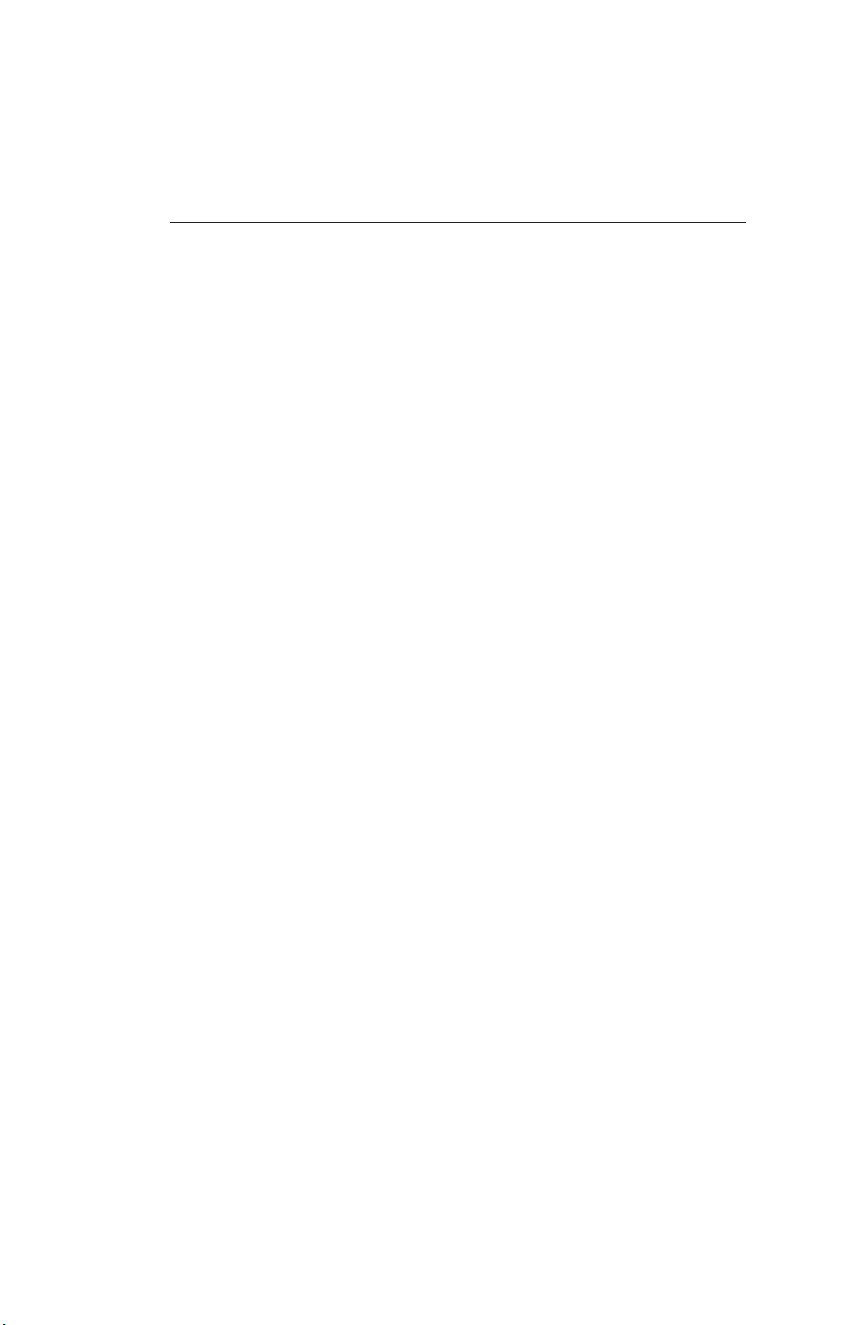
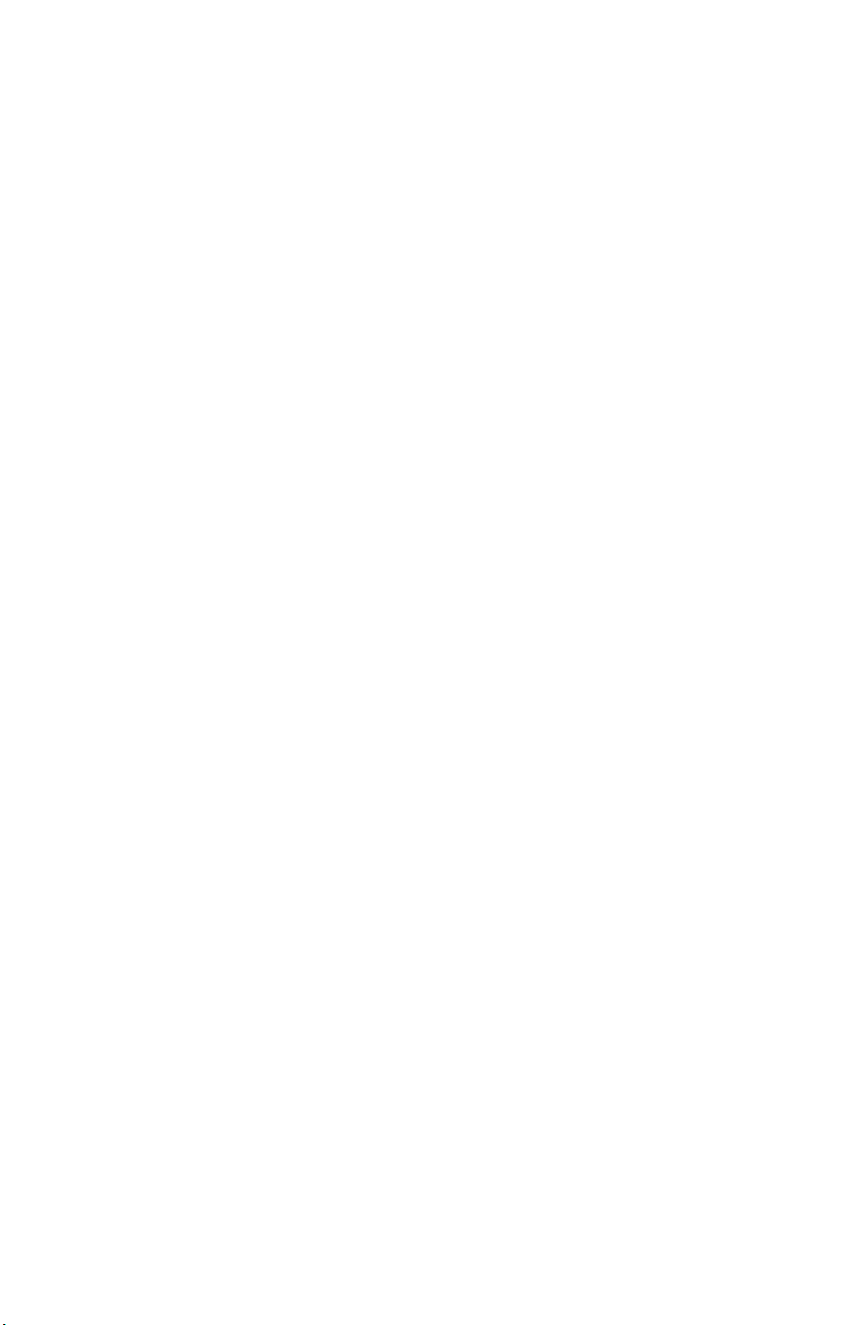
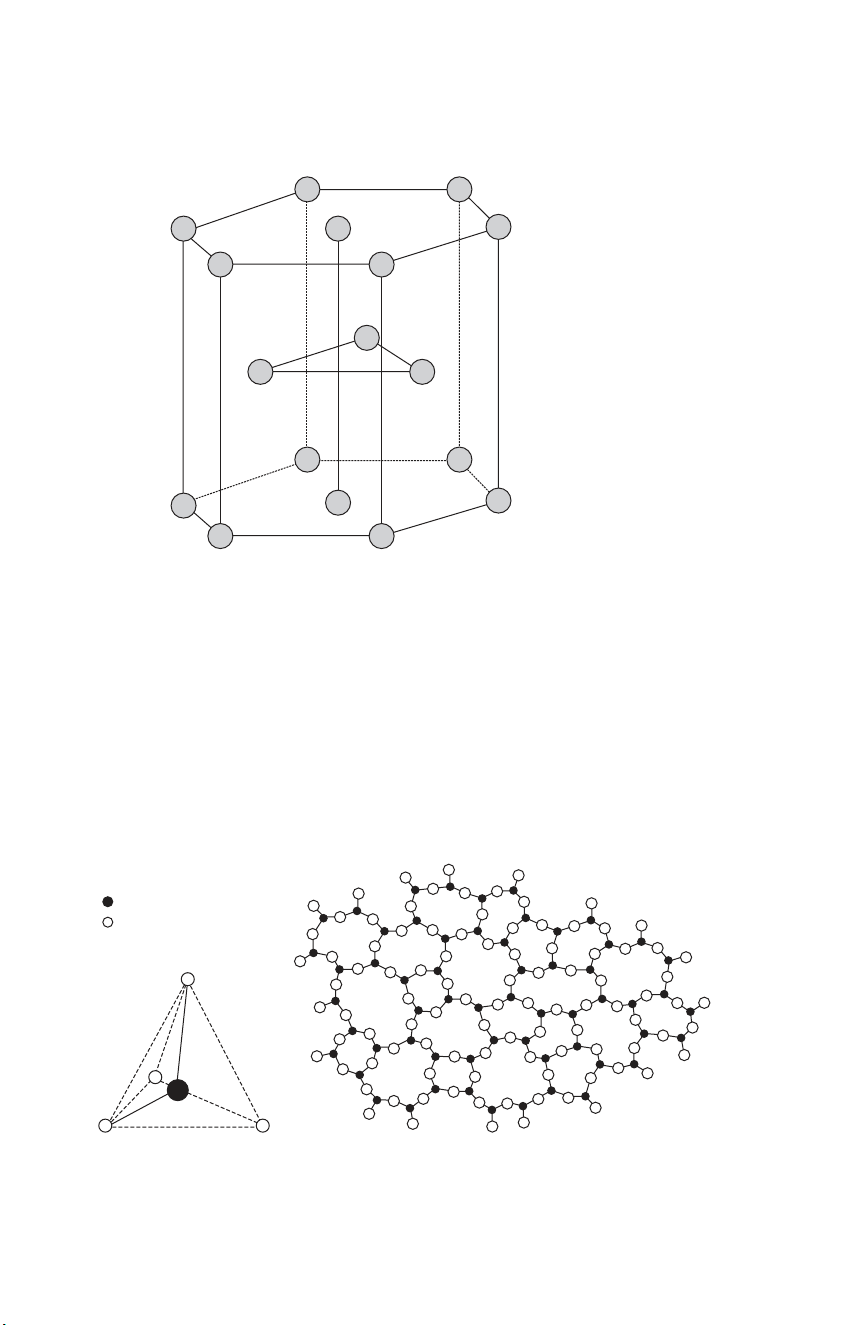
