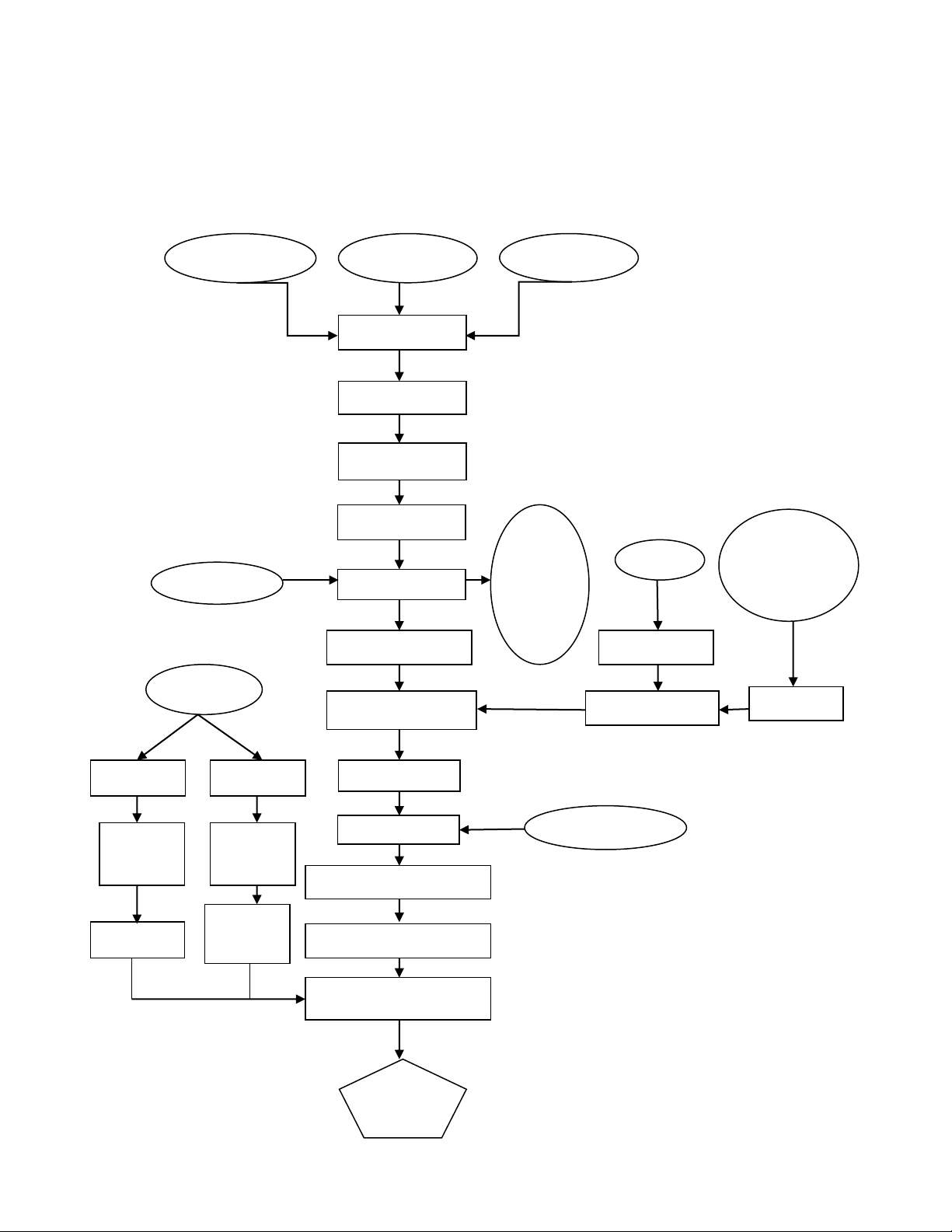
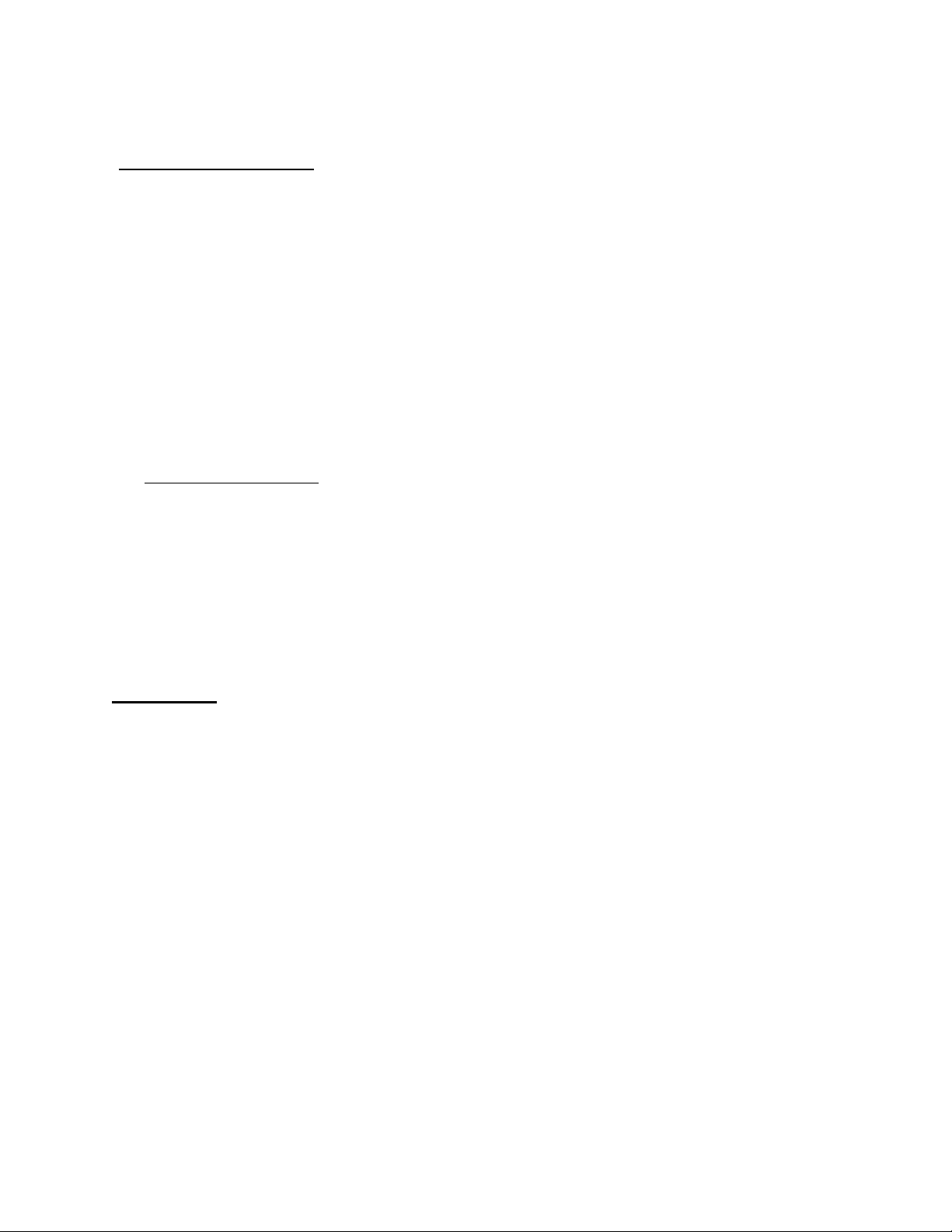

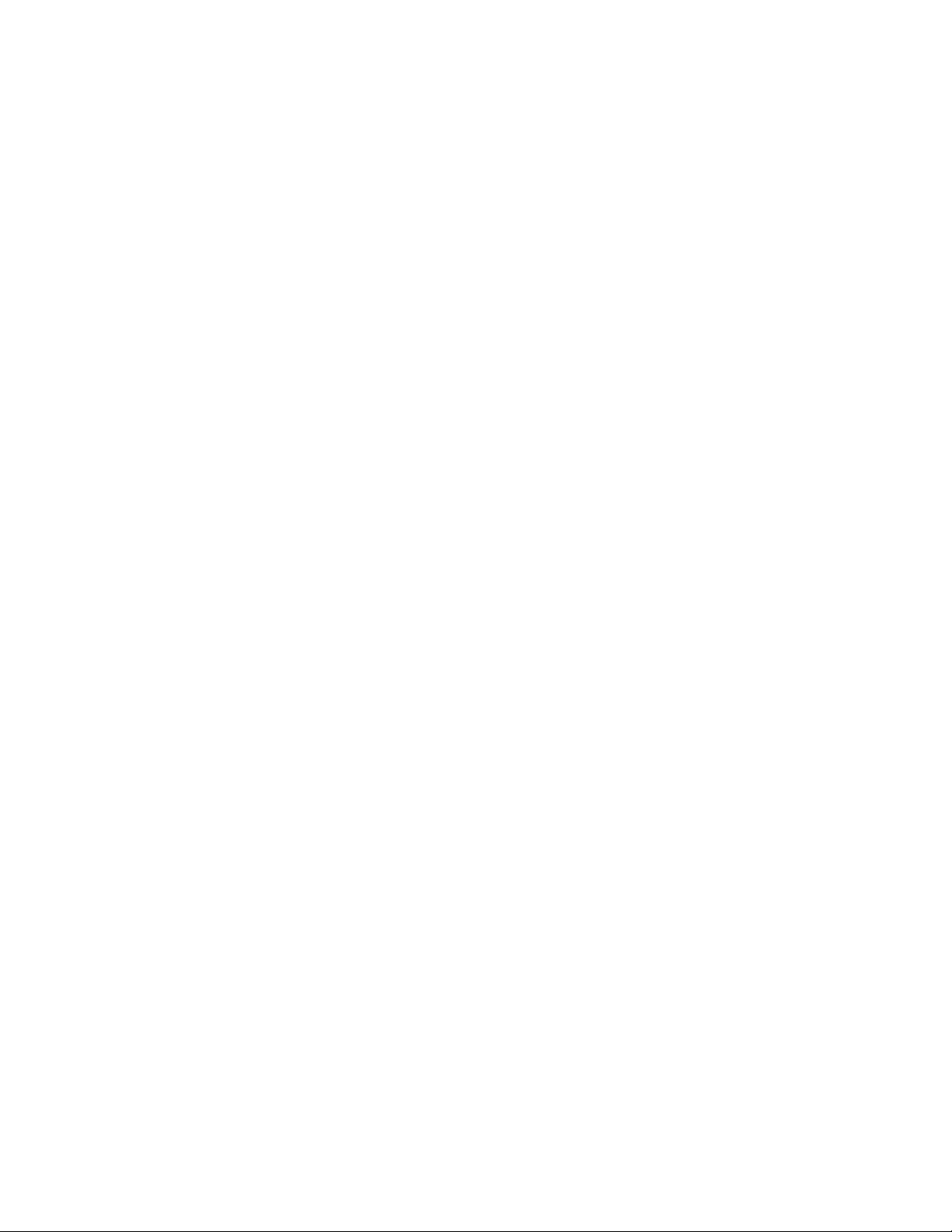
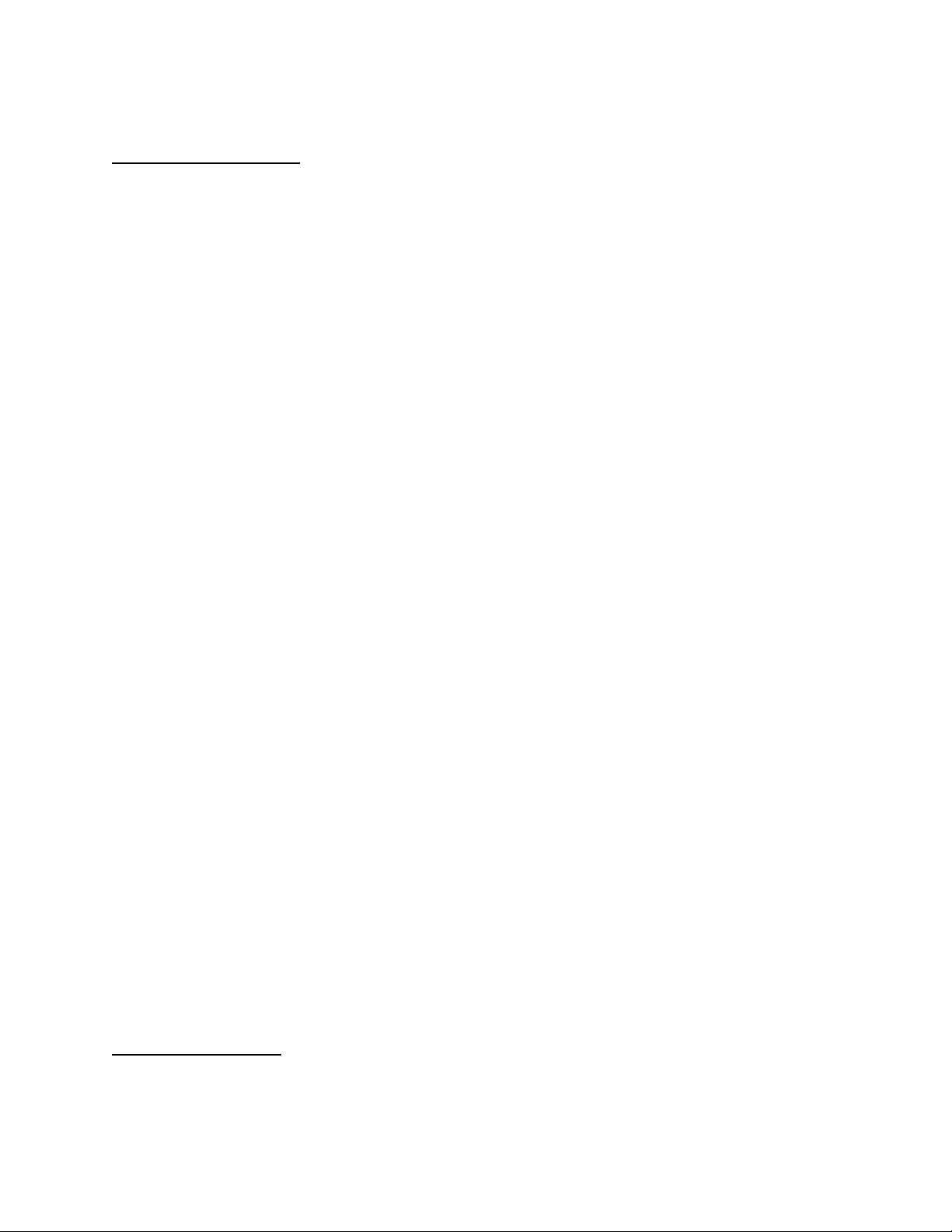
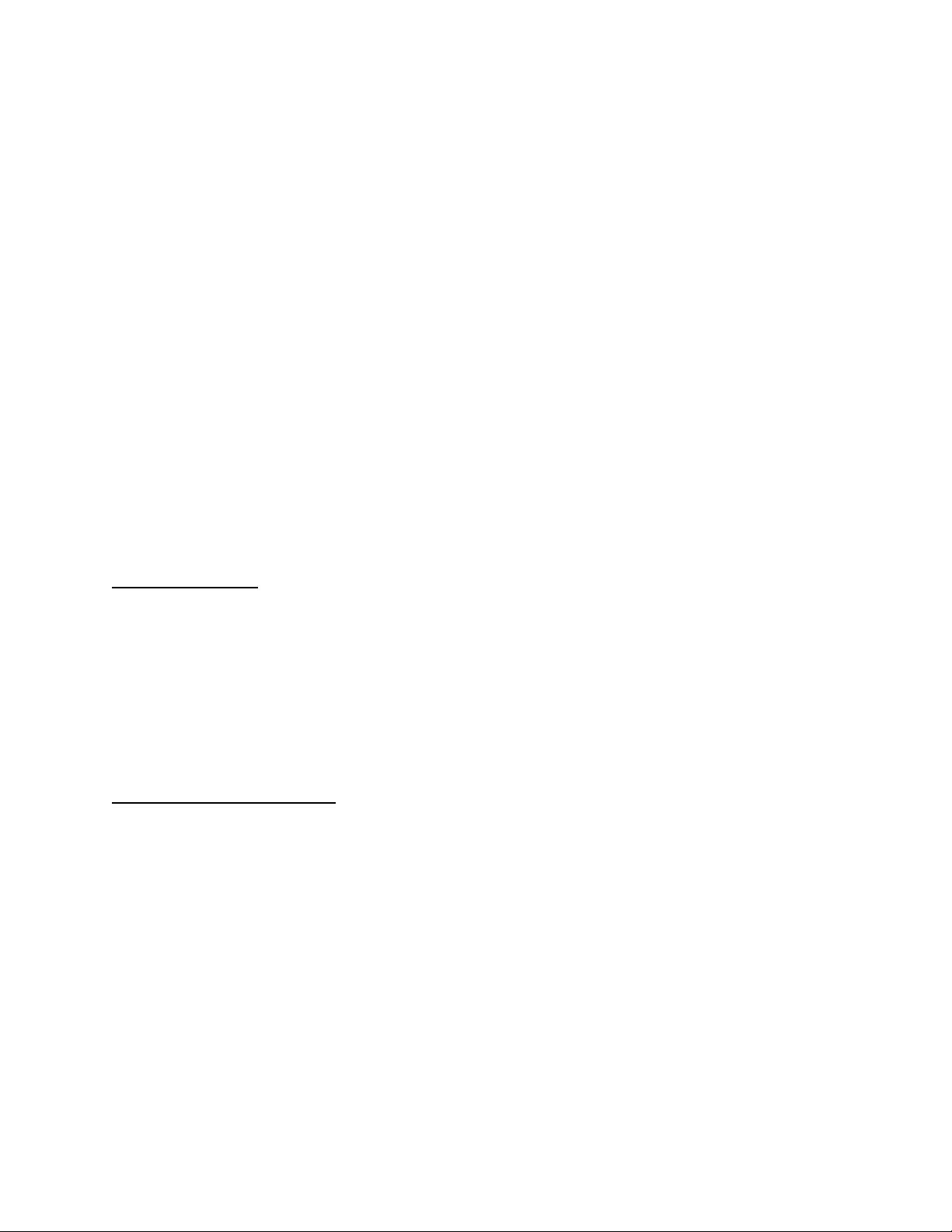
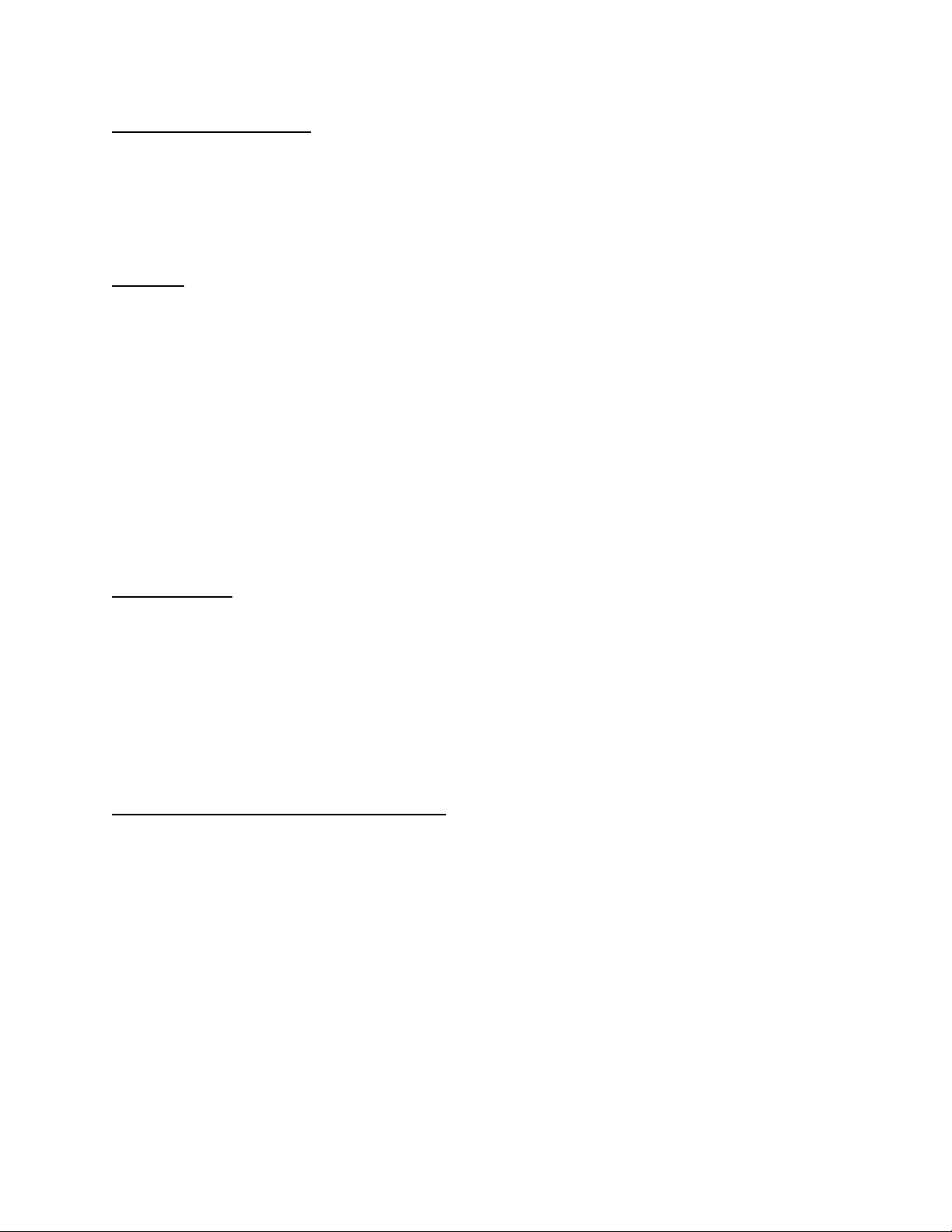
Preview text:
