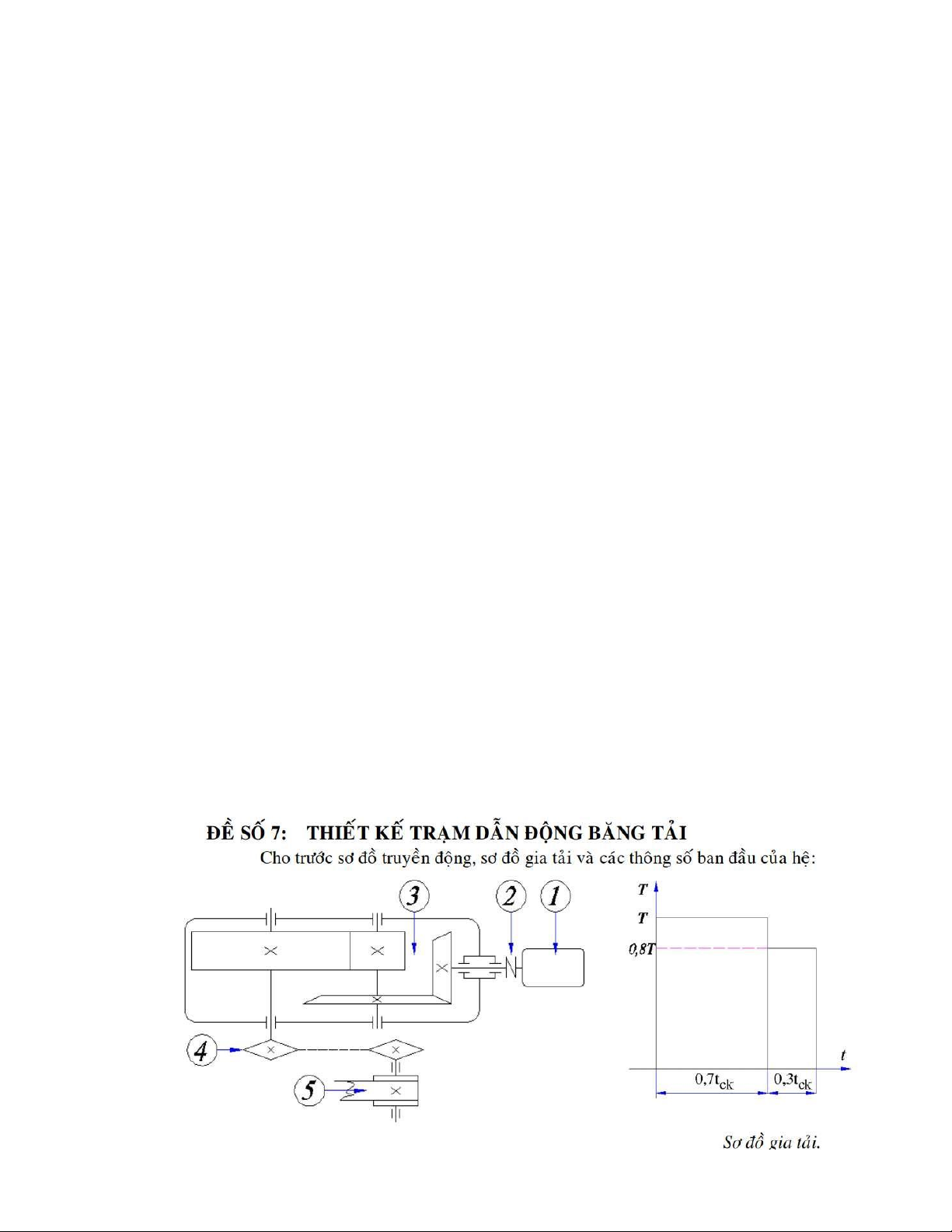
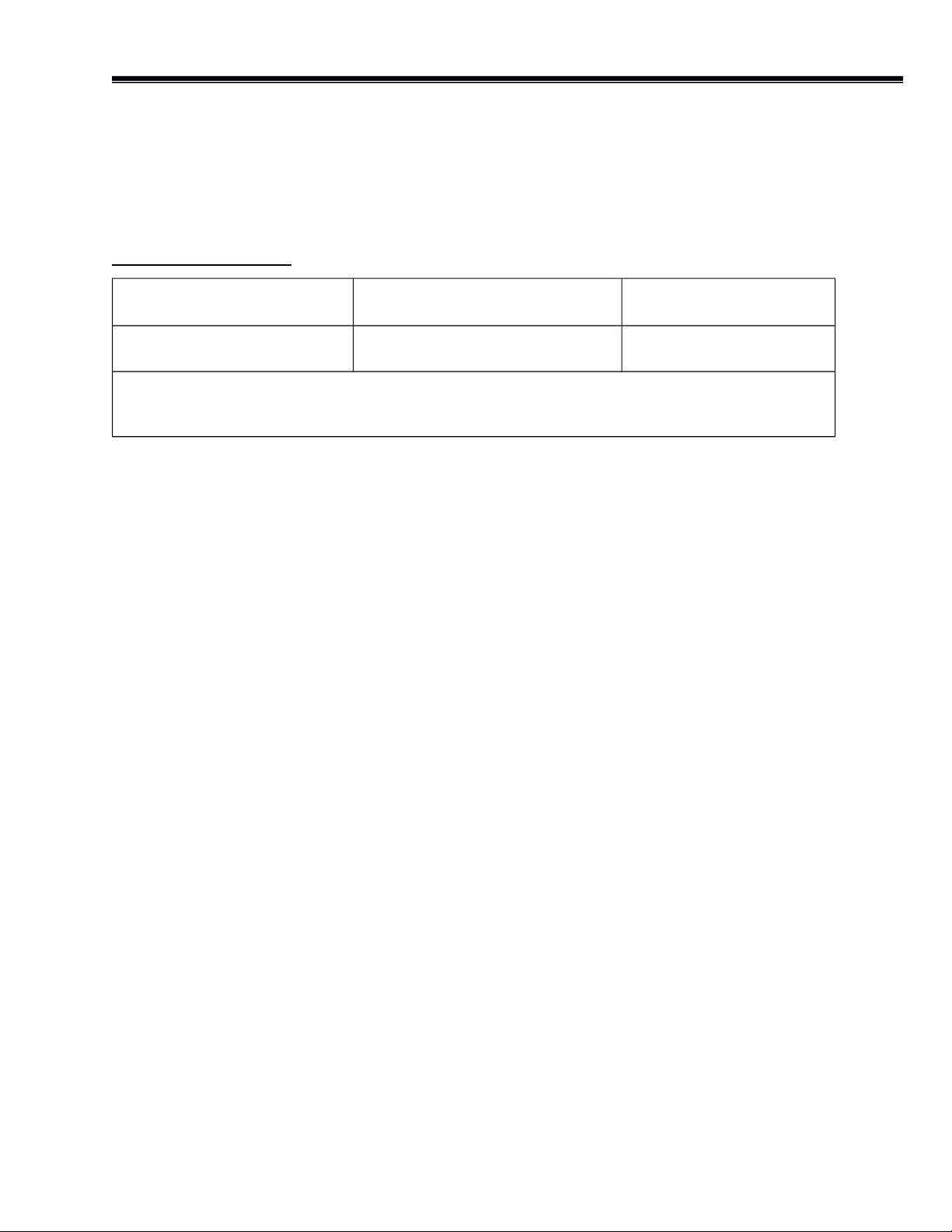
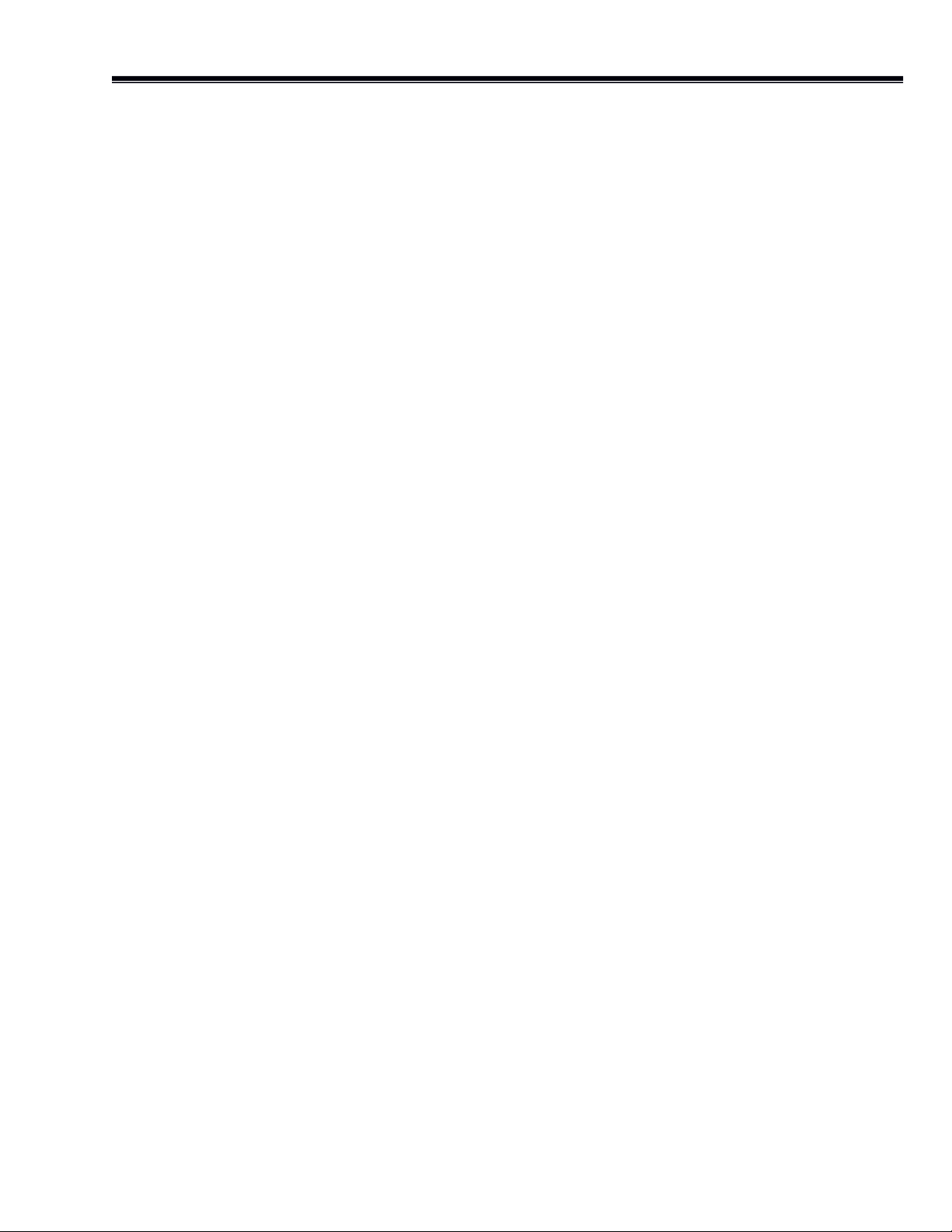
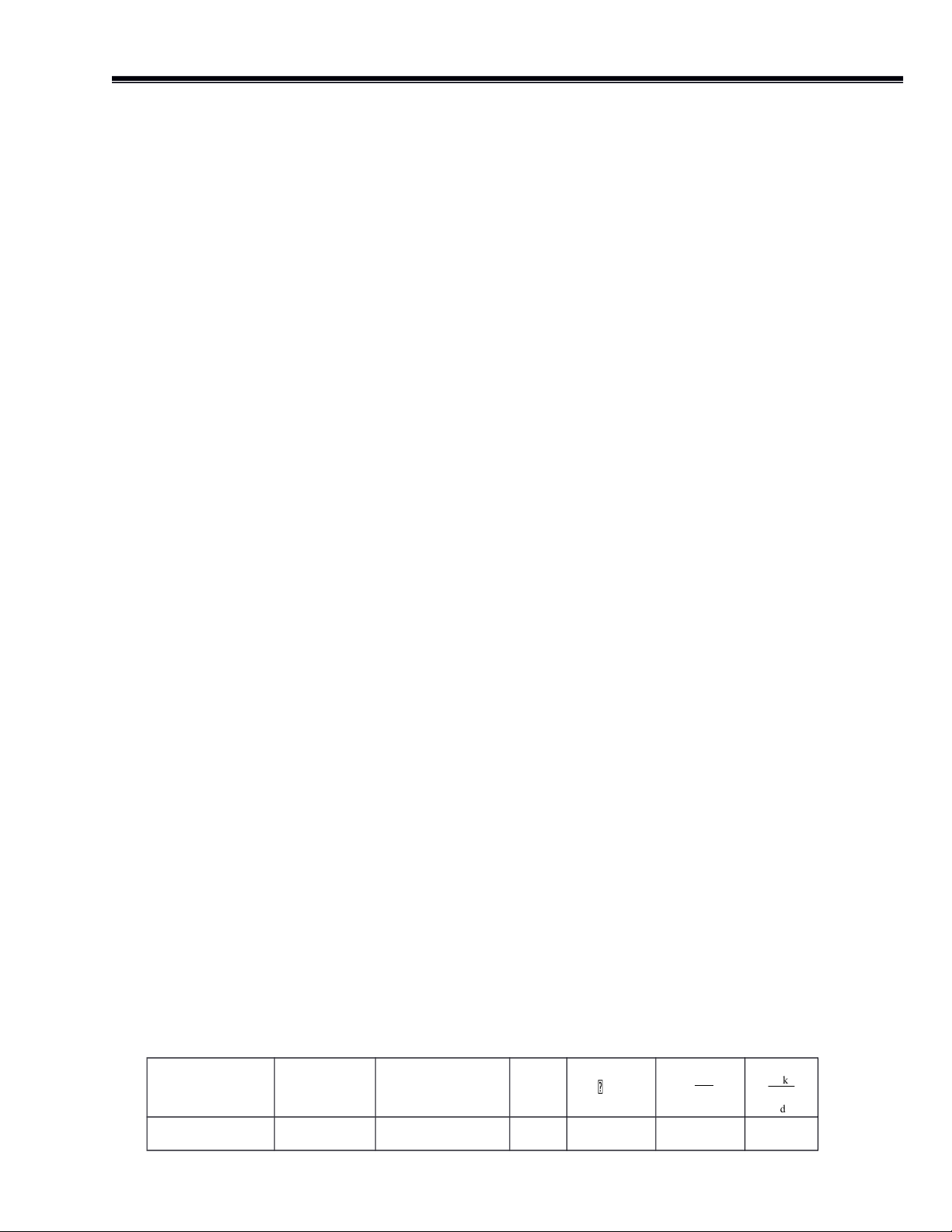
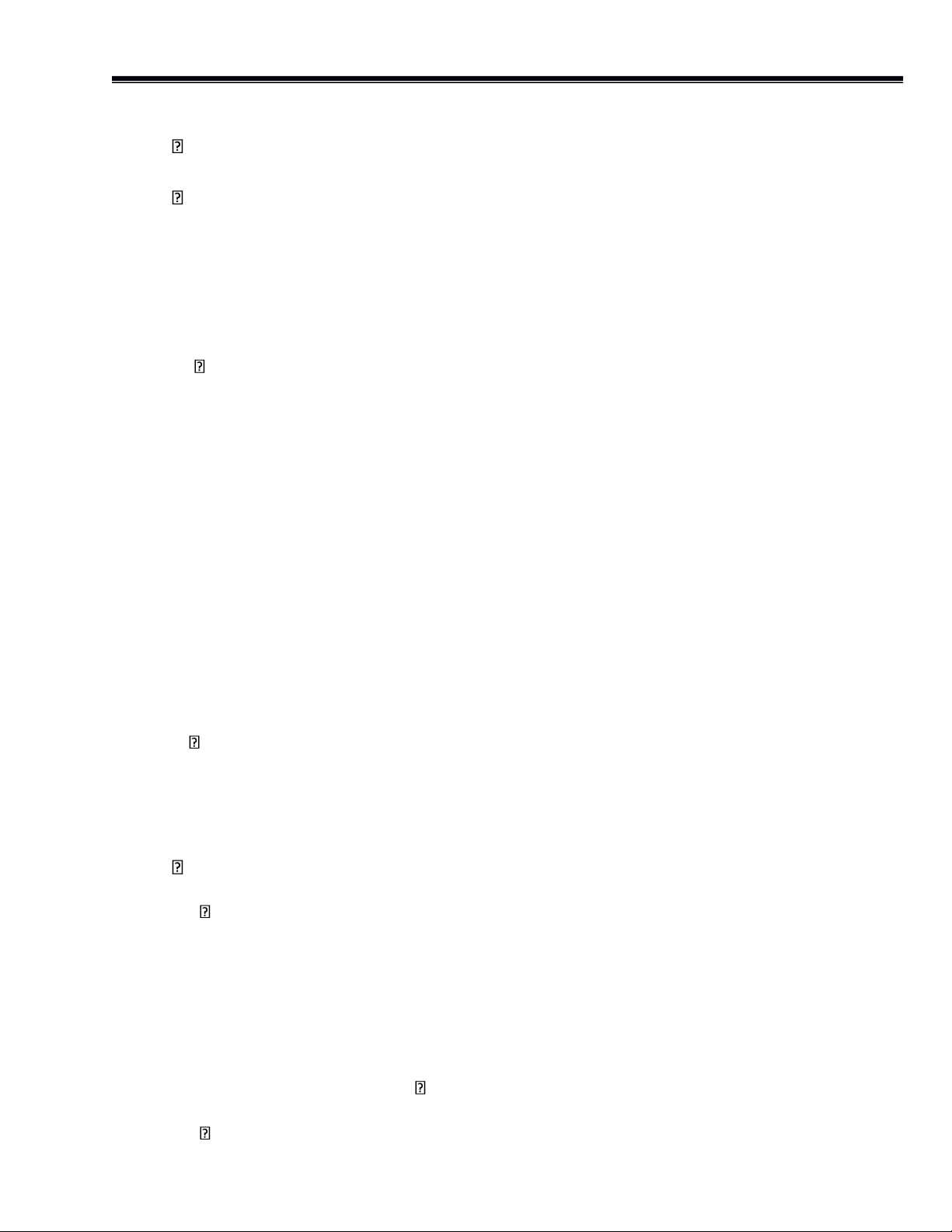
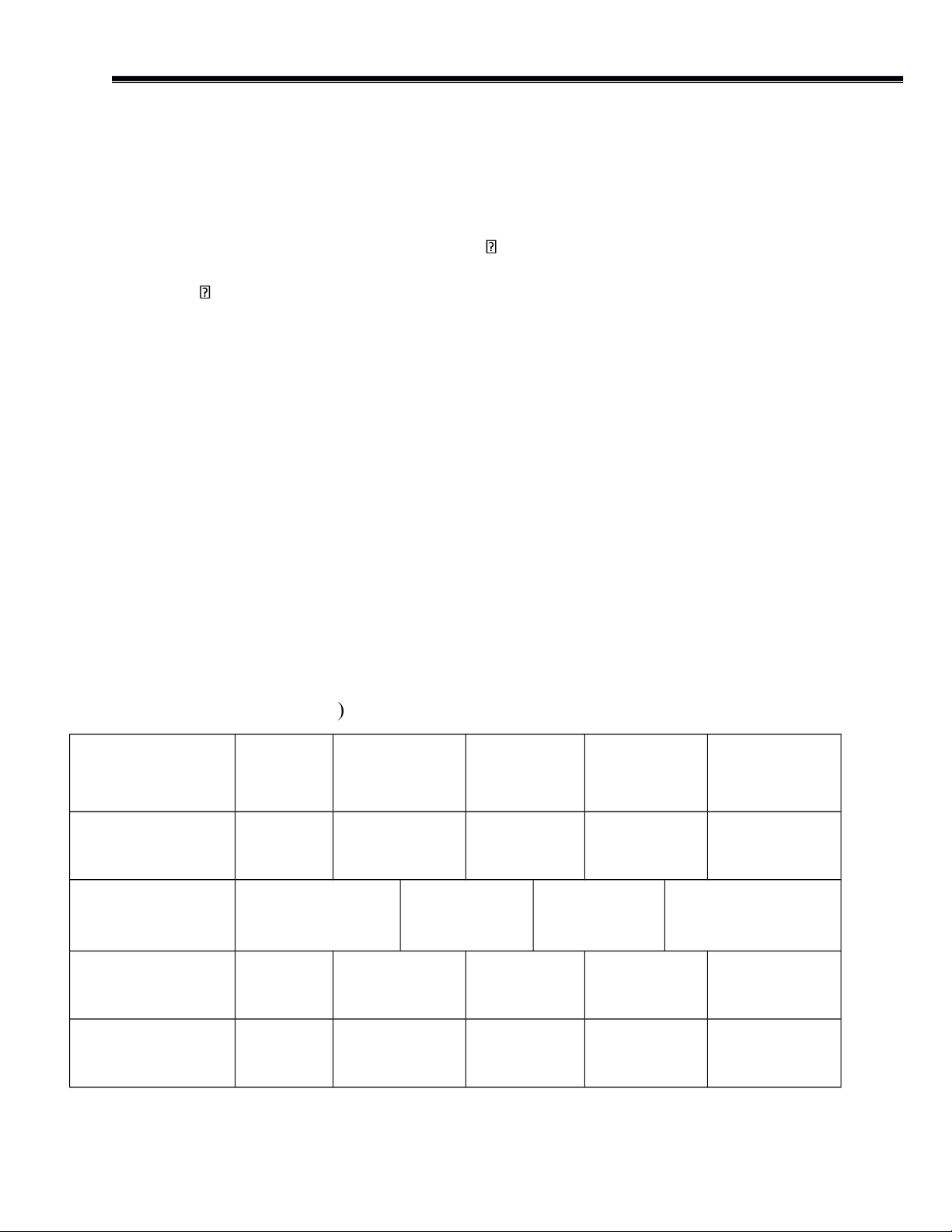
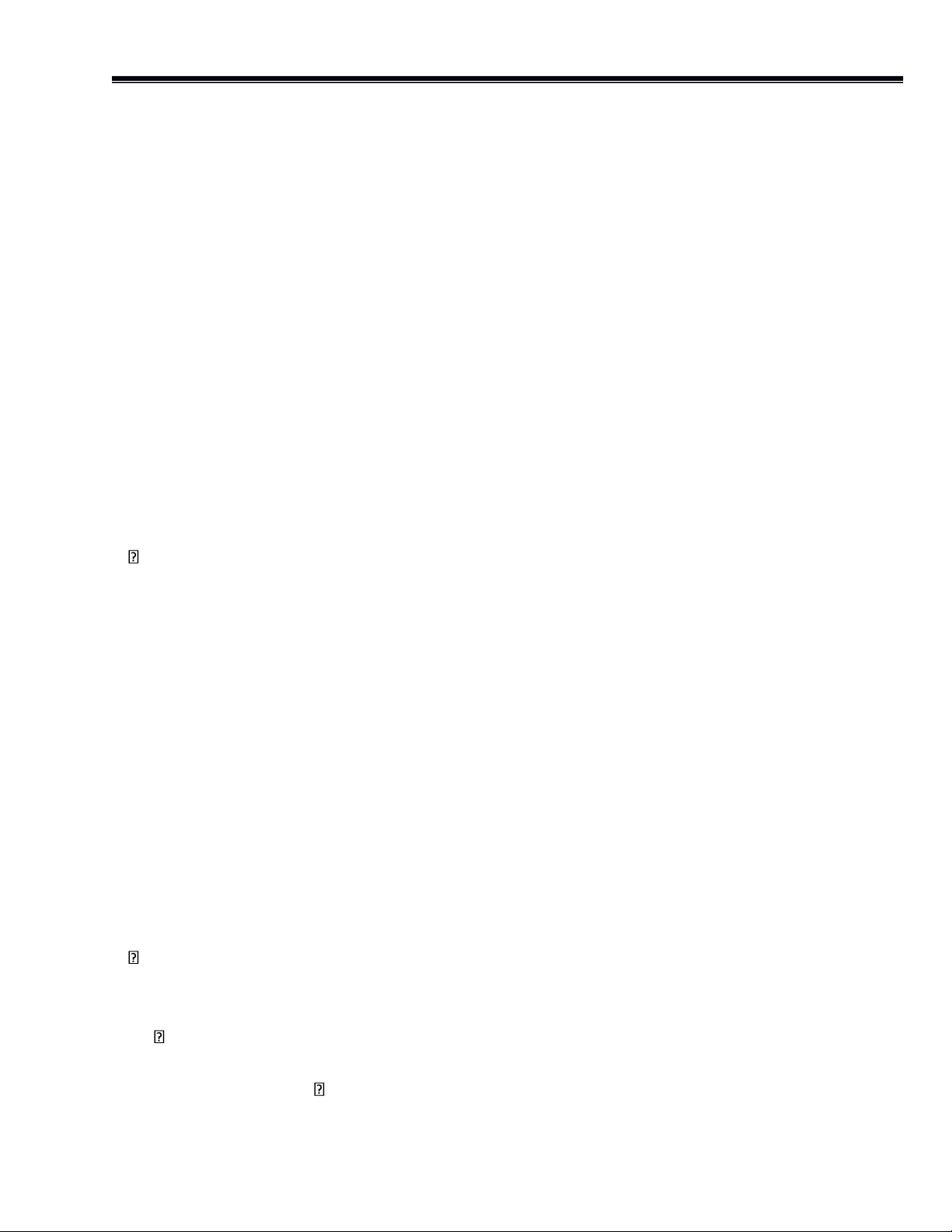
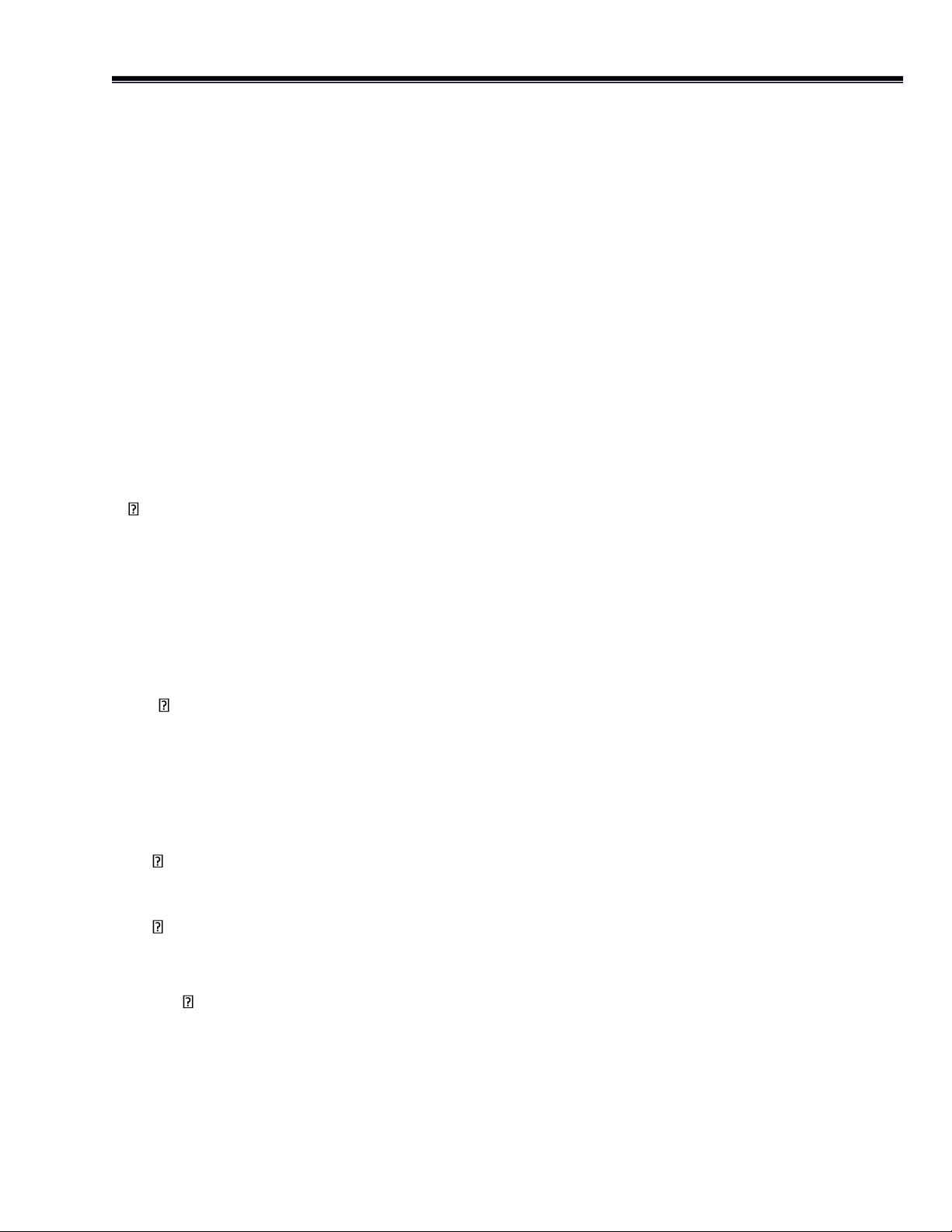
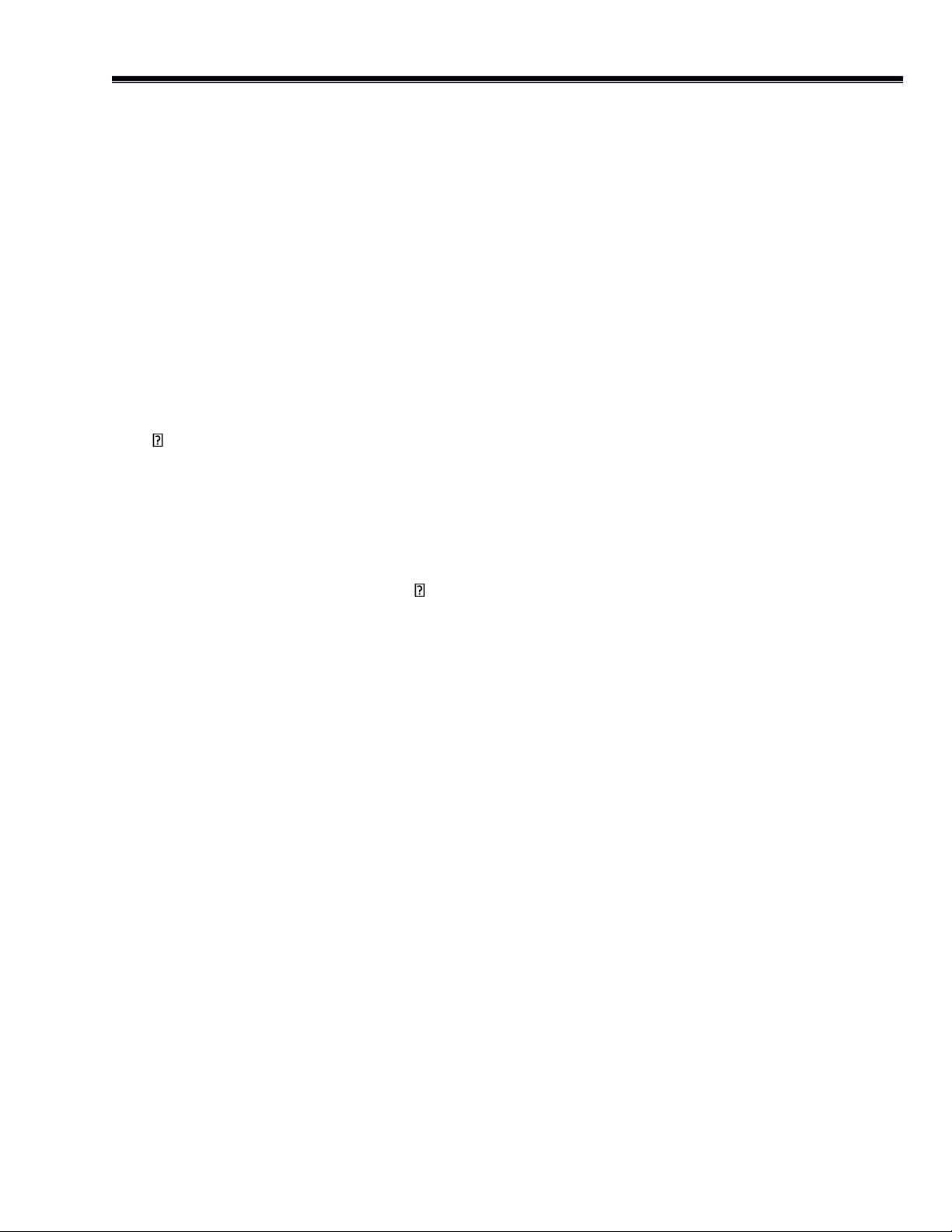
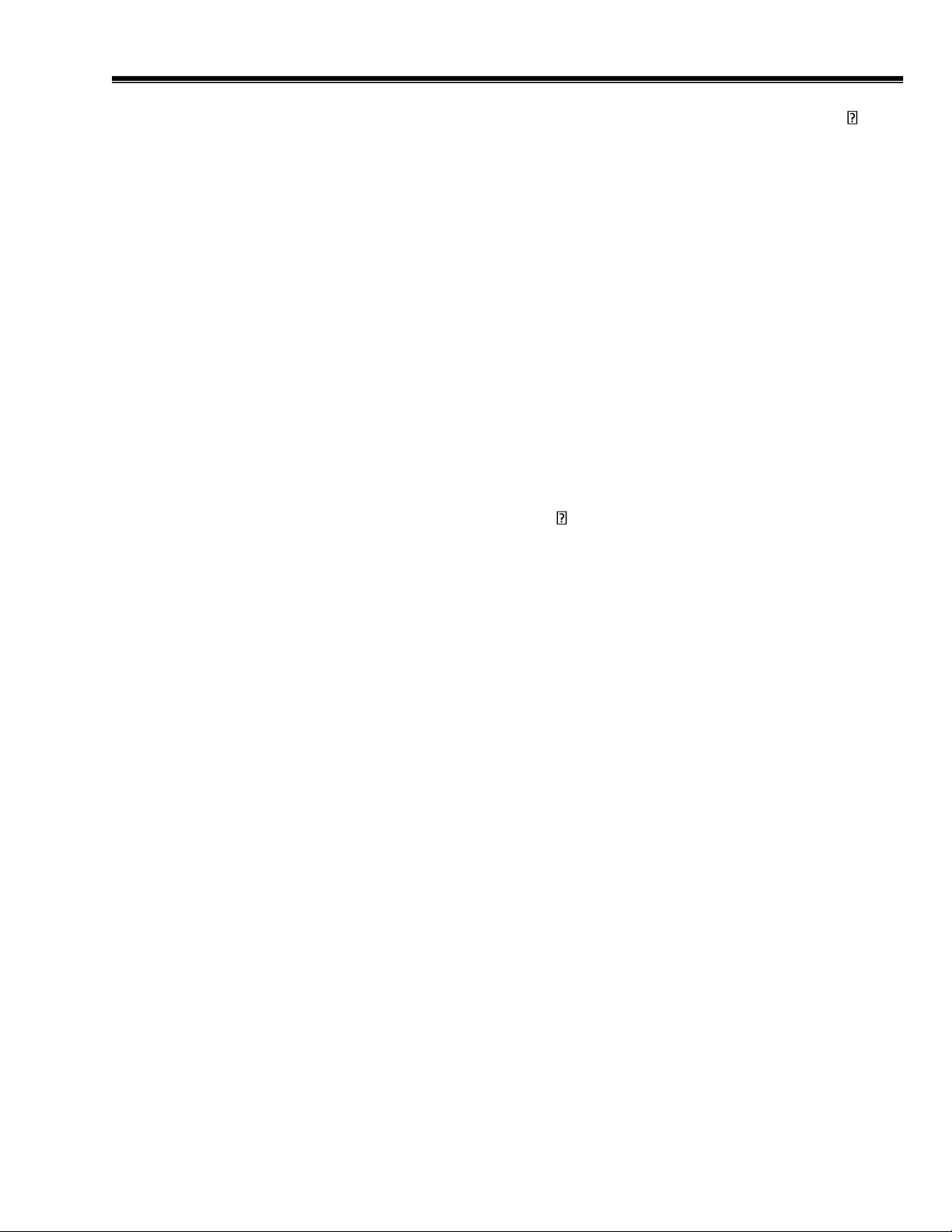
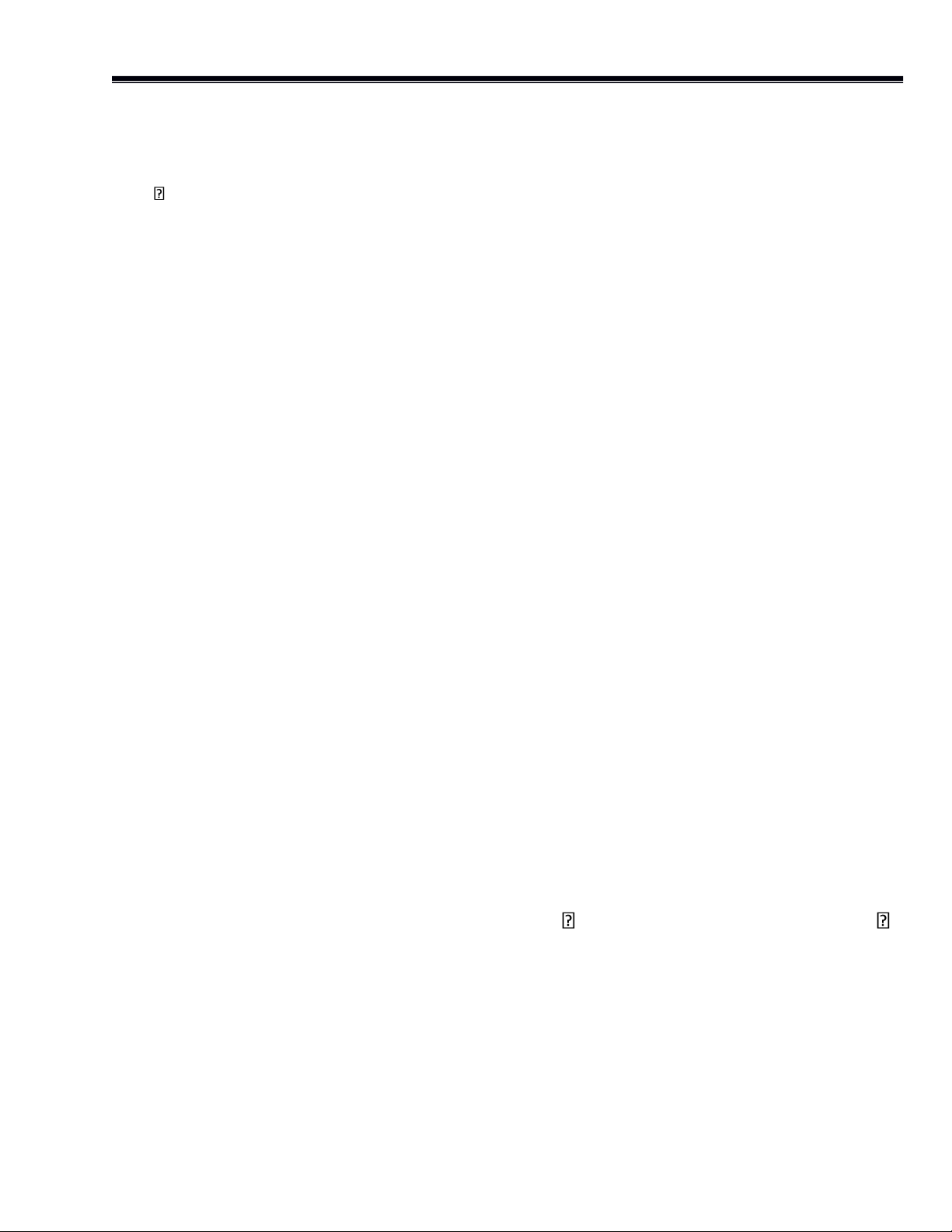
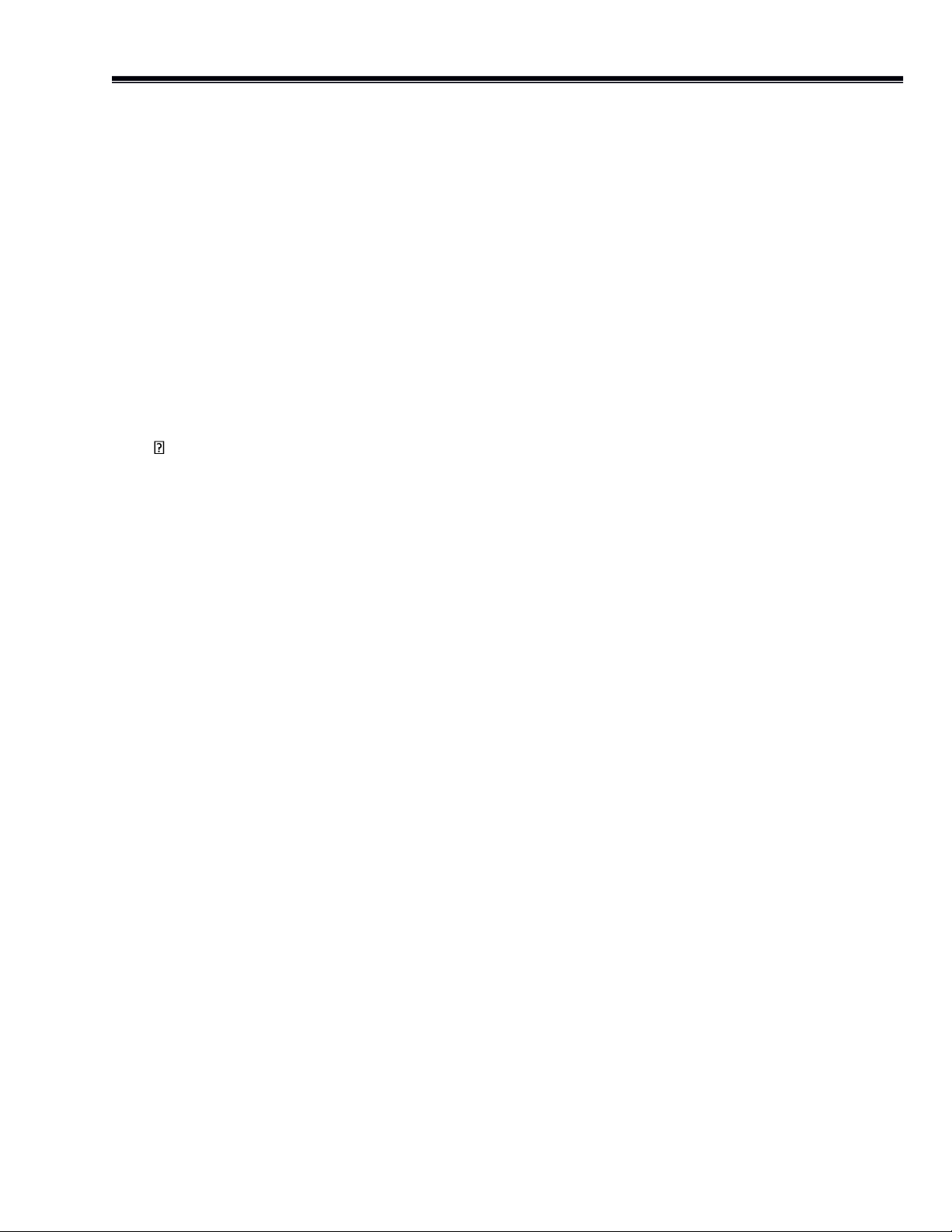
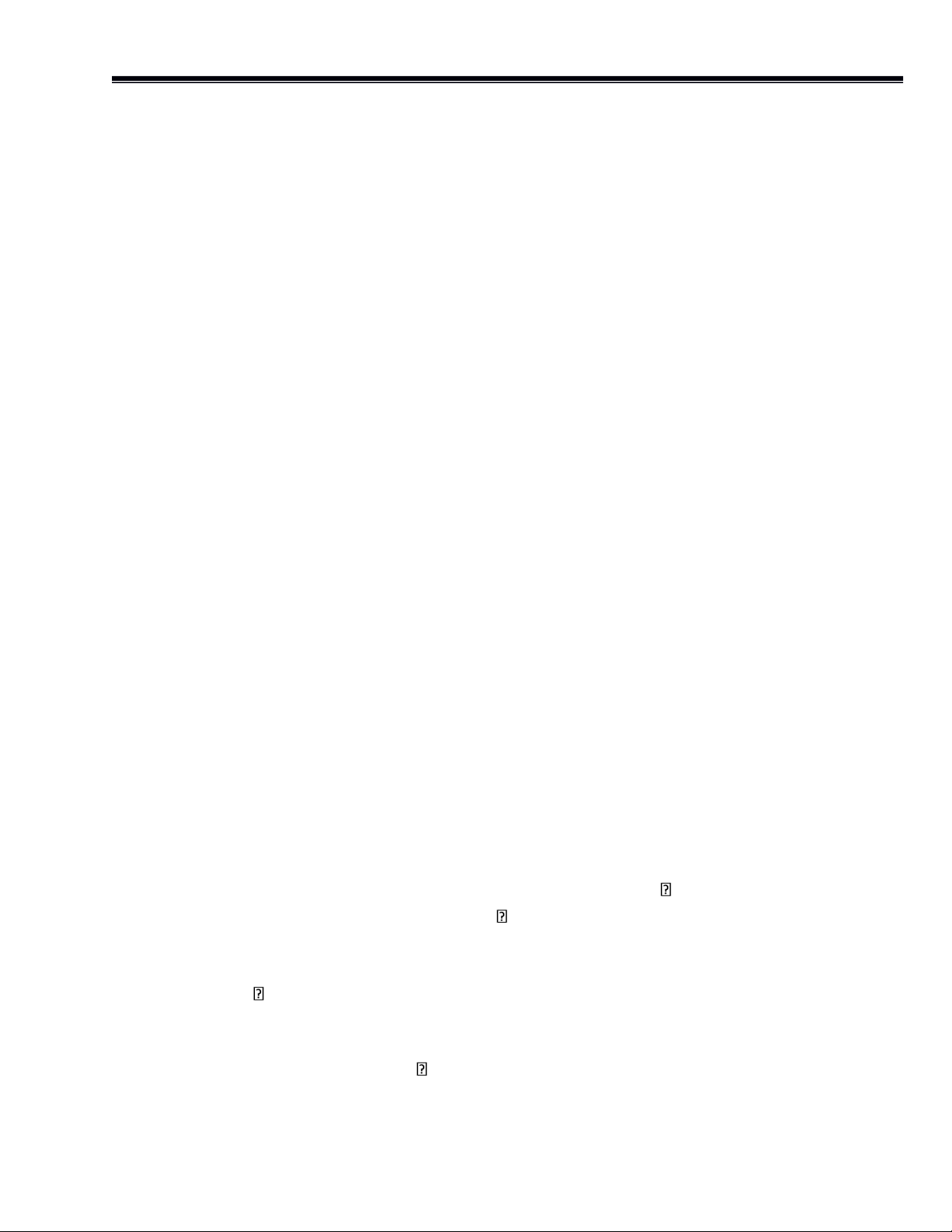
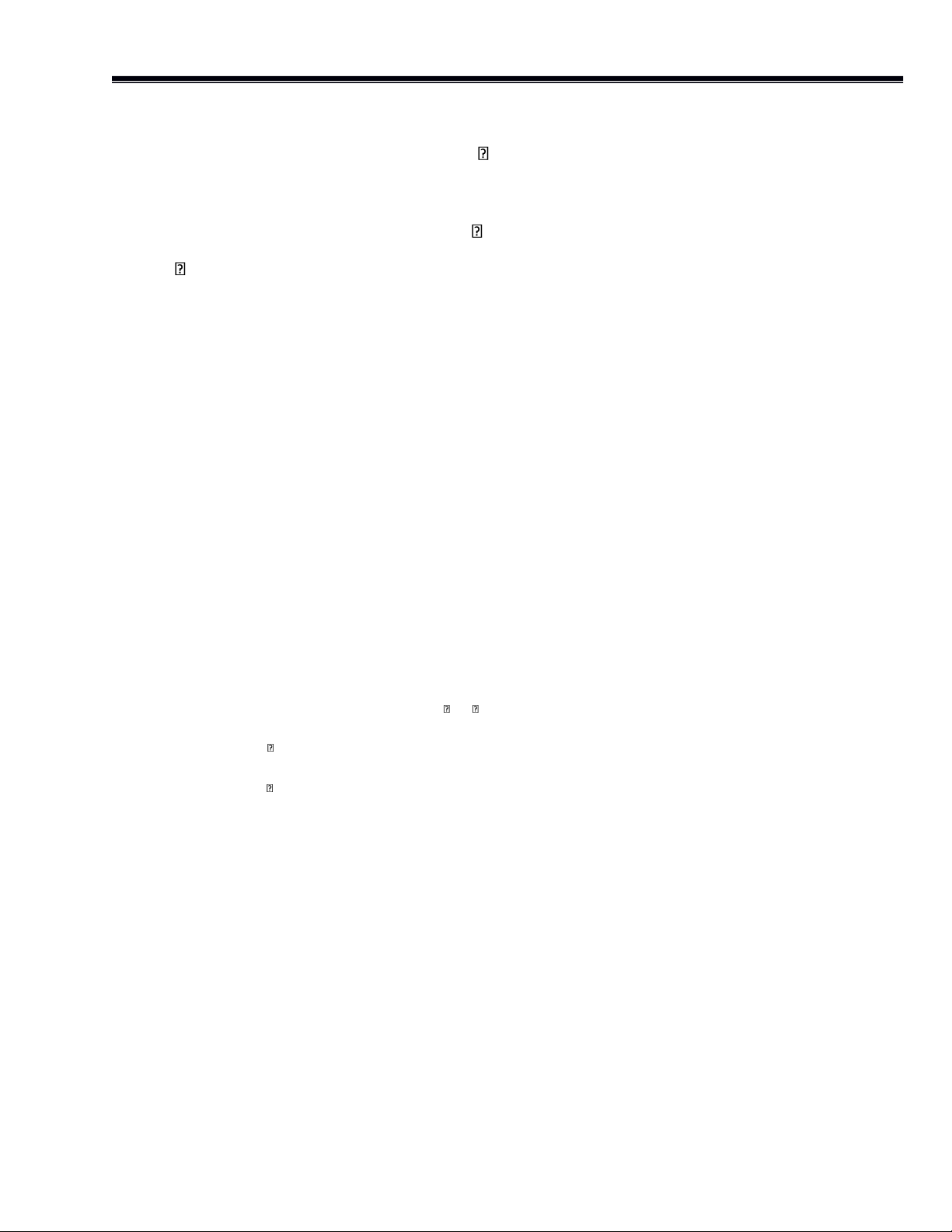
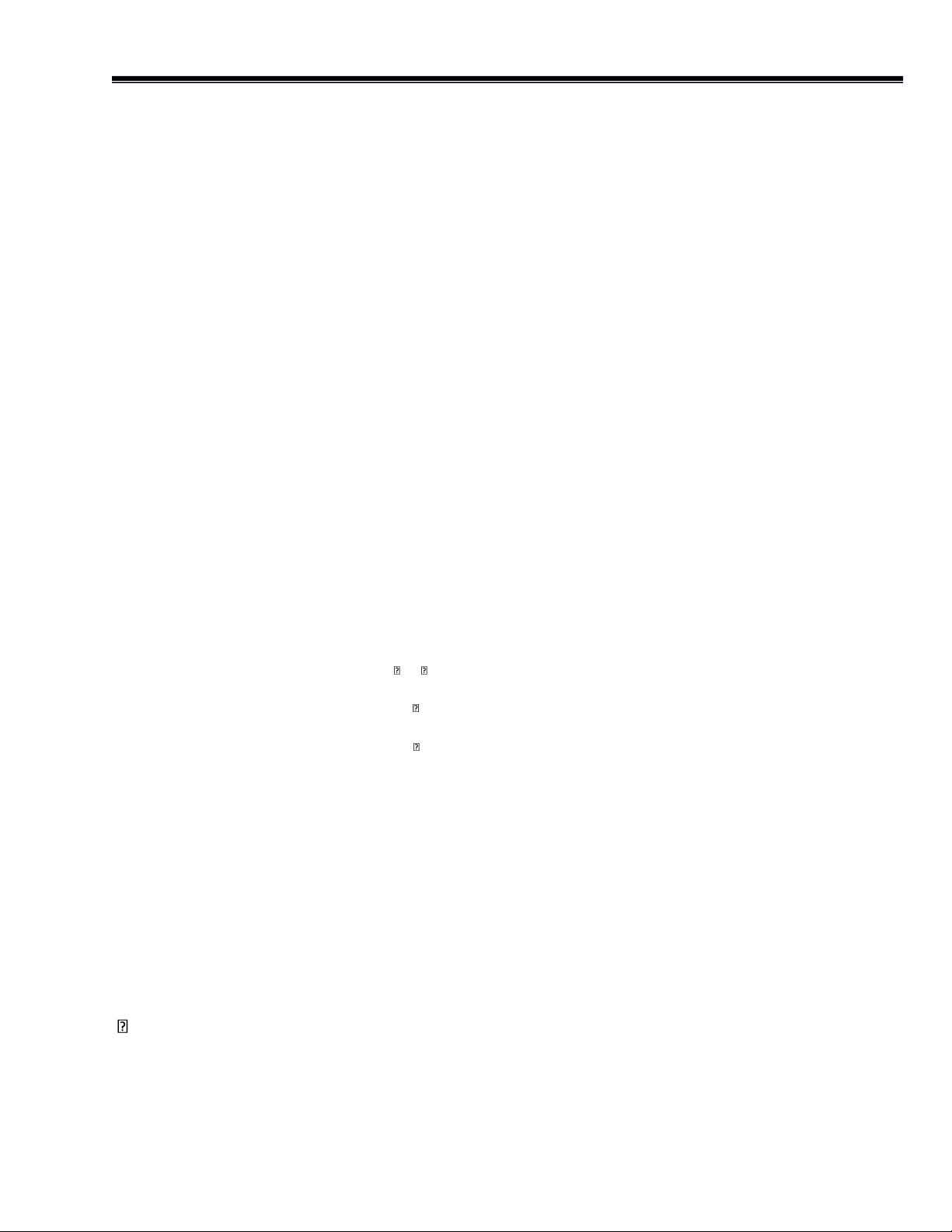
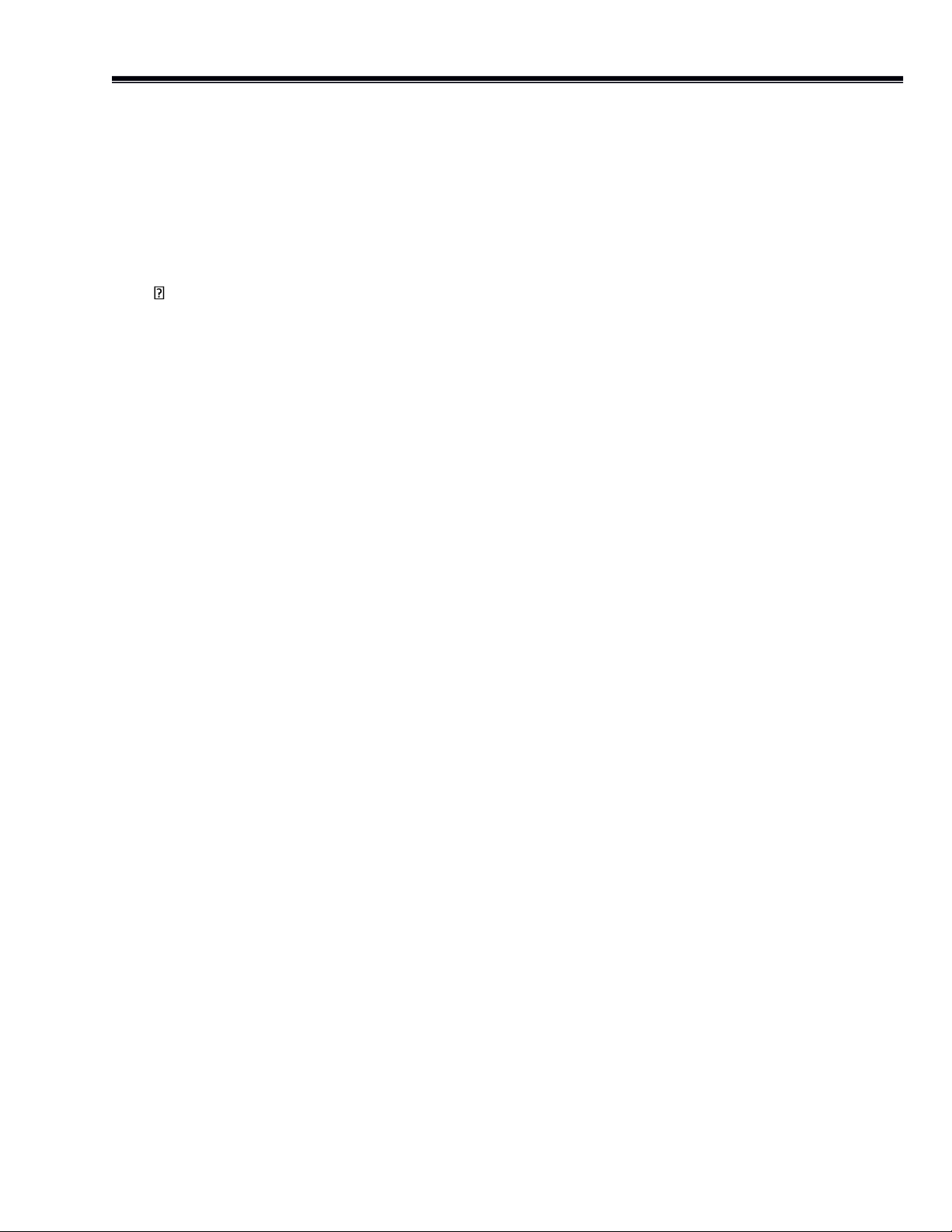
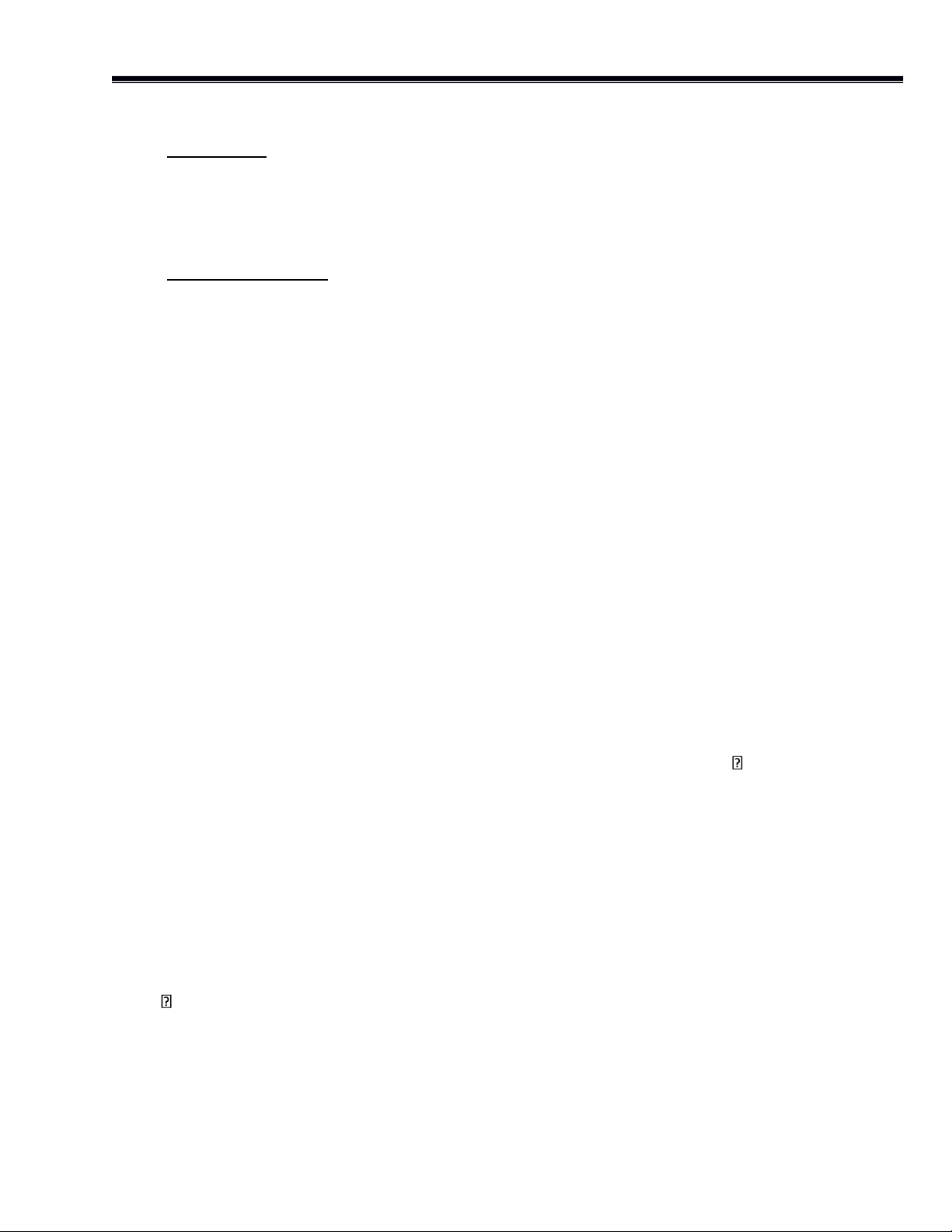
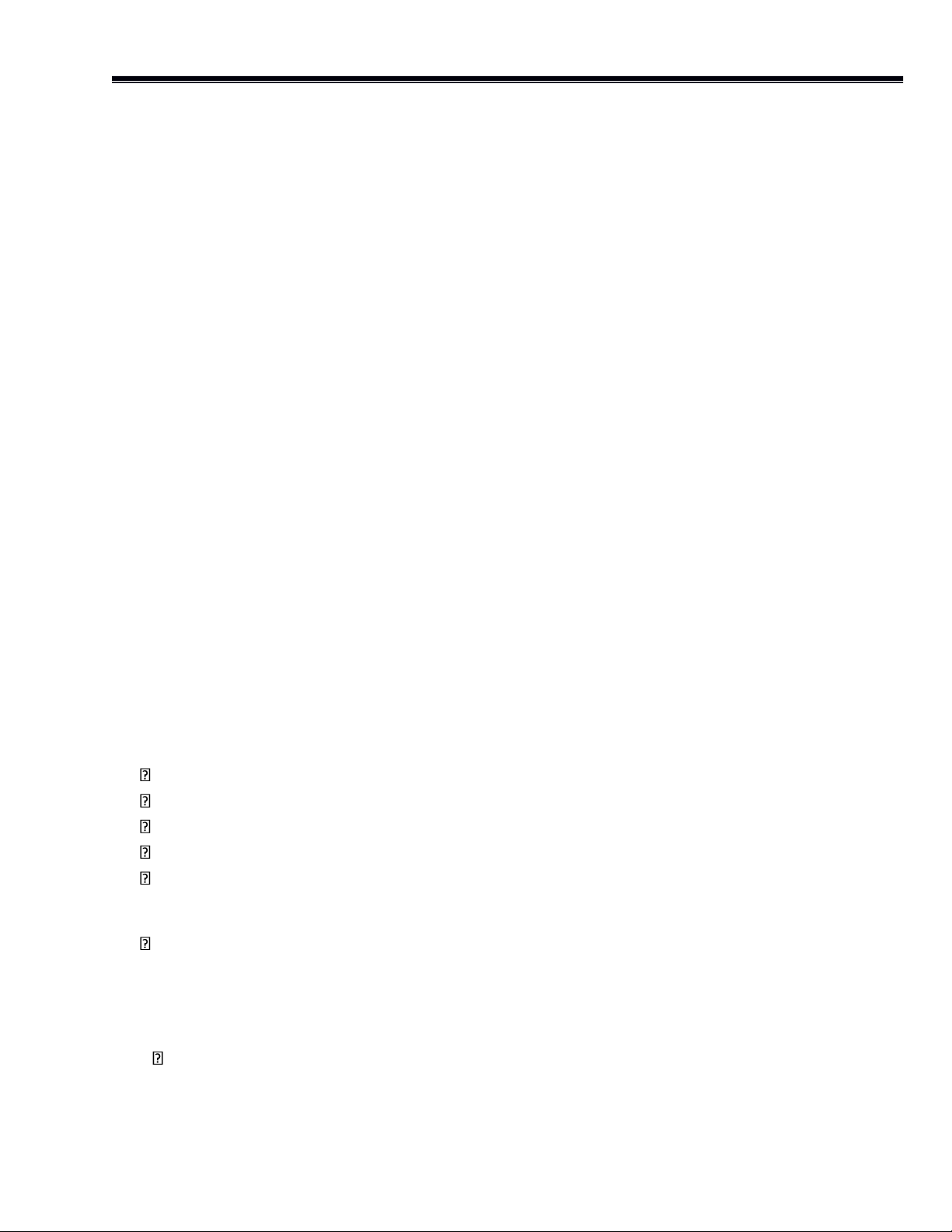
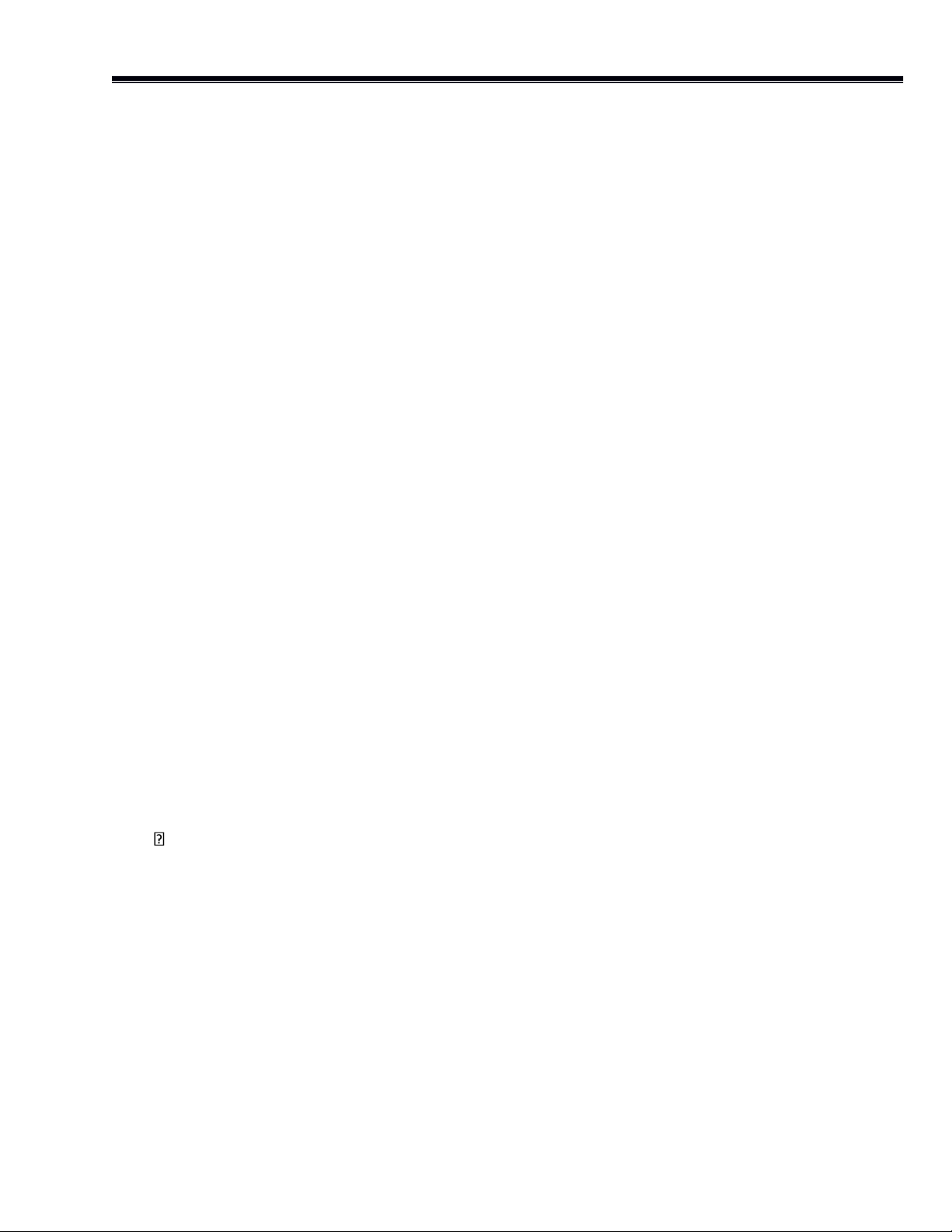
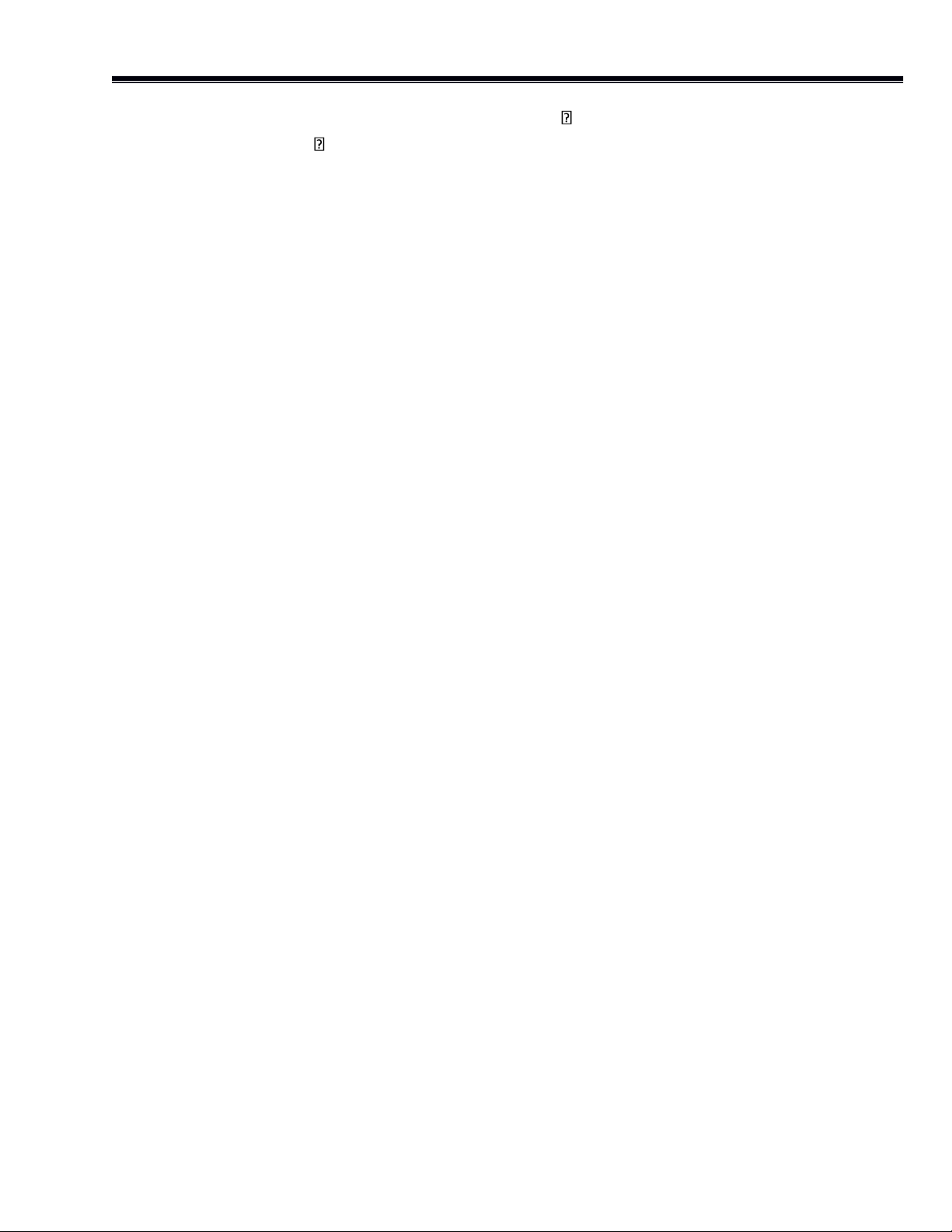
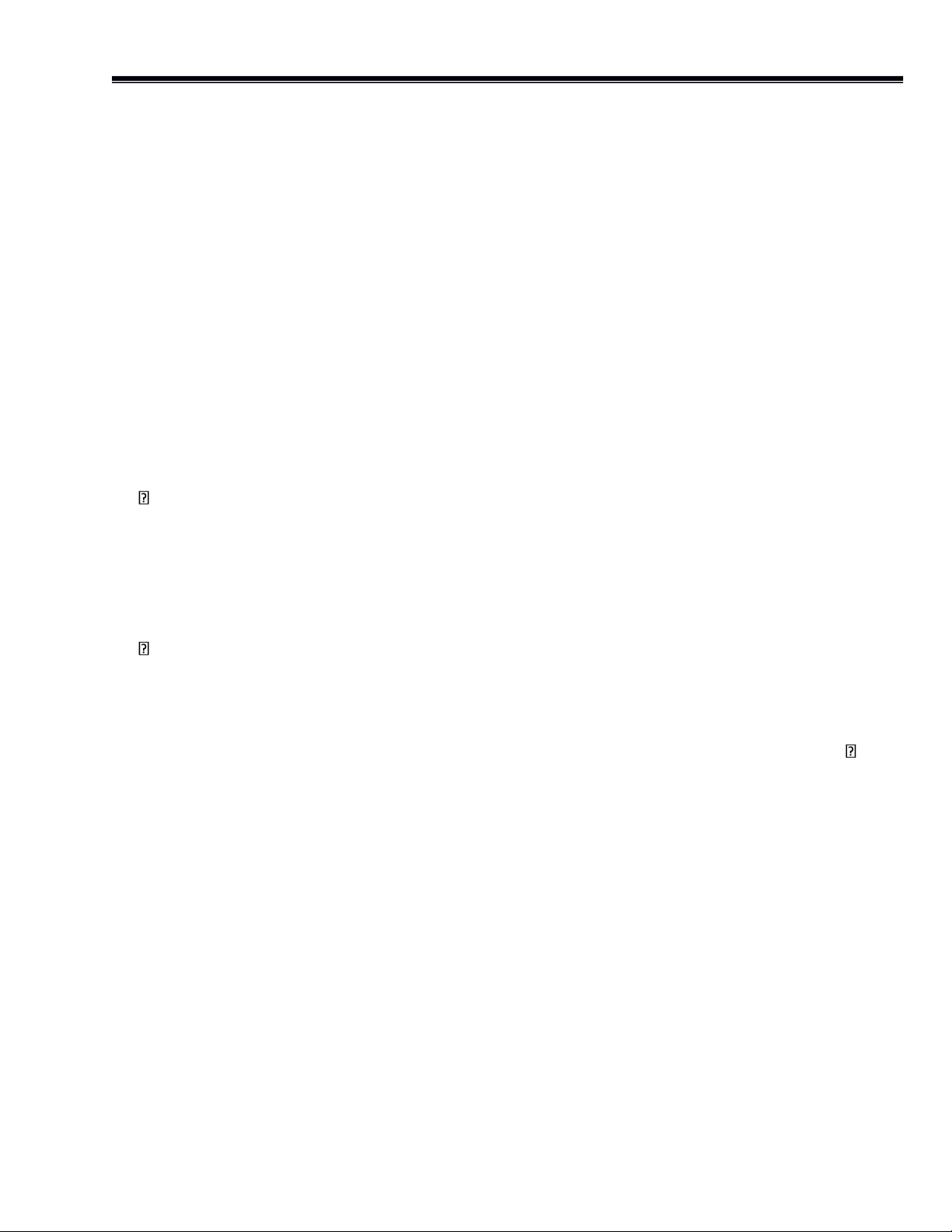
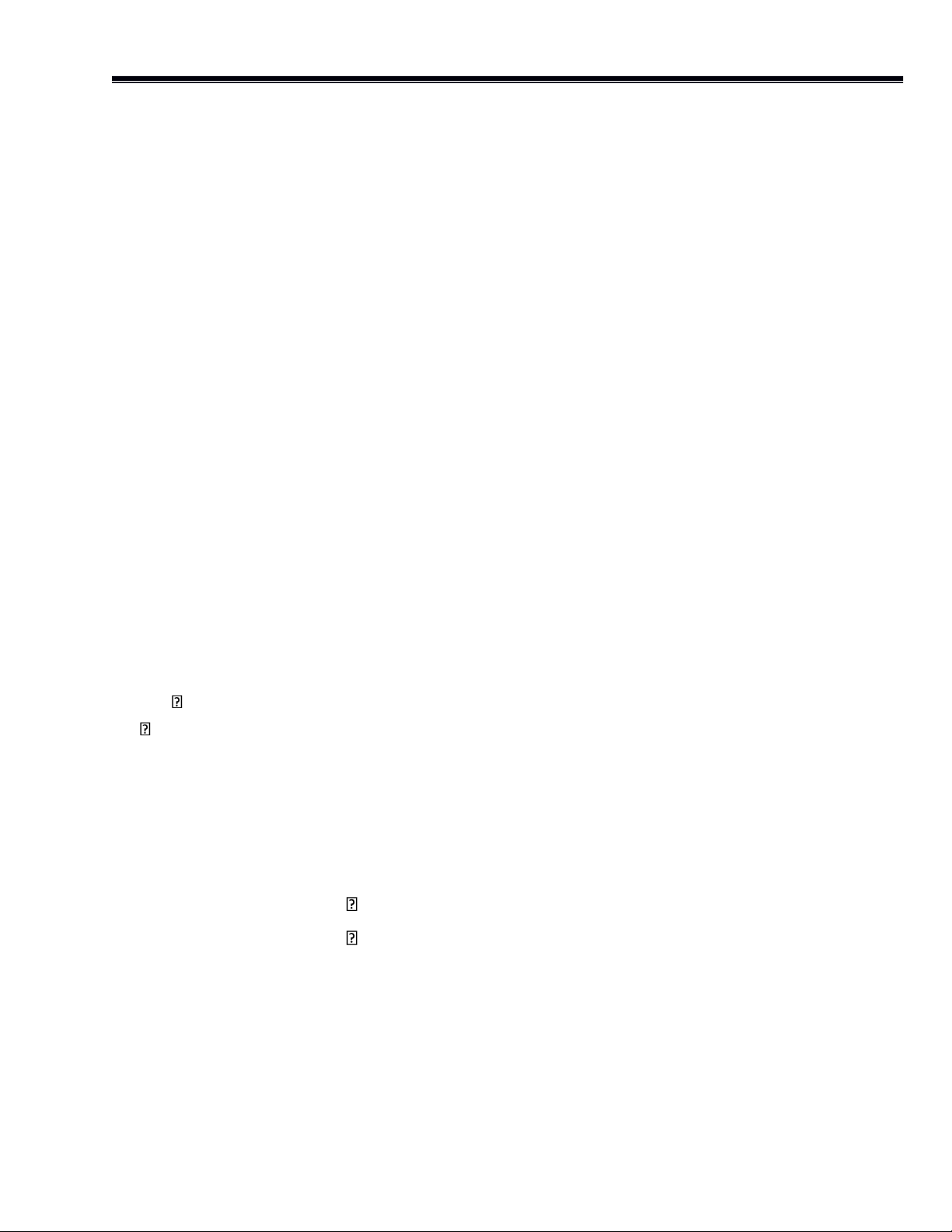
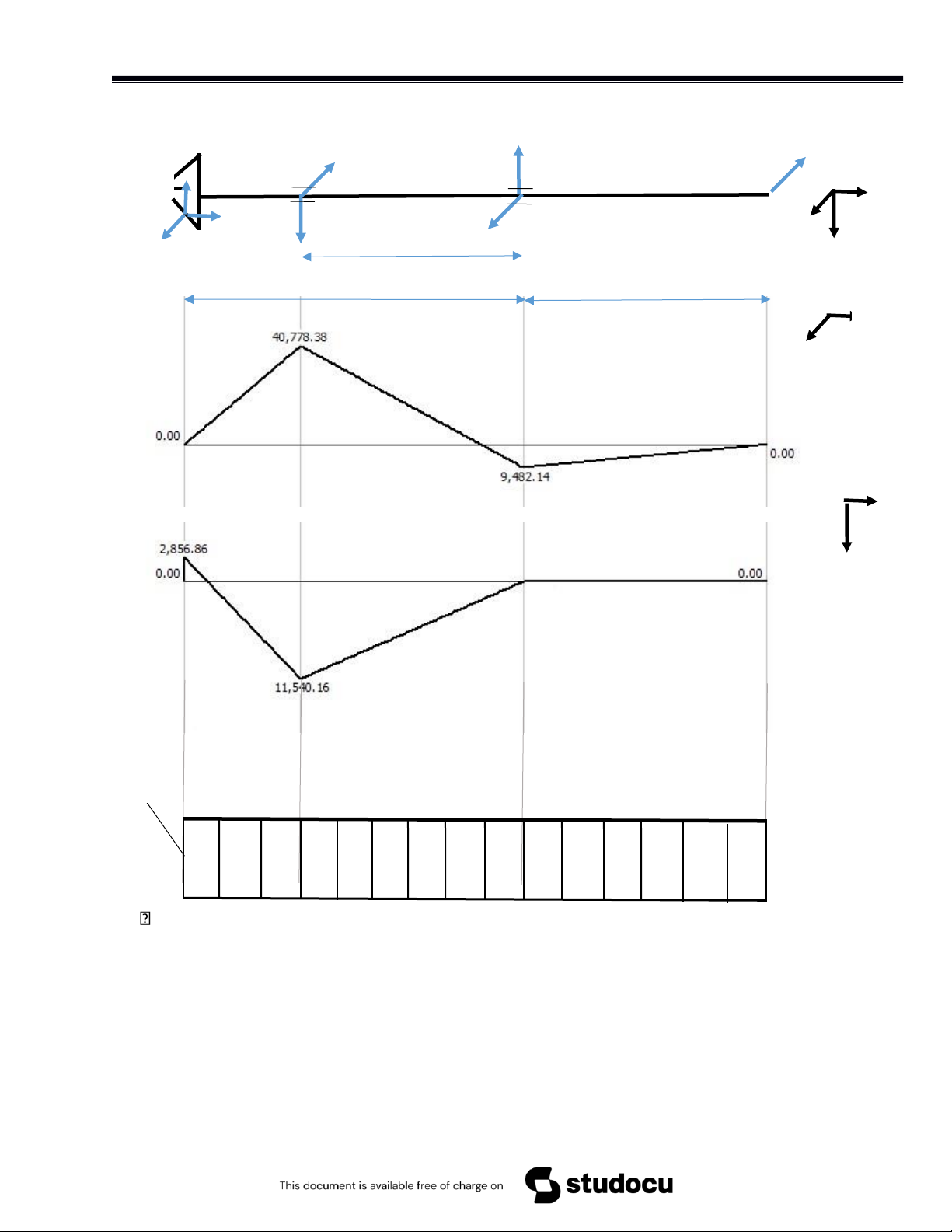
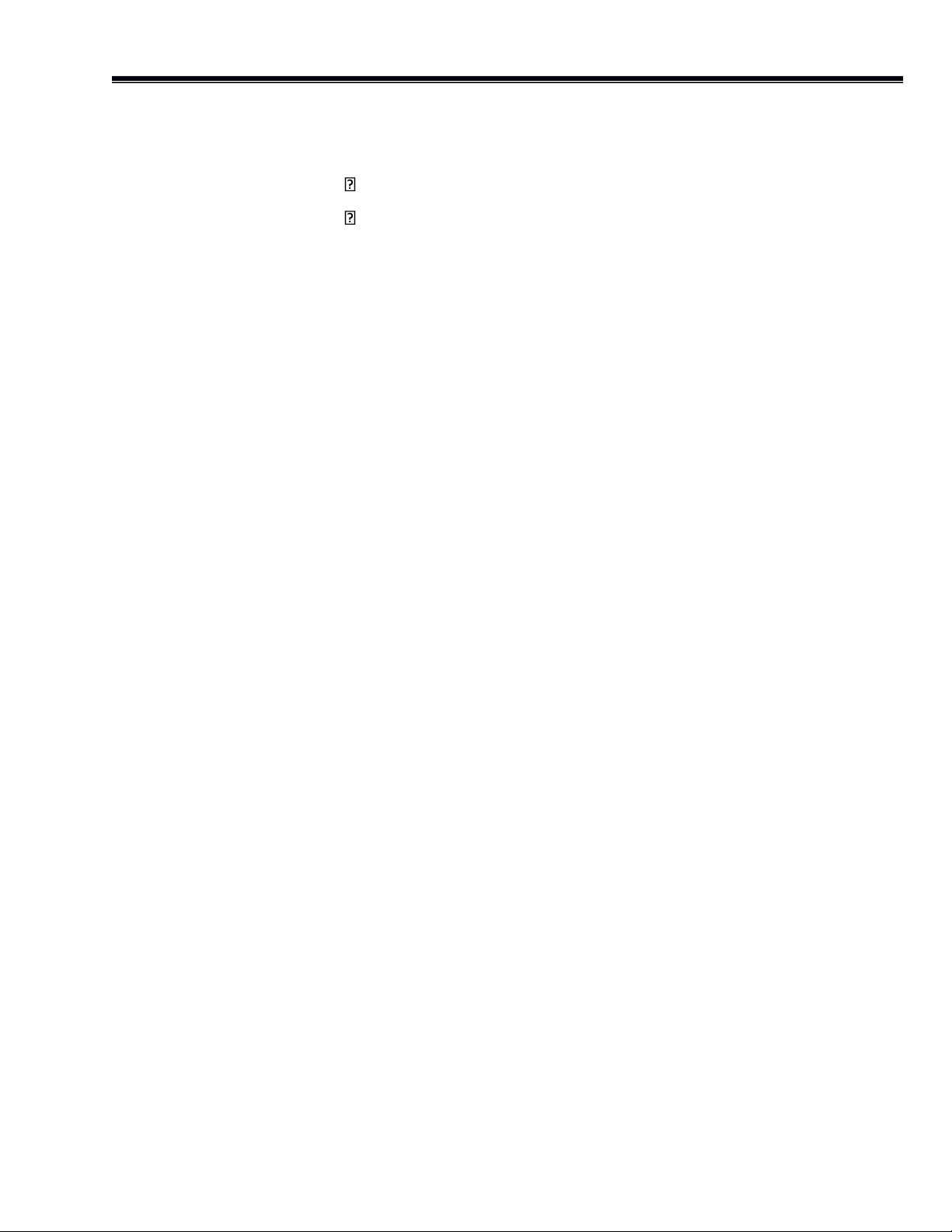
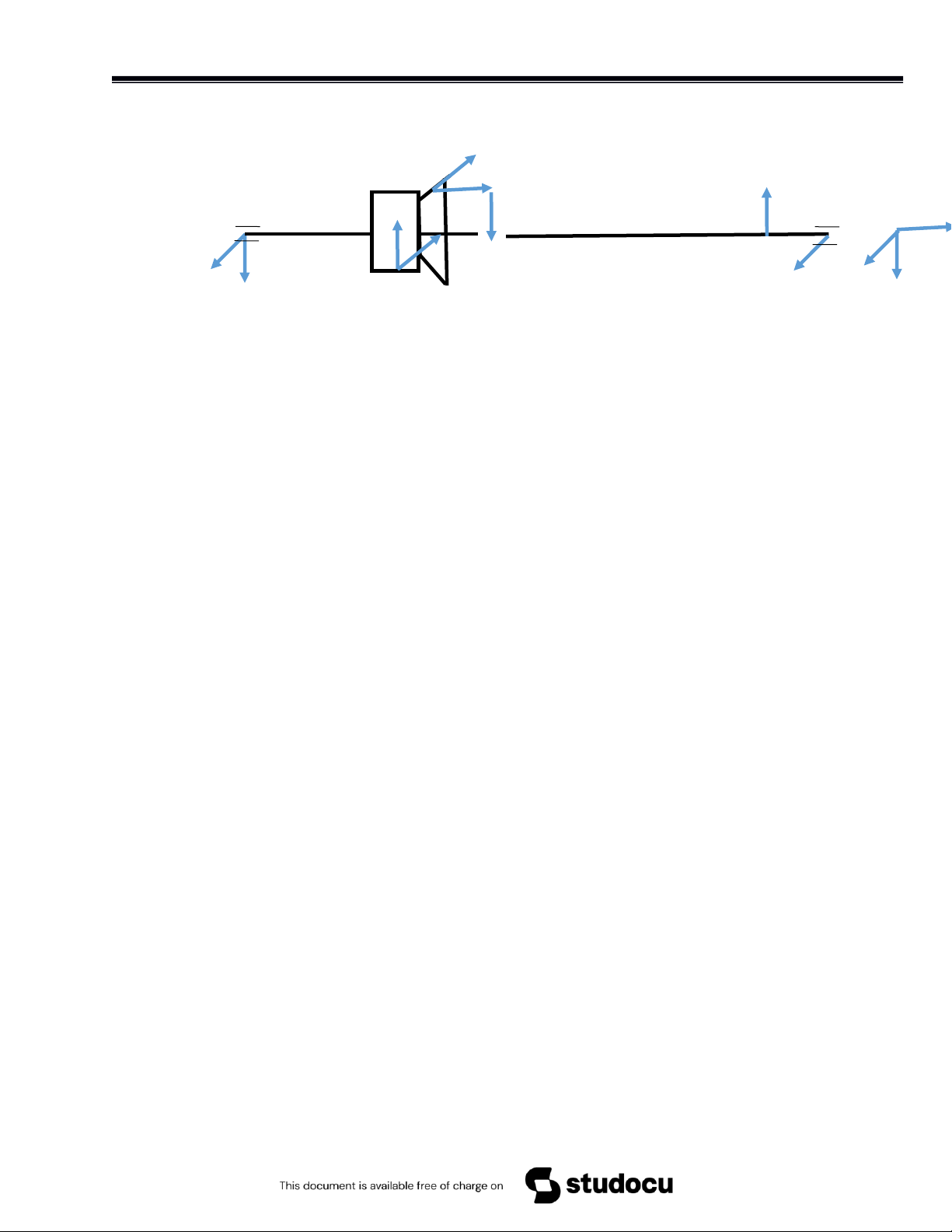
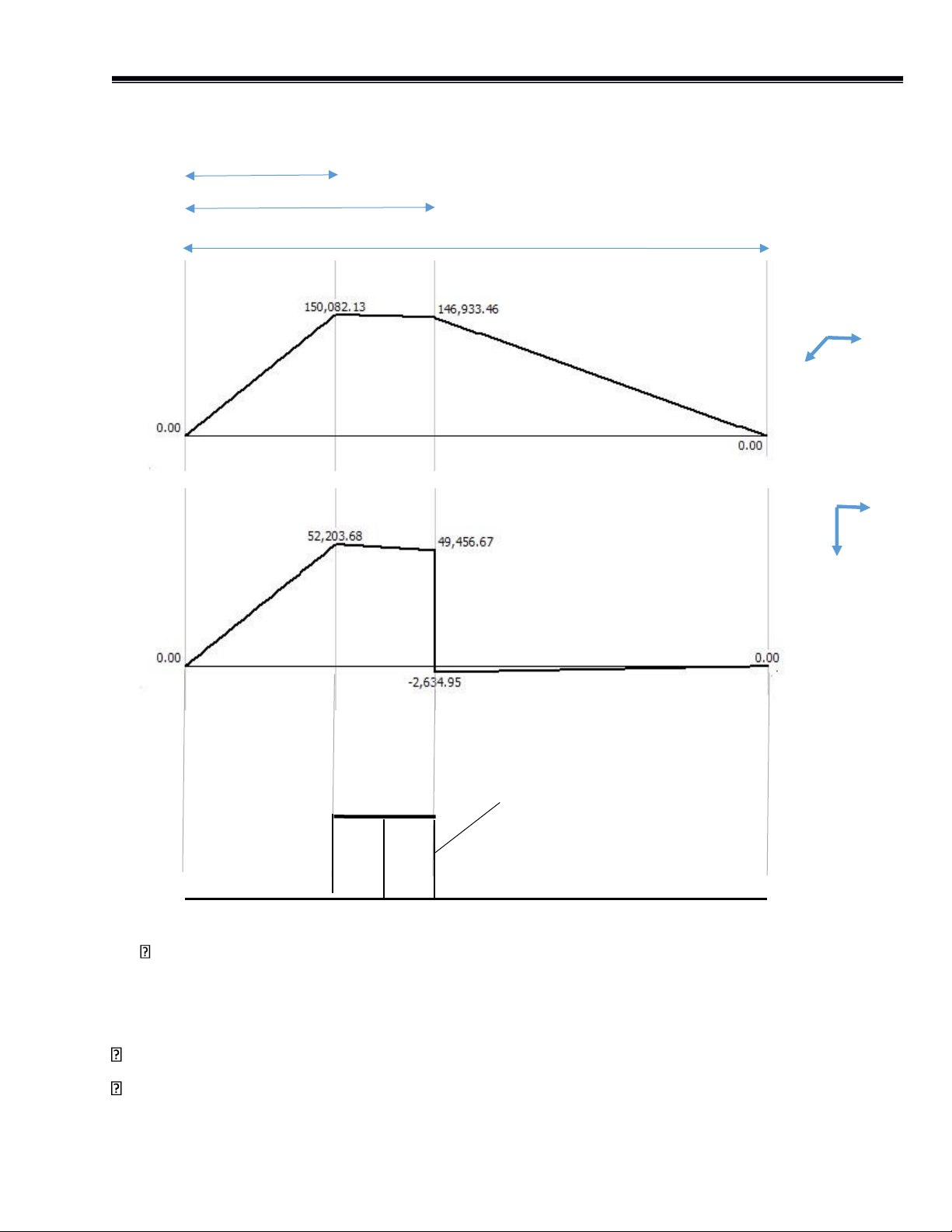
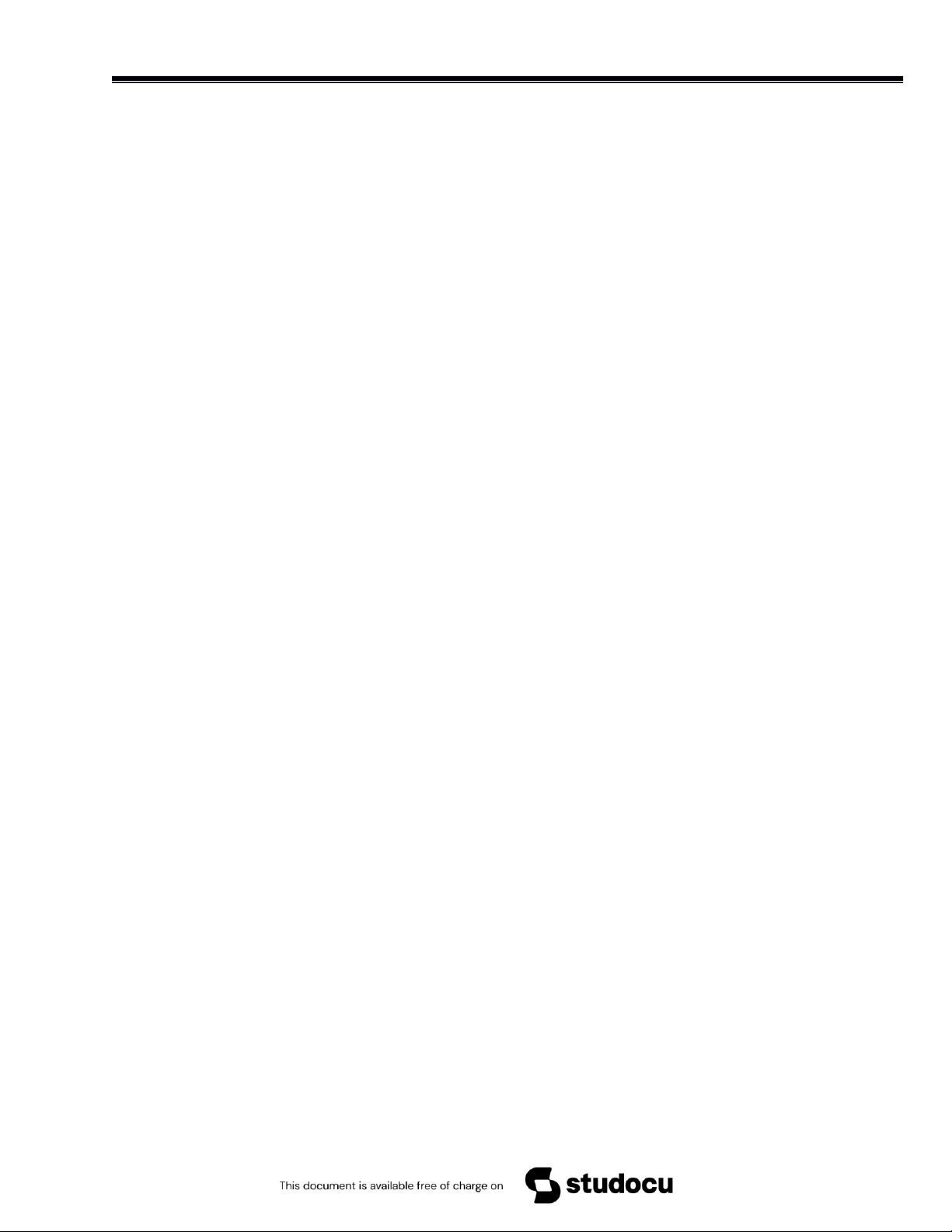
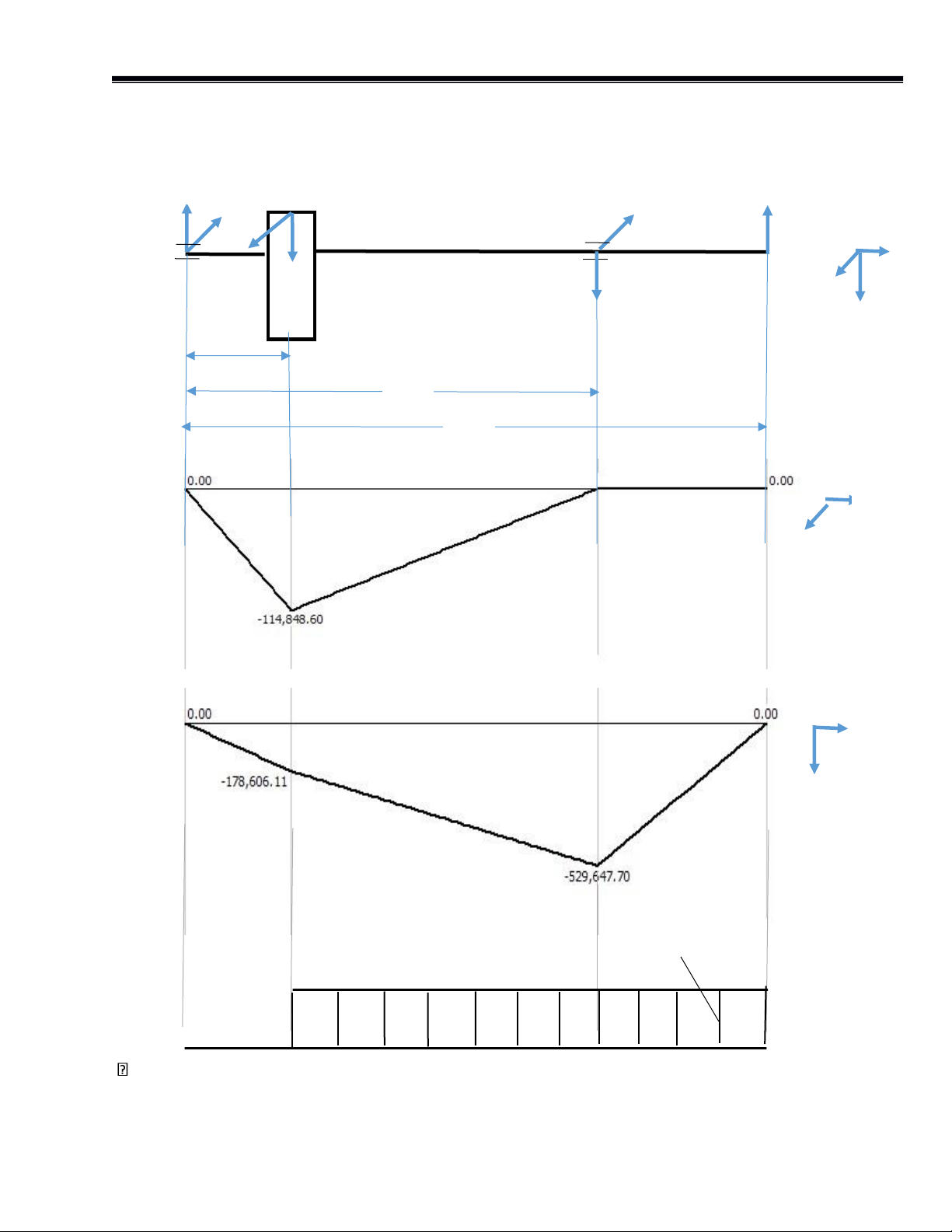
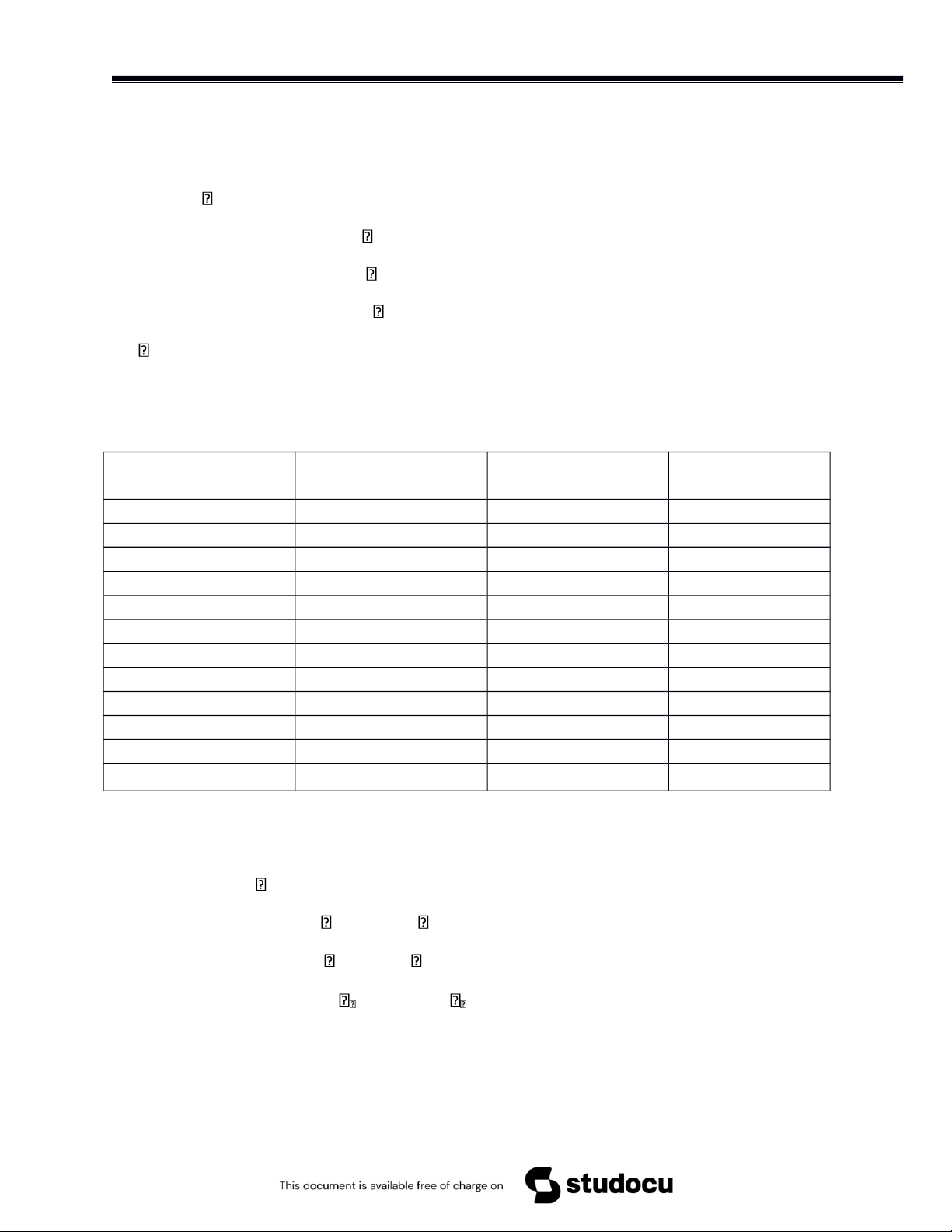
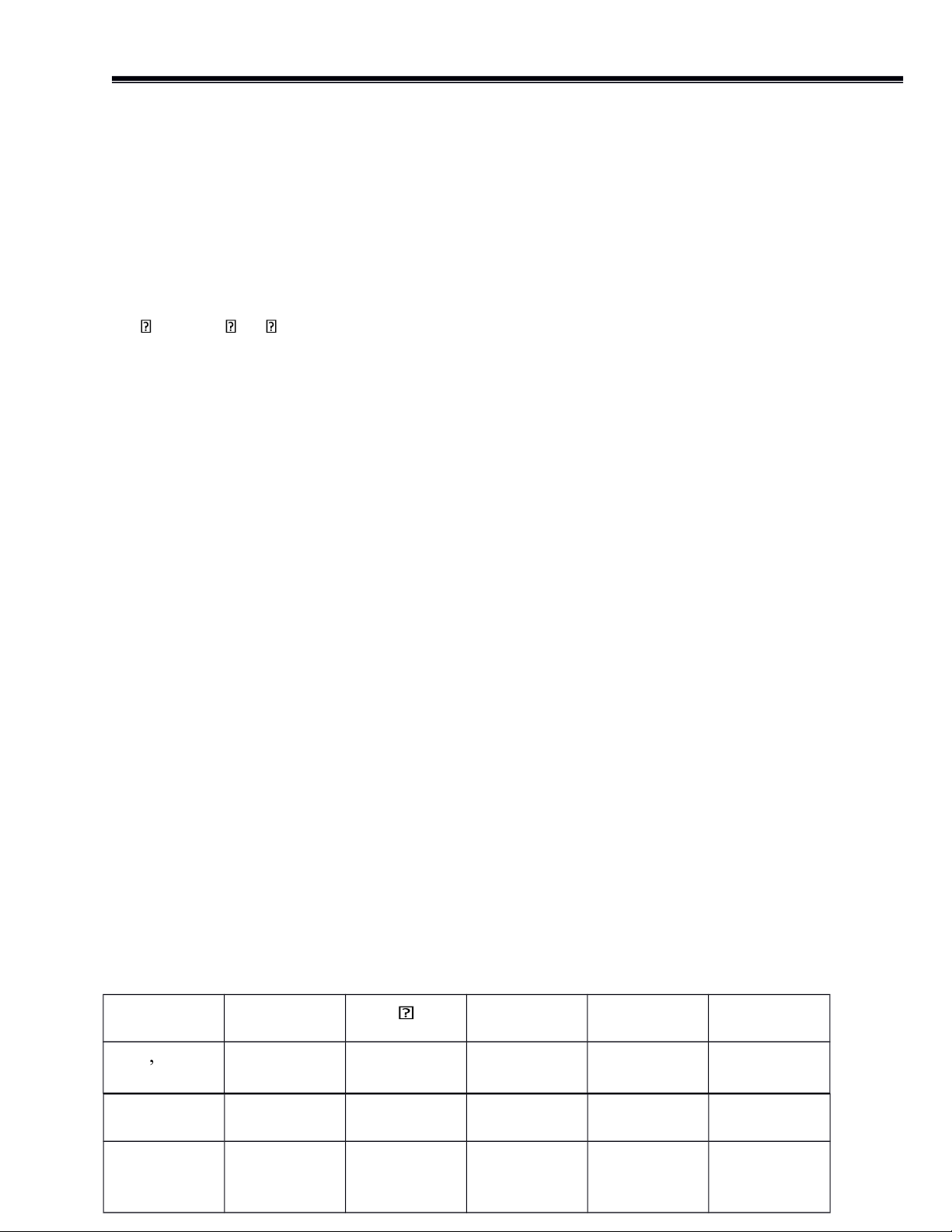
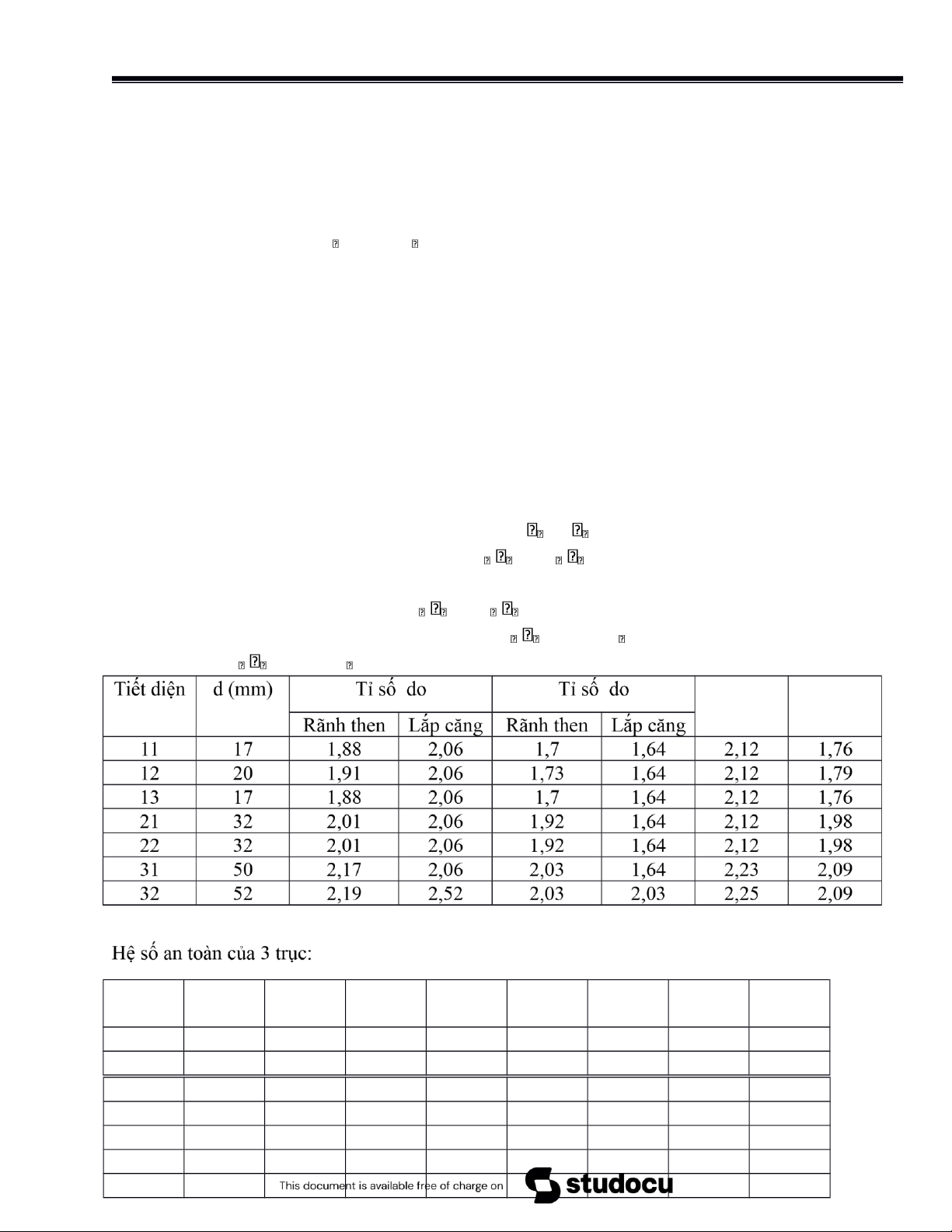
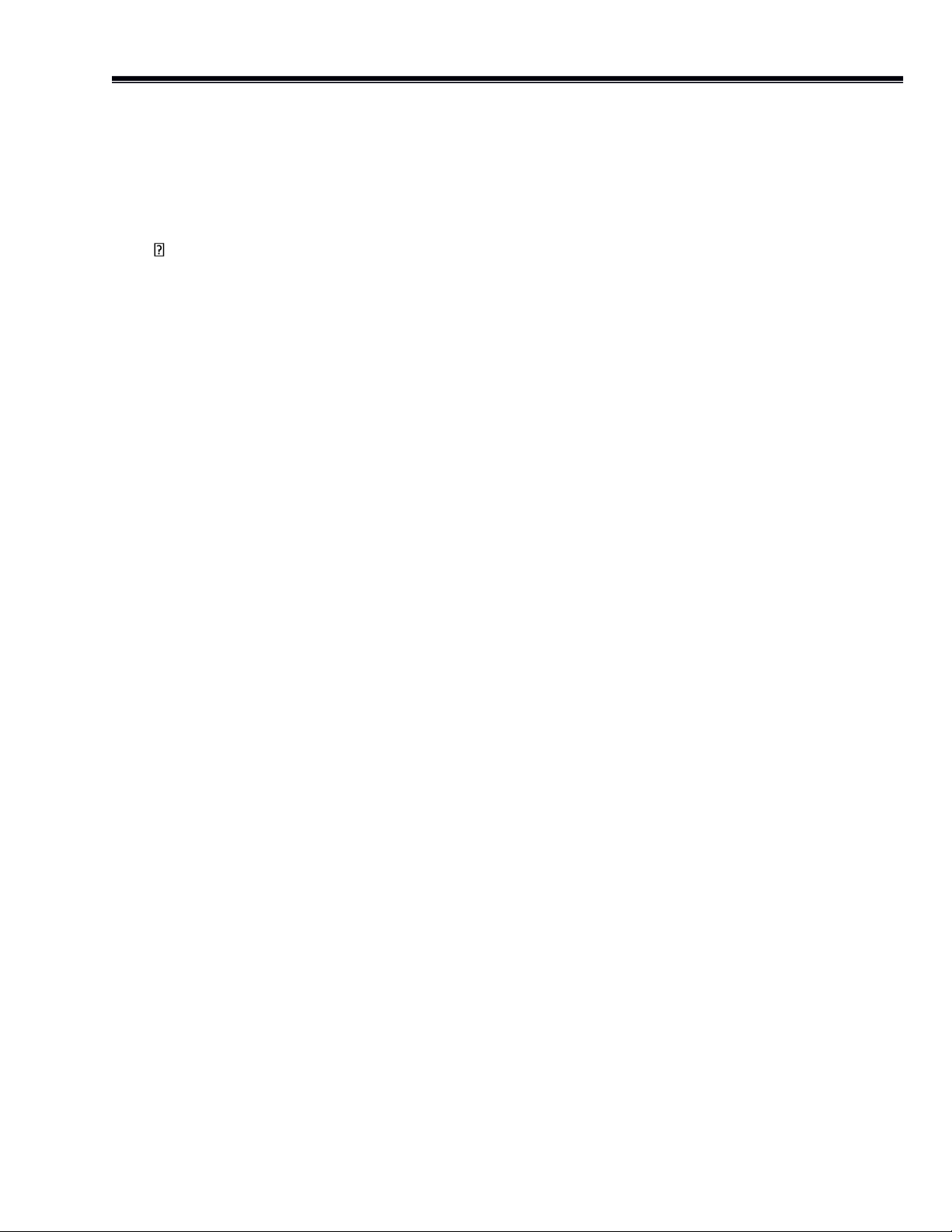
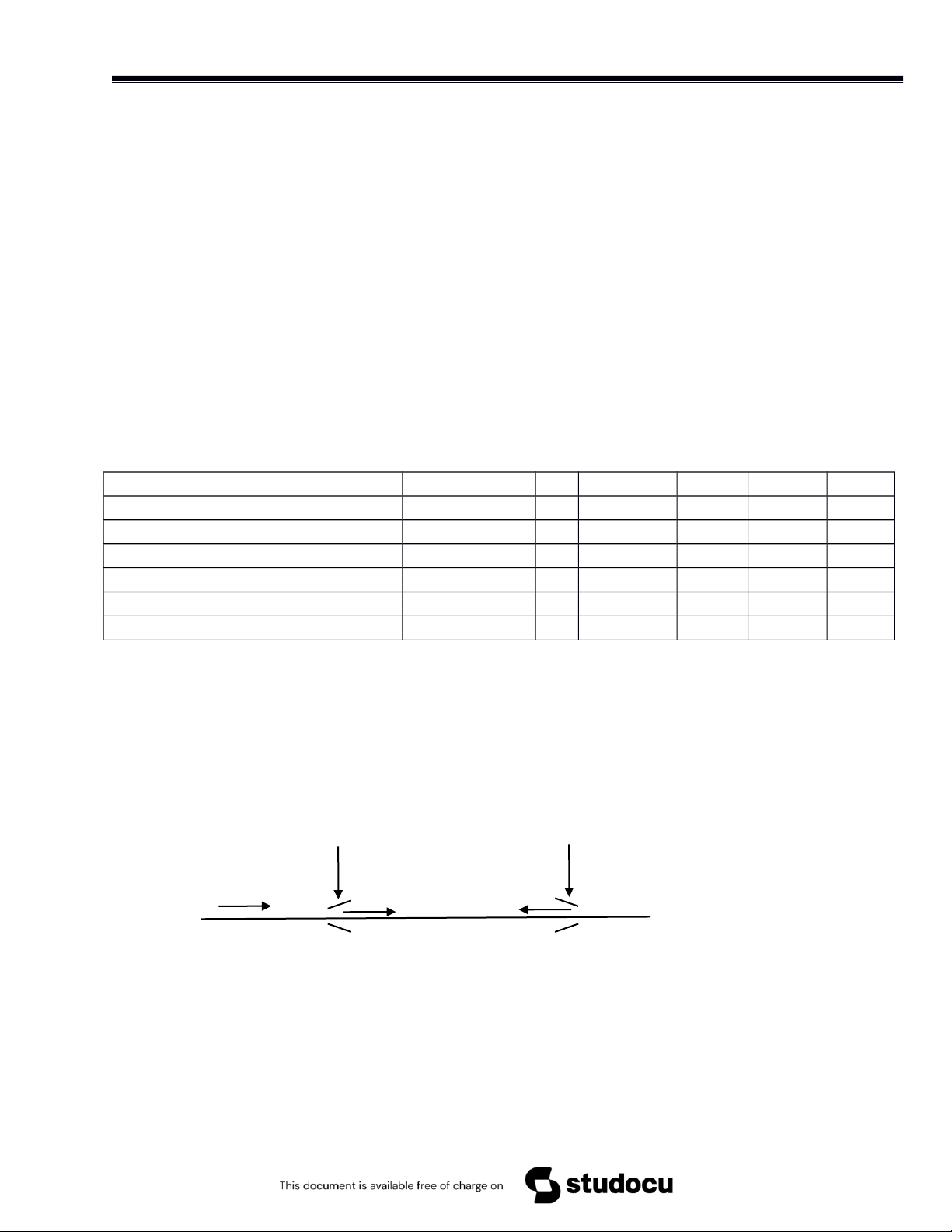
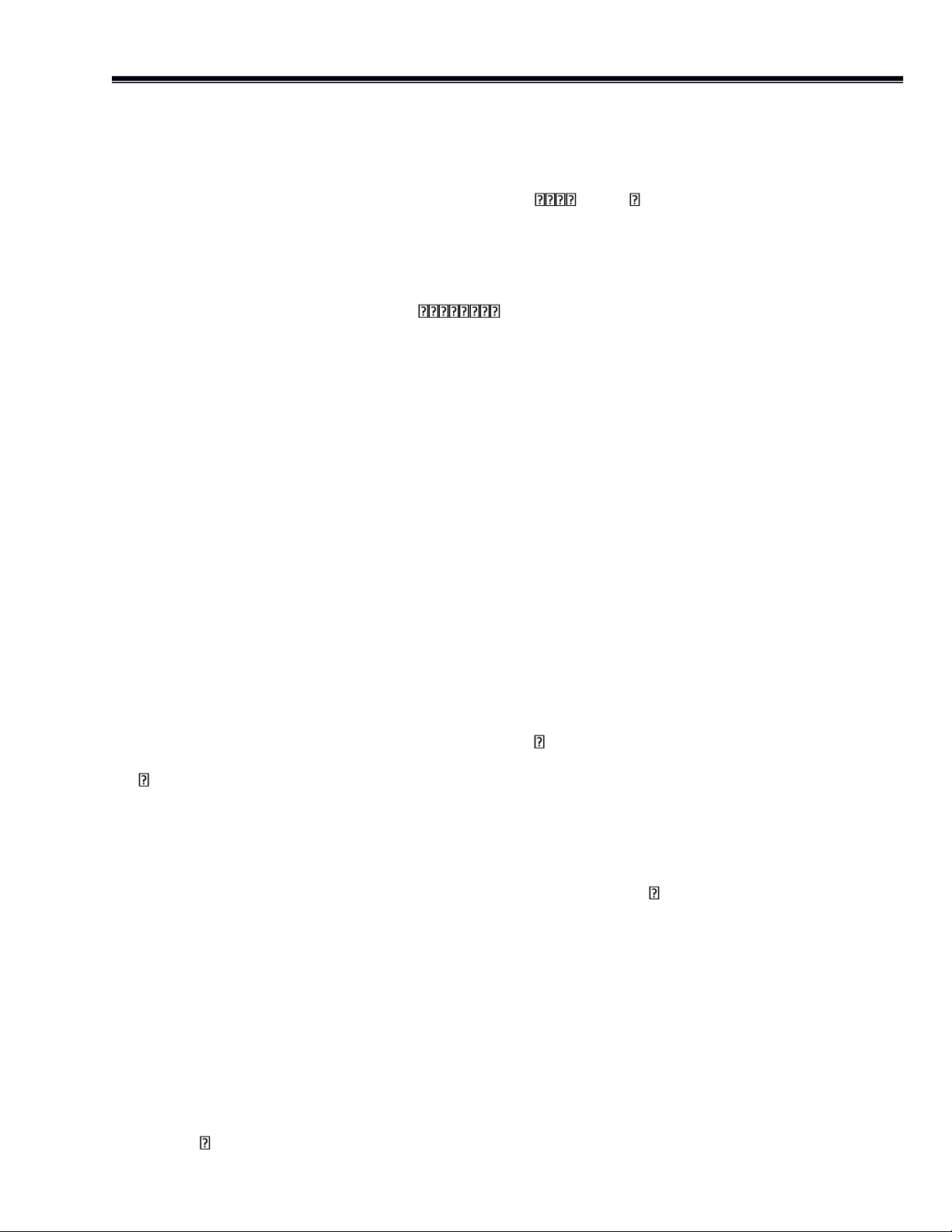
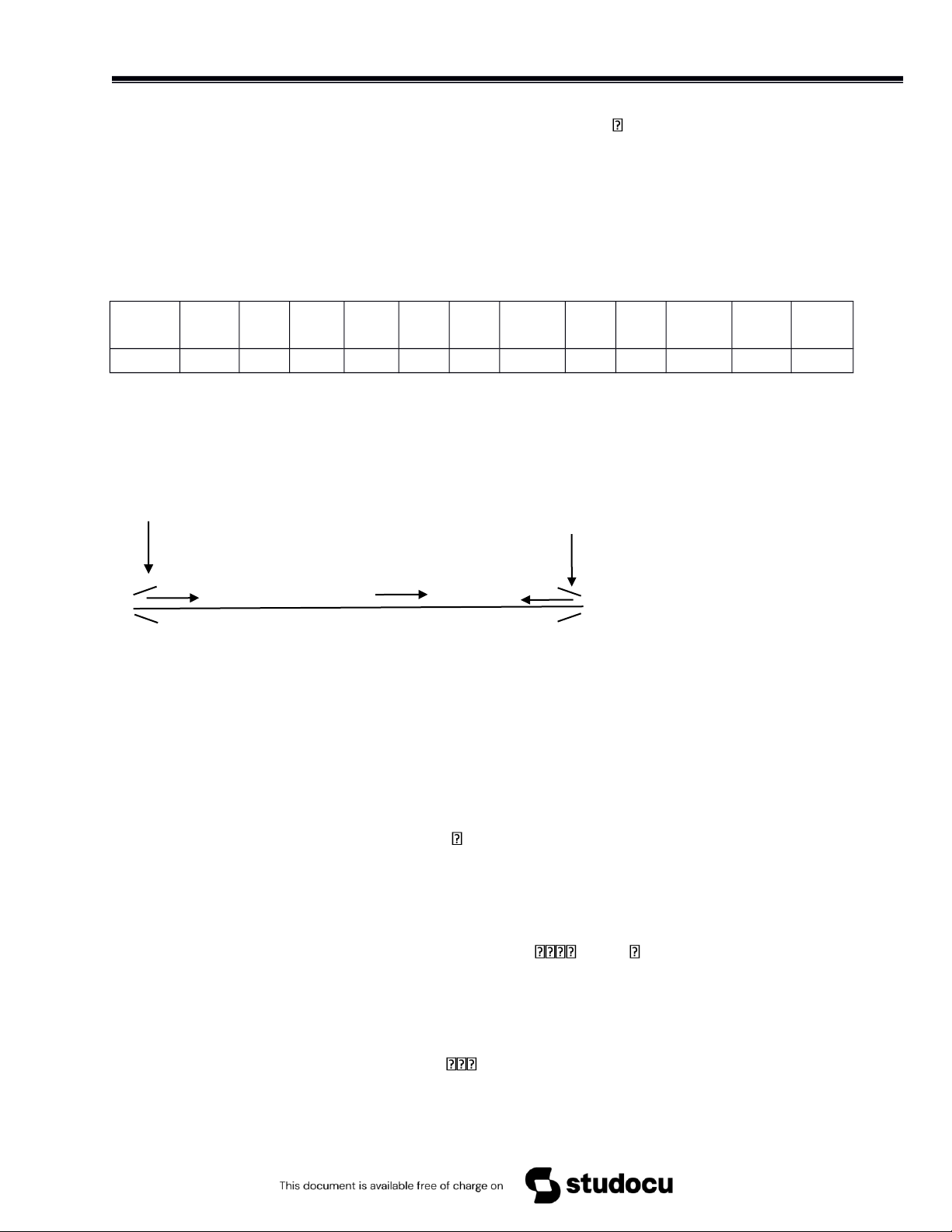
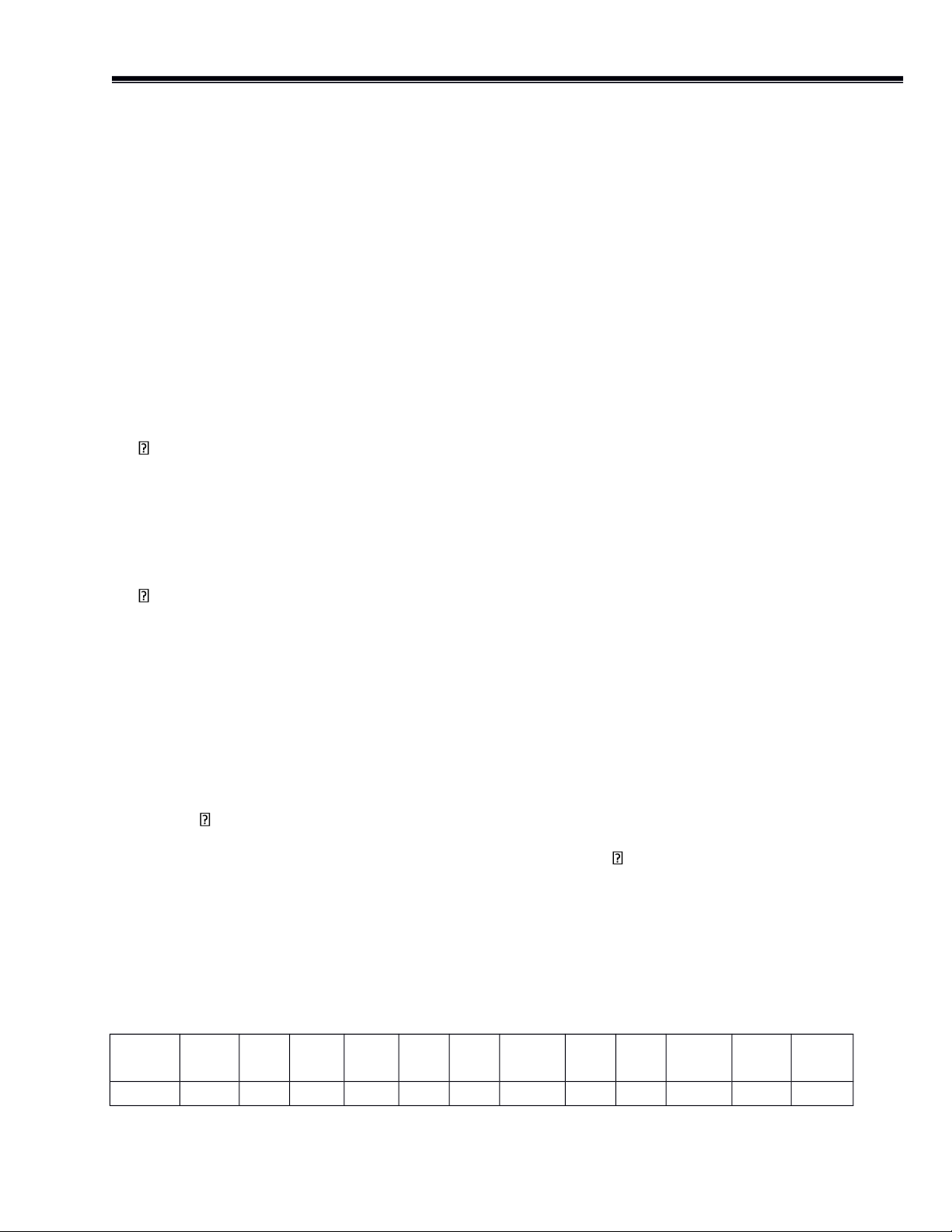
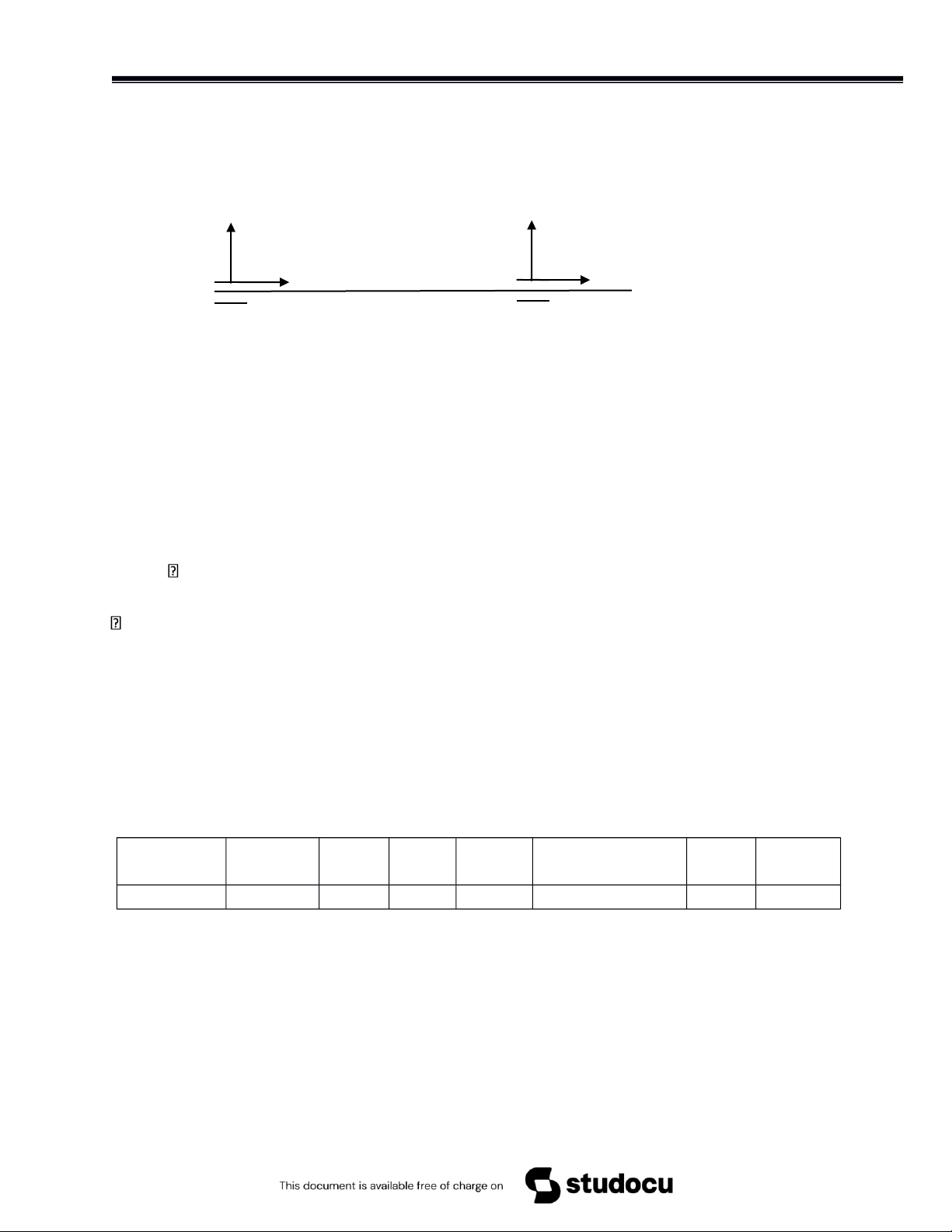
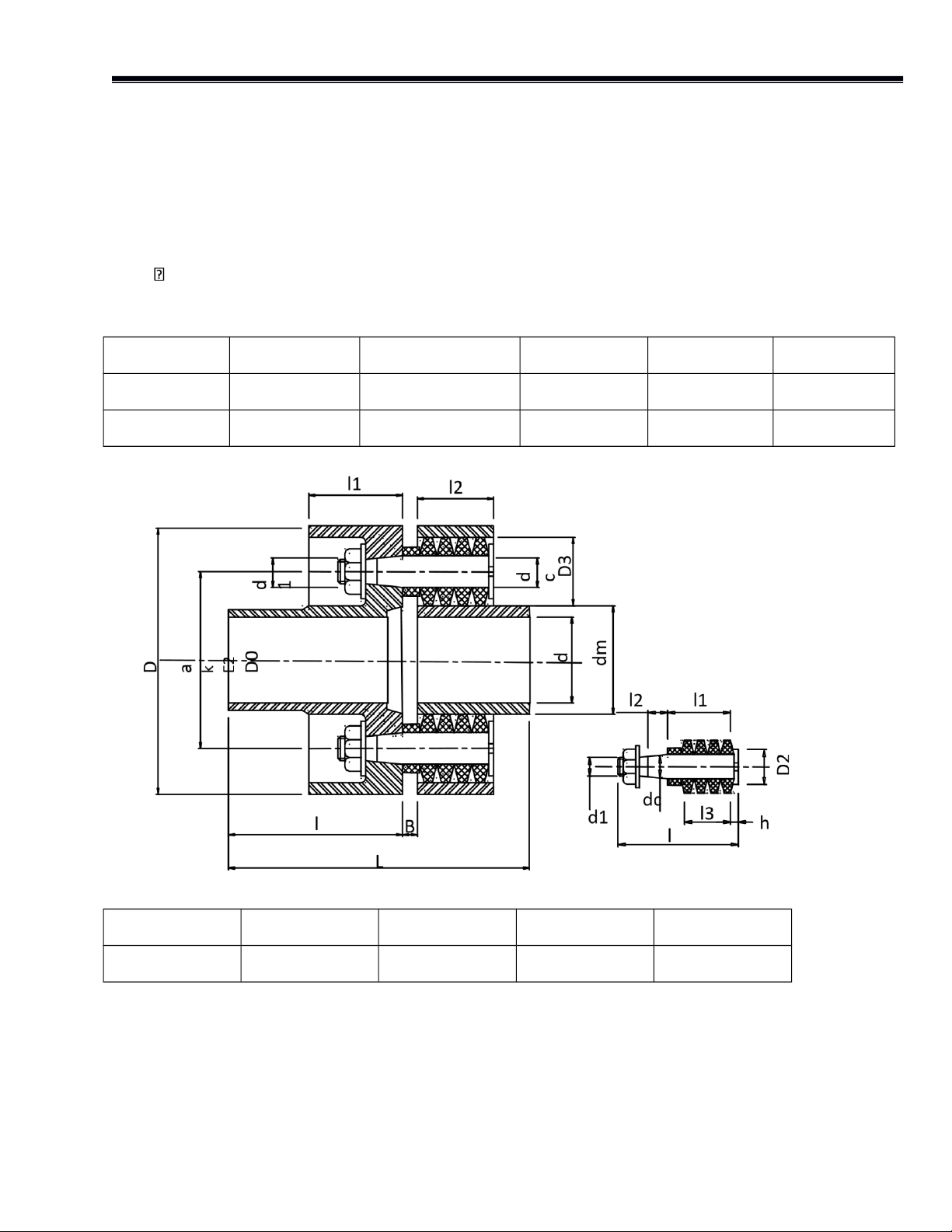
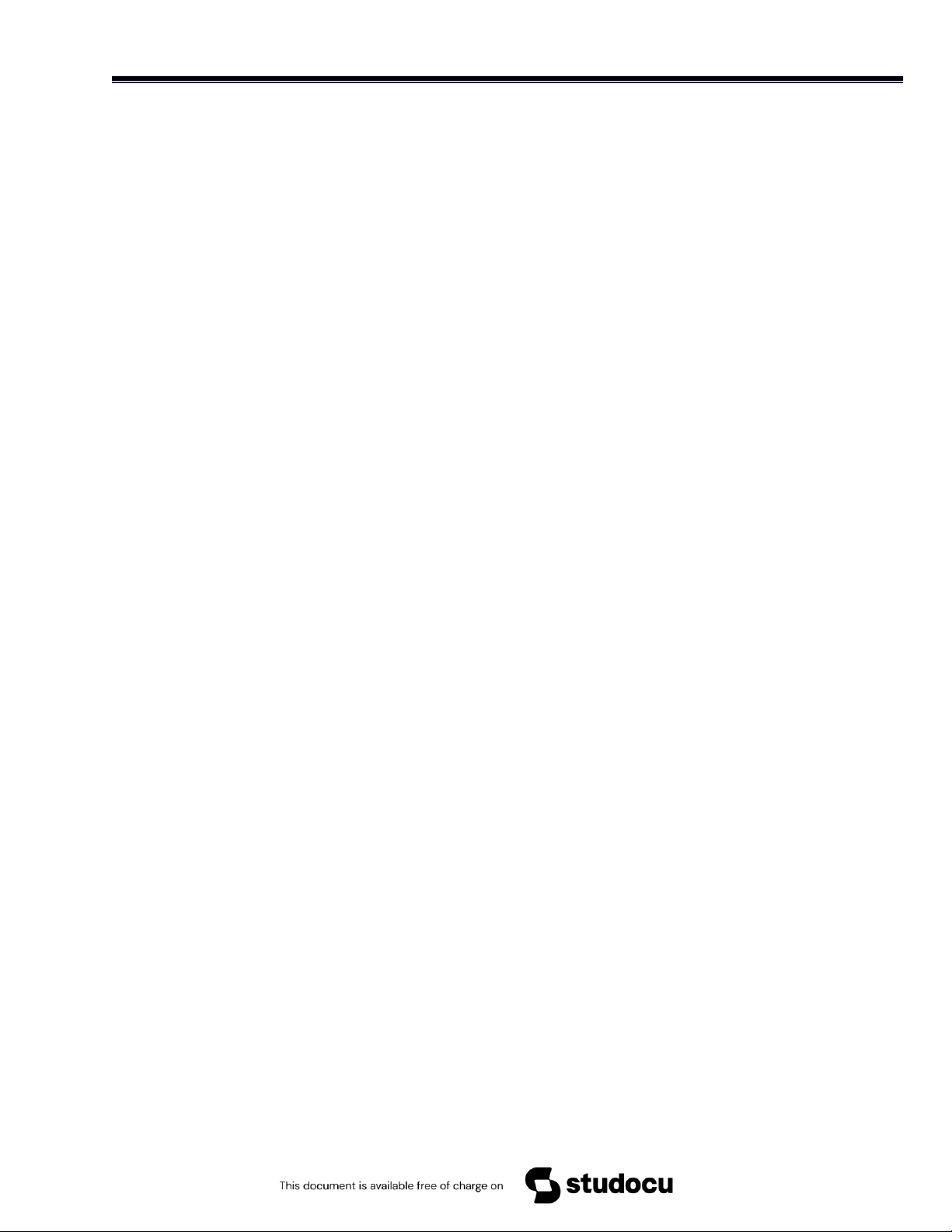
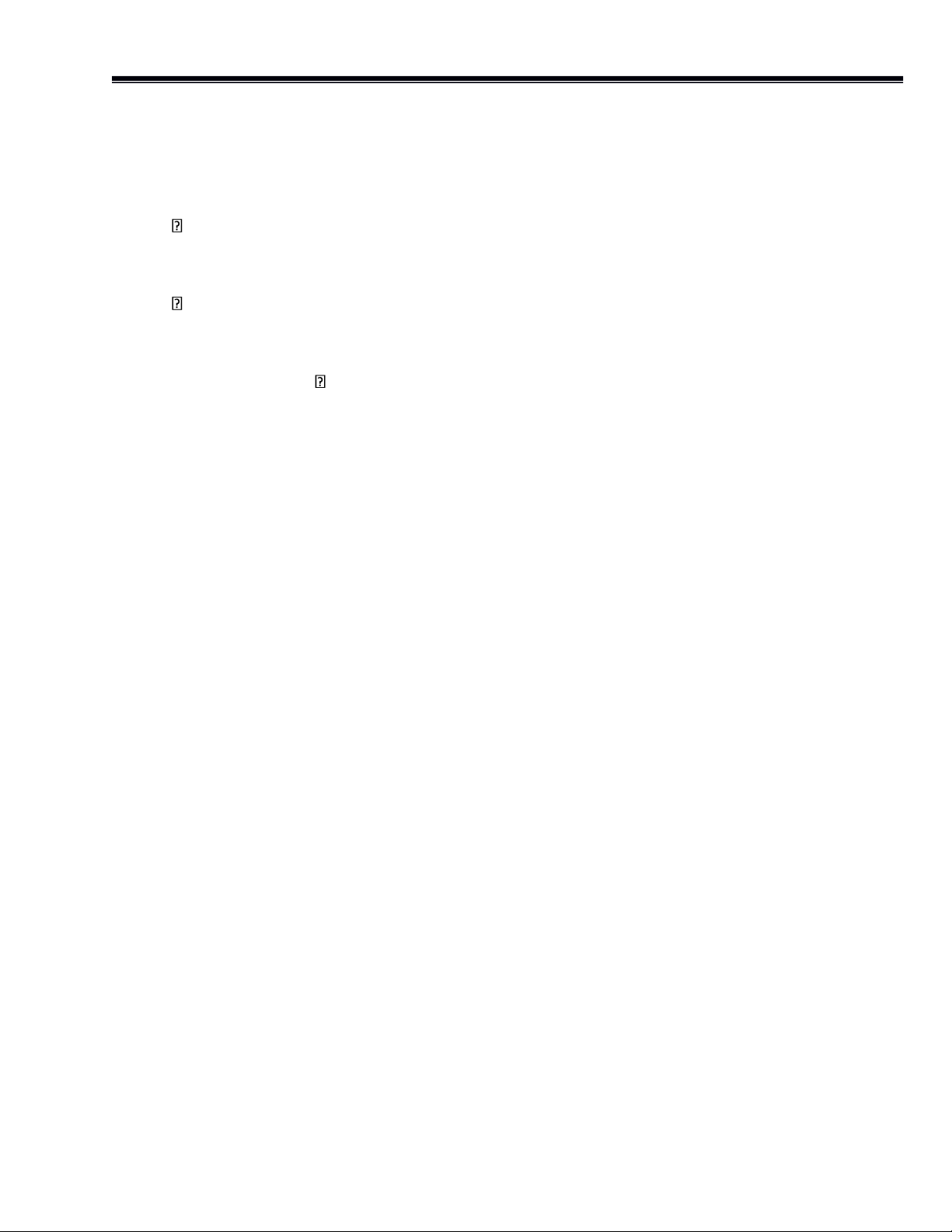
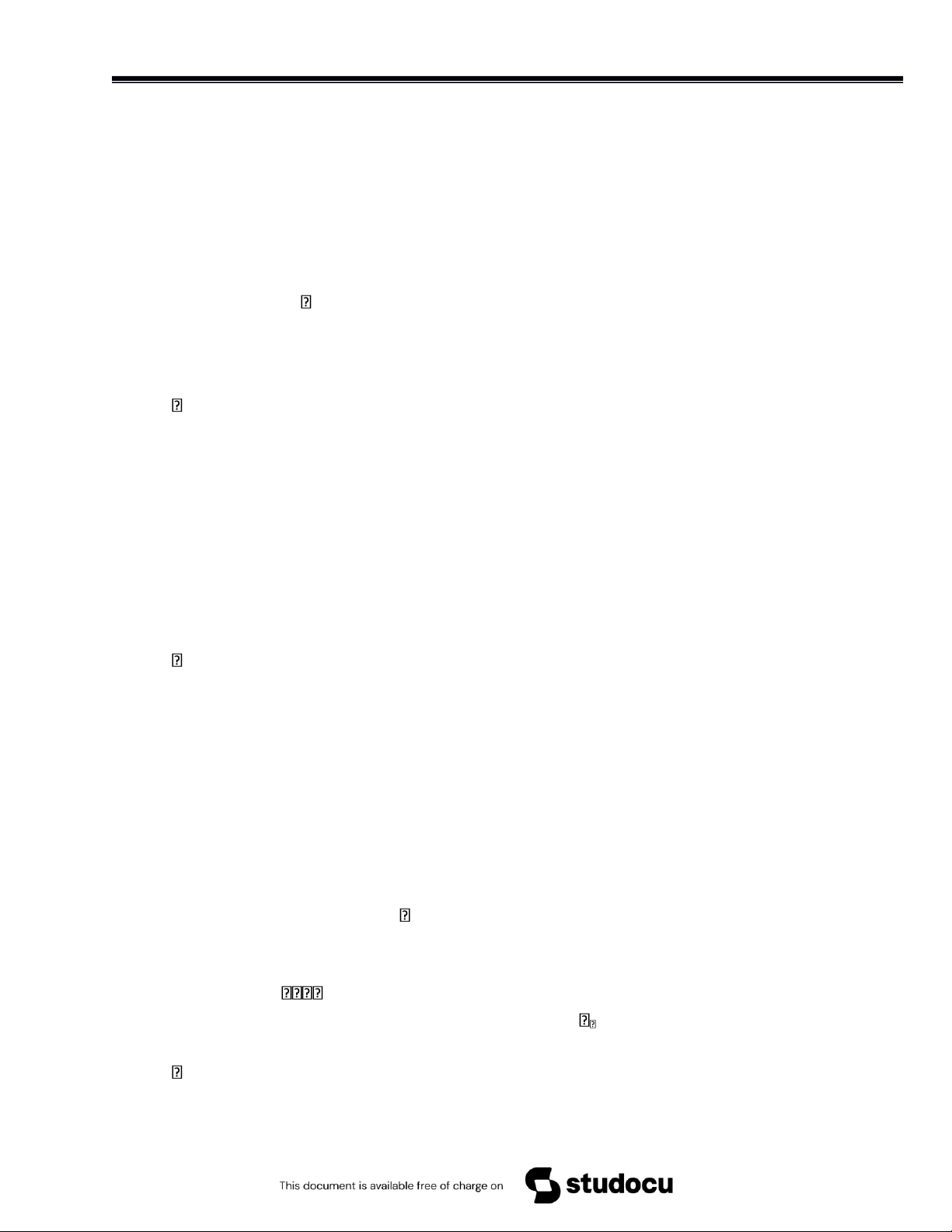
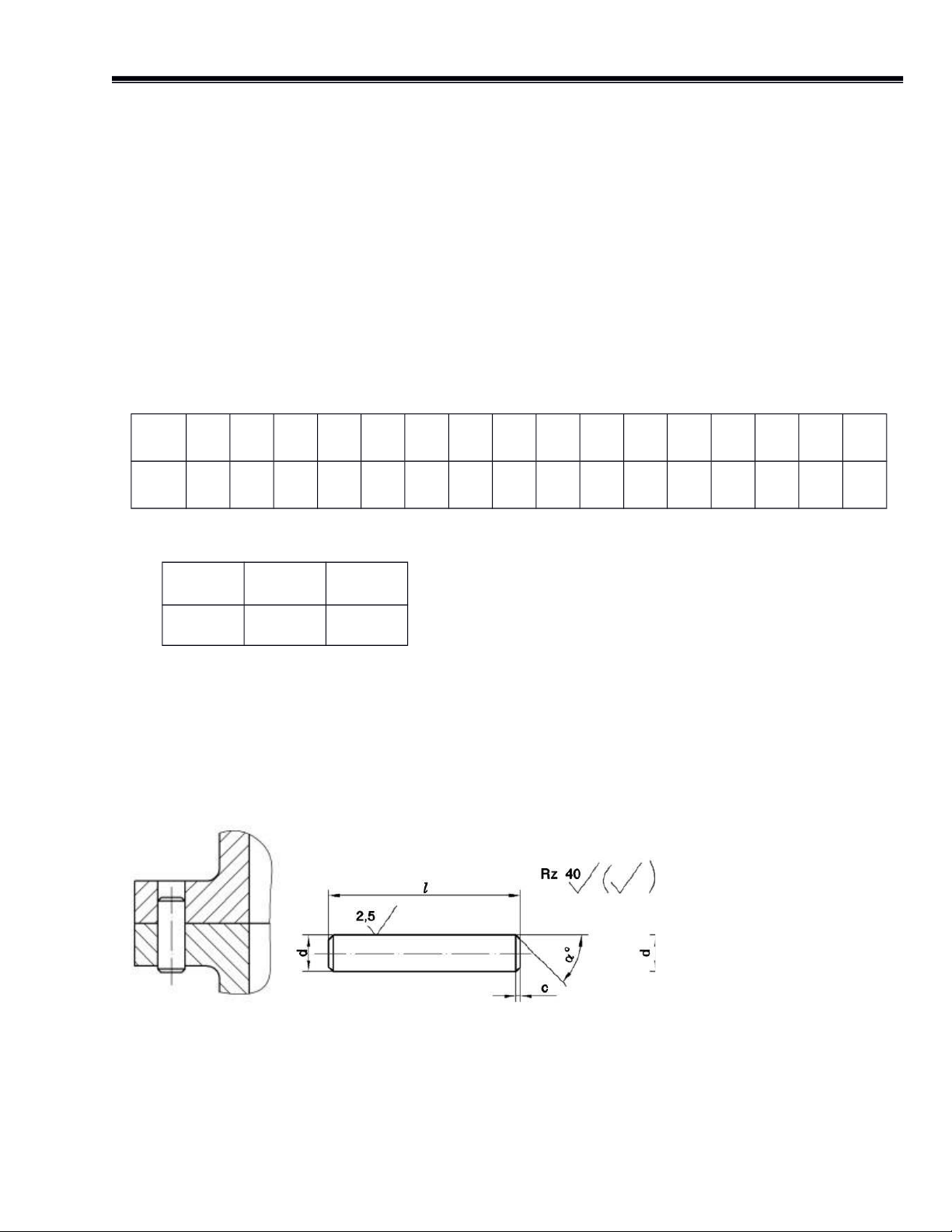
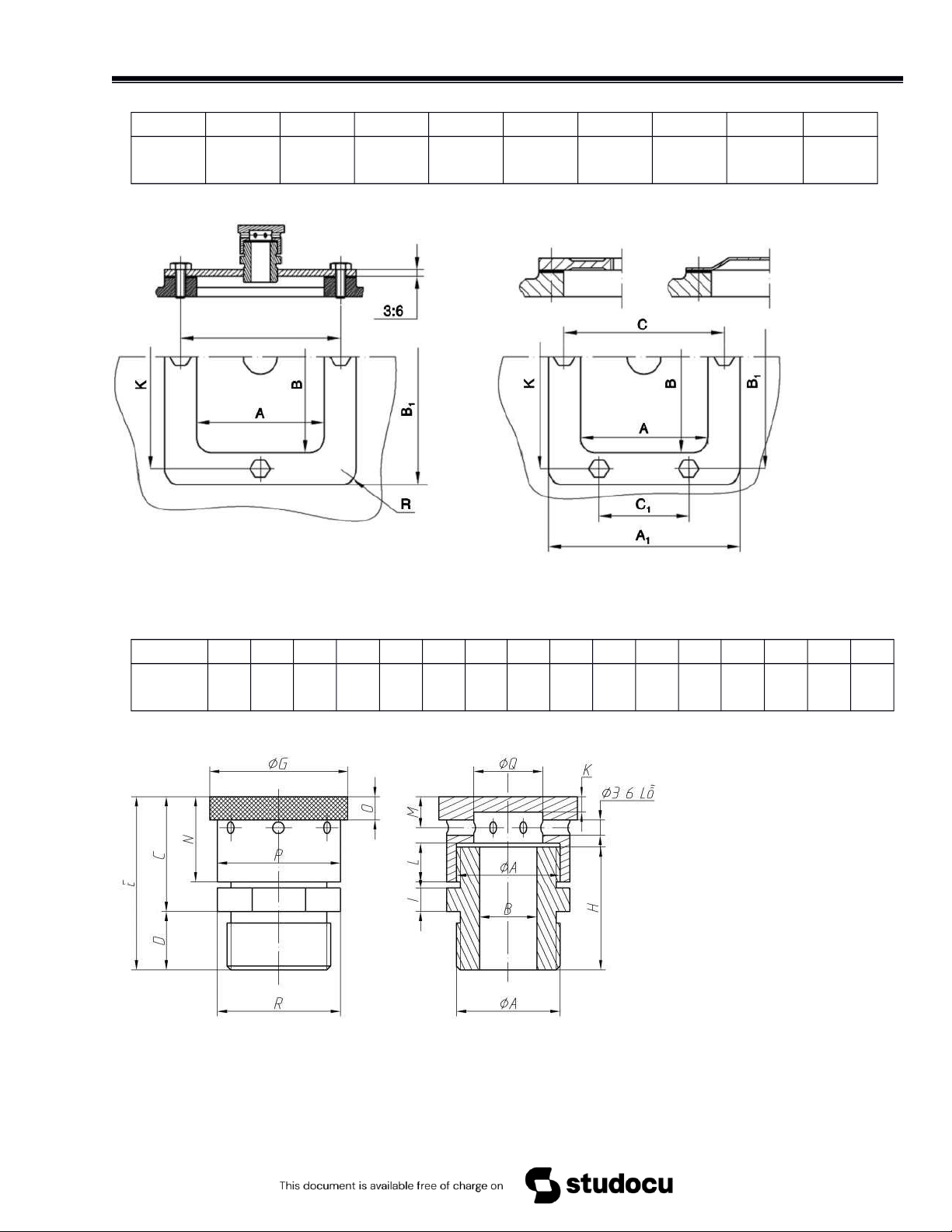
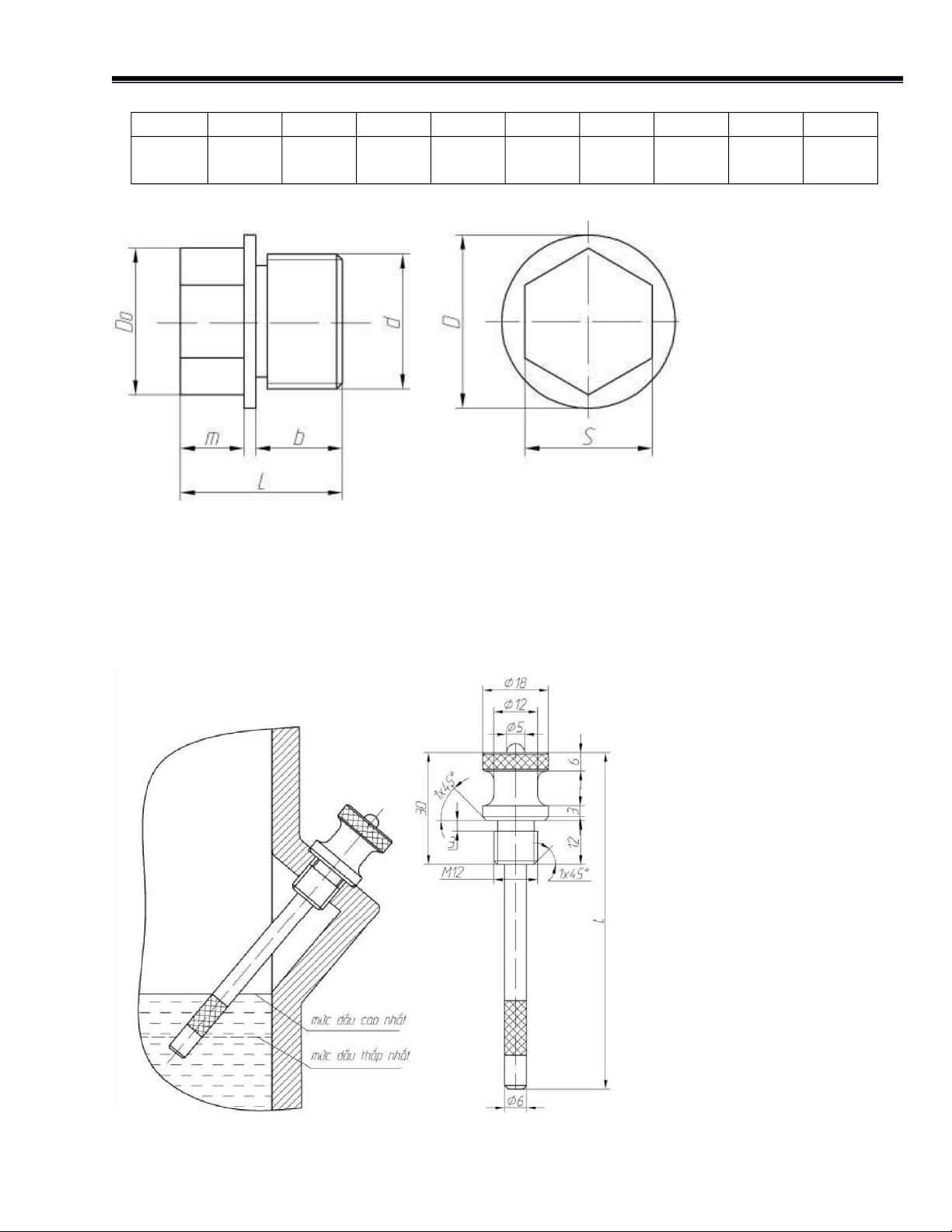
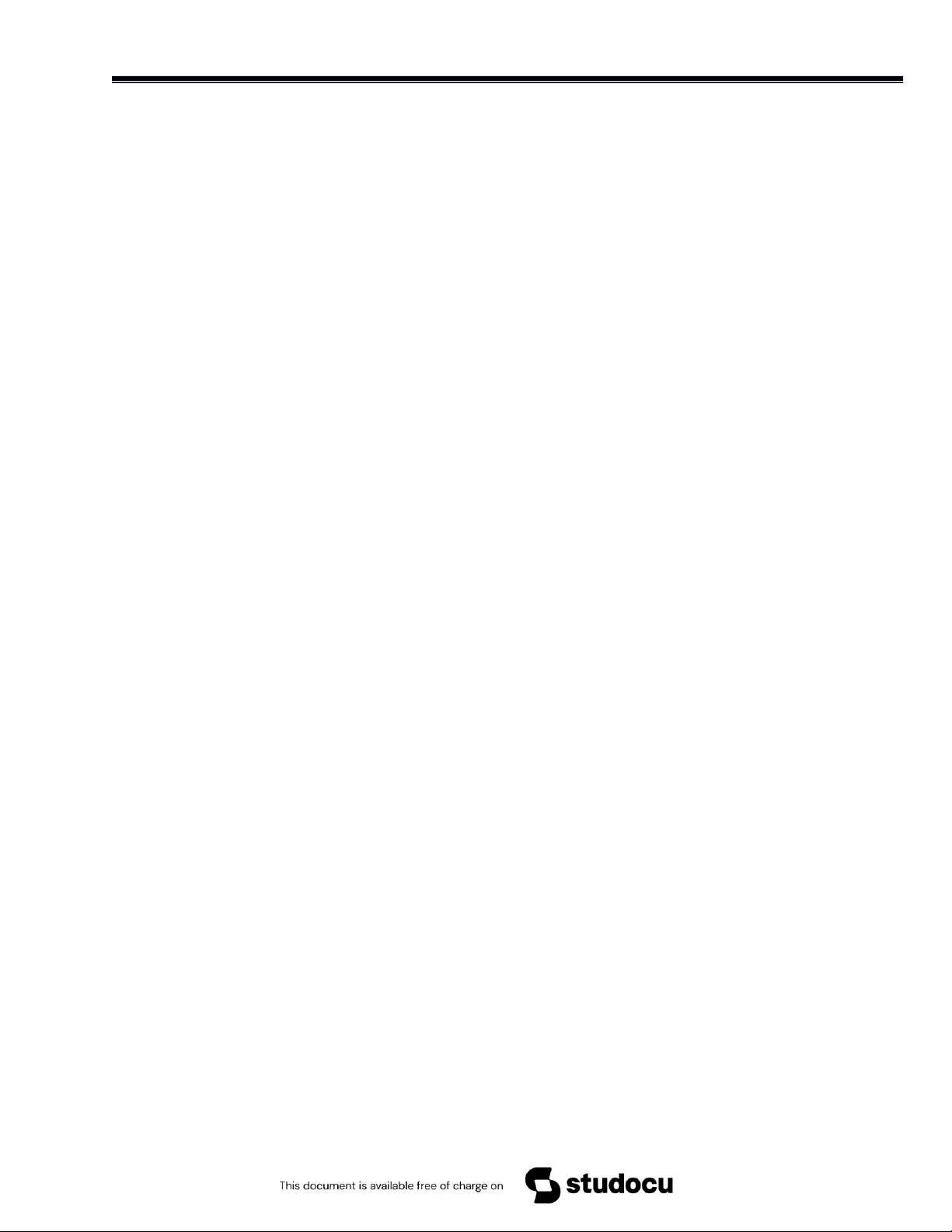
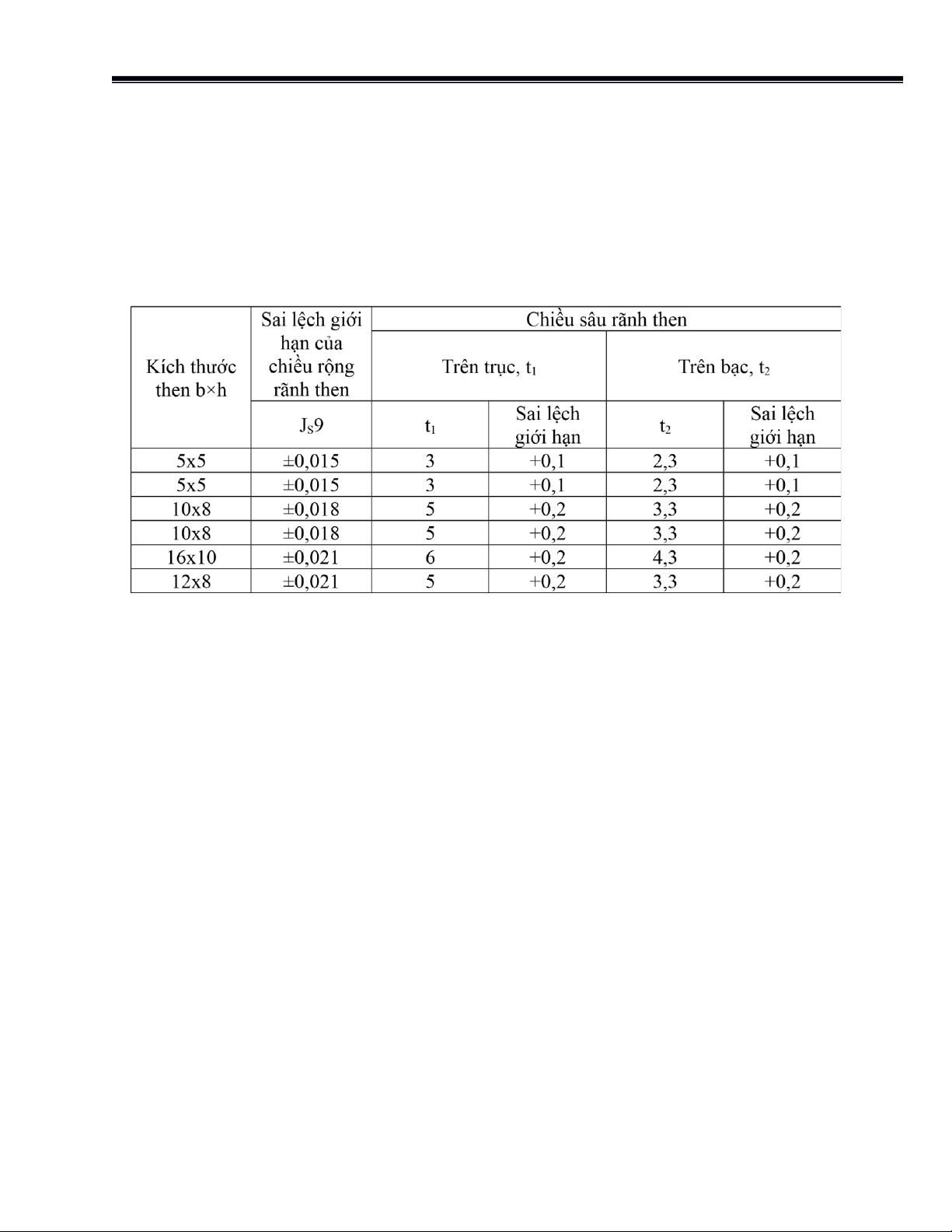
Preview text:
lOMoAR cPSD| 15962736 LỜI MỞ ĐẦU
Đồ án môn học Chi tiết máy là một trong những đồ án chuyên ngành chính đối với sinh viên
ngành cơ khí nói chung và chuyên ngành cơ khí ô tô nói riêng. Đồ án đã cung cấp cho sinh viên
kiến thức về nguyên lý, kết cấu chi tiết máy cũng như quy trình tính toán, thiết kế các chi tiết máy.
Đồ án bao gồm những nội dung cơ bản trong thiết kế máy và hệ thống dẫn động cơ khí:
tính toán thiết kế chi tiết máy theo các chỉ tiêu chủ yếu về khả năng làm việc; thiết kế kết cấu chi