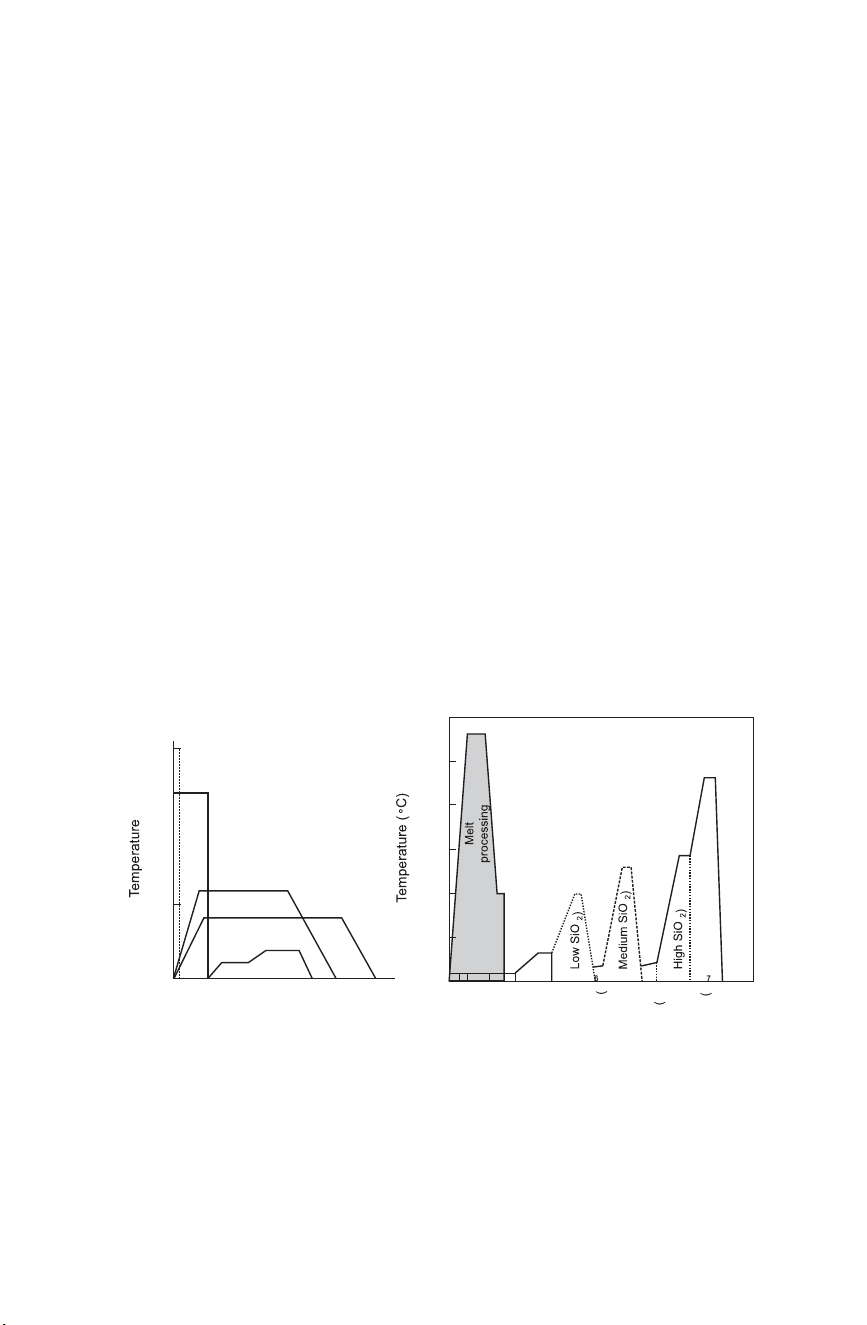
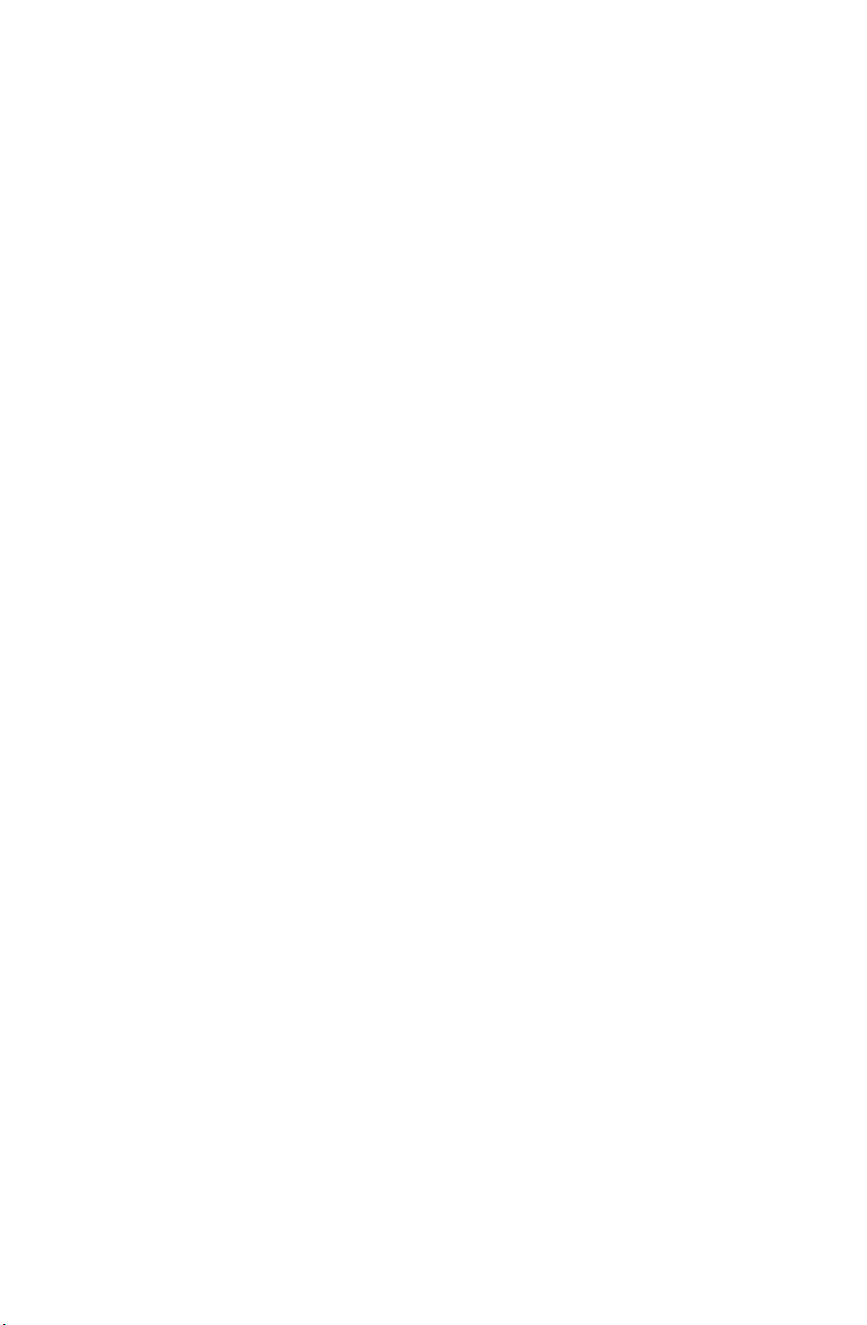
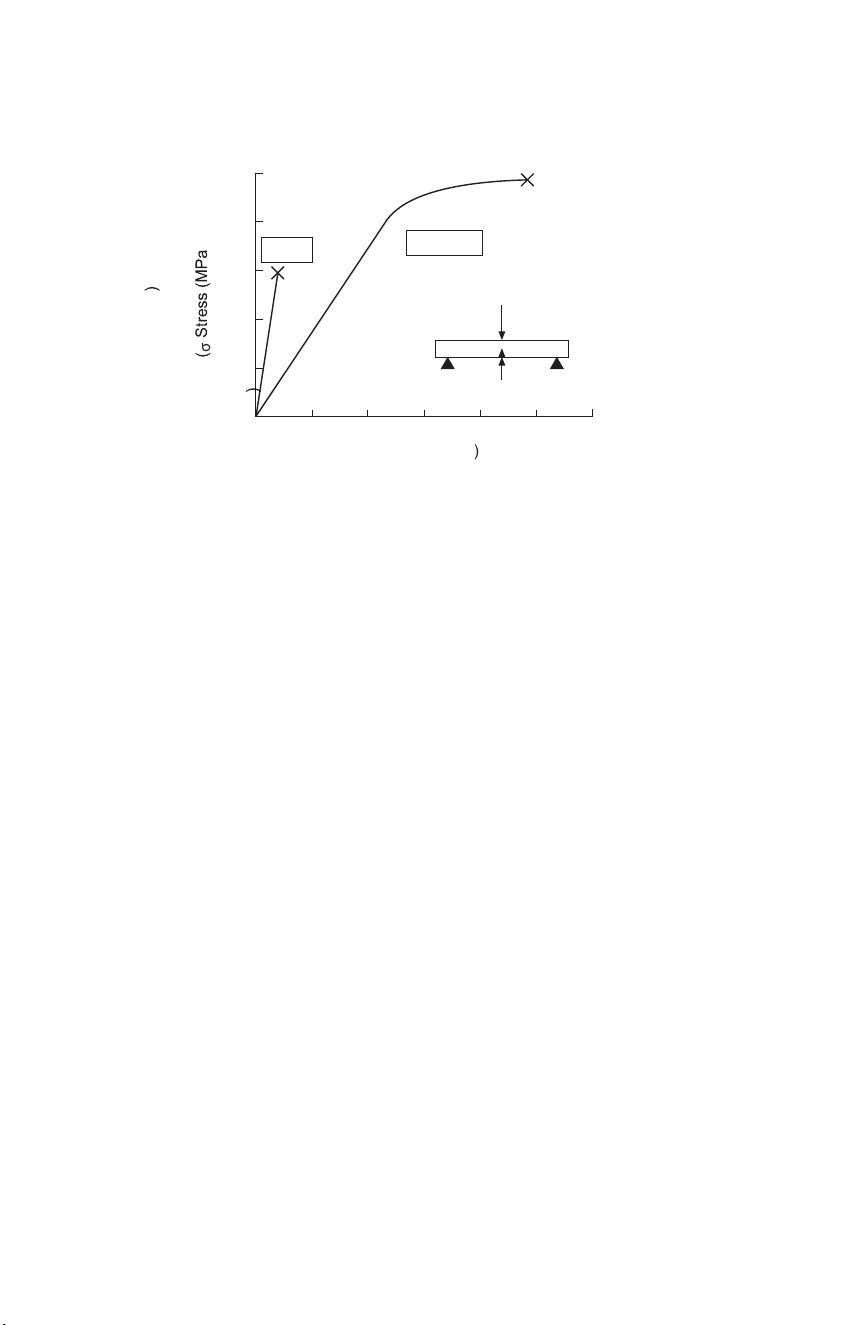
