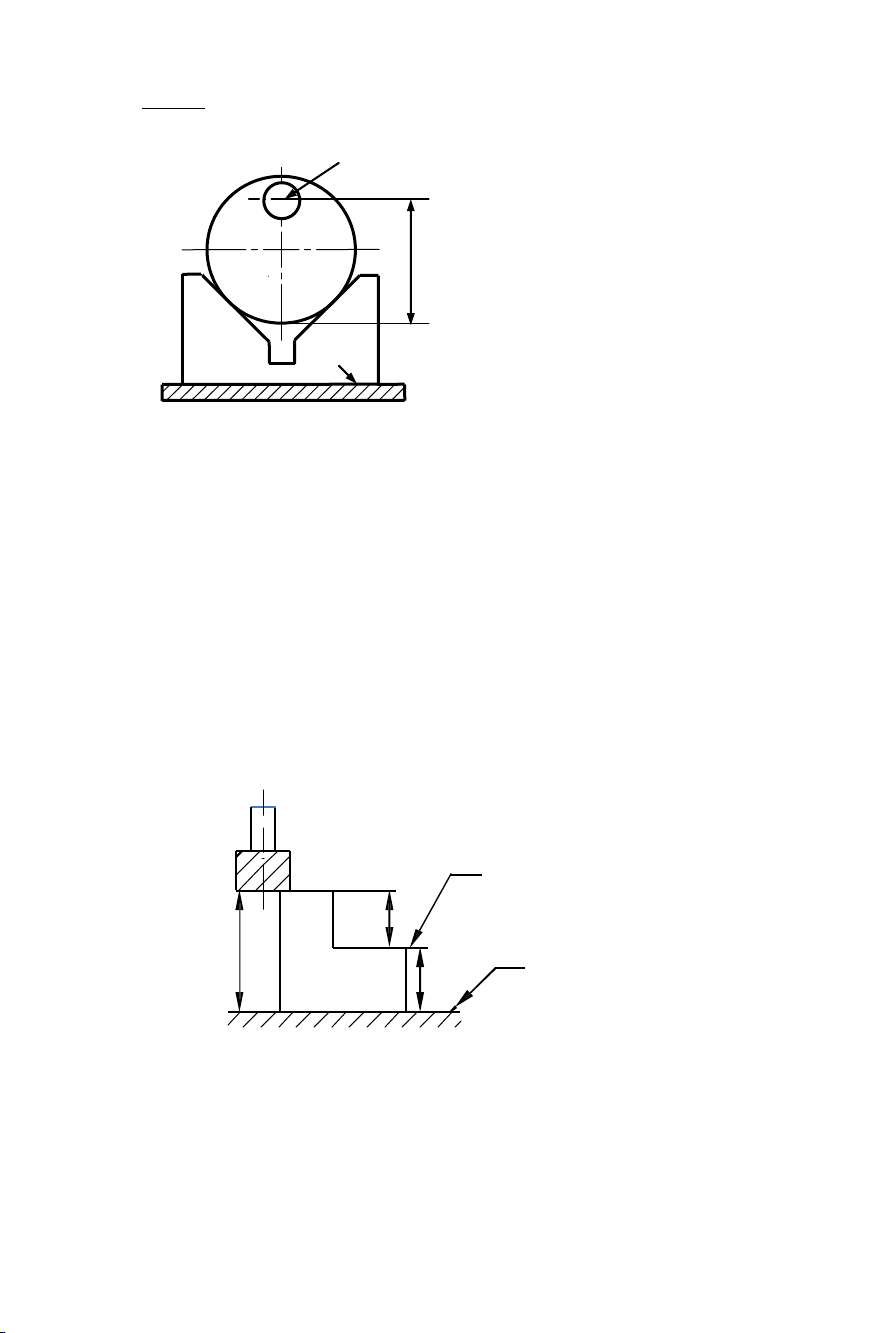
176
Ví dụ 2:
Trong ví dụ 2, chuẩn định vị, chuẩn điều chỉnh và gốc kích thước
đều nằm ở các vị trí khác nhau trong hệ thống gá đặt.
Việc phân biệt các loại chuẩn nhằm tạo điều kiện cho việc xác định
sai số chọn chuẩn chính xác hơn.
3.3.2. Sai số chuẩn
3.3.2.1. Khái niệm
Sai số chuẩn là lượng biến động lớn nhất của gốc kích thước chiếu
lên phương kích thước cần thực hiện. Sai số này phát sinh khi chuẩn định
vị không trùng gốc kích thước. Ký hiệu: ε
c
Ví dụ:
H – kích thước điều chỉnh, cố định cho cả loạt chi tiết.
h
1
– có dung sai h
1
, là kích thước hình thành ở bước công nghệ trước.
h
2
– kích thước cần đạt khi gia công.
Hình 3.2: Chi tiết gá trên khối V
A- Mặt
gia công
B- Gốc kích thước
C- Chuẩn điều chỉnh
K, K
’
- Chuẩn định vị
K
K
’
B
A
C
H
Chuẩn định vị
chuẩn điều chỉnh
(C) Gốc kích thước
H
h
1
h1
h
2
Hình 3.3: Định vị trên mặt phẳng
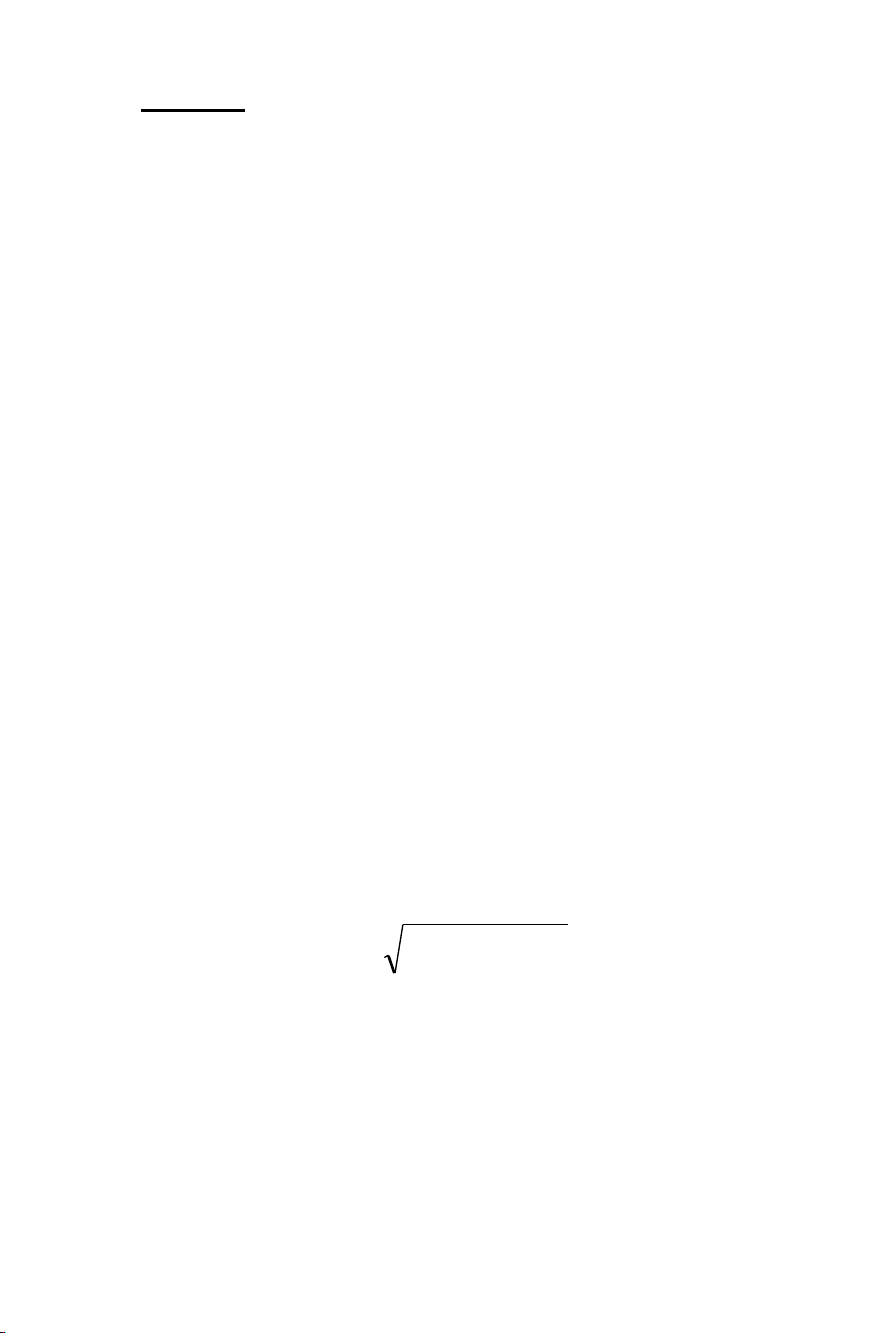
177
Nhận xét: kích thước h
2
phụ thuộc vào vị trí của bề mặt C (gốc
kích thước), mà vị trí của bề mặt C biến động một khoảng h
1
(tính cho
cả loạt chi tiết gia công).
Do đó: ε
c
(h
2
) = h
1
3.3.2.2. Mục đích tính sai số chuẩn
Kích thước hình thành khi gia công là quan trọng nhất. Sai số của
kích thước này là tổng hợp của một loạt sai số.
hdgđnmđcđh
L )(
Trong đó:
ΔL – sai số của kích thước cần thực hiện.
Δ
đh
- sai số do biến dạng đàn hồi.
Δ
đc
- sai số do điều chỉnh máy
Δ
m
- sai số do mòn dụng cụ cắt.
Δ
n
- sai số do biến dạng nhiệt của hệ thống công nghệ.
gđ
– sai số gá đặt.
Δ
hd
- sai số hình học của máy – dao – gá do chế tạo.
Hệ thống công nghệ phải đảm bảo:
ΔL < L (L: dung sai kích thước cần đạt )
Trong các sai số tạo nên ΔL, có sai số có thể điều chỉnh để khử
được, có sai số do ngẫu nhiên người công nghệ khó có thể khắc phục
được. Đối với loại sai số gá đặt (ε
gđ
) người ta cũng liệt kê vào dạng sai số
ngẫu nhiên, trị số của nó bằng:
222
đgkcgđ
Trong đó: ε
c
- sai số chuẩn
k
- sai số kẹp chặt
đg
- sai số đồ gá
Khi thiết kế đồ gá, người ta quan tâm đến các loại sai số này. Kinh
nghiệm cho thấy rằng, nếu:
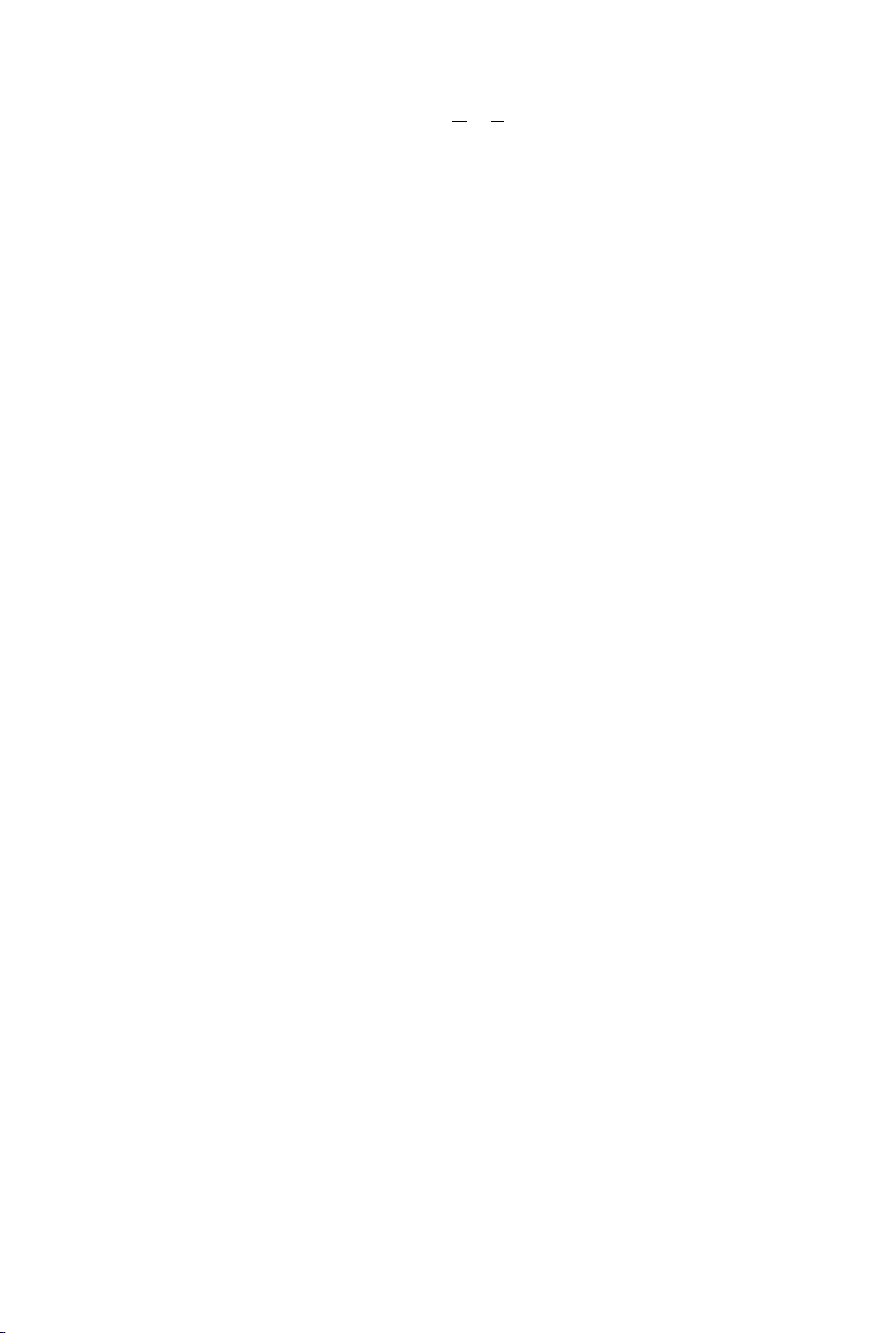
178
L
cc
3
1
2
1
thì kích thước hình thành khi gia công sẽ nằm trong phạm vi dung sai,
nghĩa là ΔL < L.
Người công nghệ khi thiết kế quy trình công nghệ phải chọn chuẩn
định vị và các phương án định vị, tính toán sai số chuẩn. Nếu thỏa điều
kiện trên thì việc chọn chuẩn đạt yêu cầu, còn nếu không thỏa thì người
công nghệ phải chọn lại chuẩn cho thỏa điều kiện trên.
Có hai phương pháp tính sai số chuẩn: tính trực tiếp và lập chuỗi
kích thước công nghệ.
3.3.2.3. Tính sai số chuẩn bằng chuỗi kích thước công nghệ
Chuỗi kích thước công nghệ gồm bốn khâu cơ bản:
Khâu 1: từ dụng cụ cắt đến chuẩn điều chỉnh (kích thước điều
chỉnh): a
Khâu 2: từ chuẩn điều chỉnh đến chuẩn định vị: x
1
.
Khâu 3: từ chuẩn định vị đến gốc kích thước: x
2
.
Khâu 4: từ gốc kích thước đến bề mặt dao (mặt gia công): L
Do sự dao động của khâu 2 (x
1
) và khâu 3 (x
2
) mà gây ra sai số chuẩn
Tức là: ε
c
(L) = Δx
1
+ Δx
2
Nếu số khâu biến động càng nhiều thì sai số chuẩn càng lớn.
Trình tự để tính sai số chuẩn cho kích thước gia công như sau:
- Vẽ sơ đồ gá đặt khi gia công.
- Xác định rõ chuẩn định vị, chuẩn điều chỉnh, gốc kích thước.
- Vẽ chuỗi kích thước công nghệ trên sơ đồ gá đặt, kích thước trong
chuỗi này có gốc và có hướng.
- Viết biểu thức quan hệ giữa các thành phần trong chuỗi kích
thước công nghệ.
- Tìm các lượng biến động của khâu x
1
và khâu x
2
.
- Sai số chuẩn của kích thước gia công chính là tổng của các lượng
biến động Δx
1
và Δx
2
.
Khi làm bài tập tính sai số chuẩn nên đọc lại chương “Chuẩn”
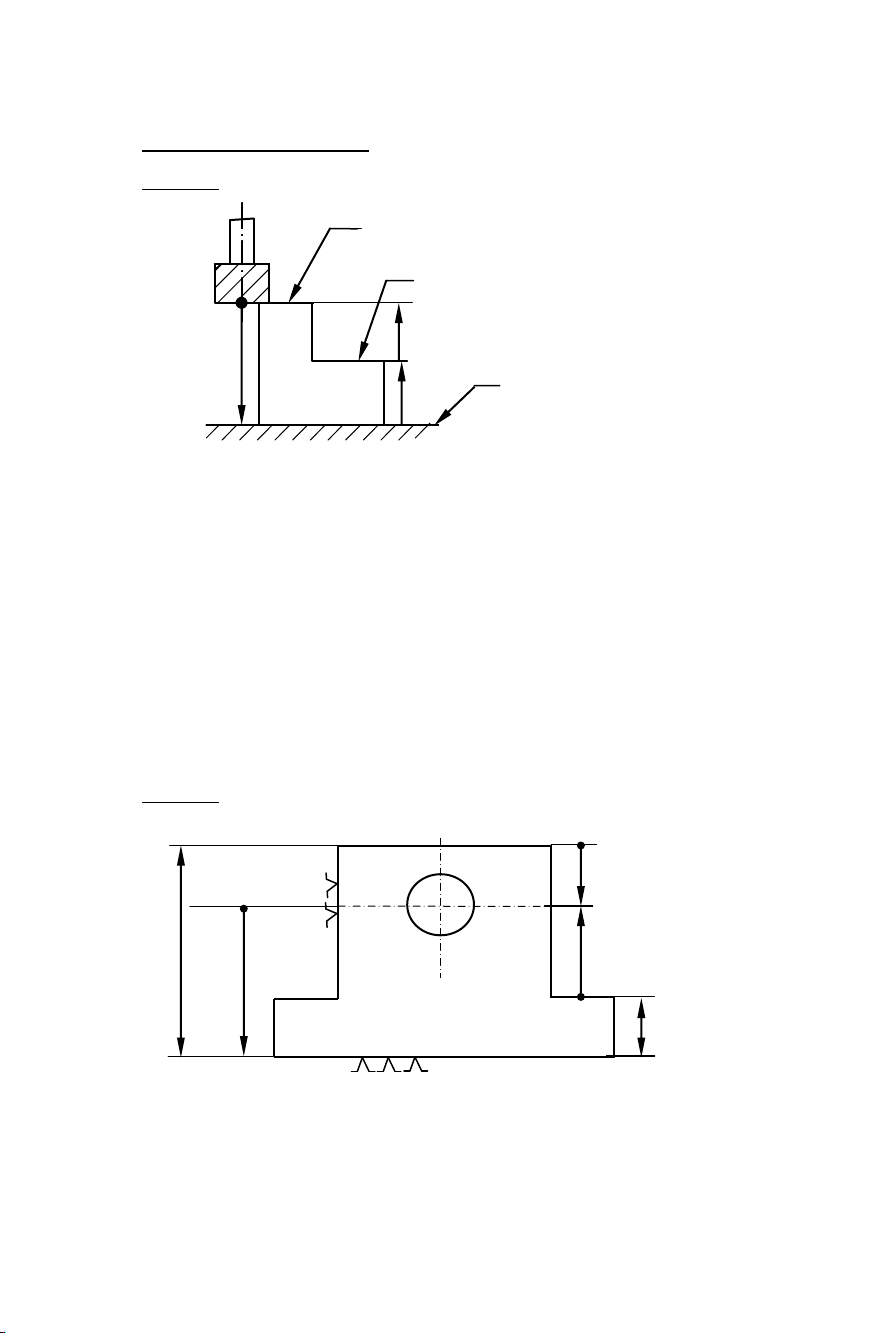
179
3.3.3. Các ví dụ về tính sai số chuẩn
Định vị vào mặt phẳng
Ví dụ 1:
Hình 3.4 là sơ đồ định vị để gia công chi tiết có chuẩn định vị trùng
với chuẩn điều chỉnh. Ta cần tính sai số chuẩn cho kích thước: h
Đối với kích thước h: gốc kích thước không trùng với chuẩn định
vị và chuẩn điều chỉnh.
Vì vậy ta có chuỗi kích thước công nghệ trong trường hợp này như sau:
a – x
2
– h = 0
h = a – x
2
Do đó:
c
(h)= x
2
Ví dụ 2:
Hình 3.5 là sơ đồ định vị để gia công lỗ, chuẩn định vị trùng với
chuẩn điều chỉnh. Ta cần tính sai số chuẩn cho kích thước: h
1
và h
2
Đối với kích thước h
1
: gốc kích thước không trùng với chuẩn định vị.
Mặt gia công
Gốc kích thước
Chuẩn định vị chuẩn
điều chỉnh
C
a
h
X
2
Hình 3.4: Định vị vào mặt phẳng
X
2
Hình 3.5 Định vị trên mặt phẳng
a
h
δh
h
1
h
2
H
δH
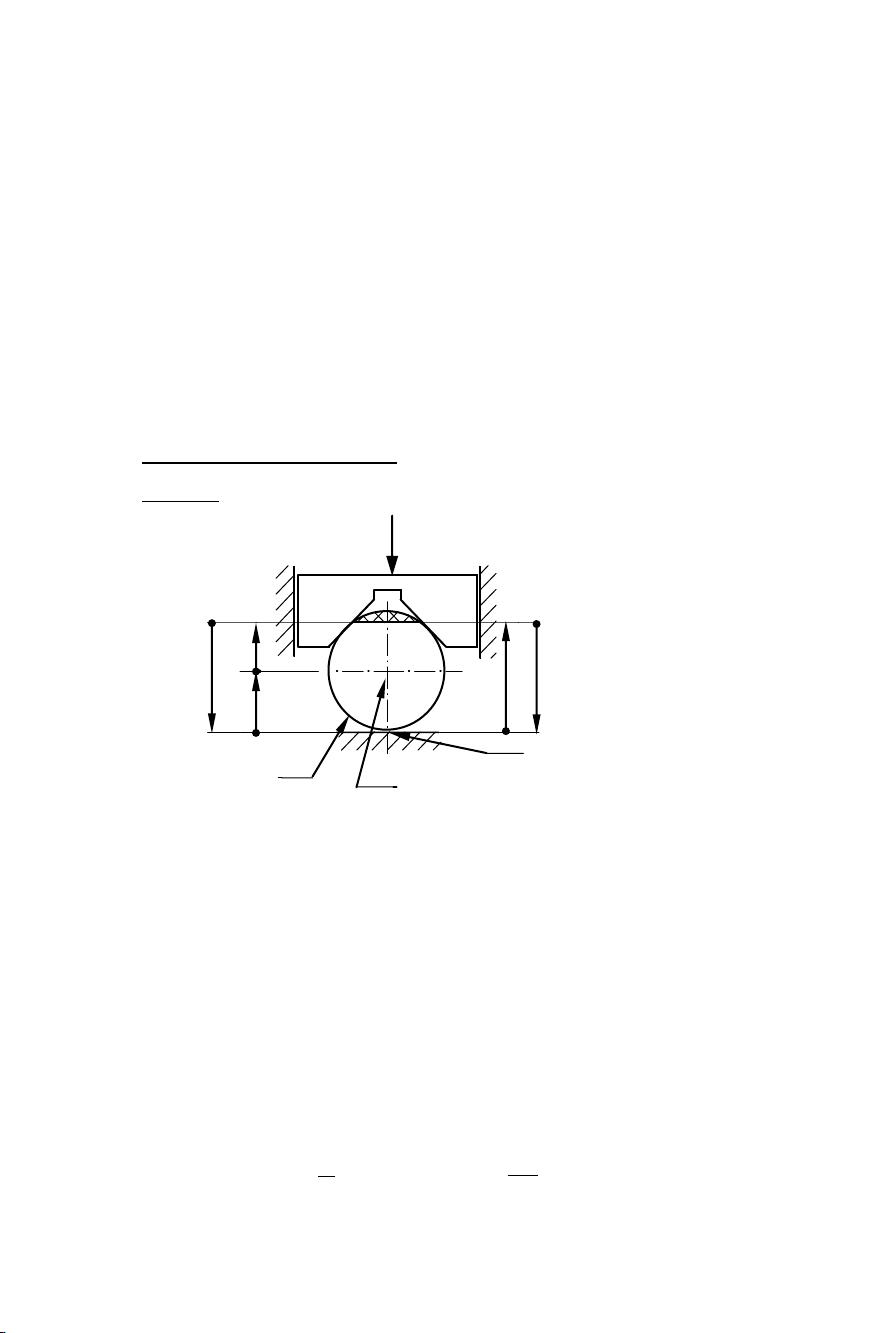
180
Vì vậy ta có chuỗi kích thước công nghệ trong trường hợp này như sau:
a – H + h
1
= 0
h
1
= H - a
Do đó:
c
(h
1
) = H
Đối với kích thước h
2
: gốc kích thước không trùng với chuẩn định
vị. Vì vậy ta có chuỗi kích thước công nghệ trong trường hợp này như sau:
a – h – h
2
= 0
h
2
= a - h
Do đó:
c
(h
2
) = h
Định vị vào mặt trụ ngoài
Ví dụ 3:
Hình 3.6 là sơ đồ định vị mặt trụ trên mặt phẳng, chuẩn định vị trùng
với chuẩn điều chỉnh. Ta cần tính sai số chuẩn cho các kích thước: H, h.
Đối với kích thước H: gốc kích thước trùng với chuẩn định vị. Do
đó:
c
(H) = 0
Đối với kích thước h: kích thước này có gốc nằm ở tâm chi tiết nên
không trùng với chuẩn định vị. Vì vậy ta có chuỗi kích thước công nghệ
trong trường hợp này như sau:
a – x
2
– h = 0
h = a – x
2
= a –
D
2
; do đó:
c
(h) =
2
D
a
h
x
2
H
a (x
1
x
2
)
W
0
Gốc kích thước h
D
D
Hình 3.6: Định vị V và mặt phẳng
Gốc kích thước H
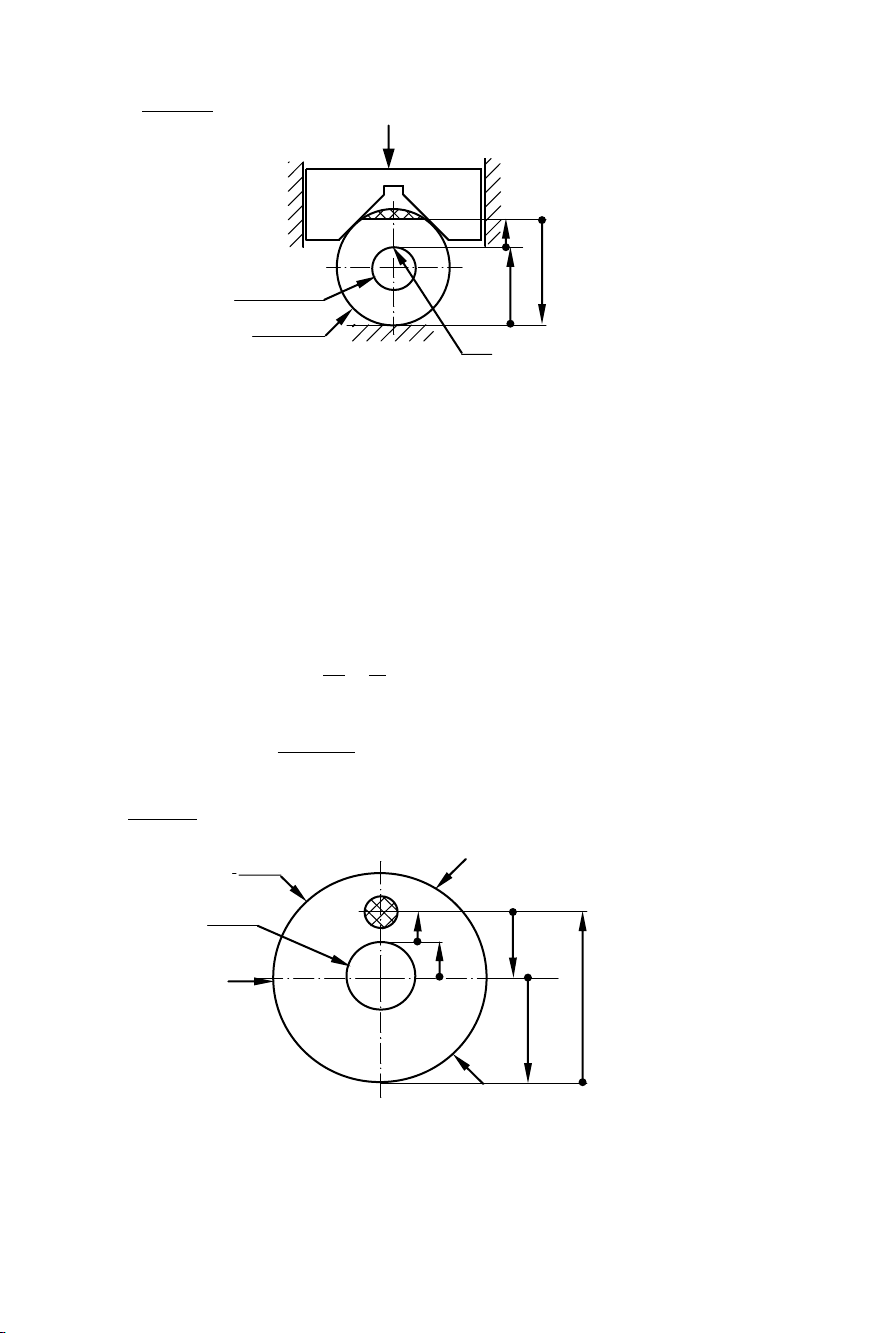
181
Ví dụ 4:
Hình 3.7 là sơ đồ định vị để gia công mặt phẳng trên chi tiết trụ có
lỗ. Tính sai số chuẩn cho kích thước h.
Ta nhận thấy chuẩn điều chỉnh và chuẩn định vị trùng nhau còn gốc
kích thước trong trường hợp này nằm ở đường sinh cao nhất của lỗ. Vì
vậy ta có chuỗi kích thước công nghệ như sau:
a – x
1
– h = 0
h = a – x = a –
22
dD
± e
Vậy:
c
(h) =
2
dD
+ 2e ( e – độ lệch tâm lỗ và trụ ngoài)
Ví dụ 5
Hình 3.8 là sơ đồ định vị chi tiết gia công trên cơ cấu tự định tâm
(mâm cặp ba chấu). Đặc điểm của cơ cấu này là chuẩn định vị tuy là mặt
trụ ngoài nhưng đại diện của nó lại là tâm O, vì vậy chuẩn định vị trùng
D
D
y
2
d
d
a
x
2
H
h
Hình 3.8: Định vị trụ trên mâm ba chấu tự định tâm
0
W
W
W
Gốc kích thước
h
x
1
a
Lỗ d
d
D
D
W
Hình 3.7: Định vị V và mặt phẳng
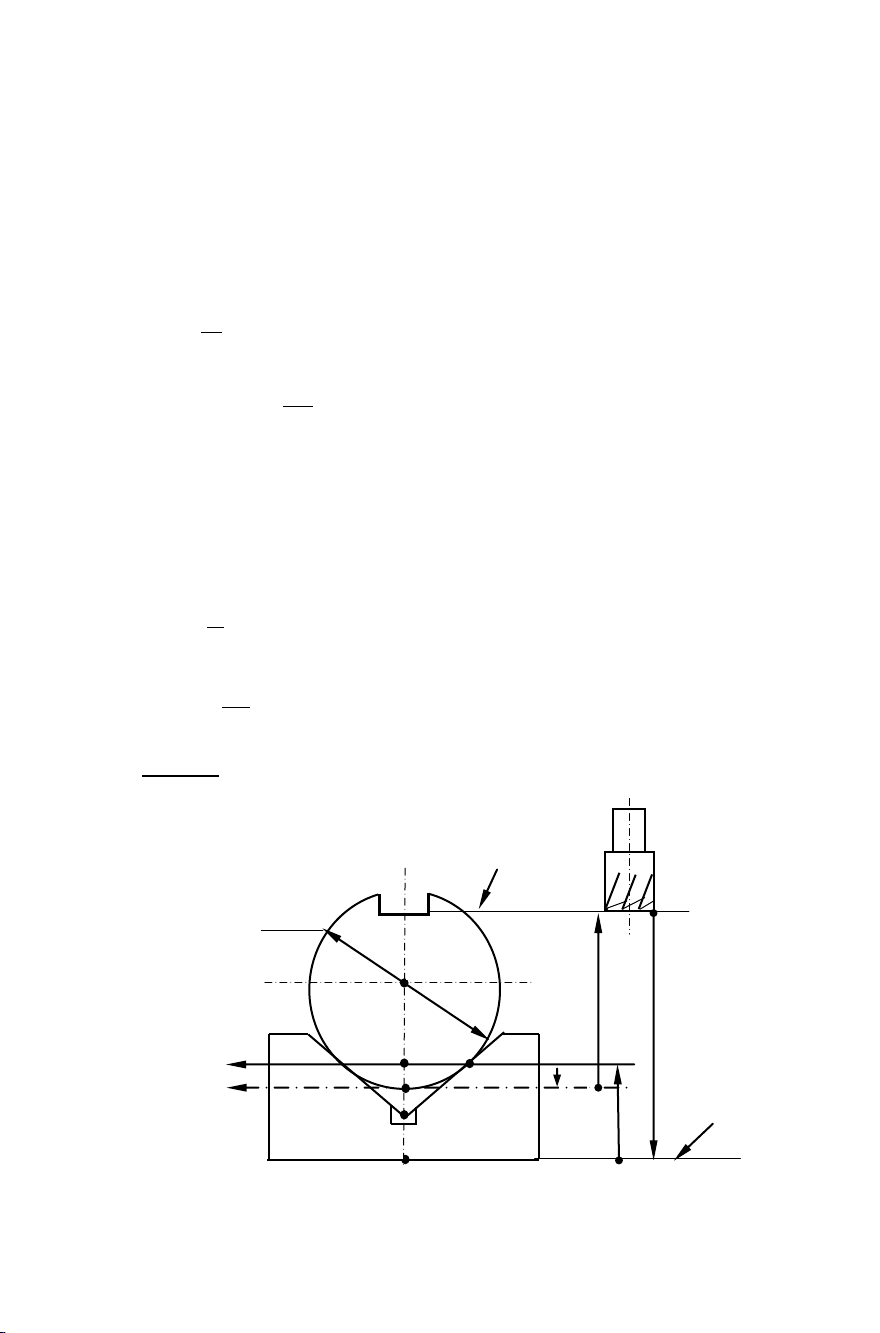
182
với chuẩn điều chỉnh (cũng là tâm O của trụ ngoài). Tính sai số chuẩn của
các kích thước: H, h.
Đối với kích thước H có gốc kích thước là đường sinh thấp nhất
của chi tiết gia công, ta có chuỗi kích thước công nghệ như sau:
a + x
2
– H = 0
H = a + x
2
2
D
a
Vậy:
2
)(
D
H
c
Đối với kích thước h có gốc kích thước là đường sinh trên cùng của
lỗ, ta có chuỗi kích thước công nghệ như sau:
a – y
2
– h = 0
h = a – y
2
)
2
( e
d
a
(e – độ lệch tâm giữa lỗ và trụ ngoài)
Vậy:
e
d
h
c
2
2
)(
Ví dụ 6: Định vị trụ trên khối V có góc là
D
δD
X
1
Mặt gia công
Chuẩn điều
chỉnh
H
1
I
Chuẩn định vị
O
M
K
J
Hình 3.9:
Sơ đồ chuỗi kích thước hình hành H
1
A
1
X
2
J
Gốc kích thước
N
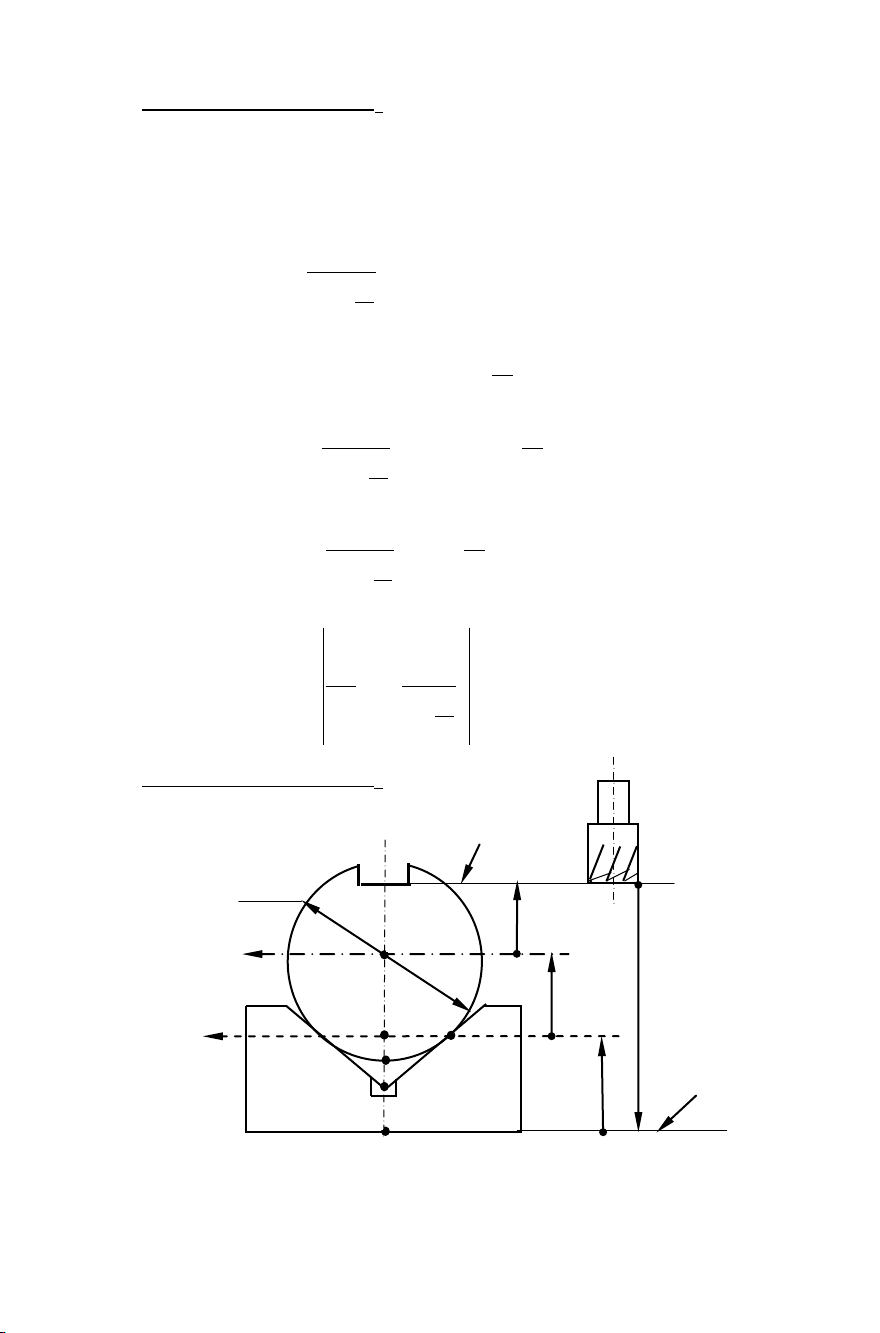
183
Tính sai số chuẩn cho H
1
(Hình 3.9)
A
1
– X
1
– X
2
– H
1
= 0
H
1
= A
1
– X
1
– X
2
Trong đó: X
1
= OJ – OM = OI + IJ – OM
=
2
sin2
D
+ IJ - OM
X
2
= MN = ON – OM =
OM
D
2
Suy ra:
OM
D
OMIJ
D
AH
2
2
sin2
11
2
2
sin2
1
D
IJ
D
A
Kết quả:
2
sin
1
1
2
)(
1
D
H
c
Tính sai số chuẩn cho H
2
(Hình 3.10)
Ta có: A
1
– Y
1
- Y
2
– H
2
= 0
D
δD
Y
1
Mặt gia công
Chuẩn điều chỉnh
H
2
I
Chuẩn
định vị
O
M
K
J
Hình 3.10:
Sơ đồ chuỗi kích thước hình hành H
2
A
1
Y
2
J
Gốc kích thước
N

184
H
2
= A
1
– Y
1
- Y
2
Trong đó:
Y
1
= OJ – OM = OI + IJ – OM
=
2
sin2
D
+ IJ - OM
Y
2
= OM
Suy ra: H
2
= A
1
–
2
sin2
D
- IJ + OM - OM
= A
1
–
2/sin2
D
+ IJ
Kết quả:
2Hc
=
2
sin2
2
sin2
DD
Tính sai số chuẩn cho H
3
Ta có: A
1
– Z
1
- Z
2
+ H
3
= 0
H
3
= - A
1
+ Z
1
+ Z
2
D
δD
Z
1
Mặt gia công
Chuẩn điều
chỉnh
H
3
I
Chuẩn
định vị
O
M
K
J
Hình 3.11:
Sơ đồ chuỗi kích thước hình hành H
3
A
1
Z
2
J
Gốc kích
thước
N
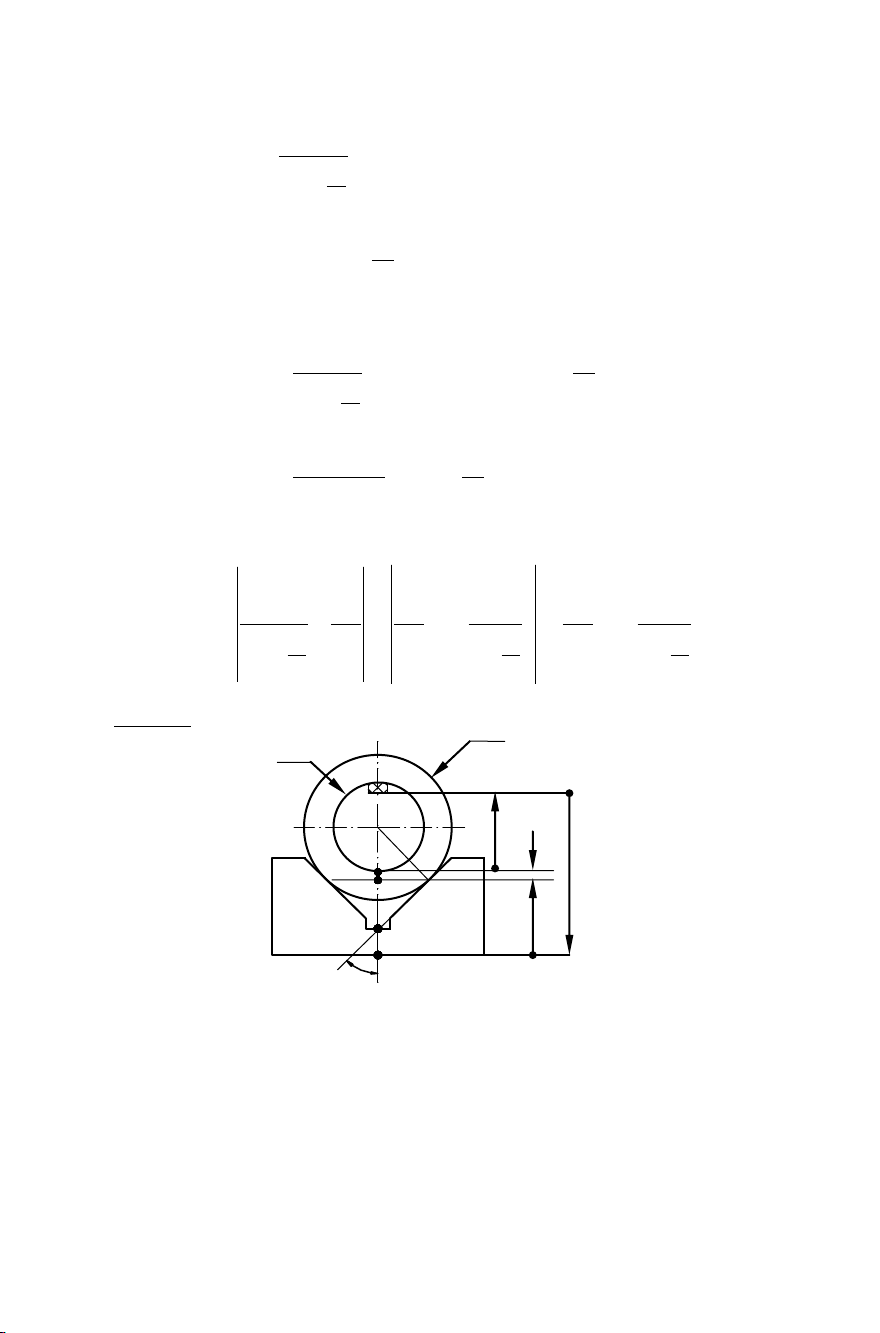
185
Trong đó: Z
1
= OJ – OM = OI + IJ – OM
=
2
sin2
D
+ IJ - OM
Z
2
= OM +
2
D
Suy ra:
H
3
= - A
1
+
2
sin2
D
+ IJ – OM + OM +
2
D
= - A
1
+
2/sin2
D
+ IJ +
2
D
Kết quả:
2
sin
1
1
2
2
sin
1
1
22
2
sin2
)(
3
DDD
D
H
c
Ví dụ 7:
Hình 3.12 là sơ đồ định vị phần trụ lớn của chi tiết trục bậc trên
khối V để gia công then trên phần trụ nhỏ. Trong trường hợp này chuẩn
định vị (2 đường sinh của chi tiết tiếp xúc với khối V) và chuẩn điều
chỉnh (mặt tựa phía dưới của khối V) là khác nhau.
Tính sai số chuẩn cho kích thức H có gốc kích thước là đường sinh
thấp nhất của phần trụ nhỏ.
Hình 3.12: Định vị trên khối V
/2
D
D
d
d
a
H
x
1
x
2
O
M
N
I
J
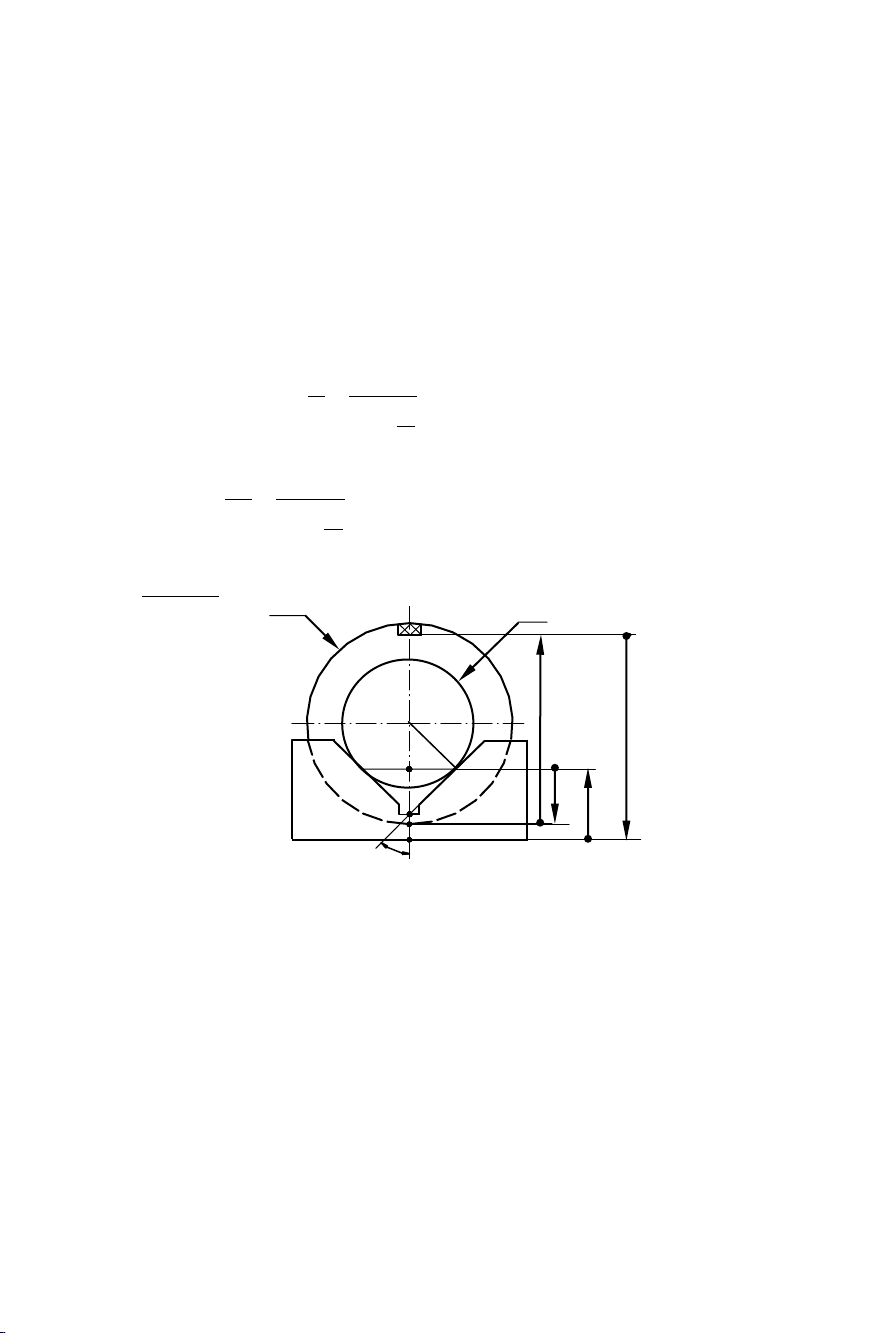
186
Ta có chuỗi kích thước công nghệ như sau:
a – x
1
– x
2
– H = 0
H = a – x
1
– x
2
Với: x
1
= OJ – ON = JI + IO – ON
x
2
= ON – OM
Nên: H = a – JI – IO + ON – ON + OM
= a – JI + OM – IO
e
Dd
JIa
2
sin2
2
Vậy:
e
Dd
H
c
2
2
sin2
2
)(
Ví dụ 8:
Hình 3.13 là sơ đồ định vị phần trụ nhỏ của chi tiết trục bậc trên khối
V để gia công then trên phần trụ lớn. Trong trường hợp này chuẩn định vị
(2 đường sinh của chi tiết tiếp xúc với khối V) và chuẩn điều chỉnh (mặt
tựa của khối V xuống dưới) là khác nhau. Tính sai số chuẩn cho kích thức
H có gốc kích thước là đường sinh thấp nhất của phần trụ lớn.
Ta có chuỗi kích thước công nghệ như sau:
a – x
1
+ x
2
- H = 0
H = a – x
1
+ x
2
Với: x
1
= OJ – OM = JN + ON – OM
x
2
= OI – OM
Hình 3.13: Định vị trên khối V
/2
d
d
D
D
H
x
2
x
1
0
M
N
I
J
a
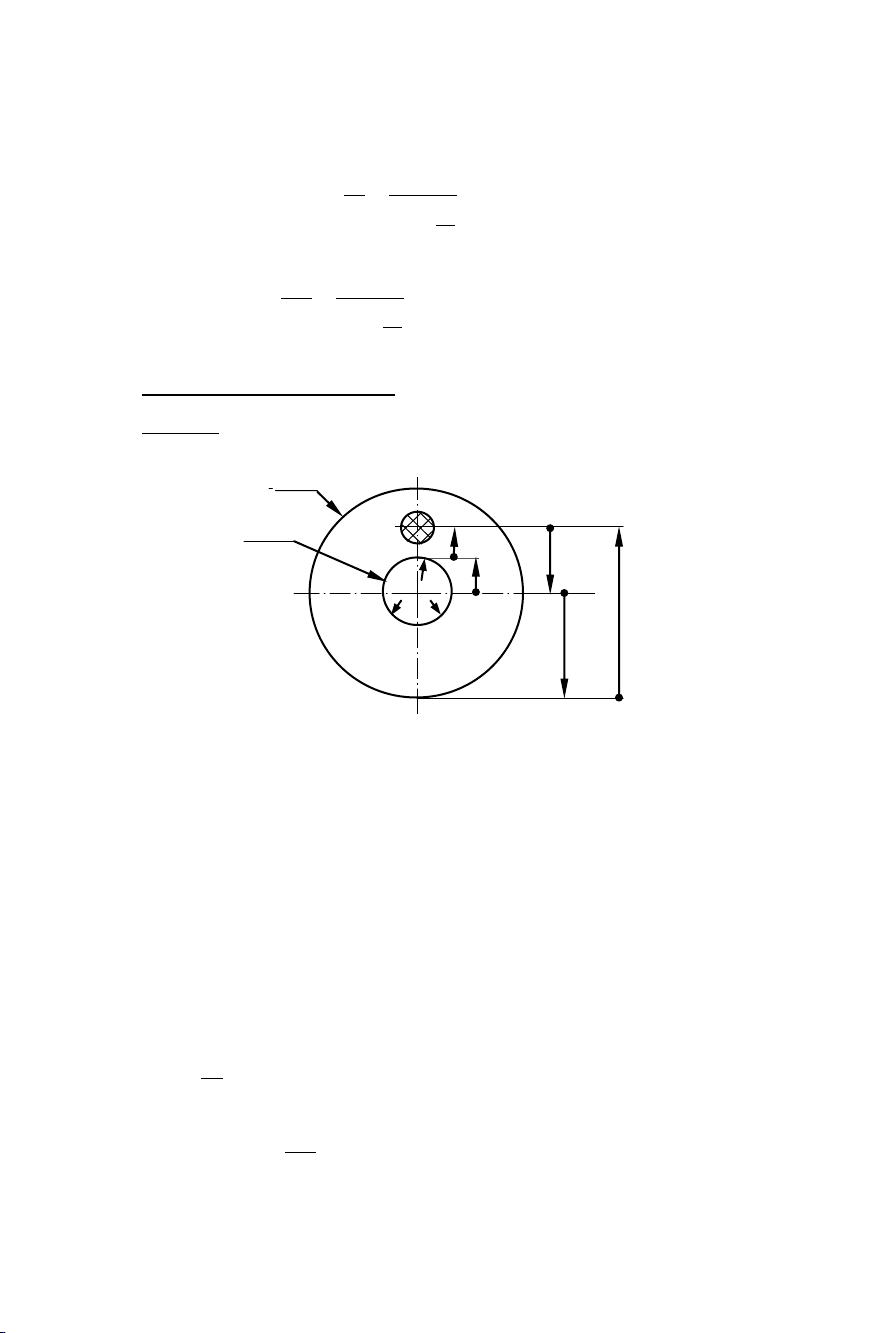
187
Nên: H = a – JN – ON + OM + OI - OM
= a – JN + OI – ON
e
dD
JIa
2
sin2
2
Vậy:
e
dD
H
c
2
2
sin2
2
)(
Định vị vào mặt trụ trong
Ví dụ 9:
Hình 3.14 là sơ đồ định vị chi tiết gia công trên cơ cấu tự định tâm
(mâm cặp ba chấu hoặc trục gá bung). Đặc điểm của cơ cấu này là chuẩn
định vị tuy là bề mặt của lỗ nhưng đại diện của nó lại là tâm O, vì vậy chuẩn
định vị trùng với chuẩn điều chỉnh (cũng là tâm O của lỗ). Tính sai số chuẩn
của các kích thước: H, h.
Đối với kích thước H có gốc kích thước là đường sinh thấp nhất
của chi tiết gia công, ta có chuỗi kích thước công nghệ như sau:
a + x
2
– H = 0
H = a + x
2
e
D
a
2
(e – độ lệch tâm giữa lỗ và trụ ngoài)
Vậy:
e
D
H
c
2
2
)(
Đối với kích thước h có gốc kích thước là đường sinh trên cùng của
lỗ, ta có chuỗi kích thước công nghệ như sau:
d
d
D
D
y
2
a
x
2
H
h
Hình 3.14: Dùng trục gá bung
0
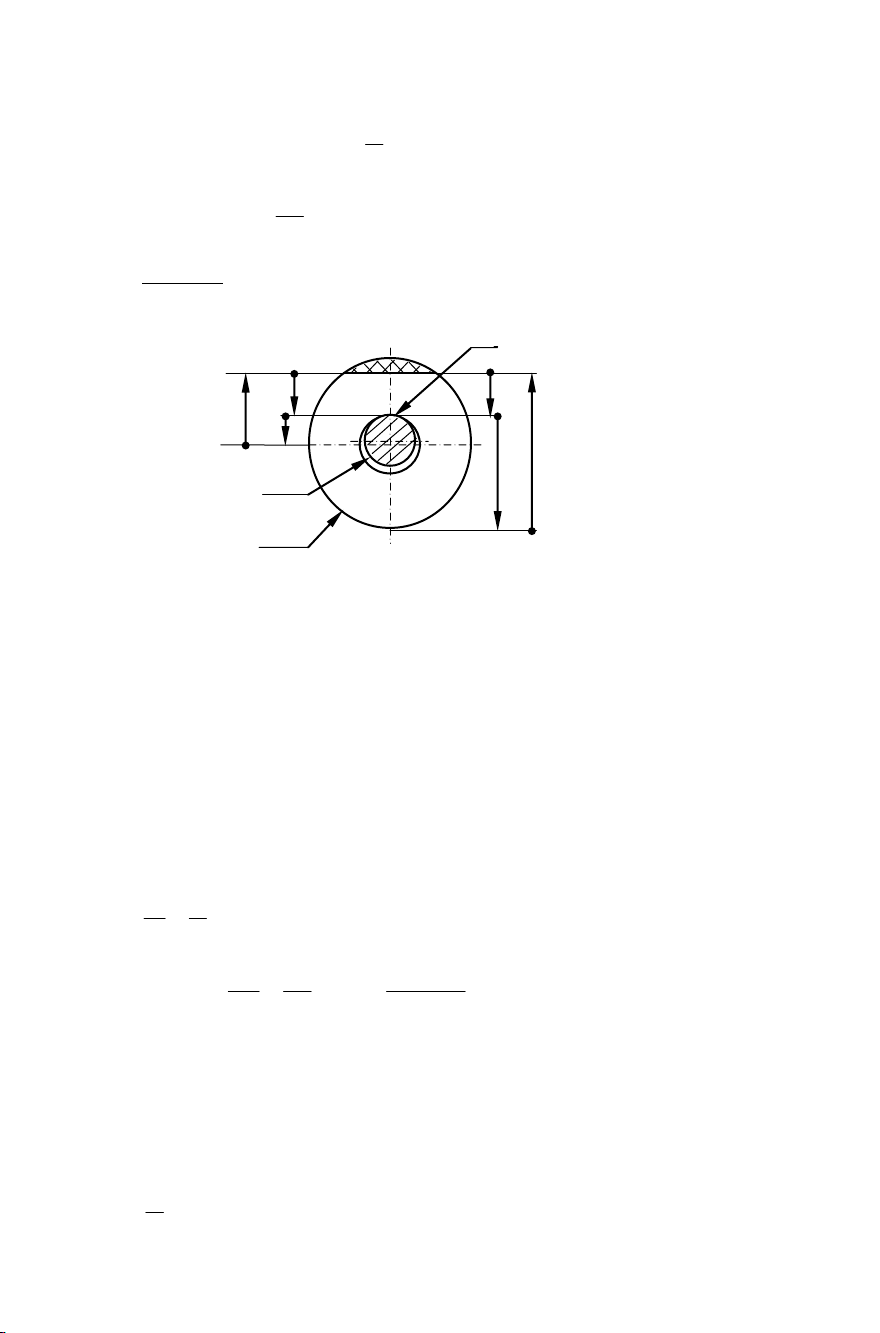
188
I
h
D
D
a
y
2
H
x
2
a
Hình 3.15: Định vị vào mặt phẳng và chốt
Chuaån ñ/c chuaån ñ/v
d
d
a – y
2
– h = 0
h = a – y
2
2
d
a
Vậy:
2
)(
d
h
c
Ví dụ 10
Hình 3.15 là sơ đồ định vị chi tiết gia công trên trục gá hoặc chốt
ngắn, giả sử khe hở phân bố về một phía, chuẩn điều chỉnh trùng với
chuẩn định vị tại điểm I. Tính sai số chuẩn cho các kích thước: H, h (cho
e là độ lệch tâm giữa lỗ và trụ ngoài,
min
= 0,
c
= 0).
Đối với kích thước H có gốc kích thước là đường sinh thấp nhất
của chi tiết, ta có chuỗi kích thước công nghệ như sau:
a + x
2
- H = 0
H = a + x
2
e
dD
a
22
Vậy:
e
dD
H
c
2
22
)(
e
dD
2
2
Đối với kích thước h có gốc kích thước là tâm O của lỗ, ta có chuỗi
kích thước công nghệ như sau:
a + y
2
– h = 0
h = a + y
2
2
d
a
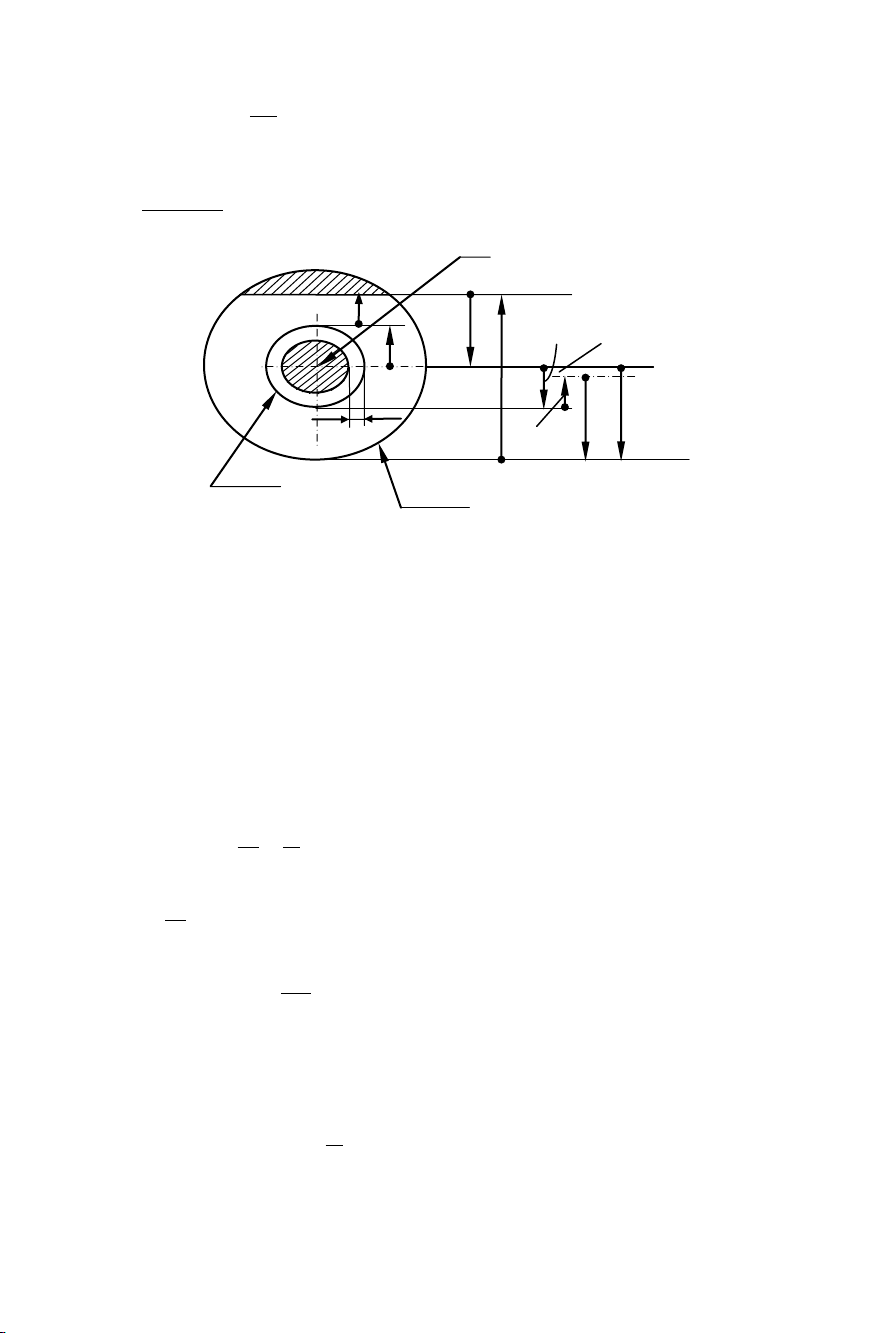
189
Vậy:
2
)(
d
h
c
(nếu h là kích thước tính từ tâm trụ ngoài thì cộng
thêm 2e)
Ví dụ 11
Hình 3.16 là sơ đồ định vị chi tiết gia công trên trục gá hoặc chốt
ngắn, giả sử khe hở phân bố bất kỳ. Tính sai số chuẩn cho các kích
thước: H, f (cho e là độ lệch tâm giữa lỗ và trụ ngoài,
min
, bỏ qua sai số
của chốt
c
= 0).
Đối với kích thước H có gốc kích thước là đường sinh thấp nhất
của chi tiết, ta có chuỗi kích thước công nghệ như sau:
a + x
2
- H = 0
H = a + x
2
Với x
2
e
dD
min
22
ed
D
22
2
min
Vậy:
ed
D
H
c
22
2
)(
min
Đối với kích thước f, ta có chuỗi kích thước công nghệ như sau:
a - y
2
– f = 0
f = a - y
2
min
2
d
a
Do tâm lỗ có thể lệch về hai phía của tâm chốt nên:
Hình 3.16 Định vị vào chốt trụ khe hở phân bố bất kỳ
D
δD
d
δd
a
H
Δ
max
f
y
2
x
2
Chuaån ñiều chỉnh
O
l
O
n
e
d/2
d/2
D/2
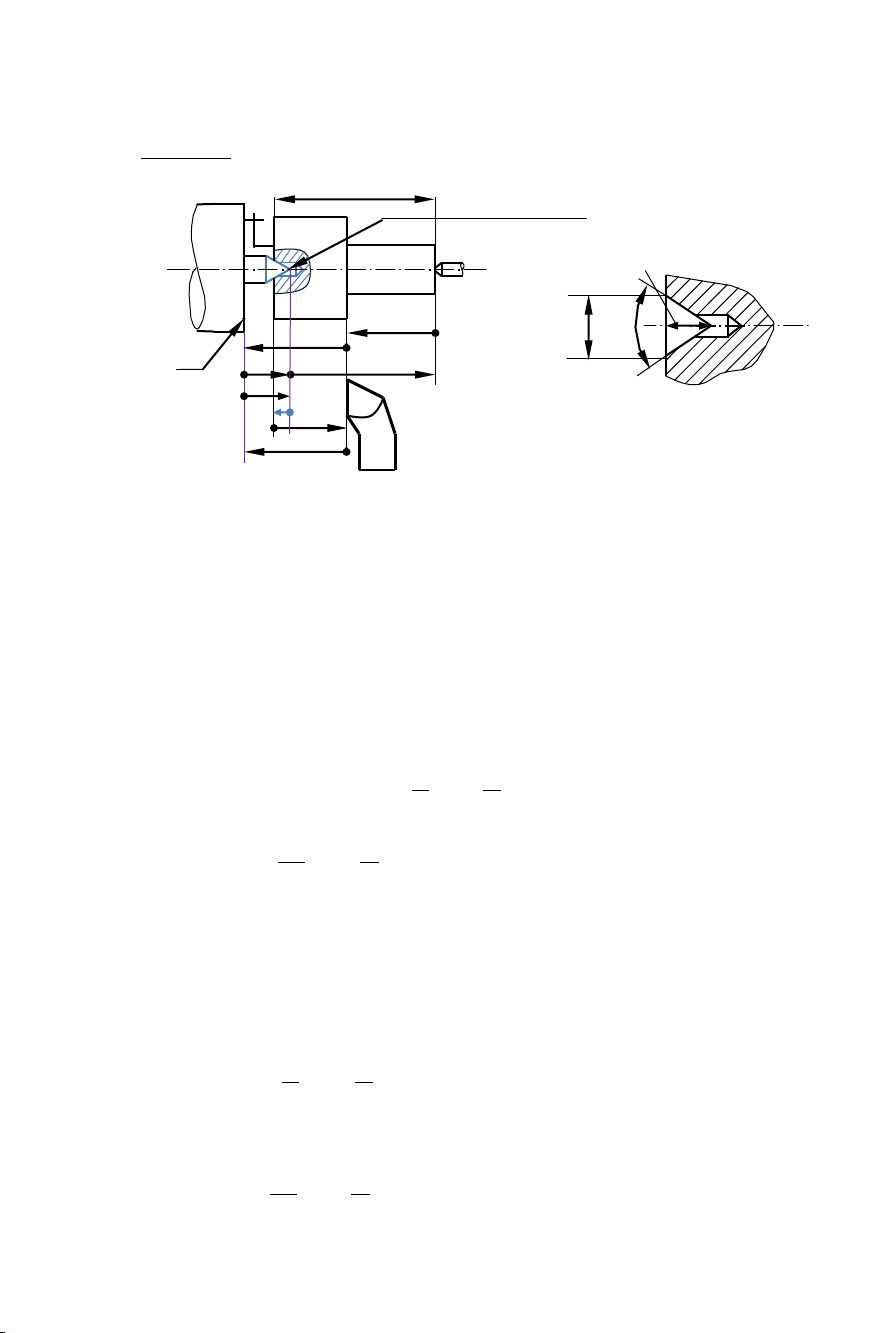
190
Vậy:
min
2)( df
c
Ví dụ 12:
Hình 3.17 là sơ đồ định vị chi tiết gia công trên hai mũi tâm, có
chuẩn định vị là mặt côn lỗ tâm và chuẩn điều chỉnh bề mặt mâm tốc, gốc
kích thước l
1
là mặt đầu bên trái của trục còn gốc l
2
là mặt đầu bên phải.
Tính sai số chuẩn cho các kích thước: l
1
, l
2
.
Đối với kích thước l
1
có gốc kích thước là mặt đầu trái chi tiết, ta
có chuỗi kích thước công nghệ như sau:
a – x
1
+ x
2
– l
1
= 0
l
1
= a – x
1
+ x
2
2
cot
2
1
g
d
xa
Vậy:
2
cot
2
)(
1
g
d
l
c
Đối với kích thước l
2
có gốc kích thước là mặt đầu phải chi tiết, ta
có chuỗi kích thước công nghệ là:
a – y
1
– y
2
+ l
2
= 0
l
2
= y
1
+ y
2
– a = y
1
– a + ( L – x
2
)
2
cot
2
1
g
d
Lay
Sai số chuẩn là lượng dao động lớn nhất của gốc kích thước nên ta có:
2
cot
2
)(
2
g
d
Ll
c
Hình 3.17: Định vị vào hai lỗ tâm
x
2
d
d
Chuaån ñònh vò
a
y
1
x
1
L
L
l
1
x
2
l
2
y
2
Chuẩn
điều
chỉnh
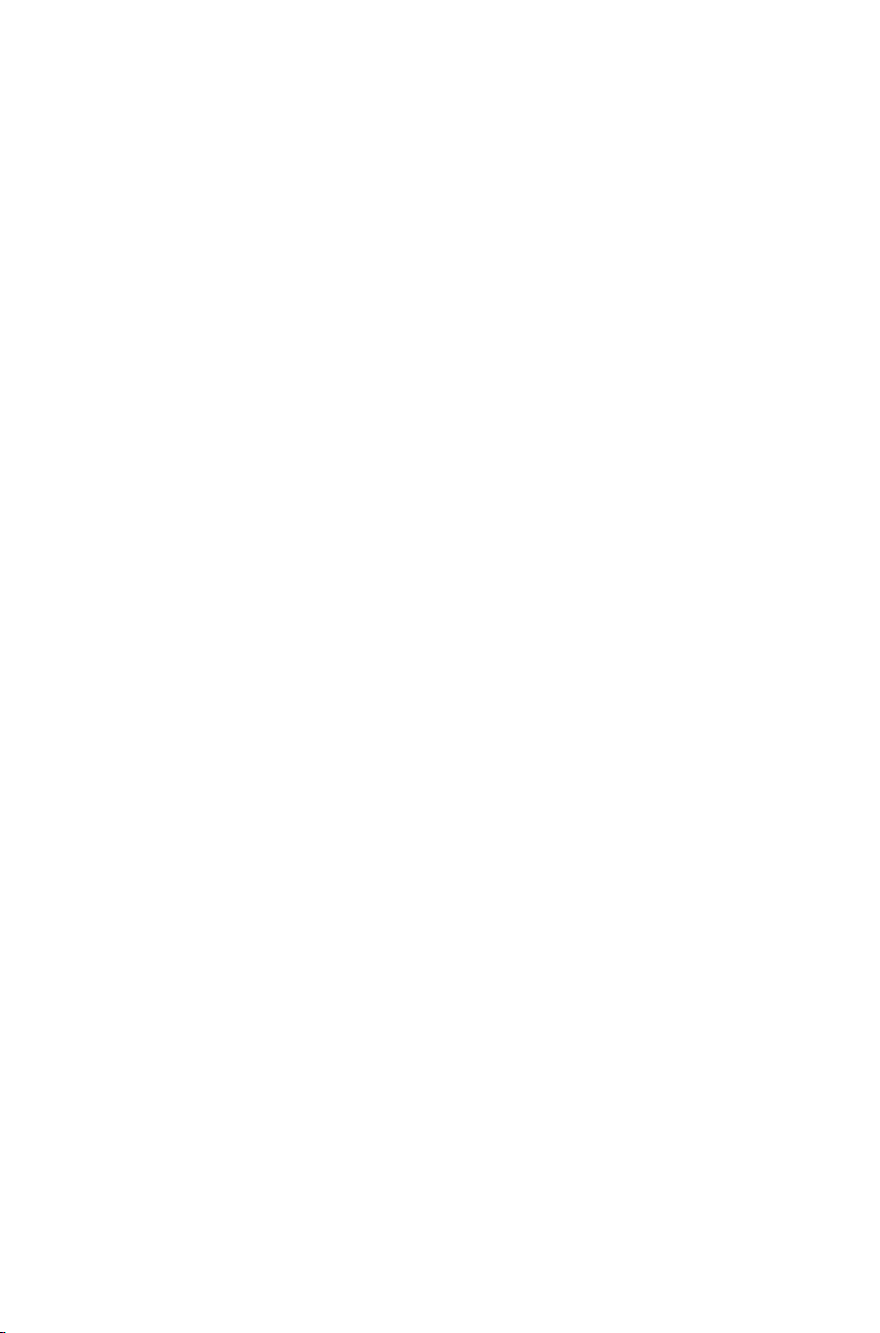
191
3.4. CÁC CHI TIẾT VÀ CƠ CẤU ĐỊNH VỊ
3.4.1. Khái niệm
Các chi tiết và cơ cấu trên đồ gá tiếp xúc với chuẩn định vị của chi
tiết gia công, thay thế cho các điểm định vị, khống chế các bậc tự do theo
nguyên tắc 6 điểm hoặc để tăng độ cứng vững chi tiết khi gia công thì
được gọi là các chi tiết và cơ cấu định vị.
Các chi tiết và cơ cấu định vị được chia làm hai loại: định vị chính
và định vị phụ.
Chi tiết định vị chính là những chi tiết có thể khống chế được một
số hoặc toàn bộ bậc tự do của chi tiết gia công, bảo đảm cho chi tiết có
một vị trí nhất định trong đồ gá.
Cơ cấu định vị phụ là những cơ cấu dùng để tăng thêm độ cứng
vững của chi tiết gia công mà không có tác dụng khống chế bậc tự do. Cơ
cấu định vị phụ không được làm thay đổi vị trí chi tiết gia công đã được
xác định, cơ cấu định vị phụ thường là điều chỉnh và di động được.
Các chi tiết định vị phụ không hạn chế bậc tự do nhưng không nên
quá nhiều làm cho đồ gá cồng kềnh phức tạp.
Các chi tiết định vị yêu cầu chế tạo chính xác, bảo đảm độ cứng và
độ chống mòn cao, dễ thay thế khi bị hư hỏng.
Để nâng cao độ chống mòn, các chốt tỳ phải làm bằng thép CD80
hoặc thép C20 qua thấm than và tôi đạt độ cứng 55 60 HRC. Các chốt
tỳ phụ chế tạo bằng thép C45 và tôi đạt độ cứng 45 50 HRC. Trong
một số trường hợp, mặt tỳ của các chi tiết định vị còn được mạ crôm
hoặc hàn đắp bằng hợp kim cứng. Các bề mặt của chi tiết định vị mài đạt
độ nhám R
a
= 0,63m(8)
3.4.2. Các chi tiết định vị chính
3.4.2.1. Chi tiết định vị vào mặt phẳng
a. Chốt tỳ cố định
Mỗi chốt tỳ định vị thay thế cho một điểm trong nguyên tắc 6 điểm
khi định vị, có thể dùng một, hai hoặc ba chốt.
