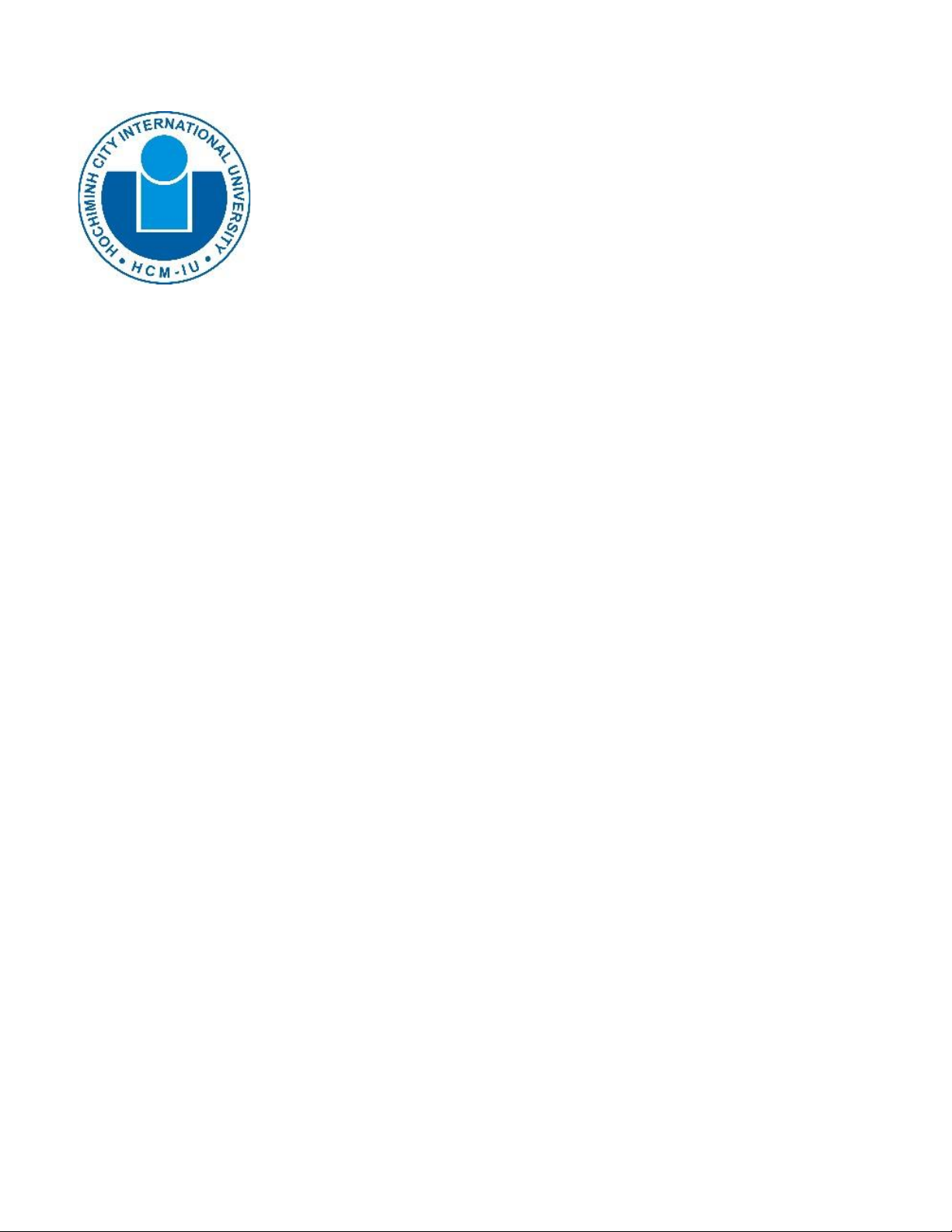
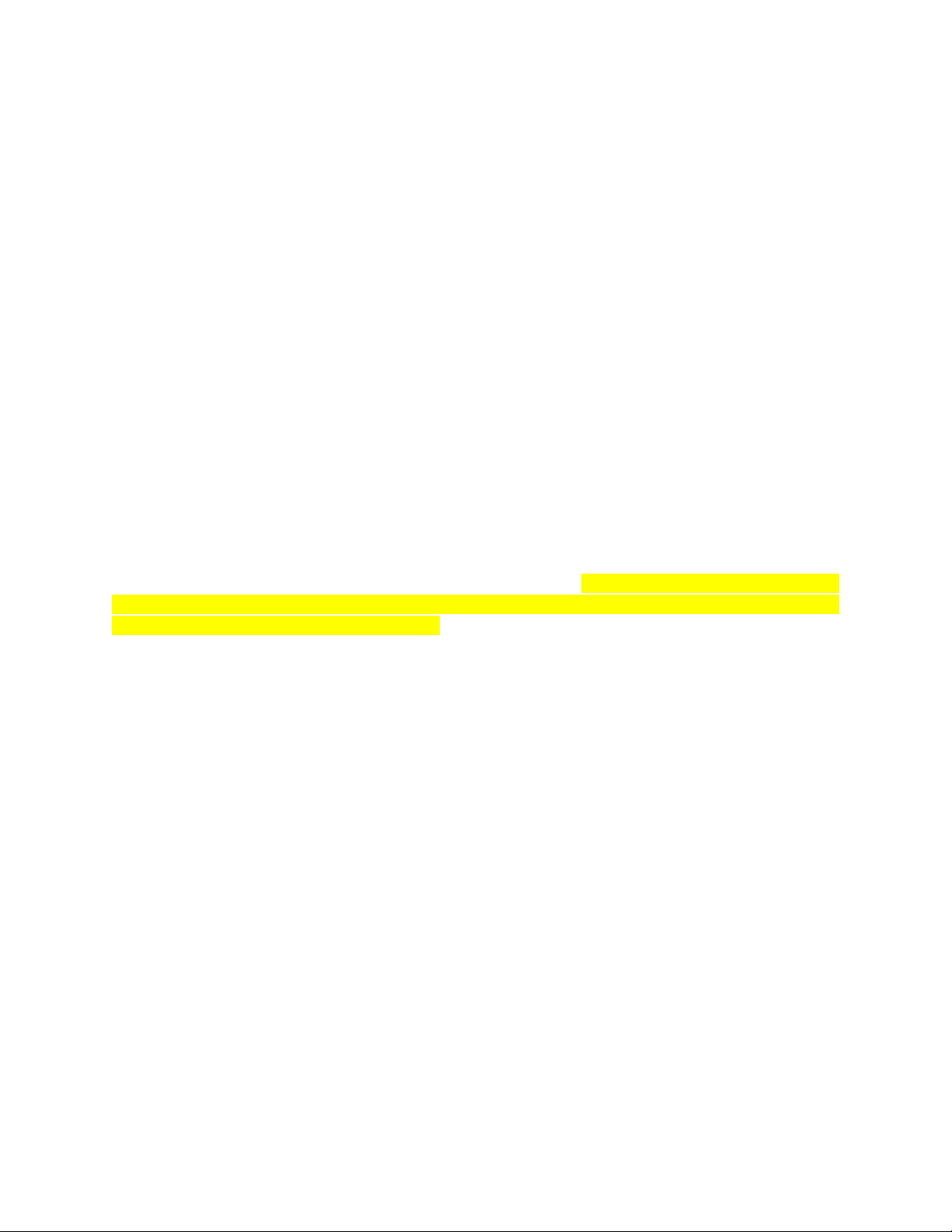

Preview text:
Vietnam National University HCMC
International University School of Business ●
Managing Organizational Change
Lecturer: PhD. Mai Ngoc Khuong
Summary Chapter 3 Core text Group 1:
1. Từ Mỹ Duyên – BABAWE17493
2. Trần Lê Thuỳ Duyên – BABAWE18498
3. Nguyễn Nữ Hoài Thư – BABAWE18621
4. Trần Thị Ánh Tuyết – BABAWE18679
5. Nguyễn Hoàng Mai Vy – BABAWE18135
Numerous occasions throughout human history have affected entire cultures, lifestyles, and customs. The
globe is changing and continuing to deal with environmental issues including political upheaval,
technological advancement, and social forces. The requirement to concentrate on both continuity and
change at once is one of management's paradoxes. Neglecting change in favor of continuity runs the risk of
succumbing to tradition and inertia. However, concentrating only on change and ignoring continuity carry
the same risk of leading to an endless cycle of disastrous re-invention. In addition, it is interesting how
mainstream academia is probably less connected to management thought and practice in the twentyfirst
century than it was in the twentieth when attempting to elucidate the interaction between theory and practice.
There are eight historical periods, and during each of those eight times, various difficulties, problems, and
theories have emerged: The Industrial Revolution (1730 – 1850), Industrial organization and the
coordination and control of work (1850s-1940s, ongoing), Change and the human aspects of work (1930s-
70s, ongoing), Sleepers wake (1940s – 80s, ongoing), Fit for purpose (1960s-1990s, ongoing), In search of
excellence (1980s-2000s, ongoing), Guru literature, popularized ideas and the re-invention of management
(1980s-ongoing), Prospective futures (2000-ongoing). This essay focused on providing overview and great
insight of the four first phases of history.
The Industrial Revolution
The enabling factors that have been identified as drivers for the British Industrial revolution include:
Utilizing skills and knowledge, government support, mechanization, migration, rich natural resources,
steam power, and transportation. The industrial revolution provides us with a useful point, as it is during
this period that new management problems emerged following the rapid expansion of the newly
industrialized towns and the rise in factory organization. The rise in commerce and the opening of markets
combined with innovations in the use and application of technology. To coordinate and control the work of
labor, employers want workers' capacity to work transformed into actual work and that the value of the
work exceeds the wages paid out for their labor.
