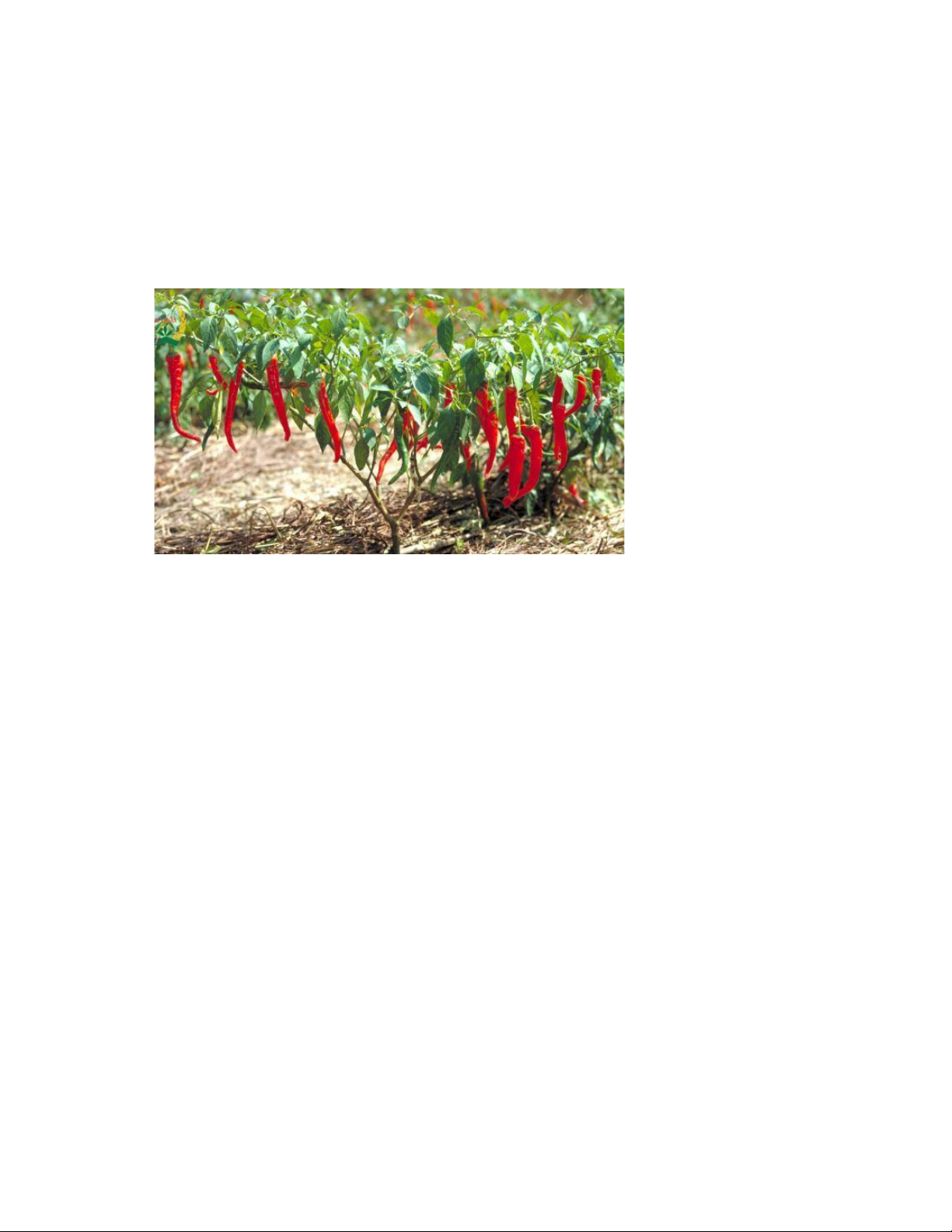
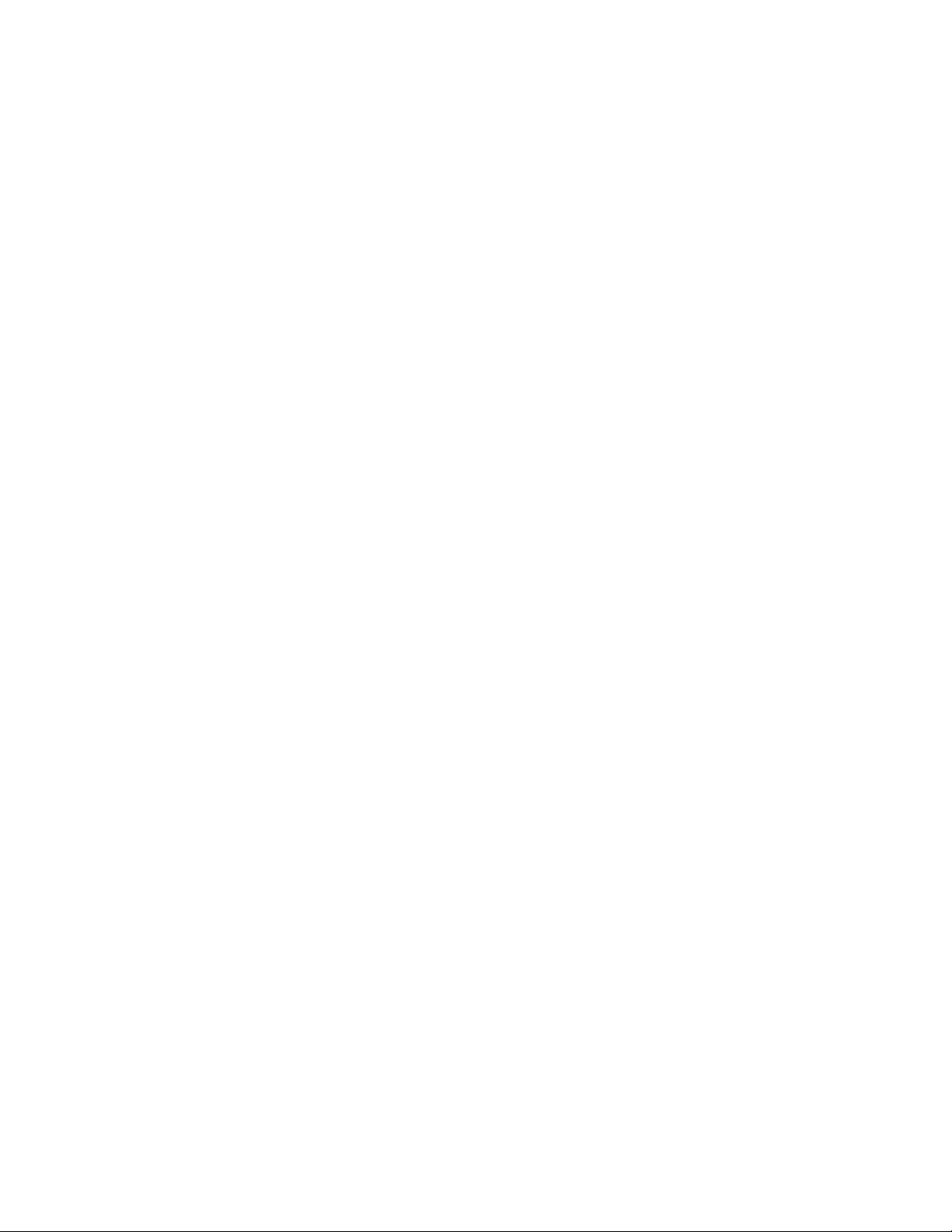
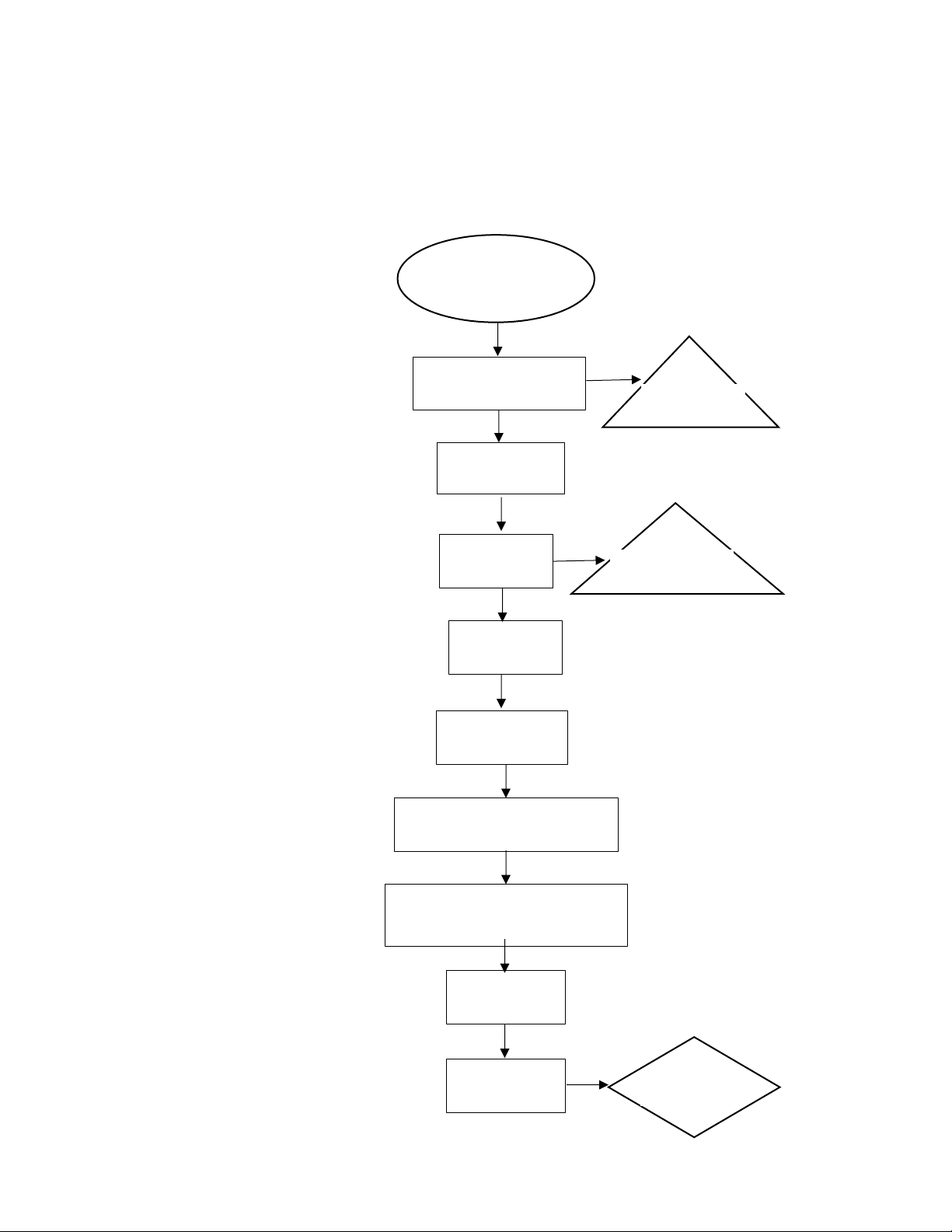
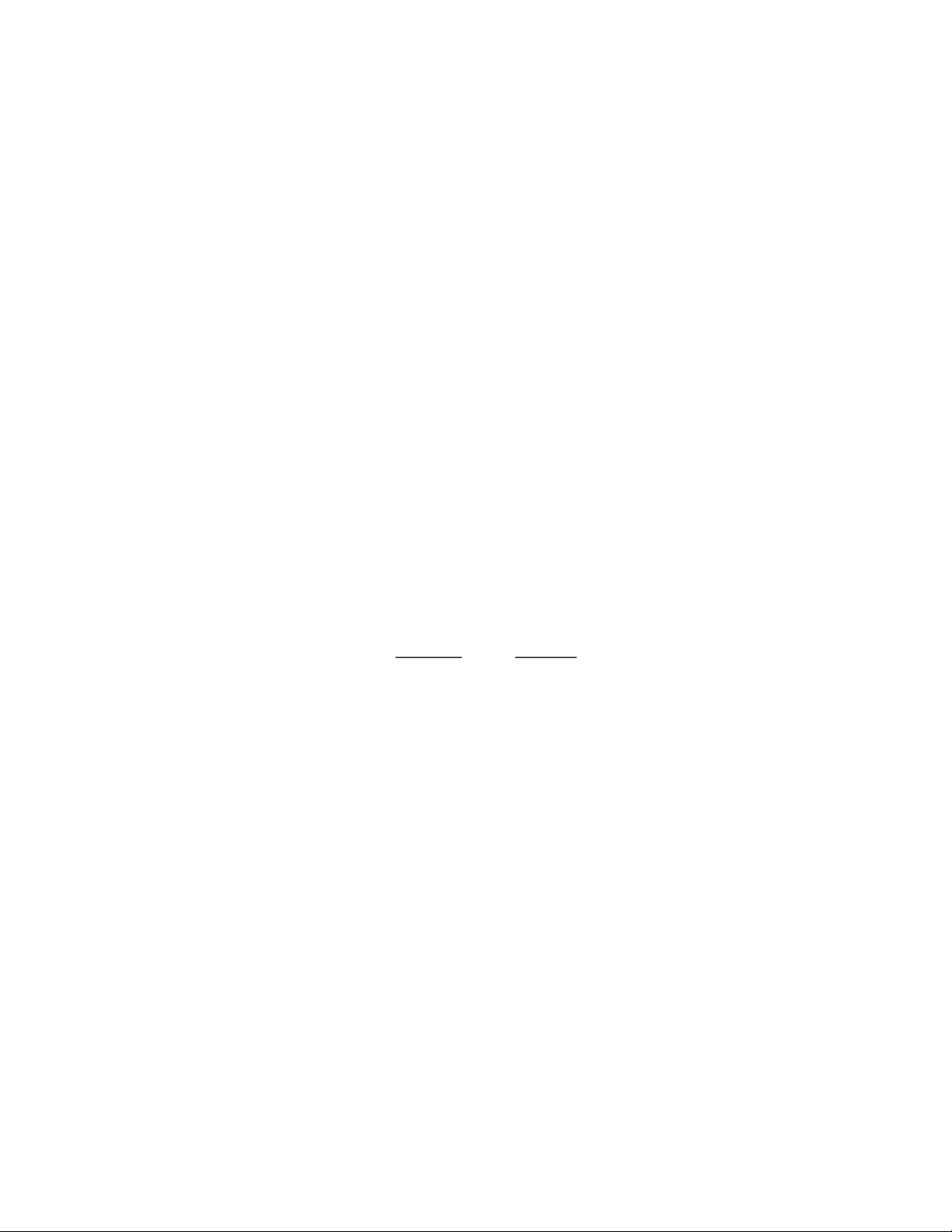
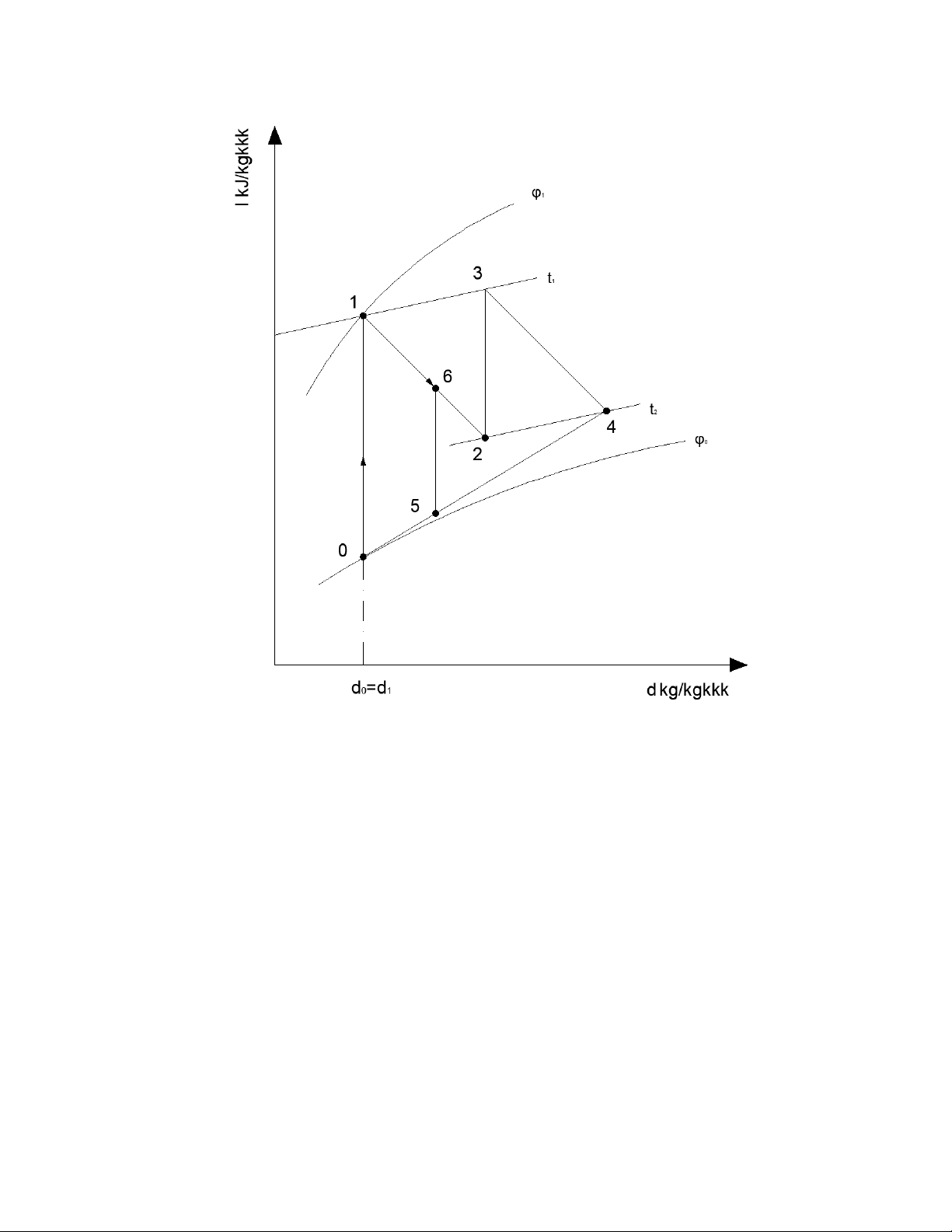
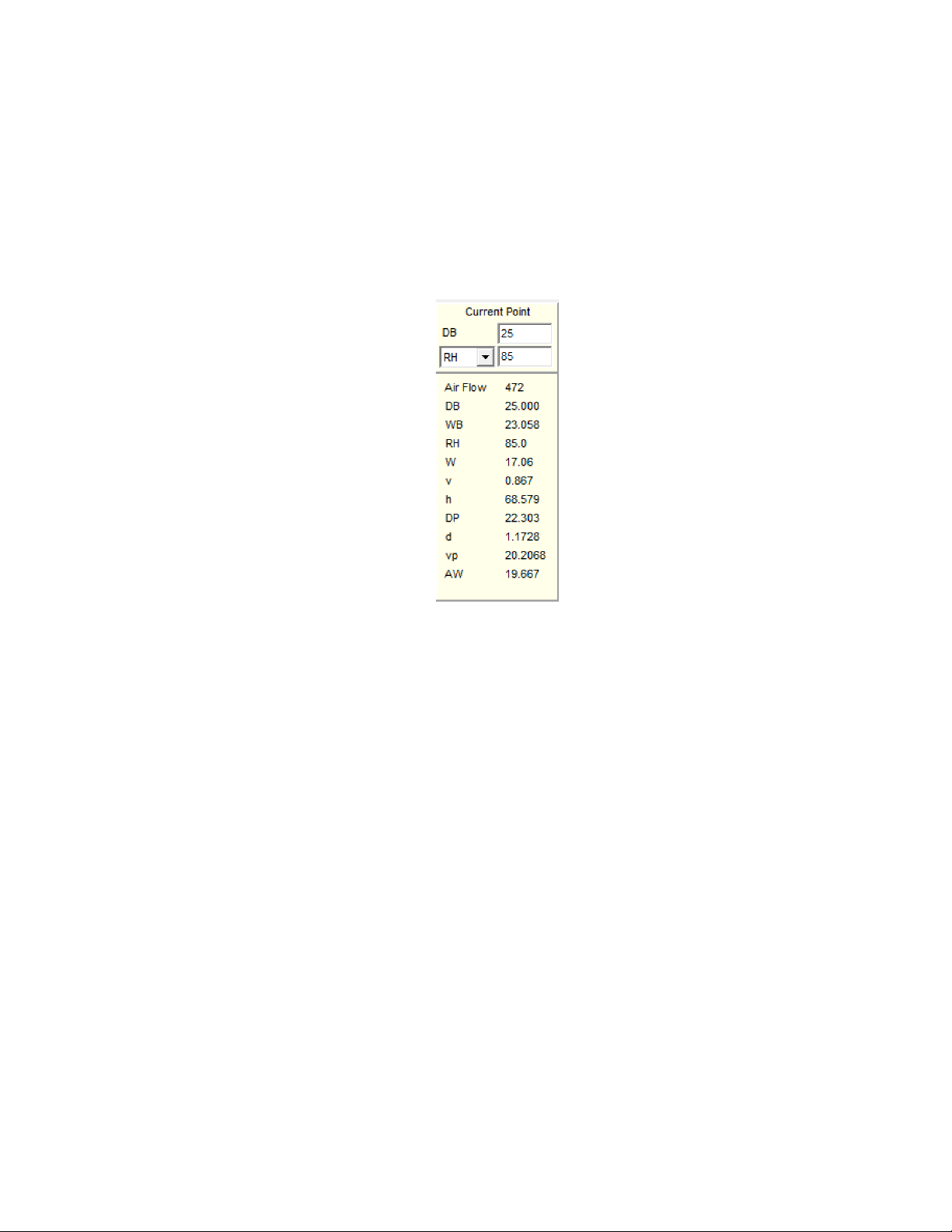
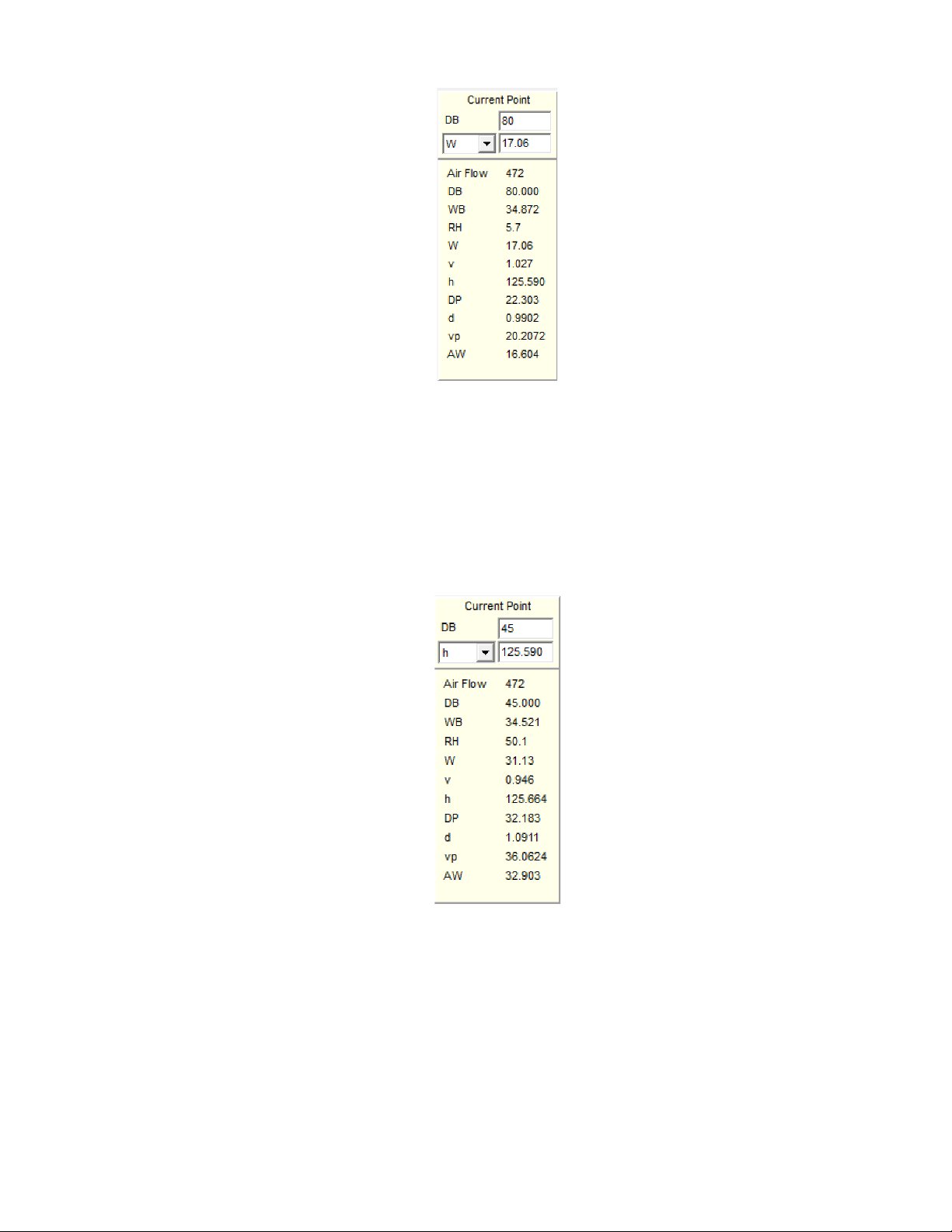
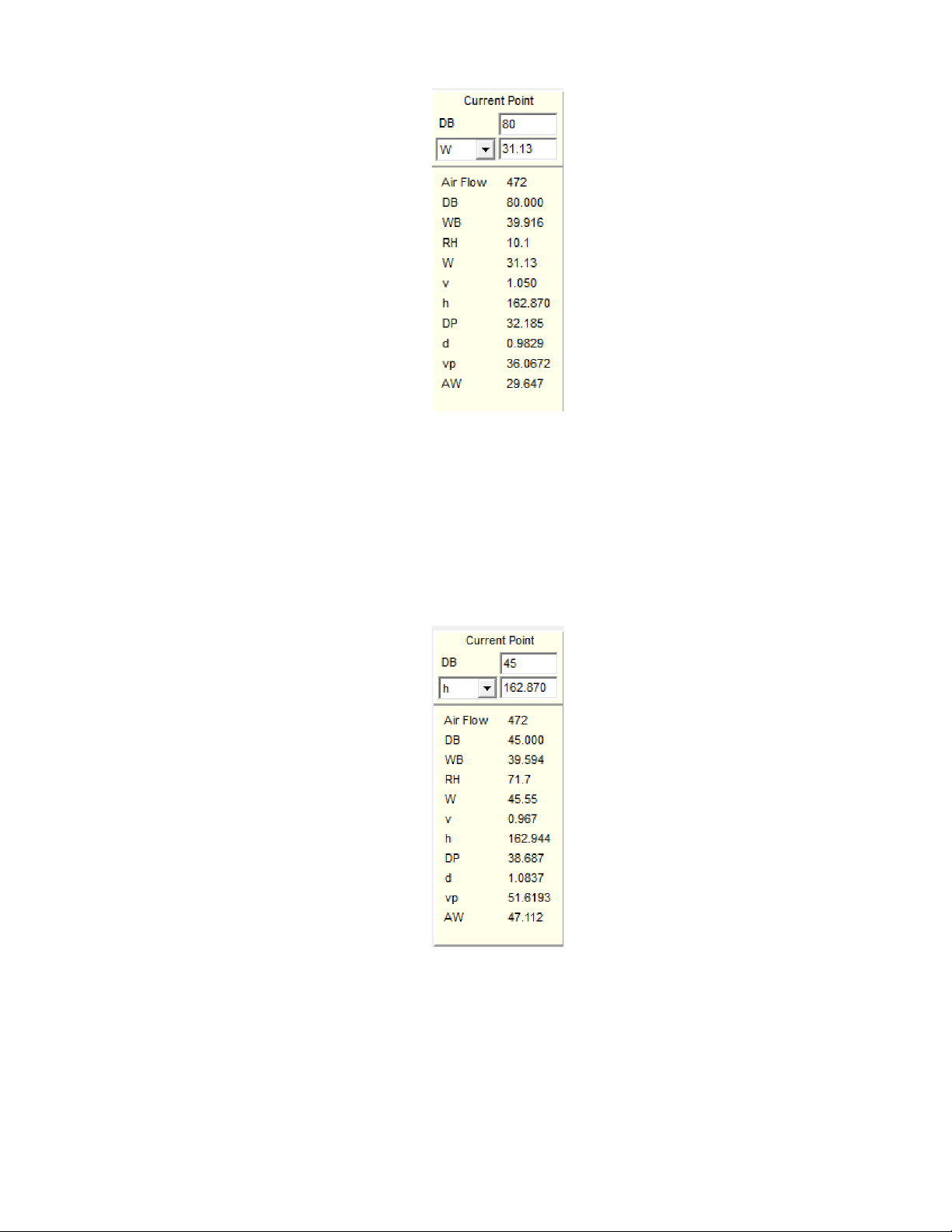
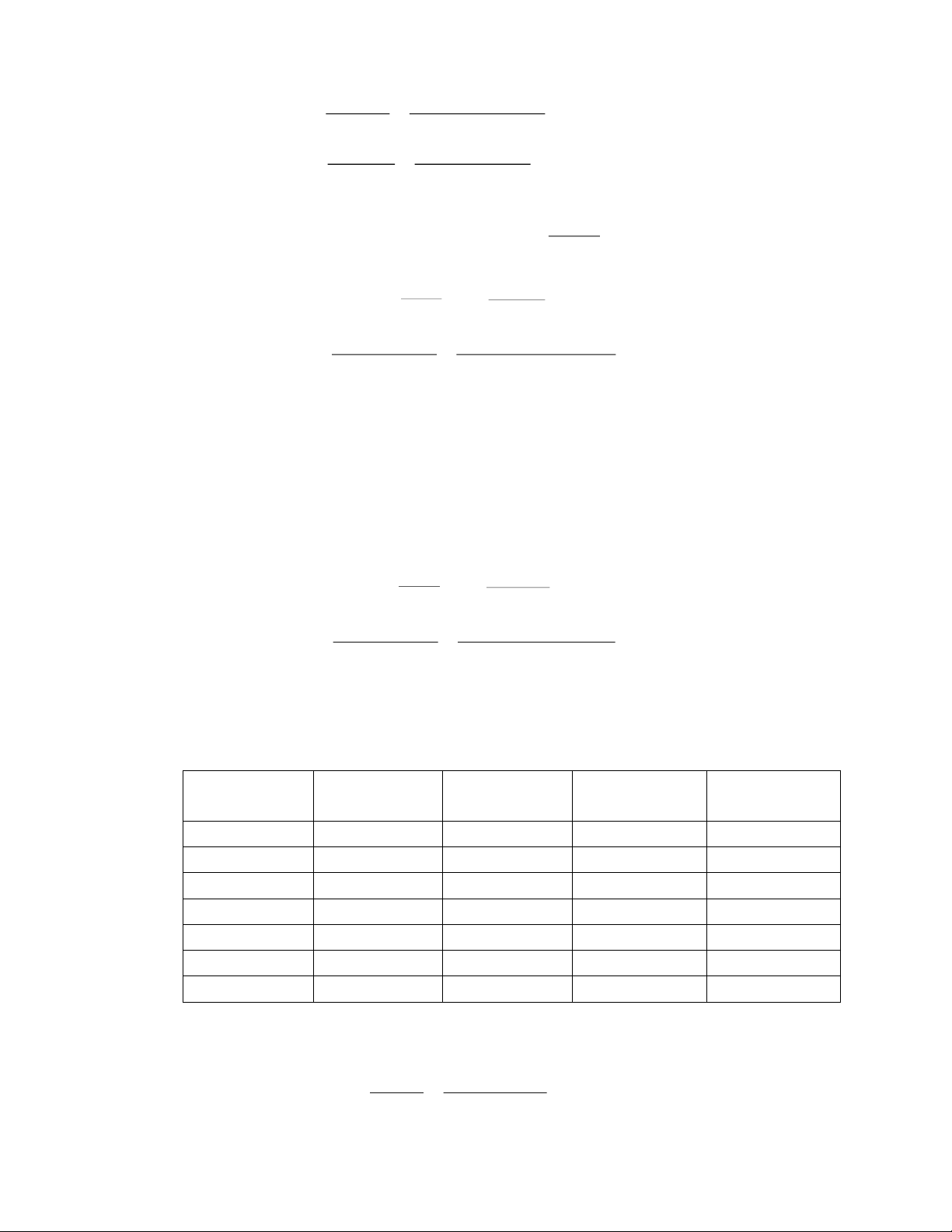
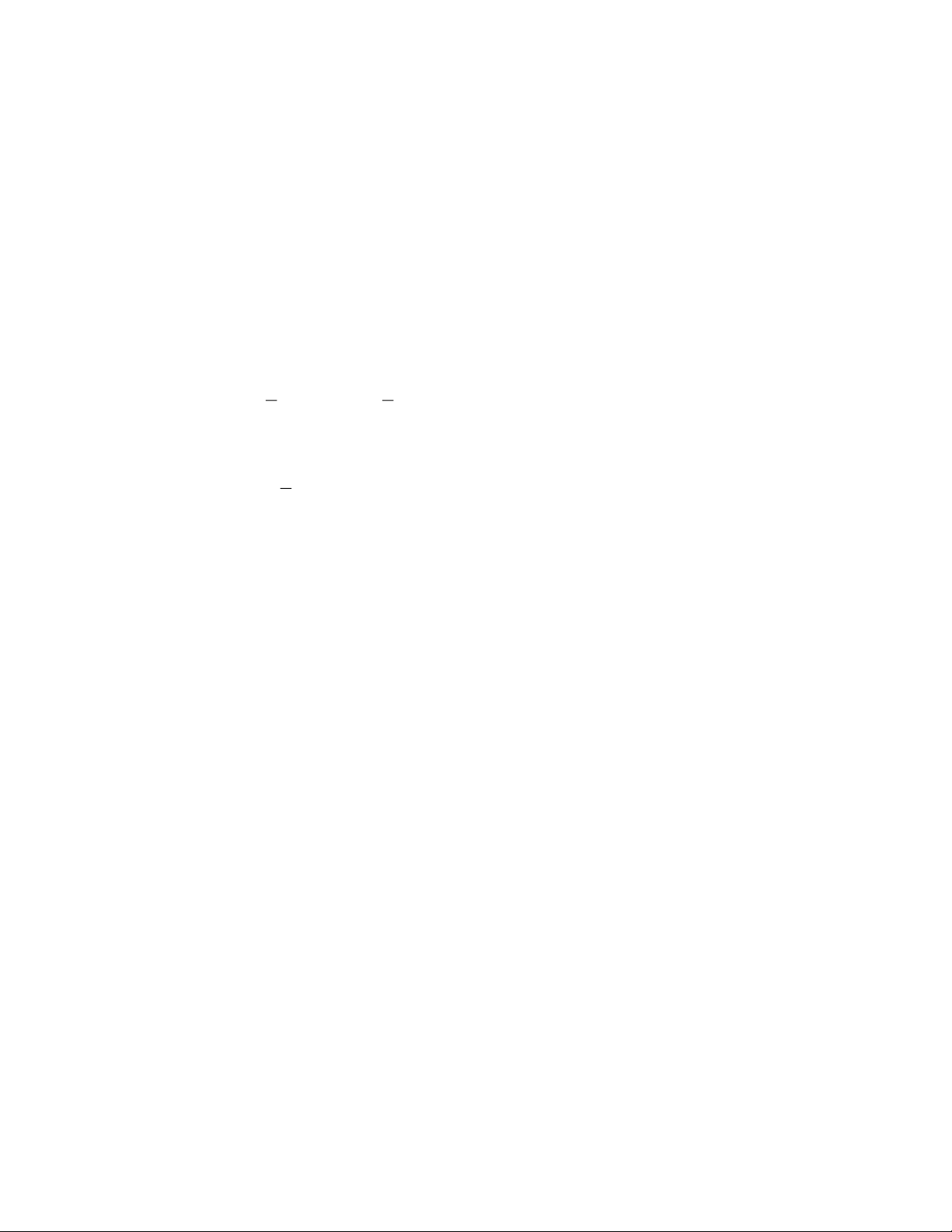
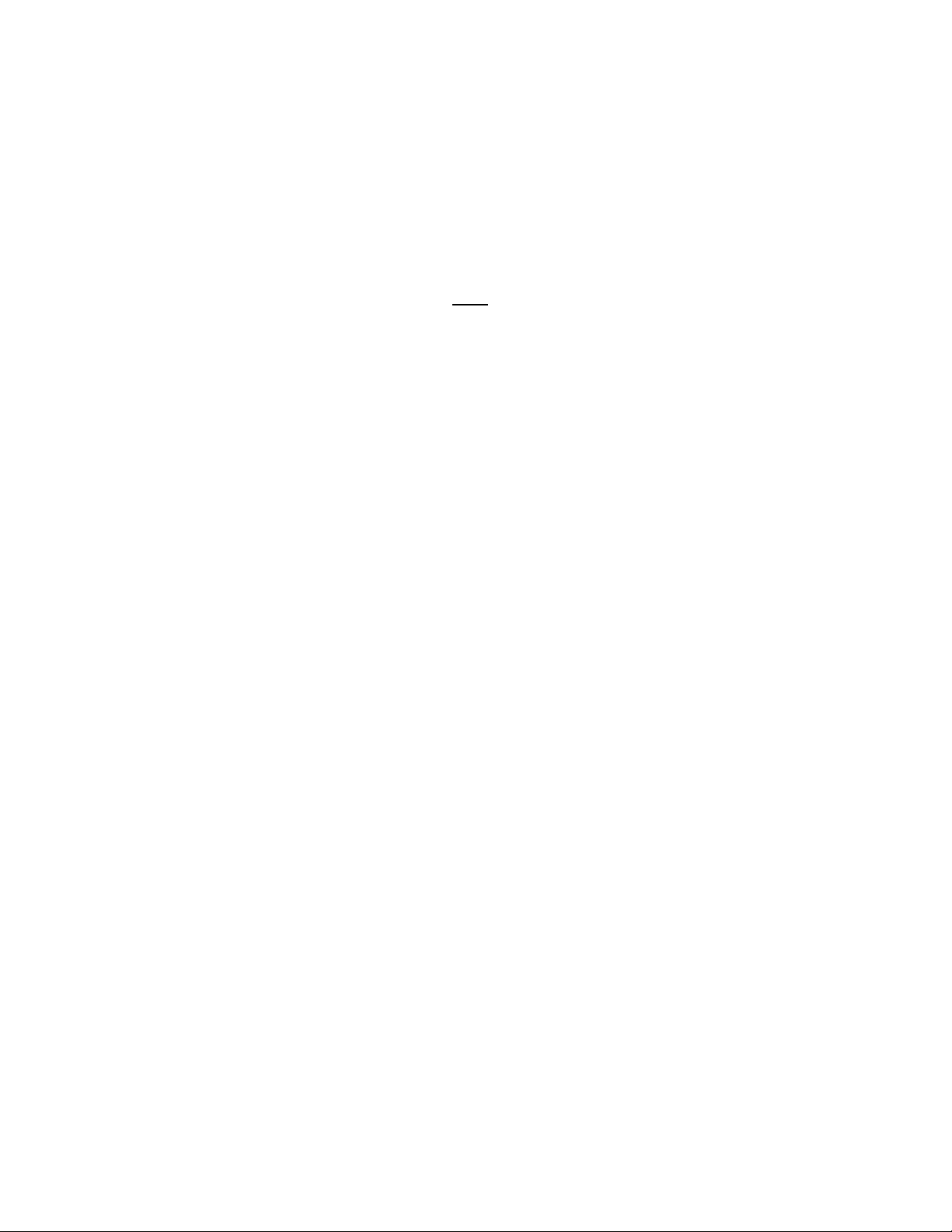
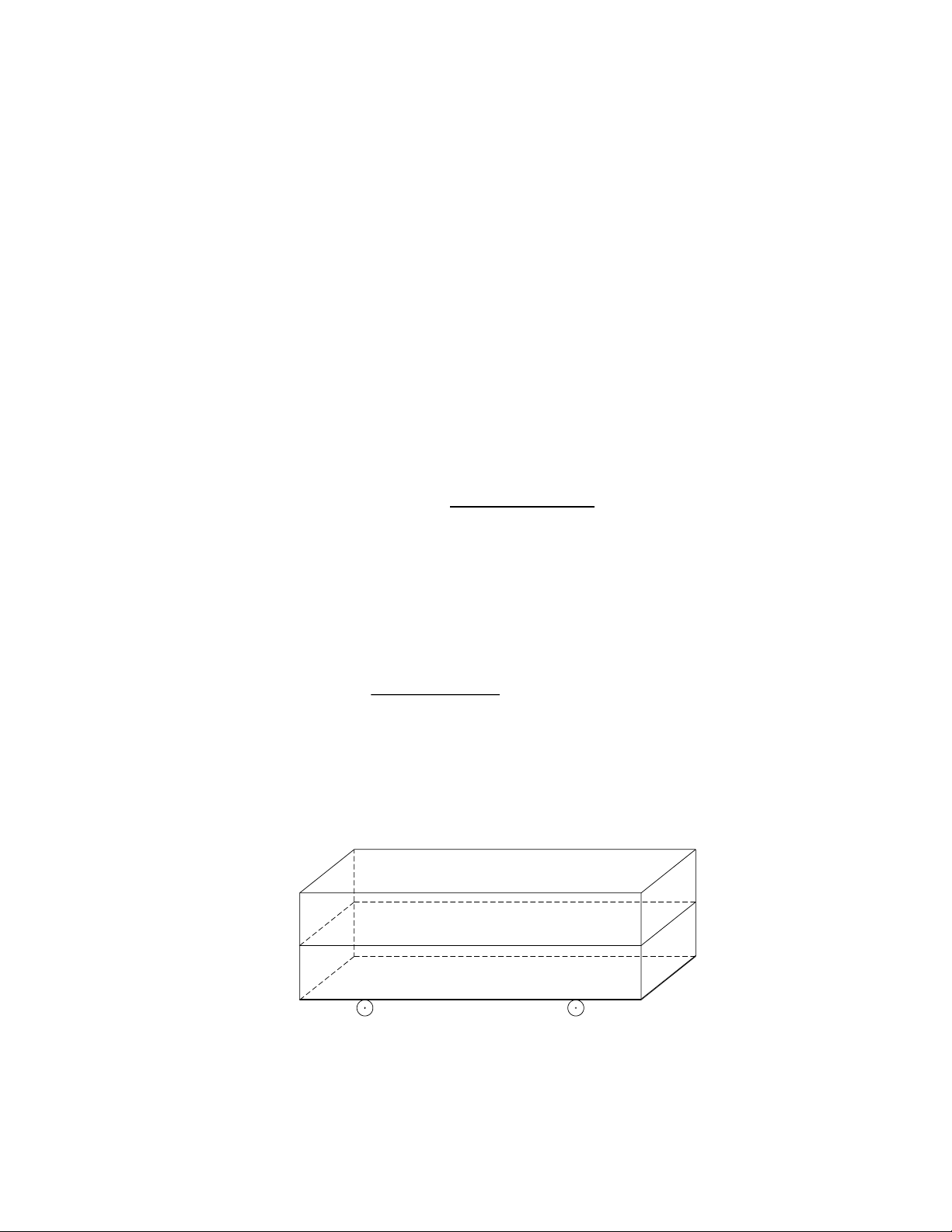
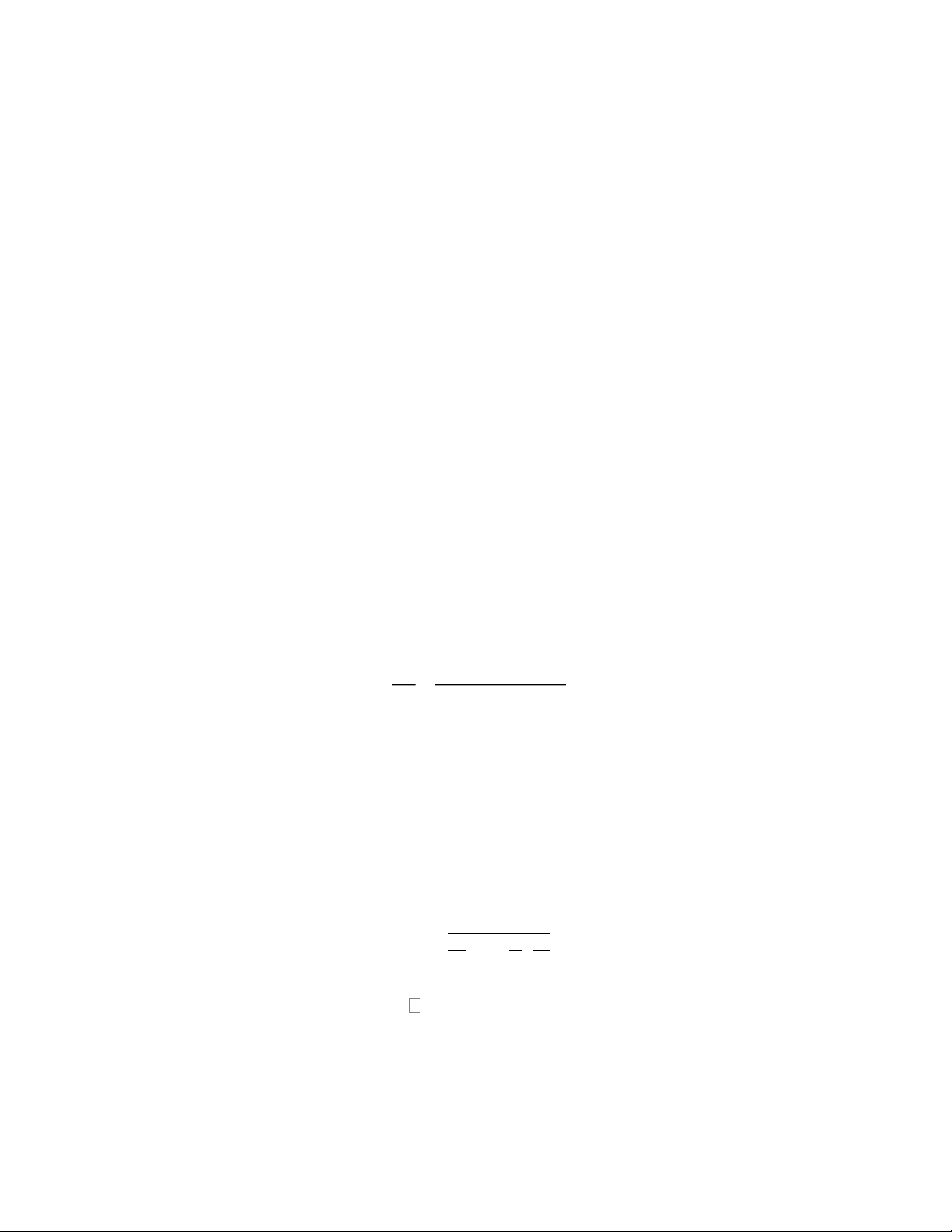
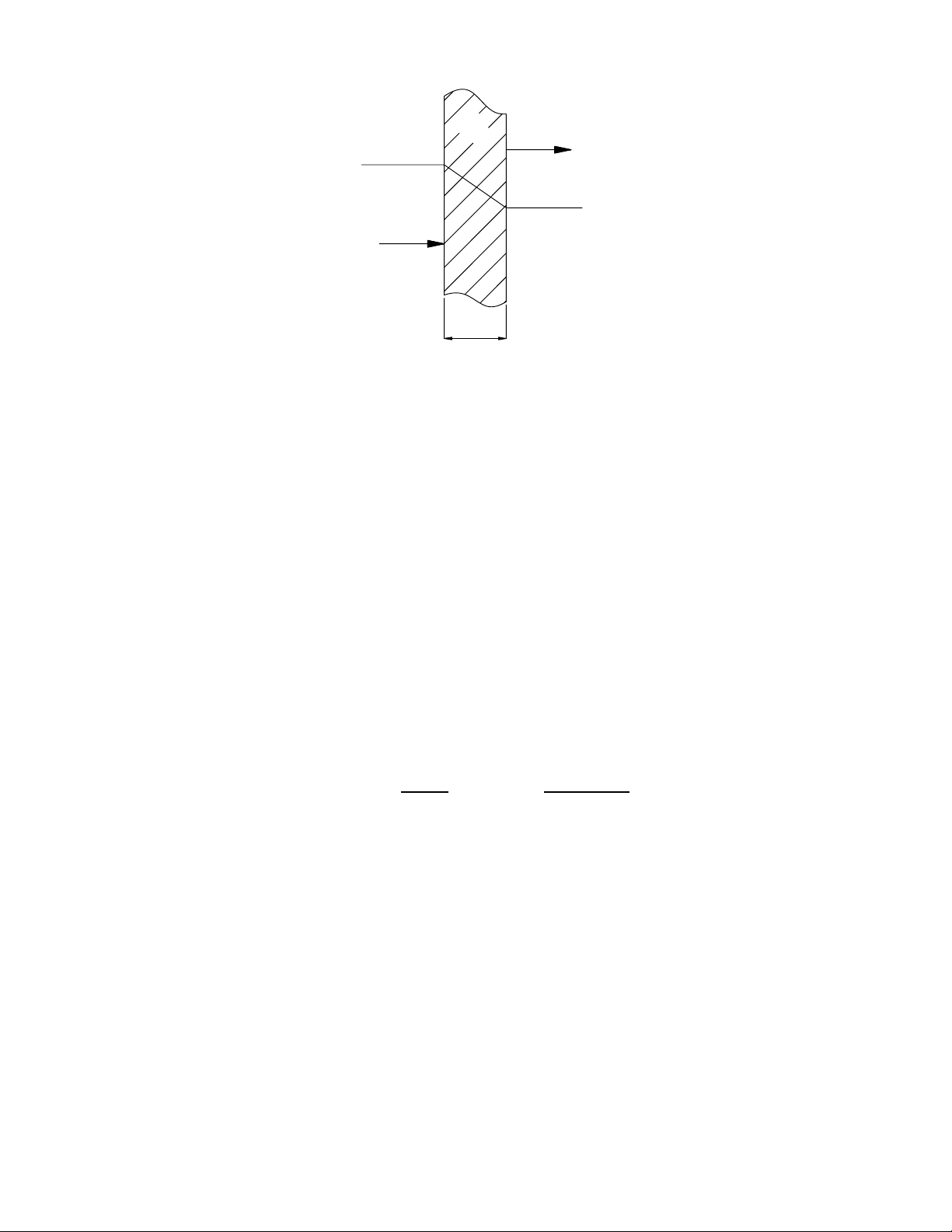
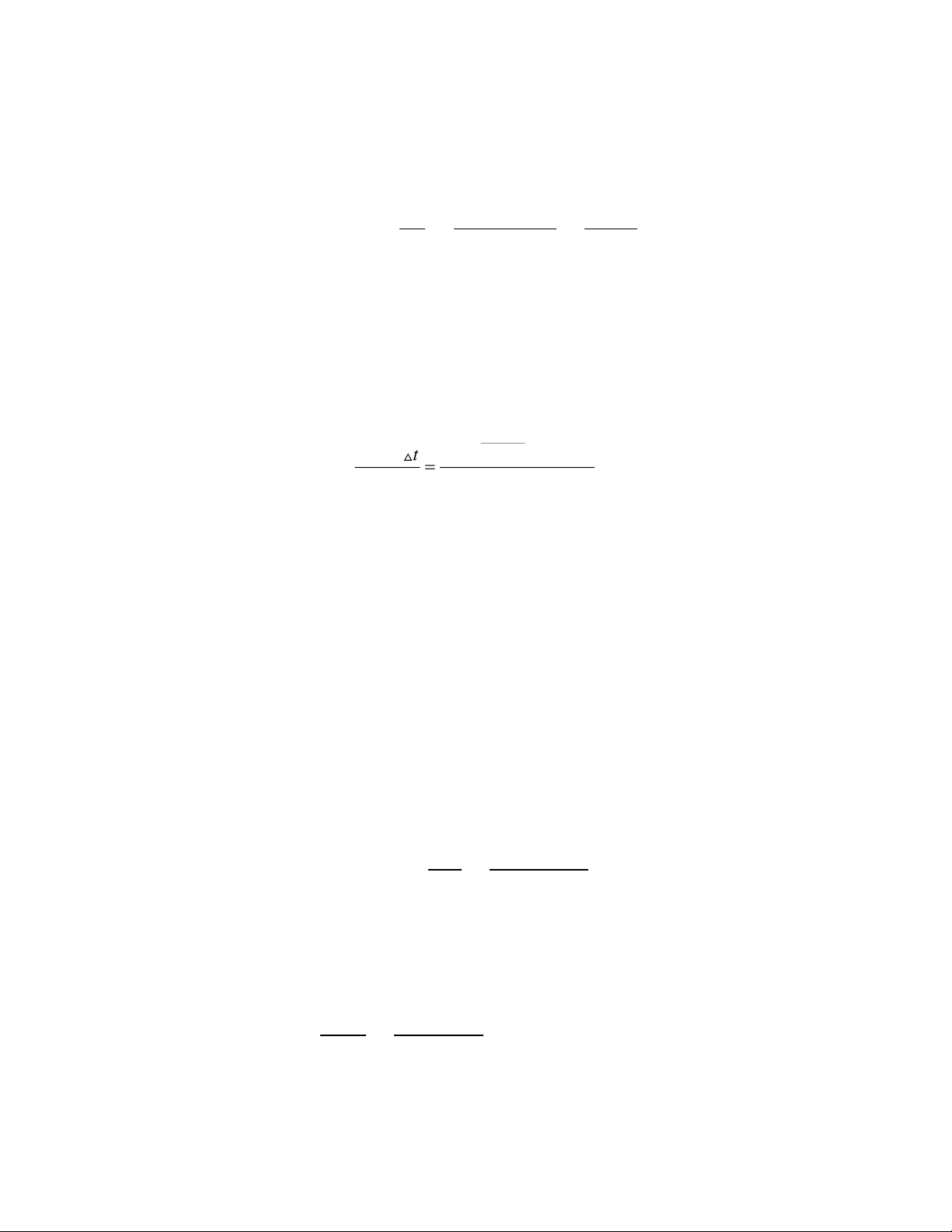
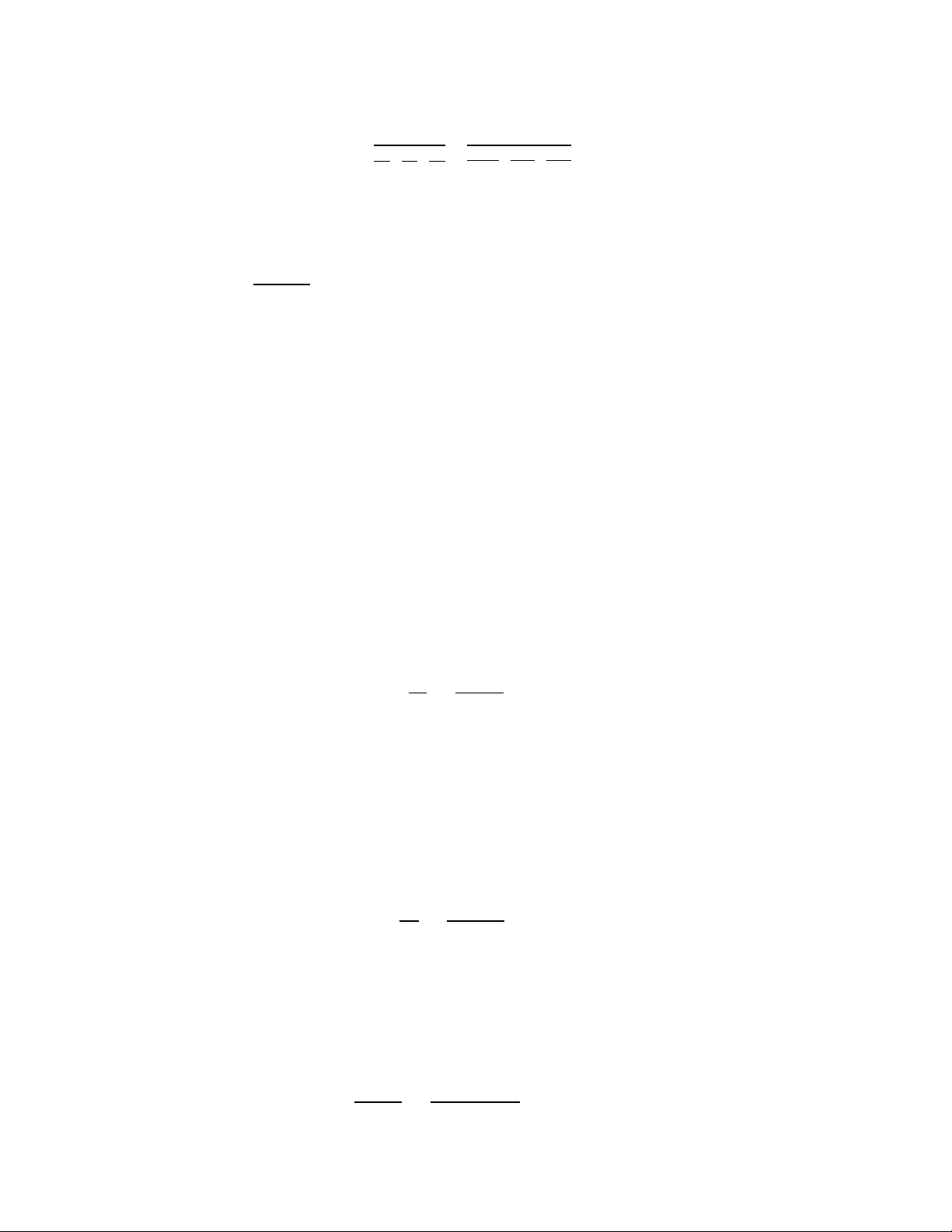
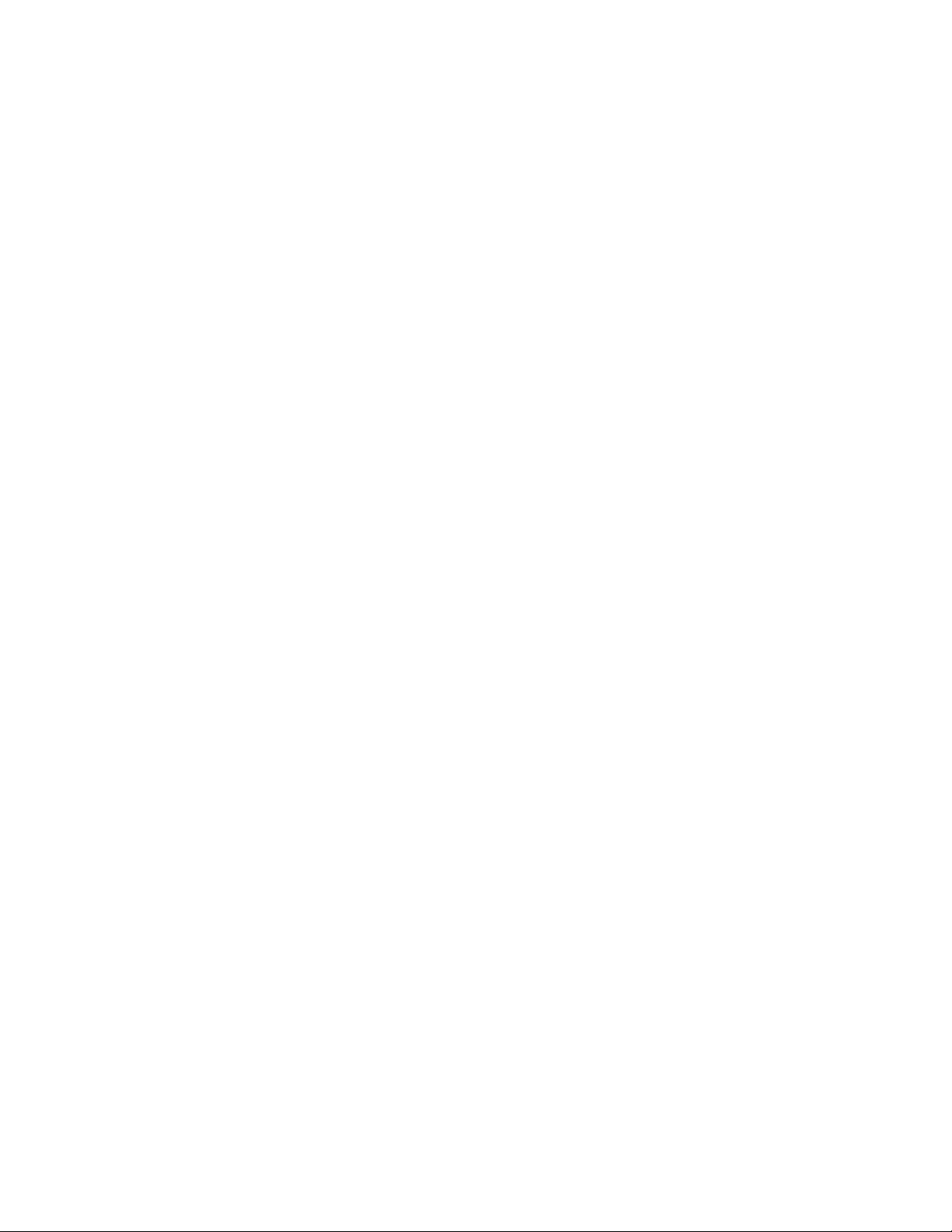