Chốt tỳ đầu phẳng (hình 3.18a) dùng để định vị mặt phẳng đã gia
công tinh.
Chốt tỳ đầu chỏm cầu (hình 3.18b) dùng để định vị mặt phẳng thô
chưa gia công, diện tích tiếp xúc có thể làm lõm mặt định vị.
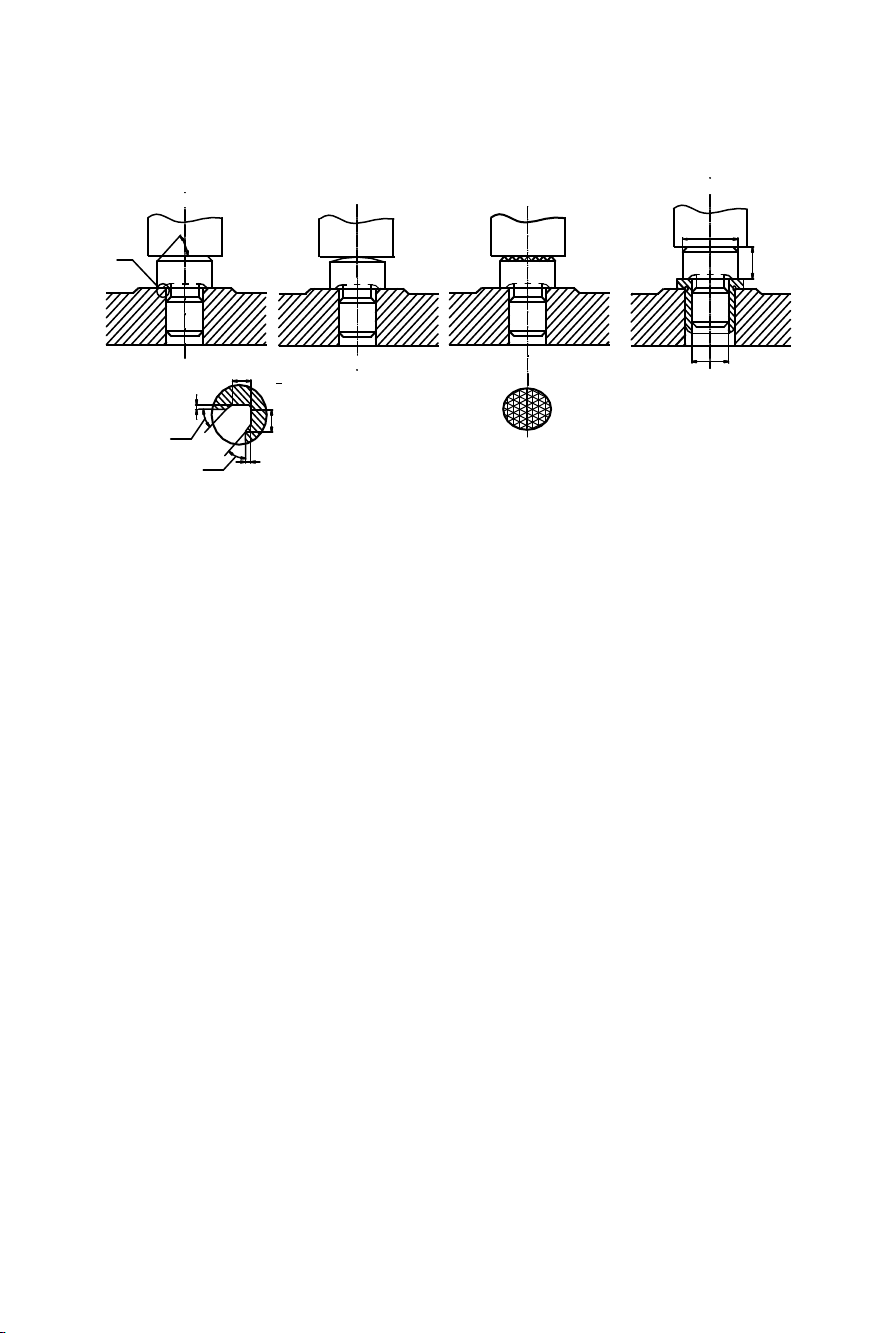
192
Chốt tỳ đầu phẳng khía nhám (hình 3.18c) dùng để định vị các mặt
phẳng thô, diện tích tiếp xúc lớn hơn loại chỏm cầu, ma sát tiếp xúc tăng
lên nhiều và lâu mòn hơn.
Loại cuống chốt có bạc lót (hình 3.18d) được dùng để khi chốt mòn
hư hỏng có thể thay thế một cách dễ dàng mà không làm hư hỏng vỏ đồ
gá, loại này được dùng trong đồ gá sản xuất hàng loạt lớn và hàng khối.
Các chốt tỳ cố định được lắp vào vỏ đồ gá bằng cuống, theo chế độ
lắp H7/r6 hoặc H7/n6 (hình 3.18a,b,c).
Lỗ lắp chốt nên làm suốt để dễ gia công và thay thế khi chốt bị
mòn. Trên vai của chốt có cắt rãnh để dễ gia công tinh cuống chốt và
mặt gờ. Kích thước của rãnh được ghi trên hình 3.18a.
Chốt có bạc lót ( hình 3.18d), thì mặt ngoài bạc lắp với đồ gá theo mối
lắp H7/r6 còn lỗ bạc lắp với chốt theo mối lắp h7/j6 hoặc H7/h6. Để đảm
bảo độ phẳng, sau khi lắp các ống lót phải đem mài lại tất cả các mặt đầu.
Các kích thước của chốt tỳ cố định nằm trong giới hạn
D = 324 mm , d = 340 mm
H = 220 mm , L = 650 mm.
(Các thông số được cụ thể hóa trong bảng 8-9 và 8-10 trang 400-401,Sổ
tay CNCTM tập 2 )
b. Chốt tỳ điều chỉnh
Là loại chốt có thể thay đổi kích thước trong quá trình định vị.
Chốt tỳ điều chỉnh dùng để định vị mặt chuẩn thô có nhiều sai lệch
về hình dáng.
0,25-0,57
0,25-0,5
0,8-2,5
0,8-2,5
45
0
45
0
I
H
45
0
I
D
H7/j6
a)
b)
c)
d)
Hình 3.18: Chốt tỳ cố định
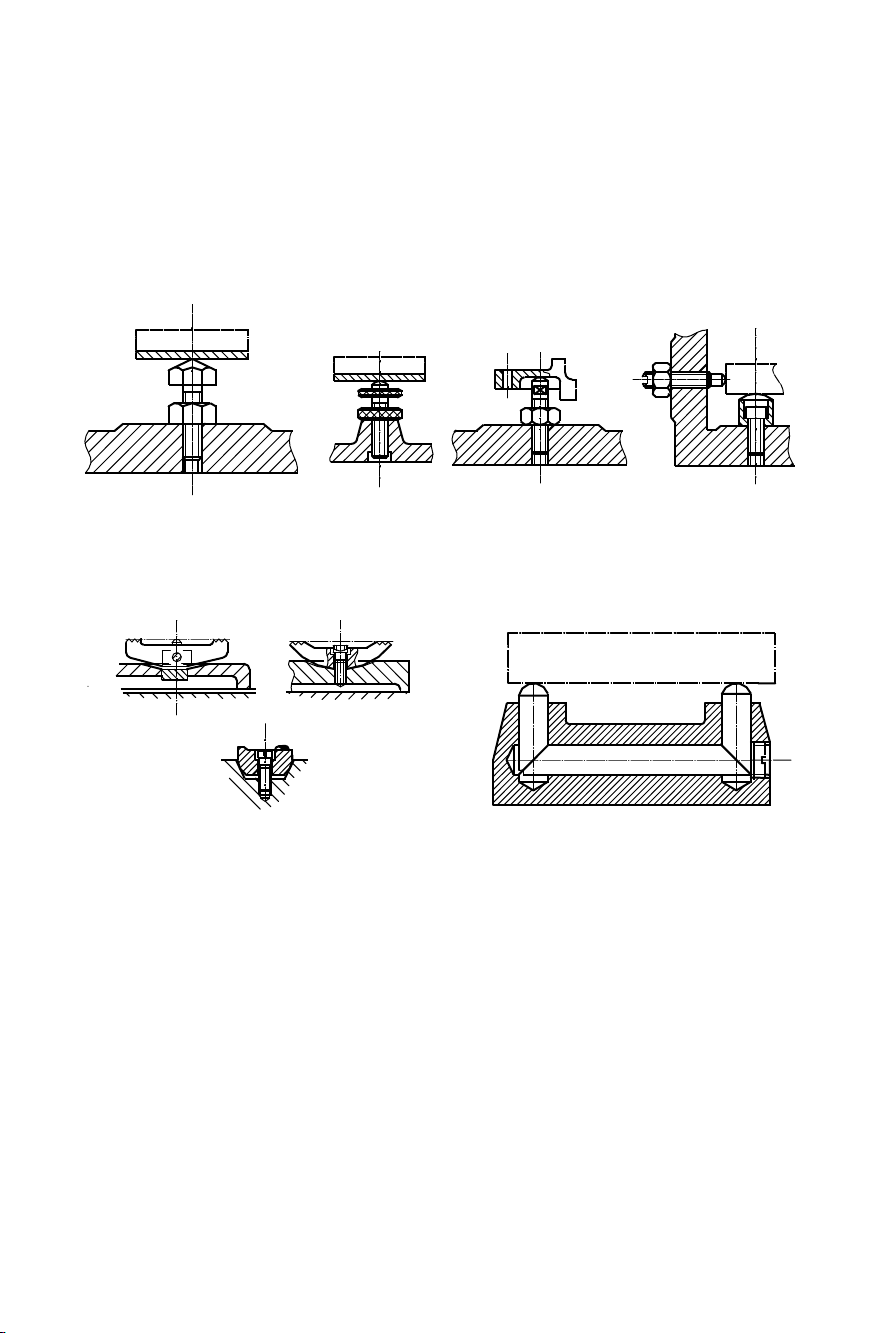
193
Chốt tỳ điều chỉnh đầu 6 cạnh dùng clê, mỏ lết,... để điều chỉnh
(hình 3.19a).
Chốt tỳ điều chỉnh đầu tròn dùng tay để điều chỉnh (hình 3.19b).
Chốt tỳ điều chỉnh có chốt vát cạnh dùng clê mỏ lết,... để điều
chỉnh (hình3.19c).
Chốt tỳ điều chỉnh lắp đặt trên mặt đứng của đồ gá (hình 3.19d).
c. Chốt tỳ tự lựa
Chốt tỳ tự lựa dùng để định vị mặt chuẩn thô của những chi tiết có
trọng lượng lớn. Dùng chốt tỳ tự lựa để thay thế một điểm định vị thành
2 hoặc 3 điểm, như vậy sẽ làm tăng độ cứng vững của chi tiết gia công
và giảm áp lực trên các điểm tỳ.
Hình 3.20a là chốt tỳ 2 điểm.
Hình 3.20b là chốt tỳ 3 điểm.
Hình 3.20c là chốt tỳ 3 điểm, giữa vít chặt và lỗ có khe lớn để lắc
tự lựa được.
Hình 3.20d là chốt tỳ 2 điểm dùng mặt nghiêng để chốt tự lựa, sử
dụng khi các điểm tự lựa cách xa nhau.
Hình 3.20: Chốt tỳ tự lựa
c)
a)
b)
d)
d)
a)
b)
c)
Hình 3.19: Chốt tỳ điều chỉnh
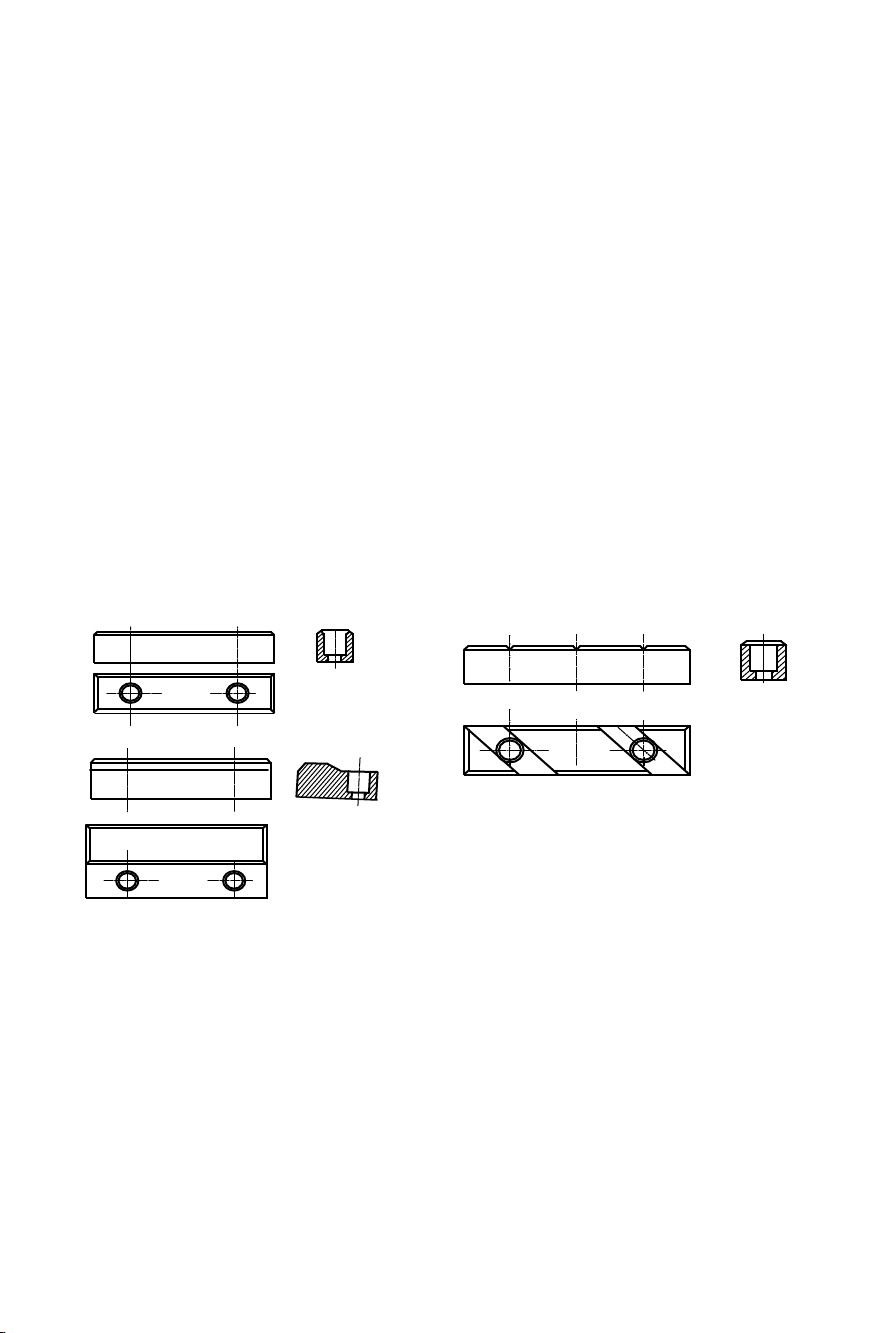
194
Ngoài các loại trên còn có rất nhiều loại chốt tỳ tự lựa làm bằng các
viên bi, bằng chất dẻo có chốt để tự lựa được dễ dàng.
Dùng chốt tự lựa thì kết cấu của đồ gá sẽ phức tạp nên chỉ dùng
trong những trường hợp thật cần thiết.
d. Phiến tỳ cố định
Phiến tỳ cố định dùng để định vị các mặt phẳng đã được gia công
của những chi tiết có kích thước lớn.
Hình 3.21a là phiến tỳ phẳng đơn giản, loại này có những lỗ bắt
vít ở giữa phiến, khó quét sạch phôi nên dùng ở các mặt thẳng đứng của
đồ gá.
Hình 3.21b là phiến tỳ bậc có chỗ bắt vít lõm xuống thấp hơn mặt
định vị 1 2mm nên dùng để quét phôi nhưng kết cấu lớn hơn nên thực
tế ít dùng.
Hình 3.21c là phiến tỳ có rãnh nghiêng thường hay dùng vì dễ quét
phôi. Rãnh làm sâu hơn mặt định vị 0,8 3 mm vì vậy chế tạo phức tạp.
Phiến tỳ cố định được bắt chặt vào thân đồ gá bằng các vít M6
M12. Chỗ lắp phiến tỳ trên thân đồ gá phải làm lồi lên chừng 1 3 và
phải gia công chính xác bằng phương pháp mài.
Phiến tỳ thường được chế tạo từ thép C20, C25 và phải thấm
cacbon cho mặt định vị có độ sâu 0,8 1,2 mm và nhiệt luyện đạt độ
cứng 55 60 HRC.
Các kích thước của phiến tỳ nằm trong khoảng:
B = 12 25 mm; b = 9 22 mm;
L = 40 210 mm; d = 6 13 mm;
Hình 3.21: Phiến tỳ cố định
c)
a)
b)
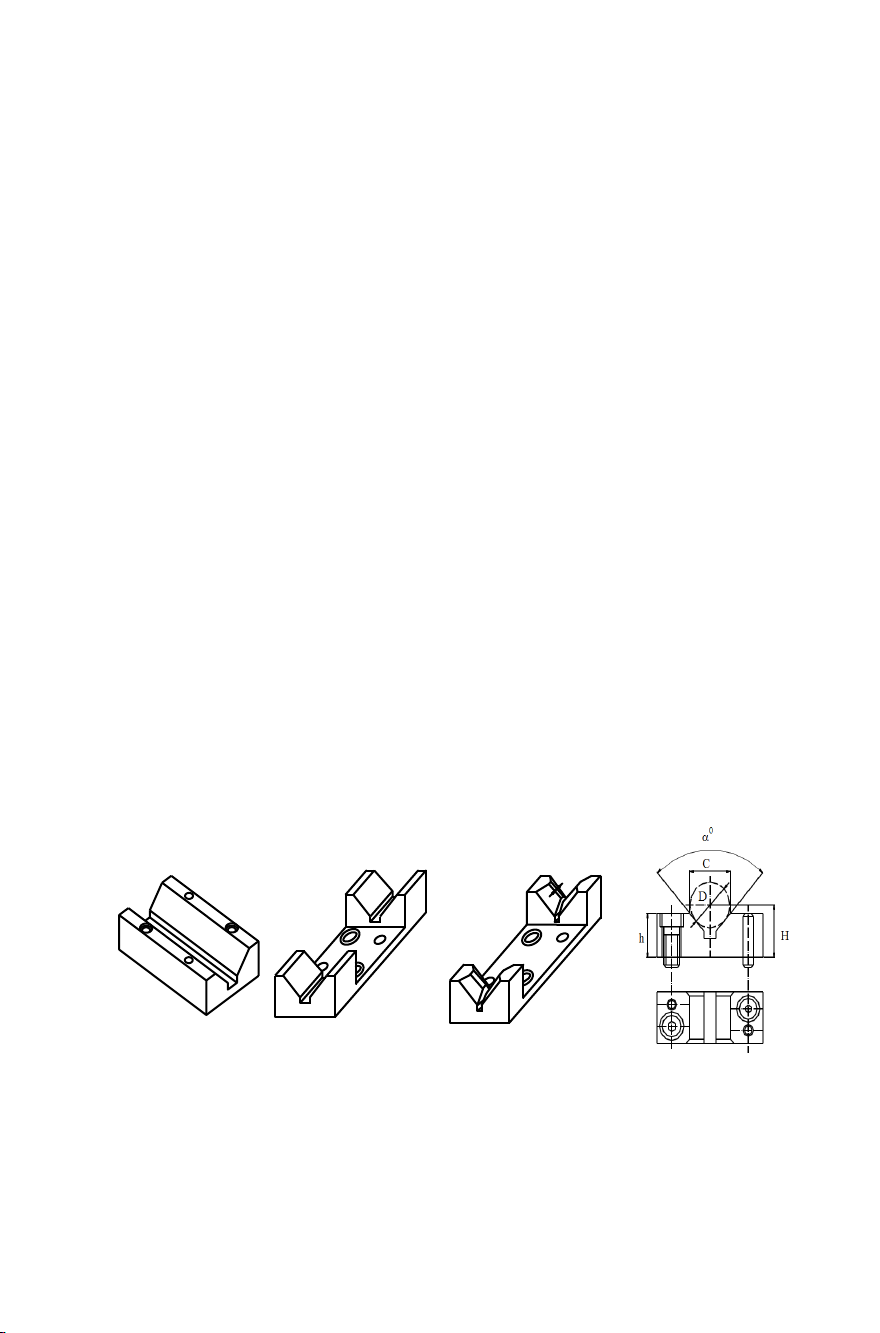
195
H = 8 25 mm; d
1
= 8,5 20 mm;
h = 4 13 mm; C = 10 35 mm;
h
1
= 0,8 3 mm; C
1
= 20 60 mm;
Khoảng cách giữa các lỗ có dung sai: 0,1 mm
3.4.2.2. Chi tiết định vị mặt trụ ngoài
Để định vị vào mặt trụ ngoài có thể dùng: mâm cặp ba, bốn chấu;
ống kẹp đàn hồi; khối V; bạc trụ hoặc bạc C; chụp côn...
a. Khối V
Chi tiết dùng để định vị vào mặt trụ ngoài khi gia công trên các
máy phay, khoan được dùng phổ biến là khối V. Khối V được phân loại
theo hai cách: góc hợp giữa hai mặt định vị ( = 60
0
, = 90
0
và =
120
0
) và chiều dài V.
Theo chiều dài có ba loại: khối V ngắn, khối V dài và khối V dài vát mép.
Hình3.22a là khối V dùng định vị các trục ngắn hạn chế hai bậc tự do.
Hình 3.22b, là khối V dùng định vị các trục dài.
Hình 3.22c là khối V có mặt định vị nhỏ hoặc khía nhám dùng định
vị vào các mặt chuẩn thô.
Vị trí của khối V quyết định vị trí của chi tiết gia công, cho nên cần
phải định vị chính xác khối V trên thân đồ gá. Khối V được định vị trên
thân đồ gá bằng hai chốt (lắp ghép theo H7/r6) và dùng vít để bắt chặt lại
(hình 3.22a).
Khối V định vị được chế tạo bằng thép 20Cr, C20 mặt định vị thấm
cácbon sâu 0,8 1,2mm, tôi đạt độ cứng 58 62HRC. Khối V dùng để định
vị các trục có đường kính D>120mm thì đúc bằng gang hoặc hàn, trên mặt
định vị được lắp các tấm thép tôi cứng, khi mòn có thể thay thế được.
Hình 3.22: Khối V
2-5mm
c)
b)
a)
d)
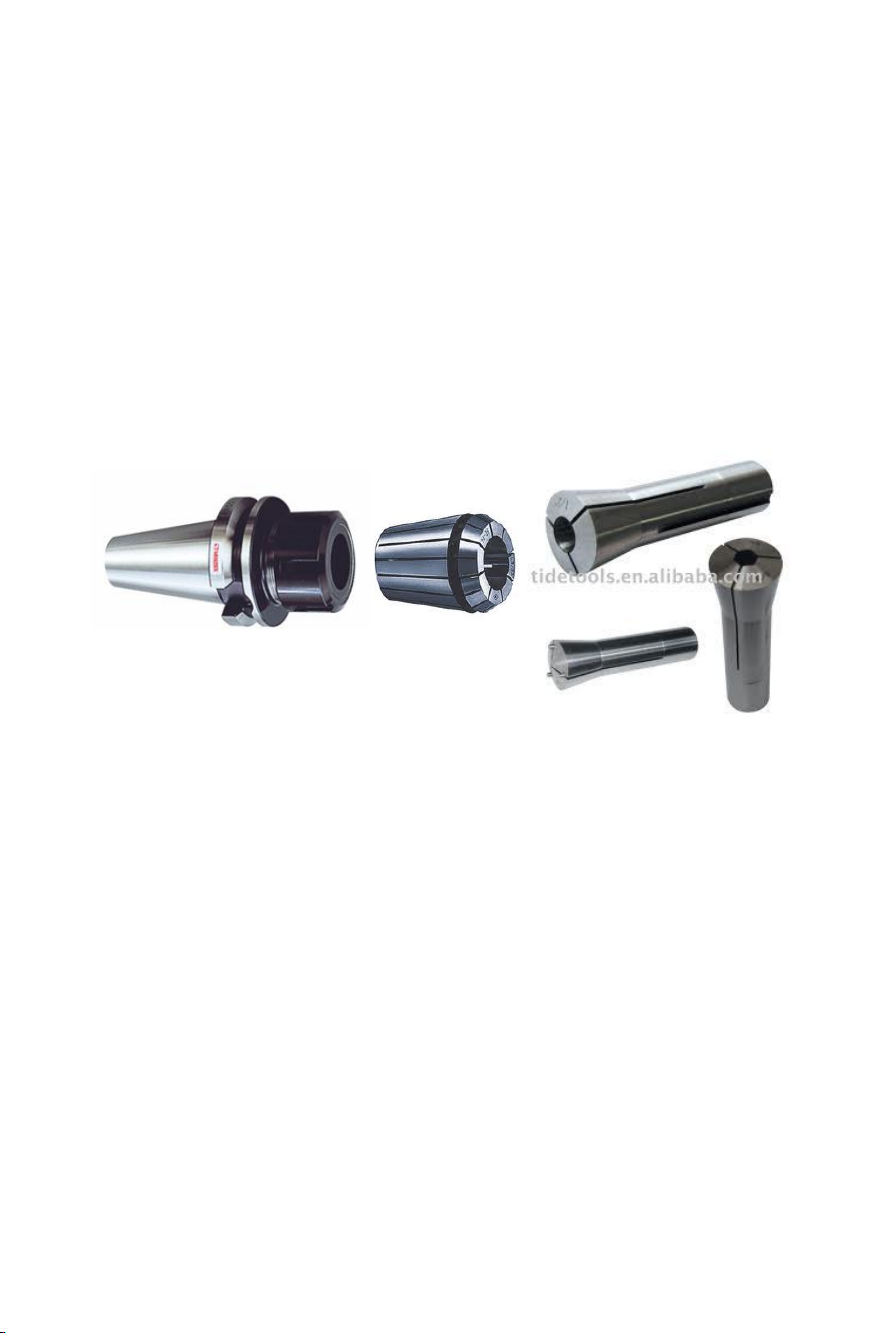
196
Khi thiết kế khối V, trước hết xác định kích thước C, rồi rút ra kích
thước H và ghi lên bản vẽ.
Quan hệ giữa H, D và C như sau:
Khi = 90
0
, thì H = h + 0,70 D – 0,5 C
Khi = 120
0
thì H = h + 0,578D – 0,289 C
b. Ống kẹp đàn hồi
Hình 3.23 trình bày một ống kẹp đàn hồi thường hay dùng trên các
loại máy tiện hoặc máy khoan. Khi vặn êcu 1, ống kẹp đàn hồi 2 sẽ bóp
chặt phôi 3, cấu tạo của ống có thể tham khảo các tài liệu về đồ gá.
Ống kẹp đàn hồi có tác dụng định vị và kẹp chặt chi tiết, ống tự
định tâm rất tốt, tuy nhiên phôi phải có độ chính xác cao.
3.4.2.3. Các chi tiết định vị mặt trụ trong chốt trụ ngắn, chốt
trám, trục gá, mũi tâm
a. Chốt trụ ngắn
Chốt trụ ngắn có mặt làm việc là trụ ngoài. Lỗ của chi tiết gia công
lắp vào chốt theo chế độ lắp lỏng, khe hở lắp ghép tùy thuộc vào yêu cầu
của độ chính xác gia công. Ví dụ có thể lắp theo chế độ: F7/h6; F7/h
Hình 3.24a là loại chốt không có vai, dùng cho lỗ có D > 16 mm,
mặt của chi tiết tỳ trực tiếp lên vỏ đồ gá làm cho đồ gá mau mòn.
Hình 3.24b là loại chốt có vai dùng cho lỗ có D 16 mm, loại này
khắc phục được nhược điểm trên.
Hình 3.24c là chốt lắp qua bạc lót và được cố định bằng mũ ốc.
Hình 3.24d là chốt trám
Hình 3.24e chốt di động dùng trong trường hợp chi tiết có trọng
lượng lớn.
Tùy theo yêu cầu sử dụng mà ta có thể sử dụng chốt trụ hoặc
chốt trám.
Hình 3.23: Ống kẹp đàn hồi
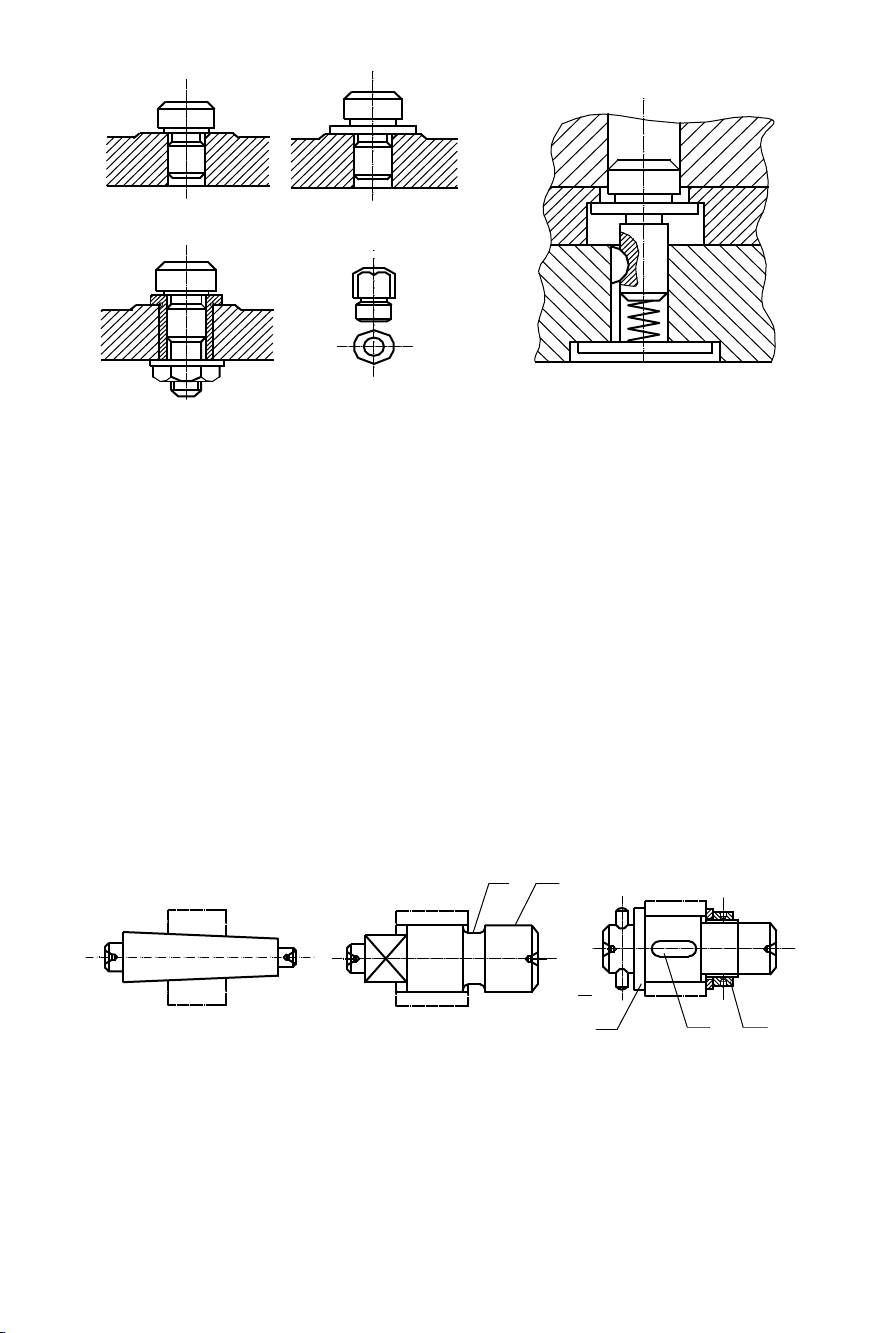
197
Trong sản xuất hàng loạt vừa và nhỏ thường dùng loại chốt cố định
và lắp vào thân đồ gá theo chế độ lắp H7/h6 (hình 3.24a,b). Trong sản
xuất hàng loạt lớn và hàng khối, để dễ thay thế chốt người ta lắp qua bạc
trung gian (hình 3.24c). Bạc trung gian lắp với thân đồ gá theo chế độ
H7/h6 còn chốt lắp với bạc theo mối lắp H7/j6 hay H7/n6.
Chốt có đường kính d 16 mm thường được chế tạo từ thép
CD70A tôi đạt độ cứng 50 55 HRC. Khi chốt có đường kính > 16 mm
thì được chế tạo từ thép 20Cr, mặt định vị thấm cacbon sâu 0,8 1,2
mm, tôi đạt độ cứng 50 55HRC.
b. Trục gá
Trục gá có 2 loại: trục gá cứng (hình 3.25) và trục gá bung (hình 3.26).
Trục gá thường được chế tạo từ thép C45 hoặc thép 40Cr nhiệt
luyện và mài đạt độ nhám Ra 0,63 m.
Hình 3.25a là trục gá côn với độ côn là từ 1/1500 1/1200 cho nên
khi lắp chi tiết chỉ cần gõ nhẹ. Nhờ tác động chêm của trục gá côn cho
nên phôi được cố định trên trục gá trong quá trình gia công.
2
1
Hình 3.25: Trục gá cứng
a)
b)
1
c)
2
3
Hình 3.24: Các loại chốt trụ ngắn
a)
b)
c)
d)
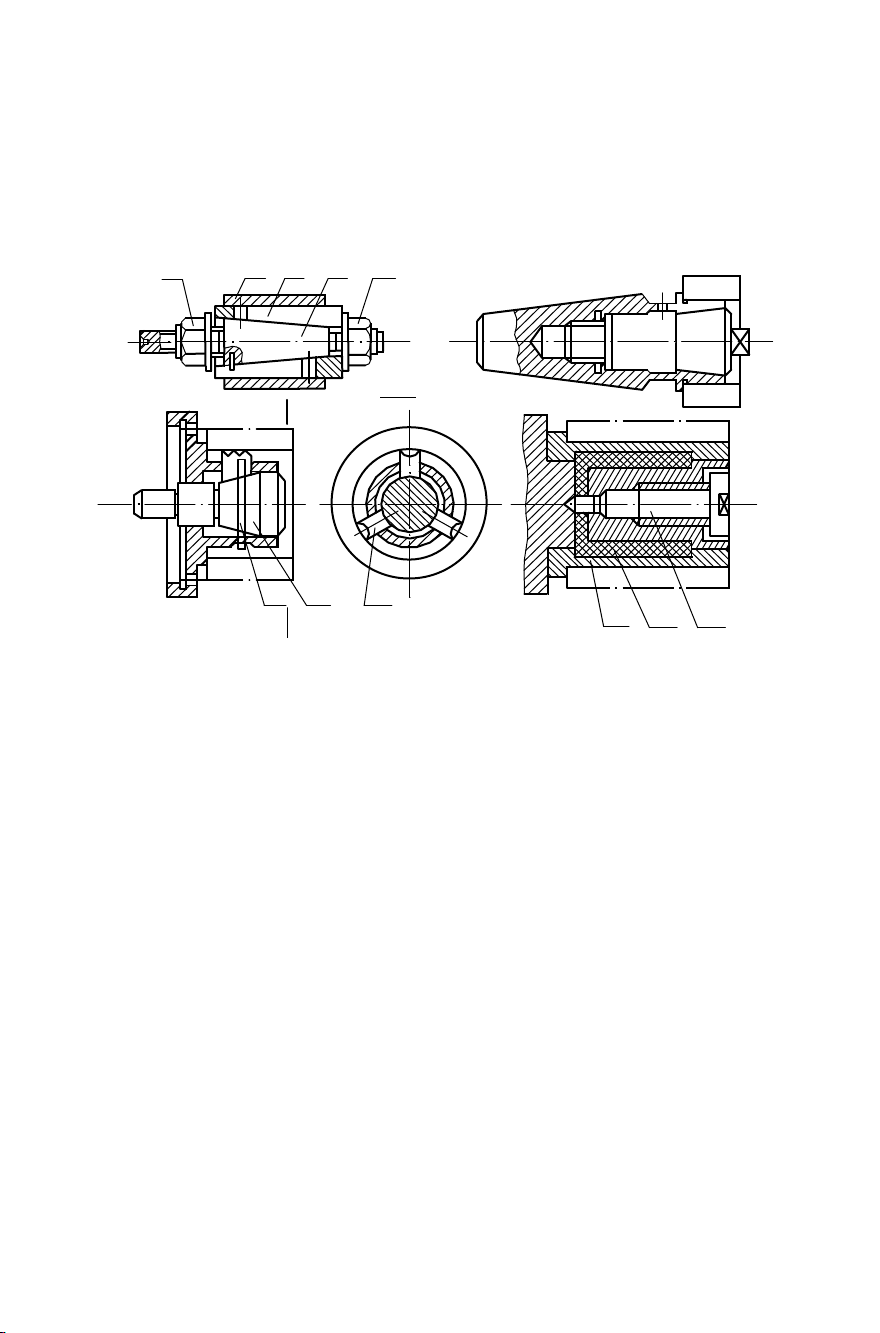
198
Hình 3.25b là trục gá để lắp có độ đôi với chi tiết gia công, chính vì
vậy mà nó định vị theo chiều dài chính xác hơn. Nhờ có rãnh 1 nên có
thể xén mặt đầu của chi tiết gia công một cách dễ dàng.
Hình 3.25c là loại trục gá có vai định vị cả chiều trục và có then để
truyền mômen xoắn cho chi tiết.
Hình 3.26a là trục gá bung. Khi xiết đai ốc 5 sẽ làm ống đàn hồi 3
dịch chuyển về bên trái, nhờ trục côn 4 mà ống đàn hồi sẽ bung ra theo
phương hướng kính và ép sát vào bề mặt lỗ của chi tiết gia công 2. Đai ốc
1 sẽ khống chế sự dịch chuyển của ống đàn hồi về phía trái.
Hình 3.26b là trục gá bung kiểu côngxôn, kẹp chặt phôi nhờ xiết
trục côn. So với trục cứng loại này có độ đồng tâm cao hơn.
Hình 3.26c Là trục gá bung kiểu chấu, loại này có ba chấu 1 được
bung ra nhờ trục côn 2. Nó thường dùng để gá đặt phôi có thành dày.
Hình 3.26d là trục gá bung kiểu chất dẻo. Khi vặn vít 3, chất dẻo 2
bị ép lại làm bung ống đàn hồi 1 ra và ép sát vào bề mặt lỗ của chi tiết gia
công. Trục gá kiểu này đảm bảo độ đồng tâm rất cao 0,005 0,01 mm.
c. Mũi tâm
Khi gia công các chi tiết trục hoặc những phôi có bề mặt chuẩn là 2
lỗ tâm hoặc vát côn thì đồ định vị là các mũi tâm.
Hình 3.27a là loại mũi tâm cứng thông dụng.
1
2
3
5
1
2
3
4
a)
b)
c)
d)
1
2
1
A-A
A
A
Hình 3.26: Trục gá bung
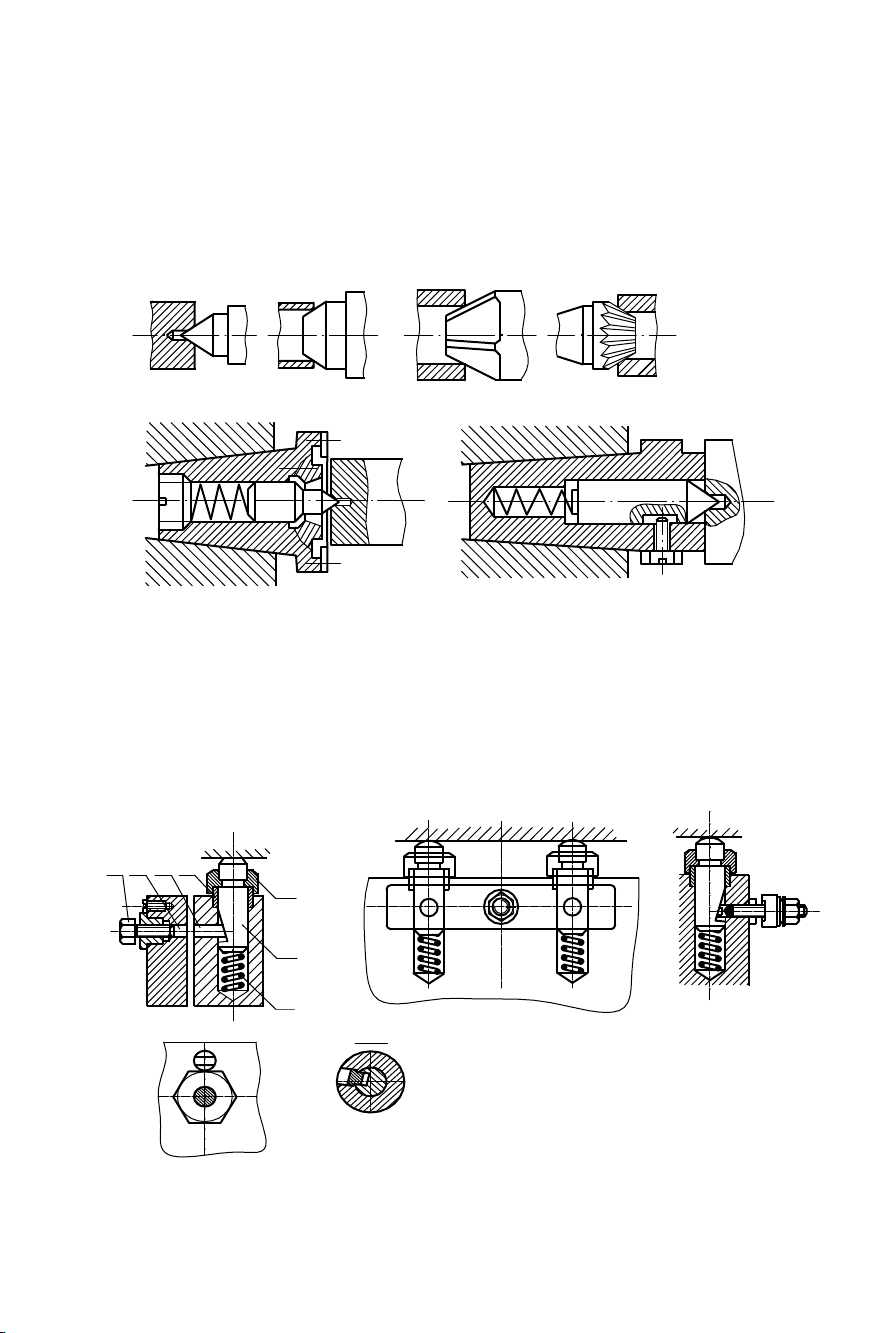
199
Hình 3.27b là loại mũi tâm lớn.
Hình 3.27c là loại mũi tâm vát.
Hình 3.27d là loại mũi tâm khía rãnh dùng để định vị và truyền
mômen quay.
Hình 3.27e,f là loại mũi tâm tự lựa dùng để chặn mặt đầu chính xác
3.4.3. Các chi tiết định vị phụ
3.4.3.1. Chốt tỳ phụ
Dùng chốt tỳ định vị để tăng độ vững chắc của chi tiết gia công, tự
nó sẽ theo đúng vị trí của chi tiết gia công đã được định vị.
Cấu tạo và nguyên tắc làm việc (hình 3.28a) như sau:
a)
b)
Hình 3.27: Các lọai mũi tâm
c)
d)
e)
f)
Hình 3.28: Chốt tỳ phụ
a)
b)
1
2
3
4
5
6
7
C-C
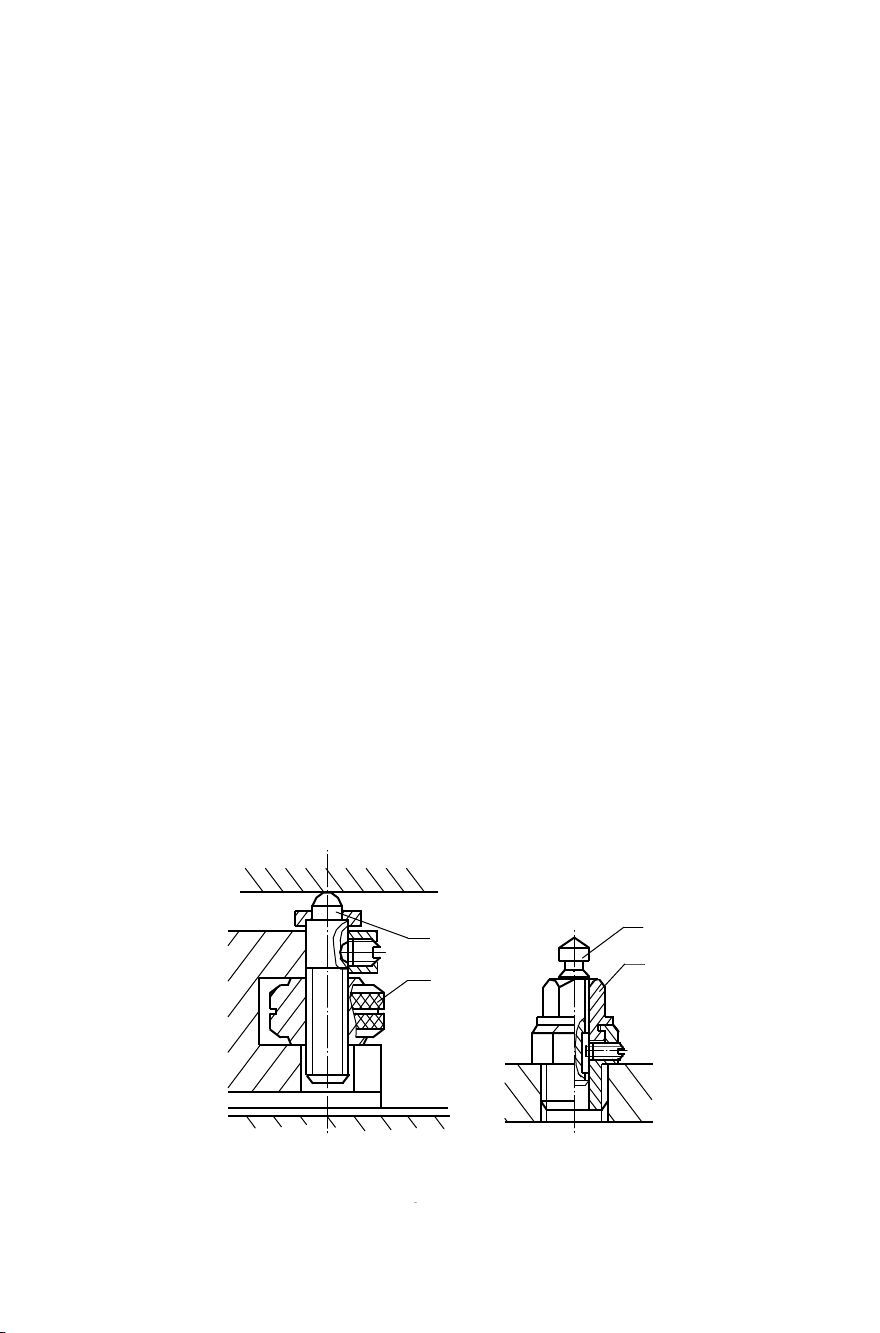
200
Dưới tác dụng của lò xo 1, chốt tỳ 2 luôn luôn tiếp xúc với chi tiết
gia công đặt trên các chi tiết định vị chính. Khi xiết vít 3, thông qua hai
chốt trượt 4 và 5 sẽ đảm bảo cố định chốt đỡ 2 lại.
Góc dốc của mặt vát trên chốt tỳ 2 phải đảm bảo tự hãm. (=5 6
0
)
nếu không chi tiết gia công sẽ bị đẩy lên khi hãm chốt. Chốt trượt 5 một
đầu trượt được vát để lồng vào rãnh dọc trên chốt 2 giữ cho chốt 2 khỏi
quay (xem tiết diện C-C) còn đầu kia có lỗ ren để lắp chốt được dễ dàng.
Để đảm bảo chốt tỳ 2 trượt được tốt, không bị ảnh hưởng của phôi,
trên thân gá còn lắp một ống lót 6 và đầu chốt đỡ nắp mũ 7.
Khi gá chi tiết gia công lên đó phải nới lỏng vít 3, lò xo 1 sẽ đẩy
chốt 2 lên cao hơn mặt định vị một ít nên khi đặt chi tiết gia công vào nó
sẽ tiếp xúc với chốt 2 trước.
Nếu chi tiết gia công quá nhẹ, phải lấy tay ép xuống trước khi hãm
chốt. Nếu trong gá lắp có dùng nhiều chốt tỳ định vị thì nên bố trí một
cơ cấu hãm chung để giảm thời gian phụ và tránh khỏi quên nới lỏng
hoặc hãm chặt một chốt tỳ nào (hình 3.28b)
3.4.3.2. Bộ phận đỡ điều chỉnh
Khi dùng bộ phận đỡ điều chỉnh, công nhân phải điều chỉnh đai ốc
1 để cho chốt 2 tiếp xúc với chi tiết gia công, sau khi đã định vị trên các
chi tiết định vị chính.
Hình 3.29a là các bộ phận đỡ điều chỉnh bằng tay, được dùng để
đỡ các chi tiết gia công nhẹ.
Hình 3.29b là bộ phận đỡ điều chỉnh dùng để đỡ các chi tiết gia
công lớn. Điều chỉnh bằng dụng cụ như cờ lê, mỏ lết,...
b)
1
2
a)
Hình 3.29: Bộ phận đỡ
điều chỉnh
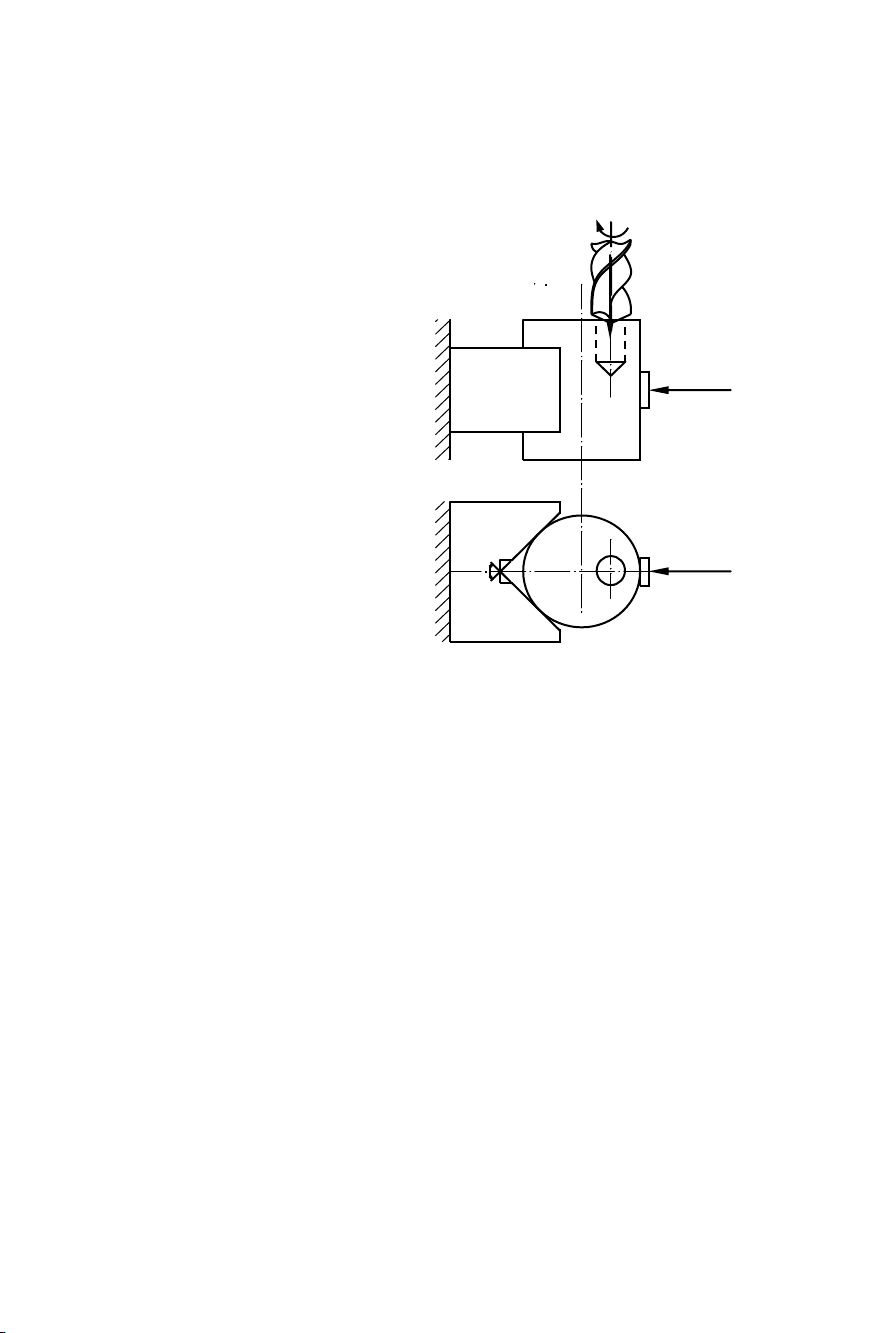
201
3.5. KẸP CHẶT VÀ NHỮNG TÍNH TOÁN VỀ KẸP CHẶT
3.5.1. Khái niệm và các yêu cầu về kẹp chặt
3.5.1.1. Khái niệm về kẹp chặt
Kẹp chặt là cố định chi tiết
đã được định vị, để trong quá
trình gia công chi tiết không bị
rung động, xê dịch hoặc biến
dạng do lực cắt hoặc do trọng
lượng bản thân của chi tiết gia
công gây ra. Lưu ý cần tránh
nhầm lẫn giữa định vị và kẹp
chặt.
Trên hình 3.30, ta thấy chi
tiết cần gia công (khoan lỗ) đã
được định vị trong khối V nhằm
hạn chế bốn bậc tự do còn hai
bậc tự do là tịnh tiến theo
phương dọc trục và xoay quanh
trục của chính bản thân nó, đó
chỉ mới là vấn đề định vị.
Ở trường hợp này, nếu lực khoan P
0
và mômen khoan M
0
thắng
được các lực ma sát sinh ra do lực kẹp chặt W thì chi tiết sẽ bị trượt và bị
xoay, không tiến hành khoan được.
Do đó, để khoan được, lực kẹp W phải đủ lớn để tránh cho chi tiết
bị trượt và bị xoay do lực cắt.
3.5.1.2. Ý nghĩa của vấn đề kẹp chặt
Việc kẹp chặt có ảnh hưởng rất lớn đến quá trình gia công chi tiết.
Nếu thực hiện tốt vấn đề kẹp chặt thì giảm được sức lao động, giảm
thời gian gia công, nâng cao độ chính xác và độ bóng gia công. Đối với
sản xuất hàng loạt lớn và hàng khối cần giải quyết được vấn đề kẹp chặt,
nó mang một ý nghĩa quan trọng, ở các dạng sản xuất này việc cơ khí hóa
và tự động hóa khâu kẹp chặt nhằm giảm sức lao động cho người công
nhân, rút ngắn thời gian lao động, sản phẩm gia công đạt được năng suất
và chất lượng cao.
Khi thiết kế cơ cấu kẹp chặt cần phải chú ý: Phương, chiều, điểm
đặt và trị số của lực kẹp, tính tự hãm của cơ cấu truyền động và kết cấu
của cơ cấu kẹp hợp lý.
3.5.1.3. Những yêu cầu cần thiết đối với cơ cấu kẹp
M
0
W
P
0
W
Hình 3. 30: Sơ đồ kẹp chặt
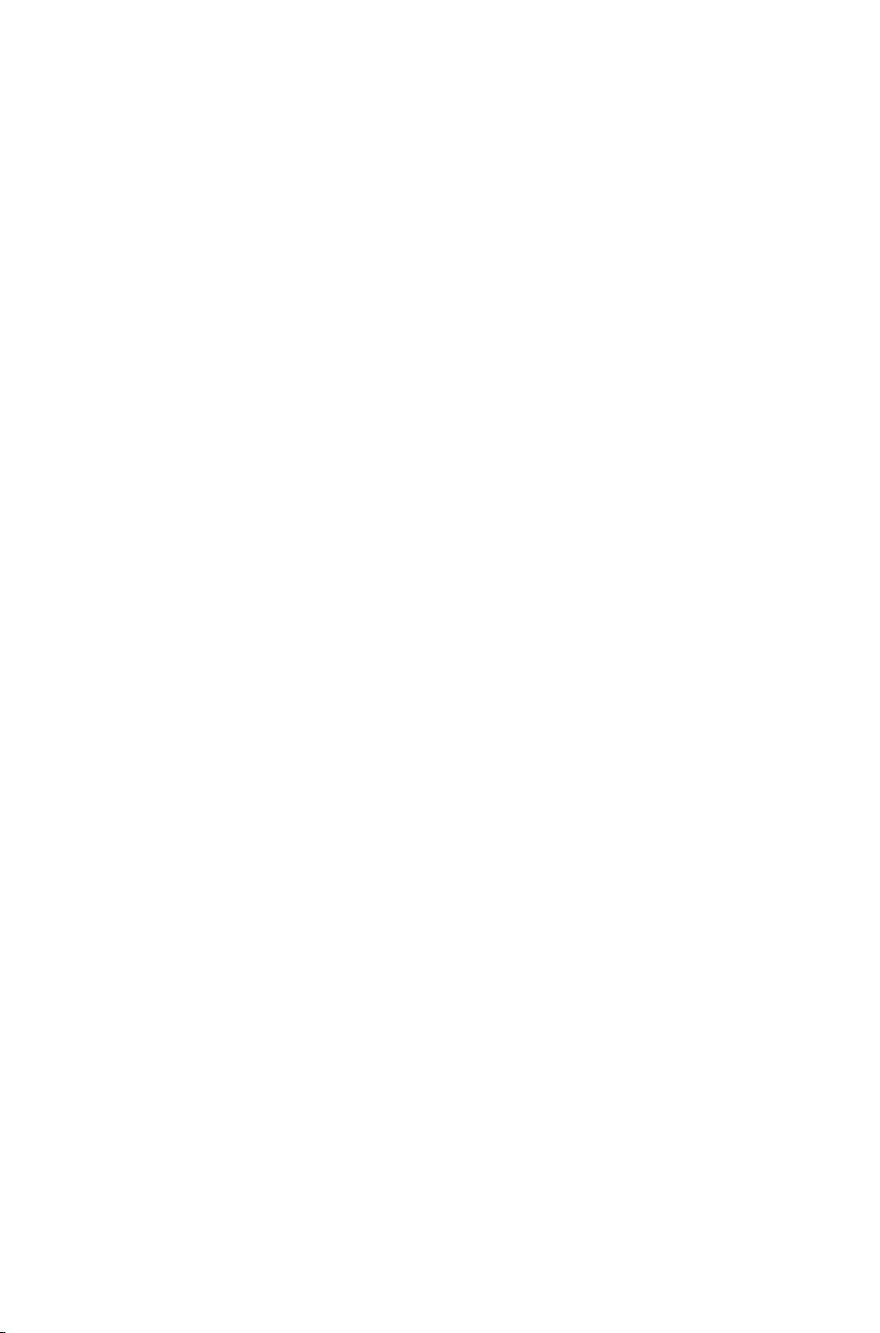
202
Không được thay đổi vị trí đã định vị của chi tiết gia công.
Lực kẹp phải vừa đủ không bé hơn lực kẹp cần thiết đồng thời
cũng không quá lớn để tránh chi tiết bị biến dạng.
Biến dạng do lực kẹp gây ra không được vượt quá giới hạn cho phép.
Đảm bảo động tác phải nhanh, nhẹ, thao tác tiện lợi, an toàn.
Cơ cấu kẹp chặt phải nhỏ gọn, đơn giản, gắn liền thành một khối.
3.5.1.4. Phương và chiều của lực kẹp
Phương và chiều của lực kẹp có liên quan mật thiết với chuẩn định
vị chính, chiều của lực cắt và chiều của trọng lượng bản thân vật gia công.
Phương của lực kẹp nên cố gắng thẳng góc với mặt chuẩn định vị
chính (mặt hạn chế ba bậc tự do), vì như thế ta có diện tích tiếp xúc lớn nhất.
Chiều của lực kẹp thì đi từ ngoài vào mặt định vị, chiều lực kẹp
không nên ngược với chiều lực cắt và trọng lượng vật gia công vì như thế
lực kẹp sẽ phải rất lớn, cơ cấu kẹp sẽ cồng kềnh, thao tác tốn sức, nhất là
khi gia công thô, lực kẹp nên cùng chiều lực cắt và trọng lượng bản thân
chi tiết gia công là tốt nhất nhưng đôi khi vì kết cấu chi tiết gia công
không cho phép thì ta chọn chúng thẳng góc với nhau.
3.5.1.5. Điểm đặt của lực kẹp
Khi kẹp vật gia công phải ít bị biến dạng nhất, vì vậy lực kẹp
phải tác dụng vào chỗ có độ cứng vững lớn.
Khi kẹp không gây ra mômen quay đối với vật gia công, muốn
vậy điểm đặt lực phải tác dụng ở trong diện tích mặt định vị hoặc ở trong
mấy điểm đỡ và phải gần mặt gia công.
Hình 3.31 chỉ ra một số trường hợp đặt lực kẹp tốt và không tốt về
phương, chiều và điểm đặt để chúng ta tham khảo.
Phân loại cơ cấu kẹp chặt
Các cơ cấu kẹp của đồ gá chia ra loại đơn giản và loại tổ hợp tức là
hợp thành bởi hai hoặc ba cơ cấu đơn giản.
Các cơ cấu đơn giản bao gồm chêm, vít, cam lệch tâm, đòn bẩy,
đòn bẩy – bản lề v.v…Các cơ cấu kẹp tổ hợp thường do liên hợp các cơ
cấu đơn giản tạo thành như vít – đòn bẩy, cam lệch tâm – đòn bẩy v.v …
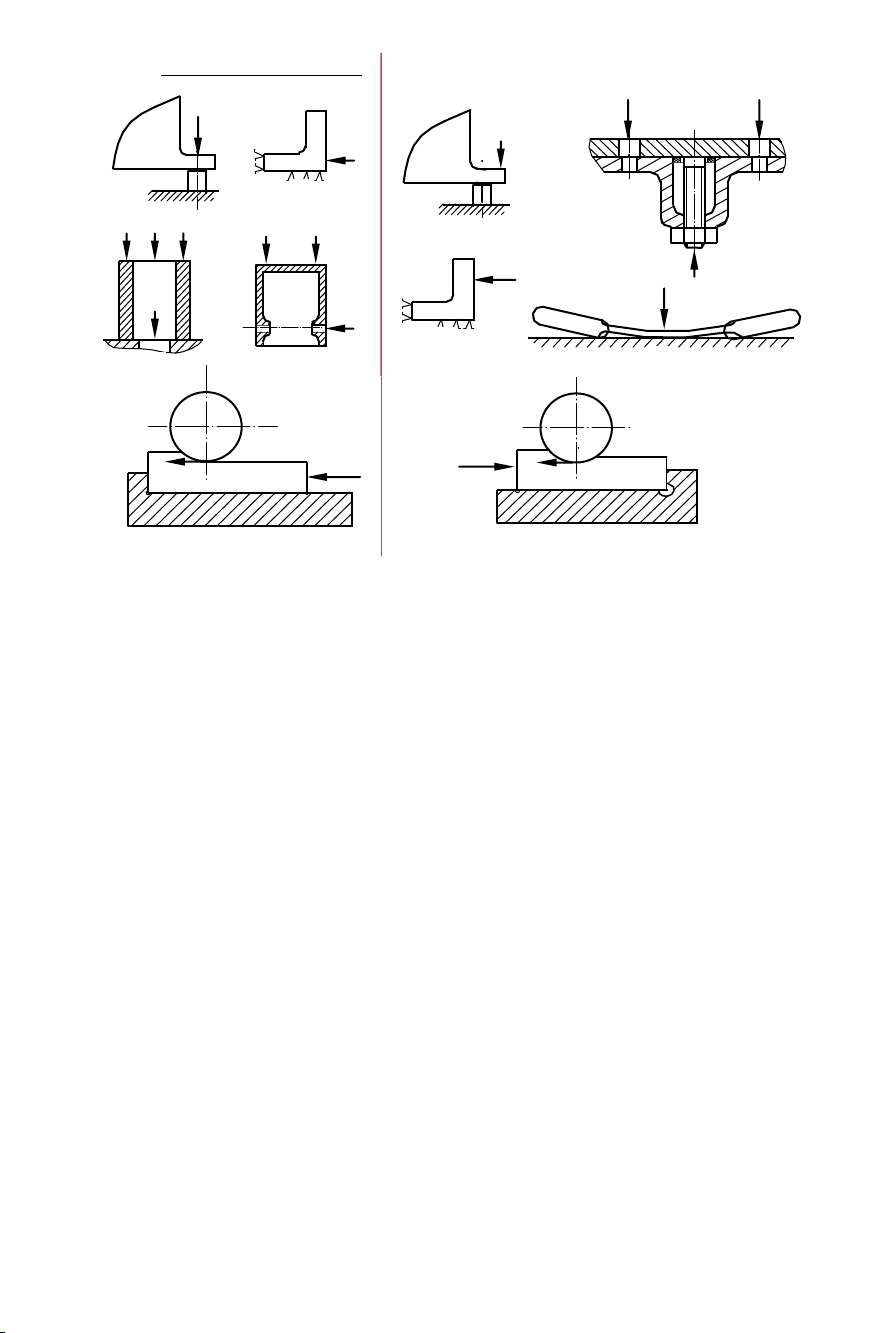
203
Theo phương pháp điều khiển, cơ cấu kẹp chặt có thể chia ra loại
thủ công, cơ khí hóa và tự động hóa.
Các cơ cấu kẹp thủ công đòi hỏi dùng sức lực con người, cho nên
năng suất thấp công nhân chóng mệt mỏi.
Cơ cấu cơ khí hóa được thực hiện từ cần truyền động, năng suất
cao, lực kẹp ổn định, chính xác.
Cơ cấu kẹp chặt tự động hóa do việc chuyển động của các bàn máy,
các gá dao, các trục chính hoặc các quán tính ly tâm của các khối lượng
quay thực hiện kẹp chặt và nới lỏng không có sự tham gia của công nhân.
Theo nguồn năng lượng, truyền động chia ra: cơ khí, khí nén, thủy
lực, điện, điện từ, chân không hoặc hỗn hợp một số loại trên.
3.5.2. Phƣơng pháp tính lực kẹp cần thiết W
ct
3.5.2.1. Đặt vấn đề
Khi lựa chọn phương án gá đặt, cần xét hai vấn đề chính:
Một là: Lựa chọn cách định vị và cơ cấu định vị sau cho hợp lý và
đủ bậc tự do.
Hai là: Lựa chọn phương chiều, điểm đặt và trị số của lực kẹp sao cho
đủ sức chống lại lực cắt và các ngoại lực khác mà vẫn nhỏ gọn, an toàn.
Điểm đặt lực kẹp tốt
P
0
W
W
G
c)
W
d)
W
P
0
a)
W
W
b)
Điểm đặt lực kẹp không tốt
m)
W
k)
W
g)
W
f)
W
P
o
P
o
j)
W
e)
P
z
W
i)
P
z
Hình 3.31: Sơ đồ so sánh điểm đặt
lực kẹp
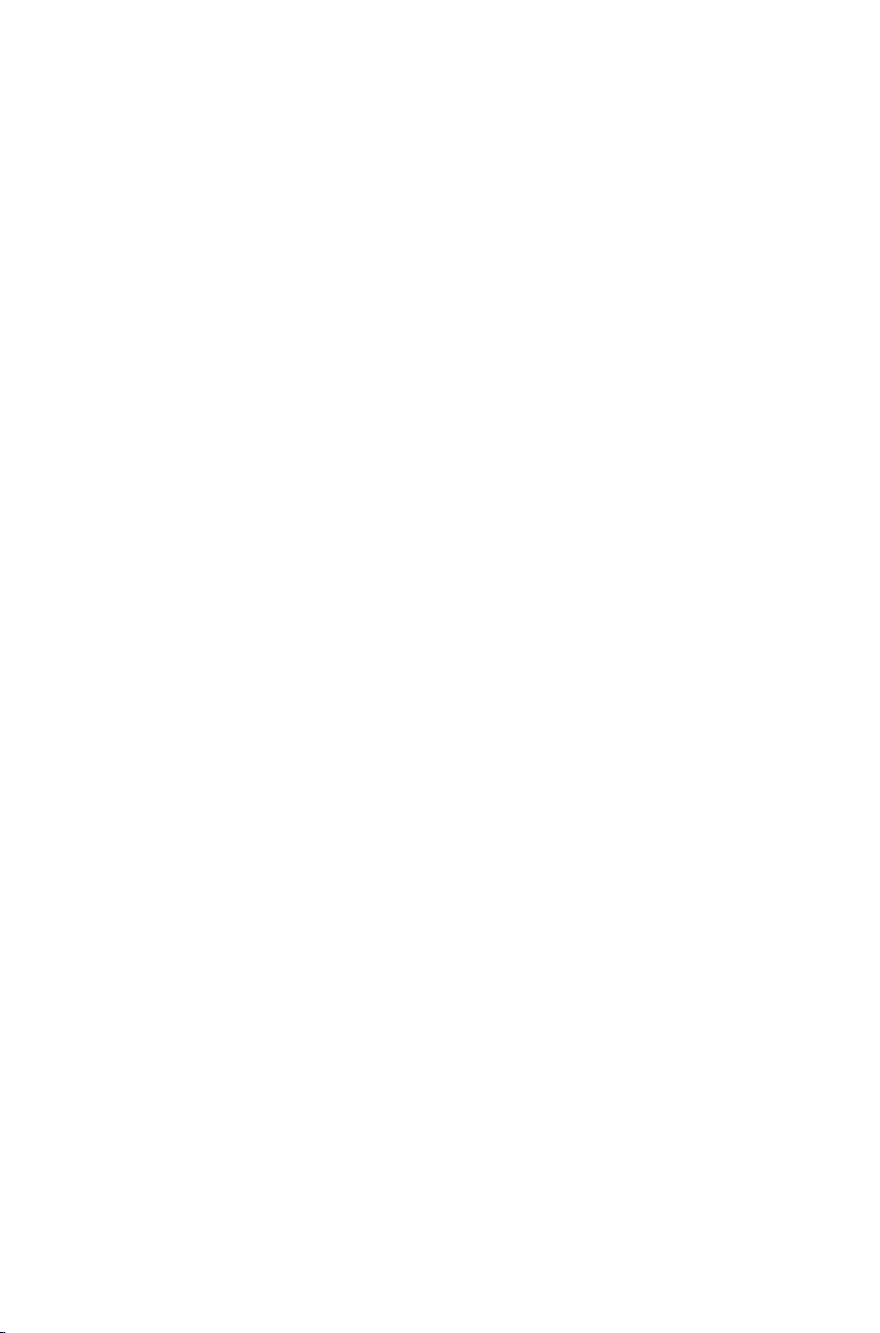
204
Trong vấn đề thứ hai, việc xác định trị số của lực kẹp chính là nội
dung của mục “Phương pháp tính lực kẹp cần thiết”.
Sau khi tính được lực kẹp cần thiết W
ct
, tiến hành chọn cơ cấu kẹp
mà cơ cấu đó tạo ra được lực kẹp W bằng trị số của lực kẹp cần thiết,
nghĩa là: W = W
ct
Phương pháp tính lực kẹp cần thiết xuất phát từ điều kiện cân bằng
tĩnh của chi tiết gia công trong đồ gá dưới tác dụng của các lực: lực cắt,
lực kẹp cần thiết, trọng lực, lực ly tâm, lực ma sát… Ta tiến hành viết
phương trình cân bằng lực hoặc cân bằng mômen, từ đó rút ra được công
thức tính lực kẹp cần thiết.
Để đảm bảo độ tin cậy khi kẹp chặt thì trị số lực cắt tính toán phải
nhân với hệ số an toàn K, thông thường K= 1,4 2,6 (khi gia công tinh
chọn K=1,4 1,6; khi gia công thô chọn K=1,7 2,6)
Hệ số an toàn K phụ thuộc vào điều kiện gia công của chi tiết trên
máy.
K = K
0
.K
1
.K
2
.K
3
.K
4
.K
5
.K
6
(3.1)
Hệ số an toàn thường lấy K
0
=1,5
K
1
– Hệ số kể đến tính bề mặt gia công (chưa được gia công hoặc
đã gia công), gia công thô K
1
= 1,2, gia công tinh K
1
= 1,1
K
2
– Hệ số kể đến việc tăng lực cắt do mòn dao, thường K
2
= 1,2 1,6
K
3
– Hệ số kể đến việc tăng lực cắt khi gia công các bề mặt không
liên tục, K
3
= 1
K
4
– Hệ số kể đến lực kẹp ổn định, kẹp bằng tay K
4
=1,3, kẹp bằng
khí ép, dầu ép K
4
=1,0
K
5
– Hệ số xét đến ảnh hưởng của mômen làm quay chi tiết quanh
trục của nó, khi kẹp bằng tay có góc quay nhỏ hơn 90
0
lấy K
5
= 1,0, góc
quay lớn hơn 90
0
thì lấy K
5
= 1,2
K
6
– Hệ số xét mômen làm phôi lật quanh điểm tựa, khi điểm tựa
có mặt tiếp xúc bé (chốt)
K
6
= 1, khi điểm tựa có mặt tiếp xúc lớn, K
6
= 1,2
3.5.2.2. Những yếu tố để tính lực kẹp cần thiết
Để tính lực kẹp cần thiết ta cần có sơ đồ nguyên công nghĩa là:
- Phương án định vị và đồ định vị.
- Phương chiều, điểm đặt lực kẹp (W
ct
).
- Phương chiều, điểm đặt và giá trị của lực cắt.
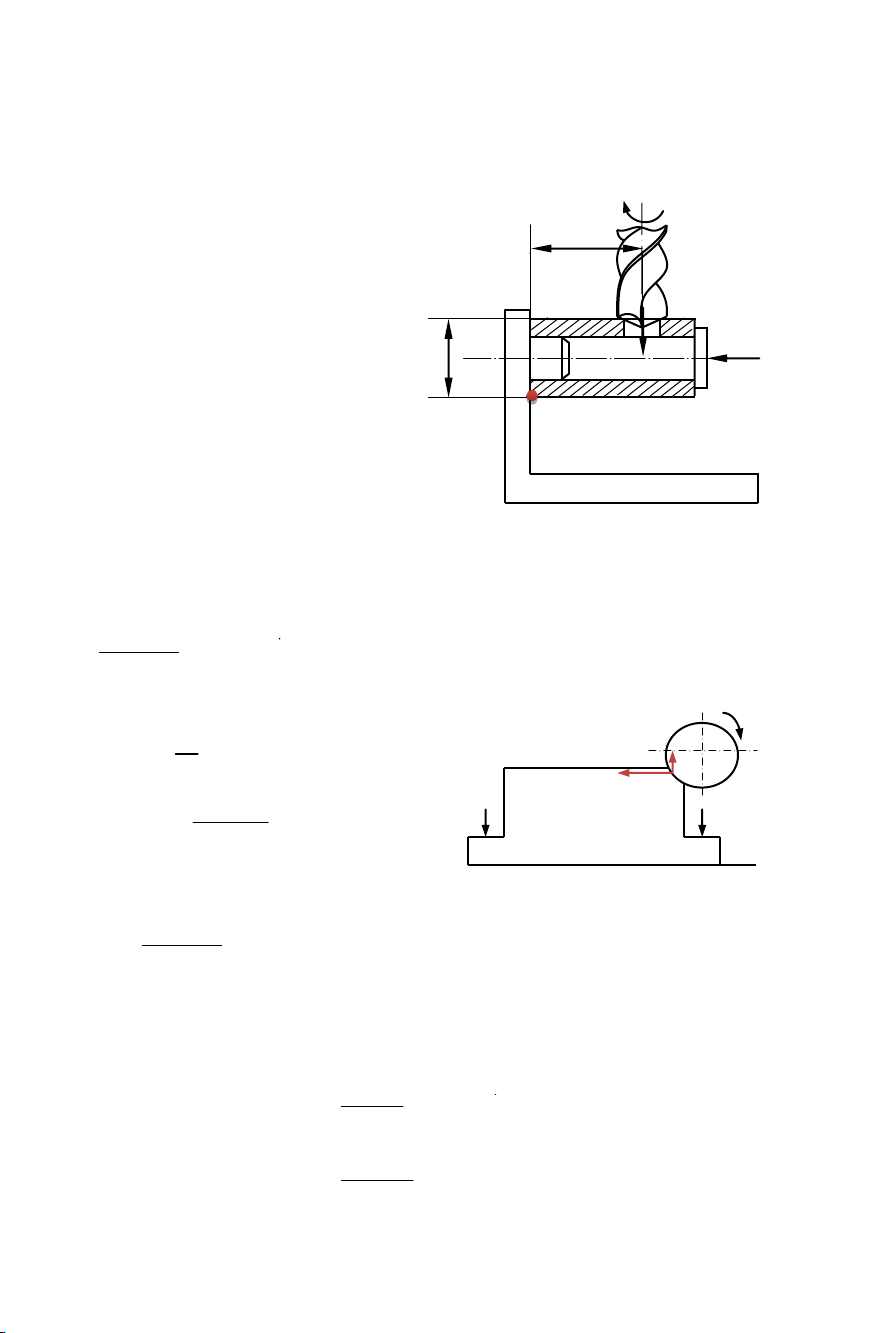
205
- Trọng lực, lực ly tâm, lực quán tính nếu có.