tiết máy; vỏ, khung và bệ máy; tính chọn các chi tiết tiêu chuẩn; chọn cấp chính xác, dung sai và
lắp ghép; trình bày bản vẽ…Các tiêu chuẩn thiết kế, thuật ngữ và các ký hiệu sử dụng trong đồ án
đều tuân theo tiêu chuẩn Việt Nam (TCVN).
Khi thiết kế đồ án Chi tiết máy, chúng ta có thể tham khảo các giáo trình như Công nghệ
chế tạo máy, Khoa học vật liệu, Nguyên lý máy, Chi tiết máy, Dung sai lắp ghép, Tính toán thiết
kế hệ dẫn động cơ khí…Ngày nay với sự phát triển mạnh của công nghệ máy tính, chúng ta còn có
sự trợ giúp của các công cụ, phần mềm tính toán thiết kê và trình bày bản vẽ. Khi đi vào thiết kế
thực tế, chúng ta phải sử dụng các tài liệu, sổ tay thiết kế kết hợp với kinh nghiệm thiết kế.
Đối với mỗi sinh viên ngành cơ khí tự động nói riêng, đồ án Chi tiết máy giúp cũng cố các
kiến thức đã học về nguyên lý máy, chi tiết máy, vẽ kỹ thuật, dung sai- kỹ thuật đo…đồng thời đây
cũng là cơ hội để sinh viên tiếp cận thực tế với một quy trình tính toán thiết kế chi tiết máy và hệ dẫn động.
Em xin chân thành cảm ơn các thầy giáo, đặc biệt là thầy Diệp Lâm Kha Tùng đã hướng
dẫn và có nhiều đánh giá, nhận xét trong quá trình em thực hiện đồ án.
Trong quá trình tính toán và thiết kế thì những sai sót là khó tránh khỏi vì vậy em mong
nhận được các ý kiến đánh giá nhận xét của các thầy để đồ án được hoàn thiện và chính xác hơn. Sinh viên thực hiện Nguyễn Tấn Lập lOMoAR cPSD| 15962736 ĐỒ ÁN CHI TIẾT MÁY
1. Động cơ điện không đồng bộ 3 pha.
2. Nối trục vòng đàn hồi.
3. Hộp giảm tốc bánh răng trụ 2 cấp nón trụ.
4. Bộ truyền xích ống con lăn. 5. Băng tải. Các thông số ban đầu:
Công suất trục công tác
Số vòng quay trục công tác Số năm làm việc P (kW) n (vòng/ phút) a (năm) 4.6 49 5
Chế độ làm việc: Quay 1 chiều, làm việc 2 ca, tải va đập nhẹ (1 năm làm việc 300 ngày, 1 ca làm việc 8 giờ) Mục lục
LỜI MỞ ĐẦU................................................................................................................................2
Mục lục...........................................................................................................................................4
CHƯƠNG 1 CHỌN ĐỘNG CƠ PHÂN PHỒI TỶ SỐ TRUYỀN..................................................6 1.1
Xác định công suất trên trục động cơ:...............................................................................6 1.2
Xác định số vòng quay sơ bộ của động cơ điện:................................................................6 1.3
