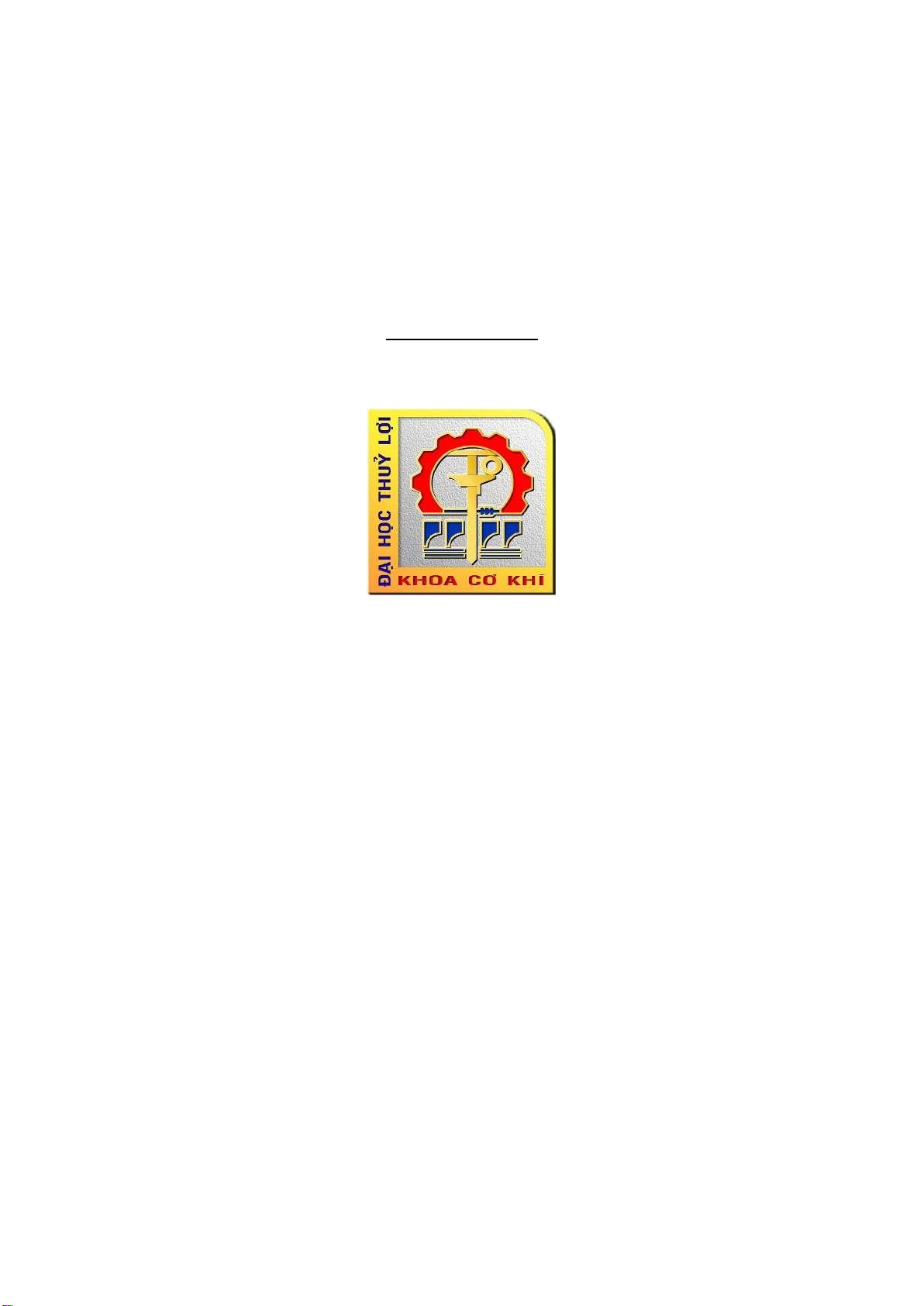













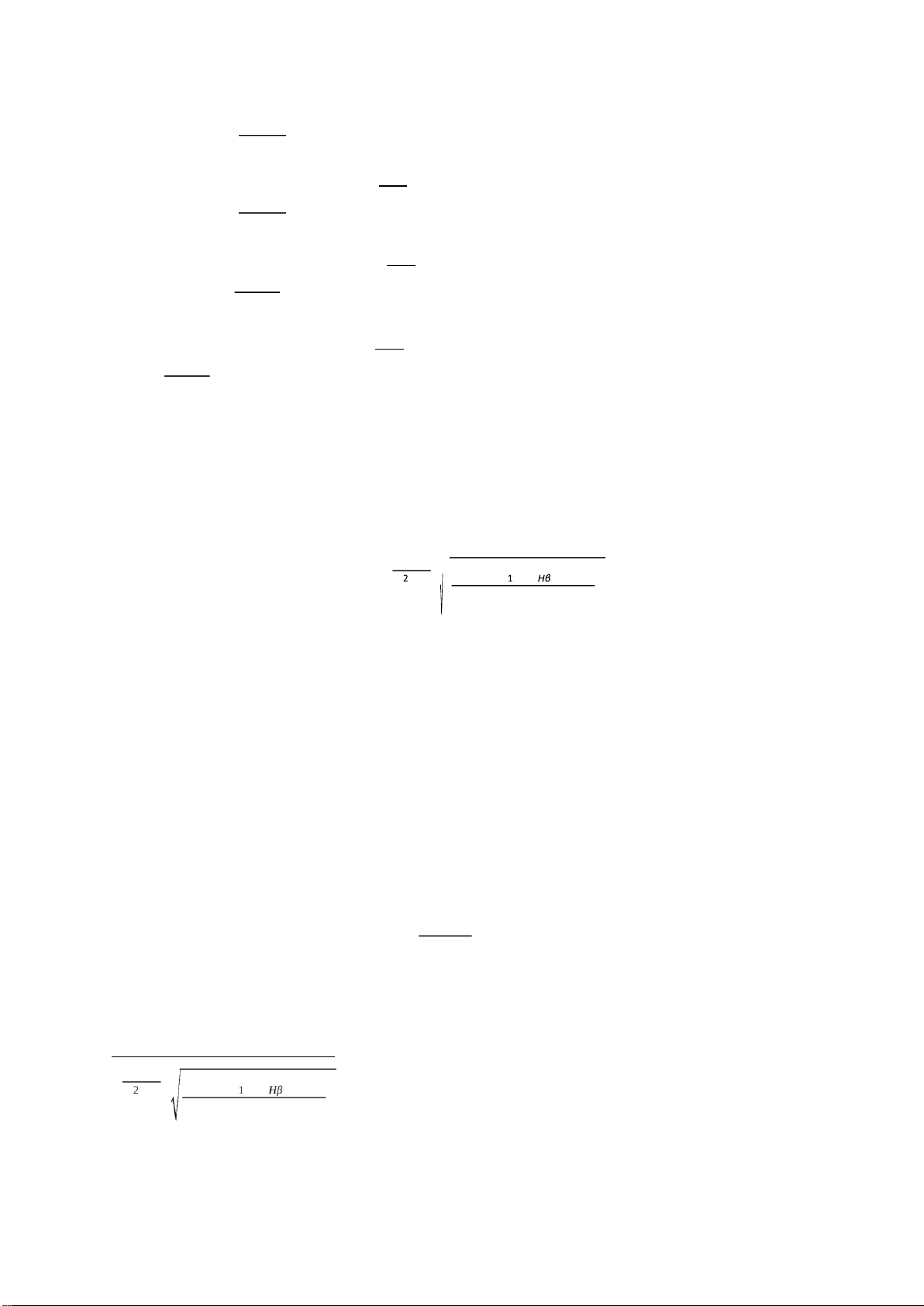



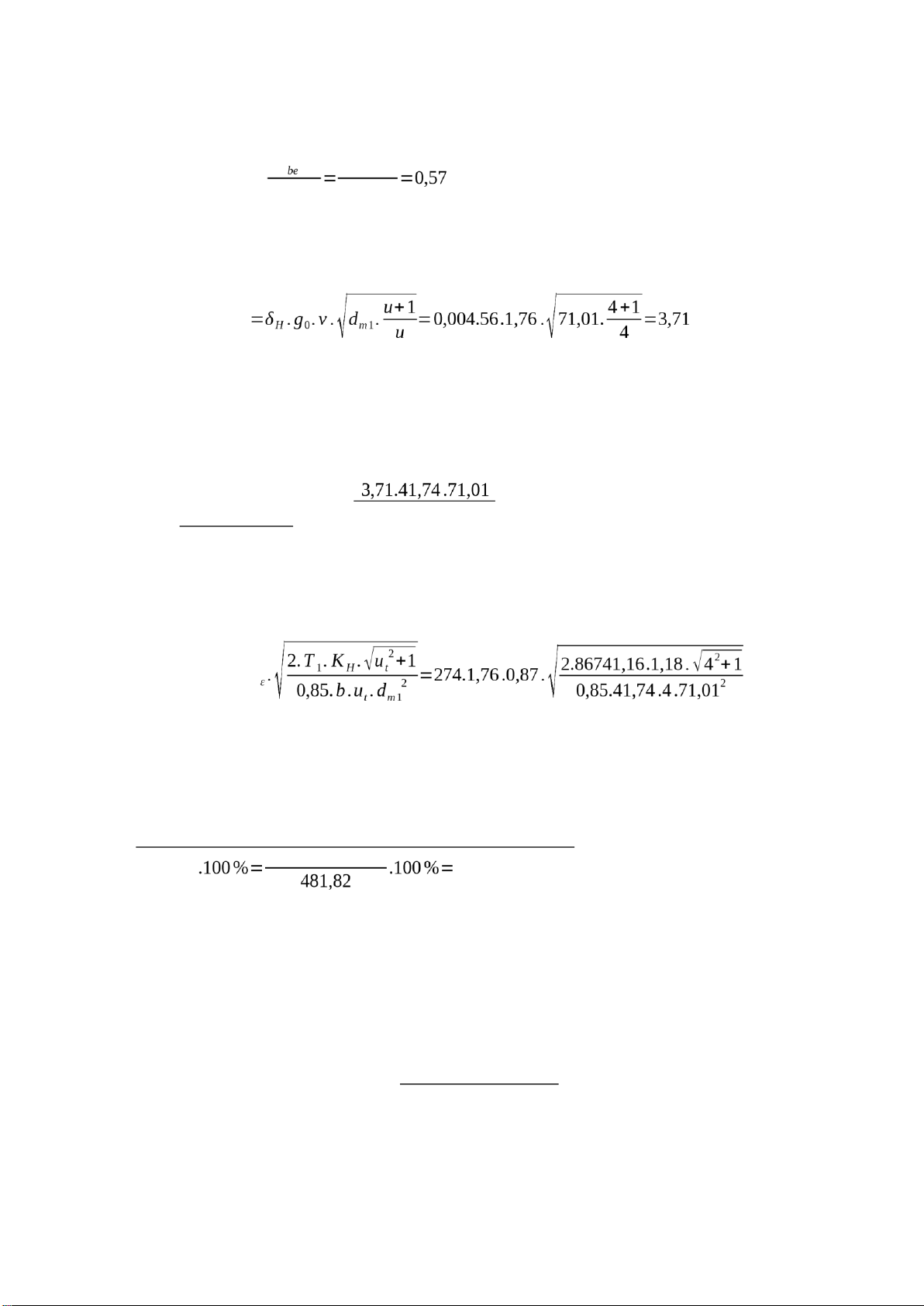




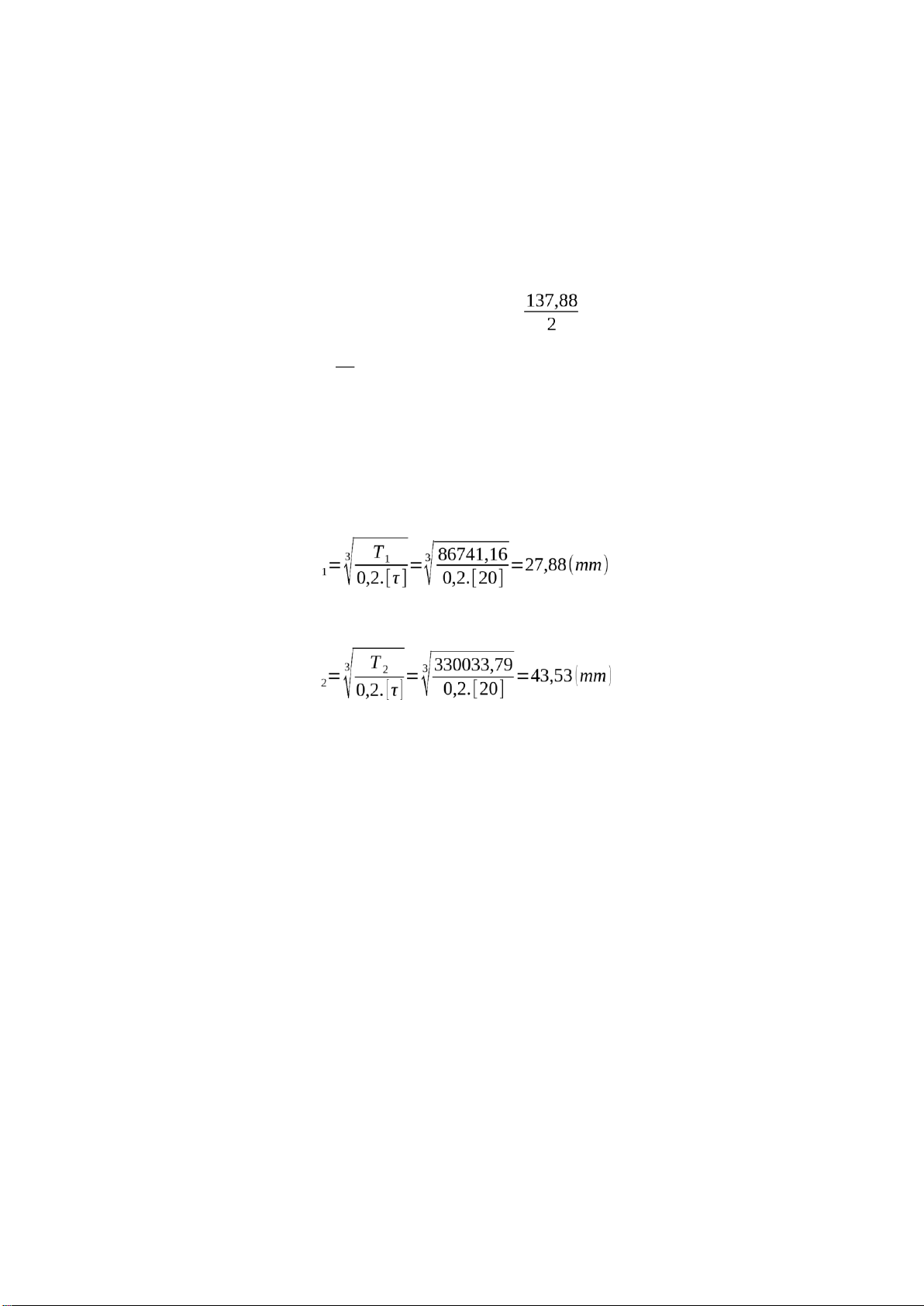
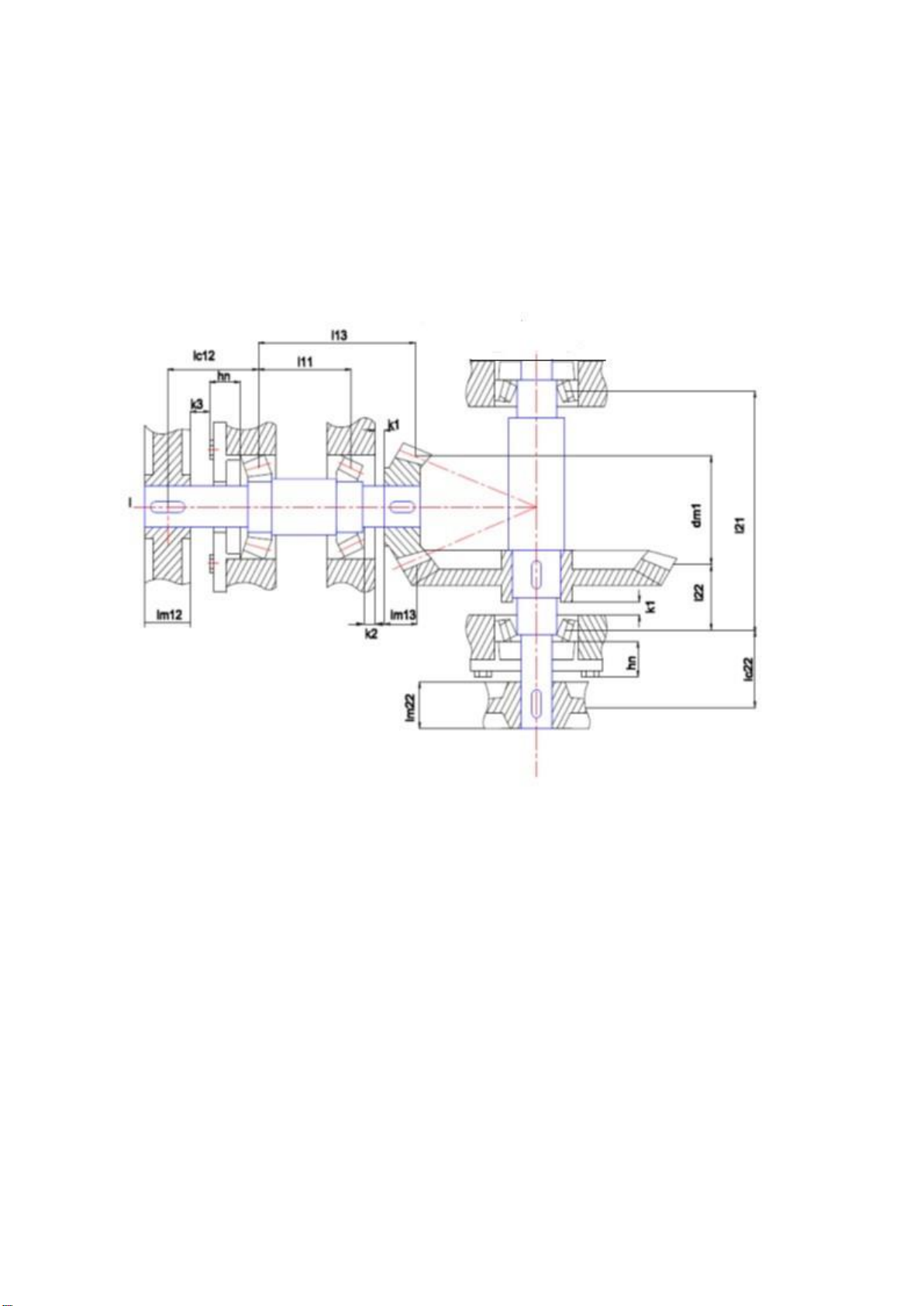

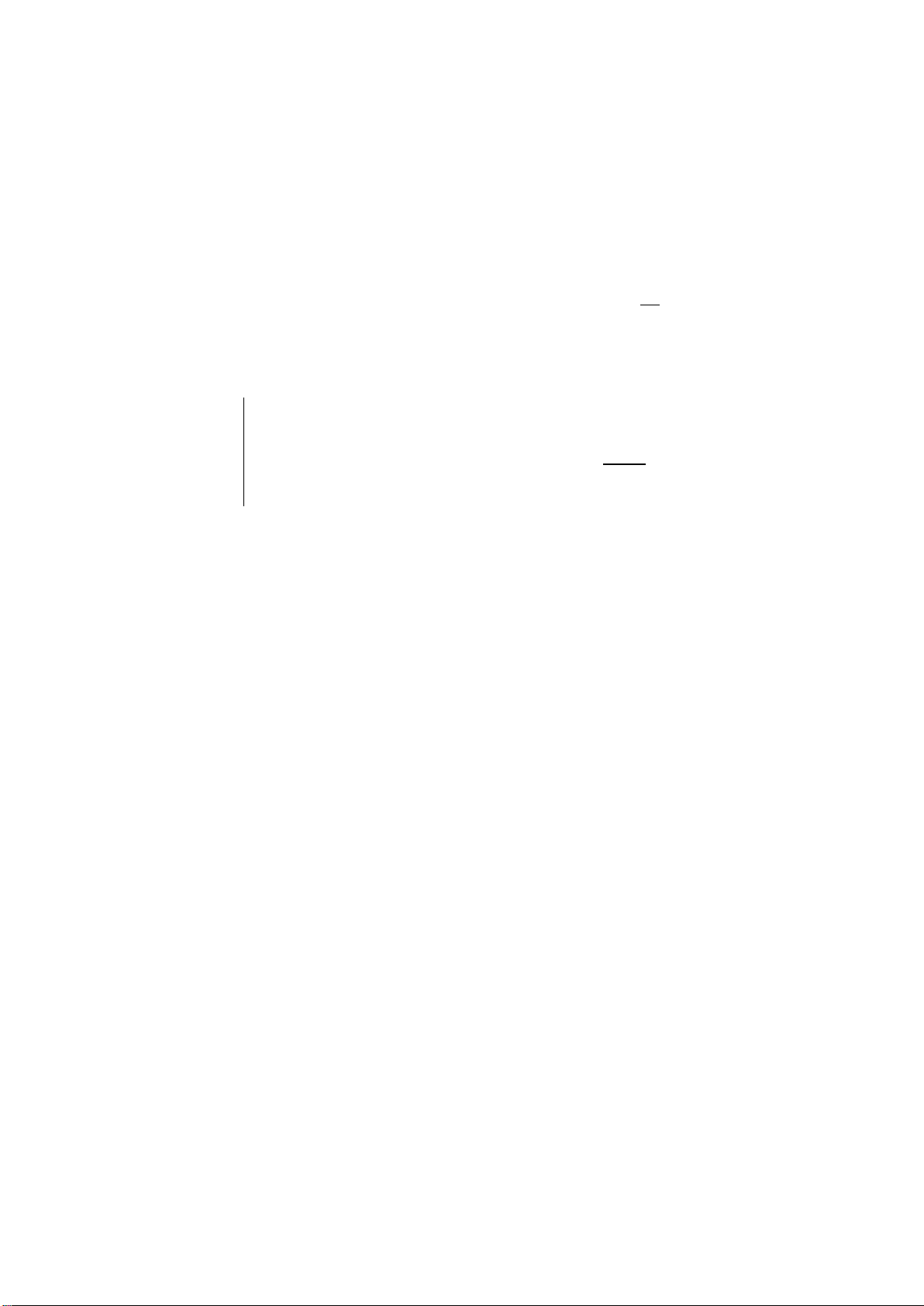





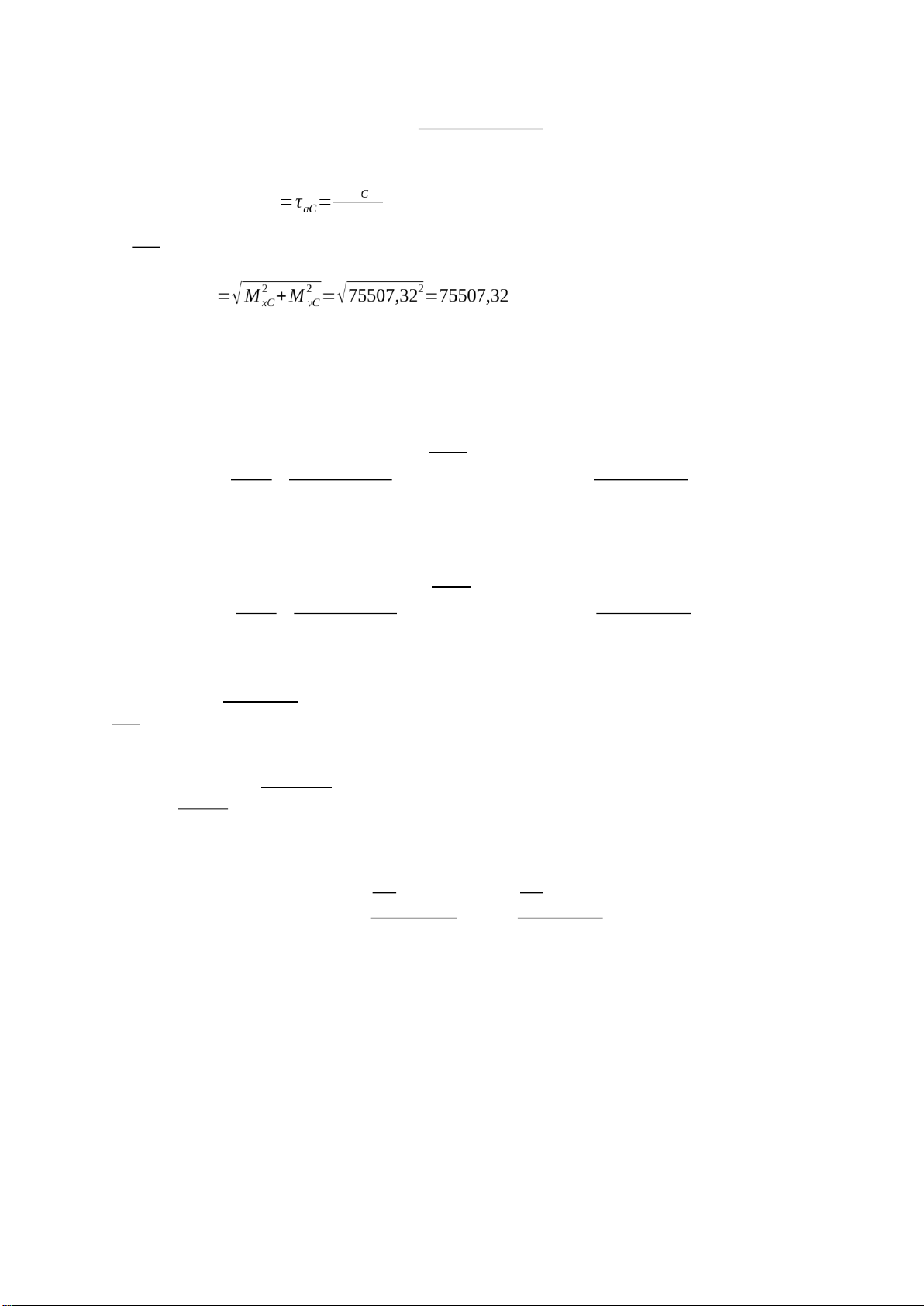










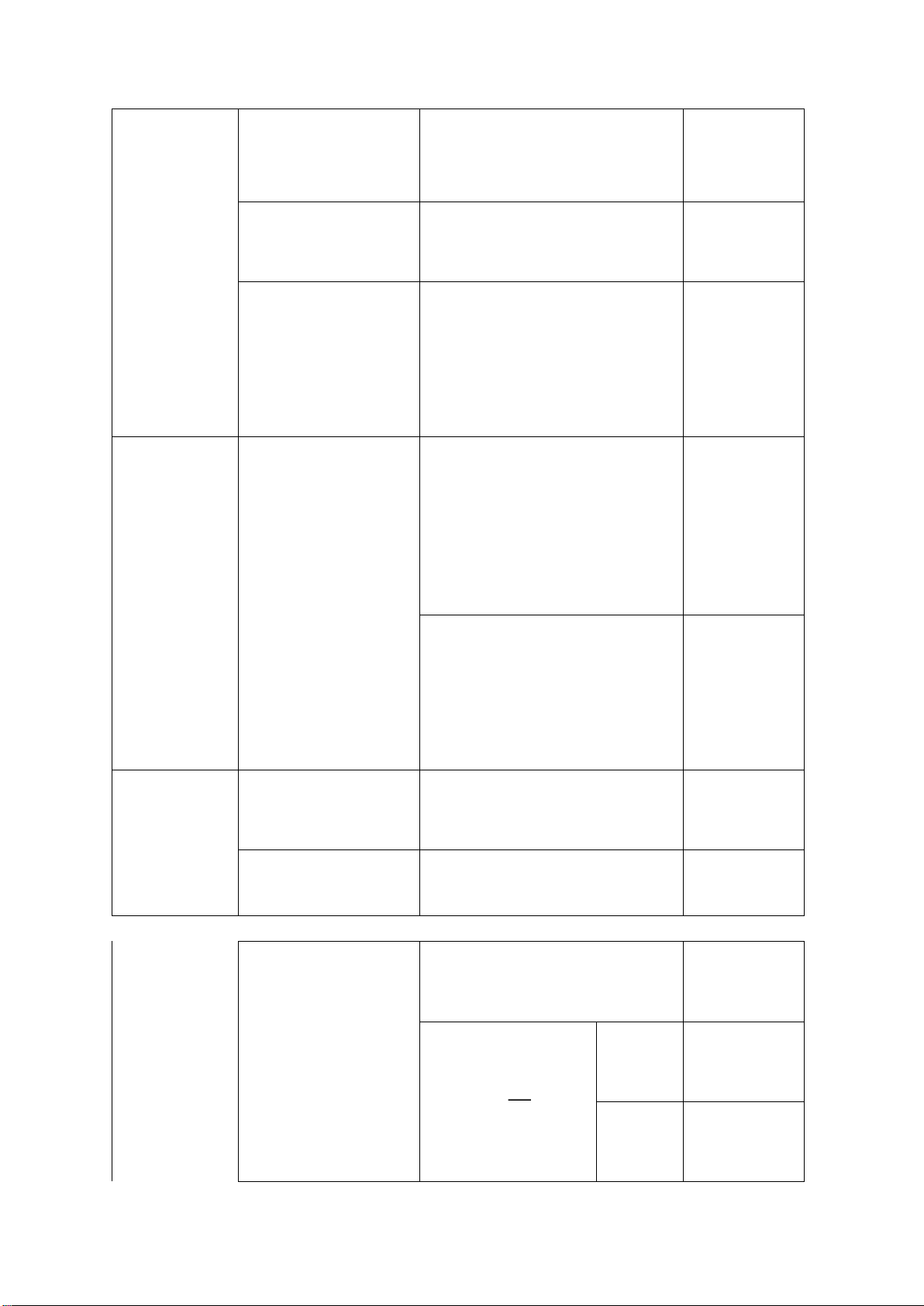







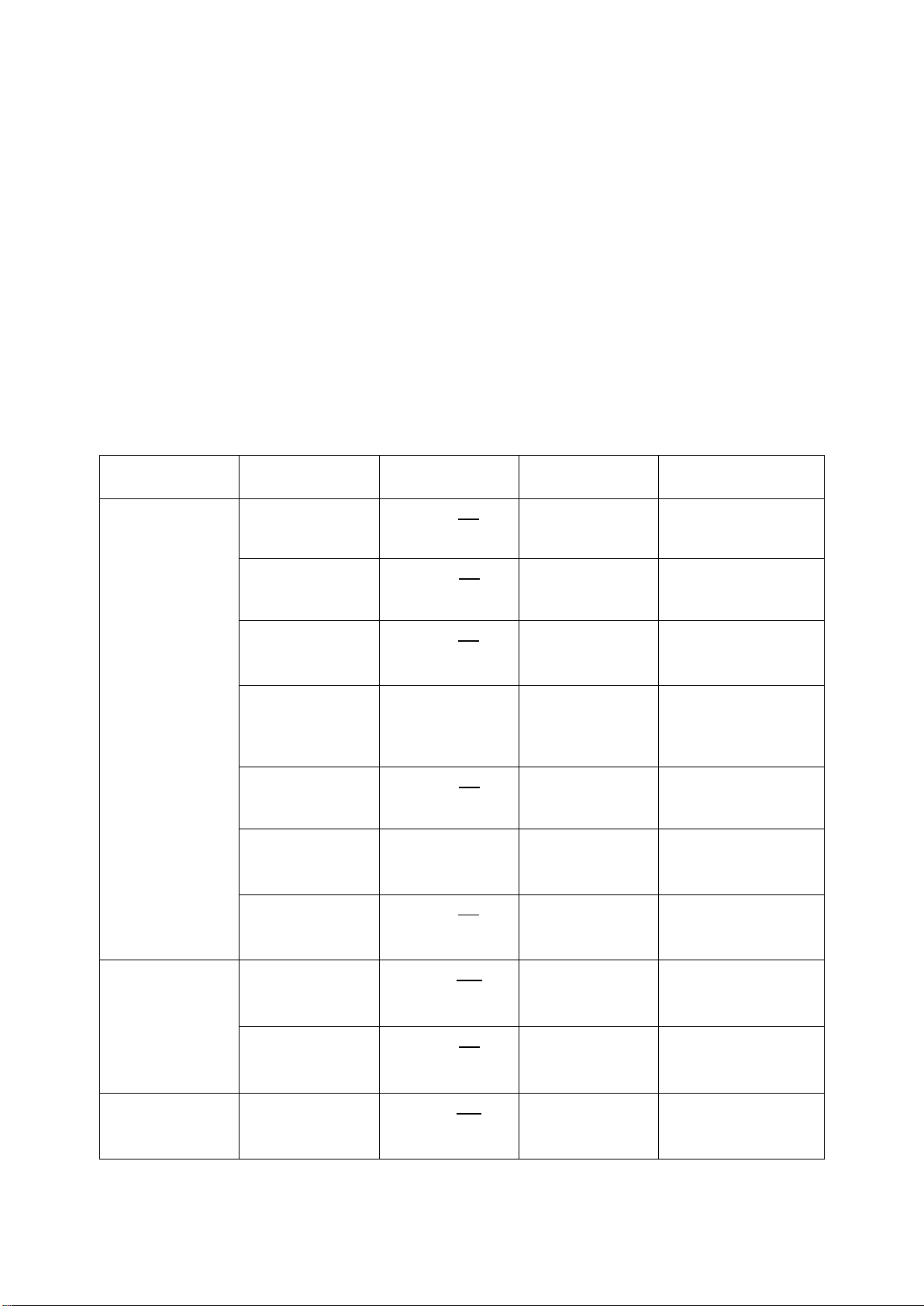

Preview text:
lOMoARcPSD| 40651217
TRƯỜNG ĐẠI HỌC THỦY LỢI KHOA CƠ KHÍ
ĐỒ ÁN CƠ SỞ THIẾT KẾ MÁY
Giảng viên hướng dẫn: ThS. Phạm Thanh Tùng
Sinh viên thực hiện : Nguyễn Mạnh Cường Lớp : 61CĐT3
Mã sinh viên : 1951201641 lOMoARcPSD| 40651217 Hà Nội, 9/2021 MỤC LỤC
LỜI MỞ ĐẦU.....................................................................................................1
PHẦN I: CHỌN ĐỘNG CƠ VÀ PHÂN PHỐI TỈ SỐ TRUYỀN..................3
1.1 Chọn động cơ......................................................................................................3
1.1.1 Xác định công suất động cơ...........................................................................3
1.1.2 Xác định số vòng quay sơ bộ.........................................................................3
1.1.3 Chọn động cơ................................................................................................4
1.2 Lập bảng thông số kỹ thuật...............................................................................4
1.2.1 Xác định tỉ số truyền của hệ dẫn động theo công thức 3.23/48[1].................4
1.2.2 Phân phối tỉ số truyền của hệ dẫn động (Ut ¿ cho các bộ truyền theo công
thức 3.24[1] ta có:..................................................................................................4
1.2.3 Xác định công suất, mômen xoắn và số vòng quay các trục..........................4
PHẦN II: TÍNH TOÁN THIẾT KẾ BỘ TRUYỀN ĐAI THANG.................5
2.1 Chọn tiết diện đai...............................................................................................5
2.2 Chọn đường kính đai.........................................................................................5
2.3 Xác định sơ bộ khoảng cách trục a...................................................................6
2.4 Xác định chính xác khoảng cách trục...............................................................6
2.5 Xác định số đai...................................................................................................7
2.6 Xác định các thông số cơ bản của bánh đai.....................................................7
2.7 Xác định lực căng ban đầu và lực tác dụng lên các trục.................................8
PHẦN III: TÍNH TOÁN BỘ TRUYỀN BÁNH RĂNG CÔN RĂNG
THẲNG................................................................................................................8