Quy trình sản xuất mì ăn liền: Quy trình: Bột mì Nước Phụ gia Định lượng Nhào trộn Cán, dát Cắt sợi Hơi Muối, Nước nước đường, bột Hơi nước Hấp chín ngưng ngọt tụ Cắt định lượng Định lượng Phụ gia Nhúng nước lèo Pha nước lèo Cân Phối trộn Phối trộn Quạt ráo Chiên Đị Shortening nh Định lượng lượng Làm nguội, ráo dầu Dầu sa Gói nêm Phân loại, kiểm tra tế Đóng gói, bảo quản Thành phẩm *Thuyết minh quy trình:
1. Chuẩn bị nguyên liệu: a.Nước trộn bột:
Đây là quá trình hòa tan các phụ gia vào nước, tạo thành một dung dịch đồng nhất, không vón
cục, không tạo màng, kéo váng.
Các chất phụ gia như đường, muối, bột ngọt, bột súp, chất màu, chất tạo dai… đều được cân
định lượng theo đúng thực đơn trước khi đồ vào bồn chuẩn bị nước trộn bột. Các thành phần
phụ gia được hòa tan bằng nước nóng trong thùng chứa nước trộn bột, sau đó thêm nước vừa đủ cho mỗi mẻ bột nhào.
Lấy nước theo tỷ lệ qui định vào bồn trộn, bật công tắc cho cánh khuấy làm việc rồi cho từ từ các
phụ gia trên vào. Đánh trộn trong 15 phút rồi tắt cánh khuấy. Lấy dung dịch đi kiểm tra nồng độ.
Nếu dung dịch đã đạt yêu cầu thì để yên bồn nước trộn 2 giờ trước khi đem nhào bột. Trước khi
đem dung dịch đi nhào bột, cần bật cánh khuấy trở lại để đảm bảo sự đồng nhất của dung dịch.
