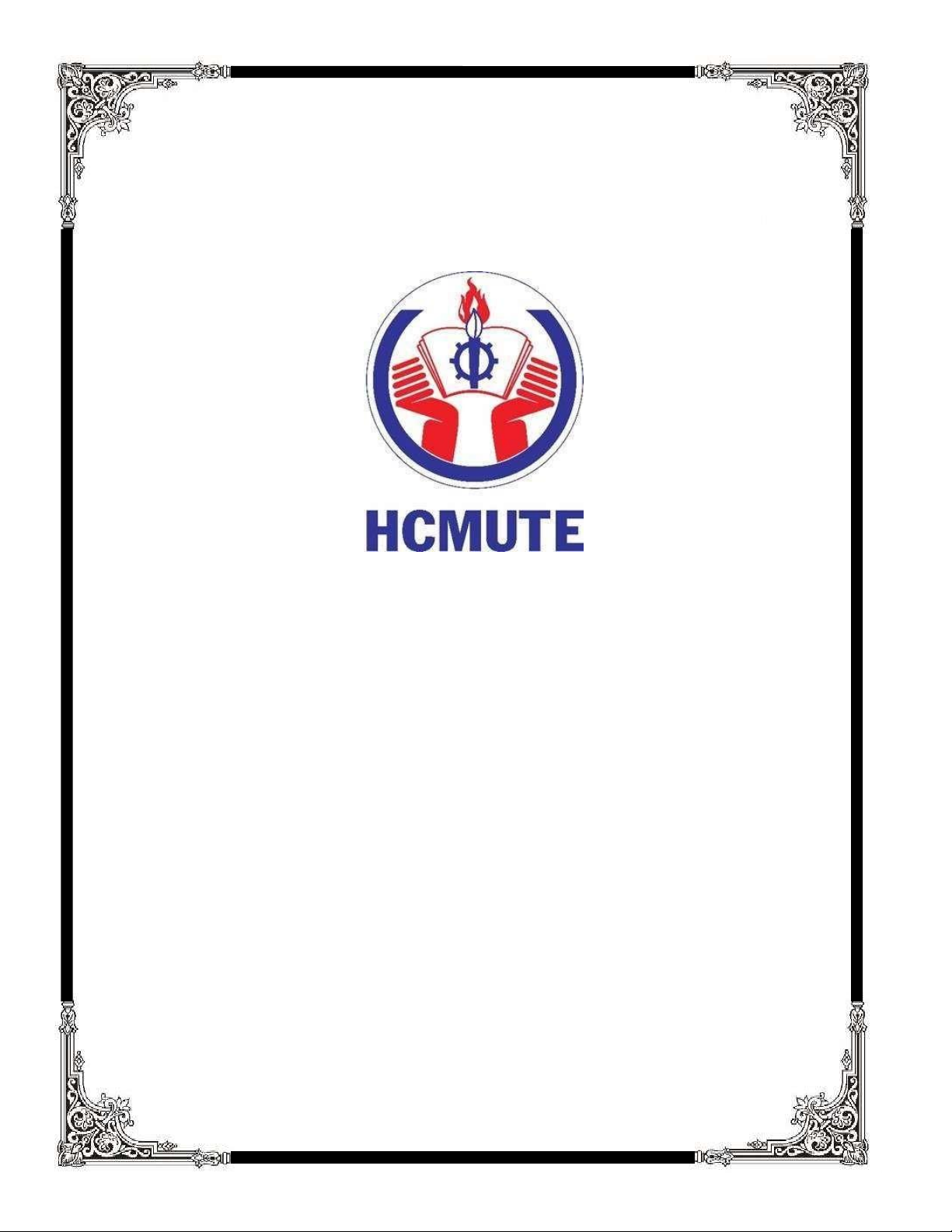
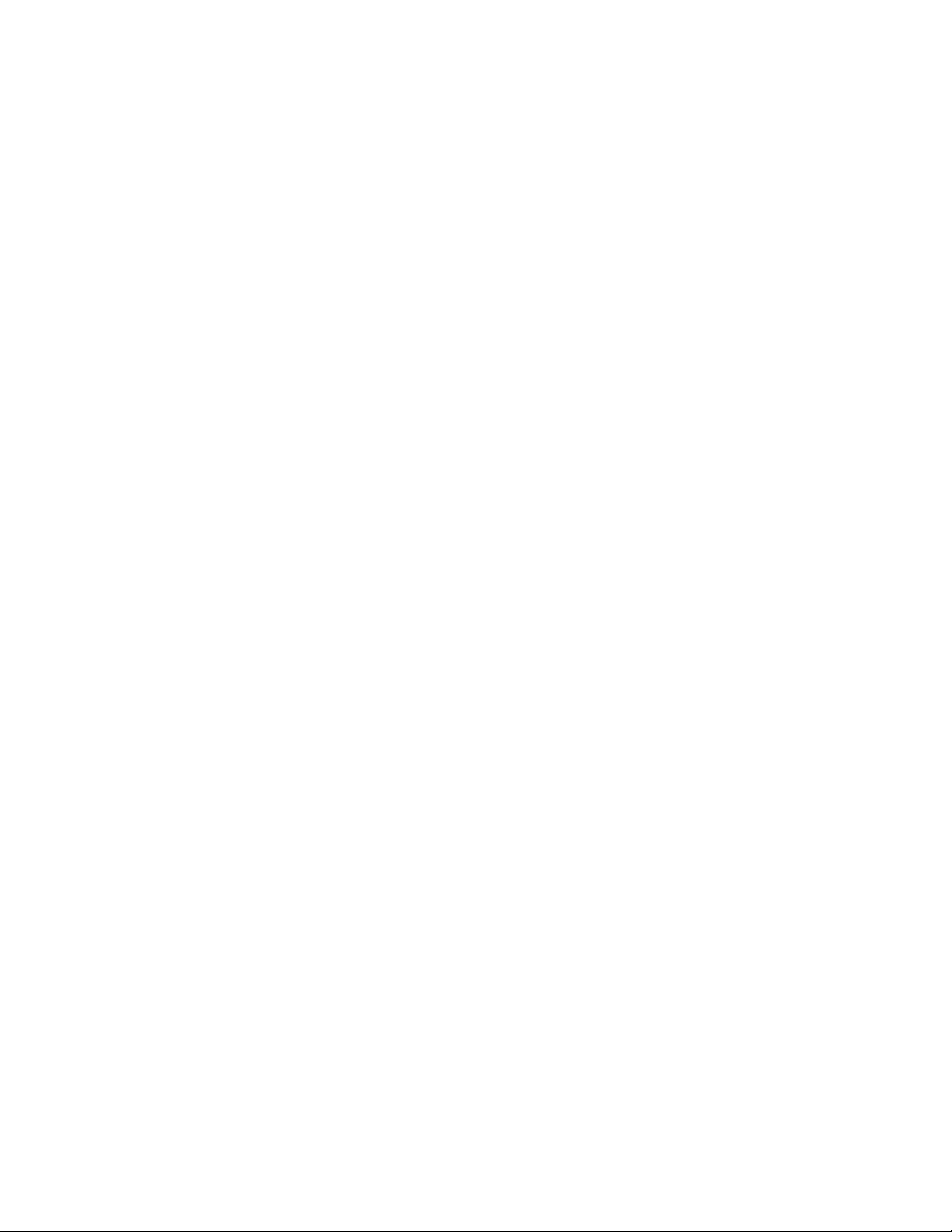
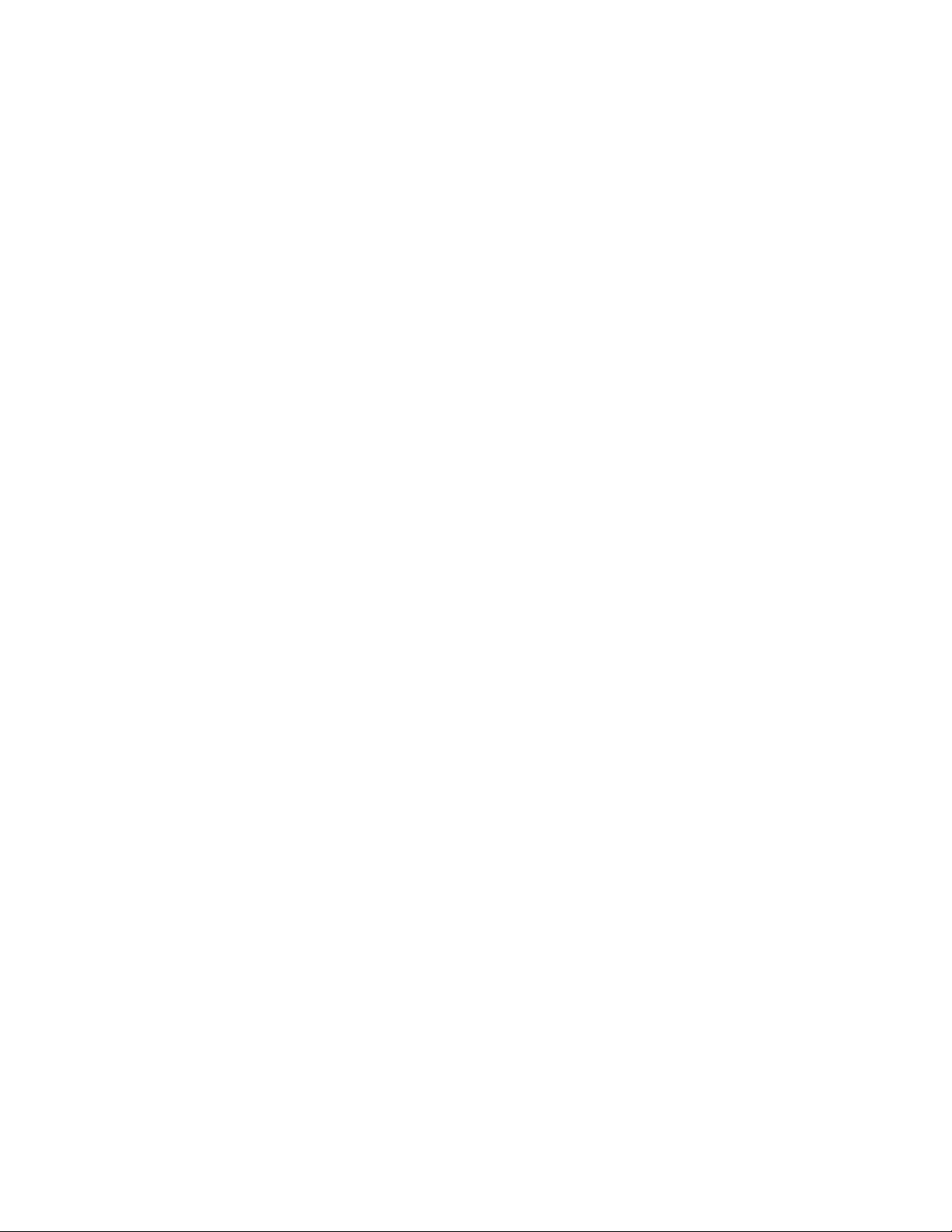
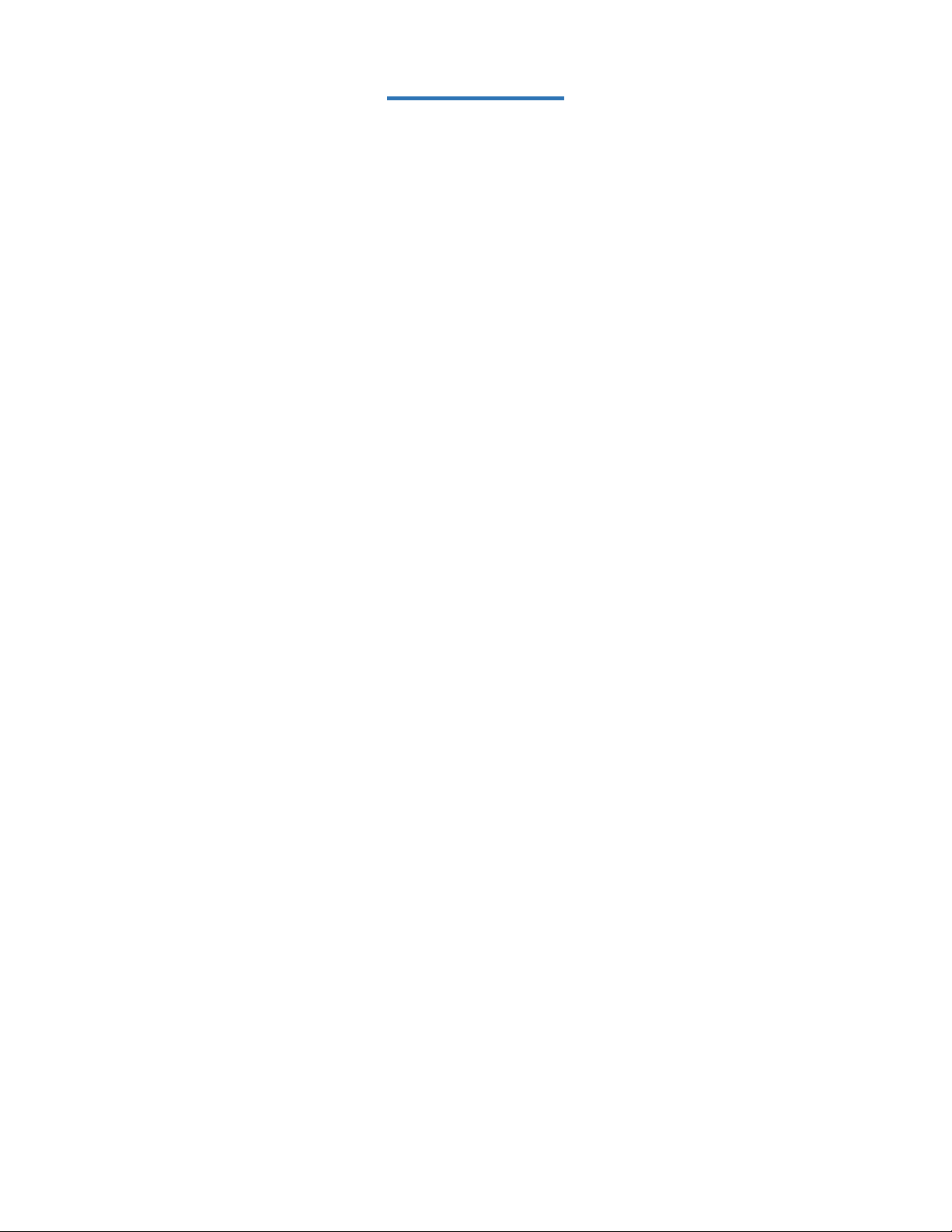
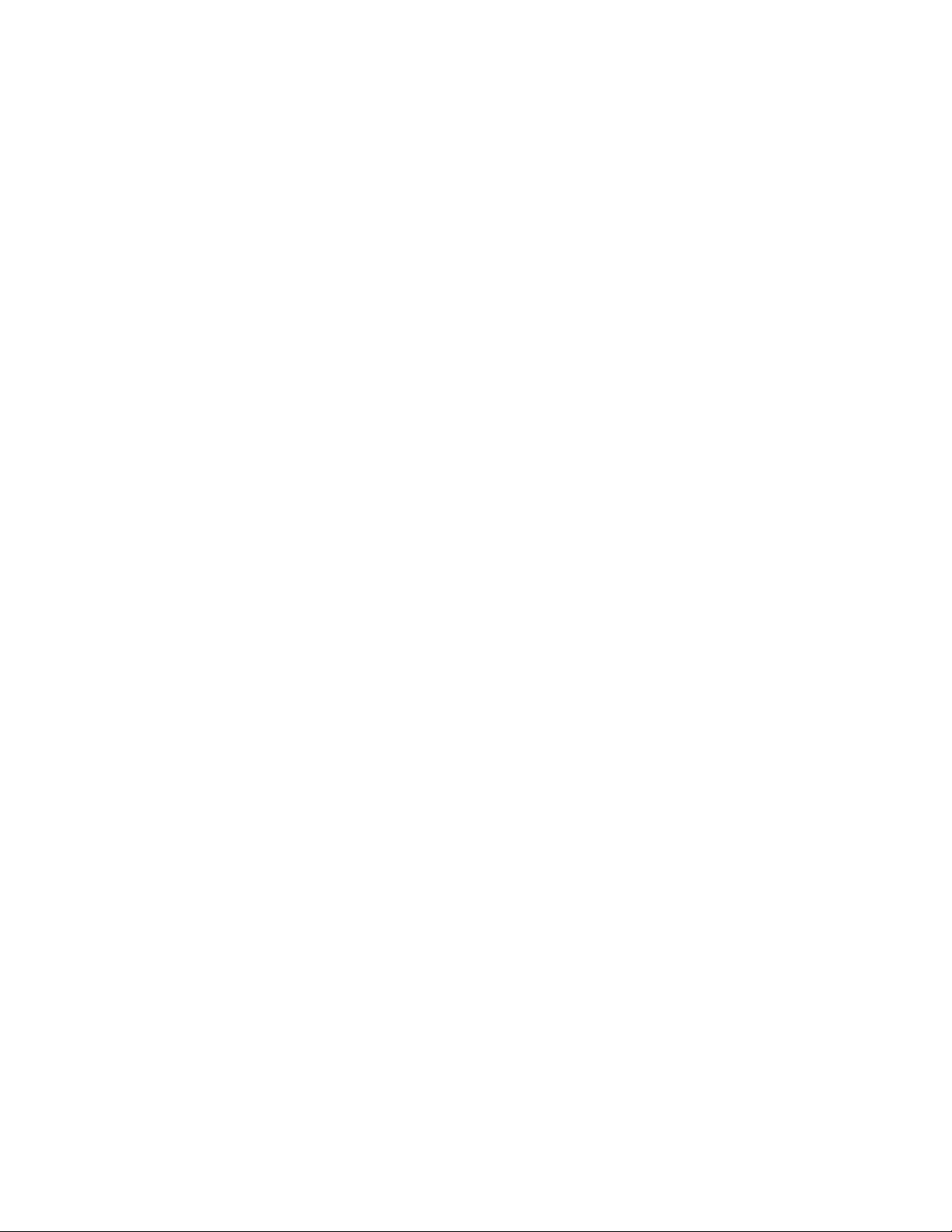
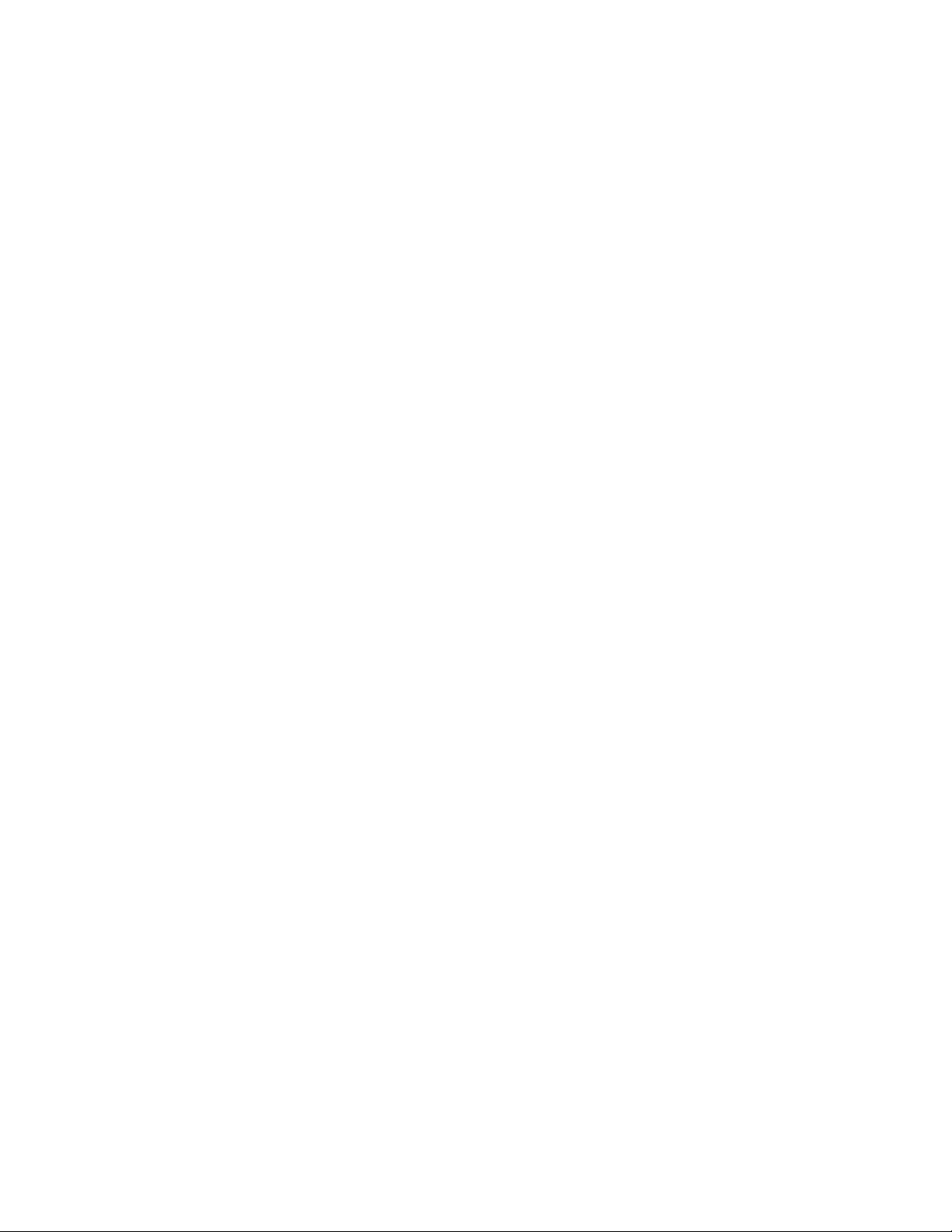

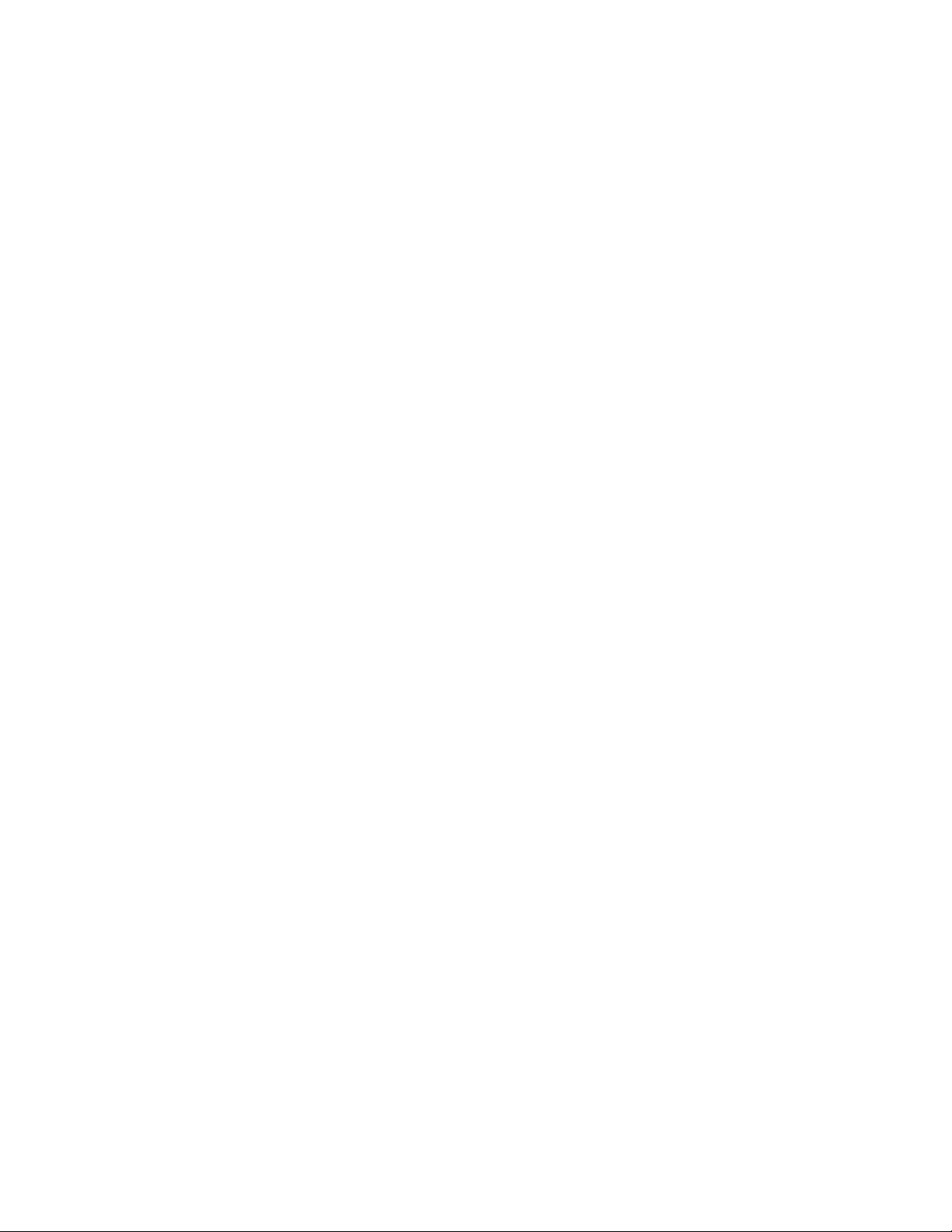
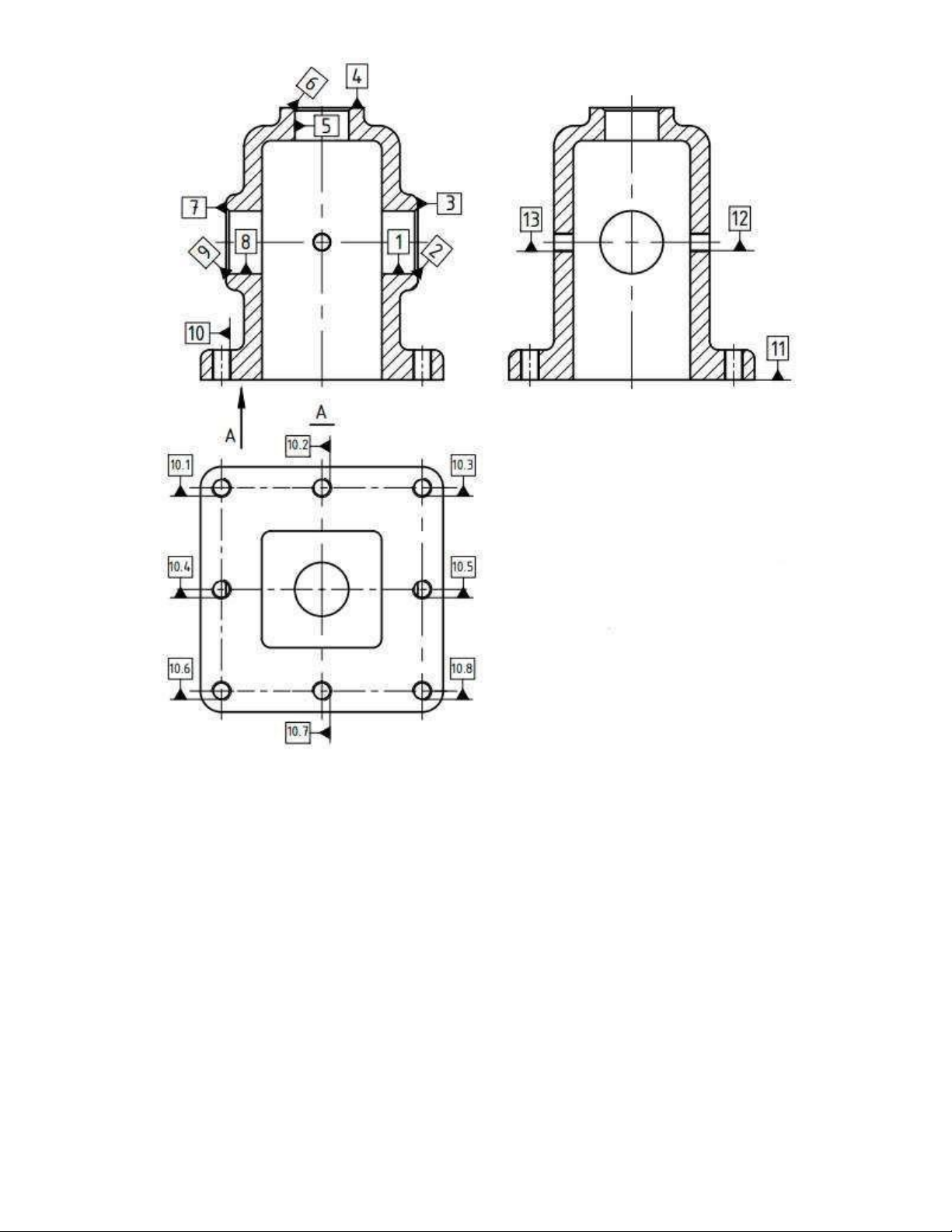
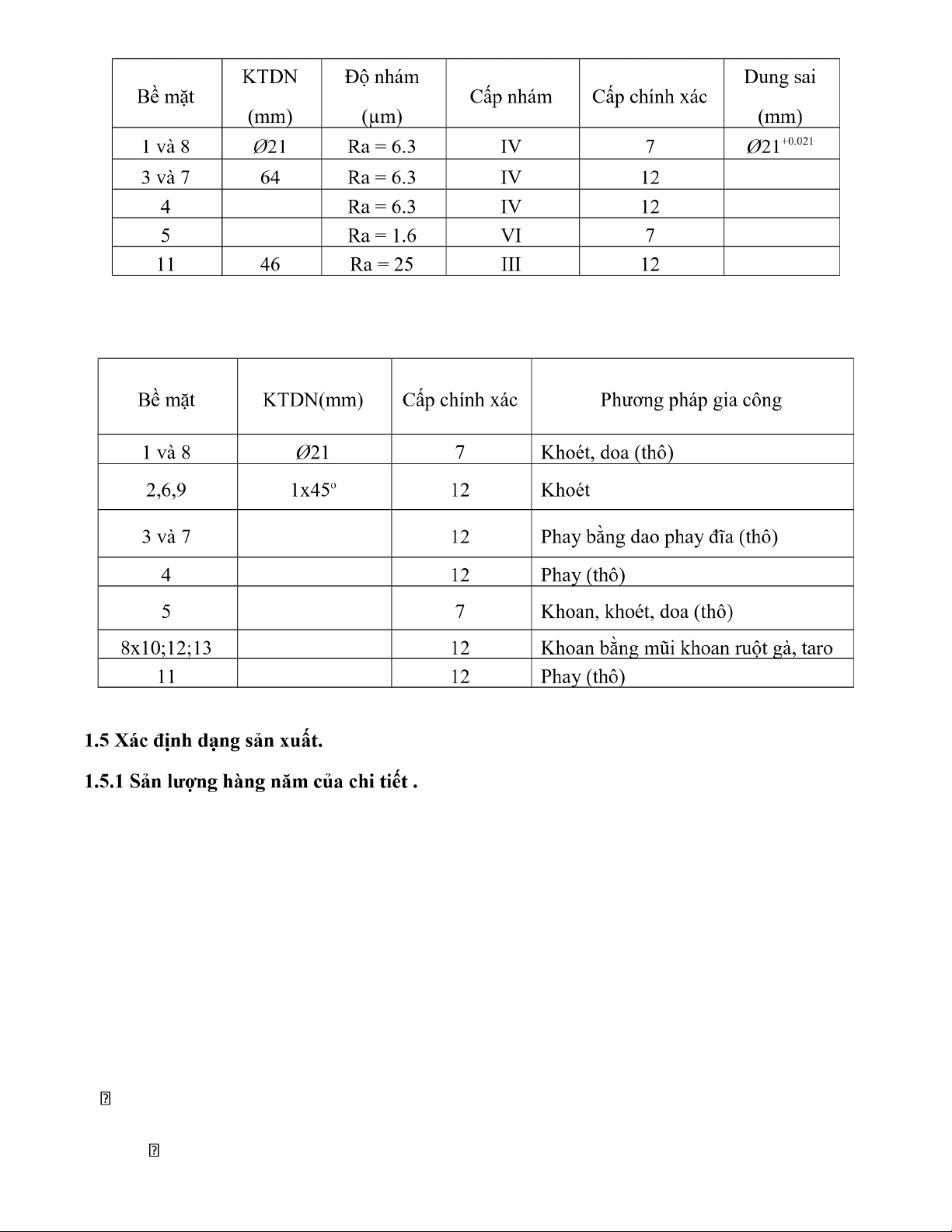
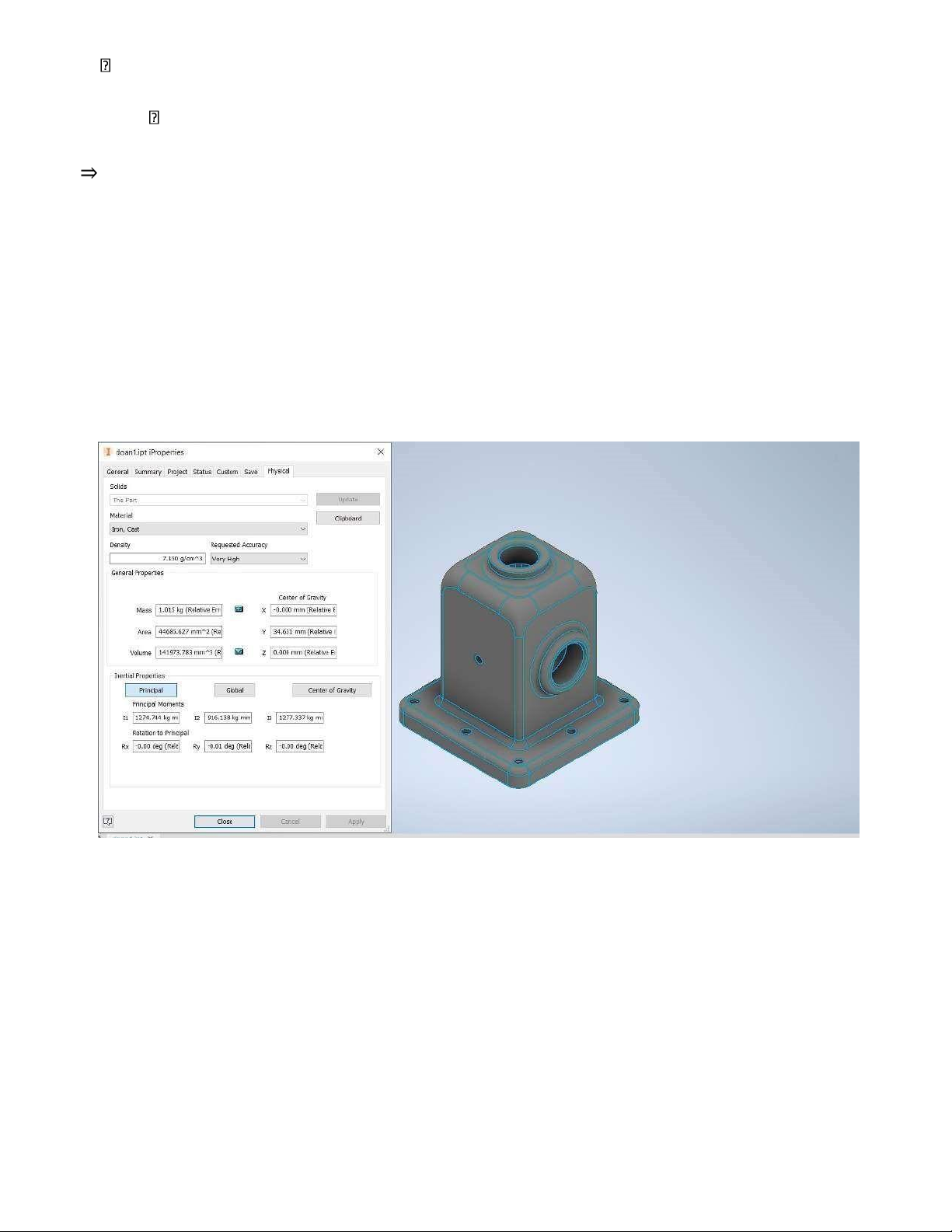
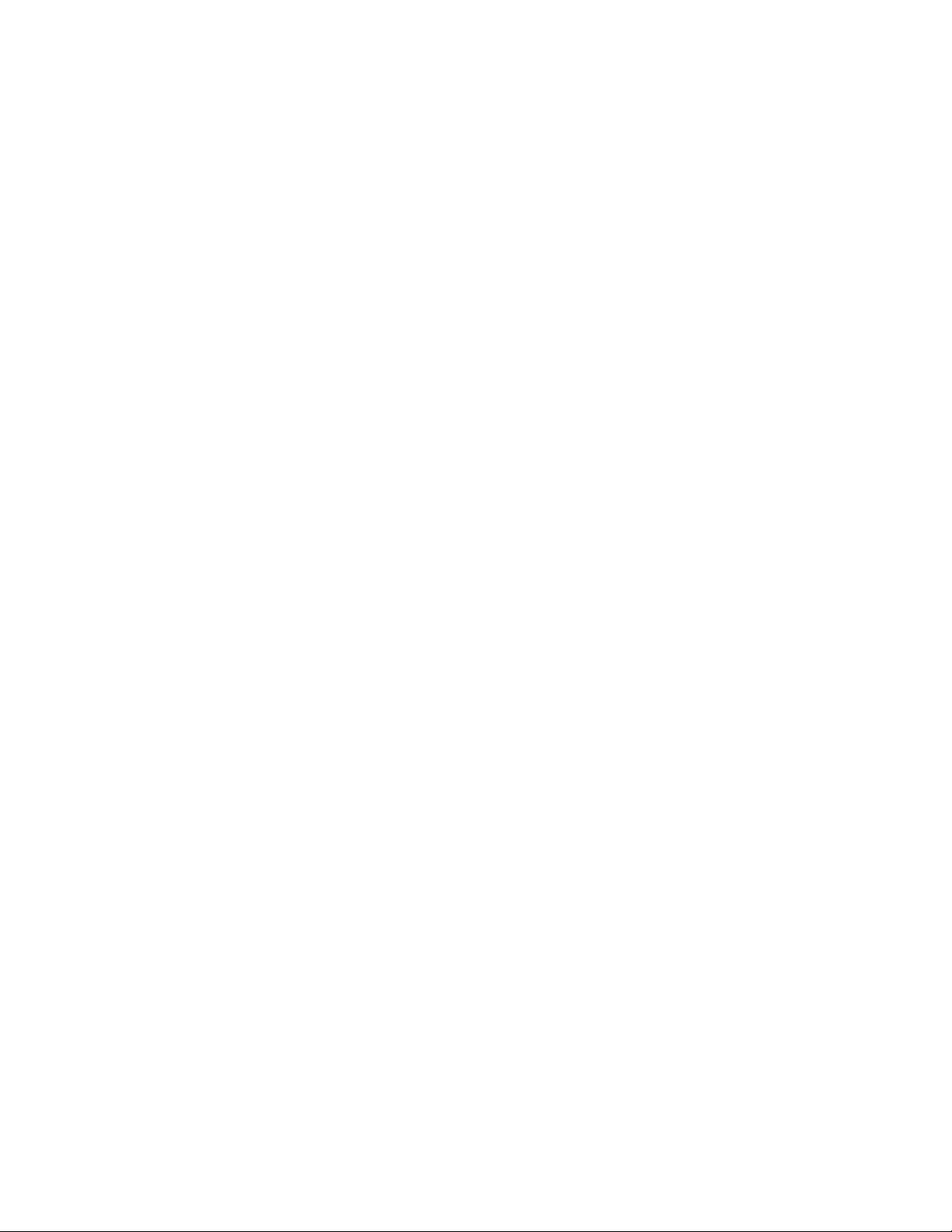
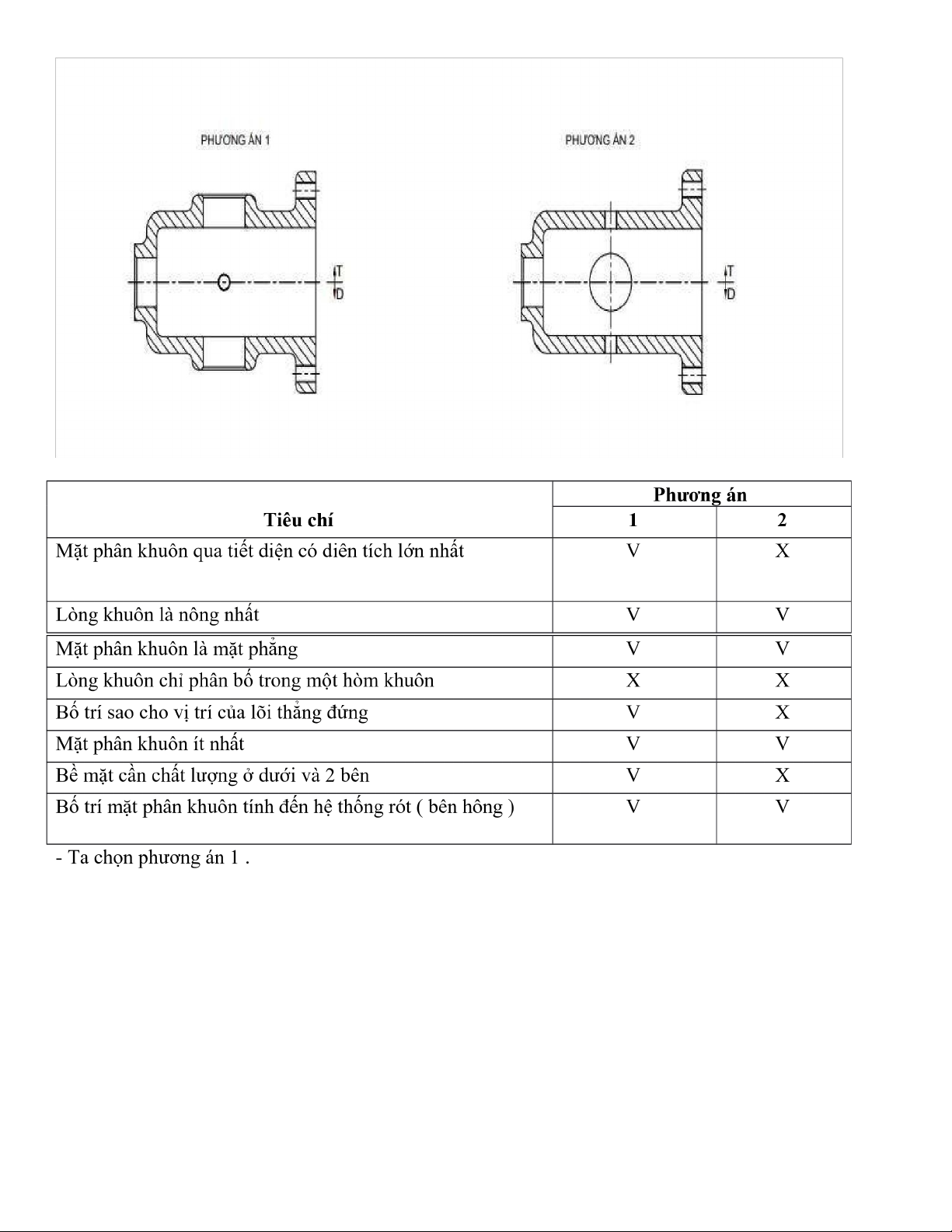
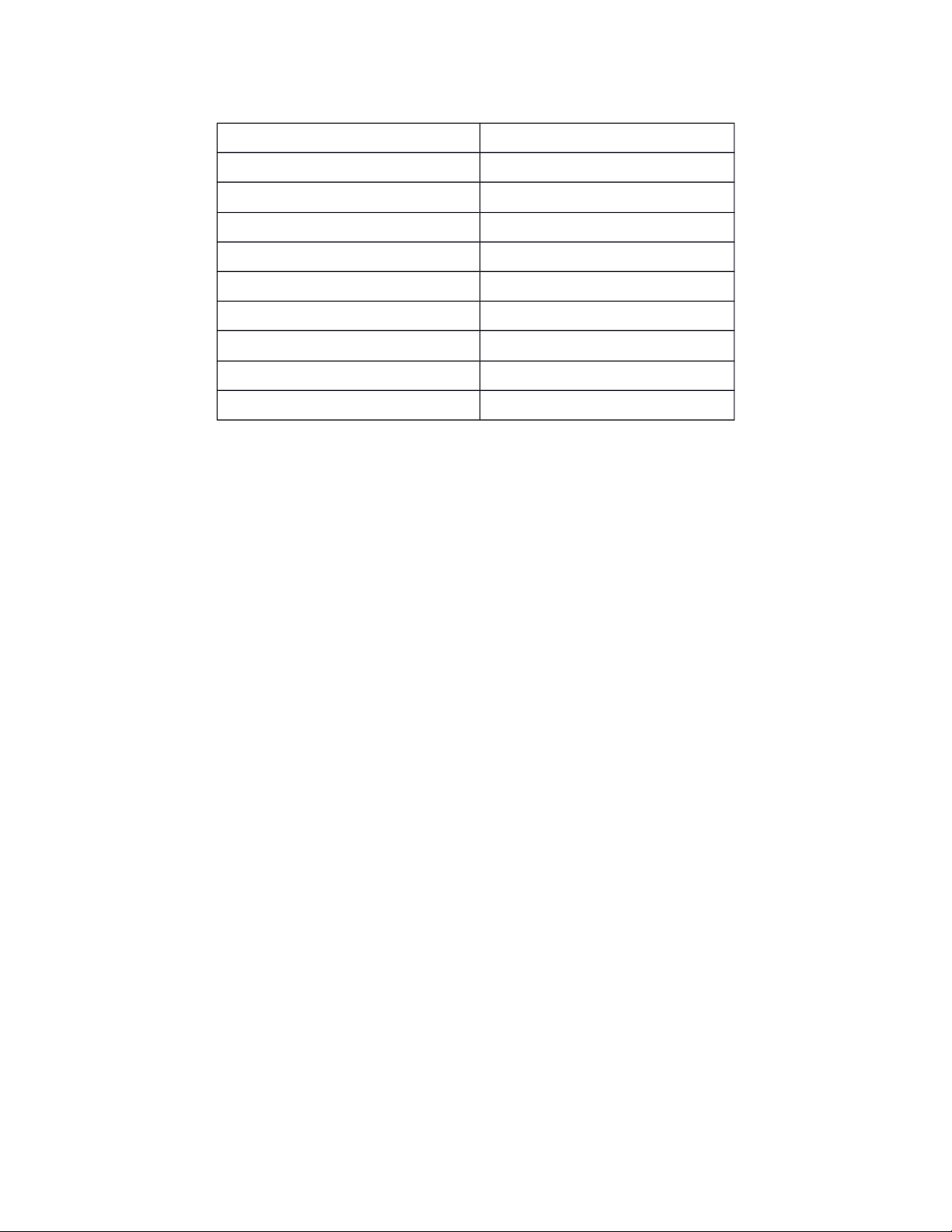
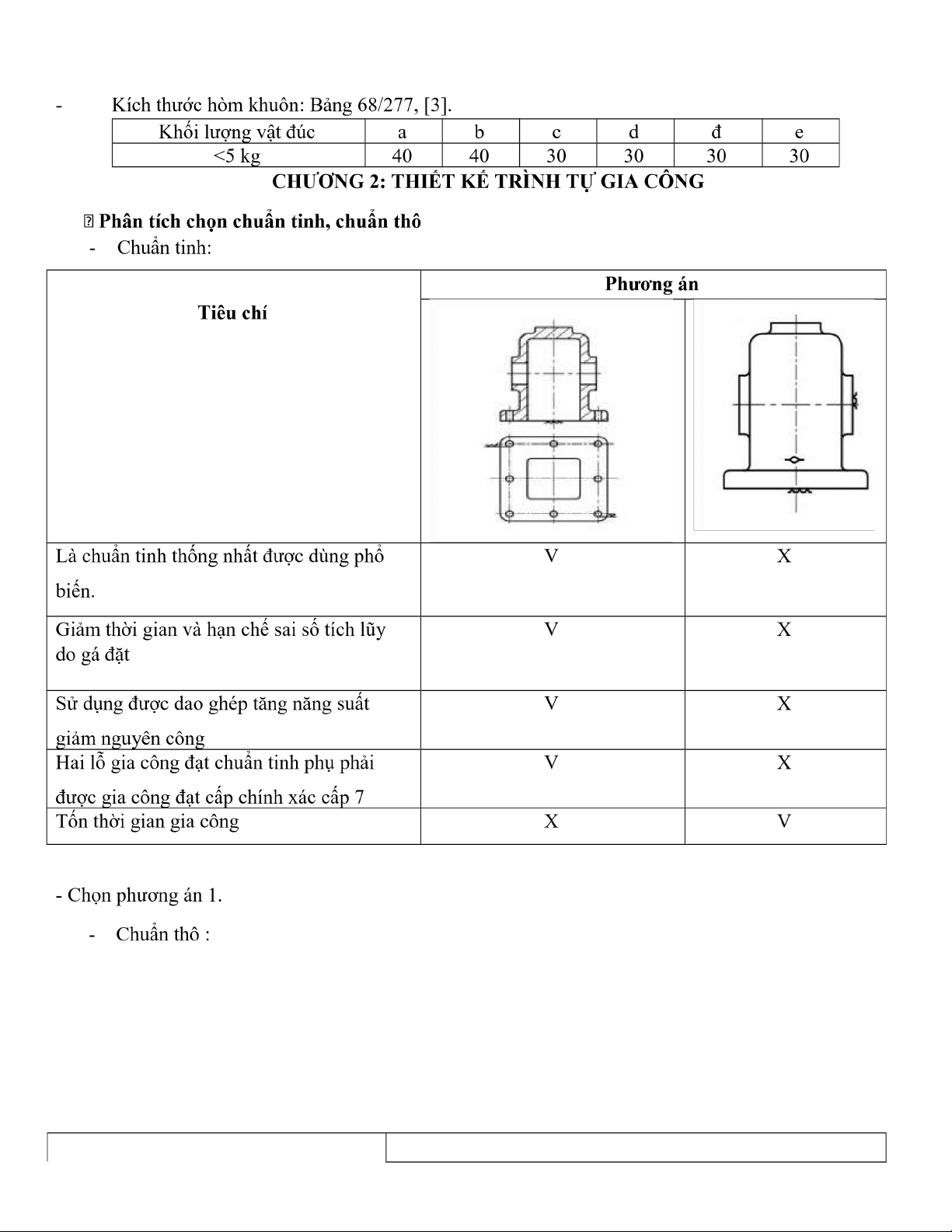
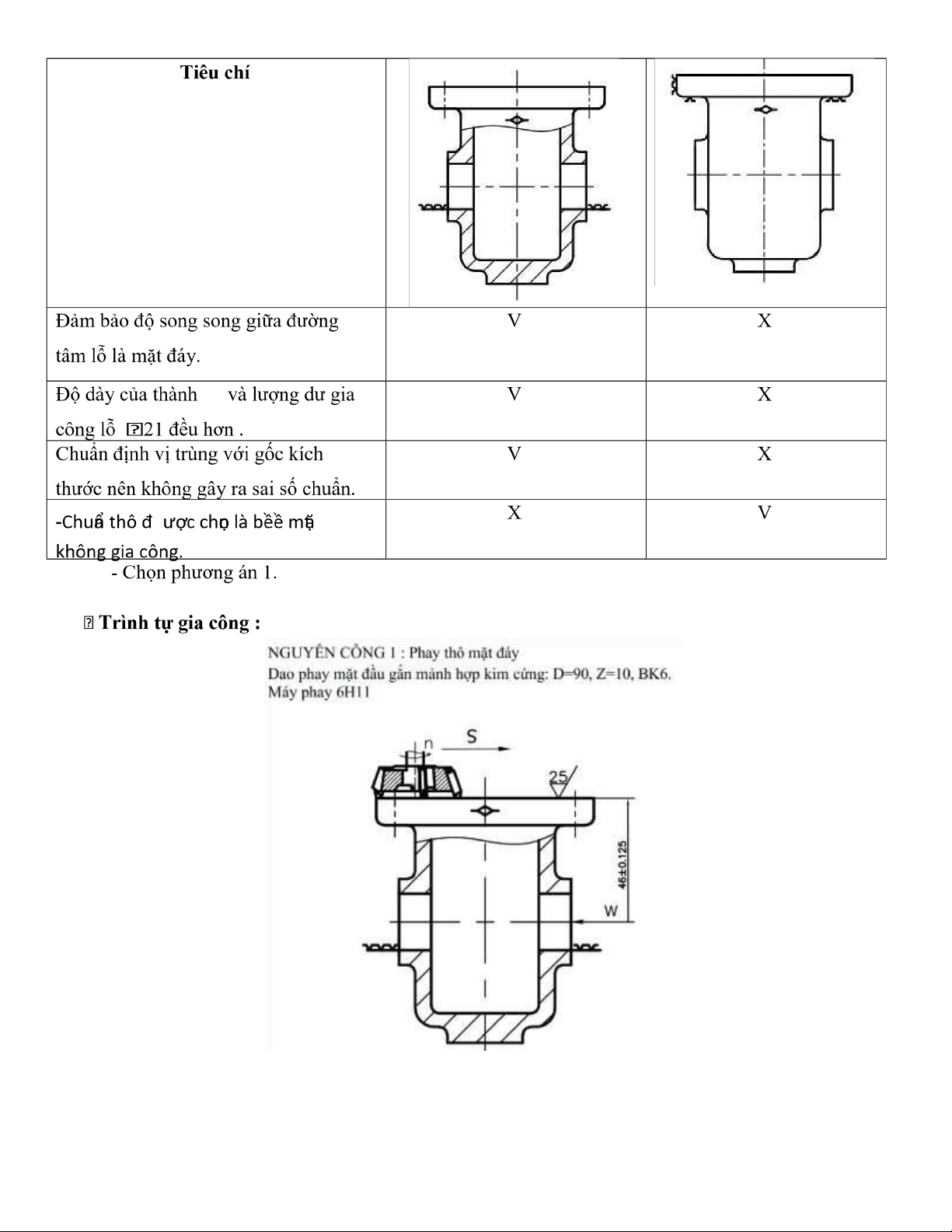
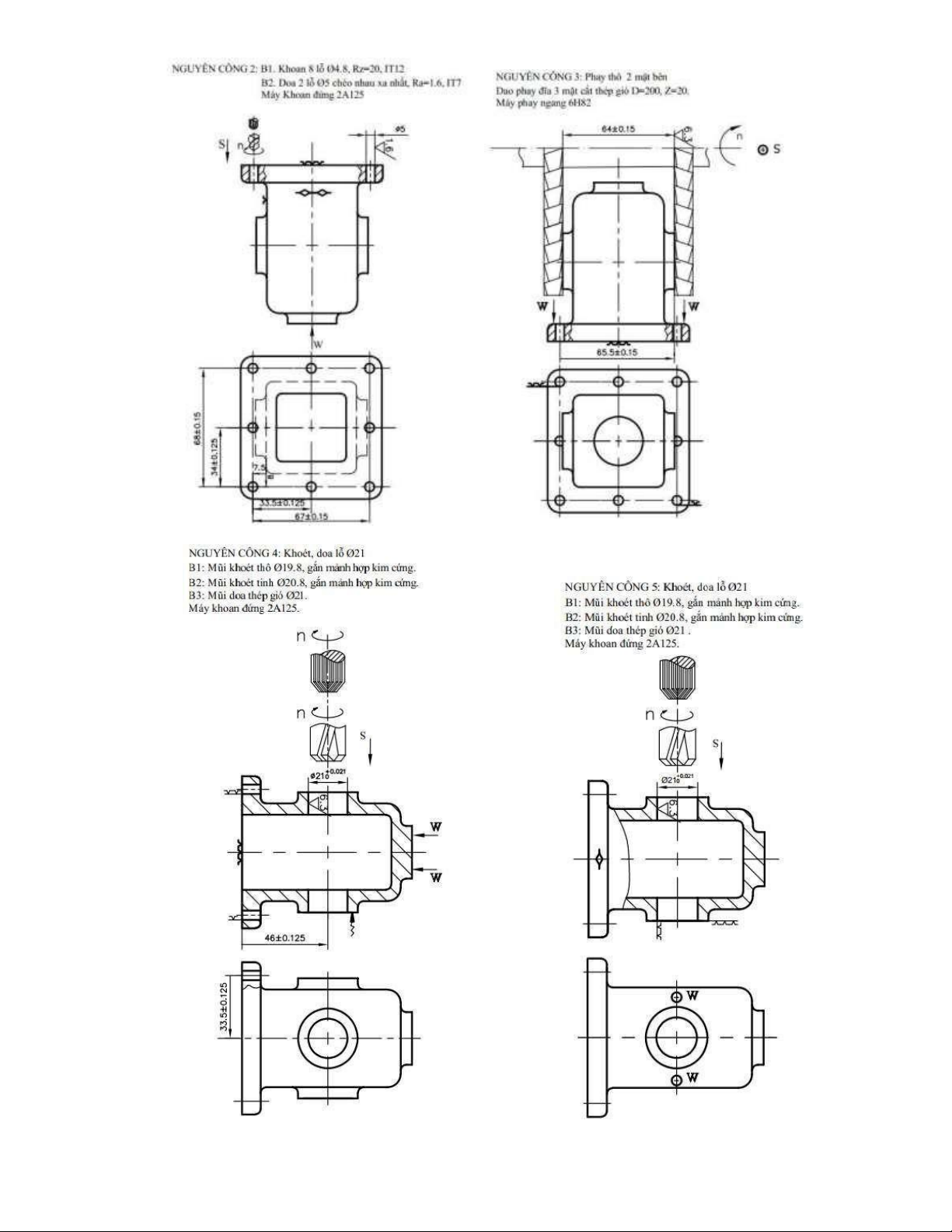
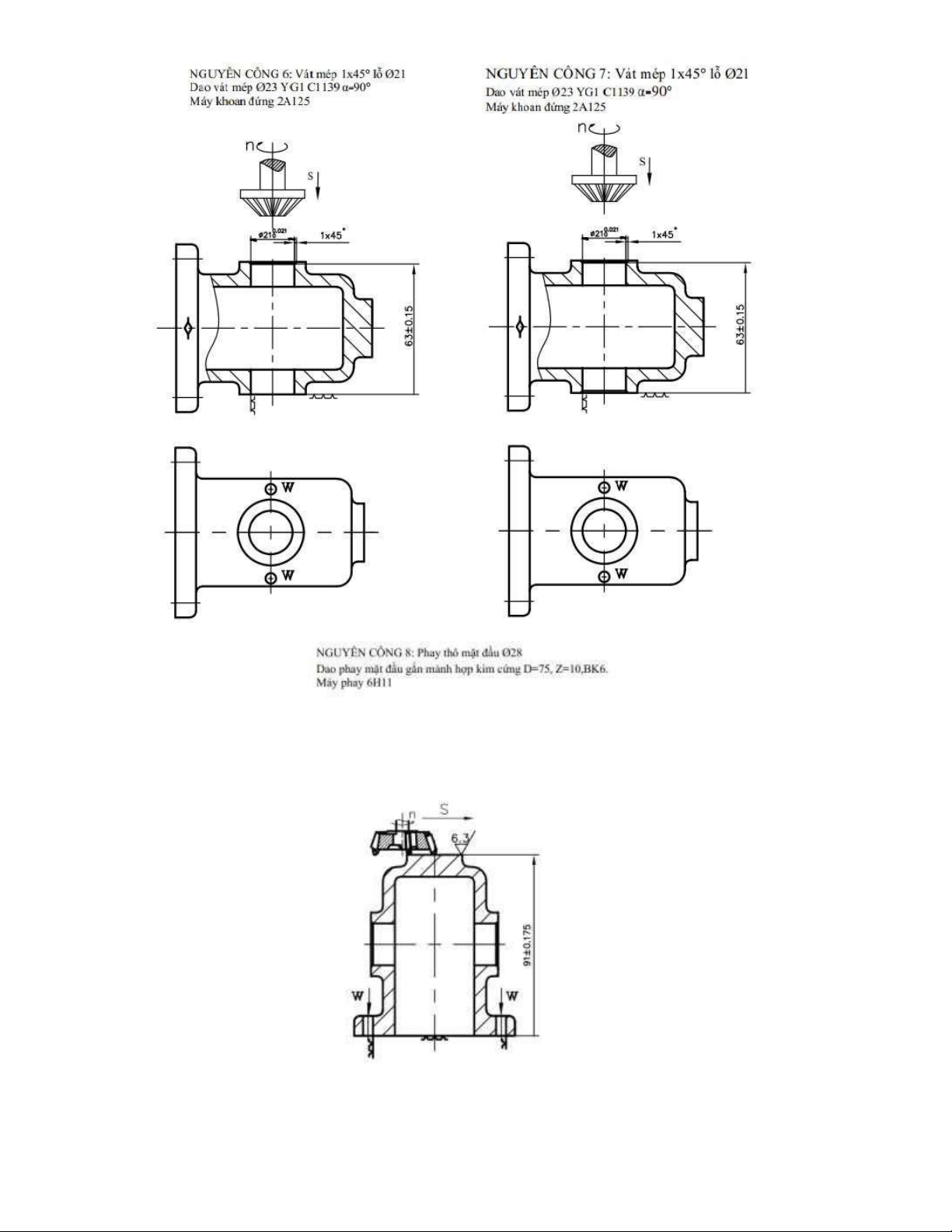