3.1 Chọn vật liệu bánh răng....................................................................................8
3.2 Xác định ứng suất sơ bộ cho phép....................................................................9
3.3 Xác định sơ bộ chiều dài côn ngoài bộ truyền bánh răng côn......................10
3.4 Xác định các thông số ăn khớp.......................................................................11
3.4.1 Xác định mô đun vòng ngoài và vòng trung bìnhmte ,mtm...........................11
3.4.2 Xác định chính xác ứng suất cho phép........................................................12 lOMoARcPSD| 40651217
3.5 Kiểm nghiệm bộ truyền bánh răng.................................................................12
3.5.1 Kiểm nghiệm độ bền tiếp xúc......................................................................12
3.5.2 Kiểm nghiệm độ bền uốn.............................................................................14
3.6 Xác định các thông số khác.............................................................................15
3.7 Bảng tổng kết các thông số của bộ truyền bánh răng...................................16
PHẦN IV: TÍNH TOÁN THIẾT KẾ TRỤC..................................................16
4.1 Chọn vật liệu chế tạo trục................................................................................17
4.1.1 Xác định lực và phân bố lực tác dụng lên trục.............................................17
4.1.2 Tính sơ bộ đường kính trục theo momen xoắn............................................18
4.2 Xác định khoảng cách giữa các điểm đặt lực.................................................18
4.3 Xác định đường kính các đoạn trục...............................................................20
4.4 Kiểm nghiệm trục............................................................................................25
4.4.1 Trục I...........................................................................................................25
4.4.2 Trục II..........................................................................................................27
PHẦN V: TÍNH TOÁN THIẾT KẾ THEN VÀ Ổ LĂN...............................28
5.1 Tính mối ghép then..........................................................................................28
5.2 Chọn ổ lăn và kiểm nghiệm ổ lăn....................................................................29
5.2.1 Trục I...........................................................................................................29
5.2.2 Trục II..........................................................................................................32
PHẦN VI: THIẾT KẾ KẾT CẤU VỎ VÀ CÁC CHI TIẾT PHỤ...............34