* Yêu cầu của nước trộn:
- Hóa chất phải được cân đủ theo đúng tỉ lệ
- Dung dịch phải đồng nhất, không vón cục, không tạo màng, kéo váng
b. Chuẩn bị bột:
Khi chuẩn bị các loại bột phải để riêng và ghi kí hiệu rõ ràng. Nguyên liệu chính để sản xuất mì
ăn liền là bột mì (82 – 84%), ngoài ra còn phối trộn thêm tinh bột để giảm giá thành sản phẩm và
tăng độ dai cho sợi mì. Nguyên liệu được cân định lượng theo công thức của từng loại mì, sau đó
đưa vào máy đánh trộn. 2. Trộn bột:
Trộn bột là khâu quan trọng của quá trình sản xuất. Yếu tố chủ yếu hình
thành nên khới bột nhào là do protein hút nước trương nở tạo thành gluten, mà cấu trúc gluten
như một cái khung gồm nhiều màng kết lại trong khối bột; các màng đó kết dính các hạt bột đã
bị trương nở. Để tăng độ kết dính của tinh bột với màng gluten, làm cho bột nhào dai và đàn hồi
cần phải nhào lâu và mạnh.
a. Mục đích của trộn bột:
- Trộn bột mì với nước thành một khối bột dẻo.
- Hòa tan các chất phụ gia như đường, muối... đồng thời phân tán chúng đều
khắp trong bột nhào, làm cho khối bột nhào trở thành một khối đồng nhất.
b. Yêu cầu của khối bột sau khi trộn: - Độ ẩm 30 – 33%
- Đạt độ đồng đều cao, không vón cục lớn, ở trạng thái bời rời khi nắm nhẹ bột
trong tay, mở tay ra bột không rời rạc, dính tay, bột mềm dẻo. c. Cách tiến hành:
- Quá trình trộn bột chia làm hai giai đoạn:
+ Trộn khô: rải đều một lượt bột mì, một lượng bột năng theo suốt chiều dài trục
nhào, cho máy trộn khô trong vòng 3 – 5 phút nhằm đảm bảo độ đồng đều của khối bột.
+ Trộn ướt: sau khi trộn bột khô đều, cho nước trộn bột vào từ từ, theo dọc chiều
dài trục nhào. Tiếp tục bật máy hoạt động, tiến hành nhào tiếp trong 15 – 20 phút.
- Quá trình nhào trộn chỉ cần đảm bảo các cấu tử trộn đều nhau, nếu kéo dài thời gian
trộn sẽ có nhiều không khí vào khối bột gây hiện tượng dễ đứt khi cán vì gluten hạn chế trương nở
- Lượng nước để nhào tính theo công thức: N= B.(W1-W2)/(100-W1)
Với: N,B: lượng nước (l) và bột (kg)
W1,W2: độ ẩm của bột nhào và bột (%)
d. Các sự cố và cách khắc phục:
- Khi trộn bột bao giờ cũng có một lượng không khí lẫn vào bột nhào. Lượng không
khí này có ảnh hưởng xấu tới sự trương nở gluten, làm cho sợi mì bị đứt khi tạo hình bằng máy đùn ép.
- Bột nhào bị nhão: bột sẽ khó cán, bông trên vắt mì khít, dầu không ngấm đều khi
chiên, làm cho vắt mì bị đốm. => KHi thấy bột nhào bị nhão do cho lượng nước trộn bột quá
mức cần thiết, thì ta cần cho bột vào thêm kết hợp với đánh trộn cho đến khi bột vừa.
- Bột nhào bị khô: làm cho bột dễ bị đứt khi cán.=> Thêm nước trộn bột kết hợp với đánh trộn.
- Đánh bột lâu bột dễ bị vón cục: cần kiểm tra bột thường xuyên để xác định đúng thời
điểm kết thúc quá trình.
- Cân thiếu hóa chất: sản phẩm sẽ không đạt yêu cầu về màu sắc, độ nở xốp ... =>
Cân định lượng chính xác các chất phụ gia khi pha nước trộn bột.
- Hóa chất không tan hết do khi pha nước trộn bột khuấy không đều: làm cho khối
bột nhào không đồng nhất. => Cần khuấy nước trộn bột trước khi sử dụng để đảm bảo sự đồng nhất cho dung dịch. 3. Quá trình cán:
Bột sau bkhi nhào trộn được xả từ cối trộn xuống thùng chứa sau đó được đưa đến hệ thống
cán nhằm cán bột ra thành các lá bột.
a. Mục đích của quá trình cán:
- Nhằm chuyển bột nhào từ trạng thái bời rời thành tấm bột có độ dày đều đặn.
- Làm đồng nhất khối bột và tăng độ đàn hồi cho khối bột nhào và giảm lượng không
khí hòa lẫn trong bột nhào.
