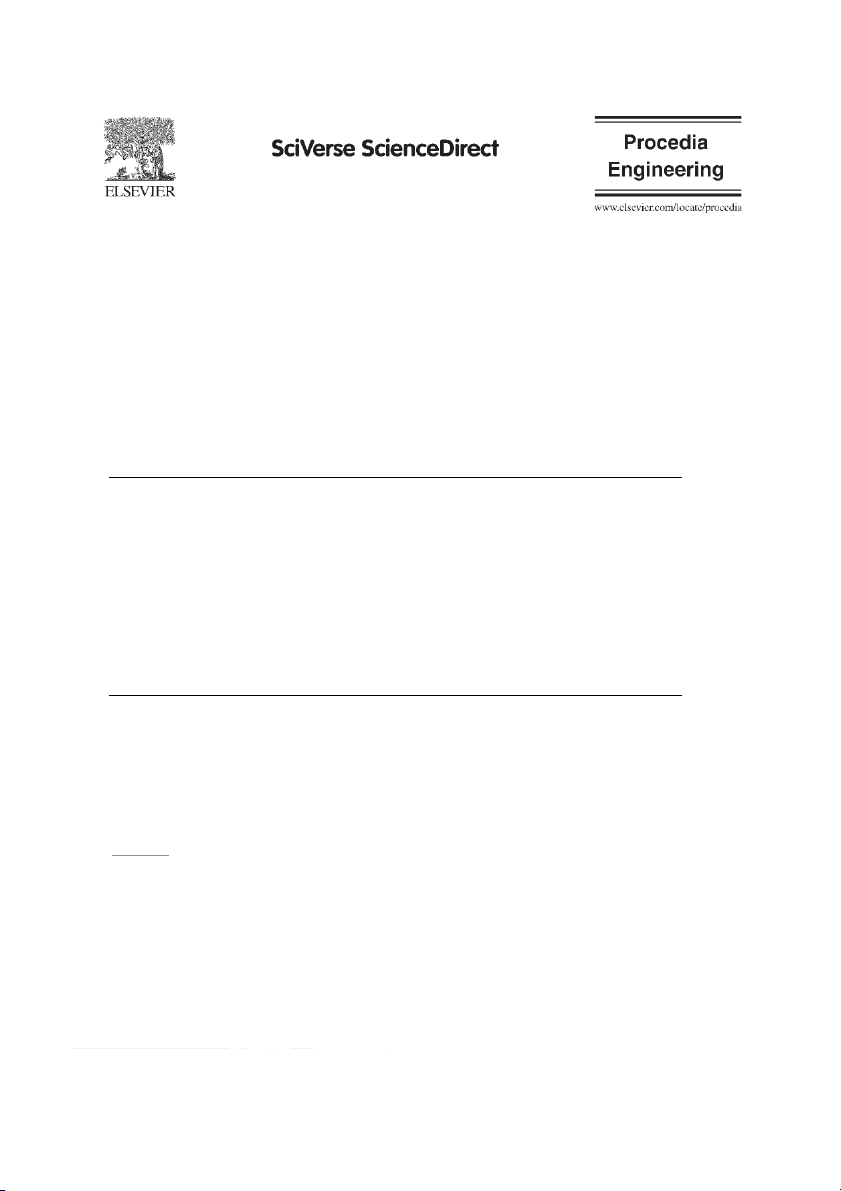
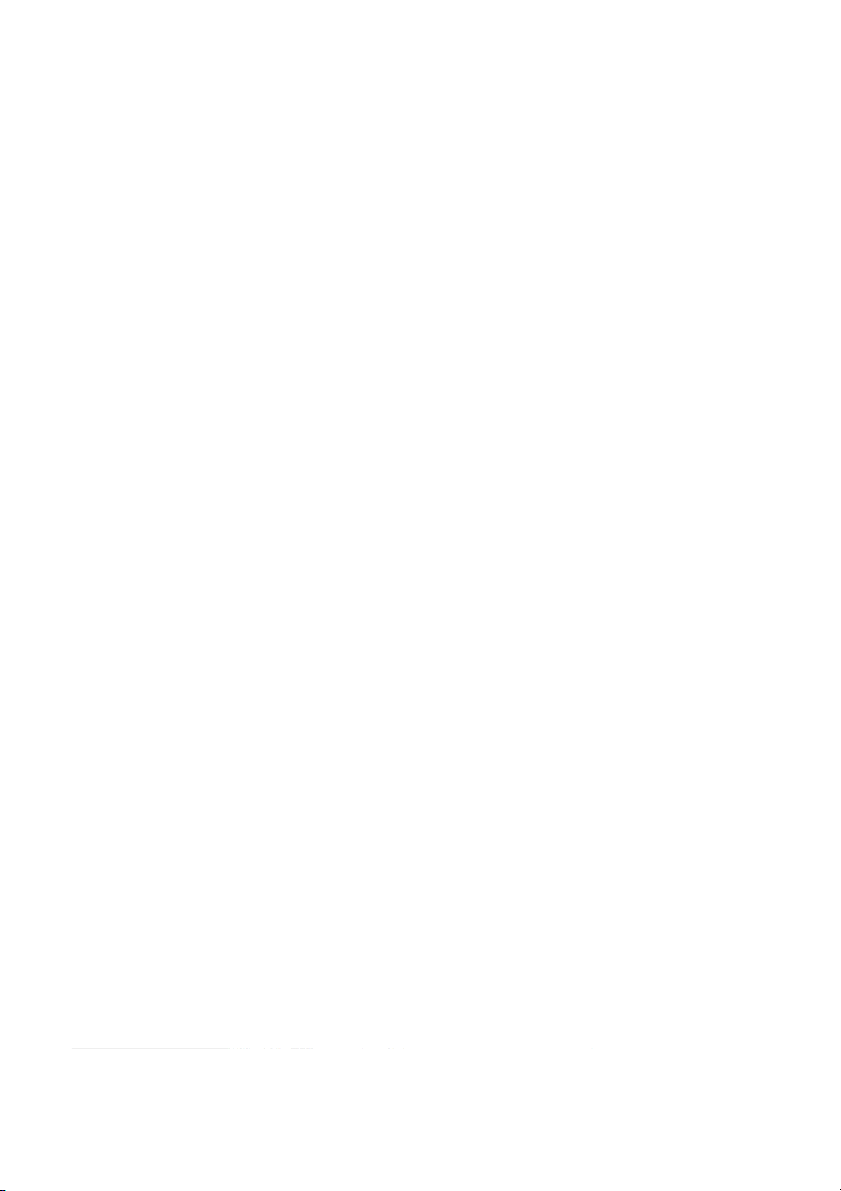
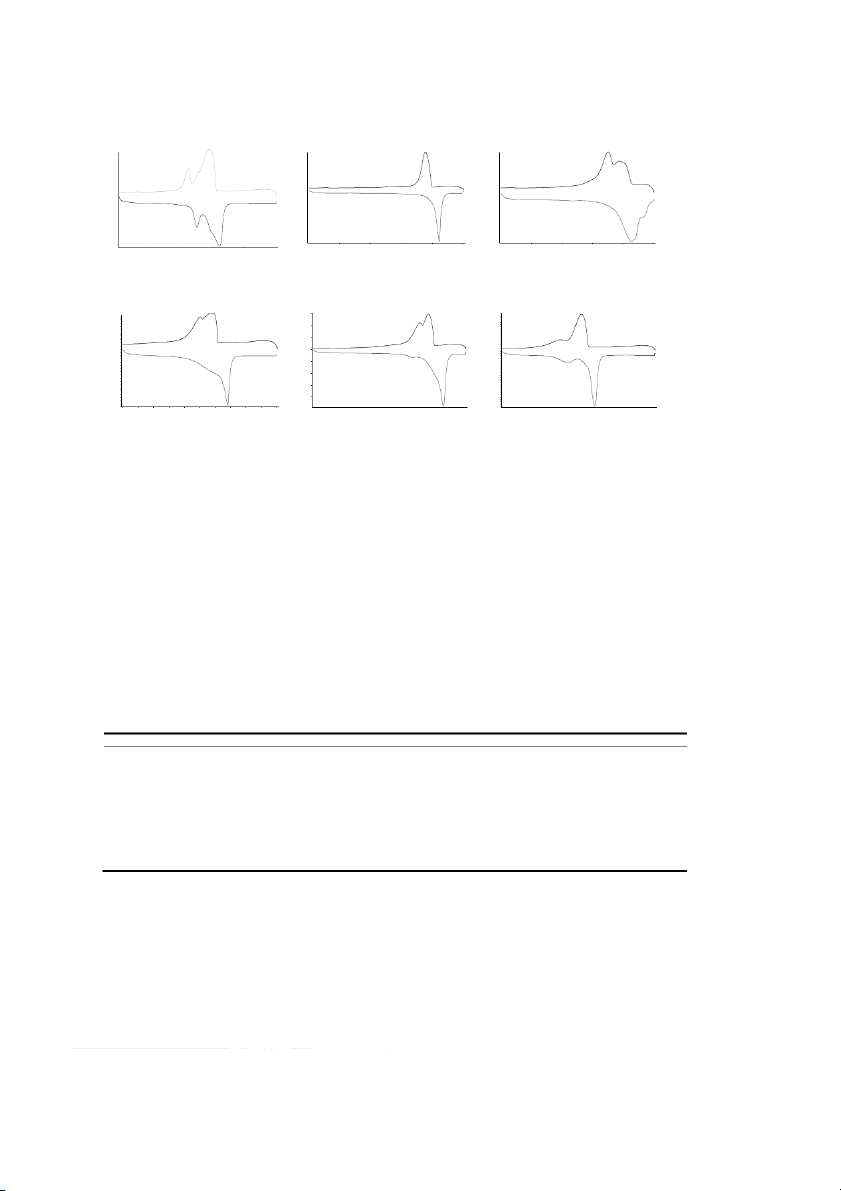
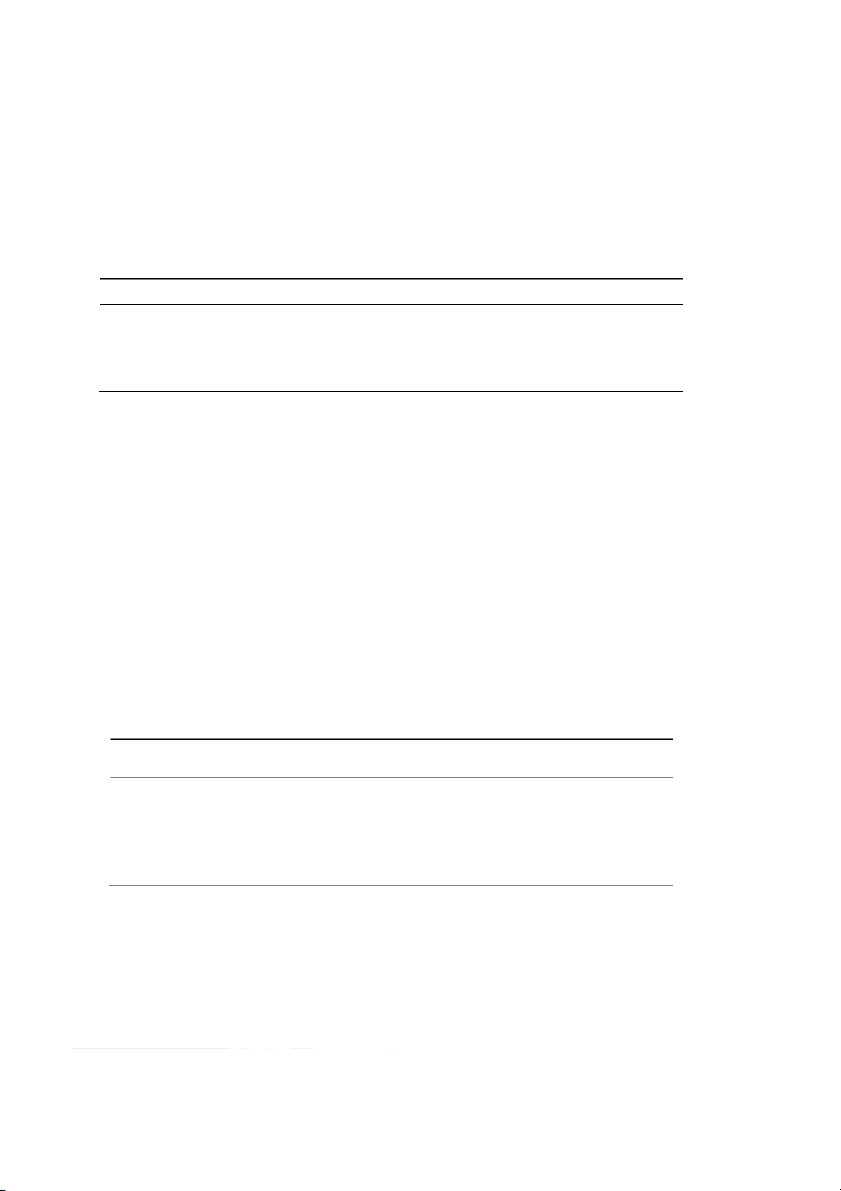
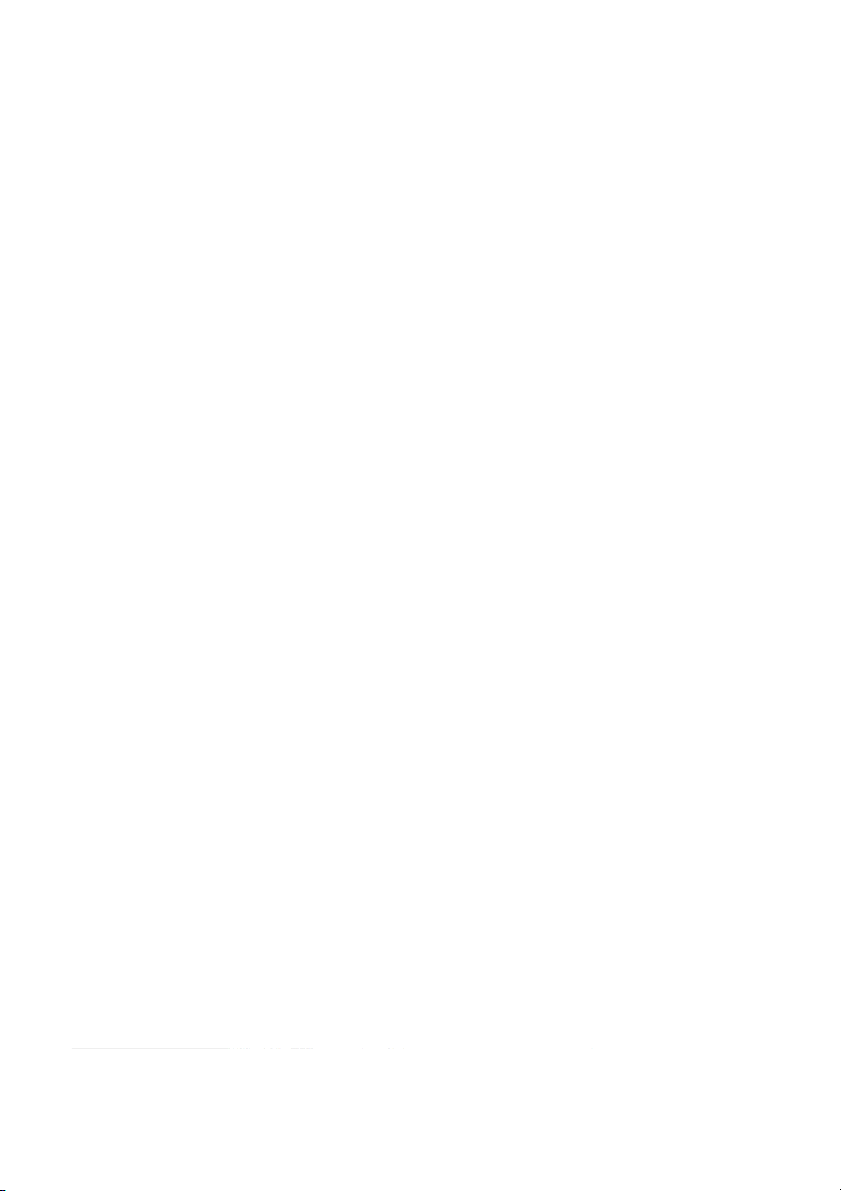
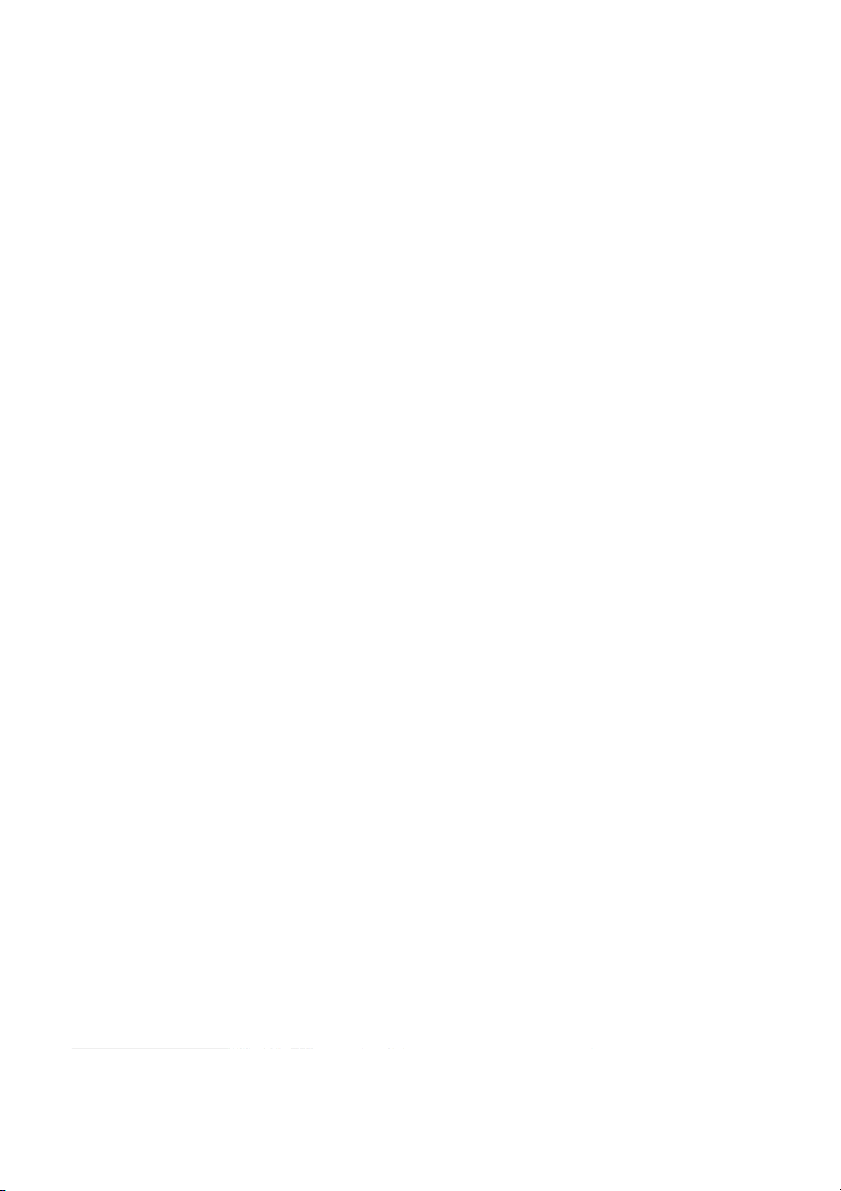
Preview text:
Available online at www.sciencedirect.com
Procedia Engineering 18 (2011) 101 – 106
The Second SREE Conference on Chemical Engineering
Thermal analysis of four insect waxes based on differential scanning calorimetry (DSC)
Zhang Ruguoa,b, Zheng Huab, Zhang Hongb,*, Feng Yingb, Li Kunb, Zhang wenwenb
aQiannan Medical College for Nationalities, Duyun, Guizhou 558003, China
bResearch Institute of Resources Insects, Chinese Academy of Forestry, Kunming, Yunnan 650224, China Abstract
For more wide development of natural wax applied in food additives industry, thermal characteristics of four insect