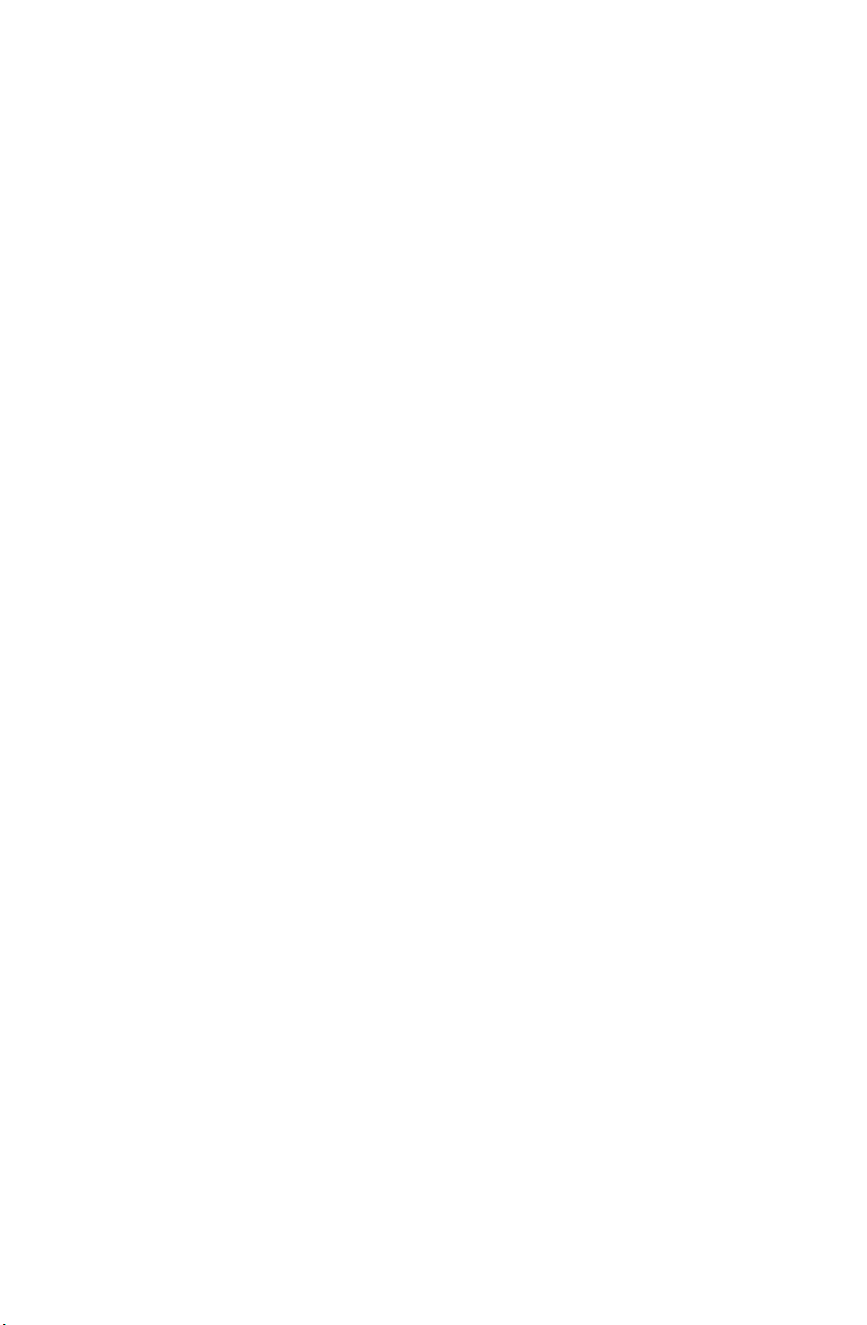
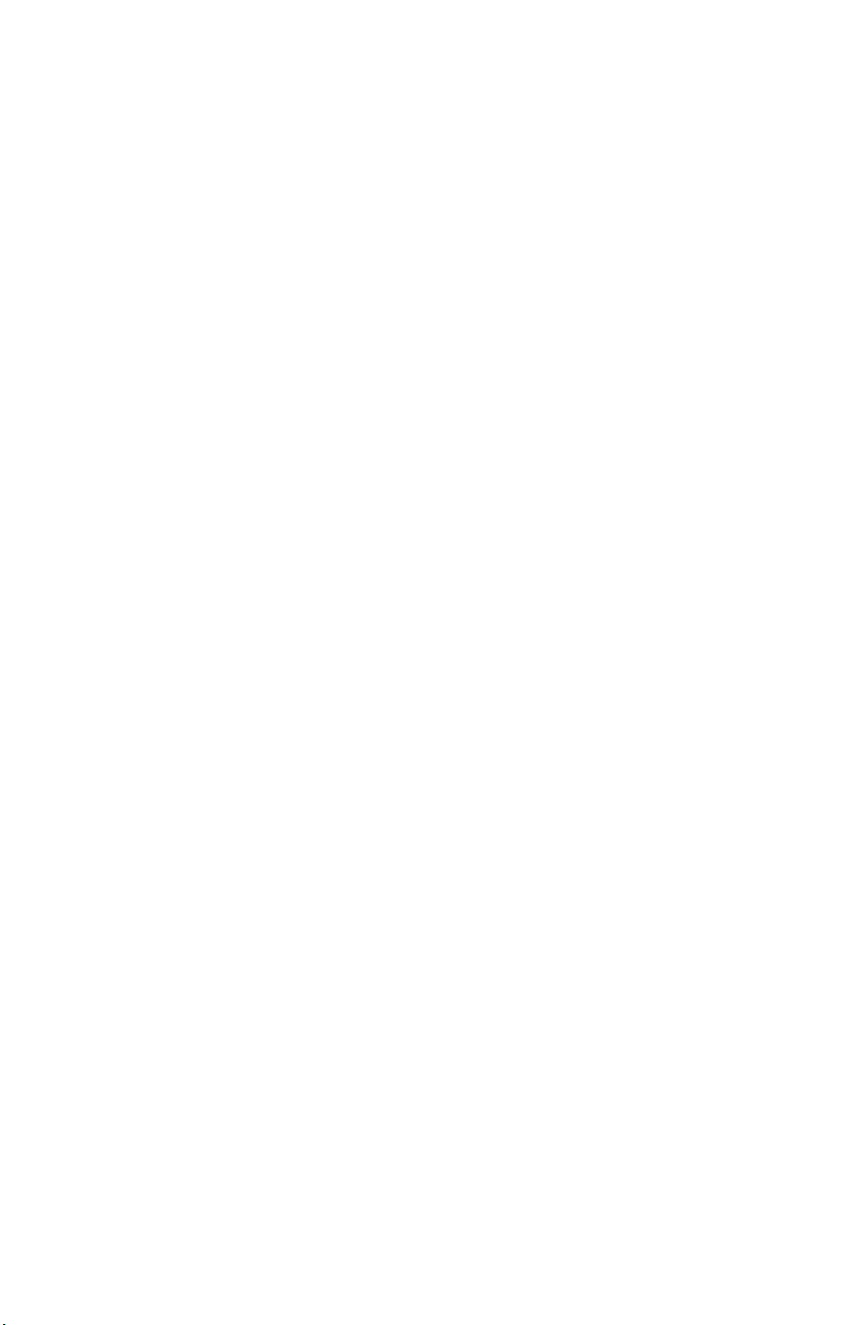
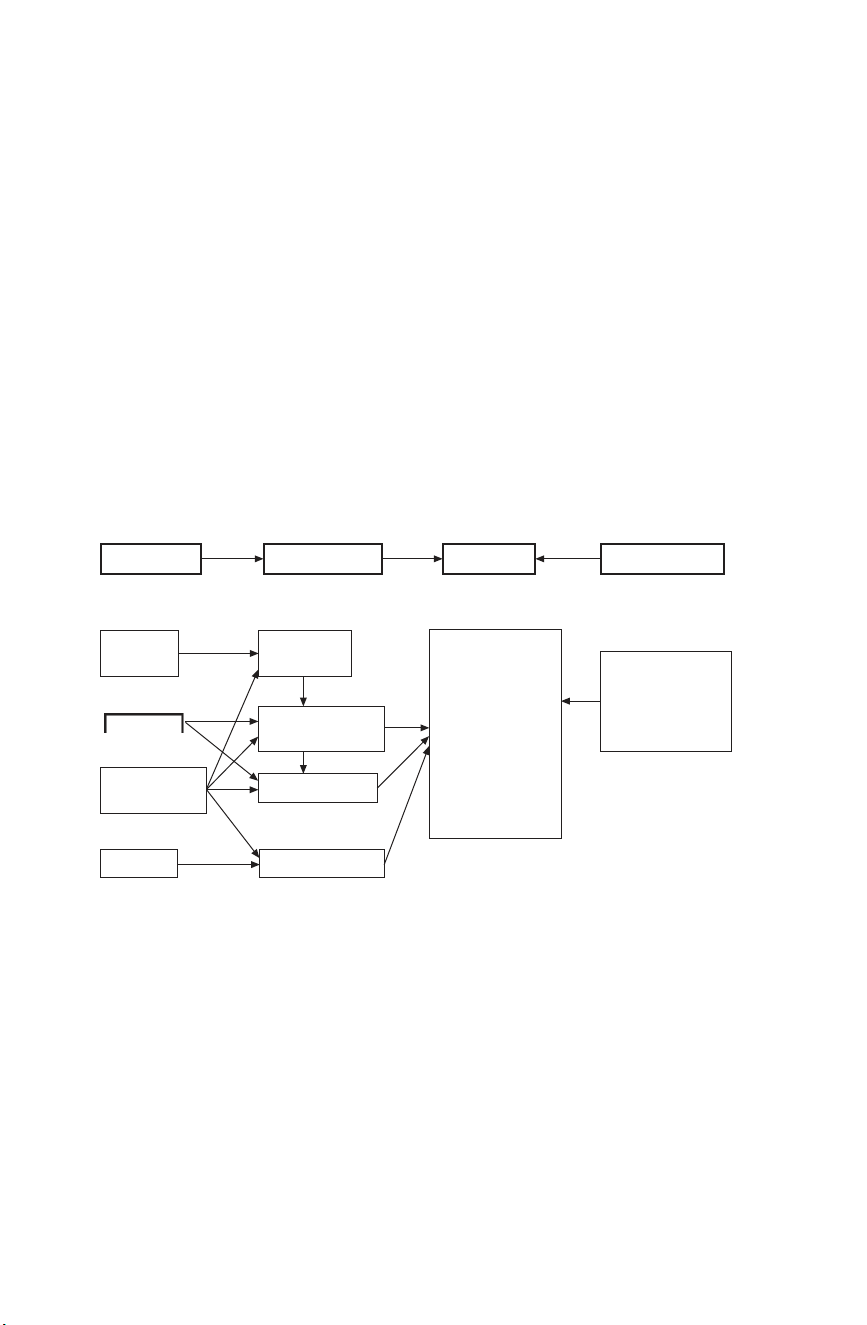
