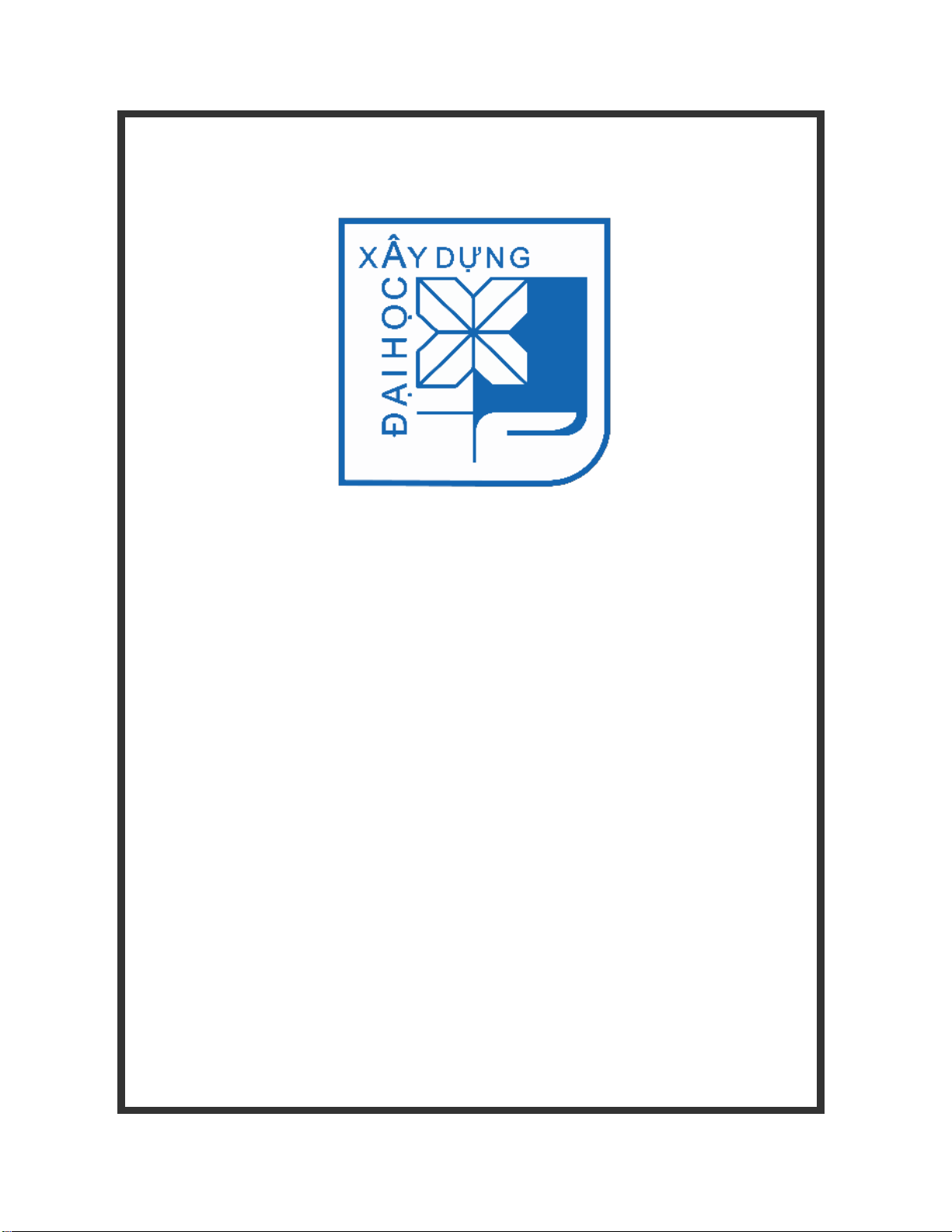
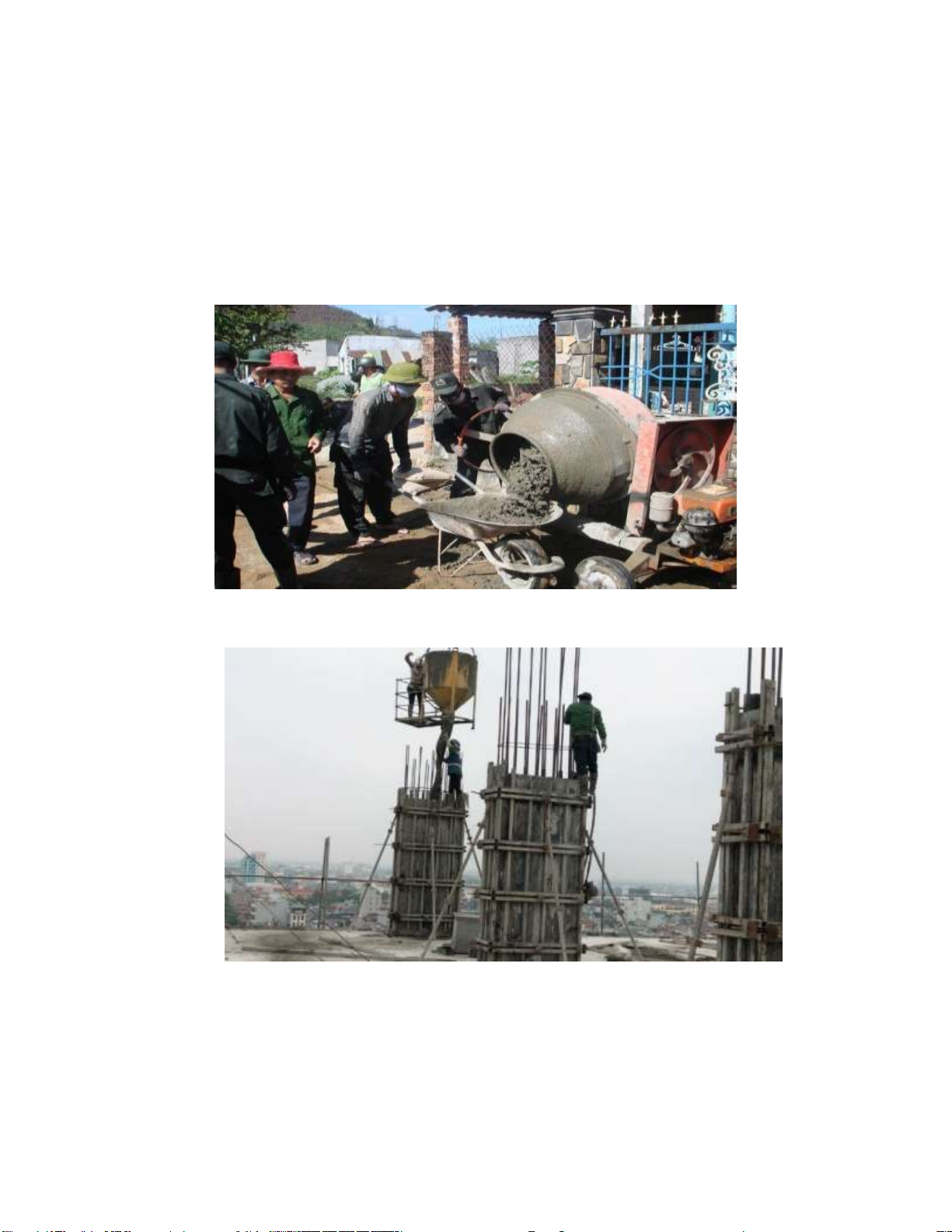
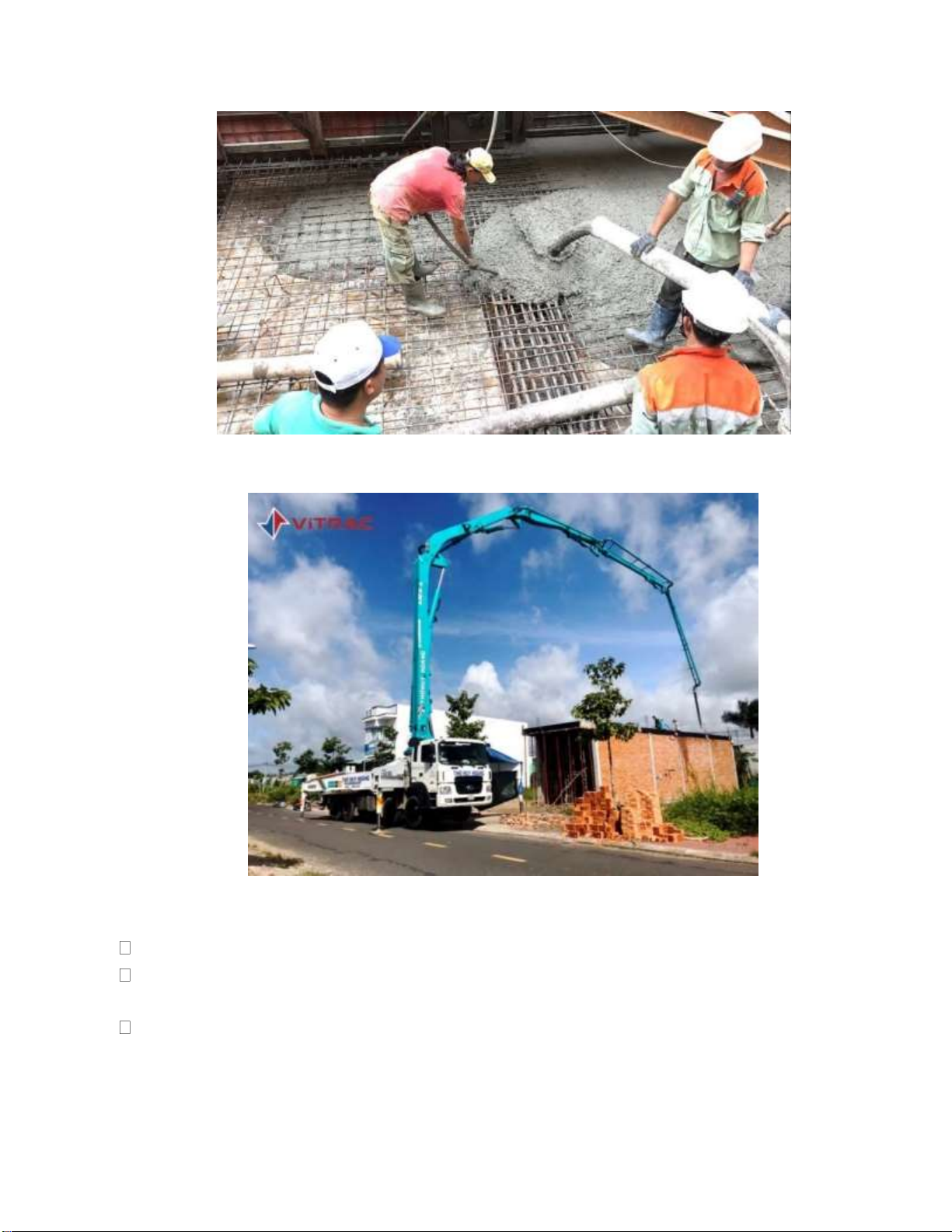
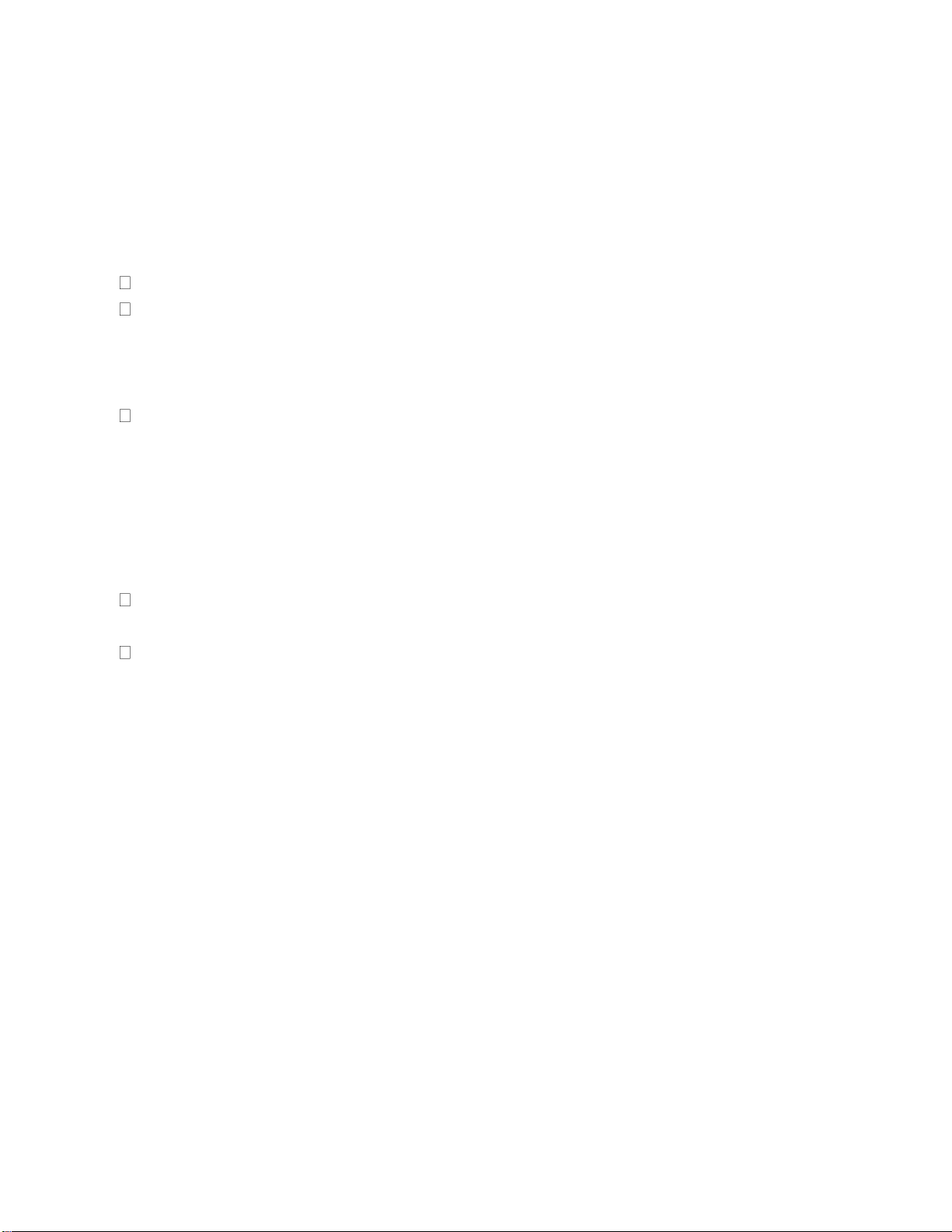
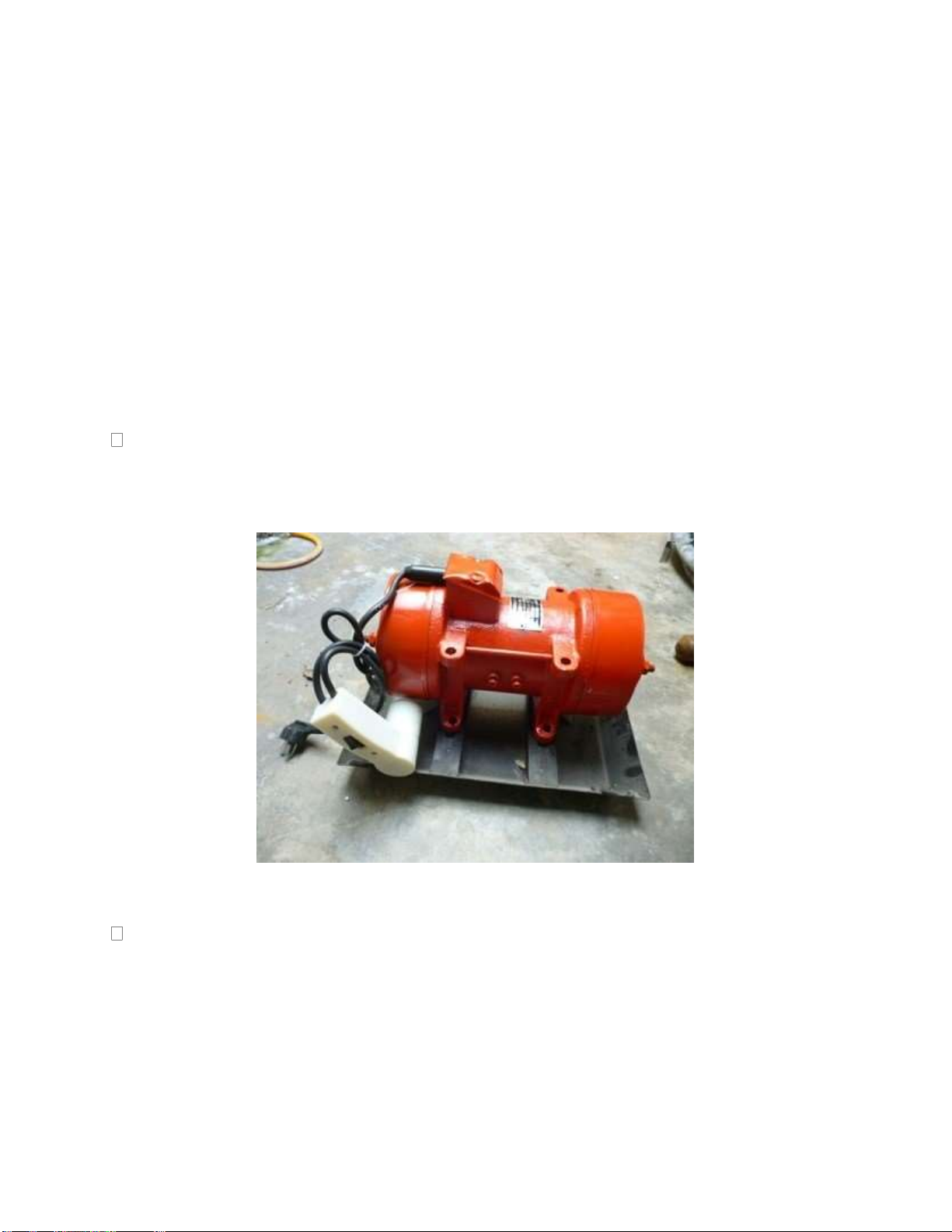
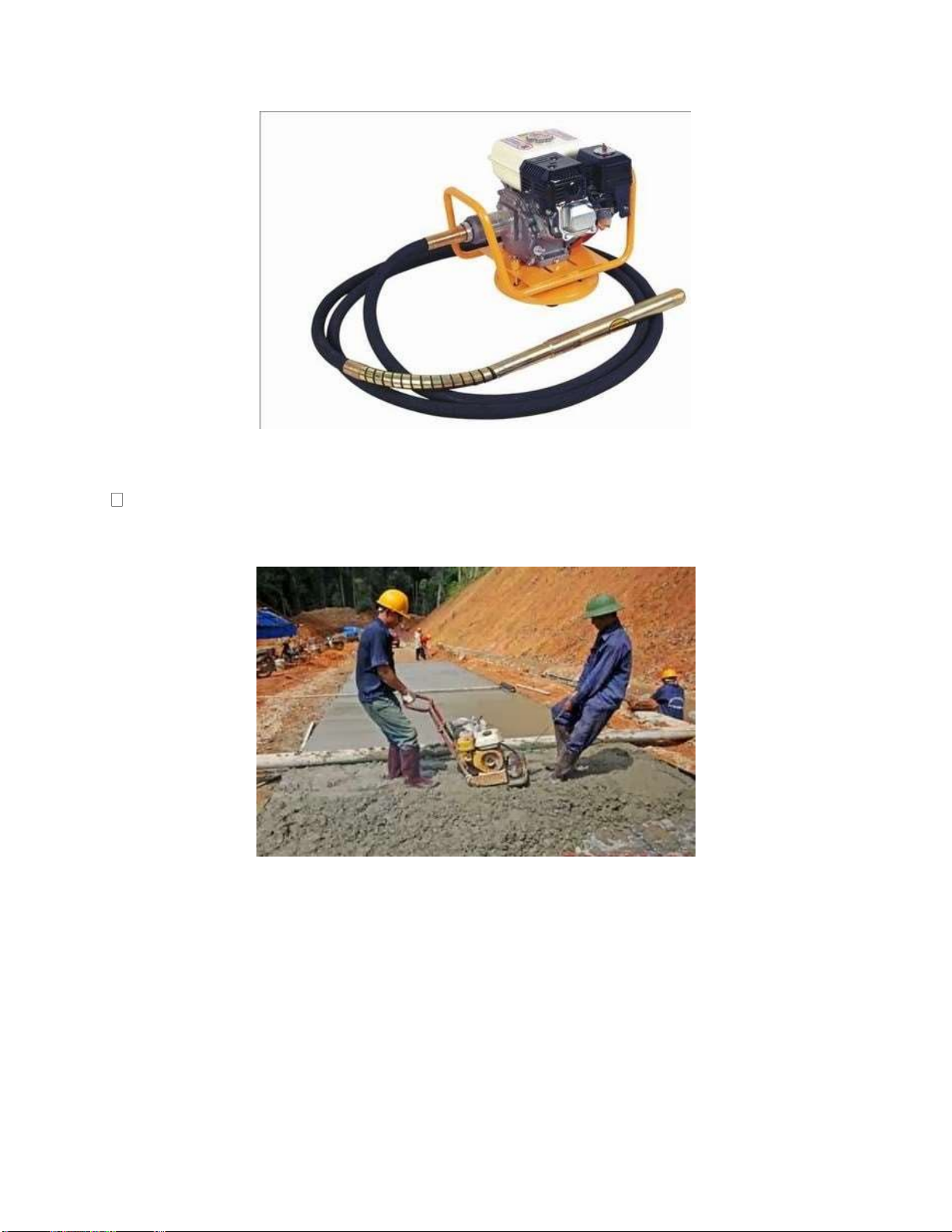
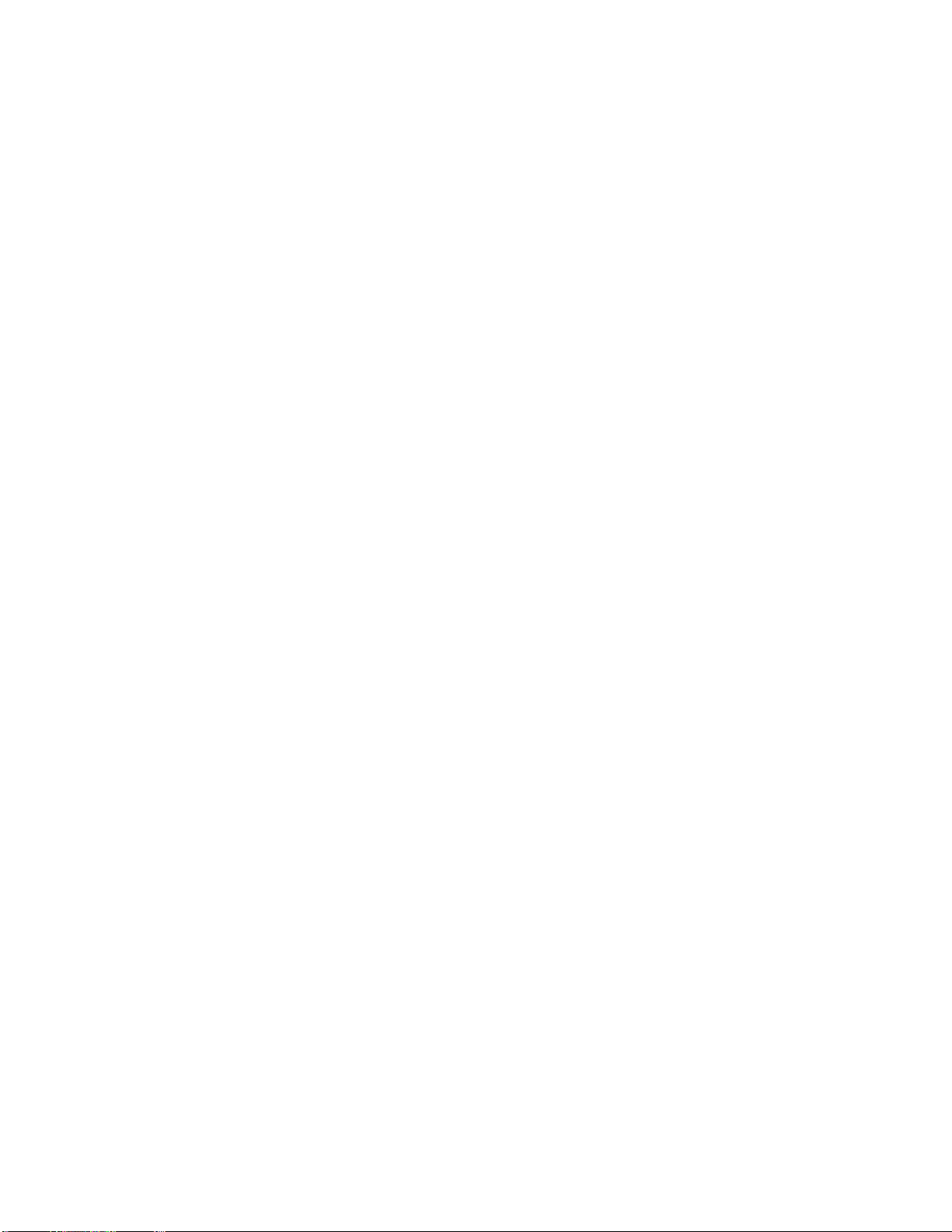
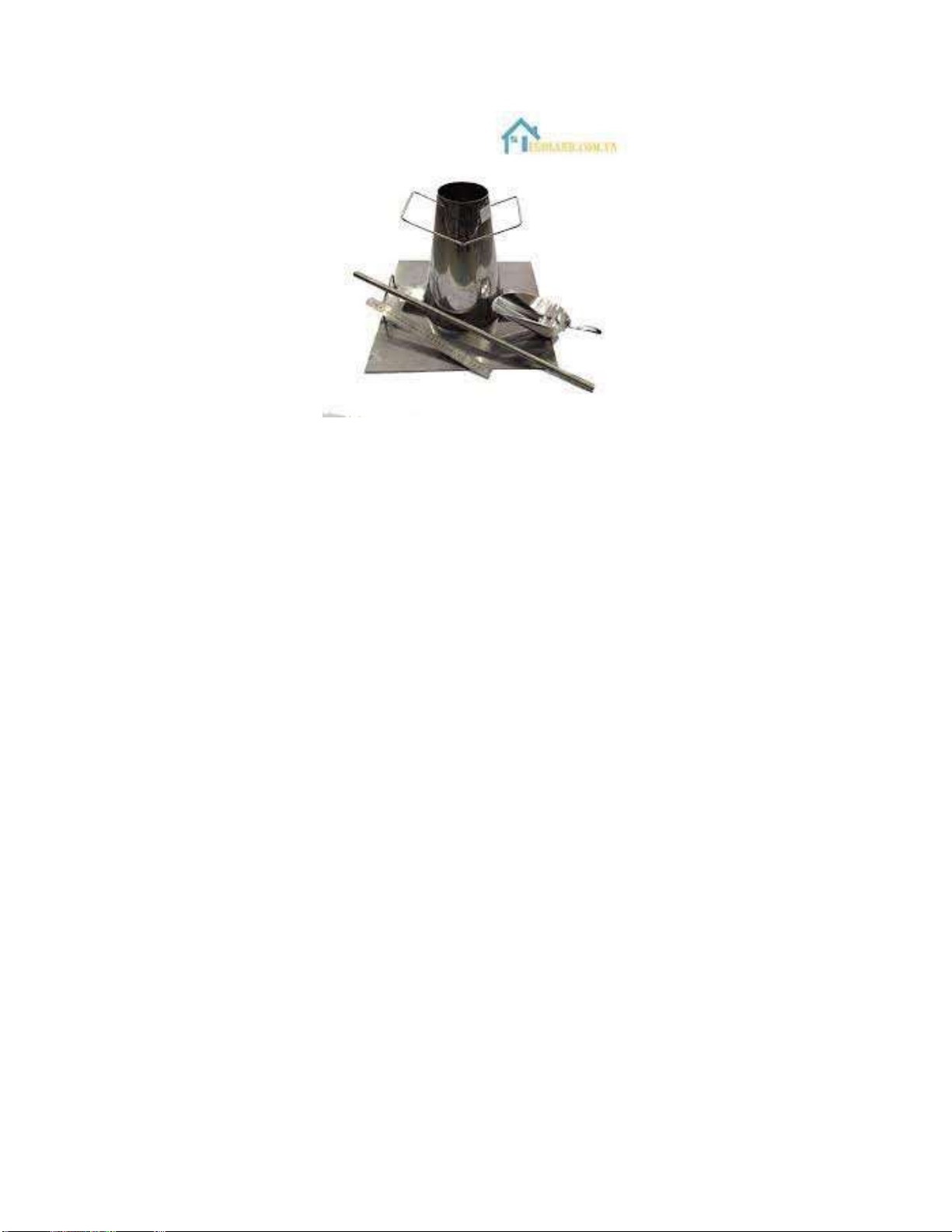
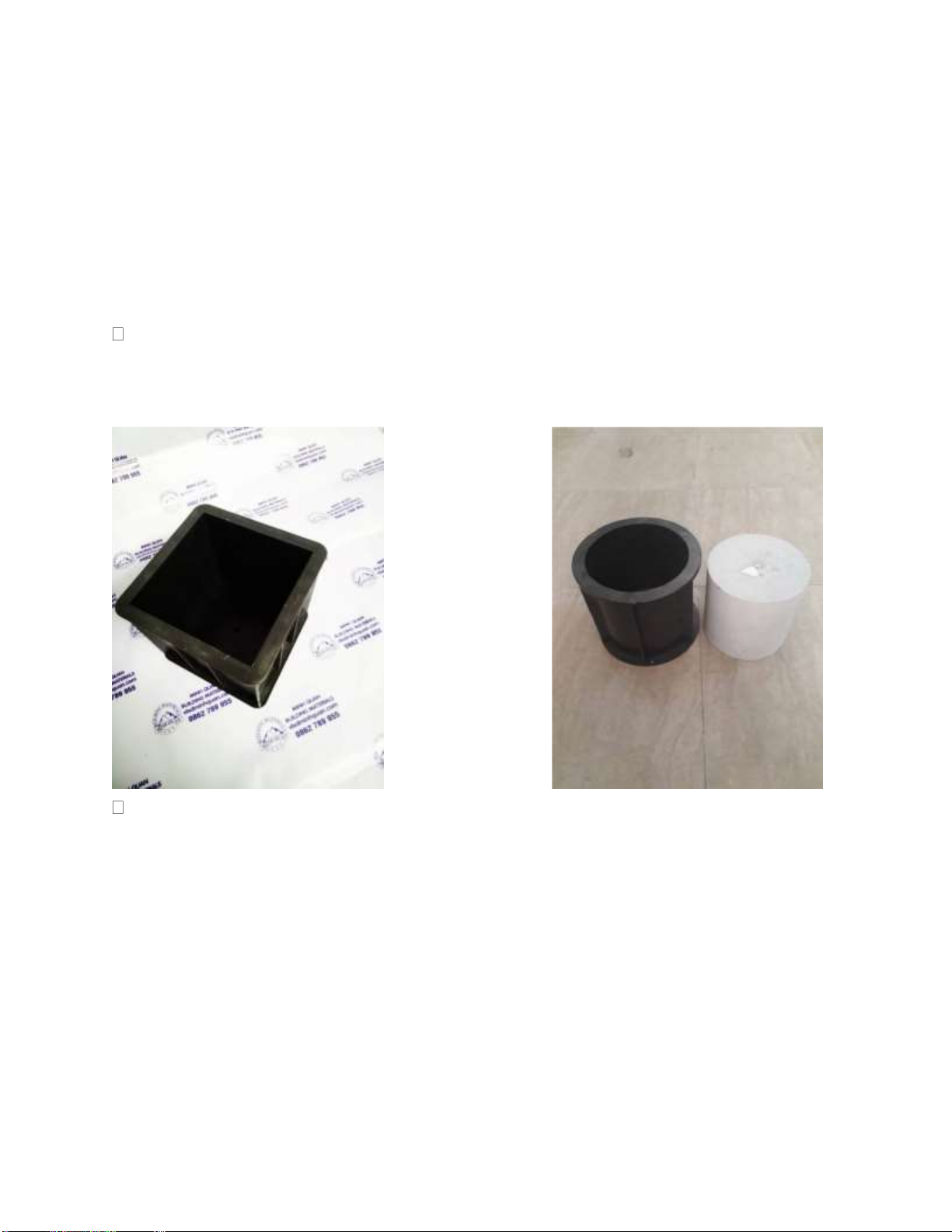
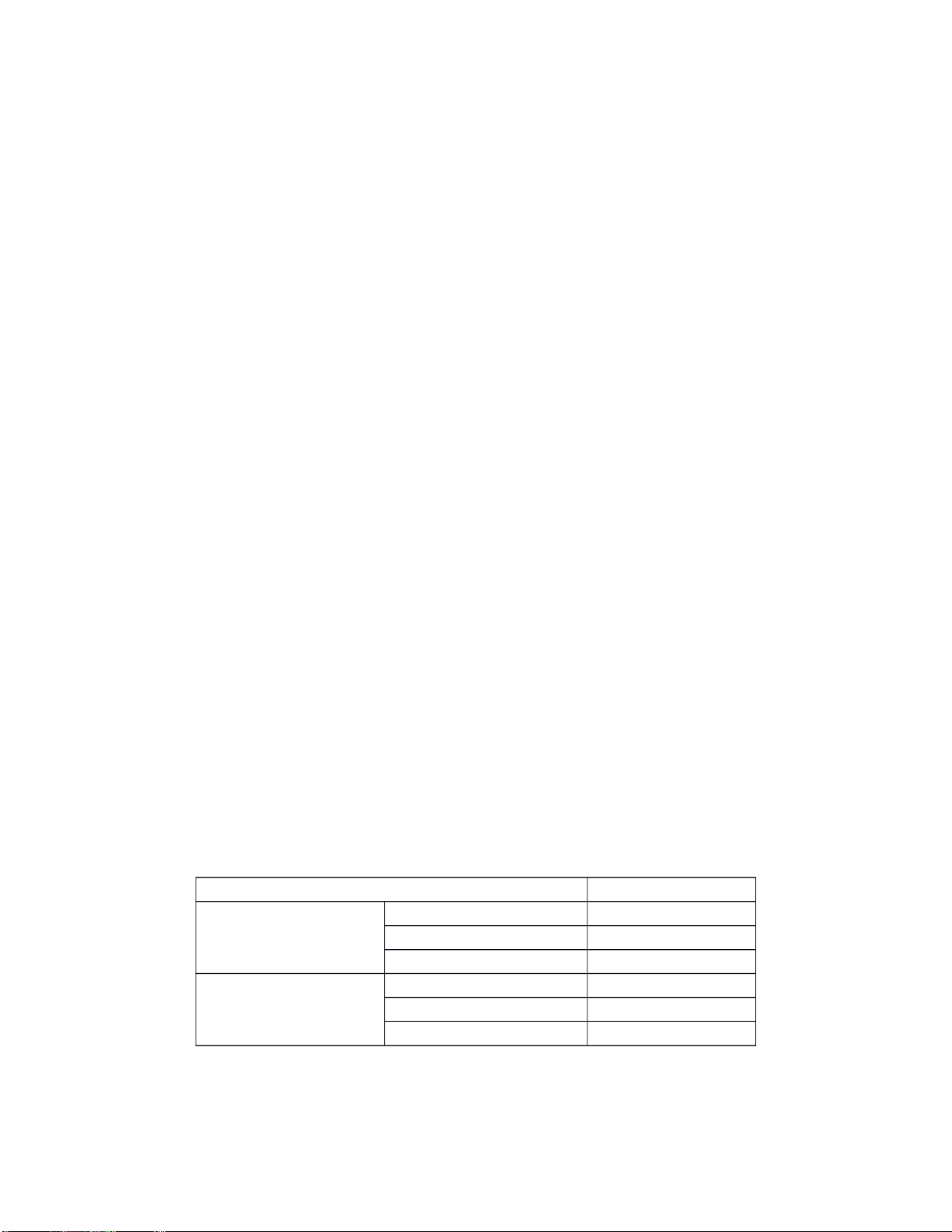
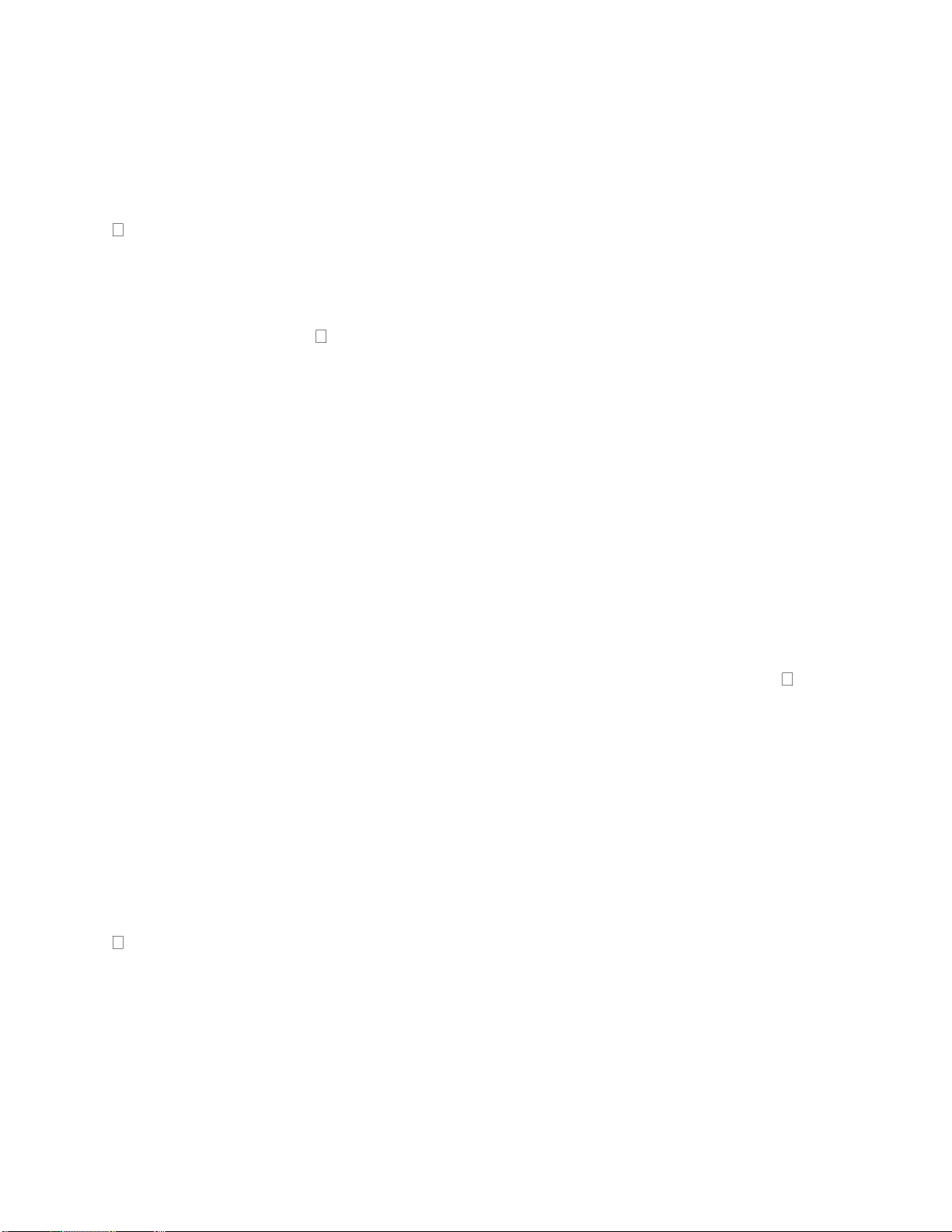
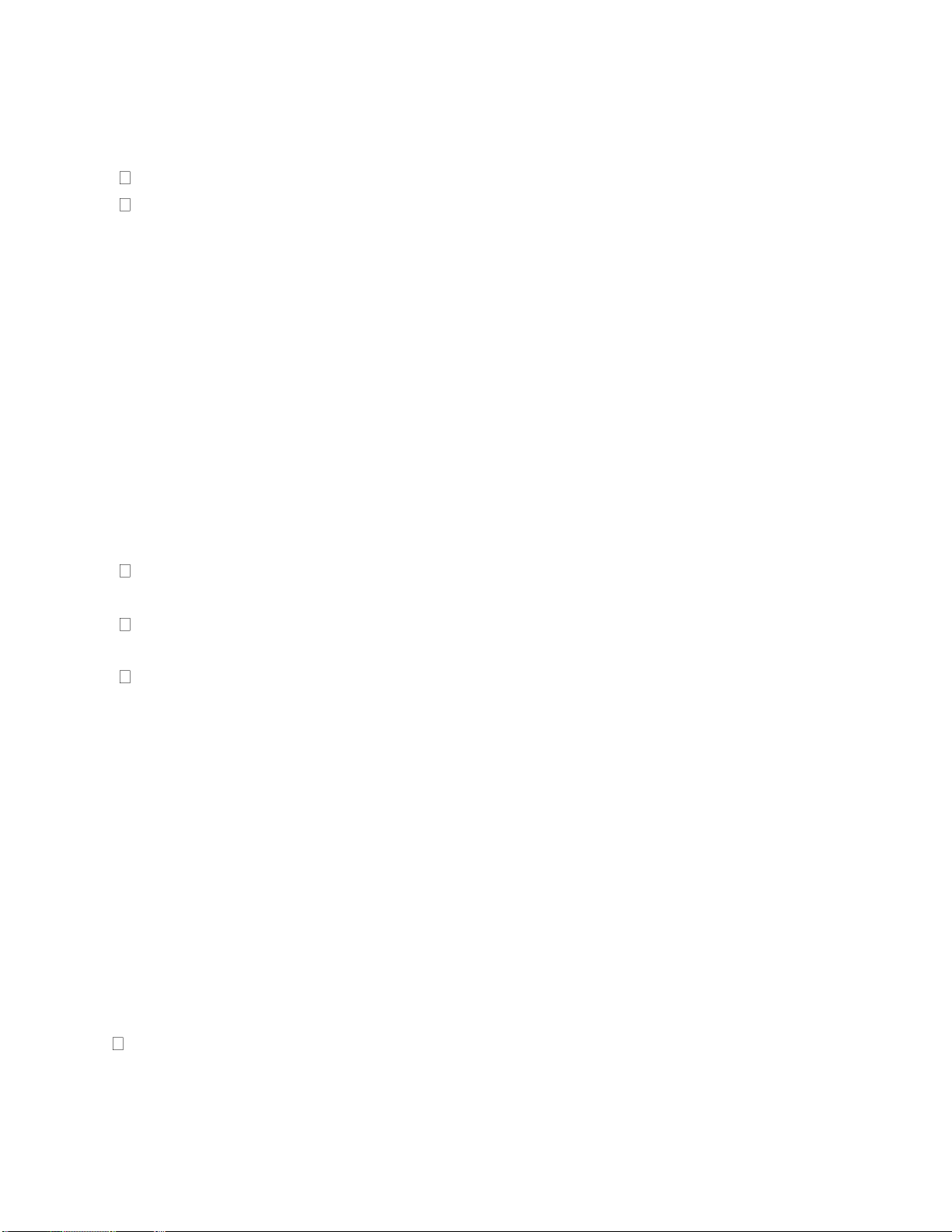
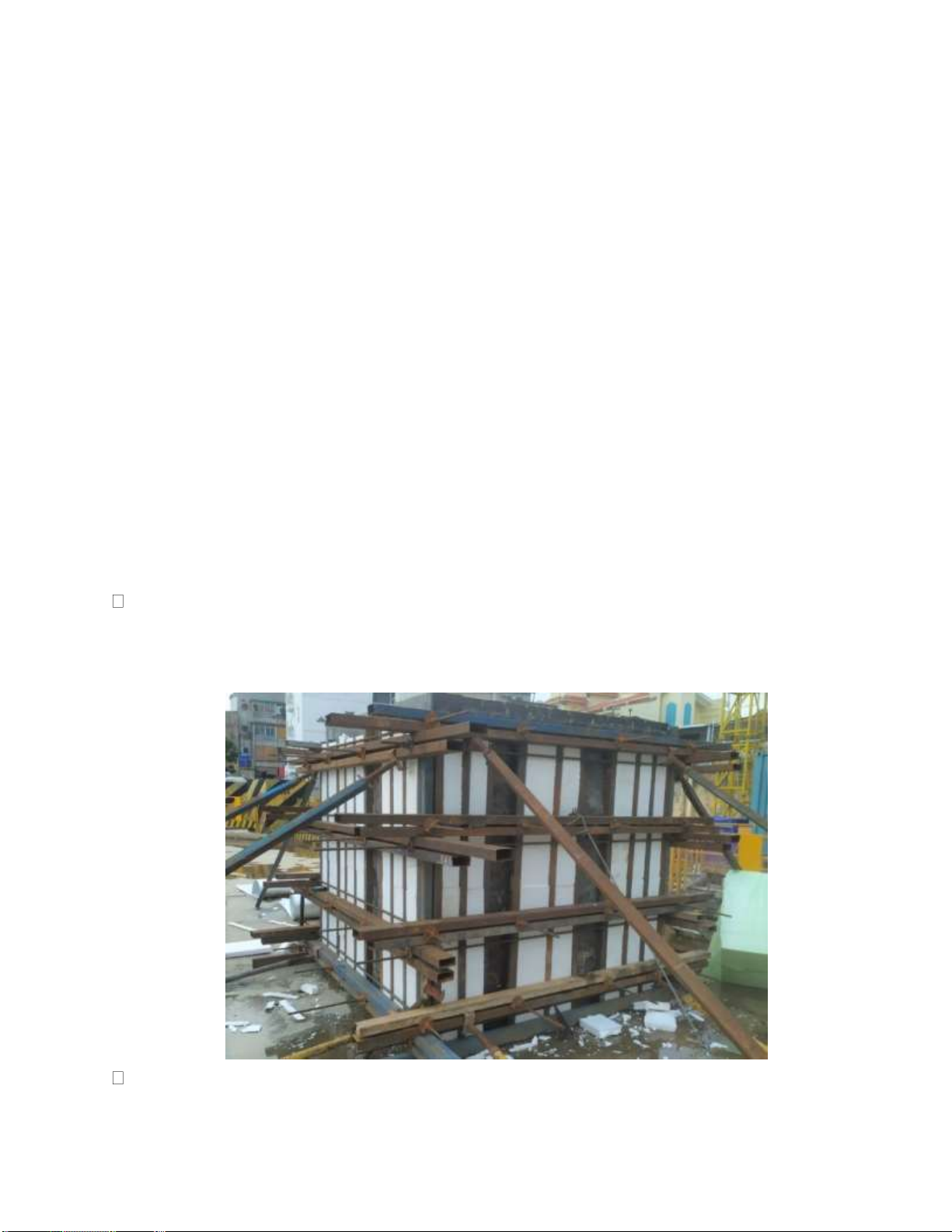