waxes were analyzed by differential scanning calorimetry (DSC), compared with paraffin (an abiological wax) and
canauba wax (a vegetal wax). It was indicated that melting point of the four insect waxes were varied at 90.42◦C of
coccerin as the highest, 70.34◦C of beeswax as the lowest, and 86.56◦C of insect white wax, 83.82◦C of shellac wax.
All of the four waxes were higher with the melting point than paraffin (63.32◦C), and the coccerin’s melting point
was even higher than that of canauba wax (87.85◦C). The melting enthalpy of insect waxes ranged at 168.1 to
203.2J/g, so did the crystallization enthalpy at 166.9 to 198.8J/g. Both melting and crystallization enthalpies were
near to other waxes such as paraffin and canauba wax. It was showed that DSC was qualitatively and quantitatively
available for thermal analysis of insect wax, and insect wax was good in thermal stability.
Keywords: insect wax; thermal analysis; differential scanning calorimetry (DSC)
Natural waxes were originated from vegetables, animals and minerals, also could be classified as
biological and abiological waxes. Biological waxes were formed as protective substances or nutrients of
the living creatures. It was no harmful of biological waxes to human health and the environment, but was
with some special properties for people’s daily life as a natural gift[1]. With safe and non-toxic quality,
insect waxes were widely used as forming, polishing and coating agents in food science and industry[2]. It