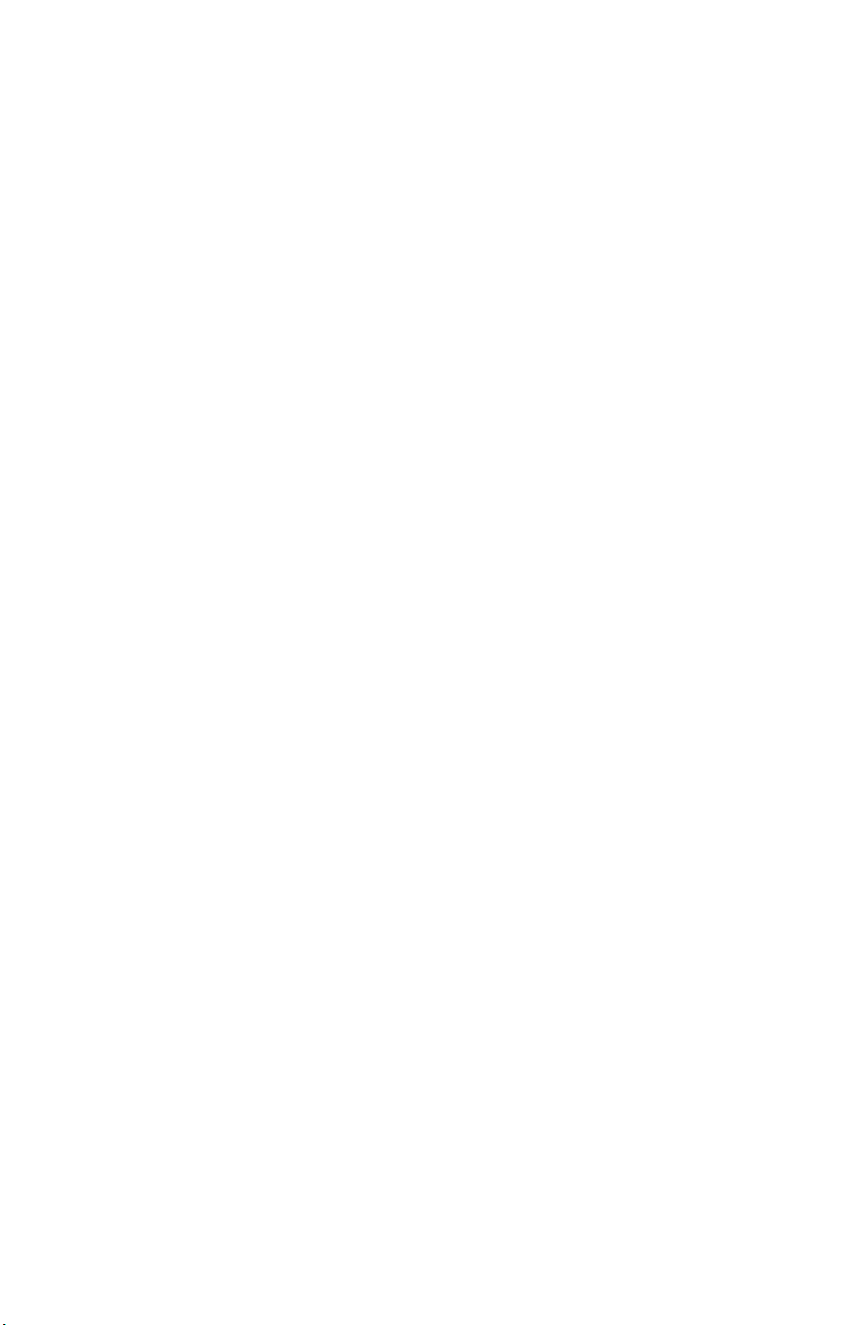
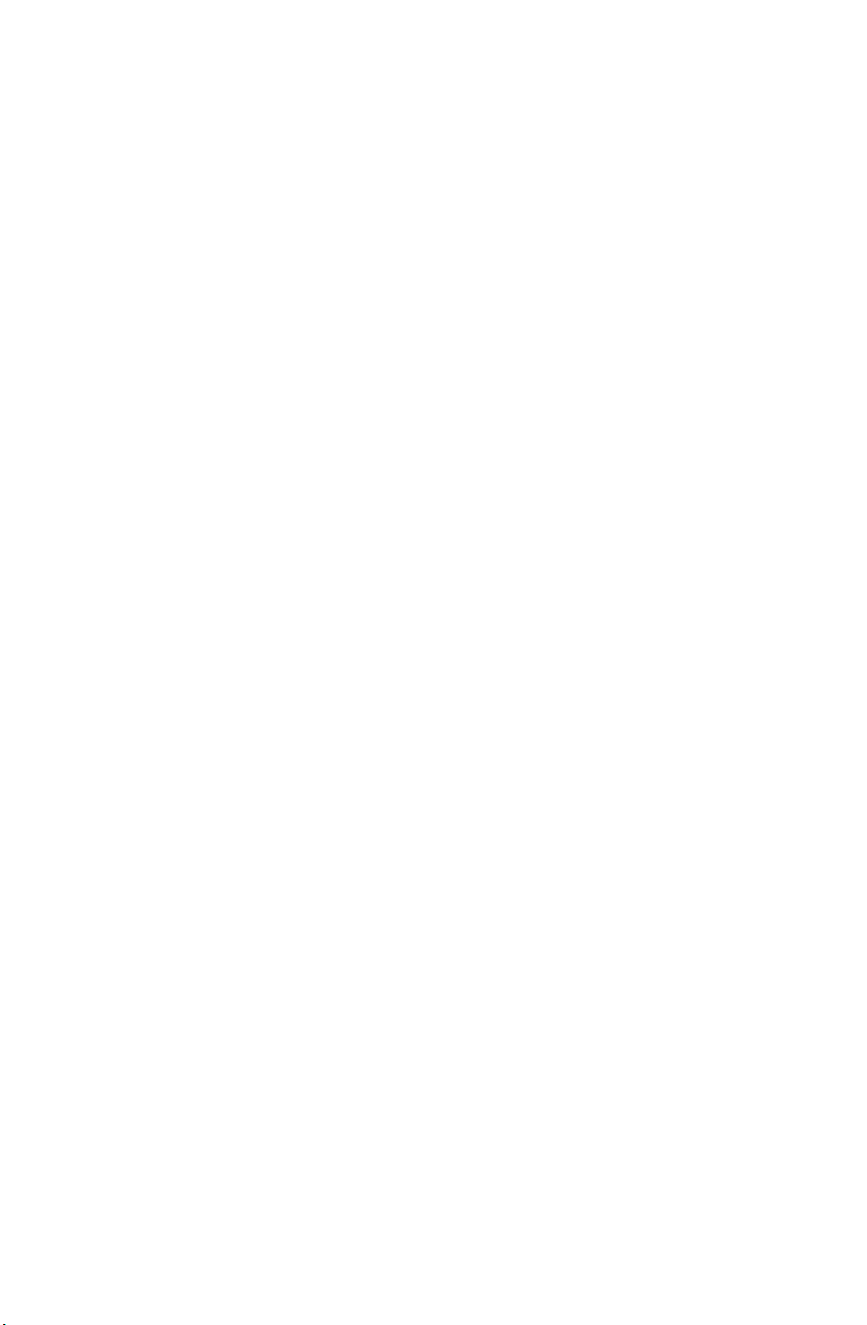
Preview text:
3 Ceramics
A L D O R. B O C C A C C I N I Imperial College London, UK 3.1 Introduction
Ceramics are solid materials composed of inorganic, non-metallic substances.