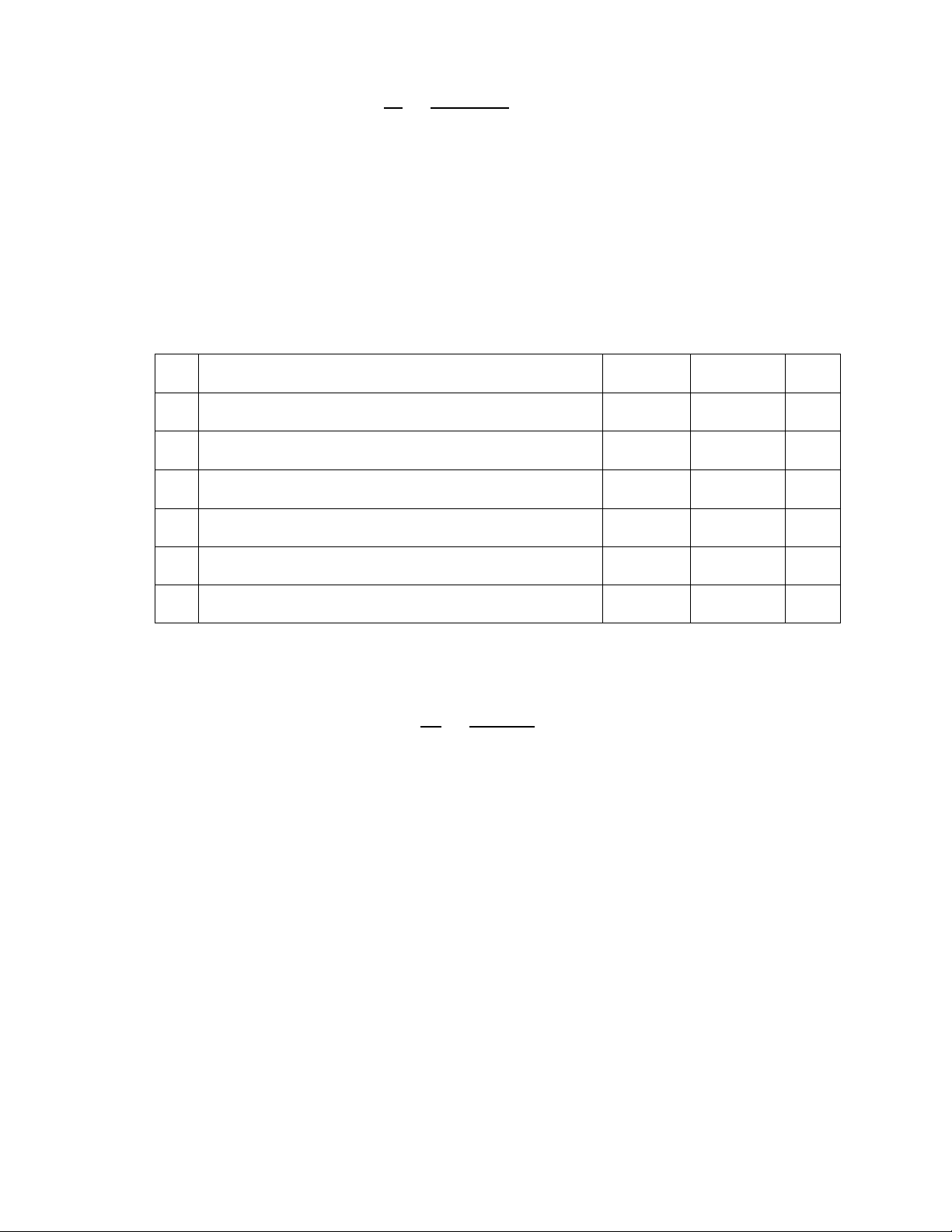
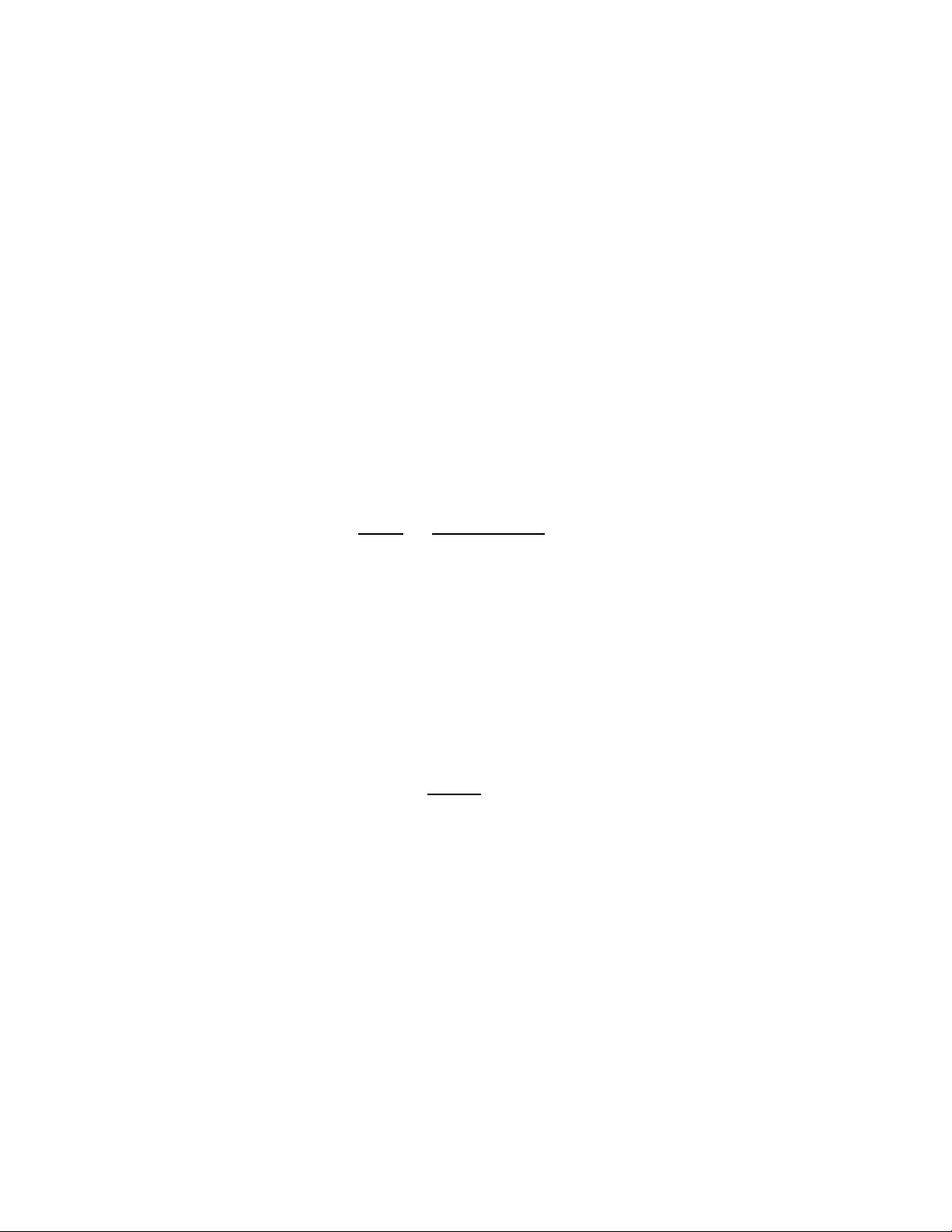
Preview text:
CHƯƠNG 1. TỔNG QUAN
1.1 Giới thiệu về cây ớt
Cây Ớt là một trong những thành phần gia vị quen thuộc trong ẩm thực hằng
ngày của con người từ xa xưa tới nay.
Ớt thuộc cây trồng lâu năm, thân dưới hóa rôc, chiều cao trung bình khoảng 40
– 70cm, phần thân có khoảng 4 cạnh, phân thành nhiều tán. Rễ có hình trụ,
nhiều nhánh phụ phát triển nhanh tạo thành rễ chùm.
Lá cây ớt là dạng lá đơn, có dạng hình trứng hoặc bầu dục, mọc thành chùm
gồm 5 – 6 giống hình hoa thị, phiến lá nhọn dần ở đâu, có màu xanh đậm, tùy
thuộc vào giống mà có loại có lông hoặc không có lông.
Hoa ớt là hoa lưỡng phái, có kích thước nhỏ,có dạng hình chén, có lá đài tương
