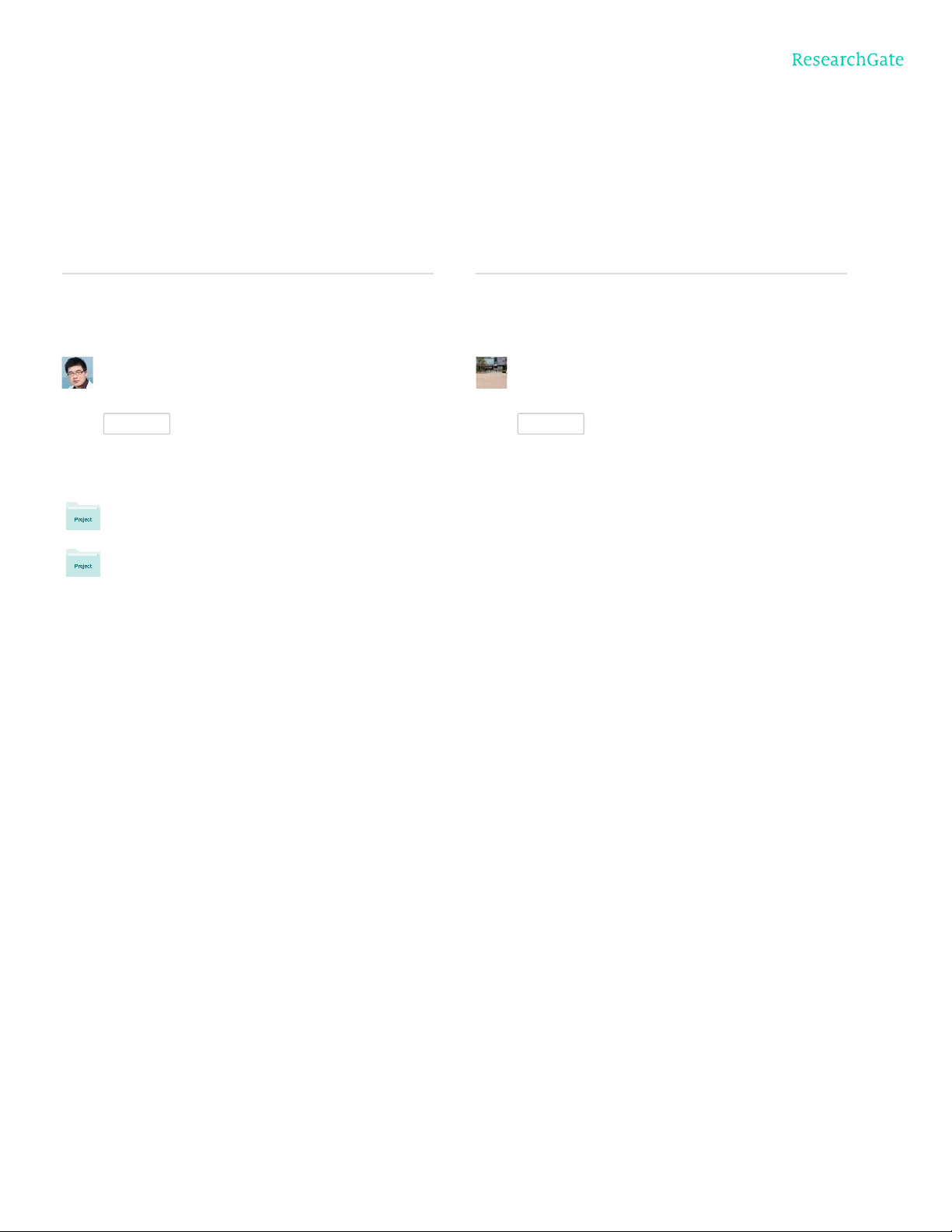
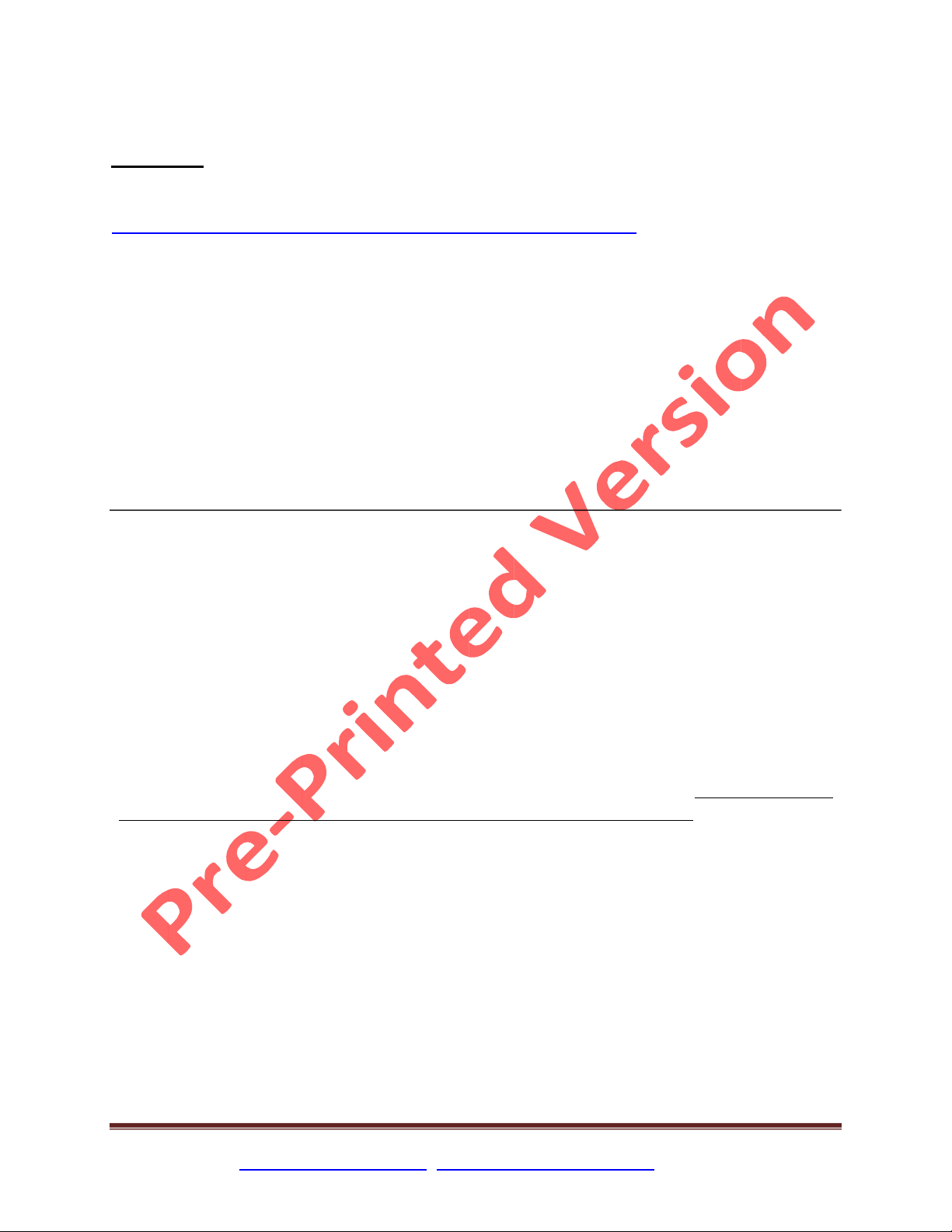
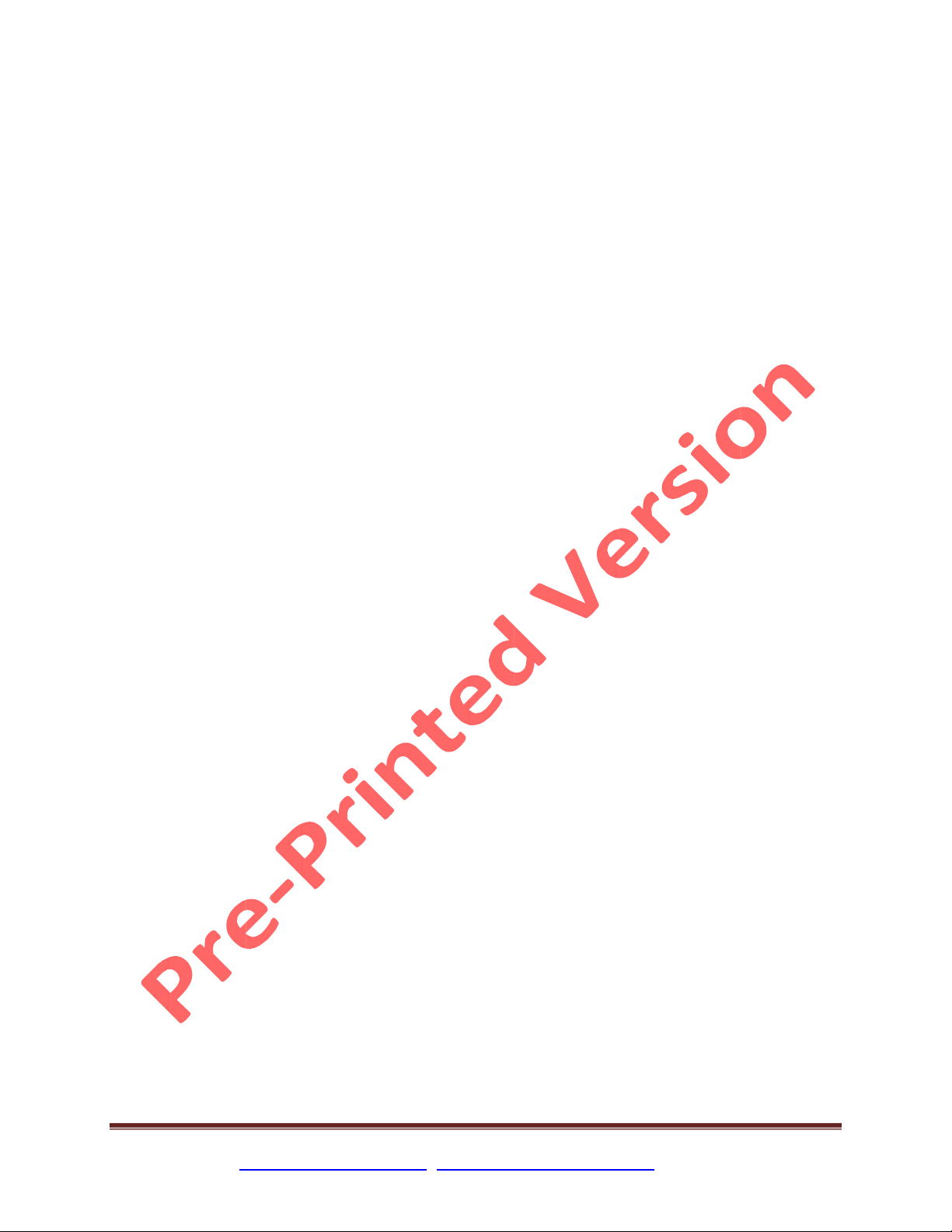
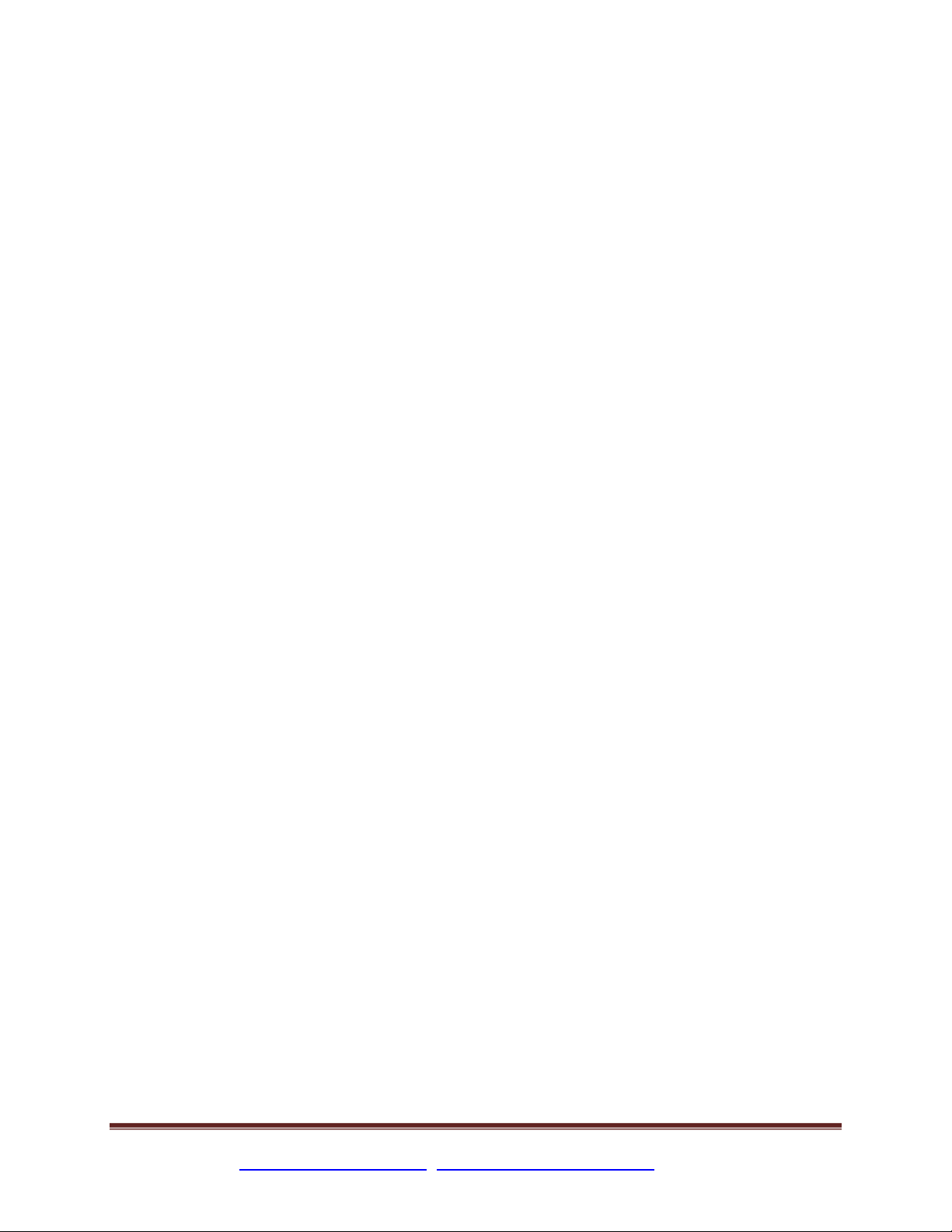

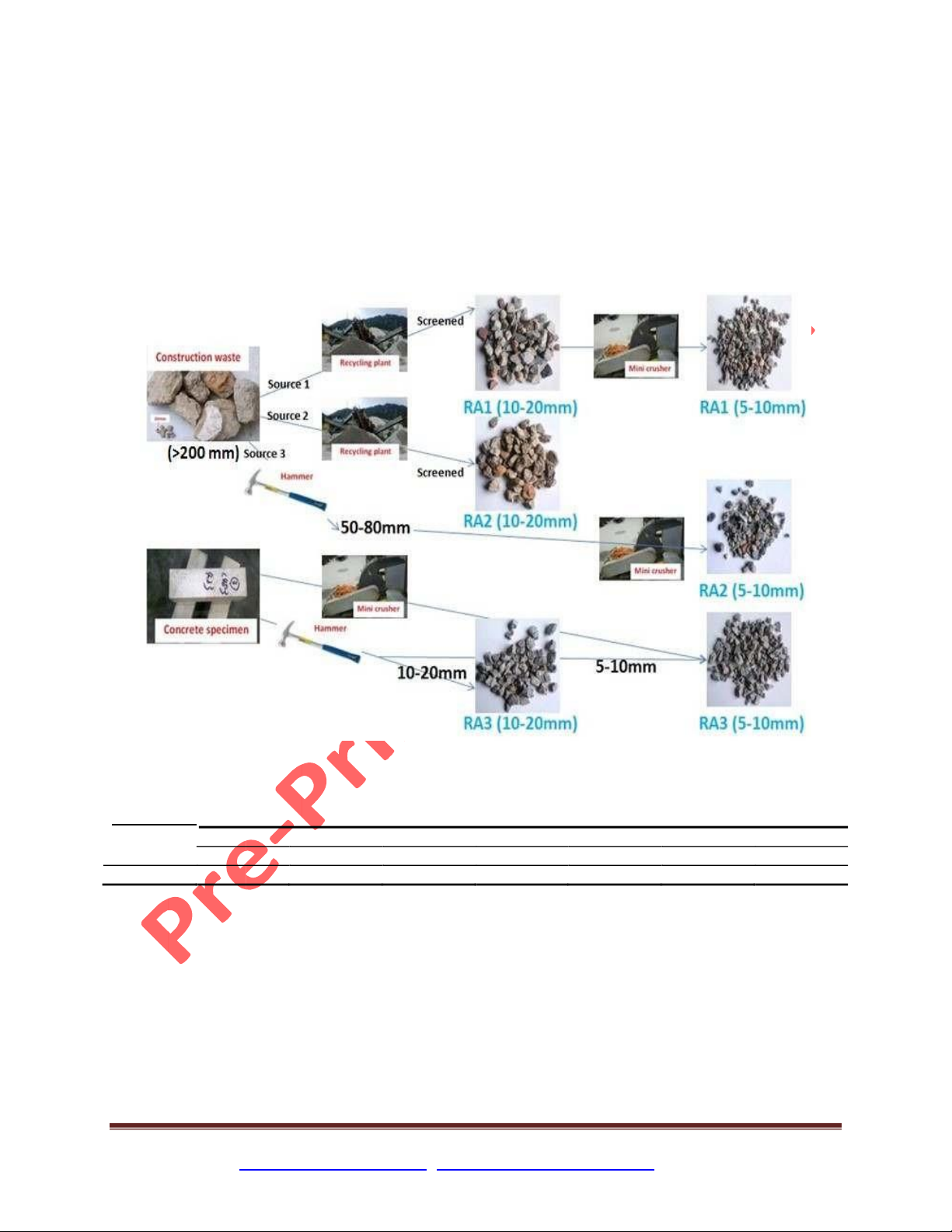
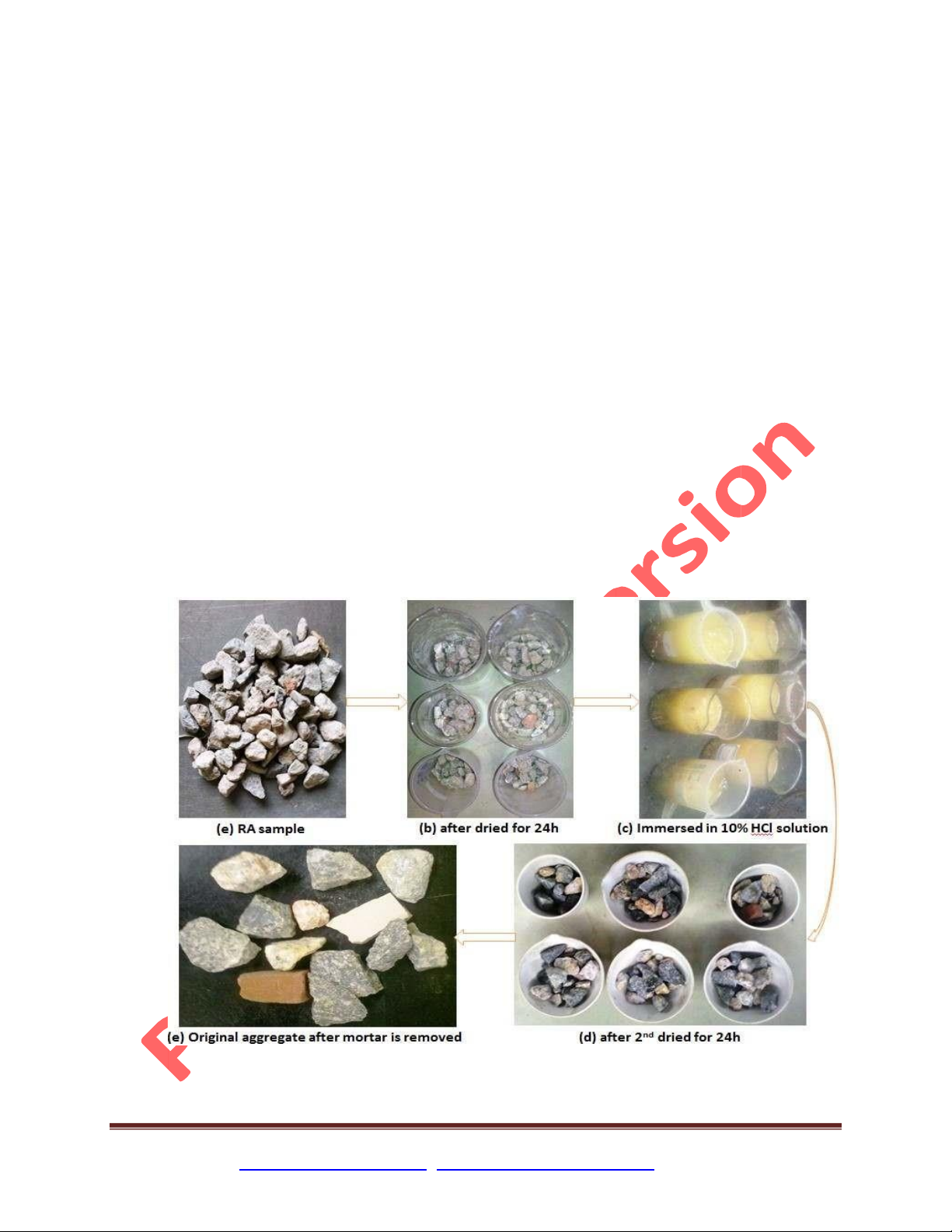
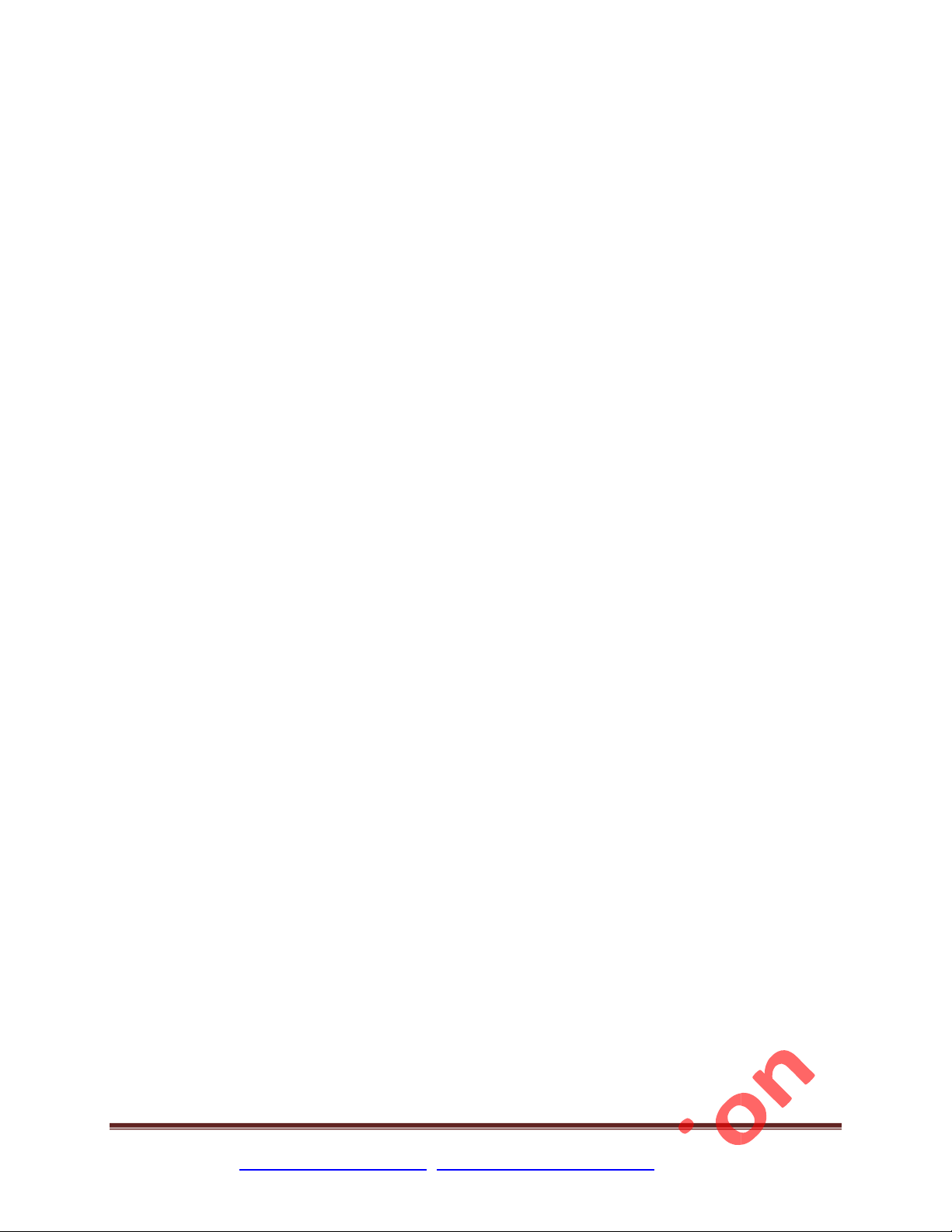
