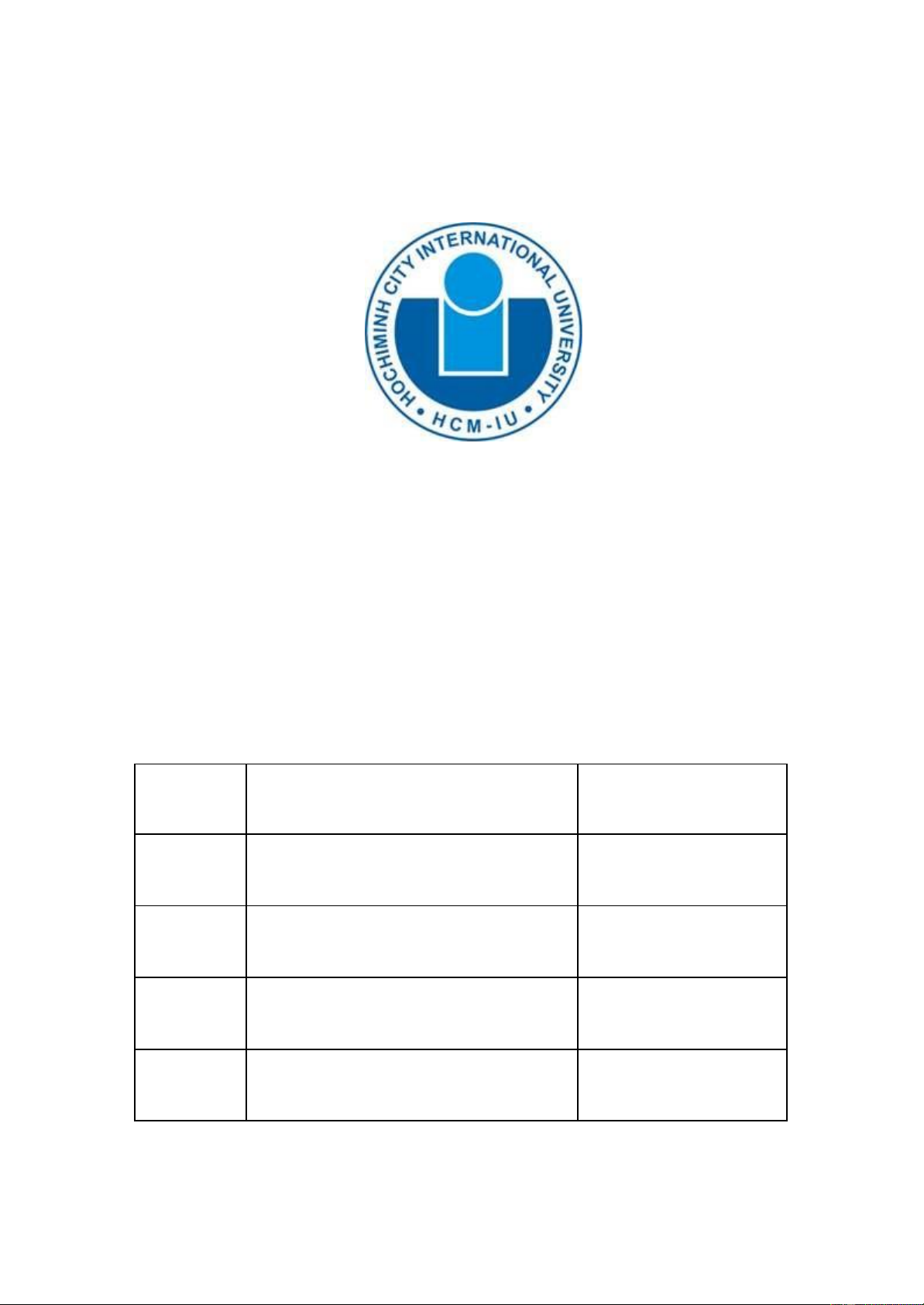
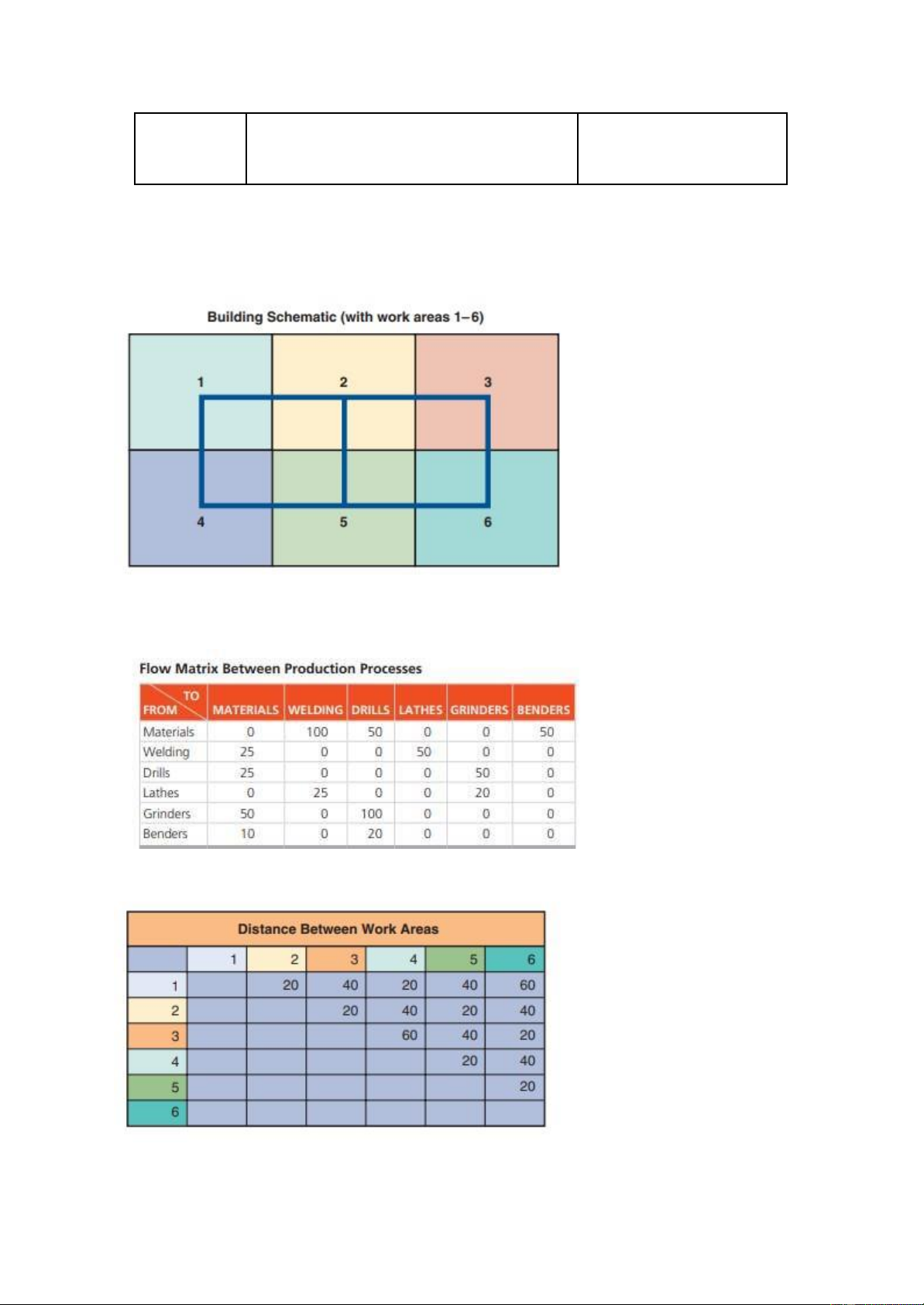
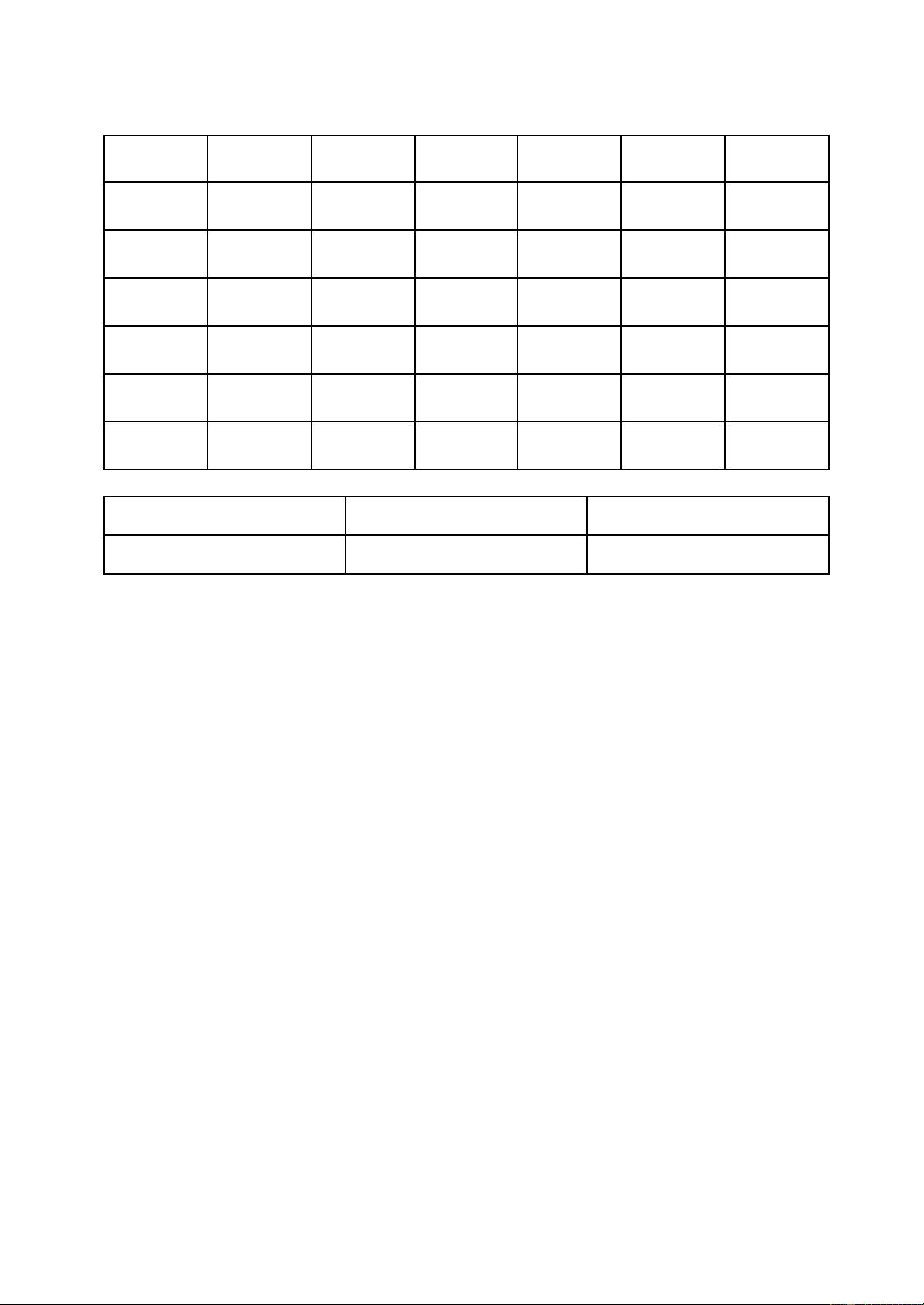
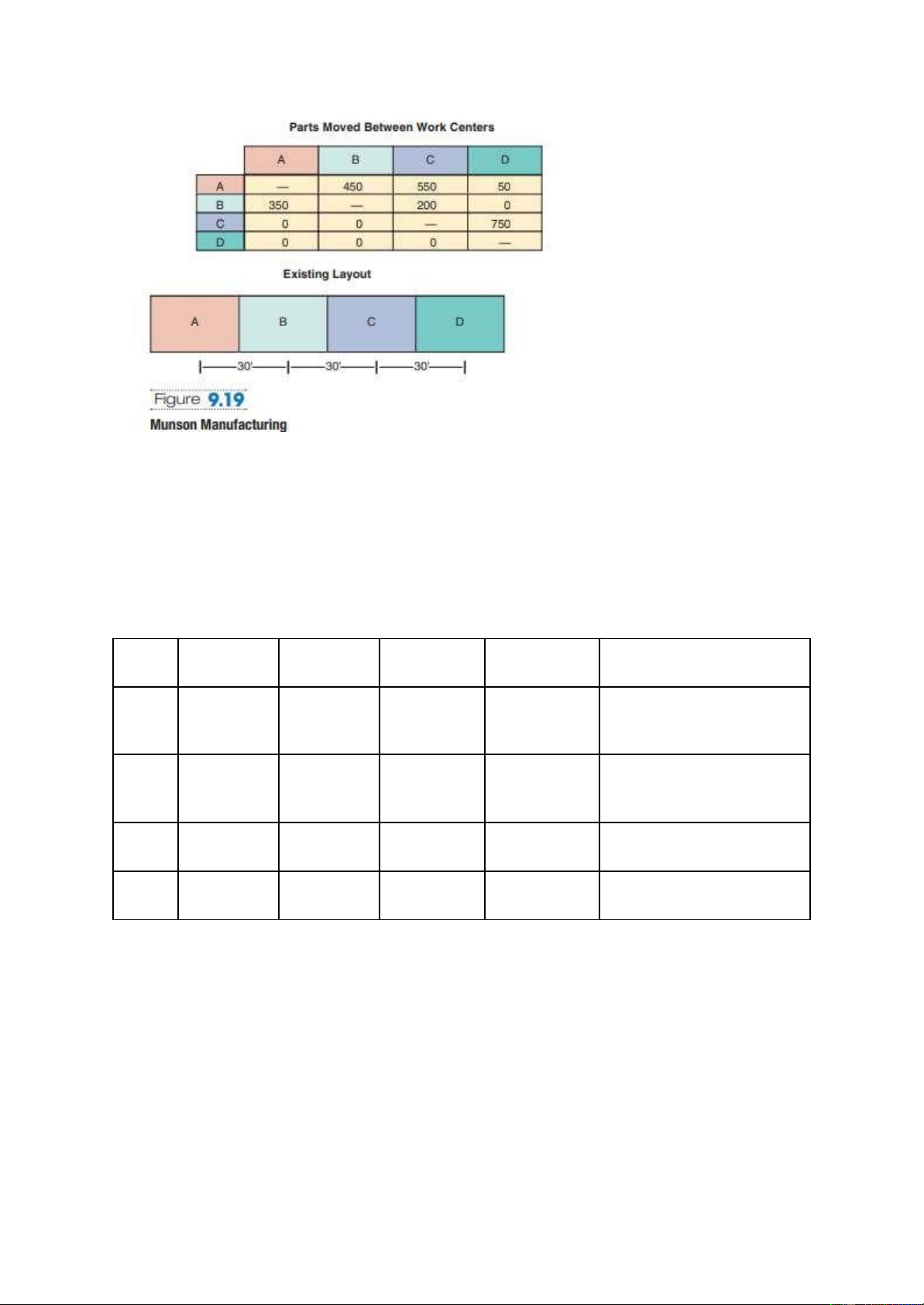
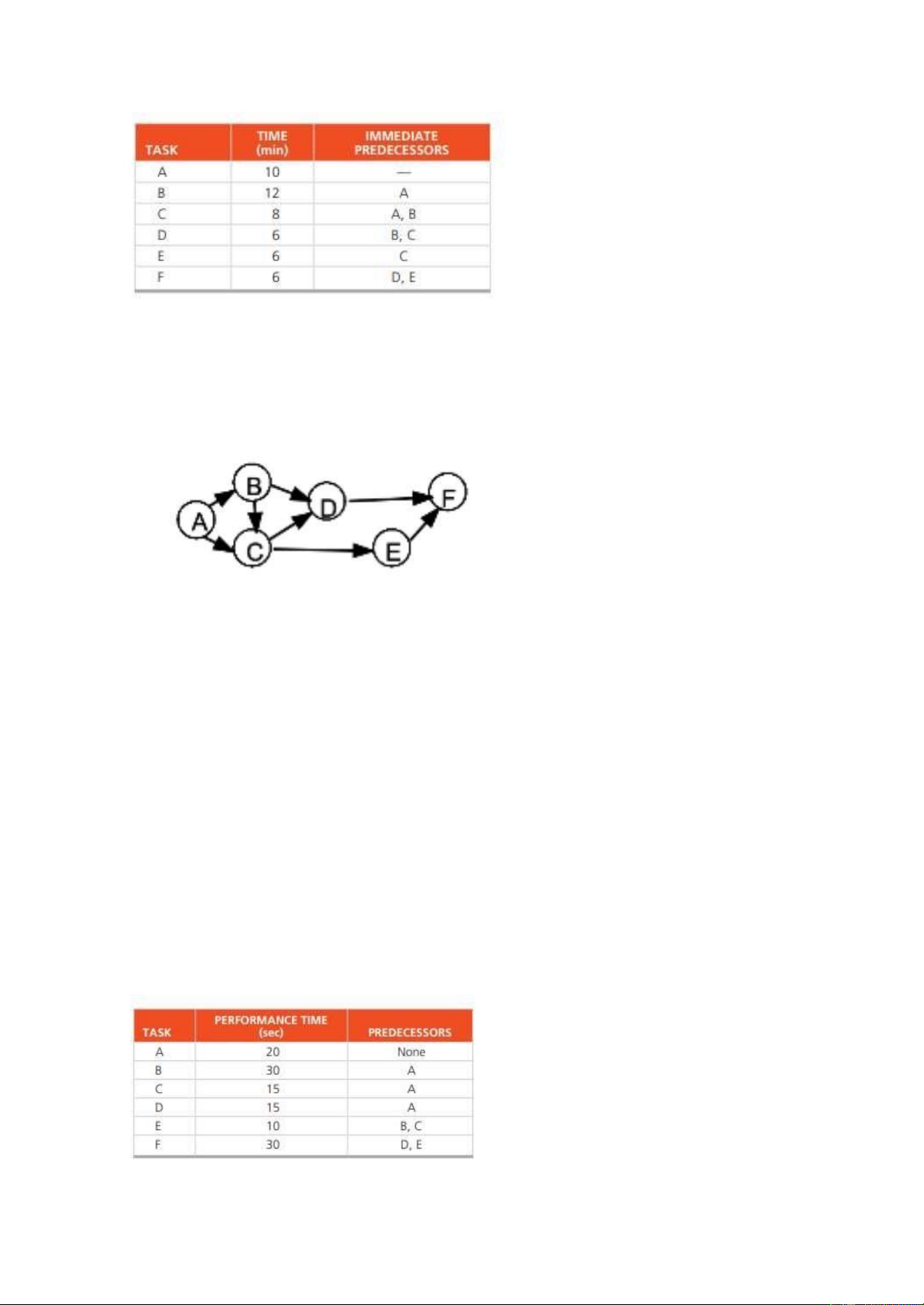
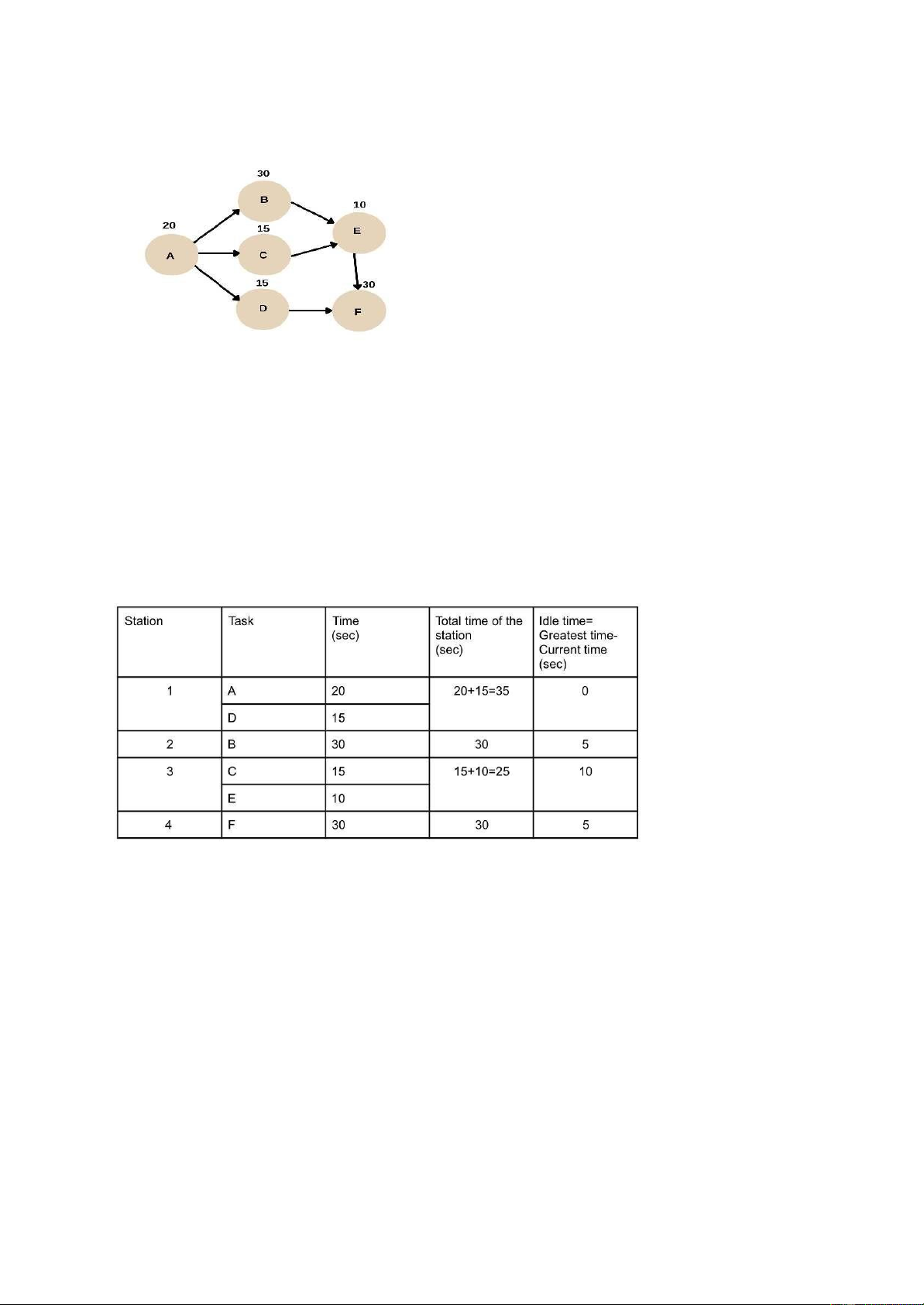
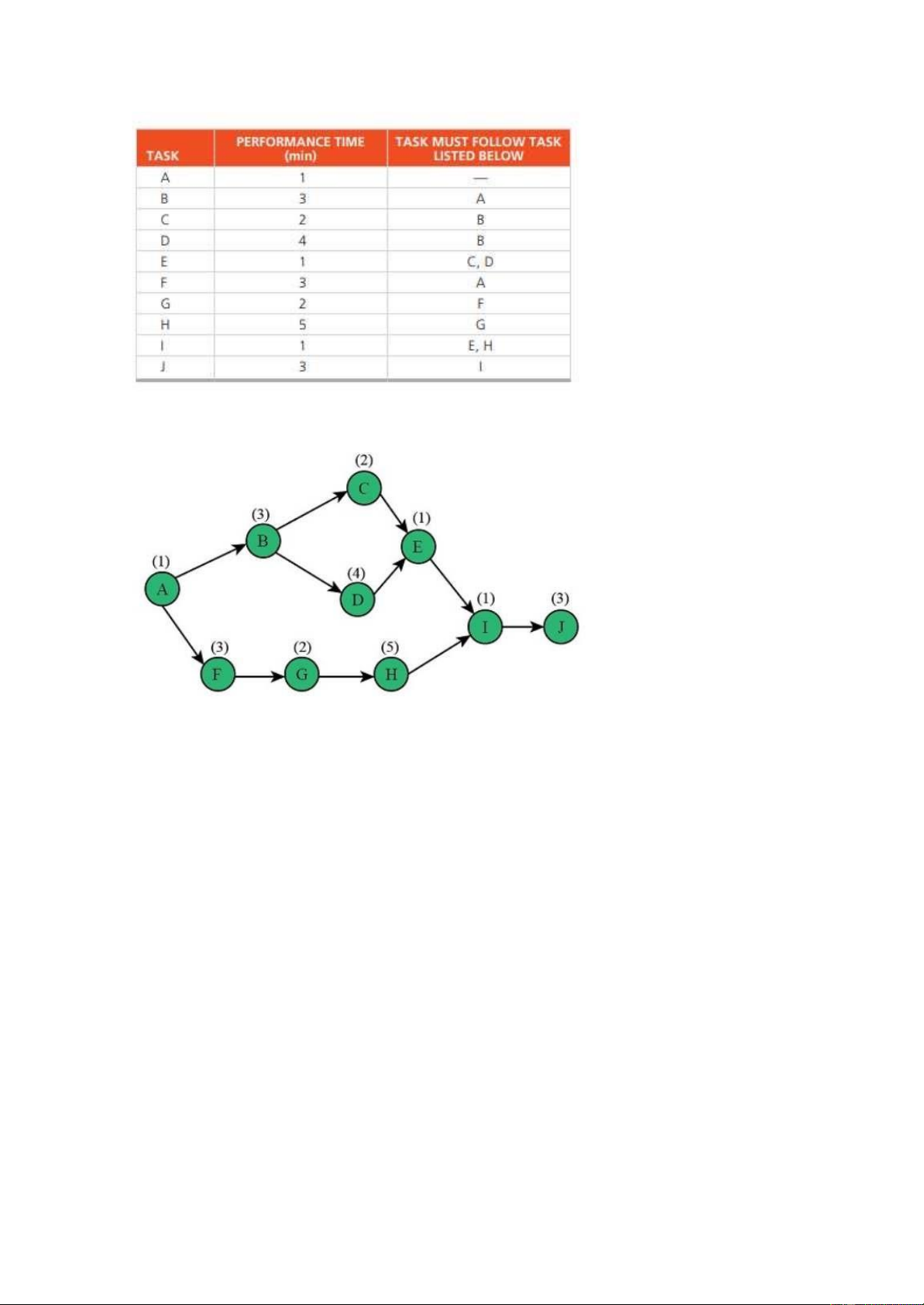