- Các kích thước liên quan về vị trí giữa các lực nói trên với nhau
và với đồ định vị.
3.5.2.3. Phương pháp tính
Khi đã có sơ đồ nguyên
công, trong thực tế, ta có thể
xem dưới tác dụng của lực cắt,
lực ly tâm… chi tiết chuyển vị
theo phương nào hay quay
quanh trục nào, lực kẹp hay lực
ma sát phải chống lại sự chuyển
vị đó, hoặc tạo ra được mômen
chống lại sự quay của chi tiết.
Trên cơ sở phân tích đó, ta có
thể viết được hai loại phương
trình cân bằng: phương trình
cân bằng lực, và phương trình
cân bằng mômen.
Ví dụ 1: Ở sơ đồ gá đặt hình 3.32, dưới tác dụng của lực khoan P
0
, chi
tiết sẽ bị lật xung quanh điểm O. Phương trình cân bằng lực được viết
theo (3.2), Từ đó rút ra lực kẹp cần thiết (3.3)
Ví dụ 2:Trên sơ đồ gia công hình 3.33, lực cắt P
z
được phân ra hai
thành phần, lực P
zd
sẽ nhắc chi tiết lên khỏi mặt định vị của đồ gá, P
zn
sẽ
làm cho chi tiết trượt trên mặt định vị của đồ gá, khi coi P
zn
= P
z
ta có các
phương trình cân bằng lực sau:
Hoặc:
f
PK
W
f
PK
W
PKfW
zđ
ct
z
ct
zct
2
.
.2
.
..2
(3.4)
ct
ct
P
zn
P
zđ
Hình 3.33: Sơ đồ tính W
ct
khi phay
Hình 3.32: Sơ đồ tính W
ct
khi
khoan
W
ct
M
c
P
0
O
D
l
D
lPK
W
lPK
D
W
ct
ct
..2
..
2
.
0
0
( 3.3)
( 3.2)
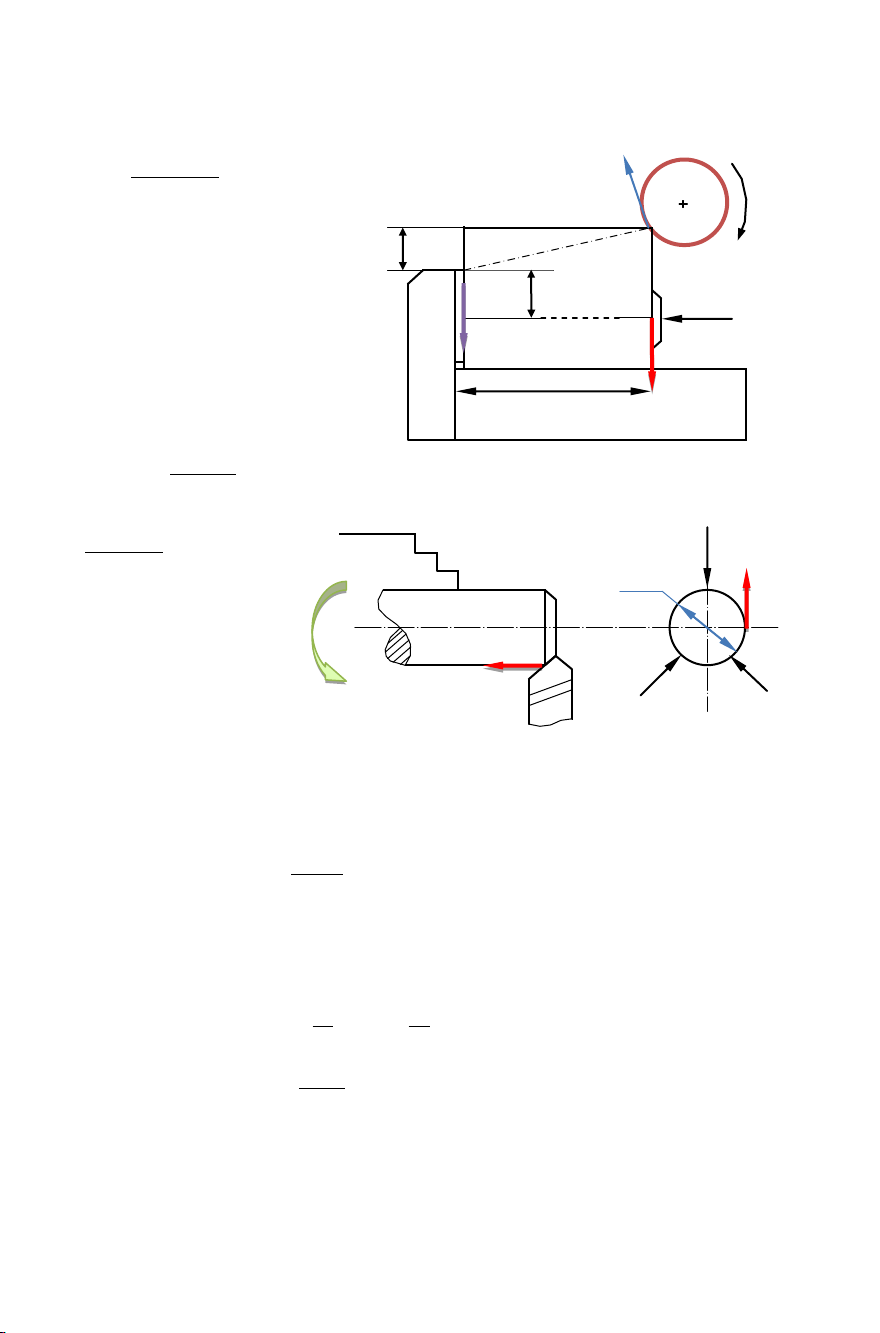
206
Thông thường lượng dư cắt nhỏ, do đó: P
zđ
<< P
zn
nên ta có thể sử
dụng công thức (3.4) để tính W
ct.
Ví dụ 3: Khi gia công
chi tiết có sơ đồ gá đặt hình
3.34, dưới tác dụng của lực
P
z
, chi tiết sẽ bị lật xung
điểm A. hương trình cân
bằng mômen sau:
Suy ra:
Ví dụ 4:
Phân tích lực
khi tiện chi tiết trên
mân cặp ba chấu có
sơ đồ công nghệ hình
3.35, ta thấy lực P
x
sẽ làm chi tiết trượt
dọc trục, phương
trình cân bằng lực là:
f
PK
W
PKfW
x
ct
xct
.3
.
..3
Lực P
z
sẽ làm chi tiết quay quanh tâm của nó ta có phương trình
cân bằng mômen:
Vì: P
z
> P
x
nên chọn W
ct
theo công thức (3.7), đó là lực trên một chấu.
f
PK
W
D
PK
D
fW
z
ct
zct
3
.
2
..
2
..3
W
ct
W
ct
W
ct
P
z
P
X
Hình 3.35: Sơ đồ tính W
ct
khi tiện
n
D
Hình 3.34: Sơ đồ tính W
ct
khi phay
l
/
A
W
ct
F
ms1
a
b
F
ms2
n
d
P
z
l
lFaWlPK
msctz
....
2
/
)5.3(
.
..
/
lfa
lPK
W
z
ct
lfWaWlPK
ctctz
.....
/
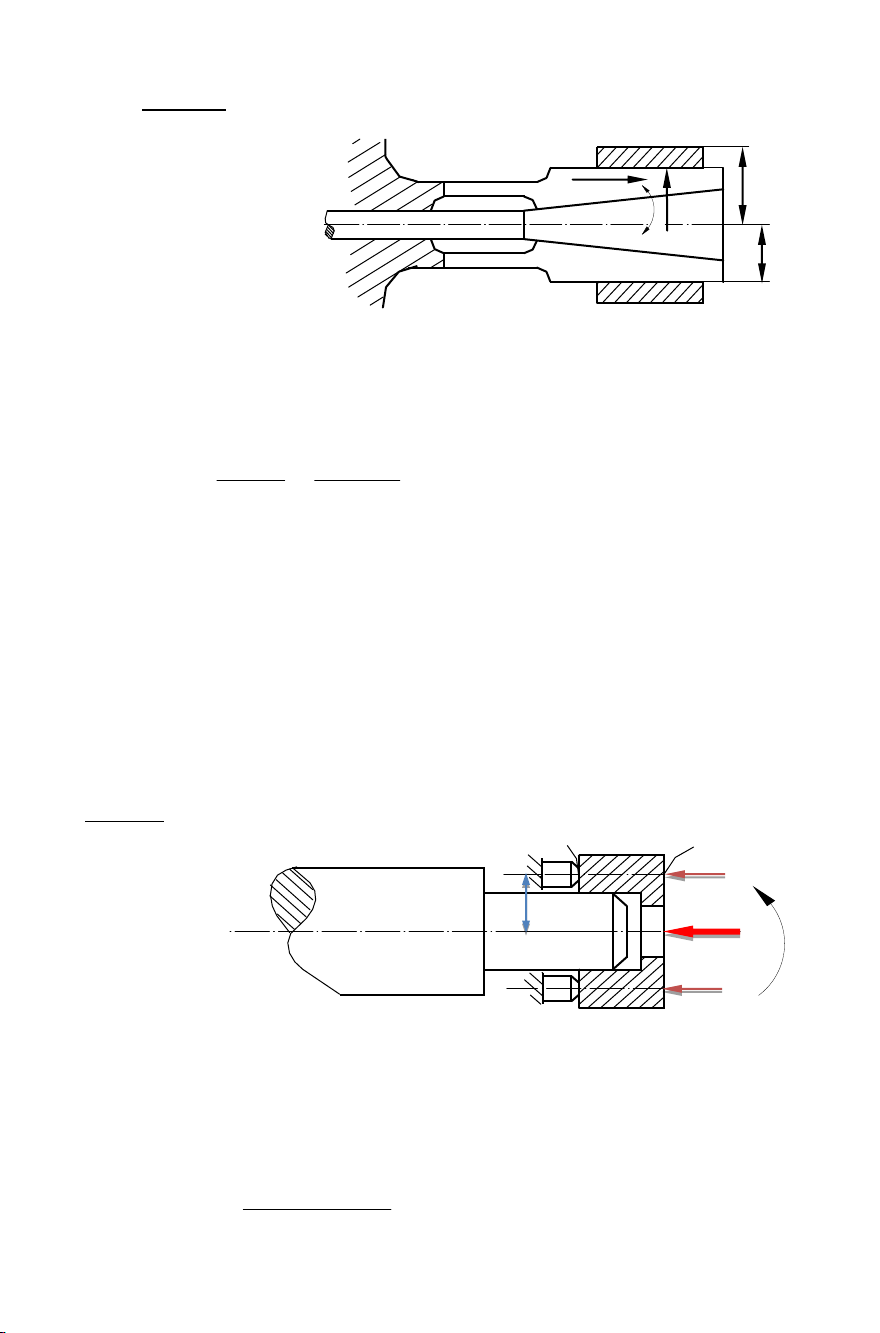
207
Ví dụ 5: Chi tiết gia công được kẹp trên ống đàn hồi hình 3.36,
mômen của lực ma sát
giữa bề mặt của chi
tiết và trục gá kẹp phải
đủ để chống lại sự
quay của chi tiết xung
quanh đường trục của
nó dưới tác dụng của
mômen lực cắt P
z,
phương trình cân bằng
mômen là:
Trong đó:
W
ct
– Lực kẹp cần thiết; tổng ( tùy theo số chấu mà phân bố );
M
c
– Mômen của lực cắt;
R – Bán kính trục gá kẹp;
R
1
– Bán kính chi tiết gia công;
f – Hệ số ma sát;
Ví dụ 6: Lỗ của chi tiết gia công hình 3.37 được định vị trên chốt của đồ
gá, còn mặt
mút trái tỳ
vào ba chốt
đỡ, chi tiết
gia công
chịu tác
dụng của
mômen M
c
và lực dọc
P
x
. Phương
trình cân bằng mômen như sau:
12
12
1212
.
..-.
.....
Rf
RPfMK
W
RPfRWfMK
xc
ct
xctc
Rf
RPK
Rf
MK
W
RPKMKRfW
zc
ct
zcct
.
..
.
.
.....
1
1
W
ct
R1
Hình 3.36: Sơ đồ tính W
ct
khi gá bung
R
M
c
W
c
t
f
1
R1
P
x
f
2
Hình 3.37: Sơ đồ tính W
ct
khi kẹp mặt đầu
R
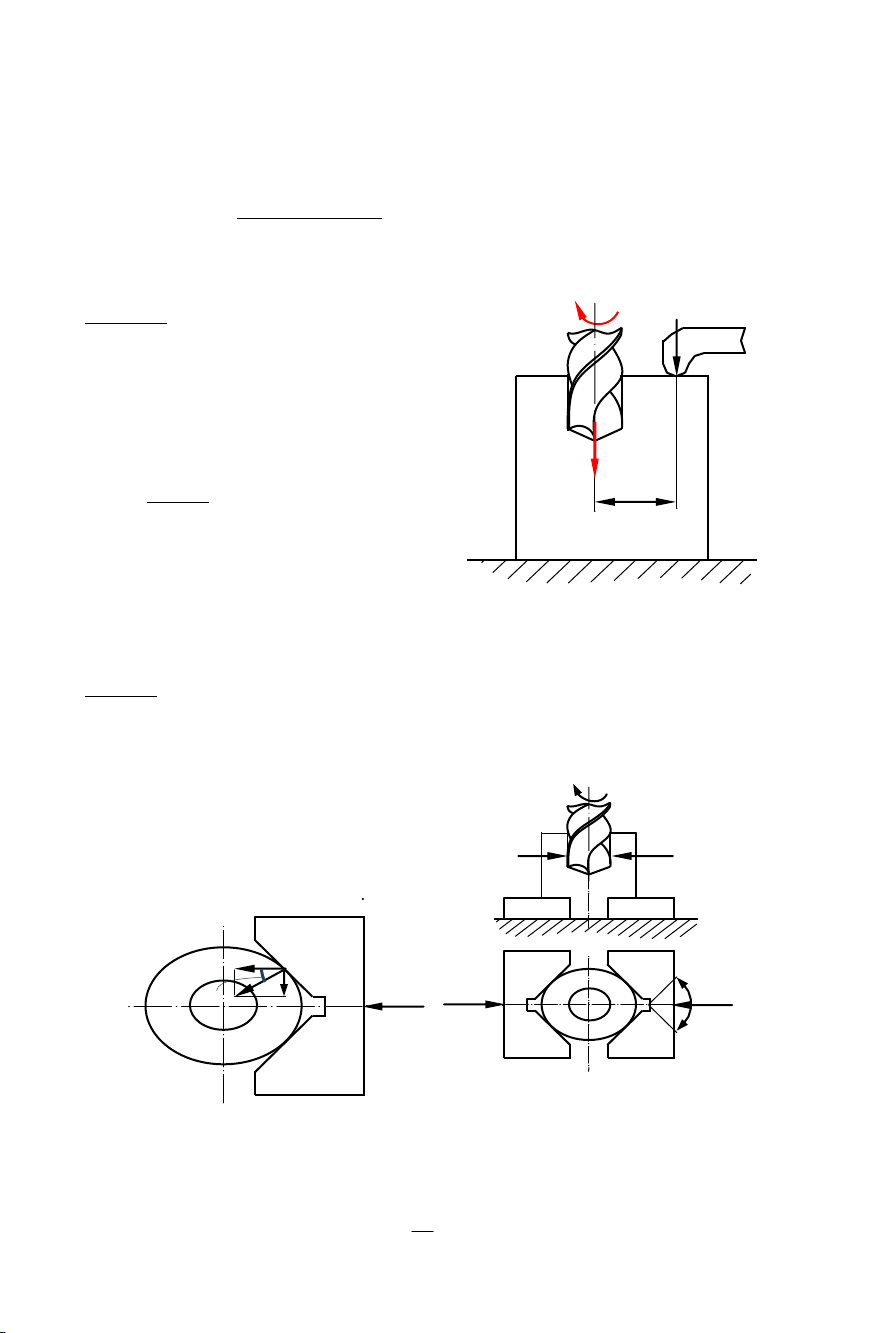
208
Nếu kể đến cả ảnh hưởng của lực ma sát giữa chi tiết gia công và
chi tiết kẹp chặt thì lực kẹp cần thiết được tính:
Ví dụ 7: Khi khoan chi tiết có sơ đồ
gá đặt như hình 3.38, phương trình
cân bằng mômen như sau:
af
MK
W
MKafW
c
ct
cct
.
.
...
Trong trường hợp này, chi tiết bị
xoay quanh tâm lỗ, nếu khoan lỗ
không thủng thì P
0
cùng tham gia vào
việc kẹp chặt, lúc đó W
ct
sẽ nhỏ đi.
Ví dụ 8: Khi khoan chi tiết được định vị trong hai khối V, có sơ đồ công
nghệ như hình 3.39, chi tiết sẽ bị xoay xung quanh tâm của nó. Lực kẹp
phải tạo ra được mômen ma sát chống lại sự xoay đó.
Dựa vào sơ đồ phân tích lực ở hình 3.39, lực pháp tuyến N được tính:
121
12
11212
..
..-.
.......
RfRf
RPfMK
W
RWfRPfRWfMK
xc
ct
ctxctc
P
0
M
c
W
ct
Hình 3.38: Sơ đồ tính W
ct
khi khoan
a
Hình 3.39: Sơ đồ tính W
ct
khi kẹp bằng 2V
W
ct
f
/2
N
W/2
W
ct
W
ct
M
c
D
c
MK
D
fN .
2
..4
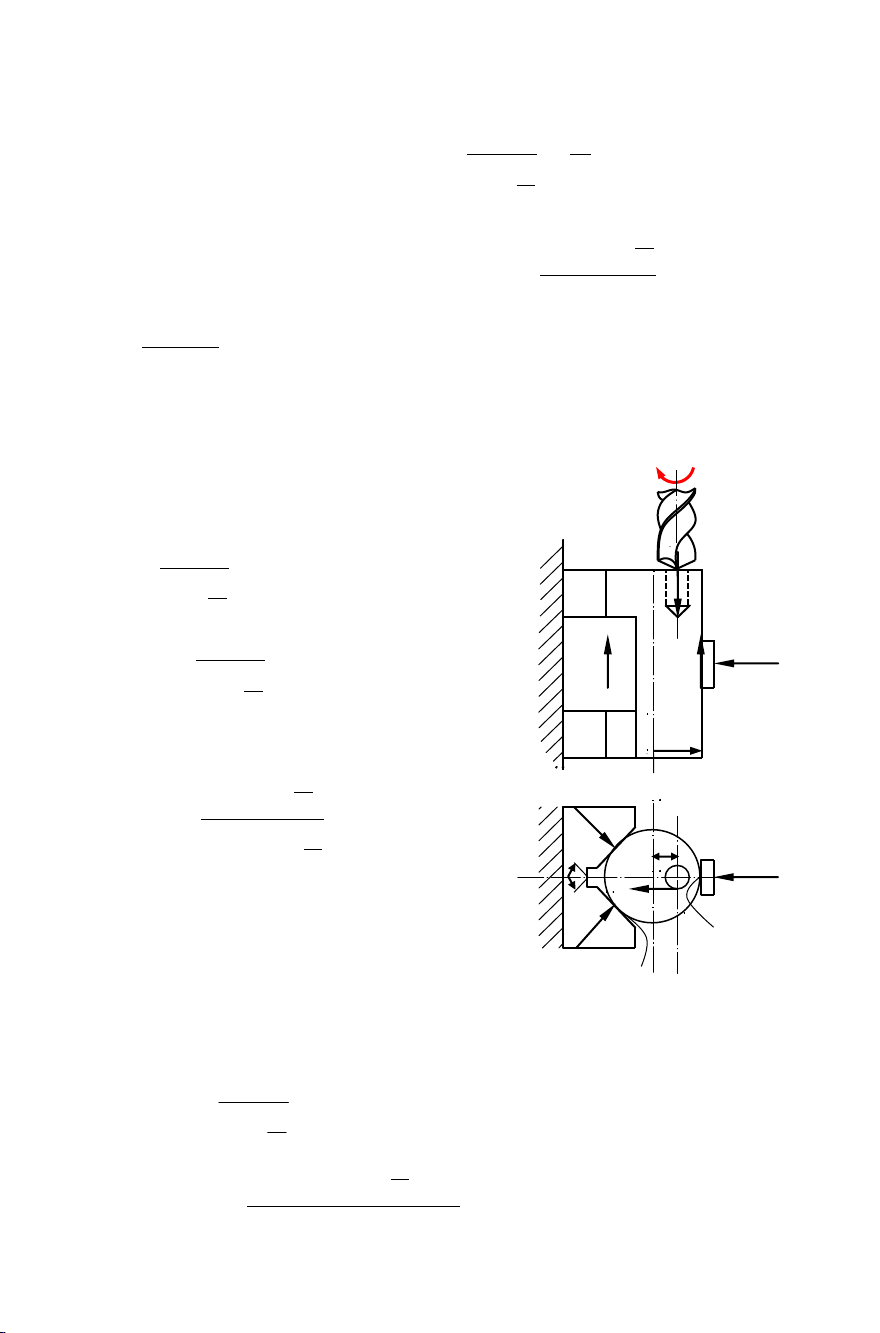
209
Phương trình cân bằng mômen:
Thế N vào ta có:
Suy ra:
Ví dụ 9: Tiến hành khoan chi tiết được định vị trên khối V, có sơ
đồ gá đặt hình 3.40, chi tiết được khoan lệch tâm và lực kẹp vuông góc
với chiều trục, khi đó chi tiết bị trượt dọc trục và xoay quanh tâm.
Điều kiện chống trượt dọc trục:
2F
ms1
+ F
ms2
= K.P
0
2N.f
1
+ W
ct
.f
2
= K.P
0
021
...
2
sin2
2 PKfWf
W
ct
ct
Suy ra:
2
sin.
2
sin..
21
0
ff
PK
W
ct
Điều kiện chống xoay (nếu xem chi
tiết quay quanh mũi khoan) ta có phương
trình cân bằng mômen:
2F
ms1
.R
ms1
+ F
ms2
.R
ms2
= K.M
c
Với: R
ms1
R + e; R
ms2
= R- e
Suy ra:
)()(
2
sin..
2121
ffeffR
MK
W
c
ct
2
sin2
ct
W
N
c
ct
MK
D
f
W
.
2
..
2
sin2
4
Df
MK
W
c
ct
.
2
sin..
Hình 3.40: Sơ đồ tính W
ct
W
ct
f
1
f
2
P
z
e
W
ct
P
0
M
c
F
ms1
F
ms2
R
cct
ct
MKeRfWeRf
W
.).(.).(.
2
sin2
2
21
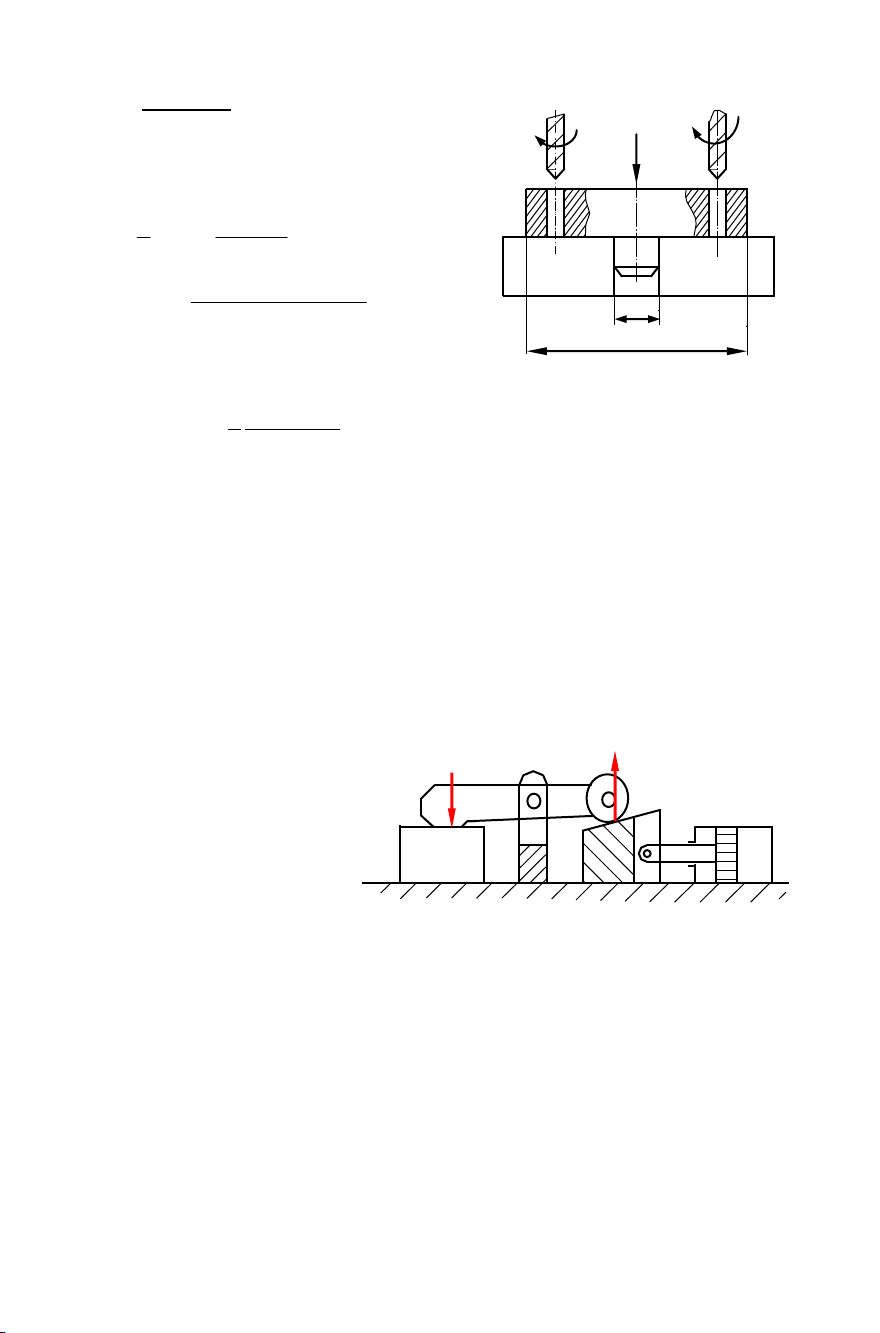
210
Ví dụ 10: Chi tiết dạng mặt
bích tròn được khoan n lỗ theo sơ đồ
hình 3.41. Để chống xoay khi khoan
chúng ta có phương trình:
Trong công thức này bán kính ma
sát là:
)(
)(
3
1
22
33
dD
dD
R
ms
3.6. CÁC CƠ CẤU KẸP CHẶT KIỂU CƠ KHÍ
3.6.1. Kẹp chặt bằng chêm
3.6.1.1. Khái niệm về kẹp chặt bằng chêm
Chêm là chi tiết kẹp chặt có hai bề mặt làm việc không song song
với nhau, khi chêm được đóng vào thì trên bề mặt làm việc tạo ra lực
kẹp. Nhờ lực ma sát giữa bề mặt chi tiết và bề mặt chêm mà trong quá
trình làm việc chêm không
bị tháo lỏng ra được, hiện
tượng này gọi là hiện
tượng tự hãm.
Chêm là dạng cơ
bản của các cơ cấu kẹp
chặt. Trong thực tế ít sử
dụng dạng chêm đơn
thuần vì lực kẹp có hạn, thường dùng trong dạng sửa chữa hoặc trong
dạng sản xuất nhỏ.Tuy nhiên được sử dụng phổ biến khi phối hợp với các
cơ cấu khác như hơi ép, dầu ép, đòn bẩy …hình 3.42 dùng chêm kết hợp
với cơ cấu đòn bẩy và hơi ép.
Ở những dạng này chêm được dùng để phóng đại lực kẹp và có khi
làm cơ cấu định tâm.
Hình 3.41: Sơ đồ tính W
ct
khi khoan nhiều lỗ
W
ct
M
c
D
d
)-(
)-.(..3
..
-
-
...
3
1
33
22
22
33
dDf
dDnMK
W
nMK
dD
dD
fW
c
ct
cct
Hình 3.42
W
W
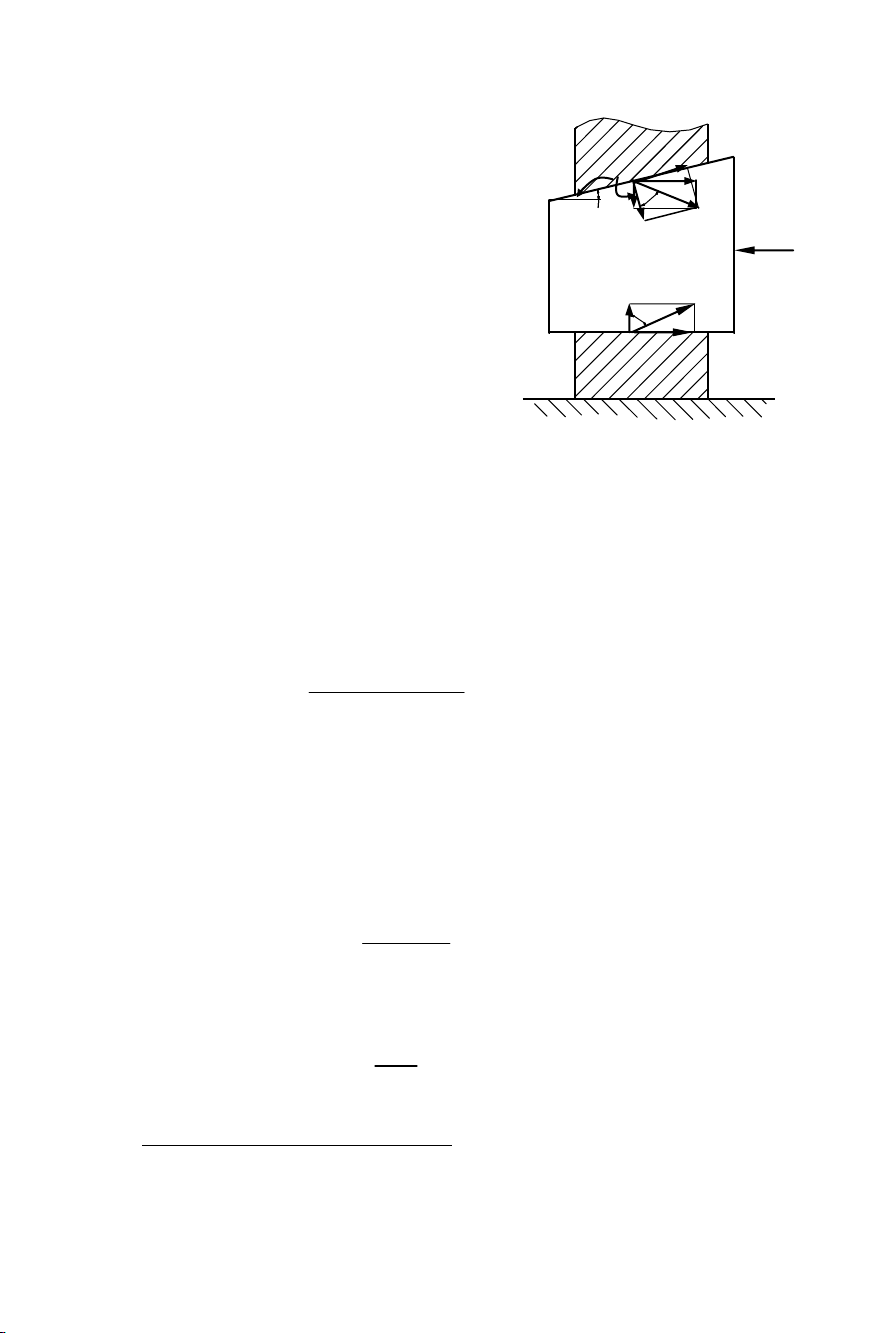
211
3.6.1.2. Lực kẹp của chêm
Chêm một mặt vát
Trên hình 3.43, khi ta dùng ngoại lực
Q đóng vào, trên mặt nghiêng sinh ra lực
ma sát F, đồng thời trên mặt ngang sinh lực
ma sát F
1
, góc ma sát lần lượt là và
1
,
góc chêm là .Từ đó sinh ra phản lực pháp
tuyến với mặt ngang là W, phản lực pháp
tuyến với mặt nghiêng là N, khi đó:
Tổng hợp hai lực N và F ta có lực R. Lực
R được phân ra thành lực thẳng đứng W và lực nằm ngang P.
Với: P = W.tg( + )
Cân bằng các lực tác dụng lên chêm theo phương ngang:
Do đó lực kẹp bằng:
Trong đó:
tg
1
– Đặc trưng cho hệ số ma sát trên mặt trượt của chêm
tg – Đặc trưng cho hệ số ma sát trên mặt vát của chêm
Nếu mặt trượt không có ma sát thì tg
1
= 0, khi đó:
Giả sử cả hai mặt không có ma sát thì lực kẹp là:
Tính tự hãm khi kẹp bằng chêm:
Trong quá trình làm việc, do rung động nên chêm có khuynh hướng
tụt ra ngoài vì thế chêm cần có tính tự hãm. Phân tích lực tác động lên
11
.
.
tgWF
tgNF
F
P
R
N
W
Hình 3.43
Q
W
F
1
R
1
1
)(..
11
tgWtgWPFQ
1
)(
tgtg
Q
W
)αφ(
tg
Q
W
αtg
Q
W
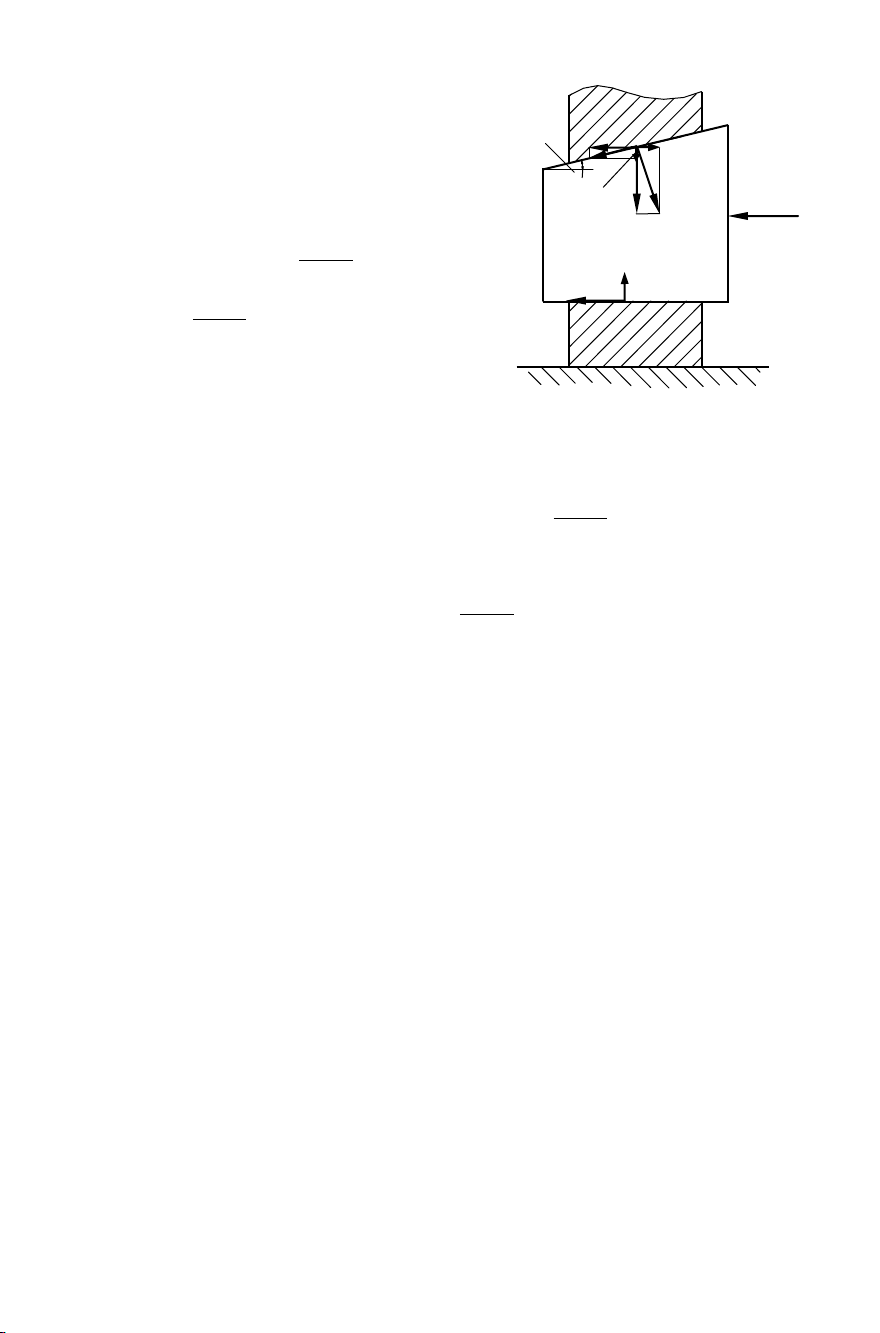
212
chêm hình 3.44, khi chêm có khuynh
hướng tụt ra, lúc đó điều kiện tự hãm là:
Ta có:
Lực F được phân ra hai thành phần:
thành phần nằm ngang là F
/
, thành phần
thẳng đứng là F.sin
Cân bằng lực theo phương đứng:
Mặt khác, thay (b) và (c) vào (a):
Từ đây rút ra được:
11
tgα tg tg tgα.tg .tg
Gần đúng:
11
tgφtgφtgα
Khi =
1
thì điều kiện tự hãm:
2
Thông thường hệ số ma sát:
(3.20)
/0/
30843φφ
0
5tg0,150,1f
(a)
F
/
+ F
1
≥ P
(b)
tgWtg
W
FF .cos.
cos
cos.
/
cos
;.
W
NtgNF
tg
W
F .
cos
)1.(
sin.
cos
sin.
/
/
tgtgWW
tg
W
WFWW
(c)
11
/
1
)..1(.
tgtgtgWtgWF
).1(...
11
tgtgtgWtgWtgWP
F
F
/
F
1
W
/
P
N
W
Q
F.sin
Hình 3.44
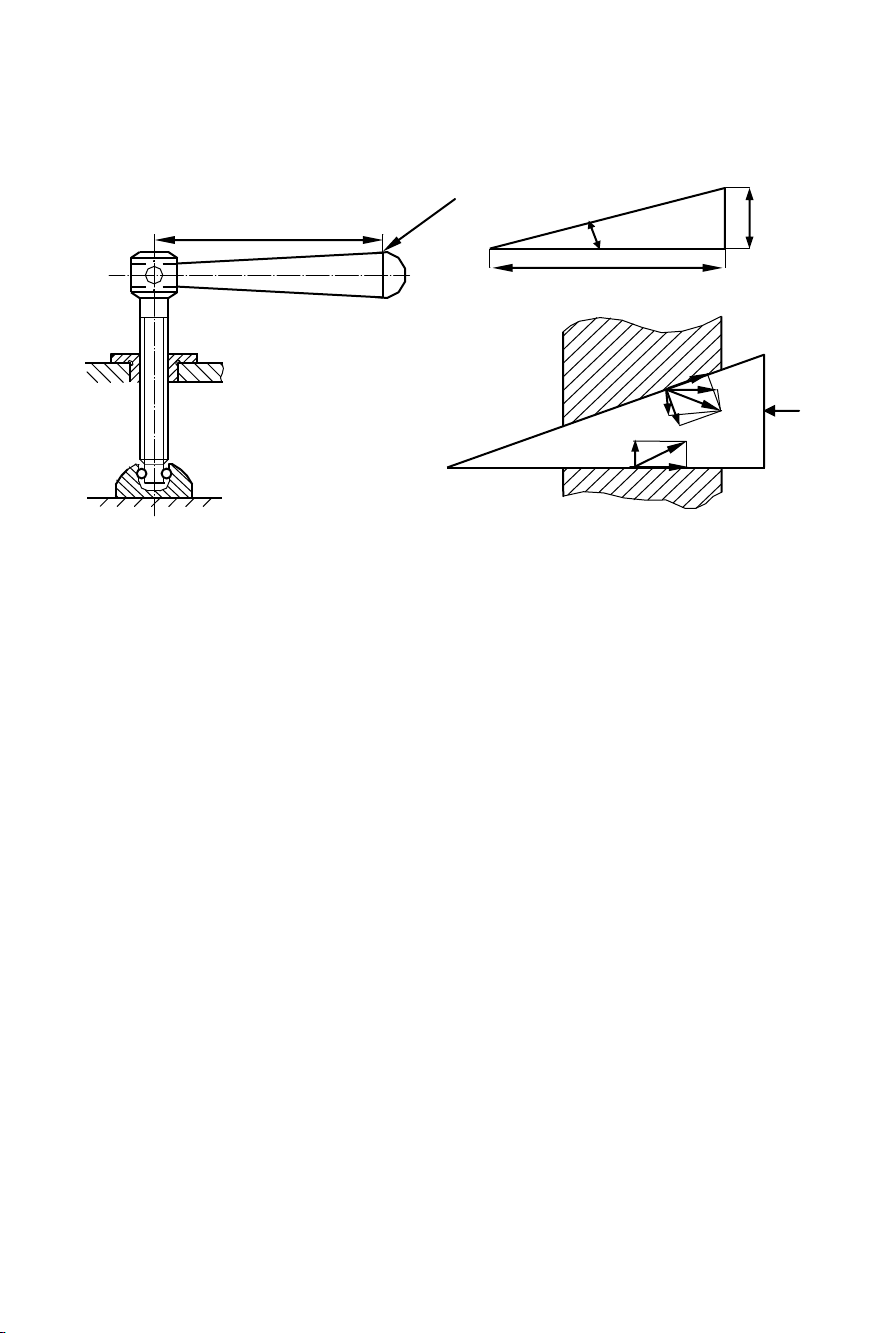
213
3.6.2. Kẹp chặt bằng ren
Kẹp chặt bằng ren vít được sử dụng phổ biến vì kết cấu đơn giản, tính
vạn năng cao và làm việc chắc chắn do lực kẹp lớn, tính tự hãm rất tốt.
Thông thường ít sử dụng trực tiếp đầu bulông để kẹp, vì dễ làm
hỏng bề mặt bị kẹp mà thường thông qua miếng đệm nhằm tăng diện tích
tiếp xúc, tránh hỏng bề mặt chi tiết, độ cứng vững của chi tiết gia công
được tăng lên.
Cụm kẹp chặt bằng ren vít thường có các phần chính là bulông, tay
quay, đai ốc và miếng đệm, các chi tiết này đã được tiêu chuẩn hóa.
Khuyết điểm cơ bản của kẹp ren là: Phải quay nhiều vòng mất thời
gian, tốn công lao động, nếu kẹp trực tiếp lên bề mặt chi tiết dễ làm cho
chi tiết bị xoay.
3.6.2.1.Tính toán lực kẹp của cơ cấu kẹp bằng ren vít
Khi ta khai triển một vòng ren, thấy nó có dạng như một cái chêm,
hình 3.45b.
Trong đó:
S – bước ren;
- góc nâng của ren
d
tb
– đường kính trung bình của ren;
Việc tính toán lực kẹp của ren vít cũng giống như tính lực kẹp của chêm.
Ở đây khác với chêm, ngoài lực Q còn có mômen ngoài (theo hình 3.45c):
Trong đó:
L – Chiều dài tay đòn;
/
1
RFrPLQ
tb
( 3.31 )
a)
L
Q
Hình 3.45
c)
b)
S
d
tb
Q
N
F
P
R
W
W
1
R
1
F
1
1
Đai ốc
Bulông
Chi tiết
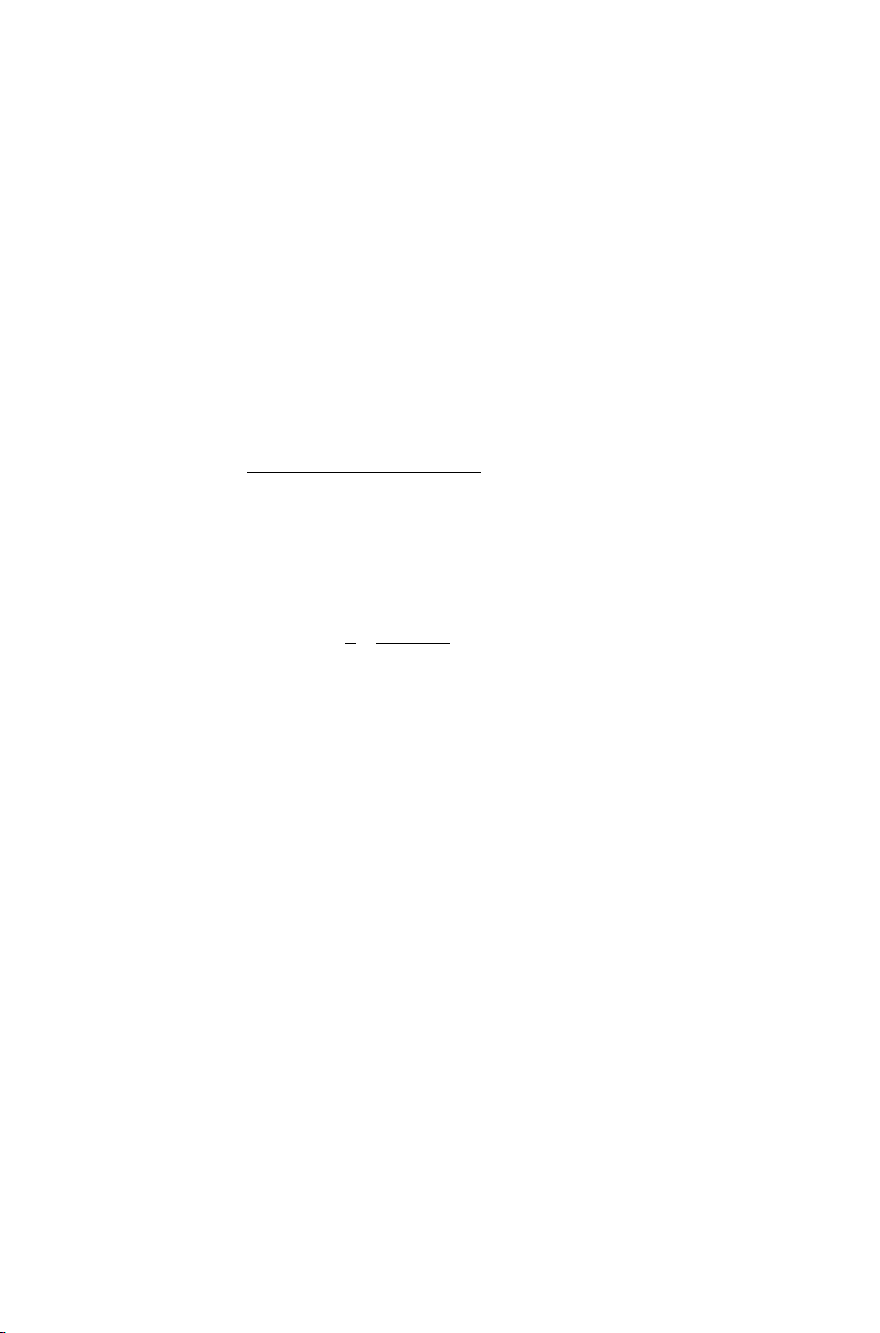
214
Q – Lực vặn tay do công nhân tác dụng;
R
tb-
Đường kính trung bình của ren;
R
/
- Bán kính tính toán của miếng đệm;
Quan hệ giữa các thành phần lực tác dụng:
Thay vào phương trình mômen ( 3.31 ) có:
Vậy khả năng sinh ra lực kẹp của vít được xác định theo công thức:
Bán kính tính toán R
/
được xác định như sau:
Đối với đầu kẹp hình vành khăn:
Đối với đầu kẹp chỏm cầu: R
/
= 0
Đối với đầu kẹp trụ: R
/
= D/3(D là đường kính đầu kẹp).
3.6.2.2. Tính sức bền cho bulông kẹp
Phần trên, ta chỉ trình bày các phương pháp tính lực kẹp của bulông,
đó chỉ là khả năng sinh ra lực kẹp của bulông, còn tính chất chịu lực của
bulông trong quá trình làm việc thì ta cần phải kiểm nghiệm lại thông qua
tính toán sức bền. Để tính toán sức bền ta phải dựa vào hình dáng, điều kiện
làm việc cụ thể, dựa vào vật liệu chế tạo bulông kẹp.
Trong quá trình làm bulông kẹp trong đồ gá có thể chịu kéo, nén, uốn,
xoắn, từ đó sinh các dạng hư hỏng thường gặp như bị cong, bị đứt thân
bulông, bị đứt các đuờng ren, để đảm bảo cho bulông kẹp đủ bền ta phải tính
toán bền cho bulông dựa vào các thuyết bền của môn sức bền vật liệu.
Riêng trường hợp bulông kẹp bị đứt chân ren, khi thiết kế ren vít
người ta phải dựa vào thuyết bền đều của ren, tức là đã kể đến mọi trường
hợp gây ra hư hỏng cho đường ren vít để tính toán thiết kế và đưa vào tiêu
chuẩn hóa của ren vít, trường hợp này ta không cần thiết phải nghiệm bền.
22
33
/
3
1
dD
dD
R
( 3.34 )
1
/
)α(
tgRtgr
LQ
W
tb
( 3.33 )
1111
)(
tgWtgWF
tgWP
( 3.32 )
/
1
)( RtgWrtgWLQ
tb
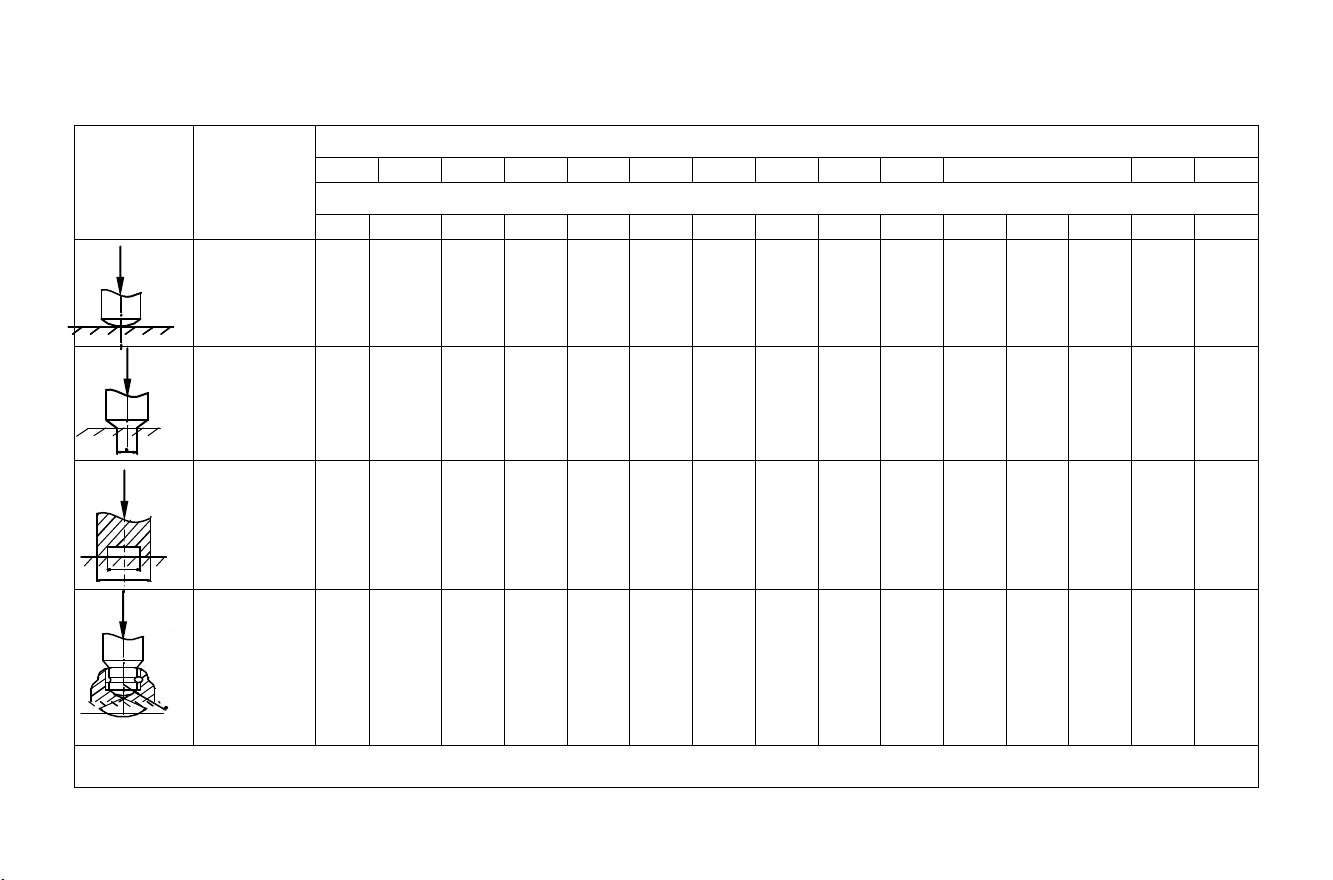
215
Bảng 3.1
Sơ đồ kẹp
Các thông số
và loại vít
Lực kẹp với các loại vít
M6
M8
M10
M12
M14
M16
M18
M20
M22
M24
M27
M30
M33
M36
M42
Bước ren
1
1,25
1,5
1,75
2
2
2,5
2,5
2,5
3
3
3
3,5
4
4,5
Chiều dài l
Lực vặn Q
Lực kẹp W
Vít đầu cầu
80
1,5
250
100
2,0
320
120
2,5
390
140
3,5
530
160
5,0
750
190
6,5
1050
220
8,5
1400
240
10,0
1600
280
12,0
2150
310
13,0
2300
360
15,0
2800
410
15,0
2900
460
15,0
3000
520
15,0
3100
600
15,0
3200
D
Chiều dài l
Lực vặn Q
Lực kẹp W
Vít đầu Phẳng
80
1,5
190
100
2,0
240
120
2,5
290
140
3,5
390
160
5,0
560
190
6,5
7600
220
8,5
1030
240
10,0
1200
280
12,0
1560
310
13,0
1700
360
15,0
2050
410
15,0
2150
460
15,0
2200
520
15,0
2350
600
15,0
3200
Chiều dài l
Lực vặn Q
Lực kẹp W
Vít đầu vành
khăn
80
2,5
220
100
3,5
290
120
4,5
370
140
7,0
550
160
5,0
460
190
6,5
650
220
8,5
860
240
10,0
1000
280
12,0
1300
310
15,0
1350
360
15,0
1400
410
15,0
1400
460
15,0
1500
520
15,0
1550
600
15,0
1600
Chiều dài l
Lực vặn Q
Lực kẹp W
Vít đầu có
miếng đệm
80
1,5
160
100
2,0
200
120
2,5
250
140
3,5
330
160
5,0
460
190
6,5
650
220
8,5
860
240
10,0
1000
280
12,0
1300
310
13,0
1400
360
15,0
1700
410
15,0
1750
460
15,0
1800
520
15,0
1850
600
15,0
1900
Trong bảng 3.1: l-tính bằng mm; Q và W tính bằng kG.
w
w w
w
w
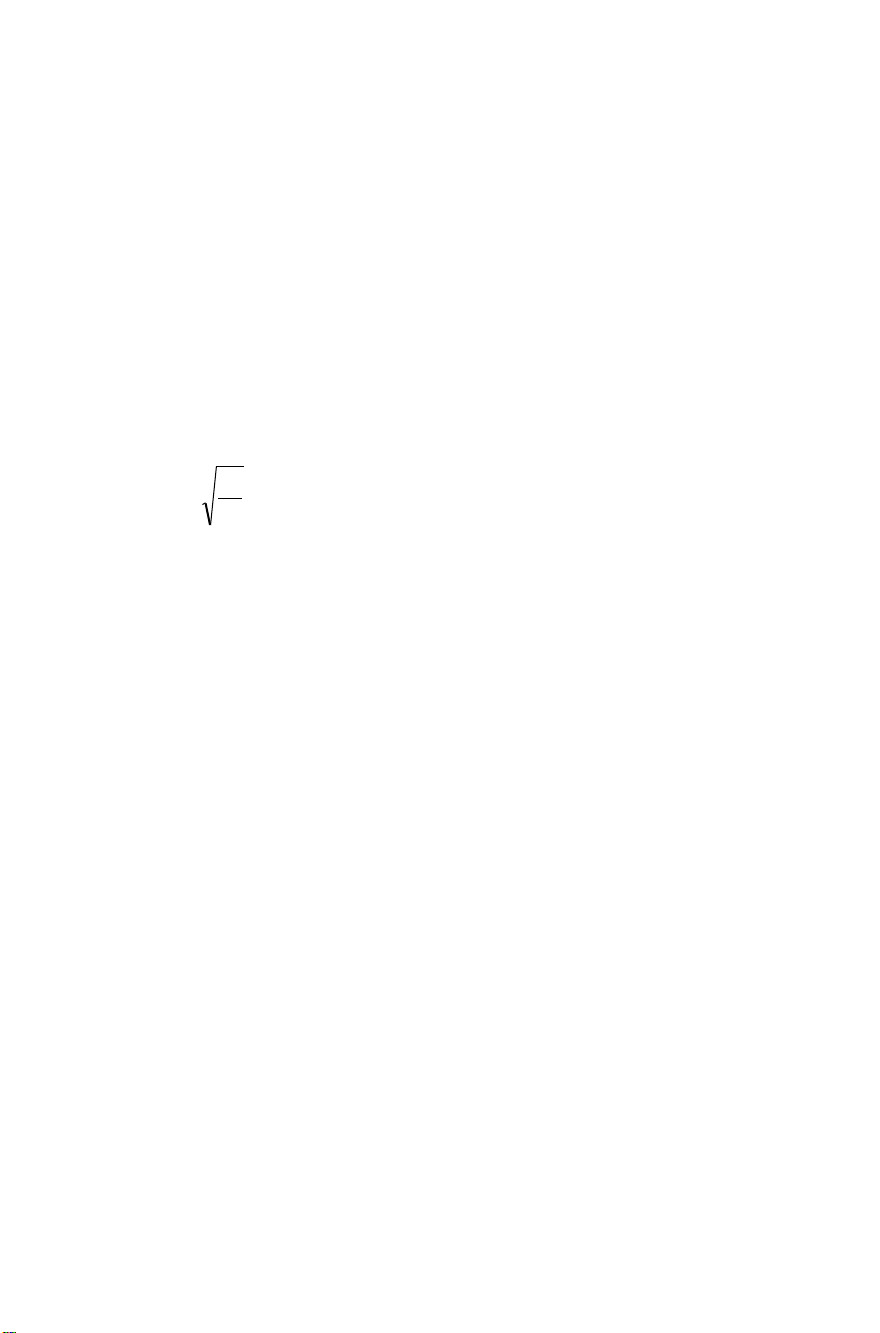
216
3.6.2.3. Cách chọn đường kính bulông
Để chọn đường kính bulông thì thông số quan trọng nhất là lực kẹp
cần thiết W
ct,
(việc xác định W
ct
đã trình bày ở phần đầu). Lúc này ta có 3
cách chọn d của bulông:
- Một là sử dụng bảng 3-1 tra ngược lại để tìm trị số của ren (M10,
M11, M12…)
- Hai là tính toán đường kính d của ren từ công thức lực kẹp do ren
tạo ra (W). Cách này thường gặp phải khó khăn do trong công thức có
nhiều ẩn, vì vậy người ta dùng công thức này để kiểm tra lại lực kẹp sau
khi đã chọn d.
- Ba là sử dụng công thức sau:
W
Cd
(mm)
Trong đó: C = 1,4 đối với ren hệ mét cơ bản;
- ứng suất kéo, (kG/mm
2
); đối với bulông bằng thép
45 thì = 8 10.
W – lực kẹp do ren tạo ra; kG
d – đường kính đỉnh ren.
3.6.3. Kẹp chặt bằng cam
Cam lệch tâm là một chi tiết kẹp có tâm quay lệch với tâm hình học
của nó, nhờ độ lệch tâm này mà nó kẹp được phôi.
Kẹp bằng cam lệch tâm có những ưu điểm như kẹp nhanh, đơn
giản, không cần các thiết bị phụ. Nhược điểm của cam lệch tâm là hành
trình kẹp nhỏ, không thích hợp với phôi có sai số lớn, tính tự hãm kém và
lực kẹp nhỏ hơn ren ốc, tính vạn năng kém và kết cấu cồng kềnh, cam
lệch tâm chỉ làm việc tốt khi chi tiết được gá cố định và khi gia công ít có
rung động.
Trong các cơ cấu kẹp bằng cam lệch tâm thường dùng hai loại:
cam lệch tâm tròn và cam lệch tâm đường cong
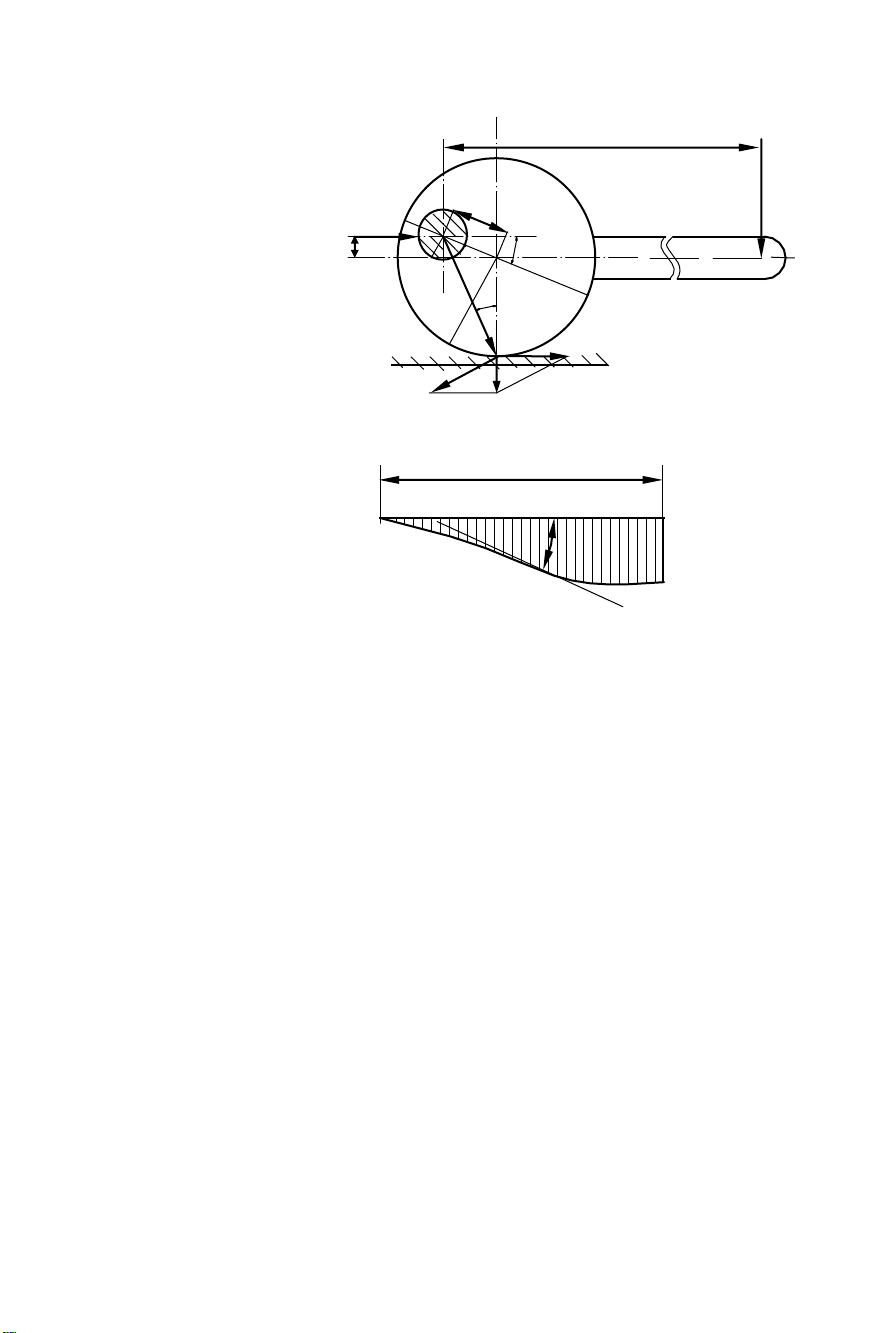
217
Thông thường
dùng các cam lệch
tâm tay quay chỉ giới
hạn 100 120
0
nên
không chế tạo mặt
cam theo cả vòng
tròn. Bề mặt của bánh
lệch tâm thường dùng
60 90
0
, bề mặt còn
lại có thể hớt đi và chỉ
cần chừa đủ để làm lỗ
lắp trên trục. Cam
lệch tâm hai phía
thường dùng trong cơ
cấu định tâm và trong
các ê-tô kẹp hai phía,
các trục lệch tâm chủ
yếu dùng trong các cơ
cấu tỳ để thực hiện
chính xác các phần
động trong đồ gá, vì
trong đó không cần
đến độ lệch tâm lớn, nên có thể dùng trục có đường kính không lớn lắm.
Muốn xác định các kích thước cơ bản của cam lệch tâm cần biết
trước các thông số sau đây: - dung sai kích phôi, từ mặt chuẩn định vị
đến điểm đặt lực kẹp ( mm ); - góc quay của bánh lệch tâm kể từ vị trí
ban đầu; W
ct
– lực kẹp cần thiết.
3.6.3.1. Cam lệch tâm tròn
Tính lực kẹp
Sử dụng cung knm là cung làm việc của cam lệch tâm hình 3.46a,
khi cam quay quanh 0
1
(tâm chốt), thì biên dạng làm việc của cung knm
có thể được khai triển theo hình 3.46b, do đó nguyên lý làm việc của nó
giống như chêm nhưng góc nghiêng của nó thay đổi từ k đến m và đạt giá
trị
max
tại n, cung mn là cung làm việc của bánh lệch tâm, ở điểm k và
điểm m góc nhỏ nhất, góc thay đổi làm cho lực kẹp ở mỗi điểm
không giống nhau, góc càng lớn thì lực kẹp càng nhỏ. Phần làm việc
của chêm thường ở hai bên điểm n, ở đó góc thay đổi chậm. Khi tác
dụng vào tay quay một lực Q sẽ tạo ra mômen truyền qua điểm tiếp xúc
A (điểm làm việc), ở điểm A chêm xuất hiện một lực Q
2
:
S
L
Q
Q
1
k
n
Q
2
F
W
e
O
O
1
A
B
a)
m
max
k
n
m
b)
Hình 3.46
D/2
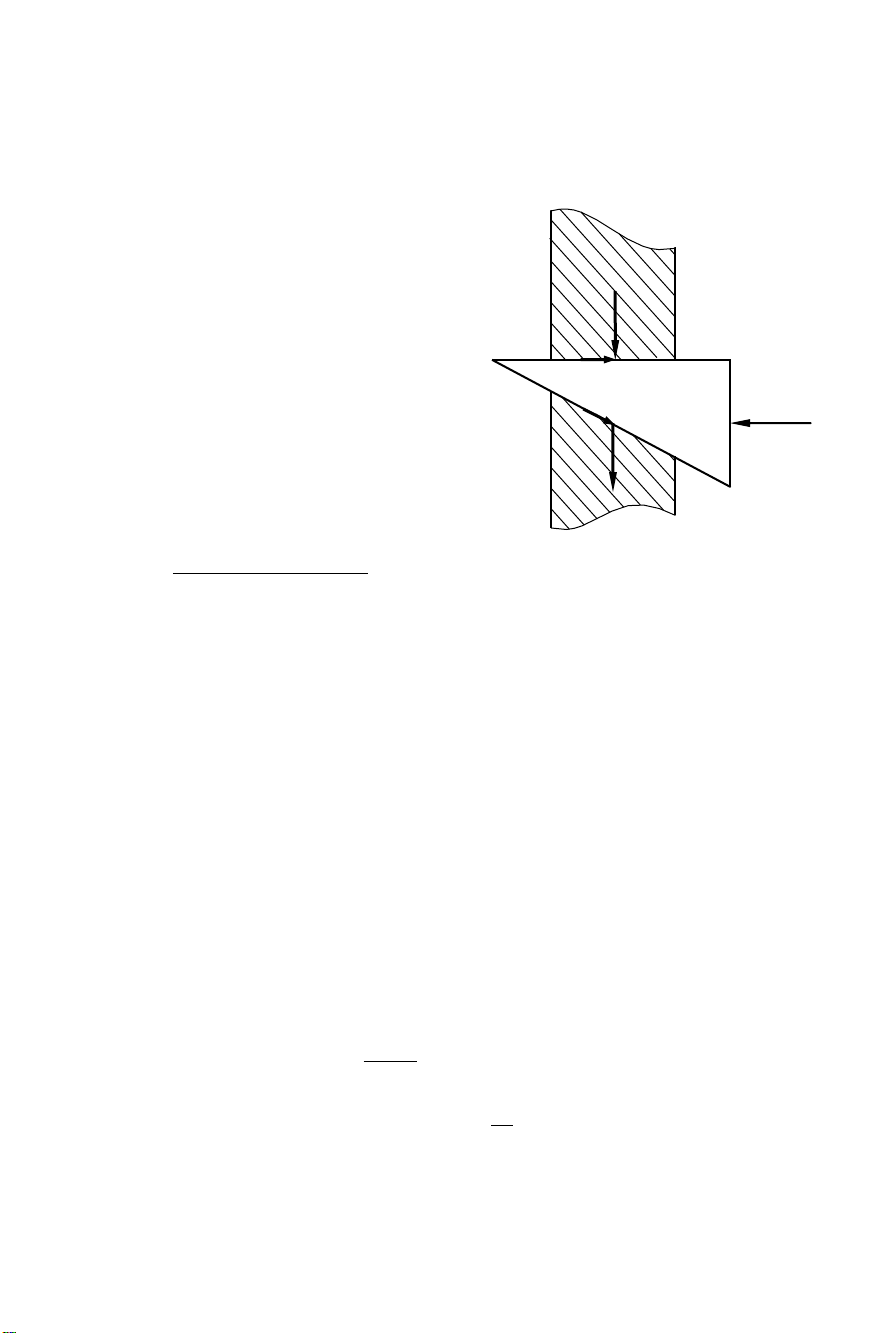
218
Với = O
1
A –bán kính làm việc của bánh lệch tâm;
Theo nguyên lý làm việc của
chêm có sơ đồ lực hình 3.47, lúc đó coi
như một chêm có góc chịu lực Q
2
đóng vào, ở điểm A sinh ra phản lực W
và lực ma sát F, ở điểm O
1
sinh ra phản
lực Q
1
, và có các giá trị sau:
Q
1
= W.tg
1
; F = W.tg(+)
Nếu coi là nhỏ ta có:
Trong đó:
Q – Lực tác dụng của công nhân, thường lấy Q = 1,5 15 kG;
L – Chiều dài cánh tay đòn bánh lệch tâm: 80 150 mm;
- Bán kính làm việc của bánh lệch tâm; mm
- Góc nâng tại điểm làm việc của bánh lệch tâm;
và
1
– Góc ma sát giữa bánh lệch tâm với bề mặt kẹp và giữa
bánh lệch tâm với chốt quay;
Tính bán kính làm việc và góc nâng tức thời
Trên hình 3.54a, xét tam giác vuông O
1
AB có:
sin
2
cos
e
D
OBAOAB
AB
Ta có :
2
QLQ
( 3.40 )
]φ)φα([ρ
]φ)φα([ρ
φ)φα(
1
1
112
tgtg
LQ
W
tgtgWLQ
tgWtgWQFQ
( 3.41)
W
Q
1
Q
2
F
W
Hình 3.47
A
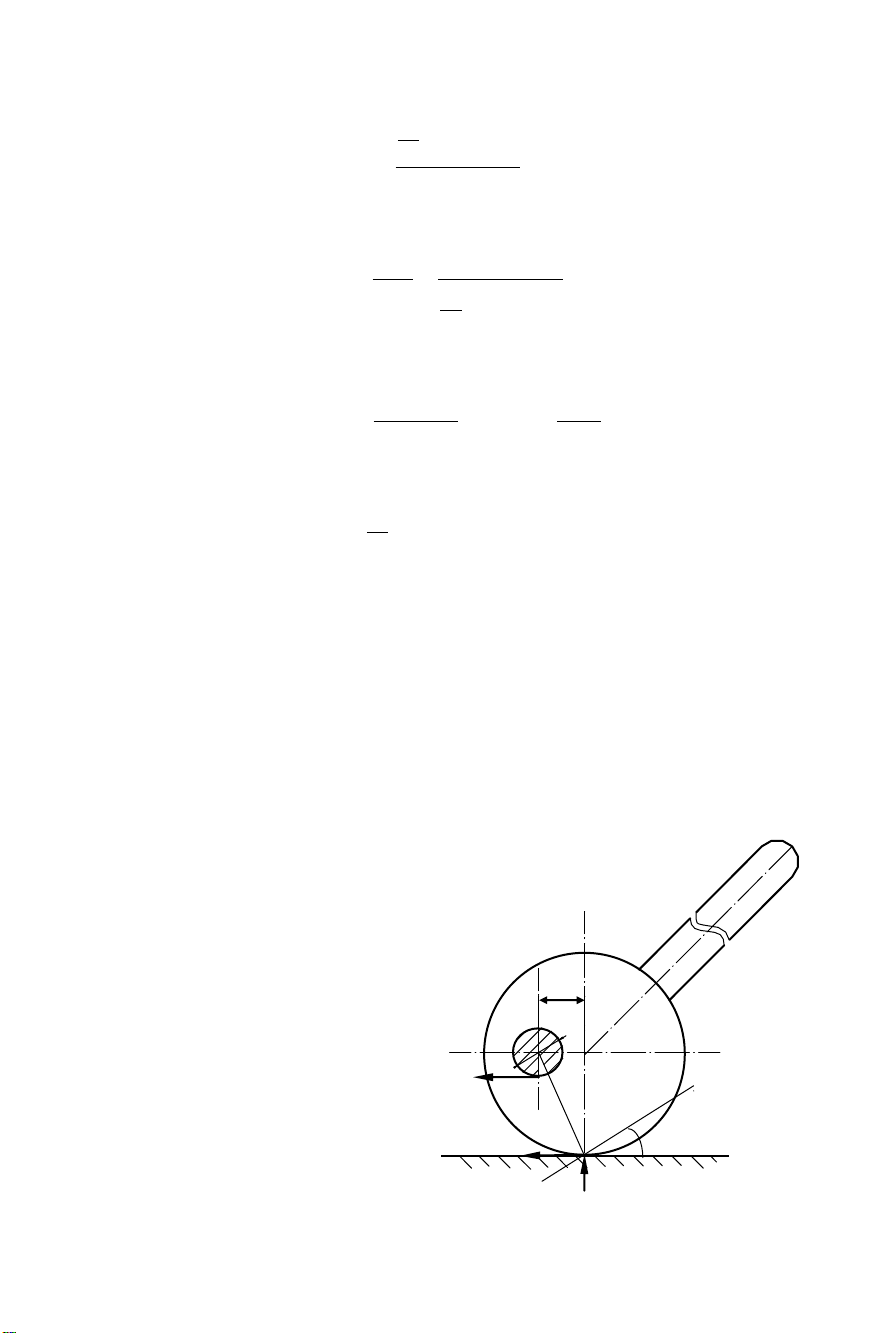
219
cos
sin
2
e
D
(3.42)
Và có :
sin
2
cos
1
e
D
e
AB
BO
tg
(3.43)
Nếu = 0 khi đó:
D
e
tg
D
2
;
cos2
max
Nếu =90
0
thì
00;
2
minminmax
tge
D
Tính hành trình kẹp:
Xét tam giác O
1
OB có:
sin eOBS
Nếu = 0 khi đó hành trình nhỏ nhất: S
min
= 0 (điểm n);
Nếu = 90
0
khi đó hành trình là lớn nhất:
S
max
= e (ở điểm m)
Việc xác định , và S phụ thuộc vào gía trị của góc , nghĩa là tùy
thuộc vào vị trí tay gạt. Các công
thức này tham khảo bảng 3.2.