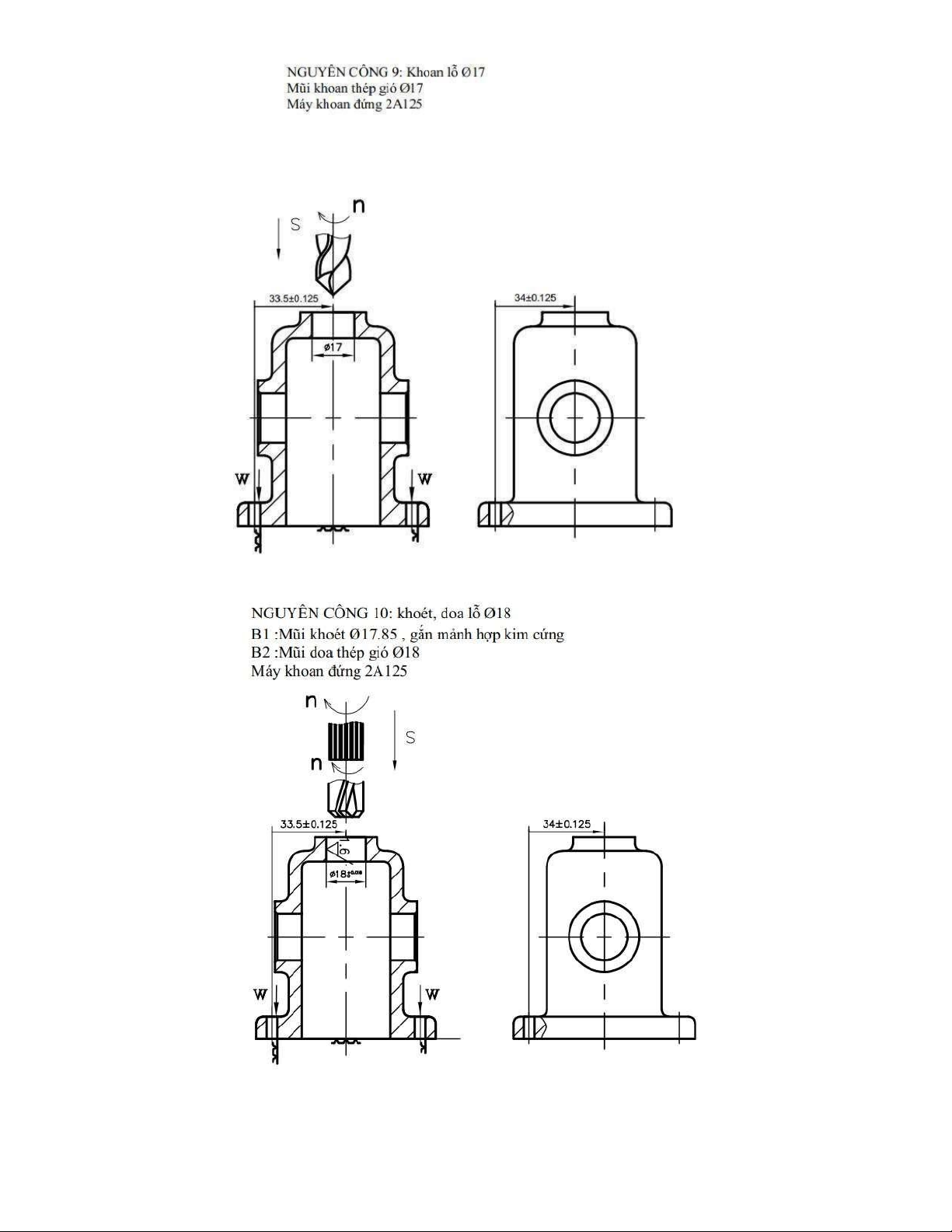
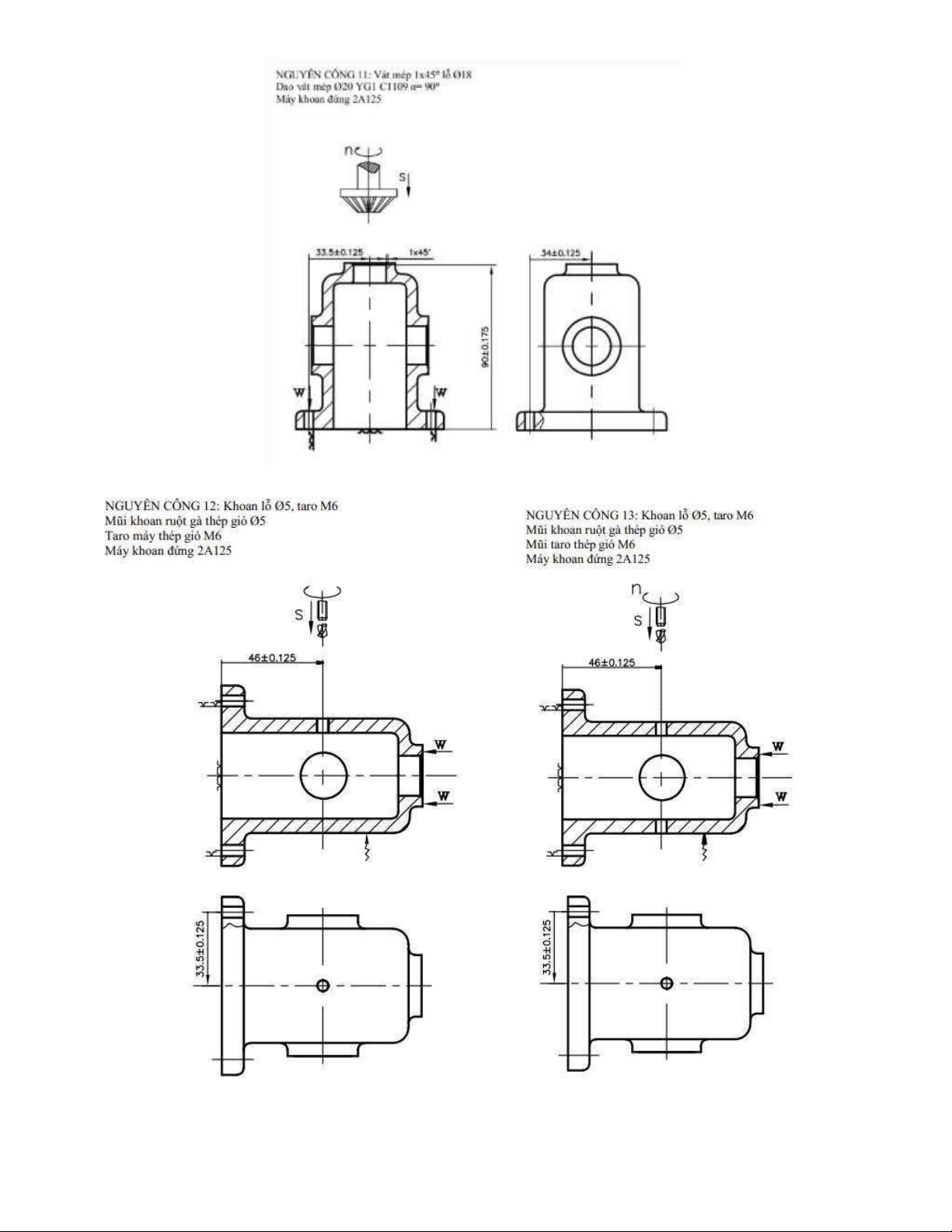
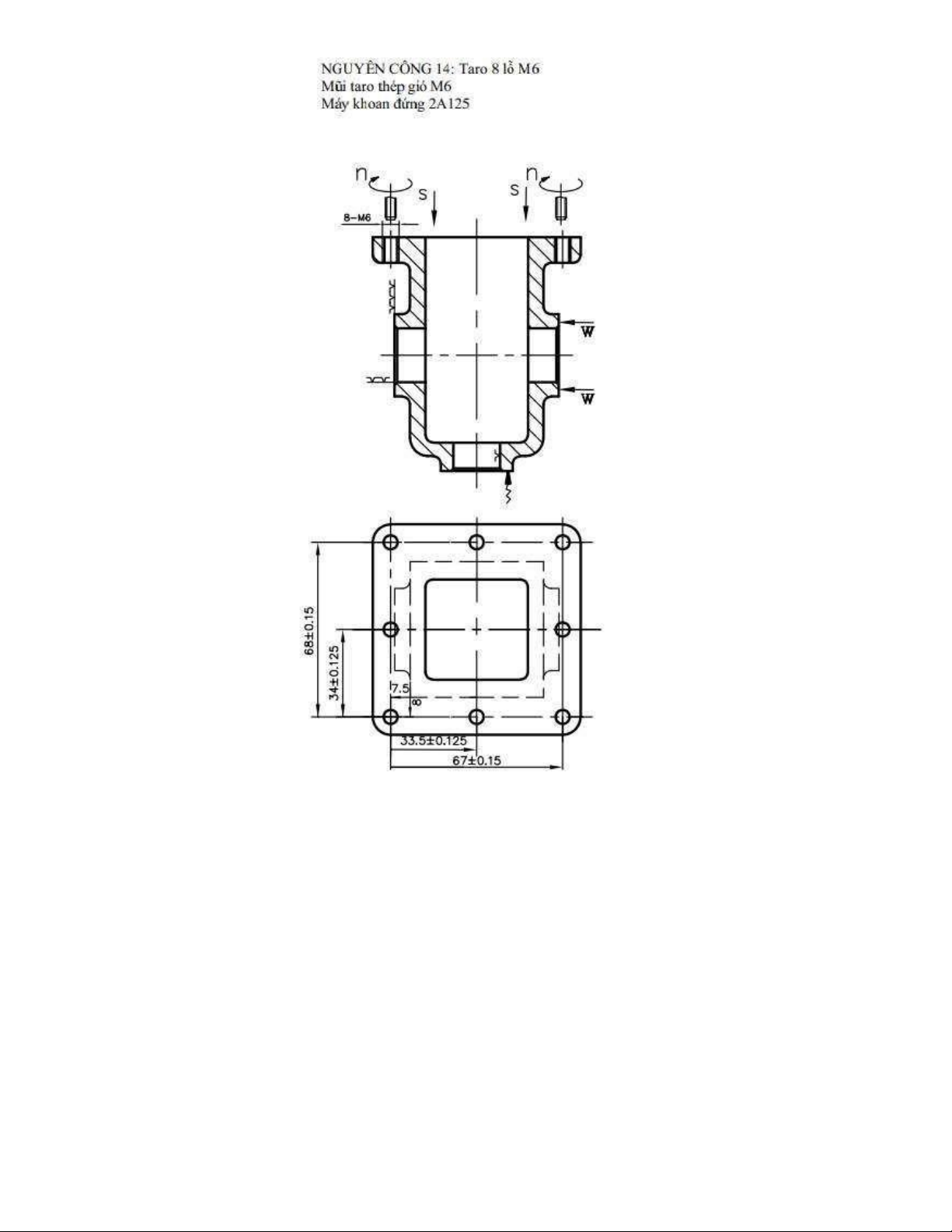
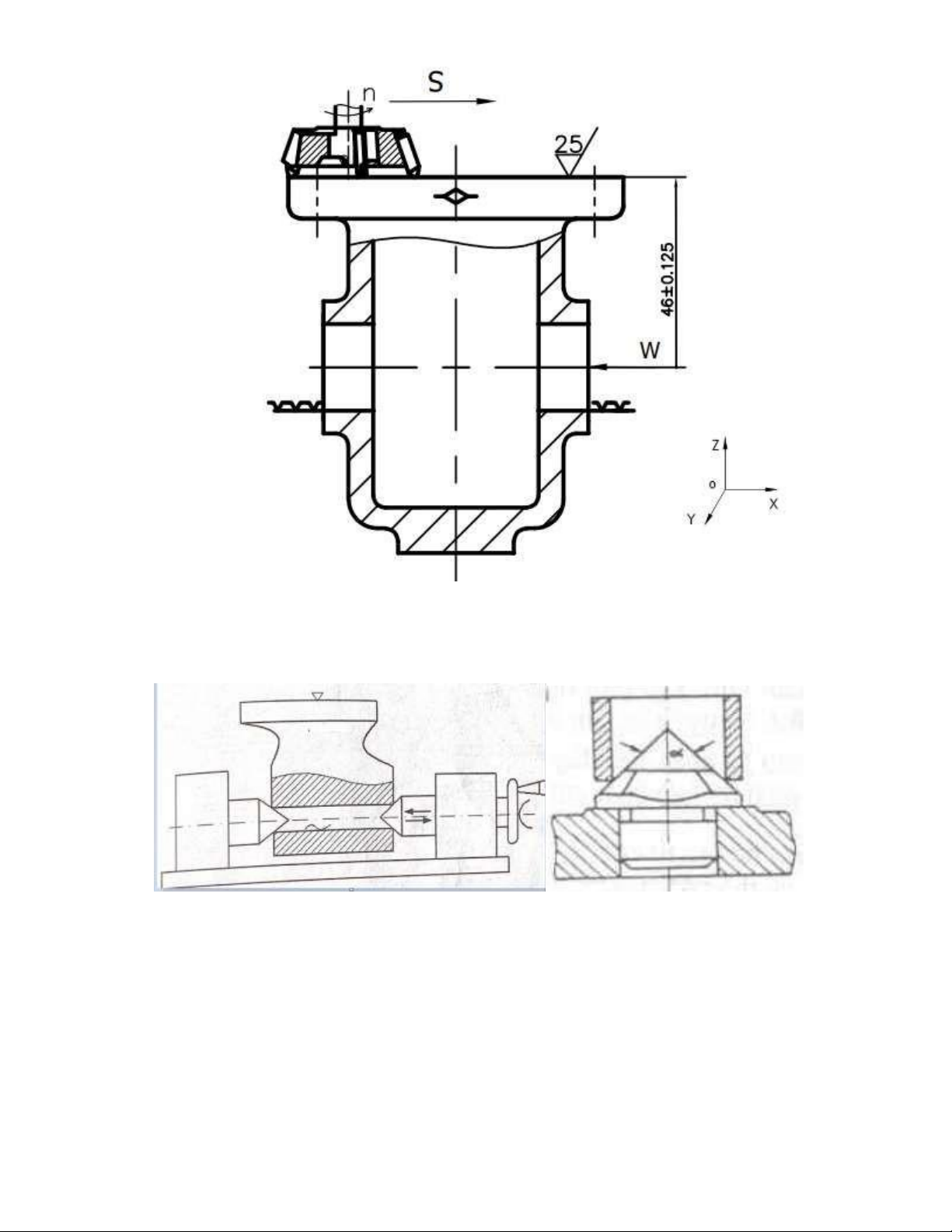
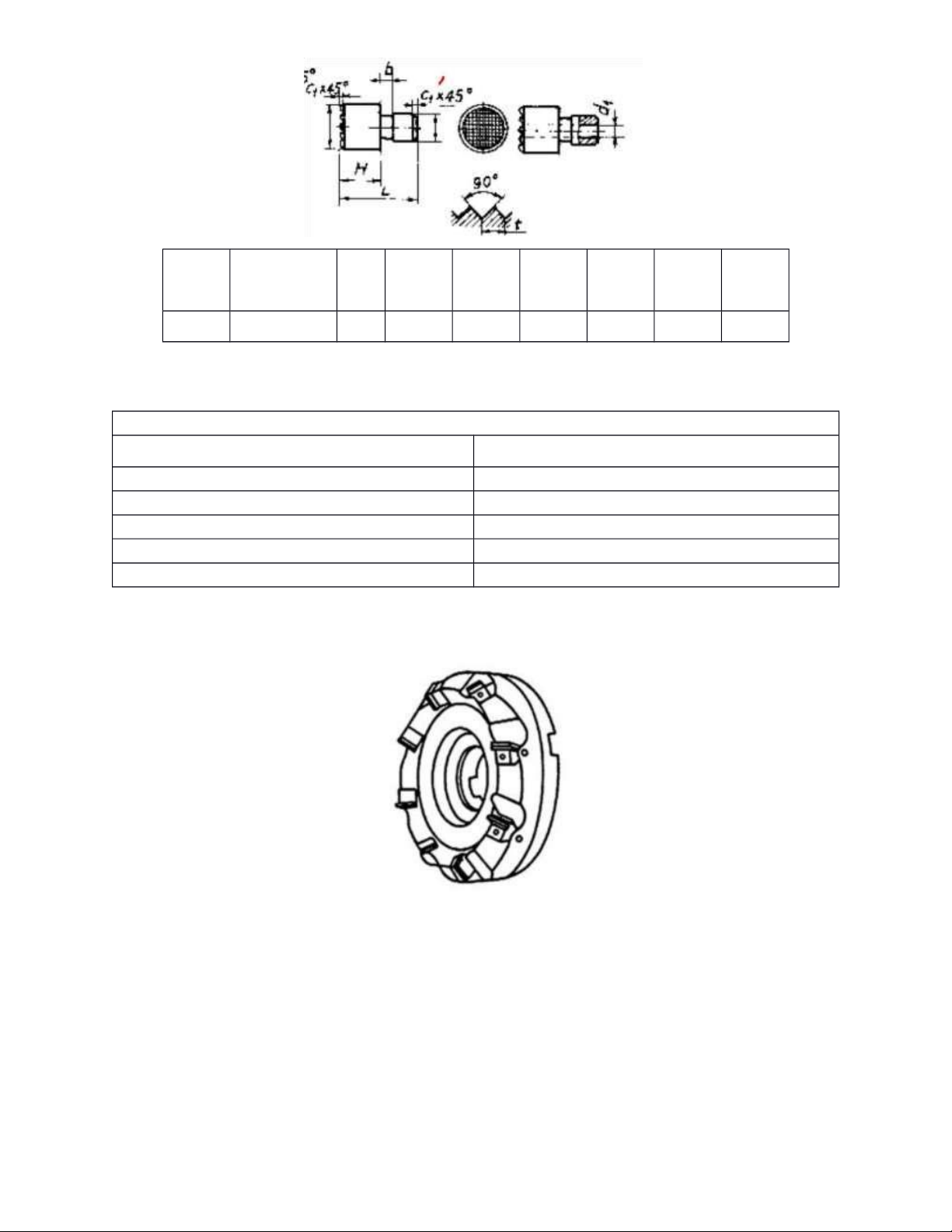
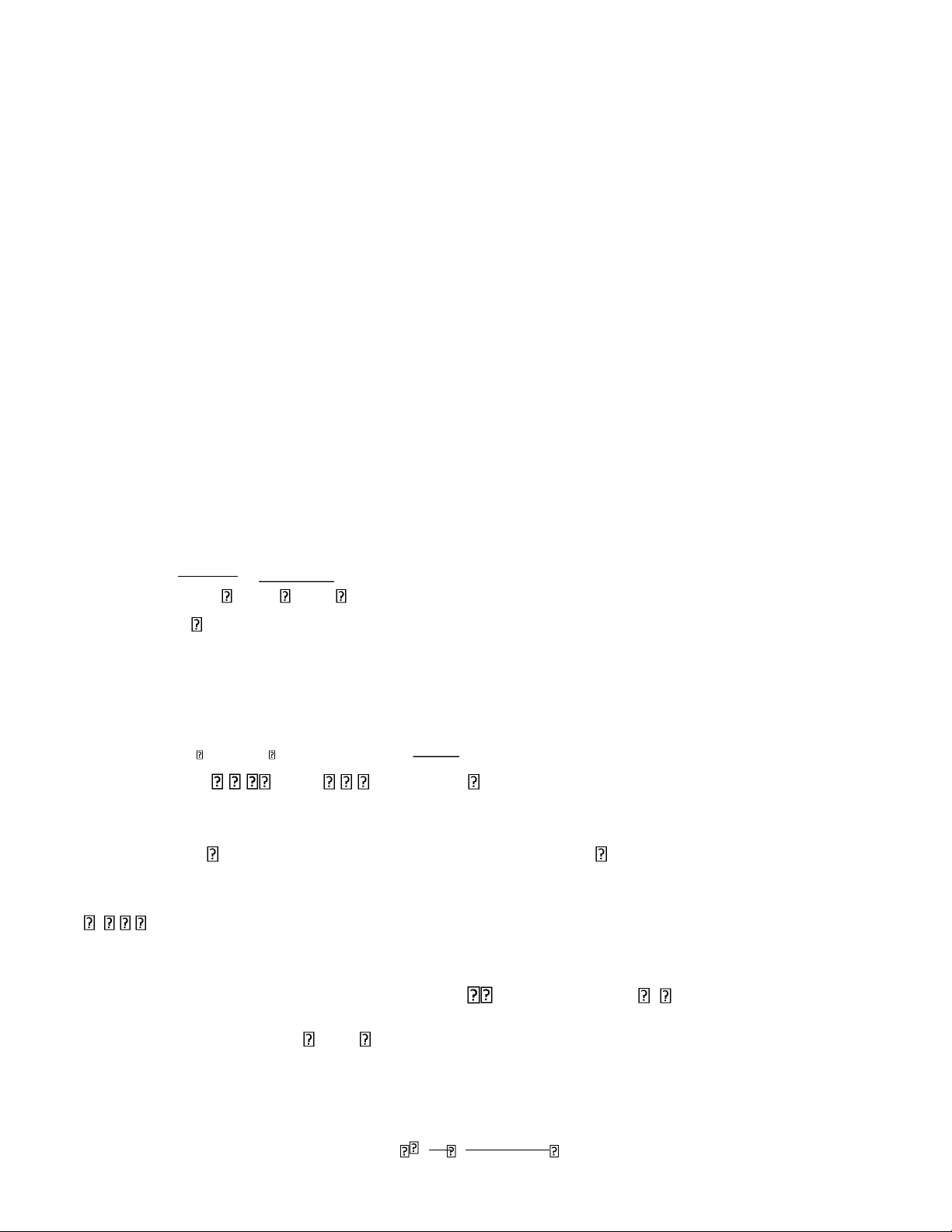
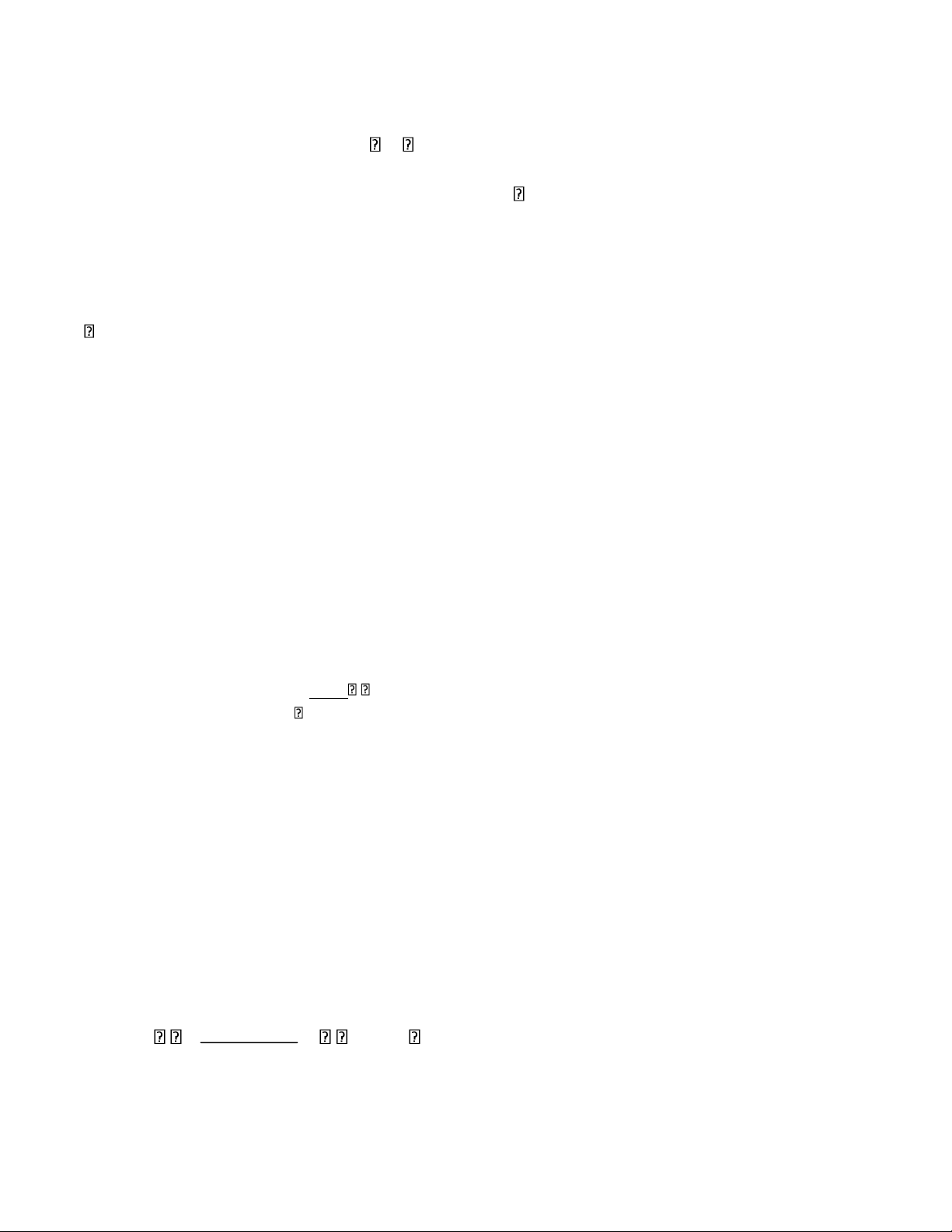
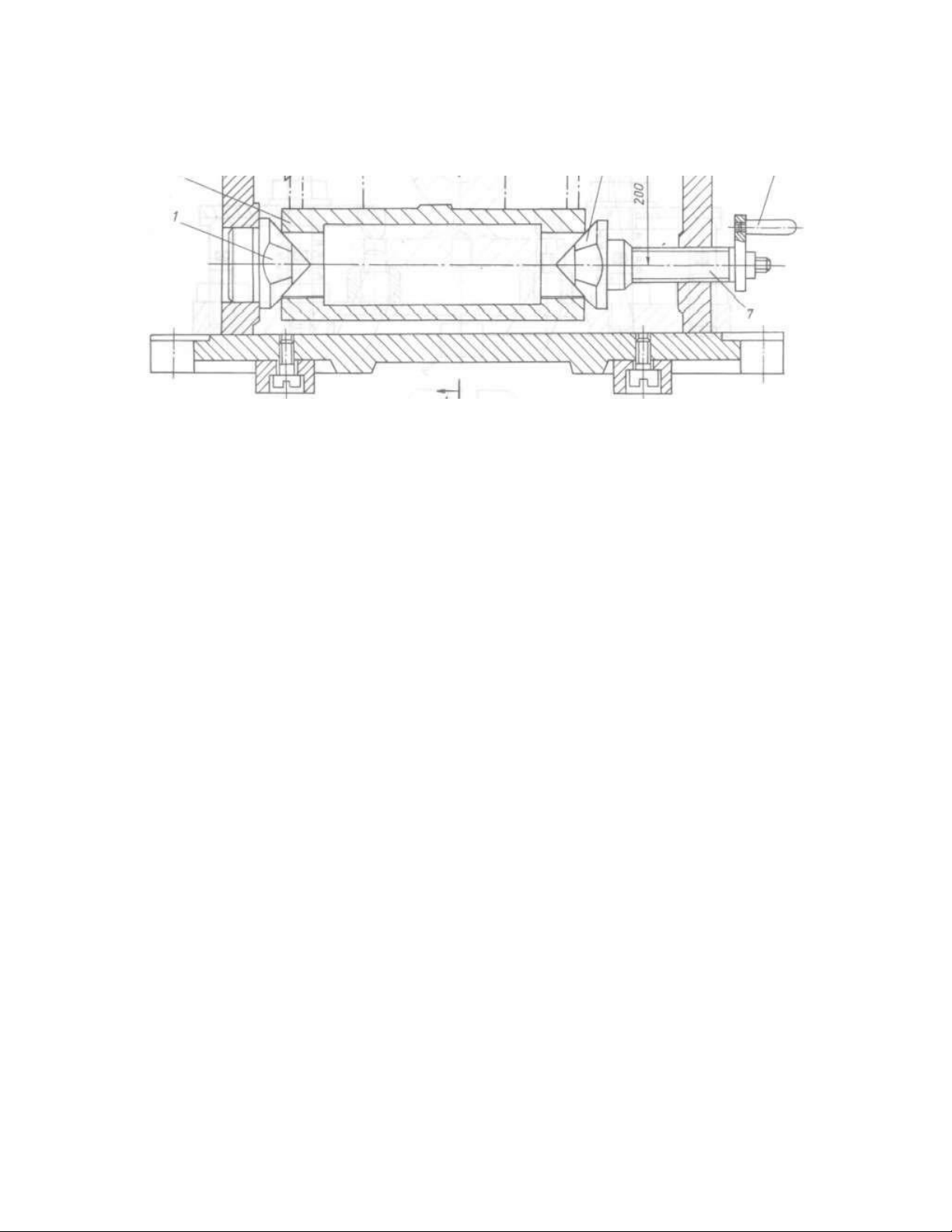
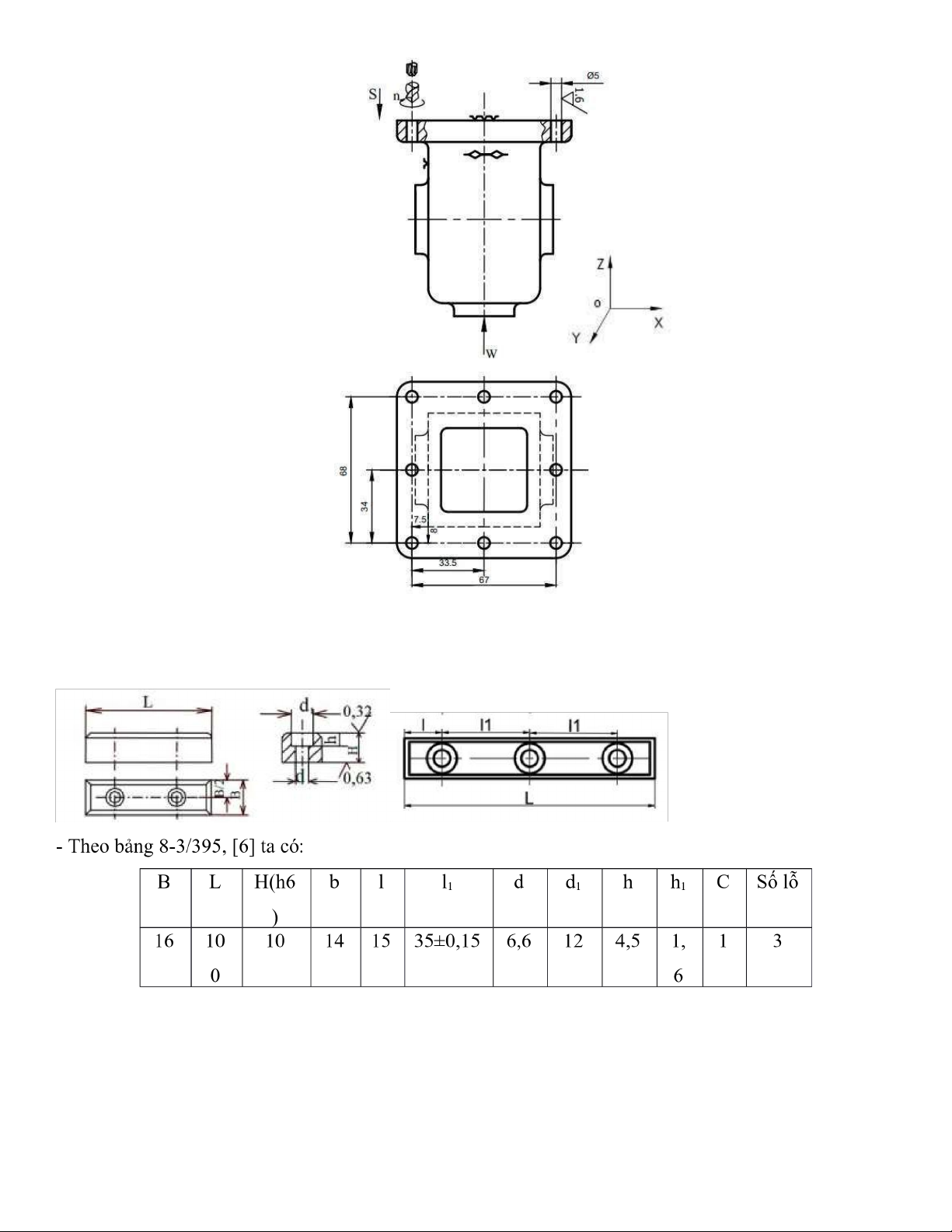
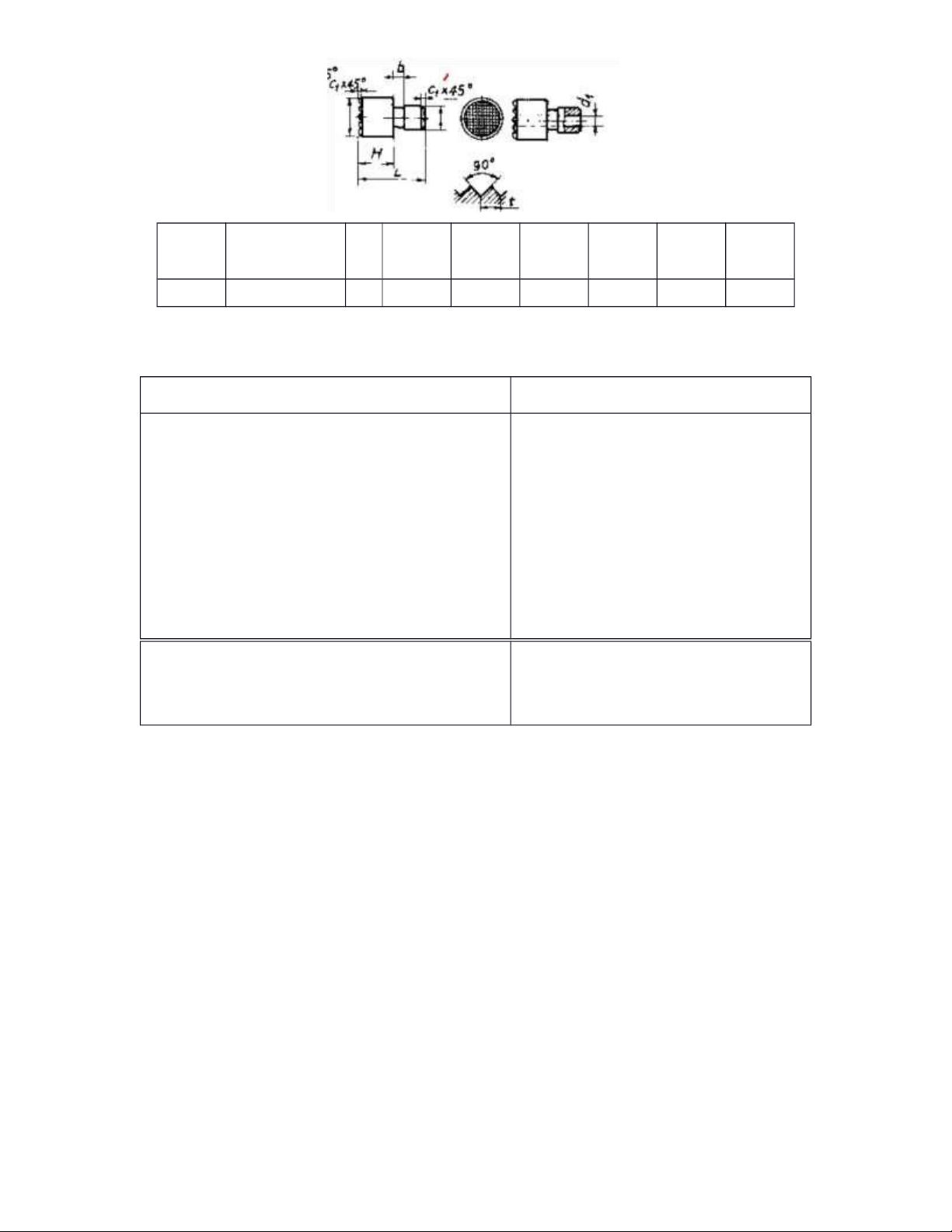
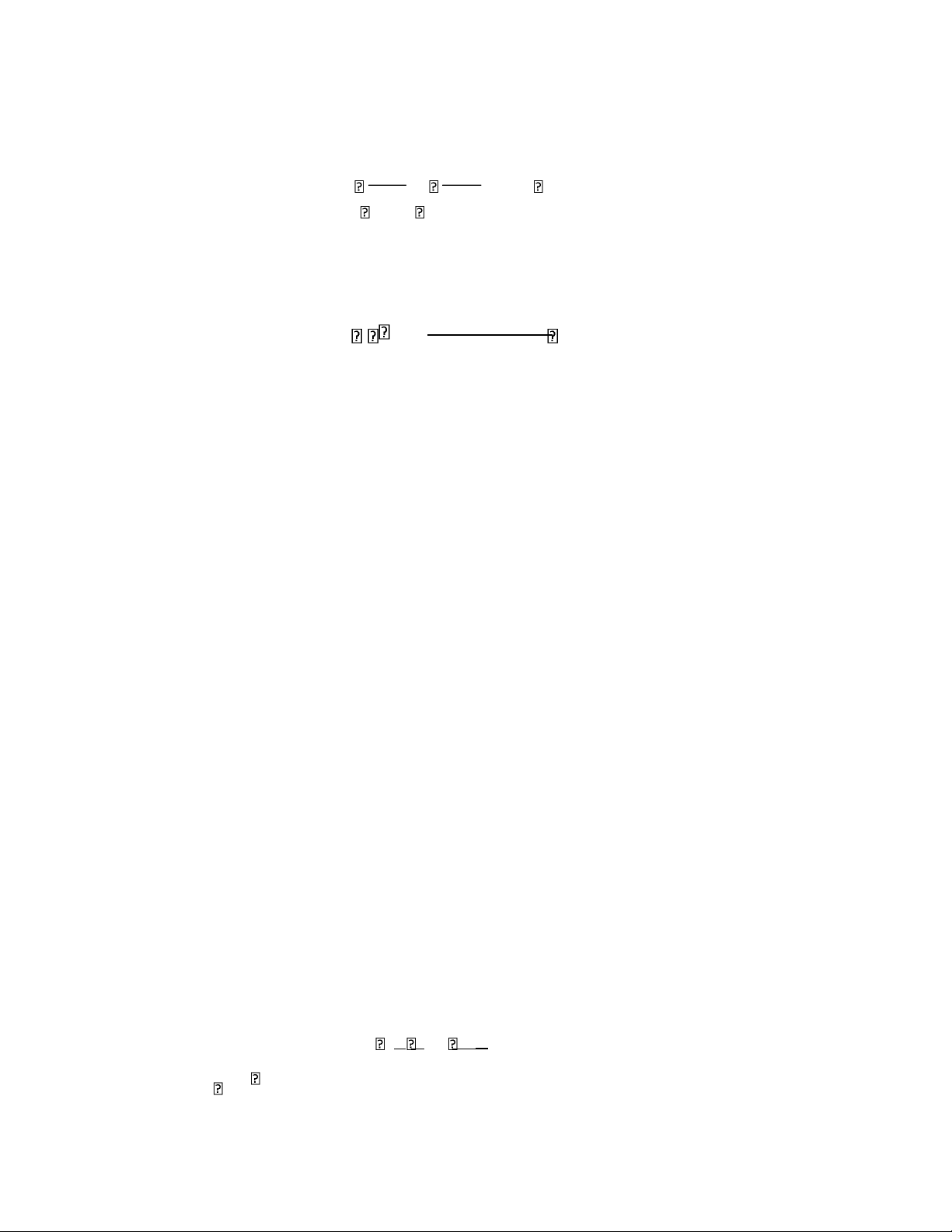
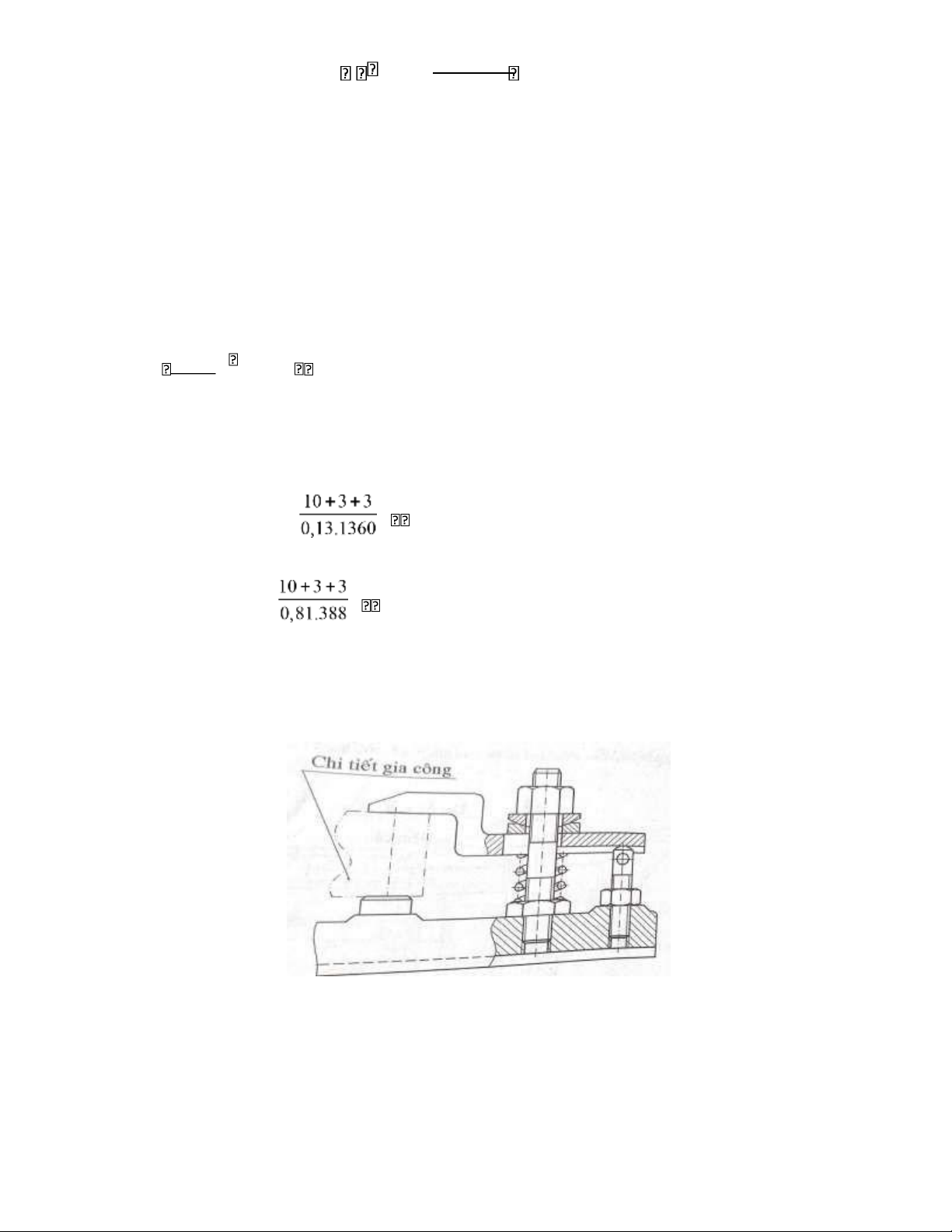
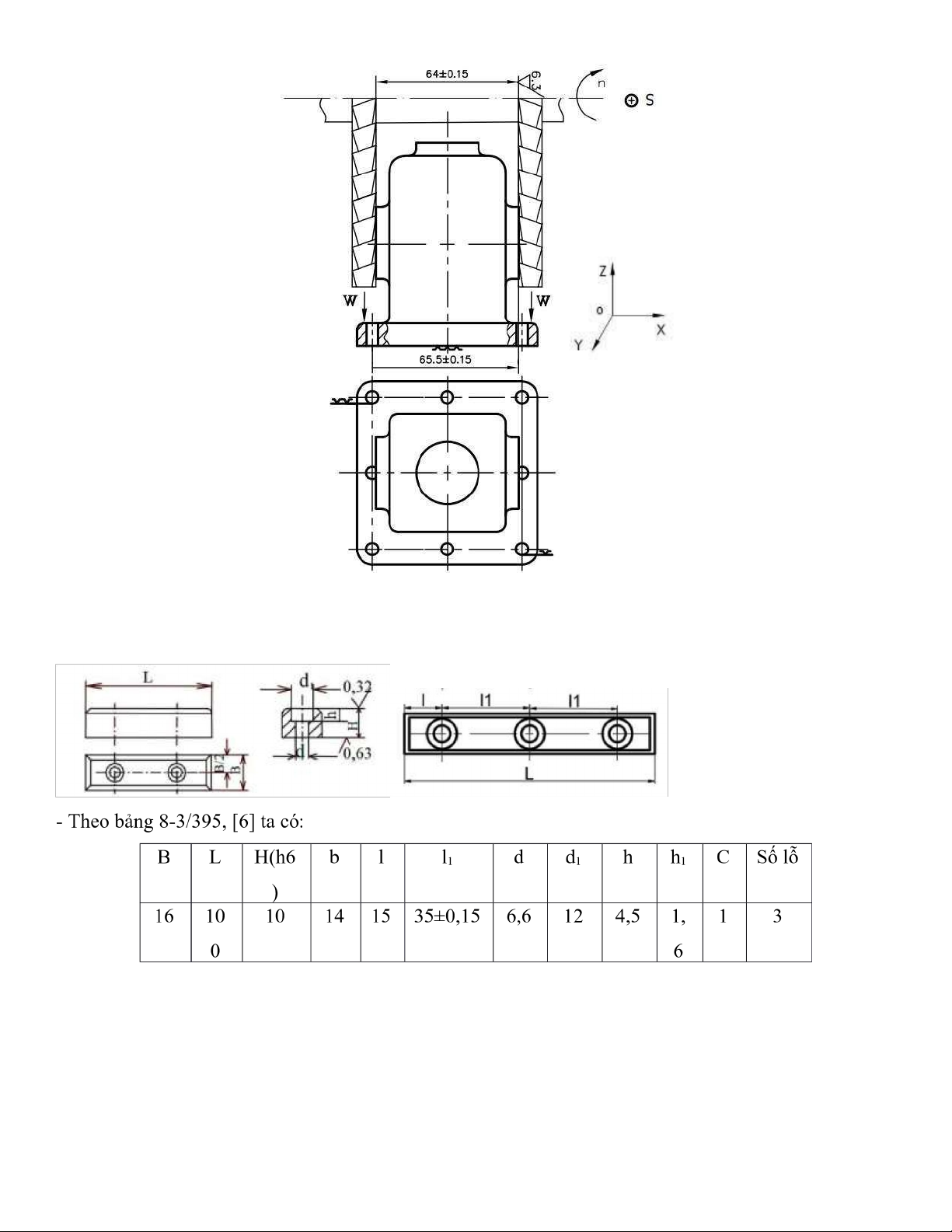
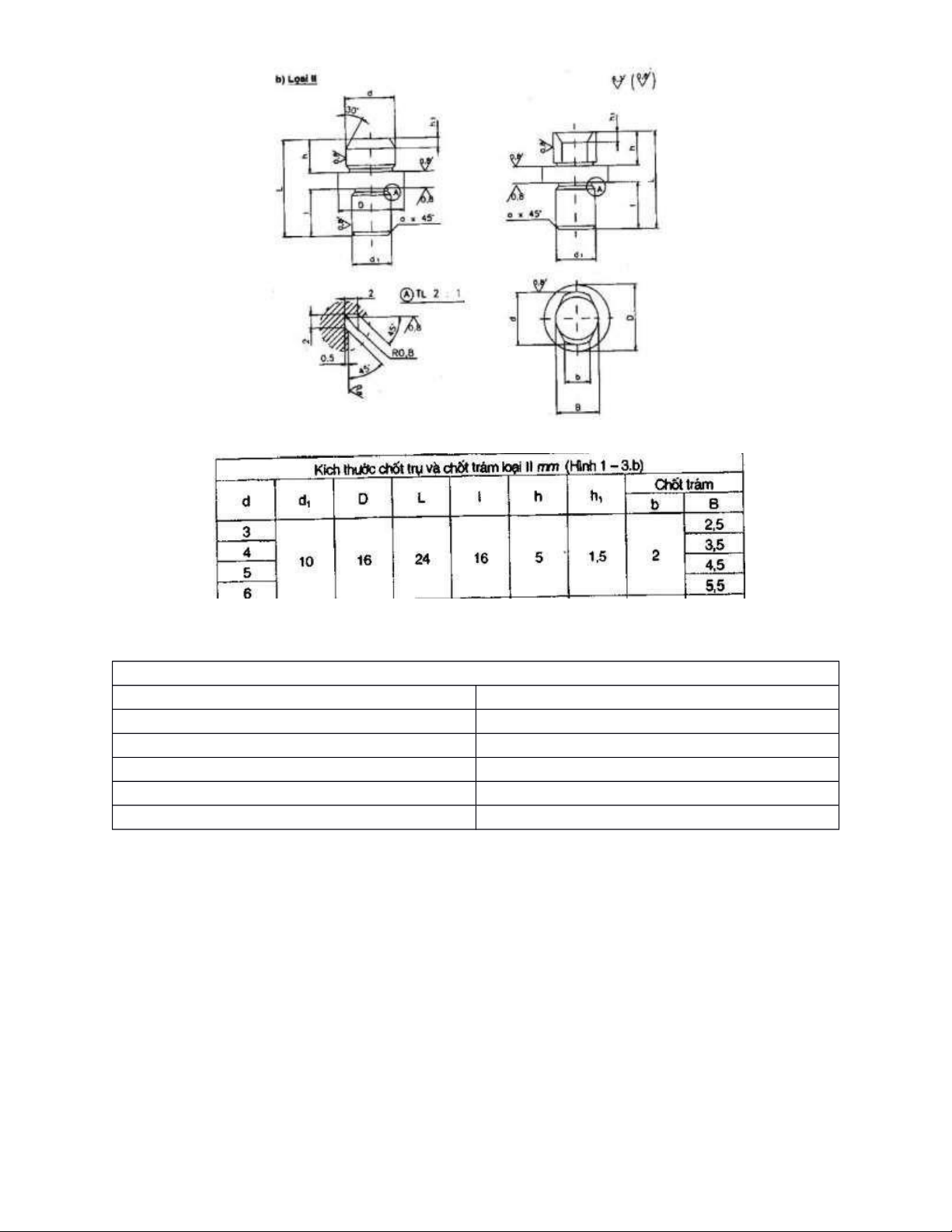
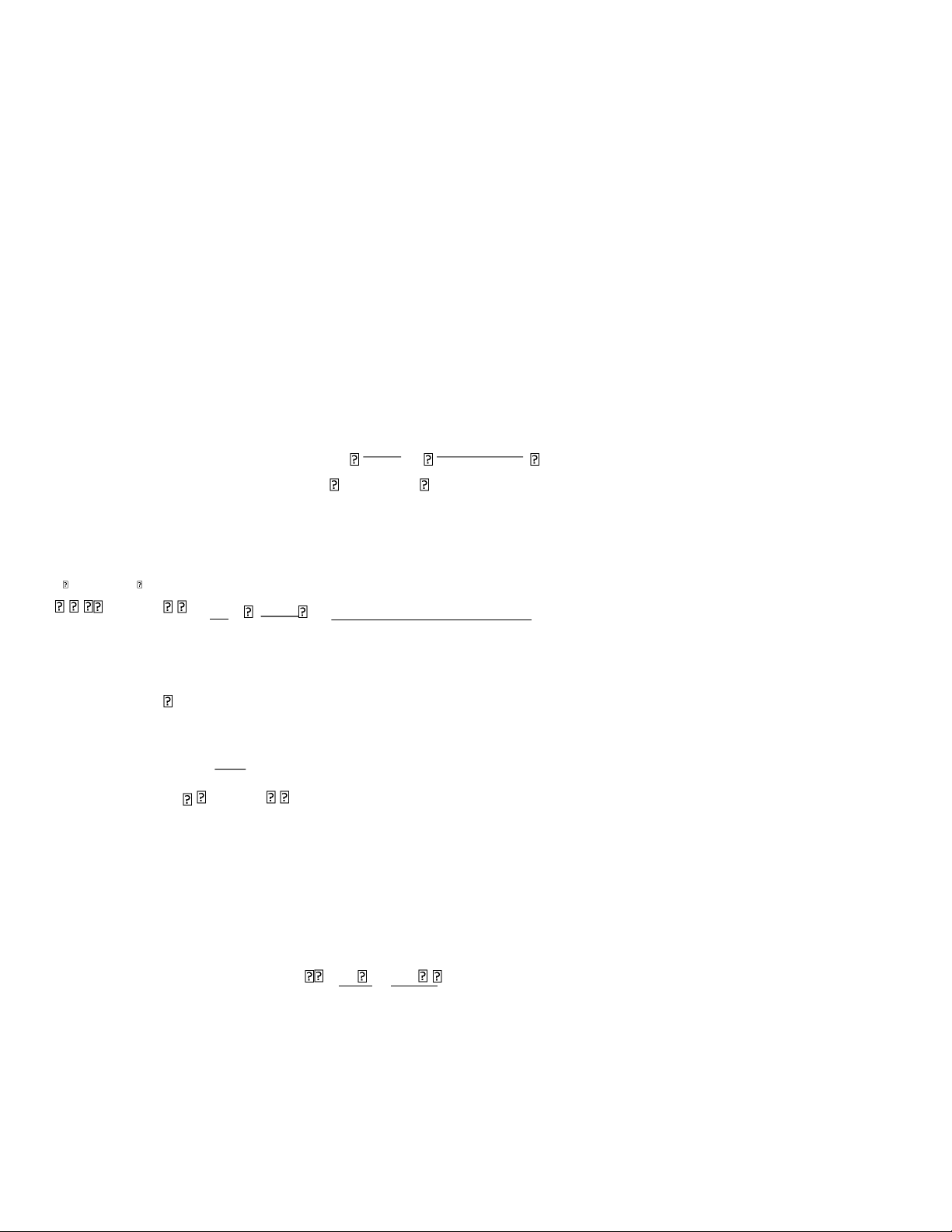
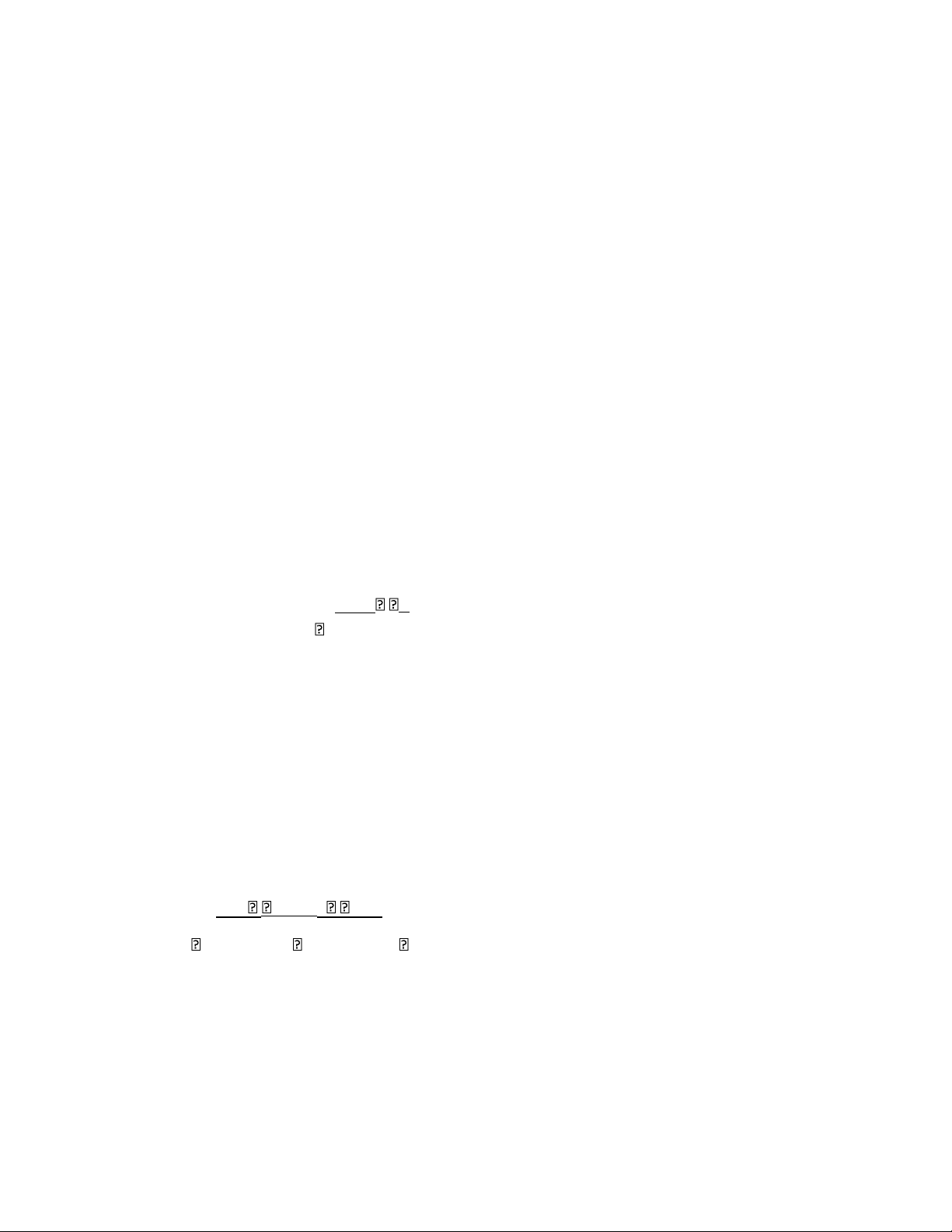

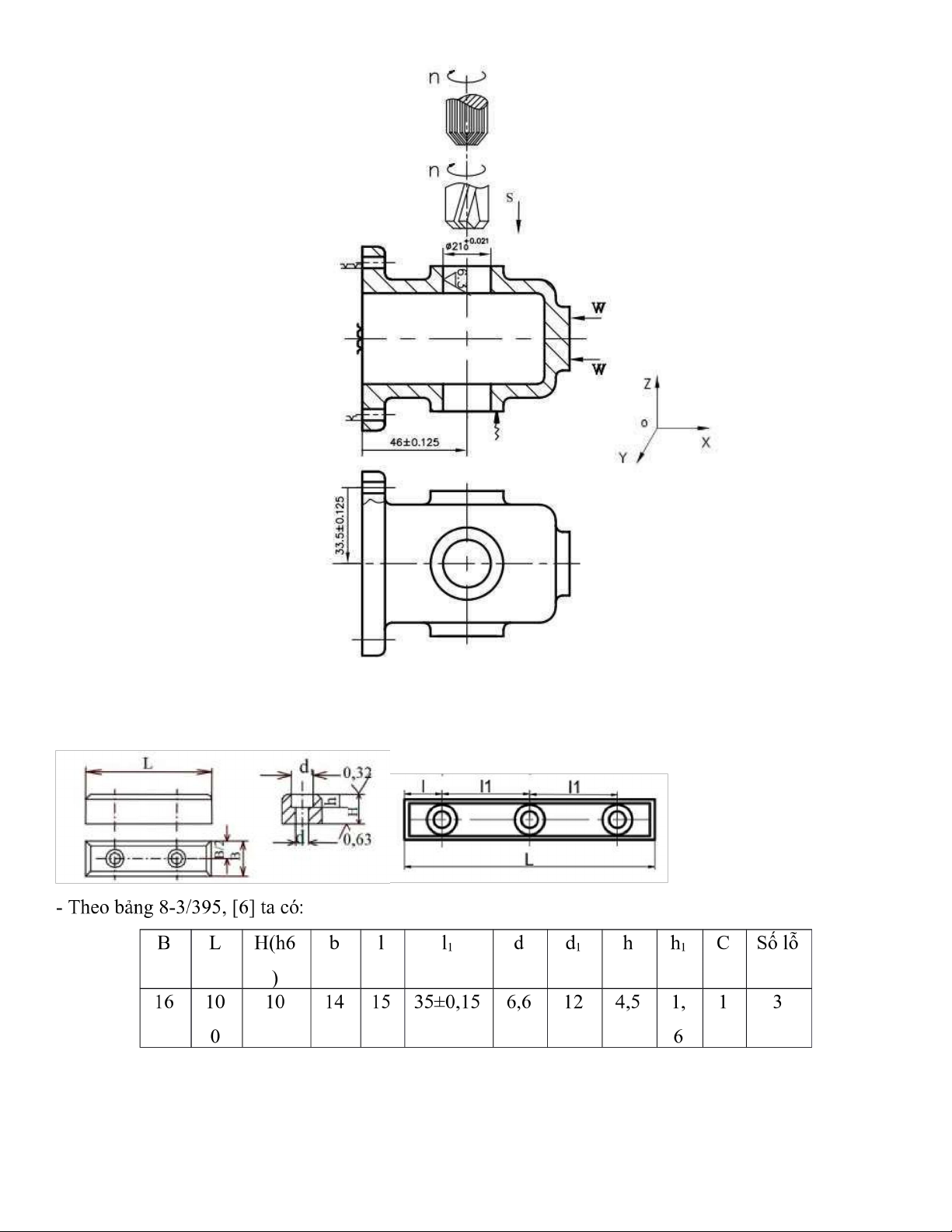