was well maintaining for fragrances and nutrients of fruits and preventing bacterial for better storage[3]. To
enlarge the processing and application field of insect waxes, shellac wax, insect white wax, beeswax and
* Corresponding author. Tel.: +86-871-386-1466; fax: +86-871-386-0021.
E-mail address: hua-zheng@sohu.com.
1877-7058 © 2011 Published by Elsevier Ltd.
doi:10.1016/j.proeng.2011.11.016 102
Zhang Ruguo et al. / Procedia Engineering 18 (2011) 101 – 106
coccerin were taken for investigation, compared with paraffin (an abiological wax) and canauba wax (a
vegetal wax), by the thermal analysis based on differential scanning calorimetry (DSC).
DSC was actually perfect for the characterization of natural solids among several thermal analysis
techniques. Thermal events such as melting, recrystallization, decomposition and glass transitions could
be measured. According to these events, heating properties of natural products such as insect waxes could
be evaluated objectively for a better developing in food, medical therapy and other industries.
1. Materials and Method
1.1. Materials and chemical r a e gents
a) Shellac wax and coccerin, purified by petroleum ether, self-experimentally achieved in the Key
Laboratory of Cultivation and Utilization of Resources Insects, State Forestry Administration; b) insect
white wax, provided by Pilot Base for Research and Development of Special Bio-resources, Research
Institute of Resources Insects, Chinese Academy of Forestry; c) beeswax, bought from market in Chiang
Mai, Thailand; d) canauba wax, Acros Organics Co., Ltd., Belgium; e) paraffin, 58-60#, bought from market in Kunming, China.