đối nhỏ, hẹp và nhọn, thường mọc thành chùm gồm 3 – 4 hoa. Tràng hoa có
khoảng 7 cánh, phân trong cánh có lỗ để tiết mật hoa. Đặc biệt hoa ớt có thể tự
thụ phấn hoặc thụ phấn chéo nhờ côn trùng đều được.
Trái ớt có rất nhiều hình dạng khác nhau từ hình cầu đến hình nón, bề mặt trái
trơn, có gợn sóng và có khía. Trái khi chín thường có màu đỏ hoặc đen vàng. Hạt
ớt dẹp có dạng hình bán cầu, vỏ hạt cứng lại khi chín.
1.2 Công dụng của quả ớt
Được sử dụng khá đa dạng trong đời sống hàng ngày. Quả ớt có mặt từ bàn ăn
của mỗi gia đình, mâm cỗ trong nhà hàng hay trong bài thuốc chữa bệnh dân gian. 1.2.1 Làm gia vị
• Ớt cay là gia vị trong các món súp, nước chấm, tương ớt… hoặc cắt tỉa trang trí món ăn.
• Ớt chuông nguyên quả và một số loại ớt ngọt khác, không có vị cay
được chế biến như một loại rau bằng cách xào hoặc làm salad.
• Ớt chuông cắt thành từng lát mỏng được sử dụng làm pizza và một số
món ăn từ cá, gà và thịt – món đặc trưng tại nhiều vùng ở châu Âu và Trung Mỹ.
• Bột ớt khô là thành phần không thể thiếu trong bột cà ri ở nhiều nước châu Á.
• Ớt ngâm sữa chua rồi phơi khô dưới nắng là một món ăn phụ ở tiểu bang miền Nam Ấn Độ. 1.2.2 Chữa bệnh
• Trong y học cổ truyền, quả ớt có vị cay, nóng, có công dụng ôn trung,
tán hàn, tiêu thực, kiện tỳ, chỉ thống. Nhờ vậy ớt có khả năng kích thích
dạ dày, lợi tiểu hay dùng ngoài làm thuốc chuyển máu. Do đó nó