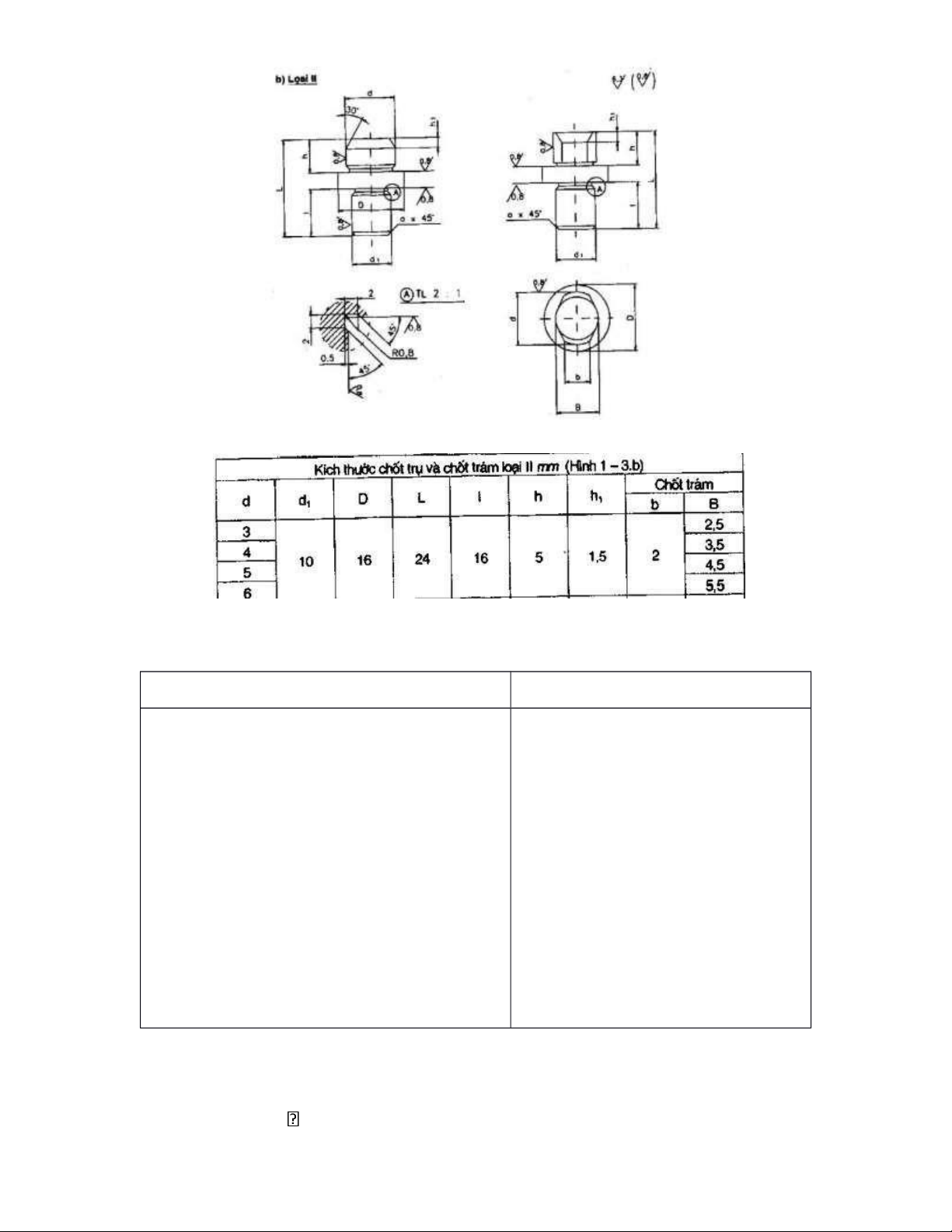
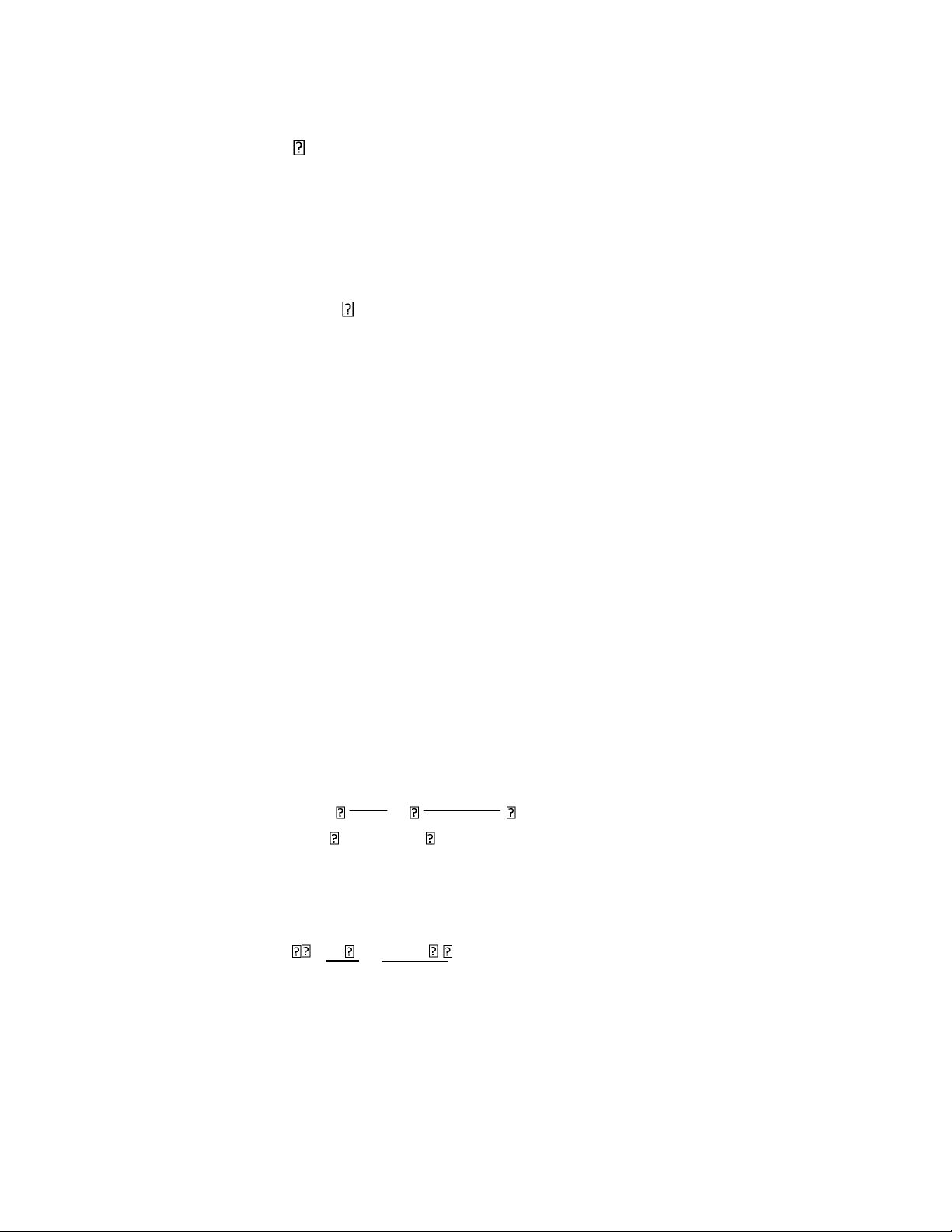
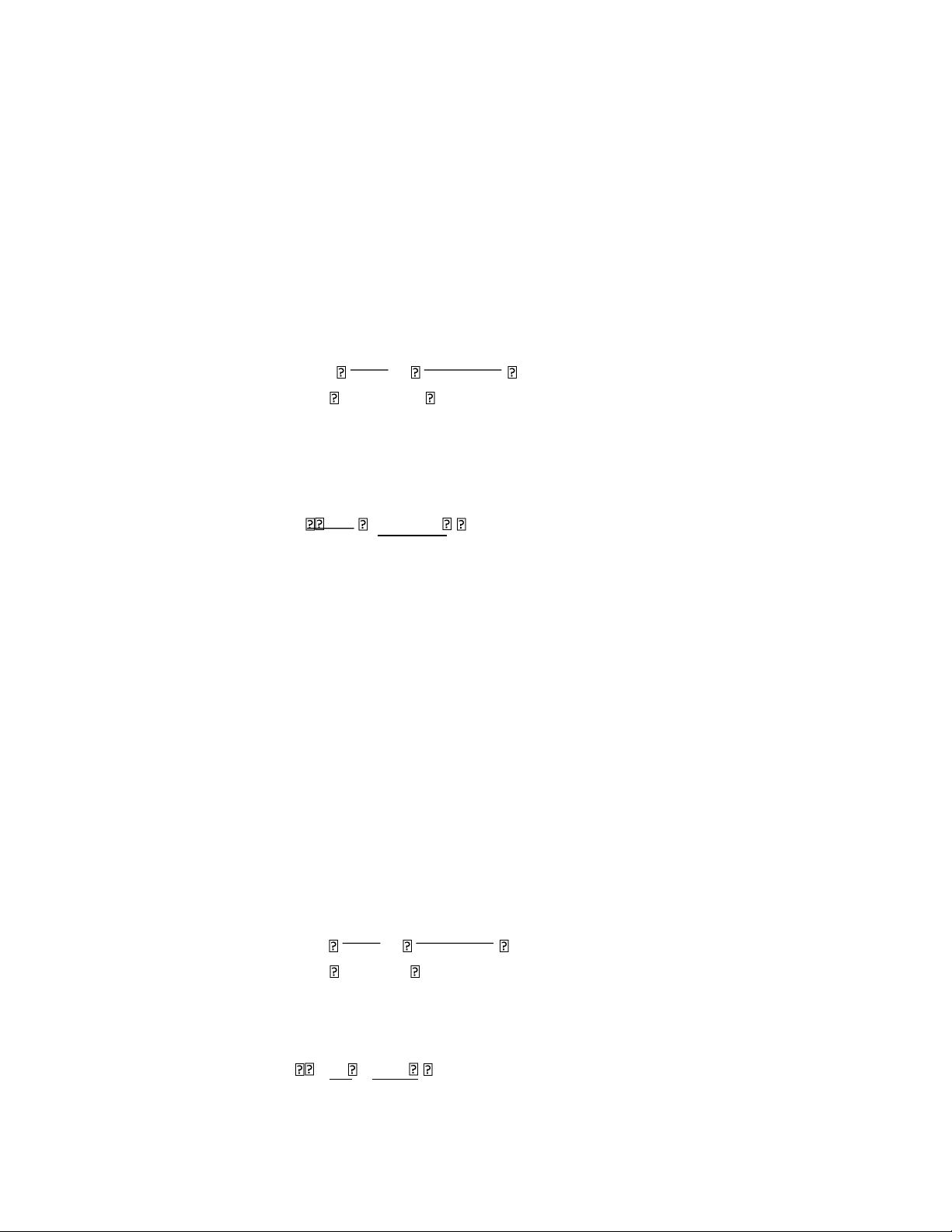
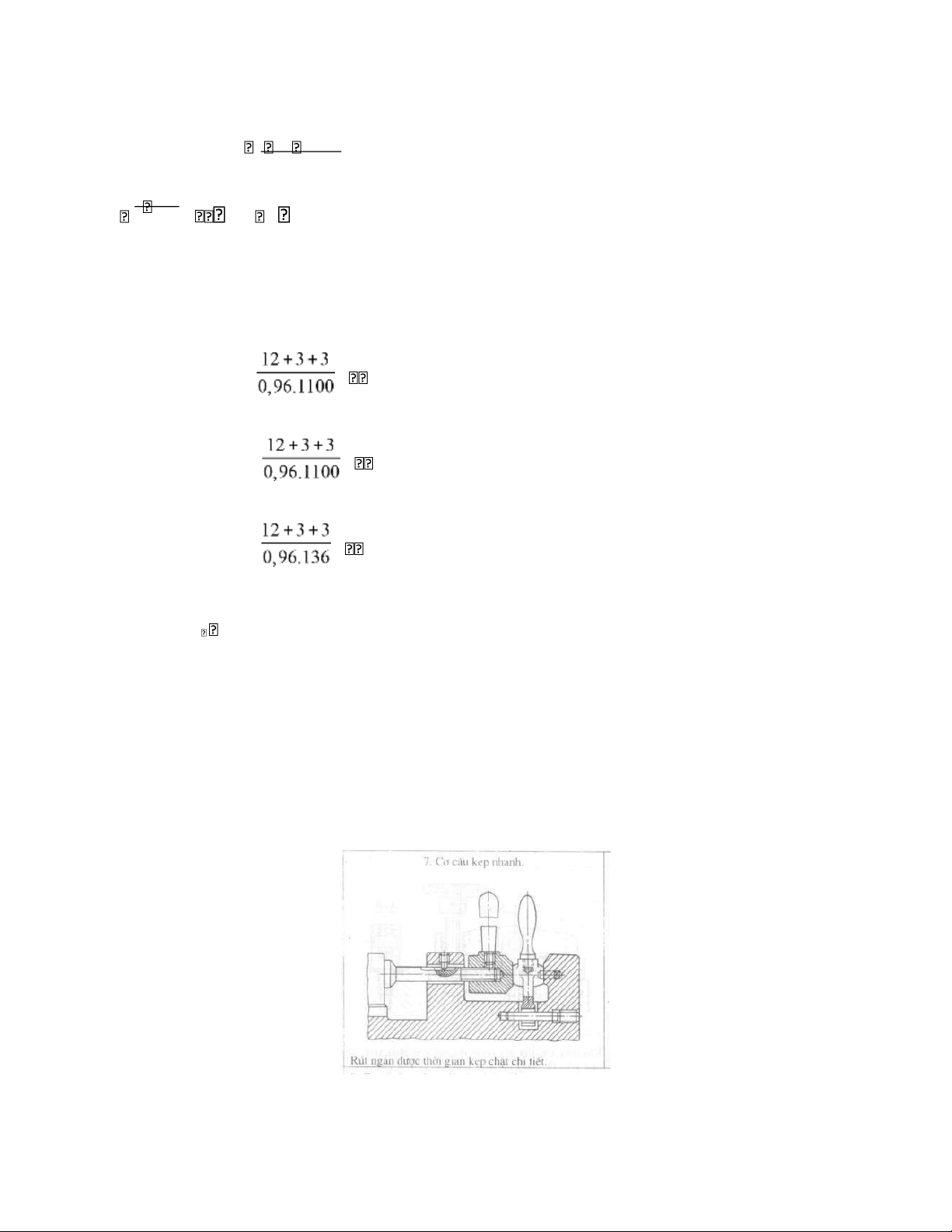
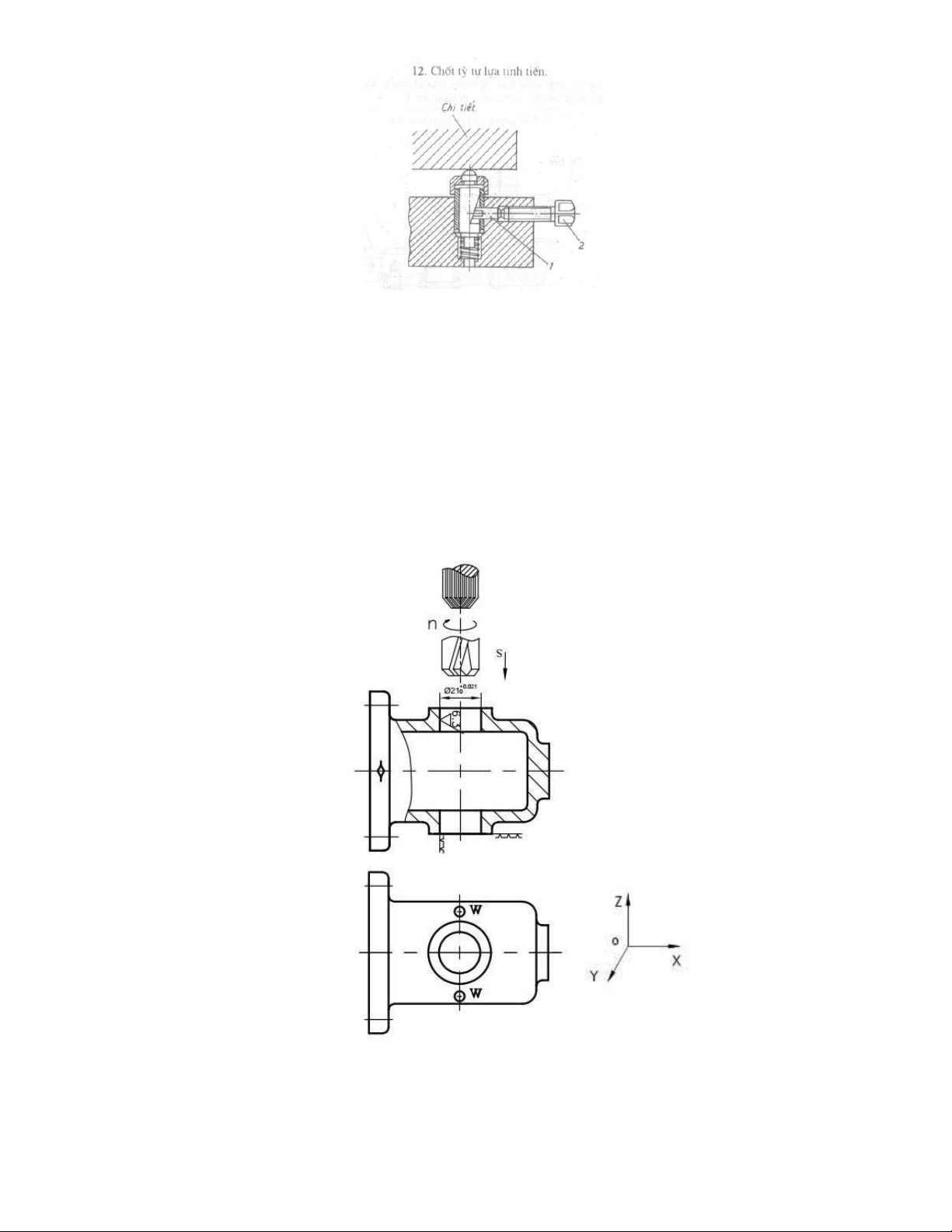
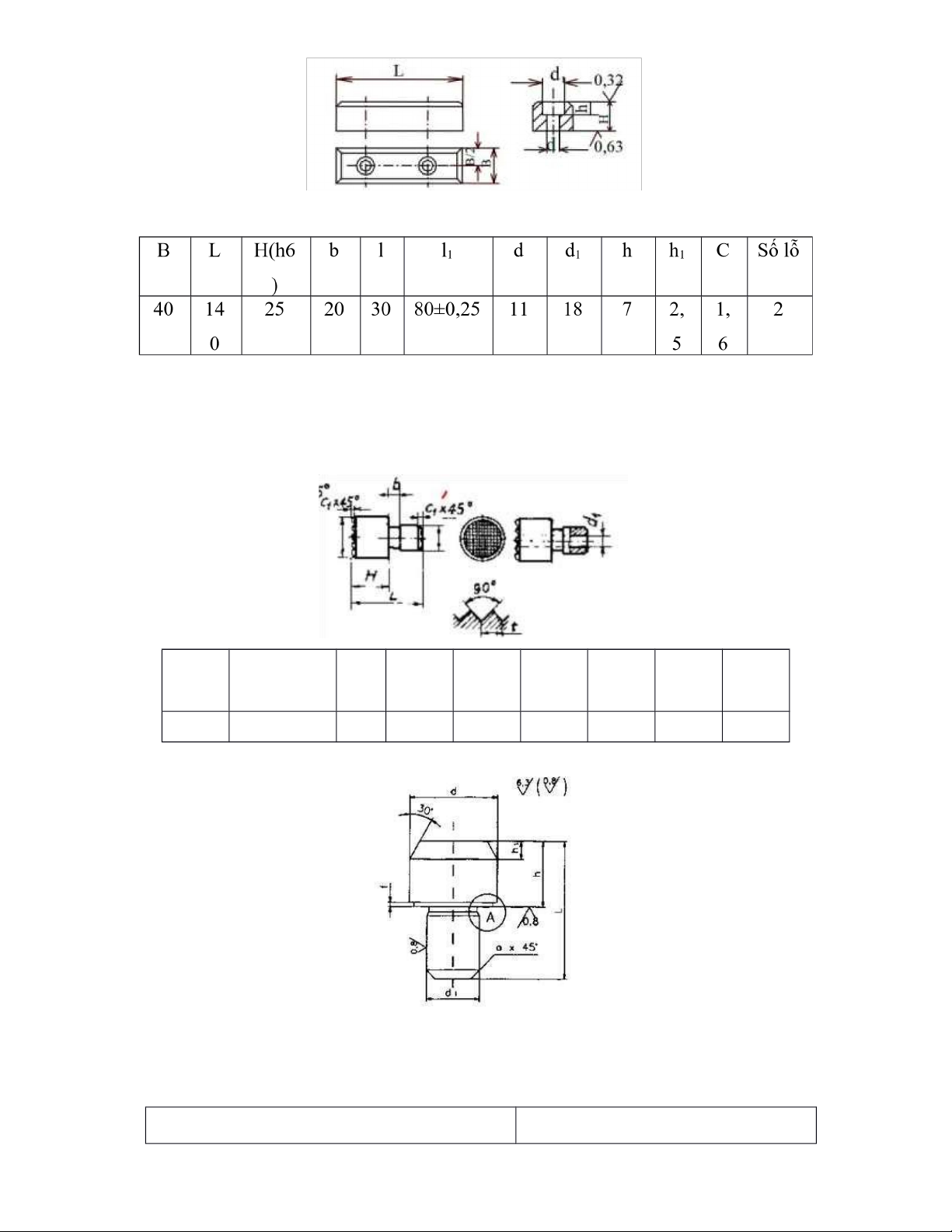
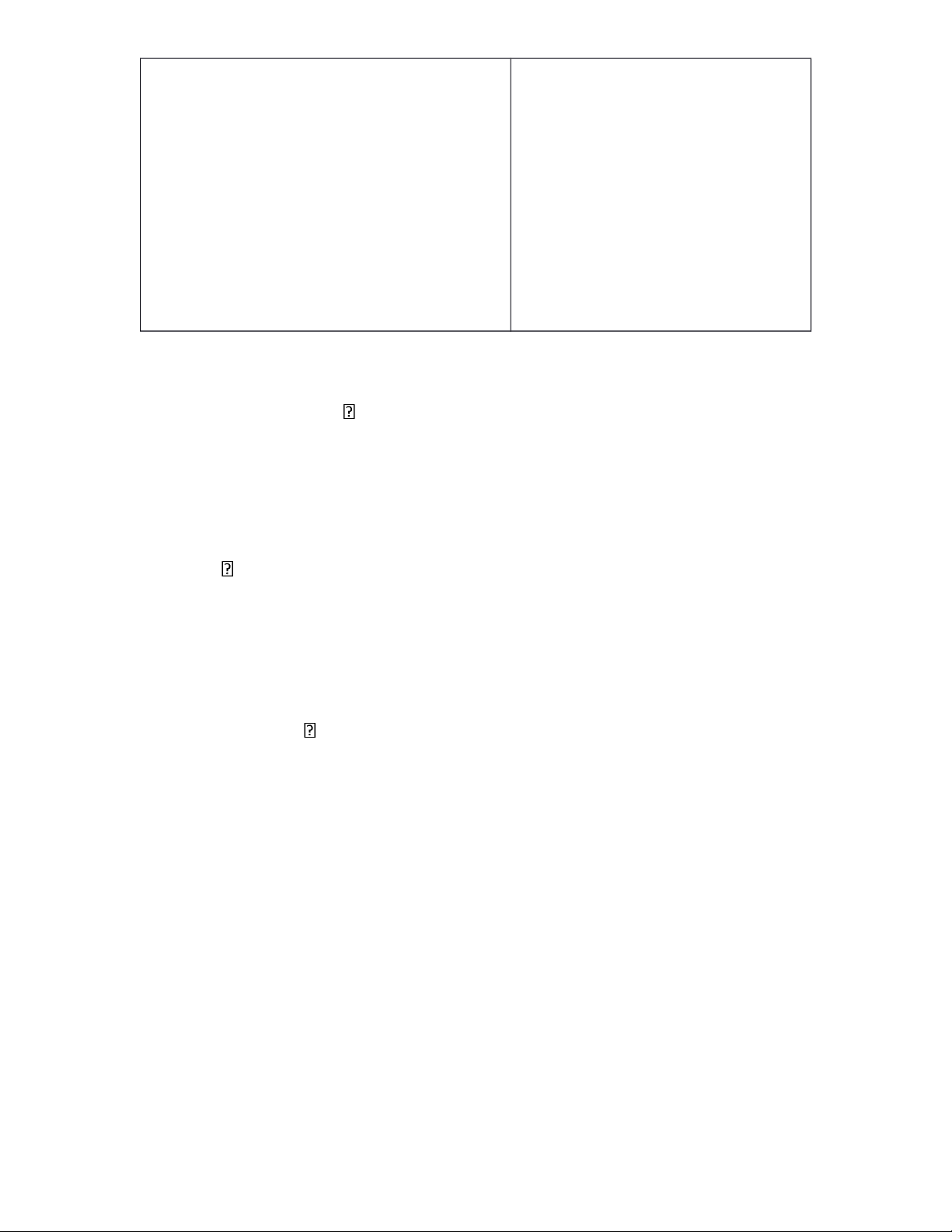
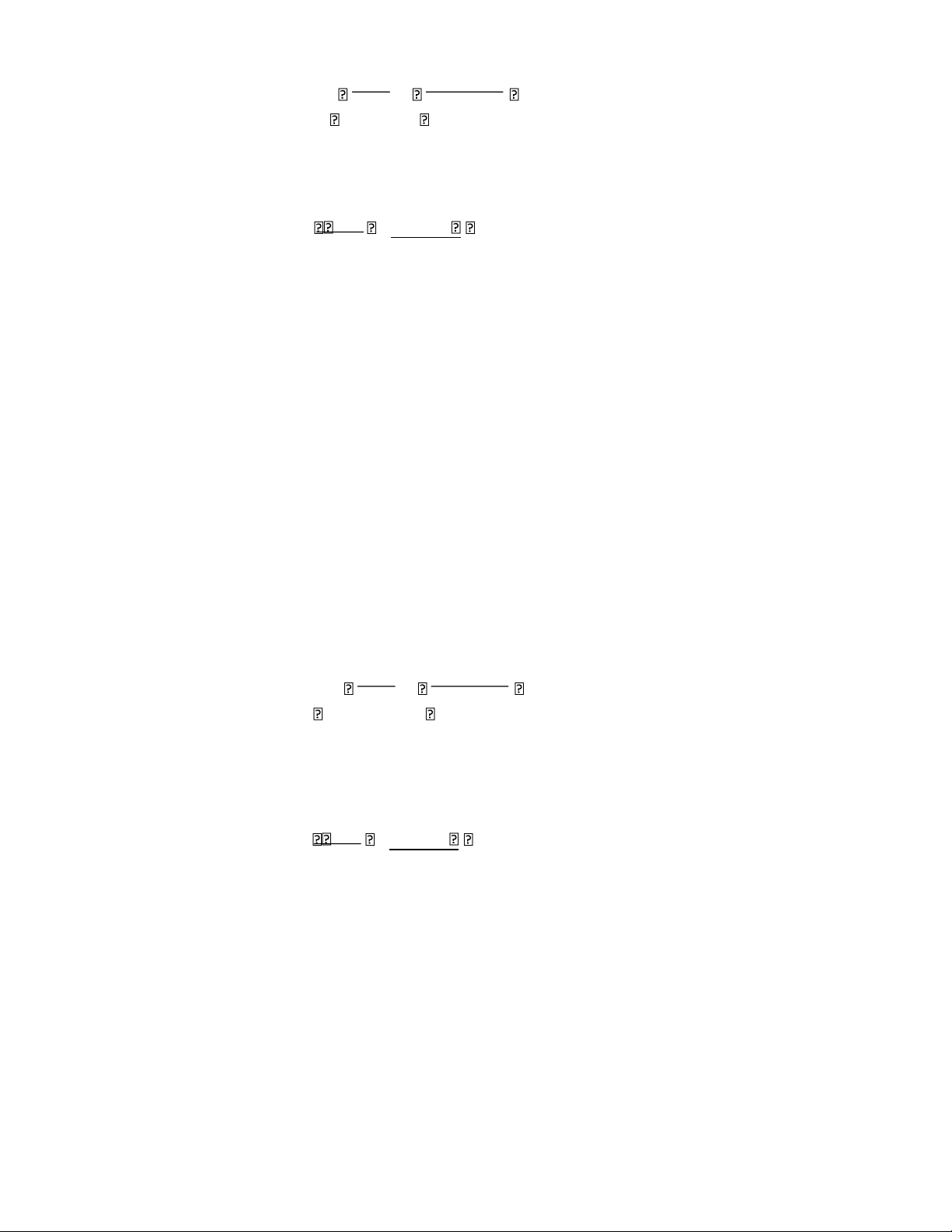
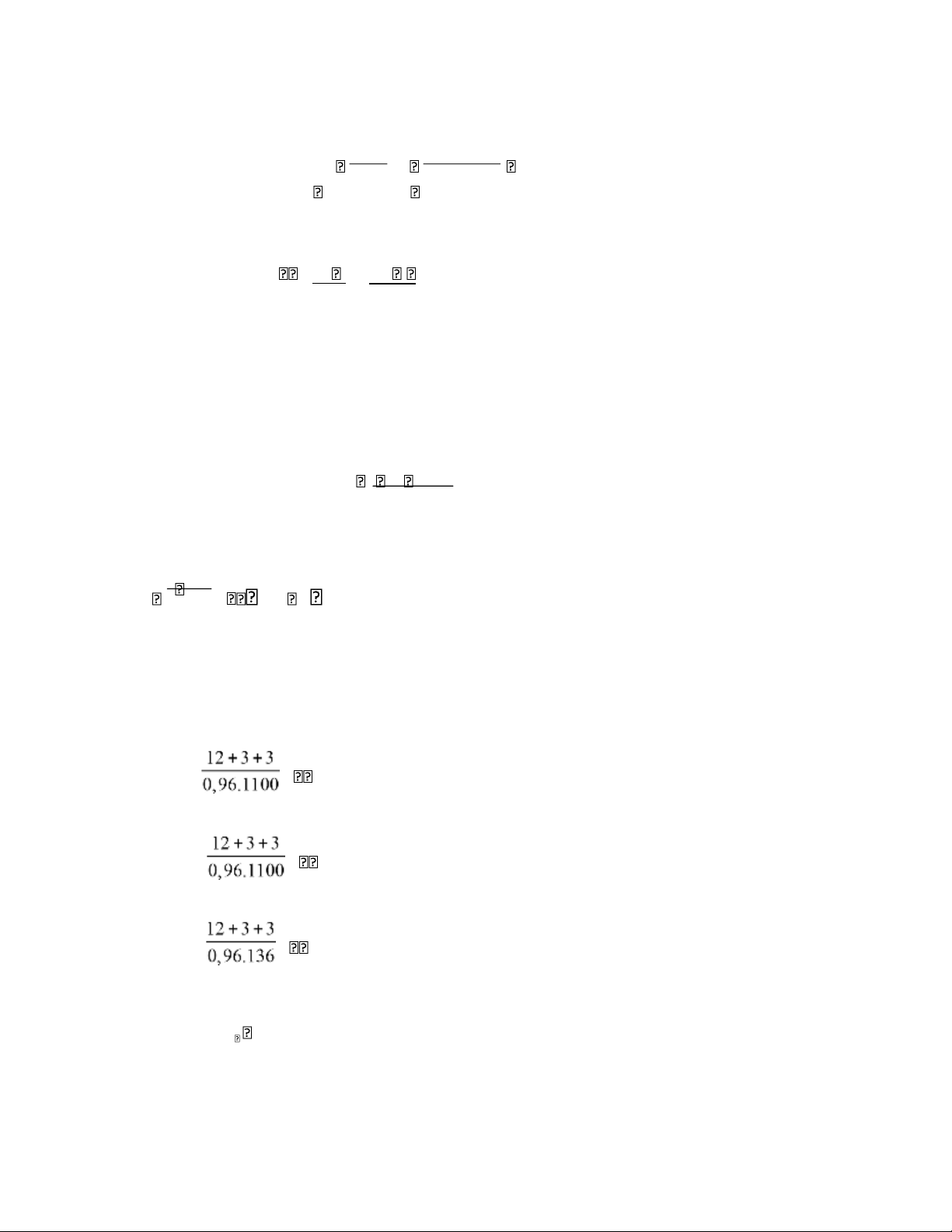
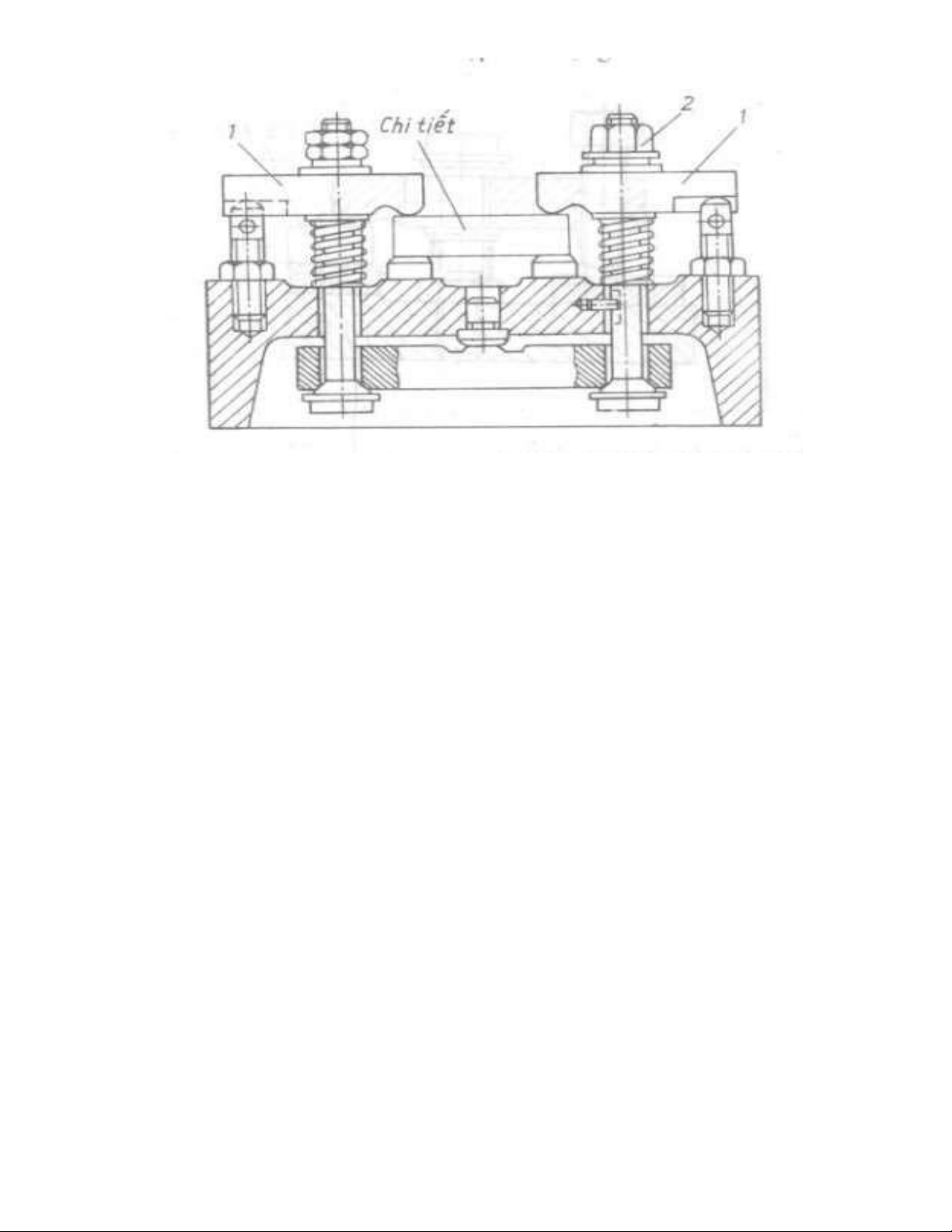
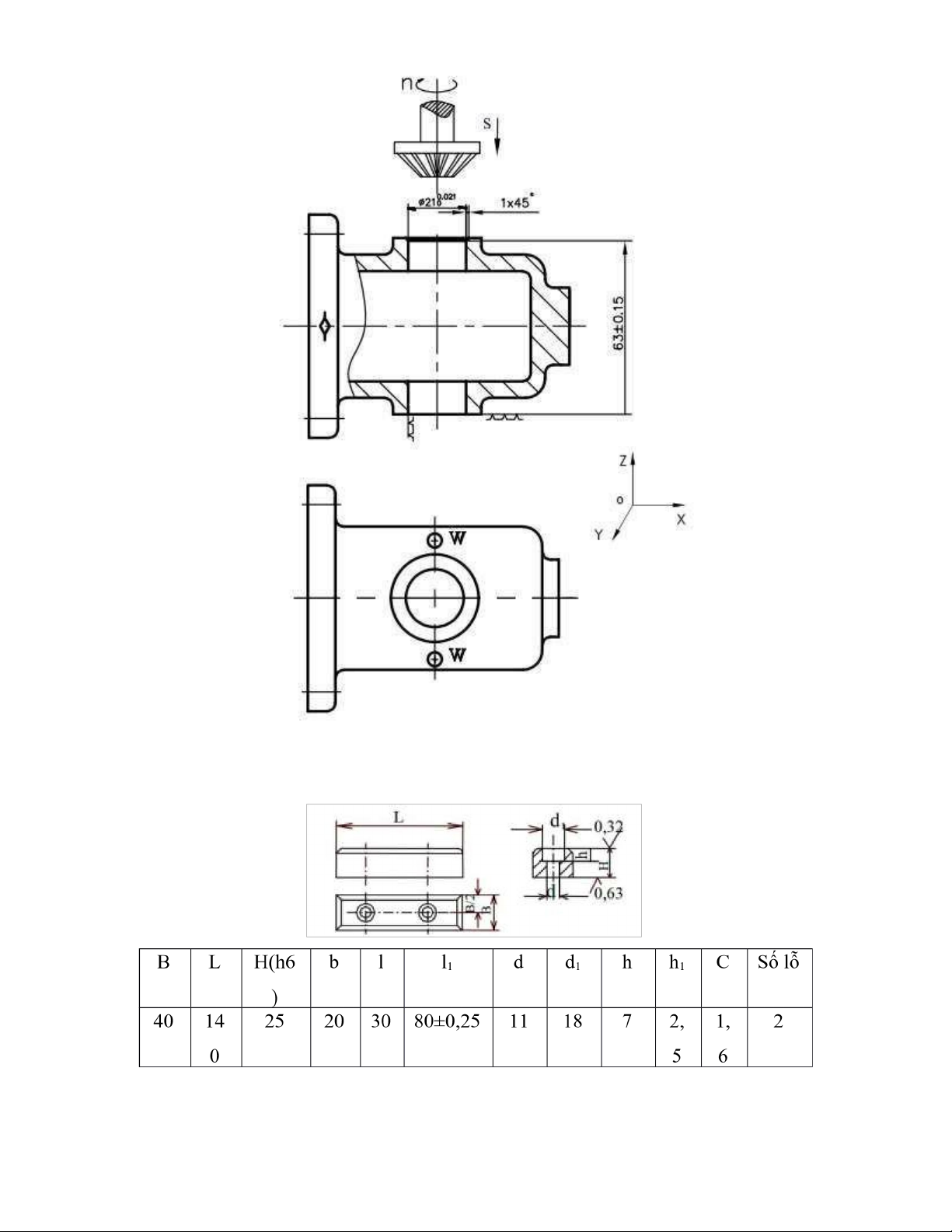
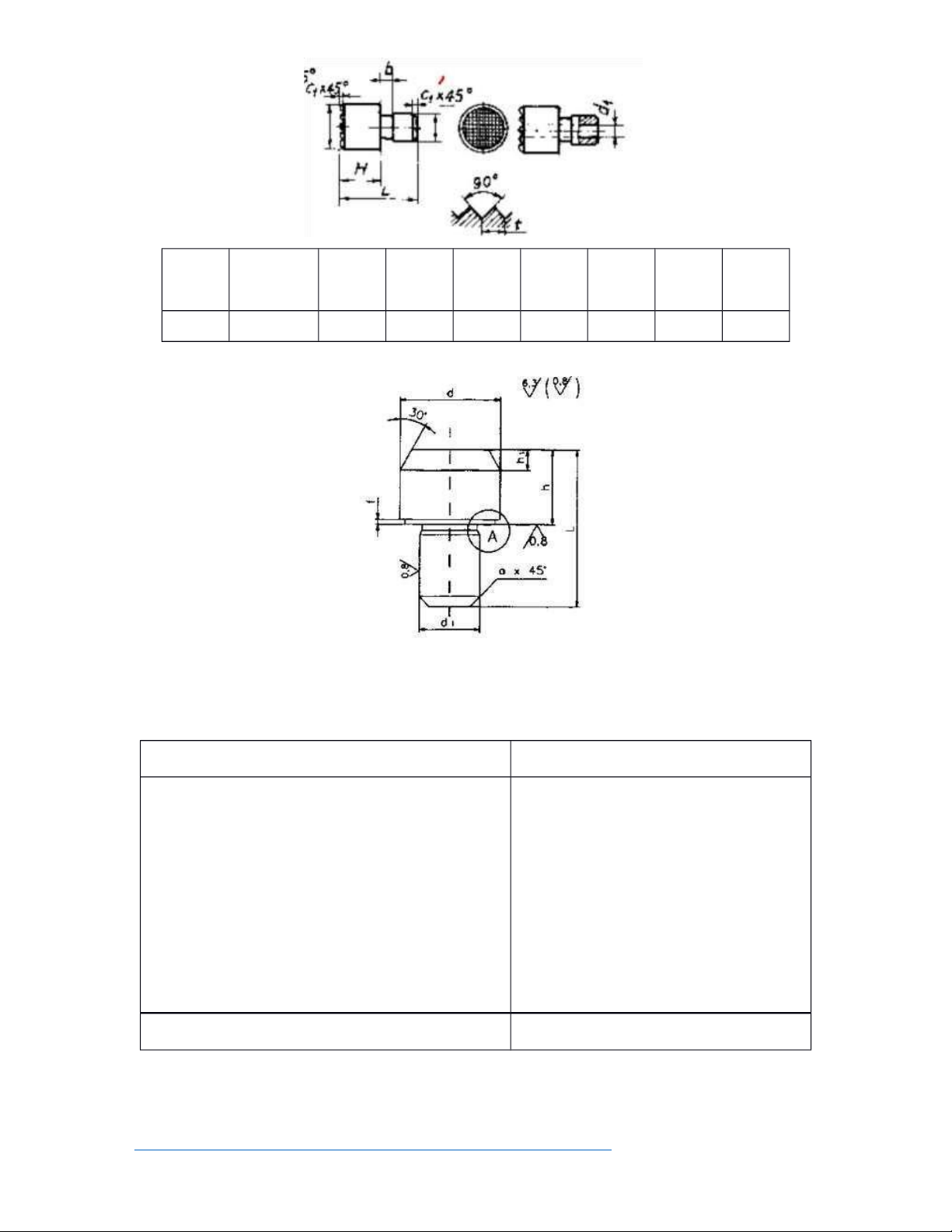
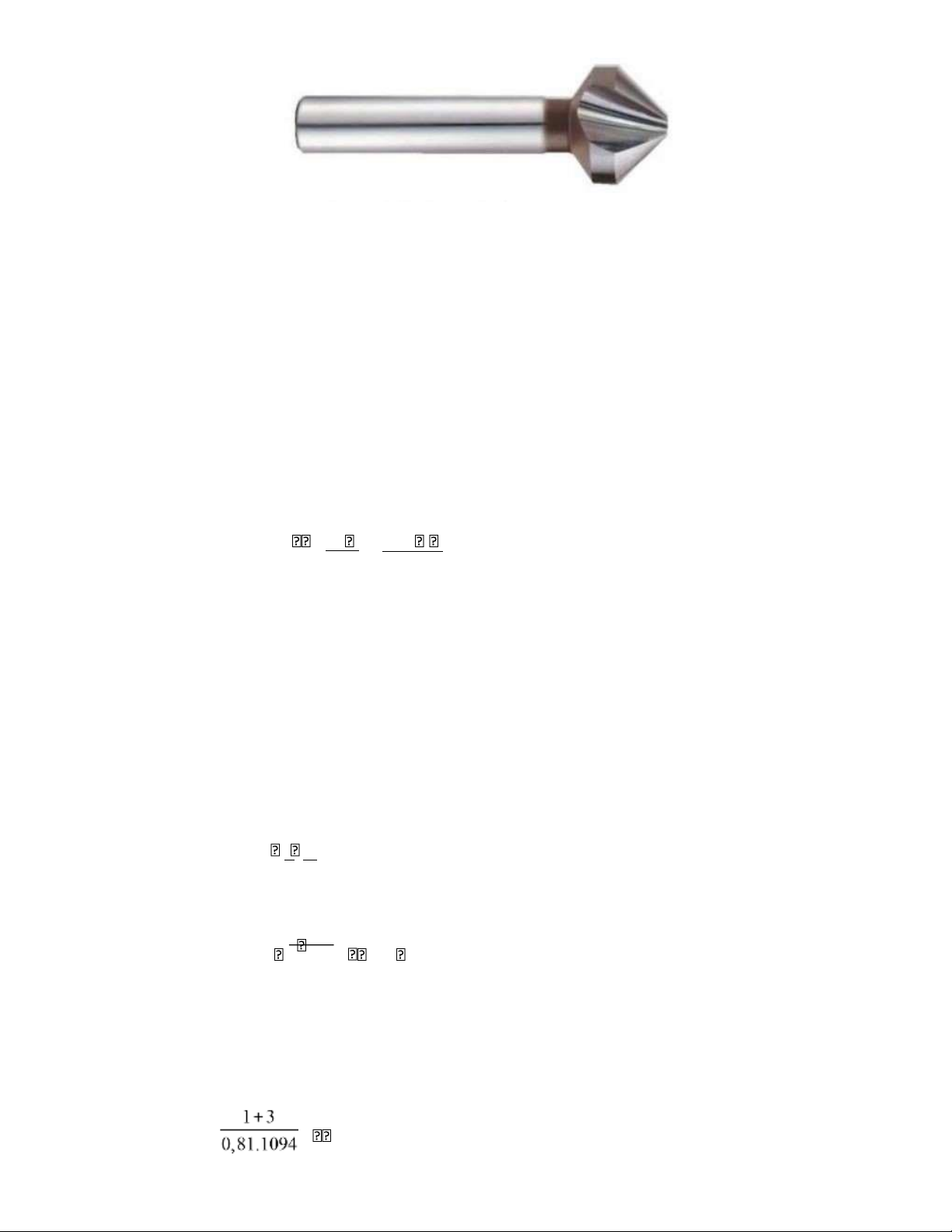
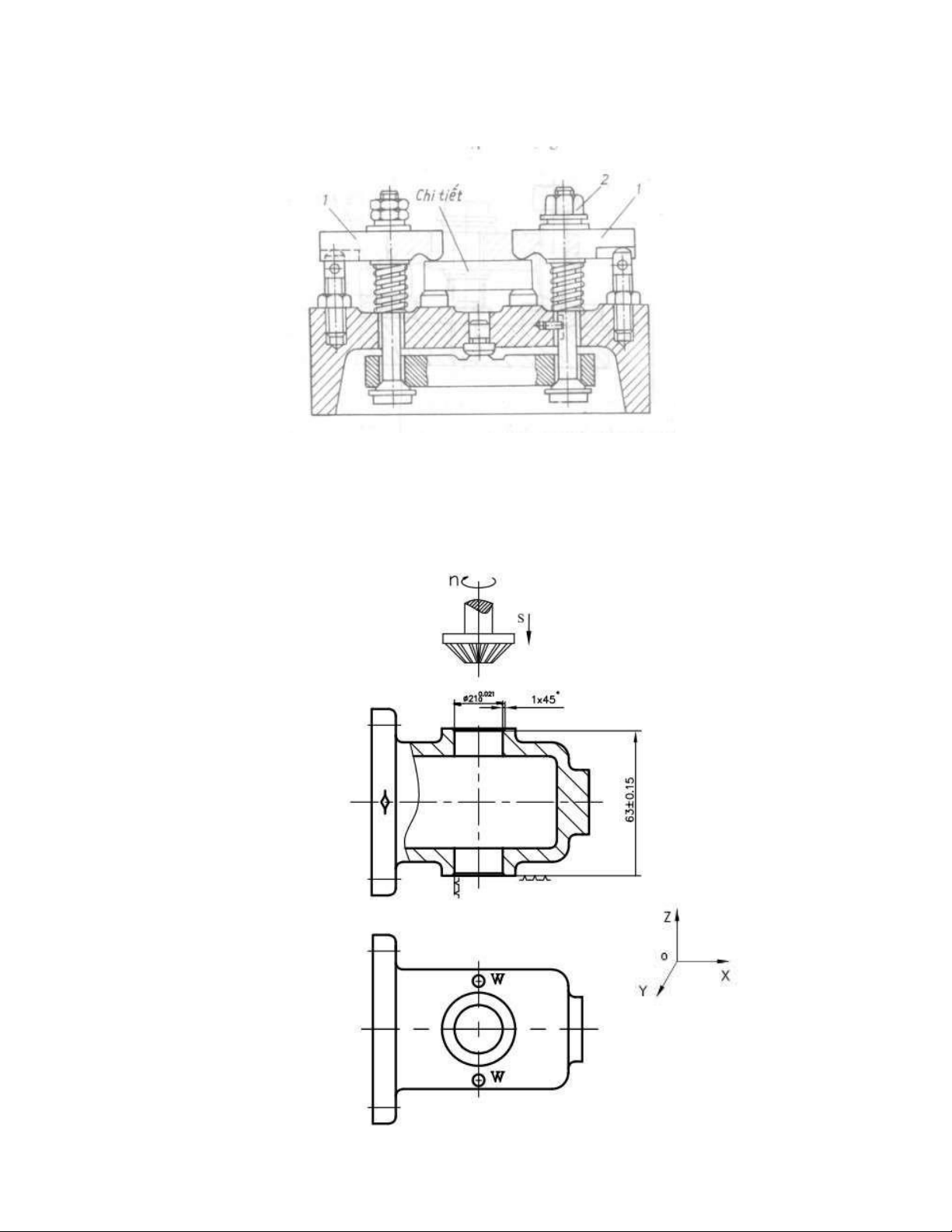
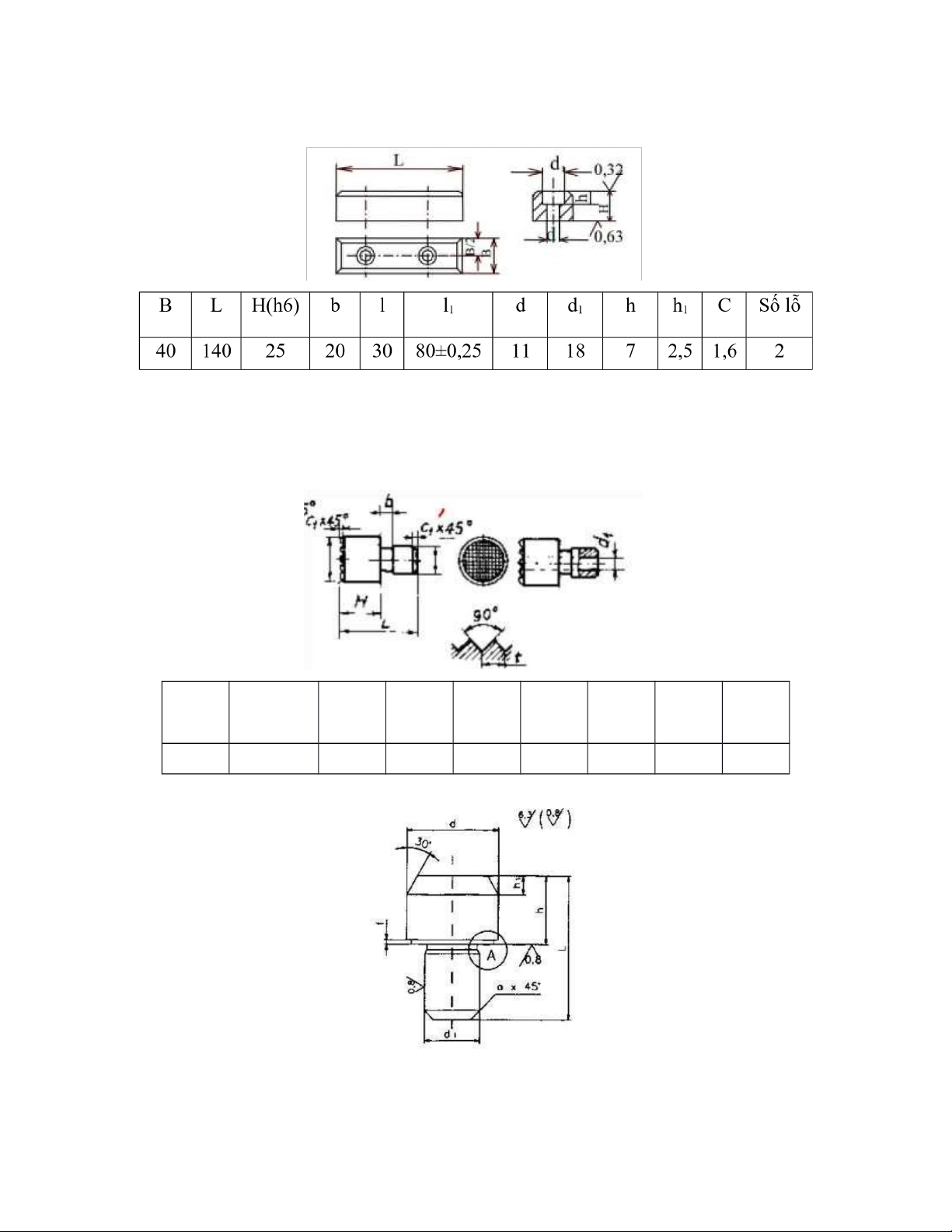
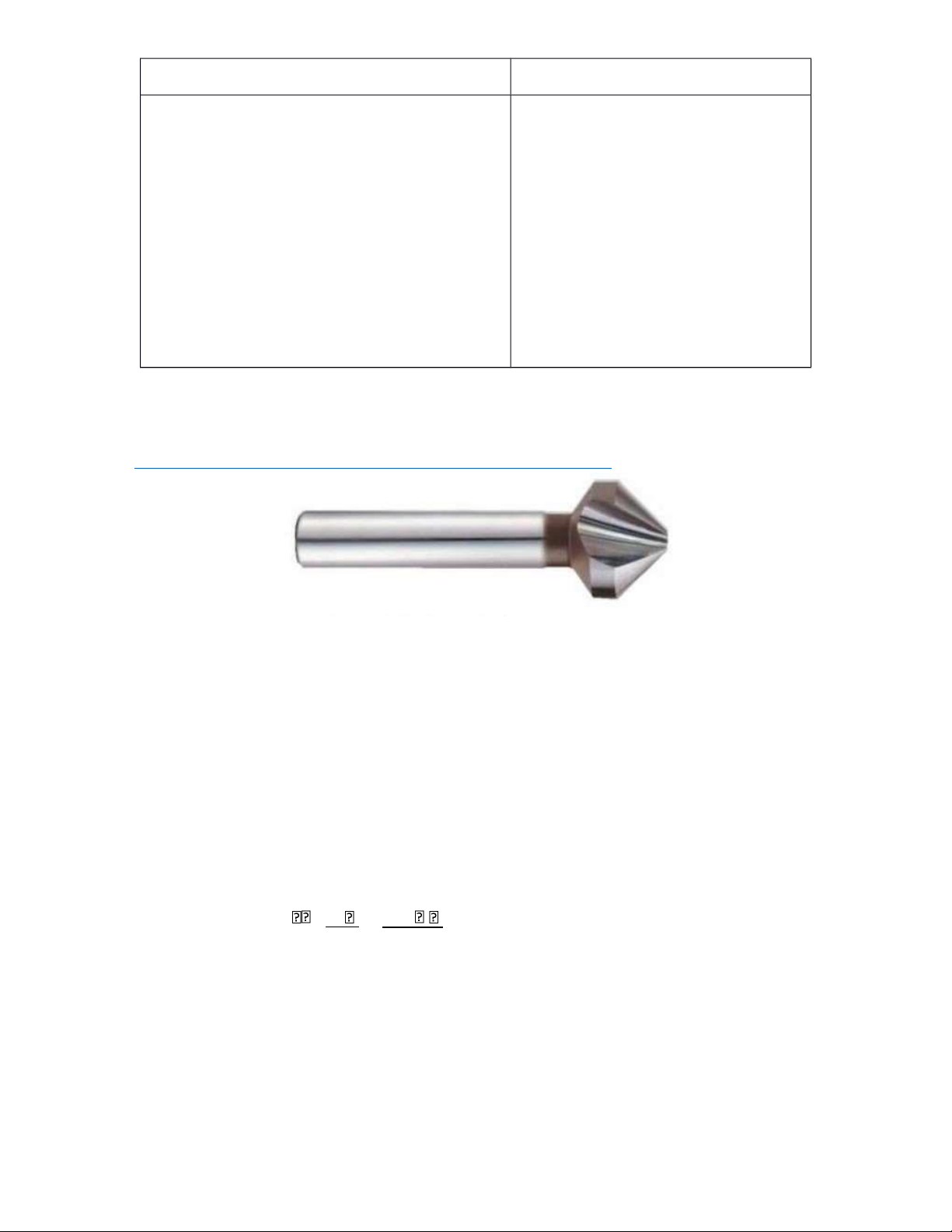
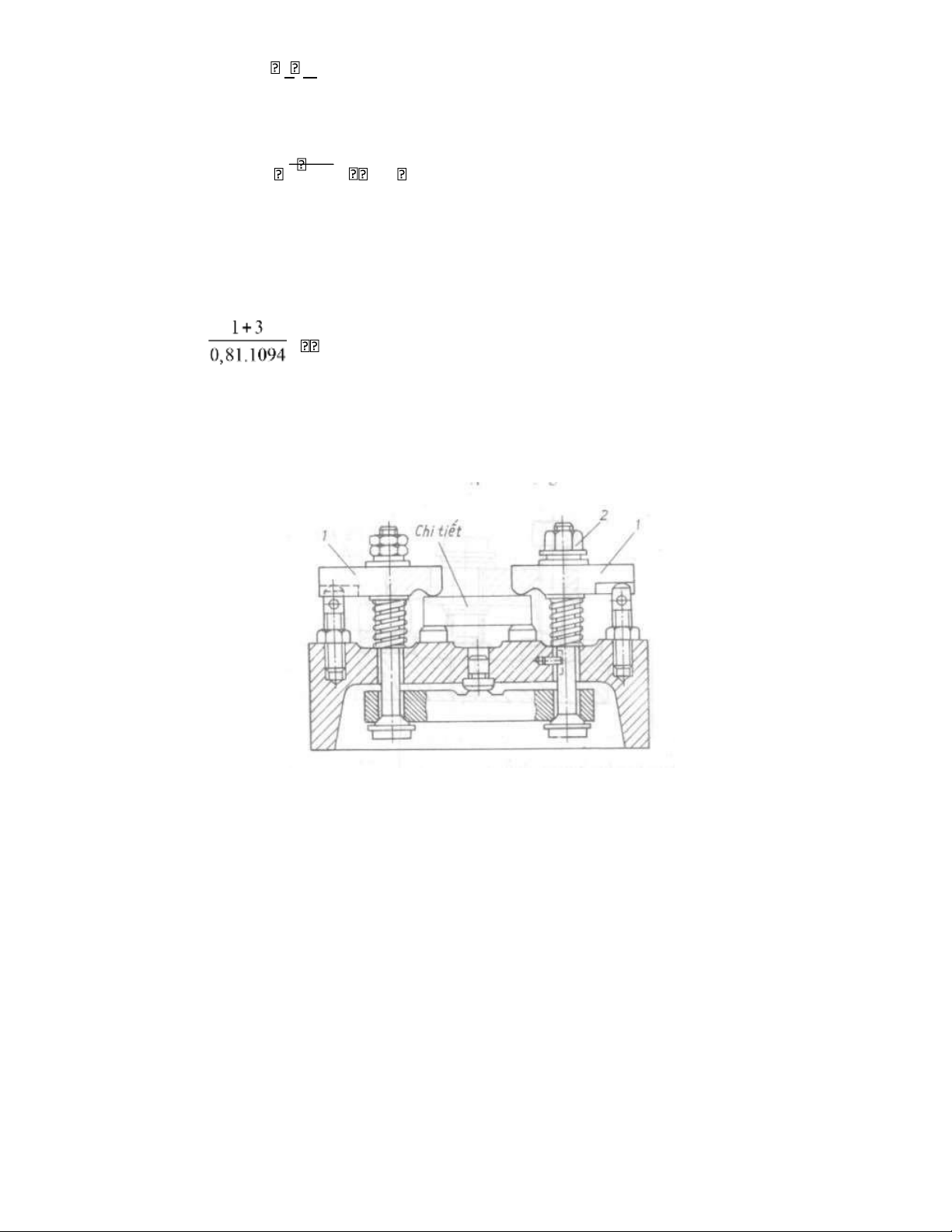
