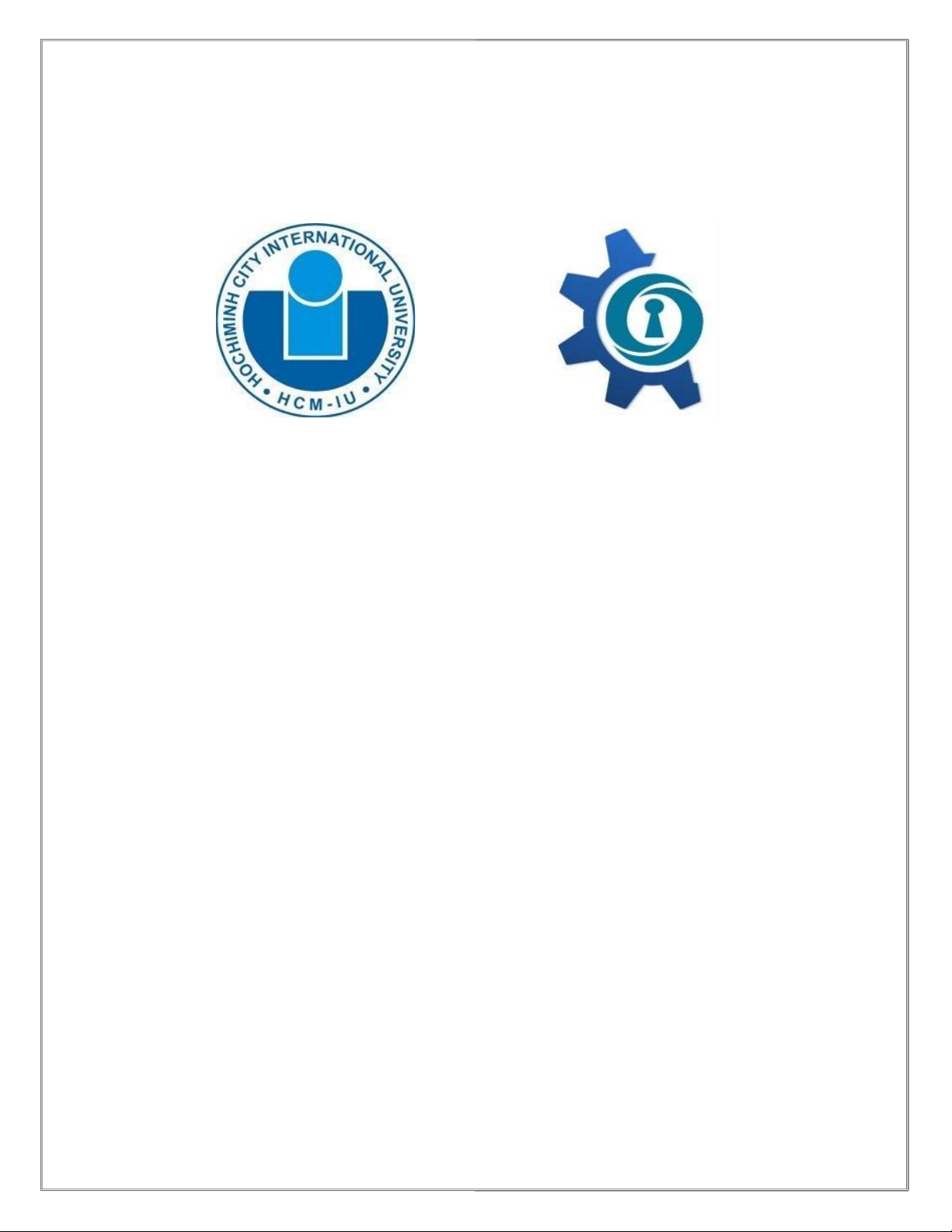
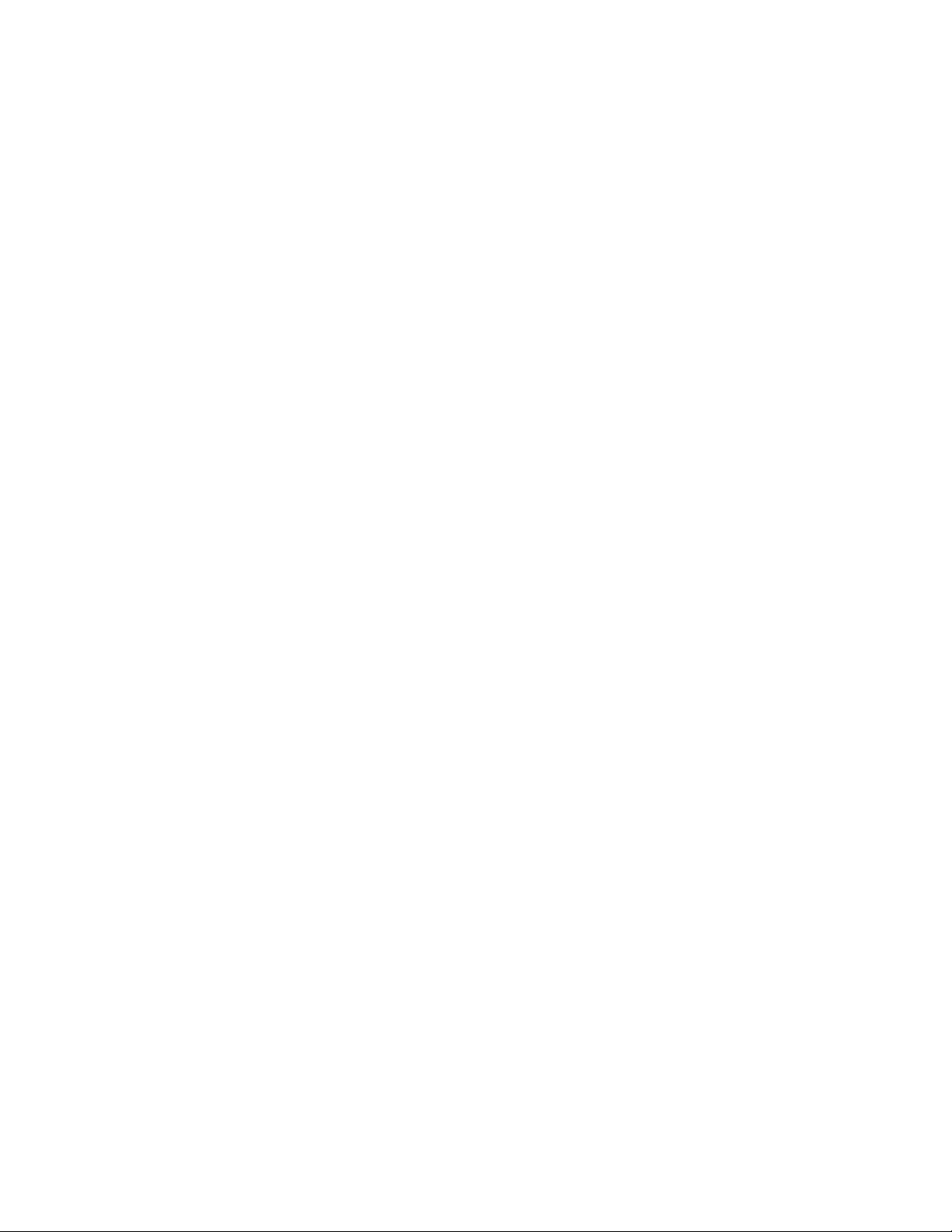
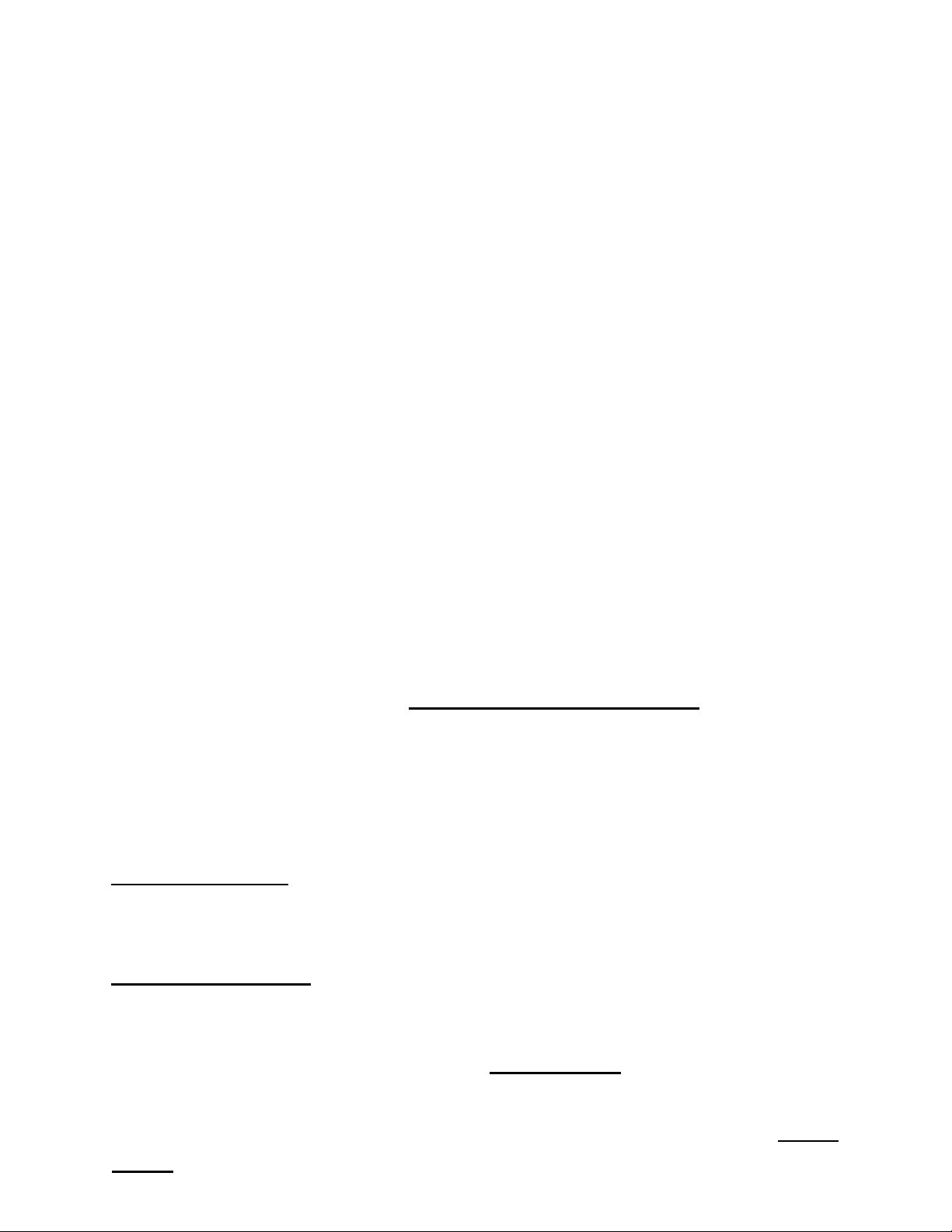
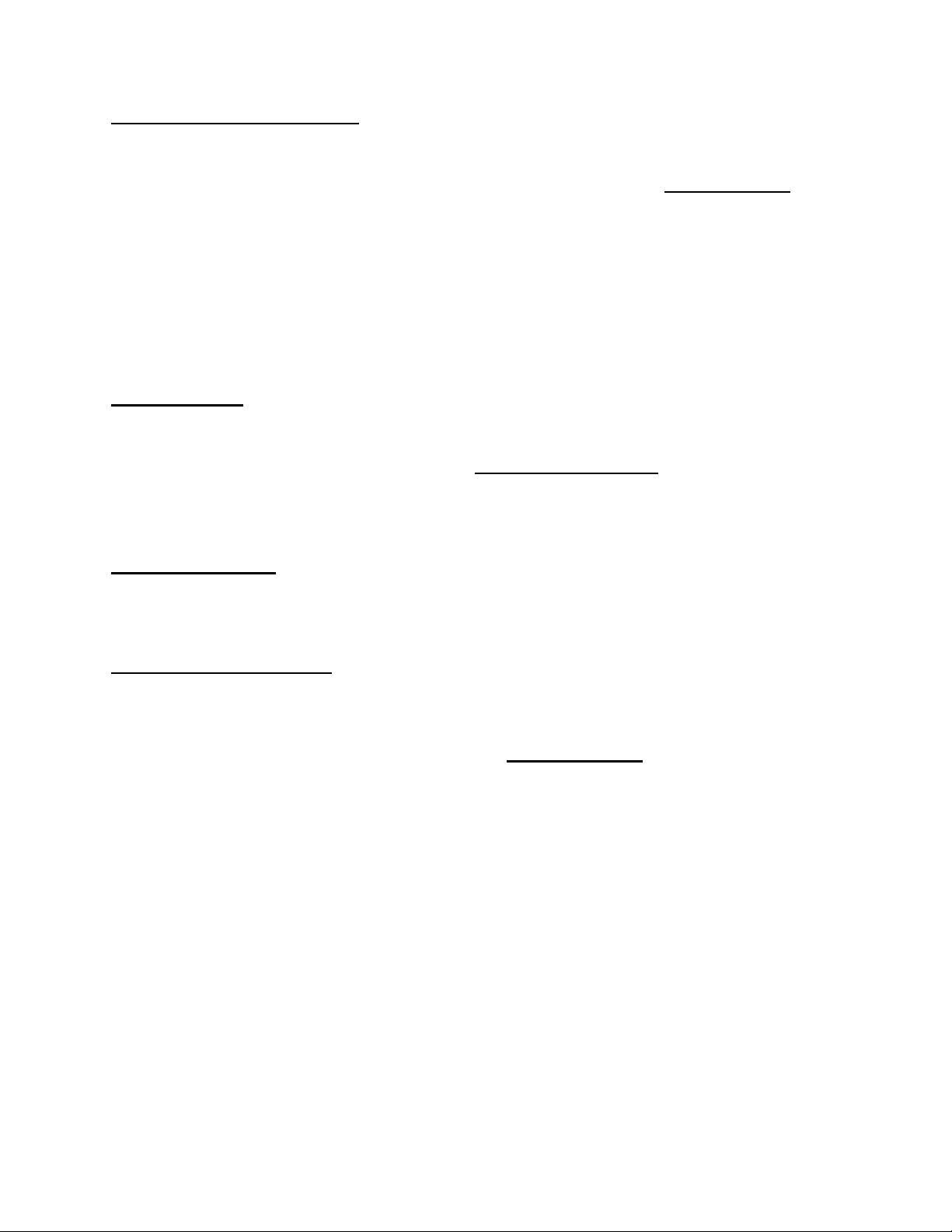
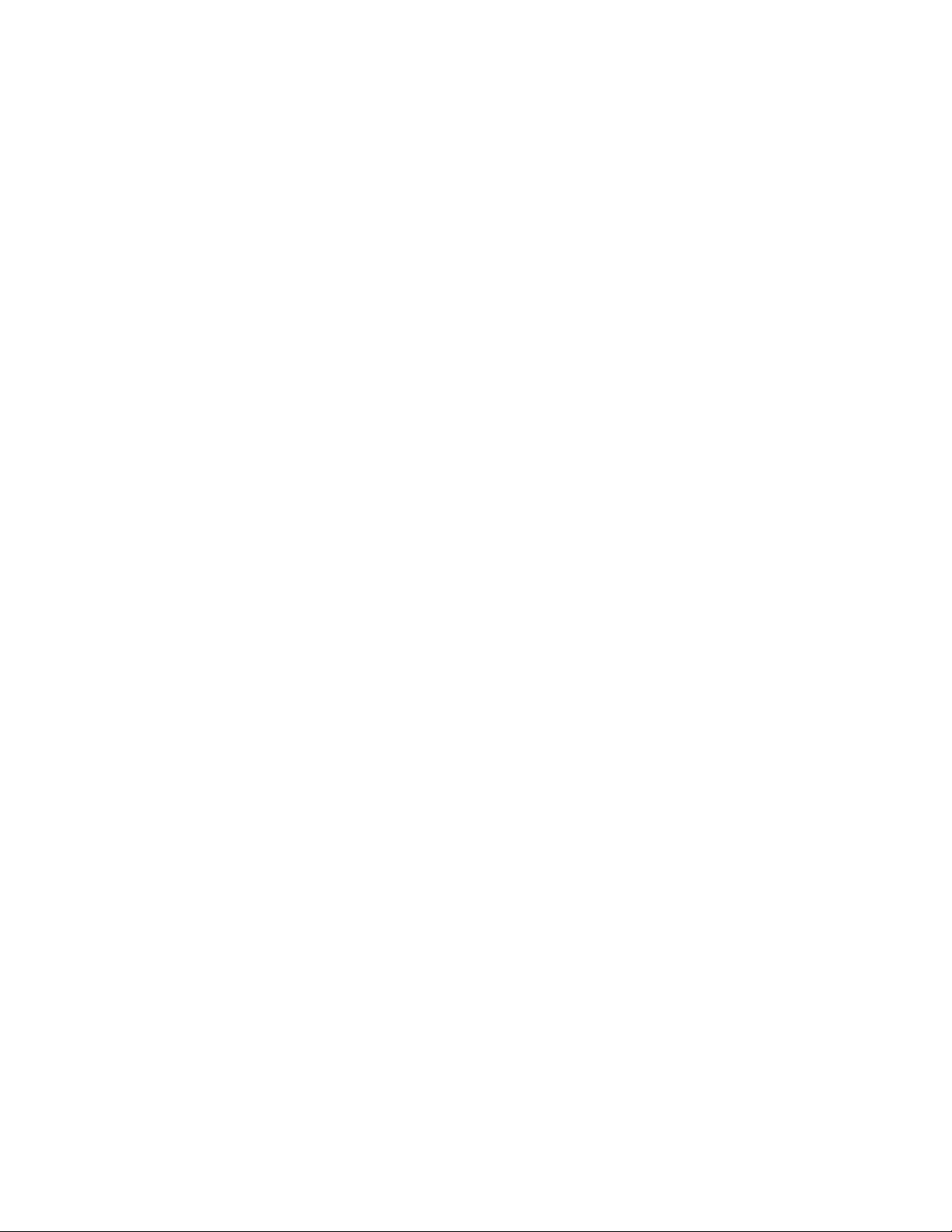
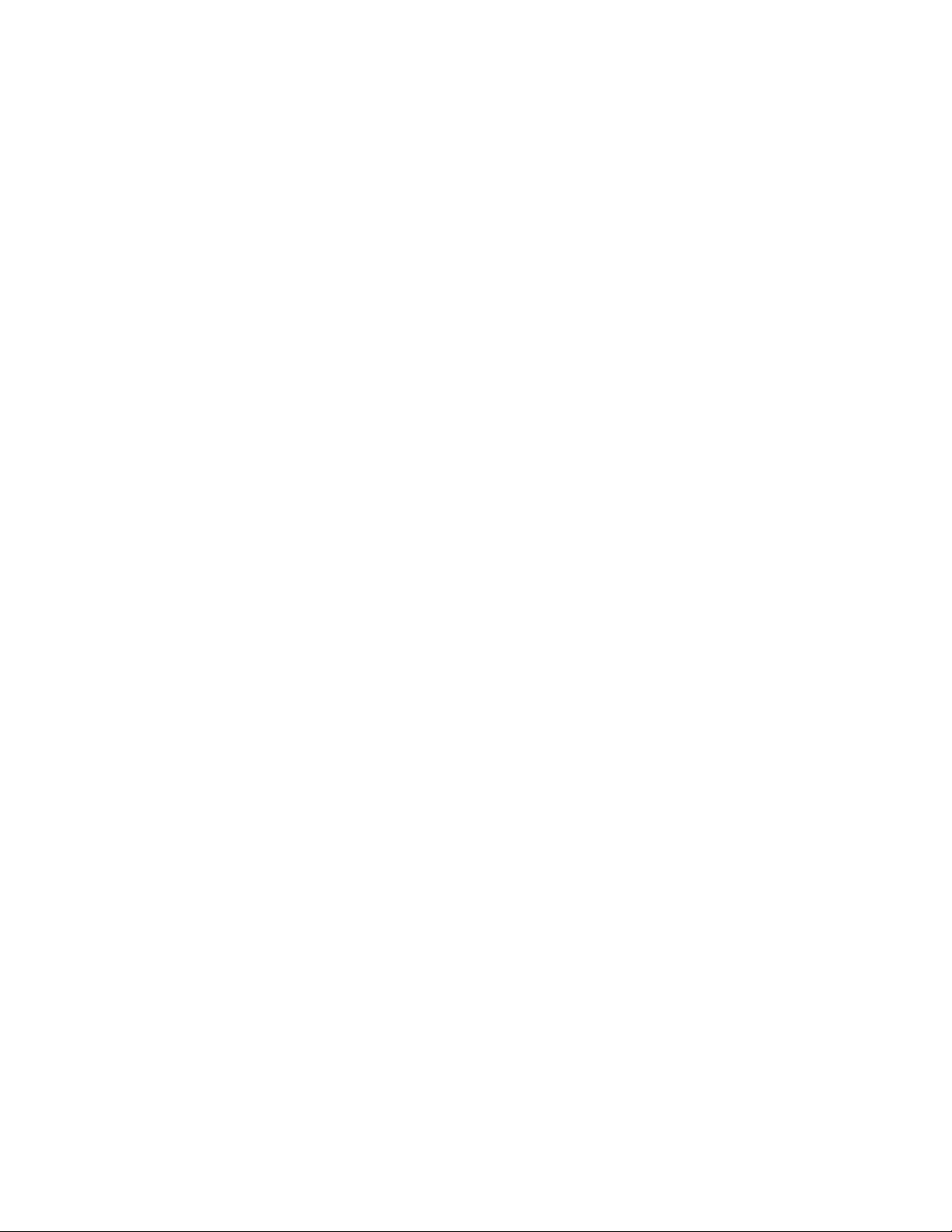
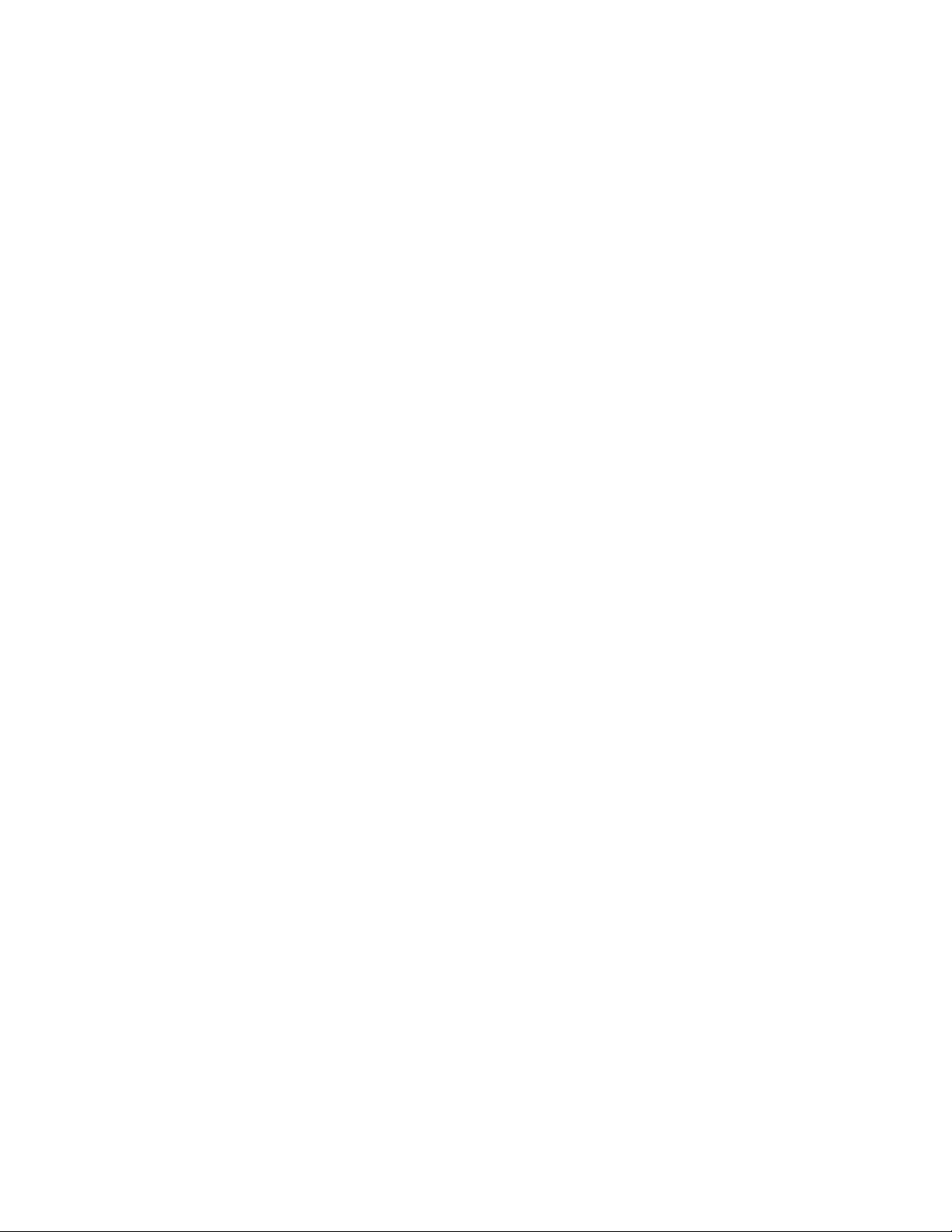
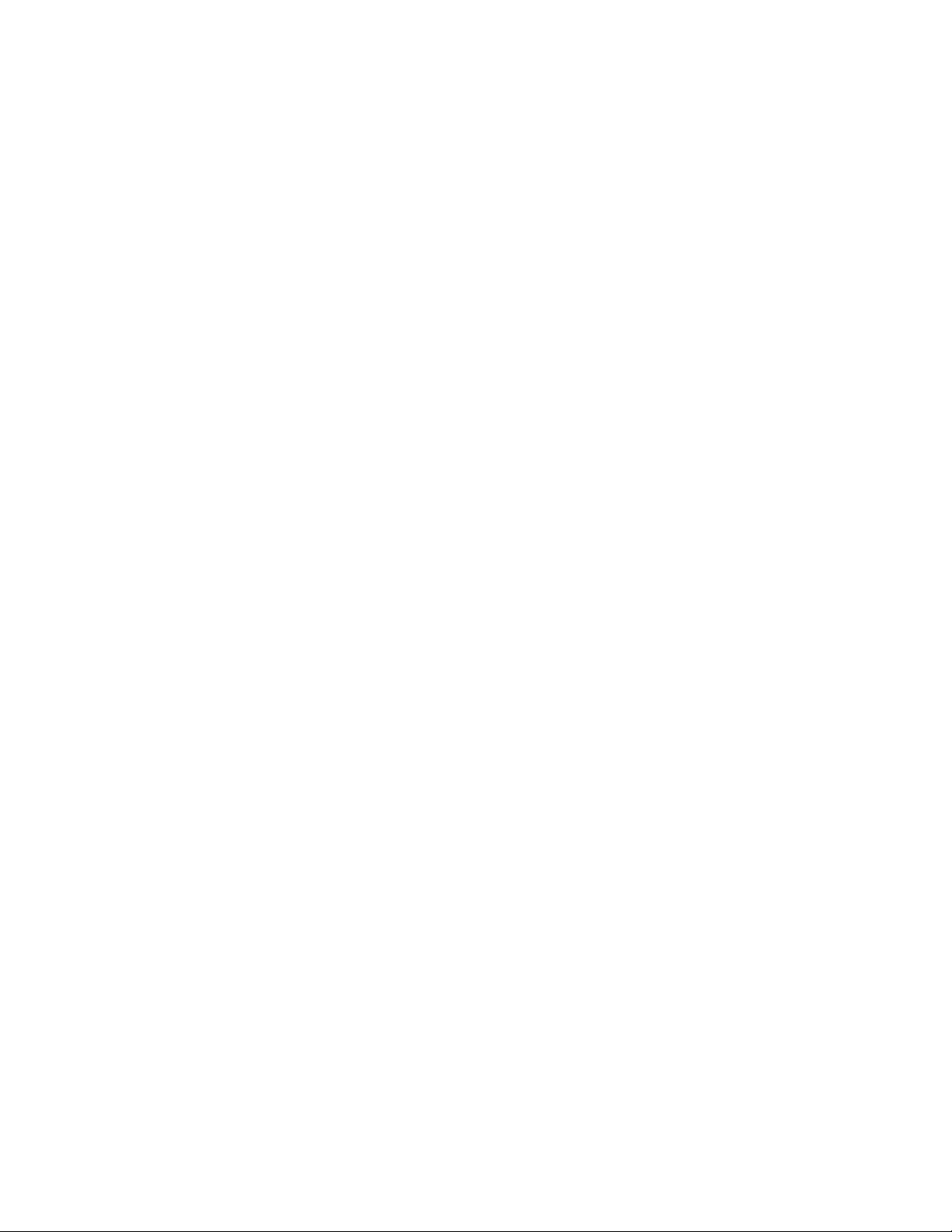
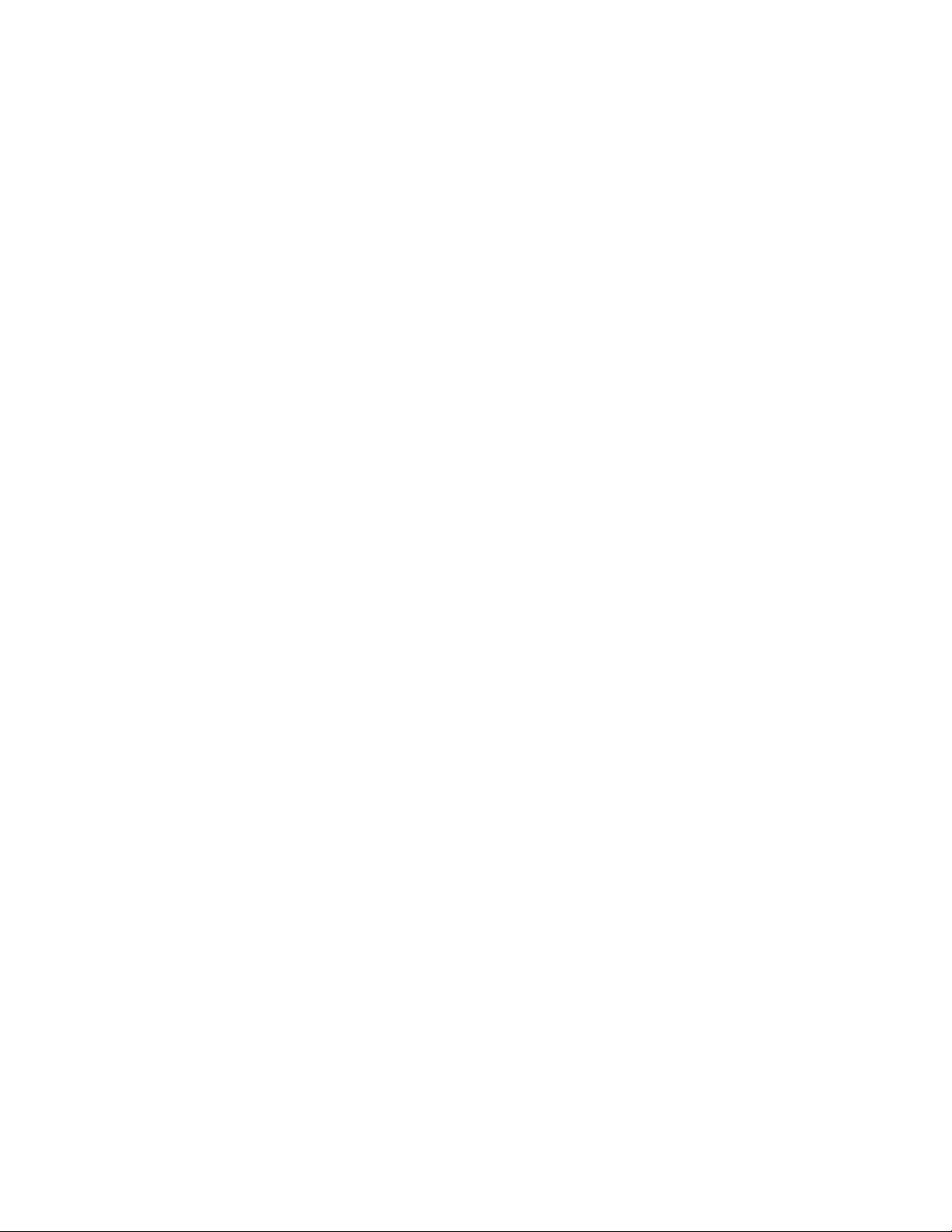