1.2. Instruments and apparatus
a) DSC200F3 differential scanning calorimetry, with Proteus data processing system, Netzsch Co.,
Ltd., Germany; b) moulding machine for DSC, Netzsch Co., Ltd., Germany; c) liquid nitrogen and
99.999% nitrogen gas, Kunming Meisaier Gas Products Co., Ltd.; d) AB204-S electronic balance,
Mettler-Toledo Group, Switzerland; e) normal experimental paraphernalia. 1.3. Method 1.3.1 Sample preparation
Pulverize insect waxes, paraffin and canauba wax and grind into 60 mesh powder as the pretreatment
for the reduction of defects such as lower melting temperature and melting enthalpy due to large size
particles or random shape samples[4].
1.3.2 Instrumental calibration
Indium (melting point 156.6◦C and melting enthalpy 28.45J/g) was chosen for standard calibration
of instrumental cell constant and temperature, in order to obtain correct and precise determination result[5]. 1.3.3 Determination condition
Weigh waxes samples precisely and transfer them into DSC aluminum smelting bowl. Capped and
packed by moulding machine, the bowl was set into DSC apparatus. After cooling by liquid nitrogen, the
sample was heated from 0◦C to 100◦C at the velocity of 10◦C/min. The maintaining time was 2min for the
adequate melting of wax and the balance of instrumental baseline. Then, cool the sample from 100◦C to
0◦C at the velocity of 10◦C/min by liquid nitrogen. Both the heating and cooling stages were running at
20mL/min purge gas and 50mL/min shield gas (nitrogen gas) ambience.
2. Results and Analyses
2.1. DSC curves of insect waxes samples
DSC curves of the 4 insect waxes, paraffin and canauba wax were showed in Fig. 1 to Fig. 6.
Zhang Ruguo et al. / Procedia Engineering 18 (2011) 101 – 106 103 DS DSC (mW/mg) DSC (mW/mg) DSC (mW/mg) 2 2 4 heat releasing heat releasing heat releasing 2 1 1 [1.3] 0 [1.3] [1.1] [1.3] 0 0 [1.1] [1.1] -2 -1 -1 heat absorbing heat absorbing heat absorbing -4 -2 -2 -6 20 40 60 80 100 20 40 100 20 40 60 80 100 temperature (◦C) temperature (◦C) temperature ( ◦C)
Fig. 1. DSC curves of shellac wax Fig. 2. DSC curves of insect white wax Fig. 3. DSC curves of coccerin DSC (mW/mg) DSC (mW/mg) D DSC (mW/mg) 3 2 3 2 2 heat releasing heat releasing heat releasing 1 1 1 [1.3 [1.3] [1.3] 0 0 [1.1] 0 [1.1 [1.1] -1 -1 -1 -2 -2 -2 heat absorbing -3 -3 heat absorbing heat absorbing -4 -3 -4 -5 0 20 40 60 80 100 20 40 60 80 100 20 40 60 80 100 temperature (◦C) temperature (◦C) temperature (◦C)
Fig. 4. DSC curves of beeswax Fig. 5. DSC curves of canauba wax Fig. 6. DSC curves of paraffin
2.2. Analyses of DSC curves and demonstration of thermal characterization of insect waxes
There were 1 to 3 heat absorbing peaks or heat releasing peaks clearly seen in the melting or
crystallizing curves of DSC diagrams according to different samples. It was usually symbolized that
different peak with different chemical composition, so it was inferred from the curves that insect waxes
were not single chemicals. For its high sensitiveness, a slight change of heat could be measured by DSC,
thus the little content of chemical constituent of insect waxes was also showed in the diagram and DSC
was able to be used as the identification on wax purity and mixture test. For instance, beeswax showed in
Fig. 4 has at least two composed chemicals, between which was one in lower content with small melting
peak at 40 to 60◦C, and another in higher content with an orderly significant peak at 60 to 70◦C. It was
known with wax composition that the change of slope in the chart during 40 to 60◦C was due to heat
absorbing from free acids and hydrocarbons, and the sharp absorbing peak was lead by fatty acid esters
which were predominant of beeswax at the content of nearly 72%. Although DSC was not a direct way
for chemical composition and structure identification, it provided thermal properties information of insect
wax that related to the state change of substances. It was showed in Table 1 of insect waxes and paraffin/
canauba wax on their main components and number of DSC melting peaks.
Table 1 Components of waxes and the number of melting peaks in DSC curves wax main components number of peaks insect white
aliphatic monobasic acid esters (93 -95%) 1 wax coccerin
esters formed with cochineal wax acids and cochineal wax alchohols 2 (with change of slop ) e 1 (with great change of beeswax
fatty acid esters (72%), free acids (13%), hydrocarbons (13%), etc. slope)
fatty acid esters (70-82%), free alchohols ( - 8 14%), free acids ( - 1 4%), shellac wax 4 hydrocarbons (1-6%) canauba wax
fatty acid esters (80-85%), free alchohols (10-15%) 2
straight chain hydrocarbons with 18 to 30 carbon atoms (80%-95%), branched paraffin 2
chain alkanes and monocycloalkanes with long side chain (≤20%) 104
Zhang Ruguo et al. / Procedia Engineering 18 (2011) 101 – 106
Thermal parameters of insect waxes could be recorded by DSC and characterized, such as melting
point[9], softening point, melting peak, melting and crystallization enthalpies[10] and change of specific heat capacity[11].