thường được sử dụng trong các bài thuốc điều trị chứng đau bụng do
lạnh, tiêu hóa kém, đau bụng do tỳ vị hư hàn, kiết lỵ, tiêu chảy, bệnh sởi
đậu ban chẩn hay đau nhức xương khớp do phong thấp, sốt rét.
• Không chỉ quả ớt mà trong Đông y, lá ớt có vị ngọt, đắng, tính mát cũng
có những lợi ích như thanh nhiệt, giải độc, lợi tiểu và sát trùng. Rễ ớt có
công dụng hoạt huyết và tán thũng giúp điều trị chứng bệnh phong thấp.
CHƯƠNG 2. QUY TRÌNH CHẾ BIẾN BỘT ỚT
Quy trình chế biến bột ớt Nguyên liệu Thiết bị rửa khô Tạp chất Phân loại Tách hạt Hạt+vỏ lụa Búa dập Máy nghiền
Thiết bị rây bột (rung)
Sấy (t=800C, có đối lưu,
gia nhiệt bằng đèn hồng ngoại Khử trùng Đóng gói Bột ớt
CHƯƠNG 3. TÍNH TOÁN
3.1. Các thông số ban đầu Vật liệu sấy
- Ớt tươi, cả quả.
- Năng suất theo sản phẩm: G2 = 500 (kg/h).
- Độ ẩm vật liệu vào: W1 = 80%.
- Độ ẩm vật liệu ra: W2 = 12%. Tác nhân sấy
- Không khí tự nhiên ngoài môi trường.
- Được gia nhiệt gián tiếp bằng khói lò.
- Hệ thống sấy có hồi lưu, được gia nhiệt bổ sung bằng đèn hồng ngoại.
- Nhiệt độ sấy: t = 80 C ; t = 45 C 1 ( ) 2 ( )
Cân bằng vật chất của thiết bị sấy
Lượng nguyên liệu ớt ban đầu vào là: W −W 80 −12 1 2 G = G . = 500. = 2200 kg / h 1 2 ( ) 100 − W 100 − 80 1
Lượng ẩm cần tách ra khỏi vật liệu sấy trong một mẻ:
W = G − G = 2200 − 500 = 1700 kg / h 1 2 ( )
3.2 Tính toán quá trình sấy lí thuyết
Đồ thị I – d của quá trình sấy lý thuyết trong hệ thống sấy
Điểm 0: Trạng thái không khí ngoài trời.