6.1 Tổng quan về vỏ hộp........................................................................................35
6.2 Thiết kế vỏ hộp.................................................................................................35
6.2.1 Chốt định vị.................................................................................................38
6.2.2 Cửa thăm.....................................................................................................38
6.2.3 Nút thông hơi...............................................................................................39
6.2.4 Nút tháo dầu................................................................................................39
6.2.5 Kiểm tra mức dầu........................................................................................40
6.3 Một số chi tiết phụ...........................................................................................40 lOMoARcPSD| 40651217
6.3.1 Các chi tiết lót bộ phận ổ.............................................................................40
PHẦN VII: DUNG SAI LẮP GHÉP VÀ BÔI TRƠN...................................42
7.1 Dung sai lắp ghép và lắp ghép ổ lăn...............................................................42
7.1.1 Lắp bánh răng lên trục.................................................................................43
7.1.2 Dung sai mối ghép then...............................................................................43
7.2 Bôi trơn hộp giảm tốc......................................................................................43
7.3 Bảng dung sai lắp ghép....................................................................................44
TÀI LIỆU THAM KHẢO................................................................................45 lOMoARcPSD| 40651217 LỜI MỞ ĐẦU
Đồ án môn học chi tiết máy với nội dung thiết kế hệ dẫn động cơ khí, cụ thể ở đây là
thiết kế hệ dẫn động băng tải, với hộp giảm tốc một cấp bánh răng côn với yêu cầu về
lực cũng như vận tốc và các đặc trưng khác.
Đồ án môn học chi tiết máy với bước đầu làm quen với công việc tính toán, thiết kế các
chi tiết máy trong lĩnh vực cơ khí nhằm nâng cao kỹ năng tính toán, hiểu sâu hơn về kiến thức đã học.
Nội dung đồ án môn học chi tiết máy bao gồm: Chọn động cơ.
Tính toán bộ truyền trong và bộ truyền ngoài.
Thiết kế trục và chọn ổ lăn.
Thiết kế vỏ hộp và bôi trơn.
Đồ án môn học chi tiết máy là tài liệu dùng để thiết kế chế tạo các hệ dẫn động cơ khí,
nhưng đây không phải là phương án tối ưu nhất trong thiết kế hệ dẫn động do những
hạn chế về hiểu biết và kinh nghiệm thực tế.
Em chân thành cảm ơn các thầy cô trong bộ môn và các bạn, đặc biệt là thầy ThS. Phạm
Thanh Tùng đã giúp đỡ em rất nhiều trong quá trình thực hiện đồ án môn học của mình.
