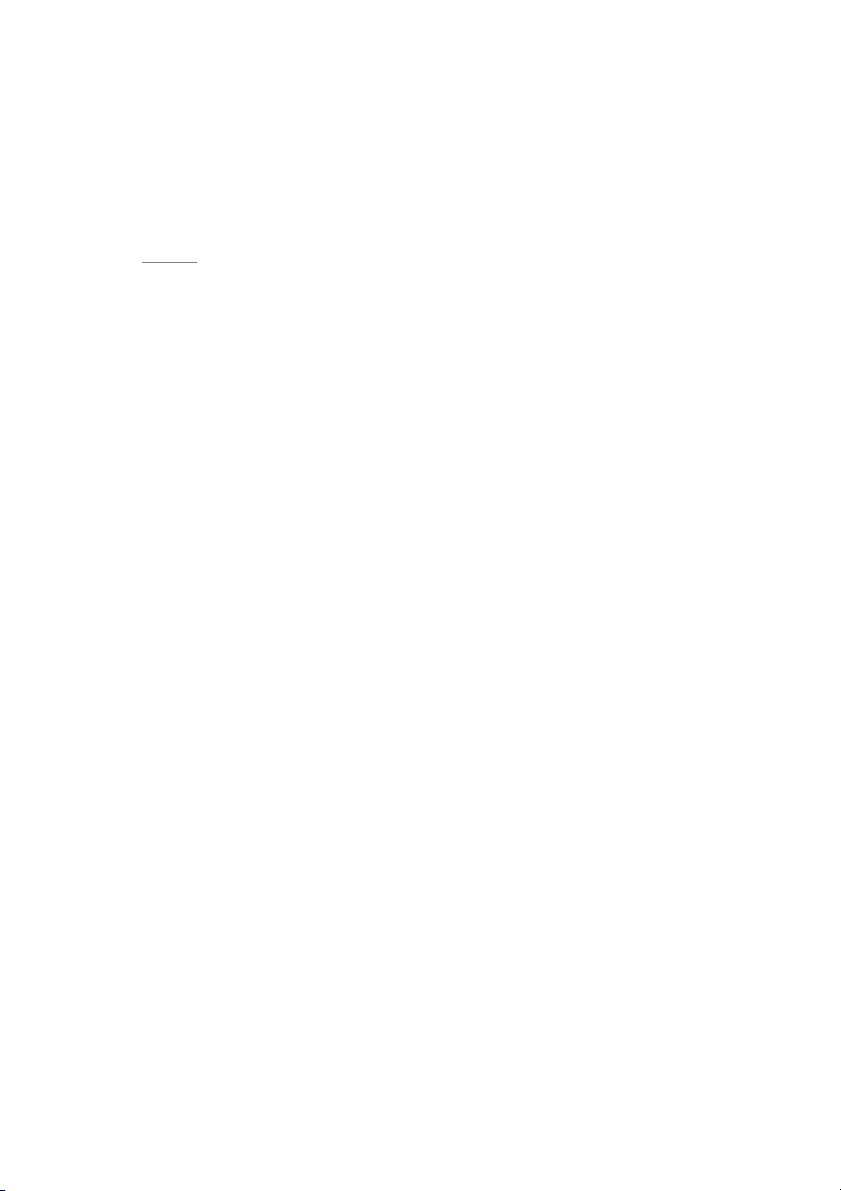
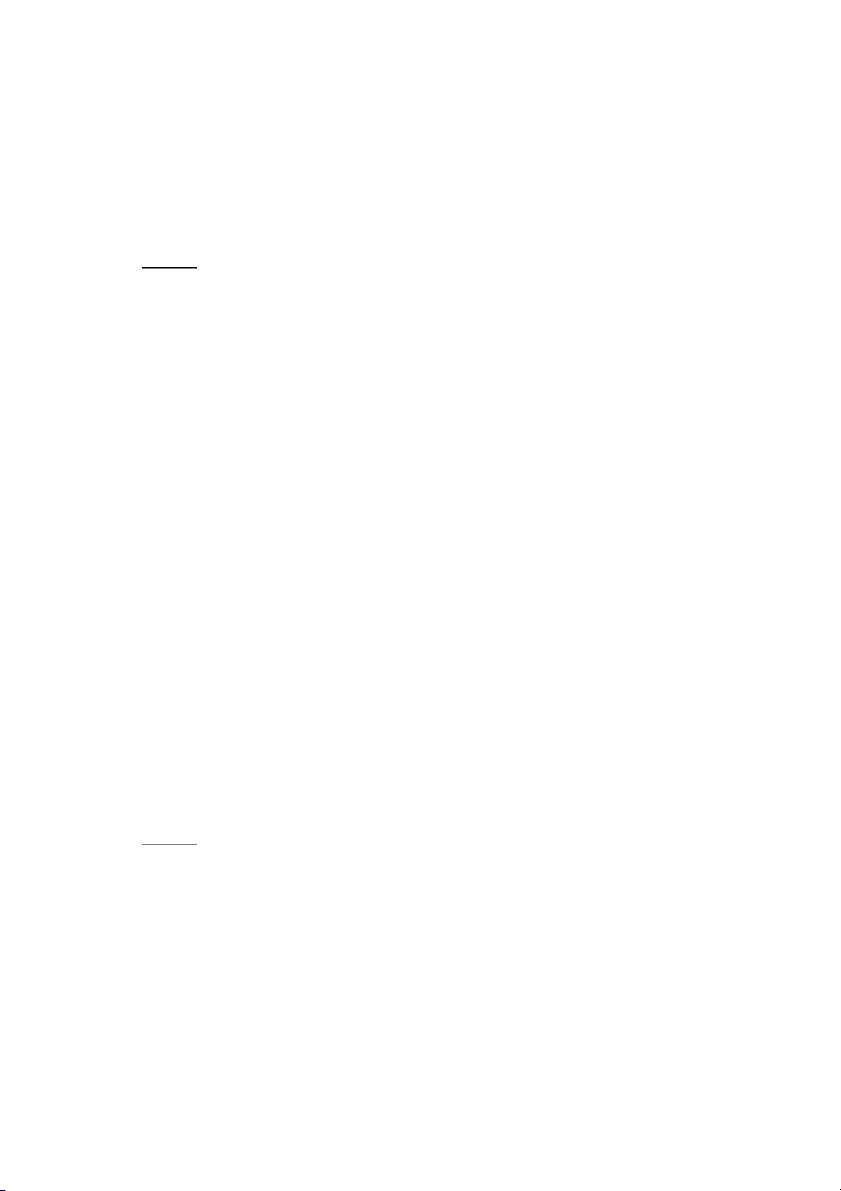
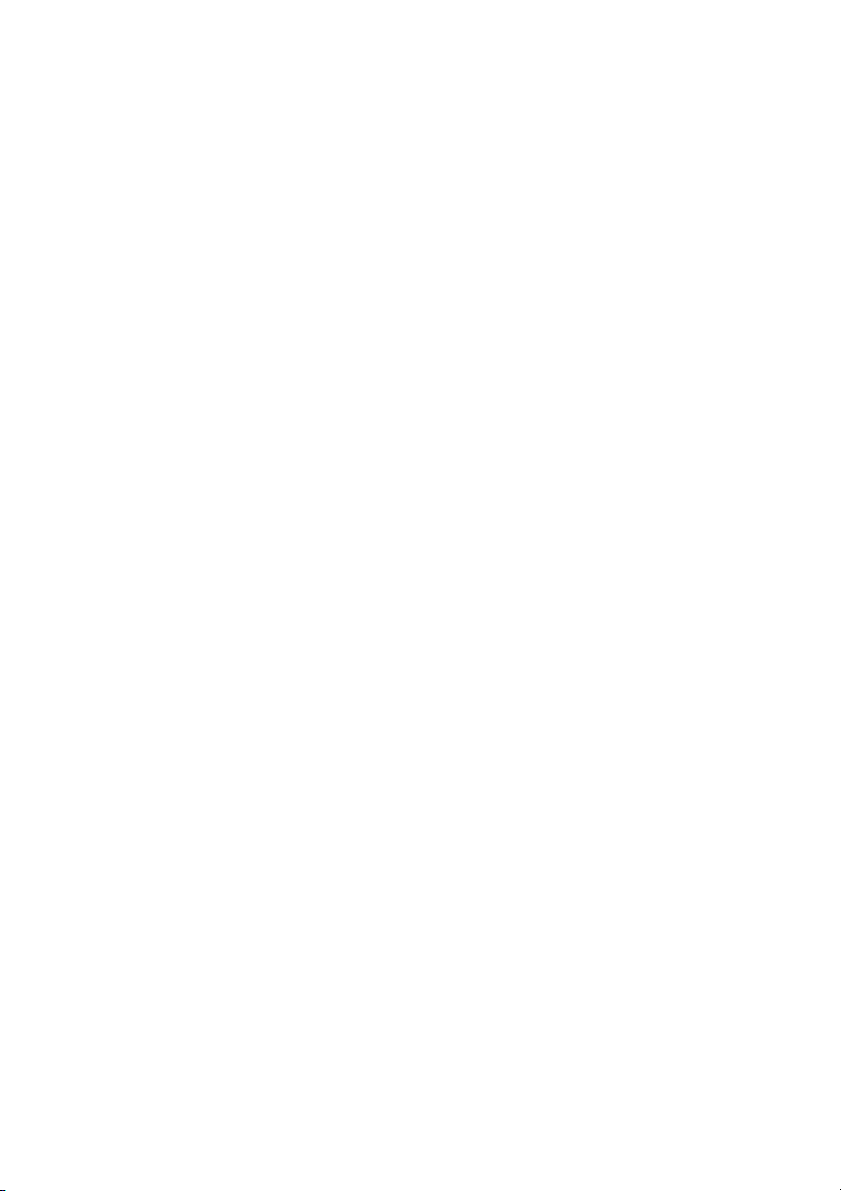
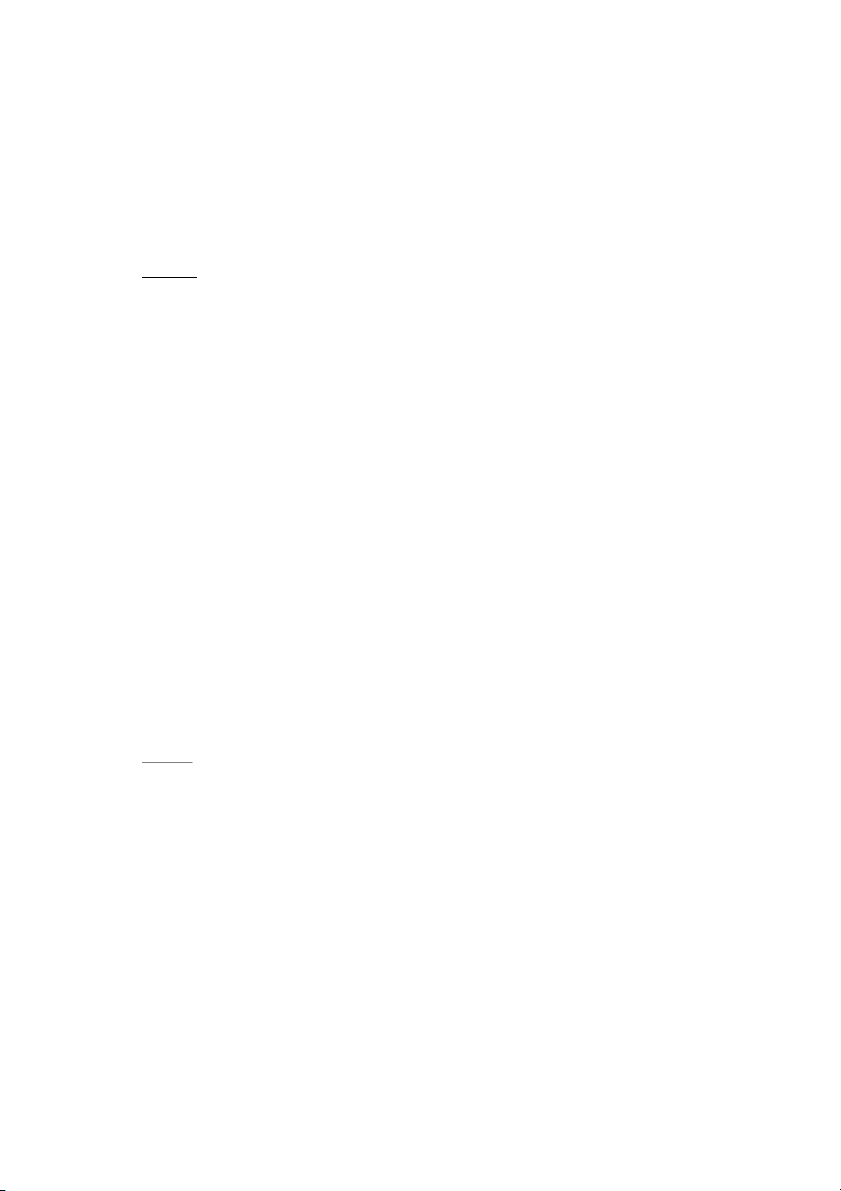
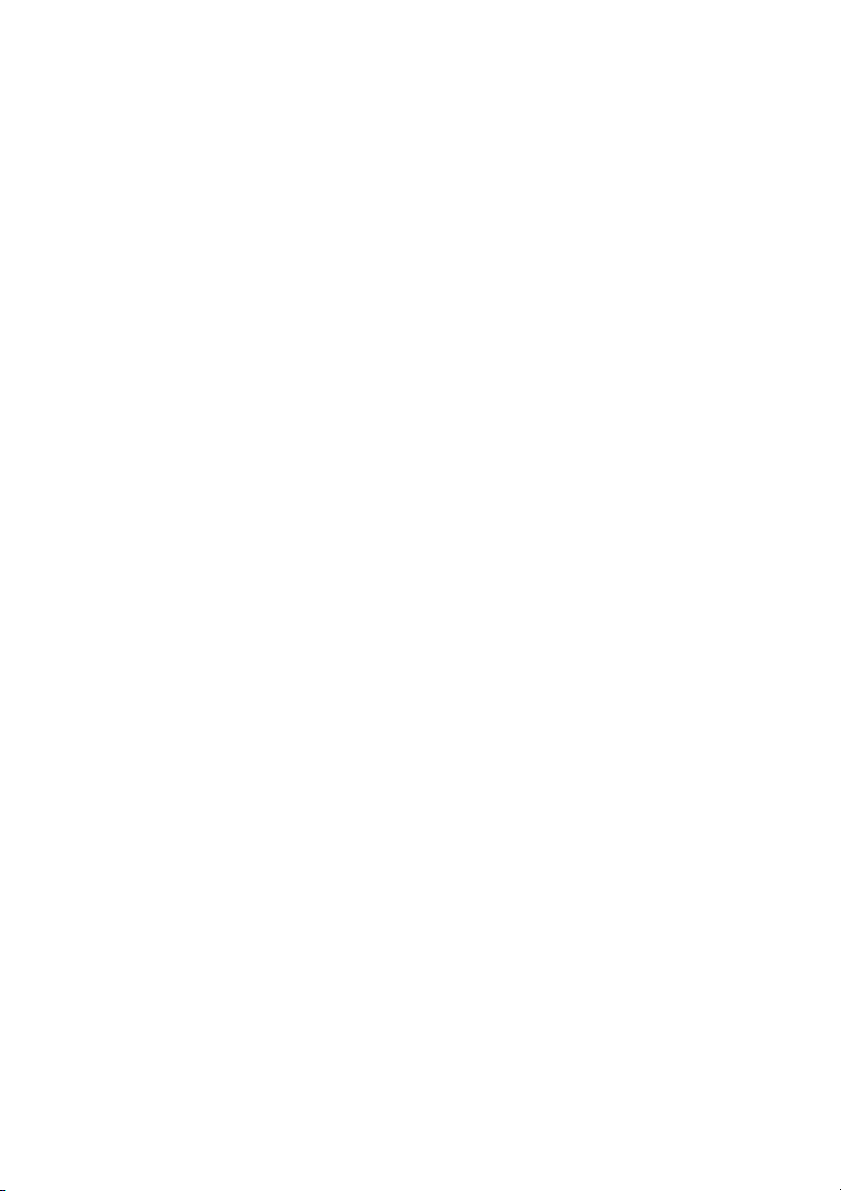
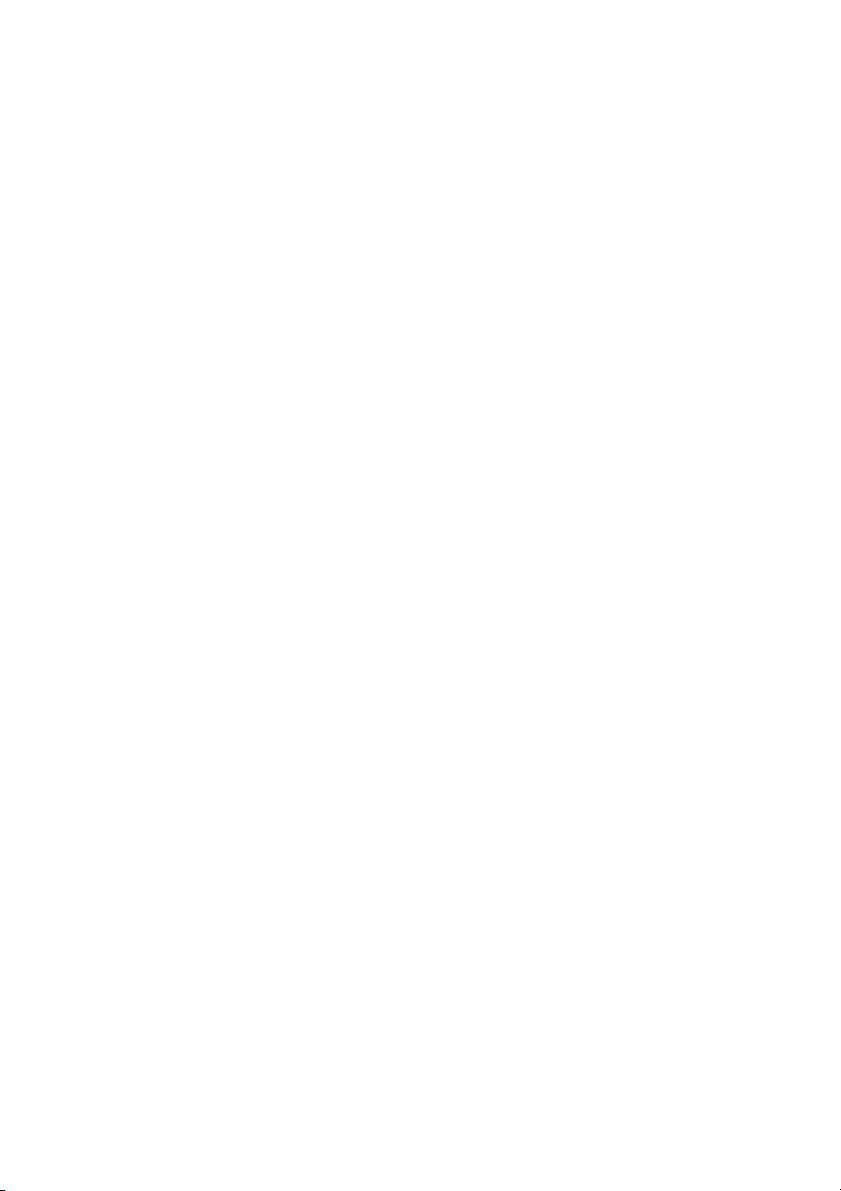
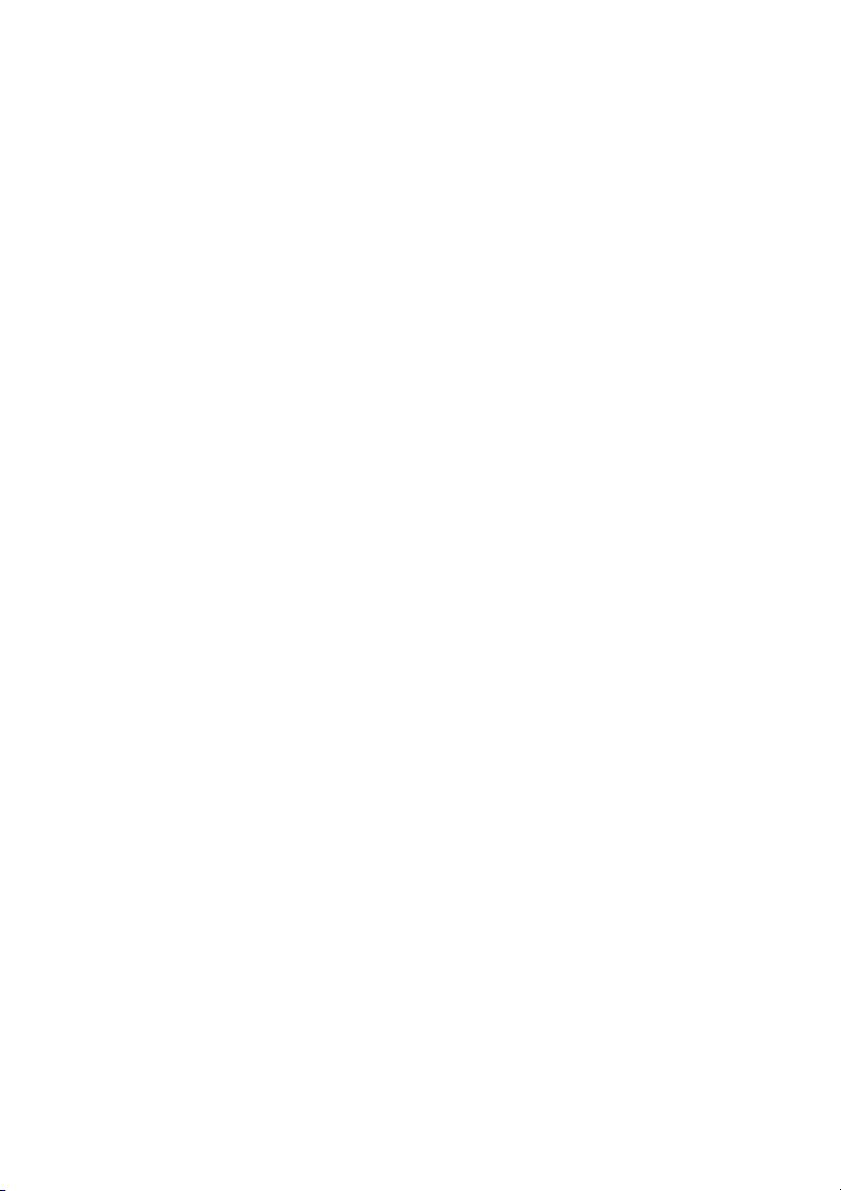
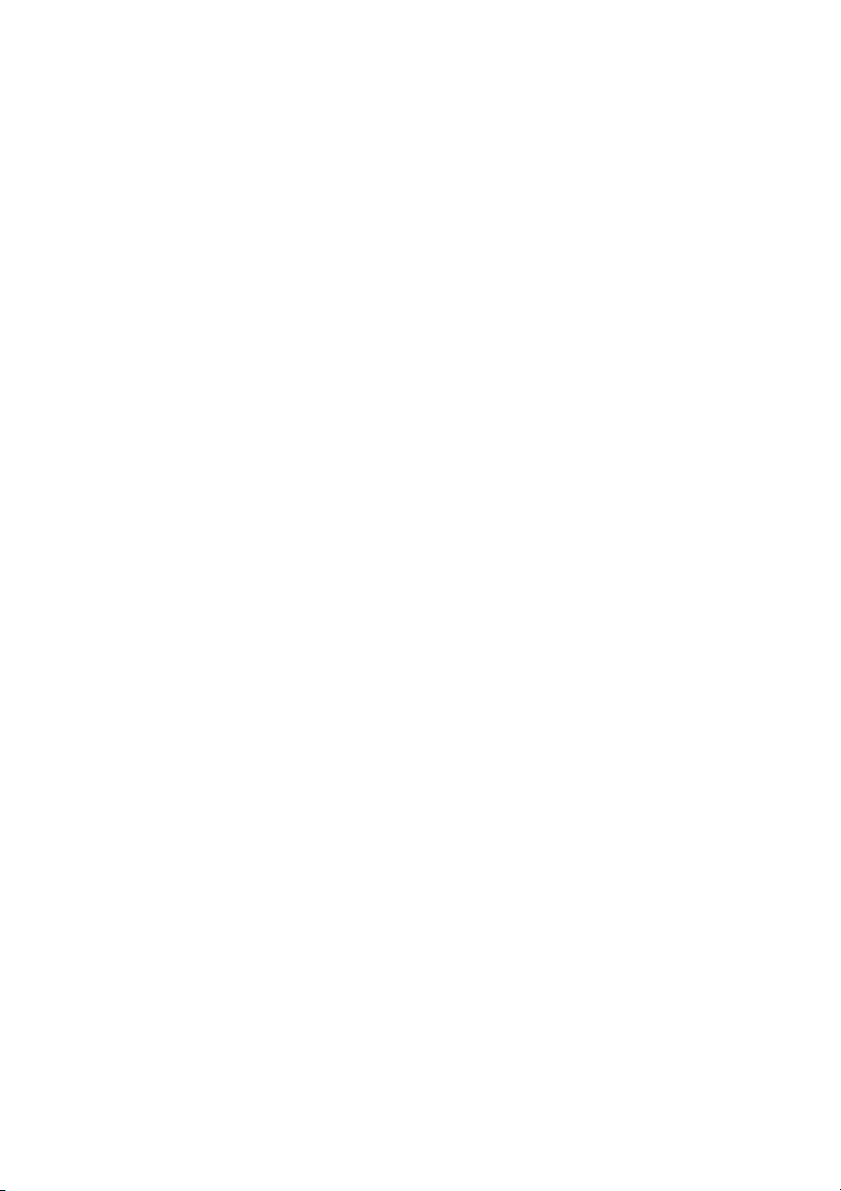
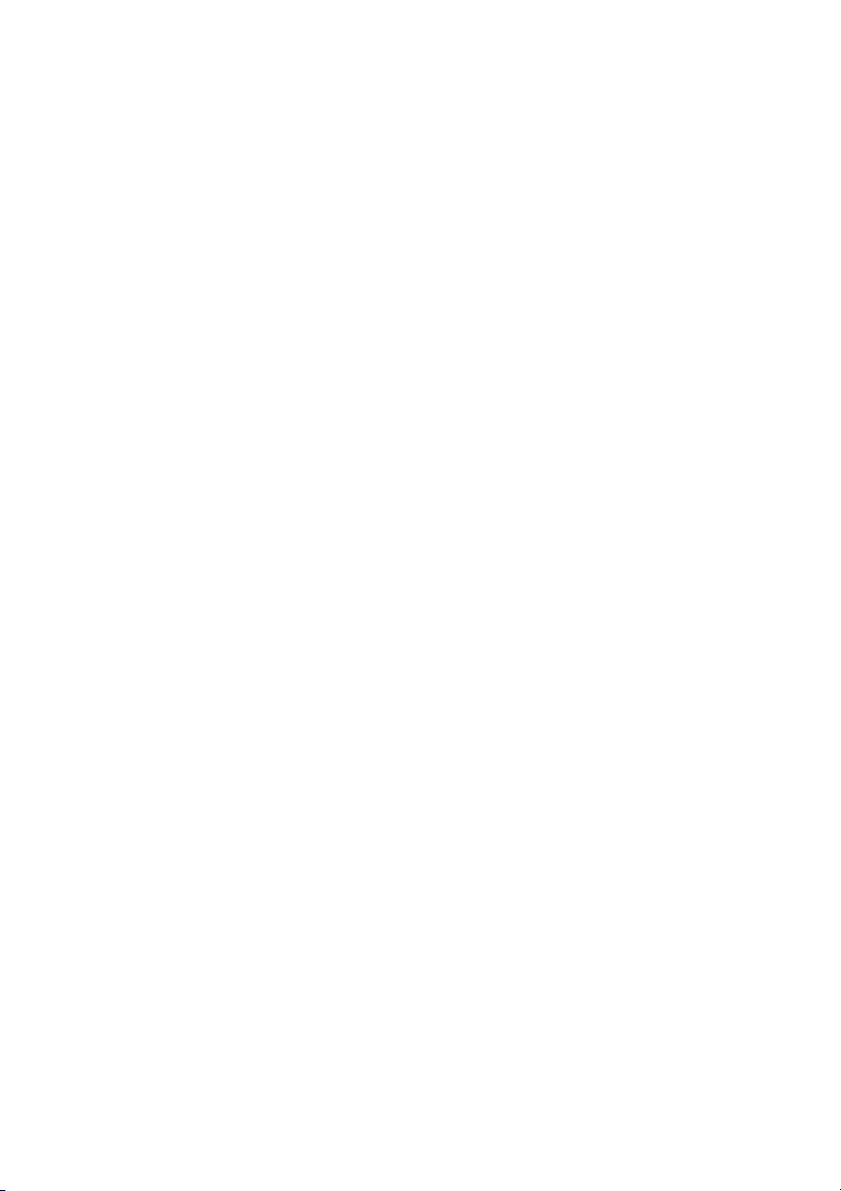
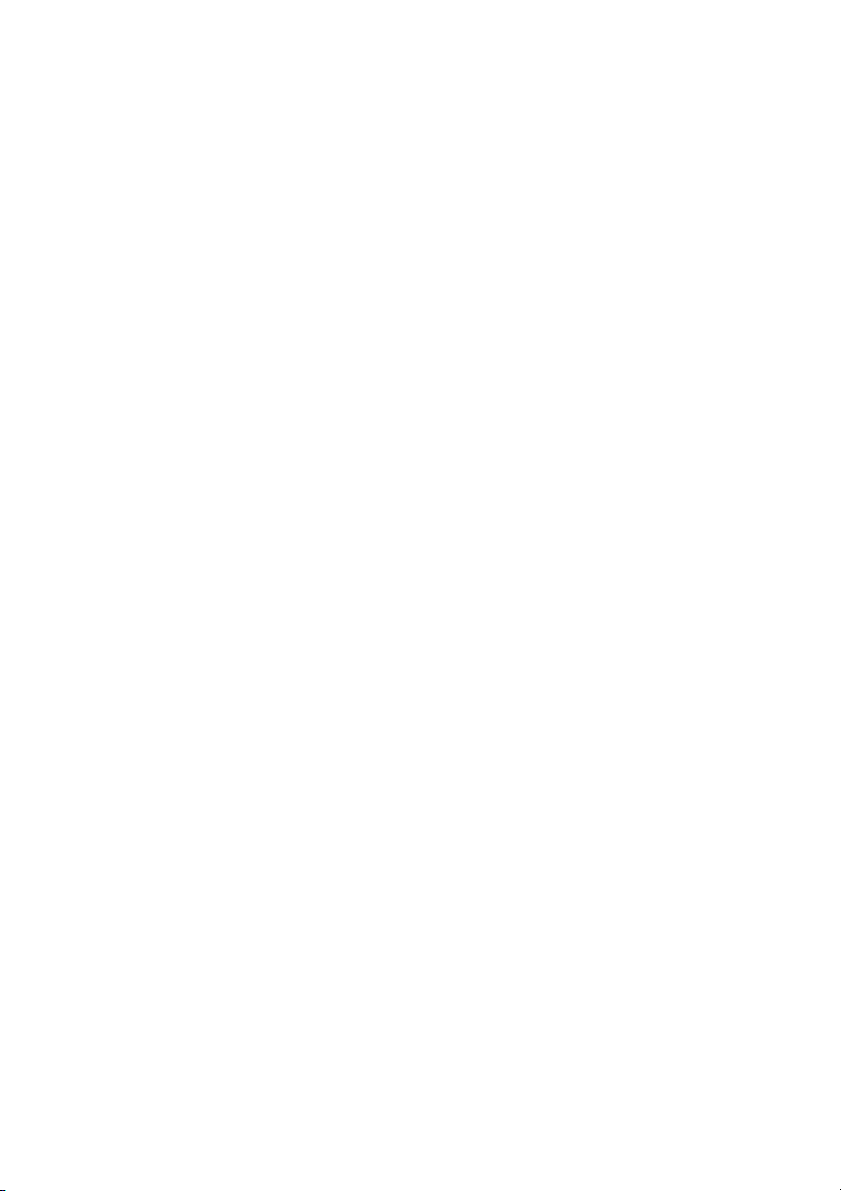
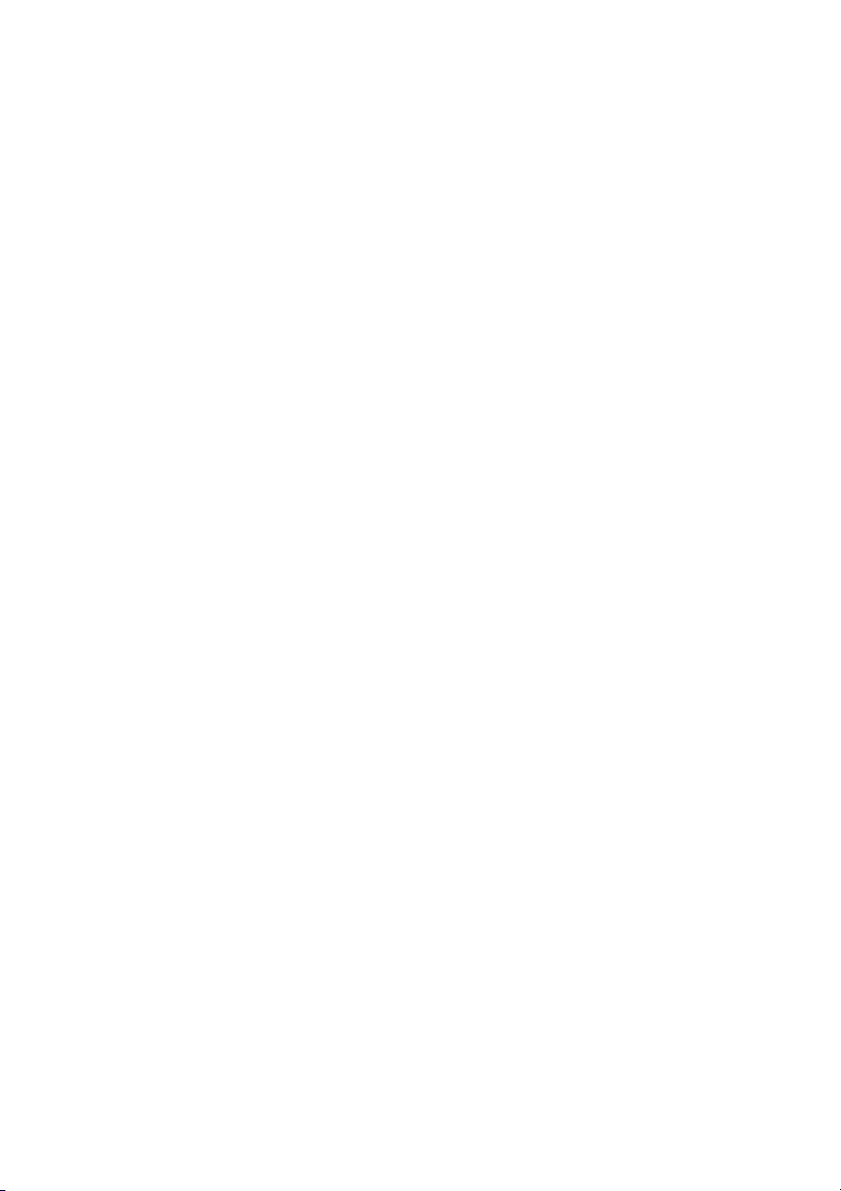
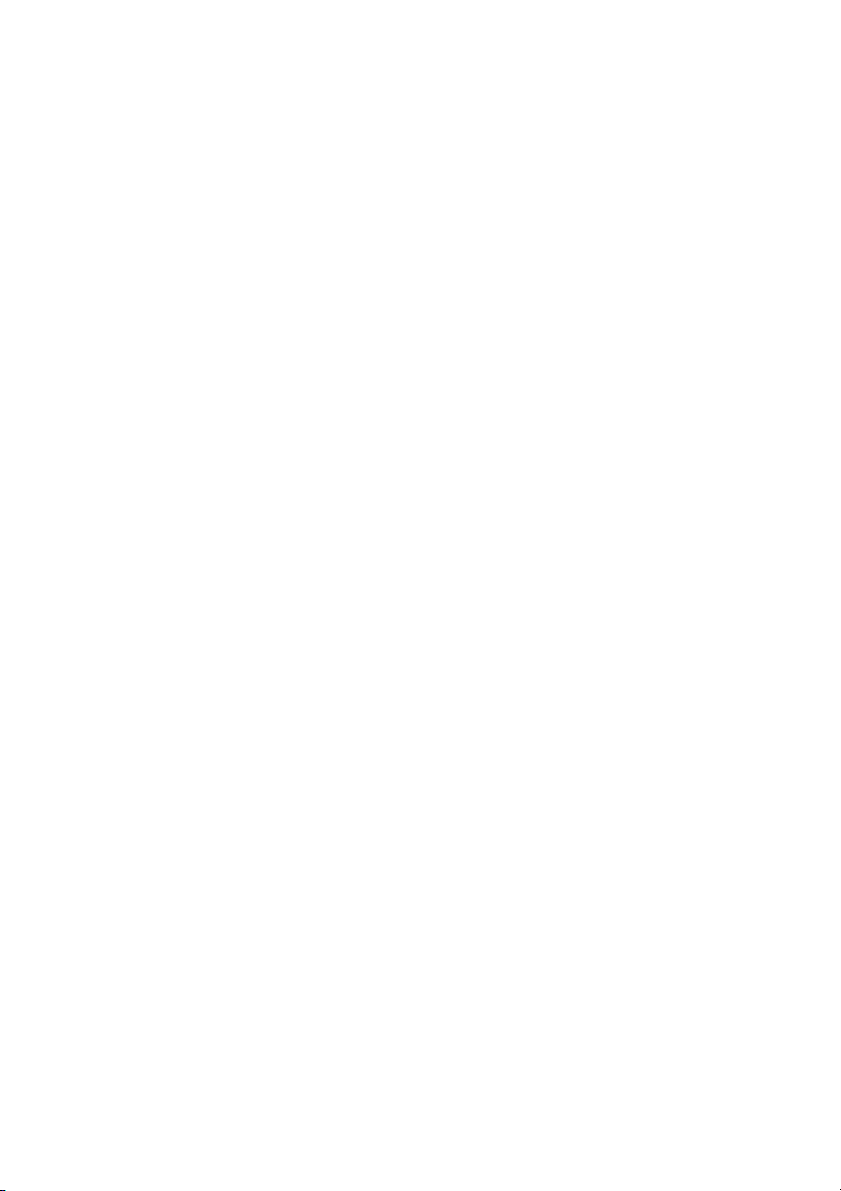
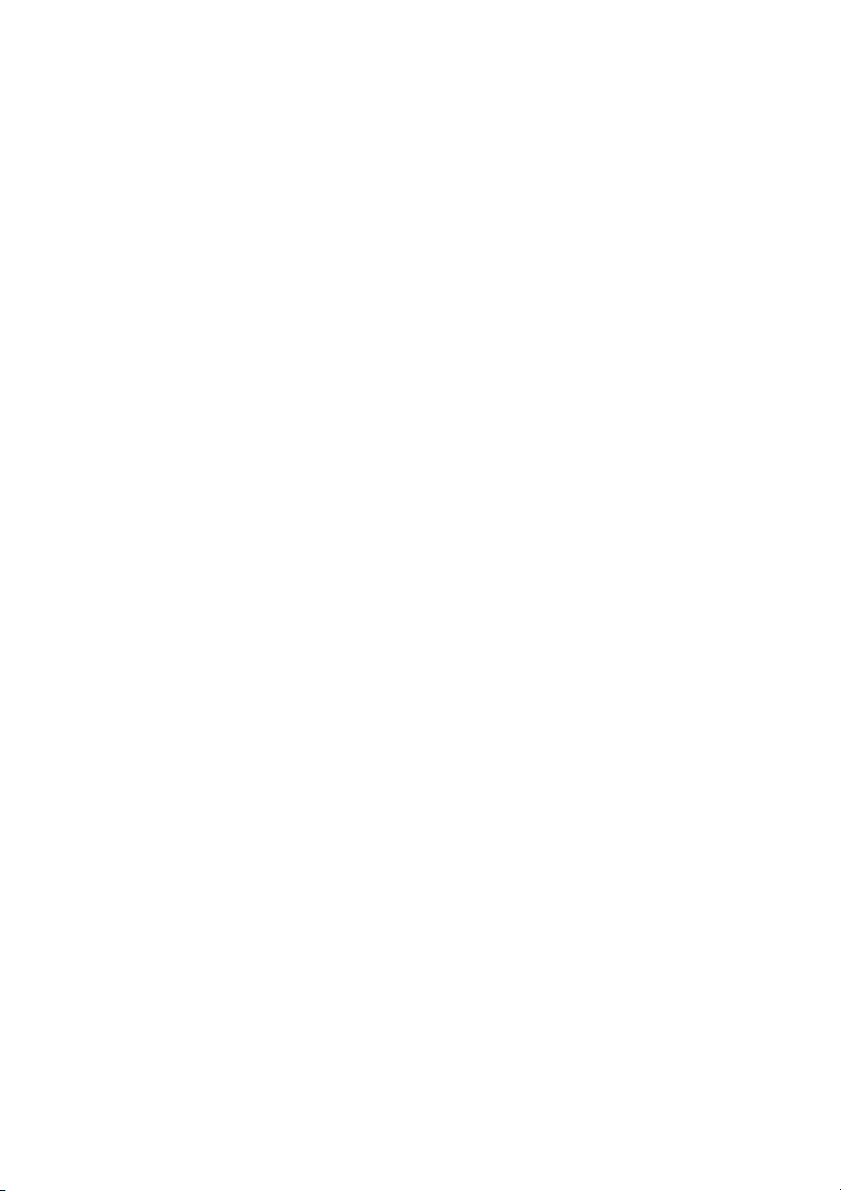