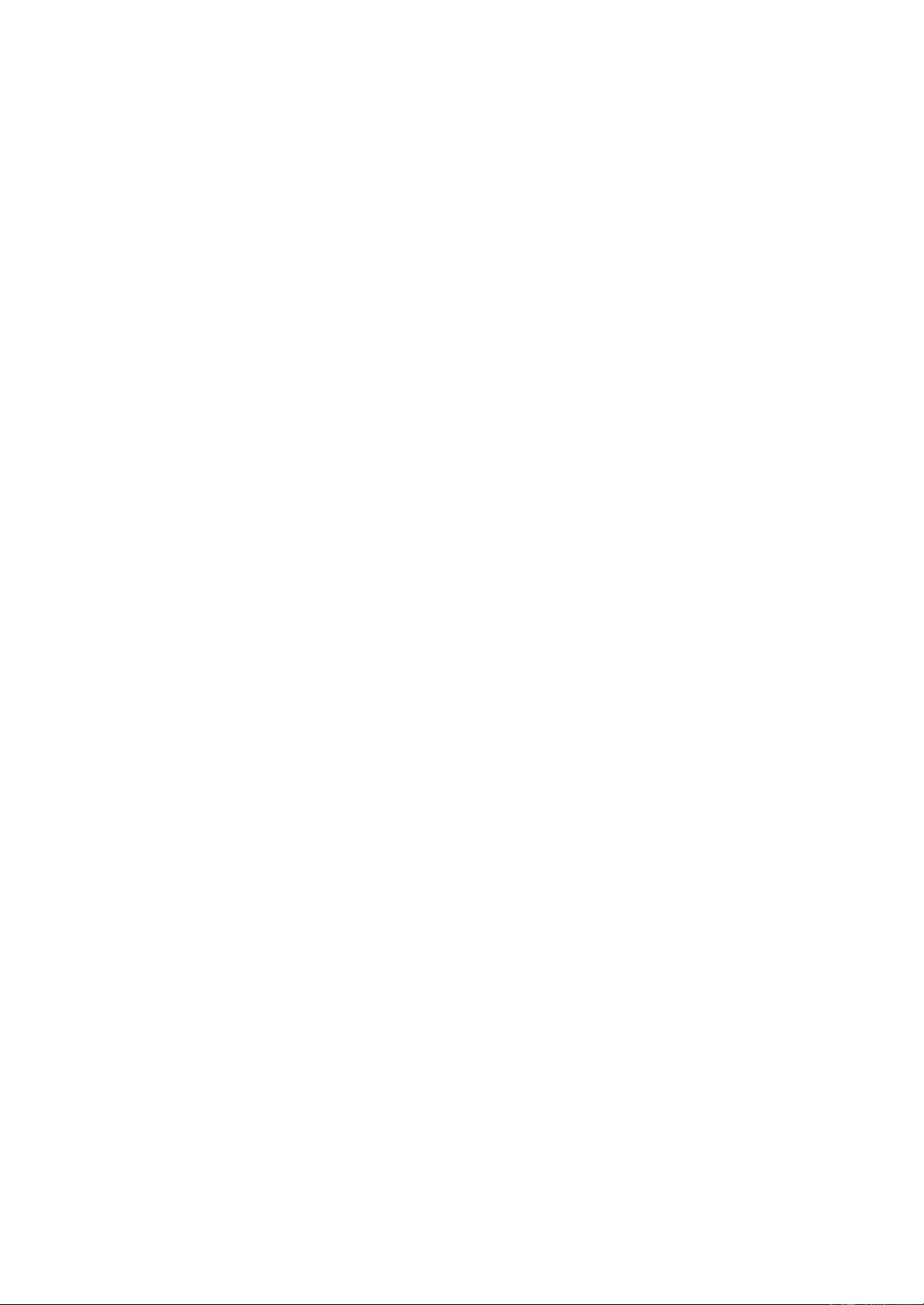
Preview text:
Vietnam National University – HCMC
International University SCHOOL OF BUSINESS
Production and Operations Management Dr. Truong Quang Duoc GROUP4 Seq. Full name Student ID 1 Trần Gia Bảo (Leader) BABAIU22355 2 Hoàng Trang Minh Anh BABAWE21465 3 Trần Hồ Gia Hy