Tính điều kiện tự hãm
của bánh lệch tâm:
Cũng giống như chêm để
cam lệch tâm đảm bảo điều kiện tự
hãm thì:
1
Trên cam lệch tâm hình 3.48
bao gồm các lực: F, F
1
, W, lúc này
cam lệch tâm có xu hướng quay
ngược lại do đó F và F
1
có chiều
e
F
1
F
W
d
A
O
max
Hình 3.48
O
1
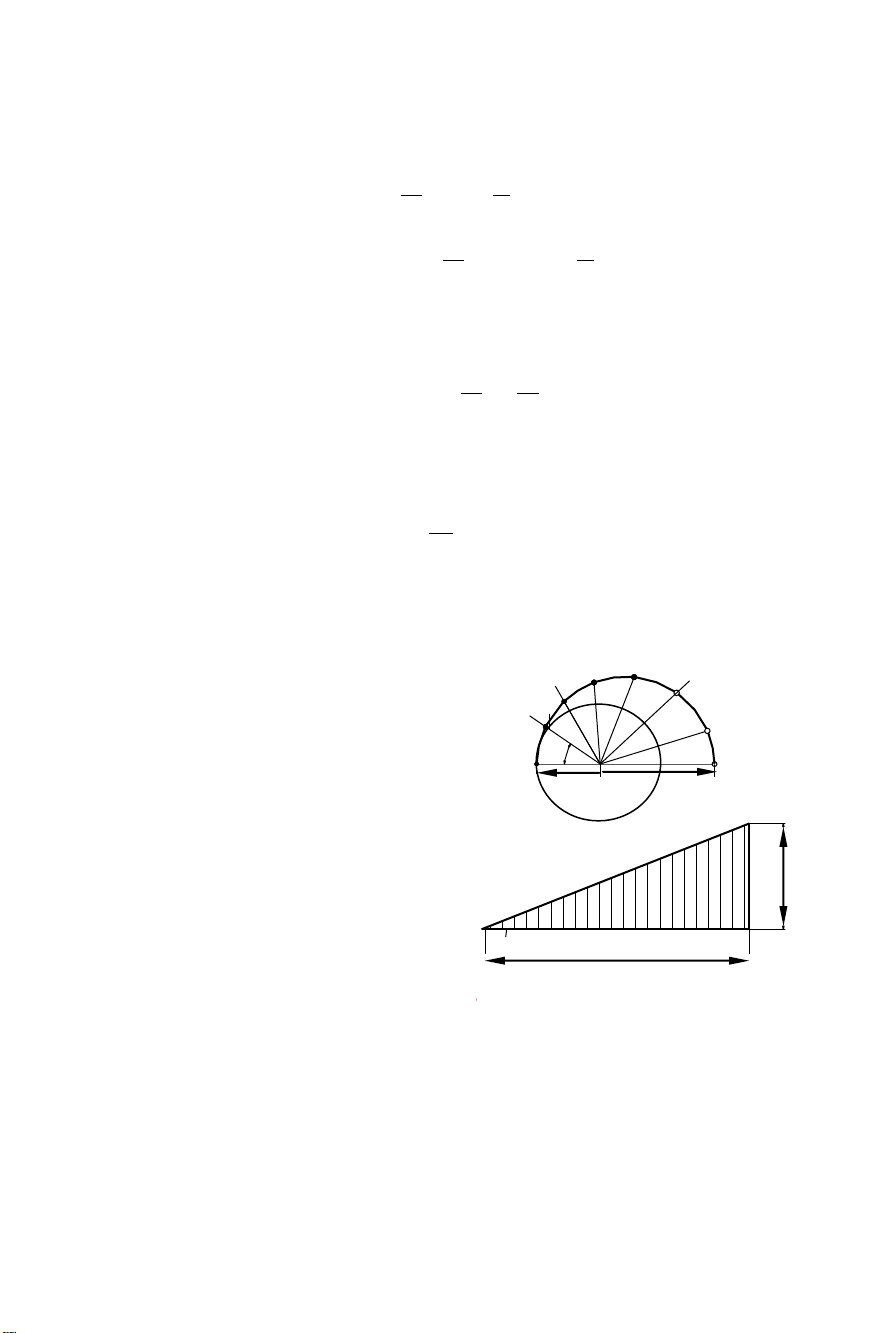
220
như hình vẽ. Lực làm cam quay ngược là W, do vậy F và F
1
phải tạo ra
được mômen chống lại mômen do W gây ra.
Nghĩa là:
Nếu: f = f
1
= 0,15 và d 10 khi đó tính gần đúng ( bỏ qua ma sát ở
trục quay ), ta có:
Đây là điều kiện tự hãm của cam lệch tâm. Nếu f=0,1 thì:
20
e
D
3.6.3.2. Cam lệch tâm đường cong
Lệch tâm đƣờng cong Ac – si – met
Việc tính toán các thông số làm
việc: lực kẹp, bán kính làm việc ,
hành trình S tương tự như cam lệch
tâm tròn xoay, góc nâng của cam
lệch tâm Ac- si- met thì không thay đổi
trong toàn bộ cung làm việc.
Xây dựng đường cong Ac- si- met:
Lấy vòng tròn cơ sở tâm O (hình
3.49a) bán kính r
o
, ta phân thành nhiều
góc bằng nhau. Sau đó, cứ qua một
góc , ta lại lấy bán kính tăng thêm
một đoạn h, nghiã là:
22
22
1
1
d
fW
D
fWeW
d
F
D
FeW
14
2
15,0
e
DD
e
hnrr
hrr
hrr
hrr
n
0
03
02
01
..............
3
2
(3.45 )
(3.44)
a)
r
1
r
2
r
i
r
n
r
0
h
r
0
b)
Hình 3.49
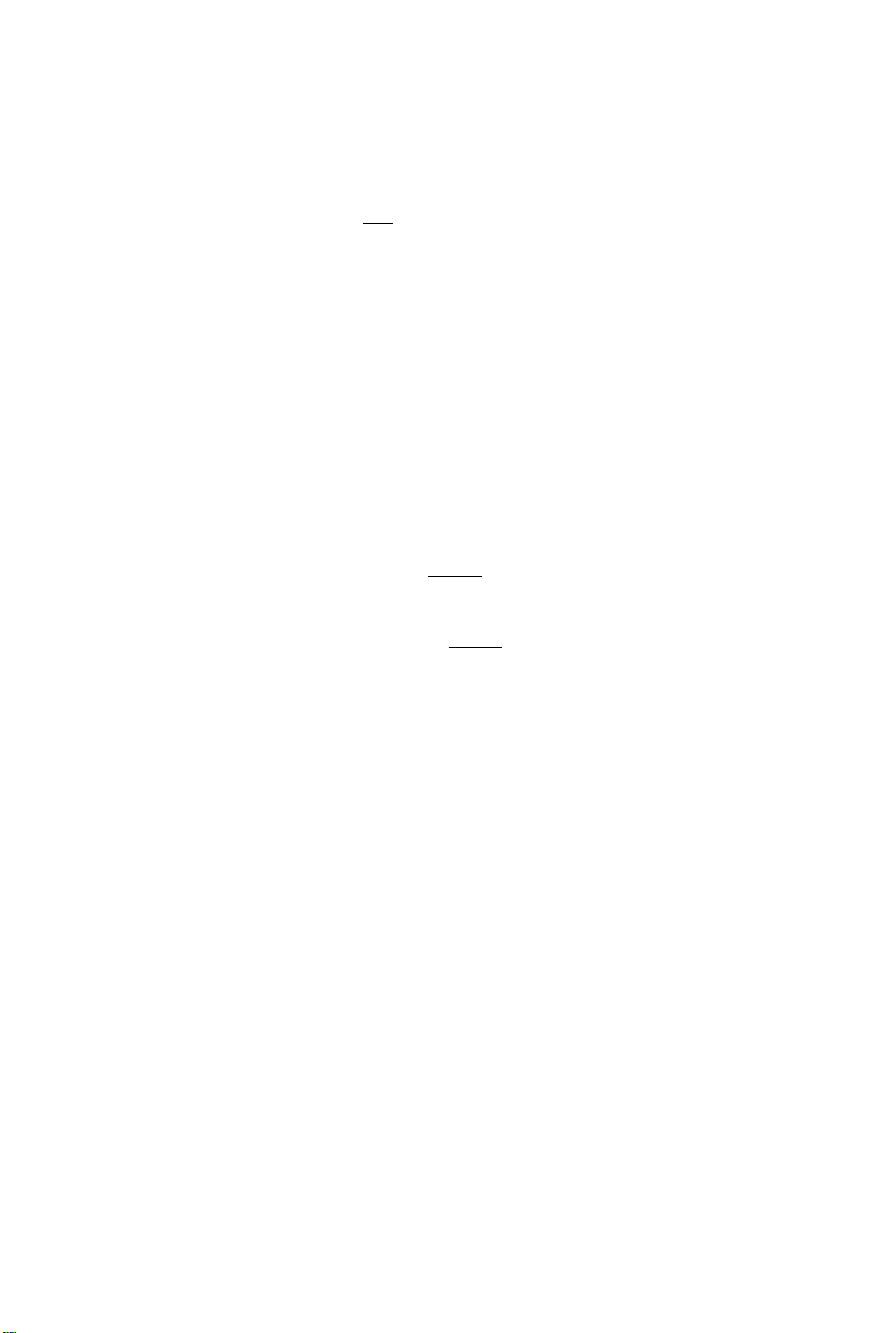
221
Nối các đầu mút bán kính lại ta sẽ được đường cong Ac- si- met.
Từ đó rút ra được phương trình độc cực của đường cong Ac- si- met:
Trong đó:
r – Bán kính một điểm bất kỳ trên đường cong;
- Góc hợp bởi hai bán kính liên tiếp nhau;
n
– Góc hợp giữa bán kính r
o
của điểm đầu và r
n
của điểm cuối;
Khi khai triển đường cong Ac- si- met, ta được một hình chêm hình
3.57b. Để xác định h ta có:
Hay:
Ở đây coi góc gần như không đổi ở bất cứ vị trí nào.
Lệch tâm đƣờng cong Lô- ga- rit
Phương pháp tính toán các thông số tương tự cam lệch tam tròn
xoay, còn các góc nâng thì không thay đổi trong suốt hành trình làm
việc của nó.
Dựa trên vòng tròn cơ sở tâm O, bán kính r
o
hình 3.50
Từ tâm O vẽ các tia phân giác chia vòng tròn thành những góc
bằng nhau, sao cho:
= 2 ( - góc ma sát của cam lệch tâm và mặt kẹp) để từ đó xác
định được r theo công thức (3.48):
)(
0
hnrr
n
( 3.46)
n
r
h
r
nh
tg
0
0
1,0
1,0
( 3.47 )
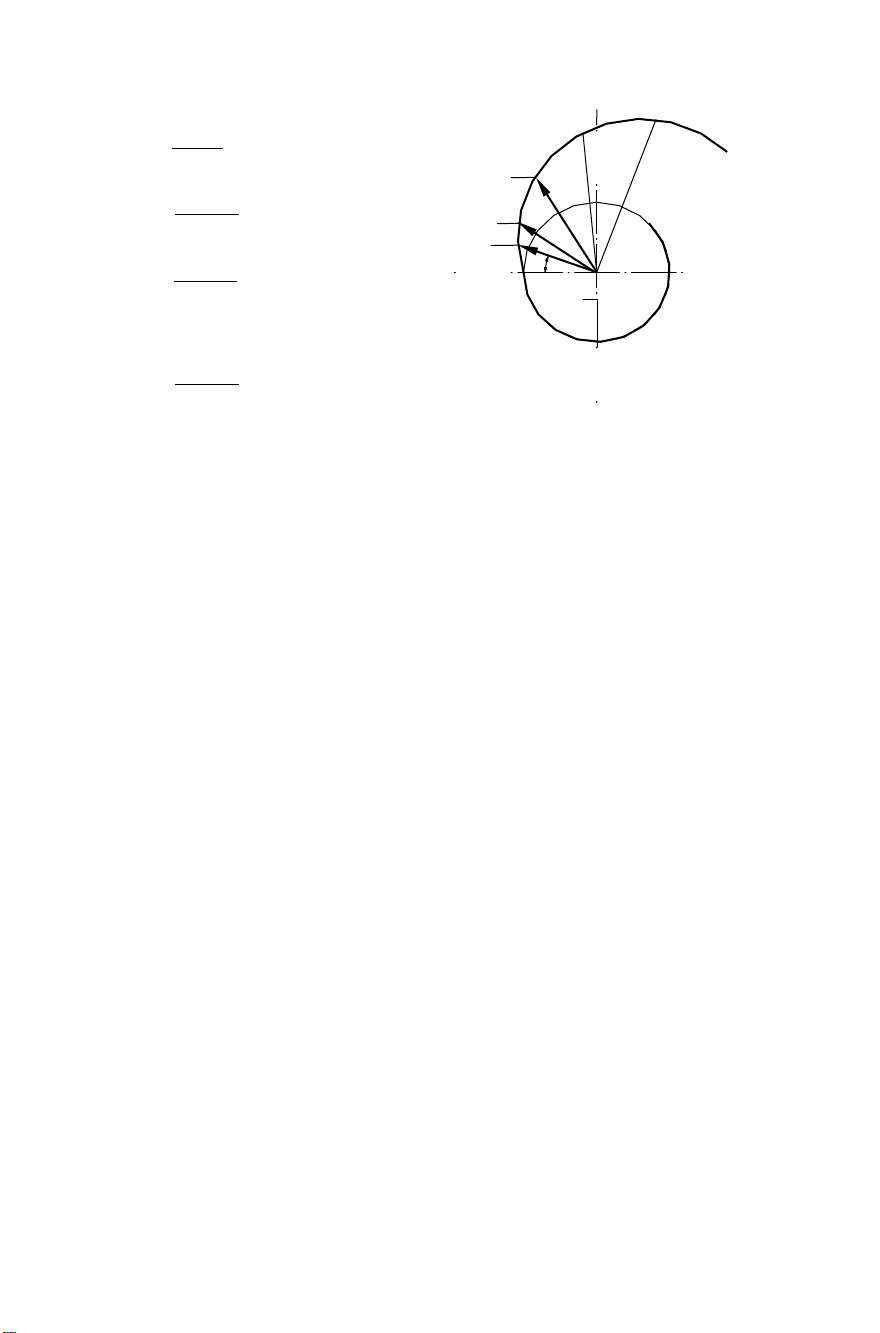
222
Nối các đỉnh bán kính lại ta sẽ được đường cong Lô- ga- rit.
Đối với đường cong Lô- ga- rit, ở bất kỳ điểm nào trên đường cong
cũng đảm bảo tính tự hãm.
Khi thiết kế cam lệch tâm, trước hết phải căn cứ kết cấu của đồ gá
để quyết định đường kính D, rồi tính khoảng lệch tâm e, sau đó xác định
tâm quay trong đồ gá, cuối cùng kiểm tra lại hành trình kẹp có đủ hay
không.
n
n
r
r
r
r
r
r
r
r
cos
.................
cos
cos
cos
0
3
0
3
2
0
2
0
1
( 3.48 )
r
1
r
3
r
2
Hình 3.50
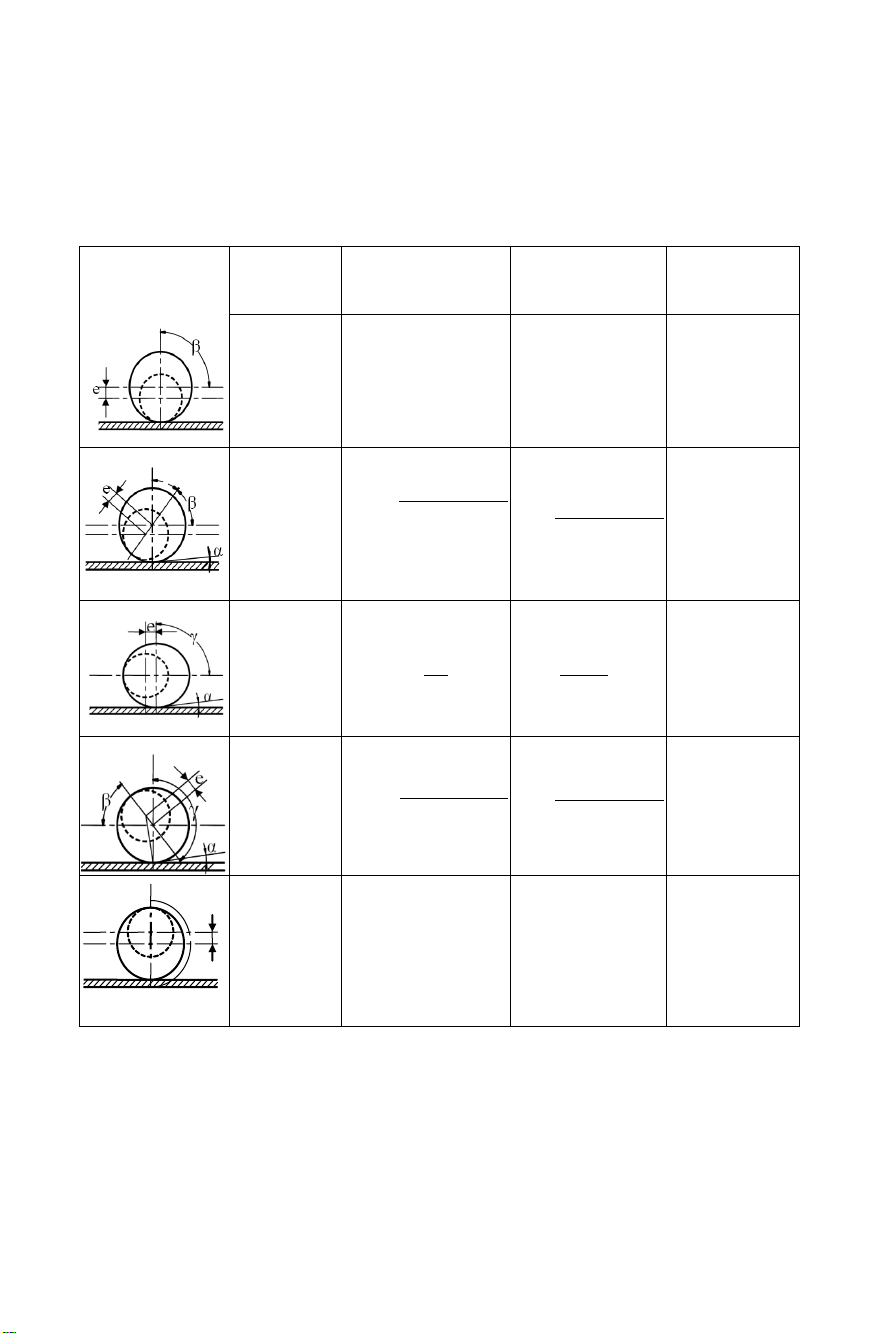
223
Sau đây là bảng công thức tính giá trị góc nâng và bán kính làm
việc khi thiết kế cam
Bảng 3.2
Sơ đồ kẹp
Góc lệch
tâm
Giá trị góc
nâng
Bán kính
làm việc
Hành
trình kẹp
0
0
tg
eD _.5,0
0S
0
900
_90
βsin._.5,0
βcos.
α
0
eD
e
tg
cos
sin._.5,0 eD
)sin_1.(
eS
0
90
D
e
tg
.2
max
cos
.5,0 D
eS =
00
18090
sin..5,0
cos.
eD
e
tg
cos
sin.5,0 eD
)sin1.(
eS
0
180
0
tg
eD .5,0
eS .2
α= 0
e
γ
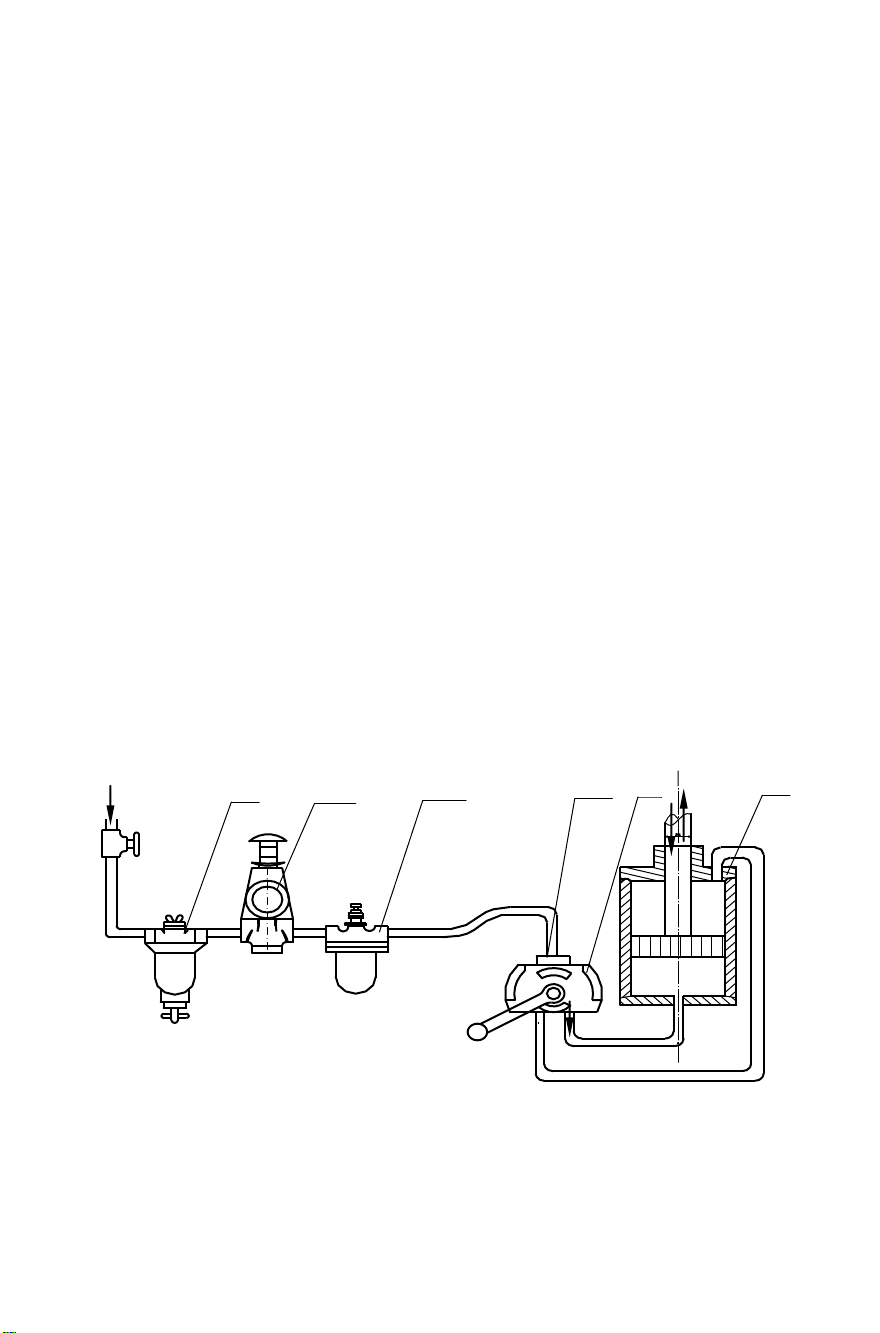
224
3.7. CÁC CƠ CẤU KẸP CHẶT THỦY, KHÍ, ĐIỆN – TỪ,
ĐIỆN - CƠ
3.7.1 Kẹp chặt bằng khí nén
3.7.1.1. Đại cương về khí nén
Khí nén ngày càng được dùng nhiều trong đồ gá vì có những ưu
điểm sau đây:
Giảm nhẹ sức lao động, đối với những chi tiết nặng thì điều này có
ý nghĩa quan trọng thao tác tiện lợi nhẹ nhàng, chỉ cần đóng mở van, rút
ngắn được nhiều thời gian phụ, lực kẹp lớn, đều, có thể điều chỉnh được,
dễ tự động hóa và điều khiển từ xa, khả năng làm việc không phụ thuộc
vào sự thay đổi nhiệt độ môi trường xung quanh.
Lực kẹp liên tục do đó đỡ tốn sức lực so với thủ công 3 4 lần, đây
là ưu điểm quan trọng khi gia công các chi tiết mỏng, dễ biến dạng khi
kẹp chặt.
Tuy nhiên kẹp chặt bằng khí nén vẫn còn một số nhược điểm: Khí
nén có tính đàn hồi nên độ cứng vững kẹp chặt không lớn vì thế đối với
các chi tiết hạng nặng ít dùng, phải có một số trang bị phụ như van, bình
lọc khí, các bộ phận điều hòa tốc độ, áp lực và lưu lượng kế… nên cồng
kềnh. Hệ thống kẹp chặt bằng khí nén gồm những bộ phận chính sau:
1 – Bộ lọc; 2 –Bộ ổn áp; 3 – Bôi trơn ( bầu phun dầu ); 4 – Van một
chiều; 5 – Van phân phối; 6 – Xylanh
Nguyên lý làm việc của bộ phận khí nén được trình bày trên hình
3.51. Khí nén từ máy nén khí đi vào thiết bị tách hơi nước 1 van giảm áp
2 (điều chỉnh áp suất), sau đó đi vào bầu phun dầu 3. Ở đây khí nén được
1
2
3
4
5
6
Hình 3.51: Hệ thống kẹp bằng khí nén
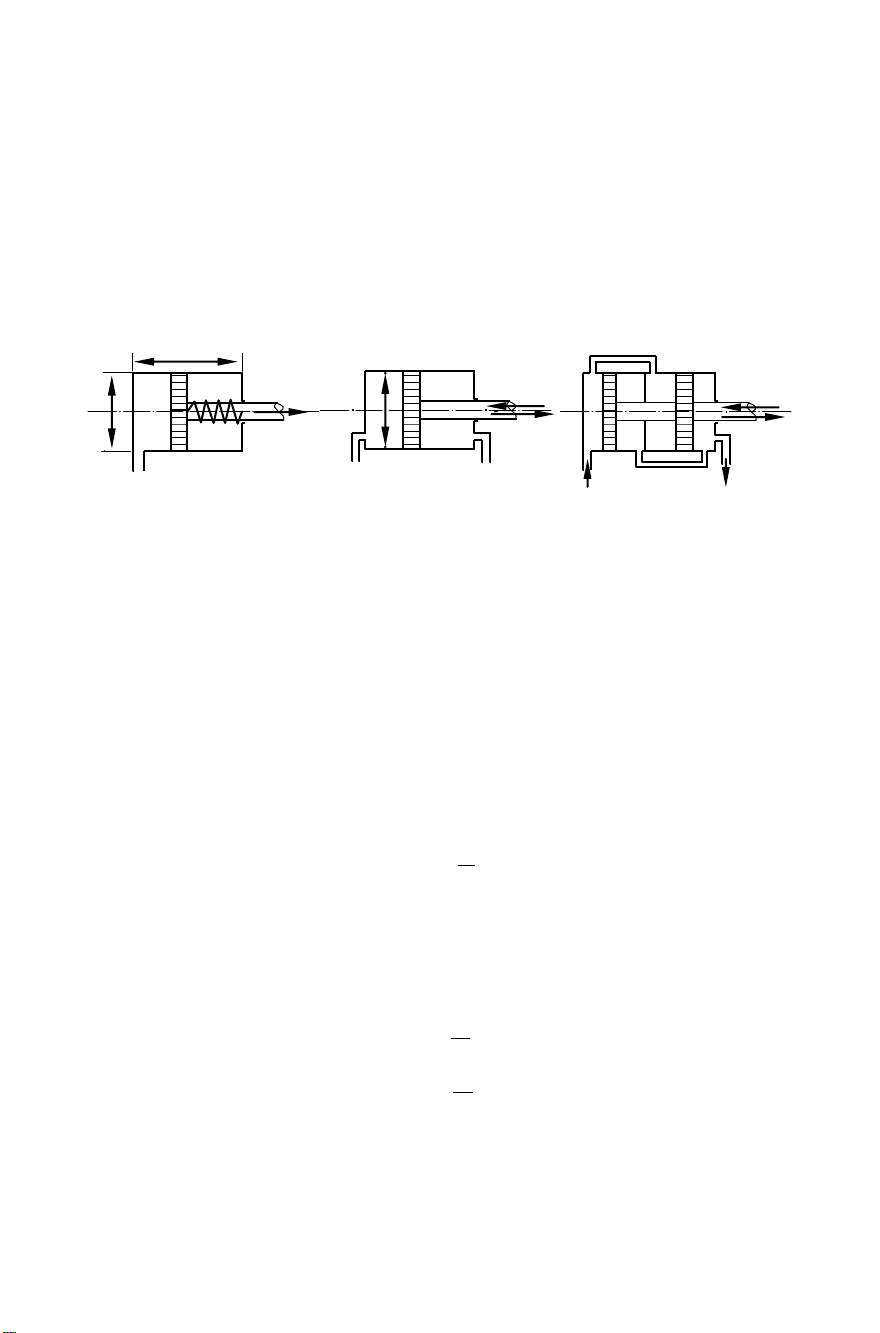
225
hỗn hợp với dầu ở dạng sương mù để bôi trơn cơ cấu truyền động. Van 5
dùng để điều khiển quá trình làm việc.Van một chiều 4 duy trì áp suất khí
nén trong truyền động không sụt áp khi xảy ra sự cố trong hệ thống khí
nén. Khi trong đồ gá có hai truyền dẫn được thực hiện liên tiếp thì ở ống
dẫn khí của một truyền dẫn cần lắp van tiết lưu, nhằm điều khiển tốc độ
khí vào để thực hiện sự làm việc tuần tự của các truyền dẫn.
3.7.1.2. Xylanh-pittông
Dựa theo kết cấu, bộ xylanh-pittông khí nén thường chia ra các
loại: cố định, đặt liền, lắc động, quay tròn. Khâu làm kín là một trong
những yêu cầu đối với xylanh khí nén, thường sử dụng các đệm bằng
các-ton dày 1mm để làm kín các mối ghép cố định với áp suất
100kG/cm
2
; Nếu áp suất lớn hơn, thì ta dùng các tấm đệm bằng đồng dày
2 3mm hoặc các vòng cao su; Khi cần lực kẹp lớn nhưng đường kính
pittông không được làm lớn, người ta dùng hai hoặc ba pittông trên cần
dẫn động hoặc dùng hệ thống đòn bẩy để tăng lực.
Trên hình 3.52a Sơ đồ pittông tác dụng dạng một chiều.
Lực kẹp Q được tính:
Đối với xylanh tác dụng hai chiều hình 3.52b hơi ép có thể vào bên
phải hoặc bên trái
Hình 3.52c là kiểu xylanh có hai pittông, hay còn gọi là hệ truyền
động kép. Hệ này có lực kẹp là:
L
Hình 3.52: Các loại pittông - xylanh
a)
b)
c)
D
D
Q
Q
1
Q
2
Q
1
Q
2
d
qpDQ
2
4
( 3.49 )
(3.50)
pdDQ
pDQ
)(
4
4
22
2
2
1
Lực sinh ra bên trái:
Lực kẹp sinh ra
bên:phải:
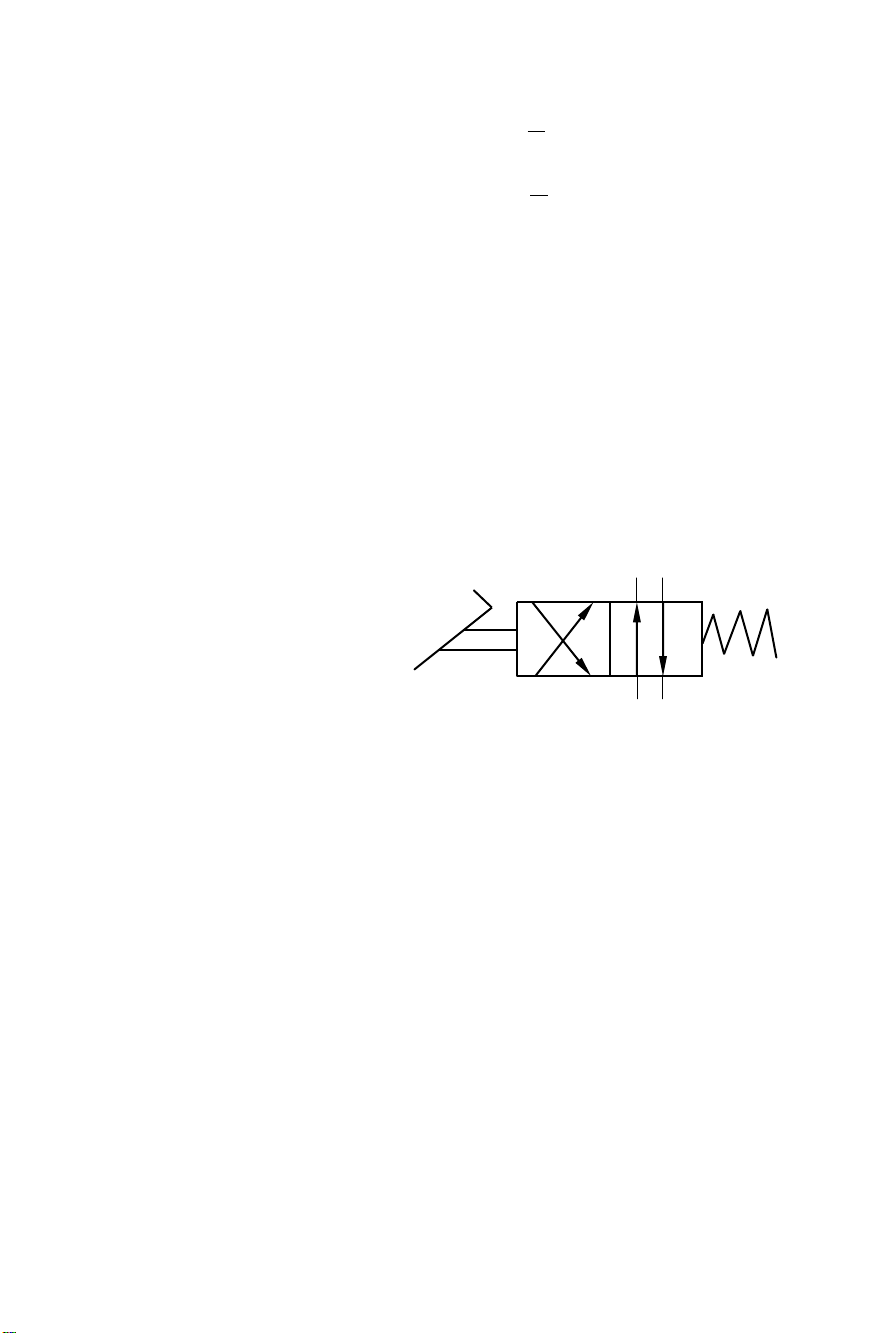
226
Chú thích:
p- Áp suất hơi ép, thông thường p = 4 at;
D- Đường kính pittông,cm;
Q- Lực kẹp, kG;
- Hiệu suất cơ khí, =0,85;
q- Lực đàn hồi của lò xo ở vị trí kẹp của pittông;
3.7.1.3. Các van đảo chiều sử dụng để điều khiển các pittông
trong quá trình kẹp chặt
Đối với pittông tác dụng
một chiều ta sử dụng van đảo
chiều 3/2, van có ba cửa P, A
và R, có hai vị trí 0 và 1, vị trí 0
bị chắn, cửa A nối với cửa R,
nếu đầu dò tác động vào, từ vị
trí van sẽ chuyển đổi sang vị trí
1, như vậy cửa P và cửa A nối
với nhau cửa R bị chặn, khi đầu dò không còn tác động nữa, thì van quay
về vị trí ban đầu, vị trí 0 bằng lực nén của lò xo. Đối với pittông tác dụng
hai chiều và xylanh nhiều pittông, ta sử dụng van đảo chiều 4/2, có thể
tác động bằng tay-bàn đạp sơ đồ nguyên lý hình 3.53, đây là loại van đảo
chiều có bốn cửa và hai vị trí.
3.7.1.4. Truyền động kiểu màng
Lực trên loại xylanh màng tác động một chiều, hình 3.54a và loại
xylanh màng tác động hai chiều hình 3.54b.
pdDQ
pdDQ
)(
2
)2(
4
22
2
22
1
Khi pittông dịch về bên trái
Khi pittông dịch về bên phải:
0
A
B
P
R
1
Hình 3.53: Van đảo chiều 4/2
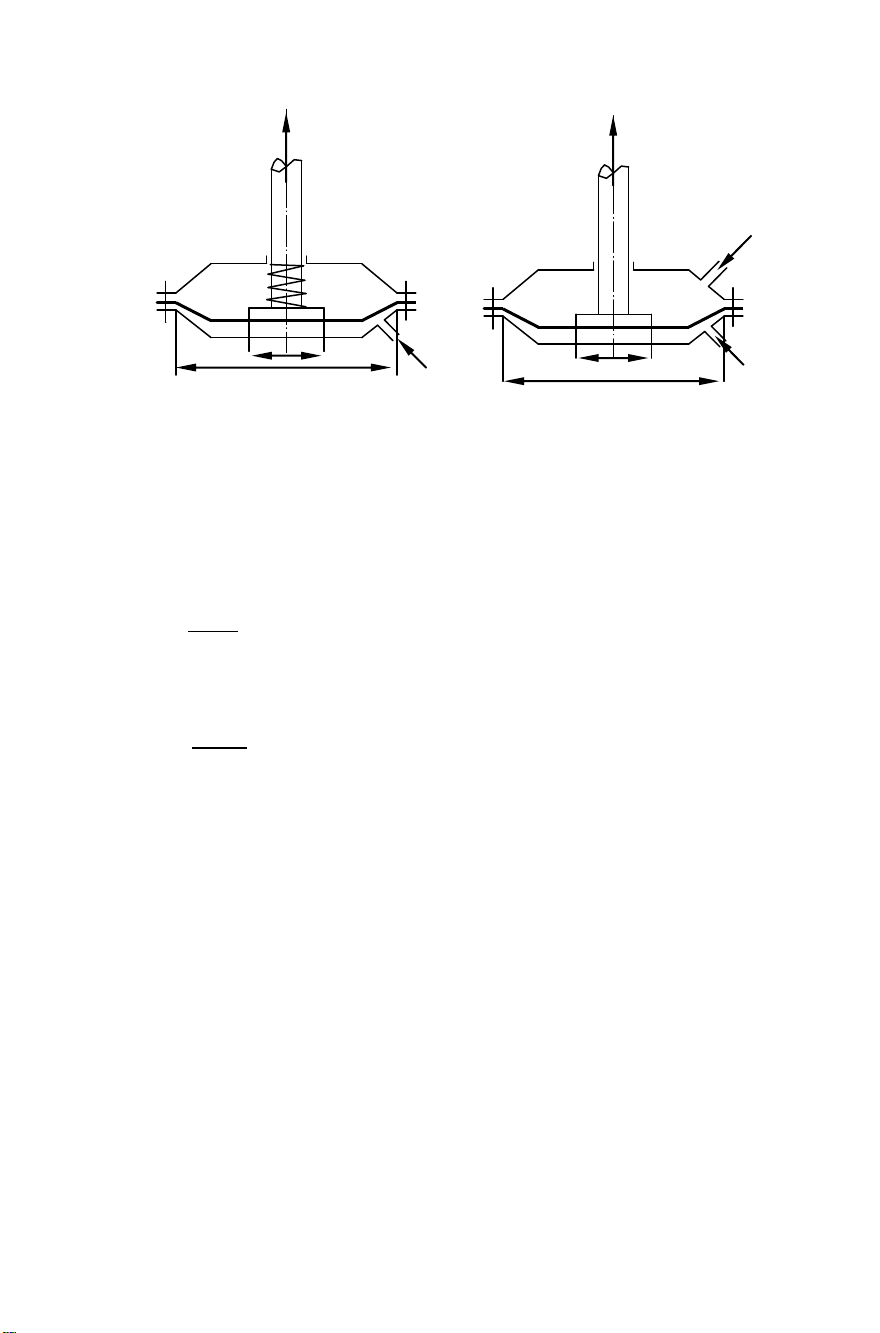
227
Ưu điểm: Tuổi thọ rất bền, sử dụng khoảng 60 lần so với pittông, ít
rò khí, thể tích bé, chế tạo rẻ hơn xylanh pittông, ít tốn hơi ép hơn.
Nhược điểm: Hành trình ngắn, chỉ dùng gia công chi tiết nhỏ.
Lực kẹp của xylanh màng tác dụng một chiều:
qddDD
p
Q
)(
12
π
22
Lực kẹp của xylanh màng tác dụng hai chiều:
)ddDD(
12
p
Q
22
π
3.7.2. Kẹp chặt bằng thủy khí
Để thực hiện chuyển động kẹp chặt trong đồ gá, người ta còn sử
dụng khí nén – thủy lực vì loại truyền dẫn này có những ưu điểm là có
thể tạo nên lực kẹp lớn, tác động nhanh, giá thành tương đối hạ, kích
thước nhỏ gọn, có thể phục vụ kẹp chặt nhiều điểm, đôi khi cách rất xa
nhau, thích hợp cho điều kiện sản xuất hàng loạt, ngoài ra còn được sử
dụng cho đồ gá có bước tiến đồng đều.
Truyền động bước tiến khí - thủy lực
Khi thực hiện bước tiến nhờ lực đàn hồi của khí nén cần phải dùng
biện pháp làm cho bước tiến điều, êm trong phạm vi tốc độ cần thiết,
điều đó có thể đạt được nhờ truyền động bước tiến khí – thủy lực, đồng
thời nó còn tạo nên truyền động không tải và phụ trợ dưới tốc độ lớn.
(3.51 )
(3. 52)
Q
D
d
d
D
Q
Hình 3.54: Xylanh màng
a)
b)
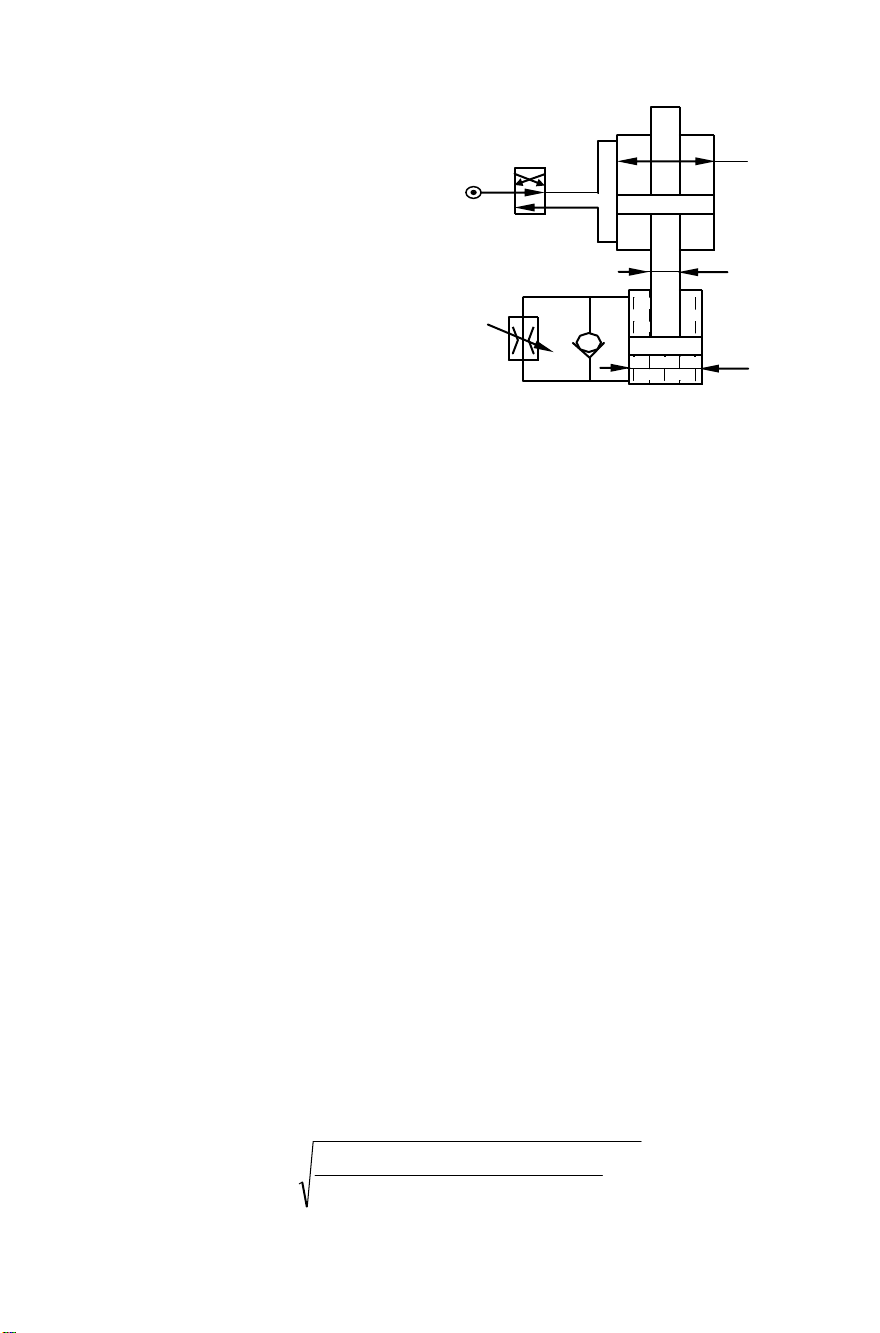
228
Trên hình 3.55 là sơ đồ truyền
động bước tiến khí - thủy lực. Ở đây,
xylanh khí nén truyền dẫn lực còn
xylanh thủy lực là bộ giảm xung, đảm
bảo hành trình êm và có thể điều chỉnh
tốc độ chuyển dịch, nhờ có van tiết lưu
để cố định tốc độ. Việc tính toán
truyền động bước tiến khí – thủy lực
theo trình tự sau.
Các số liệu ban đầu:
- Khi lực của bước tiến lớn
nhất, áp suất trước van giảm áp
không nhỏ hơn 5 6 kG/cm
2
- Áp suất trước van tiết lưu ( sau giảm áp ) trong phạm vi 1,5 2
kG/cm
2
.
- Lượng tiêu hao dầu nhỏ nhất thông qua van tiết lưu, kiểu khe là
100 cm
3
/ph
Lực Q cần thiết trên cần dẫn động của xylanh khí nén được xác
định theo công
,
22
Σ Σ ,( )
m
x
Q P p F T T kG
Trong đó:
p
2
– Áp suất dầu, kG/cm
2
;
F
2
– Diện tích có ích của pittông xylanh thủy lực, cm
2
;
P – Lực lớn nhất của bước tiến, kG;
T
m
– Lực ma sát trong cơ cấu bước tiến của máy hoặc của đồ gá, kG;
T
x
- Lực ma sát của pittông và cần dẫn động trong các xylanh khí
nén và thủy lực;
Thông thường
1) Đường kính xylanh khí nén được xác định như sau:
d
D
2
Hình 3.55
D
1
B
R
P
(3.54)
)TPFp(1,0T
m22x
ΣΣ
cm,d
p
)TTPFP(4
D
1
xm22
1
π
ΣΣ
(3.55)
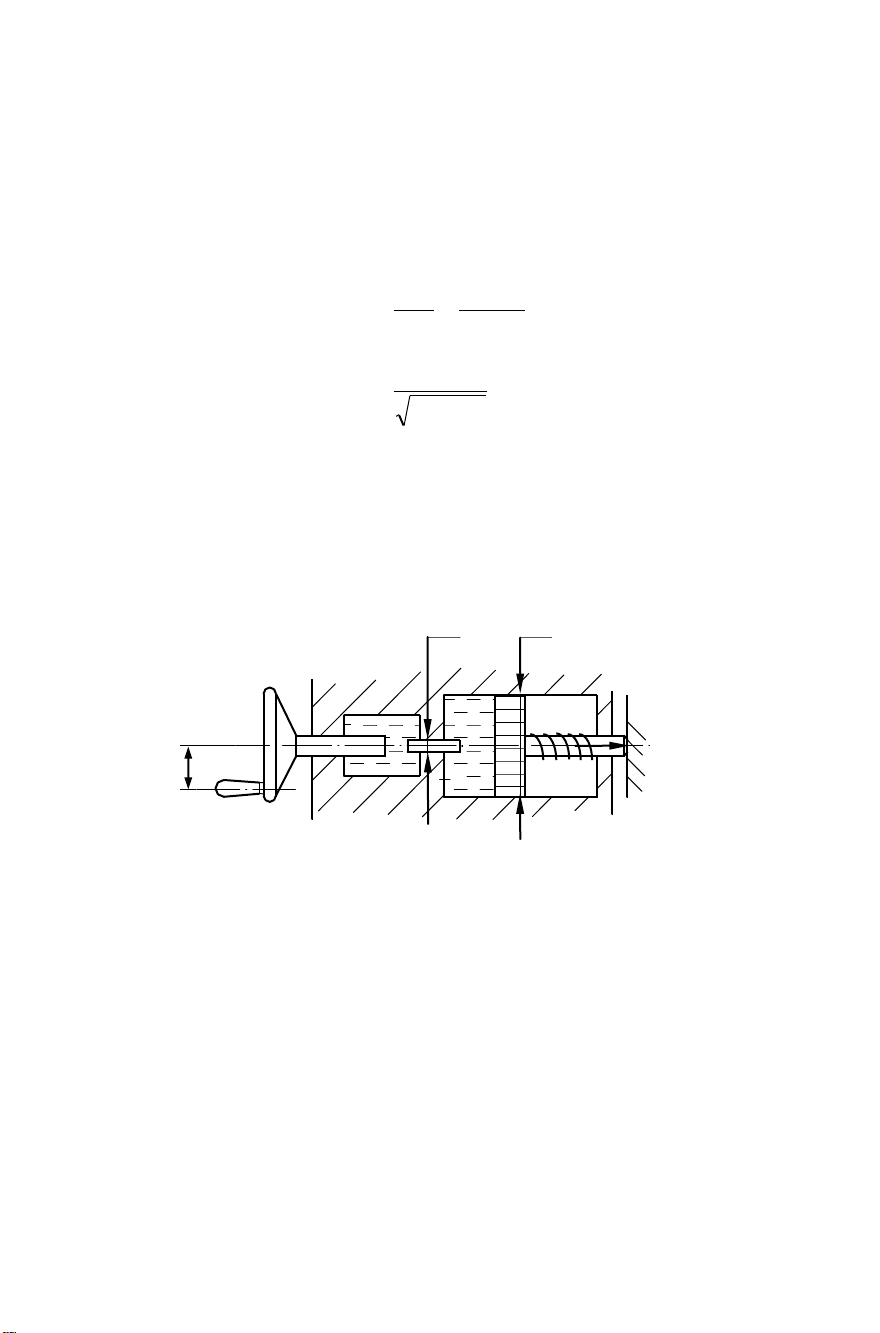
229
Với:
p
1
– Áp suất khí nén, kG/cm
2
;
d – Đường kính cần dẫn động của xylanh khí nén, cm;
2) Đường kính của xylanh thủy lực được tính theo lượng tiêu hao
dầu nhỏ nhất thông qua van tiết lưu kiểu khe:
Suy ra:
Ở đây: S
min
– Bước tiến nhỏ nhất, cm/ph;
Khi thiết kế truyền động khí - thủy lực cần tránh không để xylanh
thủy lực được thấm khí nén qua. Trong các loại máy tổ hợp, máy phay,
máy khoan dùng phổ biến truyền động bước tiến khí - thủy lực
3.7.3 Kẹp chặt bằng cơ khí – thủy lực
Dùng truyền động cơ khí - thủy lực cho các đai ốc kẹp kiểu bulông
và chìa vặn sẽ giảm thời gian phụ trong việc kẹp chặt và nới lỏng chi tiết,
dùng tay nắm để điều khiển các cơ cấu kẹp vì như thế lực điều khiển sẽ
nhỏ hơn nhiều so với lực dùng để vặn đai ốc.
Ưu điểm của việc kẹp chặt bằng cơ khí thủy lực: Không cần nguồn
năng lượng bên ngoài (máy nén khí hay bơm thủy lực), kết cấu nhỏ gọn
giá thành rẻ, thích hợp cho sản xuất hàng loạt nhỏ, có thể sử dụng nhanh
chóng và đặt trên bất kỳ máy nào.
cm
S
D ,
20
min
2
(3.56)
4
100
2
2
min
2
D
S
F
[cm/ph]
d
D
Q
Dầ
u
Hình 3.56
L
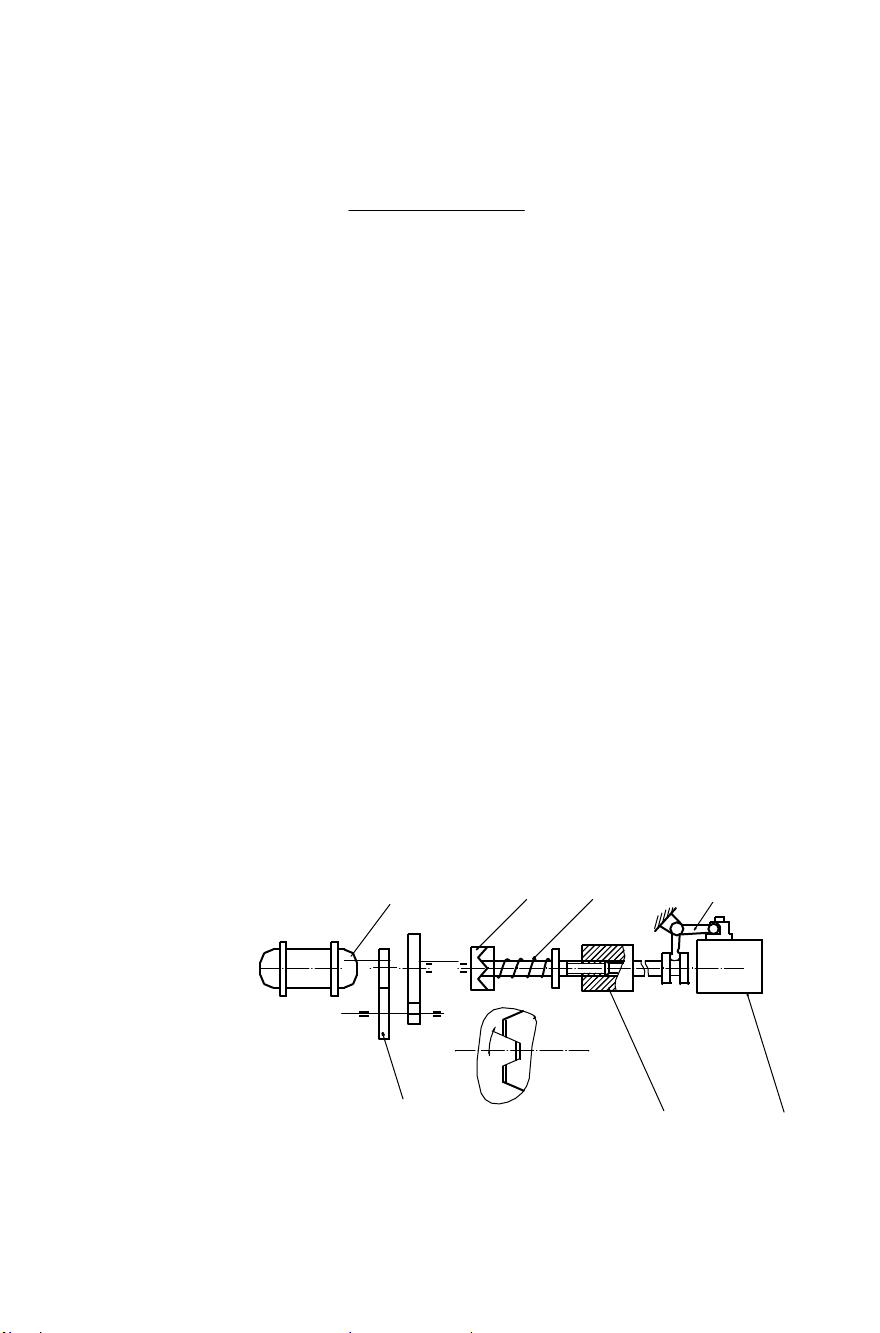
230
Trên sơ đồ hình 3.56 là nguyên lý làm việc của truyền động cơ khí
thủy lực. Khi tác động vào tay quay, lực chiều trục sẽ truyền đến pittông
thông qua môi trường dầu, lực kẹp của chi tiết phụ thuộc vào tỷ số giữa
diện tích của pittông so với diện tích của trụ trượt. Công thức xác định
quan hệ giữa lực chiều trục của vít và cần dẫn động
Trong đó: Q – Lực trên cần dẫn động, kG;
P – Lực tác động lên vô lăng (tay nắm ), kG;
L – Chiều dài cánh tay đòn từ tâm vít đến tâm nắm, cm;
r
tb
– Bán kính trung bình của ren vít, cm;
- Góc nâng ren ( = 2
0
30
’
3
0
30
’
);
- Góc ma sát trong ren, ( = 6
0
34
’
đối với ren hệ mét);
D – Đường kính pittông xylanh thủy lực, cm;
d – Đường kính trụ trượt, cm;
- Hệ số xét đến ma sát trong các đệm làm kín, ( = 0,9);
P
1
– Lực cản của lò xo, kG;
Khi chế tạo các cơ cấu kẹp chặt bằng cơ khí- thủy lực, phải chú ý
đến các đệm làm kín trong xylanh thủy lực, vì nếu rỉ dầu mà không có bổ
xung thì lực kẹp sẽ giảm.
3.7.4. Kẹp chặt bằng điện – cơ
1
7
2
3
4
5
6
Hình 3.57
1-Động cơ
2-Ly hợp
3-Lò xo
4-Vấu kẹp
5-Phôi
6-Đai ốc
7-Bộ truyền
2
2
)( dtgr
DLP
Q
tb
[cm/ph]
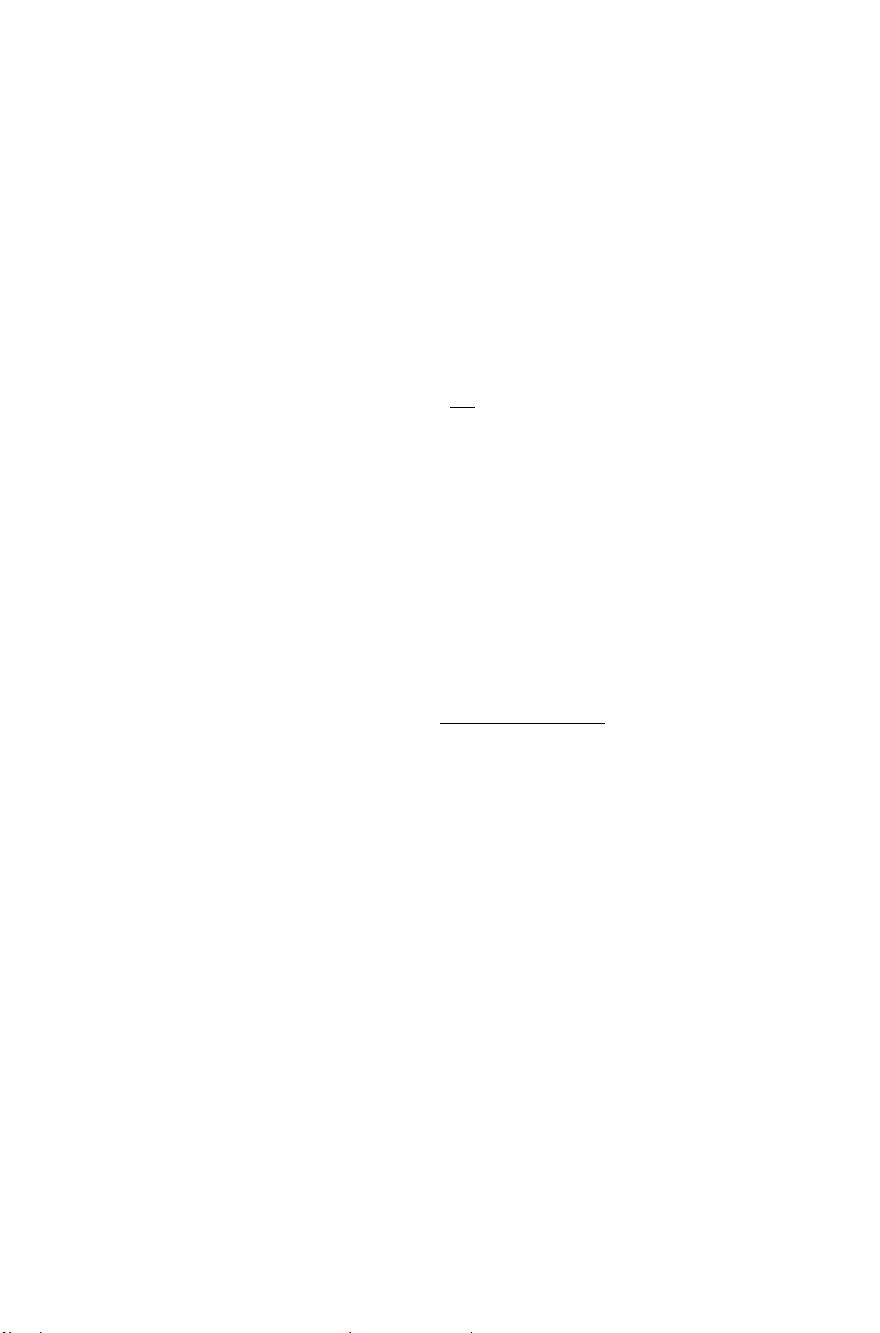
231
Các trang bị kẹp chặt với truyền động điện cơ, được dùng trong các
nhóm máy rơvonve, máy tổ hợp và đường dây tự động. Sơ đồ truyền
động điện cơ thông thường bao gồm có động cơ điện, hộp giảm tốc, bộ ly
hợp, lò xo và bộ truyền vít. Trên hình 3.57 là sơ đồ cơ cấu của loại truyền
động này.
Việc xiết lò xo sơ bộ có thể điều chỉnh mômen quay M được
truyền. Quá trình nới lỏng phôi được thực hiện bằng cách cho quay
ngược chiều động cơ, khi biết được mômen M, lực xiết lò xo sơ bộ được
tính theo công thức:
Trong đó:
r- Bán kính trung bình vị trí các vấu ly hợp;
- Góc ma sát trên mặt tiếp xúc giữa các răng ( = 6 8
0
);
- Góc nghiêng của các răng, thông thường chọn = 30 45
0
;
Lực kéo tạo bởi mômen xoắn của động cơ điện được xác định bằng
công thức:
Trong đó:
N – Công suất động cơ điện (W );
n- Số vòng quay của động cơ (vòng /phút );
r
tb
– Bán kính trung bình của ren (cm );
- Góc nâng của ren ( độ );
- Góc ma sát trong ren, ( độ );
i - Tỷ số truyền của bộ giảm tốc;
- hiệu suất của bộ giảm tốc;
3.7.5. Kẹp chặt bằng từ
3.7.5.1. Nguyên tắc làm việc
Tạo lực kẹp bằng từ để kẹp chặt các chi tiết mỏng, khó định vị và
khó kẹp.
( 3.57 )
)φ(tg
r
M
P -α×=
)(
71620
tgrn
iN
W
tb
( 3.58 )
[kG]
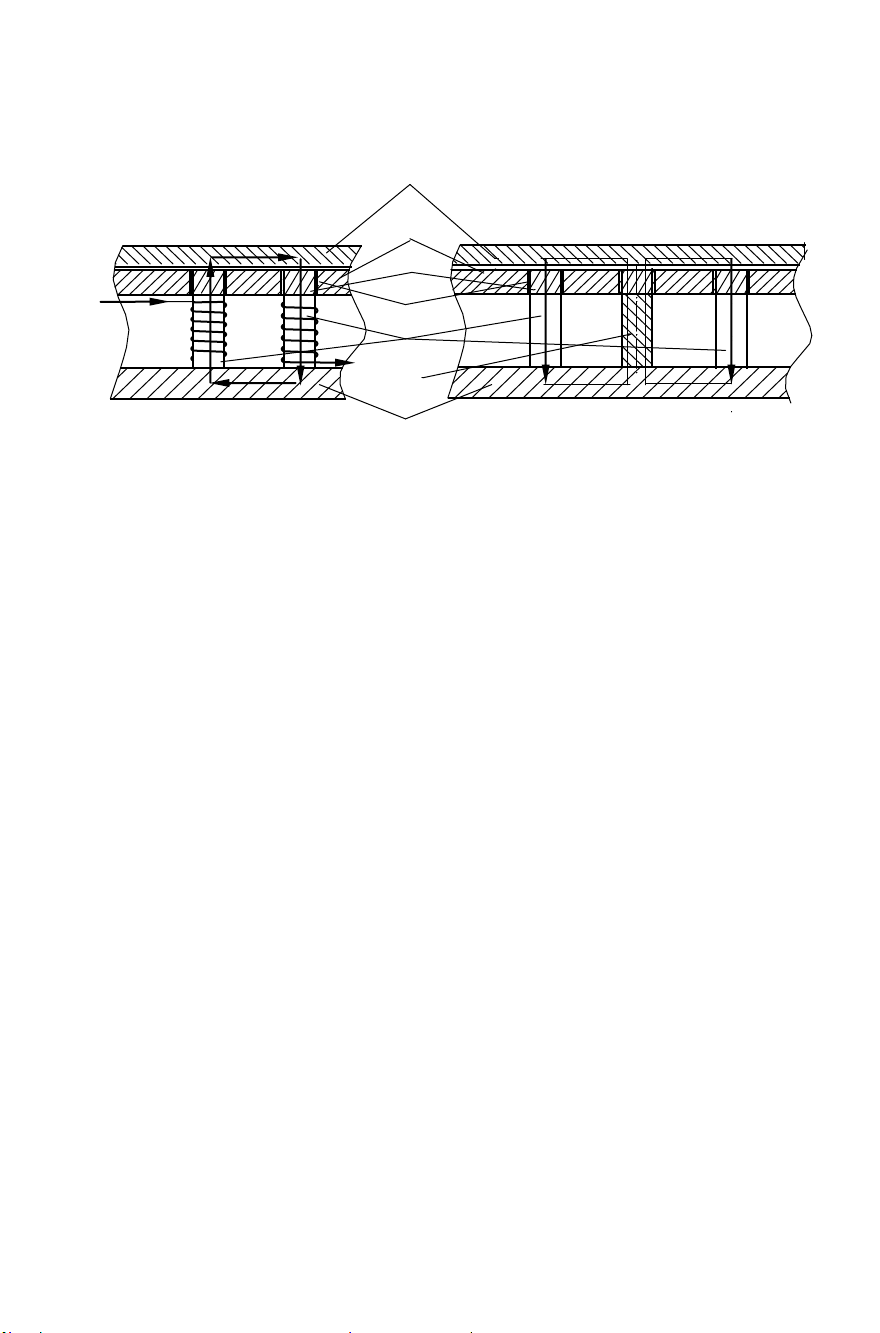
232
Đồ gá từ được phân làm hai loại:
- Đồ gá điện từ: dùng nam châm điện để tạo lực kẹp (hình 3.58a).
- Đồ gá dùng nam châm vĩnh cửu (hình 3.58b).
Mạch từ bao gồm:
Chi tiết gia công (1), các vật dẫn từ (3,6); các chi tiết không dẫn từ
(4); các cuộn dây điện từ hay nam châm vĩnh cửu (5); đế đồ gá (7).
Chi tiết gia công (1) được đặt trên bề mặt (2) của đồ gá, tại đó có từ
thông do các cuộn dây điện từ hoặc nam châm vĩnh cửu tạo ra sẽ hút chặt
chi tiết vào bề mặt định vị của đồ gá.
Đồ gá điện từ thông dụng nhất là bàn từ, mâm cặp từ. Nguồn điện
cung cấp cho các mâm cập từ, bàn từ là dòng điện một chiều có điện áp
110 hoặc 220V từ tổ động cơ máy phát hoặc các bộ chỉnh lưu từ dòng
xoay chiều thành dòng một chiều.
Đồ gá điện từ và đồ gá sử dụng nam châm vĩnh cửu dùng để gá đặt
và kẹp chặt chi tiết chế tạo từ vật liệu có độ thấm từ lớn là thép chưa tôi
và độ thấm từ nhỏ là thép tôi và thép hợp kim.
Đồ gá từ có một loạt các ưu điểm:
- Lực hút kẹp chặt phân bố đều trên toàn bề mặt tựa của chi
tiết gia công.
- Kết cấu đơn giản dễ tự động hóa hoàn toàn
- Không gian dành cho chi tiết lớn.
- Độ cứng vững của đồ gá cao, bảo đảm độ chính xác gia công.
- Điều khiển đơn giản và thuận tiện
Nhược điểm của truyền dẫn từ trong đồ gá là lực kẹp nhỏ hơn so với
các loại truyền dẫn khác, không kẹp được các chi tiết được chế tạo từ vật
liệu không dẫn từ, đồ gá từ chỉ dùng để kẹp chặt chi tiết khi gia công tinh.
Hình 3.58
2
4
3
5
6
7
N
S
N
S
b)
a)
1
S
N
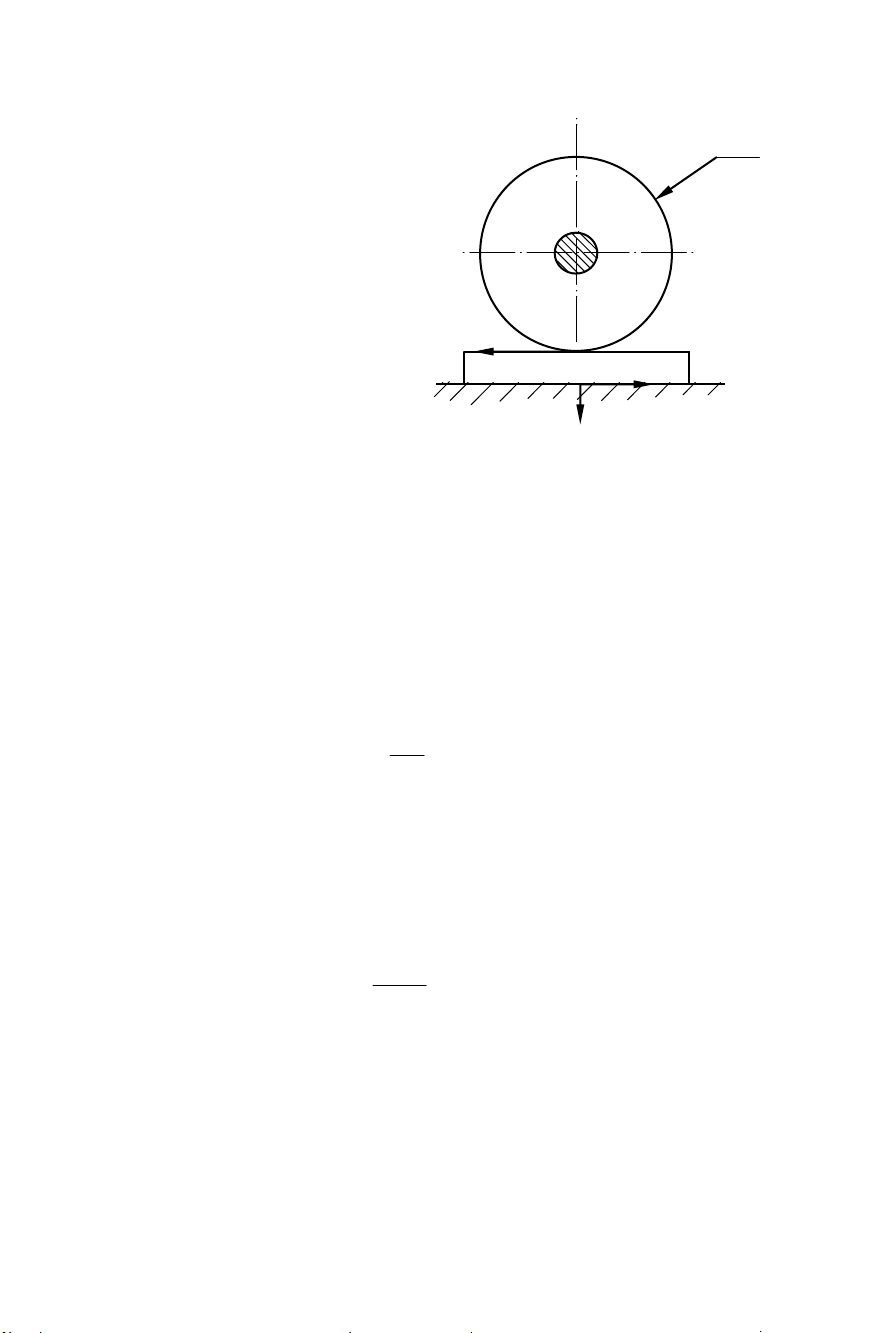
233
2.Tính lực kẹp
Lực kẹp chi tiết gia công trên
bàn từ phụ thuộc vào lực hút riêng
của bàn từ, kích thước của chi tiết
và sự bố trí chi tiết trên bàn.
Khi tăng chiều dày và diện
tích mặt cắt ngang của chi tiết, lực
kẹp sẽ tăng lên, khi độ nhám bề
mặt định vị của chi tiết tăng thì
lực kẹp giảm.
Lực hút của bàn từ phải tạo
ra được lực ma sát F lớn hơn
( hoặc bằng ):
Với:
f- hệ số ma sát giữa chi tiết gia công và bàn từ;
P
X
– lực cắt, tính theo nguyên lý cắt;
Kích thước cuộn dây được tính theo công thức:
Trong đó:
I – Cường độ dòng điện(A);
W – Số vòng của cuộn dây;
S – Từ trở, tính theo từng đoạn trong mạch mà từ thông đi qua:
- Từ thông tổng:
QB
L – Chiều dài đoạn tính từ trở;
- Hệ số dẫn từ;
Q – Diện tích mặt cắt đoạn tính ( cm);
( 3.59 )
X
PfT
( 7.60 )
Q
L
S
Đá mài
F= Tf
P
x
Hình 3.59
T
4,0
.
.
S
WI
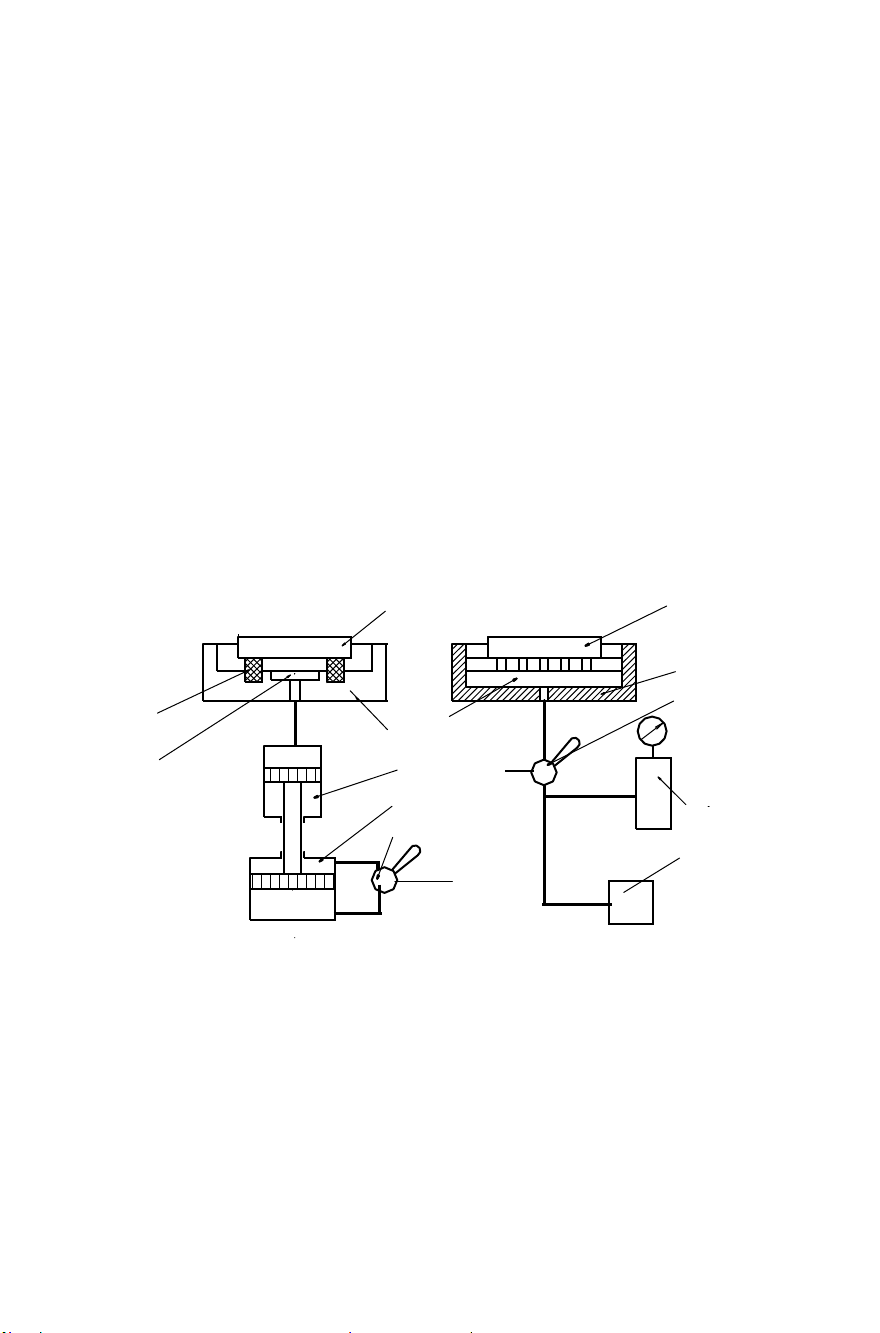
234
3.7.6. Kẹp chặt bằng chân không
3.7.6.1. Nguyên lý
Trong đồ gá truyền dẫn chân không, do ảnh hưởng của chân không
tạo ra giữa mặt định vị và chi tiết gia công và ngăn đồ gá, chi tiết được
kẹp chặt với bề mặt đồ gá bởi áp suất không khí.