This definition includes ‘traditional’ ceramics such as porcelain, pottery and
cements but also ‘advanced’ or ‘engineering’ ceramics such as ferroelectrics,
non-metallic magnetic materials, bioceramics and structural oxide and
nonoxide materials. Ceramics exist as both crystalline and non-crystalline
(amorphous) compounds. Glasses and partially crystallised glasses, known as
glass-ceramics, are therefore subclasses of ceramics.
A common characteristic of all ceramic materials is that they are subjected
to high temperatures during manufacture or use (high temperature usually
means above 500 °C). Typically, but not exclusively, a ceramic is a metallic
oxide, boride, carbide or nitride, or a mixture or compound of such materials,
i.e. it includes anions that play important roles in their atomic structure and
properties. Major characteristics of ceramics are their high hardness,
insulating properties of heat and electricity, heat and corrosion resistance and
their brittleness and fracture behaviour without deformation.
Ceramics used for implants and in the repair and reconstruction of diseased
or damaged body parts are called ‘bioceramics’. Bioceramics are used mainly
to repair hard tissues such as bones, joints or teeth. Many ceramic
compositions have been tested for use in the body; however, only few have
achieved human clinical application. Examples of bioceramics are alumina,
zirconia, titania, tricalcium phosphate, hydroxyapatite, calcium aluminates,
bioactive glasses and glass-ceramics. Depending on the type of response in
the body, bioceramics can be broadly classified as bioinert, bioactive and
resorbable, as discussed further below. Three factors influence the choice of
ceramics and glasses as biomaterials: (i) physical and mechanical properties,
(ii) degradation of the material in the body, and (iii) biocompatibility. The
microstructure of the ceramic material, its properties and the processing routes Ceramics 27
used are all very strongly interrelated. This chapter introduces the reader to
general principles that explain some of the mechanisms behind 26
these factors. These can be applied to a wide variety of ceramics and glasses
but there will be a specific emphasis on ceramics with properties and
processes relevant to biomedical applications. 3.2
Atomic bonds and atomic arrangements in ceramics
Polycrystalline ceramics are solids in which the atoms or ions are arranged in
regular arrays. In glasses (amorphous materials), the regularity (order) is only
short-range. The type of atomic bonding and the atomic arrangement affect
the properties of the materials. Atomic bonding in ceramics is mainly ionic or
covalent, and usually a hybrid of these. The tendency towards ionic bonding
increases with increasing difference in the electronegativity of the atoms. In
ionic bonding there is a transfer of electrons between the atoms making up the
compound. Positively charged ions balance out the negatively charged ions to
give an electrically neutral compound. One example is NaCl, where Na+ ions
balance the Cl– ions. In covalent bonding, electrons are shared between atoms.
The crystal structure determines how atoms are able to slip over one another
when a material is deformed. If it is difficult for the atoms to slide over one
another, the material is likely to break and is brittle, if the atoms slide easily
over one another, the material can deform and it is ductile. The characteristic
brittleness and high strength of ceramics can be traced, therefore, to the ionic
and covalent bonding types: they cause a very high inherent resistance to
dislocation motion in the lattice and thus to plastic deformation. Therefore,
unlike in metals, a stress concentration at a crack tip in a ceramic cannot be
relieved by plastic deformation and the material fails in a brittle fashion.
The spatial arrangement of individual atoms in a ceramic (the crystalline
structure) depends on the type of bonding, the relative sizes of the atoms and
the need to balance the electrostatic charges. CD Figs. 3.5–3.7 show
schematics of the unit cells of the types of crystal structures found in ceramics.
Most ceramic crystal structures are variants of the face centred cubic (f.c.c.,
CD Fig. 3.5) or hexagonal close packed (h.c.p., Fig. 3.1 and CD Fig. 3.7)
structures. Typically, the metallic cations occupy interstitial positions in a
lattice made of non-metallic ions.
The most common crystal structures in ceramics are:
1. simple cubic, e.g. CsCl, CsBr, CsI;
2. close packed cubic: this is a variant of the face-centred cubic (f.c.c.)
structure, e.g. CaO, MgO, FeO, BaO, etc;
3. closed packed hexagonal, e.g. Al2O3, Fe2O3, Cr2O3, etc. 28
Biomaterials, artificial organs and tissue engineering
Alumina (Al2O3) is the most important crystalline bioceramic as it is used in
joint replacements (Chapter 13). Its h.c.p. crystal structure is shown in Fig. 3.1 and in CD Fig 3.7. 3.1
Unit cell of a hexagonal close packed (h.c.p.) crystal latticestructure (CD Fig. 3.5).
Glasses, as a subclass of ceramics, constitute the most important group of
non-crystalline solids. Glasses are amorphous materials of very high viscosity,
which behave like solids. Glasses maintain a disordered atomic structure
characteristic of a liquid, i.e. they do not undergo transformation to a
crystalline state. Silicate glasses are made up of a network of tetrahedra of four
large oxygen ions with a silicon ion at the centre (Fig. 3.2, CD Figs. 3.15, 3.16,
19.12, 19.13). Each oxygen is, however, shared by two tetrahedra, giving the
bulk composition of SiO2. The basic silicate network can incorporate virtually = Silicon atom = Oxygen atom ( a ) ( b ) 3.2
Glassy structure. (a) A silica tetrahedron and (CD Fig. 3.15, CD Fig.19.13)
(b) a randomised network of silica tetrahedra (CD Fig. 3.16, CD Fig. 19.12). Ceramics 29
all atoms of the periodic table of elements, and thus silicate glasses of
numerous different compositions and properties can be obtained. Silicate
glasses are therefore the most common and technologically the most important
group of glasses. One of the major advantages of glasses is the ease of
fabrication, which allows processes such as melt infiltration and compression moulding to be used.
Glass-ceramics represent a special class of ceramics. They are
polycrystalline materials having fine ceramic crystallites (usually of size < 1
µm) in a glassy matrix. They are produced by the controlled crystallisation of
glasses using suitable heat treatments. Glass-ceramics of technical relevance
are, for example, in the systems Li2O–Al2O3–SiO2 (LAS), MgO–Al2O3–SiO2
(MAS), e.g. cordierite (2MgO.2Al2O3.5SiO2) and SiO2–Al2O3–MgO–K2O–F, e.g. fluoromicas.