Điểm 1: Trạng thái không khí sau calorife lần đầu tiên.
Điểm 2: Trạng thái không khí sau khi ra khỏi hầm sấy (chưa bổ sung nhiệt).
Điểm 3: Trạng thái không khí sau khi bổ sung nhiệt bởi đèn hồng ngoại.
Điểm 4: Trạng thái không khí sau khi ra khỏi hầm sấy.
Điểm 5: Trạng thái không khí sau khi hòa trộn.
Điểm 6: Trạng thái không khí sau calorife.
Trạng thái không khí ngoài trời – Điểm 0
Ta chọn thông số không khí bên ngoài trời như sau:
Giả sử thiết bị được đặt tại thành phố Hà Nội. Ta tra độ ẩm trung bình
trong năm tại Hà Nội qua các tháng, lấy tháng có độ ẩm lớn nhất là thông
số cho tác nhân sấy, để đảm bảo chất lượng quá trình sấy trong cả năm.
Theo số liệu thống kê của Tổng cục thống kê năm 2020, ta tra được:
Tháng 3 ở Hà Nội có độ ẩm tương đối lớn nhất với thông số cụ thể như sau: t = 23, 2 ( C ); = 82 (%)
Nên ta chọn thông số không khí ngoài trời ban đầu có thông số như sau: t = 25 ( C ); = 5 8 % 0 0 ( )
Sử dụng phần mềm Psycromatric Analsys, ta tìm được điểm tương ứng trên đồ thị:
Trong đó: d =17,06 g / kgkk ; h = 68,579 kJ / kg . 0 ( ) 0 ( )
Để tránh hiện tượng đọng sương trong buồng sấy, nhiệt độ thiết bị sấy
phải cao hơn nhiệt độ đọng sương của không khí. Tức nhiệt độ sấy phải cao hơn: t = 23,058 C . s ( )
Trạng thái không khí sau calorife lần đầu – Điểm 1
Không khí sau khi qua calorife, có các thông số như sau: t = 80 ( C
); d = d = 17,06 g / kgkk 1 1 0 ( )
Sử dụng phần mềm Psycromatric Analsys, ta tìm được điểm tương ứng trên đồ thị:
Trong đó: =5,7 % ; h =125,590 kJ / kg . 1 ( ) 1 ( )
Trạng thái không khí sau hầm sấy (chưa tính bổ sung nhiệt) – Điểm 2
Không khí sau khi trao đổi ẩm, nhiệt với vật liệu sấy, có các thông số như sau: t = 40 ( C
); h = h = 125,590 kJ / kg 2 2 1 ( )
Sử dụng phần mềm Psycromatric Analsys, ta tìm được điểm tương ứng trên đồ thị:
Trong đó: =50,1 % ; d = 31,13 g / kgkk . 2 ( ) 2 ( )
Trạng thái không khí sau khi được gia nhiệt bổ sung – Điểm 3
Sau khi được gia nhiệt bổ sung bằng đèn hồng ngoại, không khí có
thông số trạng thái như sau:
t = t = 80 ( C
); d = d = 31,13 g / g k k k 3 1 3 2 ( )
Sử dụng phần mềm Psycromatric Analsys, ta tìm được điểm tương ứng trên đồ thị:
Trong đó: =10,1 % ; h =1 ,
62 870 kJ / kg . 3 ( ) 3 ( )
Trạng thái không khí sau khi ra khỏi hầm sấy – Điểm 4
Sau khi trao đổi nhiệt ẩm với vật liệu sấy, không khí ra khỏi hầm sấy có thông số như sau:
t = t = 45 ( C
); h = h = 162,8 0 7 kJ / g k 4 2 4 3 ( )
Sử dụng phần mềm Psycromatric Analsys, ta tìm được điểm tương ứng trên đồ thị:
Trong đó: =71,7 % ; d = 45,55 g / kgkk . 4 ( ) 4 ( )
Trạng thái không khí sau khi khi hòa trộn – Điểm 5
Ta hồi lưu một phần khí thải với không khí tự nhiên bên ngoài môi trường theo tỉ lệ:
Khí thải/Khí tự nhiên = 1/3
Khi đó, ta có thông số tại điểm hòa trộn là: 2.h + h 2.68, 579 +162,87 0 4 h = =
= 100,009 kJ / kg 5 ( ) 3 3 2.d + d 2.17, 06 + 31,13 0 4 d = =
= 26,557 g / kgkk 5 ( ) 3 3 Lại có: 26, 557
h = 1, 004t + d . 2500 +1,842t →100,009 =1,004t + . 2500 + , 1 842t → t = 1 3 , 93 C 5 5 5 ( 5 ) 5 ( 5 ) 5 ( ) 1000 Độ ẩm tương đối: 4026,42 4026,42 12− 12− bh 235,5+t + 5 235,5 31,93 P = e = e = 0,047 bar 5 ( ) . B d 1, 013.26,557 5 → = = = 88,26 % 5 bh ( ) P .(621+ d ) 0, 047.(621+ 26,557) 5 5
Trạng thái không khí sau calorife – Điểm 6
Không khí sau khi qua calorife, có các thông số như sau:
d = d = 26, 557 ( C
); h = h = 125,590 kJ / kg 6 5 6 1 ( ) Lại có:
h = 1, 004t + d . 2500 +1,842t
→125,590 =1,004t + 26,557. 2500 +1,842t → t = 56, 223 C 6 6 6 ( 6 ) 6 ( 6 ) 6 ( ) Độ ẩm tương đối: 4026,42 4026,42 12− 12− bh 235,5+t + 6 235,5 56,223 P = e = e = 0,165 bar 6 ( ) . B d 1, 013.26,557 6 → = = = 25,19 % 6 bh ( ) P .(621+ d ) 0,165.(621+ 26,557) 6 6
Tính toán lượng tác nhân sấy và cân bằng năng lượng quá trình sấy lý thuyết
Bảng thông số trạng thái không khí trong quá trình sấy lý thuyết Trạng thái t φ h d (̊C) (%) (kJ/kgkk) (g/kgkk) 0 25 85 68,579 17,06 1 80 5,7 125,59 17,06 2 45 50,1 125,59 31,13 3 80 10,1 162,87 31,13 4 45 71,7 162,87 45,55 5 31,93 88,26 100,009 26,557 6 56,22 25,19 125,59 26,557
• Lượng không khí khô cần thiết làm bay hơi 1kg ẩm là: 1 1000 l = = = 35,1 kgkk lt ( ) d − d 45, 55 −17, 06 4 0
• Lượng không khí khô tuần hoàn trong quá trình sấy:
L = W .l = 1700.35,1 = 59670, 06 kgkk h lt lt ( / )
• Lượng không khí cần thiết ban đầu trong quá trình sấy là:
L = L .(1+ d ) = 59670, 06.(1+ 0, 01706) = 60688, 031 kgk / h lt 0 ( )
• Tổng nhiệt lượng cần thiết để làm bay hơi 1 kg ẩm là:
q = l .(h − h = 35,1. 162,87 − 68,579 = 3309, 617 kJ / kg am lt 4 0 ) ( ) ( )
- Trong đó, nhiệt lượng nhận từ calorife là: 3 q = l h − h = − = kJ kg am clf lt ( 3 . . .35,1. 125,59 100, 009 1346,823 / 6 5 ) ( ) ( ) 2 2
- Nhiệt lượng bổ sung từ đèn hồng ngoại là: 3 q =
l . h − h = − = kJ kg am bs lt ( 35,1. 162,87 125,59 1962, 794 / 3 2 ) ( ) ( ) 2
• Tổng nhiệt lượng cần thiết cung cấp cho quá trình sấy trong 1h là:
Q = W .q = 1700.3309, 617 = 5626349, 6
(kJ / h) 1563 (kW )
- Trong đó, nhiệt lượng nhận từ calorife là: Q
= W.q = 1700.1346,823 = 2289599,86 (kJ / h) 636 kW clf clf ( )
- Nhiệt lượng bổ sung từ đèn hồng ngoại là:
Q = W .q = 1700.1962, 794 = 3336749, 737
(kJ / h) 927 kW bs bs ( )
3.3 Tính kích thước khay sấy.
Vật liệu được trải trên khay sấy, khay sấy có kích thước 870 x 670 x
30(mm). Khay được xếp trên xe gòng, mỗi xe gồm 2 dãy, mỗi dãy gồm 20
khay. Trong một mẻ sấy, hầm chứa 5 xe goong, như vậy ta có tổng số 200
khay. Khoảng cách giữa 2 khay liên tiếp là 50(mm), khay được đặt lên các thanh đỡ hình chữ L.
Vậy khối lượng sản phẩm trên mỗi khay là: 500 𝑚 = = 2,5 (𝑘𝑔) 200 Ta có kích thước:
− Chiều dài: 670 x 2 + 5 x 4+ 20 x 3 = 1420 (mm).
− Chiều rộng: 870 + 5 x 2 = 880 (mm).
− Chiều cao: (30 x 20) + (50 x 21) + 150 = 1800 (mm).
3.4 Kích thước hầm sấy.
Hầm sấy chứa 5 xe sấy nên kích thước trong của hầm sấy là:
− Hai đầu hầm có hai khoảng trống 455 mm để phân gió.
− Chiều dài của hầm sấy là: 880 x 5 + 455x 2 = 5310(mm).
− Hai bên hầm có khoảng trống với thành xe gòng mỗi bên là 20(mm)
− Chiều rộng của hầm sấy là: 1420 + (2 x 20) = 1460(mm).
− Chiều cao: 1800 + 50 = 1850 (mm).
Sau khi xác định kích thước trong của hầm ta quyết định kết cấu tường, trần,
nền hầm sấy. Tường hai bên được xây bằng gạch đỏ, mỗi lớp 150(mm).
Trần hầm sấy gồm hai lớp lớp bê tông cốt thép dày 50 mm (tấm đan) và lớp xỉ cách nhiệt dày 100 (mm).
Nền hầm sấy được xử lý bình thường gồm một lớp bê tông gạch vỡ, một lớp xỉ
than cách nhiệt sau đó láng một lớp xi măng.
Cửa hầm sấy làm bằng tôn hai lớp giữa có bông thuỷ tinh cách nhiệt.
Như vậy hầm sấy có kích thước ngoài là: − Chiều dài: 5310 (mm)
− Chiều rộng: 1460 + 2 x 150 = 1760 (mm).
− Chiều cao: 1850 + 150 = 2000 (mm).
− Diện tích hai bên tường là: Ft = 2 x 5310 x 2000 = 21,24 (m2)
− Diện tích trần hầm sấy: Ftr = 5310 x 1760 = 9,34(m2).
3.5 Tính tổn thất nhiệt.
Tính nhiệt cho hầm sấy với nội dung là tính tổng tổn thất nhiệt trong tất
cả các trường hợp để từ đó biết được nguồn năng lượng loại nào và sẽ sử dụng
bao nhiêu kg để có thể cho được nhiệt lượng đã tổn thất trong quá trình sấy.
Hoặc nói một cách cụ thể là bằng tổng nhiệt sinh ra.
3.5.1 Tổn thất nhiệt do 1kg vật liệu sấy mang đi. 𝐺 𝑞
2. 𝐶𝑣𝑙(𝜃2 − 𝜃1) 2 = 𝑊 Trong đó:
G2 = 500 kg/h: lượng sản phẩm lấy ra trong thời gian một giờ.
W = 1700 kg/h: lượng ẩm bốc hơi trong 1 giờ.
Cvl: nhiệt dung riêng của ớt Cvl = 3,5 kJ/kgđộ.
, nhiệt độ vật liệu khi vào và ra: = 25˚C; =40˚C. 1 2 1 2 500.3,5.(40 − 25) q = =15,44 (kJ/kg ẩm). 2 1700
3.5.2 Nhiệt lượng tổn thất do bốc hơi W(kg ẩm) của vật liệu trong một giờ:
Q2 = q2 x 1700 = 15,44 x 1700 = 26250 (kJ/h).
3.5.3 Tổn thất do xe mang đi.
Xe làm bằng thép thẳng 20 x 20 hàn thành khung. Dưới có bốn bánh xe, mỗi xe nặng 60 kg.
Vậy 4 xe nặng: 60 x 4 = 240 kg.
Vậy nhiệt lượng để đốt nóng xe: Q3=m.C3.(t2 – t1). Trong đó:
− M = 240(kg): khối lượng của 4 xe.
− C3 = 0,44 kJ/kg độ: nhiệt dung riêng của thép hàn xe.