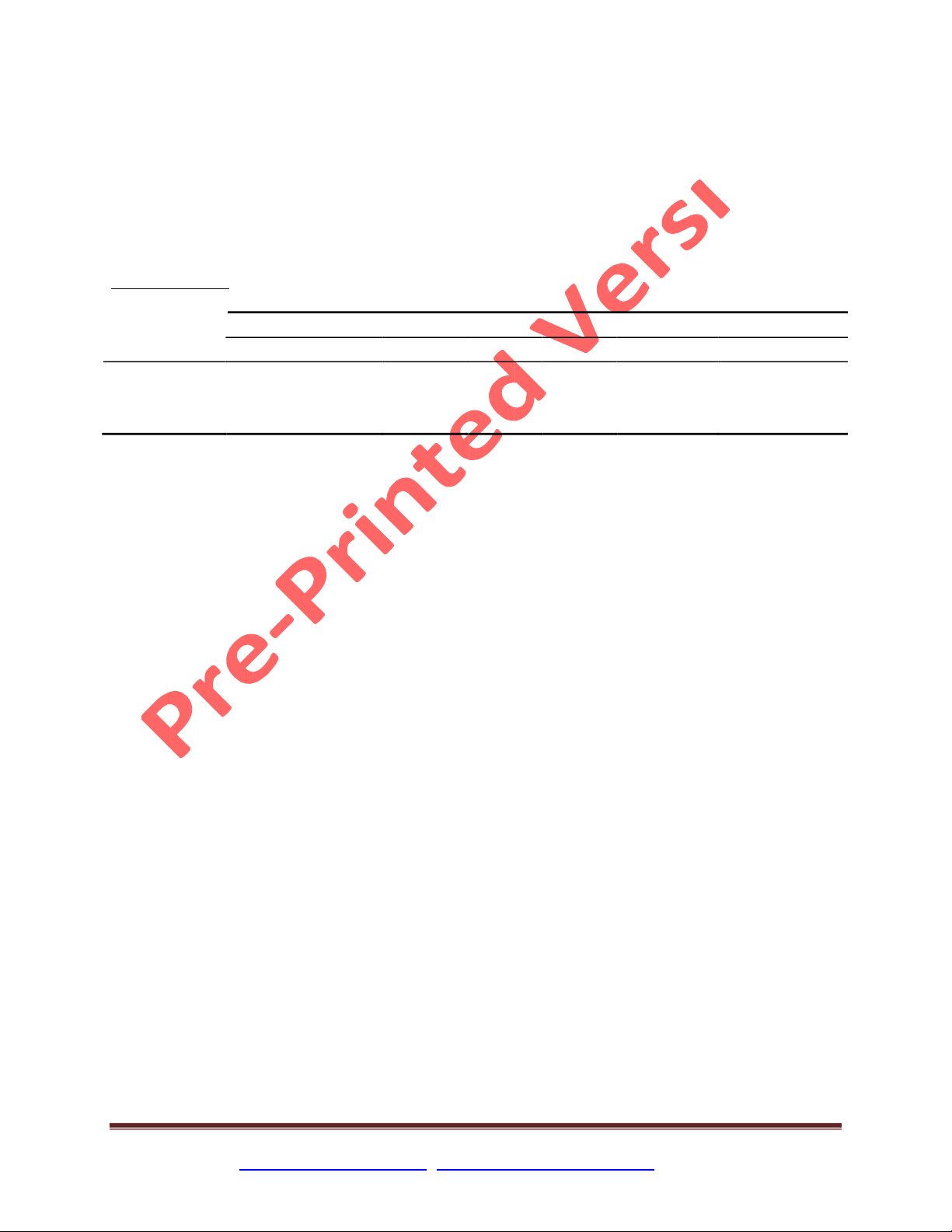
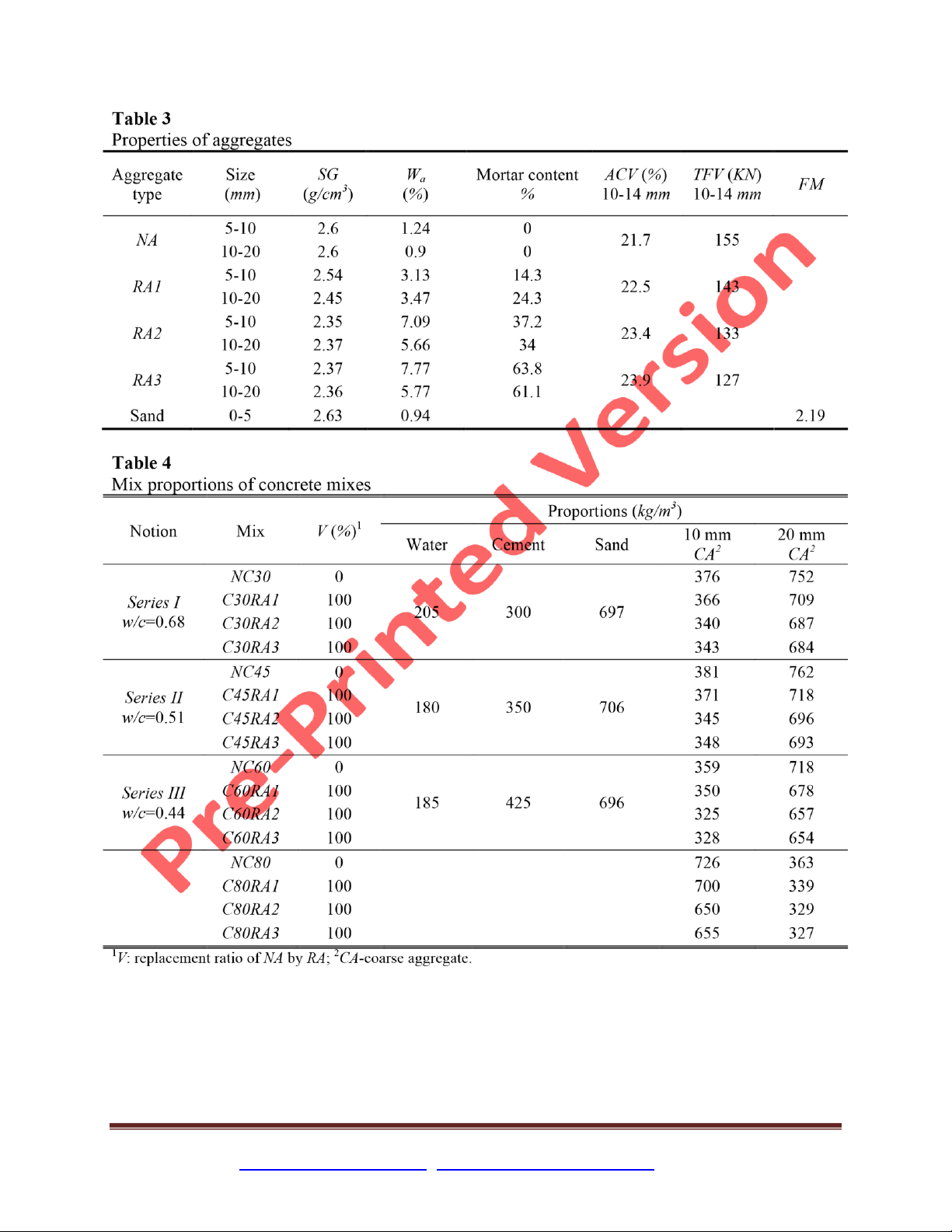
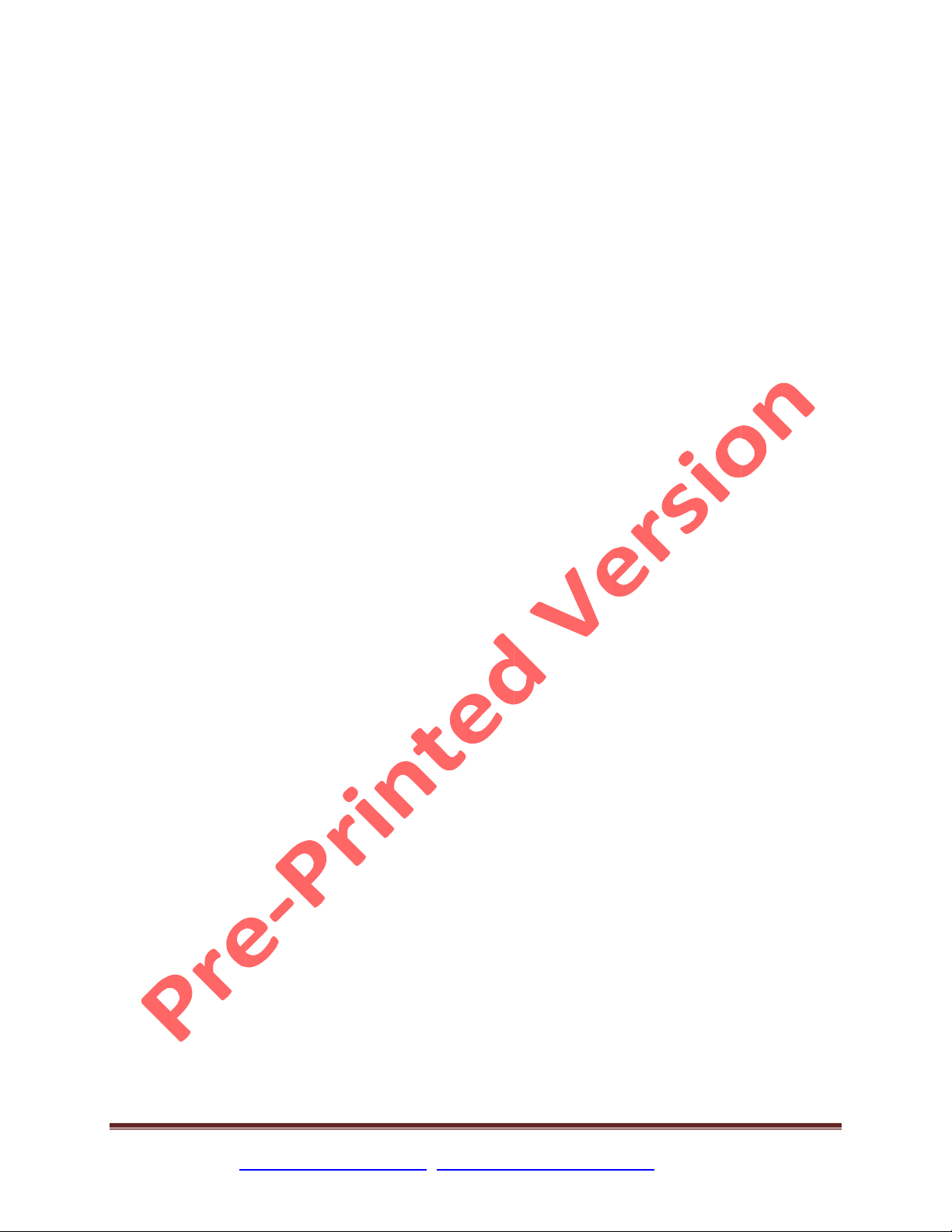
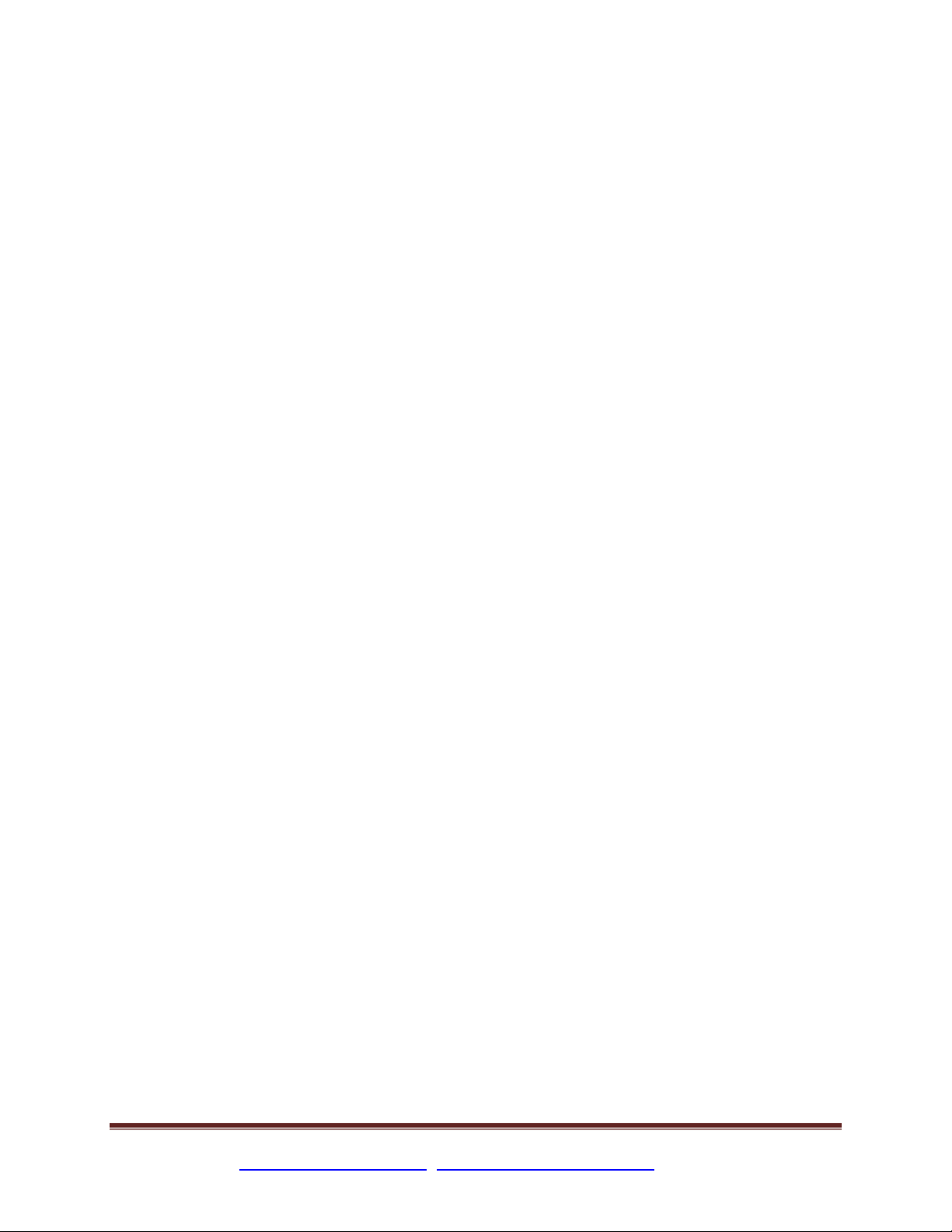
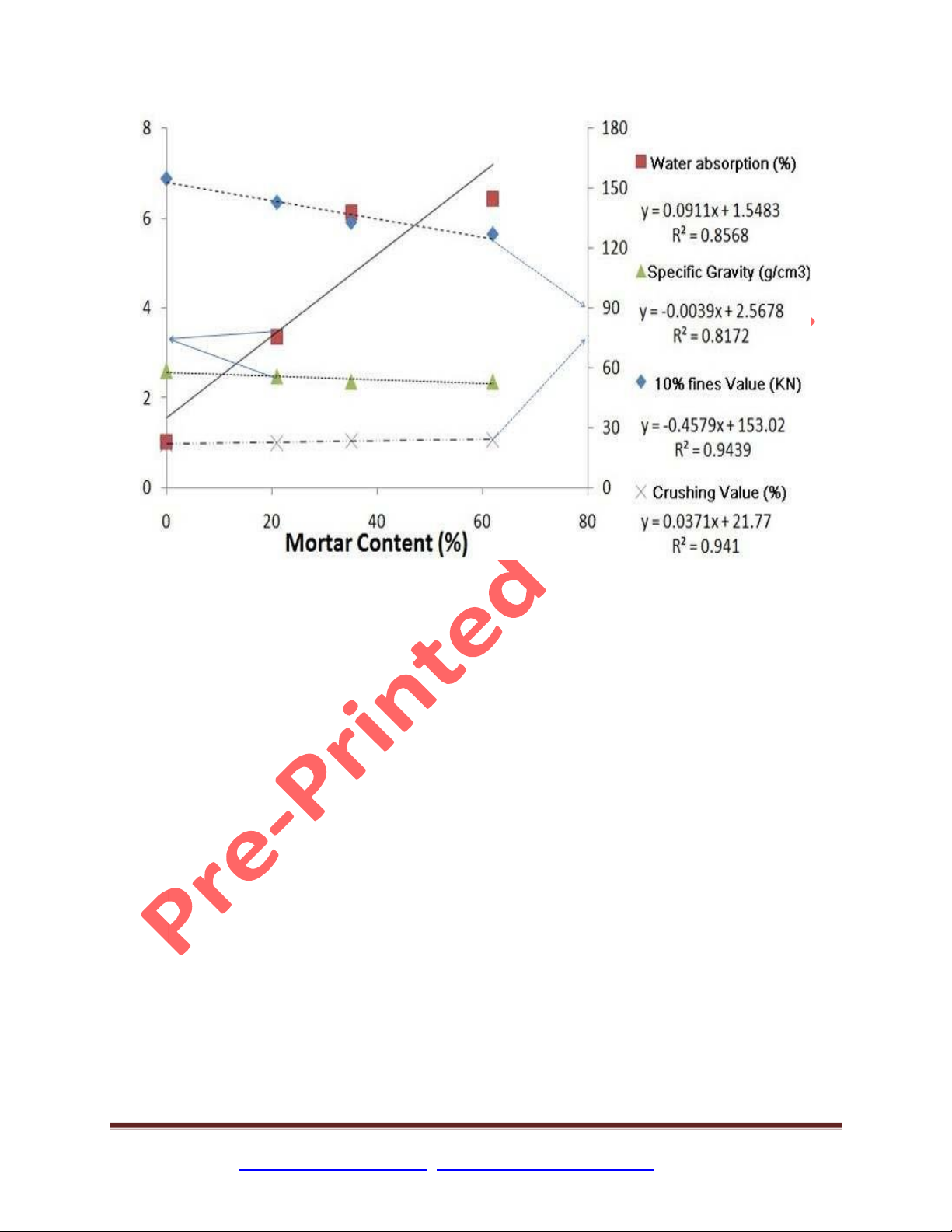
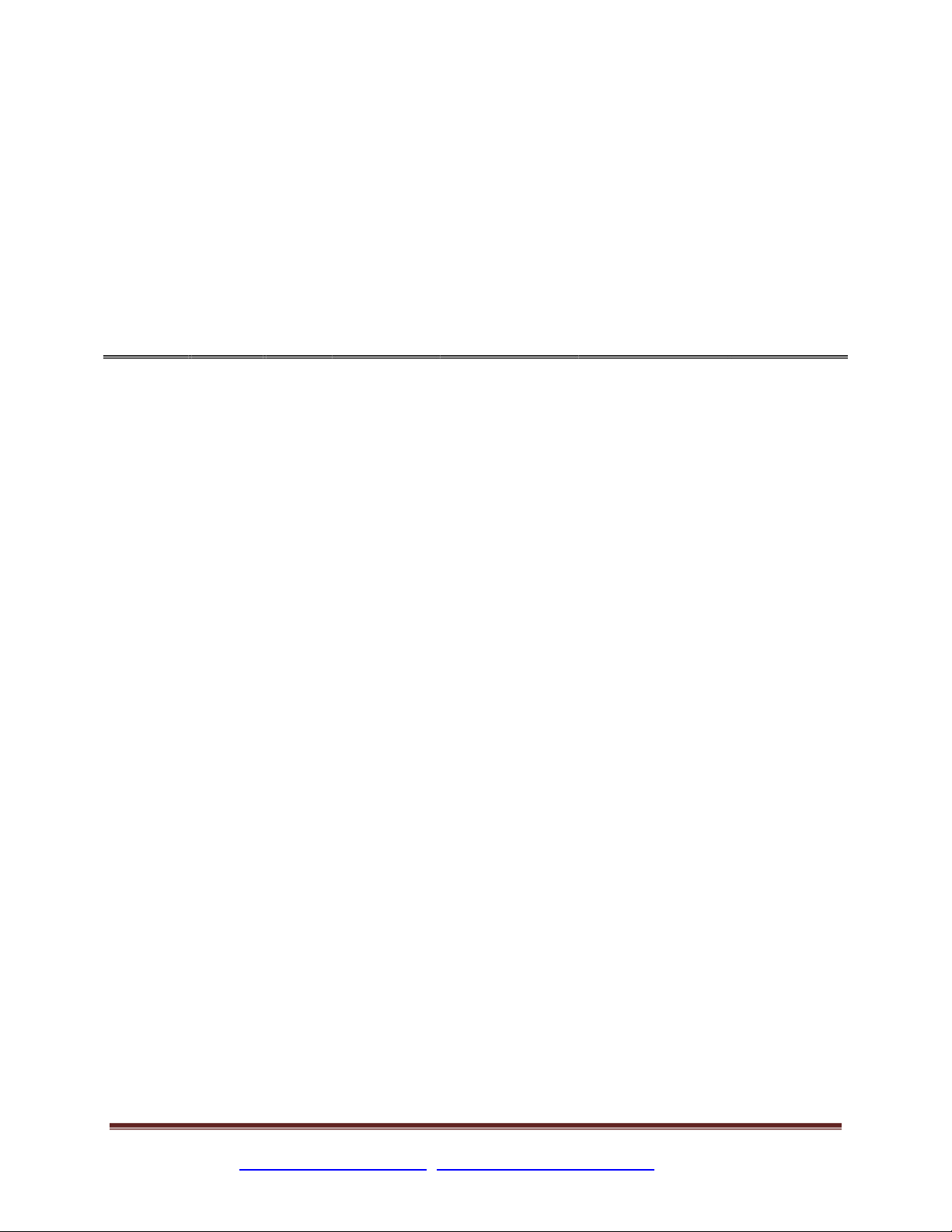
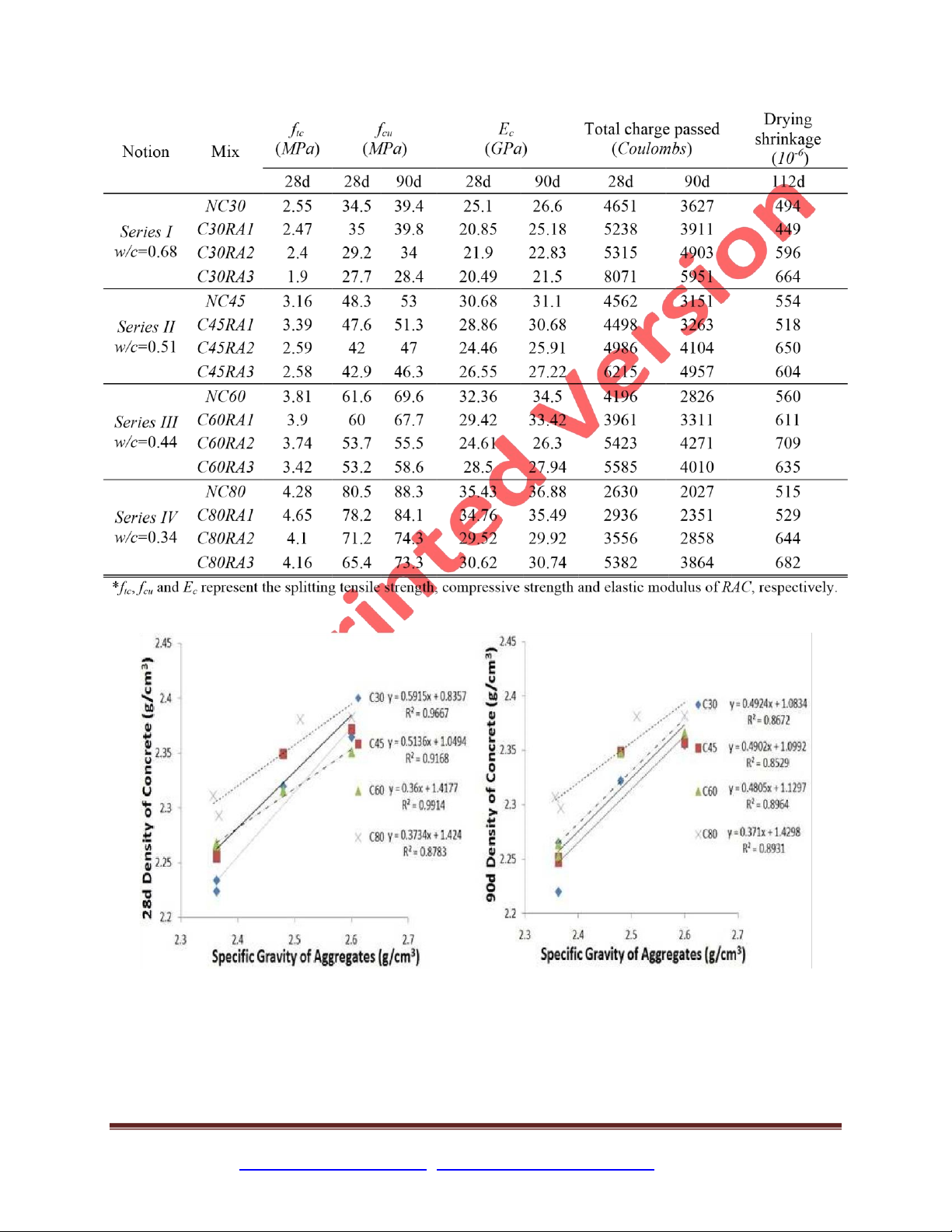
