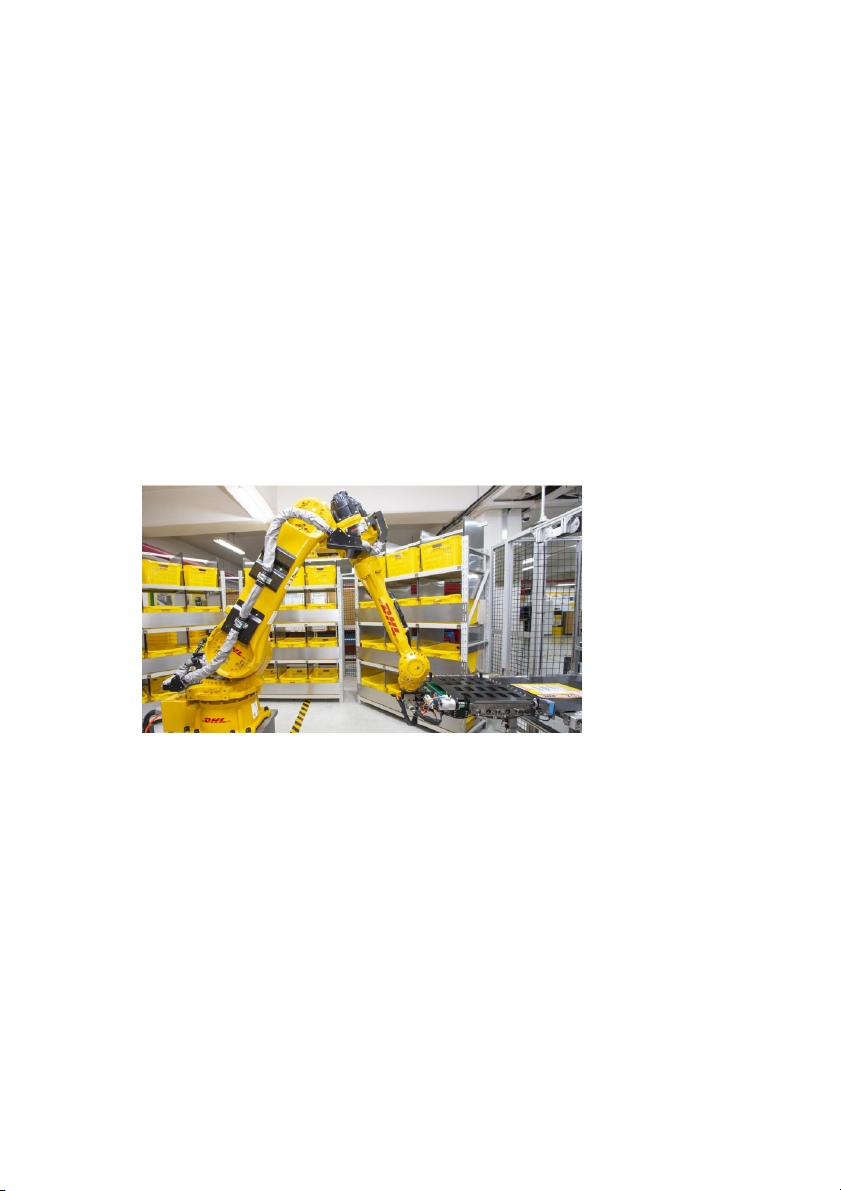
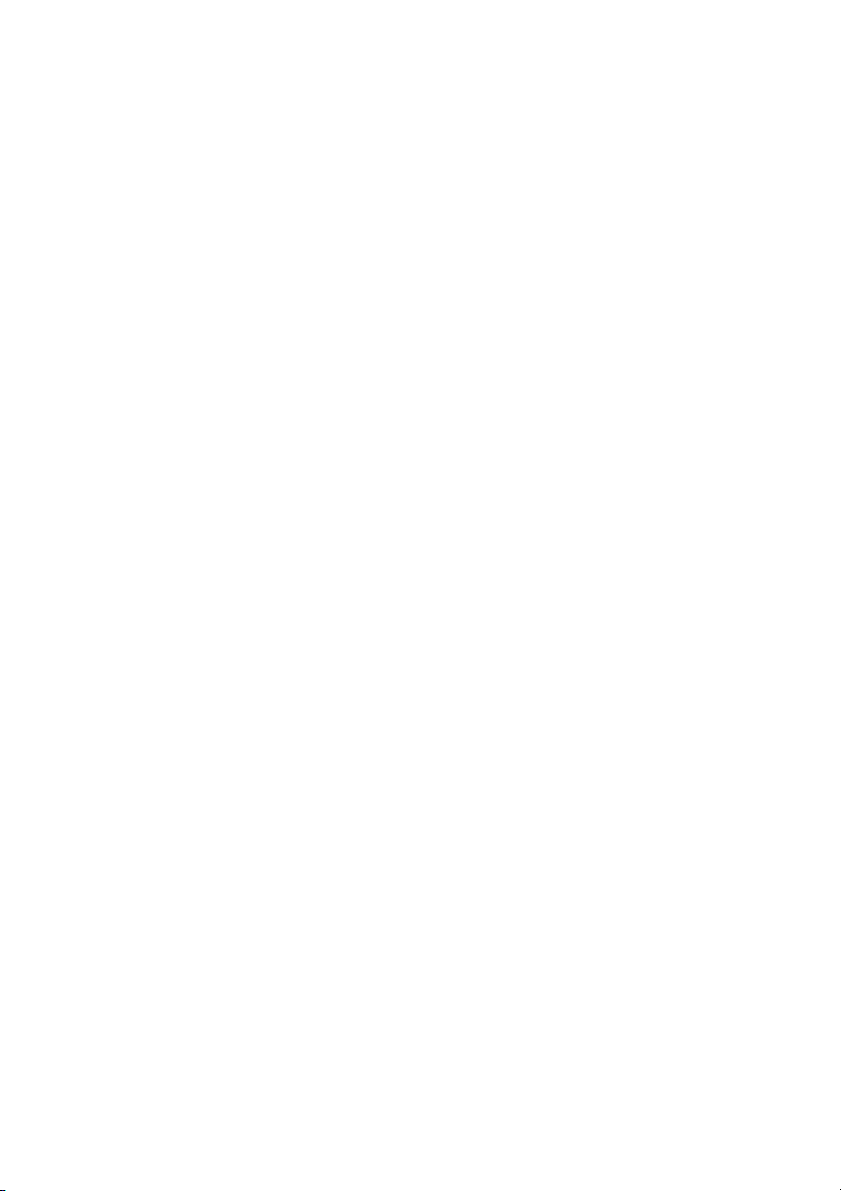
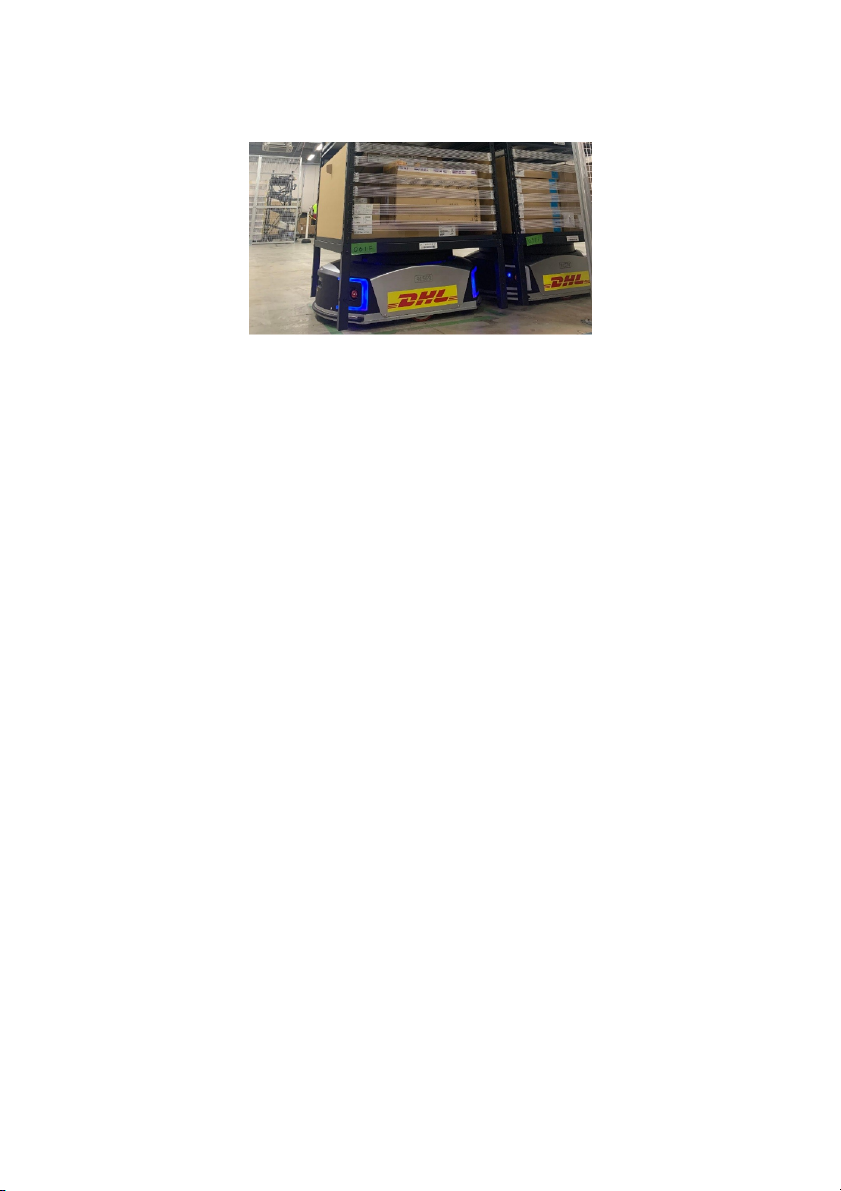
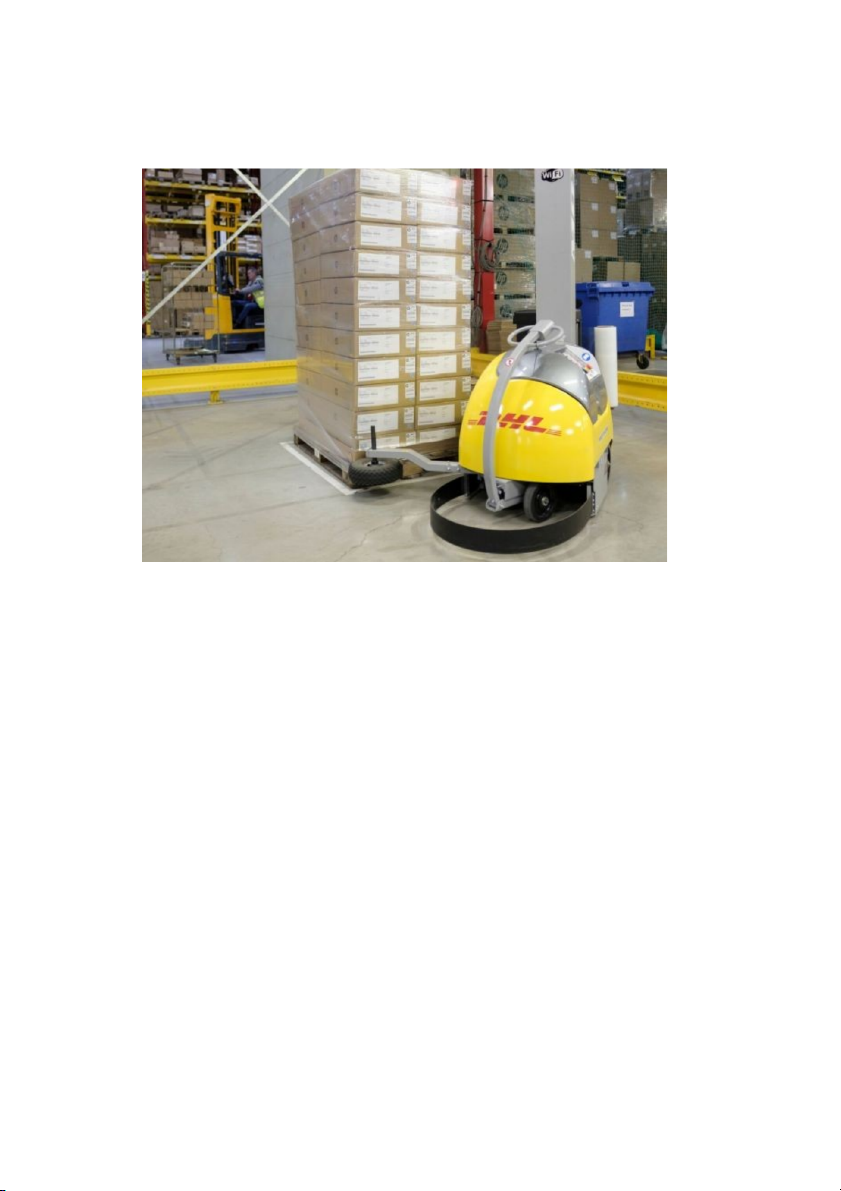
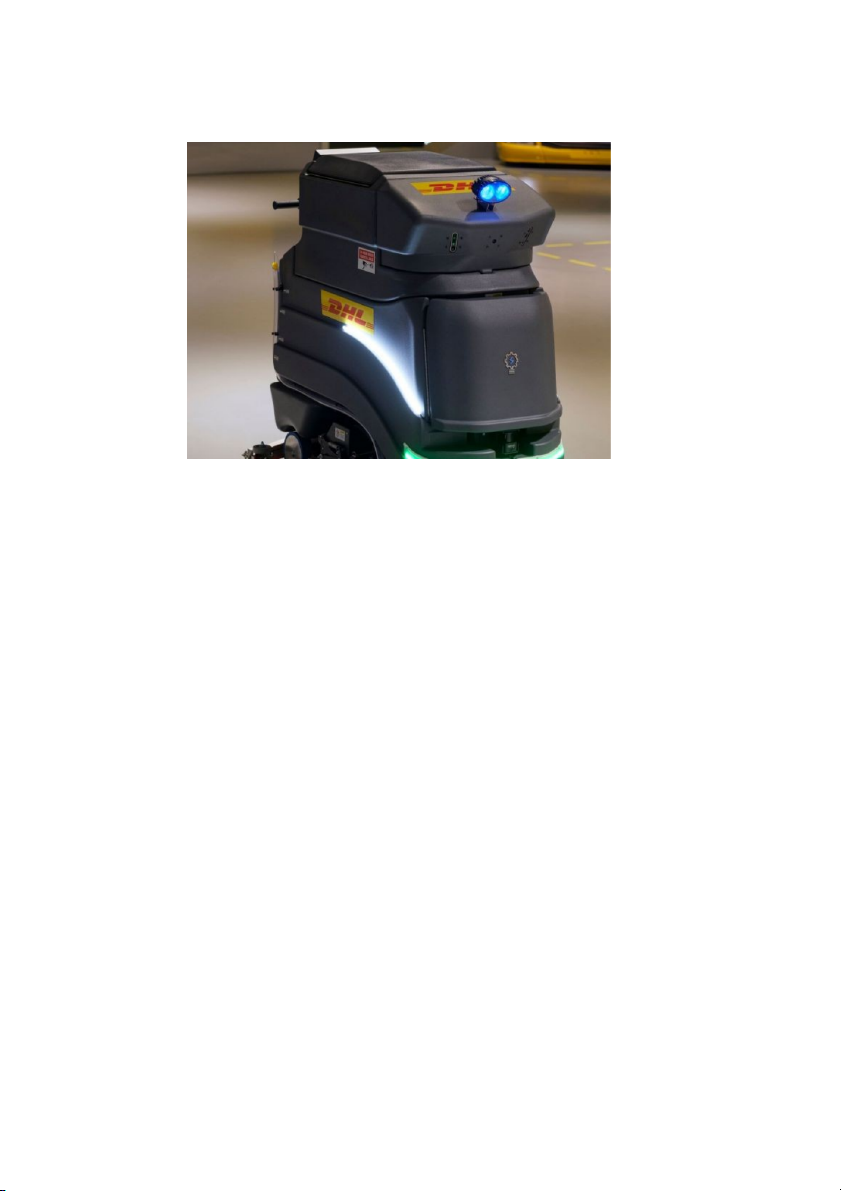
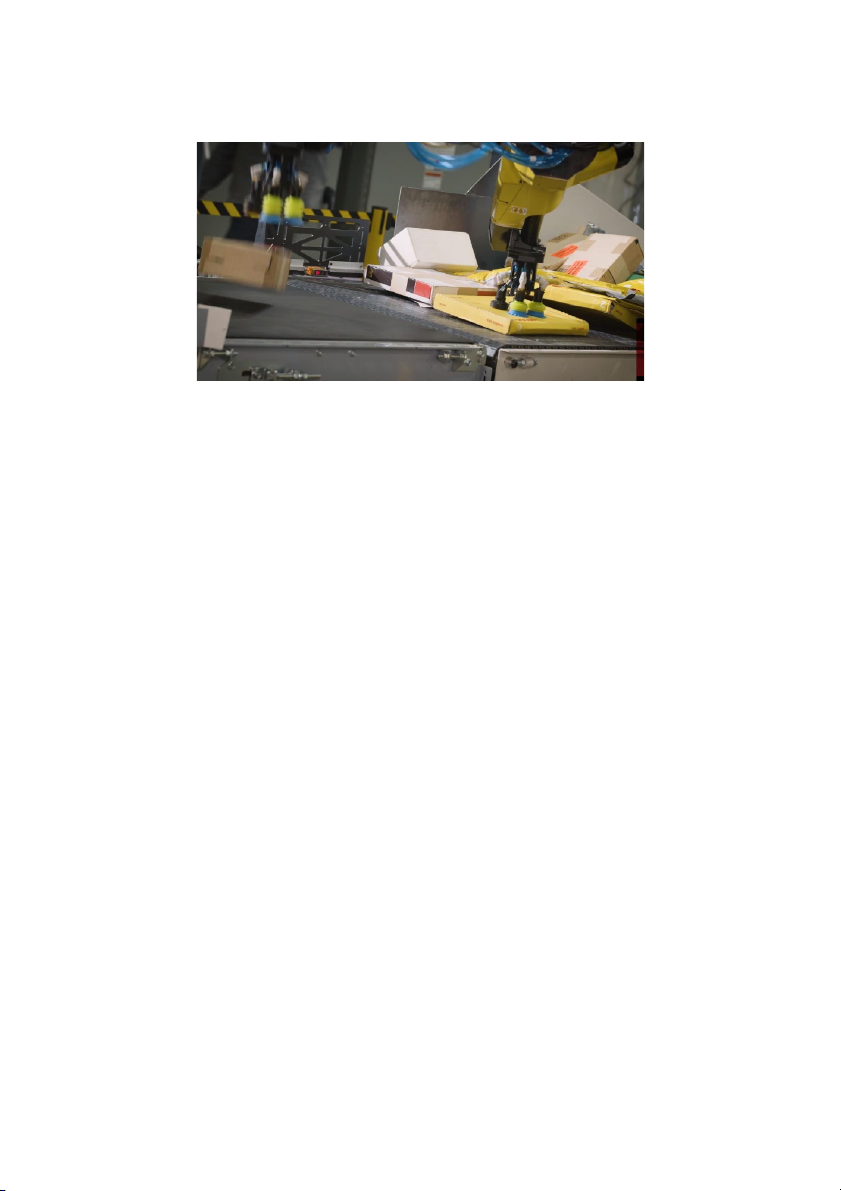