- Khi đi qua các lô cán bột lá bột sẽ được nén chặt thành lá để dễ tạo hình. Đồng thời
có tqác dụng dẫn lá bột đến thiết bị kéo sợi.
b. Yêu cấu của lá bột sau khi cán:
- Sau khi ra khỏi trục cán bột cần có bề mặt tương đối mịn, độ dày đồng đều.
- Lá bột mỏng, mềm, xốp, không rách, không bị lốm đốm (do có lẫn bột khô )
- Không có lỗ xốp, bề mặt láng đều, tráng ngà.
- Kích thước của lá bột mỏng dần khi qua các trục cán, lá bột qua trục cán tinh dày khoảng 0,8 – 1,2 mm. c. Cách tiến hành:
Quá trình cán được chia làm 2 giai đoạn:
- Cán thô: bột nhào từ thùng phân phối được đưa xuống 2 cặp trục thô có đường kính
300mm. Vận tốc trục cán thô nhỏ, tạo lực nén lớn ép bột thành tấm đưa sang cán tinh.
- Cán tinh: hệ thống cán tiknh có 5 cặp trục, vận tốc chuyển động giữa các lô tăng
dần qua các trục và khoảng cách giữa hai trục của các cặp trục nhỏ dần, khi đẩy lá bột qua lá bột
sẽ được dàn mỏng dần.
d. Yêu cầu kĩ thuật:
- Tốc của lô cán tinh: v = 90 P130 v/phút.
- Khe hở của các trục cán nhỏ dần qua các lô trục .
+ Cán thô (2 cặp trục) : L1=L2= 5mm
+ Bán thô ( 1cặp trục): L3=4mm
+ Bán tinh (3 cặp trục): L4=3P3,5mm L5= 2P2,5mm L6= 1,2P1,5mm
+ Cán tinh (2 cặp trục): L7=1 P1,2 mm L8=0,8P0,9 mm
e. Các sự cố và cách khắc phục:
- Bột nhão khi cán bị nặng, nếu bột khô khi cán dễ đứt tấm = > điều chỉnh khâu trộn.
- Các lô trục chuyển động không đều, gây ra sự cố bị đùn tấm bột hoặc bị đứt lá bột.
= > điều chỉnh lại vận tốc các lô
- Lá bột bị rách 2 bên mép = > điều chỉnh 2 bên.
- Bột dính lô cán => cần xem lại nạo.
4. Cắt sợi – Đùn bông:
Mỗi một sản phẩm không chỉ được đánh giá chất lượng bên trong mà còn phụ thuộc rất lớn
vào hình dạng, kích thước bên ngoài nên việc tạo hình cho sợi mì là cần thiết, được coi là quá
trình không thể bỏ qua trong công nghệ sản xuất mì ăn liền.
a. Mục đích của quá trình:
- Tạo hình dạng, kích thước đặc trưng cho sợi mì ăn liền
- Tạo bông để làm tăng giá trị cảm quan của vắt mì. b. Yêu cầu:
- Sợi mì láng, không bị răng cưa.
- Sợi mì rời, tạo thành gợn sóng với khoảng cách gần đều nhau.
- Bề mặt sợi mì láng, mịn.
- Sợi mì có đường kính d= 0,8 – 1mm. c. Cách tiến hành:
Tấm bột mì ra khỏi hệ thống cán tinh đã đạt yêu cầu, được đưa vào khe hở giữa 2 trục
dao cắt và được cắt thành sợi nhờ các rãnh trên trục dao. Các sợi mì được tạo thành được gỡ ra
khỏi các rãnh nhờ bộ phận lược tỳ sát vào bề mặt trục dao, tránh làm chập mì, rối sợi. Do tốc độ
mì đi ra khỏi dao cắt lớn nhưng tốc độ của băng chuyền lại nhỏ, làm cho sợi mì bị đùn lại, tạo
thành các dợn song, gọi là tạo bông cho sợi mì.
d. Yêu cầu kĩ thuật:
- Các rãnh trên 2 trục dao có: d= 0,8 – 1mm; sâu 4mm
- Vận tốc sợi mì ra khỏi dao cắt phải lớn hơn rất nhiều so với vận tốc băng chuyền tiếp nhận (lưới con)
- Vận tốc dao cắt lớn hơn rất nhiều so với vận tốc lưới con: Vdao = 0,33 – 0,48m/s; Vlưới= 0,08 – 0,1m/s
e. Sự cố và cách khắc phục:
- Chập sợi và rối sợ mì: do bộ phận lược không tỳ sát vào bề mặt trục dao
- Dợn sợi mì thấp: do chênh lệch vận tốc mì ra khỏi dao cắt và vận tốc băng chuyền
nhỏ = > giảm tốc độ băng chuyền hoặc tăng tốc độ dao cắt.