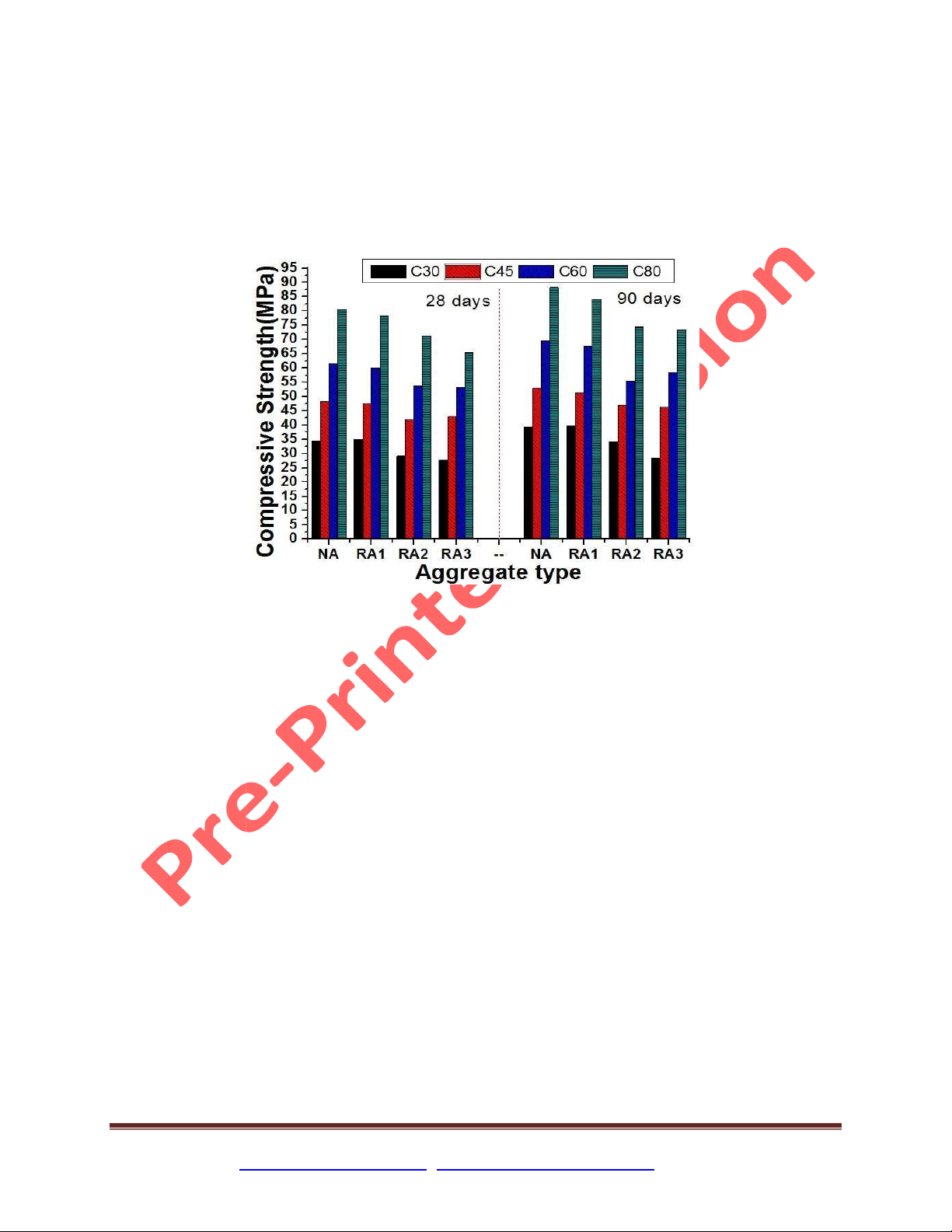
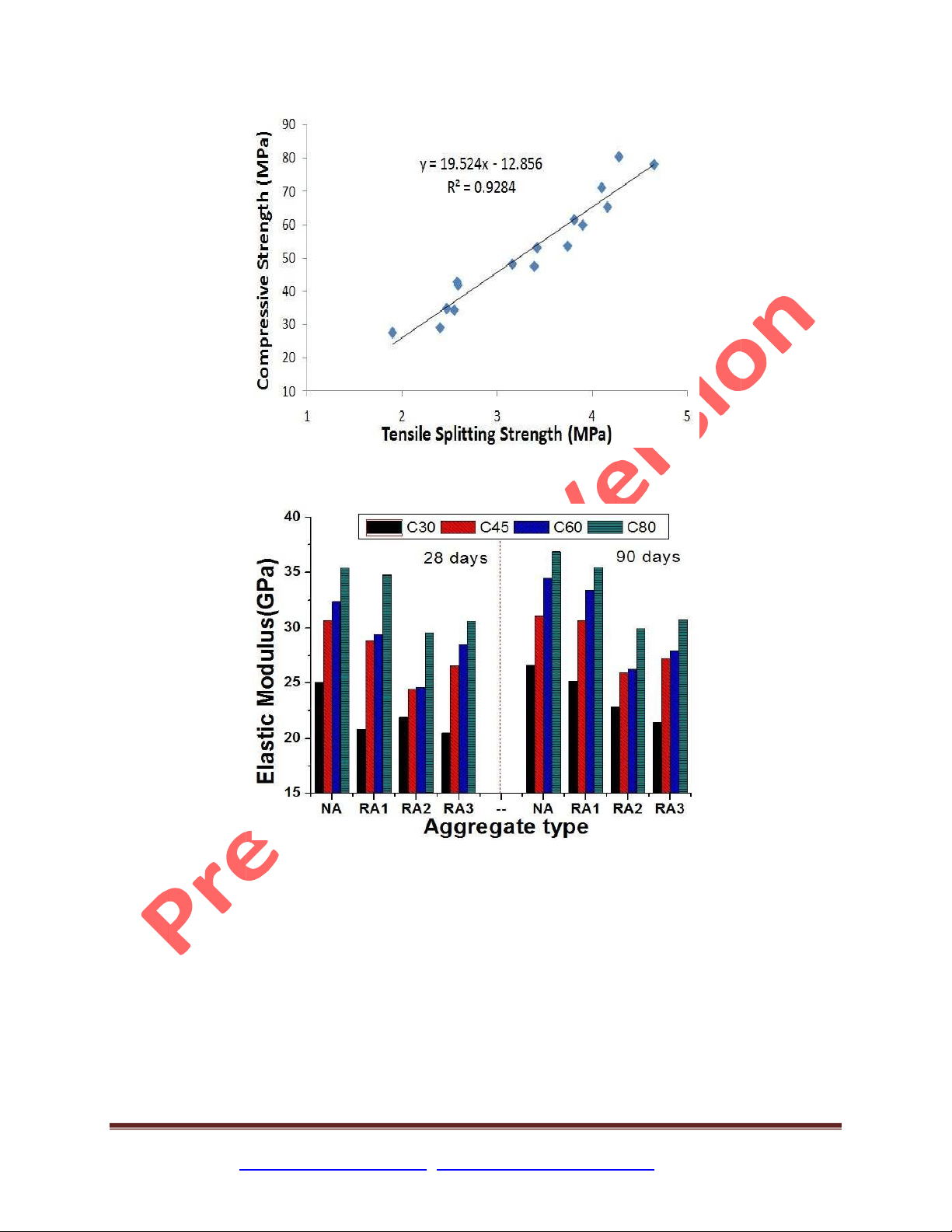
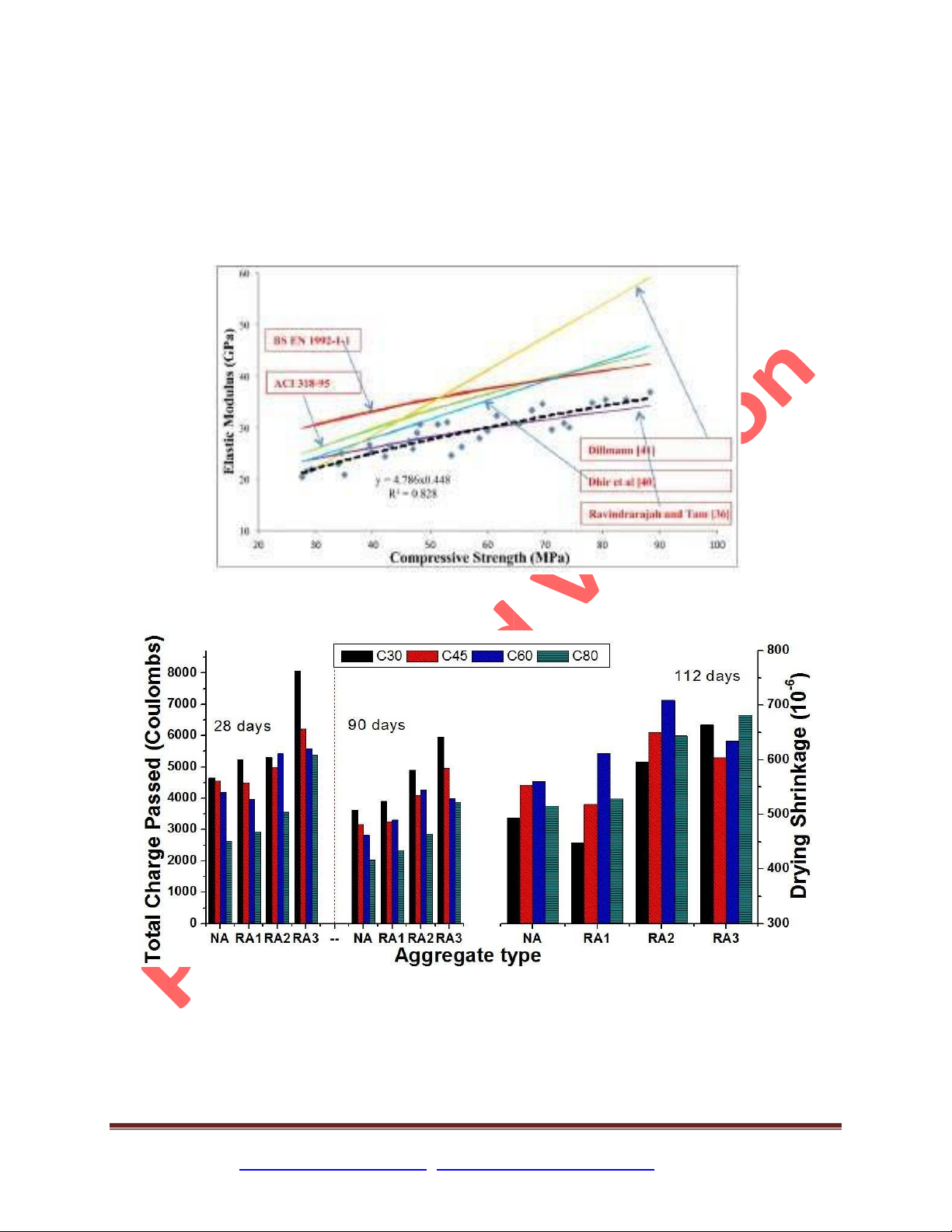
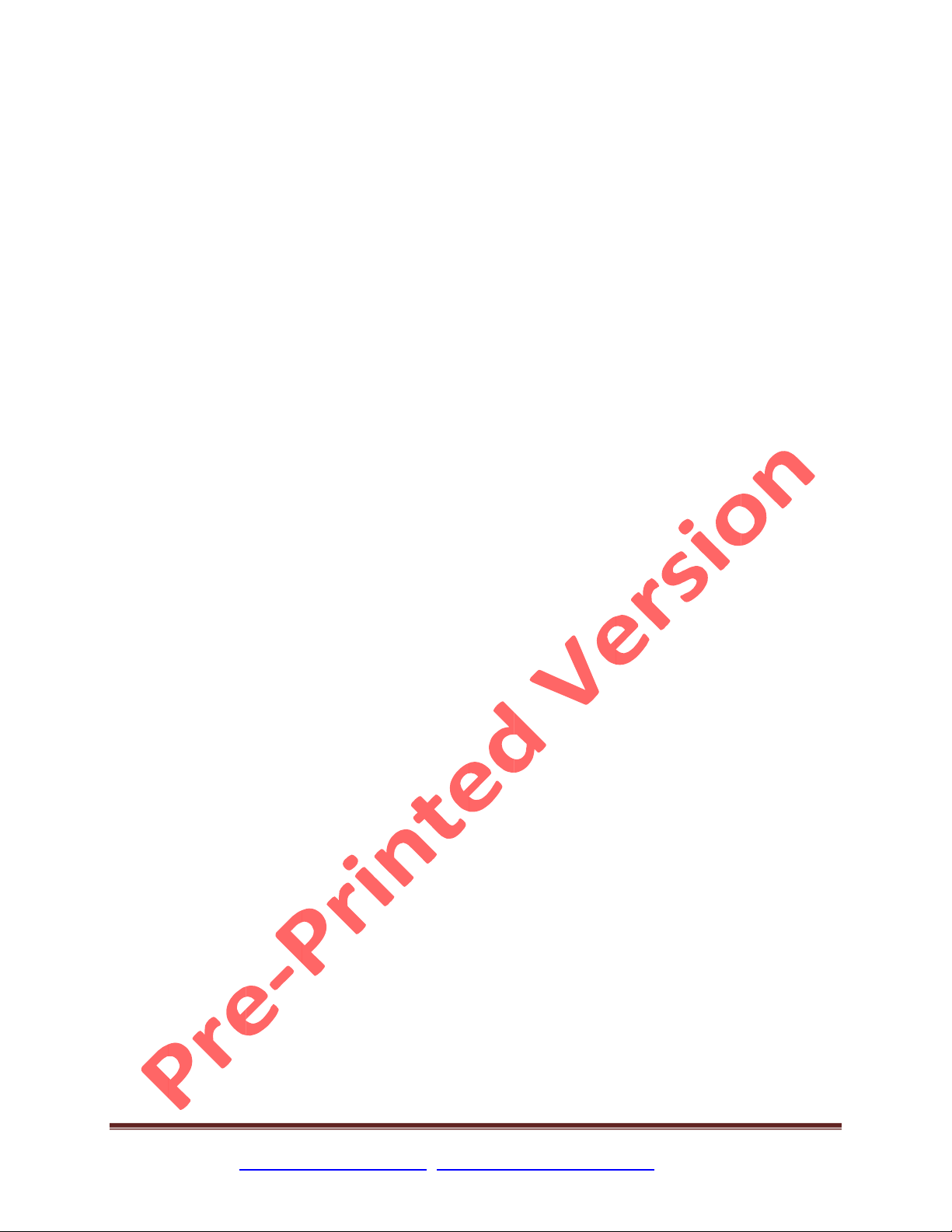
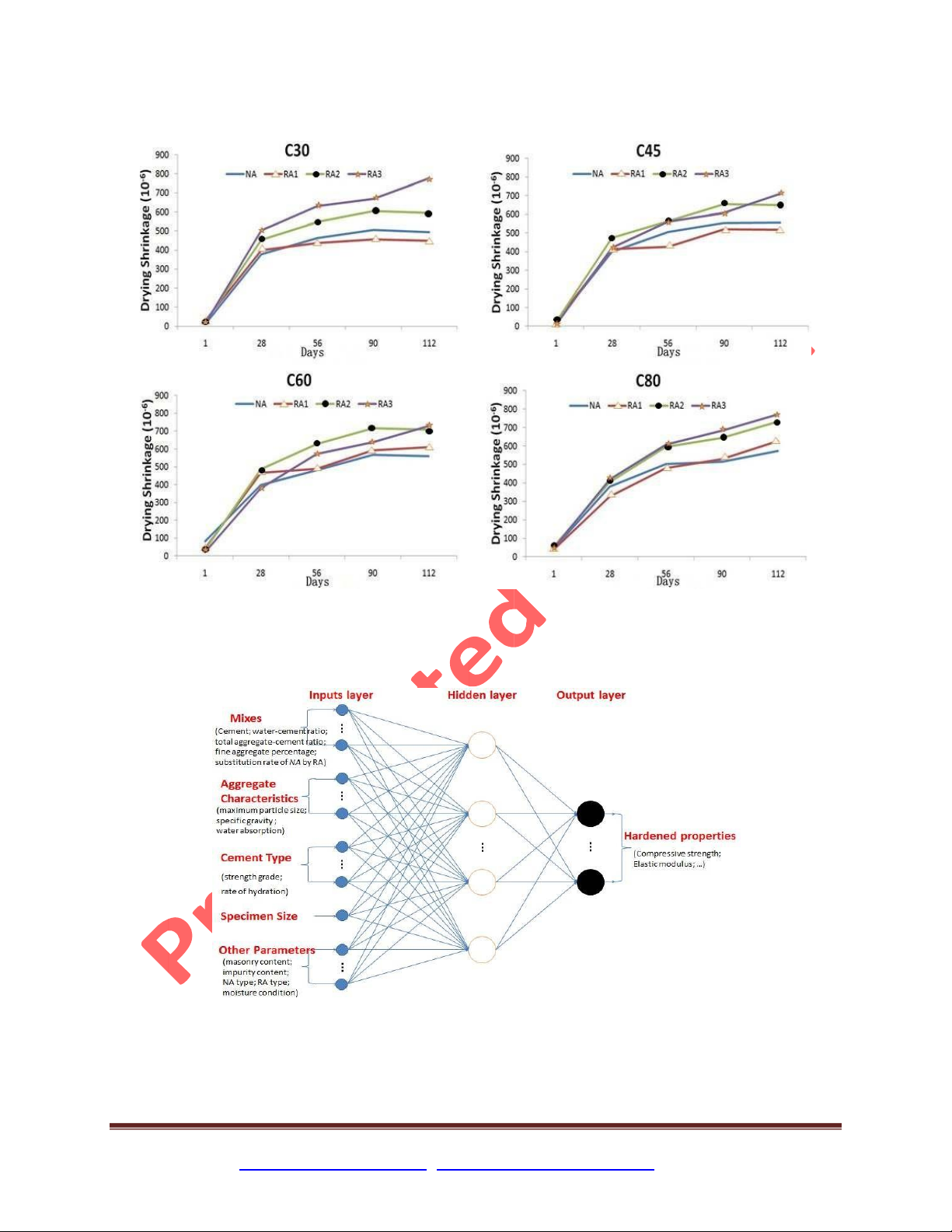
Preview text:
lOMoAR cPSD| 46560390
See discussions, stats, and author profiles for this publication at: https://www.researchgate.net/publication/260155313
Properties of recycled aggregate concrete made with recycled aggregates with different
amounts of old adhered mortars
Article in Materials & Design (1980-2015) · June 2014
DOI: 10.1016/j.matdes.2014.01.044 CITATIONS READS 391 3,296 2 authors: Zhenhua Duan Chi Sun Poon Tongji University
The Hong Kong Polytechnic University
81 PUBLICATIONS 3,592 CITATIONS
612 PUBLICATIONS 46,709 CITATIONS SEE PROFILE SEE PROFILE
Some of the authors of this publication are also working on these related projects:
Water repellent treatment and multi-functional coating for concrete structures View project
Recycling Waste Timber Formwork into Cement-bonded Particleboards View project
All content following this page was uploaded by Zhenhua Duan on 27 April 2018. lOMoAR cPSD| 46560390 !