Đối với những chi tiết kém cứng vững khi gia công tinh, khi đó ta dùng
đồ gá chân không để đặt lực kẹp lên bề mặt nhỏ dễ bị biến dạng của chúng.
Trên hình 3.60a) là kiểu đồ gá chân không dùng pittông-xylanh hút.
Van 5 sẽ có nhiệm vụ mở khí nén vào buồng 4, khí nén đẩy pittông của
xylanh 3 đi xuống tạo chân không ở buồng 6. Nhờ đệm 7 làm kín, chân
không sẽ hút chặt chi tiết 1 vào đồ gá.
Khi tháo chi tiết, ta chỉ cần xoay van 5 để khí nén vào phía dưới
của xilanh 4 đẩy pittông đi lên, buồng 6 sẽ không còn chân không nữa, ta
lấy chi tiết ra dễ dàng.
Trên hình 3.60b, người ta dùng máy hút 5 để tạo chân không, bình
4 giúp cho quá trình tạo chân không nhanh.
3.7.6.2.Tính lực kẹp
Lực kẹp được xác định:
Trong đó:
p
a
- áp suất không khí (kG/cm
2
);
P
0
= 0,01 – 0,015, là áp suất dư trong ngăn sau khi đã
tạo chân không;
( 3.61)
yoa
PF)PP(W
1
3
5
4
6
7
2
3
4
5
6
Hình 3.60
b)
a)
2
1
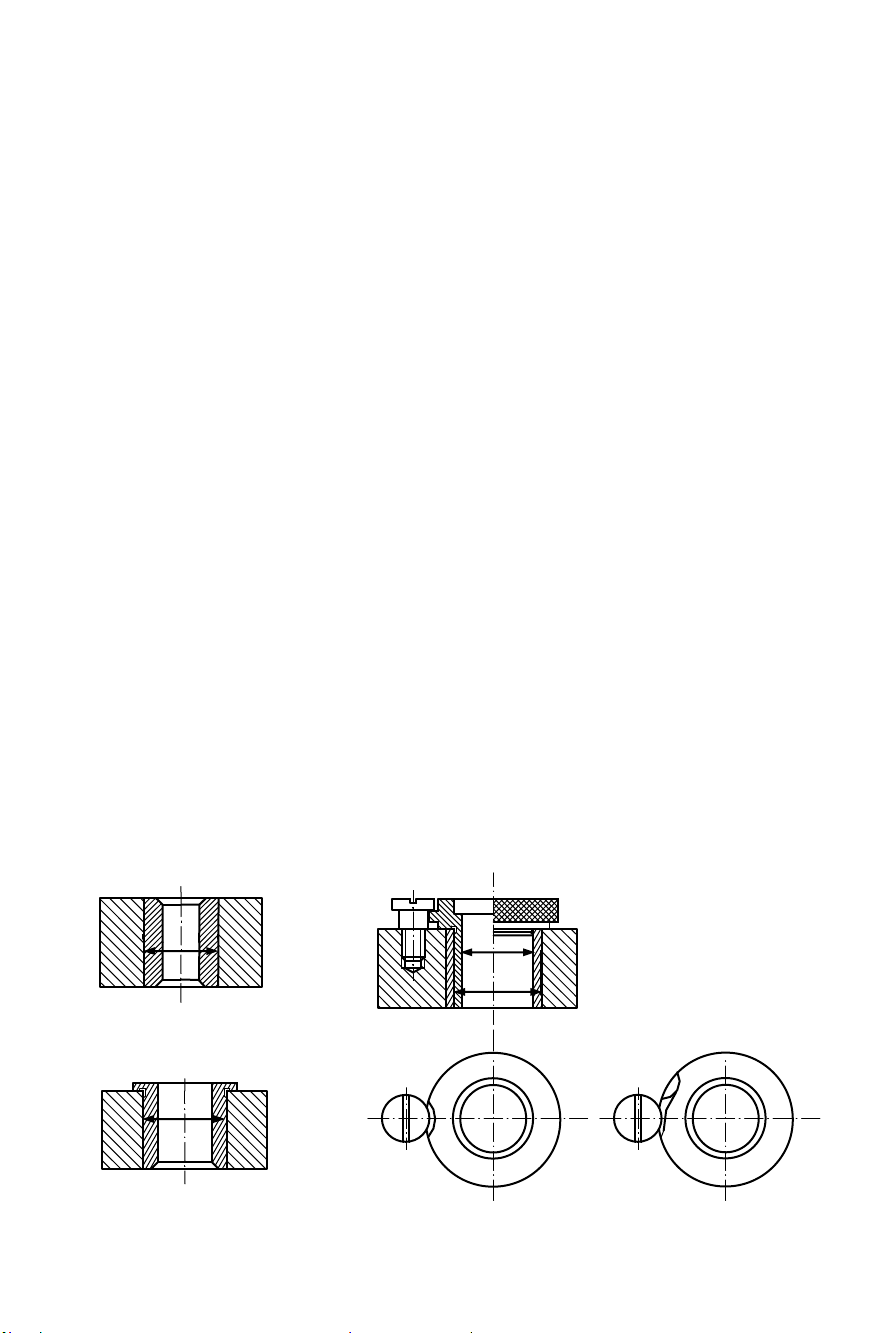
235
F – Diện tích của mặt dưới chi tiết được giới hạn bởi
đệm kín cao su (cm
2
);
P
y –
Lực đàn hồi của đệm kín cao su bị nén (kG);
Hiệu Pa-P
o
0,07 kG/cm
2
, vì nếu nhỏ hơn sẽ không đảm bảo
được độ tin cậy khi kẹp chặt.
Để phân bố đều lực kẹp, trên bề mặt gá đặt chi tiết 1 của thân 2
trên hình 3.60b, khoan nhiều lỗ nhỏ thông với ngăn chân không 6, bơm
chân không 5 qua van phân phối 3 để tạo chân không cho ngăn 6.
Lực kẹp chặt chi tiết trong đồ gá chân không được kiểm tra bằng
đồng hồ đo áp suất.
3.8. CÁC CƠ CẤU KHÁC CỦA ĐỒ GÁ
3.8.1. Cơ cấu dẫn hƣớng
3.8.1.1. Nhiệm vụ của cơ cấu dẫn hướng
Cơ cấu dẫn hướng là cơ cấu dùng để dẫn hướng dụng cụ cắt và
nâng cao độ cứng vững của nó.
Nếu không có cơ cấu dẫn hướng, dụng cụ cắt sẽ bị lệch đi, hướng
tác dụng của lực cắt không đều, vì rung động hoặc vì độ cứng vững của
dao quá kém. Cơ cấu dẫn hương thường dùng trong các nguyên công
như: khoan, khoét, tiện trong, doa ngang...
Cơ cấu dẫn hướng thường là các bạc dẫn hướng dùng trong đồ gá
để khoan, khoét, doa...
3.8.1.2. Bạc dẫn hướng
Hình 3.61: Bạc dẫn hướng
a)
b)
c)
d)
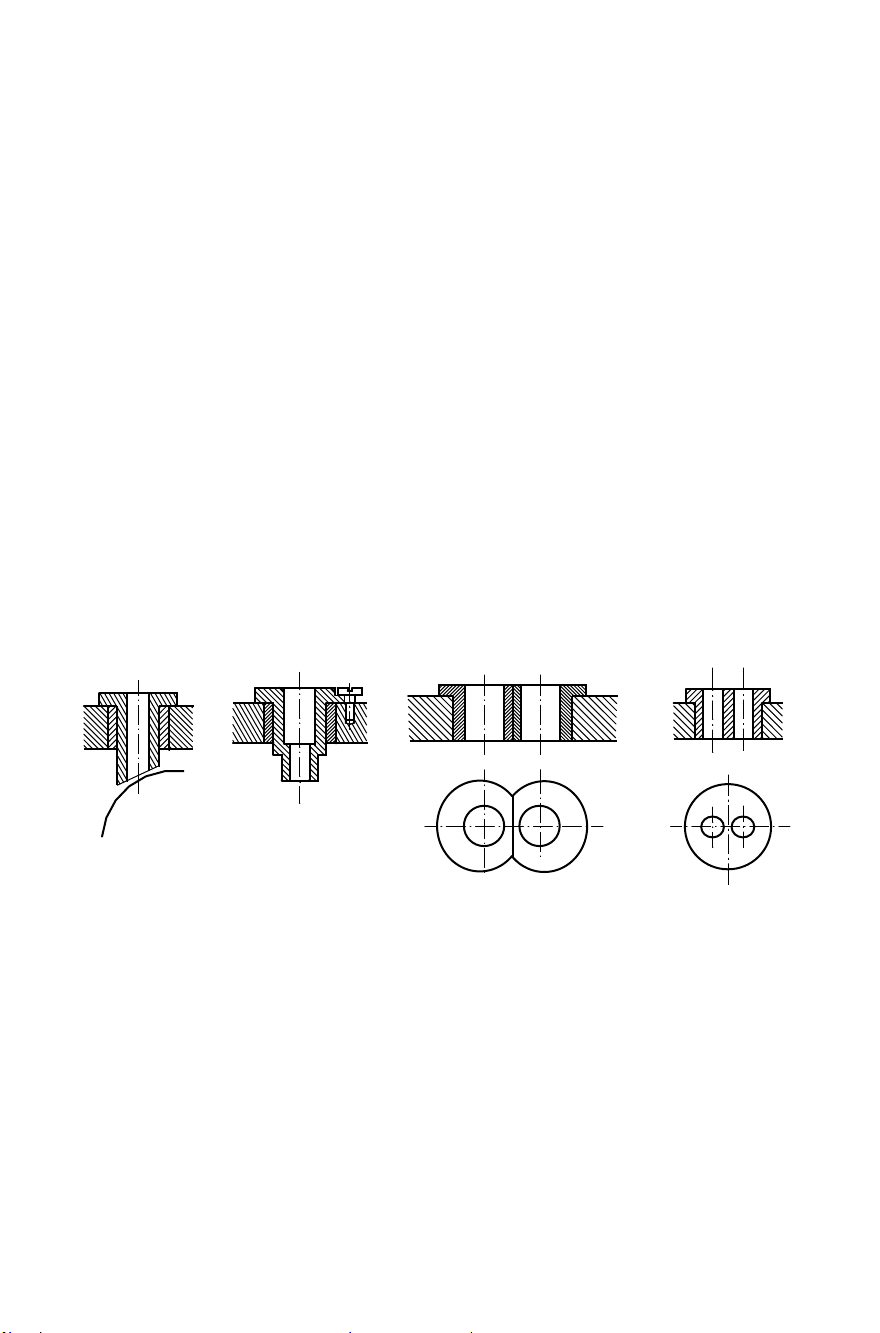
236
Hình 3.61a là loại bạc dẫn hướng cố định không có gờ.
Hình 3.61b là loại bạc dẫn hướng cố định có gờ.
Hình 3.61c là loại bạc dẫn hướng dễ thay đổi.
Hình 3.61d là loại bạc dẫn hướng tháo nhanh.
Bạc dẫn hướng cố định lắp vào đồ gá theo mối lắp thường dùng
trong sản xuất đơn chiếc để dẫn hướng một dụng cụ cắt có đường kính
không đổi.
Loại bạc dẫn hướng có gờ là để bạc khỏi bị trượt xuống trong quá
trình gia công.
Bạc dẫn hướng dễ thay thế thường dùng trong sản xuất hàng loạt
lớn và hàng khối. Khi bạc mòn, ta có thể thay bạc một cách nhanh chóng
vì nó được lắp qua một bạc lót trung gian theo chế độ H7/h6. Loại này
cũng dùng để dẫn hướng một loại dụng cụ cắt.
Khi gia công bằng nhiều dụng cụ cắt như khoan, khoét, doa...thì
phải dùng bạc tháo nhanh. Số lượng bạc tháo nhanh sẽ bằng số loại dụng
cụ cần phải dẫn hướng. Đường kính lỗ của bạc tháo nhanh sẽ tương ứng
với đường kính của dụng cụ cắt. Các bạc này sẽ lắp lên đồ gá qua bạc
trung gian theo chế độ H7/h6.
Khi gia công các bề mặt cong, lõm xuống hoặc có hai lỗ rất sát
nhau phải dùng những bạc dẫn hướng có kết cấu đặc biệt ( hình 3.62 ).
Hình 3.62a là loại bạc dẫn hướng dùng để gia công các bề mặt
cong, nghiêng.
Hình 3.62b là loại bạc dẫn hướng thò sâu xuống dùng để gia công
các bề mặt lõm xuống.
Hình 3.62c,d là loại bạc dẫn hướng dùng để gia công những lỗ
sát nhau.
c)
Hình 3.62: Bạc dẫn hướng kết cấu đặc biệt .
d)
a)
b)
c)
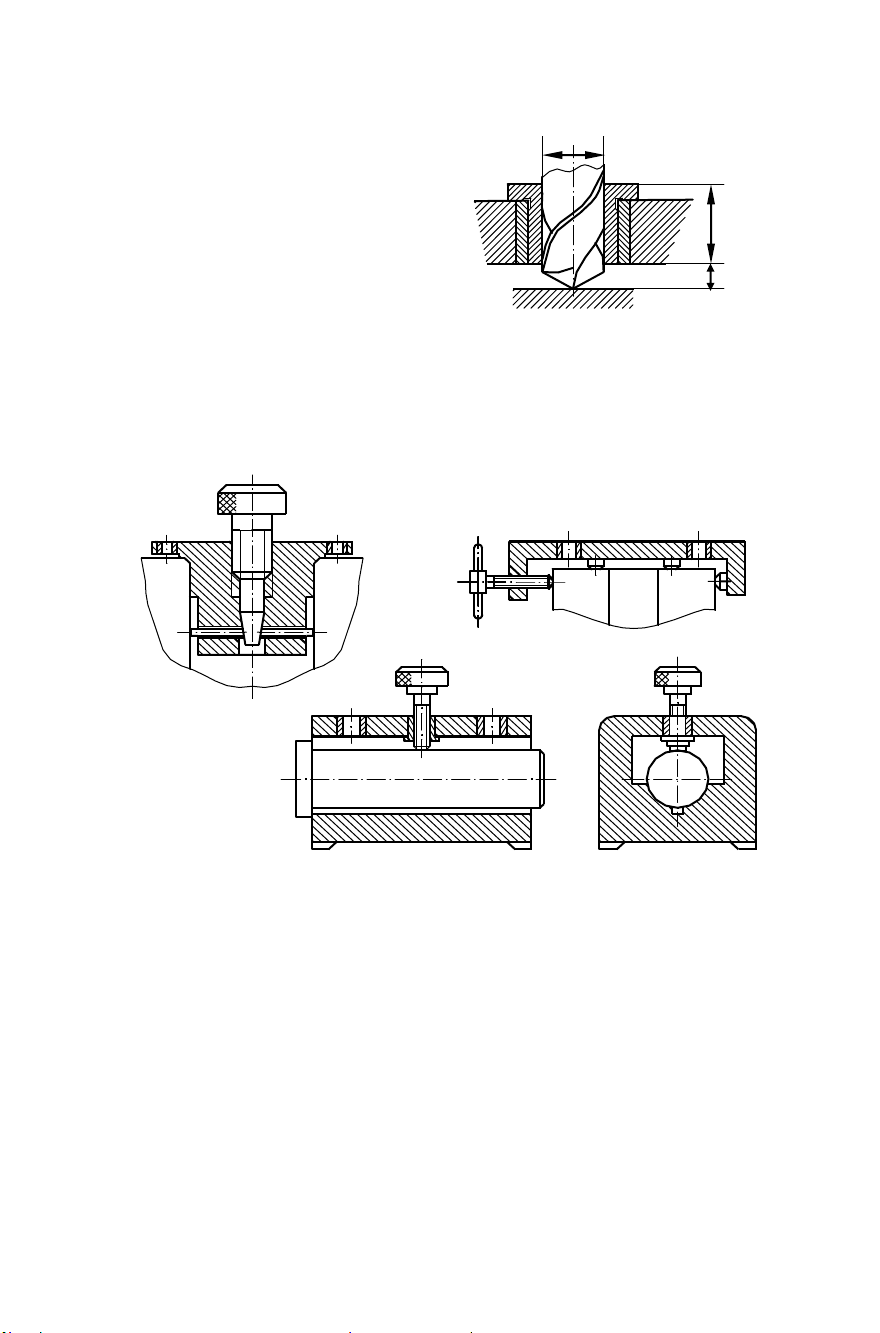
237
Để cho bạc đỡ mòn cần phải
đảm bảo các kích thước dẫn của
bạc dẫn hướng như chiều dài bạc
b và khoảng cách từ mặt đầu dưới
của bạc và bề mặt gia công a
(hình 3.63 )
Khi khoan gang a=(0,30,5)
d, còn khi khoan thép và các vật
liệu dẻo khác từ đó có thể tăng lên
đến a = ( 0,5 1 ) d, khi khoét thì a 0,3d.
Chiều dài bạc dẫn hướng chọn theo tỷ lệ sau: b = (1,5 2 ) d
Đối với các chi tiết lớn và vừa có thể dùng các phiến dẫn hướng di
động tháo lắp được cho từng chi tiết như hình 3.64a,b.
a)
c)
Hình 3.64: Phiến dẫn hướng.
b)
Hình 3.63: Kích thước bạc dẫn
a
b
d
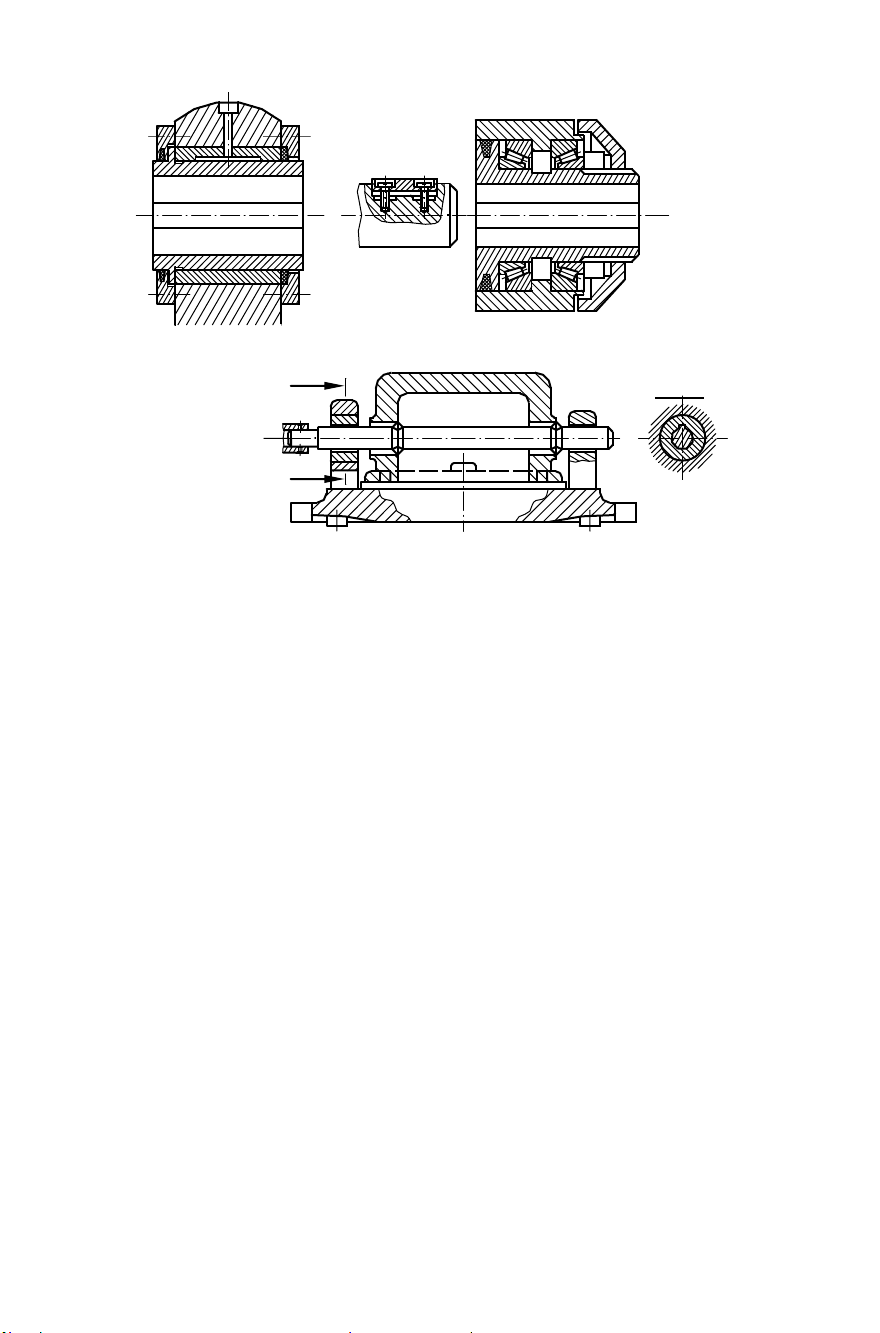
238
Khi khoan các lỗ nhỏ (d 5mm) trên các phôi nhỏ, có thể dùng
phiến dẫn hướng lắp cố định vào vỏ đồ gá như trên hình 3.64c.
Để dẫn hướng trục dao khi doa ngang có thể dùng sơ đồ trên hình
3.65.a,b,c.
Vật liệu để chế tạo bạc dẫn hướng khi khoan lỗ có đường kính D
25 mm thường dùng thép dụng cụ Y10A, Y12A hoặc 9XC tôi đạt độ
cứng 62 65 HRC. Khi khoan lỗ có đường kính D >25 mm thì dùng thép
20, 20X thấm than với chiều sâu 0,8 1,2 mm và tôi đạt độ cứng 62 65
HRC.
Tuổi thọ của một bạc dẫn hướng dùng 10.000 15.000 lỗ khi
khoan lỗ có l d. Sử dụng bạc hướng dẫn cho phép loại bỏ việc lấy dấu,
giảm độ lệch tâm khi khoan.
Độ chính xác khi dùng bạc dẫn hướng tăng khoảng 50% so với khi
không dùng.
3.8.2 Cữ so dao - cơ cấu quay và phân độ
3.8.2.1. Cữ so dao
Cữ so dao dùng để điều chỉnh cho dao cắt có vị trí chính xác tương
đối so với bàn máy và đồ gá ( tức là so với chi tiết gia công ). Cữ so dao
thường dùng trên máy phay.
Hình 3.65: Dẫn hướng trục doa ngang
a)
b)
c)
A
A
A -A
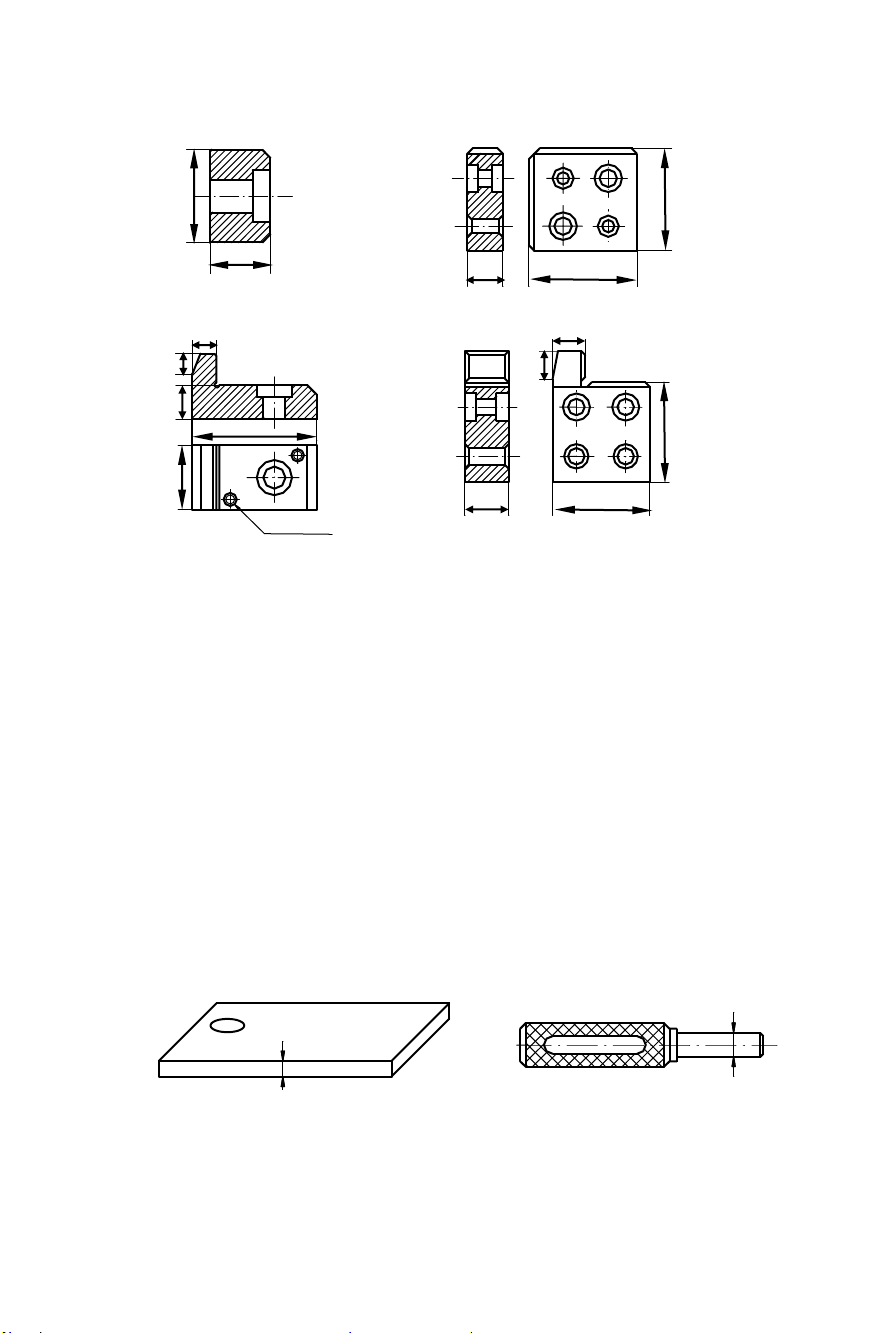
239
Cữ so dao bao gồm miếng gá các loại ( hình 3.66 ) và miếng căn.
Hình 3.66a là miếng gá dùng để gá dao khi phay mặt phẳng để đạt
kích thước chiều cao.
Hình 3.66b là miếng gá mặt đầu dùng để gá dao khi phay mặt bên
Hình 3.66c là miếng gá góc dùng để gá dao khi phay bậc, rãnh.
Hình 3.66d là miếng gá dùng để gá dao vừa phay mặt bên, vừa
phay bậc, rãnh.
Miếng căn thường dùng là loại phiến mỏng từ 3 5mm (hình
3.67a) hoặc hình trụ (hình 3.67b)
Khi điều chỉnh máy, phải dùng miếng căn đệm giữa miếng gá dao
và dao cắt để tránh dao cắt có lưới sắc sẽ làm hỏng bề mặt miếng gá dao.
Hình 3.66: Miếng gá
a)
D
H
d)
12
36
16
H
8
b)
6
12
H
40
d
1
c)
16
36
d
3 – 5
mm
a)
b)
Hình 3.67: Miếng căn
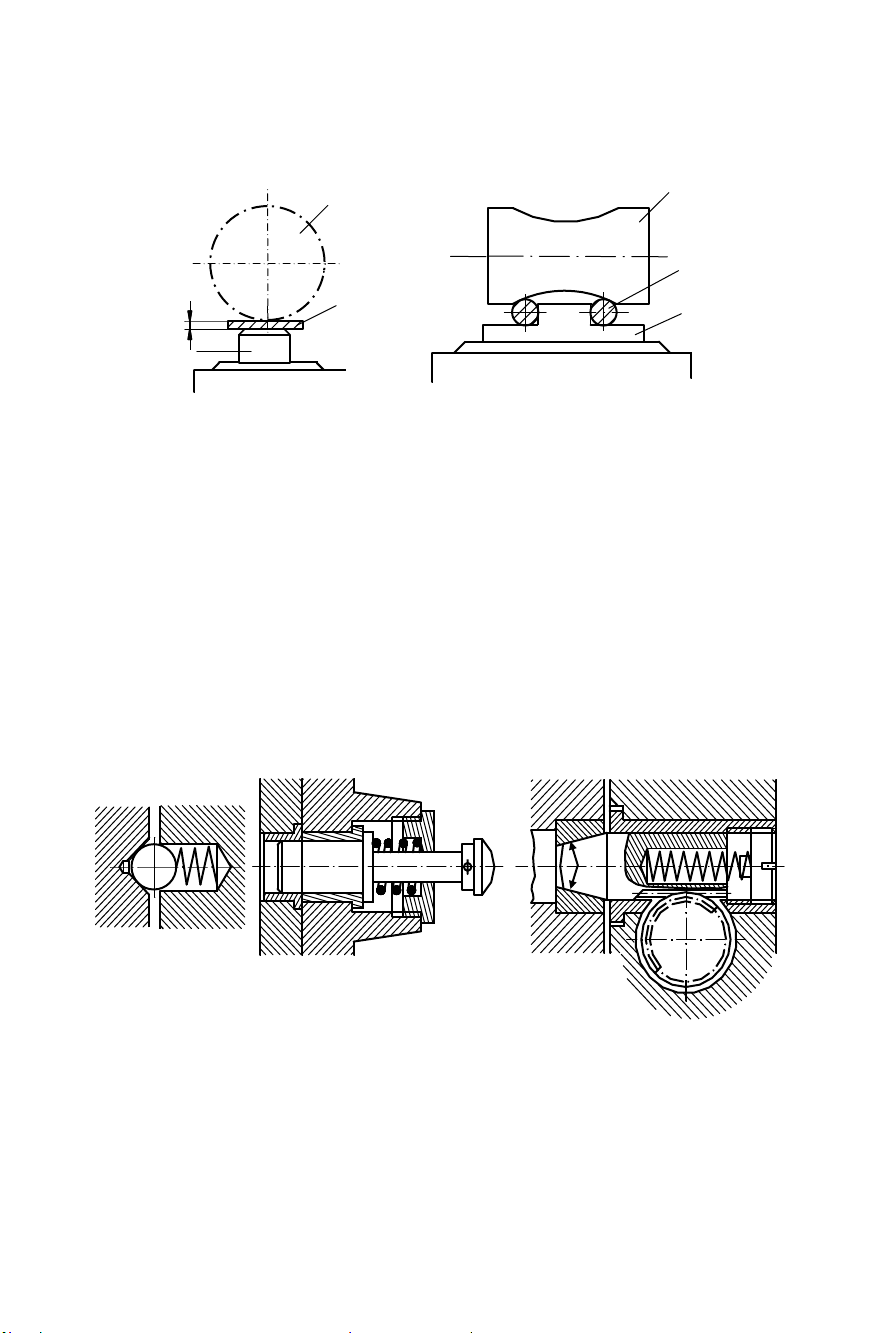
240
Ví dụ sử dụng cơ cấu gá dao trên đồ gá được trình bày trên hình 3.68.
Miếng gá dùng chốt định vị và dùng vít gắn chặt lên vỏ đồ gá ở
một chỗ thuận tiện nào đó. Sau khi lắp xong cần phải mài bề mặt làm
việc đạt độ nhám Ra = 1,25 m
Vật liệu làm miếng gá và căn thường là thép dụng cụ Y8A hoặc
thép 20 tôi đạt độ cứng 55 60 HRC.
3.8.2.2. Cơ cấu quay và phân độ
Cơ cấu quay và phân độ thường sử dụng trong những đồ gá nhiều
vị trí, dùng để tạo cho phôi có nhiều vị trí khác nhau so với dụng cụ cắt.
Các chốt phân độ có kết cấu như hình 3.69
Hình 3.69a là chốt phân độ kiểu bi có kết cấu đơn giản nhưng
không đảm bảo chính xác khi phân độ, không chịu được mômen của lực
cắt. Ta dùng tay để quay mâm quay, khi đó bi sẽ bị ấn ngược lại, khi đến
một lỗ khác sẽ bị lò xo đẩy vào lỗ.
Hình 3.68: Cơ cấu căn dao
s
Dao phay
Miếng căn
Cữ so dao
Miếng căn
Dao phay
Cữ so dao
Hình 3.69: Định vị khi phân độ
a)
b)
c)
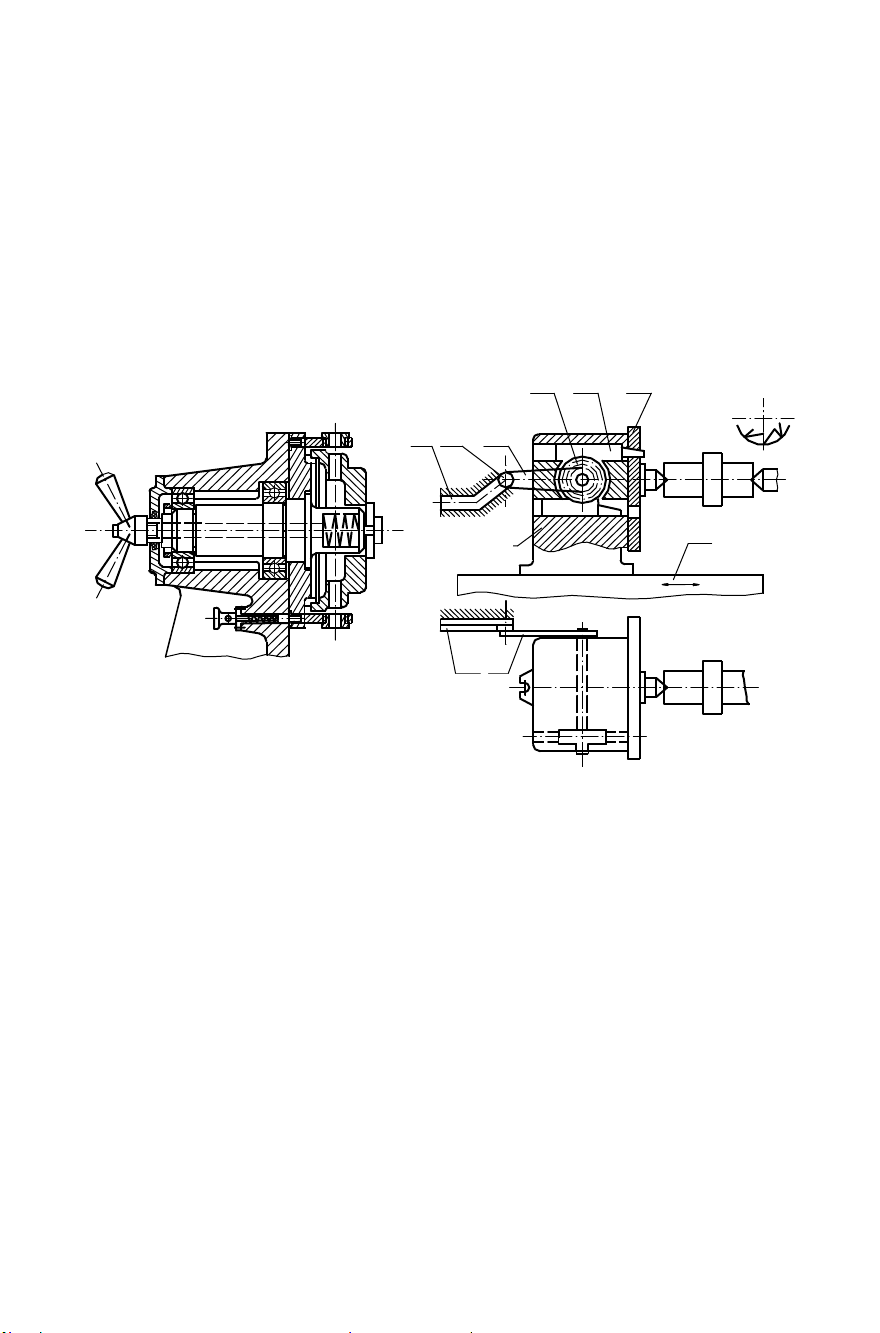
241
Hình 3.69b là chốt phân độ hình trụ có thể chịu được mômen
nhưng độ chính xác phân độ vẫn còn thấp do có khe hở giữa lỗ và chốt
phân độ.
Hình 3.69c là chốt phân độ dạng côn ( với góc côn 15
o
) đảm
bảo độ chính xác cao hơn.
Hình 3.70a là sơ đồ tổng quát của cơ cấu quay và phân độ.
Trong đồ gá tự động, việc quay và cố định phần quay được thực
hiện tự động bằng máy và không cần sự tham gia trực tiếp của con người.
Hình 3.70b là sơ đồ của đồ gá tự động dùng để phân độ thành
những bước nhỏ. Bánh răng sẽ thực hiện chuyển động lắc với góc lắc nhỏ
và truyền cho chốt 5 và 8 tịnh tiến. Các cạnh vát của chốt 5 và 8 sẽ làm
cho đĩa 6 quay một cách gián đoạn theo một hướng. Chuyển động lắc của
bánh răng thực hiện từ cách tay đòn với con lăn 2 lăn theo mẫu chép hình
cố định 1, khi bàn máy chuyển động tịnh tiến. Trong quá trình gia công,
cơ cấu khắc phục hiện tượng đĩa quay đi một góc nhỏ theo lực quán tính.
Hình 3.71a chỉ ra kết cấu của mâm quay mà phần trên của nó có thể
quay đi một góc yêu cầu khi nâng nó lên. Việc nâng bàn máy có thể thực
hiện được bằng các cơ cấu cơ khí khác nhau hoặc bằng xylanh khí nén.
Khi hạ xuống bàn máy sẽ tỳ lên mặt đầu của máy và ép sát vào đồ gá.
Một kết cấu khác được trình bày trên hình 3.71b. Phần quay trên
của đồ gá được lăn trên ổ đỡ tỳ chuyên dùng. Vì ổ lăn có kích thước lớn
cho nên nó bảo đảm ổn định khi quay và chịu được tải lớn.
b)
1
3
3
1
2
4
5
6
7
8
a)
Hình 3.70
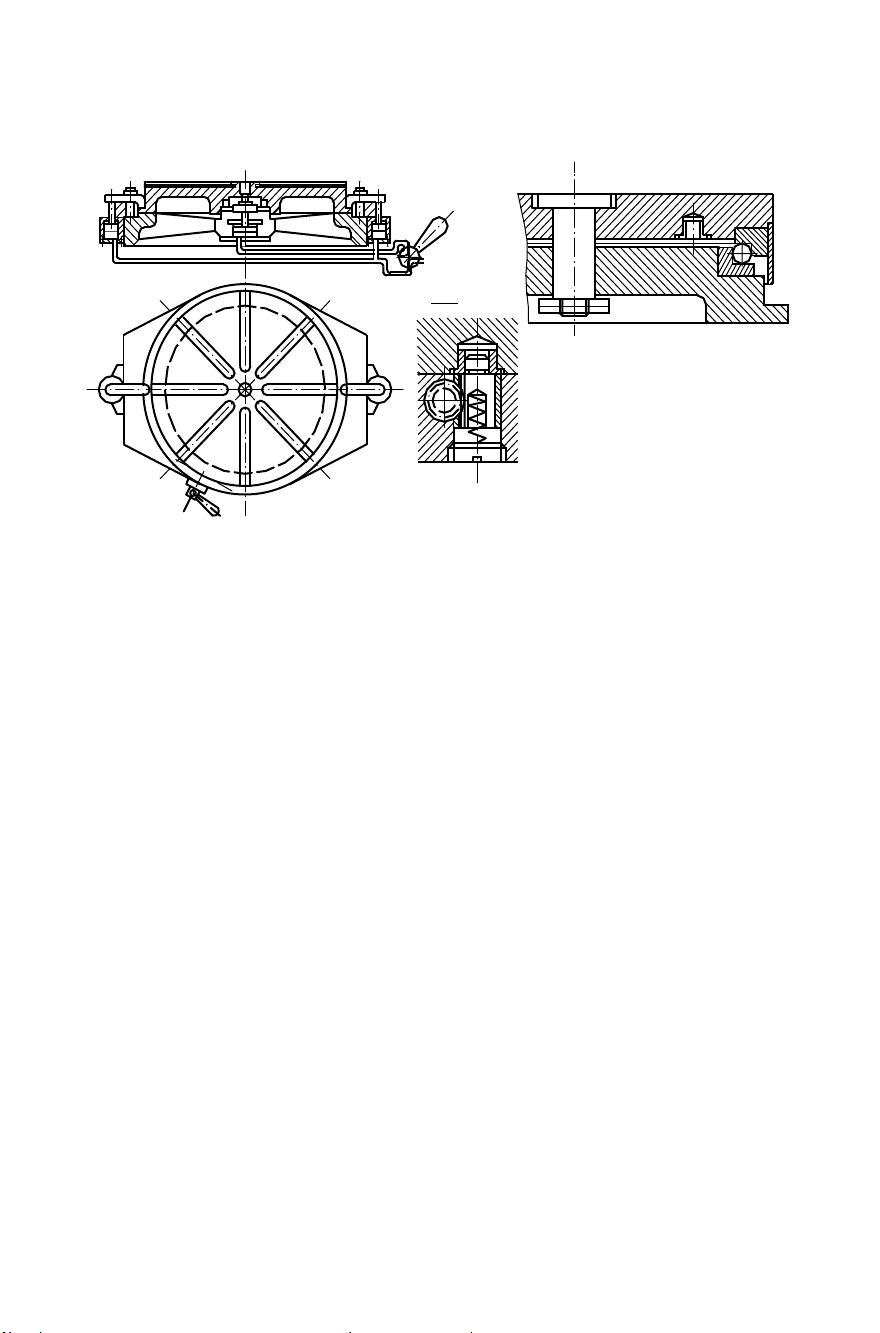
242
3.8.3. Thân đồ gá
Thân đồ gá là chi tiết cơ bản của đồ gá để lắp ráp những cơ cấu
khác còn lại như: định vị, kẹp chặt, dẫn hướng dụng cụ cắt …
3.8.3.1. Yêu cầu thân đồ gá
Thân đồ gá chịu ảnh hưởng của lực cắt và lực kẹp chặt cho nên nó
phải thoả mãn những yêu cầu sau đây:
Kết cấu phải đủ cứng vững và bền khi chịu tải trọng lực cắt và
không bị biến dạng.
Kết cấu phải đơn giản, nhẹ, dễ chế tạo, tính công nghệ cao, dễ
thao tác, dễ quét dọn phôi, dễ tháo lắp chi tiết gia công
Kết cấu phải vững chãi an toàn, nhất là đối với đồ gá quay
nhanh.
3.8.3.2. Kết cấu một số thân đồ gá
Hình 3.72a là thân đồ gá đúc từ gang xám
Hình 3.72b là thân đồ gá hàn từ thép tấm
Hình 3.72c là thân đồ gá lắp ghép từ những chi tiết chuẩn.
Hình3.72d là thân đồ gá rèn từ thép
Thân đồ gá cũng có thể phối hợp giữa phôi hàn và phôi đúc.
Hình 3.71: Kết cấu mâm quay
a)
b)
A -
A
A
A
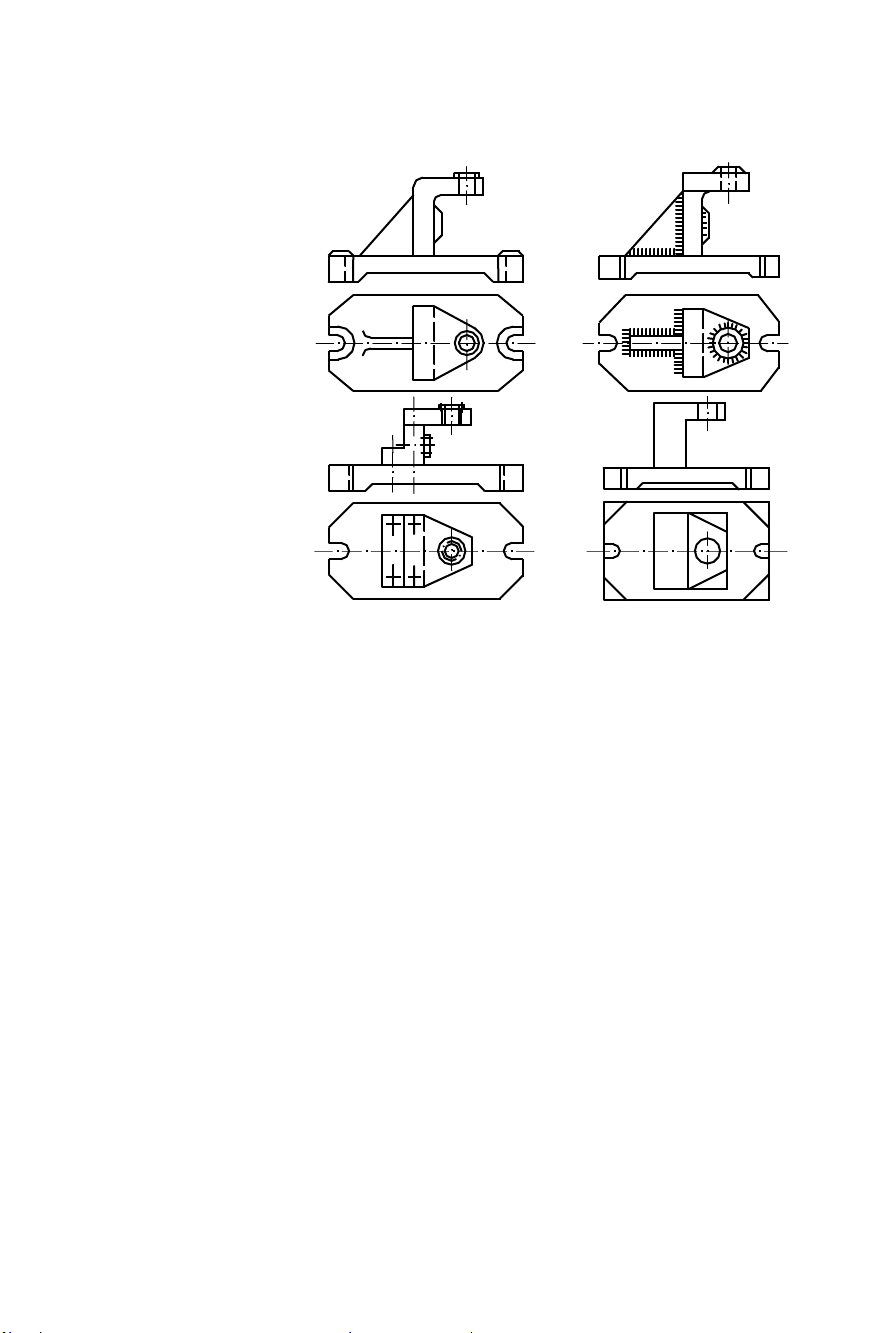
243
Bằng phương pháp đúc có thể chế tạo được thân đồ gá có kết cấu
phức tạp nhưng thời
gian chế tạo lâu và
phải khử ứng suất
dư nên giá thành
đắt. Thân đồ gá chế
tạo bằng phương
pháp hàn có độ
cứng vững kém
hơn, khó hoàn thành
kết cấu phức tạp
nhưng chế tạo
nhanh và rẻ.
Chọn
phương án chế tạo
phụ thuộc vào điều
kiện sử dụng của đồ
gá, thời hạn, giá
thành và công nghệ
chế tạo chúng.
3.9. ĐỒ GÁ TRÊN MÁY CÔNG CỤ CNC
3.9.1. Đặc điểm của đồ gá trên máy công cụ CNC
Một trong những đặc điểm chính của máy CNC là độ chính xác
của nó rất cao. Đồ gá trên máy CNC phải đảm bảo độ chính xác gá đặt
cao hơn các đồ gá trên máy vạn năng thông thường. Để đảm bảo độ
chính xác gá đặt, phải chọn chuẩn sao cho sai số chuẩn bằng 0, sai số kẹp
chặt phải có giá trị nhỏ nhất, điểm đặt của lực kẹp phải tránh gây biến
dạng cho chi tiết gia công.
Các máy CNC có độ cứng vững rất cao, do đó đồ gá trên các máy
đó không được làm giảm độ cứng vững của hệ thống công nghệ khi sử
dụng máy với công suất tối đa. Vì vậy, đồ gá trên máy CNC phải được
chế tạo từ thép hợp kim với phương pháp tôi bề mặt.
Khi gia công trên máy CNC, các dịch chuyển của máy và dao
được bắt đầu từ gốc tọa độ, do đó trong nhiều trường hợp đồ gá phải đảm
bảo sự định hướng hoàn toàn của chi tiết gia công, có nghĩa là phải hạn
chế tất cả các bậc tự do. Điều đó cũng có nghĩa phải hạn chế tất cả các
a)
b)
c)
d)
Hình 3.72: Thân đồ gá
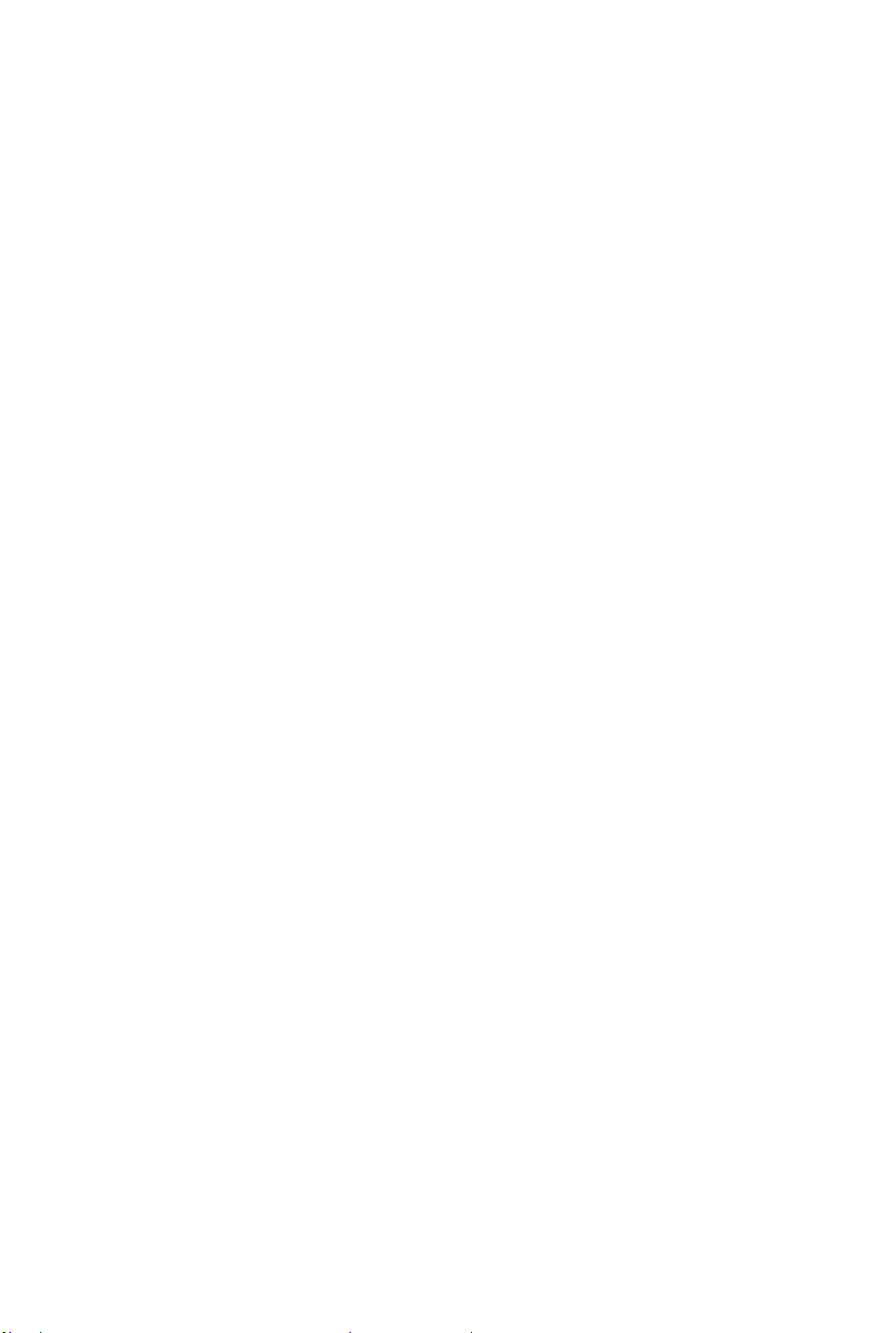
244
bậc tự do khi định vị đồ gá trên máy (phải định hướng đồ gá theo cả hai
phương ngang và dọc của bàn máy).
Đồ gá phải giảm được thời gian gá đặt và tháo chi tiết nhờ các cơ
cấu cơ khí và tự động hóa
3.9.2. Yêu cầu đối với chi tiết gia công trên máy CNC
Chi tiết gia công trên máy CNC có ảnh hưởng đến cấu trúc đồ gá,
do đó nó phải đảm bảo những yêu cầu sau đây:
Chi tiết gia công phải có những bề mặt chuẩn tốt đảm bảo độ
chính xác và độ ổn định gá đặt, đồng thời chi tiết phải có bề mặt thuận
tiện cho việc kẹp chặt, không gây biến dạng chi tiết.
Để không phải dùng đồ gá phụ, chi tiết không nên có những bề
mặt nghiêng và góc nghiêng.
Để đảm bảo độ chính xác gá đặt cao, chi tiết phải được định vị
theo ba bề mặt. Trong trường hợp này, có thể dùng các bề mặt đã qua gia
công trên các máy vạn năng để định vị.
Nếu chi tiết gia công không cho phép định vị theo ba bề mặt thì
định vị theo một bề mặt và hai lỗ, khoảng cách các lỗ phải xa nhau và có
độ bóng cấp 7.
3.9.3. Phân loại đồ gá trên máy CNC
Đồ gá trên máy CNC được phân thành các dạng sau đây:
Đồ gá vạn năng không điều chỉnh.
Đồ gá vạn năng điều chỉnh.
Đồ gá chuyên dùng điều chỉnh.
Đồ gá vạn năng lắp ghép.
Đồ gá lắp ghép điều chỉnh.
3.9.3.1. Đồ gá vạn năng không điều chỉnh
Loại đồ gá này có các chi tiết đã được điều chỉnh cố định để gá
nhiều loại chi tiết gia công khác nhau trong sản xuất đơn chiếc và loạt
nhỏ. Đó là các loại mâm cặp được dùng để truyền mômen xoắn cho chi
tiết gia công. Có ba loại mâm cặp thường dùng trên các máy CNC (ngoài
mâm cặp ba và bốn chấu thông dụng).
Mâm cặp ly tâm (mâm cặp quán tính)
Loại mâm cặp này có hai hoặc ba chấu kẹp. các chấu kẹp là những
chi tiết lệch tâm độc lập với nhau, khi quay dưới tác dụng của lực ly tâm
chúng kẹp chặt chi tiết và nhờ lực cản tự hãm mà chi tiết gia công không
bị xê dịch dù bị tác dụng của lực cắt.
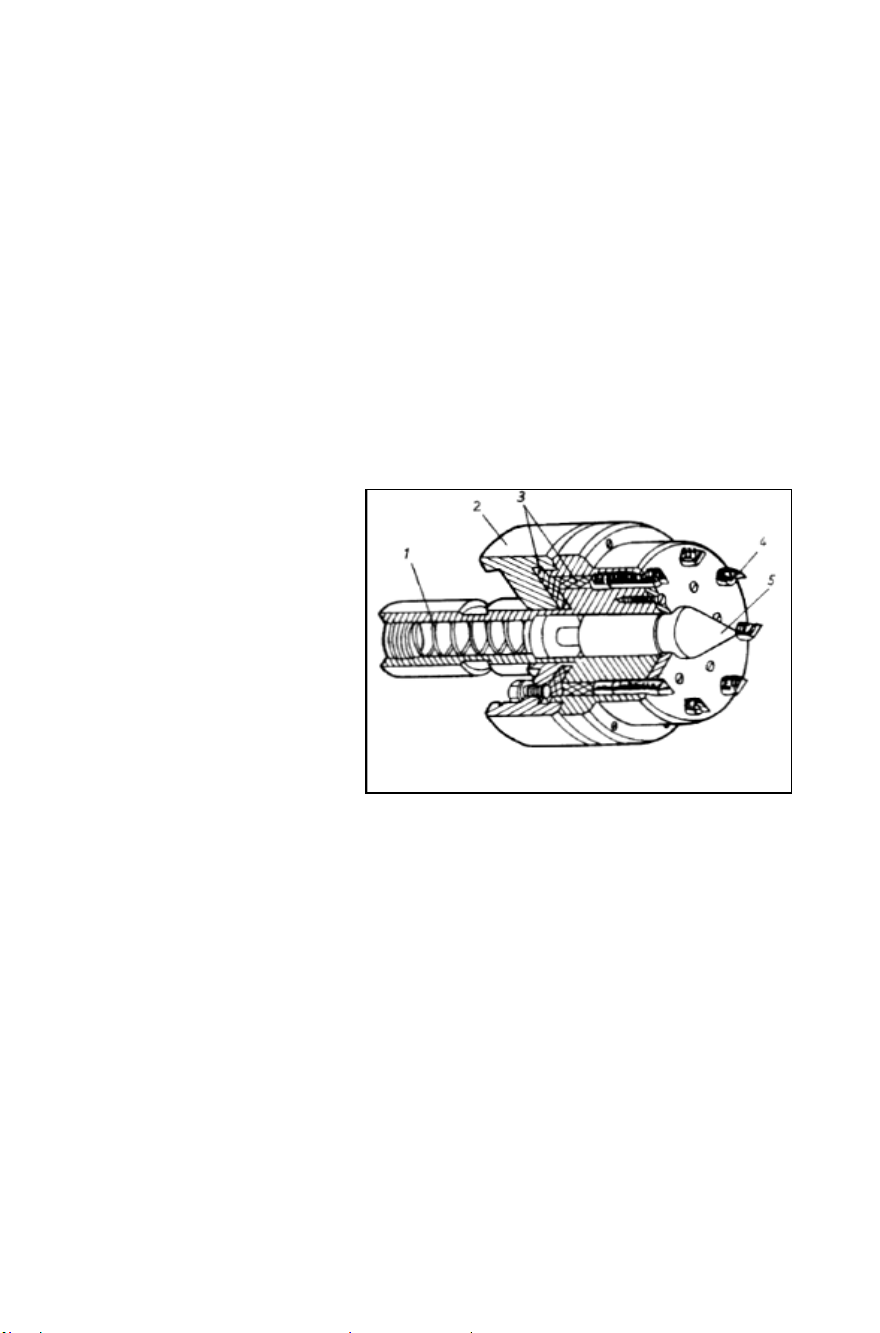
245
Mâm cặp có chân mặt đầu cứng
Mâm cặp có chân mặt đầu cứng xác định chính xác mặt đầu của tất
cả các chi tiết gia công theo trục Z. Lực kẹp chi tiết sinh ra nhờ mũi tâm
sau. Nếu mặt đầu của chi tiết không vuông góc với tâm của nó thì các
mặt đầu ăn vào chi tiết gia công không đều nhau, điều đó làm giảm
mômen xoắn được truyền từ trục chính của máy.
Mâm cặp có chân mặt đầu tùy động (hình 3.73)
Các mặt chân đầu có hình dạng tròn xoay và được lắp vào lỗ có
chứa chất dẻo. Khi chi tiết gia công được kẹp chặt từ mũi tâm sau, mặt
đầu bên trái của chi tiết đẩy các bên mặt đầu về bên trái và làm cho áp
lực chất của dẻo tăng lên. Như vậy, tất cả các chân mặt đầu đều tiếp xúc
với các mặt đầu của chi tiết gia công và lực kẹp tác động lên các chân
hầu như bằng nhau. Số chân mặt đầu có thể là 8, 10, 12, v.v
3.9.3.2. Đồ gá vạn năng điều chỉnh
Kết cấu đồ gá vạn năng điều chỉnh gồm phần đồ gá cơ sở và phần
chi tiết thay đổi điều chỉnh. Các chi tiết thay đổi điều chỉnh có kết cấu
đơn giản và giá thành chế tạo không cao. Đồ gá vạn năng điều chỉnh
được sử dụng trong sản xuất hàng loạt nhỏ, đặc biệt khi thực hiện gia
công nhóm. Trên các máy tiện CNC, đồ gá vạn năng điều chỉnh là các
mâm cặp ba chấu thay đổi điều chỉnh(thay đổi các chấu kẹp).
3.9.3.3. Đồ gá chuyên môn hóa
Đồ gá chuyên môn hóa cho phép gá đặt một số loại chi tiết điển
hình có kích thước khác nhau. Kết cấu của đồ gá gồm hai phần chính:
phần đồ gá cơ sở và phần chi tiết thay đổi. Đồ gá loại này cho phépthay
đổi chi tiết gia công ngoài vùng làm việc của máy. Phạm vi ứng dụng có
hiệu quả của đồ gá là trong sản xuất hàng loạt. Đồ gá trên hình 3.74 được
dùng để gia công các chi tiết dạng càng, dạng chấu kẹp, v.v
Hình 3.73: Mâm cặp mặt
đầu có chân tùy động
1-Lò xo;
2 – thân;
3- chất dẻo
4- chân mặt đầu;
5- mũi tâm
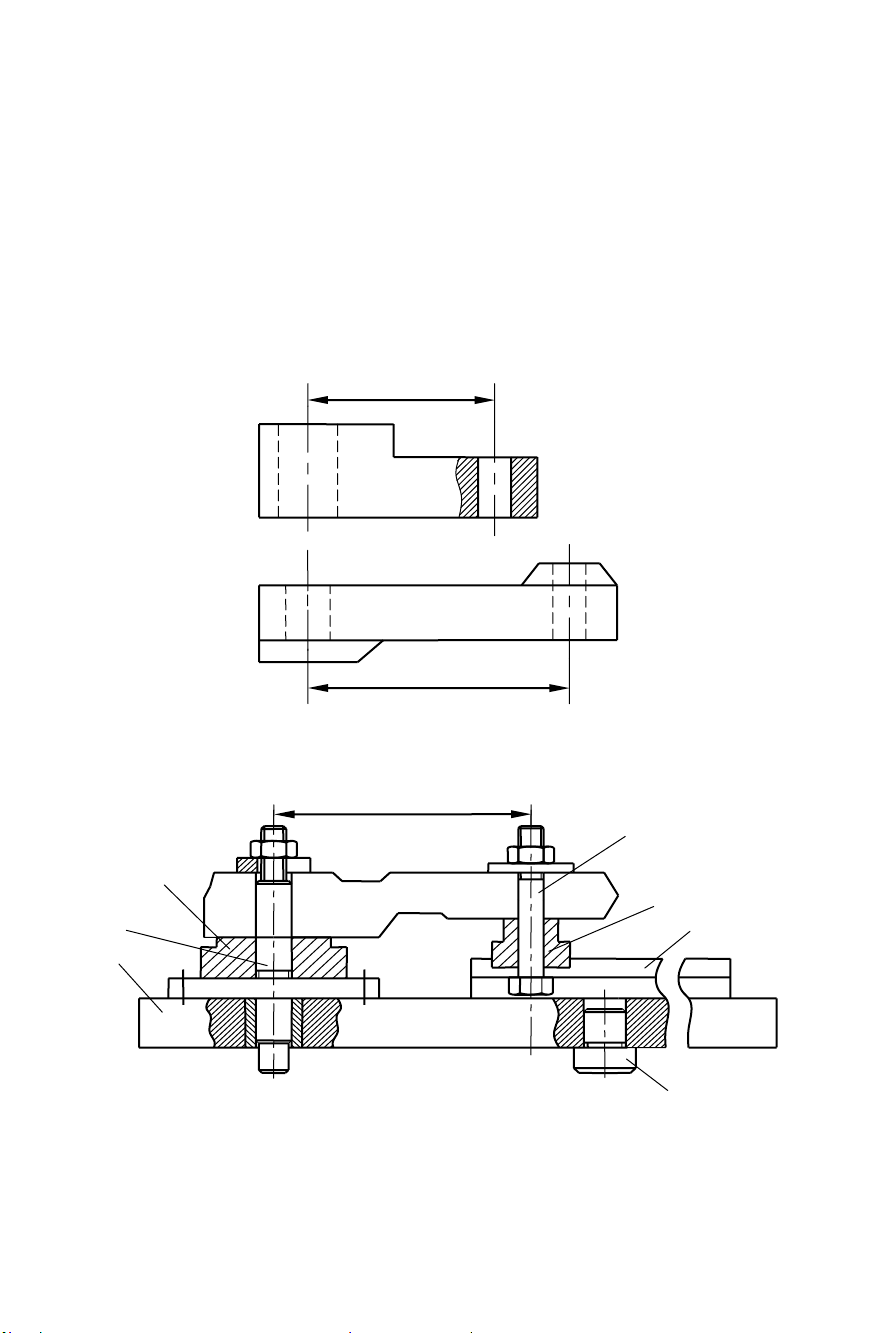
246
L
1
Hình 3.74: Các dạng chi tiết khi dùng đồ gá chuyên môn hóa
L
2
Đồ gá gồm thân đế cơ sở 1, các chi tiết thay đổi: trục gá 2, trục gá
4, các chi tiết định vị 3 và 5. Đồ gá được định vị trên bàn máy bằng một
đầu của trục gá 2 và chốt 7. Chi tiết gia công được định vị bằng mặt
phẳng trên các chi tiết định vị 3 và 5 với các mặt lỗ hai trục gá 2 và 4.
Chi tiết đươc kẹp giữa bằng hai mũ ốc. Các chi tiết thay đổi 4 và 5 được
lắp đặt và điều chỉnh theo rãnh định hướng 6 của đồ gá. Kích thước điều
chỉnh là l (khoảng cách giữa các tâm lỗ của chi tiết gia công). Nếu dùng
đồ gá để gá đặt chi tiết dạng chấu kẹp theo một lỗ và rãnh then thì dùng
trục gá 2 và chốt then.
4
L
1
2
3
5
6
7
Hình 3.75: Đồ gá chuyên môn hóa
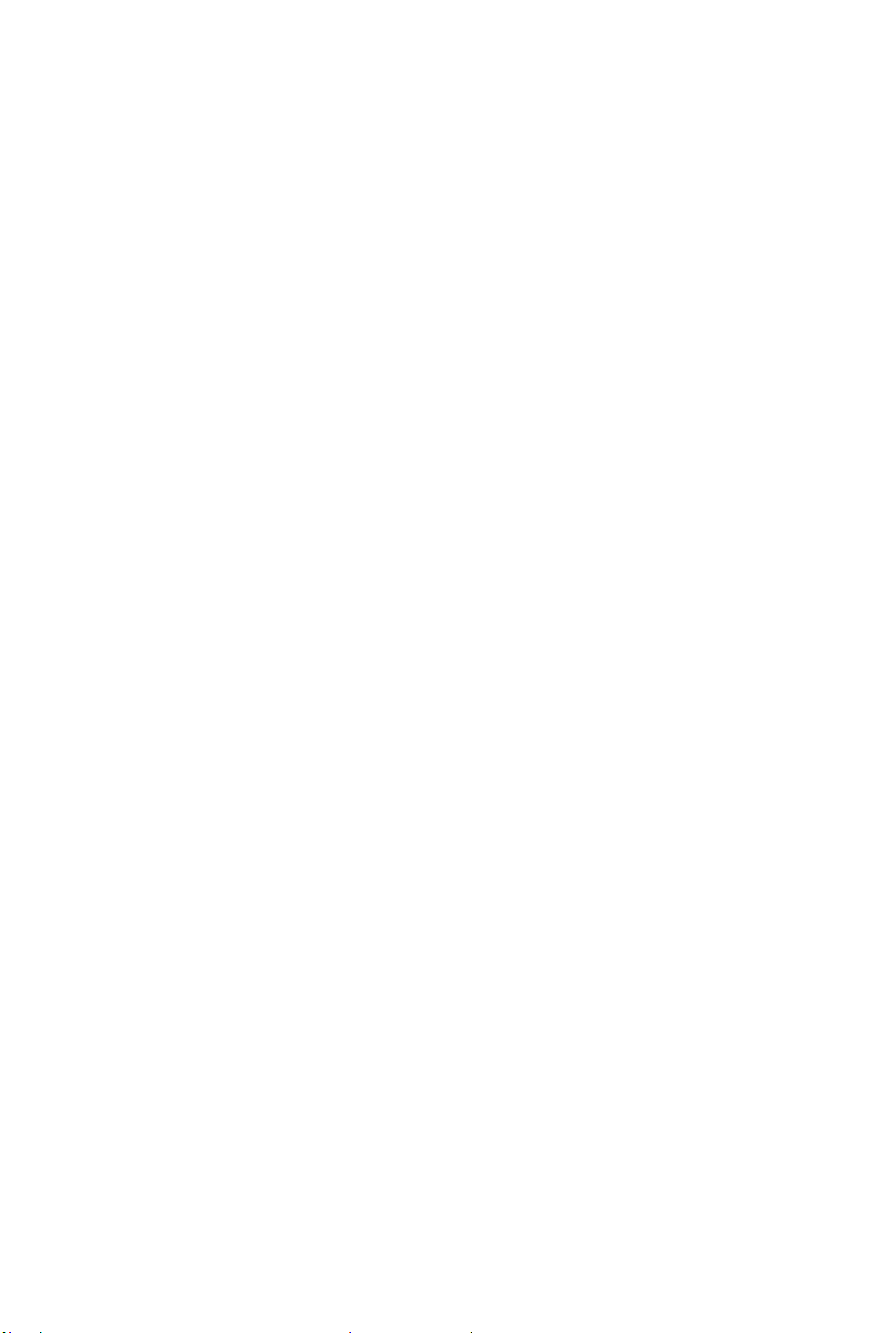
247
3.9.3.4. Đồ gá vạn năng- lắp ghép
Thành phần của đồ gá vạn năng – lắp ghép là những chi tiết chuẩn
được chế tạo với độ chính xác cao. Các chi tiết này có các rãnh then để
lắp ghép. Sau khi gia công một loại chi tiết nào đó, người ta tháo đồ gá ra
và lắp ghép lại để gá đặt chi tiết khác. Do độ chính xác của chi tiết rất cao
nên sau khi lắp ghép không phải gia công bổ sung. Thời gian để lắp ghép
một đồ gá mới khoảng 3÷4 giờ.
Hình 3.83 là đồ gá vạn năng –lắp ghép. Để tạo thành đồ gá,
người ta đem chi tiết (hình 3.83c) lắp lại với nhau và lấy để làm chi tiết
cơ sở.
Trên các máy phay, máy khoan CNC, người ta sử dụng đồ gá
vạn năng – lắp ghép cơ khí với các cơ cấu kẹp thủy lực.
Đồ gá vạn năng- lắp ghép được dùng trên các máy CNC trong
điều kiện sản xuất đơn chiếc và hàng loạt nhỏ.
3.9.3.5. Đồ gá lắp ghép điều chỉnh
Loại đồ gá này được dùng trong các máy phay CNC hoặc các máy
khoan CNC. Trên chi tiết cơ sở (đế đồ gá), người ta gia công các hệ lỗ để
lắp ghép các chi tiết định vị và kẹp chặt khi muốn tạo thành đồ gá, mới
(trên đế đồ gá vạn năng- lắp ghép có các rãnh để lắp ghép) Hệ lỗ trên đế
đồ gá lắp ghép điều chỉnh đảm bảo độ chính xác, độ cứng vững và độ ổn
định cao hơn hệ rãnh trên đồ gá vạn năng – lắp ghép. Hình 3.84 là các đế
đồ gá lắp ghép điều chỉnh.