Do đây là lần đầu em thiết kế nên việc mắc phải những thiếu sót trong bài thiết kế là
không tránh khỏi. Kính mong thầy cô và các bạn có những ý kiến phê bình, góp ý để
bài thiết kế của em được hoàn thiện hơn. Em xin chân thành cảm ơn !
Sinh viên thực hiện
Nguyễn Mạnh Cường
Khoa cơ khí – Trường Đại học Thủy Lợi 1 Downloaded by Phuong Le (lephuong0301@gmail.com) lOMoARcPSD| 40651217
Đồ án cơ sở thiết kế máy Thiết kế hệ thống dẫn động băng tải Đề 5.2: Động
cơ - bộ truyền đai - bộ truyền bánh răng côn răng thẳng – khớp nối - băng tải
Hệ thống băng tải gồm: 1. Động cơ điện 3 pha KĐBrotor lồng sóc. 2. Bộ truyền đai. 3.
Hộp giảm tốc bánh răng côn răng thẳng. 4. Nối trục đàn hồi. 5. Băng tải.
Số liệu thiết kế: Lực trên băng tải (N) 2950 Vận tốc băng tải (m/s) 1.36
Đường kính tang quay băng tải 220
Góc nghiêng đường nối tâm bộ truyền ngoài @ 135 (độ)
Thời gian phục vụ (năm) 2 1 năm làm việc (ngày) 290 Số ca làm việc (ca) 3 Thời gian 01 ca làm việc 8 (h) Đặc tính tải trọng Làm việc êm Môi trường làm việc Không bụi Điều kiện bôi trơn Đạt yêu cầu
PHẦN I: CHỌN ĐỘNG CƠ VÀ PHÂN PHỐI TỈ SỐ TRUYỀN 2
Downloaded by Phuong Le (lephuong0301@gmail.com) lOMoARcPSD| 40651217
Nguyễn Mạnh Cường, 61CĐT3 Đồ án cơ sở thiết kế máy
1.1 Chọn động cơ.
1.1.1 Xác định công suất động cơ.
- Công suất lớn nhất trong các công suất tác dụng lâu dài trên trục máy công tác:
F.v 2950.1,36 Plv=1000= 1000 =4,01( kW ) .
- Do tải trọng không thay đổi nên Pt=Plv = 4,01 (kW).
- Hiệu suất truyền động: ɳ = ɳ 3
ol .ɳđ.ɳbr.ɳkn=0,993 .0,95.0,96.0,99=0,87. Trong đó: +ɳ –
ol hiệu suất một cặp ổ lăn:ɳol = 0,99.
+ ɳđ – hiệu suất bộ truyền đai: ɳđ = 0,95.
+ɳbr – hiệu suất bộ truyền bánh răng: ɳbr = 0,96.
+ɳkn – hiệu suất khớp nối trục đàn hồi: ɳkn = 0,99.
(Trị số của hiệu suất được tra theo bảng 2.3[1]).
- Vậy công suất cần thiết trên trục động cơ là: Pt 4,01
Pct= ɳ =0,87=4,60 (kW ) (CT2.8/19[1]).
1.1.2 Xác định số vòng quay sơ bộ.
- Xác định số vòng quay của động cơ.
+ Vận tốc của băng tải: v = 1,36 (m/s).
+ Đường kính tang quay băng tải 220 mm. 60000.v 60000.1,36
nlv= π . D = π.220 =¿118,06 (vòng/phút).
+ Tỉ số truyền của bộ truyền trong: ubr = 4.
+ Tỉ số truyền của bộ truyền ngoài: uđ = 3.
U sb=ubr .uđ=4.3=12.
nsb=nlv .Usb=118,06.12=1416,7 (vòng/phút). lOMoARcPSD| 40651217
Nguyễn Mạnh Cường, 61CĐT3 Đồ án cơ sở thiết kế máy 1.1.3 Chọn động cơ.
Tra bảng P.1.3 ta có động cơ điện. Kiểu động cơ Pđc (kW) Nđc (vòng/phút) 4A112M4Y3 5,5 1425
1.2 Lập bảng thông số kỹ thuật.
1.2.1 Xác định tỉ số truyền của hệ dẫn động theo công thức 3.23/48[1]. Nđc 1425 Ut= nlv =118,06=12,07. Với: N – –
đc số vòng quay của động cơ đã chọn (vòng/phút). nlv
số vòng quay của trục máy công tác (vòng/phút).
1.2.2 Phân phối tỉ số truyền của hệ dẫn động (Ut ¿ cho các bộ truyền theo công thức 3.24[1] ta có: - Ut=12,07.
- Có Uhgt = ubr = 4 (hộp giảm tốc 1 cấp). Ut 12,07
- Tính lại tỉ số truyền bộ truyền đai: uđ = = =3,01. ubr 4
1.2.3 Xác định công suất, mômen xoắn và số vòng quay các trục.
- Công suất trục III: PIII=Plv=4.01(kW). Plv 4,01
- Công suất trục II: PII=
ɳol .ɳkn =0,99.0,99=4,09 (kW ) . PII 4,09
- Công suất trục I: PI=
ɳol.ɳbr =0,99.0,96=4,30( kW ) . PI 4,30
- Công suất thực của động cơ: Pđc=
ɳol.ɳđ =0,99.0,95=4.57(kW). Nđc 1425
- Số vòng quay trục I: nI=
uđ = 3,01 =473,42 (vòng/phút). lOMoARcPSD| 40651217
Nguyễn Mạnh Cường, 61CĐT3 Đồ án cơ sở thiết kế máy nI 473.42
- Số vòng quay trục II: nII= ubr = 4 =118,35 (vòng/phút).
- Số vòng quay trục làm việc: nlv=nII=118,35 (vòng/phút). 9,55.106 . Pi
* Mômen xoắn trên các trục: T i= ni . 9,55.106 .Pđc 9,55.106.4,57 -
Mômen xoắn thực trên động cơ: T đc= nđc = 1425 =30627,01 (N.mm). 9,55.106 .PI 9,55.106.4,30 -
Mômen xoắn trên trục I: T I= nI = 473,42 =86741,16 (N.mm). 9,55.106 . PII 9,55.106 .4,09 -
Mômen xoắn trên trục II: T II= nII = 118,35 =330033,79 (N.mm). 9,55.106 .Plv 9,55.106 .4,01 -
Mômen xoắn trên trục làm việc: T lv= nlv = 118,35 =¿323578,36 (N.mm). -
Ta có bảng thông số kỹ thuật: Thông số/Trục Động cơ I II Làm việc Tỉ số truyền u 3,01 4 1 Số vòng quay n(vòng/phút) 1425 473,42 118,35 118,35 Công suất P(kW) 4,57 4,30 4,09 4,01 lOMoARcPSD| 40651217
Nguyễn Mạnh Cường, 61CĐT3 Đồ án cơ sở thiết kế máy Mômen xoắn T(N.mm) 30627,01 86741,16 330033,7 9 323578,36
PHẦN II: TÍNH TOÁN THIẾT KẾ BỘ TRUYỀN ĐAI THANG
2.1 Chọn tiết diện đai.
- Thông số đầu vào bộ truyền ngoài: Pđc=4,57 (kW).
Nđc=1425 (vòng/phút).
T đc=¿30358,94 (N.mm).
- Chọn tiết diện đai hình thang loại: A
2.2 Chọn đường kính đai.
- Đường kính bánh đai nhỏ d1= 140 (mm) (bảng 4.13/59[1]). π .d1 .n1 π.140.1425 (m/s) < vmax=25 (m/s).
- Vận tốc đai: v == =10,44 60000 60000
→ Thỏa mãn điều kiện: v < vmax. - Đường kính bánh đai:
d2 =uđ.d1.(1 – ε) = 3,01.140.(1 – 0,02) = 412,97 (mm).
→ Chọn d2 = 400 (mm). - Tính
toán tỉ số truyền thực tế: d2 400 utt=
d1 .(1 –
ε)=140.(1– 0,02)=2,91 - Kiểm tra sai lệch tỉ số truyền: ∆ uđ|
u=|uttu−đ
.100%=|2,913,−013,01|.100%=3,32%<4 %.
→ d2 thỏa mãn điều kiện ∆u ≤ 4%.
2.3 Xác định sơ bộ khoảng cách trục a.
- Theo bảng 4.14 chọn sơ bộ khoảng cách trục. lOMoARcPSD| 40651217
Nguyễn Mạnh Cường, 61CĐT3 Đồ án cơ sở thiết kế máy asb asb=1.400=400 (mm). - =1 => d2 - Chiều dài đai: ) L = 2.a 2 sb+
π .(d21+d2)+(d4.2−adsb1 =2.400+π
.(1402+400)+(4004.400−140)2 =1690,48 (mm).
- Theo bảng 4.13/59[1] chọn chiều dài đai tiêu chuẩn: L = 1600 (mm). v
- Kiểm tra số vòng chạy: i = L= 1,6 = max= (vòng/giây).
2.4 Xác định chính xác khoảng cách trục. - Xác định: a = (mm). - Trong đó: 𝜆 = L (mm). (mm).
- Góc ôm trên bánh đai nhỏ: ) α1=180°−
57°.(da2−d1 =180°−
351,86 =137,88°>120°.
→ Góc ôm thỏa mãn.
2.5 Xác định số đai. P1 .K đ z = (CT4.16/60[1]).
[P0].Cα .CL.Cu .Cz Trong đó:
+ P1=4,57: công suất trên trục bánh đai chủ động (kW).
+ [P0 ¿: công suất cho phép từ bảng 4.19[1] Trang 62 bằng nội suy chọn [P¿¿0]=2.20¿ (kW).
+ Kđ: hệ số tải trọng động từ bảng 4.7 Trang 55 và số ca làm việc là 3 => Kđ=1,3. lOMoARcPSD| 40651217
Nguyễn Mạnh Cường, 61CĐT3 Đồ án cơ sở thiết kế máy
+ Cα: hệ số ảnh hưởng của góc ôm α1 với α1=137,88° tra bảng 4.15[1] => Cα=0,89.
+ Cu: hệ số ảnh hưởng của tỉ số truyền 4.17[1] Trang 61 => Cu=1,14. L 1600
+ CL=1: hệ số ảnh hưởng của chiều dài đai từ bảng 4.17[1](T61) với L0=1700=0,94. P1 4,57
+ C : hệ số kể đến sự phân bố không đều tải trọng giữa các dây đai, do z = =2,07 P0 2,20
Tra bảng 4.18[1] Trang 61 => Cz=0,95.
* Từ các thông số đã chọn thay vào công thức tính z, ta được: 4,57.1,3 z = 2,20.0,89.1.1,14.0,95=2,80. → Chọn z = 3.
2.6 Xác định các thông số cơ bản của bánh đai. -
Tra bảng 4.21[1] trang 63 được: h0=3,3 (mm). t
= 15 (mm). e = 10 (mm). H = 12,5 (mm). φ = 36°. -
Từ số đai z có thể xác định chiều rộng bánh đai B theo công thức:
B = (z – 1).t + 2.e = (3 – 1).15 + 2.10 = 50 (mm). -
Đường kính ngoài của bánh đai.
da1=d1+2.h0=140+2.3,3=146,6 (mm). da2=d2+2.h0=400+2.3,3=406,6 (mm). -
Đường kính đáy bánh đai.
df 1=da1−2. H=146,6−2.12,5=121,6 (mm). df
2=da2−2. H=406,6−2.12,5=381,6 (mm).
2.7 Xác định lực căng ban đầu và lực tác dụng lên các trục. -
Lực căng đai: Fv=qm .v2=0,105.10,442=11,44 (N).
Trong đó qm = 0,105 (kg/m): khối lượng 1m chiều dài đai, bảng 4.22[1]. - Lực căng ban đầu. lOMoARcPSD| 40651217
Nguyễn Mạnh Cường, 61CĐT3 Đồ án cơ sở thiết kế máy 780.P1 .K đ 780.4,57.1,3 F0=
v.Cα . z+Fv=10,44.0,89.3 +11,44=177,68 (N). -
Lực tác dụng lên trục bánh đai. α1 F )
r=2. F0. z.sin( 2 =2.177,68.3.sin( )=994,27 (N).
PHẦN III: TÍNH TOÁN BỘ TRUYỀN BÁNH RĂNG CÔN RĂNG THẲNG
3.1 Chọn vật liệu bánh răng. Tra bảng 6.1, ta chọn: -
Vật liệu bánh răng lớn. + Nhãn hiệu thép: C45. + Tôi cải thiện.
+ Độ rắn: HB2 = 230.
+ Giới hạn bền: σ b2 = 750 (MPa).
+ Giới hạn chảy: σ ch2= 450 (MPa). -
Vật liệu bánh răng nhỏ. + Nhãn hiệu thép: C45. + Tôi cải thiện.
+ Độ rắn: HB1 = 245.
+ Giới hạn bền: σ b1 = 850 (MPa).
+ Giới hạn chảy: σ ch1 = 580 (MPa).
3.2 Xác định ứng suất sơ bộ cho phép. ¿
Trong đó chọn sơ bộ: {ZYRR.Z.YVS . K.K xHxF==1.1. lOMoARcPSD| 40651217
Nguyễn Mạnh Cường, 61CĐT3 Đồ án cơ sở thiết kế máy
SH,SF – Hệ số an toàn khi tính về ứng suất tiếp xúc và ứng suất uốn.
Tra bảng 6.2 trang 94[1] với: -
Bánh răng chủ động: SH1=1,1 → SF1=1,75. - Bánh răng bị động: SH 2=1,1 → SF2=1,75. σ σ
H lim ¿0¿, F lim ¿0¿- Ứng suất tiếp xúc và uốn cho phép ứng với số chu kỳ cơ sở.