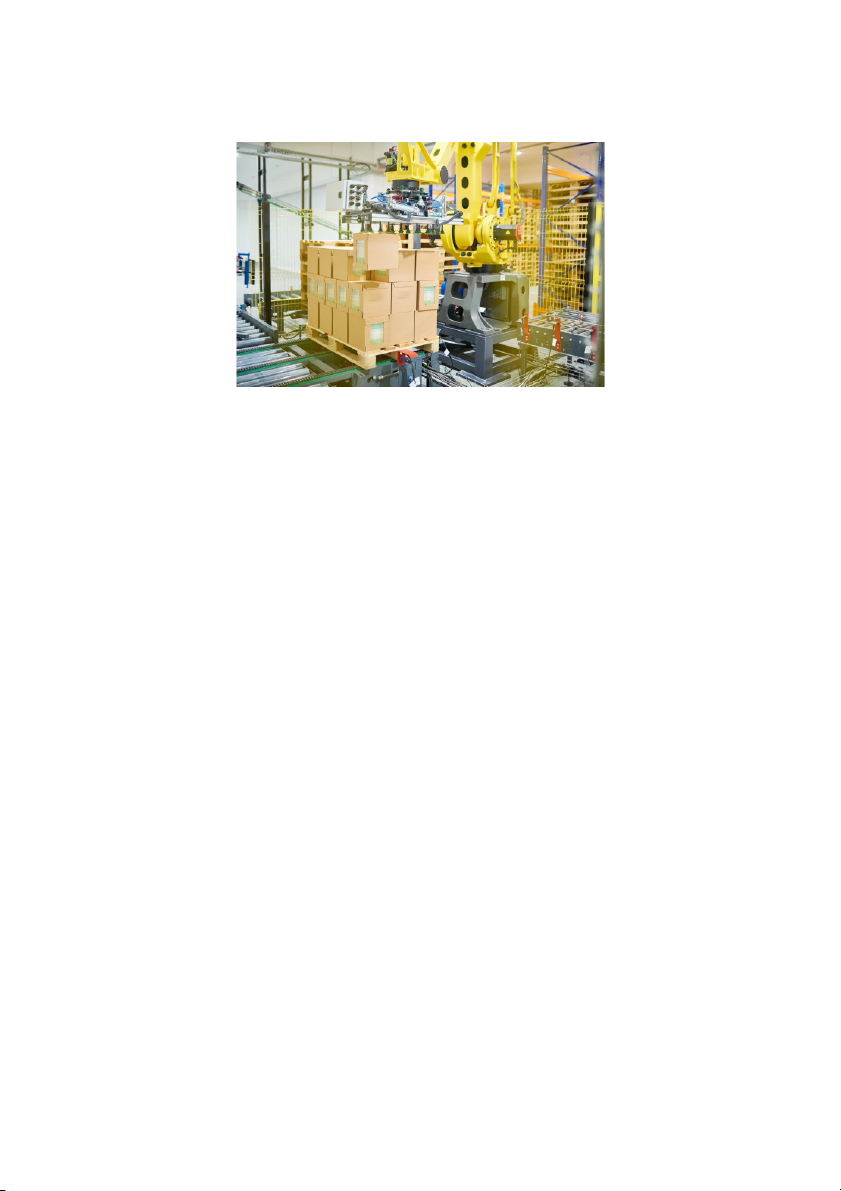
Preview text:
Inbound and outbound Process: Stocktaking Process: Loading/ Unloading Picking order process:
COVID-19 has also driven changes in the logistics industry, which includes the
acceleration of innovation, automation and digitalization in the workplace. During the
pandemic, robots increase productivity and service quality at the company’s service
centers. For example: DHL robot arm can help sort more than 1,000 piece per hour. DHL
using collaborative robots, safety measures should be reviewed before use to ensure the
health and safety of workers. For example: robot will elimate repetitive tasks, allowing
staff to perform more value – added duties. Picture :
Sorting shipments is a very repetitive, monotonous task that nevertheless requires high-
quality output. Operators who have to perform this task for hours on end in the
warehouse tend to lose concentration after a certain amount of time, making their work
error-prone and leading to additional rework costs. Sorting is therefore an ideal
application for automation, particularly the implementation of stationary sorting robots.