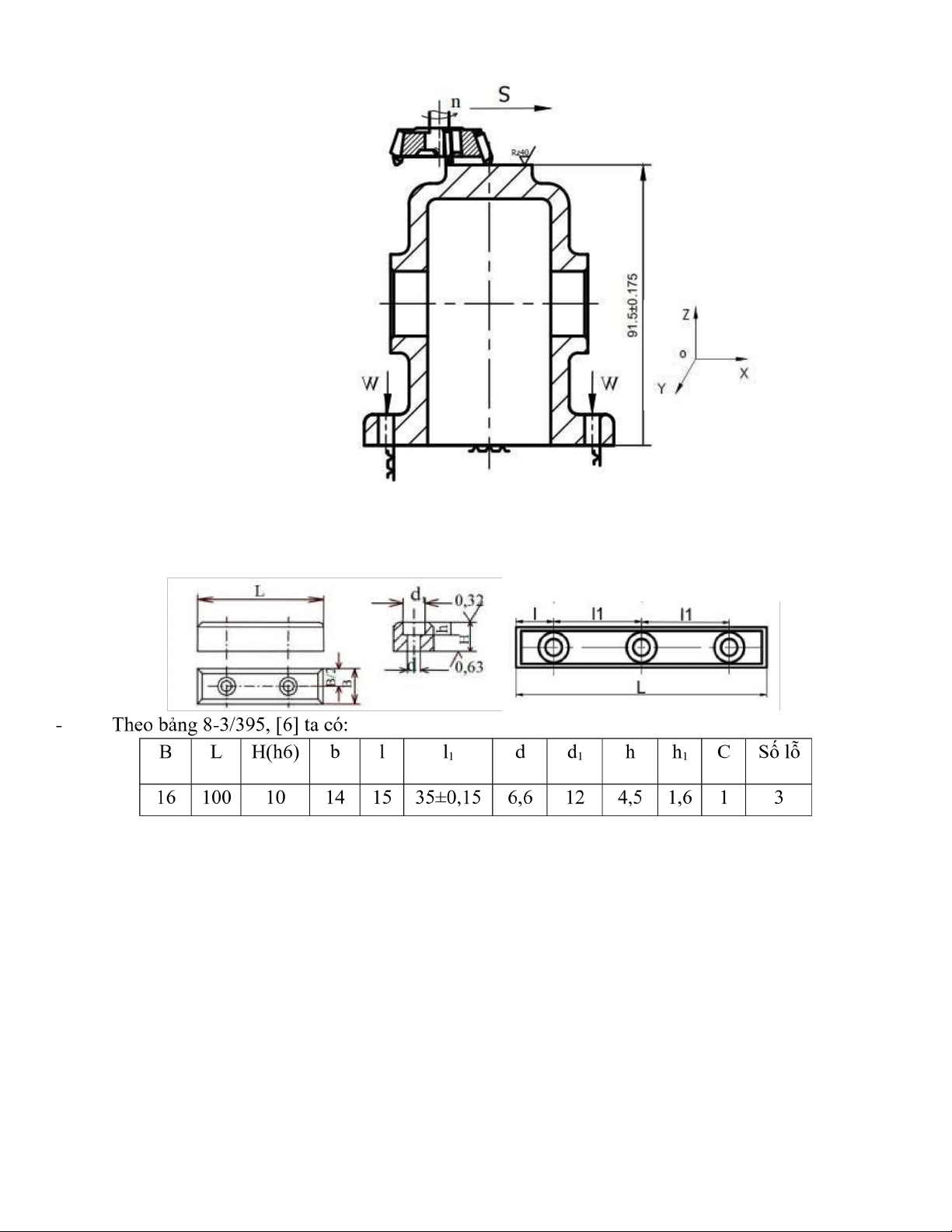
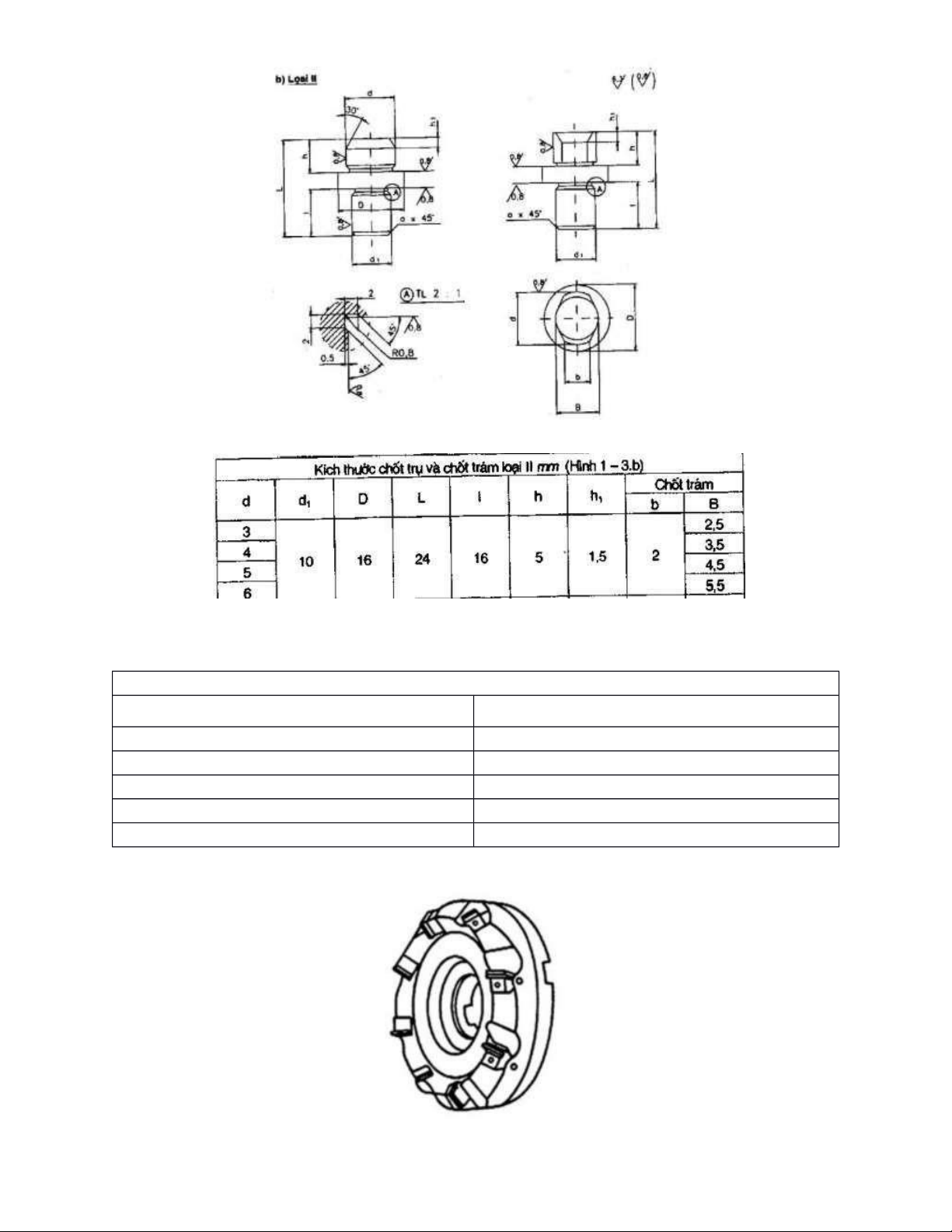
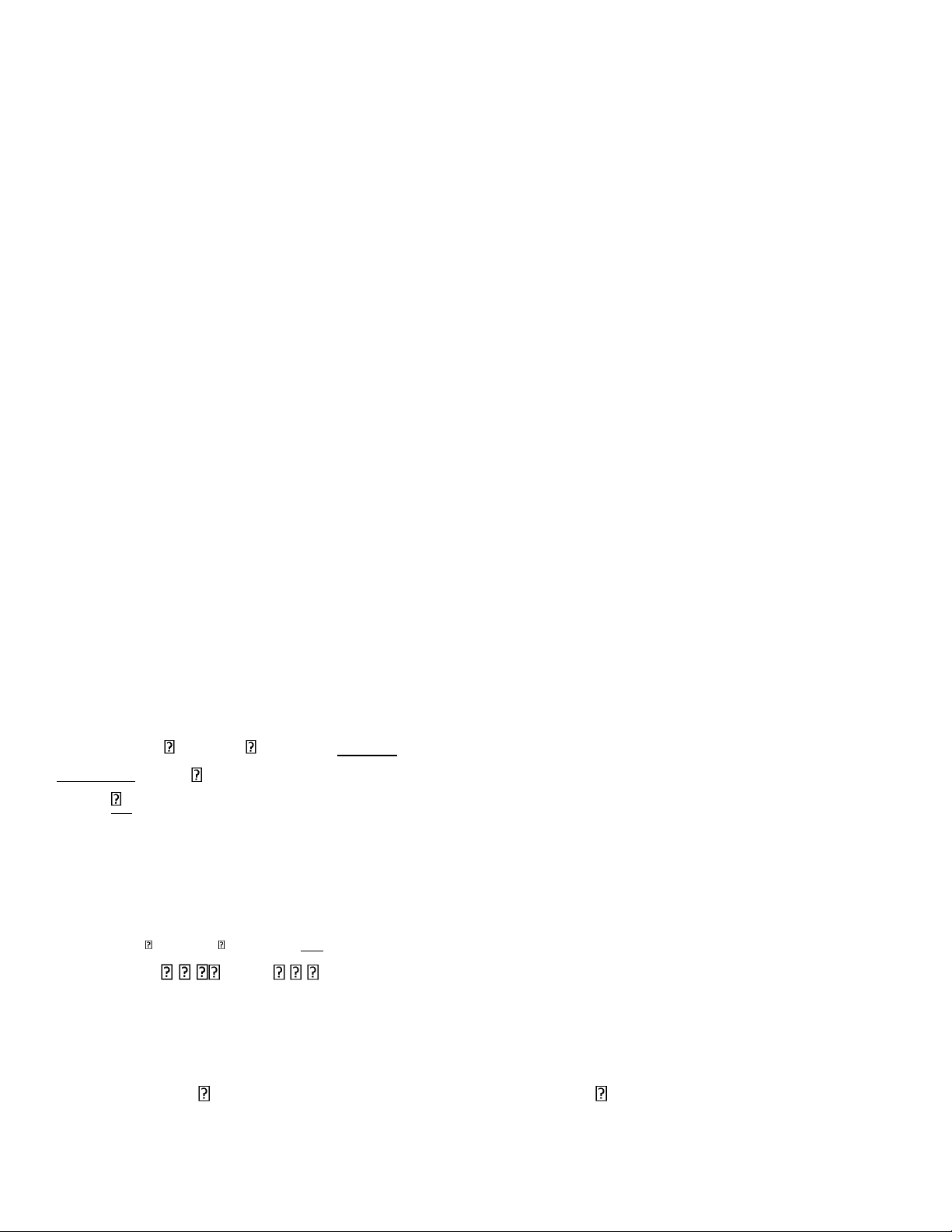
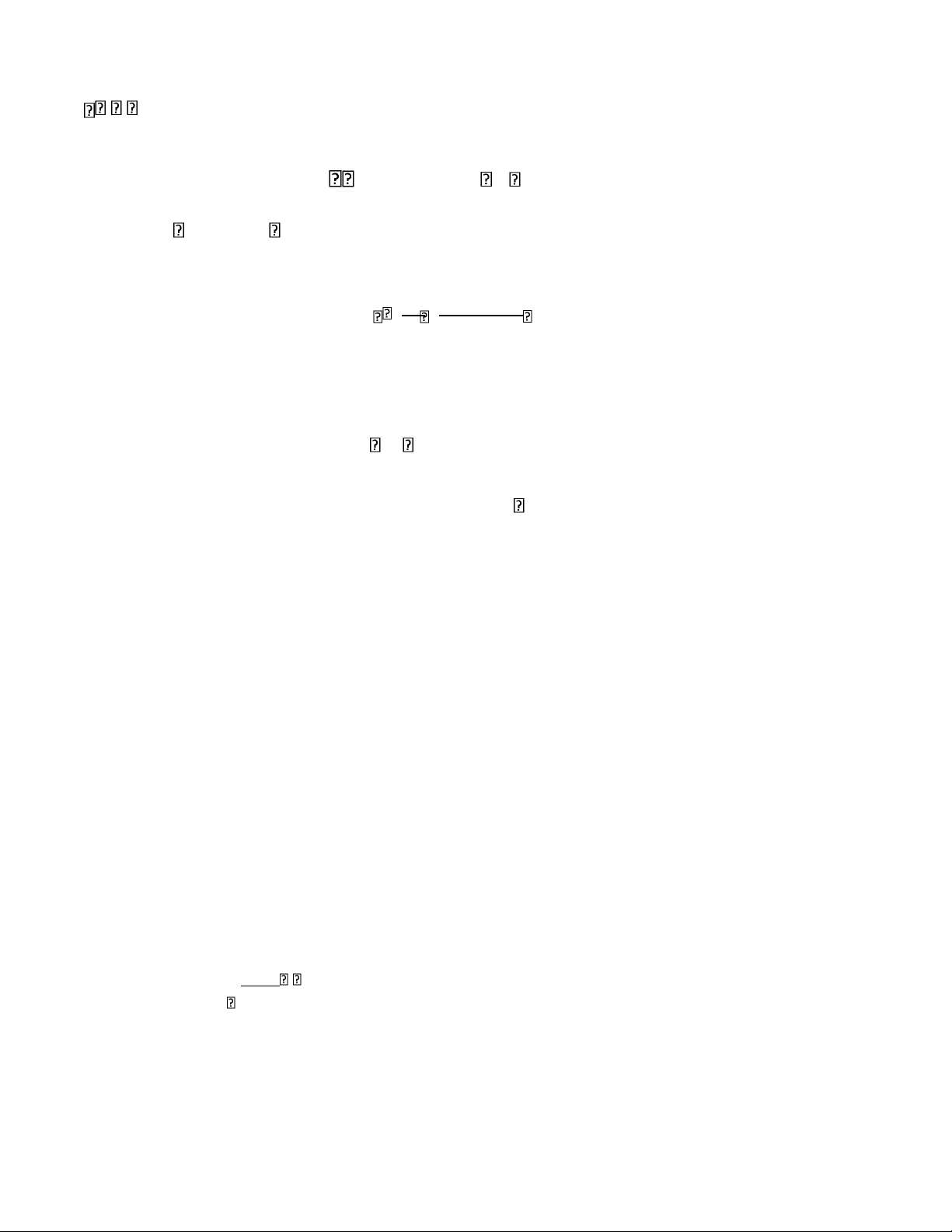
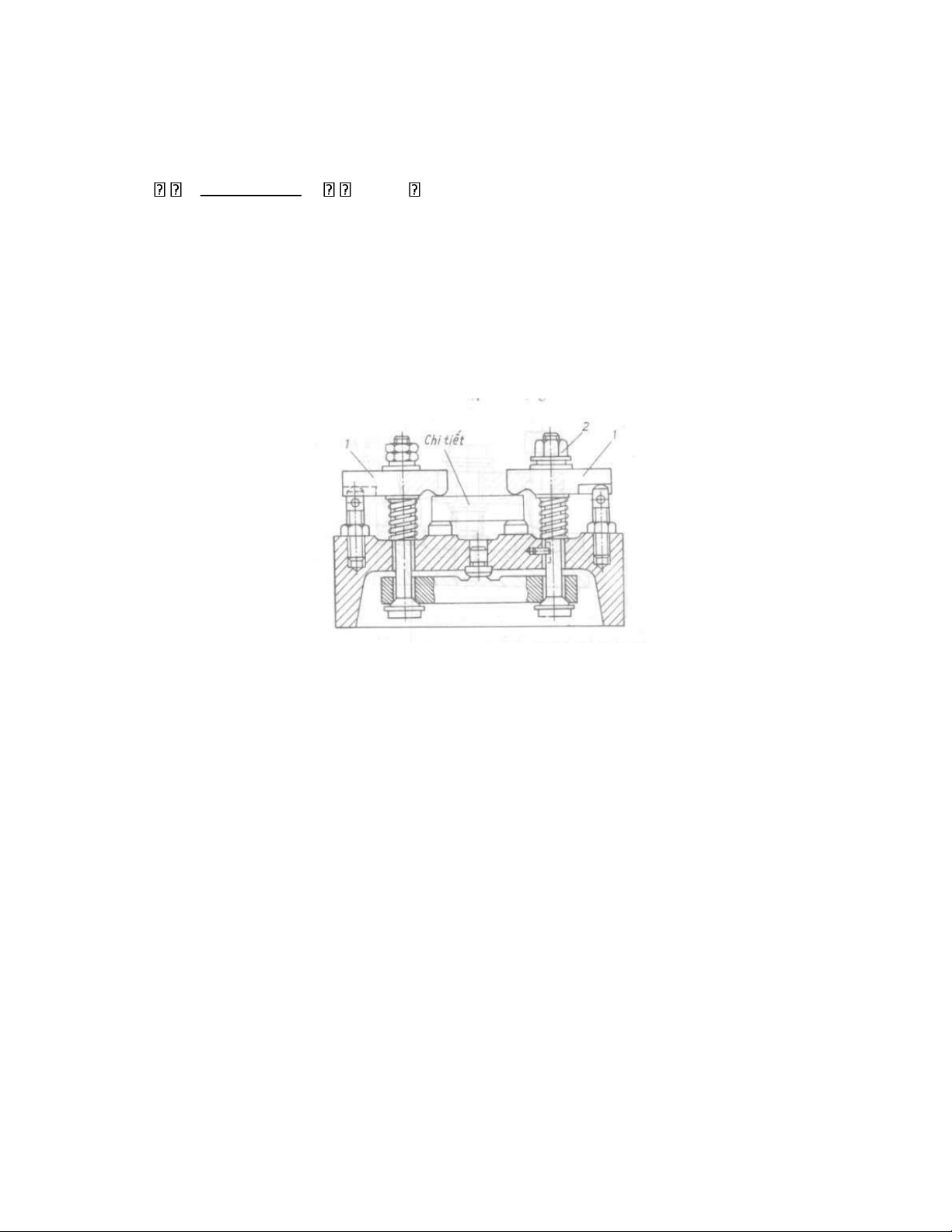
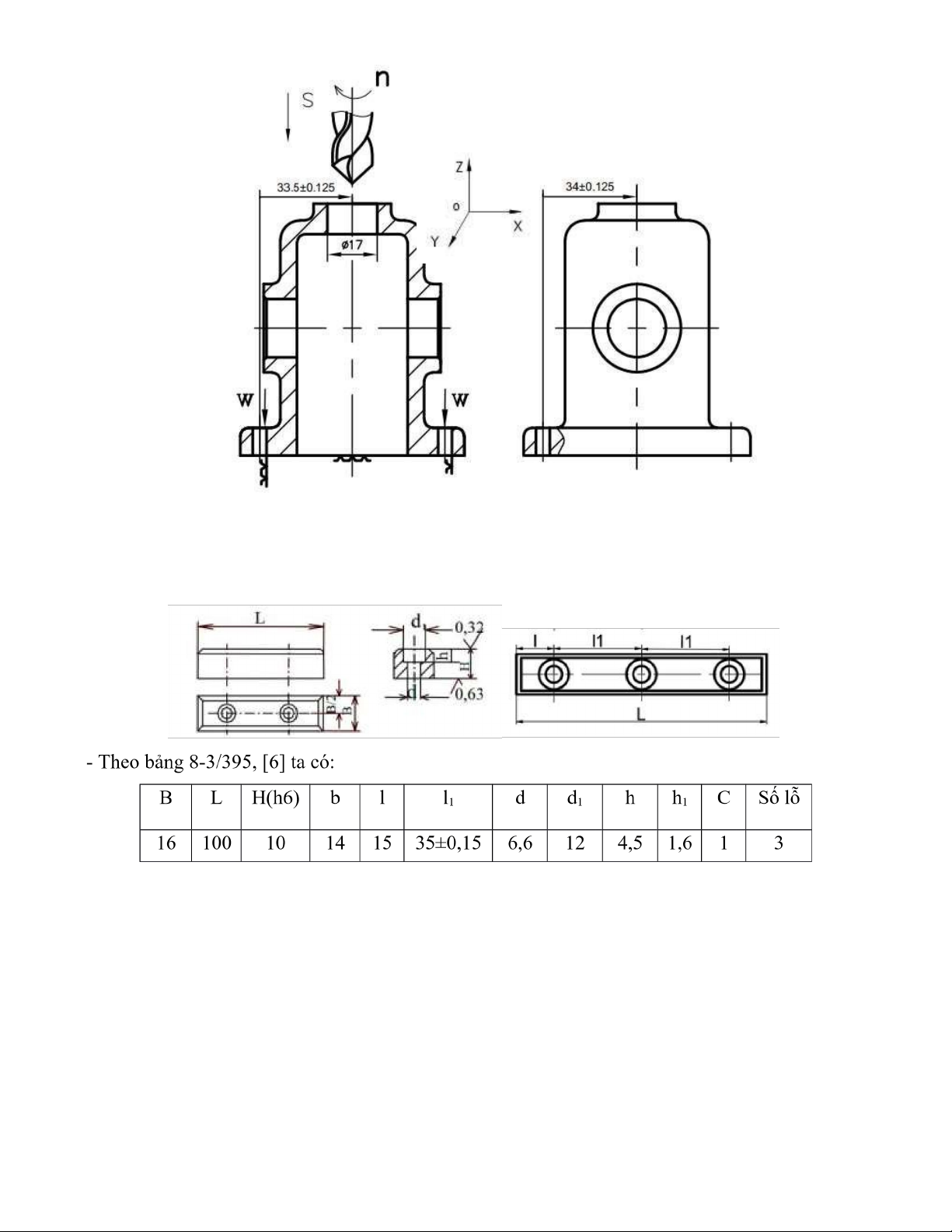
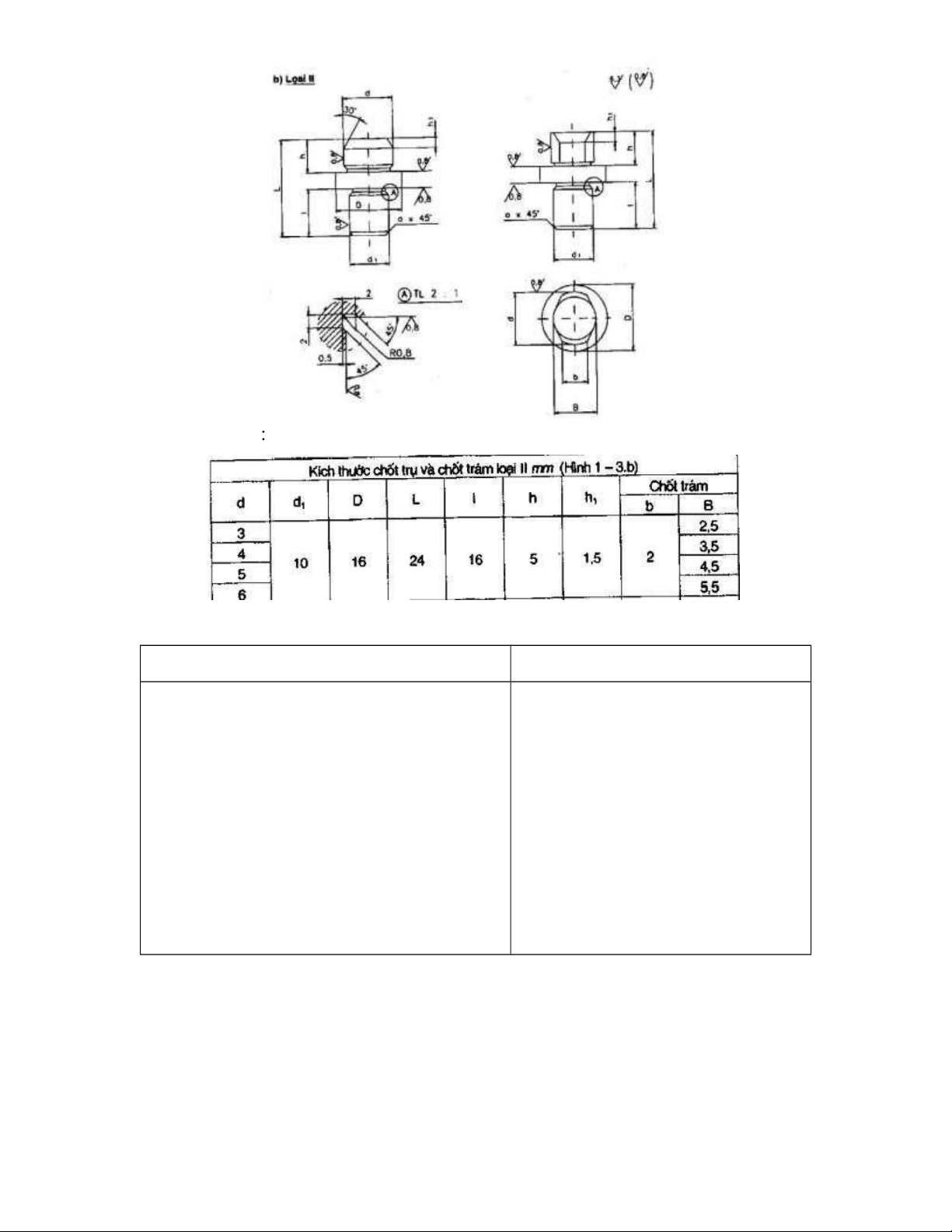
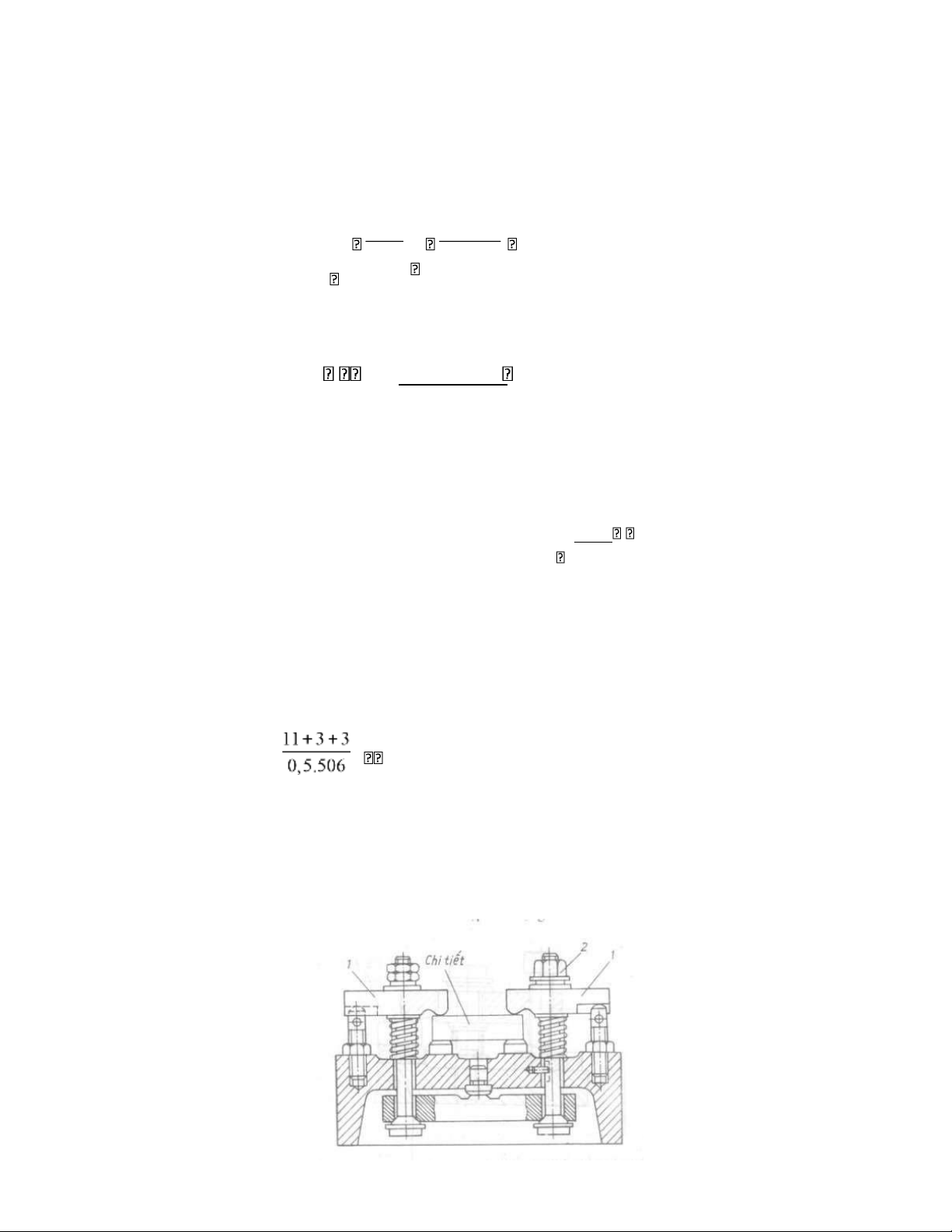
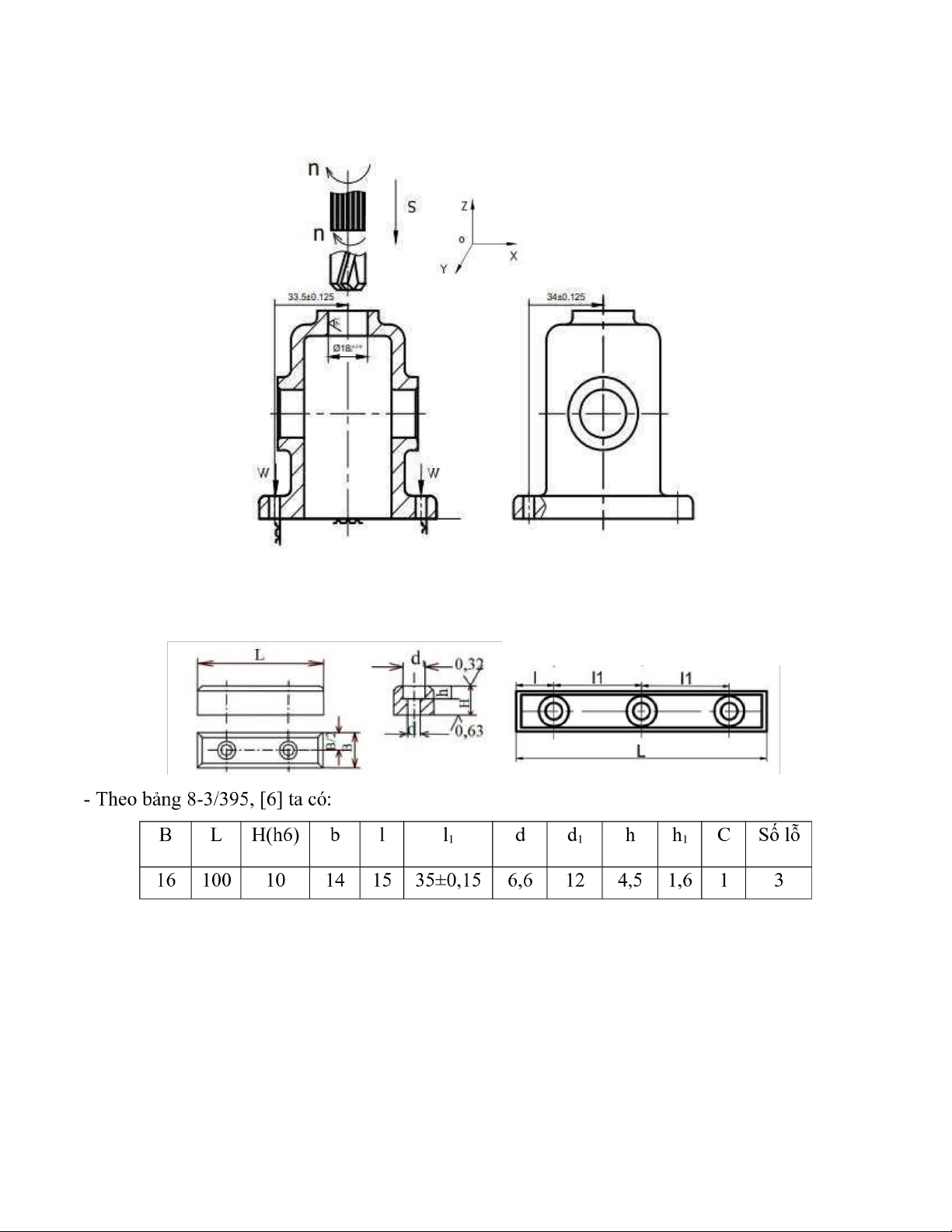
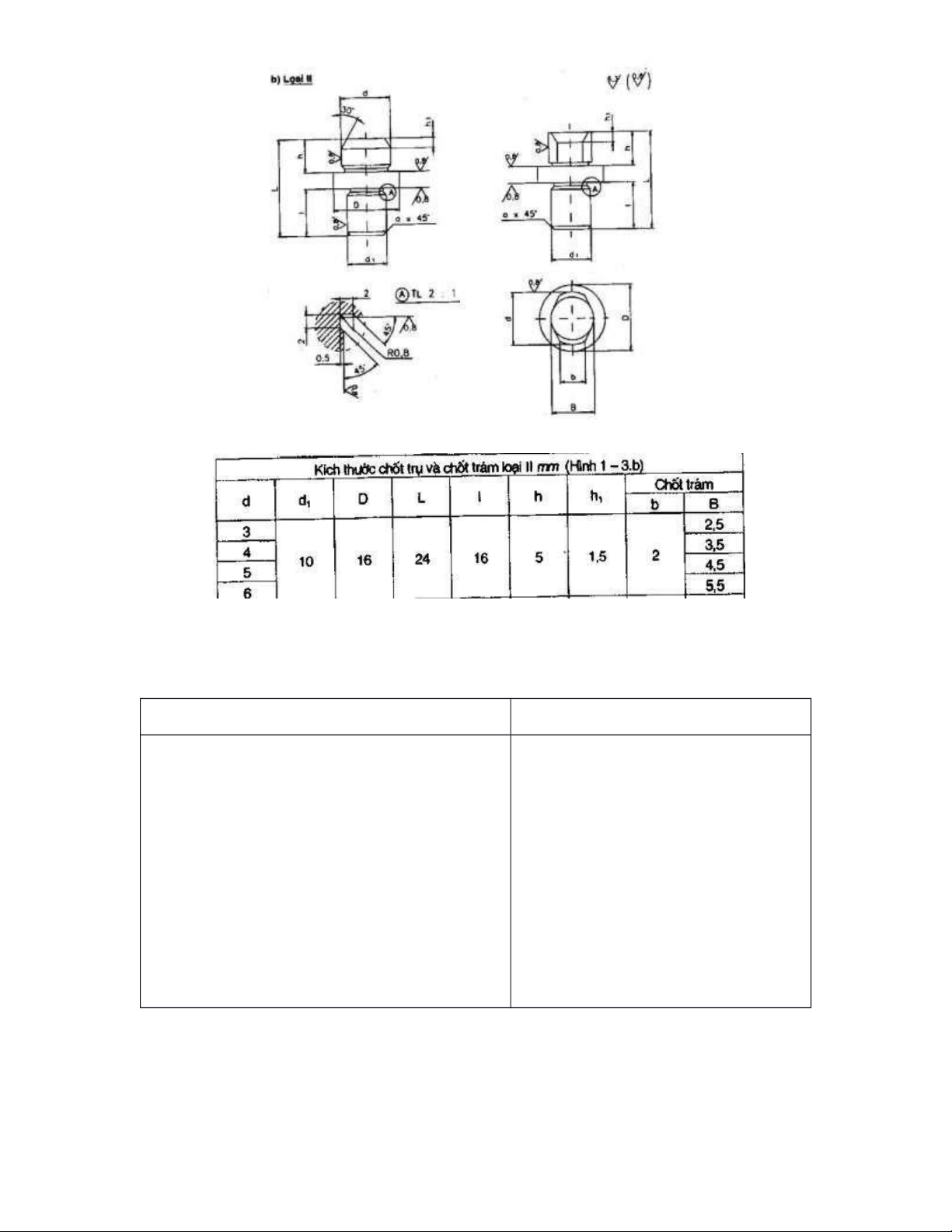
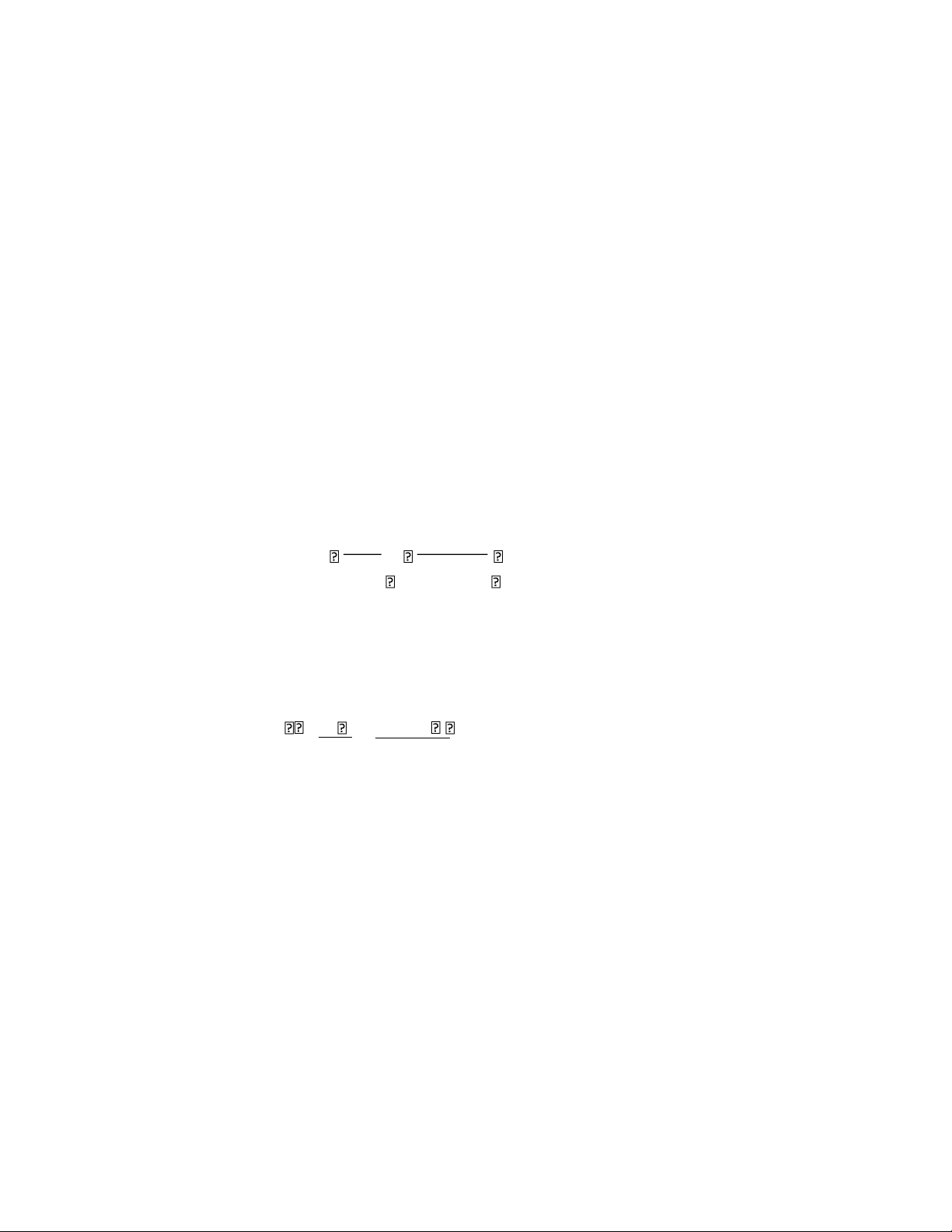
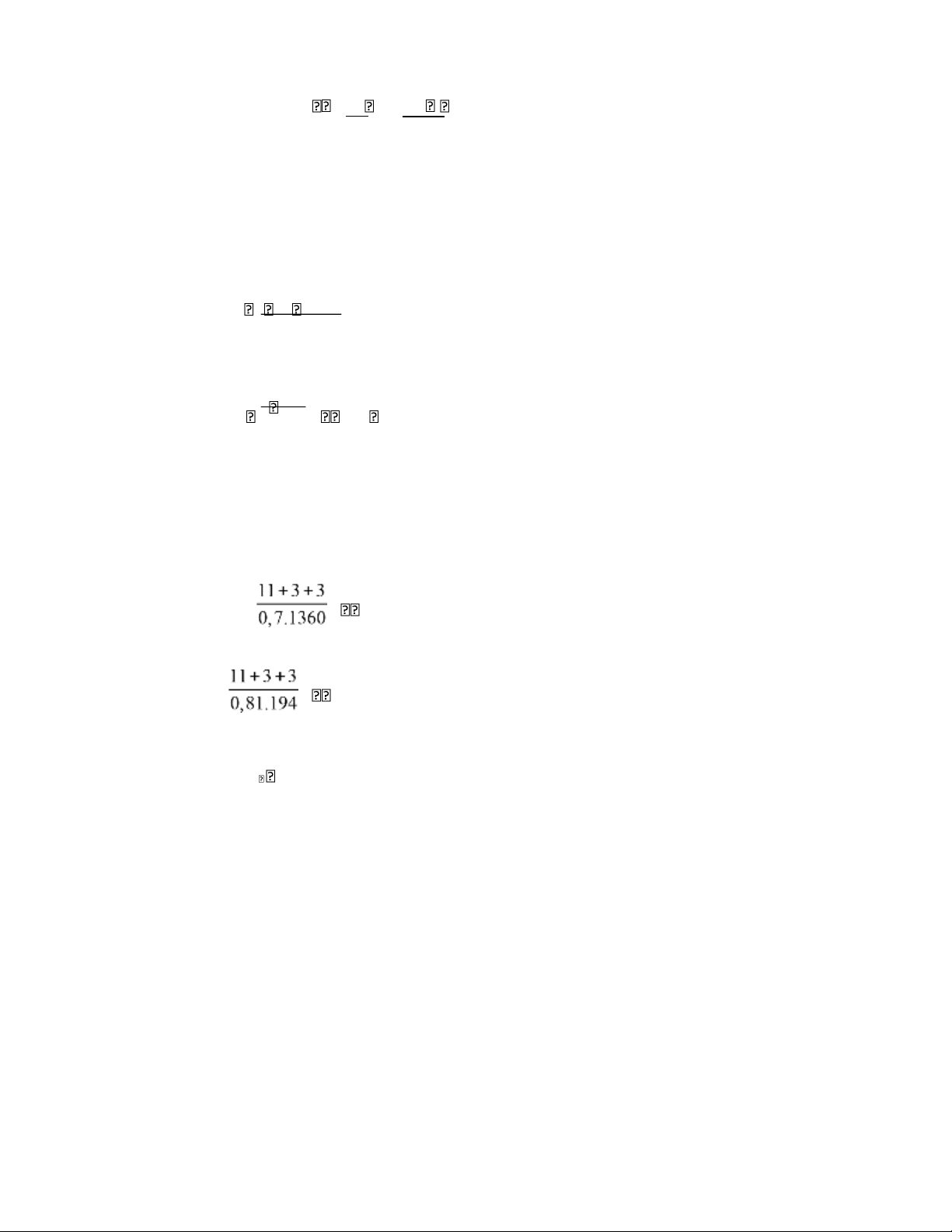
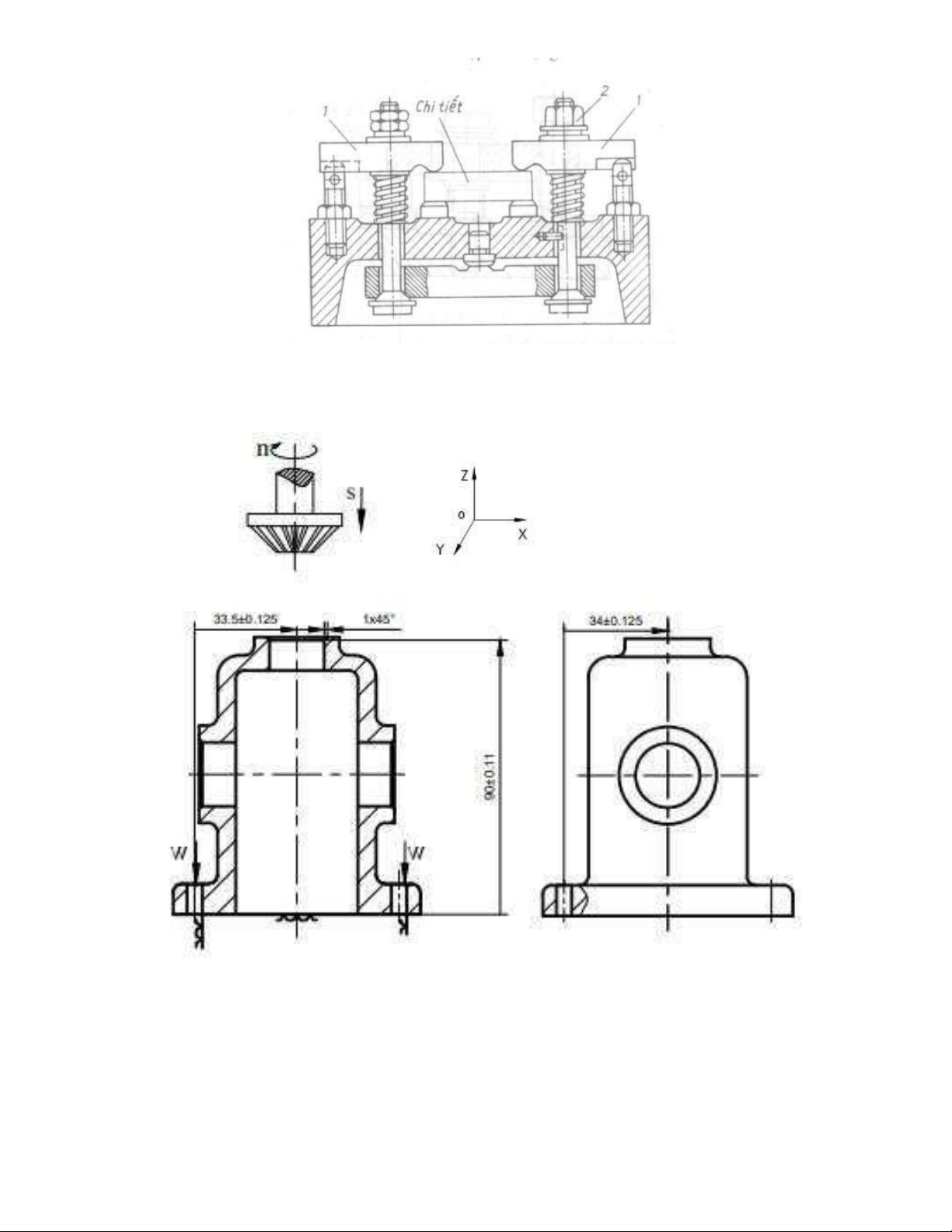
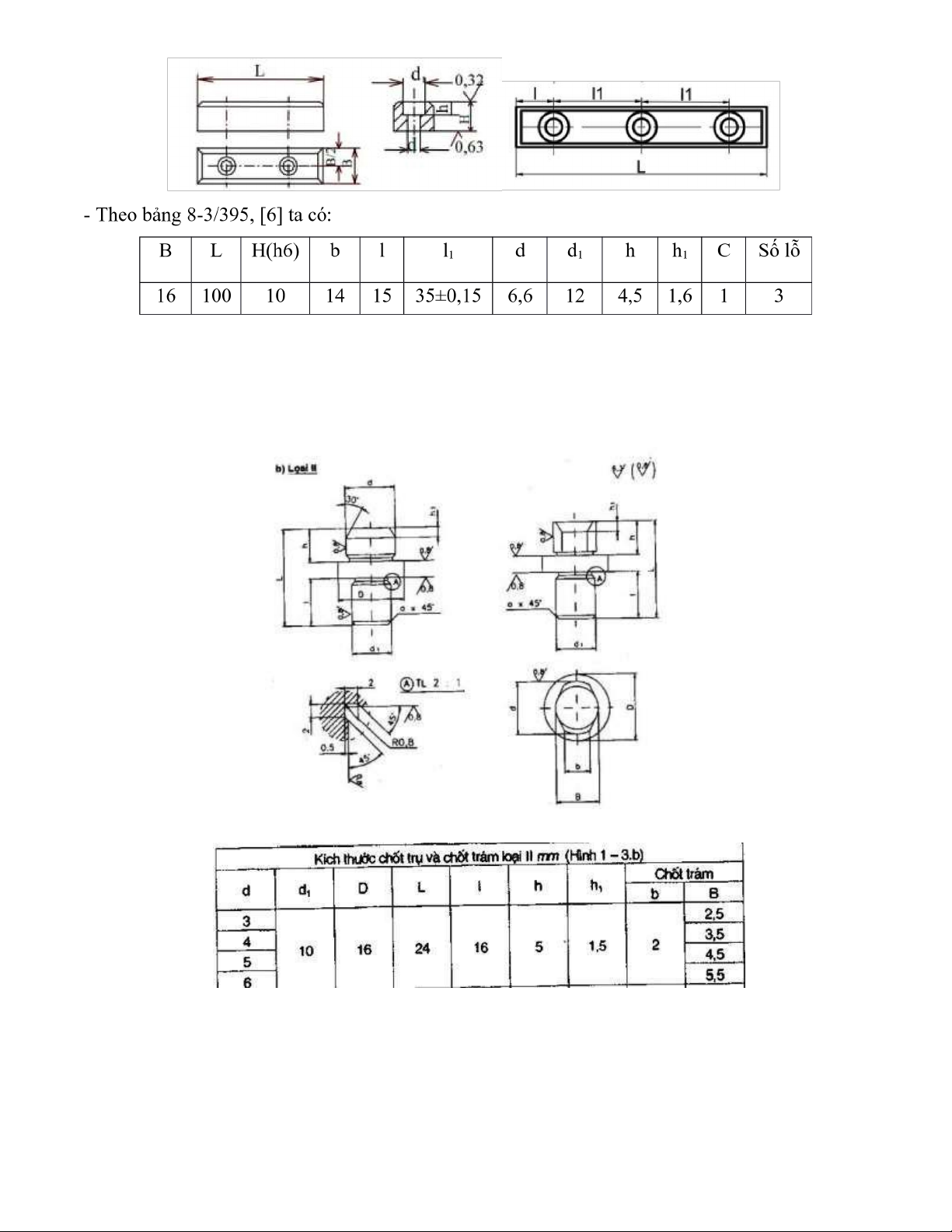
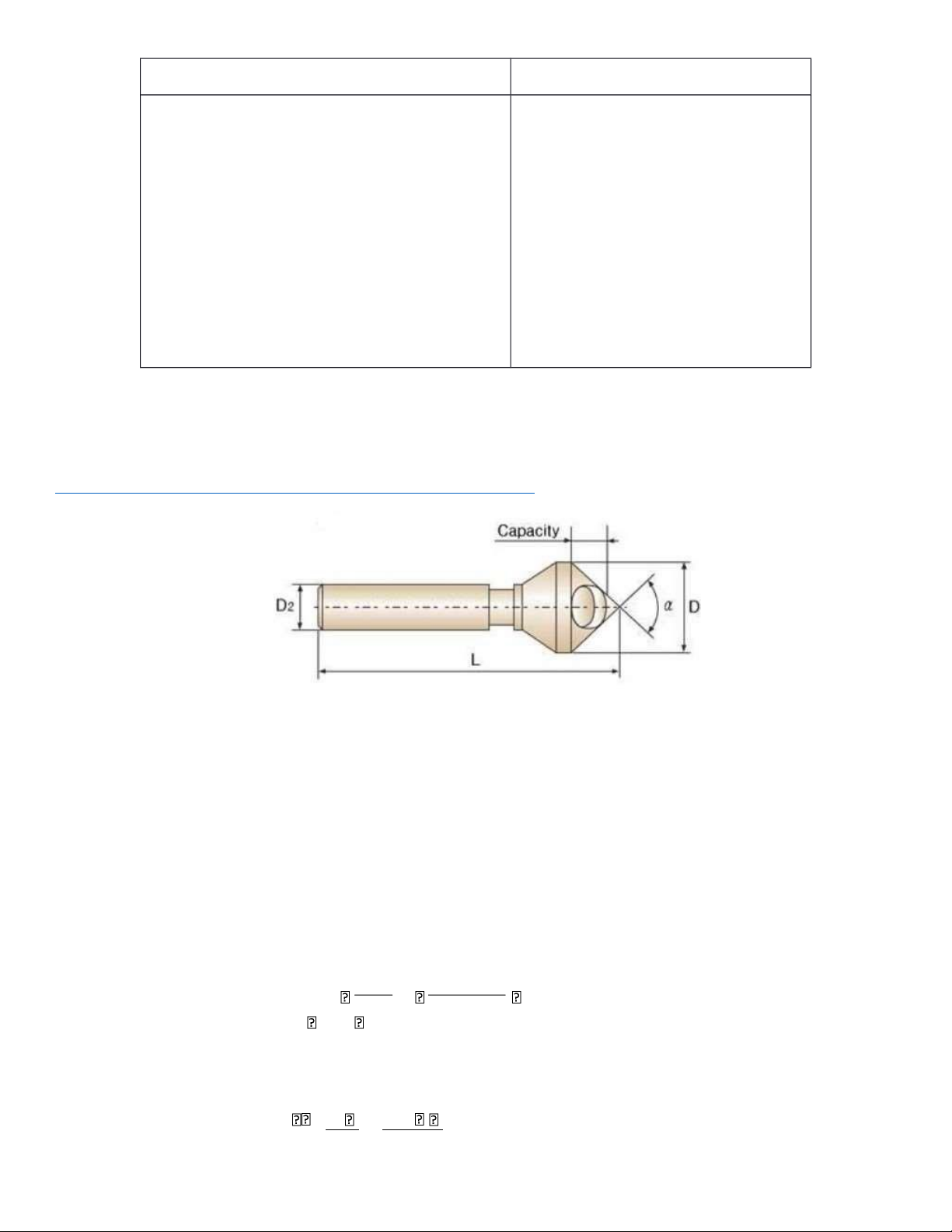
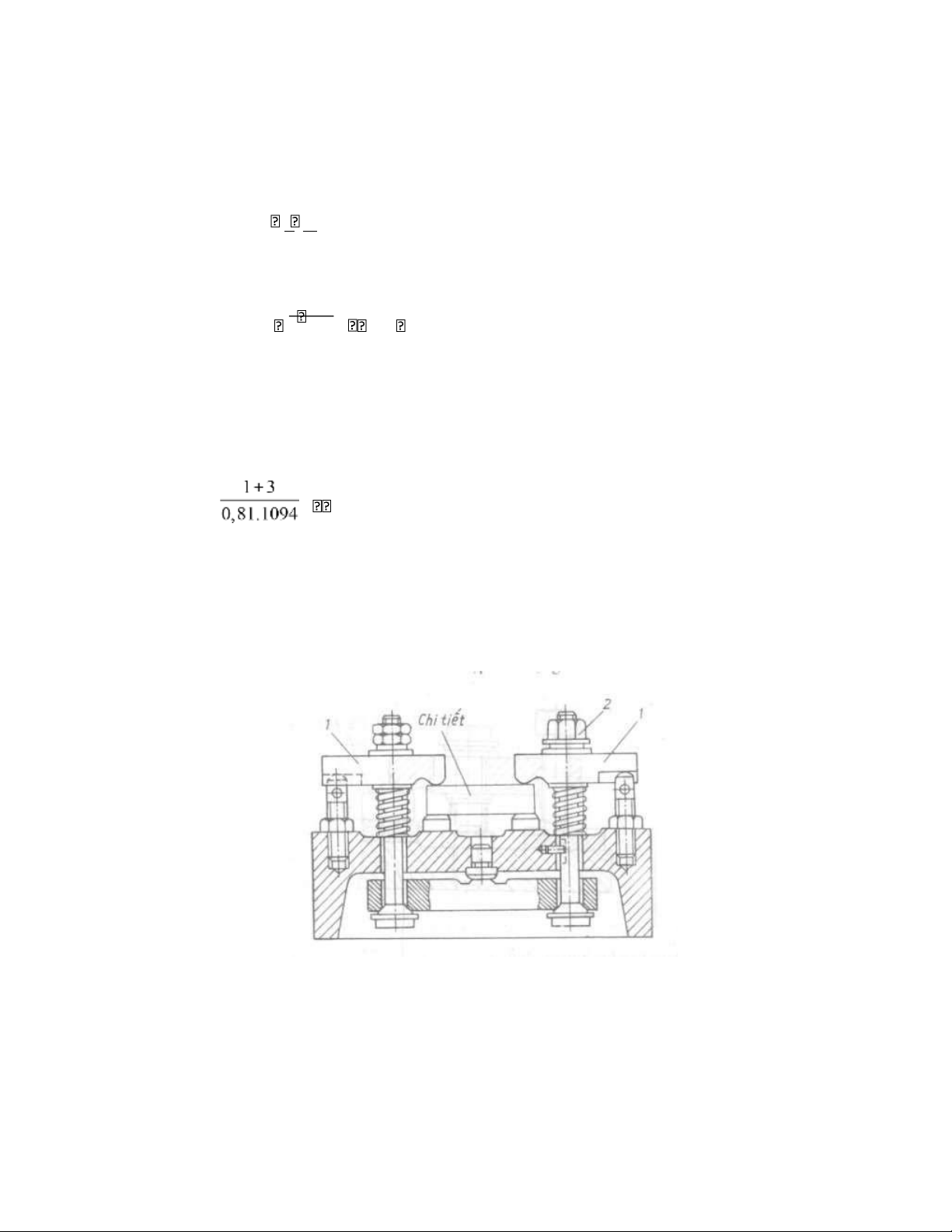