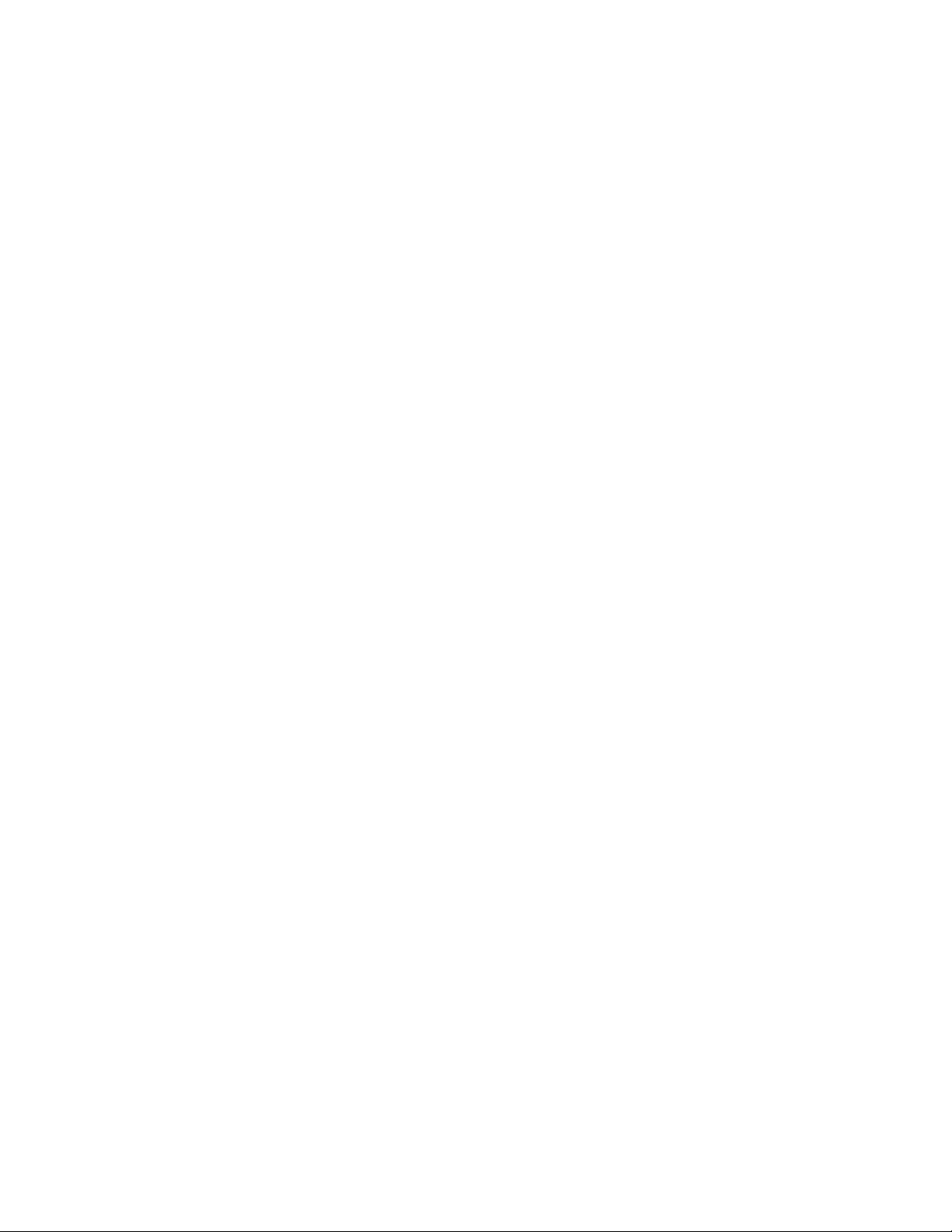
Preview text:
HOCHIMINH CITY INTERNATIONAL UNIVERSITY
SCHOOL OF INDUSTRIAL ENGINEERING & MANAGEMENT REPORT INTERNSHIP 1 Name: Võ Anh Duy ID: IEIEIU21003 Ho Chi Minh City, Vietnam /07/2023 ABSTRACT
Internship 1 is one of the mandatory courses for students at International University. The
course aims especially at students who have just finished their second year here and occurs
mainly during the months of June and July. This course involves having trips to some of
the places that are relevant to the students’ major, these places include companies, factories
and so on. For students class of 2021, they need to have exact 5 trips to 5 different places
and they are then asked to report on what they have learned during these trips.
For third-year students, this course proves to be crucial as it gives them an opportunity to
have a more detailed understanding of how the companies operate in real life, what the
working environment looks like in these places, thus giving them more information to
decide which company(ies) suit them best.
In this report, I will be presenting all the information that I have gathered during the trips
to 5 companies that our school has scheduled. These information are all factual and no personal opinions included. COMPANIES I. ACECOOK 1. Introduction
ACECOOK is a Japanese multinational company that specializes in producing all types of
instant noodles, spices and food. They currently have two subsidiary companies located in
Vietnam and Myanmar but their products have now been imported to 47 countries and territories.
Established during late 40s – early 50s, the company began their business by selling their
type of bread. Their business started to rise in popularity when they decided to sell instant
noodles with their first product of its kind in 1959. The company then changed its name to ACECOOK in 1964.