2.3. Softening point, melting peak and melting point of insect waxes and the compared samples
From DSC curves showed in Fig. 1 to Fig. 6, values of softening point, melting peak and melting point were obtained as Table 2.
Table 2 The start, end and summit temperature of melting or crystallizing peak of waxes sample weight No. sample T ◦ T ◦ ◦ ◦ ◦ ◦ m1 ( C) T T C) T C) T (mg) o ( C) f1 ( C) o2 ( m2 ( f2 ( C) insect white 1 5.3 81.01 84.82 86.56 79.82 75.85 71.27 wax 2 coccerin 5.4 74.82 85.78 90.42 85.70 70.46 62.65 3 beeswax 5.0 45.91 68.60 70.34 61.93 58.72 41.49 4 shellac wax 5.3 57.39 75.19 83.82 78.21 67.81 43.72 5 canauba wax 5.3 81.00 85.72 87.85 79.43 75.77 63.80 6 paraffin 5.3 34.80 60.64 63.32 56.45 52.00 45.58
Note: 1) To1: softening point; 2) Tm :
1 melting peak temperature; 3) Tf1: melting point (ending temperature of melting); 4) To2:
starting teperature of crystallizing; 5) Tm2: peak temperature of crystallizing; 6) Tf2: ending temperature of crystallzing.
According to DSC curves in Fig. 1 to Fig. 6 and Table 1 & Table 2, it was varied on the start, end
and summit temperature of melting or crystallizing peak of waxes due to their different composition.
Melting point among these insect waxes was the highest of coccerin, and followed by insect white wax,
shellac wax and beeswax. It was in the same order of softening point, the start, end and summit
temperature of melting or crystallizing peak to melting point. This was determined by chemical
components and molecular weight of insect waxes. It was in the order of molecular weight that
coccerin[12-13] was the highest and also followed by insect white wax[14-15], shellac wax[16-17] and beeswax.
It was suggested that DSC diagram was confirmed by wax components. In Table 2, melting points of the
insect waxes were all higher than that of paraffin because the structure of paraffin was simple with some
chain alkanes and its molecular weight was smaller than insect waxes which composed with mix esters in
high molecular weights and complicated structures. But compared to the vegetal wax——canauba wax,
only coccerin among the insect waxes was higher in the melting point. And for the same wax sample, it
was higher of the softening point, melting point and melting peak temperature than corresponding ending
temperature, starting temperature and summit peak temperature of crystallzation, which was leaded by over cryo factors.
2.4. Melting/ crystallization enthalpy and changes of specific heat capacity of waxes
Calculated according to DSC data, it was showed in Table 3 of melting/ crystallization enthalpy and
changes of specific heat capacity of waxes mentioned above.
Table 3 Melting/ crystallization enthalpy and specific heat capacity of waxes change of melting change of sample melting crystallization No. sample specific heat crystallization specific weight (mg) enthalpy (J/g) enthalpy (J/g) capacity (J/(g∙K)) heat capacity (J/(g∙K)) insect white 1 5.3 180.7 176.3 18.292 11.159 wax 2 coccerin 5.4 193.2 177.4 13.436 11.585 3 beeswax 5.3 168.1 166.9 17.960 10.006 crude shellac 4 5.0 203.2 198.8 10.351 10.100 wax 5 canauba wax 5.3 204.3 173.6 26.045 15.817 6 paraffin 5.3 193.9 193.8 27.068 18.291
Zhang Ruguo et al. / Procedia Engineering 18 (2011) 101 – 106 105
From Table 3, it was inferred that great variances were among melting/ crystallization enthalpy and
changes of specific heat capacity of waxes. The enthalpies of insect waxes from the highest to the lowest
were: Q(shellac wax)>Q(coccerin)>Q(insect white wax)>Q(beeswax). And those of melting specific heat capacity were:
ΔCp(insect white wax)>ΔCp(beeswax)>ΔCp(coccerin)>ΔCp(shellac wax); of crystallization specific heat capacity were:
ΔCp(coccerin) >ΔCp(insect white wax)>ΔCp(shellac wax)>ΔCp(beeswax). Compared with paraffin and canauba wax, most
of the melting/ crystallization enthalpy and changes of specific heat capacity of insect waxes were
relatively lower, except the enthalpies of shellac wax were higher than those of paraffin. It was known
from the above that there were some relations between the enthalpies and melting point of insect waxes.