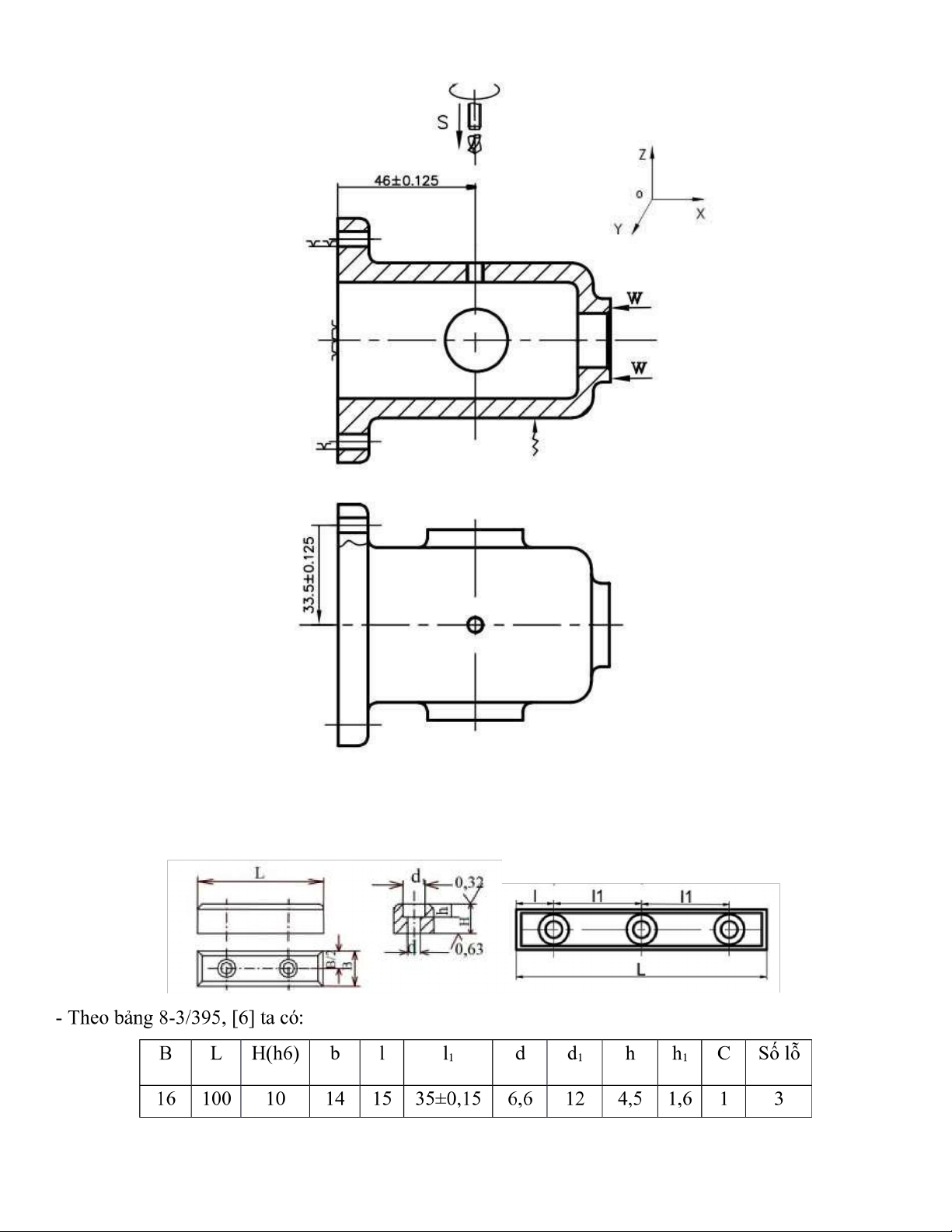
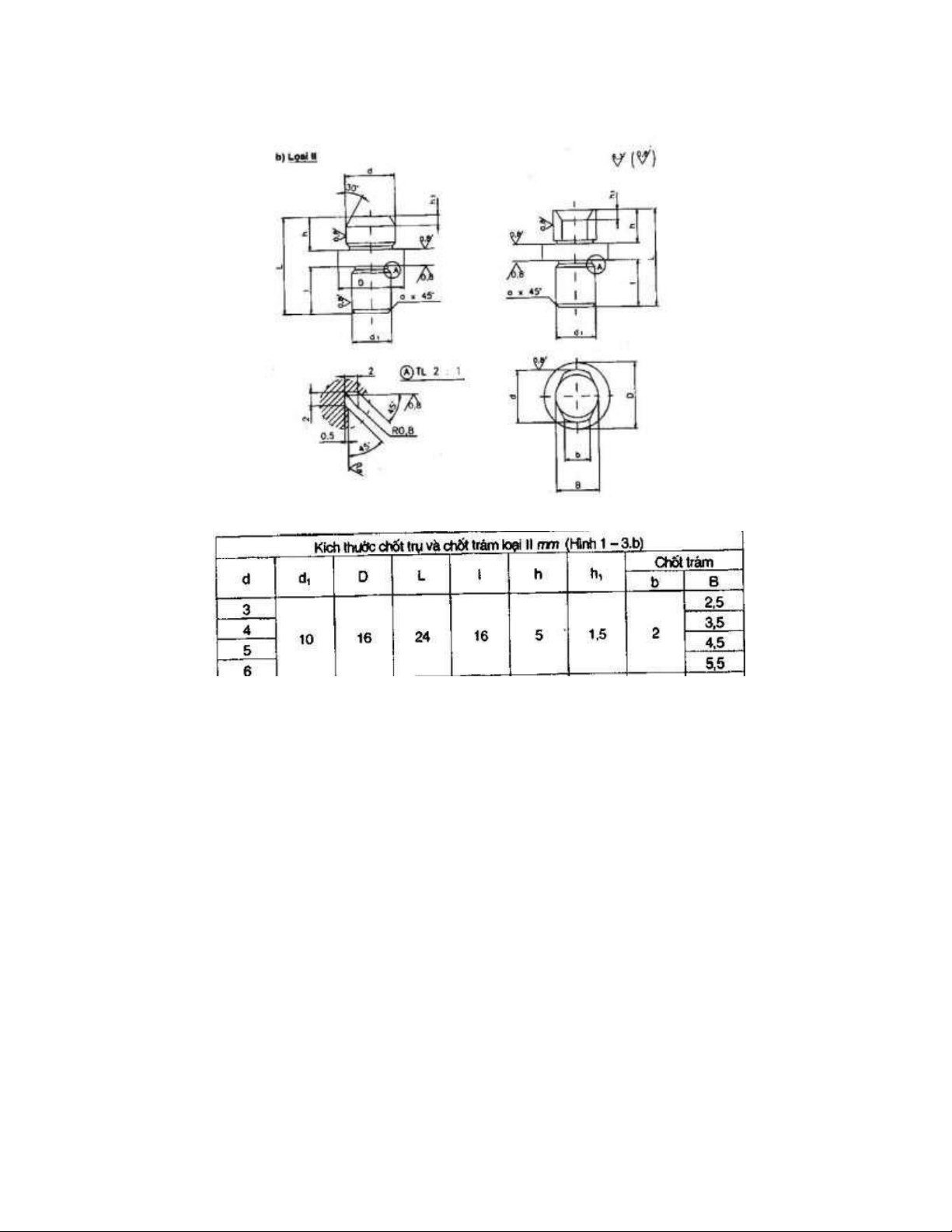
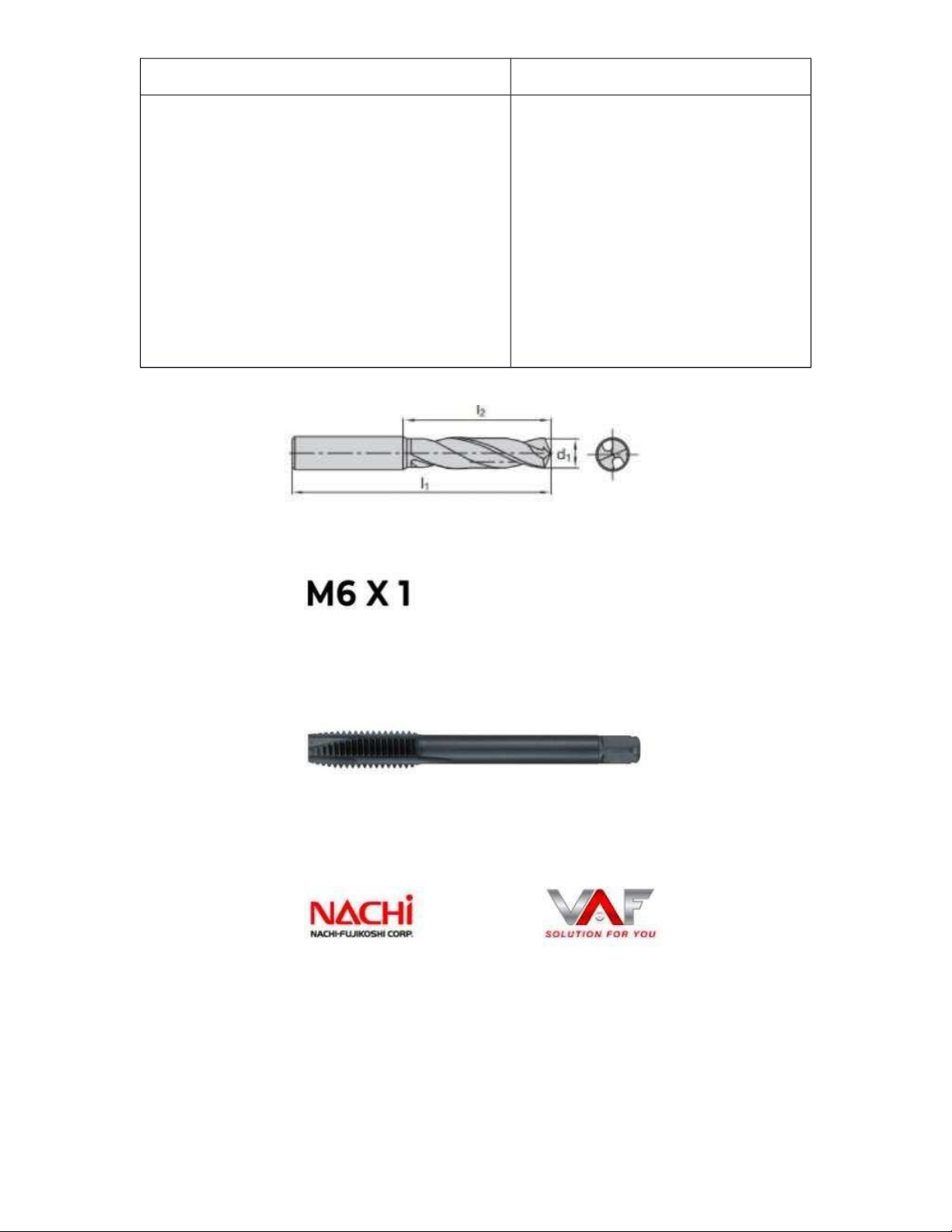
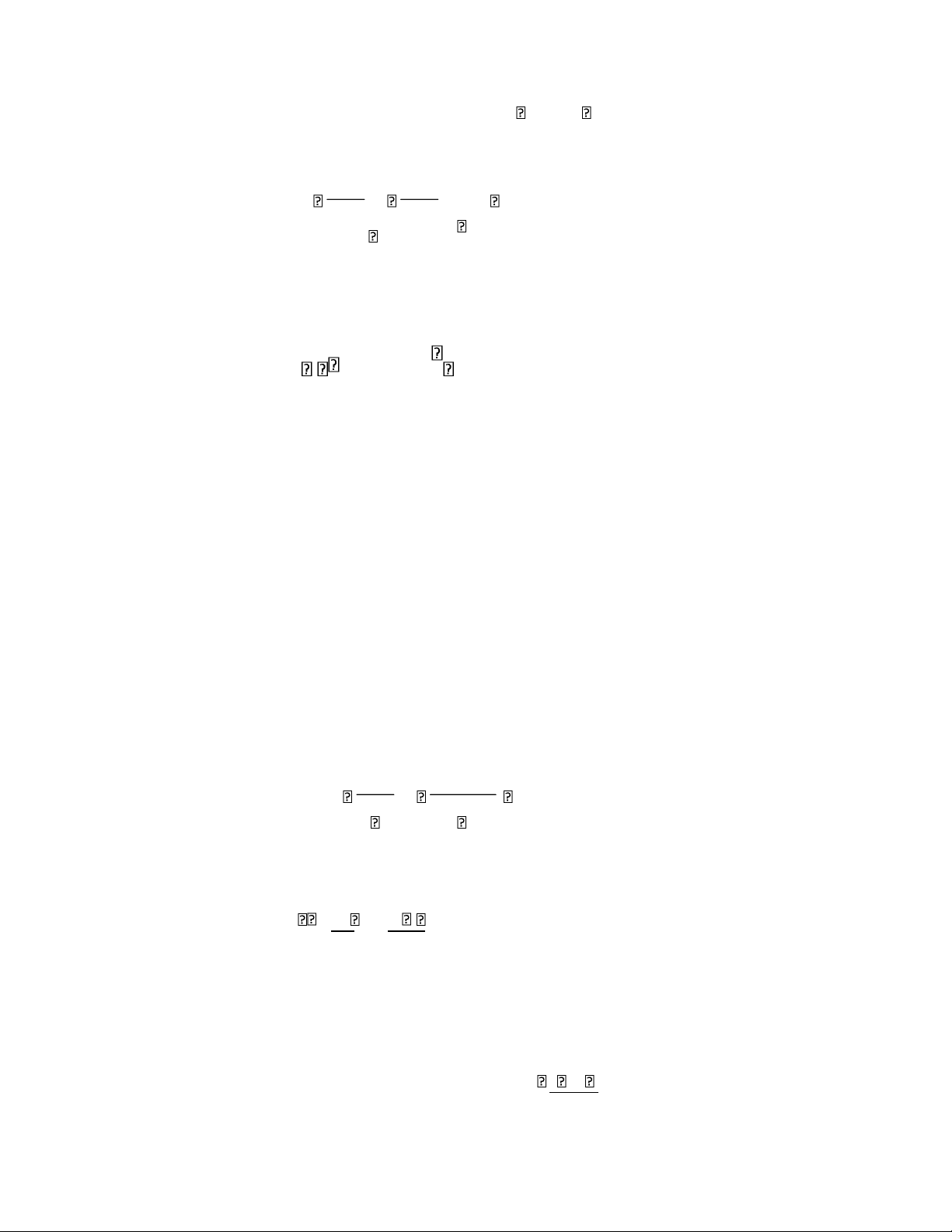
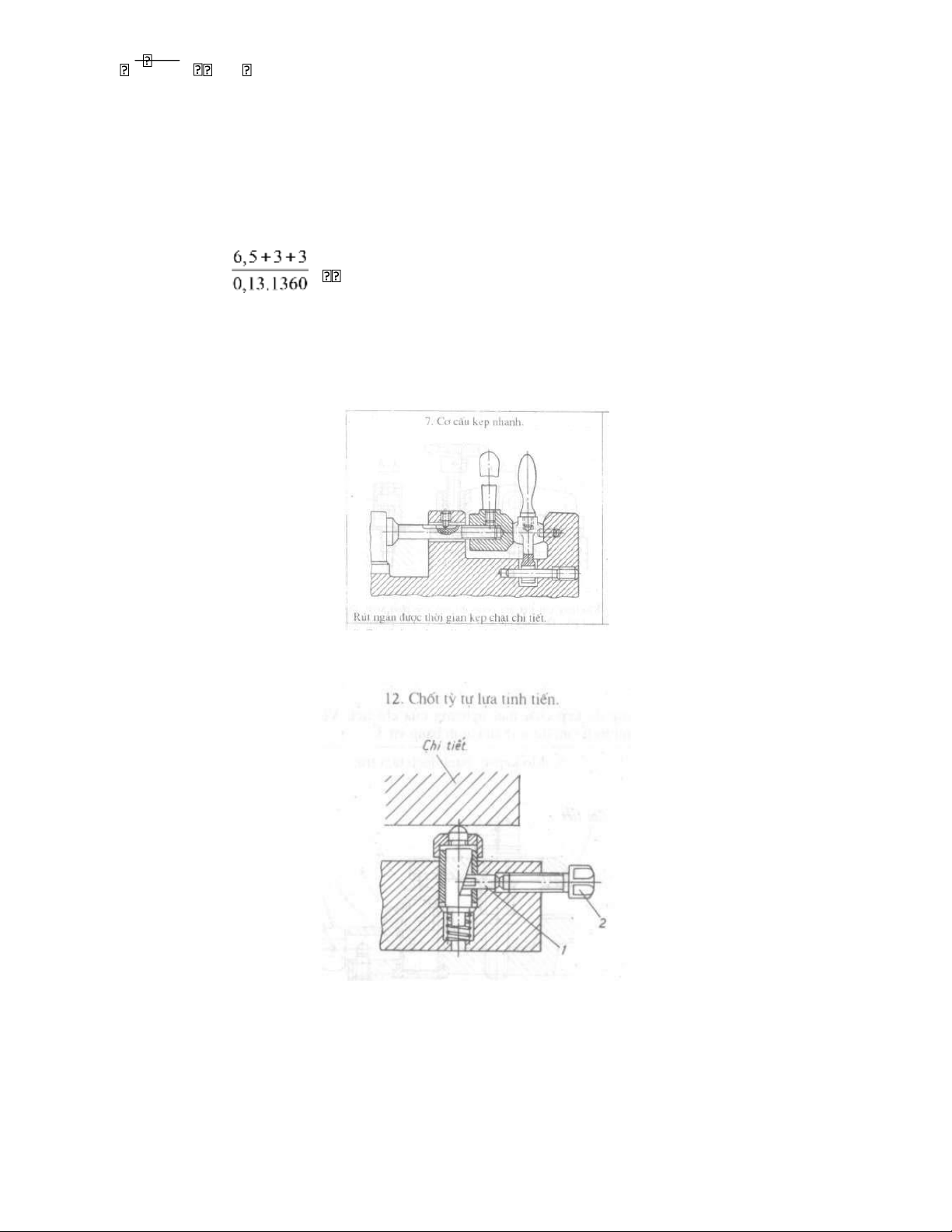
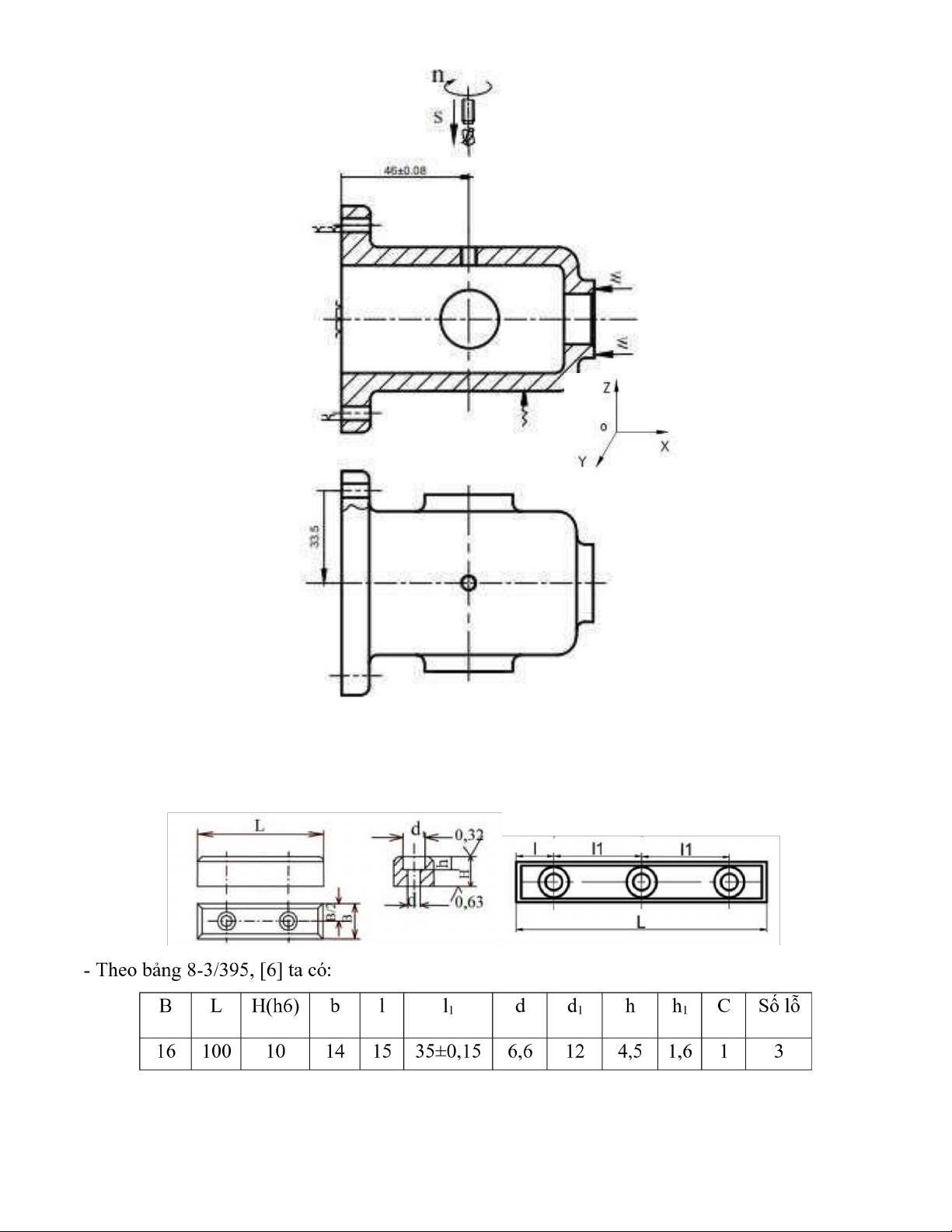
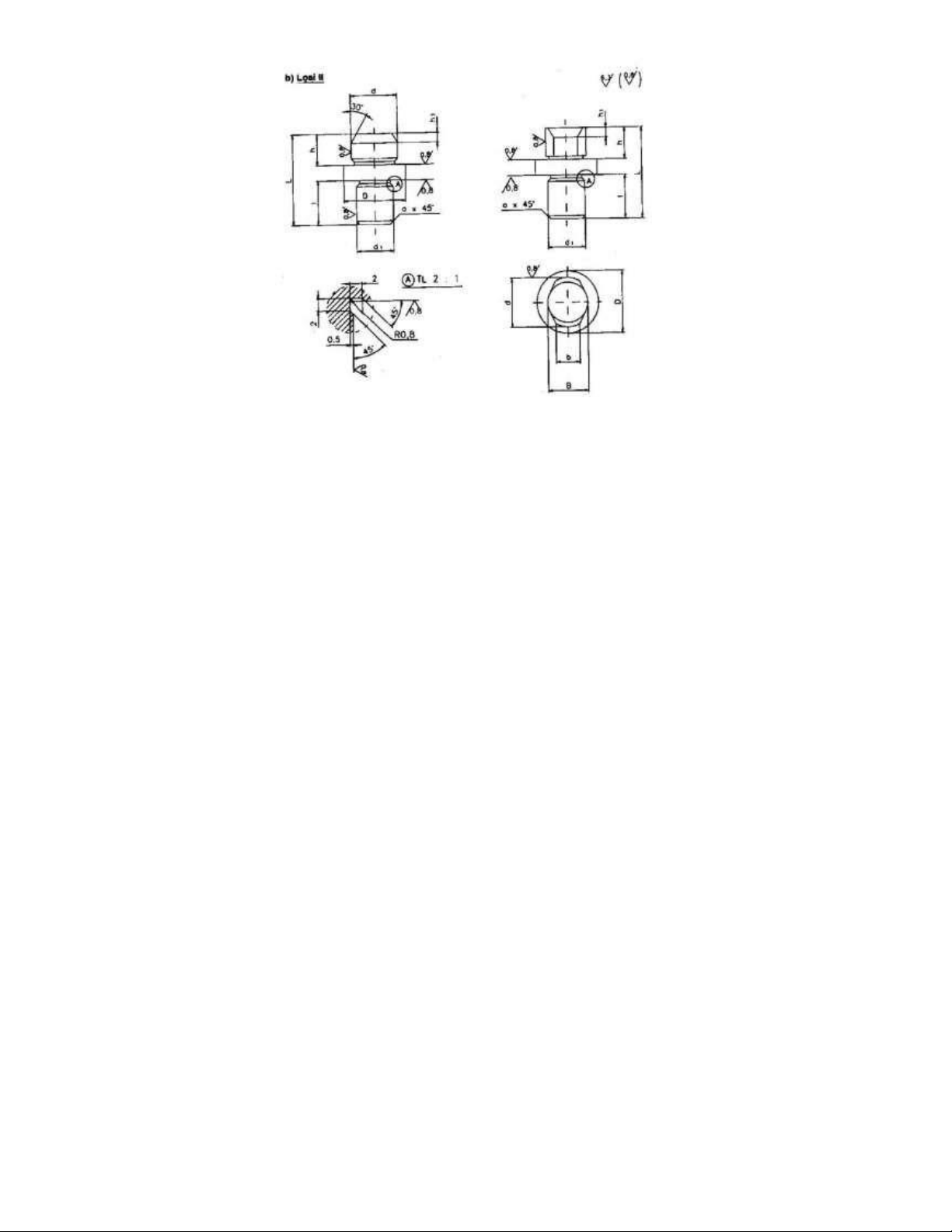
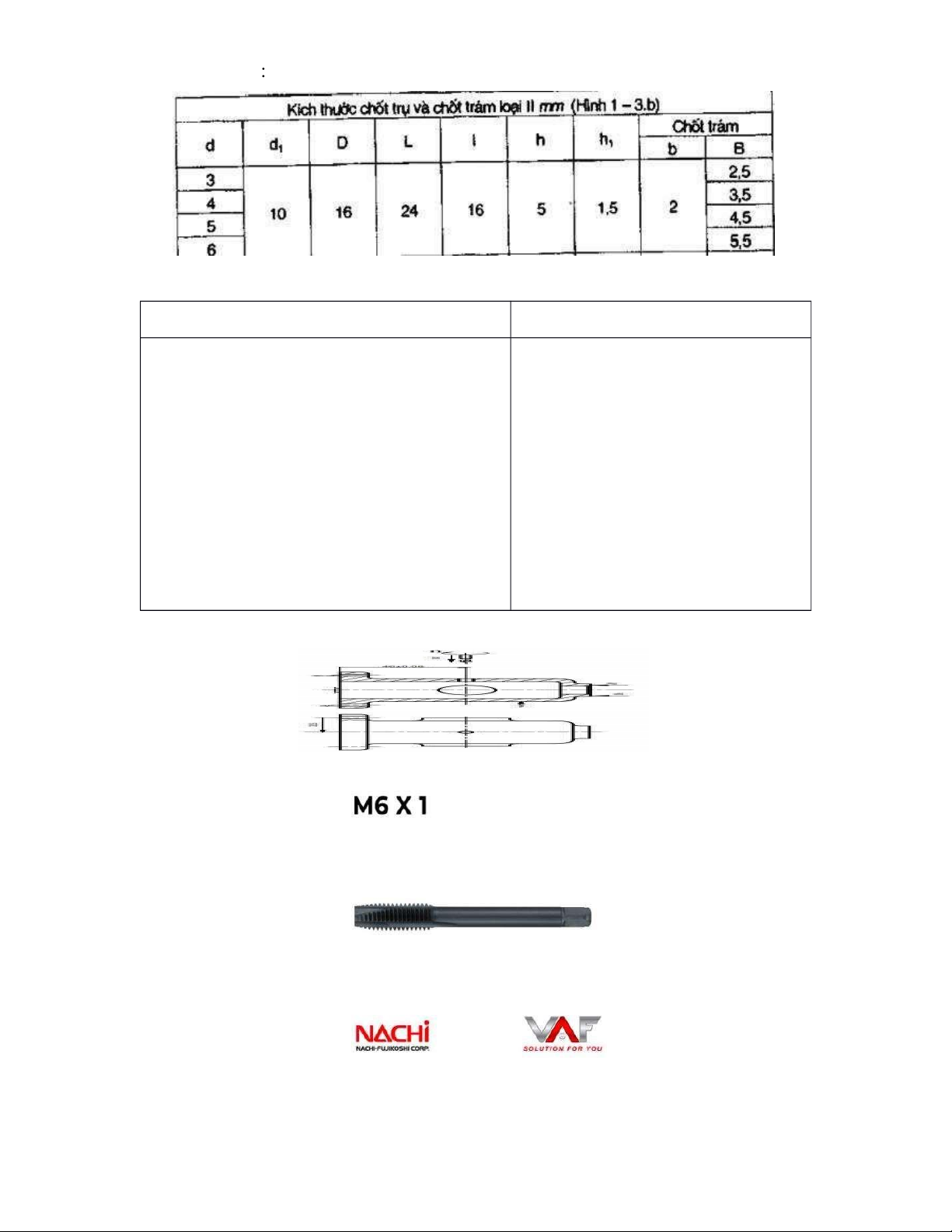
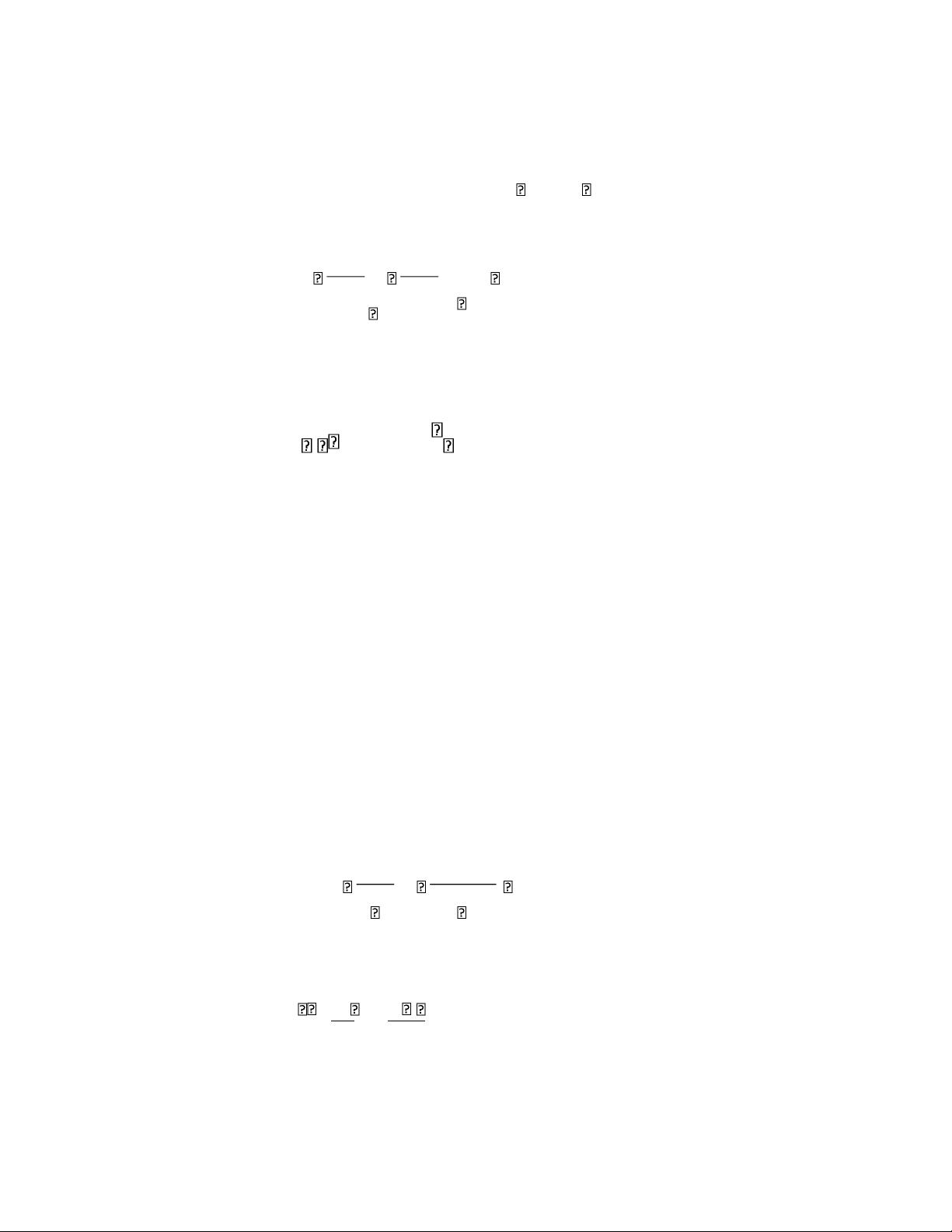
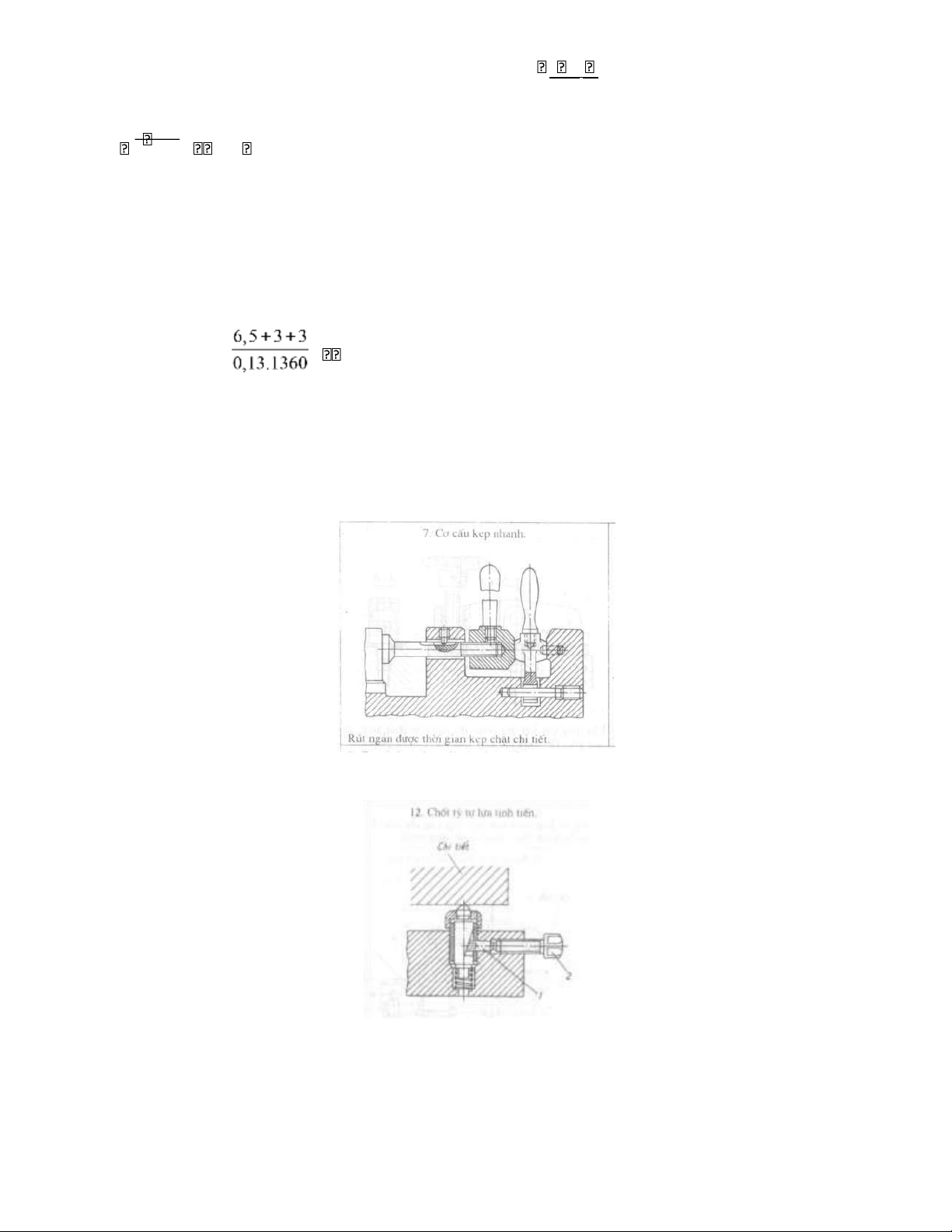
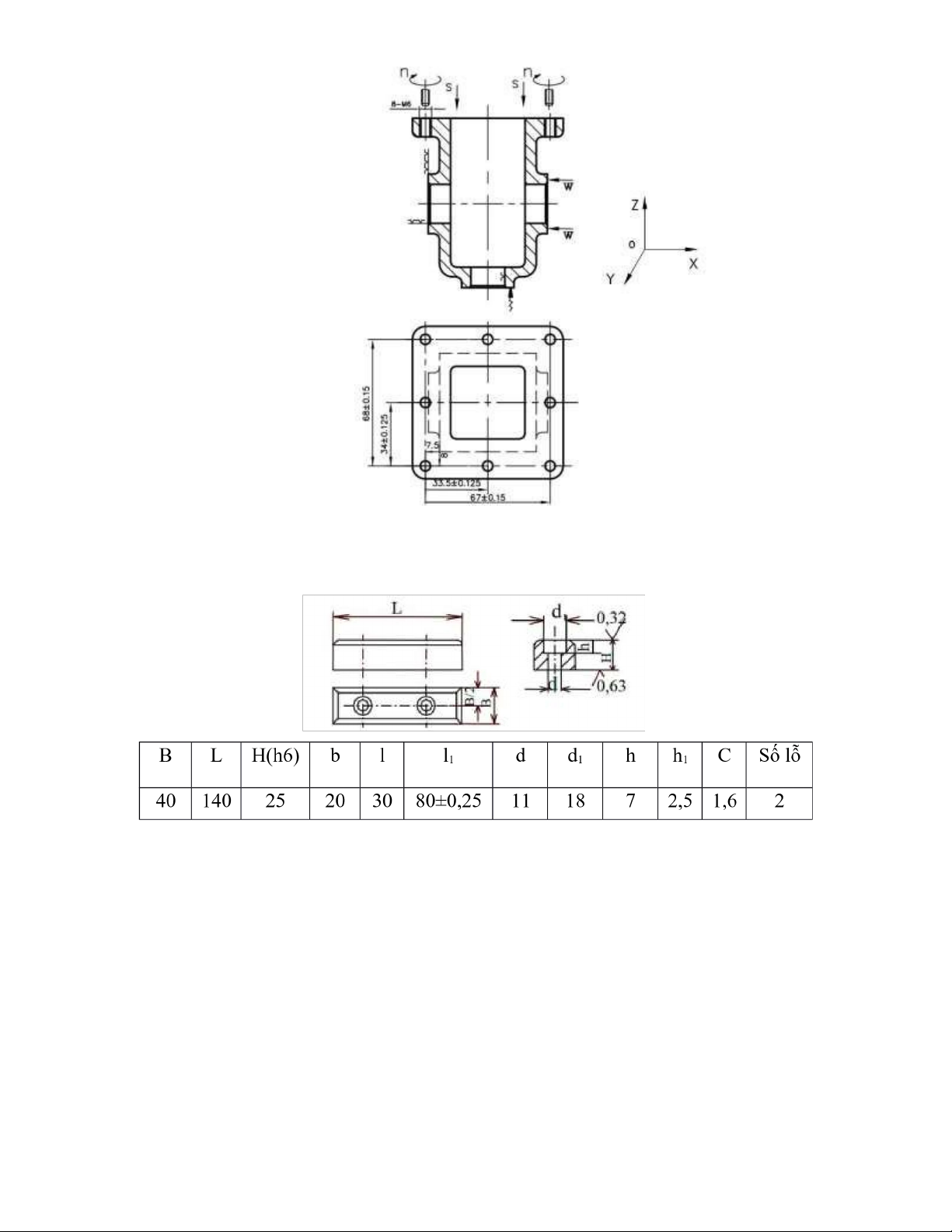
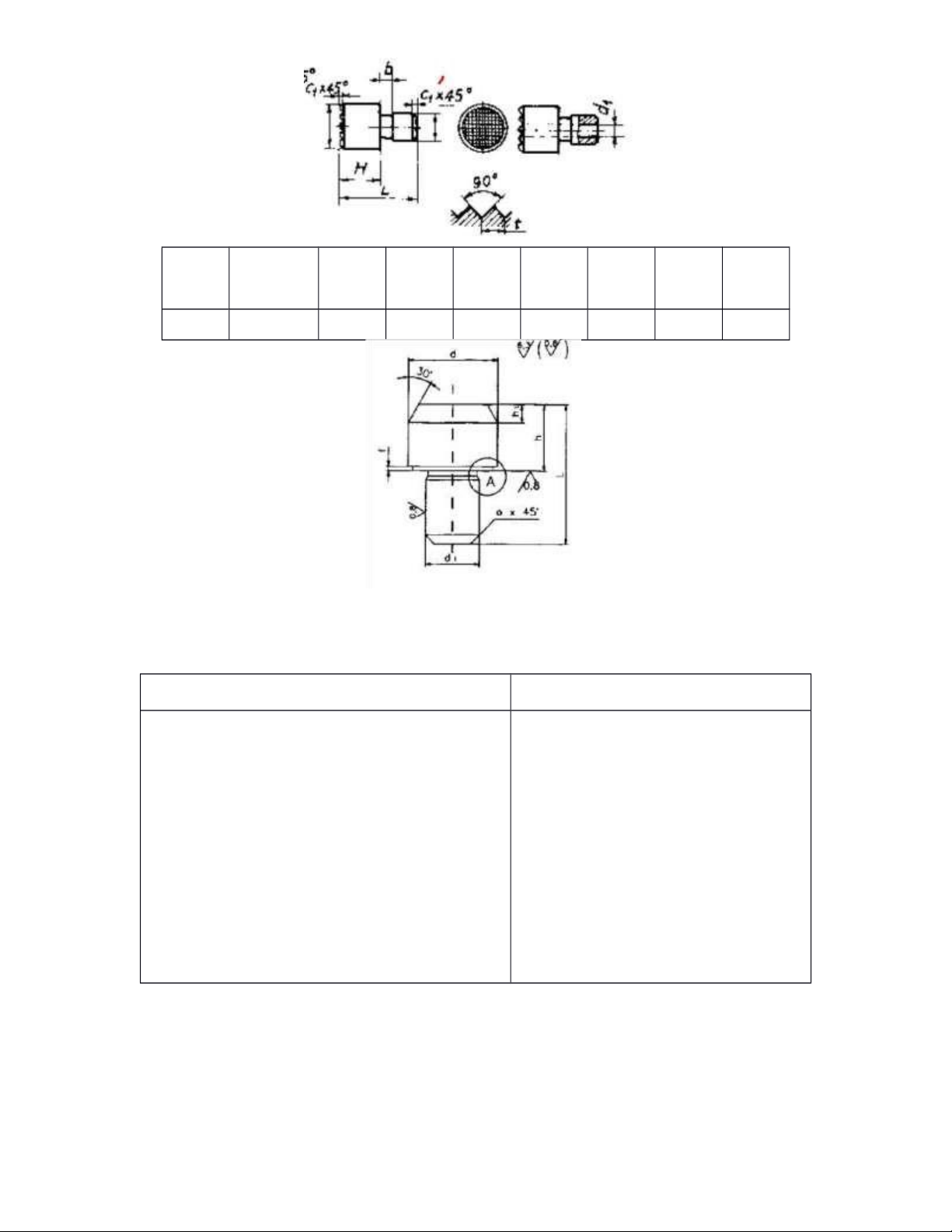
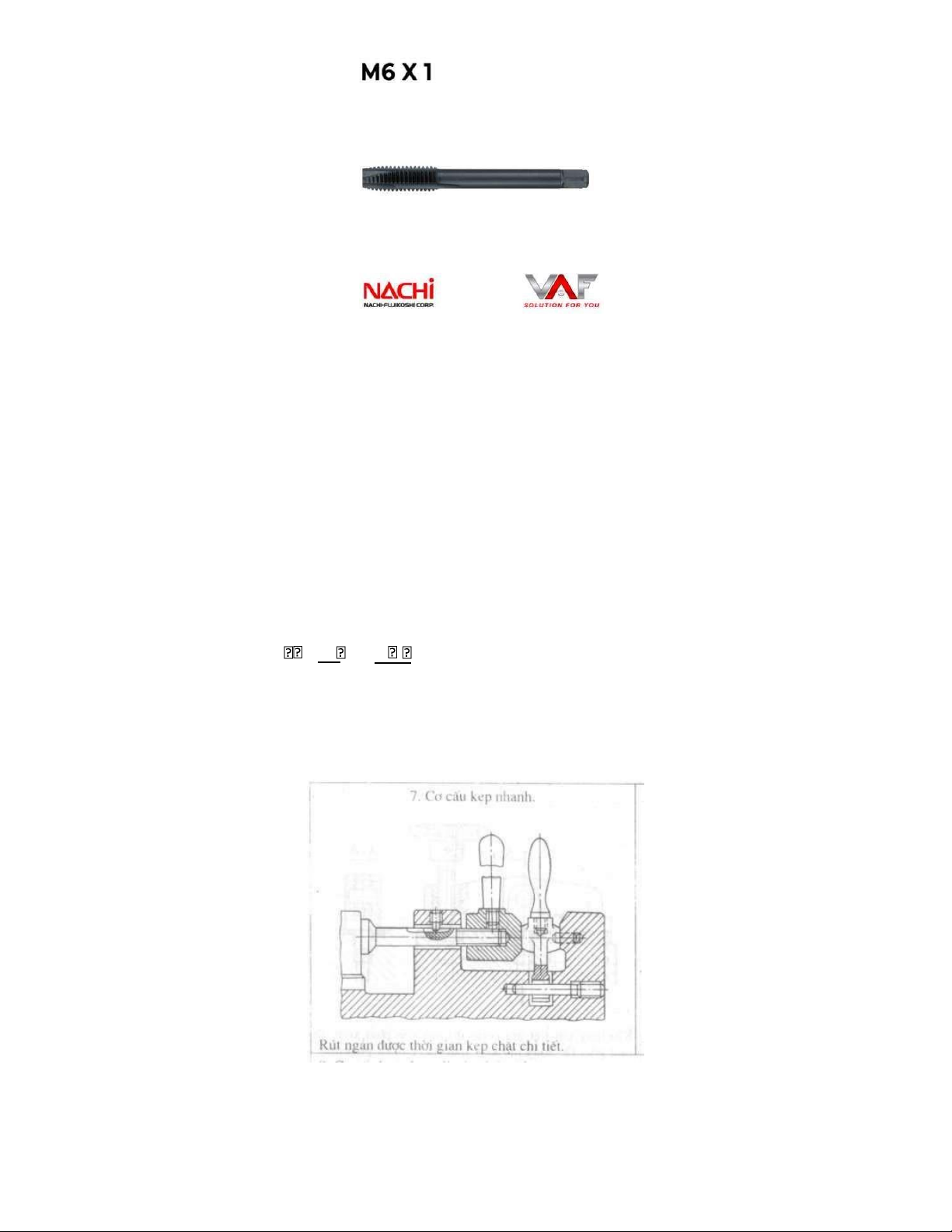
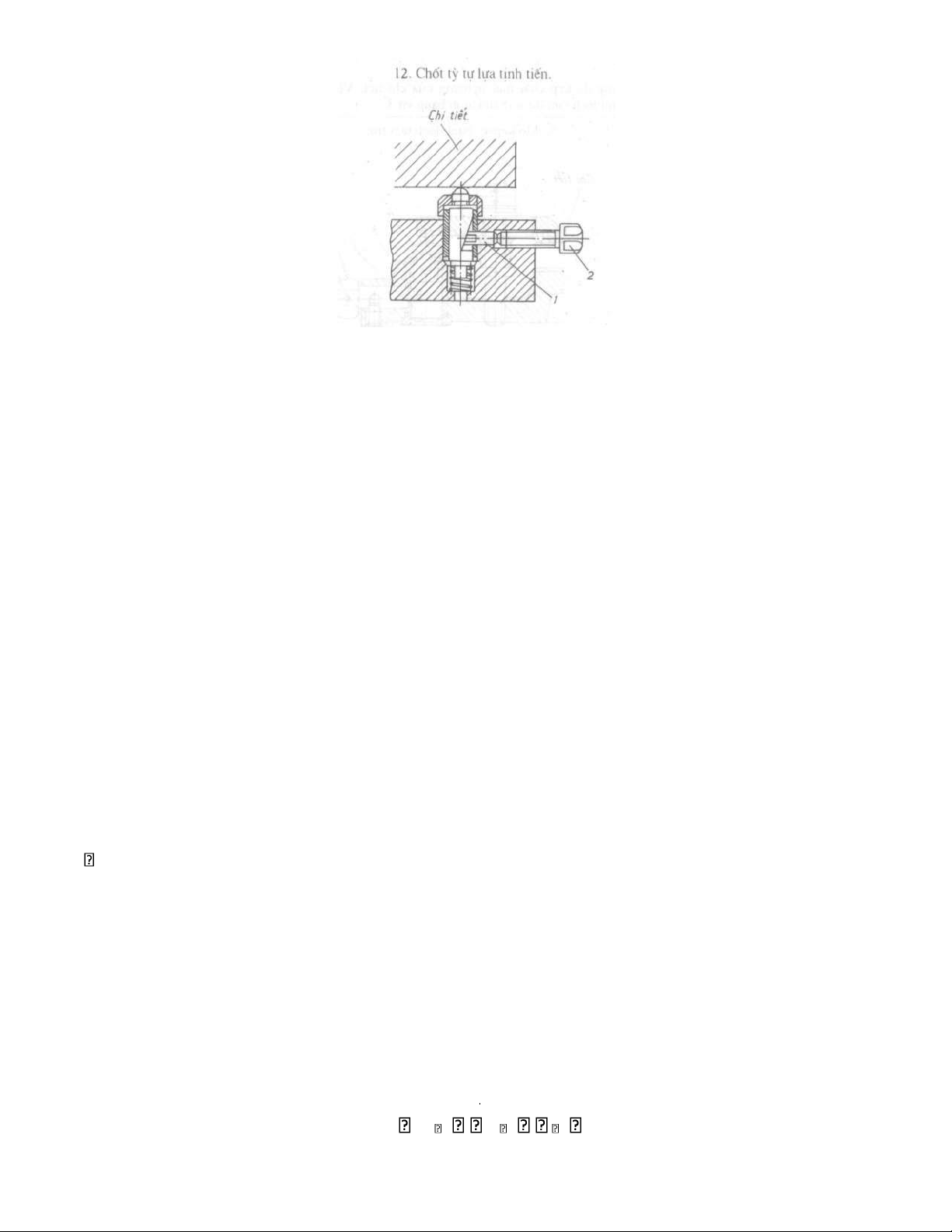

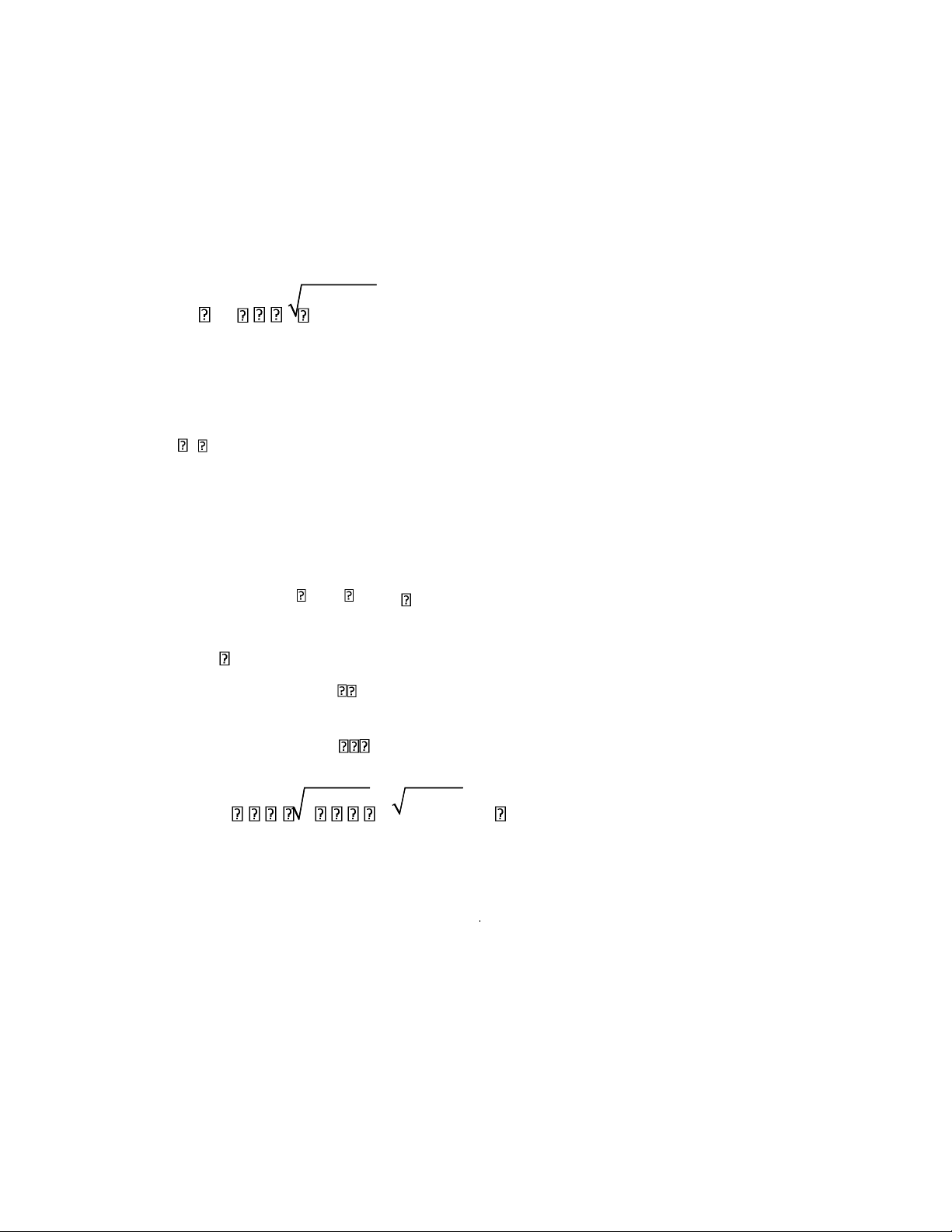
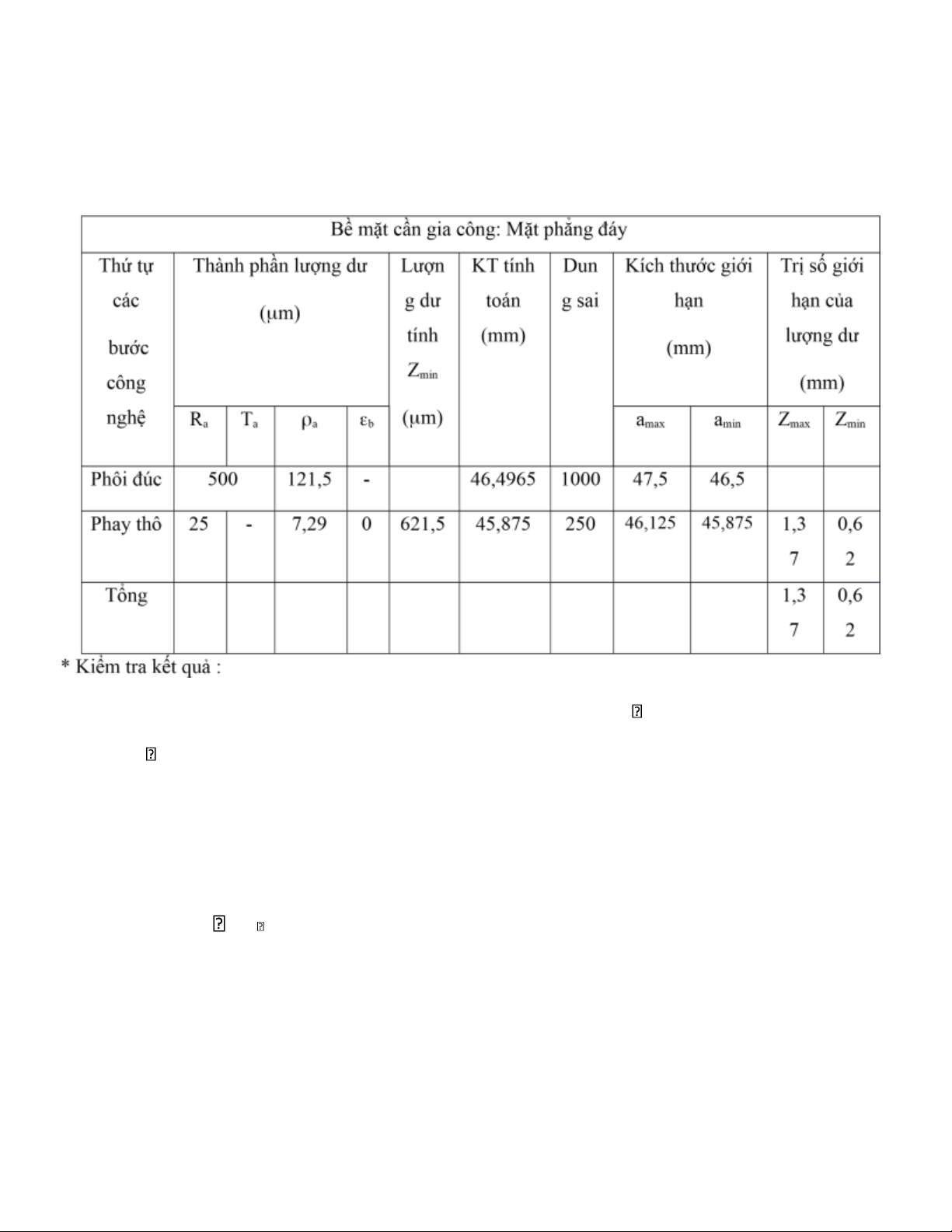
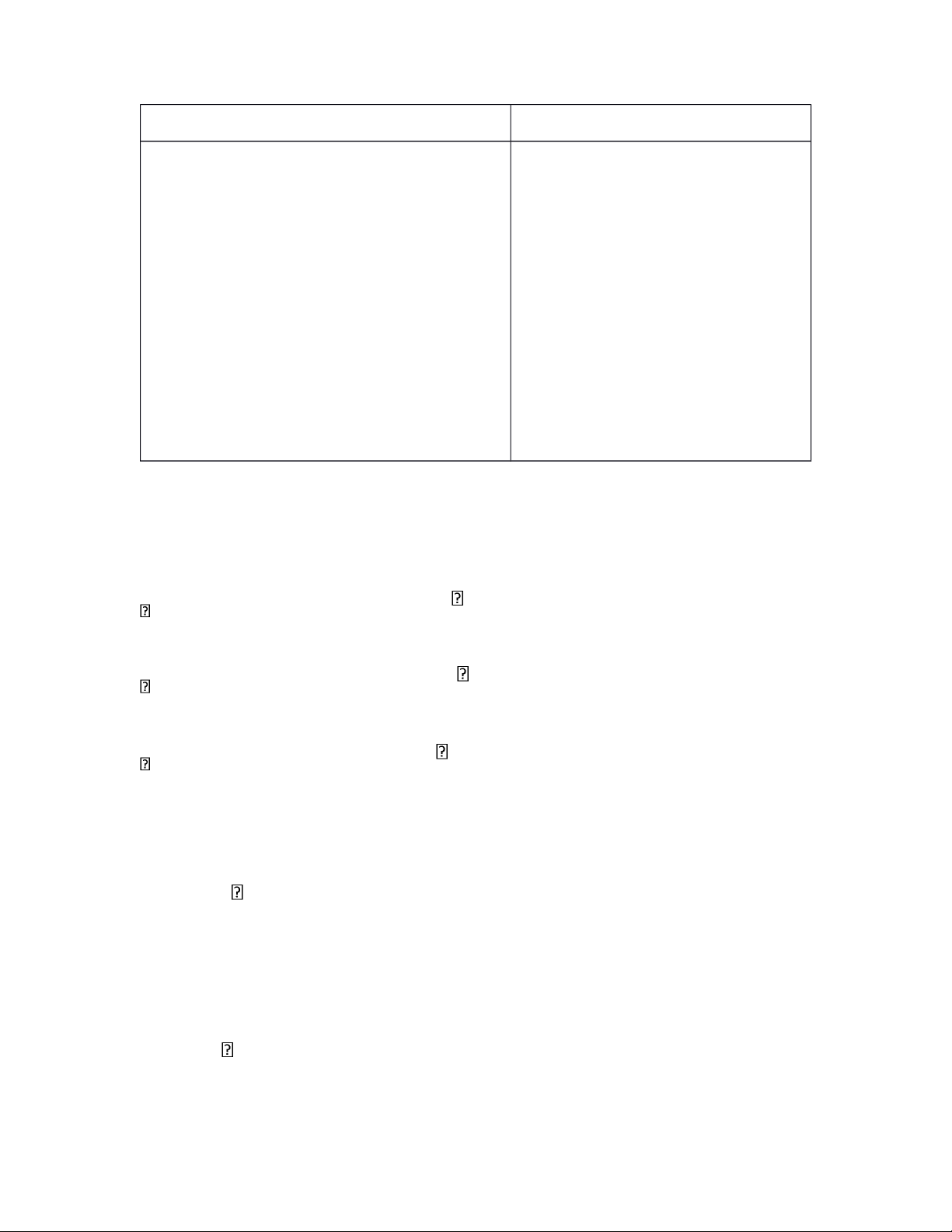