ACECOOK then thrived during the next few decades and they became well-known
internationally but their biggest deal came when they targeted at Vietnamese market
through a joint venture with Vifon in 1993.
Through the last three decades, Vifon – Acecook has taken over the Vietnamese instant
noodle market, from selling the first products in Ho Chi Minh City in 1995 to having a
complete chain of factories throughout the country and earning billions of VNĐ annually.
The factory that we visited was the first to be established in Vietnam, located in Tân Phú district 2. Observation
The process of making instant noodles at ACECOOK consisting of 12 steps that are
especially strict to ensure the quality and safety of each package before it being delivered
to consumers. The process includes: Step 1: Preparing the ingredients These include: - Flour - Oil - Soup additives - Dried vegetables - Package Step 2: Flour mixing
Flour, turmeric (to make the color) and all kinds of spice are added to a special mixer.
The ingredients are mixed in a closed environment with an automatic machine.
Step 3: Sheet flattening
The mixture flour is taken to a special machine for flattening by a conveyor belt. Right
here, the machine makes sure to process the flour until the noodle sheet meets the
requirements for its thickness and persistence. Step 4: Cutting
The sheets are then cut into different shapes, lengths and sizes according to the product. A
special system there makes sure to get the noodle to get their unique wavy shape. Step 5: Boiling
The noodle is boiled inside a complete-closed “boiler” with a temperature reaching 100 degrees Celsius
Step 6: Cutting into quantity
After being boiled, the noodle is cut by an automatic cutting system and is put into a frying
mold. Depending on the product, each mold bears a different shape. Step 7: Drying
To maintain for 5-6 months in room temperature, the noodle will be dried to lower its moisture to the lowest level.
- Fried noodle: Deep-fried in oil at 160-165 degrees Celsius for 2.5 minutes. Final moisture level: < 3%
- Non-fried noodle: “Sấy” by wind heat at 65-80 degrees Celsius for 30 minutes. Final moisture level: < 10% Step 8: Cooling
Natural airstream is purified and then blowed through pipe system to cool down the
temperature of the noodle before packaging. Step 9: Adding spices
- Packaged noodle: Added by an automatic machine
- Cup noodle: The cup-supplying system will add the spice itself Step 10: Packaging
After all the ingredients are added, the noodle will be packaged completely with its
expiration dated printed on the package.
Step 11: Quality checking
To check for defection, all packages must go thorough 3 machines: one for metal detecting,
one for weighing and one for detecting “strange” substances. Any package that fails to pass
all 3 machines will be sent away for rechecking. Step 12: Boxing
All the packages are now put in boxes. These boxes will be stored and go through quality
control again before making to the market. 3. Analysis
ACECOOK is a company that exceptionally successful in Vietnam as it targets the right
market of instant noodles, especially during the time that Vietnamese did not get to see
other types of instant noodle so ACECOOK can be considered as the “pioneer” in this field.
With the market for instant noodle keeps increasing year by year, ACECOOK can see its
success rising in the years to come. II.
FPT SOFTWARE COMPANY LIMITED 1. Introduction
FPT Software is a global IT service headquartered in Hanoi, Vietnam, being the core
subsidiary of the FPT Corporation and is considered as one of the biggest software companies in Vietnam.
Founded in 1993 by 13 members of FPT Group, the company quickly find its success
widespread to other countries. In 2000, they opened the first two oversea branches in
Silicon Valley, USA and Bangalore, India but were closed quickly afterwards.
They then decided to change over to Japan market and this turned out to be a good decision
as it boosted the growth of the company. They soon opened branches in Japan, Singapore
then expanded to Paris, France and eventually in the US. Domestically, FPT Software also
opened its delivery center in HCMC (2004), and in Da Nang (2005)
Today, the company attracts thousands of applications per year thanks to its credibility and
is currently has over 42,000 employees. The company also has annual revenue exceeds 1 billion US dollars.
The company branch that we paid a visit to located in HCMC. 2. Observation
The company is located right in the Saigon Hi-Tech Park, near to the FPT University and
many other well-known technology companies such as Intel (USA), Nidec (Japan).
The company is especially designed in a square-like shape to make it convenient to move
between deparments. They also have a big garden right in the middle the yard with bridges crossing above the garden.
FPT Company consists of various departments and each is located in a particular floor or
section of the building. One special place is called “Mekong Delta” section where they
have each room that represents a province from the Mekong Delta. This section targets at
developing technology service in the Southwest provinces.
Besides work, the company also focuses on offering many programs to attract many talents
in technology fields and even many programs for overseas working.
The company espcially concentrates on the well-being of their employees as they provide
them with almost all services and convenience. Specifically, the company has a whole
canteen, playing grounds, air-conditioning system and, most importantly, a plant to sustain
fresh atmosphere within the company. 3. Analysis
FPT Software Company is no doubt one of the most prestigious technology companies in
Vietnam. With the current policies and offers, we can expect the company to attract tens of
thousands of talents, prodigies in technology in years to come, thus, strengthening the
development path of the company in the future. III. YAKULT VIETNAM 1. Introduction
Yakult is a type of probiotic milk, known for being fermented with the bacteria
Lacticaseibacillus casei Shirota. The drink went back to the 1930s when Japanese Scientist
Minoru Shirota strenghthened and cultured the bacteria strain. Then during the same
decade, Yakult started being made in Japan in mass quantities.
Yakult became a flagship product of Yakult Honsha – a Japanese company established in
1955 to sell various products (including Yakult as well). After that, the drink gradually
started to make its name known worldwide with Yakult being sold and its factories being
built in many countries such as Taiwan, South Korea, Mexico, Australia, Great Britain and
the United States in the next few decades. Today Yakult has made its appearance in more
than 40 countries all over the world.
Yakult established branches in Vietnam in 2006 and began operation in 2007. The factory
we visited was located in Binh Duong and it was opened for operation in 2008.
Currently, Yakult has two main channels for distributing the products: Through
supermakets, retail stores and Yakult Lady delivery system 2. Observation
Binh Duong Yakult Factory is located in the Vietnam Singapore Industrial Park 1 (VSIP 1) in Binh Duong Province.
The factory is about 2.4 hectares in size and currently has thousands of employees,
including engineers to monitor the whole process of making Yakult. The process of
making and testing Yakult is exceptionally strict to ensure its quality and safety. By
Vietnamese standar, each standard bottle of Yakult must contain roughly 6.5 billion
Lacticaseibacillus casei Shirota bacteria to help maintain good health for Vietnamese people.