Preview text:
COST INFORMATION FOR DECISION MAKING QUESTION
CHAP 5 – 9 – 10 – 15 – 17 CHAP 05
5-2 Overcosting may result in overpricing and competitors entering a market and taking market
share for products that a company erroneously believes are low-margin or even unprofitable.
Undercosting may result in companies selling products on which they are in fact losing money,
when they erroneously believe them to be profitable.
5-4 An activity-based approach refines a costing system by focusing on individual activities
(events, tasks, or units of work with a specified purpose) as the fundamental cost objects. It
uses the cost of these activities as the basis for assigning costs to other cost objects such as products or services.
5-9 No. Department indirect-cost rates are similar to activity-cost rates if:
(1) a single activity accounts for a sizable fraction of the department’s costs
(2) significant costs are incurred on different activities within a department but each activity has the same cost-allocation base
(3) significant costs are incurred on different activities with different cost-allocation bases within
a department but different products use resources from the different activity areas in the same proportions.
5-11 The main costs and limitations of ABC are the measurements necessary to implement the
systems. Even basic ABC systems require many calculations to determine costs of products and
services. Activity-cost rates often need to be updated regularly. Very detailed ABC systems are
costly to operate and difficult to understand. Sometimes the allocations necessary to calculate
activity costs often result in activity-cost pools and quantities of cost-allocation bases being
measured with error. When measurement errors are large, activity-cost information can be misleading.
5-12 No, ABC systems apply equally well to service companies such as banks, railroads,
hospitals, and accounting firms, as well merchandising companies such as retailers and distributors.
5-13 No. An activity-based approach should be adopted only if its expected benefits exceed its
expected costs. It is not always a wise investment. If the jobs, products or services are alike in
the way they consume indirect costs of a company, then a simple costing system will suffice.
5-14 Increasing the number of indirect-cost pools does NOT guarantee increased accuracy of
product or service costs. If the existing cost pool is already homogeneous, increasing the
number of cost pools will not increase accuracy. If the existing cost pool is not homogeneous,
accuracy will increase only if the increased cost pools themselves increase in homogeneity vis-à- vis the single cost pool. CHAP 09
9-1 No. Differences in operating income between variable costing and absorption costing are
due to accounting for fixed manufacturing costs. Under variable costing only variable
manufacturing costs are included as inventoriable costs. Under absorption costing both variable
and fixed manufacturing costs are included as inventoriable costs. Fixed marketing and
distribution costs are not accounted for differently under variable costing and absorption costing.