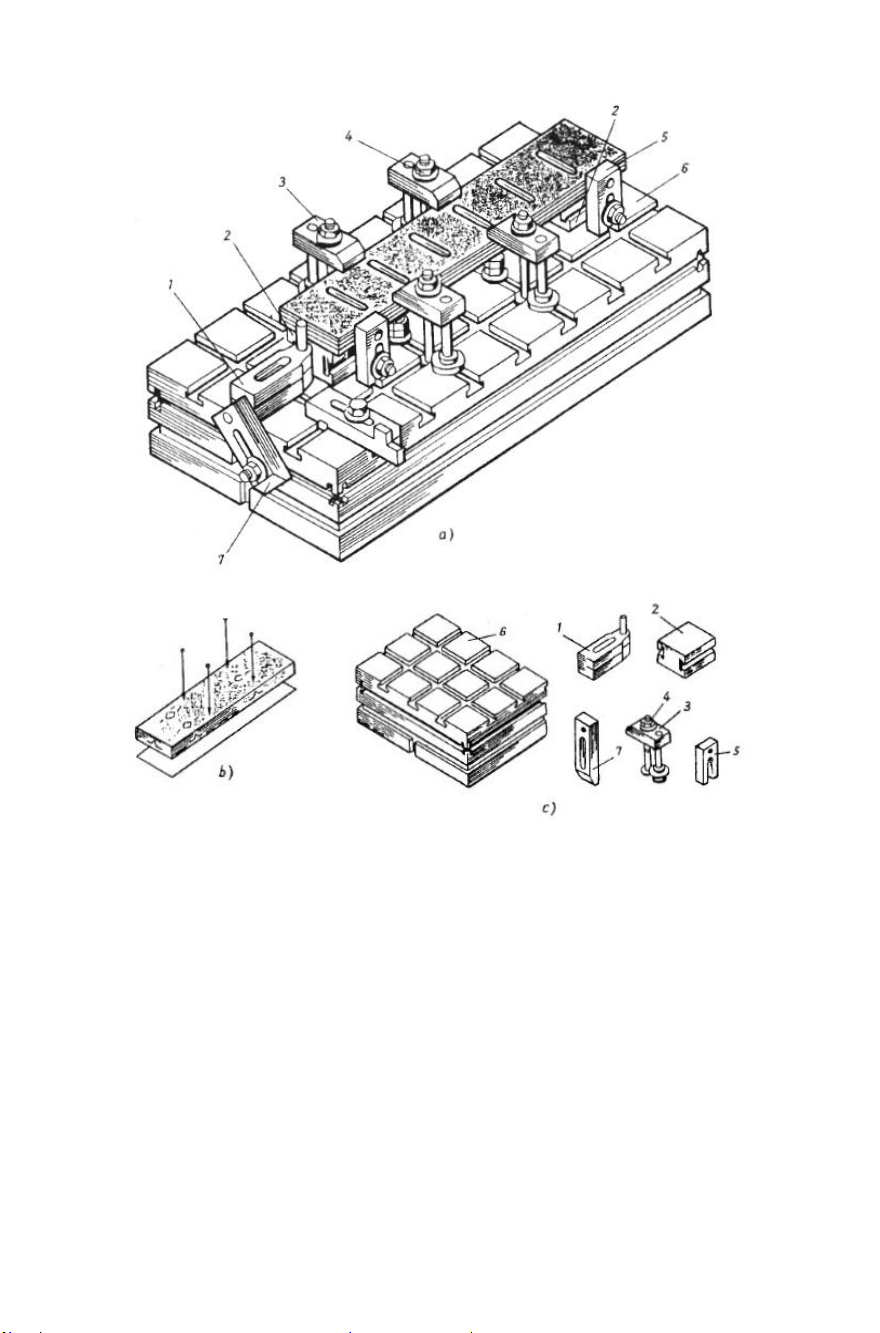
248
Hình 3.76: Đồ gá vạn năng - lắp ghép
a) Kết cấu ; b) Sơ đồ ; c) Các chi tiết
1-Cơ cấu tỳ với chốt định vị ; 2-Cơ cấu định vị ;
3-Mỏ kẹp ; 4-Đai ốc kẹp;
5-Phiến tỳ mặt bên; 6-Phiến tỳ mặt đáy;7- Phiến tỳ mặt đầu
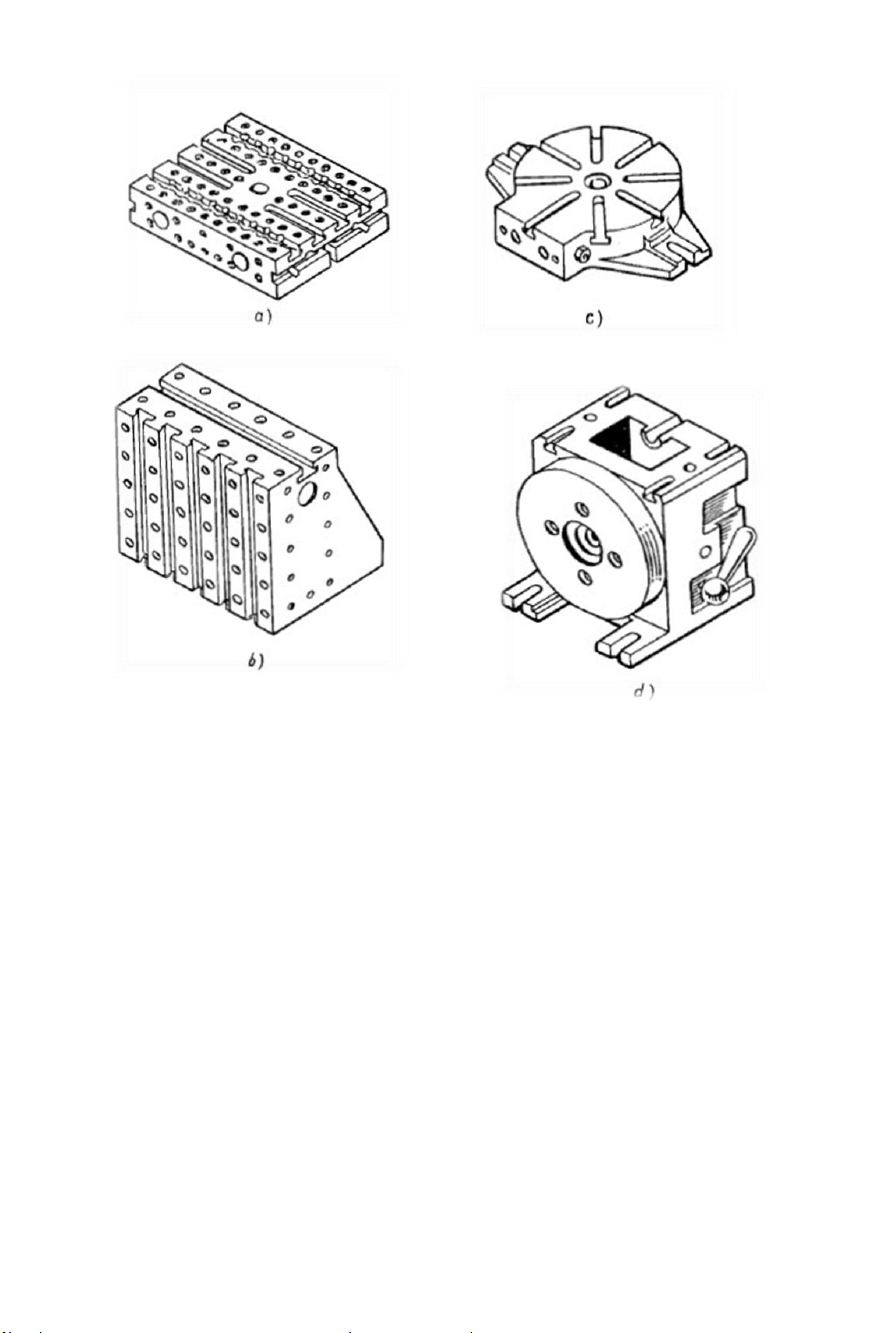
249
3.9.3.6. Đồ gá chuyên dùng
Thông thường, loại đồ gá này được sử dụng trong sản xuất hàng
loạt lớn và hàng khối. Kết cấu của đồ gá chỉ được dùng để gia công một
loại chi tiết nhất định. Trên các máy CNC, loại đồ gá này chỉ đường dùng
trong những trường hợp không thể dùng được các loại đồ gá điều chỉnh.
Kết cấu của đồ gá như vậy phải thật đơn giản để nâng cao hiệu quả kinh
tế khi sử dụng
3.9.3.7. Đồ gá quay
Nhằm mở rộng khả năng công nghệ của máy công cụ, nhất là cho
các máy CNC hai hoặc ba trục, người ta đã chế tạo một thiết bị có khả
năng tăng số trục của máy từ hai hoặc ba trục thành các máy bốn hoặc
năm trục. Thiết bị đó chính là bàn xoay (Rotory Table). Thực ra bàn xoay
chẳng qua là một loại đồ gá đặc biệt và chúng chủ yếu được sử dụng trên
các máy phay CNC, trung tâm gia công đứng, trung tâm gia công ngang
và máy doa ngang.
Hình 3.77: Đế đồ gá lắp ghép điều chỉnh
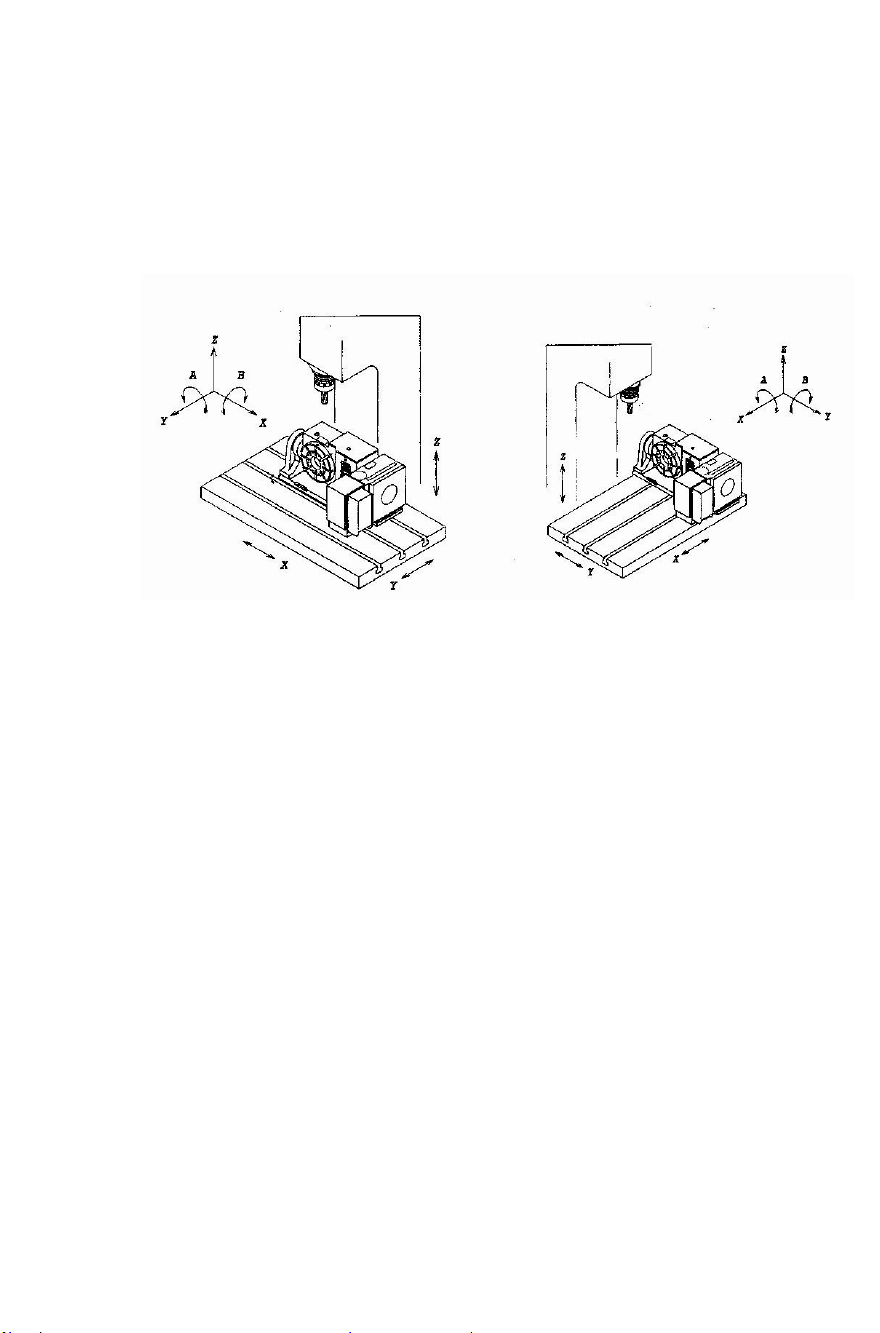
250
Lập trình gia công với bàn xoay CNC
Bàn xoay thường được lắp trên các máy phay CNC hoặc trung tâm
gia công. Đối với loại bàn xoay không nghiêng, nó có vai trò như trục thứ
4 của máy. Đối với loại bàn xoay nghiêng thì nó đóng vai trò như trục
thứ 4 và thứ 5 của máy CNC. Tùy theo định nghĩa của nhà sản xuất mà
các trục này có thể có tên là A và B như hình 3.85
Khi lập trình gia công cho máy CNC có sử dụng bàn xoay ta sử
dụng câu lệnh có cú pháp như sau:
A_._ hoặc B_._
Câu lệnh này sẽ hướng dẫn trục A hoặc B của bàn xoay quay đi
một góc nào đó.
Ví dụ:
G90 G00 A90.0: trục A của bàn xoay quay nhanh đến vị trí góc 90
độ theo chiều kim đồng hồ trong hệ tọa độ tuyệt đối.
G91 G00 B-180.0: trục B của bàn xoay quay 180 độ theo ngược
chiều kim đồng hồ từ vị trí hiện tại (hệ tọa độ tương đối).
Phân loại bàn xoay:
Bàn xoay trên máy phay CNC và các trung tâm gia công có thể
được phân ra làm các loại như sau:
Loại tiêu chuẩn:
Là loại bàn xoay này dùng để gá đặt chi tiết sao cho tâm của chi tiết
trùng với tâm trục chính. Có thể gia công được nhiều dạng bề mặt khác
Hình 3.78: Các trục của bàn xoay và máy phay CNC.
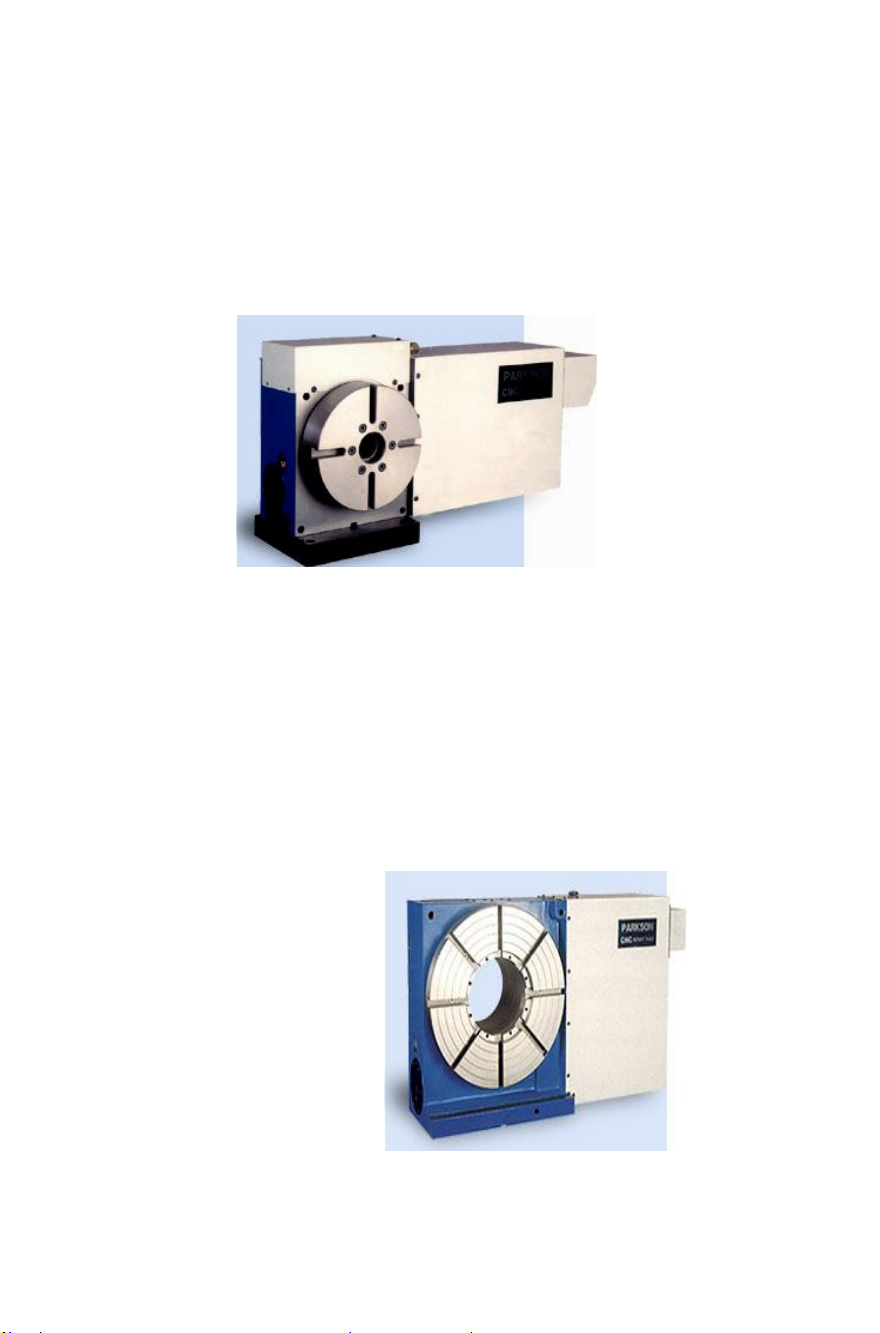
251
nhau như gia công mặt phẳng, gia công rãnh thẳng hoặc rãnh xoắn và gia
công các mặt định hình với dao định hình, đôi khi dùng để cắt bánh răng
với dao phay môđun.
Loại bàn xoay tiêu chuẩn có thể phân ra làm hai loại:
+ Loại có trục chính nằm ngang.
+ Loại có trục chính thẳng đứng.
Loại bàn xoay có lỗ trục chính lớn:
Loại bàn xoay này có trục chính có lỗ lớn, dùng để gia công các
phôi dài hoặc các ống. Kích thước lỗ trục chính của chúng có khả năng
được mở rộng để mở rộng phạm vi làm việc cho máy. Loại này thích hợp
cho việc sản xuất hàng khối. Tương tự như loại bàn xoay tiêu chuẩn, loại
bàn xoay này cũng loại trục chính nằm ngang và loại trục chính thẳng
đứng.
Loại bàn xoay
nghiêng:
Loại bàn xoay này
có hai trục. Bàn xoay có
thể nghiêng đi nhờ xoay
quanh được một trục nào
đó. Do đó, loại này có khả
năng công nghệ cao, có
thể sử dụng làm đồ gá để
gia công các mặt phẳng,
các rãnh các gờ lồi và đặt
biệt là gia công các bề
mặt nghiêng ở nhiều góc
Hình 3.80: Bàn xoay có lỗ trục chính lớn
Hình 3.79: Bàn xoay tiêu chuẩn trục nằm ngang
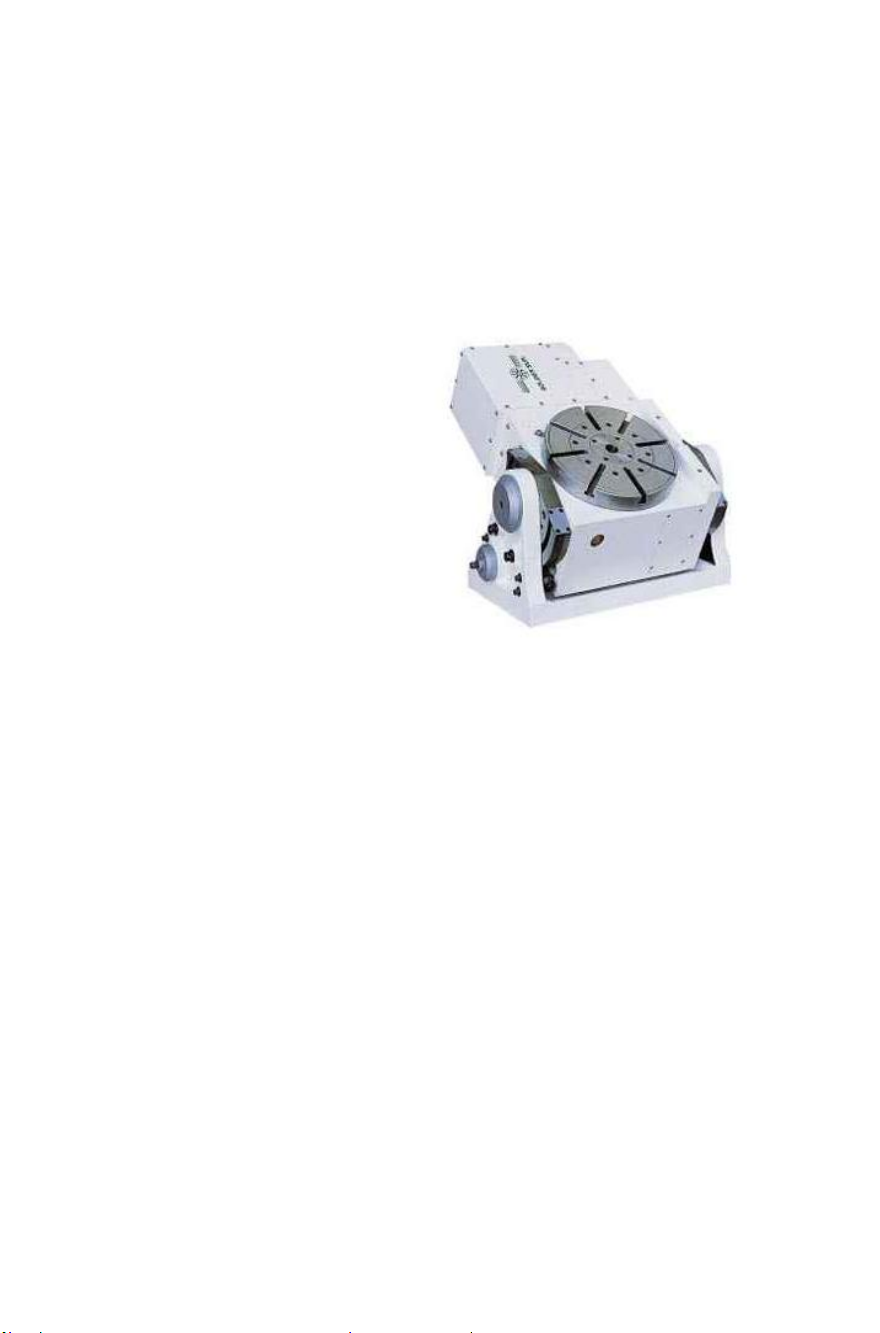
252
độ khác nhau. Loại bàn xoay này được phân ra hai loại như sau:
+ Loại điều khiển nghiêng tự động: cả hai trục của bàn xoay được
điều khiển hoàn toàn tự động từ hệ thống CNC.
+ Loại điều khiển nghiêng bằng tay: chuyển động làm nghiêng trục
được thực hiện bằng tay.
Ứng dụng của bàn xoay
Bàn xoay CNC có tác
dụng làm tăng thêm tính vạn
năng cho máy CNC. Đối với
các bàn xoay hai trục, nhờ
khả năng nghiêng bàn xoay
đi một góc nào đó, nên cho
phép máy CNC ba trục gia
công được các bề mặt phức
tạp như cánh tua bin, cánh
chân vịt tàu thủy. Nói chung
chúng có phạm vi sử dụng
rất rộng, nhưng chủ yếu là
dùng để gia công các chi tiết
có các dạng bề mặt sau:
+ Mặt phẳng.
+ Các bề mặt định
hình (như bề mặt cam, cối dập, khuôn ép …).
+ Cắt ren vít trong và ngoài.
+ Gia công bánh răng và dao cắt nhiều lưỡi có răng thẳng hoặc
xoắn.
+ Cắt rãnh thẳng và xoắn…
+ Các bề mặt nghiêng.
Đối với bàn xoay nhiều trục, có thể tiến hành gia công cùng một
lúc nhiều chi tiết. Điều này làm:
+ Tăng khả năng công nghệ của máy,.
+ Tăng năng suất gia công.
+ Giảm thời tháo lắp và điều khiển dụng cụ.
+ Giảm thời gian gia công cơ bản.
Hình 3.81: Bàn xoay CNC điều khiển
nghiêng bằng tay.
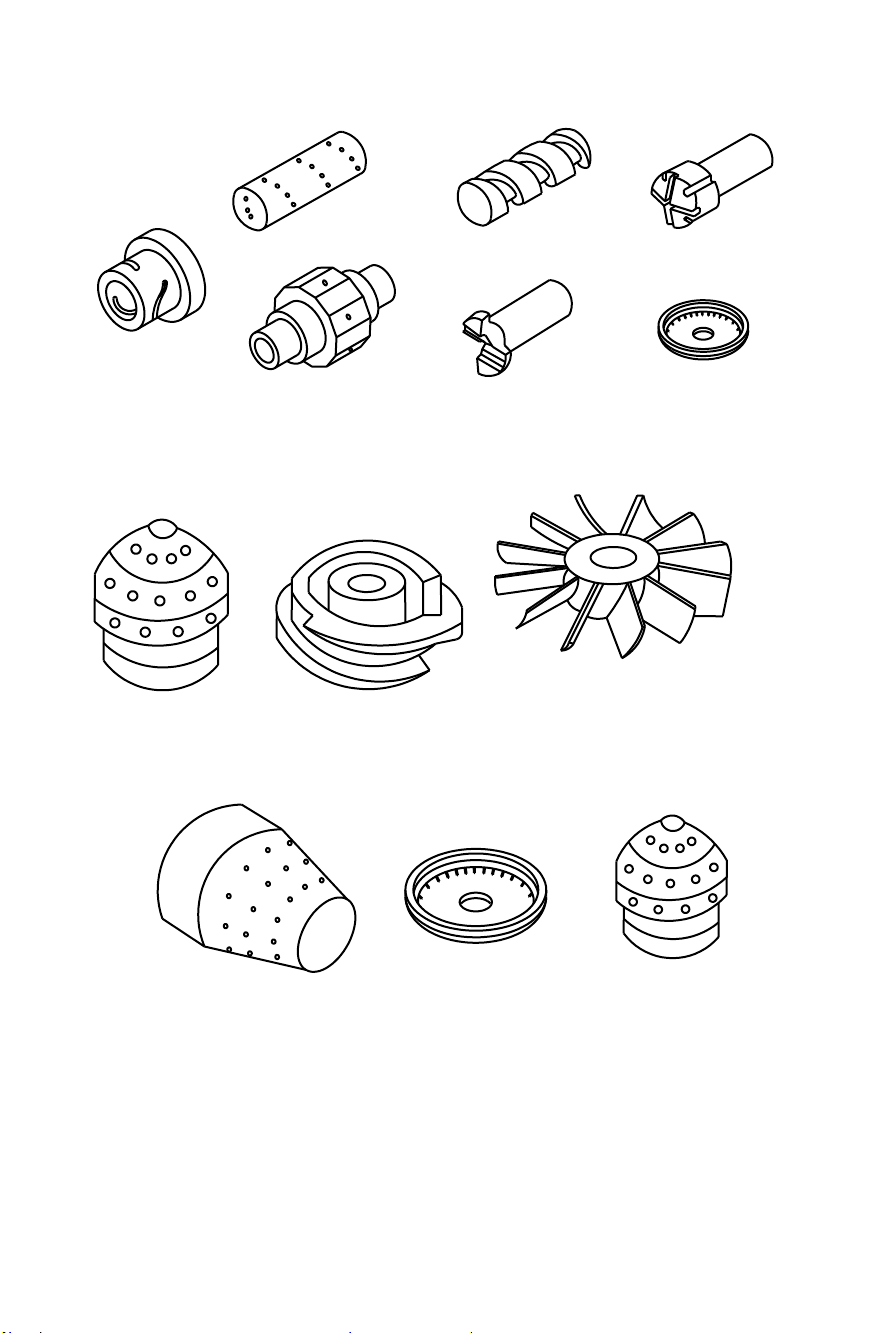
253
Hình 3.84: Một số dạng chi tiết được gia công trên bàn xoay nghiêng
Hình 3.82: Một số dạng chi tiết được gia công trên bàn xoay không
nghiêng.
Hình 3.83: Một số dạng chi tiết được gia công trên bàn xoay nghiêng
tự động.
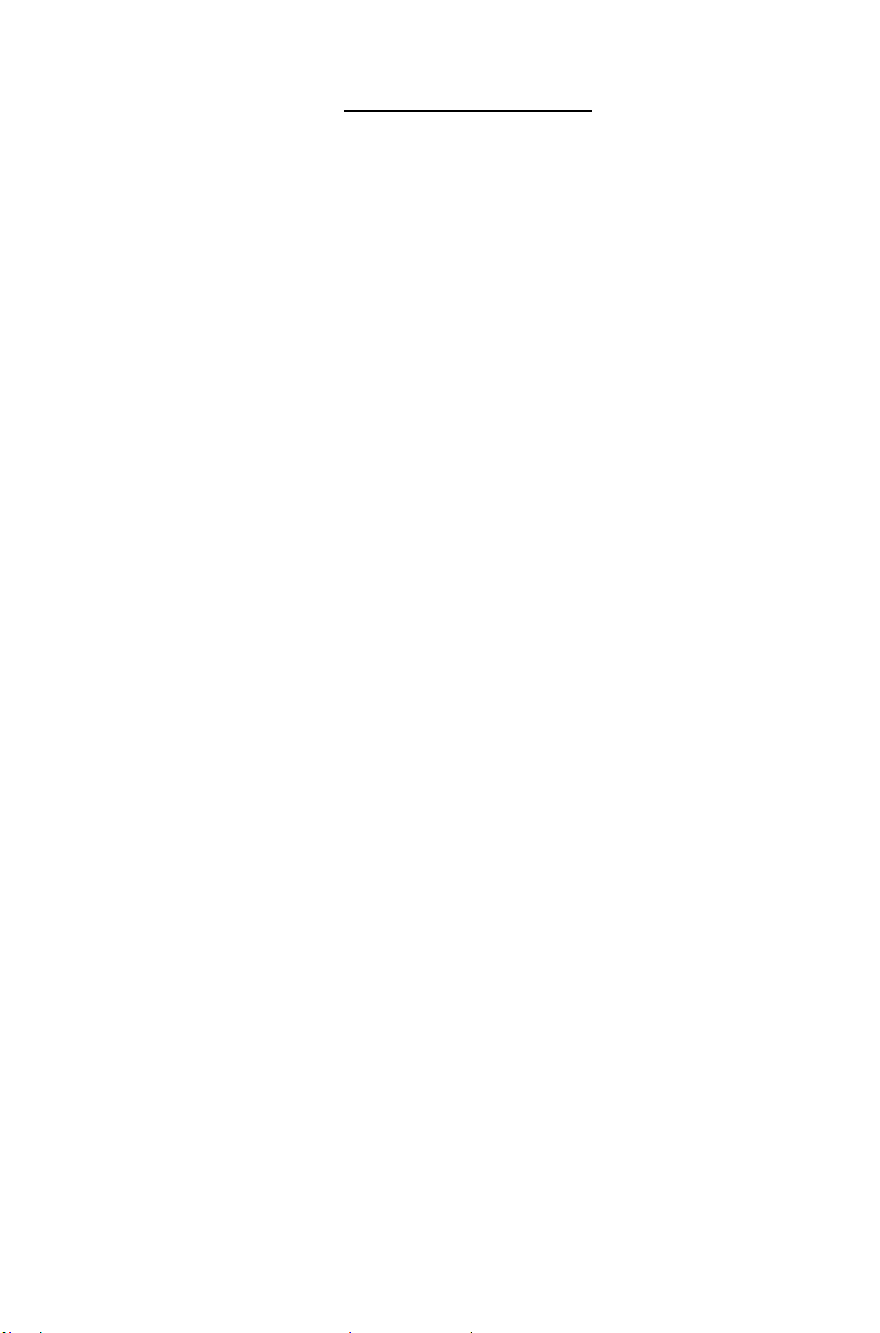
254
CÂU HỎI VÀ BÀI TẬP
1. Tác dụng của đồ gá trong việc gia công chi tiết máy ?
2. Yêu cầu gì khi thiết kế đối với đồ gá ?
3. Phân loại đồ gá theo nhóm máy gồm những loại nào ?
4. Theo mức độ chuyên môn hóa thì được phân loại như thế nào ?
Ứng dụng của từng loại ?
5. Trình bày phương pháp và trình tự thiết kế đồ gá ?
6. Khi thiết kế đồ gá cần tính toán những gì ?
7. Chuẩn là gì ? Phân loại chuẩn và cho ví dụ minh họa ?
8. Thế nào là sai số chuẩn ? Sai số chuẩn phát sinh khi nào ? Mục
đích của việc tính sai số chuẩn ?
9. Trình bày phương pháp tính sai số chuẩn bằng chuỗi kích thước
công nghệ ?
10. Thế nào là chi tiết định vị chính và định vị phụ ?
11. Liệt kê các chi tiết định vị mặt phẳng, định vị mặt trụ ngoài và
các chi tiết định phụ ?
12. Thế nào là kẹp chặt ? Ý nghĩa của việc kẹp chặt ? Cho biết
những yêu cầu cần thiết đối với cơ cấu kẹp ? Ảnh hưởng của phương và
chiều lực kẹp ?
13. Nêu những yếu tố để tính lực kẹp cần thiết ? Phương pháp tính ?
14. Cơ cấu dẫn hướng có nhiệm vụ gì ? Phân loại bạc dẫn hướng ?
15. Cho biết tác dụng của cữ so dao ? Cho biết các loại cữ so dao ?
16. Thế nào là đồ gá tổ hợp tháo lắp nhanh ? Hãy chia nhóm cho hệ
thống đồ gá tổ hợp ?
17. Đồ gá tổ hợp tháo lắp nhanh có những ưu điểm gì ?
18. Cho biết các thành phần của đồ gá tổ hợp tháo lắp nhanh ?
19. Đặc điểm của đồ gá trên máy công cụ CNC ? Phân loại đồ gá ?
20. Đồ gá xoay được sử dụng khi nào ? Phân loại bàn xoay trên máy
CNC khi gia công ? Ứng dụng từng loại ?
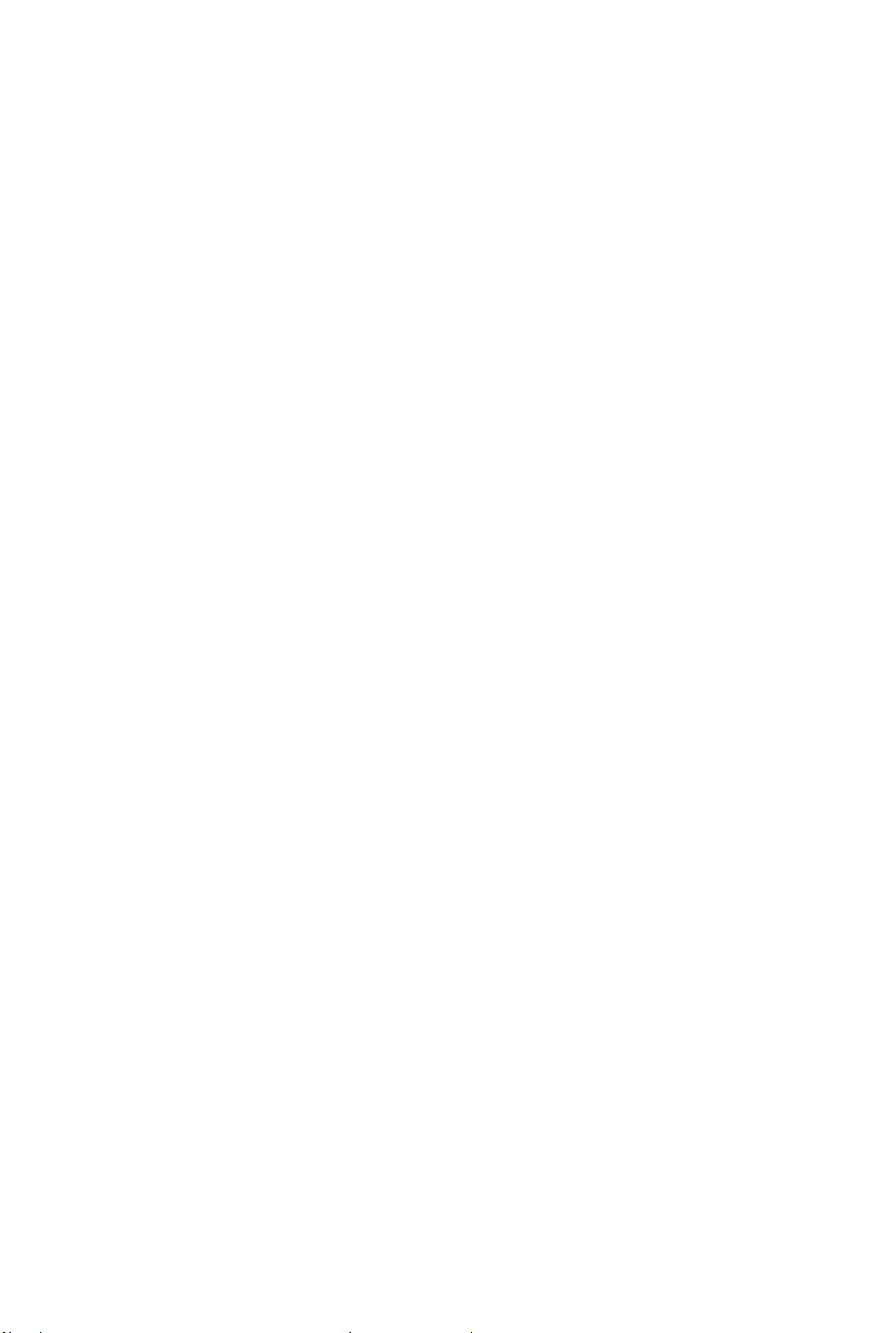
255
Chương 4
CÔNG NGHỆ LẮP RÁP CÁC SẢN PHẨM
CƠ KHÍ
Mục tiêu :
- Định nghĩa được công nghệ lắp ráp và nhiệm vụ của công nghệ lắp
ráp.
- Trình bày được các phương pháp lắp ráp
- Trình bày được trình tự thiết kế quy trình công nghệ lắp ráp
- Thiết kế được quy trình công nghệ lắp ráp, lập sơ đồ lắp ráp của
cụm sản phẩm cơ khí.
- Kiểm tra được chất lượng mối lắp, độ ổn định cân bằng tĩnh và
động , kiểm tra chất lượng sản phẩm.
4.1. KHÁI NIỆM VỀ CÔNG NGHỆ LẮP RÁP
4.1.1. Vị trí của công nghệ lắp ráp
Một sản phẩm cơ khí do nhiều chi tiết hợp thành. Những chi tiết
máy đã được gia công đạt chất lượng ở phân xưởng cơ khí sẽ được lắp
thành các bộ phận hay thiết bị hoàn chỉnh. Nếu quá trình gia công cơ khí
là giai đoạn chủ yếu của quá trình sản xuất, thì quá trình lắp ráp là giai
đoạn cuối cùng của quá trình sản xuất ấy. Vì sau quá trình lắp ráp, sản
phẩm đạt được chất lượng yêu cầu và vận hành ổn định, thì quá trình sản
xuất ấy mới có ý nghĩa, các sản phẩm cơ khí mới có tác dụng thiết thực
cho nền kinh tế quốc dân.
Quá trình lắp ráp là một quá trình lao động kỹ thuật phức tạp. Mức
độ phức tạp, cũng như khối lượng lắp ráp có liên quan chặt chẽ tới quá
trình công nghệ gia công cơ và cả quá trình thiết kế sản phẩm. Gia công
cơ các chi tiết máy có độ chính xác cao, thì lắp ráp chúng càng nhanh,
giảm được thời gian sửa chữa điều chỉnh. Mối quan hệ giữa khối lượng
gia công và lắp ráp như sau:
Trong dạng sản xuất hàng khối, khối lượng lao động lắp ráp chiếm
từ 10 –15% khối lượng lao động gia công cơ. Trong sản xuất hàng loạt:
20-35% và trong sản xuất đơn chiếc khoảng 30-45% khối lượng lao động
gia công cơ khí.
Mặt khác, khối lượng lao động lắp ráp cũng có quan hệ mật thiết
với quá trình thiết kế sản phẩm. Công nghệ lắp ráp phải đảm bảo những
yêu cầu kỹ thuật khi nghiệm thu do bản thiết kế đề ra, phải đạt yêu cầu
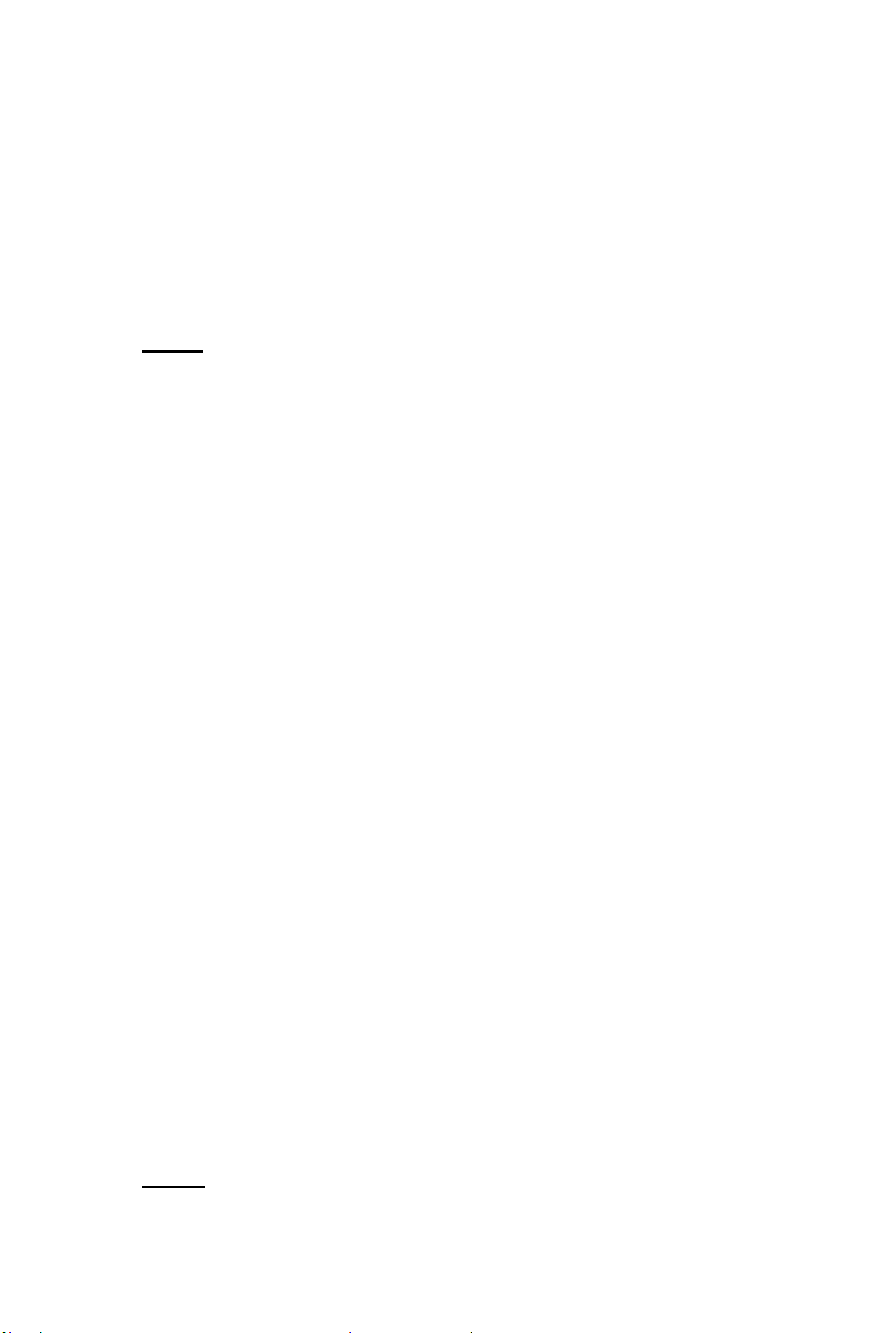
256
của các mối ghép, các chuỗi kích thước lắp ráp đạt chính xác về truyền
động. Bởi vậy, khi có bản thiết kế sản phẩm hợp lý về kết cấu và sự hình
thành chuỗi kích thước thì giảm được khối lượng lao động lắp ráp.
Tóm lại công việc lắp ráp là khâu cơ bản quyết định chất lượng của
sản phẩm. Trong nhiều trường hợp, giai đoạn gia công có chi tiết đạt mọi
điều kiện kỹ thuật nhưng công nghệ lắp ráp sản phẩm không hợp lý thì
chất lượng của sản phẩm không những không đạt được điều kiện kỹ thuật
nghiệm thu, mà còn ảnh hưởng tới cả tuổi thọ của sản phẩm.
Ví dụ: Khi lắp ráp ụ động của máy tiện không đảm bảo độ trùng tâm
của ụ động với tâm trục chính, sẽ ảnh hưởng tới độ chính xác của chi tiết gia
công khi định vị bằng chống tâm hai đầu, hay gá trên mâm cặp và chống
tâm. Sai lệch không trùng tâm theo phương ngang khi tiện, chi tiết bị côn,
sai lệch theo phương thẳng đứng sẽ gây cho chi tiết bị dạng yên ngựa.
Lắp ráp trục bánh răng không song song, làm cho các bánh răng ăn
khớp không tốt, truyền động gây tiếng ồn, tuổi thọ thấp …
Vì vậy, nghiên cứu hợp lý hóa công nghệ lắp ráp phải được quán
triệt từ giai đoạn gia công cơ khí, để sản xuất ra những sản phẩm có chất
lượng cao và giá thành hạ.
4.1.2. Nhiệm vụ của công nghệ lắp ráp
Nhiệm vụ của công nghệ lắp ráp là căn cứ vào những điều kiện kỹ
thuật của bản vẽ lắp sản phẩm mà thiết kế quy trình công nghệ lắp ráp
hợp lý, tìm các biện pháp kỹ thuật và tổ chức lắp ráp nhằm thỏa mãn hai
yêu cầu sau:
- Đảm bảo tính năng kỹ thuật của sản phẩm, theo yêu cầu nghiệm thu.
- Nâng cao năng suất lắp ráp, hạ giá thành sản phẩm.
Để đạt được những yêu cầu nói trên, cần phải giải quyết các nhiệm
vụ sau:
1. Nghiên cứu kỹ yêu cầu kỹ thuật của sản phẩm, phân biệt độ
chính xác của các mối lắp và đặc tính làm việc của chúng để trong quá
trình lắp, sai lệch không vượt quá giới hạn cho phép. Nắm vững nguyên
lý hình thành chuỗi kích thước lắp ráp, từ đó có biện pháp công nghệ lắp,
kiểm tra, điều chỉnh và cạo sửa nhằm thỏa mãn yêu cầu kỹ thuật của sản
phẩm. Bởi vậy, người thợ lắp ráp phải có kiến thức tổng hợp về công
nghệ lắp ráp và trình độ tay nghề nhất định để thực hiện những nội dung
cơ bản của công nghệ lắp ráp.
Ví dụ: Thực hiện cụm lắp ghép (hình 4.1). Sau khi gia công cơ có
các chi tiết lắp ráp sau: bạc (4) có các vai A
1
, A
3
; thân hộp (1) có kích
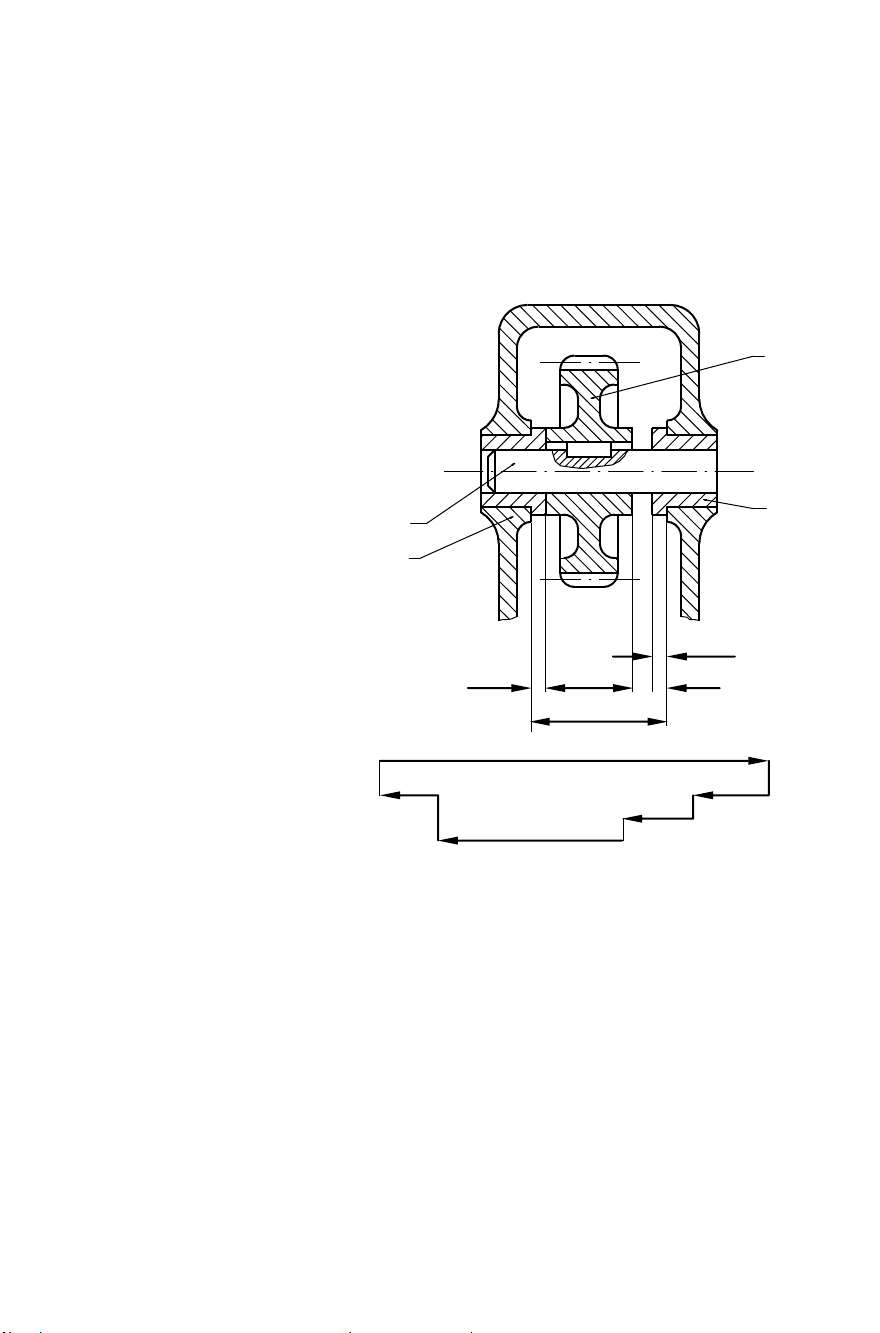
257
thứơc A
4
; bánh răng (3) có kích thước A
2
. Khi lắp ráp phải đảm bảo khâu
khép kín A
, đây là khe hở cần thiết cho bánh răng làm việc.
Đây là một ví dụ đơn giản cho chuỗi kích thước lắp theo một
phương. Thực ra trong công nghệ lắp ráp ta thường gặp những chuỗi kích
thước phức tạp theo các phương khác nhau. Như chuỗi kích thước đường
thẳng, chuỗi kích thước góc, chuỗi kích thước không gian v.v… và việc
giải quyết các yêu cầu của chúng gặp nhiều khó khăn.
2. Cần thực hiện quy
trình công nghệ lắp theo
một trình tự hợp lý, thông
qua việc thiết kế sơ đồ lắp.
Chọn tuần tự việc lắp ráp
các chi tiết, các bộ phận
máy khác nhau thực hiện
quá trình lắp tuần tự hay
song song … Trình tự lắp
không hợp lý trong nhiều
trường hợp sẽ không lắp
được hoặc ảnh hưởng tới
năng suất lắp ráp.
3. Cần nắm vững công
nghệ lắp ráp, sử dụng hợp lý
các trang bị đồ gá, các thiết
bị dầu ép, khí ép, các dụng
cụ đo kiểm, vận chuyển
v.v… để giảm nhẹ lao động
và nâng cao năng suất, chất
lượng lắp ráp.
Giải quyết tốt các
nhiệm vụ của công nghệ lắp
ráp sẽ góp phần nâng cao
năng suất, chất lượng sản
phẩm và hiệu quả kinh tế của quá trình sản xuất trong các nhà máy chế
tạo cơ khí.
4.2. CÁC PHƢƠNG PHÁP LẮP RÁP
4.2.1 Phân loại các mối lắp
Đối tượng của quá trình sản xuất là sản phẩm. Sản phẩm của nhà
máy chế tạo cơ khí bao gồm:
Hình 4.1: Những thành phần của một
chuỗi kích thước lắp ráp.
1. Thân hộp 2. Trục
3. Bánh răng 4. Bạc
A
1
1
2
3
4
A
1
A
4
A
2
A
A
3
A
3
A
2
A
A
4
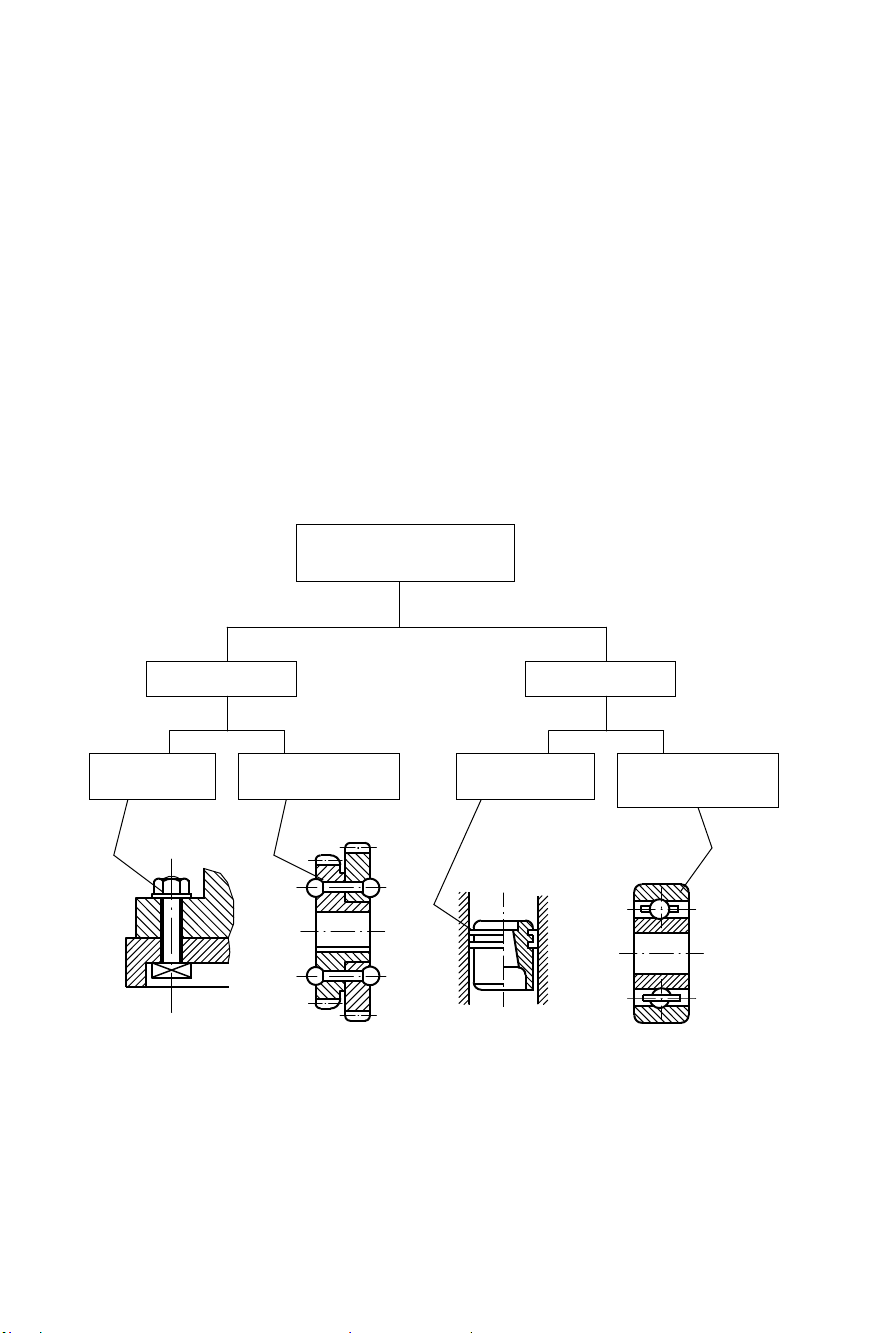
258
Các chi tiết lẻ không lắp ráp, thường là những chi tiết tiêu chuẩn
như dụng cụ cắt, bánh răng, vòng bi, ốc vít …
Cụm các chi tiết hay bộ phận máy sẽ được lắp ráp tại nơi sử dụng,
vận hành (tuabin, động cơ, hộp tốc độ, đầu lực cho các máy tổ hợp …)
Các thiết bị lắp hoàn chỉnh như máy công cụ, ôtô, máy kéo, máy
dệt …
Sản phẩm lắp ráp của nhà máy cơ khí thường được thực hiện tại
một phân xưởng riêng. Trong các dạng sản xuất lớn như ngành chế tạo
ôtô, máy kéo, sản phẩm của nó được lắp hoàn chỉnh từ những bộ phận
hay các chi tiết do nhiều xí nghiệp vệ tinh khác chế tạo.
Trong công nghệ lắp ráp, yếu tố được quan tâm đầu tiên là thực hiện
các mối lắp ghép. Dựa vào các đặc tính của nó, người ta phân các mối lắp
thành hai loại chính: mối lắp ghép cố định và mối lắp ghép di động.
1. Mối lắp cố định là mối lắp mà vị trí tương đối giữa các chi tiết
không đổi. Mối lắp cố định được phân thành mối lắp cố định tháo được
và mối lắp cố định không tháo được.
Mối lắp cố định tháo được như mối lắp ren, chêm, chốt, then …
Những dạng lắp ghép
của chi tiết máy
Cố định
Tháo được
Không tháo được
Di động
Tháo được
Không tháo
được
Hình 4.2: Sơ đồ phân loại các mối ghép.
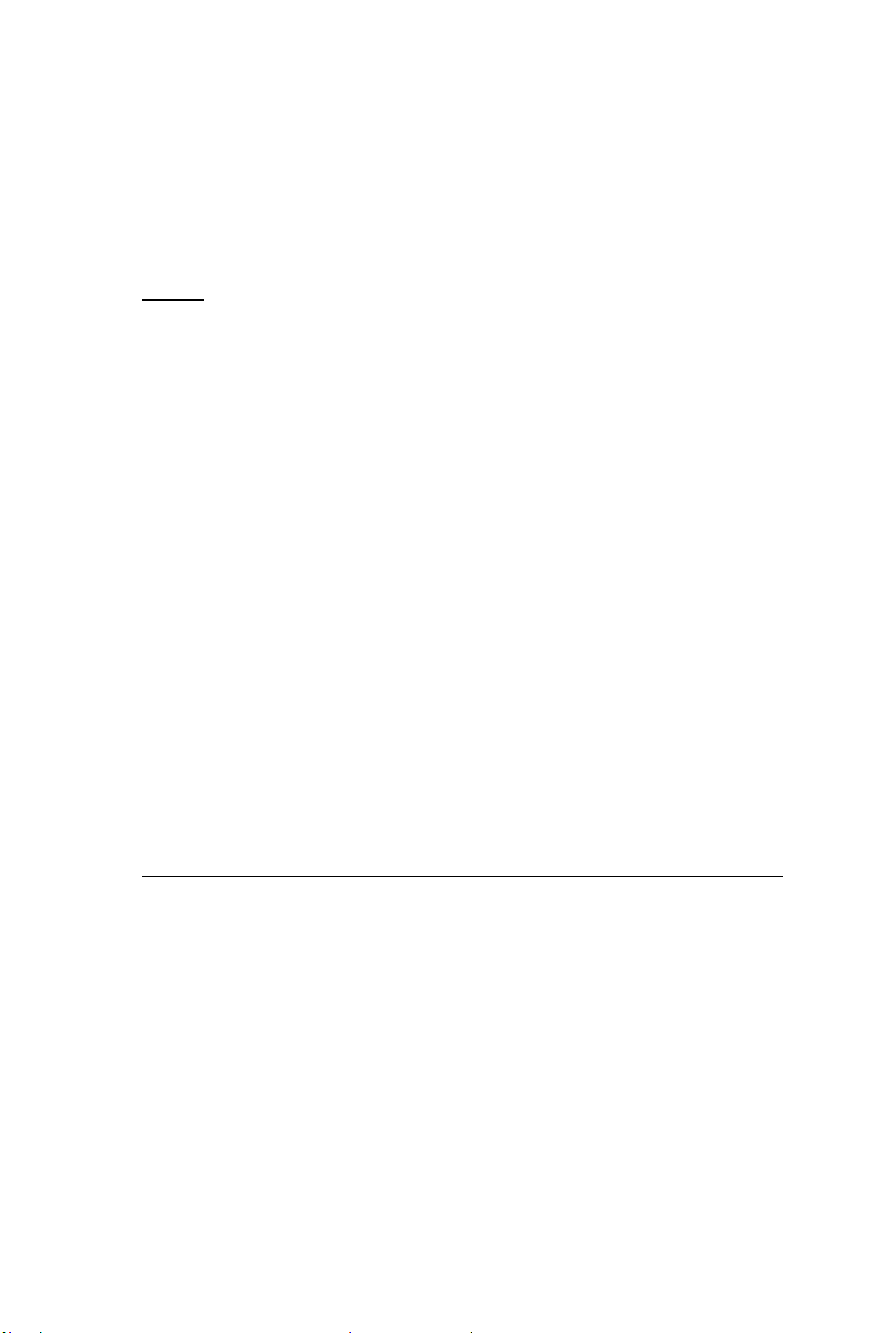
259
Mối lắp cố định không tháo được là các loại mối lắp bằng đinh tán,
hàn, ép nóng, ép nguội và dán … Các loại mối lắp này thường gặp trong
kỹ nghệ vỏ tàu thủy, vỏ máy bay, cầu, phà …
2. Mối lắp di động là các mối lắp mà các chi tiết có khả năng
chuyển động tương đối với nhau. Nó cũng được phân thành hai loại: mối
lắp di động tháo được và không tháo được.
Ví dụ: Mối lắp di động không tháo được như vòng bi …
4.2.2. Khái niệm về độ chính xác lắp ráp
Độ chính xác lắp ráp được đặc trưng bằng các yếu tố sau:
+ Độ chính xác của mối lắp như: độ dôi, khe hở … giữa hai chi tiết
lắp với nhau mà dung sai lắp ghép đã quy định.
+ Độ chính xác về vị trí tương quan giữa các chi tiết hoặc giữa các
cụm chi tiết, ví dụ: vị trí giữa hai trục cùng lắp lên thân hộp, hay vị trí
của cụm bánh răng côn di động so với cụm bánh răng côn cố định.
Các yếu tố ảnh hưởng đến độ chính xác lắp ráp gồm:
- Độ chính xác gia công của các chi tiết máy không đảm bảo:
những sai số về kích thước, hình dáng, vị trí tương quan của các bề mặt
bản thân chi tiết lắp, chất lượng bề mặt gia công. Những yếu tố trên làm
thay đổi trị số tính toán về khe hở, vị trí đã xác định theo thiết kế.
- Do ứng suất xuất hiện trong quá trình lắp làm biến dạng, gây nên
sự dịch chuyển vị trí giữa các chi tiết trong bộ phận lắp.
- Thực hiện quá trình lắp và kiểm tra không đúng quy trình công
nghệ v.v…
Đảm bảo độ chính xác lắp ráp nghĩa là phải đạt được ba yêu cầu sau:
1. Các chi tiết máy được lắp ghép với nhau giữa chúng sẽ hình
thành các mối lắp tĩnh hay động, ta phải đảm bảo tính chất của từng mối
lắp đó theo các yêu cầu của thiết kế.
2. Các mối lắp ghép liên tiếp tạo thành những chuỗi kích thước lắp,
sao cho khi làm việc các chi tiết và bộ phận máy chịu lực vẫn đảm bảo
mối quan hệ của các khâu với nhau, thỏa mãn được tính năng và ổn định
của máy.
3. Trong quá trình làm việc ở các mối lắp di động, các bề mặt tiếp
xúc của chi tiết và cụm sẽ bị mài mòn làm tăng dần khe hở, làm thay đổi
vị trí của chi tiết và bộ phận máy. Cho nên công nghệ lắp ráp cần tìm
cách giảm khe hở ban đầu và có khả năng hiệu chỉnh vị trí của chi tiết và
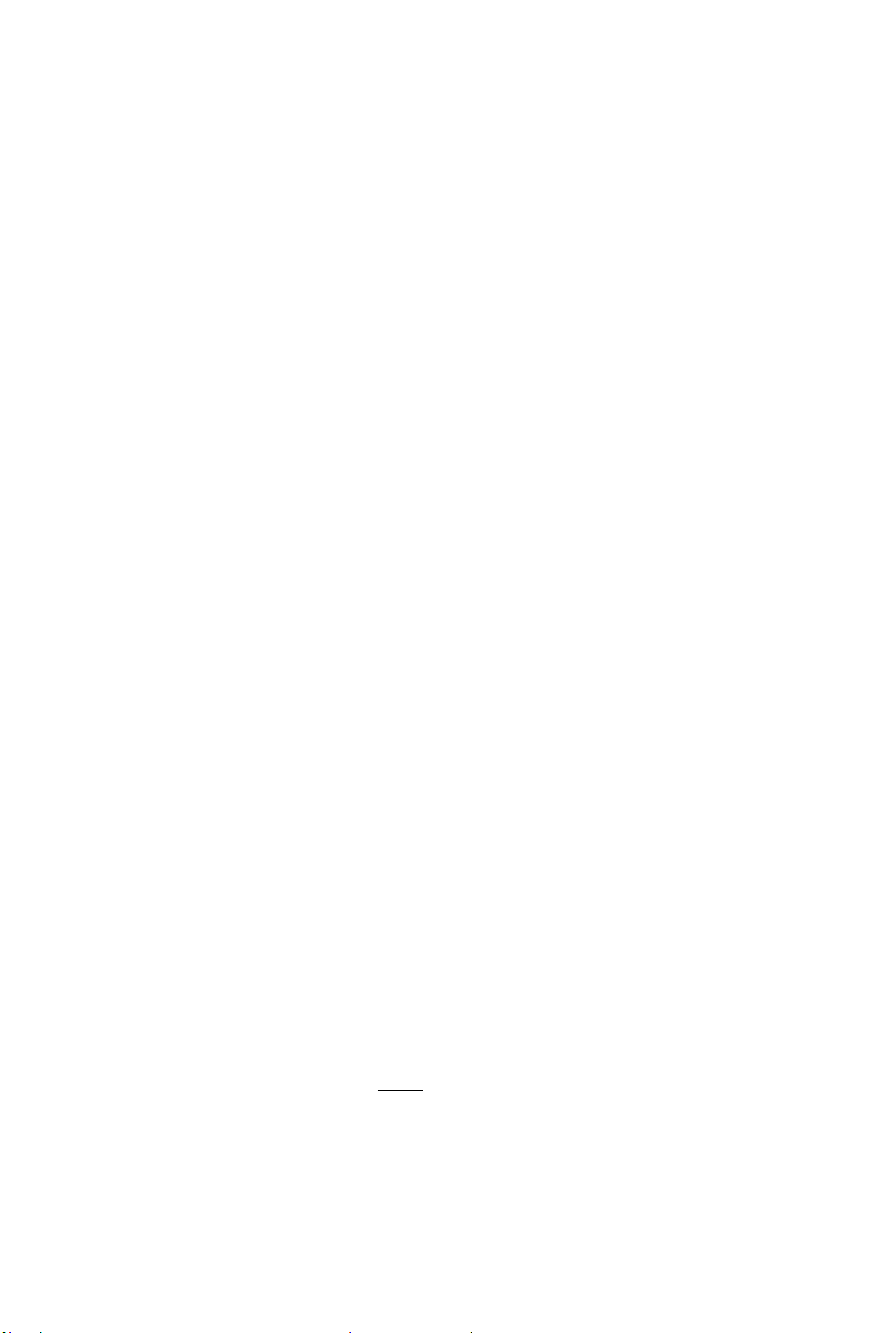
260
bộ phận khi bị mài mòn, nhằm nâng cao thời gian và hiệu quả sử dụng
thiết bị.
4.2.3. Các phƣơng pháp lắp ráp
Để đảm bảo độ chính xác lắp ráp trong các nhà máy cơ khí thường
sử dụng các phương pháp lắp ráp sau đây:
- Phương pháp lắp lẫn hoàn toàn.
- Phương pháp lắp lẫn không hoàn toàn.
- Phương pháp lắp chọn.
- Phương pháp lắp sửa.
- Phương pháp lắp điều chỉnh.
Những phương pháp lắp ráp nói trên được áp dụng tùy theo dạng
sản xuất của sản phẩm, tính chất của chúng và độ chính xác mà xí nghiệp
có khả năng gia công được cũng như các trang thiết bị và trình độ công
nhân phục vụ cho quá trình lắp ráp.
4.2.3.1. Phương pháp lắp lẫn hoàn toàn
Nếu ta lấy bất kỳ một chi tiết nào đó, đem lắp vào vị trí của nó
trong cụm hay sản phẩm lắp, mà không phải sửa chữa điều chỉnh mà vẫn
đảm bảo mọi tính chất lắp ráp của nó theo yêu cầu thiết kế thì phương
pháp này được gọi là phương pháp lắp lẫn hoàn toàn.
Phương pháp này lắp đơn giản cho năng suất lắp ráp cao, không đòi
hỏi trình độ công nhân cao, dễ dàng xây dựng những định mức kỹ thuật
nhanh chóng và chính xác, kế hoạch lắp ổn định.
Có khả năng tự động hóa và cơ khí hóa quá trình lắp. Mặt khác rất
thuận tiện cho quá trình sửa chữa thay thế sau này.
Song điều kiện để thực hiện phương pháp lắp lẫn hoàn toàn phụ
thuộc vào:
- Độ chính xác gia công của các chi tiết lắp.
- Số khâu trong chuỗi kích thước lắp.
- Dung sai khâu khép kín trong chuỗi lắp ráp được thể hiện bằng
biểu thức
Trong đó:
T
CT –
dung sai chế tạo của các khâu thành phần.
T
- dung sai của khâu khép kín.
1
n
T
TCT
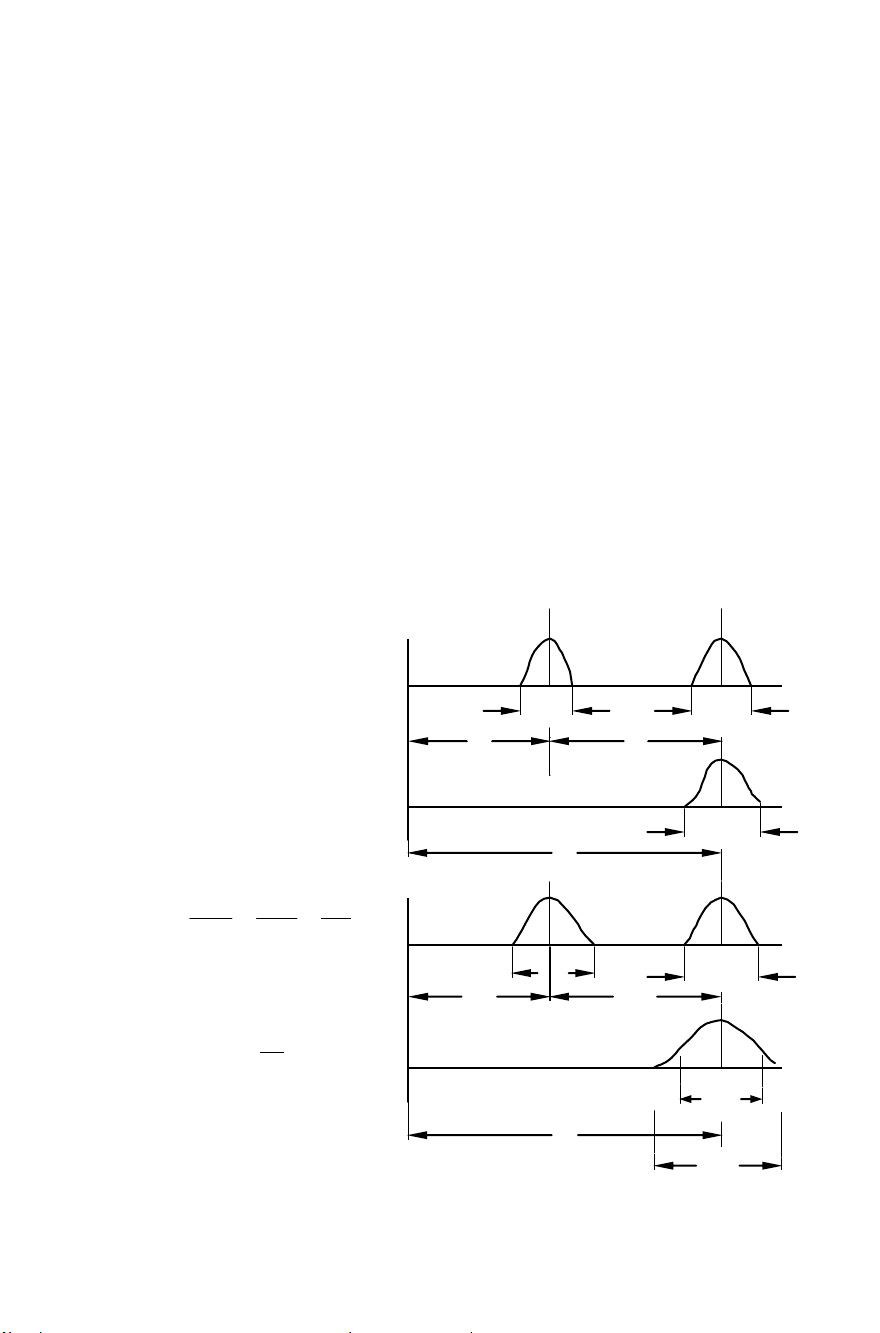
261
n - số khâu trong chuỗi kích thước lắp.
Như vậy, ta thấy nếu yêu cầu dung sai của khâu khép kín cao (T
bé) với số khâu trong chuỗi lớn thì việc thực hiện lắp lẫn hoàn toàn rất
khó khăn, nhiều khi không thể thực hiện được hoặc nếu thực hiện được
thì giá thành sản phẩm cao, vì đòi hỏi phải chế tạo các chi tiết trong sản
phẩm lắp có độ chính xác cao. Trong một số trường hợp, người ta phải
chịu một tỷ lệ phế phẩm nhất định.
Vì thế, phương pháp lắp lẫn hoàn toàn thích hợp đối với dạng sản
xuất hàng loạt lớn, hàng khối và các sản phẩm đã được tiêu chuẩn hóa.
Khi thực hiện lắp theo phương pháp lắp lẫn hoàn toàn cho hiệu quả
kinh tế thấp, ta sử dụng phương pháp lắp lẫn không hoàn toàn như lắp
chọn, lắp sửa.
4.2.3.2. Phương pháp lắp lẫn không hoàn toàn
Phương pháp lắp ráp này cho phép mở rộng phạm vi dung sai của
các khâu thành phần để dễ chế tạo. Nhưng khi lắp phải đảm bảo những
yêu cầu của khâu khép kín.
Giả sử sản phẩm có
ba khâu A
1
, A
2
, A
(có các
giá trị dung sai tương ứng là
T
A1
,T
A2
, T
A
) lắp ráp với
nhau phải thỏa mãn:
A
1
+ A
2
+ A
= 0. Giả
thiết T
A 1
= T
A 2
, theo phương
pháp lắp lẫn hoàn toàn thì:
dung sai các khâu là:
Nếu T
A
khá bé thì
việc chế tạo các khâu A
1
và
A
2
thỏa mãn
2
T
TA
rất khó
khăn, năng suất thấp, giá
thành cao, phế phẩm lớn.
Dùng phương pháp
lắp lẫn không hoàn toàn ta
có thể tăng dung sai các
Hình 4.3: Lắp lẫn không hoàn toàn.
T'A
1
T'A
2
TA
TA
A
1
TA
1
TA
2
A
2
A
A
1
A
2
A
T'A
2131
21
AAA
AA
TT
n
T
TT
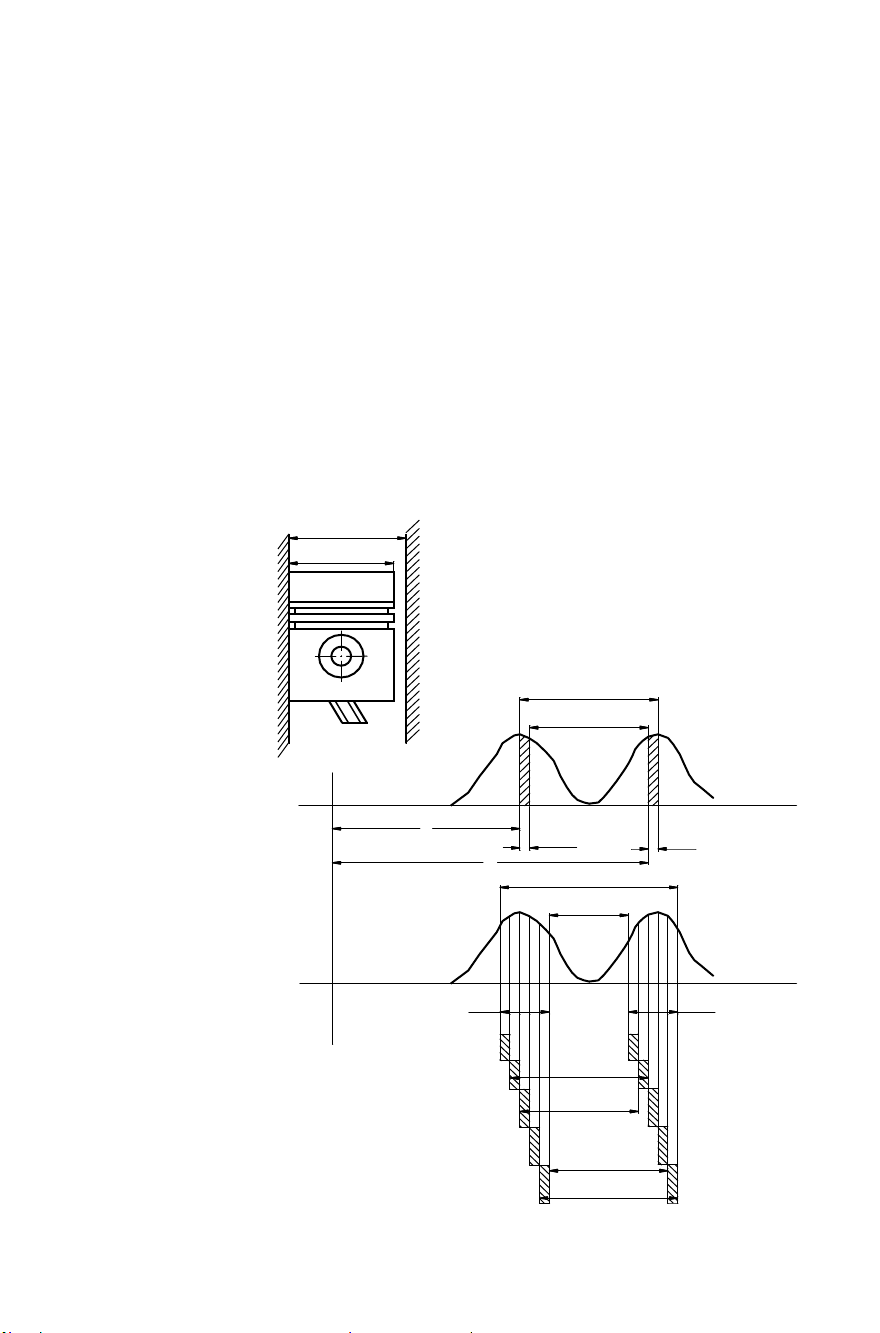
262
khâu thành phần T
A1
tới giá trị T’
A1
và T
A2
tới giá trị T’
A2
. Bây giờ chế
tạo các khâu A
1
và A
2
dễ dàng hơn. Vậy khi lắp sẽ có một lượng chi tiết
phế phẩm nhất định (hình 4.3) vì có số chi tiết không thỏa mãn yêu cầu
lắp ráp. Tỷ lệ phần trăm phế phẩm phụ thuộc vào quy luật và dạng đường
cong phân bố: nếu số khâu lớn thì T
A
có thể bù trừ cho nhau mà không
tăng tỷ lệ phần trăm phế phẩm cho các khâu theo tỷ lệ. Bởi vậy phương
pháp lắp lẫn không hoàn toàn có thể áp dụng cho sản phẩm lắp có độ
chính xác cao và số khâu lại nhiều.