With a capacity of 11000 products/hour, the factory must make sure that quality must be
ensured in as many products as possible. An 18-step procedure is executed in this factory,
from collecting world-class ingredients to producing the drinks, to packaging and even
testing, all to meet the requirements of Yakult. The process includes:
Step 1: Ingredients preparation
These include skim milk powder, glucose sugar and white sugar.
Step 2: Dissolving tank
The tank dissolves skim milk powder with glucose sugar and white sugar in hot water.
Step 3: Steritizing machine
The solution is steritized at high temperature.
Step 4: Fermenting tank
Yakult “yeast” is put into a tank which has steritized milk. The fermentation process can
take up days until billions of bacterias come to existence. The milk solution now becomes really dense.
Step 5: Another steritizing machine
This machine is connected to the fermenting tank above to make sure the milk is steritized.
Step 6: Homogenization device
Milk after being fermented will be pumped into an equipment where it is homogenized.
Step 7: Storage tank with steritized sugar
The homogenized mixture above will be pumped into a storage tank and mixed with sugar
solution to create the selling product.
This process is done with the help of the following machines/system:
Step 8: Water processing system
Step 9: Storage tank for steritized water Step 10: Mixing device Step 11: Another
water processing system
Yakult factories also produce their own bottle:
Step 12: Bottle-producing machine
The bottle is made of polystyrene – a type of plastic. The plastic “beads” are heated to its
melting point and the mixture is poured into a mold with a bottle-like shape to create bottles.
After that, they are all steritized, preparing for the milk to be poured into.
Step 13: Bottle storage tank Step 14: Bottle lining machine
This machine takes all the bottles in the storage tank and puts them on a conveyor belt.
Step 15: A machine that prints expiration date and product information on bottles
Step 16: Filling machine
This machine fills the bottles with milk from step 7 and cover them with aluminium foil. Step 17: Packaging
The final products are packed into 5-bottle package using polypropylene plastic. Step 18: Boxing
Each box has 10 packages from step 17.
Step 19: Quality testing
The packages are then stored inside a cold storage (< 10 degrees Celsius) and then get
checked by professionals to ensure the quality and safety of each product. Step 20: Delivering
All the products that make it through the quality test are then loaded on cold truck and get
delivered to retail stores, supermarkets and eventually to consumers. 3. Analysis
Yakult can be considered as the “pioneer” in creating and distributing probiotic milk, which
undoubtedly plays a crucial role in its success, prevailing all of their opponents. Especially
in Vietnamese market, during this time when food quality and hygiene is a big issue and
people often get digestion problems, Yakult product definitely helps consumers maintain a
healthy digestive system and makes metabolism much easier.
Yakult also succeeds in establishing its brand, getting recognized by most consumers.
However, in terms of reaching more customers, Yakult still needs to improve in some parts
of their operating system, such as the lack of choices in flavor of Yakult milk, the dull
apperance of the bottles and the unefficiency of the Yakult-lady delivery system in certain rural areas. IV. AJ TOTAL 1. Introduction
AJU Group is a large South Korean conglomerate that offers chemical, industry, logistics,
financial, hotel and rental products. It was originally establised by Honorary President Tae-
shik Moon in 1960. The company was then seperated into several afiliated companies
which are AJU Group, SINAJU and AJ
AJ Total is a branch in AJ companies and AJ Total Vietnam operates the largest and most
advanced temperature-controlled warehousing facility in Vietnam. It has many utilities
such as Checking room, Repacking room, numerous forklift trucks and flexible inventory
management system, all for different purposes depending on the services. At the moment,
AJ Total Vietnam offer various services such as Storage, Handling, Sorting, Labelling,
Repacking, Weighting, Cross docking, Distribution Center and so on
AJ Total Vietnam currently has 3 cold storage in Vietnam, one in Long An, one in Dong
Nai and the last one in Hung Yen. The cold storages are built as a solution to tackle the
cold chain challenge in Vietnam. The storages operate simply based on a principle that
combine handling in logistics and temperature control. The one we paid a trip to was the one in Long An province. 2. Observation
AJ Total Long An is located specifically in Long Hau Industrial Area, Long A (a few
kilometers away from border with Ho Chi Minh City).
The building currently has 44 docks, together making the area up to roughly 25,600m2. The
building also has a capaity of 32,000 ton (32,024 pallets) with approximately 25,200 pallets
for robotic automation: Automatic Storage & Retrieval System (ASRS). There are also
forklift operation in 6 rooms with about 6,824 pallets.
AJ Total Long An has a system of storages with different sizes, temperatures and conditions
to store different type of food, cold package. For instance:
- Dry storage: Used for containing some products that do not need to be maintained
in cold condition. Besides, storaging the products here help saving transporting cost and air conditioning cost.
- Cool storage: At a temperature of 5 degrees Celsius (±3¿, this storage is for some types of fruit and vaccines.
- Cold storage: This storage can get as low as -22 degree Celsius and is used for
storing some high-standard products, cold package and especially Halal products:
milk, honey, cereals,... (which need to be separated from Haram products: pork, seafood, alcohol,...)
AJ Total has a system of automatic machinery and robots that help with delivering,
checking, storing all the products until importing. 3. Analysis
Overall, AJ Total’s system of sorting and storing different types of products, food in cold
conditions in different environments prove to be sufficient as all products usually meet the
requirements in quality. Personally, I think AJ Total is doing well, if I could suggest one
thing, it would be to have more safety precautions available in the cold storages in case of emergency. V. BEST LOGISTICS
FPT University is a private university in Vietnam. The university is a member of the FPT
Group and currently has campuses in Hanoi, Ho Chi Minh City, Da Nang, Can Tho along
with another one in Quy Nhon (in progress)
Founded in 2006, FPT University was the first private university to be opened in Vietnam
and Associate Professor Truong Gia Binh, the then chairman of FPT Corp was in charge
of FPT University chairman. Currently, there are about 20,000 students at FPT University
studying full academic bachelor, partnership program, postgraduate, polytechnic and high school.
All instructors need to have at least 2-year experience in IT industry and have to pass an
entrance examination. The university also aims at foreign language teaching, especially
in English so students here may need to spend the first year broadening their English
knowledge. Besides English, FPT University is also working to establish a program in Japanese.
Finally, the university offers a wide variety of opportunity for overseas study. They run a
collaborative program with the University of Greenwich, England, the UK and is the only
program in Vietnam that awards Aptech graduates a U.K bachelor's degree.
The campus we paid a visit to was in Ho Chi Minh City, located in Thu Duc City.