BABAIU22360 4 Nguyễn Thị Ngọc Tiên BABAWE21635 5 Phan Lê Quỳnh Vy BABAIU21592
9.5 Roy Creasey Enterprises, a machine shop, is planning to move to a new, larger location. The
new building will be 60 feet long by 40 feet wide. Creasey envisions the building as having six
distinct production areas, roughly equal in size. He feels strongly about safety and intends to
have marked pathways throughout the building to facilitate the movement of people and
materials. See the following building schematic.
His foreman has completed a month-long study of the number of loads of material that have
moved from one process to another in the current building. This information is contained in the following flow matrix.
Finally, Creasey has developed the following matrix to indicate distances between the work
areas shown in the building schematic.
What is the appropriate layout of the new building?
This matrix include flows from both directions, hence, we calculate the “from-to-matrix" as below: M W D L G M - 125 75 0 50 60 W - 0 75 0 0 D - 0 150 20 L - 20 0 G - 0 B -
We develop the space requirements for each departments: BENDERS (1) MATERIALS (2) WELDING (3) DRILLS (4) GRINDERS (5) LATHES (6)
Determine the cost of this layout by calculating movement - distance: M -> W: 125 x 20 = 2500 M -> D: 75 x 40 = 3000 M -> G: 50 x 20 = 1000 M -> B: 60 x 20 = 1200 W -> L: 75 x 20 = 1500 D -> G: 150 x 20 = 3000 D -> B: 20 x 20 = 400 L -> G: 20 x 20 = 400
Total: 13 000 => optimum layout with minimum cost for the new building.