4.2.3.3. Phương pháp lắp chọn
Phương pháp này cho phép mở rộng dung sai chế tạo của các chi
tiết lắp. Sau đó dựa vào kích thước của chúng để lắp chọn, sao cho đạt
được yêu cầu của khâu khép kín.
Lắp chọn có thể tiến hành theo hai phương pháp:
- Chọn lắp
từng bước:
Phương pháp này,
ta đo kích thước
của một chi tiết
rồi căn cứ vào yêu
cầu của mối lắp
để xác định kích
thước chi tiết cần
lắp với nó. Từ đó
ta chọn chi tiết lắp
phù hợp với kích
thước đã xác định
ở trên.
Nhược điểm
của phương pháp
chọn lắp từng
chiếc là mất rất
nhiều thời gian
đo, tính toán và
lựa chọn chi tiết
phù hợp với mối
lắp, vì vậy năng
suất rất thấp, chi
phí lắp ráp tăng.
A
B
max
B
min
A
TA
T'B
T'A
max
min
min
max
TB
'min
'max
Hình 4.4: Sơ đồ phân nhóm khi chọn lắp
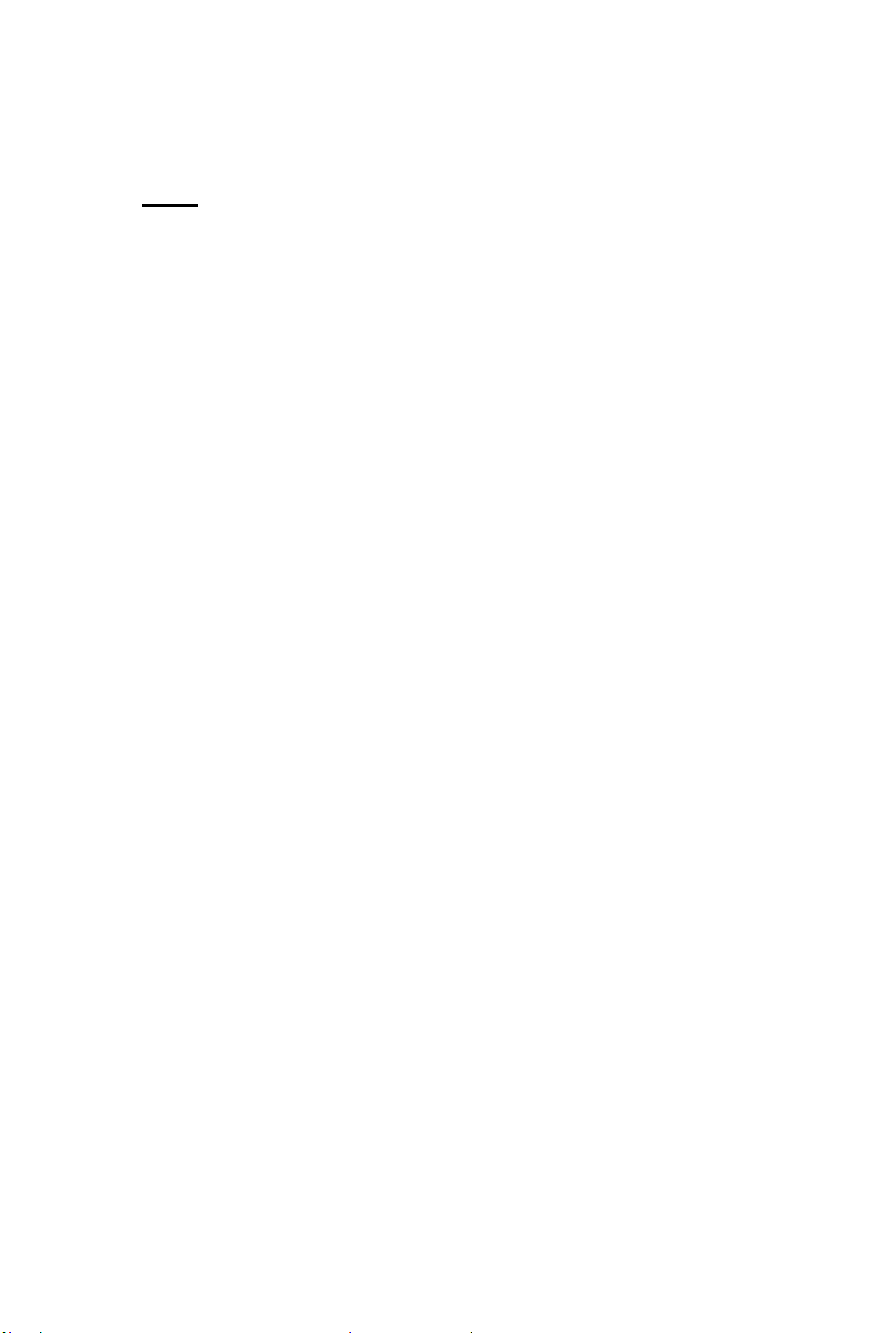
263
- Chọn lắp theo nhóm: trong quá trình lắp ráp, ta tiến hành phân
nhóm các chi tiết lắp, sau đó thực hiện quá trình lắp các chi tiết theo
nhóm tương ứng.
Ví dụ: Khi lắp ghép piston với các xylanh của động cơ đốt trong.
Với dung sai kích thước xylanh (lỗ) là T
A
, của trục (piston) là T
B
, khi lắp
phải đảm bảo khe hở là . Nếu ta tăng dung sai chế tạo cho các chi tiết bị
bao và chi tiết bao n lần thì:
T’
A
= n.T
A
và
T’
B
= n.T
B
(hình 4.4)
Sau khi chế tạo ta phân các chi tiết gia công ra n nhóm và thực hiện
quá trình lắp ráp các sản phẩm theo nhóm sẽ thỏa mãn yêu cầu kỹ thuật
của mối lắp. Như vậy trong từng nhóm, việc lắp ráp được thực hiện theo
phương pháp lắp lẫn hoàn toàn.
Phương pháp chọn lắp theo nhóm có khả năng nâng cao được năng
suất của quá trình gia công, giảm được giá thành chế tạo sản phẩm.
Phương pháp lắp chọn này, thường ứng dụng trong công nghệ chế tạo các
bộ đôi có yêu cầu dung sai của các mối lắp khắt khe như bộ đôi bơm cao
áp, van trượt thủy lực v.v.. có khe hở làm việc từ 1-3 micromet.
Tuy vậy, phương pháp chọn lắp theo nhóm còn một số tồn tại:
- Phải thêm chi phí cho việc kiểm tra và phân nhóm chi tiết, đồng
thời phải có biện pháp bảo quản tốt, tránh nhầm lẫn giữa các nhóm.
- Thường số chi tiết trong mỗi nhóm của chi tiết bao và bị bao
không bằng nhau nên xảy ra hiện tượng thừa và thiếu các chi tiết lắp của
nhóm này hay nhóm khác. Trong điều kiện gia công với sản lượng đủ
lớn, ta sử dụng phương pháp điều chỉnh máy để đảm bảo sự phân bố của
trường dung sai đối xứng hay phân bố theo quy luật giống nhau (đồng
dạng). Như vậy sẽ giảm số lượng chi tiết lắp thừa của nhóm này hay
nhóm kia. Đối với dạng sản xuất nhỏ, sản lượng quá ít phương pháp lắp
chọn có hiệu quả kinh tế thấp, có lúc không thể chấp nhận được.
Trong phương pháp lắp theo nhóm, số nhóm được chia tùy theo
yêu cầu kỹ thuật của mối lắp và điều kiện làm việc của thiết bị. Bởi vậy,
tùy theo đặc tính của chúng mà xác định số nhóm cho các mối lắp một
cách hợp lý. Ngoài việc phân nhóm theo kích thước lắp, đối với chi tiết
có chuyển động tịnh tiến khứ hồi với tốc độ cao (piston, con trượt, biên),
cần phải phân nhóm theo trọng lượng nhằm tránh hiện tượng mất cân
bằng trong quá trình làm việc, giảm rung động đảm bảo chất lượng của
thiết bị.
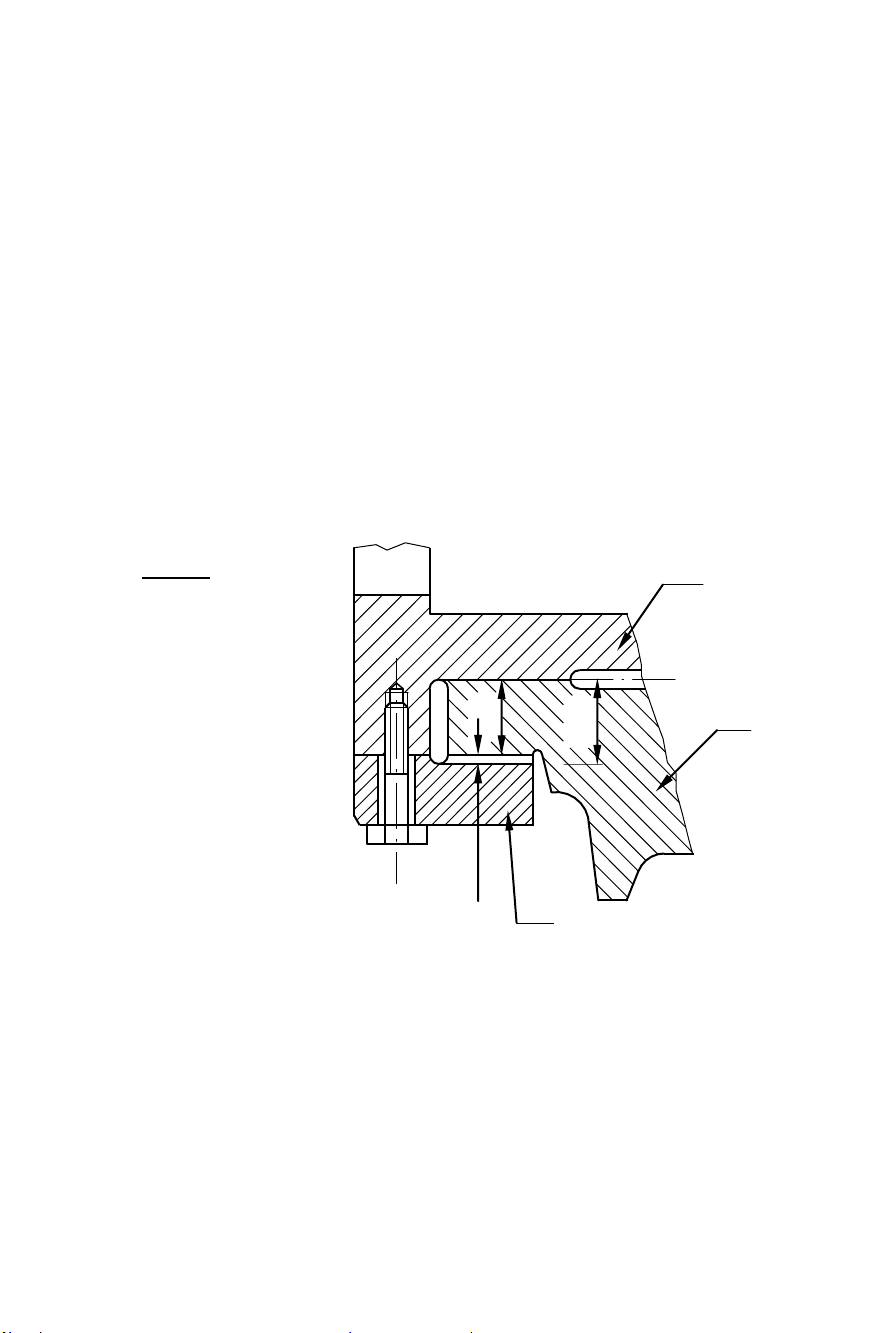
264
Trong thực tế, để phân loại chi tiết, thường dùng các dụng đo vạn
năng hay chuyên dùng. Trong sản xuất loạt lớn, hàng khối thường dùng
các dụng cụ đo chuyên dùng có thể có thể cho năng suất cao và đạt độ
chính xác tới 0,5 micromet.
4.2.3.4. Phương pháp lắp sửa
Trong một đơn vị lắp có n khâu, dung sai chế tạo của các khâu là T
1
,
T
2
…T
n
và T
là dung sai của khâu khép kín. Để gia công các chi tiết dễ
dàng, giảm giá thành chế tạo ta tăng dung sai các khâu thành phần, thành
T’
1
, T’
2
…T’
n
. Việc đảm bảo dung sai của khâu khép kín T
sẽ được thực
hiện trong quá trình lắp ráp, nghĩa là bớt đi lượng thừa ở một khâu nào đó
trong chuỗi kích thước. Khâu đó gọi là khâu bồi thường.
Vậy phương pháp lắp sửa là sửa chữa kích thước của một khâu
chọn trước trong các khâu thành phần của sản phẩm lắp bằng cách lấy đi
lượng kim loại (Z) trên bề mặt lắp ghép của nó để đạt được yêu cầu của
mối lắp (T
).
Ví dụ: Khi lắp hệ
trượt dẫn hướng (hình
4.5), hay cơ cấu tự định
tâm, ta lắp ráp số chi tiết
cơ bản 1, 2, 3 … thỏa
mãn kích thước A
TA
và
khe hở T
ở mặt dẫn
hướng. Lúc này ta chọn
khâu A
2
trên chi tiết 3
làm khâu bồi thường với
lượng dư bồi thường là Z.
Trong quá trình lắp, ta
cạo lớp kim loại cần thiết
Z ở khâu bồi thường,
nhằm thỏa mãn khe hở
mối lắp T
.
Sử dụng phương pháp lắp sửa cần chú ý một số đặc tính sau:
1. Không chọn khâu bồi thường là khâu chung của hai chuỗi kích
thước liên kết, bởi lẽ khi sửa chữa cho đạt yêu cầu của chuỗi kích thước
này thì lại có thể phá vỡ điều kiện của chuỗi kích thước kia. Hình 4.6 mô
tả chuỗi kích thước lắp ghép có một khâu chung là A
2
= B
3
. Nếu chọn nó
làm khâu bồi thường để sửa chữa cho thỏa mãn chuỗi A thì có thể làm sai
lệch chuỗi B.
A
A1
Hình 4.5: Lắp hệ dẫn hướng bằng cạo sửa
T
A
1
2
3
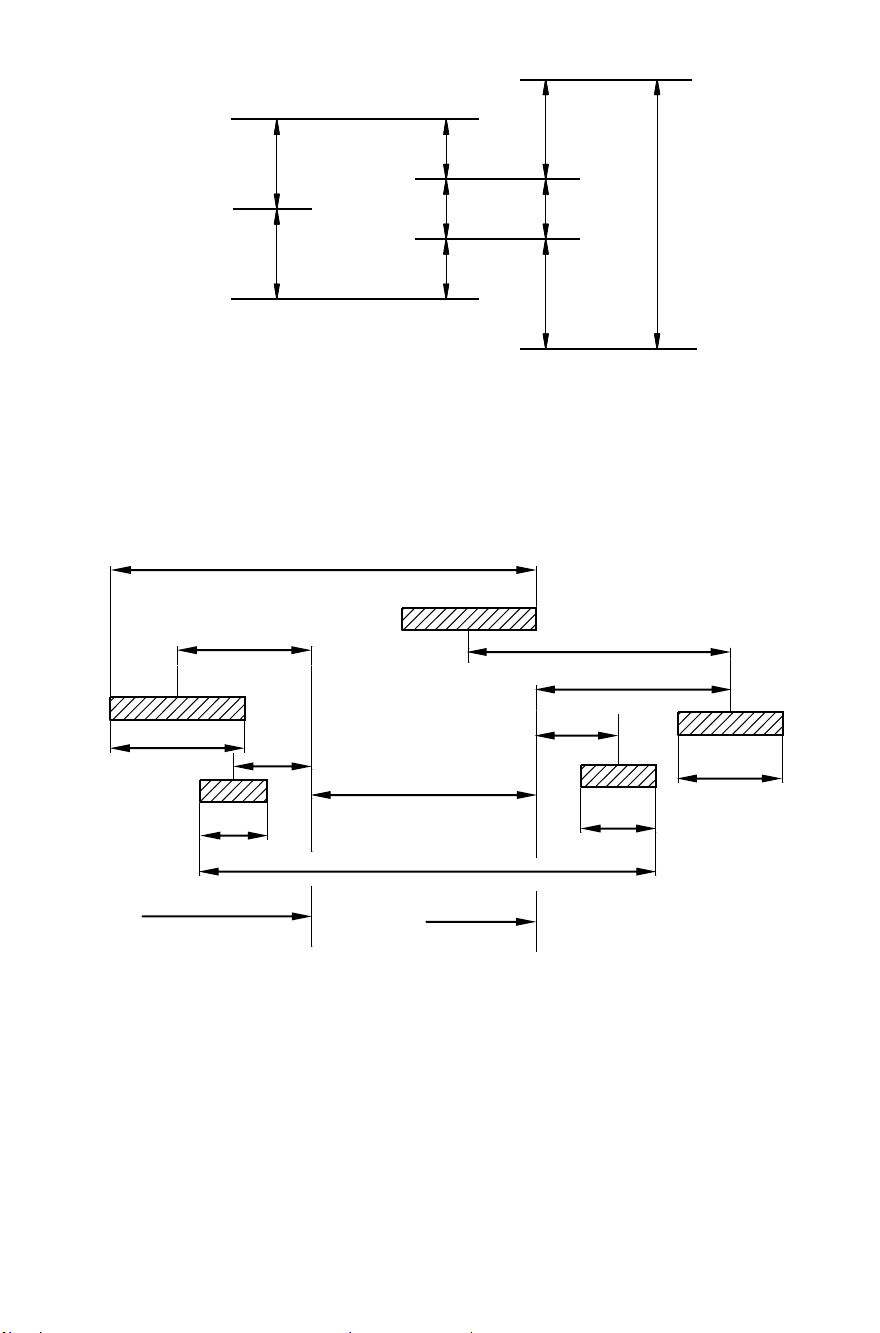
265
2. Cần xác định lượng dư sửa chữa ở khâu bồi thường một cách
hợp lý. Nếu để lượng dư bé có thể hụt kích thước, ngược lại để lượng dư
quá lớn thì tốn công sửa chữa, tăng phí tổn, giảm năng suất lắp ráp.
Cách tính lượng dư, điều chỉnh vị trí trung tâm dung sai của khâu
bồi thường được thể hiện ở trên hình 4.7.
Nếu ta gọi lượng điều chỉnh là K và giả sử ta có chuỗi kích thước
lắp ráp là:
A
1
+ A
- A
2
= 0 thì đảm bảo được yêu cầu kỹ thuật của mối lắp ráp.
Ta biết:
A4
A2
A1
A3
B2
B3
B4
A
B1
Hình 4.6: Liên kết hai chỗi kích thước lắp A và B.
D
A2
D
A1
T
A1
T'
A2
T
A2
Hình 4.7: Sơ đồ bố trí dung sai để tính
K.
A
max
D'
A'1
T'
A1
D
K
D'
A'2
A
max
A
A
1
A
2
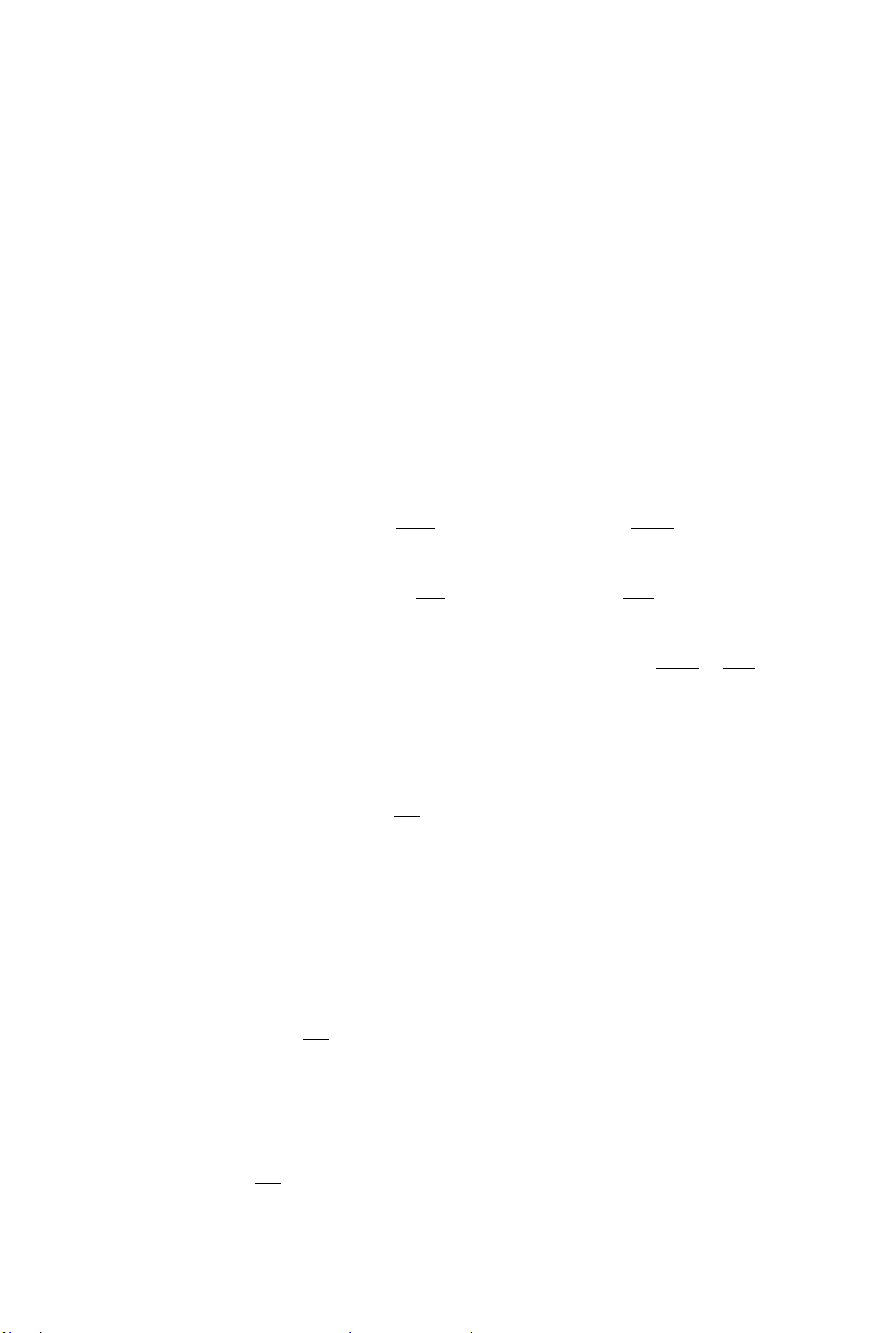
266
22
2
21
1
max
A
AA
A T
A
T
A
TA
1
và TA
2
là dung sai của kích thước A
1
và A
2
ban đầu.
T’A
1
; T’A
2
là dung sai mở rộng của kích thước A
1
; A
2
.
A1
;
A2
là tọa độ dung sai của các khâu A
1
; A
2
.
A’1
;
A’2
là tọa độ trung tâm dung sai mở rộng của các khâu A
1
; A
2
.
Mở rộng dung sai để dễ chế tạo, nhưng khi lắp ráp phải đảm bảo
dung sai của khâu khép kín không đổi. Vậy ta phải giữ cận trên, hay cận
dưới của miền dung sai mở rộng của một khâu là không đổi và điều chỉnh
cận dưới, hoặc cận trên của khâu kia, sao cho mối lắp vẫn có khe hở A
max
không đổi. Lượng điều chỉnh đó là K. Ở đây, ta chọn khâu A
2
là khâu
bồi thường và giữ cận dưới của khâu A
1
không đổi, rồi điều chỉnh cận trên
của khâu A
2.
Vậy K được xác định như sau:
Trong đó:
Suy ra ta có:
Đặt: T
K
= T’
A
- T
A
.
T
K
– sai lệch giữa dung sai khâu khép kín khi mở rộng và dung sai
khâu khép kín khi chưa mở rộng cuả các khâu thành phần.
Do đó ta có:
Từ trên ta có thể suy rộng ra là:
1. Các toạ độ tâm dung sai ở công thức trên có thể làm cho giá trị
A
tăng hoặc giảm. Nếu nó làm cho khâu khép kín tăng thì mang dấu
cộng (+) và làm cho khâu khép kín giảm thì mang dấu trừ (-). Vậy ta có
công thức tổng quát sau:
2. Công thức trên chỉ xét cho chuỗi có ba khâu, nếu chuỗi có nhiều
khâu thì K được xác định theo biểu thức sau:
)()''(
2
2121 AAAA
KT
K
max
2
21
1
2
'
''
2
'
A
T
A
T
K
A
AA
A
22
'
)()''( 2121
AA
AAAA
TT
K
)()''(
2
2121 AAAA
KT
K
m
i
n
mi
m
i
n
mi
ii
K
AAAA
T
K
1
1
1 1
1
1
)()''(
2
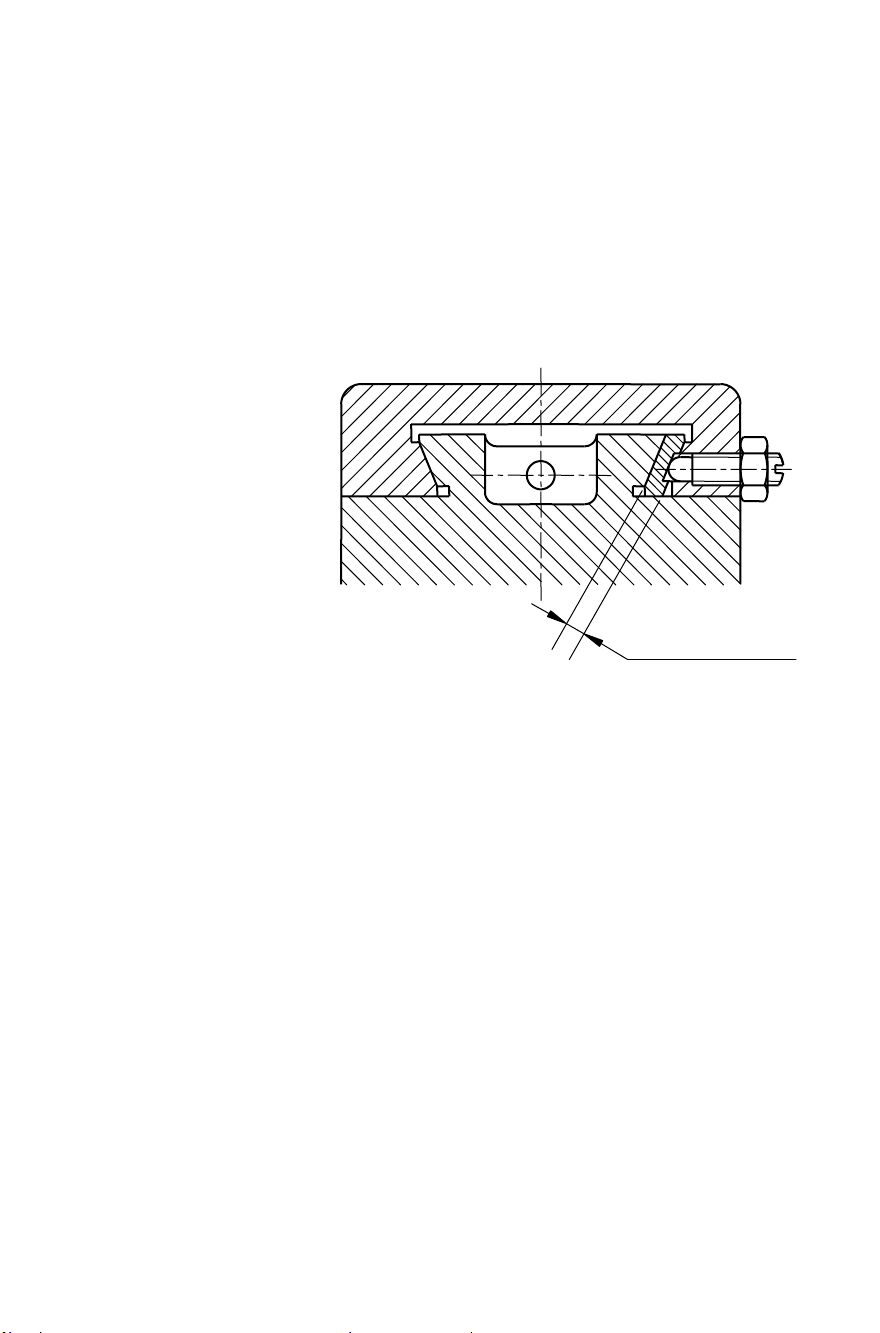
267
Trong đó:
m - số khâu tăng.
n - tổng số khâu của chuỗi.
5. Phương pháp lắp điều chỉnh
Phương pháp lắp điều chỉnh về cơ bản giống phương pháp lắp sửa.
Nghĩa là độ chính xác của khâu khép kín đạt được nhờ thay đổi vị trí của
khâu bồi thường bằng việc dịch chuyển hay điều chỉnh nó hoặc thay đổi
kích thước của chúng như bạc chặn, vòng đệm.
Từ yêu cầu của
mối lắp, ta có thể
tính ra giá trị phải
điều chỉnh ở khâu
bồi thường theo dung
sai của các khâu
thành phần đã mở
rộng và dung sai của
khâu khép kín.
Phương pháp lắp
điều chỉnh cho khả
năng phục hồi độ
chính xác của mối
lắp sau thời gian làm việc và thuận tiện trong sửa chữa thiết bị.
Phương pháp lắp sửa và lắp điều chỉnh được dùng phổ biến trong
chuỗi kích thước lắp ráp có nhiều khâu, mà khâu khép kín đòi hỏi độ
chính xác cao.
Hai phương pháp lắp ráp kể trên thường dùng trong sản xuất đơn
chiếc và loạt nhỏ, đôi khi còn dùng đối với cả dạng sản xuất hàng loạt.
4.3. CÁC HÌNH THỨC TỔ CHỨC LẮP RÁP
Chọn hình thức tổ chức lắp ráp sản phẩm, phụ thuộc vào nhiều yếu
tố như:
- Dạng sản xuất của sản phẩm.
- Mức độ phức tạp của sản phẩm.
- Độ chính xác đạt được của các chi tiết lắp.
- Tính chất của mối lắp, phương pháp lắp.
Khâu điều chỉnh
Hình 4.8: Sơ đồ lắp điều chỉnh.
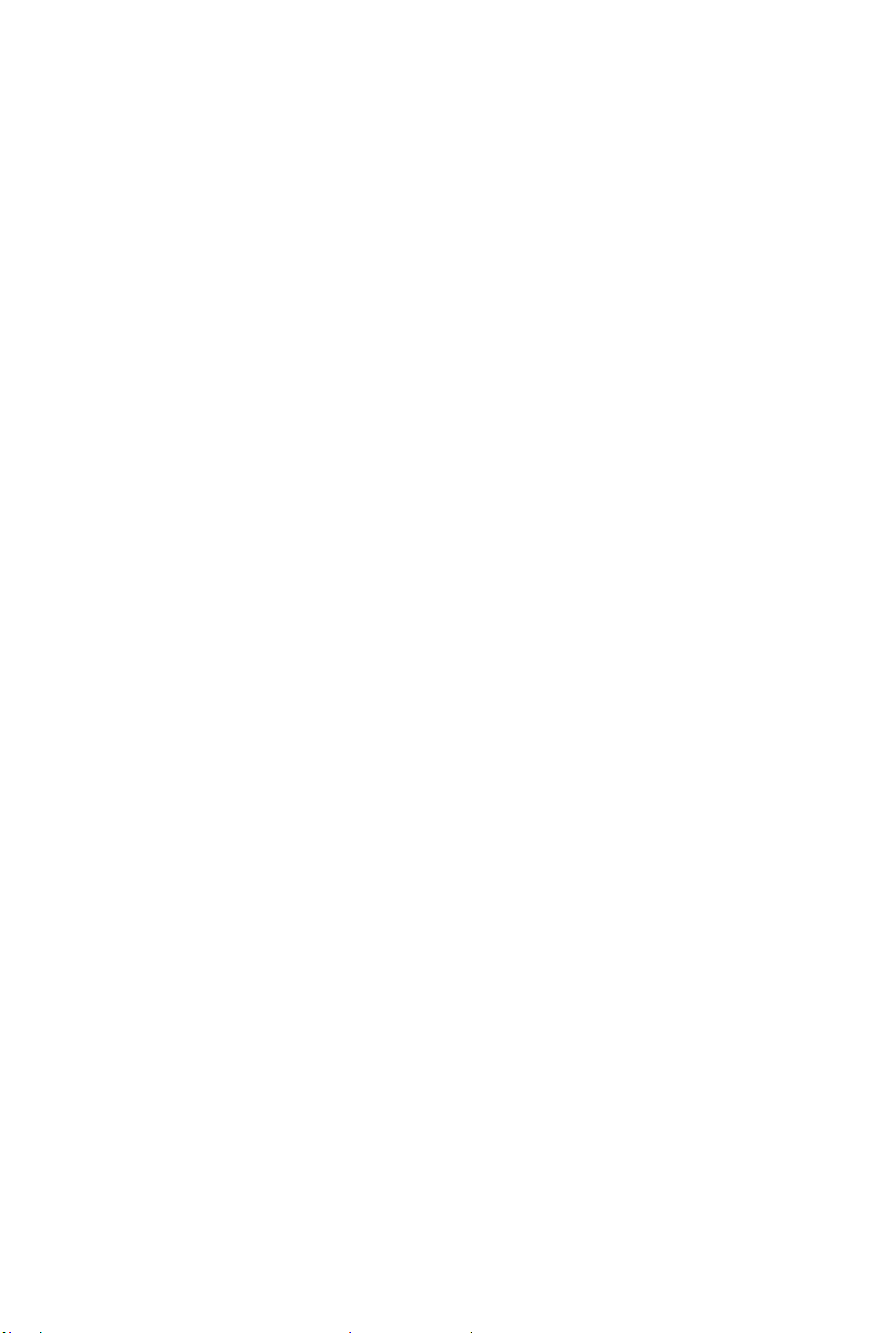
268
- Trọng lượng của sản phẩm.
Vận dụng hình thức tổ chức lắp ráp hợp lý có ảnh hưởng tới năng
suất của quá trình lắp và chất lượng của sản phẩm lắp.
Căn cứ vào trạng thái và vị trí của đối tượng lắp, người ta phân
thành hai hình thức tổ chức lắp ráp là:
- Lắp ráp cố định.
- Lắp ráp di động.
4.3.1. Lắp ráp cố định
Lắp ráp cố định là một hình thức tổ chức lắp ráp mà mọi công việc
lắp được thực hiện tại một hay một số địa điểm. Các chi tiết lắp, cụm hay
bộ phận được vận chuyển tới địa điểm lắp.
Lắp ráp cố định còn được phân chia thành lắp ráp cố định tập trung
và lắp ráp cố định phân tán.
4.3.1.1. Lắp ráp cố định tập trung
Đây là một hình thức tổ chức lắp ráp, mà đối tượng lắp được hoàn
thành tại một vị trí nhất định, do một hay một nhóm công nhân thực hiện.
Hình thức lắp ráp cố định tập trung đòi hỏi diện tích mặt bằng làm việc
lớn, trình độ thợ lắp ráp cao, tính vạn năng cao, đồng thời có chu kỳ lắp
ráp một sản phẩm lớn, năng suất lắp ráp thấp, bởi vậy thường sử dụng để
lắp các máy hạng nặng như máy cán, máy hơi nước, tàu thủy v.v ... Nó
còn được sử dụng trong dạng sản xuất đơn chiếc, loạt nhỏ để lắp những
sản phẩm đơn giản, số nguyên công ít. Trong nhà máy chế tạo cơ khí,
hình thức lắp ráp này sử dụng ở phân xưởng dụng cụ, cơ điện để lắp các
sản phẩm chế thử hay dụng cụ, thiết bị chuyên dùng.
4.3.1.2. Hình thức tổ chức lắp ráp cố định phân tán
Hình thức lắp ráp này thích hợp với những sản phẩm phức tạp, có thể
chia thành nhiều bộ phận lắp ráp, thực hiện ở nhiều nơi độc lập. Sau đó mới
tiến hành lắp các bộ phận lại thành sản phẩm ở một địa điểm nhất định.
So với lắp ráp cố định tập trung, hình thức này cho năng suất cao
hơn, không đòi hỏi trình độ tay nghề và tính vạn năng của công nhân lắp
ráp cao, bởi vậy hạ được giá thành chế tạo sản phẩm.
Nếu sản lượng càng lớn thì có thể càng phân nhỏ sản phẩm lắp
thành nhiều bộ phận và cụm. Mỗi vị trí lắp chỉ có số nguyên công nhất
định. Công nhân lắp ráp được chuyên môn hóa cao theo nguyên công.
Hình thức tổ chức lắp ráp cố định phân tán thường dùng trong nhà
máy cơ khí với quy mô sản xuất trung bình.
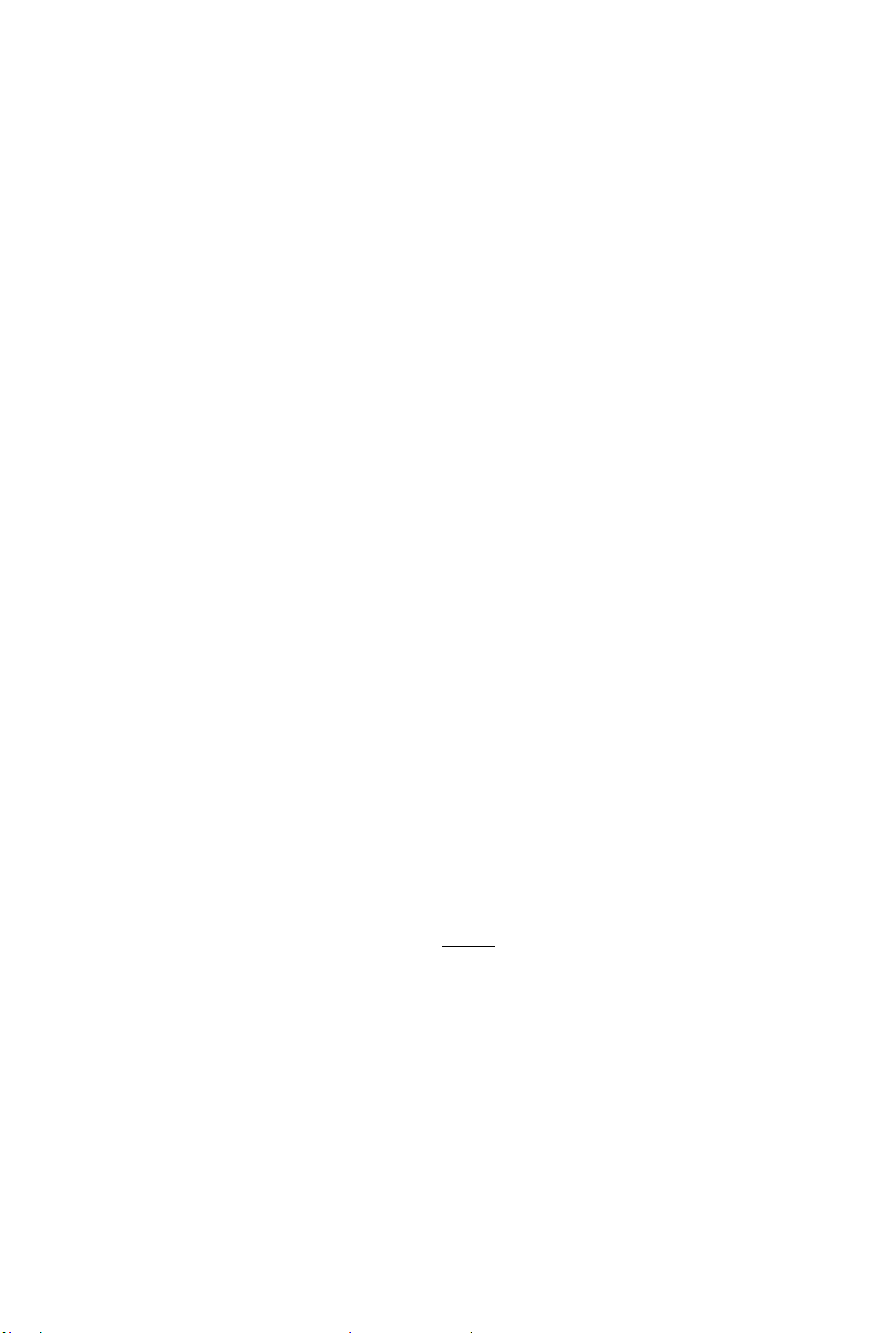
269
4.3.2. Lắp ráp di động
Trong hình thức lắp ráp di động, đối tượng lắp được di chuyển từ vị
trí này sang vị trí khác phù hợp với quy trình công nghệ lắp ráp, đối
tương được thực hiện một hoặc một số nguyên công nhất định. Theo tính
chất di động của đối tượng lắp ráp ta phân thành hai loại:
- Lắp ráp di động tự do.
- Lắp ráp di động cưỡng bức.
4.3.2.1. Lắp ráp di động tự do
Đây là hình thức tổ chức lắp ráp mà tại mỗi vị trí lắp ráp được thực
hiện hoàn chỉnh một nguyên công lắp ráp xác định, sau đó đối tượng lắp
mới được di chuyển tiếp tới vị trí lắp tiếp theo của quy trình công nghệ
lắp, chứ không theo nhịp của chu kỳ lắp. Sự di chuyển đối tượng lắp
được thực hiện bằng các phương tiện như xe đẩy, cần trục v.v.
4.3.2.2. Lắp ráp di động cưỡng bức
Đây là hình thức tổ chức lắp ráp mà quá trình di động của đối
tượng lắp được điều khiển thống nhất – phù hợp với nhịp độ của chu kỳ
lắp – nhờ các thiết bị như băng chuyền, xích tải, xe ray, bàn quay v.v …
Theo hình thức di động, người ta chia lắp ráp di động cường bức
thành hai dạng lắp ráp di động cưỡng bức liên tục và lắp ráp di động
cưỡng bức gián đoạn.
Trong hình thức tổ chức lắp ráp di động cưỡng bức liên tục, đối
tượng lắp được di chuyển liên tục và công nhân thực hiện các thao tác lắp
trong khi đối tượng lắp chuyển động liên tục. Bởi vậy, trong hình thức
lắp ráp di động cưỡng bức liên tục, cần phải xác định vận tốc chuyển
động của đối tượng lắp hợp lý, để đảm bảo yêu cầu của chất lượng lắp và
hoàn thành nguyên công lắp ráp thỏa mãn chu kỳ lắp:
Trong đó: L – đoạn đường để công nhân đi theo lắp.
l
1
– đoạn đường phụ để dự.
T
M
– chu kỳ lắp.
Lắp ráp di động cưỡng bức gián đoạn là phương pháp lắp ráp mà
đối tượng lắp được dừng lại ở các vị trí lắp để công nhân thực hiện các
nguyên công lắp ráp trong khoảng thời gian xác định, sau đó tiếp tục di
chuyển tới vị trí lắp tiếp theo. Tổng thời gian dừng lại ở các vị trí lắp và
di chuyển tương ứng với thời gian nhịp sản xuất.
MT
lL
V
1
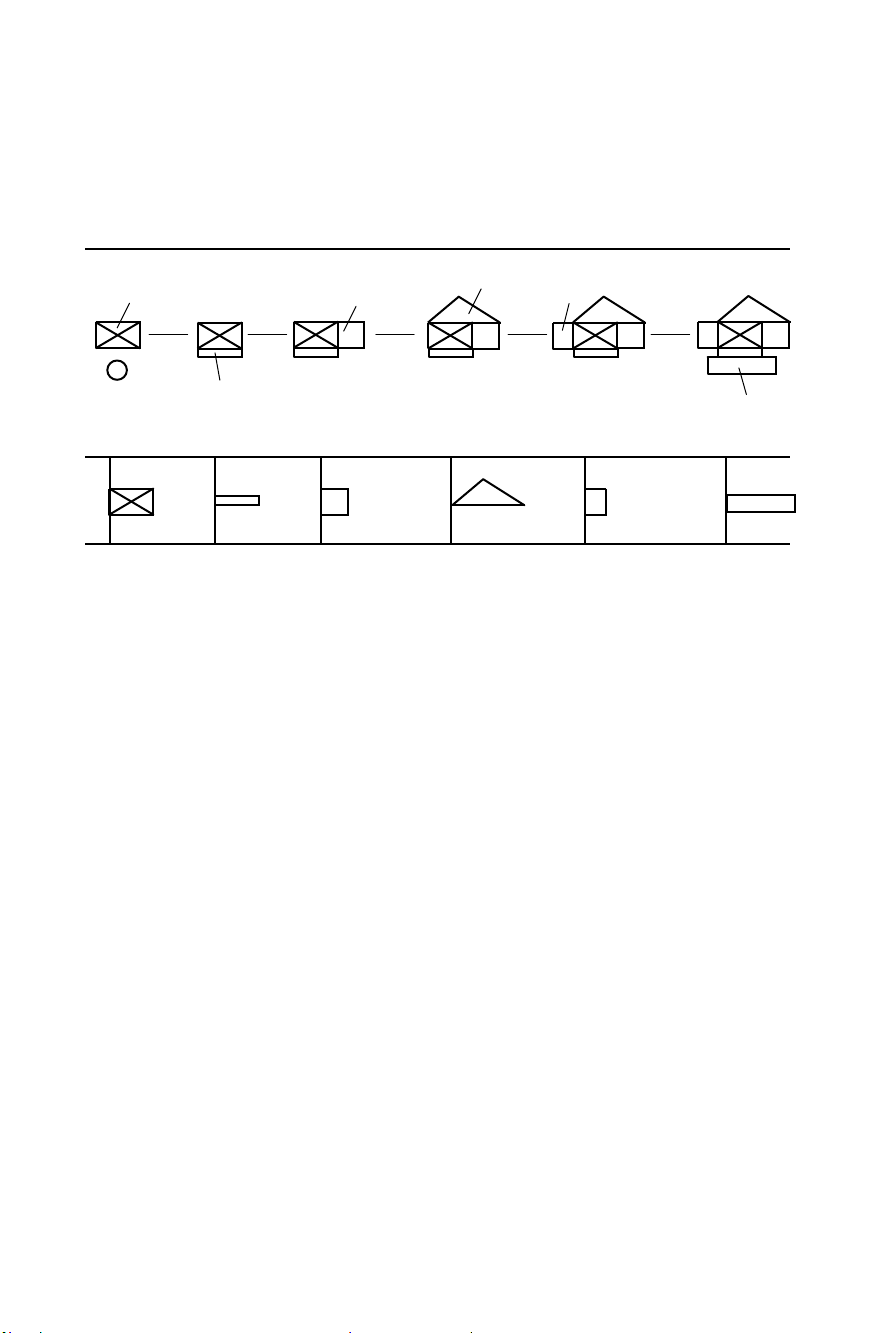
270
Lắp ráp di động cưỡng bức liên tục có năng suất cao hơn nhưng độ
chính xác lại thấp hơn so với lắp ráp di động cưỡng bức gián đoạn, vì
trong quá trình lắp và kiểm tra chất lượng bị ảnh hưởng của chấn động
của cơ cấu vận chuyền. Bởi vậy để đạt được độ chính xác và năng suất
lắp ráp, thường sử dụng hình thức lắp ráp di động cưỡng bức gián đoạn.
Hình thức lắp ráp di động tạo thành dây chuyền lắp ráp.
Trong dây chuyền lắp ráp, sản phẩm lắp được thực hiện một cách
liên tục qua các vị trí lắp ráp trong một khoảng thời gian xác định. Theo
hình thức này, các sản phẩm lắp di động cưỡng bức gián đoạn hay di
chuyển cưỡng bức liên tục.
Lắp ráp dây chuyền là cơ sở tiến tới tự động hóa quá trình lắp ráp.
Để thực hiện lắp ráp dây chuyền, cần có những điều kiện sau đây:
1. Các chi tiết lắp phải thỏa mãn điều kiện lắp lẫn hoàn toàn, loại
trừ việc sửa chữa, điều chỉnh tại các vị trí lắp của dây chuyền.
2. Cần phải phân chia quá trình lắp ráp thành các nguyên công sao
cho thời gian thực hiện gần bằng nhau hoặc bội số của nhau. Đảm bảo sự
đồng bộ của các nguyên công và nhịp sản xuất để dây chuyền làm việc
liên tục và ổn định.
3. Cần xác định chính xác số lượng công nhân với trình độ tay
nghề phù hợp với tính chất lắp ở vị trí nguyên công lắp. Lựa chọn trang
thiết bị, đồ gá và các dụng cụ phù hợp và cần thiết cho mỗi nguyên công.
4. Để cho dây chuyền làm việc liên tục, phải đảm bảo cung cấp
đầy đủ và kịp thời tới chỗ làm việc các chi tiết, cụm hay bộ phận phục vụ
cho quá trình lắp ráp.
Hình 4.9: Sơ đồ lắp ráp di động cưỡng bức liên tục.
1- 6. Thứ tự lắp ráp trong dây chuyền.
1
2
3
4
5
6
1
2
3
4
5
6
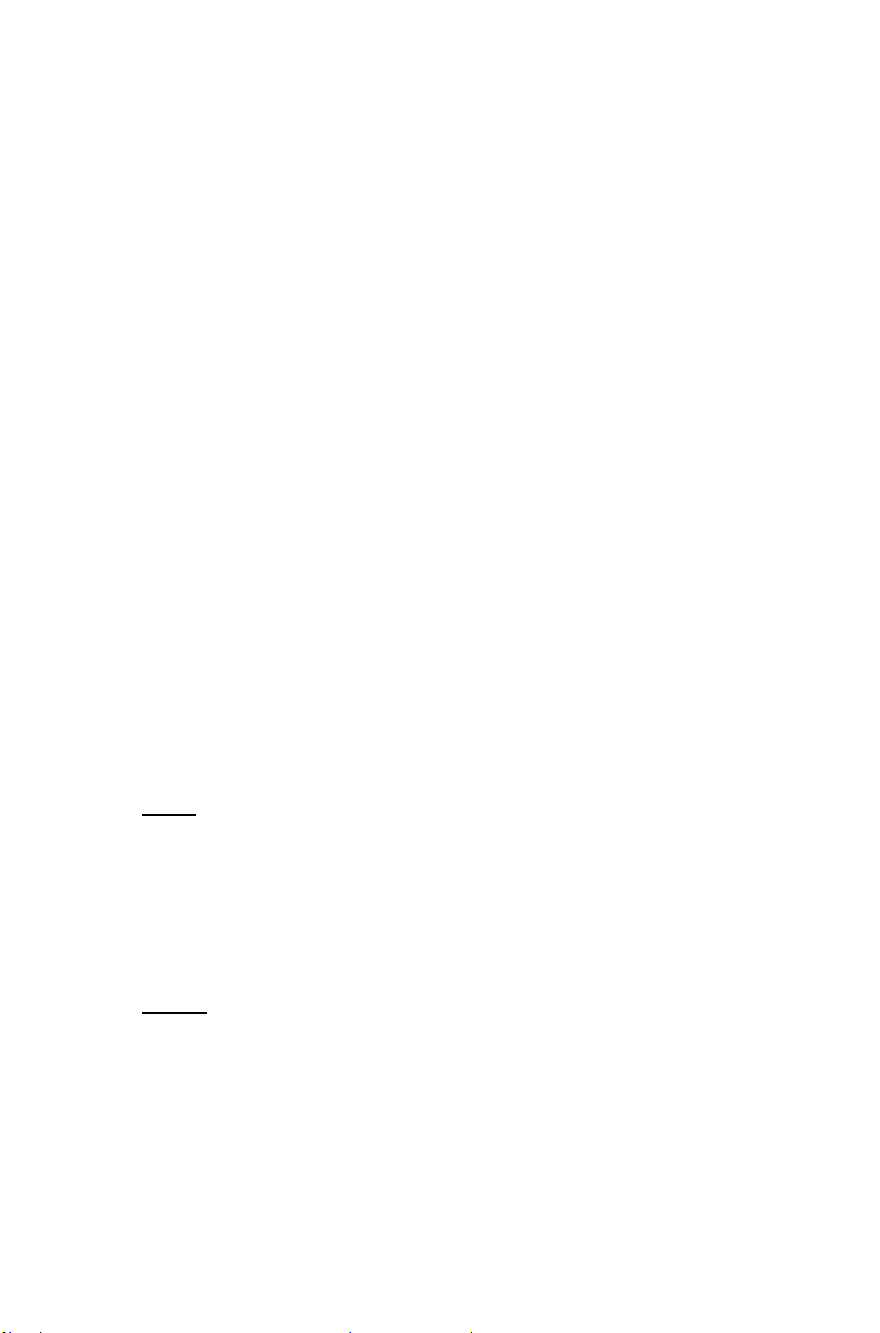
271
Thiết kế quy trình công nghệ lắp ráp theo dây chuyền đòi hỏi khối
lượng tính toán lớn, tỉ mỉ và chính xác tùy theo quy mô sản xuất, mức độ
phức tạp của những động tác lắp và điều kiện công nghệ lắp ráp. Công
nghệ lắp ráp theo dây chuyền có những ưu điểm sau:
- Công nhân lắp ráp được chuyên môn hóa, sử dụng hợp lý, giảm
thời gian lắp ráp.
- Nâng cao năng suất, giảm phí tổn, giá thành hạ.
4.4. THIẾT KẾ QUY TRÌNH CÔNG NGHỆ LẮP RÁP
4.4.1. Khái niệm và định nghĩa
Quy trình công nghệ lắp ráp là xác định trình tự và phương pháp
lắp ráp các chi tiết máy để tạo thành sản phẩm, thỏa mãn các điều kiện kỹ
thuật đề ra một cách kinh tế nhất.
Quá trình lắp ráp sản phẩm cũng được chia ra thành các nguyên
công bước vào động tác.
1. Nguyên công lắp ráp là một phần của quá trình lắp được hoàn
thành đối với một bộ phận hay sản phẩm, tại một chỗ làm việc nhất định,
do một hay một nhóm công nhân thực hiện một cách liên tục. Ví dụ: lắp
bánh răng, bánh đà lên trục hay lắp ráp máy v.v…
2. Bước lắp ráp là một phần của nguyên công, được quy định bởi
sự không thay đổi vị trí dụng cụ lắp.
Ví du: Lắp bánh đai lên đầu trục bao gồm các bước:
a. Cạo sửa và lắp then lên trục.
b. Lắp bánh đai.
c. Lắp vít hãm.
3. Động tác là thao tác của công nhân để thực hiện công việc lắp ráp.
Ví dụ: lấy chi tiết lắp, đặt vào vị trí lắp, kiểm tra chất lượng mối
lắp …
4.4.2. Những tài liệu ban đầu để thiết kế quy trình công nghệ
lắp ráp
Để thiết kế quy trình công nghệ lắp cần có các tài liệu sau:
1. Bản vẽ lắp chung toàn sản phẩm hay bộ phận với đầy đủ các yêu
cầu kỹ thuật.
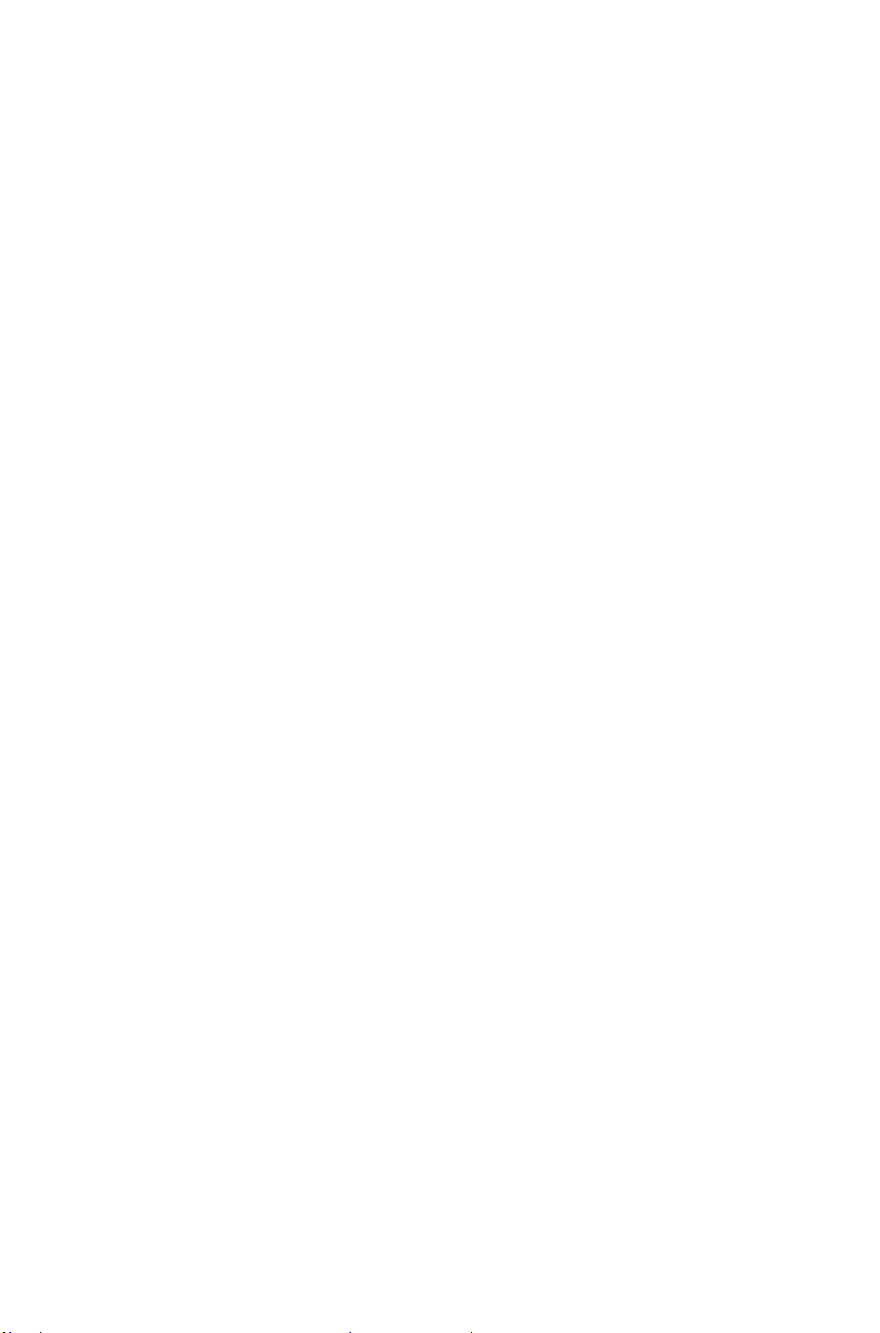
272
2. Bảng thống kê chi tiết lắp của bộ phận hay sản phẩm với đầy đủ
số lượng, quy cách, chủng loại của chúng.
3. Thuyết minh về đặc tính của sản phẩm, các yêu cầu kỹ thuật
nghiệm thu, những yêu cầu đặc biệt trong lắp ráp sử dụng.
4. Sản lượng và mức độ ổn định của sản phẩm.
5. Khả năng về thiết bị, dụng cụ và đồ gá lắp khả năng thực hiện
của xí nghiệp.
4.4.3. Trình tự thiết kế quy trình công nghệ lắp ráp
Thiết kế quy trình công nghệ lắp ráp cần thực hiện các công việc
theo trình tự sau:
- Nghiên cứu bản vẽ lắp chung sản phẩm, kiểm tra tính công nghệ
trong lắp ráp. Nếu cần phải giải chuỗi kích thước lắp ráp, sửa đổi kết cấu
để đạt tính công nghệ lắp cao.
- Chọn phương pháp lắp ráp sản phẩm.
- Lập sơ đồ lắp.
- Chọn hình thức tổ chức lắp ráp, lập quy trình công nghệ lắp.
- Xác định nội dung công việc cho từng nguyên công và bước lắp ráp.
- Xác định điều kiện kỹ thuật cho các mối lắp, bộ phận hay cụm lắp.
- Chọn dụng cụ, đồ gá, trang bị cho các nguyên công lắp ráp hay
kiểm tra.
- Xác định chỉ tiêu kỹ thuật, thời gian cho từng nguyên công. Tính
toán, so sánh phương án lắp.
- Xác định thiết bị, hình thức vận chuyển qua các nguyên công.
- Xây dựng những tài liệu cần thiết: bản vẽ, sơ đồ lắp, thống kê,
hướng dẫn cách lắp, kiểm tra …
Khi thiết kế quy trình công nghệ lắp ráp, cần chú ý các vấn đề sau:
1. Chia sản phẩm thành cụm, bộ phận lắp hợp lý; tận dụng lắp bộ
phận, cụm ở ngoài địa điểm lắp sản phẩm.
2. Cố gắng sử dụng trang thiết bị gá lắp chuyên dùng, cơ khí hóa và
tự động hóa việc lắp ráp để giảm nhẹ cường độ lao động, nâng cao năng
suất và chất lượng sản phẩm.
3. Giải quyết hợp lý khâu vận chuyển trong quá trình lắp cũng như
quá trình cung cấp chi tiết và bộ phận lắp ráp.
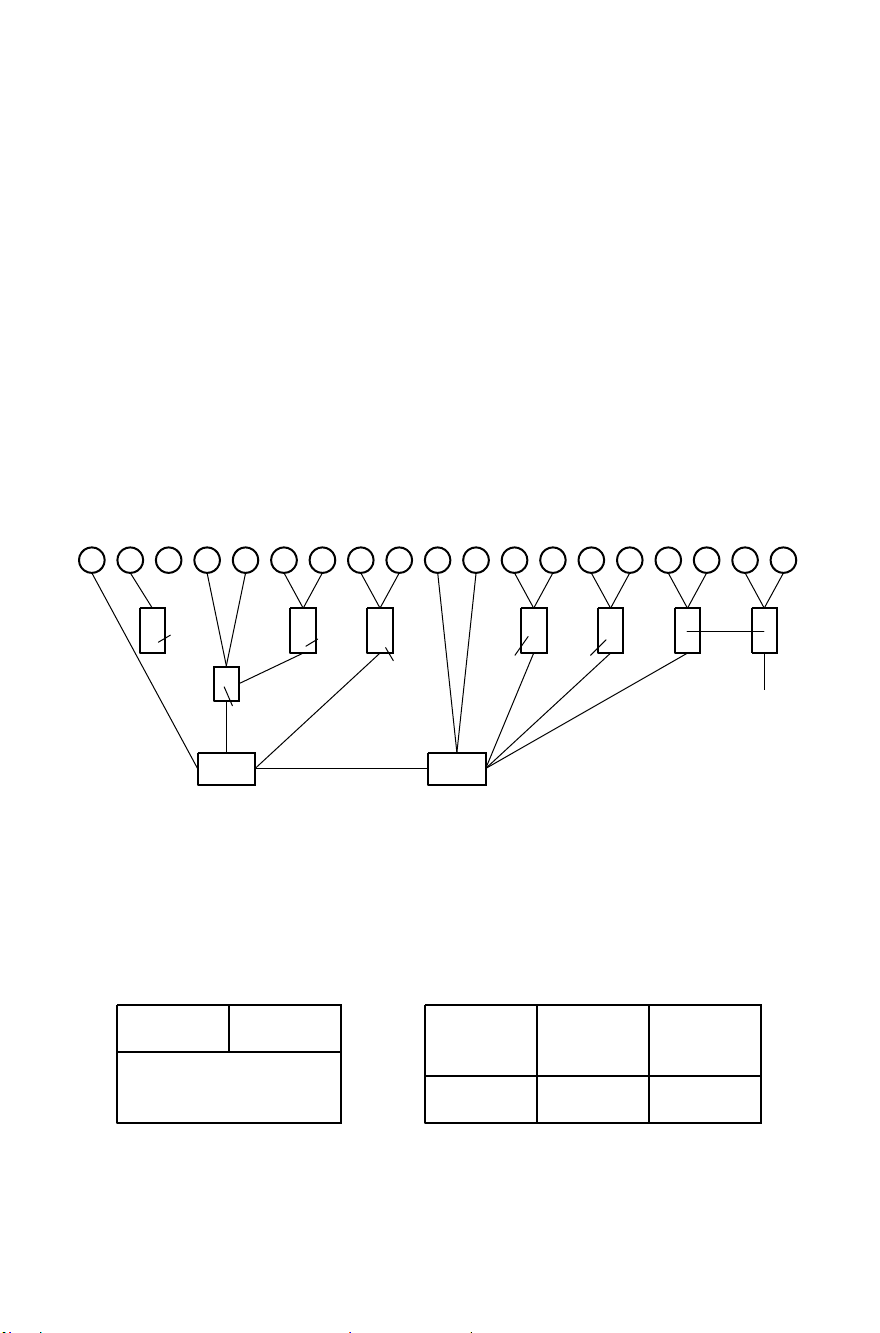
273
4.4.4. Lập sơ đồ lắp ráp
Trong một sản phẩm thường có nhiều bộ phận, mỗi bộ phận có
nhiều cụm, mỗi cụm còn có thể chia thành nhiều nhóm. Mỗi nhóm chia
nhỏ đó được coi là một đơn vị lắp. Vậy đơn vị lắp có thể là một nhóm
hay một cụm hoặc là một bộ phận của sản phẩm. Trong mỗi đơn vị lắp, ta
tìm một chi tiết mà trong quá trình lắp ráp các chi tiết khác (có thể cả
nhóm, cụm, thậm chí cả bộ phận máy) sẽ lắp lên nó. Chi tiết đó gọi là chi
tiết cơ sở.
Từ đấy, ta tiến hành xây dựng sơ đồ lắp. Trong số các chi tiết của
một đơn vị lắp ta tìm chi tiết cơ sở theo một thứ tự xác định. Như vậy có
những chi tiết được lắp thành các nhóm, các cụm, sau đấy lắp các nhóm,
cụm và những chi tiết độc lập khác lên chi tiết cơ sở tạo thành sản phẩm
lắp (hình 4.10).
Nhìn vào sơ đồ lắp (hình 4.10) ta có thể biết các đơn vị lắp và trình
tự lắp ráp sản phẩm.
Mỗi chi tiết, hoặc đơn vị lắp được biểu diễn trên sơ đồ lắp bằng
một khung chữ nhật, trong đấy ghi rõ tên, ký hiệu và số lượng (hình
4.11).
.
Ký hiệu
Số lượng
Tên chi tiết
(hay nhóm)
Ký hiệu
Tên chi tiết
(hay nhóm)
Số lượng
Hình 4.11: Ký hiệu biểu diễn trên sơ đồ lắp.
ct
ct
ct
ct
ct
ct
ct
ct
ct
ct
ct
ct
ct
ct
ct
ct
ct
ct
ct
Nhóm
Nhóm
Nhóm
Nhóm
Nhóm
Nhóm
Cụm
Cụm
Bộ phận
Sản phẩm
Hình 4.10: Sơ đồ lắp.
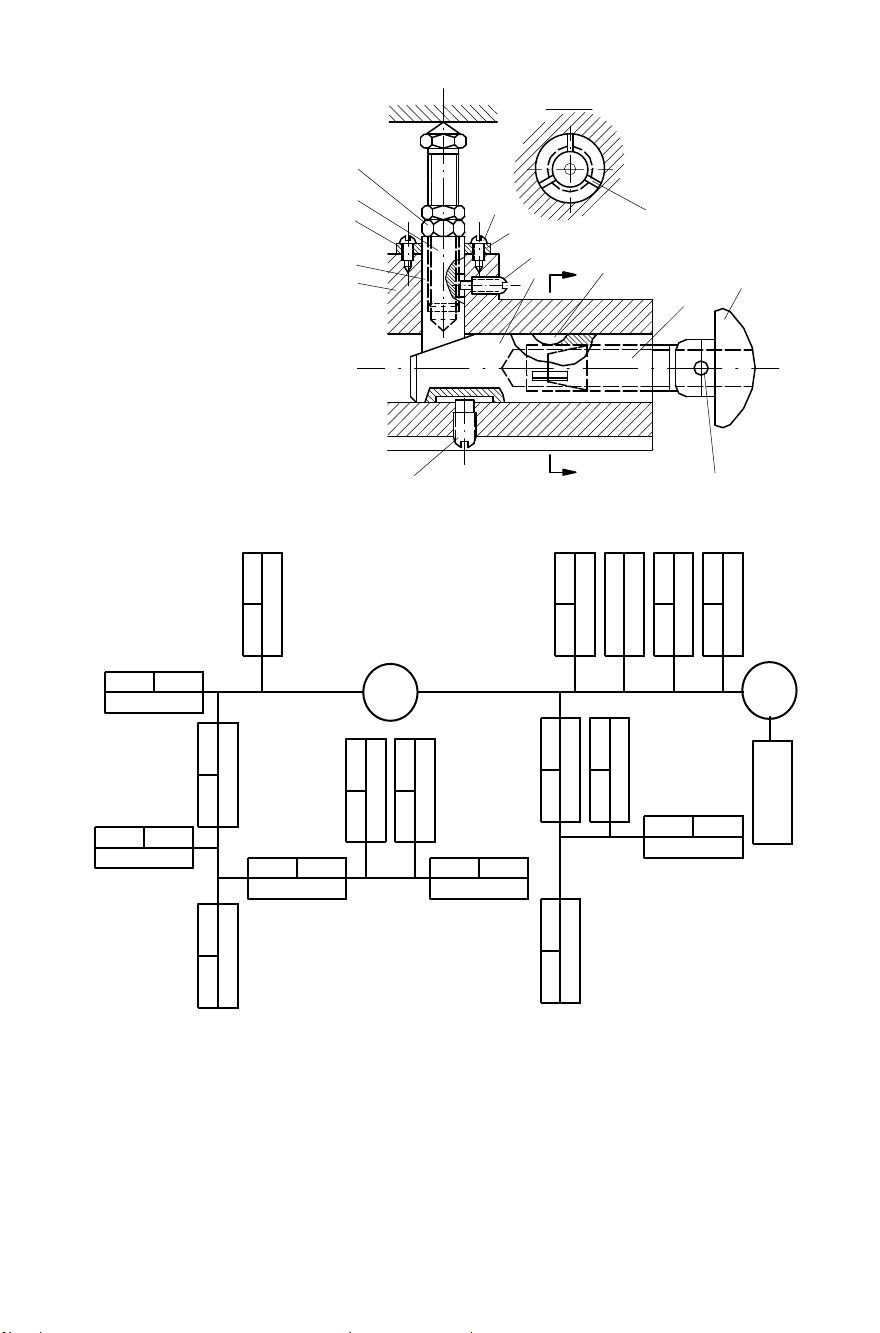
274
Trên hình 4.12 là bản vẽ lắp của cơ cấu tỳ phụ, còn hình 4.13 là sơ
đồ lắp cơ cấu đó
Khi lập sơ đồ lắp cần chú ý các vấn đề sau:
Các đơn vị lắp không nên chênh lệch nhau quá lớn về số lượng chi
tiết lắp, trọng lượng và kích thước của chúng. Làm được như vậy định
Hình 4.12: Cơ cấu tỳ phụ.
1. Thân; 2. Ống dẫn;
3. Bulông; 4. Êcu;
5. Vít hãm; 6. Chêm;
7. Then; 8. Vít hãm;
9. Vít; 10. Tay vặn;
11. Chốt; 12. Joăng;
13. Nắp; 14. Vít.
1
A
A-A
7
14
13
5
6
7
9
10
11
8
4
3
12
2
A
1
1
Thân
6
1
Chêm
1
6
Cụm
7
3
Then
Nhóm
9
1
Tay vặn
10
1
Chốt
11
1
Vít
9
1
Ống dẫn
2
1
Vít
8
1
5
Vít hãm
1
12
Gioăng
1
13
Nắp
4
14
Vít
1
2
Nhóm
4
Ê cu
1
Bulông
3
KCS
KCS
Sản phẩm
Hình 4.13: Sơ sơ đồ lắp cơ cấu tỳ phụ.
1
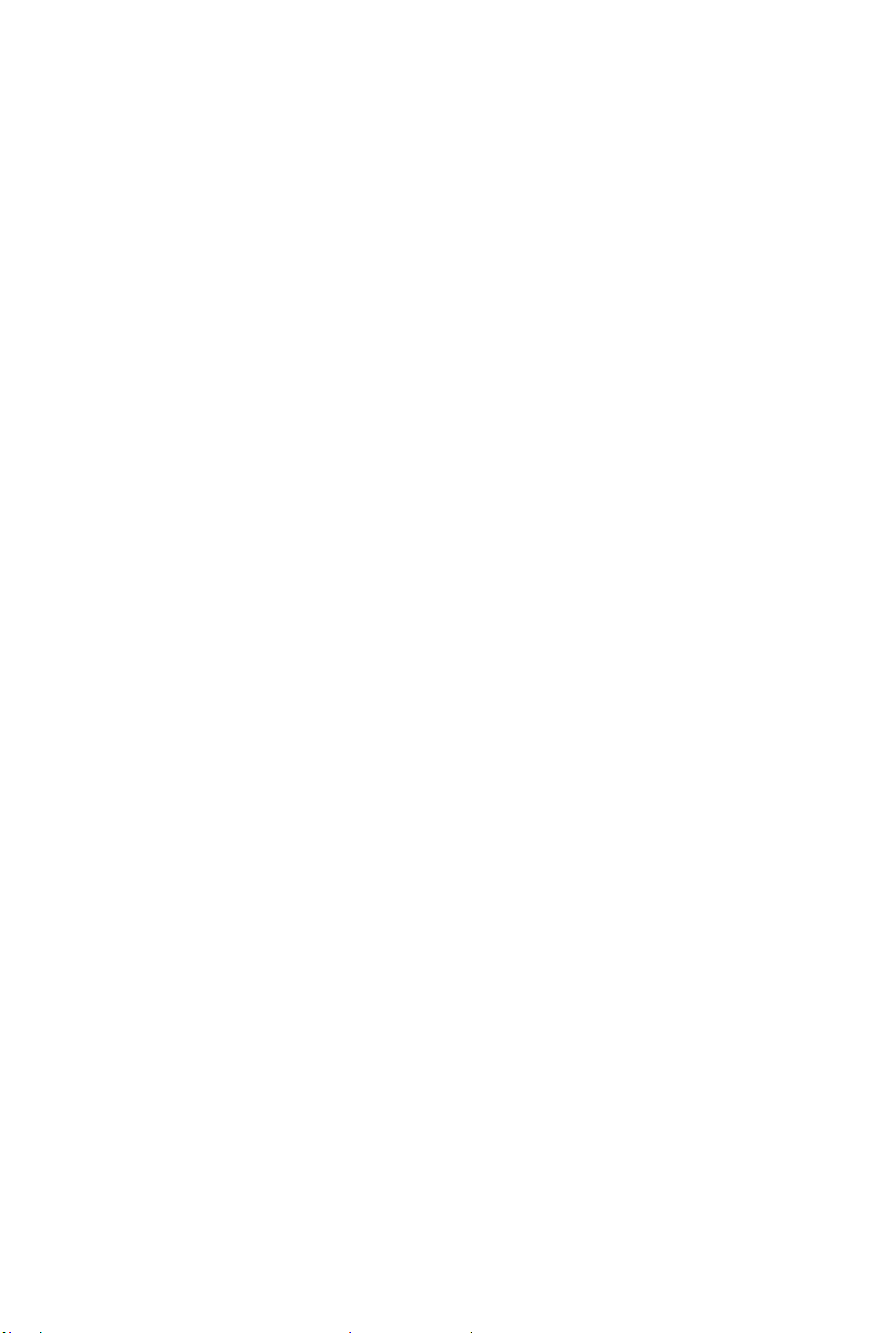
275
mức lao động cuả các đơn vị lắp sẽ gần bằng nhau, tạo điều kiện nâng
cao năng suất và tính đồng bộ khi lắp ráp dây chuyền.