¿ ⇒ - Bánh chủ động: ¿ - bánh bị động: ¿ Ta có: N ,4
H 01=30. HB21 =30.2452,4=1,6.107 . N ,4
H 02=30. HB22 =30.2302,4=1,39.107 .
NF 01=NF 02=4.106 -
N HE1=60.c.n1 .tΣ=60.1.473,42.13920=3,95.107. -
N HE2=60.c.n2 .tΣ=60.1.118.35.13920=9,88.107. -
N FE1=NHE1=3,95.107 . -
N FE2=NHE 2=9,88.107. ⇒ Ta có:
• N HE1>N H 01⇒K HL1=1.
• N HE2>N H 02⇒K HL2=1.
• N FE1>N F01 ⇒KFL 1=1. N FE2>N F02 ⇒KFL 2=1. Do vậy ta có: σ0H lim 1 560 lOMoARcPSD| 40651217
Nguyễn Mạnh Cường, 61CĐT3 Đồ án cơ sở thiết kế máy [σ H 1]=
SH 1 .ZR .ZV . K xH. K HL1= 1,1 .1.1=509,09 ( MPa) . 0 σH lim 2 530 [σ H 2]=
SH 2 .ZR .ZV . KxH . K HL2= 1,1 .1.1=481,82 ( MPa) . σ F0 lim 1 441
{[ σ F1]= SF 1 .Y R .Y S .K xF .K FL1=1,75 .1.1=252 ( MPa) . σ0F lim 2 414 [σ F2]=
SF 2 .Y R .Y S .K xF. K FL2=1,75 .1.1=236,57 ( MPa) . -
Do đây là bộ truyền bánh răng côn răng thẳng. ⇒σH=min¿¿.
3.3 Xác định sơ bộ chiều dài côn ngoài bộ truyền bánh răng côn. 1T . K
Re=K R .√u +1.¿
Kbe .(1−K be).u.¿¿
K R – Hệ số phụ thuộc vật liệu làm bánh răng và loại răng: Đối với bộ truyền bánh răng
côn răng thẳng làm bằng thép ⇒ K R=50(MPa)1/3.
T 1 – Mômen xoắn trên trục chủ động: T 1=86741,16 ( N .mm ).
[σ H ] - Ứng suất tiếp xúc cho phép: [σ H ]=481,82( MPa
). u – Tỉ số truyền: u = 4.
Kbe – Hệ số chiều rộng vành răng: chọn sơ bộ Kbe=0,25. K be .u ⇒ =0,57. 2−Kbe 1 3 T . K
Re=K R .√u +1.¿
Kbe .(1−K be).u.¿¿ lOMoARcPSD| 40651217
Nguyễn Mạnh Cường, 61CĐT3 Đồ án cơ sở thiết kế máy
K Hβ,K Fβ – Hệ số kể đến sự phân bố không đều tải trọng trên hiều rộng vành răng khi
tính về ứng xuất tiếp xúc và uốn: tra bảng 6.21 trang 133[1] với: tra bảng 6.21 với sơ đồ
1 trục lắp trên ổ đũa HB < 350 ⇒ K Hβ=1,13. Do vậy: =
3.4 Xác định các thông số ăn khớp.
3.4.1 Xác định mô đun vòng ngoài và vòng trung bìnhmte ,mtm.
- Đường kính vòng chia ngoài: de
Tra bảng 6.22 trang 114[1] với de 1=82,56(mm) và tỉ số truyền u = 4 ta được số răng Z1 p=17.
Ta có: với HB < 350 ⇒ Z1=1,6.Z1p=1,6.17=27,2. dm1=¿.Kbe ¿.de
1=(1−0,5.0,25 ).82,56=72,24 (mm). dm1 72,24 mtm=
Z1 = 27,2 =2,65 (mm) . mtm 2,65 mte= 1−0,5.Kbe
=1−0,5.0,25=3,02 (mm) .
Tra bảng 6.8 chọn me tiêu chuẩn: mte=3( mm) . mtm=mte
.¿.Kbe ¿=3. (1−0,5.0,25)=2,63( mm). dm1 72,24
Z1=mtm = 2,63 =27 (răng ) .
⇒ Z2=u.Z1=4.27=108 (răng ). - Tỉ số truyền thực. Z2 108 ut= Z1 = 27 =4 lOMoARcPSD| 40651217
Nguyễn Mạnh Cường, 61CĐT3 Đồ án cơ sở thiết kế máy
- Kiểm tra sai lệch tỉ số truyền. ∆u=|
ut−u u|=|4−4 4|=0<4%. - Góc côn chia. Z1 δ ) 1=arctg( Z2 =arctg( )=14°.
δ2=90°−δ1=90°−14°=76°.
Với u = 4; Z1= 27 răng ⇒ tra bảng 6.20 ⇒x1=0,33;x2=−0,33.
- Đường kính trung bình.
dm1=mtm .Z1=2,63.27=71,01(mm ). dm2=mtm
.Z2=2,63.108=284,04 (mm) . - Chiều dài côn ngoài. mte Re . .
3.4.2 Xác định chính xác ứng suất cho phép.
- Vận tốc vòng của bánh răng:
π .dm1 .n1 π.71,01.473,42 v = =
=1,76(m/s). 60000 60000
[σ H ¿=[σ H]sb. ZR .ZV .K xH Trong đó:
+ [σ H ¿=481,82Mpa.
+ Độ nhám 1,25…0,63 → ZR=1.
+ HB ≤350,v<5m/s→ZV =1. + K xH=1. lOMoARcPSD| 40651217
Nguyễn Mạnh Cường, 61CĐT3 Đồ án cơ sở thiết kế máy
→[σ H ¿=481,82( MPa ).
[σ F1 ¿=[σ F]1sb .Y R .Y S . KxF Trong đó:
+ [σ F]1sb=252 MPa. +Y R=1. + Y S=1.
→ [σ F1 ¿=252MPa, tương tự như thế ta được [σ F2 ¿=236,57 MPa.
3.5 Kiểm nghiệm bộ truyền bánh răng.
3.5.1 Kiểm nghiệm độ bền tiếp xúc.
Do bánh răng làm việc trong điều kiện bôi trơn tốt nên dạng hỏng chủ yếu là tróc rỗ =>
kiểm nghiệm bánh răng theo độ bền uốn. σ H=ZM .Z H .Z .
[σ H ] - Ứng suất tiếp xúc cho phép.
ZM – Hệ số kể đến cơ tính vật liệu của các bánh răng ăn khớp: Tra bảng 6.5 Trang 96[1].
=> ZM=274(MPa)1/3.
ZH – Hệ số kể đến hình dạng hình học của bề mặt tiếp xúc: Tra bảng 6.12 Trang 106[1]
với x1+¿ x2 = 0 và β = 0° ta được: ZH=1,76.
Zε – Hệ số trùng khớp của răng: Z ,Với:
εα – Hệ số trùng khớp ngang: ⇒ Z - Chiều rộng vành răng.
b = Kbe . Re=0,25.166,98=41,74.
K H – Hệ số tải trọng khi tính về tiếp xúc. lOMoARcPSD| 40651217
Nguyễn Mạnh Cường, 61CĐT3 Đồ án cơ sở thiết kế máy
K H=K Hα . KHβ . K Hv K .u 0,25.4 ⇒K Hβ=1,13. Tra bảng 6.21 với: 2−Kbe 2−0,25
- Bánh răng côn thẳng ⇒ K Hα=1. V H .
Với v = 1,76 (m/s), chọn cấp chính xác 8. + δH =0,004. + g0=56. V H .b.dm1 ⇒ K Hv=1+
2.T 1. KHβ . K Hα =1+ 2.86741,16.1,13.1=1,05.
⇒ K H=1.1,13.1,05=1,18. Vậy ta có: σ H=ZM .Z H .Z
¿455,64 (MPa ).
⇒ σ H=455,64≤[σ¿¿ H]=481,82(MPa).¿
[σ¿¿H ]−σ H ⇒ 481,82−455,64 ¿
[σ¿¿ H]5,43%<10%.¿
⇒ Vậy vật liệu làm răng thỏa mãn về độ bền tiếp xúc.
3.5.2 Kiểm nghiệm độ bền uốn.
2.T 1. K F .Y ε .Y β .Y F 1
σ F= 0,85.b.dm1 .mtm Trong đó: lOMoARcPSD| 40651217
Nguyễn Mạnh Cường, 61CĐT3 Đồ án cơ sở thiết kế máy
K F=K Fα . K Fβ. K Fv K be .u 0,25.4 =
=0,57⇒K Fβ=1,25. 2−Kbe 2−0,25
Với v = 1,76 (m/s) tra bảng 6.14 trang 107[1] ⇒ cấp chính xác 8 ⇒ K Fα=1,22.
V F=δF .g0. v.dm1.
u+1 u Với v = 1,76 (m/s), chọn cấp chính xác 8. + δF=0,011. + g0=56. ⇒ V F . ⇒ K . Fv
2.T1 . KFβ . KFα 2.86741,16.1,25.1,22
⇒ K F=K Fα . K Fβ. K Fv=1,22.1,25.1,11=1,69.
Y ε=εα =1,73=0,58. β 0
Y β=1−140°=1−140°=1. Z1 27
⇒trabảng6.18trang109 [1 ] ⇒Y F1=3,54. = = ZV
1 cosδ1 cos14°=27,82 Z1 27
⇒trabảng6.18trang109 [ 1] ⇒Y F2=3,63. = = ZV
2 cosδ2 cos76°=446,42
2.T1 . KF .Y ε .Y β .Y F1 2.86741,16.1,69.0,58.1.3,54 σ F1=
0,85.b.dm1 .mtm = 0,85.41,74.71,01.2,63 =90,85 ( MPa) .
⇒ σ F1=90,85(MPa)<[σ ¿¿F 1]=252 ( MPa) .¿ σF 1.Y F 2 90,85.3,63 lOMoARcPSD| 40651217
Nguyễn Mạnh Cường, 61CĐT3 Đồ án cơ sở thiết kế máy σ F2= Y F1 = 3,54 =93,15 (MPa
)<[σ¿¿F2]=236,57 ( MPa) .¿
⇒ Vậy vật liệu làm răng thỏa mãn điều kiện về độ bền uốn.
3.6 Xác định các thông số khác.
- Đường kính vòng chia ngoài.
de 1=mte .Z1=3.27=81 (mm). de
2=mte .Z2=3.108=324 (mm).
- Chiều cao đầu răng ngoài.
hae1=(h¿¿te+x1.cosβ).mte=(cosβ+0,33.cosβ ).3=3,99¿ (mm).
hae2=(h¿¿te+x2.cosβ).mte=(cosβ−0,33.cosβ ) .3=2,01¿ (mm).
- Chiều cao chân răng ngoài.
hfe1=he−hae1=2,2.mte−3,99=2,61 (mm).
hfe2=he−hae2=2,2.mte−2,01=4,59 (mm).
- Đường kính đỉnh răng ngoài.
dae 1=de1+2.hae 1.cosδ1=81+2.3,99.cos14°=88.74 (mm). dae 2=de
2+2.hae2.cos δ2=324+2.2,01.cos76°=324,97 (mm).
- Lực ăn khớp trong bộ truyền bánh răng côn. 2.T 1 2.86741,16 Ft1=Ft2= dm1 = 71,01 =2443,06 (N).
Fr1=Fa2=Ft 1. tan20°.cos δ1=2443,06.tan20°.cos14°=862,78 (N).
Fa1=Fr 2=Ft 1. tan20°.sin δ1=2443,06.tan20°.sin14°=215.11 (N).
3.7 Bảng tổng kết các thông số của bộ truyền bánh răng. Thông số Ký hiệu Giá trị lOMoARcPSD| 40651217
Nguyễn Mạnh Cường, 61CĐT3 Đồ án cơ sở thiết kế máy Chiều dài côn ngoài Re 166,98 (mm) Mô đun vòng ngoài mte 3 Chiều rộng vành răng b 41,74 (mm) Tỉ số truyền ut 4 Góc nghiêng của răng β 0° Z1 27 Số răng của bánh răng Z2 108 x1 0,33
Hệ số dịch chỉnh chiều cao x2 - 0,33 δ1 14° Góc côn chia δ2 76° Chiều cao răng ngoài he 6,6 (mm) hae1 3,99 (mm)
Chiều cao đầu răng ngoài hae2 2,01 (mm) hfe1 2,61 (mm)
Chiều cao chân răng ngoài hfe2 4,59 (mm) de 1 81 (mm)
Đường kính vòng chia ngoài de 2 324 (mm)
Đường kính đỉnh răng ngoài dae 1 88,74 (mm) 324,97 (mm) dae 2
PHẦN IV: TÍNH TOÁN THIẾT KẾ TRỤC
* Tổng quan về tính toán thiết kế trục. -
Trục để đỡ các chi tiết quay bao gồm trục tâm và trục truyền. Trục tâm có thể quay
cùng với các chia tiết lắp trên nó hoặc không quay chỉ chịu được lực ngang và momen uốn. -
Trục truyền luôn quay có thể tiếp nhận đồng thời cả momen uốn và momen xoắn.
Các trục trong hộp giảm tốc là những trục truyền. -
Chỉ tiêu quan trong nhất phần lớn với các trục là độ bền, ngoài ra còn có độ cứng
vàđối với trục quanh nhanh là độ ổn định dao động. [1-182].
Tính toán trục bao gồm các bước sau đây: + Chọn vật liệu.
+ Tính thiết kế trục về độ bền. lOMoARcPSD| 40651217
Nguyễn Mạnh Cường, 61CĐT3 Đồ án cơ sở thiết kế máy
+ Tính kiểm nghiệm trục về độ bền mỏi.