The user has requested enhancement of the downloaded file. Original citation:
Duan, Z.H., and Poon, C.S. (2014), "Properties of recycled aggregate concrete made with recycled
aggregates with different amounts of old adhered mortars". Materials and Design, Vol. 58, pp.19-29.
http://www.sciencedirect.com/science/article/pii/S0261306914000703
Properties of recycled aggregate concrete made with recycled aggregates with
different amounts of old adhered mortars
Zhen-Hua Duan, Chi-Sun Poon*
Department of Civil and Environmental Engineering The Hong Kong Polytechnic University, Hung
Hom, Kowloon, Hong Kong Abstract:
This paper presents the experimental results of a study on comparing the difference in properties
of recycled aggregates (RAs) with varying amounts of old adhered mortar obtained from
different sources and evaluating the influence of the different RAs on the mechanical and
durability properties of recycled aggregate concrete (RAC). Four concrete mixes (one with
natural aggregate and three others with recycled aggregates) with 28 day target compressive
strength varying from 30 MPa to 80 MPa are designed by using each RA to fully replace NA.
The properties of RAC are also modeled by using the artificial neural networks (ANN) method.
The experimental results show that the performance of RAs from different sources varied greatly
and RA of good quality can be used to produce high strength concrete with hardened properties
comparable to those of the corresponding natural aggregate concrete (NAC). The comparison of
the predicted results based on the ANN models and the experimental values indicated that the
ANN method could be used to evaluate the properties of RAC made with RAs derived from
different sources. This will facilitate the wider application of RA in concrete.
Keywords: recycled aggregate; mechanical properties; durability; recycled aggregate concrete, artificial neural networks. 1. Introduction
Reuse of recycled aggregates (RAs) to fully or partially substitute natural aggregate (NA) has been
extensively studied. Although the potential of using RA in concrete has been demonstrated
successfully in laboratory studies, the use of RA in practical application is generally limited to non-
structural concrete, and the replacement ratio of NA by RA is recommended not to exceed 30% [1].
"#$%&!’(&)*$+!,(’-.)/-)(’0123405678*9:!.)/-)7,(’-48*--/8&7;*<=(7)>!! ! lOMoAR cPSD| 46560390 !
Old cement mortar attached to RA is generally considered as the main cause of poorer properties of
RA compared with those of NA [2,3,4,5], which are reflected in higher water absorption (Wa), !0!
porosity (p), crushing value (ACV) and Los Angeles abrasion value (LA), and lower specific
gravity (SG) and 10% fines value (TFV). The properties of RA obtained from different sources
vary significantly due to the fluctuationsin compositions and qualities of the parent concrete and attached mortar.
The difference in properties of RAs derived from different sources, together with their influence
on the properties of recycled aggregate concrete (RAC) of various grades, has received increasing
research interest. In a previous study [6], eight kinds of RAs were prepared by crushing old
concretes prepared with four types of NA as coarse aggregates and with designed 28th day
compressive strengths of 45 MPa and 65 MPa. The aggregates used differed in shape, composition
and surface texture. Test results indicated that the type of virgin aggregate played a more important
role than the water-cement ratio (w/c) of the parent concrete in affecting the properties of RA. Tam
et al. [7] conducted a study on RAs obtained from ten demolition sites and the results showed that
the properties of the different RAs varied greatly and the compressive strength of the new concrete
made with such RAs ranged from 50 to 63 MPa. Besides, the quality of parent concrete [8,9,10,11]
and crushing process [12,13] also influenced the properties of RA and RAC significantly and RA
crushed from higher quality old concrete was more suitable to produce RAC with comparable properties [14].
Current specifications generally imposethe maximum allowable quantityof impurities in RA, such
as bricks, tiles, glass, asphalt, plastic, wood, gypsum, clay, etc, to ensure the properties of RAC
can be comparable with that of natural aggregate concretes (NAC). A number of studies [15,16,17]
have been done on assessing the effect of mixed recycled aggregates on the properties of RAC and
the results suggested a higher level of masonrycontent in RAcanbe allowed for concrete
applications but the possible adverse effect of the impurities ontheperformance of RAC, especially
the durability, should not be ignored [17,18,19].
However, the above studies did not quantify the effect of the amount of attached old cement mortar
on RA and RAC. This paper reports the experimental results of a comprehensive study on how the
properties of RAC are affected by RAwith different amounts of adhered mortars which were
derived from three different sources. Four series of concrete mixes with 28 day target strengths
from 30 MPa to 80 MPa are designed by using different types of RA to fully replace NA.
It has been demonstrated by the authors previous studies [20,21] that the artificial neural networks
(ANN) method is able to predictthe mechanical properties of RAC through a gradual
approximation of the nonlinear function. The ANN method is also used in this study to evaluate
the mechanical performance of RAC made with RAs from different sources.
2. Objectives and methodology
"#$%&!’(&)*$+!,(’-.)/-)(’0123405678*9:!.)/-)7,(’-48*--/8&7;*<=(7)>!! ! lOMoAR cPSD| 46560390 !
In the RA, the original virgin aggregate with attached old cement mortar is usually its main
component, and the properties of the RA are determined by both the type and the quality of the
virgin aggregates [1,11], and the quality and amount of attached cement mortar [5,22,23].
Besides, RAs derived from different sources may consist of unbound stone, original aggregate !5!
with attached old cement mortar, hardened mortar (Fig. 1). Besides, there are also some impurities
present in the RA, such as bricks, tiles, glass, asphalt, plastic, wood, gypsum, clay, etc.
"#$%&!’(&)*$+!,(’-.)/-)(’0123405678*9:!.)/-)7,(’-48*--/8&7;*<=(7)>!! ! lOMoAR cPSD| 46560390 !
( a) RA from recycling plant (b) RA from laboratory
Fig.1. RAs from different sources
This experimental study aimed to study the influence of RAs from different sources, in particular
with different amountsof old cement mortar, on the mechanical and durability properties of RAC.
Different target strength of concrete mixtures from 30 MPa to 80 MPa were designed by using
RA to fully replace NA, and the experimental test results were then compared with the predicted
values by ANN method to examine whether the ANN method can be used to model the
mechanical performance of RAC made with RAs from different sources.
Fig.2. Full experimental program !?!
"#$%&!’(&)*$+!,(’-.)/-)(’0123405678*9:!.)/-)7,(’-48*--/8&7;*<=(7)>!! ! lOMoAR cPSD| 46560390 !
3. Experimental program
Fig. 2 shows the full experimental program undertaken and itwas consisted of two parts: (1) an
investigation on the properties of concrete made from RAs obtained from different sources, and
evaluation of the mechanical performance by using ANN method; (2) explore alternative methods
to improve the properties of RAC. The results of the first part of this comprehensive study are presented in this paper.
Fig.3. Sources and crushing procedures of different RA Table 1
Chemical c ompositions of cement Composition w/% Materials LOI SiO 2 Fe 2 O 3 Al 2 O 3 CaO MgO SO 3 Cement 2.9 7 19.6 1 3.32 7.33 63.15 2.5 4 2.1 3 3.1 . Materials 3.1.1 . Cement
An ASTM Type I Portland cement, with a density of 3.15 g/cm3, was used in this study. The
chemical compositions of the cement are shown in Table 1. 3.1.2. Aggregates
"#$%&!’(&)*$+!,(’-.)/-)(’0123405678*9:!.)/-)7,(’-48*--/8&7;*<=(7)>!! ! lOMoAR cPSD| 46560390 !
The fine aggregate (0-5 mm) used was a natural river sand with a fineness modulus (FM) of 2.19.
Recycled fine aggregate was not used in this study due to its high water absorption capacity, which
would affect the performance of the concrete seriously [24,25,26]. !@!
Crushed granite with sizes ranged from 5-10 mm and 10-20 mm were used as the natural coarse
aggregate to prepare the control mixes. The sources and preparation methods of the RAs used in
this study are shown in Fig. 3 and described as follows:
RA1: RA1 (10-20 mm) was collected from a construction waste recycling plant which processed
both crushed concrete and excavated rock from construction and demolition activities. The plant
utilized a range of crushing and sieving processes to produce the RA; RA1 (5-10 mm) was obtained
from further crushing the RA1 (10-20 mm) by a laboratory mini crusher;
RA2: RA2 (10-20 mm) was also collected from the same recycling plant, but the source of the
construction waste was different, so the composition and properties of RA1 (10-20 mm) and RA2
(10-20 mm) were not the same; RA2 (5-10 mm) was obtained by crushed concrete lump obtained
from a demolition site, which was originally larger than 200 mm in size, manually (using a
RA3: RA3 (10-20 mm and 5-10 mm) was obtained from crushing (manually and by a laboratory
mini-crusher) old concrete prisms that had been previously prepared in our laboratory with an
hammer) crushed to 50-80 mm and then by a laboratory mini-crusher.
"#$%&!’(&)*$+!,(’-.)/-)(’0123405678*9:!.)/-)7,(’-48*--/8&7;*<=(7)>!! ! lOMoAR cPSD| 46560390 !
original 28th day compressive strength of about 45 MPa.
Fig.4. Test procedures of mortar content of coarse aggregates
The test of aggregate properties, such as fineness modulus, water absorption, specific density,
aggregate crushing value and ten percent fine value were performed in accordance with BS 812-
103.2 [27], BS 812: Part 2 [28], BS 812-110 [29] and BS 812-111 [30]. As there is no standard method
in measuring old cement mortar amounts in RAs, the test of the mortar content (Fig. 4) was based
on a hydrochloric acid dissolution method [31] as follow: !3!
Firstly, the aggregate samples with particle size of 5-10 mm or 10-20 mm, after washing by distilled
water and sieving to remove the fine particle, were dried in an oven at a temperature of 105¡C for 24h.
Then, appropriate amount of each sample (m1), about 100g, was taken and immersed in a solution
of 10% hydrochloric acid for 8 h.
Next, the sample was washed again by water to remove the loose particles, and dried in an oven at
a temperature of 105 ¡C for 24 h.
In this way, most of the attached cement mortar on the recycled aggregates could be easily removed,
and the remaining mortar could be removed by a hammer and a steel brush.
The sample was sieved through a 5 mm sieve to obtain the mass of the original aggregate (m2).
The mortar content was calculated using Eq. (1). For each type of aggregate, 6 samples were tested to obtain the average value.
"#$%&!’(&)*$+!,(’-.)/-)(’0123405678*9:!.)/-)7,(’-48*--/8&7;*<=(7)>!! ! lOMoAR cPSD| 46560390 !
Mc (%) = (m1- m2) / m1 × 100 (1)
The constituents and properties of the aggregates used are shown in Tables 2 and 3, respectively. Table 2
Constituents of recycled aggregates Aggregate
Constituents (% by mass) type Rock/Concrete Brick Tile Clay Metal Other impurities RA1(20mm) 98.2 0.8 0.6 0.2 0.15 0.05 RA2(20mm) 96.05 2.1 0.75 0.35 0.15 0.65 RA3(20mm) 99 0.8 0.2 0 0 0
3.1.3. Superplasticizer
The superplasticizer (Grace, ADVA-109) used was obtained from Hong Kong Grace Construction Products Limited. 3.2. Concrete mixes
Four series of concrete mixes were prepared using NA and three types of RA. In each series, four
concrete mixes with different 28 day target cube strength between 30 MPa and 80 MPa were
prepared, and the corresponding water to cement ratios were ranged from 0.68 to 0.34. For each
concrete mix, a control concrete (NC) was prepared with 100% NA, while RC1, RC2 and RC3
were made with 100% RA1, RA2 and RA3, respectively. For concrete made with different types
of aggregates, appropriate amounts of superplasticizer were used to achieve a similar slump value
of 70-90 mm for Series I to Series III and 120-150 mm for Series IV. The details of the mix
proportions are shown in Table 4.
All the 16 concrete mixes were designed using the absolute volume method with the aggregates at
the saturated surface-dried (SSD) condition, and the actual proportions of the mixes at mixing were
adjusted according to the moisture contents of the aggregates. For Series I to Series III (C30-C60)
mixes, the coarse aggregates of 5-10 mm and 10-20 mm fractions were added in a !6!
ratio of 1:2, while for Series IV (C80) mixes, the coarse aggregates of 5-10 mm and 10-20 mm
fractions were added in a ratio of 2:1.