− t1=250℃; t2=600℃: nhiệt độ đầu và cuối của xe. Do đó:
Q3 = 240 x 0,44 x (60 - 25) = 3696 (kJ/kg ẩm).
3.5.4 Tổn thất nhiệt ra môi trường xung quanh.
Tổn thất nhiệt ra hai tường bên.
❖ Giả thiết tốc độ tác nhân sấy:
Để tính tổn thất ra môi trường chúng ta giả thiết tốc độ tác nhân sấy trong hầm
thông qua kết cấu của hầm đã xác định và kích thước của xe goòng đã chọn, ta
tính được tiết diện tự do của hầm sấy bằng:
− Tiết diện hầm sấy: FH = BH.HH = 1460 x 1850 = 2,7 m2/T (mặt cắt ngang)
− Tiết khay chiếm: 40 x 30 x 670 = 804000 = 0,804 (m2)
− Tiết diện khung xe chiếm: (1650 x 2 + 1380 x 2) x 20 = 0,12(m2).
− Tiết diện bánh xe và tấm chắn dưới: 1000 x 200 = 200000 = 0,2(m2)
− Tiết diện chiếm tổng: Fe = 0,804 + 0,12 + 0,2 = 1,124 (m2)
− Tiết diện tự do: F = 2,7 – 1,124 = 1,576(m2) v 60688, 031 0 w = = =1,426(m / s) 0 F 1,576.3600.1, 293 td
Vì lượng tác nhân sấy trong quá trình sấy thực phải lơn hơn lưu lượng tác
nhân sấy trong quá trình sấy lý thuyết nên tốc độ tác nhân sấy giả thiết để
tính toán các tổn thất cũng phải lớn hơn w0. Ta giả thiết trước tốc độ tác
nhân trong hầm sấy v = 1,6(m/s).
Tính tổn thất nhiệt ra môi tr¬ường xunh quanh, ta sử dụng công thức: Q4 = 3,6.K.F.Δt [1] Trong đó:
F: Diện tích hai bên t¬ường sấy. Ta có F = 2,301(m2) 1
K: hệ số truyền nhiệt: 𝐾 = [4] 1 𝛿 1 +∑𝑛 𝑖 𝛼1 𝑖= 𝜆 1 + 𝑖 𝛼2
Tính α1 : Hệ số cấp nhiệt từ trong hầm đến mặt trong của tường.
Với giả thiết v = 1,6 m/s, 1 đư¬ợc tính như¬ sau: t 1 tT1 tT2 t 2
• Tính 𝛼1 : Hệ số cấp nhiệt từ trong hầm đến mặt trong của tường.
Với giả thiết v = 1,6 m/s, a1 được tính như sau:
a1 = 6,15 + 4,17.v = 6,15 + 4,17.1,6 = 12,8 (W/m20K)
Dòng nhiệt do tác nhân truyền cho mặt trong của tường hầm sấy bằng: q1=𝛼1(t2 - t1).
Ở đây: t1 : nhiệt độ trung bình trong hầm sấy( 500C)
tT1: nhiệt độ mặt tường trong hầm sấy.
Giả sử t1 và tT1 chênh lệch nhau 3,5 0C và tT1=50 - 3,5 = 46,50C Ta có: q1=12,8 x 3,5 = 44,8 W/m2
• Tính 𝛼2: Nhiệt độ mặt ngoài tường tính theo công thức: 𝑞 44,8.0,15 𝑡 1. 𝛿𝑡 𝑇2 = 𝑡𝑇1 − = 46,5 − ≈ 410𝐶 𝜆𝑡 1,45 Ở đây
• 𝛿t : chiều dày tường gạch 𝛿t =0,15 m. • 𝜆 =1,45 W/mđộ
t : hệ số dẫn nhiệt của gạch: 𝜆t
Biết nhiệt độ trong phòng đặt thiết bị t2 = 30 0C và nhiệt độ mặt ngoài
tường hầm sấy tT2 = 410C.
Ta tìm được nhiệt độ chênh lệch giữa mặt tường ngoài và môi trường là: tT2 - t2 = 41 - 30 = 110C.
Nhiệt độ trung bình không khí gần ngoài mặt tường ngoài là: tm = (41 + 30)/2 = 35,50C.
Từ nhiệt độ này ta tìm được các thông số của khí: 1 1 1 𝛽 = = = 𝑇𝑚 273 + 35,5 308,5
Theo tài liệu [3] ta tìm được các thông số của không khí: 𝜆 = 2,65.10-2 W/mđộ n = 15,8.10-6 m2/s Pr = 0,70 1 3 9,81. .(1,5) .11 3
g..l . t 308,5 9 G = = = 4,72.10 r 2 6 − 2 v (15,8.10 ) Trong đó: -
g: gia tốc tự do g = 9,81 m/s. -
𝛽: hệ số trao đổi nhiệt -
𝛥𝑡: hiệu nhiệt độ tường và môi trường Dt = 110C -
𝜐 : độ nhớt động học. -
l: chiều cao hầm. l = 1,5(m).
Tiêu chuẩn Nuxen trong truyền nhiệt đối lưu tự nhiện bằng:
Nu = C.(Gr.Pr)n = 0,135.(4,72.109.0,7)1/3= 202
Vậy hệ số truyền nhiệt 𝛼2 bằng: 𝑁 202.2,65.10−2 𝛼𝑇 𝑢.𝜆 2 = = =3,57 W/m20K 𝑙 1,5
Như vậy dòng nhiệt truyền từ mặt ngoài tường hầm sấy vào môi trường bằng:
q2 = 𝛼2.𝛥𝑡2 = 3,57.11 = 39,5 W/m2.
Sai số giữa dòng nhiệt từ hầm sấy ra tường và từ mặt ngoài tường ra môi trường: 𝑞 39,5−39,025 Dq% = 2−𝑞1 = . 100=1,2%. 𝑞2 39,5
Sai số này < 5% nằm trong giới hạn cho phép của công thức trên nên ta chấp
nhận giả thiết trên là đúng.
Thay số vào cho trường hợp một vách, ta tính được hệ số truyền nhiệt K: 1 1 𝐾 = = = 2,13(W/m2 độ) 1 𝛿 1 1 0,15 1 + 1+ + + 𝛼1 𝜆1 𝛼2 11,15 1,45 3,57
Tổn thất qua hai tường bên là:
QT =3,6.KT.FT𝛥t =3,6 x 2,13 x 21,24 x (60 - 40) = 3257,37 kJ/h 3257,37 Hay: 𝑞𝑇 = = 1,92 kJ/kg ẩm 1700
3.5.5 Tổn thất nhiệt qua nền.
Công thức tính nhiệt lượng tổn thất qua nền: Qn = 3,6.Fn.qn [2]
Qn = 3,6 x 9,34 x 10 = 336,24 kJ/h. Trong đó: − Fn = Ftr = 9,34(m2)
3.5.6 Tổn thất nhiệt qua kết cấu bao che. Q4=QT + Qtr + Qc + Qn
Q4 = 3257,57 + 1291 + 291,6 + 336,24 = 5176,4(kJ/h). Hay: 𝑄 5176,4 𝑞 4 4 = = = 3,045 (kJ/kg ẩm) 𝑊 1700
3.5.7 Tổng các tổn thất nhiệt. QS =Q2 + Q3 + Q4 Thay số vào, ta được:
QS = 26250 + 3696 + 5176,4 = 45122,4 (kJ/h) Hay: 𝑄 45122,4 𝑞 𝛴 𝛴 = = = 26,54( kJ/kg ẩm). 𝑊 1700
3.6. Tính toán quá trình sấy thực.
3.6.1 Xác định lượng không khí thực tế cần cho quá trính sấy.
a> Lượng không khí.
+ Lượng không khí khô cần bốc hơi 1 kg ẩm: 1 1000 𝑙 = = = 71,07 kg kk/kg ẩm. 𝑑2−𝑑𝑜 31,13−17,06
+ Lượng không khí khô cần để bốc hơi W kg ẩm trong một giờ.
L = l.W = 71,07 x 1700 = 120819 kg kk/kg ẩm.
+Lượng tác nhân đi vào hầm sấy ( sau calorifer): L 1 = (1 + d0).L
L1 = (1 + 0,01706).120819 = 122880,2 kg/h.
+ Tương tự lượng tác nhân ở điểm 2 được tính: L 2= (1 + d2).L
L2 = (1 + 0.03113).120819 = 124580,1 kg/h.
b> Thể tích tác nhân trước và sau sấy:
V1 = L1.v1 = 122880,2 x 0,867 = 106537,1 m3/h.
V2 = L2.v2 = 124580,1 x 0,946 = 117852,8 m3/h.
Thể tích trung bình của tác nhân sấy trước và sau quá tình sấy thực là:
VTB = (V1 + V2)/2 = (106537,1 +117852,8)/2 = 112194,95 m3/h
VTB = 112194,95 /3600 = 31,16 m3/s
3.6.2 Cân bằng nhiệt và hiệu suất buồng sấy.
a> Cân bằng nhiệt.
Trước hết ta tính tổn thất nhiệt do tác nhân sấy mang đi Q5 và q5: Q5 = V.Ck(t2- t0) Trong đó:
• L- lượng tác nhân trung bình trước và sau hầm sấy; V=112194,95 m3/h
• Ck - nhiệt dung riêng của không khí; Ck = 1,005 kJ/kg độ.
• t2 - nhiệt độ không khí ra khỏi hầm sấy.
• t1 - nhiệt độ không khí ra ngoài trời
Thay các giá trị vào công thức trên ta có: nhiệt tổn thất do tác nhân mang đi:
Q5= 112194,95 x 1,005 x (45 - 25) = 2255118,5 kJ/kg ẩm. Hay: 𝑄 2255118,5 𝑞 5 5 = = = 1326,54 kJ/kg ẩm 𝑊 1700
3.6.3 Nhiệt lượng cần thiết để bốc hơi 1kg ẩm:
q1 = l.(h2 – h0) = 71,07.(125,59 – 68,579) = 4050 kJ/kg ẩm.
Hoặc nhiệt lượng cần thiết để bốc hơi W kg ẩm trong 1 giờ sẽ là:
Q1 = W x q1 = 1700 x 4050 = 6885000 kJ/h.
Ta có bảng cân bằng nhiệt sau đây: TT Đại lượng Ký hiệu kJ/kgẩm % 1 Nhiệt lượng có ích q1 4050 64,8 2
Tổn thất nhiệt do tác nhân sấy q5 1326,54 28,8 3
Tổn thất nhiệt do vật liệu sấy mang ra q2 15,44 1,4 4
Tổn thất nhiệt do xe mang ra q3 2,174 2,1 5
Tổn thất nhiệt ra môi trường xung quanh q4 3,045 2,9 6 Tổng nhiệt tiêu hao q 26,54 100 Hiệu suất hầm sấy: 𝑞 2396 𝜂 = 1 = . 100 ≈ 64,8% 𝑞 3695,4
3.7 Tiêu thụ năng lượng
Khối lượng than cung cấp cho calorife
Nếu lấy hiệu suất của buồng đốt là 𝜂 = 60% = 0,6.
Nhiên liệu ta sử dụng là than có các thành phần tính theo phần trăm như sau: • C = 36,70; • H = 2,70; • S = 3,2; • N = 0,7; • O = 11,1; • A = 20,60; • W = 25
Nhiệt dung riêng của nhiên liệu Cnl = 0,5 kcal/kg độ.
Nhiệt trị cao của nhiên liệu xác định theo công thức sau: Qc= 81.C+300.H - 26.(O - S) Thay số vào ta có:
Qc = 81 x 36,7 + 300 x 2,7 - 26 x (11,1 - 3,2) = 3577 kcal/kg. Qc = 14952 kJ/kg.
Chúng ta đã có nhiệt lượng tiêu hao cần cho quá trình sấy là: Q = 2289599,86kJ/h.
Vậy lượng than cần cho quá trình sấy là: 𝑄 2289599,86 𝑇 = = ≈ 235,6 𝑘𝑔/ℎ 𝑄𝐶. 𝜂 14952.0,65
Lượng đèn halogen sử dụng
Tổng năng lượng cần cung cấp cho quá trình nhận nhiệt từ bức xạ là 927 kW
Chọn loại đèn halogen 2000W, với hiệu suất chuyển đổi nhiệt n1= 0,95 , hiệu
suất chuyển đổi của bức xạ nhiệt n2= 0,7 .
Suy ra nhiệt lượng hữu ích của mỗi bóng đèn Qđèn = 2000.0,95.0,7 = 1330 W 927000
Số bóng đèn cần lắp đặt Nđèn = = 697 bóng đèn. 1330