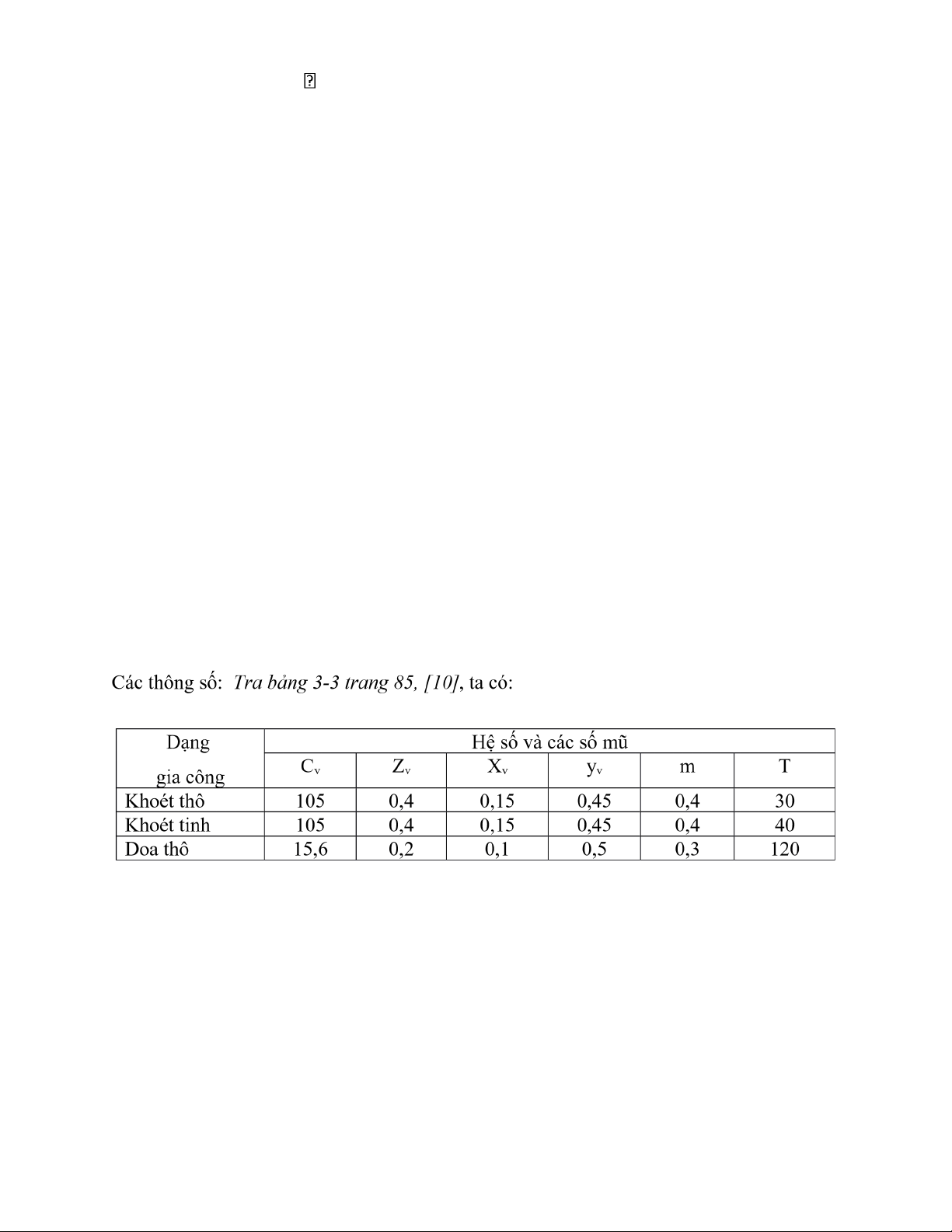
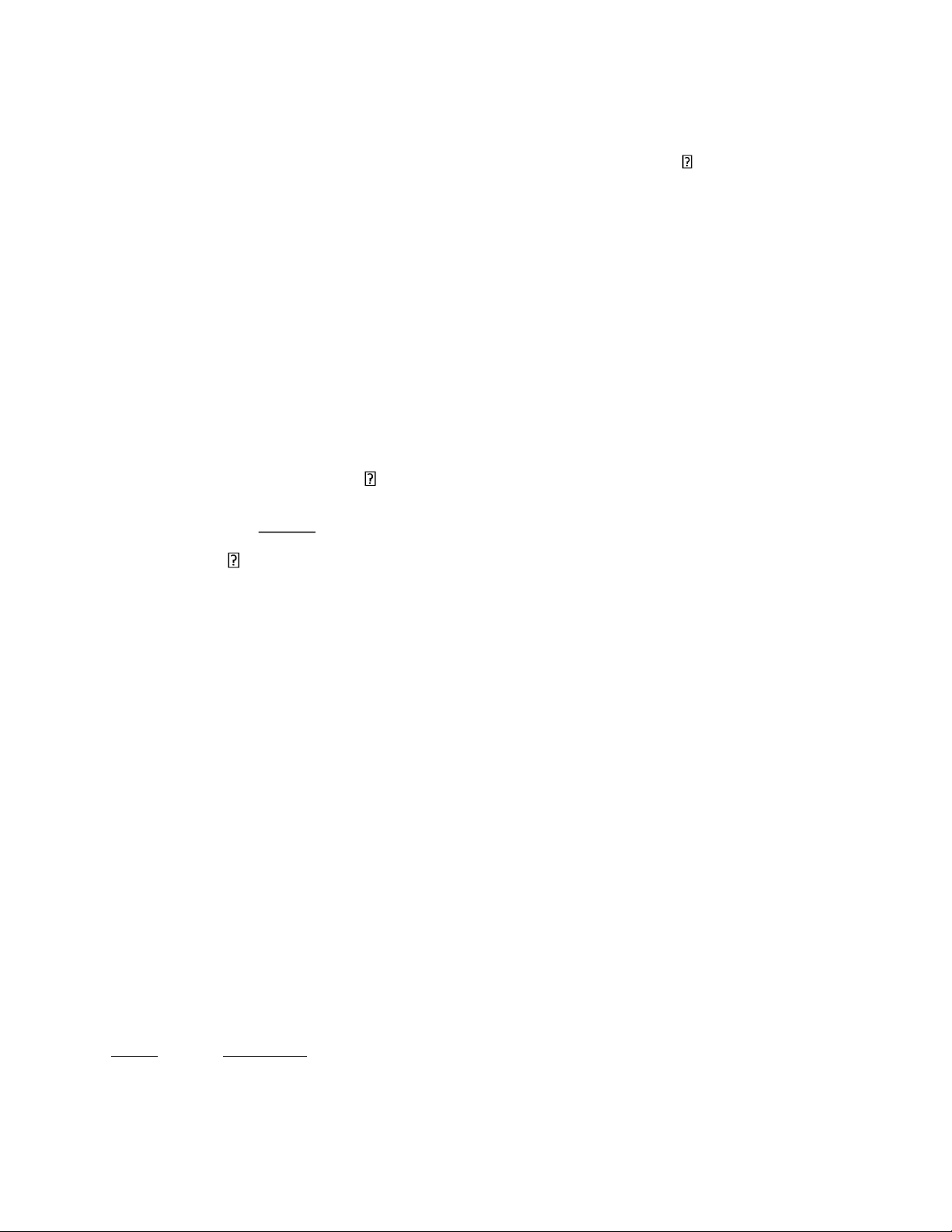
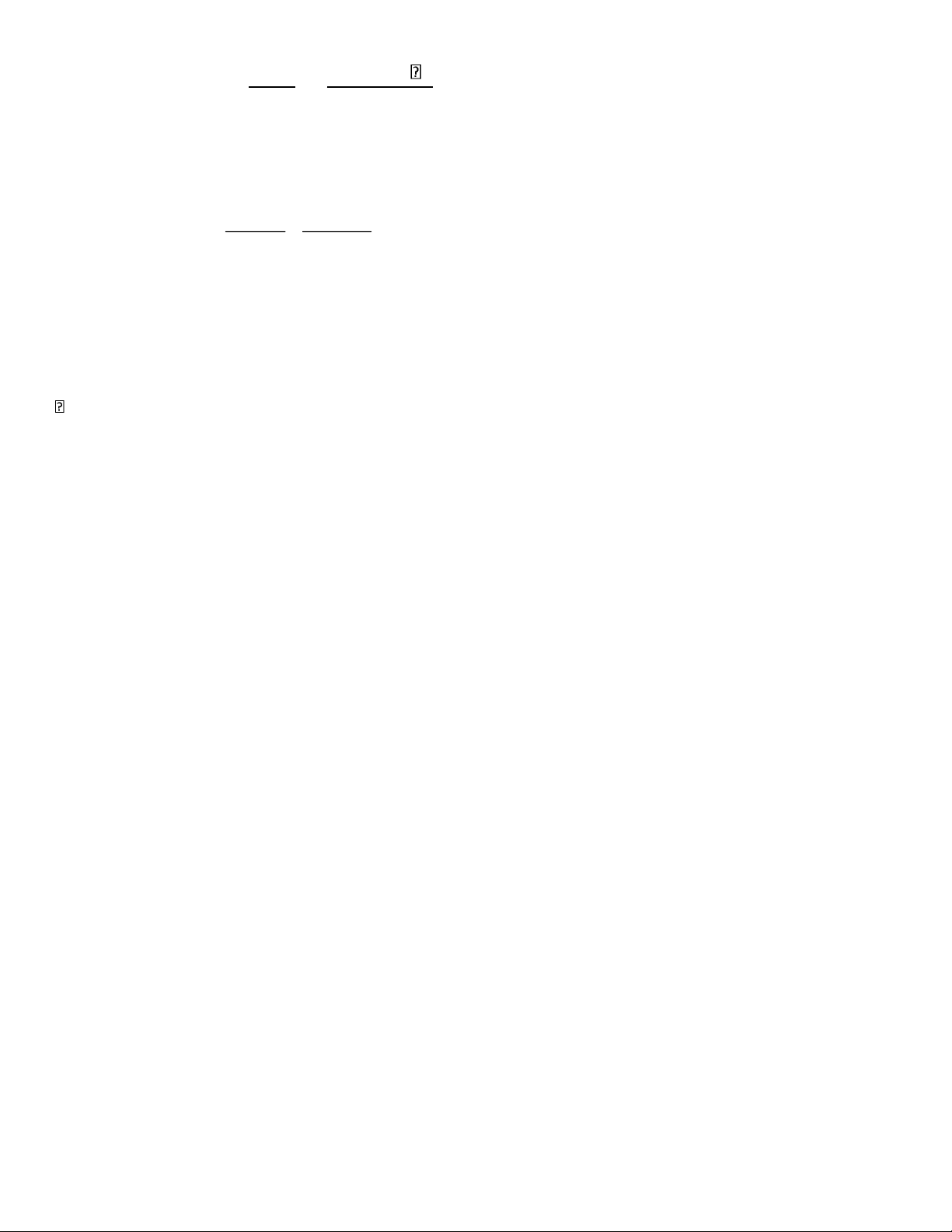
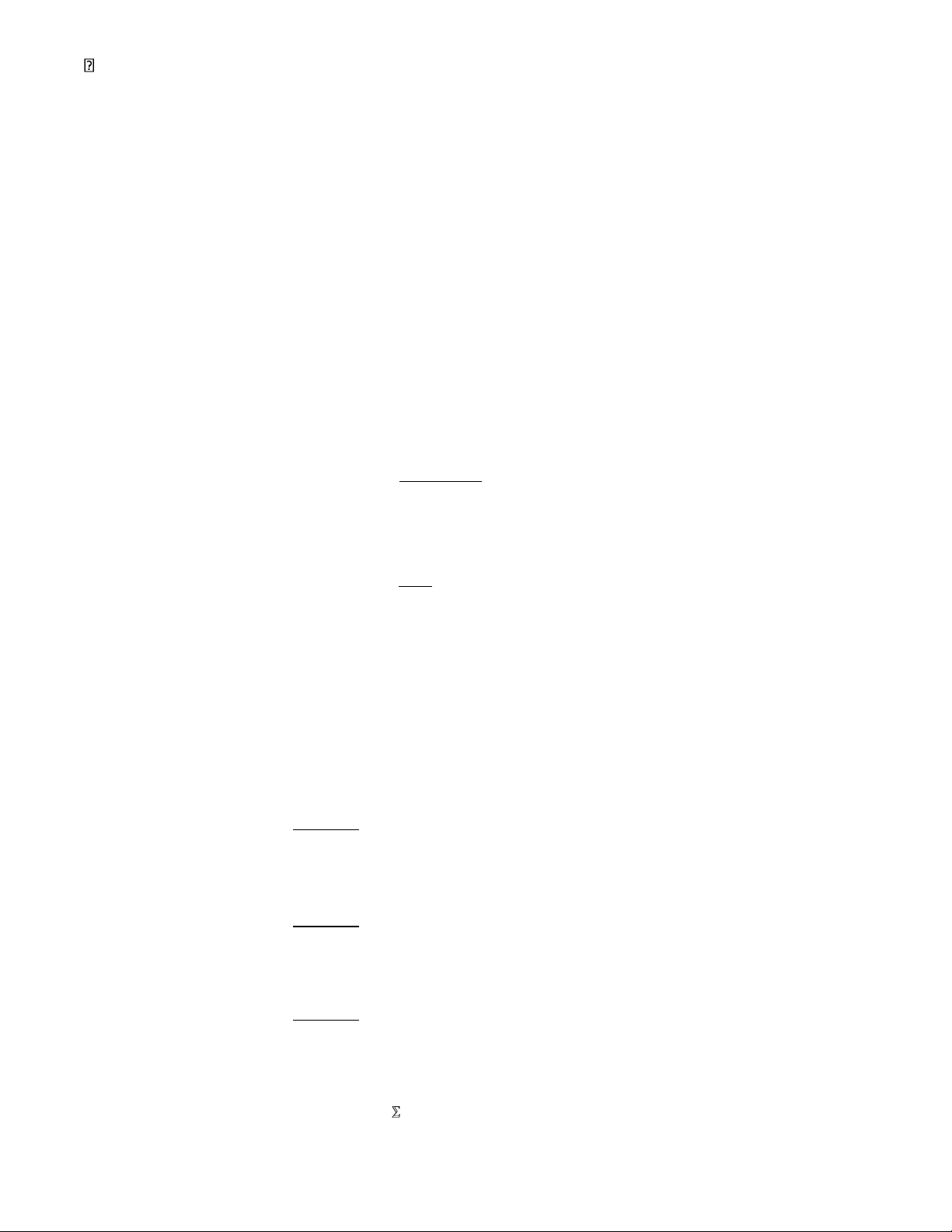
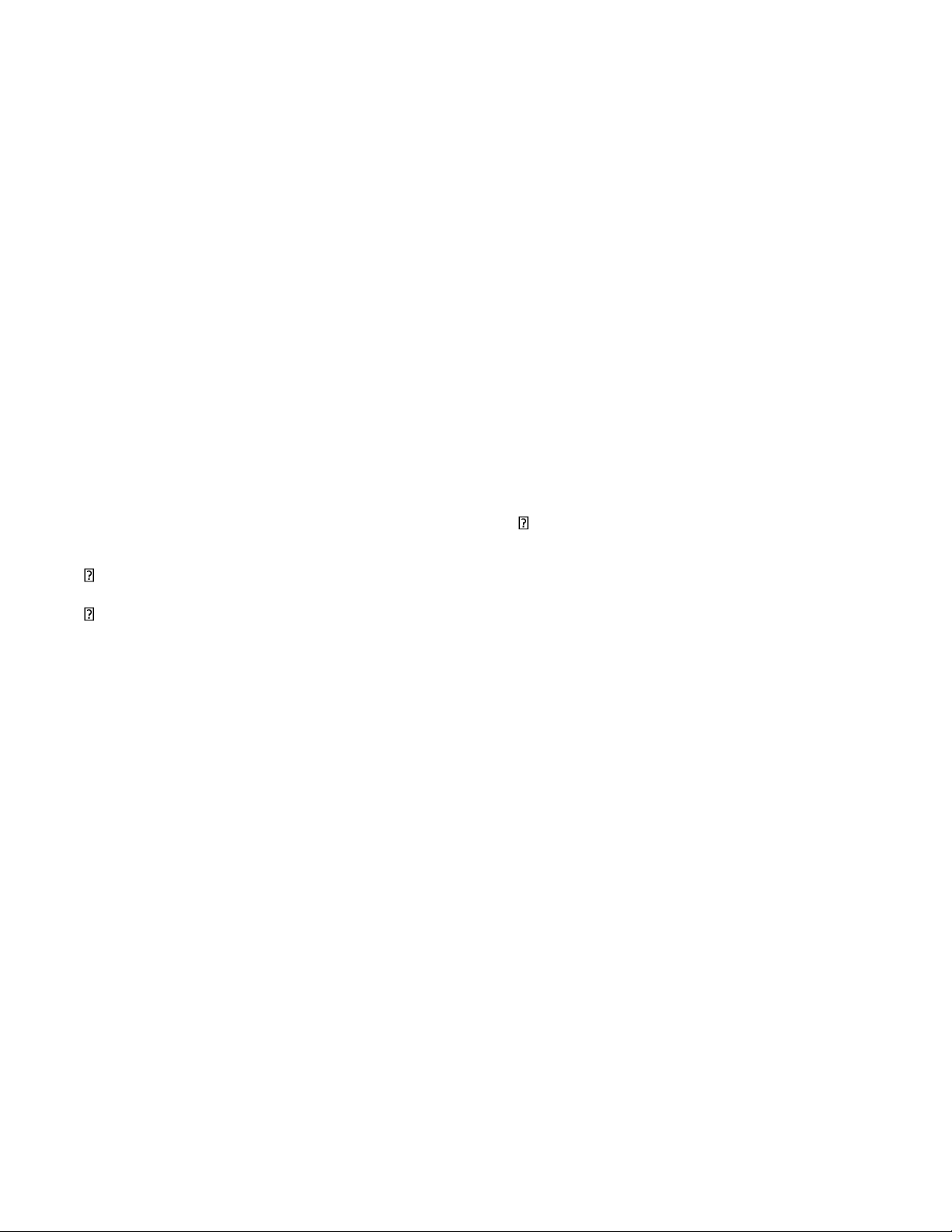
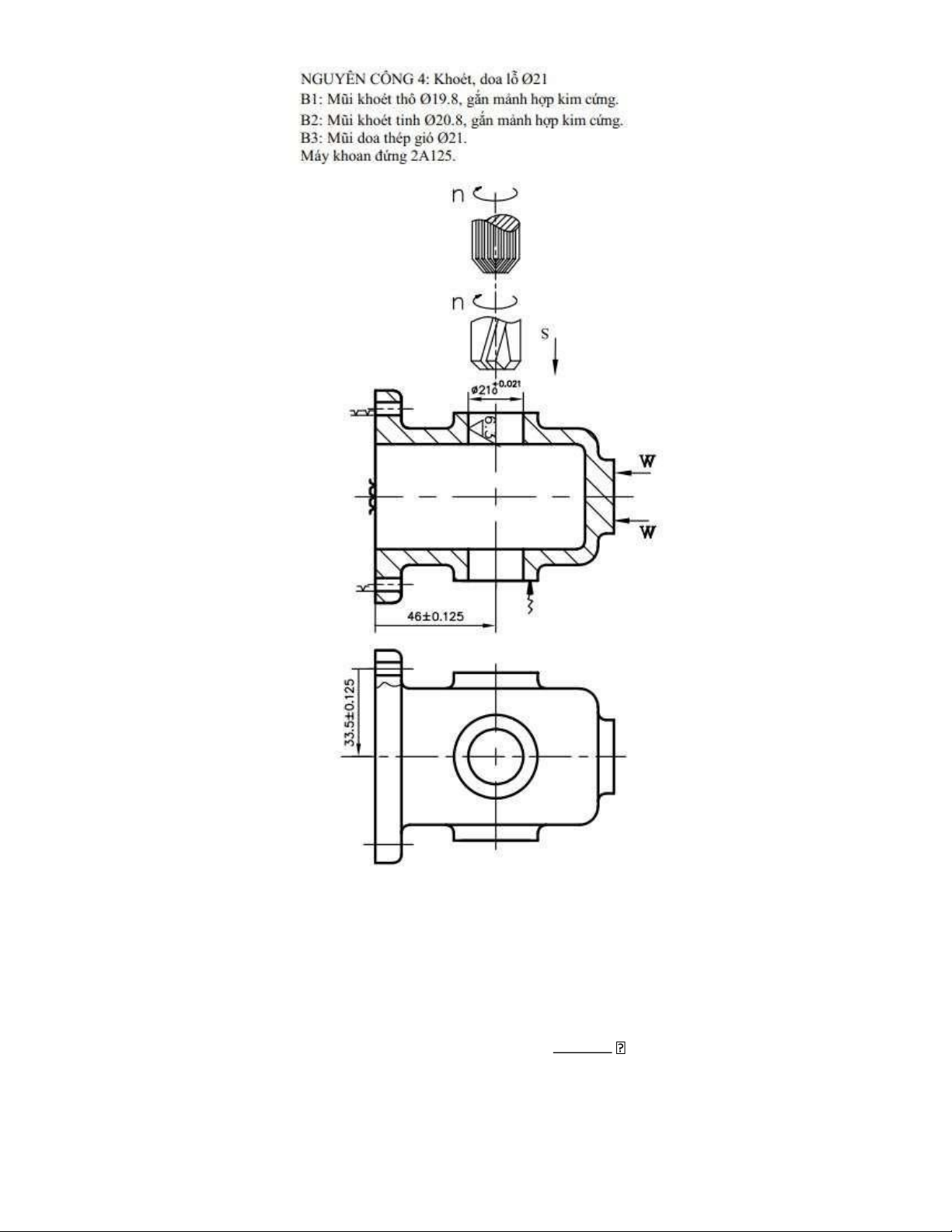
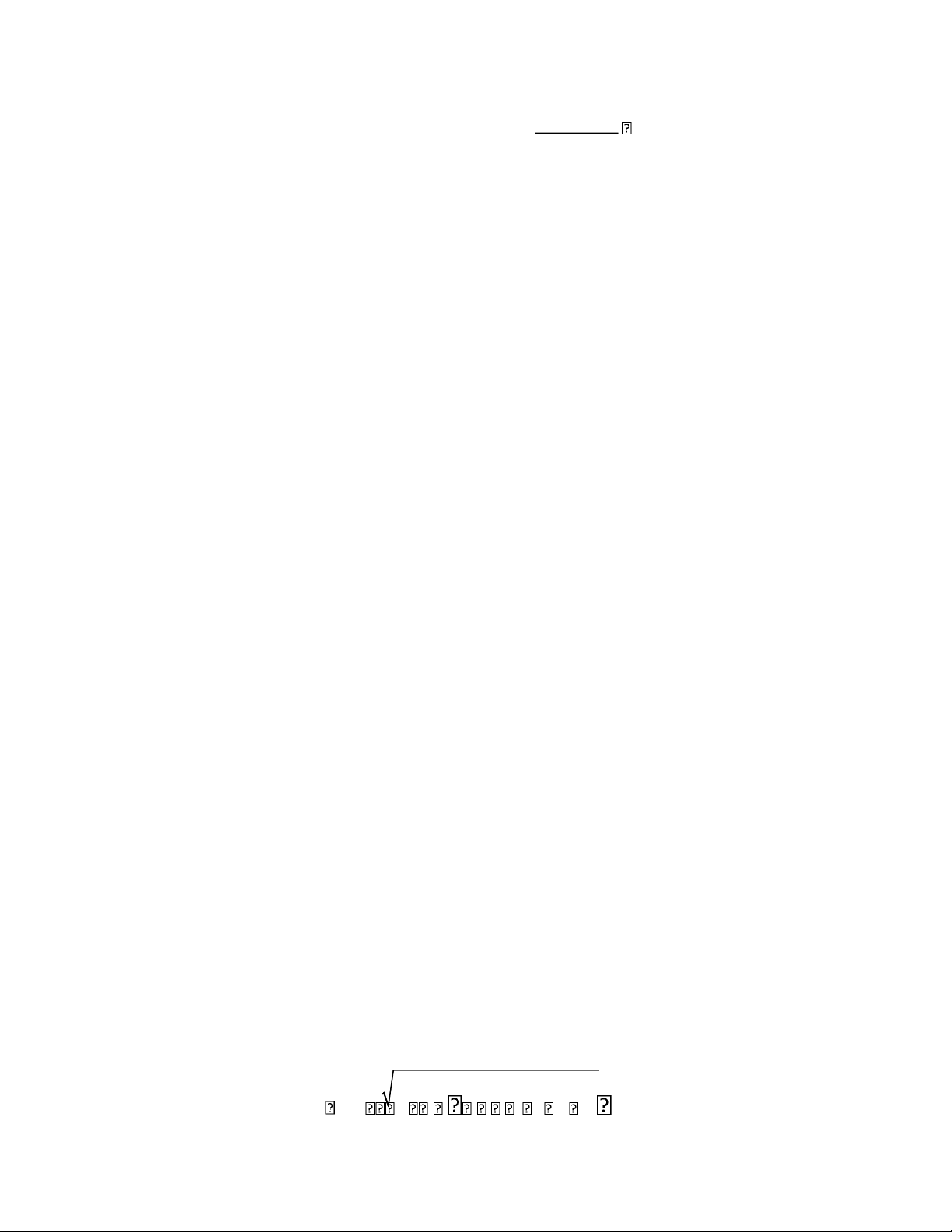
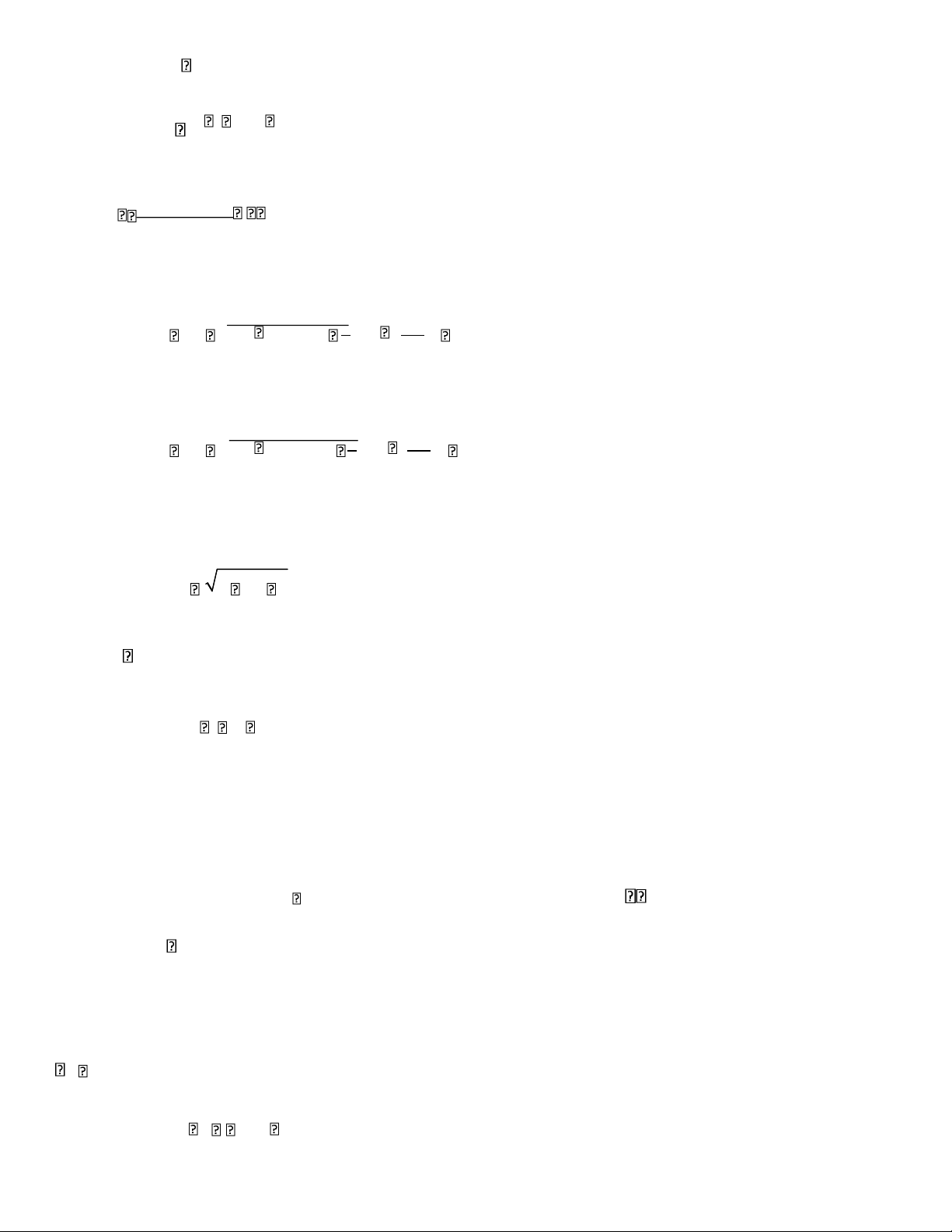
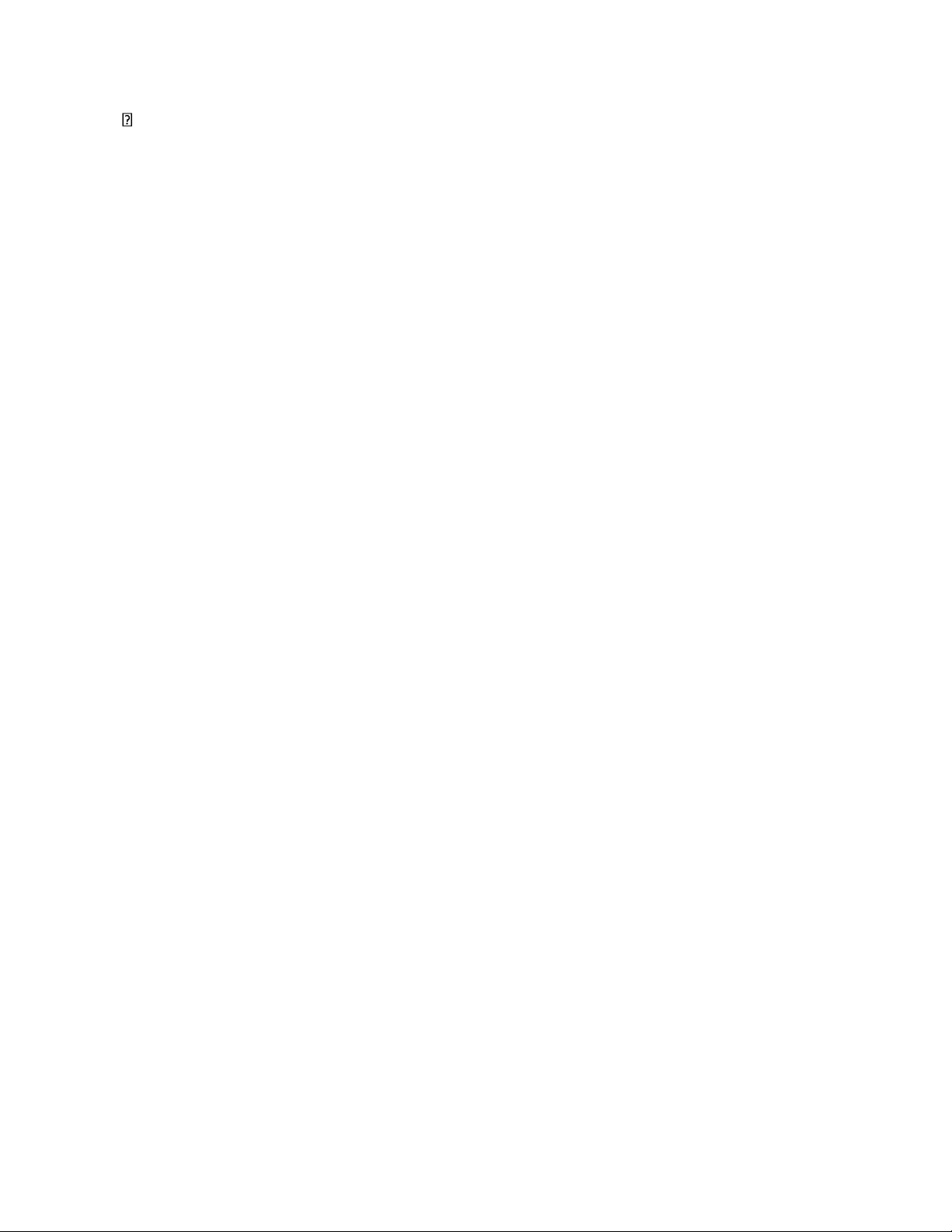
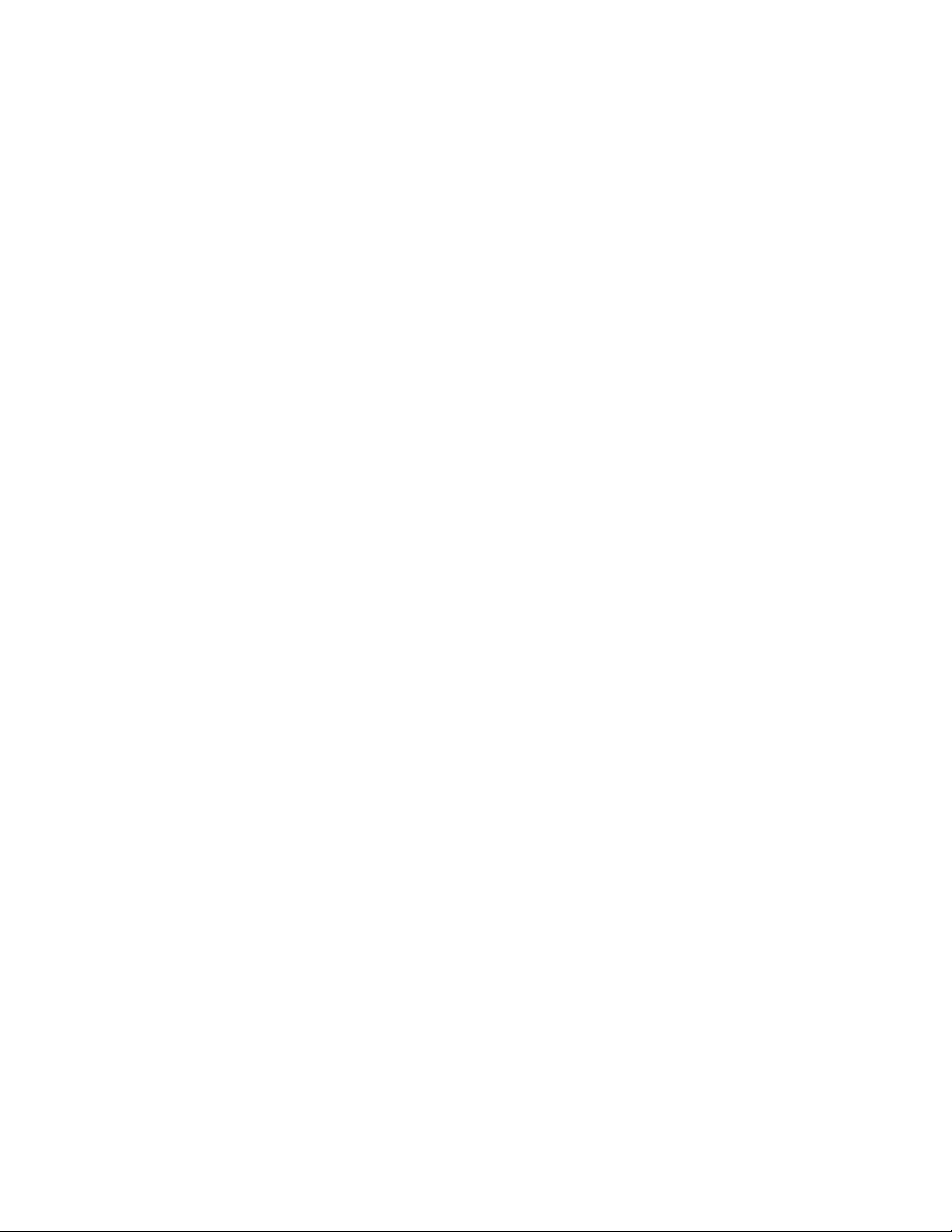
Preview text:
lOMoARcPSD|36625228 `
TRƯỜNG ĐẠI HỌC SƯ PHẠM KỸ THUẬT TP.HCM
KHOA CƠ KHÍ CHẾ TẠO MÁY TIỂU LUẬN
ĐỀ TÀI: THIẾT KẾ QUY TRÌNH CÔNG NGHỆ
GIA CÔNG THIẾT BỊ TRUYỀN ĐỘNG LỆCH TÂM GVHD: NGUYỄN HOÀI NAM SVTH: BÙI NHẬT KHÁNH LỚP : 191432B NGÀNH: CÔNG NGHỆ CTM HỌC KỲ: II lOMoARcPSD|36625228