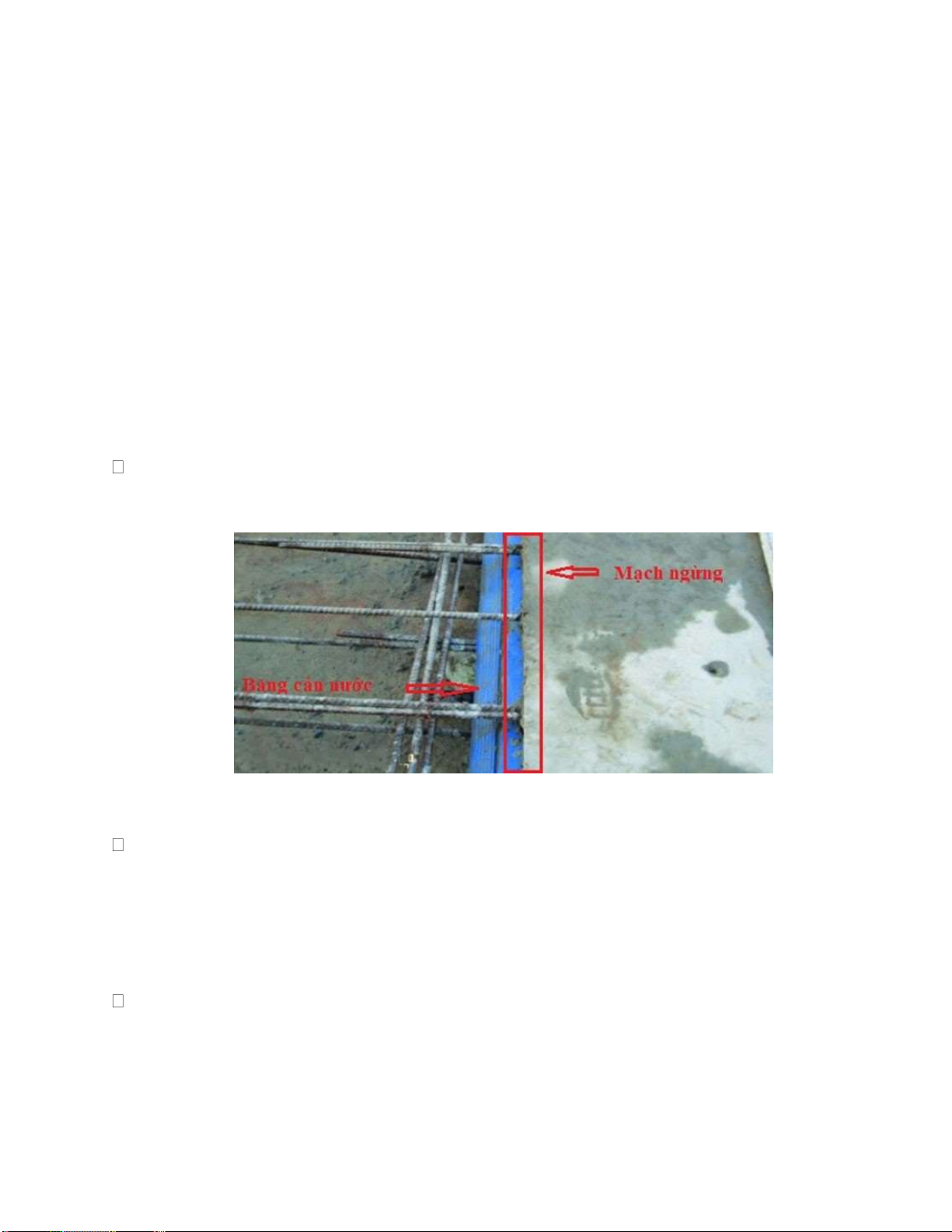

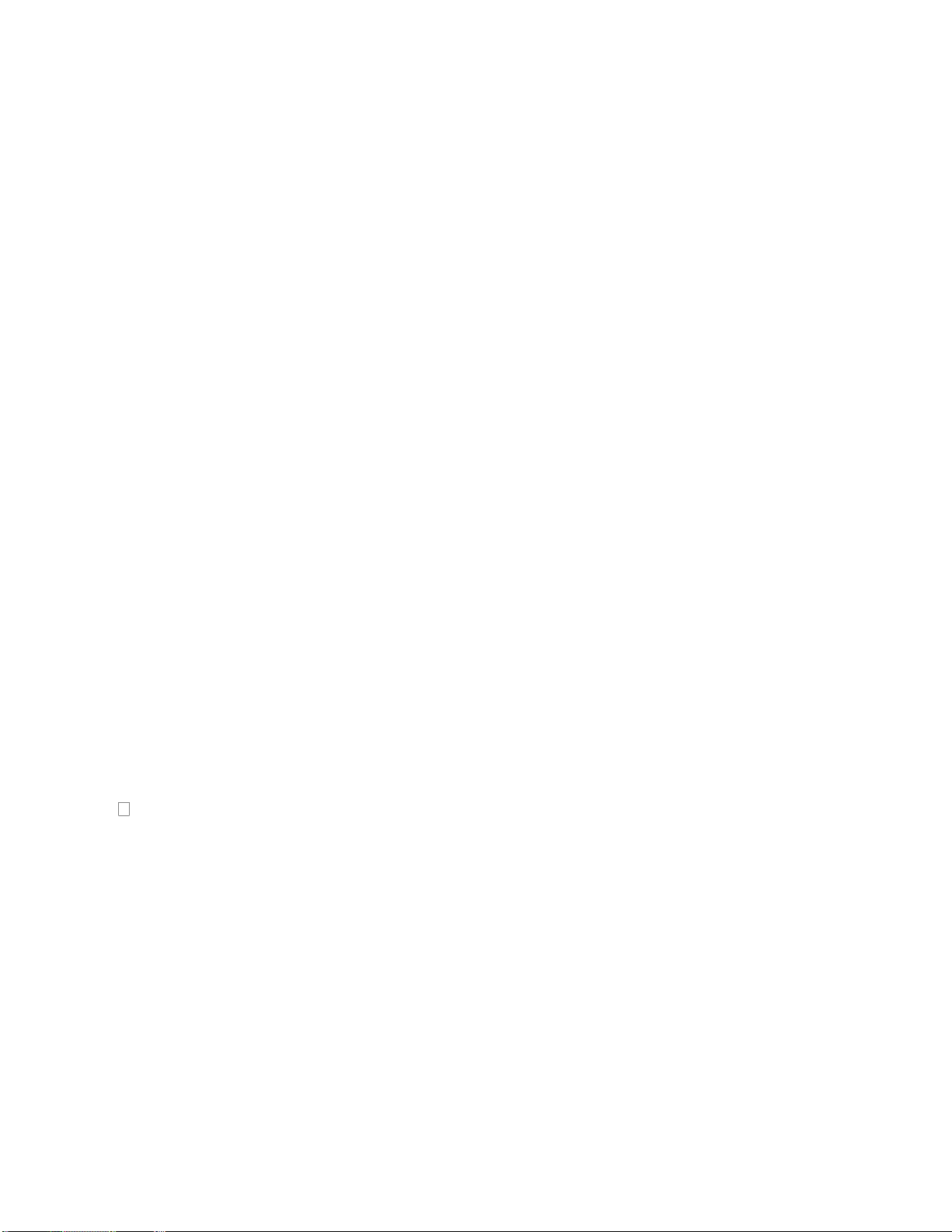
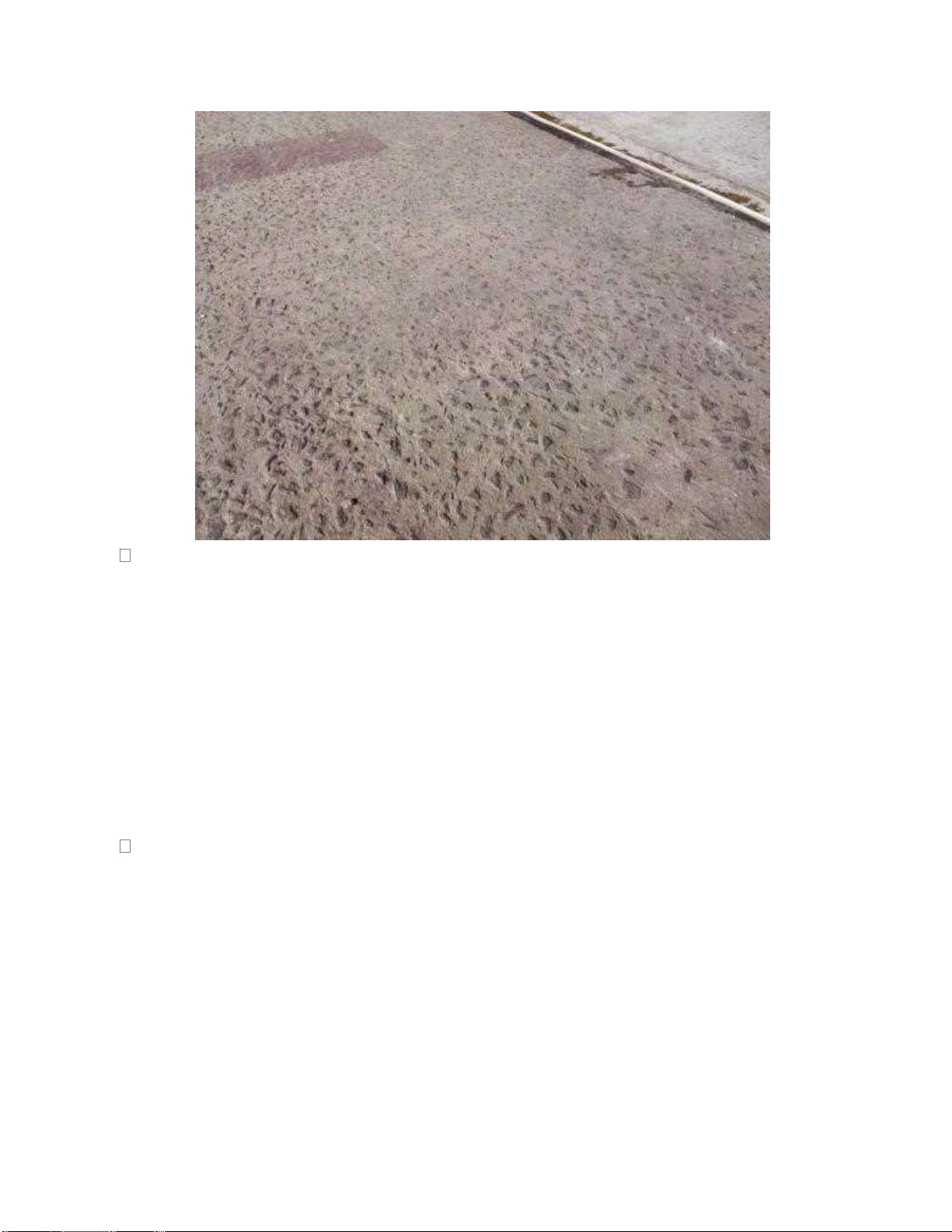
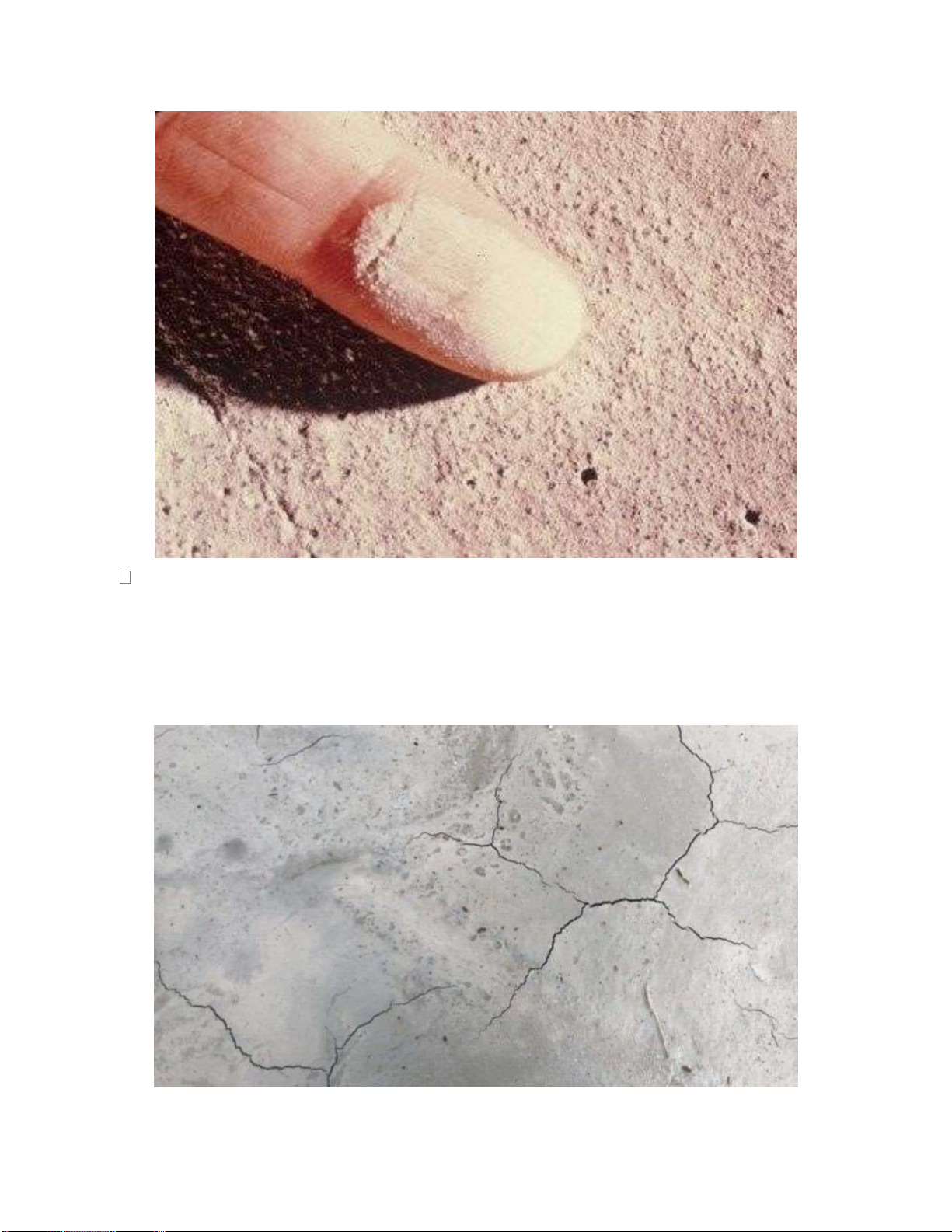
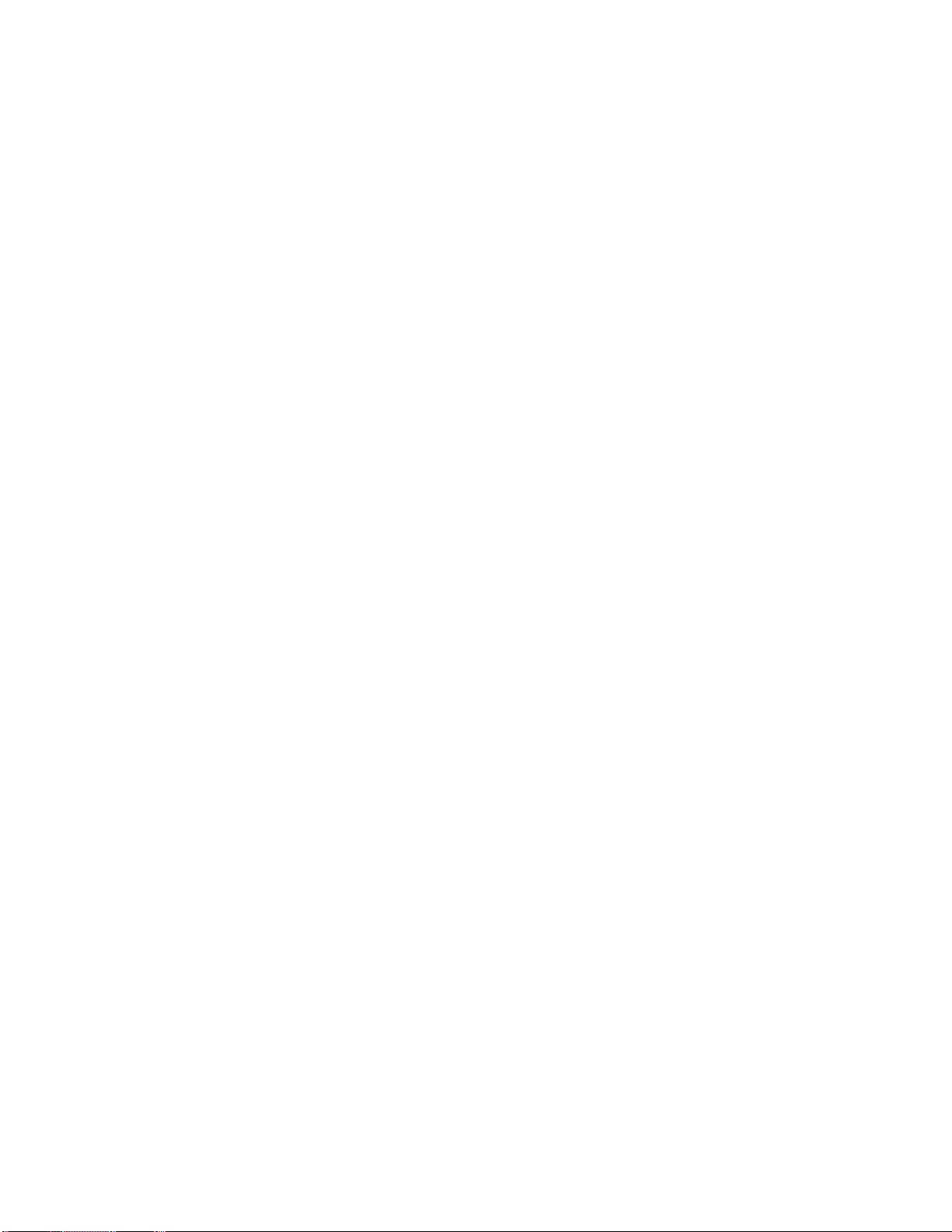
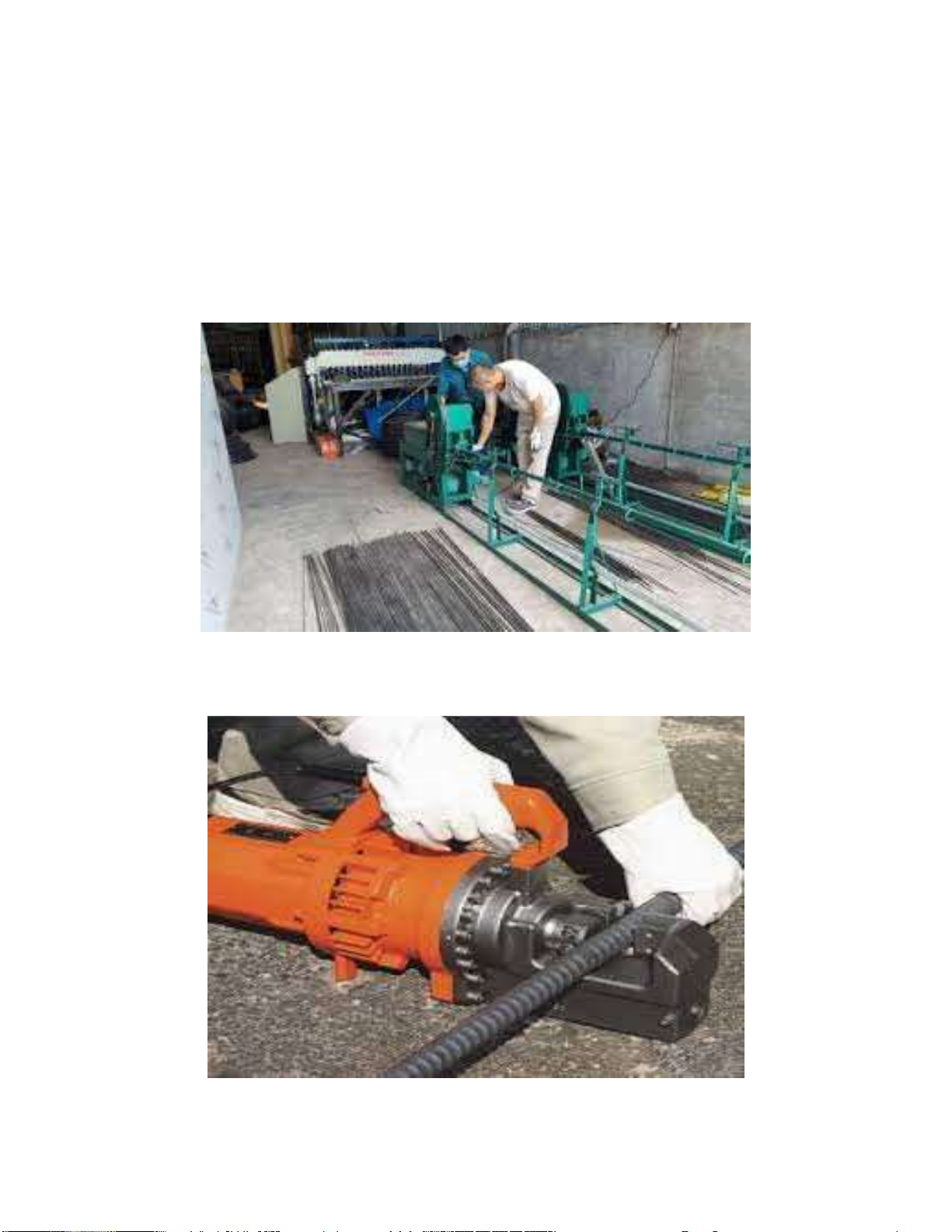
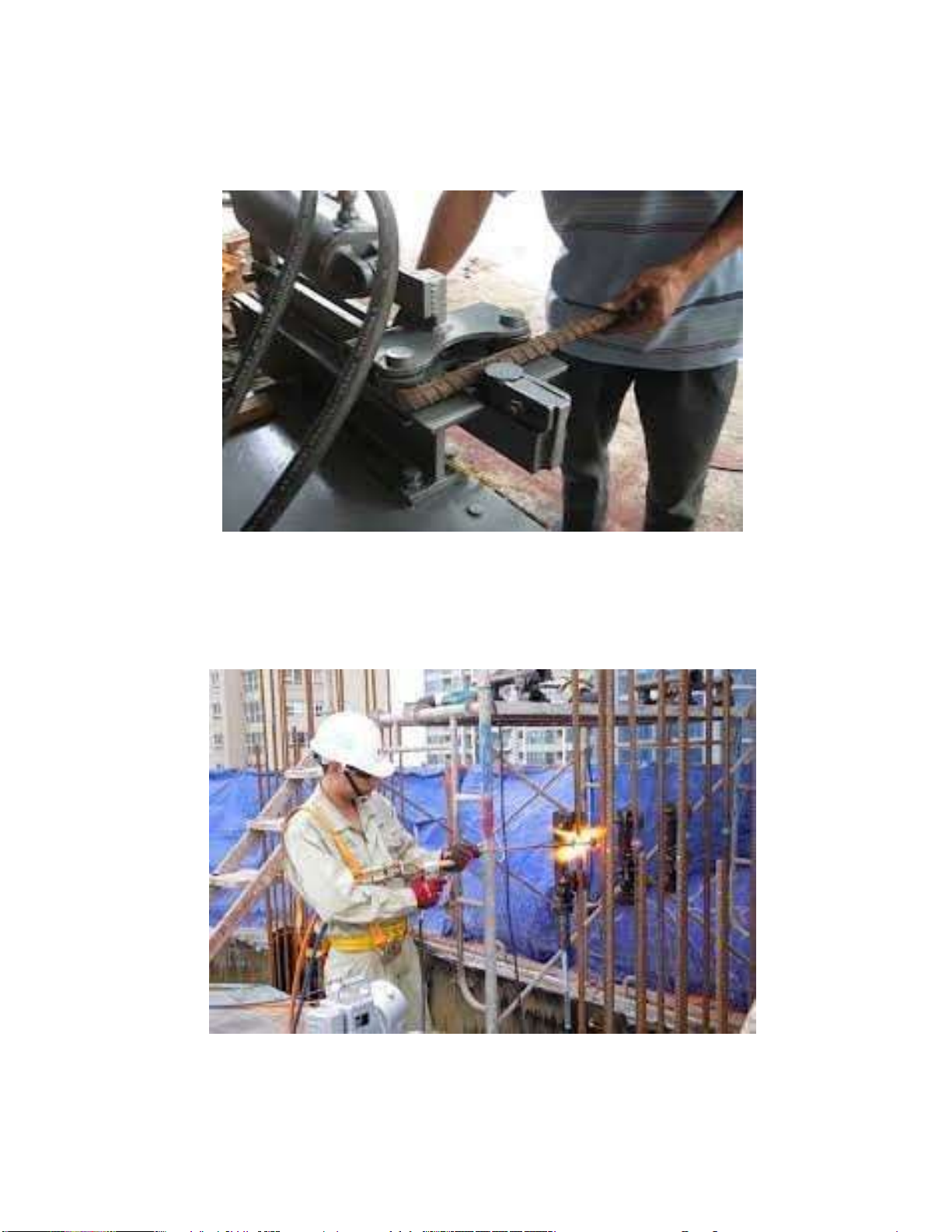
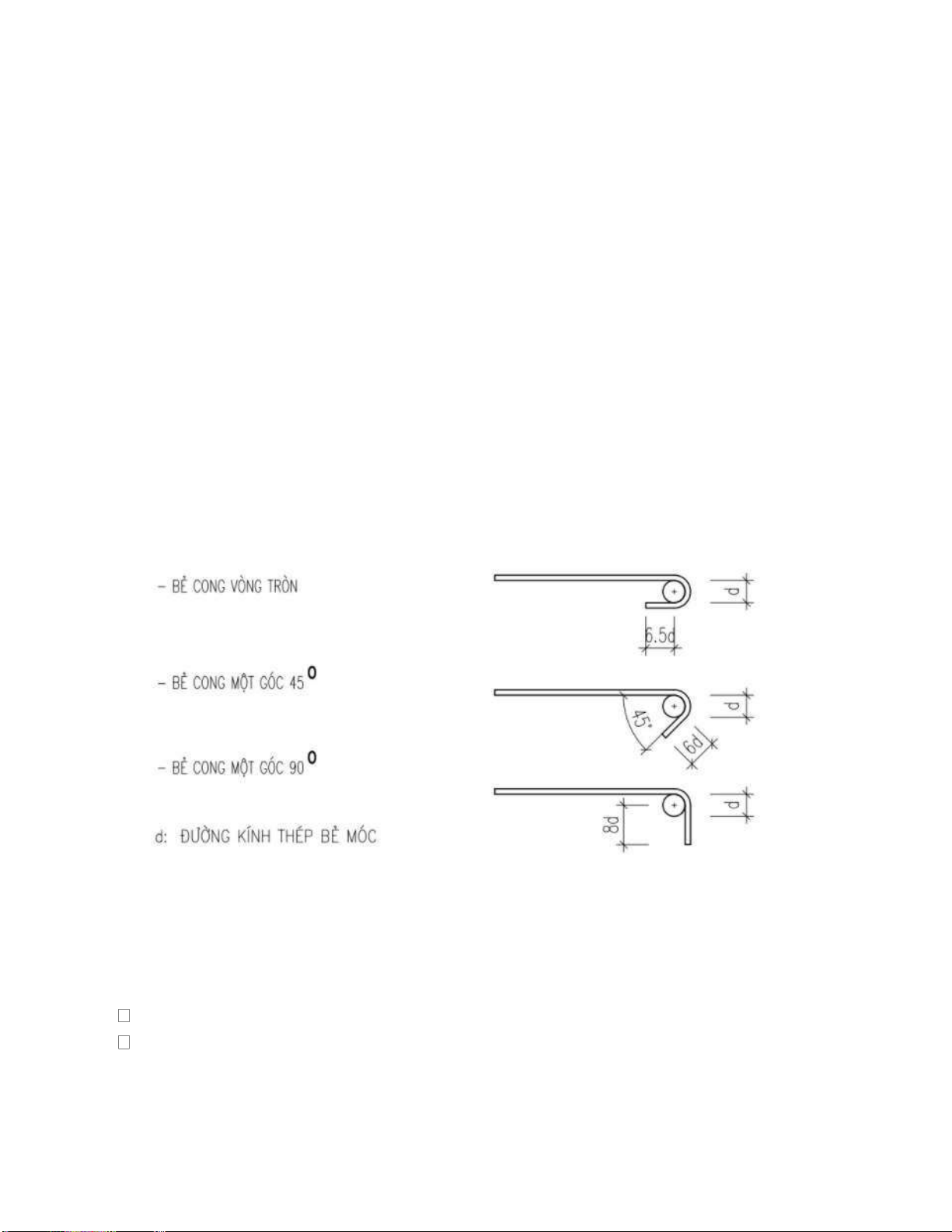
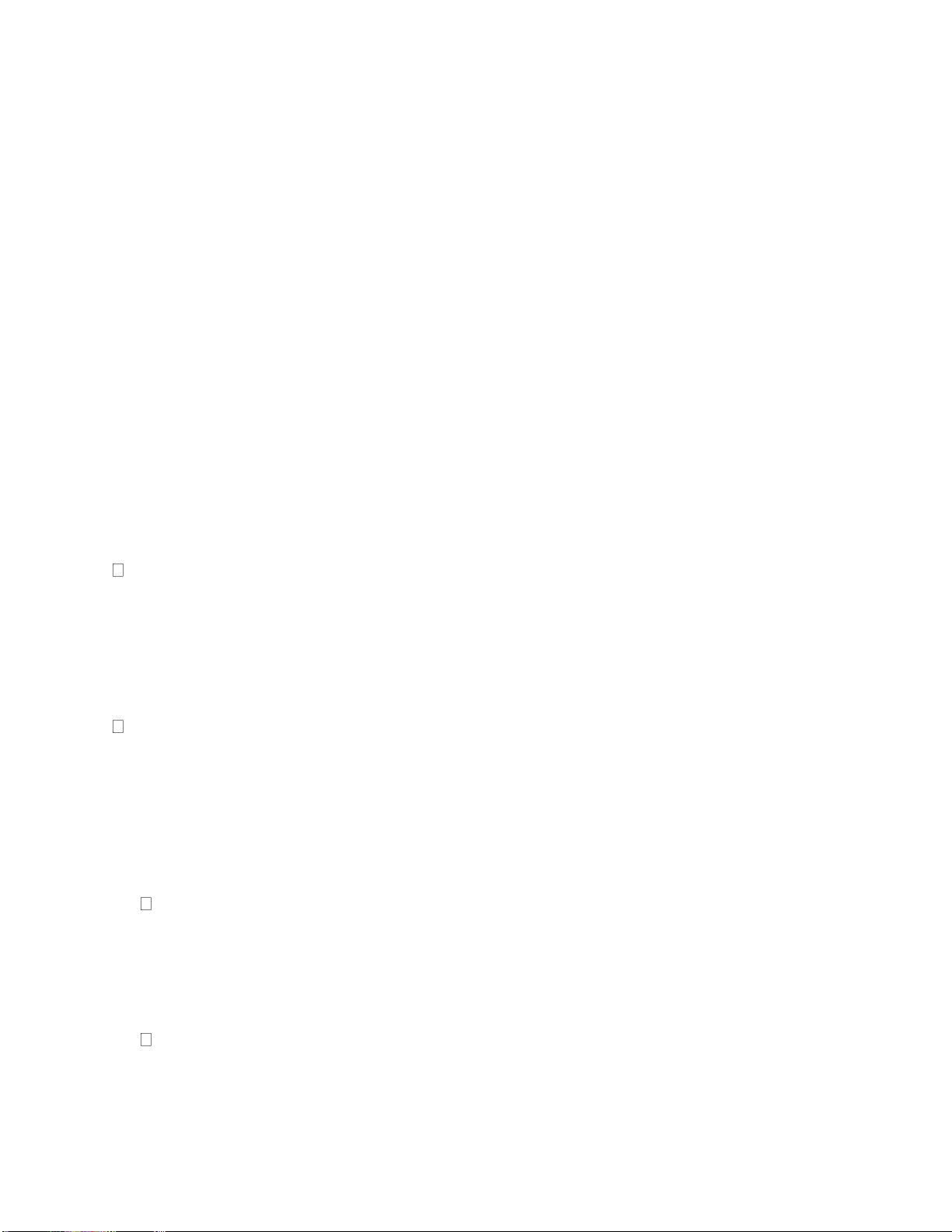
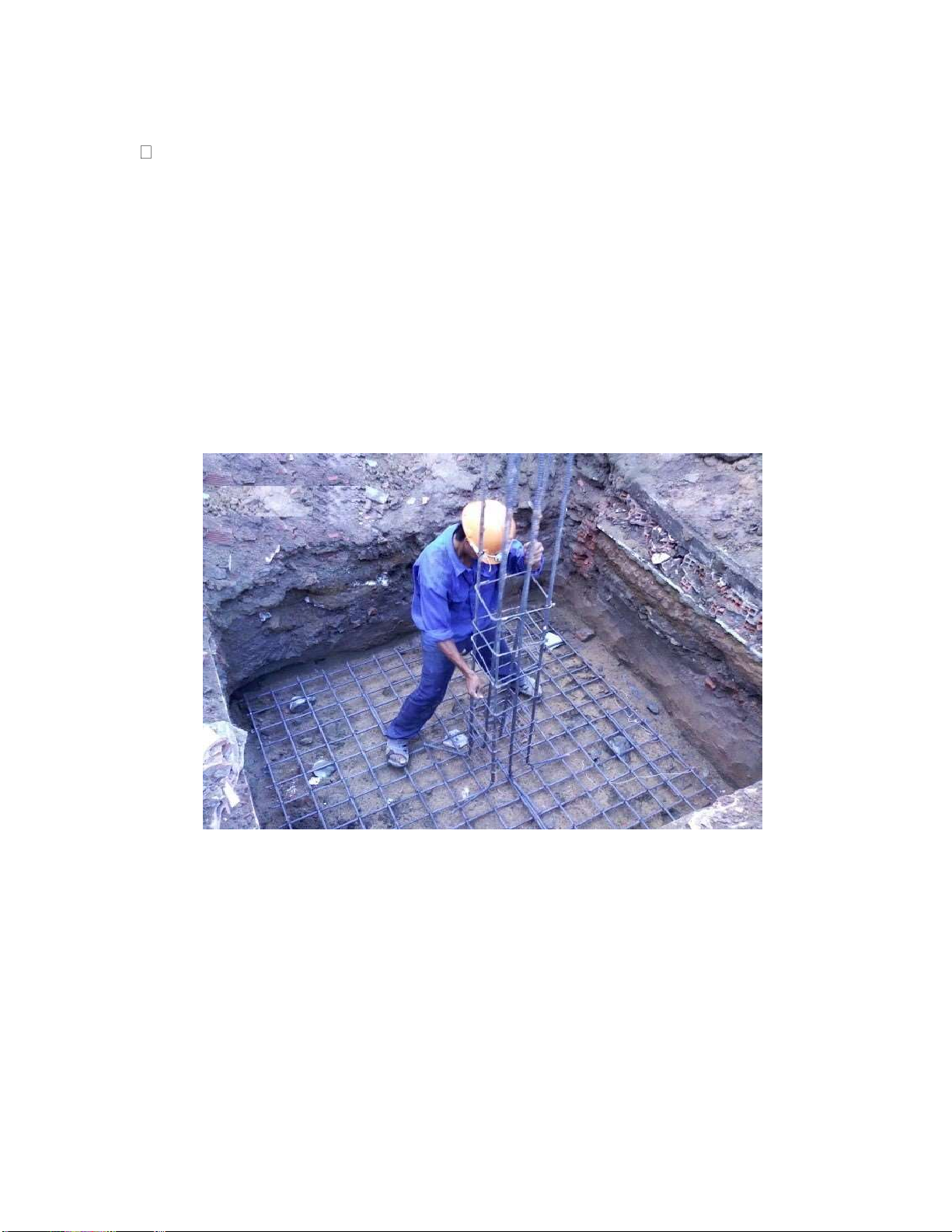
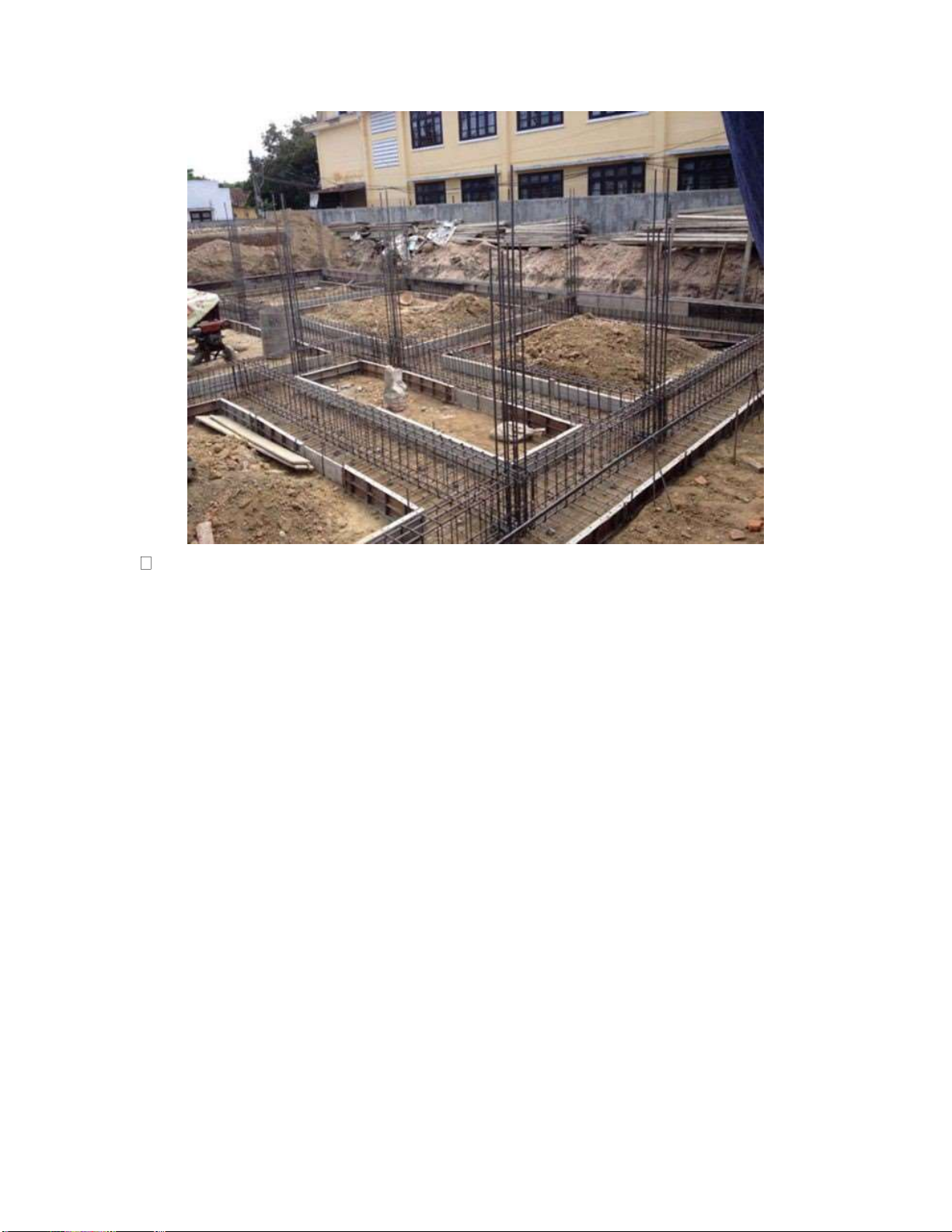
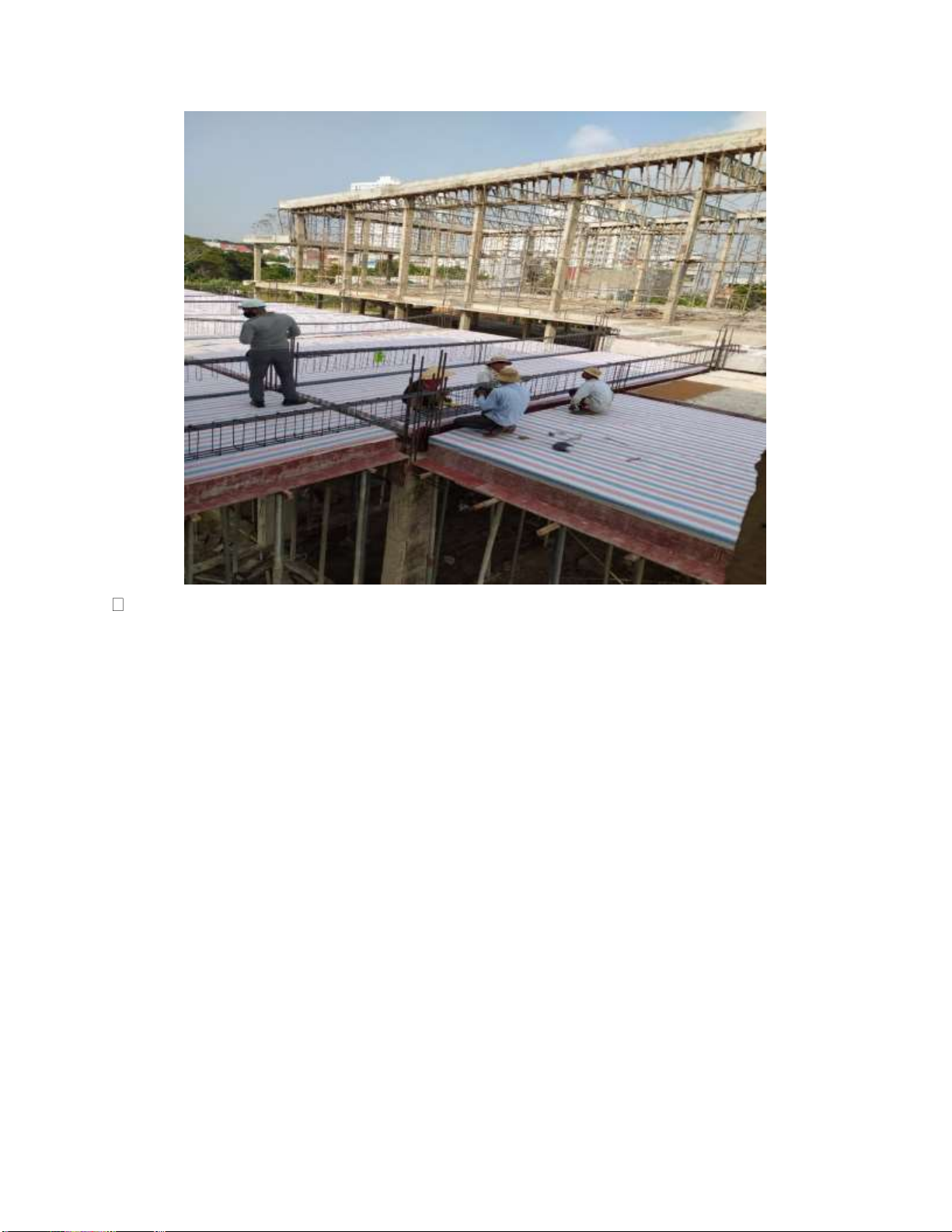
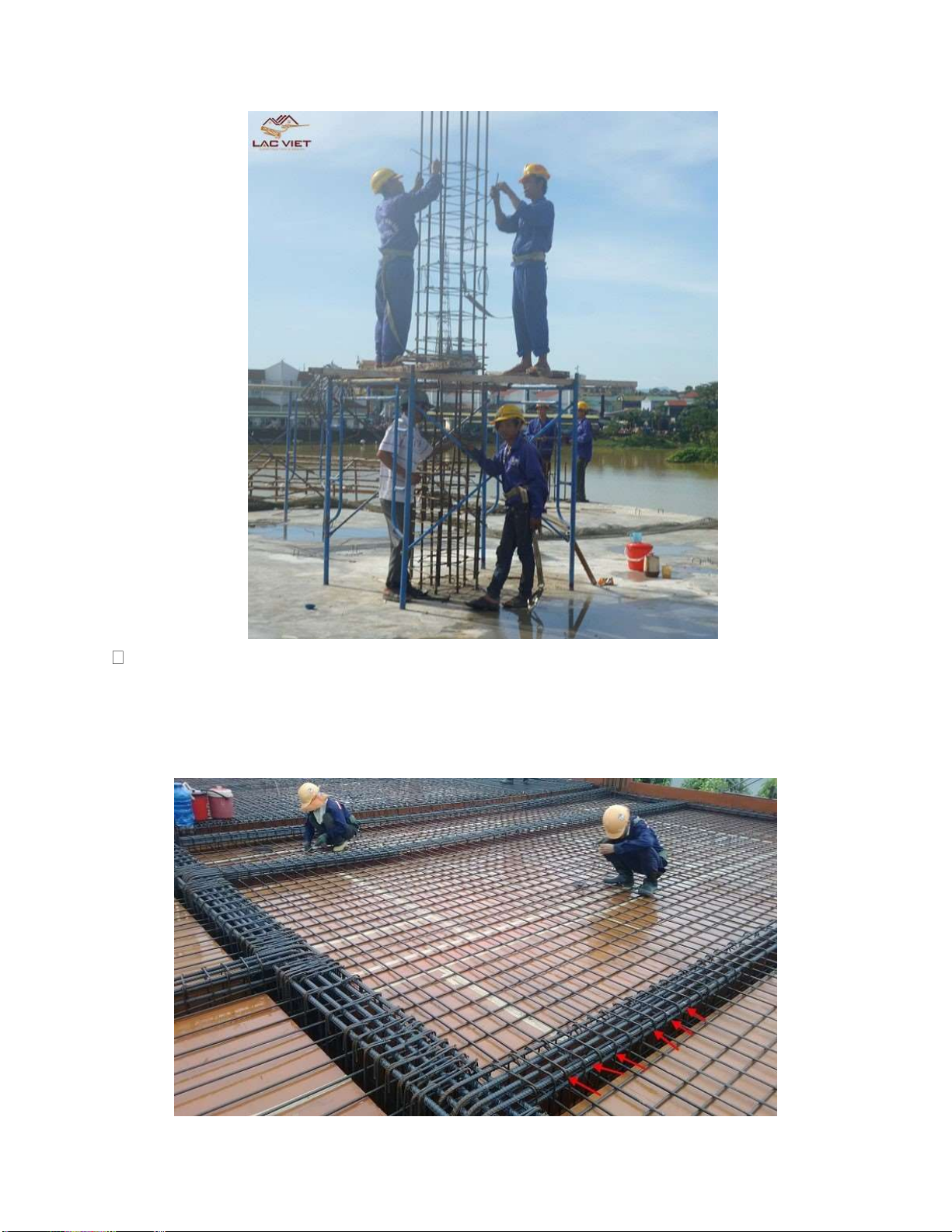