- Mì không đứt hẳn: do khe hở giữa 2 trục dao nhỏ hơn không nhiều so với lá bột, có
thể khắc phục bằng cách điều chỉnh khe hở.
- Sợi mì không bóng => kiểm tra lại các rãnh trên dao cắt.
5. Hấp và làm nguội : a. Mục đích:
- Nhằm hồ hóa bề mặt sợi mì.
- Nhằm biến tính protein dể giữ vững nát của sợi mì.
- Tăng độ dai của sợi mì trong nước sôi, tăng độ bóng.
- Làm sợi mì vàng hơn, rút ngắn thời gian chiên. b. Yêu cầu:
- Sợi mì vàng hơn, dai hơn, mền hơn.
- Sau khi hấp sợi mì chín đều tới 80- 90%.
- Sợi mì không bị biến dạng, không bị nhão, không bị kết dính lại trên băng tải.
c. Các sự cố và biện pháp khách phục:
- Hấp chín quá độ: do kéo dài thời gian hấp, áp lực hơi cao khó đảo mì biện pháp xử
lý: tăng vận tốc của băng chuyền, giảm thời gian hấp hoặc giảm áp lực hơi.
- Mì sống: do thời gian hấp ngắn, áp lực hơi không đủ do thiếu nước lò hơi sẽ làm cho vắt
mì xóp, sợi mì bởgiảm vận tốc băng chuyền đẻ tăng thời gian hấp hoặc thêm nước vào lò đẻ tăng áp lực.
- Lưới hấp hỏng do hỏng bạc đạn, lưới bị cạ thùng hấp thay lưới.
* Thổi nguội: Sau khi ra khỏi buồng hấp, sợi mì được quạt gió thổi nguội để giảm nhiệt
độ xuống dồn thời gian làm khô sợi mì, tạo điều kiện thuận lợi cho các công đoạn sau.
6. Cắt định lượng: a. Mục đích:
- Đảm bảo đúng khối lượng.
- Chiều dài sợi mì đúng qui định. b. Yêu cầu:
- Tùy theo mục đích mà sợi mì có kích thước 20 -25 cm.
- Chiều dài và trọng lượng mì sau khi cắt phải đảm bảo đồng đều và đúng qui định.
7. Nhúng nước lèo- làm ráo: a.Mục đích:
- Tạo hương vị đặc trưng cho sản phẩm.
- Tạo cho sợi mì có chất lượng cao hơn. b. Yêu cầu:
- Nước lèo phải ngấm đều trong vắt mì.
- Sau khi qua nước lèo sợi mì phải mềm, không bị biếng dạng.
c. Cách tiến hành: Sau khi hấp và thổi nguội mì có xu hướng háo nước, lợi dụng điều
này người ta đưa sợi mì qua các chất phụ gia trong thời gian 15 -20 giây đẻ tăng vị ngọt và mặn cho thích hợp.
8. Tạo khuôn cho vắt mì:
a. Mục đích: Tạo hình dáng và kích thước nhất định cho vắt mì. b. Yêu cầu:
- Vắt mì vuông vắt và đều đặn.
- Sợi mì bông lên làm dầu dễ len vào khi đưa vào chiên. 9. Chiên: a. Mục đích:
- Nhằm thuận lợi cho quá trình bảo quản ( do quá trình chiên đã tiêu diệt phần lớn vi sin vật, loại bỏ bớt nước).
- Thay thế một phần nước bằng một lượng chất béo thích hợp nhằm làm tăng giá trị dinh
dưỡng,tạo màu, mùi thơm, vị đặc trưng cho vắt mì.
b. Yêu cầu của vắt mì:
- Vắt mì sau khi chiên có độ ẩm < 4.5%.
- Màu vàng đều không có đốm trắng quá 2 cm, mì không cháy khét, không gãy nát, không có mùi lạ.
- Hàm lượng chất béo tăng, có mùi vị đặc trưng của mì. 10. Làm nguội:
a. Mục đích: Sau khi chiên, mì theo băng tải vận chuyển theo hướng lên cao để thu hồi
lượng dầu hư trong mì và tiếp tục đưa vào hệ thống thổi nguội đẻ hạ nhiệt độ của vắt mì đén
nhiệt độ môi trường. Ngoài ra giai đoạn này còn có tác dụng làm khô dầu trên vắt mì, kéo dài thời gian bảo quản. b. Yêu cầu:
- Đảm bảo nhiệt độ của vắt mì ở nhiệt độ tương đương nhiệt độ môi trường.
- Bề mặt vắt mì khô và ráo.
11. Phân loại kiểm tra trước khi đóng gói:Trước khi bao gói sản phẩm cần phải được kiểm tra
và phân loại, loại bỏ những vắt mì không đạt tiêu chuẩn ( bể vụn, cháy khét, vàng không đều,
không đúng trọng lượng…) đưa gói mì đạt chuyển qua đóng gói.