BỘ GIÁO DỤC VÀ ĐÀO TẠO
CỘNG HÒA XÃ HỘI CHỦ NGHĨA VIỆT NAM
Trường Đại Học Sư Phạm Kỹ Thuật
Độc Lập – Tự Do – Hạnh Phúc ----------***---------- ---------o0o----------
KHOA CƠ KHÍ CHẾ TẠO MÁY – BỘ MÔN CÔNG NGHỆ CHẾ TẠO MÁY
NHIỆM VỤ ĐỒ ÁN MÔN HỌC CÔNG NGHỆ CHẾ TẠO MÁY
Họ và tên: Bùi Nhật Khánh MSSV: 19143264
Ngành: Công nghệ chế tạo máy Lớp: 191432B
Tên đề tài: Thiết kế quy trình công nghệ gia công thiết bị truyền động lệch tâm
I. Số liệu cho trước - Sản lượng: 16.500 chiếc/năm.
- Điều kiện thiết bị: tự chọn. II.
Nội dung thuyết minh và tính toán
1. Nghiên cứu chi tiết gia công: chức năng làm việc, tính công nghệ của kết cấu…
2. Xác định dạng sản xuất.
3. Chọn phôi và phương pháp tạo phôi, tra lượng dư cho các bề mặt gia công.
4. Lập tiến trình công nghệ: thứ tự gia công, gá đặt, so sánh các phương án, chọn phương án hợplý. 5. Thiết kế nguyên công • Vẽ sơ đồ gá đặt
• Chọn máy, kết cấu dao
• Trình bày các bước: chọn dao (loại dao và vật liệu làm dao), tra chế độ cắt: s, v, t; tra lượng dư
cho các bước và tính thời gian từng chiếc cho từng bước công nghệ.
• Tính lượng dư gia công cho nguyên công: phay thô mặt đáy (nguyên công 1).
• Tính chế độ cắt cho nguyên công: khoét, doa lỗ ø21 (nguyên công 4). 6. Thiết kế đồ gá
- Vẽ sơ đồ nguyên lý, thiết kế cơ cấu và trình bày nguyên lý làm việc của đồ gá.
- Tính lực kẹp cần thiết, lực kẹp của cơ cấu kẹp.
- Tính sai số chế tạo cho phép của đồ gá và ghi các yêu cầu kỹ thuật.
- Tính sức bền cho các chi tiết chịu lực. III. Các bản vẽ
- Bản vẽ chi tiết:………………………………………1 bản (A3). lOMoARcPSD|36625228
- Bản vẽ chi tiết lồng phôi:……………………………1 bản (A3).
- Bản vẽ mẫu đúc:…………………………………….1 bản (A3). - Bản vẽ lắp khuôn
đúc:………………………………1 bản (A3). -
Tập bản vẽ sơ đồ nguyên
công:……………………. 4 bản (A3). -
Bản vẽ tách chi tiết từ đồ gá:………………………. 1 bản (A3). -
Bản vẽ thiết kế đồ gá:……………………………….1 bản (A1). IV.
Giáo viên hướng dẫn: Nguyễn Hoài Nam
Chủ nhiệm bộ môn
Giáo viên hướng dẫn lOMoARcPSD|36625228 MỤC LỤC
CHƯƠNG 1: NGHIÊN CỨU CHI TIẾT GIA CÔNG VÀ TẠO PHÔI. . . . . . . . . . . . . . . . . . . . . . . . . .8
1. Phân tích chi tiết gia công. . . . . . . . . . . . . . . . . . . . . . . . . . . . . . . . . . . . . . . . . . . . . . . . . . . . . . . . .8 1.1 Công
dụng. . . . . . . . . . . . . . . . . . . . . . . . . . . . . . . . . . . . . . . . . . . . . . . . . . . . . . . . . . . . . . . . . .8
1.2 Phân tích tính công nghệ trong kết
cấu. . . . . . . . . . . . . . . . . . . . . . . . . . . . . . . . . . . . . . . . . . . . 8
1.3 Yêu cầu kỹ thuật của chi tiết
. . . . . . . . . . . . . . . . . . . . . . . . . . . . . . . . . . . . . . . . . . . . . . . . . . . 8
1.4 Phân tích các bề mặt chi
tiết. . . . . . . . . . . . . . . . . . . . . . . . . . . . . . . . . . . . . . . . . . . . . . . . . . . . 8 1.5 Xác định dạng sản
xuất. . . . . . . . . . . . . . . . . . . . . . . . . . . . . . . . . . . . . . . . . . . . . . . . . . . . . . .10
1.6 Vật liệu và phương pháp chế tạo
phôi. . . . . . . . . . . . . . . . . . . . . . . . . . . . . . . . . . . . . . . . . . . .12 CHƯƠNG 2: THIẾT KẾ TRÌNH
TỰ GIA CÔNG. . . . . . . . . . . . . . . . . . . . . . . . . . . . . . . . . . . . . . . . 15
CHƯƠNG 3: THIẾT KẾ NGUYÊN CÔNG. . . . . . . . . . . . . . . . . . . . . . . . . . . . . . . . . . . . . . . . . . . . . 22 3.1
Nguyên công I: Phay thô mặt phẳng đáy chi tiết bằng gang xám,
190HB. . . . . . . . . . . . . . . . . . 22 3.2
Nguyên công II: Khoan 8 lỗ, doa 2 lỗ
Ø5. . . . . . . . . . . . . . . . . . . . . . . . . . . . . . . . . . . . . . . . . . .26 3.3
Nguyên công III: Phay 2 mặt bên Chi tiết bằng gang xám,
190HB. . . . . . . . . . . . . . . . . . . . . . . 29 3.4
Nguyên công IV: Khoét, doa lỗ
Ø21. . . . . . . . . . . . . . . . . . . . . . . . . . . . . . . . . . . . . . . . . . . . . . .34 3.5
Nguyên công V: Khoét doa lỗ Ø21 còn
lại. . . . . . . . . . . . . . . . . . . . . . . . . . . . . . . . . . . . . . . . . 40 3.6
Nguyên công VI: Vát mép 1x45 lỗ Ø21 chi tiết bằng gang xám,
190HB. . . . . . . . . . . . . . . . . . 44 3.7
Nguyên công VII: Vát mép 1x45 lỗ Ø21 chi tiết bằng gang xám,
190HB. . . . . . . . . . . . . . . . . . 48 lOMoARcPSD|36625228 3.8
Nguyên công VIII: Phay thô mặt đáy chi tiết bằng gang xám
190HB. . . . . . . . . . . . . . . . . . . . .51 3.9 Nguyên công IX: Khoan lỗ
Ø17:. . . . . . . . . . . . . . . . . . . . . . . . . . . . . . . . . . . . . . . . . . . . . . . . .56 3.10
Nguyên công X: Khoét doa lỗ
Ø18:. . . . . . . . . . . . . . . . . . . . . . . . . . . . . . . . . . . . . . . . . . . . . . 59 3.11
Nguyên công XII: Vát mép 1x45o lỗ
Ø18:. . . . . . . . . . . . . . . . . . . . . . . . . . . . . . . . . . . . . . . . . 63 3.12 Nguyên công XII: Khoan Taro
M6:. . . . . . . . . . . . . . . . . . . . . . . . . . . . . . . . . . . . . . . . . . . . . . 66 3.13 Nguyên công XIII: Khoan Taro
M6:. . . . . . . . . . . . . . . . . . . . . . . . . . . . . . . . . . . . . . . . . . . . . .71 3.14 Nguyên công XIV: Taro 8 lỗ
M6:. . . . . . . . . . . . . . . . . . . . . . . . . . . . . . . . . . . . . . . . . . . . . . . .75 CHƯƠNG 4: TÍNH LƯỢNG DƯ
GIA CÔNG. . . . . . . . . . . . . . . . . . . . . . . . . . . . . . . . . . . . . . . . . . . 79
CHƯƠNG 5: TÍNH CHẾ ĐỘ CẮT. . . . . . . . . . . . . . . . . . . . . . . . . . . . . . . . . . . . . . . . . . . . . . . . . . . .82
CHƯƠNG 6: THIẾT KẾ ĐỒ GÁ KHOÉT – DOA. . . . . . . . . . . . . . . . . . . . . . . . . . . . . . . . . . . . . . . .87
TÀI LIỆU THAM KHẢO. . . . . . . . . . . . . . . . . . . . . . . . . . . . . . . . . . . . . . . . . . . . . . . . . . . . . . . . . . . 91 lOMoARcPSD|36625228 LỜI NÓI ĐẦU
Đồ án môn học công nghệ chế tạo máy là đồ án chuyên ngành của sinh viên ngành cơ khí chế tạo
máy, là kết sau cùng của nhiều môn học như Công Nghệ Chế Tạo Máy và Công Nghệ Kim Loại, Dung
sai kỹ thuật đo,… Qua đồ án này giúp cho sinh viên làm quen với những quy trình công nghệ trước khi làm đồ án tốt nghiệp.
Việc thiết lập quy trình công nghệ gia công chi tiết nhằm ứng dụng được những công nghệ gia
công mới, loại bỏ những công nghệ lạc hậu không đảm bảo yêu cầu kỹ thuật, chất lượng kém. Ngoài ra
việc thiết lập quy trình công nghệ gia công giúp người chế tạo giảm được thời gian gia công và tăng
năng suất làm việc để đáp ứng sản phẩm theo yêu cầu sử dụng.
Một sản phẩm có thể có nhiều phương án công nghệ khác nhau. Việc thiết lập quy trình công
nghệ gia công còn là sự so sánh có chọn lựa để tìm ra một phương án công nghệ hợp lý nhằm đảm bảo
những yêu cầu chất lượng, giá thành, thời gian gia công cho sản phẩm nhằm đáp ứng nhu cầu xã hội.
Sau thời gian được trang bị các môn lý thuyết về công nghệ chế tạo máy và được tiến hành làm đồ
án môn học công nghệ chế tạo máy với đề tài:“Thiết kế quy trình công nghệ gia công THIẾT BỊ
TRUYỀN ĐỘNG LỆCH TÂM”.
Do thời gian có hạn và chưa có kinh nghiệm thực tế nhiều nên không tránh khỏi thiếu sót, kính
mong quý thầy cô và các bạn đóng góp ý kiến để đạt kết quả tốt nhất.
Em xin chân thành cảm ơn sự hướng dẫn tận tình của thầy Nguyễn Hoài Nam, và các thầy cô
trong khoa cơ khí chế tạo máy trường Đại học Sư Phạm Kỹ thuật Thành Phố Hồ Chí Minh. Sinh viên thực hiện Bùi Nhật Khánh
NHẬN XÉT CỦA GIÁO VIÊN HƯỚNG DẪN
……………………………………………………………………………………………………………
……………………………………………………………………………………………………………
……………………………………………………………………………………………………………
……………………………………………………………………………………………………………
…………………………………………………………………………………………………………… lOMoARcPSD|36625228
……………………………………………………………………………………………………………
……………………………………………………………………………………………………………
……………………………………………………………………………………………………………
……………………………………………………………………………………………………………
……………………………………………………………………………………………………………
……………………………………………………………………………………………………………
……………………………………………………………………………………………………………
……………………………………………………………………………………………………………
……………………………………………………………………………………………………………
……………………………………………………………………………………………………………
……………………………………………………………………………………………………………
……………………………………………………………………………………………………………
……………………………………………………………………………………………………………
……………………………………………………………………………………………………………
……………………………………………………………………………………………………………
……………………………………………………………………………………………………………
……………………………………………………………………………………………………………
……………………………………………………………………………………………………………
……………………………………………………………………………………………………………
……………………………………………………………………………………………………………
……………………………………………………………………………………………………………
…………………………… Chữ ký của GVHD
CHƯƠNG 1: NGHIÊN CỨU CHI TIẾT GIA CÔNG VÀ TẠO PHÔI
1. Phân tích chi tiết gia công 1.1 Công dụng -
Chi tiết gia công là chi tiết dạng hộp, bề mặt làm việc chính là bề mặt 2 lỗ Ø 21 mà tâm của
chúng song song với mặt đáy và lỗ Ø 18 -
Chi tiết dùng để đỡ trục truyền chuyển động quay thành chuyển động tịnh tiến.
1.2 Phân tích tính công nghệ trong kết cấu. lOMoARcPSD|36625228 -
Chi tiết thiết kế lỗ Ø 21 thông suốt dễ gia công, có mặt đáy và các lỗ vuông góc với mặt đáy
thuận tiện cho việc chọn chuẩn tinh thông nhất. -
Các lỗ được bố trí vuông góc và song song với mặt phẳng của vách dễ gia công, các lỗ kẹp chặt
chitiết là lỗ tiêu chuẩn (M6). -
Chi tiết có kết cấu đơn giản , có tiết diện ngang chữ U dễ làm khuôn trong việc tạo phôi. -
Chiều dày thành 6 mm phù hợp với vật đúc trung bình. (Bảng 3/24 ,[3]).
1.3 Yêu cầu kỹ thuật của chi tiết . -
Dung sai độ vuông góc giữa đường tâm lỗ Ø18 đối với đường tâm lỗ Ø21 là 0.1 mm (Bảng 2.15/95, [4]). -
Dung sai độ song song của đường tâm lỗ Ø21 so với bề mặt đáy A là 0.12 mm (Bảng 2.15/95, [4]).
1.4 Phân tích các bề mặt chi tiết. - Đánh số : lOMoARcPSD|36625228 -
Lỗ Ø21: lắp với ống lót, chế độ lắp H7/h6 (Bảng 3.1/122,[4]), cấp chính xác 7, phương pháp gia
công : khoét thô, tinh và doa thô, Ra=6.3 , Ø21+0.021 ( Bảng 1.14/34 , 2.29/113, [4] ). -
Lỗ Ø18: lắp với ống lót, chế độ lắp H7/h6 (Bảng 3.1/22, [4]), cấp chính xác 7, phương pháp gia
công :khoan, khoét và doa thô , Ra=1.6 , Ø18+0.018 ( Bảng 1.14/34 , 2.29/113, [4] ). -
Kích thước 64: phương pháp gia công: Phay thô, Ra= 6.3, IT 12 => 64±0,15 ( Bảng 1.4/11, [4]). -
Kích thước 91: Phương pháp gia công: Phay thô, Ra= 6.3, IT 12 => 91±0.175 -
Kích thước 10, 46: Phương pháp gia công: Phay thô, Ra= 25 , IT12 =>10± 0.075, 46±0.125
Bảng 1.1: Mối quan hệ giữa sai lệch giới hạn kích thước và độ nhám lOMoARcPSD|36625228
Bảng 1.2: Mối quan hệ giữa sai lệch giới hạn kích thước và phương pháp gia công
Sản lượng chi tiết cần chế tạo trong một năm: N = NO.( 1+ (chiếc/năm) Trong đó:
N : Số chi tiết sản xuất được trong 1 năm.
N0 : Số sản phẩm (số máy) được sản xuất trong 1 năm.
Theo đề bài N0= 15000(chiếc/năm).
: Số % chi tiết dự trữ. Chọn : = 5%. lOMoARcPSD|36625228 : số % phế phẩm Chọn =5 %
N=15000.[1+(5+5)/100]= 16500(chiếc/năm)
1.5.2 Tính khối lượng chỉ tiết. -
Khối lượng của chi tiết được xác định theo công thức: Q = V. (kg)
+Q: Khối lượng chi tiết (kg)
+V: Thể tích của chi tiết (dm3), sử dụng phần mêm Creo 7.0 ta đo được V= 0.1428 (dm3)
Q = 1.015 (kg) => Dạng sản xuất hàng khối.
1.6 Vật liệu và phương pháp chế tạo phôi. 1.6.1 Vật liệu
Chi tiết là gang xám, GC250 (theo tiêu chuẩn Hàn Quốc), theo trang 1849, [5] ta có: -
Giới hạn bền kéo: 250 N/mm2 -
Giới hạn bền uốn: 250 N/mm2 - Độ cứng 200 – 269 HB lOMoARcPSD|36625228
=> Chọn vật liệu chế tạo chi tiết là GX 28-48 ( TCVN 1659 – 75 ) có : -
Giới hạn bền kéo: 280 N/mm2 -
Giới hạn bền uốn: 480 N/mm2 - Độ cứng : 170-241 HB
1.6.2 Phương pháp chế tạo phôi. -
Chi tiết được chế tạo bằng vật liệu gang xám , dạng sản xuất hàng khối , chọn phương pháp
tạophôi là đúc trong khuôn cát làm khuôn bằng máy, mẫu gỗ, cấp chính xác đúc cấp II , Cấp chính xác
kích thước phôi IT15. Độ nhám về mặt Rz=80. ( Trang 23, [1]). Mặt phân khuôn : lOMoARcPSD|36625228 Thông số đúc : -
Độ xiên thoát khuôn: h= 14 => 3o , h= 40,5 => 1o 30 ( Bảng 24/93, [3]) -
Sai lệch lớn nhất về khối lượng (±): 7 % ( Bảng 17/82, [3]) -
Độ co: 1% (Bảng 23/89, [3]) -
Tuổi thọ mẫu gỗ: sản lượng ~1500, đúc mỗi đợt 100 cái. lOMoARcPSD|36625228 -
Bán kính góc lượn : R= 3 mm -
Lượng dư: (Bảng 19/84, 20/86, [3])
Các bề mặt gia công Lượng dư (mm) 1 3 2 3.5 3 3 4 Đặc 5 2.5 6 Đặc 7 3 8 Đặc 9 Đặc -
Tra bảng 30/106, [3] ta có được chiều cao của đầu gác ruột thẳng đứng:
Với L= 64 và d= 15 ta có h= 25 và h1= 15. Tra bảng 32 trang 108 ta có độ nghiêng của đầu gác α= 10o;
β= 15o. Tra bảng 33 trang 109 ta có khe hở S2=0,25. -
Tra bảng 28/104, [3] với (a+b)/2= (39+40)/2 = 39.5 và ruột có đầu gác dưới ta có l= 35, khe hở
phíatrên của khuôn là 1,5 và độ xiên đầu gác 10o.
Thiết kế khuôn đúc : -
Xác định hệ thống rót :
+ Ta có chiều dày thành vật đúc g= 6mm xác định được tiết diện rãnh dẫn Fd = 0.6 cm2, chiều dài 20 mm. (Bảng 37/139, [3])
+ Lấy quan hệ đối với vật đúc bằng gang : Fd : Fx : Fr = 1:1,2:1,4 ( Trang 140, [3])
Ta có : tiết diện rãnh lọc xỉ Fx = 0.72 cm2. Tiết diện ống rót : Fr = 0.84 cm2.
+ Cốc rót: Sử dụng cốc rót có cấu tạo như hình 2.I.92c (Trang 141,[3]). Kích thước (Bảng 39/141, [3]) :
d= 25mm, L= 120mm, M= 40mm, h= 70mm, R1= 25mm, R2= 20mm, R3= 35mm, R4= 30mm, r= 10mm, r1= 5mm.
+ Ống dẫn: Sử dụng ống là hình trụ tròn côn 3 độ trên to (theo đường kính d của cốc rót) dưới nhỏ, loại
này dễ làm khuôn lại bảo đảm dòng kim loại chảy đều vào rãnh lọc xỉ. lOMoARcPSD|36625228
+ Rãnh dẫn: tiết diện là hình thang thấp có kích thước h=3mm, a=21mm, b=19mm (Bảng 39/143, [3]). Phương án lOMoARcPSD|36625228 lOMoARcPSD|36625228 lOMoARcPSD|36625228 lOMoARcPSD|36625228 lOMoARcPSD|36625228 lOMoARcPSD|36625228
CHƯƠNG 3: THIẾT KẾ NGUYÊN CÔNG
3.1 Nguyên công I: Phay thô mặt phẳng đáy chi tiết bằng gang xám, 190HB. 1. Sơ đồ gá đặt lOMoARcPSD|36625228 2.
Định vị: Hạn chế 5 bậc tự do: tịnh tiến Oy; tịnh tiến Oz; quay Oz; tịnh tiến Ox; quay Oy bằng
chống tâm cố định hạn chế 3 bậc tự do , chống tâm di động định vị 2 bậc tự do :
- Chốt tỳ khía nhám chống xoay hạn chế 1 bậc tự do quay Ox .(Trang 392, [6]) - Kẹp chặt bằng ren lOMoARcPSD|36625228 D d (H7/js6) H L C t d1 b C1 12 8 6 16 0,6 2 2 3 1
3. Chọn máy: Máy phay 6H11 (Tra bảng 9-38, [7]). Máy phay đứng 6H11 Đặc tính kỹ thuật Thông số
Kích thước làm việc bàn máy (mm) 250x1000 Công suất động cơ (kW) 4,5
Số cấp tốc độ trục chính 16
Phạm vị tốc độ trục chính (v/ph) 65-1800
Số cấp bước tiền bàn máy 16
4. Chọn dụng cụ cắt : Chọn dao phay mặt đầu gắn mảnh hợp kim cứng.
- Các thông số của dao: (tra bảng 5-127, [6]).
- Đường kính dao: D = 90; Số răng Z = 10; Vật liệu BK6. - Tuổi bền dao T=120.
- Dụng cụ đo: Thước kẹp 150mm, độ chính xác 0,05.
5. Tra chế độ cắt và công suất cắt Nc:
Chia bước: Phay thô Z=2.5mm. Phay Thô : lOMoARcPSD|36625228 - Chiều sâu cắt t = 3 mm
- Lượng chạy dao răng: Sz=0,14 mm/răng (5-125 CNCTM 2)
- Tốc độ cắt Vb=232 m/phút (bảng 5-127 sổ tay CNCTM 2 tr. 128)
- Vậy tốc độ tính toán Vt=Vb.K1.K2.K.3K4.K5.K6 = 132 m/ph Với:
+ Hệ số điều chính phụ thuộc vào độ cứng của gang K1 = 1 vì độ cứng vật liệu HB= 190 + Hệ
số điều chỉnh phụ thuộc vào chu kì bền của dao K2=0,8 vì muốn tuổi bền thực tế cao gấp 2 lần
tuổi bền cho trong sổ tay.
+ Hệ số điều chỉnh phụ thuộc vào mác hợp kim cứng K3=1.
+ Hệ số điều chỉnh phụ thuộc vào bề mặt gia công (gang đúc có vỏ cứng) K4=0,8.
+ Hệ số điều chỉnh phụ thuộc vào chiều rộng phay K5=0,89.
+ Hệ số điều chỉnh vào góc nghiêng chính K6=1.
- Số vòng quay theo tính toán là: 1000.Vt 1000.132 467 nt .D 3,14.90 (v/ph)
- Máy 6H11 có nmin=65; nmax=1800, số cấp tốc độ m=16, tìm công bội φ như sau: m 1 16 1 15 nmin 65 15 -
Ứng với có giá trị là 32 gần với 27,69 tương ứng với =1,26. Mặc khác x nt 467 7,18 nmin 65
Theo bảng 4.1 (sách HD DACNCTM) ứng với
1,26 ta có giá trị 9 8 gần với 7,56 Vậy số n 65.8 520
vòng quay theo máy là: m (v/ph) Vtt Dn 3,14.90.520 117 lOMoARcPSD|36625228 -
Như vậy tốc độ cắt thực tế là: 1000 1000 (m/ph) -
Lượng chạy dao phút Sph= 0,14. 10. 520= 728(mm/ph) -
Lượng chạy dao của máy là: Sm 35 980mm ph/ , với lượng chạy dao 728mm/ph là quá
nhanh cho bề mặt gia công quá nhỏ vì thế ta chọn Sm 270mm ph/ - Công suất cắt khi phay thô:
Với chi tiết là gang xám có độ cứng 190HB, dùng dao HKC, ta có công suất cắt Nc = 3.8 (kW) (Bảng 5-130, [6]).
Vậy máy hoạt động tốt.
6.Thời gian gia công khi phay thô: -
Thời gian thực hiện nguyên công là: Ttc = T0 + Tp + Tpv + Ttn=T0+0,26T0 Với:
Ttc : thời gian từng chiếc T0 : thời gian cơ bản Tp : thời gian phụ Tpv :thời gian phục vụ Ttn : thời gian nghỉ ngơi L L L 1 T0 2 -
Thời gian cơ bản: Sph (phút) Với :
L=81 mm (chiều dài bề mặt gia công)
L1= 0,5D+3= 48 mm (chiều dài ăn dao)
L2= 3 mm (chiều dài thoát dao)
S=270 mm/phút (lượng chạy dao vòng) T0 81 48 3 0,49 270 (phút) = 0,49.1,26 = 0,62 (phút) lOMoARcPSD|36625228
Chế độ cắt khi phay thô: t= Z= 3mm; Sph= 270 mm/phút; nm= 520 v/ph; N= 3,8 kW
7. Đồ gá và trang bị phụ
7.1 Kẹp chặt: Cơ cấu kẹp bằng ren, lực kẹp hướng từ phải qua . -
Nguyên lý kẹp chặt :Chi tiết được định vị trên 2 mũi tâm vát (do hai lỗ chưa được gia
công ) và chốt tỳ đầu khía nhám. Chi tiết được kẹp chặt bằng tay quay thông qua bulong.
3.2 Nguyên công II: Khoan 8 lỗ, doa 2 lỗ Ø5
Chi tiết bằng gang xám có 190HB, lỗ đúc đặc sẵn, khi gia công đạt CCX7, độ nhám Ra=1,6. Theo
bảng 3.3, cần phải qua các bước sau: - Khoan thô đạt Ø4.8 -
Doa thô đạt Ø5 1. Sơ đồ gá đặt. lOMoARcPSD|36625228 2.
Định vị: Hạn chế 6 bậc tự do gồm 3 bậc tự do : tịnh tiến Oz, xoay quanh Oy, xoay quanh Ox ở
mặt đáy bằng hai phiến tì.
- 2 chốt tỳ khía nhám hạn chế 2 bậc tự do và chốt tỳ khía nhám 1 bậc tự do ở mặt bên như hình.( Trang 392, [6]) lOMoARcPSD|36625228 D d (H7/js6) H L C t d1 b C1 12 8 6 16 0,6 2 2 3 1
2. Chọn máy: Máy khoan đứng 2A125: (phụ lục/183, [1]). Đặt tính kỹ thuật Thông số máy Công suất động cơ (kw) 2,8
Đường kính gia công (max) 25
Giới hạn vòng quay trục chính(v/phút) 97-1360 Số cấp chạy dao 9 Số cấp tốc độ 9
Giới hạn chạy dao (mm/vòng) 0,1-0,81 Hiệu suất máy 0,8
4. Chọn dụng cụ cắt: -
Mũi khoan thép gió Ø4.8 mm tuổi bền T=20 phút -
Mũi doa thép gió Ø5mm tuổi bền T=60 phút - Dụng cụ đo: Calip
5. Tra chế độ cắt và công suất cắt Nc:
Chế độ cắt khi khoan
Chiều sâu cắt: t = 2.4 (mm) -
Lượng chạy dao: S = 0,12 (mm/v) (bảng 5-89). Chọn theo máy S= 0,1. -
Tốc độ cắt: Vb = 48 (m/ph) (bảng 5-90) -
Các hệ số hiệu chỉnh vận tốc 0,91 với chu kỳ bền thực tế mong muốn gấp 2 lần. lOMoARcPSD|36625228 -
Hệ số điều chỉnh theo mác của vật liệu mũi khoan là 1. -
Vậy tốc độ tính toán: Vt = 48.0,91 = 43,68 m/ph 1000 1000 Số vòng quay tính toán - Chọn nm= 1360 vòng/phút Vtt Dn 3,14.4,8.1360 20,5 -
Tốc độ cắt thực tế là: 1000 1000 (m/ph) -
Công suất cắt: N = 1 (kW) (Bảng 5- 92) -
Kiểm tra công suất máy: N = 1 (kW) < Nm = 2,8 (kW) -
Vậy máy hoạt động tốt. 68 2898 - D 4,8 (v/ph)
Chế độ cắt khi doa. -
Chiều sâu cắt: t = 0,1 (mm) -
Lượng chạy dao: S = 0,85 (mm/vòng) (bảng 5-112). -
Theo máy chọn: S= 0,81 (mm/ vòng). -
Tốc độ cắt: Vb = 6,5 (m/ph) (bảng 5-114) -
Với các hệ số điều chỉnh bằng 1 nên vận tốc tính toán Vt=6,5 m/ph 1000 1000
nt Vt 6,5 414 - Số vòng quay
tính toán là: D 5 (v/ph) - Chọn theo máy nm= 388 v/ph. lOMoARcPSD|36625228 Vtt
Dn 3,14.5.388 6,1 - Tốc
độ cắt thực tế là: 1000 1000 (m/ph) -
Công suất doa rất nhỏ, nên không cần tra.
6. Thời gian gia công: -
Theo bảng 4.8, thời gian thực hiện được xác định (phút) -
Chiều dài gia công: L= 10 mm L1 D d cot g 2 -
2 φ hníhc tắc iỡưl aủc gnêihgn cóg iớv 06= ֯ nên lấy L1=3 - Chiều dài thoát dao: L2 = 3 mm. T0 0,09 - Khi khoan thô: (ph) T0 0,05 - Khi doa thô: (ph) -
Thời gian cơ bản của 2 bước trên: T = 0,09 + 0,05 = 0,14 (ph).
7. Đồ gá và trang bị phụ - Kẹp bằng ren.
3.3 Nguyên công III: Phay 2 mặt bên Chi tiết bằng gang xám, 190HB 1.Sơ đồ gá đặt lOMoARcPSD|36625228
2. Định vị: hạn chế 6 BTD do gồm 3 bậc tự do : tịnh tiến Oz, xoay quanh Ox, xoay quanh Oy ở mặt
đáy bằng hai phiến tỳ : -
Chốt trụ ngắn 2 bậc tự do : tịnh tiến Oy, tịnh tiến Ox ở bề mặt lỗ Ø5, chốt trám 1 bậc tự do quay quanh Oz ở mặt lỗ Ø5 : lOMoARcPSD|36625228 - Trang 125, [8] ta có :
3. Chọn máy: Máy phay ngang 6H82. Tra bảng 9-38, [7] ta có : Máy phay ngang 6H82 Đặc tính kỹ thuật Thông số
Kích thước làm việc bàn máy (mm) 320x1250 Công suất động cơ (kW)
7 Số cấp tốc độ trục chính 18
Phạm vị tốc độ trục chính (v/ph) 30 – 1500
Số cấp bước tiền bàn máy 18
4.Chọn dụng cụ cắt: Chọn dao phay đĩa 3 mặt răng thép gió.
- Các thông số của dao: (Tra bảng 5-172, [6]).
- Đường kính dao: D = 200 ; Số răng Z = 20 . - Tuổi bền dao T=180.
- Dụng cụ đo: Thước kẹp 150mm, độ chính xác 0,05.
5. Tra chế độ cắt và công suất cắt Nc Phay thô Z = 3mm Phay Thô : lOMoARcPSD|36625228
- Chiều sâu cắt: t = 3 (mm)
- Lượng chạy dao răng: SZ = 0,18 (mm/răng) (bảng 5-170, [6])
- Tốc độ cắt: Vb= 30 (m/ph ) (bảng 5-127, [6]). Trị số này tương ứng với chiều sâu cắt là 25mm. -
Vậy tốc độ tính toán Vt=Vb.K1.K2 .K3 .K4 = 20,25 m/ph
+ Hệ số điều chính phụ thuộc vào độ cứng của gang K1=1 vì độ cứng vật liệu là gang có HB=190.
+ Hệ số điều chỉnh phụ thuộc vào chu kì bền của dao K2=0,9 vì muốn tuổi bền thực tế cao gấp 2
lần tuổi bền cho trong sổ tay.
+ Hệ số điều chỉnh phụ thược vào dạng gia công thô K3= 1
+ Hệ số điều chỉnh phụ thuộc vào bề mặt gia công : K4= 0,75 .Ứng với bề mặt có vỏ cứng, HB =190 1000 1000.20,25 nt Vt - Số vòng quay tính toán 200 v/ph là: D
- Máy 6H82 có nmin=30; nmax=1500, số cấp tốc độ m=18, tìm công bội φ như sau: m 1 18 1 17 nmax 1500 50 nmin 30
-Ứng với 17 có giá trị gần 50 với 50,65 tương ứng φ=1,26 ( Bảng 4.7, [1]) n nt 40 1,3 Mặc khác: nmin 30
- Theo bảng 4.7 ứng với φ=1,26 ta có giá trị φ2=1,58 gần vs 1,3 - Vậy số vòng quay theo máy là nm=30×1,58 =47 vòng/ph vtt Dnm 200.47 29,5
- Tốc độ cắt thực tế là: 1000 1000 (m/ph)
- Lượng chạy dao máy : Sph = Sz .Z .n = 0,18 x 20 x 47= 169 (mm/phuùt) lOMoARcPSD|36625228
- Lượng chạy dao của máy là : SM = 86 ÷870 (mm/phút ), với lượng chạy dao 169 mm/ph - Công
suất cắt khi phay thô: chi tiết là gang xám có độ cứng 190HB, dùng dao phay đĩa ba mặtrăng thép
gió, có công suất cắt Nc = 1 (kW) (Bảng 5-175, [6]) - Vậy máy hoạt động tốt.
6.Thời gian gia công khi phay thô:
Thời gian thực hiện nguyên công là : Ttc = T0 + Tp + Tpv + Ttn = T0 + 0,26T0 Với :
Ttc : thời gian từng chiếc (Thời gian nguyên công)
T0 : thời gian cơ bản, là thời gian cần thiết để biến đổi trực tiếp hình dạng, kích thước và tính chất cơ lý của chi tiết.
Tp: thời gian phụ, là thời gian để gá, kiểm tra kích thước, tháo chi tiết. .Giá trị gần đúng TP = 10%T0
Tpv: thời gian phục vụ chỗ làm việc , gồm: thời gian phụ vụ kỹ thuật.
(Tpvkt = 8%T0) và thời gian phụ vụ tổ chức (Tpvtc = 3%T0)
Ttn : thời gian nghỉ ngơi tự
nhiên của công nhân (TTN = 5%T0) L L L 12 To Với: thời gian cơ bản: Sph (ph)
Chiều dài về mặt gia công : L = 32 (mm)
Khoảng cách tiến vào của dao: L1 = 0,5D+3 = 0,5.200+3 = 103
Chiều dài thoát dao: L2 = 5 L L L 1 2 32 103 5 0,83 To Sph 169 (ph)
Ttc = 0,83 +0,26.0,83 = 1,04 (phút)
Chế độ cắt khi phay: t = 3mm, Sph=169 mm/ph, nm=47 vòng/ph, N=1 kW Ttc=1,04 phút
7. Đồ gá và trang bị phụ lOMoARcPSD|36625228
- Cơ cấu kẹp liên động :
3.4 Nguyên công IV: Khoét, doa lỗ Ø21
Chi tiết bằng gang xám có 190HB, lỗ đúc sẵn Ø15 khi gia công đạt CCX7, độ nhám Ra=6,3. Theo
bảng 3.3, cần phải qua các bước sau: - Khoét thô đạt Ø19,8 - Khoét tinh đạt Ø20.8 - Doa thô đạt Ø21 1. Sơ đồ gá đặt lOMoARcPSD|36625228 2.
Định vị: hạn chế 6 BTD do gồm 3 bậc tự do tịnh tiến Ox, xoay quanh Oy, xoay quanh Oz ở mặt
đáy bằng hai phiến tỳ : -
Chốt trụ ngắn 2 bậc tự do tịnh tiến Oz, tịnh tiến Oy ở mặt lỗ Ø5, chốt trám 1 bậc tự do xoay quanh Ox ở mặt lỗ Ø5 : lOMoARcPSD|36625228 - Trang 125, [8] ta có :
3. Chọn máy: Máy khoan đứng 2A135: (phụ lục/183, [1]). Đặt tính kỹ thuật Thông số máy Công suất động cơ (kw) 6
Đường kính gia công (max) 35
Giới hạn vòng quay trục chính(v/phút) 68-1100 Số cấp chạy dao 11 Số cấp tốc độ 9
Giới hạn chạy dao (mm/vòng) 0,11-1,6 Hiệu suất máy 0,8
4. Chọn dụng cụ cắt: 19,8 -
Mũi khoét thô gắn mảnh hợp kim cứng chuôi côn K40 (BK8) với các thông số: lOMoARcPSD|36625228
L=180 mm, l= 85 mm, tuổi bền dao: T= 30 phút. (bảng 4-47/332, [9]). 20,8 -
Mũi khoét tinh gắn mảnh hợp kim cứng chuôi côn K40 (BK8) với các thông số:
L=180 mm, l= 85 mm, tuổi bền dao: T= 40 phút. 21 -
Mũi doa thô thép gió với các thông số: L=138 mm, l= 26 mm, tuổi bền dao: T= 120 phút. (bảng 4-49/336, [9]). - Dụng cụ đo: calip
5. Tra chế độ cắt và công suất cắt Nc
- Chiều sâu cắt : Khi khoét thô t=2,4mm.
- Lượng chạy dao: khi khoét thô S=1mm/vòng (theo bảng 5-107/98, [6]) chọn theo máy 2A135 nên ta có S=0,96 mm/vòng.
- Vận tốc cắt Vb=97 m/phút (theo bảng 5-109, [6]) - Các hệ số hiệu chỉnh vận tốc:
Tuổi bền thực tế chọn bằng tuổi bền danh nghĩa, chọn K1=1 Phôi có vỏ cứng: K2=0,8
Mác hợp kim cứng BK8: K2=1
- Vậy tốc độ tính toán: Vt=97.0,8=77,6 m/phút. 1000 1000.77,6 nt Vt D 19,8
- Số vòng quay tính toán v/ph là:
- Số vòng quay tính toán là: nm = 1100 v/ph vtt Dnm 19,8.1100 68,39
- Tốc độ cắt thực tế là: 1000 1000 m/ph
- Công suất cắt khi khoét thô : Nc =2,5 (kW) < Nđc = 6 (kW) (Bảng 5-11, sổ tay CNCTM 2)
- Vậy máy hoạt động tốt.
Chế độ cắt khi khoét tinh: lOMoARcPSD|36625228
- Chiều sâu cắt: doa tinh t=0,5mm
- Lượng chạy dao: khi khoét thô S=1mm/vòng (bảng 5-107/98, [6])
- Vận tốc cắt Vb=97 m/phút (theo bảng 5-109, [6]) - Các hệ số hiệu chỉnh vận tốc:
- Tuổi bền thực tế chọn bằng tuổi bền danh nghĩa. K1=1
- Phôi có vỏ cứng. K2=0,8
- Mác hợp kim cứng BK8. K3=1
- Vậy tốc độ tính toán: Vt=97.0,8=77,6 m/phút. 1000 1000.77,6 ntt Vt D 20,8
- Số vòng quay tính toán v/ph là:
- Chọn số vòng quay theo máy nm = 1100 v/ph vtt
Dnm 20,8.1100 68,38 -
Tốc độ cắt thực tế là: 1000 1000 (m/ph)
- Công suất cắt khi khoét tinh : Nc =2,5 (kW) < Nñc = 6 (kW) (Bảng 5-111, [6])
- Vậy máy hoạt động tốt.
Chế độ cắt khi doa thô:
- Chiều sâu cắt : doa thô t = 0,1mm;
- Lượng chạy dao khi doa thô S=2 mm/vòng (bảng 5-116, [6]).
Chọn theo máy S= 1,6 mm/vòng
- Vận tốc cắt: Vb=10,4 m/phút (bảng 5-116, [6]) Hệ số điều chỉnh vận tốc bằng 1 nên : 1000 1000.10,4 n Vt
- Số vòng quay tính toán 21 v/ph là: D
- Chọn số vòng quay theo máy nm = 136 v/ph vtt Dnm 21.136 8,97
- Tốc độ cắt thực tế là: 1000 1000 m/ph
- Công suất cắt khi doa rất nhỏ nên không cần tra lOMoARcPSD|36625228
6. Tính thời gian nguyên công:
Theo bảng 4.8, [1] công thức tính thời gian cơ bản khi khoét , doa theo công thức:
T0 L L1 L2 S n. ph L1 D d ctg , 0 5 2 2 Với: mm; L2= (1-3) mm; L=12 mm
φ hníhc tắc iỡưl aủc gnêihgn cóg iớV06= ֯ nên lấy gần đúng L1=3mm và L2=3mm, ta có thời gian cơ bản như sau: T0 0,017 Khoét thô: ph T0 0,017 Khoét tinh: ph T0 0,14 Khoét tinh: ph
Tổng thời gian: T00,17ph
Thời gian cho nguyên công: T= 0,17.1,26= 0,22 ph
7. Đồ gá và trang bị phụ Kẹp chặt:
- Cơ cấu kẹp nhanh:
- Chốt tỳ phụ: tăng độ cứng vũng cho chi tiết khi gia công lOMoARcPSD|36625228
3.5 Nguyên công V: Khoét doa lỗ Ø21 còn lại
Chi tiết bằng gang xám có 190HB, lỗ đúc sẵn Ø15, khi gia công đạt CCX7, độ nhám Ra=6,3. Theo
bảng 3.3, cần phải qua các bước sau:
- Khoét thô đạt Ø19,8
- Khoét tinh đạt Ø20,8 - Doa thô đạt Ø21 1. Sơ đồ gá đặt
2. Định vị: : Hạn chế 6 bậc tự do gồm 3 bậc tự do tịnh tiến Oz, xoay quanh Ox, xoay quanh Oy ở mặt Ø32 bằng phiến tì : lOMoARcPSD|36625228
- Chốt trụ ngắn hạn chế 2 bậc tự do tịnh tiến Oy, tịnh tiến Ox; chốt tỳ khía nhám 1 bậc tự do chốngxoay quanh Oz. D d (H7/js6) H L C t d1 b C1 12 8 6 16 0,6 2 2 3 1 - Chốt trụ ngắn d= 21 mm
3. Chọn máy: Máy khoan đứng 2A135: (phụ lục/183, [1]). Đặt tính kỹ thuật Thông số máy lOMoARcPSD|36625228 Công suất động cơ (kw) 6
Đường kính gia công (max) 35
Giới hạn vòng quay trục chính(v/phút) 68-1100 Số cấp chạy dao 11 Số cấp tốc độ 9
Giới hạn chạy dao (mm/vòng) 0,11-1,6
4. Chọn dụng cụ cắt: 19,8 -
Mũi khoét thô gắn mảnh hợp kim cứng chuôi côn K40 (BK8) với các thông số:
L=180 mm, l= 85 mm, tuổi bền dao: T= 30 phút. (bảng 4-47/332, [9] ). 20,8
Mũi khoét tinh gắn mảnh hợp kim cứng chuôi côn K40 (BK8) với các thông số: L=180 mm, l=
85 mm, tuổi bền dao: T= 40 phút. 21
Mũi doa thô thép gió với các thông số: L=138 mm, l= 26 mm, tuổi bền dao: T= 120 phút. (bảng 4-49/33, [9]). - Dụng cụ đo: calip
5. Tra chế độ cắt và công suất cắt Nc Tra chế độ cắt khi khoét thô:
- Chiều sâu cắt : Khi khoét thô t=2,4mm.