Figure 3.3(a) (CD Fig. 3.8(b)) summarises the time–temperature profiles
used in processing melt-derived glasses and ceramics and glass-ceramics that
have been produced by melt processing, sintering or hot pressing. Figure
3.3(b) (CD Fig. 3.9) shows the time-dependent processing steps for sol–
gelderived glass production and compared to melt processing. The thermal
processing of sol–gel-derived glasses and ceramics involves much lower
temperatures, but melt processing is less time consuming, due to the carefully
controlled thermal processing required to create crack-free sol–gel derived glasses. 1500 Process steps T 1 Mixing M 2 Casting 3 Gelation 4 Ageing T M Path 5 Drying 1000 (1) (2) (5) 6 Stabilisation (6) 7 Densification Bioactive glass (3) powder T 500 S (2) (4) 5b 5 (1) a 1 2 3 4 5 6 6 6 7 0 Log time Relative time ( a ) ( b) 3.3
(a) Time–temperature profiles of processing steps for (1) glass, (2)cast
polycrystalline (large grained) ceramic, (3 and 4) solid-state sintered ceramic, (5)
polycrystalline glass-ceramic, (6) polycrystalline coating from liquid, Tm is the
melting temperature, Ts is the solidus line of the phase diagram (CD Fig. 3.8(b)). (b)
Processing steps for sol–gel-derived glass production compared to melt processing (CD Fig. 3.9). 30
Biomaterials, artificial organs and tissue engineering 3.3
Microstructure of ceramics
Ceramics are rarely used as single crystals. They are more commonly
polycrystalline and may be mixtures of two or more different crystalline
phases. Sometimes, a glassy phase is also present. Each phase is physically
and chemically distinguishable from the next. Different phases vary in crystal
structure and/or composition. The arrangement of the crystals (grains) and of
the different phases constitutes the microstructure of the material. The
microstructure depends on the initial fabrication techniques, raw materials
used, phase changes, chemical reactions and grain growth occurring during
the high temperature processing (see Section 3.5). In general, ceramic
microstructures consist of individual crystals (grains) separated by boundary
layers, often containing a glassy phase, the grain boundaries, and gas filled
pores. A wide range of grain sizes is observed, generally 1–1000 µm. Porosity
may be fine or coarse, open or closed. Ceramic microstructures can be
observed after polishing the materials by using optical microscopes. One
particular phase, or the grain boundaries, may be highlighted by chemical or
thermal etching. Features smaller than ~ 1 µm on polished sections and
fracture surfaces can be observed using electron microscopes.
The microstructure of any material is important as it affects the material’s
mechanical and physical properties. In particular, the grain size and shape,
grain size distribution, nature of grain boundaries and pore structure are very
important parameters. In contrast to polycrystalline ceramics, there are no
microstructural features in glasses, which appear homogeneous under optical
or electron microscopes, whereas glass-ceramics microstructures are
characterised by a dispersion of crystals, usually of micrometre size, dispersed
in a continuous glassy matrix. 3.4
Mechanical properties of ceramics
Elastic modulus, fracture strength, fracture toughness
When a force is applied to a material, an opposing force exists within the
material. This opposing force is measured as a force per unit area giving the
stress in the material. The stress causes the material to deform. The ratio of
the deformation to the original dimension is the strain (CD Fig. 3.19). Initially,
there is a linear relationship between the stress and the strain (Fig. 3.4). The
gradient of the stress–strain dependence is the elastic modulus or Young’s
modulus and this is a material property. If the stress is removed during this
(initial) stage of the deformation, the material will return, instantaneously, to
its original dimensions. This reversible behaviour is called elastic
deformation. The elastic properties of ceramics determine their mechanical
behaviour and are closely related to the crystal structure and atomic bonding. Ceramics 31
Elastic constants are also strongly dependent on the microstructure. In particular, porosity has Fracture 1000 Yield 800 Ti 6 Al 4 V Al 2 O 3 600 Fracture Tensile or bending strength 400 200 Fracture 0 0 2 4 6 8 10 12 ( ε ) Strain (% )
3.4 Stress–strain graph for an alumina ceramic compared with a metal alloy.
a significant effect on elastic constants, which decrease with increasing pore
content. Besides pore content, pore shape and pore orientation also affect the
elastic behaviour of ceramics and glasses.
Ceramics and glasses break immediately after they have undergone a
critical amount of elastic deformation; metals, however, begin to undergo a
second stage of plastic deformation before fracture (see Chapter 2). The
maximum tensile stress that can be applied to a material before it fractures is
called the tensile strength of the material. The common strengths of ceramics
are one or two orders of magnitude less than the theoretical values calculated
from interatomic forces. This is because the fracture of ceramics and glasses
normally occurs by the propagation of cracks or flaws existing in the materials,
as discovered by Griffith in 1920. These cracks have a stress concentrating
effect, which weakens the material. The ease with which a sheet glass can be
‘cut’ after light scribing with a sharp diamond tip is a demonstration of this
effect. The concentrated stress at the tip of a narrow crack is inversely
proportional to the radius of curvature at the crack tip; thus sharp cracks are
more detrimental to tensile strength than rounded flaws. Typical flaws in ceramics are:
1. processing-induced flaws, such as inclusions, pores, isolated large grains,
glassy grain boundaries and machining-induced surface cracks;
2. design-induced flaws, such as sharp corners, holes, etc;
3. service-induced flaws, mainly due to environmental degradation, thermal
stresses, impact loads and wear.
Porosity is one of the most common defects in ceramics, which also negatively
affects strength. Careful processing can eliminate many flaws or reduce the
flaw size. The size of the crack strongly affects the strength of the material. 32
Biomaterials, artificial organs and tissue engineering
The fracture strength (σ) of a ceramic or glass material containing an
internal crack of length 2c is given by the Griffith’s relationship:
σ = (2E γ/c)1/2 [3.1]
where E is the Young’s modulus and γ is the surface energy of the crack surface.
There are other important properties that can be read from the graph of
stress against strain. Toughness is a measure of the resistance of a material to
crack propagation and one way of measuring toughness is as the area under
the stress–strain graph. This area is proportional to the energy required to
fracture the specimen. A low energy is found for brittle materials, such as
ceramics and glasses, which often fail with little or no warning. The
relationship between fracture toughness (KIc) and tensile strength in a ceramic
containing a crack of length 2c is given by the following relationship: KIc = σYc1/2 [3.2]
where Y is a dimensionless constant which depends on the geometry of the
loading and the crack configuration.
The incorporation of particles or fibres into ceramic and glass matrices,
forming composite materials, is a common method used to increase the
toughness of these brittle materials (Chapter 5). Ceramic composites are also
more resistant to sudden impact loads. The low fracture toughness of ceramics
and glasses is the greatest impediment to their broader use in load-bearing
orthopaedic applications in the human body. However, bioceramics find broad
applications as coatings on metallic implants in load-bearing orthopaedic
applications and in a variety of other areas in the muscoskeletal and dental
fields not involving high loads. Subcritical crack growth
Time under stress is a very important parameter when considering the strength
of ceramics. The strength of ceramics under constant load changes with time.
The time dependence of strength is due to subcritical crack growth occurring
under stress, which is often assisted by environmental factors, such as water
from the environment. Below a certain value of stress intensity factor, KI0, no
crack growth occurs. At higher values of KI, subcritical crack growth occurs
at a constant rate, which depends mainly on the diffusion of corrosive species
from the environment (e.g. body fluids in case of a bioceramic) to the crack
tip. Safe operation of ceramic components is under conditions leading to stress
intensity factors below KI0. Ceramics 33 Hardness and wear
The hardness of a material is a measure of its resistance to localised
deformation by indentation or scratching and is one of the easiest mechanical
properties to measure. A small indentor is pressed into the surface of the
material and the size of the indent formed is measured to calculate a hardness
value. The hardness and fracture toughness of a ceramic influence its wear
behaviour when there is relative motion between two surfaces. The wear will
also depend on the presence of any lubrication, the roughness of the sliding
surfaces, the chemical environment and the loading conditions. Wear is
important not only due to the damage caused to the component but also due
to the generation of undesirable debris, which, in the case of bioceramics, can
lead to failure of the component (implant) and/or inflammatory responses in the surrounding tissue. 3.5 Processing of ceramics
There are several methods for producing glasses and ceramics. The following
steps are involved in the conventional processing of ceramic components:
1. The starting material is usually in the form of a powder, slurry or a colloidal suspension.
2. A preliminary component is formed, which is called a green body. The
green body has the shape of the final component but is generally of lower
strength. In the case of powders, this is done by pressing to produce a
powder compact. In the case of colloidal suspensions and slurries, several
methods can be used, e.g. tape and slip casting, injection moulding,
pressure filtration and electrophoretic deposition.