Industrial organization and the coordination and control of work
The five-step process for the coordination and control of work rested on: identifying 10-15 of the most
productive workers; studying their work behavior, methods, and their use of implement in carrying out
tasks; Timing the movements made in the completion of tasks; designing a working system that is
streamlined in ensuring that all unnecessary movements are eliminated; Equipping employees with the best
implements to carry out a prescribed set of movements in the accomplishment of clearly defined work tasks.
The differential piece-rate system (Taylor) comprised setting a low rate up to a set standard based on time-
and-motion studies, after which a bonus would be payable upon reaching the standard with a higher rate
payable above that standard. The aim was to enable employees to reach their highest level of efficiency to
maximize output, productivity and enable them to benefit from higher levels of pay. This change and
innovation in the way in which work was organized replaced “rule of thumb” methods with standard rates
of output fixed to set financial rewards. The strong industrial economies of the twentieth century were
characterized by a healthy car manufacturing sector. Integral to these developments was the continuous-
flow assembly line, which refers to the industrial arrangement of machines, equipment, and workers that
allows for the continuous flow of work-pieces along a moving line of assemblies in the mass manufacture
of products. All movement of material is simplified, with no cross-flow or backtracking, and the worker
remains in position on the line carrying out a simplified set of repetitive tasks. Throughout the 20 century,
the manufacture of automobiles was a key industry that served as a leading example of technological
advancement, innovation, and change. Blauner (1964) investigated four industries that represented different
levels of technological sophistication; these were printing, cotton-spinning, motor cars, and petrochemicals.
He found that under traditional craft-style industries work retained social meaning; under mass production
jobs became meaningless and employees felt increasingly isolated, selfestranged, and powerless.
Change and the human aspects of work
After the Second World War, the 'problem' of dissatisfaction, alienation and industrial unrest became an
organizational concern. Since the late 691940s, people could find employment and switch jobs and
consequently felt less compelled to employment of management (Roethlisberger, 1945: 283-98). The classic
study by Roethlisberger and Dickson (1939) were used to show the benefits of 'democratic' leadership that
encouraging employee participation in decision-making. The importance of consulting and listening to
employees. In viewing industrial organization as a complex social system: Distrust and resistance to change
was expressed changes were introduced too rapidly or without sufficient consideration of their social
implications. Too rapid interference is likely to lead to feelings of frustration and an irrational exasperation
with technical change in any form. (Roethlisberger and Dickson, 1939: 567-8). The social context of change
and the meaning that attach to their work remain an important area of concern (see McCabe, 2007).
However, attention switched from more sociological concerns towards a barrage of psychological studies
that examined job satisfaction, motivation and leadership. Knights and McCabe (2003: 19) provided fertile
ground for the development of 'management innovation based on a neo-behaviourist model’ with the
'Hawthorne understanding of worker subjectivity was much more complex than the conceptualizations that
flowed from those in the new-human relations school'.
Sleepers wake: The spectre of technology and innovation
Trist and Bamforth (1951: 37) conclude that a greater intolerance of unsatisfying or difficult working
conditions, or systems of organization, among miners, even though they may not always be clear as to the
exact nature of the resentment or hostility which they often appear to feel. Trist and Bamforth set out to test
two hypotheses: that output shortfall was essentially a technical problem associated with innovation and
that it was the social shortcomings of the long-wall method of coal mining that was restricting output note
that prior to mechanization the technical process of coal-getting had the following cycle of stages:
preparation, getting, advancing. The Tavistock researchers argued that there was a misalignment between
the technical and social aspects of work. These studies were argued that change initiatives that focus on
either the purely technical or social aspects of work are likely to have limited 'success' as they create a
situation where the whole is sub-optimized for developments in one dimension. In spite of these criticisms,
activity has continued in this area and with the growing uptake of team-based manufacturing, many of these
original STS idea have been further developed (see Clarke et al.,2010; Willcocks and Mason, 1987). It is
not only necessary to address the interdependent and interpenetrating nature of the technical and the social,
but also the change process through which these elements are reconfigured (Badham, 1995: 81). a more
contextual and negotiated model in which individuals and groups may shape processes and outcomes of
change (Badham, 1995). there can be a tendency towards less theoretical and more prescriptive models,
which may mask a more rigorous analysis of the contextual shaping process and limit theoretical insight
(Knights and Murray, 1994: 12).
In conclusion, it is obvious that people and the environment are continually evolving and regenerating
when we look on this time in history. Since the dawn of time, mankind has created its own machines to
increase productivity and the standard of living. We must create a goal to guide ourselves through the
process of changing because of the obligation of change in order to adapt. This goal should not be a dramatic
one or demand us to change quickly. We should go through this procedure step by step so that we may
observe and identify our own capabilities and adjust the strategy for the following phase.