"#$%&!’(&)*$+!,(’-.)/-)(’0123405678*9:!.)/-)7,(’-48*--/8&7;*<=(7)>!! ! lOMoAR cPSD| 46560390 ! Series IV 165 485 685 w/c=0.34
"#$%&!’(&)*$+!,(’-.)/-)(’0123405678*9:!.)/-)7,(’-48*--/8&7;*<=(7)>!! ! lOMoAR cPSD| 46560390 ! !A!
3.3. Specimens casting and curing
For each concrete mix, 100 mm cubes, fl100 × 200 mm cylinders and 70 × 70 × 285 mm prisms
were cast. The 100 mm cubes were used to determine the compressive strength. Some of the
cylinders were used to evaluate the splitting tensile strength and static modulus of elasticity; the
rest of the cylinders were cut to fl50×100 mm slices to test the chloride-ion penetration. The
70×70×285 mm prisms were used to determine the drying shrinkage. All the specimens were cast
in steel moulds and compacted using a vibrating table. The specimens were demolded after curing
for 24 hours at a controlled laboratory environment, and then the cubes and cylinders were cured
in a water-curing tank at 27 – 2 …C, while the concrete prisms were stored at a constant
temperature (23 – 2 ¡C) and relative humidity (50 – 5%) chamber until the age of testing. 3.4. Test methods
At the ages of 28th and 90th day, the hardened density, compressive strength and elastic modulus
of the concrete were measured according to BS EN 12390-7 [32], BS EN 12390-3 [33] and BS
1881-121 [34], respectively, while the chloride penetrability of concrete was tested in accordance with ASTM: C1202.
The tensile splitting strength of concrete was determined based on BS EN 12390-6 [35] after 28
days of curing. As regards to the dry shrinkage, ASTM: C157 was followed. The initial lengths of
the specimens were measured and the initial dry shrinkage values were recorded after the
specimens were demolded. Then the specimens were conveyed to a drying-chamber with a
constant temperature of 23 ¡C and a relative humidity of 55% until further measurement at 1, 28,
56, 90 and 112 days, respectively.
4. Results and discussion 4.1. Aggregate properties
Table 3 shows the experimental results of the physical and mechanical properties of the aggregates
investigated, including the mortar content, water absorption, specific gravity (SSD), aggregate
crushing and 10% fines values.
Compared with NA, it can be noticed from Table 3 that the density and 10% fines value of RAs
were lower, but the corresponding water absorption and aggregate crushing value were higher.
As mentioned above, RAs used in this study can be regarded as a composite material containing
unbound stone, virgin aggregate with attached old mortar, hardened mortar and some impurities.
The amount of old mortar in RA1 was the lowest as it contained more crushed rock and was
"#$%&!’(&)*$+!,(’-.)/-)(’0123405678*9:!.)/-)7,(’-48*--/8&7;*<=(7)>!! ! lOMoAR cPSD| 46560390 !
processed at a recycling plant. For RA2, especially the (5-10 mm) fraction, the mortar content was
higher due to its major source was from old concrete, RA3 had the highest mortar content as it
only underwent one crushing process in the laboratory. !2!
"#$%&!’(&)*$+!,(’-.)/-)(’0123405678*9:!.)/-)7,(’-48*--/8&7;*<=(7)>!! ! lOMoAR cPSD| 46560390 !
Fig.5. Relationships between mortar content and other properties of aggregates
The influence of the quantity of attached mortar on aggregate properties can be seen clearly from
Fig. 5 . The most noticeable influences of the attached mortar are on the water absorption and the
ten percent fines values (TFV). The water absorption values of RA increased drastically while
the TFV decreased gradually with the increase in mortar content. For evaluating the strength of
the recycled aggregates, it seems that the TFV value is more sensitive than the aggregate
crushing value, because the weaker materials in the RA were crushed before the specified load
(400 KN) was reached. Based on the test results, it seems that RA1 was of the best quality
among all the RAs used; while the properties of RA2 and RA3 were nearly the same. It is noted
that RA2 had more impurities and clay bricks while RA3 contained more attached mortar,
rendering both of them weaker and more porous. 4.2 . Concrete properties
Table 5 lists the test results of different grades of concrete mixtures.
4.2.1 . Density
As shown in Fig. 6, the densities of the hardened concrete made with RA were lower than those
prepared with NA. Good relationships can be established between the density of the concrete and
the specific gravity of the corresponding aggregates used, with the correlation coefficients R2 all exceed 0.85.
"#$%&!’(&)*$+!,(’-.)/-)(’0123405678*9:!.)/-)7,(’-48*--/8&7;*<=(7)>!! ! lOMoAR cPSD| 46560390 !
4.2.2. Compressive strength
The compressive strength of concrete made with NA and RAs are shown in Fig. 7. As expected,
the compressive strength of the concrete made with RA were mostly lower than that made with !1!
NA, regardless of the w/c ratio used; besides, the strength of the concrete made with NA and RA all increased with age. Table 5
Properties of concrete mixes
"#$%&!’(&)*$+!,(’-.)/-)(’0123405678*9:!.)/-)7,(’-48*--/8&7;*<=(7)>!! ! lOMoAR cPSD| 46560390 !
Fig.6. Relationship between specific gravity of aggregates and density of concrete !0B!
It can be noticed from Fig. 7 that there were large reductions in compressive strength when RA2
and RA3 (over 10% at both 28th and 90th day) were used to fully replace NA to produce the
concrete, which might be due to the large amounts of old mortar attached to them. With the
"#$%&!’(&)*$+!,(’-.)/-)(’0123405678*9:!.)/-)7,(’-48*--/8&7;*<=(7)>!! ! lOMoAR cPSD| 46560390 !
decrease in w/c ratio, it was increasingly difficult for RA2 and RA3 to produce concrete that can
satisfy the target strength. For Series IV, the strength values were about 11% and 18% lower than
the target strength of 80 MPa when RA2 and RA3 were used, respectively. This might be due to
the porous nature of RA2 and RA3 with a larger amount of cracks and attached mortar.
Fig.7. Effect of different aggregates on compressive strength of concrete mixes
For the concrete made with RA1, the compressive strength was comparable to that of the control
mix (and even exceeded the control in the case of C30 concrete). With the increase in target
strength, the difference between the strength of concrete made with NA and RA1 increased
gradually to about 2.9% and 4.8% for C80 at 28 days and 90 days, respectively. However, it can
be noticed from Table 5 that the concrete made with RA1 was still able to reach the target strength
of 60 MPa. So RAs of high quality may beused for producing concrete with comparable strength
to that of natural aggregates.
4.2.3. Tensile splitting strength
The results in Table 5 indicate that the concrete made with RA1 had higher tensile splitting strength
(except C30) than the corresponding natural aggregate concrete. The improved strength may be
due to the presence of the attached cement mortar, which would enhance the bonding between the
RA and the new cement paste [36]. Furthermore, the rough surface of the RAs might also further
improve the microstructure of the interfacial transition zone (ITZ) [37], and enhanced the splitting tensile strength.
Although RA2 and RA3 also had higher amounts of attached mortar than NA, the excessive
amounts of porous mortar led to a decrease in tensile strength. !00!
"#$%&!’(&)*$+!,(’-.)/-)(’0123405678*9:!.)/-)7,(’-48*--/8&7;*<=(7)>!! ! lOMoAR cPSD| 46560390 !
Fig.8. Relationship between 28d compressive strength and tensile splitting strength
Fig.9. Effect of different aggregates on elastic modulus of concrete mixes
As shown in Fig. 8 , the tensile splitting strength of concrete had a good correlation with the
corresponding compressive strength, and the correlation coefficient R2 reached as high as 0.93.
4.2.4. Static modulus of elasticity
The results of the static modulus of elasticity tests are shown in Fig. 9. A decline of elastic modulus
values is noted for the concrete made with RAs and the decrease is more obvious in concrete made with RA2 and RA3.
"#$%&!’(&)*$+!,(’-.)/-)(’0123405678*9:!.)/-)7,(’-48*--/8&7;*<=(7)>!! ! lOMoAR cPSD| 46560390 !
The elastic modulus values of the concrete made with RA1 were almost as good as those made
with NA in all the mix series at both 28 and 90 days of curing. As the elastic modulus of !05!
concrete is related to the quality of coarse aggregate, a comparison between mechanical strength
(TFV and ACV) of NA and RA1 in Table 3 further proves that good quality RA is able to fully
replace NA to produce even high strength concrete.
Fig.10. Relationship between compressive strength and elastic modulus
Fig.11. Effect of different aggregates on chloride ion penetration and shrinkage of concrete mixes
Fig. 10 shows the relationship between elastic modulus and compressive strength of all mixes at
both 28 and 90 days. The relationship stipulated by ACI 318-95 [38] and BS EN 1992-1-1 [39],
together with some empirical relationships (Eqs.2-4) that have been proposed by other researchers
"#$%&!’(&)*$+!,(’-.)/-)(’0123405678*9:!.)/-)7,(’-48*--/8&7;*<=(7)>!! ! lOMoAR cPSD| 46560390 !
[36,40,41] based on their laboratory studies on testing concrete produced with RA, are also plotted
to compare the present findings with that of the relationships. !0?! Ravindrarajah and Tam [36]: Ec= 7.77fcu0.33 (2) Dhir et al [40]: Ec= 0.37 fcu+ 13.1 (3) Dillmann [41]: Ec= 0.63443fcu+ 3.0576 (4)
The regression equation based on the 28 and 90 days experimental results in this study can be expressed as follow: Ec= 4.7863fcu0.4485 R2=0.828 (5)
where fcu and Ec are expressed in MPa and GPa, respectively.
It can be noticed from Fig. 10 that most of the codes and established empirical relationships
overestimate the elastic modulus of the RAC. This may be due to that only one parameter,
compressive strength, was used to evaluate the corresponding elastic modulus value in such
relationships. More parameters, such as aggregate characteristics and cement type, should be
considered to be included for better estimation of the properties of recycled aggregate concrete.
4.2.5. Chloride ion penetrability
Fig. 11 shows the effect of different types of aggregates and w/c ratios on the resistance of chloride
ion penetration of the concrete. The results show that concrete made with RAs generally had poorer
resistance to chloride ion penetrability, and it decreased with the trend: RA1 > RA2 > RA3.
However, it should be noted from the Figure that the resistance to chloride ion penetration of the
concrete made with RA1 was the best in all mix series, and it can be comparable with those
prepared with NA, especially in Series II and III mixes at 28 days. 4.2.6. Drying shrinkage
Fig. 11 also illustrates the effect of RA on the drying shrinkage of the concrete at 112 days and the
trends are similar to that of the chloride ion resistance test results. For concrete made with the
better quality of RA, lower shrinkage values were recorded generally.
The drying shrinkage development of concrete made with different coarse aggregates in all series
is presented in Fig. 12. As expected, the drying shrinkage of concrete increased with the curing
days in all series. Similar to the chloride penetration test, the drying shrinkage of concrete made
with RA1 was the best in all series, and can be comparable with those with NA.
"#$%&!’(&)*$+!,(’-.)/-)(’0123405678*9:!.)/-)7,(’-48*--/8&7;*<=(7)>!! ! lOMoAR cPSD| 46560390 ! !0@!
Fig.12. Drying shrinkage of concrete made with different types of aggregates 4.3 . Modeling by ANN
Fig.13. Constructed ANN model
ANN model with a 16-40-1 structure (Fig. 13), proved previously to be capable of predicting the
properties of concrete made with RAs derived from different sources after training and testing [20],
was also used in this study to model the compressive strength and elastic modulus values.
"#$%&!’(&)*$+!,(’-.)/-)(’0123405678*9:!.)/-)7,(’-48*--/8&7;*<=(7)>!! !