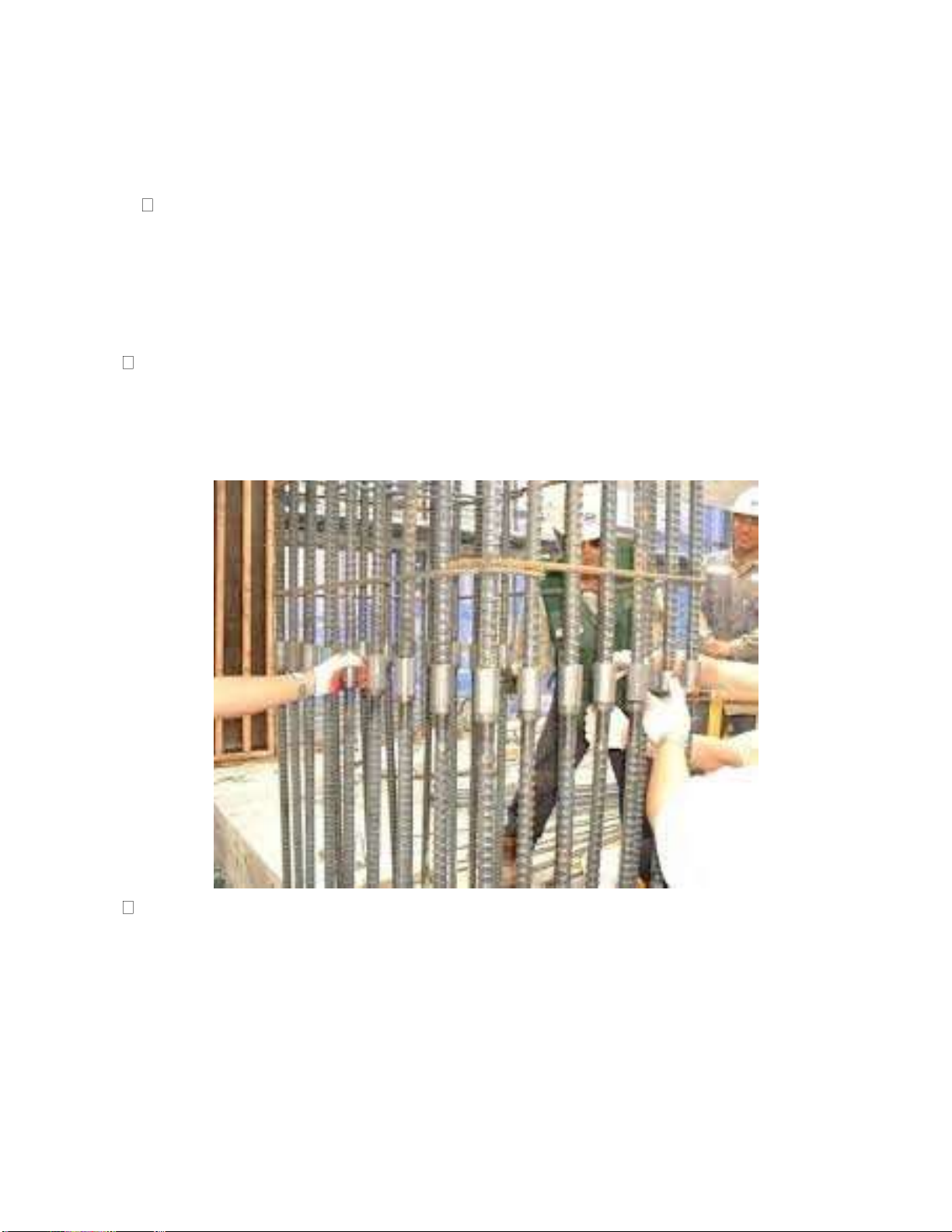
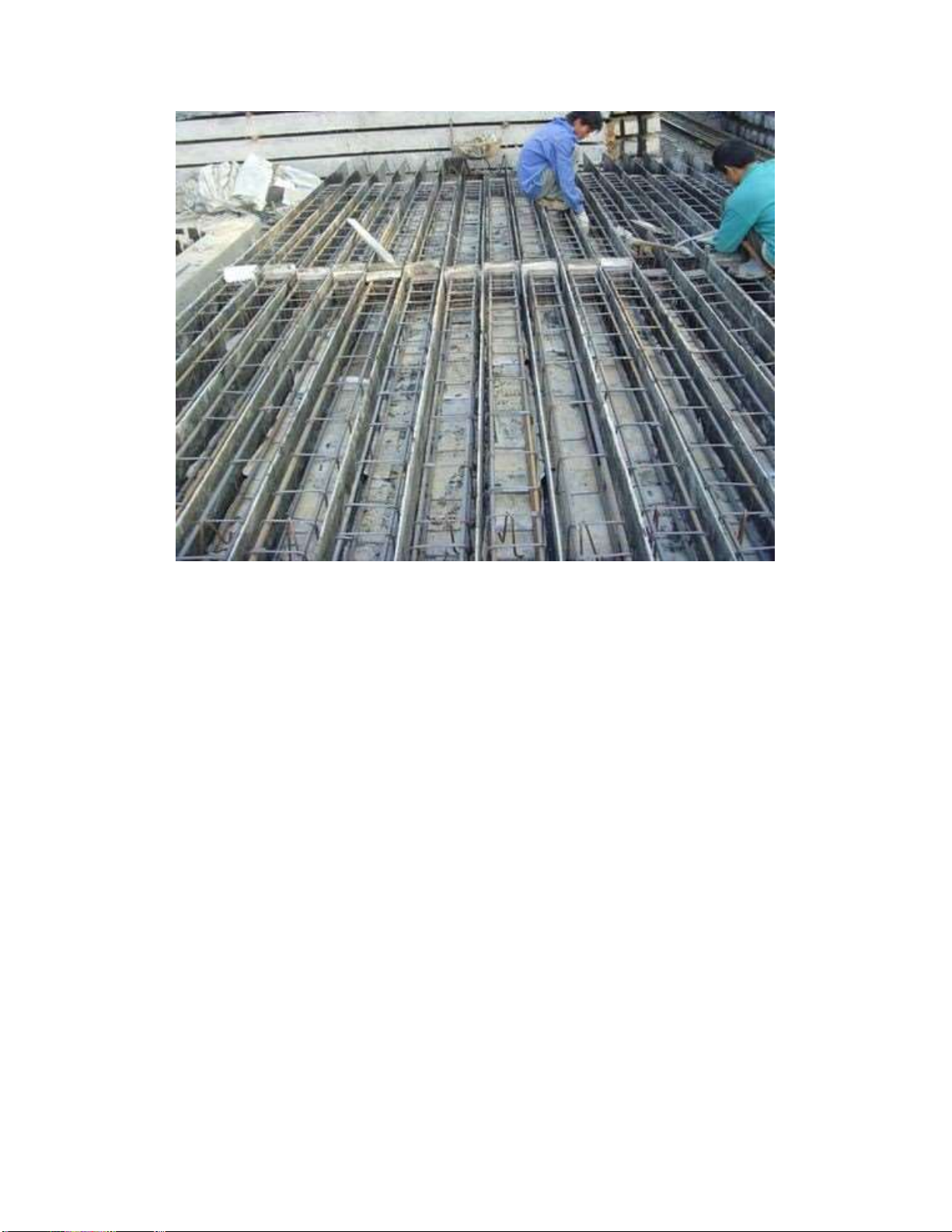
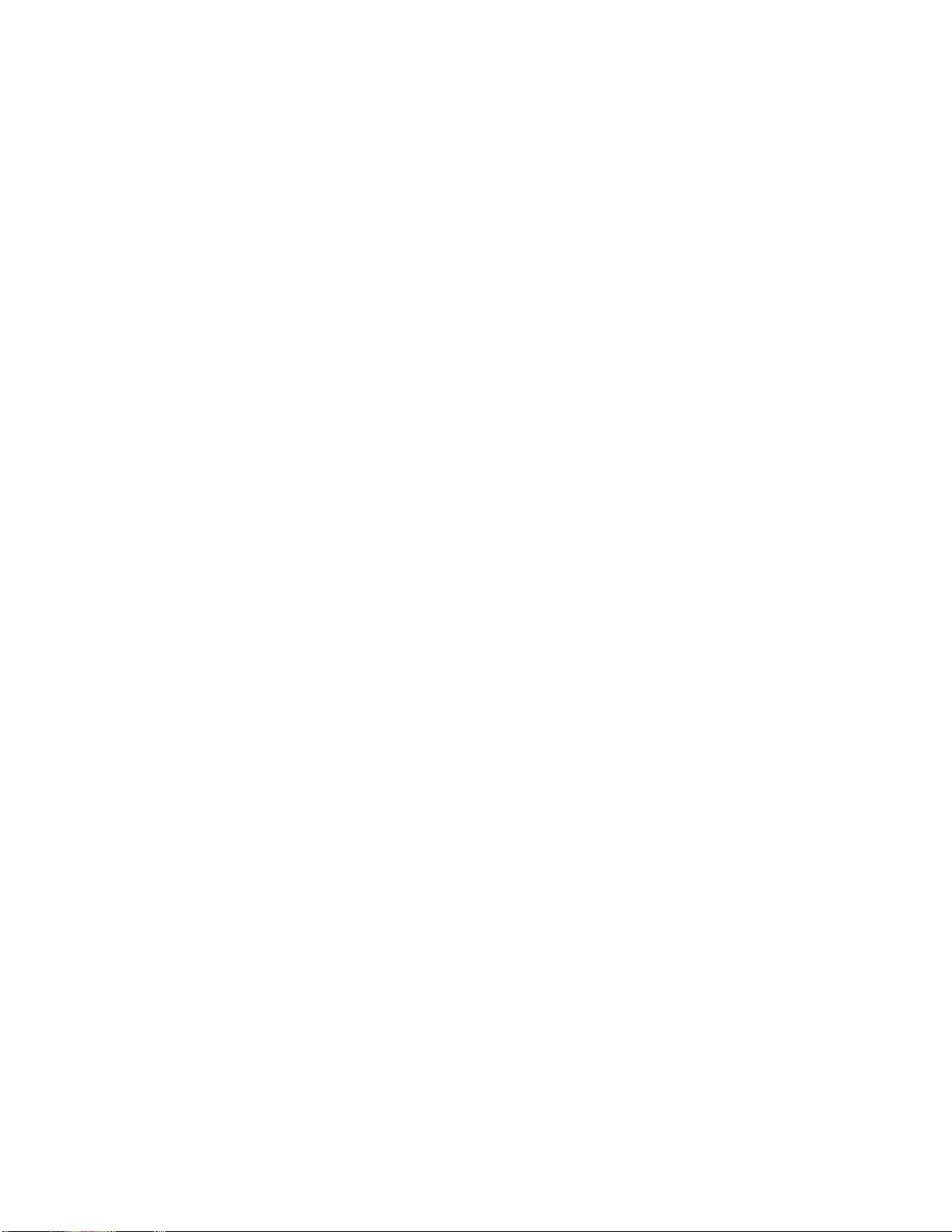
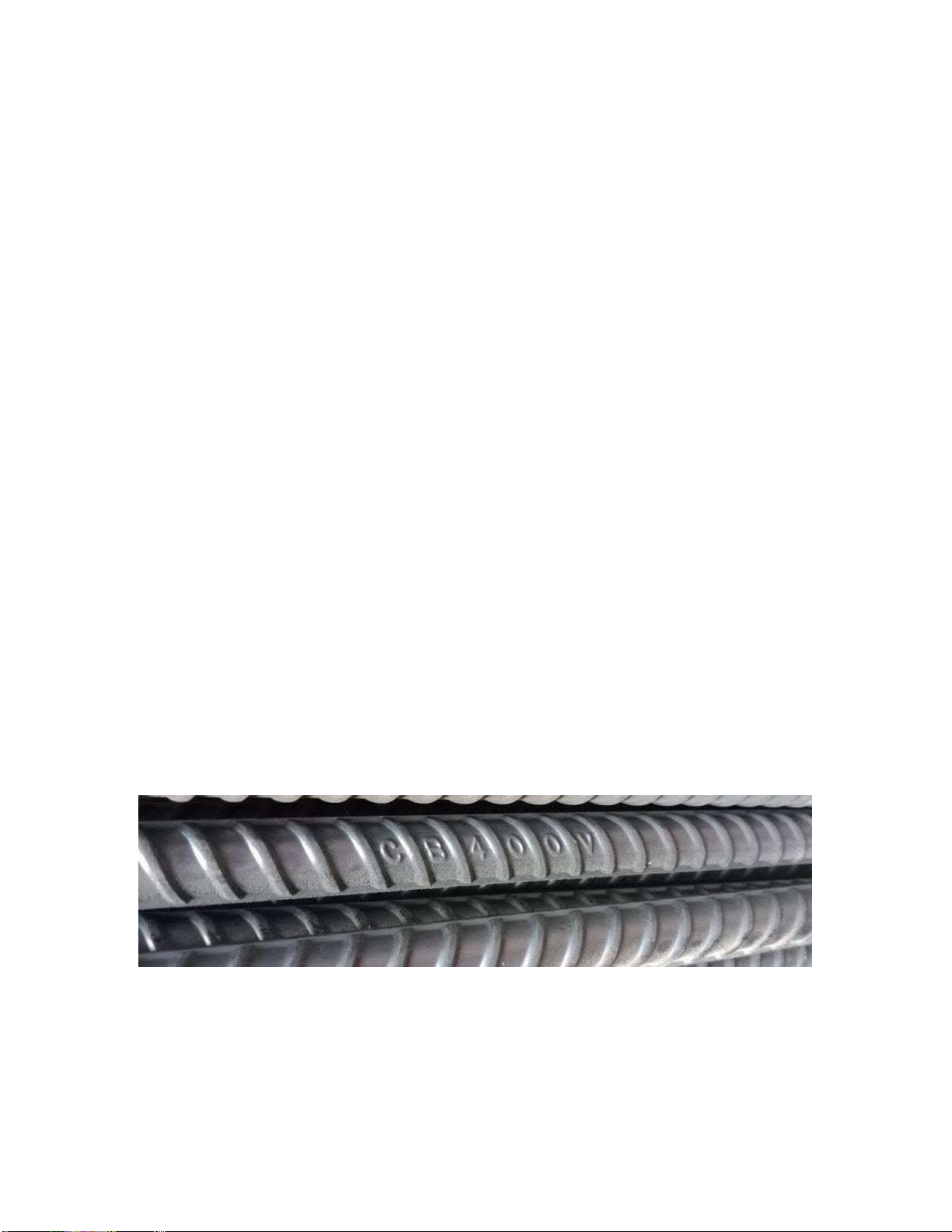
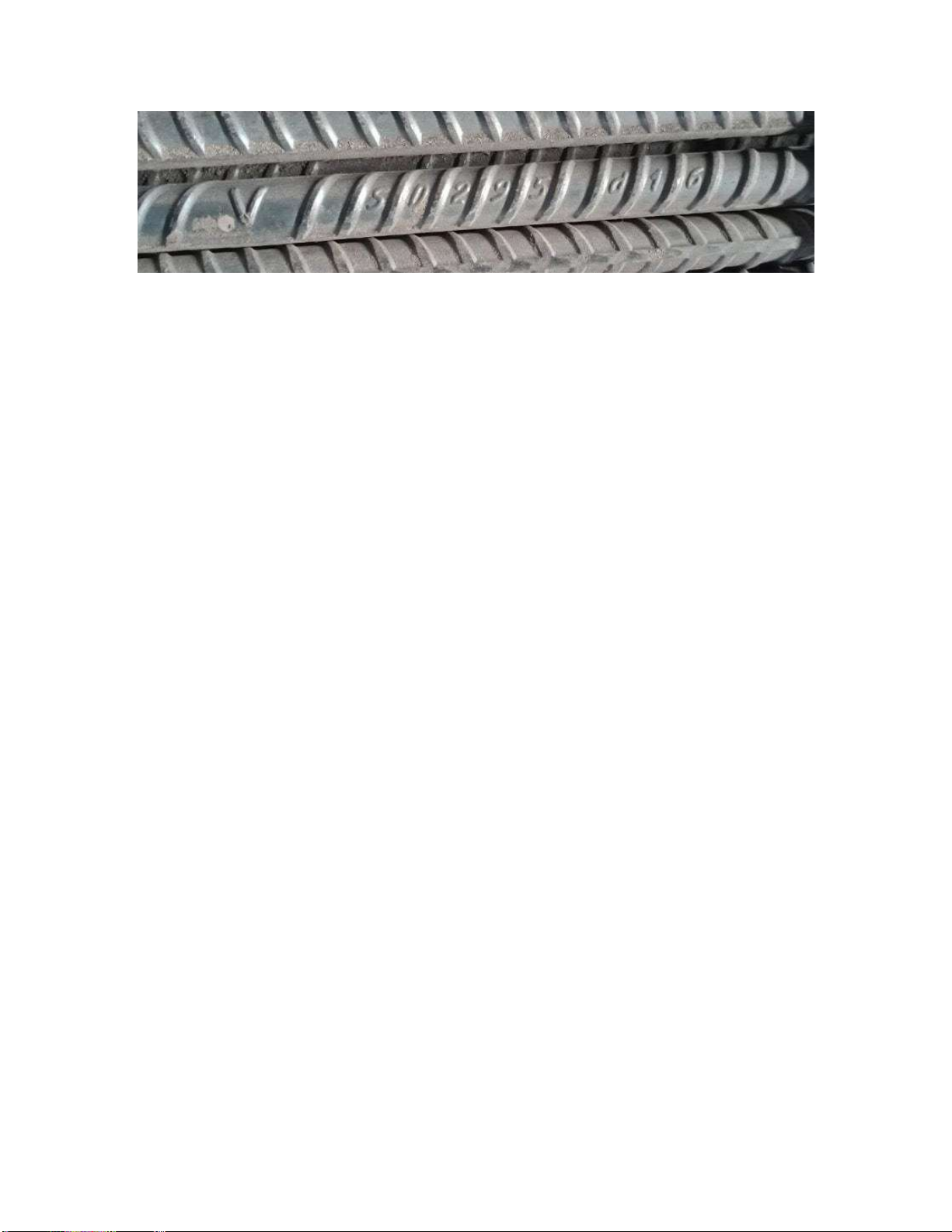
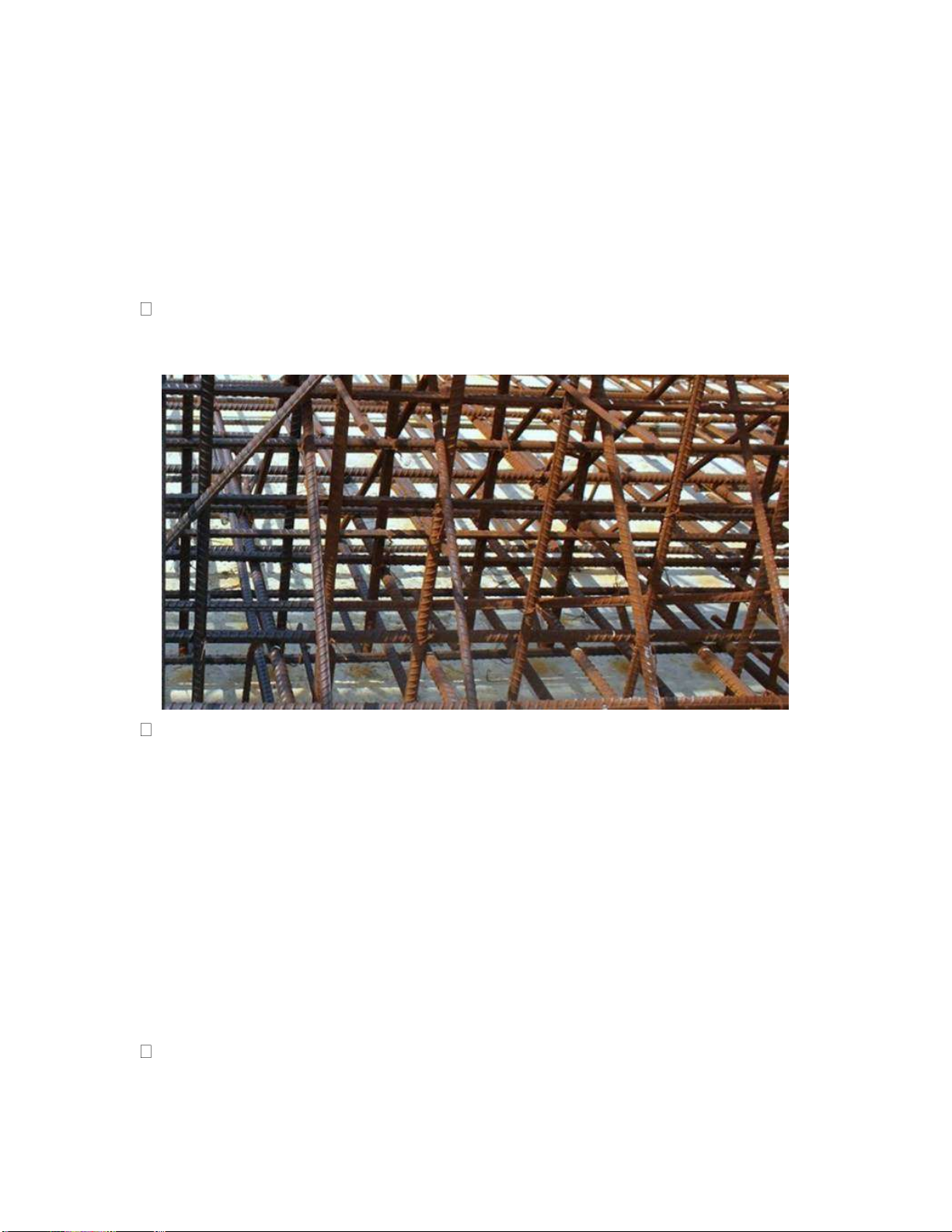
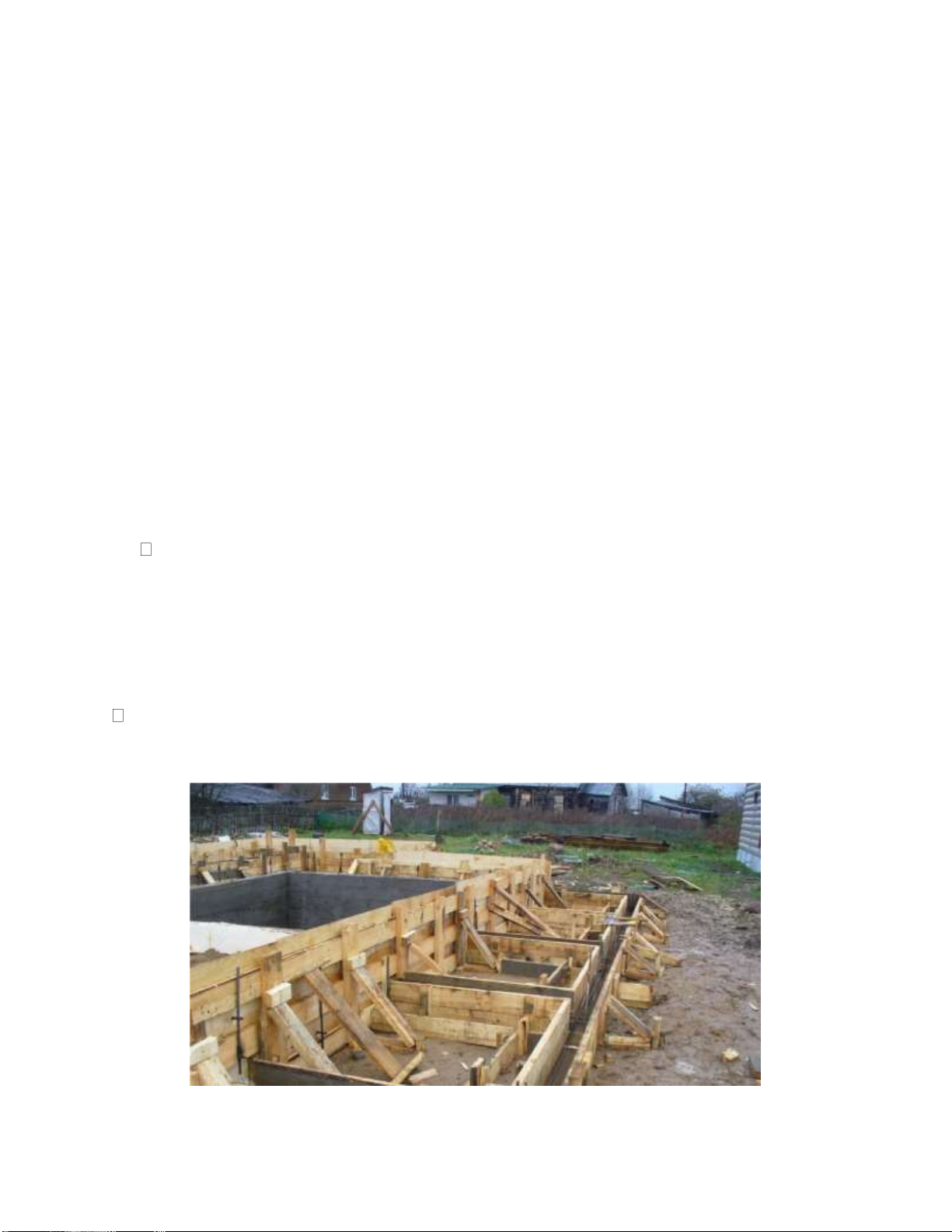
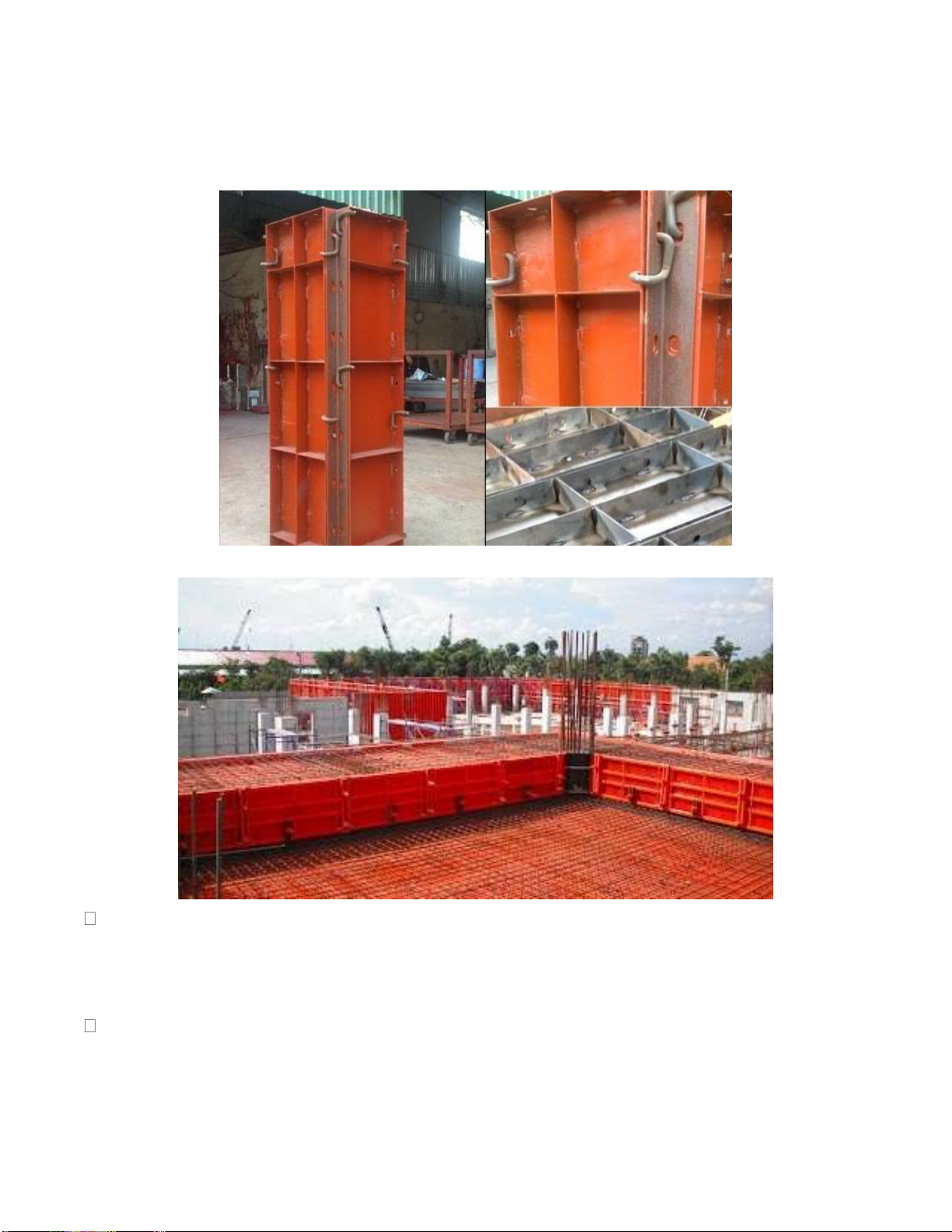
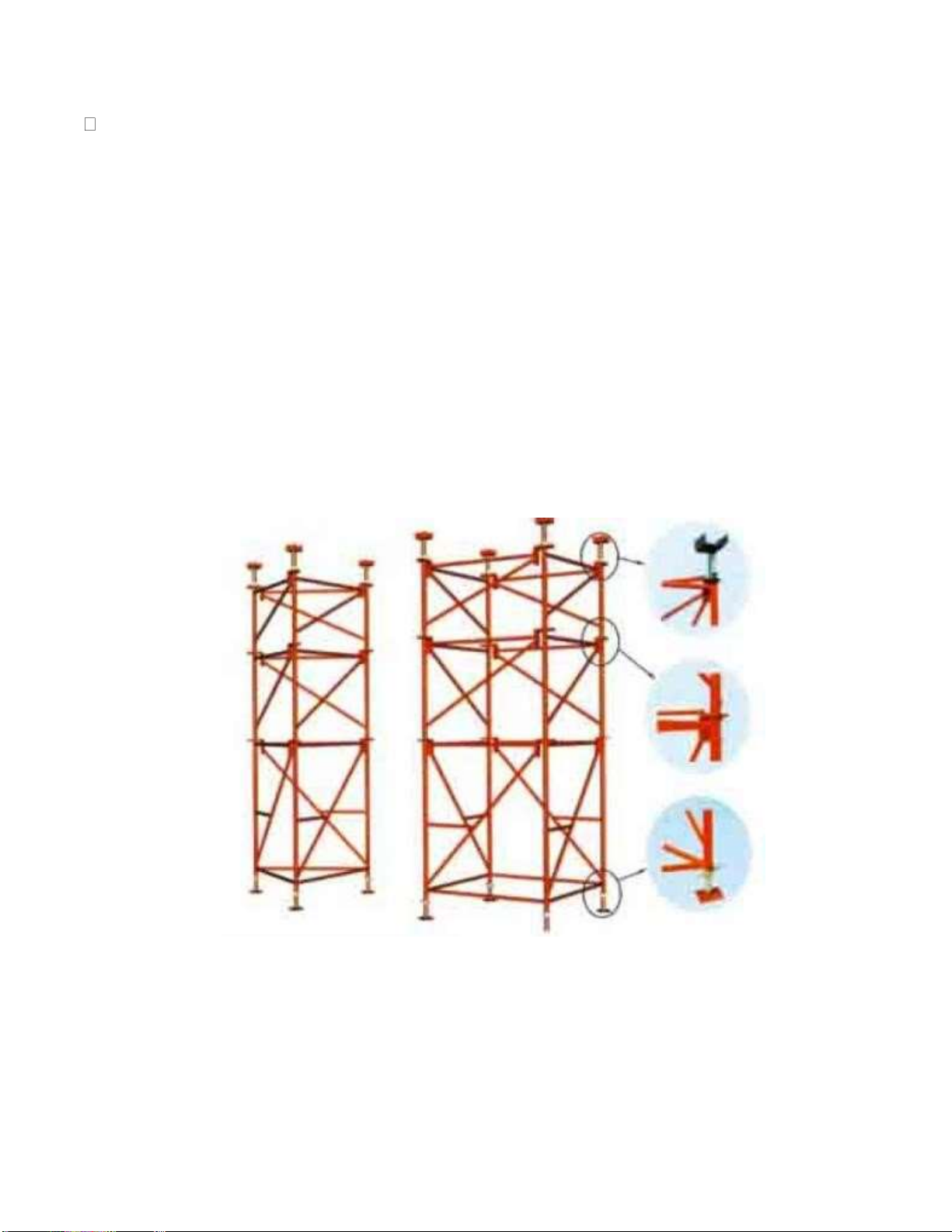
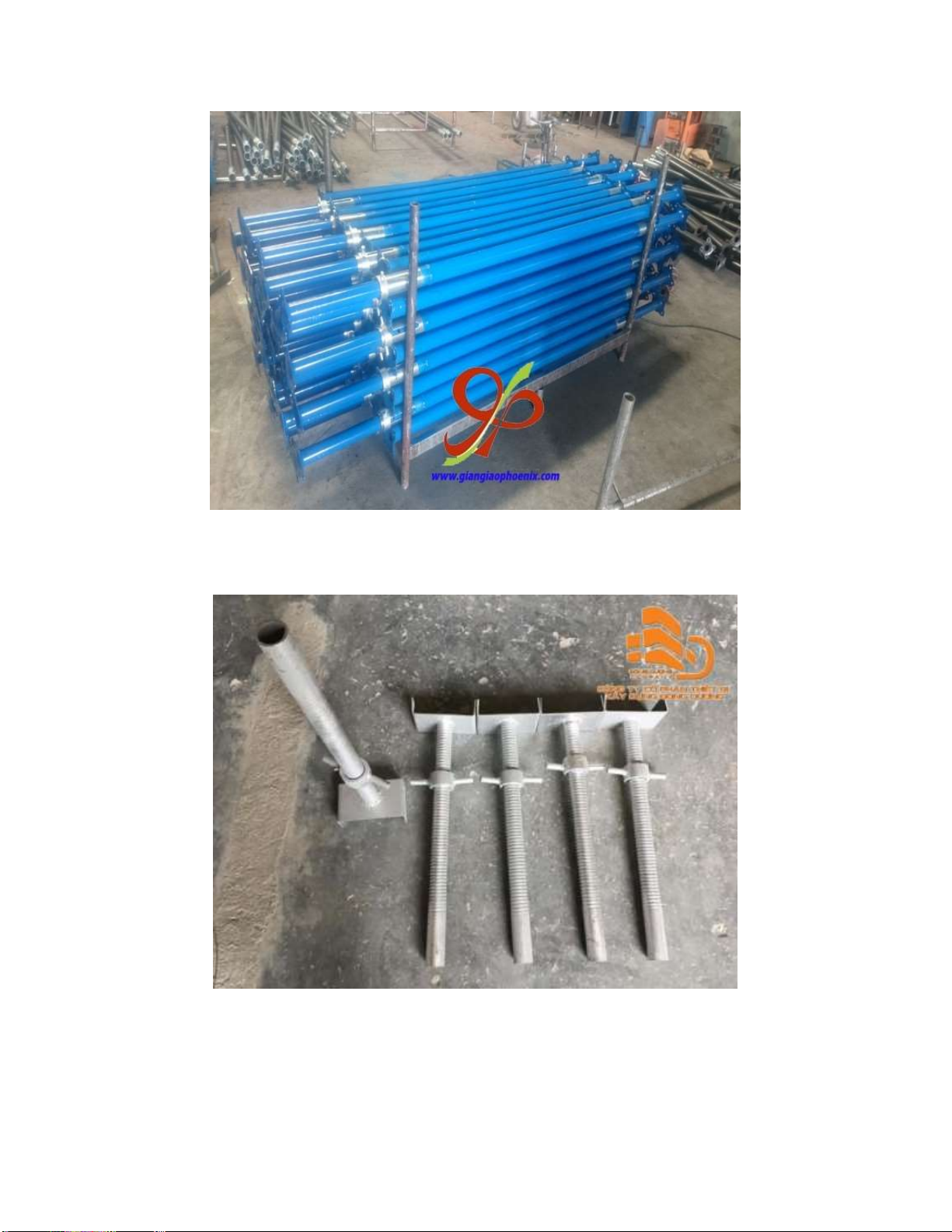
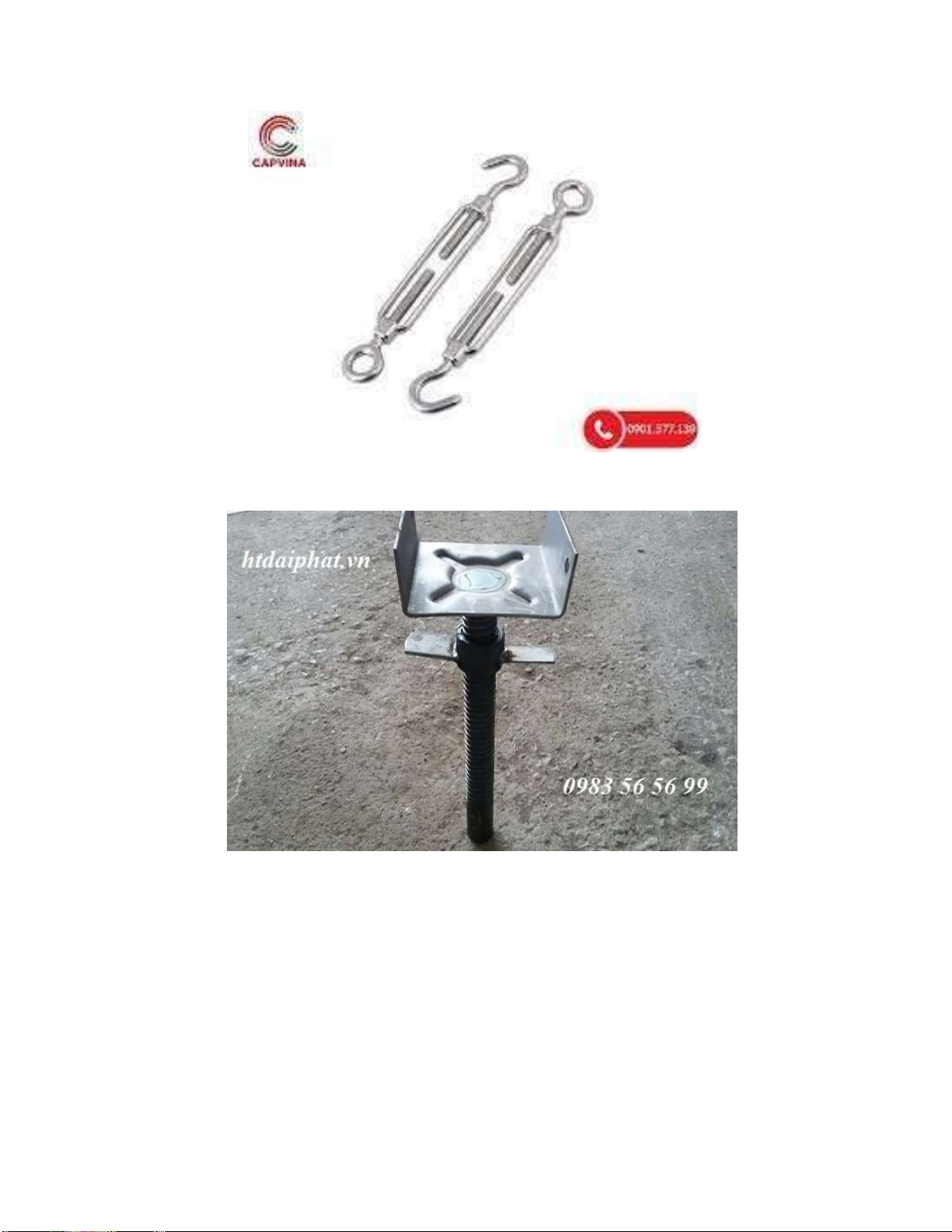
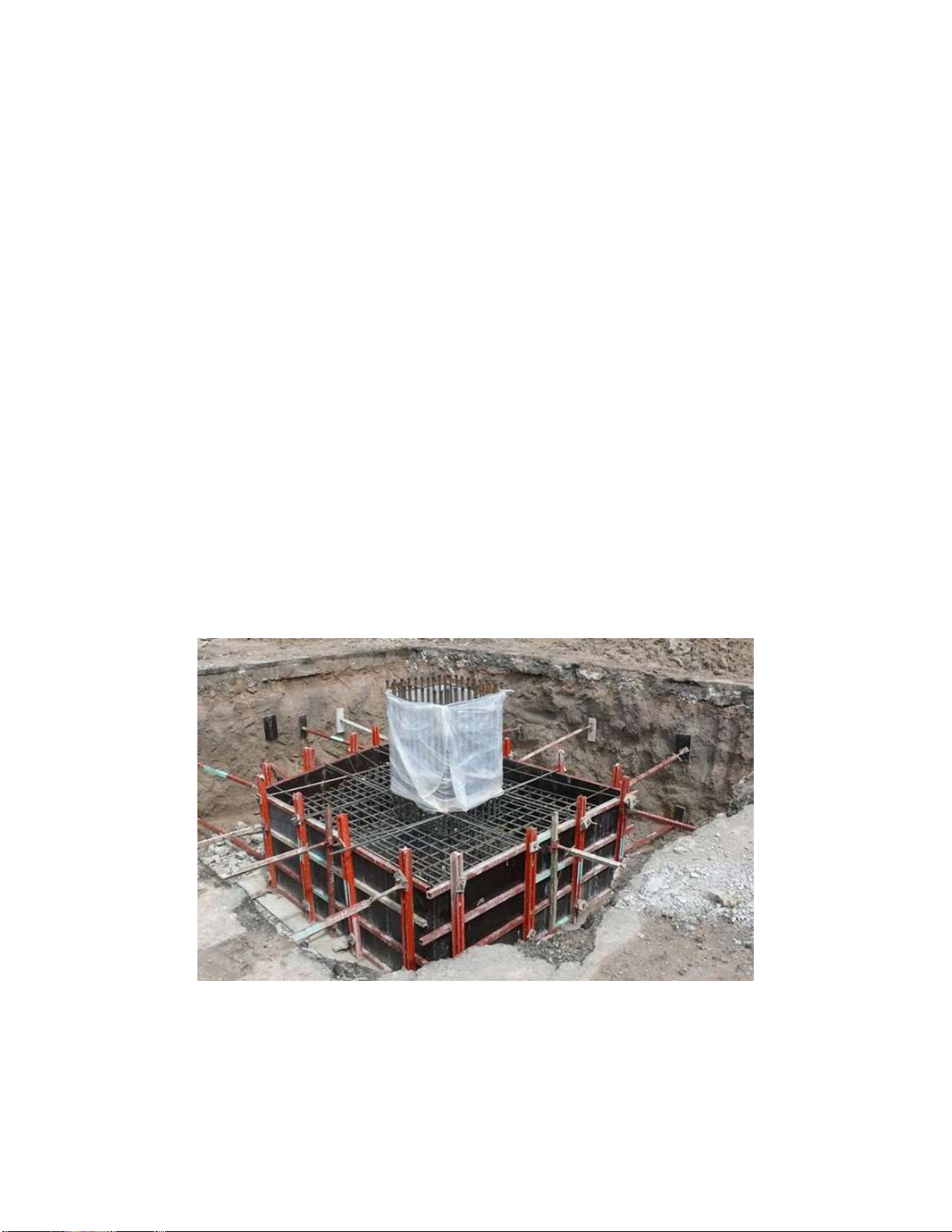
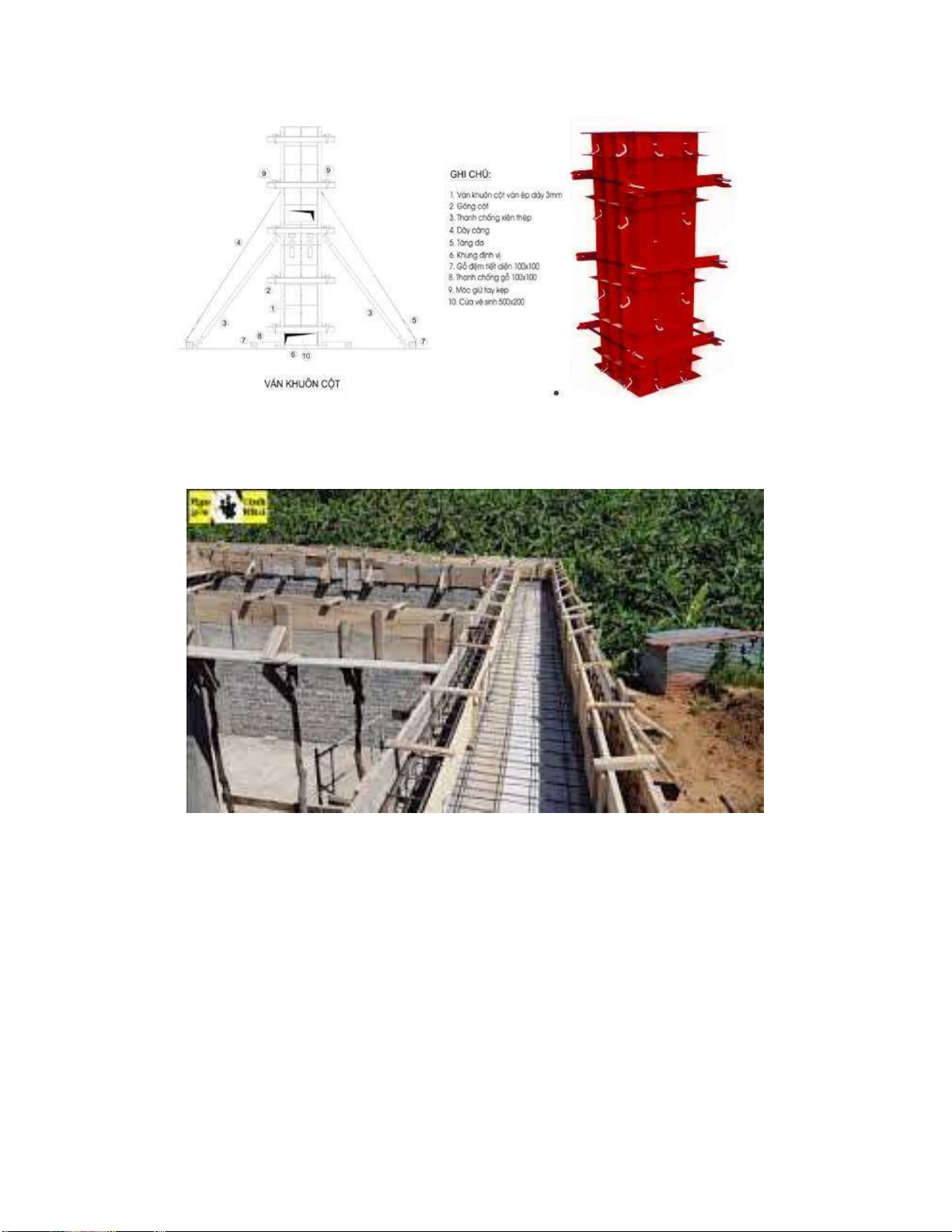