These devices often use cameras and AI capabilities to differentiate items for shipment
and use pre-defined characteristics to classify and sort them.
One example of such a device, used at a DHL eCommerce Solutions facility in Atlanta,
Georgia, USA is the DoraSorter sorting robot from Dorabot. This device uses a tray with
a clamp instead of a specialized end-of-arm tool to support the specifics of each
operation, ensuring even delicate shipments and irregularly shaped items are not crushed or destroyed.
The use of sorting robots like the DoraSorter can help to further drive human-robot
collaboration. It also provides valid business cases especially for greenfield facilities.
Pictures: The Atomatic Robot DHL inbound and outbound in Japan
https://www.dhl.com/jp-en/home/press/press-archive/2019/dhl-supply-chain-deploys-
intelligent-robot-solutions-in-one-of-its-largest-warehouses-in-japan.html
The integrated warehousing system, designed to facilitate deployment of advanced
robotics solutions, seamlessly combines robots that fully automate the inbound, outbound
and cycle-counting processes 24/7. Optimized to carry out automated Goods-to-Person
storing, picking and cycle-counting for multi-stock keeping unit (SKU) of various sizes,
the robots can be scheduled to lift and carry shelves weighing up to 600 kilograms and
navigate the designated areas for warehousing activities with obstacle-avoidance capability. Picture: The Wrapping Robot
The Wrapping Robots boost the stretch-wrapping process, decrease potential product
damage and save on film waste. They come equipped with several programs allowing
larger and oddly shaped items to be safely and efficiently wrapped for shipping or storage. PICTURES: SUPPORTING ROBOT
Improved mapping of environments, better path planning, longer lasting batteries,
efficient electric motors and the development of omnidirectional wheels have
revolutionized the category of supporting robots.
PICTURE: ROBOT PICKING & PLACING
The manual separation and alignment of parcels, letters, cartons, and flyers to prepare
them for further processing downstream is very monotonous and labor intensive. The
automation of this process via stationary robots has gained a lot of traction in recent
years. Robotic induction, the act of picking an item and placing it with a specific
orientation on a conveyer belt as well as identifying its characteristics, is a very scalable
solution given its widespread applicability.
PICTURES: Robotics_Palletizing_and_Depalletizing
The automation of palletizing and depalletizing in inbound and outbound warehouse or
hub operations holds great potential for stationary robotics. A distinction should be made
between uniform and mixed palletizing.
While uniform palletizing is the movement of same-shaped, unvarying goods from and
onto a pallet, mixed palletizing describes the handling of pallets with items of various
sizes and weights. In general mixed palletizing is more complex than uniform palletizing
as it requires much more powerful AI to stack disparate, unwieldy packages as securely
and efficiently as possible. However, the company Dexterity provides software that can
be used with any robot size or configuration to enable flexible handling and optimal stacking of mixed boxes.