The higher the melting point, the higher the enthalpies. But the crude shellac wax was irregular in such
relations due to high content of impurities in the crude sample. And for the same wax sample, it was
slightly higher of melting enthalpy than crystallization enthalpy, because chemical components of waxes
were crystal transferred during recrystallization[18]. 3. Conclusion
3.1. DSC was available for thermal characteristic determination of insect waxes qualitatively and
quantitatively, with better accuracy and repeatablity than traditional mercury surface measurement.
3.2. According to DSC investigation on insect waxes, melting point of them from the highest to the
lowest were: coccerin, insect white wax, shellac wax and beeswax, so were the orders of softening point,
the start & end temperature and the summit temperature of melting/ crystallization peaks.
3.3. It was dominated on melting point and DSC curves of insect waxes by chemical compositions and molecular weight.
3.4. All the studied insect waxes were higher with their melting point than paraffin. Melting points of
insect white wax, shellac wax and beeswax were lower than that of canauba wax, but coccerin’s melting
point was rather higher than that of canauba wax. These were also caused by molecular composition and weight.
3.5. There were some relations between melting/ crystallization enthalpies and melting point of insect
waxes, except crude shellac wax. The higher the melting point, the higher the melting/ crystallization enthalpies.
3.6. For the same wax, it was slight higher of melting enthalpy than crystallization enthalpy. Acknowledgements
This investigation was supported by Fund Program in Conversion of Agricultural Science and
Technology Achievement, Ministry of Science and Technology of the People’s Republic of China
(2010GB24320619) and State Forestry Project on Promotion of Scientific and technical achievement,
SFA, China ([2010]11). We gratefully thank the contributions of everyone who joined in these research projects mentioned above. References
[1] Wang YQ, Duan QF, Zhao H, Sun L. Bio-wax: a green product. Quart Fore By-prod Special Chin 2002; (3 : ) 28–29 .
[2] Ling GT. Natural Food Additives Handbook. Beijing: Chemical Industry Press; 2000 .
[3] Zheng H, Tang LY, Zhang RG, Zhang H. Bio-wax and human health. Nat Prod Res De
v 2009; 21: 313–316 .
[4] Wang F. Studies on the effect of DSC parameters on melting point of medication. J Nanjing Nor Uni (Engin Tech) 2004; 4 (4): 58–60.
[5] Ji L, Sun ZS, Wang Y, Cui H. Determination of purity of inositol by DSC method. Chin J Phar Ana 2002; 22 (2 : ) 498–500. 106
Zhang Ruguo et al. / Procedia Engineering 18 (2011) 101 – 106
[6] Sun Y. Determination of purity of crystallization organic compounds by DSC thermal analysis technolog . y Guangxi Chem Indu s 2002; 31 (2): 29–31.
[7] Yang XY, Gu XY, Zhang L. Application of beeswax in traditional Chinese medicinal agents. Gansu J Tradi Chin Med 2005; 18 (8): 42–43 .
[8] Zhang RG, Zheng H, Zhang H, Gan ,
J Yu LS, Zhang WW. Differential scanning calorimetric study of thermal characteristics of
lac wax. Food Sci 2009; 30 (17 : ) 137–140 .
[9] GB/T 5536—1985, Inspection of vegetable oils: methods for determination of melting point.
[10] Zhang XW, Liu Z, Yang CY. Determination of wax melting point by DSC. Petrochem Tech 2003; 32 (6): 521–524. [11] Guo J. Superficiall y analyz e tha t differentia l scannin g calorimetry measurement tes t the specifi c hea t capacity of the materia . l
Taiyuan Sci Tech 2007; (10 : ) 10–20 . [12] Zheng H, Zhang H, Gan ,
J Tang LY, Zhao H, Lu YM, et al. Extraction and preliminary purification of cochineal wax. Food Sci
2009; 30 (16): 162–165 .
[13] Zhang JY, Li ZG, Bao SL, Zhao J ,
J Yang SY, Luo X. Optimization of extraction technology for cochineal wax by orthogonal
design. J Northeast Fore Uni 2009; 37 (3): 95–96 .
[14] Chen XM, Feng Y. An Introduction to Resource Entomology. Beijing: Science Press Beijin ; g 2008 .
[15] Zhang H, Chen J, Zheng H. Design on pilot-technology for fine processing product of white wax. Fore Cons 2005; (5): 3–5.
[16] Chen XM, Chen YQ, Zhang H, Shi L. Cultivation of Lac Insect and Processing of Shellac. Beijing: China Forestry Press; 2008 .
[17] Zhang H, Zheng H, Chen J, Chen XM, Shi L, Zhao H. A Method for Lac Wax Extraction and a Prepared Lac Wax by this
Method. Chinese Patent ZL200710198438.5; 2008.
[18] Li WB, Xue F, Ding EY, Cheng S. Accurate determination of latent heat via differential scanning calorimetry. J Instru Ana l 2006; 25 (2): 16–19.