+ Trường hợp cần thiết thì kiểm nghiệm trục về độ cứng, trục quay nhanh kiểm nghiệm
về độ ổn định dao động.
4.1 Chọn vật liệu chế tạo trục. -
Chọn vật liệu chế tạo các trục là thép 45 có σ b=600(MPa), có ứng suất xoắn cho
phép [ τ ]=12÷20(MPa).
4.1.1 Xác định lực và phân bố lực tác dụng lên trục.
* Khớp nối: Khớp nối đàn hồi, chi tiết tiêu chuẩn, dựa vào momen xoắn tính toán.
- Momen xoắn trên khớp nối. T t=k .T
+ Tra bảng 16.1/58[2] ta có: k=1,2÷1,5 đối với băng tải Chọn k=1,5.
⇒ T t=k .T=1,5.330033,79=495050,68 ( N .mm )=495,05(N .m).
+ T t<[ T ]=1000 (N .m), với [T] = 1000 (N.m).
- Tra bảng 16.10a/68[2], ta có:
Dt=D0=130(mm)
- Lực vòng trên khớp nối. 2.T 2.330033,79 Ft= Dt = 130 =5077,44(N)
- Lực hướng tâm tác dụng lên trục.
Fkn=0,3. Ft=0,3.5077,44=1523,23 ( N ) .
* Bộ truyền bánh răng côn thẳng. - Ta có lực vòng: 2.T 1
2.86741,16 Ft1=Ft2= dm1 = 71,01 =2443,06 (N). lOMoARcPSD| 40651217
Nguyễn Mạnh Cường, 61CĐT3 Đồ án cơ sở thiết kế máy
- Lực hướng tâm và lực dọc trục.
Fr1=Fa2=Ft 1. tan20°.cos δ1=2443,06.tan20°.cos14°=862,78 (N).
Fa1=Fr 2=Ft 1. tan20°.sin δ1=2443,06.tan20°.sin14°=215,11 (N). * Bộ truyền đai. α1 F )
r=2. F0. z.sin( 2 =2.177,68.3.sin( )=994,27 (N).
4.1.2 Tính sơ bộ đường kính trục theo momen xoắn.
- Tra bảng P1.7/242[1] với động cơ 4A112M4Y3 ta có: ddc=32(mm).
Theo công thức 10.9 trang 188[1], ta có: - Đường
kính trục xác định chỉ bằng momen xoắn. d
⇒ Chọn d1sb=30(mm ). d
⇒ Chọn d2sb=45 (mm) .
- Chiều rộng ổ lăn trên trục, tra bảng 10.2/189[1].
Với {dd12sbsb==3045((mmmm)) ⇒ {bb0201==2519 ((mmmm ))..
4.2 Xác định khoảng cách giữa các điểm đặt lực.
* Xác định chiều dài may ơ.
- May ơ bánh đai: lm12=(1,2…1,5 ).d1=36÷45(mm).
⇒ Chọn lm12=45 (mm ).
- May ơ bánh răng côn nhỏ: lm13=(1,2…1,4) .d1=36÷42(mm).
⇒ Chọn lm13=40( mm). lOMoARcPSD| 40651217
Nguyễn Mạnh Cường, 61CĐT3 Đồ án cơ sở thiết kế máy
- May ơ nối trục đàn hồi: lm22=(1,4…2,5) .d2=63÷112,5(mm).
⇒ Chọn lm22=70 (mm) .
- May ơ bánh răng côn lớn: lm23=(1,2…1,4) .d2=54÷63 (mm) .
⇒ Chọn lm23=55 (mm) .
* Xác định khoảng cách giữa các điểm đặt lực và chiều dài đoạn trục: Trong đó: -
k: số thứ tự trục trong hộp giảm tốc, k = 1…2 (hộp giảm tốc 1 cấp ). -
i: số thứ tự của tiết diện trục lắp các chi tiết tham gia truyền tải trọng.
• i = 0 và 1 các tiết diện trục lắp ổ.
• i = 2…s, với s là số chi tiết quay. -
lkl – Khoảng cách giữa các gối đỡ 0 và 1 trên trục thứ k. -
lki – Khoảng cách từ gối đỡ 0 đến tiết diện thứ i trên trục k. -
lmki – Chiều dài may ơ của chi tiết quay thứ i lắp trên trục k. -
lkci – Khoảng công xon trên trục k, tính từ chi tiết thứ i ở ngoài hộp giảm tốc đến
gối đỡ: lcki=0,5. (lmki+b0)+k3+hn. lOMoARcPSD| 40651217
Nguyễn Mạnh Cường, 61CĐT3 Đồ án cơ sở thiết kế máy -
bki – Chiều rộng bánh răng thứ i trên trục thứ k.
Tra bảng 10.3/189[1], ta được:
⇒ Chọn k1=10 (mm) ,k2=5 (mm) ,k3=10 (mm ),hn=15 (mm) . * Trục I.
l12=0,5. (lm12+b01)+k3+hn=0,5.( 45+19)+10+15=57 (mm) . l11=(2,5÷3
).d1=(2,5÷3) .30=75÷90 (mm) ⇒chọnl11=75(mm) .
l13=l11+k1+k2+lm13+0,5.(b01−b13 .cosδ1)=75+10+5+40+0,5. (19−41,74.cos14 )=119,24 (mm) ⇒ Chọn l13=120 (mm). * Trục II.
lc 22=0,5.(b02+lm22)+hn+k3=0,5.(25+70 )+15+10=72,5 (mm) .
l22=0,5. (lm22+b02)+k1+k2=0,5.(70+25 )+10+5=62,5 (mm ). ⇒ Chọn l22=63(mm).
l21=2.l22+dm1=2.63+71,01=197,01⇒Chọnl21=198(mm)
4.3 Xác định đường kính các đoạn trục. * Trục I. - Sơ đồ đặt lực: - Tính lực:
Frx=Fr .cos (180−@)=994,27.cos (180−135)=703,05(N .mm)
Fry=Fr .sin (180−@)=994,27.sin (180−135)=703,05(N .mm) ΣFxΣFy==0
FFryrx−+FFAxAy−+FFByBx−+FFtr11==00 0 lOMoARcPSD| 40651217
Nguyễn Mạnh Cường, 61CĐT3 Đồ án cơ sở thiết kế máy { ΣMBy =0⇒
Frx . (57+75 )+F Ax . (75)−Ft1 . (45)=( 0 ) ΣMBx =0
Fry .(57+75 )−F Ay. (75)+Fr1. ( 45)−Fa1. dm1 =0 2
703,05+F Ax−FBx+2443,06=0
703,05−F Ay+F By−862,78=0
703,05. (57+75)+F Ax .75−2443,06.45=0 71,01 703,05.(57+75
)−F Ay.75+862,78.45−215,11.( 2 )=0 FBx=3374,57(N)
⇒FBy=1812,93(N)
{ FAx=228,46 ( N ) FAy=1653,20(N)
- Biểu đồ nội lực trục I. lOMoARcPSD| 40651217
Nguyễn Mạnh Cường, 61CĐT3 Đồ án cơ sở thiết kế máy
- Tính Mtđ tại các vị trí mặt cắt.
Mtđ=√M x2+M y2+0,75.T z2 MtđO ( N .mm) . MtđA ( N .mm) . MtđB ( N .mm ). MtđC (N .mm) .
- Xác định kích thước các đoạn trục. d
Tra bảng 10.5/195[1] ta có: với thép 45 tôi cải thiện, σ=600 ( MPa)⇒ [σ ¿=63 (MPa). lOMoARcPSD| 40651217
Nguyễn Mạnh Cường, 61CĐT3 Đồ án cơ sở thiết kế máy dO
⇒ChọndO=25 (mm) . d A
⇒Chọnd A=30( mm) . d B
⇒ChọndB=30 (mm) . dC
⇒Chọndc=25 (mm ). - Mô phỏng trục I. * Trục II. - Sơ đồ đặt lực. - Tính lực.
ΣFyΣFx==00 FknF+EyF−ExF−r2F−t 2F+GyF=Gx0=0 lOMoARcPSD| 40651217
Nguyễn Mạnh Cường, 61CĐT3 Đồ án cơ sở thiết kế máy { ( ΣM Ey=0⇒
Fkn .(72,5)−Ft2 .(63 )+) FGx.
(198)=0 ΣM Ex=0 −Fr2. (63 )+Fa2 . dm2 −FGy. (198)=0 2
1523,23+FEx−2443,06+FGx=0 FEy−215,11−FGy=0
1523,23. (72,5)−2443,06.63+FGX . (198)=0 −215,11.(63 )+862,78.( )−FGy. (198)=0 FEx=700,25(N)
⇒FEy=765,51(N)
{F Gx=219,58 ( N ) FGy=550,40(N)
- Biểu đồ nội lực trục II. lOMoARcPSD| 40651217
Nguyễn Mạnh Cường, 61CĐT3 Đồ án cơ sở thiết kế máy
- Tính Mtđ tại các vị trí mặt cắt.
Mtđ=√M x2+M y2+0,75.T z2 MtđD ( N .mm) . MtđE ( N .mm ). MtđH (N .mm) .
MtđG=0 ( N .mm) .
- Xác định kích thước các đoạn trục. d lOMoARcPSD| 40651217
Nguyễn Mạnh Cường, 61CĐT3 Đồ án cơ sở thiết kế máy
Tra bảng 10.5/195[1] ta có: với thép 45 tôi cải thiện, σ=600 ( MPa)⇒ [σ ¿=63 (MPa). d D
⇒ChọndO=36 (mm ). d E
⇒Chọnd A=40( mm). d H
⇒ChọndB=45 (mm) .
dG=40 (mm ). - Mô phỏng trục II.
4.4 Kiểm nghiệm trục.
Kết cấu trục vừa thiết kế đảm bảo được độ bền mỏi yêu cầu nếu hệ số an toàn tại các chi
tiết nguy hiểm thỏa mãn điều kiện sau:
- Với vật liệu là thép 45 tôi cải thiện có σ b=600 MPa.
σ−1=0,436.σb=0,436.600=261.6(MPa)
τ−1=0,58.σ−1=0,58.261,6=151,72(MPa) 4.4.1 Trục I.
- Tại vị trí lắp bánh răng. S .S SC2 SτC
Trong đó [S]: hệ số an toàn cho phép, thông thường [S] = 1,5…2,5. Với: σ−1
SσC=k τdC .σaC+ψσ .σmC τ−1 lOMoARcPSD| 40651217
Nguyễn Mạnh Cường, 61CĐT3 Đồ án cơ sở thiết kế máy
SτC=k τdC.τ aC+ψ τ .τmC MC T σ mC=0;σ aC=
WC ;τmC 2.W oC . Trong đó: Mc N .mm.
T C=T 1=86741,16 N .mm.
Tra bảng 10.7[1] trang 197 → ψσ=0,05;ψτ=0 MPa. π .d3C
b.t1.(dC−t1)2 π .253 8.4. (25−4)2 WC= 32 − 2.dC = 32 − 50 =1251,74 N .mm
π .d3C b.t1.(dC−t 1)2 π .253 8.4. (25−4)2 WoC = 16 − 2.dC = 16 − 50 =2785,72 N.mm MC 75507,32 σ aC= WC = 1251,74 =60,32. T C 86741,16 τ mC=τ aC=
2.WoC =2.2785,72=15,56. Kσ K τ +K −1 +K −1 εσ x ετ x KσdD= K y ;KτdD= K y
Trong đó: tra bảng 10.8[1] trang 197.
- Tiện Ra 2,5…0,63; σ b=600 MPa ⇒ K x=1,06.
Tra bảng 10.9[1] trang 197 ⇒ K y=1,7.
Tra bảng 10.10[1] trang 198 ⇒ εσ=0,88; ετ=0,81.
Tra bảng 10.12[1] trang 199 ⇒ Kσ=1,76; Kτ=1,54. lOMoARcPSD| 40651217
Nguyễn Mạnh Cường, 61CĐT3 Đồ án cơ sở thiết kế máy Kσ 1,76 +K −1 +1,06−1 εσ x 0,88 KσdD= K y = 1,7 =1,21 K KτdD →S σC
kτdC .σ aC+ψσ .σmC 1,21.60,32+0,05.0 →S τC
kτdC .τaC+ψτ .τmC 1,15.15,56+0.15,56 SσC .SτC 3,58.8,47 ⇒SC 3,29 S 2,5 4.4.2 Trục II.
- Tại vị trí lắp bánh răng. SσH .SτH SH 2 2 S Với: σ−1
SσH=kτdH .σ aH+ψσ .σmH τ−1
SτH=kτdH .τaH +ψτ .τmH M H
T H σ mH=0;σ aH= W H ;τmH=τaH= 2.W oH . Trong đó: MH N .mm
T H=T 2=330033,79 N .mm.
Tra bảng 10.7[1] trang 197 ⇒ ψσ=0,05;ψτ=0 MPa. lOMoARcPSD| 40651217
Nguyễn Mạnh Cường, 61CĐT3 Đồ án cơ sở thiết kế máy π .d3 b.t1
.(dH −t1)2 π .453 14.5,5.( 45−5,5)2 W H 32 2.d H 32 90 N .mm π .d3H
b.t1.(dH−t1)2 π .453 14.5,5. (45−5,5)2 WoH= 16 − 2.dH = 16 − 90 =16557,47N .mm
M H 255113,35 σ aH= WH = 7611,29 =33,51. T H 330033.79 τ mH=τaH=
2.WoH =2.16557,47=9,96. K σ Kτ +K −1 +K −1 εσ x ετ x KσdH= K y ;KτdH= K y
Trong đó: tra bảng 10.8[1] trang 197.
- Tiện Ra 2,5…0,63; σ b=600 MPa ⇒ K x=1,06.