PHÂN PHỐI TỶ SỐ TRUYỀN:.......................................................................................7
CHƯƠNG 2 THIẾT KẾ BỘ TRUYỀN BÁNH RĂNG TRONG HỘP GIẢM TỐC....................10 2.1
Chọn vật liệu bánh răng:.................................................................................................10 2.2
Xác định ứng suất cho phép............................................................................................10 2.3
Tính toán cấp nhanh: Bộ truyền bánh răng côn răng thẳng.............................................12 2.4
Tính toán cấp chậm: Bộ truyền bánh răng trụ răng thẳng:...............................................18
CHƯƠNG 3 THIẾT KẾ BỘ TRUYỀN XÍCH.............................................................................23 3.1
Chọn loại xích:................................................................................................................23 3.2
Xác định các thông số của xích và bộ truyền..................................................................23 3.3
Tính toán các thông số của bộ truyền xích:.....................................................................24 3.4
Kiểm nghiệm số lần va đập của xích trong 1 giây:..........................................................24 3.5
Kiểm nghiệm xích về độ bền...........................................................................................24 3.6
Đường kính đĩa xích........................................................................................................25 3.7
Kiểm nghiệm độ bền tiếp xúc đĩa xích:...........................................................................26 3.8
Xác định lực tác dụng lên trục:........................................................................................26
2SVTH: Nguyễnễ Tấấn L pậ lOMoAR cPSD| 15962736 ĐỒ ÁN CHI TIẾT MÁY
CHƯƠNG 4: TÍNH TOÁN THIẾT KẾ TRỤC.............................................................................27 4.1
Chọn vật liệu:..................................................................................................................27 4.2
Xác định dường kính trục:...............................................................................................27 4.3
Xác định khoảng cách giữa các gối đỡ và điểm đặt lực:..................................................27 4.4
Trị số các lực chi tiết quay tác dụng lên trục:..................................................................29 4.5
Tính kiểm nghiệm trục về độ bền mỏi:............................................................................36 4.6
Tính kiểm nghiệm độ bền của then đối với các tiết diện của 3 trục:................................40
CHƯƠNG 5: TÍNH TOÁN CHỌN Ổ LĂN.................................................................................41 5.1
Trên trục 1:....................................................................................................................41 5.2
Trên trục 2:......................................................................................................................43 5.3
Trên trục 3:......................................................................................................................45
CHƯƠNG 6 CHỌN KHỚP NỐI..................................................................................................46
CHƯƠNG 7: THIẾT KẾ VỎ HỘP VÀ CÁC CHI TIẾT CỦA HỘP GIẢM TỐC........................48 7.1
Kết cấu vỏ hộp giảm tốc:.................................................................................................48 7.2
Chọn bề mặt lắp ghép:.....................................................................................................48 7.3
Xác định các kích thước của vỏ hộp:...............................................................................48 7.4
Các chi tiết của hộp giảm tốc:.........................................................................................50 7.5
Chốt định vị:....................................................................................................................51 7.6
Cửa thăm dầu:.................................................................................................................51 7.7
Nút thông hơi:.................................................................................................................51 7.8
Nút tháo dầu:...................................................................................................................52 7.9
Chọn que thăm dầu và bôn trơn:......................................................................................53
CHƯƠNG 8: BÔI TRƠN, ĐIỀU CHỈNH ĂN KHỚP VÀ DUNG SAI LẮP GHÉP....................54 8.1.
Bôi trơn:..........................................................................................................................54 8.2.
Điều chính ăn khớp bánh răng:........................................................................................54 8.3.
Dung sai lắp ghép:...........................................................................................................54
8.4. Dung sai và lắp ghép mối then........................................................................................55
TÀI LIỆU THAM KHẢO............................................................................................................56
CHƯƠNG 1 CHỌN ĐỘNG CƠ PHÂN PHỒI TỶ SỐ TRUYỀN
1.1 Xác định công suất trên trục động cơ:
- Công suất trên trục công tác: kW - Ptđ = kW
3SVTH: Nguyễnễ Tấấn Lập lOMoAR cPSD| 15962736 ĐỒ ÁN CHI TIẾT MÁY
- Công suất trên trục động cơ điện: (1)
- Từ bảng tra 2.3 trang 19 tài liệu [1] ta có: + Hiệu suất khớp nối:
+ Hiệu suất 1 cặp ổ lăn:
+ Hiệu suất bộ truyền bánh răng côn:
+ Hiệu suất bộ truyền bánh răng trụ:
+ Hiệu suất bộ truyền xích:
Hiệu suất chung của bộ truyền là: (CT 2.9 tài liệu [1]) =.1.0,96.0,98.0,95 = 0.86 Thay vào (1) ta được: kW
1.2 Xác định số vòng quay sơ bộ của động cơ điện: Trong đó
+ : số vòng quay sơ bộ của động cơ
+ : số vòng quay của trục công tác = 49 (vòng/phút)
+ : tỷ số truyền chung của hệ thống dẫn động Mà
Trong đó: (theo bảng 2.4 TL[1])
- Tỉ số truyền bộ truyền xích = 2 (2 ÷ 5)
- Tỉ số truyền bộ hộp giảm tốc 2 cấp bánh răng nón trụ = 12 (8 ÷ 40) Vậy = 49.24 = 1176 (vg/ph)
Chọn động cơ điện thỏa
Theo bảng P1.3 phụ lục trang 236 tài liệu [1] ta chọn động cơ: 4A112M4Y3 Công suất Vận tốc quay T T Kiểu max k cos φ % ( kW ) ( vòng/phút ) T T dn dn
4 A112M4Y 3 5.5 1425 0.85 85.5 2.2 2.0
4SVTH: Nguyễnễ Tấấn L pậ lOMoAR cPSD| 15962736 ĐỒ ÁN CHI TIẾT MÁY
1.3 PHÂN PHỐI TỶ SỐ TRUYỀN: Tỷ số truyền
Phân tỷ số truyền của hệ dẫn động:
Tra bảng 2.4 TL[1] theo tiêu chuẩn chọn trước ux = 2 Suy ra tỷ số truyền: Xác định u1, u2
Với u1 là tỷ số truyền của cặp bánh răng côn (cấp nhanh)
u2 là tỷ số truyền của cặp bánh răng trụ (cấp chậm)
Ta chọn Kbe = 0.3 (0.25-0.3) = 1.2 [K01] = [K02] Ck = 1.1 (1-1.4) Ta tính được giá trị
Từ đồ thị h3.21 TL[1] ta chọn được: u1 = 4,1 u2 = 3,5
Xác định công suất, moment và số vòng quay trên các trục :
Công suất trên các trục:
• Công suất trên trục công tác:
• Công suất trên trục III: P3 =
• Công suất trên trục II: P2 =
• Công suất trên trục I: P1 = Công suất trục trên động cơ: Pđc =
Số vòng quay trên các trục:
5SVTH: Nguyễnễ Tấấn Lập lOMoAR cPSD| 15962736 ĐỒ ÁN CHI TIẾT MÁY
• Số vòng quay của trục động cơ: nđc = 1425 (vg/ph)
• Số vòng quay của trục I: (vg/ph)
• Số vòng quay của trục II: 347,56 (vg/ph)
• Số vòng quay của trục III: (vg/ph) Số vòng quay của trục công tác: (vg/ph)
Mômen xoắn trên các trục:
• Mômen xoắn trên trục động cơ: (N.mm)
• Mômen xoắn trên trục I: (N.mm)
• Mômen xoắn trên trục II: 127494,53 (N.mm)
• Mômen xoắn trên trục III: (N.mm)
• Mômen xoắn trên trục công tác: ( N.mm) Trục Trục công Động cơ Trục 1 Trục 2 Trục 3 Thông số tác Công suất P 4 , 93 4 , 88 4 , 64 4 , 5 4 , 23 ( kW ) Tỷ số truyền u 1 4.1 3.5 2 Số vòng quay n 1425 1425 347.56 99.3 49.65
( vg/ph ) Momen xoắn T 33039,65 32704,56 127494,53 432779,46 813625,38 (N.mm )
6SVTH: Nguyễnễ Tấấn L pậ lOMoAR cPSD| 15962736 ĐỒ ÁN CHI TIẾT MÁY
CHƯƠNG 2 THIẾT KẾ BỘ TRUYỀN BÁNH RĂNG TRONG HỘP GIẢM TỐC Thông số đầu vào: P1 = 4,88 (kW) u1 = 4,1 n1 = 1425 (vg/ph) T1 = 32704,56 (N.mm)
2.1 Chọn vật liệu bánh răng:
Do không có yêu cầu gì đặc biệt nên theo 6.1 TL [1]
Bánh nhỏ: thép 45 tôi cải thiện đạt độ rắn HB = 241…285 Có = 850 Mpa = 580 Mpa
Bánh lớn: thép 45 tôi cải thiện đạt độ rắn HB=192…240 Có = 750 Mpa = 450 Mpa
2.2 Xác định ứng suất cho phép
Theo bảng 6.2 TL [1] với thép tôi cải thiện đạt độ rắn HB=180…350 ta có:
Chọn độ rắn bánh nhỏ HB1 = 245
Chọn độ rắn bánh lớn HB2 = 230 Khi đó:
lần lượt là ứng suất tiếp xúc cho phép và ứng suất uốn cho phép ứng với số chu kì cơ sở
NHO là số chu kì thay đổi ứng suất cơ sở khi thử về uốn N 2.4 HO1=30.HB1 =30.2452.4 =1,6.107 N 2.4 HO2=30.HB2 =30.2302.4 =1,39.107
Số chu kì thay đổi ứng suất tương đương Theo công thức 6.5 TL [1]: NHE = 60c. NHE1 = 60c.
= 60.1.(13.0,7+0,83.0,3).1425.24000 =17,5.108 NHE2 = 60c.
= 60.1..24000.(13.0,7+0,83.0,3)
7SVTH: Nguyễnễ Tấấn Lập lOMoAR cPSD| 15962736 ĐỒ ÁN CHI TIẾT MÁY =42,7.107 NFO = NFO1 = NFO2 = 4.106
Với c=1 là số lần ăn khớp của răng trên mỗi vòng quay
Thời gian làm việc: 5 năm, 1 năm làm việc 300 ngày, 1 ca làm việc 8 tiếng, 1 ngày làm 2 ca ti =5.300.16=24000 giờ
Vì NHE1 > NHO1 do đó KHL1 = 1 và NHE2 > NHO2 do đó KHL2 = 1
Như vậy theo công thức 6.1a TL [1], sơ bộ xác định được: [ Suy ra: [ [
Với cấp nhanh sử dụng bánh răng côn răng thẳng nên: [’= [
Tính ứng suất uốn cho phép
Ta có NFE số chu kì thay đổi ứng suất tương đương NFE1 =60c.
=60.1.(16.0,7+0,86.0,3).1425.24000=1,6.109
Theo bảng 6.4 TL [1] ta có mF = 6. NFE2 = 60c.
Vì NFE1 > NFO1 do đó KFL1 = 1
và NFE2 > NFO2 do đó KFL2 = 1. Theo 6.2a TL [1]: [
Với bộ truyền quay một chiều nên KFC = 1. [ = [ =
Ứng suất quá tải cho phép theo 6.13 và 6.14 TL [1]: [ [ [
2.3 Tính toán cấp nhanh: Bộ truyền bánh răng côn răng thẳng
8SVTH: Nguyễnễ Tấấn L pậ lOMoAR cPSD| 15962736 ĐỒ ÁN CHI TIẾT MÁY
a. Xác định chiều dài Môđun vòng ngoài:
Theo công thức 6.52a TL [1]: Trong đó:
+ là hệ số phụ thuộc vào vật liệu bánh răng và loại răng. Với truyền động bánh răng côn răng thẳng có:
+ là hệ số kể đến sự phân bố không đều tải trọng
+ là hệ số chiều rộng vành răng = 0,3 (đã chọn ở trên) Theo bảng 6.21 TL [1]:
Trục bánh răng côn lắp trên ổ bi, sơ đồ HB < 350 ta tra được Suy ra
b. Xác định các thông số ăn khớp: Số bánh răng nhỏ:
Tra bảng 6.22 TL [1] ta được: Z1p = 16
Với HB < 350 ta có số răng côn nhỏ Z1 = 1,6 Z1p =1,6.16 = 25,6 Chọn Z1 = 26 răng.
• Đường kính trung bình: CT 6.54 TL [1]
• Môđun vòng trung bình: CT 6.55 TL [1]
• Môđun vòng chia ngoài: CT 6.56 TL [1]
Theo bảng 6.8 TL [1] chọn trị số theo tiêu chuẩn:
• Xác định lại môđun trung bình: Suy ra: Z1 = Chọn Z1 = 26 răng
9SVTH: Nguyễnễ Tấấn Lập lOMoAR cPSD| 15962736 ĐỒ ÁN CHI TIẾT MÁY
• Số răng bánh lớn Z2 = u1.Z1 = 4,1.26 = 106,6 Chọn Z2 = 107 răng Tỉ số truyền thực: Góc côn chia:
Theo bảng 6.2 TL [1], ta chọn hệ số dịch chỉnh: x1 = 0; x2 = 0
• Đường kính trung bình bánh nhỏ: • Chiều dài côn ngoài:
c. Kiểu nghiệm răng về độ bền tiếp xúc: Theo 6.58 TL [1]:
Theo bảng 6.5 TL [1]: ZM = 274 Mpa1/3 hệ số xét đến cơ tính vật liệu bánh răng
Theo bảng 6.12 TL [1], với xt = x1 +x2 = 0
Suy ra: ZH = 1,76 hệ số kể đến hình dạn tiếp xúc
Hệ số kể đến sự trùng khớp của răng: Theo 6.59a TL [1]:
• Hệ số trùng khớp ngang: theo CT 6.6 TL [1]: Suy ra:
• Hệ số tải trọng khi tính về tiếp xúc: Theo CT 6.61 TL [1]:
+ hệ số kể đến sự phân bố không đều tải trọng vành răng.
+ (bánh răng côn răng thẳng) – hệ số kể đến sự phân bố không đều của tải trọng cho các đôi răng đồng thời ăn khớp.
• Vận tốc vòng (theo CT 6.62 TL [1]):
Theo bảng 6.13 TL[1] chọn cấp chính xác là 8 Theo CT 6.64 TL [1]:
Trong đó theo bảng (6.15) và (6.16) TL[1] có: và Theo CT 6.63 TL [1]:
10SVTH: Nguyễnễ Tấấn L pậ lOMoAR cPSD| 15962736 ĐỒ ÁN CHI TIẾT MÁY 1,24
Trong đó b = Kbe.Re = 0,3.137,64= 41,3 mm KH = 1,26.1,24=1,56 Vậy
• Ứng suất tiếp xúc cho phép:
+ v = 3,75 m/s < 5 m/s => Zv = 1 hệ số ảnh hưởng của vận tốc vòng; chọn cấp chính xác tiếp xúc 7, + Ra = 0,63...1,25
Vậy : đảm bảo độ bền tiếp xúc.
d. Kiểm nghiệm răng về độ bền uốn:
• Hệ số tải trọng khi tính về uốn: Tra bảng 6.21 TL [1]: bánh răng thẳng Với
Trong đó theo bảng (6.15) và (6.16) TL[1] có: ; Suy ra: KFv = 1 + Do đó: KF = 1,62.0,53.1= 0,86
• là hệ số kể đến độ nghiêng của răng, với răng thẳng hệ số kể đến sự trùng khớp của răng Số răng tương đương:
• Hệ số dạng răng: Tra bảng 6.18 TL [1]: YF1 = 3,86, YF2 = 3,6
11SVTH: Nguyễnễ Tấấn Lập lOMoAR cPSD| 15962736 ĐỒ ÁN CHI TIẾT MÁY Suy ra: 33,27 Mpa < [ MPa Mpa < [ Mpa Ta thấy ,
Như vậy độ bền uốn được đảm bảo.
e. Kiểm nghiệm răng về quá tải: Theo CT 6.48 TL [1]: Kqt = 1
Đảm bảo điều kiện quá tải f.
f. Bảng tóm tắt các thông số bánh răng côn: Chiều dài côn ngoài Re = 137,64 mm Môđun vòng ngoài mte = 2,5 mm Chiều dài vành răng b = 41,3 mm Tỉ số truyền um = 4,1 Góc nghiêng của răng = 0 Số bánh răng z1 = 26, z2 = 107
Hệ số dịch chỉnh chiều cao x1 = 0; x2 = 0 Đường kính chia ngoài de1 = 59,71 mm, de2 = 267,5 Đường kính trung bình
dm1 = 50,75 mm, dm2 = 227,37 mm Góc chia côn Chiều cao răng ngoài he = 5,5mm
Chiều cao đầu răng ngoài hae1 = 2,5 mm; hae2 = 2,5 mm
Chiều cao chân răng ngoài hfe1 = 3 mm; hfe2 = 3 mm
Đường kính đỉnh răng ngoài
dae1 = 64,4 mm; dae2 = 272,2 mm
2.4 Tính toán cấp chậm: Bộ truyền bánh răng trụ răng thẳng:
a. Tính sơ bộ khoảng cách trục: Khoảng cách trục 6.15a
12SVTH: Nguyễnễ Tấấn L pậ lOMoAR cPSD| 15962736 ĐỒ ÁN CHI TIẾT MÁY
+ Bảng 6.5, Ka = 49,5 Mpa1/3 hệ số phụ thuộc vật liệu cặp bánh răng
+ Bảng 6.6 = 0,315 (theo tiêu chuẩn) Ta có:
+ Bảng 6.7 TL [1], sơ đồ 5, Suy ra: Chọn aw = 176 mm
Xác định các thông số ăn khớp:
• Môđun: Theo 6.17 TL [1]: m = (0,01 ÷ 0,02)aw = 2 ÷ 4
Theo quan điểm thống nhất hóa trong thiết kế, chọn môđun tiêu chuẩn của bánh răng cấp chậm
bằng môđun ở cấp nhanh m = 3 mm. + Số bánh răng dẫn: z1 = Chọn z1 = 26 răng
+ Số răng bị dẫn z2 = u2.z1 = 3,5.26 = 91 Chọn z2 = 91 răng
• Tỉ số truyền thực: um = b. Góc ăn khớp Theo CT 6,27 TL [1], Suy ra
c. Khoảng cách trục thực tế:
d. Các thông số chủ yếu của bộ truyền bánh răng trụ thẳng: Chiều rộng báng
răng: bw = .aw = 0,315.176 = 55,44 mm
Đường kính vòng chia: d1 = m.z1 = 3.26 =
78 mm d2 = m.z2 = 3.91 = 273 mm
• Đường kính vòng lăn: dw1 = 2aw/(um + 1) = 2.176/(3,5+1) = 78.22 mm dw2 = dw1.u = 78,22.3,5
= 273,77 mm Đường kính đỉnh răng:
da1 = d1 + 2m = 78+2.3 = 84 mm
da2 = d2+ 2m = 273+2.3 = 279mm Đường kính vòng chân răng:
13SVTH: Nguyễnễ Tấấn Lập lOMoAR cPSD| 15962736 ĐỒ ÁN CHI TIẾT MÁY
df1 = d1 – 2,5m = 78 – 2,5.3 = 70,5 mm
df2 = d2 – 2,5m = 273 – 2,5.3 = 265,5 mm Xác định các lực: + Lực vòng:
+ Lực hướng tâm: FrT1 = FtT1.tg = 1189,86 N = FrT2 Với = góc ăn khớp.
e. Kiểm nghiệm răng về độ bền tiếp xúc: Công thức kiểm nghiệm: Trong đó:
+ Bảng 6.5 TL [1]: ZM = 274 MPa1/3 – Hệ số kể đến cơ tính vật liệu của các bánh răng ăn khớp.
+ Bảng 6.12 TL [1]: ZH = 1,76 – Hệ số kể đến hình dạng bề mặt tiếp xúc
+ Hệ số kể đến sự trùng khớp của răng:
Với hệ số trùng khớp ngang:
+ Hệ số tải trọng khi tính về tiếp xúc: KH = KH KH KHv Trong đó: KH = 1 bánh răng thẳng KH = 1,05
Vận tốc vòng bánh răng: (m/s)
Theo bảng 6.13 TL [1] chọn cấp chính xác là 9.
Do đó theo bảng 6.15 và 6.16 TL [1], ta được: và g0 = 73 Theo CT 6.42 TL [1]: (m/s) Suy ra: Vậy KH = 1,05.1.1,07 = 1,12 Suy ra: Mpa • Ứng suất cho phép:
14SVTH: Nguyễnễ Tấấn L pậ lOMoAR cPSD| 15962736 ĐỒ ÁN CHI TIẾT MÁY
+ v = 1,47 m/s < 5m/s nên Zv = 0,85.2,070,1 = 0,91
+ Với cấp chính xác về mức tiếp xúc là 9, khi đó gia công đạt độ nhám Rz = 10...40μm, do đó ZR = 1 + da < 700 mm nên KxH = 1 Do đó: Mpa
Vậy : đảm bảo độ bền tiếp xúc.
f. Kiểm nghiệm theo độ uốn: Công thức kiểm nghiệm: •
- Hệ số kể đến sự trùng khớp của răng Với: • Số răng tương đương: Zv1 = Zv2 =
Vì sử dụng răng không dịch chỉnh nên hệ số dịch chỉnh x=0. • Hệ số dạng răng: YF1 = 3,88, YF2 = 3,6 • KF = KF KF KFv
+ Bảng 6.7 TL [1], sơ đồ 5: KF = 1,045 + Báng răng thẳng: KF = 1 Theo CT 6.47 TL [1], ta có:
Thay vào CT 6.46 TL [1], ta có: Suy ra: KF = 1,2.1,045.1=1,25 MPa MPa
+ YR =1 hệ số ảnh hưởng của độ nhám mặt lượn chân răng
+ YS = 1,08 - 0,0695ln(m) = 1 – hệ số xét đến độ nhậy của vật liệu đối với tập trung ứng suất.
15SVTH: Nguyễnễ Tấấn Lập lOMoAR cPSD| 15962736 ĐỒ ÁN CHI TIẾT MÁY
+ KxF = 0,95 ( da < 700 mm ) – hệ số xét đến kích thước bánh răng ảnh hưởng đến độ bền uốn. Suy ra: [ MPa [ MPa Vậy ;
Đảm bảo điều kiện uốn.
g. Kiểm nghiệm răng về quá tải Kqt = 1
h. Các thông số cơ bản của bộ truyền bánh răng trụ răng thẳng: Khoảng cách trục aw = 176 mm Môđun m = 3 mm Chiều rộng vành răng bw = 55,44mm Tỉ số truyền um = 3,5 Góc nghiêng của răng β = 0 Số răng bánh răng Z1 = 26; Z2 = 91 Hệ số dịch chỉnh x1 = 0; x2 = 0 Đường kính vòng chia d1 = 78 mm; d2 = 273 mm Đường kính đỉnh răng da1 = 84 mm; da2 = 279 mm Đường kính đáy răng df1 = 70,5 mm; df2 = 265,5 mm Đường kính vòng lăn
dw1 = 78,22 mm; dw2 = 273,77 mm
16SVTH: Nguyễnễ Tấấn L pậ lOMoAR cPSD| 15962736 ĐỒ ÁN CHI TIẾT MÁY
CHƯƠNG 3 THIẾT KẾ BỘ TRUYỀN XÍCH Các số liệu: Công suất dẫn P = 4,5 kW Số vòng quay trục dẫn n3 = 99,3 vg/ph Tỷ số bộ truyền xích ux = 2
Tính toán thiết kế:
3.1 Chọn loại xích:
Do điều kiện làm việc chịu tải va đập nhẹ và theo đề yêu cầu nên xích ống con lăn.
3.2 Xác định các thông số của xích và bộ truyền
Ứng với tỷ số truyền ux= 2 chọn sơ bộ số răng đĩa xích nhỏ Z1=26. Do đó số răng đĩa lớn
Z2 =u.Z1 = 2.26 =52 < zmax = 120.
- Theo CT 5.3 TL [1], công suất tính toán: Pt = P.k.kz.kn Trong đó: với Z1 = 26, kz = Với n01 = 50 vg/ph
Theo CT 5.4 và bảng 5.6 TL[1]: k = k0.ka.kđc.kđ.kc.kbt Trong đó:
k0 = 1 - hệ số ảnh hưởng của vị trí bộ truyền,ứng với đường tâm các đĩa xích làm với
phương ngang 1 góc < 400 .
ka = 1 - hệ số kể đến khoảng cách trục và chiều dài xích_với a = (30 50)p.
kđc = 1 - hệ ảnh hưởng của việc điều chỉnh lực căng xích ( trục điều chỉnh = 1 trong các đĩa xích).
kđ = 1,3 - hệ số tải trọng động ứng với tải va đập nhẹ. kc = 1,25 - hệ
số kể đến chế dộ làm việc của bộ truyền (làm việc 2 ca).
kbt = 0,8 hệ số kể đến ảnh hưởng của bôi trơn (môi trường không có bụi, chất lượng bôi trơn I_bảng 5.7[1]). k = 1.1.1.1,3.1,25.0,8 = 1,3 Như vậy:
Pt = 4,5.1,3.0,96.0,5 = 2,81 kW
Theo bảng 5.5 TL[1], với n01=50 vg/ph, chọn bộ truyền xích 1 dãy có bước xích p = 25,4 mm
thỏa mãn điều kiện bền mòn Pt < [p] = 3,2 kW
17SVTH: Nguyễnễ Tấấn Lập lOMoAR cPSD| 15962736 ĐỒ ÁN CHI TIẾT MÁY
Đồng thời theo bảng 5.8 TL [1], p < pmax
3.3 Tính toán các thông số của bộ truyền xích:
• Chọn khoảng cách trục sơ bộ a = (30÷50)p = 40.25,4 = 1016 mm Chọn a = 40p
• Số mắt xích: theo CT 5.12 TL [1]: =
Lấy mắt xích chẵn ta chọn: X = 120 mắt xích. Chiều dài xích: L = p.X = 25,4.120 = 3048 mm
• Ta tính lại khoảng cách trục theo CT 5.13 TL [1] = 0,25.25,4.1023 mm
Do đó khoảng cách trục a = 1020 mm
3.4 Kiểm nghiệm số lần va đập của xích trong 1 giây:
Với [i] = 30 số lần va đập cho phép của xích trong một giây, bảng 5.9 TL[1].
3.5 Kiểm nghiệm xích về độ bền. Theo 5.15 TL [1] Trong đó:
Theo bảng 5.2 TL[1], tải trọng phá hỏng Q = 56700 N; khối lượng 1 mét xích q=2,6 kg.
kđ = 1,7 – tải trọng mở máy bằng 2 lần tải trọng danh nghĩa. m/s Lực vòng:
Lực căng do lực ly tâm sinh ra: Fv = q.v2 = 2,6.0,52 = 0,65 N
Lực căng do trọng lượng nhánh xích bị động sinh ra:
Fo = 9,81.kf.q.a = 9,81.6.2,6.1020 = 156096,72 N
Với kf – hệ số phụ thuộc vào độ võng của xích, khi xích nằm ngang kf =6
Theo bảng 5.10 TL [1] với n=50 vg/ph nên [s] = 7
Vậy s < [s] bộ truyền xích đảm bảo đủ bền.
18SVTH: Nguyễnễ Tấấn L pậ lOMoAR cPSD| 15962736 ĐỒ ÁN CHI TIẾT MÁY
3.6 Đường kính đĩa xích
Theo CT (5.17) TL[1] và bảng 13.4:
Với: 0,5025.15,88+0,05 = 8,03 mm (xem bảng 5.2 TL [1]) 3.7
3.7 Kiểm nghiệm độ bền tiếp xúc đĩa xích: Theo CT 5.18 TL [1]: Trong đó:
Z1 = 26 => kr = 0,41 - hệ số kể đến ảnh hưởng của số răng đĩa xích.
E = 2,1.105 MPa – Môđun đàn hồi.
A = 180 mm2 - bảng 5.12 TL [1] - diện tích chiếu của bản lề.
kd = 1 (xích 1 dãy)- hệ số phân bố tải trọng không đều giữa các dãy.
kđ = 1,3 bảng 5.6 TL[1] - hệ số tải trọng động.
Lực va đập trên tải 1 xích (m=1) Theo 5.19 TL [1]:
Fvđ =13.10-7.n1.p3.m = 13.10-7.46.25,43.1 = 1,14.10-2 N MPa
Như vậy dùng thép 20X thấm cacbon đạt độ rắn HRC60 sẽ đạt được ứng suất tiếp xúc cho phép [
MPa => , đảm bảo được độ bền tiếp xúc cho răng đĩa 1.
Tương tự Z2 = 52 => kr = 0,24 => MPa < [, đảm bảo được độ bền tiếp xúc cho răng đĩa 2.
3.1 Xác định lực tác dụng lên trục: Theo 5.20 TL [1]: N
Trong đó : kx – hệ số kể đến trọng lượng của xích, kx=1,15 đối với bộ truyền nằm ngang hoặc
nghiêng một góc nhỏ hơn 400.
CHƯƠNG 4: TÍNH TOÁN THIẾT KẾ TRỤC
4.1 Chọn vật liệu:
19SVTH: Nguyễnễ Tấấn Lập lOMoAR cPSD| 15962736 ĐỒ ÁN CHI TIẾT MÁY
Chọn vật liệu chế tạo các trục là thép 45 thường hóa có b = 600 MPa, độ rắn HB = (170...217),
ứng suất xoắn cho phép [ ] = 15...30 MPa, lấy trị số nhỏ đối với trục vào, trị số lớn đối với trục ra của hộp giảm tốc.
4.2 Xác định dường kính trục:
Theo CT 10.9, đường kính trục thứ k: - Trục I: T1 = 32704,56 N.mm mm chọn d1 = 20 mm - Trục II: T2 = 127494,53 N.mm mm chọn d2 = 30 mm - Trục III: T3 = 432779,46 N.mm mm chọn d3 = 45 mm
4.3 Xác định khoảng cách giữa các gối đỡ và điểm đặt lực:
Theo bảng 10.2 TL[1] ta xác định chiều rộng ổ lăn: d1 = 20 mm => b01 = 15 mm d2 = 30 mm => b02 = 19 mm d3 = 45 mm => b03 = 25 mm
Theo bảng 10.3 TL [1] ta có các thông số sau:
- Khoảng cách từ mặt mút của chi tiết quay đến thành trong của hộp hoặc khoảng cách giữa các chi tiết quay: k1 = 10
- Khoảng cách từ mặt mút ổ đến thành trong của hộp: k2 = 6
- Khoảng cách từ mặt mút của chi tiết quay đến nắp hộp: k3 = 15
- Chiều cao nắp ổ và đầu bulông: hn = 18 Chiều dài mayơ bánh răng côn nhỏ:
Im13 = (1,2...1,4)d1 = (24...28) mm Chọn Im13 = 26 mm
Chiều dài mayơ bánh răng côn lớn:
Im23 = (1,2...1,4)d2 = (36...42) mm Chọn Im23 = 40 mm
Chiều dài mayơ bánh răng trụ răng thẳng nhỏ:
Im22 = (1,2...1,5)d2 = (36...45) mm
20SVTH: Nguyễnễ Tấấn L pậ lOMoAR cPSD| 15962736 ĐỒ ÁN CHI TIẾT MÁY Chọn Im22 = 44 mm
Chiều dài mayơ bánh răng trụ răng thẳng lớn:
Im32 = (1,2...1,5)d3 = (54...67,5) mm Chọn Im32 = 60 mm
Chiều dài mayơ khớp nối:
Imkn = Im12 = (1,4...2,5)d1 = (28...50) mm Chọn Imkn = 50 mm
Chiều dài mayơ đĩa xích:
Imx = Im33 = (1,2...1,5)d3 = (54...67,5) mm Chọn Imx = 60 mm Trục I: •
I12 = - Ic12 = k3 + hn = + 15 + 18 = 65,7 mm •
I11 = (2,5...3)d1 = (50...60) mm, chọn I11 = 60 mm •
I13 = I11 + k1 + k2 + Im13 + 0,5(b01 – b13)
= 60 + 10 + 6 + 26 + 0,5(15 – 40cos(13)) = 91,35 mm Trục II: •
I22 = 0,5(Im22 + b02) + k1 + k2 = 0,5(44 + 19) + 10 + 6 = 47,5 mm •
I23 = I22 + 0,5(Im22 + b13) + k1 = 47,5 + 0,5(44 + 40cos(77)) + 10 = 78,88 mm
Khoảng cách giữa hai ổ lăn trên trục thứ II: •
I21 = Im22 + Im23 + b02 + 3k1 + 2k2 = 44 + 78,88 + 19 +3.10 + 2.6 = 183,88 mm Trục III: • I32 = I22 = 47,5 mm •
I33 = I31 + Ic33 = 183,88 + 75,5 = 259,38 mm Với:
Ic33 = 0,5(Im33 + b03) + k3 + hn = 0,5(60 + 25) + 15 + 18 = 75.5 mm I31 = I21 = 183,88 mm
4.4Trị số các lực chi tiết quay tác dụng lên trục:
a. Xác định các lực tác dụng:
• Lực tác dụng lên trục bánh răng côn răng thẳng: Ft1 = N N = N = Trong đó:
21SVTH: Nguyễnễ Tấấn Lập lOMoAR cPSD| 15962736 ĐỒ ÁN CHI TIẾT MÁY
dm1 là đường kính trung bình của bánh nhỏ
: là góc ăn khớp là gốc côn chia bánh nhỏ
• Lực tác dụng lên trục bánh răng thẳng: Ft3 = N N Trong đó:
dw1 là đường kính vòng lăn của báng răng trụ 1 là góc ăn khớp
• Lực từ khớp nối tác dụng lên trục:
Với: N – lực vòng trên khớp nối
Trong đó: Dt là đường kính vòng tròn qua tâm các chốt (nối trục vòng đàn hồi).
Tra bảng 16.10 [TL2] : Dt = 90,38 mm.
• Lực tác dụng từ bộ truyền xích: Frx = 7015 N
b. Xác định các phản lực và đường kính tại các đoạn trục:
Các biểu đồ momen: Trục 1
Momen do lực dọc trục Fa1 gây ra: Ma1 = N.mm + Trong mặt phẳng Oxz: + Trong mặt phẳng Oyz:
22SVTH: Nguyễnễ Tấấn L pậ lOMoAR cPSD| 15962736 ĐỒ ÁN CHI TIẾT MÁY R By F k R Ax F r1 z x F a1 R Ay R Bx l 11 F t1 y l 13 l 12 z x M y ( N.mm ) z y M x N ( .mm ) 32704,56 M z ( N.mm ) Trục 2
Momen do lực dọc trục Fa2 gây ra: Ma2 = N.mm Trong mặt phẳng Oxz: 23SVTH:
Nguyễnễ Tấấn Lập Downloaded by H?u Mai Th? (choemosoeul@gmail.com) lOMoAR cPSD| 15962736 ĐỒ ÁN CHI TIẾT MÁY
Sơ đồ đặt lực và biểu đồ momen: Trong mặt phẳng Oyz:
24SVTH: Nguyễnễ Tấấn L pậ
Downloaded by H?u Mai Th? (choemosoeul@gmail.com) lOMoAR cPSD| 15962736 ĐỒ ÁN CHI TIẾT MÁY F t2 R By F a2 z R Ax F r3 F r2 R Ay y F t3 x R Bx l 22 25SVTH:
Nguyễnễ Tấấn Lập Downloaded by H?u Mai Th? (choemosoeul@gmail.com) lOMoAR cPSD| 15962736 ĐỒ ÁN CHI TIẾT MÁY
Sơ đồ đặt lực và biểu đồ momen: l 23 l 21 z x M y N.mm z y M x N.mm 127494,53 T N.mm Trục 3 Trong mặt phẳng Oxz:
26SVTH: Nguyễnễ Tấấn L pậ
Downloaded by H?u Mai Th? (choemosoeul@gmail.com) lOMoAR cPSD| 15962736 ĐỒ ÁN CHI TIẾT MÁY Trong mặt phẳng Oyz: 27SVTH:
Nguyễnễ Tấấn Lập Downloaded by H?u Mai Th? (choemosoeul@gmail.com) lOMoAR cPSD| 15962736 ĐỒ ÁN CHI TIẾT MÁY
Sơ đồ đặt lực và biểu đồ momen: R Ay R Ax F rx R Bx F r4 z F t4 R x By y l 32 l 31 l 33 M y N.mm z x M x N.mm z y 432779,46 T N.mm
Xác định đường kính tại các tiết diện trục:
28SVTH: Nguyễnễ Tấấn L pậ
Downloaded by H?u Mai Th? (choemosoeul@gmail.com) lOMoAR cPSD| 15962736 ĐỒ ÁN CHI TIẾT MÁY Theo CT 10.17 TL [1]:
Trong đó: [ ] – trị số ứng suất cho phép , theo bảng 10.5 TL[1]: + Trục I: [ ] = 63 MPa + Trục II: [ ] = 63 MPa + Trục III: [ ] = 53,25
Tính momen uốn tổng Mj và momen tương đương Mtdj tại các tiết diện j: Momen uốn tổng: CT 10.15 TL [1] Momen tương đương: CT 10.16 TL [1] Momen uốn tổng Momen tương đương Đường kính tiết Đường kính tiêu (N.mm) (N.mm) diện (mm) chuẩn M10 = 0 Mtd10 = 28322,98 d10 = 16,5 17 M11 = 9509,1285 Mtd11 = 29876,66 d11 = 16,8 17 M12 = 41985,3 Mtd12 = 50645,4 d12 = 20,03 20 M13 = 2856,21 Mtd13 = 28466,7 d13 = 16,53 17 M20 = 0 Mtd20 = 0 d20 = 0 20 M21 = 154605 Mtd21 = 189983,81 d21 = 31,13 32 M22 = 157872,59 Mtd22 = 192652,27 d22 = 31,27 32 M23 = 0 Mtd23 = 0 d23 = 0 20 M30 = 0 Mtd30 = 374798 d30 = 39,04 40 M31 = 529632,5 Mtd31 = 648832,9 d31 = 46,87 50 M32 = 212351,24 Mtd32 = 430774,41 d32 = 40,89 42 M33 = 0 Mtd33 = 0 d33 = 0 50
4.5 Tính kiểm nghiệm trục về độ bền mỏi: Với thép 45 có b = 600 MPa
Giới hạn mỏi uốn: -1 = 0,436. b = 0,436.600 = 261,6 N/mm2.
Giới hạn mỏi xoắn -1 = 0,58. -1 = 0,58.261,6 = 151,7 N/mm2. Theo bảng 10.7 = 0,05; = 0
a. Kết cấu trục vừa thiết kế đảm bảo được độ bền mỏi nếu hệ số an toàn tại các mặt cắt nguy
hiểm đều thỏa mãn điều kiện sau: 29SVTH:
Nguyễnễ Tấấn Lập Downloaded by H?u Mai Th? (choemosoeul@gmail.com) lOMoAR cPSD| 15962736 ĐỒ ÁN CHI TIẾT MÁY CT 10.19 TL [1]
[s]: Hệ số an toàn cho phép, thông thường [s] = 1,5…2,5
: hệ số an toàn chỉ xét riêng ứng suất pháp, hệ số an toàn chỉ xét riêng ứng suất tiếp tại tiết diện j.
Tất cả các trục đều quay làm việc theo 1 chiều nên ứng suất pháp (uốn) thay đổi theo chu kỳ đối xứng, do đó: mj = 0;
aj = max = Mj/Wj theo CT 10.22 TL [1] Theo CT 10.20 TL [1]: Theo CT 10.21 TL [1]:
Tất cả các trục đều quay 1 chiều nên ứng suất tiếp (xoắn) thay đổi theo chu kỳ mạch động: Theo CT 10.23 TL [1]
b. Xác định hệ số an toàn ở các tiết diện nguy hiểm của trục:
Ta tiến hành kiểm nghiệm trục tại các tiết diện nguy hiểm, đây là các tiết diện cần phải kiểm tra về độ bền mỏi:
- Trên trục I: các tiết diện 10 (lắp khớp nối); 11,12 (lắp ổ lăn); 13 (lắp bánh răng côn nhỏ);
- Trên trục II: các tiết diện 22 (lắp bánh răng thẳng); 21 (lắp bánh răng côn);
- Trên trục III: các tiết diện 32 (lắp bánh răng thẳng); 31 (lắp ổ lăn);
c. Chọn lắp ghép: các ổ lăn lắp lên trục theo k6, lắp bánh răng,đĩa xích, nối trục theo k6 kết hợp với lắp then.
Công thức tính momen cảm uốn Wj và momen xoắn Woj : bảng 10.6 TL[1]: Momen cản uốn: Momen xoắn:
Kích thước của then (bảng 9.1 TL[1]), trị số của momen cản uốn và momen cản xoắn ( bảng
10.6) ứng với các tiết diện trục ta tính được như sau: Tiết diện Đường kính b h t 1 W j (mm 3 ) W oj (mm 3 ) trục ,1 10 1, 13 17 5 x 5 3 395,86 878,19 12 20 6 x 6 3 , 5 642,47 1427,87 20,23 20 6x6 3,5 642,47 1427,87 21,22 32 10x8 5 2647,46 5864,45
30SVTH: Nguyễnễ Tấấn L pậ
Downloaded by H?u Mai Th? (choemosoeul@gmail.com) lOMoAR cPSD| 15962736 ĐỒ ÁN CHI TIẾT MÁY 30 40 12x8 5 5364,44 11647,62 31,33 50 14x9 5,5 10747,05 23018,9 32 52 16x10 6 11850,93 25655,09
d. Xác định các hệ số K dj dj và K dj đối với các tiết diện nguy hiểm 3 trục theo CT (10.25) và (10.26) TL[1]:
- Các trục được gia công trên máy tiện, tại các tiết diện nguy hiểm yêu cầu đạt Ra = 2,5…
0,63 μm, do đó theo bảng 10.8 [TL1], hệ số tập trung ứng suất do trạng thái bề mặt Kx = 1,06.
- Không dùng các phương pháp tăng bền bề mặt, do đó hệ số tăng bền Ky = 1
- Theo bảng 10.12 TL[1], khi dùng dao phay ngón, hệ số tập trung ứng suất tại rãnh then
ứng với vật liệu có σb = 600 MPa là Kσ = 1,76, Kτ = 1,54.
- Theo bảng 10.10 TL[1] tra hệ số kích thước và ứng với đường kính của tiết diện
nguy hiểm, từ đó xác định được tỉ số K / và K / tại rãnh then trên các tiết diện này.
Theo bảng 10.11 TL[1], ứng với kiểu lắp đã chọn, σb = 600 MPa và đường kính của tiết
diện nguy hiển tra được tỉ số K / và K / do lắp căng tại các tiết diện này, trên cơ sở đó
dùng giá trị lớn hơn trong hai giá trị của K / để tính K d và giá trị lớn hơn trong hai giá
trị của K / để tính K d Tiết d (mm) S j diện 11 17 24 , 02 18 , 62 , 2 12 1 , 76 5 , 14 4 ,63 3 , 44 12 20 65 , 35 11 , 45 2 , 12 , 1 79 1 , 89 7 , 4 1 , 83 13 17 7,22 18,62 2,12 1,76 17,09 4,63 4,47 21 32
58,4 10,87 2,12 1,98 2,11 7,05 2,02 22 32 59,63
10,87 2,13 1,98 2,06 7,05 1,98 31SVTH:
Nguyễnễ Tấấn Lập Downloaded by H?u Mai Th? (choemosoeul@gmail.com) lOMoAR cPSD| 15962736 ĐỒ ÁN CHI TIẾT MÁY 31 50 49,28 9,4 2,23 2,09 2,38 7,72 2,27 32 52 17,92 8,43 2,25 2,09 6,49 8,6 5,19 Ta thấy Sj = 1,5...2,5
Như vậy các tiết diện nguy hiểm trên cả 3 trục đều đảm bảo an toàn về độ bền mỏi. 6.
32SVTH: Nguyễnễ Tấấn L pậ
Downloaded by H?u Mai Th? (choemosoeul@gmail.com) lOMoAR cPSD| 15962736 ĐỒ ÁN CHI TIẾT MÁY
4.6 Tính kiểm nghiệm độ bền của then đối với các tiết diện của 3 trục:
Điều kiện bền dập và điều kiện cắt: CT (9.1) và (9.2) TL[1]
với [ = 150 MPa (bảng 9.5 TL [1]) với = 60...90 MPa - ứng suất cắt Với lt = (0,8 ÷ 0,9)lm (l m – chiều dài mayơ)
+ Tại đĩa xích l = (0,80,9).60 = (4854) =>Chọn l = 50 mm
+ Tại bánh răng côn nhỏ: l = (0,80,9).26 = (23,4) =>Chọn l = 22 mm
+ Tại bánh răng côn lớn: l = (0,80,9).40 = (3236) =>Chọn l = 35 mm
+ Tại bánh răng trụ nhỏ: l = (0,8,9).44 = (35,239,6) =>Chọn l = 36 mm
+ Tại bánh răng trụ lớn: l = (0,80,9).60 = (4854) =>Chọn l = 50 mm + Tại khớp nối: l = (0,80,9).50 = (4045) =>Chọn l = 40 mm Vị trí d (mm) lt bxh t1 Khớp nối 17 40 5x5 3 48,09 19,24 Bánh răng côn nhỏ 17 22 5x5 3 87,45 34,98 Bánh răng côn lớn 32 35 10x8 5 75,89 22,77 Bánh răng trụ nhỏ 32 36 10x8 5 73,78 22,13 Bánh răng trụ lớn 52 50 16x10 6 83,23 20,81 Đĩa xích 40 50 12x8 5 144,26 36,06
Ta thấy và nên tất cả các mối ghép then đều đảm bảo độ bềndập và độ bền cắt.
CHƯƠNG 5: TÍNH TOÁN CHỌN Ổ LĂN
- Thời gian các ổ làm việc trên các trục là như nhau và thời gian làm việc là 5 năm.
- Thời gian làm việc tính bắng giờ là: Lh = 5.300.2.8 = 24000 giờ 5.1 Trên trục 1: F r1 F r0 at F F s1 s0 F A B
• Tại gối A: RAx = 2120,76 N, RAy = 645,18 N + Lực hướng tâm tại gối A:
• Tại gối B: RBx = 976,65 N, RBy = 190,15 N + Lực hướn tâm tại gối B: Tỉ số: 33SVTH:
Nguyễnễ Tấấn Lập Downloaded by H?u Mai Th? (choemosoeul@gmail.com) lOMoAR cPSD| 15962736 ĐỒ ÁN CHI TIẾT MÁY
Vì trục lắp bánh răng côn nên cần nâng cao độ cứng với d = 20 mm, ta chọn ổ đũa côn cỡ trung.
Theo bảng P2.11 TL [1] ta có các thông số:
Kí hiệu: 7304 d = 20 mm; C = 25 kN; C0 = 16,6 kN; 11,170 Kiểm
nghiệm khả năng tải động của ổ:
• Lực dọc trục do lực hướng tâm tác dụng lên ổ sinh ra: Fs = 0,83.e.Fr
Theo bảng 11.4 TL [1], e = 1,5.tan tan11,170 = 0,3
• Lực dọc tác dụng lên ổ thứ i: Vì nên = Fs0 = 551,97 N Vì nên = 664,55 N
• Vì tải trọng tĩnh nên kđ = 1, vòng trong quay nên V = 1, kt = 1 (t0 < 1000) Ta có:
Tra bảng 11.4 TL [1] ta được: X0 = 1; Y0 = 0
Tra bảng 11.4 TL [1] ta được: X1 = 0,4; Y1 = 0,4cotg = 0,4.cotg11,170 = 2,02 Tải động quy ước:
Q0 = (X0VFr0+Y0Fa0)kđ.kt = (1.1.2216,73+0.551,97).1.1 = 2216,73 N
Q1 = (X1VFr1+Y1Fa1)kđ.kt = (0,4.1.995+2,02.664,55).1.1 = 1740,39 N
Ta thấy Q0 > Q1 nên chọn Q0 để tính toán cho 2 ổ, Q0 = 2216,73 N
Thời hạn, tính bằng triệu vòng quay: (triệu vòng)
• Khả năng tải động tính toán: CT 11.1 TL [1]: Cd= Q.
với m = 10/3 đối với ổ đũa.
= 2216,73. N = 21,85 kN < C0 = 25 kN
Vậy ổ đảm bảo khả năng tải động.
Kiểm nghiệm khả năng tải tĩnh
34SVTH: Nguyễnễ Tấấn L pậ
Downloaded by H?u Mai Th? (choemosoeul@gmail.com) lOMoAR cPSD| 15962736 ĐỒ ÁN CHI TIẾT MÁY
Theo bảng 11.6 TL [1], với ổ đũa côn X0 = 0,5, Y0 = 0,22.cotg = 0,22.cotg11,170 = 1,11 Theo CT 11.19 TL [1]:
Qt = X0.Fr + Y0.Fa = 0,5.2216,73+1,11.551,97 = 1721,05 N < Fr0
Như vậy Qt = Fr0 = 2216,73 N = 2,22 kN < C0 = 16,6 kN
Kích thước của ổ:
Kí d, D, D1, d1, B, C1, T, r, r1, α, C, C0, hiệu mm mm mm mm mm mm mm mm mm mm kN kN 7304 20 52 42 35,4 15 13 16,25 2 0,8 11,33 25 16,6 5.2 Trên trục 2:
Sơ đồ bố trí tải trọng như sau: F r0 F at F s0 F s1 Fr1 A B
• Tại gối A: RAx = 3153,75 N, RAy = 1049 N Lực hướng tâm Fr0 = N
• Tại gối B: RBx = 1395 N, RBy = 24,92 N Lực hướng tâm Fr1 = N
• Lực dọc trục: Fat = Fa2 = 458,21 N Tỉ số:
Vì trục lắp bánh răng côn nên cần nâng cao độ cứng với d = 20 mm, ta chọn ổ đũa côn cỡ trung.
Theo bảng P2.11 TL [1] ta có các thông số:
Kí hiệu: 7304 d = 20 mm; C = 25 kN; C0 = 16,6 kN; 11,170 Kiểm
nghiệm khả năng tải động của ổ:
• Lực dọc trục do lực hướng tâm tác dụng lên ổ sinh ra: Fs = 0,83.e.Fr
Theo bảng 11.4 TL [1], e = 1,5 tan 0,3
Fs0 = 0,83.0,3.3323,63 = 827,58 N
Fs1 = 0,83.0,3.1395,22 = 347,41 N 35SVTH:
Nguyễnễ Tấấn Lập Downloaded by H?u Mai Th? (choemosoeul@gmail.com) lOMoAR cPSD| 15962736 ĐỒ ÁN CHI TIẾT MÁY
• Lực dọc trục tác dụng vào ổ thứ i: • N
Vì < Fs0 nên Fa0 = Fs0 = 827,58 N • N
Vì > Fs1 nên Fa1 = Fs1 = 369,34 N
• Vì tải trọng tĩnh nên kđ = 1, vòng trong quay nên V = 1, kt = 1 (t0 < 1000) Ta có:
Tra bảng 11.4 TL [1]: ta có X0 = 1; Y0 = 0
Tra bảng 11.4 TL [1]: ta có X0 = 1; Y0 = 0 Tải trọng qui ước:
Q0 = (X0VFr0 + Y0Fa0)kđkt = (1.1.3323,63+0.827,58).1.1 = 3323,63 N
Q1 = (X1VFr1 + Y1Fa1)kđkt = (1.1.1395,22+0.369,34).1.1 = 1395,22 N
Ta thấy Q0 > Q1 nên chọn Q0 để tính toán cho 2 ổ, Q0 = 3323,63 N
Thời hạn, tính bằng triệu vòng quay: (triệu vòng)
• Khả năng tải động tính toán: CT 11.1 TL [1]: Cd = Q.
với m = 10/3 đối với ổ đũa.
= 3323,63. N = 21,44 kN < C =25 kN
Vậy ổ đảm bảo khả năng tải động.
Kiểm nghiệm khả năng tải tĩnh
Theo bảng 11.6 TL [1], với ổ đũa côn X0 = 0,5, Y0 = 0,22.cotg = 0,22.cotg11,170 = 1,11 Theo CT 11.19 TL [1]:
Qt = X0.Fr + Y0.Fa = 0,5.3323,63 + 1,11.827,58 = 2580,43 N < Fr0
Như vậy Qt = Fr0 = 3323,63 N = 3,32 kN < C0 16,6 kN
Kích thước của ổ:
Kí d, D, D1, d1, B, C1, T, r, r1, α, C, C0, hiệu mm mm mm mm mm mm mm mm mm mm kN kN 7304 20 52 42 35,4 15 13 16,25 2 0,8 11,33 25 16,6
36SVTH: Nguyễnễ Tấấn L pậ
Downloaded by H?u Mai Th? (choemosoeul@gmail.com) lOMoAR cPSD| 15962736 ĐỒ ÁN CHI TIẾT MÁY 6.2 5.3 Trên trục 3:
Sơ đồ bố trí tải trọng: F y1 F x0 F x1 Fy0 A B
• Tại gối A: RAx = 2417,8 N, RAy = 3760,33 N Lực hướng tâm Fr0 = N
• Tại gối B: RBx = 842,1 N, RBy = 9588,82 N Lực hướng tâm Fr1 = N
Vì Fr1 > Fr0 nên ta tính toán chọn ổ B.
• Do không có lực dọc trục nên X = 1; Y = 0 (bảng 11.4 TL[1])
• Vì tải trọng tĩnh nên kđ = 1, vòng trong quay nên V = 1, kt = 1 (t0 < 1000) Tải trọng quy ước:
Q = (XVFr1 + YFa)kđkt = (1.1.9625,73+0.0)1.1 =9625,73 N
Thời hạn, tính bằng triệu vòng quay: (triệu vòng)
• Khả năng tải động tính toán: CT 11.1 TL [1] Cd = QE. với m = 3 đối với ổ bi. Cd = 9625,73. N =50,34 kN
Theo bảng 2.7 ta chọn ổ bi đỡ 1 dãy cỡ nặng 410 với C = 68,5 kN, C0 = 53 kN
Kích thước của ổ: Kí hiệu ổ d,mm D,mm B,m Đường kính bi, C,kN C 0 ,kN m mm 410 50 130 31 3 , 5 25 , 4 68 , 5 53
CHƯƠNG 6 CHỌN KHỚP NỐI
Trong nối trục đàn hồi, hai nửa gối trục nối với nhau bằng bộ phận đàn hồi. Nhờ có bộ phận
đàn hồi cho nên nối trục đàn hồi có khả năng: giảm va đập và chấn động, đề phòng cộng hưởng
do dao động xoắn gây ra và bù lại độ lệch trục. Nối trục vòng đàn hồi có cấu tạo đơn giản dễ chế
tạo, dễ thay thế. Nó dùng để truyền momen xoắn nhỏ và trung bình. Có thể làm việc với độ lệch tâm 0,2 ÷ 0,6 (mm). Momen xoắn tính toán: Tt = k.T Trong đó: 37SVTH:
Nguyễnễ Tấấn Lập Downloaded by H?u Mai Th? (choemosoeul@gmail.com) lOMoAR cPSD| 15962736 ĐỒ ÁN CHI TIẾT MÁY
+ T: momen xoắn trên trục vào của hộp giảm tốc.
T = T1 = 32704,56 N.mm = 32,7 N.m
+ k: hệ số chế độ làm việc, phụ thuộc vào loại máy công tác
Tra bảng 16.1 TL [2], máy công tác là xích tải, k = 2 Tt = 2.32,7 = 65,4 N.m
Dựa vào Tt = 65,4 N.m tra bảng 16.10a, ta chọn kích thước của nối trục vòng đàn hồi: d = 20 mm D = 100 mm dm = 36 mm L = 104 mm l = 50 mm d1 = 36 mm
D0 = 71 mm Z = 6 nmax =5700 v/ph B = 4 mm
B1 = 28 mm l1= 21 mm D3 = 20 mm l2 = 20 mm
Hình vẽ của nối trục vòng đàn hồi: Hình 16.6 TL[2]:
Kích thước cơ bản của vòng đàn hồi: dc = 10 mm d1 = M8 D2 = 15 mm l = 42 mm l1 = 20 mm l2 = 10 mm l3 = 15 mm h = 1,5 mm
Điều kiện sức bền dập của vòng đàn hồi:
Trong đó: MPa_ứng suất dập cho phép của vòng cao su
38SVTH: Nguyễnễ Tấấn L pậ
Downloaded by H?u Mai Th? (choemosoeul@gmail.com) lOMoAR cPSD| 15962736 ĐỒ ÁN CHI TIẾT MÁY
=> Đảm bảo sức bền dập của vòng đàn hồi.
Điều kiện sức bền của chốt: Trong đó: mm
[ MPa_ứng suất cho phép của chốt
=> Đảm bảo sức bền của chốt.
CHƯƠNG 7: THIẾT KẾ VỎ HỘP VÀ CÁC CHI TIẾT CỦA HỘP GIẢM TỐC
7.1 Kết cấu vỏ hộp giảm tốc:
- Vỏ hộp giảm tốc đúc có thể có nhiều dạng khác nhau, xong chúng
đều có chung nhiệm vụ:
bảm bảo vị trí tương đối giữa các chi tiết và bộ phận máy, tiếp nhận tải trọng do các
chi tiết lắp trên vỏ truyền đến, đựng dầu bôi trơn bảo vệ các chi tiết máy tránh bụi bặm. -
Thành phần bao gồm: thành hộp, nẹp hoặc gân, mặt bích, gối đỡ… - Chi tiết cơ bản:
độ cứng cao, khối lượng nhỏ.
- Vật liệu làm vỏ phổ biến nhất: gang xám GX15-32
- Phương pháp gia công: đúc
- Mặt đáy về phía lỗ tháo dầu với độ dốc 2% và ngay tại chỗ tháo dầu lõm xuống.
7.2 Chọn bề mặt lắp ghép:
- Bề mặt ghép của vỏ hộp thường đi qua đường tâm các trục, nhờ đó
việc lắp ghép các chi tiết sẽ thuận tiện hơn. Sau khi lắp ghép trên các
trục các chi tiết như bánh răng, ổ… sau đó từng trục sẽ được đặt vào vỏ hộp.
- Bề mặt ghép thường chọn song song với mặt đế. Tuy nhiên có thể
chọn bề mặt không song song với mặt đế nếu nhờ đó có thể giảm
được trọng lượng và kích thước của hộp giảm tốc cũng như tạo điều
kiện bôi trơn tốt cho các cặp bánh răng bằng phương pháp ngâm dầu.
7.3 Xác định các kích thước của vỏ hộp:
- Hình dạng của nắp và thân chủ yếu được xác định bởi số lượng và
kích thước của bánh răng, vị trí mặt ghép và sự phân bố của các trục
trong hộp, đồng thời còn phụ thuộc vào chỉ tiêu kinh tế, độ bền, độ cứng. 39SVTH:
Nguyễnễ Tấấn Lập Downloaded by H?u Mai Th? (choemosoeul@gmail.com) lOMoAR cPSD| 15962736 ĐỒ ÁN CHI TIẾT MÁY
- Nhìn chung, vỏ hộp do các mặt trụ và mặt phẳng tạo thành. Mặt
phẳng thuận tiện khi làm khuôn mẫu nhưng làm tăng khuôn khổ, kích
thước và trọng lượng vỏ hộp. Dựa vào hình 18.2 và bảng 18.1, ta xác
định các kích thước như sau: Chiều dày:
- Chiều dày thân hộp: mm mm > 6 mm
- Chiều dày nắp hộp: mm lấy mm Gân tăng cứng:
- Chiều dày e: mm => chọn e = 7 mm
- Chiều cao h: h < 58 mm, chọn h = 55 mm
- Độ dốc khoảng 20 Đường kính:
- Bu lông nền, d1 d1 > 0,04a + 10 = 0,04.150,765 + 10 = 16,03 mm => chọn d1 = 18 mm -
40SVTH: Nguyễnễ Tấấn L pậ
Downloaded by H?u Mai Th? (choemosoeul@gmail.com) lOMoAR cPSD| 15962736 ĐỒ ÁN CHI TIẾT MÁY
- Bu lông cạnh ổ, d2 d2 = (0,70,8)d1 = (0,70,8).18 = 12,614,4 mm => chọn d2 = 14 mm
- Bu lông ghép bích nắp và thân, d3 d3 = (0,80,9)d2 = (0,80,9).14 =
11,212,6 mm => chọn d3 = 12 mm
- Vít ghép nắp ổ, d4 d4 = (0,60,7)d3 = (0,60,7).12 = 7,28,4 mm => chọn d4 = 8 mm
- Vít ghép nắp cửa thăm, d5 d5 = (0,50,6)d4 = (0,50,6).8 = 44,8 mm =>
chọn d5 = 4 mm Mặt bích ghép nắp và thân:
- Chiều dày bích thân hộp, S3 mm => chọn S3 = 21 mm
- Chiều dày bích nắp hộp, S4 mm => chọn S4 = 20 mm
- Bệ rộng bích và thân, K3 mm
Kích thước gối trục:
- Đường kính ngoài và tâm lỗ vít: D3, D2 xác định theo kích thước lắp ổ:
Trục I: D = 17 mm, mm mm => chọn D2 = 32 mm Trục II: D = 20
mm, mm mm => chọn D2 = 35 mm Trục III: D = 50 mm, mm mm => chọn D2 = 60 mm
- Bề rộng mặt ghép bu lông cạnh ổ: K2 mm
- Tâm lỗ bu lông cạnh ổ: E2 (k là khoảng cách từ tâm bu lông đến mép
lỗ) mm (không kể chiều dày thành hộp) Và mm chọn R2 = 18 mm mm chọn k = 16 mm - Chiều cao h:
h xác định theo kết cấu, phụ thuộc vào tâm lỗ bu lông kích thước mặt tựa Mặt đế hộp: - Chiều dày:
+ Khi không có phần lồi S1 mm => chọn S1 = 26 mm
+ Khi có phần lồi: Dd, S1 và S2 Dd
xác định đường kính dao khoét
mm => chọn S1 = 30 mm mm => chọn S2 = 19 mm
- Bề rộng mặt đế hộp, K1 và q: mm mm => chọn q = 69 mm
Khe hở giữa các chi tiết:
- Giữa bánh răng và thành hộp: mm => chọn 8 mm
- Giữa đỉnh bánh răng lớn là đáy hộp: mm => chọn = 36 mm
- Giữa mặt bên các bánh răng với nhau: mm
Số lượng bu lông nền Z: mm 41SVTH mm :
Nguyễnễ Tấấn Lập Downloaded by H?u Mai Th? (choemosoeul@gmail.com) lOMoAR cPSD| 15962736 ĐỒ ÁN CHI TIẾT MÁY Chọn Z = 2
Với L, B: chiều dài và rộng của hộp.
7.4 Các chi tiết của hộp giảm tốc:
a. Bu lông vòng hoặc vòng móc:
Để nâng và vận chuyển hộp giảm tốc (khi gia công, khi lắp ghép…) trên nắp và thân thường
lắp thêm bulông vòng hoặc vòng móc.
Theo bảng 18.3b ta có khối lượng gần đúng của hộp giảm tốc là:
Với Re = 125,53 mm, aw = 176 mm => Q = 258 kg
Theo bảng 18.3a ta có kết quả kích thước bulông vòng như sau: Ren d 1 d 2 d 3 d 4 d 5 h h 1 h 2 l≥ f b c x r r 1 r 2 d M1 45 25 10 25 15 22 8 6 21 2 12 1 , 5 3 2 5 4 0
Trọng lượng nâng được: a b c 200 250 125 b.
7.5 Chốt định vị:
Để đảm bảo vị trí tương đối của nắp và thân trước và sau khi gia công cũng như khi lắp ghép
dùng hai chốt định vị. Nhờ có chốt định vị, khi xiết bulông không làm biến dạng vòng ngoài của
ổ, do đó loại trừ được một trong các nguyên nhân làm ổ chóng bị hỏng. Ta chọn chốt định vị hình
côn cỡ kích thước sau: d = 6 mm; c = 1 mm; l = mm 7.6 Cửa thăm dầu:
Để đổ dầu vào hộp và quan sát các chi tiết trong hộp khi lắp ghép cần có cửa thăm. Theo bảng
18.5 ta chọn cửa thăm có các kích thước như sau:
42SVTH: Nguyễnễ Tấấn L pậ
Downloaded by H?u Mai Th? (choemosoeul@gmail.com) lOMoAR cPSD| 15962736 ĐỒ ÁN CHI TIẾT MÁY A B A 1 B 1 C C 1 K R Vít Số vít M8×2 100 75 150 100 125 - 87 12 4 2 7.7 Nút thông hơi:
Khi làm việc nhiệt độ trong hộp tăng lên, để giảm áp suất và điều hòa không khí trong và ngoài
hộp nên ta dùng nút thông hơi. Kích thước nút thông hơi chọn theo bảng 18.6 A B C D E G H I K L M N O P Q R S M27× 15 30 15 45 36 32 6 4 8 22 6 32 18 36 32 2 10 7.8 Nút tháo dầu:
Sau một thời gian làm việc, dầu bôi trơn chứa trong hộp bị bẩn (do bụi bặm và do bụi mài), hoặc
bị biến chất, do đó cần phải thay dầu mới. Để tháo dầu cũ, ở đáy hộp có lỗ tháo dầu. Lúc làm việc
lỗ được bịt kín bằng nút tháo dầu. Kết cấu và kích thước của nút tháo dầu: Theo bảng 18.7 43SVTH:
Nguyễnễ Tấấn Lập Downloaded by H?u Mai Th? (choemosoeul@gmail.com) lOMoAR cPSD| 15962736 ĐỒ ÁN CHI TIẾT MÁY d b m f L c q D S D 0 M20× 15 9 28 2 , 5 17 , 8 30 25 2 3 22 , 4
7.9 Chọn que thăm dầu và bôn trơn:
Khi vận tốc bánh răng v < 12 m/s, thì bánh răng được ngâm trong dầu. Chiều cao mức dầu trong
hộp được kiểm tra qua thiết bị chỉ dầu. Ta có que thăm dầu:
44SVTH: Nguyễnễ Tấấn L pậ
Downloaded by H?u Mai Th? (choemosoeul@gmail.com) lOMoAR cPSD| 15962736 ĐỒ ÁN CHI TIẾT MÁY
CHƯƠNG 8: BÔI TRƠN, ĐIỀU CHỈNH ĂN KHỚP VÀ DUNG SAI LẮP GHÉP 8.1. Bôi trơn:
8.1.1. Bôi trơn các bộ truyền trong hộp:
Trong phần thiết kế bánh răng, điều kiện bôi trơn đã được thỏa mãn vì vậy ta chọn phương
pháp bôi trơn bằng dầu. Để kiểm tra mức dầu trong hộp, đảm bảo tốt công việc bôi trơn cho bộ
truyền của hộp giảm tốc với vận tốc 1…2,5 (m/s). Theo bảng 18.11 (sách 2) dùng dầu nhớt ở t0 =
50° (100°) C có độ nhớt 186. Theo bảng 18.13 với dầu AK15. Độ nhớt ≥ 135. Khối lượng riêng ở
20°C là 0,886…0,926 (g/cm3).
8.1.2. Bôi trơn ổ lăn:
Khi ổ được bôi trơn đúng kỹ thuật, nó sẽ không bị mài mòn bởi vì chất bôi trơn sẽ giúp tránh
không để các chi tiết kim loại trực tiếp tiếp xúc với nhau. Ma sát trong ổ sẽ giảm, khả năng chống
mòn của ổ tăng lên, khả năng thoát nhiệt tốt hơn, bảo vệ bề mặt không bị han gỉ, đồng thời giảm
được tiếng ồn. Ta sử dụng mỡ bôi trơn bởi vì so với dầu thì mỡ được giữ trong ổ dễ dàng hơn,
đồng thời có khả năng bảo vệ ổ tránh tác động của tạp chất và độ ẩm. Mỡ có thể dùng cho ổ làm
việc lâu dài (khoảng 1 năm), độ nhớt ít bị thay đổi khi nhiệt độ thay đổi nhiều. Theo bảng 15.15a
( sách 1) ta chọn loại mỡ có ký hiệu LGMT2 do hãng SKF sản xuất. Mỡ tra vào ổ chiếm 1/2 thể tích của bộ phận ổ.
8.2. Điều chính ăn khớp bánh răng:
Sai số về chế tạo các chi tiết theo kích thước chiều dài và sai số về lắp ghép làm cho vị
trí bánh răng trên trục không chính xác. Trong hộp giảm tốc bánh răng trụ, để bù vào sai số
đó thường lấy chiều rộng bánh răng nhỏ tăng lên 10% so với chiều rộng bánh răng lớn.
8.3. Dung sai lắp ghép:
Ổ lăn lắp trên trục theo hệ thống lỗ, lắp có độ dôi, lắp theo kiểu k6. Lắp bánh răng, bánh
đai và nối trục theo hệ thống lỗ, mối ghép có độ dôi theo kiểu k6.
• Lắp ghép giữa trục bánh răng với ổ bi: H7/k6
• Lắp ghép giữa thân bánh răng với trục: H7/k6
• Lắp ghép giữa khớp nối với trục: H7/k6
• Lắp ghép giữa vòng chắn mỡ với trục: K7/h6
• Lắp ghép giữa nắp ổ và vỏ hộp: H7/k6 • 45SVTH:
Lắp ghép giữa vòng ngoài ổ lăn: H7
Nguyễnễ Tấấn Lập Downloaded by H?u Mai Th? (choemosoeul@gmail.com) lOMoAR cPSD| 15962736 ĐỒ ÁN CHI TIẾT MÁY
• Lắp ghép giữa mặt bích với vỏ hộp: H7/d11
• Mối ghép then: Then cố định trên trục theo kiểu lắp ghép có độ dôi, thường lắp theo hệ
thống lỗ với sai lệch của then là k6. 8.4. Dung sai và lắp ghép mối then.
Bộ truyền làm việc với chế độ tải thay đổi, chịu va đập nhẹ nên chọn kiểu lắp then bình thường.
Sai lệch giới hạn của chiều rộng và chiều sâu rãnh then. (Bảng 20.6 trang125)
TÀI LIỆU THAM KHẢO
1. Tính toán thiết kế hệ dẫn động cơ khí (tập 1,2) , Trịnh Chất – Lê Văn Uyển, nhà xuất
bảnGiáo dục Việt Nam – 1999.
2. Cở sở Thiết kế máy - Nguyễn Hữu Lộc, nhà xuất bản Đại học Quốc gia Tp. Hồ ChíMinh.
3. Đồ án môn học Chi tiết máy – Ngô Văn Quyết, nhà xuất bản Hải Phòng.
4. Dung sai và lắp ghép – Ninh Đức Tốn, nhà xuất bản Giáo dục Việt Nam.
5. Vẽ cơ khí – Vũ Tiến Đạt, nhà xuất bản Đại học Quốc gia Tp. Hồ Chí Minh.
46SVTH: Nguyễnễ Tấấn L pậ
Downloaded by H?u Mai Th? (choemosoeul@gmail.com)