- Lượng chạy dao: khoét thô S=1mm/vòng (theo bảng 5-107/98, [6])
- Vận tốc cắt Vb=97 m/ph (theo bảng 5-109, [6]) - Các hệ số hiệu chỉnh vận tốc:
K1=1: tuổi bền thực tế chọn bằng tuổi bền danh nghĩa. K2=0,8: phôi có vỏ cứng
K3=1: mác hợp kim cứng BK8
- Vậy tốc độ tính toán: Vt= 97.0,8= 77,6 m/phút. lOMoARcPSD|36625228 1000 1000.77,6 nt Vt D 19,8 1248
- Số vòng quay tính toán là : v/ph
- Chọn số vòng quay theo máy nm = 1100 v/ph vtt Dnm 19,8.1100 68,39
- Tốc độ cắt thực tế là: 1000 1000 m/ph
- Công suất cắt khi khoét thô: Nc =2,5 (kW) < Nm = 6 (kW) (Bảng 5-111, [6]) - Vậy máy hoạt
động tốt Chế độ cắt khi khoét tinh:
- Chiều sâu cắt: doa tinh t=0,5mm
- Lượng chạy dao: khi khoét thô S=1mm/vòng (bảng 5-107/98, [6])
- Vận tốc cắt Vb=97 m/ph (theo bảng 5-109, [6]) - Các hệ số hiệu chỉnh vận tốc:
- Tuổi bền thực tế chọn bằng tuổi bền danh nghĩa. K1=1
- Phôi có vỏ cứng. K2=0,8
- Mác hợp kim cứng BK8. K3=1
- Vậy tốc độ tính toán: Vt=97.0,8=77,6 m/phút. ntt Vt D 20,8 - Số vòng quay tính toán v/ph là:
- Chọn số vòng quay theo máy nm = 1100 v/ph vtt Dnm 20,8.1100 68,38
- Tốc độ cắt thực tế là: 1000 1000 (m/ph)
- Công suất cắt khi khoét tinh : Nc =2,5 (kW) < Nñc = 6 (kW) (Bảng 5-111, [6])
- Vậy máy hoạt động tốt.
Chế độ cắt khi doa thô:
- Chiều sâu cắt : doa thô t = 0,1mm;
- Lượng chạy dao khi doa thô S=2 mm/vòng (bảng 5-116, [6]). lOMoARcPSD|36625228
- Chọn theo máy S= 1,6 mm/vòng
- Vận tốc cắt: Vb=10,4 m/ph (bảng 5-116, [6]) Hệ số điều chỉnh vận tốc bằng 1 nên : nt Vt - Số vòng quay tính toán 21 v/ph là: D
- Chọn số vòng quay theo máy nm = 136 v/ph vtt Dnm 21.136 8,97
- Tốc độ cắt thực tế là: 1000 1000 m/ph
- Công suất cắt khi doa rất nhỏ nên không cần tra
6. Tính thời gian nguyên công:
- Theo bảng 4.8, [1]) công thức tính thời gian cơ bản khi khoét , doa theo công thức:
T0 L L1 L2 S n. ph L1 D d ctg 0,5 2 - Với: 2 mm; L2= (1-3) mm; L=12 mm
-φ hníhc tắc iỡưl aủc gnêihgn cóg iớV 06= ֯ nên lấy gần đúng L1=3mm và L2=3mm, ta có thời gian cơ bản như sau: T0 0,017 Khoét thô: ph T0 0,017 Khoét tinh: ph T0 0,14 Khoét tinh: ph
- Tổng thời gian: T00,17ph
7. Đồ gá và trang bị phụ Kẹp chặt:
- Cơ cấu kẹp liên động : lOMoARcPSD|36625228
3.6 Nguyên công VI: Vát mép 1x45 lỗ Ø21 chi tiết bằng gang xám, 190HB 1.Sơ đồ gá đặt: lOMoARcPSD|36625228
2. Định vị: : Hạn chế 6 bậc tự do gồm 3 bậc tự do tịnh tiến Oz, xoay quanh Ox, xoay quanh Oy ở mặt Ø32 bằng phiến tì : -
Chốt trụ ngắn hạn chế 2 bậc tự do tịnh tiến Oy, tịnh tiến Ox;chốt tỳ khía nhám 1
bậc tự do chốngxoay quanh Oz. lOMoARcPSD|36625228 D d H L C t d1 b C1 (H7/js6) 12 8 6 16 0,6 2 2 3 1 - Chốt trụ ngắn d= 21 mm
3. Chọn máy: Máy khoan đứng 2A125: (phụ lục/183,[1]). Đặt tính kỹ thuật Thông số máy Công suất động cơ (kw) 2,8
Đường kính gia công (max) 25
Giới hạn vòng quay trục chính(v/phút) 97-1360 Số cấp chạy dao 9 Số cấp tốc độ 9
Giới hạn chạy dao (mm/vòng) 0,1-0,81
4. Chọn dụng cụ cắt :
Dao vát mép lỗ Ø23 YG1 C1139 có α= 90o , L= 67 mm, C3139230
Link tra : https://www.sieuthietbi.com.vn/dao-vat-mep-lo-yg1-c1139 lOMoARcPSD|36625228
5. Tra chế độ cắt và công suất cắt Nc
- Chiều sâu cắt: t = 1 ( mm )
- Lượng chạy dao: khi khoét thô S=1mm/vòng (bảng 5-107/98, sổ tay CNCTM 2)
- Vận tốc cắt Vb=97 m/phút (theo bảng 5-109, [6]) - Các hệ số hiệu chỉnh vận tốc: K2=0,8- phôi có vỏ cứng
- Vậy tốc độ tính toán: Vt=97.0,8=77,6 m/phút.
- Số vòng quay tính toán là : nt = Vt 1074 vòng/ph0út
- Chọn số vòng quay theo máy nm = 1094 v/ph vtt Dnm 23.1094 79
- Tốc độ cắt thực tế là: 1000 1000 m/ph
Công suất cắt khi khoét côn: vì nguyên công này không yêu cầu cao về kỹ thuật, và chỉ khoét với
kích thước 1x45o nên lực cắt rất nhỏ, dẫn đến công suất nhỏ.
Với công suất máy 2,8 kW đủ để thực hiện nguyên công.
6. Tính thời gian nguyên công:
- Theo bảng 4.8, công thức tính thời gian cơ bản khi khoét theo công thức:
T0 L L1 S n. ph
L1 D d ctg (0,5 2) 2 mm
-φ hníhc tắc iỡưl aủc gnêihgn cóg iớV06= ֯ nên lấy gần đúng L1=3mm và L=1mm, ta có thời gian cơ bản như sau: T0 0,004 lOMoARcPSD|36625228 - Khoét thô: ph
7. Đồ gá và trang bị phụ Kẹp chặt - Cơ cấu kẹp liên động :
3.7 Nguyên công VII: Vát mép 1x45 lỗ Ø21 chi tiết bằng gang xám, 190HB 1.Sơ đò gá đặt: lOMoARcPSD|36625228
2. Định vị: : Hạn chế 6 bậc tự do gồm 3 bậc tự do tịnh tiến Oz, xoay quanh Ox, xoay quanh Oy ở mặt Ø32 bằng phiến tì : -
Chốt trụ ngắn hạn chế 2 bậc tự do tịnh tiến Oy, tịnh tiến Ox;chốt tỳ khía nhám 1 bậc tự do chốngxoay quanh Oz. D d H L C t d1 b C1 (H7/js6) 12 8 6 16 0,6 2 2 3 1 - Chốt trụ ngắn d= 21 mm
3. Chọn máy: Máy khoan đứng 2A125: (phụ lục/183, [1]). lOMoARcPSD|36625228 Đặt tính kỹ thuật Thông số máy Công suất động cơ (kw) 2,8
Đường kính gia công (max) 25
Giới hạn vòng quay trục chính(v/phút) 97-1360 Số cấp chạy dao 9 Số cấp tốc độ 9
Giới hạn chạy dao (mm/vòng) 0,1-0,81
4. Chọn dụng cụ cắt:
Dao vát mép lỗ Ø23 YG1 C1139 có α= 90o , L= 67 mm, C3139230
Link tra : https://www.sieuthietbi.com.vn/dao-vat-mep-lo-yg1-c1139
5. Tra chế độ cắt và công suất Nc:
- Chiều sâu cắt: t = 1 ( mm )
- Lượng chạy dao: khi khoét thô S=1mm/vòng (bảng 5-107/98, sổ tay CNCTM 2) - Vận tốc cắt
Vb=97 m/phút (theo bảng 5-109, [6]) - Các hệ số hiệu chỉnh vận tốc: K2=0,8- phôi có vỏ cứng
- Vậy tốc độ tính toán: Vt=97.0,8=77,6 m/phút.
- Số vòng quay tính toán là : nt = Vt 1074 vòng/ph0út
- Chọn số vòng quay theo máy nm = 1094 v/ph vtt Dnm 23.1094 79
- Tốc độ cắt thực tế là: 1000 1000 m/ph
Công suất cắt khi khoét côn: vì nguyên công này không yêu cầu cao về kỹ thuật, và chỉ khoét với
kích thước 1x45o nên lực cắt rất nhỏ, dẫn đến công suất nhỏ.
Với công suất máy 2,8 kW đủ để thực hiện nguyên công.
6. Tính thời gian nguyên công:
Theo bảng 4.8, công thức tính thời gian cơ bản khi khoét theo công thức: lOMoARcPSD|36625228
T0 L L1 S n. ph L1 D d ctg (0,5 2) 2 mm
φ hníhc tắc iỡưl aủc gnêihgn cóg iớV06= ֯ nên lấy gần đúng L1=3mm và L=1mm, ta có thời gian cơ bản như sau: T0 0,004 Khoét thô: ph
7. Đồ gá và trang bị phụ Kẹp chặt:
- Cơ cấu kẹp liên động :
3.8 Nguyên công VIII: Phay thô mặt đáy chi tiết bằng gang xám 190HB 1.Sơ đồ gá đặt: lOMoARcPSD|36625228
2. Định vị: hạn chế 6 BTD do gồm 3 bậc tự do : tịnh tiến Oz, xoay quanh Ox, xoay quanh Oy ở mặt
đáy bằng hai phiến tỳ : -
Chốt trụ ngắn 2 bậc tự do : tịnh tiến Oy, tịnh tiến Ox ở bề mặt lỗ Ø5, chốt trám 1 bậc tự do quay quanh Oz ở mặt lỗ Ø5 : lOMoARcPSD|36625228 - Trang 125 [8]ta có :
3. Chọn máy: Máy phay 6H11 Tra bảng 9-38, [7] Máy phay đứng 6H11 Đặc tính kỹ thuật Thông số
Kích thước làm việc bàn máy (mm) 250x1000 Công suất động cơ (kW) 4,5
Số cấp tốc độ trục chính 16
Phạm vị tốc độ trục chính (v/ph) 65-1800
Số cấp bước tiền bàn máy 16
4. Chọn dụng cụ cắt : Chọn dao phay mặt đầu gắn mảnh hợp kim cứng.
- Các thông số của dao: (tra bảng 5-127, [6]). lOMoARcPSD|36625228
- Đường kính dao: D = 75; Số răng Z = 10; Vật liệu K20 (BK6). - Tuổi bề dao T=120.
- Dụng cụ đo: Thước kẹp 150mm, độ chính xác 0,05.
5. Tra chế độ cắt và công suất Nc:.
- Chiều sâu cắt: t = 3 (mm).
- Lượng chạy dao răng: SZ = 0,14 (mm/răng) (bảng 5-125).
- Tốc độ cắt: Vb= 204 (m/ph) ( bảng 5-127).
- Vậy tốc độ tính toán Vt=Vb.K1.K2.K.3K4.5.K6 = 147 m/ph Với:
+ Hệ số điều chính phụ thuộc vào độ cứng của gang K1 = 1 vì độ cứng vật liệu là gang có HB= 190
+ Hệ số điều chỉnh phụ thuộc vào chu kì bền của dao K2= 0,8 vì muốn tuổi bền thực tế cao gấp
2 lần tuổi bền cho trong sổ tay.
+ Hệ số điều chỉnh phụ thuộc vào mác hợp kim cứng K3= 1.
+ Hệ số điều chỉnh phụ thuộc vào bề mặt gia công (gang đúc có vỏ cứng) K4= 0,8.
+ Hệ số điều chỉnh phụ thuộc vào chiều rộng phay K5= 1,13.
+ Hệ số điều chỉnh vào góc nghiêng chính K6= 1.
- Số vòng quay theo tính toán là: 1000.Vt 1000.147 .D 624 nt 3,14.75 (v/ph) -
Máy 6H81 có nmin=65; nmax=1800, số cấp tốc độ m=16, tìm công bội φ như sau: m 1 16 1 15 nmax 1800 nmin 65
- Ứng với 15 có giá trị là 32 gần với 27,69 tương ứng với =1,26. Mặc khác x nt 624 lOMoARcPSD|36625228 9,6 nmin 65
- Theo bảng 4.1 [1] ứng với
1,26 có giá trị 1010,08 gần với 9,6 - Vậy số vòng quay theo n 65.10,08 655 máy là: m (v/ph) Vtt Dn 3,14.75.655 154
- Như vậy tốc độ cắt thực tế là: 1000 1000 (m/ph)
- Lượng chạy dao phút Sph= 0,14. 10. 655= 917 (mm/ph)
- Lượng chạy dao của máy là: Sm 35 980mm ph/ , với lượng chạy dao 917mm/ph là quá nhanh
cho bề mặt gia công quá nhỏ vì thế ta chọn Sm 270mm ph/
- Theo bảng 5-139 ([6]) ta có công suất cắt là Nc= 3,8 Kw < Nm =4,5 Kw - Vậy máy hoạt động tốt.
6.Tính thời gian nguyên công
Thời gian thực hiện nguyên công là: Ttc = T0 + Tp + Tpv + Ttn=T0+0,26T0 Với:
Ttc : thời gian từng chiếc T0 : thời gian cơ bản Tp : thời gian phụ Tpv :thời gian phục vụ Ttn : thời gian nghỉ ngơi L L L 1 T0 2 Sph Thời gian cơ bản: (phút) Với :
L=28 mm (chiều dài bề mặt gia công) lOMoARcPSD|36625228
L1= 0,5D+3= 40,5 mm (chiều dài ăn dao)
L2= 4 mm (chiều dài thoát dao)
S=270 mm/phút (lượng chạy dao vòng) T0 28 48 4 0,27 270 (ph) = 0,27.1,26 = 0,34 (phút)
Chế độ cắt khi phay: t= Z= 3mm; Sph= 270 mm/phút; nm= 655 v/ph; N= 3,8 kW.
7. Đồ gá và trang bị phụ Kẹp chặt:
- Cơ cấu kẹp liên động :
3.9 Nguyên công IX: Khoan lỗ Ø17: 1. Sơ đồ gá đặt : lOMoARcPSD|36625228 2.
Định vị: hạn chế 6 BTD do gồm 3 bậc tự do : tịnh tiến Oz, xoay quanh Ox, xoay quanh Oy ở
mặt đáy bằng hai phiến tỳ :
- Chốt trụ ngắn 2 bậc tự do : tịnh tiến Oy, tịnh tiến Ox ở bề mặt lỗ Ø5, chốt trám 1 bậc tự do quay quanh Oz ở mặt lỗ Ø5 : lOMoARcPSD|36625228 - Trang 125, [8] ta có :
3. Chọn máy: Máy khoan đứng 2A125: (phụ lục/183, [1]) Đặt tính kỹ thuật Thông số máy Công suất động cơ (kw) 2,8
Đường kính gia công (max) 25
Giới hạn vòng quay trục chính(v/phút) 97-1360 Số cấp chạy dao 9 Số cấp tốc độ 9
Giới hạn chạy dao (mm/vòng) 0,1-0,81
4. Chọn dụng cụ cắt :
- Mũi khoan thép gió Ø17 tuổi bền T=60 phút - Dụng cụ đo: calip
5. Tra chế độ cắt và công suất Nc . lOMoARcPSD|36625228
Chế độ cắt khi khoan :
- Chiều sâu cắt: t = 8,5 (mm)
- Lượng chạy dao: S = 0,5(mm/vòng) (bảng 5-89, sổ tay CNCTM 2)
- Tốc độ cắt: Vb = 27 (m/ph) (bảng 5-90,[6]), với hệ số điều chỉnh 1 nên V=27 mm/ph nt Vt - Số vòng quay tính toán 17 (v/ph) là: D
- Chọn số vòng quay theo máy nm= 547 vòng/phút Vtt Dn 3,14.17.547 29 -
Tốc độ cắt thực tế là: 1000 1000 (m/ph) -
Công suất cắt: N= 1,3 (kW) kiểm tra với công suất máy: N= 1,3< Nđc =
2,8(kW) - Vậy máy hoạt động tốt 6.Thời gian gia công : L L L 1 T0 2 -
Theo bảng 4.8, thời gian thực hiện được xác định: Sn. (phút) -
Chiều dài gia công: L = 11 mm
-φ hníhc tắc iỡưl aủc gnêihgn cóg iớv :oad nă iàd uềihC 06= ֯ nên lấy gần đúng L1=3mm -
Chiều dài thoát dao: L2 = 3 mm T0 0,06 - Khi khoan thô: (ph) -
Thời gian từng chiếc cho nguyên công này: T=0,06.1,26=0,076 ph 7. Đồ gá
và trang bị phụ 7.1 Kẹp chặt: -
Cơ cấu kẹp liên động : lOMoARcPSD|36625228
3.10 Nguyên công X: Khoét doa lỗ Ø18: 1.Sơ đồ gá đặt:
2. Định vị: hạn chế 6 BTD do gồm 3 bậc tự do : tịnh tiến Oz, xoay quanh Ox, xoay quanh Oy ở mặt
đáy bằng hai phiến tỳ : -
Chốt trụ ngắn 2 bậc tự do : tịnh tiến Oy, tịnh tiến Ox ở bề mặt lỗ Ø5, chốt trám 1 bậc tự
do quay quanh Oz ở mặt lỗ Ø5 : lOMoARcPSD|36625228 - Trang 125, [8] ta có :
4. Chọn máy: Máy khoan đứng 2A125: (phụ lục/183, [1]) Đặt tính kỹ thuật Thông số máy Công suất động cơ (kw) 2,8
Đường kính gia công (max) 25
Giới hạn vòng quay trục chính(v/phút) 97-1360 Số cấp chạy dao 9 Số cấp tốc độ 9
Giới hạn chạy dao (mm/vòng) 0,1-0,81
4. Chọn dụng cụ cắt :
- Mũi khoét thô Ø17,85 gắn mảnh hợp kim cứng chuôi côn K40 (BK8) với các thông số:
L=180mm, l= 85 mm, tuổi bền dao: T= 30 phút. (bảng 4-47/332, [9]), tuổi bền T=30 phút. lOMoARcPSD|36625228
- Mũi doa thô Ø18 với các thông số: L=138 mm, l= 26 mm, tuổi bền dao: T= 120 phút. (bảng 4- 49/336, [9]).T=60 phút - Dụng cụ đo: calip
5. Tra chế độ cắt và công suất Nc .
Chế độ cắt khi khoét thô:
- Chiều sâu cắt : Khi khoét thô t=0,425mm.
- Lượng chạy dao: khi khoét thô S=0,7 mm/vòng (theo bảng 5-107/98, [6])
- Vận tốc cắt Vb=138 m/phút (theo bảng 5-109, [6]) - Các hệ số hiệu chỉnh vận tốc:
K1=1: tuổi bền thực tế chọn bằng tuổi bền danh nghĩa. K2=0,8: phôi có vỏ cứng
K3=1: mác hợp kim cứng BK8
- Vậy tốc độ tính toán: Vt=138.0,8=110 m/phút. 1000 1000.110 nt Vt 1963
- Số vòng quay tính toán là: D 17,85 v/ph - Chọn số vòng quay theo máy: nm= 1360 vòng/phút vtt Dnm 17,85.1360 76,22
- Tốc độ cắt thực tế là: 1000 1000 m/ph
- Công suất cắt khi khoét thô: Nc =1,8 (kW) < Nñc = 2,8 (kW)(5-111, [6])
Vậy máy hoạt động tốt
Chế độ cắt khi doa thô:
- Chiều sâu cắt : doa thô t = 0,075 mm;
- Lượng chạy dao khi doa: doa thô S=2 mm/vòng (bảng 5-112, [6]) chọn theo máy 2A125 nên tacó S= 0,81mm/vòng.
- Vận tốc cắt: Vb= 11,7 m/phút (bảng 5-114 , sổ tay CNCTM2).
Các hệ số điều chỉnh vận tốc đều bằng 1, vì thế số vòng quay tính toán là:
- Số vòng quay tính toán là : nt = Vt 207 v/ph lOMoARcPSD|36625228
- Chọn số vòng quay theo máy: nm= 194 v/ph vtt Dnm 18.194 11 -
Tốc độ cắt thực tế là: 1000 1000 (m/ph)
- Công suất cắt khi doa rất nhỏ nên không cần tra.
6. Tính thời gian nguyên công:
- Theo bảng 4.8, công thức tính thời gian cơ bản khi khoét , doa theo công thức:
T0 L L1 L2 S n. ph L1 D d ctg (0,5 2) 2 mm L2= (1-3) mm
-φ hníhc tắc iỡưl aủc gnêihgn cóg iớV 06= ֯ nên lấy gần đúng L1=3mm và L2=3mm,L=11mm ta có
thời gian cơ bản như sau: T0 0,02 Khoét thô:ph T0 0,1 Doa thô: ph
Tổng thời gian: T00,12ph
Thời gian cho nguyên công: T=0,12.1,26= 0,15 ph
7. Đồ gá và trang bị phụ Kẹp chặt:
- Cơ cấu kẹp liên động : lOMoARcPSD|36625228
3.11 Nguyên công XII: Vát mép 1x45o lỗ Ø18:
1.Sơ đồ gá đặt : 2.
Định vị: hạn chế 6 BTD do gồm 3 bậc tự do : tịnh tiến Oz, xoay quanh Ox, xoay quanh Oy ở
mặt đáy bằng hai phiến tỳ : lOMoARcPSD|36625228 -
Chốt trụ ngắn 2 bậc tự do : tịnh tiến Oy, tịnh tiến Ox ở bề mặt lỗ Ø5, chốt trám 1
bậc tự do quay quanh Oz ở mặt lỗ Ø5 : - Trang 125, [8] ta có : 3.
Chọn máy: Máy khoan đứng 2A125: (phụ lục/183, [1]). lOMoARcPSD|36625228 Đặt tính kỹ thuật Thông số máy Công suất động cơ (kw) 2,8
Đường kính gia công (max) 25
Giới hạn vòng quay trục chính(v/phút) 97-1360 Số cấp chạy dao 9 Số cấp tốc độ 9
Giới hạn chạy dao (mm/vòng) 0,1-0,8 4.
Chọn dụng cụ cắt :
Dao vát mép lỗ Ø20 YG1 C1109 có α= 90o , L= 65 mm, C3109200 Link tra :
https://www.sieuthietbi.com.vn/mui-vat-mep-lo-yg1-c1109 5.
Tra chế độ cắt và công suất Nc: -
Chiều sâu cắt: t = 1 ( mm ) -
Lượng chạy dao: khi khoét thô S=1mm/vòng (theo bảng 5-107/98, [6]) chọn theo máy
2A125 nên ta có S=0,81 mm/vòng. -
Vận tốc cắt Vb=97 m/phút (theo bảng 5-109, [6]) - Các hệ số hiệu chỉnh vận tốc: K2= 0,8: phôi có vỏ cứng -
Vậy tốc độ tính toán: Vt=97.0,8=77,6 m/phút. nt Vt - Số vòng quay tính toán v/ph là: D 23
- Chọn số vòng quay theo máy nm = 1094 v/ph vtt Dnm 23.1094 79
- Tốc độ cắt thực tế là: 1000 1000 m/ph lOMoARcPSD|36625228
- Với công suất máy 2,8 kW đủ để thực hiện nguyên công. 6.
Tính thời gian nguyên công:
- Theo bảng 4.8, công thức tính thời gian cơ bản khi khoét theo công thức:
T0 L L1 S n. ph
L1 D d ctg (0,5 2) 2 mm
-φ hníhc tắc iỡưl aủc gnêihgn cóg iớV 06= ֯ nên lấy gần đúng L1=3mm và L=1mm, ta có thời gian cơ bản như sau: T0 0,004 - Khoét thô: ph 7.
Đồ gá và trang bị phụ Kẹp chặt:
- Cơ cấu kẹp liên động :
3.12 Nguyên công XII: Khoan Taro M6:
1.Sơ đồ gá đặt : lOMoARcPSD|36625228
2. Định vị: hạn chế 6 BTD do gồm 3 bậc tự do : tịnh tiến Ox, xoay quanh Oz, xoay quanh Oy ở mặt
đáy bằng hai phiến tỳ : lOMoARcPSD|36625228 -
Chốt trụ ngắn 2 bậc tự do : tịnh tiến Oz, tịnh tiến Oy ở bề mặt lỗ Ø5, chốt trám 1 bậc tự do quay quanh Ox ở mặt lỗ Ø5 : - Trang 125, [8]ta có :
3. Chọn máy: Máy khoan đứng 2A125: (phụ lục/183, [1]). lOMoARcPSD|36625228 Đặt tính kỹ thuật Thông số máy Công suất động cơ (kw) 2,8
Đường kính gia công (max) 25
Giới hạn vòng quay trục chính(v/phút) 97-1360 Số cấp chạy dao 9 Số cấp tốc độ 9
Giới hạn chạy dao (mm/vòng) 0,1-0,81
4. Chọn dụng cụ cắt : - Mũi khoan thép gió HSS Ø5 LMT, l1= 86 mm,l2= 52 mm tuổi bền T=20 phút.
- Mũi taro NACHI M6x1 STP06M1R L6868 chiều dài đoạn ren dẫn hướng 5P.
5. Tra chế độ cắt và công suất Nc .
Chế độ cắt khi khoan : -
Chiều sâu cắt : t = 2,5 ( mm ) -
Lượng chạy dao: S=0,15 mm/vòng (theo bảng 5-89/86, [6]) -Tốc độ cắt : Vb = 48 ( m/v ) ( bảng 5-90, [6]) lOMoARcPSD|36625228 -
Hệ số điều chỉnh vận tốc 0,91 theo chu kỳ bền thực tế mong muốn gấp 2 lần. Hệ
số phụ thuộc vào mác vật liệu 1 nên vận tốc tính toán là : Vt 48.0,91 43,68 m/ph 1000 1000 nt Vt 43,68 2782 -
Sôố vòng quay tính toán D 5 (v/ph) - Chọn nm= 1360 vòng/phút Vtt Dn 5.1360 21,35 -
Tốc độ cắt thực tế là: 1000 1000 (m/ph) -
Công suất cắt: N = 1 (kW) (Bảng 5- 92) -
Kiểm tra công suất máy: N = 1 (kW) < Nm = 2,8 (kW) -
Vậy máy hoạt động tốt.
Chế độ cắt khi Taro: -
Chiều sâu cắt : t = 0.5 ( mm ) -
Tốc độ cắt: Vb = 8 (m/ph) ( bảng 5-188, sổ tay CNCTM 2) -
Hệ số điều chỉnh vận tốc phụ thuộc vào vật liệu gia công 1,1 nên vận tốc Vt= 8.1,1= 8,8 (m/phút) 1000 1000.8,8 nt Vt 467 -
Số vòng quay tính toán là: D v/ph 6 -
Số vòng quay chọn theo máy : nm= 388 v/ph vtt
Dnm 6.388 7,31 - Tốc độ
cắt thực tế là: 1000 1000 m/ph
6.Tính thời gian gia công : Khoan:
T0 L L1 L2 -
Theo bảng 4.8, thời gian thực hiện được xác định: S n. ph lOMoARcPSD|36625228 L1 D d ctg (0,5 2) - 2 mm - L2= (1-3) mm -
=φ hníhc tắc iỡưl aủc gnêihgn cóg iớV 06 ֯ nên lấy gần đúng L1= 3mm và L2= 3mm, L=
6,5mm ta có thời gian cơ bản như sau: T0 0,071 - Khoan thô: ph
7. Đồ gá và trang bị phụ Kẹp chặt:
- Cơ cấu kẹp nhanh:
- Chốt tỳ phụ: tăng độ cứng vũng cho chi tiết khi gia công
3.13 Nguyên công XIII: Khoan Taro M6:
1.Sơ đồ gá đặt : lOMoARcPSD|36625228
2. Định vị: hạn chế 6 BTD do gồm 3 bậc tự do : tịnh tiến Ox, xoay quanh Oz, xoay quanh Oy ở mặt
đáy bằng hai phiến tỳ :
- Chốt trụ ngắn 2 bậc tự do : tịnh tiến Oy, tịnh tiến Oz ở bề mặt lỗ Ø5, chốt trám 1 bậc tự
do quay quanh Ox ở mặt lỗ Ø5 : lOMoARcPSD|36625228 lOMoARcPSD|36625228 - Trang 125, [8] ta có :
3. Chọn máy: Máy khoan đứng 2A125: (phụ lục/18, [1]) Đặt tính kỹ thuật Thông số máy Công suất động cơ (kw) 2,8
Đường kính gia công (max) 25
Giới hạn vòng quay trục chính(v/phút) 97-1360 Số cấp chạy dao 9 Số cấp tốc độ 9
Giới hạn chạy dao (mm/vòng) 0,1-0,81
4.Chọn dụng cụ cắt : - Mũi khoan thép gió HSS Ø5 LMT, l1= 86 mm,l2= 52 mm tuổi bền T=20 phút. -
Mũi taro NACHI M6x1 STP06M1R L6868 chiều dài đoạn ren dẫn hướng 5P.
5.Tính thời gian gia công :
Chế độ cắt khi khoan :
- Chiều sâu cắt : t = 2,5 ( mm ) lOMoARcPSD|36625228
- Lượng chạy dao: S=0,15 mm/vòng (theo bảng 5-89/86, [6]) -Tốc độ cắt : Vb = 48 ( m/v ) ( bảng 5-90, [6])
- Hệ số điều chỉnh vận tốc 0,91 theo chu kỳ bền thực tế mong muốn gấp 2 lần. Hệ số phụ
thuộc vào mác vật liệu 1 nên vận tốc tính toán là : Vt 48.0,91 43,68 m/ph 1000 1000 nt Vt 43,68 2782
- Sôố vòng quay tính toán D 5 (v/ph) - Chọn nm= 1360 vòng/phút Vtt Dn 5.1360 21,35 -
Tốc độ cắt thực tế là: 1000 1000 (m/ph) -
Công suất cắt: N = 1 (kW) (Bảng 5- 92) -
Kiểm tra công suất máy: N = 1 (kW) < Nm = 2,8 (kW) -
Vậy máy hoạt động tốt.
Chế độ cắt khi Taro: -
Chiều sâu cắt : t = 0.5 ( mm ) -
Tốc độ cắt: Vb = 8 (m/ph) ( bảng 5-188, sổ tay CNCTM 2) -
Hệ số điều chỉnh vận tốc phụ thuộc vào vật liệu gia công 1,1 nên vận tốc Vt= 8.1,1= 8,8 (m/phút) 1000 1000.8,8 nt Vt 467 -
Số vòng quay tính toán là: D v/ph 6 -
Số vòng quay chọn theo máy : nm= 388 v/ph vtt
Dnm 6.388 7,31 - Tốc độ
cắt thực tế là: 1000 1000 m/ph
6.Tính thời gian gia công : Khoan: lOMoARcPSD|36625228
T0 L L1 L2 -
Theo bảng 4.8, thời gian thực hiện được xác định: S n. ph L1 D d ctg (0,5 2) - 2 mm - L2= (1-3) mm -
=φ hníhc tắc iỡưl aủc gnêihgn cóg iớV 06 ֯ nên lấy gần đúng L1= 3mm và L2= 3mm, L=
6,5mm ta có thời gian cơ bản như sau: T0 0,071 - Khoan thô: ph
7. Đồ gá và trang bị phụ 7.1 Kẹp chặt: - Cơ cấu kẹp nhanh :
- Chốt tỳ phụ : tăng độ cứng vũng cho chi tiết khi gia công
3.14 Nguyên công XIV: Taro 8 lỗ M6: 1. Sơ đồ gá đặt: lOMoARcPSD|36625228 2.
Định vị: : Hạn chế 6 bậc tự do gồm 3 bậc tự do tịnh tiến Ox, xoay quanh Oz, xoay quanh Oy ở
mặt Ø32 bằng phiến tì : -
Chốt trụ ngắn hạn chế 2 bậc tự do tịnh tiến Oy, tịnh tiến Oz;chốt tỳ khía nhám 1 bậc tự do chốngxoay quanh Ox. lOMoARcPSD|36625228 D d H L C t d1 b C1 (H7/js6) 12 8 6 16 0,6 2 2 3 1 - Chốt trụ ngắn d= 21 mm 3.
Chọn máy: Máy khoan đứng 2A125: (phụ lục/183, [1]). Đặt tính kỹ thuật Thông số máy Công suất động cơ (kw) 2,8
Đường kính gia công (max) 25
Giới hạn vòng quay trục chính(v/phút) 97-1360 Số cấp chạy dao 9 Số cấp tốc độ 9
Giới hạn chạy dao (mm/vòng) 0,1-0,81 4.
Chọn dụng cụ cắt :
- Mũi taro NACHI M6x1 STP06M1R L6868 chiều dài đoạn ren dẫn hướng 5P. lOMoARcPSD|36625228
5.Tra chế độ cắt khi Taro:
- Mũi taro NACHI M6x1 STP06M1R L6868 chiều dài đoạn ren dẫn hướng 5P.
- Chiều sâu cắt: t = 0.5 ( mm )
- Tốc độ cắt : Vb = 8 ( m/v ) ( bảng 5-188, [6])
- Hệ số điều chỉnh vận tốc phụ thuộc vào vật liệu gia công 1,1 nên vận tốc tính toán là : Vt=8.1,1=8,8 (m/phút)
- Số vòng quay tính toán là : nt = Vt 467 vòng/phút - Số vòng quay chọn theo máy : nm= 388 vòng/phút vtt Dnm 6.388 7,31
- Tốc độ cắt thực tế là: 1000 1000 m/ph
6. Đồ gá và trang bị phụ Kẹp chặt: - Cơ cấu kẹp nhanh : -
Chốt tỳ phụ : tăng độ cứng vũng cho chi tiết khi gia công lOMoARcPSD|36625228
CHƯƠNG 4: TÍNH LƯỢNG DƯ GIA CÔNG
Tính lượng dư cho nguyên công 1: Phay thô mặt đáy -
Tính lượng dư gia công bề dày kích thước 46 ±0,125 -
Nguyên công phay thô: Hạn chế 6 bậc tự do gồm 3 bậc tự do bằng chống tâm cố định, chống
tâm diđộng định vị 2 bậc tự do và 1 chốt tỳ khía nhám chống xoay hạn chế 1 bậc tự do.
Bề mặt gia công không đối xứng dùng công thức:
Lượng dư nhỏ nhất một phía : Zimin Rzi 1 Ti 1 i 1 i Trong đó : lOMoARcPSD|36625228
Zimin: Lượng dư bề mặt của bước công nghệ thứ i.
Rzi-1: chiều cao nhấp nhô tế vi do bước công nghệ sát trước để lại,
Ti-1: Chiều sâu lớp hư hỏng bề mặt do bước công nghệ sát trước để lai. i 1
: là tổng sai lệch về vị trí không gian do bước công nghệ sát trước để lại ( độ cong vênh, độ
lệch tâm, độ không song song,…), Ta có: =
Với + c: sai số do công vênh bề mặt gia công.
+ cm: sai số vị trí tổng quan giữa bề mặt gia công và mặt định vị , m.
i : là sai số gá đặt chi tiết ở bươc công nghệ đang thực hiện. i = Với: c là sai số chuẩn, k là sai số gá đặt, đg là sai số của đồ gá.
Áp dụng cho phay mặt phẳng, với phôi là phôi đúc có khối lượng, giá trị cần thiết cho các bước gia công:
Bước : Phay thô, CCX 12, độ nhám Ra=25, chiều sâu lớp hư hỏng h = 0. Bước : Phay thô
Phôi được chọn là phôi đúc bằng khuôn cát có :
Phôi : Rz +T =500 m . (Bảng 3-65/235, [9]).
Dung sai phôi khi đúc là phôi = 800 m (Bảng 3-98/253, [9]).
- Sai lệch vị trí không gian của phôi : Phôi 2c vt2 c = k L = 1,5.81 = 121,5 (). lOMoARcPSD|36625228 Trong đó:
k: Độ cong vênh đơn vị giới hạn phôi đúc k = (0,3 ÷ 1,5) ( mm).
L: chiều dài của mặt gia công. Ta có: L = 81 mm. vt: sai lệch vị trí tương quan giữa
mặt gia công và mặt định vị. Do sai lệch này bằng với độ lệch khuôn.
Ta có: vt =0 chuẩn thô là lỗ chính (chống tâm hai đầu). Vậy ta có: Phôi 2c vt2 = 121,5 ().
- Sai lệch vị trí sau khi phay thô : 1 = 0,06. phôi = 7,29 - Sai số gá đặt:
C 0 , do chi tiết định vị bằng 2 mũi chống tâm nên gốc kích thước trùng với chuẩn định Sai số chuẩn: vị.
Sai số kẹp chặt : kc (ymax ymin )cos
Trong đó là góc hợp bởi phương của lực kẹp với phương của kích thước.
Trong nguyên công này 90o kc = 0 Suy ra sai số gá đặt: i c2 k2 02 02 0 m .
- Lượng dư cho bước gia công phay thô: Z1min = 500+121,5= 621,5 () - Kích thước tính toán:
+ Kích thước sau khi phay thô: 45,875 mm;
+ Kích thước phôi: 45,875+0,6215 = 46,4965 mm; - Kích thước giới hạn: lOMoARcPSD|36625228
+ Kích thước sau khi phay thô: hmin = 45,875 mm; hmax = 46,125 mm;
+ Kích thước phôi: hmin =46,5 mm; hmax = 47,5 mm;
- Lượng dư giới hạn phay thô : Zmin= 46,5 – 45,875 = 0,62 mm ;
Zmax= 47,5 – 46,125 = 1,37 mm
- Phay thô : Zmax – Zmin= 1,37 - 0,62= 0,75 mm phôi - thô= 1 – 0,25 = 0,75 mm
CHƯƠNG 5: TÍNH CHẾ ĐỘ CẮT
5.1 Yêu cần đạt của nguyên công: - Kích thước: 210 0,021 - Cấp chính xác: cấp 7. - Độ nhám: Ra= 6,3.
5.2 Vật liệu chi tiết: gang xám 28-48 lOMoARcPSD|36625228
5.3 Chọn máy: Máy khoan đứng 2A135: Đặt tính kỹ thuật Thông số máy Công suất động cơ (kw) 6
Đường kính gia công (max) 35
Giới hạn vòng quay trục chính(v/phút) 68-1100 Số cấp chạy dao 11 Số cấp tốc độ 9
Giới hạn chạy dao (mm/vòng) 0,11-1,6 Hiệu suất máy 0,8
5.4 Trình tự làm việc: 19,8 Bước
1: Khoét thô lỗ đạt kích thước (mm). 20,8
Bước 2: Khoét tinh lỗ đạt kích thước (mm). 21
Bước 3: Doa thô lỗ đạt kích thước (mm). 5.5 Chọn dao: 19,8 -
Mũi khoét thô gắn mảnh hợp kim cứng chuôi côn K40 (BK8) với các thông số: L=180 mm, l=
85 mm, tuổi bền dao: T= 30 phút. (bảng 4-47/332, [9]). 20,8
Mũi khoét tinh gắn mảnh hợp kim cứng chuôi côn K40 (BK8) với các thông số: L=180 mm, l=
85 mm, tuổi bền dao: T= 40 phút. lOMoARcPSD|36625228 21
Mũi doa thô thép gió với các thông số: L=138 mm, l= 26 mm, tuổi bền dao: T= 120 phút. (bảng 4-49/336, [9]).
5.6 Xác định chế độ cắt bằng phương pháp phân tích khi khoét – doa: - Chiều sâu cắt: + Khoét thô: t = 2,4 (mm). + Khoét tinh: t = 0,5 (mm). + Doa thô: t = 0,1 (mm). - Lượng chạy dao:
+ Khoét thô: S =Cs.D0,6=0,15.19,80,6= 0,9 (mm/vòng), chọn theo máy 2A135 ta có S=0,8
mm/vòng. (Tra bảng 1-3/83, [10], Cs=0,15).
+ Khoét tinh: S = Cs.D0,6= 0,075.20,80,6= 0,46 (mm/vòng), chọn theo máy 2A135 ta có S=0,44
mm/vòng. (Tra bảng 1-3/83, [10], Cs=0,075).
+ Doa thô: S = Cs.D0,7 =0,1.210,7= 0,84 (mm/vòng), chọn theo máy 2A135 ta có S=0,88
mm/vòng. (Tra bảng 2-3/83, [10], Cs=0,1). - Vận tốc cắt V(m/phút): V =
Hệ số hiệu chỉnh chung về tốc độ cắt:
Kmv. Knv. Klv. Kuv=1. 0,8.1.0,83= 0,664 Kv=
Kmv: hệ số phụ thuộc vào vật liệu gia công (bảng 5-3, [10]). Kmv=1 lOMoARcPSD|36625228
Kuv: hệ số phụ thuộc vào vật liệu dụng cụ cắt (bảng 8-1, [10] ). =0,83
Klv: hệ số phụ thuộc vào chiều sâu lỗ gia công (bảng 6-3, [10] ).Kl 1v
Kn v: hệ số phụ thuộc vào tình trạng bề mặt phôi (bảng 7-1, [10] ).Knv= 0,8 Vậy vận tốc cắt:
- Khoét thô: V = = (m/phút).
- Khoét tinh: V = = (m/phút). - Doa thô : V = = (m/phút). 1000v n D - Số vòng quay n: (vòng/phút).
- Khoét thô: nt = V 882 (vòng/phút)
- Khoét tinh: nt = V 1480 (vòng/phút)
- Doa thô: nt = V 165 (vòng/phút)
Theo thông số máy 2A135: (phục lục/183, [1]).
Chọn số vòng quay theo máy:
+ Khoét thô: n = 882 (vòng/phút), theo máy ta chọn n =750 (vòng /phút).
+ Khoét tinh: n = 1480 (vòng/phút), theo máy ta chọn n = 1100 (vòng /phút).
+ Doa thô : n = 165 (vòng/phút), theo máy ta chọn n = 135 (vòng /phút).
Vậy tốc độ cắt thực tế: π.D.nm 19,8.750π v = = =46.65 ( m/ph ) - Khoét thô : 1000 1000 lOMoARcPSD|36625228 π.D.nm 20,8.1100 v = = =71,8 ( m/ph ) - Khoét tinh : 1000 1000 π.D.nm 21.135π v = = =8,91 ( m/ph ) - Doa thô : 1000 1000
- Momen xoắn và lực dọc trục:
Khoét thô : P0=CP.Dzp.SYp.txp.Kmp=1.19,8.0,8.2 .2,4 .11 1 1 1 76 (kG)
Moment xoắn khi khoét thô được tính theo công thức: , KGm
Với các thông số (tra bảng 11-1,[10] ) như sau: Cpz= 92, Xpz= 1, Ypz= 0,75
Tra bảng (12-1, [10]) và (13-1, [10]) ta có : Kmp== 1
Tra bảng (15-1, [10]) : Kφp= 0,94; K p ֯=1,1 Vậy : Kp= 1.0,94.1,1= 1,034 Khoét tinh :
Moment xoắn khi khoét tinh được tính theo công thức: , KGm
Với các thông số (tra bảng 11-1, [10]) như sau: Cpz= 92, Xpz= 1, Ypz= 0,75
Tra bảng (12-1, [10]) và (13-1, [10]) ta có : Kmp== 1
Tra bảng (15-1, [10]) : Kφp= 0,94 ; K p ֯=1,1 Vậy : Kp= 1.0,94.1,1= 1,034 lOMoARcPSD|36625228
Khi doa momem xoắn và lực dọc trục bé nên có thể bỏ qua.
- Công suất cắt của máy khi khoét thô: Ta có: = 5,88 (kW).
Thử lại kết quả: N =5,88 (kW) < Nđc = 6 (kW).
- Công suất cắt của máy khi khoét tinh: Ta có: = 1,2 (kW).
- Xác định thời gian gia công:
Công thức tính thời gian cơ bản khi khoét, doa: (bảng 4.8/60, [1]). L+L +L12 T =0 S.n ph D-d L =1 ctgf+(0,5-2)mm 2 . L =(1÷3)mm2 .
- φ hníhc tắc iỡưl aủc gnêihgn cóg iớV06= ֯ nên lấy gần đúng L1= 3mm và L2= 3mm, ta có thời gian cơ bản như sau: 12+3+3 T =0 = 0,03 - Khi khoét thô: 0,88.750 ph 12+3+3
- Khi khoét tinh: T =0 0,43.1100 = 0,037 ph 12+3+3 T =0 = 0,15 - Khi doa thô: 0,88.135 ph
- Thời gian cơ bản của 3 bước là: T0 = 0,217 (phút).
- Thời gian từng chiếc cho nguyên công này là : T= 0,217.1,26= 0,27 phút lOMoARcPSD|36625228
CHƯƠNG 6: THIẾT KẾ ĐỒ GÁ KHOÉT – DOA
6.1. Nhiệm vụ của đồ gá
-Đồ gá có nhiệm vụ tạo ra khả năng tự lựa vị trí tương quan giữa lỗ cần gia công và đầu khoan, khoét.
6.2. Kết cấu và nguyên lí làm việc
- Đồ gá dùng cơ cấu kẹp bằng ren để kẹp chặt chi tiết, định vị bằng phiến tỳ và chốt trụ ngắn,
cómột chốt trám để chống xoay cho chi tiết trong quá trình gia công, trên đồ gá có gắn bạc gẫn
hướng thay nhanh giúp quá trình gia công được thuận lợi và tăng độ cứng vững của dụng cụ cắt.
- Nguyên lí kẹp chặt : Đặt chi tiết lên phiến tỳ, điều chỉnh lỗ định vị của chi tiết khớp với chốt trụ.
- Lỗ chéo ở vị trí xa nhất khớp với chốt trám, chi tiết được kẹp bằng cơ cấu kẹp nhanh.
6.3. Xác định phương pháp định vị
- Đồ gá được thiết kế trên cơ sở định vị 6 bậc tự do Chốt trụ ngắn: không chế 2 bậc tự do.
Phiến tỳ: Không chế 3 bậc tự do.
Chốt trám: Không chế 1 bậc tự do.
6.4. Xác định các kích thước và yêu cầu kĩ thuật
- Chiều dài của đồ gá là: L= 470mm
- Chiều cao của đồ gá là: H= 240mm
- Chiều rộng của đồ gá là: L= 240mm
6.5. Tính lực hướng trục P0= 76 (kG)
6.6. Tính toán lực kẹp cần thiết lOMoARcPSD|36625228
- Khi khoét lực chiều trục P0 sẽ làm chi tiết trượt dọc hoặc lật, từ đó ta có hai phương trình cân bằng
Phương trình cân bằng lực: 3,71.76 2169 K.P0 /f= 0,1 (kG)
= Fms =Wct.f; suy ra Wct = K.Po lOMoARcPSD|36625228
- Phương trình cân bằng momen: 3,71.76.46 320 K.P0.L
= Wct.H Suy ra Wct = K.Po.L/H= 40,5 (KG) Chọn Wct=2169 (kG).
Với K: hệ số an toàn (Theo trang 144-145, [1]) ta có:
Với: K0= 1.5 : hệ số an toàn cho tất cả các trường hợp
K1= 1.2 : hệ số tính đến trường hợp khi dộ bóng thay đổi
K2= 1,2 : hệ số tăng lực cắt khi dao mòn
K3= 1,2 : hệ số tăng lực cắt khi gia công gián đoạn
K4= 1,3: hệ số xét đến sai số của cơ cấu kẹp chặt
K5= 1: hệ số tính đến mức độ thuận lợi của cơ cấu kẹp bằng tay
K6= 1,2: hệ số tính momen làm quay chi tiết
Vậy: K= 1,5.1,2.1,2.1,2.1.1.1= 3,71
Hệ số ma sát f: Bề mặt chi tiết đã gia công và các chốt tỳ, phiến tỳ: 0,15
Chọn kích thước cơ cấu kẹp *Chọn đường kính ren
Sử dụng công thức : d= C = 1,4 = 20 (mm)
6.7 Tính sai số chế tạo của đồ gá
Theo (Trang 148 , [1]) ta có sai số chế tạo cho phép của đồ gá được tính theo công thức : 2 2 2 2 ct = gd c k m dc 2 lOMoARcPSD|36625228 -
Sai số gá đặt: gđ = 0,0833 mm (Bảng 7.3/36, [2]). -
Sai số chuẩn C: cLtg.
Với L=12(mm): chiều dài lỗ gia công tan 1max 2max L1
1max dlomax dchottrumin 5,012 4,992 0,01 Trong đó 2 2 (mm)
2max dlomax dchottrammin 5,012 4,992 0,01 2 2 (mm)
L1 là khoảng cách giữa hai chốt trụ, trám L1 672 682 95,46(mm) Vậy C=0,0025 - Sai số kẹp chặt: 80 k m (Bảng 5.13, [1]). -
: sai số do đồ gá bị mòn gây ra:
Với: N là số lượng chi tiết gia công trên đồ gá, lấy N = 10000 0,1
Do dùng chốt định vị lỗ
nên: = 0,1- 0,5 (Theo trang 148, [1]) ,Chọn ; Vậy: m =0,1. = 0.01 mm -
Sai số điều chỉnh : dc0,005mm : sai số phụ thuộc vào khả năng điều chỉnh và dụng cụ được dùng
để điều chỉnh khi gá lắp. Thường lấy 5 10 m dc (Trang 149, [1]). lOMoARcPSD|36625228 -
Vậy sai số chế tạo cho phép của đồ gá là: ct = mm
6.8 Tính sai số chế tạo của đồ gá
Vậy yêu cầu kỹ thuật của đồ gá -
Độ không vuông góc giữa tâm bạc dẫn hướng và mặt đáy đồ gá ≤ 0,02. -
Độ không vuông góc giữa phiến tỳ và mặt đáy đồ gá ≤ 0,02mm. -
Độ không đồng tâm giữa bề mặt lắp bạc dẫn hướng và bề mặt lắp chốt trụ ≤ 0,02mm TÀI LIỆU THAM KHẢO
[1]. Hồ Viết Bình – Phan Minh Thanh
Hướng dẫn thiết kế đồ án Công nghệ chế tạo máy – Nhà xuất bản Đại học Quốc gia TP. Hồ Chí Minh.
[2]. PGS. TS. Trần Văn Địch
Sổ tay & Atlas đồ gá – Nhà xuất bản Khoa học và Kỹ thuật HÀ NỘI – năm 2000.
[3]. Nguyễn Xuân Bông – Phạm Quang Lộc
Thiết kế đúc – Nhà xuất bản Khoa học và Kỹ thuật. [4]. Ninh Đức Tốn
Sổ tay Dung sai lắp ghép – Nhà xuất bản Giáo dục.
[5]. GS. TS. Trần Văn Địch – PGS. TS. Ngô Trí Phúc
Sổ tay Thép thế giới – Nhà xuất bản Khoa học và Kỹ thuật.
[6]. GS. TS. Nguyễn Đắc Lộc – PSG. TS. Lê Văn Tiến – PGS. TS. Ninh Đức Tốn – PGS. TS. Trần Xuân Việt
Sổ tay CÔNG NGHỆ CHẾ TẠO MÁY TẬP 2 – Nhà xuất bản Khoa học và Kỹ thuật.
[7]. GS. TS. Nguyễn Đắc Lộc – PSG. TS. Lê Văn Tiến – PGS. TS. Ninh Đức Tốn – PGS. TS. Trần Xuân Việt
Sổ tay CÔNG NGHỆ CHẾ TẠO MÁY TẬP 3 – Nhà xuất bản Khoa học và Kỹ thuật.
[8]. Hồ Viết Bình – Lê Đăng Hoành – Nguyễn Ngọc Đào
Đồ gá gia công cơ khí Tiện – Phay – Bào – Mài – Nhà xuất bản Đà Nẵng. lOMoARcPSD|36625228
[9]. GS. TS. Nguyễn Đắc Lộc – PSG. TS. Lê Văn Tiến – PGS. TS. Ninh Đức Tốn – PGS. TS. Trần Xuân Việt
Sổ tay CÔNG NGHỆ CHẾ TẠO MÁY TẬP 1 – Nhà xuất bản Khoa học và Kỹ thuật.
[10]. Nguyễn Ngọc Đào – Trần Thế San – Hồ Viết Bình
Chế độ cắt gia công cơ khí – Nhà xuất bản Đà Nẵng 2002.
Document Outline
- MỤC LỤC
- nmax1800 27,69
- 81 48 3 0,49
- 19,8
- 20,8
- 21
- 19,8
- 20,8
- 21
- 1000.Vt 1000.147 624 nt
- 1800 27,69
- 9,6
- n65.10,08 655
- T028 48 4 0,27
- Vtt Dn 3,14.17.547 29
- Vtt Dn 5.136021,35
- Vtt Dn 5.136021,35
- Vtt Dn 3,14.17.547 29
- 19,8
- 20,8
- 21
- 1000v n
- π.D.nm 20,8.1100
- 12+3+3
- 12+3+3
- nmax1800 27,69