9.6 Munson Manufacturing, in Gainesville, Florida, wants to arrange its four work centers so as
to minimize interdepartmental parts handling costs. The flows and existing facility layout are shown in Figure 9.19.
a) What is the “load × distance,” or “movement cost,” of the layout shown?
The movement cost for each center:
Center A = (450* 30) + (550* 60) + (50* 90) = 51,000
Center B = (350* 30) + (200* 30) = 16,500
Center C = 750* 30 = 22,500 The total movement cost:
51,000 + 16,500 + 22,500 = 90,000 feet
b) Provide an improved layout and compute its movement cost
We can improve this layout by swapping Center A and Center B, center C and center D B A D C Movement cost A 450 - 50 550 450* 30 + 550* 30 +50* 60 = 33,000 B - 350 0 200 350* 30 + 200* 30 = 16,500 C 0 0 750 - 750* 30 = 22,500 D 0 0 - 0 0
The total cost after improved:
33,000 + 16,500 + 22,500 = 72,000 feet
After improved, we can reduce movement cost by 18,000 feet
9.11 Sue Helms Appliances wants to establish an assembly line to manufacture its new product,
the Micro Popcorn Popper. The goal is to produce five poppers per hour. The tasks, task times,
and immediate predecessors for producing one Micro Popcorn Popper are as follows:
a) What is the theoretical minimum for the smallest number of workstations that Helms can
achieve in this assembly line?
b) Graph the assembly line and assign workers to workstations. Can you assign them with the theoretical minimum?
c) What is the efficiency of your assignment?
a) The desired output is 5 units per 60 mins =60/5=12 mins per unit
Totaltasktime=9+11+10+11+7+5=53mins
Minimum no. of work station= Total task time / Cycle time = = 53 12 = 4.4 or 5(rounded)
b) Theoretical minimum no. of workstations is 5
Line balancing, the required cycle time is 12 mins per workstation. But the sum of task times cannot
be more than cycle time in a workstation
c) if the no. of workstation= 5 cycle time = 12 mins Total task time =53mins
Efficiency= total task time / no. of workstation* cycle time = 53/(5*12)= 0.8833 or 88.33%
9.15 The Action Toy Company has decided to manufacture a new train set, the production of
which is broken into six steps. The demand for the train is 4,800 units per 40-hour workweek:
a) Draw a precedence diagram of this operation
b) Given the demand, what is the cycle time for this operation?
- The demand is 4,800 units per 40-hour workweek.
- The available time is 40 hours per week converted to seconds: 40 (hours/week) x 60
(minutes/hour) x 60 (seconds/minute) =144,000 (seconds/week)
=> Cycle time = Available time / Demand =144,000 (seconds/week) / 4,800 (units/week)= 30 (seconds/unit)
c) What is the theoretical minimum number of workstations?
The total task time is the sum of all the task times : 20+30+15+15+10+30=120 seconds
Theoretical minimum number of workstations= Total task time / Cycle time = 120 / 30= 4 workstations
d) Assign tasks to workstations.
e) How much total idle time is present each cycle?
- Total idle time = 5+10+5= 20 seconds
f) What is the efficiency of the assembly line with five stations? With six stations?
- With five stations => Largest asigned cycle time ís 30
- With six stations => Largest asigned cycle time ís 30
9.17 Tailwind, Inc., produces high-quality but expensive training shoes for runners. The
Tailwind shoe, which sells for $210, contains both gas- and liquid-filled compartments to
provide more stability and better protection against knee, foot, and back injuries.
Manufacturing the shoes requires 10 separate tasks. There are 400 minutes available for
manufacturing the shoes in the plant each day. Daily demand is 60. The information for the tasks is as follows:
a) Draw the precedence diagram. Ans:
b) Assign tasks to the minimum feasible number of workstations according to the
“rankedpositioned weight” decision rule. Ans: Revised Workstations:
Workstation 1: Task A (1 min), task B (3 min). Total: 4 minutes
Workstation 2: Task C (2 min), task D (4 min). Total: 6 minutes
Workstation 3: Task E (1 min), task F (3 min). Total: 4 minutes
Workstation 4: Task G (5 min). Total: 5 minutes
Workstation 5: Task H (5 min), task I (1 min). Total: 6 minutes
Workstation 6: Task J (3 min). Total: 3 minutes
c) What is the efficiency of the process you completed in (b)?Ans:
The cycle time = Total Time Available / Daily Demand = 400 / 60 = 6.67 minutes/unit
Efficiency = Sum of Task Times / Number of Workstations × Cycle TimeSum of Task Times = 28 / (6 × 6.67) = 0.7
So the efficiency of the process is approximately 70%.
d) What is the idle time per cycle? Ans:
Idle Time = (Number of Workstations × Cycle Time) − Sum of Task Times = (6 × 6.67) − 28 = 12.02 minutes
The idle time per cycle is 12.02 minutes.