3. The green body is heat treated (sintered) to increase density and strength
of the component. Frequently, a combination of high temperature and
pressure (hot-pressing and hot isostatic pressing) is used.
4. The sintered dense compact is machined to the final required shape.
The conventional processing of glass involves the melting of raw materials,
followed by casting; however, several products for biomedical applications,
made, for example, of bioactive glasses, are prepared by the ‘ceramic powder
methods’ described above. Sintering is the most important process used for
consolidating ceramic and glass powders. This technique involves atomic
diffusion processes in the case of polycrystalline ceramics and viscous flow
in the case of amorphous glasses. Other techniques used for producing
ceramic and glass components involve chemical routes, which usually lead to
a high degree of homogeneity on a molecular scale and consequently high
purity products can be obtained. The sol–gel process belongs to this category.
The sol–gel process has extensive application for production of porous and
foamlike bioactive glasses, ceramics and ceramic coatings. This process 34
Biomaterials, artificial organs and tissue engineering
involves the hydrolysis of silicon alkoxide in solution to form a colloidal
solution (sol) and the subsequent chemical polymerisation (condensation
reaction) of the silica units to form gel. The gel is heat treated to dry it and
form a glass or ceramic structure at temperatures much lower than those used for powder sintering. 3.6
Impact of fabrication on microstructure and properties
The microstructure and composition of a material determines many of its
physical, and all of its mechanical, properties. The microstructure is
determined by the processing conditions and the composition. The evolution
of the microstructure during processing (for example, densification during
sintering) may limit the processing operations that can be performed.
Alternatively, microstructures that may result in poor properties of the finished
component may form in the work piece. The complex interaction between
fabrication, microstructure, mechanical properties and external factors (e.g.
temperature, environment conditions) is given in Fig. 3.5. Fabrication Microstructure Properties External factors Raw Chemical Fracture strength material composition Temperature, Elastic modulus environment and test Processing Phase distribution Fracture conditions and grain size toughness Wear resistance Heat treatment Pores and cracks ( e.g. sintering ) Hardness etc. Finishing Surface condition
3.5 The interaction between fabrication conditions, microstructure, mechanical
properties and external factors in ceramic materials (modified from Davidge, 1979). 3.7 Clinical requirements
Bioceramics are used mainly for repair and reconstruction of diseased or
damaged parts of the musculoskeletal system. The choice of a particular
bioceramic for a given application will depend on the type of bioceramic/
tissue attachment required. Dense, non-porous, almost inert ceramics such as
Al2O3 and ZrO2 attach by bone growth into surface irregularities by cementing
the device into the tissue, or by press-fitting into a defect (mechanical
fixation). If these implants have pores with diameters in excess of 100 µm,
bone ingrowth can occur, which anchors the bone to the material (biological Ceramics 35
fixation). In surface reactive ceramics, such as hydroxyapatite and certain
compositions of silicate glasses and glass-ceramics are used, the materials
attach directly by chemical bonding with the bone (bioactive fixation).
Bioactive ceramics are also used as coatings on metallic implants. Resorbable
ceramics and glasses in bulk or powder form are designed to resorb in the
body at the similar rate of formation of new bone. Some bioactive glass
compositions, particularly in the system SiO2–CaO–Na2O–P2O5 also bond to
soft tissues. Bioceramics, therefore, have high potential to be used as porous
scaffolds for tissue engineering applications (Chapter 19).
For a ceramic material to be used as a biomaterial, it must have adequate
physical, biological and mechanical properties to perform its function. The
major challenge facing the use of ceramics in the body as permanent implants
is to replace old, deteriorating bone with a material that can function for the
remaining years of the patient’s life. Survivability of a bioceramic requires
formation of a stable interface with living tissue. If interfacial movement can
occur, the implant loosens rapidly. Loosening invariably leads to clinical
failure, in the form of fracture of the implant or the bone adjacent to the
implant. In case of using (almost) inert bioceramics, bone at the interface is
very often structurally weak because of disease, localised death of bone, or
stress shielding that occurs because the higher elastic modulus of the implant
prevents the bone from being loaded properly. The attachment and bonding of
(almost) inert implants (both metallic and ceramic) to bone can be enhanced
by using designed porous structures or by using bioactive ceramic materials,
such as hydroxyapatite or bioactive glasses, as coatings. The potential
advantage offered by porous ceramics is the mechanical stability of the
interface that develops when bone grows into the pores. Lower mechanical
strength and brittleness are the disadvantages associated with porous ceramic
implants that have restricted their uses primarily to non-load-bearing applications.
Resorbable bioceramics are designed to degrade gradually over time and
be replaced by the natural host tissue. In fact, this could be seen as the optimal
solution to biomaterials problems. However, developments of resorbable
ceramics present complications, mainly due to problems related to matching
the rate of resorption with the replacement by the natural host tissue and
maintenance of strength and stability of interfaces during the degradation
period. The rate of tissue growth varies from patient to patient and with tissue type.
Another approach to the solution of the problems of interfacial attachment
is the use of bioactive materials. These are materials that elicit a specific
biological response at the interface of the material, which results in the
formation of a bond between the tissues and the material. As mentioned above,
hydroxyapatite and selected compositions of silicate glasses (e.g. Bioglass®)
and apatite–wollastonite glass-ceramics are bioactive. In fact, bioceramics that
are both resorbable and bioactive constitute the ‘thirdgeneration’ biomaterials, 36
Biomaterials, artificial organs and tissue engineering
which find applications as scaffolds in osseous and soft tissue engineering. In
these applications, the bioactive ceramic can be formed into a porous (foam-
like) structure with tailored pore size and orientation or it can be used as a
filler or coating in resorbable polymers, forming optimal scaffolds exhibiting
both resorbability and bioactivity (Chapter 19).
The mechanical properties of bioceramics, in particular their low fracture
toughness are disadvantages for their direct use as bone replacement in
loadbearing applications. Usually, bioceramics are combined with polymers
and metals effectively forming composite materials with enhanced mechanical
properties and elastic constants matched to those of bone. 3.8 Summary
This chapter has introduced the reader to ceramics (and glasses), describing
some of their distinguishing properties due to the nature of the atomic bonds
and, in the case of polycrystalline ceramics, their crystalline structure. The
concept of a microstructure within a ceramic material was introduced, paying
attention to grain size, porosity and flaws existing in all ceramics used in
practical applications. The definition and measurement of several mechanical
properties including elastic modulus, fracture strength, fracture toughness,
subcritical crack growth, hardness and wear were described, focussing on the
brittle and flaw-sensitive nature of the ceramic fracture mode. Processing
methods for ceramics were discussed and the influence of processing
conditions on the microstructure and hence the properties of ceramic materials
was emphasised. Finally, general clinical requirements and examples of
ceramics used in biomedical applications were mentioned. 3.9 Reading list
Chawla K.K., Ceramic Matrix Composites, London, Kluwer Academic Publishers, 2003.
Davidge R.W., Mechanical Behaviour of Ceramics, Cambridge, Cambridge University Press, 1979.
Green D.J., An Introduction to the Mechanical Properties of Ceramics, Cambridge,
Cambridge University Press, 1998.
Hench L.L. and Wilson J., An Introduction to Bioceramics, Singapore, World Scientific, 1993.
Kingery W.D., Introduction to Ceramics, New York, J. Wiley & Sons, 1976.
Rice R.W., Mechanical Properties of Ceramics and Composites: Grain Size and Particle
Effects, New York, Marcel Dekker, 2000.