9-3 No. The difference between absorption costing and variable costs is due to accounting for
fixed manufacturing costs. As service or merchandising companies have no fixed manufacturing
costs, these companies do not make choices between absorption costing and variable costing.
9-4 The main issue between variable costing and absorption costing is the proper timing of the
release of fixed manufacturing costs as costs of the period: a. at the time of incurrence, or b. at
the time the finished units to which the fixed overhead relates are sold. Variable costing uses (a)
and absorption costing uses (b).
9-6 Variable costing does not view fixed costs as unimportant or irrelevant, but it maintains that
the distinction between behaviors of different costs is crucial for certain decisions. The planning
and management of fixed costs is critical, irrespective of what inventory costing method is used.
9-7 Under absorption costing, heavy reductions of inventory during the accounting period might
combine with low production and a large production volume variance. This combination could
result in lower operating income even if the unit sales level rises.
9-11 The theoretical capacity and practical capacity denominator-level concepts emphasize
what a plant can supply. The normal capacity utilization and master-budget capacity utilization
concepts emphasize what customers demand for products produced by a plant
9-15 No. The costs of having too much capacity/too little capacity involve revenue opportunities
potentially forgone as well as costs of money tied up in plant assets. CHAP 10
10-1 The two assumptions are 1. Variations in the level of a single activity (the cost driver)
explain the variations in the related total costs. 2. Cost behavior is approximated by a linear cost
function within the relevant range. A linear cost function is a cost function where, within the
relevant range, the graph of total costs versus the level of a single activity forms a straight line.
10-4 No. High correlation merely indicates that the two variables move together in the data
examined. It is essential also to consider economic plausibility before making inferences about
cause and effect. Without any economic plausibility for a relationship, it is less likely that a high
level of correlation observed in one set of data will be similarly found in other sets of data.
10-5 Four approaches to estimating a cost function are
1. Industrial engineering method. 2. Conference method. 3. Account analysis method.
4. Quantitative analysis of current or past cost relationships
10-7 The account analysis method estimates cost functions by classifying cost accounts in the
subsidiary ledger as variable, fixed, or mixed with respect to the identified level of activity.
Typically, managers use qualitative, rather than quantitative, analysis when making these costclassification decisions.
10-8 The six steps are
1. Choose the dependent variable (the variable to be predicted, which is some type of cost).
2. Identify the independent variable or cost driver.
3. Collect data on the dependent variable and the cost driver. 4. Plot the data.
5. Estimate the cost function.
6. Evaluate the cost driver of the estimated cost function.
Step 3 typically is the most difficult for a cost analyst.
10-9 Causality in a cost function runs from the cost driver to the dependent variable. Thus,
choosing the highest observation and the lowest observation of the cost driver is appropriate in the high-low method.
10-10 Three criteria important when choosing among alternative cost functions are: 1. Economic plausibility. 2. Goodness of fit.
3. Slope of the regression line.
10-13 Four key assumptions examined in specification analysis are 1. Linearity of relationship
between the dependent variable and the independent variable within the relevant range. 2.
Constant variance of residuals for all values of the independent variable. 3. Independence of
residuals. 4. Normal distribution of residuals. CHAP 15
15-2 The dual-rate method provides information to division managers about cost behavior.
Recognizing the different behavior or fixed costs and variable costs is useful in decision making.
15-3 Budgeted costs rates motivate the manager of the support department to improve
efficiency because the support department bears the risk of any unfavorable cost variances.
15-4 Give examples of allocation bases used to allocate aupport-department cost pools to operating departments.
Examples of bases used to allocate support department cost p pools to operating departments
include the number of employees, square feet of space, number of direct labor hours, and machine-hours.
15-8 The reciprocal method is theoretically the most defensible method because it fully
recognizes the mutual services provided among all departments, irrespective of whether those
departments are operating or support departments.
15-11 All contracts with U.S. government agencies must comply with cost accouting standards
issued by the Cost Accouting Standards Board (CASB).
15-12 Areas of dispute between contracting parties can be reduced by making the “rules of the
game” explicit and in writing at the time the contract is signed.
15-13 Companies increasingly are selling packages of products or services for a single price.
Revenue allocation is required when managers in charge of developing or makerting individual
products in a bundle are evaluated using product-specific revenues. CHAP 17
17-1 Indutries using process costing in their manufacturing area include chemical processing, oil
refining, pharmaceuticals, plastics, brick and tile manufacturing, semiconductor chips,
beverages, and breakfast cereals.
17-4 The accuracy of the estimates of complietion depends on the care and skill of the
estimator and the nature of the process. Semiconductor chips may differ substantially in the
finishing necessary to obtain a final product. The amount of work necessary to finish a product
may not always be easy to ascertain in advance.
17-6 Three inventory methods associated with process costing are: - Weighted average - First-in, first-out - Standard costing
17-7 The weighted-average process-costing method calculates, the equivalent-unit cost of all
the work done to date (regardless of the accounting period in which it was done), assisgns this
cost to equivalent units completed and transferred out of the process, and to equivalent units in
ending work-in-process inventory.
17-9 FIFO should be called a modified or departmental FIFO method because the goods
transferred in during a given period usually bear a single average unit cost (rather than a distinct
FIFO cost for each unit transferred in) as a matter of convenience.
17-10 A major advantage of FIFO is that managers can judge the performance in the current
period independently from the performance in the preceding period.
17-11 The journal entries in process costing are basically similar to those made in job-costing
systems. The main difference is that, in process costing, there is often more than one work-in-
process account – one for each process. 17-4 The accuracy of the estimates of completion depends on the care and skill of the estimator and the nature of the process. Semiconductor chips may differ substantially in the finishing necessary to obtain a final product. The amount of work necessary to finish a product may not always be easy to ascertain in advance. 17-5 The five key steps in process costing follow: Step 1: Summarize the flow of physical units of output. Step 2: Compute output in terms of equivalent units. Step 3: Summarize total costs to account for. Step 4: Compute cost per equivalent unit. Step 5: Assign total costs to units completed and to units in ending work in process. 17-6 Three inventory methods associated with process costing are: Weighted average. First-in, first-out. Standard costing. 17-7 The weighted- average process-costing method calculates the equivalent-unit cost of all the work done to date (regardless of the accounting period in which it was done), assigns this cost to equivalent units completed and transferred out of the process, and to equivalent units in ending work-in-process inventory 17-4 The accuracy of the estimates of completion depends on the care and skill of the estimator and the nature of the process. Semiconductor chips may differ substantially in the finishing necessary to obtain a final product. The amount of work necessary to finish a product may not always be easy to ascertain in advance. 17-5 The five key steps in process costing follow: