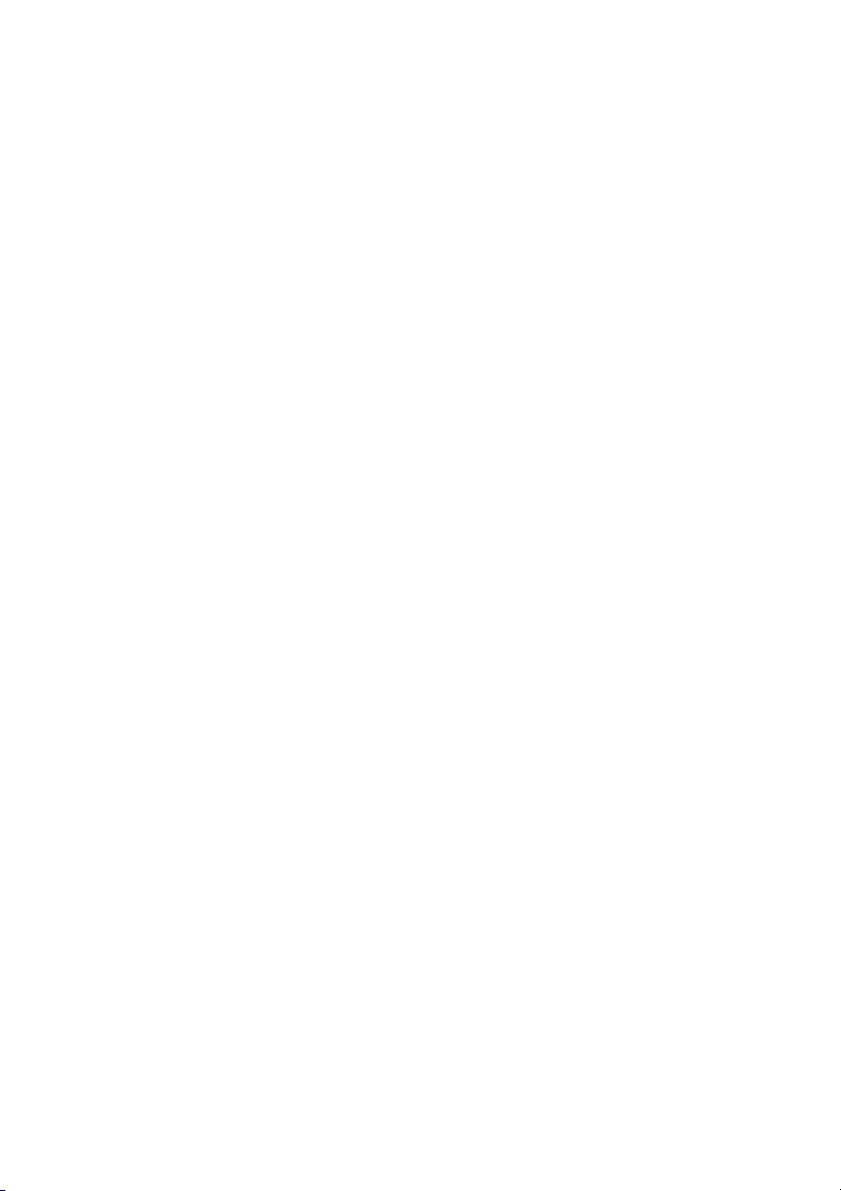
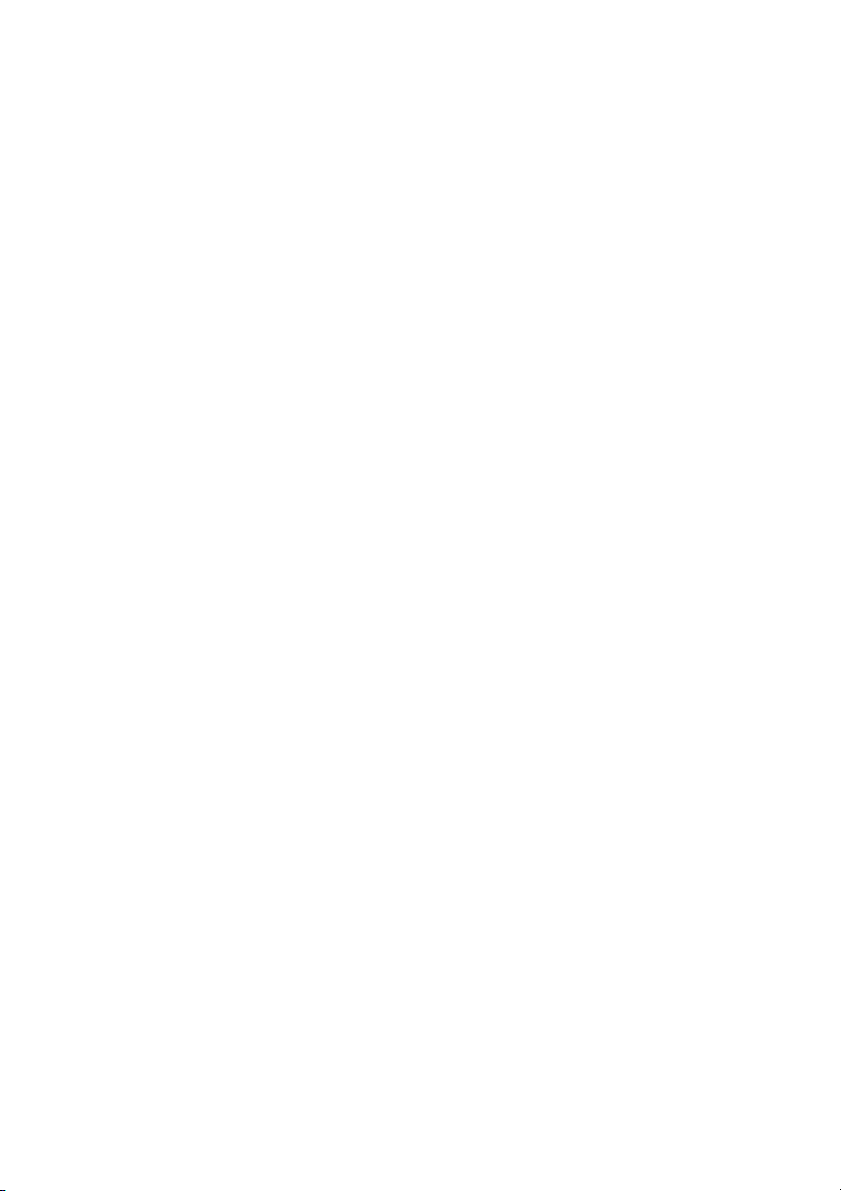
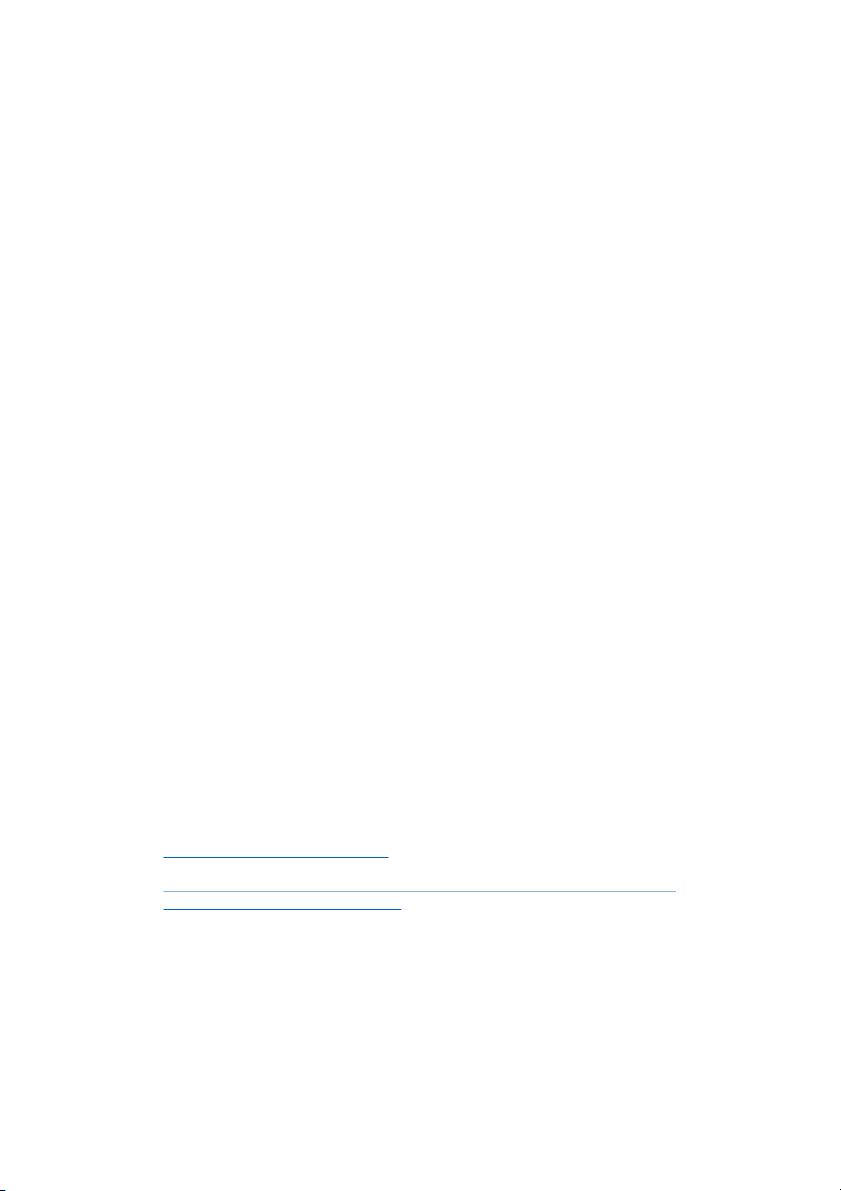
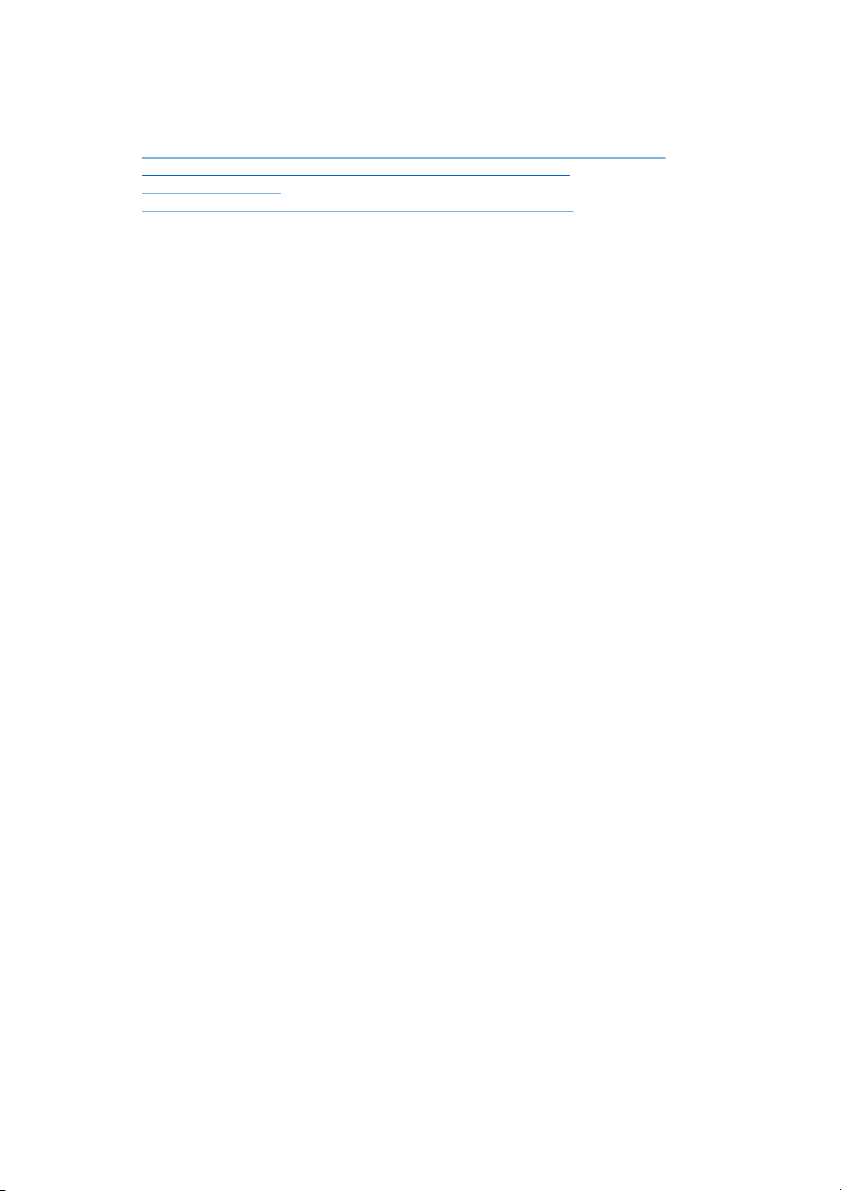
Preview text:
2. INVENTORY COSTS:
• Coca-Cola's inventory for the financal year ending December 2018 through 2022 averaged $3.473 billion.
• CocaCola inventory for 2022 was $4,233B, a 23.99% increase from 2021.
• Looking back over the past 5 years, Coca-Cola's inventory peaked in June 2023 at 4,646 billion USD. 2.1.
Inventory carrying cost:
Inventory carrying cost, also known as storage cost, is the total cost a business must
pay to store goods for a certain period of time before selling them. This cost includes
both tangible and intangible costs.
Storage costs of coca cola include
• Warehouse rental costs: Coca-Cola owns a number of factories and warehouses
around the world. This helps the company reduce warehouse rental costs.
• Labor costs for warehouse management.
• Cost of cargo insurance: Coca-Cola buys cargo insurance to protect against risks
such as natural disasters, fire, and theft. This helps the company reduce inventory risk costs.