Tra bảng 10.9[1] trang 197 ⇒ K y=1,7.
Tra bảng 10.10[1] trang 198 ⇒ εσ=0,85; ετ=0,78.
Tra bảng 10.12[1] trang 199 ⇒ Kσ=1,76; Kτ=1,54.
K σ +K −1 1,76+1,06−1 εσ x 0,85 KσdH= K y = 1,7 =1,25 K KτdH →S σH
kτdH .σaH +ψσ .σ mH 1,25.33,51+0,05.0 lOMoARcPSD| 40651217
Nguyễn Mạnh Cường, 61CĐT3 Đồ án cơ sở thiết kế máy →SτH
kτdH .τaH+ψτ .τmH 1,19.9,96+0.9,96 SσH .SτH 6,24.12,80 ⇒SH 5,60 S 2,5
Kết luận: Cả hai trục thỏa mãn điều kiện bền mỏi.
PHẦN V: TÍNH TOÁN THIẾT KẾ THEN VÀ Ổ LĂN
5.1 Tính mối ghép then.
* Chọn then bằng theo bảng (bảng 9.1[1]).
- Tại vị trí lắp bánh răng: Đường Kích thước tiết Chiều sâu rãnh
Bán kính góc lượn Chiều diện then then của rãnh r dài then kính b h Trên Trên lỗ Nhỏ Lớn nhất lt trục d, trục t1 t2 nhất mm O 8 7 4 2,8 0,16 0,25 32 C 8 7 4 2,8 0,16 0,25 32 D 10 8 5 3,3 0,25 0,4 50 H 14 9 5,5 3,8 0,25 0,4 40
* Tính kiểm nghiệm then. 2.T σ d= ≤[σ d]
[d .lt .(h−t1)] 2.T τ
c=d.<.b ≤[τc] Trong đó:
T – Mômen xoắn trên trục. d – Đường kính trục.
lt, b, h, t – Kích thước then.
[σd ] - Ứng suất dập cho phép (MPa). [σ d] = 150 MPa. lOMoARcPSD| 40651217
Nguyễn Mạnh Cường, 61CĐT3 Đồ án cơ sở thiết kế máy
[τ¿¿c]¿ - Ứng suất cắt cho phép (MPa).
[τ¿¿c]¿ = 90 MPa. Bảng kiểm nghiệm then. Vị trí tại
Ứng suất dập σ d (MPa)
Ứng suất cắt τ c (MPa) O 72,28 27,10 C 72,28 27,10 D 122,23 36,67 H 104,77 26,19
Kết luận: Then thỏa mãn.
5.2 Chọn ổ lăn và kiểm nghiệm ổ lăn. 5.2.1 Trục I. Ta có d = 30 mm 0,05 < 0,3.
Do yêu cầu độ cứng cao, độ chính xác giữa vị trí trục và bánh răng côn thẳng chọn ổ
đũa côn tra bảng P2.11 và dựa vào đường kính ngõng trục là d = 30 mm ta chọn sơ bộ ổ đũa côn cỡ nhẹ.
- Kí hiệu 7206 có các thông số sau: d (mm) D (mm) ∝(°) C (kN) C0 (kN) 30 62 13,67 29,80 22,30
* Kiểm nghiệm khả năng tải động của ổ lăn.
- Khả năng tải động Cd được tính theo công thức: 11.1 trang 213[1].
Cd=Q. m√L lOMoARcPSD| 40651217
Nguyễn Mạnh Cường, 61CĐT3 Đồ án cơ sở thiết kế máy Trong đó :
m – Bậc của đường cong mỏi: m = 10/3 (ổ đũa côn).
L – Tuổi thọ của ổ: L = 60.n.Lh .10−6 = 60.473,42.13920.10−6 = 395,40 (triệu vòng).
Q – Tải trọng động quy ước (KN) được xác định theo công thức 11.3 trang 114[1].
Q=( X .V . Fr+Y . Fa).kt .kd Trong đó:
V – Hệ số kể đến vòng nào quay, ở đây vòng trong quay: V = 1 kt
– Hệ số ảnh hưởng của nhiệt độ k t=1
kđ – Hệ số kể đến đặc tính tải trọng, tải trọng tĩnh, hộp giảm tốc công suất nhỏ: k đ=1
e = 1,5 tan (∝(°)) = 0,36 -
Tính lực Fr và Fs: Ổ lăn A: FrA N
FsA=0,83.e.FrA=498,67 N Ổ lăn B: FrB N
FsA=0,83.e .FrB=1144,61 N
∑FaA=FsB+Fat=1144,61+215,11=1359.72 N
∑FaB=FsA−Fat=498,67−215,11=283,56 N
- Theo bảng 11.4 Với ổ đũa côn: X
– Hệ số tải trọng hướng tâm Y
– Hệ số tải trọng dọc trục- Tính tỷ số: FaA
V . FrA =0,81>e; X A=0,4;Y A=1,64 FaB
=0,07<e ; XB=1;Y B=0 lOMoARcPSD| 40651217
Nguyễn Mạnh Cường, 61CĐT3 Đồ án cơ sở thiết kế máy V . FrB
- Tải trọng quy ước tác dụng vào ổ:
Q=( X A .V .FrA+Y A .FaA ).kt .kd=(0,4.1.1668,91+1,64.1359,72).1.1=2897,50 N
Q=( XB .V .FrB+Y B . FaB).kt .k d=(1.1.3830,72+0.283,56) .1.1=3830,72N ⇒
Q=max (QA ,QB)=QB=3830,72N
- Khả năng tải động của ổ lăn. Cd kN
Cd<C ⇒ Thỏa mãn khả năng tải động.
* Kiểm nghiệm khả năng tải tĩnh của ổ lăn.
- Tra bảng B11.6 trang 221[1] cho ổ đũa côn 1 dãy ta được: X0=0,5 { Y 0=0,9
- Kiểm nghiệm khả năng tải tĩnh của ổ:
QtA=X0 .Fr+Y 0 .Fa=0,5.1668,91+0,9.1359,72=2058,20 N
⇒ Q0=2058,20N<C0 ⇒ Thỏa mãn khả năng tải tĩnh. 5.2.2 Trục II. Ta có: d = 40 mm. lOMoARcPSD| 40651217
Nguyễn Mạnh Cường, 61CĐT3 Đồ án cơ sở thiết kế máy Ổ lăn E: F N Ổ lăn G: FrG N Fa ⇒ =0<0,3 Fr
Do yêu cầu độ cứng cao, độ chính xác giữa vị trí trục và bánh răng côn thẳng chọn ổ
đũa côn tra bảng P2.11 và dựa vào đường kính ngõng trục là d = 40 mm ta chọn sơ bộ
ổ đũa côn cỡ nhẹ rộng.
- Kí hiệu 7508 có các thông số sau: d (mm) D (mm) ∝(°) C (kN) C0 (kN) 40 80 14,25 53,90 44,80
* Kiểm nghiệm khả năng tải động của ổ lăn.
- Khả năng tải động Cd được tính theo công thức: 11.1 trang 213[1].
Cd=Q. m√L Trong đó:
m – Bậc của đường cong mỏi: m = 10/3 (ổ đũa côn).
L – Tuổi thọ của ổ: L = 60.n.Lh .10−6 = 60.473,42.13920.10−6 = 395,40 (triệu vòng).
Q – Tải trọng động quy ước (KN) được xác định theo công thức 11.3 trang 114[1].
Q=( X .V . Fr+Y . Fa).kt .kd Trong đó:
V – Hệ số kể đến vòng nào quay, ở đây vòng trong quay: V = 1 kt – Hệ số ảnh
hưởng của nhiệt độ kt=1 kđ – Hệ số kể đến đặc tính tải trọng, tải trọng tĩnh, hộp
giảm tốc công suất nhỏ: k đ=1 lOMoARcPSD| 40651217
Nguyễn Mạnh Cường, 61CĐT3 Đồ án cơ sở thiết kế máy
e = 1,5 tan (∝(°)) = 0,4 -
Tính lực Fr và Fs: Ổ lăn E: F N
FsE=0,83.e. Fℜ=344,44N Ổ lăn G: FrG N
FsG=0,83.e. FrG=196,73N
∑FaE=FsG−Fat=196,73−862,78=−666,05 N
∑FaG=FsE+Fat=344,44+862,78=1207,22 N
- Theo bảng 11.4 Với ổ bi đỡ:
X – Hệ số tải trọng hướng tâm
Y – Hệ số tải trọng dọc trục - Tính tỷ số:
Theo bảng B11.4 trang 216[1] ta có FaE
=−0,64<e;X E=1;Y E=0 V . Fℜ FaG
V . FrG =2,03>e; XG=0,4 ;Y G=1,44
- Tải trọng quy ước tác dụng vào ổ:
Q=( X E.V .F ℜ+Y E .FaE).kt .kd=(1.1.1037,47).1.1=1037,47 N
Q=( XG .V . FrG+Y G .FaG).kt .kd=(0,4.1.592,58+1,44.1207,22).1.1=1975,42N ⇒ Q=max
(QE ,QG)=QG=1975,42 N
- Khả năng tải động của ổ lăn. Cd kN
Cd<C ⇒ Thỏa mãn khả năng tải động.
* Kiểm nghiệm khả năng tải tĩnh của ổ lăn. lOMoARcPSD| 40651217
Nguyễn Mạnh Cường, 61CĐT3 Đồ án cơ sở thiết kế máy
- Tra bảng B11.6 trang 221[1] cho ổ bi đỡ 1 dãy ta được: X0=0,5 { Y 0=0,8
- Tải trọng tĩnh tương đương tác dụng vào ổ nguy hiểm nhất:
QtE=X0. Fℜ+Y 0 .FaE=0,5.1037,47+0,8.(−666,05)=−14,10kN ⇒
Q0=−14,10kN<C0=44,80kN
QtG=X0 .FrG+Y 0. FaG=0,5.592,58+0,8.1207,22=1,26kN
⇒ Q0=1,26 kN<C0=44,80kN
⇒ Ổ lăn thỏa mãn khả năng tải tĩnh.
PHẦN VI: THIẾT KẾ KẾT CẤU VỎ VÀ CÁC CHI TIẾT PHỤ
6.1 Tổng quan về vỏ hộp. * Nhiệm vụ.
- Bảo đảm vị trí tương đối giữa các chi tiết, bộ phận máy.
- Tiếp nhận tải trọng các chi tiết lắp trên vỏ.
- Đựng dầu bôi trơn, bảo vệ các chi tiết. * Chỉ tiêu thiết kế. - Độ cứng cao. - Khối lượng nhỏ.
* Cấu tạo, vật liệu và phương pháp gia công. -
Cấu tạo: thành hộp, nẹp hoặc gân, mặt bích, gối đỡ,…- Vật liệu: gang xám GX15-32. -
Phương pháp gia công: Đúc
* Chọn bề mặt lắp ghép và thân. lOMoARcPSD| 40651217
Nguyễn Mạnh Cường, 61CĐT3 Đồ án cơ sở thiết kế máy -
Bề mặt lắp ghép của vỏ hộp (phần trên của vỏ là nắp, phần dươi là thân) thường
điqua đường tâm các trục. -
Bề mặt ghép song song với trục đế.
6.2 Thiết kế vỏ hộp.
Dựa vào bảng 18.1 trang 85[2] ta có bảng các kích thước cơ bản của vỏ hộp. -
Với Re=166,98mm. Tên gọi Biểu thức tính toán Giá trị Chiều dày Thân hộp: δ
δ=0,03. Re+3=¿ δ=8mm 0,03.166,98+3=8,00mm Nắp hộp: δ1
δ1=0,9.δ=0,9.8=7,2mm δ1=8mm Gân tang Chiều dày gân: e
e = (0,8 ÷ 1). δ = 0,8.8 = 6,4÷ e = 8 mm cứng 8 Chiều cao gân: h h < 58 mm h = 50 mm Độ dốc Khoảng 2° 2° Bu lông nền: d1
d1>0,04.Re+10=¿ d1 = 18 mm 0,04.166,98+10=¿ (M18) 16,67mm Đường
d2=(0,7÷0,9 ).d1=¿ d2 = 16 mm kính 12,6÷16,2mm (M16)
Bu lông cạnh ổ: d2 Bu lông ghép mặt d 3 = 12 mm
bích thân và nắp: d3 (M12)
d3=(0,8÷0,9 ).d2
Vít ghép nắp ổ: d4 d4 = 10 mm
d4=(0,6÷0,7) .d2 (M10) Vít ghép nắp của
d5=(0,5÷0,6 ).d2 d5=¿8 mm thăm dầu (M8) lOMoARcPSD| 40651217
Nguyễn Mạnh Cường, 61CĐT3 Đồ án cơ sở thiết kế máy Chiều dày mặt bích
S3=(1,4 ÷1,8 ).d3 S3=¿20 mm thân: S3 Chiều dày mặt bích
S4=(0,9÷1).S3 S4=¿ 20 mm nắp: S4 Bề rộng mặt bích:
K3 ≈ K2−(3÷5) K3=¿45 mm K3 Mặt bích ghép nắp và thân D2=100 mm D Trục I: D = 62 mm 3=122 mm
D2 ≈D+2.δ+(1÷2) .d4 Đường kình ngoài
D3 ≈ D+2.δ+4,4.d4 Kích thước gối trục
và tâm lỗ vít D2, D3 D2=121 mm D3=145 mm Trục II: D = 85 mm Bề rộng mặt ghép
K2=E2+R2+(3÷5) mm K2=50 mm
bu lông cạnh ổ: K2
E2=1,6.d2=1,6.16=25,6 E2=25 mm
R2=1,3.d2=1,3.16=20,8 R2=20 mm Tâm bu lông cạnh Trục I C = 61 mm ổ: E2, C D C= 3 2 Trục II C = 72,5 mm lOMoARcPSD| 40651217
Nguyễn Mạnh Cường, 61CĐT3 Đồ án cơ sở thiết kế máy Khoảng cách từ tâm bu lông đến mép lỗ:
k>1,2.d2=1,2.16=19,2 k k = 20 mm Chiều dày khi
S1=(1,3÷1,5) .d1 S1=25 mm không có phần lồi: S1
S1=(1,4÷1,7 ).d1 S1=27 mm
S2=(1÷1,1).d1 S2=19 mm
Chiều dày khi có Dd Xác định theo đường kính Mặt đế hộp phần lồi: dao khoét.