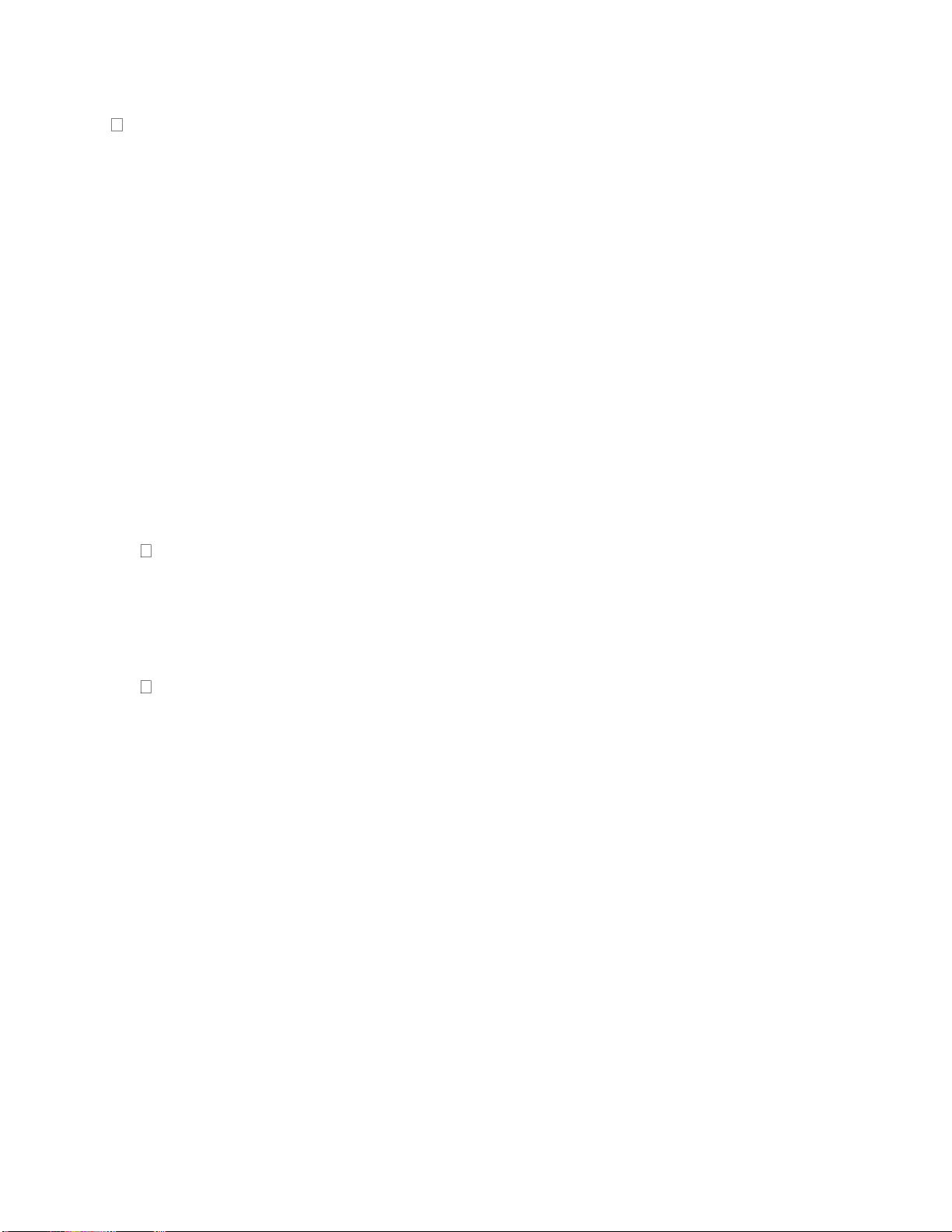
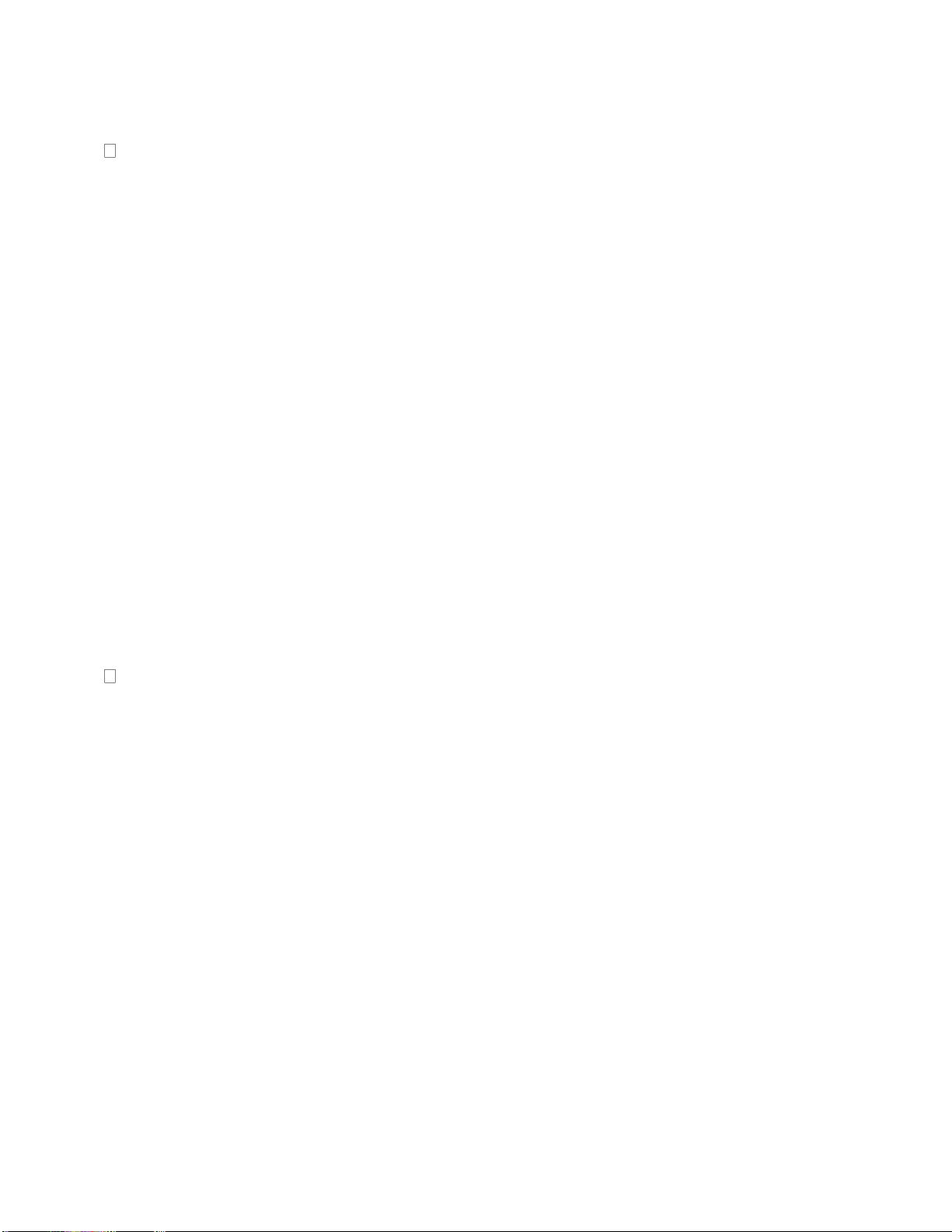
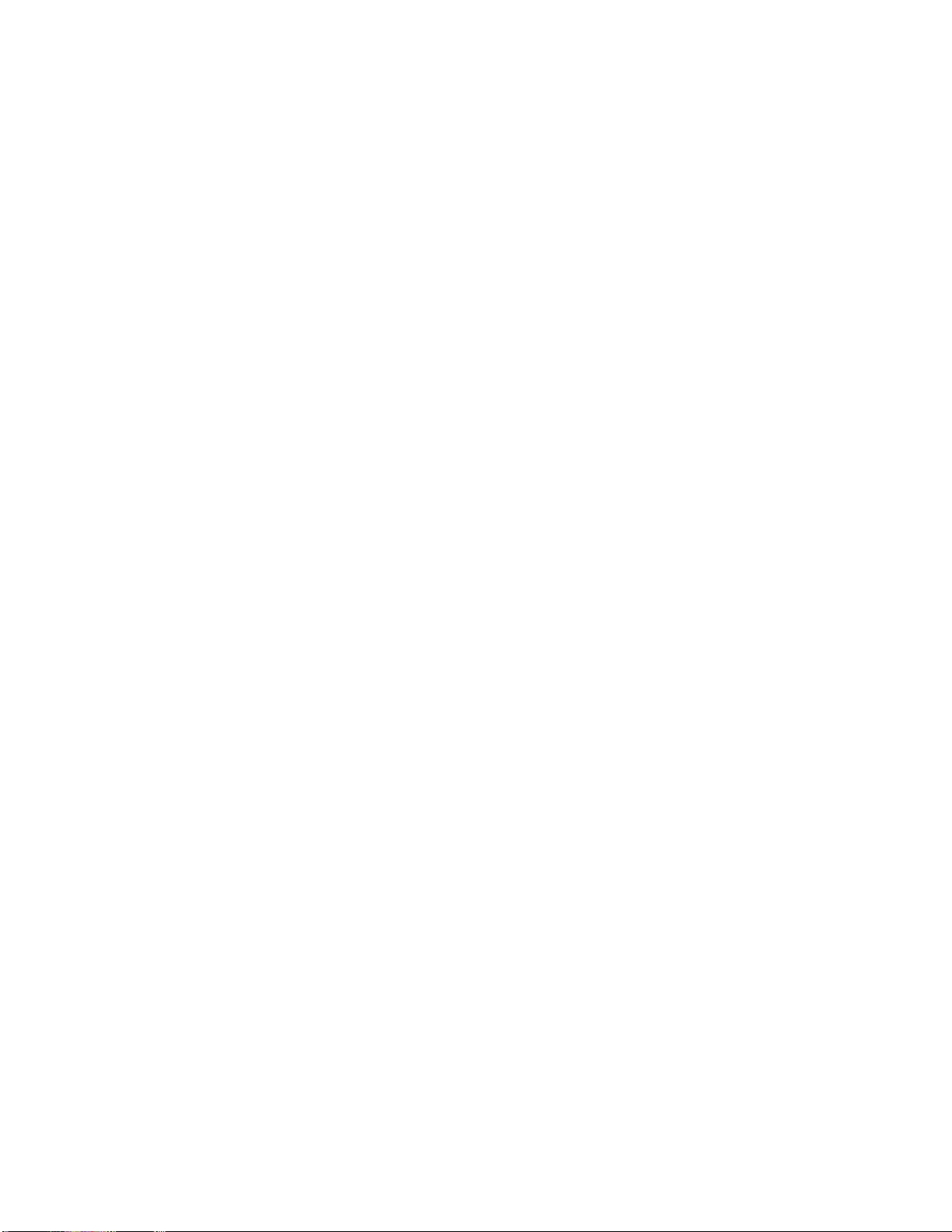
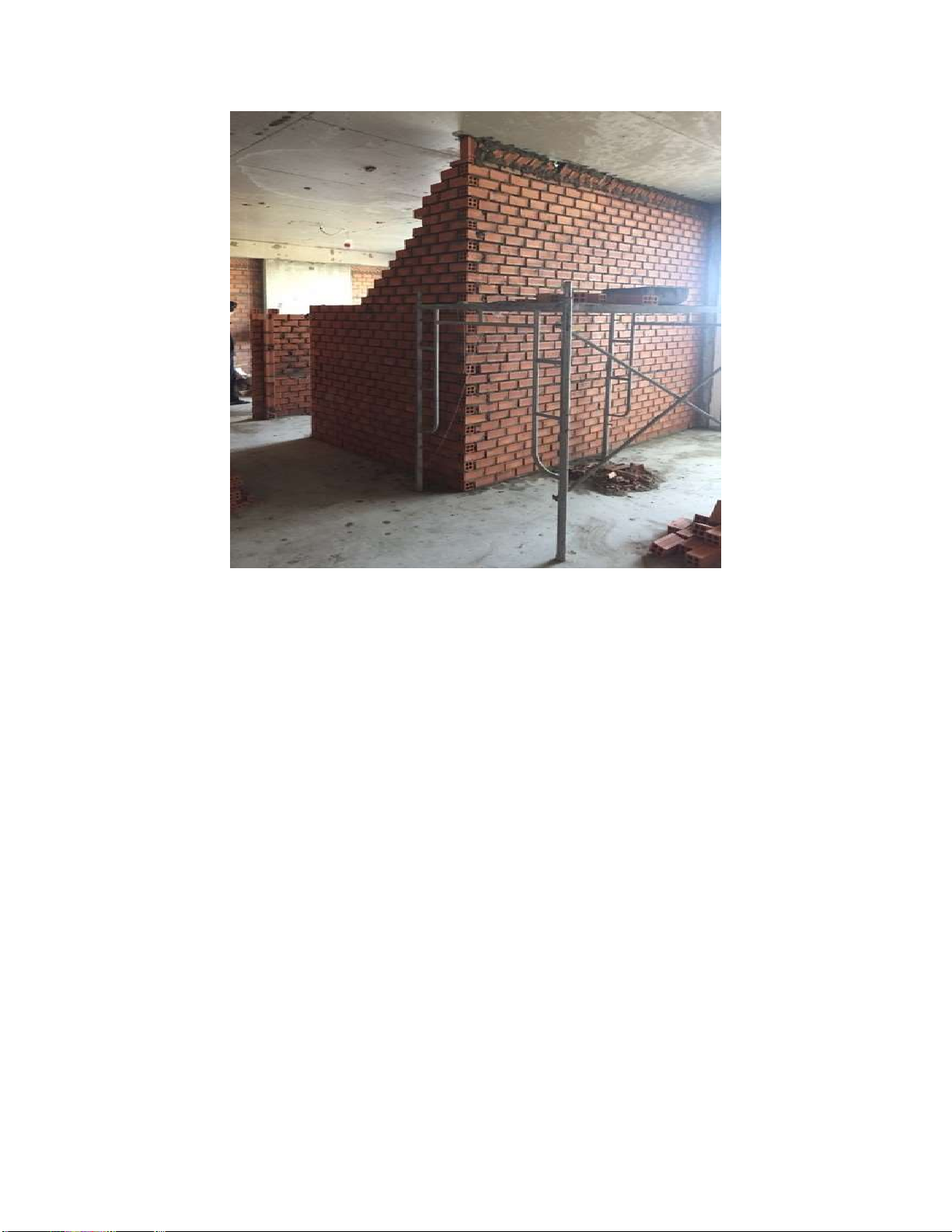
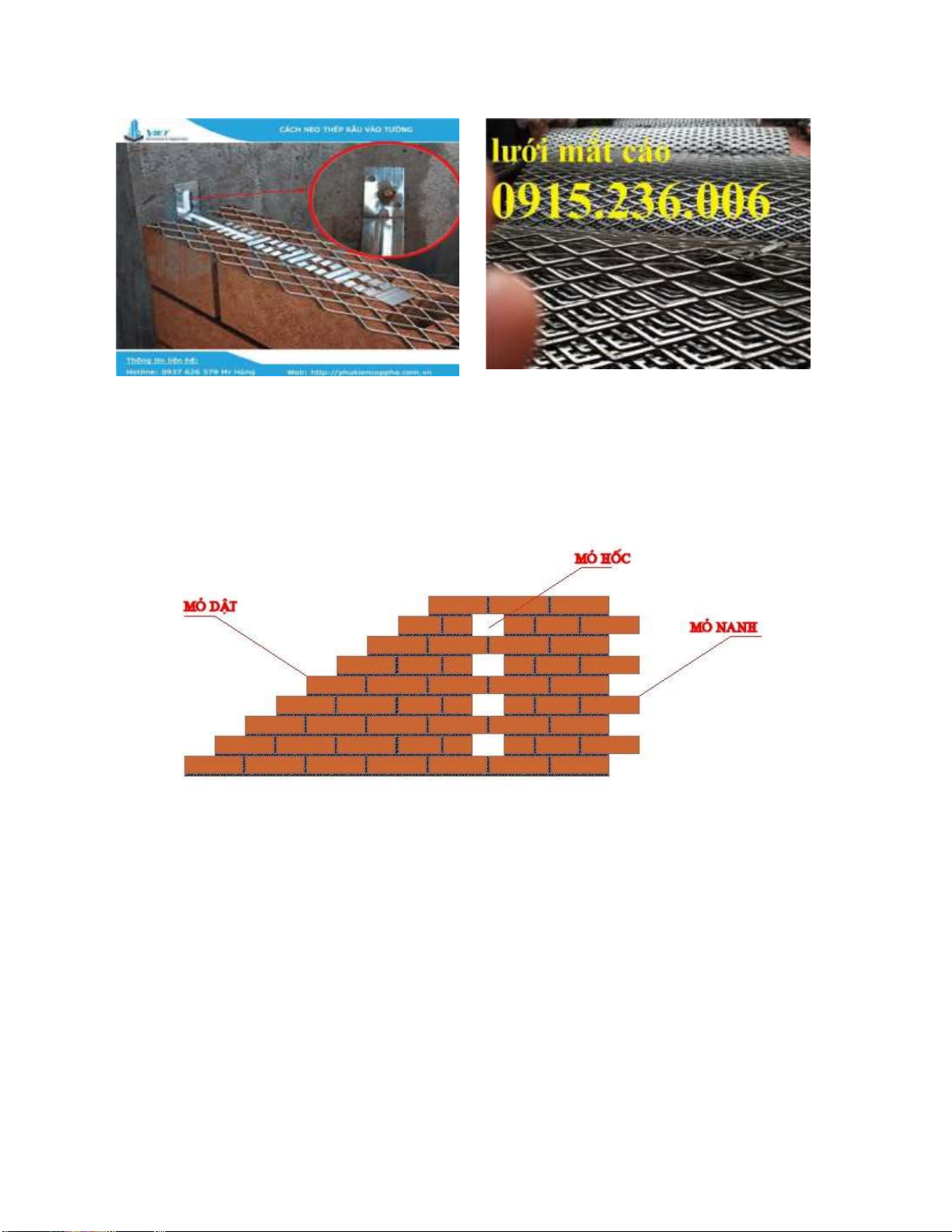
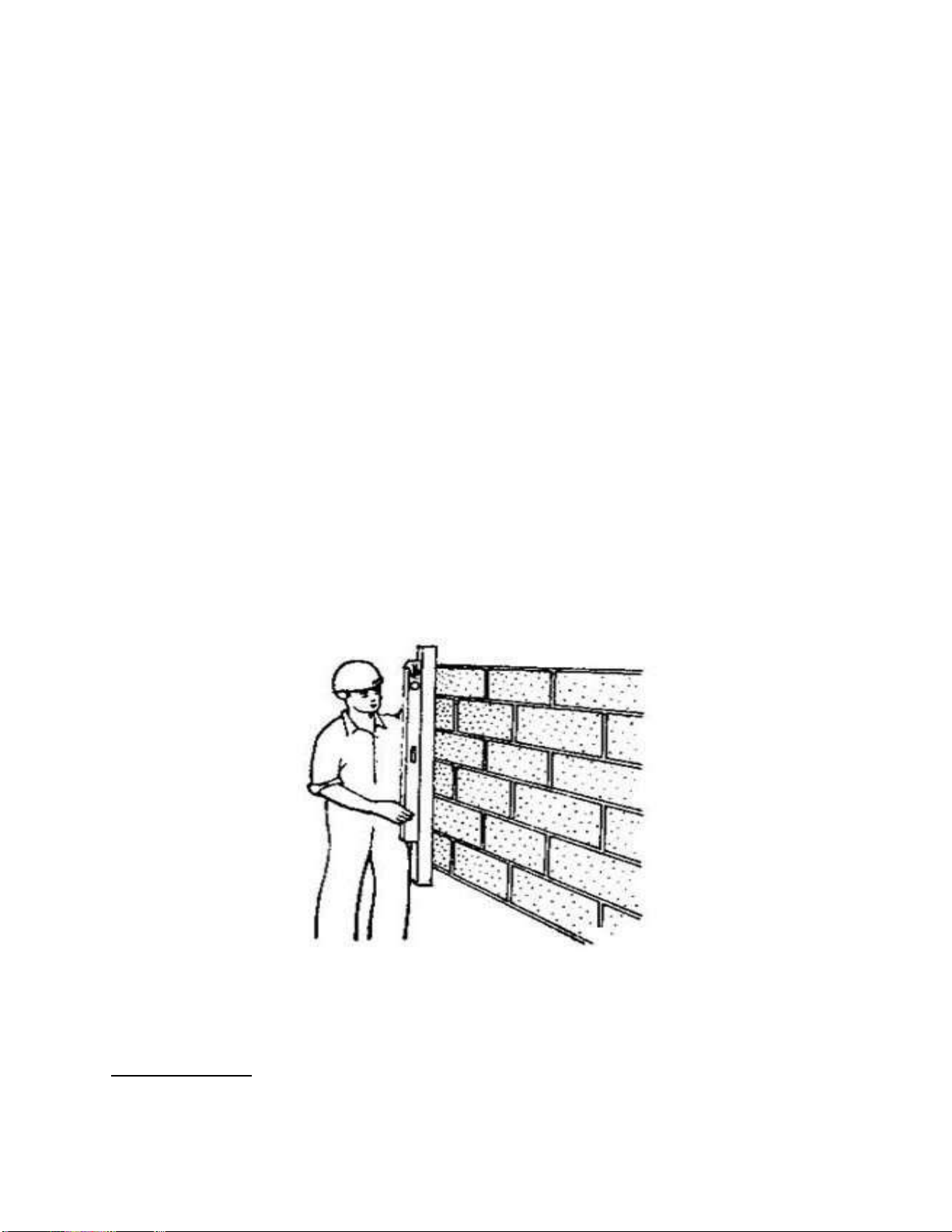
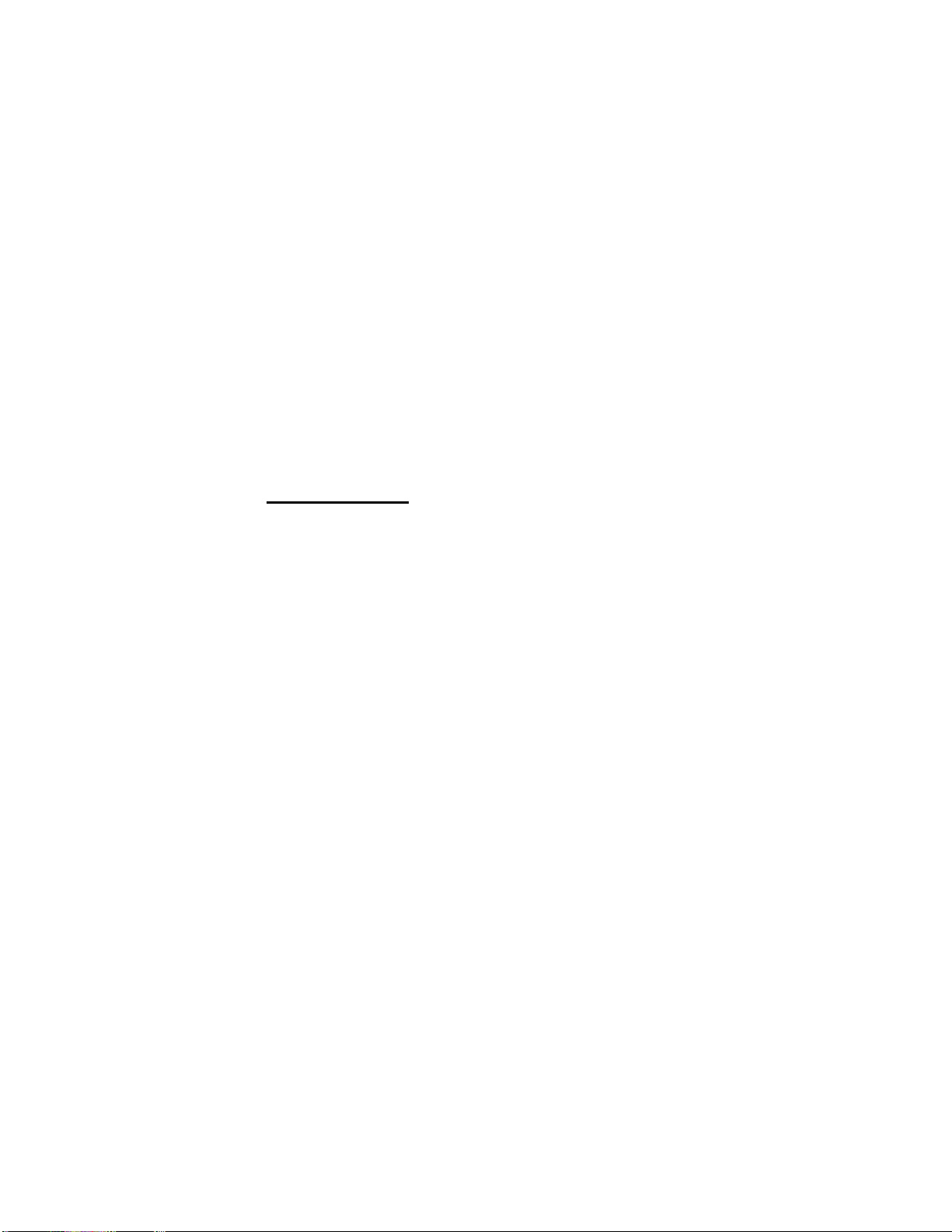
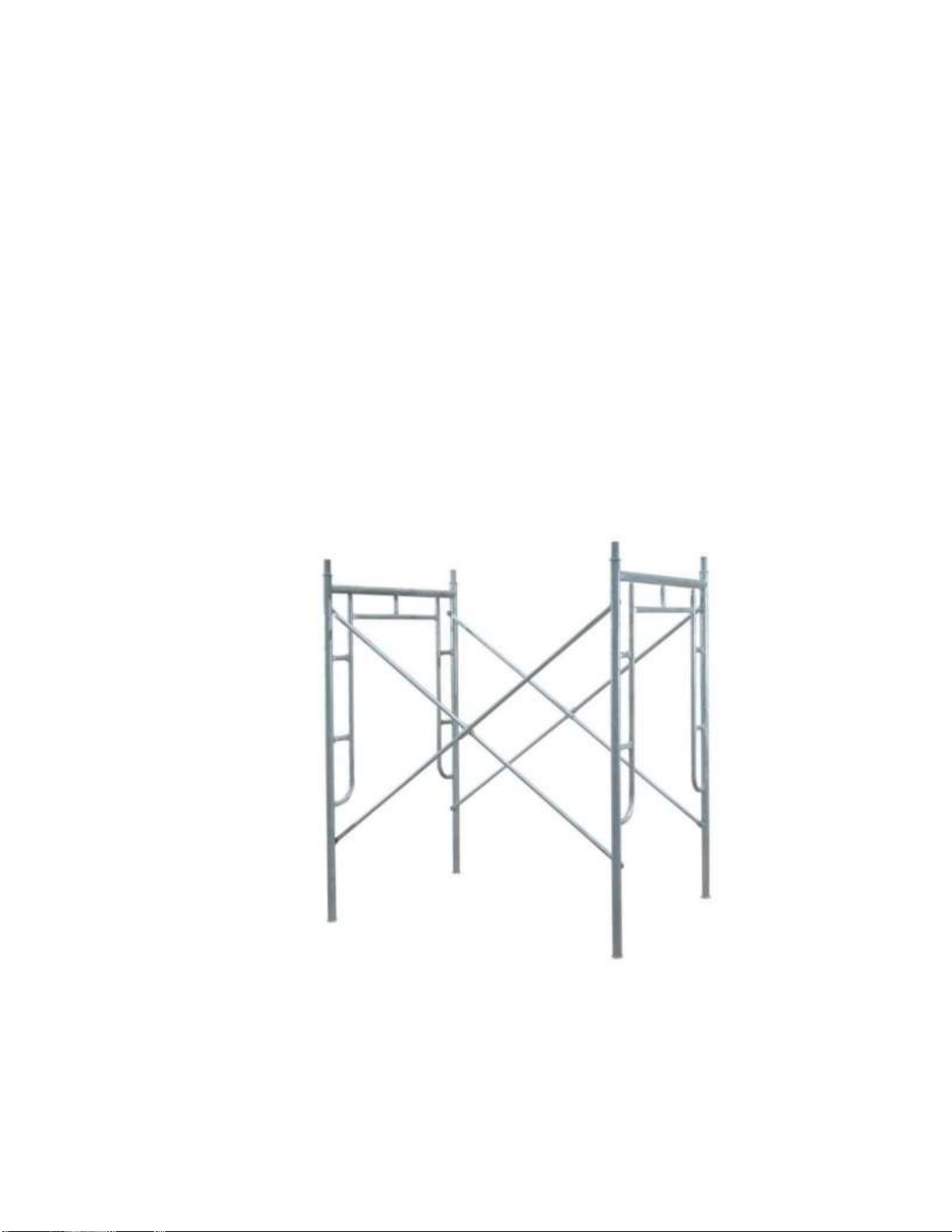
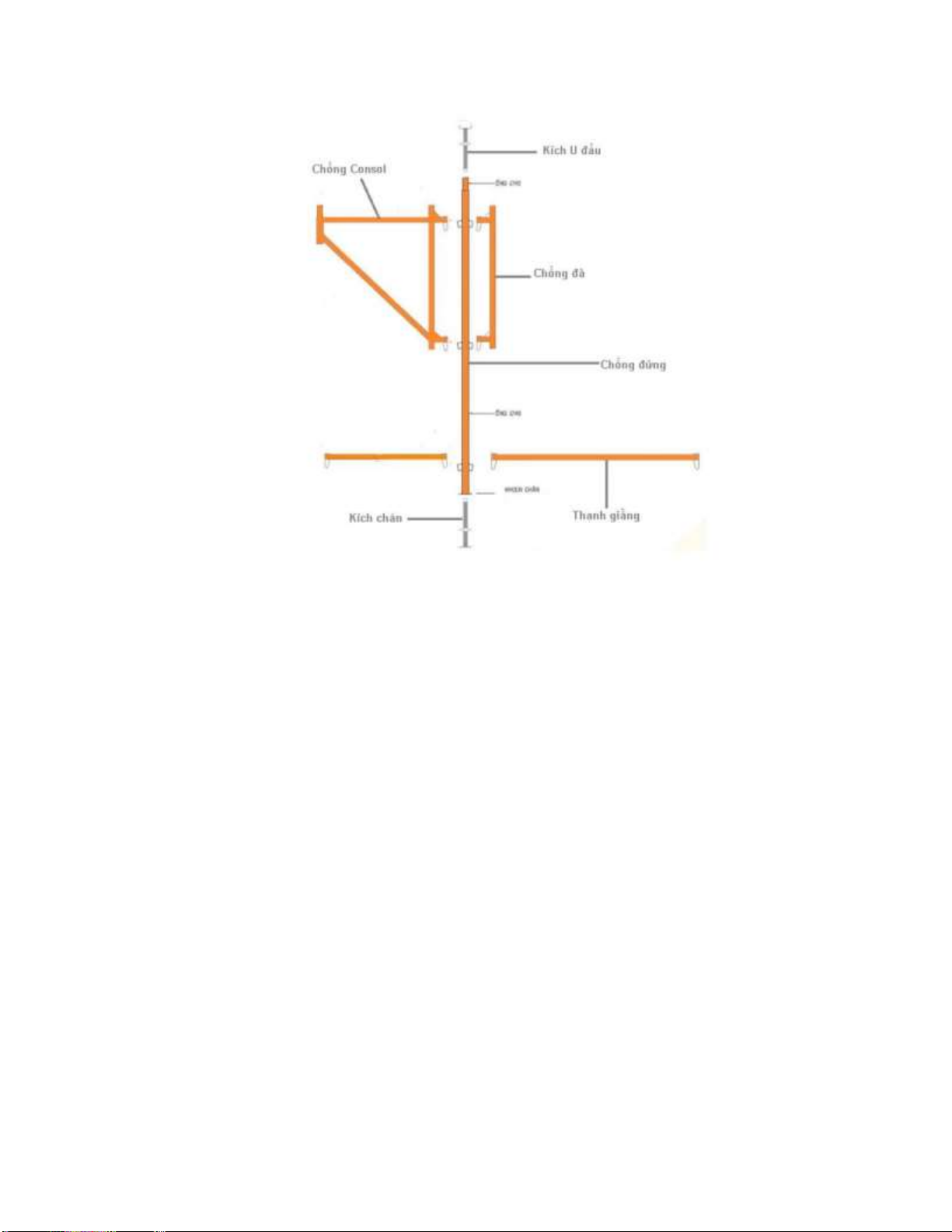
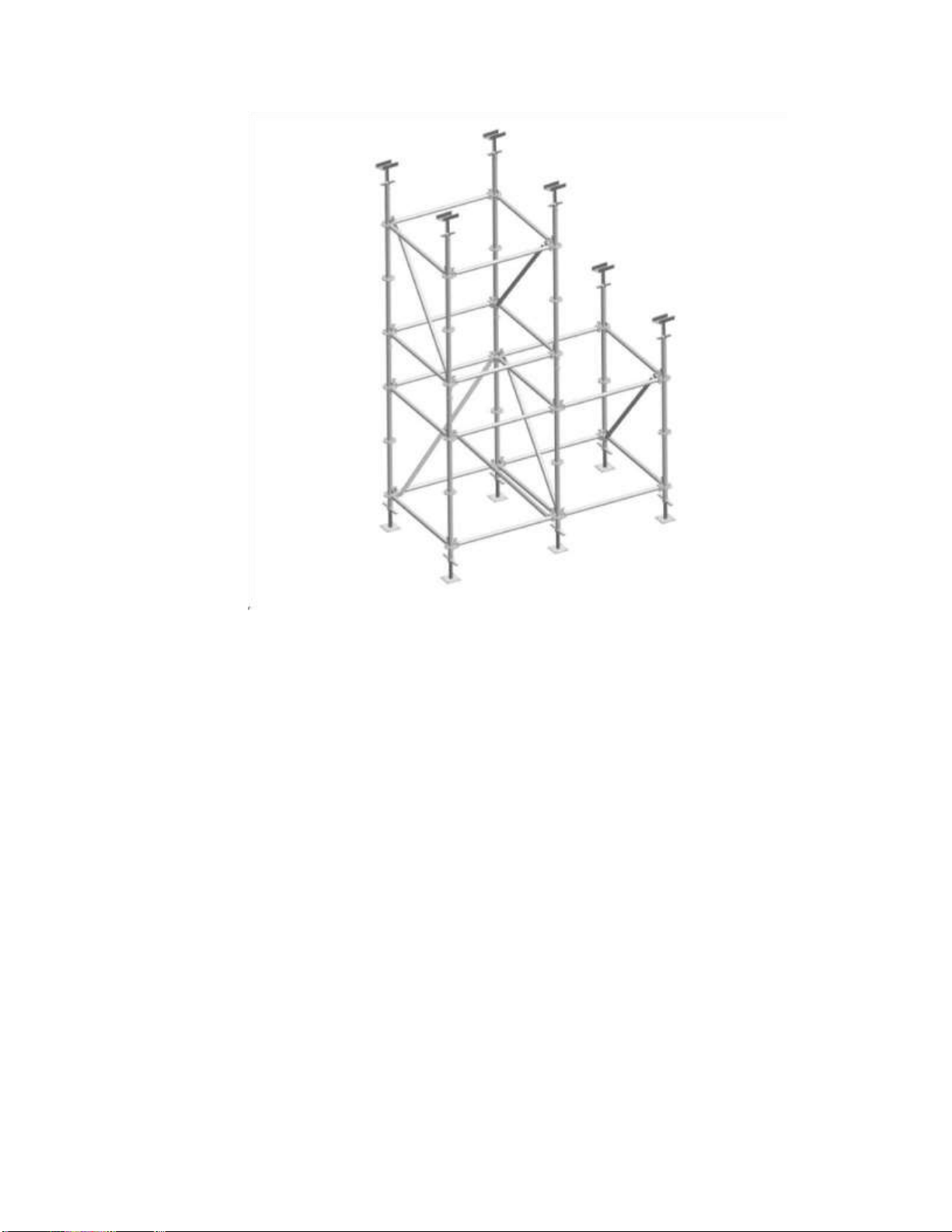
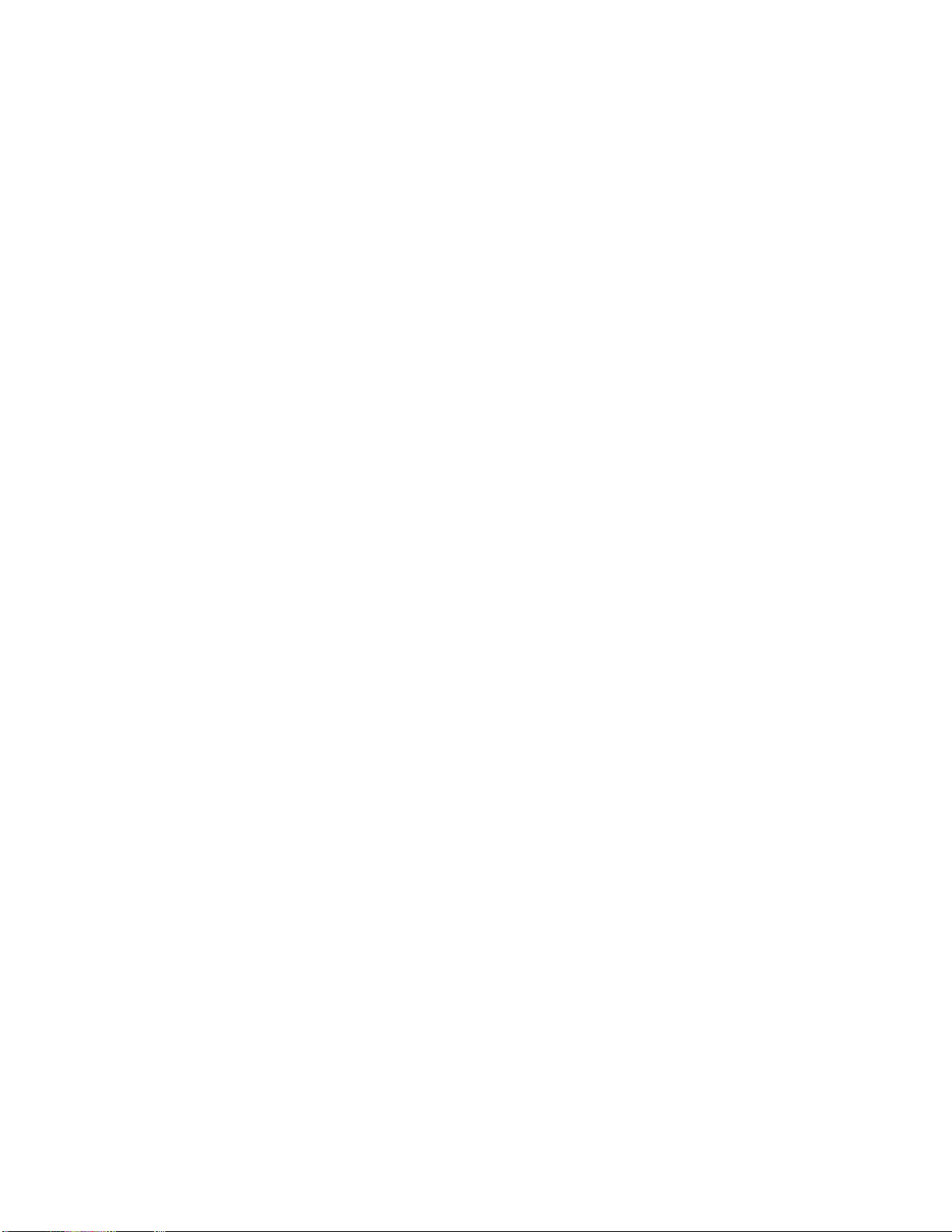
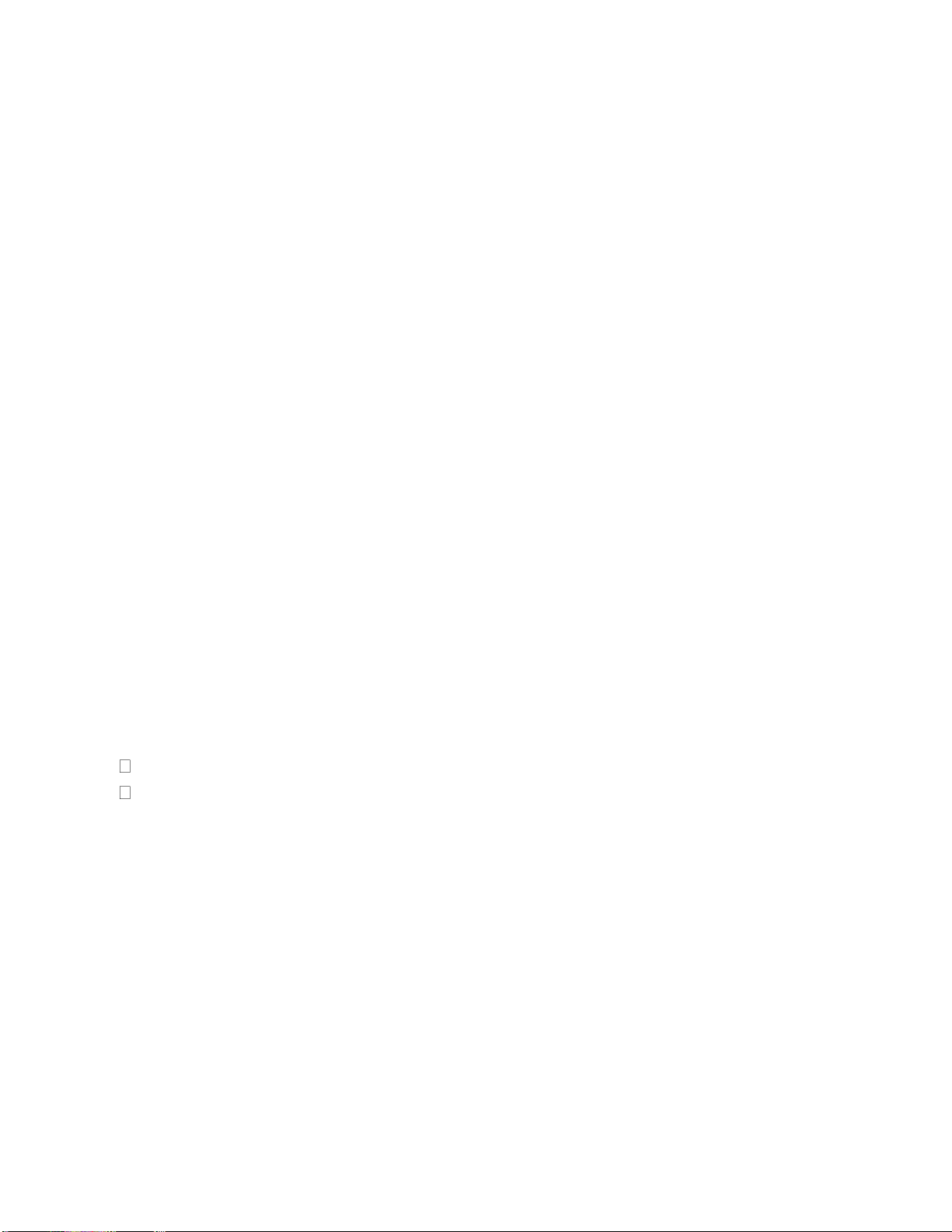
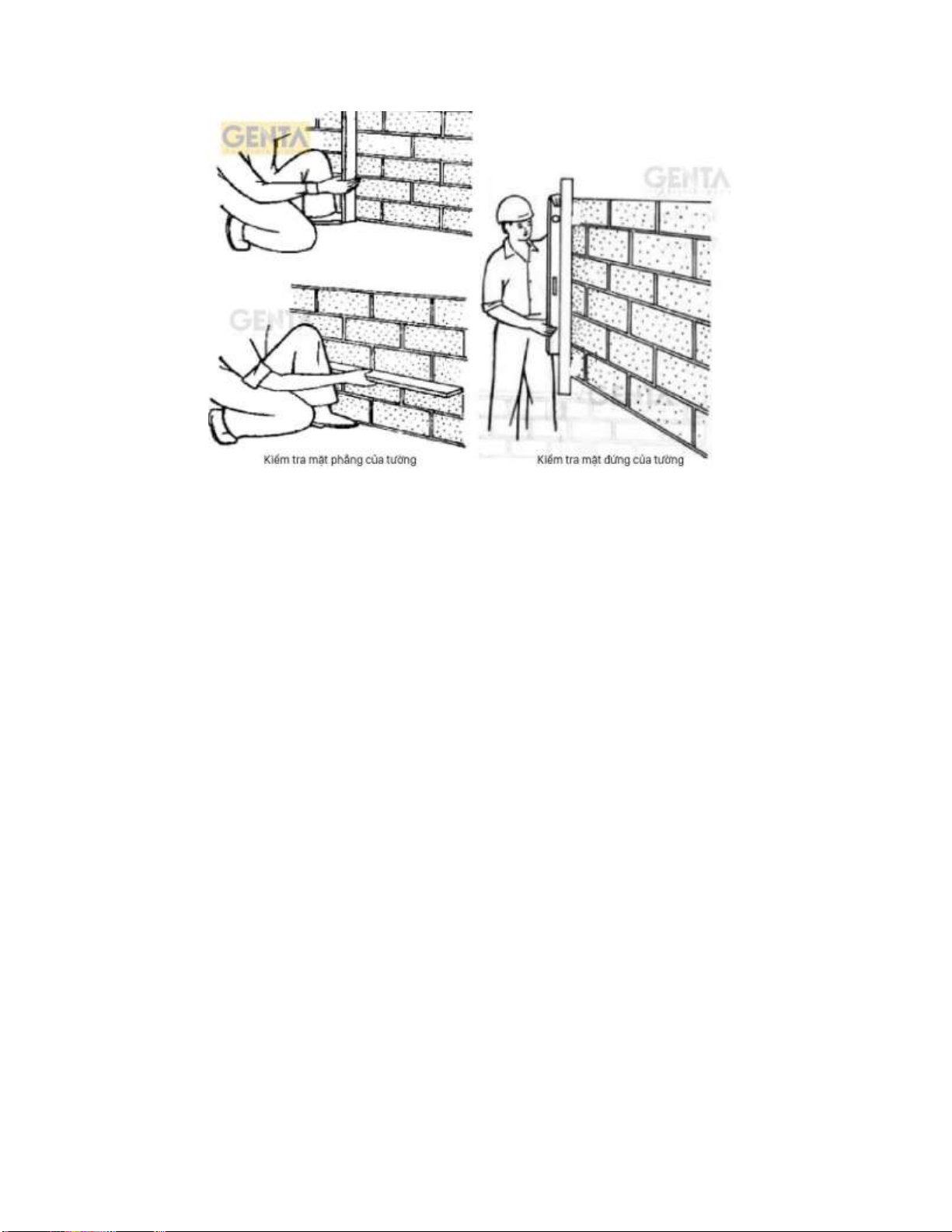
Preview text:
M
TRƯỜNG ĐẠI HỌC XÂY DỰNG HÀ NỘI BÁO CÁO THỰC TẬP CÔNG NHÂN
HỌ VÀ TÊN SINH VIÊN: NGUYỄN MINH HIỂN MÃ SỐ SINH VIÊN: 66663 LỚP : 63KT6
GIẢNG VIÊN HƯỚNG DẪN: ĐỖ HỮU KHOA HÀ NỘI – 02/2022
BÁO CÁO THỰC TẬP CÔNG NHÂN
I. Công tác bê tông
1. Tìm hiểu về các thành phần công việc trong một quá trình đổ bê tông, biên chế
tổđội đổ bê tông (số lượng, thành phần cấp bậc):
1.1. Phương pháp đổ và biên chế tổ đội:
a) Các phương pháp đổ bê tông thường dùng là:
- Đổ bê tông thủ công: thường dùng cho các công trình nhà dân.