• Storage time: Coca-Cola's storage time is 35 days in 2022. This is a short storage
time compared to other businesses in the beverage industry.
Currently, Coca Cola has applied warehouse automation. uses Automated Storage and
Retrieval Systems (ASRS) in many of its factories. In addition to automating its
warehouses, Coca-Cola is using robotics and automation to revamp its supply chain and logistics.
In this way, the facilities are designed to accommodate and automatically move nearly
30,000 pallets through the warehouse. This doubles the warehouse's storage capacity
and allows all manufactured products to be shipped directly to customers. The goal is to lower carrying costs. 2.2. Ordering Cost
Ordering Cost: Coca-Cola's ordering cost is the cost related to ordering Coca-Cola
products. Including labor costs, paperwork, procedures and fees incurred when place an order.
In 2022, Coca-Cola's ordering costs may have increased due to inflation.
Transportation and handling costs have increased significantly over the past year,
driven by rising fuel prices and labor costs.
Some estimates of Coca-Cola's ordering costs in 2022:
For example, the cost of producing a can of Coca Cola:
It costs the Coca-Cola Company about $0.26 to produce a can of Coca-Cola. This
includes the cost of raw materials, packaging and shipping. The Coca-Cola Company
then sells the Coca-Cola can to a distributor for approximately $0.50. The distributor
then sells the Coca-Cola can to a retailer for about $0.75. The retailer then sells the
can of Coca-Cola to the consumer for about $1.51
So, the total cost to produce one can of Coca-Cola is about $1.51. 2.3. Stockout cost:
Cost when an order is stockout (out of stock) and cannot be filled. It is often difficult
to measure the amount of these fees, so it is often measured as a % of the number of
orders delivered to the customer.
Coca-Cola's stockout cost is not publicly announced by the company.
Based on Coca Cola's sales of 30 billion USD per year and low inventory, this can
show that Coca Cola's stockout cost also reaches hundreds of millions of USD per year. 2.4.
Trade-off between carrying costs and ordering costs:
=> Inventory cost = Carrying cost + Ordering cost
Coca-Cola needs to consider trade-off between these two types of costs to determine
the optimal inventory level. If inventory levels are too high, Coca-Cola will incur high
storage costs. If inventory levels are too low, Coca-Cola could experience inventory
shortages, leading to lost sales and increased costs.
Coca Cola can apply some measures to consider:
• Reduce the number of suppliers: Coca-Cola cooperates with a number of large
suppliers such as Coca-Cola European Partners, Coca-Cola Bottling Company United
States,... or Coca-Cola Beverages Vietnam: This is an exclusive distributor Coca- Cola's rights in Vietnam.
In Vietnam, Coca-Cola Beverages Vietnam is the largest supplier of Coca-Cola. This
company has 11 manufacturing plants and 1 bottling center nationwide. Coca-Cola
Beverages Vietnam provides Coca-Cola with beverage products including Coca-Cola,
Sprite, Fanta, Dasani spring water, Mountain Dew energy drink, Lipton tea, Nestea coffee,...
• Coca-Cola uses a number of automated ordering methods: Ordering based on
minimum inventory levels, ordering based on demand forecasts: Coca-Cola uses
demand forecasting tools to predict demand of cutomer. 2.5.
Trade-off between carrying and stockout cost:
If companies store too much inventory, they will incur high storage costs. However, if
companies carry too little inventory, they risk running out of stock, which can lead to lost sales and other costs.
• Demand: To improve its procurement efficiency, Coca-Cola has partnered with
Keelvar, a technology company that uses AI to provide solutions to procurement
sourcing problems.Collaboration between the two companies initially started with
logistics procurement but later expanded its scope to include Coca-Cola procurement.
• Delivery time: Coca-Cola needs to consider the time it takes to place orders and
receive inventory from its suppliers. Coca-Cola HBC enables customers to track
deliveries in real time by partnering with Shippeo.
• Safety inventory: Coca-Cola needs to store a certain amount of safety inventory to
compensate for demand fluctuations or unexpected delivery times.
For example: Coca-Cola has increased the price of its products in some markets. The
decision was made after the company suffered increased costs for raw materials, packaging and transportation.
This price increase is an example of how Coca-Cola weighs inventory costs against shortage costs.
https://www.coca-colacompany.com
https://www.ajot.com/news/coca-cola-hbc-enables-real-time-delivery-tracking-for-
customers-by-partnering-with-shippeo
https://finbox.com/NYSE:KO/explorer/inventory/#:~:text=Analysis&text=Coca
%2DCola's%20inventory%20for%20fiscal,June%202023%20at %204.646%20billion.
https://www.icsid.org/uncategorized/can-of-coke-production-cost/