- Chọn đơn vị lắp sao cho khi lắp ráp thuận tiện nhất. Số chi tiết
lắp trực tiếp lên chi tiết cơ sở càng ít càng tốt. Thiết kế quy trình lắp ráp
hợp lý sẽ tránh được việc tháo ra, lắp vào nhiều lần trong quá trình lắp.
- Bộ phận nào cần phải kiểm tra khi lắp ráp nên tách thành đơn vị
lắp riêng để kiểm tra dễ dàng, thuận tiện.
4.5. KIỂM TRA CHẤT LƢỢNG LẮP RÁP
Trong quá trình lắp ráp sản phẩm có thể gây nên những sai lệch do
các nguyên nhân sau:
- Xác định khe hở của các mối lắp không chính xác.
- Điều chỉnh vị trí tương quan của các chi tiết lắp không đúng.
- Lực tác dụng khi lắp hay lực kẹp làm cho chúng bị biến dạng.
Trong quá trình vận chuyển làm thay đổi vị trí hay biến dạng cụm hay bộ
phận của sản phẩm lắp v.v…
Những sai lệch do quá trình lắp ráp làm giảm chất lượng của sản
phẩm. Bởi vậy trong quá trình lắp ta cần kiểm tra theo các điều kiện kỹ
thuật của chúng, thực hiện cân bằng các chi tiết, bộ phận có chuyển động
quay cũng như kiểm tra chất lượng của sản phẩm theo các điều kiện
nghiệm thu. Dưới đây sẽ trình bày một số phương pháp kiểm tra chất
lượng lắp ráp sản phẩm.
4.5.1. Kiểm tra chất lƣợng của mối lắp
Để đảm bảo chất lượng của mối lắp, cần kiểm tra điều kiện kỹ thuật
của chúng cũng như các bộ phận và cụm sản phẩm lắp. Đồng thời dựa
vào kết quả kiểm tra, có lúc phải điều chỉnh lại những yêu cầu kỹ thuật
đã đề ra khi thiết kế.
Tùy theo mức độ phức tạp của sản phẩm lắp mà bố trí các nguyên
công kiểm tra trong dây chuyền lắp ráp, thông thường bố trí ở những vị
trí có khả năng gây nên sai lệch hoặc sau khi hoàn thành lắp một bộ phận
hay một cụm của sản phẩm.
Đối với những mối lắp quan trọng, thường bắt buộc phải kiểm tra
100%, còn những mối lắp không quan trọng, chỉ kiểm tra định kỳ sau
từng loạt lắp ráp.
Tùy theo điều kiện kỹ thuật của mối lắp và điều kiện sản xuất, có
thể áp dụng một trong các phương pháp kiểm tra sau đây.
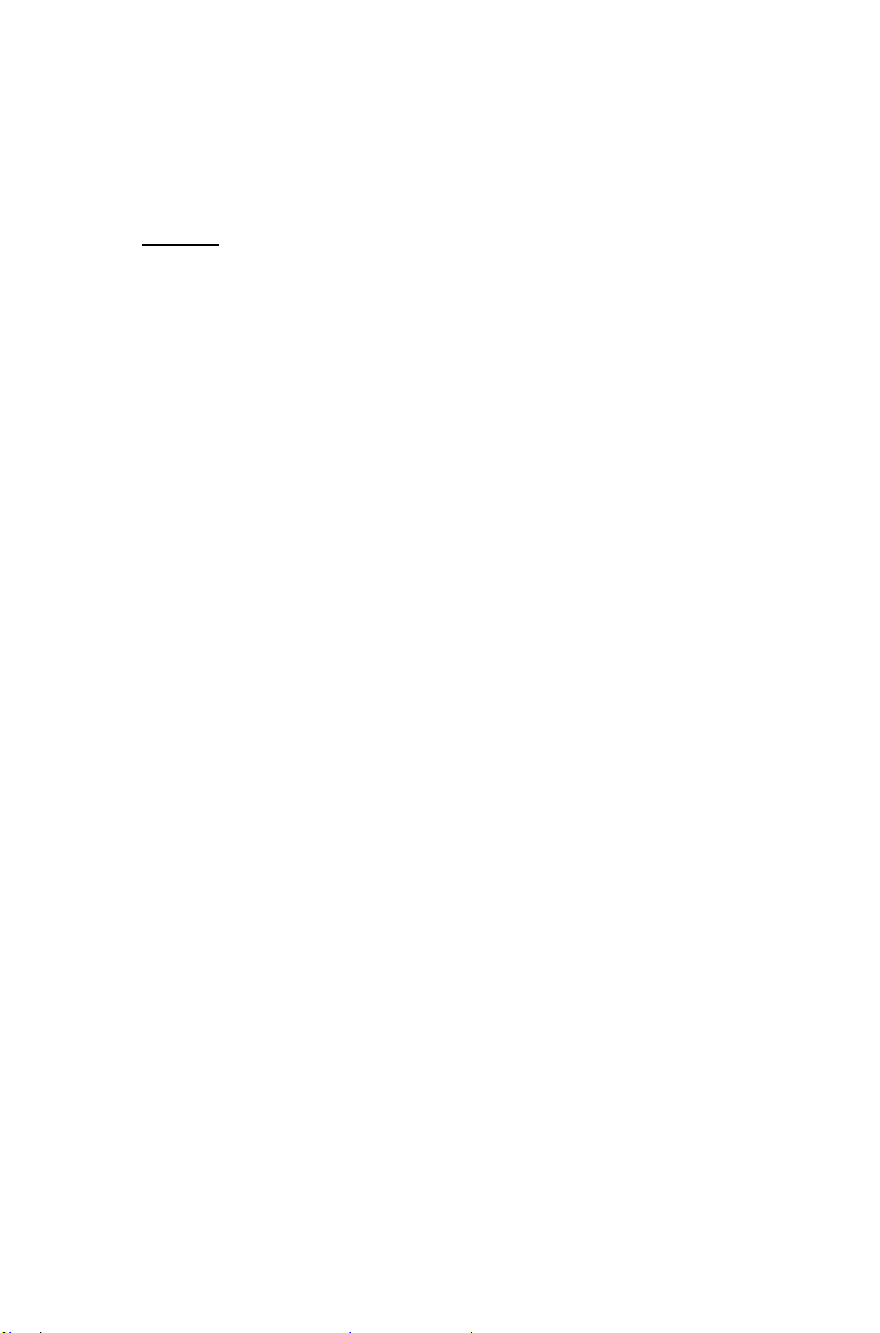
276
4.5.1.1. Kiểm tra trực tiếp
Phương pháp này không cần dùng thiết bị hay dụng cụ đo lường
phức tạp, mà chủ yếu dựa vào kinh nghiệm của công nhân để đánh giá
chất lượng của mối lắp.
Ví dụ: Kiểm tra bằng mắt, cho chạy thử nghe tiếng ồn của bộ
truyền bánh răng ăn khớp. Phương pháp này dùng để kiểm tra các mối
lắp yêu cầu chất lượng không cao. Nó có năng suất cao nhưng tồn tại một
số nhược điểm sau:
- Độ chính xác thấp và chất lượng kiểm tra không đều.
- Chất lượng mối lắp phụ thuộc nhiều vào trình độ và kinh nghiệm
của công nhân lắp ráp.
- Kết quả kiểm tra chỉ là định tính, không cho chúng ta giá trị định
lượng .
Phương pháp kiểm tra trực tiếp chỉ áp dụng đối với dạng sản xuất
nhỏ cho các sản phẩm yêu cầu chất lượng thấp.
4.5.1.2. Kiểm tra cơ khí
Đây là phương pháp kiểm tra có sử dụng các dụng cụ cơ khí, đo
lường hay đồ gá để đánh giá chất lượng của mối lắp.
Những phương tiện kiểm tra thường dùng là các dụng cụ đo vạn
năng, thước panme, đồng hồ so, căn mẫu, trục kiểm, thước, dưỡng mẫu
v.v…
Phương pháp này cho ta biết được giá trị định lượng mối lắp,
thường áp dụng trong sản xuất hàng loạt.
4.5.1.3. Kiểm tra tự động
Phương pháp này thường sử dụng trong lắp ráp dây chuyền và lắp
ráp tự động. Việc kiểm tra chất lượng lắp ráp được tự động hóa nhờ các
thiết bị chuyên dùng.
Phương pháp này đạt được độ chính xác và năng suất cao. Cơ sở lí
thuyết của kiểm tra tự động được giới thiệu trong các tài liệu về tự động
hóa đo lường.
4.5.2. Cân bằng máy
Những thiết bị có các bộ phận chuyển động quay, nếu không cân
bằng trong quá trình làm việc sẽ phát sinh lực quán tính li tâm hay các
ngẫu lực, tạo nên rung động làm giảm độ chính xác. Không đạt được chỉ
tiêu kỹ thuật và làm giảm tuổi thọ của thiết bị.
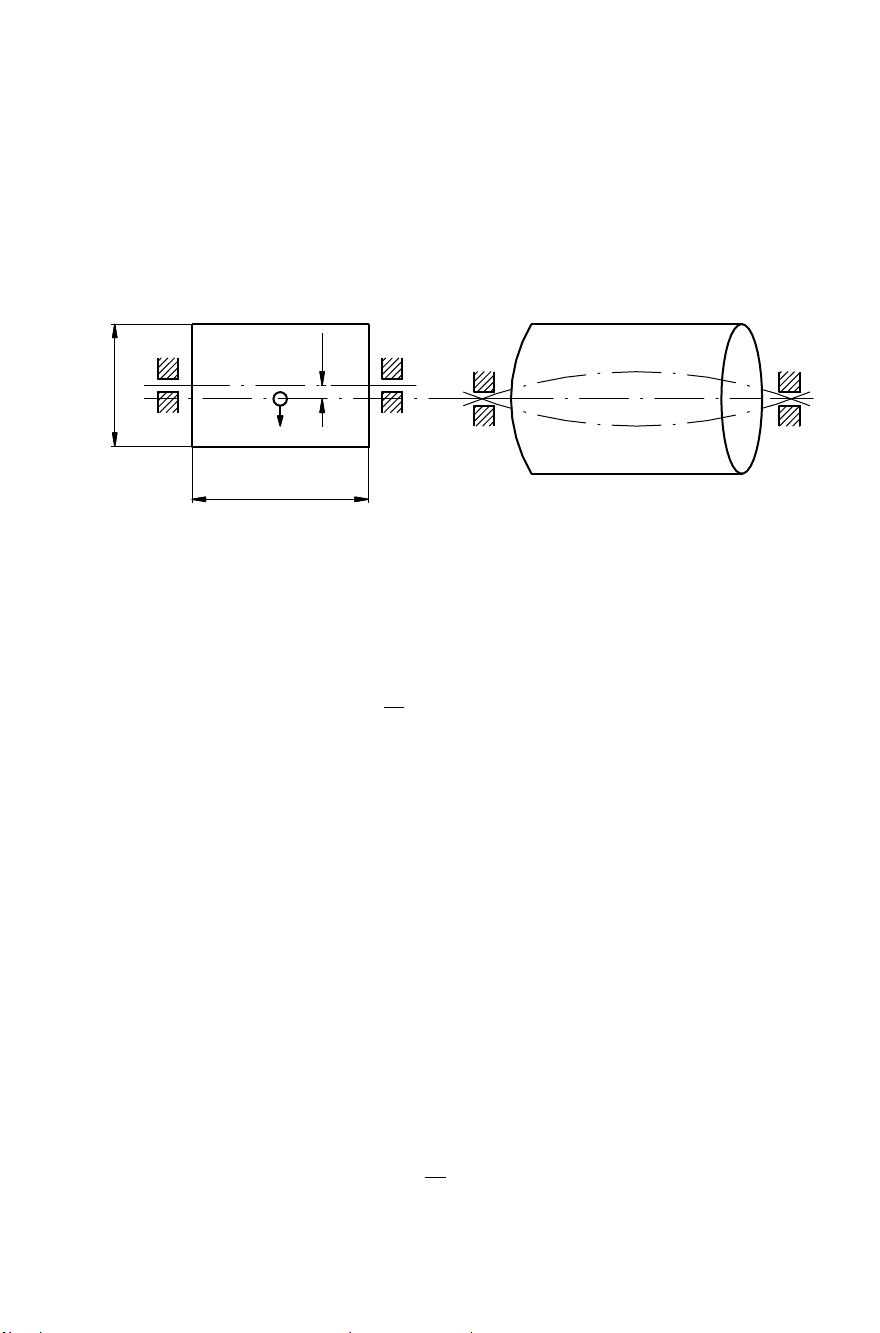
277
Vì vậy cân bằng máy phải được coi là một thông số của độ chính
xác lắp ráp. Máy có yêu cầu độ chính xác càng cao thì phải thực hiện quá
trình cân bằng càng nghiêm ngặt.
Nguyên nhân gây nên sự mất cân bằng là do sự sai sót trong quá
trình chế tạo, lắp ráp làm cho trục quay không trùng với trục quán tính
trung tâm.
Hình 4.15 là sơ đồ sự không cân bằng của chi tiết quay.
Giả sử khi lắp puli có trục quay là OO lệch với trục quán tính trung
tâm O
1
O
1
một khoảng là a. Khi chuyển động quay sẽ sinh ra lực quán
tính ly tâm là:
2
.
a
g
Q
J
Trong đó: Q – trọng lượng của vật quay,
g – gia tốc trọng trường,
a – độ lệch tâm,
– vận tốc góc.
Nguyên lý cân bằng máy đã được trình bày kỹ trong giáo trình
“Nguyên lý máy và các vấn đề dao động trong kỹ thuật”. Ở đây chỉ giới
thiệu một cách khái quát quá trình cân bằng bằng cách thêm hay bớt khối
lượng trên chi tiết quay không cân bằng.
Có hai phương pháp cân bằng là cân bằng tĩnh và cân bằng động.
1. Cân bằng tĩnh
Thực hiện quá trình cân bằng ở trạng thái tĩnh. Phương pháp này áp
dụng cho các chi tiết quay có tỉ lệ:
1
D
L
L – chiều dài và D – là đường kính vật quay.
d
L
a
o
o
1
j
o
o
1
Hình 4.15: Sơ đồ biểu thị sự không cân bằng của chi tiết quay.
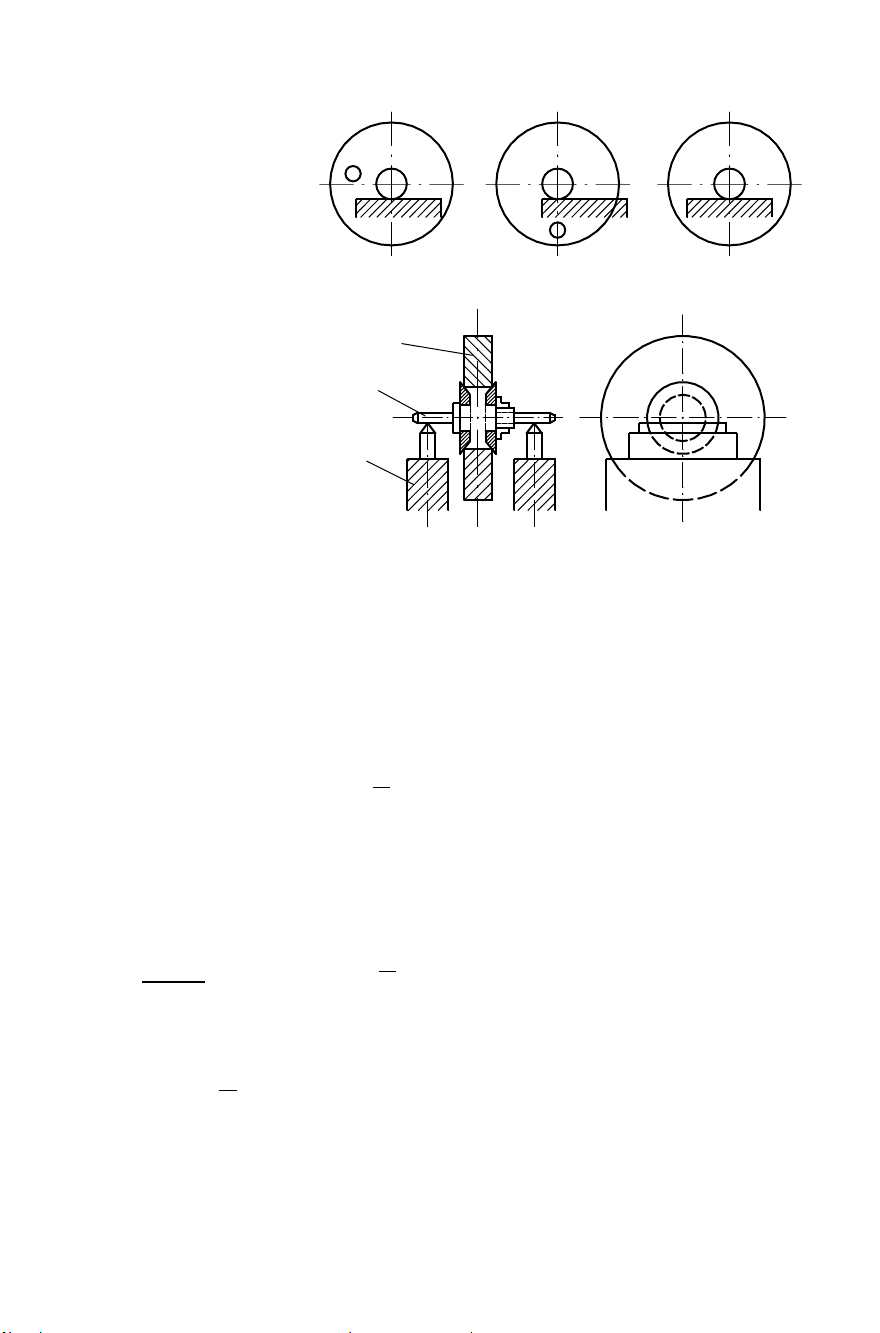
278
Trong điều kiện
sản xuất nhỏ, có thể
cân bằng tĩnh với một
thiết bị đơn giản gồm
hai gá đỡ song song
với nhau trong mặt
phẳng ngang. Gá chi
tiết lên trục gá và đặt
trên hai lưỡi đỡ của
giá rồi lăn nhẹ chi tiết
để xác định trọng tâm
của vật.
Nếu vật không
cân bằng thì trọng
tâm luôn nằm ở vị trí
thấp nhất. Từ đấy, ta
sẽ bớt khối lượng ở
phần dưới hay thêm
khối lượng vào phía
đối diện qua tâm quay
cho đến khi vật đạt được giá trị cân bằng. Hình 4.16 trình bày sơ đồ
nguyên lý quá trình cân bằng tĩnh.
2. Cân bằng động
Những chi tiết có tỉ lệ
d
l
lớn nếu mất cân bằng, khi chuyển động
quay sẽ tạo ngẫu lực lớn do các khối lệch tâm tạo nên trên chiều dài của
trục. Nếu vận tốc quay càng lớn thì ảnh hưởng do mất cân bằng càng lớn,
có tác hại tới ổn định và chất lượng của thiết bị, bởi vậy những loại chi
tiết dạng trên trong quá trình lắp ráp cần phải kiểm tra cân bằng động.
Ví du: Với loại chi tiết
3
d
l
với vận tốc quay V= 5m/s. Nếu nền
móng vững chắc thì chỉ cân bằng tĩnh. Còn khi V 6m/s thì nhất thiết
phải cân bằng động. Với vận tốc quay tương tự nếu nền móng kém vững
chắc với tỉ lệ
1
d
l
cũng phải thực hiện quá trình cân bằng động.
Chưa cân
bằng
Tìm vị trí cân
bằng
Đã cân
bằng
Hình 4.16: Sơ đồ cân bằng tĩnh.
1. Chi tiết, 2. Trục gá, 3. Giá đỡ.
1
2
3
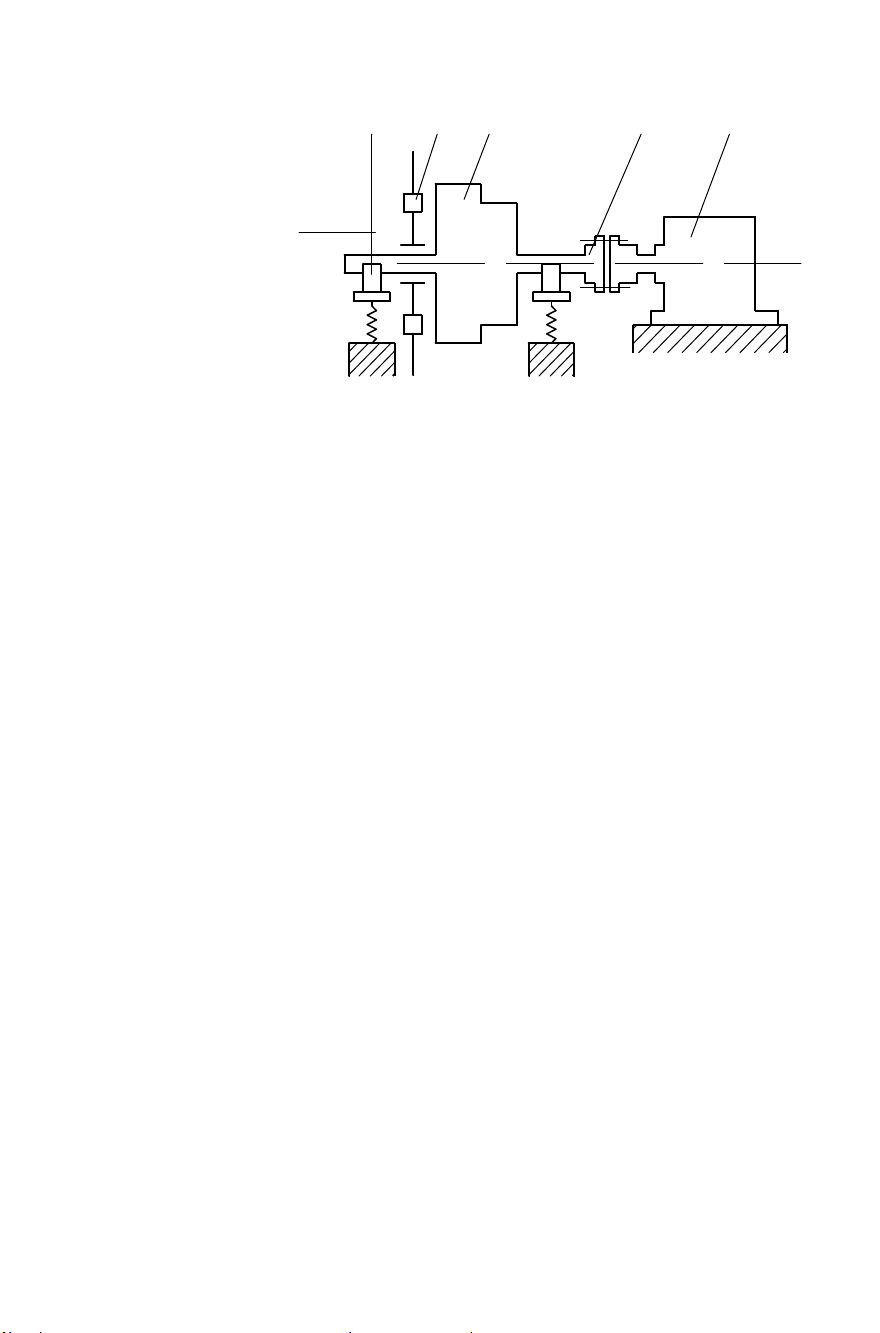
279
Phương
pháp cân bằng
có khả năng
khắc phục được
cả hai dạng mất
cân bằng do lực
li tâm và ngẫu
lực, bởi vậy nó
thay thế cho cả
phương pháp cân
bằng tĩnh.
Hiện nay
người ta đã chế
tạo ra nhiều loại
máy khác nhau
để thực hiện cân
bằng động chi
tiết quay. Một trong những nguyên lý đó được thể hiện trên hình 4.17.
Chi tiết cân bằng 3 được thực hiện trên hai giá đỡ đàn hồi 2. Đối
trọng 1 có thể dịch chuyển hướng trục và hướng kính. Nhờ bộ truyền
động vô cấp 5 kéo chi tiết quay, có thể đạt tới số vòng quay cộng hưởng.
Căn cứ vào vị trí của đối trọng khi quay với số vòng quay cộng hưởng n
để thêm hay bớt đi một phần trọng lượng của chi tiết cần được cân bằng.
4.5.3. Kiểm tra chất lƣợng sản phẩm
Sau khi lắp ráp hoàn chỉnh, chuẩn bị xuất xưởng sản phẩm phải
được kiểm tra theo các điều kiện kỹ thuật và các chỉ tiêu nghiệm thu do
nhà thiết kế đề ra. Kết quả kiểm tra được ghi vào văn bản nghiệm thu sản
phẩm chế tạo.
Thông thường có ba nhóm thông số cần kiểm tra.
- Kiểm tra các thông số hình học.
- Kiểm tra các thông số động học.
- Kiểm tra các thông số động lực học.
4.5.3.1. Kiểm tra các thông số hình học
Đó là việc kiểm tra độ chính xác về vị trí tương quan giữa các chi
tiết và bộ phận máy.
2
1
3
4
5
Hình 4.17: Sơ đồ nguyên lý cân bằng động
1. Đối trọng, 2. Giá đỡ đàn hồi,
3. Chi tiết cân bằng, 4. Khớp nối trục,
5. Bộ truyền động vô cấp.
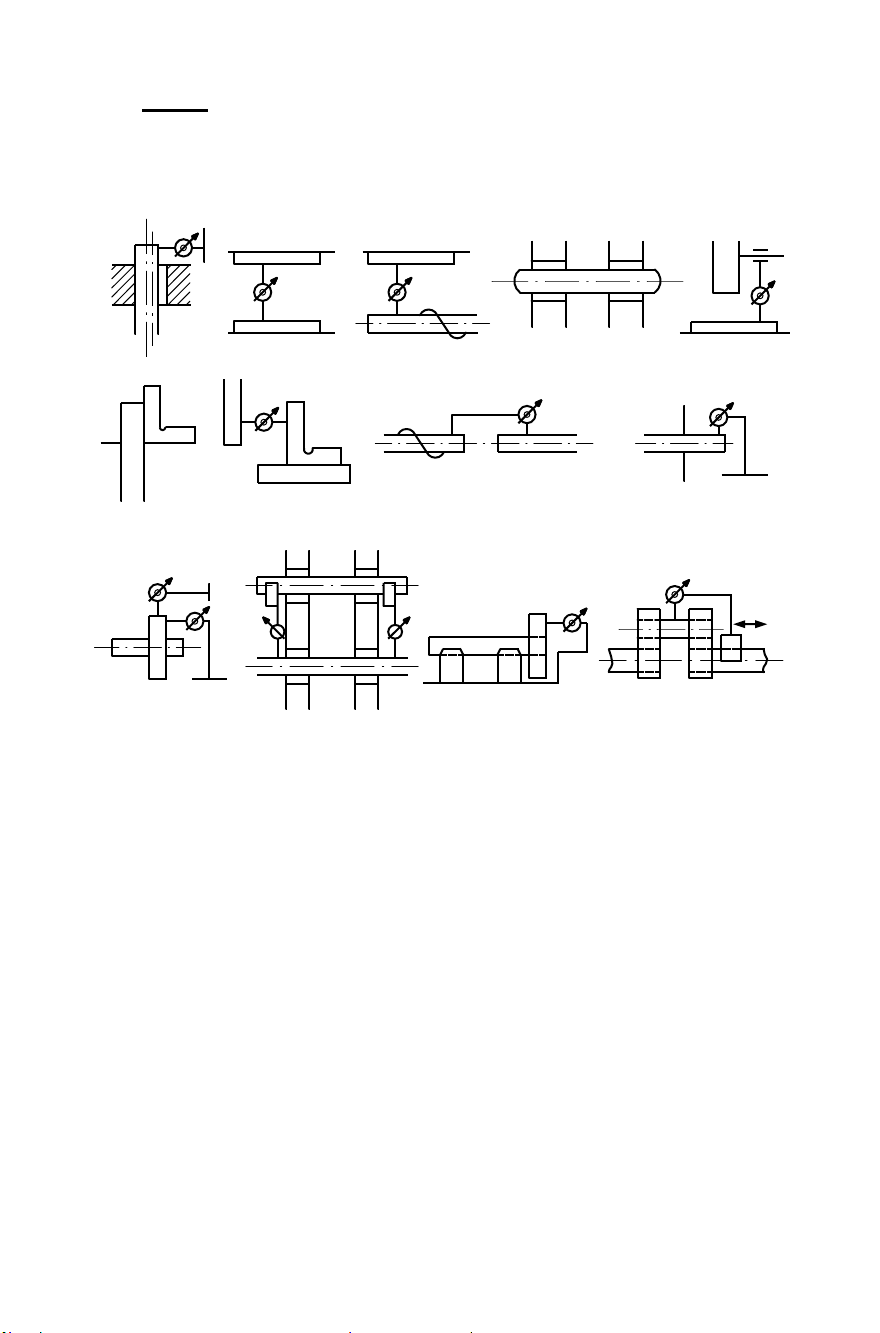
280
Ví dụ: Đối với các máy công cụ như máy tiện cần kiểm tra độ
chính xác hình học như độ song song của băng máy, độ song song của
trục chính với băng máy theo theo hai phương, độ trùng tâm của ụ sau
với trục chính v.v…
4.5.3.2. Kiểm tra động học
Kiểm tra độ chính xác của từng bộ phận hay của toàn máy trong
điều kiện không tải, đồng thời thực hiện chạy rà các bề mặt làm việc.
Nếu kiểm tra từng bộ phận riêng của máy, thì chúng được gá trên
những đồ gá chuyên dùng và dẫn động bằng các động cơ riêng. Bắt đầu
từ tốc độ thấp và tăng dần tới tốc độ tới hạn. Trong quá trình thử nghiệm
sẽ quan sát đánh giá tình trạng làm việc của các bề mặt, tình trạng của ổ
lăn, ổ trượt, sống trượt, bộ truyền ăn khớp bánh răng, vítme, cam v.v …
Đo tốc độ, đo vòng quay đảm bảo quan hệ về tỉ số truyền và sự làm việc
tin cậy của các bộ phận máy như: các bơm dầu, bơm thủy lực, hệ thống
làm mát, hệ thống bôi trơn trước khi thử nghiệm có tải.
1)
2)
3)
4)
5)
6)
7)
8)
9)
10)
12)
13)
11)
Hình 4.18: Sơ đồ kiểm tra các sai lệch hình học khi lắp.
1. Kiểm tra khe hở, 2-3-5-11-13. Kiểm tra độ song song,
4-8. Kiểm tra độ đồng tâm, 6-7. Kiểm tra độ thẳng góc,
9-10-12. Kiểm tra độ đảo hướng kính và hướng trục.
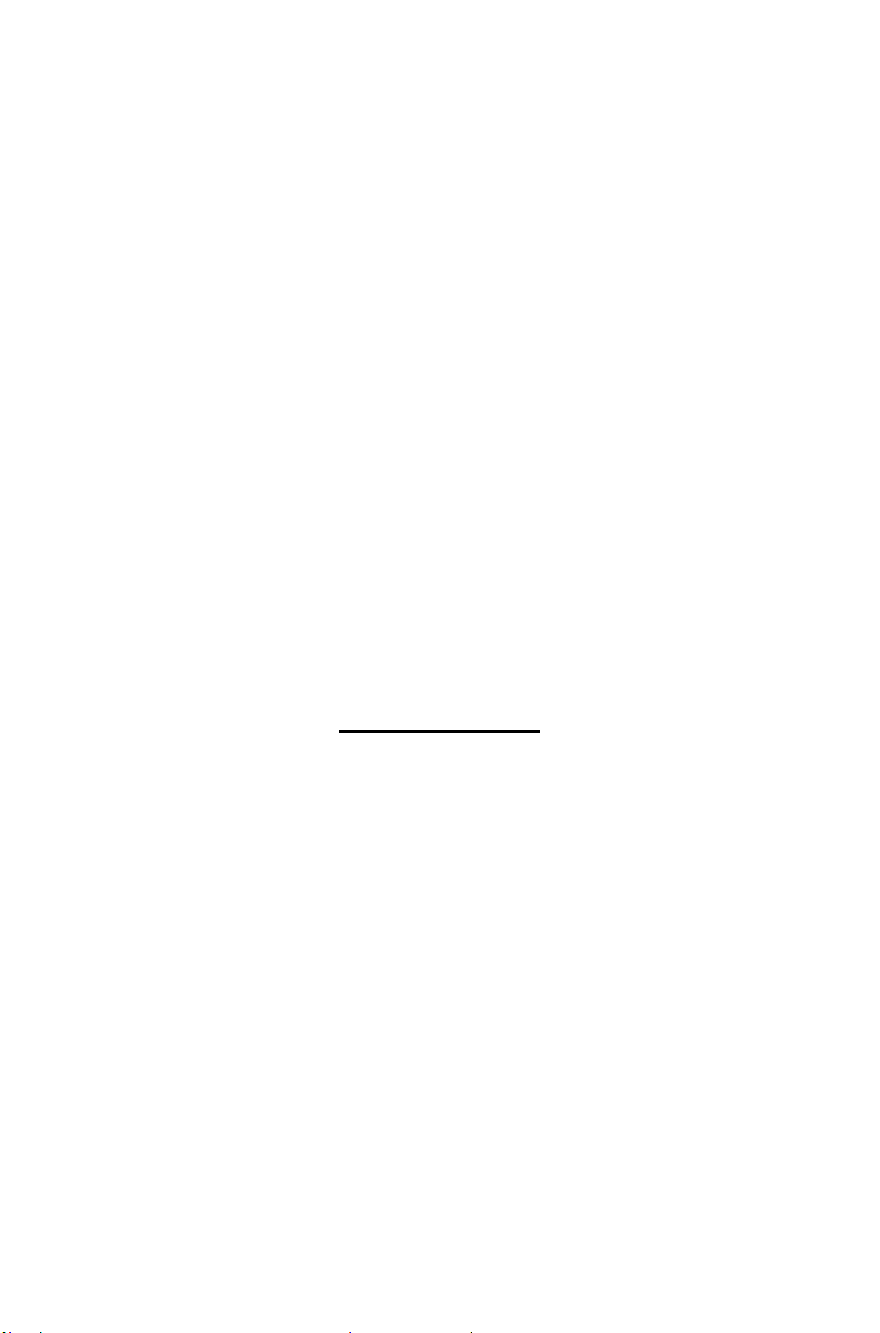
281
4.5.3.3. Kiểm tra động lực học
Kiểm tra động lực học là kiểm tra sự làm việc có tải của thiết bị
trong điều kiện làm việc của chúng với công suất toàn phần trong khoảng
thời gian mà điều kiện kỹ thuật đã quy định.
Nếu sản phẩm là các loại động cơ như: động cơ điện, máy phát
điện, động cơ nhiệt, máy hơi nước tuabin v.v… thì cũng phải thử nghiệm
với các dụng cụ năng lượng và công suất tương ứng.
Trong quá trình thử nghiệm, ta phải đo các thông số về: lực, công
suất, lượng tiêu hao nhiên liệu, nhiệt độ phát sinh và độ biến dạng ở
những bộ phận quan trọng. Quan sát quá trình làm việc của các chi tiết và
bộ phận máy, đánh giá về rung động và tiếng ồn.
Cuối cùng ghi các số lượng đo đạc, quan sát được vào văn bản yêu
cầu đối với việc nghiệm thu sản phẩm.
Trong quá trình thử nghiệm nếu có thông số nào nghi ngờ thì phải
tiến hành kiểm tra lại.
Những sản phẩm đạt chất lượng là những sản phẩm thỏa mãn mọi
yêu cầu nghiệm thu và các điều kiện kỹ thuật do thiết kế đề ra và sẽ được
xuất xưởng, kết thúc quá trình chế tạo lắp và ráp chúng.
CÂU HỎI ÔN TẬP
1. Thế nào là quy trình lắp ráp ? Cho biết mối quan hệ giữa khối
lượng gia công và lắp ráp? Cho ví dụ minh họa
2. Hãy nêu các yêu cầu của nhiệm vụ lắp ráp ? Để đạt được các
yêu cầu đó cần phải giải quyết các nhiệm vụ gì ?
3. Cho biết các loại sản phẩm của nhà máy chế tạo cơ khí sản
xuất gồm những gì ? Từ đó cho biết người ta phân mối lắp ra làm những
loại nào ? Cho ví dụ
4. Thế nào là độ chính xác lắp ráp ? Yếu tố nào làm ảnh hưởng
đến độ chính xác lắp ráp ?
5. Để đảm bảo được độ chính xác lắp ráp cần phải đạt được
những yêu cầu gì ?
6. Để đảm bảo được độ chính xác lắp ráp trong các nhà máy cơ
khí thường sử dụng các phương pháp lắp ráp nào ? Cho biết ứng dụng
từng loại khi nào ?
7. Hình thức tổ chức lắp ráp sản phẩm phụ thuộc vào những yếu tố
gì? Căn cứ vào đâu để có thể phân hình thức lắp ráp ra thành những loại nào?
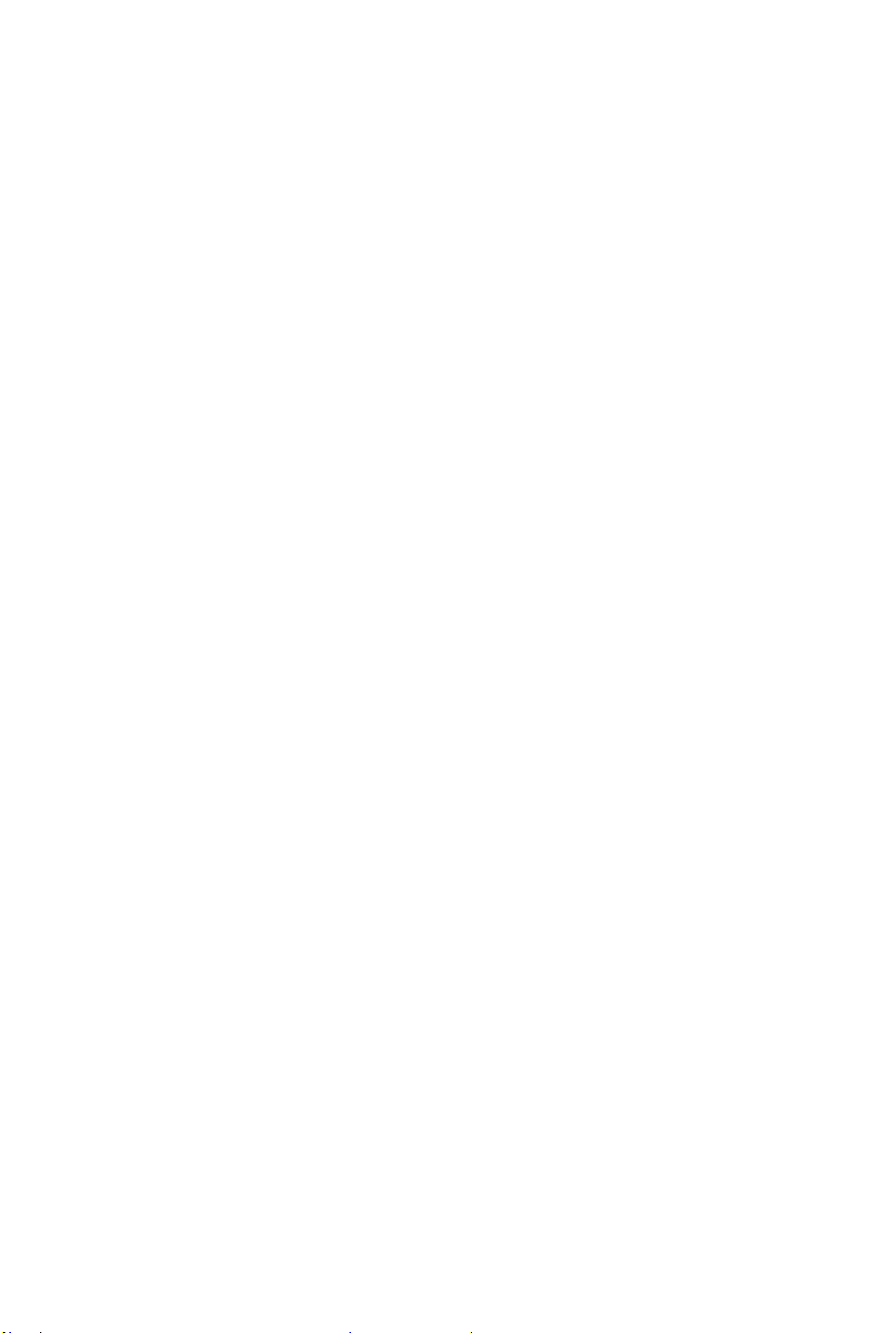
282
8. Thế nào là lắp ráp cố định ? Lắp ráp cố định được chia thành
các kiểu nào ? Mục đích của việc chia này có ưu điểm gì ?
9. Thế nào là lắp ráp di định ? Lắp ráp cố định được chia thành
những loại nào ? Mục đích của việc chia này có ưu điểm gì ?
10. Hãy nêu các điều kiện để thực hiện việc lắp ráp dây chuyền ?
11. Quy trình công nghệ lắp ráp là gì ? Nêu các thành phần của
quy trình lắp ráp sản phẩm ? Cho ví dụ minh họa
12. Trình bày trình tự thiết kế quy trình công nghệ lắp ráp ?
13. Hãy nêu những nguyên nhân gây nên sai lệch trong quá trình
lắp ráp sản phẩm ?
14. Trình bày các phương pháp kiểm tra chất lượng mối lắp ?
15. Mục đích của việc cân bằng máy là gì ? Trình bày các phương
pháp kiểm tra cân bằng máy?
16. Kiểm tra chất lượng sản phẩm bởi các thông số nào ? Cho biết
nội dung của từng phương pháp kiểm tra ? Cho ví dụ ?
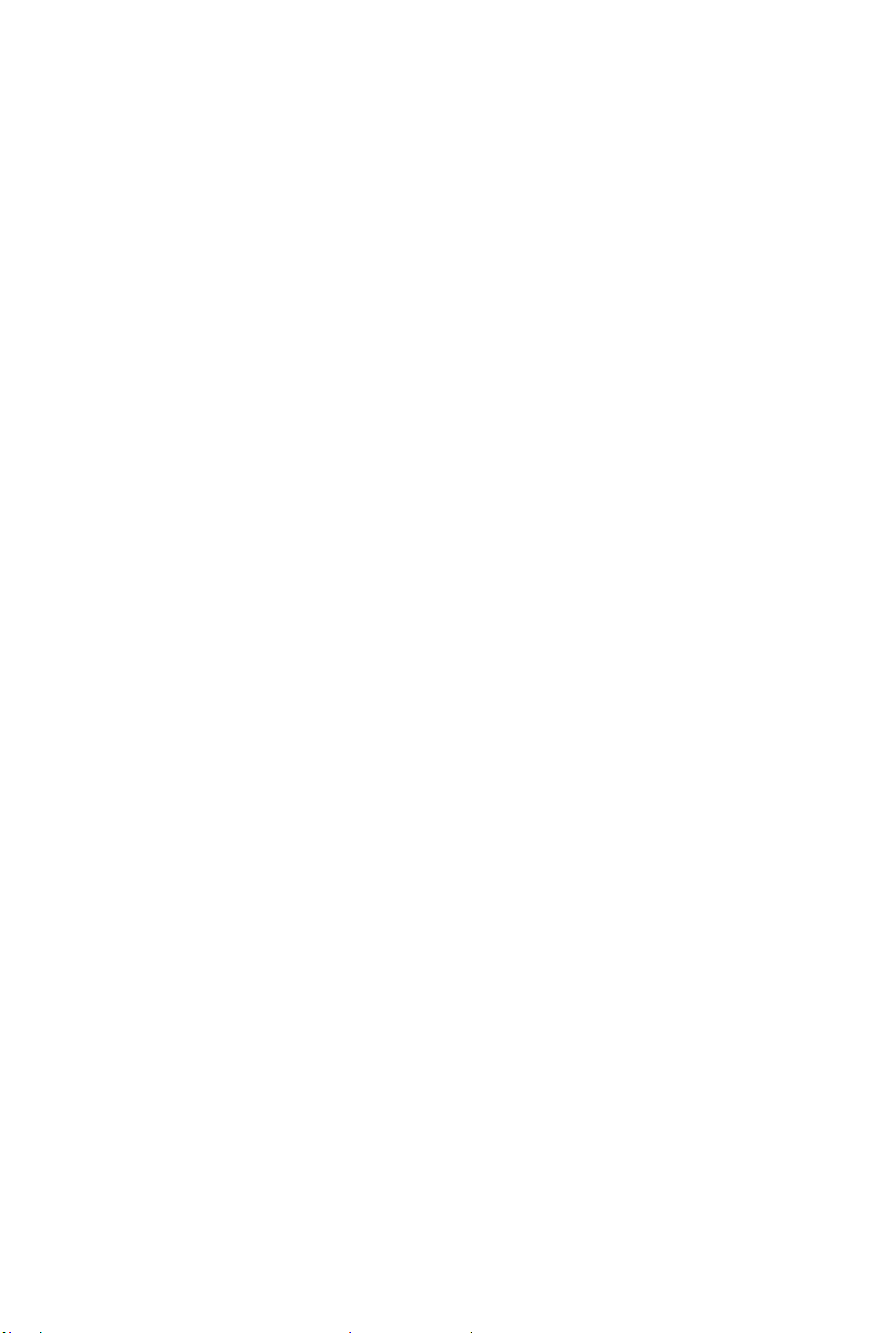
283
TÀI LIỆU THAM KHẢO
[1]. Hà Văn Vui – Nguyễn Văn Long
Đồ gá trên máy cắt kim loại.Tập 1 và 2 - Nhà xuất bản Khoa học và kỹ
thuật Hà Nội. 1987.
[2]. Lê Văn Tiến – Nguyễn Đắc Lộc …
Công nghệ chế tạo máy (2 tập). Nhà xuất bản Giáo dục. 1998.
[3]. Ancepob.
Đồ gá trên máy cắt kim loại(Tiếng Nga) - Nhà xuất bản Khoa học và kỹ
thuật Moscow. 1985.
[4]. B.E. Antonuk
Giúp đỡ bạn trẻ thiết kế đồ gá .(Tiếng Nga) - Nhà xuất bản Minck. 1985.
[5]. Barơbasôp.
Kỹ thuật phay - Nhà xuất bản “MIR” Moscow. 1984.
[6]. Hồ Viết Bình – Nguyễn Ngọc Đào – Lê Đăng Hoành;
Đồ gá gia công cơ khí – Tiện, Phay, Bào, Mài – Nhà xuất bản Đà Nẵng. 2000.
[7]. Trần Văn Địch (chủ biên)
Công nghệ chế tạo máy – Nhà xuất bản Khoa học kỹ thuật. 2008.
[8]. GS. TS. Trần Văn Địch
Đồ gá gia công cơ - Nhà xuất bản khoa học và kỹ thuật. 2002.
[9]. E. Paul DeGarmo; JT. Black; Ronald A. Kohser; Barney E.
Klamecki
Materials and Processes in Manufacturing Copyright 2004 Exclusive
rights by John Wiley & Sons(Asia) Pte. Ltd
[10] V.M.Kovan, V.S. Korsakov, …M.D. Solodov Fundamentals
of Manufacturing Engineering, Mir Publishers Moscow. 1987.
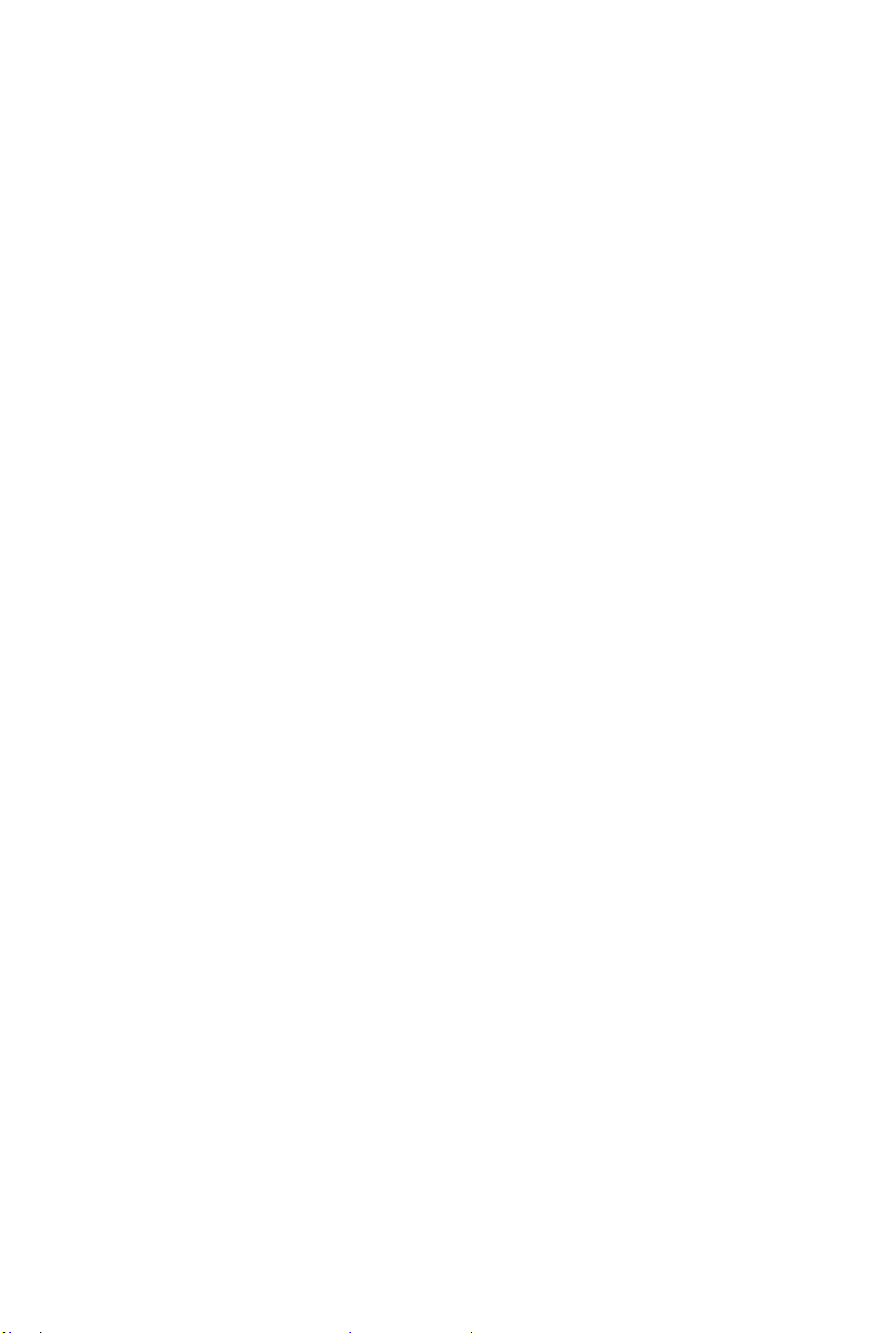
285
MỤC LỤC
Lời nói đầu .............................................................................................. 3
Chương 1:THIẾT KẾ QUY TRÌNH CÔNG NGHỆ GIA CÔNG CHI
TIẾT MÁY ............................................................................................. 5
1.1. Phương pháp thiết kế quy trình công nghệ gia công cơ ................. 5
1.1.1.Tài liệu ban đầu ......................................................................... 5
1.1.2.Trình tự thiết kế QTCN ............................................................. 6
1.1.3.Nghiên cứu bản vẽ và kiểm tra tính công nghệ trong kết cấu ... 6
1.1.4.Xác định trình tự gia công hợp lý và thiết kế nguyên công ...... 13
1.1.5. Xác định lượng dư gia công hợp lý .......................................... 17
1.2. Thiết kế quy trình công nghệ trên máy CNC .................................. 31
1.3. So sánh các phương án công nghệ .................................................. 32
1.4.Tiêu chuẩn hóa quy trình công nghệ ........................................... 35
1.4.1.Khái niệm .................................................................................. 35
1.4.2.Công nghệ điển hình ................................................................. 35
1.4.3.Công nghệ nhóm ....................................................................... 36
1.4.4.Công nghệ tổ hợp ...................................................................... 37
Câu hỏi ôn tập chương 1 ........................................................................ 38
Chương 2: CÔNG NGHỆ GIA CÔNG CHI TIẾT ĐIỂN HÌNH ............ 39
2.1.Quy trình công nghệ chế tạo các chi tiết dạng hộp .......................... 39
2.1.1. Những yêu cầu kỹ thuật chủ yếu của chi tiết dạng hộp .......... 40
2.1.2. Tính công nghệ trong kết cấu của chi tiết hộp ........................ 41
2.1.3. Vật liệu và phôi để chế tạo các chi tiết dạng hộp .................... 42
2.1.4. Quy trình công nghệ gia công chi tiết hộp .............................. 43
2.1.5. Biện pháp thực hiện các nguyên công chính ........................... 45
2.2.Quy trình công nghệ gia công các chi tiết dạng càng ....................... 60
2.2.1.Điều kiện kỹ thuật .................................................................... 61
2.2.2.Vật liệu và phôi ........................................................................ 62
2.2.3.Tính công nghệ trong kết cấu của càng ................................... 62
2.2.4.Quy trình công nghệ chế tạo các chi tiết dạng càng ................ 63
2.2.5.Biện pháp thực hiện các nguyên công ..................................... 65
2.2.6. Quy trình công nghệ gia công tay biên ................................... 71
2.3.Quy trình công nghệ gia công các chi tiết dạng trục ....................... 73
2.3.1.Điều kiện kỹ thuật chi tiết dạng trục ........................................ 74
2.3.2.Vật liệu và phôi chế tạo trục .................................................... 74
2.3.3.Tính công nghệ trong kết cấu của trục ..................................... 75
2.3.4.Quy trình công nghệ chế tạo các chi tiết dạng trục .................. 76
2.3.5.Kiểm tra trục ......................................................................... .. 99
2.4.Quy trình công nghệ gia công các chi tiết dạng bạc ..................... 100
2.4.1.Điều kiện kỹ thuật ................................................................. 101
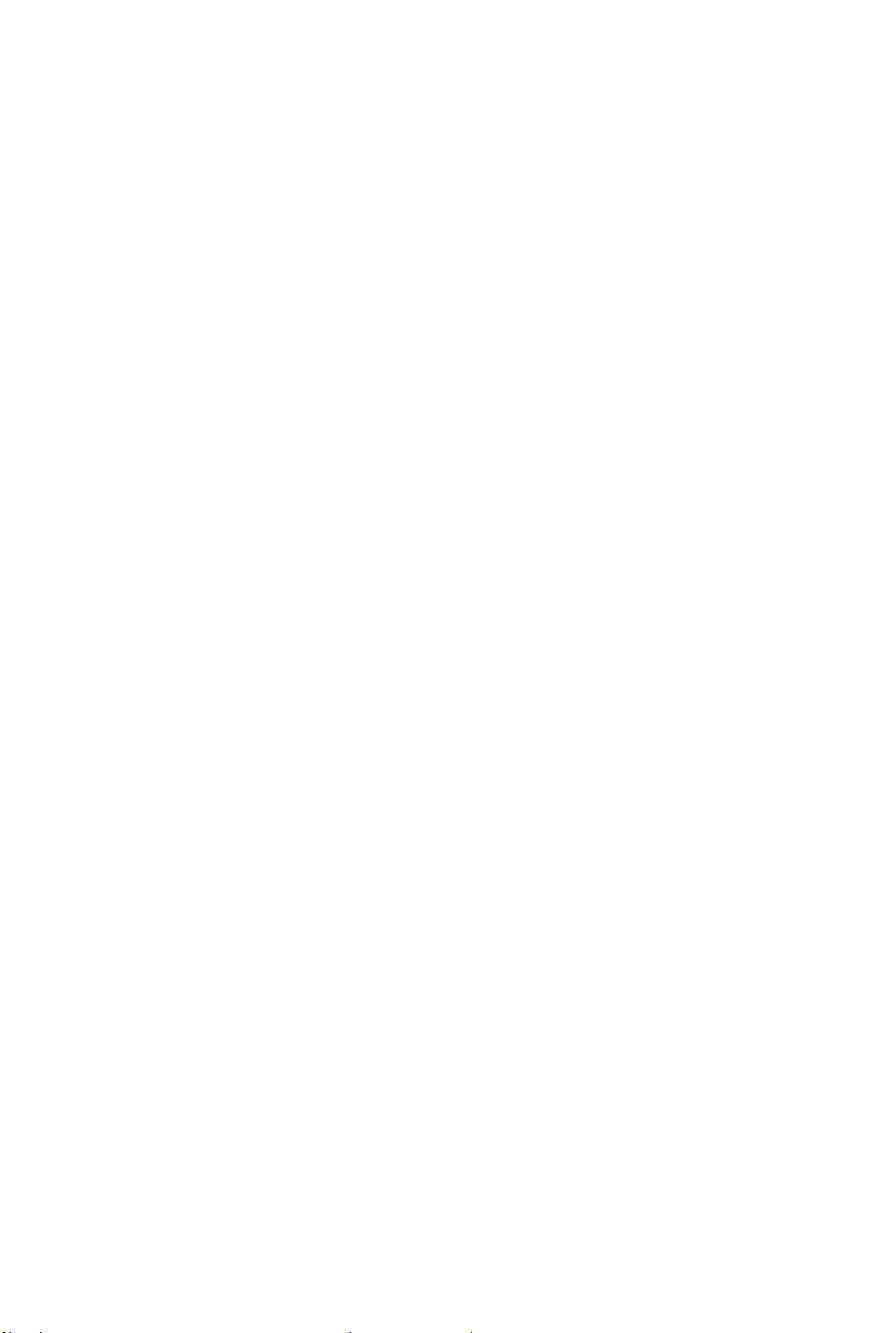
286
2.4.2.Vật liệu và phôi ..................................................................... 102
2.4.3.Tính công nghệ trong kết cấu của bạc .................................. 102
2.4.4.Quy trình công nghệ khi gia công bạc .................................. 103
2.4.5.Biện pháp thực hiện các nguyên công .................................. 105
2.5. Gia công bánh răng ..................................................................... 111
2.5.1 Phân loại và độ chính xác bánh răng .................................... 113
2.5.2 Vật liệu và phôi bánh răng .................................................... 114
2.5.3 Yêu cầu kỹ thuật và nhiệt luyện bánh răng ........................... 115
2.5.4 Chuẩn định vị và quy trình công nghệ trước khi gia công răng .. 116
2.5.5 Các phương pháp gia công răng của bánh răng .................... 117
2.5.6 Kiểm tra bánh răng ................................................................ 155
Chương 3 : THIẾT KẾ ĐỒ GÁ ................................................. 167
3.1. Khái niệm chung về đồ gá ........................................................... 167
3.1.1. Khái niệm về trang bị công nghệ ......................................... 167
3.1.2. Phương pháp trang bị cho QTSX ......................................... 167
3.1.3. Cấu tạo tổng quát của đồ gá ................................................. 168
3.1.4. Tác dụng của đồ gá .............................................................. 168
3.1.5. Yêu cầu đối với đồ gá .......................................................... 169
3.1.6. Phân loại đồ gá ..................................................................... 169
3.2. Phương pháp thiết kế đồ gá ......................................................... 171
3.2.1. Phương hướng chung ........................................................... 171
3.2.2. Tài liệu ban đầu để thiết kế đồ gá ........................................ 172
3.2.3. Phương pháp và trình tự thiết kế đồ gá ................................ 172
3.2.4. Những tính toán cần thiết khi thiết kế đồ gá ........................ 173
3.3.Chuẩn và sai số chuẩn ................................................................... 174
3.3.1.Chuẩn .................................................................................... 174
3.3.2.Sai số chuẩn .......................................................................... 176
3.3.3. Các ví dụ về tính sai số chuẩn .............................................. 179
3.4. Các chi tiết và cơ cấu định vị ....................................................... 191
3.4.1. Khái niệm ............................................................................. 191
3.4.2. Các chi tiết định vị chính .................................................... 191
3.4.3. Các cơ cấu định vị phụ ......................................................... 199
3.5. Kẹp chặt và những tính toán về kẹp chặt ..................................... 201
3.5.1.Khái niệm và các yêu cầu về kẹp chặt .................................. 201
3.5.2.Phương pháp tính lực kẹp cần thiết ....................................... 203
3.6. Các cơ cấu kẹp chặt kiểu cơ khí .................................................. 210
3.6.1 Kẹp chặt bằng chêm ............................................................. 210
3.6.2 Kẹp chặt bằng ren ................................................................ 213
3.6.3 Kẹp chặt bằng cam ............................................................... 217
3.7. Các cơ cấu kẹp chặt kiểu thuỷ khí, điện từ, điện cơ .................... 225
3.7.1 Kẹp chặt bằng khí nén ........................................................... 225
3.7.2 Kẹp chặt bằng thủy khí ......................................................... 228
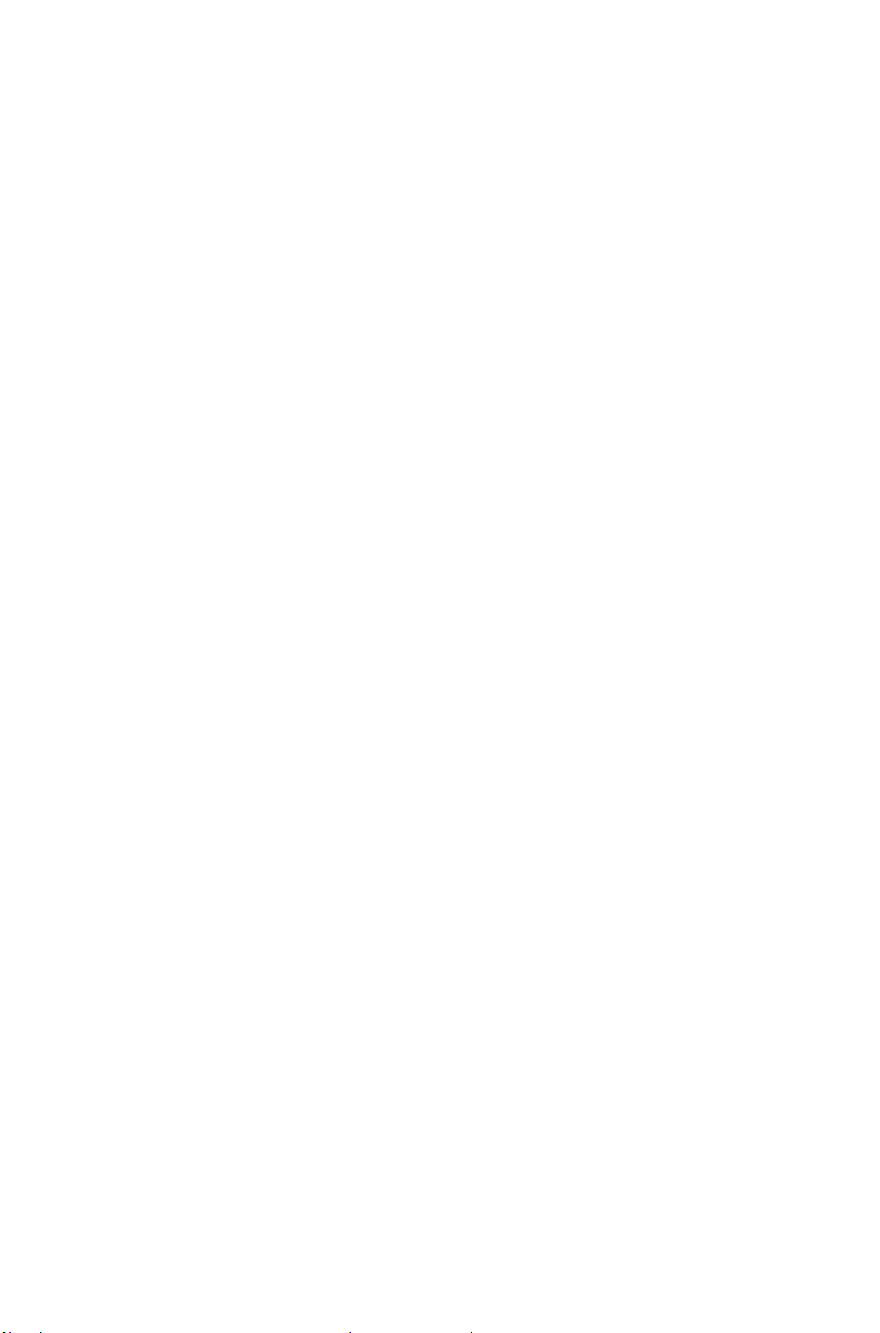
287
3.7.3. Kẹp chặt bằng cơ khí – thủy lực .......................................... 230
3.7.4 Kẹp chặt bằng điện – cơ ....................................................... 231
3.7.5 Kẹp chặt bằng điện từ .......................................................... 232
3.7.6 Kẹp chặt bằng chân không .................................................... 235
3.8. Các cơ cấu khác của đồ gá ........................................................... 236
3.8.1 Cơ cấu dẫn hướng ................................................................ 236
3.8.2 Cữ so dao - Cơ cấu quay và phân độ ................................... 239
3.8.3 Thân đồ gá ............................................................................ 243
3.9. Đồ gá trên máy CNC ................................................................... 244
3.9.1 Đặc điểm đồ gá trên máy công cụ CNC ............................... 244
3.9.2 Yêu cầu chi tiết khi gia công trên máy CNC ........................ 245
3.9.3 Phân loại đồ gá trên máy CNC ............................................. 245
Câu hỏi và ôn tập ................................................................................ 255
Chương 4: CÔNG NGHỆ LẮP RÁP CÁC SẢN PHẨM CƠ KHÍ ..... 255
4.1 Khái niệm về công nghệ lắp ráp .................................................. 255
4.1.1.Vị trí của công nghệ lắp ráp .................................................. 255
4.1.2.Nhiệm vụ của công nghệ lắp ráp ........................................... 256
4.2 Các phương pháp lắp ráp ............................................................. 257
4.2.1.Phân loại các mối lắp ............................................................ 257
4.2.2.Khái niệm về độ chính xác lắp ráp ........................................ 259
4.2.3.Các phương pháp lắp ráp ...................................................... 260
4.3 Các hình thức tổ chức lắp ráp ...................................................... 267
4.3.1 Hình thức tổ chức lắp ráp cố định ......................................... 268
4.3.2 Hình thức tổ chức lắp ráp di động ......................................... 269
4.4 Thiết kế quy trình công nghệ lắp ráp ........................................... 271
4.4.1 Khái niệm và định nghĩa ....................................................... 271
4.4.2.Tài liệu ban đầu ..................................................................... 271
4.4.3 Trình tự thiết kế QTCN lắp ráp ............................................. 272
4.4.4 Lập sơ đồ lắp ......................................................................... 273
4.5.Kiểm tra chất lượng lắp ráp .......................................................... 275
4.5.1.Kiếm tra chất lượng mối lắp ................................................. 275
4.5.2. Cân bắng máy ...................................................................... 276
4.5.3. Kiểm tra chất lượng sản phẩm ............................................. 279
Câu hỏi ôn tập ..................................................................................... 281
Tài liệu tham khảo ............................................................................... 283
Mục lục ................................................................................................ 285
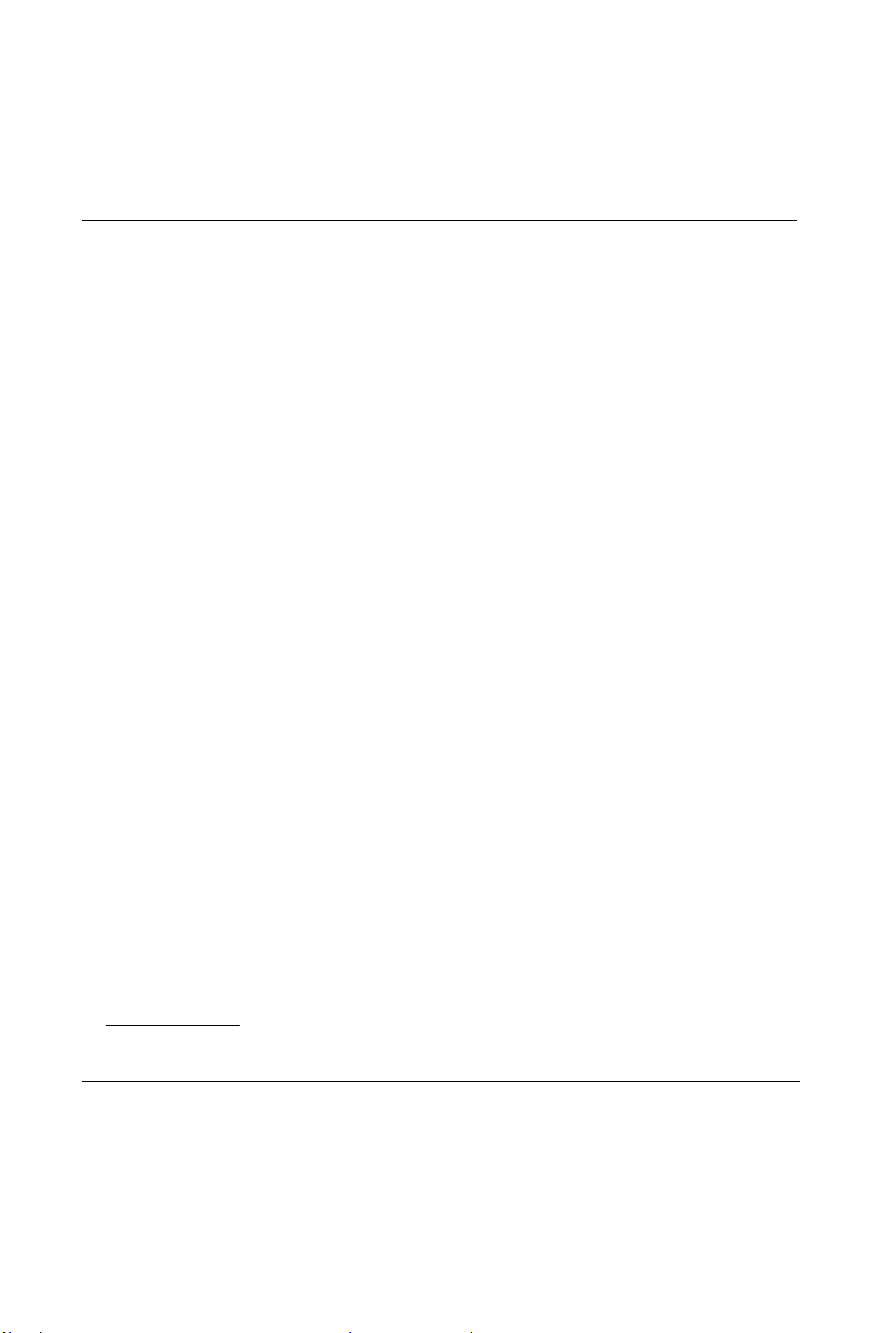
Giáo trình
CÔNG NGHỆ CHẾ TẠO MÁY
ThS. Hồ Viết Bình - ThS. Phan Minh Thanh
NHÀ XUẤT BẢN ĐẠI HỌC QUỐC GIA TP HỒ CHÍ MINH
Khu phố 6, Phường Linh Trung, Quận Thủ Đức, TPHCM
Số 3 Công trường Quốc tế, Quận 3, TP. HCM
ĐT: 38 239 172 - 38 239 170
Fax: 38 239 172
E-mail: vnuhp@vnuhcm.edu.vn
Chịu trách nhiệm xuất bản
TS. HUỲNH BÁ LÂN
Tổ chức bản thảo và chịu trách nhiệm về tác quyền
TRƯỜNG ĐẠI HỌC SƯ PHẠM KỸ THUẬT TP. HCM
Biên tập
NGUYỄN ĐỨC MAI LÂM
Sửa bản in
THUỲ DƯƠNG
Thiết kế bìa
TRƯỜNG ĐẠI HỌC SƯ PHẠM KỸ THUẬT TP. HCM
GT.01.KT(V)
ĐHQG.HCM-13
155-2012/CXB/547-08/ĐHQGTPHCM
KT.GT.135 – 13 (T)
In 300 cuốn khổ 16 x 24cm, tại Công ty TNHH In và Bao bì Hưng
Phú. Số đăng ký kế hoạch xuất bản: 155-2012/CXB/547-
08/ĐHQGTPHCM. Quyết định xuất bản số: 34/QĐ-ĐHQGTPHCM cấp
ngày 04/3/2013 của Nhà xuất bản ĐHQGTPHCM. In xong và nộp lưu
chiểu Quí II, 2013.
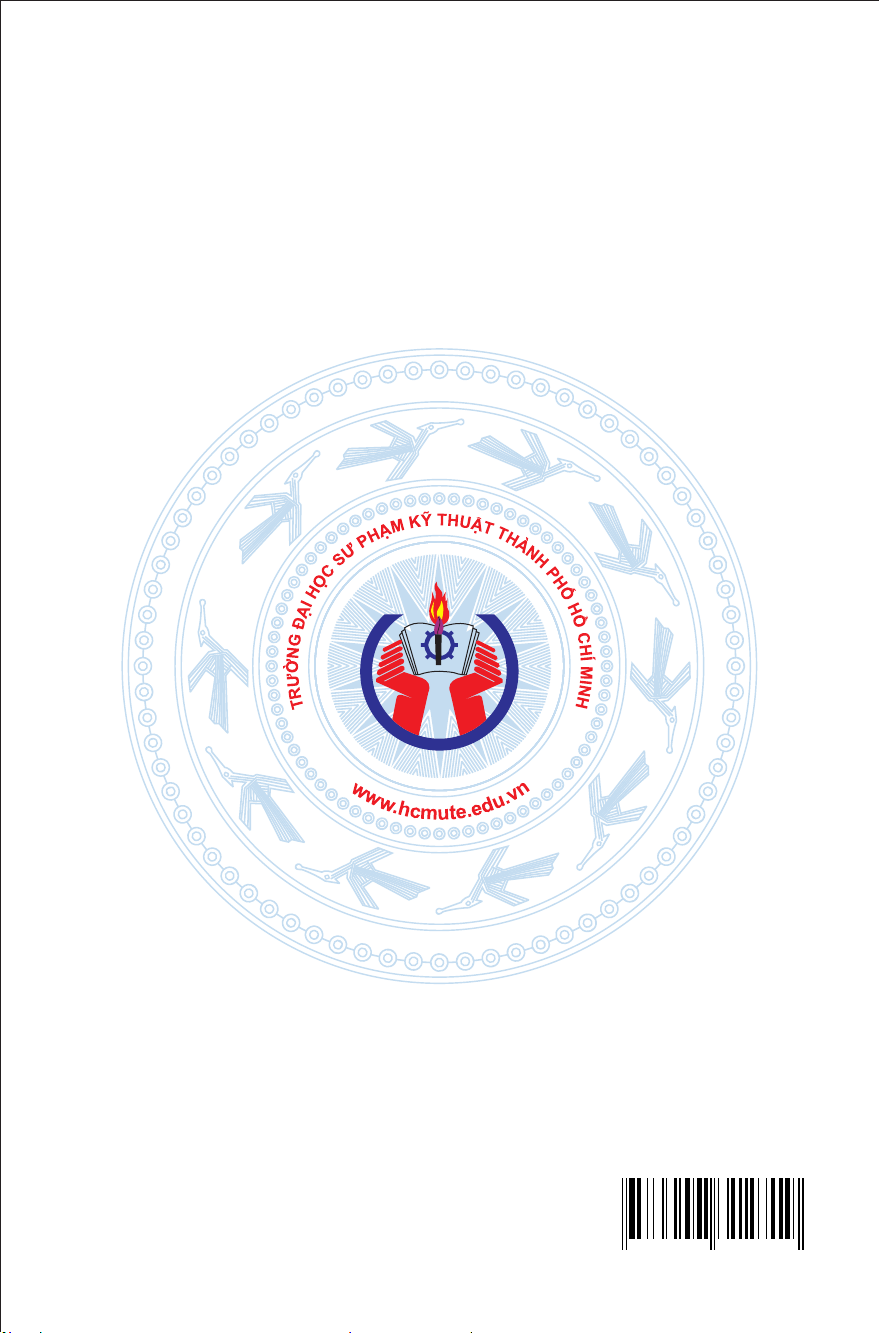
9 78604 7 3127 1 9
ISBN: 978-604-73-1271-9
Bấm Tải xuống để xem toàn bộ.