- Đổ bê tông bằng cần trục tháp: thường dùng cho các công trình nhiều tầng, các dự án
xây dựng với quy mô lớn,…
- Đổ bê tông bằng bơm tĩnh: thường dùng cho các công trình cao ốc hoặc nhà ở trong ngõ hẻm sâu.
- Đổ bê tông bằng bơm cần: thường dùng cho các công trình có chiều dài, nhà cao dưới
5 tầng, khá phổ biến hiện nay.
b) Thành phần công việc cho một quá trình đổ bê tông:
Thông thường thì phần việc cho 1 quá trình đổ bê tông thường gồm:
Chuẩn bị vật liệu và xác định thành phần cấp phối bê tông
Trộn bê tông : có thể bằng máy trộn, thủ công bằng tay hoặc sử dụng bê tông thương phẩm từ nhà máy.
Vận chuyển bê tông từ nơi trộn đến nơi đổ: với mỗi phương pháp đổ bê tông thì lại có
mỗi cách vận chuyển bê tông khác nhau
- Đổ bê tông thủ công: dùng xe rùa hoặc xô cùng máy tời để chuyển bê tông đến vị trí đổ.
- Đổ bê tông bằng cần trục tháp: đổ đầy bê tông từ máy trộn vào phễu đổ bê tông, sau
đó cần trục sẽ cẩu phễu đổ lên và đưa đến vị trí đổ.
- Đổ bê tông bằng bơm tĩnh: thông qua máy bơm bê tông và đường ống dẫn để đưa bê tông đến vị trí đổ
- Đổ bê tông bằng bơm cần: bê tông lấy từ máy trộn, thông qua xe bơm bê tông cần để
đưa bê tông đến vị trí đổ. Đổ bê tông và đầm Bảo dưỡng bê tông
c) Biên chế tổ đội công nhân
Tùy theo từng phương pháp và quy mô công trình xây dựng mà số công nhân cần thiết khác nhau. Phương pháp thủ công:
- Đổ bê tông móng, dầm sàn: 1-2 người trộn bê tông, 4-5 người vận chuyển, đổ bê
tông đến khu vực thi công, 1 người đầm dùi, 1-2 người xoa mặt bê tông (đối với
thi công dần sàn trên cao cần 1 người làm vị trí điều chỉnh tời để vận chuyển bê tông lên cao).
- Đổ bê tông cột: 1- 2 người vận chuyển bê tông, 1 người trộn bê tông, 1 người đổ
bê tông, 1 người đầm dùi
Phương pháp cơ giới: 5-6 người cho toàn bộ công tác từ nối ống bơm bê tông đến điều
chỉnh vận chuyển bê tông tới khu vực đổ, 1 người đầm dùi, 1 người xoa mặt.
Số công nhân tối thiểu: phương pháp cơ giới: 6 người; phương pháp thủ công: 8 người 1.2.
Khối lượng bê tông thi công cho mỗi ca:
Khối lượng bê tông thi công cho mỗi ca làm việc phụ thuộc vào dung tích máy trộn, vị trí
cần đổ (dầm, sàn, cột, móng, khoan nhồi,…), điều kiện thời tiết, số lượng công nhân tham gia đổ,… 1.3.
Bê tông cọc nhồi, tường vây, cọc barrett đổ khác so với công tác đổ bê tông
móng, cột dầm sàn phần thân là:
- Đổ bê tông cọc nhồi, tường vây, cọc barrett thích hợp với công trình có tải trọng lớn.
Phương pháp này có khả năng tạo ra các cây cọc lớn và có chiều dài đạt mức tối đa ,
có thể thi công cọc xuyên qua các tầng địa chất cứng nằm xen kẽ, không gây chấn
động đến các công trình xung quanh trong điều kiện cho phép có thể mở rộng đáy cọc
với các hình dạng khác nhau.
- Đổ bê tông móng, dầm cột sàn phần thân ưu điểm là có tiến độ nhanh, chi phí không
cao, có lực ma sát với thành đất ca hơn, phù hợp với các công trình nhỏ.
- Bê tông cọc nhồi, tường vây, cọc barrett đổ khác gì so với công tác đổ bê tông móng,
dầm cột sàn phần thân ở chỗ là người ta không đầm mà trút trực tiếp bê tông xuống
nên yêu cầu bê tông phải có độ sụt cao hơn bê tông móng, dầm cột sàn. 1.4.
Tổ chức mặt bằng sản xuất:
- Sau thi công công tác cốp pha, cốt thép và vệ sinh được nghiệm thu thì tiến hành thi
công mạch ngừng sàn (nếu có). Sử dụng các hộp 5x5, 10x10, xà gồ, gỗ dán, lưới mắt
cáo giăng (nếu có), xốp,…. để thi công mạch ngừng. Tận dụng tối đa năng suất để
công việc đổ bê tông được thực hiện một cách liên tục.
- Khi đổ bê tồn gặp trời mua thì phải có biện pháp che chắn để nước mưa không lẫn
vào bê tông, cần phải chuẩn bị tấm bạt, nilon cỡ lớn để che chắn nước mưa, bố trí hệ
thống thoát nước mưa một cách hợp lý. Nếu phải ngừng đổ bê tông thì phải đợi bê
tông đạt cường độ tối thiểu 25KG/cm2 mới được tiếp tục, trước khi đổ lại phải xử lý
mạch ngừng lẫn bề mặt ở vị trí dừng lại đó. 1.5.
Máy đầm bê tông:
Các loại máy đầm bê tông phổ biến trong xây dựng: Đầm rung:
Máy đầm rung là một loai máy xây dựng làm các công việc đầm bê tông nhờ lực rung của
động cơ tạo ra giúp hỗn hợp vữa bê tông trở nên đặc chắc, nhanh thoát nước và nhanh đông
cứng làm tăng chất lượng khối bê tông.
Máy đầm rung được sử dụng khi đổ bê tông trong ván khuôn như các chi tiết bê tông dạng cột, trụ, tấm,… Đầm dùi:
Máy đầm dùi là một loại máy đầm bê tông co có động cơ và bộ rung tách biệt nhau. Đầu
rung được kết nối với động cơ thông qua dây dùi, động cơ hoạt động truyền lực rung vào
đầu rung, đầu rung tiếp xúc trực tiếp với hỗn hợp vữa bê tông tạo ra rung động trong lòng
khối vữa bê tông, giúp bê tông đặc chắc.
Máy đầm dùi được sử dụng khi đổ bê tông có diện tích mặt thoáng lớn với chiều dày lớn
hơn 25cm như đổ bê tông sàn, mái, cột, móng,…. Đầm bàn:
Đầm bàn là máy đầm được sử dụng để đầm mặt bê tông với những vị trí bê tông có diện
tích mặt thoáng lớn và chiều dày nhỏ hơn 25cm.
Máy đầm bàn thường sử dụng cho đầm sàn, nền, mái,…
2. Phương pháp cân, đong các loại vật liệu khi trộn vữa, thành phần cấp phối: 2.1.
Đối với trộn bê tông bằng thủ công hoặc trộn bằng máy trộn quả lê:
Cần phải sử dụng sàng lọc cát hoặc máy sàng cát để loại bỏ tạp chất như đá, sỏi nhỏ ra khỏi
cát. Rửa đá để loại bỏ các tạp chất bụi bẩn khỏi đá chuẩn bị trước cho công tác đổ bê tông.
Chuẩn bị sẵn xi măng đúng mác và đúng tiêu chuẩn chất lượng.
Trên mỗi bao xi măng nhà sản xuất đều đưa ra tỉ lệ cấp phối cho từng loại xi măng, nên
thường người ta hay sử dựng thùng, xô để cân đong cũng như quy đổi để trộn bê tông.
Cân đong vật liệu theo mac BT cần đúng với tỉ lệ in trên bao bì XM .Đá và cát dùng thùng
18l, nước dùng thùng 18l, xi măng dùng bao. 2.2.
Bê tông sản xuất bằng trạm trộn tại hiện trường hoặc bê tông thương phẩm:
Khối lượng vật liệu thành phần được xác định :
- Xi măng: Xi măng phải được cân theo trọng lượng, sai số cho phép ±1% lượng xi măng yêu cầu.
- Cốt liệu: Cốt liệu phải được cân theo trọng lượng. Trọng lượng cốt liệu trong cấp
phối bao gôm trọng lượng cốt liệu khô cộng thêm trọng lượng nước chứa trong cốt
liệu với độ chính xác ±3% trọng lượng hỗn hợp.
- Nước: Nước trộn bê tông bao gồm nước cho vào mẻ trộn, nước do độ ẩm của vật
liệu và nước trong phụ gia cho vào bê tông. Nước phải đong theo thể tích với độ
chính xác ±1% tổng lượng nước yêu cầu.
- Phụ gia bê tông: Phụ gia ở dạng bột phải được cân theo trọng lượng. Phụ gia ở dạng
lỏng được cân theo trọng lượng, hoặc đong theo thể tích. Độ chính xác khi cân đong
phụ gia được lấy trong khoảng ±1% trọng lượng yêu cầu. 2.3.
Thành phần cấp phối bê tông:
Cấp phối bê tông là tỷ lệ thành phần các vật liệu cho 1m³ bê tông. Cấp phối bê tông phụ
thuộc vào mác bê tông, kích thước cốt liệu, chất kết dính, thành phần phụ gia. Với bê tông
thường cấp phối bê tông thường được hiểu là tỷ lệ các thành phần: xi măng, đá, cát, nước cho 1m³ bê tông.
Tỷ lệ trộn xi măng với nước thường sẽ là khoảng 7:11 theo thể tích, hoặc 13:7 theo khối
lượng. Chúng có quan hệ mật thiết với nhau và ảnh hưởng trực tiếp đến các tính chất của bê tông:
- Ảnh hưởng đến quá trình thủy hóa của bê tông: Khi nước gặp xi măng, quá trình thủy
hóa sẽ được diễn ra; xi măng tác dụng với nước sẽ tạo ra kết dính thủy lực để gắn kết
các hỗn liệu khác như cát, đá, sỏi... lại với nhau. Tuy nhiên, nếu quá nhiều nước sẽ
làm loãng quá trình, bề mặt yếu và bở và có khả năng chịu lực kém hơn.
- Ảnh hưởng đến cường độ bê tông: hỗn hợp ít nước hơn thì độ sụt bê tông thấp hơn
cũng như mang lại cường độ bền cao hơn so với hỗn hợp có nhiều nước hơn.
3. Phương pháp kiểm tra chất lượng vữa trộn: 3.1.
Độ sụt bê tông:
Độ sụt bê tông được hiểu là việc đo độ cứng hỗn hợp bê tông, tính ẩm ướt, tính lỏng. Hay
đo chiều cao của hỗn hợp bê tông sau khi được được đổ trong nón sụt giảm khác nhau với
những mẫu khác. Độ sụt được xác định theo TCVN 3105-93 hoặc ASTM C143-90A. Ký hiệu là SN.
Dụng cụ đo là hình nón cụt của Abrams, gọi là côn Abrams. Có kích thước 203x102x305
mm, đáy và miệng hở. Que đầm hình tròn có đường kính bằng 16mm dài 600mm.
Các bước kiểm tra độ sụt bê tông:
- B1: đặt chảo hỗn hợp lên sàn nhà, trước đó làm ẩm chảo từ trong ra ngoài. Cố định
chảo để giữ vững cho hình nón cụt bằng cách sử dụng cả 2 chân giữ tại chỗ. Sau đó
chèn hỗn hợp đã trộn vào 1/3 hình nón, đầm chặt mỗi lớp bê tông được đổ. Có tổng
cộng 25 lớp, đảm bảo rằng không để bị khuấy.
- B2: lần lượt thêm bê tông đã trộn vào để đánh dấu 2/3, cứ lặp lại cho đến 25 lần nén.
Đầm chặt lớp bê tông để không bị đổ vỡ, làm kỹ từng lớp cho đến khi nón sụt đầy.
- B3: sau lớp nén cuối thì từ từ lột bỏ nón sụt bằng cách nâng nón theo chiều dọc trong
khoảng thời gian 5s + hoặc – 2s. Khi tháo nón thì không được để khối bê tông đã nén chuyển động.
Sau đó tiến hành đo độ sụt bê tông: đo độ sụt giảm bằng chiều cao. 3.2.
Độ sụt cho cọc khoan nhồi, tường vây:
- Độ sụt của bê tông cọc khoan nhồi thường có độ sụt cao hơn so với các cấu kiện khác
như bê tông tường vây hay bê tông cột , đài móng , dầm móng , dầm sàn và bê tông
lót bởi bê tông cọc khoan nhồi thường là bê tông tươi thương phẩm nên cần có độ
linh hoạt cao để vận chuyện và đổ dễ dàng , kèm theo đó thì bê tông cọc khoan nhồi
sẽ khó để có để đầm dùi được nên cần có độ sụt cao nhằm tránh cho bê tông bị rỗ .
- Độ sụt của bê tông đài móng , dầm sàn cũng cao hơn bê tông dầm móng, cột bởi độ
sụt của bê tông cũng chính là độ lưu động của bê tông lên để dễ dàng cho quá trình
bê tông phủ khắp bề mặt của dầm sàn hay đài móng thì độ sụt của bê tông tường cao
hơn , còn đối với cột hay dầm móng thì cần có độ sụt thấp hơn để bê tông có thể đóng
rắn nhanh hơn tránh làm hư hại kết cấu sau khi đã tháo ván khuân , bởi bê tông của
cột thường có số ngày tháo ván khuân sớm hơn bê tông dầm sàn .
- Vị trí đổ bê tông có ảnh hưởng đến độ sụt đổ bê tông vì tùy theo yêu cầu thiết kế sẽ
có yêu cầu về độ sụt riêng , ví dụ như đổ mái bằng thì độ sụt sẽ cao hơn đổ bê tông
mái chảy vì khi đổ mái chảy bê tông cần hóa rắn nhanh hơn nên cần có độ sụt thấp
hơn . Hay như khi đổ bê tông thương phẩm đối với nhà thấp tầng thì độ sụt sẽ thấp
hơn đối với nhà cao tầng bởi với nhà cao tầng bê tông cần vận chuyển lên cao hơn
nên cần có độ lưu động cao hơn để vận chuyển và cào phẳng khi đổ nếu không bê
tông khi để ở bồn chứa quá lâu sẽ bị đông cứng . Hoặc như đã giải thích ở trên thì tùy
từng vị trí của kết cấu cũng sẽ có yêu cầu độ sụt riêng . Như vậy tùy theo mục đích
của thiết kế và vị trí đổ bê tông thì độ sụt sẽ có các yêu cầu khác nhau. 3.3.
Kiểm tra cường độ bê tông bằng phương pháp đúc tổ mẫu: a) Khuôn đúc mẫu:
Khuôn đúc mẫu gồm 2 loại: mẫu lập phương và mẫu hình trụ.
- Mẫu lập phương kích thước (mm) gồm 100x100x100; 150x150x150; 200x200x200; 300x300x300.
- Mẫu hình trụ kích thước dxh (mm) gồm 71,4x 143; 100x200; 150x300; 200x400.
Mỗi tổ mẫu gồm 2-3 viên mẫu. Ý nghĩa:
- So sánh các giá trị cường độ nén max và min với cường độ nén của viên mẫu trung
bình nếu 2 giá trị đó đều không chênh lệch quá 15% so với cường độ nén của viên
mẫu trung bình thì cường độ nén của bê tông tính bằng trung bình của 3 kết quả thử
trên 3 viên mẫu. Nếu 1 trong 2 giá trị đó chênh lệch quá 15% so với cường độ nén
của viên mẫu trung bình thì bỏ 2 kết quả đó -> cường độ nén bê tông là cường độ
nén của viên mẫu còn lại.
- Nếu tổ mẫu chỉ có 2 viên thì cường độ nén của bê tông được tính bằng trung bình
của kết quả thử 2 viên mẫu đó. b) Cách xác định:
Lấy mẫu bê tông theo tiêu chuẩn TCVN 4453-1995:
- Trong quá trình thi công xây dựng cán bộ giám sát của Chủ đầu tư và cán bộ kỹ
thuật thi công của nhà thầu xây dựng phải lấy mẫu bê tông tại hiện trường, cán bộ
kỹ thuật của Chủ đầu tư ký xác nhận trên tem và dán lên mẫu ngay sau khi vừa đúc
mẫu bê tông (khi bê tông còn ướt). Thí nghiệm ép mẫu bê tông ở tuổi từ 07-28 ngày.
- Mỗi loại cấu kiện bê tông phải lấy một tổ mẫu gồm 03 viên mẫu được lấy cùng một
lúc ở cùng một chỗ theo quy định của TCVN 3105-1993. Kích thước viên mẫu
10x10x10 cm hoặc 150x150x150 Mm. Số lượng tổ mẫu được quy định theo khối lượng như sau:
+ Đối với bê tông khối lớn: cứ 500m3 lấy 01 tổ mẫu khi khối lượng bê tông trong
một khối đổ lớn hơn 1000m2 và cứ 250m3 lấy 01 tổ mẫu khi khối lượng bê tông
trong một khối đổ ít hơn 1000m3.
+ Đối với các móng lớn: cứ 100m3 bê tông lấy 01 tổ mẫu nhưng không ít hơn một
tổ mẫu cho một khối móng.
+ Đối với bê tông móng bệ máy có khối lượng đổ lớn hơn 50m3 thì cứ 50 m3 lấy
01 tổ mẫu nhưng vẫn lấy một tổ mẫu khi khối lượng ít hơn 50m3.
+ Đối với kết cấu cấu khung cột, dầm, sàn cứ 20m3 lấy 01 tổ mẫu, nhưng khi khối
lượng ít hơn thì vẫn phải lấy một tổ mẫu cho mỗi loại cấu kiện.
+ Đối với các kết cấu đơn chiếc khác có khối lượng ít hơn thì vẫn phải lấy một tổ mẫu.
+ Đối với bê tông nền, mặt đường ô tô, đường băng sân bay… cứ 200m3 lấy 01 tổ
mẫu nhưng nếu khối lượng bê tông ít hơn 200m3 thì vẫn phải lấy một tổ mẫu.
- Phương pháp thí nghiệm trực tiếp trên cấu kiện. Dùng phương pháp kiểm tra hiện
trường bằng súng bắn bê tông (phương pháp thử bằng súng bật nẩy), siêu âm, khoan
cắt bê tông tại hiện trường để thí nghiệm đánh giá, xác định cường độ chất lượng bê tông. 3.4.
Kiểm tra mác bê tông:
- Kiểm tra mác bê tông bằng phương pháp ép mẫu bê tông ở 28 ngày ninh kết hoặc
khoan bê tông tại hạng mục thi công để lấy mẫu để kiểm tra.
- Hệ số của các loại kích thước mẫu thử: Hình dạng mẫu Hệ số quy đổi 10 x 10 x10 cm 0,91 Hình lập phương 15 x 15 x 15 cm 1,00 20 x 20 x 20 cm 1,05 10 x 20 cm 1,17 Hình trụ 15 x 30 cm 1,2 20 x 40 cm 1,24
- Trường hợp thí nghiệm mác bê tông không đạt thì nên làm lại mẫu bê tông, có cho
thêm phụ gia, bảo quản thật tốt rồi thí nghiệm lại.
- Chi phí thí nghiệm mẫu bê tông do bên nhà thầu chịu, được tính vào khoản mục chi phí trực tiếp khác.
4. Phương tiện và phương pháp vận chuyển vữa (vận chuyển ngang và vận chuyển
lên cao), thời gian vận chuyển cho phép của bê tông:
Các phương tiện dùng để vận chuyển vữa trên cồng trường là:
- Theo phương ngang: thùng xô, xe rùa, xe cút kít, băng chuyền, xe ben, xe có gắn thùng trộn phía sau,…
- Theo phương đứng: tời, cần trục thiếu nhi, cần trục tự hành, cần trục tháp, xe bơm
cần, vận thăng,… Phạm vi sử dụng:
- Dùng cần trục tháp cho công trình cao tầng lớn và ngoài việc đổ bê tông ra nó được
tận dụng sử dụng vận chuyển nhiều vật liệu khác nên khi sử dụng phải lưu ý tận
dụng khả năng của cần trục tháp mốt cách tối ưu nhất.
- Dùng bơm tĩnh khi dùng bê tông thương thẩm và công trình > 7 tầng hoặc vị trí đổ
xa (trong ngõ, ngách) xe bơm không tiếp cận được.
- Dùng bơm động khi dùng bê tông thương phẩm và công trình ≤ 7 tầng, có chỗ đứng
kiến cố cho xe bơm cần.
- Dùng tời vận chuyển lên cao cho công trình nhỏ H<10m (từ 2-3 tầng), lượng vận
chuyển vữa bê tông ít, yêu cầu chất lượng vữa bê tông không cao.
- Dùng phương tiện thủ công: gánh khi vận chuyển 10-15m; xe cút kít khi vận chuyển
50-100m đường vận chuyển kín, đường thẳng gồ ghề; dùng xe ba gác cho công trình
nhỏ; ròng rọc và giàn đội khi khối lượng vận chuyển không nhiều, yêu cầu chất
lượng vữa bê tông không cao, chiều cao vận chuyển từ 2-3 tầng (H<10m). Các
phương pháp vận chuyển vữa là: theo phương ngang, theo phương đứng.
- Ý nghĩa phương pháp vận chuyển theo pheo phương ngang là để vận chuyển vữa từ
nơi trộn hoặc vận chuyển vữa từ các phương tiện vận chuyển khác đến nơi cần đổ
khi nơi lấy vữa và nơi đổ vữa cách xa nhau một khoảng; từ đó ta phải xác định
khoảng cách sau đó chọn phương tiện vận chuyển theo phương ngang hợp lý để
trong quá trình vận chuyển hỗn hợp vữa bê tông không phân tầng và mất nước.
- Ý nghĩa phương pháp vận chuyển theo phương đứng là vận chuyển vữa đến nơi đổ
khi nơi lấy và đổ vữa chênh lệch nhau về cao trình 1 khoảng đủ lớn; từ đó ta xác
định được khoảng cách chọn phương tiện vận chuyển hợp lý.
Thời gian cho phép vận chuyển vữa bê tông được phép tối đa đến 4h. Cứ sau 0,5 giờ
phải trộn lại 1 lần và trước khi đổ phải trộn lại bê tông. Nếu vận chuyển bằng bơm thì
trong thời gian chờ bê tông cứ 0,5 giờ lại phải đẩy bê tông trong ống bơm dịch đi khoảng
20cm. Có thể tăng thời gian vận chuyển lên được, thời gian tăng lên phụ thuộc vào thỏa
thuận của người tiêu dùng, nếu tăng thêm thì phải báo cho nhà máy và thêm phụ gia dẻo cho bê tông.
5. Phương pháp đổ và đầm bê tông của các kết cấu khung cột, dầm, sàn, cầu thang.
Các biện pháp tránh phân tầng, biện pháp kiểm tra chất lượng đổ bê tông: 5.1.
Đổ bê tông bằng bơm tĩnh và bơm động:
Bê tông có thể được bơm bằng cả 2 loại bơm tĩnh và bơm động tùy từng trường hợp.
Những loại cấu kiên như móng, dầm, sàn,... thì cần đổ bằng bơm. ̣
- Bơm tĩnh thích hợp những công trình cao ốc hoặc nhà ở những vị trí hẹp như trong
hẻm sâu vì kích thước nhỏ gọn, bơm đông thường dành cho những công trình có ̣ lối
ra vào rông rãi vì kích thước khá lớn và cồng kềnh. Bơm tĩnh khá nhỏ gọn nêṇ có
thể phục vụ được các công trình trong ngõ hẹp nhưng bơm lại chỉ có phần máy bơm
chính, không có kèm theo đường ống bơm bê tông và thông thường không thể tự di
chuyển, chính vì thế, mỗi lần cần vận chuyển máy bơm bê tông tĩnh, người ta phải
sẽ phải gắn máy vào xe đầu kéo để kéo đi, tương tự như một chiếc rơ-moóc;
- Bơm đông thì có thiết kế phần cần trục dài giúp bơm bê tông được ở các vị trí trêṇ
cao, máy bơm bê tông động luôn được gắn theo ống dẫn, ống dẫn này rất bền, có độ
bền khá cao và có thể gấp lại được, phần cần trục của máy bơm bê tông tĩnh có thể
được điều khiển từ xa và vươn xa để bơm bê tông vào đúng vị trí mong muốn tuy
nhiên vì kích thước to lớn cồng kềnh nên không thể phục vụ cho các công trình nằm sâu trong ngõ hẹp.
Biên chế tổ đội khi đổ bê tông bằng bơm là: thường gồm từ 3 – 5 người. 5.2.
Đổ bê tông đổ bằng cần trục tháp:
Sử dụng cần trục tháp để đổ bê tông đối với những cấu kiện ở trên cao, mà máy bơm
không bơm bê tông lên được.
Biện pháp tránh phân tầng bê tông:
- Để tránh phân tầng thì chiều cao rơi tự do của bê tông không vượt quá 1,5m. Nếu
chiều cao rơi tự do lớn hơn 1,5m phải dùng ống vòi voi hoặc máng nghiêng.
- Đổ bê tông một cách liên tục, với khối lượng nhơ hơn 200m3 thì thời gian đổ liên tục không quá 4h.
- Nên chọn loại bê tông tươi, bê tông thương phẩm được trôn theo tiêu chuẩn kỹ ̣ thuât.
Sử dụng bê tông tươi, không sử dụng loại bê tông đã được trộ n nhưng để lâu,̣
không được sử dụng loại bê tông đã bắt đầu có đô ninh kết, cũng không trộ n lại bệ
tông đã được trôn lần 1 nhưng chưa kịp sử dụng ̣
- Tiến hành san, đầm bê tông đúng phương pháp
- Bê tông chỉ trôn 1 lần , trong quá trình trộ
n không đổ thêm cốt liệ u: nước, đã, xị măng,...
- Chọn bê tông mác phù hợp với từng hạng mục công trình. Biên chế tổ đội:
Bộ phận gồm có thợ chính và thợ phụ. Tổ thợ gồm từ 3 đến 6 người hoặc hơn:
- Thợ chính ( 1 người ) : điều khuyển cần trục tháp giúp đưa mẻ trộn từ dưới lên sàn để đổ bê tông.
- Thợ phụ (3 - 5 người ) : thợ phụ số 1 (1 người) điều khuyển xe bơm bê tông đổ bê
tông vào phểu đổ bê tông của cần trục tháp . Thợ phụ số 2 (1 người) thả chốt dưới
miệng bê tông để xả bê tông xuống, thợ phụ số 3 (2 – 3 người) di chuyển phếu đổ bê tông . 5.3.
Đổ bê tông bằng máy trộn quả lê, đổ thủ công:
- Đổ bê tông thủ công : khối lượng mẻ trộn ít không có mặt bằng trộn.
- Bê tông trộn bằng máy trộn quả lê : cho ra chất lượng bê tông đồng đều , khối lượng mẻ trộn lớn.
- Biên chế tổ đội trộn bê tông bằng máy trộn quả lê (2-4 người thợ): cho các vật liệu trộn theo tỉ lệ.
- Đổ bê tông thủ công :
+ Trộn bê tông : 2 - 4 người
+ Vận chuyển bê tông từ nơi trộn đến nơi hoàn thiện (1-3 người )
+ Thi công bê tông cào, cáng bề mặt bê tông , xoa bề mặt bê tông, rải Hardener, lăn
rulo tạo nhám, cắt ron chống nứt, xoa bề mặt bê tông (nếu có) 4-10 người. 5.4.
Bê tông khối lớn:
Bê tông khối lớn có sự kết hợp giữa hỗn hợp bê tông và cốt thép khối lớn, là một khối
bê tông có cạnh nhỏ nhất là và chiều cao phải lớn hơn 2m. Theo quy định ban hành của
bộ trưởng bộ xây dựng ở nghị định số 09 vào ngày 10 tháng 05 năm 2004 thì tiêu chuẩn
của bê tông khối lớn có trong TCXDVN 305.
Khi đổ bê tông khối lớn, cần lưu ý:
- Chiều cao mỗi lần đổ không quá 1.5m và thời gian chờ để đổ lượt tiếp theo không ít
hơn 4 ngày tính từ lúc đổ xong đợt trước. Mỗi lần đổ cần được đầm liên tục quay vòng
cho đến khi đạt đủ chiều cao và thời gian mỗi lần đổ không quá 1h vào mùa hè và 2h vào mùa đông.
- Mỗi đợt đổ tiếp theo cần làm sạch và tưới nước lên bề mặt trước, xong đổ lớp vữa xi
măng cát dày khoảng 1.5cm có thành phần giống trong bê tông.
- Khi chia kết cấu thành nhiều khối đổ theo chiều cao thì mặt tiếp giáp giữa các khối
đổ phải đc đánh xờm để đảm bảo tính liền khối.