Dd, S1, S2 Bề rộng mặt đế K1=3.d1=3.18=54 K1=54 mm hộp: K1, q
q=K1+2.δ=54+2.8=70 q = 70 mm Giữa bánh răng và
∆≥ (1÷1,2) .δ=8÷9,6 ∆ = 10 mm thành hộp Giữa bánh răng và ∆ Khe hở giữa
1≥ (3÷5 ).δ=24÷40 ∆1 = 36 mm đáy hộp các chi tiết
(phụ thuộc loại hộp giảm tốc) Giữa mặt bên các ∆≥δ=8 ∆ = 10 mm bánh răng với nhau Z Z = 4 = (L+B) Số lượng bu (200÷300) lông nền Z
L, B – Chiều dài và chiều rộng của hộp. - Chiều dày vòng móc. lOMoARcPSD| 40651217
Nguyễn Mạnh Cường, 61CĐT3 Đồ án cơ sở thiết kế máy
S=(2÷3) .δ=(2÷3) .8=16 mm - Đường kính vòng móc.
D=(3÷ 4) .δ=(3÷ 4) .8=24 mm 6.2.1 Chốt định vị. -
Tên chi tiết: Chốt định vị. -
Chức năng: Nhờ có chốt định vị, khi xiết bu lông không làm biến dạng vòng
ngoàicủa ổ (do sai lệch vị trí tương đối của nắp và thân) do đó loại trừ được các nguyên
nhân làm ổ chóng bị hỏng. -
Chọn loại chốt định vị là chốt côn. -
Thông số kích thước: Tra bảng [18.4b,2-91] ta được: d = 6 mm, c = 1 mm, L = 20 ÷ 110 mm Chọn L = 45 mm. 6.2.2 Cửa thăm. - Tên chi tiết: Cửa thăm -
Chức năng: Để kiểm tra quan sát các chi tiết trong hộp khi lắp ghép và để đồ dầu
vàohộp, trên đỉnh hộp có làm cửa thăm. Cửa thăm được đậy bằng nắp, trên nắp có nút thông hơi. -
Thông số kích thước: Tra bảng [18.5,2-92] ta được: A B A1 B1 C C1 K R Vít Số lượng lOMoARcPSD| 40651217
Nguyễn Mạnh Cường, 61CĐT3 Đồ án cơ sở thiết kế máy 100 75 150 100 125 - 87 12 M8× 22 4 6.2.3 Nút thông hơi.
Tên chi tiết: Nút thông hơi. -
Chức năng: Khi làm việc nhiệt độ trong hộp tăng lên. Để giảm áp suất và diều
hòakhông khí bên trong và bên ngoài hộp người ta dùng nút thông hơi. -
Thông số kích thước: Tra bảng 18.6 Trang 93[2] ta được: A B C D E G H I K L M N O P Q R S
M 27×2 15 30 15 45 36 32 6 4 10 8 22 6 32 18 36 32 6.2.4 Nút tháo dầu. -
Tên chi tiết: Nút tháo dầu. -
Chức năng: Sau 1 thời gian làm việc dầu bôi trơn có chứa trong hộp bị bẩn (do
bụibẩn hoặc hại mài…) hoặc dầu bị biến chất. Do đó cần phải thay dầu mới, để tháo dầu
cũ, ở đáy hộp có lỗ tháo dầu, lúc làm việc lỗ này bị bít kín bằng nút tháo dầu. -
Thông số kích thước (số lượng 1 chiếc): tra bảng 18.7 Trang 93[2] ta được: lOMoARcPSD| 40651217
Nguyễn Mạnh Cường, 61CĐT3 Đồ án cơ sở thiết kế máy d b m f L c q D S Do M20 15 9 3 28 2,5 17,8 30 22 25,4 × 2 6.2.5 Kiểm tra mức dầu. -
Tên chi tiết: Que thăm dầu. -
Chức năng que thăm dầu: Dùng để kiểm tra mức dầu, chất lượng dầu bôi trơn
tronghộp giảm tốc. Để tránh sóng dầu gây khó khăn cho việc kiểm tra, đặc biệt khi máy
làm việc 3 ca, que thăm dầu thường có vỏ bọc bên ngoài. - Số lượng: 1 chiếc.
6.3 Một số chi tiết phụ.
6.3.1 Các chi tiết lót bộ phận ổ. -
Ổ lăn làm việc trung bình và bôi trơn bằng mỡ ta chọn làm kín dộng gián tiếp bằngvòng phớt. * Chi tiết vòng phớt. -
Đặc điểm: Dễ thay thế, đơn giản và chống mòn. -
Phân loại: Cố định và điều chỉnh được khe hở. -
Chức năng: Bảo vệ ổ lăn khỏi bám bụi, chất lỏng hạt cứng và các tạp chất xâm
nhậpvào ổ, những chất này làm ổ chóng bị mài mòn và han gỉ. lOMoARcPSD| 40651217
Nguyễn Mạnh Cường, 61CĐT3 Đồ án cơ sở thiết kế máy -
Thông số kích thước tra bảng 15.17 trang 50[2] ta được: d d1 d2 D a b S0 Trục I 30 31 29 43 6 4,3 9 (mm) Trục II 45 46 44 64 9 6,5 12 (mm)
* Chi tiết vòng chắn dầu. -
Chức năng: Vòng chắn dầu quay cùng với trục, ngăn cách mỡ bôi trơn với dầu
tronghộp, không cho dầu thát ra ngoài. -
Thông số kích thước vòng chắn dầu.
a=6÷9 (mm) ,t=2÷3 (mm) ,b=2÷5(mm) (lấy bằng gờ trục) * Ổ lăn. -
Tên chi tiết: Ổ đũa côn. -
Chức năng: Đỡ trục và các chi tiết trên trục và chịu lực dọc trục làm cho trục
quayổn định và cứng vững. - Vật liệu: Thép ổ lăn. - Thông số kích thước: lOMoARcPSD| 40651217
Nguyễn Mạnh Cường, 61CĐT3 Đồ án cơ sở thiết kế máy Kí d D D1 d1 B C1 T r r1 α C C0 Số hiệu lượng (mm) ° (kN)
Trục 30 62 50,6 45,6 16 14 17,25 1,5 0,5 13,67 29,80 22,30 2 I Trục 45 85 69 65,4 23 9 24,75 2 0,8 15,50 51,60 42,60 2 II * Cốc lót. - Tên chi tiết: Cốc lót. -
Chức năng: Dùng để đỡ ổ lăn tạo thuận lợi cho việc lắp ghép và điều chỉnh bộ
phậnổ cũng như điều chỉnh ăn khớp của bánh răng côn. -
Vật liệu: Gang xám GX15÷32. -
Thông số chi tiết: Chọn chiều dày cốc lót: δ=8mm.
Chọn chiều dày vai và bích cốc lót: δ1=δ2=δ=8 (mm).
PHẦN VII: DUNG SAI LẮP GHÉP VÀ BÔI TRƠN
7.1 Dung sai lắp ghép và lắp ghép ổ lăn. -
Lắp vòng trong của ổ lên trục theo hệ thống lỗ cơ bản và lắp vòng ngoài vào vỏ
theohệ thống trục cơ bản. -
Để các vòng không trượt trên bề mặt trục hoặc lỗ khi làm việc, ta chọn kiểu lắp
trunggian với các vòng không quay và lắp có độ dôi với các vòng quay. -
Chọn miền dung sai khi lắp các vòng ổ. -
Tra bảng 20-12, 20-13 ta được: lOMoARcPSD| 40651217
Nguyễn Mạnh Cường, 61CĐT3 Đồ án cơ sở thiết kế máy
+ Lắp ổ lên trục là: k6.
+ Lắp ổ lên vỏ là: H7.
7.1.1 Lắp bánh răng lên trục. -
Để truyền momen xoắn từ trục lên bánh răng và ngược lại, ta chọn sử dụng
thenbằng. Mối ghép then thường không được lắp lẫn hoàn toàn do rãnh then trên trục
thường được phay thường thiếu chính xác. Để khắc phục cần cạo then theo rãnh then để lắp. -
Lắp bánh răng lên trục theo kiểu lắp trung gian: H 7
7.1.2 Dung sai mối ghép then.
Tra bảng B20.6 Trang 125[2] với tiết diện then trên các trục ta được.
Sai lệch giới hạn của chiều rộng then:
Trục I:b×h=12×8chọn:P9(12− 0,018 − 0,061)
{Trục II :b×h=14×9chọn:P9(14− 0,018 −
0,061) Sai lệch chiều sâu rãnh then:
Trục I:t=5,0mm⇒Nmax=+0,2mm {Trục II
:t=5,5mm⇒Nmax=+0,2mm
7.2 Bôi trơn hộp giảm tốc. * Bôi trơn trong hộp. -
Theo cách dẫn dầu bôi trơn đến các chi tiết máy, người ta phân biệt bôi trơn
ngâmdầu và bôi trơn lưu thông, do các bánh răng trong hộp giảm tốc đều có vận tốc v <
12 (m/s) nên ta bôi trơn bánh răng trong hộp bằng phương pháp ngâm dầu. -
Với vận tốc vòng của bánh răng côn răng thẳng: v = 2,80 (m/s). -
Tra bảng 18.11 Trang 100[2], ta có được độ nhớt để bôi trơn là:
Centistocứngvớinhiệt độ50℃ -
Theo bảng 18.13 Trang 101[2] ta chọn được loại dầu AK-20. * Bôi trơn ngoài hộp. lOMoARcPSD| 40651217
Nguyễn Mạnh Cường, 61CĐT3 Đồ án cơ sở thiết kế máy
Với bộ truyền ngoài hộp do không có thiết bị nào che đậy nên dễ bị bám bụi do đó bộ
truyền ngoài ta thường bôi trơn định kỳ.
- Bôi trơn ổ lăn: Khi ổ lăn được bôi trơn đúng kỹ thuật, nó sẽ không bị mài mòn, ma sát
trong ổ sẽ giảm, giúp tránh không để các chi tiết kim loại tiếp xúc trực tiếp với nhau,
điều đó sẽ bảo vệ được bề mặt và tránh được tiếng ồn.
Thông thường các ổ lăn đều có thể bôi trơn bằng dầu hoặc mỡ, nhưng trong thực tế thì
người ta thường bôi mỡ vì so với dầu thì mỡ bôi trơn được giữ trong ổ dễ dàng hơn,
đồng thời có khả năng bảo vệ ổ tránh tác động của tạp chất và độ ẩm. Ngoài ra mỡ được
dùng lâu dài ít chịu ảnh hưởng của nhiệt độ theo bảng 15.15a Trang 44[2] ta dùng loại
mỡ LGMT2 và chiếm 1/2 khoảng trống trong ổ.
7.3 Bảng dung sai lắp ghép. Trục Vị trí lắp Kiểu lắp Lỗ Trục Trục I Trục lắp bánh H7 Ø25++0,0030 Ø25++0,0150,002 đai Ø25 k 6 Trục và bạc D8 Ø25++0,0980,065 Ø25++0,0150,002 lót Ø25 k 6 Cốc lót và vỏ H7 Ø78+00,035 Ø78−0 0,022 Ø78 h6 Vòng ngoài Ø 62H 7 Ø 62+00,035 của ổ và cốc lót Trục và vòng D8 Ø25++0,1190,080 Ø25++0,0180,002 chắn dầu Ø25 k 6 Trục và vòng Ø30 k6 Ø30++0,0180,002 trong ổ Trục và bánh H7 Ø25+00,025 Ø25++0,0180,002 răng Ø25 k 6 Vỏ và nắp ổ H 7 Ø 85+00,035 Ø 85−0 0,022 Ø 85 h6 Trục và vòng D8 Ø 40++0,1460,100 Ø 40++0,0210,002 chắn dầu Ø 40 k 6 Trục II Trục và bánh H 7 Ø 45+00,030 Ø 45++0,0210,002 răng Ø 45 k 6 lOMoARcPSD| 40651217
Nguyễn Mạnh Cường, 61CĐT3 Đồ án cơ sở thiết kế máy Trục và vòng Ø 40k 6 Ø 40++0,0210,002 trong ổ Vỏ và vòng Ø 85H 7 Ø 85+00,035 ngoài ổ Trục và bạc D8 Ø36++0,1460,100 Ø36++0,0210,002 lót Ø36 k6 Trục và khớp Ø36 k 6 Ø36++0,0210,002 nối
TÀI LIỆU THAM KHẢO 1.
Tính toán thiết kế hệ dẫn động cơ khí – tập 1 – Nhà xuất bản giáo dục;PGS.TS
– Trịnh Chất – TS Lê Văn Uyển. 2.
Tính toán thiết kế hệ dẫn động cơ khí – tập 2 – Nhà xuất bản giáo dục;PGS.TS
– Trịnh Chất – TS Lê Văn Uyển. 3.
Dung sai lắp ghép - Nhà xuất bản giáo dục; PGS.TS Ninh Đức Tốn. 4.
Trang web: http://thietkemay.edu.vn