- Đổ bê tông khép kín các khối chèn được thực hiện ngay khi các khối đổ trước đã co
ngót và nhiệt độ đã giảm tương ứng với quy định trong thiết kế thi công. - Bê tông
phải đổ liên tục thành nhiều lớp có chiều dày đều nhau.
6. Mạch ngừng bê tông: 6.1.
Mạch ngừng bê tông:
Mạch ngừng bê tông là vị trí bị gián đoạn trong thi công bê tông được bố trí ở những
nơi nhất định .Tại những vị trí này lớp bê tông sau được đổ khi lớp bê tông trước đã đó đông cứng.
Có mạch ngừng thi công nằm ngang; mạch ngừng thi công thẳng đứng; mạch ngừng thi công ở cột.
Dầm có kích thước lớn và liền khối vói bản thì mạch ngừng thi công bố trí cách mặt
dưới của bán 2-3 cm. Khi đổ bê tông sàn phẳng thì mạch ngừng thi công có thể đặt ở
bất kì vị trí nào nhưng phải song song với cạnh ngắn nhất của sàn; khi đổ bê tông ở các
tấm sàn có sườn song song với dầm phụ thì mạch ngừng thi công bố trí trong khoảng
1/3 đoạn giữa nhịp của dầm, song song với dầm chính thì mạch ngừng bố trí ở trong
khoảng giữa nhịp dầm và sàn (mỗi khoảng dài 1/4 nhịp).
Xử lý mạch ngừng: Để 2 lớp bê tông cũ và mới bám dính vào nhau, bạn cần xử lý thật
kỹ bằng những biện pháp sau:
- Vệ sinh sạch sẽ và tưới nước xi măng lên bề mặt lớp bê tông cũ trước khi đổ lớp mới.
- Đối với mạch ngừng đứng, bạn đánh mòn bề mặt và đục hết những phần bê tông
không đạt chuẩn rồi tưới nước xi măng.
- Đối với mạch ngừng ngang, sau khi đánh mòn bề mặt, phủ một lớp xi măng mác cao
khoảng 2-3cm trước khi đổ lớp bê tông mới.
- Sử dụng các phụ gia kết dính dùng cho mạch ngừng.
- Khi thi công lớp bê tông đầu, bạn nên đặt sẵn lưới thép tại vị trí mạch ngừng. 6.2.
Phân đợt, phân đoạn bê tông:
Phân đoạn thi công bê tông còn gọi là phân khu thi công bê tông là phân chia mặt bằng
thi công bê tông cốt thép toàn khối thành từng khu vực thi công, sao cho tổ đội công
nhân chuyên môn làm việc một cách độc lập trong một ca làm việc. Phân đoạn thi công
bê tông chính là khoang đổ bê tông trong một ca làm việc.
Ý nghĩa: giảm độ phức tạp trong thi công khi những kết cấu có hình dạng phức tạp việc
đổ bê tông liên tục rất khó khăn. Tăng hiệu quả kinh tế (tăng tỷ số vòng quay ván khuôn).
7. Bảo dưỡng bê tông sau khi đổ:
Bảo dưỡng bê tông mới đổ là tạo điều kiện thuận lợi cho sự đông kết của bê tông, mục
đích là không cho nước bên ngoài thâm nhập vào vữa mới đổ, không làm mất nước bảo
vệ, không cho ngoại lực tác dụng lên bê tông khi bê tông chưa đủ khả năng chịu lực,
không gây rung động làm long cốt thép bên trong.
Bảo dưỡng bê tông ngay khi vừa đổ bê tông xong:
- Sử dụng vải, bạt, nilon lớn để phủ lên lớp bê tông che chắn bởi mưa và nắng.
- Tưới nước thường xuyên để giữ ẩm (chỉ tiến hành tưới nước khi kết thúc đổ bê tông
từ 4 – 6h để tránh phá hoại).
- Thời gian tưới nước dưỡng ẩm kéo dài đến khi bê tông đạt cường độ 50% R28. Thời
gian bảo dưỡng phụ thuộc vào khí hậu và theo mùa.
- Trong suốt quá trình bảo dưỡng không được để bê tông khô trắng mặt.
8. Thời gian phát triển cường độ bê tông:
- Cường độ bê tông được tính từ lúc đổ bê tông cho đến khi bê tông đủ khả năng chịu lực.
- Cường độ bê tông tăng theo tuổi của nó. Trong quá trình rắn chắc cường độ bê tông
không ngừng tăng lên: từ 7 đến 14 ngày đầu cường độ phát triển nhanh, sau 28 ngày
chậm dần và có thể tăng đến vài năm gần như theo quy luật logarit.
Rn/R28 = lgn/lg28 với n >3
Trong đó : Rn, R28 cường độ bê tông ở tuổi n và 28 ngày (Kg/Cm2)
n: tuổi của bê tông (ngày)
- Trong quá trình bê tông phát triển cường độ cần lưu ý về điều kiện thời tiết (nắng,
mưa, gió,..), tránh những tác động mạnh đến bề mặt .giữ nguyên cốp pha, phun nước
và ngâm nước giữ độ ẩm.
Đối với bê tông khối lớn, bảo dưỡng khối bê tông bằng lớp vật liệu cách nhiệt (dày
tối thiểu 5cm) để kháng lại việc mất nhiệt tại bề mặt khối đổ. Không tưới nước
(khi cần kiểm soát co ngót khô thì sau 5 ngày có thể được áp dụng)
- Thời gian sau khi đã hoàn thành xong việc đổ bê tông,làm mặt xong không nên đi lại
hay tác động mạnh đến các cấu kiện cột chống , các ván khuôn xung quanh. Khi tầng
trên mới đỏ bê tông xong thì tầng dưới của tầng mới đổ chưa được tháo các cột
cống,ván khuôn đáy ra luôn , chỉ nên tháo ván khuôn 4 xung quanh .còn các tầng bên
dưới nếu bê tông đủ cường độ thì có thể tháo các ván khuôn ra.
9. Các biện pháp khắc phục bê tông bị phình, rỗ, trắng mặt, nứt chân chim: 9.1.
Bê tông bị phình:
- Nguyên nhân gây phình bê tông là do ván khuôn cong vênh, ván khuôn đáy không
chịu đủ tải trọng của bê tông, đóng nêm chốt, gông chống không đúng biện pháp.
- Biện pháp: kiểm tra lại ván khuôn cột chống xem đủ tại trọng của khối bê tông, các
nêm chốt, gông đóng có chắc không. 9.2.
Bê tông bị rỗ: Nguyên nhân:
- Ván gỗ có độ hút ẩm cao, trước khi đổ bê tông không tưới nước đủ ẩm nhất là vào
thời tiết hanh khô nên mặt bê tông bị rỗ đổ gỗ đã hút nước của bê tông.
- Đầm đối, đầm sót, đầm không tới độ sâu cần thiết. Nhất là tại vị trí có mặt độ thép dầy.
- Cấp phối đá không hợp lý, cỡ đá to nhỏ không đều.
- Đổ trộn bê tông không đều.
- Đổ bê tông quá khô.
- Cốp pha không kín khít làm chảy mất vữa xi măng, nhất là dưới chân móng, chân cột, đáy dầm. Biện pháp:
- Đối với rỗ mặt: dùng xà beng, que sắt hoặc bàn chải sắt tẩy sạch các viên đá nằm
trong vùng rỗ. Sau đó dùng vữa bê tông sỏi nhỏ mác cao hơn mác thiết kế trát lại, sau
đó xoa đều phẳng mặt.
- Đối với rỗ sâu: dùng đục sắt và xà beng cậu sạch các viên đá nằm trong vùng rỗ, sau
đó ghép ván khuôn (nếu cần) đổ vữa bê tông sỏi nhỏ có mác cao hơn mác thiết kế và đầm chặt lại.
- Đối với rỗ thấu suốt: trước khi sửa chữa cần chống đỡ kết cấu (nếu cần), sau đó ghép
ván khuôn và đổ bê tông có mác cao hơn mác thiết kế và đầm kĩ. Có thể dùng máy
bơm vữa bê tông để đổ bê tông. 9.3.
Bê tông bị trắng mặt: Nguyên nhân:
- Hoàn thiện bề mặt quá sớm, trước khi bê tông se mặt hoặc do hoàn thiện dưới trời mưa.
- Bảo dưỡng không đúng cách, hay bề mặt bị khô quá nhanh. - Bản
thân bê tông quá yếu, chịu mài mòn kém. Biện pháp:
- Đợi bê tông se mặt trước khi làm mặt, hoặc quét nước mặt khi trời tiết lạnh. Bảo dưỡng đúng cách.
- Bảo vệ bê tông tránh bị khô quá nhanh trong thời tiết nóng và gió.
- Đắp bao tải cát hoặc mùn cưa, tưới nước thường xuyên từ 5 -7 ngày. 9.4.
Bê tông bị nứt chân chim:
- Nguyên nhân: pha trộn vật liệu không đúng tỉ lệ, bảo dưỡng bê tông không đúng cách,
rung động trong quá trình ninh kết bê tông, co ngót vữa bê tông,…
- Biện pháp: dùng nước xi măng quét và trát lại, sau đó phủ bao tải, tưới nước và bảo dưỡng.
10.Các biện pháp an toàn khi đổ bê tông:
- Chuẩn bị, tính toán nhân lực, máy móc thiết bị đảm bảo cho quy trình đổ bê tông.
- Tính toán thời gian đổ bê tông.
- Tính toán mặt bằng thi công đổ bê tông.
- Đảm bảo về mặt an toàn khi thi công trong quá trình tiến hành đổ bê tông cột, dầm, sàn.
- Dọn dẹp, dội nước làm sạch cốt pha, cốt thép.
- Kiểm tra các khuôn đúc về các tiêu chuẩn hình dáng, kích thước, thời gian sử dụng.
Kiểm tra cốt thép, giàn giáo, sàn thao tác, chuẩn bị ván gỗ để làm sàn.
- Đảm bảo an toàn khi đổ bê tông đối với người lao động. Công nhân được trang bị đầy
đủ bảo hộ lao động khi thi công.
- Kiểm tra số lượng và chất lượng vật liệu xây dựng: cát, đá, xi măng, sắt thép,… để
đảm bảo rằng chúng đáp ứng đủ yêu cầu kỹ thuật của công trình. Nếu chất lượng của
cát, đá, xi măng,… không tốt thì chất lượng của bê tông cũng bị ảnh hưởng rất nhiều.
- Kiểm tra máy móc, thiết bị phục vụ công đoạn thi công như máy đầm bê tông, máy
trộn bê tông, máy bơm bê tông, máy mài sàn bê tông, máy xóa nền phải đảm bảo tiêu
chuẩn kỹ thuật. Nên sử dụng máy đầm bàn khi đổ bê tông sàn mỏng hơn 30cm hoặc
dầm sàn. Sử dụng đầm rung, đầm dùi chạy xăng hoặc chạy điện đối với sàn có chiều
dày lớn hơn 30cm. Các chi tiết bê tông như cột, tường, vách.
- Kiểm tra sàn đổ bê tông phải đạt tiêu chuẩn nhẵn, không ngập nước.
- Khi thi công ở trên cao, phải kiểm tra kĩ lưỡng các khu vực lan can an toàn xung
quanh, mép các sàn, lỗ trống cầu thanh, giếng trời,… và phải dùng lưới an toàn ở những vị trí đó.
- Chi phí biện pháp an toàn được tính vào khoản mục chi phí: II.
Công tác cốt thép.
1. Thành phần công việc trong quá trình gia công và lắp đặt cốt thép, biên chế tổđội: 1.1.
Phần việc để lắp 1 thanh thép vào vị trí thiết kế:
- Lựa chọn thép, kéo thép, cắt thép theo đúng yêu cầu kỹ thuật.
- Vệ sinh, đánh gỉ thép.
- Gia công cốt thép.
- Lắp dựng cốt thép vào vị trí thiết kế. - Nối thép.
- Kê thép tạo lớp bê tông bảo vệ. 1.2.
Thao tác chính gia công cốt thép:
Cốt thép trước khi gia công cần đảm bảo bề mặt sạch, không bị dính bùn đất, dầu mỡ,
không có vẩy sắt và các lớp gỉ. Thao tác chính gồm:
- Nắn thẳng cốt thép: Nếu khối lượng cốt thép ít, đường kính cốt thép nhỏ có thể nắn
thẳng bằng thủ công: dùng búa, vam khuy. Nếu khối lượng cốt thép nhiều, đường kính
cốt thép lớn nên bảo đảm mức độ cơ giới phù hợp để nâng cao năng suất lao động và chất lượng sản phẩm.
- Đo cắt cốt thép: Trước khi cắt cốt thép phải tính được chiều dài thanh thép cần cắt.
Cốt thép khi uốn sẽ bị đãn dài ra. Khi đo đạc, lấy dấu phải trừ di độ đãn dài trên đế
tiết kiệm thép và bảo đảm cốt thép không chạm vào cốp pha.
- Uốn cốt thép: Uốn để thanh thép có hình dạng đúng với hình dáng và kích thước của
nó rrong bảng thống kê cốt thép. Uốn cốt thép có thể dùng bàn uốn thủ công hoặc
dùng máy uốn tùy theo khối lượng thép uốn nhiều hay ít và đường kính cốt thép.
- Hàn nối cốt thép: Liên kết hàn có thể thực hiên theo nhiều phương pháp khác nhau,
nhưng phải đảm bảo chất lượng mối hàn theo yêu cầu thiết kế. Khi nối bước, cốt thép
ở vùng chịu kéo phải uốn móc đối với thép tròn trơn, cốt thép có gờ không uốn móc;
dây bước dùng loại đây thép mềm có đường kính lmm; trong các mối nối cần bước ít
nhất là 3 vị trí (ở giữa và hai đầu). 1.3.
Các loại máy gia công cốt thép:
Các loại máy dùng để gia công thép là máy hàn, máy cắt thép, máy nắn thẳng cốt thép,
máy uốn cong cốt thép... Công dụng:
- Máy hàn: Dùng để hàn các loại thép kết cấu.
- Máy cắt thép: Cắt thép một cách nhanh chóng, cho đường cắt gọn đẹp không làm hư
hại khu vực xung quanh vùng cắt.
- Máy nắn thẳng cốt thép: nắn thẳng các loại thép cuộn xây dựng. - Máy uốn cong
cốt thép: uốn cong các loại thép theo yêu cầu. 1.4.
Thép chủ, thép đai, thép cấu tạo:
- Thép chủ có tác dụng: dùng để chống lại lực kéo trong các cấu kiện bị uốn như dầm
hoặc trong các cấu kiện chịu lực kéo.
- Thép đai: có tác dụng cố định vị trí cốt thép dọc khi đổ bê tông, chịu các ứng suất khi
co ngót và thay đổi nhiệt độ, tăng khả năng chịu nén của bê tông, hạn chế nở ngang, chịu lực cắt.
- Thép cấu tạo: dùng để giữ vị trí các thanh thép chịu lực và làm toàn bộ cốt thép thành
một bộ khung vững chắc, tăng sự ổn định của sàn hay dầm. Phát huy hết khả năng chịu lực của bê tông. 1.5.
Bẻ mỏ thép:
- Các hình thức bẻ mỏ thép: bẻ cong vòng tròn, bẻ 1 góc 45 độ và bẻ 1 góc 90 độ.
- Móc tròn dùng cho cốt thép có đường kính >= 12mm; móc xiên dùng cho đường kính
d < 12 mm, móc vuông dùng cho cốt thép chịu nén và cốt thép sàn.
- Khi uốn, chiều dài thanh thép giãn dài thêm 1 khoảng tương ứng với các mỏ: mỏ tròn,
mỏ xiên, mỏ thẳng lần lượt là: 6,5d; 6d; 8d. 1.6.
Chiều dài cây thép tiêu chuẩn và cách tổ hợp cắt thép:
Chiều dài cây thép tiêu chuẩn hiện nay là 11,7m.
Cách tổ hợp cắt thép tiết kiệm: ưu tiên cắt những thanh thép có chiều dài lớn hơn trước
rồi mới cắt các thanh theo thứ tự độ dài giảm dần.
- Đối với thép dầm tăng cường lớp trên (thép momen âm tăng cường ở dầm, ở các gối):
Liệt kê sắp xếp theo các cấp đường kính, rồi xếp các thanh đó theo các loại đường
kính rồi trong các loại đường kính đó ta phân loại các kích thước chiều dài thép, rồi
tổ hợp các kích thước với nhau để cho vào 1 thanh 11.7m để sao cho có số dư là nhỏ
nhất (có thể tổ hợp bởi chính 1 loại chiều dài thép hoặc nhiều loại chiều dài thép,
nhưng cuối cùng vẫn là xếp vào đủ 11.7m). Xong phần thép dầm tăng cường momen
âm. rồi dựa vào số lượng các cấu kiện ;từ đó tính ra số lượng các loại chiều dài đó mà
tính ra cắt bao nhiêu thanh 11.7 m.
- Đối với thép dầm tăng cường lớp dưới (Thép momen dương ở giữa nhịp ) : Tương tự
cách cắt như thép tăng cường mô men âm. Chú ý nếu thép tăng cường momen âm và
momen dương cùng loại đường kính thì có thể tổ hợp lẫn nhau để có thêm 1 sự lựa
chọn cho việc cắt để sao thép vụn là nhỏ nhất.
- Thép sàn: thì thì bố trí và tính dễ dàng hơn vì không yêu cầu vị trí nối và chiều dài
sàn cũng lớn nên dễ tính thép.
- Thép cột: Dễ dàng tổ hợp và tính thép tương tự như cách tổ hợp các thanh cùng đường kính sao như ở trên. 1.7.
Biên chế tổ đội gia công cốt thép và vận chuyển thép ra vị trí lắp dựng:
Vận chuyển cốt thép đã gia công ra công trường bằng thủ công, xe chở vật liệu, cần
trục tự hành, cần trục tháp, xe cẩu,… Quá trình vận chuyển cần phải cố định hoặc neo
giữa kết cấu cố định lại, tránh hiện tượng bị xô dịch gây móp méo hay biến dạng.
Phương tiện vận chuyển cũng cần được đảm bảo về mặt tải trọng để không gây ra sự
cố trong lúc di chuyển, khi vận chuyển tới công trường nếu chưa được sử dụng thì cần
phải được che chắn và bảo quản cẩn thận. Biên chế tổ đội:
- 2 người thợ cắt thép;
- 2 người thợ uốn thép;
- 4 người vác thép từ vị trí cắt ra vị trí uốn gần nhất.
2. Lắp dựng cốt thép: 2.1.
Quy trình lắp dựng cốt thép:
Quy trình thi công lắp dựng cốt thép tường vây trên mặt đất:
- B1 : Lắp dựng thép chủ.
- B2 : Lắp dựng thép đai. - B3 : Đặt con kê bê tông.
- B4 : Lắp ống siêu âm.
- B5 : Lắp thép chờ + xốp bảo vệ.
Quy trình thi công lắp dựng cốt thép cọc nhồi trên mặt đất:
- B1 : Lắp đặt chép chủ.
- B2 : Lắp dựng thép đai.
- B3 : Đặt con kê + ống siêu âm.
Quy trình lắp dựng cốt thép móng:
- Đối với lắp dựng cốt thép móng cột: thường được nối buộc hoặc hàn tại xưởng gia
công. Nếu sử dụng mối nối buộc, phải buộc trái chiều để lưới cốt thép không bị xộc
xệch khi vận chuyển. Sau khi nghiệm thu xong cốp pha móng thì đặt lưới thép vào,
chú ý vị trí thép đặt trên và thép đặt dưới. Khoảng cách các con kê tạo lớp bảo vệ cốt
thép 70cm theo cả hai phương. Trước khi đặt cốt thép chờ. cần xác định các đường
tim trục cột theo hai phương và đóng khung định vị cốt thép. Đầu các cốt thép chờ cột
phải cao hơn mặt phẳng của lưới cốt thép trên cùng ít nhất là 30d,chân cốt thép chờ
tại 4 góc cột nên đặt thế chân vịt chĩa ra ngoài theo hướng đường chéo của tiết diện
cột để cho khung thép cột đứng vững. Nếu cột thấp nên buộc hoặc hàn thành khung
sẵn rồi đem đặt vào vị trí, cần chống đỡ cột thật chắc chắn, đúng vị trí không xê dịch
trong quá trình đổ bê tông.
- Lắp dựng cốt thép móng băng nhà xây: thường được lắp dựng trước khi lắp dựng cốp
pha và đà giáo. Sau khi đã vệ sinh sạch sẽ lớp lót móng và truyền tim cột xuống đáy
hố móng tiến hành đặt cốt thép móng băng. Nếu mặt bằng hố móng chật hẹp nên hàn
hoặc buộc cốt thép thành lưới sẵn rồi mới hạ xuống hố móng. Nếu mặt bằng hố móng
đủ rộng lắp dựng cốt thép ngay trên đáy hố móng xuống dưới rồi mới đặt cốt thép
phân bố lên trên, dùng thanh cữ ướm, bước các mắt lưới. Các con kê lớp bê tông bảo
vệ cốt thép, tùy theo mặt độ cốt thép đặt cách nhau 0,7- 1m theo hai phương.
Quy trình lắp dựng cốt thép dầm:
- Đầu tiên khi lắp dựng cốt thép dầm sàn thì cần lắp dựng ván khuôn dầm, sàn.
- Sau đó tới công đoạn lắp ghép thép dầm vào các vị trí dầm và kiểm tra cường độ thép
ở vị trí dầm có đủ tải trọng không , rồi đến rải thép sàn đếu nên các vị trí sàn.
- Sau khi điều chỉnh rải thép xong dùng thép 1-2 ly để buộc cố định thép lại với nhau.
- Cuối cùng là kiểm tra các bề mặt và kê các thanh thép dầm sàn lên khỏi ván khuôn
khoảng 1-2cm và chờ đổ bê tông.
Quy trình lắp dựng cốt thép cột:
- Trước khi lắp đặt cốt thép cột cần phải kiểm tra lại vị trí cột.
- Cốt thép có thể gia công thành khung sẵn rồi đưa vào ván khuôn đã ghép trước 3 mặt,
khi lắp khung cần chú ý đặt những miếng kê.
- Đặt cốt thép đúng vị trí rồi nối bằng phương pháp buộc hay hàn.
Quy trình lắp dựng thép sàn:
- Đặt cốt thép dầm chính trước, cốt thép dầm phụ sau, cốt thép sàn sau cùng.
- Cốt thép sàn thường luồn qua khung cốt thép dầm, cho nên sau khi đã buộc xong cốt
thép dầm mới rải và buộc cốt thép sàn. Nên vạch trước các dấu định vị cốt thép trên ván sàn. 2.2.
Mối nối thép:
Theo Tiêu chuẩn Việt Nam TCVN 4453-1995 về kết cấu bê tông và bê tông toàn khối –
quy phạm thi công và nghiệm thu, việc nối cốt thép phải tuân theo các tiêu chuẩn sau:
Thép dầm: Nếu sử dụng phương pháp nối buộc truyền thống cho cốt thép thì:
- Thép có gờ phải đảm bảo cùng mặt cắt không được nối quá 50% lượng thép.
- Không được nối thép tại các vị trí chịu lực lớn và những vị trí uốn cong. Những vị trí
chịu lực lớn (ví dụ các vị trí như thép giữa nhịp – thép dưới; thép gối – thép trên) là
những vị trí phải chịu lực lớn nhất trong dầm nên không được thực hiện nối thép tại
những vị trí này để tránh việc vị tuột mối nối rất nguy hiểm.
Thép cột:đối với thép có gờ thì cùng mặt cắt không được nối quá 50% lượng thép; tại
các vị trí phải chịu lực lớn và những vị trí cần uốn cong không được nối thép; tại cột
của các công trình dân dụng thì chân cột nhà – vị trí sát mặt dầm và đầu cột – vị trí
dưới mặt dầm là hai vị trí phải chịu lực lớn nhất vì vậy không được thực hiện việc nối
thép để tránh việc thép bị tuột nối buộc.
Thép sàn: việc nối thép sàn về cơ bản phải tuân thủ theo các quy định như việc nối
thép dầm do sàn bê tông cốt thép về bản chất giống như là những đoạn dầm. Không
nối thép tại những điểm, vùng phải chịu lực lớn.
2.2.1. Nối hàn:
Nối hàn bắt buộc với thép có đường kính lớn hơn 16mm.
Quy định về đường hàn cho mối nối: theo TCVN 9392:2012
Chiều dài đoạn nối hàn :Phải đảm bảo theo yêu cầu thiết kế:
- Nếu hàn về 1 phía thì chiều dài thép chồng để hàn lớn gấp 10 lần đường kính thanh thép.
- Nếu hàn về 2 phía chiều dài ghép chồng để hàn lớn gấ 5 lầ đường kính thanh thép.
2.2.2. Nối buộc:
Khi cốt thép có đường kính nhỏ hơn hoặc bằng 16mm hoặc sủ dụng với các kết cấu nằm
ngang như dầm, sàn, móng.
- Với nối buộc dùng dây buộc loại: dây thép mềm đường kính 1 mm.
- Quy định về nối buộc cho từng loại kết cấu:
+ Nối buộc cho thép sàn: không nối thép tại những điểm, vùng phải chịu lực lớn. +
Nối buộc cho thép dầm: Thép có gờ phải đảm bảo cùng mặt cắt không được nối quá
50% lượng thép; không được nối thép tại các vị trí chịu lực lớn và những vị trí uốn
cong. Những vị trí chịu lực lớn (ví dụ các vị trí như thép giữa nhịp – thép dưới; thép
gối – thép trên) là những vị trí phải chịu lực lớn nhất trong dầm nên không được thực
hiện nối thép tại những vị trí này để tránh việc vị tuột mối nối rất nguy hiểm.
+ Nối buộc cho thép cột: Đối với thép có gờ thì cùng mặt cắt không được nối quá
50% lượng thép; Tại các vị trí phải chịu lực lớn và những vị trí cần uốn cong không được nối thép.
- Chiều dài đoạn nối chồng giữa 2 thanh thép:
+ Đối cốt thép chịu lực trong các khung và lưới không nhỏ hơn 250mm đối với thép
chịu kéo, không nhỏ hơn 200mm đối với thép chịu nén.
+ Đối với thép tròn trơn: Nếu cốt thép dùng để đặt ở vùng bê tông chịu kéo thì hai
đầu cốt thép phải được uốn cong thành móc (uốn 180 độ) và đặt chập lên nhau một
đoạn dài từ 30-45d, sau đó dùng dây kẽm quấn quanh chỗ uốn; Nếu dùng để thi công
ở những vùng bê tông chịu nén thì không cần uốn móc mác thép nhưng cần phải uốn
dây thép quanh chỗ nối, đoạn chập nhau của hai mác thép phải đảm bảo có độ dài từ 20-40d.
2.2.3. Nối ren: Dùng cho dầm
Quy trình thực hiện 1 mối nối ren:
- Thực hiện tiện ren cốt thép;
- Cắt bỏ lớp gân đầu cốt thép bằng máy tạo ren sau đó tiện đầu ren cốt thép bằng máy tạo ren;
- Nối hai đầu cốt thé bằng ống nối thép có ren.
Mối nối ren so với hai hình thức nối hàn và nối buộc có:
- Ưu điểm : thực hiện đơn giản , nhanh , chất lượng cao có tính tiện dụng cao và mang
lại hiệu quả kinh tế cao.
- Nhược điểm :yêu cầu kĩ thuật cao. Nếu tạo ren bằng thép lại suy giảm tiết diện nên
chỉ thực hiện được tại ví trí nội lực nhỏ không sử dụng hết hàm lượng cốt thép. 2.3.
Một vài lưu ý về lắp dựng cốt thép:
- Trong ô sàn momen căng thớ trên ở đầu sàn và căng thớ dưới ở giữa sàn nên ở giữa ô
sàn đặt thép chịu lực ở dưới và đầu ô sàn đặt thép mũ (thép lớp trên) để chịu lực do
vậy với ô sàn sàn lớn đặt thép ở giữa lớp trên là không cần thiết và gây tốn kém nên
ta không đặt thép tại vị trí giữa các ô sàn lớn.
- Lắp thép xong mới lắp ván khuôn khi các cấu kiện tiết diện nhỏ hẹp nếu lắp ván khuôn
trước không có không gian để lắp thép và ghép các mối nối (Ví dụ: cột, tường,…).
Lắp ván khuôn xong mới lắp dựng thép khi cấu kiện hình dạng lớn và lắp ván khuôn
trước tạo sàn công tác có không gian cho người thợ thao tác (Ví dụ: dầm, sàn,…).
- Vị trí giữa dầm giao với cột phải dùng thép đai dầm, vì lực cắt rất lớn ở chỗ đấy, ta
phải dùng để tăng khả năng chịu lực.
3. Kiếm tra chất lượng cốt thép: 3.1.
Kiểm tra số lượng thép:
- Thép mua theo hình thức trọng lượng: kiểm tra bằng cách tính toán khối lượng thép
của từng cấu kiên sau đó tổng hợp khối lượng thép cần cho cả công trình , so sánḥ với
khối lượng thép nhâp về công trường để biết được hàng nhậ p thép về là đủ haỵ chưa.
- Thép mua theo hình thức eteket (theo bó, theo cây ): tính toán số cây thép cho từng
cấu kiên và tổng hợp cho cả công trường cần bao nhiêu cây thép. Tính toán số thép ̣
có trong môt bó, sau đó nhân với số bó đã nhậ p về. Đem so sánh với số cây thép cầṇ
thiết đã tính toán để biết được lượng hàng nhâp về là đủ hay chưa.̣ 3.2.
Trọng lượng riêng của thanh thép:
Trọng lượng riêng của thép hiện nay là 7850 kg/m3
Cách tính trọng lượng 1md của từng loại thép :
- Thép Tấm Trọng lương thép tấm(kg) = Độ dày (mm) x Chiều rộng (mm) x Chiều dài (mm) x 7.85 (g/cm3).
- Thép Ống Trọng lượng thép ống(kg) = 0.003141 x Độ dày (mm) x Đường kính ngoài
(mm) – Độ dày (mm)} x 7.85 (g/cm3) x Chiều dài (mm).
- Thép hộp vuông Trọng lượng thép hộp vuông (kg) = [4 x Độ dày (mm) x Cạnh (mm)
– 4 x Độ dày (mm) x Độ dày (mm)] x 7.85(g/cm3) x 0.001 x Chiều dài(m).
- Thép hộp chữ nhật Trọng lượng thép hộp chữ nhật (kg) = [2 x Độ dày (mm) x {Cạnh
1(mm) +Cạnh 2(mm)} – 4 x Độ dày(mm) x Độ dày (mm)] x 7.85 (g/cm3) x 0.001 x Chiều dài(m).
- Thép tấm thanh la Trọng lượng thanh la (kg) = 0.001 x Chiều rộng (mm) x Độ dày
(mm) x 7.85 (g/cm3) x Chiều dài(m).
- Thép cây đặc vuông Trọng lượng thép đặc vuông(kg) = 0.0007854 x Đường kính
ngoài (mm) x Đường kính ngoài (mm) x 7.85 (g/cm3) x Chiều dài (m). 3.3. Mác thép:
Mác thép là thuât ngữ chuyên ngành kĩ thuậ t để phân biệ t các sản phẩm khác nhau. tùỵ
từng vào tiêu chuẩn mà mác thép kể đến khả năng chịu lực (cường đô)̣ , hay thành phần hóa học có trong thép.
- Với thép xây dựng: SD 295, SD 390, CII, CIII, Gr60, Grade460, SD49,(CT51), CIII,
SD295,SD390, CB300-V, CB400-V, CB500-V. Mác thép CB Mác thép SD
- Với thép kết cấu: trên thị trường Việt Nam hiện tại sử dụng thép SS400, Q235, Q345B,
hay trong các bản vẽ ta thấy ghi chú thép CCT34, CCT38...
Kí hiêu: Trên thị trường có nhiều ký hiệu về mác thép làm cho người tiêu dùng bối rối và ̣
không biết nên sử dụng loại nào cho phù hợp. Tuy nhiên mỗi ký hiệu đều có ý nghĩa riêng
của nó. Ký hiệu của mác thép gắn với “tiêu chuẩn sản xuất được áp dụng” của thép đó. Có
nhiều tiêu chuẩn mà nhà sản xuất áp dụng để sản xuất như Tiêu chuẩn Việt nam TCVN,
tiêu chuẩn Nhật Bản JIS, tiêu chuẩn Nga vv.. Mỗi tiêu chuẩn sẽ có một ký hiệu khác nhau.
Tiêu chuẩn áp dụng khi sản xuất là: Tiêu chuẩn TCVN 1651-1985, TCVN 1651-2008, JIS
G3112 (1987) JIS G3112 – 2004, TCCS 01:2010/TISCO, A615/A615M04b, BS 4449 – 1997. 3.4.
Kiểm tra chất lượng thép:
Làm 3 thí nghiệm: uốn thép, kéo thép, dãn dài.
- Thí nghiệm uốn, kéo, giãn dài (so sánh với TCVN 1651-2:2018).
- Tiến hành cắt 3 thanh thép có chiều dài bằng nhau, tiến hành cân để tính trọng lượng riêng của thép.
- Thí nghiệm kéo: cho thanh thép vào máy kéo thép theo dõi và ghi số liệu thu được
khi thanh thép bị đứt rồi chập lại để đo độ dãn dài của thép.
- Thí nghiệm uốn: cho thanh thép vào máy uốn tiền hành uốn, ghi số liệu so sánh với TCVN 1651-2:2018.
- Trường hợp thép không đạt yêu cầu thì tiến hành tham khảo đơn vị tư vấn, trong quá
trình thép quá kém không đạt yêu cầu về thi công thì trả về
Chi phí thí nghiệm thép được tính vào khoản mục chi phí nguyên vật liệu, Nhà thầu cần
chịu chi phí này vì nhà thầu cần thí nghiệm để biết kết quả ra sao và nên sử dụng vật liệu
như thế nào để phù hợp với công trình.
4. Biện pháp phòng chống và xử lý cốt thép bị xâm thực: 4.1.
Mức độ xâm thực của môi trường với thép:
- Mức độ xâm thực của môi trường với thép hiện nay là rất mạnh dẫn tới ăn mòn và
phá huỷ các công trình bê tông. Mức độ xâm thực phụ thuộc vào vị trí và điều kiện
làm việc cụ thể của từng kết cấu công trình. So với các nước khác môi trường biển
Việt Nam có khí hậu nóng ẩm, mưa bão nhiều tạo ra sự ăn mòn mạnh hơn đối với thép.
- Ảnh hưởng của xâm thực tới chất lượng thép là : Thiết kế thi công bê tông cốt thép
dự kiến độ bền 50-60 năm nhưng thực tế chỉ chỉ đạt 20-30 năm nhiều cái hư hỏng
nặng sau 7-15 năm , tốc độ ăn mòn ở mức báo động gây hư hỏng nhanh hơn và khả
năng sửa chữa rất tốn kém. 4.2. Gỉ thép:
Nguyên nhân gây gỉ thép: Do tiếp xúc với oxy và độ ẩm trong không khí một thời
gian dài gây ra phản ứng hóa học gọi là oxy hóa. Trong xây dựng có thể do chúng
ta bảo quản thép chưa tốt dẫn đến thép bị ăn mòn hóa học. Biện pháp phòng chống:
- Sử dụng hợp kim.
- Sử dụng dầu chống gỉ
- Sử dụng một lớp phủ khô - Sơn thép
- Lưu trữ, bảo quản thép tránh tiếp xúc với nước - Mạ kẽm - Nhuộm xanh - Sơn tĩnh điện - Bao bì VCI
Trong xây dựng thép thường được sử dụng bằng cách bảo quản đúng cách và có thể phủ 1
lớp dầu để chống gỉ.
Khi bị gỉ sét, ăn mòn thì biện pháp xử lý là:
Sử dụng các công cụ, thiết bị làm sạch gỉ bằng các tác động cơ học như chà sát, va đập
hoặc làm sạch gỉ bằng dòng điện dựa trên phản ứng điện phân hoặc sử dụng các hóa chất
có tham gia phản ứng hóa học với gỉ sét.
Có 3 phương pháp sử lý gỉ thép (cơ học, điện hóa, hóa học).
- Phương pháp cơ học:
+ Ưu điểm: là làm sạch gỉ tốt, dụng cụ và thiết bị sử dụng đơn giản, lao động phổ
thông không cần kỹ thuật cao.
+ Nhược điểm: thép thanh bị tái gỉ trở lại, gây ô nhiễm môi trường, gây ảnh hưởng
đến sức khỏe người lao động - Phương pháp địên hóa:
+ Ưu điểm: làm sạch gỉ tốt , có khả năng làm gỉ ở các vị trí phức tạp.
+ Nhược điểm: Chỉ làm sạch được các kết cấu có kích thước nhỏ, khó áp dụng ngoài
công trường, thiết bị và máy móc phức tạp.
- Phương pháp hóa học:
+ Ưu điểm: có khả năng làm sạch gỉ ở các vị trí phức tạp, dễ áp dụng trong xưởng lẫn
ngoài công trường, tạo màng bảo vệ lâu dài.
+ Nhược điểm: Chất lượng làm sạch gỉ phụ thuộc nhiều vào hóa chất sử dụng.
Thay thế thép bị gỉ khi ở mức độ D (bề mặt thép có nhiều vảy gỉ lớn bong ra, xuất
hiện nhiều vết lõm nhỏ, dễ nhìn thấy bằng mắt thường).
III. Công tác ván khuôn:
1. Thành phần công việc trong quá trình gia công và lắp đặt ván khuôn, giàn giáo.
Biên chế tổ đội ván khuôn: 1.1.
Phân loại ván khuôn:
Ván khuôn phân loại theo vật liệu:
- Ván khuôn gỗ: ván khuôn gỗ xẻ dày 25 – 30mm; ván khuôn gỗ dán có kích thước
1,2x2,4 m2 và chiều dày từ 1 – 2,5 cm.
- Ván khuôn kim loại: ván khuôn thép (chiều dày 2-2.5cm, hệ sườn dốc, ngang đỡ phía
dưới để tăng độ cứng cho ván khuôn dày 2.8mm, hệ số dử dụng lớn hơn hoặc bằng 50 lần).
- Ván khuôn nhựa: kích thước tấm lớn, bề mặt nhẵn, vật liệu giòn, dễ lắp đặt.
Ván khuôn phân loại theo hình dạng: - Ván khuôn cột:
- Ván khuôn dầm: - Ván khuôn sàn: 1.2.
Quy trình lắp dựng ván khuôn:
Ván khuôn dầm sàn toàn khối: lắp dựng cột chống -> xà gồ (chống đỡ ván khuôn, chống
đỡ hệ sàn, xà gồ có 2 lớp: lớp chính và lớp phụ vuông góc với lớp chính -> lắp ván khuôn
đáy dầm -> lắp dựng cốt thép dầm -> lắp ván khuôn thành dầm -> lắp ván khuôn đáy sàn
-> lắp dựng cốt thép sàn -> lắp dựng ván khuôn thành sàn -> nghiệm thu Ván khuôn móng cột
- Căng dây theo trục tim của cột (theo 2 phương);
- Ghép ván khuôn thành hộp theo kích thước từng bậc thang;
- Xác định trung điểm của các cạnh ván khuôn, qua các trung điểm đó đóng 2 thước gỗ vuông góc với nhau;
- Lắp đặt hộp ván khuôn, thả dọi theo dây căng xác định tim cột, sao cho cạnh thước đi
qua trung điểm đó trùng với đường đóng của dây dọi;
- Cố định ván khuôn bằng những thanh chống, cọc cữ. Các đợt trên cũng tiến hành tương tự. 1.3.
Giáo chữ A, cây chống tăng, bát đầu, kích chân, đà, tăng đơ,..
- Giáo chữ A: Giàn giáo chữ A hay còn gọi là giàn giáo Pal, được thiết kế trên nguyên
tắc một khung giàn tam giác. Khi lắp ráp các đoạn chồng lên nhau tạo thành cột giáo
có chân đế hình vuông hay hình tam giác với kích thước 1200mm x 1200mm. Hiện
nay, hệ giàn giáo Pal được sử dụng khá phổ biến bởi nó đảm bảo tính an toàn và tiết kiệm về kinh phí.
- Cây chống tăng (hay còn gọi với những cái tên khác như: cây chống giàn giáo, cột
chống tăng, cây chống đơn, cây chống thép, cột chống,…): chúng được dùng để chống
sàn, chống các loại cốp pha đổ cột cũng như cốp pha đổ dầm. Là bộ phận không thể
thiếu trong công tác đổ bê tông vì đảm bảo độ vững chắc. Hơn thế nữa, chúng là bộ
phận có thể điều chỉnh độ cao thích hợp khi chống đỡ cốp pha sàn.
- Kích chân (hay kích tăng): là thiết bị được lắp đặt cùng với giàn giáo, có nhiệm vụ
chống và điều chỉnh độ cao tùy ý cho hệ giàn giáo để đảm bảo an toàn cho công trình xây dựng.
- Tăng đơ: là công cụ mang đến tác động hỗ trợ tích cực cho các kết cấu cần dùng tới
dây cáp thép. Cụ thể, chúng đóng vai trò điều chỉnh sức căng dây, mang đến sự liên
kết giữa cáp thép với các khung cố định hay giữa các sợi cáp thép với nhau tùy theo
đặc tính của các công trình.
- Bát đầu: là 1 loại kích sử dụng ở trên đầu của giàn giáo, có công dụng đỡ xà gồ, tạo
sự ổn định cho xà gồ. 1.4.
Biên chế tổ đội:
Thường gồm từ 18 – 20 người
- Lắp dàn giáo: 7 – 10 người
- Lắp ván khuôn: 3 – 5 người đóng ván khuôn; 3 – 5 người gia công ván khuôn. -
Vận chuyển ván khuôn: 3 người
2. Các loại máy móc thiết bị, công cụ thi công và các thao tác trong quá trình gia
công và lắp đặt ván khuôn:
- Vật tư chính: cốp pha 12 – 18mm, hộp 5x5, hộp 10x10, hộp 5x10, giáo chống tam
giác 0,75m – 1m - 1,5m; ống nối; chân kích; bát kích; giằng ngắn – dài; giáo hoàn
thiện, tôn định hình;…
- Vật tư phụ: đinh các loại, búa, ti chuẩn, vít gỗ,tiren các loại, tăng đơ, dây cáp, xà gồ, cọc cừ tràm,…
- Máy móc: máy khoan, máy bắt vít, máy hàn, cần trục, máy cắt gỗ,…
- Dùng bật mực hoặc bút để lấy kích thước của ván khuôn cần lấy để thi công, sau đó
dùng cưa để cưa đoạn ván khuôn cần dùng để thi công, cố định ván khuôn bằng gông
và thanh chống, với ván khuôn sàn thì cố định ván bằng cách đóng đinh cố định với xà gồ ở dưới.
3. Phương pháp ghép và điểu chỉnh ván khuôn các loại kết cấu chủ yếu: móng, cột, dầm, sàn: 3.1.
Lấy tim cốt cột, ván khuôn dầm sàn:
Sử dụng 2 máy kinh vĩ đặt theo 2 phương vuông góc để định vị vị trí, công việc định vị tim
cột của cột, những mốc đặt ván khuôn, sơn và đánh dấu những vị trí này để những tổ đội
thi công dễ dàng xác thực những mốc, ví trí yêu cầu. 3.2.
Biện pháp chống đỡ ván khuôn:
- Ván khuôn móng: sử dụng các thanh chống lên thành đất (phải được kê lên tấm gỗ
dày ít nhất 3cm để giảm lực xô ngang khi đổ bê tông); liên kết các tấm ván khuôn
bằng nẹp ngang và nẹp đứng; sử dụng các thanh chống xiên;…
- Ván khuôn cột: sử dụng các gông cột để cố định ván khuôn không bị bung ra khi đổ
bê tông; dùng thanh chống xiên, dây căng để cố định vị trí ván khuôn cột thằng đứng.
- Ván khuôn dầm: có thể chống giữ ván thành bằng gong mặt, thanh chống xiên bên
ngoài, hoặc néo bằng dây thép kết hợp với những thanh văng chống tạm bên trong,
tuỳ theo chiều cao của dầm.
- Ván khuôn sàn: dùng ván khuôn thép đặt trên hệ dàn giáo chữ A chịu lực bằng thép
và hệ xà gồ bằng gỗ, dùng tối đa diện tích ván khuôn thép định hình, với các diện tích
còn lại thì dùng kết hợp ván khuôn gỗ. 3.3.
Tổ hợp các tấm ván khuôn định hình:
- Thường dùng cho các công trình có thiết kế giống nhau ở các tầng, khi lắp ghép cho
các ô sàn, dầm giống nhau, thậm chí cả 1 tầng. -
Thường dùng ván khuôn nhôm.
4. Các biện pháp án toàn trong quá trình thao tác: 4.1.
An toàn khi thi công trên cao, các vị trí biên công trình:
a) Biên pháp an toàn khi thi công trên cao:̣
Đối với người lao đông:̣
- Nhất thiết phải đeo dây an toàn tại những nơi đã qui định.
- Việc đi lại, di chuyển chỗ làm việc phải thực hiện theo đúng nơi, đúng tuyến quy định,
cấm leo trèo để lên xuống vị trí ở trên cao, cấm đi lại trên đỉnh tường, đỉnh dầm, xà,
dàn mái và các kết cấu đang thi công khác.
- Lên xuống ở vị trí trên cao phải có thang bắc vững chắc. Không được mang vác vật
nặng, cồng kềnh khi lên xuống thang.
- Cấm đùa nghịch, leo trèo qua lan can an toàn, qua cửa sổ.
- Không được đi dép lê, đi giày có đế dễ trượt.
- Trước và trong thời gian làm việc trên cao không được uống rượu, bia, hút thuốc lào,…
- Công nhân cần có túi đựng dụng cụ, đồ nghề, cấm vứt ném dụng cụ, đồ nghề hoặc bất
kỳ vật gì từ trên cao xuống.
- Lúc tối trời , mưa to, giông bão, hoặc có gío mạnh từ cấp 5 trở lên không đươc làm
việc trên dàn giáo cao, ống khói, đài nước, cột tháp, trụ hoặc dầm cầu, mái nhà 2 tầng trở lên, vv.
Yêu cầu đối với các phương tiện làm việc trên cao:
- Để phòng ngừa tai nạn ngã cao, một biện pháp cơ bản nhất là phải trang bị dàn giáo
(thang, giáo cao, giáo ghế, giáo treo, chòi nâng, sàn treo,…) để tạo ra chỗ làm việc và
các phương tiện khác bảo đảm cho công nhân thao tác và đi lại ở trên cao thuận tiện và an toàn.
- Để bảo đảm an toàn và tiết kiệm vật liệu, trong xây dựng chỉ nên sử dụng các loại dàn
giáo đã chế tạo sẵn theo thiết kế điển hình.
- Chỉ được chế tạo dàn giáo theo thiết kế riêng, có đầy đủ các bản vẽ thiết kế và thuyết
minh tính toán đã được xét duyệt:
b) Biên pháp an toàn khi thi công ơꄉ vị tr椃Ā biêṇ :
- Công nhân không được uống rượu bia, sử dụng chất kích thich... khi làm viêc ̣
- Bồi dưỡng kiến thức về an toàn khi thi công ở vị trí biên, và tuyên truyền các tại nạn
đáng tiếc và biên pháp an toàn cho công nhân.̣
- Giàn giáo phải vững chắc, đảm bảo về kết cấu.
- Vị trí biên phải được đánh dấu, để biển báo nguy hiểm. 4.2.
An toàn khi hàn nối, sử dụng điện:
Yếu tố nguy hiểm khi hàn nối và sử dụng điện là:
- Điện giật do rò, chạm, chập vào các bộ phận dẫn điện;
- Bức xạ có hại do hồ quang điện;
- Khí, bụt độc hại;
- Bỏng do hạt kim loại nóng chảy, kim loại có nhiệt độ cao; - Cháy, nổ.
Các biện pháp an toàn là:
- Thợ hàn phải phải có hiểu biết về điện.
- Người lao động phải được trang bị đầy đủ đồ bảo hộ lao động.
- Mỗi máy hàn phải có 1 cầu dao riêng biệt không được đấu chung tất cả máy hàn vào 1 công tắc.
- Ngắt nguồn điện cấp cho máy hàn khi di chuyển máy hàn, ngừng công việc, sửa chữa đầu dây của máy hàn.
- Các công tắc điện trên máy hàn hoặc ở trạm điện cung cấp cho máy hàn phải hoạt
động tốt, có thiết bị bảo vệ.
- Trong quá trình hàn cần đảm bảo khu vực hàn không có chất dễ bắt lửa; dụng cụ hàn
chất lượng tốt; không hàn tại những thùng đóng kín, thùng trước đây đựng chất dễ
cháy nhưng chưa được làm sạch; không để cáp hàn tiếp xúc với nước, hóa chất ăn
mòn; nếu vị trí đặt máy hàn có nhiều người qua lại thì phải có lớp cách điện cho cáp hàn.
- Khi xong việc phải tháo các dây dẫn. Sau đó, để máy hàn và dụng cụ hàn ở nơi sạch
sẽ, tránh ẩm ướt, có nhiều ánh nắng để sản phẩm có tuổi thọ cao. 4.3.
An toàn hệ thống giáo đỡ, các biện pháp neo giằng, kê kích,…
Các biện pháp an toàn hệ giáo chống đỡ: đảm bảo chịu lực và đả bảo ổn định về kết cấu giàn giáo.
- Vật liệu làm giàn giáo còn đủ tốt để sử dụng được. Cần kiểm tra chặt chẽ chất lượng
vật liệu sử dụng làm giàn giáo. Tre, gỗ, đã bị mục, bị mối xông hoặc bị khuyết do các
tác động cơ học con người tạo nên, không được tiếp tục sử dụng. Thanh, ống kim loại
trong giàn giáo thép nếu bị ăn mòn, gỉ sét hoặc bị biến hình do va đập, móp, bẹp cũng không được sử dụng.
- Cấu trúc đỡ dưới dàn giáo phải đủ sức chịu tải, không bị chuyển dịch do trơn trượt
hay bị chuyển dịch cưỡng bức khác.
- Hệ giàn giáo phải neo, gắn với công trình bảo đảm chống chuyển dịch toàn hệ thống
do các tải trọng ngang như gió, lốc hay các rung chuyển đất vì những lý do khác nhau
(nổ mìn gần, xe trọng tải lớn đi gần, những lý do tạo rung khác…).
- Vật liệu để liên kết phải mới, bảo đảm các tiêu chí thiết kế và những vị trí liên kết
phải được thi công tốt, chặt, bền.
- Vật liệu làm giàn giáo phơi lộ mưa, nắng cần được kiểm tra định kỳ và thường xuyên.
Kỳ kiểm tra nên là 10 ngày vào mùa khô và 7 ngày vào mùa mưa.
- Thanh giằng và kết cấu giằng tạo ổn định cho hệ giàn giáo, chống biến hình và mất ổn định.
- Giàn giáo phải chắc chắn. Tay vịn lan can phải phải có chiều cao từ 0,9 - 1,15m so
với mặt sàn. Khoảng cách giữa giàn và tàu không quá 200mm.
Các biện pháp neo giằng, kê kích:
- Dùng dây cáp :các đầu giàn giáo chồng lên nhau phải cố định chắc chắn bằng dây thép, dây cáp;
- Sử dụng chân kích giàn giáo để kích giàn. IV. Công tác xây
1. Thành phần công việc trong quá trình xây, biên chế tổ đội (thành phần và cấp bậcthợ). 1.1.
Quy trình thực hiện 1 khối xây:
- Vận chuyển vật liệu;
- Bắc giáo: để đảm bảo có sàn công tác tốt thì khi xây lên cao, cần phải bắc giáo làm
sàn công tác; một bức tường xây thường cao từ 3-3,6m; người ta thường chia làm
3 đợt công tác: đợt 1 từ mặt sàn đến 1-1,2m; đợt 2 từ cao độ 2-2,4m; đợt 3 xây hết
chiều cao bức tường (chiều cao tầng nhà); - Căng dây mực;
- Chuyển và đặt gạch lên tường; - Chặt, đẽo gạch; - Miết mạch;
- Kiểm tra kích thước và độ chính xác của khối xây: cần có bản vẽ thiết kế; kiểm tra
mác gạch, mác xi măng; nghiệm thu tim cốt khối xây; sử dụng quả rọi, máy thuỷ
bình,… Để kiểm tra chiều ngang và đứng của khối xây; mặt khối xây không được
lồi lõm, không nghiêng lệch, góc khối xây phải vuông, mạch đứng hàng trên không trùng hàng dưới. 1.2.
Biên chế tổ đội xây:
Tùy thuộc vào khối lượng tường xây mà biên chế tổ đội có số lượng người khác nhau.
Thường sẽ 6 người trong 1 nhóm: 2 thợ phụ và 4 thợ chính -
Thợ phụ : vận chuyển gạch, trộn vữa phục vụ thợ chính. -
Thợ chính: xây, căng dây, kiểm tra chất lượng vữa xây.
2. Quy cách, chất lượng khối xây: 2.1.
Chiều cao tối đa của 1 đợt xây (đối với từng loại tường 110, 220, 330,..):
- Tường 110 thì chiều cao tối đa là 1,5m
- Tường 220 thì chiều cao tối đa là 1,8m
- Tường 330 thì chiều cao tối đa là 2m 2.2.
Một số lưu ý với tường xây 220 trở lên:
- Với tường xây từ tường 220 trở lên, để khối xây đặc chắc, ổn định thì xây theo kiểu
5 dọc 1 ngang; hàng gạch dưới cùng bao giờ cũng phải quay ngang. Viên gạch quay
ngang sẽ phân bố lại mạch xây, chia đều tải trọng sang 2 bên và tạo thành khối đặc chắc.
+ Ưu điểm: có thể xây gạch có kích thước ko được đồng đều lắm; xây được tường
khong trát, mặt tường phẳng và đẹp; cách xếp gạch đơn giản, mỗi lớp gạch đều đặt theo
1 chiều nên công nhân thao tác dễ; cường độ chịu lực của tường đảm bảo tốt. + Nhược
điểm: có những lớp gạch trùng qua 3 hay 5 hàng, cường độ chịu lực của tường xây sẽ bị giảm đi 5-6%.
- Hàng ngang dùng gạch đặc để chống thấm cho tường và tránh hiện tượng bị tụt đinh.
2.3. Lưu ý khi xây hàng xây cuối cùng:
Đối với vị trí tiếp giáp đỉnh tường, nếu xây ngang thì độ bám chặt của gạch với sàn sẽ yếu,
lớp vữa sát sàn dễ bị co ngót không bám sát được vào sàn nhà, đồng thời độ võng của sàn
và dầm thường gây ra vết nứt ở vị trí tiếp giáp. Vì vậy để dễ thi công và liên kết tốt ở vị trí
tường và sàn dầm thì lớp gạch cuối được xây nghiêng và miết hồ dầu ở vị trí tiếp giáp.
2.4. Lưu ý khi xây ở vị trí má cửa:
Vị trí má cửa nên dùng gạch đặc vì khi hoàn thiện vị trí má cửa ta phải khoan bắt bản lề
cho cửa và nếu gạch rỗng trong quá trình trát má sẽ có một lượng vữa hao hụt do chui vào trong lỗ của gạch.
2.5. Cách liên kết giữa tường xây với cột, vách bê tông của công trình:
- Khung cột bê tông cốt thép là cấu kiện chịu lực chính và thường được thi công trước
nên sẽ là cấu kiện bị co ngót trước; tường gạch khi đc xây với công trình có khung
cột dầm sàn thì chủ yếu có chức năng bao che, phân chia không gian, cách âm cách
nhiệt,.. và thường được xây sau khi đã hoàn thành các cấu kiện cột, dầm sàn.
- Vì giai đoạn thi công không đồng nhất, vật liệu không đồng nhất mà dẫn đến sự co
ngót không đều dễ dẫn đến nứt ở phần liên kết giữa cột và tường vì vậy người ta bố
trí râu thép chờ để liên kết giữa cột và tường và đóng lưới mắt cáo khi trát giáp lai giữa tường và cột. 3. Các loại mỏ xây:
Mỏ xây là gián đoạn kỹ thuật trong khối xây theo phương mặt bằng, giữa hai phân đoạn
xây trước và sau, đồng thời là mối nối giữa hai phân đoạn đó. Mỏ xây nằm ở hai đầu mỗi
phân đoạn, là nơi kết thúc một phân đoạn. Có ba loại mỏ xây là: mỏ nanh, mỏ hốc, mỏ giật cấp.
- Mỏ giật cấp chất lượng tốt ở điều kiện tầm thấp và trung bình nhưng nhược điểm của
việc để mỏ giật là diện xây của mỗi phân đoạn giảm dần theo chiều cao khi để mỏ
dật, (diện xây có dạng hình thang càng lên cao càng nhỏ dần), dẫn tới năng suất xây
giảm dần theo chiều cao khi để mỏ giật., nên đc áp dụng ở vị trí công trình thấp và trung bình.
- Mỏ nanh và mỏ hốc: chất lượng phần khối xây tại vị trí để các loại mỏ này không
được tốt: khi để mỏ các viên gạch tạo thành các nanh chìa thường có dạng conson,
mà lại chỉ được giữ bởi một lớp vữa mạch nằm còn tươi và ở dạng lỏng khi xây, nên
thường bị gục xuống, không đảm bảo cho lớp xây ngang bằng tại vị trí mỏ; đồng thời
các mạch vữa tại vị trí các mỏ này thường không thể no đầy, tạo ra các khe rỗng gây
giảm yếu cho khối xây tại vị trí mỏ. Tuy nhiên, ưu điểm của hai loại mỏ này là diện
xây không đổi theo chiều cao nên áp dụng khi xây phân đoạn mới nối tiếp phân đoạn
xây cũ, trên tầm cao hơn thì ở phân đoạn cũ để mỏ hốc còn phân đoạn mới được nối vào đó bẳng mỏ nanh
4. Các phương pháp và thao tác lấy mốc xây:
4.1. Cách định vị tim cốt tường xây và kiểm tra chất lượng vữa xây:
- Dùng 2 máy kinh vĩ đặt lên 2 phương vuông góc để xác định vị trí định vị tim cốt tường xây.
- Dựa vào bản vẽ theo thiết kế dùng máy đo laser xác định định tim cột, tiến hành bật
mực theo đường laser để giữ lại vị trí tim cốt tường xây.
4.2. Cách làm phẳng hàng dây và đảm bảo độ thẳng đứng của tường xây:
- Để đảm bảo độ bằng phẳng của khối xây, người thợ dùng thước tầm. Cách thực hiện:
Đặt thước tầm lên mặt trên của khối xây, chồng ni vô lên thước. Nếu bọt nước của
ống thủy nằm ngang vào giữa thì tường nằm ngang và ngược lại. Trị số sai lệch nằm
ngang là khe hở giữa đầu thước và mặt tường khi điều chỉnh bọt nước vào giữa.
- Để đảm bảo độ thẳng đứng của khối xây, người thợ dùng thước tầm hoặc thước đo
góc. Cách thực hiện áp thước tầm theo phương thẳng đứng vào bề mặt khối xây, áp
ni vô vào thước tầm. Nếu bọt nước ống thủy lệch về 1 phía thì tường nghiêng, muốn
biết độ nghiêng là bao nhiêu thì chỉnh thước sao cho bọt nước ống thủy nằm giữa.
Khe hở giữa thước và tường chính là độ nghiêng. Thước góc dùng để bắt góc khối
xây (kiểm tra độ vuông góc của tường).
5. Mác gạch xây và mác vữa xây 5.1.
Mác gạch xây và cách xác định mác gạch xây: (thông tư 12,13/2021/BXD)
Mác gạch xây căn cứ vào cường độ nén và cường độ uốn (theo TCVN-6355-1-1998)
Thí nghiệm nén: - Chuẩn bị mẫu:
+ Lấy 5 viên gạch ngẫu nhiên đã đạt tiêu chuẩn ngoại hình, cưa đôi viên gạch bằng máy cưa
+ Ngâm các nửa viên gạch vào nước trong 5 phút.
+ Vớt gạch ra khỏi nước, trát vứa lên mạch để gắn 2 nửa viên chồng lên nhau, 2 đầu
cắt nằm về 2 phía khác nhau.
+ Bảo dưỡng mẫu tự nhiên trong không khí 72 giờ - Thử nén:
+ Mẫu được thử nén ở độ ẩm tự nhiên trong không khí.
+ Đo kích thước diện tích chịu lực nén, mỗi kích thước được tính trung bình 3 giá trị.
+ Đặt mẫu vào máy ép ở tâm điểm mâm nén, cho máy làm việc với tốc độ tăng lực
0,2-0,3 N/mm2. giây cho đến khi mẫu bị phá hoại.
+ Thí nghiệm với 5 mẫu và kết quả tính trung bình từ 5 giá trị Rn thí nghiệm được,
nếu có 1 trong 5 giá trị lệch quá 35% gtri trung bình thì bỏ gtri trung bình đó và tính trung
bình 4 gtri còn lại, nếu 2 trong 5 gtri lệch quá 35% thì bỏ tất cả các kết quả để thí nghiệm
lại với 5 mẫu khác Thí nghiệm uốn: - Chuẩn bị mẫu:
+ Lấy 5 viên gạch ngẫu nhiên đã đạt tiêu chuẩn ngoại hình.
+ Ngâm các viên gạch vào nước trong 5 phút.
+ Trát vữa lên viên gạch nguyên thành 3 giải vữa ở 2 vị trí đặt gối 2 đầu viên gạch và
1 vị trí đặt lực giữa nhịp ở mặt đối diện.
+ Bảo dưỡng mẫu tự nhiên trong không khí 72 giờ - Thí nghiệm uốn:
+ Đo kích thước tiết diện uốn, mẫu thử được thí nghiệm ở độ ẩm tự nhiên tròng phòng.
+ Đặt giá uốn gạch lên máy ép, đặt mẫu uốn lên giá uốn sao cho 2 gối tựa trùng với
tâm giải vữa gắn trên mẫu gạch, đặt gối truyền lực lên mặt trên mẫu, trùng với tâm
giải vữa thứ 3, hạ mâm nén trên xuống sát gối truyền lực rồi chỉnh gối lần cuối. + Cho
máy ép vận hành với tốc độ gia tải 0,5 N/mm2.giây. Ghi nhận giá trị tải trọng phá hoại P.
+ Thí nghiệm với 5 mẫu và kết quả tính trung bình từ 5 giá trị thí nghiệm được, nếu
có 1 trong 5 giá trị lệch quá 50% gía trị trung bình thì bỏ gía trị trung bình đó và tính
trung bình 4 gía trị còn lại, nếu 2 trong 5 gía trị lệch quá 50% thì bỏ tất cả các kết quả
để thí nghiệm lại với 5 mẫu khác. 5.2.
Lập cấp phối vữa xây và kiểm tra mác vữa xây:
a) Cách lập cấp phối vữa xây
- Vữa xi măng: Tính khối lượng xi măng cho 1m3 cát theo công thức:
Với: Rv : Mác vữa cần thiết kế, kG/cm2
Rx : cường độ của xi măng, kG/cm2
K : hệ số chất lượng vật liệu - Vữa tam hợp:
+ Tính khối lượng xi măng cho 1m3 cát theo công thức như trên.
+ Thể tích vôi nhuyễn cho 1m3 cát: Vv = 0,17*(1-0,002X) m3
Trong đó: V : thể tích vôi nhuyễn, m3 v
b) Xác định mác vữa xây:
Mác vữa xây được xác định theo trị số giới hạn cường độ chịu nén trung bình cảu những
mẫu vữa hình khối lập phương kích thước 7,07 x 7,07 x 7,07 cm, được chế tạo và bảo
dưỡng 28 ngày trong điều kiện tiêu chuẩn hoặc cũng có thể sử dụng các nửa mẫu dầm kích
thước 4 x 4 x 16cm sau khi chịu uốn.
6. Các loại giàn giáo công cụ phục vụ công tác xây:
- Giàn giáo khung chữ H: giàn giáo khung thường được sản xuất với chất liệu thép phi
42, dày 2mm, trọng lượng cơ bản của 1 bộ khung giàn giáo 1,7m là 12,5kg. Hệ giàn
giáo khung bao gồm: khung giàn giáo, giằng chéo, kích tăng, cây chống tăng, cầu thang, mâm giàn giáo.
- Giàn giáo nêm: có tác dụng chống sàn sử dụng chủ yếu trong công tác chịu lực khi
đổ bê tông, kết cấu bê tông, giải pháp tối ưu cho đổ dầm, sàn, cột,.. giàn giáo nêm
được lựa chọn sử dụng phù hợp với các công trình lớn. Cấu tạo hệ giàn giáo nêm bao
gồm: chống đứng, giằng ngang, giằng chéo, hệ chống đà biên. Các phụ kiện được liên
kết qua các linh kiện như: chốt nêm, U liên kết,…
- Giàn giáo đĩa: cấu tạo tương tự với giàn giáo nêm tuy nhiên chỉ khác nhau ở các mối
liên kết được thiết kế đặc biệt, giống với mâm đĩa nhưng lại có nhiều ưu điểm hơn.
Hệ giàn giáo đĩa cấu tạo bao gồm các bộ phận: thanh giằng, đà chống, chống consol,..
So với các loại giàn giáo khác thì thanh chống đứng của giàn giáo đĩa rất chắc chắn
có thể chịu được trọng tải rất lớn, hơn nữa các điểm kết nối trong hệ giàn giáo chắc
chắn tới mức có thể giàn thanh chống đà ở giữa để có không gian hơn cho công trình
những vẫn đảm bảo được độ chắc chắn an toàn.
7. Các biện pháp an toàn lao động.
7.1. Khi xây móng:
- Trước khi xây móng phải kiểm tra tình trạng vách đất, hệ thống chống đỡ vách đất,
đặc biệt chú ý hố đào ở nơi đất tơi xốp, ẩm ướt, gần đường giao thông chịu tác động của xe cộ.
- Dọc theo hố móng phải chừa 1 dải đất trống ít nhất 0,5m, trên đó ko đc chất vật liệu và máy móc thi công.
- Đưa gạch xuống hố móng bằng ván trượt, đưa vữa bằng ván nghiêng.
- Khi thi công nếu hố móng bị ngập nước phải dừng thi công.
- Khi lấp đất hố móng phải lấp đều 2 bên, lấp đến đâu phải đầm đến đó.
7.2. Khi xây tường:
- Trước khi xây phải kiểm tra tình trạng của móng hoặc phần tường đã xây cũng như
tình trạng các phương tiện làm việc trên cao: giàn dáo,….
- Khi xây tường dưới 7m phải làm rào ngăn ở phía ngoài dọc theo chu vi công trình
cách tường 1,5 m để phòng ngừa dụng cụ vật liệu rơi xuống.
- Phải che chắn những lỗ tường từ tầng 2 trở lên nếu lỗ đó người chui qua được.
- Không đứng trên mặt tường để xây, không dựa thang vào tường mới xây để lên xuống.
- Khi đưa vật liệu lên cao phải dùng các thiết bị nâng: thang tải, tời, ..
- Không ném gạch bừa bãi xuống mặt đất.
- Trang bị các phương tiện phòng hộ lao động như giầy, mũ nhựa, dây an toàn, găng
tay, ủng đầy đủ cho công nhân.
- Cấm dùng bia rượu trong khi làm việc.
- Công nhân làm việc trên cao phải đảm bảo sức khoẻ tốt, không bị chóng mặt. V. Công tác trát:
1. Dụng cụ: bay, bàn xoa, thước, nivô, dây nhợ……
2. Nguyên tắc khi trát:
- Bề mặt cần trát cần phải đạt một độ cứng ổn định, chắc chắn rồi mới tiến hành trát.
Tường xây sau 2 ngày là có thể trát được.
- Bề mặt cần trát quá khô thì phải phun nước làm ẩm trước khi trát.
- Quy trình trát: Trát trần trước rồi tới tường và cột.
- Cũng giống như bê tông, vữa trát cũng có quá trình phát triển cường độ, và cũng có
hiện tượng mất nước do sự bốc hơi nước. Vì vậy cúng ta cũng cần tuân thủ quy trình
bảo dưỡng lớp trát. Yêu cầu sau khi trát 24h tiến hành phun ẩm bảo dưỡng tránh nứt,
thời gian bảo dưỡng tối thiểu 3 ngày.
3. Các phương pháp và thao tác lấy mốc trát:
Cách tạo mốc và lấy các mốc trát:
Làm mốc trát tường gồm 2 phần việc chính: đắp các mốc chính - mốc phụ (điểm) và dải
mốc (đường nối các điểm với nhau).
- Bước 1: Chuẩn bị dụng cụ và vật liệu
+ Dụng cụ thường dùng
+ Bay, búa, đinh, dây + Thước tầm, nivo
+ Quả dọi, máy laser, thước dây
+ Nguyên vật liệu:Hồ dầu (hỗn hợp xi măng và nước); các miếng gạch vỡ hoặc
miếng vữa khô có mặt nhẵn (Thường công trường người ta đổ vữa xi măng lên một
tấm ván phẳng. Dùng bay khía thành các phần đều nhau khoảng 5x5cm. Sau đó phơi
khô. Cuối cùng bẻ nhỏ thành các miếng mốc trát).
- Bước 2: Kiểm tra tường trước khi trát
Bề mặt trát được kiểm tra tổng thể bằng cách:
+ Kiểm tra độ phẳng của bề mặt tường: Bạn cần dùng dây căng và thước để kiểm tra.
+ Thử độ thẳng đứng, ngang bằng: Dùng thước tầm, nivô.
+ Xác định được mức độ lồi lõm, nghiêng của tường là bao nhiêu -> giúp xác định
được độ dày của mốc.
- Bước 3: Đắp các mốc chính
+ Định vị mốc chính phía trên:
+ Đầu tiên, bạn cần định vị 2 diểm cách trần và tường bên 15- 20cm tại vị trí 2 góc
trên của mặt tường trát.
+ Sau đó, thực hiện đóng đinh theo điểm vừa định vị, đầu đinh nhô ra cách
tường một khoảng bằng chiều dày lớp trát. + Gióng xuống mốc chính ở phía dưới:
+ Xác định bằng cách thả dọi từ 2 mốc chính trên xuống. Tường có chiều cao nhỏ chỉ
cần dùng thước tầm và nivô để xác định mốc chính phía dưới.
- Bước 4: Đắp các mốc phụ
Cần làm mốc phụ khi chiều dài thước cán nhỏ hơn khoảng cách giữa 2 mốc chính, hoặc ở
vị trí tương ứng với chiều cao đợt giáo. Như vậy các mốc trát sẽ phân bố thành hàng ngang,
hàng dọc trên tường với khoảng cách thông thường là từ 1.5-2.5m (trừ các khu vực hẹp có
thể nhỏ hơn). Số lượng mốc phụ sẽ tùy theo diện tích trát.
Cách làm mốc phụ như sau: dùng dây căng giữa 2 mốc chính theo chiều đứng ta định vị
được vị trí cần đắp mốc phụ.
Với cách làm tương tự ta cũng xác định được các vị trí trên bề mặt nằm ngang để đặt mốc phụ.
- Bước 5: Đắp dải mốc
+ Làm dải mốc: theo phương song song với chiều cần cán thước, thực hiện nối
các dải mốc bằng vữa. Sau đó, dựa vào 2 mốc ở 2 đầu dùng thước cán phẳng. +
Hệ thống dải mốc: sử dụng thước tầm cán phẳng theo 2 cạnh của dải mốc, dùng
bay cắt vát cạnh ta được hệ thống dải mốc trát.
Các mốc trát sẽ phân bố thành hàng ngang, hàng dọc trên tường với khoảng cách thông
thường là từ 1.5-2.5m (trừ các khu vực hẹp có thể nhỏ hơn)
4. Phương pháp kiểm tra chất lượng bề mặt được trát:
Kiểm tra độ đặc chắc: gõ trực tiếp, tất cả những chỗ bộp phải phá ra làm lại.
Kiểm tra độ bằng phẳng:
- Kiểm tra bằng đèn chiếu laser: Chiếu tia laser vào tường nếu tường thẳng thì tia laser
nhìn thấy sẽ là đường thẳng còn những vị trí không phẳng ta thấy tia laser sẽ gãy.
- Kiểm tra bằng thước nhôm: Thước dài 2m đặt trên tường kiểm tra xem tiếp xúc giữa
tường và thước có kẽ hở không dê thước trên mặt phẳng tường để kiểm tra độ phẳng.
5. Phương pháp kiểm tra chất lượng của vữa trộn: -
Kiểm tra bằng mắt thường: xem bê tông có bị vón cục, chảy nước,
… - Kiểm tra độ sụt. Bê tông đạt thì mới cho đổ - Lấy mẫu thí nghiệm.